2 minute read
A New System
We knew 2020 would be a year of transition—transitioning from building to operating. We want Serve Denton to be known for operational excellence. One organization that is known for excellence in this area is the Toyota Motor Corporation. Their years of manufacturing experience had taught them that small improvements can make a big difference. Toyota’s team members across North America use this philosophy to find better ways of doing things each day. Over time, they had learned this approach can help other organizations, too.
For 25 years, Toyota has shared their knowledge — known as the Toyota Production System — with nonprofits and community organizations to enable them to develop better ways of doing their day-to-day work. So we reached out to them, and together, found solutions to help us become more productive, maximize available resources and improve quality and safety.
The Toyota Production System Support Center (TSSC) is a not-for-profit corporation affiliated with Toyota Motor Engineering & Manufacturing North America, Inc., headquartered in Plano, Texas.
We told them about our challenges, then rolled up our sleeves and met them on the “shop floor” to learn more. They took a close look at how we operate so we could work together to improve. In learning Toyota’s approach, we made it our own and use it every day. We call it the Serve Denton Business System (SDBS). This system is depicted as a house in the figure to the right.
Our customers, the nonprofit partners, have told us the four things they value most from Serve Denton are:
Quality and functional physical spaces to accomplish their mission. Low costs so more funds can go toward programs. Responsiveness when problems occur. A supportive community where people are treated with dignity and respect.
The Serve Denton Business System is an organizational culture created and sustained by four elements:
1. Philosophy — long-term systems thinking. Our management decisions are based on what is best for our nonprofit partners and Serve Denton in the long-term even at the expense of short-term goals.
2. Process — the right process will produce the right results. Work like the tortoise, not the hare. We stop to fix problems, to get quality right the first time. Any employee at Serve Denton has the authority to stop operations when they identify a quality issue. We use standardized processes that enable continuous improvement from the people doing the work. We seek to incorporate visual control into everything we do so no problems are hidden.
3. People — respect, challenge and grow our people toward a vision of excellence. We grow leaders who thoroughly understand the work, live the philosophy and can teach it to others. We will continue to develop exceptional people and teams who follow Serve Denton's philosophy. We respect our extended network of partners and suppliers by challenging them and helping them improve.
4. Problem-Solving — think and act scientifically to improve toward the desired future. Directors are expected to "go-and-see" operations. Without experiencing the situation firsthand, directors will not have an understanding of how it can be improved. We make decisions slowly by consensus, thoroughly considering all options; then implement decisions rapidly. We seek to become a learning organization through relentless reflection.
We want Serve Denton to be known for operational excellence.
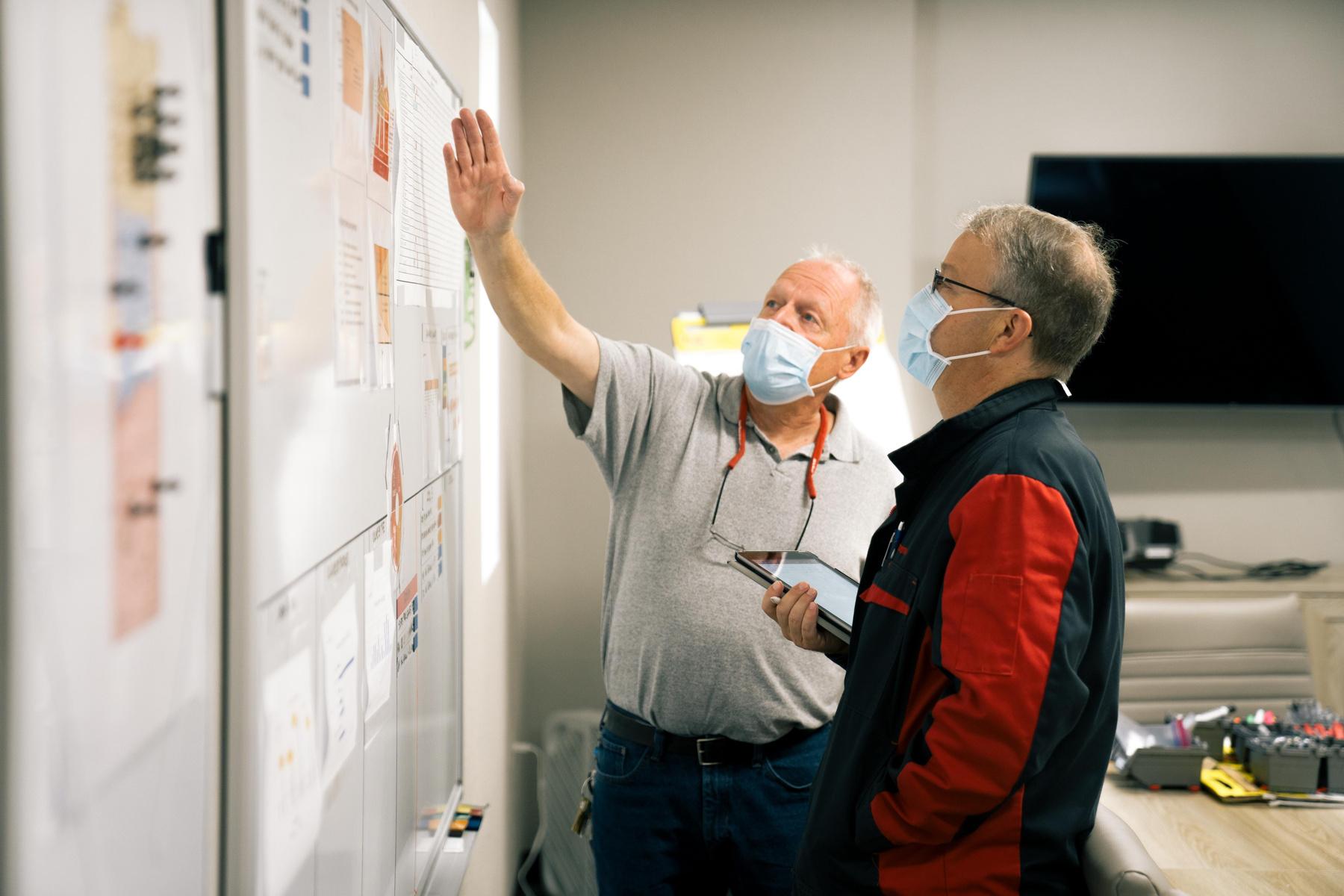