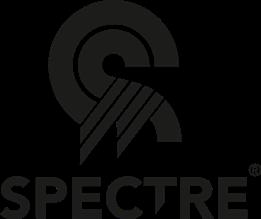
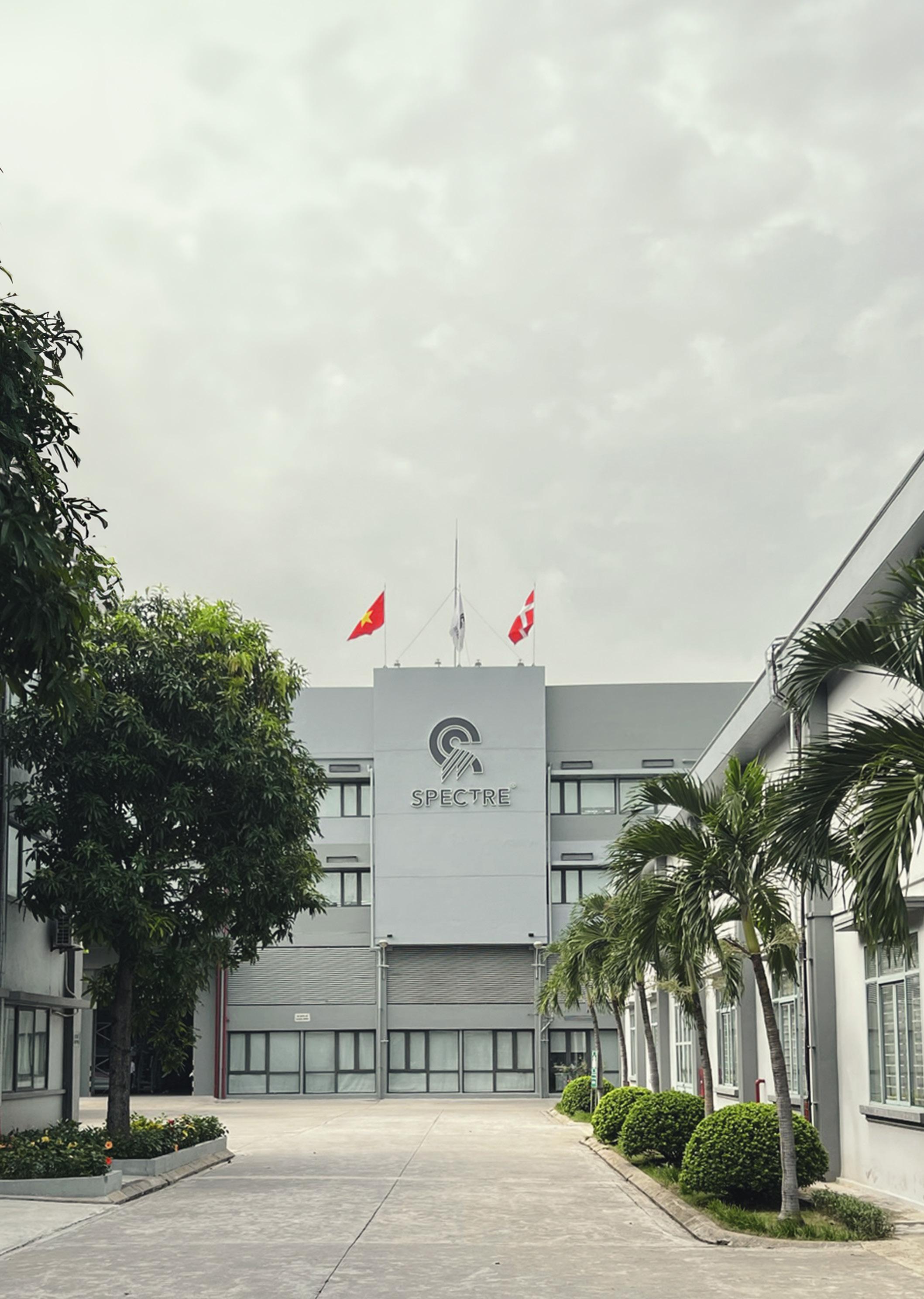
2023/2024
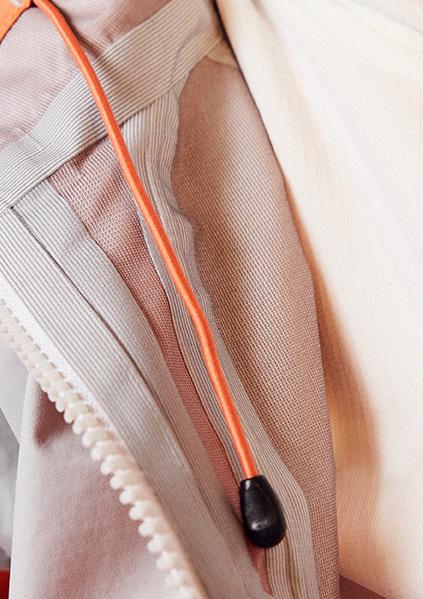

2023/2024
Reflecting on the 2023/2024 year, it presented a unique set of challenges for the apparel industry, particularly for the outdoor segment in which we specialize. The global landscape was marked by conflicts, a volatile macroeconomic environment, and persistent supply chain disruptions. Rising inflation rates and surging interest rates led to a significant reduction in disposable income, resulting in overstock issues for brands and subsequently reduced orders for manufacturers like Spectre. In such a manufacturing environment, where capacity exceeds demand and customers are grappling to balance their finances, sourcing decisions become hyper-focused on price. These conditions led to two main sustainability challenges for Spectre in 2023/24.
The first challenge was managing temporary excess capacity in terms of workforce as responsibly as possible. The market downturn meant that we had to reduce our workforce by 20% compared to the previous year and implement a shortened workweek for extended periods to preserve jobs for our employees and retain important skills within the company while working to secure orders that would restore us to previous output levels.
The second challenge was maintaining our strong commitment to sustainability, while experiencing intense pressure to reduce the prices of our services. Our commitment is to uphold high standards of social and environmental performance and address common challenges together with our customers and supply chain partners even during tough times.
Despite these challenges, the past year marked great milestones for sustainability at Spectre. In December 2023, we reaffirmed our commitment to being a responsible company and proudly became a certified B Corp, highlighting our ongoing efforts to meet the highest standards of social and environmental performance. This includes also updating how we think and speak about sustainability in our organization and therefore we have named this year’s report the Responsible Business Report, reflecting Spectre’s aspiration, transparency and commitment.
Our factories in Nam Dinh and Thai Binh achieved Fair Trade certification in addition to our other social and environmental standards, reinforcing our dedication to fair and safe working conditions, while empowering employees to make collective decisions on community projects financed through the worker premium fund.
In March 2024, by committing to set net zero Science Based Targets, we underscored our proactive approach to addressing climate change. Tangible actions, such as transitioning to 100% renewable electricity in our Vietnamese factories, significantly contributed to our goal of reducing our carbon footprint. Consequently, we closed the year with a 46% lower carbon emission intensity per production unit.
We are ambitious about our responsible business targets for 2030 and have been diligently developing a detailed yet focused approach, ensuring that responsibilities and needed resources are assigned through a thorough action plan. We aim to publish our 2030 responsible business strategy by the end of 2024, along with validated near-term and net zero Science Based Targets.
The year 2023/24 was characterized by significant challenges and transformative progress. Despite the turbulent landscape, Spectre not only maintained but strengthened our commitment to being a responsible company. As we look to the future, we remain dedicated to integrating responsible business practices into our core business strategy, improving transparency, and fostering collaborations that drive meaningful change. We hope this report provides valuable insights into our journey and inspires continued efforts toward a more sustainable and resilient future.
Jesper Klausen Co-owner, Chief Manufacturing & Sustainability Officer
2023/2024
2,999,329 garments produced
1,154 tons of fabric used 40% of fabric composed of recycled materials
7,603 m3 of water consumed
8,621 MWh of energy consumed
3,182 employees worldwide (year average)
The environmental footprint from Spectre’s manufacturing of a JACKET¹ compared to last year
2.75 kWh of energy consumed: +10% 2.43 liters of water used: +30%
0.10 kg of CO2e emitted in Spectre’s operations: -91%
320 g of waste: 0%
1 For a typical jacket requiring 70 attributable minutes in production
Business taken over by Anny and Evald Klausen
Spectre founded by Thomas Poulsen, mayor of Ikast
Third branch in Latvia opened in Rezekne
Second branch in Latvia opened in Kalnciems
Spectre signs UN Global Compact
LEAN production system implemented
New factory built in Ikast
Production moved from Denmark to Latvia
Generational change to next generation - Jacob Klausen and Jesper Klausen
Hot-air bonding technology implemented.
Ground-breaking technology for new laminated details in knitted fabrics developed in Latvia.
Joint venture company established in Vietnam
Our vision
We want to become the outdoor sports and activity brands’ preferred development and manufacturing partner for functional garments.
Our mission
We work to strengthen our customers’ brand value through our competence in the development and manufacturing of high-quality functional clothing in a sustainable and responsible way.
Our business operates at the intersection where we purchase materials and trims from various suppliers across the globe to be assembled into finished products, which are then packaged, quality assured and shipped to our customers’ warehouses. Thus, it is our concern and responsibility that working conditions are good and that we have as little negative impact on the local environment as possible. We collaborate with our customers to fine-tune designs for optimal production and performance.
Our apparel brand partners design, sell, and distribute the garments to retailers or end consumers, assuming responsibility for consumer relations and placing the product on the market. Most materials used in our products, and thus the suppliers we work with, are selected, and nominated by the brands. Therefore, we share with them the responsibility of building responsible supply chains.
In our position within the value chain, we engage in daily interactions with both upstream and downstream supply chain partners. This includes coordinating and ensuring compliance with quality, social, and environmental requirements throughout the value chain, developing products in time for bulk production, ensuring cost efficient and responsible material deliveries, and planning deliveries of readymade garments to customers. We must be proactive in smoothing out any delays or deviations—whether in our operations or elsewhere in the value chain. These pressure points need to be carefully managed to account for their impact on workers and the environment.
We set high standards for ourselves and, as the industry faces increased regulatory requirements from EU and US regulators, we must be proactive in responding and leading by example.
At Spectre, we produce garments that our customers market to consumers worldwide through both brick-and-mortar stores and e-commerce distribution channels. We produce apparel for companies based in Europe (primarily Switzerland, Germany, Sweden, the United Kingdom, and Spain), the United States and Canada. Indirectly, garments from our factories are sold and distributed to stores and consumers across Europe, North America and Asia.
At Spectre, we are dedicated to achieving excellence in our role as a tier 1 supplier to outdoor brands. It is with great pride that we announce our recent recognition as the Best Supplier – Apparel by one of our longstanding, strategic partners, Mammut Sports Group (MSG). MSG places a high value on corporate social responsibility and evaluates supplier performance not only based on quality, delivery, and price, but also on sustainability impacts.
SPECTRE A/S
Ikast, Denmark (Group HQ)
SPECTRE GMBH Münich, Germany
Three in Latvia and three in Vietnam.
SPECTRE GARMENT TECHNOLOGIES VCL
Nam Dinh, Vietnam
Thai Binh, Vietnam
SPECTRE GARMENT TECHNOLOGIES AN GIANG VCL
An Giang, Vietnam
SPECTRE LATVIA SIA
Kalnciems, Latvia
Auce, Latvia
Rezekne, Latvia
Europe and Asia – the perfect combination
At Spectre, we uphold a set of long-standing core company values that reflect our approach to work and our attitude towards colleagues, customers, and other business partners. Our work is driven by the ambition to achieve the best possible results, create a high-quality working environment, and ensure our customers are always satisfied.
We believe that satisfied customers are the foundation for strong, long-term partnerships, stable jobs for our employees, and a positive working environment.
We show passion and commitment in everything we do. We strive to perform tasks to the best of our ability and remain loyal to the company and our colleagues. We always go the extra mile for our customers. Through our passion and commitment, our partners experience the clear benefits of collaborating with us.
We care about sustainability and act with integrity. We take responsibility for our workplace and the external environment, solving tasks responsibly to achieve the best results for our company, customers, and business partners. This includes finding balanced solutions for long-term sustainable business practices.
Show passion and commitment in whatwe do
We trust and help each other and live our values
We care for sustainability and act with honesty
Our performance exceeds expectations “not just to be good, but to be the best”
Integrity
We trust and support each other, staying true to our values, company policies, and guidelines in our work and interactions with business partners and colleagues. By trusting and helping each other, we form a strong team capable of achieving our goals.
Our performance exceeds expectations—not just to be good, but to be the best. By anticipating situations, we strive to find the best solutions and leverage the advantages of being one step ahead. Our ambition to be the best sets us apart, as our customers seek the best business partners in the market.
Setting the course for responsible business
As a company with nearly eight decades of history, “doing the right thing” has always been central to Spectre’s ethos. Spectre became a B Corp in December 2023, which marked a milestone of adopting a framework for responsible business practices.
Becoming a B Corp means publicly committing to considering the interests of all stakeholders in our decision-making processes, a responsibility now enshrined in our board of directors’ mandate and embedded into our purpose in our Articles of Association.
B
The B Corp community aims to create outstanding solutions to social & environmental problems
Looking for ways for Spectre to create value with least environmental impact and creating good jobs
Becoming a B Corp means joining a community of businesses all on the same mission, sharing knowledge and ideas about how to use business as a force for good
B Corps believe that business can be a force for good and operate their business in a way that achieves this
Working with other B Corps through initiatives and networks is how we can contribute to solving the biggest challenges
B Corps are driving positive change through their supply chain, consumers, environmental management
Besides governments, NGOs and each person individually, businesses have an enormous opportunity to be part of the solution
Only by engaging with our stakeholders we can achieve significant changes
The B Impact Assessment (BIA) evaluates numerous impact topics across five ‘Impact Areas’: Workers, Environment, Governance, Community, and Customers. The median score for an ordinary company in the BIA is 50.9. Spectre achieved a score of 81.2, which we view as a strong starting point in our journey to become a more responsible company.
The material topics included in the BIA allow us to track our progress on the B Corp journey. We have integrated BIA sub-scores as metrics in Spectre’s responsible business strategy, guiding our action plans with B Corp principles in mind.
How a business contributes to employee well-being, financial security, career development, and worker satisfaction.
The enrionmental management practices and how they affect the climate, biodiversity, water, air, and land throughout their operations.
Spectre is transparent about its business and its mission is aligned with business responsibility. Company bylaws obligate Spectre to create benefit to stakeholders throughout the value chain.
Spectre creates new jobs, empowers local management, gender balance in management positions and has a robust code of conduct for suppliers and supplier assessment.
How well a business takes care of its customers through its products and services, marketing techniques and maintenance of privacy.
Our Score 28.4 Our Score 16.3
Our Score 15.6 Our Score 3.1 Our Score 17.6
In Spectre we pay no less than living wage, we have bonus systems, solid health and safety practices, availability of social services, career development, employee satisfaction and involvement, providing jobs and training for unskilled workers
We have a robust environmental management system, energy/ emissions performance, water management practices, responsible waste management
Our transparency initiatives, as well as our mission lock is where these points primarily come from. A declaration in our bylaws define our company to create benefit to stakeholders throughout our value-chain and not only for shareholders
The points come from our ability to create new jobs, having local management instead of from HQ country, our code of conduct for suppliers and supplier assessment, and the fact that we also have women in management positions
We have strong quality management systems and processes, while we currently have limited impact on material selection
We take pride in enabling people to experience the great outdoors in high-quality apparel designed for demanding environments. However, we recognize that our value creation comes with social and environmental impacts. A materiality assessment helps us understand where we have the greatest impacts and identifies our stakeholders’ concerns, forming the basis of Spectre’s responsible business strategy.
double materiality approach, based on European
Reporting Standards (ESRS), aligns closely with the B Impact Assessment data points. This ensures that both frameworks work together to provide transparency on Spectre’s sustainability performance.
We assess not only our impacts on stakeholders and the environment but also the potential financial risks of sustainability topics for the company.
Our stakeholders inform the assessment of material impacts through various engagement methods. We conducted a sustainability priority survey among our customers and hold regular sustainability-dedicated meetings to align with customer expectations on social and environmental standards. Participating in supplier events and training organized by industry organizations like Cascale and EOG keeps us informed about relevant sustainability topics.
The B Impact Assessment performed as part of attaining B Corp certification was crucial for engaging with Spectre’s internal stakeholders and identifying previously unconsidered material topics. An annual employee satisfaction survey is a key tool for making employee concerns transparent to management. Suggestion and grievance channels provide ongoing information about employee needs and issues, while elected employee representatives and trade unions serve as mediators to communicate employee concerns.
GHGemissions(own & value chain)
Material flows (i ncoming material, outgoing product,waste)
Pollution in thevalue chain
Water impacts in thevalue chain
Living wage and conditions(own & value chain)
Working time (own & value chain)
S
Surrounding communities
H&S in thevalue chain
Measures against violence and harassment
Worker rights in thevalue chain
Supplier management G
Upon presenting Spectre’s 2030 responsible business strategy we will provide a more detailed analysis of Spectre’s double materiality assessment and how that translates into our targets for 2030 and more immediate action plans.
Addressing the impacts identified in the materiality assessment requires a long-term strategic approach. Only through collaboration with our customers and suppliers can we make significant progress toward improving our impacts and addressing global challenges. Over the past year, we have defined the focus areas for our sustainability efforts, the outcomes we aim to achieve, and the action targets and KPIs that contribute to these goals. Making these targets SMART (specific, measurable, attainable, relevant, time-bound) is essential. Developing action plans is the first step toward successful implementation and fine-tuning the values we set for the targets.
We plan to complete the action plan development within 2024 and then publish our full 2030 Responsible business strategy. A crucial part of this will be developing and validating our climate targets for 2030 and net zero with the Science Based Targets initiative.
Assessing and addressing our impacts
Climate change is evident and felt worldwide. Melting glaciers, increasingly frequent extreme weather events such as droughts, storms, and floods, along with rising sea levels, all endanger the delicate balance of the world in which humans live, as well as the ecosystems and biodiversity that rely on predictable and stable climatic patterns. Spectre acknowledges its role in this global challenge and is committed to playing its part in addressing climate change.
Submit a letter establishing your intent to set a science-based target
Therefore, In May 2023, Spectre committed to setting near-term science-based targets, and in March 2024, the company also pledged to establish net-zero Science-Based Targets.
Develop Work on an emissions reduction target in line with the SBTi’s criteria
Submit
Present your target to the SBTi for official validation
Communicate
Announce your target and inform your stakeholders
Disclose
Report company-wide emissions and progress against targets on an annual basis
There is a growing acknowledgment within the industry of the urgent need for climate change mitigation and adaptation. Membership requirements such as Cascale’s validation of climate targets and EOG’s commitment to the Race to Zero initiative serve as indicators of this recognition. However, there remains a lack of clarity among stakeholders regarding how to translate commitments into actionable plans.
We are committed to actively engage with upstream suppliers and customers through multi-stakeholder initiatives to craft Spectre’s decarbonization plan within 2024. We will do so in collaboration with like-minded value chain partners.
This is a key task to align ourselves with the needed pace of greenhouse gas emissions reduction.
› Supplier energy efficiency and switch to renewables
› Customer switch to preferred materials
› Recycled fibers, packaging
› More efficient production technologies
› Local sourcing
› Material efficiency
› Reduction of leftovers
› Incoming material quality means less waste
› Waste recycling in own operations and supply chain
› Sustainability services: 3D product development, repair, product developement/enviromental optimization as service etc.
› Switch to renewable energy
› Energy efficiency improvement
Transport
› Route optimization
› Reduction of airfreight
› Switch to biofuels
› Incentivizing better commute options
Through initiatives such as installing an additional solar rooftop on factory in Vietnam, purchasing grid electricity covered by renewable energy certificates and transitioning gradually to electric company vehicles, we have bolstered the proportion of renewable energy reaching 93% across the entire group in 2023/24. Energy consumption in
Spectre’s total energy consumption in 2023/24 decreased by 9.1% compared to the previous year, primarily attributed to reduced production output. Moving forward, we intend to intensify efforts to enhance the energy efficiency of our factories, thereby reducing our reliance on energy resources. An energy audit conducted at our Nam Dinh factory in October 2023 furnished us with actionable steps toward improving energy efficiency, many of which have already been implemented, while others necessitate significant investment over the long term.
Business operations and manufacturing inherently require energy. To reduce our climate impact, we focus on enhancing energy efficiency in our operations and transitioning to renewable energy sources.
Electricity predominates as the primary energy source in Spectre’s factories in Vietnam. Air conditioning, crucial for maintaining a comfortable working environment, represents the largest electricity consumer, followed by production equipment such as sewing machines, air compressors, and a vast range of specialized machinery. Hence, transitioning to renewable electricity has been pivotal in reducing our climate impact.
An Giang became Spectre’s second facility generating solar power through rooftop solar panels, successfully connecting to the grid in October 2023. Rooftop solar now covers a 11% of Spectre’s electricity consumption in Vietnam.
Given the limited rooftop space for electricity generation, since 2023/24, we have procured renewable energy certificates (RECs) to ensure the entirety of our electricity consumption becomes renewable.
By combining on-site solar power generation with RECs, we have achieved a complete transition to renewable electricity in our Vietnam factories.
The only remaining non-renewable energy usage pertains to fuel for company cars or other combustion engines, constituting 2% of total energy consumption in Vietnam.
Types of energy consumed in Spectre’s factoriesin Vietnam, MWh, 2023/24
In 2023, An Giang became Spectre’s first factory to achieve LEED certification. It marked a significant milestone as the first purpose-built factory for Spectre, enabling us to incorporate sustainability principles into its design from inception.
Existing buildings that meet high sustainability standards can attain LEED Operations & Maintenance certification.
Leed O&M covers the same topics as new buildings certificate but more emphasis on energy efficiency and materiales used in maintenance:
› Integrative process
› location and transportation
› sustainable sites
› Water efficiency
› Energy and atmosphere
› Materials and resources
› Indoor environmental quality
› Innovation
We view this LEED certification not as an isolated achievement, but as part of an ongoing commitment to sustainability, also regarding our manufacturing buildings.
Accordingly, we are actively pursuing LEED certification for our existing factories.
An Giang factory, Vietnam: employee football pitch and charging points for electric scooters have been added in 2023/24
An energy audit conducted at our Nam Dinh factory in the autumn of 2023 allowed us to identify actions and opportunities for investments aimed at substantially enhancing energy efficiency and thereby reducing environmental impacts. The next steps involve further assessing current performance and identifying areas for improvement regarding accessibility, water efficiency, waste management, and indoor environment.
Spectre achieved a major 46% reduction in GHG emissions intensity (per production output) in 2023/24 compared to the previous financial year. Several factors contributed to this significant drop. First, the reduction is due to large one-off investments occurring in the reference year due to the opening of the An Giang factory in 2022/23 and purchasing the production and office equipment.
The second largest contributor was our purchase of renewable energy certificates (RECs) and the operation of rooftop solar systems as part of our switch to renewable electricity. The third significant area of change was logistics: in 2023/24, there were fewer disruptions in global logistics chains, resulting in fewer shipments expedited by airfreight instead of sea freight. Additionally, our long-term logistics partner, DSV, switched to using at least 30% biofuel for shipping.
“During 2023/24 we have strengthened our company relations, and we will now, with more energy, continue to optimize the supply chain with sustainable solutions for Spectre.”
Keld Søgaard, Strategic Account Manager, DSV Global Transport and Logistics
Lastly, an increasing share of recycled fabrics in our garments led to incremental emissions reduction that we expect to continue in the coming years. Other initiatives, such as switching to electric company vehicles, also marginally reduced emissions.
Therefore, the total reduction in carbon emissions can be attributed to a mix of various factors—some under Spectre’s control, some influenced by our customers’ choices, some driven by global events in the supply chain, and some due to one-off investments in the reference year. The development of a decarbonization plan will help us set a trend for further reductions in the coming years.
Spectre team visiting main logistics partner DSV, January 2024
Fabrics alone accounted for 56% of Spectre’s total GHG emissions in 2023/24. This significant figure makes fabrics the focal point of Spectre’s decarbonization strategy, a challenge we must solve in close cooperation with our customers and material and trims suppliers. Improving energy efficiency and switching to renewable energy in material production are the highest-impact actions. This requires a similar mindset in the value chain where our focus will be working with customers and suppliers who share our climate goals and are willing to invest in this transition and inspire others to do the same.
Improving energy efficiency and switching to renewable energy in material production are the highest-impact actions. This requires a similar mindset in the value chain where our focus will be working with customers and suppliers who share our climate goals and are willing to invest in this transition and inspire others to do the same.
Further improvements involve switching to preferred materials, which also contribute to making the industry more circular.
› Supplier energy efficiency and switch to renewables
› Customer switch to preferred materials
› Recycled fibers packaging
› More efficient production technologies
› Local sourcing
› Material efficiency
› Reduction of leftovers
› Incoming material quality means less waste
› Waste recycling in own operations and supply chain
We expect that redesigning garments with preferred materials will be a major focus for our customers, as about half of Spectre’s customers, by turnover, have committed to the United Nations Fashion Industry Charter for Climate Action (Fashion Charter), which includes a commitment to fully switch to preferred materials by 2030.
We aim to reduce emissions by sourcing more materials locally from producers in Vietnam for our Vietnam factories. That should lead to shorter distances for materials deliveries and would also make use of energy options available in Vietnam that are cleaner than in some of the current sourcing countries.
Additional opportunities to reduce material use include improving purchasing and planning to minimize leftover materials, collaborating with suppliers to enhance fabric quality, and ensuring first-time quality in Spectre’s production to reduce rejects and waste. Moreover, enhancing waste treatment processes to maximize recycling is the final step in this chain. On the product development side, there are reduction potentials by applying 3D technology to replace physical samples and reduce courier shipments of samples.
Fabric
Trims
Processing and packaging materials
Other
Subcontractor
Distribution of GHG emissions in Scope 3 category 1 “Purchased Goods and services”, tons CO2e, 2023/24
Materials choices can enable circular business models
Next business year (2024/25), we also aim to pursue certifications like the Global Recycled Standard, allowing brands to switch to preferred materials in a verifiable way with chain of custody certifications.
This ensures that players in the supply chain, and ultimately consumers, can trust the information provided about the product and make conscious decisions that contribute to emissions reduction. Fabrics sourced in 2023/24 consisted of 40% recycled fibers, resulting in an increase from 37% in the previous year.
Fabrics made of a single type of fiber, like 100% polyester, are generally easier to recycle into usable raw materials than blends of different fibers. However, the mix of different fibers is often what provides desirable and functional characteristics, and therefore new innovations in the field of fabric performance or within the waste handling industry are required to move boundaries further.
The share of mono-material fabrics remained stable at 44% in 2023/24, even though switching to mono-material fabrics has the potential to reduce carbon emissions from fabric waste in production (pre-consumer) and at the end of the garment’s lifecycle (post-consumer).
Distribution of amounts of fabric disaggregated by composition fibers by circularity properties, tons, 2023/24
Spectre on its part has been working to switch to recycled polyester sewing thread. All such changes involve assessing not only the environmental impact of the material but also its performance qualities and the responsible business practices of the supplier. To switch to a different thread, we have to get approval from each of our customers so in 2023/24 we managed to reach 12% share of recycled thread and expect that to significantly increase in the next year.
This stability likely reflects most brands’ focus on reducing emissions embedded in materials through upstream processing in the value chain. The development of post-consumer garment recycling services and technologies that can recover the most value from synthetic fabric garments needs industry-wide support before we see brands prioritizing this emissions source. Moreover, emissions from processing fabric waste at Tier 1 producers are not included in emissions accounting of the brands according to the GHG protocol, further disincentivizing focus on this area for brands. Bearing in mind fabric waste during garment production easily reaches around 20% of total fabric consumption, this is an obvious area to investigate for the industry in the future.
The decrease of total waste volume in 2023/24 is primarily driven by a lower production quantity than the previous year, as a direct consequence of a general market slow-down. We saw a modest increase in the share of waste repurposed, reaching 28% from 26% in the previous year.
During the year, we explored new partnerships with potential recyclers and waste contractors, and we anticipate a significant rise in the share of repurposed waste by switching to a new waste contractor at our Nam Dinh factory in the next fiscal year.
Performing our due diligence included verifying the vendor’s setup to ensure that materials are recycled as promised and that proper social and environmental standards are maintained by the waste contractor and their partners. If successful, we plan to extend this cooperation to our Thai Binh factory, further improving our waste management performance.
We are continuing exploration of partnerships to feed the fabric scrap from cutting processes or leftovers into a textile-to-textile recycling setup. The technologies, such as mechanical and chemical recycling processes, are continuing to develop and the different requirements depending on the fabric type and recycling method add to the complexity. However, the growing push by society, regulators and industry towards solving the obvious problem of textile waste is likely to lead to rapid development and scaling of new and improved technologies. Spectre wants to be at the forefront of adopting those solutions that become mature and viable.
Our production process does not involve the use of hazardous chemicals. We use chemicals for tooling and maintenance, R&D and sparingly some spot cleaning products on the garments themselves which we choose with great care for it being safe.
Chemicals are managed according to legal requirements and Higg FEM best practices for health and safety, pollution and waste management, and ensuring consumer safety. Procedures have been set up to control any possible impacts on the environment, and we provide regular training for our workers on safe and proper handling. This involves procedures for evaluating and approving any of the chemicals used at our facilities.
Sources of hazardous waste are also limited to maintenance (expired, used chemicals, empty cans, used rags, fluorescent light bulbs), regular office appliances (batteries, electronic waste, ink cartridges) and spent or expired first aid medical supplies. Waste generated in Spectre’s operations by type in tons, 2023/24 Waste generated in 2023/24
At Spectre, water is primarily used for household purposes by employees (hygiene, drinking), maintenance (cleaning of premises), watering greenery and water features, and minor production processes such as sample washing. Therefore, our direct impact on water resources is quite limited.
Features like the rainwater harvesting system for greywater use at our An Giang factory contribute to reducing this impact.
A total of 17’358 m3 of rainwater were harvested in 2023/24. Water consumption rose in 2023/24 as the An Giang factory operated for a full year compared to the previous year when the factory was newly opened. Water consumption is the difference between water inflows (municipal water and harvested rainwater) and amount of water directed towards sewage. Water is consumed mostly for watering greenery, refilling water evaporated from decorative water basins, water used in cleaning and maintenance of premises etc.
The main impacts on water resources in Spectre’s business model lie upstream in the supply chain, particularly in the fabric dyeing process. We are implementing water risk screening of our material suppliers, and our efforts to gain access to supplier Higg FEM assessments are providing valuable insights into their water impacts. These insights will form the basis for Spectre setting targets and actions to reduce these negative impacts.
Screening with the WWF Water Risk Filter reveals that regions in the north and south of Vietnam, where Spectre’s factories are located, are exposed to flooding risks and pollution risks from untreated wastewater. South Vietnam, and to a limited extent Latvia, experience seasonal drought. Thereby the best way Spectre can address these risks is to focus on proper management of facility wastewater, while also defining an approach to mitigate potential future flooding damage in the region, especially considering rising sea levels due to climate change.
Ensuring a fair, safe and engaging work environment
Spectre has always aimed to apply the most rigorous social and labor management systems at our factories. For over a decade, SA8000 has been Spectre’s framework of choice, with all factories currently certified under this standard. Additionally, we undergo regular social audits adhering to other frameworks such as Fair Wear, SMETA, FLA-aligned, or customer-specific codes of conduct. As a proud member of Cascale, we also conduct third-party verified Higg assessments at all our factories annually (read in more detail in the section on the Spectre Factory Model).
Factory Production Standard
1. Empowering workers to manage the spending of the premium
2. Ensuring fundemental rights at work
3. Fair conditions of employment for workers
4. Occupational health and safety
5. Responsible management of environmental impacts
6. Transparency and traceability of Fair Trade product
7. Robust internal management system
The latest addition to our responsible business initiatives is the Fair Trade Certification, implemented at our Nam Dinh and Thai Binh sites. The Fair Trade USA Factory Production Standard not only sets requirements for social, labor, and OH&S aspects but also covers environmental and chemical management.
What sets this standard apart is the worker premium scheme, where brands in the Fair Trade program contribute a share of the value of garments produced at the factory directly to an account managed by a worker-elected representative committee. This committee then decides on community benefit activities funded by this money. We see this program as benefiting the local community while empowering workers by building social capital and decision-making skills. We are pleased to be part of this program together with Arc’teryx.
In 2023/24, Spectre recorded zero major workplace accidents (those resulting in more than three days of absence) and saw a significant reduction in minor incidents. We are proud of these results achieved by our employees, which reflect Spectre’s strong commitment to providing a safe working environment.
Achieving a safe working environment is not the result of a one-off campaign but is primarily a mindset rooted in our values, reinforced by proper processes and management systems. Spectre aims to maintain and build on this achievement, continually striving towards zero accidents.
In addition to conducting work safety risk assessments, providing instructions, and implementing procedures, we also monitor our employees’ perception of how safety values are prioritized compared to other incentives, such as achieving high efficiency. This helps us identify areas where these values may be at risk and require additional attention.
Disagree & mostley disagree
The past year demanded adaptation to extraordinary shifts in market demand. A surge in consumer demand during the COVID-19 pandemic was followed by a sharp drop as conflicts and uncertainty globally, as well as hiking interest rates and inflation, coincided with reduced government market stimulation in the core markets of our customers. Retailers and brands found themselves overstocked, leading to reduced orders for manufacturers like Spectre. This situation left us with excess production capacity, presenting the unenviable challenge of reducing the workforce across our factories.
As a result, the number of employees decreased by 20% compared to the previous year, though it remains significantly above the levels of 2021/22.
Number of minor and major accidents in Spectre’s operations
We employed various approaches to manage this adjustment, from downsizing the workforce to shortening the workweek to four or five days instead of the standard six-day workweek in Vietnam. The reduction affected male employees more (-25%) than female employees (-18%). This difference is attributed to male employees generally being more likely to seek employment elsewhere when faced with reduced income due to a shorter workweek.
Employee turnover rate by country, by gender, 2023/24
Employee satisfaction overall remained stable compared to the previous year, but the survey highlighted several site-specific concerns.
The main concerns for workers at the Nam Dinh and Thai Binh factories, were related to the quality of amenities, such as the availability of parking. We are investing in improving these amenities year by year to address employee concerns.
Workers in An Giang expressed below-average levels of satisfaction with interpersonal relations, particularly with managers. In response, we launched a worker empowerment program (WE program) in An Giang in January 2024. This program facilitates collaboration between factory management and workers to raise awareness about human rights, improve employee representation, and foster respectful and efficient communication between workers and management.
The reduced workweek and downsizing have led to a drop in satisfaction with remuneration and certainty about job roles, as well as communication about these changes.
Spectre strives to be an inclusive and supportive workplace. We believe that leveraging the full potential of our employees in all their diversity is our path towards sustainable growth and success. Gender and age are the first lenses through which we have begun analyzing the impacts of diversity on our employees and organization.
Distribution of employees by gender and age group across locations, 2023/24
Women make up 72% of all employees in Spectre group companies. Our Vietnamese production facilities have the youngest workforce, with the youngest employees located at our newest factory in An Giang. Conversely, the highest share of older employees is found in our Danish and German offices. The greatest gender disparity by location is in Latvia, where 91% of employees are women, while our offices in Denmark and Germany have the most balanced gender distribution. Vietnam boasts the most equal gender distribution in senior management positions.
These varying age and gender distributions present different challenges and opportunities. To note some examples, the underrepresentation of women in management in some units requires us to prioritize gender-sensitive communication practices. An older workforce in some locations represents the high level of experience and competency acquired through many years working at Spectre while aging also necessitates a more accommodating regime for more frequent sick leave and addressing succession planning and making full use of the accrued experience by efficiently sharing it with newcomers in the organization. Spectre aims to enable our employees to create better results for the company and themselves irrespective of their age while leveraging their different perspectives.
Meanwhile, the very small representation of male employees in Latvia, and their concentration in certain roles, skews gender pay gap indicators.
The lack of female employees in top management positions highlights the need for more targeted approaches to career advancement and recruitment.
These are some of the issues to be addressed in our 2030 responsible business strategy action plan, which is under development and will be launched in 2024.
LV 28,9%
DE 34,0%
DK 56,4%
ND -2,7%
TB -3,1%
AG -0,34%
Gender pay gap across locations in sample periods within 2023/24.
We also see that the gender pay gap manifests differently across locations. The highest gender pay gap is in the headquarters in Denmark and Germany which is due to higher share of management positions held by male employees.
Top management (board of directors) gender balance currently is 20% with a target of 33% by 2025/26. In other management levels women make up 43%.
Gender pay and equal pay are not the same. Equal pay deals with the pay differences between men and women who carry out the same job, similar jobs or work of equal value. Gender pay gap shows the difference in the average pay between all men and women in a workforce.
Spectre Vietnam donated 700 T-shirts for participants of an annual wildlife restoration event at several national parks in southern Vietnam.
Picture: Volunteers working to restore wildlife at Bu Gia Map National Park, 2023
Spectre Vietnam organized donations together with other local partner companies for pre-school children in the remote highland commune of Long Pu in the very North of Vietnam on the border with China.
Picture: Representatives of Spectre Vietnam and partners visiting kindergarten in Long Pu commune, May 2023
Closing out the year with a big celebration for all employees before the Lunar New Year (Tet) holiday break is already a long-standing tradition for Spectre Vietnam
Picture: Lunar New Year celebrations in Nam Dinh, January 2024
The new factory in An Giang fields a football pitch accessible to company employees.
An evening football game on the football pitch at the An Giang factory
Building a system to ensure high standards
Spectre is committed to maintaining equally high social, environmental, quality, and efficiency standards across all our factories. This commitment is encapsulated in the Spectre Factory Model. Core parts of the model are certified management systems:
› SA8000 or Fair Trade for human rights, labor relations, and occupational health and safety.
› ISO 14001 for environmental management.
› ISO 9001 for quality management.
Undergoing third-party verified Higg FEM and Higg FSLM assessments is the second cornerstone of the sustainability standards.
Third-party verified Higg FEM and Higg FSLM assessments were completed in Spectre’s factories that account for 92% of produced minutes in 2023/24.
Completion of SA8000 certification and Higg assessment verification at An Giang during 2023/24 were milestones of implementing the Spectre Factory Model at this new factory. We have also onboarded our partner factory in Ukraine to the Higg FEM and plan to implement Higg FSLM there in 2024.
The Spectre Factory Model is evolving as we improve our approach to being a responsible business and align with customer needs. In 2023, Spectre became a certified B Corp, a certification that applies to the entire group. Our next step is to implement LEED certification at our Nam Dinh factory , furthering the principles of the Spectre Factory Model. We aim to produce an ESRS-based Responsible Business Report for the 2024/25 financial year.
With growing customer demand for verified product content claims, we are working to add GRS and potentially other content claims scope certifications to our model. As we are adding new certifications, we will also be looking to consolidate the certifications that we already hold to avoid overlap and best align with customer needs.
rights, labour conditions, H&S standard
labour conditions, H&S standard, worker premium management
rights, labour conditions, H&S standard for brands
rights, labour conditions, H&S standard for brands
claims, social & labour, environmental & chemical standard
responsible business
- workers, community, environment, customers, governance
Spectre has always aspired to be a responsible business, embedding sustainability as a core consideration in our sourcing and purchasing decisions. We continually strive to improve our upstream sourcing and minimize our social and environmental impacts through dedicated due diligence efforts.
To this end, we have intensified our focus on ensuring compliance from our suppliers by conducting factory audits at selected partners. Insights gained from these audits enable us to act swiftly to mitigate any red flags detected at our supplier factories. In 2023, Spectre’s supply chain team audited 10 materials suppliers in Vietnam and Taiwan. Additional audits were conducted in February 2024 to ensure ongoing due diligence.
Created under the guidance of Cascale, Worldly is a comprehensive impact intelligence platform trusted by more than 40,000 major brands, retailers, and manufacturers across various industries, including fashion, outdoor gear, home goods, and toys.
Another key focus is local sourcing in Vietnam. By prioritizing Vietnamese sourcing, we can reduce our CO2 emissions while also supporting local communities through increased business. Governance is the foundation for ensuring a responsible supply chain, and we will continue to set new, higher targets.
Employing the tools available through Cascale membership provides us with additional insight into the social and environmental impacts of our suppliers. Engaging with suppliers using Worldly’s facility tools, such as the Facility Environmental Module (FEM) and the Facility Social and Labor Module (FSLM) provides us with detailed insights into the operations of our suppliers. In 2023/24 we engaged with 28% of our immediate suppliers by spend through Worldly tools.
However, this does not provide a complete picture of our suppliers’ performance.
Therefore, we are working to implement a new due diligence framework. This will help us better manage supplier sustainability risks and enable us to recommend preferred suppliers from a social and environmental perspective, as well as preferred materials from an emissions reduction perspective.
Most materials by spend are sourced from Taiwan and Hong Kong, each with distinct social and environmental contexts that must be considered in the due diligence process. Additionally, each type of supplier and material category presents different risks. However, the main challenge lies in gaining sufficient insight into the supply chain beyond our immediate suppliers. Addressing this will require the cooperation of all actors across the value chain, including brands, Spectre, and material suppliers.
One challenge in tracing global supply chains is the identification of factories in a uniform way, as the spelling of supplier company names and addresses can vary in an international context. This is where the Open Supply Hub (formerly known as the Open Apparel Registry) comes in. Using supply chain data from various organizations, brands, and retailers, OSH has mapped over 90,000 facilities.
Since 2022, Spectre voluntarily contributes information about our owned factories and subcontractors used in garment production to the OSH platform to provide transparency about our operations.
Data in the Open Supply Hub is contributed to and use by organizations worldwide, including major global brands, civil society organizations, multi-stakeholder initiatives, certification schemes, and factory groups. OS Hub’s vision is to build a world there supply chain data is open, trusted, and harnessed to benefit people and the planet.
As part of a global value chain, Spectre recognizes that many of the impacts we face are global and complex, requiring collaborative solutions across the industry. Therefore, we have joined several organizations and initiatives dedicated to promoting sustainability worldwide.
As members of Cascale, we are committed to making the apparel value chain more socially and environmentally responsible by deploying Higg tools. Our membership in the European Outdoor Group (EOG) allows us to exchange experiences on managing sustainability with peers and stay informed about sustainability policy developments affecting the industry.
Since 2010, we have been proud members of the UN Global Compact, a movement based on ten principles in the areas of human rights, labor standards, environment, and anti-corruption. The Global Compact provides a platform for private businesses to contribute to the Sustainable Development Goals. Membership requires submitting an annual Communication on Progress report, ensuring transparency in our efforts towards these principles. Additionally, the Global Compact offers valuable training courses on sustainability topics, supporting our ongoing responsible business initiatives.
Spectre is a member of the Danish Fashion and Textiles Industry Association (Dansk Mode & Tekstil or DM&T) with Spectre co-owner Jacob Klausen serving on its board. The association represents more than 375 companies and provides industry-specific and personal advice in HR law, trade law, corporate responsibility, technology and more. Spectre is also a member of Business Council Herning & Ikast-Brande (Erhvervsrådet), representing interests of more than 800 businesses in Central Jutland, Denmark, with co-owner Jesper Klausen as deputy chairman. The organization is involved in lobbying on a local, regional and national level to improve the business environment for local businesses. Spectre has not made any political contributions.
We focus our efforts to contribute to four selected Sustainable Developement Goals: Climate action, Decent work and economic growth, Responsible consumption and production, Partnerships for the goal.
In the upcoming year of 2024/25, we aim to strengthen the management of Spectre’s environmental and social impacts. Finalizing the development of our 2030 responsible business strategy and publishing these commitments will be a significant milestone. This strategy, aligned with the B Corp framework, will become the cornerstone for managing our impacts, building a common understanding, and establishing a shared vocabulary across the organization to address these impacts with a clear, unified vision.
Part of this initiative includes renaming our annual sustainability impact report to the Responsible Business Report. As a responsible business, Spectre’s aspiration is to reduce the harm resulting from our business model, build a higher-quality business, and provide meaningful work that people seek—to create a better business by doing good.
We structure our report along the three pillars of ESG— environment, social, and governance. While ESG refers to how company sustainability performance is measured, we use the term ‘responsible business’ to better capture our philosophy, which aligns with Spectre’s DRIVe values and the values of B Corp. This term signifies our ambition to operate in a way that positively contributes to our employees, the wider society, and the environment based on the best knowledge we have.
We will work to better integrate sustainability into the organization, breaking down silos between human resources, sourcing, research and development, quality management, production, supply chain, sales, and other functions. This requires a thorough review of our governance structure to empower the organization through clear areas of responsibility, resource allocation, and skills training where necessary to meet future targets.
Our efforts to develop and strengthen the Spectre Factory Model will involve implementing new management standards and discontinuing others to align optimally with customer needs and consolidate our efforts, as discussed in this report. We look forward to updating you on our progress in our next Responsible Business Report.
The reporting period covers the business year from April 1, 2023, to March 31, 2024. This report includes information on material ESG topics as well as key events from previous years for additional context and comparison.
Spectre’s previous report on responsible business was based on GRI standards. However, with the EU’s adoption of the European Sustainability Reporting Standards (ESRS), Spectre is now in a transition process to apply ESRS. As a result, part of disclosures included in this align with ESRS, while others still align with GRI standards. Therefore, the Responsible Business Report 2023/24 does not claim compliance with either of standards during this transition to avoid confusion.
Spectre’s assessment of EU Taxonomy alignment in 2023 revealed that the main activity of Spectre - the manufacturing of apparel — is not included in the EU Taxonomy scope. However, Spectre engages in other applicable activities that fall under the EU Taxonomy reporting, specifically economic activity 7.3: Installation, maintenance and repair of energy efficient equipment. Our goal is to improve the Do No Significant Harm (DNSH) risk assessment before the next report to enable our EU Taxonomy alignment reporting.
Data on previous years is provided for KPIs and other performance indicators where possible. This data has been updated where methodological changes have occurred since the previous reporting year. The previous CSR report covering the year 2022/23 was published in June 2023.
For further inquiries on responsible business at Spectre, feel free to contact group CSR manager Krišjānis Dzalbe via email krisjanis.dzalbe@spectre.lv.