Maximising Efficiency and Quality in Craft Beer Making Through the Latest Machineries
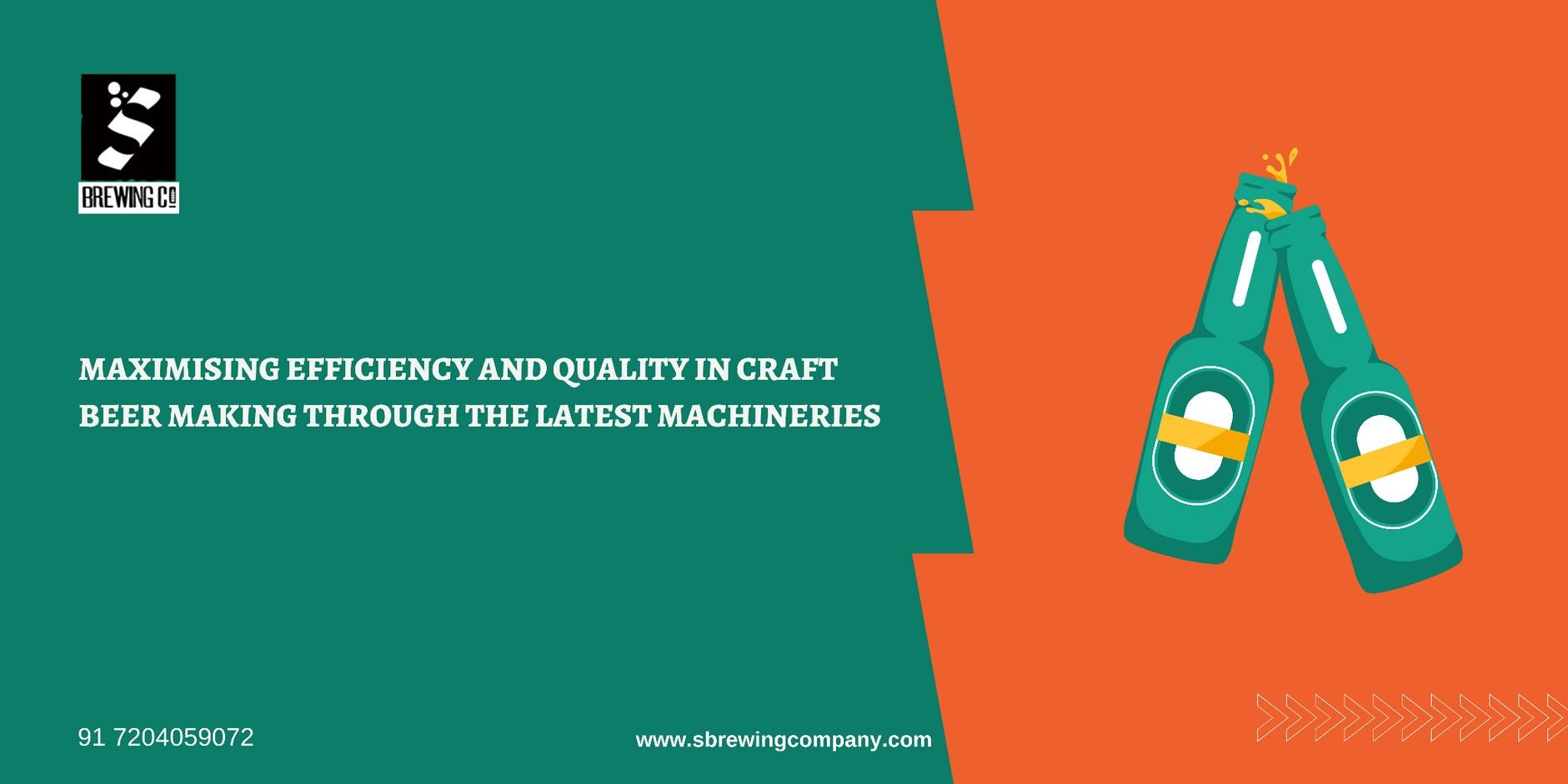
Introduction:
Craft beer has gained immense popularity in recent years, with beer enthusiasts and connoisseurs seeking unique flavours, innovative recipes, and high-quality brews. Craft breweries, both small and large, are constantly striving to improve their production processes to meet the growing demand and maintain the highest standards of quality. In this document, we will explore how the latest machineries can significantly enhance efficiency and quality in craft beer making.
Automated Brewing Systems:
One of the most significant advancements in craft beer production is the emergence of automated brewing systems. These cutting-edge machines integrate various processes such as mashing, lautering, boiling, and fermentation into a single streamlined system. Automated brewing systems offer several benefits:
a. Time Efficiency: These systems eliminate the need for manual labor and reduce the time required for each brewing cycle. Precise temperature control and automated recipe management ensure consistent results, saving valuable time for brewers.
b. Consistency and Quality Control: The automation of critical brewing parameters guarantees consistency in flavor, aroma, and quality across batches. Automated systems can accurately control variables such as temperature, pH levels, and fermentation times, leading to a more refined and predictable brewing process.
c. Data Monitoring and Analysis: Advanced automated brewing systems are equipped with sensors and software that continuously monitor crucial data points during the brewing
process. Brewers can access real-time data and make informed decisions to optimize the production process and maintain quality standards.
Inline Quality Control Systems:
Maintaining consistent quality is paramount for craft breweries, and inline quality control systems play a crucial role in achieving this objective. These systems integrate with the production line, allowing real-time analysis and monitoring of various parameters. Benefits of inline quality control systems include:
a. Enhanced Quality Assurance: Inline systems can automatically detect deviations in key quality parameters, such as colour, pH levels, turbidity, and alcohol content. By identifying and rectifying issues in real-time, breweries can prevent the production of subpar batches and ensure that only top-quality beer reaches the market.
b. Increased Efficiency: Inline quality control systems eliminate the need for manual sampling and laboratory testing, reducing time-consuming processes and improving overall efficiency. By automating quality checks, breweries can expedite production timelines and minimise wastage.
c. Data-Driven Decision Making: These systems generate comprehensive data sets that can be analysed to identify trends, patterns, and areas for improvement. Breweries can use this data to refine recipes, optimise production parameters, and make informed decisions to enhance product quality and consistency.
Yeast Propagation Systems:
Yeast plays a vital role in the fermentation process and has a significant impact on the flavour profile of craft beers. Traditional methods of yeast propagation involve timeconsuming and labour-intensive procedures. However, the latest yeast propagation systems offer numerous advantages:
a. Consistency in Fermentation: Yeast propagation systems ensure consistent and healthy yeast populations, which directly influence fermentation. With precise control over yeast propagation conditions, breweries can achieve reliable and repeatable results in terms of flavour, aroma, and alcohol content.
b. Reduced Contamination Risks: The use of automated yeast propagation systems minimises the risk of contamination from unwanted microorganisms. These systems provide a sterile environment and employ strict protocols, eliminating the potential for off-flavours or spoilage.
c. Scalability: Craft breweries experiencing growth can benefit from yeast propagation systems designed for scalability. These systems allow for the efficient production of larger yeast volumes to meet increasing production demands while maintaining consistency.
Canning and Bottling Technologies:
Packaging plays a vital role in preserving the quality and extending the shelf life of craft beers. The latest canning and bottling technologies offer several advantages over traditional methods:
a. Oxygen Control: Modern canning and bottling systems incorporate advanced technology to minimise oxygen exposure during the packaging process. By reducing oxygen ingress, breweries can maintain the freshness and flavour stability of their beers, resulting in a superior drinking experience for consumers.
b. Increased Speed and Efficiency: Automated canning and bottling systems can handle high volumes of production with minimal manual intervention. These machines can rapidly fill, seal, and label containers, improving overall efficiency and reducing labour costs.
c. Customization and Flexibility: Craft breweries often value the ability to personalise their packaging. The latest canning and bottling technologies offer customizable labelling options, allowing breweries to create unique designs and communicate their brand identity effectively.
Conclusion:
In the dynamic and competitive craft beer industry, maximising efficiency and quality is crucial for success. By embracing the latest machineries, craft breweries can streamline their production processes, reduce manual labour, and achieve consistency and precision in every batch. Automated brewing systems, inline quality control systems, yeast propagation systems, and advanced packaging technologies offer numerous benefits, including time savings, improved quality assurance, data-driven decision making, and enhanced consumer experiences. As the craft beer market continues to evolve, investing in the latest machineries becomes increasingly essential for breweries aiming to stand out and thrive in this vibrant industry.