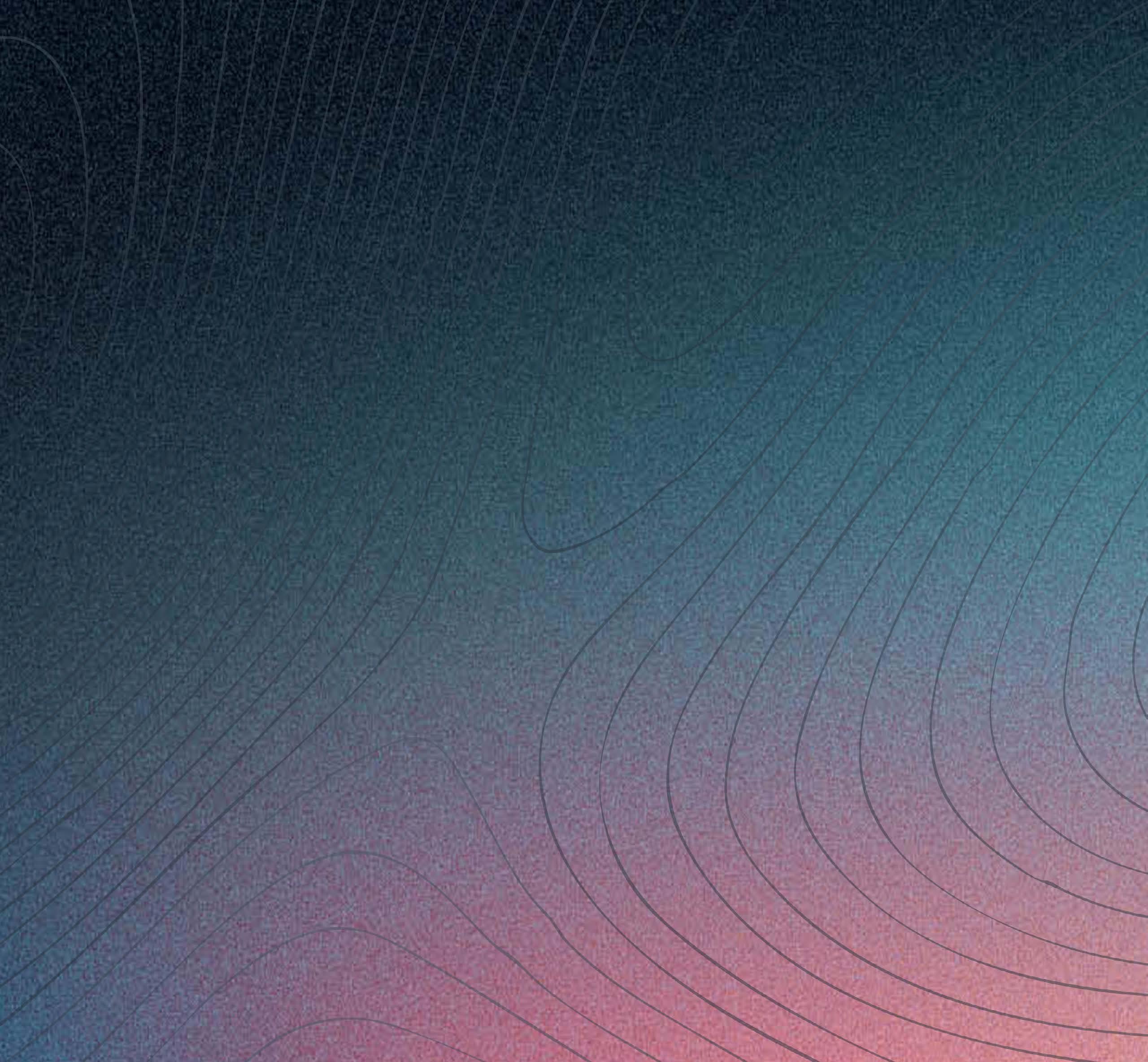

A 3D FULFILLMENT SOLUTION INSPIRED BY NATURE TO OVERCOME SUPPLY CHAIN CHALLENGES
A 3D FULFILLMENT SOLUTION INSPIRED BY NATURE TO OVERCOME SUPPLY CHAIN CHALLENGES
Now more than ever, consumers’ demands are changing at lightning speeds. Warehouses need to be flexible in order to adapt to these unexpected changes quickly.
The Attabotics solution offers optimal flexibility and scalability. The grid can be expanded if more storage is needed, while additional robots and workstations can be added if more throughput is desired. All without significantly disrupting operations.
DIRECT ACCESS TO EVERY BIN
No digging, no re-slotting
INTEGRATED PORTS
No need for conveyors
INTEGRATED SEQUENCING
By utilizing the bottom of the structure (basement)
FLEXIBLE AND SCALABLE
Add robots, workstations, or extend the grid
NO SINGLE POINT OF FAILURE
Every robot can access every bin and every workstation
HIGH STORAGE DENSITY
Market leading density up to 9M of total system height
Companies with fulfillment operations face increasingly complex challenges. As businesses rapidly grow, customers’ requirements are also getting more and more difficult to match. On top of that, there is a prevalent labor shortage, common to most industries.
NaTURe
The Attabotics solution is based on a unique vertical grid structure that mimics nature. “I had this crazy idea of reconfiguring warehouse space after watching a documentary about how leaf cutter ants access their colonies vertically. A 3D system just makes sense.”, says Scott Gravelle, CEO and founder of Attabotics.
Robots can travel the grid in all 3 dimensions
Each robot has access to every bin and to every workstation
Speeds up top 2.7m/s
Payload max 45kg bin
The robots are powered by long-life ultra capacitors and are charged each cycle, while climbing
The innovative vertical grid structure has allowed Attabotics to create a solution that is the perfect fit for single-item fulfillment.
Attabotics robots can travel in all 3 dimensions of the grid, including the attic (top), basement (bottom) and vertical access throughout. This allows robots to have direct access to each bin without the need for re-slotting, making the system’s performance independent of the order structure. There is also no need to have a specific Pareto curve in your assortment. Furthermore, the Attabotics solution can handle rush orders with ease, as bins arrive at the workstation within 90 seconds of the request.
Manual sequencing is a task often required in fulfillment operations whenever orders are small or items need to be packed in a specific sequence to prevent damage. The Attabotics solution provides automatic sequencing by leveraging short retrieval times in combination with intelligent use of the space below the storage area, known as the basement.
With growing assortments, warehouse space can be an issue. Attabotics grid can be built up to 9m high, optimally utilizing the available vertical space in the warehouse. And while the solution allows direct access to every bin, the structure ensures a class-leading storage density.
Compared to a manual pick-from-shelf warehouse layout, it represents a reduction in space of up to 85%.
While labor shortages continue to be an ongoing challenge in the industry, there is an increased need for efficient and ergonomic order picking. Each individual Attabotics workstation can present more than 300 bins per hour to the operator. With advancements in the new Workstation 2.0, presentations can increase to 400-500 bins per hour. Workstations can be placed anywhere on the perimeter of the system. Unlike external legacy conveyor systems, Attabotics workstations are fully integrated into existing structure geometry to allow each robot to move freely to any workstation, providing ultimate flexibility.
2 BIN TYPES AVAILABLE
Outer dimensions ( l x b x h)
Interior dimensions ( l x b x h)
Empty weight
Maximum payload
Material
Dividers
614 x 614 x 275mm
614 x 614 x 435mm
571 x 571 x 249mm
571 x 571 x 405mm
Approx. 4.4kg (medium bin)
45kg (including bin weight)
Polypropylene, UNIPOL 2135
Multiple configurations possible with removable dividers. Up to16 compartments per bin
Attabotics has successfully deployed its system in North America and Canda, from systems with less than 5,000 bins, to high end solutions with over 190,000 stored bins.
See it moving
SYSTEM
Runs in the background regardless of the state of the HMI or other Central Nexus functions ensuring system operates safely in all events. Manages all emergency stop functions (light curtain, E-stop button) and manages safe shutdowns in the event of a power outage.
WMS + CENTRAL NEXUS:
To the WMS the Attabotics system is treated as one storage location capable of storing endless SKUs. The WMS sends an order to the Central Nexus, and Attabotics delivers the order out the workstation and a confirmation back to WMS signaling the completion of the order.
01 02 03 04 05 06
WMS sends orders to Central Nexus.
Order Processor validates orders, adds them to prioritized order processing queue.
As capacity opens, Order Processor sends highest priority Pick Requests to Planner ensuring all business rules are followed.
Planner divides Pick Requests into tasks to maximize productivity of all robots and active workstations.
Planner sends bin assignments to Attabot Simulator and Task Assignments to HMI.
Attabot Simulator sends Route Request to Route Finder.
Order Processor sends Order Completion Confirmation to WMS. 07 08 09 10 11 12
Route Finder calculates lowest cost path considering all existing path reservations and returns path to Attabot Simulator.
A simulation is computed to validate path and once validated trip segment instruction is sent to Radio Task.
Radio Task transmits path wirelessly to Attabot.
Attabot retrieves bin and brings bin to Workstation, while continuously reporting its progress to Radio Task.
Once task is completed, HMI notifies Order Processor of completion.
Attabotics stands apart from competing automation solutions with its combination of storage density, flexibility, and efficiency.
Take a closer look at five key areas to see how Attabotics is leading the automation industry when it comes to innovation and performance.
ATTABOTICS
The cubed, 3-D structure of the Attabotics solution provides high storage density and allows robots to move above, below, and vertically through the structure to access bins without any digging or re-slotting.
COMPETITORS
Legacy 2-D vertical aisles and shuttle systems have much lower storage density by footprint and lack the agility needed for rush orders. Competing 3-D cubed designs also require extensive digging and re-slotting to access bins, which reduces efficiency and throughput.
ATTABOTICS
Orders can be automatically sequenced and sorted in the basement of the grid structure before presenting at a workstation, eliminating the need for external conveyor systems.
COMPETITORS
Most automation solutions still utilize legacy conveyer systems for sequencing and sortation, which greatly expands the overall warehouse footprint.
ATTABOTICS
Since every robot can reach every bin stored with the 3-D grid, if a single robot goes down, it does not effect the efficiency of the remaining robots in the structure.
COMPETITORS
A malfunction in a 2-D vertical aisle or shuttle solution can render entire rows of bins inaccessible until repairs are made. External conveyor system shutdowns can also disrupt the sequencing and sortation process.
ATTABOTICS
The high-density automation footprint delivers high throughput rates with the potential to achieve higher presentations per hour simply by adding more robots and workstations.
COMPETITORS
Automation solutions not designed specifically for machines offer a slower throughput and can only achieve higher presentations per hour by greatly expanding their footprint.
ATTABOTICS
The 3D Attabotics grid can be built up to 9m high to optimize available warehouse space. Sequencing and sortation are incorporated into the structure, further reducing the solution footprint by as much as 85% compared to traditional warehouse layouts.
COMPETITORS
Automated shuttle systems require a large footprint to achieve acceptable throughput rates. Other automated 3-D cubed and 2-D vertical aisle solutions require external sequencing and sortation systems that greatly increase their footprint.
Attabotics is the world’s first 3D robotics supply chain system for modern commerce. Inspired by the framework of ant colonies, Attabotics replaces the rows and aisles of traditional fulfillment centers with a patented storage structure and robotics shuttles that utilize both horizontal and vertical space, reducing companies’ warehouse needs by 85%.
By empowering retailers to place fulfillment centers near high-density urban areas, Attabotics helps to create jobs and decrease carbon emissions by closing the last-mile delivery gap. Attabotics has been adopted by major retailer brands across apparel, food & beverage, and home goods.
Attabotics is based in Calgary, Alberta, Canada with fulfillment centers across the United States and Canada.
www.attabotics.com Visit us