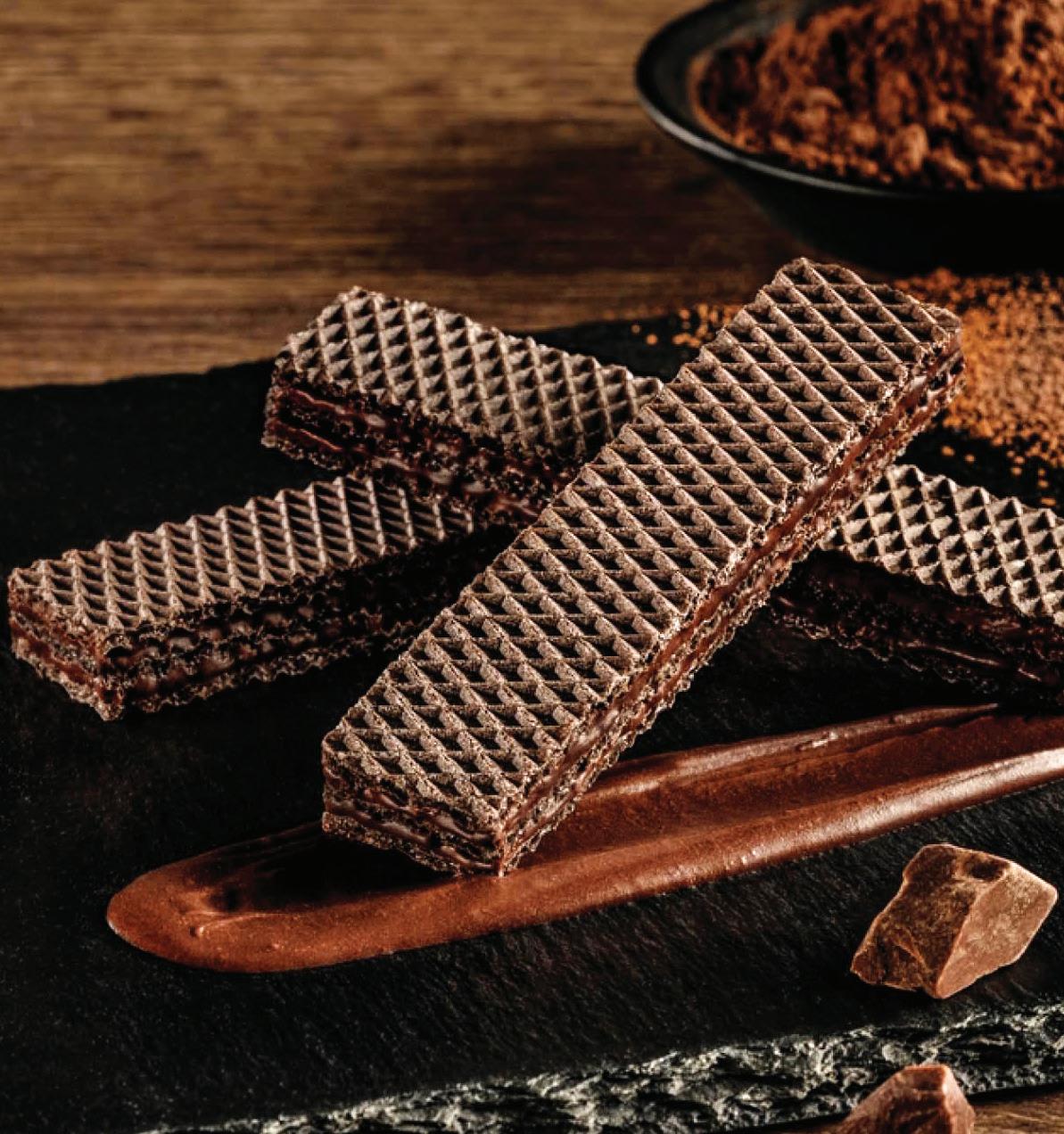
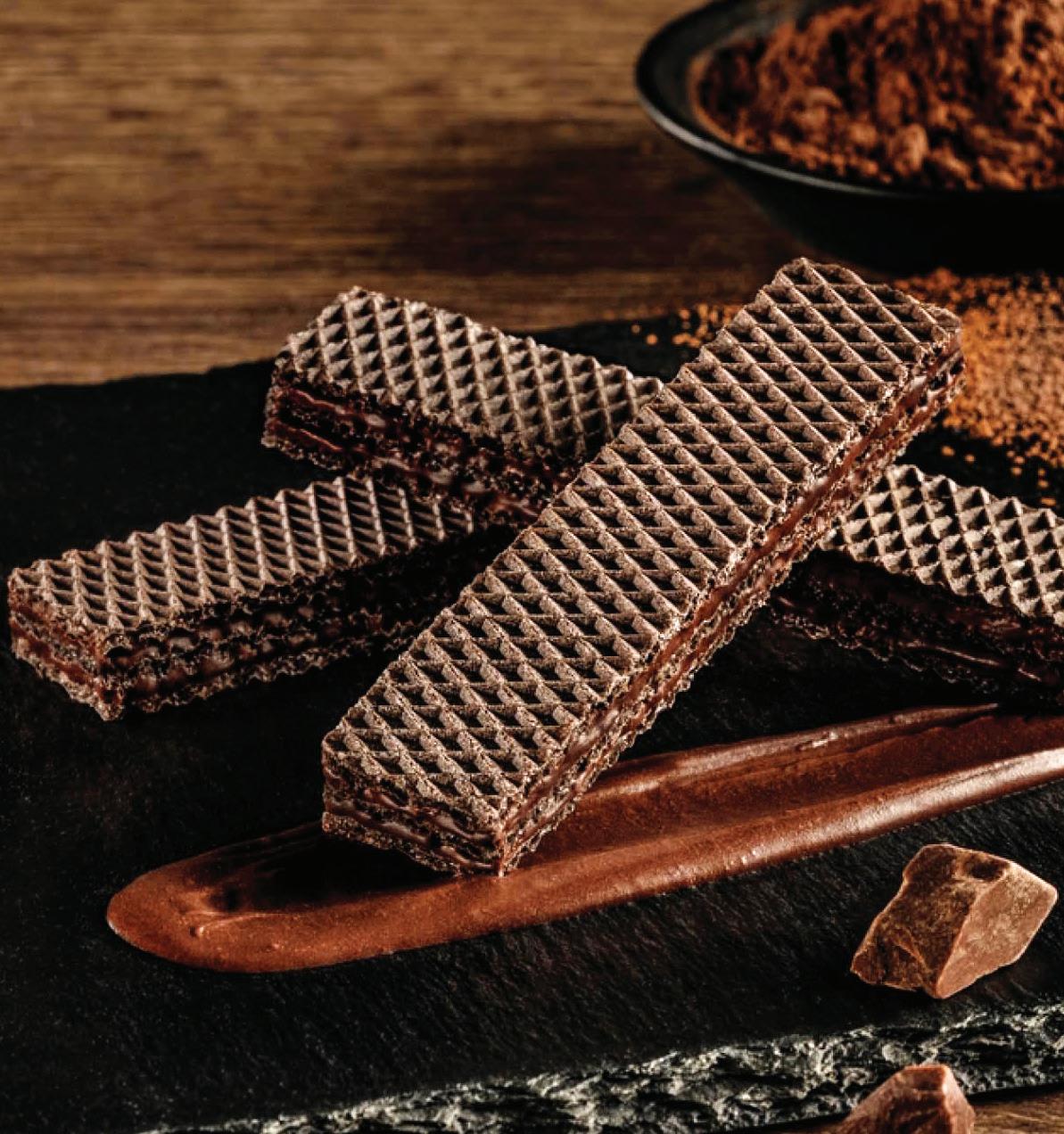
editor ’ s note
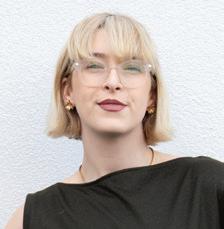
Caitlan Mitchell Editor-in-Chief caitlan@reviewmags.com
When Innovation Doesn’t Stand Still
Inspire+ NZ Artisan Awards season is always a highlight.
Every year, we’re reminded how far local brands can go when passion meets perseverance. Many of these journeys begin in home kitchens, on family farms, or at weekend farmers’ markets, where ideas are tested, refined, and brought to life.
The product that might have started in a recycled jar or hand-stamped paper bag is now beautifully branded, supermarket or foodservice ready, and, in many cases, making its way onto the global stage.
What’s most inspiring is that the journey doesn’t end at the shelf or in the restaurant kitchen. The best brands never stand still. They adapt, rethink, and ask what
contents
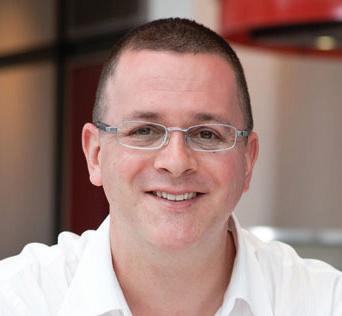
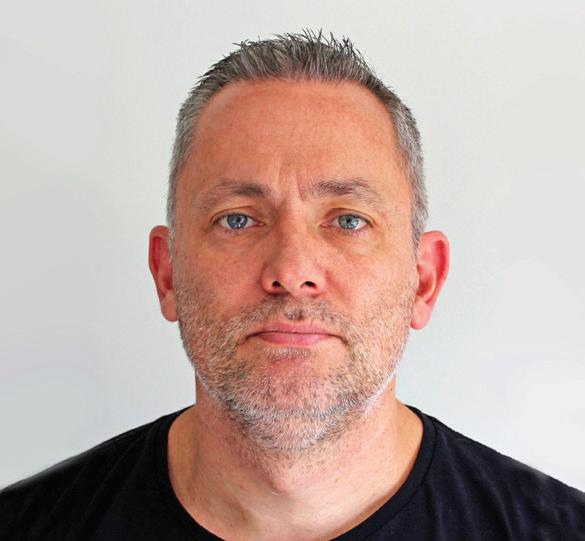
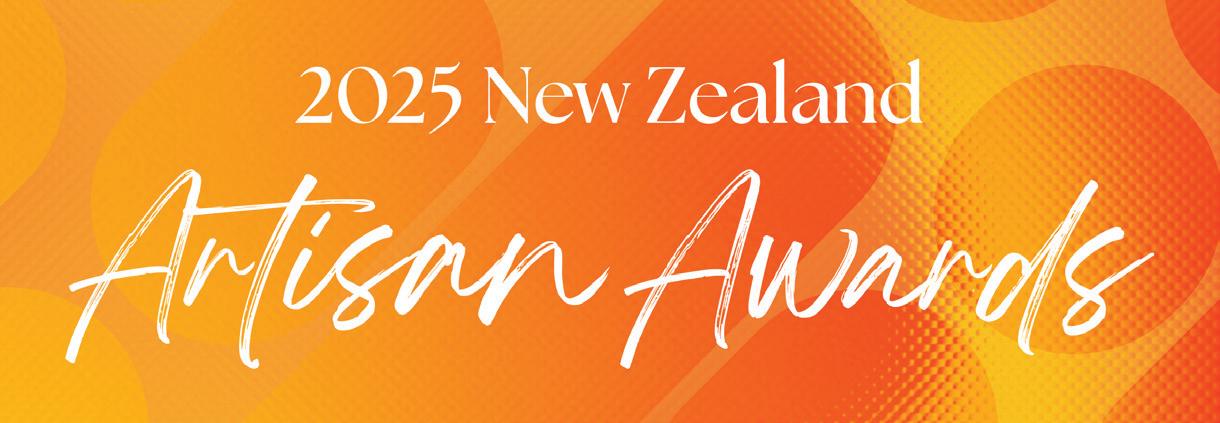
comes next. That could mean reformatting for foodservice, exploring aged care, scaling into convenience channels, or tapping into new consumer trends.
This year, we’re proud to return as innovation judges at Anuga where packaging continues to be one of the most talkedabout aspects of product design. It's not just about visual appeal. It's about mouth-feel, function, and fit, how a product is used, stored, and experienced. From the shape of a bottle to how easily it pours, great
packaging strikes a balance between beauty and practicality.
Across this year’s Artisan entries, we’re seeing brands thinking bigger, asking smarter questions, and designing for the real world. Taste and concept remain essential, but so does usability.
Innovation isn’t a moment. It’s a mindset. The brands that keep asking how they can do better are the ones that thrive, grow, and make a lasting impression.
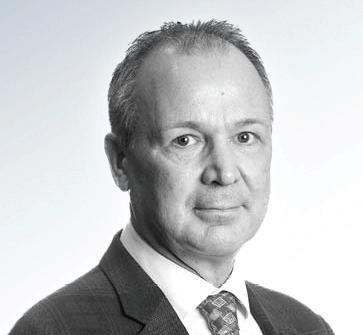
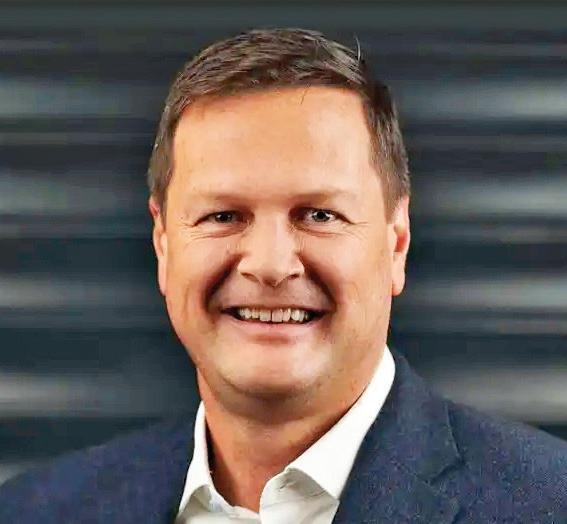
PUBLISHER Tania Walters
GENERAL MANAGER Kieran Mitchell
BRAND MANAGER Sarah Mitchell
EDITOR-IN-CHIEF Caitlan Mitchell
EDITORIAL ASSOCIATES Jenelle Sequeira, Sam Francks
ADVERTISING SALES caroline@reviewmags.com, daniel@reviewmags.com
SENIOR DESIGNER Raymund Sarmiento
GRAPHIC DESIGNER Raymund Santos
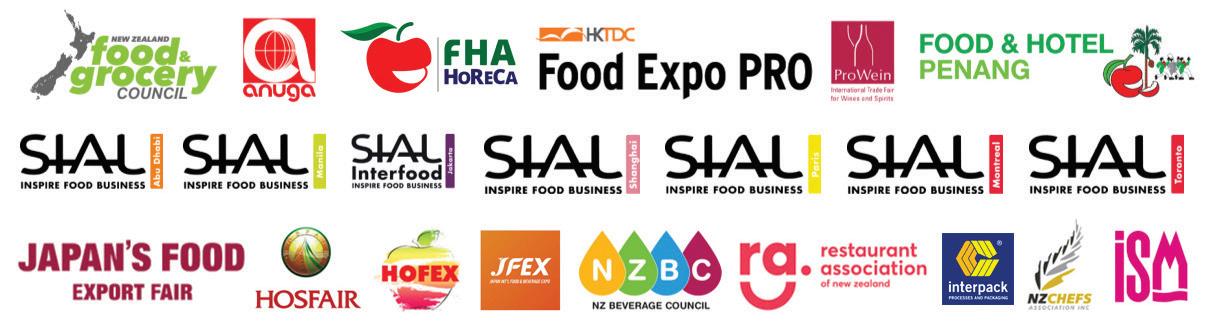
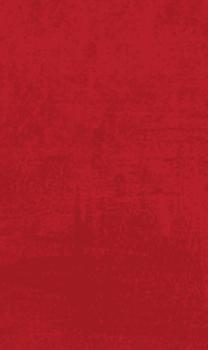
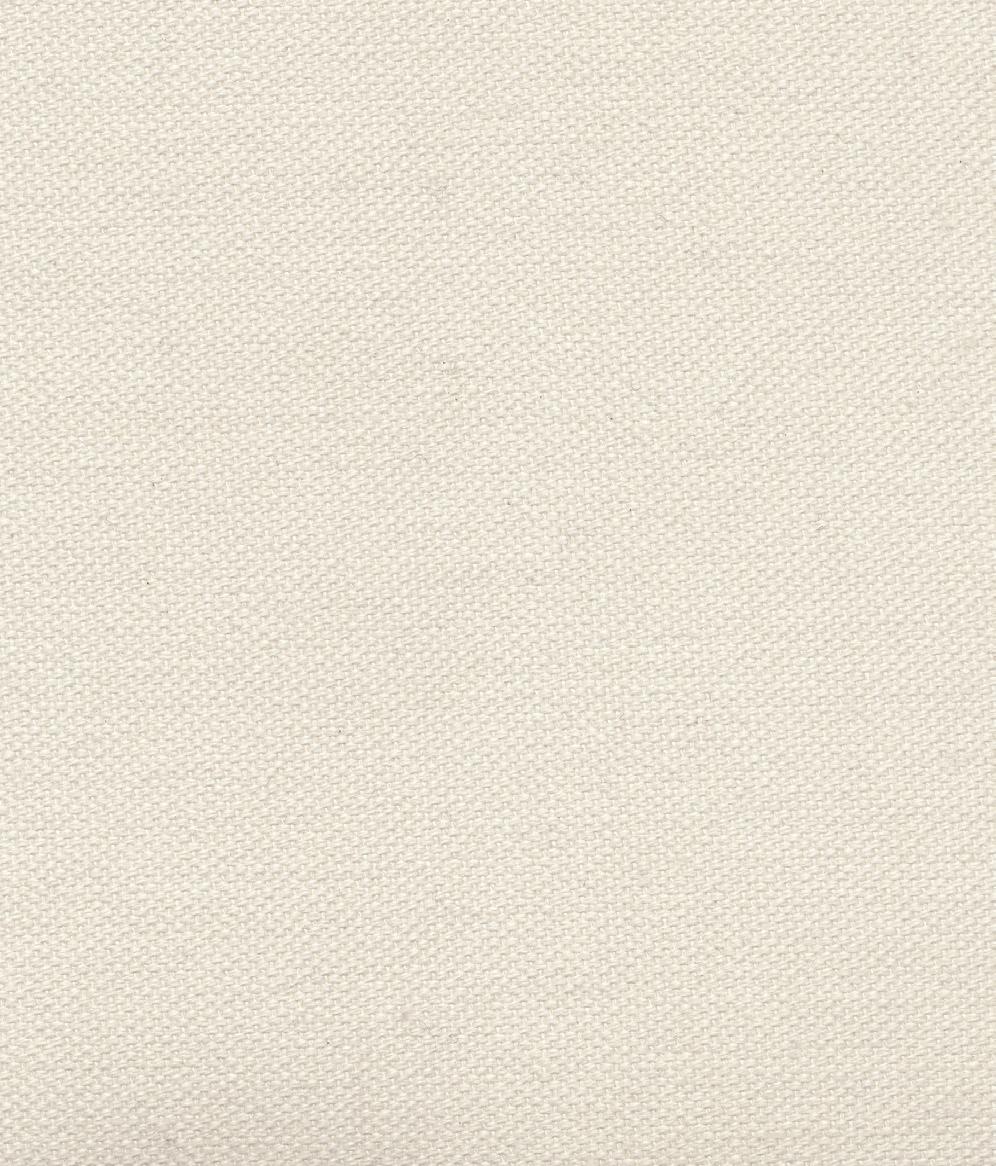
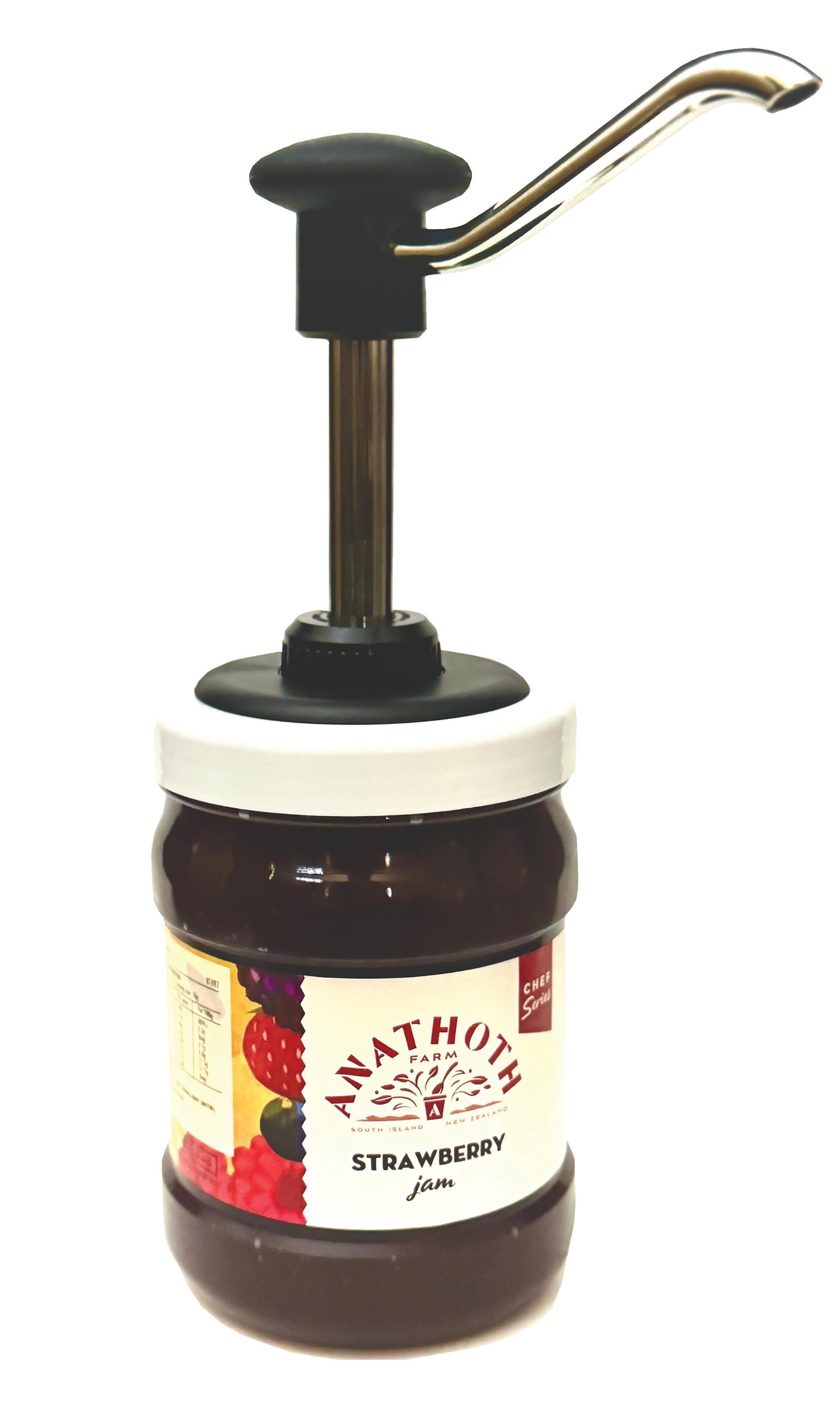
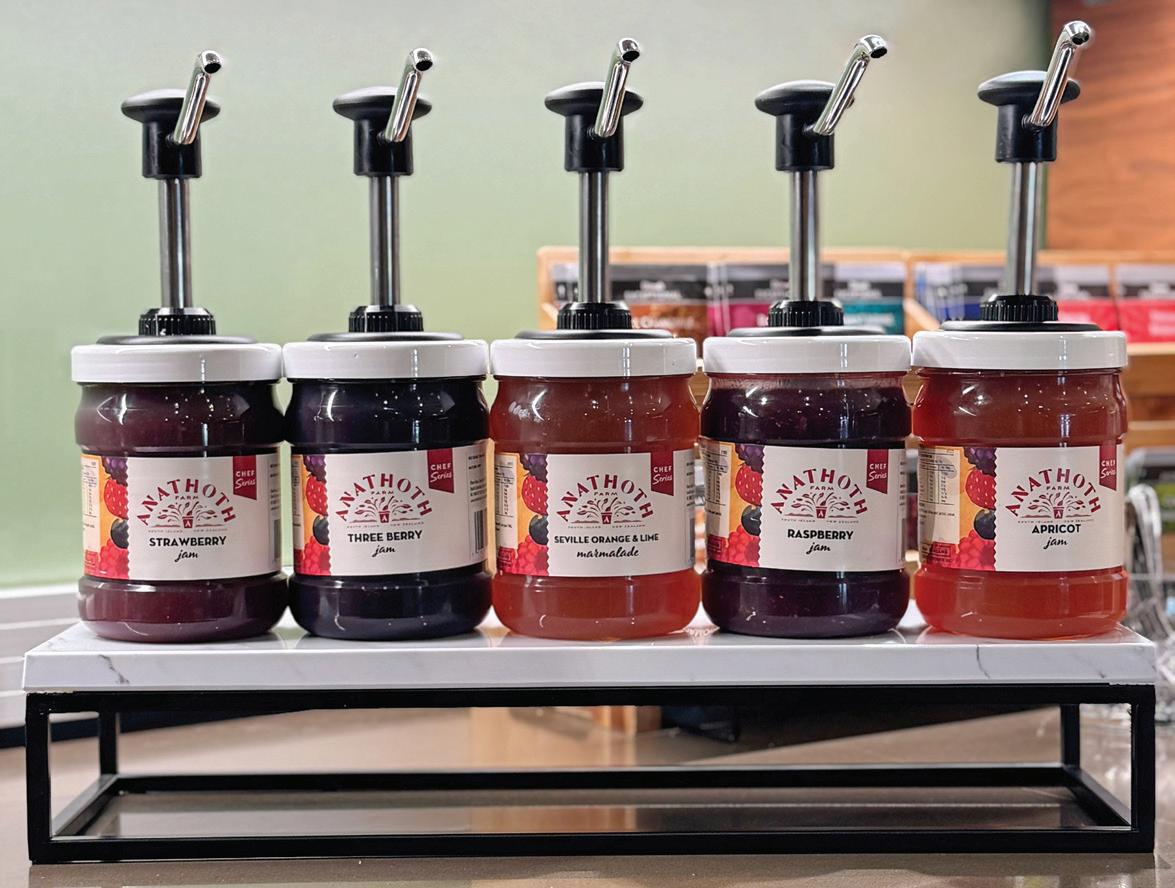
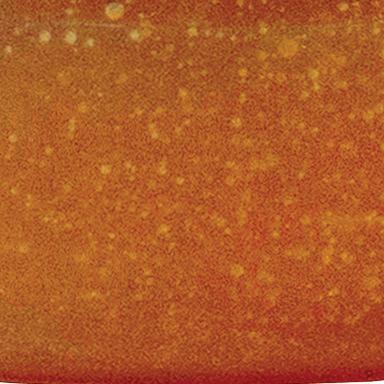
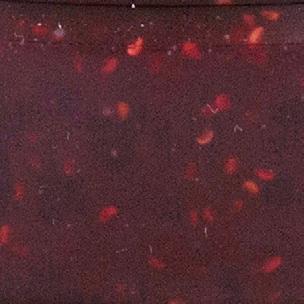
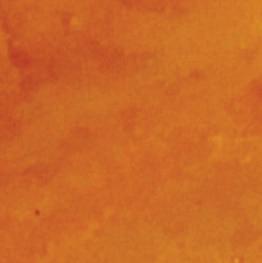
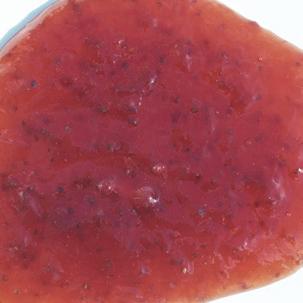
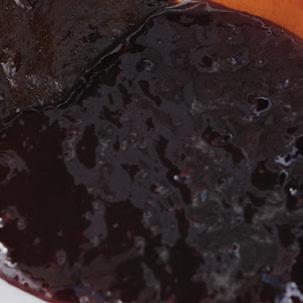
local news
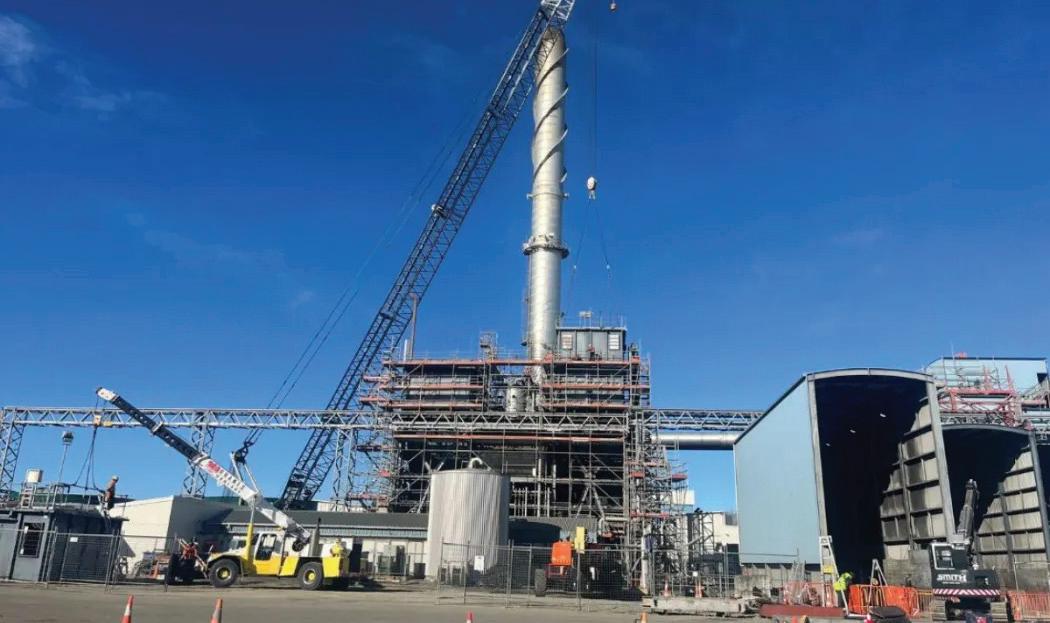
Fonterra’s Clandeboye Decarbonisation Project On Track
Fonterra’s largest decarbonisation project to date – the conversion of two boilers to run on wood pellets at its Clandeboye site – is progressing well.
The conversion will help the Co-op achieve a 50.4 percent reduction in absolute Scope 1 and 2 emissions by 2030, from a 2018 baseline.
Read more here
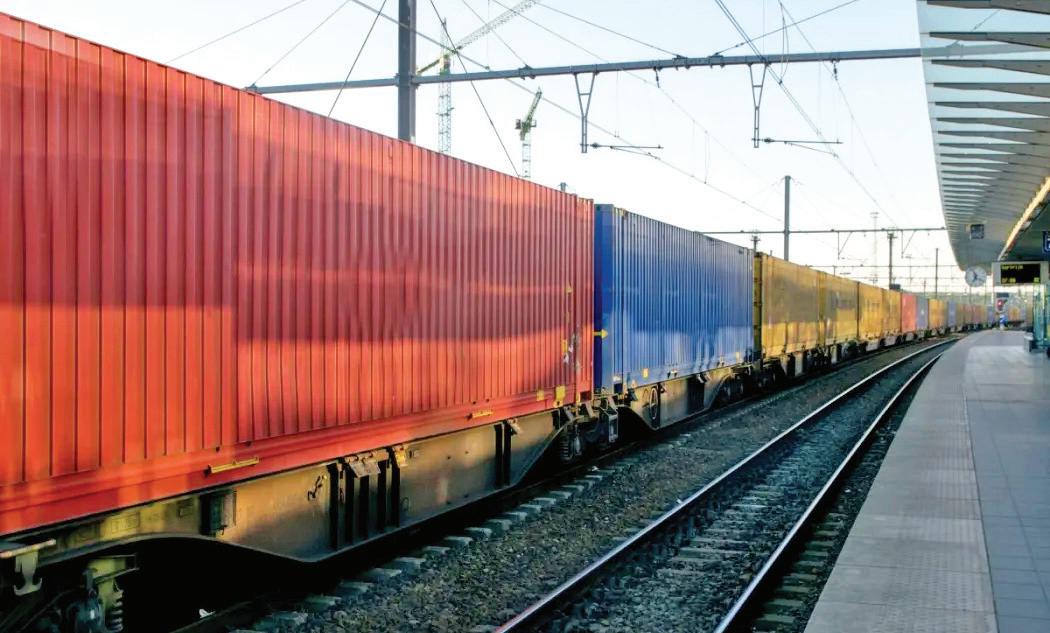
New Director On KiwiRail Board
The appointment of Scott O’Donnell to the KiwiRail board will bolster its freight expertise.
Minister for Rail Winston Peters said railways have no shortage of potential for New Zealand, and he expected to see sustained growth in earnings, revenue, volumes, reliability, and safety to turn this business into something extraordinary. Read more here
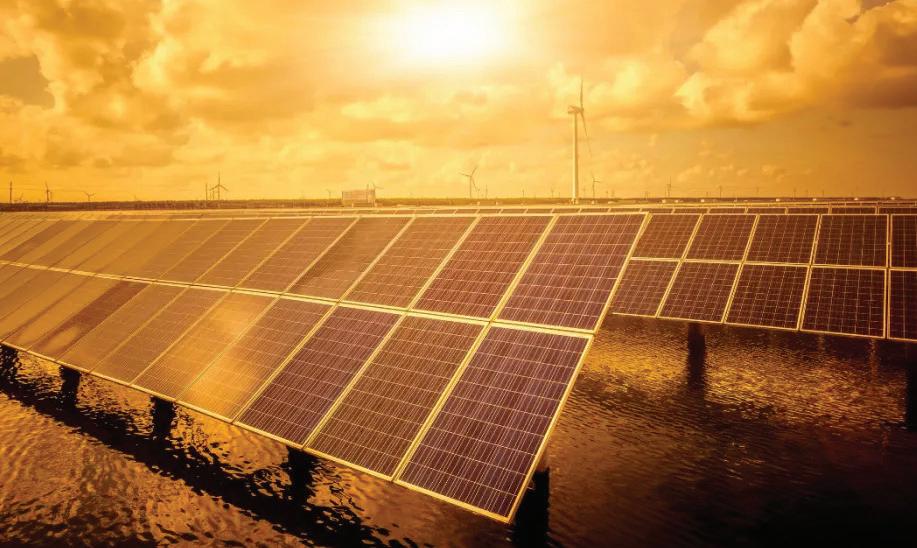
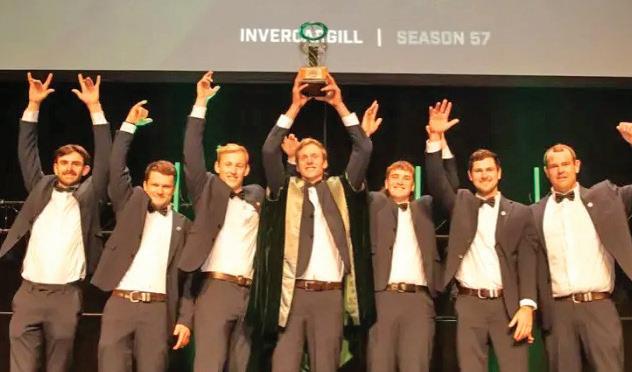
Hugh Jackson Crowned 2025 FMG Young Farmer of the Year
Waikato Bay of Plenty Young Farmer Hugh Jackson has secured the title of New Zealand’s top young farmer.
A community gem and dedicated Young Farmers member, the 26-year-old sheep and beef farmer was crowned the 57th FMG Young Farmer of the Year after a nail-biting Grand Final event in Invercargill.
Read more here
Backing Innovation To Grow King Salmon Exports
The Government is backing innovation to grow New Zealand’s high-value aquaculture exports, with a NZD 455,000 investment from the new Primary Sector Growth Fund.
The NZD 1.2 million project, led by global aquafeed company Skretting, will design feed tailored specifically for New Zealand’s King salmon, supporting the growth of open-ocean farming and
Regional Infrastructure Fund
Backs Solar Energy
Three solar projects in regional New Zealand will receive loans of up to NZD 28.1 million combined from the Regional Infrastructure Fund to ensure security of local energy supply and community resilience.
Regional Development Minister Shane Jones and Energy Minister
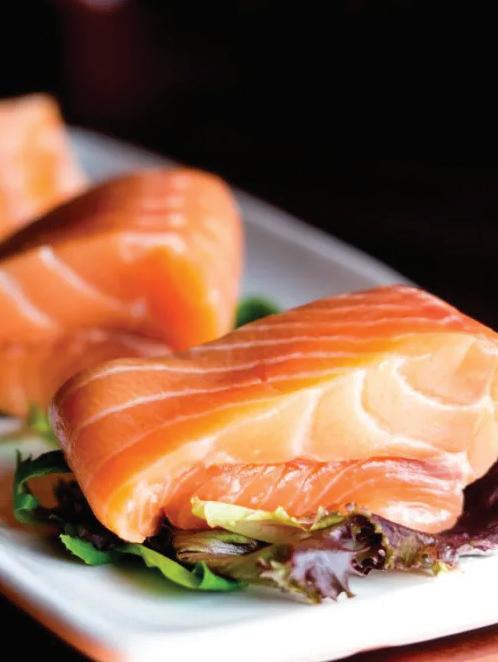
helping reduce costs for local producers.
Read more here
Simon Watts said the loans for these projects in Bay of Plenty, Hawke’s Bay and Rakiura/Stewart Island will allow them to get underway this year, helping them to improve economic prosperity and resilience. They will also create up to 150 jobs during construction.
Read more here
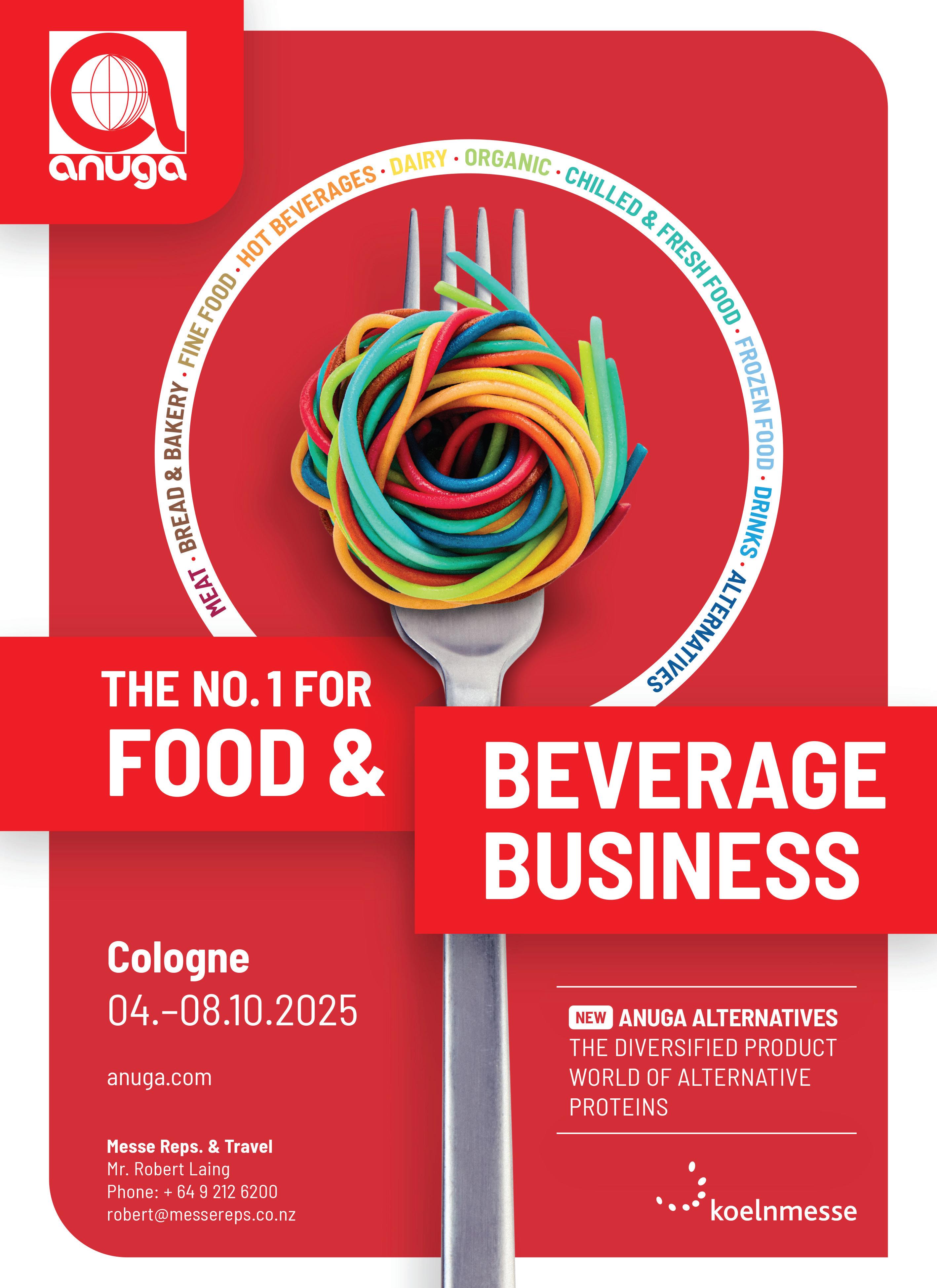
global news
The Ocean Cleanup x Coca‑Cola Malaysia Launch Waste Sorting Facility
The Ocean Cleanup, together with its partners Landasan Lumayan Sdn Bhd (LLSB), J&K Wonderland Foundation, and Coca-Cola Malaysia, officially unveiled a new waste sorting facility on the Klang River.
The waste sorting facility was officiated by YBhg. Dato' Haji Abd. Hamid Hussain, Mayor of Klang Royal City Council (MBDK), witnessed by YBhg. Datuk Dr. Ching Thoo, Secretary-General of the Ministry of Natural Resources and Environmental Sustainability (NRES), in recognition of his contribution to strengthening local waste management and environmental sustainability efforts.
Read more here
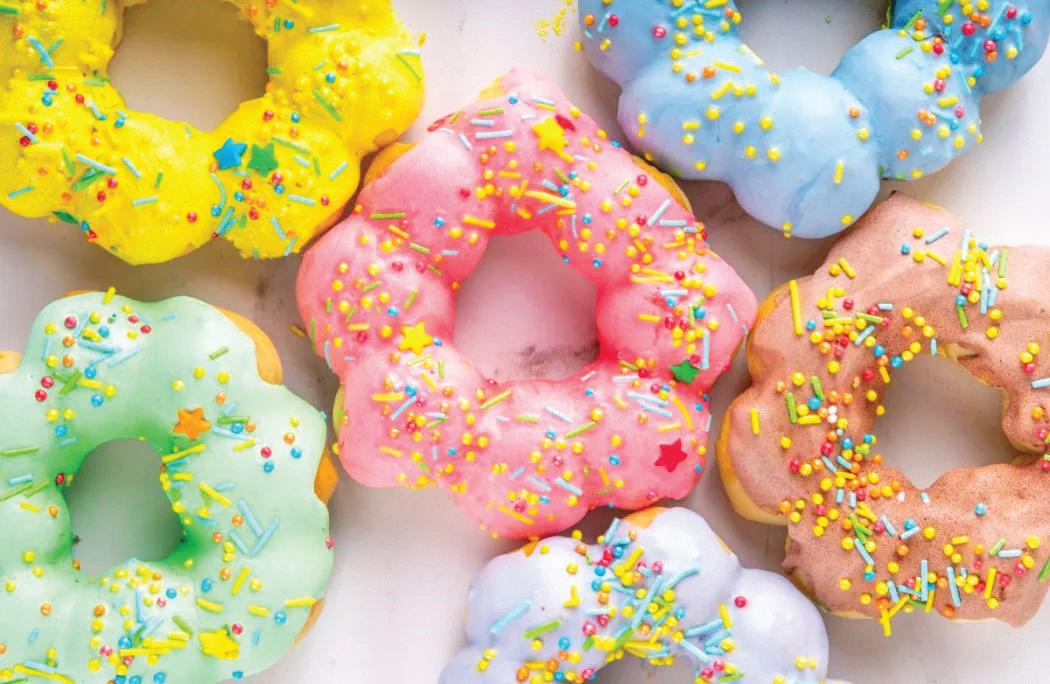
Nestlé USA to Eliminate Use of FD&C Colours by Mid 2026
Nestlé USA has shared its timeline to fully eliminate FD&C colours in its U.S. food and beverage portfolio by mid-2026.
Over the last decade, the company has been actively removing synthetic colours from its products and working to identify alternative solutions in recipes where they are still used. The work is scheduled to be completed within the next 12 months.
Read more here
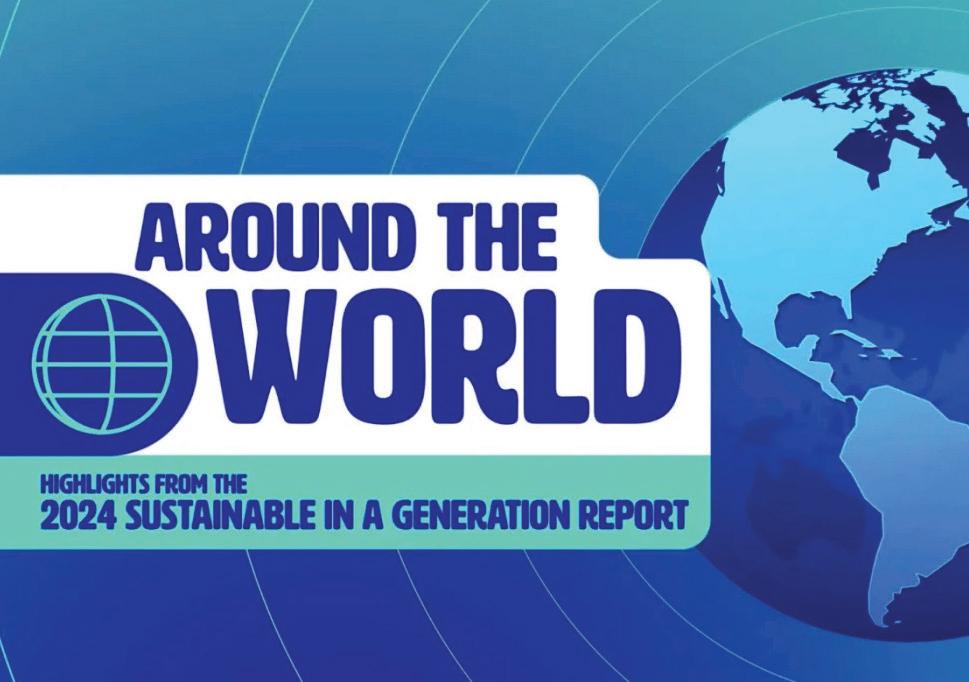
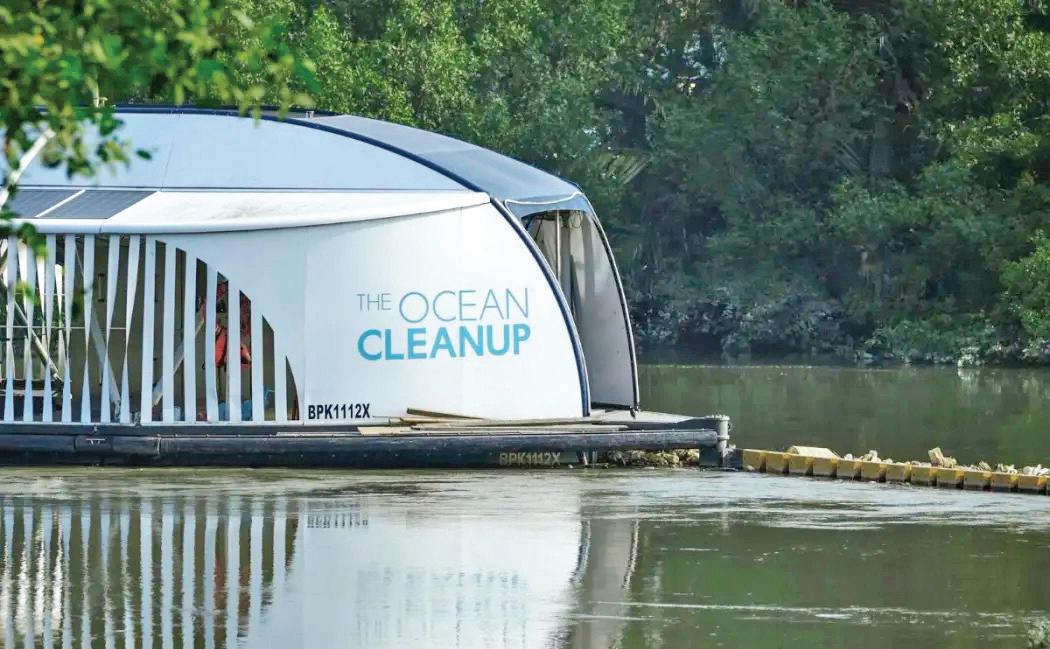
General Mills To Remove Certified Colours from All U.S. Cereals & K 12 Foods
General Mills announced plans to remove certified colours from all its U.S. cereals and all K-12 school foods by summer 2026.
For nearly 160 years, General Mills has been providing families with quality, great-tasting products across its beloved portfolio of brands. Additionally, the company will work to remove certified colours from its complete U.S. retail portfolio by the end of 2027.
Read more here

Mars Decouples Carbon Emissions
Mars, Incorporated released the 2024 Mars Sustainable in a Generation Report, announcing continued progress towards its goal of reducing its carbon footprint.
By the end of 2024, Mars achieved another 1.9 percent reduction in absolute greenhouse gas (GHG) emissions compared to its 2015 baseline, while growing the business over 69 percent to approximately USD 55 billion in annual sales during the same period.
Read more here
Our team will help you do it right
The Ministry for Primary Industries’ Exporter Help team supports new and established New Zealand exporters with advice and ongoing support on regulation and certifications. We make it easier to understand exporting requirements so you can reach more markets overseas and grow your sales with confidence.
Telecommunication
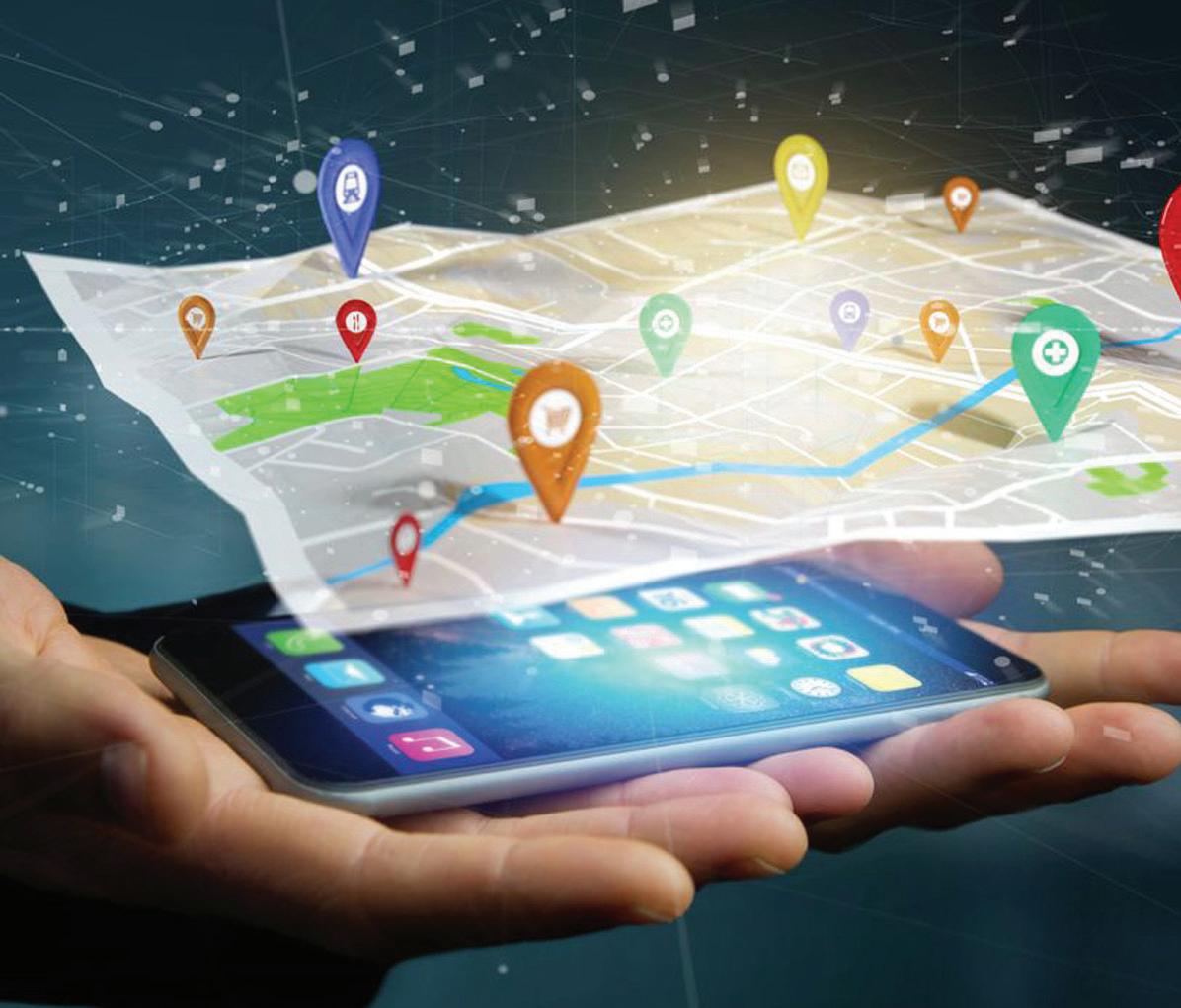
Ready for the end OF 3G
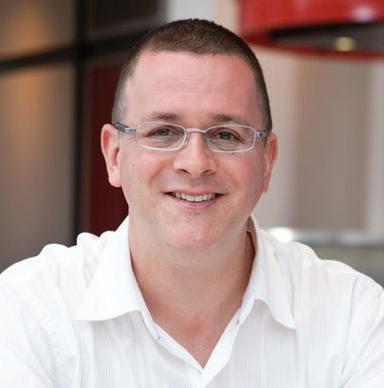
PAUL BRISLEN CEO, NZ Telecommunications Forum
Paul Brislen, CEO of the New Zealand Telecommunications Forum, has been at the forefront of guiding businesses through the 3G shutdown.
From farms to freight, the shift is already underway, and those who aren’t prepared risk getting left behind.
“Probably the most obvious sector at risk is vehicle tracking, but it’s also the most prepared as it’s done this before,” said Brislen.
“Vehicle tracking has evolved with every network generation, starting back in the GPRS days. Most enterprise customers, those who use mobile services for more than just phone calls, were alerted to this change at least
18 months ago, if not earlier. They’re already well down the path.”
Still, Brislen stressed that any service relying on a mobile connection should conduct a telco audit, knowing what technology they run and what the upgrade path is.
For businesses managing large fleets or devices in rural areas, the outlook is reassuring. All three mobile network operators have been collaborating with equipment manufacturers to support their customers. The first step should always be to contact the device’s supplier.
When it comes to patchy coverage, the closure of 3G is offset by the rollout of more 4G, and in some regions, 5G too. Many areas that are currently 3G-only will have at least 4G by the time the shutdown takes effect.
While sectors like supermarkets and manufacturing aren’t usually reliant
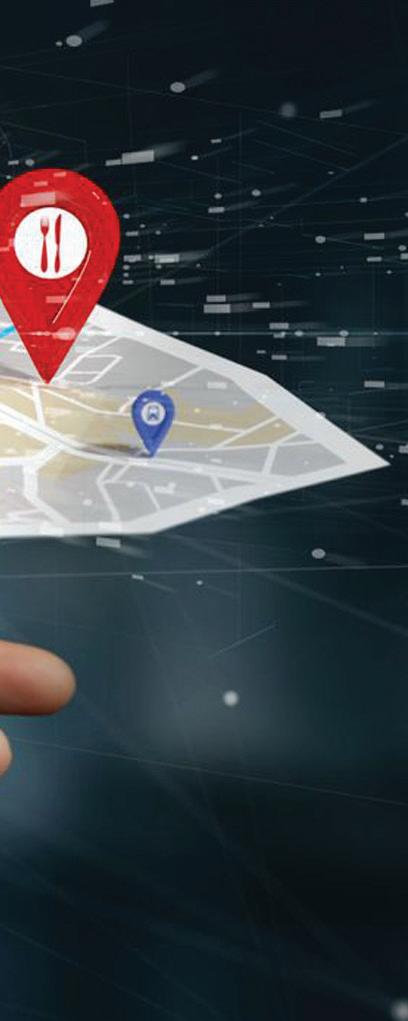
on 3G, Brislen encouraged everyone to double-check. The role the TCF has been asked to play is to raise mass market awareness and ensure that key stakeholder groups have access to the information they need about the transition.
Brislen himself has been speaking to a variety of stakeholder groups, including Field Days, the Facilities Management Association, Age Concern, and several others, and will continue to do so for anyone who wants to hear from him.
He also dismissed any concerns about panic surrounding IoT transitions for device types such as vehicle trackers, alarms, and sensors. Most providers have been working with customers for many years to transition them to newer technology, so they’re generally wellpositioned to make a smooth transition.
However, he said that the real problem areas were likely to be
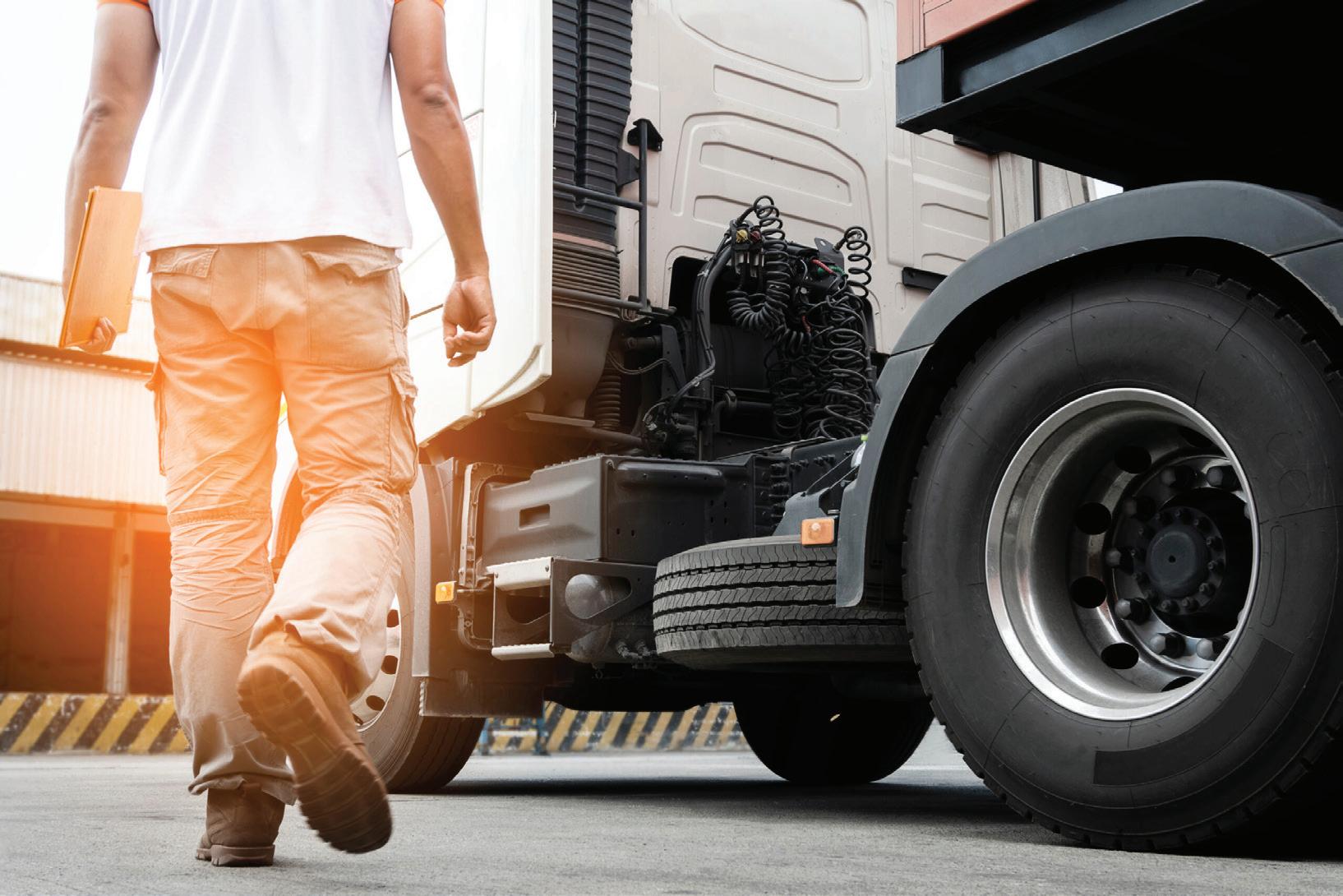
The equipment suppliers will be able to guide customers more accurately than the telcos can – we don’t necessarily see what type of device you might be using, just that it connects to the network. That makes support very difficult.
handsets bought overseas, which may or may not support New Zealand’s 4G and 5G bands properly.
“The telecom sector has no control over customers bringing such devices into the country, but we can’t be sure they’ll work fully after the 3G networks are turned off. This is an area we are observing.”
When it comes to diagnosing risk, the popular ‘text 550’ checker is only suitable for mobile phones, not IoT or embedded systems. Because there are numerous types of devices in the IoT space, ranging from burglar alarms to EFTPOS terminals, security systems to smart meters, and more, the best course of action is for businesses to contact their suppliers and determine which network their devices use.
“The equipment suppliers will be able to guide customers more accurately than the telcos can – we don’t necessarily see what type of device you might be using, just that it connects to the network. That makes
support very difficult.”
Although it’s early days in the public campaign, Brislen has started seeing success stories. He has already observed ads from fleet tracking companies promoting upgraded 4G/5G devices with additional features and improved performance.
Compared to 3G, which is slower and supports fewer users, 5G are a major leap. The move to 4G will enable more customers to use multiple services simultaneously, which will particularly benefit drivers in overcoming those black spots they encounter.
Brislen’s advice to all was to talk to the suppliers and mobile providers, as no telco wants to lose customers, so they’re all on board to help smooth the transition.
“This won’t be the last upgrade. By 2030, Chorus will have shut down its copper network as well. So even if you get through the 3G switch-off unscathed, you’ll want a plan for what comes next.”


Telecommunication
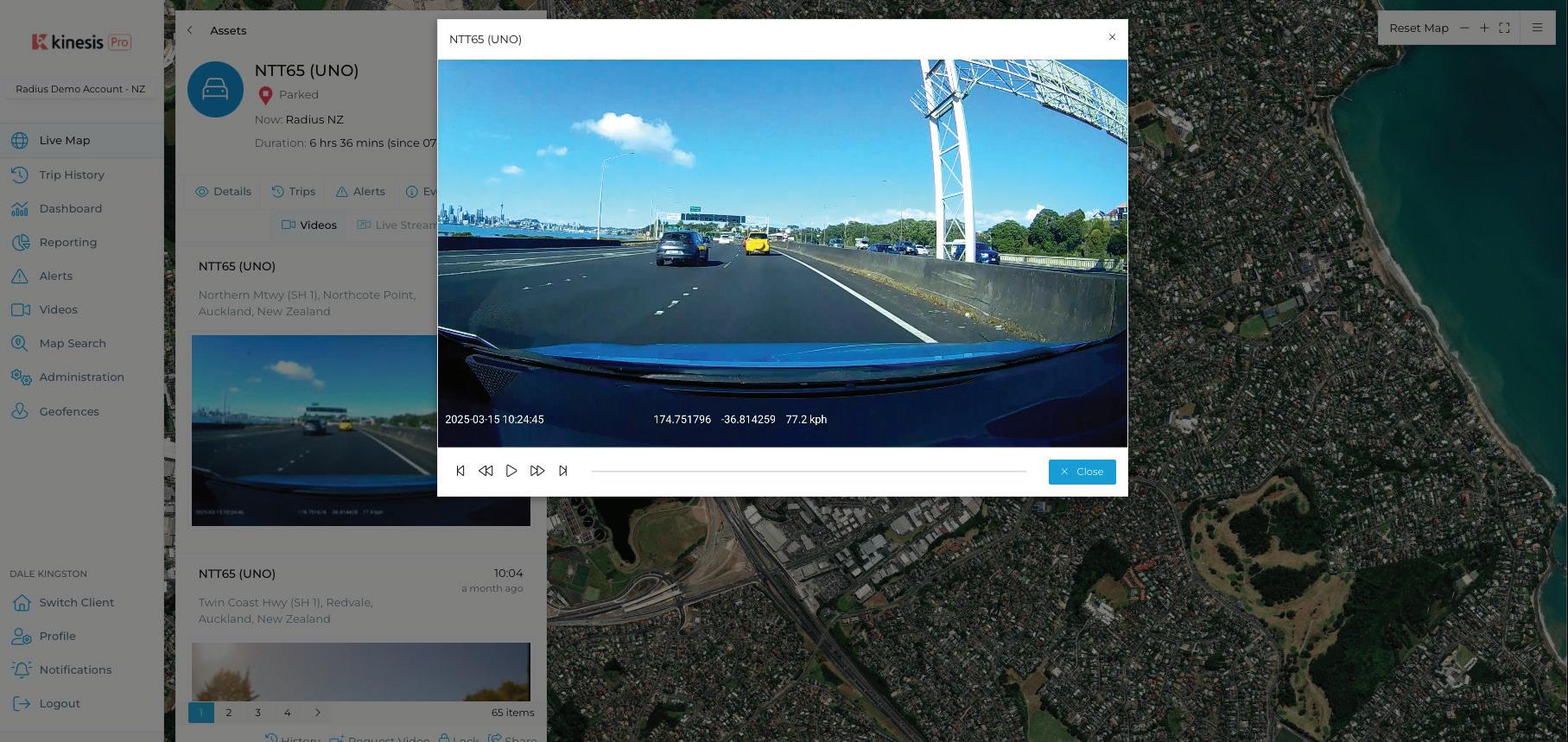
Staying Ahead OF THE GAME
Radius Telematics NZ has been ahead of the curve and currently has no devices operating on 3G.
Its focus now is entirely on supporting its 4G client base and helping new customers make a smooth transition to 4G-enabled solutions. The result has been a seamless shift, with clients fully future-proofed and unaffected by the shutdown of the 3G network.
Dale Kingston, New Zealand Country Manager for Radius, identified industries with large, distributed fleets, such as logistics, cold chain transport, and field services, as being most vulnerable to the impact of legacy tracking units.
These sectors depend on real-time data for compliance, safety, and operational efficiency, so any lapse in connectivity could have a ripple effect on service delivery and customer satisfaction.
To help businesses, especially small to medium-sized enterprises (SMEs), transition smoothly without downtime or added pressure on budgets, Radius has offered a range of tailored telematics solutions.
“In almost every case, we’re able to deliver cost savings while upgrading clients to our advanced 4G platform. Our approach is consultative; we assess each client’s needs and provide a solution that not only ensures continuity but also enhances operational efficiency and visibility,”

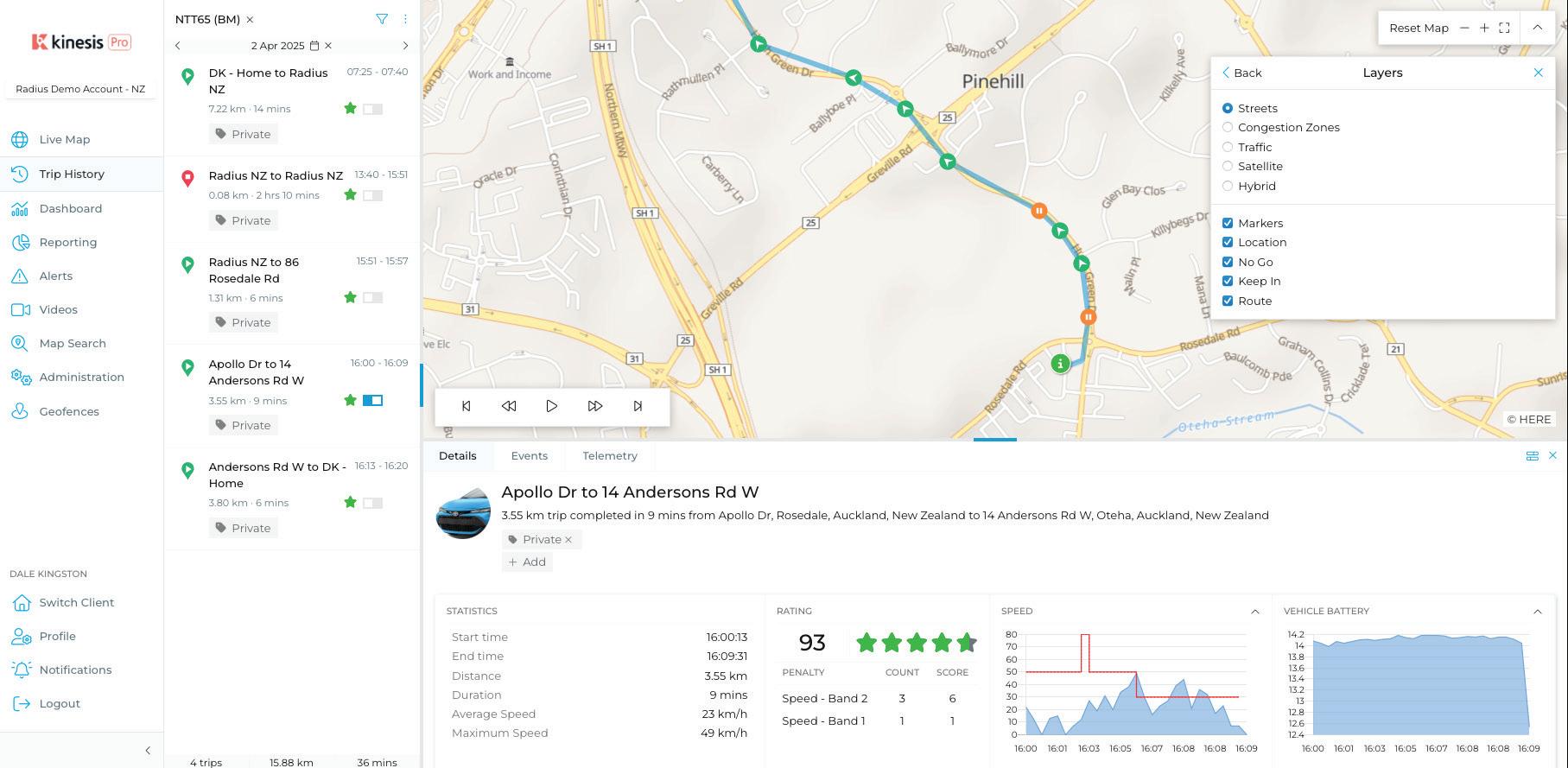
said Kingston.
Since Radius clients are already operating on 4G, Kingston confirmed there would be no disruption in real-time tracking, driver behaviour monitoring, or delivery performance.
He said that a key benefit of this
transition was the adoption of a modern technology platform, which has enabled Radius to support new solution features and enhance functionality to meet evolving fleet management needs.
For businesses in rural or remote
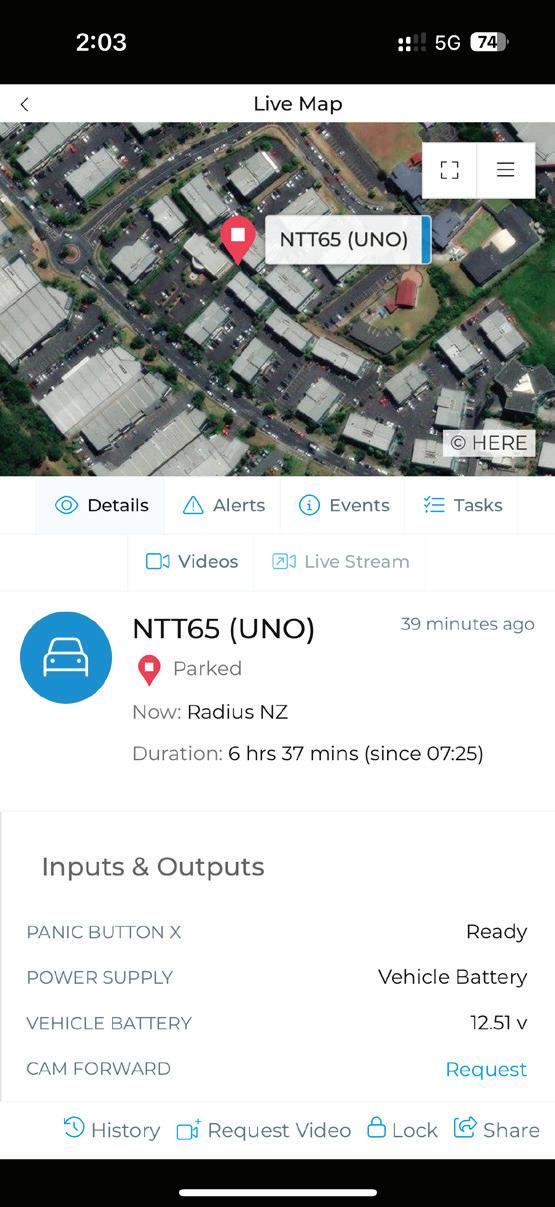
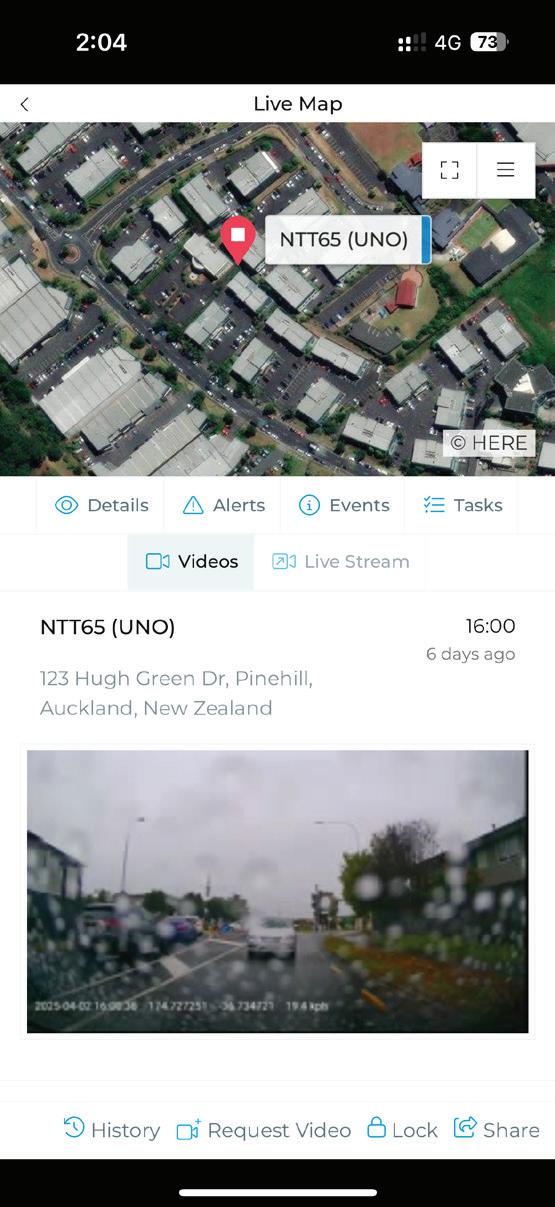
areas where 4G coverage may be variable, Radius devices come with built-in dualnetwork capability.
This means they can switch between Spark and One networks, significantly reducing the risk of connectivity loss. Leveraging multiple 4G networks ensures consistent performance and data availability for clients, regardless of location.
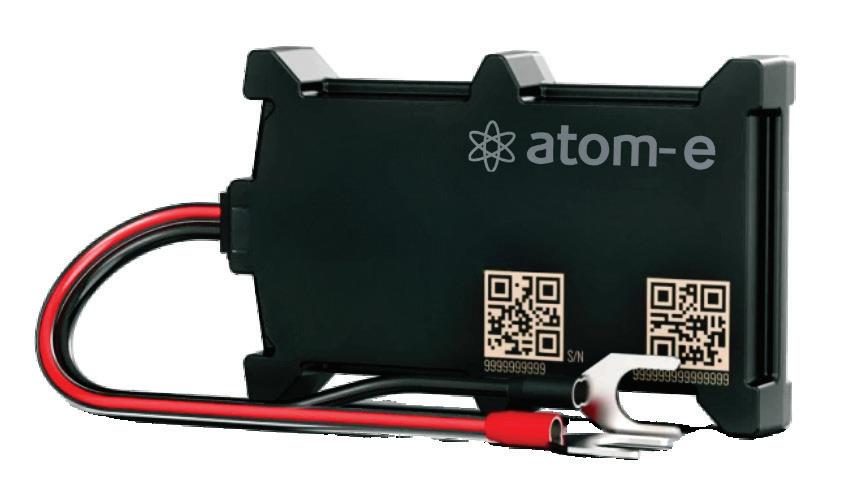
Looking ahead, Kingston noted that while Radius is monitoring the development of 5G in New Zealand, it is not a current focus for telematics.
“From a fleet management perspective, businesses don’t need to be concerned about 5G at this stage. The priority right now is ensuring robust, reliable 4G solutions that meet today’s operational demands.”
“The current focus across the industry is on the 3G shutdown, which is freeing up spectrum to enhance 4G services.”
At Radius, the emphasis remains on ensuring clients have access to futureready 4G technology that supports their evolving needs, with the flexibility to adopt 5G when it becomes commercially relevant and delivers clear benefits.
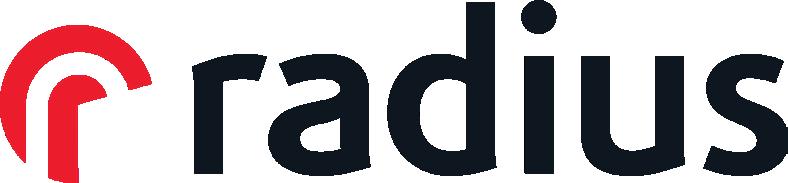
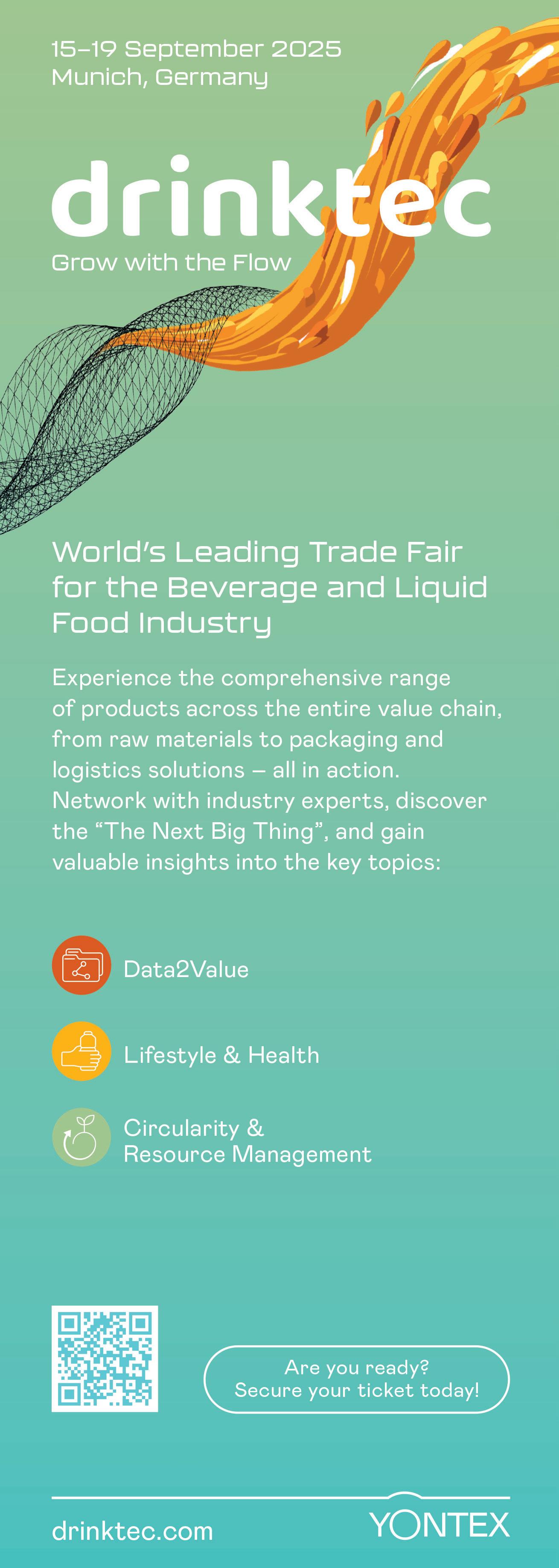


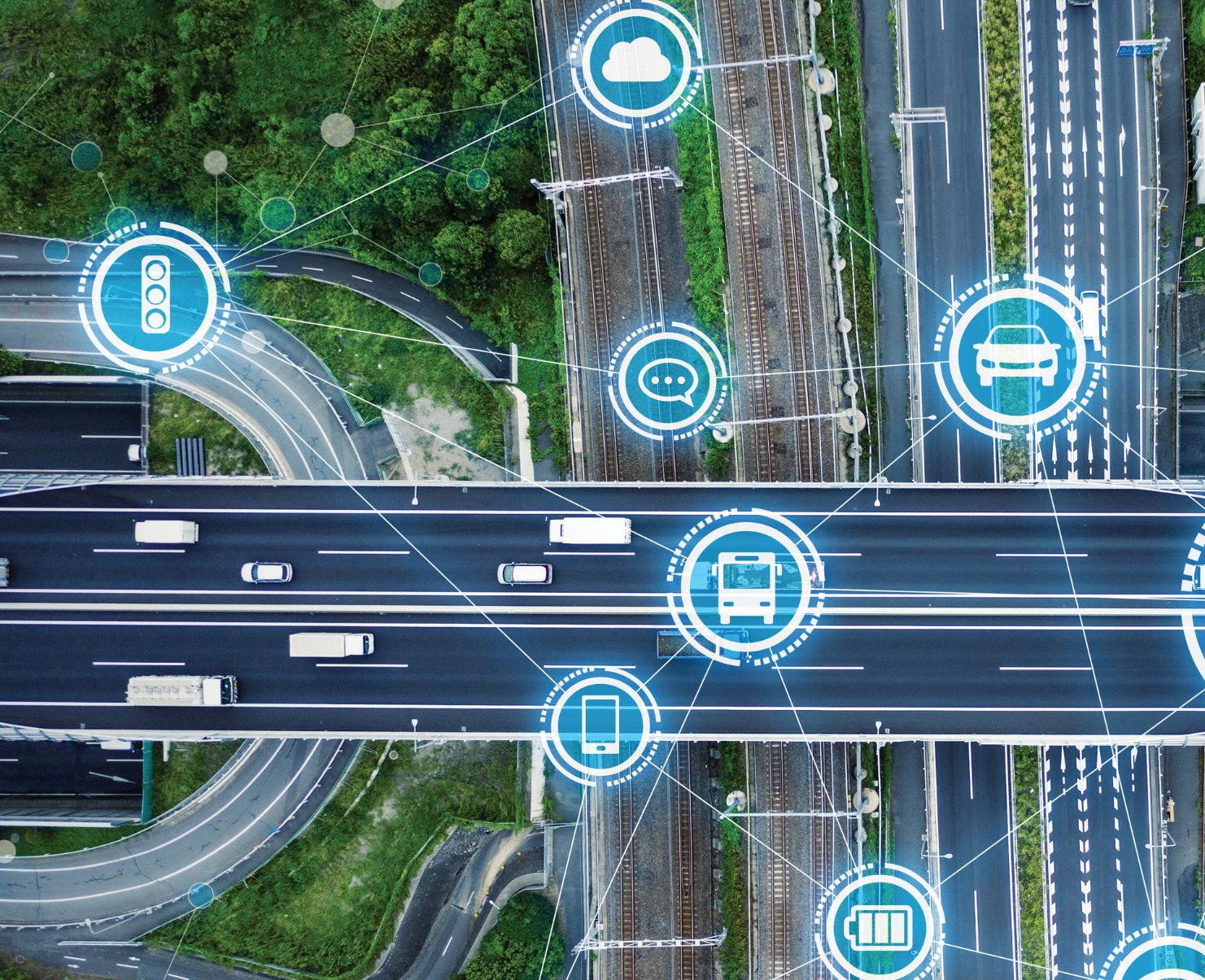
FuturePROOFING FLEETS
With the nationwide 3G network shutdown on the horizon, Argus Tracking has already taken steps to ensure its customers experience a seamless transition to newer technologies.
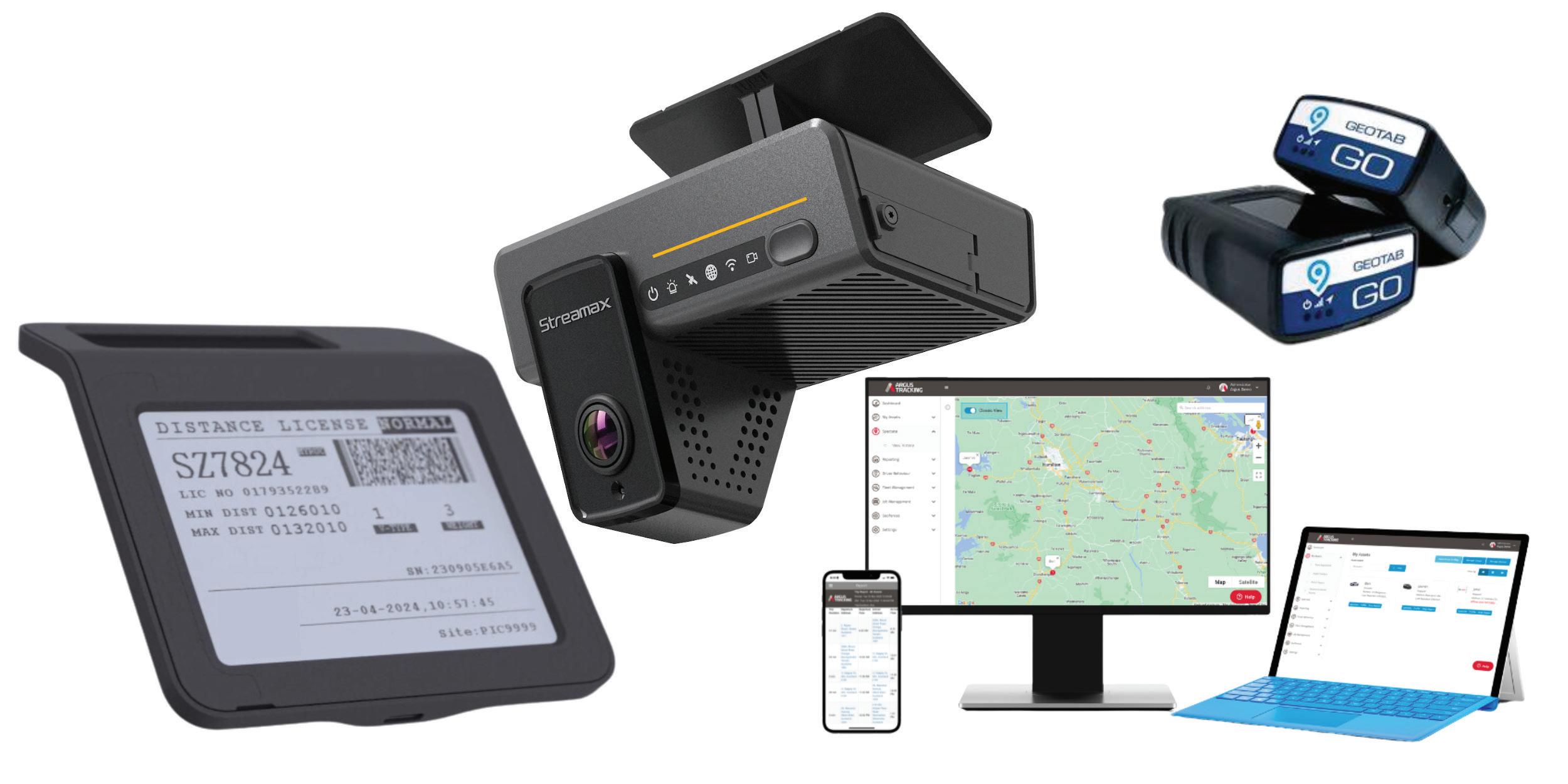
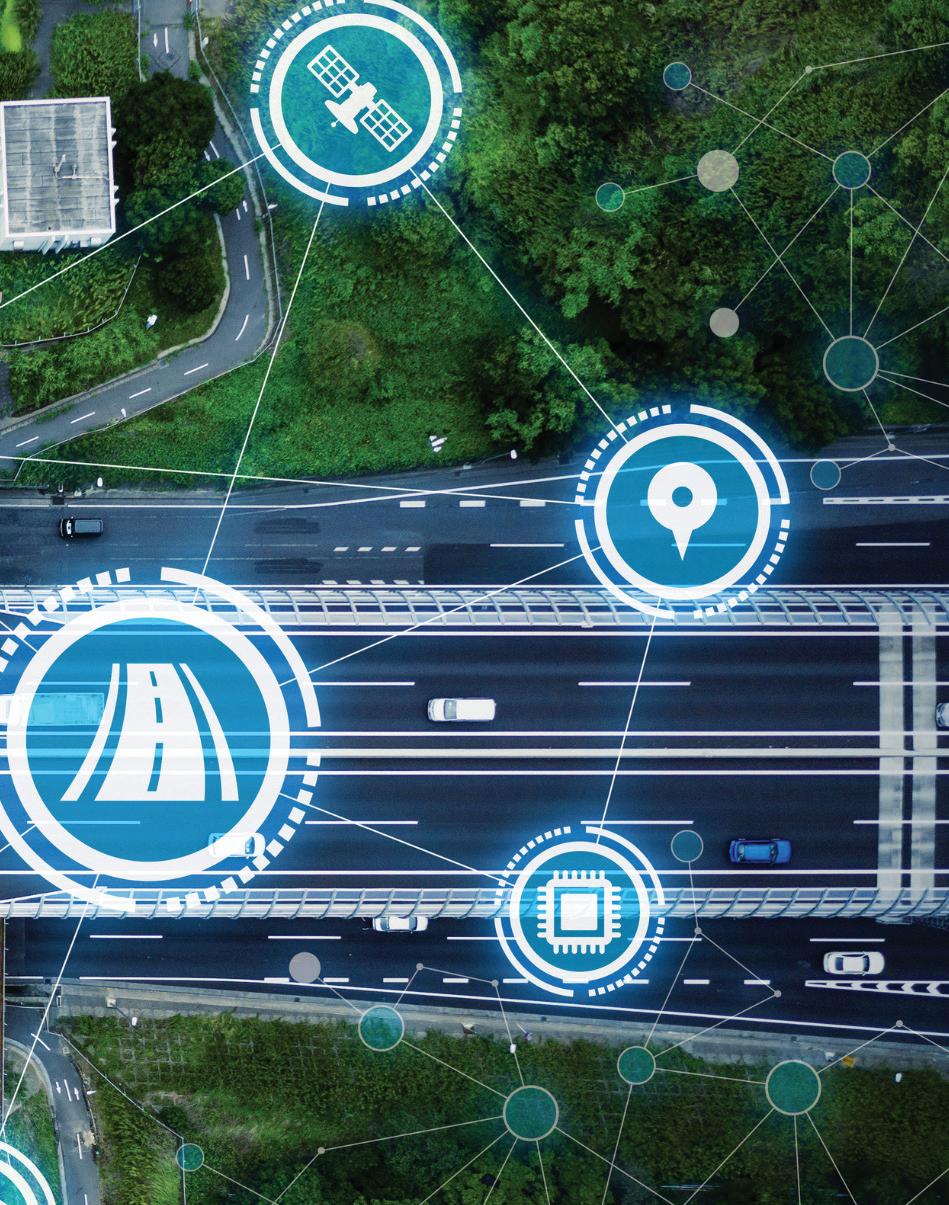
While a small number of 3G units remain active, the team has proactively identified those still in use and begun upgrading them to more advanced models compatible with 4G and beyond.
“All our customers will be fully prepared,” said Andy Patrick, CEO of Argus Tracking.
“We’ve made it a priority to raise awareness and support the transition, especially for commercial fleets that rely on GPS tracking for day-to-day operations.”
Industries with heavy transport, logistics, or fleet operations are particularly vulnerable to disruption, especially those still running older tracking hardware. Real-time data transmission, driver behaviour monitoring, and performance reporting all depend on live connectivity, which will be compromised when 3G is switched off.
“The shutdown will create blind
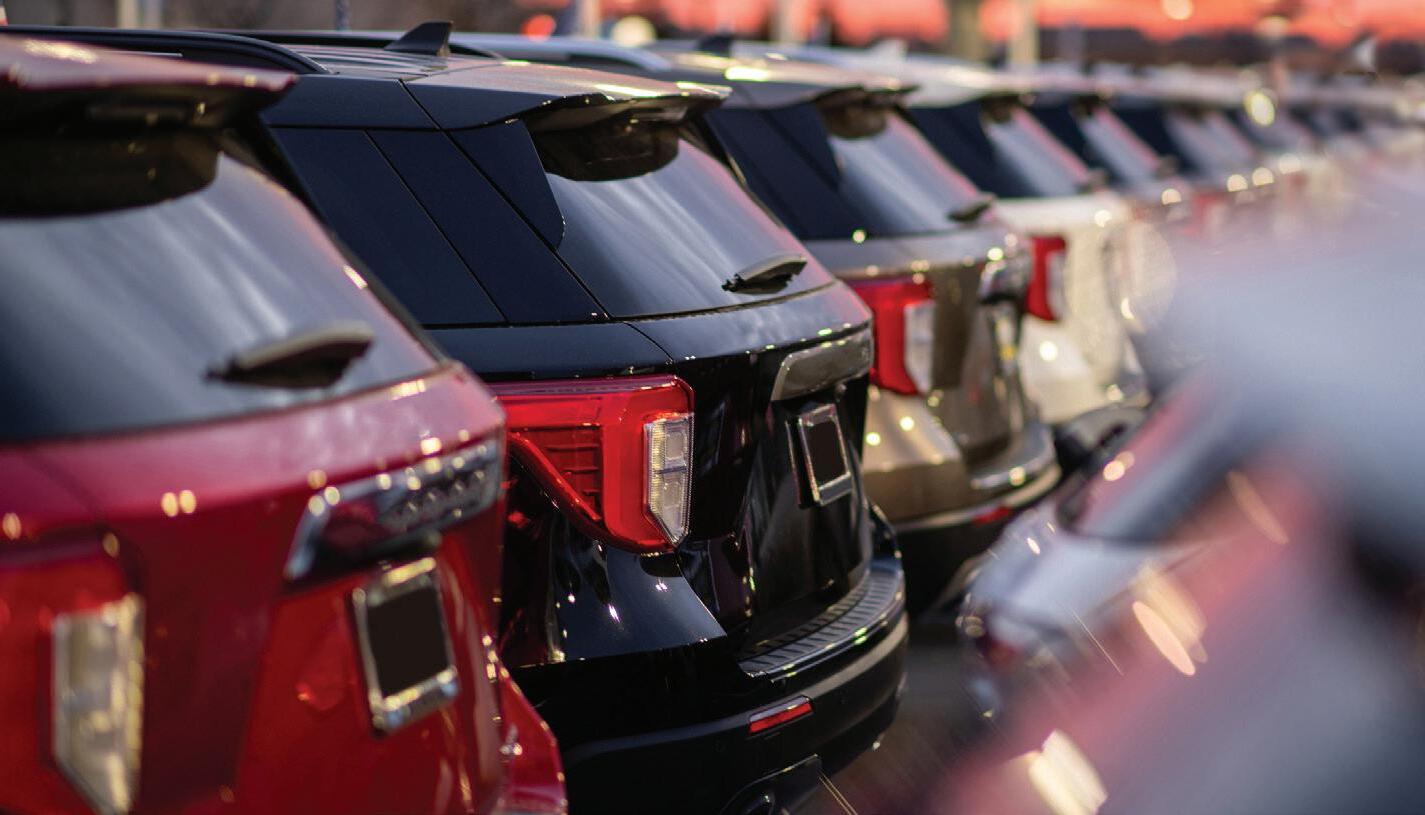
ensures uninterrupted coverage in rural areas or areas with patchy network coverage. Designed for customers working in off-grid or remote locations, it automatically switches between mobile and Iridium satellite networks, providing consistent tracking even when 4G or 5G signals are weak or unreliable.
For industries like food and beverage, the stakes are even higher. Reliable GPS tracking supports not just delivery accuracy but also compliance, cold chain integrity, and customer trust.
spots for fleets still using 3G devices.
We’ve been directly contacting affected customers and walking them through the upgrade process to avoid unexpected service interruptions.”
To alleviate the financial burden on businesses, particularly small and medium-sized enterprises, Argus Tracking is offering a complimentary device swap for fleet owners with outdated tracking units.
Patrick said it's a stark contrast to some providers who are trying to pass on full hardware costs to customers. The goal is to make the transition affordable, minimise downtime, and help businesses continue running smoothly.
“We know it’s a tough economic climate for many SMEs. Argus has been a trusted partner for over 18 years, and we remain committed to supporting Kiwi businesses with smart, cost-effective solutions.”
One of these solutions is SATRACKS, a satellite-enabled service that
With that in mind, Argus has been helping fleet managers reassess their technology stacks and upgrade to smarter systems.
Among its advanced offerings are Smart ERUCs, which automate road user charges and reduce admin workload, and AI-powered dashcams that enhance driver safety, provide real-time footage, and help control insurance and compliance costs.
“With the 3G shutdown underway, it’s the perfect time to future-proof your fleet. Upgrading now means fewer disruptions later and full access to the benefits of modern fleet management.”
From free upgrades to satellite connectivity and compliance tech, Argus Tracking continues to deliver the tools and support businesses need to stay ahead in a fast-changing transport landscape.
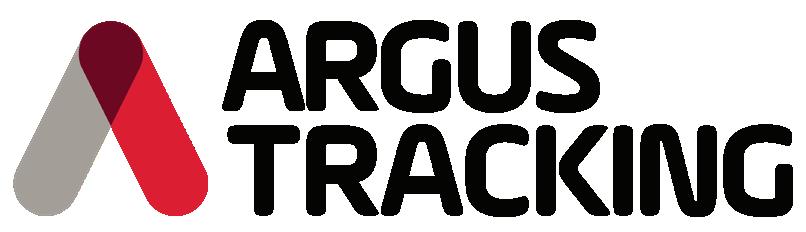


Telecommunication
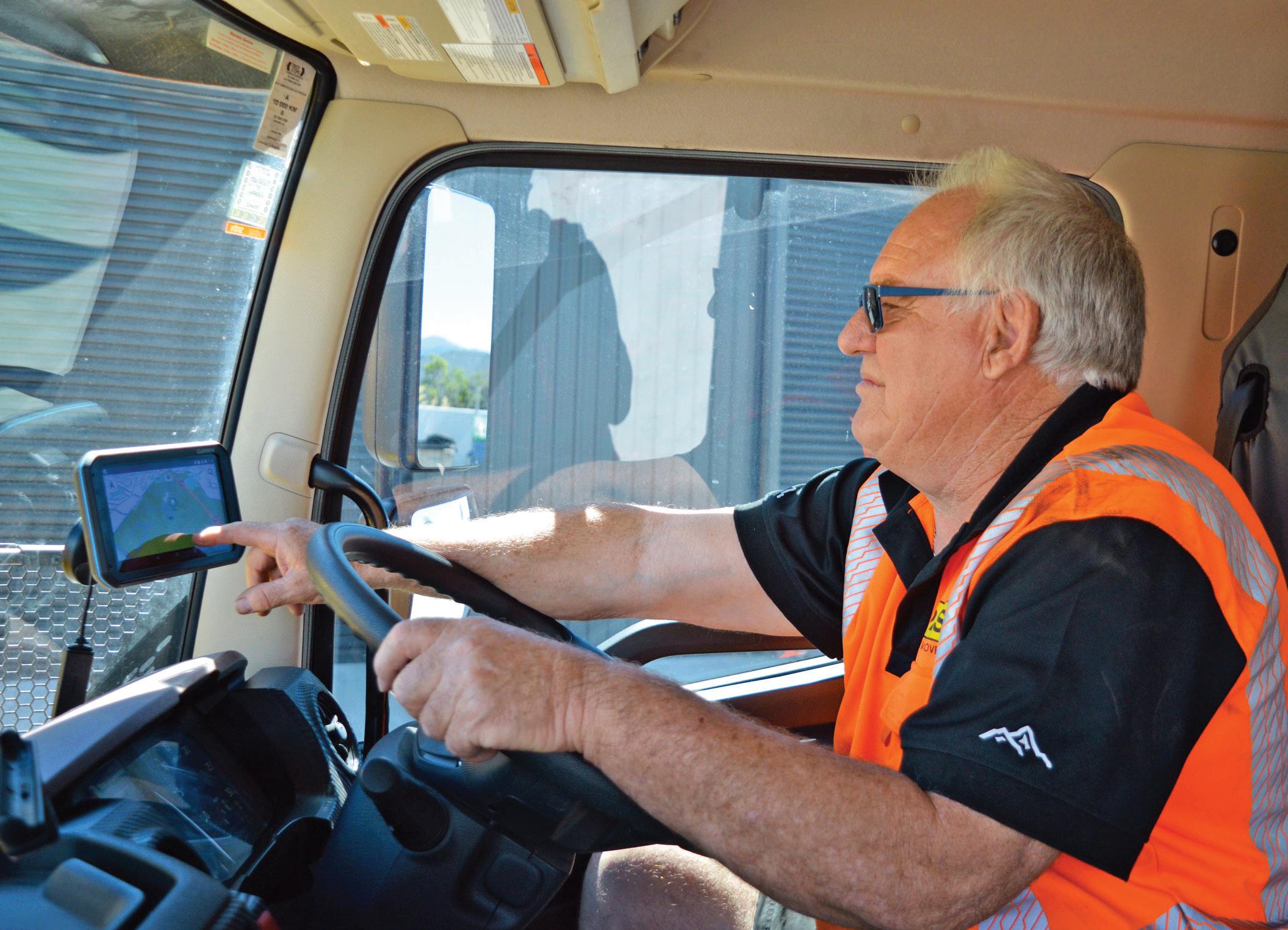
Telecommunication Changes COME WITH BENEFITS
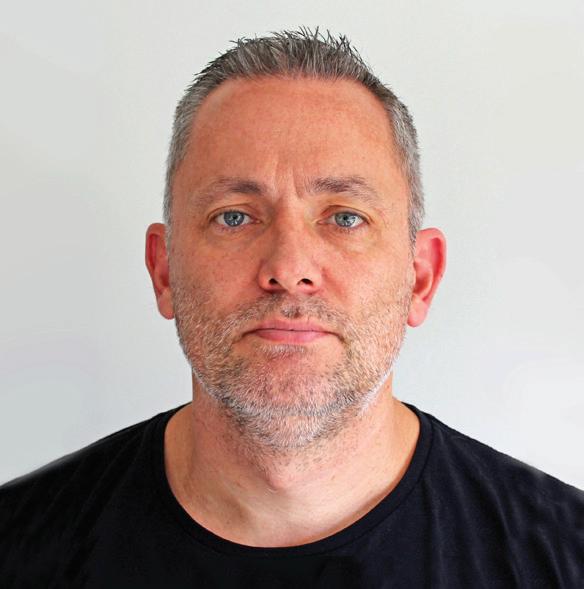
SIMON
Head of Customer Implementation, TeleTrac Navman
Given that the shutdown of the 3G network will render 3G-enabled devices across New Zealand inoperable, Teletrac Navman has been actively working with customers and the industry at large to educate and raise awareness about the steps required to help fleet businesses make this transition.
Many of its New Zealand customers have been using 3G devices as part of, or across their whole fleet. Simon McCaughan, Head of Customer Implementation for Teletrac Navman, has been leading the team’s 3G migration project across New Zealand.
“We’re actively helping these customers update and upgrade their systems before the 3G network shutdown, helping them understand the benefits 4G will offer through faster speeds, better coverage, and more efficient use of spectrum. Ultimately, articulating the benefits this telecommunications system change will bring,” said McCaughan.
“One of the biggest challenges arises when clients delay their
McCAUGHAN
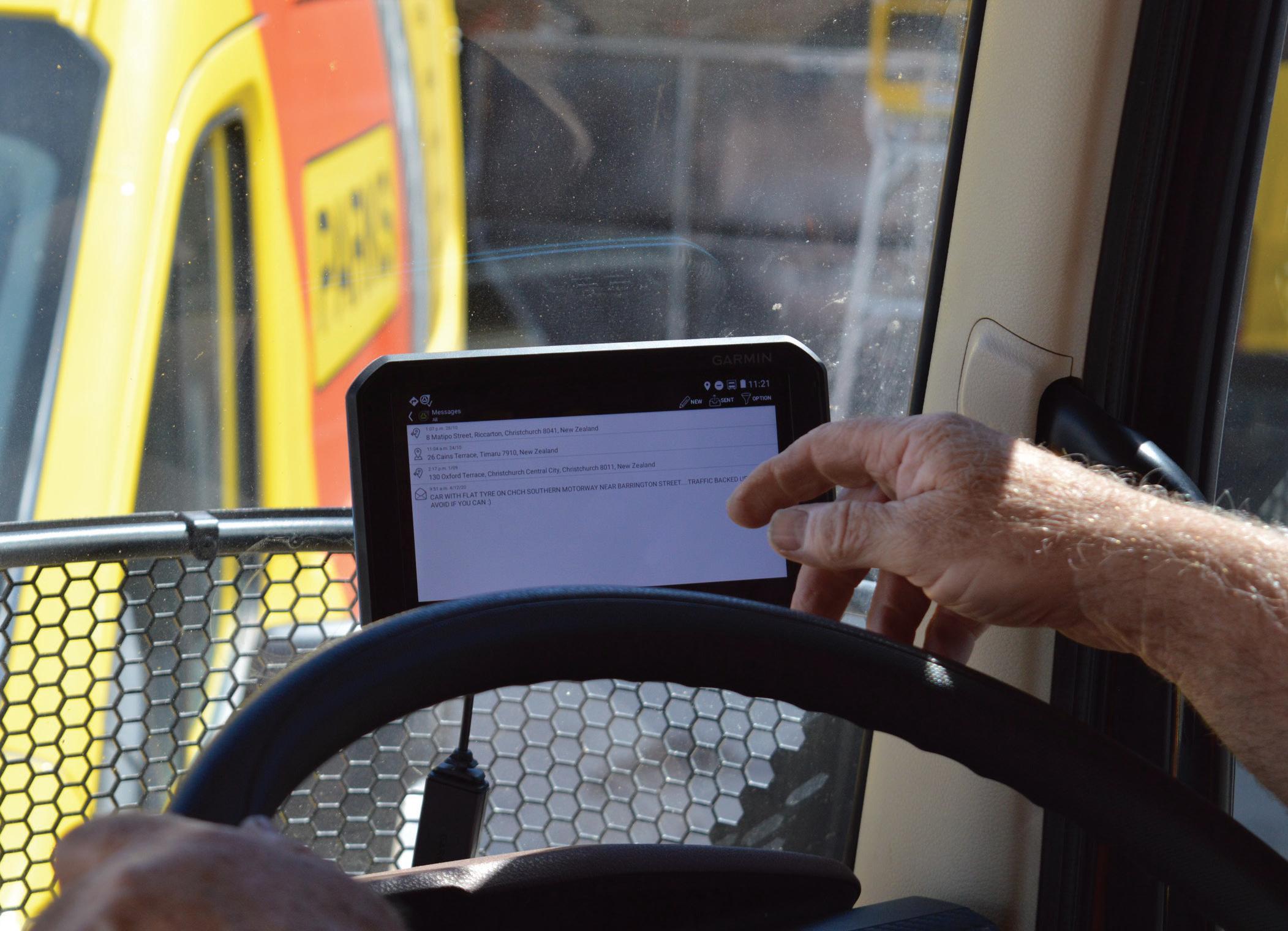
We’re actively helping these customers update and upgrade their systems before the 3G network shutdown, helping them understand the benefits 4G will offer through faster speeds, better coverage, and more efficient use of spectrum.
decision-making. Technological progress is inevitable, and forwardthinking businesses are staying informed about these changes to make progressive investments that can come at a greater expense.”
McCaughan added that delaying the migration from 3G to modern devices hinders the ability to install the replacement devices in a timely manner.
In both Australia and the US, Teletrac Navman has observed many clients postponing their decisions until the last minute, which has led to entire fleets, or portions of them, potentially going ‘dark’ because they couldn’t guarantee service after the network was scheduled to shut down.
This is a significant operational issue that impacts both driver safety
and the bottom line, a key reason why NZ fleet businesses should be working today to map out their migration plans.
“If you are relying on real-time tracking to monitor your staff on the road, it simply won’t be possible with 3G telemetric devices once the network is switched off. This is a critical business continuity issue, and we encourage businesses to plan for a seamless transition.”
Teletrac Navman teams have been working closely with customers to ensure they understand the requirements of the device swap. This collaboration has encouraged the development of change management plans and strategies to help businesses manage the transition with their teams. The business
also introduced self-installation options and streamlined installation processes.
The transition to 4G technology as a whole means that data speeds and bandwidth will improve significantly in New Zealand, enabling faster and more efficient tracking, monitoring, and management of driver safety and efficiency on the road.
Teletrac Navman’s devices and platform capabilities will continue to evolve as telecommunications infrastructure, such as network speeds, improves.
“The speed and quality of data fleet businesses can track today will continue to improve tomorrow, for customers in New Zealand and across the world.”


packaging .
Preparing Customers FOR CHANGE
With the 3G shutdown looming, Andrew Josefsen from SENSERI has taken a proactive approach to support their fleet customers, half of whom are already covered through leasing agreements.
“Approximately half of our customers are on a leasing contract with us, so they’ll receive the new 4G units at no additional hardware cost,” he said.
“For the rest, we’ve put together a special discounted offer to help ease the transition.”
He added that there was nothing to worry about, as there was no change in functionality when moving from 2G/3G to 4G. Based on current 4G
installations, there is no noticeable difference in coverage, so operations won’t be disrupted.
His only concern was customer urgency.
“We do see some leaving it until the last minute, and that could lead to
installation bottlenecks, but we’ve prepared for that too.”
SENSERI offers plug’n play units that are simple for customers to install themselves, and the team can also help coordinate with autoelectricians or any third parties that customers prefer to use.
The tech is ready, the support is in place, and for customers willing to act now, the transition will be smooth.
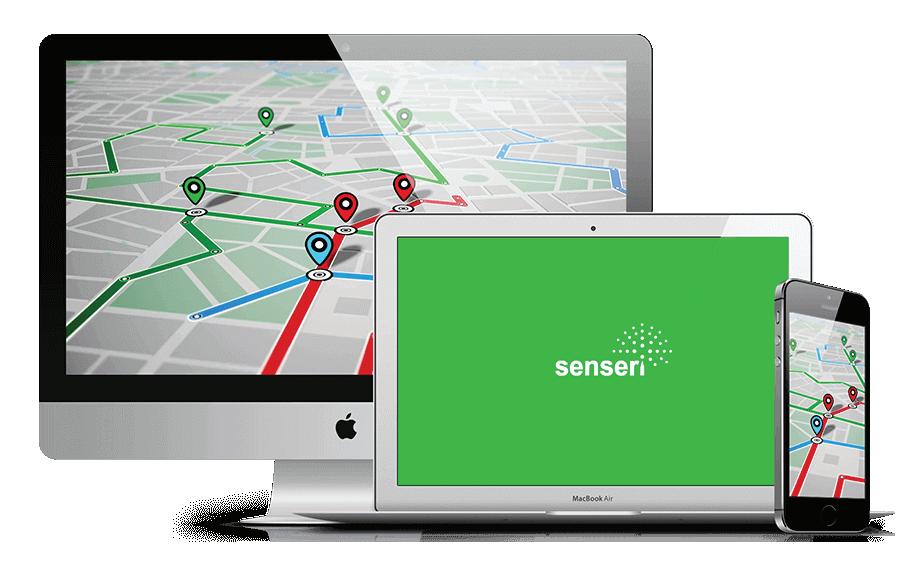
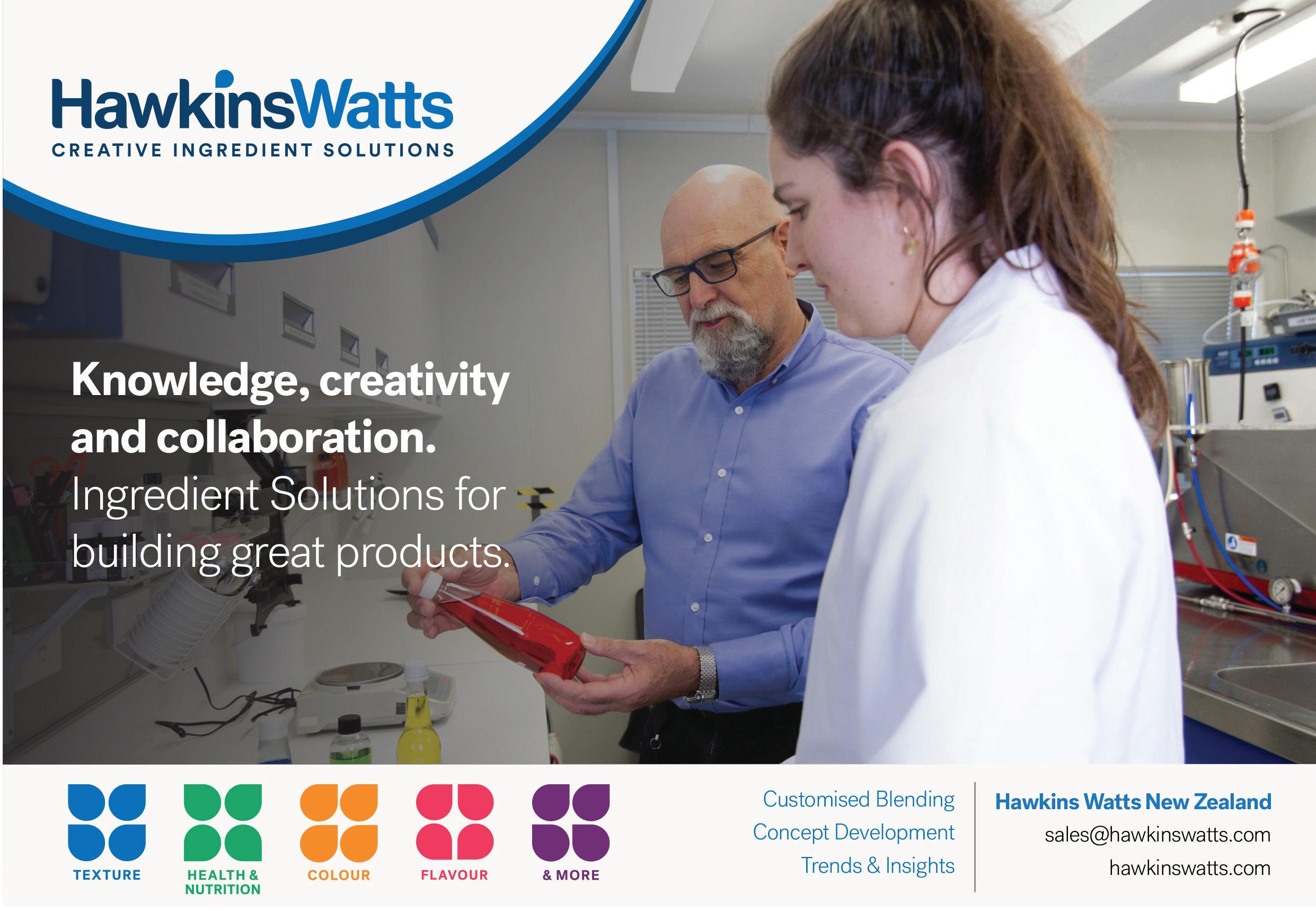
Igniting New Zealand’s most famous FMCG brands for 20 years.
Where did those 20 years go? It seems like only yesterday that we set up shop.
To all our clients, industry colleagues, and team members down the years, thank you for helping us reach this landmark occasion. Now here’s to the next 20 years.
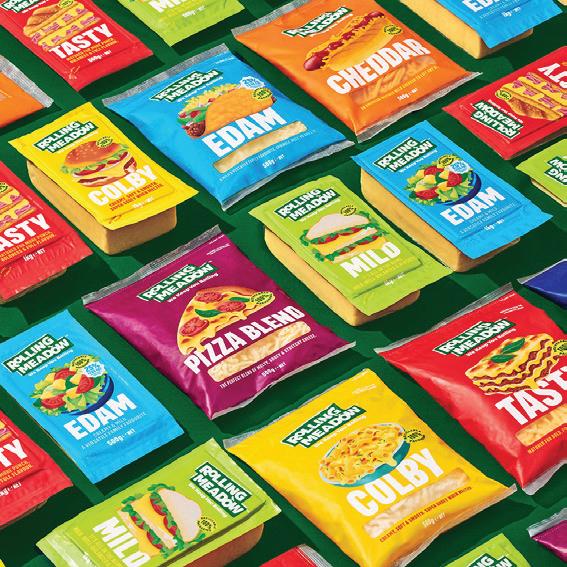
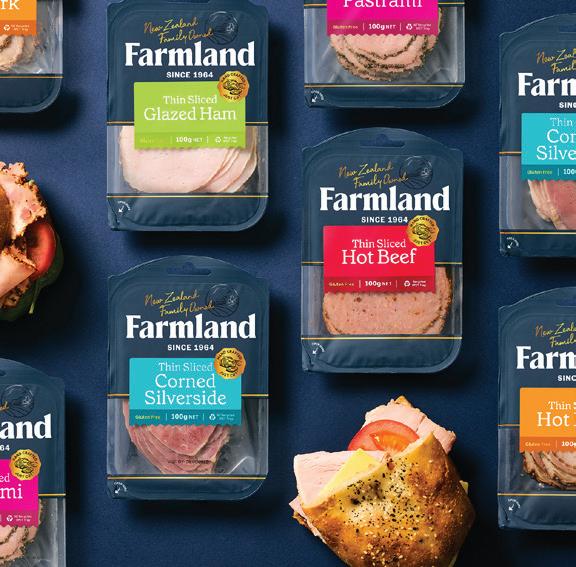
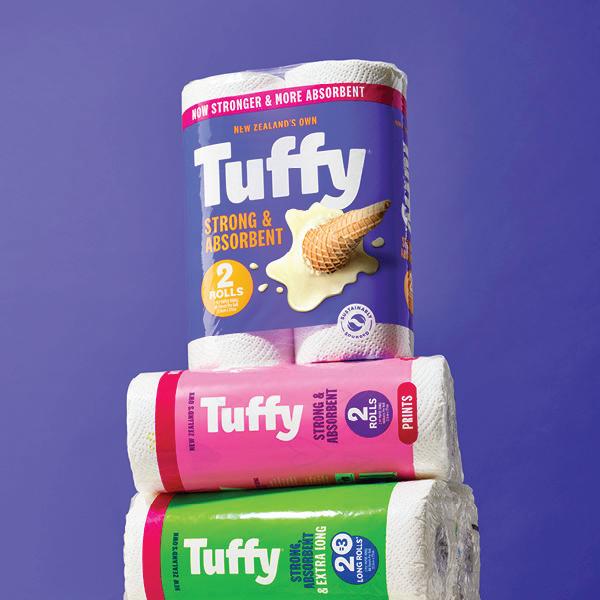
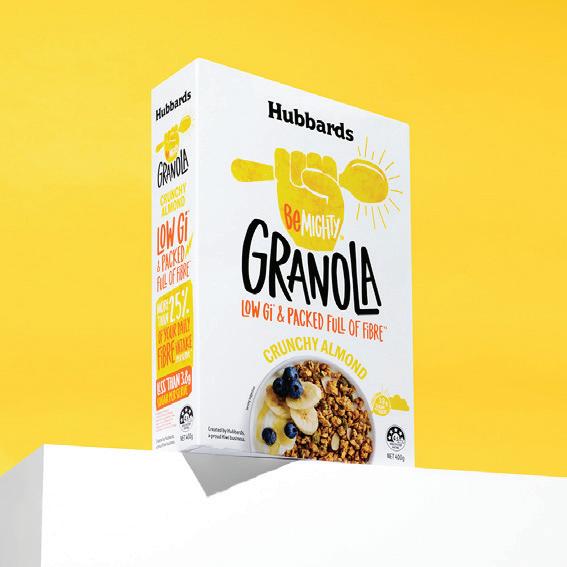
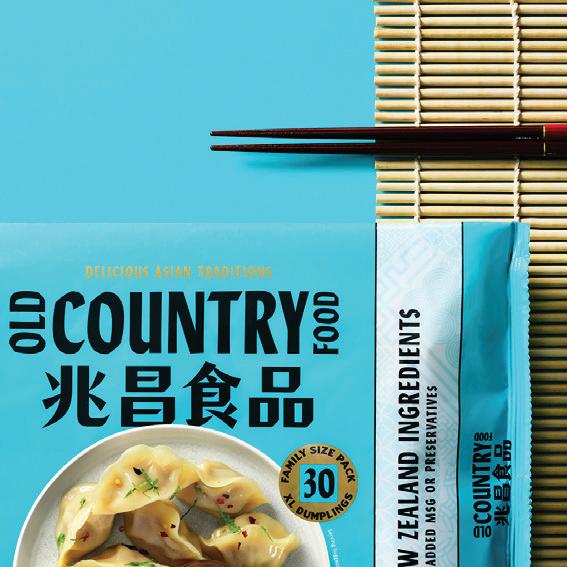
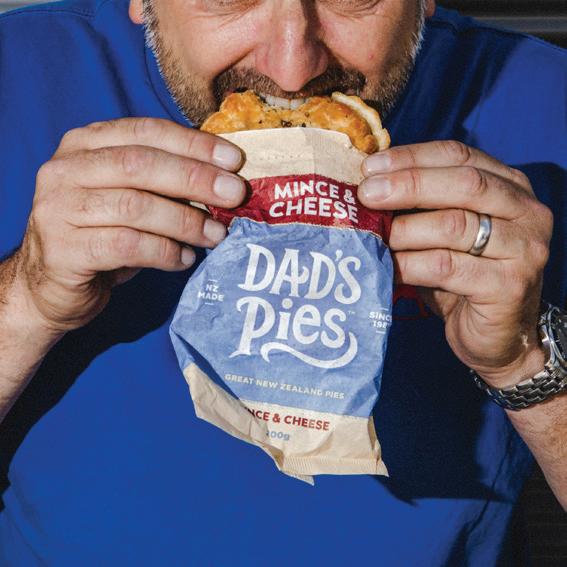
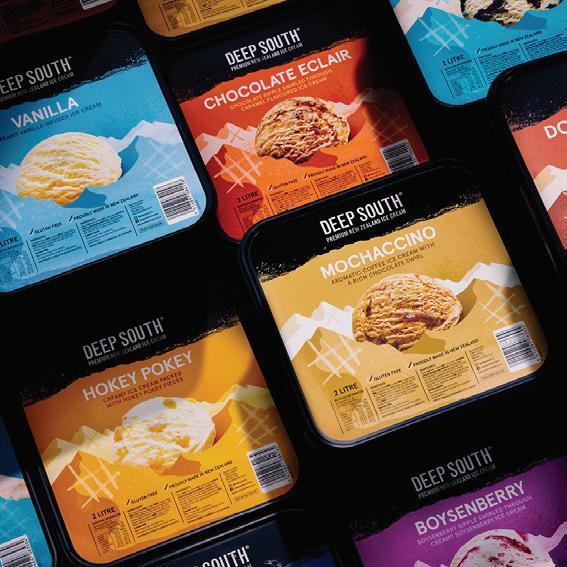
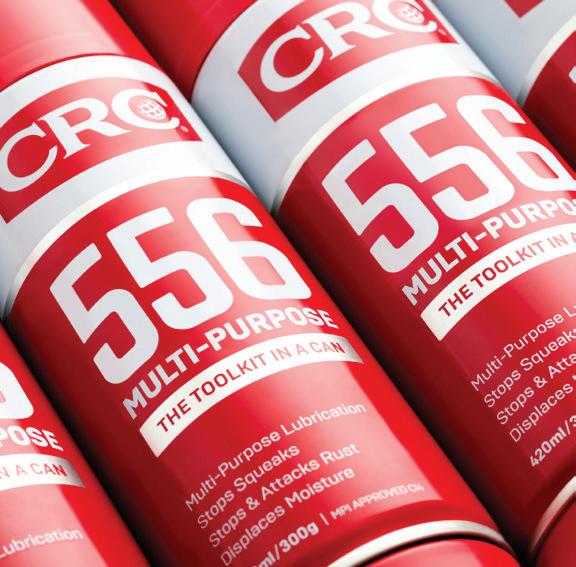
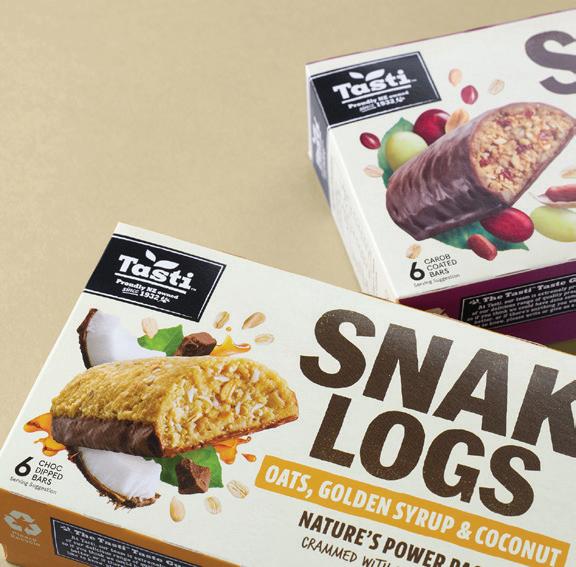
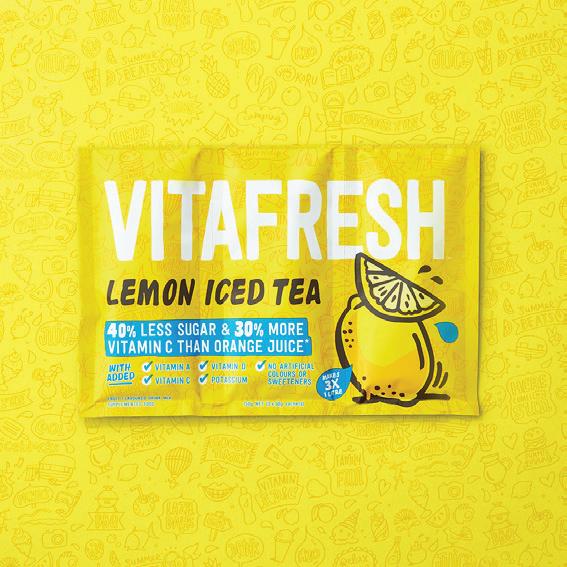
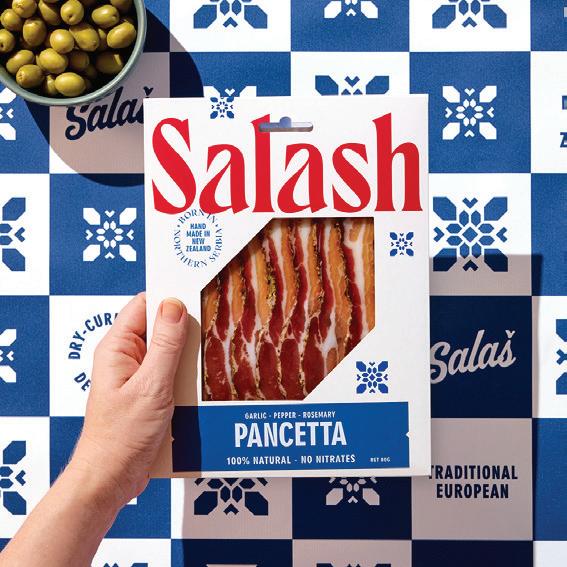
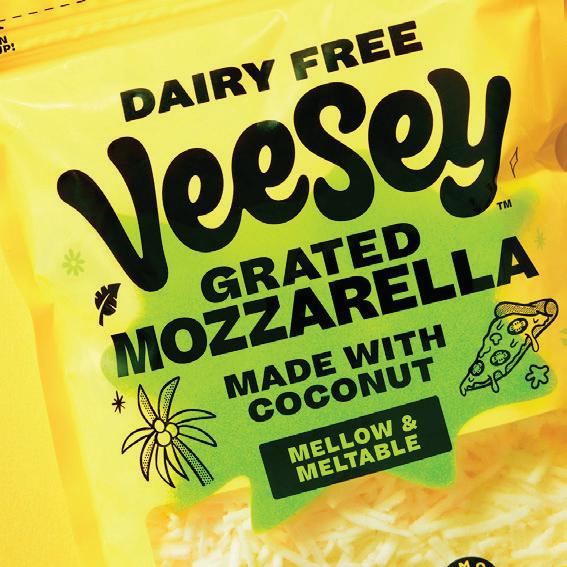
Ignite your brand now. Call Sam Allan, Managing Director, on 021 608 204 or sam@weareonfire.co.nz.


20 minutes with...
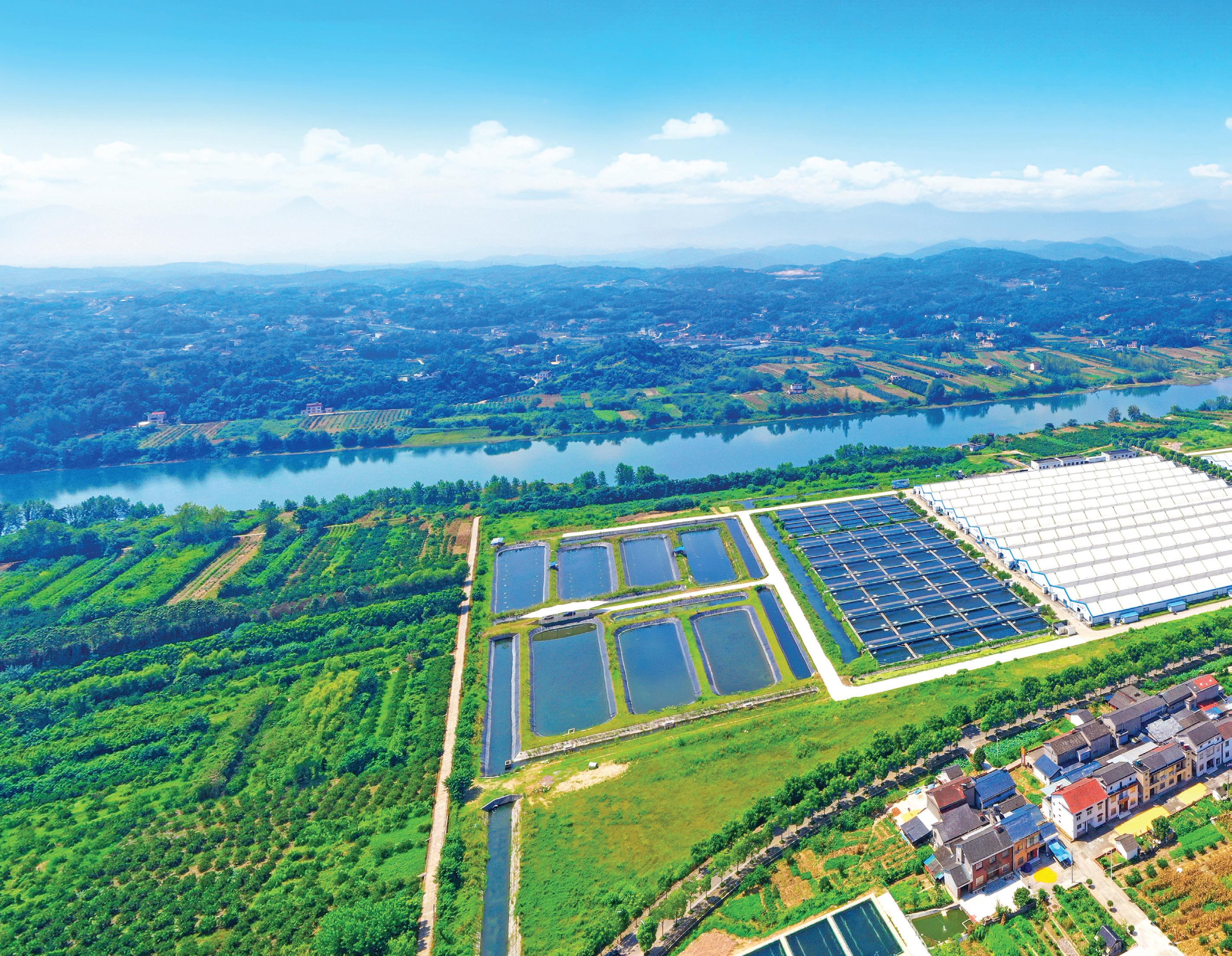
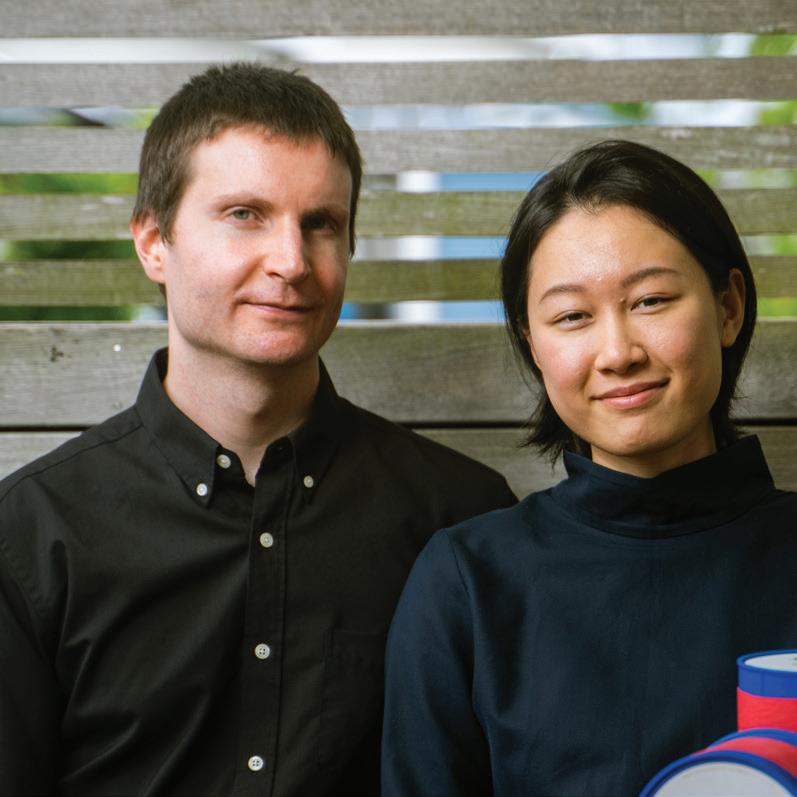
NICHOLAS LONG & XINYUE WAN
Co-founders & Directors, Sturgeon Valley Ltd
A Taste of Luxury, CRAFTED IN ROTORUA
From advanced water filtration systems and rooftop solar arrays to the clean, hands-on approach, Nicholas Long and Xinyue Wan, co-founders and directors of Sturgeon Valley Limited, were struck by the entire sturgeon lifecycle, from hatchlings to mature fish, during their visit to an aquaculture farm in China.
It was their first time tasting caviar, and experiencing it ultra-fresh, directly at the source, left a lasting impression, especially the farm’s commitment to sustainability and innovation, advancing the science of sturgeon aquaculture.
“That visit opened our eyes to both the integrity behind the product and the potential of bringing caviar of that
calibre to New Zealand,” said Long.
“We left the aquafarm filled with questions and a genuine curiosity, which quickly evolved into focused research on sturgeon, roe handling, and global caviar standards.”
Over the following year, the duo was fortunate to work closely with the farm, learning directly from industry experts and receiving hands-on
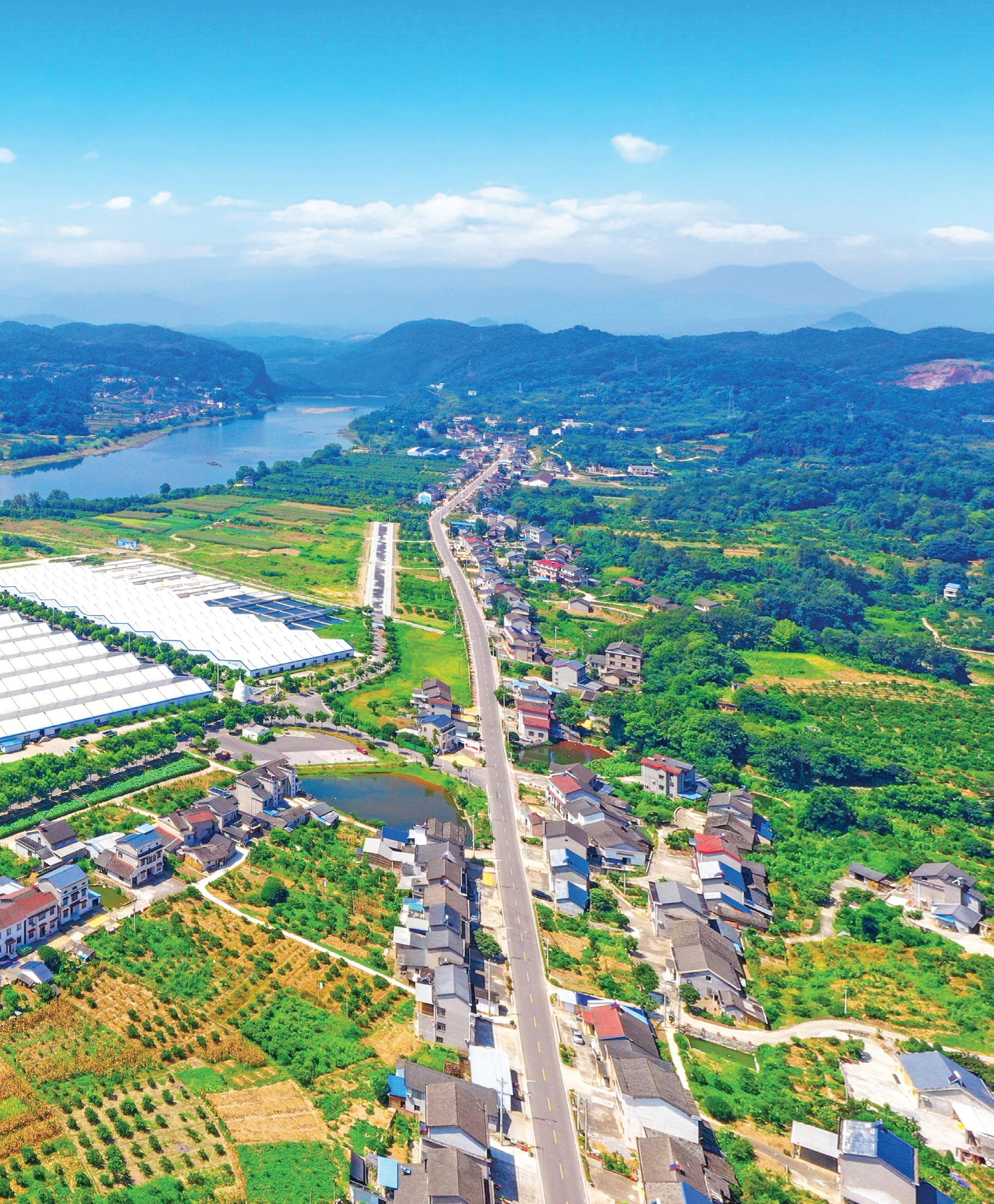
training as caviar technicians.
From the outset, they were determined to be involved in the process as much as possible, maturing and packing the roe themselves rather than importing a finished product. This level of involvement allowed them to fine-tune the ageing process in-house and shape the final flavour profile with intention and consistency.
A combination of formal training, technical research, and iterative testing provided a deep understanding of the maturation process.
“Once we felt confident in both our technical understanding and handson capabilities, we began importing sturgeon roe to trial our storage, maturation, and packaging processes.”
The Sturgeon Valley team only orders what they need, with no substitutions allowed, which is an essential step in maintaining consistency. During the maturation process, the team regularly tastes the product and applies a detailed evaluation system. Each batch is scored using a structured scale to reference previous evaluations
and maintain a consistent standard.
Sturgeon Valley offers four distinct grades of Kaluga sturgeon caviar. Its core varieties - Classic (from 8-year-old sturgeon) and Signature (from 10-year-old sturgeon) come from a naturally occurring Kaluga hybrid (Huso dauricus × Acipenser schrenckii). These are consistently available and celebrated for their nuanced flavour and texture.
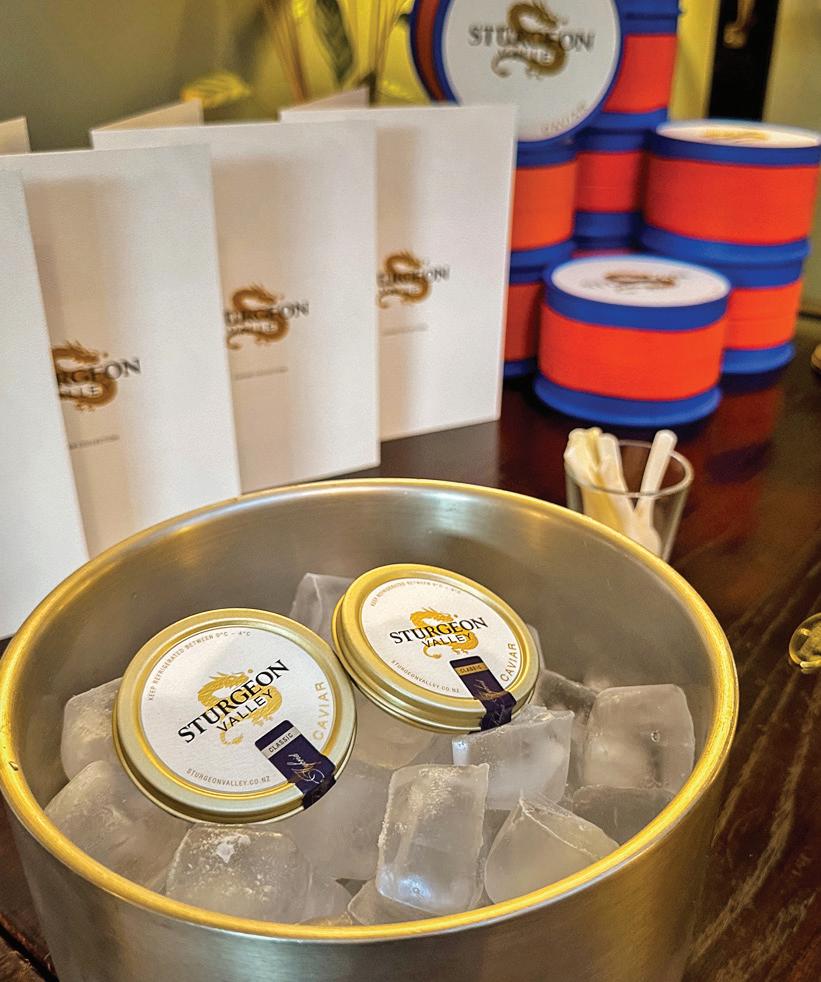
and versatility, making it ideal for both fine dining establishments and a broader range of customers.
Native to China, the Kaluga sturgeon is widely celebrated in the culinary world for its rich umami flavour and smooth, buttery texture. In addition, it offers a well-balanced price point, making it a popular choice among top restaurants.
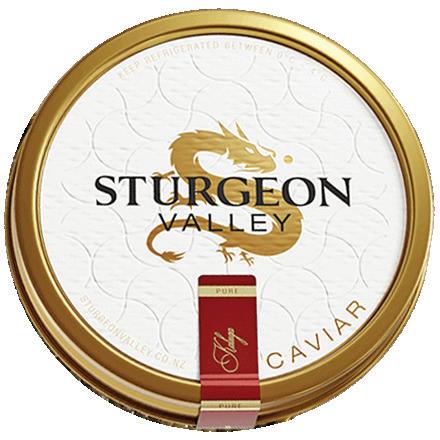
“The farm we work with has done an outstanding job refining its breeding practices, successfully improving both sturgeon survival rates and caviar quality. This makes Kaluga roe a reliably sustainable option and ensures a consistent, quality product year after year.”
The farm also adheres to some of the highest environmental standards in the industry. It’s a land-based facility that employs recirculating aquaculture systems, eliminating any impact on wild sturgeon populations and surrounding waterways.
The seasonal grades are more difficult to secure and highly sought after. Special Reserve, from the same 10-year-old Kaluga hybrid, is scarce as only one in 10,000 fish produces this golden roe, and it occurs entirely by chance.
Pure, the final grade, comes from a 12-year-old purebred Kaluga (Huso dauricus), sometimes referred to as the River Beluga, a close cousin of the true Beluga sturgeon.
Long mentioned that the Kaluga roe was chosen for its excellent quality
Significant investment has been made in advanced water recycling and filtration systems, which have greatly reduced waste and helped protect local ecosystems. Renewable energy has also played a role, with solar-powered systems supporting filtration and oxygenation, contributing to a minimal carbon footprint.
It is also CITES-registered, meaning every step complies with strict international regulations designed to protect endangered species
Continued


20
minutes

from page 19.
and promote sustainable farming practices.
“Every time we asked about their environmental practices, they had a well-considered answer, and often, they’d already taken things a step further. They’re not simply ticking boxes; they actively collaborate with researchers on sturgeon conservation and are engaged in major global conversations around sustainable aquaculture.”
Closer to home, Long mentioned that they have been experimenting with natural materials, such as bull kelp, as an alternative vessel for maturing caviar. Digital tools, such as AI, have also helped streamline communications and storytelling, which are crucial to educating and connecting with an audience in new and engaging ways.
Setting up a facility and navigating New Zealand’s regulatory landscape presented various challenges. The biggest challenge was that, since no one had done this before, there were no established guidelines for the situation.
Explaining the process to CITES NZ required extensive research, precise documentation, and ongoing communication. Because of the novelty of the request, it took time to clarify the applications of specific regulations.
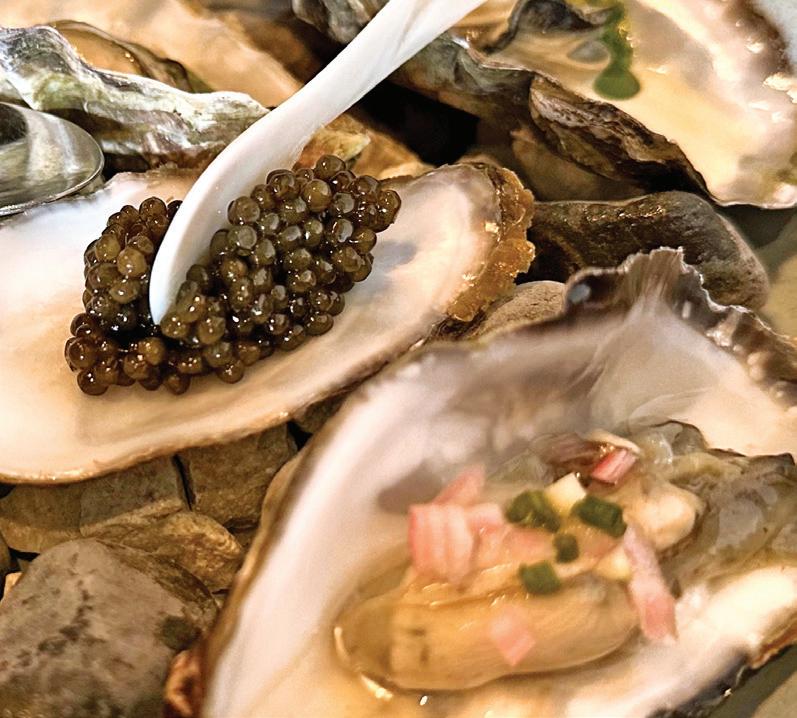
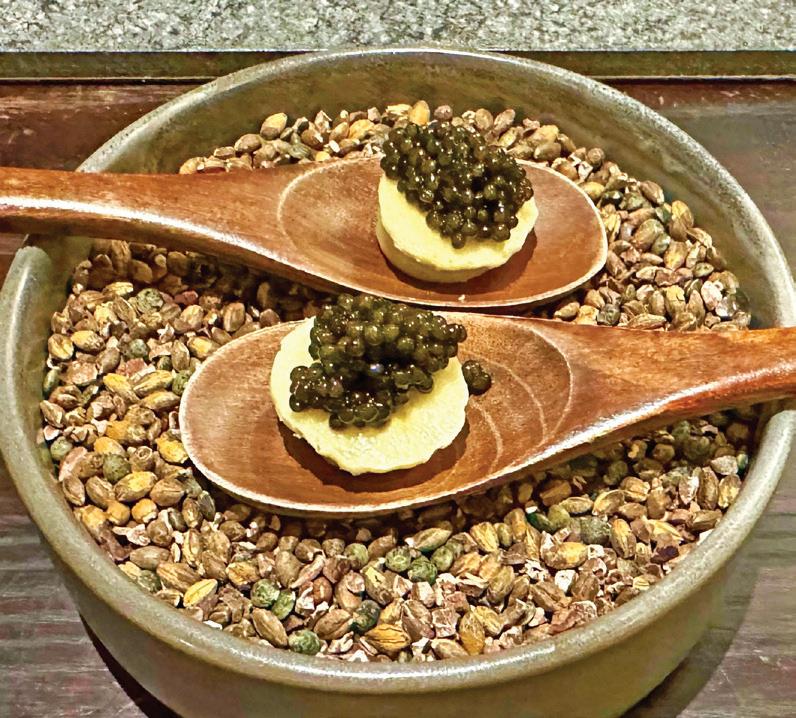
“Their support throughout was invaluable, and after working closely with them, we ultimately received permission to import sturgeon roe, repack it locally, and sell it on the domestic market.”
Becoming New Zealand’s first approved caviar repackaging plant under CITES has set a precedent,
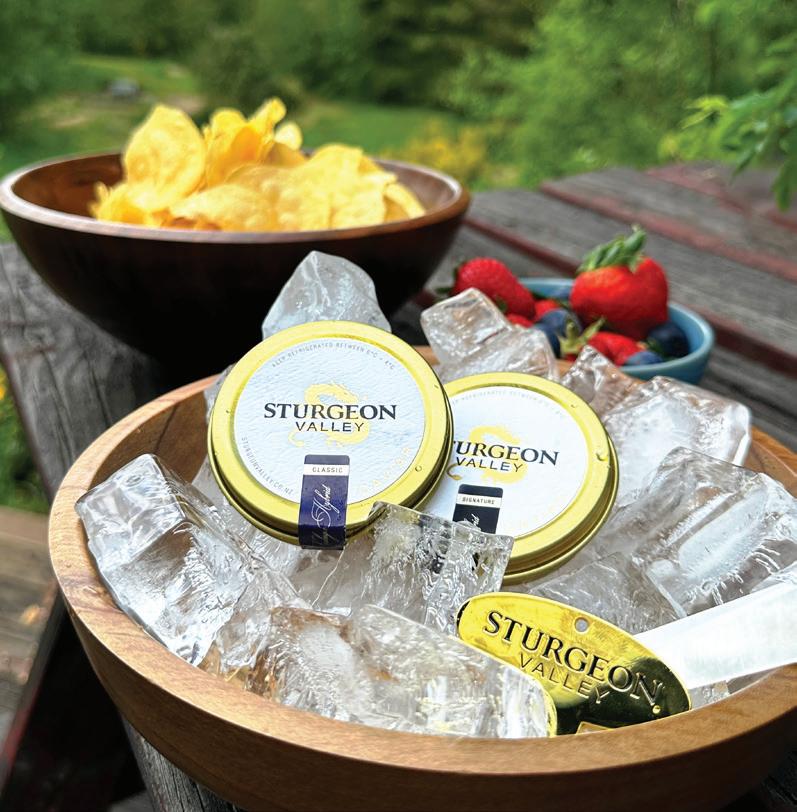
and Long said he was proud to have helped establish a pathway for this niche industry.
Having a base in Rotorua has put Sturgeon Valley within easy reach of many of New Zealand’s top restaurants, allowing us to build strong relationships with chefs and stay hands-on.
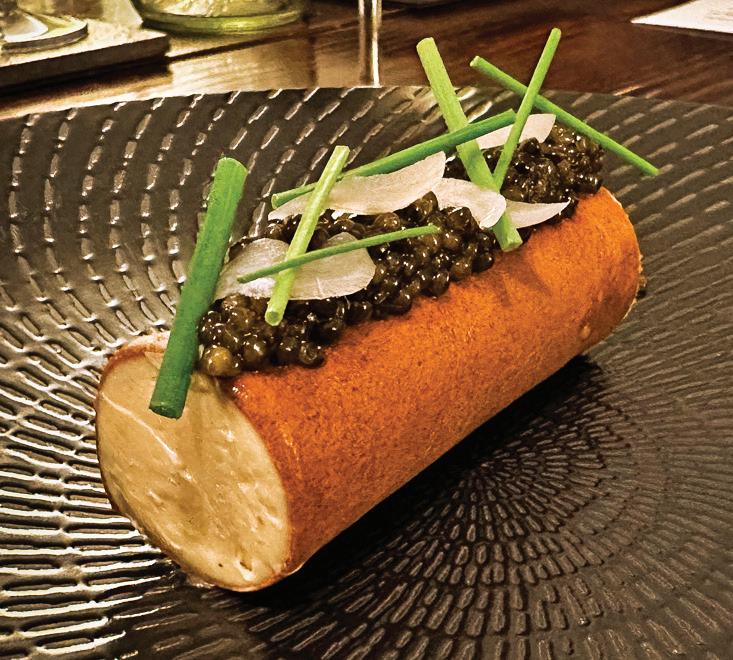
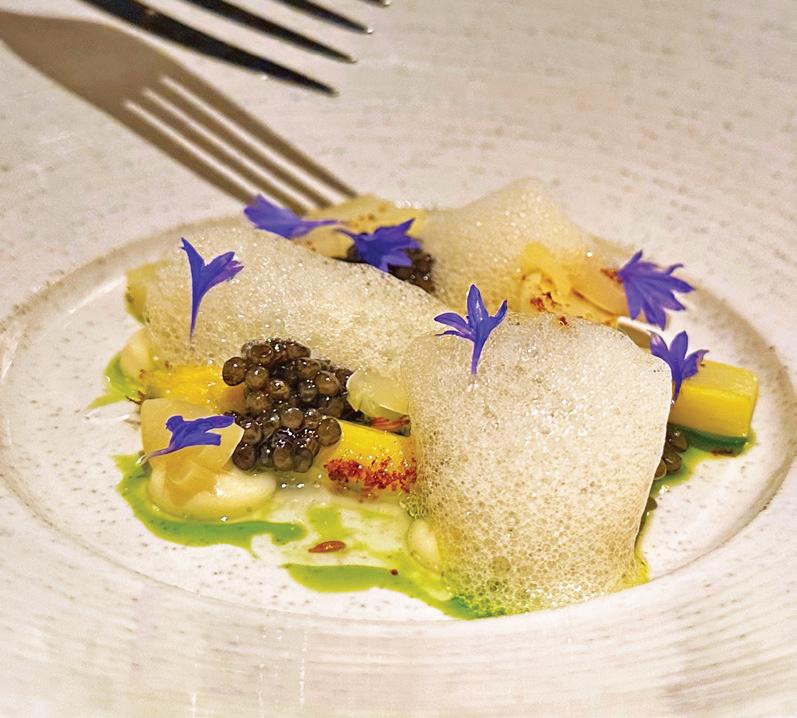
Although the location has surprised people, it has reinforced the business’s connection to New Zealand’s clean, green, and eco-conscious values, setting it apart.
The response from New Zealand’s fine dining community has been fantastic. Word of mouth has played a significant role, and Sturgeon Valley has had the privilege of being introduced to many incredible people who have expressed genuine appreciation for its caviar.
Long said that many renowned New Zealand chefs have described the caviar as top-tier, and it was exciting to be featured on the menus of some of the country’s best restaurants.
According to Long, one of the most exciting collaborations was with Jano Bistro, where Chef Pierre-Alain Fenoux curated a special dégustation menu featuring Sturgeon Valley caviar in every course, from starters to dessert.
“It was our first event, and it completely sold out. The menu was mind-blowing; Chef Pierre’s inventive use of caviar opened our eyes to its potential.”
Long added that it was an unforgettable evening and a milestone moment, demonstrating how caviar could elevate each dish in unexpected ways. He mentioned that caviar also fits naturally into New Zealand’s culinary culture, which has
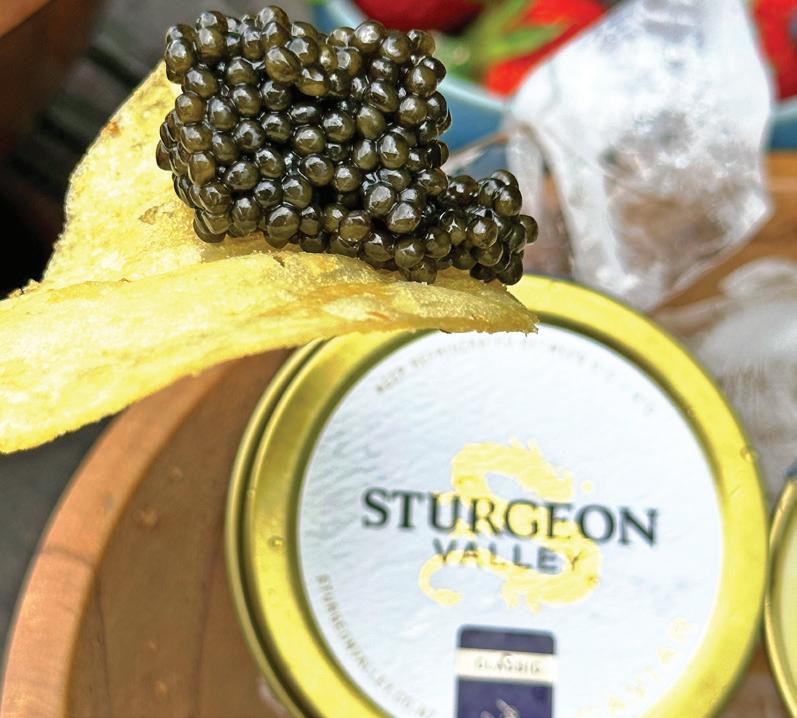
Continued
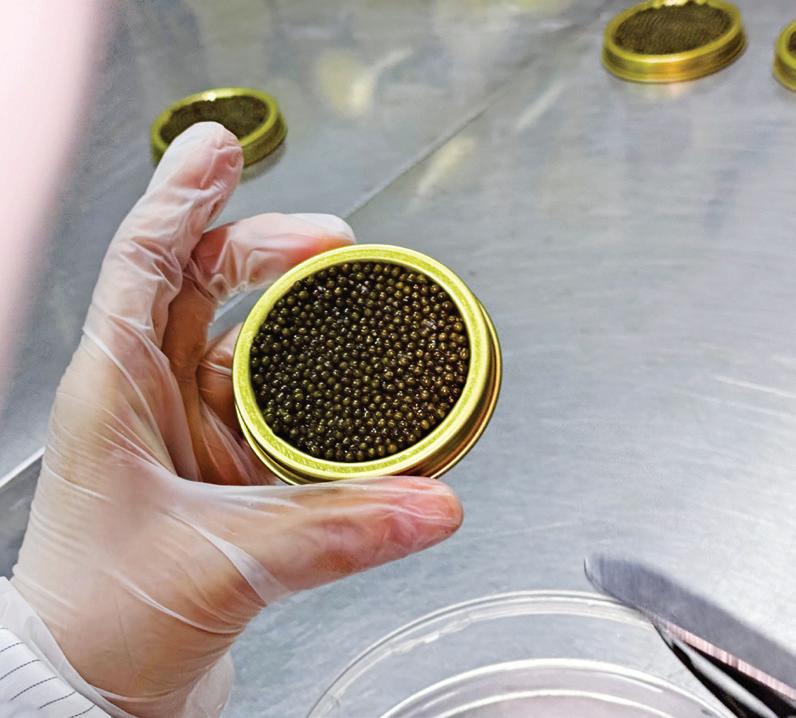
been centred on fresh, high-quality ingredients and responsible farming practices.
He said that New Zealanders value food with a story and appreciate the passion and dedication that go into it. With the country being home to some of the world’s best produce, Sturgeon Valley caviar has resonated with local chefs and diners who are deeply committed to authenticity and quality.
“We’re incredibly grateful to be recognised by the culinary community here and proud to be part of a culture
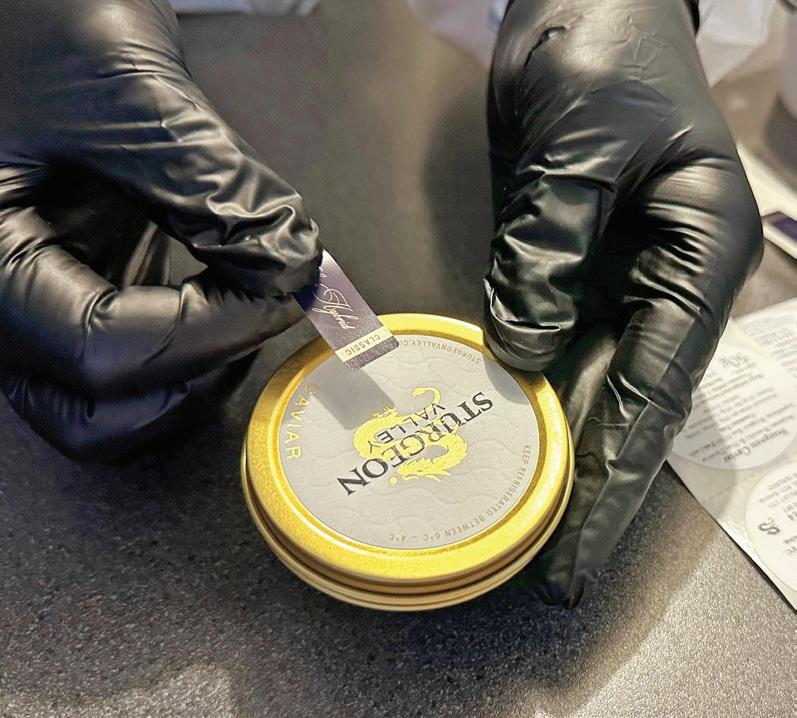
that values not only delicious food, but also the people who bring it to life.”
Despite officially starting trading in December 2024, Sturgeon Valley has already seen strong interest beyond the hospitality sector, particularly from private clients eager to enjoy premium, locally matured caviar.
While the current economic climate has resulted in more cautious spending, Long said the demand is growing, and he was optimistic that, over time, more people will recognise the value of quality and care in what they eat.
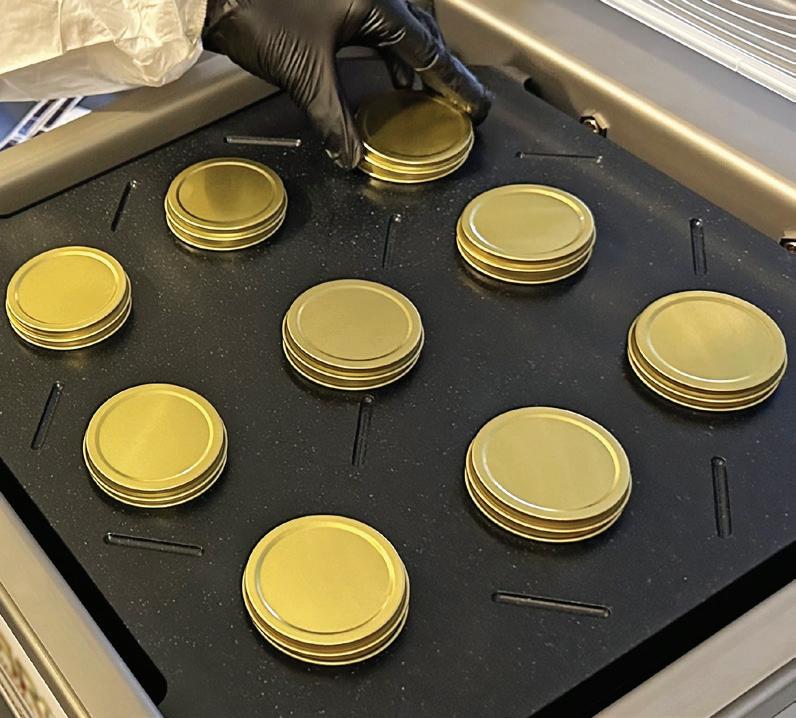
Looking ahead, the immediate priority for the business is to build strong local relationships and ensure the quality, consistency, and accessibility of the product remain exceptional.
At the same time, Sturgeon Valley is steadily expanding through events and collaborations, working with CITES NZ to help establish the regulatory framework necessary to support transparent and wellregulated exports in the future, and actively exploring export opportunities.
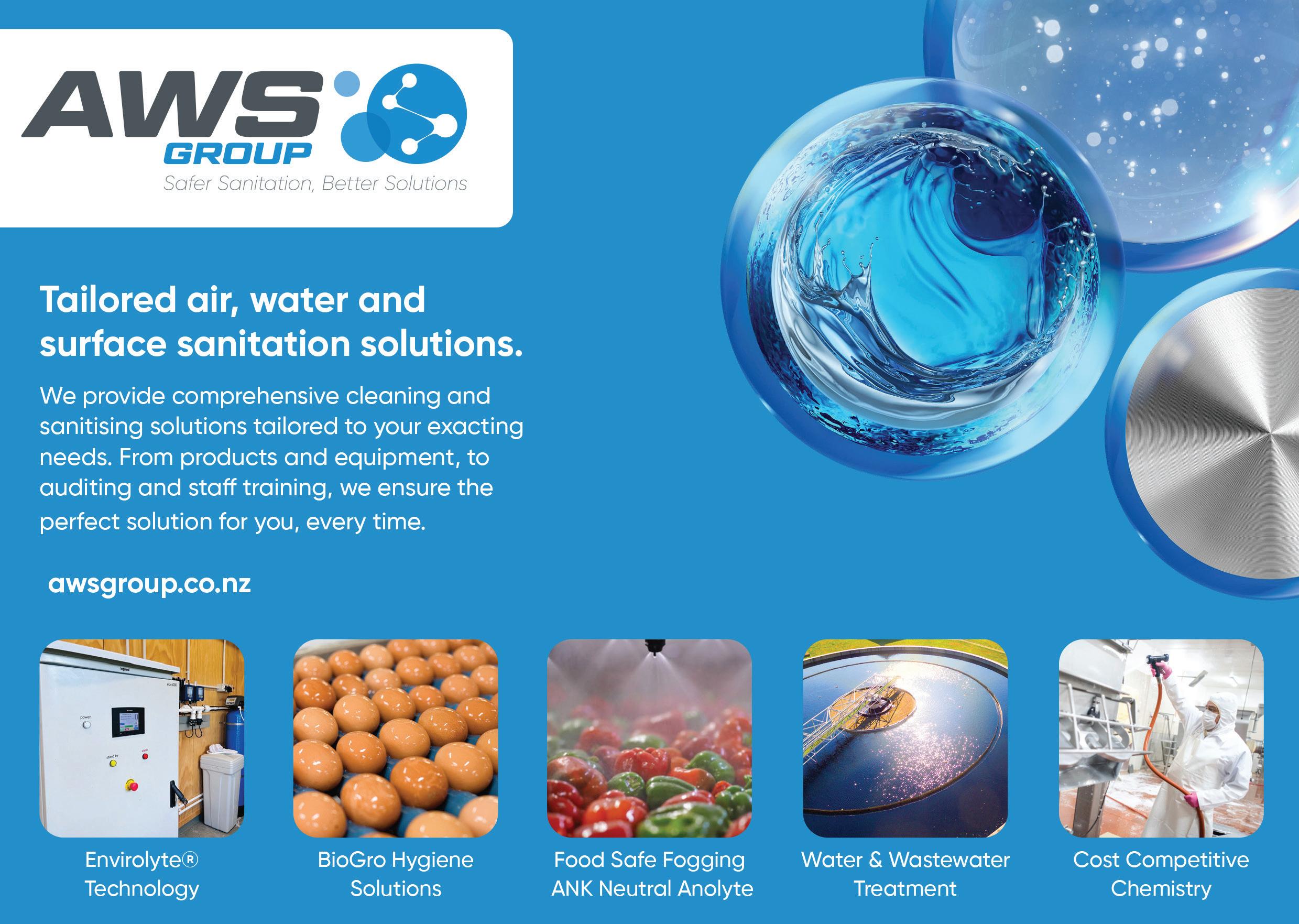


fluid management
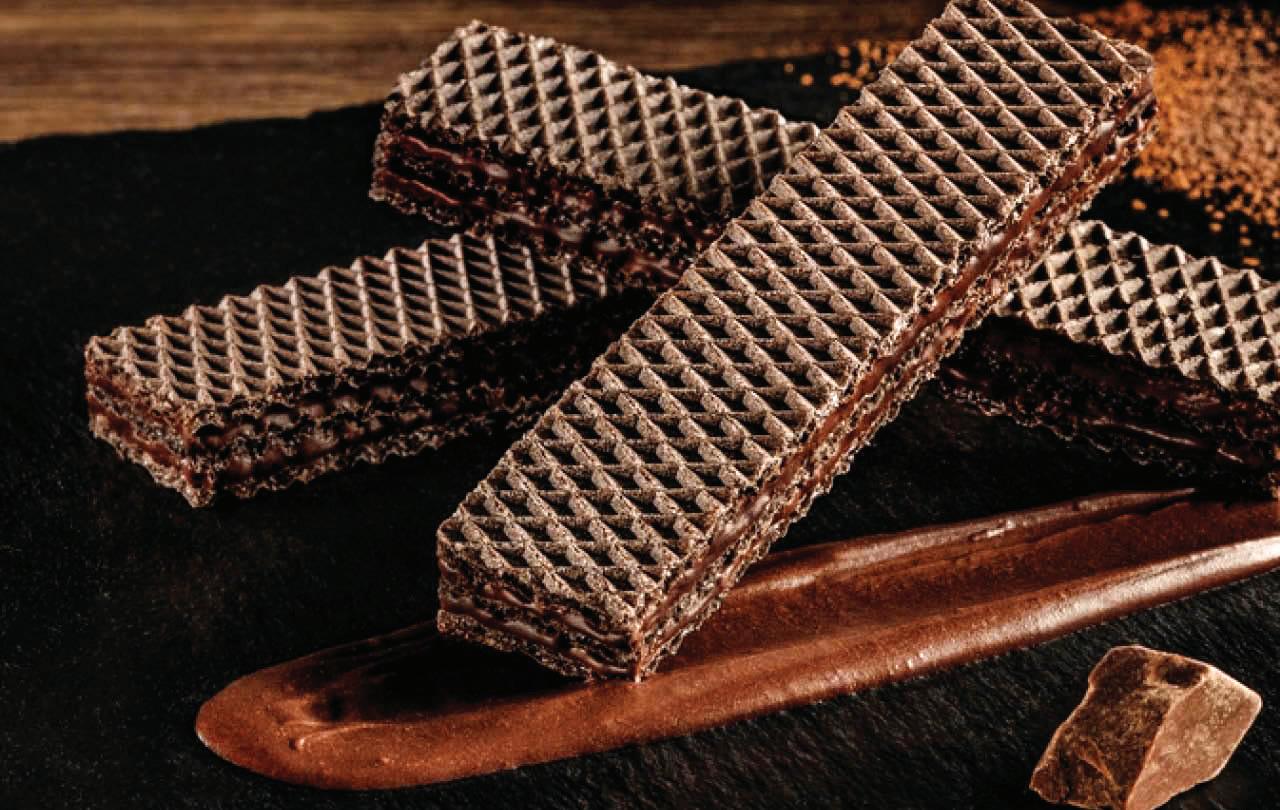
A Sweet Solution for Chocolate WAFER PRODUCTION
Pumping chocolate with wafers can present a unique set of challenges in the confectionery sector. Maintaining a consistent product texture while preventing caramelisation and avoiding pump failure is essential for maintaining production efficiency.
According to an All Pumps Australia case study, a confectionery manufacturer discovered specific issues with traditional lobe pumps in this scenario.
While commonly used in chocolate production for its gentle handling, the lobe pump had been introducing excess heat into the mix. That heat caused the chocolate and wafer blend to caramelise prematurely, compromising texture, reducing quality and creating a residue build-up inside the pump casing.
Over time, this hardened residue increased friction and eventually caused the pump to seize. The impact on production was immediate, with unscheduled downtime, emergency maintenance, and inevitable financial setbacks.
To address the issue, All Pumps that recommended transitioning to a Graco sanitary flap valve diaphragm pump.
Unlike the lobe system, the diaphragm pump operates with minimal heat generation, effectively eliminating the risk of caramelisation. The flap valve design also enabled the pump to handle wafer pieces without breaking them down or causing clogs, thereby maintaining the integrity of
the product and ensuring a smooth transfer.
The Graco pump also featured cleanin-place (CIP) functionality, enabling simplified maintenance and enhanced hygiene compliance, crucial in foodgrade processing environments.
Since installation, the manufacturer has not experienced a single incident of pump-related downtime. Operators noted the difference, not just in operational stability but also in ease of cleaning and overall product quality.
By eliminating the issues of overheating and residue accumulation, the production line has consistently produced batches of chocolate wafer products without compromise. The long-term cost savings from reduced maintenance, improved output, and minimised waste justified the initial investment in the pump.
The case highlighted the importance of selecting application-specific equipment in the food and beverage manufacturing industry. For any manufacturer dealing with chocolate or other viscous substances combined with inclusions such as wafers, nuts, or fruit, a diaphragm pump with a flap valve design can make a significant difference.
MANAGING ENERGY EFFICIENTLY
HRS Heat Exchangers
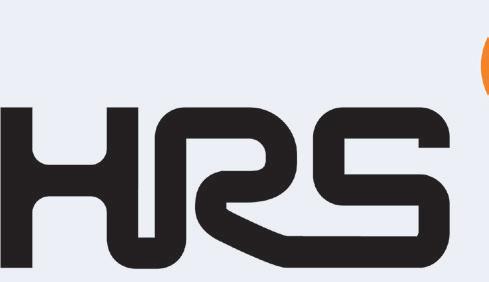
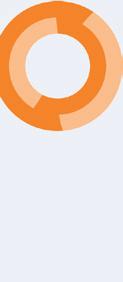
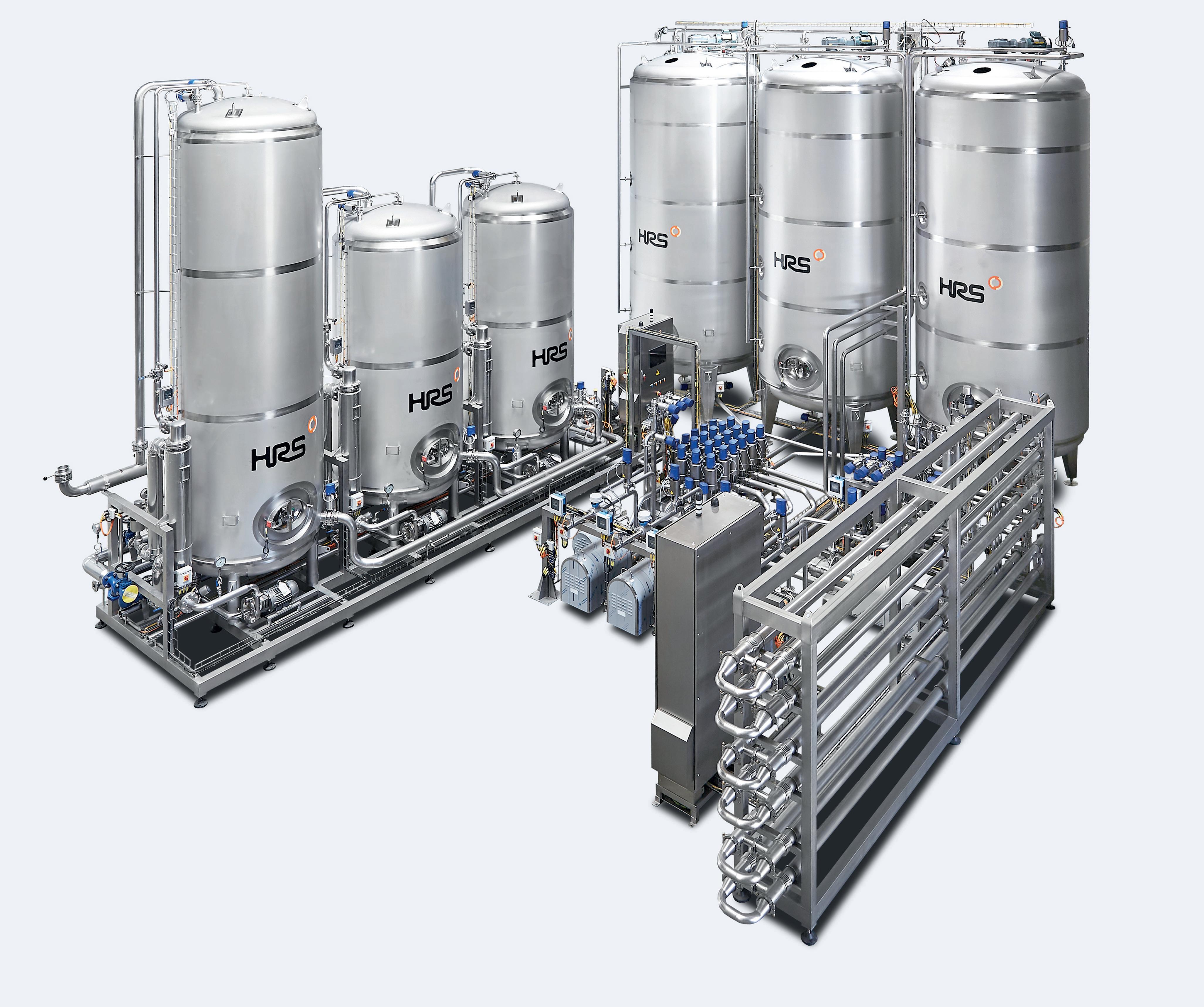
Pasteurisation
Sterilisation
Aseptic Filling
Direct Steam Injection
Evaporation
CIP Kitchens
Process Skids
Juice Crushing and Remelting


fluid management
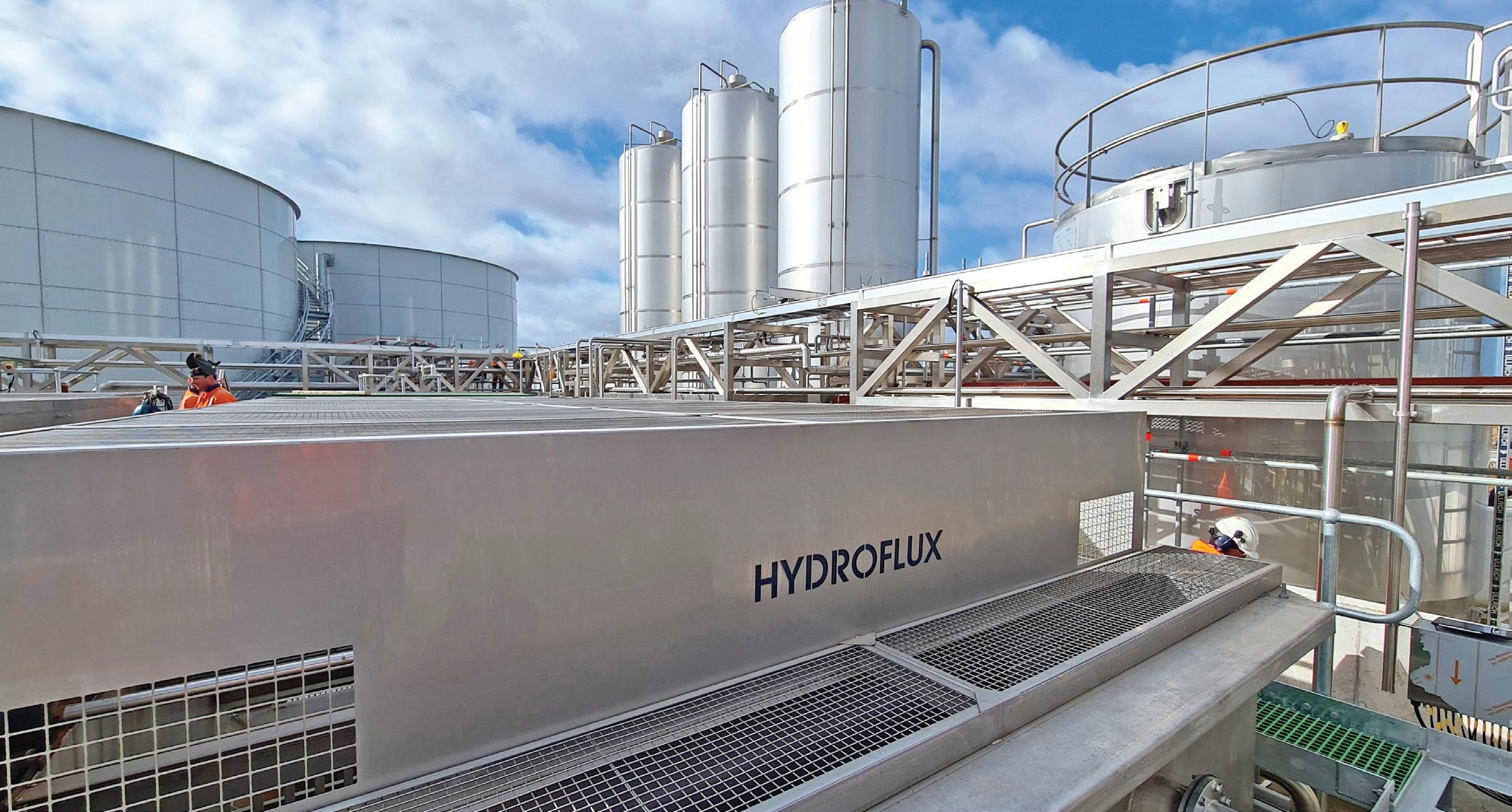
Proactive Approach to WATER MANAGEMENT
Many New Zealand food producers experience seasonal fluctuations in wastewater flow and pollutant loads, which require treatment systems that are both flexible and responsive.
Similarly, process water must often meet extremely stringent quality standards, especially for international brands that demand uniformity and consistency in taste across all regions.
Hydroflux is a locally active group working across New Zealand, Australia, and the Pacific, specialising in water, wastewater, and sustainability solutions for industries, councils, and utilities.
It has engineered hygienic water systems that deliver precise quality parameters to suit specific product and compliance requirements. Every solution is tailored to the client’s operational needs, including layout, capacity, materials of construction, automation, and control.
“At Hydroflux, being a ‘fluid thinking’ group means we approach every food
and beverage project with agility, creativity, and a deep understanding of the industry’s specific challenges. In practice, it’s about thinking beyond offthe-shelf solutions,” said Andrew Miley, co-founder of Hydroflux.
“Instead, we collaborate closely with clients to design and deliver tailored process water and wastewater treatment systems that meet stringent hygiene standards, reduce water and energy use, and support sustainability goals.”
The team closely monitors updates to discharge consents, freshwater reform, climate-related reporting, and sustainability frameworks that affect the food and beverage sector.
Closed-loop water systems, advanced biological treatment processes, membrane bioreactors (MBRs), HyX Ion exchange systems and the HyPure range for high-purity water treatment are key to many of its projects. These technologies help clients improve wastewater quality and maximise opportunities for reuse.
Miley has observed that water costs and availability are at the forefront of many businesses’ minds, particularly in regions where freshwater allocation is heavily scrutinised. Breweries, dairies,
and meat processors have sought systems that recycle water for noncritical uses, thereby easing demand on town supplies.
He added that complete net-zero water systems are still rare, but interest has grown as sustainability targets become more ambitious.
“Water is becoming a strategic resource, not just a utility. In the food and beverage sector, taking a proactive approach to water management now will pay dividends later in resilience, compliance and brand reputation.”
Hydroflux recently delivered a state-of-the-art aerobic wastewater treatment plant for Frucor Suntory’s new AUD 400 million beverage manufacturing facility in Swanbank, Queensland. This project showcased Hydroflux’s commitment to innovation and sustainability, aligning directly with Frucor Suntory’s vision to lead the FMCG sector in sustainable manufacturing.
Designed to operate entirely carbon-neutral, the Swanbank facility is powered by 11 GWh of publicly owned renewable energy through a partnership with CleanCo. This initiative supports Queensland’s target of achieving 70 percent renewable energy by 2032.
As Frucor Suntory CEO Darren Fullerton emphasised, the facility aimed to set a new benchmark for sustainable investment in the region, operating from day one on 100 percent green energy.
Miley said that Hydroflux’s role in
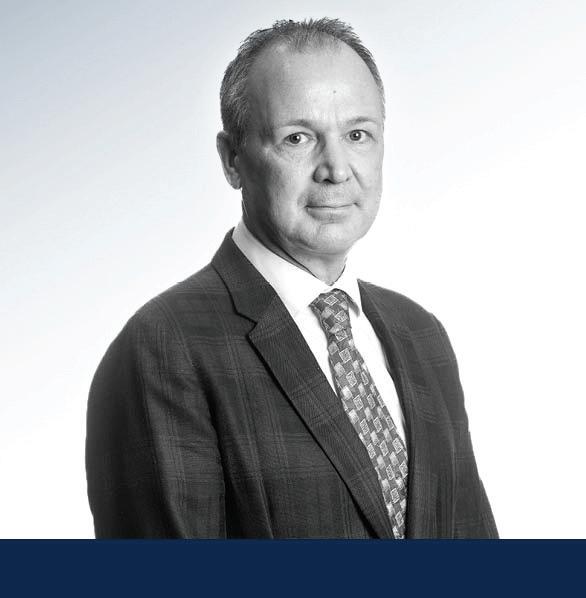
the project was to deliver a highperformance, low-impact wastewater treatment solution that complements this sustainability focus. The system features advanced aerobic Moving Bed Biofilm Reactor (MBBR) technology, designed to manage high-strength wastewater with high efficiency while reducing energy consumption and minimising chemical use.
The modular, scalable design supports future plant expansion and enables integration with additional resource recovery initiatives, such as water reuse or enhanced solids handling.
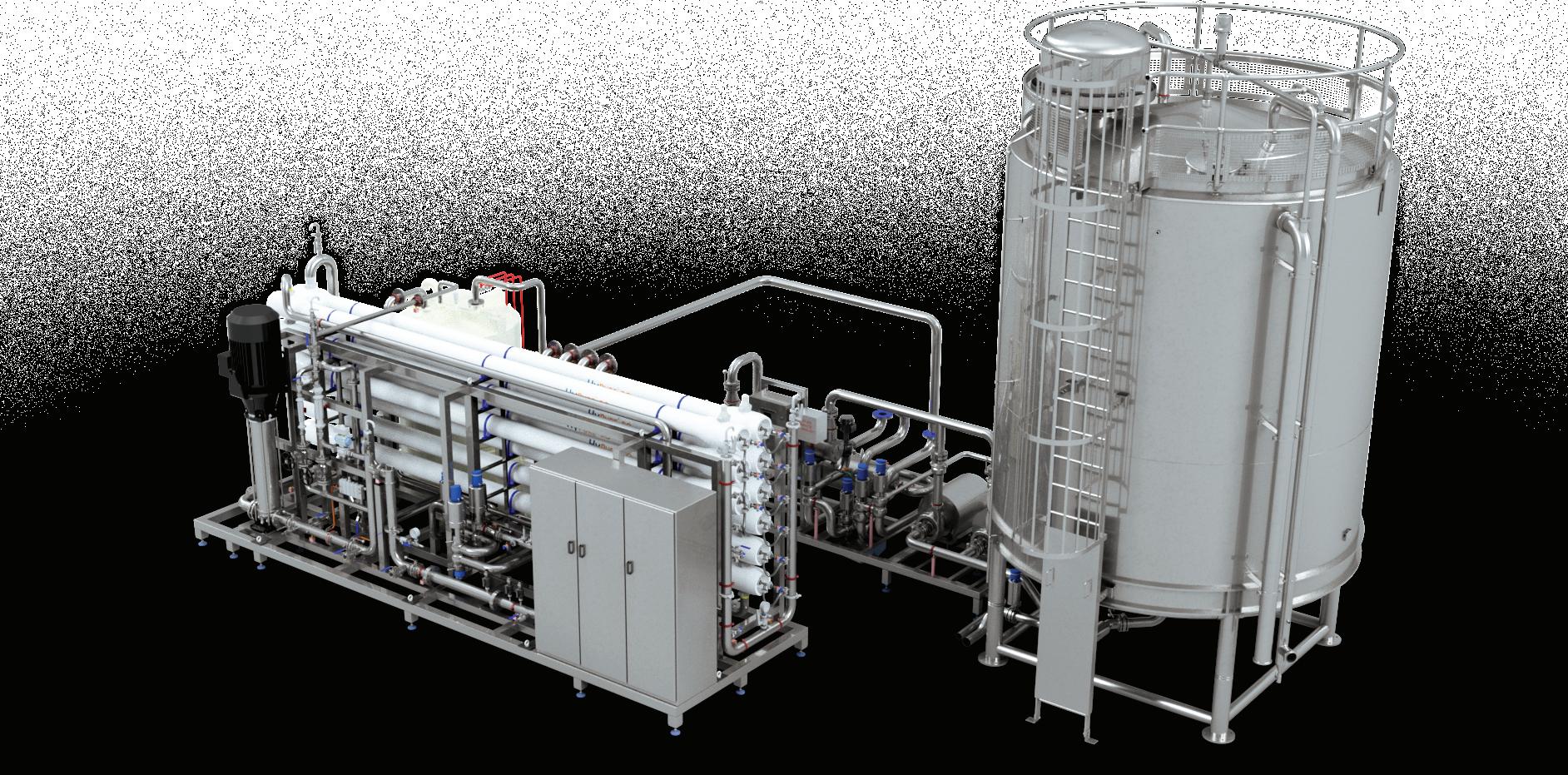
“What makes this installation unique is not only its technical capability but also the fact that it was delivered under Hydroflux’s certified carbonneutral delivery model,” added Miley.
“While our contribution formed just one part of the broader project, it played a vital role in helping Frucor Suntory deliver a future-ready, environmentally responsible facility that sets a new benchmark for sustainable manufacturing in Australia.”
This collaboration is a leading example of how industrial infrastructure can be developed
to meet both performance and environmental objectives.
For F&B manufacturers who are just beginning to review their fluid management processes, Miley advised starting by understanding water balance and usage. He said that even a simple audit can uncover savings or risks. From there, work with a partner who understands both the engineering and regulatory landscape.
“It is not just about compliance. Smarter water management can lower costs and strengthen your environmental credentials.”
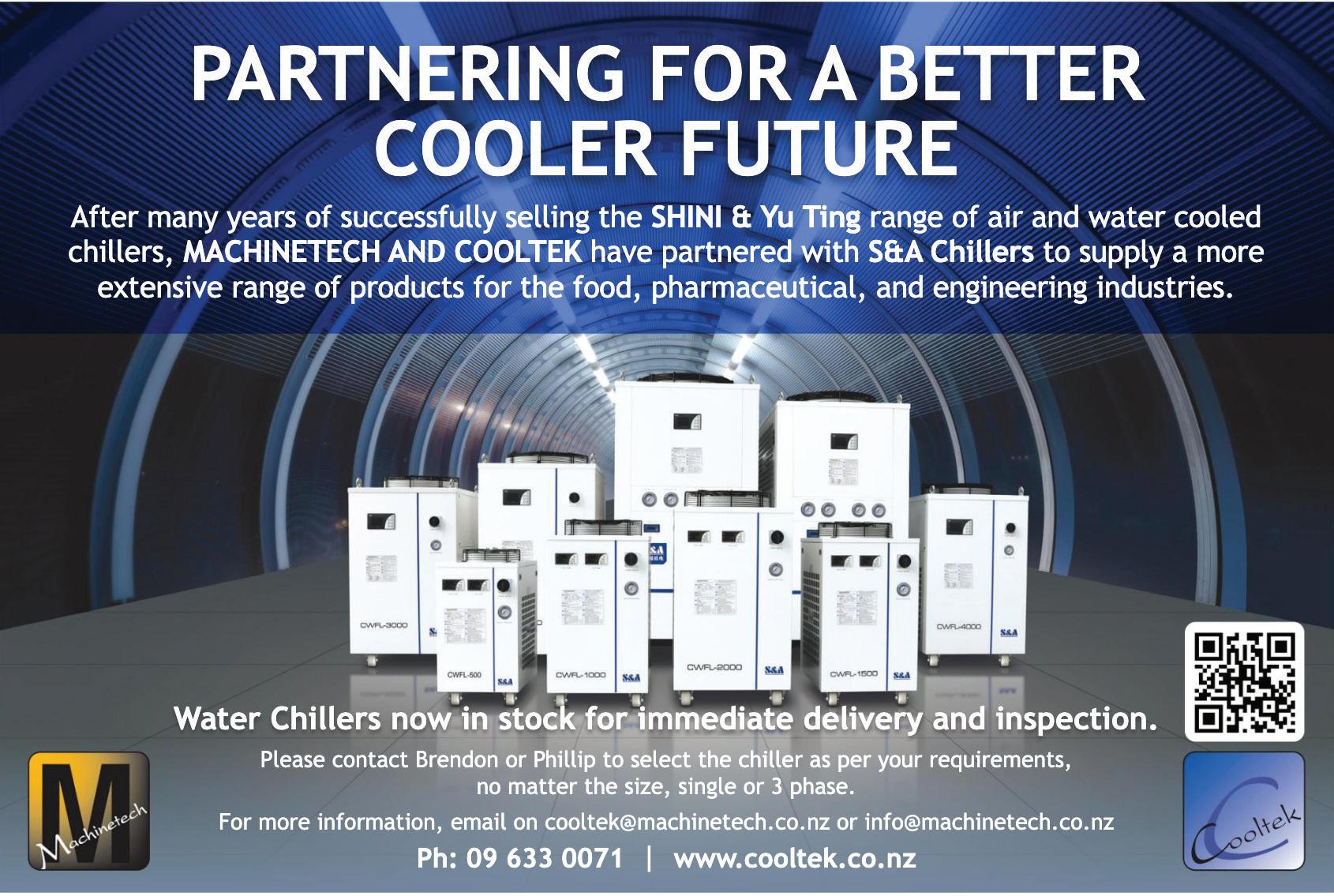


Andrew Miley, Hydroflux co-founder
fluid management
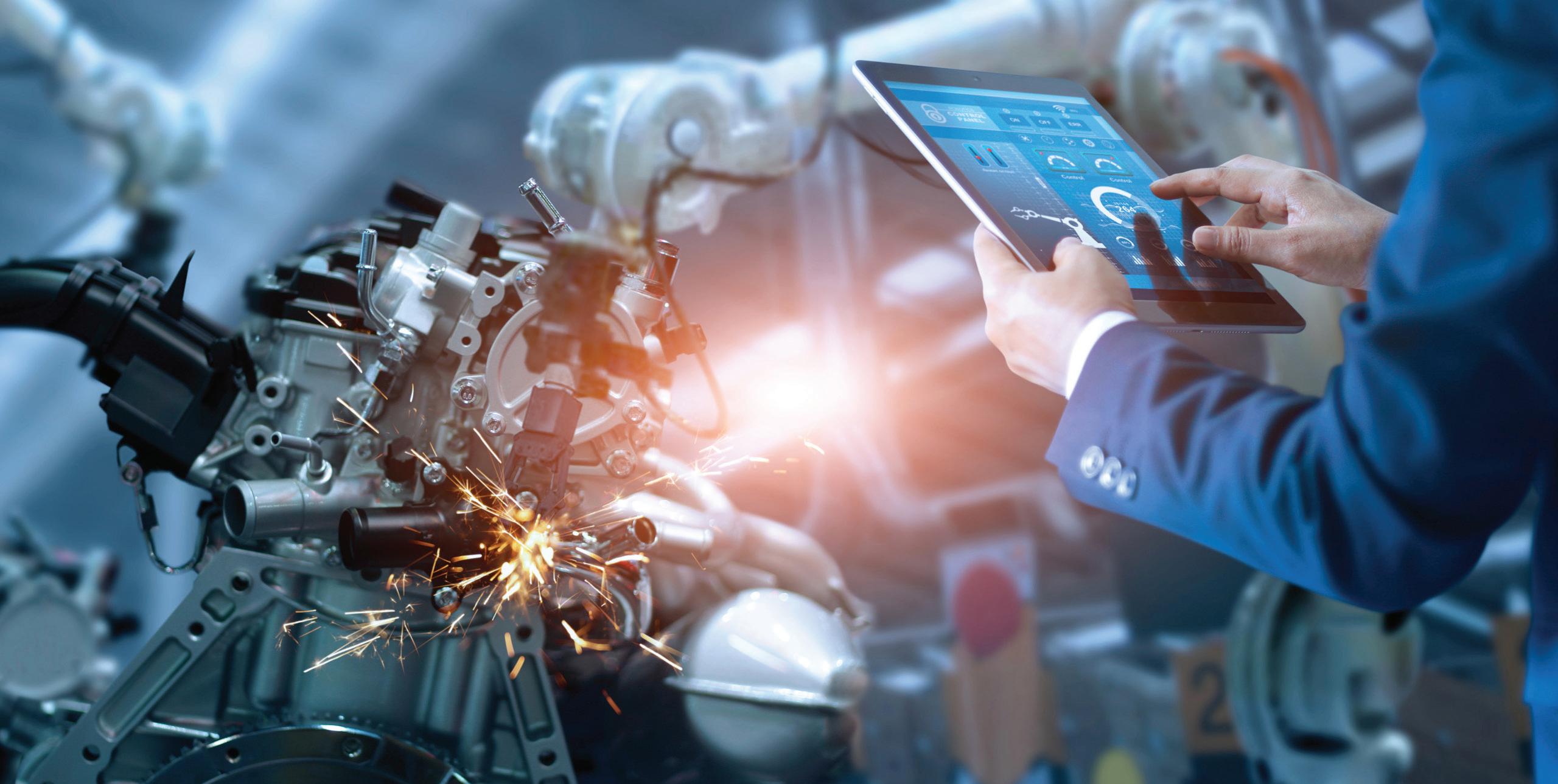
Daniel Coetzee Leads INDUSTRIAL AUTOMATION GROWTH
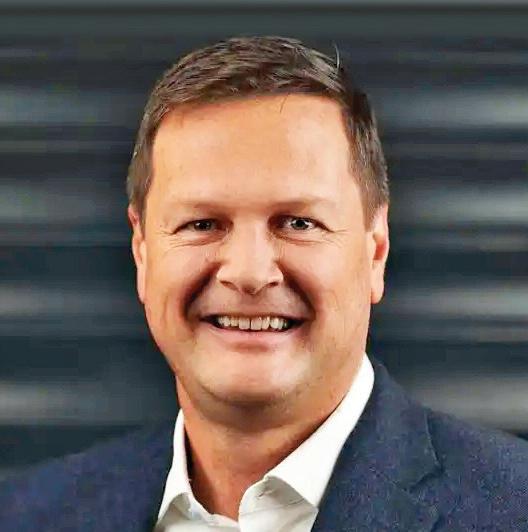
IMI Norgren has welcomed Daniel Coetzee as Vice President of Growth for its Industrial Automation division.
With over 25 years of experience in senior leadership roles, Coetzee will bring extensive expertise to help drive innovation and deliver enhanced support to customers, across a wide range of industries. With leadership experience from organisations such as GE, Emerson, and Luffy AI, he has worked across a variety of industries, including power,
oil and gas, life sciences, automotive, green energy, and food and beverage, making significant contributions to innovative solutions and operational efficiency.
His expertise spans advanced technologies and digital transformation strategies, including Artificial Intelligence, Manufacturing Execution Systems (MES), Asset Performance Management (APM), robotics, Industrial Internet of Things (IIoT), cyber security, and Industry 4.0.
He has been focused on addressing the challenges faced by modern industries, ensuring companies can successfully adopt and benefit from digital and automation solutions. He will lead the M&A and Commercial functions for the Industrial Automation division.
His priorities include strengthening customer engagement, pursuing market-led innovation, and enhancing the Industrial Automation digital ecosystem to serve its global customer base better.
Coetzee will play a central role in enabling businesses to adapt to the demands of digital transformation, focusing on productivity, sustainability, and cost management. His strategic approach will reinforce IMI’s
commitment to delivering practical, future-focused solutions for customers across various sectors, including water treatment, healthcare, and manufacturing.
“Digital transformation is reshaping how industries operate, driving efficiencies and enabling organisations to meet critical challenges like sustainability and cost control,” said Coetzee.
“IMI has a solid foundation for supporting customers through these changes, and I’m excited to build upon it, further strengthening our partnerships and solutions for a continually evolving market.”
IMI Norgren will remain dedicated to helping its customers succeed in an increasingly digital and automated world. With Coetzee leading the business’ growth initiatives, its Industrial Automation division is positioned to deliver even greater value and innovation.
Coetzee’s appointment represents the next step in IMI Norgren’s efforts to offer dependable, customer-focused solutions while driving its Industrial Automation division forward. His expertise and leadership are central to the mission of advancing industrial automation in ways that are both practical and forward-looking.
DANIEL COETZEE Vice President of Growth for Industrial Automation Division
MORE FLUID THINKING
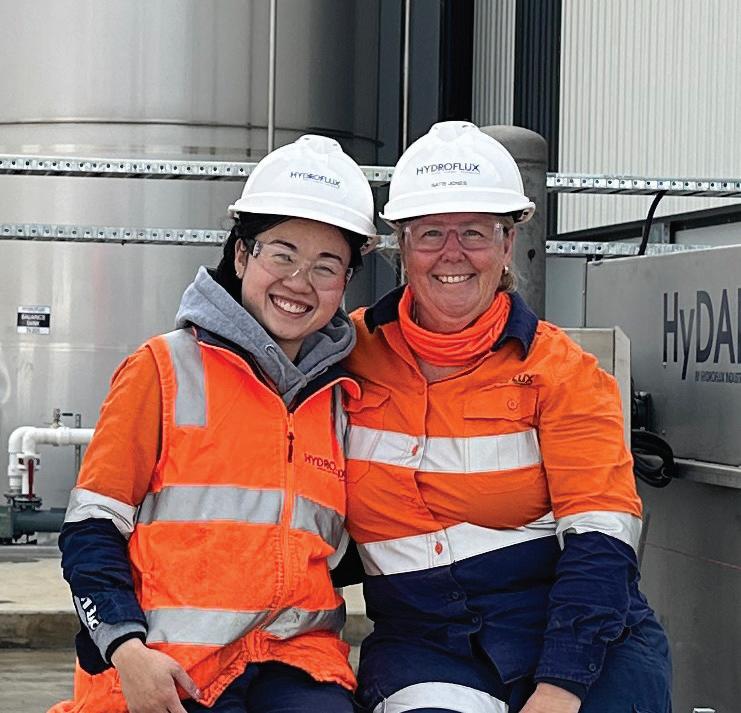

The world of water is evolving faster than ever, and every challenge is unique.
We are a fluid-thinking team of engineers, scientists, project designers, and sustainability specialists, committed to protecting our most valuable resources. We deliver tailored flexibility with innovative agility across the ANZ-Pacific water sector.
Whether you’re a local municipality or a global manufacturer, think of us as your performance partner. Here to help you maximise project lifecycle value and drive sustainable change.
Our in-depth hydro expertise, world-leading technology, and carbon-neutral services enable us to achieve exactly this—together.
Discover what more fluid thinking can do for you | hydroflux.nz


WATER WASTEWATER RENEWABLE ENERGY
HYDROGEN TRANSITION ENVIRONMENTAL PROTECTION
New Expertise in LEVEL MEASUREMENT
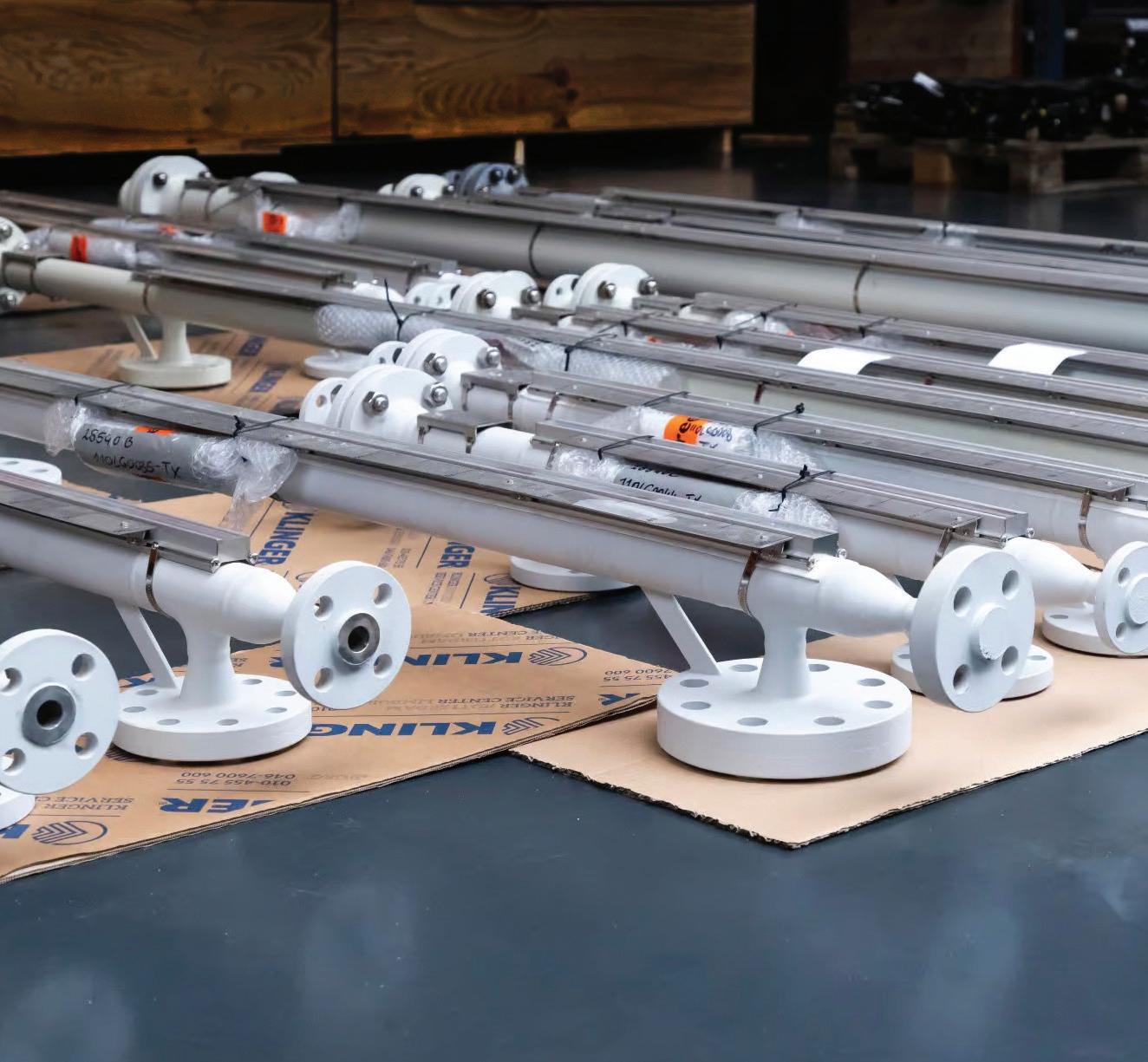
KLINGER, a globally respected name in industrial sealing and fluid control, has taken another step toward consolidating expertise in level instrumentation by bringing Hadro Techniek under its roof.
With a clear focus on expanding its product offerings in process instrumentation, KLINGER The Netherlands has acquired the Dutch manufacturer Hadro Techniek.
The Hadro team, which works at the production site in Moordrecht, only 20 kilometres from KLINGER The Netherlands, will remain with KLINGER The Netherlands, ensuring continuity of service.
Jasper Drost, the former owner of Hadro Techniek, will remain as a consultant and work closely with Ton van Erkelens, Managing Director at KLINGER The Netherlands, and Gijs
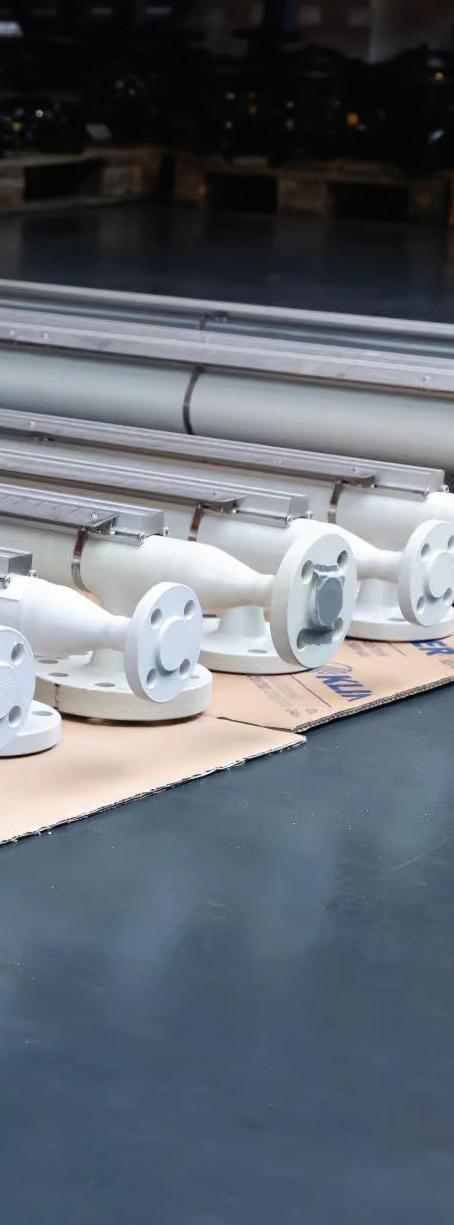
de Bakker, Project Manager for Fluid Control & Steam Solutions at KLINGER The Netherlands. This setup guarantees technical continuity and ensures the seamless integration of Hadro into the KLINGER Group.
“We see Hadro as a perfect strategic fit. Their products, quality standards, and commitment to customer solutions align perfectly with KLINGER values,” said Ton van Erkelens, Managing Director of KLINGER The Netherlands. With certifications such as PED, ATEX/IECEx, and maritime approvals from Lloyd’s Register and Bureau Veritas, Hadro has established a strong position in the highly specialised magnetic level gauge market. The
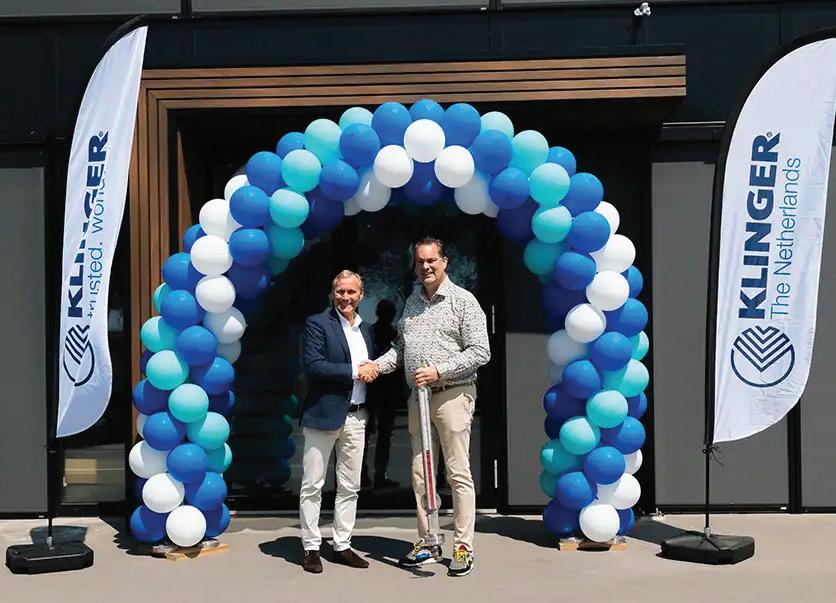
It’s a win-win situation. The acquisition of Hadro sets the stage for further advancements in the KLINGER instrumentation portfolio.
acquisition enables KLINGER to strengthen its level gauge business further and make it directly accessible to all companies within the KLINGER Group.
As the inventor of the glass reflex level gauge in 1891, KLINGER has long been associated with excellence in visual level indication. Now, with Hadro joining the KLINGER family, the Group is poised to strengthen and expand its instrumentation portfolio, guided by a long-term vision.
“By joining KLINGER The Netherlands, we secure the expertise of our company while opening up exciting new possibilities for innovation and growth on an international scale,” said Jasper Drost, former owner of Hadro Techniek.
The acquisition has opened up
new opportunities for all KLINGER subsidiaries by providing direct access to high-performance, tailor-made level indicators and engineering expertise.
Hadro’s experienced team and extensive technical knowledge allow KLINGER to better support customers in applications where safety, customisation, and certification are paramount.
“It’s a win-win situation. The acquisition of Hadro sets the stage for further advancements in the KLINGER instrumentation portfolio,” said Daniel Schibli, CEO of the KLINGER Group. With shared values and a focus on quality, as well as the benefits of local production, the collaboration will not only support existing customers but also unlock new markets worldwide.


fluid management

Future-Proofing Fluid Systems with MITSUBISHI’S FLUOROSINT MATERIALS
Mitsubishi Chemical Group has continued to lead in the field of advanced fluid management by engineering material solutions that prioritise durability, efficiency, and safety across high-demand industrial applications.
Designed to optimise the performance of systems that convey and process gases and liquids, its portfolio of high-performance polymers and components is tailored to meet the evolving needs of sectors such as energy, chemical processing, and manufacturing.
With a vertically integrated operation and global manufacturing footprint, Mitsubishi delivers endto-end support, from early concept development through to component production and delivery.
Its advanced R&D capabilities and extensive material testing ensure products that not only meet global OEM specifications but also push the boundaries of long-term equipment reliability and environmental performance.
One standout innovation within its offering is the Fluorosint family of enhanced PTFE materials. Developed to close the performance gaps left by unfilled and conventionally filled PTFE polymers, Fluorosint is chemically
engineered by bonding synthetic mica to virgin PTFE, resulting in a series of materials with significantly elevated mechanical properties.
Each grade within the Fluorosint range is specifically tailored to meet the performance requirements of challenging bearing and sealing applications. These materials exhibit chemical resistance and low friction while also providing enhanced wear performance, load-bearing strength, and dimensional stability.
By incorporating these high-spec materials into fluid handling systems, manufacturers benefit from safer, longer-lasting components that support continuous operation and reduce the risk of failure in critical applications.
This proactive approach to fluid management aligns with Mitsubishi’s broader KAITEKI commitment to sustainable innovation, circular economy goals, and reducing environmental impact, delivering value across both operational and ecological dimensions.
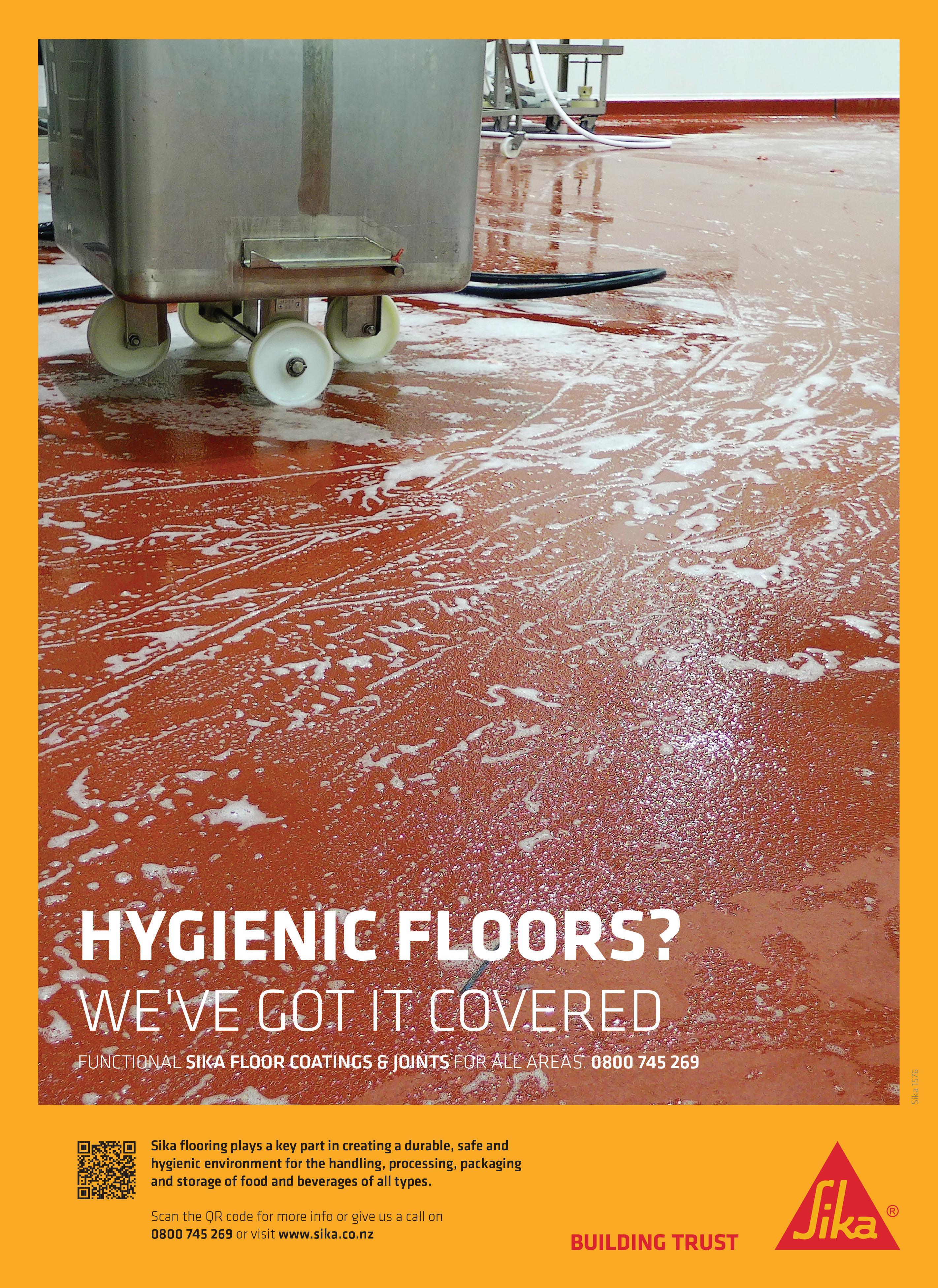
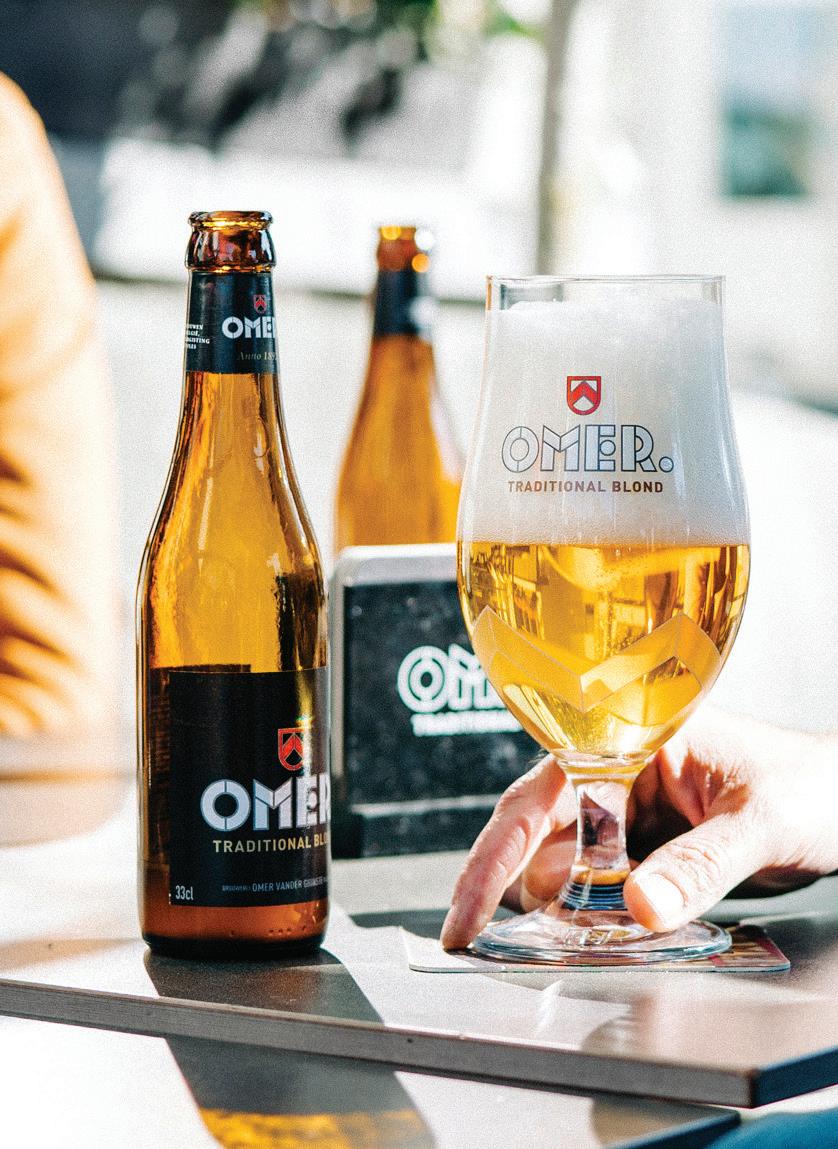
fluid management
Transforming Wastewater Into RESOURCES AT HISTORIC BELGIAN BREWERY
Veolia Water Technologies has been chosen by the Omer Vander Ghinste Brewery for the expansion of the wastewater treatment plant (WWTP) at its historic brewery close to Kortrijk, Belgium.
Since 1892, Brewery Omer Vander Ghinste has been a fixture in Belgian brewing. The brewery is now focusing on sustainable growth, balancing expansion with responsible practices. Veolia’s extension of the WWTP is designed to support the brewery’s growing operational needs while significantly reducing its environmental footprint.
The comprehensive upgrade incorporates advanced technologies, including a ZeeWeed 500 membrane bioreactor system, an anaerobic Biobed Advanced EGSB, and CaptuRO, a high-recovery reverse osmosis system.
The bio-factory concept, where wastewater is transformed into valuable resources, is at the heart of this project. Veolia’s EGSB technology plays a pivotal role in producing high-quality biogas from wastewater.
This green source of renewable energy is subsequently processed and used to heat water and buildings, creating a sustainable energy recovery cycle that annually prevents the emission of 548 tons of CO2.
Furthermore, the advanced CaptuRO technology ensures that 70 per cent of the water used in the brewing process is efficiently and securely recycled and reused for cooling water, bottle washing, and cleaning of vessels, saving a volume of freshwater equivalent to the annual consumption of nearly 3,000 Belgian residents. This approach not only minimises waste but also exemplifies Veolia’s vision for a circular economy in the industrial sector.
“We are very proud to collaborate with the historic Omer Vander Ghinste brewery on this project that perfectly illustrates how our advanced technologies can improve both the sustainability and efficiency of an industrial site. By allowing 70 percent of water reuse and creating a renewable energy cycle, we
By allowing 70 percent of water reuse and creating a renewable energy cycle, we demonstrate that ecological innovation can go hand in hand with operational efficiency, in connection with our GreenUp strategic plan.
demonstrate that ecological innovation can go hand in hand with operational efficiency, in connection with our GreenUp strategic plan.”
Veolia group aims to become the benchmark company for ecological transformation. Present on five continents with nearly 218,000 employees, the Group designs and deploys practical solutions for managing water, waste, and energy that contribute to a radical turnaround of the current situation. Through its three complementary activities, Veolia helps to develop access to resources, preserve existing resources, and renew them.


fluid management
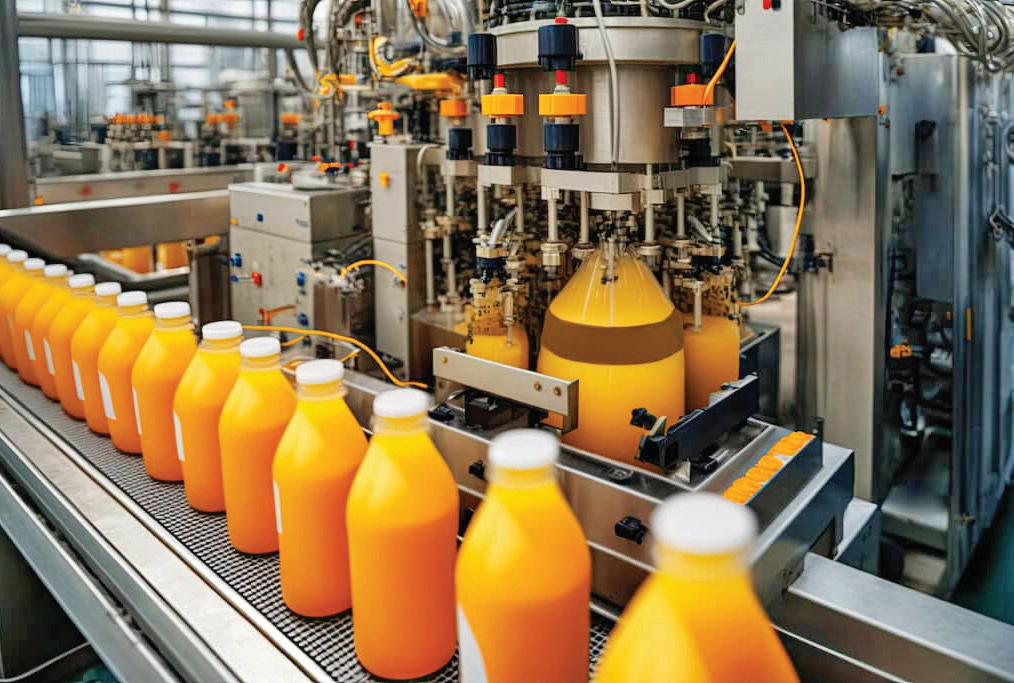
Reliable Solution FOR CITRUS BEVERAGES
The production of citrus beverages presents its own set of complex challenges. From managing naturally high acid levels to meeting hygiene requirements, manufacturers need equipment that can deliver both strong performance and compliance.
The acidic nature of citrus juice, while essential for flavour and preservation, can degrade traditional rubber-lined hoses over time. This often results in leaks, product contamination, and costly replacements.
Juice manufacturers must also meet stringent food safety standards. Any hose with internal grooves or uneven linings risks harbouring residue, which can create hygiene issues, waste, and extended cleaning downtime.
Slickflex, a premium PTFE-lined hose from Pacific Hoseflex, has been designed to overcome these challenges.
The PTFE lining delivers resistance to acidic ingredients, maintaining structural integrity where standard hoses fail. The smooth inner bore reduces the risk of product buildup, promoting cleaner flow, easier sanitation, and reduced product waste.
Built to handle acidity, high pressure, and repeated cleaning cycles, Slickflex lasts longer than conventional alternatives, saving time and maintenance costs. It also ensures safety and reliability.
For citrus beverage producers, hose failure can be a risk to product integrity and production schedules. Slickflex provides a reliable and efficient solution that aligns with the high standards of the food and beverage sector.

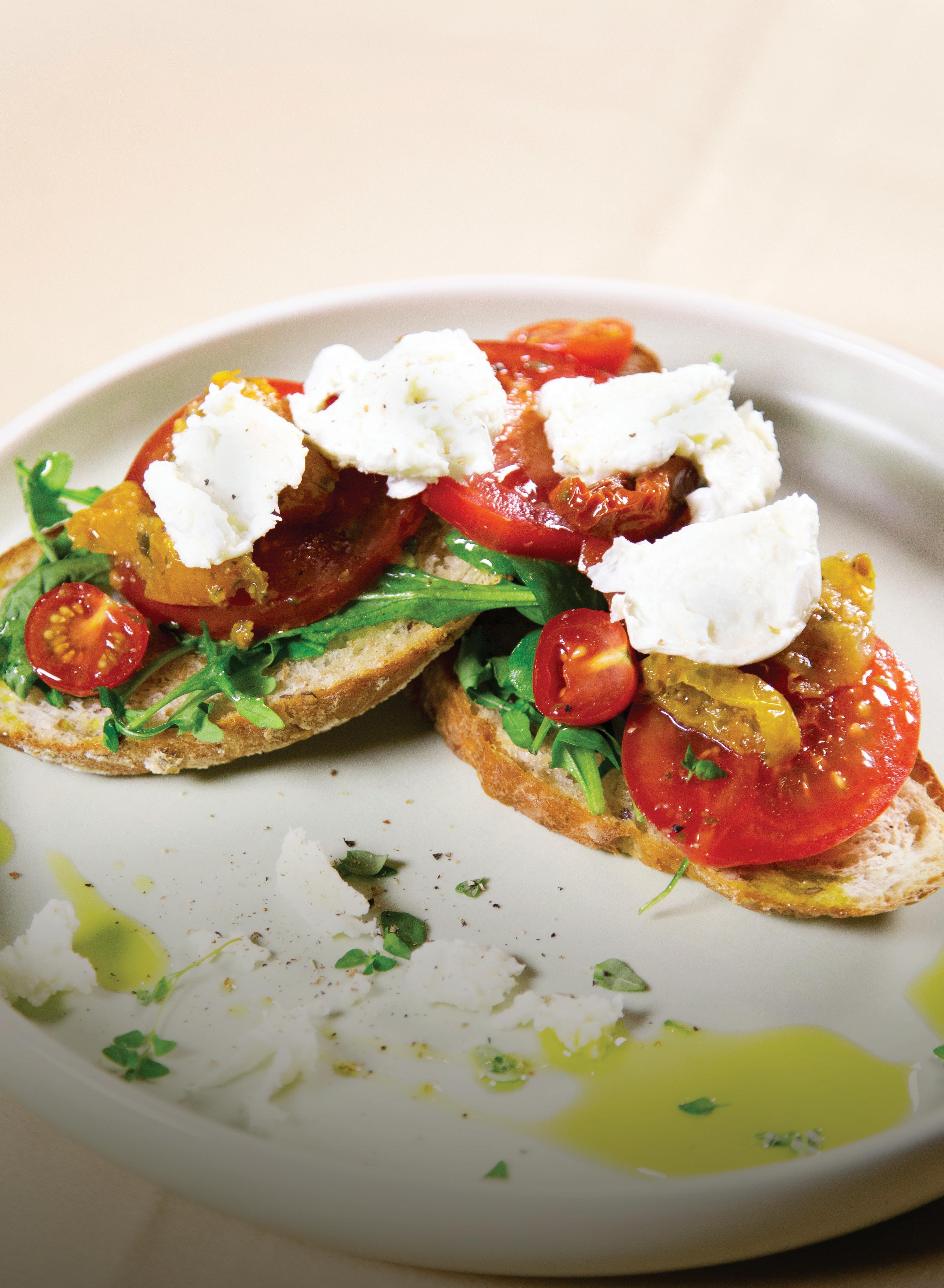
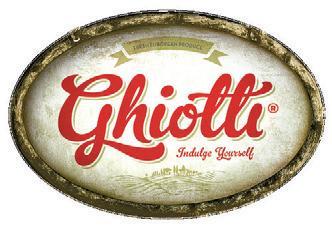
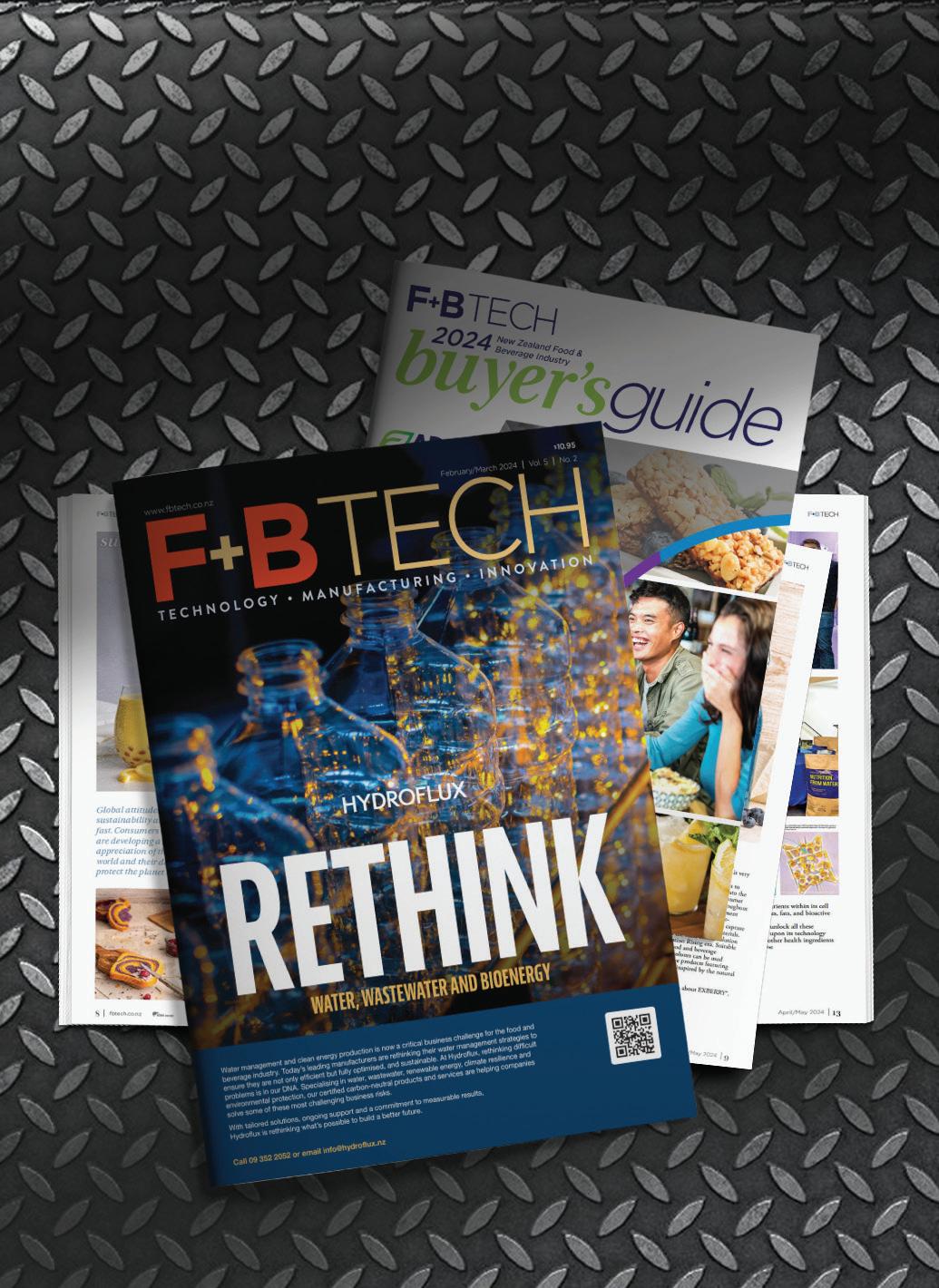