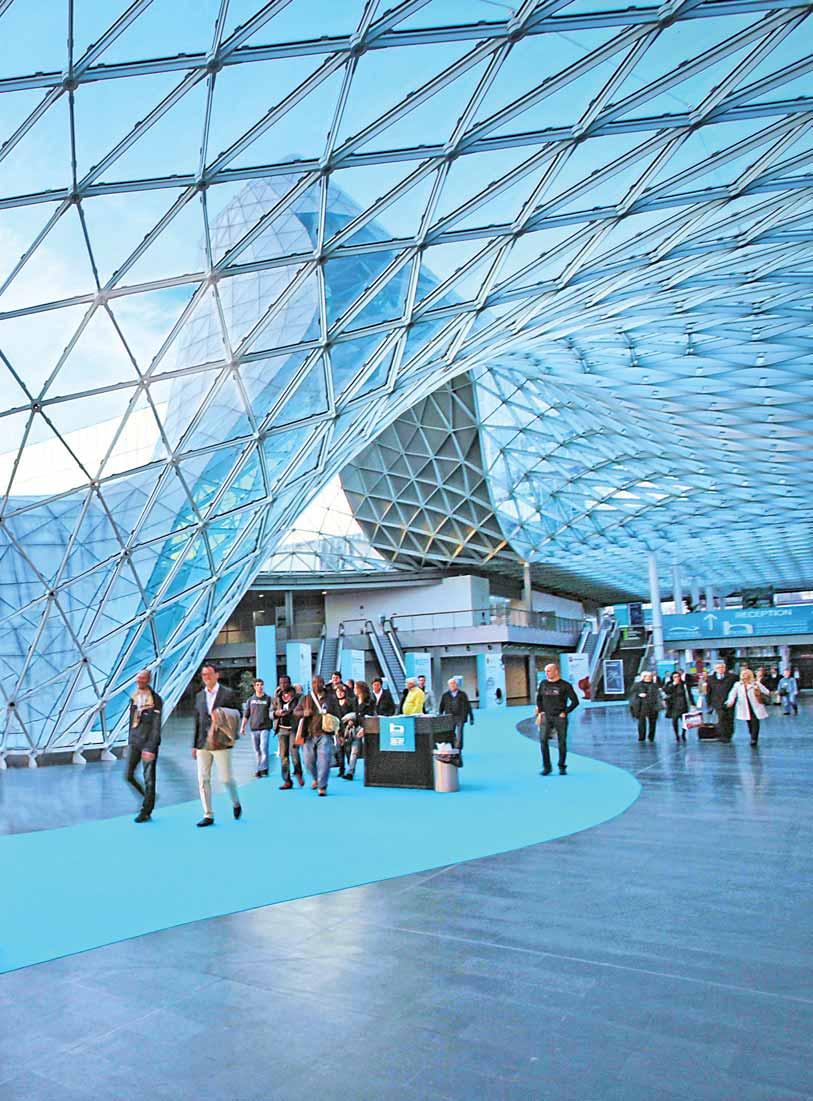




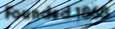











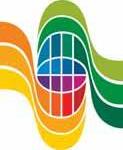
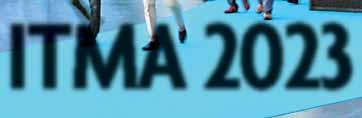
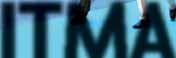
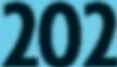
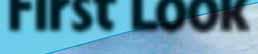


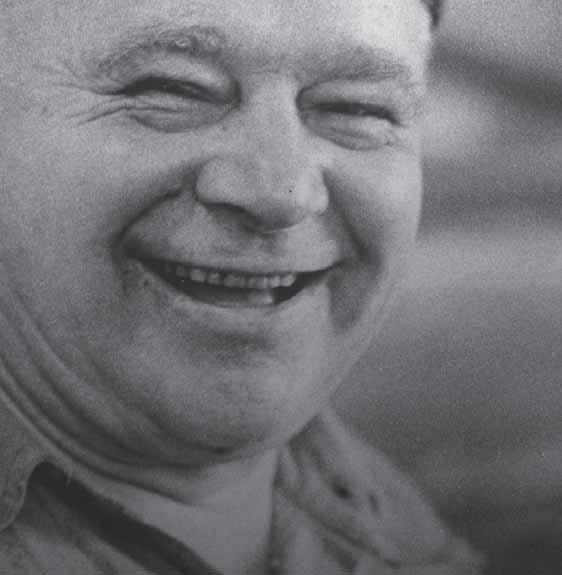


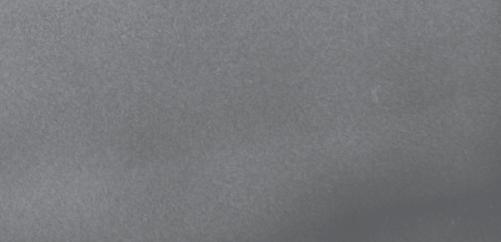
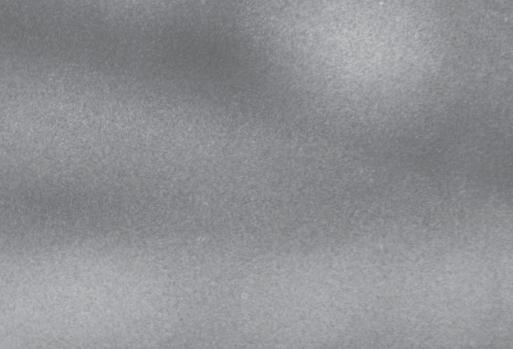
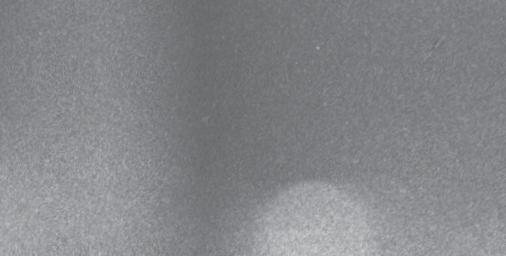

29 Sustainable Denim Production Using Open-End Versus Spun Yarn Kontoor Brands is examining its manufacturing processes to look for ways to reduce energy and its carbon footprint.
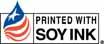
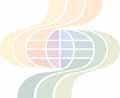
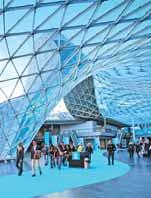
29 Sustainable Denim Production Using Open-End Versus Spun Yarn Kontoor Brands is examining its manufacturing processes to look for ways to reduce energy and its carbon footprint.
CComing off the challenging but strong year in 2022,the textile industry faces additional challenges and opportunities in 2023.
This issue of Textile World features a review of investments made last year in the industry — and it is an impressive list.Companies large and small in a variety of diverse industry sectors clearly illustrate an appetite for investing in U.S.textiles.
Large,historic companies like Mount Vernon Mills and Milliken & Company continue to invest in capacity.On the other hand,family owned business Beverly Knits is creating new opportunities with Creative Dyeing & Finishing LLC.The acquisition gives Beverly the ability to provide solutions from knitting all the way to a completed garment.
Yes,there are headwinds in the economy with rising interest rates,inflation and faltering economies around the globe.But there also are positive trends like near-shoring and the clear demonstration that global supply chains are vulnerable —a fact made evident during the pandemic.
The year 2023 also is a year jam packed with industry events with something for everybody —ITMA 2023,INDEX™23, JEC World 2023,Techtextil North America/ Texprocess Americas and the Advanced Textiles Expo,just to name just a few.But the schedule begs the questions: Has COVID changed the show and sales environment significantly? Will people want to participate? Will exhibitors invest? Will attendees travel?
The consensus seems cautious,but optimistic on both fronts.There are many people who miss the networking and sense of discovery that trade shows bring,as well as the search for and discovery of new technologies that can be leveraged or considered in a company’s investment plans.
The strong dollar may hurt U.S.exports but compared to recent years,it creates a buying
opportunity for U.S.companies to purchase equipment from euro-denominated suppliers.
In addition,there is investment chasing new dominant trends in the industry that are tied to green and sustainable manufacturing — things that measurably reduce the carbon footprint of textile manufacturing. Technologies that reduce consumption of water,energy,use more environmentally friendly chemistries,and less of them,are sought after.And new materials that have a “greener”story than traditional products are being explored.
It seems that brands and retailers continue to drive demand.And demand parameters have changed over the past five years. The cheap needle and a blind eye to sources have shifted to a place of valuing things such as traceability,authenticity and ethical origins of manufacture.More and more,companies are appointing a chief sustainability officer or vice president of sustainability.It may not be a bad thing to see these initiatives and investments valued in the supply chain.
Surely,2023 will see accelerating changes in the industry.The one thing that has always stood out about U.S.textiles is the companies that are successful have found success because of quick and smart adoption of innovations and acceptance of change.By all counts those qualities remain important today.
Fingers crossed that a negative black swan doesn’t shift the gears of the post-COVID recovery,and just maybe 2023 will yield more opportunities and fewer challenges.
James M. Borneman jborneman@TextileWorld.comEDITOR IN CHIEF James M. Borneman
EXECUTIVE EDITOR Rachael S. Davis
TECHNICAL EDITORS Dr. Lisa Parillo Chapman
Dr. Peter J. Hauser
Dr. Trevor J. Little
Dr. William Oxenham
Dr. Behnam Pourdeyhimi
Dr. Abdel-Fattah Seyam
Dr. Andre West
CONTRIBUTING EDITORS Jim Kaufmann
Stephen M. Warner
INTERNET CONTENT EDITOR Rachael S. Davis
CIRCULATION MANAGER Julie K. Brown-Davis
ADVERTISING BUSINESS MANAGER Denise Buchalter
ART & PRODUCTION MANAGER Julie K. Brown-Davis
OWNER/PUBLISHER James M. Borneman
ADVERTISING REPRESENTATIVES
UNITED STATES/CANADA Turner Marketing & Media, LLC
+864-594-0921 • sturner@textileworld.com
MEXICO, CENTRAL & SOUTH AMERICA Virgilio L. González
+ 58-412-622-2648 • Fax +58-212-985-7921 • vlgonzalezp@gmail.com
EUROPE (except ITALY) Sabine Dussey
+49-171-5473990 • sabine.dussey@dussey.de
ITALY Ferruccio & Filippo Silvera
+39-022-846716 • Fax +39-022-8938496 • info@silvera.it
ASIA James M. Borneman
+678-483-6102 • jborneman@textileworld.com
INTERNET & CLASSIFIEDS OPPORTUNITIES Julie Davis
+678-522-0404 • jdavis@textileworld.com
PO Box 683155 | Marietta, GA 30068, USA
Telephone +678-483-6102 | www.TextileWorld.com
Pearl River,N.Y.-based Anellotech has announced plans to start advanced lab testing and scale-up of its Tex-TCat™ mixed textile waste recycling technology. The solution is a fluid bed catalytic pyrolysis process that effectively recycles mixed waste textiles directly into the same chemical feedstocks such as benzene,toluene and xylenes.The closed-loop, fiber-to-fiber process then uses these compounds to make virgin polyester and nylon.According to the company,lab-scale studies have shown that Tex-TCat is capable of handling a variety of textile materials including cotton, polyester,nylon,elastane, acrylic and polyurethane. The technology is one solution to the mixed waste stream that ends up in landfills since it tackles single fiber garments as well as blends and traditionally non-recylable blends.
“Tex-TCat has the potential to divert large quantities of previously unrecyclable textiles from landfills and provide major brands,through their existing suppliers, with recycled content,”said David Sudolsky,president and CEO of Anellotech. “The technology promises to be a key enabler of the textile industry’s work to become more sustainable.”
Advanced materials manufacturer Hollingsworth & Vose (H&V), headquartered in East Walpole,Mass.,has announced a $40.2 million expansion project in Floyd County,Va.The expansion includes a 28,000-squarefoot addition to existing facilities and will add 25 new jobs.Governor Youngkin approved a $558,700 grant from the Commonwealth’s Opportunity Fund to assist Floyd County with the project.
“Hollingsworth & Vose has generated positive economic impact and job opportunities in Floyd County for more than four decades,and this significant investment further solidifies the company’s commitment to Virginia,” Governor Youngkin said.
“We’ve been a part of the Floyd,Virginia,community since 1976,”said Josh Ayer, H&V CEO.“This facility is essential to serving both our global and domestic customers.We chose Virginia for this expansion because of its positive business environment and strong support from the Commonwealth of Virginia and Floyd County.”
Warp knit fabric producer Apex Mills,Inwood,N.Y.,has announced plans to acquire a former HanesBrands facility in Patrick County,Va.The
revalyu Resources,a Germany-based chemical polyethylene terephthalate (PET) recycling company, has announced plans to open its first U.S.based PET recycling plant in Statesboro,Ga.The $50 million investment covers the initial phase of the development,which when complete,will result in capacity to process more than 225,000 pounds per day of post-consumer plastic bottles into sustainable esters and rPET chips. The facility will employ 70 associates initially.Eventually,the facility will have capacity to process up to 450,000 pounds per day. revalyu reports its proprietary chemical recycling process has processed more than 6 billion bottles into recycled PET of the highest purity.According
$3.1 million investment will retain 96 jobs and create 44 additional positions. Apex will maximize the full capacity of the facility to fulfill contracts for the Hanes basic apparel brand.Virginia Governor Glenn Youngkin approved a $300,000 grant from the Commonwealth’s Opportunity Fund to assist the county with the project. Apex Mills also is eligible to receive state benefits from the Virginia Enterprise Zone Program as well as funding and services to support employee training through the Virginia Jobs Investment Program.
“The Apex Mills family of companies has been
to the company,its process uses 91-percent less energy and 67-percent less water than conventional polyester recycling processes.revalyu’s rPET chips may be used in any sustainable PET product, but are mostly used in the textile industry.
“We thank all our U.S. customers,partners,and the Statesboro community for their support,trust, and confidence in us,”said Jan van Kisfeld,managing director of revalyu.
”Expanding our operations to the U.S.is an important milestone for our global expansion strategy.It brings us closer to our target of recycling more than two million pounds of used PET bottles per day by 2026 and contributes to solving the plastic waste problem.”
manufacturing Made in the USA textiles for 80 years,and as part of our dedication to support and grow the domestic textile industry we are continually seeking facilities and communities committed to this same goal,”said Jonathan Kurz,president and CEO,Apex Mills.
“When we became aware of the imminent closing of the HanesBrands Woolwine operation and learned more about the rich tradition of textile manufacturing in Patrick County we ultimately made the decision that this was where we wanted to locate our next fabric formation facility.” TW
It’s the technology that produced your fabric that makes your product so special.
The Itema weaving machines guarantee to worldwide weavers the most innovative technology tailored on the latest market trends: superior performances, eco-efficiency and textile mastery are the features you immediately feel when relying on Itema.
DISCOVER MORE
The global textile industry will converge on Milan in June for the 19th edition of ITMA.
TW Special Report
SSince 1951, the European Committee of Textile Machinery Manufacturers (CEMATEX) has organized what is generally regarded as the largest and most comprehensive textile machinery trade show in the world. Held once every four years, ITMA has become a platform for emerging trends and innovative solutions, new knowledge and best practices, and establishing relationships with textile industry leaders. The next edition of the show will be held June 8-14, 2023, at the Fiera Milano Rho fairgrounds in Milan, Italy. Milan is hosting ITMA for the sixth time since its inception at the now 19th edition of the show.
ITMA is owned by CEMATEX, and is organized by ITMA Services.
The overall theme for ITMA 2023 is “Transforming the World of Textiles.” Four sub-themes under this umbrella title include advanced materials, automation and digital future, innovative technologies, and sustainability and circularity.
ITMA’s quadrennial schedule somewhat insulated the event from pandemic-related effects. The last show took place in 2019, and now, 4 years later, the 2023 event is on track to occur with minimal disruption for organizers. CEMATEX President Ernesto Maurer noted in a recent interview with Textile World that the
industry has been very supportive of the event and strong participation is expected in June (See sidebar on page 10).
As of TW ’s press time, exhibition space is almost sold out and more than 1,570 exhibitors from 42 countries have booked exhibit space. Italy, Germany and Spain form the top three countries based on the number of exhibiting companies; and the top sectors are finishing, spinning, weaving, printing, knitting, winding and nonwovens.
“We are also pleasantly surprised that a number of exhibitors have taken up larger stand surface,” Maurer said. “On average, we see a more than 10 percent increase in the space booked by exhibitors.” Companies with the largest exhibit space include Epson, Groz-Beckert, Karl Mayer/Stoll, Lonati, Muratec, Oerlikon, Pai Lung, Picanol, Reggiani Macchine, Rieter, Saurer, Savio, Stäubli, Trützschler and Vandewiele.
“After weathering over two years of the pandemic, the global business community is eager to get down to real business,” noted Charles Beauduin, chairman of ITMA Services. “Businesses are looking at longterm investments in key technologies to remain competitive. As the world’s most established showcase of its kind, ITMA is the quintessential platform for the industry to buy and sell, and to collaborate face-to-face.”
Fiera Milano Rho is one of the largest fairgrounds in the world, spanning 345,000 square meters of covered gross exhibition space over 20 pavilions. The venue is well equipped with conference rooms, as well as a host of restaurants, bars and coffee houses. The fairground is located in the west of Milan and connected to the city center via a metro station, Rho Fiera. It is also served by railway and there are 14,000 parking spaces for visitors.
• Chapter 1 : Machinery for spinning preparation, man-made fiber production, spinning, auxiliary machinery and accessories
• Chapter 2 : Machinery for winding, texturing, twisting, auxiliary machinery and accessories
• Chapter 3 : Machinery for web formation, bonding and finishing of nonwovens and felting, auxiliary machinery and accessories
• Chapter 4 : Weaving preparatory machinery, weaving, tufting machinery, auxiliary machinery and accessories
• Chapter 5 : Knitting and hosiery machinery, auxiliary machinery and accessories
• Chapter 6 : Embroidery machinery, auxiliary machinery and accessories
• Chapter 7 : Braiding machinery and accessories
• Chapter 8 : Washing, bleaching, dyeing, drying, finishing, cutting, rolling and folding machinery, auxiliary machinery and accessories
• Chapter 9 : Printing machinery, digital printing machinery, auxiliary machinery and accessories
ITMA has added one new category to its list of exhibit “chapters” for 2023 — Chapter 11, which is focused on machinery for textile reinforcement structures for composites. This brings the total number of chapters to 20 (See Table 1)
CEMATEX has also launched the Start-Up Valley, a new initiative featuring companies in early stages of developments “with new and game changing solutions and technologies to support and inspire innovation for the textile, garment and fashion industry.” Sixteen startups were selected by an expert panel from a pool of applicants. Successful companies received a grant to help cover the costs of exhibiting at the Start-Up Valley during the exhibition, and also are invited to participate in the Innovator Xchange, ITMA Sustainable Innovation Award and Innovation Showcase. See the March/April 2023 issue of TW for more information about these show features and other events and education offerings for participants during the 2023 exhibition.
“CEMATEX is excited to launch the Start-Up Valley initiative to attract innovative, young companies
• Chapter 10 : Garment making machinery, other textile processing machinery, auxiliary machinery and accessories
• NEW Chapter 11 : Machinery for textile reinforcement structures for composites, auxiliary machinery and accessories
• Chapter 12 : Laboratory testing and measuring equipment and accessories
• Chapter 13 : Transport, handling, logistics, storing and packing equipment and accessories
• Chapter 14 : Equipment for recycling, waste reduction and pollution prevention and accessories
• Chapter 15 : Software for design, data monitoring, processing and integrated production
• Chapter 16 : Colorants and chemical auxiliaries for the textile industry
• Chapter 17 : Equipment and products to ensure machinery and plant operations
• Chapter 18 : Services for the textile industry
• Chapter 19 : Research and educational institutions
• Chapter 20 : Fibers, yarns and fabrics
to ITMA 2023,” Maurer said. “As the largest textile technology exhibition attracting leading textile and garment manufacturers from around the world, ITMA offers start-ups a useful
Table 1
platform to put their innovations in front of a global audience, to find investors and collaborators, and to leverage industry connections and professional networks.”
Some of the more famous visitor attractions found in Milan include (clockwise from top left): The Galleria Vittorio Emanuele II shopping arcade; Santa Maria delle Grazie church (photograph courtesy of Marcin Bialek), which houses The Last Supper by Leonardo da Vinci; and the Duomo di Milano, Italy’s largest church.
Use the QR to visit Textile World ’s collection of ITMA 2023 exhibitor previews or TextileWorld.com/category/textile-world/itma/ Exhibitors, submit your ITMA 2023 press releases and images for online coverage to rsdavis@TextileWorld.com
Visitor registration is currently open. To encourage visitors to register ahead of time, ITMA is offering an early bird rate through May 7, 2023, on its website. Visitors may purchase a one-day pass for 40 euros and an eight-day pass for 80 euros. Students are welcomed June 10-14 at a discounted rate of 25 euros for a five-day badge.
Beginning March 8, registered visitors will gain access to ITMAcon-
nect, an online platform that connects visitors with exhibitors and industry partners to make appointments for in-person meetings during the show, as well as enable discussions before and after the event.
“Even before the COVID-19 pandemic, we have been exploring ways to add value to our participants in the digital space,” Maurer remarked. “We are excited that with the launch of ITMAconnect, we now offer the global textile
ITMA is owned by the European Committee of Textile Machinery Manufacturers (CEMATEX), an organization that represents Europe’s national textile machinery associations.
Ernesto Maurer, president of the Swiss Textile Machinery Association (Swissmem), currently is serving a four-year term as CEMATEX president.
T e x t i l e W o r l d recently had the opportunity to speak to Maurer about ITMA 2023.
TW : A lot has changed in the world since the last ITMA show held in Barcelona in 2019. Has the COVID-19 pandemic affected ITMA2023 at all in terms of planning and organizing the event?
Maurer : We are fortunate that the COVID-19 pandemic started after we had successfully completed ITMA 2019. Since ITMA is held every four
years, the pandemic has minimal impact on the organizing of the exhibition as preparations only intensify two years before the exhibition. By the close of our space application, many countries have lifted COVID-19 restrictions and companies are eager to take their business back on track. Nevertheless, the pandemic has a vast impact on the global economy and disrupted supply chains, which has affected our participants adversely. Despite this, we are grateful for the support of the industry which has helped us secure a strong participation rate for ITMA 2023.
TW : Barring any unforeseen issues, what is the outlook for the show in terms of exhibitors and visitors?
Maurer : We are very optimistic about the outcome of the exhibition, as every-
community enhanced opportunities that extend beyond the physical exhibition. We hope exhibitors will make full use of this online platform to keep their contacts engaged while generating new leads to grow their businesses.”
The show is open June 8-13 from 10 a.m. until 6 p.m. each day. On June 14, the show opens at 10 a.m. and closes at 4 p.m.
Located in the northwestern section of the Po Valley, Milan is the second-largest city in Italy with a population of approximately 1.3 million. The city is the main financial, industrial and commercial center of Italy, housing the Borsa Italiana — Italy’s main stock exchange — and the headquarters of major banks and corporations.
body — exhibitors, visitors and organizers alike — are really enthusiastic.
Our exhibitor promotions have yielded favorable response and virtually all exhibition space has been fully booked. Although we may not reach the number of exhibitors as in 2019, many exhibitors are booking more space. In terms of exhibition space, we have already surpassed the 2019 size, and this is what counts in the end.
Generally, the industry is looking forward to having face-to-face interactions again and we are positive that there will a good turnout of visitors from around the world, barring unforeseen circumstances.
TW : What are the areas of strength in technologies and markets for machinery?
Maurer : The world is pivoting to digital and there are also urgent demands for sustainable and circular solutions. Textile machinery that will help textile manufacturers transform digitally and automate processes to increase productivity will be in great demand. On the sustainability front, green technologies that reduce carbon footprint or use less water and energy are currently trending.
The pandemic has also spawned demand for machinery for the manufacturing of
The city has a long history as a fashion, clothing and textile producer and is widely recognized as one of the world’s fashion capitals, making it the perfect backdrop for a textile machinery trade show.
Famous must-see sights while in Milan include the Duomo di Milano, La Scala, and Leonardo da Vinci’s The Last Supper mural.
The Duomo di Milano,— or Milan Cathedral — took nearly six centuries to build. It is the largest church in Italy and the fifth largest in the world. The Duomo is dedicated to St. Mary of the Nativity and acts as the seat of the Archbishop of Milan.
Teatro alla Scala, or La Scala as it’s more commonly known, is an opera house opened in 1778. Throughout its history, many great operatic artists and singers have appeared at the
nonwovens, especially for hygiene and medical uses.
TW : Are there any emerging areas of interest for the textile industry?
Maurer : There are two broad areas the industry is interested in: digitalization and automation; and sustainability and circularity. These are the main forces shaping the future of manufacturing for many industries, including the textile and garment industry. Both digitalization and sustainability require a long-term commitment that reshapes the entire approach to business. At the same time, they need to have mind-changing inputs at a technological, as well as economical level. Increasingly, digitalization can be used as a powerful tool in the journey towards sustainable manufacturing.
TW Does the show’s Milan location offer any benefits in terms of international travel?
Maurer : A cosmopolitan city, Milan is a very popular
venue, which is still considered one of the leading opera and ballet theatres in the world. The La Scala Theatre Chorus, La Scala Theatre Ballet and La Scala Theatre Orchestra are all housed at the opera house.
For ITMA visitors interested in a little shopping during their time in Milan, the Galleria Vittorio Emanuele II is a can’t miss stop. This four-story double arcade connecting the Duomo and La Scala, is one of the world’s oldest shopping malls built between 1865 and 1877. Today, the arcade features a variety of luxury retailers, restaurants, cafés and bars.
The Last Supper, da Vinci’s late 15th century mural, can be found in the refectory of the Convent of Santa Maria delle Grazie in Milan. The painting has seen better days after
destination for exhibitions and conventions. As it has three airports, it is extremely wellconnected to Europe and the rest of the world. Participants can make the most out of their ITMA 2023 experience by combining business with leisure. They can also take the opportunity to explore nearby picturesque cities and towns, art and culture, and gastronomic delights.
TW : Are there any new show features visitors should be aware of?
Maurer : For this edition, we have value-added to the ITMA experience by introducing ITMAconnect, a one-stop sourcing platform and knowledge hub. The platform connects the global textile community before ITMA, and extends the engagement after the exhibition.
Our exhibitors will be setting up digital spaces to showcase their exhibits, and registered visitors will be able to learn more about these
enduring repeated damage, years of neglect and various restoration attempts over time, but it is still a very popular tourist attraction.
Traveling around Milan is easy thanks to the city’s extensive transportation system comprising an underground metro, trams, buses, link lines and taxis. The underground lines offer cheap and quick movement around the city, and bus routes follow the four metro lines M1, M2, M3, M4 as well as the most popular routes between the city center and outskirts. Bus service also runs all night on Friday and Saturday nights.
For more information about ITMA 2023, visit itma.com. T e x t i l e W o r l d will continue its pre-show coverage in the March/April 2023 issue complete with an A-Z exhibitor list and show floor plan.
products and schedule onsite meetings with them from March 8. With this platform, both exhibitors and visitors can plan their participation more effectively and be more productive during the exhibition.
Another new initiative is Start-Up Valley which spotlights companies in its early stages of development with game changing solutions. Sixteen companies have been awarded a CEMATEX grant to defray their participation costs. You can find out more about these start-ups and their innovative solutions from www.itma.com.
Last, but not least, we have expanded our index of products by introducing textile composites. Visitors will be able to source machinery for textile reinforcement structures for composites, auxiliary machinery and accessories.
TW : Please give a quick synopsis of ITMA 2023. Tell readers what to expect and why they should attend.
Maurer : ITMA 2023 will be the first major exhibition for the textile and garment industry to be held after the coronavirus pandemic. The industry is looking forward to the face-to-face interactions with their industry colleagues and customers in Milan.
The theme of ITMA 2023 is “Transforming the World of Textiles.” It is underscored by four trending topics: automation and digital future, advanced materials, sustainability and circularity, and innovative technologies.
Well-known as the launchpad for innovative products, you can expect many exhibitors to take advantage of the largest industry gathering to showcase the latest innovations from across the entire manufacturing value chain.
With greater emphasis on collaboration among various stakeholders, ITMA 2023 will present great opportunities for dialogues and sharing of knowledge among industry groups. TW
EEvery three years Belgium-based EDANA — the international association serving the nonwovens and related industries — and show organizer Palexpo bring together the entire nonwovens industry at the INDEX™ trade show. The event, with its unique nonwovens focus and highly vertical format, offers four intensive days of insights, networking and rewarding business activities, according to EDANA.
However, the pandemic seriously impacted the triennial schedule for INDEX with the March 2020 edition of the show eventually taking place in October 2021 after several postponements and rescheduled dates.
This left a decision to make about when to host future editions of the show. After polling stakeholders including EDANA members and exhibitors, it was determined that the show should remain on its previously announced schedule with the next editions taking place in 2023 and 2026.
“We have heard our key stakeholders’ voice, and the leading position of INDEX among global nonwovens exhibitions gives us full trust in the industry’s favorable response to both INDEX 23 and INDEX 26,” said Michael Staal Axelsen, chair of the EDANA board and CEO of Fibertex Personal Care.
Currently, organizers are getting ready for the 2023 edition, which will be held April 18-21, at its usual loca-
Based on favorable feedback from a stakeholder poll, INDEX™ 23 returns to Geneva in 2023 despite pandemic-related disruptions to last edition
TW Special Report
tion — Palexpo in Geneva. Dates for 2026 have yet to be announced.
The atypical show schedule makes it hard to predict visitor numbers, but organizers report they expect 2023 figures to be somewhere between 9,000 and 13,000 based on 2017 and 2021 attendance. The 2021 edition hosted 500 exhibitors with an additional 200 exhibitors participating via the show’s virtual platform.
Exhibits are organized into six groups: Filtration; Geotextiles & Civil Engineering; Hygiene & Cleaning; Medical: Infection Prevention; Transportation; and Packaging.
Alongside the exhibit floor, the show will host a seminar program focused on the topics of:
•Sustainable use of geosynthetics in mega projects in civil and environmental engineering;
•A look into the future of sustainable nonwovens;
•Nonwovens are essential for the mobility transition;
•Why nonwovens are indispensable in healthcare; and
The INDEX 23 awards will be presented to winners during the exhibition, and visitors will be able to view all nominated products from each of the six award categories in a dedicated space on the show floor.
In addition, INDEX 23 will continue to offer a virtual option for participants unable to visit Geneva in person. The tool allows visitors to watch presentations, as well interact with speakers, exhibitors and other participants.
The exhibition is open April 18-20 from 9 a.m. until 6 p.m., and on April 21 from 9 a.m. until 4 p.m. A fourday ticket is available for 100 euros ($110). No daily tickets will be available. Participation in the virtual event will be free to all.
“The three year-cycle provides an ideal frequency to keep the momentum and eagerness for visitors and exhibitors alike to live the unique INDEX experience, reconnect with their business contacts and rediscover Geneva’s scenery again,” said Magali Fakhry, exhibition director, Palexpo. “We are looking forward to welcoming them again in April 2023 …” TW
For more information about INDEX ™23 including details about the seminars, events and virtual options, please visit indexnowovens.com.
DDubbed by organizer JEC Group as the “festival of composites,” the annual trade show JEC World returns to the Paris Nord Villepinte Exhibition Centre, April 25-27, 2023.
JEC World is a global show attracting visitors from around the world to view what’s new in the composites arena. Established firms as well as startups join research and development personnel, scientists, academics and other experts to do business, share insights, learn and network.
The 2022 edition of the show hosted more than 1,200 exhibitors covering the entire composites value chain from raw materials through to end-users and integrators. More than 36,000 visitors are expected in 2023.
Some exhibits will be grouped in variety of regional and international pavilions to highlight regional or national expertise in composite technologies. In addition, JEC World is offering dedicated tours for the first time.
Besides exhibitor booths, attendees can visit special show displays including the 3D Printing Village,
Comprehensive composites showcase JEC World returns to Paris in April for the 2023 edition.
TW
Special ReportPlanets highlighting real-world composite applications in the Mobility and Industry sectors. The exhibits are designed to inspire and present current trends in the composites sector.
JEC World participants also can use the Business Meetings program to plan and organize meetings. The program offers team support preshow as well as a digital platform to connect industry buyers with JEC World exhibitors.
Across the three-day event, keynotes and conference sessions on two stages will present developments and innovations impacting the composites industry.
For the sixth time, JEC World will host the JEC Composites Startup
Booster, a competition designed to gain exposure for innovations in composites and advanced materials, and help startups grow their businesses. JEC World and its partners Airbus and Mercedes-Benz will select 20 finalists from the pool of applicants that will pitch their innovations during the show. Three winners will be selected after the pitches in Materials & Products; Process, Manufacturing & Equipment; and Sustainability categories.
Each year, JEC Group confers honors on deserving, cutting-edge projects that demonstrate the value of composite materials. The JEC Composites Innovation Awards will be presented during a ceremony on March 2.
The early bird rate for visitors who register for the event before March 1 is 55 euros ($60). The price increases to 85 euros ($92) after March 1. The “late bird” rate for attendees who wait to register on site is 110 euros ($120).
The show is open from 9 a.m. until 6 p.m. each day. TW
For more information about JEC World 2023 and to register, please visit www.jec-world.events.
TTe x t i l e W o r l d ’s annual review of textile investments highlights a broad-ranging investment horizon including what may be described as traditional textile investments — spinning, weaving, dyeing and finishing — as well as apparel and on to leather alternatives for sustainable automotive interiors.
A review of TW ’s 2022 “New Plant & Equipment, M&A” news section yields interesting insight into where investors see the future opportunities in the U.S. textile industry and what areas may possibly be reinvigorated in a post-pandemic world.
Well established textile companies continued to invest in 2022. Mauldin, S.C.- based Mount Vernon Mills announced that it has agreed to acquire Wade Manufacturing Co.’s yarn spinning and weaving facility located in Rockingham, N.C. The company stated that with the acquisition, Mount Vernon Mills will be vertically integrated from yarn production to finished fabric in certain
products and will be in greater control of the company’s supply chain.
“The Rockingham facility is a modern, cost-efficient operation with an experienced and stable workforce, making it a great fit as we increase the amount of control that we have over our yarn supply, weaving operations and overall costs,” said Bill Duncan, CEO, Mount Vernon Mills. “We are also proud to expand our footprint in the U.S. and build upon our made in America commitment and heritage.”
The company stated that initially, the Rockingham facility will produce open-end spun yarn for Mount Vernon Mills and woven greige goods for the company’s flame resistant (FR) products.
Spartanburg, S.C.-based Milliken & Company made two significant announcements this year leading off with the acquisition of one of the Frontier yarn plants located in Mayodan, N.C. The company said that this acquisition from Gildan will expand Milliken’s open-end yarn production for its protective fabrics, workwear,
government and defense, industrial, and napery textile business units.
Frontier Spinning Plant #3, which will be renamed the Two Rivers Plant as a nod to its dedicated team and the community it serves, will become a spinning hub for Milliken. Multiple Milliken textile plants throughout the Southeast will source their yarn needs from the Two Rivers Plant.
Milliken also announced a plan to expand operations at its Magnolia Finishing plant in Cherokee County, S.C. The company plans a $27.4 million investment that will create 75 new jobs. The expansion will include newly added production lines to increase manufacturing capacity. The facility specializes in workwear, military and FR apparel.
Additionally, Milliken launched a new polypropylene clarifier plant in Blacksburg, S.C., that will enhance access to the Millad® NX® 8000 additive for customers worldwide. This facility will enable Milliken to meet increasing demand for plastic additives and colorants well into the future.
Albemarle, N.C.- based Beverly Knits Inc. purchased the assets of Gentry Mills. The new business — Creative Dyeing & Finishing LLC — will continue to provide dyeing & finishing services to the textile industry. The operation complements the Beverly Knits group of companies — Creative Fabrics, Creative Ticking, Altus Finishing and Hemingway Sewing Solutions.
At the time of the announcement, Ron Sytz, CEO of Beverly Knits Inc. said: “A combination of factors led to the decision to invest and expand. We have been producing quality circular knit textile products for over 42 years in Gastonia, North Carolina. We feel that this is the right time to further expand our capabilities into dyeing and finishing of fabrics. This continues to support the re-shoring of textile production and to strengthen our
capability to produce goods ‘Made in the USA.’ With this addition, Beverly Knits companies have the ability to provide solutions from knitting all the way to a completed garment.”
The Creative Dyeing and Finishing operation will provide fabric dyeing, finishing, napping and printing services to the apparel, industrial and bedding markets.
Hemingway Sewing Solutions — a subsidiary of Beverly Knits, announced plans to establish operations in Williamsburg County, S.C. The company’s $3.3 million investment was slated to create 242 new jobs. Hemingway Sewing Solutions plans to manufacture a variety of textile products for brands including Purple Mattress, Indigo and Vapor Apparel, as well as the U.S. Department of Defense.
In other acquisition news, Faribault, Minn.-based brand Faribault Woolen Mill Co. — maker of handcrafted blankets, decorative throws, apparel and accessories — added cotton to its product line up with the acquisition of Brahms Mount, a Monmouth, Maine-based manufacturer of high-quality cotton blankets, throws and other textiles. Terms of the deal were not disclosed.
“This acquisition is a great extension of our strategic focus on building Made in USA jobs,” said Faribault Mill President and CEO Ross Widmoyer. Brahms Mount will continue its cotton product manufacturing in Maine and retain the current employee base.
As part of the acquisition, Faribault Woolen Mill Co. will rebrand as Faribault Mill to reflect the product offering expansion. A new line called The Brahms Mount Collection by Faribault Mill will launch later in the spring.
Piana Technology, the 439-yearold Italy-based textile company known for innovations within the fiber and nonwovens textiles markets, has gone live with a solar panel system at its nonwovens facility in Cartersville, Ga.
The facility specializes in verticallyand crosslapped nonwovens. Since 2016, the facility has manufactured a variety of intermediate products that are behind many of the common household products used today.
Piana partnered with Southern View Energy, a local solar electrical design and solar installation company, to carefully review the facility’s energy profile and pilot an installment project. The new 471 kiloWatt system is poised to supply more than 622,000 kiloWatt hours each year and avoid an estimated 460 tons of carbon dioxide per year, which is equivalent to 125 acres of trees. Although most of this energy will go towards the facility, on days where there is overproduction, energy will go back to the city of Cartersville for redistribution.
Fab-Con Machinery Development Corp. , is a manufacturer of textile finishing equipment that has relocated to Salisbury, N.C. The company announced a $5.3 million investment to relocate its headquarters and manufacturing operation to Rowan County. Serving the knitwear industry for more than five decades, Fab-Con designs, builds, and exports finishing machines for men’s, women’s, and children’s clothing, outerwear and underwear. Fab-Con has a global footprint that supports a major market share of more than 200 customers in Asia, and North, South, and Central Americas. This relocation will be the new home of the
company’s global headquarters in a 90,000 square-foot facility as well as its machine manufacturing, administration, and sales operations.
“By relocating to North Carolina, Fab-Con will be more competitively positioned to operate at a lower cost,” said Chris Snyder, vice president, FabCon Machinery. “Several recently obtained U.S. and E.U. patents have given us a strong competitive advantage over our competitors both domestically and internationally.” The new positions, including machinists and fabricators, have a combined average annual salary of $73,081, which exceeds Rowan County’s overall annual wage of $48,360. Once filled, these new jobs have the potential to create an annual payroll impact of more than $1.9 million for the community.
New York City-based Ferrara Manufacturing , a family-owned apparel manufacturer announced the launch of Ferrara Uniform. Ferrara Manufacturing produces garments worn on the runways of New York and Paris-as well as by American Olympians and the U.S. military. Located in Manhattan’s Garment District, Ferrara Uniform is a new division of the company focusing specifically on uniforms made in the USA.
With the addition of Ferrara Uniform, the company now is made up of three specialized divisions serving diverse markets — tailoring, uniforms, and protective garments. Ferrara Supply Co. was one of the first
federal partners to provide domestically madepersonal protective equipment (PPE) as part of the 2021 American Rescue Plan, and made millions of gowns and masks in the U.S. during the pandemic for the U.S. government.
Los Angeles-based BELLA+ CANVAS announced a $11.9 million investment to establish an advanced fabric-cutting facility in Wetumpka, Ala. The operation was to open in a portion of an 890,000square-foot building vacant since 2013, when Russell Brands departed from the Elmore County city.
BELLA+CANVAS produces clothing for the retail and wholesale markets, while also offering clothing design and manufacturing services. The company is known for its domestic manufacturing mission, the development of innovative new fabrics and its sustainability practices.
At the time of the announcement, Chris Blakeslee, president of BELLA+CANVAS, said, “We are thrilled to be part of the community and look forward to creating jobs and opportunities for many in Alabama.
“After a comprehensive search, we ultimately concluded that our new location in Wetumpka, Alabama was not only optimal to enhance our manufacturing footprint and technologically advanced operations levels, but also ideal in terms of support from the local government and access to great new team members.”
BELLA+CANVAS employs more than 1,000 people at a Los Angeles cutting facility it reports is North America’s most advanced, thanks to proprietary software and specialized cutting tables. The Wetumpka facility is expected to be modeled after this operation.
New York City-based Sentinel Capital Partners , a private equity announced the acquisition of L2 Brands, a designer, manufacturer, and marketer of custom apparel and headwear for the collegiate, destination and leisure, and corporate markets.
With a heritage dating back more than 30 years, L2 Brands has grown into a diversified business with a successful history of long-term profitable growth. L2’s two brands — League and Legacy — offer widely recognized lines of premium apparel and headwear.
“L2 has a three-decade reputation for offering leading brands, excellent customer service, and high-quality products,” said Sentinel Partner John Van Sickle. “Sentinel is excited to partner with L2 and its talented management team for its next chapter of growth.”
League was founded in 1991 and Legacy was launched one year later and has become the brand of choice in customized headwear and winter knits. These brands include more than 150 styles for men and women that are sold into the collegiate, destination and leisure, and corporate markets.
Dahlonega, Ga.-based RefrigiWear , a supplier of insulated work apparel for the cold chain, announced its acquisition of Samco Freezerwear Co. (Samco) . Founded in 1968, Samco is a provider of freezerwear, insulated industrial workwear, and other insulated industrial apparel and accessories for workers in the food-related cold chain.
“We are excited to welcome Samco to the RefrigiWear family. This acquisition will help us serve our customers with a broader range of choices,” explained Ryan Silberman, RefrigiWear CEO. “For us, it’s all about the customer and gaining capabilities to serve the ever-changing and demanding environments they face in the cold chain.”
Both companies offer a selection of products that keep workers warm and safe in temperature-controlled distribution and production facilities, which can sometimes operate in temperatures well-below freezing. RefrigiWear and Samco continue to operate under separate brand names with diverse product offerings for customers both small and large.
Michael Southard, managing director of Beachwood, Ohio-based Elvisridge Capital LLC, announced the acquisition of Glacier Outdoor Inc. (Glacier Glove). Based in Reno, Nev., Glacier Glove manufactures gloves and other apparel for the fishing and hunting industries. Glacier now joins Elvisridge Capital’s other fishing-related brands, Blackfin Rods and fishing line manufacturer BBS (FINS Fishing).
“Glacier fits well with our existing portfolio companies in this space,” Southard stated. “Our strategy will be to continue to add distribution points, as well as increase the speed and quantity of product development.”
Memphis, Tenn.-based Radians® — a manufacturer of personal protective equipment including Radwear ® high visibility apparel,
rainwear, hand protection, head gear, cooling products, heated jackets, workwear, N95 respirators and face masks/gaiters among other products —announced the expansion of its Memphis campus.
“We’re very happy that the new space is conveniently located next door to our Discover buildings and very close to our Distriplex headquarter buildings,” said CEO Mike Tutor. “The increase in space is significant because the expansion represents a 20 percent increase in Radians’ overall square footage, bringing our Memphis campus footprint to approximately eight acres under roof.”
According to Tutor, the expansion allows Radians to have more inventory in-house strengthening its supply chain capabilities and provides the needed space required for its growing warehousing operations and workforce.
“Our employees are ecstatic about
having a larger and more efficient workspace at Mineral Wells,” said President Bill England. “Thanks to our employees, sales team, large distributor networks, and product innovations, we have experienced explosive growth in multiple product lines. It was time for more space and resources to support this growth.”
Headquartered in Conover, N.C., furniture manufacturer Vanguard Furniture Company Inc. announced an investment of more than $5.9 million for an expansion of its upholstery manufacturing operations to Morganton, N.C.
“North Carolina continues to be the global leader for furniture manufacturing,” said North Carolina Governor Roy Cooper in a press release.
Vanguard Furniture is a manufacturer and marketer of high-end case goods and upholstery. It is a familyheld company, employing 680 asso-
ciates operating out of seven manufacturing facilities in Conover, N.C., and Hillsville, Va., with flagship showrooms showroom in High Point, N.C., and Las Vegas.
Sausalito, Calif.-based high-end furniture company Serena & Lily announced it will locate its first East Coast operation with a new $55 million, 1.2-million-square-foot distribution facility located at the Georgia International Trade Center in Effingham County, Ga.
“Our unmatched logistics infrastructure through air, land, and sea is an asset to any company that chooses to locate here,”said Governor Brian Kemp. “We are home to the nation’s fastest-growing port, and Georgia has established itself as the logistics hub of the Southeast. We are excited Serena & Lily chose Georgia to grow their business, and
we look forward to helping them reach markets all over the world.”
Sean Connelly, COO of Serena & Lily said, “With its proximity to the Port of Savannah and our East Coast customers, this facility will play an integral role in supporting our infrastructure network to shorten lead times and ultimately enhance our customer experience.”
Biotechnology company MycoWorks , a firm that specializes in mycelium-based materials as sustainable, luxury-quality leather alternatives, has announced plans to establish operations in Union County, S.C. The company’s $107 million investment will create 400 new jobs.
Established in 2013, MycoWorks’ patented Fine Mycelium ™ process produces materials including Reishi™ — a globally recognized breakthrough in materials science — that mimics the performance of animal leathers and lowers environmental impacts. The material offers creative solutions and new design possibilities for fashion and luxury brands while offering relief to supply chain constraints.
MycoWorks also announced its newest investor GM Ventures —the investment arm of General Motors Co. — and their long-term agreement to co-develop Fine Mycelium materials for potential use in a range of applications within automotive design. MycoWorks’ collaboration with GM marks the exploration of its entry into one of the largest end-use markets for leather and demonstrates the significant opportu-
nity to create more sustainable materials for the automotive space.
Hillside, N.J.-based technical textile manufacturer Ronald Mark Associates Inc. (RMA), a producer of custom resin and vinyl fabric formulations and technical services, announced a $13.5 million investment to establish a manufacturing operation in Tazewell County, Va.
“Ronald Mark Associates has selected the State of Virginia to expand their operations in advanced fabric coating. The progressive talent of Tazewell County is a perfect place to start, create, and produce infrastructure fabrics and technical textiles for our Ronald Mark customers,” said RMA President Michael Satz.
RMA has been marketing, distributing, and packaging PVC resin since 1971 and manufacturing vinyl films and technical textiles since 1979. RMA has positioned itself as an innovator and streamlined manufacturer in the flat roof membrane market as well as critical proprietary fabrics for infrastructure.
St. Louis-based Baldwin Technology Co. Inc. has announced the installation of its state-of-the-art TexCoat G4 finishing system
Using Baldwin’s cost-efficient and highly sustainable spray finishing technology, Graniteville Specialty Fabrics will be able to increase production efficiency, and minimize chemical and water waste.
Based in Graniteville, S.C., Graniteville Specialty Fabrics produces coatings and coated fabrics that are resistant to water, fire, ultraviolet rays and weather for the military, marine and tent markets, among other markets. The company excels in developing and sourcing custom coatings, and creating specialized technical solutions to meet specific, and often unique, end-user requirements. The installation of Baldwin’s TexCoat G4 is part of a major facility upgrade to maximize production efficiency and capacity in the durable water-repellent finishing and coating line to meet growing customer demand for advanced engineered products.
“We are pleased to be a key partner in Graniteville Specialty Fabrics’ modernization project,” said Rick Stanford, Baldwin’s vice president of Global Business Development, Textiles. “The team reached out to us, and it was clear that the TexCoat G4 was the right tool to help them minimize waste and increase productivity.”
New York City-based Victor Capital Partners announced that an affiliate has entered into a definitive agreement to sell PrimaLoft Inc. to Compass Diversified . PrimaLoft is a developer of advanced insulations and fabrics that global brands use to deliver high performance and comfort while also reducing impact on the environment. Based in Latham, N.Y., PrimaLoft technologies are integral components that balance innovation, performance, and sustainability, and have been widely adopted in the finished products of over 950 brands.
Victor Capital acquired a majority interest in PrimaLoft in 2017 in partnership with the management team, which maintained a significant investment in the business.
The more than 950 global brand partners of PrimaLoft include outdoor brands Patagonia, Helly Hanson, LL Bean, and Arc’teryx; athletic brands Nike, Adidas, lululemon and Athleta; fashion/lifestyle brands Polo Ralph
Lauren, Stone Island, J.Crew and Prada; and home goods brands The Company Store and Boll & Branch. PrimaLoft also offers a licensing program, providing its technologies and branding to an expanded set of nonwoven and other textile markets.
Cleveland-based Avient Corp. completed its purchase of the protective materials business of DSM (including the Dyneema ® brand), which will now be called Avient Protective Materials and reported within the company’s Specialty Engineered Materials segment.
“With the addition of the Protective Materials business, we have significantly increased the size of our fastest growing platform and firmly established Avient as a leader in the advanced composites space,” said Chris Pederson, president, Specialty Engineered Materials, Avient.
The foundation of Avient Protective Materials is the renowned technology and globally admired brand of Dyneema, the World’s Strongest Fiber ™ . The ultra-lightweight specialty fiber is 15 times stronger than steel and is used in demanding applications, such as ballistic personal protection, marine and sustainable infrastructure, renewable energy, industrial protection and outdoor sports. The business includes six production facilities, four research and development centers and approximately 1,000 employees located around the world.
Bast Fibre Technologies Inc. (BFT) , a manufacturer of premium natural fibers, completed its purchase of Georgia-Pacific’s Lumberton Cellulose LLC . The Lumberton, N.C., site is a highly automated state-of-the-art manufacturing facility with approximately 25 employees that will now operate under the new name of BFT Lumberton.
BFT plans to significantly expand capacity to over 30,000 metric tons
per year, establishing BFT Lumberton as one of the largest fully integrated natural fiber processing parks in North America.
“As changes in consumer preferences and single-use plastics legislation drive demand for alternatives to synthetic fibers, consumer brand companies are seeking to manufacture products using fiber with minimal ecological impacts,” said BFT President Jim Posa. “The BFT Lumberton plant will produce all-natural, clean, soft, compostable fibers that are capable of displacing synthetics fibers in many nonwoven and textile applications and will bring valuable cleantech sector jobs to the local community.”
In addition to the planned capacity increase, the acquisition of the Lumberton facility diversifies BFT’s natural fiber offerings allowing entry into complementary product categories for cosmetic cotton, filtration, hygiene, and other nonwoven applications.
FyberX Holdings, a developer of technology to process raw agricultural biomass into refined natural fibers, will invest $17.5 million to establish its U.S. headquarters and production operation in the former Kinderton Distribution Center building in Mecklenburg County, Va. The new facility will process hemp and other agricultural products, producing fibers to supply the textile industry, and will create 45 new jobs.
“Industrial hemp fiber has great potential in Virginia, and FyberX can unlock that potential and create a sustainable market for the Commonwealth’s hemp producers, with its investments into the processing infrastructure for this crop,”said Secretary of Agriculture and Forestry Matthew Lohr.“I commend FyberX for their bold vision and commitment to bringing this needed infrastructure to Southern Virginia.”
“Southern Virginia is strategically positioned to play a vital role in unlocking the economic potential of industrial hemp fiber in a variety of markets including textiles, construction, packag-
ing, automotive, and bioplastics,”said Ben Young, FyberX CEO.
FyberX was founded in 2019 to build the foundational infrastructure required to process raw agricultural biomass into refined natural fibers, creating more environmentally friendly manufacturing solutions. The company focuses on industrial hemp sources in the United States. and will use its technology to process hemp for use in sustainable replacements for the textile, packaging, and construction industries.
The year 2022 was a healthy year for textile investment and the preceding announcements are just a snapshot to illustrate the breadth of interest in U.S. textile investment. There were many additional investments in fiber though finishing — like the investment in retrofitting at TSG Finishing’s plant in Hickory, N.C.
Still many other investments go unreported because of privacy requests and the competitive nature of the business.
TW editors try to report what they can, and if textile investment is of particular interest, keep an eye on T W ’s “New Plant & Equipment, M&A” section under the news menu on TextileWorld .com.
Let’s see if 2023 — an ITMA year — shows continued growth and strength. TW
Stein Fibers LLC,Albany,N.Y., has purchased the North American fiber operation of Fibertex Corp. The combined operation will benefit both companies and expand the North America fiber product portfolio.
“I am excited to partner with the Stein Fibers organization,which shares the same core values and believe the combination will provide an opportunity to grow our relationships with both customers and suppliers.”
“We are truly excited to work with Ernest as Fibertex and Stein Fibers have similar histories rooted in a deep family commitment to the textile industry that has stretched generations,”said Stein Fibers’ COO Robert Taylor.
Kraig Biocraft Laboratories Inc., Ann Arbor,Mich.,reports it has delivered the first two hybrid-cross Dragon Silk™ silkworm strains to its third-party production partner in Vietnam.The current issue limiting large-scale production is robustness of the silkworms in a large-scale production environment.The new hybrid strains were developed to address this hurdle and combine the mechanical performance of the company’s original Dragon Silk worms with the size and robustness of native production silkworm strains.
“Work with our production partner in Vietnam has accelerated the identification of challenges and opportunities in scaling up production to metric tonnage
MMI Textiles,Brooklyn,Ohio, recently inked an agreement with Milliken & Company to supply Milliken Tegris® thermoplastic composite fabric.Tegris is a lightweight,but stiff material design to protect from blasts and projectiles.It also is suitable for plate carriers and belt applications.
MMI is positioned as a Tegris expert and can now offer the material at quantities previously unavailable.
“Being able to offer Tegris and partner with a leader in the textile industry like Milliken further illustrates MMI’s commitment to provide innovative products to the end customer,especially those that protect our warfighters,”said Joey Smith,MMI’s director of business development.
Germany-based Trützschler
Card Clothing (TCC) reports it will invest 12 million euros to expand its Neubulach,Germany,card clothing production facility.Production,warehouse and offices will be upgraded, which will expand the range of services offered at the site.The company has seen increased demand for its card clothing products that are used in carding processes in nonwovens as well as spinning applications.
Bangkok-based nonwovens company Avgol® has announced an investment in a new high-speed, high-capacity flexible multiple beam Reicofil 5 line for its Mocksville,N.C.,
levels,”said Jon Rice,COO,Kraig Biocraft Laboratories.
Israel-based Nilit recently introduced a version of its SENSIL® EcoCare recycled nylon 6,6 that is produced at its North American facility in Martinsville,Va.,using only U.S.materials.SENSIL EcoCare is made using post-industrial recycled nylon 6,6.According to the company, its recycling process retains the properties of virgin fiber for highquality nylon fibers and yarns.The new yarns are compliant with the Berry Amendment as well as the United States-Mexico-Canada Agreement and Dominican Republic-Central America Free Trade Agreement rules. TW
plant.The line,supplied by Germanybased Reifenhäuser Reicofil GmbH & Co.KG,is the sixth line in Mocksville.
“The addition of this new line enables us to have even greater production capacity,delivering component materials that are Made in America and offering more sustainable options for the growing North America market and around the world,”said Avgol CEO Tommi Bjornman.“This additional new line also enables the Mocksville facility to deliver additional meltblown nonwovens,ensuring we have extra capacity to meet market demand.
In other company news,Avgol was recently honored for the first time with a Supplier Excellence Award from Procter & Gamble (P&G) as a notable and valuable supplier to the company’s Baby Care business unit. TW
TTo loosely quote Marcus Aurelius, “Looking back over the past, one can foresee the future.” This same idea applies to fiber research and development. For insight on where fiber developments might go in the future, the best indicator is the past. There is no crystal ball and no way to truly predict the future, only a “guess-o-meter.” But the past suggests possible future direction. Some developments are more near-term and less of a leap of faith, while some other developments are longer-term projects that may or may not come to fruition.
The distance between a great idea and commercialization is very long and unfortunately there is a lot of opportunity for things to go wrong.
Sometimes, the greatest ideas just don’t pan out.
If we compare the fiber industry of today to that of 20 to 30 years ago, not much has changed. Today, polyester is still king and poly/cotton blends are still woven and knit into fabrics. Some 20 to 30 years ago, perhaps people thought everyone would be wearing nonwovens in a few decades and that hasn’t happened yet, although it still eventually could. Obviously, research and development is ongoing and things that are in development today will change the face of the industry in the next few decades. But it’s important to remember that change is slow and in probably the next 20 to 30 years things that are important now are still going to be important in the fiber industry.
Also, the big developments that have taken place have mostly been on the margins. If history is a straight line — and of course it never is — but if the future is like the past, then the margins are where most of the new developments will remain.
If that’s the case, then why focus on those innovations? The answer is because that’s where the money is. Even if a company is working on a development that is going to remain in the margins, it’s where producers can make money instead of competing solely on price and volume. It’s one of the reasons why companies chase innovations and new developments.
There also is always the dream that not only can research create something that is profitable, but perhaps it will result in a “new polyester” that fundamentally changes the industry. Polyester has been king for decades, but it didn’t exist 100 years ago, and change will happen eventually.
Bicomponent fibers are not new, but one of the still untapped uses is in binder fiber applications. There is new technology coming online that will allow for expanded performance of binder fibers. People are fairly familiar with standard binder fibers. With new polymer developments, there are new melt temperatures available to tailor the fiber to the application. The ability to chose between an amorphous or a crystalline binder also can better tailor a product to do the job that’s needed.
In addition, one newer possibility is a binder that will bond the fabric together initially and then at whatever time is needed for the application, the bonds may be released. Those are potentially near-term possibilities in binder fiber innovations.
Taggant technologies are another currently available bicomponent technology that is underutilized and there is a lot of value in these type of
fiber technologies. An identifier like a 2D barcode can be created, or materials can be used that light up the fiber when viewed using different wavelengths of light.
A 2D barcode provides a lot of information where forensic approach of sorts is required to determine the cross section and extract the information in the barcode. In comparison, a tag that is revealed using a certain wavelength of light is more of a simplistic, binary technology that only identifies the fiber if it’s present. There’s not a whole lot of information in this type of tag, but it can be useful in certain applications such as a point-of-sale scan.
It’s possible in the future some sort of taggant technologies may be required in order to have downstream accountability. Such applications offer a way to extend bicomponent technology beyond where it is today.
Using a DNA additive is a newer approach to these taggant technologies. DNA can be inserted into a fiber now that contains a lot of information similar to the 2D barcode. One advantage of using DNA is extracting the information is more straightforward and forensic methods aren’t necessary. This technology is not cheaper, but a more straightforward way of embedding lots of information into a fiber.
Beyond taggants, splittable fibers also offer some expansion possibilities for bicomponent fibers in the market. When producing spun yarns, microfibers pose a problem in the carding machine. However, with control of the cross section of a bicomponent fiber, the splittability of the fiber also can be controlled,
which offers a way to incorporate microfibers into spun yarns. The splittability property is important because carding processes are all different, and the design and application may require a different mix of splittable microfibers and nonmicrofibers. With all of the different cross sections that can be produced in combination with the many different types of polymers available, it is possible to manufacture a really broad range of splittable fiber.
Cardable, splittable bicomponent fibers include (See Figure 1):
•Hollow;
•Hollow partial wrap;
•Standard;
fiber mix to carry all the fiber through the process. But this technique allows microfibers to be blended in spun yarns. This expansion of bicomponent fiber applications may require some additional downstream work, but it’s a fairly low hanging fruit that is available and ripe for development in the short-term.
Another short-term development on the fiber future “guess-o-meter” is environmentally advantaged fibers. The term “green” fiber can mean many different things, and there is much more to “green” fibers than just sustainability or carbon dioxide mitigation including microplastic concerns, toxicity and landfill issues. Different fiber technologies address different environmental concerns and the term environmentally advantaged is a fitting term to use to cover many scenarios.
One of the first things that is already underway is an expanding role for natural fibers. It’s clear from a consumer’s point of view that these fibers are greener than a plastic. However, despite demand, natural fibers are not 100-percent of what is used in textiles because they don’t deliver the properties that polyester in particular delivers.
•Standard partial wrap; and
•Hollow full wrap.
With a range of splittabilities, it’s possible to tailor a fiber to a process and card a blend where the bicomponent fibers split during carding. The caveat is that there has to be some non-splittable, non-microfibers in the
For use of natural fibers to expand much more than it has already, there may need to be some work done to chemically modify the fibers to expand their property envelope. Also, at some point in the future, there will be a debate about whether to use our land to produce something that isn’t food. Producers of polylactic acid (PLA) fibers already have seen some push back on the polymer because they are using corn and are therefore consuming some of the food supply. So, the expansion of natural fibers may hinge on the question “fibers or food?” Ultimately the battle —if it is even a battle —between natural and synthetic fibers is going to be one that is potentially limited by the evolution of plastics. There is a lot of
work taking place in the plastics industry to address some of the environmental problems that plastics present, and solutions are becoming compelling. Not many of the solutions are cost effective yet, but at least technologically there are a lot of answers to environmental issues. The speed of development and the ultimate cost of new solutions may very well may limit the impetus to focus more on natural fibers.
One newer technology developed in the plastics industry that delivers a lot of bang for the buck is degradation enhancing additives (DEAs). CiCLO® is one such technology offered by Intrinsic Advanced Materials, a joint venture between Intrinsic Textiles Group and Parkdale Advanced Materials. There are other technologies in the market, and they work in basically the same way. When DEAs are added to just about any plastic, the material will degrade in a microbe-rich environment in two to three years and not in 200 or 300 years.
One of the appealing things about these technologies is the relative low cost compared to biopolymers, which are often sought after to solve environmental issues. Biopolymers offer a lot of technical advantages, but none of them is cheap. DEAs are relatively low cost and can be put into a product right away. Another big advantage is that biopolymers require a significant sacrifice in properties in the application or processing, or both. DEAs allow an environmental benefit at low cost, quickly with essentially no sacrifice in properties. In addition, some biopolymers require composting to degrade, and DEAs allow a fiber to degrade in any microbe-rich environment without requiring composting.
One drawback is that the degradation may not occur as fast as it does in some of the other polymers such as PLA. But there is a compelling proposition for the use of DEAs when comparing a product that degrades quickly but is expensive and costs a lot in terms of properties versus a fiber with DEAs that doesn’t degrade right away, but
degrades in a couple of years versus centuries and the technology exists today. DEAs likely will become an important technology in a fairly short amount of time.
Polyethylene furanoate (PEF) is a new biopolymer being developed primarily by Avantium in the Netherlands, among other companies. PEF is an exception in the biopolymer world because choosing biobased ingredients does not mean sacrificing fiber properties as it does with other biopolymers.
Fully biobased polyethylene terephthalate (PET) is not yet a reality because biobased ethylene is an available feedstock, but the terephthalate part is really tricky. In PEF, the furanoate monomer —2,5-furandicaboxylic acid —combines with biobased ethylene glycol to make a polymer that is very similar to PET, but the furanoate monomer also is biobased so the resulting PEF polymer is 100-percent biobased. The fiber has some natural degradability, but is not spontaneously biodegradable, which is useful because many applications require durability. PEF is inbetween the two extremes —it doesn’t degrade right away, but it can be made to degrade if necessary. The fiber properties are comparable to polyester, but the fiber is biodegradable in the medium-term and may be
recycled in typical PET recycling streams, which is a significant advantage. Another upside is that PEF may be produced in an existing PET plant. The reaction kinetics are different, but fundamentally, manufacturers just need to swap the terephthalate monomer for the furanoate monomer. In addition, PEF in particular would be a good polymer to use in combination with DEAs.
One drawback to PEF is its cost. This is due in part to the fact that it’s early in the development stage, so the price will come down. Avantium has shared projections for the cost, and it is predicting that with scale the price will be comparable to PLA, maybe a little higher. But that is a significant premium, which has frankly hampered the adoption of PLA in mass markets.
On the price front, there are other reasons to believe the cost will get to an acceptable level. Some research is taking place to develop a polymerization process that may cut the cost of making PEF to about 20 percent of what it is now. In addition, the oxygen barrier of PEF is fantastic. This property means nothing in fibers, but is very important in the plastic bottle market. Coca-Cola, among other companies, is investing a lot of money to develop bioplastic bottles, which will drive the development of PEF.
The other option is to make a 100percent biodegradable PET, which can be done, but it’s expensive and despite large investments that nut has not yet been cracked. And with the property differences in mind, PEF has a chance to be the winner over biodegradable polyester. If it is, the volumes will be enormous and the cost will be driven down. PEF is a fiber to watch. The research is not quite there yet, but the first pilot scale plant is in the works.
Polyhydroxy alkanoates (PHAs) is another class of biopolymers that bears watching. They are still not quite ready for prime time as a textile fiber, but the technology is getting closer to commercialization. PHAs have many advantages over some other materials. They are 100-percent biobased and are spontaneously biodegradable. As previously mentioned, it’s an advantage that PEF has some durability to it — that’s something that will be desired in many applications. But there are other applications where spontaneous degradability is important. Anywhere there are microbes, PHAs will degrade. That doesn’t mean it will degrade hanging in the closet. But when left on the ground, degradation is quick; and the polymer is also marine degradable, which makes it a promising solution to the marine plastics and microplastics issues. PHAs are likely to be available at relatively low cost at scale — possibly even cheaper than polypropylene, which is a tremendous advantage over other biopolymers. PHAs also can be made
from just about any biomaterial or carbon dioxide so sugars from corn or other food sources are not impacted. Factories can even use carbon dioxide captured by a scrubber on a smokestack as the raw material for a PHA — how green is that? PHAs are not quite there yet in terms of processability, but this is chemistry base that has wide tailorability. There are many ways to tailor the properties of the polymer, and this, plus the compelling environmental advantages, will hopefully drive development forward to a solution.
Chemical recycling also is potentially a big deal in the environmentally advantaged fibers category. Years ago, BASF looked into depolymerizing nylon. Back then, it wasn’t an environmental issue, it was more cost-driven research, but the company determined it was cost prohibitive. It’s interesting to see renewed activity in this area today. Polyester and polypropylene recycling plants are being built many places in the world now, and it’s hard to imagine that kind of capital would be invested unless it was going to be a profitable endeavor.
Chemical recycling also eliminates downcycling so conceivably a polyester can be recycled eternally.
There is a debate about recycling versus using biopolymers because recycling seems so simple —it’s just a mechanical process —and biopolymers seem more exotic and advantageous. But in terms of delivering an environmental advantage,
recycling, in the right context, can be more powerful than a polymer that easily degrades. In the future, there will be a lot more focus on chemical recycling efforts.
There are things that can be done with fibers and textiles that haven’t been adequately developed yet, including electrical applications. Electrically functional apparel — adding wires to textiles —has been in development for some time, but it hasn’t yet taken the industry by storm. But innovation is ongoing, and it is likely the challenges will be resolved.
More so, electrically activated substrates hold a lot of promise and could be very useful. Think about an electrical stimulus activating motion in a substrate, for example. Or other types of activation include photovoltaic textiles that may be useful in garments, window blinds or roofing substrates. Such technologies also could be used to create foldable or rollable display screens that would eliminate the need for a separate projector. This sort of technology is not something that could be produced tomorrow – a lot of work and investigation would need to go into how exactly it would work – but materials are available that are appropriate for the job, and there is enough value there that the research is worthwhile.
Textiles also can be conductors. There is one naturally conductive polymer, a polyaniline, that has limited conductivity. But the fact that it exists suggests that there could be development work done to create a more conductive fiber that is more valuable than the currently available polyaniline.
Conductive fibers also can be created using conductive additives such as carbon nanotubes, or by using vapor deposition technologies.
Carbon nanotubes may be used to produce a yarn that is more conductive, but what’s most interesting is that single wall carbon nanotubes are not just conductive, they are super conductors. If these microscopic car-
bon nanotubes could be embedded in a matrix of polyester, for example, and it was possible to make something with practical length, these new materials could offer a lot of value as super conductors.
It is possible to deposit metal on polymers —for example, silver deposition on nylon —but those fibers get very expensive because of the amount of silver that is involved. However, silver cannot be deposited on polyester using the same process used to deposit silver on nylon. So, imagine a bicomponent fiber with just a sliver of nylon running throughout. Silver could be deposited only on the nylon to create a fiber that offers 100 percent of the conductivity for a fraction of the cost.
Further for the electrical applications, polyvinylidene fluoride is melt extrudable so it can be made into fibers. And when stretched and drawn during production in a properly oriented electrical field, the result is a fiber that is piezoelectric. There must be value in a piezoelectric fiber for use in sensors, actuators or synthetic muscles as just a few examples. This is an untapped, valuable opportunity in the fiber arena waiting for someone to find a solution.
Moving into another territory with regards to fantasy future fibers, are solvent-spun protein fibers. The horizon in this category is almost limitless. The goal is to use proteins and solvent spin them — ideally using water as the solvent to ensure an environmentally safe process — to make something similar to a synthetic spider silk that has all the properties you could ever want in a fiber — lightweight, strong and with stretch.
There is lots of research in this area and things are getting closer to commercialization every day. Once a solution is found to produce a commercially useable protein fiber, spider silk is just the beginning because there is an entirely new landscape of chemistries to work with that offer an enormous range of new proper-
ties. Not just improved properties, but different properties. The field is ripe for picking if the fundamental technology can be mastered. A Wallace Carothers moment in protein fibers is needed, and once that happens, a whole new world will open up that could completely change the fiber landscape in a way not seen in the past 20 to 30 years.
Almost maxing out the future “guess-o-meter” are 3D fibers. Innovation first mastered one dimension — how long a fiber is —and that was the only variable. Then research made it possible to control variation in the second dimension to produce bicomponent fibers and non-circular cross sections. But examining the third dimension in fibers may bring lots of value. For example, perhaps it’s possible to change the way a fiber is shaped or its composition along the length — so there is one cross section here and a different cross section further along; or you have one material here and then another material or different combination of materials further along the length. Maybe in 20 or 30 years the industry will be closer to producing such fibers.
One possible application is in synthetic goose down. Goose down,
which has little barbules along the length (See Figure 2) , is one of the most expensive fiber products there is. When a goose down batting is compressed, the barbules catch on perpendicular fibers and the fiber bends instead of pushing past. When pressure is released, the down expands back and insulative properties are maintained. A synthetic goose down would be a valuable product, but the technology first has to exist to change the shape of the fiber along the length.
This is just one view of where the future may lie in fibers if the “guess-o-meter” is correct. It might work out that way, or it might not, but past development suggests future direction. TW
Editor’s Note: Jeff Dugan is the cofounder of Fiber Innovation Technology and he served as vice president of research up until his recent retirement. He still helps people with new fiber projects as a consultant on an occasional basis. During his 39-year career, Dugan authored numerous papers and is named on almost 50 patents. He also presented the first and only TED Talk on the subject of fibers. This article is based on content from Dugan’s presentation, “Future Fibers,” given at the last Synthetic Yarn and Fabric Association (SYFA) conference.
Sunbrella fabrics can be applied throughout the entire boat, from Bimini tops that provide comfort from the sun to soft seating, pillows and durable covers that keep boats clean and free of debris when stored so boaters can leave the dock at a moment’s notice. (Photograph © Steve Exum)
hopes that by sharing its knowledge, it can educate and inspire those that are part of the marine community because the future is bright for all.
TThe post-pandemic surge in recreational boating activity reignited the marine industry with new opportunities for innovation and connection. Ongoing research from the National Marine Manufacturers Association affirms this momentum will continue, which is why it has become increasingly important for marine textile companies to understand evolving consumer habits and apply those insights to develop new marine products and enhance existing ones to meet the needs of boaters today and tomorrow.
From commercial yachts that require premier textiles with a soft and luxurious hand to consumer fishing boats, pontoons and catamarans with seating crafted to protect against challenges such as microbial pinking, there has never been such an exciting opportunity for textile companies that serve the boating industry. How can
we help boaters with different desires create memorable experiences on the water? How can we best serve each of our stakeholders — from boaters to manufacturers to fabricators — based on their specific needs? These are some of the questions posed every day at Sunbrella since the company entered the market more than 60 years ago—but these words now have new meaning.
As the Sunbrella team approaches 2023 at full throttle, they also are taking time to reel it back and reflect on how far Sunbrella has come as a brand with a purpose and ethos the company feels proud to stand behind. For decades, the company’s success has been centered on a legacy of complete performance, from fabrics that stand the test of time in demanding environments to the service and support that Sunbrella extends to customers. The company
Sunbrella began in 1961 when the brand’s founders identified an opportunity to develop an awning canvas with a substantially longer lifespan than cotton. The patented material that was created not only delivered on that longevity, but also offered an unprecedented resistance to fading. Sunbrella fabric was the first of its kind and the company quickly began to lead the awning market.
It wasn’t long before Sunbrella realized that its performance fabrics could extend beyond shade structures. In the years that followed, the founders brought the innovative spirit of Sunbrella into several new environments and applications, including marine. From superyachts to speedboats, the state-of-the-art fabrics began appearing on vessels of all sizes around the world as a result of the protection they offered against the elements. The company feels proud to have redefined what consumers could expect from performance textiles in those initial years.
Ever since Sunbrella entered the marine market, it has been a priority for the brand to deliver premium fabric that gives boaters, manufacturers and fabricators the materials they need to create the extraordinary in textile design, whether that be a vibrant color palette or niche function. Sunbrella is founded on the belief that fabrics should be beautiful, comfortable and functional. For marine appli-
Following the company’s ethos that fabrics should be beautiful, comfortable and functional, Sunbrella marine fabrics are designed and engineered to meet the needs of boaters today and tomorrow.
cations, this translates to a luxurious experience on the water with Bimini tops that provide comfort from the sun, soft seating and pillows that deliver worry-free performance and are engineered to stand up to everything from splashes to spills, and last but not least, durable covers that keep boats clean and free of debris when stored so boaters can leave the dock at a moment’s notice. It also means producing fabric offerings in a wide range of colors and patterns to reflect a consumer’s unique style. The expansive Sunbrella portfolio includes textiles that are all woven with careful attention to detail. The brand stand behind its textiles with industry-leading warranties. This has been critical to earn and maintain the trust of trade partners and consumers in the marine space.
Today, the term “performance fabric” is used broadly to refer to any textile designed to be easily cleanable and withstand wear and tear, but not all performance fabrics are created equal. Some rely on a sprayed-on topcoat or finish that wears away over time or after consistent exposure to ultraviolet (UV) rays from the sun. The proprietary performance of Sunbrella is engineered into the core of its fabrics with yarns saturated at the fiber level with exclusive UV-stable pigments. For example, Sunbrella marine canvas fabrics block 98 percent of harmful UV light. Sunbrella shade fabrics are further recommended by the Skin Cancer Foundation as part of a complete sun protection regimen alongside regular use of sunscreen to aid in preventing sun-induced skin damage.
Sunbrella continues to push the boundaries with its formulations to ensure the innovative fabrics exceed the expectations of modern life, including new products that work harder and smarter for boaters to combatmarine-specific phenomena like microbial pinking or salt residue. From sourcing raw materials to manufacturing to distribution, the company adheres to strict standards to ensure its fabrics perform and the company’s vertically integrated pro-
duction process aligns with company values. All fabrics must pass an extensive combination of 33 rigorous in-house and third party-certified tests to ensure they provide exceptional quality and durability to perform in the harshest of environments. These tests gauge things such as colorfastness, flame retardancy, abrasion resistance, weathering and more.
Most recently, the company launched Sunbrella Horizon marine vinyl — the company’s first nonwoven upholstery fabric. Horizon offers revolutionary resistance against microbial pinking, four-way stretch and recovery and lasting performance for years of worry-free enjoyment. It also features aknit-backed construction that prevents misshaping.This soft vinyl fabric is suitable for numerous marine upholstery applications, including captain’s chairs, cushions, bench seating and sunpads, and is designed to complement and coordinate with gelcoat and Sunbrella marine canvas fabrics. Additionally, Horizon is weather-, mold- and mildew-resistant, resists cold cracking and is easy to clean — even with bleach — so boaters can spend more time on the water and less time on maintenance and care. Horizon also features highly UV-stable pigments for optimal color retention over time with strong protection against fading from sunlight. The product is now available in more than 30 styles, 25 colors and two embossing patterns, and is being used by a growing number of boat manufacturers.
Sunbrella customers always have been more than a purchase order to the company and over the years, the company has learned that by making a commitment to product excellence, it is investing in their success. Customers deserve the best for their customers — and everyone must work with the greater success of the industry in mind.
To keep up with early and ongoing success across a growing number of industries, the parent company of Sunbrella, Glen Raven, significantly expanded its manufacturing facilities over the past few decades to have a global footprint across three continents. While the Sunbrella headquarters and primary production facilities are located in the United States, there are additional manufacturing facilities in Lille, France, and Suzhou, China —two strategic locations that have enabled the company to deliver on the growing demand.
Today, these capital investments span new technologies such as B2B portals for customers to see inventory in real time, as well as a multiphase $250+ million capacity expansion plan —75 percent of which is focused on Glen Raven’s U.S. footprint — to continuing to increase production, warehousing and testing capabilities.
In the marine industry, relationships are everything. Sunbrella takes a holistic approach to supporting the industry and by sharing more about
its approach, the company hopes it can inspire other companies to consider similar tactics. The industry is a close-knit group of good people who trust each other. Word of mouth is an invaluable learning tactic in this industry, but more importantly, these conversations allow Sunbrella to better support its partners and understand their needs.
For decades, Sunbrella has partnered with regional, national, advocacy and trade associations that reach various sectors of the business and at all levels. These associations are central to the marine industry as they provide fabricators, distributors, manufacturers, companies and their customers with support and education to make informed business and purchasing decisions. This approach has brought immense value not only to the company’s research and product development, but to its customer relationships as well.
Sunbrella also has benefitted from involvement with trade associations such as the Advanced Textiles Association (ATA) and Marine Fabricators Association. Through regional events, workshops and conferences, a longstanding partnership with ATA has helped Sunbrella build strong and lasting relationships with the fabricators that are critical to its business and the industry at large. The Marine Fabricators Conference each January is an annual highlight for the Sunbrella team.
The company also takes pride in its involvement with regional associations like the North East Canvas Products Association and the Chesapeake Marine Canvas Fabricators Association. These associations help Sunbrella reach awning and marine canvas dealers and fabricators in the places where they have operated for years. These connections give Sunbrella the opportunity to learn about its trade partners, hear feedback and determine how the company can continue to provide support and help them address their unique challenges.
In addition to its relationships with associations, Sunbrella always has pri-
oritized attending and exhibiting at boat shows across the country. These events are one of the most effective ways to promote brand awareness. The company sees the events as opportunities to demonstrate its category leadership for Sunbrella alongside other key players in the industry. From Seattle to Miami to Newport, in-person conversations at these shows with consumers and the trade help Sunbrella communicate important messages about the design excellence and top performance for which Sunbrella is known in a setting that promotes trust.
Being a good corporate citizen and steward of the environment has defined Glen Raven for decades. The company is committed to the greater good of its people, its communities and the planet. Sustainability practices are being increasingly evaluated and prioritized across industries, including marine, but these practices have always been part of the company’s DNA.
The performance woven into Sunbrella fabrics allows them to maintain their color through wear and tear and in the harshest marine environments, delivering not only a superior product but also one that needs to be replaced less often, providing a more sustainable option and ultimately reducing waste over time.
This learning goes back to the idea that word of mouth and authenticity are critical in driving brand awareness for marine textiles. When consumers can pair the tactile feel of a soft vinyl fabric like Sunbrella Horizon with advice they’re receiving in real time based on experience, they are more likely to walk away with trust in that product.
As individualization in design is increasingly sought after, consumers must start by understanding their fabric options to best personalize their boat. That understanding should also incorporate knowledge of the brand they are choosing and what it stands for. In the case of Sunbrella, the brand’s goal is to support consumers with the education and tools they need to choose Sunbrella with confidence to enjoy their experience on the water.
In addition to longstanding sustainable practices, Sunbrella is passionate about two philanthropic marine partnerships. The first is with SeaCleaners, a nonprofit association that encourages coordinated joint action against plastic pollution in the oceans. The second partnership is with Bonefish & Tarpon Trust, a science-based organization with a mission to conserve bonefish, tarpon and permit species, their habitats and associated fisheries. By working with SeaCleaners, Sunbrella has been able to make a direct impact on preserving oceans and marine environments; and with Bonefish & Tarpon Trust, the company has been able to promote healthy fisheries and their marine environments for the long term.
The marine industry is dynamic, filled with a storied history and brimming with growth opportunities. Sunbrella has many exciting projects on the horizon and the company will continue to meet the needs of its customers while respecting the planet. Led by relationships and best-in-class textiles, Sunbrella looks forward to championing the growth of the marine industry in 2023 and beyond. TW
Kontoor
IIt is unequivocal that anthropogenic carbon dioxide (CO2) emissions are causing climate change. The rate of these emissions is unmatched in the last 2,000 years of human history1 Consequently, the world has been experiencing unprecedented climate extremities. From devastating flooding in Pakistan and the United States, to a record-breaking heat wave in the United Kingdom, 2022 saw many climate anomalies2.
The consensus among scientific communities is that the global temperature rise needs to be kept below a 1.5°C rise from preindustrial levels during the period 1850-1900. Beyond this point, the world may experience far more catastrophic climate change effects on its people and ecosystems1. Keeping the temperature rise at less
than 1.5°C requires halving global carbon emissions by 2030 from 2010 levels and achieving net zero by 2050. In plain terms, this decade — from 2020 to 2030 — is the last window of opportunity for humanity to redefine the climate future.
Kontoor Brands — owner of iconic Wrangler® and Lee® brands, among other brands — recognizes this urgency and sustainability is an endto-end commitment included in the company’s strategic priorities. It is aware that the global fashion industry contributes roughly 2 percent of carbon emissions — approximately 1.05 gigatons of CO2 equivalents — every year3. Hence, Kontoor constantly is looking for ways to improve any part of the processes used to manufacture its products to reduce the impact on
the planet and the people living on it. At the end of 2022, Kontoor submitted its Science-Based Targets (SBTs) to align its emissions reduction strategy with the 1.5°C climate target. SBTs are enterprise-wide binding commitments to reduce CO 2 emissions, overseen by the Science-Based Targets initiative (SBTi)4
Through a corporate carbon footprint assessment, Kontoor has found that product related emissions account for approximately 78 percent of its carbon footprint, excluding consumer use of product (See Figure 1). This refers specifically to the emissions associated with the extraction, development, and processing of products’ raw materials as well as the assembly of final products including packaging. Breaking it down further, spinning accounts for about 20 percent or one-fifth of the total product related emissions (See Figure 2). Therefore, it is beneficial to explore alternative options to reduce emissions from spinning, and Kontoor is currently examining the feasibility to expand open-end spinning in all denim and related products.
Open-end (OE) yarn is a type of yarn that can be produced without using a spindle. In OE spinning, the roving process is omitted, and the
sliver is fed directly into a rotor after the drawing process. The fineness of the yarn can be altered by adjusting the rate at which the fibers are drawn out of the rotor relative to the rate at which fibers are fed into the rotor. The process is based on principles of centrifugal force. Imagine the fibers are pressed into a groove on the inside of the rotor until the desired count is achieved.
The primary difference between OE yarns and ring-spun (RS) yarns is the process used to form the yarn. RS yarn is formed by inserting twist into a continuous strand of fibers. A piece of OE yarn is formed by collecting individual fibers from the inside surface of a rotor and combining them using centrifugal forces. RS yarn may be described as formed from the outside in, while OE yarn is formed from the inside out.
OE yarns often are found across multiple product categories in basic apparel. However, use of OE yarn remains in the minority, with RS yarn accounting for around 70 percent of the yarn used for clothing purposes today5. OE yarns are often found in towels, where the yarn works well for both feel and water absorption. As technologies and processes continue
to evolve, the applications for OE yarns also are evolving. With the sustainability gains of OE yarns, more opportunities for application are on the horizon.
Less Time and Energy — The primary difference that makes OE spinning a better process than ring spinning is its high efficiency. OE spinning has fundamentally fewer steps in its process than ring spinning. Since OE spinning only requires one pass of drawing — versus two passes for ring spinning — and no roving frame procedure, it is a faster process than ring spinning.
Cem Yalcin, head of Sales and Marketing for Switzerland-based Saurer AG, described OE spinning as “unbeatable in productivity and energy savings.” Considering only the spinning process of OE compared to ring spun, it is simply faster in this area as ring spinning machines are relatively slower. The OE process is faster because of the remarkably high rotor speed in OE machines. Figure 3 shows a direct comparison of the output of a ring spinning machine versus an OE spinning machine using a typical denim yarn in the timeframe of one
minute. The graph illustrates the glaring difference in speed. The elimination of roving and winding steps leads to yarn production speeds that are six to eight times faster than ring spun yarns 6,7,8 . Also, with fewer steps, the floorspace required is less for the OE spinning process.
Along with improving efficiency, having less steps in the process also results in reduced workforce requirements. Brad Johnson, vice president of Manufacturing at Cone Denim, estimated that for the full ring spinning process, approximately three to four times as many operators are needed than are required for OE spinning. Despite the need for fewer operators for OE spinning, the output is still considerably higher. Great advances actively are being made in the automation stages of OE spinning, requiring even fewer operators. For example, optical and capacitance systems are able to continually assess fiber characteristics, such as linear density, making it possible to quickly identify and remove faults or mistakes, often automatically. A study from Das and Alagirusamy9 predicts that there are possibilities of full automation of the yarn spinning process within the world of OE spinning. This concept also typically results in tighter statistical controlled processes from a quality perspective. While full automation of mills has not yet been realized, full automation is much closer with OE spinning than it is with ring spinning, according to experts at Saurer.
The shortened process and improved efficiency greatly affects the energy consumed during OE spinning, which creates a meaningful sustainability advantage when compared to ring spinning. There are multiple publications and reports that compare the energy usage of the two spinning methods (See Table 1). OE spinning consistently uses less energy than ring spinning, with reductions as high as 57 percent.
Based on the most recent numbers from the United States Energy Information Administration 10 , the OE spinning energy savings are equivalent to a minimum of thirteen cents per kilogram of yarn produced. When that number factors towards the hundreds of thousands of kilograms mills produce weekly, it becomes significant.
Less Waste Generated Besides energy savings, OE spinning generates less fiber waste when compared to ring spinning. Cheryl Smyre, director of Advanced Materials at Parkdale Mills, shared the variance in waste between OE spun yarn and RS yarn (See Figure 4).
Recycled Fiber Usage and Circularity — The OE spinning process also offers advantages when it comes to compatible fiber types. OE spinning can utilize shorter fibers, while ring spinning can only use fibers of a minimum length and high uniformity. The use of shorter or lower grade cotton fiber in OE spinning processed does not compromise yarn integrity and allows yarns of the same quality
to be produced using less expensive cotton than the ring-spinning process. In addition, it is easier to process recycled fibers in the OE spinning process. Although ring frames can process almost all fiber types, more short fiber content tends to result in a higher number of yarn breaks and higher wastage. Therefore, the quantity of recycled fibers used in RS yarns is considerably lower compared to OE yarns. Switzerland-based Rieter 11 evaluated the unevenness of RS and OE yarns as a function of torn recycled fibers (See Figure 5) . Figure 6 shows the range of acceptable fiber sizes for different spinning methods.
For acceptable yarn quality and operational reliability, a blend containing up to 75-percent recycled content is possible in OE spinning. With ring spinning, recycled content is typically kept below 25 percent 6 . OE spinning offers the opportunity to better utilize recycled materials versus ring spinning where recycled fiber use is more limited.
The need to recycle fabrics already is on the rise in some regions. France recently passed a law to combat waste that makes the destruction of unused textiles illegal. Such waste must be recycled or donated12. Other regulations have been proposed in the European Union that call for a mandatory minimum use of recycled fibers for fashion companies by the year 2030. Circular material flows — such as reuse and recycling — also is recommended in IPCC’s 13 climate
change mitigation strategy. The ability to utilize recycled fiber for apparel products is something that will become increasingly important in the coming years and OE spinning will be a helpful strategy.
One of the main obstacles of OE yarn relates to its strength and durability. A study from Cary, N.C.-based Cotton Incorporated14 found that OE spun yarn was 10- to 30-percent weaker than RS yarn on average. In addition, light man-made fibers such as polyester cannot be effectively spun alone using the OE spinning process. For instance, a durable, but exceptionally lightweight garment likely could not be produced using OE spun yarn.
Another common concern when comparing OE to RS yarn is the fact that RS yarn is easily placed on a core while OE yarn is not. Core spinning is the process of spinning fibers around a pre-existing yarn core. The core can be comprised of different yarns. For example, a polyester core would add strength to the garment, while an elastic core would allow the garment to stretch. This stretch property is especially important when making modern slim fit and skinny jeans because certain level of stretch often is incorporated for comfort as well as the ability to expand and adjust. The required stretch can be conferred by a spandex
core yarn in the center of the cotton. Though this is one of the drawbacks of OE, technology is being developed that enables stretch yarns to be produced on OE spinning machines.
One example of this technology is the Rotona process developed by Rieter. The process involves wrapping OE-spun yarn around a core that can be elastic or non-elastic 15 . Another solution to this problem is to use a combination of OE and RS yarn in products that require a degree of stretch. While it is no argument that a garment made entirely out of ring-spun yarn with an elastic core would certainly stretch more, the combination of OE yarn and
elastic RS yarn may be sufficient for some consumers and products.
One non-technical drawback to this combined option would be to address consumer perception, as most consumers are used to the feel of the standard RS fibers. OE spinning produces a slightly coarser yarn count, and the structure of the yarn itself is slightly different than RS, with OEspun yarn having fewer parallel fibers. An OE-spun yarn cannot currently be produced in the same caliber of fineness that a RS yarn can. It is difficult to produce finer yarns above 40 Ne with this system; this does not pose a major challenge in denim manufacturing, as denim yarns range from 10 to 30 Ne. These variances result in a slightly different hand — one that the consumer may notice when purchasing products. For a heavier fabric, such as denim, these attributes of OE-spun yarn are not as much of a concern.
Kontoor has submitted a sciencebased target in line with a 1.5°C temperature reduction scenario. As shown in Figure 2, yarn spinning accounts for roughly 20 percent of Kontoor’s product related emissions. Hence, innovation in cotton spinning processes would produce a notable reduction to the company’s overall carbon footprint. For example, an internal analysis from Quantis revealed that replacing
50 percent of Kontoor’s current ring spun volume with an OE process can potentially save 6 percent emissions from scope 3, which are defined as value chain emissions. Therefore, the potential impact of OE spinning cannot be ignored.
OE spinning offers advantages in a wide array of distinct aspects of the garment-making process. The process requires fewer workers, less energy and factory floor space, and produces less waste, while increasing efficiency, opportunities for automation, and opportunities to recycle fibers. When viewing all these advantages, OE spinning is a more sustainable choice when producing garments. In addition, overall cost savings, including the cost of lower grade cotton, makes it a financially viable strategy.
Kontoor encourages spinning machine manufacturers to continue innovating. The future of the spinning process relies on finding ways to
References
increase efficiency to decrease waste and emissions. Kontoor also encourages other brands to consider the possibilities related to using OE spinning for some or all of their product lines. The potential positive environmental impact is substantial. At Kontoor, sustainability is defined as the dynamic process of continual improvement for its people, product, and planet. In support of this, the company is always searching for innovation and activities that can improve performance relative to these objectives. Kontoor views OE spinning as an area that can impact the sustainability of apparel products. As a good steward in the sustainability space, Kontoor hopes to see other brands pursue these same types of initiatives.
Limiting global warming to less than a 1.5°C rise would require accelerated and far-reaching transitions in
1 IPCC (2021). Summary for Policymakers. In: Climate Change 2021: The Physical Science Basis. Contribution of Working Group I to the Sixth Assessment Report of the Intergovernmental Panel on Climate Change. https://www.ipcc.ch/report/ar6/wg1/downloads/report/IPCC_AR6_WGI_TS.pdf
2 NCEI (2022, Sep 14). Assessing the Global Climate in August 2022. NOAA. https://www.ncei.noaa.gov/news/ global-climate-202208
3 Ley, K., Perkins, L., van Mazijk, R., Gaines, R. & Hugil, R. (2021). Unlocking the trillion-dollar fashion decarbonization opportunity: existing and innovative solutions. Apparel Impact Institute & Fashion for Good. https://apparelimpact.org/wp-content/uploads/2021/11/Aii_UnlockingTheTrillion-DollarFashionDecarbonisation Opportunity_Report_v11.pdf
4 https://sciencebasedtargets.org/
5 Singh, M. K., & Nigam, A. (2013). Effect of various ring yarns on fabric comfort. Journal of Industrial Engineering, 2013.
6 Goyal, A., & Nayak, R. (2020). Sustainability in yarn manufacturing. In Sustainable Technologies for Fashion and Textiles (pp. 33-55). Woodhead Publishing.
7 Kiron, M. I. (2021, January 28). An overview of open-end rotor spinning. Textile Learner. https://textilelearner.net/ an-overview-of-open-end-rotor-spinning/#:~:text=The%20production%20rate%20of%20rotor,used%20in%20 cotton%20carded%20spinning.
8 Dr. Tai Mac, Saurer, personal communication, 2022
9 Das, A., & Alagirusamy, R. (2010). Fundamental principles of open end yarn spinning. In Advances in yarn spinning technology (pp. 79-101). Woodhead Publishing.
10 United States Energy Information Administration. (2022, July 26). Electric Power Monthly. U.S. Energy Information Administration (EIA). https://www.eia.gov/electricity/monthly/epm_table_grapher.php?t=epmt_5_6_a
11 Rieter (2021). The Increasing Importance of Recycling in the Staple-Fiber Spinning Process. Switzerland: Rieter Spinning
12 Casert, R. (2022, March 30). EU to propose new rules to discourage consumers against Fast Fashion. PBS. https://www.pbs.org/newshour/world/eu-to-propose-new-rules-to-discourage-consumers-against-fast-fashion# :~:text=New%20rules%20proposed%20by%20the,conditions%20in%20the%20garment%20industry.
13 IPCC (2022). Summary for Policymakers. In: Climate Change 2022: Mitigation of Climate Change. Contribution of Working Group III to the Sixth Assessment Report of the Intergovernmental Panel on Climate Change. https://www.ipcc.ch/report/ar6/wg3/downloads/report/IPCC_AR6_WGIII_SPM.pdf
14 Cotton Incorporated. (2003). Introduction to open end Spinning - Cotton Incorporated. Retrieved August 5, 2022, from https://www.cottoninc.com/wp- content/uploads/2017/12/TRI-1004-Introduction-to-Open-End-Spinning.pdf
15 Hehl, R. (2004). Rotona: An open-end core yarn, especially suitable for denim. 59-61.
16 Rieter (2015). Processing Indian Raw Cotton. Switzerland: Rieter Spinning
17 ITMF (2008). International Comparison of Manufacturing Costs, Spinning/Weaving/Knitting, Sweden: International Textile Manufacturers Federation.
18 ITMF (2010). International Comparison of Manufacturing Costs, Spinning/Weaving/Knitting, Sweden: International Textile Manufacturers Federation
19 ITMF (2018). International Comparison of Manufacturing Costs, Spinning/Weaving/Knitting, Sweden: International Textile Manufacturers Federation.
20 Kaplan, E., & Koç, E. (2010). Investigation of Energy Consumption in Yarn Production with Special Reference to Open-End Rotor Spinning. Fibres & Textiles in Eastern Europe.
21 Kaplan, E. & Koç, E. (2007). An Investigation on Energy Consumption in Yarn Production with Special Reference to Ring Spinning. Fibres & Textiles in Eastern Europe, (4 (63)), 18-24.
energy and industrial systems. It is a global issue, and everyone needs to pull together in every possible way. Each action towards emission reduction counts, no matter how big or small. From reduction in fossil fuel use to deployment of low-emission energy sources to energy efficiency and conservation, every opportunity needs to be seized in order to fight climate change. OE yarn spinning is just one of the many solutions available. Kontoor is hopeful that this will catalyze others and that the fashion industry will be able to do its fair share to deliver on climate targets. TW
Editor’s Note: The following people contributed to this article Brad Johnson, vice president of Manufacturing at Cone Denim; Carole McFee, senior director of Quality Assurance and Product Stewardship of Jeanswear at Kontoor Brands; Cem Yalcin, vice president, head of Sales and Marketing at Saurer; Cheryl Smyre, director of Advanced Materials at Parkdale Mills; Dhruv Agarwal, vice president –Sustainability, Innovation, Development at Kontoor Brands; Jacob Knego, developer, Textile Research at Kontoor Brands; Jeff Frye, head – Sustainability, Innovation, Product Development, Procurement at Kontoor Brands; Jordan Brewster, manager of Global Sustainability Engagement at Kontoor Brands; Lauren Fields, senior manager of Global Sustainability Data and Reporting at Kontoor Brands; Logan Fortenberry, Sustainability intern at Kontoor Brands; Matthew Hawthorne, Sustainability consultant at Quantis; Randy Fortenberry, Former Supply Chain executive; Dr. Sarif Patwary, senior Sustainability Analyst at Kontoor Brands; Dr. Tai Mac, vice president, director of Business Line Open-End Spinning at Saurer.
In addition, the paper was reviewed by Dr. Rong Yin, assistant professor, Textile Engineering, Chemistry and Science, Wilson College of Textiles, North Carolina State University; and Larry Hubbard, associate director, Fiber Processing and Spinning, Cotton Incorporated.
TThomas Jefferson University (Jefferson), based in Philadelphia, and Heriot-Watt University (Heriot-Watt) based in Edinburgh, Scotland, together recently announced a partnership to offer an exclusive joint Master of Science (M.S.) degree in Global Textile Design.
“This program is being positioned to enlighten students about the opportunities and issues which this global industry is currently facing,” said Marnie Collins, co-director of the Global Textile Design program and assistant professor, program director of Studies-Design for Textiles at Heriot-Watt. “We’ll also support the students in navigating their own leadership pathway in the field.”
“It is the first program of its kind in textile design that will offer joint masters degrees from each institution,” added Marcia Weiss, also co-director of the Global Textile Design program
and director, Textile Design Programs, at Jefferson’s Kanbar College of Design, Engineering and Commerce. Though the co-directors didn’t know each other in college, Weiss and Collins — both graduates of the textile design program at the then Philadelphia College of Textiles and Sciences which is now part of Jefferson (See “A Study in Collaboration,” TW , September/October 2020) — have followed similar career paths and passions. Each maintains a love of textile design, and both worked in various aspects of the textile industry before joining academia, albeit in different countries. “We’ve worked together for several years overseeing the longstanding international student exchanges between our Universities,” Collins said. “We learned we had common interests beyond woven textile design and higher education in artisanal textiles and the heritage and provenance
of textiles.” A co-authored research paper, “The Role of Provenance in Luxury Textiles,” that focused on cultural similarities and differences in the perceptions and importance of design origins between U.K. and U.S. consumers formed the basis for a mutual friendship and interest in finding other ways to collaborate.
Ultimately, the women found themselves at what both Weiss and Collins agree “was the most enjoyable ‘business’ meeting ever!” “At various times, we’d have informal discussions on different ways to collaborate. Then in June 2016, Marnie was visiting family along the Jersey Shore and invited me out to Beach Haven, N.J., where we sat on the beach, looked out at the ocean, and inevitably started to piece together the program’s general scope and structure,” Weiss said. “I believe it was Marcia who came up with the idea of the joint master’s program which led to the ‘wouldn’t it be great’ question being asked quite often,” Collins added. “With such an inspiring location, it was inevitable for us to day-dream about what the most amazing joint master’s program would look like.”
The first of its kind program for both universities has been finalized and will welcome its first class of students in the fall of 2023. “This program is structured to educate students about the opportunities and issues currently being faced throughout the contemporary textile industry and to support them in navigating their own leadership pathway in the field,” Weiss said. “Textile design creativity, sustainability, artisanal heritage as well as entrepreneurship will be emphasized.”
Structured as an 18-month-long master’s program, all students in the class will follow the same program path. It will begin with a full fall semester held at Jefferson in Philadelphia. After the traditional
holiday/New Year break, students will spend the first half of the spring semester at Jefferson and then collectively move to Scotland during spring break to complete the second half of the spring semester at Heriot-Watt.
A key aspect of the joint program is the incorporation of a credit-bearing summer internship that will provide students with unprecedented opportunities because of the quality of industry partners and potential placement options offered. Each internship could be completed at select companies literally anywhere in the world. “Marnie and I have both worked directly in the textile industry prior to joining academia and with various other segments through university and industry collaborations. We both are focused on our student’s career opportunities and there are a high level of industry contacts and networks available that can be engaged specific to potential internships,” Weiss noted.
The final fall semester will be completed in full at Heriot-Watt. According to Weiss: “The sequencing and location of semesters were chosen based on the proximity of textile industry tradeshows occurring throughout the duration of the program.” A comprehensive tuition package will cover travel within courses, but not the back-and-forth between Scotland and Philadelphia. Students will need to be prepared for a considerable amount of travel as part of this global program which will also afford them the opportunity to visit and participate in a variety of international textile events both in the United States and Europe.
The program initially will be limited to a class size of 12 students. Because of the small class size, careful consideration will be given to the selection process ensuring a high quality of participants. Qualifications for those interested in enrolling will require a bachelor’s degree from an accredited institution and a level of creative experience, which doesn’t necessarily have to be specifically in textiles or textile design. “We are
really looking for a demonstrated passion and interest in creative pursuits from the candidates,” suggested Weiss. Prospective students will also be asked to submit a portfolio of their work, a resume or curriculum vitae, as well as letters of recommendation. Decisions on acceptance will be made jointly by both Universities.
“The textile industry is obviously global,” Collins said. “There are aspects of the industry that have local challenges and concerns. However, the vast majority of modernday issues facing the textile industry are shared across the world, including sustainability, ethical practices and artisanal skills preservation.”
“We view this program in a similar way to the ‘farm to table’ philosophy found in the restaurant industry,” Weiss noted. “People increasingly want to know the provenance of their textiles as well. So, the textile industry is pivoting towards thinking global, yet living local in order to meet the changing attitudes of consumers globally.”
There are numerous similarities between Jefferson and Heriot-Watt and their textiles and design programs. They each represent two of the world’s oldest textile institutions — The School of Textiles and Design at Heriot-Watt was formerly the Scottish College of Textiles, while Jefferson’s textile program was founded in 1884 as the Philadelphia Textile School. “The heritage and reputation of both institutions are widely known and highly respected,” stated Collins. “Both have expert staff who provide high quality support for their students for undergrad and post grad. And both have amazing facilities including textile processing labs and testing facilities, excellent historical archives and fantastic links with the industry. Graduates will find themselves with an expanded network and a much more varied experience to draw upon post degree.”
Differences between the two are
subtle, but significant. Jefferson has better digital facilities and industrial machinery, while Heriot-Watt has prolific analog facilities and handweaving equipment. Given the different environments where each university is located, students also will be exposed to a variety of not
only different cultures, but also industry networks. “There are so many great textiles globally. We hope to build on the legacy of both institutions with the arrival of this program and the international community it will foster,” stated Weiss.
Earning a degree from two of the world’s most prestigious and respected textile institutions can only provide a major benefit to the program’s graduates as they enter or reenter the workplace. The plan was to introduce the program for the 2019/2020 school year, but the COVID pandemic hit and postponed its launch. On the bright side, this allowed for more discussions on and fine-tuning of the program details, the meshing of institutional regulations into one cohesive program, and additional time to attract national and international students. Now, both Weiss and Collins are ready to get this program off the ground. “We’re super excited for the opportunities it will bring to the students and to further connect our two schools,” said Weiss. “It’s going to be great fun!” TW
Switzerland-based Rieter reports Norbert Klapper, Rieter CEO for the past nine years, plans to leave the company to pursue other professional challenges. Thomas Oetterli will succeed Klapper as CEO of Rieter on March 13, 2023.
Web Industries Inc., Marlborough, Mass., has named John Madej CEO and Amy Reardon Doherty vice president, Legal.
Helsinki-based Ahlstrom has named Helen Mets president and CEO. She succeeds Hans Sohlström who is leaving the company.
Gunnar Meyer was named managing director of A. Monforts Textilmaschinen GmbH & Co. KG, Germany.
Jessica Adler has joined outdoor performance and lifestyle brand Merrell® as vice president of U.S. sales. She reports directly to Merrell’s Global Brand President Chris Hufnagel.
Sonobond Ultrasonics Inc., West Chester, Pa., announced Manning Smith IV is the new president. He replaces Janet Devine who recently retired. She will operate in an advisory position during a transition period.
Effective April 30, 2023, John Hrdlick will retire from INX International Ink Co., Schaumburg, Ill., at which time Bryce Kristo will take over as president and CEO.
Standard Textile Co. Inc., Cincinnati, announced Alex Heiman will succeed his father Gary Heiman as president of the company. He will be the fourth-generation family member to be president of the company. Gary Heiman will continue as chairman and CEO.
Darn Tough Vermont® , Northfield, Vt., has hired Kristen Graf as global director, Environmental and Social Responsibility.
Christopher Bernat was appointed general manager of North America and the Caribbean markets for Italybased MS Printing Solutions and JK Group. He is based in Charleston, S.C.
Cornell
of Integrative Plant Science Scientist and Professor Dr. Michael Gore was awarded the 2022 Cotton Genetics Research Award at the recent 2023 Beltwide Cotton Improvement Conference.
Paul Cleary is the new president and CEO of Momentum Textiles & Wallcovering, Irvine, Calif.
Singapore-based DyStar named Yalin Yu managing director and president of DyStar Group; and Eric Hopmann was named chief commercial officer with a focus on sales and marketing reporting to Xu.
Südwolle Group GmbH, Germany, has appointed Stéphane Thouvay managing director, sales and marketing. Effective April 1, 2023, he also will lead the company’s global marketing organization.
The Cary, N.C.-based Association of the Nonwoven Fabrics Industry (INDA) has named MaryJo Lilly Market Intelligence Leader.
Humbolt, Tenn.-based Jones Family of Companies has named former Executive Chairman Ralph Jones III chairman and CEO. In addition, Scott Butler was promoted to president and John French has joined the senior leadership team CFO.
England-based Pincroft has hired Louise Sheridan as the company’s business development manager.
Aquafil USA, Cartersville, Ga., has welcomed back Ian Burt as its director of sales and marketing.
London-based Eco-Age has promoted Harriet Vocking from chief strategy officer to CEO.
David Heiman has joined Milliken & Company, Spartanburg, S.C., as account manager for the outdoor fabrics category on the Textile Businesses’ Décor team.
New York City-based PVH Corp. has appointed Eva Serrano global brand president of Calvin Klein.
The board of directors at the United States Fashion Industry Association (USFIA) has chosen Chris Lucas, senior director, associate general council at American Eagle Outfitters Inc. as its new chair.
Jyl Davis has joined StandardFiber, Burlingame, Calif., as vice president, sales and merchandising.
Simon WhitmarshKnight was named textile global marketing director for Seoul-based Hyosung.
Steve Rendle has decided to retire from his position as chairman, president and CEO of Denver-based VF Corp.Benno Dorer has been named interim president and CEO, and Richard Carucci will serve as interim chairman of the board. TW
22 :Southern Textile Association (STA) Winter Seminar,Textile Technology Center at Gaston College,Kimbrell Campus, Belmont,N.C.Visit southerntextile.org.
23 :Americas Apparel Producers’ Network (AAPN) Los Angeles Regional,FIDM Los Angeles campus. Visit aapnetwork.net.
28-March 3 :Introduction to Spunbond and Meltblown Technology, organized by INDAand The Nonwovens Institute (NWI),NWI,NC State University,Raleigh,N.C.Visit inda.org/training/advanced-training.php.
1-3 :Advanced Textiles Association (ATA) Women in Textiles Summit,Francis Marion Hotel,Charleston,S.C.Visit textiles.org/events.
21 :STA Southern Division Spring Meeting, Embassy Suites by Hilton Greenville Golf Resort & Conference Center.Visit southerntextile.org.
28-30 :National Council of Textile Organizations (NCTO) Annual Meeting, Washington.Visit ncto.org.
11-12 :Smart Fabrics Summit,organized by ATA and NC State’s Wilson College of
Textiles,NC State Campus,Raleigh,N.C. Visit smartfabricssummit.com.
17-20 :SAMPE 2023,organized by the North America Society for the Advancement of Material and Process Engineering (SAMPE),Washington State Convention Center,Seattle,Wash. Visit 365.sampe.org/events.
18 :STA Northern Division Spring Meeting,location tbd. Visit southerntextile.org.
18-21 :INDEX™ 2023,organized by the European Disposables and Nonwovens Association (EDANA),Palexpo,Geneva, Switzerland.Visit indexnonwovens.com. TW
CONTACTS:
For more information about Nuyarn® Merino, visit nuyarn.com
New Zealand-based TMC Ltd.’s twist-free spinning technology allows wool’s natural properties to shine through for highperformance applications.
New Zealand has long been associated with wool, so it’s not surprising that New Zealand-based company TMC Ltd. is responsible for developing a new twist-free spinning technology for producing performance wool yarns.
Dubbed Nuyarn® Merino, the spinning method drafts a superfine merino wool yarn with a high-performance nylon filament carrier yarn. The result is an ultrafine, two-ply yarn with more volume and aeration than merino yarns produced using traditional worsted spun-yarn technologies.
The company considers itself to be an ingredient brand and it works with all its partners to create unique products — modifying the merino to nylon ratio, weight, and feel, among other parameters, to meet performance criteria —and then controls the supply chain from fiber to end garment on behalf of the brand.
Go online to TextileWorld.com for archived Quality Fabric articles.
According to Nuyarn Founder Andy Wynne, the technology “unleashes the natural performance of merino wool,” and doesn’t “twist the life out of the fiber.” The idea behind the technology was to create wool products that perform as close as possible to wool in nature. Spun yarn processes compress natural air pockets, introduce tension, create loops and restrict natural fiber movement —all of which reduce the wool fiber’s inherent advantages and impart scratchiness to a garment.
Independent testing performed by Intertek® Vietnam and AgResearch, New Zealand, showed compared to a conventional ring-spun 100-percent merino spun yarn, Nuyarn yarns:
•Dry five times faster;
•Are 85-percent more elastic;
•Offer 35-percent more thermal retention as a result of the increase in natural air pockets;
•Are 35-percent more air resistant;
•Feature a 50-percent increase in tensile strength;
•Are 8.8 times more resistant to abrasion; and
•Produce 120-percent stronger seams in garments. These enhanced performance benefits all last for the lifetime of the garment because they are created using a mechanical versus a chemical process.
Nuyarn is suitable for a wide variety of applications, however, the light weight and softness of the yarns make them perfect candidates for next-to-skin applications in baselayer garments in particular. Multiple brands have collaborated with Nuyarn to create baselayer products including Artilect, Trew, KUIU, Outdoor Vitals, Odlo, Black Diamond, Wuru Wool, Mosko Moto and Universal Colours.
“The problem with most traditional merino wool is you have to use higher weight fabrics to get an acceptable level of durability, and Nuyarnsolves that basically by reinventing the way the yarn is created,” said Chris Pew, Trew co-founder and CEO. “Nuyarn construction is lighter, stronger, and more durable than anything that we've seen before it's also stretchier, loftier, and has more thermoregulating capabilities.”
The ODLO team also noted: “While everyone at ODLO loves pure, natural merino, it does have one fatal flaw; once it reaches peak saturation, it ceases to wick sweat, and the fabric structure retains moisture. This is where Performance Wool powered by Nuyarn stands apart.”
According to Wynne, some of the limitations related to wool use in the performance apparel industry were related to how the yarns are spun. The Nuyarn innovation removes those limitations and gives brands an opportunity to harness the natural attributes of wool along with weight and performance advantages in both winter and summer performance garments. TW