


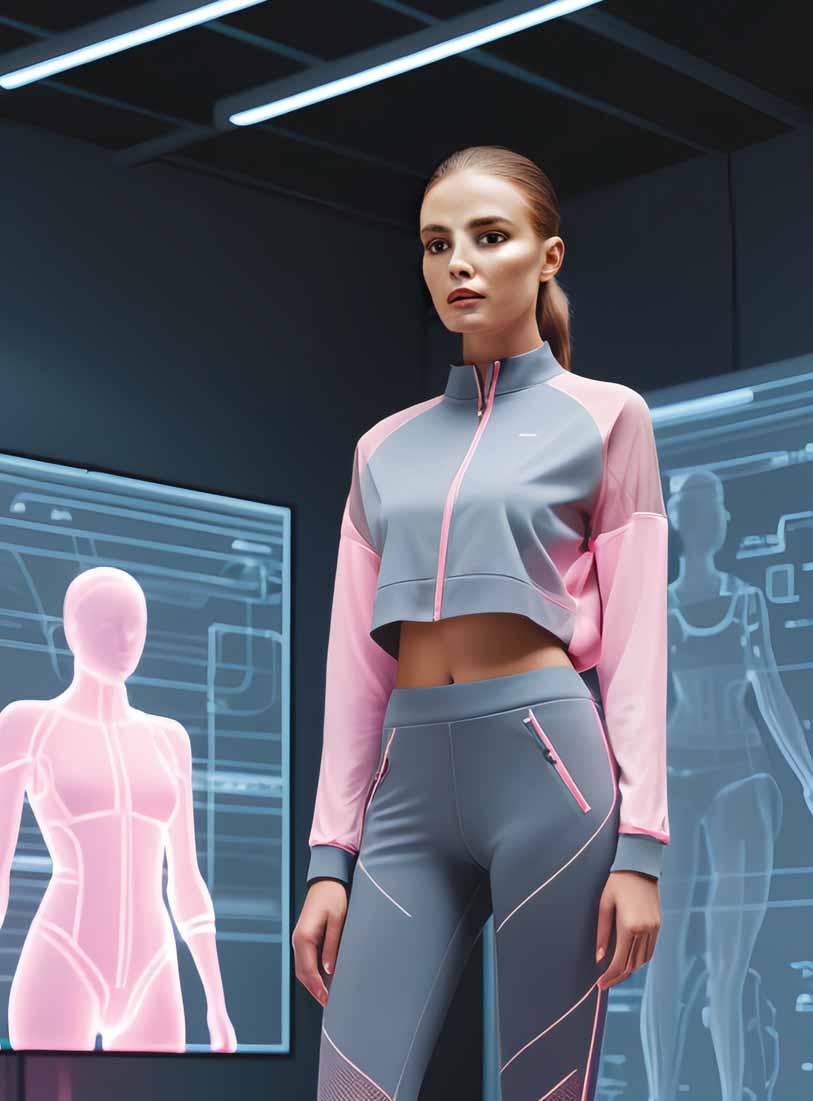

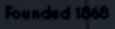
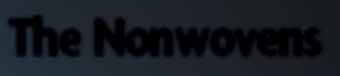
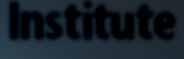
The Nonwovens Institute
Enabling Future Materials

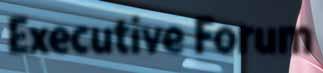
Executive Forum
Unifi’s Meredith Boyd
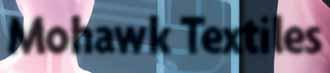
Mohawk Textiles
New Greenfield Plant

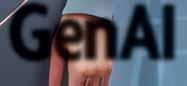
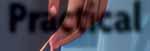
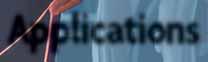

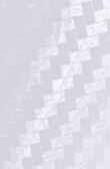
Enabling Future Materials
Unifi’s Meredith Boyd
New Greenfield Plant
Featuring hundreds of suppliers, onfloor educational Tech Talk sessions, and the acclaimed Symposium. Discover new technology, learn from experts on economic trends, and explore business growth opportunities.
Mark Your Calendars for the 2025 Edition of Techtextil North America!
Co-located with Incorporated with
MAY 6 – 8, 2025
Scan the QR code for more attendee information!
Generative artificial intelligence (GenAI) technologies are getting better by the day and companies should consider embracing these technologies and growing with them. Image GenAI technologies have improved tremendously and are capable in some cases of producing photo-realistic quality images given the right prompt.
10 Executive Forum: Meredith Boyd
UNIFI’s Meredith Boyd talks about her career in the fiber industry and her role as president of the Synthetic Yarn & Fabric Association.
13 Executive Forum: Greybull Stewardship
Mason Myers recently spoke to Textile World about investments in “pre-middle” market businesses and textile companies.
Industry Events Coverage
16 Uzbekistan Showcases Modern Textile Investment
The International Textile Manufacturers Federation’s 2024 annual conference was hosted in partnership with the International Apparel Federation in Samarkand, Uzbekistan.
20 Highlights From TTNA 2024
Raleigh, N.C., provided the backdrop for networking and learning at the recent Techtextil North America (TTNA) trade show.
21 RISE® 2024: Driving Innovation In Engineered Fabrics
The 14th RISE conference brought new innovations to light, conferred awards and highlighted student research.
22 Three Perspectives On The North American Composites Industry
The composites industry benefited from three composites-related events that recently took place in the space of four weeks.
26 SYFA Conference Highlights Industry Resilience & Future Trends
Presentations and panel discussion were held under the theme “Innovation: A Catalyst for the Future.”
28 Generative AI: Understanding Fears & Embracing The Innovations
There is no time better than the present to embrace artificial intelligence (AI) technologies. 32 Mohawk Textiles Celebrates New Greenfield Facility
Mohawk Textiles aims to follow in the footsteps of Mohawk Fabric Co. as it begins its journey as a 100-year-old technical textile “start up.”
Office. All rights, including translation into other languages, reserved. Subscription rates for one year are: $65 (US); $85 (Canada and Mexico); $130 (Other International). Single copy rates are: $15 per copy. All prices are in U.S. dollars and all orders must be prepaid. Questions may be submitted to jdavis@textileworld.com. To obtain electronic copies of print articles, please contact ProQuest at www.proquest.com. To obtain microform copies, please contact NA Publishing at www.napubco.com. POSTMASTERsend address changes to: Textile Industries Media Group, LLC, PO Box 683155, Marietta, GA 30068. Send Canadian address changes to: Textile World, c/o The Mail Group, P.O. Box 25542, London, ON N6C 6B2, Canada. Customer #7007632 Publications Agreement #40612608.
55 Rieter’s Autoconer X6 Multilink: Energy & Cost Savings
MKAS Textile selected the Autoconer X6 Multilink from Rieter for an economical boost to production.
56 Marine Textile Trends: 2025 & Beyond
Marine fabrics, combining durability with aesthetics, influence, and are influenced by, partner and peer industries.
36 Executive Forum: Advancing Textile Circularity
Reju™ CEO Patrik Frisk spoke with TW about the company’s new Regeneration Hub Zero and the drive for circular polyester.
News
39 Medical Textiles: Navigating Regulation Challenges & Testing
Success in global medical textile markets requires an understanding of global regulatory standards and testing protocols.
42 The Nonwovens Institute: Enabling Materials Of The Future
The Nonwovens Institute’s success is driven by creating measurable goals in line with a long-term vision.
47 Modern Meadow: Where Leather Goes To Dye
The textile industry is developing ways to combine material science and manufacturing processes to pave the way for a more sustainable future.
50 ETV Looks To The Future With Monforts
At a time when European commission finishers are encountering extremely high overheads, ETV is going from strength-to-strength, alert to new opportunities going forward.
52 Executive Forum: World Emblem —Embracing AI
CEO Randy Carr talks to TW about the use of AI at embroidered patch maker World Emblem and how it has helped his company.
Founded 1868
Quality Fabric: Seaweed Reinvented
Read about Keel Labs’ first Kelsun™ fiber commercial product introduction —the Kelsun Universal Blanket Shirt from Oakland, Calif.based sustainable brand OuterKnown.
NEXT ISSUE:
• Technical Textiles Focus
• Knitting/Apparel Update
• Executive Forum
EDITOR IN CHIEF
James M. Borneman
EXECUTIVE EDITOR
Rachael S. Davis
TECHNICAL EDITORS
Dr. Lisa Parillo Chapman
Dr. Peter J. Hauser
Dr. Trevor J. Little
Dr. William Oxenham
Dr. Behnam Pourdeyhimi
Dr. Abdel-Fattah Seyam
Dr. Andre West
CONTRIBUTING EDITORS
Jim Kaufmann
INTERNET CONTENT EDITOR
Rachael S. Davis
CIRCULATION MANAGER
Julie K. Brown-Davis
ADVERTISING BUSINESS MANAGER
Denise Buchalter
ART & PRODUCTION MANAGER
Julie K. Brown-Davis
OWNER/PUBLISHER
James M. Borneman
ADVERTISING REPRESENTATIVES
UNITED STATES & CANADA Turner Marketing &Media, LLC +864-594-0921 sturner@textileworld.com
EUROPE (except ITALY) Sabine Dussey +49-171-5473990 sabine.dussey@dussey.de
ITALY
Ferruccio & Filippo Silvera +39-022-846716 info@silvera.it
ASIA
James M. Borneman +678-483-6102 jborneman@textileworld.com
MEXICO, CENTRAL & SOUTH AMERICA
Virgilio L. González +58-412-622-2648 vlgonzalezp@gmail.com
INTERNET & CLASSIFIEDS
Julie Davis +678-522-0404 jdavis@textileworld.com
PO Box 683155 | Marietta, GA 30068, USA
Telephone +678-483-6102 | www.TextileWorld.com
IIt is over.With the 2024 election in the books,the road is clear — or clearer — to chart a course into 2025 and beyond.
Whether the candidate you supported won or lost,it is reassuring to know the election was held without any major disruptions; a definitive outcome was achieved with both the electoral college and popular vote — for the first time in a very long time — aligning; and all signals now pointing to a peaceful transition of the government.
The table is set for clarity and reduced risk in planning short-term,mid-term and long-term strategies — from raw material suppliers,manufacturers and retailers — through all sectors associated with today’s integrated supply chains.
Sure,there is always room for a political discussion,but with a known quantity — of either stripe — set to take charge for the next four years,strategic risks are reduced and there is an improved ability to anticipate the business climate affecting the industry.
For manufacturers,this may be a bright spot.The opinion that lower energy costs, a pro-U.S.manufacturing sentiment and improved emphasis on nearshoring may be in the cards is palpable.
Retailers and sectors that have chosen to rely on imports may need to reevaluate their positions.And suppliers of inputs,machinery and technology may need to shift gears to realign with changing industry forecasts.
It is an opportunity to reboot.Consider the level of certainty entering decision making, mitigating planning risk and — probably — a business-friendly environment for many.
There will undoubtedly be some dustups on the way,with tariff talk on the horizon, regulation and taxation front and center, and globalism’s effects under scrutiny.
However,this clearer environment coincides with a plethora of game-changing
technologies maturing – think artificial intelligence (AI),machine learning and commercialized circularity.
This could in fact be the forefront of a new era of manufacturing boosted by the lessons learned during the pandemic,the awareness of supply chain vulnerabilities and the giant steps made in technology influencing all facets of daily life.
It is a time to be embraced — one of openness to opportunity and of acknowledgment of the persistence of technology to innovate and reinvent the future.
Of course,it is not all hearts and flowers. The realities of making manufacturing work in the current environment is not for the faint of heart.The promise of technology is not always easy to manifest and make an immediate impact,but the potential is there,and the test cases have shown positive results.
Will AI make your company more efficient, more responsive to the marketplace,and a better place to work for your employees?
Will confidence in a firmer planning horizon make your ability to commit financial resources embolden a growth story for your company? Will the company have fresh eyes on the future and embrace opportunities with confidence?
As the nation enters 2025,there is no doubt that the environment has changed. Impacts on various sectors of the industry will differ and need adjustment.
Maybe — just maybe — the question won’t be to invest in new machines and technologies or not,but rather,to pay in cash or bitcoin!
James M. Borneman jborneman@TextileWorld.com
Hundreds of exhibitors, 3 days of education, and unlimited networking. Join the premier event for sewn products, designed for manufacturers and innovators in apparel, footwear, home furnishings, and more.
Mark Your Calendars for the 2025 Edition of Texprocess Americas!
MAY 6 – 8, 2025
Scan the QR code for more attendee information!
Co-located with Co-produced by
Shawmut Infinite,a newly created affiliate of Shawmut LLC,West Bridgewater,Mass.,recently acquired warp knitter Fairystone Fabrics,Burlington, N.C.Shawmut Infinite plans to continue Fairystone’s contract knitting and warping service operation in Burlington retaining both the management team and 100-percent of the workforce.Over the next two years,Shawmut plans to invest $8 million to retrofit the facility with new, digitally controlled
prototyping,knitting and warping technologies.The transaction was structured as a purchase of assets.
“The Fairystone acquisition marks the realization of Shawmut’s long-standing vision for operating a fully integrated textile and textile composite supply chain in North America,and for deploying new digital tools that enable big leaps forward in productivity and innovation.”said Shawmut CEO James Wyner.“It’s just one more way in which Shawmut is enhancing its position as a preferred global partner to automotive and industrial OEMs”.
The Brickle Group, based in North Smithfield, R.I.,and operating as Hyman Brickle and Son Inc.,has acquired Family Yarns based in Etna,Maine. Brickle provides berets, blankets and other coldweather gear to the U.S. Department of Defense in addition to providing industrial nonwovens, trading raw materials and recycling waste fiber.The purchase of Family Yarns, which specializes in coarser count yarns in a variety of
fiber types,adds 1 million pounds of woolen spinning capacity to support the company’s yarn needs.
Brickle also recently opened a yarn plying operation in North Smithfield that offers 2-for-1 twisting up to 4-ply to cater to companies requiring specialized yarns.
“Our commitment to vertical integration and enhancing our valueadded services continues with these investments,” said President Max Brickle. “We are excited about the opportunities that the Family Yarns acquisition and our new plying
Textile industry associations want the textile industry to know they are talking.With a desire to work more collaboratively on industry initiatives and events that are beneficial to all their respective members,11 associations — Advanced Textiles Association (ATA),American Textile Machinery Association (ATMA),Americas Apparel Producers’Network (AAPN), American Association of Textile Chemists and Colorists (AATCC),Association of the Nonwovens Fabrics Industry (INDA),the Nonwovens Institute (NWI),North American Linen Association (NALA), SEAMS – The Association & Voice of the U.S.Sewn Products Industry,Southern Textile Association (STA),Sewn Products Equipment and Suppliers of the Americas (SPESA),and
“Alphabet
Synthetic Yarn & Fabric Association (SYFA) — recently got together to discuss ways to benefit the industry.
“We all represent various segments of the textiles and sewn products industry,”said Maggie McDonald,vice president,Communications,SPESA.
“But we all agree that collaboration and building on synergies is what will propel our industry into its next chapter.”
This “Alphabet Soup Collective,”as the group has affectionately named itself,was officially launched during Techtextil North America (TTNA) 2024 held in Raleigh.N.C.
One of the first ideas for the collective was to co-host a social event open to all members of the textile industry including current association members as well as nonmembers wanting to learn
more.The result,the inaugural Alphabet Soup Shindig,was held at the Whiskey Kitchen during TTNA.This first-of-itskind,sold-out event gathered people from all aspects of the industry in one place at the same time to network,learn and collaborate.Attendance far exceeded expectations, illustrating a hunger for these types of cross-industry networking opportunities.
Twelve sponsors were instrumental in making the shindig happen:
•American & Efird;
•Asheboro Elastics Corp. (AEC);
•Baxter Mill Archives;
•Better Than Found;
•Coker & Associates; •Contempora Fabrics; •Danbartex; •Gribbin Strategic; •Itema America Inc.;
•MajorSage Business Coaching;
•MMI Textiles;and •North Carolina Textile Foundation at NC State University.
Ben Talbert,president and CEO of Greenville,S.C.-based Better Than Found Search Group,one of the event sponsors,said:“Better than Found Search Group (BTF) was proud to sponsor this event.The textile community is a family,and this felt like our reunion.”
As McDonald noted:“Good people,good networking,good vibes,AND good weather. Doesn’t get much better.”
The Alphabet Soup Collective will continue its conversations as it looks for ways to collaborate,streamline events and gather the industry in productive,beneficial ways for all involved.
operation will bring to our clients and partners in the textile industry.”
Cone Denim®,Greensboro,N.C., has inaugurated its first rooftop solar panel installation in Jiaxing,China. The action will generate 9 megawatt hours of electricity per year and reduce the plant’s annual greenhouse gas emissions by 17 percent,according to Cone,which is in line with the company’s 2030 sustainability goals.
“This project is a great accomplishment for Cone towards our sustainability efforts,”said Cone Denim Vice President of Manufacturing Brad Johnson.“The solar panel installation demonstrates our commitment to continued innovation across our manufacturing facilities and platforms to reduce greenhouse gas (GHG) emissions. This launch provides Cone Denim the opportunity to scale our efforts on clean energy and carbon reduction,all on-site in Jiaxing.By implementing this on our industrial site,we are preserving the natural landscape without requiring any additional surrounding land resources.”
Bondex,based in Columbia,S.C., has invested $18.8 million to add a new needlepunch line to its facility located in Trenton,S.C.The investment created 13 new jobs and will serve growing demand from global customers for filtration,automotive and laundry felt products,among other products.
“At Bondex,we are proud to deepen our roots in Edgefield County with this expansion,”said Bondex President Brian Little.“This investment is a testament to our team’s dedication to innovation and to the growing demand for our high-quality products.Our reputation in the area as a great place to work is something we take seriously,and we’re excited to continue building that legacy by creating new opportunities for growth and employment.We look forward to advancing both our capabilities and the local community as we grow in South Carolina.” TW
Non-contact precision spray technology and plasma treatment for sustainable finish applications.
Providing jet, jigger, beam and cold pad batch dyeing machines with IR lab dyeing equipment. Continuous scouring, bleaching, mercerizing and singeing ranges.
Finishing and coating lines for woven and knit fabrics, technical textiles and nonwovens.
Detwisting, opening and web guiding for all fabric constructions.
Textile calenders for softening, lustre change, embossing and recalipering of textile substrates.
Foam generators, in line chemical mixing and blending systems.
Water treatment and water recovery plants in textile facilities.
Fabric surface finishing equipment: napping, sueding and shearing.
Circular knitting machines for apparel, mattress, home furnishings and footwear markets.
Turbotex Scrim Fabric machine.
In-line vision systems for weaving and warp knitting machines, tenter frames, compactors, coating/laminating ranges.
Slitting, spooling and rewinding machines. Ultrasonic slitting for loom state and finished fabrics.
Automatic dispensing of powder dyestuffs and liquid chemicals for laboratory, and bulk textile production.
Automated inspection and packaging systems for rolled goods.
Textile Coating ranges, digital, flat bed and rotary screen printing and loop steamers.
For additional information on these companies contact Ian Mills at imills@fi-tech.com.
UNIFI’s Meredith Boyd talks about her career in the fiber industry and her new role as president of the Synthetic Yarn & Fabric Association (SYFA).
MMeredith Boyd has been involved in the textile industry now for some 17 years.Her first job,after her time at NC State University’s Wilson College of Textiles and UNC-Charlotte,was with Unifi Kinston LLC, part of Unifi Inc.,Greensboro,N.C.,where Boyd has carved a successful career in the fiber industry.Most recently,she was promoted to executive vice president and chief product officer at Unifi.
Boyd also took the helm of the Synthetic Yarn and Fabric Association (SYFA) this past spring where she will serve a two-year term as president.She was initially encouraged to engage with SYFA by Unifi
colleagues — including past SYFA President Pat Murray,Joel Cornelius, Terry Turner and Charlie King — as a way to gain more understanding of key technical topics,customer needs and opportunities for collaboration.
Textile World recently spoke with Boyd about her career in the fiber industry and her new role as SYFA president.
TW : What has your career trajectory looked like? Where did you start at Unifi and what steppingstones brought you to your current position of executive vice president and chief product officer?
Boyd: Unifi has afforded so many opportunities for
exposure and learning in my years.I started at the Unifi Kinston site in Kinston,N.C.This was Unifi’s continuous polymerization site and was originally DuPont’s first plant dedicated to the commercial production of polyester fiber.
I started in the quality lab.I then had the opportunity to move to Unifi’s Yadkinville,N.C.,site at an exciting time — just as we were commercializing the REPREVE® recycled polyester product.I worked in the partially oriented yarn (POY) spinning plant focusing on our specialty additive and polymer products including Repreve.I was fortunate to be involved as we worked on the technol-
ogy backward integration of Repreve and opened our own recycling center.
I then had the chance to move into the product development team.This was my first big move to work across business units within the company.I gained exposure to all of Unifi’s core businesses and supported our new product efforts and gained a lot of customer-facing experience.
My next role was in global business development — ultimately leading that team.This role worked on expanded new markets, leveraged strategic partnerships,and worked on expanding our production footprint particularly in Asia.
I then took a role as vice president of our Brand
Sales division.This role helped me further develop my understanding of the key role of the customer in our development and communication processes.
I then had the opportunity to return wholly to the technical side in 2019 as senior vice president of Global Innovation,gaining responsibility for leading — and learning from! — a brilliant team of material scientists,engineers and technicians for all of our new process and product development initiatives. The role further expanded into leading our plant technology and sustainability teams.
My current role as executive vice president and chief product officer encompasses so much of what I have loved and provides the continuing opportunity to learn every day.Beyond innovation and plant technology, I now have the chance to lead business development and our marketing and communication teams.
TW : What skills brought you success and what skills did you need to attain to continue your career progress?
TW : As an executive who has crafted a multifaceted career in the synthetic fiber industry, what do you consider the milestones?
Boyd : So many of my career milestones have been cultivated by advancements in Unifi and in the industry.The global expansion of Repreve and its worldwide production has been fascinating and energizing on which to work.The role of environmental sustainability as a cohesive part of corporate strategies has been exciting — not only at Unifi — but at so many companies.
And I’d be remiss not to mention the COVID-19 pandemic.The pandemic challenged all of us to think differently and be innovative.We realized how important supply chain security really is — the need to ensure that U.S.and regional manufacturing only strengthen — not only for “nice to haves” but also for our own national security.
Boyd: Curiosity is probably what comes the most in handy because it is tied into my love of learning,embracing innovation,and growth. Embracing others and the talents and ideas they bring is another key facet of success — always surrounding oneself with people who know more than you do and have different talents and expertise is an amazing way to build a team.
TW : How have the demands of the industry changed? For instance, what education and skills did you need to help address Unifi’s focus on sustainability?
Boyd: There are art and science aspects to this industry.Many things can be learned in school,but so much of this industry is experiential in nature. Certain areas like the roles of automation,machine learning,and artificial intelligence are becoming critically important.Sustainability was an area of immense interest but also naivete on my part.I sought out thought leaders,conferences,mentors,and resources that could help me learn.I have also been fortunate to work with a number of talented hires and interns with specialized expertise in this area that helped me to learn key facets of how to generate data and communicate opportunities in this space.
TW : Synthetic fibers and fabrics often are regarded to be at the center of sustainability issues yet are growing in importance to the textile industry.What is your vision/answer to those who question the sustainability of synthetics and their future in the industry?
Boyd: Synthetic fiber, filament and spun yarns, and resins are so critical across a multitude of industries.Polyester fiber is the largest volume synthetic fiber produced globally.1 Synthetic fibers as a whole represent approximately 65 percent of the global textile fiber input volume.2 It’s imperative to focus on making the materials that are most widely utilized the best we can for the environment.This is how we can collectively have the most positive impact on the environment and the people who inhabit it. There are solutions now — that are at scale — that can offer lower environmental impact materials. Eliminating materials is not a sustainable solution — materials are fundamental to our very lives — from apparel to homes to our cars,in industrial applications and much more. Rather,utilizing solutions available today will help us all mutually invest in the technology we need for solutions for the future.
TW : You have always given your time and talents in support of the SYFA.During your tenure as president,what would
you like to see SYFA accomplish/support/ focus on?
Boyd: We will emphasize and promote the importance of the industry particularly in the United States and regionally.As an industry,we have tremendous capabilities at all points of production that need to be leveraged across all markets.Ensuring that our membership,and those outside of it,know the manufacturing powerhouse that is here is critical to our mission.Additionally,we have always emphasized the technical nature of our conferences.We want to be a destination for emphasizing innovation and information sharing for the betterment of the industry. We also have to grow our membership.Increasing exposure to new companies and colleagues within new and existing member companies,is critical for the organization but also for the industry.It is important that young people — as well as those more seasoned! — feel a core connection to the industry.
TW : How do you view the role of SYFA, and what does the organization mean to the U.S.textile industry?
Boyd: SYFA is a common thread amongst key manufacturers through the value chain. We link together fabric and fiber producers, chemical manufacturers, technology providers and more.Giving awareness to our membership,and
UNIFI has converted more than 40 million bottles into REPREVE®.
those outside of it,regarding the capabilities of this industry is a key role we need to play.Additionally, we support other key resources in the industry including scholarships for workforce development.
TW : Give a quick value synopsis for a first-time conference attendee.What can they expect to see and learn at an SYFA conference?
Boyd: The conference is focused on offering two key benefits for all attendees — valuable information that is relevant to the industry and companies attending,as well as the opportunity to network beyond one’s own company.We integrate industry and beyond-industry speakers with valuable networking times to ensure that both goals can be met.
TW: For textile industry leaders who step forward to serve in elected positions,there is an added commitment of time and brain power to the duties involved.How will you balance those new
demands with your responsibilities at Unifi?
Boyd: There is never success without a great team.I’m fortunate to be surrounded by mentors and leaders of experience — both in the membership but also on the SYFA board.The directors on the board are all serving in a volunteer function — we are all investing time into providing the support and services of the organization to the industry.We work collectively on activation of key events and execution of the conferences twice yearly.Additionally,we have our SYFA director, Rodney Turner,and tremendous support from Sheree Turner.Their dedication to the membership is a tremendous support.
TW : Anything else you would like to share with TW readers about SYFA and its conferences?
Boyd: We recently introduced new opportunities like our annual golf tournament to support scholarship opportunities at the Textile Technology Center.
In addition,feedback is always valued.We want to hear from our members,as well as those who aren’t yet members regarding how the organization can provide the most value for what every company needs.
TW : Lastly,as the industry focuses on developing and attracting new talent,what picture can you paint for young people about the rewards of a career in textiles and the synthetic fiber industry?
Boyd: I believe the same reasons that drew me to this industry will draw young people in today. This industry is globally engaged and regionally critical.We are an industry of makers — we make products that can protect our armed forces,clothe newborn babies,and line our first cars.The upstream and downstream value chain gives an opportunity for real collaboration and exposure. TW
References:
1Polyester fibers — New Jersey Institute of Technology (njit.edu).
2Global textile fiber market share by type 2022 / Statista.
Mason Myers recently spoke to Textile World about investments in “pre-middle” market businesses and textile companies.
TW Special Report
ason Myers is the founder and CEO of Jackson,Wyo.based Greybull Stewardship,a private equity firm that focuses on investments in the “premiddle”market.Myers defines this market as businesses with less than $5 million in profit.
Myers founded the business in 2010 with the goal of supporting these pre-middle market business owners and entrepreneurs to strengthen and scale their companies.“I’ve been involved in small businesses since my twenties,” Myers noted.“As a former small business owner myself,I see tremendous opportunity in this space to help these high potential businesses become stronger,bigger and better.”
Myers’first business was an early Internet company he founded with a friend. The company eventually merged with another company and obtained $20 million in venture financing before going public.“We were acquiring smaller companies and,in doing so,discovered the abundance of overlooked, solid businesses that are
too small for larger private equity firms,”Myers said. “The traditional venture capital model was not a good fit for their needs.I really love small businesses — I have lived the experiences,challenges and opportunities of these companies.It is so fun to support them because you can see the direct impact you’re having on the customers and employees by improving the businesses and helping them create tremendous value.”
Myers recently shared some insights on his investment strategies and recent textile industry investments with Textile World
TW : What makes a company attractive as an investment? What parameters attract you?
Myers: The most important factor we look for in companies is an attractive business model and the potential to grow and become a solid larger company – whether their business has strong bones. That strong foundation and opportunity for scale are what Greybull is here to support.To us,an attractive business model is
recurring or highly repeating revenue,has attractive margins and a business that can scale without requiring a lot of additional capital for working capital or capital expenditures.
Our team is comprised of many functional experts who came from these types of businesses and have grown their own.They have the firsthand experience to help founders who may have never done something like this before.
For us,it’s about the people.First and foremost, we strive to build relationships with the owners and leaders of these companies, work with them to understand their visions and then collaborate and leverage our expertise to execute on that with their partnership.
TW : What drew you to explore textiles?
Myers: The textiles industry is poised for major growth in the next few years,and we see exciting investment opportunities in the space.Issues of supply chain efficiency,manufacturing,sustainability and technological innovation continue to be top-ofmind for the industry.
The demand for innovation and push for a greener future creates opportunities for unique companies to fill whitespace and offer differentiated solutions.We have identified some small businesses with nuanced capabilities and forward-looking visions that focus on addressing customer needs. We’re keeping an eye on numerous developments in the space as the industry continues to evolve.
Our current investments in the space — Clothes Bin,Green Earth Cleaning and Reclaimed Textiles — have great potential for expansion in the industry. Through our partnerships with these companies,we get to tap into this dynamic market and be a part of the ongoing innovation.
TW : What textile-related investments has Greybull pursued?
Myers: Greybull first entered the textiles space in 2021 with our investment in Clothes Bin,a U.S.-based textile recycling franchisor that helps people conveniently recycle their clothes,shoes and textiles to make it easier to keep these materials out of
noticeable impact in an industry that is evolving to be more green-focused.
With our expertise in textile recycling combined with our functional experts that know how to assist and support businesses of this size,we are the perfect partner for a company in this space that has potential to get to the next level.
TW : When do you enter and when do you exit an investment? What is the strategy to achieve an exit?
landfills.Local franchises place bins at schools and other accessible locations and manage the collection of the items to recycle.
We acquired Green Earth Cleaning in 2022, a company that provides environmentally friendly solvent to dry cleaners around the world.The industry is moving away from petroleum-based solvents because Green Earth works better and is better for the environment.
We acquired Reclaimed Textiles Co.in 2023. Reclaimed Textiles repurposes a range of textile products to give them new life, promote sustainability and help address unique,evolving needs in the industry.
TW : As an investor, how do you see your role?
Myers: I see Greybull’s role as supporting the smaller pre-middle market business owners and founders to help their companies reach their maximum potentials.We have a long history of demonstrated success in this space – we know how to create
value and avoid potential pitfalls.Our goal is to partner with business leaders to fully understand their operations,business practices and strategies to help them further strengthen their businesses and have a greater impact.Aligning with their visions enables us to effectively identify how we can best support and scale their businesses while maintaining their visions and core missions.
We have functional expertise in accounting, finance,strategy,technology,sales,marketing,planning,operations and more so that we can lend and apply our knowledge.Our involvement is also about the emotional investment of empowering owners,so they feel confident to work alongside us and take their businesses to the next level.
TW : How does Greybull’s pre-middle market investment strategy differ from more traditional private equity models,and why is this focus particularly valuable in the textiles and recycling sectors?
Myers: Our pre-middle market investing strategy focuses on smaller,growing businesses where we believe our team’s operational expertise and resources can have the greatest impact and value-add.
We use pre-middle market to mean businesses with revenues of $5 to $50 million and profits of less than $5 million — a segment of the market that is often overlooked and underserviced by traditional private equity.We see enormous value in this space,and there are many companies that fall in this category and do not have any capital focused on supporting them.This is the need that Greybull is stepping in to fill; we partner with these companies and help them grow and scale to the middle market.
For textiles specifically, we see particular opportunity to have a distinct impact.The pre-middle market includes companies that significantly benefit from operational,strategic, and financial guidance. We are able to make a
Myers: We enter when the company matches our investment criteria — revenues of $5 to $25 million, profit under $5 million — and has a proven and high-potential model with a clear opportunity to add value through operational improvements and capital injection.The business must show promising growth prospects with a need for our niche support capabilities.
While private equity investments typically have hold periods of around four years,the Greybull model is built around the idea that longer investments can create greater scale and position businesses to sustain growth in the long term. Our average hold period is approximately eight years, and we have held companies for up to 11 years.We see tremendous value in enabling these businesses to develop practices at a pace that will help them thrive long after our investment ends.An ownership change can be disruptive to the customers and employees,so we prefer a model where we provide stability
over a long time horizon so that the company can focus on creating value in the business.We want to avoid unnecessary disruption wherever possible.
Most often,we will consider an exit when the management recommends that we do so.We do not like to bring arbitrary timelines and constraints to our companies,and we prefer to hold and allow the value creation to compound.We do not have a requirement to exit on any certain timeframe,and so we are motivated to focus on what is best for the business.
TW : With the textile recycling market expected to grow significantly by 2028,how do you see private equity playing a role in driving innovation and expansion in this space?
Myers: For every company,there comes a time when the opportunity is so big or attractive that the company needs additional expertise and capital to achieve its potential.That is where we step in.This is likely to happen more and more in the textile recycling market,and we will be there to support good companies with potential who want a collaborative partner alongside them as they pursue their maximum potential.
Although different from Greybull’s strategy, traditional private equity will also be there for businesses who want help with a quick flip of their company in three to five years.Depending on the company,that strategy can be the right fit.
TW : Can you elaborate on Greybull’s long-term partnership with Clothes Bin?
Myers: To have a sustainable environmental impact,it is important to have strong systems and a sustainable business model.Clothes Bin was an excellent business for both the franchises in the system and the franchisor. We were able to make it even better and help them build the systems to scale the business,which makes the entire system and every franchise stronger.
As Clothes Bin becomes larger,it is easier for the franchises and the company overall to partner with cities and states to have even more environmental impact.These entities want to help keep materials out of landfills and it is easier for them to engage with a larger company like Clothes Bin.In this way,Clothes Bin is able to impact environmental policy and more.
TW : What lessons from your work with Clothes Bin could apply to other growing businesses in the textile space?
Myers: We have experience growing textile businesses of this size and the specific knowledge of textile recycling and other environmentally friendly efforts and industries that can all help a growing good business with potential in this market.
One lesson is to work on the infrastructure of your business before you want to scale.Important factors of that include
accounting,technology and people,all of which enable businesses to handle significant growth and size.You cannot shortcut that process.It has to be done well before you can scale,or you are asking for difficulty down the road.
Another lesson is to be constantly looking to improve efficiency in your systems and processes to make the business model better and more sustainable.This is critical not just for the environment,but also for the long-term growth of the business.
To scale beyond a certain size also requires focus and trade-off decisions.What got your company to one level will not be what gets your company to the next level.In the entrepreneurial phase of developing a business,it is important to consider every opportunity and be constantly on the look-out for the best opportunity.In the scaling phase,it becomes impor-
tant to focus on only a few opportunities in the optimal sequence and focus on internal execution and systems.This is often a different skill than the entrepreneurial phase and achieving this transition through different phases is critical.
TW : What is your opinion of the U.S. textile industry?
Myers: It's a highly fragmented industry between traditional manufacturing and a growing segment of textile recycling organizations that are evolving to adopt more modern and sustainable practices.Consumer preferences are beginning to lean toward more sustainable operations and companies are finding ways to prioritize waste reduction.
We are optimistic on the U.S.textile industry’s continued growth and expansion and anticipate further innovation in the space. TW
Themed “Innovation, Cooperation, and Regulation — Driving Forces of the Textile and Apparel Industry” the ITMF’s recent annual conference was hosted in partnership with the International Apparel Federation (IAF) in Samarkand, Uzbekistan.
By James M. Borneman, Editor In Chief
Approximately 400 delegates from 40 countries gathered in Samarkand, Uzbekistan, for three days of discussions and presentations covering a broad array of textile topics.
textile production to continue a growth trajectory in the industry.
The first day of the conference concluded with a session titled “Audit Fatigue — Progress Made & Way Forward” that addressed the challenges associated with international compliance. Anne Sutanto of Indonesia-based Pan Brothers moderated the panel featuring Janet Mensink, SLCP; Michael Cai, Décor; and Nate Herman, American Apparel and Footwear Association (AAFA).
Day two of “Innovation, Cooperation, and Regulation” opened with a keynote address by Uzbekistan Deputy Prime Minister Jamshid Khodjaev. Khodjaev’s focus was the positive effect of moving past the cotton boycott that Uzbekistan had faced in recent years and embracing Better Work and Better Cotton Initiatives.
TThe Zurich-based International Textile Manufacturers Federation (ITMF) recently held its annual conference in conjunction with The International Apparel Federation (IAF) World Fashion Convention in Samarkand, Uzbekistan.
The three-day event included discussions and presentations covering a broad array of topics affecting the future of the global textile supply chain.
“The conference convened with 400 delegates for three days with 40 presentations by as many industry experts,” noted Dr. Christian Schindler, ITMF director general. “Participants came to Samarkand from 40 countries from around the globe. The general theme of the conference, ‘Innovation, Cooperation & Regulation — Drivers of the Textile & Apparel Industry,’ served as a framework for presentations covering a broad tapestry of important issues facing global textile manufacturing.”
The opening day of sessions took a deep dive into global issues facing cotton and man-made fibers.
The Cotton Fiber session, moderated by Muhammad Anees Khawaja, of Pakistan-based Mahmood Group featured presentations by Uday Gill, Indorama Corp.; Nezihi Aslankeser, Cotton Council International; Rama Janarthanan, Arise; Terry Townsend, Cotton Analytics; and Corin WoodJones, Better Cotton.
The Man-Made session, moderated by Stefan Hutter, of Singaporebased Saentis Textiles featured presentations by Alexei Sinitsa, Wood Mackenzie; Nezihi Aslankeser, Cotton Council International; Jay Sardana, Reliance; and Florian Heubrandner, Lenzing. An interesting take-away was the realization of how far Uzbekistan has come with cotton cultivation and textile manufacturing, as well as the need to develop the man-made fiber component of Uzbek
As a matter of context, the meeting occurred in the Uzbekistan post-cotton-ban-era. This global boycott of Uzbek cotton, a time also known as the Cotton Pledge, was initiated in 2010 by the Cotton Campaign. At the heart of the matter was child labor, a State-Run system of forced labor as well as human rights violations. During the ban, more than 330 companies, including brands like Gap and C&A, pledged not to use Uzbek cotton. Cotton was a significant export for Uzbekistan, and the boycott significantly negatively impacted exports. The boycott lasted 11 years, from 2010 to 2022.
According to sources, following President Shavkat Mirziyoyev's rise to power in 2016, Uzbekistan implemented significant reforms to address forced labor.
With campaigns by The World Bank and International Labor Organization, by 2021 it was determined by
independent monitors that systemic forced labor had been effectively eliminated from the cotton harvest in Uzbekistan. In March 2022, the Cotton Campaign officially ended the boycott, allowing companies to reengage with the Uzbek cotton sector.
Some of the major effects of the reforms were privatization and a transformation in cotton textiles from simply producing raw cotton for export to the domestic creation of higher value textile products.
By 2022, 100 percent of the cotton grown in Uzbekistan was further processed domestically — and the country no longer exported raw cotton. Textile product exports, on the other hand, rose from hundreds of millions of dollars during the ban to $3.2 billion dollars in 2022.
Wages grew within the industry, foreign investors showed interest, and the shift into manufacturing/ processing cotton created new jobs.
Uzbekistan’s focus turned to the 130 newly established private cotton clusters embracing quality control, innovation and establishing inroads throughout the textile value chain.
Embracing the latest technologies as well as practices regarding sustainability and traceability are key elements in rebuilding Uzbekistan’s reputation from its tarnished past. These ideas were center stage in
Deputy Prime Minister Khodjaev’s presentation.
Uzbek Textile & Apparel Industry Association (UZTS) Chairman Mirmukhsin Sultanov, ITMF president K. V. Srinivasan and IAF President Cem Altan welcomed delegates and dignitaries from around the globe to the 2024 event.
Major sessions included presentations regarding:
•Textile & Apparel Industry in Uzbekistan;
•Sustainability & Regulation;
•Digitalization;
•Artificial Intelligence in the Textile Value Chain; and
•Collaboration
The first session titled, “Textile &
Apparel Industry in Uzbekistan” was moderated by Aziz Akhrarov of Uzbekistan-based Samarkand Apparel and featured presentations by Kihak Sung, Youngone; Abu Yousuf, Better Work; Karim Shafei, Gherzi; Muzaffar Razakov, Global Textile; and Mirmukhsin Sultanov, UZTS. This session was a showcase of the host country’s textile transformation and vision for a textile focused future.
The “Sustainability & Regulation” session, moderated by Mustafa Denizer of Turkey-based Diktas, featured presentations by Dirk Vantyghem, EURATEX; Kenichi Tomiyoshi, JTF; Yan Yan, CNTAC; and Steve Lamar, American Apparel and Footwear Association (AAFA). The session drove home the point that there is a burgeoning regulatory environment brewing in Europe; Environmental, Social and Corporate Governance (ESG) compliance continues as a hot button issue globally; and regarding the United States, exporters need to keep an eye on state as well as federal regulations. The THREADS Fashion Protocol also was discussed in the context of creating harmonized regulations.
The “Digitalization” session, moderated by Stefano Festa Marzotto of Italy-based Miles Manifattura, featured presentations by Nate Herman, AAFA; and Christian Lott, DMIx. Herman highlighted the need for the adoption of digital garment labeling, while Lott presented the DMIx SamplR — an intriguing technology that “creates precise digital replicas of flat
physical materials.” Lott also hammered home the need to pay attention to the coming regulations of the Digital Product Passport (DPP), offering a stern warning that those who are not in compliance could find themselves “out-of-business” in Europe.
The “Artificial Intelligence in the Textile Value Chain” session, moderated by Rafael Cervone of Brazilbased ABIT, featured presentations by Thomas Gries, ITA Group; and Povilas Sugintas, Euromonitor.
The final day of the conference opened with a session titled “Collaboration.” Fazlee Shamim Ehsan of Bangladesh-based Fatullah Apparel moderated a panel featuring Felix Poza Peña, Inditex; Akila Fernando, Epic Group; and Femi Akinrebiyo, International Finance Corporation (IFC) — the financial arm of the World Bank.
The speakers highlighted how companies were working together to affect a range of issues from microplastic pollution to climate change and the complexity of the supply chain. IFC’s Akinrebiyo explained that the IFC was less of a bank and more
of a development partner focused on waste reduction opportunities in the textile value chain.
The ITMF Startup Awards honored companies breaking new ground in textiles.
Tae Jin Kang of Seoul National University, Korea, moderated the first panel which featured the following innovations:
•Bylon — scalable, melt-spun fibers without oil or waste developed by Sci-Lume Labs, Oklahoma City, Okla.;
•SYCORE-TEX — materials of topological softgel for ultra-thermal insulation from China-based Sycoretec CAS;
•RE&UP — scalable recycling technologies for high-performance fibers developed by RE&UP Recycling Technologies, the Netherlands; and
•Syre — hyperscale textile-to-textile recycling from Syre Impact, Sweden.
Juan Pares of Spain-based Textil
Santanderina presented the winners of the ITMF Innovation & Sustainability Award 2024, which were:
•High-Technique Fiber Co., China, for low-carbon & sustainable innovation in PET fiber industry;
•HeiQ AeoniQ, Switzerland, for Hyperscaling HeiQ AeoniQ; and
•Samsara Eco, Australia, for Infinite plastic recycling — a solution for end-of-life textiles.
Winners of the ITMF International Cooperation Award 2024 included:
• Next generation cellulosic filaments from hemp — DITF, Germany & RBX Creations, France; and
• Open lab . HKRITA, Hong Kong, China.
Although every presentation deserved to be highlighted, the quality of the work was difficult to present in such an abridged fashion. However, the presentations were catalysts for further discussions, networking, and in-depth analysis.
“The presentations provided the participants with relevant insights thus assisting them to better assess the current and especially the future business environment,” said Dr. Schindler. “It was important to see how regulation will shape the evolution of the textile value chain around the world. Likewise, to see all the innovation presented in the session about the various ITMF Awards Winners 2024 was impressive — recycling, circularity, sustainability are important forces driving innovation and collaboration.”
Muzaffar Razakov, CEO of Uzbekistan-based Global Textile presented “From tradition to innovation — how Uzbekistan is expanding its textile horizons” in the first session — a fitting topic for Global Textile. According to the company, Global Textile has been at the forefront of Uzbekistan’s textile transformation and development of the cotton “cluster” model.
This model integrates the production value chain from cotton field through finished products.
Global Textile is a fully integrated textile company managing the entire production cycle from cotton cultivation to garment manufacturing. Global cultivates 12,960 hectares of cotton fields, primarily in Uzbekistan’s Fer-
gana region, producing 160,000 metric tons of cotton annually.
It spins 47,000 metric tons of yarn, processes 21,000 metric tons of fabric in its knitting facilities, and dyes 10,000 metric tons of fabric each year.
Global also has garment manufacturing capacity that produces 3 million items annually
According to Razakov: “Uzbekistan’s textile industry has seen remarkable growth, driven by reforms aimed at creating a competitive, investor-friendly environment. Global Textile has capitalized on these reforms, adopting value-added production processes that meet international standards and facilitating expansion into new global markets.
“The government’s support through tax incentives, financing programs, and modernization subsidies has allowed companies like Global Textile to embrace cutting-edge technologies, particularly in sustainability, he added. “Our company has benefited from export support and modernization assistance, making us more competitive on the global market.”
Regarding Uzbekistan’s selection as the host for the ITMF IAF Joint Conference Razakov commented, “This is a significant milestone for Uzbekistan, demonstrating that the global textile community once again trusts our industry.
“The conference provides a platform for Uzbekistan to showcase its achievements and potential to an international audience, further
strengthening its role in the global textile landscape.”
“The ITMF & IAF Conference 2024 in Samarkand showcased in an impressive manner how much the Uzbekistan’s cotton, textile and apparel industry was transformed since the start of the reform policy initiated in 2017 by President Mirziyoyev,” Dr. Schindler noted. “A statemonopoly that focused on exporting most of the cotton was transformed to a market-driven private economy that is adding value by producing yarns, fabrics, garments, and home textiles.”
As the event closed, Dr. Schindler acknowledged the extraordinary hospitality that was extended to the conference participants by the host associations, the Uzbek Textile and Apparel Industry Association and the Chamber of Commerce and industry in Uzbekistan.
“In completing a successful ITMF & IAF Conference 2024, the ITMF and IAF have decided to jointly hold their events also in 2025 which will be hosted by the Indonesian Textile and Apparel Industry Association (API) in the city of Yogyakarta from October 23-25, 2025,” Dr. Schindler shared at the end of the conference.
“We are very much looking forward to gathering in Indonesia in October 2025 back-to-back with ITMA+CITME Asia 2025 in Singapore October 28 through 31, 2025.” TW
TECHTEXTIL NORTH AMERICA 2024 REVIEW
TECHTEXTIL NORTH AMERICA 2024 REVIEW
Raleigh, N.C., provided the backdrop for networking and learning at the recent TTNA trade show.
TW Special Report
ticket (See “ Textile World News,” TW , this issue).
Attendee Steve Zawislak Engineering director, Norfab & Amatex, Davlyn Group companies both based in Norristown, Pa., thought Techtextil North America 2024 was a worthwhile endeavor. “Techtextil, over the years, has always been a show to connect on a personal level with current, former, and potential suppliers and customers,” Zawislak reported. “The most recent show in Raleigh lived up to that standard in a big way. Traveling with a sales colleague, we were consumed with meetings, planned and impromptu, for the two days we had scheduled to walk at the show.Many of the meetings were impactful on the success of our business.We plan to make the show an annual event on our calendar. I really enjoy seeing old friends and making new ones amongst the best minds in the textile industry.”
TThe technical textiles industry recently convened in Raleigh for the 2024 edition of Techtextil North America (TTNA). The event, held at the Raleigh Convention Center, was the first tradeshow after the summer lull, and it seemed participants were glad to see old friends, network and make new connections.
The event, organized by Atlantabased Messe Frankfurt Inc., runs in opposite years to the North American flagship Techtextil show held in Atlanta every two years. As such, Raleigh was a smaller show, but just as worthwhile.
“Back in Raleigh after two editions, Techtextil North America 2024 was a great success,” stated Kristy Meade, vice president, Technical Shows, Messe Frankfurt. “We were thrilled to return to the heart of the textile industry, exceeding expectations in exhibitor support and overwhelming visitor satisfaction.Techtextil North
America continues to be the platform for product solutions, industry advancements and networking.”
The show was filled with the buzz of symposium sessions, Tech Talks on the show floor, a student poster program, as well as the bustling exhibit floor. In conjunction with the 125th anniversary of the Raleighbased Wilson College of Textiles at NC State University, the show floor featured the “History of Textiles Museum,” showcase. The exhibits comprised early technology and artifacts through modern innovations and textile creations to illustrate the historical beginnings and possible future inventions.
The “Alphabet Soup Collective” — composed of 11 industry organizations who recently opened discussions as a group to find ways to better serve the industry — also hosted an evening shindig open to all TTNA attendees who bought a
Messe Frankfurt is busy planning the collocated Techtextil North America 2025 and Texprocess Americas 2025 events that will take place in Atlanta May 6-8, 2025, at the Georgia World Congress Center. Exhibitors are booking booth space and in a few short months, visitor registration will begin.
“Techtextil North America 2025 will once again be collocated with Texprocess Americas, the event for Equipment and Technology for the Development, Sourcing, and Production of Sewn Products,” Meade said. “The collocation creates an unmatched opportunity for attendees to experience the full production and sourcing pipeline under one roof. With new features on the show floor, cutting-edge technology on display, forward-thinking education sessions, and a powerhouse lineup of industry experts we are confident and excited to address the current challenges, deliver solutions and set the stage for the future of our industry.” TW
RISE ® 2024 REVIEW
The 14th RISE® conference brought new innovations to light, conferred awards and highlighted student research.
TW Special Report
Arnold Wilkie received the INDA Lifetime Technical Achievement Award (far left) and Matthew Mead, founder and CEO, Hempitecture Inc., with the 2024 RISE Innovation Award (far right).
from a variety of nonwoven, textile and fiber programs — had the opportunity to share their work and engage in attendees about their research.
“An exciting addition to RISE was inclusion of more than 30 posters from students & faculty from multiple leading universities,” O’Sickey said.“RISE is unique in sharing both immediately actionable innovation as well as fundamental enabling research.”
TThe Cary, N.C.-based Association of the Nonwoven Fabrics Industry (INDA) recently held the 14th iteration of its RISE ® Research, Innovation & Science for Engineered Fabrics — conference at a new location on the NC State campus —the James B. Hunt Jr. Library on Centennial Campus, Raleigh, N.C. The two-day event was coorganized by INDA and The Nonwovens Institute (NWI).
RISE focuses on emerging technologies and ideas with the aim of connecting innovations with realworld applications for professionals in the nonwoven/engineered fabrics industry.
Speakers included experienced industry, government and academic personnel. Topics covered sustainability and biobased materials, plastic regulation, circular economy strategies, and process technologies and product design, among other topics.
“Two highlights really stood out at this year’s RISE conference,” said Matt O’Sickey, director of Education & Technical Affairs.“The program brought together presenters that shared varied but surprisingly complementary views on end-of-life con-
siderations for fabrics.They emphasized that there is no ‘silver bullet’ solution for all end-of-life questions and that some combination of mechanical recycling, chemical recycling, advanced recycling, up-cycling, biodegradation and compostability will be necessary to most advantageously address and utilize the endof-life input streams.”
Hempitecture Inc. was the winner of the 2024 RISE Innovation Award for its PlantPanel™ insulation material made using 100-percent biobased and recycled material. INDA also conferred its Lifetime Technical Achievement Award to Arnold Wilkie, president and owner of Hills Inc., Melbourne, Fla. Wilkie has more than 40 patents and applications relating to yarns, fibers, filaments, nonwovens and polymer processing innovations.
Other RISE related events included a golf tournament, tour of The Nonwovens Institute to view the analytical labs and pilot lines, and an evening reception featuring graduate student posters. The students — who came
“While environmental responsibility is frequently highlighted in marketing materials, RISE provided direct access to the scientists and thought leaders — from innovative startups and emerging companies to established Fortune 500 firms — who are driving meaningful change from a technical perspective,” said Rishi Gurnani, director of Software Engineering & Algorithms, Atlanta-based Matmerize; first time RISE attendee and speaker. “The conference offered invaluable learning and networking opportunities. I believe Artificial Intelligence will play a significant role in addressing the ongoing challenges in the nonwovens sector, particularly in advancing sustainable solutions.”
“I was honored to be an invited speaker at the INDA RISE conference,” said Aaron Hall, founder and CEO, Intropic Materials Corp., Oakland, Calif. “At Intropic Materials, we are developing enzyme-based additives enabling plastics and fibers to self-degrade at end of life without producing microplastics — unlocking high performance and more sustainable products. The crowd at RISE was engaged, motivated, and so many wonderful innovations were showcased. It was my first time attending, and I’m excited for continued collaboration with INDA, the Nonwovens Institute, and companies in the space.”
RISE will return to NC State University for the 15th edition of the event October 14-15, 2025. TW
COMPOSITES
The composites industry benefited from three composites-related events that recently took place in the space of four weeks.
By Jim Kaufmann, Contributing Editor
The CAMXshow floor was busy with visitors who came to view the latest the composites industry has to offer.
tance and growth of composites as legitimate structural materials and versatile design elements both in North America and globally.
Perhaps fittingly given its 10th anniversary, the expo kicked off with a forward-thinking keynote speaker, Maurice Conte, a futurist and advisor to several Fortune 500 companies. Conte’s commentary around the “Augmented Age” that we all find ourselves living and doing business in, centered on how the increasing presence of artificial intelligence (AI) in industry feels relevant to the issues, challenges, fears and concerns that many face. Conte made the point that AI is simply another tool in the toolbox created to augment, complement and enhance work that is already being done.
GGiven the continuing growth and expansion of North America’s composites industry it would stand to reason that a bevy of local and international conferences, expos and related industry events would also emerge to provide avenues for interested parties to converge and engage in the related opportunities provided. This fall saw several events staged in quick succession. CAMX, the largest composites trade event in North America led the procession, followed by the IBEX “boat” show, and then the Carbon Fiber Conference, as well as other regional events held the following week.
CAMX, the Composites and Advanced Materials Expo, held this year held in San Diego, Calif., was organized jointly by the American Composites Manufacturers Association (ACMA) and the Society for the
Advancement of Material and Process Engineering (SAMPE). It was an all-encompassing event highlighting virtually all facets of the composites and advanced materials marketplace. Similar in scope to JEC World, which is held annually in Paris (see “A Legitimate Glimpse into the Future of Composites,” T W , May/June 2023) , the markets and applications on display targeted aerospace, marine, wind energy, construction and infrastructure, medical and sports and leisure segments, among other exhibits.
The 2024 event, CAMX’s 10th anniversary, comprised of more than 500 exhibitors and more than 6,300 attendees — an 11-percent increase from 2023’s attendance numbers. Much has happened in the 10 years since the first CAMX in 2014. Since the inaugural event, the composites industry and the CAMX show have not rested on their laurels. Both have continued along a journey of evolution, driven by the continued accep-
That “work already being done” was again demonstrated by the wide array of products and technologies on display along with the technical conference offering a full array of topical presentations and various education sessions held throughout on the CAMX show floor. The diversity of technologies, applications and conversations competing for favor to a wide array of potential customers attending was apparent in most every direction. Campfire Sessions, technical papers and poster presentations were geared to growing one’s knowledge about various industry aspects and developments.
A popular feature of the CAMX show floor, Composites One’s “Closed Mold Alliance Demo Zone” and learning space, once again presented expertly hosted demonstrations of molding techniques and new technologies while showcasing numerous featured products.
Observations and discussions generated while wandering through the show floor included:
•This year’s West Coast location, as in previous West Coast expos, produced a noticeable increase in
attendees from the Silicone Valley technology sector and the West Coast-based aerospace industries that effectively mixed in well with the usual general industries regulars.
•In general, the vibe on the show floor was very positive in regards to the direction, stability and continued growth of the composites industry in North America, however concerns persist which included:
º The pending U.S. election and general uncertainty it brings regardless of any political leanings;
º Influx of low-cost imports that has again risen as the world comes out of the COVID crisis with travel and shipping restrictions easing; and
º Increasing shipping costs and logistics issues both within North America and internationally.
•Sustainability, circularity and recyclability continues to make inroads into the composites industry and its applications in North America and is finally receiving a growing level of the attention that it deserves. Unfortunately, many questions, concerns and technology issues still persist, but encouraging signs abound.
•The competition between thermoplastic and thermoset resin systems also continues to evolve as thermoplastics are finding preference by drafting upon recycling and sustainability’s inroads. In many applications, thermoplastics are viewed as the future because of their increased flexibility, improved processability and greater potential for recyclability over thermosets. According to one knowledgeable composites industry veteran, “Thermosets currently have 70 percent of the market compared to thermoplastics, but the trend is definitely moving quickly in the other direction towards thermoplastics.”
•Processing technologies continue to advance in ongoing efforts to
(clockwise from top): CAMXwrapped up with the Good Day CAMX session in the exhibit hall, featured a conference with more than 130 speakers, and also conferred CAMX Awards across a variety of categories.
reduce the manufacturing costs and efficiencies associated with all aspects of composite part production. Robotics, automated placement technologies, AI augmented systems for not only production but also for product design, advanced chemistries and good old-fashioned creativity are all directly contributing to these efforts.
•Natural fibers and plant-based resin systems are gaining more visibility with improvements in performance and cost, while slowly gaining a toehold in composite applications. Again, these advances are being fueled by the drive for sustainability.
•More and more colleges and universities are developing and promoting their materials engineering and composites programs and platforms, not to mention prototyping and development laboratories to fill the growing needs for materials sciences and composites engineers, which is encouraging to see.
The CAMX website suggests “We Form the Future,” which seems appropriate given the breadth of thoughts that fill one’s brain when exploring all there was to see at this 10th anniversary event. Over the past 10 years, CAMX, like the industry it represents has only continued to grow and evolve. Given the industry and its potential, there doesn’t appear to be an end in sight for the advancements CAMX continues to showcase. It really is all about the journey.
The 2025 iteration of CAMX will be held September 8-11, 2025, in Orlando, Fla., and will undoubtedly provide the opportunity to address any curiosities and perhaps generate a few business opportunities, not to mention getting a further glimpse of the future.
The International Boat Builders’ Exhibition and Conference (IBEX) — held in Tampa, Fla., and organized by the National Marine Manufacturers Association (NMMA) and RAI
Amsterdam — is simply all about boats and the marine industry. Just about any related component of work and leisure watercrafts were in some way represented during the event. IBEX took place this year the week in-between two devastating hurricanes that originated in the Gulf of Mexico and created havoc in various locations across the Southeastern states. Somehow, both storms managed to skirt the Tampa area allowing the show to go on as originally planned to the surprise of many.
The IBEX show floor and education halls sported many components that involve the use of composites. Several of the exhibitors — including Chomarat, Composites One, Metyx, SAERTEX, V2 Composites, Vectorply, Wolff Industries — had to quickly pack up most all or parts of their CAMX booths and ship them to Tampa, only to reassemble them again in the IBEX Composites Pavilion, which was a segment of the show floor devoted to the composites industry. Various other textile products were also represented on
the show floor including Sunbrella’s Marine fabrics line.
Similar to the CAMX show, it is obvious that IBEX has continued to evolve and grow in depth, breadth and content from previous iterations. Every possible item that can be found on or added to a boat was represented at one or more of the display booths and/or boats available throughout the grounds. This included the IBEX Docks conveniently located at the estuary of the Hillsborough River with the Hillsborough Bay, just outside and behind the convention center. Featuring live demos and “test it for yourself” opportunities, the IBEX Docks allowed attendees to see the new technologies in action and on the water.
Also similar to the CAMX show, numerous speakers and learning opportunities flourished throughout. An industry breakfast, the first of several planned networking events, opened the first day. Charlie Cook, a non-partisan political analyst provided an intriguing keynote address regarding the run up to the election.
Time will tell how correct his comments turned out to be. In addition, NMMA President and CEO Frank Hugelmeyer presented a “State of the Industry” address during the breakfast. He outlined trends, sales data and reaching untapped audiences in the recreational boating industry, among other topics.
After the breakfast, the show floor opened and the seminar series began, leaving attendees free to listen, wander and wonder.
As with most events like this, there was a lot of catching up to do by the industry regulars, while the first-time visitors could be seen coveting many of the products on display. The election was again a popular topic, as was the state of the boating industry and how it may be affected by whoever won the assorted local, state and national races. On the bright side, the weather held out throughout the show and all present seemed to remain in good spirits throughout. Next year’s event is scheduled to take place again in Tampa October 7-9, weather permitting, of course.
The three-day Carbon Fiber Conference, held in Charleston, S.C., addressed a variety of carbon fiber/composites related topics, markets, processing technologies and applications. There was an adjacent room for tabletop displays that featured 22 different exhibitors and was available to attendees during breaks and meals.
A scheduling quirk had some of the attendees shuttling in and out of the conference because as luck would have it, two additional composite industry events — the SAMPE Carolinas Chapter’s Material Expo and the Fall Technical Exchange Meeting of The Composites Consortium (TCC) —also were held on the same dates in the same city. This scheduling boon made it easier to be in two places at the same time for attendees.
A pre-conference seminar featured two sessions specifically addressing the supply and demand
of carbon fiber. The first session highlighted the quickly increasing Chinese manufacturing capacity for carbon fiber, while the second focused more on the dynamics of the global carbon fiber market. Attendees found both sessions to be informative, but more than a few came away with increased concerns about a possible future glut of low cost, and presumably lower quality, carbon products entering the marketplace as additional projected capacity begins to come online.
Richard Apps and Joanne Zhang from Counterpoint Market Intelligence kicked off the formal conference sessions with a keynote address focusing on carbon fiber usage in the aerospace industry. Their commentary also provided several interesting contrasts between Boeing and Airbus, by far the biggest players in the aerospace industry. Several in the audience later remarked about the directness of their comments specific to the issues Boeing in particular is facing due to recent quality and labor issues. The speakers also offered that Airbus has recovered faster than Boeing from the industry and travel slowdowns resulting from the COVID pandemic. Two standout comments in particular were that: “Composites usage is not only about reducing weight, it is also directly about optimizing the entire structure’s design” and “Composite structures are currently 40- to 100percent more expensive than metal counterparts, but this delta is partially offset by the fact that a 20-percent reduction in weight translates into 1 to 2 percent in fuel cost savings,” which translates into a rather
large number over the aircraft’s lifetime. Definitely one of the more interesting and informative keynote presentations encountered in years. Additional facts from the 16 conference presentations and panel discussion sessions included the following:
•India and Southeast Asia combined have more than 1.9 billion people with a young and growing population. This results in a trend for labor intense composites manufacturing to be moved to the lower labor cost markets found there.
•Interest in carbon fiber composites only continues to grow. Aerospace markets are the primary driver, though commercial segments also are gaining traction. Carbon fiber composite growth is projected to be five to seven percent, while the carbon fiber market shows a projected growth of seven to 10 percent over the next seven to 10 years.
•A potential oversupply of carbon fiber capacity could push prices down, though this is not expected to be equal across all market segments based on quality, consistency and performance parameters.
•Basalt fiber continues to be presented as an alternative to carbon fiber though issues still persist in finding a consistent quality and reliable sourcing for the raw material inputs and manufacturing of the actual fiber.
•Pressure vessels for hydrogen and compressed natural gas storage remain growing markets for carbon fiber because of its performance characteristics as these
The Carbon Fiber Conference addressed a variety of carbon fiber/composites related topics, markets, processing technologies and applications.
alternative fuel sources realize increased usage. “Hydrogen is not yet ready for mass adoption, but compressed natural gas is,” said one speaker.
•The wind industry is seen as a potential growth market for carbon fiber because of the continued increases in turbine blade size — now approaching 140-meter blade lengths for off-shore applications — requiring carbon fiber’s high strength and stiffness to weight ratios compared to other materials. “There’s just not enough carbon fiber available yet for the wind market,” noted one speaker.
•“The overall trend is that consumers do generally care about sustainability, but ‘sustainability’ still lacks the substance to legitimately move forward.”
•“Cost is still king!” and “Cost remains a big deal!”
The next Carbon Fiber Conference is scheduled for November 4-6, 2025, in Wichita, Kan. and is surely a should attend event for those interested in learning more about the carbon fiber industry and its premier status in the composites world.
Three-plus national events in the span of four weeks can certainly be challenging, not to mention tiring. Fortunately, for exhibitors and attendees alike, the products seen, people met, stories told and lessons learned were ultimately all beneficial to those involved in the composites industry. Most wouldn’t have it any other way. TW
(left to right): SYFAPresident Meredith Boyd; Brian Moore, Unifi’s executive vice president and president of Unifi Manufacturing Inc.; Symtech Owner Per Olofsson; and Aquafil O’Mara President Jason Hickman, participated in an “Industry Leader Panel” during the recent SYFAmeeting, which attracted 96 attendees.
MMeredith Boyd, president of the Synthetic Yarn and Fabric Association (SYFA), gave an impassioned speech to kick off the recent fall conference held at the Sheraton Charlotte Airport Hotel in Charlotte, N.C. She spoke of the industry’s resilience, adaptability and innovation, as well as the pressures and challenges. In addition, Boyd touched on the future opportunities, sustainability, digital transformation and artificial intelligence — all topics that carried over into an “Industry Leader Panel” discussion —among Brian Moore, Unifi, Per Olofsson, Symtech, and Jason Hickman, AquafilO’Mara with Boyd as the moderator — held at the end of the first day of proceedings. The panel also talked about ways to attract talent, an often-discussed topic in the textile industry as the workforce is aging out.
The first day’s presentations began with a “Fiber and Yarn Update” from Consultant Laura Murphy. She was followed by Jenn Hanna, director of Innegra Sales, Quantum Materials LLC, who discussed Innegra, a highperformance lightweight fiber featuring patented micro voids and nano bridges for enhanced performance.
The second day of proceedings included a focus on water-repellent
The conference, under the theme “Innovation: A Catalyst for the Future,” offered a broad range of presentations, as well as a panel discussion all relevant to the synthetic fiber and fabric industry.
TW Special Report
finishes by Jerrod Flanagan, R&D manager, Staple and Nonwovens, Goulston Technologies, who presented “Novel Solutions for Fluorine-Free Water Repellency;” a look at a more sustainable elastane fiber from Lycra Consultant Jean Hegedus who offered a talk on “From Farm to Fiber: Developing Elastane with 70% Renewable Content;” and least, but not least, a presentation by Andrew Fraser with e.dye Americas, who presented the “e.dye Waterless Color System” to attendees.
Conference sponsors included Diamond Sponsor Premier Fibers Inc.; Gold Sponsors Goulston Technologies and Jomar Softcorp International Inc.; Silver Sponsors Pulcra Chemicals LLC and Unifi Inc.; Bronze Sponsor Polyspintex; and
Patron Sponsors Milliken & Company and the Economic Partnership Development of North Carolina.
“The SYFA conference was a solid success,” Boyd said after the event. “Our theme, ‘Innovation: A Catalyst for the Future,’ was felt throughout all of the presentations.The membership offered a great reception to the technical presentations on new materials, the fiber market update, and the panel that highlighted leaders from their industry.The conference left me energized and determined to find even more opportunities to leverage innovation and collaboration to promote our industry and our capabilities among our membership.”
The next edition of the SYFA conference will be held April 10-11, 2025, at the Sheraton Charlotte Airport Hotel. The association also will host its third annual golf outing the day before the conference, on April 9, to raise money for the SYFA Scholarship Fund for Gaston Community College’s textile program. Mark your calendar! TW
Editor’s Note: Also see “Executive Forum: Meredith Boyd: Unifi Leader & SYFA President, TW, this issue” to learn more about Boyd and her role as president of the SYFA, as well as her career at Unifi.
stand and interact with GenAI, leaders can reshape their organizations to maximize the strengths and value of both their human and machine workers.”
BCG’s survey also revealed that engagement with AI in the workplace is increasing. Almost twothirds of leaders report they are beginning to use GenAI tools in their organizations and more than twice as many frontline employees reported using AI tools on a regular basis this year compared to 2023.
For some, the mere idea of Artificial Intelligence (AI) conjures up fears of robots and computers taking over the world in some future dystopian nightmare. This futuristic idea seems less and less far-fetched as generative AI (GenAI) technologies — a subset of AI that creates text, images, videos or other forms of content based on data it has learned —are starting to take off. GenAI often produces output as a response to specific prompts, or requests, given by a user, with ChatGPT one example of such a technology.
But in the shorter term, perhaps the most common fear expressed is a more basic, “Will AI take my job?”
Half of regular AI users think their
job may disappear within the next decade according to a report, “AI at Work: Friend and Foe,” released by the Boston-based Boston Consulting Group. The company’s BCG X Tech Build and Design Division surveyed 13,000 employees in 15 countries and regions about AI use and adoption.
“Our survey exposes the doubleedged nature of GenAI,” said the report’s co-author Sylvain Duranton, a managing director and senior partner at BCG. “Familiarity correlates with both comfort and fear. GenAI is a revolutionary technology, so these opposing reactions should not be surprising. By recognizing the complex ways in which humans under-
Joe Parrish, founder of WinstonSalem, N.C.-based award-winning ad agency The Variable Agency, doesn’t think AI will take jobs. “However, a big qualifier to that is a person with AI experience may take your job,” Parrish conjectured during his presentation “Leveraging AI In Your Business — Apparel or Otherwise,” given at an AI Executive Workshop hosted recently by the Atlanta-based Americas Apparel Producers’ Network (AAPN) for its members. AAPN is a huge proponent of using AI and wants its members to embrace the technology sooner rather than later (See sidebar on page 30)
Parrish views AI as a transformative technology, with the potential to be more impactful than steam power was during the industrial revolution. “If programmers were to stop developing the current AI technologies tomorrow, I predict it could still take a good 10 years to fully realize the capabilities of the existing technology,” he said. “We have tons of capability at our fingertips, but we have a utility problem. Generally, people don’t know how to use AI. But I truly believe there isn’t a problem that AI as it exists today couldn’t help us solve.”
AI technology is evolving rapidly, and to illustrate the rapid pace of change, Parrish introduced ChatGPT’s brand new voice feature to the audience during his presentation.
Because of this rapidly changing technology landscape, Parrish recommends jumping in and using AI now. Start small, and grow with the technology. “The best time to dive into AI was yesterday.” But the good news according to Parrish is that the second-best time to jump in is today. “There will never be a smaller gap between an AI beginner and an AI expert than there is right now,” Parrish added.
AI may be used in a variety of ways in industry, academia and even one’s personal life. Some of the applications include image generation and recognition, language translation and processing, machine learning, computer vision, and decision making — analyzing data to find patterns and offer insights to aid informed decisions —among many, many applications for AI.
Ethan R. Mollick, associate professor at the University of Pennsylvania’s Wharton School, collaborated with a team of social scientists at BCG on an experiment to assess the future of professional work in the age of AI. Mollick shared that when consultants were given 18 different tasks designed as realistic examples of the type of work performed at elite consulting companies, “… consultants
using ChatGPT-4 outperformed those who did not, by a lot,” Mollick said. “On every dimension. Every way we measured performance.” Specifically, consultants using AI completed 12 percent more tasks on average, were 25 percent faster and produced 40 percent higher quality results than consultants not using AI.
As a comparison, steam power increased productivity by approximately 18 to 22 percent. And today, companies spend huge amounts of money on massive software installations to see perhaps a 3 to 4 percent increase in productivity. In studies such as the one from The Wharton School, AI is exceeding these productivity gains. By a lot.
Parrish recommends assuming AI can help whatever the situation. “Try it, and let it prove you wrong,” he said. He notes it can take at least 10 hours to understand what the technology can do and how it can help. “But too many people try using AI a few times, don’t like what they see and give up,” Parrish said. “Use AI as a thought partner. Let AI take on tasks that take you lots of time, sort of like a grad school intern.”
He also suggests taking work tasks that are time consuming and creating a ChatGPT to solve the problem or reduce the time needed for a task.
Two of the biggest AI breakthroughs, according to Parrish, are ChatGPT and Midjourney. “There are other facets to AI, but these are more expensive and more specific,” Parrish said. “Chat GPT and Midjourney are tools everyone can see value in.”
During the AAPN workshop, Parrish talked in-depth about both technologies and how and when to use them, among other AI technology options (See Figure 1).
Different AI technologies have certain strengths, and the ultimate end result may be best generated using multiple GenAI technologies. For example, “ChatGPT 4o is fairly terrible at generating images, but is great for creating prompts to give to Midjourney,” Parrish said. According to Parrish, Midjourney is one of the best AI image generation tools to choose. But a user can utilize ChatGPT to create a prompt for an image, then take that prompt over to Midjourney to obtain a different, better result.
According to Parrish, ChatGPT 01 is very good at math as well as thought and reasoning, and step-bystep problem solving. Claude AI is a great all round Gen AI tool; Complexity is adept for research; and Google’s NotebookLM is great at condensing and summarizing lots of information into study guides, FAQs, timelines or even a podcast you can listen to, among other ideas.
GenAI also is popping up in software that is already commonly used. Gemini is Google’s AI. It may be used to write text or to create images within a Google slides presentation, for example. Microsoft Edge also now includes a button for Copilot — the name for its GenAI technology — in the browser. Save time reading a long article and use Copilot to summarize a story, for example.
Some GenAI technologies are free, or have a free version, while others are paid only or offer additional services with a paid subscription. Most are available with low monthly fees or team/group rates for a company wishing to offer access to all its employees.
Engineering a prompt for GenAI is a skill that needs to be developed. AI is intelligent, but the wrong prompt may not generate the answer that is sought. An individual’s value comes from the ability to write the correct prompt. “No two people will get the same result from AI, because the inputs are not the same,” Parrish said. In addition, the more a person can incorporate expertise from their vertical, the better a prompt will be.
To start, break down any job into a series of smaller tasks. AI cannot write an entire movie, but it can generate ideas for a scene in a movie, for example.
Parrish introduced an analytical method of writing a prompt he defined using the RTEF acronym, which stands for Role, Task, Example and Format. The mnemonic “Robots Teach Everything Funny” is a helpful way to remember these four prompt requirements.
• Role —who. Give AI a role — teacher, engineer or writer, for example.
• Task —what is the problem, what is needed?
• Example — perhaps suggest some examples to consider.
• Format —state the desired output format. For example, “Give me a title for the story and a one paragraph summary.”
Prompts also may simply be conversational in nature. Conversational prompting lets you build expertise by uncovering insights gradually,
adapting questions based on responses. “It’s a longer process that deepens your understanding over time, allowing you to refine your knowledge through each interaction,” Parrish said.
Parrish breaks down Midjourney prompts for images into three levels of Atomic Prompting. The first, or organism level, level is a basic image prompting consisting of an art direction and the subject of your prompt. The second, or molecular level, is a more detailed approach to prompting that includes descriptors like inspiration and shot type for reference. The third, or atomic, prompt is a highly specific prompt to control every aspect of your image from environment to styling. He demonstrated the quality of the images generated as he refined and perfected his Midjourney prompts during the AAPN AI workshop.
If Midjourney isn’t producing what you are looking for, reprocess
the prompt. Parrish showed that Midjourney will produce images that are very different given the same prompt (See Figure 2)
AI is generally viewed as an analytical tool that is not creative. “But it’s not true,” Parrish said. “If AI is not creative, that’s because the user is not giving it the right prompt.” To illustrate this, he noted that the best test is an alternative uses test.
When asked for ideas of things a pencil can do other than its basic function of writing, on the low end, humans can come up with three to five mostly obvious uses. On average humans generate between 5 and 10 ideas, while a few exceptional people specifically trained in divergent thinking may manage to exceed 15 ideas. When asked, AI suggested 100 alternate uses, far surpassing humans in this creative task. “Given the right prompt, AI can be very creative,” Parrish said.
Perhaps this may not appear to be creative in a human sense, however, answering a prompt decisively is AI’s relentless mission.
During the workshop, Parrish spent some time explaining popular AI tools, showing participants ways to exploit the technologies in various aspects of the apparel industry.
You are an experienced fashion designer at an apparel manufacturing company focused on sustainable, high-quality clothing. You’ve been tasked with conceptualizing a new clothing line that embodies versatility and minimal environmental impact, while still appealing to modern consumers’desire for style and adaptability. You could design a line of reversible garments with multiple looks in one piece. Or maybe a modular collection where pieces can be layered or connected for different styles and uses. Describe the concept for the clothing line,including the name and a short description of its unique features and environmental benefits.
— R T E F prompt example for a fashion designer
The Americas Apparel Producers’ Network (AAPN) is an Atlanta-based association serving the apparel industry supply chain “from the dirt to the shirt”. Its member companies are located in North America, the Caribbean, Central and South America, as well as Europe and Asia. AAPN believes sourcing in this hemisphere makes sense — it’s easier, faster, safer and more stable, among other benefits.
AAPN is looking at ways to integrate and use AI in the apparel industry. It wants its members to embrace, implement and use AI to its benefit. To AAPN, it’s not about taking jobs away, but about making them better.
"AI represents a pivotal moment for our membership, many of whom are leaders in the textile and apparel industry,” said Lynsey Jones, executive director, AAPN. “At theAAPN, we view AI as a powerful tool that can provide a competitive edge, helping our members further solidify their leadership positions. Whether it's automating routine tasks to free up time for more
AI can be used to create trend presentations, mood boards and even apparel designs. Parrish created a theoretical apparel collection using a variety of AI tools all the way to photographic-like images of a model wearing the designs (See Figure 3)
Ad agency executive Parrish also demonstrated using AI to develop a new product including brand name, logo, related photographic images, a song generated using Suno or udio AI, and finally a video to showcase just some of the capabilities of GenAI. “AI can create commercials from start to finish and it’s only getting better,” Parrish said.
ChatGPT can handle the mammoth task of analyzing data sets such as shirt sales for the year, for example. Once the data is uploaded, ask
meaningful work or leveraging AI to enhance customer experiences and support data-driven decision-making, the potential is vast. Importantly, we don't see AI as a replacement for people, but as a catalyst for productivity, creating opportunities for members to focus on higher-impact initiatives."
Jones scheduled a call with Joe Parrish and his team after a conversation with an AAPN member who had engaged him to walk their company through the AI revolution. “From my very first conversation with the team, I was captivated,” Jones said. “Their enthusiasm for AI and its practical applications was contagious. Joe made something as complex and daunting as AI feel accessible and approachable.”
AAPN initially brought Parrish in as a speaker at its 2024 pro:Americas Annual Conference. “The entire room was just as impressed and inspired as I had been during that initial call,” Jones noted. The feedback and response prompted AAPN to put together the AI workshop to continue the learning.
ChatGPT questions like “What are the different ways I can analyze this data,” “Let’s do a comprehensive analysis of stock turnover and back orders,” or “I have to prepare a report using this data. Outline the report and create the charts I will need to look great in front of my boss.” AI can examine the numbers and see patterns, trends and outliers quickly and effectively.
It may feel daunting to share large, private data sets with AI technologies, but the data is safe. AI uses the data to learn and analyze, but does not share this information with anyone else.
Bringing a company into the AI era may at first seem daunting. But apply the proverbial “eating the elephant” idea and start with small
“bites” applying AI to small tasks. As a company or an individual, breaking down a collective fear of AI may ease the transition and spark a broader corporate adoption.
Parrish suggests companies can think about the following five things to encourage the adoption of AI:
• Cultivate curiosity —In the age of AI, foster a culture of continuous questioning and exploration. Employees should be encouraged to ask “what if” and “why not,” pushing boundaries and seeking new applications for AI rather than settling for the status quo.
• Reward innovation — Recognize and incentivize employees who propose novel ways to leverage AI, even if not all ideas are implemented. This encourages a culture of forward-thinking and helps the organization stay ahead of AI trends.
• Focus on augmenting, not replacing, humans — Frame AI adoption as a way to enhance human capabilities rather than a threat to jobs. This approach not only eases adoption but also leads to more effective human-AI collaboration, leveraging the strengths of both.
• Prioritize adaptability —AI technologies evolve rapidly. Companies need to build flexibility into their workflows and be ready to pivot quickly. This means valuing employees who can learn and adapt swiftly, and creating systems that can be easily modified as new AI capabilities emerge.
• Value skills that complement, not compete, with AI — Rather than focusing solely on technical skills that AI might replicate, organizations should prize uniquely human abilities like emotional intelligence, creative problem-solving, and ethical decision-making. These skills work in tandem with AI to produce superior outcomes.
Parrish suggest individuals consider the following four things related to AI:
• Value the impact, not work hours —Working hard is important — it offers the experience to learn and become an expert at something. But once a task is learned, the path to scaling impact without scaling work hours is significantly clearer thanks to AI. When deciding what to work on, it’s increasingly important to find the areas that create the most value.
• Assume the skills to solve the problem are present — Consider learning something new from ChatGPT. It may be surprising how AI cuts the time required to learn a new skill down to a fraction, or even a fraction of a fraction, of previous efforts. With the explosion of content online and the accessibility that AI offers, learning a new skill and solving a problem has never been easier.”
• Be resourceful — When resourcefulness is present, AI serves as the ultimate resource. Thanks to AI, the primary limitation to achieving dreams is likely internal. People are launching
software companies without prior coding experience. What accomplishments could AI support?”
• Specialize and dig in deep Expertise is rising in value as AI commoditizes average. By design, AI generates the average of human intelligence on any task. Being a generalist may become easier, leading to an average skill level in everything with minimal effort. This trend will likely apply universally.
“We are entering a new era for GenAI which is less about optimism and curiosity and more about confidence and value realization,” said Vinciane Beauchene, a managing director and partner at BCG and a coauthor of the “AI at Work: Friend and Foe” report. “Adoption has increased, and individuals are starting to see the benefits. Companies are also starting to realize that getting the value out of their investment will require them to think beyond productivity and take a more holistic
and proactive approach to redirect the time saved to the most valuable and joyful activities, to reskill their employees to do so, and to reshape their organizations and operating models as a consequence.”
Some companies in the textile industry are already embracing the use of AI in their day-to-day operations such as World Emblem, an embroidered patch manufacturer based in Fort Lauderdale, Fla. (See “World Emblem: Embracing AI,” TW,this issue) And AAPN hopes many more textile companies will take the leap and at least dabble to get more comfortable with the idea of using AI in their businesses.
And maybe, just maybe, GenAI contributed to this article. TW
Editor’s Note: This feature is based on information presented by Joe Parrish at the Americas Apparel Producers’ Network (AAPN) AI Executive Workshop —“Leveraging AI In Your Business — Apparel or Otherwise.” Parrish is the founder of The Variable Agency in Winston-Salem, N.C.
Mohawk Textiles recently held a ribbon-cutting ceremony for its new greenfield plant.
(images courtesy of Honey &Bee Photography unless otherwise noted)
SSpend five minutes speaking with Dominic Wade, president, Gallatin, Tenn.-based Mohawk Textiles, and you’ll very quickly learn that you are speaking with a driven and relatively fearless individual. He is passionate about his family, the people he works with, investing in the future of textiles and cares deeply about the country he’s served.
After attending Lafayette College where he earned a degree in business economics on an Army ROTC scholarship, Wade was assigned to the 118th Military Police Company Airborne located at Fort Bragg in Fayetteville, N.C. Post 9/11, Wade served two years overseas in the Iraqi Theater supporting anti-terrorism and was responsible for high-value detainees.
After his first deployment from 2002-2003 Wade attended Lehigh University and earned an MBA with a concentration in entrepreneurship.
In January 2006, Wade started at Mohawk Fabric Co., in Amsterdam, N.Y., as general manager and minority owner. And so, the journey began — a journey that forms a compelling
Mohawk Textiles aims to follow in the footsteps of Mohawk Fabric Co. as it begins its journey as a 100-year-old technical textile “start up.”
By James M. Borneman, Editor In Chief
story of a textile business with a long history with Wade’s determined eye on the future.
Mohawk Fabric Co. was founded in 1922 in the Mohawk Valley of Upstate New York. The tricot warp knitter focused on processing yarn with twisting and warping, as well as knitting, in the city of Amsterdam where it still operates today.
Under Wade’s leadership, the company has embarked on an ambitious expansion and Wade has been instrumental in shaping the company’s growth.
Supported by his brother Schuyler Wade and fellow army veteran Blaine Harvey, the team envisioned building a state-of-the-art greenfield facility in Middle Tennessee. After a decade of dreaming, Mohawk Textiles was founded in 2020 in Gallatin, Tenn., as a sister company to the deeply rooted Mohawk Fabric.
The team added the technically gifted Christopher Ripp, who migrated South to bolster Mohawk’s capabilities and drive the Mohawk vision forward.
Today, Mohawk Textiles specializes in knitting and weaving technical textiles with a focus on singlestep twisting, warping, knitting, weaving, braiding and finishing. The new venture marks a significant milestone in Mohawk’s journey of expansion and reflects its commitment to innovation and quality.
Harvey, Ripp, the Wade brothers, and their families now gladly call Sumner County, Middle Tennessee, home. It’s more than just a job. According to Wade, Mohawk Textiles
is a “family first” business for all stakeholders and has constructed a “Bold Facility” in the community. Wade eagerly explained the numerous amenities established for Mohawk team members and their families to enjoy that go above and beyond the traditional workplace.
To Wade it is all a function of the founding business principles that drive the Mohawk forward: “Treat all people the way you want to be treated. Communicate often and truthfully. Produce the highest quality product possible. Operate at a fair and sustainable profit. Innovate products with customer collaboration.” And the most important principle: “Invest in and develop your people.”
“With these guidelines, we manufacture knit and woven technical textile products that support the most important American and global industries,” Wade. “They are core to who we are and how we are.”
Mohawk Textiles’ products are, in Wades words, “critical” to technical applications globally. As a manufacturing center of excellence, Mohawk Textiles focuses on production of high-quality fabrics that meet their customers rigorous demands. “We support all major industries in the USA manufacturing arena — automotive, industrial, medical, aerospace, and military — and are developing soon-to-be-released braided products that focus on recycled, reused, and upcycled waste,” Wade added.
During the opening ceremony for the Mohawk Textiles greenfield facility in the Gallatin Industrial Center, Wade described the experience of committing to a greenfield expansion.
“Four years ago today, we were 100 yards from here for our groundbreaking,” Wade recalled.
“I know some of you were here that day. Going back in time to that day, we were at the height of COVID with new mask protocols, millions of companies hemorrhaging cash by the
day, if they were allowed to operate at all. As I woke up that morning 1,000 miles from home, contemplating the future, and if this was the right time for the Mohawk Textiles expansion to Middle Tennessee, I was scared, nervous, and questioned if I was out of my mind.
“But I had planned, checked it over with everyone that would listen — it was sound in normal times — but these were not normal times. They were challenging times. And I made commitments to team members, banks, and customers, as well as the City of Gallatin.
“So, my family and I drove from New York to the Gallatin Industrial
Center for our groundbreaking,” Wade continued. “My plan was to hide my fears and face the challenges as they came — I was expecting about 10 people I knew, and possibly a few others — but boy, was I wrong! The Southern Hospitality was strong that day, and almost 100 people were present. The grit and grace of Gallatin’s business community was in full force.
“Mayor Brown’s welcoming and inspiring words made all the fear, worry and anxiety disappear in an instant, I knew we had made the right choice — the millions of dollars earmarked and spent for state-ofthe-art equipment, a cutting-edge facility that spoke to anyone who would visit — that focused on the best experience for employees possible, seemed so right.
“And through the chaos of the pandemic, I could see the opportunities that would be there in the future,” Wade said.
Tennessee was one of about six states that were considered for the new Mohawk facility.
“In other states we could have gotten a free building, but Gallatin had the perfect blend of work, play, and quality of life standards — all 30 minutes from downtown Nashville,” Wade said. “The schools and amenities that are in Sumner County are so family friendly and community oriented that it made sense to give it a try. It also was a growing community that our employees could also afford to live.”
While finishing his MBA, Wade wrote a white paper outlining a 10-year plan putting himself in the shoes of the Mohawk Fabric Co. owner. These ideas in the white paper have continued to influence and guide Wade after he earned his diploma. The highlights of the plan were:
•Engage and understand customer needs and why they buy from us and what we can do together to improve;
•Understand the textile manufacturing process and modernize to current standards from the working museum that we were in 2005;
•Build stronger relationships with suppliers and vendors and leverage their knowledge and resources to grow and better the company; and
When asked her thoughts on the matter, Gallatin Mayor Paige Brown noted: “Mohawk has a culture that fits so well in our city and in the state of Tennessee. Mohawk exemplifies the Made in Tennessee spirit, and we are grateful they chose Gallatin. Our philosophy, much like Mohawk’s, is when Gallatin does well by our businesses, our businesses do well and that helps everyone.”
Gallatin Economic Development Agency Executive Director Rosemary Bates shed some light on shared economic goals. “Mohawk represents
•Get to know the employee base and invest in them and provide the resources for them to build a stronger foundation for the future of the company.
In 2014, when Blaine Harvey and Schuyler Wade joined the company, together they worked on another 10-year plan, which formed the basis for Mohawk Textiles.
the type of manufacturing we envisioned several years ago in our strategic planning — high tech and visionary with an emphasis on taking care of their employees,” she said.
“My predecessor, James Fenton, deserves much of the credit for forging an initial relationship with Mohawk, visiting them in New York to better understand their operations and, of course, to share how Gallatin would like to be a second home for them. When James walked around the shop there with Dominic, he noticed that Dominic knew every employee by name and usually something about their families. That is the type of employer we embrace in Gallatin.
“Mohawk’s facility here is a neighbor to Beretta USA, a meta hyperscale data center, and Axem, which is a company that pursues advanced technology like Mohawk does. Gallatin is also home to Gap Inc.’s Southeast distribution center — also focused on advancing technology.
“Dominic and Mohawk think in big ideas, creative ideas and innovation. They speak our language. The Gallatin Economic Development Agency, Tennessee’s Department of Economic and Community Development, along with TVA — our regional power provider and partner in economic development — also pursue innovation, collaboration, and ingenuity to create a better environment for manufacturing, research and development.”
Tennessee State Representative William Slater (Rep.-Gallatin) offered his thoughts on the selection and commitment by Mohawk to Gallatin. “I am extremely proud that a timetested business-like Mohawk has expanded to Gallatin,” Slater said. “Our skilled workforce and booming economy have helped many compa-
(Below left): Robert Norris demonstrates the Ratti R325 NF twisting machine. (Below right): Director of Operations, Blaine L. Harvey, U.S. Army retired, discusses a Karl Mayer HKS-2-M with EL Drive during the grand opening.
nies flourish, and I’m confident Mohawk will similarly thrive here.
“Working with Dominic has been a pleasure, and I appreciate his forward-thinking approach and dedication to innovation and precision.
“Tennessee’s business-friendly environment has proven once again to be a powerful draw for top-tier companies, and I’m grateful that Dominic decided to invest in our community,” said Slater, who spoke at the grand opening celebration and was joined by suppliers that were key to executing Wade’s plan for the new plant.
Of course, when setting up a new manufacturing plant, machinery and technology companies play a key role in providing guidance. “Mohawk comes across as a very modern-led organization that not only talks about being customer-centric and employee-friendly but actually is so to its core,” said Per Olofsson, CEO of Spartanburg, S.C.-based Symtech Inc., a distributor of textile machinery and equipment in the United States and Canada. “Mohawk is very open to customers’ requirements and finds ways to deliver them,” he said. “With the new facility, a very skilled and motivated team and investments in world-class technology, Mohawk is a force to be reckoned with.
“At SYMTECH, we are convinced that Dominic and his team are just at the beginning of their growth journey, and we are excited to do as much as we can to support them.”
Greensboro, N.C.-based textile machinery manufacturer KARL MAYER North America president Mariano Amezcua echoed Olofsson’s sentiments. “Dominic Wade and the Mohawk team have established the new standard for textile mills in North America in collaboration with Karl Mayer,” Amezcua said. “Through the years, Mohawk has steadily moved towards making that vision a reality. Mohawk remains at the forefront of Karl Mayer technology by continually
During plant tours at the grand opening, Director of Operations Blaine Harvey presented the Karl Mayer Direct Warper and Weaving technician Julia Whitaker shared details on a Picanol OptiMax-i weaving machine.
investing in the latest cloud-connected warp knitting machines. Mohawk is firmly recognized as a sustainable and innovative leader through ensuring a warp knit infrastructure prepared for the market demands of today and the future demands of tomorrow.”
Tom Johnston, sales manager, Greenville S.C.-based weaving machinery manufacturer Picanol of America, offered some insight into Mohawks commitment to innovation. “I was impressed from the first time that I met Dominic in June 2019,” Johnston said. “The vision he has of building a company with total employee involvement and family values is part of the reason for the company’s success. Dominic is not afraid of change. He and his team are willing to work outside of the box of his current product line. This is why he and his company are a success.
On the challenges of investing Johnston offered: “Not only did Dominic invest in a greenfield plant, but as he grows, he continues to invest back into the company. Dominic has made multiple weaving investments with Picanol and has the
state-of-the-art weaving machines with the capability of producing fabrics for many different segments.”
Mohawk Textiles aims to follow in the footsteps of Mohawk Fabric Co. as it begins its journey as a 100-yearold start-up. At the opening celebration, Wade punctuated his remarks, saying: “I believe conducting business better is the only path to ensure our success in the future. That future is founded in taking care of Mohawk’s team members while also supporting their families. I’m honored to have this opportunity to share with you, my fellow business partners, and leaders, that there is a better way to treat people in the workplace compared to that of the past.”
Wade follows the motto “lead by example, join an amazing community, add more than we take.”
“I followed this path and as a result we are here together, celebrating the hard work of the Mohawk Team — North and South, and all our partners,” Wade said. “I am grateful to have this opportunity showcase our version of the future workplace that prioritizes its people, community, and business relationships.” TW
Reju™CEO Patrik Frisk spoke with Textile World about the company’s new Regeneration Hub Zero and the drive to make meaningful progress towards circular polyester.
TW Special Report
CCircularity in textiles — reusing materials instead of turning them into waste — is possible and getting closer. Innovative companies are developing methods to recycle various types of textile waste,keeping clothing out of the landfill and reducing the reliance on virgin polymers.
Reju™ is a new company entering the circular conversation.This Parisbased start-up intends to offer a circular recycled polyester (rPET) chip that can be recycled an infinite number of times.Reju also is expected to have a 50-percent lower carbon footprint than virgin polyester confirmed via a life cycle assessment conducted by Deloitte.
“What has been holding the world back in textile circularity is not a lack of demand for textile recycling, but the lack of a solution that makes recycling of textiles economical on an industrial scale,”said Arnaud Pieton,CEO of
Technip Energies,the France-based parent company of Reju.
Reju,led by CEO Patrik Frisk and COO Alan Poincheval,is capitalizing on a glycolysis polyester recycling technology named VolCat that was originally co-developed in a collaborative venture among partners IBM,Under Armour and Technip Energies, although Under Armour is no longer involved.Reju broke ground on its demonstration plant located in Frankfurt,Germany,in the fall of 2023.The facility, known as Regeneration Hub Zero,recently opened, and it is expected to begin delivering polyester chip in 2025.There also are plans for additional hubs in the United States and Europe.
“We’re starting with the most urgent problem in textile waste — polyester,” Frisk said in a press release about the launch of Reju. “The world produces 92 million tons of textile waste each year,yet less than 1 percent is recycled.It is
a system that extracts finite resources creating textile waste with no responsibility for end-of-life.Reju is going to change that by unlocking a new system through critical partnerships around the world. We will build infrastructure, scale technology,comply with regulation and,in the end,help the textile industry evolve and enable a change in behavior.Our Regeneration Hub Zero in Frankfurt is a significant milestone,showcasing how this advanced technology addresses the global textile waste problem.”
Textile World recently had the opportunity to speak with Reju CEO Frisk to learn more about the company.Frisk is a Swedish-American textile industry veteran who began his career in the industry with W.L.Gore & Associates as a fabric salesman.His career path took him through the doors of storied companies and brands including VF Corp.,The North Face,
Timberland,Aldo and Under Armour in the United States as well as in Europe.Frisk first became involved with VolCat during his time at Under Armour,so it was a natural progression for him to take the job as CEO of Reju.
TW : What’s the biggest misconception about polyester fiber and apparel that you would like to address?
Frisk: One question often asked is why don't we just stop using polyester and switch to more natural materials or something else? Unfortunately,that’s currently not possible.Polyester is a useful material for the textile industry,carpet industry, automotive and airline industries,bedding, packaging,and others. We can’t live without it for the foreseeable future.At the same time,polyester is the biggest contributor to global textile waste — only 15 percent of the polyester we make is even recycled,
So,we need to understand how to live with it in a much smarter way,which is why we’re breaking it down and regenerating it. We’re finding new ways to use the resources we have.
TW : How does IBM’s VolCat technology play a pivotal role in Reju? How does the company’s process differ from that of other companies working to recycle polyester?
Frisk: Reju’s proprietary technology,which originated with IBM research,is the key to unlocking the circular textile system we are building.Reju is developing the infrastructure to take textile waste and regenerate it at scale, starting with polyester. The technology is the key to making this a reality.
Our work is focused on solving one of the largest societal problems of the future which is textile waste.Our approach and technology are different in that we are able to handle and are focused on mixed post-consumer waste and the extraction of polyester from this waste,something
our technology is uniquely able to do.
TW : What are the biggest challenges facing Reju as the company scales up its recycling efforts,and how is Reju preparing to address any challenges?
Frisk: Our biggest challenge is that the new system to enable circularity does not exist,so we need to help build this out while we continue to build our own part of this new economy and system. We have been working to identify how the entire new system and its infrastructure needs to come together to ensure a steady feed stream for our regeneration hubs.It requires specialized knowledge in waste management and reverse logistics in combination with an understanding of textile fiber composition and chemistry. At Reju,this is part of our unique approach and talent of our organization.
TW : How does Reju contribute to the circular economy,and what steps are being taken to close the loop on polyester recycling?
Frisk: Reju is working to close the loop between upstream feedstock partners and downstream brand offtake partners by regenerating the collected materials. The industry has been on a linear model for decades and it will take a lot of work to make
it circular,but we are optimistic that it can be done.
TW : Reju is promoting an open supply chain with 100-percent traceability. What technologies will be employed to ensure the process is traceable?
Frisk: We are working with our partner IBM to create a traceability platform that will support our Reju guarantee of textile-to-textile regenerated polyester, where we never lose chain of custody from textile waste to regenerated polyester.
TW : What are your main priorities for the company in the coming year? How do you see the role of advanced technology such as Reju’s in transforming the polyester apparel recycling industry over the next 10 years?
Frisk: We recently announced the opening of our first operating unit — Regeneration Hub Zero — in Frankfurt,Germany.This is Reju’s first major milestone after being incorporated just 12 months ago in Paris,France.The Hub was built in record time and is expected to begin deliveries in 2025.We have plans to build more Regeneration Hubs in other markets, including in the United States.It’s going to take the entire polyester ecosystem working together to solve the problems created.And we know this is going to take time to build the circular system — we’re talking about a generational change — but it doesn’t mean we shouldn’t start.
TW : How important is collaboration between recycling technology providers and the collective textile industry in order to have the biggest global impact?
Frisk: The massive size and global nature of the problem we’re trying to solve makes it impossible for any single organization to make meaningful progress on its own.Our goal is to create an industry where textiles aren’t wasted,but recirculated. Partnerships are critical to ensuring we can accomplish this at scale and that we can drive global awareness and adoption.
TW : What excites you the most about the work being done at Reju?
Frisk: At Reju,we have a wide variety of expertise, but there's one thing we have in common — we're all radical pragmatists.We’re staying grounded in reality, dealing in facts and the truth — even when it’s hard to swallow — and we’re working across engineering, technology,and textiles to solve one of the hardest problems of our time. TW
Editor’s Note:Since the interview with Frisk,Reju has announced plans for a multi-year initiative with Goodwill ® and WM ® to advance textile recycling in North America.The plan includes a collaborative model for regional textile collection, sorting,reuse and recycling with the goal of diverting nonwearable textiles from the waste stream.
Germany-based Trützschler Nonwovens and Italy-based Texnology S.r.l. are partnering to provide a complete needlepunching and thermobonding line to Peruzzo Productions Group company O.R.V. Manufacturing S.p.A., Italy. The production line will be used to manufacture filter media, among other products.
O.R.V. selected the machinery after customer trials conducted at Trützschler’s Nonwoven Customer Testing Center in Germany. “With Trützschler Nonwovens and Texnology, we are pleased to have found two partners with whom we can realize this major project based on the shared values of a familyowned business,” said O.R.V. Manufacturing CEO Gabriele Zanella.
“We strive to set new industry standards while implementing environmentally conscious solutions,” added Nicola Olivo, co-owner, Texnology. “Together, we leverage the unique strengths of each company and transform these values into high-quality products.”
DILO Group, Germany, was bestowed with a 2024 Innovation Award for its MicroPunch nonwoven needling development during the CINTE Techtextil China trade fair held recently in Shanghai. Winners are selected based on the “calibre and contribution potential of their products,” according to event organizer Messe Frankfurt (HK) Ltd.
Dilo’s new MicroPunch intensive needling technology allows a wide variety of lightweight nonwoven fabrics to be produced using only a mechanical process incorporating a needle board containing approximately 45,000 needles per meter per board. According to Dilo, the tech-
nology produces a nonwoven with properties similar to those of hydroentangled nonwovens using up to 75-percent less energy compared to other bonding technologies.
The Association of the Nonwoven Fabrics Industry (INDA), Cary, N.C., recently signed a letter of intent (LOI) with Brussels-based EDANA, the Voice of Nonwovens, to explore a strategic alliance and leverage the combined resources and expertise of the two organizations. The hope is the alliance will enhance scope and value to members, offer joint advocacy and representation, bring operational synergies, and enhance innovation and growth. INDA and EDANA are in a due diligence phase to evaluate the prospect.
“This potential alliance represents an opportunity to combine our strengths while openly engaging on the global issues affecting the industry,” said INDA President and CEO Tony Fragnito. “Better coordination will enhance our ability to serve the industry and our members while retaining our regionally focused support and representation.”
Nonwovens manufacturer Shalag U.S. Inc., Oxford, N.C., and parent company Israel-based Shalag Industries Ltd. have announced plans to invest $16.6 million for a new production facility in South Hill, Va. The plant will create 52 jobs. Shalag specializes in through-air bonded and carded thermobonded nonwovens that are used in diapers, feminine hygiene products, air filtration and wipes products, among other applications.
“Shalag US Inc., and ownership are looking forward to adding a nonwovens line in South Hill, Virginia,” said CEO
Germany-based Freudenberg Performance Materials (FPM) recently acquired the core business of the Germany-based Heytex Group including three production locations, as well as headquarters-related functions including sales and research and development. The assets, purchased from private equity investor Bencis Capital Partners, employ 400 associates and generated approximately $100 million euros in 2023.
“The acquisition of major parts belonging to the Heytex Group complements our business in coated technical textiles ideally: we are expanding our technology platform, our market exposure and R&D capabilities,” said Dr. Andreas Raps. “… At the same time, we are gaining access to new, attractive product segments and strengthening our capabilities in the field of coated technical textiles.”
In related news, Bondcote® engineered fabrics producer HeyTex USA Inc., Pulaski, Va., was purchased by XFS Global LLC, a service-disabled, veteranowned fabric shelters and support technologies company. HeyTex USA has been renamed BondCote Performance Textiles LLC and will continue to operate as a separate company under the leadership of XFS Global.
and general manager Rodney Clayton. “When our new line is complete and running at anticipated levels, it will increase our overall production capacity in the U.S. by 25 percent. Some factors in the purchase of the South Hill location are the strategic location, the company’s objective to reach more customers, and the ability to diversify its portfolio.” TW
Textiles used in the medical industry are subject to rigorous testing and regulation.
Success in global medical textile markets requires an understanding of global regulatory standards and testing protocols.
By Dr. Timo Hammer
AAround the world, millions of people a day receive medical care in hospitals and clinics. Most take for granted that the bandages, gowns and other materials they encounter are safe. But what are the criteria that govern those standards?
Advancements in technology and a burgeoning demand for specialized textile applications continues to drive exponential growth in the medical textile industry. From wound care to surgical garments to filtration systems in medical devices such as ventilators, the scope of medical textiles reaches every corner of the healthcare industry. As these products become increasingly vital in hospital and healthcare settings, manufacturers must navigate the complex landscape of global regulations and testing protocols to ensure safety and efficacy.
Medical textiles encompass a wide range of products designed for specific health-related uses. These can be broadly categorized into two types: disposable items, which are often uti-
lized in hospital settings; and reusable items, such as surgical clothing and medical compression stockings.
Disposable products are typically designed for single use, promoting sanitation and reducing the risk of infection. Common examples include surgical drapes and sterile wound dressings. These items are used in operating rooms and during patient care procedures, where hygiene is paramount. The materials used in these textiles must meet stringent regulatory requirements, ensuring they are safe for immediate contact with patients.
In the other category, reusable items like surgical clothing and compression stockings are engineered for repeated use, requiring longevity and comfort as well as rigorous cleaning and sterilization processes. Surgical gowns, for instance, are designed to withstand repeated laundering while maintaining their protective qualities. Medical compression stockings are designed to provide consistent pressure, improving circulation in patients with various medical conditions. The durability and efficacy of
these products are essential for their continued use in healthcare settings.
The application of textiles in medical settings extends beyond garments — they also play a critical role in filtration systems used in ventilators, blood purification devices and sanitation equipment. Such innovations highlight the transformative power of textiles in enhancing patient care and operational efficiency in healthcare facilities.
One of the most significant challenges facing medical textile manufacturers centers around the varying regulatory frameworks in the United States and the European Union. While the outcomes are similar, the differing classifications for medical devices can complicate the introduction of products to different markets.
In the European Union, medical devices are classified under the Medical Device Regulation (MDR) 2017/745. This regulation categorizes devices into four classes — Class I,
Class IIa, Class IIb, and Class III — based on the level of risk they pose to patients and operators.
•Class I includes low-risk devices, which are non-invasive and may be sterile or reusable, such as wound dressings and thermometers.
•Class IIa comprises medium-risk devices like catheters, surgical clamps and hearing aids.
•Class IIb devices represent middle-to-high risks found in defibrillators and lasers.
•Class III devices are considered high-risk and require extensive evaluation, including heart valves and joint implants.
For Class I devices, manufacturers can self-declare compliance using the CE marking process, allowing for a streamlined market entry. A CE marking, or “Conformite Europeenne” label, shows that a product meets safety, health and environmental standards set forth by the EU, and is a requirement for many products sold in the European Union.
Class II and higher necessitate verification by a notified body. However, all classes involve assessment and documentation, including the preparation of a Technical File.
The U.S. Food and Drug Administration (FDA) employs a similar riskbased classification system for medical devices. For Class I exempt devices, there is no requirement for independent audits before market release, allowing manufacturers to proceed with a self-declaration process. Most devices require manufacturers to submit a 510(k) premarket notification to demonstrate substantial equivalence to a legally marketed device by providing clinical data and other relevant information. Medical devices that are critical (typically Class III) and for which there are no comparator products require a more rigorous premarket approval process (PMA), demanding extensive clinical trial data to establish safety and efficacy.
These regulatory differences highlight the challenges and complexities manufacturers face in ensuring compliance and achieving market access for medical textiles across both regions.
“It can be tricky for medical device manufacturers seeking to participate in multiple markets,” said Ben Mead, managing director at Hohenstein Institute America, Ligonier, Ind. “Learning the differences early on can save time and money.”
Biocompatibility is a key consideration in the development and marketing of medical textiles, as it determines how materials interact with the human body. Testing typically involves both in vitro —testtube or culture dish — and in vivo — animal or human — studies, depending on the potential risk associated with the textile.
The ISO Standard 10993-1 outlines the necessary evaluations for biocompatibility, focusing on factors such as the type of body contact and the duration of exposure.
Three biological endpoints are standard for biocompatibility assessments in nearly all medical devices:
• Cytotoxicity : Evaluates the potential of a material to cause cell damage. The in vitro test uses liv-
ing cells to detect damaging substances (cytotoxins) from a sample, measuring the material hazard potential at the cellular level.
• Irritation : Assesses whether a material induces a localized inflammatory response. This in vitro test utilizes 3D human skin models, which are composed of different cellular layers that mimic human epidermis. Measuring irritation specific to mucosal damage to the eyes, nose and lungs still requires testing on animals. In vitro alternatives are under development.
• Sensitization: Determines whether exposure to a material can lead to allergic reactions. There are several types of testing for sensitization, as sequential events lead to a skin sensitizing effect in humans. Although the regulations still require animal testing, the international trend is toward the use and further development of meaningful animal-free methods. In the US, the FDA mandates specific regulations and standards related to biocompatibility testing, that align with the EU’s required standard, ISO 10993. However, it does not fully recognize all ISO 10993 standards, and manufacturers must provide biocompatibility data with their regulatory submissions for FDA clearance or approval.
A notable challenge in biocompatibility testing arises from the textile supply chain. Manufacturers often lack detailed information about the materials used, complicating the assessment of compatibility. It is prudent to conduct biocompatibility evaluation early in the development process, allowing manufacturers to identify suitable materials before finalizing the product. Additional testing can be done for evaluation on the finished textile device —as well as the packaging for sterile items — to meet ISO 10993-18, the chemical characterization. Failure to adequately assess biocompatibility can lead to adverse patient outcomes and regulatory repercussions.
“Biocompatibility testing can be useful not only to meet regulations, but to protect consumers and reduce litigation risk,” Mead continued. “It is the safest way to prove compliance.”
Eliminating microbes and germs is critical to ensuring patient safety and preventing healthcare-associated infections. Both the European Union and the United States have established regulations and guidelines that address the cleanliness and disinfection of medical products, though their approaches and specifics vary.
The MDR emphasizes the importance of biocompatibility and microbial limits, necessitating compliance with standards such as EN ISO 13485, which outlines quality management systems for medical devices. Reprocessing and disinfection protocols are guided by the European Committee for Standardization (CEN) in standards like EN ISO 17664 and EN 14885. EN 13795, which specifies the requirements for the performance of surgical drapes and gowns in terms of cleanliness and microbial barrier properties, focuses on the product performance regarding its application. Likewise, DIN SPEC 13257 specifies requirements for singleuse foot bandages and defines corresponding test procedures.
The FDA regulates medical textiles under a similar framework, but the focus on cleanliness and disinfection is articulated through the Quality System Regulation (QSR) and specific guidance documents. The QSR mandates that manufacturers establish and maintain procedures for ensuring the cleanliness of products throughout their lifecycle, including stringent requirements for cleaning, disinfection and sterilization processes. The FDA also references standards from organizations like the Association for the Advancement of Medical Instrumentation (AAMI), which provides guidelines for the cleaning and disinfection of reusable medical devices.
Manufacturers are responsible for validating cleaning processes, and they must provide detailed information regarding the recommended cleaning and sterilization methods on product labels. Various types of testing, including measurement of biological residues left behind after washing and porousness of packaging, can help manufacturers verify claims and meet the requirements for both regions.
As the demand for medical textiles continues to grow, manufacturers must remain vigilant and adaptable.
Understanding the intricacies of the regulatory frameworks in the European Union and the United States is essential for successful market entry and product acceptance.
While it can seem overwhelming, a proactive approach to biocompatibility and microbial testing can help guide product development and innovation and enhance product safety and efficacy. Many medical device manufacturers partner with a testing laboratory already familiar with the labyrinth of global regulations, developing a plan specific to their needs and budget.
“Meeting global testing requirements can be daunting, but there are ways to optimize the process,” coun-
sels Jaime Griggs, Brand Partnership director at Hohenstein. “Not every medical device or textile needs the same approach.”
The evolving landscape of medical technology continues to bring better, faster solutions for improving patient care. Manufacturers seeking to succeed in global markets must take a big-picture view that includes adhering to multiple standards — not only to ensure that medical textiles meet regulatory standards but also to fulfill their intended purpose: To keep people safe in a vulnerable setting. TW
Editor’s Note: Dr. Timo Hammer is the CEO of Life Science & Care at Hohenstein Laboratories, a Germanybased global textile testing laboratory that serves brands and manufacturers. He holds a Ph.D. from the University of Stuttgart-Hohenheim and advanced his knowledge of the medical device industry as Product manager and Medical Marketing manager at Germany-based Xenios AG.
TTechnology Readiness Level (TRL) is a measurement system developed by the National Aeronautics and Space Administration (NASA) in the 1970s to manage the process of translating fundamental knowledge into technology ready for deployment. In NASA’s case, the goal was to use TRL to enable the development of “flight-proven” technology ready to stand up to the challenges of space travel. TRL has also been employed by industry to evaluate the maturity of a technology or invention as it progresses along the tortuous path toward commercialization.
A comprehensive description of TRL is one recently articulated by the U.S. Department of Energy (See Figure 1).
The Nonwovens Institute (NWI), based on the Centennial Campus of North Carolina State University in Raleigh, N.C., has leveraged the TRL system to shape its pillar service offerings with the aim of providing value to the entire nonwovens industry value chain.
While university-based programs have historically focused on basic research problems (TRL 1-2), NWI is unique in that it focuses on the full TRL range (TRL 1-9), facilitating col-
The Nonwovens Institute’s success is driven by creating measurable goals in-line with a long-term vision.
TW Special Report
laboration among industry, government, and academia to enable the development of next-generation nonwoven solutions to mission-critical challenges.
NWI is the world’s first accredited academic program for the interdisciplinary study of engineered fabrics. NWI works with experts from industry, government, and academia to facilitate experimental trials and engage in problem-solving for nonwovens-relevant applications, while also providing hands-on training and guidance to the field’s future leaders and industry professionals.
NWI traces its history back to 1991 when the Nonwovens Cooperative Research Center (NCRC) was established at NC State University as a State/Industry-University Coopera-
tive Research Center (IUCRC) with matching grants from the National Science Foundation (NSF), the State of North Carolina, and several industry partners. NCRC was one of the first five State/IUCRC’s funded by NSF, which would contribute more than $2 million over nine years to the Institute.
In 1999, NCRC graduated from NSF and became self-sustaining. NCRC transitioned into The Nonwovens Institute in 2007, establishing the Institute as a university-wide activity that touches at least three colleges and more than seven departments. NWI continued to grow its capability to collaborate with industry and government research agencies to deliver relevant results. NWI’s success is the product of its diligent attention to understanding the needs of the industry and developing the five pillars of NWI’s capability to meet those needs. NWI’s pillar focus areas range from fundamental, precompetitive research through to technology commercialization.
Pillar 1 : Knowledge Creation — NWI views education, research, and outreach as critical components of its
mission. Pre-competitive research conducted as part of NWI’s Knowledge Creation pillar initiative falls in the TRL 1-3 categories and is often described as “core projects.” These research activities engage the Institute’s network of faculty and students and are a means by which NWI trains the future leaders of the nonwovens and affiliated industries. Graduate students who participate in the NWI research program are equipped with the knowledge required to succeed in the corporate environment, while the results of NWI research projects enable NWI member companies to innovate by finding solutions to grand challenges in nonwovens-relevant subject matter areas.
Pillar 2 : Knowledge Transfer/ Workforce Development — NWI leverages the insight gained from its Knowledge Creation pillar initiative to inform its extensive array of training content. These training programs are formalized into various course offerings, with regularly scheduled in-person short courses, presented in partnership with INDA, The Association of the Nonwoven Fabrics Industry, custom courses and online training modules available to meet the professional development needs of the industry. NWI’s Workforce Development pillar initiative covers TRL 4-9, with course content ranging from material characterization and testing to product development and commercialization.
Pillar 3 : Fabrication and Testing — NWI has continued to build and update its facilities since 2000, and today has the most extensive set of lab- and large pilot-scale nonwoven production equipment found anywhere in the world. NWI’s Fabrication and Testing pillar initiative (TRL 3-6) plays a key role in the development and transformation of the latest innovations into marketable fiberbased systems ready for shipment to commercial, consumer, and industrial users around the world. NWI’s facilities include lab-scale systems dedicated to polymer characterization, fiber extrusion, and meltblown, with
large pilot facilities for bicomponent spunbond and meltblown, staple fiber, fiber spinning, needlepunching, hydroentangling, thermal bonding, and web composite capability. Analytical and filtration testing facilities offer the ability to analyze and evaluate material performance according to a wide range of industry-specific standard test methods.
Pillar 4 : Problem Solving — NWI’s Problem Solving pillar initiative is rooted in sponsored research that is funded by industry or government agencies. The work performed in this area of NWI’s service offering is confidential to the sponsors and provides an option to license any intellectual property (IP) generated using a standard joint development agreement (JDA).
NWI conducts activities in the Problem Solving area utilizing the stage-gate development process (TRL 4-6) with a focus on bridging sponsors from innovation development to practical demonstration and the reduction of engineering risk — the so-called developmental “valley of death.” Working hand-in-hand with NWI’s in-house production, testing, and product development team — who bring decades of experience in the full range of nonwovens production processes and test methods —
sponsors can elevate exciting new discoveries relevant to nonwovens.
Pillar 5: Product Incubation — In the Product Incubation pillar area, NWI has created a non-profit affiliate entity of NC State University called Leaders in Nonwoven Commercialization (LINC LLC). LINC helps commercialize new products and technologies with manufacturing capability, specializing in small-tomedium scale production runs. In parallel, LINC works with companies to establish long-term supply chains and transfer the technology to support their ongoing operation. In this way, attention is focused on TRL 7-9 — effectively bridging the valley of death and validating market acceptance for new products. LINC adheres to the highest standards of quality under NWI’s Quality Management System.
Aligning with NWI’s plans for growth going forward, the Institute recently announced the appointment of Dr. Raoul Farer to the role of executive deputy director.
Farer, who will also serve as a professor in NC State’s Wilson College of Textiles’ Department of Textile Engi-
neering, Chemistry and Science (TECS), joins the Institute’s leadership team and will work closely with NWI’s Executive Director Dr. Behnam Pourdeyhimi and Operations Director Tom Daugherty to manage the implementation of NWI’s strategic vision.
Farer comes to NWI and NC State following a 24-year career with Freudenberg Performance Materials with various assignments in Germany, Spain and the United States. Farer brings extensive knowledge in textile technologies with a specialization in nonwovens. He earned his Master of Science in Textile Management and Technology in 1996 and a doctorate in Fiber and Polymer Science in 1999 from NC State. Farer also participated in NWI’s fundamental nonwovens research program as a student, studying novel dispersion technologies for wet-laid nonwovens and the formation of 3D meltblown structures via a robotic system.
During his tenure at Freudenberg Performance Materials, Farer also served on NWI’s Industrial Advisory Board (IAB), most recently as chair of its Executive Committee (2022-2024).
“Having worked with Raoul from the time he was a student researcher at NC State and watching him progress in his career with Freudenberg Performance Materials, I am thrilled to have him join us here at NWI,” Pourdeyhimi said. “I look forward to working with Raoul once again and seeing NWI continue to grow with the benefit of his contributions.”
“Returning to my alma mater and NWI is a dream come true,” Farer
said. “After a long career in industry at one of the world’s leading nonwoven manufacturers, I couldn’t be more excited about the opportunity to give back to the students, NWI, the Wilson College of Textiles, and NC State. Nonwovens have been my passion from the moment when I first took an introductory course as an undergraduate student. I feel very fortunate to be able to join the teams at NWI and TECS and look forward to helping our students learn and grow in their journeys toward becoming future researchers and innovators and to further strengthening our industry partnerships to help build the NWI of the future.”
NWI continues to build upon its strong foundation of quality-based manufacturing practices by pursuing the Brand Reputation Compliance Global Standard (BRCGS) Certification for Packaging Materials, which is recognized under the Global Food Safety Initiative (GFSI). NWI is on schedule to complete this certification process in 2024, enabling the Institute to meet the needs of producers of nonwovens for food packaging.
NWI has been following good
manufacturing practices (GMP) requirements since 2019, and its most recent audit resulted in a rating of “Excellent” with a score of 962/1000, according to an independent thirdparty auditor. NWI’s Analytical, Filtration Testing, Spunbond and Hydroentangling, and Meltblown labs are all ISO 9001:2015 accredited.
“Here at NWI we are continuously striving to improve our quality measures,” said Jamie Plummer, lab research specialist. “Over the past several years, we’ve implemented a full suite of standard operating procedures, not only in our labs, but across all our operations. Our goal with BRCGS Packaging Materials Certification is to align our business with GFSI to meet the needs of our current and prospective customers who are serving the food and beverage industry.”
NWI also recently announced its newly expanded Filtration Testing Lab, featuring services for facemasks and respirators, along with filter media for automotive, HEPA, and HVAC applications, among others. Importantly, NWI’s Filtration Testing Lab is outfitted with equipment to perform ASTM F2299 testing for the
measurement of Particle Filtration Efficiency (PFE) at 0.1 microns.
Testing equipment available in NWI’s Filtration Testing Lab includes:
•PALAS MFP-3000-S fractional aerosol filter test;
•Two TSI 8130 machines for filtration efficiency;
•Two TSI 3160 machines for filtration efficiency;
•Two offline charging and discharging units;
•Two environmental chambers for aging and conditioning masks and filter media;
•TSI Portacount respirator fit tester;
•Testex TN 139 synthetic blood tester;
•Testing apparatus for the measurement of fluid resistance for surgical masks; and
•Prototyping facility to produce masks per NIOSH Standard Test Protocol.
NWI’s Filtration Testing Lab is managed by Amy Minton, who has more than 20 years of experience in administering a wide variety of analytical, physical, and filtration test methods for nonwoven materials.
“NWI’s Filtration Testing Lab is an important addition to the Institute’s impressive nonwoven fabrication and testing capabilities,” said Minton, who also manages the NWI Analytical and Physical Testing Lab.
“Our decades of testing experience and our strict adherence to GMP and Standard Operating Procedures provide our industry partners assurance that the tests they conduct at NWI will be executed with the highest level of quality and accuracy.”
NWI recently announced a collaboration agreement with INDA, the Association of the Nonwoven Fabrics Industry, to provide continuing education to the nonwoven industry. This agreement expands upon the ongoing partnership between INDA and NWI, whereby the two organiza-
tions have successfully presented training programs, covering the full spectrum of the nonwovens value chain from raw materials to processes to products.
Under the terms of the agreement, INDA and NWI will develop and present a full roster of training courses, featuring a combination of classroom learning supported by hands-on activities in NWI’s world-class nonwoven production and testing labs.
“As we enter into this new phase of our partnership, NWI and INDA are excited to leverage our diverse perspectives and industry contacts to create an unmatched training and education program,” Daugherty said. “This will ensure the nonwoven industry remains competitive and is equipped with the latest skills. With the pace of change in our industry heightened due to the rapid rise of such megatrends as sustainability and machine learning, we believe continuing education in nonwovens is more
important than ever — and NWI and INDA are well positioned to serve the needs of our industry in this regard.”
“The Nonwovens Institute is the most successful non-medical research institute that began with NSF funding based on longevity and research, education, and industry service impact,” Pourdeyhimi said. “This success is driven by creating measurable goals that are consistent with NC State and NWI’s long-term vision.
“As we’ve recently completed our ‘2030 Strategic Plan,’ we have set ambitious targets in each of our pillar service areas, and we are already making positive strides toward these goals,” Pourdeyhimi continued. “We look forward to continuing to serve nonwovens-affiliated organizations, with high-value offerings that touch on the full range of our industry’s needs from fundamental understanding to technology commercialization.”
Modern Meadow’s BIO-VERA® material can be used to make items traditionally made using leather such as handbags and pouches.
Under intense scrutiny for its ecological footprint, the textile industry is developing ways to combine material science and existing manufacturing processes to pave the way for a more sustainable future.
By Dr. David Williamson
FFor nearly as long as humans have lived, they have dyed materials. Early craftsmen discovered that natural dyes found in the bodies of insects, mollusks and plants could be isolated and used to transform common textiles into culturally defining works of art. Tyrian purple, for example, was so difficult and costly to produce that few in the ancient world could afford it, and so the color purple became an iconic symbol of Roman royalty. To this day, the significance of color as a medium for personal and cultural expression has not faded. Whether it’s the deep indigo of Japanese textiles or the vibrant reds of ancient Peruvian fabrics, color tells stories — of status, geography, and tradition — that words often cannot.
What began as a niche art has since evolved into a multi-billiondollar global industry. Modern dyeing practices, powered by synthetic chemicals and large-scale production facilities, allow manufacturers to dye materials at a rate and scale unimaginable to the dyers of antiquity. Yet, this growth has come at a significant environmental cost. The global textile industry is now under intense scrutiny for its ecological footprint. The apparel and footwear sectors alone are responsible for up to 8 percent of the world’s greenhouse gas (GHG) emissions and significant amounts of water used and effluent produced, creating stress on regions given how water is already a diminishing resource. The demand for color has become entangled with
some of the most pressing sustainability challenges of our time.
Next-generation materials have emerged as a potential solution for the industry. These advanced materials, many created through biomanufacturing, are designed to both reduce the environmental cost of textile production and decrease contribution to landfills. Though there are many exciting applications for nextgeneration materials, one noteworthy opportunity lies in leather production, where there is opportunity to reduce its environmental footprint and not many alternate solutions exist.
The leather tanning process relies heavily on water- and chemicalintensive processes to achieve the richly dyed hides that are so often associated with luxury. Consumer demand for animal-free, responsibly produced leather has steadily risen, causing many to look to next-generation materials. However, leather is an ancient material that has been crafted by artisans for millennia. The material’s charm comes not from its resilience and water-resistant properties, but from its distinct look and feel.
A viable alternative to leather will thus have to be more than just ecologically friendly, it will have to inspire reverence among consumers, becoming a material that’s worth showing off. Next-generation materials have largely failed to achieve this, in part because the look of leather is so hard to replicate. But where others have failed, Modern Meadow is poised to succeed. Using a proteinbased material known as Bio-Alloy® as a starting point, Modern Meadow has developed a leather-like material that not only matches many of leather’s tensile properties but allows tanners to tell their ancient and colorful stories on a new canvas.
To appreciate the significance of Bio-Alloy, it’s important to first understand how leather gets its color. The final color of any material
is determined by many factors, including the quantity and arrangement of dye molecules that have bound the material, as well as the overall structure of the material.
Leather is rich in type 1 collagen proteins, which provide a unique canvas for dye binding. Collagen’s triplehelix structure, along with the various functional groups present on its amino acid backbone, create ample opportunities for interaction between dye and protein. If this interaction is strong, the dye molecules will be retained in the material and contribute to its final color.
The fastness of the material’s color depends on how the dye-protein interaction is formed, with the strongest occurring through covalent bonds. While leather can be dyed with most types of dye, it is typically done using acid dyes, which carry a net negative charge and are attracted to the positive charge of collagen fibers. This electrostatic force causes the dyes to penetrate far into the material creating an ionic bond and enabling a deep, rich color to be achieved.
This process is a delicate one that requires careful consideration from start to finish. How the hide is treated from the moment it’s received can affect the collagen’s structure and
charge, as well as the hide’s permeability — all of which can affect the dye-collagen interaction and subsequent color of the hide. Similarly, contamination of tanning reagents by chelated metals in factory pipes can greatly affect dye properties. Therefore, the quality of the dyeing process — and by extension, the leather — depends on a meticulously designed tanning and post-tanning process.
In recent years, the textile industry has sought alternative materials that can rival natural leather in performance while improving on its environmental impact. These next-generation materials, often made from bio-based or synthetic components, are designed to minimize animal, water and chemical usage during production. However, creating a truly viable leather alternative is no simple task.
One of the biggest challenges is replicating the structure and look of natural leather. The complex collagen matrix in animal hides doesn’t just dictate how dyes bind to the material; it also affects properties like breathability, water permeability and resilience. To be commercially successful, any alternative material
must match or exceed these qualities while achieving the rich look of leather. Simply put, leather’s value is more than skin-deep — it’s a product of its structure.
Many leather-like materials are constructed using synthetic fibers, which possess chemical properties very different from those of collagen. To achieve the desired color, such materials would have to be treated with a significantly different dyeing process that may not be compatible with tannery infrastructure. The infrastructure for dyeing and processing leather has been optimized over centuries, with significant investments in equipment and processes. Introducing a material that requires bespoke manufacturing workflows can be prohibitively expensive for manufacturers, leading to slow market adoption. This has been a stumbling block for many synthetic leather alternatives, which, despite their promise, have failed to penetrate the market on a large scale.
This is where Modern Meadow’s Bio-Alloy technology comes in.
Bio-Alloy has a molecular blend composed of biopolymers and plantderived proteins. Modern Meadow has explicitly designed Bio-Alloy to
contain a soy protein blend that is enriched with dye-binding sites, enabling the materials that contain Bio-Alloy to achieve deep and fast color properties.
To emulate leather, Bio-Alloy is combined with a nylon meshwork formed from upcycled rubber and consumer waste. The structure provided by the nylon, combined with the protein matrix of Bio-Alloy results in a remarkably hide-like material, known as BIO-VERA® that can be seamlessly dropped into leather tanning workflows at the dyeing stage.
BIO-VERA offers several advantages for tanneries looking to develop a leather alternative. Firstly, the material is produced without livestock which greatly reduces the amount of GHG emissions associated with material production. Preliminary life cycle assessment studies show significant reductions in greenhouse gas emissions with approximately 7 kilograms of carbon dioxide equivalents per square meter of material. Additionally, BIO-VERA is drop-in ready, meaning no bespoke infrastructure is needed — it can simply integrate into existing tannery workflows. Notably, because BIOVERA does not need to be delimed or tanned, it also requires at least 90 percent less water than natural hides.
As discussed, look is a critical feature of leather. BIO-VERA is capable of achieving a highly-leather-like look and feel thanks in large part to Bio-Alloy, whose protein composition is akin to that of leather’s. This means that BIO-VERA can be dyed using the same acid dyes that work on leather. However, BIO-VERA has also been designed to offer a wider range of dye options for tanners. For example, now it can also be dyed using reactive dyes, bringing an entirely new color palette to the leather industry or the bronze metallic sheen that comes with basic dyes.
Put another way, the availability of different binding chemistries in Bio-Alloy opens up a new level of design flexibility for tanners using BIO-VERA.
The leather industry is at a crossroads. On one hand, the demand for sustainable practices is undeniable. On the other, the challenge of developing a viable leather alternative has proven elusive — until now. With BIO-VERA and its underlying BioAlloy technology, Modern Meadow has developed a material that not only addresses the environmental concerns of traditional leather but also meets or exceeds its performance characteristics. By enabling manufacturers to use traditional dyeing techniques, while also opening the door to new possibilities, Bio-Alloy represents a breakthrough in the field of next-generation materials.
As the textile industry continues to evolve, innovations like Bio-Alloy are paving the way for a more sustainable future. By combining the best of both worlds — advanced material science and compatibility with existing manufacturing processes — Modern Meadow’s protein-based technology is set to make a lasting impact on the world of leather dyeing. TW
Editor’s Note: Dr. David Williamson is CEOof Nutley, N.J.-based sustainable materials company Modern Meadow.
Pictured during her visit to ETV is Germany’s Economics and Climate Protection Minister Mona Neubaur (third from left), with members of the ETV and Monforts management teams, including Dirk Tunney (far left) and Gunnar Meyer (far right). (Image courtesy of ETV)
At a time when European commission finishers are finding it increasingly difficult to operate due to extremely high overheads, Germanybased ETV is going from strength-to-strength, alert to new opportunities going forward.
By Adrian Wilson
FFounded in 1950, ETV Eing TextilVeredlung GmbH & Co. KG — a privately held company based in Germany — is currently installing a third Monforts Montex 8500 finishing range with a working width of 3.2 meters, fully equipped with a Montex®Coat coating unit, an EcoBooster heat recovery unit, crash calender and computer-controlled winders and unwinders engineered by Germany-based A. Monforts Textilmaschinen GmbH & Co. KG.
For ETV Managing Director Dirk Tunney, the company’s longevity is in part due to a timely move away from traditional textile applications such as clothing and home textiles 25 years ago, to focus on adding value and functionality to technical textiles, films and membranes.
“The large discounters now dominate the procurement markets, particularly in the home textiles sector,” Tunney said. “Stationary retail hardly exists anymore, and the market is characterized by the price structure of cheap imports from non-European countries.”
Since repositioning itself in 1999, ETV has grown into a powerhouse in its selected fields, dyeing and finishing around 1,500 tons of yarn and 1.6 million linear meters of fabric each year. In addition, the company annually prints around 4 million linear meters of fabrics, foils and membranes, along with coating up to 40 million linear meters of fabrics and nonwovens.
ETV also was early in addressing the need for sustainable processes with a thermal exhaust air aftertreatment unit, a printing paste recycling
station and the use of 100-percent recycled industrial water as a result of its own in-house water and sewage treatment plant.
Escalating energy costs in Germany, however, have understandably been a cause for concern for the company.
“Up to and including 2020, our energy expenditure was less than 10 percent of our total overheads which ensured we were competitive on the market, but at their peak in 2022, gas prices in Germany had increased tenfold and electricity prices increased fivefold,” Tunney noted. “Our industry today has to live with electricity prices that are approximately twice as high and gas prices that are approximately three-and-a-half times higher than before 2021. In the future, we are assuming a level of 12 to 13 percent so we are talking about additional expenditure of up to 400,000 euros depending on our future product production program, which as a contract processor we have only a limited influence on.
“Energy is certainly no longer cheap in Germany, and we have moved from being an exporter of electricity to an importer and will no longer be able to supply ourselves in the future if we don’t change anything. It’s worrying that without our European neighbors our lights would sometimes go out.”
Monforts Montex tenters are now industry standard for the fabric finishing industry, providing many advantages in terms of production throughput and especially in energy efficiency and savings.
The Monforts Eco Booster, integrated into the chamber design of ETV’s Montex tenter, is a single heat recovery system with automatic cleaning that can further save up to 35 percent in energy costs. The Eco Booster consumes only minimal amounts of water during
the cleaning cycle and the entire process is controlled and monitored automatically.
The Montex Coat serves a very diverse number of markets and enables full coatings, pigment dyeing or minimal application surface and low penetration treatments to be carried out. Knife coating, roller coating or screen printing can also all be accommodated with this system. In addition, the Montex Coat provides the ultimate in flexibility and the ability to switch quickly from one fabric run to the next, without compromising on the economical use of energy or raw materials.
“We certainly anticipate energy savings in addition to increased productivity and process reliability with this latest line and in addition, we will be working with Monforts on alternative energy options,” Tunney said.
Monforts currently is leading a consortium of industrial partners and universities in the three-year WasserSTOFF project, launched in November 2022, to explore all aspects of this fast-rising new industrial energy option.
The target of the governmentfunded project is to establish to what extent hydrogen can be used in the future as an alternative heating source for textile finishing processes. This will first involve tests on laboratory equipment together with associated partners and the results will then be transferred to a tenter frame at the Monforts Advanced Technology Center in Mönchengladbach, Germany.
“Green hydrogen’s potential as a clean fuel source is tremendous, but there is much we need to explore when considering its use in the textile finishing processes carried out globally on our tenter dryers and other machines,” said Monforts’ Managing Director Gunnar Meyer. “Everybody knows that textile finishing is a high energy consuming process and to make the processes more efficient, we already offer several
solutions, but as a technology leader we are also rising to the challenge of exploring alternative heating options to be ready for the future.”
ETV’s relative proximity to the Monforts headquarters in Mönchengladbach makes it an ideal site for the WasserSTOFF project.
“The project for a hydrogen-powered coating tenter frame is very suitable for our region,” Tunney said. “Germany’s textile industry has a long tradition and with more than 1,400 companies, is not unimportant to the country, but without support from politics, both ideologically and financially, something like this cannot be done.
“If we want decarbonization, paths must be identified and funds made available. We absolutely have to remain open to technology in order to position ourselves in the best possible way. Otherwise, it will result in deindustrialization, which none of us want. We look forward to a closer collaboration with Monforts and its project partners going forward.”
On September 6 this year, Germany’s Economics and Climate Protection Minister Mona Neubaur visited ETV to get a first-hand view of how the textile industry is rapidly adapting to a changing landscape.
“The future of German industry will be decided in North RhineWestphalia,” Neubaur said. “This requires courageous companies to move forward. Innovative ideas strengthen our competitiveness and make a significant contribution to becoming the first climate-neutral industrial region in Europe. Green hydrogen will play an important role in this, and I am very pleased that through companies like ETV and Monforts and their partners, we are now moving quickly from preparation to action.” TW
Editor’s Note: Adrian Wilson is an England-based analyst and writer specializing in the technical textiles, nonwovens and composites industries. He is the owner of AWOL Media.
CEO Randy Carr talks to Textile World about the use of AI at embroidered patch maker World Emblem and how it has helped his company.
TW Special Report
WWorld Emblem,Fort Lauderdale,Fla., was founded in 1993 by Jerold Carr.Led today by Carr’s two sons — Randy and Jamie — this familyowned business has blossomed into one of the largest patch and emblem producers in the world. World Emblem manufactures and ships some 250 million products each year that are produced on its 4,250 embroidery heads located in 1 million square feet of manufacturing space in the United States, Mexico,Canada and Europe.The company employs 1,200 associates, and its embroidered patches are used for sports headwear,footwear,sports garments and uniforms, among other applications.
Randy Carr became World Emblem’s president in 1998.As the current CEO,he said: “I try to embody passion,insight, and a forward-thinking approach that I believe has helped transform the industry and positions World Emblem at the forefront of innovation.I strive to be
more than just a CEO,but also a driver of motivation — a testament to what one can achieve with hard work, a supportive family,and the will to always aim higher.”
Part of Carr’s forwardthinking approach includes the use of artificial intelligence (AI) technologies in his business.More and more textile companies are beginning to embrace the use of AI to give them a competitive edge,and industry organizations such as the Atlanta-based Americas Apparel Producers’Network are encouraging their members to jump in and get started using AI sooner,rather than later (See “Generative AI: Understanding Fears & Embracing The Innovations,” TW ,this issue)
Carr recently spoke with TW about World Emblem’s use of AI and the ways it helps the company.
TW : You’ve stated that AI will make the manufacturing apparel industry unrecognizable in the next three to five years.Can you share specific examples of how you foresee AI
transforming key processes within the industry?
Carr: Absolutely.AI will indeed dramatically transform the manufacturing apparel industry.Firstly,AIpowered predictive maintenance tools will analyze machine data in real time to predict equipment failures before they occur.AI also will revolutionize supply chain management by optimizing inventory levels, predicting demand,and identifying potential disruptions.The industry also will be able to make use of robotic process automation (RPA) and cobots to take over repetitive,manual tasks.AI-driven computer vision systems will enhance quality control processes by automatically detecting defects in products on production lines.In addition, AI will enable hyper-personalized and on-demand manufacturing by analyzing customer preferences, market trends,and product feedback in real time.
TW : What areas of apparel manufacturing have you already integrated AI into,and what
measurable impacts have you observed so far?
Carr: For starters,all of this is still very new. However,we have selected four areas of the business we are enhancing using AI:
• Customer experience — AI chatbots and virtual assistants are used to handle customer inquiries,provide real time access,assist in ordering processes and offer personalized product recommendations based on past orders.
• Production efficiency and automation — AI will be crucial in connecting production machines,sensors,and systems to analyze performance data in real time.This can help optimize production lines,reduce defects and adjust for bottlenecks.
• Quality control — AIbased computer vision systems can inspect emblems and labels for imperfections in real time.These systems are capable of detecting misprints,alignment issues,and color mismatches at a faster rate
than human inspection, leading to fewer rejected batches and higher product consistency.
• Customization —
AI is already enabling our designers to use intelligent software for creating custom emblems and labels.
TW : Can you talk about backend processes that AI can optimize,and how that translates into cost savings or operational efficiencies?
Carr: AI is revolutionizing backend processes in numerous ways,from demand forecasting to personalized customer interactions.By predicting inventory needs and optimizing pricing through data analysis,AI enhances inventory and supplier management.Production schedules are now generated automatically based on order priorities,machine availability, and workforce capacity, streamlining operations.
Predictive maintenance enables machinery performance monitoring,addressing issues before they result in downtime.Financial tasks
such as bookkeeping,cash flow forecasting,and managing accounts payable and receivable are automated, reducing errors and ensuring timely payments.Customer communication is more personalized,with automated follow-ups and tailored recommendations. In human resources,AI scans resumés,shortlists candidates,and even assesses interview responses,expediting the hiring process.Real-time data analysis and reporting offer decision-makers valuable insights,while business intelligence tools identify trends and inefficiencies.
Through predictive analytics,companies can anticipate future production, sales,and market conditions.Order processing,
fulfillment,and tracking are fully automated,minimizing errors and providing realtime updates to both customers and teams,ensuring a smoother,more efficient operation overall.
TW : How do you think AI will impact the speed-to-market in the apparel industry?
Carr: Logo design to completion is already getting disrupted.However,we believe that rather than taking anywhere from one to two weeks,sometimes even longer,for a client to complete their logo project,this will be done in real time.
TW : What key advantages do you think companies leveraging AI will have over those that don’t, and how soon do you expect this divide to become apparent?
Carr: Companies that leverage AI will reap several advantages over those that do not.Operational efficiency advantages include streamlined repetitive tasks,reduced human error and improved speed of processes across the board using AI-Driven automation.Companies using AI can reduce costs and improve productivity
by optimizing resource allocation and minimizing downtime.
There also is a data advantage that improves decision making.AI enables companies to process and analyze large amounts of data in real-time,offering insights that lead to better decision making.
AI provides a personalization and customer experience advantage since it allows businesses to offer personalized experiences at scale.
There also is a cost reduction and scalability advantage because AI can reduce labor costs by automating manual tasks and enabling scalability.
The impact of these advantages is immediate.
TW : In terms of customer satisfaction,on what specific AI-driven innovations are you focusing?
Carr: At World Emblem, we are implementing several AI-driven initiatives to greatly enhance the customer experience.We can offer automated order tracking and notifications using AI.Real-time order tracking and status updates can be powered using AI giving customers more transparency throughout production and shipping.
World Emblem’s associates help create patches that are used in garment, headgear and footwear applications among other end-uses.
AI also can analyze past customer interactions to predict when customers might need help and preemptively offer solutions. Chatbots or virtual assistants can answer common questions,resolve simple issues and escalate more complex problems to human agents efficiently.
In addition,AI tools can assist customers in the design and customization process,offering suggestions for colors,layouts, and patterns based on current trends or customer preferences.AI can also generate previews in realtime to show what the finished product will look like.
TW : Why have you chosen to invest heavily in AI technology?
Carr: World Emblem has always been about investing in the best technologies to improve the customer experience and drive our business forward. We believe our investment in AI will reap benefits in operational efficiency and automation,an enhanced customer experience,datadriven decision making, and in product innovation and customization.
AI-powered design tools
allow for greater customization giving our clients more control over the final product.
TW : What challenges have you faced in adopting AI and how have you overcome these hurdles?
Carr: World Emblem, like most forward-looking companies,has experienced some minor challenges with the adoption of AI. We have experienced some issues with technical implementation. Challenges integrating AI systems with existing infrastructure and processes is complex.Data quality and availability is also a hurdle as AI models need vast amounts of high-quality data to be effective.However,we are overcoming it with phased rollouts,improved data management,and partnering with experts.
Employees also resist AI adoption due to fears of job loss or a lack of understanding of how AI will impact their roles.However,we are overcoming the same with education and training, clear communication,and involvement in the process.
AI adoption often requires a cultural shift in
how decisions are made, and this cultural change has been challenging.
Additionally,there are cost and return on investment (ROI) concerns. These upfront costs of AI technology and the uncertainty around the ROI were overcome through pilot projects with measurable outcomes,focusing on high-impact areas.
TW : Looking ahead, what new technologies or AI-driven solutions are you excited about that have the potential to reshape the industry?
Carr: We are very excited about the potential of AI and see great promise for its utilization in areas such as AI-powered sustainable manufacturing, AI-driven customization and on-demand production,3D design,smart supply chains with AI and blockchain,and generative design and AI creativity tools.AI can optimize the use of materials and energy leading to more sustainable manufacturing practices.It also can enable hyper-personalized products and on-demand manufacturing allowing customers to design and
order customized labels and emblems in real time. AI-powered 3D design tools are already making an impact by enabling designers to create virtual prototypes and run simulations.In addition,AI tools that use generative design algorithms can assist in creating new designs by exploring all possible combinations of shapes,materials,and patterns based on certain design constraints.AI can also learn from historical design data and customer feedback to suggest new trends.
TW : For companies that are hesitant or slow to adopt AI,what do you think are the most significant risks they face over the next few years?
Carr: Companies must continually adapt to the times,including changing customer preferences and technical innovations. They must always be forward-looking,otherwise they will fall behind.Those that don’t change could face the following issues: loss of competitive advantage; decreased operational efficiency; missed opportunities for datadriven decision making; inefficiency in customer experience and personalization; and an inability to scale effectively.Companies not embracing AI also may have to find themselves competing with a company like World Emblem that is embracing the technology. TW
MKAS Textile selected the Autoconer X6 Multilink from Rieter for an economical boost to production.
TW Special Report
S. Mohamed Suhil, managing director, MKAS Textile Pvt. Ltd., reports he is highly satisfied with the Autoconer X6 Multilink installation.
that he is highly satisfied with the Autoconer X6 Multilink installation. “The lower investment costs and, above all, up to 25 percent lower energy costs in operation, are extremely important aspects for us, for a profitable business,” Suhil added. “This allows us to establish ourselves as a new spinning company with high-quality products in a difficult and demanding market.”
The investment costs of 2:1 Multilink mill installation of 442 winding units, tailored to their layout specification, were significantly lower than as 1:1 direct single-link of 442 winding units, due to optimum quantities of machines, components and aggregates.
IIndia-based MKAS Textile Pvt. Ltd. entered the country’s fine yarn spinning business in 2021 and now achieves a production capacity of 4.5 tons per day. The company sells 100-percent cotton yarns made from high-quality cotton fibers in the yarn count range between Ne 80 to 100 for weaving applications. As part of its strategy to establish itself in this market, MKAS Textile chose Switzerland-based Rieter’s winding machine Autoconer X6, type V Multilink as a highly economical, energy-saving automation solution.
Given limited resources like skilled operators and high-quality raw materials, it is a major challenge to ensure a consistently high level of quality. Rising energy costs further make it difficult to achieve acceptable production costs when meeting the demanding requirements of the market.
MKAS Textile opted for a high degree of automation with the Autoconer X6 Multilink system. To plan the most effective and optimal spinning
mill layout, Rieter experts discussed the requirements with the company’s management and technicians. Due to the attractive benefit on investment and operating costs, MKAS chose eight winding machines Autoconer X6, type V with automatic material flow as 2:1 Multilink for 52 winding units each. This means that two ring spinning machines are linked to one Autoconer. To respond to MKAS Textile’s individual needs for maximum space utilization one winding machine was added as 1:1 direct single-link — 26 winding units. On specification, the company chose the underfloor link where the cops and spinning tubes move underground between the ring spinning machine and the winding machine. This creates a passageway for operators between the two machines and makes the machine handling easily manageable.
The spinning mill now runs at full production. Mohamed Suhil, MKAS Textile’s managing director, stated
Recently, MKAS Textile conducted an energy study comparing its 1:1 single-link machine and 2:1 Multilink system. Around 25 percent lower energy consumption in favor of the Multilink machines was measured. This means savings of 238,750 kiloWatt hours (kWh) per year, which corresponds to an annual energy cost saving of 1,910,000 Indian rupees ($22,630) based on the company’s daily production of 4.5 tons, 362 working days per year, and 8 rupees per kWh.
Furthermore, the Multilink system achieves major benefits in terms of labor saving thanks to the longer winding machines and optimized mill layout. Instead of four operators, it now only takes two operators to manage the tasks for the eight Multilink winding machines. This means one operator can handle four Autoconers —seven 296 ring spinning spindle production — which translates into a doubling of the working area. TW
Marine fabrics, combining durability with aesthetics, influence and are influenced by partner and peer industries.
By Anne Bushell
MMarine fabrics play a specialized yet defining role within the textile industry. First and foremost, they’re designed for resiliency and durability, so some of the most cutting-edge performance innovations show up in this space first. And when it comes to aesthetics, marine textiles serve a wide range of style needs, from sporty power boats to recreational pontoon boats to high-end yachts needing the most elevated designs.
The trends and positioning within the marine textile space can signal larger evolutions on the horizon for all fabrics. From trending colors and textures to technological advancements, there’s no shortage of exciting developments for 2025 and beyond.
When predicting how marine textile design will evolve in both the near and long term, there are a few key indicators that inform a forecast. Developers look to partners, peer industries and evolving cultural behaviors and preferences to understand the larger-scale influences that may affect the look, feel and style of the marine industry. The Sunbrella design team keeps a close
eye on the industry through trade shows, consumer feedback and marine influences seen while traveling. Perhaps the most valuable resource is the relationships with partners and customers. Sunbrella keeps an ongoing dialogue to understand what they’re hearing from their customers, where their needs are and how it can provide even better, more beneficial products to them. The global design and research team that develops fabrics for a wide range of applications at Sunbrella has a multifaceted understanding of the textile industry and the nuances of specific fields.
One industry with a broad influence on marine design is automotive design. Some specific automotive trends influencing the marine sector include the rise of mid-tone neutrals such as shades of putty and mid-tone blues. When it comes to hardline elements, trends show movement toward flatter paints in place of pearlescent finishes. Ultra-matte paints are in growing demand, especially for high-end cars and boats.
Beyond automotive, other industries — big and small — can have a meaningful impact on marine design. Even in an area as niche as wristwatch design, the ways the hardware, leather band and watch face details are intricately paired together for a big impact can spark inspiration for new material pairings on a boat.
Take sports apparel, from shoes to activewear, as another example. The color palettes in this industry are meant to paint a picture of functionality, with softer colors used for everyday life but added pops of color through trim or labeling that are meant to communicate the product is meant for a sportier purpose.
While these exact textures or pops of lime greens and sporty reds may not make it directly onto most boats, this principle influences how all boats are designed. At boat shows in the past, there were more solid, plain approaches to seating, but boat shows are now filled with intricate seating details, from quilted finishes to pops of color.
Interior design and its tenets can lend inspiration to the marine market
as well, particularly when it comes to a cohesive palette for the full boat design. Interior designers take a holistic approach to a room, considering how the drapery, rugs, seating and throw pillows all relate to one another. Even in a more industrial application, Sunbrella can think like its peers in the décor area to create a more impactful product. Holding frequent one-on-one consultations with OEMs and fabricators can help lend a new perspective to the design processes. It seems like this interiorsinfused approach is on the rise and will continue in the years ahead.
Technological advances have allowed for significant movement in what’s possible in performance upholstery fabrics, including bouclé and chenille yarns that maintain performance attributes. This texture-forward approach extends to more industrial design as well, and while the marine fabric industry doesn’t have these decorative yarns to work with, it has other creative ways to imbue texture into these palettes, including embossing patterns or new weaving structures. More and more, textures layered throughout the boat with complementary colors and finishes are observed. Rather than a full helm chair in a bold texture, fabricators are bringing in strong texture through piping details to add even more depth. Texture can convey a story in boaters’ minds, even if they don’t realize it, such as a perforated look signaling a high-tech breathability or a leatherlike finish reading as a more luxurious fabric.
As marine design trends move toward these neutral, less lustrous palettes, expect an even heavier reliance on textile elements to add depth and dimension, especially as a way to subtly elevate the boat design.
Marine textile performance elements are non-negotiable due to the harsh conditions on the water. Marine textiles must retain their
color through ultraviolet (UV) exposure and be resistant to water, mildew and microbial pinking, and that performance should be backed by a comprehensive warranty. However, superior performance shouldn’t compromise the importance of comfortable fabrics that help make a boat look and feel luxurious.
Ultimately, comfortable fabrics lead to a more pleasant boating experience that allows boat owners to stay out on the water longer. That means a continued interest in pop-up shade structures and a focus on fabrics that create a more comfortable ride even when bracing for impact over choppy waters. As the aesthetic elements of marine textiles evolve, designers and product development teams are working hand-in-hand to make sure they not only maintain their performance attributes but also improve them to make for an even better experience on the water.
Now also is the time to reinforce the importance of sustainability in marine design. When looking to other elements of the boat, electric motors are beginning to enter this industry in full force, and other sustainable elements are beginning to be incorporated in boat design, including biodegradable boat wraps.
When it comes to marine textiles, recycled content continues to be introduced into fabrics. It’s become
much more common in décor fabrics and even in some of the canvas fabrics seen on boats, but reclaimed fibers are starting to be included in more industrial fabrics as well. Even the sheer quality of marine textiles is inherently a question of sustainability, as the more durable, long-lasting, warranty-backed options will require less frequent replacement and contribute less waste over time.
Per- and polyfluoroalkyl substances (PFAS) chemicals are also a hot topic when it comes to performance fabrics and their impact on the environment, especially as state and federal bodies begin regulating these chemicals more and more. Some brands, such as Sunbrella, have been shifting to non-PFAS production backed by years of research to ensure minimal impact on the performance capabilities of the fabric.
Anchored in innovation, marine textiles are an essential part of the broader textile industry, with technology and design changes set to reverberate across industrial fabrics and beyond. As recreational boating grows and as the marine market continues to influence and be influenced by partners and peer industries, the innovations and design trends in marine textiles will keep making waves. TW
Editor’s Note: Anne Bushell is design director of product development, Sunbrella, Burlington, N.C.
7-9 :Advanced Textiles Association (ATA) Tent Conference 2025,Hyatt Regency Louisville,Louisville,Ky. Visit textiles.org/ events.
9-11 :ATA’s Marine Fabricators Conference 2025,Omni Corpus Christi,Corpus Christi, Texas.Visit textiles.org/events.
14-15 :Première Vision New York, Tribeca 360°,New York City. Visit newyork.premiere vision.com.
14-16 :2025 Beltwide Cotton Conferences,New Orleans Marriott, New Orleans.Visit cotton.org/beltwide.
14-17 :Heimtextil 2025,Messe Frankfurt Fairgrounds,Frankfurt,Germany. Visit heimtextil.messefrankfurt.com.
20-22 :FESPA Middle East,Dubai Exhibition Centre (DEC),Dubai. Visit fespamiddleeast.com.
21-22 :SpinExpo™ Spinclub Paris, Bastille Design Center,Paris. Visit spinexpo.com/paris.
21-23 :Texworld New York City/ Apparel Sourcing New York City, Javits Center,New York City. Visit texworld-usa.us.messefrankfurt.com.
21-24 :IM Intermoda,Expo Guadalajara,Guadalajara,Mexico. Visit intermoda.com.mx.
28-30 :Colombiatex de las Americas 2025, Plaza Mayor,Medellín,Colombia. Visit colombiatex.com.
10-12 :Texworld Paris/Apparel Sourcing Paris,Le Bourget Exhibition Center,Paris. Visit texworld-paris.fr.messefrankfurt.com.
10-12 :Sourcing at MAGIC,Las Vegas Convention Center,Las Vegas. Visit sourcingatmagic.com
11-13 :Première Vision Paris, Paris Nord Villepinte,Paris. Visit paris.premierevision.com.
19 :Southern Textile Association (STA) Winter Seminar,Textile Technology Center at Gaston College,Belmont,N.C. Visit southerntextile.org.
25-27 :44th SpinExpo Shanghai,Shanghai World Expo Exhibition and Convention Center,Shanghai.Visit spinexpo.com/shanghai.
26-27 :63rd Edition of FILO,International Exhibition of Yarns and Fibres,Allianz Mico,Milan,Italy.Visit filo.it.
26-28 :21st International Istanbul Yarn Fair, Tüyap Istanbul Fair and Congress Center, Istanbul,Türkiye.Visit iplikfuari.com.
2-5 :ATA’s Geotechnical Frontiers,Kentucky International Convention Center,Louisville, Ky.Visit textiles.org/events.
4-6 :JEC World 2025,International Composites Show,Paris Nord Villepinte, Paris.Visit jec-world.events.
5-6 :Performance Days Munich, Messe München,Munich,Germany. Visit performancedays.com.
5-7 :American Apparel & Footwear Association(AAFA) 2025 Executive Summit,InterContinental Washington D.C. — The Wharf.Visit aafaglobal.org.
11-13 :Intertextile Shanghai Apparel Fabrics,Yarn Expo Spring and Intertextile Shanghai Home Textiles Spring Edition, National Exhibition and Convention Center,Shanghai.Visit intertextile-shanghai-
apparel-fabrics-spring.hk.messefrankfurt.com, yarn-expo-spring.hk.messefrankfurt.com and intertextile-shanghai-hometextiles spring.hk.messefrankfurt.com.
17-20 :FESPA Brazil,Expo Center Norte,Sao Paulo,Brazil. Visit fespabrasil.com.br.
19 :STA Southern Division Spring Meeting,Hyatt Regency,Greenville, S.C.Visit southerntextile.org.
25 :EDANA Filtrex™,Hilton Waterfront Hotel,Vienna.Visit edana.org/events/filtrex.
25-26 :National Council of Textile Organizations (NCTO) 21st Annual Meeting,Washington.Visit ncto.org.
31-April 2 :ATA’s Women In Textiles Summit 2025,Fashion Institute of Technology,New York City. Visit textiles.org/events.
8-10 :Emitex 2025,La Rural Trade Center,Buenos Aires,Argentina. Visit emitex.ar.messefrankfurt.com.
8-10 :Heimtextil Colombia licensed by Messe Frankfurt GmbH,Plaza Mayor,Medellín,Colombia. Visit heimtextilcolombia.com.
8-11 :Americas Apparel Producers’ Network (AAPN) Carolina Mill Tour. Visit aapnetwork.net.
14-16 :Functional Fabric Fair powered by Performance Days,Oregon Convention Center,Portland,Ore. Visit functionalfabricfair.com.
9 :Synthetic Yarn & Fabric Association (SYFA) Annual GolfTournament, Rocky River Golf Course,Concord,N.C. Visit thesyfa.org.
10-11 :SYFA 2025 Spring Conference, Sheraton Charlotte Airport Hotel, Charlotte,N.C.Visit thesyfa.org.
29-May 1 :IDEA® 2025,organized by the Association of the Nonwoven Fabrics Industry (INDA),Miami Beach Convention Center,Miami Beach,Fla. Visit ideashow.org.
29-May 1 :INDA’s FiltXPO™,Miami Beach Convention Center,Miami Beach,Fla.Visit filtxpo.com.
6-8 :Techtextil North America 2025, Georgia World Congress Center, Atlanta.Visit techtextil-north-america.us. messefrankfurt.com.
6-8 :Texprocess Americas 2025, Georgia World Congress Center, Atlanta.Visit texprocess-americas.us. messefrankfurt.com.
6-9 :FESPA Global Print Expo, Messe Berlin,Berlin.Visit fespaglobal printexpo.com.
12-14 :AAPN’s 2025 pro:Americas Annual Conference,Marriott Harbor Beach,Fort Lauderdale,Fla. Visit aapnetwork.net.
19-22 :SAMPE 2025,Indiana Convention Center,Indianapolis. Visit 365.sampe.org/events.
2-4 :ATA’s Outlook® Conference, Lambeau Field,Green Bay,Wis. Visit textiles.org/events.
11-12 :Furniture Manufacturing Expo,Hickory Metro Convention Center,Hickory,N.C.Visit furniture manufacturingexpo.com
11-13 :Intertextile Shenzhen Apparel Fabrics,Shenzhen Convention & Exhibition Center,Shenzhen,China.Visit intertextileshenzhen.hk.messefrankfurt.com.
18-20 :Outdoor Retailer,Salt Palace Convention Center,Salt Lake City,Utah. Visit outdoorretailer.com.
20-22 :STA Annual Meeting,Sonesta Resort,Hilton Head Island,S.C. Visit southerntextile.org.
21-23 :Functional Fabric Fair powered by Performance Days,Javits Center, New York City.Visit functionalfabric fair.com.
21-24 :INDA’s WOW® World of Wipes, Hilton Columbus Downtown,Columbus, Ohio.Visit worldofwipes.org.
22-24 :Texworld New York City/Home Textiles Sourcing/Apparel Sourcing New York City,Javits Center,New York City. Visit texworld-usa.us.messefrankfurt.com.
29-31 :Texworld Los Angeles,California Market Center,Los Angeles.Visit texworld-la.us.messefrankfurt.com.
20-22 :Intertextile Shanghai Home Textiles Autumn Edition,National Exhibition and Convention Center, Shanghai.Visit intertextile-shanghai-hometextiles-autumn.hk.messefrankfurt.com.
2-4 :Intertextile Shanghai Apparel Fabrics Autumn Edition,National Exhibition and Convention Center, Shanghai.Visit intertextile-shanghaiapparel-fabrics-autumn.hk. messefrankfurt.com.
15-16 :INDA’s RISE® 2025,McKimmon Center,NC State University,Raleigh,N.C. Visit riseconf.net.
16-18 :Première Vision Paris, Paris Nord Villepinte,Paris. Visit paris.premierevision.com.
23-25 :EDANA Outlook™,Marriott Hotel, Budapest,Hungary.Visit edana.org/events/ outlook/outlook-2025.
8-11 :CAMX Conference and Exhibition, Orange County Convention Center, Orlando,Fla.Visit thecamx.org.
10-11 :64th Edition of FILO,International Exhibition ofYarns and Fibres, Allianz Mico,Milan,Italy.Visit filo.it.
TBD :AAPN Triad Tour, Greensboro/Winston-Salem,N.C. Visit aapnetwork.net.
23-24 :SYFA 2025 Fall Conference, Sheraton Charlotte Airport Hotel, Charlotte,N.C.Visit thesyfa.org.
28-31 :ITMA Asia + CITME Singapore 2025,Singapore Expo,Singapore. Visit itmaasiasingapore.com.
29-30 :Performance Days Munich, Messe München,Munich,Germany. Visit performancedays.com.
4-7 :AT Expo 2025 and Emerging Technologies Conference,Indiana Convention Center,Indianapolis. Visit advancedtextilesexpo.com.
19-21 :Techtextil India,Bombay Exhibition Center,Mumbai,India. Visit techtextil-india.in. messefrankfurt.com . TW
The American Association of Textile Chemists and Colorists (AATCC), Research Triangle Park, N.C., has announced Gregg Woodcock as its new executive director. In addition, Christina Rapa was named president-elect. Her term begins January 1, 2025, and lasts for two years.
Dario Aguilar was appointed managing director, Latin America, for San Francisco-based Levi Strauss & Co.
Helsinki-based Suominen has named Minna Rouru chief people and communications officer.
Dr. David Williamson has transitioned from president and COO to CEO of sustainable materials company Modern Meadow, Nutley, N.J.
Natalia Scherbakoff has joined Houstonbased Orion S.A. as chief technology officer. She succeeds David Deters who is retiring.
Beaulieu International Group (B.I.G.), Belgium, named Jean-Baptiste De Ruyck CEO.
Natureworks, Plymouth, Mass., has appointed Roger Tambay chief growth officer, and Roger Kempa CFO.
Milliken & Company, Spartanburg, S.C., recently named Allen Jacoby president of the Textile
Business and company executive vice president. He replaces David Smith who is retiring after 45 years of service to Milliken. In other Milliken appointments, Marcio Manique has joined the textile business as senior vice president, Protective Fabrics. Manique will oversee the fire service, workwear and napery businesses, as well as manage Westex: A Milliken Brand.
Wolverine World Wide Inc., Rockford, Mich., named Susie Kuhn president of the company’s Active Group. She is responsible for the Merrell, Saucony and Chaco Brands.
Stefan Lux is the new managing director of Germanybased KM.ON GmbH as well as the KM.ON business unit of the Germanybased Karl Mayer Group He succeeds interim director Carla Janz
Raul Thomas recently retired after a 37-year career with Switzerlandbased Uster Technologies AG. He was honored at a celebration held at the Gaston College Textile Technology Center in Belmont, N.C. In honor of his legacy, Uster has awarded a transfer scholarship at the Technology Center and NC State University’s Wilson College of Textiles.
Charlotte, N.C.-based Elevate Textiles has named Elizabeth K. “Liz” Ren head of Corporate Development and Strategy.
The Board of Directors at Albany International, Rochester, N.H., has appointed Christopher Stone president of Albany Engineered Composites Inc. In addition, Merle Stein was named president of the Machine Clothing business segment.
Nike Inc., Beaverton, Ore., announced that Elliott Hill has returned to the company as president and CEO. He replaces John Donahoe who is retiring. In addition, Tom Peddie was named vice president and general manager of the North America Geography at Nike.
Doug McBurney is the new Global Procurement executive at MMI Textiles, Brooklyn, Ohio.
Jay Hertwig has joined Atlanta-based industrial yarn and fabric solution provider Hamilton International as vice president of Sales and Marketing.
Jonathan Horton has joined the direct sales team as Western Regional manager for Herculite Products, Emigsville, Pa.
Dan Bugaj was named head of Business Development for American Cord and Webbing (ACW), Woonsocket, R.I.
Eric Liedtke has joined Baltimorebased Under Armour as executive vice president of brand strategy.
Dr. Raoul Farer recently joined The Nonwovens Institute, Raleigh, N.C., as executive director. He also serves as a professor in the Wilson College of Textiles’ Department of Textile Engineering, Chemistry and Science (TECS) at NC State University
Israel-based Delta Galil Industries has appointed Yaniv Benedek CFO. TW
Geneva-based testing, inspection and certification company SGS has unveiled a comprehensive suite of per-and polyfluoroalkyl substances (PFAS) testing services.
Q-Lab,Westlake,Ohio, has launched a redesigned website.Located at Q-Lab.com,the site offers new tools and resources to visitors to simplify searches,among other improvements.
Switzerland-based Heberlein Technology and Indonesia-based Busana Apparel Group have both joined the Zurich-based International Textile Manufacturers Federation (ITMF) as a corporate members.
Germany-based Monforts recently celebrated its 140th anniversary under the motto “140 Years of Performance,Innovation and Partners.”
Forbo Flooring Systems has introduced the first collection in its Evolve+ series,Tessera Topology, which features Thrive ® matter low-carbon-footprintyarn from Bristol,Va.based Universal Fibers®
Vancouver-based denim and lifestyle apparel brand Duer has launched a performance flannel buttondown shirt made using a graphene nanofiber.The graphene fights static,keeps
the fabric fresh,is cooling when hot,and confers warmth without weight.
Italy-based Thermore has introduced Invisiloft®, a slim insulation product that offers high warmth with minimal thickness.
Spartanburg,S.C.-based Polartec ,a Milliken & Company brand,won the 2024 R&D 100 Award in Mechanical/Materials for its Power Shield™ Pro fabric. TW
RESPONSIBILITIES
• Visit customers’facilities and gain knowledge of their parts needs
• Expand existing and develop prospective accounts • Enhance and maintain strong customer relations and promptly resolve customers’ concerns • Prepare and submit reports on customer visits
QUALIFICATIONS
• Experience in the textile industry,preferably with technical knowledge of weaving machines • Strong communication and customer relations skills • Excellent problem solving and troubleshooting skills
• Willing to travel • Proficient in the use of computer systems including word processing,email software,and spreadsheets • Self-motivated,and able to work both independently and as a team member EMAIL:Larry@probityproducts.com
Specific Responsibilities Include:
•Hire and lead team members — with a knowledge of and the ability to perform and coach the primary sales functions.
•Help develop, implement and evaluate performance goals and strategic plans for each product line and sales associate.
•Efficiently and effectively manage active and prospective accounts and actively engage with issues &/or opportunities to consistently meet goals and increase sales.
•Gain and apply knowledge about the customer’s needs and help refine our product lines, markets, applications, specifications, pricing and customer benefits.
•Help manage customer service, marketing and promotions.
•Coordinate with other departments as part of the executive team to maximize our progress and success.
Very Helpful Would Be:
•5+ years sales management experience.
•Strong skills with: MS Office, ERPsoftware
AND/OR — Strong knowledge of and/or experience working in sewn products and/or fabric & trim design, production, merchandising, selling or buying AND/OR — Existing relationships with sewn products manufacturers, and/or brands, designers, merchandisers, catalogs &/or retailers. Apply today to Donna Knight HR 423-305-7211
By Rachael S. Davis, Executive Editor
Sustainable fashion brand OuterKnown has launched the first commercial product featuring Keel Labs’ Kelsun™ fiber.
The Kelsun™ Universal Blanket Shirt from OuterKnown
For more information, see @keel.labs, @kelsun.fiber, or visit keellabs.com.
To view the shirt, visit outerknown.com. Go online to TextileWorld.com for archived Quality Fabric articles.
Slippery and slimy are words that come to mind when describing seaweed, not soft, smooth and comfortable like natural textile fibers. But Keel Labs, formerly known as AlgiKnit and the creator of Kelsun™ fiber, has harnessed alginate — a biopolymer found in seaweed — and developed a process to turn it into an environmentally friendly textile fiber. The fiber, designed as a plug-and-play replacement for conventional fibers, may be used in applications throughout the textile industry, according to Keel Labs.
The company was founded by Tessa Callaghan and Aleks Gosiewski. As design students, they wanted to tackle waste in the fashion industry and took on the mission of creating a material solution that is as environmentally friendly as possible. Kelsun is 100-percent biobased, and also is biodegradable in wastewater. The seaweed used also is responsibly sourced.
After years in development, Keel Labs is excited to announce the first commercial product launch for Kelsun fiber. The Kelsun Universal Blanket Shirt was developed in partnership with OuterKnown, a Culver City, Calif.-based apparel brand. The fabric is a 30-percent Kelsun/70-percent regenerative organic certified (ROC™) cotton, which retains the look, feel and performance of the original Universal Blanket Shirts in OuterKnown’s product line.
OuterKnown was founded by pro surfer Kelly Slater and John Moore, Creative director, with a commitment to sustainable choices. The brand focuses on high-quality, responsibly sourced materials including organic, recycled or regenerated fibers, and biobased materials.
“The Blanket Shirt was one of the first products in our line, and it remains one
of my favorite pieces,” Slater said. “From the beginning, it was important to me to design and build a shirt that was high quality, made from sustainable materials, but felt vintage soft. … It’s been 10 years since we made the first one, and we are proud to be partnering with Keel Labs on the next generation of this shirt with a version made from Kelsun, a 100-percent biobased fiber derived from seaweed. Working with suppliers that share our love for the ocean is a great fit for Outerknown. I’m excited to see this grow.”
“We are thrilled to announce our partnership with Outerknown for the first commercial launch of Kelsun fiber,” said Keel Labs Co-Founder and CEO Callaghan. “At Keel Labs, we are deeply committed to our mission of harnessing the potential of our oceans to create better products for people and the planet alike. Working alongsidea brand like Outerknown, that shares our dedication to creating a better world, and our steadfast love of the sea to bring our products to life couldn’t be more fitting. This is a pivotal moment, not just for Keel Labs, but for the industry as a whole, standing as a marker for what lies ahead when conviction, action and collaboration combine. This garment is the first — though not last — of its kind, and we can’t wait to continue sharing the evolution and expansion of our partnership.” TW