CONTENTS
RMIT- INSTITUTIONAL BUILDING
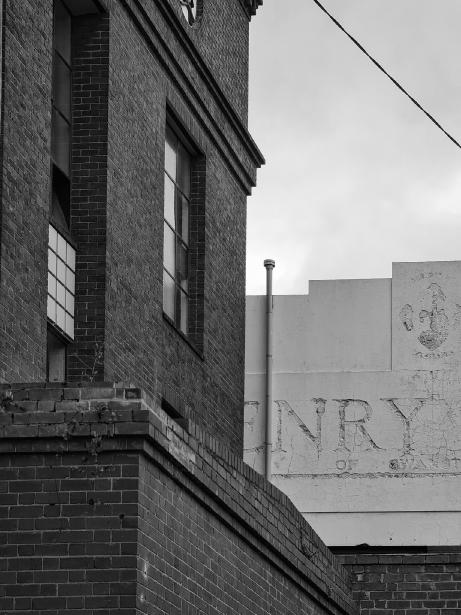
PLASTIC COBWEB
RURBAN ACUPUNCTURE
MEDICAL CENTRE
ART GALLERY PROJECT
INTERIOR WORK
RMIT - INSTITUTIONAL BUILDING
Year-3
ADV. DIPLOMA OF BUILDING DESIGN
“Looking for a great teacher who can tell you what will happen in the future? Ask the ancient ruins what will happen!”
- Mehmet Murat Idan

Relation to context
The pre-design process was a collaborative endeavour. The area also contains the work of our team members; we were tasked with planning and constructing a building for class 9b, which is an RMIT institutional facility.
As we were informed to highlight the link between our buildings and our colleagues, each team member presented suggestions that had to connect with their neighbouring members.
The precinct has undergone changes as a result of its reliance on sustainability. Inside the building, amenities such as green space and common space were created to encourage social interaction.
Some heritage buildings were demolished to make way for the proposed improvements, although ancient RMIT buildings such as 51, 56, and 57 were preserved.

Artwork
The concept is based on the conceptual work of Sol Lewitt. The model is characterised by a concern to investigate and describe basic geometric shapes. The artwork is achieved by the variation of incomplete open cubes. The paradigm reflects the trend of irrational reasoning, and Sol Lewitt explains how to follow it completely and objectively.
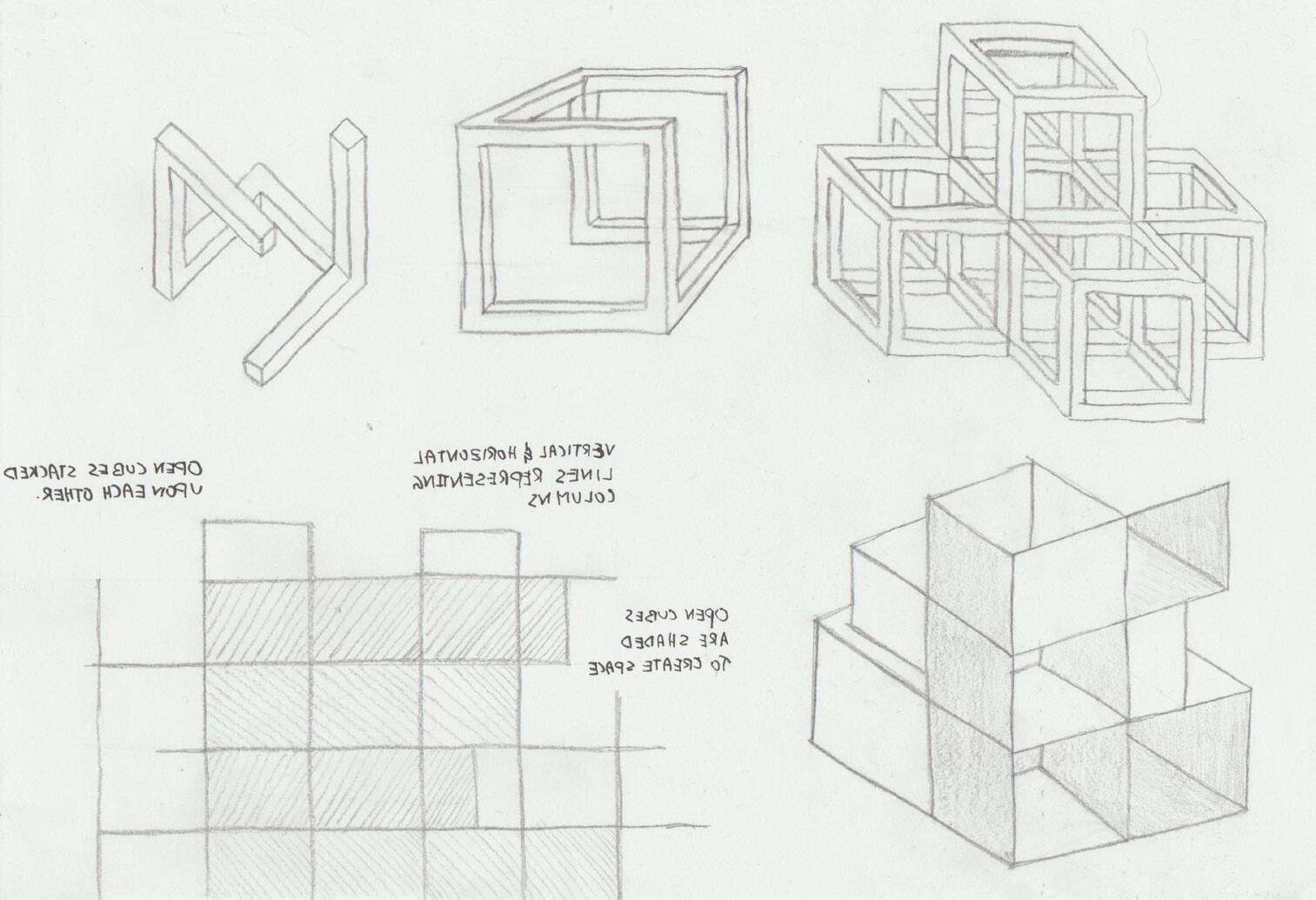
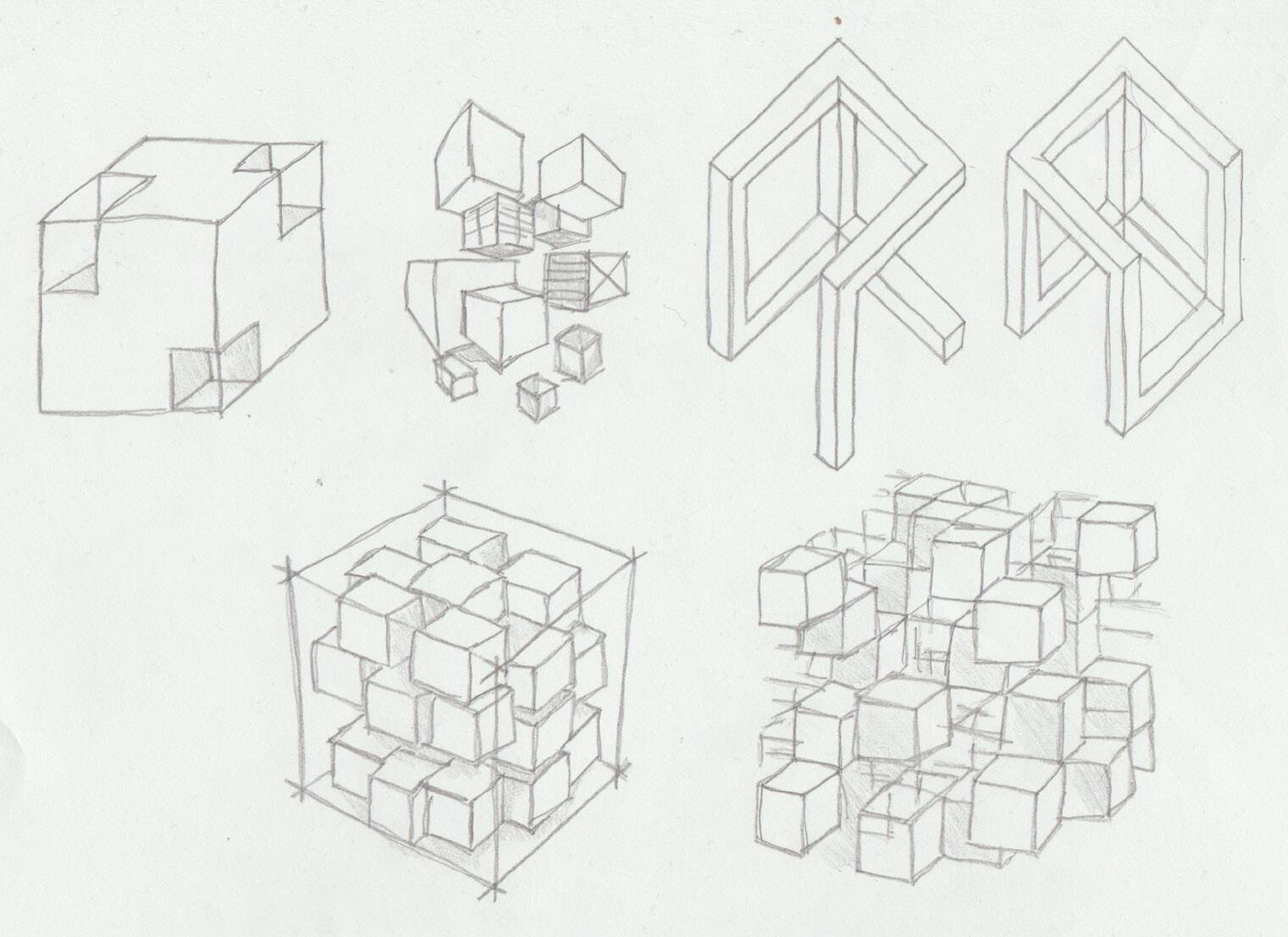
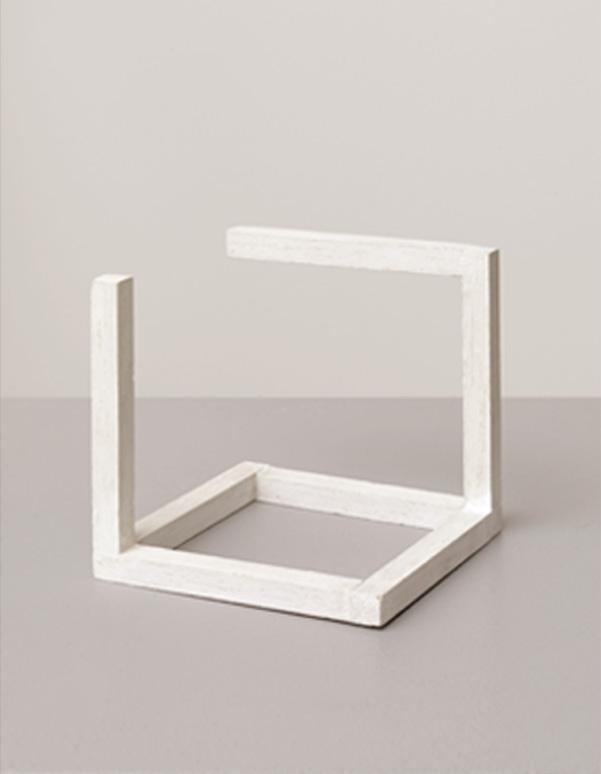



Just as Sol Lewitt descirbes that It is as if, having found the square through a combination of idle play and thorough alchemical discovery, a terribly chaotic, systematic quest for possibilities and combinations leading him to a hermetic proof of the triangle, and eventually to the multi-cubic form.
Concept
The shape is the sum of basic building and structural elements, distorted and leaving many empty spaces to stress the idea of unfinished.
Design Outcome
This is a modernist open cube design; the layout and approach were basic, however the structuring was intricate. Multiple voids have been created to demonstrate the concept’s openness. The timber columns appear to be tree trunks, and climbing plants have been planted on each external column to simulate a tree. The plan was to create a vegetation-filled wood jungle to promote building sustainability. Other environmentally friendly materials, such as repurposed window frames and breeze blocks, were employed.
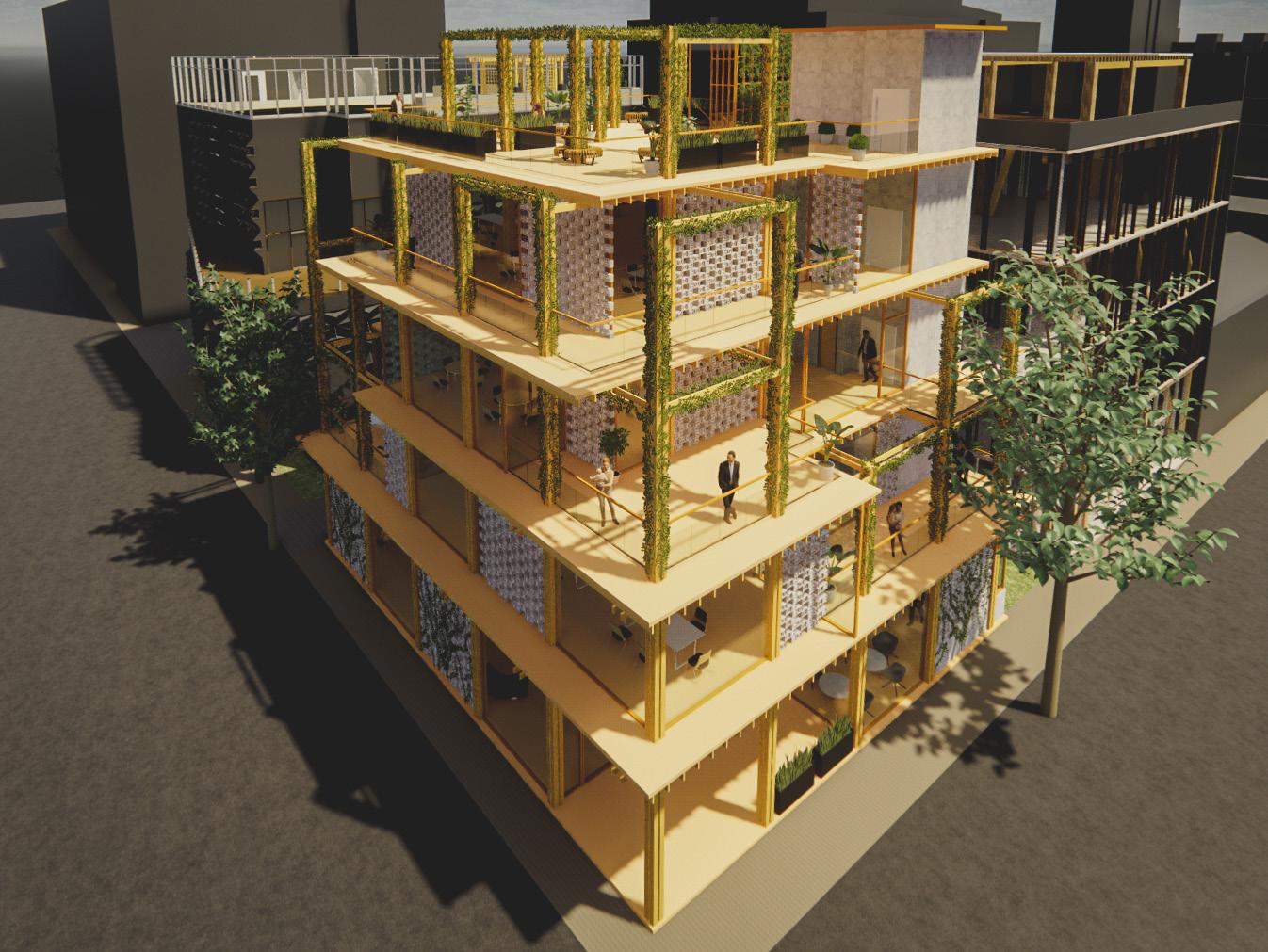

The subject property is situated on the intersection of Lygon Street and Victoria Street, both of which are prominent thoroughfares with a large level of foot activity and road traffic. There are several parking spots around the property that are occupied the most of the day, implying that a car park is required for the occupier.
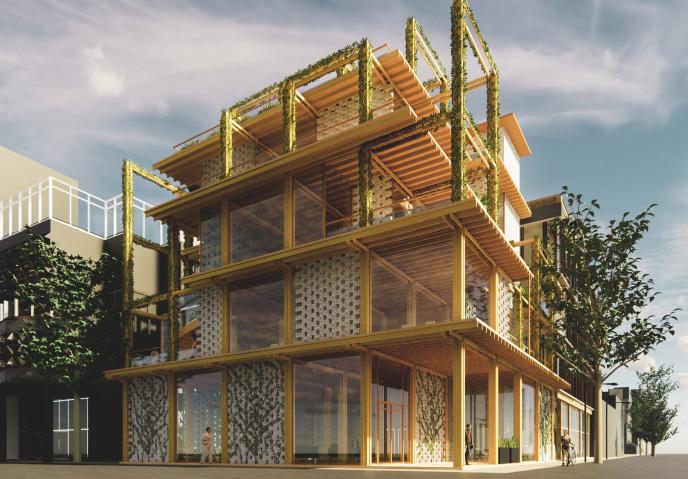
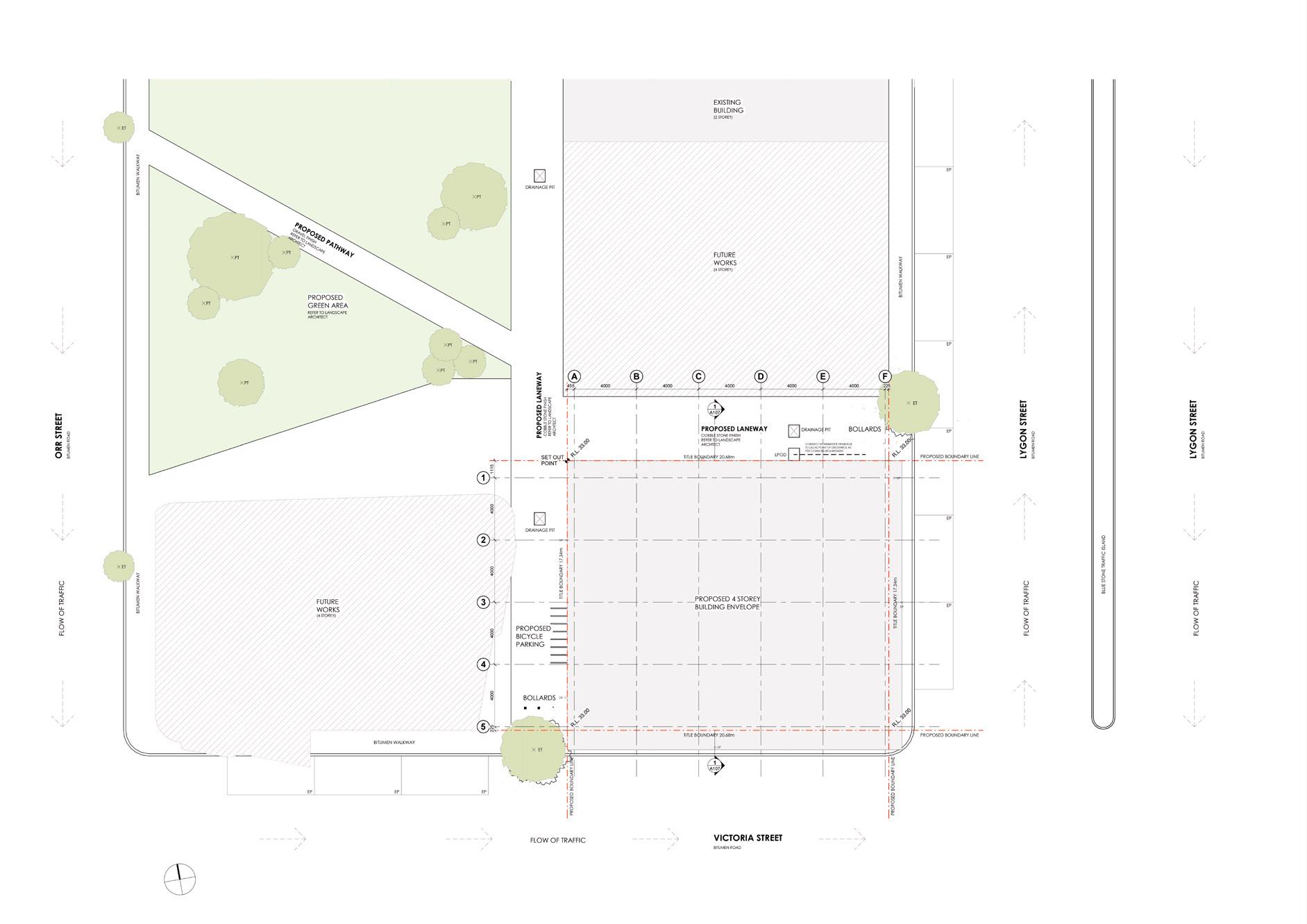

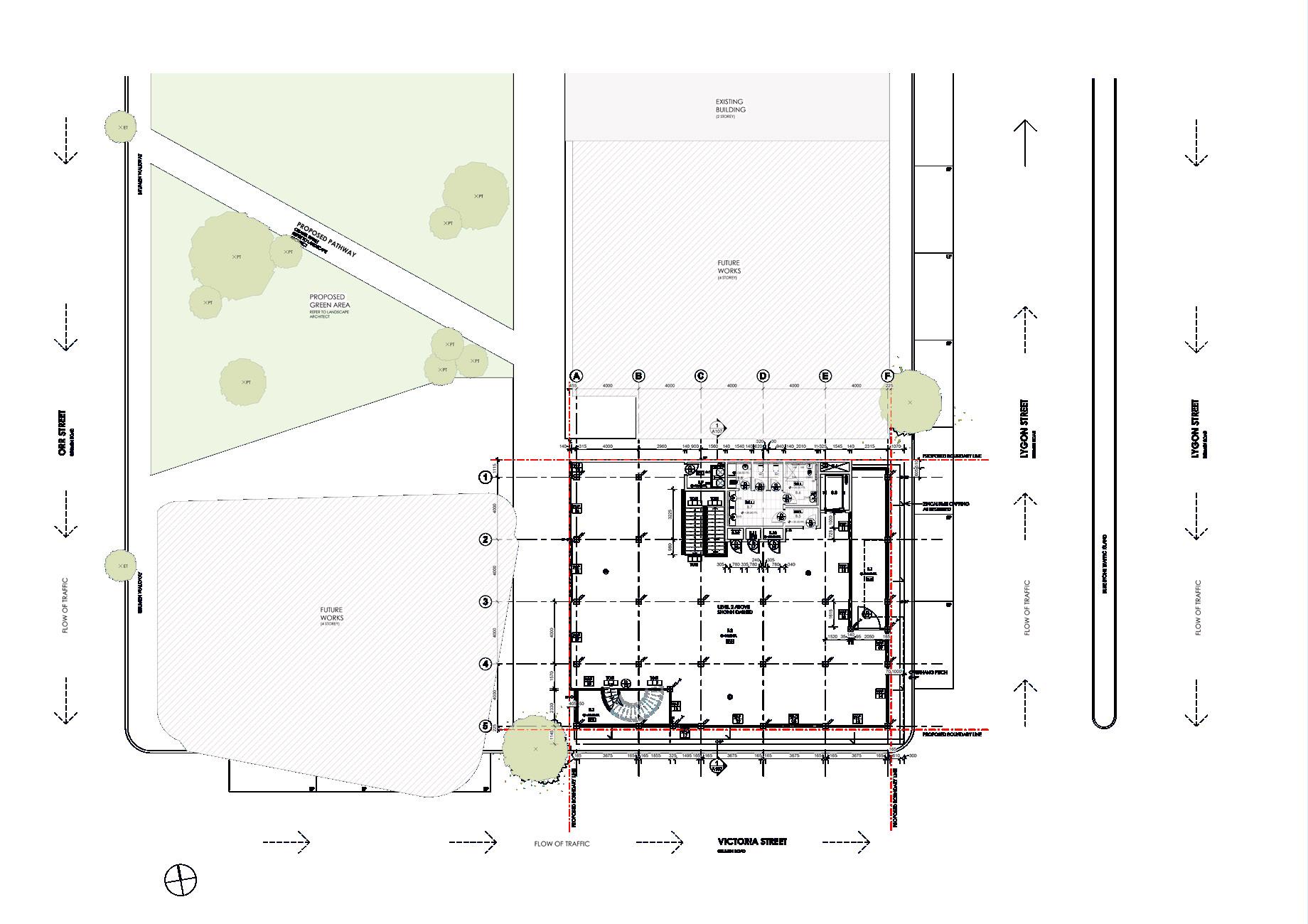
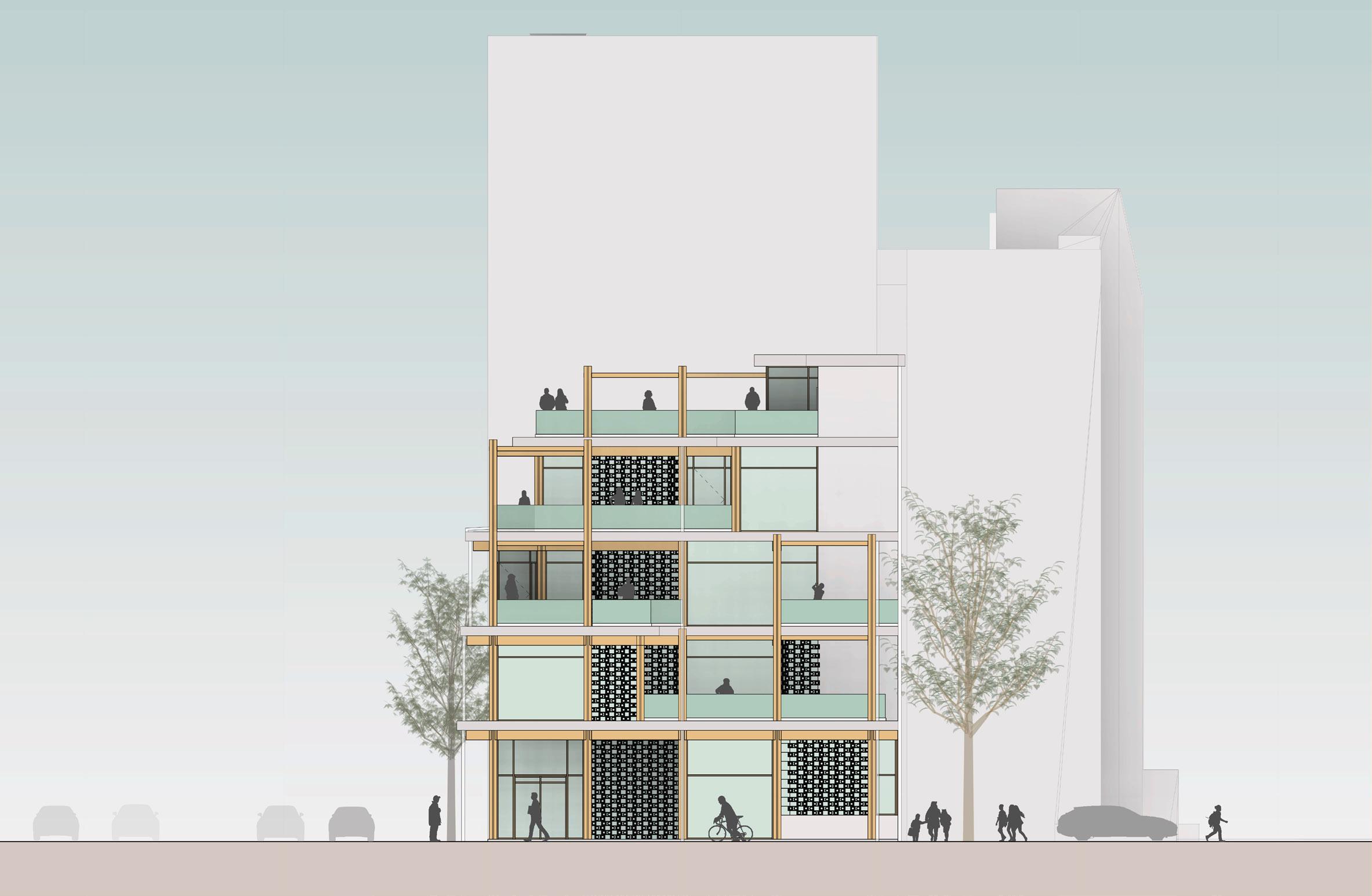

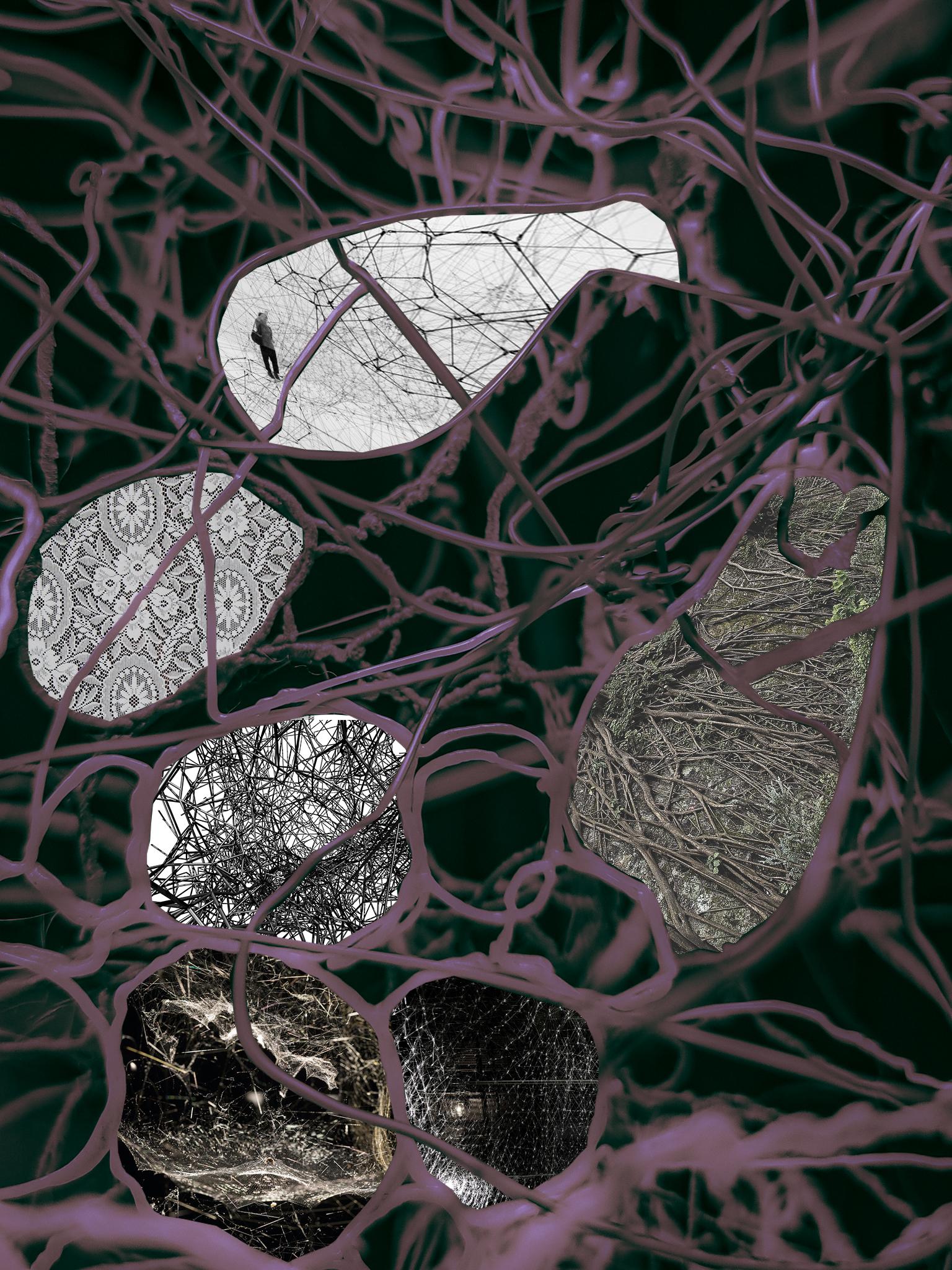
“I alone cannot change the world, but I can cast a stone across the waters to create many ripples.”
- Mother Teresa
BACHELOR OF ARCHITECTURAL DESIGN
Relation to context
Extensive research was done for the location during the Pre-Design stage because the Proposed Model would link with the communal space. It would serve as a transition from a residential area to green space.

The Brief was to create an identity of architecture where people would go and take a part of the architecture and keep it as memorabilia since the type of material used in this project is exotic and can be created by anyone using a 3D pen and be operated with a power bank, the brief was changed to suit what the material wants to do and how it wants the people to perceive it, which is to create an architectural concept and let people drive it using their creativity.
After various experiments, very few things were added to the brief, the model would stand as a temporary model that would only sit for 5 years, because temperatures in Australia can reach 38C or 40C, and because the model is made of plastic, the material can deform with temperature during the summertime and people can add more stuff to it during the wintertime, the model would look different in each coming season.
Concept:

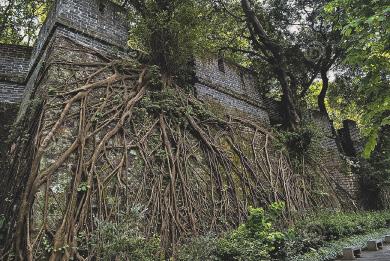
The researchers investigated how 3D pens and holographic imaging may be utilised to drive the manufacturing of the lacework model. We were tasked with developing ways for concurrently producing complicated goods with a pen, plastic filament, and a heat gun. The images above show what we can expect from 3D printing; the top left image is one of Tomas Saraceno’s “Courtesy of the Shed” models, which he created by putting different species of spiders in a glass box and then having them create all the webs; the cobwebs were then scanned and fabricated using plastic material. Bottom right is the outcome of 3D scanning the spider webs and then creating the spider web design using threads. To produce the parabolic shape for the plastic lace to hang loose, the concept of Peter Luigi Nervi’s arch was thought upon.
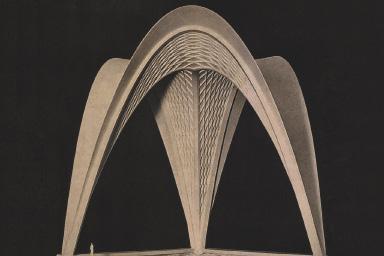
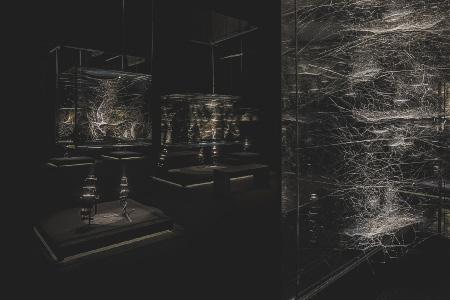
3D PRINTED PAVILLION
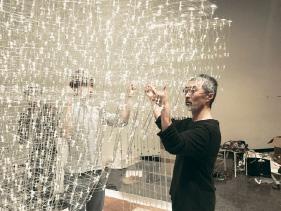
Crafting Technique:
The mini crafts were made using a MYNT3D Pen, which can extrude 1.75mm diameter filament. Variations in the figure were created by using different colours of plastic PLA filaments. The pen can alter both the operating temperature and the rate at which the filament is produced. The temperature can be varied between (130 and 140)°C, which helps manage the stiffness or flexibility of the model. Layering a single strand of extruded plastic with the 3D pen can reinforce it; layers of three or four can make it exceedingly hard, decreasing the possibility of deformation.
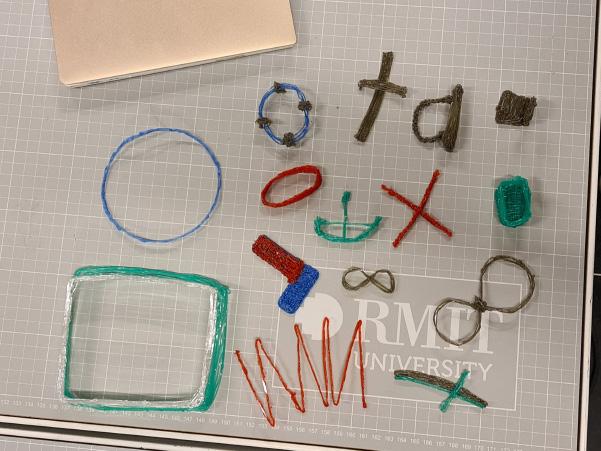
The image, which consists of little hand-made 3D objects, is the result of an experiment undertaken to assess the material’s stress, strength, and durability; each trial was completed with varying temperature and speed measures. If the extrusion speed is increased, the density of the extruded material may be increased, and if the extrusion speed is decreased, the pen can be used to make any object with accuracy since it gives the user more control over the extruded plastic.
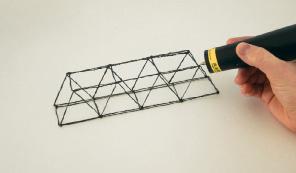
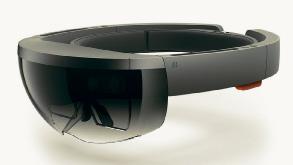
Final Project:
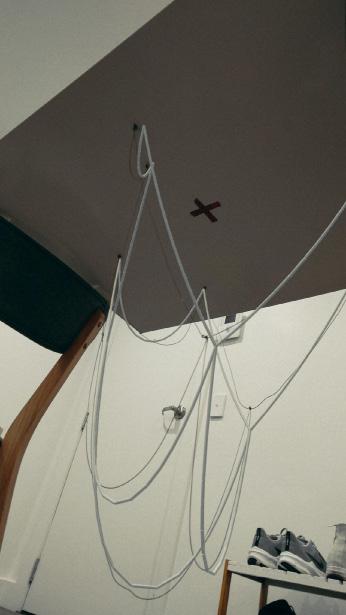
3D software such as Rhino and Grasshopper were used to create the model, and advanced technology known as Microsoft Hololens was used to create these models. The Hololens guides the user through the process of developing their desired model by displaying an augmented model in front of the lens screen at the same time as reality.
The hologram is there to help us throughout the production process, but it proved challenging to recreate the augmented models in reality since the material shrinks and deforms with temperature change. Because the Hololens has difficulty identifying shaded sections in real life and thus becomes slightly glitchy when in use, it was advised that we utilise white panels so that it can identify the surface and decrease the amount of objects that we want to produce to reduce latency.
After creating the augmented model with 3D software, we use Fologram, a programme co-founded by our professor Gwyllim Jahn that allows us to see the augmented model in real-time using the hololens or a smartphone as we are building the model.
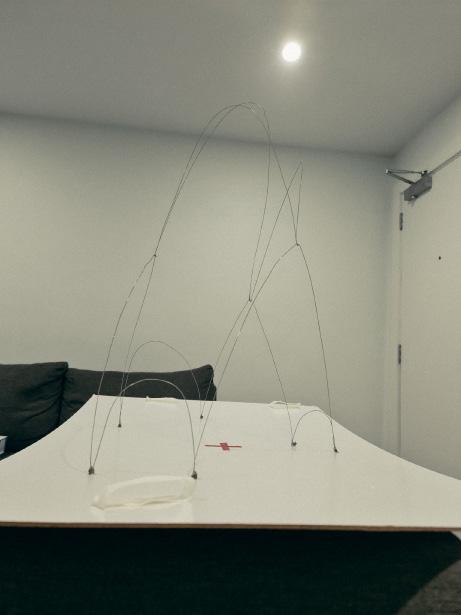

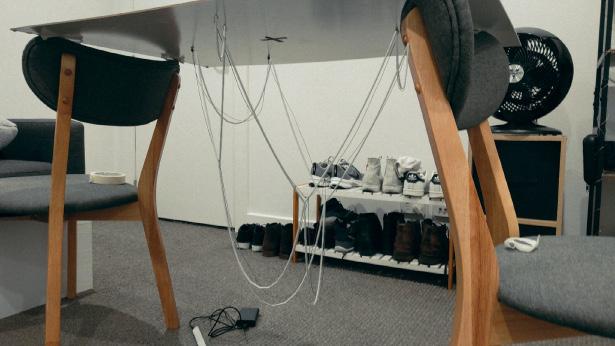
Failed Prototypes:
The prototypes shown above were created as part of the process of developing the final product. Because the extruded material was difficult to regulate, these models did not match our expectations. The spherical balls acted as a guide, the lace structure was made 2D on a non-stick surface, and then a heat gun was used to deform the lacework and create a lace spherical object. Later, the aluminium spheres would have been removed, and only the spherical lacework would have remained connected with the other lacwork. However, this procedure was inefficient and time-consuming.
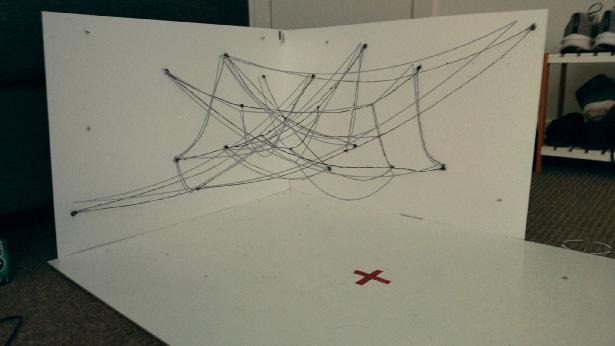
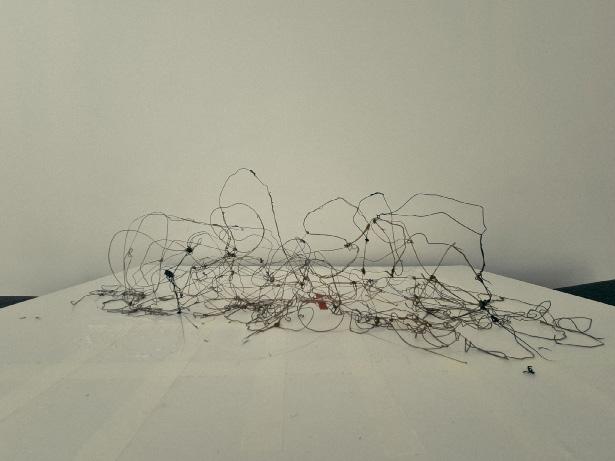


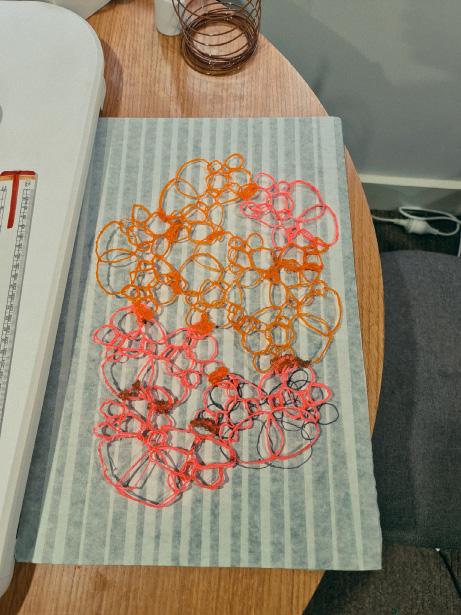
Because of the weight, the freehand 3D printing in the second row of images was difficult to control because the extruded plastic kept falling owing to gravity and would not stay firm or straight when fresh laces were inserted or linked to that particular lace. The model had been attached to the surface to hold it in place, but this was deemed inadequate. In the third row of images, the enhanced model was inverted upside down to deal with gravity, as advised by my professor Gwillim Jahn. We were able to move the model by building it upside down, but the arches were too small to form corridors, so we changed our design from having panels to allow us to create a web-like structure to a gothic long arch on a single panel.

Fabrication & Render:
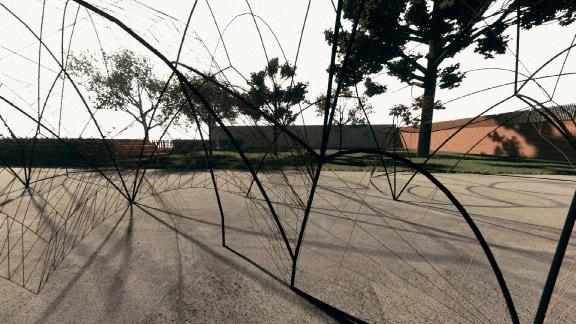
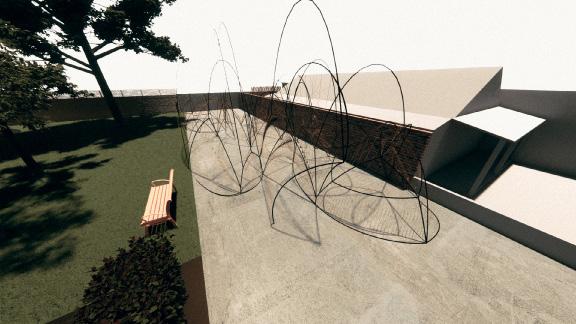
Considering our brief required us to build a shelter with rooms, we developed dense laceworks for privacy in the bedrooms and additional openings for natural light penetration in the living, dining, and kitchen areas. The method used to build the prototype is shown in the photos above; the augmented model was built normally, but when it came time to fabricate it, it was turned upside down so that we could use gravity to make those arches with the 3D pens. 2 to 3 layers of plastic filament were added to the arches to give longevity and structural support, ensuring that the sculpture does not bend.
To provide apertures and variation, colourful laces were drawn on the model to form a façade; the laces highlight the difference between the white surfaces and the coloured facade, giving the figure a distinct character. The single-layer laces also functioned as a brace to hold the arches together. The laces were drawn crisscrossed or chevron-style using the hololens. A force was applied to the model several times to evaluate its durability and strength; no deformation occurred, and the model was flexible enough to withstand the pressure.
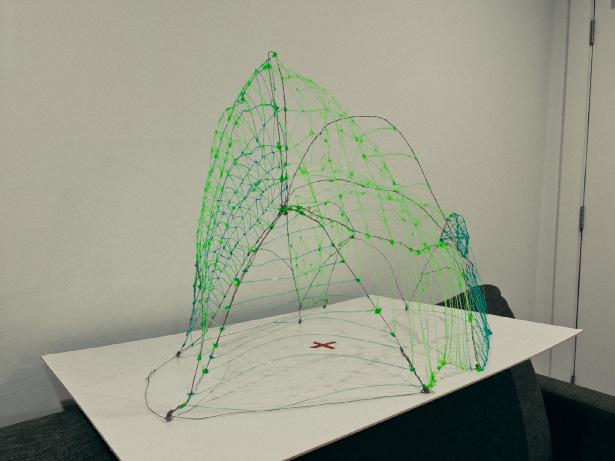


“Under trees, the urban dweller might retsore his troubled soul and find the blessing of a creative space.”
- Walter GropiusBACHELOR OF ARCHITECTURAL DESIGN
Relation to context
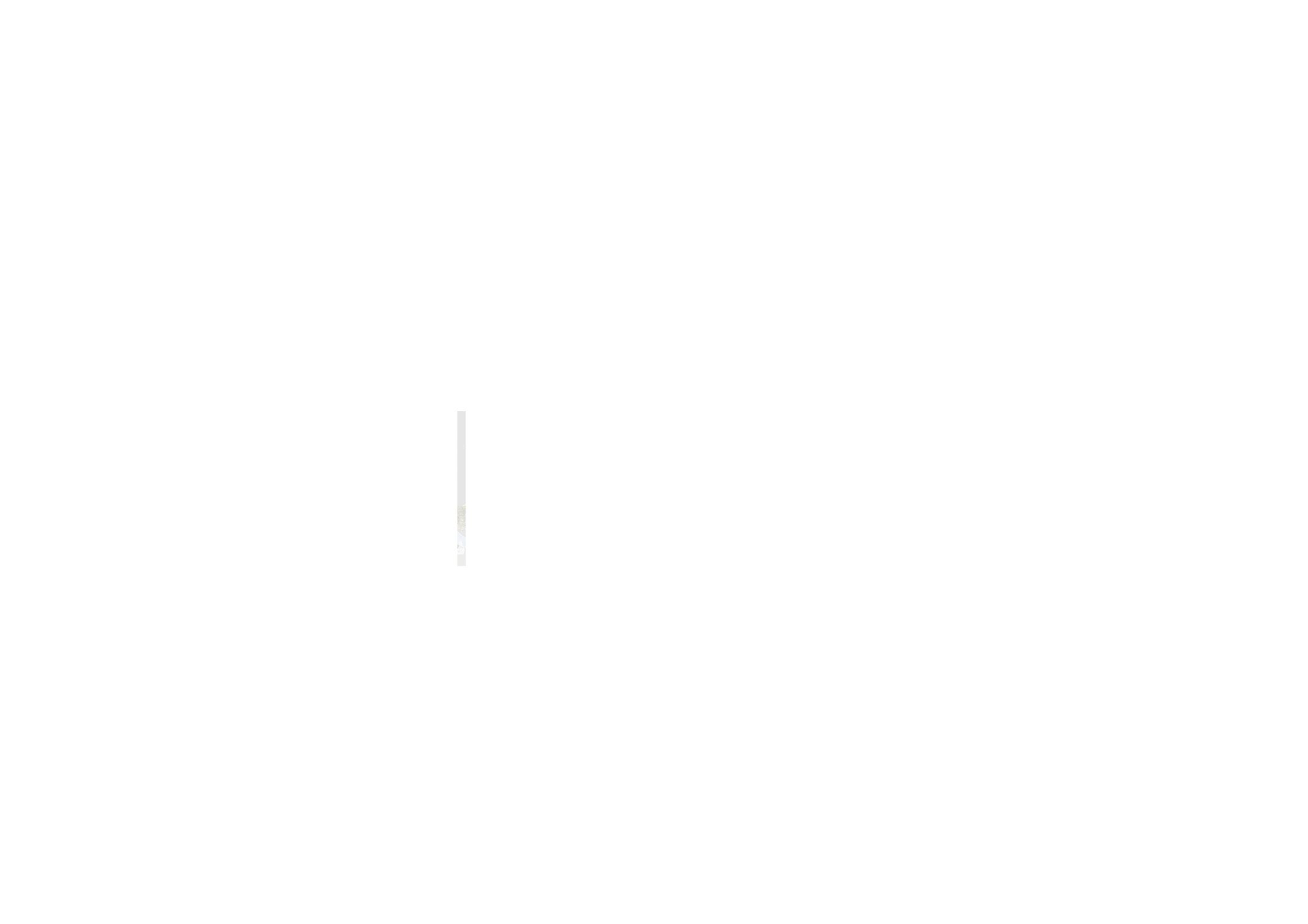
The site is in Indonesia, specifically Yogyakarta, the capital city of the island of Java’s south-central region. With a rapidly growing population, the city was vulnerable to increased traffic, and slower movements would interrupt the flow of people and logistics. A complex concept has been developed that will house entertainment, a fresh market, logistics, and transportation all in one location.
The site chosen is Giwangan Bus Terminal, which is located in the south-east of Yogyakarta and handles 20,000 people and 850 buses each day on average.

Shade is another idea that has been considered for implementation because Indonesia is closer to the equator where temperatures can rise and it would be difficult for people to commute and attend any events due to the heat. Tensile structures have been implemented on the first floor of the proposed building to provide shade.
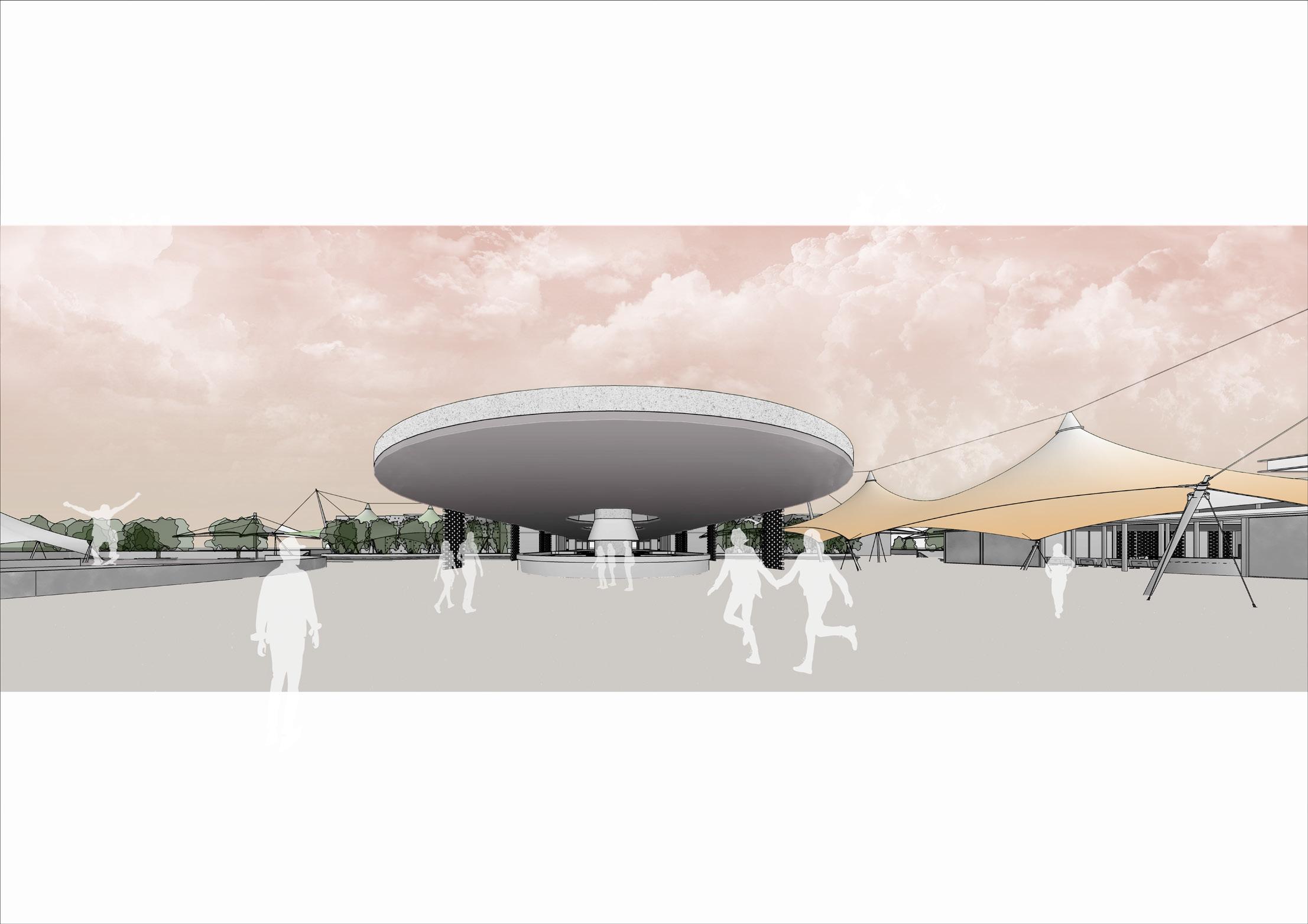
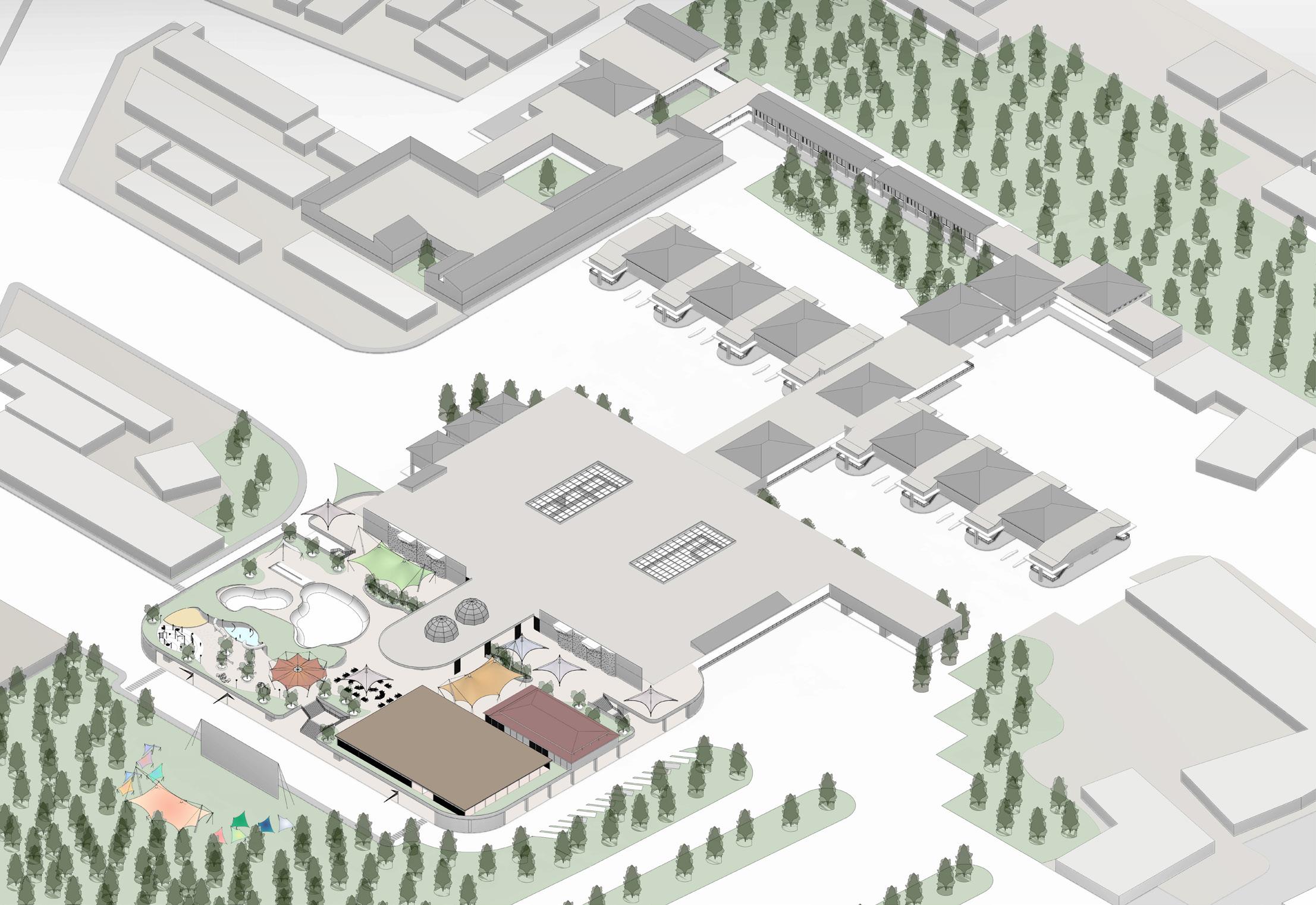
o y a c p a p c a R g o o o y a n n o e n e u h- n a pa h a d a
Design Research:
For the past two centuries, industrialisation has been inextricably associated with widespread migration from rural areas to increasing metropolitan areas. For the first time, the world population was majority urban in 2007. While this method has significantly reduced poverty, it has also resulted in tremendous environmental devastation and great income disparity in many areas.
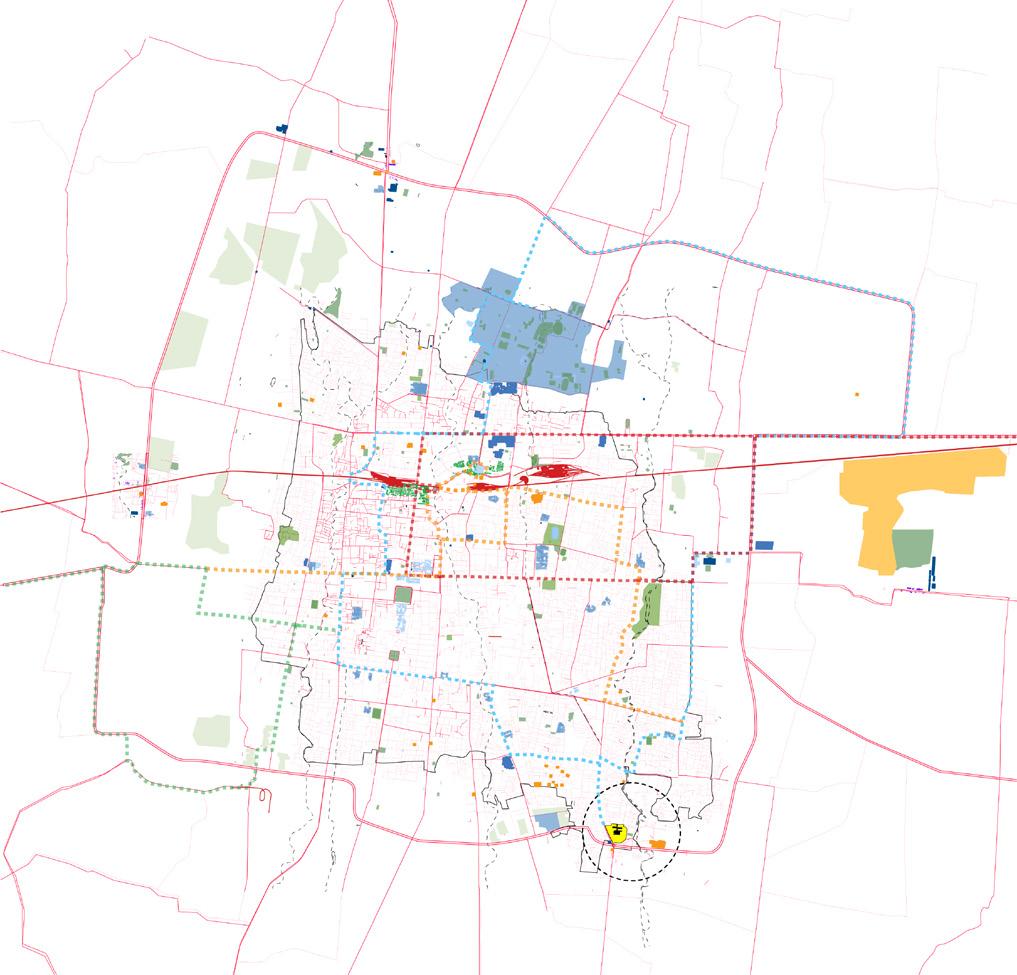
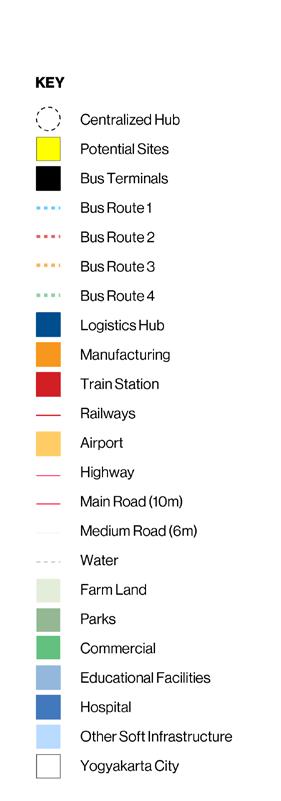
We generated research from post-capital and Java predicament studies in the Pre-design stage, studying hard and soft infrastructure, local benefits, macro benefits, financial investments, and the UN SDG, among other things. Using this research, considerable information was obtained about Java, namely Yogyakarta. Based on Yogyakarta statistics, it was discovered that the city was densely inhabited with heavy traffic, yet the city has big hard infrastructures such as bus terminals, airports, and train stations. Using the existing hard infrastructure, new soft infrastructures such as the entertainment centre and farmers market were built on top of the existing building.
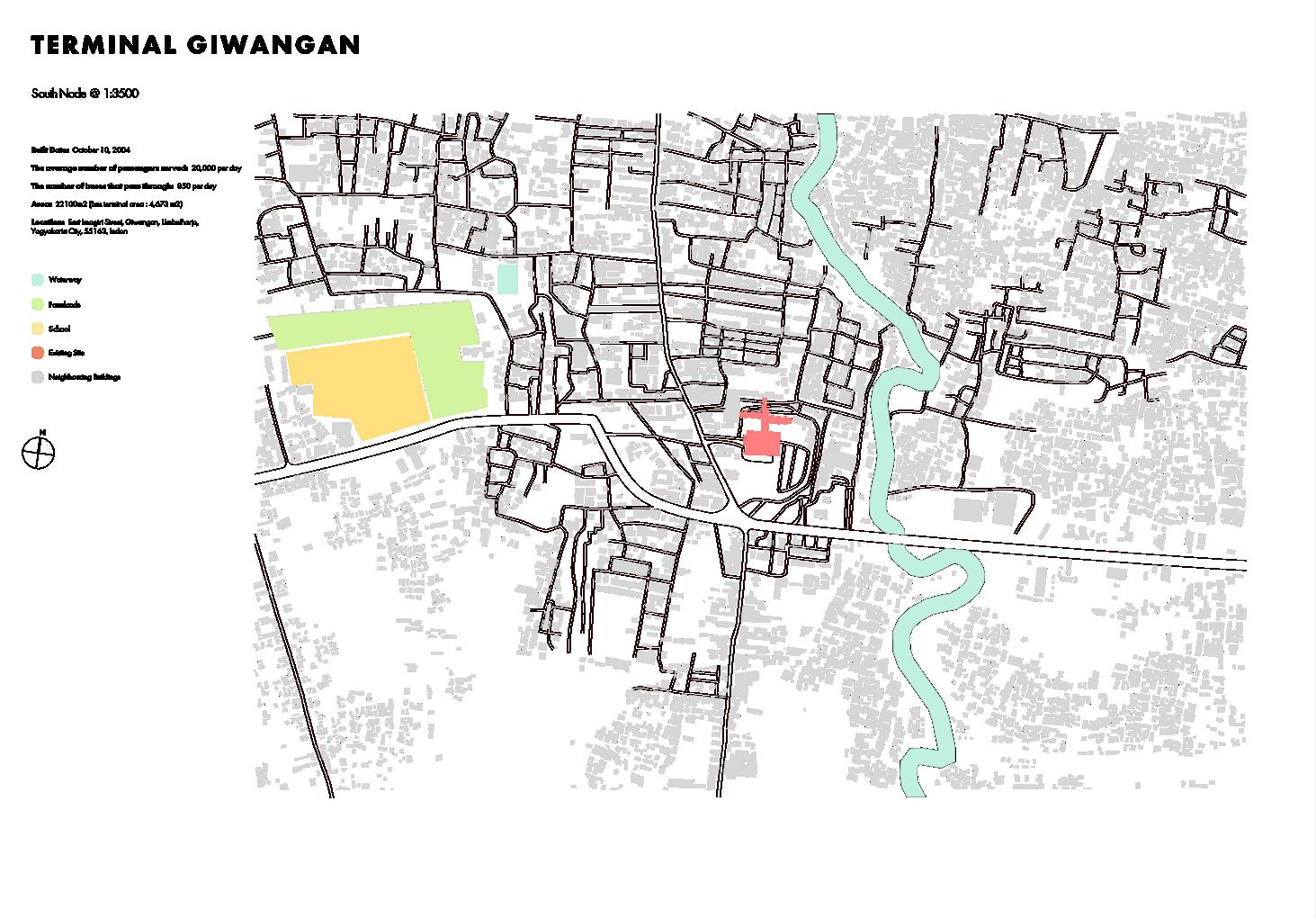
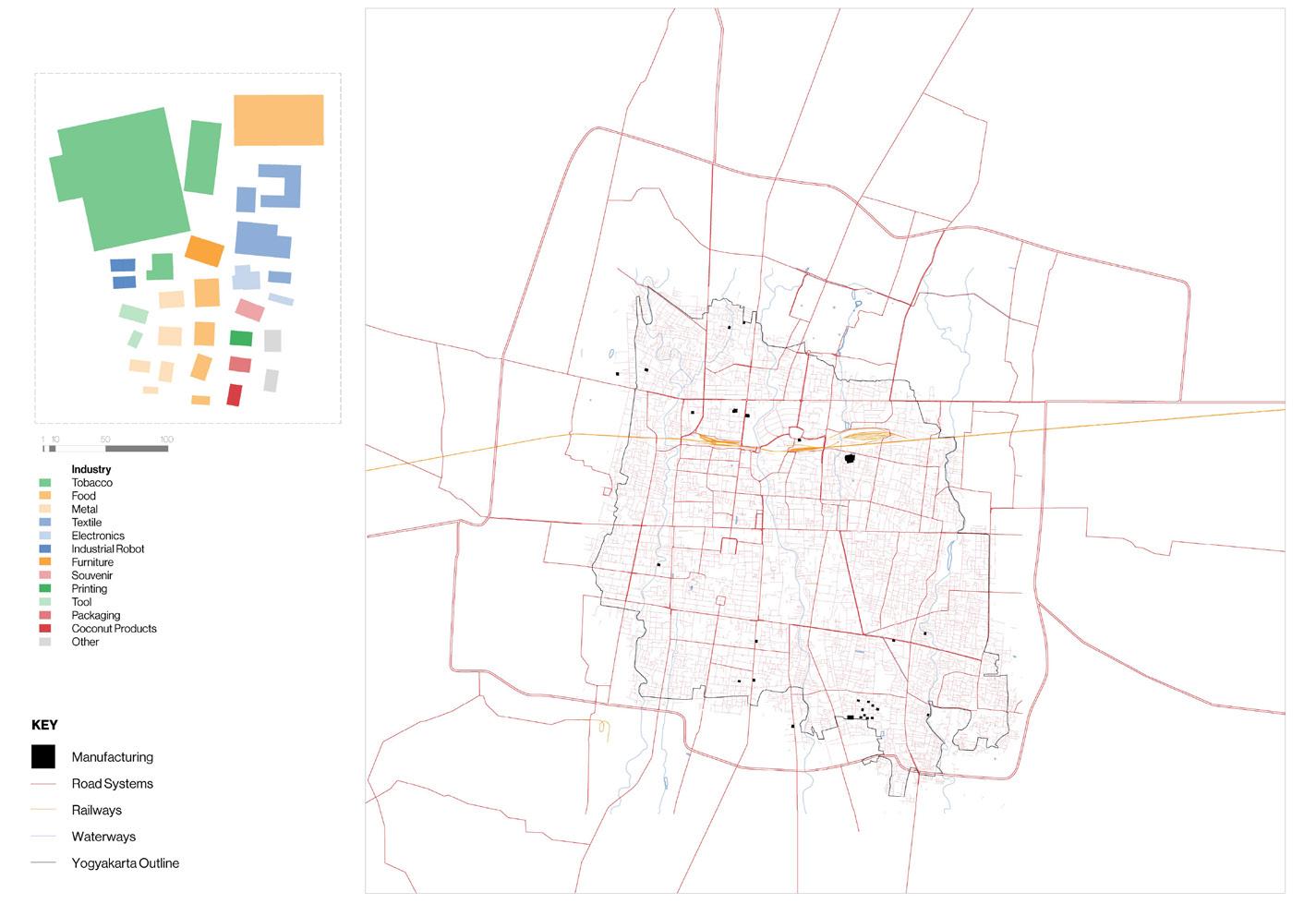
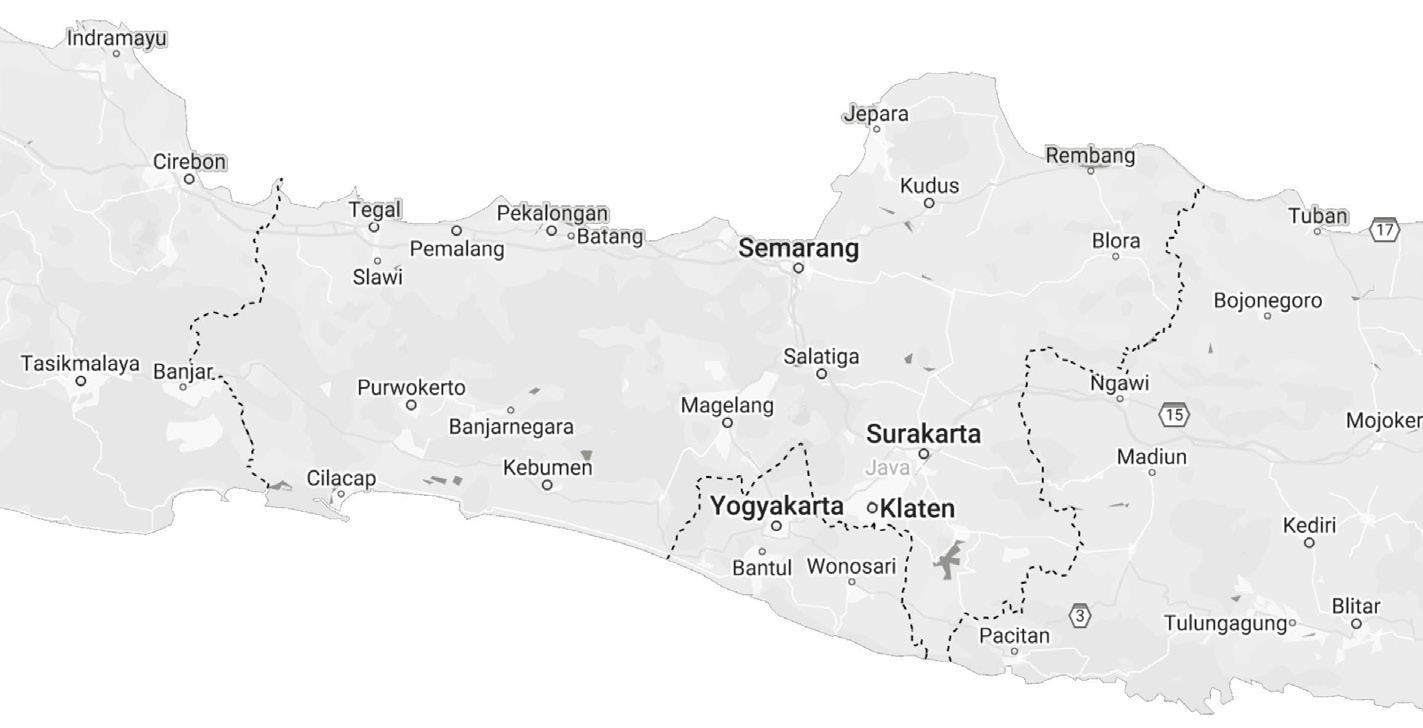
-- A Ad s o n e a n A p e m e omme c a p n Rail Y y k S v de u a g S o e e o o a n b h a n e c e n h e h Bus e a e e y a g n w o h u h e m e o Yo y k m w o e a e e e n m e omb u Te m n n h o h o h G w n a B m
a u h