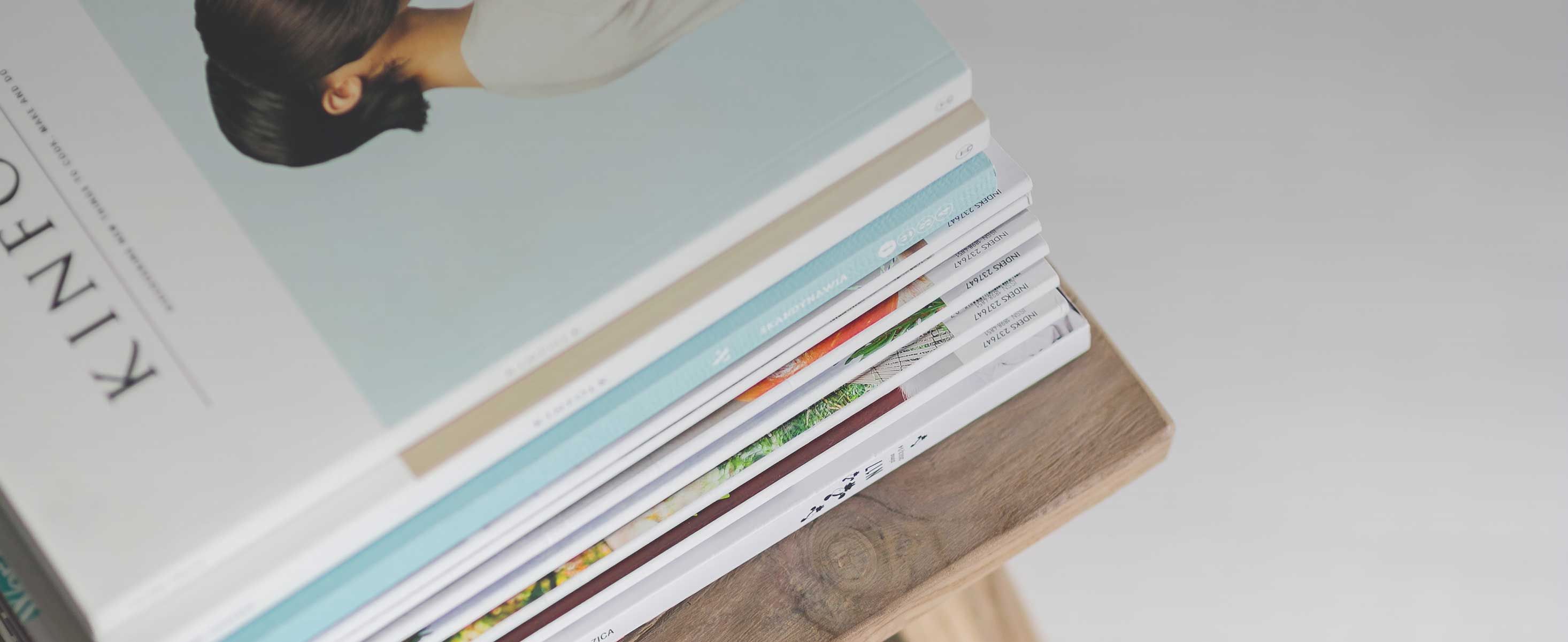
22 minute read
Project
Barbara Lopez Santander – Master of Business Administration
Sebastian Sarquis – Master of Business Administration (MBA)
Advertisement
PROJECT SPONSOR:
Sarah Klemsz – Director, Process Engineering
FACULTY ADVISORS: Len Middleton – Ross School of Business Ray Muscat – College of Engineering
AMAZON'S Process Engineering Team has partnered with the Tauber Institute for Global Operations to improve process speed and safety in their fulfillment centers. The Tauber team will assess the current operations and propose a strategy that includes financial impact analysis, equipment needed, and safety requirements to identify and validate investments.
Amazon Robotics
Exploring use cases for Amazon’s new Autonomous Mobile Robot
STUDENT TEAM:
Bruno Simao Da Silva Nascimento – Master of Business Administration
Vivien Wei – Master of Business Administration
PROJECT SPONSORS:
Gustavo Frattini – Senior Engineer, Advanced Manufacturing Engineering
Paul Seay – Senior Manager, Advanced Manufacturing Engineering
FACULTY ADVISORS: Max Z. Li – College of Engineering
Ruslan Momot – Ross School of Business
AMAZON ROBOTICS (AR) is the division of Amazon.com Inc. responsible for developing and providing robotic automation to empower a more efficient and consistent customer experience through automating Amazon’s overall operation process in fulfillment and delivery. With the Covid-19 pandemic highlighting the importance of Amazon in customers' lives, the company recognizes the need to continually innovate its complex logistical infrastructure to fulfill customers' needs. Consequently, Amazon Operations faces the challenge of shifting from high-volume to highmix production, which requires increased flexibility and efficiency. To address some of these challenges, Amazon has developed its first Autonomous Mobile Robot, Proteus.
While Proteus was primarily designed to move Go-Carts, a core component of Amazon’s logistics operations, Amazon recognizes the potential for Proteus to serve many other purposes. To meet this need, AR tasked the Tauber team with identifying new use cases for Proteus, both internal and external to Amazon. Overall, the team concluded that in the short term, Amazon’s internal opportunities have much greater return on investment compared to external ones. This conclusion was derived from the observation that the net cost savings of the top five internal opportunities is greater than the projected operating profit of the entire AMR market segment for manufacturing in 2027.
The Tauber team identified 28 different potential internal use cases through six site visits and 30+ interviews, then selected two use cases to prioritize. The final deliverable for each use case includes: (1) gap analysis, (2) layout, (3) technical requirements, (4) implementation roadmap, (5) financial analysis, (6) risks and issues assessments, (7) next steps.
The first use case proposed involves utilizing a Proteus fleet to automate the replenishment of parts to the stations in the AR production lines. The team estimated that the use case can result in an annual cost savings of ~$450K based on current demand forecasts. When considering AR full production capacity, the annual savings is estimated at $2.3M.
The second use case proposed involves using Proteus to replenish Totes in the Amazon fulfillment centers (FC). The team estimated that this use case can bring $2.84M of labor savings per year for a single FC, with an 8.6-month payback period compared to the current manual handling process. Considering all new fulfillment centers in the pipeline, the use case has a potential impact of $76.7M in three years.
Overall, the two use cases the team presented could save up to $79M in three years.
American Industrial Partners
Optimized Design of Steel Joist Production Scheduling System
STUDENT TEAM:
Christian George – EGL (BSE/MSE Computer Science)
Ziyu Han – EGL (BSE/MSE Industrial and Operations Engineering)
PROJECT SPONSOR:
Almira Dogruyol – Senior Industrial Engineer, Canam Steel corporation
Scott Redmond – Director of Quality and Engineering Services, Canam Steel Corporation
FACULTY ADVISORS:
Izak Duenyas – Ross School of Business
Oleg Gusikhin – College of Engineering
AMERICAN INDUSTRIAL PARTNERS, a results-driven middle-market private equity firm, has made a strategic investment in Canam Steel Corporation (CSC), a prominent manufacturer of steel joists and decks in the United States.
The Tauber Team, situated at CSC’s headquarters in Point of Rocks, MD, took on a pivotal role in creating a robust algorithmic framework for optimizing the scheduling of steel joist production. The complexity of steel joist scheduling cannot be overstated. Currently, each CSC plant employs a dedicated scheduler responsible for managing the entire scheduling process within a two-week timeframe. Compounded by the highly customized nature of CSC’s steel joist orders, with variations in specifications like length, depth, thickness, and quantity, these demands present significant challenges. Schedulers must strive for maximum production line efficiency while factoring in changeover, manpower, material flow, estimated time, and critical deadlines to avoid potential financial penalties.
Across plants, existing scheduling practices differ due to institutional knowledge, leading to scheduling becoming a potential single point of failure.
The Tauber Team addressed this challenge by conducting comprehensive interviews with schedulers from two plants, gaining insights into their methodologies. To support and improve the current scheduling process, the Tauber Team developed a robust Job Scheduling Optimization Model to efficiently schedule and sequence incoming job orders. Proposed optimizations and future integrations included streamlining material flow and developing a standardized procedure. This proposed coherent framework and the developed scheduling optimization model are designed to be adopted by any individual and seamlessly integrated, even automated, into future Enterprise Resource Planning (ERP) upgrades.
Understanding the paramount role of time estimates, the team undertook a rigorous validation process. Analyzing ten years’ worth of historical data across all six facilities, they revealed a tendency for CSC to underestimate time estimates. By extracting job design data from legacy tools, the team identified patterns within underestimated jobs, pinpointing two critical components contributing to estimation inaccuracies. Furthermore, detailed time studies on three bottleneck workstations resulted in questions regarding current estimation practices.
In conclusion, the Tauber Team synthesized a comprehensive framework for a steel joist scheduling optimization model. Coupled with recommendations to enhance estimation precision and overall scheduling efficiency, this effort addresses the intricate challenges CSC faces in its production processes.
BECTON, DICKINSON AND COMPANY
Capital equipment forecast accuracy improvement project
STUDENT TEAM:
Maria Fernanda Guerrero Pineiro - Master of Business Administration (MBA)
Farzad Siraj - EGL (BSE/MSE Computer Science)
PROJECT SPONSORS:
Nilesh Bodade – Director, Data Science and Process Digitalization - Business Process
Kate Wetzel – Vice President, Business Process Excellence
FACULTY ADVISORS:
Christian Lastoskie – College of Engineering
Joline Uichanco – Ross School of Business
BECTON DICKINSON, renowned as BD, stands as a preeminent American multinational in the realm of medical technology. The company’s indelible mark extends to pioneering the very technologies that drive forward medical research and elevate clinical laboratories. Within the realm of Becton Dickinson, the compass of forecasting outlines the course for financial budgets, production blueprints, sourcing endeavors, procurement strategies, and other pivotal business trajectories. The Tauber project, a transformative initiative engineered to elevate BD’s capital equipment forecast accuracy, colloquially termed “instruments”.
Embarking on a voyage of inquiry, we performed extensive interviews, amassing insights from over 50 respondents from three regions. The first facet of this approach hinged on meticulous analysis, looking for specific areas of enhancement. By benchmarking best practices from a plethora of industries, this endeavor sought to provide the organization with refined strategies. The second facet, a data-driven approach of modeling and refining the existing inventory policy. These approaches aimed to elevate precision and efficacy became the cornerstone of the project.
In this pursuit of excellence, these improvement opportunities and inventory policy modeling stand as beacons guiding BD toward a horizon marked by elevated efficiencies, harmonized cross-functional collaboration, and a resolute commitment to unwavering progress. With a potential of $4-12M in revenue increase, up to 40% Inventory Savings, 50% Backorder Reduction with 10% increased Service Levels, based on a HBR Study and our analysis.
The Boeing Company
777X Restart Readiness
STUDENT TEAM:
Daniel Cotton – Master of Business Administration (MBA)
Nick Tran – EGL (BSE/MSE Industrial and Operations Engineering)
Claudia Zimmerman – EGL (BSE-ME/MSE Systems)
PROJECT SPONSOR:
Jeff Dillaman – Senior Manufacturing Manager, 777 Interiors
Kartik Raju – Sustainable Aviation Fuel Aircraft Compatibility Leader, Product Development
FACULTY ADVISORS:
Richard Hughes – College of Engineering
Mohamed Mostagir – Ross School of Business
This report summarizes the findings and recommendations of the Tauber’s 2023 BOEING 777X project team. The team was tasked with observing early production restart activities at Boeing’s main factory in Everett, WA to benchmark and identify best practices and improvements for the 777-9 airplane, which is Boeing’s new largest twin aisle long-haul passenger model. These best practices will provide frameworks to improve operations management for the 777 Program in the areas of staff training, quality assurance, and fulfillment processes, which will be critical to Boeing’s continued success as it increases production rates for the 777 Program.
This final report provides background on the project’s problem statement, a summary of the project’s scope and strategic goals, a description of the team’s approach to research and findings, final recommendations, and plans for implementation of these recommendations.
The team began gathering information by conducting over 40 qualitative interviews, performing relevant metric data analysis, surveying Boeing employees & stakeholders, and observing daily operations to gain an in-depth understanding of the production process for the 777. Since 777X production had not restarted prior to our project’s start, we relied on qualitative information and historical production data to determine potential improvement opportunities.
From our initial analysis we identified significant improvement opportunities related to mechanic training, quality assurance processes, and fulfillment practices. We also compiled a list of best practices for immediate implementation, including early material inspection and buyoff, skill development monitoring, and tooling refresher training. Next, the team conducted additional benchmarking activities, including a trip to Boeing’s 787 production facility in Charleston, SC, to determine specific improvement pathways in the three focus areas. Next, the team provided recommendations to improve the processes to determine new mechanic learning pathways via gap analysis as well as those to improve quality checks and balances by providing a formal framework for intervention. Finally, the team provided a dynamic framework to determine optimal fulfillment strategies on the factory floor based on evolving supply chain and production conditions.
The gap analysis and Individual Learning Plan revisions have the potential to increase Certification Levels for new mechanics by approximately 50%, significantly decreasing non-value-added time for these mechanics and accelerating early on-the-job training adaptations. The quality assurance process interventions proposed by our team will provide a framework to quickly identify and prevent defect propagation along the production value stream, with potential for a 40% reduction in rework hours in sampled production centers for the 777-9. Finally, the fulfillment practices framework will reduce factory floor space requirements by at least 25%, decreasing the likelihood that the factory floor reaches capacity for point-of-use fulfillment as well as helping to reduce set-up times in fulfillment and manufacturing. These recommendations combine to prepare Boeing for success through promotion of talent development, quality management, and continuous improvement as the 777 Program expands its market presence.
The Boeing Company
Early Warning Systems
STUDENT TEAM:
Delenn Bauer – EGL (BSE/MSE Aerospace)
Roxana Martinez-Bernal –- EGL (BSE-Biomedical/MSE Industrial and Operations Engineering)
Aidan Fitzgerald – EGL (BSE/MSE Industrial and Operations Engineering)
PROJECT SPONSOR:
Kimberly Brock – System Engineering Manager
Wendi Folkert – Director for Supply Chain Propulsion Strategy
FACULTY ADVISORS:
W. Monroe Keyserling – College of Engineering
Stewart Thornhill – Ross School of Business
BOEING COMMERCIAL AIRPLANES tasked the Tauber Team to consult on the development of a predictive heatmap for FAA delegate’s interference. The team was able to effectively benchmark three airlines and consolidate internal resources to synthesize 12 concise recommendations that can effectively transition the heatmap to a minimum viable product. This heatmap will enable Boeing to ensure less stressful working conditions for FAA delegates in charge of enforcing federal safety standards thereby improving safety for the 100,000s of passengers who use Boeing’s products every day.
The Boeing Company
Supply Chain Reminder And Notifications
STUDENT TEAM:
Joshua Geller – Bachelor of Business Administration/Master of Supply Chain Management
Paulina Rajski – EGL (BSE-Industrial and Operations Engineering/MSE Design Science)
PROJECT SPONSORS:
Joshua Cypher – Supply Chain Engineering Initiatives Senior Manager
Peter Lohrman – Supply Chain Engineering Initiatives Manager
FACULTY ADVISORS:
David Kaufman – Ross School of Business
Prakash T. Sathe – College of Engineering
BOEING COMMERCIAL AIRPLANES oversees the production of commercial airplanes. Their demand has increased over the past couple of years in accordance with global activity increasing as well. It is essential for Boeing to have an efficient supply chain while supporting rapid production rates of which only 20% are delivered on time. Due to a demographic shift within the work force, The Boeing Company and its suppliers have experienced high employee turnover leading to gaps in knowledge transfer. This has also been experienced by the supply base at large and consequently has led to noncompliance and misunderstandings of Boeing requirements. Furthermore, this gives rise to Notices of Escapement which contribute to production stoppages. A Notice of Escapement occurs when The Boeing Company suspects or identifies a part that was noncompliant to engineering requirements and is still installed on aircraft or even delivered to the customer. Notice of Escapements often occur due to a supplier’s lack of understanding of product standard requirements. The Boeing Company invited the Tauber team to study this strategic issue. The team was tasked with evaluating various supplier communication channels used by Boeing, and for each, recommending advantages and disadvantages, optimum frequency, and target audiences.
To understand the current state of communication processes between engineering and suppliers, the team identified different methods of communication used by The Boeing Company. These were then evaluated by sending communication to suppliers using these processes followed by a survey to test the following criteria: content retention, supplier communication preferences, and frequency for sending reminders. Communications were sent out to 4000+ suppliers. The Tauber team then surveyed suppliers to determine the most effective methods for communicating requirements and the frequency of communicated.
The key findings the team discovered were that suppliers like to participate in communication methods that are comprised of human interactions over systems. This allows for a two-way conversation between Boeing engineering and the supply base, for which its implications are immense. Furthermore, the team uncovered the potential for an outdated system to send reminders to the supply base whenever there are changes to standard requirements, increasing compliance.
The summarized results from the project were documented in The Boeing Company Enterprise Playbook commons. This playbook, which incorporates the various processes for communicating between The Boeing Company and suppliers, is now accessible to the entire company. Short-term, the tool can be used to track reminders sent out by the team and streamline processes for communicating with suppliers. In the long term, it ensures that the communication methods are documented clearly to prevent future knowledge gaps. In addition, the information gathered in the playbook will be used to program the One Data Management System, which is a central system for communication workflows being developed by the Supply Chain Engineering Team. Through streamlined reminders, the number of future Notices of Escapement can be proactively reduced by sending effective communications to the supply base, realizing projected costs savings of $6.5 million by 2028.
Brandsafway
Inventory Management and Operational Optimization in Forming and Shoring
STUDENT TEAM:
Charles Bienert – EGL (BSE/MSE Industrial and Operations Engineering)
Richard Shu – Bachelor of Business Administration/ Master of Supply Chain Management
PROJECT SPONSOR:
Mark Choe – EVP/Chief Technical Officer
John Lucas – Director of Commercial Operations
FACULTY ADVISORS:
Debra Levantrosser – College of Engineering
Anyan Qi – Ross School of Business
BRANDSAFWAY is a global leader in scaffold and access solutions, forming and shoring equipment, and specialty services with over 650 branches across six continents and $3.5 billion in rental assets. Aluma Systems is a smaller but highly profitable subsidiary, specializing in forming and shoring, the structural support equipment for concrete pours and temporary load bearing. The company is jointly owned by private equity firms Brookfield and CD&R (Clayton, Dubilier, & Rice) and prioritizes Earnings Before Interest, Taxes, Depreciation, and Amortization (EBITDA) as the primary financial metric. BrandSafway contracted Tauber to create scalable EBITDA improvement in the Atlanta Forming and Shoring branch.
While identifying 10 key improvement opportunities, the Tauber team observed and participated in 112 hours of yard operations, interviewed 42 stakeholders, conducted detailed data analysis across 8 databases, and developed end-toend process mapping of sales and operations. Of the 5 opportunities that had successful output, the 3 most impactful initiatives involved creating and piloting tools across the Yard Operations, Inventory, and Sales functions. The team:
• Initiated Forklift Telematics: optimizing safety and efficiency, collecting data
• Created Inventory Simulation Model: capturing untapped demand and minimizing internal costs
• Built Sales Dashboard: creating information streams to support job closeout negotiations
Forklift Telematic tracking provides visibility on forklift uptime and runtime, routing, and maintenance status. Inventory in the outbound and returns process requires frequent forklift touches. The Tauber team sourced and implemented the trackers in 2 branches and unlocked the potential for improved inventory placement and more lean operational processes.
The Inventory Simulation is an adjusted M/M/1 queueing model that uses historical demand data to quantify optimal inventory levels for an SKU. It outputs simulated revenue and cost metrics at a specific inventory level, including interbranch freight and subrent cost forecasts, and provides an efficient frontier for decision-makers to better inform purchasing decisions. The team created the simulation to operate at the branch level, but with further integration and development, the model can be expanded for handling a more precise network-wide forecast.
The team built a Sales Dashboard to create a job-level information stream between operations and sales. This dashboard will provide salespeople with direct access to relevant documentation, better facilitate the job closeout process, and improve visibility on customer job statuses.
The project is projected to save $1.25 million locally in Atlanta, save $6.83 million when scaled across the 13 Aluma Forming and Shoring branches, and grow annual EBITDA by 1.3%.
Conagra Brands
Conagra Brands
Optimizing Synergies Across Conagra’s Supply Chain
STUDENT TEAM:
Rachel Karaban – Master of Business Administration
Isabel Rolfe – EGL (BSE & MSE Industrial and Operations Engineering)
PROJECT SPONSORS:
Sam Beadle – Sr Director Productivity
Craig Weiss – Senior Vice President of Supply Chain
FACULTY ADVISORS:
Ravi Anupindi – Ross School of Business
Wei Lu – College of Engineering
CONAGRA BRANDS, a food company that produces popular brands such as Marie Calendar’s, Bird’s Eye, and Slim Jim, is focused on optimizing their inbound logistics for their frozen meal network. Currently, there are five plants, all of which are regionally consolidated: Council Bluffs in Iowa, Macon and Marshall in Missouri, and Fayetteville and Russellville in Arkansas, that produce frozen meals. The inbound logistics of the frozen meal network is rather spread out as there is need for external warehousing located far away, sometimes as far away as Wisconsin to service Arkansas.
Even though these plants are all Conagra-owned, they operate almost as individual entities, leading to a lot of redundancies across the network, from labor to purchase orders to suppliers. By bringing raw materials and packaging into the network through a hub, there is the potential to consolidate tasks, purchases, and shipments for the plants in scope. At the hub, tasks that are completed at each plant individually can be done in larger quantities by less labor overall. These tasks include quality assurance, mixing, and material planning. While doing tasks at a larger scale can mean mistakes become more costly, there are rarely any mistakes within quality assurance and mixing for this to be a viable risk.
One issue plaguing the network is high working capital, which is stored in an expensive external warehousing network, there are more materials within the network, and thus more money tied up.
By creating a hub-and-spoke model, which consolidates external warehousing to a centralized distribution center, Conagra will realize reduced labor cost and working capital and logistics efficiencies. Additionally, a hub will enforce a culture of cohesion and unity between these five plants with orders and planning happening centrally rather than separately. This solution would also allow the network to operate in a “just in time”/Kanban system that would facilitate a reduction in inventory levels.
Ford Motor Company
Scaling Additive Manufacturing
STUDENT TEAM:
Brendan Biache – Master of Business Administration
Elizabeth Hoyt – EGL (BSE Chemical/MSE Industrial and Operations Engineering)
PROJECT SPONSORS:
Jay Haubenstricker –Additive Manufacturing Engineering Supervisor
Jason Ryska – Director, Manufacturing Technology Development
FACULTY ADVISORS:
Lennart Baardman – Ross School of Business
Judy Jin – College of Engineering
The goal of this FORD MOTOR COMPANY was to build an excel model to identify the cost and value differences between additive manufacturing and plastic injection molding at different scales of production. The purpose of this project is to develop a comprehensive cost/value model (henceforth the Tauber Model) that can be used to estimate the total cost and hidden value of additive manufacturing.
The project team used a variety of data sources, including previous Ford cost models, interviews with engineers, interviews with suppliers, previous price quotes, and market research to develop a detailed cost model. The accuracy of the model was then verified by comparing the Tauber Model to other pricing models and known values used by Ford.
The model was designed to be flexible and adaptable so users can update variables and add new information that was not considered at this time. The team also developed a sensitivity analysis to identify the key drivers of costs and to assess the impact of changes in these variables on total production costs.
The Tauber Model was utilized to compare various scenarios that involved automation and different part sizes. These scenarios provided valuable strategic insights that either justified or ruled-out further investment in automation and certain production parts.
The results of the project show that the cost model is a valuable tool for estimation production costs and identifying potentially cost saving opportunities. The model can be used to optimize production processes and forecast production costs for different vehicle volumes.
Overall, this project demonstrates the importance of developing a comprehensive cost model for additive manufacturing in the automotive industry. The Tauber Model provides valuable insights into the cost structure of production and can help managers make informed decisions about resource allocation and production planning.
MILLERKNOLL, INC.
An Assessment & Recommendations for Automation Opportunities in MillerKnoll’s Warehousing Operations
STUDENT TEAM:
Won Young Kang – EGL (BSE/MSE Industrial and Operations Engineering)
Rachael B. White – Master of Business Administration
PROJECT CHAMPION:
Richard Scott – Chief Global Manufacturing & Operations Officer
PROJECT SUPERVISOR:
Beau Seaver – Vice President Engineering, Automation, and EHS
FACULTY ADVISORS:
Raymond Muscat – College of Engineering
Eric Svaan – Ross School of Business
With over fifteen unique brands under the MILLERKNOLL umbrella,MillerKnoll is the largest high-end furniture manufacturer in the world. With a vision and purpose to ‘design for the good of humankind,’ MillerKnoll places a strong emphasis and focus on people from its customers to its own associates throughout the organization. Our Tauber project with MillerKnoll this year focused on the company’s warehousing operations, more specifically the Midwest Distribution Center in Holland, Michigan. Our team defined the following two goals for our project.
1. Reduce the human struggle in warehousing operations
2. Roadmap the integrated technology ecosystem for the future state of warehousing
Our Tauber team set out to achieve these goals by conducting benchmarking research and site visits to understand what industry leaders are doing in the warehousing technology ecosystem. In parallel to this benchmarking, the team planned and executed a series of trials for process improvements and technology solutions to inform final recommendations for the DC excellence journey that MillerKnoll has embarked on. Based on the knowledge gained from the benchmarking research and trial execution, the team defined recommendations in the form of a phased implementation plan to take the Midwest Distribution Center from its current state operations to a desired future state with an integrated technology and data-driven system.
As MillerKnoll continues the DC excellence journey with the guidance of the recommendations and detailed analysis our team was able to complete and provide at the end of this project, we expect the Midwest Distribution Center to implement an integrated, technology ecosystem in the next 3-4 years that will yield compounding annual savings up to an estimated $2 million. In addition, we expect MillerKnoll to utilize our learning to continue the ongoing DC excellence journey to identify more opportunities to reduce the human struggle and gain additional operational efficiencies.
Mayo Clinic
Improving End-to-End Supply Chain Reliability
Student Team: Joseph Kearney – Master of Business Administration
Jared Pavlick – EGL (BSE Biomed/MSE Industrial and Operations Engineering)
Jayantha Tatkionda – EGL (BSE Biomed/MSE Industrial and Operations Engineering)
Project Champion: Joe Dudas – Strategy & Innovation Division Chair
Project Liaison / Supervisor: Jared Featherstone – Operations Manager
Faculty Advisors:
Hyun-Soo Ahn – Ross School of Business
Tom Buchmueller – Ross School of Business
MAYO CLINIC is a nonprofit organization committed to clinical practice, education, and research, that provides expert, whole-person care to everyone who needs healing. The Mayo Clinic Supply Chain Division supports physicians at Mayo Clinic and elsewhere by procurement and distribution of close to $4B in supplies annually including medical supplies and devices, pharmaceutical, lab supplies, medical and lab equipment as well as purchased services. In the past two years, backorders have increased 300%.
Backorders affect patients directly as well as lead to waste in the supply chain. The current state is not sustainable, and a new solution needs to be deployed.
The Tauber team studied the causes of the increase in backorders, the financial costs incurred by backorders and potential solutions to decrease backorders. The research discovered an annual cost of over $17.48M spent resolving backorders with substitutes.
The team developed a framework to provide leverage to improve existing supplier relationships. First, the team developed an implementation of Collaborative Planning Forecast and Replenishment (CPFR) program with existing suppliers. Second, the team developed a dashboard to automate the costs incurred by backorders and enable Mayo Clinic to leverage these costs into their future contract language and rebates. In doing so, the monetary impact is predicted to save $90M over the next 5 years; the quantity of backorders is expected to be reduced by 82.5%. This framework is the initial foundation to provide Mayo Clinic the opportunity to completely change the health care supply chain industry through supplier relationships.
Modine Manufacturing Company
Developing a Standard Rough Cut Capacity Planning (RCCP) Model for Modine’s Air-Cooled Applications Business
STUDENT TEAM:
Griffin Riley – Bachelor of Business Administration / Master of Supply Chain Management
Abrajeedhan (AB) Rajagopalan Srilatha – Master of Business Administration
PROJECT CHAMPION:
Jason Ulett – General Manager - Power Generation
PROJECT SUPERVISOR:
Vatsal Gandhi – Director of Strategic Materials Planning - Air Cooled Applications
FACULTY ADVISORS:
Damian Beil – Ross School of Business
Debra Levantrosser – College of Engineering
MODINE MANUFACTURING COMPANY is a global leader in thermal management solutions for a wide range of industries, including automotive, agriculture, construction, data centers, HVAC, and industrial equipment. As part of its transformation to a high-performing, diversified industrial organization, Modine’s strategic initiatives target the development of an 80/20 culture by segmenting the company into clearly defined, market-focused business verticals. The Air-Cooled Applications vertical provides air-cooled thermal management and currently operates multiple legacy plants across the globe that produce similar products.
Even though Modine is a global player, each plant operates without a standardized Rough Cut Capacity Planning (RCCP) tool, making it difficult for the company to meet customer demand and drive asset utilization. The project was directed towards creating a connected view of global capacity for the Air-Cooled Applications business vertical in Modine’s portfolio by developing a standard RCCP model. This model will be integrated into Modine’s Sales, Inventory, and Operations Planning (SIOP) process and propel the organization towards optimizing asset utilization to better meet customer demand.
The deliverables for the project include a full RCCP model dashboard designed for Modine’s Lawrenceburg, TN plant, as well as a comprehensive instruction manual that explicates the process of refreshing the data in the model on a monthly basis. The Tauber team developed the model in Power BI and successfully communicated its purpose and capabilities to the executive and plant leadership, initiating the use of Rough-Cut Capacity Planning as part of Lawrenceburg’s monthly operations.
With the refinement and expansion of the model to other Air-Cooled Applications businesses in North America, the team estimates a 15-20% increase in operational efficiency from optimizing station-level workloads and long-term materials planning. Furthermore, the deployment of the model will reduce overtime by 20-30% via synchronization of production schedules with demand patterns. Trapped inventory is also expected to drop by 10-15% through enhanced management of Work-In-Progress materials and reduction of idle periods. Ultimately, RCCP model developed by the Tauber team will serve as the foundation for global long-term capacity planning in the Air-Cooled Applications vertical and other verticals thereafter. This will unlock further tangible and intangible value at the company-level as Modine drives asset utilization and increases revenues throughout their transformation.
Nestl Purina
Optimizing the Inbound Supply Chain Network
STUDENT TEAM:
Hanna Chapin – EGL (BSE Computer Engineering / MS Robotics)
Joshua Phan-Gruber – MBA and MS Environment & Sustainability
PROJECT SPONSORS:
Roger Brecht – Vice President of Digital Manufacturing Nestlé Purina North America
Christopher Micena – Director of Innovation, Digital Manufacturing at Nestlé Purina North America
FACULTY ADVISORS:
Raed Al Kontar – Assistant Professor Industrial & Operations Engineering, College of Engineering
Sanjeev Kumar – Lecturer of Technology and Operations, Ross School of Business
NESTLÉ PURINA is a global Fortune 500 company and is the leading pet food brand in the United States. Purina has seen strong growth over the past several years driven by the surge in pet adoptions during the Covid-19 pandemic, and with the domestic pet food market projected to have a 9.3% CAGR through 2027, Purina has more demand than it can currently meet. Purina reported $19.5B in revenue in 2022, a 16.4% increase from 2021, with continued expansion expected in 2023
Maximizing available resources is a top priority for Purina, and the Tauber project aligns with that strategic focus. The project is focused on the supply chain of “Ingredient X”, an input for Purina wet dog and cat foods. Ingredient X is a raw product with a shelf life of a few days, with hundreds of millions of pounds purchased annually from over a dozen supplier locations going to seven Purina facilities. With such large volumes moving across a geographically dispersed network, getting the required supply of Ingredient X to the right Purina facility on time requires a transparent and dynamic supply chain. The Tauber team was given a broad mandate to analyze current processes used to manage Ingredient X and to identify opportunities to reduce expense, lower risk, and increase the availability of raw materials
The project team spent three weeks in a discovery phase, traveling to factory locations and having conversations with procurement, technical applications, logistics, and external stakeholders. Supplier communications, internal data availability, and product rendering were identified as key opportunities to be addressed with a unified approach in order to achieve the desired efficiencies.
The Tauber team considered several approaches and ultimately decided to design and initiate the build of a custom application developed in Microsoft PowerApps. This application will allow real-time visualization of the tanker network, centralize communications and data within the network, reduce the volume of renders due to inefficient communications and information flows, and allow for future optimization of the supply chain based on the data it generates. Designs were created in close coordination with the future end users of the application, and it is estimated that once implemented, this tool will save $12.8M over the next three years in reduced raw material and rendering costs, with greater future savings likely once the data generated by the application can be analyzed internally to identify trends and inefficiencies that are invisible with current capabilities.