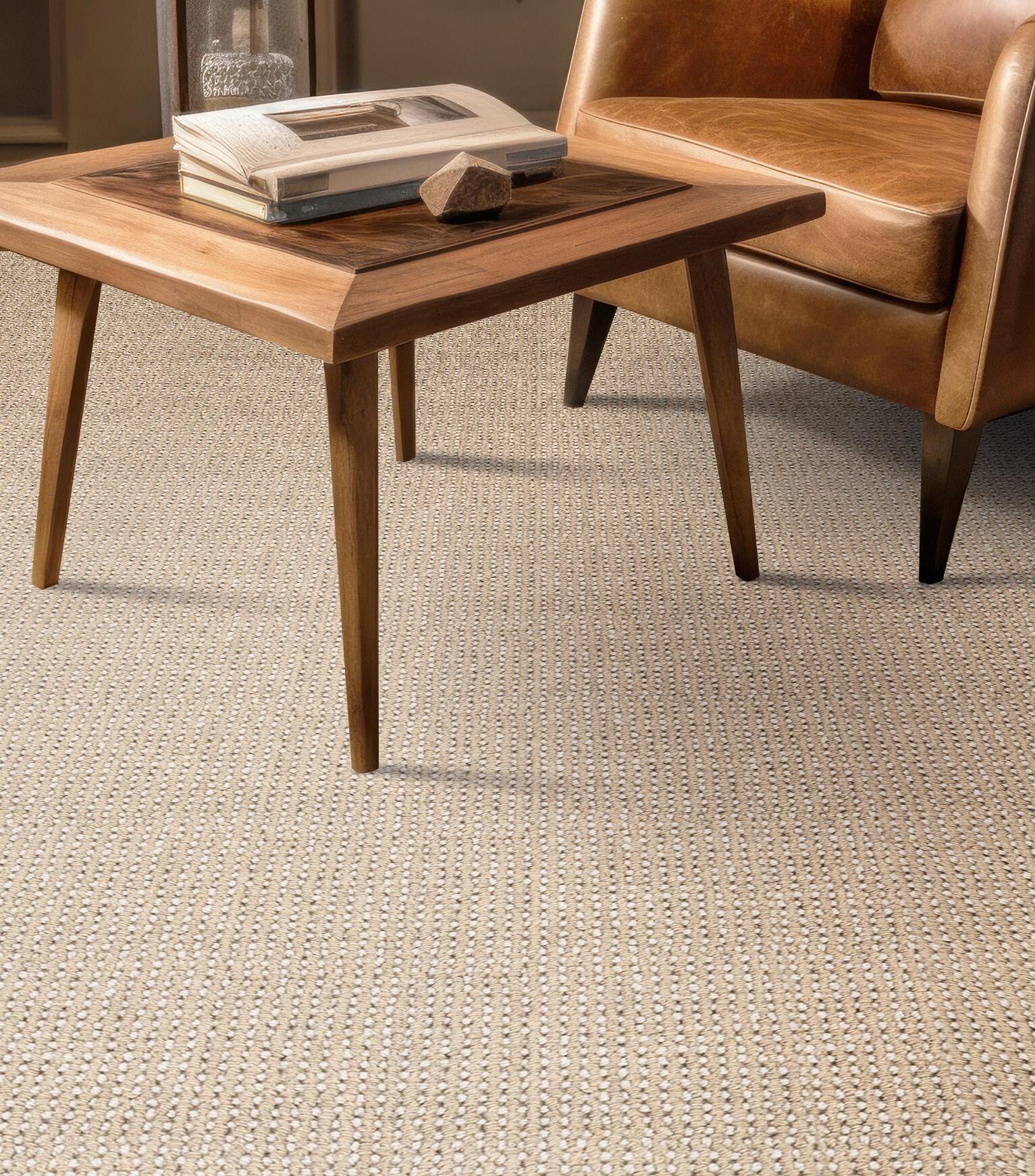
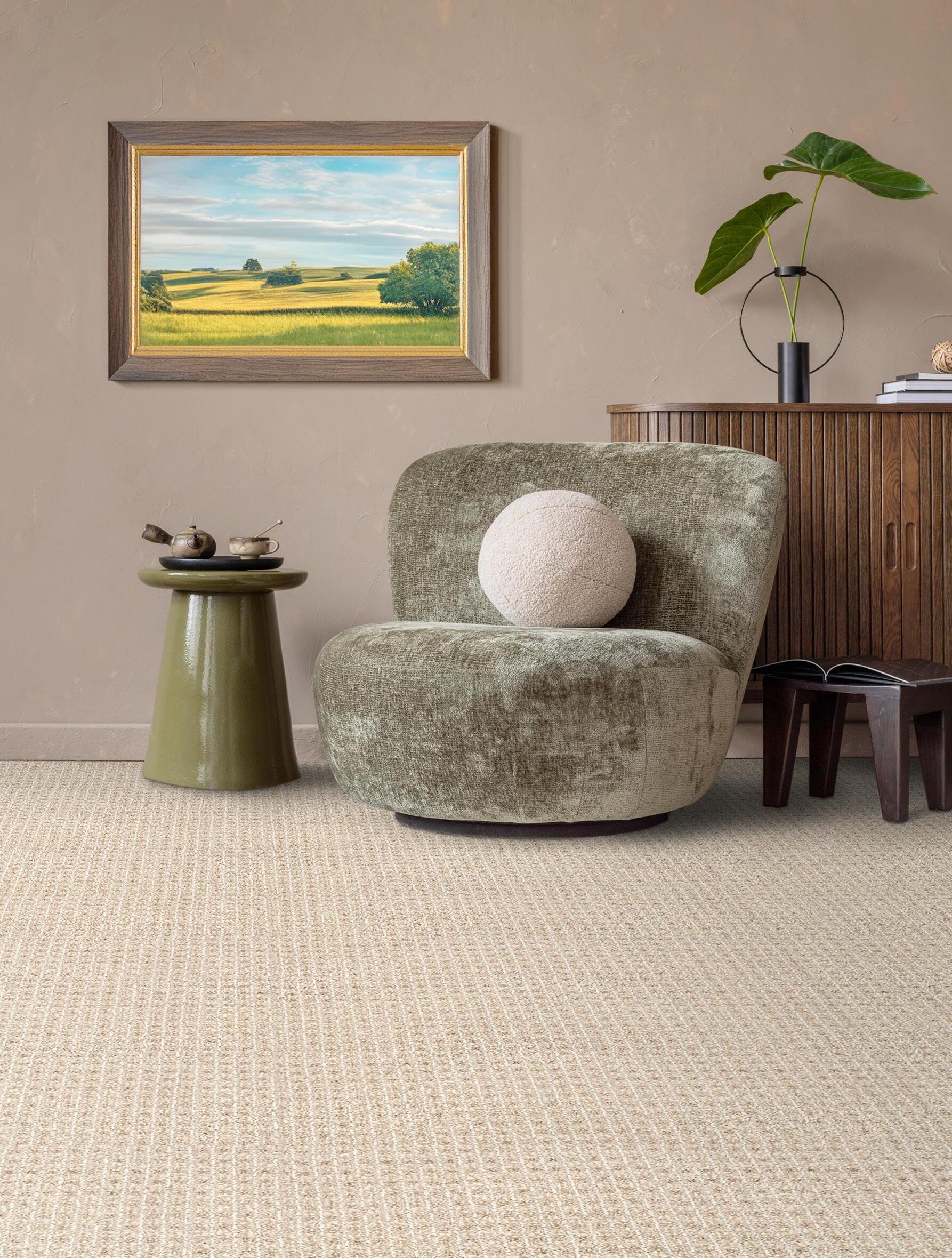
• Given the nature of this construction, no seam will be invisible. End-user should be made aware of this prior to installation.
• It is absolutely critical that every cut edge, including seams, perimeters and openings are sealed. Sealer should be applied with a 1/8” bead. This should be done immediately after cutting, but latex should still be “tacky” when creating a seam.
• Allow carpet to acclimate to room conditions for at least 12 hours. Stanton recommends 24 hours when possible.
• All products with repetitive patterns require that installations involving multiple rolls be sequenced, installing rolls with the longest pattern repeat first and moving towards installing rolls with short repeats last. This allows shorter pattern repeats to be stretched to fit longer ones. Match all patterns in center of seam and work towards the ends.
• Recommended under lays for these products include flat solid rubber (18 lb minimum density) or fiber cushions (synthetic felts) with a minimum weight of 40 oz/sy.
• Attach proper cushion to the floor, ensuring that no carpet seam will be traveling parallel within 6” of the cushion seam. Stanton requires architectural tackless strips to be used (J pins). Strips should be placed 3/16” from walls.
• Specific flat weaves can be cut from the top using a cushion back cutter.
• In the event of pins protruding through the surface of the carpet, use thin felt pressed over the tacks to “build up” the base on the tackless strip until pins cannot be felt at surface prior to attaching carpet.
• Ensure that patterns are squared and aligned during the initial layout and maintain alignment throughout the seaming and power stretching procedure.
• Planning and care should be taken in determining the proper location for the lengthwise cut for a seam. Depending on the style (pattern), the cut should be made so as to cut through as few weft (widthwise) accent yarns as possible. When viewed from the back, you will notice a white line running in the length direction. The first cut should be made next to this line. This will eliminate most fraying, but this edge still requires latex.
• To greater ensure the durability of seams when installing patterns with top warp yarns that are spaced ¼” or greater, the following steps need to be followed:
• Strip 1 ½” inches of warp yarns away from the seam edge on either side of the seam.
• Trim away filler weft yarns without disturbing weft accent yarns.
• Fold under exposed accent weft yarns and glue to the back of the carpet to ensure the accent yarns will not fray after the seam is made.
• Complete seam using standard CFI installation guidelines.
• When welding the seam, all loose yarn must be worked down into the seam.
• Stanton recommends premium seaming tape to attain a good bond at seam areas and to avoid seam peaking.
• Conventional seaming irons should be set no higher than 2.5 to avoid burned or distorted seams. A non-heat conductive weight should be used to smooth the seam. Star tractors are not recommended.
• When installing via direct glue down, the substrate should be clean and dry. A high quality, latex adhesive with high solids content should be used, applied with a 1/8” x 1/16” “U” shaped trowel at a spread rate of 10 -12 square yards per gallon, and should be allowed to flash off before laying the carpet into it to prevent the glue from coming through the material and onto the face. It should be stringy or tacky before adhering the carpet to the substrate. The carpet should never be laid in wet. The material should be rolled with no more than a 35-pound roller.
Please contact Stanton’s Technical Department at 706-624-9385 with any questions or concerns.
• End user should be made aware of applicable, natural characteristics of the construction being installed prior to installation.
• IMPORTANT BEFORE CUTTING: The carpet should be visually inspected for any defect or flaw. The carpet should be checked against the shipping papers, labels, and store sample to ensure it is the correct pattern, color, and size. Any noted defect of discrepancy should be immediately reported to the Stanton Claims Department.
• Carpet should be allowed to acclimate to room conditions at least 24 hours before installation. Ideally, the temperature should be between 65 – 95 degrees F (18 – 35 C). Extreme variances in temperature can cause difficulties during installation.
• It is the owner or general contractor’s responsibility to check concrete subfloors for excessive levels of alkaline and for moisture. According to CRI guidelines the recommended pH is between 5 and 9. Readings greater than 9 will result in adhesive failure. Moisture levels can be checked by a calcium chloride testing kit. Readings between 3 – 5 pounds are in the accep able range.
• Stanton’s recommended pad or cushion is 40 oz. synthetic felt pad or a flat rubber pad with minimum density of 18 pounds.
• The cushion should be attached to the floor, making sure that all cushion seams fall perpendicular to carpet seams.
• Stanton requires architectural tackless or double rows of 1” tackless. Strips should be placed ¼” from the walls.
• All cut edges (seams, transitions, openings) should be sealed with a premium latex seam sealer to avoid unraveling and fraying. Seam sealer is required on both stretch-in and glue-down installations.
• Stanton recommends premium 4” seaming tape to attain a good bond at seam areas and to avoid seam peaking.
• Note: A layer of Monk’s cloth prevents the secondary backing from imprinting onto the carpet face of delicate products. See below for installation directions.
• To assure a strong seam on handmade products with Monk’s cloth covering the secondary backing; construct the seam as follows on the next page:
(i) Cut back and remove the Monk’s cloth 3 ¼“from the edge to be seamed.
(ii) Seal both of the edges to be seamed.
(iii) Join the edges to be seamed with the seaming tape and seaming iron.
This procedure ensures that the thermoplastic adheres to the carpet, resulting in a stronger bond.
• On specific styles, seams can be row cut from the face. After determination is made on where the seams are to be trimmed, use an awl or flat screwdriver to open a row. Use a cushion back cutter to trim seam edges. If row cutting is not possible, cut from the back using a straight edge as a guide. All seams should be sealed.
• To greater ensure the durability of seams when installing patterns with top warp yarns that are spaced ¼” or greater, the following steps need to be followed:
• Strip 1 ½” inches of warp yarns away from the seam edge on either side of the seam.
• Trim away filler weft yarns without disturbing weft accent yarns.
• Fold under exposed accent weft yarns and glue to the back of the carpet to ensure the accent yarns will not fray after the seam is made.
• Complete seam using standard CFI installation guidelines.
• Seams should be constructed on a hard flat surface.
• Conventional seaming irons should be set no higher than 2.5 and adjusted as needed to avoid burned or distorted seams. A non-heat conductive weight should be used to smooth the seam. Star tractors are not recommended.
• Direct glue down and double glue installations require premium adhesives. Follow the adhesive supplier’s recommendation on trowel size and pad requirements for double glued installs. In both procedures, the adhesive must be given proper open time and allowed to set up. It should be stringy or tacky before laying in the carpet. The carpet should never be laid in wet.
• Seams on patterned carpet should be matched in the center of the seam first and then stretched to match from the center outward to both sides. Side matching is achievable but can be challenging. Seams may require trimming, shearing, or color balancing. This is not a defect, as this is a handmade product. No seams are invisible; consumer expectation should be realistic.
• For optimum side match and finished seam appearance, this product should be installed with the seams running perpendicular to major (outside) lighting sources.
• Whether tackless or glue down, the installation should conform to all CRI 104 or CRI 105 guidelines.
• Use a knee kicker for positioning the carpet only. Use a power stretcher with the appropriate head fitted to stretch the carpet evenly across its length and width. Gradually apply pressure when stretching handmade products.
• Stanton recommends using an installer qualified to work with hand loomed carpet and who understands its inherent characteristics.
• Please contact Stanton’s Technical Department at 706.624.9385 with any questions or concerns.
When installing Stanton’s natural flooring it is important to follow our basic guidelines. These materials are woven from natural plant fibers and tend to expand and contract according to climate and moisture conditions. It is our recommendation that this material be acclimated for at least 24 to 48 hours, open at the installation site, before it is cut to fit.
Approved installation methods include direct glue-down installation or double glue-down installation. Stanton does not recommend stretch-in installation or loose laid wall-to-wall installation for sisals.
Temperature and humidity: It is very important that the indoor temperature be kept between 65 – 95 degrees with a relative humidity of 65% or less. If the ambient temperatures are outside these parameters, installation should not begin until the HVAC system is operational. The conditions must be maintained for at least 48 hours before installation and 72 hours after completion.
Floor preparation: Carpet must be installed over properly prepared substrates that are suitable for the method of installation and product selected. Concrete floors, even with adequate curing time, can present an unacceptable moisture condition by allowing excessive amounts of moisture vapor to pass through to the surface. This can be a problem even on suspended concrete floors. Test all concrete floors for moisture emission rates using an anhydrous calcium chloride moisture test kit. As a general guideline an emission rate of 3.0 lbs or less is acceptable. Testing for alkalinity, a pH range of 7 – 9 is satisfactory. A reading above 9 requires corrective measures.
Direct Glue Down (complete transfer of adhesive required)
Use a premium multi-purpose adhesive. Adhesive should be spread evenly using a spread rate of approximately 7 square yards per gallon. This requires a 1/8” x 1/8” U-notched trowel. The back of these materials, even with latex, has a considerable amount of texture. Getting complete contact between the flooring and the floor requires much more adhesive than typical carpeting to fill in all voids created by the texture. Failure to apply the proper amount of adhesive will result in a poor or loose bond to the floor and will allow the material to shrink, bubble, or wave.
General Installation Procedures for Sisal products:
1. Remove existing trim before beginning installation.
2. Dry fit the pre-cut floorcovering into the room, laying it out so that you have 3 – 4 inches surplus to lap up the walls evenly. Allow the material to acclimate for 24 – 48 hours. Natural grass materials tend to shrink in the length as they acclimate because this is the direction of the grain of the weave.
3. Side seams will provide the best results. Always trim the factory woven edge off before seaming.
4. Seal the edges of the seam with an appropriate seam sealer taking care so as not to contaminate the face yarns.
5. Make sure the trowel lines are heavy enough to be busted and the glue has enough time to flash off before laying the material into the glue.
6. The “trim in” should be one of the last steps, allowing the adhesive to start to grab.
7. Make sure all transition areas are protected.
8. Use a 35 – 75 lb. roller to insure complete transfer of adhesive.
9. Floor moulding, quarter-round, etc. is recommended to complete the installation.
Please contact Stanton’s’ Technical Department at 706-624-9385 with any questions or concerns.
• End user should be made aware of applicable, natural characteristics of the construction prior to the carpet being installed.
• We recommend this product be installed by a professional, qualified installer according to CRI 104/CRI 105 standards.
• IMPORTANT; Before cutting, the carpet should be visually inspected for any defect or flaw. The carpet should be checked against the shipping papers, labels, and store sample to ensure it is the correct pattern, color, and size. Any discrepancy should be reported to the Stanton Claims Department.
• Allow the carpet to acclimate to room conditions for at least 24 hours before installation. Ideally, the temperature should be between 65 to 95 degrees F(18 to 36 degrees C). Extreme variances in temperature can cause difficulties during installation.
• It is the owner’s or general contractor’s responsibility to check concrete sub floors for excessive levels of alkaline and for high moisture levels. Based on CRI standards, the ph reading should be between 5 and 9; readings higher than 9 will result in adhesive failure. Moisture levels can be checked by a calcium chloride testing kit. Readings should be between 3 to 5 pounds.
• Stanton’s recommended pad or cushion is a 40 oz. synthetic felt, or a flat solid rubber, min density 18 lbs.
• The cushion should be attached to the floor ensuring that no cushion seam falls in the same direction under a carpet seam.
• Stanton requires architectural tack strip or a double row of standard strip. The tack strip should be at least ¼ inch from the wall.
• For optimum seam appearance, major seams should be run into the any prominent light source, such as a bay window or sliding door, they should never be run across the light source.
• Ensure that patterns are squared and aligned during the initial layout and continue throughout the seaming and power stretching process.
• All cut edges (seams, transitions, and openings) should be sealed with a latex sealer to prevent raveling and fraying. Seam sealer is required on both stretch-in and glue-down installations.
• The use of a dead man, crab stretcher, and stay nails may be required to properly align patterned carpet and to correct bow and skew. Bow/Skew, pattern elongation of 1.5 inches is correctable. No seams are invisible, the end users expectation should be realistic.
• For a conventional seaming iron a 6 inch tape should be used to attain a good bond and minimize peaking. The iron should not be set over 2.7 on the heat dial.
• Seams should be row cut from the face. After the determination is made on where the seams are to be cut, use an awl or flat head screwdriver to open a row. Use a loop pile or cushion back cutter to trim the seam on both sides. All seams should be sealed.
• The seaming iron should be set low to begin and gradually increased as needed. Carpets should be seamed in the direction of the pile lay on top of a hard surface like a seaming board. A non heat conductive weight should be used to smooth the seam behind the iron. Star tractors are not recommended.
• Direct glue down and double glue installations require premium all-purpose adhesives. Follow the adhesive supplier’s instructions on trowel size, spread rate, and open time. In both procedures the adhesive needs to flash off, become tacky or stringy before laying the carpet. The carpet should never be laid in wet.
• Whether tackless or glued down the installation should conform to CRI 104/CRI 105 guidelines.
• Contact Stanton Carpet’s Technical Department at 800-452-4474 with any questions or concerns.
• End user should be made aware of applicable, natural characteristics of the construction being installed prior to installation.
• We recommend this product be installed by a professional CFI qualified installer using CRI104 or CRI105 guidelines unless otherwise specified in this document.
• IMPORTANT: Before cutting, the carpet should be visually inspected for any defect or flaw. The carpet should be checked against the shipping papers, labels, and store sample to ensure it is the correct pattern, color, and size. Any noted defect or discrepancy should be immediately reported to the Stanton Claims Department.
• Allow carpet to acclimate to room conditions for at least 24 hours before installation. Ideally, the temperature should be between 65 to 95 degrees F (18 to 35 degrees C). Extreme variances in temperature can cause difficulties during installation.
• It is the owner or general contractor’s responsibility to check concrete sub floors for excessive levels of alkaline and for moisture. According to CRI guidelines the recommended ph for alkalinity is between 5 and 9. Readings greater than 9 will result in adhesive failure. Moisture levels can be checked by a calcium chloride testing kit, Readings between 3 to 5 pounds are in the acceptable level.
• Stanton’s recommended pad or cushion is 40 ounce synthetic felt pad or a flat rubber pad with minimum density of 18 pounds.
• The cushion should be attached to the floor, ensuring that no carpet seam will be traveling parallel within 6” of the cushion seam.
• Stanton requires commercial or architectural tackless to be used (either C or D pin). Strips should be placed ¼” from walls.
• All products with repetitive patterns require that installations involving multiple rolls be s quenced, installing rolls with the longest pattern repeat first and moving towards installing rolls with shorter repeats last. This will allow shorter pattern repeats to be stretched to fit longer ones.
• For optimum side match and finished seam appearance, this product should be installed whenever possible with the seams running perpendicular to major (outside) lighting sources.
• Ensure that patterns are squared and aligned during the initial layout and maintain alignment throughout the seaming and power stretching procedures.
• All cut edges (seams, transitions, and openings) should be sealed with a premium latex seam sealer to prevent raveling and fraying. Seam sealer is required on both stretch-in and glue-down installations.
• Using a double head power stretcher or dead man, pre-stretch the seam area if needed to get a proper pattern match. Use stay nails to hold the pattern match and begin the seaming.
• Stanton recommends that a high quality seaming tape be used to attain a good bond at the seam and to lessen peaked seams.
• Face to Face seams should be cut from the back of the carpet following the pattern. Wilton seams should be cut from the face taking care to avoid cutting loops whenever possible. All cut edges should be sealed immediately.
• Seaming iron setting should be set initially on a low setting, then gradually increased as needed. Carpets should be seamed with the lay of the carpet on top of a hard surface, such as a seaming board. A non heat conductive weight should be used to smooth the seam. Star tractors are not recommended.
• Once the seam has cooled, the carpet can be stretched in and installed.
• Some seams may require spot tacking or sewing in extreme cases of pattern stretch. Stanton woven carpets can safely be stretched 1% - 1.5% in the length.
• Direct glue down and double glue installations require premium adhesives. Follow the adhesive supplier’s recommendation on trowel size, and pad requirements for double glued installs. In both procedures, the adhesive must be given proper open time and allowed to set up. It should be stringy or tacky before laying in the carpet. The carpet should never be laid in wet.
• Seams on patterned carpet should be matched in the center of the seam first and then stretched to match from the center outward to both sides. The use of a dead-man, crab stretcher, double-headed power stretcher, and stay nails may be required. No seams are invisible, consumer expectation should be realistic.
• Whether tackless or glue down, the installation should conform to all CRI 104 or CRI 105 guidelines.
• Please contact Stanton’s’ Technical Department at 706-624-9385 with any questions or concerns.
Make sure you inspect this carpet prior to installation. No claim will be honored if carpet is installed with visible defects. Read all instructions prior to beginning any installation.
DO NOT ROW CUT. The pattern is printed on the carpet after tufting and finishing. Tufted rows are “not” aligned with the pattern and the method below “must” be used to trim the patterns. No claim will be accepted for any installation that is ROW-CUT.
How to trim printed patterns:
Printed carpet is manufactured using an overprinting process; that is, the patterns are actually printed on the face of the carpet yarns, not tufted into the pattern. Because these patterns are printed on, the row cutting method should not be used for trimming seams. Rows and patterns do not run true. Cut 24 hours in advance if possible. This allows the carpet to relax.
The following should be used to trim seams and align patterns; after determination is made on where the seams are to be trimmed:
1. Using a razor knife, make slits into the face of the carpet on the exact point of the pattern you wish to follow. Make these cuts every 3 to 4 feet for the entire length of the seam and at the seam point of the pattern. NOTE: Always use center of diamonds for pattern match; for other patterns use heavy accent lines.
2. Fold carpet over and use straightedge to cut from the back. Following slits every 3 to 4 feet will assure patterns are trimmed at the same point on each pattern.
3. Trim second seam edge using the same procedure. Half diamonds will line up with half diamonds to form a complete diamond.
If patterns are not cut in this fashion, they will not match. Chalk line, free-hand, or trace cutting is not recommended and will not achieve a match. All seams should be sealed.
How to match pattern (and correct for pattern elongation):
Once the printed carpet has been trimmed in the proper fashion:
1. An easy way to determine which cuts will match best is to count off 30 patterns and compare the measurements to determine sequence. You will stretch the short side, not shrink the long side. Experience has shown that most carpets easily stretch 2% with a power stretcher.
2. Dry fit all pieces prior to beginning installation.
3. Match all patterns in the center of the seam and work toward the ends.
Installation:
Remember, we can only stretch the short side (not shrink the long side). Lay out all work so this can be accomplished. Never glue the short side first.
1. The best way to determine pattern match is to stand back and sight down diagonals formed by pattern.
2. Loose lay all drops in place in proper sequence. Allow to relax for 24 hours if possible.
3. Trim and prepare seams per instructions (this sheet).
4. Once long and short sides are determined, use two-head power stretcher on short side of match pattern.
5. Begin pattern matching in center of drop. This divides the pattern elongation and makes for less work.
6. Seal seam edges with high-quality latex seam adhesive. Apply latex sealer at base of primary backing.
7. Run seaming iron making minor adjustments with knee kicker. Run short lengths of seam if necessary. Allow to cool and readjust as needed.
1. All Double Glue Installation’s require the seams be constructed with seaming tap designed for double glue installations
2. All Double Glue Installation’s require the carpet cushion be designed for double glue installations with its own warranty and installation guidelines.
3. All Adhesives must be designed for double glue and pattern slip installation.