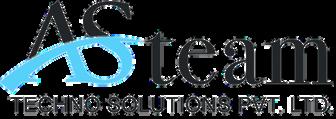
WeprovidesolutionsinAllenBradley(RockwellAutomation), AVEVA(formerlyWonderware), Siemens,Schneider,ABB, PhoenixContact,MOXA,Advantech, Weidmullerandmanymore.....
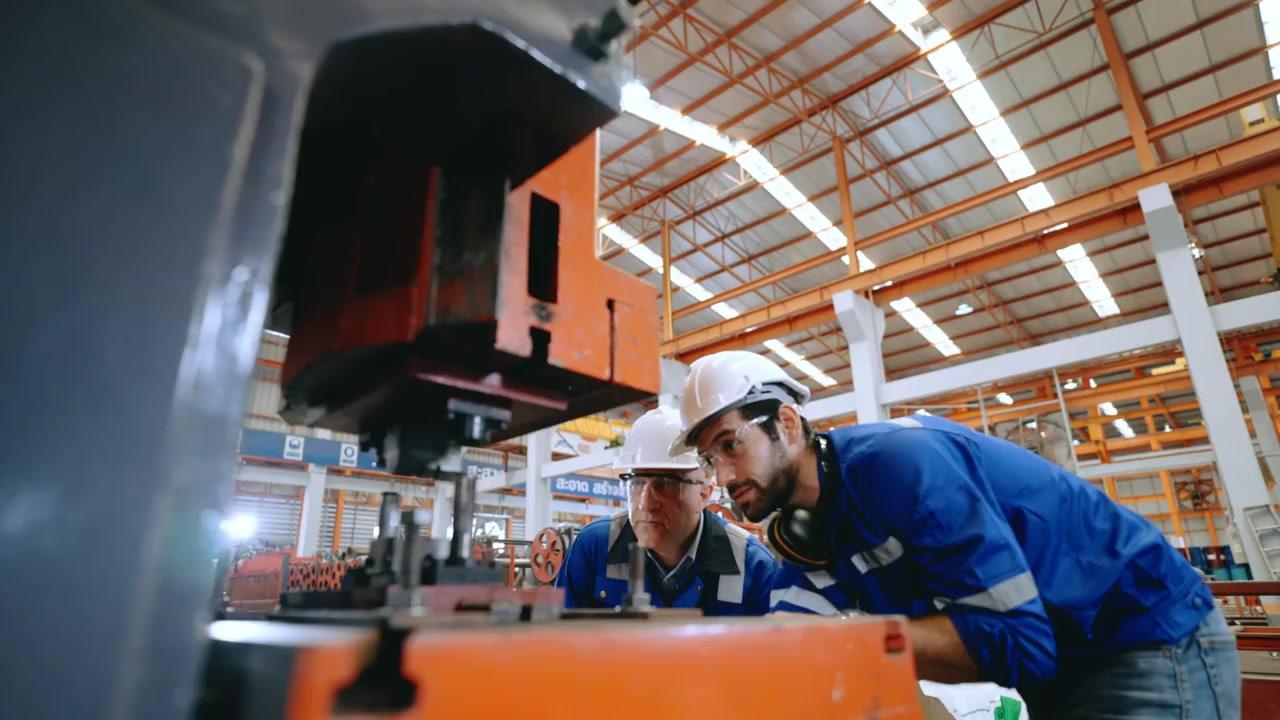
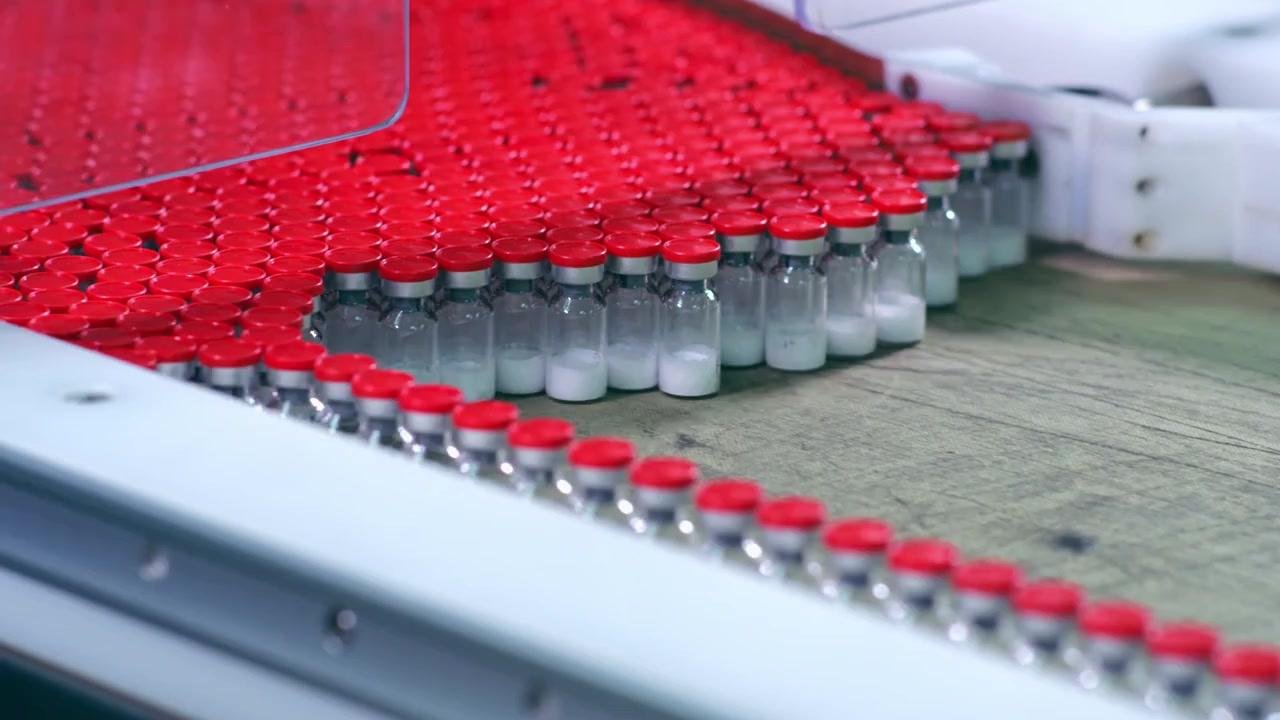
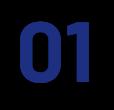
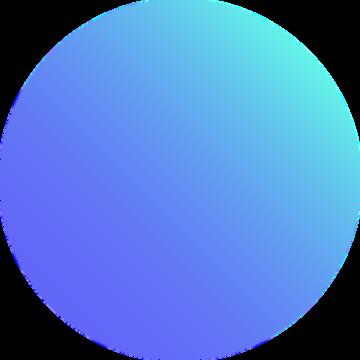
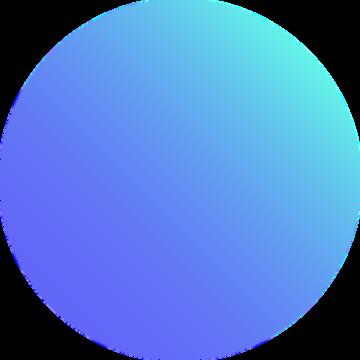
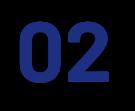
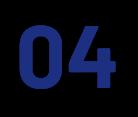
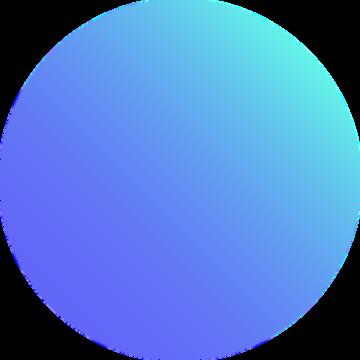
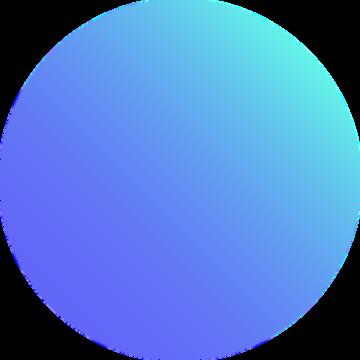
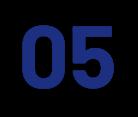
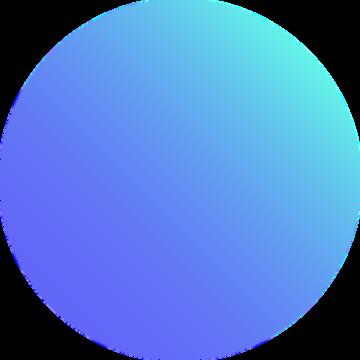
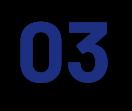
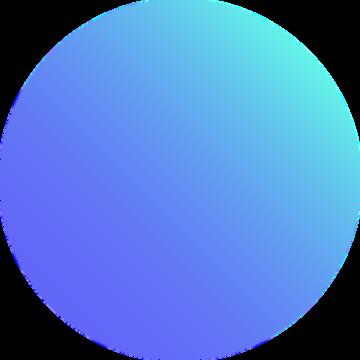
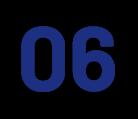
WeprovidesolutionsinAllenBradley(RockwellAutomation), AVEVA(formerlyWonderware), Siemens,Schneider,ABB, PhoenixContact,MOXA,Advantech, Weidmullerandmanymore.....
Kinetix 5500 Servo Drive overview
OffersinnovativesharedAC/DCbusconnectiontoconfiguremulti-axisapplications
Includesdual-portEthernet
Providesdigitalfeedbackthroughasinglecable
Providesdisturbanceobserverthatallowsupto80-1inertiamismatch
Letsyourunservoandinductionmotorsononedriveplatform
SafeTorque-offiscertifiedatISO13849-1PLd/SIL2
UsesLoadObserverreal-timetuningtechnology
Helpssavetimebymitigatingtheneedfortuningeachaxis
Automaticallycompensatesforunknownmechanics,andcompliance,suchasinbelts,flexiblecouplings,andshafts
2198-H003-ERS
2198-H008-ERS
2198-H015-ERS
Kinetix 5500 Servo Drive, 2.5 Amp peak current output, 1 and 3 phase 190 - 528 VAC input Kinetix 5500 Servo Drive, 6.3 Amp peak current output, 1 and 3 phase 190 - 528 VAC input Kinetix 5500 Servo Drive, 12.5 Amp peak current output, 1 and 3 phase 190 - 528 VAC inputOffers innovative shared AC/DC bus connection to configure multi-axis applications
Includes dual-port Ethernet
Provides digital feedback through a single cable
Provides disturbance observer that allows up to 80-1 inertia mismatch
Lets you run servo and induction motors on one drive platform
Safe Torque-off is certified at ISO 13849-1 PLd/SIL 2
Uses Load Observer real-time tuning technology
Helps save time by mitigating the need for tuning each axis
Automatically compensates for unknown mechanics, and compliance, such as in belts, flexible couplings, and shafts
Perform SIL3 Ple Safe Torque Off safety functions over EtherNet/IP
connection
Complete project integration in Studio 5000 Logix Designer for control, safety, and motion
Decrease wiring of safety circuit
Lessen number of components required
Validate your safety system through code reuse
Reduce cabinet space requirements
Perform SIL3 Ple Safe Torque Off safety functions over EtherNet/IP
connection
Complete project integration in Studio 5000 Logix Designer for control, safety, and motion
Decrease wiring of safety circuit
Lessen number of components required
Validate your safety system through code reuse
Reduce cabinet space requirements