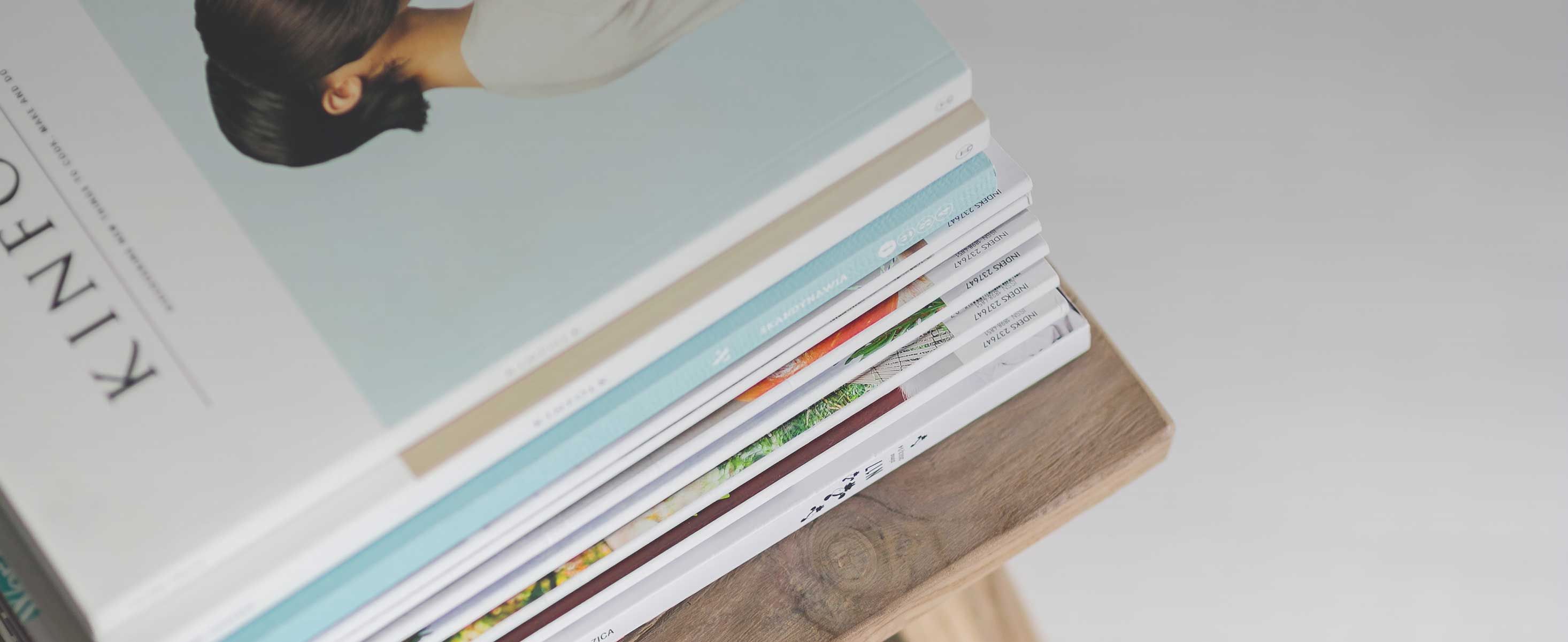
6 minute read
STANLEY BLACK AND DECKER, INC.
Optimizing Advanced Manufacturing of Fasteners
STUDENT TEAM:
Advertisement
Jessica Dillon - EGL (BSE & MSE in Mechanical Engineering)
Neal Sinha - EGL (BSE & MSE in Mechanical Engineering)
PROJECT CHAMPION:
Nate Dietrich – Director of Advanced Manufacturing & Engineering Processes
Danny Nicolino – Continuous Improvement Manager
FACULTY ADVISORS:
Stefanus Jasin – Ross School of Business
Brian Love – College of Engineering
STANLEY BLACK & DECKER (SBD) is a globally recognized Fortune 500 company responsible for over $15.6B in revenue and is present in over 60 countries. SBD is the industry leader in the power tools and fasteners sectors. Stanley Engineered Fasteners (SEF) is a subsidiary of SBD in the Industrial division with a revenue of $2.5B from fastener and assembly technologies.
SEF tasked the Tauber team with examining and improving operations at its West Ridge Plant in Elyria, OH. The company has a goal of producing around 600,000 parts daily through its cumulative operations at multiple plants in Northeast Ohio. However, due to heightened trends of machine downtime, the plants have consistently fallen short of their targets. Using root cause analyses to identify waste, define value, and improve flow, the team was tasked with developing new sustainable strategies for operational improvements that would result in at least $1.3 million of value and a payback of 2 years. The team also aimed to implement at least one physical change and find quick wins while examining scalability to other sites.
Over the course of the summer, our team analyzed the previous state of production to deliver three main solutions after conducting 36 stakeholder interviews, over 150 Gemba walks, and developing a map for internal material and tooling flow. The first solution the team piloted was a data visualization program providing downtime tracking and analysis at a granular level. After tracking over 256,000 hours of downtime, the team determined downtime from waiting for tooling was the primary reason for unexpected productivity inefficiencies. The second solution focused on improving tool crib management through a plant redesign transformation of the flow of tooling to achieve an 85% reduction in unnecessary tooling waiting times and a 65% reduction in non-value added setup times. The third solution centered on the management of installing a new thread roller machine. Through conversations with vendors and the development of layouts, the machine has been fully installed and is ready for a mid-September run date.
The team calculated the value of these solutions—productivity increases, hard cost savings, and revenue growth—to be $7.2M over three years, exceeding the financial target value and implementing physical change. Additionally, the team identified several quick wins and opportunities for scalability of the tooling management project to other plants.
Starbucks Corporation
US Licensed Store Asset Tracking: Developing an asset tracking strategy for US Licensed Store business division
STUDENT TEAM:
Yuzhou Judy Liu – EGL (BSE/MSE Industrial and Operations Engineering)
Clark Yidi Wang – EGL (BSE/MSE Industrial and Operations Engineering)
PROJECT SPONSOR:
Hailey Imperato – Director of Strategy and Programs
Courtney Perkerewicz – Program Manager, LS Strategy and Programs
FACULTY ADVISORS:
Ekaterina Astashkina – Ross School of Business Mark Brehob – College of Engineering
The US Licensed Store (USLS) business unit is a division of STARBUCKS CORPORATION. It supports nearly 7,000 Starbucks locations in the US, almost half of Starbucks’s domestic portfolio. The LS business employs a licensing business model, like franchising, where other large corporations license the right to establish a Starbucks location inside their own. Notable clients in the USLS portfolio include Target, Kroger, Albertsons, Aramark, and HMS Host.
A comprehensive asset tracking strategy has been developed in response to the imperative need for accurate and upto-date asset data within Starbucks LS. A successful implementation of this strategy will lead directly to a conservative estimate of US$1.4 million in cost savings annually. The strategy is designed to streamline asset data investigation, ensure data accuracy, increase employee productivity, reduce waste and overhead, and improve profitability and customer experience. It encompasses both short-term solutions and a long-term vision to strengthen the support of the licensees and meet Starbuck's business teams’ operational goals. The central components of this framework are dichotomous- acquiring precise and current asset data for all LS locations, and establishing a sustainable and cost-effective auditing cadence. However, the strategy also envisions a gradual transition from third-party to internal capabilities, aligning with Starbucks’s commitment to innovation.
In conclusion, the Licensed Store asset tracking strategy presents a holistic and sustainable approach to data collection and management. By addressing immediate collection and planning for long-term projections, Starbucks ensures operational and data excellence.
Target Corporation
Optimizing Freight Presentation and Sequencing criteria of CONS freight for ART Inbound Receipt
STUDENT TEAM:
Alexios Avrassoglou – EGL (BSE/MSE Industrial and Operations Engineering)
Santiago Currea – EGL (BSE/MSE Industrial and Operations Engineering)
Austin Tauber – EGL (BSE Chemical/MSE Industrial and Operations Engineering)
PROJECT SPONSOR:
Dave Carruth – Lead Process Manager Inbound
Kyle Murphy – Director GSCL Field Operations
Lei Ying – College of Engineering
FACULTY ADVISORS:
Andrew Wu – Ross School of Business
Lei Ying – College of Engineering
TARGET CORPORATION is a prominent retail giant renowned for its extensive network of locations across the United States, with 1,948 stores located in urban and suburban locations nationwide. Target has grown to become one of the largest retailers in the country, boasting a diverse range of products including apparel, clothing, electronics, home goods, and groceries that can be delivered to guests through stores, curbside pickup, or online delivery formats. The expansive supply chain network used to service Target’s stores features 26 regional distribution centers (RDCs) that are used to receive, sort, store, and deliver goods to their many locations. The Tauber team’s project focused on Automated Receiving Technology (ART), an inbound receipt automation technology used across the entire RDC network to convey, sort, and store cartons.
In recent years, Target’s RDC Inbound department is falling short of ART throughput goals by 15-25% across the network. Root cause analysis from the 2022 Tauber Project found that the lack of defined load sequencing and freight presentation criteria from 3PL Consolidator and De-consolidator (CONS) facilities contributes to lower processing speeds. Trailers coming from these 3PL facilities make up 43% of the RDC network’s volume, and often contain unpredictable loads that do not group like items, mix conveyable and non-conveyable cartons, and generally slow down team members from unloading and processing. It is estimated that over $20MM can be saved annually in labor by processing freight faster through better-sequenced trailers. The Tauber team spent the summer developing solutions to improve the Carton per Minute (CPM) throughput by developing the optimal freight presentation criteria to improve productivity in ART.
The team conducted waste observations and performed time studies on the floor in a Target RDC to identify current issues with loads coming from CONS facilities. After hypothesizing improved load sequencing criteria, the team performed historical data analysis in Python and SQL on over 200,000 CONS trailers and simulated ART processes in Emulate3D to quantify the estimated impact of each suggested criterion. Using these results, the team determined the ideal trailer loading criteria, developed solutions to introduce the new criteria and more 3PL accountability, and began the implementation of the recommendations, successfully handing off the project to Target’s 3PL team which manages requirements with upstream partners.
Target’s continued implementation of the optimal freight presentation criteria and strategies are expected to generate $60.7MM in labor savings over the next three years by sorting like items, floor loading, and separating conveyable and non-conveyable freight. The recommendations of the Tauber Team will improve adherence to existing 3PL requirements and communication between Target and 3PL partners. Finally, the project introduced a longer-term framework for what functionality the ideal Consolidator should have to inform future site expansion and strategies to better suit Target’s downstream processes.
Washington Gas
Optimizing Low Carbon Energy Portfolio Solutions for Data Centers
STUDENT TEAM:
Gabriel Correa - Bachelor of Business Administration/Master of Supply Chain Management
Allen Zhao - EGL (BSE & MSE Materials Science & Engineering)
PROJECT SPONSORS:
Mallik Angalakudati - Senior Vice President, Strategy and Innovation
Amit Nagpal - Director, Strategy and Innovation
FACULTY ADVISORS:
Christian Lastoskie - College of Engineering
Vijay Pandiarajan - Ross School of Business
WASHINGTON GAS is a regulated natural gas utility that has been providing safe and reliable energy to residential, commercial, and industrial customers throughout Washington D.C. and parts of Maryland and Virginia for 175 years. Washington Gas is currently undergoing a transformation to decarbonize its operations and align with the global shift towards clean energy.
The company has identified an opportunity to serve an energy-intensive hyperscale data center campus customer by providing a pathway to a reliable low-carbon energy portfolio. The goal is to leverage the company’s existing expertise and infrastructure in renewable natural gas distribution to offer low-carbon energy solutions to the customer. Given the favorable regulatory landscape, Washington Gas is developing a framework for investment strategies in hydrogen and other energy alternatives, based on market opportunities and risks.
The Tauber team was tasked with assessing the landscape of low-carbon energy sources and evaluating optimal methods to leverage these technologies in order to generate reliable, low-carbon energy solutions to serve the regional data center market. This required an analysis of the hydrogen production and stationary power generation value chain, and exploration of regulatory policy and incentives.
The efforts of this project helped Washington Gas have a better idea of how to serve this specific demand segment with production designs that better suit the customer profile. The Tauber team demonstrated that Washington Gas has the ability to provide this data center customer with reliable low-carbon energy for a considerably lower cost than initially expected. The energy solution proposed by the Tauber team will reduce operational costs, and lower the capital expenditure by roughly $200 million. The use of renewable natural gas in tandem with innovative production models will help Washington Gas serve this customer segment, along with other potential customers in industries that are hard to decarbonize.