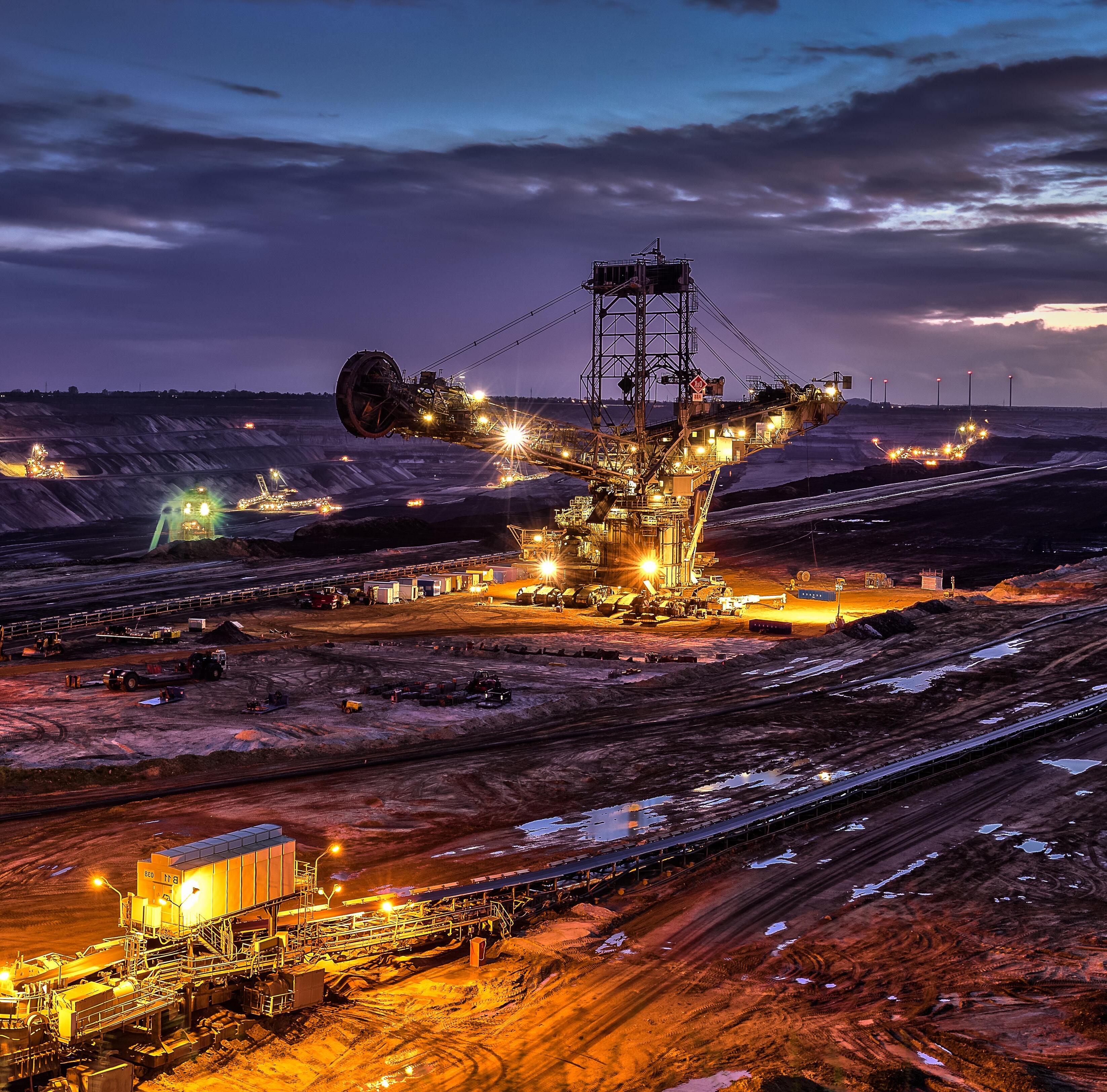

The Southern African Institute of Mining and Metallurgy (SAIMM) is committed to fostering a more diverse and inclusive minerals industry. As part of this commitment, we have relaunched the SAIMM Diversity and Inclusion Committee that seeks to advance the diversity and inclusion in the industry through initiatives and activities that support the professional growth and aspirations of people actively pursuing a career in the minerals industry.
The vision of the Diversity and Inclusion Committee is to :
• Drive Change
• Raising Awareness
• Creating Inclusion
Our purpose is to promote:
• Growth and Progress
• Being part of a solution
• Influence Making changes
• Collaboration
We believe that alone, we can achieve much, together, our potential becomes limitless.
OFFICE BEARERS AND COUNCIL FOR THE 2024/2025 SESSION
President E. Matinde
President Elect
G.R. Lane
Senior Vice President
T.M. Mmola
Junior Vice President
M.H. Solomon
Incoming Junior Vice President
S.J. Ntsoelengoe
Immediate Past President
W.C. Joughin
Honorary Treasurer
W.C. Joughin
Ordinary Members on Council
W. Broodryk M.C. Munroe
Z. Fakhraei S.M. Naik
B. Genc G. Njowa
K.M. Letsoalo S.M. Rupprecht
S.B. Madolo A.T. van Zyl
M.A. Mello E.J. Walls
K. Mosebi
Co-opted Council Members
A.D. Coetzee
L.T. Masutha
Past Presidents Serving on Council
N.A. Barcza C. Musingwini
R.D. Beck S. Ndlovu
Z. Botha J.L. Porter
V.G. Duke M.H. Rogers
I.J. Geldenhuys G.L. Smith
R.T. Jones
G.R. Lane – TP Mining Chairperson
Z. Botha – TP Metallurgy Chairperson
K.W. Banda – YPC Chairperson
C.T. Chijara – YPC Vice Chairperson
Branch Chairpersons
Botswana K. Mosebi
DRC K.T. Kekana (Interim Chairperson)
Johannesburg N. Rampersad
Limpopo M.S. Zulu
Namibia T. Aipanda
Northern Cape Vacant
North West Vacant
Pretoria P.G.H. Pistorius
Western Cape Vacant
Zambia N.M. Kazembe
Zimbabwe L. Shamu
Zululand Vacant
*Deceased
* W. Bettel (1894–1895)
* A.F. Crosse (1895–1896)
* W.R. Feldtmann (1896–1897)
* C. Butters (1897–1898)
* J. Loevy (1898–1899)
* J.R. Williams (1899–1903)
* S.H. Pearce (1903–1904)
* W.A. Caldecott (1904–1905)
* W. Cullen (1905–1906)
* E.H. Johnson (1906–1907)
* J. Yates (1907–1908)
* R.G. Bevington (1908–1909)
* A. McA. Johnston (1909–1910)
* J. Moir (1910–1911)
* C.B. Saner (1911–1912)
* W.R. Dowling (1912–1913)
* A. Richardson (1913–1914)
* G.H. Stanley (1914–1915)
* J.E. Thomas (1915–1916)
* J.A. Wilkinson (1916–1917)
* G. Hildick-Smith (1917–1918)
* H.S. Meyer (1918–1919)
* J. Gray (1919–1920)
* J. Chilton (1920–1921)
* F. Wartenweiler (1921–1922)
* G.A. Watermeyer (1922–1923)
* F.W. Watson (1923–1924)
* C.J. Gray (1924–1925)
* H.A. White (1925–1926)
* H.R. Adam (1926–1927)
* Sir Robert Kotze (1927–1928)
* J.A. Woodburn (1928–1929)
* H. Pirow (1929–1930)
* J. Henderson (1930–1931)
* A. King (1931–1932)
* V. Nimmo-Dewar (1932–1933)
* P.N. Lategan (1933–1934)
* E.C. Ranson (1934–1935)
* R.A. Flugge-De-Smidt (1935–1936)
* T.K. Prentice (1936–1937)
* R.S.G. Stokes (1937–1938)
* P.E. Hall (1938–1939)
* E.H.A. Joseph (1939–1940)
* J.H. Dobson (1940–1941)
* Theo Meyer (1941–1942)
* John V. Muller (1942–1943)
* C. Biccard Jeppe (1943–1944)
* P.J. Louis Bok (1944–1945)
* J.T. McIntyre (1945–1946)
* M. Falcon (1946–1947)
* A. Clemens (1947–1948)
* F.G. Hill (1948–1949)
* O.A.E. Jackson (1949–1950)
* W.E. Gooday (1950–1951)
* C.J. Irving (1951–1952)
* D.D. Stitt (1952–1953)
* M.C.G. Meyer (1953–1954)
* L.A. Bushell (1954–1955)
* H. Britten (1955–1956)
* Wm. Bleloch (1956–1957)
* H. Simon (1957–1958)
* M. Barcza (1958–1959)
* R.J. Adamson (1959–1960)
* W.S. Findlay (1960–1961)
* D.G. Maxwell (1961–1962)
* J. de V. Lambrechts (1962–1963)
* J.F. Reid (1963–1964)
* D.M. Jamieson (1964–1965)
* H.E. Cross (1965–1966)
* D. Gordon Jones (1966–1967)
* P. Lambooy (1967–1968)
* R.C.J. Goode (1968–1969)
* J.K.E. Douglas (1969–1970)
* V.C. Robinson (1970–1971)
* D.D. Howat (1971–1972)
* J.P. Hugo (1972–1973)
* P.W.J. van Rensburg (1973–1974)
* R.P. Plewman (1974–1975)
* R.E. Robinson (1975–1976)
* M.D.G. Salamon (1976–1977)
* P.A. Von Wielligh (1977–1978)
* M.G. Atmore (1978–1979)
* D.A. Viljoen (1979–1980)
* P.R. Jochens (1980–1981)
* G.Y. Nisbet (1981–1982)
A.N. Brown (1982–1983)
* R.P. King (1983–1984)
J.D. Austin (1984–1985)
* H.E. James (1985–1986)
H. Wagner (1986–1987)
* B.C. Alberts (1987–1988)
* C.E. Fivaz (1988–1989)
* O.K.H. Steffen (1989–1990)
* H.G. Mosenthal (1990–1991)
R.D. Beck (1991–1992)
* J.P. Hoffman (1992–1993)
* H. Scott-Russell (1993–1994)
J.A. Cruise (1994–1995)
D.A.J. Ross-Watt (1995–1996)
N.A. Barcza (1996–1997)
* R.P. Mohring (1997–1998)
J.R. Dixon (1998–1999)
M.H. Rogers (1999–2000)
L.A. Cramer (2000–2001)
* A.A.B. Douglas (2001–2002)
* S.J. Ramokgopa (2002-2003)
T.R. Stacey (2003–2004)
F.M.G. Egerton (2004–2005)
W.H. van Niekerk (2005–2006)
R.P.H. Willis (2006–2007)
R.G.B. Pickering (2007–2008)
A.M. Garbers-Craig (2008–2009)
J.C. Ngoma (2009–2010)
G.V.R. Landman (2010–2011)
J.N. van der Merwe (2011–2012)
G.L. Smith (2012–2013)
M. Dworzanowski (2013–2014)
J.L. Porter (2014–2015)
R.T. Jones (2015–2016)
C. Musingwini (2016–2017)
S. Ndlovu (2017–2018)
A.S. Macfarlane (2018–2019)
M.I. Mthenjane (2019–2020)
V.G. Duke (2020–2021)
I.J. Geldenhuys (2021–2022)
Z. Botha (2022-2023)
W.C. Joughin (2023-2024)
Editorial Board
S.O. Bada
R.D. Beck
P. den Hoed
I.M. Dikgwatlhe
M. Erwee
B. Genc
R.T. Jones
W.C. Joughin
A.J. Kinghorn
D.E.P. Klenam
D.F. Malan
D. Morris
C. Musingwini
P.N. Neingo
S.S. Nyoni
M. Phasha
P. Pistorius
P. Radcliffe
N. Rampersad
Q.G. Reynolds
I. Robinson
S.M. Rupprecht
K.C. Sole
T.R. Stacey
International Advisory Board members
R. Dimitrakopolous
R. Mitra
S. Ndlovu
A.J.S. Spearing
E. Topal
D. Tudor
F. Uahengo
D. Vogt
Editor /Chairperson of the Editorial Board
R.M.S. Falcon
Typeset and Published by
The Southern African Institute of Mining and Metallurgy
PostNet Suite #212 Private Bag X31 Saxonwold, 2132
E-mail: journal@saimm.co.za
Printed by Camera Press, Johannesburg
Advertising Representative
Barbara Spence
Avenue Advertising
Journal Comment: Past, Present and Future Insights to be shared by G.R. Lane
President’s Corner: Navigating the complexity of retrenchments and layoffs in the mining industry: In search of a collective ubuntu-based approach by E. Matinde ..................................................................
THE INSTITUTE, AS A BODY, IS NOT RESPONSIBLE FOR THE STATEMENTS AND OPINIONS ADVANCED IN ANY OF ITS PUBLICATIONS.
Copyright© 2025 by The Southern African Institute of Mining and Metallurgy. All rights reserved. Multiple copying of the contents of this publication or parts thereof without permission is in breach of copyright, but permission is hereby given for the copying of titles and abstracts of papers and names of authors. Permission to copy illustrations and short extracts from the text of individual contributions is usually given upon written application to the Institute, provided that the source (and where appropriate, the copyright) is acknowledged. Apart from any fair dealing for the purposes of review or criticism under The Copyright Act no. 98, 1978, Section 12, of the Republic of South Africa, a single copy of an article may be supplied by a library for the purposes of research or private study. No part of this publication may be reproduced, stored in a retrieval system, or transmitted in any form or by any means without the prior permission of the publishers. Multiple copying of the contents of the publication without permission is always illegal. U.S. Copyright Law applicable to users In the U.S.A. The appearance of the statement of copyright at the bottom of the first page of an article appearing in this journal indicates that the copyright holder consents to the making of copies of the article for personal or internal use. This consent is given on condition that the copier pays the stated fee for each copy of a paper beyond that permitted by Section 107 or 108 of the U.S. Copyright Law. The fee is to be paid through the Copyright Clearance Center, Inc., Operations Center, P.O. Box 765, Schenectady, New York 12301, U.S.A. This consent does not extend to other kinds of copying, such as copying for general distribution, for advertising or promotional purposes, for creating new collective works, or for resale.
Honorary Legal Advisers
M H Attorneys Auditors
Genesis Chartered Accountants Secretaries
The Southern African Institute of Mining and Metallurgy 7th Floor, Rosebank Towers, 19 Biermann Avenue, Rosebank, 2196
PostNet Suite #212, Private Bag X31, Saxonwold, 2132 E-mail: journal@saimm.co.za
Telephone (011) 463-7940 . E-mail: barbara@avenue.co.za ISSN 2225-6253 (print) . ISSN 2411-9717 (online)
Assessing the impact of prereduction parameters on Mn ore from the Kalahari Manganese Field by B.M.V. Baloyi, D. Chetty, D. Mchabe ...................................................................................
This paper considers the effect of methane, anthracite, and holding time at a fixed temperature, on the extent of reduction of Mamatwantype manganese ore, primarily from a mineralogical perspective. The aim was to carburise the monoxide Mn phase to Mn carbide, as this is less energy intensive than producing metallic Mn from the monoxide. The ore and products from three experiment sets were analysed. The results show promise for reducing energy consumption for Mn smelting in ferromanganese production.
Plasma soup for the pyrometallurgist’s soul by Q.G. Reynolds, B. Bowman, M.W. Erwee, I.J. Geldenhuys, C. Sandrock, G.A. Venter, B.S. Xakalashe, J. Zietsman
Understanding the behaviour of plasma arcs is an important part of the direct current electric arc furnace smelting processes. In this paper the authors describe the ‘minplascalc’ tool that has been in development for several years. It is a workflow using thermochemistry software to predict the expected gas phase composition through a given process, followed by plasma property calculations using an open-source software tool. The workflow is applied to the calculation of plasma properties for a variety of historical and current pyrometallurgical processes, and the results are compared.
Design and development of lightweight Fe-Mn alloys for storage and transportation of liquified natural gas (LNG) —
Computational materials modelling study by M. Phasha, L. Mampuru, D. Mkhonto, J. Moema
In seeking to find suitable alternative materials to build infrastructure for cryogenic applications, this study employed density functional theory (DFT) based first-principles computational materials modelling technique to investigate the structural, thermodynamic and magnetic properties of binary Fe-Mn alloy composition in competing FCC, HCP, and BCC crystal structures. It was possible to unravel the key underlying elastic properties that are directly correlated to experimental tensile strength and high toughness in binary Fe-Mn alloys. The current predicted properties and the deployed approach will serve as a benchmark from which further alloying will be conducted.
A macro-scale approach to computational fluid dynamics modelling of the reduction of manganese ore by hydrogen by M.I. Khama, Q.G. Reynolds, B.S. Xakalashe
This research investigates hydrogen as an alternative source for the reduction of manganese ore. Hydrogen results in the structural changes in the intermediate products, which might limit the diffusion of the reactant gases through the pores. The current work uses CFD models to predict the degree of reduction in a shaft furnace under hydrogen reducing conditions. The results indicate that advection contributes significantly towards the overall transport of hydrogen to the reaction sites. Porosity of the final product was found to be higher than porosity of the raw material.
121
129
Evaluating the corrosion resistance of different materials used in friction rock stabilisers in different underground environments by T.P. Chidakwa, T.R. Stacey ............................................................................................ 161
This study investigated the corrosion rates of various steel types and coatings used for friction rock stabilisers in a deep-level gold mine under diverse underground environmental conditions. Results revealed that environmental variations significantly influence the corrosion performance of different materials and coatings. Duplex coatings demonstrated the highest corrosion resistance. Zinc-based coatings provided moderate protection, while 3CR12 stainless steel and uncoated S420 carbon steel exhibited comparatively poor resistance.
Analysis of pressure drop and hold-up during vertical transport of limestone slurry in lean phase and heterogeneous regime by P.K. Senapati, J.K. Pothal, A. Dubey, R. Barik, S. Basu 173
The aim of this paper was to study the characteristics of limestone particles during their transportation from open cast mines through pipes. The influence of four different size fractions of limestone on pipe flow characteristics during vertical transport in a 100 mm hose pipe was investigated. Results indicated that there was no substantial increase in pressure drop of slurry samples in the range of concentrations studied, particle size, and low to medium range mixture velocities with respect to water run head loss data. The hold-up for the larger size fractions was found to be significant as compared to smaller size fractions, possibly due to terminal settling velocities of individual fractions of the studied samples.
As the incoming President of SAIMM, I have been reflecting on my 34-year career in the mining industry and the lessons I have learned; lessons I can leverage to lead SAIMM and support the industry during my tenure. Writing this month’s journal comment provides an opportunity to share part one of some of these insights.
Each role, as well as the individuals and teams I have worked with throughout my career, have shaped and expanded my experience and perspectives on how to make a difference and add value.
I began my journey as a young engineer, developing and commissioning new mining operations in Africa for a multinational mining house. Later, I pivoted to mine optimisation modelling and software development, aiming to transform mine planning as the co-founder of multiple startup businesses.
This experience reinforced my understanding of the technical and safety challenges in the mining industry, the inherent risks and variability in ore body characteristics, and the complexities of managing a dynamic, interconnected value stream of activities to mine and process ore. Additionally, a lack of management focus, caused by an overwhelming number of improvement projects and initiatives that are often poorly implemented, means that many of these efforts fail to add value.
Later in my career, after being exposed to the tools of Lean Six Sigma and the Theory of Constraints, I learned that using the right decision-making tools enables management to focus on the right leading indicators that add value. However, it would be remiss of me not to mention that none of these methodologies alone adequately address the challenges in mining. In fact, some principles of Lean can limit performance due to the inherent variability in ore and processing.
The mining industry also faces significant challenges in implementing new technology. We often underestimate the people-related challenges involved and fail to effectively design and manage the necessary changes in work processes, roles, and employee buy-in. The promises of Big Data and Industry 4.0 (IR4) are recent examples of this. In my opinion, current change management thinking and execution is not adequate for our rapidly changing future business landscape.
A common phrase I have heard over the years is: ‘Our mine is unique and more challenging, so what worked at mine XYZ won’t work here’.
To determine whether we can learn from other industries, I explored insights from the automotive sector, particularly Toyota’s leadership in systems thinking, which leverages Lean Six Sigma and a people-centric approach. The automotive industry has seen massive productivity increases over the past decade, whereas the mining industry has experienced a decline over the same period. A recording of my keynote address, ‘Has Technology Generated ROI?’, from the 2015 International MPES Conference, is available on YouTube, where I discuss these insights further. https://www.youtube.com/watch?v=qDN3lGriJas
Over the past eight years, in a new business venture, I have been able to test and refine these hypotheses across multiple industries worldwide. Whether in chocolate or biscuit manufacturing, a tissue paper mill and converting line, the production of lab-grown diamonds, product lifecycle management for high-tech equipment R&D and manufacturing, or ore moving through a value stream, the challenges remain the same. Each industry has its own technical requirements, whether in chemical engineering, metallurgy, or mining engineering, but the fundamental challenge of managing and maximizing the flow of material through a complex system of interconnected activities, as well as the impact of performance variability on this flow, is identical across industries.
What was even more revealing was that these challenges persist regardless of technological sophistication. Whether in a greenfield digital manufacturing facility equipped with expert control and real-time data reporting in dedicated operating centres or a brownfield operation reliant on paper and Excel spreadsheets for data collation and reporting, the same issues exist. In fact, we found that, in many instances, more real-time data creates more noise, uncertainty, and reactive responses to variance, leading to a further dilution of management focus – leadership time in a day is also a constraint. In many cases, general managers of production facilities spend over 75% of their time explaining yesterday’s poor performance.
In every example, production success is driven by individual effort; people working hard across all engineering disciplines and business functions, often relying on a handful of ‘heroes’ to achieve equipment reliability and production targets. One clear symptom of this is the excessive number of meetings employees at all levels attend weekly; meetings that serve no clear purpose and produce no agreed upon outcomes.
With all the technological advances in the world, we have neglected to focus on the people within this increasingly complex business system. The advent of artificial intelligence will also have a profound impact and must be designed into the future operating model.
In my next journal comment I will begin to unpack the learnings and requirements of an integrated operating model that addresses these challenges.
G.R. Lane
TNavigating the complexity of retrenchments and layoffs in the mining industry: In search of a collective ubuntu-based approach
he mining industry is an integral part of the South African economy. According to the Minerals Council of South Africa, the mining industry contributed around 425 billion rands (or 6.2%) to the country’s GDP in 2023. In the same period, the mining industry also employed over 470,000 people, thereby contributing significantly to the socioeconomic wellbeing of mining and nearby communities. More details on the most recent statistics are available here: https://www.mineralscouncil.org.za/reports/2023/. As has been in the past, the mining industry remains a cornerstone and plays an inseparable role in the economy through multiplier contributions, such as investing in social projects and infrastructure, training and skills development, health and education.
The cyclical nature of mining sector profitability presents unprecedent challenges to the long term stability of the industry. Despite the net-positive impact of the clean energy transition on some commodities, domestic and global headwinds such as capital scarcity, declining commodity prices, disruptive technologies, rising operating costs, and harsh domestic economic conditions, among others, continue to present long-term viability challenges to most mining operations in the mining sector. These industry headwinds naturally affect the mining sector differently, with some operations being affected more adversely than others. The platinum group metal (PGM) industry, for example, was severely impacted by the long-term decline in commodity basket prices for PGMs in the global markets, mostly driven by the growing concerns about the demand disruption from electrical vehicles.
In order to survive these headwinds, the mining industry finds itself with the need to cut costs and implement drastic restructuring strategies. The recent cost cutting and restructuring measures implemented by some companies in the South African mining industry naturally resulted in the significant reduction in the workforce through retrenchments and layoffs. Within the last two years, notable retrenchments and layoffs were observed across the various commodities in the sector, with the PGM sector being the most affected. Being one of the largest employers within the South African mining industry, employing over 38% of the total mining workforce in 2023, any impact on the PGM industry will have an oversized weighted impact on the overall employment statistics and perception of the mining sector. Regrettably, retrenchments and layoffs are not common to the mining sector alone, but are also being experienced across the other core segments of the economy. Recent public reports attest to this painful reality in the manufacturing sector as well.
Retrenchments and layoffs can be viewed as an inevitable consequence of every bad business cycle. While retrenchments and layoffs might seem inhumane, they can sometimes be necessary, albeit drastic, measures to ensure the survival of the company during economic downturns. This means that implementing cost reduction and restructuring decisions can sometimes be a matter of survival and a necessary step to ensure long-term business continuity. However, if managed properly and conducted in good faith, retrenchments and layoffs can result in improved efficiency and profitability growth in the long term, leading to future protection of jobs and improvement in employee welfare.
Retrenchments and layoffs represent some of the most challenging and delicate decisions any organisation can make. Nonetheless, retrenchments and layoffs should be used as a last resort and should not be used as a tool to solve challenges emanating from temporary economic shifts, Trump-like
geoeconomic disruptions, and poor strategic decisions by management. Due to the irreversible damage to organisational brand and the emotional and socioeconomic wellbeing of employees and affected communities, there is a strategic need to balance humanity over short-term profits. Although easier said than done, a more feasible approach would be to focus on cutting costs through improving operational efficiency and business model innovation, rather than arbitrarily reducing the employee headcount. In the worst case scenario, it is also important to explore alternative and more humane strategies to reducing headcount, such as natural attrition, voluntary separation, and early retirement, among others. Open communication and taking collective responsibility beyond what are mandated by national labour laws and company policies are crucial requirements to navigating the complexity and impact associated with a retrenchment process.
Job loss is always an emotive process. In addition to the usual feelings of anger, resentment, and sense of inadequacy, the feelings associated with a lack of job security often leads to the poor physical and mental health of affected individuals and their families. Since the impact of retrenchments and layoffs extend beyond the affected employees to their families and communities, there is a need for a collective approach to explore viable ‘beyond the fence’ support to assist affected individuals and communities to cope with the changes and losses. For example, collaborative efforts involving the state institutions, mining companies and their suppliers, industry bodies, organised labour, communities and local municipalities, among others, can have significant impact in assisting the affected individuals through community based social and enterprise development projects. It is also important to retain an active register of affected employees and giving them first preference in case of a successful turnaround.
A people oriented strategy is also required to support those affected by restructuring processes leading to a reduction in the workforce. For example, a longer term view on career transition support, through reskilling and multi-skilling the individuals who are at risk to acquire artisanry, technical and enterprise skills, can help to mitigate the socioeconomic impact of retrenchments and layoffs. Reskilling the workforce through artisanal, professional, and postgraduate training also increases employability of effected individuals in transversal industries. These approaches can only be successful if implemented early in one’s career so as to increase the chances of internalisation of the knowledge and skills, which in themselves are core determinants to building individual self-efficacy and the likelihood of entrepreneurial success. As SAIMM, we offer a wide variety of self-mastery and industry relevant CPD-accredited training courses, conferences, and webinars that can assist individuals to navigate the complex self-learning space. Self-learning through the various open access online platforms can also increase one’s ability to acquire new skills and adapt to shifting employment trends.
In conclusion, retrenchments and layoffs are very emotive issues. Thus, the purpose of my article is neither to take a moral position against retrenchments and layoffs, nor is it an attempt to glorify workforce reduction as a viable and moral corporate cost-cutting measure. Rather, the sole purpose of this article is to stimulate a healthy and constructive debate on how we can collectively navigate the complex needs for business continuity while mitigating the emotional and socio-economic impact on affected colleagues and communities.
E. Matinde President, SAIMM
Affiliation:
Mintek, Randburg, South Africa
Correspondence to:
B.M.V. Baloyi
Email: BebertoB@mintek.co.za
Dates:
Received: 25 Oct. 2024
Published: March 2025
How to cite:
Baloyi, B.M.V., Chetty, D., Mchabe, D. 2025. Assessing the impact of prereduction parameters on Mn ore from the Kalahari Manganese Field. Journal of the Southern African Institute of Mining and Metallurgy, vol. 125, no. 3, pp. 121–128
DOI ID:
https://doi.org/10.17159/2411-9717/770/2025
ORCiD:
B.M.V. Baloyi
http://orcid.org/0000-0003-1332-8374
D. Chetty
http://orcid.org/0000-0002-1913-7598
D. Mchabe
http://orcid.org/0000-0002-9422-6750
This paper is based on a presentation given at the Mintek@90 Conference 2024, 11-12 November 2024, Sandton Convention Centre, Johannesburg, South Africa
by B.M.V. Baloyi, D. Chetty, D. Mchabe
Abstract
South Africa accounts for the largest global manganese ore production share, primarily from its Kalahari Manganese Field deposit. Despite this, domestic smelting is beset by energy constraints, resulting in most ore being exported for smelting. Mintek is investigating energyefficient pathways for ore reduction, specifically undertaking prereduction tests to reduce energy consumption for manganese smelting. The present contribution considers the effect of methane, anthracite, and holding time, at a fixed temperature, on the extent of reduction of Mamatwan-type ore, primarily from a mineralogical perspective. In particular, the aim was to carburise the monoxide Mn phase to Mn carbide, as this is less energy intensive than producing metallic Mn from the monoxide. Based on thermogravimetric test results, the ore and products from three experiment sets were analysed using X-ray diffraction and scanning electron microscopy to assess the phases and textures present. The findings show that carburisation of manganese monoxide and its equivalents is most advanced under conditions of 8% anthracite, 10% methane, and 60 minutes of holding time, thus confirming with the thermogravimetric data. These results show promise for reducing energy consumption for Mn smelting in ferromanganese production.
Keywords manganese, prereduction, mineralogical characterisation and low energy
Manganese is an important metal used in a wide range of industries (battery, steel, electronics, and alloys). South Africa, with its world-class manganese resources, is a significant contributor to the global production of manganese. The country's large manganese mine operations over the recent years have further solidified its position in the industry. While most of the manganese produced globally is sourced from South Africa, most of this ore is exported to other countries for beneficiation. The remainder of the ore not exported is used to feed the local smelters. South Africa also has the potential to become a major player in the smelting space, but key data show that there are issues that have delayed the initiative to expand this industry. For example, the data show that South Africa has reduced its smelting capacity, where previously, 50% of the ore produced was smelted locally compared to only 16% of the ore smelted locally, as recorded in 2014 (Steenkamp et al., 2018). The decrease in the amount of ore processed locally is also linked to the increased mine production over the years, whereas the expansion of local smelting industries did not keep up to accommodate the increased mine production. The non-growth of this industry was mostly due to the instabilities in global manganese prices, energy costs, and availability. Over the years, these issues affected the industry, leading to the closure of some operations and, in some cases, resulted in job losses. In addition to that, the power utility company in the country has been struggling to meet the demand, which is projected to increase over the coming years. This is because of the projected increase in the population and the creation of new industries to power up the economy. As stated, a considerable amount of energy is required to produce manganese alloys, which comes with high cost implications. South Africa is currently facing energy issues related to the continuous increase in electricity tariffs and the unavailability of energy. In addition, the increased carbon taxes and environmental impact issues have contributed to a reduction in domestic smelting capacity. Finding new ways, or improving existing processes, to recover ferromanganese and silicon manganese alloys is much needed. A research project at Mintek aims to contribute to finding efficient ways to achieve higher recoveries of ferromanganese and manganese alloys from prereduced manganese using a CH4-H2-Ar gas mixture while lowering energy consumption. The present contribution focuses on the mineralogy of a selected low-grade ore from the Kalahari Manganese Field (KMF), aiming to understand the effect
of different parameters (temperature, holding time, and methane concentration) during its prereduction on various products derived from a series of tests.
The Kalahari Manganese Field (KMF) in South Africa, is a giant ore body that accounts for ~75% of the world's land-based manganese ore resources. This region alone produces most of the mined Mn ore globally, at ~38% annually, compared to other countries (USGS, 2024). The Mn ore is hosted within the Hotazel Formation, occurring in three distinct layers interbedded with banded iron formation and hematite lutite layers. The KMF is characterised by three ore types based on their mineral assemblages and associated alteration styles. The Wessels ore type is high-grade (> 45% Mn), predominantly made up of Mn oxides, and represents a hydrothermally altered ore. The Mamatwan ore type is a low grade ore of Mn at ~38% and appears to be the least altered ore type, comprising Mn oxide and carbonate mineral assemblages. Intermediate characteristics of the Wessels and Mamatwan ore types characterise the supergene ore type. This ore has a variable Mn grade of 38% to 45% and is rich in both Mn-bearing carbonates and oxides, as well as containing oxyhydroxides typical of supergene ore. The Mamatwan type represents the largest portion of the resource, at ~97%, followed by the Wessels type at ~3%, and Supergene type at ~1%. Geographically, the Mamatwan type occurs throughout the ore body, whereas the Wessels type is restricted to the northern part of the deposit, and the Supergene type occurs along the eastern and northern sub-outcrops of the KMF. The Mn carbonate assemblages include kutnohorite, Ca(Mn,Mg)(CO3)2, Mn-calcite, (Ca,Mn)CO3, and Mn oxide phases include hausmannite, Mn2+Mn23+O4, bixbyite, (Mn,Fe)2O3, and braunite II, Ca(Mn3+Fe3+)14SiO24. The supergene phases include manganomelane, KMn4+7Mn3+O16, manganite, MnO(OH) and pyrolusite, MnO2.
Prereduction of Mn ores
Pyrometallurgical processing of manganese ore is an energyconsuming activity. Over the past years, new processes have been introduced to curb the high energy consumption during this process. One of these new ways was to introduce a prereduction stage prior to the final stage of ore smelting. Considering that the reduction of stable oxides requires higher energy inputs, the prereduction of Mn ores using gas reductants such as CH4-H2Ar gas mixtures allows for reduction to take place at relatively lower temperatures (Bhalla, 2018). The reduction of the Mn ore at lower temperatures translates to lower energy inputs. In addition, during the traditional smelting process, mineralogical data is not necessarily required; rather, elemental chemistry data is preferred for assessing the ore feedstock. This manner of operation does not consider the type of minerals that host Mn. Besides that, ore body variability is generally quite common due to different geological processes that take place, as is evident from the different ore types present in the KMF, as well as variability within specific ore types (e.g., Chetty, 2008). These processes may result in the ore containing variable mineralogical compositions in terms of the Mn host mineral contributions to the grade. As such, the use of elemental chemistry data alone will not be able to account for the types of minerals present at any given geographical location of the ore body. The formation and decomposition of minerals is an energyconsuming activity; each mineral phase has unique requirements. Given that each mineral phase requires a variable amount of energy to decompose, it is thus necessary to understand the behaviour of mineral phases in the feed sample prior to processing. The
typical reactions that may take place during the reduction stage, as presented by Reactions 1 to 10 (Wellbeloved et al., 1990; Tangstad et al., 2015; Chetty, Gutzmer, 2018) are provided in the following. Based on these reactions, the reduction of higher Mn oxides occurs exothermically as opposed to the endothermic reaction associated with the lower Mn oxides.
The desirable carbothermic reduction reactions for higher Mn oxides in Reaction 1 to 8 show that their reduction is accompanied by the release of CO2 at temperatures above 800 ⁰C. Since the ore also consists of other phases such as carbonates, etc., the following Reactions 9 and 10 for calcite and dolomite may take place, respectively. Generally, the reactions are highly endothermic, and carbonate decomposition results in the release of CO2.
Reactions 1 to 10 represent the prereduction of higher manganese oxide and the decomposition of carbonates. These reactions take place in the prereduction zone. Reactions 11 to 15 represent the carburisation of MnO species using methane gas (Rankin, Van Deventer, 1980; Rankin, Wynnyckyj, 1997). These carburisation reactions take place at temperatures ranging from 1000⁰C to 1300⁰C (Kuo, Persson, 1954). The most likely carbide to be formed under these conditions is Mn7C3. However, Mn5C2 also forms, as given by Reaction 15.
Methodology
Raw material
Low-grade, Mamatwan-type manganese ore from the KMF, anthracite, and organic binder (Alcotac@ CB6), which is a copolymer of acrylic acid and acrylamide (from BASF, South Africa), were subjected to pelletisation. Before pelletising, the respective raw materials were characterised with regard to proximate analysis (anthracite – using the ASD-MET-C16/26 method) and chemical analyses (manganese ore – using the Mintek internal methods of ICP FEMN and XRF Q SCAN).
Thermogravimetric analysis
A series of thermogravimetric experiments to measure the mass loss during the prereduction of manganese composite pellets was conducted in a top loading thermogravimetric analyser housed in Mintek’s Pyrometallurgy Division Laboratories. The schematic representation of the experimental setup can be seen in Figure 1, where the vertical type resistance furnace is connected to a proportional-integral-derivative (PID) controller. The temperature of the hot zone was maintained at ± 5 °C.
A continuous flow of argon gas at a rate of 1 L/min was introduced into the furnace to control the atmosphere. Pellet samples (5 g–15 g) were placed in a basket positioned retort fixed on a balance with high accuracy (0.1 mg). The data logging computer recorded the mass changes of samples. The temperature was ramped to a desired temperature (1000°C, 1200°C, or 1300°C) at a rate of 10°C/min, where it was kept constant. At a set temperature,
the reaction gas (consisting of 5–10 vol % CH4, 50 vol % H2, and balance Ar) was introduced and allowed to flow at a set flow rate (2 L/min) until no mass change was observed. After the prereduction experiment, the prereduced pellets were cooled to room temperature in an inert argon environment (i.e., the TGA was flushed with argon flowing at 1 L/min until room temperature was attained). The processes that are considered to take place are moisture removal, devolatilisation of anthracite, pyrolysis of the binder, pyrolysis of anthracite, reduction of manganese ore, and carburisation of oxides derived from manganese ore.
Mineralogical analysis was carried out on a total of 11 samples. Of those, one was the ore sample, sourced from the KMF, and the others were prereduced samples. The prereduced samples are made up of 3 batches representing product sets from different experimental conditions (Table 1). Two representative portions for all the samples were obtained post-splitting. The first portion was pulverised and subjected to qualitative XRD analysis for relative modal abundances, with quantitative mineral abundance determined on the ore sample only. This is because prereduced samples were expected to contain intermediate phases of poor or illdefined structure. The other portions were prepared into a polished section and subjected to the SEM to obtain backscattered electron (BSE) images and energy dispersive spectrometry (EDS) analysis to track changes between the baseline ore sample and prereduced samples.
Experimental set-up for the different parameters investigated with the controlled parameters
Results and discussion
TGA results
The observed results from the TGA experiments are summarised in Figure 2. In the experiments to establish the optimum holding time, the weight-loss percentages were observed (Figure 2(a)) to reach a plateau at holding times of around 50 minutes. This observation informed that the tests in this study be carried out at a holding time of 60 minutes. This holding time agrees with the holding times of Anacleto et al. (2004), who reported that the formation of ferromanganese carbide was completed in 120, 60, and 45 min at 1000°C, 1100°C, and 1200°C, respectively. Despite the reduction being considered to increase with the increasing temperature (Ostrovski et al., 2004; Kononov et al., 2009), the temperature of 1200°C was observed to be optimum (Figure 2(b)). The decrease in the rate and extent of reduction on increasing the temperature to 1300°C can be associated with sintering and formation of semiliquid silicate slags. Under the experimental conditions of this study, the effect of increasing anthracite content was observed to be insignificant. This observation is consistent with the results reported by Kononov et al. (2009) for carbon content ranging from 12 to 30 w/w%.
Ore characterisation
As observed in Tables 2 and 3, the ore sample has chemical and mineralogical concentrations consistent with a Mamatwan ore type. The major manganese-bearing minerals include braunite, hausmannite, and kutnohorite. Based on observations made from SEM, the sample can be set apart from the prereduced samples
because of the well-preserved distinct textures observed (Figures 3A and B). Meanwhile, the prereduced samples display irregular textures. In the ore sample, the hausmannite phase appears to occur interstitially in a matrix of kutnohorite and serpentine. (Figure 3A). The SEM observations are aligned with the quantitative XRD analysis, which includes similar phases such as kutnohorite, hausmannite, calcite, and bixbyite (Figures 3A and B), identified in both techniques.
Mineralogical characterisation of the prereduced products
It is clear from the mineralogy of the prereduced samples that reduction has taken place. The extent to which reduction has
Table 3
Bulk mineralogy of the ore sample
Table 4
Qualitative relative phase proportions in four prereduced samples, investigating the effect of methane concentration on reduction extent
Compound Name
Manganosite MnO x x x
Iron manganese oxide (Fe,Mn)O xx
Manganese magnesium oxide (Mg,Mn)O
Manganese carbide A Mn7C3
Manganese carbide B Mn5C2
Iron manganese
Gehlenite
Bredigite
Kirschsteinite
Fe0.3Mn0.7 x
Ca2Al(AlSiO7) xx
Ca7Mg(SiO4)4 xxx
Graphite C
Trace (< 5% wt.% x), minor (5-15 wt.% xx), intermediate (15-30 wt.% xxx), major (30-50 wt.% xxxx) and predominant (>50 wt.% xxxxx)
taken place is reflected by the presence of manganese oxides and manganese carbides in accordance with Reactions 1 to 8 and 11 to 15, respectively. The extent of reduction for samples investigating the effect of methane concentration on prereduction was confirmed through XRD analysis. The relative abundances of phases identified during reduction for the methane samples are given in Table 4. The 0% methane sample is primarily made up of bredigite, with gehlenite, manganese carbides, iron manganese oxide, and manganese magnesium oxide that range from minor to intermediate concentrations. Meanwhile, the 10% methane sample has a higher relative abundance of manganese carbides in major to minor proportions, with lower abundances of bredigite present. Based on these results, the concentration of methane does influence reduction extent, and this is shown by the variable relative
abundances of reduction indicator phases such as manganese carbides (Mn7C3 and Mn5C2), iron manganese, and manganosite (MnO), with its solid solution equivalents manganese magnesium oxide and iron manganese oxide.
Table 5 presents the relative mineral abundances of the samples, investigating the effect of anthracite concentration on the prereduction of Mn ores. The XRD analysis reveals a relatively high presence of reduction indicator phases (as defined in the aforementioned). Similar to the trend reported for the methane samples, the relative abundances of phases present in the anthracite samples are variable with increasing abundances of anthracite. The 0% anthracite sample records a relatively lower combined abundance of the reduction indicator minerals as opposed to the relative higher abundance recorded in the 12% anthracite sample.
Table 5
Qualitative relative phase proportions in three pre-reduced samples investigating the effect of anthracite concentration on reduction extent
Compound Name Ideal
Manganosite
manganese oxide (Fe,Mn)O
Manganese magnesium oxide (Mg,Mn)O
Manganese carbide A
Manganese carbide B Mn5C2
Iron manganese
Gehlenite
Bredigite
Kirschsteinite
Fe0.3Mn0.7
Ca2Al(AlSiO7)
Ca7Mg(SiO4)4
CaFe2+SiO4
Graphite C
Iron Silicon Fe11Si5
Not detected (-), trace (< 5% wt.% x), minor (5-15 wt.% xx), intermediate (15-30 wt.% xxx), major (30-50 wt.% xxxx) and predominant (>50 wt.% xxxxx)
Figure 3—Backscattered electron images of the ore and prereduced samples under different conditions (A-F). (A-B) Ore sample with original textures. (C-D) Manganese carbides, manganese magnesium oxides, and iron-manganese with silicate phases for the methane and anthracite samples respectively, in an altered texture from that of the ore. (E-F) Reaction rims of manganese carbides and oxides with enclosed phases of manganese calcium oxides represent partially reduced particles. He – hematite, Br – braunite, Kut – kutnohorite, Ha – hausmannite, Ca – calcite, Bx – bixbyite, Rom – romanechite, Serp - serpentine, Mn – manganese carbide, MMO – manganese magnesium oxide, G – gehlenite, Bred - bredigite, IM – iron manganese, MnO – manganese oxide, and MnCaO – manganese calcium oxide phases
The vice versa applies to other of the phases present in the samples. Furthermore, the results reveal that the increase in anthracite concentrations corresponds with the formation of new phases. These phases are in the 8% anthracite sample where graphite is observed, and the 12% anthracite sample, in which the iron silicon phase is observed.
The relative phase abundances in the samples investigating the effect of holding time are presented in Table 6. The observations made are in line with the reduction reactions presented in this paper. The relative abundances of the reported phases are variable, and it is evident that reduction has occurred. The XRD analysis does not detect the presence of manganosite, magnesium manganese oxide, and iron manganese oxide in the 60- and 90-minutes samples, as opposed to the 20-minute sample where these phases were detected. Higher relative abundances of manganese carbides and iron manganese phases are recorded instead, which could suggest the additional time allowed for more extensive reduction to take place. As such, the absence of manganosite and its solid solution equivalents may be due to the carburisation process, as given by Reactions 11 to 15. Additionally, a slight decrease in the relative abundance of Mn7C3 is observed from the 60-minute to the 90-minute sample, possibly due to a change in environment. A change in environment over time may favour the formation of other phases in the sample, such as the increased relative abundances of iron manganese and other alloy phases.
Overall, the XRD analysis confirmed that reduction had taken place, and that the manganese ore was predominantly reduced to Mn7C3 and Mn5C2. The relative abundance of Mn7C3 was higher than that of Mn5C2 across all the prereduced samples analysed. Other species associated with reduction include iron manganese, manganese iron carbide, manganosite, and the solid solution equivalents of manganosite. The XRD highlights that the increase of methane gas and anthracite concentrations during reduction corresponds to optimal results through the formation of carbides. Finally, the extent of reduction of manganese oxides based on the results appears to depend on the holding time, hence the high relative abundance of manganese carbides in the 60-minute sample, similar to the study conducted by Bhalla and Eric (2015).
Observations made through the SEM-EDS analysis for the prereduced samples highlight the presence of textures different from those of the ore sample, with various phases representing the original minerals, reduced oxides, and increased silicate formation compared with the ore. All the identified phases host Mn in varied concentrations (refer to Table 6 for the abundances of the phases identified). The calcium manganese oxide is characterised by a porous texture, indicative of CO2 loss from original carbonates, and consistent with reduction textures with rims of manganese oxide and carbides (Figures 3E and F). The phases that form part of the reduced material include manganese carbides, iron manganese, manganese magnesium oxide, and manganese oxides characterised
Table 6
Qualitative relative phase proportions in three prereduced samples investigating the effect of holding time concentration on reduction extent
Compound
Manganosite
Manganese magnesium oxide (Mg,Mn)O
Manganese carbide A
Manganese carbide
Manganese
Gehlenite Ca2Al(AlSiO7)
Bredigite Ca7Mg(SiO4)4
Kirschsteinite
Calcium silicate
CaFe2+SiO4
Ca(SiO3)
Not detected (-), trace (< 5% wt.% x), minor (5-15 wt.% xx), intermediate (15-30 wt.% xxx), major (30-50 wt.% xxxx) and predominant (>50 wt.% xxxxx)
by a high concentration of Mn and intergrown with silicate (Figures 3 C and D). Of all the materials identified, the silicate material is characterised by low Mn concentrations as opposed to the high Mn concentrations in the feed and reduced materials. The gehlenite and bredigite comprise the silicate materials occurring interstitially to the carbides, iron manganese, and manganese oxides (Figures 3C to F).
Overall, the samples display porous textures and smooth surfaces, representing the modification of structures and morphologies observed in the ore sample, similar to observations by Kononov (2008). In addition to the textural differences, the samples have variable oxide, alloy, and carbide coalescence, with the silicates representing the glass phase. The carbonates recorded in ore samples were completely decomposed by Reactions 9 and 10, since these phases were not observed in the prereduced products. The extent of the reduction in this study is determined by the presence of monoxides and carbides.
The carbides (Mn7C3, Mn5C2, and (Fe1.8Mn1.2)C), oxides (MnO, FeO, FeO0.198(MnO)0.802, SiO2, and MgO), and complex silicates (Ca3Mg(SiO4)2, Ca2Al(AlSiO7), Ca7Mg(SiO4)4, and CaFe2+SiO4) identified in this study are quite similar to those typically found during the production of HCFeMn, MCFeMn, and LCFeMn, despite differences in carbon sources and operating conditions. Olsen et al. (2007) reported the HCFeMn producers typically produce alloy containing 78% Mn and 7% C, and slag containing around 40% MnO. The primary objective of HCFeMn/MCFeMn/ LCFeMn is to create a manganese-rich alloy that enhances the strength, toughness, and wear resistance of steel. The carbon content in these alloys contributes to the mechanical properties of steel. Tangstad (2013) reported typical compositions of major commercial manganese alloys to have Mn ranging from 70 wt% to 82 wt% for
HCFeMn, 75 wt% to 95 wt% for MCFeMn, and 85 wt% to 95 wt% for LCFeMn, with the corresponding C contents ranges being 6 wt% to 7.5 wt% , 1 wt% to 2 wt%, and 0.2 wt% to 0.5 wt%, respectively. Producing carbides is more energy-efficient and cost-effective compared to producing pure manganese metal. The energy required to fully reduce MnO to metallic manganese without forming carbides is significantly higher (Coetsee, 2021), making it less economically viable for large-scale production. This is because the temperatures used in HCFeMn and MCFeMn production – around 1500 °C (Kononov et al., 2010) – favours the formation of carbides, with their Gibbs free energy being lower than that of metallic manganese (Kononov et al., 2009). Manganese's affinity for carbon and the reducing environment (high CO partial pressure) further stabilise carbides over oxides.
The study explored the mineralogical assessment of prereduced KMF Mamatwan-type manganese ore under different conditions using the CH4-H2-Ar gas mixture. The parameters investigated included understanding the effect of anthracite and methane concentration, as well as the effect of holding time on reduction extent. The mineralogical analysis highlights that the manganese ore was primarily reduced to manganese carbides, Mn7C3 and Mn5C2, which are preferred for the production of pure manganese metal. Other reduced phases included iron manganese and manganese oxide with their solid solution equivalents. Generally, the reduction using the CH4-H2-Ar gas mixture was effective and based on the results, the most desirable conditions for reduction are 8% anthracite, 10% methane, and 60 minutes of holding time, in agreement with the observations from the TGA tests. The overall results observed prove to be beneficial to the quest of lowering energy consumption and improving the overall efficiency of the smelting process.
Acknowledgements
The authors would like to thank Mintek for providing funding for this project.
References
Anacleto, N., Ostrovski, O., Ganguly, S. 2004. Reduction of manganese ores by methane-containing gas. ISIJ international, vol. 44, no. 10, pp. 1615–1622.
Bhalla, A., Eric, R.H. 2015. Reduction behavior of manganese ore using methane gas. In The fourteenth international ferroalloys congress, pp. 461–469.
Bhalla, A. 2018. Hydrocarbon reduction of manganese ores University of the Witwatersrand (South Africa).
Chetty, D. 2008. A geometallurgical evaluation of the ores of the northern Kalahari Manganese Deposit, South Africa. University of Johannesburg (South Africa).
Chetty, D., Gutzmer, J. 2018. Quantitative mineralogy to address energy consumption in smelting of ores from the Kalahari Manganese Field, South Africa. INFACON XV, Cape Town, South Africa, pp. 25–28.
Coetsee, T. 2021. The Role of Metallic Iron in Low Temperature Carbothermic Reduction of MnO: Phase Chemistry and Thermodynamic Analysis. Minerals, vol. 11, no. 11, p. 1205.
Kononov, R. 2008. Carbothermal solid state reduction of manganese oxide and ores in different gas atmospheres (Doctoral dissertation, UNSW Sydney).
Kononov, R., Ostrovski, O., Ganguly, S. 2009. Carbothermal solid state reduction of manganese ores: 2. non-isothermal and isothermal reduction in different gas atmospheres. ISIJ international, vol. 687, no. 49, pp. 1107–1114.
Kononov, R., Ostrovski, O., Ganguly, S. 2010. June. Low temperature carbothermal reduction of siliceous manganese fines. In Twelfth
international ferroalloys congress sustainable future, Helsinki, Finland, pp. 6–9.
Kuo, K., Persson, L.E. 1954. A contribution to the constitution of the ternary system Fe-Mn-C. Isothermal sections at, 1050(910), pp.3 9–44.
Olsen, S.E., Olsen, S., Tangstad, M., Lindstad, T. 2007. Production of manganese ferroalloys. Tapir academic press.
Ostrovski, O., Anacleto, N., Ganguly, S. 2004. February. Reduction of manganese ores by methane containing gas. In Proceedings Tenth International Ferroalloys Congress (pp. 173–183).Rankin, W.J. and Van Deventer J.S.J. 1980. Journal of the Southern African Institute of Mining and Metallurgy, vol. 80, pp. 239–47.
Rankin, W.J., Wynnyckyj, J.R. 1997. Kinetics of reduction of MnO in powder mixtures with carbon. Metallurgical and Materials Transactions B, vol. 28, pp. 307–319.
Steenkamp, J.D., Bam, W.G., Ringdalen, E., Mushwana, M., Hockaday, S.A.C., Sithole, N.A. 2018. Working towards an increase in manganese ferroalloy production in South Africa-a research agenda. Journal of the Southern African Institute of Mining and Metallurgy, vol. 118, no. 6, pp. 645–654.
Tangstad, M. 2013. Manganese ferroalloys technology. In Handbook of ferroalloys, pp. 221–266. Butterworth-Heinemann.
Tangstad, M., Ichihara, K. and Ringdalen, E. 2015. Pretreatment unit in ferromanganese production. The Fourteenth International Ferroalloys Congress. Energy efficiency and environmental friendliness are the future of the global ferroalloy industry, Kiev, Ukraine, 31 May-4 June 2015, pp. 99–106.
U.S. Geological Survey. 2024. Mineral commodity summaries 2024: U.S. Geological Survey, 202 p., https://doi.org/10.3133/mcs2024
Wellbeloved, D.B., Craven, P.M., Waudby, J.W. 1990. Manganese and Manganese Alloys. In: Elvers, B., Hawkins, S. and Schulz, G. (Eds.) Ullmann’s Encyclopedia of Industrial Chemistry. 5th Edition. vol. A16, pp. 77–121. u
Affiliation:
1Pyrometallurgy Division, Mintek, South Africa
2Department of Chemical Engineering, Stellenbosch University, South Africa
3Independent Consultant, USA
4Samancor Chrome Ltd, South Africa
5Independent Consultant, South Africa
6Independent Consultant, South Africa
7Department of Chemistry, University of Cape Town, South Africa
8Ex Mente Technologies, South Africa
9Department of Metallurgical Engineering, University of Pretoria, South Africa
Correspondence to:
Q.G. Reynolds
Email: QuinnR@mintek.co.za
Dates:
Received: 22 Oct. 2024
Published: March 2025
How to cite:
Reynolds, Q.G., Bowman, B., Erwee, M.W., Geldenhuys, I.J., Sandrock, C., Venter, G.A., Xakalashe, B.S., Zietsman, J. 2025. Plasma soup for the pyrometallurgist’s soul. Journal of the Southern African Institute of Mining and Metallurgy, vol. 125, no. 3, pp. 129–144
DOI ID: https://doi.org/10.17159/2411-9717/758/2025
ORCiD:
Q.G. Reynolds http://orcid.org/0000-0002-5196-8586
This paper is based on a presentation given at the Mintek@90 Conference 2024, 11-12 November 2024, Sandton Convention Centre, Johannesburg, South Africa
by Q.G. Reynolds1,2, B. Bowman3, M.W. Erwee4, I.J. Geldenhuys2,5, C. Sandrock6, G.A. Venter7, B.S. Xakalashe1, J. Zietsman8,9
Abstract
Understanding the behaviour of plasma arcs is an important part of the design and operation of direct current electric arc furnace smelting processes, which are used in the industrial production of many metallurgical commodities. In recent years numerical and computational modelling techniques have begun to illuminate the complexity of arc behaviour and how it is deeply connected to the thermodynamic and physical properties of the arc plasma. Plasma properties may be estimated from first principles using statistical mechanics methods, but this requires as input some knowledge of the composition of the gas phase that occurs over the process during smelting. In this paper the authors describe a workflow using thermochemistry software to predict the expected gas phase composition through a given process, followed by plasma property calculations using an open-source software tool that has been in development for several years. This tool, 'minplascalc' has been in development for several years and is also described in detail here. The workflow is then applied to the calculation of plasma properties of interest for a variety of historical and current pyrometallurgical processes, and the results are compared. The plasma property data are published in an open-access database for general use.
Keywords plasma, arc furnace, simulation, Mmaterial properties, software
Introduction
Over the past five decades Mintek has conducted extensive applied research into a wide range of pyrometallurgical processes using direct current (DC) electric arc furnace technology. Many of these processes have been successfully developed through to large pilot-plant or industrial scales and include commodities such as ferrochromium, ferronickel, high-titania slag, zinc, magnesium, cobalt, and platinum group metals (Barcza, 1986; Jones, Curr, 2006).
As shown in Figure 1, DC arc furnaces consist of a cylindrical refractory-lined vessel, which is used to contain the molten process products, which are typically immiscible slag (metal oxide) and alloy phases at temperatures in excess of 1400°C. Raw material, fluxes, and reductants are introduced through feedports in the furnace roof, with the feed rate carefully controlled to match the power input in order to maintain an open bath surface. The furnace is usually operated in semi-batch mode, with continuous feed and periodic removal of products by tapping. Power is supplied to the unit from a transformer and rectifier combination – one or more graphite electrodes enter through the roof of the vessel, and the electrical circuit is completed either through a hearth anode in the base of the furnace or, less commonly, between anode and cathode electrodes.
The plasma arc, which gives the furnace its name bridges the gap between the tip of the electrode and the molten bath surface (see Figure 2). The arc acts as the engine room of the furnace, driving intense transfer of thermal and mechanical energy to the metallurgical process. Understanding and managing the arc is an important aspect in the successful running of any DC arc furnace plant (Geldenhuys, 2017).
Arcs are formed from process gases in the freeboard, which have been heated to the point that they decompose into a mixture of molecules, atoms, charged ions, and electrons – a plasma. This 'plasma soup' renders the arc electrically conductive, and powerful coupling between the electric, magnetic, thermal, and momentum fields shapes the arc into a high temperature, high velocity jet, which can reach tens of thousands of Kelvin and travel at kilometres per second (Bowman, Krüger, 2009).
Like any good soup, changing the ingredients can have an effect on the properties of the final result, ranging from subtle to strong; likewise, the composition of the freeboard gases over different metallurgical processes influences the electrical and thermal behaviour of the resulting arc.
Experimental studies on plasma arcs in situ are very challenging due to the extreme conditions inside operating furnaces. Due to this, the development of mathematical and numerical models of arc
behaviour has been an important aspect of research in this area for many years, and measurements must often be supplemented with such models to improve the understanding of arc behaviour and generate useful insight. Models fall into a range of categories from lumped parameter steady-state or dynamic approaches such as Bowman’s empirical models for DC and Cassie-Mayr models for AC, through to more complex 1D dynamic formulations such as channel arc models, and finally up to 2D and 3D spatial magnetohydrodynamic models, which directly simulate the electromagnetic, temperature, and velocity fields from the fundamental governing equations. The pros and cons of different models are well documented in (Bowman, Krüger, 2009) and (Haraldsson et al., 2021).
All arc modelling requires input information about the thermodynamic, transport, and radiation properties of the plasma material for the problem in question. These are sometimes simply bulk-averaged values of properties like electrical conductivity, but particularly in more sophisticated models detailed knowledge of the dependence of properties on plasma temperature and pressure is also needed. Direct measurement of plasma properties is again extremely difficult even in controlled laboratory conditions, but it is possible to calculate them from first principles using methods from branches of physics such as statistical mechanics. These calculations are very complex and tedious, and their implementation is nontrivial. Results of some such calculations have previously been published for materials such as pure noble gases, simple gases such as pure hydrogen, and selected binary mixtures such as ArH2 and CO2-Cu (Boulos et al., 1994; Yang et al., 2016). However, typical pyrometallurgical process gases may contain a variety of hydrogen, oxygen, carbon, and sulphur compounds combined with many metallic elements, and data for such complex mixtures are not readily available in open literature. This, combined with
the difficulty of implementing first-principles plasma property calculations, has led to many previous authors, including those of this paper (Reynolds, 2018; Reynolds et al., 2010), to develop detailed arc models, which rely on highly oversimplified or approximated plasma property data from literature sources; the question arises of whether the results obtained in such work translate to the real industrial operations that such modelling is intended to represent. Recent work by (Makgoale et al., 2021) has comprehensively highlighted the sensitivity of arc models to approximations and simplifications, including material properties.
In this paper, a full methodology for calculating plasma properties from first principles for arbitrary mixtures is presented together with an open source software implementation developed for the Python programming language. The plasma property calculator is combined in a workflow together with traditional thermochemical process calculation tools, and applied to a number of Mintek DC arc furnace projects to demonstrate how processspecific plasma property data sets can be generated for use in further modelling.
Plasma property calculations are generally part of broader workflows, which connect metallurgical process information to practical aspects of DC furnace operation such as thermal performance and electrical behaviour. A typical example is shown in Figure 3.
The first step involves calculations using thermochemistry calculation tools such as FactSage (Bale et al., 2016) to obtain the composition of the gas phase in the furnace freeboard as a function of process parameters. This is followed by plasma property calculations as described in this paper to determine the behaviour of this gas at conditions inside the arc. Finally, this property information can be passed on to models of the arc to predict its behaviour for furnace design and operation purposes. In this paper the focus is primarily on the second step, for which the methods described here have been developed. The calculations are then demonstrated by application to a variety of DC arc furnace smelting processes.
Thermal plasmas of the sort found in the arcs of DC furnaces are often assumed to be in local thermodynamic equilibrium (LTE), meaning that the heavy particles such as ions and atoms are in thermal equilibrium with the much lighter electrons, and a single unique temperature can be assigned to all species (Boulos et al., 1994). A major advantage of the LTE approximation is that all thermophysical properties of a mixture of an arbitrary number of plasma species can be expressed as (complicated) functions of temperature, pressure, and initial composition only – the equilibrium composition is itself a function of these variables since it is uniquely determined by the state parameters and mass conservation, and the properties are in turn determined by the equilibrium composition.
Given temperature, pressure, and a set of species present in a plasma (and some information about the elemental composition of the mixture if more than one element is present), the number density of each species at thermodynamic equilibrium can be calculated using the principle of Gibbs free energy minimisation (Boulos et
al., 1994). This is an important intermediate step in calculating the thermophysical properties and may also be useful in, its own right, if one is interested in the relative proportions of different species in complex plasmas. To start, recall the definition of Gibbs free energy:
Where G is the Gibbs free energy of a system, G0 is a reference value depending only on temperature and pressure, μi is the chemical potential of species i, and Ni is the absolute number of particles of species i present. In statistical mechanics, μi in J per particle is represented as:
Where T is absolute temperature, kB is the Boltzmann constant, Q is a statistical quantity called the partition function in m-3, V is the volume of the system, and is a reference energy in J per particle of the species relative to its constituent uncharged atoms. For uncharged monatomic species and electrons = 0, for uncharged polyatomic species it is the negative of the dissociation energy, and for charged species it is of the species with one fewer charge number.
Consider, for example, a simple plasma system for hydrogen containing species H2, H, H+, and e-. In this case = = 0, De,H2→2H, and + = is Ie,H where De,H2→2H is the dissociation energy of the diatomic hydrogen molecule, and Ie,H is the ionisation energy of the hydrogen atom.
It is possible to substitute volume out of the equations by using the ideal gas law:
Where P is the specified pressure of the system. A system at equilibrium is characterised by a minimum stationary point in G, giving an independent equation for each species i, which simplifies to:
This set of equations must be solved subject to constraints supplied by the conservation of mass of each element present:
Where νij is the stoichiometric coefficient representing the number of atoms of element j present in species i, and is the (fixed) total number of atoms of element j present in the system, specified by the initial composition. Together with this, one additional constraint is supplied by the requirement for electroneutrality of the plasma: [6]
Where zi is the charge number of species i. The set of Equations in 4, 5, and 6 are solved using an iterative Lagrange multiplier approach to obtain the set of Ni, and hence number density ni = Ni/V, at LTE starting from an initial guess.
Partition functions
The partition function for a particular species is a description of the statistical properties of a collection of atoms or molecules of that species at thermodynamic equilibrium. Partition functions are normally presented as the sum of weighted state probabilities across the possible energy states of the system. In general, at moderate
plasma temperatures up to a few 10⁴ K, a species’ total partition function can be written as the product of several unique partition functions arising from different quantum mechanical phenomena (assuming weak state coupling and no contribution from nuclear states):
[7]
Here, Qt is the translational partition function due to the species’ ability to move around in space, Qint is the internal partition function due to various energy states internal to the particles of the species, Qe is the electronic partition function due to different possible arrangements of the electronic structure of the species, Qv is the vibrational partition function due to the ability of the bonds in a polyatomic species to vibrate at different energy levels, and Qr is the rotational partition function due to a species’ ability to rotate around its center of mass at different energy levels.
Four different types of species are distinguished here: monatomic for charged or uncharged single atoms, diatomic for charged or uncharged bonded pairs of atoms, polyatomic for charged or uncharged bonded groups of three or more atoms, and free electrons. The formulae used for the various partition functions for each type are shown in Table 1 (Boulos et al., 1994; Herzberg, 1945; McQuarrie, 1973). Here mi and me are the mass of one particle of the species concerned, ℏ is the reduced Planck constant, g j and Ej are the quantum degeneracy and energy (in J) of electronic energy level j with j=0 being the ground state, σs is the symmetry constant of a molecular species, and ωe,j, Ar, Br, and Cr (all converted to J equivalent) are the vibrational, symmetry, and rotational constants, respectively, for a diatomic or polyatomic molecule.
In this study complete electronic energy level sets are implemented for single atoms and ions, but only the ground state level is considered for diatomic and polyatomic molecules. This is assumed to be a reasonable approximation, since these species are generally present only at low temperatures where electronic excitation is limited compared to vibrational and rotational states. Ionisation energy lowering
The ionisation energy required to remove a single electron from a particle is a constant for that particular species when considered in isolation. However, in a mixture of different species and free electrons, the ionisation energy is lowered by a small amount due to local electrostatic shielding effects. This affects both the calculation of the partition functions (the summation of electronic state contributions for monatomic species ignores states with energies above the lowered ionisation energy) and the calculation of equilibrium plasma compositions (the equilibrium relationships are defined using the reference energy levels for each species, which in turn depend on the lowered ionisation energies). Ionisation energy lowering is a complex problem in plasma physics, but there exist many approximate methods for quantifying this effect using the theory of Debye-shielded potentials. Provided the same method is used for all species, the calculation errors generally remain small (Boulos et al., 1994).
In the present work an approximate analytical solution is used (Stewart, Pyatt, 1966). In this method, the ionisation energy lowering for each charged species is calculated explicitly using: [8]
Here, δIe,i is the ionisation energy lowering of species i (in J), ai is the ion-sphere radius of species i, lD is the Debye sphere radius, z* is the effective charge number in a plasma consisting of a mixture of species of different charges, zj is the charge number of species j, nj is the number density (particles per cubic meter) of species j, and e is the elementary charge.
It should be noted that the method of Griem has been used extensively for previous work in the field (Griem, 1964), and slight differences may exist compared to the method of Steward and Pyatt used here.
Thermodynamic properties
Given a plasma composition in terms of number densities ni, the mass density ρ, the enthalpy H, and the heat capacity CP can be calculated directly.
Plasma density
The plasma mass density is a straightforward calculation:
Where Mi is the molar mass of species i in kg/mol, and NA is Avogadro’s constant.
Plasma enthalpy
[9]
Calculation of the plasma enthalpy at a particular temperature, pressure, and species composition is performed using the statistical mechanics definition of internal energy:
Where Hi is the enthalpy of species i in J per particle. Summing over all component species of a plasma and dividing by the density then gives the specific enthalpy of the mixture in J/kg:
[13]
It is important to note that the values obtained may be relative to an arbitrary non-zero value in general, and caution should be exercised when comparing enthalpy calculations for different mixtures.
Heat capacity
Direct calculation of CP given an arbitrary plasma composition is possible if some knowledge of the reaction paths between species is also supplied. Although any set of consistent reaction paths will give the same result at equilibrium, choosing one actual set of paths from the many possible options implies that it represents reality, and this is certainly open to some debate. It is therefore simpler to avoid the need for any such choices by calculating heat capacity using a numerical derivative of the mixture enthalpy around the temperature of interest:
Transport properties
[10]
Where U is the internal energy in J for a single particle of a particular species, Qj are the various kinds of partition functions making up Qtot for the species, and β = 1/kB T. Formulae for U of various plasma species are thus readily produced using the partition function expressions given earlier. Once the internal energy is known, enthalpy can be calculated from its definition:
[14]
Transport properties of plasmas are calculated using ChapmanEnskog theory developed from the principles of statistical mechanics. This is well described in (Chapman, Cowling, 1990; Devoto, 1966).
Collision integrals
[11]
When multiple species are present, the relative reference energy for each species must also be included. Application of the ideal gas law to the pV term then gives:
For the calculation of transport properties of a mixture of particles in a dilute phase such as gas or plasma as a function of temperature and pressure, information is needed about both the composition of the mixture in terms of the species present, and the nature of collisions between pairs of particles. The former is obtained from free energy minimisation procedures described in the aforementioned, and the latter is described using quantities called collision integrals. Collision integrals are calculated as the effective geometric cross section between a given pair of particles, which is in general dependent on the physical nature of each particle as well as their closing velocity.
The collision integral in terms of integer moments l and s is derived from the gas-kinetic cross section σij (χ,g) by two successive integrations as follows (Chapman, Cowling, 1990):
Where χ is the collision deflection angle, g is the closing velocity, and:
Where mr is the reduced mass of the colliding pair, and mi are the particle masses. In general, collision integrals depend in complex ways on the interaction potential between the colliding pair, which may have both classical and quantum mechanical components. As they are often difficult to calculate efficiently in closed forms, this has led to the development of many approximate or empirical expressions for various types of collisions. In the present work we distinguish different collision-pair types as shown in Table 2.
Elastic collision integrals Θnn/in for collisions between neutral heavy species or neutrals and ions are calculated using the empirical formulae of Laricchiuta et al. (2007). These were obtained by fitting to classical trajectory models using an extended and generalised Lennard-Jones type potential. The Laricchiuta expressions have the advantage of depending on only a few fundamental properties of the colliding species: their polarisability, the effective number of electrons contributing to polarisation, and the charge number in the case of neutral-ion collisions.
In these expressions rLJ and єLJ are parameters related to the Lennard-Jones potential used and are defined in terms of the colliding species' polarisabilities, effective electrons, and charge if applicable. Ai are polynomials in a parameter called 'softness', which is determined from the species' polarisabilities. A full description of the model including tabulations of the polynomial coefficients for (l,s) in the range 1 to 4 is available in (Laricchiuta et al., 2007).
The inelastic resonant charge transfer integral Θtr is only used for collisions between first ions and neutrals of the same species. It is obtained from approximate quantum mechanical calculations of an electron moving in the potential between two identical nuclei (Devoto, 1967; Rapp, Francis, 1962; Smirnov, 1971):
Table 2
Collision integrals for interaction between different particles
Neutral Ion Electron
Neutral
Ion
Electron
R is the universal gas constant, M is the molar mass of the species, and Ie is its first ionisation energy in eV.
For collisions between charged particles, the collision integral Θc is calculated from classical trajectories of charges moving in a Coulombic potential. This is found to depend on a quantity called the Coulomb logarithm, In Λ Approximate empirical expressions are available for In Λfor three important classes of collisions: electron-electron, electron-ion, and ion-ion. For the temperature ranges of interest in thermal plasma calculations, and assuming LTE conditions, these are (Richardson, 2019:
[20] [21] [22]
The appropriate expression for l Λ is then used to calculate the overall collision integral for charged particles (Devoto, 1967), where γ is the Euler gamma constant: [23]
Calculation of the electron-neutral collision integral Θe from first principles is an extremely complex process and requires detailed knowledge of quantum mechanical properties of the target species. The complexity also increases rapidly as the atomic mass of the target increases and multiple excited states become relevant. For the present work a simple empirical formulation was developed instead, which can be fitted to experimental or theoretical data to obtain an estimate of the collision integral for the neutral species of interest:
[19]
[24]
In cases where insufficient data is available, a very crude hard sphere cross section approximation can be made by specifying only D1 and setting the remaining Di to zero. In all other cases, the Di are fitted to momentum cross section curves obtained from literature sources. Performing the second collision integral integration step from Equation 16 then yields:
[25]
In the Chapman-Enskog formulation, the solutions to the Boltzmann transport equation are found to depend on quantities called bracket integrals. The bracket integrals are expanded using associated Laguerre polynomials, approximated to a specified number of terms indicated by integers m and p (Chapman, Cowling, 1990). This produces expressions, which are functions of the particle masses, concentrations, and collision integrals. These expressions are then combined in a matrix representing the set of binary collisions between all species in the plasma at a given level of approximation. For example, the matrix entries for the lowest approximation level are given by:
[26]
Where δij is the Kronecker delta. Full q matrix entry expressions for m and p from 0 to 3 are available in the appendices of Devoto (1966). Different expressions are used depending on whether the property being calculated is related to mass or momentum transport – in the present work Devoto’s convention is adopted and they are indicated as and , respectively.
Mass and thermal diffusion coefficients
Although not generally of direct interest in equilibrium calculations where diffusion kinetics do not play a role, the binary and thermal diffusion coefficients are an important intermediate calculation step for other properties of interest. As per Devoto (1966) we have:
Where the a and c values are calculated by solution of the linear systems:
The indices i, j, h, and k range over the number of species present in the plasma and indices m and p range from 0 to M`, the maximum q-matrix approximation level.
Plasma viscosity
As per Devoto (1966), viscosity μ of a plasma mixture is given by: [31]
Where values for b are obtained from the solution of the linear system: [32]
Plasma electrical conductivity
Although conduction by ions does contribute to the overall electrical conductivity σ of a plasma mixture, the effect is generally very small due to the large mass difference between electrons and
ionic species and can be neglected. Using this approximation, we have per Devoto (1966):
Where n is the total number density of the plasma in particles per m3, and Dej are the binary diffusion coefficients of electrons relative to the heavy species
Plasma thermal conductivity
The effective heat flux in equilibrium plasmas is a combination of several terms describing molecular transport, thermal diffusion, and chemical reaction. These can be rearranged in a variety of ways depending on the application, but one of the forms given in Devoto (1966) is particularly useful:
If we consider an equilibrium system at constant pressure and with no external forces, we have:
Where xj are the mole fractions of the species present in the plasma. By substituting Equation 35 into 34, the total thermal conductivity κ can be expressed as the pre-multiplication factor to ∇T in the heat flux expression: [36]
The molecular thermal conductivity κ' is determined using the a values obtained from Equation 30: [37]
As in the case of the plasma heat capacity it is possible to develop analytical expressions for the term if some assumptions are made about reaction pathways, but as before this can be avoided simply by evaluating the derivative numerically at the temperature of interest: [38]
Radiation properties
Thermal radiation in plasmas is an extensive topic of study on its own and covers a broad range of phenomena including line emission and absorption, continuum radiation, quantum mechanical effects, and many others. These are well documented in references such as (Boulos et al., 1994). Calculation of radiation behaviour becomes highly complex when absorption effects are considered – in the present work these effects are not explored, and only an estimate of the total emission coefficient is calculated. It should be noted that particularly in the case of metallic atoms and ions, line broadening and the associated absorption effects can be very strong indeed and the results here should therefore be taken as indicative of relative behaviour only.
For certain analyses, radiation emission can be combined with thermal conductivity to produce a lumped effective thermal conductivity κeff. This is a useful approximation for simple analytical calculations in optically thick plasmas where reabsorption of emitted radiation is high, and a rigorous treatment of the radiation transport is not practical. In such cases, κeff values including radiation diffusion terms can be orders of magnitude higher than the true thermal conductivity (Howell et al., 2020).
Total radiation emission coefficient
To a good first approximation in the temperature ranges of interest to thermal plasma applications, the total emission from a plasma mixture can be assumed to be purely line radiation from transitions between excited states in the constituent species. This can be calculated simply by integrating over wavelengths between 0 and ∞ for each line in the emission spectrum for each species and summing the results. As per Boulos et al. (1994), the formula for atomic species is:
Line wavelengths λj,L, state degeneracies g j,L, transition probabilities , and energy levels Ej,L are readily available for most elements in atomic spectroscopy databases.
Similar expressions can be developed for molecular species, but these are neglected here as they are only present at very low plasma temperatures where the total emission is relatively small, and some inaccuracy can be tolerated. The emission spectrum for molecules is also predominantly from rotational and vibrational modes, and these generally have much smaller values than those of the electronic emission lines of atoms and ions.
Software implementation
The plasma properties calculations described in the aforementioned have been implemented in an open source software package for the Python programming language, 'minplascalc'. The package uses a flexible object-oriented representation of plasma species and mixtures to perform a range of LTE calculations on arbitrary mixtures, assuming data for the constituents are available. Direct calculation of plasma properties is implemented using high-level functions, improving repeatability and providing a simple and straightforward user experience. The code is under active development, and along with documentation and usage instructions, is available online (Reynolds, Sandrock, 2024).
Results and discussion
In this section we present new results from thermochemical modelling and plasma property calculations for a range of DC arc furnace smelting processes, all of which were tested to large pilot plant scale at Mintek during the period from 1970 to 2020.
In each case the procedure was to first calculate the equilibrium gas composition over the process using FactSage software, and then pass the elemental gas composition into the minplascalc
Table 3
Data sources for monatomic species
Ar, Arz+
C, Cz+, Cu, Cuz+, H, H+, Mg, Mgz+, O, Oz+
Al, Alz+; Ca, Caz+; Co, Coz+; Cr, Crz+; Fe, Fez+; Mn, Mnz+; Ni, Niz+; Pb, Pbz+; S, Sz+; Si, Siz+; Ti, Tiz+; Zn, Znz+
software to calculate the thermophysical properties of the plasma at arc temperatures. The FactSage calculations are performed at a range of different slag temperatures between the typical operating temperature for the process and the effective vaporisation temperature (the lowest temperature at which all process material is in the gas phase). This reflects the possibility of very large temperature gradients in the slag bath in the vicinity of the arc attachment zone in DC furnaces (Barcza et al., 1990).
Thermochemical simulations were done using FactSage 8.3. In all simulations, the FactPS database was used to represent selected pure solid species, while the gas phase was modelled with the gaseous ions option enabled. For the slag phase in all simulations, the FTOxid database was used. For the ferrochromium, ilmenite, and ferronickel processes the SGTE alloy solution database was employed, while for the Conroast, Enviroplas, and Mintek Thermal Magnesium processes, the metallic and/or matte solutions were approximated using the FTmisc database.
Species data for plasma property calculations in minplascalc was obtained from various sources as listed in Table 3 and Table 4:
(a) NIST Atomic Spectra Database (Kramida and Ralchenko, 1999).
(b) NIST CCCBDB (Johnson, 2022).
(c) New ab initio calculations conducted for the present work (see further description in the following).
(d) LXCat (Carbone et al., 2021).
(e) Estimated using empirical polarisation potentials (Laricchiuta et al., 2007).
Additional information was also sourced from NIST Chemistry Webbook (Linstrom, 1997).
Data flagged as (c) were obtained from computations using density functional theory employing the PBE0 hybrid exchange functional (Adamo, Barone, 1999) and the aug-cc-pVTZ basis sets (Balabanov, Peterson, 2005; Hill, Peterson, 2017; Kendall et al., 1992; Prascher et al., 2011; Woon, Dunning, 1993). Pseudopotentials comprising aug-cc-pVTZ-PP basis functions (Peterson, 2003) for valence electrons and the associated relativistic small-core Stuttgart/ Cologne pseudopotential functions (Metz et al., 2000) were used to describe the elements Sn and Pb. Basis sets and pseudopotentials not available by default in the software were obtained from online databases (Feller, 1996; Pritchard et al., 2019; Schuchardt et al., 2007). All computations were performed using Gaussian 16 (Frisch et al., 2016).
Static polarisabilities were calculated analytically using the Kohn-Sham equivalent of the Coupled Perturbed Hartee-Fock equations. Adiabatic ionisation energies Ie were calculated at 0 K from electronic energies of the neutral (Eneutral) and cationic (Ecation) form of each plasma species, corrected for zero-point energy (ZPE), as Ie = Ecation – Eneutral
Dissociation energies at 0 K were likewise calculated from the difference in the ZPE-corrected energies of the constituent atoms and the parent molecule, each in their lowest energy spin states.
Table 4
Data sources for diatomic and polyatomic species
Species
CO, CO2, H2O, O2, SO2
AlO, CaO, CrO, FeO, MgO, NiO, OH, PbO, SO, SiO, TiO
ZPE and fundamental vibrational frequencies were scaled by a factor of 0.962 to correct for anharmonicity and deficiencies in the level of theory (Johnson, 2022).
DC ferrochromium process
DC arc furnace smelting technology for the production of ferrochromium has been in industrial use for over forty years, with its first implementation dating back to 1984 (Barcza, 1986). This technology evolved to address the ‘fines problem’ encountered by South African ferrochrome producers, where the availability of traditional lumpy ore was diminishing, and the friable nature of the remaining ores led to the generation of high proportions of fines. DC smelting offered an efficient solution by processing these fine materials without the need for agglomeration. The process can be optimised for high efficiencies due to the high-intensity arc attachment zone in the open-arc furnace. Ferrochrome production occurs at very high temperatures, where chromite ore, along with fluxes such as lime and silica, reacts with a carbonaceous reducing agent. Slag modifiers are used to adjust the liquidus temperature and viscosity of the slag, ensuring optimal metal recovery. In a DC operation, maintaining a continuous balance of power and feed is crucial, with the arc attachment zone acting as the engine room where these elements are harmonised to meet the smelting objectives. The bulk chemistry of the slag and metal bath in the DC smelter is fairly uniform, enabling high metal conversion, while the configuration minimises metal entrainment in the slag, resulting in high metal recoveries. Because the power input in a DC arc smelting furnace is relatively independent of slag properties, it is possible to adjust the slag composition to optimally recover metal and produce a desired product, such as one with lower or higher silicon content. Over the years DC smelting for ferrochrome production has matured, with power ratings of installations increasing from 12 MW to 72 MW.
Thermochemical simulations in FactSage were based on the composition of South African MG ore (42.9% Cr2O3), for which the full composition can be found in (Geldenhuys, 2013). Anthracite with a dry fixed carbon content of 83.5%, 6.5% volatiles, 10% ash, and 2% moisture was assumed to be the reductant for the process; the detailed composition of the reductant ash can be found in the
patent of Denton and Schoukens (1993). For these simulations the small amounts of Na, K, P, and V oxides in the ore and reductants were ignored. For 100 kg of ore, it was assumed that 13 kg of CaO, 8.6 kg of SiO2, and 22 kg of anthracite reacts in the DC furnace at slag temperatures between 2023 K and the vaporisation temperature of 3590 K, with a simulated step size of 25 K. The choice of fluxing was guided by slag composition targets from Geldenhuys (2013). Volatiles were approximated as CH4. In FactSage, the option to calculate all transitions was also enabled; this aids in finding appropriate points where phase transitions such as boiling take place.
For calculation of the plasma properties the minplascalc species set included Al, C, Ca, Cr, Fe, H, Mg, O, Si, Ti, Al+, C+, Ca+, Cr+, Fe+, H+, Mg+, O+, Si+, Ti+, Al2+, C2+, Ca2+, Cr2+, Fe2+, Mg2+, O2+, Si2+, Ti2+, Al3+, C3+, Ca3+, Cr3+, Fe3+, Mg3+, O3+, Si3+, Ti3+, SiO, FeO, MgO, CaO, CrO, AlO, CO2, H2O, CO, O2, OH, and H2. For a selection of slag temperatures over the range shown in Figure 4, the calculations were run between 2000 K and 30000 K at a pressure of one atmosphere. The results are given in Figure 5, with properties of pure CO plasma as a reference.
In ferrochromium smelting there is a clear distinction in plasma properties generated by gas formed by slag at temperatures Ts > 2400 K, and those for Ts < 2400 K. This is because very few of the metallic species apart from magnesium evaporate below this temperature, and the plasma gas is mainly carbon monoxide with some hydrogen from moisture and volatiles in the feed. The properties in this range are quite close to those of pure CO, with the exception of the radiation emission coefficient and electrical conductivity – these both show significant deviations at plasma temperatures of 3000 K to 7000 K, which are important for arc behaviour. This is likely due to the presence of trace amounts of magnesium in the gas phase even at relatively low process slag temperatures.
Ilmenite is smelted to produce TiO2-containing titania slag, primarily for pigment production (Pistorius, 2008). In South Africa, ilmenite from beach sands is a prime example of deposits not amenable to direct processing due to their high iron content. The smelting process acts as a concentration step at high temperatures
whereby iron is rejected through carbothermic reduction, yielding an economically valuable by-product, while the stable titania oxide is concentrated in the slag. Initially developed from ironmaking processes, the smelting of titaniferous feedstocks saw significant advancement in the 1950s with the commissioning of large electric furnaces at Sorel in Canada, designed to smelt low-grade titaniferous deposits in Quebec into titania-rich slag. The high electrical conductivity of titania slags and the need for precise slag composition control make conventional submerged-arc technology unsuitable, as carbon-based electrodes would come into direct contact with the melt. This high conductivity also limits heat generation through resistance, leading to the adoption of openarc mode for large-scale smelting of titania-rich slags. The Sorel process was replicated in South Africa at Richards Bay Minerals in the mid-1970s for processing beach sand concentrate in six-in-line rectangular AC furnaces.
The application of DC smelting for ilmenite emerged in the mid-1990s as an alternative to the Sorel and Richards Bay furnace technologies. Led by Mintek and the Anglo American Corporation, DC technology was first implemented at Namakwa Sands on the West Coast of South Africa. These DC smelters, despite their smaller furnace capacities compared to the larger six-in-line furnaces, are economically viable and offer a flexible alternative to mega-scale furnace technology, enabling new producers to enter the slag market and providing operations with the flexibility that multiple smaller units offer. The metallurgical process is technologically agnostic, but with a single electrode and DC power, the control of the openarc operation is arguably simpler in the DC units compared to the larger six-in-line furnaces. Unlike ferrochrome production, the selection of DC technology for ilmenite smelting is not driven by substantial process benefits, but the DC furnace offers a smaller footprint and greater operational flexibility. This has made it an attractive alternative, especially in South Africa, where four such furnaces operate with power ratings ranging from about 25 MW to 35 MW (Geldenhuys et al., 2021).
For FactSage simulation of the ilmenite process the composition of the ore and anthracite as per the patent of Denton and Schoukens
(1993) was used, excluding the small amounts of V, Na, K, and P oxides that were used as inputs to the simulation. Test series C in the patent was chosen as an example case, normalised to 100 kg of ore and 13.9 kg anthracite. This process is considered fluxless. Simulations were done from 1873 K to the vaporisation temperature of 3659 K in this case, with the same step size as for other simulations.
For calculation of the plasma properties the minplascalc species set included Al, C, Ca, Cr, Fe, H, Mg, Mn, O, Si, Ti, Al+, C+, Ca+, Cr+, Fe+, H+, Mg+, Mn+, O+, Si+, Ti+, Al2+, C2+, Ca2+, Cr2+, Fe2+, Mg2+, Mn2+, O2+, Si2+, Ti2+, Al3+, C3+, Ca3+, Cr3+, Fe3+, Mg3+, Mn3+, O3+, Si3+, Ti3+, SiO, FeO, AlO, TiO, CO2, H2O, CO, O2, OH, and H2. For a selection of slag temperatures over the range shown in Figure 6, the calculations were run between 2000 K and 30000 K at a pressure of one atmosphere. The results are given in Figure 7, with properties of pure CO plasma as a reference.
In ilmenite smelting the process gas composition at low slag temperatures is again close to pure carbon monoxide, with some added hydrogen from contaminants in the feed material. The plasma properties are very similar to those of pure CO up to Ts ≈ 2300 K, after which they deviate significantly as metallic species begin to evaporate in significant quantities. It is interesting to note the appearance of multiple peaks in the plasma CP and κ curves as Ts increases – this is likely due to the introduction of Ti species into the gas at high slag temperatures.
Laterites and other oxidised nickel ores constitute a significant portion of global nickel reserves and typically require calcining prior to smelting, which generates calcine consisting of fine particles as the ores decompose during calcining. Smelting nickel laterite ores to produce ferronickel involves a trade-off between recovery and grade. A carbonaceous reductant is added to calcined laterite ore to reduce both iron and nickel. By selectively reducing iron, the slag and alloy composition can be adjusted to optimise nickel recovery while minimising excessive iron reduction. Increased reduction enhances nickel recovery but can dilute the nickel grade with iron.
l) Thermochemical calculation of elemental composition of the gas phase during DC ilmenite smelting, (r) example plasma species composition calculation at Ts = 2766 K with Fe and Ti species highlighted
The degree of reduction and the nickel-to-iron ratio of the feed material determine the alloy product grade and generally the tradeoff considers, nickel recovery, slag properties (especially for low Fe ores), the mass of the metal product, and the grade. A notable feature of ferronickel smelting is the high slag-to-metal ratio, which means that a significant portion of the smelting energy is used to generate the nickel-depleted slag.
In the early 1990s, a DC smelting route for producing unrefined ferronickel from nickel-containing laterite was developed at Mintek (Lagendijk, Jones, 1997). In this process, lateritic material, along with a carbonaceous reducing agent, is fed into the central region of the molten bath in a cylindrical DC arc furnace. The high-intensity arc attachment zone in the DC furnace allows for processing nickel laterites with a wide compositional range, making high-intensity processing of fines a key feature of this technology. The DC arc efficiently attracts fines into the smelting zone, where high-intensity smelting is maintained through power-to-feed balance.
Traditional ferronickel smelting in rectangular furnaces also evolved to use arc smelting but with what is described as a shielded arc operation. These operations manage feed cavity formation around the electrodes using multiple feed zones and experience. The shift to high-voltage operation was driven by the need to increase smelting intensity, which was limited in immersed mode (Matyas et al., 1993). The transition to open-arc (high-voltage) operation significantly enhanced smelting intensity for ferronickel smelters
who opted for this type of operation. DC smelting represents a high-intensity version of current technology, offering an alternative flowsheet with direct smelting of hot, prereduced fine calcine. This approach reduces electrical energy requirements and offers a high intensity smelting unit. As is the case for ilmenite smelting, DC technology for ferronickel offers a high-intensity alternative to mega-scale six-in-line rectangular furnaces, but the metallurgical basis is the same. The single-electrode design of the DC furnace is mechanically less complex while providing intense processing capabilities with proven capacity to pull fines into the high intensity arc zone.
For the ferronickel case, FactSage simulations were performed based on information by Lagendijk and Jones (1997). The composition of the nickel laterite fines (1.96% NiO) and charcoal given in aforementioned paper was used as is. The feed used in simulations was 100 kg ore, with 5 kg of charcoal. The amount of charcoal was adjusted slightly from the paper to match the simulated composition of metal with that in the paper, which in this case, was 23.3% Ni, condition D5 from Lagendijk and Jones (1997). Simulations were run from 1873 K to the vaporisation temperature of 3646 K with the same step size as for other simulations.
For calculation of the plasma properties the minplascalc species set included Al, C, Ca, Cr, Fe, H, Mg, Mn, Ni, O, Si, Al+, C+, Ca+, Cr+, Fe+, H+, Mg+, Mn+, Ni+, O+, Si+, Al2+, C2+, Ca2+, Cr2+, Fe2+, Mg2+, Mn2+, Ni2+, O2+, Si2+, Al3+, C3+, Ca3+, Cr3+, Fe3+, Mg3+, Mn3+,
Ni3+, O3+, Si3+, SiO, NiO, FeO, MgO, CaO, CrO, AlO, CO2, H2O, CO, O2, OH, and H2. For a selection of slag temperatures over the range shown in Figure 8, the calculations were run between 2000 K and 30000 K at a pressure of one atmosphere. The results are given in Figure 9, with properties of pure CO plasma as a reference.
As another traditional carbothermic oxide smelting process, ferronickel shows somewhat similar behaviour to the previous two cases. For Ts < 2300 K the species present are again predominantly carbon, oxygen, and hydrogen, albeit in different ratios due to the higher moisture content of the feed material in this case. Due to the different ratios, the properties already deviate quite substantially from those of pure CO in this region. For slag temperatures above 2300 K, a familiar pattern is seen where increasing evaporation of metallurgical atomic and molecular species results in drastic changes in the plasma properties, especially for important parameters like σ and εtot, which have a large influence on the electrical and thermal behaviour of the arc.
The ConRoast process is designed to significantly reduce or eliminate sulphur emissions from sulphide smelting by roasting sulphide-bearing ores prior to smelting (Jones, 2015). This process can be applied to various ores such as nickel sulphides and precious metal sulphides, and is particularly relevant in South Africa’s PGM industry where traditional matte smelting is commonly used.
In conventional PGM smelting, PGM-bearing sulphide concentrates are typically melted without the addition of a reductant. Base metal sulphides separate from gangue oxides and PGM concentrate in the matte phase, which is then tapped for further processing – this includes slow cooling, converting, and refining. The ConRoast process offers an alternative approach by roasting (oxidising) the concentrate before the reductive smelting step. The premise is to selectively reduce iron oxide and associated base metal oxides (such as nickel, copper, and cobalt) to the metallic state, and collecting the PGM in the iron-rich alloy. Due to their high affinity for iron, high recoveries can be achieved for PGM. In addition, by removing sulphur before the smelting and converting stages ConRoast effectively eliminates downstream sulphur emissions associated with traditional PGM smelting operations. The iron alloy produced in the ConRoast process has a higher liquidus temperature than traditional matte. A major contributor to the higher slag liquidus in South African concentrates is the presence of UG2 concentrates, which result from dual production streams of chromite and PGM mining. UG2 concentrates are lower in sulphur and base metals and contain significant residual chromite, which raises the slag's liquidus temperature. Traditional matte smelters manage this 'chrome problem' by increasing the temperature and controlling the chrome content in the feed blend. In the reductive environment of the ConRoast process, chromium predominantly reports to the slag, effectively rejecting chrome during smelting without the adverse effects associated with matte
smelting. The mild reducing conditions required for high PGM and base metal recoveries do not lead to extensive chromium oxide reduction, ensuring that chrome remains in the slag phase.
By roasting the concentrate upfront, most of the sulphur emissions can be contained at a single point. This also allows for hot-feeding the furnace directly from the roaster, which reduces the electrical energy requirement. This process also increases the potential for using a higher ratio of oxide-rich ores in the blend, unlocking access to potentially lower cost feed stocks. DC furnace technology is the preferred embodiment for implementing the ConRoast process due to the ultra-fine nature of PGM ores, where dust losses have a significant economic impact due to the value of the precious metals content. The alloy smelting process provides a high-intensity, efficient smelting method to process PGM-bearing ores without the environmental and health impacts associated with sulphur emissions throughout the plant and addresses several of the typical challenges faced by the industry.
For FactSage simulation of the DC furnace reductive smelting step of the ConRoast process, it was assumed that 100 kg of roasted concentrate reacted with 5 kg of high-grade coke (99.5%C, 0.5% volatiles). The concentrate composition was based on the roasted concentrate analysis with 0.25% S as reported by Jones (2002). Simulations were run from 1923 K to the vaporisation temperature of 3716 K with the same step size as for other simulations.
For calculation of the plasma properties the minplascalc species set included Al, C, Ca, Co, Cr, Cu, Fe, H, Mg, Ni, O, S, Si, Al+, C+, Ca+, Co+, Cr+, Cu+, Fe+, H+, Mg+, O+, Ni+, S+, Si+, Al2+, C2+, Ca2+,
Co2+, Cr2+, Cu2+, Fe2+, Mg2+, Ni2+, O2+, S2+, Si2+, Al3+, C3+, Ca3+, Co3+, Cr3+, Cu3+, Fe3+, Mg3+, O3+, Ni3+, S3+, Si3+, SiS, SiO, NiO, FeO, MgO, CaO, CrO, AlO, CO2, H2O, SO2, CO, O2, OH, SO, and H2
For a selection of slag temperatures over the range shown in Figure 10, the calculations were run between 2000 K and 30000 K at a pressure of one atmosphere. The results are given in Figure 11, with properties of pure CO plasma as a reference.
Due to the presence of sulphur compounds in trace amounts, the ConRoast smelting process generates chemically complex gas phases and resulting plasmas. Despite this, a similar pattern to the previous three cases is observed as Ts increases, with properties initially tracking close to those of pure CO (with the exception of σ and εtot at low plasma temperatures – silicon evaporation contaminates these plasmas from relatively low slag temperatures and affects these two properties disproportionately). At Ts > 2500 K multiple metallic species begin to evaporate, and this produces a large amount of nonlinearity in the heat capacity and thermal conductivity curves particularly.
The Enviroplas process is designed for the treatment of solid waste products from the metallurgical industry without requiring agglomeration before smelting (Abdel-latif, 2002). The process is based on the carbothermic reduction of selected metal oxides in these undesirable by-product materials (e.g., nickel, chrome, and zinc oxides). The smelting step occurs at high temperatures and with the preferred implementation using a DC arc furnace offers a
flexible solution across a wide range of problematic materials. The primary objectives of the process are to produce a non-hazardous disposable slag and, when processing undesirable by-products from stainless steel operations (e.g., AOD dust or similar), to recover chromium and nickel into a crude ferroalloy. Both the metal and slag are tapped from the furnace in liquid form.
For materia ls with high zinc content, such as lead blast furnace slags and EAF dusts, the goal is to recover zinc in the furnace off-gas fume while ensuring low levels of zinc in the discard slag. Zinc-rich fume can either be combusted to produce solid ZnO or routed through a condenser to recover metallic zinc, and the slag can be conditioned to achieve the same basicity index as typical blast furnace slag, making it potentially suitable for use as a cement extender when granulated. Both process routes were successfully demonstrated at Mintek in the 1990s.
The DC arc furnace fuming stage for the Enviroplas zinc process was simulated in FactSage based on the parameters and composition for a premelter slag given in the patent for the process (Barcza et al., 1996). It was assumed that 100 kg of premelter slag is fed to the DC furnace with 3 kg coke. The temperature range for simulations was 1723 K to the vaporisation temperature of 3769 K.
For calculation of the plasma properties the minplascalc species set included Al, C, Ca, Cu, Fe, H, Mg, O, Pb, Si, Zn, Al+, C+, Ca+, Cu+, Fe+, H+, Mg+, O+, Pb+, Si+, Zn+, Al2+, C2+, Ca2+, Cu2+, Fe2+, Mg2+, O2+, Pb2+, Si2+, Zn2+, Al3+, C3+, Ca3+, Cu3+, Fe3+, Mg3+, O3+, Pb3+, Si3+, Zn3+, SiO, FeO, MgO, CaO, AlO, PbO, CO2, H2O, CO, O2, OH, and H2. For a selection of slag temperatures over the range
shown in Figure 12, the calculations were run between 2000 K and 30,000 K at a pressure of one atmosphere. The results are given in Figure 13, with properties of pure CO plasma as a reference. The Enviroplas process intentionally recovers the primary product, zinc, to the gas phase in the DC fuming furnace step. As a result of this, the plasma properties are considerably different to those of pure carbon monoxide across the entire range of Ts. In particular, the electrical conductivity is higher at plasma temperatures between 5000 and 12,000 K, and the radiation emission is stronger by up to four orders of magnitude in the same range. This is likely to have a large effect on arc behaviour and cause some aspects of the electrical and thermal operation of Enviroplas furnaces to be significantly different from traditional smelting processes.
The thermal production of magnesium at atmospheric pressure was first demonstrated in the late 1980s, with initial test work conducted in a DC arc furnace at a scale of 50 kVA to 100 kVA. This work paved the way for the development of the Mintek Thermal Magnesium Process (Abdel-latif, 2011). Mintek's use of a DC open-arc furnace to produce magnesium vapor allows for operation at temperatures of 1700°C or higher. These elevated temperatures provide a broader selection of slag compositions and feed materials. Operating at atmospheric pressure, instead of under a vacuum as required by conventional magnesium production processes, enables continuous or semi-continuous operation and the possibility of scaling up beyond the 10 MW batch units typical of traditional
methods. By avoiding the use of vacuum conditions, the MTMP reduces the risk of air leakage and the subsequent reoxidation of magnesium.
The process involves the smelting of calcined dolomite in the presence of ferrosilicon at atmospheric pressure. The MTMP is not limited by the electrical properties of the slag, allowing the furnace to operate at relatively high voltages. The volatilised magnesium is captured as liquid metal in a surface condenser unit, which allows for periodic tapping of crude magnesium. The ability to operate under atmospheric pressure facilitates continuous (or semicontinuous) operation in large-scale facilities. The MTMP has been demonstrated on a 1 MW scale, producing high-purity magnesium metal in continuous operation with periodic online cleaning. The DC magnesium process is distinct in that the atmosphere of the sealed furnace is carefully controlled to minimise oxygen in the system. While the Enviroplas process, used for zinc fuming, also operates with metallic vapor, it does not require the same level of sealing and oxygen evacuation as is necessary for magnesium smelting.
The thermochemical simulations for the MTMP were carried out in FactSage based on compositions and parameters stated in the original process patent (Barcza, Schoukens, 1986). The feed consists of 77% calcined dolomite, 13% FeSi, and 10% Al2O3. Simulations were carried out assuming the pressure of 85 kPa stated in the patent, and the mole fraction of Ar gas was 0.5 at the normal operating temperature. Simulations were run from 1923 K to the vaporisation temperature of 3873 K with the same step size as for other simulations.
For calculation of the plasma properties the minplascalc species set included Al, Ar, C, Ca, Fe, Mg, O, Si, Al+, Ar+, C+, Ca+, Fe+, Mg+, O+, Si+, Al2+, Ar2+, C2+, Ca2+, Fe2+, Mg2+, O2+, Si2+, Al2+, Ar2+, C3+, Ca3+, Fe3+, Mg3+, O3+, Si3+, SiO, FeO, MgO, CaO, AlO, CO, and O2. For a selection of slag temperatures over the range shown in Figure 14, the calculations were run between 2000 K and 30,000 K at a pressure of one atmosphere. The results are given in Figure 15, with properties of pure CO plasma as a reference.
As mentioned, the MTMP is a somewhat unique case. Similarly to Enviroplas, it recovers its primary product – magnesium – as a vapour in the gas phase. Unlike any of the preceding cases it uses a metallic reductant, which generates no additional gas from the reduction reactions, and argon is used as an inert carrier gas. The gas phase composition is therefore completely different to CO across the entire range of slag temperatures, and the resulting plasma properties show this clearly. There is also not much variation in the properties over the range of Ts, which is likely due to the dominating effect of magnesium, which is present in large fractions. Electrical conductivity between 3000 and 12,000 K is extremely high, as is the total emission coefficient. Arcs in MTMP furnaces are therefore likely to operate very differently indeed, compared to traditional carbothermic smelting processes.
The raw data used to produce the graphs in the aforementioned is available online (Reynolds, 2024). This data set includes the elemental gas-phase compositions at different process slag
temperatures Ts calculated using FactSage 8.3, and plasma compositions and properties as a function of plasma temperature T calculated using minplascalc.
Conclusions
As the pyrometallurgy industry advances toward more sustainable processing, large step changes in the design and operation of established unit operations such as DC arc furnaces are expected. These may include variations such as novel ore pretreatment technologies, alternative reductants, energy recovery systems, and complex secondary raw materials such as urban and electronic wastes. In this context, digital modelling tools for rapid prototyping and optimisation will be critical to support effective and agile decision-making; plasma properties calculation methods and workflows such as those described here can potentially be of some value in this ecosystem.
A review of DC arc furnace projects conducted at Mintek over the past five decades has shown how plasma calculations can provide new ways to look at the thermal and electrical behaviour of processes, and by linking such calculations forward into arc models it is likely that even more case-specific insight can be gained in the future. The authors trust that these results have demonstrated that plasma soup truly can be good for the arc furnace pyrometallurgist’s soul.
Acknowledgements
This paper is published with the permission of Mintek. The authors acknowledge the Centre for High Performance Computing (CHPC), South Africa, for providing computational resources to this research project.
References
Abdel-latif, M.A. 2011. Review of the development work on the Mintek Thermal Magnesium Process (MTMP). Journal of the Southern African Institute of Mining and Metallurgy, vol. 111, no. 6, pp. 393–399.
Abdel-latif, M.A. 2002. Fundamentals of zinc recovery from metallurgical wastes in the Enviroplas process. Minerals Engineering, vol. 15, pp. 945–952. https://doi.org/10.1016/S0892-6875(02)00133-4
Adamo, C., Barone, V. 1999. Toward reliable density functional methods without adjustable parameters: The PBE0 model. The Journal of Chemical Physics. vol. 110, pp. 6158–6170. https://doi.org/10.1063/1.478522
Balabanov, N.B., Peterson, K.A. 2005. Systematically convergent basis sets for transition metals. I. All-electron correlation consistent basis sets for the 3d elements Sc–Zn. The Journal of Chemical Physics. vol. 123, no. 064107. https://doi. org/10.1063/1.1998907
Bale, C.W., Bélisle, E., Chartrand, P., Decterov, S.A., Eriksson, G., Gheribi, A.E., Hack, K., Jung, I.-H., Kang, Y.-B., Melançon, J., Pelton, A.D., Petersen, S., Robelin, C., Sangster, J., Spencer, P., Van Ende, M.-A. 2016. FactSage thermochemical software and databases, 2010–2016. Calphad 54, pp. 35–53. https://doi.org/10.1016/j.calphad.2016.05.002
Barcza, N.A. 1986. The development of large-scale thermal plasma systems. Journal of the South African Institute of Mining and Metallurgy, vol. 86, no. 8, pp. 317–333.
Barcza, N.A., Curr, T.R., Jones, R.T. 1990. Metallurgy of open-bath plasma processes. Pure and Applied Chemistry. vol. 62, pp. 1761–1772. https://doi.org/10.1351/pac199062091761
Barcza, N.A., Schoukens, A.F.S. 1986. The thermal production of magnesium. South African Patent Application no. 867102.
Barcza, N.A., Schoukens, A.F.S., Denton, G.M. 1996. The processing of zinc bearing materials. South African Patent no. 95/4963.
Boulos, M.I., Fauchais, P., Pfender, E. 1994. Thermal Plasmas: Fundamentals and Applications. Plenum Press, New York, USA. Bowman, B., Krüger, K. 2009. Arc Furnace Physics. Verlag Stahleisen GmbH, Düsseldorf, Germany.
Carbone, E., Graef, W., Hagelaar, G., Boer, D., Hopkins, M.M., Stephens, J.C., Yee, B.T., Pancheshnyi, S., Van Dijk, J., Pitchford, L. 2021. Data Needs for Modeling Low-Temperature NonEquilibrium Plasmas: The LXCat Project, History, Perspectives and a Tutorial. Atoms 9, 16. https://doi.org/10.3390/atoms9010016
Chapman, S., Cowling, T.G. 1990. The Mathematical Theory of Non-uniform Gases: An Account of the Kinetic Theory of Viscosity, Thermal Conduction and Diffusion in Gases, Cambridge Mathematical Library. Cambridge University Press.
Denton, G.M., Schoukens, A.F.S. 1993. The production of high titania slag from ilmenite. South African Patent Application no. 935072.
Devoto, R.S. 1967. Transport Coefficients of Partially Ionized Argon. Physics of Fluids, vol. 10, no. 2, pp. 354–364. https://doi.org/10.1063/1.1762115
Devoto, R.S. 1966. Transport Properties of Ionized Monatomic Gases. Physics of Fluids, vol. 9, no. 6, pp. 1230–1240. https://doi.org/10.1063/1.1761825
Feller, D. 1996. The role of databases in support of computational chemistry calculations. Journal of Computational Chemistry vol. 17, pp. 1571–1586. https://doi.org/10.1002/(SICI)1096987X(199610)17:13<1571::AID-JCC9>3.0.CO;2-P
Frisch, M.J., Trucks, G.W., Schlegel, H.B., Scuseria, G.E., Robb, M.A., Cheeseman, J.R., Scalmani, G., Barone, V., Petersson, G.A., Nakatsuji, H., Li, X., Caricato, M., Marenich, A.V., Bloino, J., Janesko, B.G., Gomperts, R., Mennucci, B., Hratchian, H.P., Ortiz, J.V., Izmaylov, A.F., Sonnenberg, J.L., Williams-Young, D., Ding, F., Lipparini, F., Egidi, F., Goings, J., Peng, B., Petrone, A., Henderson, T., Ranasinghe, D., Zakrzewski, V.G., Gao, J., Rega, N., Zheng, G., Liang, W., Hada, M., Ehara, M., Toyota, K., Fukuda, R., Hasegawa, J., Ishida, M., Nakajima, T., Honda, Y., Kitao, O., Nakai, H., Vreven, T., Throssell, K., Montgomery, J.A., Jr., Peralta, J.E., Ogliaro, F., Bearpark, M.J., Heyd, J.J., Brothers, E.N., Kudin, K.N., Staroverov, V.N., Keith, T.A., Kobayashi, R., Normand, J., Raghavachari, K., Rendell, A.P., Burant, J.C., Iyengar, S.S., Tomasi, J., Cossi, M., Millam, J.M., Klene, M., Adamo, C., Cammi, R., Ochterski, J.W., Martin, R.L., Morokuma, K., Farkas, O., Foresman, J.B., Fox, D.J. 2016. Gaussian 16 Revision C.01.
Geldenhuys, I.J. 2017. The Exact Art and Subtle Science of DC Smelting: Practical Perspectives on the Hot Zone. JOM 69, pp. 343–350. https://doi.org/10.1007/s11837-016-2171-z
Geldenhuys, I.J. 2013. Aspects of DC chromite smelting at Mintek - an overview, in: Efficient Technologies in Ferroalloy Industry: Proceedings of the Thirteenth International Ferroalloys Congress, International Ferroalloys Congress. Presented at the 13th International Ferroalloys Congress, Public Association INFACON XIII, Almaty, Kazakhstan, pp. 31–47.
Geldenhuys, I.J., Akdogan, G., Reynolds, Q.G. 2021. Towards sustainable processing of vanadium-bearing titaniferous magnetite deposits - an overview of barriers and opportunities, in: International Minerals Processing Congress. Presented at the IMPC 2020: XXX International Mineral Processing Congress, The Southern African Institute of Mining and Metallurgy, Cape Town, South Africa, pp. 2566–2581.
Griem, H.R. 1964. Plasma Spectroscopy. McGraw-Hill.
Haraldsson, H., Tesfahunegn, Y.A., Tangstad, M., Sævarsdóttir, G.A. 2021. Modelling of Electric Arcs for Industrial Applications, a Review. SSRN Electron. J. https://doi.org/10.2139/ssrn.3927158
Herzberg, G. 1945. Infrared and Raman Spectra of Polyatomic Molecules, Molecular spectra and molecular structure. Van Nostrand.
Hill, J.G., Peterson, K.A. 2017. Gaussian basis sets for use in correlated molecular calculations. XI. Pseudopotential-based and all-electron relativistic basis sets for alkali metal (K–Fr) and alkaline earth (Ca–Ra) elements. Journal of Chemical Physics. vol. 147, no. 244106. https://doi.org/10.1063/1.5010587
Howell, J.R., Mengüç, M.P., Daun, K., Siegel, R. 2020. Thermal Radiation Heat Transfer, 7th ed. CRC Press, Seventh edition. | Boca Raton : CRC Press, 2021. | Revised edition of: Thermal radiation heat transfer / John R. Howell, M. Pinar Mengüç, Robert Siegel. Sixth edition. 2015. https://doi.org/10.1201/9780429327308
Johnson, R. 2022. Computational Chemistry Comparison and Benchmark Database, NIST Standard Reference Database 101. https://doi.org/10.18434/T47C7Z
Jones R.T. 2015. Fundamental aspects of alloys melting in a DC arc furnace (Ph. D.). University of the Witwatersrand, Johannesburg.
Jones R.T. 2002. ConRoast: DC arc smelting of dead-roasted sulphide concentrates, in: Sulfide Smelting ’02. Presented at the Third International Sulfide Smelting Symposium, TMS Annual Meeting, Seattle, Washington, USA, p. 22 (Mintek Paper no. 8527).
Jones, R.T., Curr, T.R. 2006. Pyrometallurgy at Mintek, in: Southern African Pyrometallurgy 2006. Presented at the Southern African Pyrometallurgy 2006, The South African Institute of Mining and Metallurgy, Johannesburg, South Africa, pp. 127–150.
Kendall, R.A., Dunning, T.H., Harrison, R.J. 1992. Electron affinities of the first-row atoms revisited. Systematic basis sets and wave functions. Journal of Chemical Physics, vol. 96, pp. 6796–6806. https://doi.org/10.1063/1.462569
Kramida, A., Ralchenko, Y. 1999. NIST Atomic Spectra Database, NIST Standard Reference Database 78. https://doi.org/10.18434/T4W30F
Lagendijk H., Jones R.T. 1997. Production of ferronickel from nickel laterites in a DC-arc furnace, in: Nickel-Cobalt 97. Presented at the 36th Annual Conference of Metallurgists, Sudbury, Canada, pp. 151–162.
Laricchiuta, A., Colonna, G., Bruno, D., Celiberto, R., Gorse, C., Pirani, F., Capitelli, M. 2007. Classical transport collision integrals for a Lennard-Jones like phenomenological model potential. Chemical Physics Letters, vol. 445, pp. 133–139. https://doi.org/10.1016/j.cplett.2007.07.097
Linstrom, P., 1997. NIST Chemistry WebBook, NIST Standard Reference Database 69. https://doi.org/10.18434/T4D303
Makgoale, T., Bogaers, A., Zietsman, J., Akdogan, G. 2021. Momentum Transfer from Arc to Slag Bath in a DC Ilmenite Smelting Furnace: A Computational Analysis. JOM 73, pp. 2682–2697. https://doi.org/10.1007/s11837-021-04792-x
Matyas, A., Francki, R.C., Donaldson, K.M., Wasmund, B. 1993. Application of new technology in the design of high-power electric smelting furnaces. CIM Bulletin, vol. 86, pp. 92–99. McQuarrie, D.A. 1973. Statistical Mechanics, Harper’s chemistry series. Harper and Row.
Metz, B., Stoll, H., Dolg, M. 2000. Small-core multiconfigurationDirac–Hartree–Fock-adjusted pseudopotentials for post-d
main group elements: Application to PbH and PbO. Journal of Chemical Physics, vol. 113, pp. 2563–2569. https://doi. org/10.1063/1.1305880
Peterson, K.A. 2003. Systematically convergent basis sets with relativistic pseudopotentials. I. Correlation consistent basis sets for the post- d group 13–15 elements. Journal of Chemical Physics, vol. 119, pp. 11099–11112. https://doi. org/10.1063/1.1622923
Pistorius, P.C. 2008. Ilmenite smelting: the basics. The Journal of the Southern African Institute of Minining and Metallurgy, vol. 108, pp. 35–43.
Prascher, B.P., Woon, D.E., Peterson, K.A., Dunning, T.H., Wilson, A.K. 2011. Gaussian basis sets for use in correlated molecular calculations. VII. Valence, core-valence, and scalar relativistic basis sets for Li, Be, Na, and Mg. Theoretical Chemistry Accounts, vol. 128, pp. 69–82. https://doi.org/10.1007/s00214-010-0764-0
Pritchard, B.P., Altarawy, D., Didier, B., Gibson, T.D., Windus, T.L. 2019. New Basis Set Exchange: An Open, Up-to-Date Resource for the Molecular Sciences Community. Journal of Chemical Information and Modeling, vol. 59, pp. 4814–4820. https://doi. org/10.1021/acs.jcim.9b00725
Rapp, D., Francis, W.E. 1962. Charge Exchange between Gaseous Ions and Atoms. Journal of Chemical Physics. vol. 37, pp. 2631–2645. https://doi.org/10.1063/1.1733066
Reynolds, Q.G. 2024. Composition and thermophysical properties of metallurgical plasmas - LTE calculations (1.0.0) [Data set]. https://doi.org/10.5281/zenodo.13337769
Reynolds, Q.G. 2018. Influence of the power supply on the behaviour of DC plasma arcs - a modelling study. J. South. Afr. Inst. Min. Metall. vol. 118, no. 6, pp. 655–660. http://dx.doi.org/10.17159/2411-9717/2018/v118n6a14
Reynolds, Q.G., Jones, R.T., Reddy, B.D. 2010. Mathematical and computational modelling of the dynamic behaviour of direct current plasma arcs. Journal of the Southern African Institute of Mining and Metallurgy, vol. 110, no. 12, pp. 733–742.
Reynolds, Q.G., Sandrock, C. 2024. minplascalc (commit 967faf3), https://github.com/quinnreynolds/minplascalc.
Richardson, A.S. 2019. NRL Plasma Formulary. United States Naval Research Laboratory, Washington D.C., United States of America.
Schuchardt, K.L., Didier, B.T., Elsethagen, T., Sun, L., Gurumoorthi, V., Chase, J., Li, J., Windus, T.L. 2007. Basis Set Exchange: A Community Database for Computational Sciences. Journal of Chemical Information and Modeling. vol. 47, pp. 1045–1052. https://doi.org/10.1021/ci600510j
Smirnov, B.M. 1971. The Classical Theory of Resonance Charge Exchange. JETP 32, pp. 670–672.
Stewart, J.C., Pyatt, K.D., Jr. 1966. Lowering of Ionization Potentials in Plasmas. Astrophysical Journal, vol. 144, p. 1203. https://doi.org/10.1086/148714
Woon, D.E., Dunning, T.H. 1993. Gaussian basis sets for use in correlated molecular calculations. III. The atoms aluminum through argon. Journal of Chemical Physics, vol. 98, no. 2, pp. 1358–1371. https://doi.org/10.1063/1.464303
Yang, A., Liu, Y., Zhong, L., Wang, X., Niu, C., Rong, M., Han, G., Zhang, Y., Lu, Y., Wu, Y. 2016. Thermodynamic Properties and Transport Coefficients of CO2–Cu Thermal Plasmas. Plasma Chemistry and Plasma Processing, vol. 36, pp. 1141–1160. https://doi.org/10.1007/s11090-016-9709-2 u
Affiliation:
Advanced Materials Division, Mintek, South Africa
Correspondence to: M. Phasha
Email: majep@mintek.co.za
Dates:
Received: 15 Oct. 2025
Published: March 2025
How to cite:
Phasha, M., Mampuru, L., Mkhonto, D., Moema, J. 2025. Design and development of lightweight Fe-Mn alloys for storage and transportation of liquified natural gas (LNG) — Computational materials modelling study.
Journal of the Southern African Institute of Mining and Metallurgy, vol. 125, no. 3, pp. 145–150
DOI ID:
https://doi.org/10.17159/2411-9717/761/2025
ORCiD:
M. Phasha
http://orcid.org/0000-0003-4295-9247
L. Mampuru
http://orcid.org/0000-0003-2009-2665
D. Mkhonto
http://orcid.org/0000-0003-0329-8095
J. Moema
http://orcid.org/0000-0002-9517-9749
This paper is based on a presentation given at the Mintek@90 Conference 2024, 11-12 November 2024, Sandton Convention Centre, Johannesburg, South Africa
by M. Phasha, L. Mampuru, D. Mkhonto, J. Moema
Abstract
The global liquified natural gas (LNG) storage market size is projected to reach USD17.5 billion by 2025. Currently, owed to its high toughness, tensile strength, and excellent weldability, the 9% nickel steel is the most used in building infrastructure for cryogenic applications such as the construction of tanks and pipes for storage and transportation of LNG. However, this alloy is not readily available because of its complex production process and high cost. This provides an opportunity for suitable alternative materials to build infrastructure for cryogenic applications. Among strong contenders is the Fe-Mn based alloys, which have sparked global interest due to their desirable properties such as relatively lower density, low cost, high toughness and strength, due to a high manganese (Mn) content. These attractive properties render Fe-Mn based alloys preferred candidates to replace traditional steels in engineering applications in which strengthweight ratio is critical. In response, as a build-up to designing and developing austenitic FeMn alloys, the present study employed density functional theory (DFT) based first-principles computational materials modelling technique to investigate the structural, thermodynamic, and magnetic properties of binary Fe-Mn alloy composition in competing FCC, HCP, and BCC crystal structures. Using this approach, it was possible to unravel the key underlying elastic properties that are directly correlated to experimental tensile strength and high toughness in binary Fe-Mn alloys. Besides successfully validating the existing experimental data, the current predicted properties and the deployed approach will serve as a benchmark from which further alloying required to improve other properties will be conducted.
Keywords liquefied natural gas, 9% nickel steel, binary Fe-Mn alloys, first-principles calculations
In the quest to meet the greenhouse gas (GHG) emission targets set out in the Paris Agreement (2015), there is worldwide exploration of viable sustainable and environmentally friendly energy options, aimed at the effective curbing of global warming. Amongst alternative, relatively cleaner energy sources that have attracted much attention in the effort to diversify energy supply in what is termed ‘energy-mix’, is the liquified natural gas (LNG). The global LNG storage market size is projected to reach USD17.5 billion by 2025 (GlobalEnergyWorld, 2020). Storage and distribution of LNG is conducted at a cryogenic temperature of -196 °C (77 K). As a result, very few commercial alloys are able to withstand such sub-zero temperatures while maintaining the required impact toughness of 100 J. Currently, owing to their high toughness, tensile strength, and excellent weldability, the 6–9% nickel (Ni) steel alloys are the most used in building infrastructure for cryogenic environment (77 K) applications such as the construction of tanks and pipes for storage and transportation of LNG (Hickmann, et al. 2005, Kim, et al.2021) . The most successful and readily available being the 9% Ni steel alloy that is comprised of face-centred-cubic (FCC) and body-centred-cubic (BCC) dual phase microstructure and referred to as γ+α or γ+α´. Although the undesired ε-hexagonal-close-packed (HCP) martensite that is detrimental to toughness forms upon forging due to small stacking fault energy (SFE), it is eliminated by applying an appropriate heat treatment process in the γ+α region. However, this material is not readily available because of its complex production process and high cost of Ni. This poses an opportunity for suitable alternative alloyed materials to build infrastructure for such cryogenic environments. Among the strong frontrunners in this pursuit are the Fe-Mn based alloys that have sparked global interest in many engineering applications due to their desirable properties such as lower density than traditional steels,
low cost, high toughness and strength, due to the high manganese (Mn) content (Kim et al., 2021; Lee et al., 2014; Sohn et al., 2015; Chowdhury et al., 2017; Guerrero et al., 2017; Bleck and Haase, 2019; Bastidas et al., 2021). These attractive properties render Fe-Mn based alloys preferred candidates to replace traditional steels in engineering applications in which strength-weight ratio is critical. Moreover, South Africa endows high-grade iron (Fe) ore and is home to more than 70% of the global Mn ore reserves (U.S. Geological Survey, 2020). Consequently, the development of Fe-Mn based alloys is seen as a great downstream beneficiation opportunity capable of not only unlocking, but also stimulating local economic growth.
As a build-up to designing and developing dual phase Fe-Mn alloys consisting of FCC (γ)+BCC (α or α´) crystal structures, the present study employed the ab initio computational materials modelling technique to generate structural, thermodynamic, and magnetic properties of binary competing FCC, HCP, and BCC Fe-Mn phases in various alloy compositions. In addition, the elastic properties of non-magnetic (NM) FCC and ferromagnetic (FM) BCC Fe-Mn alloy compositions are presented. Using this computational tool, that has become more reliable in predicting properties of solids, it was possible to identify compositions and elastic properties that can be linked to yield strength and high toughness at cryogenic temperature (0 K). Similar studies on binary Fe-Mn alloys have previously been carried out, however, the focus was on the structural and thermodynamic properties (Gebhardt et al., 2010 ; Lintzen et al., 2013) with very limited research on magnetic (Gebhardt et al., 2010) and elastic properties. Thus, in the current study, the first-principles calculations were conducted to generate structural, thermodynamic, and magnetic property data of binary FCC, HCP and BCC Fe-Mn alloys using the supercell approach. In some cases, the elasticity data for cubic Fe-Mn alloy compositions is also presented. The overal intent of this work is to unravel the key underlying properties of various Fe-Mn alloy compositions that could be directly correlated to available experimental data for validation purposes.
All calculations reported in this study were performed on 2x2x2 FCC, HCP, and BCC supercells comprised of 32, 16 and 16 atoms, respectively, to represent Fe1-xMnx alloy compositions from Fe32-xMnx and Fe16-xMnx supercells. This work was carried out using the density functional theory (DFT)-based CASTEP code embedded in the Materials Studio software package (Clark et al., 2005). The robust Vanderbilt ultrasoft pseudopotentials (Vanderbilt, 1990) were used to describe the ion-electron interaction within the generalised gradient approximation (GGA) (Perdew and Wang, 1992) with PW91 functional (Perdew et al., 1992), with spin polarisation (SP) for FCC, HCP, and BCC as well as the non-spin polarisation (NSP) for FCC (NM) Fe-Mn alloy compositions. A plane wave cutoff energy of 500 eV and k-points set of 6x6x6, 12x12x6, 8x8x8, and 8x8x8 were sufficient to converge the total energy of the considered system in a non-magnetic state. The ground-state structures were optimised using the BroydenFletcher-Goldfarb-Shanno (BFGS) minimisation scheme. The convergence criterion of less than 1 × 10-5 eV/atom, the maximum residual forces of 0.03 eV/Å, maximum residual bulk stress of 0.05 GPa and maximum atomic displacement of 1 × 10-3 Å were utilised.
The heat of formation calculated using Equation 1 was used to determine the thermodynamic stability of the alloy compositions considered in this study:
where is the total energy of the alloy composition, and are the total energies of the ground-state structures of elemental Fe and Mn, respectively, whereas x and 1 - x refer to the fractional concentrations of the constituent elements; the total number of atoms in the structure is represented by n
The stress-strain relation may be used to distinguish the elastic and plastic regimes of solid materials. The elastic moduli are the fundamental physical parameters that establish the stress-strain relation in the elastic regime. For an isotropic polycrystalline solid, the two independent elastic parameters are the bulk modulus (B) and the trigonal shear modulus (G). The ratio of B/G predicts the brittleness of metals, depending on the threshold value of 1.75 (ductile if above 1.75) (Pugh, 1954). These elastic moduli are calculated from elastic constants computed from applying an appropriate set of strains to the geometrically relaxed unit cell. Elastic constants are then determined from the resulting change in total energy on the deformation. For the cubic structures, there are only three independent elastic constants, namely, C11, C12, and C44 The mechanical stability criteria for a cubic crystal is given by the expressions in Equations 2 and 3:
where E is the modulus of elasticity, C the tetragonal shear modulus, and Poisson’s ratio ν
Results and discussion
Phase stability
The lattice constants of the geometrically relaxed FCC, HCP, and BCC crystal structures of considered binary Fe-Mn alloy compositions are presented in Table 1. As a consequence of Mn having slightly larger atomic radius than Fe, the lattice constant a0 of all phases increases gradually with an increase in Mn composition, as observed in Table 1. However, for FCC Fe-Mn alloy compositions in AFM state, the increase is a bit rapid until at 15.625 at.% Mn, followed by fluctuation thereafter, while the increase in lattice constant of FCC (NM) is linear. This anomaly could be attributed to non-linear antiferromagnetic behaviour, as is demonstrated in Figure 1. With the exception of FCC (AFM), the lattice constant trends established in this work are similar to those of theoretical results reported by and experimental data therein. This is the case, despite the fact that the lattice constants predicted in the current study are much smaller, in agreement with other predicted results (Bleskov et al., 2016) and in line with the experimentally observed lattice contraction in BCC Fe (FM→NM) upon heating, prior to α→γ phase transition. According to the present authors, it is this lattice contraction that is responsible for the onset non-magnetic Fe.
Table 1
Equilibrium lattice constants of binary FCC, HCP and BCC Fe-Mn alloy compositions
The heat of formation of considered binary Fe-Mn alloy compositions in FCC, HCP, and BCC crystal structures, as well as the corresponding magnetic moments of FCC (AFM) and BCC (FM) phases are presented in Figures 1(a) and (b), respectively. It is evident from Figure 1(a) that the austenitic (FCC) Fe-Mn alloy compositions are the least thermodynamically stable at lower Mn
compositions ≤ 12.5 at.%. This is in accordance with literature (Okamoto, 1992), as BCC (FM) remains the most stable from 0 to just below 7 at.% Mn, after which the HCP phase is dominant for a broad range of compositions with highest stability 12.5 at.% Mn. The HCP (NM) phase is in competition with FCC (AFM) only at 15.625% and 21.875.% Mn in terms of stability, with FCC (AFM) being the most stable at 21.875.% Mn. On the other hand, the stability of BCC (FM) decreases sharply with an increase in Mn composition. The current predicted phase stability trends are in excellent agreement with other theoretical predictions (Lintzen et al., 2013). As shown in Figure 1(b), it is worth noting that the FCC (AFM) has the highest magnetic moments at the aforementioned two Mn compositions with higher thermodynamic stability. The magnetic moment is zero at 0, 18.75 and 25 at.% Mn, the compositions at which the thermodynamic stability is the lowest. On the other hand, although it remains strongly magnetic, the magnetic moments of BCC (FM) reduce gradually with an increase in Mn composition.
The driving force behind the key deformation mechanisms such as transformation-induced plasticity (TRIP) and twinninginduced plasticity (TWIP) in the high-Mn steels is the stacking fault energy (SFE) (Welsch et al., 2016). It is reported that TRIP is dominant at low SFE (< 20 mJ-2), whereas TWIP occurs if SFE is much higher to suppress any possible martensitic transformation. Since the SFE corresponds directly to FCC-HCP phase transition, it is therefore directly proportional to the total energy difference between these two phases. Hence, due to its strong influence on the hardening mechanisms in Fe-Mn alloys, the calculated structural energy difference between FCC and HCP is plotted against Mn composition in Figure 2. Clearly, there is not much in energy difference when FCC is at NM or AFM state with respect to the HCP phase, except at 12.5 at.% Mn composition where there a significant polarised difference with FCC (NM) enjoying the largest energy difference to HCP than FCC (AFM). However, the predicted energy difference trend is not so linear as others have reported (Gebhardt et al., 2010 ; Guerrero et al., 2020).
Figure 2—The structural energy difference between FCC and HCP binary Fe-Mn alloy compositions
Elastic properties
The calculated elastic constants of the binary FCC (NM) and BCC (FM) Fe-Mn alloy compositions are presented in Tables 2 and 3,
Table 2
respectively. As shown in Table 2, in general, the increase in Mn composition results in a gradual decrease in C11 and C44 elastic constants while there is a slight increase in C12. The resulting elastic moduli (Cʹ, B, and E) also decrease with an increase in Mn composition although the decrease in bulk modulus is very small. In accordance with the Hall-Petch effect, it is evident from Tables 2 and 3, that the Young’s modulus (E) values of polycrystalline alloys are much higher than that of the single crystalline counterpart due to grain-size strengthening effect (Cordero et al., 2016). This results in a larger value of the trigonal shear modulus (G) calculated using an expression, as expressed in Equation 4. Subsequently, the B/G ratio decreases leading to a smaller Poisson’s ratio (ν), both indicative of reduction in ductility. Thus, the mechanical properties of single crystal material may be viewed as the lower bound whereas those of polycrystalline material are upper bound. For example, single crystal FCC Fe is predicted to be ductile as the values of B/G ratio and Poisson’s ratio (ν) are all far above threshold values of 1.75 and 0.26, respectively. However, its polycrystalline counterpart may become brittle if the lowest values of 1.65 and 0.2478 for B/G and
Computed elastic properties of FCC (NM) Fe-Mn alloy compositions
Mn comp. Crystal-type Elastic constants Cij (GPa)
Table 3
Computed elastic properties of BCC (FM) Fe-Mn alloy compositions
Poisson’s ratio (ν), respectively, are reached by obtaining smallest grains. It is evident from Table 2 that as materials’
stiffness (E) decreases with the addition of Mn, the ductility increases, as shown by B/G and Poisson’s ratios. Polycrystalline FCC (NM) starts to be ductile upon adding 12.5 at.% Mn. On the other hand, due to its soft nature, the stiffness (E) of all considered BCC (FM) Fe-Mn alloy compositions in both single crystal and polycrystalline states is much smaller than even the single crystal of FCC (NM). Thus, BCC phase will be key to ensure toughness while FCC phase will provide strength, a property combination required in dual phase Fe-Mn alloys. Therefore addition of Mn much higher than 12.5 at.% will not only ensure that the ductile to brittle transition (DBT) is suppressed at cryogenic temperature but provides room for solid-solution-strengthening of FCC Fe-Mn alloys by adding other alloying in an attempt to increase its stiffness (E), which is directly proportional to yield strength as well as improving its thermodynamic stability.
First-principles calculations were successfully conducted to generate structural, thermodynamic, and magnetic property data of binary FCC, HCP, and BCC Fe-Mn alloys using the supercell approach. In general, the predicted equilibrium lattice constants increased slightly with an increased Mn composition. The highest thermodynamic stability is obtained at Fe-Mn alloy compositions with 12.5 and 21.875 at.% Mn for HCP and FCC (AFM) phases, respectively. An increase in magnetic moment seem to influence the thermodynamic stability of FCC (AFM) phase. While the thermodynamic stability of ferromagnetic BCC Fe-Mn decreases sharply with an increase in Mn composition, its magnetic strength drops gradually. The trends for structural energy difference between FCC and HCP phases of binary Fe-Mn alloy compositions are not linear, as reported elsewhere. Elasticity data reveal that a minimum of 12.5 at.% Mn is required to meet the minimum ductility threshold in FCC (NM) Fe-Mn alloys, while the BCC (FM) alloys maintain its soft character shown by lower Young’s modulus (stiffness) and high ductility indicated by B/G and ν values way higher than the threshold values. Thus, BCC phase will be key to ensure toughness while FCC phase will provide strength, a property combination required in dual phase Fe-Mn alloys. Therefore addition of Mn much higher than 12.5 at.% will not only ensure that the ductile to brittle transition (DBT) is suppressed at cryogenic temperature, but provides room for solid-solution-strengthening of FCC Fe-Mn alloys by adding other alloying in an attempt to increase its stiffness (E), which is directly proportional to yield strength as well as improving its thermodynamic stability.
Acknowledgements
The authors would like to thank MINTEK and the Advanced Metals Initiative (AMI) of the Department of Science and Innovation (DSI) for financial support. Gratitude is also extended to the Centre for High-Performance Computing (CHPC) in Cape Town for allowing us to carry out the calculations using their remote computing resources.
References
GlobalEnergyWorld. 2020. https://www.globalenergyworld.com/ news/traditional-energy [accessed 27 Feb 2020].
Hickmann, K., Kern, A., Schriever, U., Stumpfe, J. 2005. Production and properties of high strength nickel alloy steel plate for low temperature applications. ThyssenKrupp Stahl AG, Division Metallurgy/Heavy Plate, Profit Center Heavy Plate, Germany.
Kim, T-Y., Yoon, S-W., Kim, J-H., Kim, M-H. 2021. Fatigue and Fracture Behavior of Cryogenic Materials Applied to LNG Fuel Storage Tanks for Coastal Ships. Metals, vol. 11, no. 1899.
Lee, J., Sohn, S.S., Hong, S., Suh, B-C., Kim, S-K., Lee, B-J., Kim, N.J., Lee, S. 2014. Effects of Mn Addition on Tensile and Charpy Impact Properties in Austenitic Fe-Mn-C-Al-Based Steels for Cryogenic Applications. Metallurgical and Materials Transactions. A, vol. 45, no. 5419.
Sohn, S.S., Hong, S., Lee, J., Suh, B-C., Kim, S-K., Lee, B-J., Kim, N.J., Lee, S. 2015. Effects of Mn and Al contents on cryogenictemperature tensile and Charpy impact properties in four austenitic high-Mn steels. Acta Materialia, vol. 100, no. 39.
Chowdhury, P., Canadinc, D., Sehitoglu, H. 2017. On deformation behavior of Fe-Mn based structural alloys. Materials Science and Engineering R, vol. 122, no. 1.
Guerrero, L.M., La Roca, P., Malamud, F., Baruj, A., Sade, M. 2017. Composition effects on the fcc-hcp martensitic transformation and on the magnetic ordering of the fcc structure in Fe-Mn-Cr alloys. Materials Design, vol. 116, no. 127.
Bleck, W., Haase, C. 2019. Physical Metallurgy of High Manganese Steels. Metals, vol. 9, no. 1053.
Bastidas, D.M., Ress, J., Bosch, J., Martin, U. 2021. Corrosion Mechanisms of High-Mn Twinning-Induced Plasticity (TWIP) Steels: A Critical Review. Metals, vol. 11, no. 287.
U.S. Geological Survey. 2020. Mineral commodity summaries 2020 U.S. Geological Survey, 200, https://doi.org/10.3133/ mcs2020
Gebhardt, T., Music, D., Hallstedt, B., Ekholm, M., Abrikosov, I.A., Vitos, L., Schneider, J.M. 2010. Ab initio lattice stability of fcc and hcp Fe–Mn random alloys. Journal of Physics: Condensed Matter, vol. 22, no. 295402.
Lintzen, S., Von Appen, J., Hallstedt, B., Dronskowski, R. 2013. The Fe–Mn enthalpy phase diagram from first principles. Journal of Alloys and Compounds, vol. 577, no. 370.
Clark, S., Segall, M.D., Pickard, C.J., Hasnip, P.J., Probert, M.J., Refson, K., Payne, M.C. 2005. First principles methods using CASTEP. Zeitschrift für Kristallographie, vol. 220, no. 567. Vanderbilt, D. 1990. Soft self-consistent pseudopotentials in a generalized eigenvalue formalism. Physical Review B, vol. 41, no. 7892.
Paris Agreement to the United Nations Framework Convention on Climate Change, Dec. 12, 2015, T.I.A.S. No. 16-1104.
Perdew, J.P., Wang, Y. 1992. Accurate and simple analytic representation of the electron-gas correlation energy. Physical Review B, vol. 45, no. 13244.
Perdew, J.P., Chevary, J.A., Vosko, S.H., Jackson, K.A., Pederson, M.R., Singh, D.J., Fiolhais, C. 1992. Atoms, molecules, solids, and surfaces: Applications of the generalized gradient approximation for exchange and correlation. Physical Review B, vol. 46, no. 6671.
Pugh S.F. 1954. Relations between the elastic moduli and the plastic properties of polycrystalline pure metals. Philosophical Magazine and Journal of Science, vol. 45, no. 367, p. 823.
Bleskov I., Hickel T., Neugebauer J., Ruban A. 2016. Impact of local magnetism on stacking fault energies: A first-principles investigation for fcc iron. Physical Review B, vol. 93, no. 214115. Okamoto, H. 1992. Phase Diagrams of Binary Iron Alloys, ASM International.
Welsch, E., Ponge, D., Hafez Haghighat, S.M., Sandlöbes, S., Choi P., Herbig, M., Zaefferer, S.D., Raabe, D. 2016. Strain hardening by dynamic slip band refinement in a high-Mn lightweight steel. Acta Materialia, vol. 116, no. 188.
Guerrero, L.M., La Roca, P., Malamud, F., Baruj, A., Sade, M. 2020. A Short Review on the Effect of Cr on the fcc–hcp Phase Transition in Fe–Mn-Based Alloys. Shape Memory and Superelasticity, vol. 6, no. 202.
Cordero, Z.C., Knight, B.E., Schuh, C.A. 2016. Six decades of the Hall–Petch effect – a survey of grain-size strengthening studies on pure metals. International Materials Reviews, vol. 61 no. 8, p. 495. u
Whatever terminology you wish to use, it is obvious the world of work is changing rapidly.
The Mining Industry, along the Mining Value Chain, is a part of this; seeking to take advantage of digital opportunities in the quest for competitiveness, sustainability and Zero Harm.
Mining businesses in Africa, as globally, are on this journey purposefully or by default. This event adds to purpose by being a showcase and learning experience for everyone associated with the Mining Industry. We will learn about Global Best Practices, network with global leaders in mining and other businesses, and do so in an exciting and interactive format.
Be prepared to be challenged and informed and to leave excited and better equipped for today’s digital journey.
Affiliation:
1Mintek, Randburg, South Africa
2University of Stellenbosch, Department of Chemical Engineering, Matieland, South Africa
Correspondence to: M.I. Khama
Email: mopelik@mintek.co.za
Dates:
Received: 9 Sept. 2024
Accepted: 12 Nov. 2024
Published: March 2025
How to cite:
Khama, M.I., Reynolds, Q.G., Xakalashe, B.S. 2025. A macro-scale approach to computational fluid dynamics modelling of the reduction of manganese ore by hydrogen. Journal of the Southern African Institute of Mining and Metallurgy, vol. 125, no. 3, pp. 151–160
DOI ID:
https://doi.org/10.17159/2411-9717/3559/2025
ORCiD:
M.I. Khama
http://orcid.org/0000-0003-1443-6262
Q.G. Reynolds
http://orcid.org/0000-0002-5196-8586
B.S. Xakalashe
http://orcid.org/0000-0003-0069-7082
by M.I. Khama1, Q.G. Reynolds1,2, B.S. Xakalashe1
Abstract
The carbonaceous reduction of manganese ore is an energy-intensive process that releases large amounts of pollutant gases. In an attempt to circumvent the greenhouse gas emissions, this research investigates hydrogen as an alternative reductant. The reduction of manganese ore with hydrogen results in the structural changes in the intermediate products, which might limit the diffusion of the reactant gases through the pores. Computational fluid dynamics (CFD) models capture the structural changes and predict the rate controlling mechanism and this is key in designing the prereduction reactors. The current work uses CFD models to predict the degree of reduction in a shaft furnace under hydrogen reducing conditions. Manganese ore is described as a collection of scalar and tensor fields such as thermal conductivity of the porous medium, density, and viscous resistance. The results indicate that advection contributes significantly towards the overall transport of hydrogen to the reaction sites. Porosity of the final product was found to be higher than porosity of the raw material.
Keywords
CFD, diffusion limitations, kinetic limitations, solid-state reduction, hydrogen
The production of high carbon ferromanganese is achieved through the reduction of manganese ore in a submerged arc furnace (SAF) and utilises carbon as a reductant. The process is energy-intensive and this is particularly evident in carbonate rich manganese ores. This is because the thermal decomposition of carbonates is highly endothermic, and this increases the energy requirements. However, some furnace operations charge manganese sinter in the electric furnace resulting in the reduction of the smelting energy consumption (Liu et al., 2024). This is because manganese sinter does not have carbonates as they decompose during sintering. In cases where sinter is not used, the high-energy requirements coupled with high greenhouse gas emissions necessitated a need to explore alternative reductants. Several researchers have investigated the solid-state reduction using H2 as a potential reductant for prereduction (Patisson et al., 2020; Wu et al., 2024; Ma et al. 2022). Prereduction offers advantages such as reduced energy consumption in the downstream smelting. Furthermore, prereduction of carbonate rich manganese ores by H2 results in the acceleration of the carbonate decomposition (Davies et al., 2023).
The reduction behavior of manganese ores is non-uniform since manganese ores contain minerals with different compositions of manganese and iron (Coetsee et al., 2015). The heterogeneous nature of manganese ores requires that the reaction mechanism and kinetic data for each ore be determined before process equipment design. In the context of solid-state prereduction of manganese ore with H2, a shaft furnace can be used, and the kinetic parameters are key for the design and upscale of the shaft furnace.
The prereduction of manganese lumps or pellets with H2 in a shaft furnace represents a reacting flow problem that is susceptible to mass transfer limitations. However, H2 has a small molecular size and diffuses easily into the ore. The diffusion of H2 happens through three mechanisms namely, physisorption, chemisorption, and H2 uptake (Li et al., 2024). Physisorption happens due to the Van der Waals forces between H2 and the manganese ore surface and is influenced by temperature and pressure. Chemisorption concerns the formation of covalent bond between molecules (Christmann, 1988). H2 uptake involves incorporation of H2 into the metal oxide lattice structure through desorption.
The knowledge of reaction mechanism in the pre-reduction of manganese ores with H2 is crucial. Owing to the importance of understanding the kinetics and reaction mechanism for prereduction
with H2, Rukini et al. (2022) carried out some studies aimed at understanding this phenomenon. These researchers state that lattice oxygen in the oxide is removed, and the process is driven by H2O removal. The diffusion of H2 into the metal oxide structure, which results in the breaking of metal oxide bonds is facilitated by the transformation of molecular H2 into atomic state (Kung, 1989). Upon breaking the metal oxide bonds, the formation of a hydroxyl group and metal hydride follows. The resultant metal hydride is volatile and subsequently releases H2 to form H2O with hydroxyl followed by water vapour desorption (Rukini et al., 2022).
The chemical reactions might be fast enough to facilitate the desired reduction and conversion, however, the transport of H2 from the bulk gas phase to the reaction sites affects the reaction concentration. Therefore, the reduction kinetics are strongly coupled with heat and mass transfer and a numerical model needs to capture this phenomenon. This is particularly evident in the solid-state reduction of a packed bed of pellets in a shaft furnace (Hamadeh et al., 2018). It is vital to characterise several performance indicators of industrial heterogeneous reactors in order to gauge the optimum operating conditions. However, the performance of industrial heterogeneous reactions at high temperatures is difficult to measure during the operation. This shortcoming is addressed by using the CFD models, which are able to capture the dynamic features of industrial heterogeneous processes. The fixed bed reactor performance and productivity is influenced by the gas-solid reactions, therefore, the development of robust, coupled reaction kinetics and transport models is of paramount importance.
Several researchers have developed reaction models for gassolid reactions (Hamadeh et al., 2018; Li et al, 2023; Kinaci et al., 2020). These models include the shrinking core model and the grain model. The shrinking core model works for simplified cases and its applicability is confined to cases where the inward diffusion controls the reaction (Ahn et al., 2017). In most cases, the heterogeneous reaction system constitutes a multi-step and multi-species process, and this renders the shrinking core model unsuitable. This is because the condition of multiple reaction steps and equilibrium reactions, among other factors, result in model deviations (Wesenauer et al., 2020). A more accurate reaction modelling approach is the one that considers the pellet as a porous spherical agglomerate of composite grains. The robustness and generality of such a model can manifest in its predictive capability of prereduction behavior of a bed of pellets or lumps in a shaft furnace.
A shaft furnace is by design a complex reactor that involves multiphase flows coupled with high temperature and pressure. It is crucial to measure parameters that influence the process performance. However, it is difficult to measure them during operation. Numerical models that consider multiphase flows and couple chemical kinetics with transport phenomena circumvent these shortcomings. An example of such a model is a shaft furnace model developed by Li et al. (2023), which uses the well-established volume-averaged multiphase Navier Stokes equations to describe the gas phase in a reacting gas-solid system. The authors assumed a steady state and considered the momentum, mass, and energy conservation for the two phases. Their continuum-based model was validated against performance indicators measured from plant operation based on production using H2 and natural gas.
The gas-solid dynamics in a shaft furnace can be captured through modelling approaches such as Eulerian two-phase models, plug flow models, direct numerical simulation (DNS), and computational fluid dynamics and discrete element methods (CFDDEM). DNS does not require closure models, and its predictions
result in the highest resolution of gas and particle flow. However, it is computationally expensive and limited to low Reynolds numbers and a finite number of fluid elements, rendering it unsuitable for most real applications. CFD-DEM model is able to capture the particle descent and flow patterns in a furnace due to its ability to account for drag force (Fei et al., 2024). The larger number of particles in the furnace coupled with longer spatial and temporal scales including non-linear equations impose high computational expense on CFD-DEM models. The plug flow models are unable to resolve the particles and assume a constant axial velocity and this allows for faster evaluation of gas-solid flow in industrial shaft furnaces. Given the high computational expense of CFD-DEM and DNS models and inaccuracy of plug flow models, further research is needed to develop computationally efficient and accurate heterogeneous reacting flow models.
Liu et al. (2023) developed a 3D CFD model to investigate the influence of reducing gas temperature on physical quantities in a shaft furnace with the view to optimise the operating conditions. Their model assumes that the moving bed of pellets has uniform porosity and ignores the interaction between particles in the furnace charge. The heat transfer between gas and solid phase considers convection and chemical reaction heat. In the cases where the reactions take place at high temperatures, the effects of radiative heat transfer are significant and have to be included in the energy equation.
The current work utilises the CFD reacting flow models developed by Jan Źuk et al. (2022) to investigate the reduction behaviour of manganese ore under H2 in a shaft furnace. The approach utilises a standalone CFD solver that couples fluid flow, heat transfer, and heterogeneous reactions in a porous medium. The geometry of the porous medium is taken into account by its physical characteristics. The inclusion of ore particles into the computational domain is done by using the special form of the immersed boundary method named the fictitious domain (Jan Źuk et al.,2022). In this study, the porous medium in the fictitious domain is defined by its physical characteristics that include scalar porosity and tensor viscous resistance. As mentioned above, the models used to predict the gas-solid dynamics are computationally expensive. However, the current approach is an efficient and easy implementation that allows for rapid numerical computation, particularly for cases where there is need to change the physical characteristics of the geometry or flow during calculation time without remeshing the domain and rewriting the corresponding boundary conditions. The study considers a fixed bed of particles with uniform porosity, and predicts the species mass fractions and the structural changes as the products are formed from gas-solid reactions.
A bed of particles as depicted in Figure 1, is described by its physical properties that include density, thermal conductivity, and porosity. The CFD model developed by Jan Źuk et al. (2022) represents the porous medium as a volume field within a computational domain. To simplify the implementation, the porous medium is assumed to be either entirely inside or outside the computational cell. This is done to minimise the need to use two or more computational cells to resolve porous medium.
The gas flow through the porous medium is integrated with heterogeneous reactions. In the heterogeneous reactions where there is a possibility of mass transfer limitations, the CFD model must incorporate the effects of diffusion limitations. In this study, Damkohler number (Dai) is used to determine whether the reaction
rates are controlled by diffusion or chemical reactions. Dai is defined by the ratio of characteristic diffusion time to characteristic surface reaction time as depicted in Equation 1.
[1]
In the diffusion-controlled regime, Dai →∞ because in this case, diffusion is slower than the reaction at the surface, whereas in the chemical reaction-controlled regime, Dai→0 since the reactions at the surface are slower than diffusion. The other way to gauge the operating regime is to evaluate the ratio of diffusion flux to reaction rate flux. The diffusion flux is calculated from Fick’s law and the reaction rate based on species diffusion is modelled according to Equation 2:
Where Kg (m/s) is mass transfer coefficient, SAV (m-1) is the ratio of surface area to volume, Rdifs (kg m-3 s-1) is the volume averaged reaction rate, ρG (kg m-3) is the fluid density, YiG is the bulk mass fraction of the reduction gas, and YiS is the surface mass fraction of the reducing gas. Mass transfer coefficient depends on the intensity of the energy dissipation in the fluid and is evaluated from the correlation by Comiti et al. (2000) as shown in Equation 3:
Where Sh is Sherwood number, Sc is Schmidt number, ε is porosity, Y is particle aspect ratio, Xew is wall energetic criterion, and τ is tortuosity.
Schmidt number (Sc) is calculated from the ratio of momentum diffusivity to mass diffusivity. Sutherland’s law is used to calculate dynamic viscosity as a function of temperature and Sutherland coefficient, and this allows for the evaluation of Sc (Sutherland 1893) . The Sutherland coefficients for H2O and H2 are as follows:
both exothermic and endothermic and the heat of the reaction is presented in Equation 5. Reaction 6 is exothermic while reaction 7 is endothermic. It should be noted that, although the enthalpy of formation in this section is calculated at standard conditions (1 atm, 298 K), the heat of reaction at the operating temperature in the study was calculated from Equation 17.
[6] [7]
The governing equations for gas flow through a homogeneous porous medium are presented in Equations 8 to 11, which represent momentum, continuity, species conservation, and energy balance, respectively. In these equations, Cp is the specific heat, ρ represents density, p is pressure, ε is porosity, u is fluid velocity, µeff is the effective viscosity, Deff is the diffusion coefficient, D is Darcy’s resistance to flow, and F is the Forchheimer’s term. The superscript G refers to gas phase. In Equation 8, a non-Darcy term is included to address the limitations in Darcy’s law. Darcy’s law is only applicable to creeping flow regimes or low Reynolds number regime, since it neglects the effects of inertial forces on fluid flow and heat transfer (Vafai, Tien, 1981). On the other hand, the Forchheimer model is applicable to flows with Reynolds numbers greater than 10 since, in this regime, the inertial effects are significant. The inertial effects are more pronounced near the boundary and in high porosity media rendering the application of Darcy’s law invalid. The Forchheimer model adds the inertial term to the Darcy equation to account for the non-linear behaviour of pressure drop versus flow velocity. The Darcy’s equation is presented in Equation 12 while the Forchheimer model is presented in Equation 13.
Where As is Sutherland coefficient and Ts is Sutherland temperature. Dynamic viscosity is calculated as shown in Equation 4. [4]
The energy requirement for the heterogeneous reactions depends on whether the reactions are exothermic or endothermic. The heat of reaction for each reaction step is evaluated from the enthalpy of formation of the species involved in a chemical reaction as shown in Equation 5:
[5]
Where is the enthalpy of formation at standard conditions. In this study, the prereduction of manganese ore with H2 is represented by Equations 6 and 7. In this case, the global reactions are used as opposed to the multi-step reactions. This study considers isothermal process at a chosen temperature. The reactions are
The solid phase is described by continuity, species conservation, and energy balance equations as shown in Equation 14 to 16. The solid phase does not include the momentum equation since the particles are immobile. The solid and gas phase interact through the reactions between the gas and solid and heat transfer, and the coupling between the phases is achieved through the reaction rate source term R:
[14]
[15]
[16]
[17]
Where denotes reduction rate of solid species and denotes reduction rate of gas species. The reduction rate is presented in Equation 18:
[18]
Where vi,k is the stoichiometric coefficient, ks is the number of elementary reactions, Ng is the number of gas phase species, and Ns is the number of solid phase species. Kf is the rate constant and v’j,k is reaction order. The rate constant depends on temperature and is described by Equation 19:
[19]
Where Ta is the activation temperature and A is the pre-exponential factor.
Initial and boundary conditions
At the inlet boundary condition, temperature, velocity and composition of gas (YiG), and solid (Yks) are known. A no slip boundary condition is imposed for velocity at the walls and at the
A summary of initial and boundary conditions
Initial condition
inlet, gas velocity is specified. The reactions take place at the ore surface, and the boundary condition at the interface is described by Equation 20. At the outlet boundary, heat flux and mass flux are assumed to be zero as shown in Equation 21 to 22. The heat and mass flux are assumed to be zero at the outlet because the flow is assumed to be fully developed. The flow regime is laminar and the assumption of a fully developed flow for shorter domains is valid. A summary of initial and boundary conditions is presented in Table 1.
The convective heat transfer at the interface is defined by Equation 23:
Where SAV denotes the surface area to volume ratio, h is the convective heat transfer coefficient, Tg the gas phase temperature, and Ts is the solid phase temperature.
Geometry and meshing
The dimensions of a shaft furnace considered in the study are presented in Table 2. Gmsh mesh generator was used to generate the mesh for a 3D and 2D axisymmetric geometry as presented in Figure 2. The manganese particles are packed in the furnace from 1.2 m to 1.85 m as observed in Figure 2. The porous medium is
Boundary conditions
Inlet Outlet Walls
Volumetric flowrate 0 l/min 100 l/min zero gradient 0 l/min
Pressure 101300 Pa zero gradient 101300 Pa zero gradient
Temperature (solid phase) 800oC zero gradient zero gradient zero gradient
Temperature (gas phase) 800oC 800oC zero gradient zero gradient
Table 2
Reactor
and operating conditions Reactor
Reactor
Cone
Cone
Inlet
Outlet
Bed
Initial
Inlet
Inlet
Inlet gas flow rate (l/min)
MnO2
Fe2O3
usually inhomogeneous however, it was assumed that porosity is uniformly distributed through a bed of particles.
A solution approach to any numerical problem must achieve convergence, consistency, and numerical stability in order to be considered accurate. The criterion for convergence is a close agreement between the numerical solution and the exact solution as grid spacing tends to zero. In the current work, mesh sensitivity analysis on the 2D-axisymetric model was undertaken and the results are presented in Figure 2. The species mass fraction profiles at various grid sizes reveal that at grid 1, the mass fraction profiles are resolution dependent. Refining the mesh size to grid sizes larger than grid 2 resulted in no difference in the predicted mass fraction,
thus revealing grid 2 as the optimum mesh size. The number of cells in Grid 1, Grid 2, and Grid 3 is 5 241, 10 482, and 31 446, respectively. For the 3D geometry, the number of cells in Grid 1, Grid 2 and Grid 3 is 23 807, 47 614, and 71 421, respectively.
The computational solution to Navier-Stokes and transport equations was carried out in OpenFOAM® 8. The coupling of chemistry and transport processes was done by using the OpenFOAM® solver for heterogeneous reacting flows developed by Jan Źuk et al. (2022). These authors developed their framework at the top of OpenFOAM® wherein the mesh and discretisation of Navier-Stokes equations is managed through the OpenFOAM® framework, while their CFD code focused on the reaction mechanisms and gas-solid reactions as the reducing gas flows through the porous medium.
This study investigates prereduction in a shaft furnace with the dimensions and operating conditions shown in Table 2. A 2D-axisymetric and a 3D model results are compared to investigate whether their predictions are similar. 2D-axisymetric models are not computationally expensive when compared to 3D models, and if their predictions are found to be viable, this will result in faster evaluation of shaft furnace performance indicators. However, the inability to predict asymmetry of flow patterns and transversal fluid flow constitute some limitations inherent to 2D-axisymmetric models (Mezhericher et al., 2009). The mass fraction profiles for a 3D geometry are presented in Figures 3 to 6. The mass fraction profiles of reactants and products indicate that at 2450 seconds (40.8 minutes), reduction is complete. At 1100 seconds (18.3 minutes), only a fraction of the 0.65 m bed height is reduced, and this indicates that mass transfer controls the rate of reduction. To circumvent this limitation, the flowrate of the H2 needs to be increased. The increase in the reducing gas flow rate results in the
increased diffusion through the boundary layer, and as a result, an increased rate of reduction. Increasing H2 partial pressure increases the rate of adsorption, which ultimately results in an increased rate of reduction. In order to elucidate the spatial distribution of the rate of reduction, the shaft furnace was compartmentalised and the mass fraction profiles at each compartment are shown in Figure 7.
The species mass fraction profiles at 1.3 m, 1.5 m, and 1.8 m are shown in Figure 7. A total mass balance was performed as a way to gauge whether the model is consistent in its predictions. The consistency tests on each compartment reveal that the mass balance is closed. The mass fraction results show that at 1.3 m, the reduction to metallic iron and MnO is complete at 500 seconds (8,33 minutes), while the reduction at 1.8 mm is complete at 2450 seconds (40,83 minutes). This is attributed to the effects of mass transfer limitations more pronounced at longer bed heights.
A change in particle density and porosity as products are formed, is presented in Figure 8. Formation of products results in the particle density changes and subsequently changes in porosity. Generally, the increase in bulk density at constant particle density results in the decrease in porosity (Kurgan, 2014). However, in this study, particle density increases as metallic iron and MnO are formed from reduction reactions and, given that the total mass does not change, porosity is expected to increase. The results in Figure 8 show that a change in porosity and the density is rapid on the lower section of the particles’ bed because the lower compartment is the first point of contact with the reducing gas. It is crucial that a CFD model predicts structural changes during the phase transformation. This is important because the formation of intermediate products may result in the formation of dense phase with low porosity, thus blocking the access of reducing gases to the reaction interface.
Chemical reactions and diffusion normally play a role in controlling the rate of reactions. If chemical reactions are slow, the rate of reactions are controlled by chemical reactions and, if diffusion is slow, the process is diffusion controlled. In this study, Equation 24 is used to determine the operating regime. The equation evaluates the fraction of diffusion flux and, whenever the fraction is less than 0.5, it can be concluded that diffusion is slower than chemical reactions. As observed in Figure 9, when the reducing gas reaches a compartment of interest, the diffusion flux fraction is always less than 0.5, indicating that diffusion is rate limiting. When reduction is complete or not yet started, the fraction of diffusive flux is unity as the reaction rate flux is zero.
The rate of H2 transport from the bulk phase to reaction sites influences the reaction concentration, and owing to this, the analysis of the effect of diffusion and convection is performed. Péclet number (Pe) is used to determine the effect of diffusion and advection. Pe is defined as shown in Equation 25. The results in Figure 10 reveal that convective transport contributes significantly towards overall mass transport because Pe is always greater than unity. The results indicate that the effect of axial dispersion is insignificant.
The mass fraction profiles predicted from a 2D-axisymetric model are presented in Figures 11 to 14. Similar to the 3D model, the reactor is compartmentalised to allow for the description of the spatial distribution of mass fraction profiles. In this case, the reduction is complete in all compartments at 600 seconds (10 Minutes), while the 3D model results in complete reduction at 2450 seconds (40,83 minutes). Therefore, the computational accuracy of the two models is different and for a more accurate description of prereduction behaviour in a shaft furnace, a 3D model should
be used. Although the 2D-axisymetric model overestimates the reaction rates, the manifestation of mass transfer limitations is still as apparent as in the 3D model. The 3D model results were validated against experimental results already presented, therefore, it is postulated that the 2D-axisymetric model overestimates the reaction rates.
The effect of H2 flowrate on the rate of prereduction was investigated, and the results are presented in Figure 15. As observed, the higher H2 flowrates result in an increased rate of reduction. This is because an increase in the reducing gas flow rate leads to increased diffusion through the boundary layer, as a result an increased rate of reduction.
Model validation
There are no experimental data for prereduction of manganese in a shaft furnace, however, there are experimental data for prereduction in a thermogravimetric analysis furnace (TGA). Therefore, to
validate the predictions of the CFD model, experimental percentage mass loss data from the TGA were used. In this case, the CFD model was used to predict the prereduction behaviour of manganese under H2 reducing atmosphere in a TGA furnace. The CFD predictions for a TGA furnace were compared with the experimental measurements from the TGA by Sarkar et al. (2023). The results presented in Figure 15 concern prereduction in the TGA with 4.5 cm diameter and 48 cm in height at 700oC at the H2 flow rate of 4 l/min. As observed, there is a close agreement between experimental and model percentage mass loss data up to 2500 seconds (41,66 minutes), and thereafter a discrepancy is observed with a maximum error of 1%. The discrepancy can be attributed to the decomposition of carbonates in the experimental measurements, which results in CO2 evolution and increased mass loss. On the other hand, the CFD model only describes mass loss from reduction reactions and does not take into account mass loss due to carbonate decomposition.
Conclusions
Conclusions
The CFD modelling of prereduction of manganese ore in a shaft furnace has demonstrated that longer bed heights require high H2 flowrate to facilitate faster rates of reduction. At low flowrates and long bed heights, the effect of diffusion limitations on the reactions is more pronounced. This is attributed to a long boundary layer thickness at low gas flowrates and slower rates of mass transfer. The computational accuracy of the 2D-axisymmetric and the 3D model is different and this results in the overestimation of the rate of reduction in the 2D-axisymmetric case. The 3D models are required to predict the dynamic features of a shaft furnace and evaluate performance indicators. The CFD models are able to predict whether mass transfer or kinetics control the reaction rates and this is crucial in the design and optimisation of heterogeneous
The CFD modelling of prereduction of manganese ore in a shaft furnace has demonstrated that longer bed heights require high H2 flowrate to facilitate faster rates of reduction. At low flowrates and long bed heights, the effect of diffusion limitations on the reactions is more pronounced. This is attributed to a long boundary layer thickness at low gas flowrates and slower rates of mass transfer. The computational accuracy of the 2D-axisymmetric and the 3D model is different and this results in the overestimation of the rate of reduction in the 2D-axisymmetric case. The 3D models are required to predict the dynamic features of a shaft furnace and evaluate performance indicators. The CFD models are able to predict whether mass transfer or kinetics control the reaction rates and this is crucial in the design and optimisation of heterogeneous
reactors. However, the CFD model does not include the effects sintering and future work will incorporate this. Sintering has a retarding effect on reduction since it results in the blockage pores, hindering the transport of reducing gases to the reaction sites. Future work will incorporate sintering by utilising discrete element method (DEM) and assigning to particles models such as inter-particle bond formation, grain coalescence models, breakage models, heat transfer models, contact models, and consideration of mass transport due to surface and grain boundary diffusion. Currently, the models assume homogeneous porous medium, however, in the future, the inhomogeneity of the porous medium will be captured by considering a non-uniform porosity distribution, and a micro CT based method will be used to validate porosity of prereduced product predicted by the CFD model.
reactors. However, the CFD model does not include the effects of sintering and future work will incorporate this. Sintering has a retarding effect on reduction since it results in the blockage of pores, thus hindering the transport of reducing gases to the reaction sites. Future work will incorporate sintering by utilising discrete element method (DEM) and assigning to particles models such as inter-particle bond formation, grain coalescence models, breakage models, heat transfer models, contact models, and consideration of mass transport due to surface and grain boundary diffusion. Currently, the models assume homogeneous porous medium, however, in the future, the inhomogeneity of the porous medium will be captured by considering a non-uniform porosity distribution, and a micro CT based method will be used to validate porosity of prereduced product predicted by the CFD model.
Notation
Notation
Ts solid phase temperature K
Ts solid phase temperature
Tg gas phase temperature K
Tg gas phase temperature
Cp specific heat
Cp specific heat J kg-1K-1
Da Damkohler number, dimensionless
Da Damkohler number, dimensionless
Kg mass transfer coefficient
Kg mass transfer coefficientm s
Rdifs volume averaged reaction rate
Rdifs volume averaged reaction rate
ρG gas density
ρG gas density
YiG bulk mass fraction of the reduction gas, dimensionless
YiG bulk mass fraction of the reduction gas, dimensionless
Yis surface mass fraction of the reducing gas, dimensionless
Yis surface mass fraction of the reducing gas, dimensionless
Sh Sherwood number, dimensionless
Sh Sherwood number, dimensionless
Sc Schmidt number, dimensionless
Sc Schmidt number, dimensionless
Y particle aspect ratio, dimensionless
Y particle aspect ratio, dimensionless
Xew wall energetic criterion, dimensionless
Xew wall energetic criterion, dimensionless
τ tortuosity, dimensionless
τ tortuosity, dimensionless
As Sutherland coefficient kg m-1s-1K-1/2
As Sutherland coefficient kg m-1s-1K-1/2
Ts Sutherland temperature
μ dynamic viscosity
Sutherland temperature .................................K dynamic viscosity kg m-1s-1
hf0 enthalpy of formation
hf0 enthalpy of formation kJ mol-1
p pressure ............................... Pa
p pressure
u fluid velocity
u fluid velocity
m s-1
D Darcy’s resistance to flow
Kung, H.H. 1989. Transition Metal Oxides: Surface Chemistry and Catalysis. vol. 45. 1st ed.
Kung, H.H. 1989. Transition Metal Oxides: Surface Chemistry and Catalysis. vol. 45. 1st ed.
D Darcy’s resistance to flow m-2
-2 reduction rate of solid phase species
reduction rate of solid phase species kg m-3s-1
reduction rate of gas phase species .................... kg m-3s-1
m-3s-1 reduction rate of gas phase species
A pre-exponential factor
A pre-exponential s-1
Ta activation temperature
Ta activation temperature K
Pe Péclet number, dimensionless
Pe Péclet number, dimensionless
Acknowledgments
Acknowledgments
This paper is published with the permission of Mintek. The authors acknowledge the Centre for High Performance Computing (CHPC), South Africa, for providing computational resources to this research project. The authors are grateful to Mintek (PDR-24023) and HAlMan (PDE-23002) for financial support.
paper the Mintek. The acknowledge the Centre for High Performance Computing (CHPC), South Africa, for providing computational resources to this research project. The authors are grateful to Mintek (PDR-24023) and HAlMan (PDE-23002) for financial support.
Conflicts of Interest: The authors declare no conflict of interest
Conflicts of Interest: The authors declare no conflict of interest.
References
References
Ahn, Hyungjun, Sangmin Choi. 2017. “A Comparison of the Shrinking Core Model and the Grain Model for the Iron Ore Pellet Indurator Simulation.” Computers and Chemical Engineering, vol. 97, pp.13–26. doi: 10.1016/j.compchemeng.2016.11.005
Ahn, Hyungjun, Sangmin Choi. 2017. “A Comparison of the Shrinking Core Model and the Grain Model for the Iron Ore Pellet Indurator Simulation.” Computers and Chemical Engineering, pp.13–26. doi: 10.1016/j.compchemeng.2016.11.005.
Christmann, K. 1988. Interaction Of Hydrogen With Solid Surfaces Vol. 9. Armsterdam.
Christmann, K. 1988. Interaction Of Hydrogen With Solid Surfaces Vol. 9. Armsterdam.
Coetsee, T., Reinke, C., Nell, J., Pistorius, P.J. 2015. “Reduction Mechanisms in Manganese Ore Reduction.” Metallurgical and Materials Transactions B: Process Metallurgy and Materials Processing Science, vol. 46, 6 doi: 10.1007/s11663-015-0414-y.
Coetsee, T., Reinke, C., Nell, J., Pistorius, P.J. 2015. “Reduction Mechanisms in Manganese Ore Reduction.” Metallurgical and Materials Transactions B: Process Metallurgy and Materials Processing Science, vol. 46, no. 6 pp. 2534–52. doi: 10.1007/s11663-015-0414-y
Comiti, J., Mauret, E., Renaud, M. 2000. “Mass Transfer in Fixed Beds: Proposition of a Generalized Correlation Based on an Energetic Criterion.” Chemical Engineering Science, vol. 55, pp. 5545–54.
Comiti, J.,Mauret, E., Renaud, M. 2000. “Mass Transfer in Fixed of Correlation an Energetic Criterion.” Chemical Engineering Science, pp. 5545–54.
Davies, J., Tangstad, M., Schanche, T.L., Du Preez. S.P. 2023. “PreReduction of United Manganese of Kalahari Ore in CO/CO2, H2/H2O, and H2 Atmospheres.” Metallurgical and Materials Transactions vol. 54, no. 2 pp. 515–35. doi: 10.1007/s11663-022-02705-0
Davies, J., Tangstad, M., Schanche, T.L., Du Preez. S.P. 2023. “PreReduction of United Manganese of Kalahari Ore in CO/CO2, H2/H2O, and H2 Atmospheres.” Metallurgical and Materials Transactions B, vol. 54, no. 2 pp. 515–35. doi: 10.1007/s11663-022-02705-0
Fei, Yang., Guan, X., Kuang, S., Yu, A., Yang, N. 2024. “A Review the Furnace Metallurgy: A Chemical Engineering Perspective.” vol. 4, no. 2, pp. 45–65. doi: 10.1021/acsengineeringau.3c00033
Fei, Yang., Guan, X., Kuang, S., Yu, A., Yang, N. 2024. “A Review on the Modeling and Simulation of Shaft Furnace Hydrogen Metallurgy: A Chemical Engineering Perspective.” ACS Engineering Au, vol. 4, no. 2, pp. 45–65. doi: 10.1021/acsengineeringau.3c00033
Hamadeh, H., Mirgaux, O., Patisson, F. 2018. “Detailed Modeling of the Direct Reduction of Iron Ore in a Shaft Furnace.” Materials, vol. 11, no. 10. 10.3390/ma11101865
Hamadeh, H., Mirgaux, O., Patisson, F. 2018. “Detailed Modeling of the Direct Reduction of Iron Ore in a Shaft Furnace.” Materials, vol. 11, no. 10. doi: 10.3390/ma11101865
Jan Pawel, Rymarz, Kwiatkowski, Marek Dudynski, Flavio C. C. Galeazzo, and Guenther C. Krieger. 2022. “OpenFOAM Solver for Thermal and Chemical Conversion in Porous.” Computers and Physics Communications, 10.1016/j.cpc.2022.108407
Jan Źuk, Pawel, Bartosz Tuźnik, Tadeusz Rymarz, Kamil Kwiatkowski, Marek Dudynski, Flavio C. C. Galeazzo, and Guenther C. Krieger. 2022. “OpenFOAM Solver for Thermal and Chemical Conversion in Porous.” Computers and Physics Communications, vol. 278, no. 1–19. doi: 10.1016/j.cpc.2022.108407
Kinaci, M.E., Lichtenegger, T., Schneiderbauer, S. 2020. “A CFDDEM Model for the Simulation of Direct Reduction of Iron-Ore in Fluidized Beds.” Chemical Engineering Science, vol. 227. doi: 10.1016/j.ces.2020.115858
Kinaci, M.E., Lichtenegger, T., Schneiderbauer, S. 2020. “A CFDDEM Model for the Simulation of Direct Reduction of Iron-Ore Beds.” Chemical Engineering Science, vol. doi: 10.1016/j.ces.2020.115858.
Kurgan, N. 2014. “Effect of Porosity and Density on the Mechanical and Microstructural Properties of Sintered 316L Stainless Steel Implant Materials.” Materials and Design, vol. 55, pp. 235–41. doi: 10.1016/j.matdes.2013.09.058.
Kurgan, N. 2014. “Effect of Porosity and Density on the Mechanical and Microstructural Properties of Sintered 316L Stainless Steel Implant Materials.” Materials and Design, vol. 55, pp. 235–41. doi: 10.1016/j.matdes.2013.09.058
Li, Q., Ghadiani, H.,Jalilvand, V., Alam, T., Farhat, Z., Aminul Islam, Md. 2024. “Hydrogen Impact: A Review on Diffusibility, Embrittlement Mechanisms, and Characterization.” Materials, vol. 17, no. 4.
Li, Q., Ghadiani, H.,Jalilvand, V., Alam, T., Farhat, Z., Aminul Islam, Md. 2024. “Hydrogen Impact: A Review on Diffusibility, Embrittlement Mechanisms, and Characterization.” Materials, vol. 17, no. 4.
Liu, W., Zhu, D., Pan, J., Wei, Z., Yang, C., Guo, Z., Zhang, W., Ruan, Jiang, “Study of Ore Fines Strengthened by Pellet-Sintering Process.” Journal of Sustainable Metallurgy, vol. 10, 3 10.1007/s40831-024-00866-7
Liu, W., Zhu, D., Pan, J., Wei, Z., Yang, C., Guo, Z., Zhang, W., Ruan, Z., Jiang, L. 2024. “Study on Sintering Technology of Manganese Ore Fines Strengthened by Pellet-Sintering Process.” Journal of Sustainable Metallurgy, vol. 10, no. 3 pp. 1415–27. doi: 10.1007/s40831-024-00866-7
Liu, Z., Lu, S., Wang, Y., Zhang, J., Cheng, Q., Ma, Y. 2023. “Study on Optimization of Reduction Temperature of Hydrogen-Based Shaft Furnace—Numerical Simulation and Multi-Criteria Evaluation.” International Journal of Hydrogen Energy, vol. 48, no. 42, pp.16132–42. doi: 10.1016/j.ijhydene.2023.01.057
Liu, Z., Lu, S., Wang, Y., Zhang, J., Cheng, Q., Ma, Y. 2023. “Study on Optimization of Reduction Temperature of Hydrogen-Based Shaft Furnace—Numerical Simulation and Multi-Criteria Evaluation.” International Journal of Hydrogen Energy, vol. 48, no. 42, pp.16132–42. doi: 10.1016/j.ijhydene.2023.01.057
Li, Z., Qi, Z., Zhang, L.,Guo, M.,Liang, D., Dong, Q. 2023. “Numerical Simulation of H2-Intensive Shaft Furnace Direct Reduction Process.” Journal of Cleaner Production, vol. 409. doi: 10.1016/j.jclepro.2023.137059
Li, Z., Qi, Z., Zhang, L.,Guo, M.,Liang, D., Dong, Q. 2023. “Numerical Simulation of H2-Intensive Shaft Furnace Direct Reduction Process.” Journal of Cleaner Production, vol. 409. doi: 10.1016/j.jclepro.2023.137059
Ma, Y., Isnaldi R., Souza F., Yang, B., Schenk, J., Patisson, F., Beck, A., Jeroen, A., Van Bokhoven, M., Willinger, G., Li, K., Xie, D., Ponge, D., Zaefferer, S., Baptiste, G., Jaber, R., Mianroodi, Raabe, D. 2022. “Hierarchical Nature of Hydrogen-Based Direct Reduction of Iron Oxides.” Scripta Materialia, vol. doi: 10.1016/j.scriptamat.2022.114571
Ma, Y., Isnaldi R., Souza F., Yang, B., Schenk, J., Patisson, F., Beck, A., Jeroen, A., Van Bokhoven, M., Willinger, G., Li, K., Xie, D., Ponge, D., Zaefferer, S., Baptiste, G., Jaber, R., Mianroodi, Raabe, D. 2022. “Hierarchical Nature of Hydrogen-Based Direct Reduction of Iron Oxides.” Scripta Materialia, vol. 213. doi: 10.1016/j.scriptamat.2022.114571
Mezhericher, M., Levy, A., Borde, I. 2009. “Modeling of Droplet Drying in Spray Chambers Using 2D and 3D Computational Fluid Dynamics.” Drying Technology9, vol. 27, no. 3, pp. 359–70. doi: 10.1080/07373930802682940
Mezhericher, M., Levy, A., Borde, I. 2009. “Modeling of Droplet Drying in Spray Chambers Using 2D and 3D Computational Fluid Dynamics.” Drying Technology9, vol. 27, no. 3, pp. 359–70. doi: 10.1080/07373930802682940
Patisson, F., Mirgaux, O. 2020. “Hydrogen Ironmaking: How It Works.” Metals, 7, 10.3390/met10070922
Patisson, F., Mirgaux, O. 2020. “Hydrogen Ironmaking: How It Works.” Metals, vol. 10, no. 7, pp. 1–15. doi: 10.3390/met10070922
Rukini, A., Rhamdhani, M.A., Brooks, G.A., Van den Bulck, A. 2022. “Metals Production and Metal Oxides Reduction Using Hydrogen: A Review.” Journal of Sustainable Metallurgy, vol. 8, 1.
Rukini, A., Rhamdhani, M.A., Brooks, G.A., Van den Bulck, A. 2022. “Metals Production and Metal Oxides Reduction Using Hydrogen: A Review.” Journal of Sustainable Metallurgy, vol. 8, no. 1.
Sarkar, A., Schanche, T.L.,Jafar Safarian, J. 2023. “Isothermal Pre-Reduction Behavior of Nchwaning Manganese Ore in H2 Atmosphere.” Pp. 2–9 in Material Proceedings. MDPI AG.
Sarkar, A., Schanche, T.L.,Jafar Safarian, J. 2023. “Isothermal Pre-Reduction Behavior of Nchwaning Manganese Ore in H2 Atmosphere.” pp. 2–9 in Material Proceedings. MDPI AG.
Vafai, K., Tien, C.L. 1981. “Boundary And Inertia Effects On Flow And Heat Transfer In Porous Media.” International Journal of Heat and Mass Transfer, vol. 195–203.
Vafai, K., Tien, C.L. 1981. “Boundary And Inertia Effects On Flow And Heat Transfer In Porous Media.” International Journal of Heat and Mass Transfer, vol. 24, pp. 195–203.
Wesenauer, F., Jordan, C., Pichler, M., Frei, A., Azam, M., Jahromy, S.S., Harasek, M., Winter, F. 2020. “An Unreacted Shrinking Core Model Serves for Predicting Combustion Rates of Organic Additives in Clay Bricks.” Energy and Fuels, vol. 34, no. 12, pp. 16679–92. doi: 10.1021/acs.energyfuels.0c03075
Wesenauer, F., Jordan, C., Pichler, M., Frei, A., Azam, M., Jahromy, S.S., Harasek, M., Winter, F. 2020. “An Unreacted Shrinking Core Model Serves for Predicting Combustion Rates of Organic Additives in Clay Bricks.” Energy and Fuels, vol. 34, no. 12, pp. 16679–92. doi: 10.1021/acs.energyfuels.0c03075
Wu, S., Zhang, Y., Li, H., Zhang, S., Kasai, E., Wang, C. 2024. “Hydrogen-Based Pre-Reduction of Chromite: Reduction and Consolidation Mechanisms.” International Journal of Hydrogen Energy, pp. 397–410. doi: 10.1016/j.ijhydene.2023.09.026 u
Wu, S., Zhang, Y., Li, H., Zhang, S., Kasai, E., Wang, C. 2024. “Hydrogen-Based Pre-Reduction of Chromite: Reduction and Consolidation Mechanisms.” International Journal of Hydrogen Energy, vol. 50, pp. 397–410. doi: 10.1016/j.ijhydene.2023.09.026 u
Affiliation:
School of Mining Engineering, University of the Witwatersrand, South Africa
Correspondence to:
T.R. Stacey
Email:
Thomas.Stacey@wits.ac.za
Dates:
Received: 28 May 2024
Revised: 6 Oct. 2024
Accepted: 24 Feb. 2025
Published: March 2025
How to cite:
Chidakwa, T.P., Stacey, T.R. 2025. Evaluating the corrosion resistance of different materials used in friction rock stabilisers in different underground enviroments. Journal of the Southern African Institute of Mining and Metallurgy, vol. 125, no. 3, pp. 161–172
DOI ID:
https://doi.org/10.17159/2411-9717/3415/2025
ORCiD:
T.P. Chidakwa
http://orcid.org/0009-0009-9568-8760
T.R. Stacey
http://orcid.org/0000-0003-3763-9193
by T.P. Chidakwa, T.R. Stacey
Abstract
This study investigated the corrosion rates of various steel types and coatings used for friction rock stabilisers in a deep-level gold mine under diverse underground environmental conditions. Testing was conducted in situ within ramps, intake airways, and exhaust airways, and through simulated laboratory experiments. Results revealed that environmental variations significantly influence the corrosion performance of different materials and coatings. Duplex coatings, made up of galvanised steel with an organic paint layer, demonstrated the highest corrosion resistance. Zinc-based coatings provided moderate protection, while 3CR12 stainless steel and uncoated S420 carbon steel exhibited comparatively poor resistance under both aqueous and atmospheric conditions.
Keywords friction rock stabilisers, corrosion, coupon tests
Introduction
Ground stabilisation support elements used in most deep underground mines are susceptible to corrosion due to the harsh environmental conditions. These harsh conditions are a result of the wet conditions due to groundwater, the presence of corrosive ions such as chloride (Cl-) and sulphate (SO42-), and the high temperatures and high humidity due to mining depth and high virgin rock temperatures. According to Preston, et al. (2019), the high atmospheric temperatures, combined with the presence of pollutants and high humidity, promote the corrosion of exposed ground support elements.
Corrosion of ground stabilisers is of great concern as it causes deterioration of ground support elements, which may cause support failure. Support failure contributes significantly to falls of ground, which then adversely impact the mining operations. Dorion, et al. (2009), described the corrosion of support systems as a major safety and economic concern in underground hard rock mines. According to Potvin, et al. (2001), corrosion is responsible for 25% of all cable bolt failures and 29% of all rock bolt failures in the Australian mining industry. Potvin, et al. (2001) also discovered that 27% of the rockfalls where support had been installed, were supported using friction stabilisers. The corrosion resistance of ground stabilisers plays a crucial role in determining support regimes for mining operations.
This study was conducted at a South African underground gold mine where friction rock stabilisers and yielding mechanical hybrid rockbolts serve as primary ground reinforcement. The friction rock stabilisers being used are susceptible to corrosion due to their design and support mechanism. According to Tilman, et al. (1984), the large surface area, thin tube wall, full column contact with the rock mass, and lack of protective grouting make friction rock stabilisers prone to corrosion failure. This corrosion compromises the structural integrity of rock bolts, leading to loss of support capacity, bolt failure, and rock falls. The mine faces challenges with falls of ground, some of which have been attributed to localised corrosion of ground support. Of the five falls recorded in 2018, one was attributed to support element failure due to corrosion.
The importance of determining the corrosion rates for various metals and coatings has long been recognised in the mining industry. Preston, et al. (2019), evaluated the effectiveness of several coatings, carbon steel alternatives, barrier protection, and combinations of these in different mining environments. Chen, et al. (2022), have also evaluated the impact of different coatings in protecting rock bolts from stress corrosion cracking in underground mines. Hadjigeorgiou, et al. (2023), focused on the impact of rock bolt properties such as chemical composition, configuration, and material hardness on the corrosion resistance of friction rock stabilisers. It is recognised that different coatings lead to different
corrosion in different conditions, as established by Hadjigeorgiou, et al. (2019), when investigating the corrosion resistance of six proprietary coatings used for expandable bolts.
In South Africa, several materials, including S420 carbon steel, 3CR12 stainless steel, and galvanised steel are used in the manufacture of friction rock stabilisers. S420 carbon steel is one of the most common materials, but it suffers from poor corrosion resistance. S420 steel is a high-strength low-carbon steel that contains small amounts of alloying elements such as manganese (1.6%), silicon (0.5%), carbon (0.12%), phosphorus (0.025%), and sulphur (0.015%), which improve its strength and other mechanical properties (Thomas, 2013). As pointed out by Pedeferri (2018), the porous and non-protective rust layer formed on the surface of S420, owing to its carbon steel composition, makes it susceptible to atmospheric corrosion. In contrast, 3CR12 stainless steel is a preferable choice for challenging acidic environments due to the chromium content, which reacts with oxygen to establish a protective oxide layer (Pedeferri, 2018). The 3CR12 was originally developed by Columbus Stainless, which designated the registered trademark ‘3CR12’. Official designations of this grade include UNS S40977/S41003 and 1.4003, ASME SA240 grades, ASTM A240/A240M grades and EN 10088.2. According to Azo Materials (2014), 3CR12 stainless steel is a low-cost grade chromium-containing corrosion resisting ferritic steel fabricated by modifying the properties of grade 409 steel. Its composition typically includes chromium (11.6%), titanium (0.2%), nickel (0.6%), carbon (0.025%), silicon (0.4%), manganese (0.5%), phosphorus (0.025%), and sulphur (0.020%) (Thomas, 1981). Some compositions of 3CR12 have molybdenum, which further enhances corrosion resistance due to molybdenum’s effectiveness in improving pitting and crevice corrosion resistance, (Schweitzer, 2007). However, this stainless-steel variant is susceptible to pitting corrosion in the presence of chloride solutions and oxidising agents (Mursalo, et al., 1988). To mitigate corrosion, zinc-based coatings are increasingly being used on friction rock stabilisers, due to Zn exhibiting a corrosion rate 10 to 30 times lower than that of carbon steel, contingent on environmental conditions (Pedeferri, 2018). Zinc coatings also provide dual protection consisting of barrier and sacrificial protection, and are also more resistant to mechanical damage, (Kania, 2022). Despite the protective nature of galvanised coatings, caution should be exercised regarding their effectiveness in reducing corrosion rates in that it is limited to short-term periods due to the inherent thinness of the coatings (Stimpson, 1998).
Due to the wide variety of rock bolts used and the differences in underground mining environments, it has been difficult to gather enough information to inform different mines on their choice of the best coatings for support elements to suit different conditions. The objective of the research described in this paper was to assess corrosion rates for different types of materials used for friction rock stabilisers in diverse underground environments. The goal was to provide valuable insights for mines in selecting appropriate support elements based on specific conditions.
The research utilised both quantitative and qualitative methodologies aimed at quantifying the corrosion resistance of various steel types and coatings used in the manufacturing of friction rock stabilisers in South Africa, (Chidakwa, 2023). The study consisted of underground corrosion testing conducted at an underground gold mine, and testing at an external laboratory under controlled conditions referred to as simulated underground
corrosion testing (SUCT). These two tests aimed to evaluate corrosion under atmospheric and aqueous environments, respectively.
Underground testing was confined to coupon testing, whilst the SUCT was expanded to include both rock bolt and coupon testing. Coupon testing is a widely accepted procedure for the determination of the type and rate of corrosion in underground environments. It can be described as an in-line monitoring method where coupons are placed directly in the process stream and later removed for assessment; an approach that offers a direct measurement of metal loss, enabling the calculation of the general corrosion rate (Orth, 1997). This method was used by Hadjigeorgiou, et al. (2008), in Quebec underground mines, whilst Villaescusa, et al. (2007), used it in Australian underground mines.
The final evaluation of corrosion for the different materials was based on visual qualification of corrosion, weight loss analysis, and corrosion rate.
Corrosion testing underground was designed to test for atmospheric corrosion. Six different types of steel and coatings were selected for testing in three different types of underground environments i.e., ramps, intake airways, and exhaust airways. These were identified as having distinct atmospheric conditions impacting corrosion. Corrosion coupons made from the materials under investigation were sourced from four different local suppliers who manufacture friction rock stabilisers. The coatings investigated were all proprietary coatings designed in-house by the suppliers. These coupons were manufactured as rectangular slabs measuring approximately 120 mm x 30 mm x 3 mm, as shown in Figure 1.
A total of 288 coupons, made of the different materials under investigation, were installed in 12 different underground locations distributed equally among ramps, intake airways, and return airways. Each location had four sets of coupons from each of the different materials, securely attached to the hanging wall using cable ties.
The materials selected for investigation were:
➤ Hot dip galvanised S420 carbon steel (‘hot dip galvanised’).
➤ S420 carbon steel with a black paint coating (‘black paint’).
➤ Hot-dip galvanised S420 carbon steel with a powder coating (‘powder coating’).
➤ Zinc electroplated S420 carbon steel.
➤ 3CR12 stainless steel (hot rolled with a black finish).
➤ Uncoated S420 carbon steel.
Coupon retrieval was done at 6-, 12-, and 24-month intervals. After retrieval, the coupons were mechanically cleaned to remove dust, photographed at high resolution, and analysed visually before
being bagged individually and despatched to an external laboratory for further analysis. At the laboratory, the coupons were chemically cleaned according to (ISO 9226, 2012) and (ASTM G1-03(2017)e1, 2017), standards before the assessment of mass loss and dimensional changes due to corrosion. Microstructure evaluation was also conducted to determine the nature and extent of the corrosion.
The SUCT was created to assess aqueous corrosion in an environment where temperature, humidity, and water chemistry were controlled. The experiments took place in a custom-built corrosion test chamber at an external laboratory. The environmental conditions for the SUCT were maintained at a temperature of 30 ± 2°C and humidity of 95 ± 5%. An electrolyte solution to simulate underground mine water was used and it comprised 3.5% sodium chloride (NaCl), 2% sodium sulphate (Na2SO4), 0.1% calcium chloride (CaCl2), 0.01% sodium carbonate (Na2CO3), and 0.01% sodium nitrate (NaNO3). The average pH of the solution was 8.27 with a 1.7 range. It is important to note that, whilst there has been water testing conducted at the mine for other projects, there was no water testing conducted for this particular investigation.
A total of 136 coupons and 138 friction rock stabilisers were used for the investigation, distributed across six different materials as follows:
➤ Hot-dip galvanised S420 carbon steel (‘hot dip galvanised’).
➤ Thermal-diffusion Zn-Fe coated S420 carbon steel (‘Distek’).
➤ White (Duplex) coated galvanised S420 carbon steel.
➤ Zinc electroplated S420 carbon steel.
➤ 3CR12 stainless steel (hot rolled with a black finish).
➤ Uncoated S420 carbon steel.
The duplex coating investigated consists of a galvanised S420 carbon steel with a layer of white organic paint. Villa (2012), describes a duplex system as consisting of steel protection with a zinc coating and a non-metallic coating such as paint applied on top to provide additional protection where galvanising alone does not provide the required corrosion durability. The galvanising acts as both a barrier and sacrificial coating, whilst the paint acts as an additional barrier coating.
During friction rock stabiliser installation, the outer layer comes into contact with drilled hole walls, causing potential damage that may impact the rate and type of corrosion. Thus, half of the rock bolts in each category were pressed through a custom-made rigid steel assembly containing compacted stone to simulate scuffing or scratching that occurs during underground installation, as shown in Figure 2.
Before placement in the test chamber, coupons were tagged, weighed, and measured. Specimens, including both coupons and bolts, were then exposed to a controlled environment in the test chamber for a total of 1440 hours, divided into six ten-day cycles. The friction rock stabilisers were subjected to water spray conditions, whilst the test coupons were completely submerged in water in plastic pans on the floor as shown in Figure 3. The friction rock stabiliser test specimens underwent daily rotation, with regular water sample collection to monitor various parameters. After each cycle, at least two coupons for each material type were retrieved, chemically cleaned, and measured according to ASTM G1 procedures. The rest of the coupons and rock bolts were analysed visually. Visual classification of both coupons and friction rock stabilisers was done according to the European rust scale. Microscopic analysis was also conducted on friction rock stabilisers at the end of the investigation.
Visual corrosion qualification
Visual corrosion evaluation for all coupons and friction rock stabilisers was conducted based on the European Rust Grade Scale (ASTM D610) and a chart by Dorion and Hadjigeorgiou (2013). These charts were used to provide a reference point to compare the severity of corrosion for the coupons and rock bolts under investigation. The rust scale and the visual corrosion chart are presented in Figure 4 and Table 1, respectively.
The rust scale assigns a corrosion grade based on the percentage of surface corroded as well as the degree of corrosion. A rust grade
of 5 means that approximately 8% to 14% of the surface is corroded, whilst a rust grade of 9 means that 95% to 100% of the surface is corroded.
The visual corrosion chart was used to assign a corrosion level based on the percentage of the surface corroded as well as the nature of that corrosion and corrosion product. It assigns a corrosion level on a scale of C1 to C6, with C6 being the last or highest level representing extreme corrosion. The chart is comprised of examples adapted from Dorion and Hadjigeorgiou (2013) in column A, and comparable underground coupon specimens obtained from the mine corrosion investigation in column B.
Table 1
Visual Corrosion chart combining local underground specimens and guidelines adapted from Dorion and Hadjigeorgiou, (2013)
Level ID Level of corrosion Description A B
C1 Negligible corrosion Steel is in excellent condition and corrosion signs only on the surface. A few localised spots, less than 10% of the surface is corroded.
C2 Localised corrosion
C3 Surface corrosion
C4 Advanced corrosion
Corrosion is characterised by localised spots on the surface. Between 10% and 75% of the surface is corroded. The steel is in good condition.
Corrosion over 75% of the surface. Corrosion is only on the surface. If a corrosion crust is present it is very thin. Can identify blisters.
100% of the surface is corroded. Can identify blisters. Thin corrosion crust
C5 Very advanced corrosion
C6 Extreme corrosion
100% of the surface is corroded. Thick corrosion crust (> 1 mm) and flaky.
Corrosion goes through the steel. The integrity of the steel has been damaged. Pieces are easily breakable by hand.
Quantifying the rate of corrosion
The rates of corrosion for the different types of steel and coatings were determined using the following equation, where:
CR = (W*K)/(ρ*A*T) [1]
CR is the corrosion rate (mm/y), W is the weight loss (g); K is the constant (8.75*10⁴) when the area is in square centimetres (cm2), ρ is the alloy density (g/cm3), A is the exposed area (cm2), and T is the exposure time (hrs).
Results and discussion
The study involved the investigation of corrosion properties of different materials under different environmental conditions underground, and under simulated conditions at an external laboratory.
Environmental impact on corrosion
Temperature and humidity measurements were taken by the mine environmental department in all the underground locations under investigation. Two measurements were done in each location throughout the study. The average temperature and humidity are shown in Figure 5.
The study established that the different underground environments, i.e., intake airways, ramps, and return airways were sufficiently distinct in terms of temperature and humidity. Return airways (RAW) had the highest average temperature and the lowest relative humidity. Intake airways and the ramps only showed a small variation in terms of average conditions, however, both temperature and humidity were more varied in the ramp areas. It needs to be noted that these conditions are not static and likely fluctuate with mining activities such as a change in ventilation fan locations and capacity, as well as changes in the designated roadways for trackless mobile machinery, among other operational factors.
The corrosion severity of the different materials after 24 months in the different underground environments is shown in Figure 6.
Corrosion severity was the highest in the return airways for all materials. The conditions in the return airways impacted more aggressively on all materials, compared to those in the ramps and intake airways. However, galvanised materials, i.e., zinc electroplated, hot-dip galvanised, and powder coated hotdip galvanised surfaces were the most affected. However, 3CR12 stainless steel, black paint coated, and S420 uncoated steel materials did not show much variation between environments. Overall, the galvanised materials exhibited the best corrosion performance in all environments after 24 months.
Corrosion coupons installed underground were retrieved after 12 and 24 months, and subjected to visual and laboratory testing. The corrosion severity of the different materials based on the visual corrosion scale is shown in Figure 7.
All materials, except the hot-dip galvanised with a powder coating, experienced a significant increase in corrosion severity with time. Zinc electroplated, hot-dip galvanised, and powder coated materials demonstrated the highest corrosion resistance. The 3CR12 stainless steel and black paint coatings performed much worse compared to the Zn-based coatings, but slightly better than S420 uncoated steel, which exhibited the worst corrosion performance. There is also a notable decrease in the rate of corrosion when comparing corrosion severity at 12 and 24 months, which could be as a result of the accumulated corrosion product acting as a protective barrier against further corrosion.
Zn electroplated coatings exhibited varying degrees of corrosion, ranging from being completely unaffected, to small patches of shallow pitting corrosion. Localised shallow corrosion with a whitish-to-greenish-white corrosion product (zinc hydroxide) was also observed. Hot-dip galvanised coatings displayed corrosion ranging from tiny localised patches of shallow corrosion with no product buildup, to localised corrosion with a whitish corrosion product buildup. The corrosion of both zinc electroplated and hot-dip galvanised coupons is shown in Figure 8.
Powder coated coupons exhibited corrosion ranging from spot or localised corrosion to shallow corrosion with a yellowish-brown product, progressing to surface corrosion with a reddish-black corrosion product. The 3CR12 stainless steel coupons showed corrosion mechanisms ranging from shallow uniform corrosion to advanced deep corrosion with an accumulation of a reddish-brown corrosion product. Figure 9 shows the different corrosion levels for powder coated and 3CR12 coupons.
Both black paint coated coupons and S420 uncoated coupons experienced corrosion mechanisms ranging from extensive shallow surface corrosion to advanced deep corrosion with a reddish-black corrosion product. S420 uncoated steel also exhibited very advanced deep corrosion with a layer of corroded material flaking off. Figure
Figure 8—Observed corrosion: (a) unaffected Zn electroplated, (b) localised shallow corrosion on Zn electroplated, (c) unaffected hot-dip galvanised, (d) localised patches on hot-dip galvanised
9—Observed corrosion: (a) localised corrosion on powder coating, (b) surface corrosion on powder coating, (c) shallow uniform corrosion on 3CR12 stainless steel, (d) advanced corrosion on 3CR12 stainless steel
10—Observed corrosion: (a) shallow surface corrosion on black coating, (b) advanced deep corrosion on black coating, (c) shallow surface corrosion on S420 carbon steel, (d) advanced corrosion on S420 carbon steel
10 shows the different forms of corrosion on black painted coupons and S420 uncoated carbon steel.
A weight loss analysis was conducted on the coupons from underground. The average weight loss was calculated for each type of coating and steel, providing a quantitative measure of the extent of corrosion of each material.
The average weight loss for the different types of coatings and substrate materials is shown in Figure 11.
The results of the weight loss analysis showed that the Zn electroplated coating displayed the smallest average percentage weight loss, indicating the best corrosion resistance. The galvanised and powder coatings exhibited similar performance, whilst the uncoated S420 carbon steel showed the highest average percentage weight loss, indicating the worst corrosion resistance.
Corrosion rates were calculated for each steel type and coating, and are presented in Figure 12. Uncoated S420 steel displayed the worst rate of corrosion, whilst Zn electroplated coating showed the lowest rate of corrosion, followed by powder coated hot-dip galvanised steel and then hot-dip galvanised steel. However, to note is the wider range in the corrosion rate of black paint coated and uncoated S420 carbon steel specimens, with some coupons experiencing mild corrosion whilst some experienced advanced corrosion with serious loss of metal, as can be seen in Figure 10(d), which shows a layer or metal flaking off due to corrosion.
All three Zinc coatings, i.e., Zn electroplated, Zn hot-dip galvanised, and Zn hot-dip galvanised with a powder coating, provided effective protection against corrosion in the short term. The corrosion resistance of 3CR12 is generally expected to be significantly better than that of S420 carbon steel, due to its chromium content.
However, in this testing, the performance of 3CR12 was only slightly better than S420 carbon steel, which could be a result of its chemical composition, surface finish, and manufacturing quality control. What is important to note is that all coatings tested in this study were applied to an S420 carbon steel substrate, which has lower corrosion resistance than 3CR12 stainless steel. Therefore, the rate of corrosion is expected to increase significantly after the initial coating deteriorates.
Corrosion behaviour under aqueous conditions
The simulated underground corrosion test was conducted to evaluate the performance of different types of steel and coating under aqueous conditions.
Figure 13 shows the final corrosion severity for coupons from the different types of steel and coatings, based on the rust scale grading system. The white (Duplex) coating was the best coating based on visual observation, followed by the trio of zinc-based coatings, i.e., zinc electroplated, thermal diffusion (Distek) coating and hot-dip galvanised. The 3CR12 stainless steel and S420 carbon steel were the worst performers, with 3CR12 stainless steel being slightly better at a rust grade of 8 compared to S420, which reached the maximum rust grade of 9 with very advanced corrosion.
Hot-dip galvanised specimens exhibited corrosion ranging from light to moderate, characterised by white and red rust and staining progressing to severe reddish-brown rust. Microscopic analysis of
rock bolts indicates localised corrosion with black oxide deposits and slight pitting. The level of corrosion for both coupons and rock bolts is shown in Figure 14.
Thermal diffusion Zn-Fe coated samples displayed corrosion from moderate to severe rusting, featuring reddish-brown rust and white rust/staining. Evidence of localised corrosion and slight
pitting was observed through microscopic evaluation of rock bolts. Figure 15 shows the corrosion of thermal diffusion ZN-Fe coupons and rock bolts.
Zinc electroplated specimens demonstrated varying corrosion mechanisms, from moderate rusting and staining to severe rusting and staining. Microscopic observations on rock bolts show localised corrosion, reddish-black oxide deposits, and slight to moderate pitting corrosion. The corrosion mechanisms for zinc electroplated coupons and rock bolts are shown in Figure 16.
The duplex coated samples were affected by corrosion, ranging from very light rusting to light rusting with reddish-black oxide. Coating delamination was observed after 480 hours, in the form of blistering and flaking of the white paint coating. Localised corrosion, slight pitting corrosion, and the presence of black oxide deposits were also observed during the microscopic analysis of rock bolts. This can be seen in Figure 17, which shows the corrosion of both white duplex coated coupons and rock bolts.
3CR12 stainless steel displayed corrosion initiation in the form of severe red rust and staining, evolving into deep advanced uniform corrosion, pitting corrosion, and notable metal loss after 1200 hours. Microscopic analysis of rock bolts indicates deep advanced corrosion and severe pitting corrosion. Figure 18 shows
the advanced corrosion of coupons and rock bolts for 3CR12 stainless steel. Pitting corrosion can be seen clearly in Figure 18d.
Uncoated S420 carbon steel exhibited corrosion starting as severe red rusting, progressing to advanced deep corrosion with signs of pitting and metal loss, which can be observed in Figure
19. Microscopic analysis revealed severe deep penetrative general and pitting corrosion, which can be seen in Figure 19c, along with exfoliation of the steel surfaces.
After the removal of the corrosion product, S420 carbon steel experienced the biggest loss of material, whilst Zn electroplated exhibited the smallest loss, which can be seen in detail in Figure 20. However, to note is that the loss of weight for the white duplex coating was a combination of corrosion and the paint flaking off, thus it is exaggerated and not representative of its performance.
Corrosion rates for the different types of coatings were subsequently calculated. Figure 21 shows the corrosion rates for the different types of steel and coatings after each 10-day cycle.
There is a gradual decline in the rate of corrosion over time for most of the coatings and steel types. The average rates of corrosion after 1440 hours are shown in Figure 22.
Zinc-based coatings performed the best overall. Zinc electroplated steel had the lowest corrosion rate. The next best was thermal diffusion (Zn-Fe) coating, followed by hot-dip galvanised and white duplex coating, all of which exhibited significantly higher corrosion rates than the Zn electroplated coating. In contrast, 3CR12 stainless steel showed very poor performance. Whilst it
performed worse than all the Zn-based coatings, it was slightly better than S420 carbon steel, which exhibited the poorest corrosion resistance, registering a rate 9% higher than 3CR12 stainless steel, and 80% higher compared to zinc electroplated coating.
Coating damage, simulated to replicate abrasion encountered during underground installation, adversely affected the corrosion resistance of coated materials, as depicted in Figure 23. Conversely, the impact on uncoated materials, namely 3CR12 stainless steel, and uncoated S420 carbon steel, was found to be insignificant. It is noteworthy that while surface damage may not significantly impact uncoated materials, it could potentially trigger other forms of corrosion, such as crevice corrosion for some materials. This, in turn, has the potential to accelerate the corrosion rate for both coated and uncoated materials.
The diminished corrosion resistance observed in coated materials following surface damage is attributed to the exposure of the weaker S420 carbon steel substrate to corrosive elements. Hadjigeorgiou, et al. (2019), also noted that scratching or mechanical damage allows exposure of the underlying substrate to corrosion. Uncoated bolts like 3CR12 and S420 carbon steel exhibit limited susceptibility to abrasion damage, as their surface material is of the same composition as the substrate. Nevertheless, surface damage fosters alternative corrosion forms, notably crevice corrosion, which may not be immediately apparent. Pedeferri (2018), noted that crevice corrosion can arise as a result of the presence of gaps and cracks on a metal surface and that this type of
corrosion is a concern for active-passive alloys such as stainless steel in chloride containing solutions.
Approximately 10% to 15% of the bolt surfaces were damaged in this experiment. If damage surpasses this threshold during underground installations, the corrosion resistance of coated bolts is expected to decline rapidly, given the poor corrosion resistance of the exposed S420 carbon steel substrate. In such instances, the zinc electroplated bolt is anticipated to be the most affected due to its thin coating. Conversely, the white duplex coated bolt is expected to perform better due to its dual coating mechanism, as the paint coating, which forms the outer layer, is likely to suffer most of the surface damage, whilst still leaving the galvanised coating to protect the bolt. According to Jaroslav, et al. (2021), the duplex system has a longer service life than both service lives of two coatings applied separately, thus, in the duplex system, there is a mutual synergistic effect of the zinc coating and organic paint coating. Additionally, 3CR12 stainless steel bolts are expected to outperform S420 carbon steel owing to their superior corrosion resistance.
A ranking of the corrosion resistance of diverse steel types and coatings was conducted after 1440 hours of exposure, considering factors like final corrosion severity, corrosion nature, type, and impact on coating damage for both coupons and friction rock stabilisers rock bolts. The white duplex coating exhibited the best performance due to its dual protective mechanism combining galvanising and painting. Electroplated zinc coating performed slightly better than the other zinc coating methods, including
hot-dip galvanising and thermal diffusion zinc coatings. While the latter two offered thicker, more adherent, more durable coatings, and were expected to have better resistance to aqueous corrosion, inconsistent quality control during manufacturing might explain the electroplated coating's superior performance. The 3CR12 stainless steel performed worse than all the galvanised coatings, but slightly better than S420 carbon steel, which exhibited the worst performance.
Four steel types and coatings were tested under both atmospheric and aqueous conditions. These were Zn electroplated, Zn hot-dip galvanised, 3CR12 stainless steel, and uncoated S420 carbon steel. All coatings corroded at a faster rate under aqueous conditions, as shown in Figure 24.
Conclusions
This study examined different steel types and coatings to identify the best options for corrosion resistance of friction rock stabiliser support in various underground environments. The results obtained determined that the different environments have a quantifiable impact on the corrosion rates of the various steel types and coatings. Corrosion rates were consistently higher in the return airways, compared to ramps and intake airways. This can be attributed partly to the higher dust content in the exhaust air. According to Schweitzer (2007), dust on metallic surfaces,
especially in the presence of moisture, can accelerate corrosion by creating hygroscopic galvanic or differential cells. Particles, such as chlorides, sulphates, carbon compounds, and metal oxides in the dust, combine with moisture to initiate corrosion.
When exposed to atmospheric corrosion, the Zn electroplated coating offered the best corrosion resistance, followed by hot-dip galvanised steel and then hot-dip galvanised steel with powder coating. All three displayed good resistance, with some coupons remaining unaffected after 24 months. Hassell (2008), claimed that zinc offers triple protection by acting as a physical barrier, preferentially corroding to shield the underlying metal, and forming a protective film from its corrosion by-products. The protective film consists of basic salts such as carbonates as a form of resistance to atmospheric corrosion, (Schweitzer, 2007). The 3CR12 stainless steel performed poorly, with most coupons experiencing advanced corrosion within the same period. Uncoated S420 carbon steel displayed the worst resistance, with most specimens reaching very advanced corrosion after 24 months.
In the test for aqueous corrosion, the white duplex coating performed best, followed by all zinc-based coatings (electroplated, thermal-diffusion Zn-Fe-coated, and hot-dip galvanised), which all demonstrated good corrosion resistance. The 3CR12 stainless steel performed slightly better than uncoated S420 carbon steel, but both reached very advanced corrosion after 24 months. The corrosion rates for all steel types and coatings were much higher under aqueous conditions compared to atmospheric conditions.
Overall, considering both atmospheric and aqueous conditions, the duplex coating is considered the overall best option due to its double protection mechanism only if the paint layer application is improved to reduce delamination. Zinc-based coatings also offered comparable protection. Thus, several factors such as cost, availability, damage susceptibility during installation, and impact on support capacity should be considered in selecting the best material for use. All zinc-based coatings are suitable for permanent structures like accessways and workshops of which their lifespan is long. However, to note is that zinc galvanised coatings have been proven to be ineffective in acidic environments (Preston, et al., 2019). Both 3CR12 and S420 carbon steel are not suitable for permanent excavations with a long lifespan and highly corrosive environments, however, both can be used for low to moderately corrosive settings in temporary excavations such as production areas.
Lastly, coating damage during installation significantly affects corrosion resistance. Coatings that are thicker, harder, and have better adhesion to the substrate are expected to offer more protection to the substrate due to better damage resistance during the installation of friction rock stabilisers. Further research could explore optimised zinc-based coating options and specific environmental factors influencing corrosion.
Acknowledgements
This paper is an extract from the extensive corrosion research conducted at South Deep Gold Mine with funding from the WitsGoldfields bursary for postgraduate students. South Deep Gold Mine is thanked for its permission to publish this paper.
Credit author statement
TPC: conceptualisation, methodology, investigation, validation, formal analysis, writing of original draft, visualisation, project, TRS: writing: review and editing preparation, supervision. University of the Witwatersrand: resources, project administration, funding acquisition.
References
Arunachalam, N. 2002. Photograph Booklet of European Scale of Rusting for Anti-corrosive Paints. [Online] Available at: https://www.scribd.com/document/497829787/RE-code
ASTM International. 2017. ASTM G1-03 (2007)e1: Standard Practice for Preparing, Cleaning, and Evaluating Corrosion Test Specimens. [Online] Available at: www.astm.org
Azo Materials. 2014. Stainless Steel - Grade 3CR12 (UNS S40977) [Online] Available at: https://www.azom.com/article.aspx?ArticleID=11048
Chen, H. 2022. The environmentally induced corrosion failure of cable bolts in underground coal mines. Wollongong. Proceedings of the 2022 Resource Operators Conference (ROC 2022), University of Wollongong.
Chidakwa, T. P. 2023. Ground Support Corrosion - Case Study: South Deep Mine, Johanessburg: University of the Witwatersrand.
Dorion, J. F., Hadjigeorgiou, J. 2013. Corrosion considerations in the design and operation of rock support systems. Mining Technology: Transactions of the Institutions of Mining and Metallurgy: Section A, vol. 123, (2014 - Issue 2), pp. 59–68.
Dorion, J.F., Hadjigeorgiou, J., Ghali, E. 2009. Quantifying the rate of corrosion in selected underground mines. Toronto, Proceedings of the 3rd CANUS Rock Mechanics Symposium. Hadjigeorgiou, J., Dorion, J.F., Ghali, E. 2008. Support system performance under different corrosion conditions. The Southern African Institute of Mining and Metallurgy, vol. 108, no. 6, pp. 359–365.
Hadjigeorgiou, J., Savguira, Y., Thorpe, S.J. 2019. Comparative Susceptibility to Corrosion of Coated Expandable Bolts. Rock Mechanics and Rock Engineering, vol. 52, pp. 2665–2680.
Hadjigeorgiou, J., Thorpe, S.J., Cole, K.M. 2023. Quality assurance considerations for friction rock stabilizers. Mining Technology, vol. 132, no. 1, pp. 17–29.
Hassell, R.C. 2008. Corrosion of Rock Reinforcement in Underground Excavations, Perth: Curtin University of Technology.
International Organization for Standardization. 2012. ISO 9226:2012 Corrosion of metals and alloys — Corrosivity of atmospheres — Determination of corrosion rate of standard specimens for the evaluation of corrosivity. [Online] Available at: https://www.iso.org/
Jaroslav, L., Votava, J., Smak, R. 2021. Duplex Anti-Corrosion Protection of Steel Using a Combination of Hot-Dip Galvanising and Water-Soluble Paints. Acta Technologica Agriculturae, vol. 3, pp. 129–135.
Kania, H. 2022. Structure and Corrosion Resistance of Coatings Obtained by the Batch Double Hot Dip Method in Eutectoid ZnAl Bath with the Addition of Mg and Si. Coatings, vol. 12, no. 1207.
Martinez, C. 2012. New approaches and technologies to manage external corrosion and CUI. [Online] Available at: https://www.icorr.org/wp-content/uploads/2020/06/Shell-IcorrPresentation-28-05-2014
Mursalo, N., Tullmin, M., Robinson, F.P.A. 1988. The corrosion behaviour of mild steel, 3CR12, and AISI type 316L in synthetic minewaters. Journal of the Southern African Institute of Mining and Metallurgy, vol. 88, no. 8, pp. 249–256.
National Paints. 2003. Decorative Coatings General Technical Data Sheet. [Online] Available at: https://www.aeconline.ae/13/resourcefile/30/53/05/Sec-a-2.pdf
Orth, J.E. 1997. Corrosion coupon testing. Water Management International, pp. 47–50.
Pedeferri, P. 2018. Corrosion Science and Engineering. 1st ed. Milan: Spinger.
Potvin, Y. 2001. Toward the elimination of rockfall fatalities in Australian mines, East Perth: MERIWA.
Preston, R., Roy, J., Bewick, R. 2019. Rusty Bolts: Planning for Corrosion of Ground Support in Underground Mines. Sudbury, Ontario, Canada. Proceedings of the Ninth International Symposium on Ground Support in Mining and Underground Mine Construction Australian Center for Geomechanics, pp. 423–436.
Schweitzer, P.A. 2007. Fundamentals of Metallic Corrosion: Atmospheric and Media Corrosion of Metals. 2nd ed. Boca Raton Florida: CRC Press Taylor Francis Group.
Stimpson, B. 1998. Split set fiction stabilizers: An experimental study of strength distribution and the effect of corrosion. Canadian Geotechnical Journal, vol. 34, no. 4, pp. 678–683.
Thomas, C. R. 1981. SX 3CR12 - A material for abrasion-corrosion control. Journal of the Southern African Institute of Mining and Metallurgy, vol. 81, no. 10, pp. 298–302.
Thomas, G. P. 2013. Structural Steel 420 - Chemical Composition, Mechanical Properties and Common Applications. [Online] Available at: https://www.azom.com/article.aspx?ArticleID=8071 Tilman, M.M., Jolly III, A. F., Neumeier, L.A. 1984. Corrosion of Friction Rock Stabilizers in Selected Uranium and Copper Mine Waters, Washington: United States Department of the Interior, Bureau of Mines.
Villa, C. S. 2012. Specifications for corrosion protection in the copper mining industry in Chile. Salvador Bahia, INTERCORR 2012. Villaescusa, E., Hassel, R., Thompson, A. 2007. Corrosion of Rock Reinforcement in Underground Excavations, East Perth: MERIWA. u
Affiliation:
CSIR-Institute of Minerals and Materials Technology, India
Correspondence to:
J.K. Pothal
Email: jkpothal@immt.res.in
Dates:
Received: 4 Oct. 2021
Revised: 22 Mar. 2024
Accepted: 18 Nov. 2024
Published: March 2025
How to cite:
Senapati, P.K., Pothal, J.K., Dubey, A., Barik, R., Basu, S. 2025. Analysis of poressure drop and hold-up during vertical transport of limestone slurry in lean phase and heterogrneous regime. Journal of the Southern African Institute of Mining and Metallurgy, vol. 125, no. 3, pp. 173–178
DOI ID:
https://doi.org/10.17159/2411-9717/1777/2025
ORCiD:
P.K. Senapati
http://orcid.org/0009-0005-1005-1690
J.K. Pothal
http://orcid.org/0009-0000-9708-4551
A. Dubey
http://orcid.org/0000-0003-3693-887X
R. Barik
http://orcid.org/0009-0007-7717-8746
S. Basu
http://orcid.org/0000-0001-7288-2370
by P.K. Senapati, J.K. Pothal, A. Dubey, R. Barik, S. Basu
Abstract
The aim of this paper is to study the characteristics of limestone particles (size varies from 4 mm to 20 mm) during its transportation from open cast mines through pipes. The influence of four different size fractions of limestone samples (4–6 mm, 6–10 mm, 10–15 mm, and 15–20 mm) on pipe flow characteristics during vertical transport in a 100 mm NB hose pipe was investigated. The flow velocities in the vertically lifting pipe was varied from 0.95 m/s to 2.78 m/s and a rotary feeder of 2 to 4 tonne/hr. capacity was employed to feed the limestone samples to the lifting pipe. The pressure drop data for the different size fractions of limestone samples at different mixture velocities were analysed. The effect of input volume fraction and superficial velocity of limestone samples on hold-up ratio were discussed. It was indicated that there was no substantial increase in pressure drop of slurry samples in the studied range of concentrations (CW = 4.22% - 12.54%), particle size, and low to medium range mixture velocities with respect to water run head loss data. The hold-up for the larger size fractions (15–20 mm) of limestone samples was found to be significant as compared to smaller size fractions, which may be due to terminal settling velocities of individual fractions of the studied samples.
Keywords limestone, vertical transport, hold-up, pressure drop, heterogeneous regime
The vertical flow of solid-liquid mixtures in pipelines finds applications mostly in mining industries. This provides a potentially cost-effective way of transporting crushed ore from opencast or underground mines to the surface. Extensive studies have been carried out to evaluate the pressure drop and other important operational parameters for designing of slurry pipeline systems, though very limited investigations have been carried out on the flow characteristics of solid-liquid mixtures in vertical pipes. Newitt et al. (1961) investigated the influence of particle size, density, size distribution, pipe diameter, slurry concentration, and velocity on the hydraulic gradient of sand-water mixtures and indicated the negligible influence of larger particles on the pressure drop during vertical transport of mixture slurry. The economic benefits of integrating the mine dewatering and hydraulic transport of solids in vertical pipes as an efficient way of using the groundwater have been investigated by Sellgren (1985). The effect of viscosity on the pipe flow behaviour of solid-liquid mixtures in a vertical pipe was studied by Tokanai et al. (2004). The contribution of both Bagnold force due to collision at the pipe wall, and liquid lifting force in the near-wall zone mainly, influencing the frictional pressure drop was explained by Matousek (2009), while conducting experimental studies on vertical transport of sand-water slurry. Using radiometric method, the phase velocities of artificial nodules and carrier fluid were measured during vertical flow of the mixture, and the interfacial slip for a particle of specific diameter was found to be of the same order as the free settling velocity of the particle (Sobota et al., 2013). A comparative evaluation of frictional pressure drop during horizontal and vertical transport of graded basalt pebbles water mixture in a 100 mm diameter steel pipe was carried out by Vlasak et al. (2014). It has been observed that the frictional pressure drop in vertical pipe were found to be less than in the horizontal pipe and the influence of larger particles on the frictional pressure drops for vertical transport of the mixture slurry could not be confirmed. Some studies on hydraulic lifting of manganese nodules have been reported in the literature (Xia et al., 2004; Park et al., 2004; Yoon et al., 2009; Chung, 2009; Song et al., 2017).
Most of the literature on solid-liquid flow are devoted to vertical transport of sand-sized particles in narrow sized pipes. Further, very limited studies have been conducted on vertical slurry transport
of large-sized particles (> 4 mm size and above). Keeping in view the various aforementioned observations made on the subject, an attempt has been made in this paper to evaluate the pressure drop of large-sized limestone particles in a 100 mm NB hose pipe and the effect of solids concentration, mixture velocity, and the hold-up in vertical flow regime has been analysed.
Experimental procedure
Characterisation studies
The crushed limestone ore samples for the studies were obtained from Lanjiburna mines, M/s Dalmia Cement Pvt. Ltd, Odisha. The material density of the samples were determined using calibrated standard specific gravity bottles and were found to be 2806 kg/m3 The chemical analysis of the bulk limestone samples was carried out by Philips PW2440-X-ray spectrometer manufactured by PANanalytical, Netherland and the composition of major elements present was CaO: 37.2%, MgO: 10.9%, SiO2: 6.85%, Al2O3: 2.5%, K2O: 0.9%, and Fe2O3: 0.97%. Limestone samples in four distinct
narrow size ranges of 4–6 mm, 6–10 mm, 10–15, mm, and 15–20 mm were prepared in the laboratory by using standard sieves for the experimental studies and are shown in Figure 1. Table 1, presents the characteristics of these four graded limestone particles.
The experimental pipe loop test set-up facility at the CSIR-Institute of Minerals and Materials Technology, Bhubaneswar, consists of a flexible hose pipe of 100 mm nominal bore with 20 m vertical height. The layout of the test loop is shown in Figure 2. A high pressure centrifugal clean water pump (Model: CW50200, Make: Crompton Greaves Ltd.) of 60 m3/hr flow capacity and comprising a discharge pressure of 6 kg/cm2 was installed in the test loop to push the solid particles discharged from the rotary waterlock feeder for conveying through the pipe. The water flow rate is controlled by a variable frequency drive connected to the drive motor. A water reservoir tank of 30 m3 capacity feeds water to the centrifugal pump. The solid water mixture, after flowing through the vertical section of the pipe, gets discharged into a slurry collecting hopper.
Characteristics of limestone samples used for the study
The solids are then separated from the water in a dewatering screen after the mixture is passed through a downcomer MS pipe. The solids and water are separately collected in a solids collecting hopper and water reservoir tank, respectively. The water collected in the reservoir tank can be further used to feed water to the water pump. In order to measure the delivered concentration of the mixture slurry, the sampling of the slurry can be carried out in a measuring bucket manually at the discharge point of the vertical pipe. An electromagnetic slurry flow meter (Krone Make, Model: OPTIFLUX 2000 DN 100) with an indicator was fixed to the vertical section of the pipe to measure the slurry flow rate. The flow meter can measure the slurry flow rates in the range of 0–125 m3/hr., with measuring accuracy of ± 0.3% mv with an IFC 100 converter and repeatability of ± 0.1 mv. The pressure drop in the vertical section of the pipe can be measured by pressure transducers (Jumo Make, Model: Jumo dTrans p30 404366) with a MASIBUS make indicator (0–6 bar), and the pressure tapping points, which are located 15 m apart. The pressure transducers can measure the pressure drop with an accuracy of 0.5%.
The experimental investigation on vertical slurry transport of limestone water mixture samples in a 100 mm NB flexible hose pipe was carried out using the aforementioned vertical test set up. The test rig is quite suitable for studying the effect of mixture velocity and concentration on pressure drop and mixture flow behaviour in vertical sections, as shown in Figure 2. Prior to conducting the pipeline studies with limestone water mixture, a water run test was conducted in the 100 mm NB flexible hose pipe (internal dia:102 mm) to determine the friction factor of the hose pipe and to ensure the satisfactory operation of the test rig and the experimental accuracy. The water run test data obtained for the 100 mm NB hose pipe were compared with the theoretical predictions using the Colebrook-White equation to validate the system. The limestone samples were introduced into the water flow system on the discharge side of the pump (1) by means of a specially designed watertight rotary waterlock feeder (3) with a 2–4 ton/hr. feeding capacity. The flow rate of both water and limestone samples were varied by variable frequency drives coupled to both the water pump and rotary waterlock feeder.
The slurry flow rate and pressure drop data for the four distinct limestone samples in solids with a concentration range of 4.22% to 12.54% by mass were collected in an AMBETRONICS make 8 channel data logger (Model No. TC 800D) by smart log software version 2.0–8. The mixture velocity, VM of limestone water mixture slurry at varying slurry flow rates were then computed to be in the range of 0.85 to 3.21 m/s for the four different size fractions of the limestone samples. The settling velocities of the four distinct limestone fractions with top sizes of 6 mm, 10 mm, 15 mm, and 20 mm were ascertained by visual observations through the transparent Perspex piping sections (5) fixed to the flexible vertical hose pipe by adjusting the water flow rate to maintain the stones suspended in the Perspex section. The delivered concentration, ØSd of limestone water mixture was determined by collecting the limestone particles and water separately for a specific period of time using a stop watch at the dewatering screening point, and was calculated by taking the ratio of volume of solids delivered at the discharge point of pipe to the total volume of mixture delivered. The
volume fraction of solids was determined from the ratio of volume of solids delivered at the discharge point of pipe to the total volume of mixture delivered.
Pressure drop during vertical transport
In the case of vertical upward hydraulic transport of large particles (> 1 mm), dispersed regimes are encountered and the total pressure drop is the cumulative effects of hydrostatic weight due to the mixture column and the frictional forces due to the wall-fluid interactions. The frictional pressure drop, Hf of a two-phase solid liquid mixture can be expressed by the following equation:
[1]
Where, ΔP is the pressure drop measured from the tapping points of the differential mercury manometer attached to the upper and lower part of the vertical pipe, L is the distance between the tapping points, g is the acceleration due to gravity, ØSt is the insitu transport volume fraction of solids, ρs and ρl are the density of solid and liquid, respectively. The density of the mixture slurry ρm can be determined by the following expression:
The concentration of limestone mixture slurry by mass, being CW, was calculated by using Equation 3:
[2]
[3]
Thus, the pressure drop velocity curve for the limestone water mixture slurry for the two narrow size fractions (4–6 mm and 15-20 mm) of particles in solids concentration (range of 4.22% to 12.52% by mass), are plotted in Figure 3, after having removed the hydrostatic weight of the vertical column. The studied range of mixture velocities for the 4–6 mm and 15–20 mm sized particles were 0.86 m/s to 2.73 m/s and 0.98 m/s to 2.78 m/s, respectively. It is observed from the plots in Figures 3(a) and (b), that the frictional pressure drop for the two sized limestone particles increased with an increase in both solids concentration and mixture
velocity. The difference in the frictional pressure drop data of both water and the limestone water mixture samples was found to be negligible at lower to medium range of mixture velocities. This may be due to the movement of the limestone particles from the pipe wall region to the core of the piping section, and the frictional pressure drop encountered mainly by pipe wall liquid friction and major contribution of particle wall friction during upward transport (Vlasak et al., 2014). Beyond a mixture velocity of 2 m/s, the difference between the water run and limestone water mixture slurry indicated a marked difference in the frictional pressure drop, which may be attributed to migration of some limestone particles to the pipe wall due to collisions among themselves and, as a result, the cumulative effect of particle wall friction and drag due to particle liquid slip increased.
Hold-up and slip during vertical transport
In a heterogeneous suspension, there is a tendency for the liquid phase to slip past the solids and there tends to be a ‘hold-up’ of solids. The existence of a velocity profile and concentration profile across the cross section of the pipe in addition to the local relative velocity between phases by gravitational effects influences the hold-up during vertical conveying of particles. The relationship between the average slip velocity VSlip, and the hold-up ratio H, for the limestone water mixture slurry was determined by using the following relationship (Govier, Aziz, 1972):
Where, VSl and VSs are the liquid and solid phase velocities in the vertical piping section and can be computed as:
The plot of the holdup ratio HR, for the four different size fractions of limestone samples, is plotted against the mixture velocity VM for the limestone water mixture slurry at a solid concentration of ~12.5% by mass and is presented in Figure 4.
From Figure 4, it is observed that the hold-up ratio for the larger size fractions (15–20 mm) of limestone samples exhibiting terminal velocity in the range of 0.92 m/s to 1.0 m/s was found to be significantly higher, as compared to the other three smaller size fractions. It can be seen from Table 1, that the terminal settling velocity of 15–20 mm size fraction limestone samples is almost double that of 4–6 mm size fractions. Thus, it is expected that the large particles with higher terminal velocities will have a significant effect on the hold-up ratio. Further, with decreasing mixture velocities, the limestone water mixture flows as a heterogeneous suspension, and there is a tendency for the fluid phase, i.e., water to slip past the limestone particles in the mixture and hence, the predominance of hold-up persists. As the limestone mixture velocity increases and approaches the fluid velocity, the hold-up ratio tends toward unity for all the four size fractions of limestone samples, as observed in Figure 4.
During upward transport of limestone water mixture, the solid and liquid water move at different velocities in the vertical pipe. The different particle fractions of the solid phase move at different velocities. By using the following correlation of Shook and Roco (1991), the slip velocities for the four different limestone particle sizes were computed:
Where, V0 is the terminal settling velocity of particle, ØSt is the transport volumetric concentration of limestone water mixture, and the exponent n is dependent on Reynolds number of the solid particle. The plot of slip velocity as a function of particle diameter for the four different limestone particle sizes at a mixture concentration of 4.3 vol% is presented in Figure 5.
It is observed from Figure 5 that the computed values of slip velocities for the limestone particles indicated higher values as compared to those of Shook and Roco (1991), and Sobota et al. (2013). The slip velocities determined for the four different size fractions of limestone samples with top sizes of 5 mm, 10 mm, 15 mm, and 20 mm at a volumetric concentration of 4.3% were 0.48 m/s, 0.63 m/s, 0.77 m/s, and 0.91 m/s, respectively. The discrepancy in obtaining higher values of slip velocities may be attributed to the solid density and particle shape of limestone samples. Besides, the evidence of reduced drag coefficients in turbulent flow conditions might have led to higher slip for the limestone samples.
[4]
Conclusion
The investigation on vertical transport of limestone water mixture slurry in a 100 m NB hose pipe indicated the following:
➤ The frictional pressure drop for the limestone samples with varying particle size fractions increased with an increase in both solids concentration and mixture velocity, and the assumption about the almost negligible influence of large particles could not be ascertained. Under moderate to high mixture velocities, the particles may migrate to the pipe wall, contributing extra frictional pressure drops in addition to pipe wall liquid friction.
➤ The predominance of hold-up at lower mixture velocities persists during vertical upward transport of limestone water mixture slurry and the larger size fractions (15–20 mm) of limestone samples with higher terminal settling velocities indicated higher hold-up ratios.
➤ The correlation of Shook and Roco (1991) was employed to determine the slip velocities for the four different limestone particle sizes, and the discrepancy, in agreement with Sobota et al. (2013), was attributed to material density and shape of limestone samples. Further systematic investigation in this aspect may be carried out to measure the phase velocities precisely for determining the slip velocity accurately with even larger size particles at higher solids concentration in turbulent regime during ascending flow of solid liquid mixture.
Acknowledgement
The authors are thankful to the Director, CSIR-Institute of Minerals and Materials Technology, Bhubaneswar, India, for giving permission to publish the paper, and indebted to CSIR, New Delhi for supporting the investigation.
References
Chung, J.S. 2009. Deep Ocean Mining Technology-III: Developments. Proceedings of the 8th ISOPE Ocean Mining Symposium, Chennai, India, September 20-24, 2009. pp.1–7.
Govier, G.W., Aziz., K. 1972. The flow of complex mixtures in pipes. Van Nostrand Reinhold Co., New York.
Matousek, V. 2009. Pipe wall friction in vertical sand- slurry flows. Particulate Science and Technology, vol. 27, no. 5, pp. 456–468. https://doi.org/10.1080/02726350903133179
Newitt, D.M., Richardson, J.F., Gliddon, B.J. 1961. Hydraulic Conveying of Solids in Vertical Pipes. Transactions Institute of Chemical Engineers , vol. 39, pp. 93–100.
Park, Y.C., Yoon, C.H., Lee, D.K., Kwon, S.K. 2004. Experimental studies on Hydraulic lifting of solid-Liquid Two-phase flow. Ocean and Polar Research Article, vol. 26, no. 4, pp. 647–653. https://doi.org/10.4217/OPR.2004.26.4.647
Sellgren, A. Mine Water-A resource for transportation of ores from underground mines. In the Proceedings of 2nd International Mine Water Association Congress, Granada 1985, vol. 2, pp. 1027–1037.
Shook, C. A., Roco, M. 1991. Slurry flow principles and practice, Butterworth-Heinemann Series in Chemical Engineering.
Sobota, J., Petryka, L, Vlasak, P., Zych, M. 2013. Slip velocities in mixture vertical pipe flow. Proceedings of the 10th ISOPE Ocean Mining and Gas Hydrates Symposium, Poland, September 22-26, 2013.
Song, Y., Zhu, X., Sun, Z., Tang, D., 2017. Experimental investigation of particle induced pressure loss in solid-liquid lifting pipe. Journal Cent. South University, vol. 24, pp. 2114–2120. 10.1007/s11771-017-3620-8.
Tokanai, H., Harada, E., Hasegawa, J., Kuriyama, M. 2004. Turbulent Transition and pressure drop in solid-high viscosity upward flow through vertical pipe. Chemical Engineering, vol. 30, no. 4, pp. 509–514. https://doi.org/10.3390/en14123485
Vlasak, P., Chara, Z., Krupicka, J., Konfrst, J. 2014. Experimental investigation of course particle-water mixture flow in horizontal and inclined pipes. Journal of Hydrology Hydromech, 62(3), pp. 241-247. DOI: 10.2478/johh-2014-0022
Xia, J.X., Ni, J.R., Mendoza, C. 2004. Hydraulic Lifting of Manganese Nodules Through a Riser. Article in Journal of Offshore Mechanics and Arctic Engineering, vol. 126, no. 1, pp. 72–77. DOI: 10.1115/1.1641385
Yoon, C.H., Park, Y.C., Park, J., Kim, Y.S., Kang, J.S., Kown, S.K. 2009. Solid-Liquid Flow Experiment with Real and Artificial Manganese Nodules in Flexible Hoses. International Journal of Offshore and Polar Engineering, vol. 19, no. 1, pp. 77–79. u
27 - 28 OCTOBER 2025 - CONFERENCE
29 OCTOBER 2025 - TECHNICAL VISIT
VENUE - SUN CITY, RUSTENBURG, SOUTH AFRICA
Building on the success of previous events since its inception in 2004, the Platinum Conference Series continues to address the opportunities and challenges facing the global platinum group metals (PGM) industry. As the sector faces increasing demand, from technological innovation and decarbonisation to cost management and market volatility, the 9th International PGM Conference offers a critical platform for addressing these challenges head-on.
Guided by an expert Organising Committee and informed by insights from the industry, this year’s conference will delve into various themes designed to spark meaningful dialogue to drive innovation at every level of the PGM value chain and maintain competitiveness in a rapidly changing global landscape. Attendees can expect high-quality technical papers and presentations, robust networking opportunities, and strategic insights that help shape the future of the industry.
Now more than ever, the platinum industry needs fresh ideas, collaborative partnerships, and forward-thinking strategies to remain relevant. Whether you’re an academic, industry professional, sponsor, or policy leader, your participation will contribute to a dynamic exchange of expertise and solutions that can safeguard the sector’s long-term success. Join us as we explore cutting-edge developments, address the industry’s most pressing issues, and shape a sustainable, competitive future for the PGM industry.
ECSA Validated CPD Activity, Credits = 0.1 points per hour attended.
Anyone interested in shaping the future of the PGM industry such as:
• Academics and Researchers
• Academics and Researchers
• Business Development Managers
• Concentrator Managers
• Consultants
• Engineers (Mining, Mechanical, Process, Ventilation)
• Exploration and Geology
• Professionals
• Fund and Investment Managers
• Innovation and Technology
• Managers
• Market Researchers and Strategy
• Analysts
• Metallurgists and Pyrometallurgists
• Planning Managers
• Production Managers (Mining and Metallurgy)
• Project Managers
• Scientists
27 June 2025 - Submission of abstracts
1 August 2025- Submission of papers
27-28 October 2025 - Conference
29 October 2025 - Technical visit
• Self-Determination, Relevance and Driving Competitiveness
• Efficient Production through Technology
• Safety and Cost Management
• Market Outlook and Strategic Positioning
• Sustainability, Social Performance and Decarbonisation
Be part of this dynamic event and help shape the future of the platinum and PGM sector. We invite you to submit your abstracts, register as a delegate, or explore sponsorship opportunities to ensure that this conference continues to be the premier platform for exchanging knowledge, ideas, and best practices.
FOR FURTHER INFORMATION, CONTACT:
Gugu Charlie, Conferences and Events Co-ordinator
E-mail: gugu@saimm.co.za
Tel: +27 011 538 0238 Web: www.saimm.co.za
7-8 April 2025 — 2ND Southern African Hydrogen and Fuel Cell Conference 2025
Southern Sun Rosebank, Johannesburg
Contact: Gugu Charlie Tel: 011 538-0238
E-mail: gugu@saimm.co.za
Website: http://www.saimm.co.za
8-10 April 2025 — 27TH International Conference on Paste, Thickened and Filtered Tailings
Swakopmund, Namibia
Website: https://acgpaste.com/2025/
19-22 May 2025 — ALTA Innovation in Mining and Metallurgical Processing
Pan Pacific Hotel, Perth, Western Australia
Website: https://www.altamet.com.au/
26-29 May 2025 — 9TH Sulphur and Sulphuric Acid Conference 2025
Protea Hotel Stellenbosch and Conference Centre, Stellenbosch
Contact: Gugu Charlie
Tel: 011 538-0238
E-mail: gugu@saimm.co.za
Website: http://www.saimm.co.za
3-5 June 2025 — Introduction to Mining Hydrology and Mine Dewatering Design Workshop
Indaba Hotel, Spa and Conference Centre, Fourways
Contact: Gugu Charlie Tel: 011 538-0238
E-mail: gugu@saimm.co.za
Website: http://www.saimm.co.za
22-25 June 2025 — European Metallurgical Conference 2025 (EMC) Hamburg, Germany
Website: https://gdmb.de/home/
25-26 June 2025 — 4TH Digital Transformation in Mining Conference 2025
Glenburn Lodge and Spa, Muldersdrift
Contact: Gugu Charlie Tel: 011 538-0238
E-mail: gugu@saimm.co.za
Website: http://www.saimm.co.za
21-25 July 2025 — AfriRock 2025
Pioneering Progress: The Future of Rock Engineering
Sun City, South Africa
Contact: Camielah Jardine
Tel: 011 538-0237
E-mail: camielah@saimm.co.za
Website: http://www.saimm.co.za
18-19 August 2025 — 13TH International Heavy Minerals Conference 2025
Sun City Resort, Rustenburg, South Africa
Contact: Gugu Charlie Tel: 011 538-0238
E-mail: gugu@saimm.co.za
Website: http://www.saimm.co.za
1-3 October 2025 — International Mineral Asset
Valuation Conference 2025
Navigating Mineral Asset Valuations in an Uncertain Future
The Maslow Hotel, Sandton
Contact: Gugu Charlie
Tel: 011 538-0238
E-mail: gugu@saimm.co.za
Website: http://www.saimm.co.za
13-16 October 2025 — Geometallurgy Conference 2025
Future-Ready Geometallurgy: Trusted Data, Advanced Tools, Smarter Decisions
Glenburn Lodge and Spa, Muldersdrift
Contact: Gugu Charlie Tel: 011 538-0238
E-mail: gugu@saimm.co.za
Website: http://www.saimm.co.za
27-29 October 2025 — 9TH International PGM Conference 2025
PGM - Enabling a cleaner world
Sun City, Rustenburg, South Africa
Contact: Gugu Charlie Tel: 011 538-0238
E-mail: gugu@saimm.co.za
Website: http://www.saimm.co.za
16-22 November 2025 — The 12TH International Copper Conference (Copper 2025)
Phoenix, Arizona, USA
Website: https://www.extractionmeeting.org/ Extraction2025/Extraction2025/Copper2025/default.aspx
The following organizations have been admitted to the Institute as Company Affiliates
acQuire Technology Solutions
AECI Mining Chemicals, a division of AECI Mining Ltd
African Pegmatite
Allied Furnace Consultants
AMIRA International Africa (Pty) Ltd
Anglogold Ashanti Ltd
Anton Paar Southern Africa
Arcus Gibb (Pty) Ltd
Becker Mining (Pty) Ltd
Bluhm Burton Engineering Pty Ltd
Buraaq mining Services (PTY) LTD
Caledonia Mining South Africa
CARBOCRAFT
Castle Lead Works
CIGroup ACE Pty Ltd
DDP Specialty Products South Africa (Pty) Ltd
De-Tect Unit Inspection (Pty) Ltd
Digby Wells and Associates
EHL Consulting Engineers (Pty) Ltd
Elbroc Mining Products (Pty) Ltd
EPIROC South Africa (Pty) Ltd
Ex Mente Technologies (Pty) Ltd
Exxaro Resources Limited
FLSmidth Minerals (Pty) Ltd
G H H Mining Machines (Pty) Ltd
Geobrugg Southern Africa (Pty) Ltd
Glencore
Gravitas Minerals (Pty) Ltd
Hatch (Pty) Ltd
Herrenknecht AG
Impala Platinum Holdings Limited
IMS Engineering (Pty) Ltd
Ingwenya Mineral Processing
Ivanhoe Mines SA
Malvern Panalytical (Pty) Ltd
Maptek (Pty) Ltd
Mech-Industries (Pty) Ltd
Micromine Africa (Pty) Ltd
Minearc South Africa (Pty) Ltd
Minerals Council of South Africa
MineRP Holding (Pty) Ltd
Mining Projection Concepts (Pty) Ltd
Mintek
MLB Investments CC
Modular Mining Systems Africa (Pty) Ltd
Murray & Roberts Cementation (Pty) Ltd
Paterson & Cooke Consulting Engineers (Pty) Ltd
Pump and Abrasion Technologies (Pty) Ltd
Redpath Mining (South Africa) (Pty) Ltd
Rosond (Pty) Ltd
Roytec Global (Pty) Ltd
Rustenburg Platinum Mines Limited - Union
Salene Mining (Pty) Ltd
Schauenburg (Pty) Ltd
Sebotka (Pty) Ltd
SENET (Pty) Ltd
Sibanye Gold Limited
Sound Mining Solution (Pty) Ltd
SRK Consulting SA (Pty) Ltd
StageFright Edutainment
Tomra (Pty) Ltd
Trans-Caledon Tunnel Authority
Ukwazi Mining Solutions (Pty) Ltd
VBKOM Consulting Engineers
Weir Minerals Africa
ZUTARI (Pty) Ltd
13 October 2025 Technical Workshops
14-15 October 2025 Conference
16 October 2025 Technical Visits
Venue: Glenburn Lodge and Spa, Muldersdrift
(1-hour drive from O.R. Tambo International Airport, Johannesburg, South Africa)
ECSA Validated CPD Activity, Credits = 0.1 points per hour attended.
Ore heterogeneity and metallurgical complexity continue to rise, while sustainability occupies an ever-prominent role. Geometallurgy offers a refined, multidisciplinary pathway to improve the value of ore deposits.
Future-Ready Geometallurgy examines strategies to generate trustworthy data through the steady application of machine learning, novel sensors, digital twins, and Industry 4.0 technologies in mining. Reliance on dependable data and innovative tools empowers the industry to make more timely and discerning decisions for mine planning and metallurgical plant optimisation.
Following the success of past SAIMM Geometallurgy conferences, the third conference in this series provides a platform to explore the latest progress in geometallurgy and to celebrate the success of its integration into the mining value chain.
• Sampling and sensor-based core logging
• Practical tools and methodologies for ore characterisation and testing
• Standardised methods for reporting to generate trusted data
• Geostatistics, data integration, smart workflows, and modelling
• Incorporation of predictive mining, processing, and environmental models into resource modelling
• Project and operational geometallurgy case studies
• 17 June 2025 - Submission of short abstracts
• 29 July 2025 - Submission of extended abstracts for peer review
• 13 October 2025 – Technical workshops
• 14-15 October 2025 - Conference
• 16 October 2025 - Technical visits
FOR FURTHER INFORMATION CONTACT: Gugu Charlie, Conferences and Events Co-ordinator E-mail: gugu@saimm.co.za | Tel: +27 11
Prospective authors are invited to submit short abstracts of not more than 500 words to: Conferences and Events Co-ordinator, Gugu Charlie, e-mail: gugu@saimm.co.za
Authors of accepted abstracts will be required to submit extended abstracts for peer review and publication in the conference proceedings.
Following the conference, full papers can be submitted to the journal for peer review and publication in an SAIMM Journal Special Issue.
Prof. Julian M. Ortiz Ph.D., P.Eng.
Mark Cutifani / Anglo American Chair in Mining Innovation, Camborne School of Mines | University of Exeter
MARCH 2026 CONFERENCE
3-4 MARCH 2026 – CONFERENCE | 5 MARCH 2026 – TECHNICAL VISIT
Indaba Hotel, Spa and Conference Centre, Fourways
ECSA and SACNASP Accredited
Supported by SAIEG In partnership with MMMA and SAICE
The SAIMM is proud to announce its upcoming 2026 conference on Tailings. Since the inaugural event, which raised the profile of tailings management and fostered collaboration among industry stakeholders, and the subsequent conference that focused on embracing the Global Industry Standard on Tailings Management (GISTM), the field has seen significant progress. We’ve deepened our understanding of GISTM requirements, advanced geotechnical knowledge of tailings dams, engaged more stakeholders, and made strides toward improved safety through GISTM compliance.
However, despite these achievements, tailings dam failures persist, signalling that there is still much work to be done and lessons to learn. As we look to the future, the 2026 conference will ask: Where to now? In a world of new standards, evolving expectations, and emerging possibilities, what opportunities lie ahead? What residual risks need addressing? How can we further reduce, reclaim, or reuse tailings? How can we accelerate the adoption of new technologies and set a new benchmark for the industry? What impacts, once considered acceptable, are no longer tolerable, and how can we best manage them?
Join us in 2026 to explore these critical questions and engage in meaningful discussions with key role players in the tailings industry.
For further information contact:
Gugu Charlie, Conferences and Events Co-ordinator E-mail: gugu@saimm.co.za | Tel: +27 11 538-0238 | Web: www.saimm.co.za