
16 minute read
Data en digitalisering essentieel bij energiebesparing
Meer energie-efficiëntie dankzij volautomatische fabriek Soudal, de Kempische specialist in siliconen, lijmen en PU-schuimen, is gestart met de bouw van een volautomatische fabriek nabij het hoofdkwartier in Turnhout. Met de nieuwbouw is een investering van 40 miljoen euro gemoeid. Dit hoopt de wereldspeler onder andere terug te verdienen met het drukken van de energierekening. Door gebruik van data, digitalisering en automatisering wil het bedrijf energiezuiniger en met minder afval produceren.

Advertisement

Chipsoven van PepsiCo verwarmt woningen De PepsiCo-fabriek in Veurne zal de nieuwe wijk ‘Suikerpark’ verwarmen met restwarmte van haar chipsoven. In de wijk ligt een netwerk van goed geïsoleerde ondergrondse leidingen, waardoor warm water tot in de woningen wordt gebracht. Een warmtewisselaar brengt de warmte over aan leidingen die naar de verwarming of de keuken en badkamer lopen. Het betreft het eerste warmtenet in ons land dat volledig draait op restwarmte van een voedingsbedrijf.
Fossiele brandstoffen raken uitgeput en dragen bij aan de opwarming van de aarde. De energietransitie staat inmiddels hoog op de agenda bij bedrijven. Door data-analyse en digitalisatie kan de energie-efficiëntie opgevoerd worden en kan ook groene energie optimaal benut worden.
België onderschrijft de Europese klimaatdoelstellingen en streeft naar een emissieloze samenleving in 2050. Om deze doelen te bereiken, is een belangrijke rol weggelegd voor de Belgische industrie, die volgens Energy Key Data van het ministerie van Economie 25 procent van de totale Belgische energieconsumptie voor haar rekening neemt.
Minder energie verbruiken is essentieel bij het halen van de energiedoelstellingen, aldus Dirk Torfs, CEO van kennisinstelling Flanders Make. Volgens hem kan deze energie-efficiëntie verbeterd worden met technologische innovatie en digitalisatie. Hij noemt het voorbeeld van de huidige generatie van vraaggestuurde moderne elektromotoren die uitgerust zijn met variabele snelheidomvormers, die een efficiëntiewinst kunnen boeken tot 40 procent afhankelijk van de status van de initiële installatie. “Ze hebben geen constante output, maar leveren het vermogen dat gevraagd wordt. Hierdoor is er minder energie nodig om dezelfde output te bereiken zodat het hele proces veel efficiënter is qua energieverbruik.” Torfs ziet een belangrijke rol weggelegd voor Industrie 4.0. Dit is het proces van automatisering en digitalisering van de maakindustrie waarbij de productie digitaal aangestuurd en bijgestuurd wordt op basis van data en data-analyse. “Er zijn steeds meer data beschikbaar en die kunnen met artificiële intelligentie gebruikt worden om het productieproces in te richten. Een optimalisatie van de productie betekent ook een optimalisatie van het energieverbruik.”
Ook energiesoftware en consultancy-specialist Condugo benadrukt het belang van data. Het bedrijf adviseert grote energieverslinders – farmaceutische en chemische multinationals – bij het verhogen van de energie-efficiëntie. Hoe groot deze multinationals ook zijn, hun energieverbruik is allesbehalve op orde. “Door een efficiëntere inrichting van de productie kan op korte termijn 2 tot 10 procent aan energie-efficiëntie gewonnen worden”, vertelt CEO Xavier De Moor.
Condugo inventariseert de beschikbare energiedata van de grote concerns. “Bedrijven hebben tegenwoordig veel data op het gebied van energiegebruik, maar het ontbreekt aan softwaresystemen om deze data te capteren en te bewerken. Er wordt veelal nog gewerkt met simpele Excel-systemen om data te registeren”, vertelt De Moor.
Door artificiële intelligentie op data los te laten kan Condugo aangeven welke parameters invloed hebben op het energiegebruik in verhouding tot de productie. “Hieruit kan bijvoorbeeld blijken dat het opvoeren van de temperatuur of druk een positieve invloed heeft op het energiegebruik per eenheid product.” Volgens De Moor worden bedrijven steeds meer gedwongen om hun energiehuishouding op orde te hebben. “De wetgever eist steeds meer gedetailleerde rapportage over het energieverbruik in verhouding tot de productie, terwijl ook de aandeelhouders en de consumenten steeds meer openheid eisen.”
Dirk Torfs sluit zich daarbij aan. “Energieverbruik is niet meer alleen een kostenpost, maar ook een onderdeel van sociaal-maatschappelijk ondernemen, waardoor energietransitie hoog op de agenda van bedrijven staat. Voor producten die met minder energie vervaardigd zijn, kun je ook meer geld vragen. Duurzaamheid is een verkoopargument geworden.”
Volgens de experts is energie-optimalisatie niet sluitend, maar moet er sprake zijn van een combinatie van maatregelen om een energieverduurzaming te realiseren. Naast een reductie of optimalisatie van energieconsumptie en de implementatie van groene energie, biedt ook een circulaire huishouding uitkomsten. Digitalisatie en automatisatie kunnen er ook voor zorgen dat groene energie, die beschikbaar is als de zon schijnt of de wind waait, beter benut wordt. “Je kunt bijvoorbeeld denken aan een datagedreven, flexibel productieproces dat inspeelt op het aanbod van wind- en zonne-energie. Is er veel energie beschikbaar, dan kunnen energie-intensieve operaties uitgevoerd worden en bij minder aanbod verschuiven de accenten naar andere activiteiten”, besluit Torfs.
Door Jerom Rozendaal
Festo maakt bedrijven klaar voor energiezuinige productie
Festo Energy Saving Services en energiebesparende producten verminderen de CO2-uitstoot
Het toenemende bewustzijn van klimaatbescherming, maar ook de hoge energieprijzen maken energie-effi ciëntie tot een kerntaak van de onderneming. Bovendien wordt milieuvriendelijk en CO2 neutraal produceren steeds meer een concurrentiefactor.
Persluchtbewaking op basis van AI
Nieuw is een bewakingssysteem dat de volledige installatie continu bewaakt. De meetwaarden worden geregistreerd, verwerkt en voor de gebruiker gevisualiseerd in een door Festo ontwikkelde softwareoplossing op basis van AI. Zo beschikt de klant over een permanente conditiebewaking van zijn installatie.
Technologieneutraal ontwerp
Festo biedt een compleet pneumatisch en een elektrisch portfolio aan. Dankzij onze pneumatische, elektrische en gecombineerde aandrijfoplossingen kunnen wij de beste en meest duurzame oplossing voor onze klanten selecteren met energie/kosten vergelijkende berekeningen. Dat is wat Festo onderscheidt!
Intelligente producten besparen energie
Digitalisering is een belangrijke enabler om de industriële productie klimaatneutraal te transformeren. Door pneumatiek intelligent te maken verhogen we de effi ciëntie voor de klant. Bijvoorbeeld met de digitale ventielterminal VTEM waarop functionele apps zijn te installeren om bijvoorbeeld bewegings- of energiefuncties toe te voegen. Of de C2M energie-effi ciëntiemodule, die het persluchtverbruik bewaakt, aan- of uitschakelt en alles rapporteert in de cloud.
Groene en circulaire chemie of géén chemie
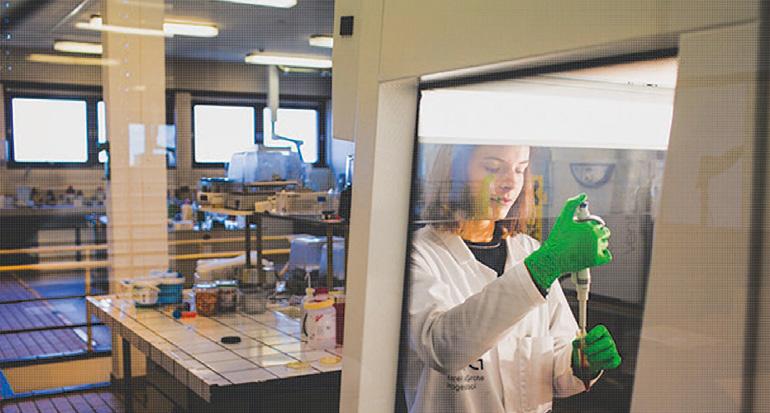
Hoe zet je afval om in grondstoffen? Hoe optimaliseer je je chemische proces of maak je het groener? Op dit soort vragen zoekt het expertisecentrum Duurzame Chemie van Karel de Grote Hogeschool samen met het bedrijfsleven antwoorden. Het expertisecentrum doet al meer dan 15 jaar praktijkgericht wetenschappelijk onderzoek om de resultaten vervolgens in te zetten in de chemische industrie. De focus ligt daarbij op de valorisatie van nevenstromen, afval dus, en op het gebruik van artificiële intelligentie voor de optimalisatie van chemische producten en processen. Afvalstromen uit de landbouw en de voedingsindustrie worden door de onderzoekers bijvoorbeeld omgezet in natuurlijke gewasbeschermingsmiddelen, antioxidanten en kleurstoffen. Spuislib, een afvalstroom uit de waterzuivering, wordt ingezet in beton- en lijmapplicaties. “Bedrijven komen met hun vragen bij ons en wij zetten onze onderzoeksexpertise in om een duurzame oplossing aan te bieden die ze direct kunnen toepassen in hun bedrijf”, vertelt Jeroen Geuens, hoofd van het expertisecentrum.
‘Daarin verschilt onderzoek aan hogescholen van onderzoek aan universiteiten. De onderzoeksvragen die we behandelen zijn rechtstreeks afkomstig van het werkveld’, vertelt Geuens. ‘We hebben een zeer nauwe band met het chemisch werkveld. Als we merken dat meerdere bedrijven met hetzelfde probleem zitten, starten we een collectief onderzoeksproject rond dit probleem. We betrekken in deze projecten steeds de hele waardeketen, dit wil zeggen bedrijven die met een bepaalde nevenstroom zitten, bedrijven die over de installaties beschikken om deze nevenstroom te verwerken en bedrijven die de chemische componenten die uit deze nevenstroom gebruiken in hun eindproducten. Als we een zeer specifieke nood capteren bij één bedrijf, starten we een zogenaamd dienstverleningsproject op, één-op-één met dat bedrijf.’
In het project Biocolor (2020-2022) worden afvalstromen uit de landbouw en uit de voedingsindustrie verwerkt tot natuurlijke kleurstoffen. Het Vlaamse Inagro en het Nederlandse Delphy, beide onderzoekscentra voor land- en tuinbouw, zorgen voor de aanlevering van de grondstoffen. Het bedrijf Add Essens uit Lokeren kan op industriële schaal extracties van kleurstoffen uitvoeren en zorgt dus voor de opschaling binnen het project. Wat betreft de toepassing van de natuurlijke kleurstoffen worden er 2 opties verkend: textiel en voeding. Voor de toepassing in textiel zijn 3 projectpartners betrokken, namelijk Masureel, Centexbel en het Fashion and Textiles Innovation Lab van HoGent. Food Pilot, onderdeel van ILVO, voert testen uit op het kleuren van yoghurt.
‘We gaan steeds op zoek naar de meest geschikte projectpartners’, zegt Geuens. ‘We beperken ons daarbij niet tot de landsgrenzen of tot de grenzen van universitaire associaties, we staan open voor samenwerking met iedereen die relevante expertise heeft en zijn schouders mee onder het project wil zetten en we werken bij voorkeur interdisciplinair, dat is enorm verrijkend.’
Annelore Wens, onderzoeker op het Biocolor project, vertelt: ‘De focus van het project ligt op duurzame technologieën om de kleurstoffen uit de afvalstromen te extraheren. We gebruiken bijvoorbeeld geen organische oplosmiddelen maar gewoon water als solvent. De resultaten zijn soms verrassend, zo geeft het extract van afval uit rode kool alles behalve een rode of paarse kleur. De eerste testen op textiel zijn veelbelovend. Momenteel wordt bij de projectpartners de kleurvastheid bestudeerd terwijl wij verder werken aan de toepassing in voeding namelijk het kleuren van yoghurt.’ Op de vraag op welke nevenstromen ze al gewerkt heeft antwoordt Wens: ‘Dat zijn er verschillende, bijvoorbeeld ajuinschillen, snoeiafval van liguster, walnoten, afval van avocado’s en mango’s, perskoek uit de fruitsapindustrie zoals van frambozen. We werken ook rechtstreeks op de planten zelf, zo hebben we bijvoorbeeld al experimenten uitgevoerd op tijm, brandnetel, meekrap, wouw en wede.’
‘Het is soms leuk te zien dat één bepaalde nevenstroom kan ingezet worden in verschillende toepassingen’, vult Geuens aan. ‘Zo kunnen we uit dezelfde nevenstroom met water een kleurstof extraheren terwijl we met superkritische CO2 componenten extraheren die als antioxidans kunnen dienen.’ ‘Dit is de toekomst’, zegt Geuens, ‘het volledig benutten van een nevenstroom, er alle waardevolle componenten uithalen. Belangrijk punt hierbij is dat naast de duurzaamheid van de grondstof ook de duurzaamheid van het hele proces niet uit het oog verloren wordt. Een proces kan immers pas duurzaam zijn als het ook economisch duurzaam is. We hebben ons de afgelopen jaren daarom gespecialiseerd in de optimalisatie van extractieprocessen. Hiervoor gebruiken we klassieke, statistische tools maar ook meer geavanceerde technieken zoals algoritmes uit de artificiële intelligentie. Een proces dat optimaal verloopt heeft een lager grondstofverbruik, kost minder energie, heeft dus een kleinere carbon footprint en kost vooral ook minder geld. Dan pas wordt het interessant en industrieel relevant.’
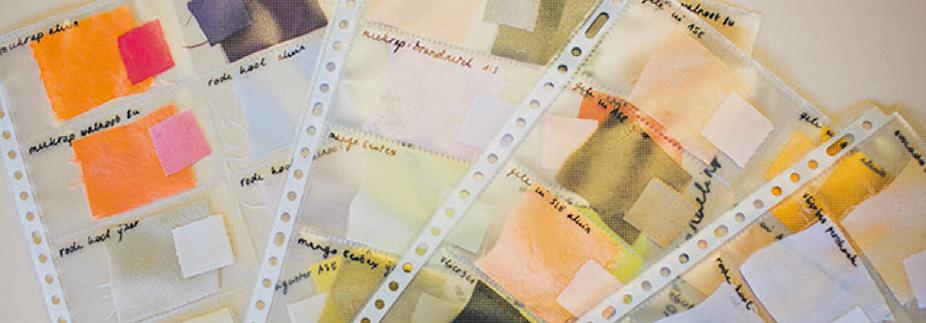
kdg.be
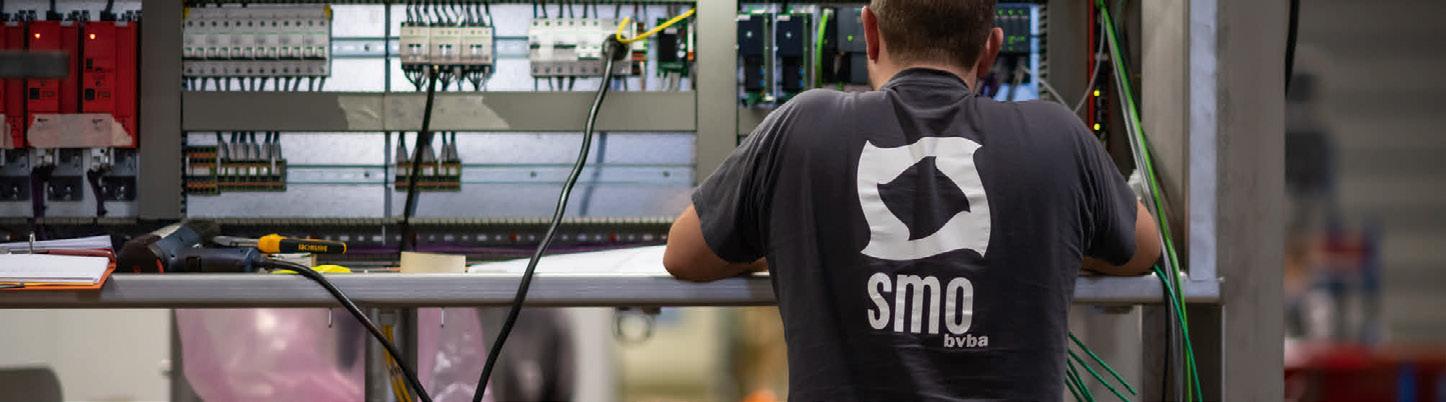
INNOVERENDE MACHINES OP MAAT VAN DE KLANT
Steeds meer bedrijven erkennen de meerwaarde van maatwerk voor hun machinebouw, automatisatie,engineering en constructiewerken. Sander Mollet, CEO van machinebouwer SMO, legt uit hoe dit bedrijf innovatieve oplossingen aanreikt bij specifieke uitdagingen, zowel groot als klein.
Elke stap in het proces in eigen beheer
“Als innovatief machinebouwer ontwerpen we industriële machines, constructies en automatisaties helemaal op maat van de specifieke behoeften van de klant. Onder het motto “Alles kan” kunnen wij in bepaalde gevallen ver gaan. Alles gebeurd in-house bij SMO. We beheersen elke tussenstap van het proces: Van concept, 3D ontwerp, sterkteberekening, laswerken, verspaning, montage, programmatie, … tot dienst na verkoop. Uiteraard kunnen we u deze diensten ook afzonderlijk aanbieden. De service van SMO loopt nog verder na de installatie van het project. Klanten kunnen ook bij ons terecht voor fine-tuning, herstellingen en opleidingen. Met een team van 20 ingenieurs en in totaal bijna 50 werknemers staan we klaar om elk project tot een goed eind te brengen.”

Automatiseren met slimme robots
“Met SMO specialiseren we ons op het vlak van verregaande automatisaties met robots en visiesystemen. Industriële automatisaties zorgen voor hogere efficiëntie of productiviteit en lagere arbeidskosten voor de klant. Bedrijfsautomatiseringen zijn doorgaans verbeteringen tijdens het productieproces die bekomen worden door standaard mechanische bewegingen in combinatie met sensoren en een sturing via PLC. Laat ons zeggen dat we helemaal mee zijn in het Industrie
4.0 verhaal.
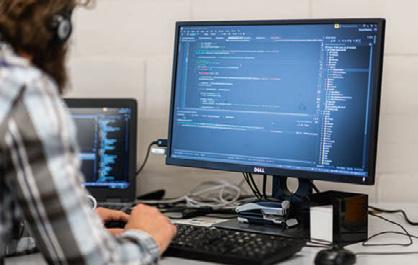
Vroeger was een robot niet flexibel in het uitvoeren van taken, tegenwoordig lossen we dit op met beeldverwerking en beeldanalyse. Camera’s in de machine voorzien de robots van informatie, die informatie wordt dan in real-time begrepen door de artificiële intelligentie. De positie herkennen van een product op een transportband en het opnemen en verplaatsen, de groei van planten analyseren en automatisch irrigeren, kwaliteitscontrole, … de mogelijkheden van robotica met beeldanalyse en beeldverwerking zijn eindeloos.”
Veelzijdigheid als troef
“Onze sterkte is onze veelzijdigheid. Van ruwe industriële machines tot spitstechnologie, of van automatische transportsystemen tot professionele laswerken. De veelzijdigheid komt ook terug in de sectoren waarvoor we reeds projecten hebben gerealiseerd. Tussen onze referenties staan onder andere multinationals als Coca-Cola, Hilti en Philips maar ook Kmo’s en startups zijn meer dan welkom met hun projecten.
Alles start bij de engineering. Elk project krijgt zijn eigen verantwoordelijke toegewezen uit ons ingenieursteam. Hierbij start een nauwe samenwerking van de eerste schetsen tot aan de installatie van de machine. Het idee wordt samen met de klant uitgewerkt tot een realistisch concept. Om de theorie met de praktijk te staven kan er ook een testopstelling gebouwd worden om de verdere uitwerking bij te sturen. Daarnaast zijn er ook 3D-simulaties mogelijk om de klant een beter inzicht te geven in het eindresultaat. SMO heeft reeds veel ervaring met het bouwen en optimaliseren van prototypes. We blijven optimaliseren totdat zowel wij als de klant tevreden zijn over de machine op maat.
Indien het prototype goedgekeurd is, kan SMO ook verder gaan. Als machinebouwer beschikken wij over al het nodige om een project volledig intern te realiseren. Onze ateliers zijn zodanig ingericht dat we nagenoeg alles zelf kunnen maken. Zo kunnen wij een korte doorlooptijd van uw project garanderen. Daarnaast beschikken we ook over de ruimte en capaciteiten om de machines op maat in ons eigen atelier op te bouwen en in orde te stellen.
Innovatie blijft de rode draad. We maken dan ook gebruik van de nieuwste software, hardware en technieken. Daarom zijn we zeer geïnteresseerd in mensen met problemen waarvoor nog geen oplossingen bestaan. Voor dit soort klanten creëren wij systemen en machines die dit probleem van de baan helpen met vernieuwende en efficiënte oplossingen. Het spreekt voor zich dat het aangaan van zulke uitdagingen een gezonde portie lef vereist. Trial and error maken deel uit van dit proces en dragen net bij tot onze verregaande expertise. Het innovatief karakter van SMO werd ook al meermaals beloond met een award.”
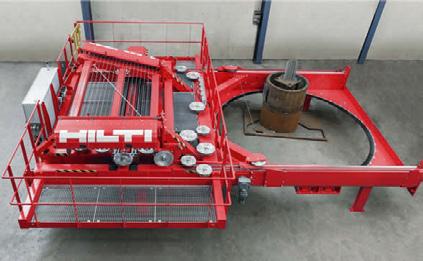
Het onvermijdelijke pad naar automatisatie en digitalisatie loopt via samenwerking
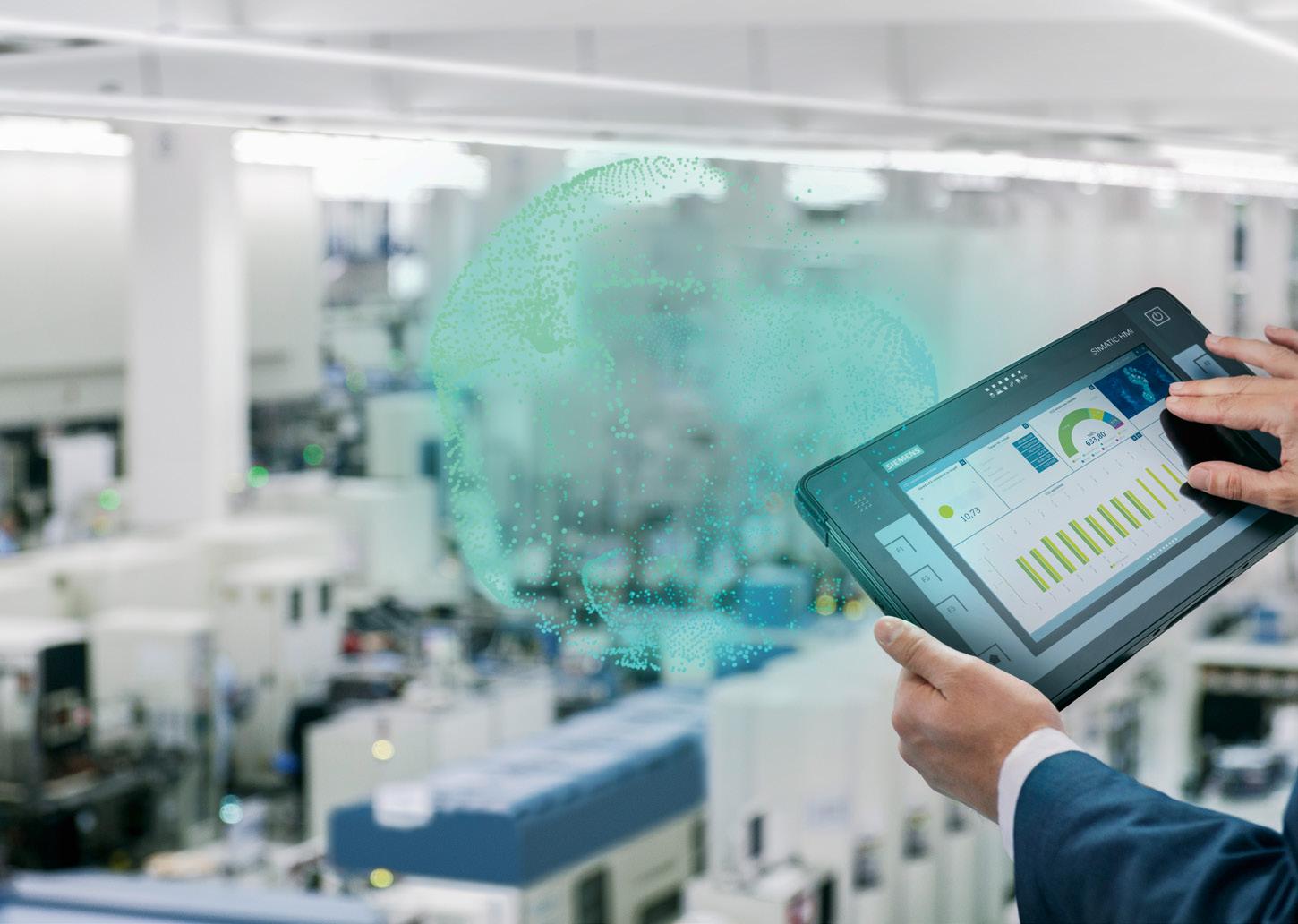
Ongeveer elke sector en bedrijfstak in ons land gaat momenteel door een stevige digitaliserings- en automatiseringsgolf. Waar komt die noodzaak vandaan? Welke rol spelen technologieën als de cloud en big data? En hoe zal dit allemaal evolueren?
Dat onze vaderlandse industrieën extra veel moeite steken in het automatiseren van hun processen heeft een eenvoudige reden, volgens Geert De Coninck, Business Unit Manager Factory Automation bij Siemens: “Het moet een antwoord bieden op de vraag die elke CEO vandaag wakker houdt: hoe zorg ik ervoor dat mijn bedrijf competitief blijft in deze razendsnel veranderende wereld? Een eerste manier is door de productiviteit te verhogen: je verhoogt de output van je installaties, maar je doet dat met minder mensen en minder engineeringuren. Je kunt ook de time-to-market versnellen, zodat je geïnvesteerde kapitaal sneller rendeert. En tot slot kun je flexibeler worden, zodat je op dezelfde productielijnen snel tussen verschillende producten kunt switchen of kosteneffectief series in kleine oplages kunt maken. Bij al die oplossingen is automatisering de hefboom die dit allemaal mogelijk maakt.”
Daarnaast brengt digitalisatie en automatisatie nog andere voordelen mee, zoals zo energie-efficiënt en milieubewust mogelijk produceren, of het concept van de ‘digital twin’. “Een digital twin is een soort digitale kopie van een product, productielijn of zelfs productieproces dat we virtueel bouwen voor we de ‘echte’, reële versie ervan installeren”, legt De Coninck uit. “Door die bouw – bijvoorbeeld van een machine – minutieus voor te bereiden, kunnen we dat sneller en goedkoper doen, maar we kunnen dan op voorhand allerlei zaken uittesten op elektrisch en mechanisch niveau. Aan de hand van simulaties op de digital twin kunnen we nagaan wat er kan gebeuren als we de machine onder een te zware belasting laten draaien. Wat als er te hoge temperaturen voorkomen? Hoe sneller een eventuele fout in het proces ontdekt wordt, hoe meer we de meerkosten kunnen drukken.”
In de echte machines zelf worden ook meer en meer sensoren ingebouwd die bijvoorbeeld bepalen wanneer er onderhoud moet gebeuren. “We kunnen bijvoorbeeld de slijtage van een motor bepalen op basis van de geluidsfrequenties die hij produceert. Of op basis van de viscositeit van de olie in de motor”, zegt De Coninck. “Door dat in de gaten te houden, moet er pas onderhoud gedaan worden precies op het moment dat het nodig is.”
Al die sensoren en machines genereren ook een machtige hoeveelheid data. Die wordt tegenwoordig ook ingezet als ‘grondstof’. “Vroeger werden de data wel opgeslagen, maar tegenwoordig zullen we die ook gebruiken en analyseren, bijvoorbeeld om er trends in te ontdekken of om voorspellingen te doen”, aldus De Coninck. “Tot voor kort stuurde men alles naar de cloud, maar de laatste jaren wordt bij veel data ook al een soort pre-analyse gedaan op de machine zelf. En pas dan worden de gefilterde data naar de cloud gestuurd. Of die data worden direct gebruikt op een zogenaamde ‘edge-applicatie’ binnen de installatie. De reden daarvoor is simpel: er is op die manier minder opslag in de cloud nodig, maar ook de rekenkracht van onze toestellen is zo hoog geworden dat die dat gemakkelijk zelf aankunnen. De meeste PLC’s (programmeerbare controllers) zijn nu uitgerust met vier cores of rekenkernen. Momenteel worden er daar vaak maar twee van gebruikt. Maar in de toekomst zullen we die alle vier gaan inzetten, om die analyses al zo veel mogelijk lokaal af te handelen.”
Heel die evolutie heeft ook zo haar invloed op technologische bedrijven, zoals Siemens zelf, zegt De Coninck. “Vroeger bestond het grootste deel van onze omzet uit hardware. Tegenwoordig wordt software minstens even belangrijk, want het is de software die de toegevoegde waarde geeft bij de hardware. En die software moet op maat van de klant gemaakt worden, want een chemisch bedrijf verwacht iets heel anders dan een glasfabriek, en die willen weer iets heel anders dan een farmabedrijf.”
Voor zowel Siemens als de industrie betekent dit dat ze zich voortdurend moeten aanpassen en zich nieuwe methodieken eigen moeten maken. Ecosystemen en samenwerkingen zijn daarop het antwoord, niet alleen om business te genereren, maar ook kennis, bijvoorbeeld bij opleidingen. De Coninck: “Drie jaar geleden hebben we samen met de KU Leuven een netwerk rond opleidingen en nieuwe technologieën opgestart: de Siemens Industry Academy. Ondertussen is ook de UGent aangesloten. Samen met 43 industriële bedrijven, zoals Puratos, Volvo en Wienerberger, stellen we lespakketten samen en stellen we de meest recente technologie ter beschikking. Dat is een van de redenen waarom we van Agoria het label ‘Employer Ready for the Future of Work’ hebben gekregen.”
Geert De Coninck
Business Unit Manager Factory Automation
Het Duitse technologieconcern Siemens heeft een geschiedenis die meer dan 170 jaar teruggaat. Het bedrijf is actief in een hele resem sectoren, van industriële installaties over energienetwerken en transportsystemen tot gebouwenbeheer. Wereldwijd heeft Siemens zo’n 293.000 mensen op de loonlijst staan en draait het een omzet van meer dan 57 miljard euro. Bijna 41.000 mensen werken bij Siemens in R&D, zij beschikken over een jaarbudget van 4,6 miljard euro.