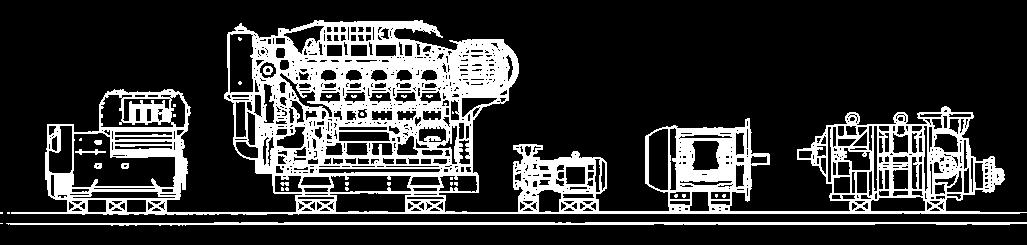
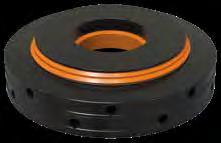
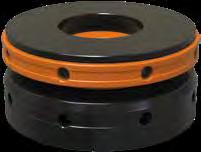
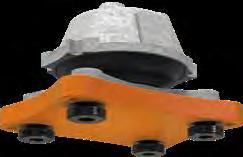
WAS IST EIN KIPPFUẞ?
Seite 2
STABILER STAND MIT ROTACHOCK® BASICLINE
Seite 9
HINWEISE FÜR KONSTRUKTEURE
Seite 18
SCHNELLE UND EINFACHE MONTAGE ELASTISCHER LAGERUNGEN
Seite 13
WIE MAN ROTACHOCK® MONTIERT
Seite 21
info@rotachock.com www.rotachock.com
® RotaChock ist eine eingetragene Marke von Chock Design B.V. © Chock Design B.V. 2024
ROTACHOCK® EINSATZBEREICHE & BRANCHEN
Seite 25
Der Inhalt dieser Publikation unterliegt dem Urheberrecht des Herausgebers und darf ohne vorherige schriftliche Genehmigung nicht (auch nicht auszugsweise) vervielfältigt werden. Die Richtigkeit der Angaben in dieser Publikation wurde mit größter Sorgfalt geprüft. Dennoch kann keine Haftung für direkte, indirekte oder Folgeschäden übernommen werden, die sich aus der Verwendung der hierin enthaltenen Informationen ergeben.
Publikation RotaChock® Informationsbroschüre Ausgabe 08/2024
90%
ALLER ROTIERENDEN MASCHINEN IM EINSATZ LAUFEN
AU ẞ ERHALB IHRER EMPFOHLENEN AUSRICHTUNGSTOLERANZEN.
70%
ALLER AUSFÄLLE ROTIERENDER MASCHINEN
WERDEN UNMITTELBAR DURCH KIPPFÜ ẞ E VERURSACHT.
Seit mehr als 35 Jahren sind wir im Ausrichtungsbereich tätig und weisen immer wieder auf die Notwendigkeit einer korrekten Ausrichtung hin. Wir wissen wie kein anderer, wie schwierig es sein kann, eine optimale Ausrichtung Ihrer rotierenden Maschinen zu erreichen. Im Laufe der Jahre mussten wir immer wieder feststellen, dass unsere Kunden
Schwierigkeiten hatten, die Ausrichtung innerhalb akzeptabler Toleranzen zu halten. Dies führt zu einer Reihe mechanischer und qualitativer Probleme:
Lärm und Vibrationen
Erhöhter Stromverbrauch
Ausfallzeiten von Maschinen
Diese Probleme mit rotierenden Maschinen stellen für die Industrie weltweit eine enorme Kostenbelastung dar. Wenn einzelne kritische Maschinen ausfallen, kommt es zu Störungen im gesamten Betrieb und einem Stillstand der Produktion. Während unserer langjährigen Erfahrung im Ausrichtungsbereich sind wir auf unzählige Maschinen gestoßen, die die oben beschriebenen Probleme aufweisen. Korrekturen an der Wellenausrichtung sind sinnvoll. Es stellt sich die Frage: Warum sollte man ein Ausrichtungs-problem korrigieren und lösen, wenn man es von vornherein vermeiden und die Leistung der Maschine verbessern kann?
Unserer Erfahrung nach sind 70% aller Ausfälle rotierender Maschinen direkt auf ein Kippfuß-Problem zurückzuführen. Eine Neuausrichtung der Maschine ohne Behebung des Kippfußes ist nur eine vorübergehende Lösung, da die Anlage wieder ihre
Verkürzte Nutzungsdauer der Kupplung
Beschleunigte Abnutzung
Verkürzte Nutzungsdauer von Lagern und Dichtungen
Ausrichtungstoleranzen überschreiten wird. Ihre Möglichkeiten für dauerhafte und nachhaltige Lösungen sind begrenzt, auch wenn geschulte Mechaniker wissen, wie sie vorübergehende Ausrichtungsprobleme beheben können. Aber Sie brauchen einen technischen Ansatz, um die Anlage zu verbessern und einen Kippfuß zu verhindern.
Sie müssen das Problem an der Wurzel packen.
Sie müssen das Kippfußproblem angehen.
Warum sollte man falschen Fuß starten?
Ein Kippfuß kann mit einer Waschmaschine verglichen werden, bei der ein Bein kürzer ist als die anderen drei. Diese Unebenheiten und der fehlende Kontakt zum Boden lassen die Waschmaschine wackeln. Das kann auch bei allen rotierenden Maschinen vorkommen und kann zum Ausfall der Maschine führen, wenn dies nicht korrigiert wird.
Mehrere Faktoren können einen Kippfuß verursachen. Vielleicht ist das darunter liegende Fundament verzogen, verbogen, uneben oder beschädigt. Dasselbe gilt für den Maschinenfuß. Der Spalt zwischen dem Fuß und dem Fundament kann bereits mit gestauchten/verbogenen oder anderweitig beschädigten Unterlegplatten gefüllt sein. In diesem Fall kann sich der Rahmen der Maschine verziehen, da der Fuß durch die Spannung der Fundamentschraube auf die Basis gezogen wird. In unserer Branche nennen wir das einen „nachgiebigen Fuß“. Sie müssen aber auch Umwelteinflüsse wie Schmutz und Ablagerungen berücksichtigen, die sich dazwischen abgelagert haben könnten. Ein komplexerer Kippfuß wird durch maschinenexterne Kräfte verursacht, z. B. durch Spannungskräfte, die in jeder Phase des Ausrichtungsprozesses entstehen.
Wahrscheinlicher ist jedoch, dass eine Kombination der oben genannten Faktoren einen Kippfuß verursacht. Die häufigsten Kippfuß-Situationen sind:
Paralleler Kippfuß: Wenn der Maschinenfuß keinen Kontakt zum Fundament hat und sich ein Spalt bildet.
Schräger Kippfuß: Wenn der Maschinenfuß nur auf einer Seite mit dem Fundament in Kontakt kommt, biegt er sich, wodurch ein Zwischenwinkel entsteht.
Um einen Kippfuß zu verhindern, benötigen Sie etwas, um den Spalt –den Raum zwischen Fundament und Maschinenfuß – zu füllen. Dies bezeichnen wir als Einbaustück.
Ein Einbaustück ist die Schnittstelle zwischen dem Fundament und dem Maschinenfuß. Der Hersteller schreibt vor, dass alle Maschinen auf einer tragenden Unterlage befestigt werden müssen. Es gibt verschiedene Optionen für Einbaustücke in diesem Sektor, wie z. B. Stahlblöcke, Unterlegplatten und Epoxidharze.
Die Verwendung von Stahlblöcken ist eine zeitaufwändige und spezifische Arbeit. Das Verfahren des Messens, Korrigierens, Einpassens und des Bearbeitens muss wiederholt werden, bis der Stahlblock eine ausreichende Kontaktfläche mit dem Maschinenfuß hat. Die Bearbeitung dieser Blöcke ist ein erheblicher Kostenfaktor, selbst wenn sie intern erfolgt.
Beim Schneiden von Unterlegplatten aus dem Material können die scharfen Grate ein Sicherheitsproblem darstellen und Fehler beim Stapeln der Unterlegplatten verursachen. Vorgeschnittene Unterlegplatten sparen zwar Zeit, aber ein Stapel von ihnen wird trotzdem zu Überstunden führen. Der schräge Kippfuß ist immer noch vorhanden und verursacht eine unzureichende Auflagefläche.
Diese Lösung besteht aus Zweikomponenten-Harz und ist eine dauerhafte Lösung. Das Vorbereiten, Gießen und Warten auf die Aushärtung ist ein zeitaufwändiger Prozess. Jedes Mal, wenn die Maschine neu ausgerichtet werden muss, muss das Epoxidharz herausgeschnitten werden. Zertifiziertes Personal muss das Material gießen, wobei es keinen Raum für Trial & Error gibt.
Ein erfahrener und geduldiger Zerspanungstechniker ist erforderlich.
Das „Trial & Error“-Verfahren kann endlos sein.
Die Kosten für Fräsmaschinen sind beträchtlich.
Relativ einfach bei parallelem Kippfuß, Schwierig zu schließen bei einem schrägen Kippfuß.
Jemand mit wenig Erfahrung kann die Arbeit erledigen.
Schnell, wenn vorgeschnitten.
Auf kurze Sicht billig, aber Stapeln ist auf lange Sicht teuer.
Fast unmöglich, bei schrägem Kippfuß zu schließen.
Zertifiziertes Personal erforderlich.
Zeitaufwändige Montage und Aushärtungszeit.
Material und Kosten für zertifizierte Arbeiter.
Erhebliches Risiko für Montagefehler.
Diese Methoden haben zwei Hauptziele: eine ebene Montagefläche für die Maschine zu schaffen und die Reaktionskraft von den Maschinenfüßen auf das Fundament zu übertragen. Leider verbleibt bei den oben genannten Methoden ein hohes Risiko für einen Kippfuß. Unsere jahrelange Erfahrung im Ausrichtungsbereich hat uns gelehrt, dass alle Anwendungen irgendwann neu ausgerichtet werden müssen. Während des Transports, der Montage oder der Nutzungsdauer der Anwendung kann viel passieren. In diesen Situationen ist Zeit von entscheidender Bedeutung, es steht Geld auf dem Spiel, und die Maschine muss so schnell wie möglich wieder in Betrieb genommen werden.
Sie brauchen eine justierbare Lösung.
ENTWICKLUNG VON ROTACHOCK®
Alle bekannten Techniken haben zwei grundlegende Ziele: die Schaffung einer ebenen Montagefläche und die Übertragung der Kräfte von den Maschinenfüßen auf das Fundament. Unser drittes Ziel war es jedoch, eine Lösung zur Verhinderung von Kippfüßen zu entwickeln, die auch später noch angepasst werden kann. Deshalb haben wir Technologien kombiniert, um die mechanische Verkeilung weiterzuentwickeln, und wir sind stolz darauf, einen technisch überlegenen Lückenfüller für Kippfüße zu präsentieren:
Der RotaChock® ist ein justierbares, selbstnivellierendes und wiederverwendbares Einbaustück für die Montage rotierender Maschinen. Der RotaChock® ist eine Mischung aus Technik und jahrelanger Praxiserfahrung, die zu einem robusten, stabilen und eleganten Lückenfüller für Endmaschinen mit Kippfuß geführt hat. RotaChock® erfüllt die primären Einbaustückziele und bietet darüber hinaus eine zusätzliche Justierbarkeit, die in der Branche unübertroffen ist.
Das Gewindeteil ermöglicht die Justierung des Einbaustücks, wodurch ein paralleler Kippfuß behoben wird.
ROTACHOCK® CONSISTS OF 3 PARTS:
Oberer Ring mit konvexer Oberfläche, der in dem konkaven mittleren Ring ruht.
Mittlerer Ring mit Außengewinde und konkavem Hohlraum auf der Oberseite.
Unterer Ring mit Innengewinde.
VORTEILE VON ROTACHOCK®
Der runde Aufsatz gleicht Winkeldifferenzen bis zu 4° aus und behebt einen schrägen Kippfuß.
In erster Linie halten wir RotaChock® aus den folgenden Gründen für die beste Lebenszykluslösung für rotierende Geräte:
› RotaChock® beseitigt Kippfüße.
› RotaChock® ist justierbar, sodass eine Ausrichtung und Neuausrichtung jederzeit möglich ist.
› RotaChock® spart Zeit und Geld im Vergleich zu anderen Verkeilungsoptionen.
RotaChock® kann in einer Vielzahl von Konfigurationen geliefert werden, um Ihre Anforderungen zu erfüllen. In dieser Informationsbroschüre werden alle verfügbaren Optionen und die Anwendungen, für die sie am besten geeignet sind, kurz vorgestellt. Alle technischen Details, Montagehinweise sowie technische Tipps und Tricks finden Sie auf den folgenden Seiten.
DESIGNPHILOSOPHIE
Das schwächste Glied in jeder RotaChock®Anwendung ist die Fundamentschraube, die den Maschinenfuß mit dem Fundament verbindet. Zur Absicherung haben wir ein wirksames Konstruktionsprinzip angewendet: die Geometrie. Der Gewindedurchmesser von RotaChock® beträgt mindestens das Zweifache des zulässigen Durchmessers der Fundamentschraube. Infolgedessen kann das RotaChock®-Gewinde nicht durch Schraubenspannung beschädigt werden.
GEWINDEDESIGN
Die Ausrichttoleranz von rotierenden Maschinen liegt bei wenigen hundertstel Millimetern (0,02-0,05 mm). Es ist wichtig, ein perfektes Gewindedesign zu haben, um Trial & Error beim Ausrichten zu minimieren. In diesen Fällen können Sie Ihr Werkzeug in die Nut einführen und ihr bis zum nächsten Einstellloch folgen.
RotaChock® verwendet einen speziellen Gewindetyp, das sogenannte Sägezahngewinde. Im Gegensatz zu den im Maschinenbau gebräuchlichen Gewindetypen metric (M) und unified national (UNC,
Sägezahngewinde Metrisches Gewinde
Innengewinde Außengewinde Innengewinde Außengewinde
Aufgrund dieses Gewindedesigns hat RotaChock® eine höhere mechanische Steifigkeit und eine höhere Belastbarkeit als ein metrisches Standardgewinde mit ähnlichem Durchmesser und ähnlicher Neigung mit einem 2x30°-Winkeldesign. Die selbstsichernden Eigenschaften des Sägezahngewindes sorgen dafür, dass keine mechanische Sicherung erforderlich ist, um den RotaChock® unter Last am Drehen zu hindern.
Verschiebung von Sägezahngewinde und metrischem Gewinde unter Last.
UNF) hat das Sägezahngewinde ein asymmetrisches Design mit einem 7°-Oberwinkel und einer 45°-Stützflanke.
Für das Design von Sägezahngewinden gibt es Standardbedingungen und -definitionen für Toleranzen nach ISO 965-1. Gemäß ISO-Norm wird ein Spiel zwischen den ineinandergreifenden Gewinden geschaffen. Bei der Herstellung von Mutter und Schraube bezeichnet man dies als Abweichung.
Gemäß unserer RotaChock®-Designphilosophie war dies nicht genug. Deshalb haben wir ein perfekt passendes Spiel geschaffen, das wir intern ständig überprüfen können. Wir haben spezielle Messverfahren und Taster entwickelt, um dieses während der Produktion zu überprüfen. Diese Methode gewährleistet eine minimale Abweichung zwischen den Gewinden und ein endgültiges Gewindespiel mit einer Gewindeeinstellung von weniger als 0,05 mm / 0,002” nach Anziehen der Fundamentschrauben.
Das Justieren von RotaChock® ist eine einfache Aufgabe, die mit einfachen Werkzeugen durchgeführt werden kann. Das einzigartige und praktische Werkzeugnutdesign macht dies möglich. Bei einigen Anlagen ist RotaChock® nicht sichtbar, weil es sich an einer komplizierten Stelle befindet. In diesen Fällen können Sie Ihr Werkzeug in die Nut einführen und ihr bis zum nächsten Einstellloch folgen.
ROTACHOCK® MA ẞ TABELLE
Jeder RotaChock®-Typ hat eine Maßtabelle, und es gibt pro Typ mehrere RotaChock®-Größen:
Typ
Typ und Größe von RotaChock®. Der Außendurchmesser in Zoll entspricht der RC-Größe. Zum Beispiel hat RC2 einen Außendurchmesser von 2 Zoll.
Nennlast
Die Nennlast, die auf den RotaChock® ausgeübt werden kann und von Klassifizierungsstellen zugelassen ist.
Gewinde Ø
Der RotaChock® Gewindedurchmesser, der sich vollständig unter dem Maschinenfuß befinden sollte.
Innerer Ø
Der Durchmesser der mittleren RotaChock® Bohrung, durch die die Fundamentschraube geführt wird.
Standard-Schraubengröße
Der bevorzugte Fundamentschrauben-Durchmesser für die Verwendung in Kombination mit RotaChock®.
Optionale Schraubengröße
Sollten Sie einen größeren Fundamentschrauben-Durchmesser verwenden wollen als es die Bohrung im RotaChock® zulässt, so ist es auch möglich, die Bohrung im RotaChock® zu vergrößern. Siehe dazu FAQ Nr. 7 auf Seite 30 für weitere Anweisungen zur Vergrösserung von Schraubenlöchern.
Reduzierte Mindesthöhe
Sollte der RotaChock® zu hoch für den zur Verfügung stehenden Platz sein, dann ist es möglich, die Höhe des RotaChock® auf einer Drehbank zu reduzieren. Denken Sie daran, dass Sie für jeden Millimeter, den Sie wegnehmen, auch 1 mm an Justierung verlieren. Siehe dazu FAQ Nr. 6 auf Seite 30 für weitere Anweisungen zur Verringerung der Höhe.
Mindesthöhe
Die RotaChock® Höhe, wenn er vollständig eingeschraubt ist.
Konstruktionshöhe
Die Höhe, in der sich der RotaChock® genau in der Mitte seines Justierbereichs befindet.
Maximale Höhe
Bei Überschreitung dieser Höhe bleibt zu wenig greifendes Gewinde, um die Last sicher zu tragen.
Neigung
Die RotaChock® Höhenverstellung nach einer kompletten Umdrehung.
Gewicht
Das Gewicht des RotaChock®
Der technische Ansatz für die Entwicklung von RotaChock® bestand darin, die höchstmögliche Tragfähigkeit zu erreichen und gleichzeitig das Material mit der niedrigsten Streckgrenze zu verwenden, die in der Industrie benötigt wird: Edelstahl 316 gemäß APIRichtlinien. Der RotaChock® Standardansatz verwendet Einbaustücke aus Kohlenstoffstahl und legiertem Stahl, die eine noch größere Sicherheitsspanne aufweisen als die unten angegebene Streckgrenze. Das Standard- und Lagersortiment von RotaChock®:
› RCx-C BasicLine Kohlenstoffstahl (DIN 1.0507 - S355) das bevorzugte Standarddesign
› RCx-SS BasicLine Edelstahl (DIN 1.4404 - 316L) für maximalen Schutz gegen Rost
› RCx-AS BasicLine Legierter Stahl (DIN 1.7225 - 42CrMo4) für extreme Maschinenkräfte
› RCx-SL SlimLine Kohlenstoffstahl & Gewin- (DIN 1.0507 - S355) für den Reparatur- und Nachrüstungsmarkt deteile aus legiertem Stahl (DIN 1.7225 - 42CrMo4) für den Reparatur- und Nachrüstmarkt
Sollten für bestimmte Anwendungen andere Materialien oder Bearbeitungen erforderlich sein, so können diese auf Anfrage bereitgestellt werden.
MECHANISCHE EIGENSCHAFTEN
Dehnung
Ermüdung
Schlagfestigkeit
VERBESSERTER KORROSIONSSCHUTZ
Eine weitere RotaChock® Innovation ist die Erforschung und Umsetzung eines Verfahrens zur Verhinderung von Rostbildung bei normalen Einbaustücken aus Stahl. Edelstahl 316L ist ein ausgezeichnetes und erforderliches Material für hochkorrosive Anwendungen – aber es hat seinen Preis. Daher haben wir das Molekulardiffusionsverfahren für Einbaustücke aus Kohlenstoffstahl und legiertem Stahl gewählt, um einen kostengünstigeren Korrosionsschutz zu bieten.
Dieses Verfahren verbessert die Verschleißeigenschaften und erhöht die Korrosionsbeständigkeit erheblich. Das Verfahren ist eine Kombination aus verschiedenen thermochemischen Prozessschritten, einschließlich Gasnitrocarburieren und Oxidieren. Es entstehen
Wir nennen dieses Verfahren Anti-Corrosion Enhanced – ACE! (verbesserter Korrosionsschutz)! Dieses Verfahren zeichnet sich durch die folgenden Merkmale aus:
1 Hohe Verschleißfestigkeit
2 Hervorragende Abriebfestigkeit Resistenz gegen Reibverschweißung
3 Bis zu 120 % verbesserte Ermüdungseigenschaften
4 Erheblich verbesserte Korrosionsbeständigkeit
5 Gute Oberflächenqualität
6 Vernachlässigbare Formverzerrung
7 Vorhersehbare Wachstumsmerkmale
8 Substitution von Legierungen – unlegierter Stahl anstelle von legiertem Stahl
Vergleiche mit Salzsprühnebeltests zeigen, dass Edelstahl 316L nach 480 Stunden und Anti-Corrosion Enhanced nach 320 Stunden, unbehandelter Kohlenstoffstahl dagegen nach 90 Minuten Markierungen aufweist.
Alle RotaChock® werden in ISO-zertifizierten Werkstätten hergestellt. Moderne CNC-Anlagen und Messgeräte auf dem neuesten Stand der Technik garantieren ein konstantes und hochwertiges Niveau.
Die Produktion wird jährlich von Zertifizierungsstellen geprüft, unterstützt durch Audits von RotaChock® Anwendern, die in der Branche führend sind. Mit den vorhandenen Qualitätssystemen können alle Märkte bedient werden, von der Schifffahrt bis zur Kernkraftindustrie.
Der Produktionsprozess wird mit selbst entwickelten Messverfahren und Tastern ständig überwacht. Die abschließende Kontrolle des Gewindespiels wird mit einem Oberflächenrauheits-/ Konturmesssystem durchgeführt. Diese Methode gewährleistet eine minimale Abweichung zwischen den Gewinden. Das endgültige Spiel von weniger als 0,05 mm / 0,002” minimiert das Einstellen des Gewindes nach Anziehen der Fundamentschrauben.
PRODUKTRÜCKVERFOLGBARKEIT
RotaChock® wird in Chargen hergestellt, wobei jede Charge einen eindeutigen Code hat, der auf dem Stahlelement eingraviert und auf der Verpackung angegeben ist. Die Chargencodes sind mit unserer Produktionsdatenbank verknüpft, die Materialzertifikate und Messberichte enthält, die auf Anfrage erhältlich sind. Diese Chargencodes enthalten die folgenden Informationen:
4 RotaChock® Größe.
C Material
TYPENZULASSUNGEN
Siehe Maßtabelle, 4 = RC4
› C Kohlenstoffstahl
› SS Edelstahl
› AS Legierter Stahl
24 Herstellungsjahr
0 Produkttyp
› 0 BasicLine
› 1 SlimLine
4 RotaChock® Größe
Siehe Maßtabelle, 4 = RC4
03 Chargennummer des betreffenden Jahres
RotaChock® wurde von verschiedenen Klassifizierungsstellen zugelassen, sodass der Einsatz von RotaChock® unter Antriebsmaschinen und Hilfsanlagen an Bord von Schiffen ohne langwieriges Planfeststellungsverfahren möglich ist. RotaChock® ist von allen großen Klassifikationsgesellschaften „typgeprüft“, wie z. B:
Dieser Typ ist die Hauptlösung für neue Konstruktionen und Anwendungen, die gebaut werden. Wenn die Spalthöhe noch auf dem Reißbrett steht, setzen Sie einfach den RotaChock® BasicLine ein. Die Fundamentschraube läuft durch das Mittelloch des RotaChock® und klemmt den Maschinenfuß, den RotaChock® und die Oberplatte des Fundamentes sicher zusammen. Wenn Ihre Maschine neu ausgerichtet werden muss, lösen Sie einfach die Fundamentschrauben und richten Sie den RotaChock® BasicLine entsprechend aus. Diese Justierbarkeit ist in der Branche unübertroffen und sorgt für entscheidende Zeitvorteile im Vergleich zu anderen Einbaustücklösungen.
SCHNELLIGKEIT
RotaChock® ist schnell montiert. Eine auf einem RotaChock® aufgestellte Maschine kann im Allgemeinen innerhalb einer Stunde neu ausgerichtet und gesichert werden. Zum Vergleich: Die Verwendung von Epoxidharz kann aufgrund der langen Aushärtungszeit Tage dauern. Das Ausmessen, die Herstellung und der Einbau von Stahlblöcken dauern sogar noch länger, und die Arbeitskosten machen das Ganze relativ teuer.
RotaChock® hat ein rundes Oberteil, das die bestmögliche Kontaktfläche gewährleistet, auch wenn Fundament und Maschinenfuß nicht parallel sind. RotaChock® ist auch höhenverstellbar. Die Kombination dieser beiden Merkmale verhindert Kippfüße.
RotaChock® verhält sich wie ein massives Einbaustück aus Stahl und ermöglicht es, die Fundamentschraube mit jedem gewünschten Drehmoment zu spannen. Einbaustücke aus Epoxidharz haben dagegen eine maximale Belastbarkeit von 5 N/mm2. Dieses relativ niedrige Drehmoment führt häufig dazu, dass sich die Fundamentschrauben fast vollständig lösen.
Der Wettbewerbsvorteil von RotaChock® ist die große Aufstandsfläche: Die Oberfläche des unteren Rings, die mit dem Fundament in Berührung kommt, ist größer, sodass der Druck, der auf diese Oberfläche ausgeübt wird, geringer ist. RotaChock® verwendet ebenfalls ein Sägezahngewinde. Diese Eigenschaften ermöglichen es RotaChock®, größere Lasten zu tragen.
Runder oberer Ring für eine Winkeldifferenz von bis zu 4° zwischen Maschinenfuß und Fundament.
Die Aufstandsfläche ist groß und verringert die Flächenpressung. ROTACHOCK®
Die Aufstandsfläche ist groß und verringert die Flächenpressung.
ROTACHOCK® BASICLINE – MA ẞ TABELLE
RotaChock® BasicLine besteht aus 10 verschiedenen Größen, die von 51 mm bis 254 mm Außendurchmesser reichen und den gesamten Bereich von M12- bis M72-Fundamentschrauben abdecken. Die RotaChock® Nennlast steigt mit dem Außendurchmesser. Werkzeugnut und Bohrungen für die Montage mit einer Vielzahl von Werkzeugen. Sägezahngewinde für maximale Festigkeit und Steifigkeit.
ROTACHOCK® BASICLINE – KONFIGURATIONEN
RotaChock® BasicLine kann in einer Vielzahl von Materialien geliefert werden. Wir empfehlen die Verwendung unserer Standard RotaChock® BasicLine, die aus S355 (DIN1.0570) hergestellt und ACE-behandelt ist – für normale Anwendungen. Für maximalen Schutz gegen Korrosion in extremen Umgebungen kann RotaChock® BasicLine in Edelstahl (316L) geliefert werden. Für maximale Festigkeit bei extremen Kräften kann RotaChock® BasicLine in legiertem Stahl (z. B. 34CrNiMo6) geliefert werden. Auf Seite 7 finden Sie weitere Informationen zu den verfügbaren Materialien und Oberflächenbehandlungen.
Lesen Sie die Auswahl- und Konstruktionshinweise auf Seite 17 oder nutzen Sie das RotaChock® Auswahltool auf www.rotachock.com, um die passende RotaChock® BasicLine-Variante zu finden.
Lesen Sie die Montagehinweise auf Seite 21 oder sehen Sie sich die Montagevideos unter www.rotachock. com an, um Hilfe bei der Montage der RotaChock® BasicLine zu erhalten.
Sie können alle Typenzulassungen und RotaChock® BasicLineZeichnungen sowohl in 2D als auch 3D online unter www.rotachock.com herunterladen.
Die FAQs zur RotaChock® BasicLine finden Sie auf Seite 29 oder online unter www.rotachock.com
Wenn die RotaChock® BasicLine nicht in den vorhandenen Raum zwischen dem Maschinenfuß und dem Fundament passt, sollten Sie die RotaChock® SlimLine verwenden. Mit einer Gesamthöhe ab 20 mm eignet sich die RotaChock® SlimLine für die meisten Nachrüstanwendungen und bietet dennoch einen Justierbereich von 10 mm.
RotaChock® SlimLine ist für die Nachrüstung von epoxidharzverfugten Anlagen konzipiert. Jedes Mal, wenn die Maschine neu ausgerichtet werden muss, muss dieses Epoxidharz wieder herausgeschnitten werden. Die Konstruktionshöhe von Einbaustücken aus Epoxidharz liegt im Bereich von 20 bis 40 mm. Aus diesem Grund wurde die SlimLine-Reihe mit denselben Höhen konzipiert. Jetzt können Sie das Epoxidharz herausschneiden und es direkt durch RotaChock® SlimLine ersetzen.
Diese Konstruktion ist nicht nur für den Nachrüstungs- und Reparaturmarkt gedacht: RotaChock® SlimLine kann in allen Anwendungen und jeder Ausführung eingesetzt werden. Wenn der Platz für die BasicLine nicht ausreicht, kann die SlimLine mit minimaler Höhe verwendet werden.
Runder oberer Ring für eine Winkeldifferenz von bis zu 2° zwischen Maschinenfuß und Fundament.
Standard ACE-Oberfläche: ACE-behandelt für kosteneffektiven Korrosionsschutz.
Die Aufstandsfläche ist groß und verringert die Flächenpressung.
ROTACHOCK® SLIMLINE – MA ẞ TABELLE
Werkzeugnut und Bohrungen für die Montage mit einer Vielzahl von Werkzeugen.
Sägezahngewinde für maximale Festigkeit und Steifigkeit.
RotaChock® SlimLine besteht aus 5 unterschiedlich großen Elementen mit einem Außendurchmesser von 76 mm bis 178 mm, die den gesamten Bereich von M16- bis M52-Fundamentschrauben abdecken. Die RotaChock®-Nennlast steigt mit dem Außendurchmesser.
RotaChock ® SlmLine
ROTACHOCK® SLIMLINE – KONFIGURATIONEN
RotaChock® SlimLine kann in einer Vielzahl von Materialien geliefert werden. Für normale Anwendungen empfehlen wir die Verwendung unserer Standard RotaChock® SlimLine. Diese wird aus S355 (DIN1.0570) hergestellt, wobei die Gewindeteile aus legiertem Stahl (42CrMo4) bestehen, und ist ACE-behandelt für kosteneffektiven Korrosionsschutz. Für maximalen Schutz gegen Korrosion in extremen Umgebungen kann RotaChock® SlimLine in Edelstahl (316L) geliefert werden. Für maximale Festigkeit bei extremen Kräften kann RotaChock® SlimLine in legiertem Stahl (z. B. 34CrNiMo6) geliefert werden. Auf Seite 7 finden Sie weitere Informationen zu den verfügbaren Materialien und Oberflächenbehandlungen.
Lesen Sie die Auswahl- und Konstruktionshinweise auf Seite 17 oder nutzen Sie das RotaChock®-Auswahltool unter www.rotachock.com, um die passende RotaChock® SlimLine-Variante zu finden.
Lesen Sie die Montagehinweise auf Seite 21 oder sehen Sie sich die Montagevideos unter www.rotachock.com an, um Hilfe bei der Montage der RotaChock® SlimLine zu erhalten.
Sie können alle Typenzulassungen und RotaChock® SlimLine-Zeichnungen sowohl in 2D als auch 3D online unter www.rotachock.com herunterladen.
Die FAQs zur RotaChock® SlimLine finden Sie auf Seite 29 oder online unter www.rotachock.com
Die Montage von elastischen Lagerungen kann eine Herausforderung sein.Die Grundplatte der Gummilagerung muss perfekt parallel zum Maschinenfuß ausgerichtet sein, um eine optimale Schwingungsdämpfung zu gewährleisten. Traditionell wird die elastische Lagerung mithilfe der vier Justierschrauben so eingestellt, dass jeder Winkel zwischen der Kappe und der Grundplatte eliminiert und dann der Spalt zwischen der Grundplatte der Lagerung und dem Fundament mit Zweikomponenten-Epoxidharz oder einem maßgeschneiderten Stahlblock ausgefüllt wird.
Die RotaChock®-Philosophie zur Behebung von Kippfüßen kann auch für die schnelle und einfache Montage dieser elastischen Lagerungen angewendet werden. Deshalb wurde die RotaChock®-Montageplatte in enger Zusammenarbeit mit führenden Entwicklern elastischer Lagerungen entwickelt. Wir haben vier RotaChock® in die Ecken einer starren Montageplatte integriert.
Die RotaChock®-Montageplatte bietet eine kostengünstige Alternative zu Epoxidharz- oder maßgeschneiderten Stahlblöcken. Die Justierschrauben in der RotaChock®Montageplatte werden verwendet, um den Winkel zwischen dem Fundament der Lagerung und der Grundplatte zu eliminieren. Nun werden die vier RotaChock® an den Ecken justiert, um den Spalt zu schließen. Die Grundplatte, die RotaChock® Montageplatte und das Maschinenfundament werden dann mit vier Fundamentschrauben fest zusammengeschraubt.
Das Montagesystem kann bei Bedarf jederzeit nachjustiert werden. Lösen Sie einfach die Fundamentschrauben und justieren Sie die RotaChock®-Montageplatte, um die gewünschte Ausrichtung zu erzielen. Die Zeit, die für die Fertigstellung einer typischen elastisch gelagerten Maschine benötigt wird, kann von mehreren Tagen auf nur wenige Stunden verkürzt werden.
Runder oberer Ring für eine Winkeldifferenz von bis zu 4° zwischen Maschinenfuß und Fundament.
Werkzeugschlitze und Bohrungen zur Erleichterung der Montage mit einer Vielzahl von Werkzeugen.
Standard ACE-Oberfläche: ACE-behandelt für kosteneffektiven Korrosionsschutz.
Sägezahngewinde für maximale Festigkeit und Steifigkeit.
VORTEILE DER ROTACHOCK®-MONTAGEPLATTE
Vorteile der RotaChock®-Montageplatte im Vergleich zu anderen Verkeilungslösungen wie Epoxidharz und Stahlblöcken:
› Der Hauptvorteil von RotaChock® ist die Einstellbarkeit. Korrekturen und Anpassungen sind jederzeit möglich. Bei der Verwendung von Epoxidharzen oder Stahlblöcken müssen Sie das Epoxidharz herausschneiden oder den Stahlblock entfernen und den gesamten langwierigen und kostspieligen Prozess neu durchführen.
› Schnelligkeit: RotaChock® ist schnell installiert. Eine auf einem RotaChock® aufgestellte Maschine kann im Allgemeinen innerhalb von Stunden neu ausgerichtet und gesichert werden. Bei der Verwendung von Epoxidharzen dauert es aufgrund der relativ langen Aushärtungszeit des Harzes von 36-48 Stunden mindestens drei Tage, bis die Maschine wieder funktioniert. Bei der Verwendung von Stahlklötzen dauern das Messen des Spalts, das Fräsen des Stahlkeils und der Schweißvorgang mehrere Tage.
› RotaChock® ist benutzerfreundlich; für den Einbau sind keine besonderen Kenntnisse erforderlich. Im Gegensatz zu Epoxidharzen sind für den Einbau keine zertifizierten Personen erforderlich, um die Garantie zu erhalten. Für das lokale Verfahren zum Messen, Korrigieren, Einpassen und
ROTACHOCK® MONTAGEPLATTE MASSTABELLE
Bearbeiten von Stahlblöcken sind erfahrene und geduldige Fräser erforderlich.
› Stahlblöcke müssen für jede elastische Halterung separat gemessen und bearbeitet werden. Die RotaChock®Lösung ist ein Standarddesign mit einem Verstellbereicheine Passung pro elastischer Halterung, die in der Höhe verstellt werden kann.
› Bei der Verwendung von RotaChock® ist kein Erhitzen erforderlich; Hitze könnte das Ausrichtungsziel negativ beeinflussen. Epoxidharze müssen zum Aushärten erhitzt werden, und in Stahl eingepasste Blöcke müssen mit dem Fundament verschweißt werden.
› RotaChock® verhält sich wie ein massiver Stahlkeil, und mit RotaChock® kann der Fundamentbolzen mit jedem gewünschten Drehmoment gespannt werden. Im Gegensatz dazu haben Epoxidharze eine maximale Belastung von 5 N/ mm2. Dieses relativ niedrige Drehmoment führt oft dazu, dass die Fundamentbolzen fast lose sind.
› RotaChock® ist umweltfreundlich; Epoxidharze enthalten gemischte und aggressive chemische Komponenten, die für die Anwender gefährlich sind.
Die Auswahl der RotaChock®-Montageplatte ist ganz einfach: Gleichen Sie einfach das Schraubenmuster Ihrer elastischen Lagerung mit der untenstehenden Tabelle ab. Die RotaChock®-Standard-Montageplatte wird aus S355 (DIN1.0570) hergestellt und ist ACE-behandelt für kosteneffektiven. Auf Seite 7 finden Sie weitere Informationen zu den verfügbaren Materialien und Oberflächenbehandlungen.
RotaChock ® Monta-geplatte Min. Höhe Konstruktionshöhe Max. Höhe
Der Zweck der Verkeilung ist die Schaffung einer perfekten koplanaren Montagefläche für die Maschine. RotaChock® gleicht den Spalt zwischen dem Maschinenfuß und dem Fundament aus und beseitigt Parallel- und Winkelversatz. Das heißt aber nicht, dass es nicht trotzdem zu fehlerhaften Beschlägen kommen kann. Ob mit RotaChock®, Epoxidharzen oder Stahlblöcken – eine unzureichende Dehnung der Schrauben durch eine falsche Ausrichtung der Beschläge bedeutet eine lose Fundamentschraube. In einigen Fällen liegen fehlerhafte Beschläge vor,
DAS PROBLEM
Im Schiffbau verlangen Klassifizierungsstellen, dass die Unterseite von Fundamenten angefräst oder aufgebohrt wird, sodass die Oberflächen parallel sind. In anderen Industrien sind extra lange Stifte erforderlich. Diese langen Stifte verringern zwar den Spannungsaufbau, sind aber für die Nutzungsdauer nicht von Vorteil. Warum das Fundament bearbeiten oder das Problem entschärfen, wenn Sie es auch anders lösen können?
Runder Abstandshalter mit glatter konkaver und konvexer Krümmung
RUNDE ABSTANDSHALTER –
MA ẞ TABELLE
Die Auswahl eines runden Abstandshalters ist einfach; sie sind speziell für die verwendete Fundamentschraube ausgelegt. Prüfen Sie einfach die von Ihnen verwendete Schraube und gleichen Sie diese mit der Tabelle ab. Die standardmäßigen runden Abstandshalter werden aus 42CrMo4 (DIN1.7225) hergestellt und sind ACE-behandelt für kosteneffektiven Korrosionsschutz. Auf Seite 7 finden Sie weitere Informationen zu den verfügbaren Materialien und Oberflächenbehandlungen.
Die runden Abstandshalter erfüllen zwei Funktionen: die Schaffung der Beschlagsebenen und die Dehnung der Schrauben. Diese Lösung besteht aus zwei Teilen mit einer glatten konkaven und konvexen Krümmung, die einen Winkelversatz von 4° ergeben, wodurch die Beschlagsebene entsteht. Die Standardhöhen verlängern die Schraube und schaffen zusätzliche Klemmlänge.
Die meisten auf dem Markt erhältlichen runden Unterlegscheiben haben einen runden x konischen Querschnitt. Aufgrund des Linienkontakts zwischen runden und konischen Konturen könnten sich diese Unterlegscheiben als problematisch erweisen, z. B. wenn Ihre Anwendung hohen Vibrationsbelastungen, seismischen Erschütterungen oder Belastungen bei Schiffsanwendungen ausgesetzt ist.
Selbst für kleinste rotierende Maschinen ist eine einfache und schnelle Ausrichtung mit RotaChock® HexLine möglich. Diese kleinformatigen Hexagon RotaChock® sind ideal für kleine Maschinen wie z. B. Pumpensätze, bei denen eine genaue Ausrichtung entscheidend ist. Diese Lösung hat das gleiche Prinzip wie alle RotaChock®-Varianten: ein justierbares Gewinde in der Mitte für parallele Differenzen und eine runde Oberseite, um Winkelunterschiede auszugleichen. Dank der sechseckigen Ausführung kann die Justierung mit einem einfachen Mutter-/Schraubenschlüssel vorgenommen werden.
Bei einigen Anwendungen gibt es Konfigurationen mit nur geringem Höhenunterschied zwischen den Wellenachsen. In vielen Fällen reicht der Justierbereich von RotaChock® aus, um die Unterschiede auszugleichen. Aber wenn 5 bis 25 mm an zusätzlicher Höhe benötigt werden, ist ein höherer oberer Ring wirtschaftlicher als andere Lösungen. Die Bevorratung von höheren oberen Ringen kann bei der Montage zu einer Zeitersparnis führen, wenn Sie feststellen, dass die vorgesehene Spalthöhe leicht überschritten wird.
Als Markt- und Technologieführer entwickeln, produzieren und vermarkten wir innovative Verkeilungslösungen für alle Arten von rotierenden Maschinen und Verkeilungsszenarien. Wenn es keine Standardlösung gibt, kann unser Ingenieurteam eine maßgeschneiderte RotaChock®-Lösung für Ihre Anwendung entwickeln. In der untenstehenden Übersicht finden Sie RotaChockLösungen, die in Nischenmärkten oder spezifischen Situationen entwickelt und eingesetzt werden: In der nachstehenden Übersicht finden Sie RotaChock®-Lösungen, die in Nischenmärkten oder einzigartigen Situationen entwickelt und eingesetzt werden:
Die Höhe der Wellenachse zwischen dem Antrieb und der angetriebenen Maschine ist in der Regel unterschiedlich. Um diese Unterschiede auszugleichen, werden meist Höhensockel am Skid angebracht. Diese Lösung ist kostspielig, da für die Montage der Stahlkonstruktion zusätzliche handwerkliche Fähigkeiten erforderlich sind. Unsere Lösung ist ein RotaChock® mit einer höheren Höhe, der die Anforderungen Ihrer Anwendung erfüllt. Einige Dinge müssen jedoch bei der Verwendung von Tall-LineKonfigurationen, berücksichtigt werden, z. B. wenn Schub- oder Querkräfte auftreten.
RotaChock®-Nuten und -Bohrungen erleichtern die Montage, und es können verschiedene Arten von Werkzeugen verwendet werden. Manche Techniker bevorzugen jedoch einen Mutter-/oder Schraubenschlüssel. Für jede RotaChock®-Größe wurde eine Reihe von Justierwerkzeugen entwickelt.
ROTACHOCK® KANN MITTELS DREI METHODEN AUSGEWÄHLT WERDEN
AUSWAHL NACH SCHRAUBENGRÖ ẞ E UND SPALTHÖHE:
Wählen Sie einen RotaChock® basierend auf dem Durchmesser der Fundamentschraube und der Spalthöhe:
Scannen Sie den QR-Code, um das Auswahlwerkzeug zu öffnen.
› Gleichen Sie den Durchmesser der Fundamentschraube mit dem RotaChock®-Standardschraubendurchmesser in der Maßtabelle ab.
Zum Beispiel: M36 = RC5 oder RC6
› Gleichen Sie Ihre Spalthöhe mit der RotaChock®-Konstruktionshöhe in der Maßtabelle ab. Zum Beispiel: M36 und Spalthöhe von 28 mm --> RC5-SlimLine. M36 und Spalthöhe von 56 mm --> RC5-BasicLine Wenn die Spalthöhe noch auf dem Reißbrett steht, verwenden Sie die Konstruktionshöhen der RotaChock® BasicLine. Diese Methode ist ein schneller und einfacher Weg, die richtige RotaChock®-Größe auszuwählen. Unter www.rotachock.com finden Sie das RotaChock®-Auswahltool, das Ihnen bei der Auswahl hilft.
Durchmesser der Fundamentschraube prüfen
Spalthöhe prüfen
RotaChock®-Größe auswählen
AUSWAHL AUF DER GRUNDLAGE DER LASTBERECHNUNG DURCH ROTACHOCK®-HÄNDLER
Wenn Sie eine detailliertere Auswahl wünschen, füllen Sie bitte das RotaChock®Datenformular aus und übermitteln Sie es an Ihren örtlichen RotaChock®-Händler. Anhand der Angaben Ihrer Maschine kann Ihr örtlicher Händler die Größenberechnung kostenlos durchführen. Laden Sie dieses Datenformular unter www.rotachock.com herunter. Auf Seite 19 finden Sie eine ausführliche Erläuterung der Formeln, die wir für diese Berechnungsmethode verwenden.
PLANFESTSTELLUNGEN
Planfeststellungen sind für Antriebs- und Hilfsanlagen bei Schifffahrtsanwendungen erforderlich, die eine Klassifizierungs-genehmigung erfordern. Für diese Anwendungen kann ein RotaChock®-Konstruktionsvorschlag mit allen Berechnungen und einer Skizze der Verkeilungsanordnung vorgelegt werden, um eine Planfeststellung von der zuständigen Klassifizierungsstelle zu erhalten.
Wenn Ihre Maschinen und Fundamente komplexeren Kräften ausgesetzt sind, kann unser Team eine gründliche Strukturanalyse durchführen, einschließlich Computermodellierung und Finite-Elemente-Analyse.
Sie können in jedem Fall die Dienste unseres Ingenieurteams in Anspruch nehmen, indem Sie Ihr ausgefülltes Formular (das Sie unter www.rotachock.com herunterladen können) mit 2D/3D-Zeichnungsdateien an engineering@rotachock.com senden.
60 - 70 % des empfohlenen Anzugsdrehmoments bei Nennlast.
Elastische Grenze Streckgrenze Zugfestigkeit
Totalausfall F
Plastischer Bereich
Elastischer Bereich Zugkraft
Dehnung
50 % auf Mutterseite
Einschnürung
10 % umgewandelt in Vorspannung
Jede Branche hat ihre eigenen Spezifikationen für die Verschraubung von Fundamenten, und jeder Hersteller hat seine eigenen Vorlieben bei der Verschraubung. RotaChock® ist um die Fundamentschrauben herum konstruiert, also folgen Sie einfach den ursprünglichen Verschraubungsanweisungen des Konstrukteurs. Jede Größe, Qualität und Art von Schrauben kann in Kombination mit RotaChock® verwendet werden. Im Allgemeinen raten wir, die Konstruktionshinweise des Herstellers zu befolgen. Wenn in der Zeichnung eine M24-Fundamentschraube angegeben ist, verwenden Sie diese. Wenn nur der Lochdurchmesser angegeben ist, wählen Sie die passende Fundamentschraube aus der Tabelle auf Seite 20 nach ISO 273 aus.
Wenn die Schraubengüte nicht angegeben ist, empfehlen wir die Verwendung von Schrauben der Güteklasse 8.8 (Streckgrenze 640 N/mm2) für RotaChock®-Anwendungen. Die Fundamentschraube muss innerhalb des elastischen Bereichs des Schraubenmaterials angezogen werden. Bei der Verwendung von Schrauben der Güteklasse 8.8 (Streckgrenze 640 N/mm2) empfehlen wir eine Spannung von 60 % - 70 % der Streckgrenze des Schraubenmaterials.
DEHNUNG
40 % in Gewinden
Reibungsverluste (trockene Stahlschraube)
Die linke Abbildung zeigt, was passiert, wenn ein Drehmoment auf eine trockene Schraube aufgebracht wird. Nur etwa 10 % der Kraft, die in den Schraubenschlüssel investiert wird, wird in die Vorspannung der Schraube umgewandelt. Die daraus resultierende Dehnung ist das Einzige, was die Schraubverbindung dicht hält. Als direkte Folge des Drehmoments, das bei der Montage auf die Fundamentschraube odermutter aufgebracht wird, ist diese Schraubendehnung entscheidend für die Lebensdauer der Maschine. Die Dehnung der Schraube muss ausreichen, um einen Dehnungsverlust aufgrund der Abflachung der Oberflächenrauhigkeit von Mutter, Schraubenkopf, Fundament und Unterlegscheiben auszugleichen.
Wenn die Dehnung der Schraube nicht ausreicht, bleibt das Verbindungselement möglicherweise nicht fest, und die Verbindung kann sich lösen. Wir empfehlen daher eine Mindestdehnung der Schraube von 0,20 mm.
Bei unzureichender Schraubendehnung kann die Klemmlänge vergrößert werden. Hierfür empfehlen wir unseren runden Abstandshalter, der auch eine perfekte Montageebene für den Schraubenkopf oder die Mutter schafft. Weitere Informationen zum runden Abstandshalter finden Sie auf Seite 15. Die Klemmlänge ist der Gesamtabstand zwischen Schraubenkopf und Mutter. Bei einer typischen RotaChock®-Montage entspricht dies der Summe aus:
› Höhe des oberen Abstandshalters
› Maschinenfußdicke
› RotaChock®-Konstruktionshöhe
› Fundamentstärke
› Höhe des unteren Abstandshalters
Schrauben der Güteklasse 8.8 (Streckgrenze 640 N/ mm2) mit einer Spannung im Bereich von 60 % - 70 % der Streckgrenze des Schraubenmaterials erfordern eine Mindestklemmlänge von 95 mm, um eine Mindestdehnung der Schraube von 0,20 mm zu erreichen.
Das RotaChock®-Berechnungstool wurde in Zusammenarbeit mit Herstellern und Klassifikationsstellen entwickelt. Wenn Sie uns Ihre Anwendungsdetails mitteilen, kann Ihr örtlicher Händler die Berechnung durchführen und eine Größenempfehlung abgeben. Nachstehend finden Sie eine Erläuterung der verwendeten Formeln.
Die folgenden Kräfte wirken auf den RotaChock® während des Maschinenbetriebs:
1 Statische Last (Gewicht der Maschine, die auf dem RotaChock® ruht)
2 Drehmoment Reaktionskraft
3 Schubkraft (z. ß. Propellerschub)
4 Kraft der Schraube
STATISCHE LAST
FWEIGHT Kraft, die durch das Gewicht der Maschine innerhalb der Erdanziehung entsteht [N].
M Masse der Maschine [kg]
G Gravitationsfeldstärke = 9,81 m/s2
N Gesamtzahl der montierten RotaChock®
DREHMOMENT-REAKTIONSLAST
FTORQUE Belastung infolge der Drehmomentreaktion [N]
P Leistung der Maschine [kW]
RPM Umdrehungen pro Minute
A Fundamentbreite von Schraubenloch zu Schraubenloch [mm]
N Gesamtzahl der montierten RotaChock®
SCHUBKRAFT-REAKTIONSLAST
FTHRUST REACTION Kraft infolge der Schubreaktion [N]
FVK Schubkraft [N]
H Vertikaler Versatz zwischen der Achse der Abtriebswelle und der Fundamentoberseite [mm]
L Länge zwischen vorderen und hinteren Schraubenlöchern [mm]
Die folgenden Formeln werden in unseren Größenempfehlungen verwendet:
5 Bei Anwendungen in der Schifffahrt, für die die Vorschriften der Klassifikationsgesellschaft gelten, ist ein C-Faktor gemäß den Klassenrichtlinien vorgeschrieben. Dieser C-Faktor ist ein kombinierter und gerundeter Wert, der auf Annahmen zu Schmierung, Reibung und Gewindedesign basiert. Bei der Berechnung nach den Klassenregeln ist die Verwendung diese C-Faktors obligatorisch.
6 Bei Anwendungen, für die keine Klassifizierungsregeln gelten, wird das Schraubendrehmoment gemäß ISO 16047 berechnet. Der Reibungskoeffizient wird bei der Auswahl der spezifischen Schraubenschmierung festgelegt.
7 Dehnung als direkte Folge des bei der Montage auf die Schraube oder Mutter ausgeübten Drehmoments.
SCHRAUBENLAST
FBOLT Kraft als Folge der Schraubenkraft [kN]
S Von-Mises-Spannung in der Schraube [N/mm2] A Schaftfläche [mm2]
SCHRAUBENDREHMOMENT BEI SCHIFFSANWENDUNGEN
NACH KLASSIFIZIERUNGSREGELN:
T Drehmoment der Schraube [Nm]
F Spannung in der Schraube [N]
D Schrauben-(Haupt-)Durchmesser (mm)
C Schrauben-(Haupt-)Durchmesser (mm)
SCHRAUBENDREHMOMENT NACH ISO 16047
T Drehmoment der Schraube [Nm]
F Spannung in der Schraube [N]
P Gewindeneigung [mm]
µTH Reibungskoeffizient im Gewinde
D2 Neigungsdurchmesser des Gewindes [mm]
µTH Reibungskoeffizient unter Schraubenkopf/Mutter
D0 Durchmesser der Reibungsfläche Kopf/Mutter [mm]
dh Durchmesser des Schraubenlochs
SCHRAUBENDEHNUNG:
Δi Dehnung der Schraube [mm]
L Länge der Schraube zwischen Schraubenkopf & Mutter [mm]
F Spannung in der Schraube [N]
E Elastizitätsmodul (210.000 für gängige Stahlsorten) [MPa]
A Schaftfläche [mm2]
CHECKLISTE
Unabhängig davon, welche Methode zur Auswahl von RotaChock® verwendet wurde, sollten Sie immer Folgendes prüfen:
Die Unterseite des ausgewählten RotaChock® sollte vollständig von dem Fundament getragen werden.
Der Gewindedurchmesser des RotaChock® sollte sich vollständig unter dem Maschinenfuß befinden.
Prüfen Sie, ob der gewählte Fundamentschraubendurchmesser dem RotaChock® entspricht.
The minimum required bolt stretch is 0,20 mm When using 8.8-grade bolts (yield strength 640 N/mm2), the necessary clamping length can be found in the below table.
The table below shows the tightening torques and clamping lengths for 8.8-grade bolts lubricated with light machine oil, ISO metric screw thread, and coarse pitch.
Bohrung im Maschinenfuß Auswahl einer Schraube der Güteklasse 8.8 nach ISO 273 Empfohlenes Schraubendrehmoment (µTH = 0,15)
Erforderliche Streckung des Schraubenmaterials
Erforderliche Mindestklemmlänge für 0,20 Schraubendehnung
Ø12M1060 70 95
Ø14M12100 70 95
Ø16M14150 70 95
Ø18M16 23070 95
Ø20
Prüfen Sie, ob sich die Spalthöhe innerhalb des RotaChock®-Justierbereichs befindet.
Ø43 M393.410
Ø66M6012.700 70 95
Ø70 M6415.350
TO INSTALL ROTACHOCK® YOU MUST COMPLETE FOLLOWING STEPS:
QR scannen, um das Montagevideo zu sehen
Reinigen Prüfen Ausrichten SPALT schließen Fundamentschrauben anbringen Endgültige Ausrichtung prüfen
VERKEILUNGSBEREICH PRÜFEN
Führen Sie eine Sichtprüfung der Unterseite des Maschinenfußes und der Oberseite des Montagefundaments durch. Reinigen Sie das Fundament und alle Maschinenoberflächen, die mit RotaChock® in Kontakt kommen, mit einem Tuch. Alle Bereiche sollten frei von Öl, Fett, Graten, Schlacke und anderem Schmutz oder Rost sein. Eine dünne Schicht Shot Primer ist akzeptabel, jedoch nicht mehr als 0,05 mm / 0,002”. Dickere Lackschichten sind nicht zu empfehlen und wirken sich negativ auf die Klemmkraft der Fundamentschraube aus.
Bestimmen Sie genau, wo RotaChock® positioniert werden soll, und prüfen Sie Folgendes:
2.1 SPALTHÖHE UND SCHRAUBENLOCH FÜR
DEN GEWÄHLTEN ROTACHOCK® PRÜFEN
Messen Sie die vorhandene Spalthöhe jeder Position und den Durchmesser des Schraubenlochs. Die Spalthöhe sollte innerhalb des Justierbereichs des gewählten RotaChock® liegen, und der Durchmesser der Fundamentschraube muss zum ausgewählten RotaChock® passen.
2.2 PRÜFEN, OB DIE ROTACHOCK® KONTAKTFLÄCHE GETRAGEN WIRD
Stellen Sie sicher, dass das Fundament mindestensgenauso breit wie der RotaChock-Durchmesser ist.
Das Fundament muss das RotaChock®Unterteil vollständig tragen. Der Maschinenfuß sollte mindestens den Gewindedurchmesser des RotaChock®Oberteilsabdecken.
2.3 PRÜFEN, OB DER ROTACHOCK® AUF DEM FUNDAMENT WACKELT
Dies bezeichnen wir als „Wackelkontrolle“. Legen Sie nach der endgültigen Positionierung des RotaChock® eine Hand auf die Oberseite des RotaChock® und versuchen Sie, den RotaChock® von einer Seite zur anderen zu bewegen. Wenn er wackelt, ermitteln Sie die Ursache und beheben Sie sie. In den meisten Fällen umfasst die Oberflächenvorbereitung nur lokales Abschleifen.
2.4 PRÜFEN, OB DER ROTACHOCK® DEN FÜHLERLEHREN-TEST BESTEHT
Drücken Sie auf den RotaChock® und wenden Sie eine Fühlerlehre von 0,05 mm / 0,002“ um den Umfang des Unterteils an. Die Prüfung der zulässigen Montagefläche ist erfolgreich, wenn die Fühlerlehre nicht vollständig durch den Schnittstellenbereich passt.
AUSRICHTUNG
Stellen Sie sicher, dass die Ausrichtung innerhalb der Zielvorgaben der Maschine für die Kaltausrichtung, das thermische Wachstum und die Durchbiegung der Kurbelwelle mithilfe von Hebevorrichtungen erfolgt. Da der RotaChock® ein mechanisches Gerät ist, richten Sie die Einheit 0,05 mm / 0,002” über dem Ziel aus. Die 0,05 mm / 0,002” sind ein Nennmaß, um die Extrusion des Schmiermittels in den RotaChock® Innenflächen zu ermöglichen.
RotaChock® ist ein Einbaustück, und wir empfehlen nicht, ihn als Hebevorrichtung für die Ausrichtung zu verwenden.
4
SPALT MIT ROTACHOCK®
SCHLIE ẞ EN UND DIE VERTIKALEN ABDRÜCKSCHRAUBEN LÖSEN
Packen Sie den RotaChock®aus; die Einheit ist zwecks Rückverfolgung mit einer Chargennummer gekennzeichnet. Platzieren Sie den RotaChock® in Position, in der Regel konzentrisch mit dem Schraubenloch, wobei die Chargennummer nach außen zeigen muss. Montieren Sie den RotaChock®, indem Sie ihn gegen den Uhrzeigersinn drehen, um den Spalt zu schließen.
Das Justieren kann manuell, mit RotaChock®Justierwerkzeugen oder Ihren eigenen Werkzeugen erfolgen.
Die erforderliche Kraft zum Anziehen des RotaChock® im Spalt ist minimal (10 - 15 Nm). Die selbstsichernden Eigenschaften des Sägezahngewindes sorgen dafür, dass keine mechanische Sicherung erforderlich ist, um zu verhindern, dass sich der RotaChock® unter Last dreht.
Sobald alle RotaChock® montiert sind, entlasten Sie die vertikalen Abdrückschrauben.
Montieren Sie die Fundamentschrauben, vorzugsweise von unten nach oben, und ziehen Sie die Fundamentschrauben gemäß der vom Hersteller empfohlenen Reihenfolge und dem empfohlenen Anzugsdrehmoment an.
Wir empfehlen eine Festigkeit der Fundamentschrauben von 70 %. In den Konstruktionshinweisen auf Seite 17 finden Sie weitere Informationen zur Auswahl der Schrauben. Die Tabelle rechts zeigt die Anzugsdrehmomente und Klemmlängen für mit leichtem Maschinenöl geschmierte Schrauben der Güteklasse 8.8, metrisches ISO-Gewinde und grobe Neigung.
Bei fehlenden Herstelleranweisungen: Ziehen Sie die erste Schraube mit dem erforderlichen Drehmoment an. Fahren Sie direkt über Kreuz fort, bis alle Schrauben angezogen sind.
Bohrung im Maschinenfuß Wählen Sie Schraube der Güteklasse 8.8 nach ISO 273 Empfohlenes Schraubendrehmoment (µTH = 0,15)
Ø12M1060
Ø14M12100
Ø16M14150
Ø18M16 230
Ø20 M18 320
Ø22M20440 Ø25M22 600 Ø27M24 760 Ø30M27 1.120 Ø33M30 1.510 Ø36 M33 2.060 Ø40 M362.640
Ø43 M393.410
Ø46 M424.220
Ø50M455.270
Ø53M48 6.340
Ø58M528.200
Ø62M5610.190
Ø66M6012.700
Ø70 M6415.350
Ø74 M6818.620
Prüfen Sie die endgültige Ausrichtung, nachdem Sie alle Fundamentschrauben auf das erforderliche Drehmoment festgezogen haben. Die Ausrichtung sollte innerhalb der Zieltoleranzen für die Kaltausrichtung liegen.
ROTACHOCK® SLIMLINE – MONTAGEHINWEISE
RotaChock® SlimLine setzt sich aus 5 Teilen zusammen:
Oberer Ring mit konvexer Oberfläche.
Mittlerer Ring mit Außengewinde und konkavem Hohlraum auf der Oberseite.Antriebsring mit Innengewinde.Basisring zur Befestigung
der Antriebsstifte. Antriebsstifte zur Arretierung des Mittelrings beim Rotieren des Antriebsrings.
Im Gegensatz zur RotaChock® BasicLine arbeitet die RotaChock® SlimLine im Uhrzeigersinn. Folgen Sie einfach den auf den vorherigen Seiten beschriebenen Schritten, aber montieren Sie in Schritt 4 die RotaChock® SlimLine, indem Sie sie im Uhrzeigersinn drehen, um den Spalt zu schließen. Die korrekte Montage verläuft wie folgt:
Denken Sie daran, die RotaChock® SlimLine durch Drehen im Uhrzeigersinn zu montieren!
ROTACHOCK®-MONTAGEPLATTE – MONTAGEHINWEISE
Die Montage der RotaChock®-Montageplatte ist ganz einfach, und die Schritte sind die gleichen wie bei anderen RotaChock®Typen. Befolgen Sie einfach die Montagehinweise Ihres Anbieters elastischer Lagerungen. Wenn es an der Zeit ist, die Einbaustücke zu montieren, befolgen Sie das RotaChock®Montageverfahren.
Überprüfen Sie zusätzlich zu den in Schritt 2 beschriebenen Kontrollen, ob Ihre RotaChock®-Montageplatte mit dem Schraubenmuster der elastischen Lagerung übereinstimmt.
QR scannen, um das Montagevideo zu sehen
Nach dem Lösen der Abdrückschrauben und vor dem Anziehen der Fundamentschrauben darf kein Spalt zwischen der RotaChock®-Montageplatte und der Bodenplatte der elastischen Lagerung sein.
Denken Sie daran, immer sicherzustellen, dass kein SPALT zwischen der RotaChock®-Montageplatte und der Bodenplatte der elastischen Lagerung verbleibt.
RotaChock® wird für die Montage aller Arten von rotierenden und kritisch ausgerichteten Maschinen verwendet. Jede Art von Anlage wurde schon einmal erfolgreich auf RotaChock® montiert. Von Wind-, Gas- und Dampfturbinen bis hin zu Motoren, Kränen, Winden und Walzwerken. Die am häufigsten montierten RotaChock®-Anwendungen sind:
Abpackbetriebe sind Hersteller von Anlagen, bei denen ein Antrieb und ein angetriebenes Bauteil auf einem Rahmen-Skid montiert sind. Es kann eine Kombination der links dargestellten Anwendungen sein. Beispiele sind ein mit einer Pumpe kombinierter Elektromotor, der als Pumpenaggregat in verschiedenen Industriezweigen – von öffentlichen Versorgungsbetrieben bis zum Bergbau – zum Einsatz kommt. Oder eine Kombination aus Verbrennungsmotor und Generator zur Notstromversorgung eines Krankenhauses.
Weltweit führende Erstausrüster wie Caterpillar, GE, Wärtsilä und Rolls Royce haben die Verwendung von justierbaren Einbaustücken in ihrem Skid-Design standardisiert. Diese Anlagen müssen im Laufe ihrer Nutzungsdauer mehrfach neu ausgerichtet werden. Dank RotaChock® können diese Skids bei der Montage und während ihrer gesamten Nutzungsdauer leicht justiert werden.
In einem Kernkraftwerk ist RotaChock® unter Generatoren mit einem Gewicht von 423.000 Kilogramm montiert, über 1.350.000 kWh erzeugen.
In der Schifffahrt ist RotaChock® die perfekte Montagelösung für Propulsionsanlagen. Wenn eine Neuausrichtung erforderlich ist, bedeutet die Möglichkeit, das Einbaustück neu zu justieren, eine erhebliche Zeitersparnis für die Schiffseigner. RotaChock® verkürzt die Wartungspausen erheblich und verlängert die Nutzungsdauer. Aber auch Werften setzen beim Bau neuer Schiffe auf RotaChock®. Es ermöglicht die endgültige Ausrichtung nach dem Stapellauf, wenn das Schiff bereits im Wasser ist.
RotaChock® wird in einer Vielzahl von Branchen eingesetzt. RotaChock® bedient Industrien von der Energieerzeugung und Offshore bis hin zur Schifffahrt und Nuklearindustrie und kommt in prestigeträchtigen Projekten zum Einsatz:
Das größte gebaute Kreuzfahrtschiff, die Oasis of the Seas, die 7.000 Passagieren Platz bietet, verfügt über mit RotaChock® ausgestattete Maschinen.
Karadeniz Powerships erzeugen Hunderte von MW an Strom mit Aggregaten, die mit RotaChock® ausgestattet sind.
Shells Appomattox nutzt mit RotaChock® ausgestattete Kompressorsätze im Golf von Mexiko.
› 1. Ich brauche Einbaustücke mit zusätzlicher Höhe
› 2. Kann unter RotaChock® ein(e) Unterlegscheibe/Platte/Ab stands halter montiert werden?
› 3. Wie montiert man RotaChock® unter einem hohlen/ U-förmigen Maschinenfuß?
› 4. Ist es möglich, RotaChock® zwischen einem AluminiumMaschinenfuß oder Fundament zu montieren?
› 5. Ich brauche einen erweiterten Justierbereich, gibt es eine Grenze für die Justierhöhe?
› 6. Wie reduziert man die RotaChock®-Höhe?
› 7. Wie vergrößert man das RotaChock®-Schraubenloch?
› 8. Wie muss RotaChock® abgestützt werden?
› 9. Welche Fundamentstärke wird empfohlen?
› 10. Was ist mit I-Trägern?
› 11. Kann ich RotaChock® an das Fundament heftschweißen?
› 12. Wie kann man Passschrauben in Kombination mit ROTA montieren?
› 13. Wie kann man Passstifte in Kombination mit ROTA montieren?
› 14. Kann ich RotaChock® auf dem Kopf stehend montieren?
› 15. Kann ich die Fundamentschraube von oben montieren?
› 16. Kann ich meine Maschine mit RotaChock® aufbocken oder ausrichten?
› 17. Kann ich zuerst die vier Ecken montieren und dann die anderen montieren?
1. ICH BRAUCHE EINBAUSTÜCKE
MIT ZUSÄTZLICHER HÖHE
Es gibt drei Möglichkeiten, wenn Sie für Ihre Anlage zusätzliche Höhe benötigen:
A HÖHERER OBERER RING
Wenn eine zusätzliche Höhe zwischen 5-25 mm benötigt wird, können wir höhere obere Ringe für die RotaChock® BasicLine/ SlimLine/Montageplatte liefern. Diese ersetzen die ursprünglich gelieferten Ringe und bieten zusätzliche Höhe. Wir führen diese höheren oberen Ringe für das gesamte Sortiment in verschiedenen Stärken für maximale Flexibilität.
B ABSTANDSRING
Falls erforderlich, kann ein Abstandsring unter die RotaChock® BasicLine & SlimLine und das Fundament platziert werden. Wir führen diese Abstandsringe für das gesamte Sortiment in verschiedenen Stärken für maximale Flexibilität.
› 18. Wie verhindert man, dass sich das Einbaustück dreht? Muss ich den RotaChock® sichern?
› 19. Was ist die größte Belastung in der Anlage?
› 20. Wieso lösen sich meine Fundamentschrauben?
› 21. Was ist der Unterschied zwischen starrer und elastischer Lagerung?
› 22. Wie leitet RotaChock® Schall im Vergleich zu Epoxidharz-Einbaustücken, Unterlegplatten oder Stahlblöcken?
› 23. Was raten Sie hinsichtlich Korrosionsschutz?
› 24. Kann man auf dem RotaChock® eine Beschichtung aufbringen?
› 25. Verwenden Sie Schmierfett für RotaChock®?
› 26. Was ist mit dem Schmieren der Fundamentschrauben?
› 27. Wie wird RotaChock® auf Beton montiert?
› 28. Was ist zu tun, wenn mein RotaChock® schwer zu bewegen oder zu drehen ist?
› 29. Sollte ich meine Maschine nach der Montage von RotaChock® auf Kippfüße montieren?
› 30. Muss ich RotaChock® während der Nutzungsdauer überprüfen?
› 31. Was ist am kosteneffektivsten: Epoxidharz, Stahlblöcke oder RotaChock®?
› 32. Wie lange ist die Nutzungsdauer von RotaChock®?
› 33. Können wir den RotaChock® oben auf einem Gewindeblock montieren?
› 34. Welches Schraubendrehmoment müssen wir anwenden?
› 35. Wie gehen wir mit Langlöchern im Maschinenfuß um?
› 36. Wie groß ist die Höheneinstellung bei einer Drehung um 60° (ein Einstellloch)?
C ROTACHOCK® TALL LINE
Für spezielle Anwendungen empfehlen wir den Einsatz der RotaChock® Tall Line, die einen verlängerten unteren Ring hat. Einige Dinge müssen jedoch bei der Verwendung von Tall-LineKonfigurationen berücksichtigt werden, z. B. wenn Schub- oder Querkräfte auftreten.
Als Faustregel für alle drei Optionen gilt: Die Höhe des Einbaustücks darf niemals den Durchmesser überschreiten. Zum Beispiel sollte die maximale Höhe der RC4-BasicLine, die einen Durchmesser von 102 mm hat, 102 mm nicht überschreiten.
Maximale Höhe = 53, was bedeutet, dass die maximal zusätzliche Höhe 49 mm beträgt. Aus Konstruktionssicht ist die beste Option A. Die Anzahl der Passflächen sollte minimiert werden, da dies die endgültige Klemmkraft beeinflusst.
2. KANN UNTER ROTACHOCK® EIN(E) UNTERLEGSCHEIBE/PLATTE/ ABSTANDSHALTER MONTIERT WERDEN?
Ja. Bei der Montage ist jedoch Vorsicht geboten. Im Folgenden finden Sie einige Szenarien, die wir im Laufe der Jahre erlebt haben:
EINE UNTERLEGPLATTE/2 EINBAUSTÜCKE MEHRERE UNTERLEGPLATTEN
VERBOGENE UNTERLEGPLATTEN VERZOGENES FUNDAMENT
Es gibt zwei wichtige Konstruktionshinweise für die Verwendung von Unterlegscheiben/Platten/Distanzstücken unter RotaChock®:
› Das Fundament und die zusätzliche Auflage müssen flach sein. Jede Verformung bedeutet, dass sich die Anlage verziehen/ verbiegen kann, was zu Kippfüßen führt. Bitte beachten Sie die erhöhte Gefahr des Verziehens/Verbiegens, wenn eine Unterlegscheibe/Platte unter mehrere Einbaustücke gelegt wird. Beim Anziehen des ersten RotaChock® kann sich die hinzugefügte Platte verziehen und verbiegen. Bitte beachten Sie, dass dies auch beim Schweißen in unmittelbarer Nähe passieren kann. Hitze kann den Stahl verformen und zu Kippfüßen führen.
› Die Anzahl der Passflächen muss so gering wie möglich gehalten werden, da dies die endgültige Klemmkraft beeinflusst. Das Hinzufügen weiterer separater Teile in der Klemmvorrichtung sollte vermieden werden.
Unsere empfohlenen Lösungen für eine größere Höhe finden Sie in FAQ Nr. 1
3.
4. IST ES MÖGLICH, ROTACHOCK® ZWISCHEN ALUMINIUM-MASCHINENFU ẞ ODER FUNDAMENT ZU MONTIEREN?
Ja, das ist möglich. Allerdings muss die Flächenpressung auf Aluminium ein akzeptables Niveau haben. Bitte wenden Sie sich an unser Ingenieurteam, um die zulässige Flächenpressung für Ihre Aluminium-Anwendung zu berechnen.
5. ICH BRAUCHE EINEN ERWEITERTEN JUSTIERBEREICH. GIBT ES EINE GRENZE FÜR DIE JUSTIERHÖHE?
Wir bieten den erweiterten Justierbereich für RotaChock® (Extended Adjustment Range = EAR), wenn mehr Justierbarkeit erforderlich ist. Wie die RotaChock® Tall Line hat der EAR einen verlängerten unteren Ring, aber auch einen verlängerten mittleren Ring. Der EAR erhöht die Flexibilität bei der Konstruktion der Anlage oder eines Systems, das sich während seiner Nutzungsdauer ändert. Bitte kontaktieren Sie Ihren RotaChock®-Händler für weitere Einzelheiten zu dieser Produktreihe und ihren Anwendungsmöglichkeiten.
6. WIE REDUZIERT MAN DIE ROTACHOCK®-HÖHE?
Die RotaChock® BasicLine und der runde Abstandshalter können leicht auf einer Drehbank bearbeitet werden. Montieren Sie zunächst das zusammengebaute Einbaustück in das Spannfutter der Drehbank (nur den unteren und mittleren Ring). Entfernen Sie dann gleichzeitig Material von der Unterseite beider Ringe, bis Sie die gewünschte Höhe erreicht haben. Das Verfahren ist Teil der Typenzulassung, sodass keine besondere Genehmigung erforderlich ist. Bitte beachten Sie. Für jeden mm, den Sie wegnehmen, verlieren Sie einen mm Justierbereich. Bei minimal reduzierter Höhe bleibt nur noch ein Millimeter Justierspielraum. Die minimalen Reduzierhöhen finden Sie in den RotaChock®-Maßtabellen. Wenn die reduzierte Höhe nicht ausreicht, verwenden Sie die RotaChock® SlimLine.
7. WIE VERGRÖ ẞ ERT MAN DAS ROTACHOCK®SCHRAUBENLOCH?
RotaChock kann unter jedem ungleichmäßig geformten Maschinenfuß montiert werden, indem eine Stahlplatte zwischen angebracht wird. Unten sehen Sie ein Beispiel für einen E-Motor mit einem U-Fuß:
In den Maßtabellen finden Sie die optionale Größe der Fundamentschraube; dies ist die maximal zulässige Schraubengröße für RotaChock®, wenn das Schraubenloch vergrößert ist. Als Faustregel gilt: Die maximale Vergrößerung ist die optionale Schraubengröße +1 mm. Zum Beispiel hat RC2-BasicLine einen Innendurchmesser von Ø17, und die optionale Schraubengröße beträgt M18. Beim Hinzufügen eines mm kann der Innendurchmesser bis zu einem Maximum von Ø19 vergrößert werden.
8. WIE MUSS ROTACHOCK® ABGESTÜTZT WERDEN?
Der untere Teil sollte immer vollständig abgestützt sein; wenn der Basisring nicht abgestützt wird, kann sich das Gewinde der Basis verziehen. Der RotaChock®-Gewindedurchmesser sollte sich vollständig unter dem Maschinenfuß befinden. Beide Durchmesser finden Sie in der Maßtabelle.
9. WELCHE FUNDAMENTSTÄRKE WIRD EMPFOHLEN?
Als Faustregel gilt, dass der Durchmesser der Fundamentschrauben dem Durchmesser des Fundaments entsprechen sollte; wenn der Schraubendurchmesser 1“ beträgt, sollte das Fundament mindestens 1“ dick sein. Achten Sie auch darauf, dass der Lastpfad durch Knotenbleche mit dem Fundament verbunden ist. Bei einer großen Motormasse sind die Knotenbleche nach außen abzuwinkeln, um die Festigkeit des Fundaments zu erhöhen.
10. WAS IST MIT I-BEAMS?
Bei einigen Anlagen müssen Ausschnitte in den Stegen der I-Träger angebracht werden, um die Fundamentschrauben zu montieren (siehe Beispiel unten).
Falsch: Die Aussparung ist zu groß für den Durchmesser des Einbaustücks. Das entfernte Stegmaterial ist zu nahe am Montageflansch. Das Ergebnis ist eine deutlich reduzierte Trägerstärke und ein System, das so wirkt, als hätte es einen Kippfuß.
Richtig: Dies ist ein verbesserter Zugangsausschnitt, bei dem die Festigkeit des Montageflansches erhalten bleibt. Fügen Sie einen Abstandshalter hinzu, um die Mutter zu erreichen und die Wartung während der gesamten Nutzungsdauer zu erleichtern.
11. KANN ICH ROTACHOCK® AN DAS FUNDAMENT HEFTSCHWEI ẞ EN?
Schweißen Sie nichts an oder um den RotaChock®. Vermeiden Sie auch Schweißarbeiten in unmittelbarer Nähe, da die Hitze die Stahlstruktur verformen kann und das Risiko von Kippfüßen birgt. Wenn geschweißt werden muss, ist auf eine ordnungsgemäße Erdung zu achten.
12. WIE KANN MAN PASSSCHRAUBEN IN KOMBINATION MIT ROTACHOCK® VERWENDEN?
Wenn gemäß den Anweisungen des Herstellers Passschrauben erforderlich sind, empfehlen wir, nur den Maschinenfuß und das Fundament aufzubohren. Wenn ein größeres Schraubenloch im Einbaustück benötigt wird, um die Schraube zu montieren, lesen Sie bitte FAQ Nr. 7.
13. WIE KANN MAN PASSSTIFTE IN KOMBINATION MIT ROTACHOCK® VERWENDEN?
Sie können einen geschweißten Anstiegsblock oder eine Mutterund Schrauben-Methode anwenden, wie unten dargestellt:
Option geschweißter Anstiegsblock
Option Mutter und Schraube
Wenn Sie alle Schritte der Montagehinweise ausgeführt haben, schweißen Sie einen Stahlblock an, der 1 mm tiefer liegt als der Spalt in der Nähe des Einbaustücks, bohren Sie ein Loch durch den Maschinenfuß in den Block und setzen Sie einen Passstift ein.
14. KANN ICH ROTACHOCK® AUF DEM KOPF STEHEND MONTIEREN?
Das ist in Ordnung; eine perfekte Lösung, wenn die Konstruktion des Fußes oder des Fundaments dies erfordert.
15. KANN ICH DIE FUNDAMENTSCHRAUBE VON OBEN MONTIEREN?
Ja, das ist möglich. Bedenken Sie aber, dass es für die Montage einfacher ist, die Muttern von oben zu montieren.
16. KANN ICH MEINE MASCHINE MIT ROTACHOCK® AUFBOCKEN ODER AUSRICHTEN?
RotaChock® ist ein Lückenfüller, und wir empfehlen nicht, ihn als Hebevorrichtung für die Ausrichtung zu verwenden. Verwenden Sie Abdrückschrauben oder andere Vorrichtungen zum Ausrichten, und füllen Sie den verbleibenden Spalt mit RotaChock®
17. KANN ICH ZUERST DIE VIER ECKEN MONTIEREN UND DANN DEN ANDEREN ROTACHOCK®?
Ja, für Ausrichtungszwecke, aber nicht für die endgültige Ausrichtung. Wir empfehlen die Verwendung der vertikalen Abdrückschrauben bei der endgültigen Ausrichtung und der Montage von RotaChock®, wie in den Montagehinweisen beschrieben.
18. WIE VERHINDERT MAN, DASS SICH DAS EINBAUSTÜCK DREHT? MUSS ICH DEN ROTACHOCK® SICHERN?
Wenn Sie die vertikalen Abdrückschrauben während der Montage lösen, drückt das Gewicht der Maschine das Einbaustück zusammen. Das RotaChock®-Gewinde wird durch die Reibung im Gewinde gesichert. Andere Sicherungsmethoden sind nicht erforderlich.
19. WAS IST DIE GRÖ ẞ TE BELASTUNG IN DER ANLAGE?
Die Schraubenspannung ist bei weitem die größte Belastung in der Anlage. Im Allgemeinen werden ca. 90 % der Gesamtbelastung des RotaChock® durch die Schraubenspannung verursacht. Alle anderen Belastungen, wie z. B. Maschinenlasten, die durch Gewicht und Drehmoment entstehen, sind weniger bedeutend.
FUNDAMENTSCHRAUBEN?
Die ersten beiden Fragen, die Sie sich stellen müssen: Haben Ihre Schrauben eine ausreichende Dehnung? Sind Ihre Schrauben gerade und nicht verbogen? Weitere Informationen finden Sie auf den Konstruktionsseiten auf Seite 17. In der Praxis erleben wir eine hohe Streuung bei Spannern, in einigen Fällen über 40 %. Auch die Schmierung der Schrauben ist ein wichtiger Faktor. Es gibt verschiedene Gründe für das Lösen von Schrauben; wenden Sie sich an unser Technikteam.
STARRER UND ELASTISCHER LAGERUNG?
STARRE LAGERUNG
Alle Maschinen, insbesondere rotierende Maschinen, müssen laut Herstellerangaben auf einer tragenden Unterlage befestigt werden. Starre Lagerung bedeutet, dass eine solide Stahlplatte (Fundament) mit einer bearbeiteten Oberfläche geschaffen werden muss, die auf einem Betonfundament eingegossen oder an eine Stahlkonstruktion geschweißt wird und die Ausrichtung der Maschine unterstützt und beibehält. Die Lücke zwischen dem Fundament und dem Maschinenfuß kann mit verschiedenen Verfahren und Produkten gefüllt werden. Gemäß der Philosophie von RotaChock® ist es unser Ziel, eine starre koplanare Oberfläche für die Maschine zu schaffen, die die Herstelleranforderungen für Kippfüße übertrifft und die die Position der Ausrüstung nach der endgültigen Ausrichtung beibehalten muss.
Körperschall und Vibrationen werden durch die beweglichen Teile eines Motors und den Verbrennungsprozess erzeugt. Diese verschiedenen Formen von Vibrationen wie Lärm, Schwingungen oder Erschütterungen stören den Komfort an Bord von Schiffen. Elastische Lagerungen sind die effektivste Option, wenn die auf den Schiffsrumpf übertragenen Geräusche und Vibrationen auf ein absolutes Minimum reduziert werden müssen. Diese Verringerung trägt erheblich zum Komfort von Besatzung und Passagieren bei, insbesondere auf Fähren, Kreuzfahrtschiffen oder Yachten.
Die Montage elastischer Lagerungen kann eine Herausforderung sein. Die Grundplatte der Gummilagerung muss perfekt parallel zum Maschinenfuß ausgerichtet sein, um eine optimale Schwingungsdämpfung zu gewährleisten. Zum Glück haben wir eine Lösung für dieses Problem. Ausführliche Informationen zu unserer RotaChock®Montageplatte finden Sie auf Seite 13.
22. WIE LEITET ROTACHOCK® SCHALL IM VERGLEICH ZU EPOXIDHARZ-EINBAUSTÜCKEN, UNTERLEGPLATTEN ODER STAHLBLÖCKEN?
Da es sich bei RotaChock® um ein mechanisch steifes Stahleinbaustück handelt, sind die Schallausbreitungseigenschaften vergleichbar mit denen von Harzeinbaustücken und Stahlblöcken. Die selbstnivellierende Oberplatte des RotaChock® bedeutet jedoch, dass die tatsächliche Schallleistung oft besser ist als die von Stahlblöcken oder Unterlegplatten.
23. WAS RATEN SIE HINSICHTLICH KORROSIONSSCHUTZ?
Die Standard-RotaChock®-Typen sind ACE-behandelt. Weitere Informationen zu diesem Verfahren finden Sie auf Seite 7. Wir empfehlen rostfreien Stahl (316L) für maximalen Schutz gegen Korrosion in extremen Umgebungen wie Offshore- und Decksanwendungen. Im Falle spezifischer Korrosionsanforderungen, wenden Sie sich bitte an unser Ingenieurteam.
24. KANN MAN AUF DEM ROTACHOCK EINE BESCHICHTUNG AUFBRINGEN?
Bei einigen Anwendungen wird die komplette Anlage beschichtet, einschließlich RotaChock®. Bitte seien Sie bei der Anwendung vorsichtig, da auf das Gewinde gespritzte Farbe den RotaChock® am Rotieren hindern kann.
25. VERWENDEN SIE SCHMIERFETT FÜR ROTACHOCK®?
Alle RotaChock®, die ACE-behandelt sind, werden abschließend in Maschinenöl getaucht. Sie können noch ölig sein, wenn sie aus der Verpackung genommen werden. Das Öl beeinträchtigt die endgültige Montage nicht und kann auf dem RotaChock belassen werden®. Falls gewünscht, kann es mit einem Tuch entfernt werden. Bei allen RotaChock® aus Edelstahl sind die Gewinde und runden Oberteile mit Molykote® D Anti-Seize-Paste oder Ähnlichem geschmiert. Diese Paste sollte nicht entfernt werden, da sie verhindert, dass sich die Teile festfressen.
Bei allen RotaChock® aus unbehandeltem (Kohlenstoff-)Stahl sind die Gewinde und das runde Oberteil mit Molykote® P-37 Anti-SeizePaste oder Ähnlichem geschmiert. Sie muss bei der Montage auf dem RotaChock® verbleiben. Die Außenflächen sind mit LPS 3® Premier Rust Inhibitor oder Ähnlichem beschichtet. Dieser sollte von der Ober- und Unterseite des Einbaustücks entfernt werden.
26. WAS IST MIT DEM SCHMIEREN DER FUNDAMENTSCHRAUBEN?
Viele Branchen und Hersteller haben ihre eigenen Präferenzen hinsichtlich Verschraubung und Schmierung. Ein Wechsel des Schmiermittels wirkt sich auf den Reibungskoeffizienten und das daraus resultierende Anzugsdrehmoment aus. Unabhängig von der verwendeten Schmierung ist zu beachten, dass die Fundamentschraube eine Mindestdehnung von 0,20 mm haben sollte.
27. WIE WIRD ROTACHOCK® AUF BETON MONTIERT?
Verwenden Sie eine Stahlplatte mit ausreichender Oberfläche und Dicke, damit die Flächenpressung auf den Beton ein akzeptables Niveau hat. Bei der Montage von RotaChock® direkt auf Beton, prüfen Sie zunächst die zulässige Flächenpressung des vorhandenen Betons.
28. WAS IST ZU TUN, WENN MEIN ROTACHOCK® SCHWER ZU BEWEGEN ODER ZU DREHEN IST?
Es kann sein, dass Schmutz oder Ablagerungen in das Gewinde des RotaChock® eingedrungen sind. Demontieren Sie das Einbaustück, prüfen Sie die Gewinde, und reinigen Sie sie mit einem Lappen und WD-40 oder Ähnlichem. In den meisten Fällen wird das Problem dadurch gelöst.
In Fällen, in denen das Einbaustück vollständig festgefressen ist (z. B. weil sich das Fett in den Gewinden aufgrund einer Reaktion mit Reinigungslösungen, die zum Entfetten der Maschine verwendet wurden, verfestigt hat), entfernen Sie das Einbaustück und wenden Sie vorsichtig Hitze an (nie mehr als 250 °C/480 F). Durch die Hitze verflüssigt sich das Fett. Reinigen Sie die Gewinde und verwenden Sie vor der erneuten Montage ein Anti-Seize-Mittel auf Nickelbasis.
Haben Sie einen Schaden am Gewinde entdeckt? Holen Sie Ersatzteile aus Ihrem Lager. Halten Sie eine Reihe von Ersatzteilen bereit. Nehmen Sie das alte Einbaustück heraus und ersetzen Sie es durch einen funktionierenden Satz. Zurück in der Werkstatt können Sie die alten Einbaustücke in aller Ruhe aufarbeiten und wiederverwenden.
29. SOLLTE ICH MEINE MASCHINE NACH DER MONTAGE VON ROTACHOCK® AUF KIPPFÜ ẞ E PRÜFEN?
Wenn die Konstruktions- und Montagehinweise von RotaChock® befolgt werden, sollte es zu keinem Kippfuß kommen. Wenn Sie jedoch eine abschließende Kippfuß-Kontrolle durchführen wollen, finden Sie hier die entsprechenden Anweisungen:
1. Bringen Sie nach der endgültigen Ausrichtung, wenn die Schrauben mit dem endgültigen Drehmoment angezogen wurden, eine Messuhr in der Nähe der Schraubenposition 1 an und stellen Sie sie auf Null.
2. Beim Lösen der Schraube sollte sich die Messuhr nicht mehr als 0,05 mm/0,002“ bewegen.
3. Wenn sich die Messuhr um mehr als 0,05 mm/0,002“ bewegt, wiederholen Sie die Ausrichtung und überprüfen Sie Ihren Verschraubungsplan.
30. MUSS ICH ROTACHOCK® WÄHREND DER NUTZUNGSDAUER ÜBERPRÜFEN?
Der RotaChock® selbst muss bei der Wartung nicht überprüft werden. Wir empfehlen, die OEM-Wartungsanweisungen und -Richtlinien für die Überprüfung des Drehmoments der Befestigungselemente zu befolgen.
31. WAS IST AM KOSTENEFFEKTIVSTEN: EPOXIDHARZ, STAHLBLÖCKE ODER ROTACHOCK®?
RotaChock® ist die kosteneffektivste und langlebigste Wahl für rotierende Maschinen. Kippfüße gehören der Vergangenheit an, und Ihre Maschine kann zu jedem gewünschten Zeitpunkt neu ausgerichtet werden. Unser Ingenieurteam verfügt über jahrzehntelange Erfahrung im Ausrichten und Montieren von Maschinen und hat bereits mit vielen anderen Verkeilprodukten gearbeitet. Wenn Sie nicht überzeugt sind, empfehlen wir Ihnen, gemeinsam mit uns einen Kostenvergleich zwischen Epoxidharzen, Stahlblöcken und RotaChock® zu erstellen.
32. WIE LANGE IST DIE NUTZUNGSDAUER VON ROTACHOCK®?
Nutzer sind oftmals skeptisch, weil sie Erfahrung mit Epoxidharzen haben, bei denen es wichtig ist, vor dem Mischen das Herstellungsdatum zu überprüfen. RotaChock ist jedoch aus Stahl gefertigt, weshalb seine mechanischen Eigenschaften nicht verloren gehen oder sich verschlechtern. Daher hat RotaChock® kein Verfallsdatum und ist unbegrenzt nutzbar. Kohlenstoffstahl ist das am häufigsten recycelte Material der Welt und kann ohne Verlust der mechanischen Eigenschaften
unbegrenzt wiederverwendet werden. Aufgrund seiner Lang lebigkeit hat RotaChock® eine lange Nutzungsdauer und kann recycelt und in anderen Produkten wiederverwendet werden, was wiederum Ressourcen spart. Hinweis: RotaChock unter trockenen Bedingungen und in der Originalverpackung gelagert werden.
33. KANN MAN DEN ROTACHOCK® AUF EINEM GEWINDESTOCK INSTALLIEREN?
Ja, das ist möglich. Als Faustregel gilt jedoch, dass die Gewindetiefe mindestens das 1,5-fache des Gewindedurchmessers betragen sollte. Zum Beispiel: Eine M30-Schraube sollte einen Gewindeeingriff von 45 mm haben.
34. WELCHES SCHRAUBENDREHMOMENT MÜSSEN WIR ANWENDEN?
Der RotaChock® selbst sollte handfest angezogen werden (10-15 Nm).Die empfohlenen Anzugsmomente für die Fundamentschraube finden Sie auf Seite 23.
35.WIE GEHT MAN MIT LANGLÖCHERN IM MASCHINENFUSS UM?
Wir empfehlen, die Anweisungen und Richtlinien des OEM für die Konstruktion der Schraube zu befolgen.Ohne OEM-Richtlinien gilt als Faustregel, dass die Dicke der Unterlegscheibe der Hälfte des Schraubendurchmessers entsprechen sollte, um das Langloch zu überdecken.
36.WIE IST DIE HÖHENEINSTELLUNG BEI EINER DREHUNG VON 60° (EIN EINSTELLLOCH)?
RC2-BasicLine 6 60161.60.26
RC3-BasicLine 6 60161.60.26
RC4-BasicLine 6 60122.1
RC4.5-BasicLine 6 60122.1
RC5-BasicLine 6 60122.1
RC6-BasicLine 6 60122.1
RC7-BasicLine 6 60 8
RC8-BasicLine 6 60 8
RC9-BasicLine 8 45 8
RC10-BasicLine 8 45 6
RC3-SlimLine 6 60161.60.26
RC4-SlimLine 6 60122.1
RC5-SlimLine 6 60122.1
RC6-SlimLine 6 60122.1
RC7-SlimLine 6 60122.1
Wie der Name schon sagt, konstruieren wir Einbaustücke (engl. chocks) – Stahleinsätze für Maschinenfundamente. Chock Design ist ein globales Powerhouse mit einer Fülle von Erfahrungen, Fachwissen und Marktkenntnissen. Wir bieten nicht nur Produkte an: Wir nutzen unsere Produkte auch, um Lösungen zu bieten. Und das können wir dank unserer langjährigen Erfahrung in einem breiten Spektrum von Unternehmen weltweit. Und was vielleicht noch wichtiger ist: Wir entwickeln unsere Produkte auf der Grundlage unserer eigenen praktischen Erfahrungen.
RotaChock® wird weltweit über ein Netz von hochqualifizierten Ausrichtungs- und Montageexperten vertrieben. Dieses weltweit flächendeckende Händlernetz gewährleistet den Zugang zu einem kompletten Support-Team – von Entwicklungsingenieuren in den Wissenszentren bis hin zu Servicetechnikern im Außendienst.
Vertriebshändler kennen und verstehen ihren lokalen Markt, ihre Kunden und ihre Herausforderungen. Dank dieser lokalen Präsenz bieten wir schnelle Reaktionszeiten und erfahrene Ingenieure. Sie verfügen über das Fachwissen und die Ausrüstung, um Probleme schnell zu erkennen und zu beheben.
Unser internationales Team von Maschinenbaukonstrukteuren und Anwendungsingenieuren meistert Ihre Herausforderungen und freut sich auf Sie. Unser Team ist der zuverlässigste Partner für Einbaustücklösungen – von Konstruktion und Technik bis hin zu Performance und Support. Gemeinsam mit Ihnen können wir die richtige Einstellung und Ausrichtung Ihrer Maschinen vornehmen.
Unser Team kann für komplexe Anlagen, bei denen sowohl die Maschinen als auch die Fundamente dynamischen Kräften ausgesetzt sind, eine eingehende Strukturanalyse durchführen, einschließlich Computermodellierung und Finite-ElementeAnalysen. Diese fortschrittlichen technischen Dienstleistungen sind hilfreich für neue Anlagen und haben sich bei der Lösung von Problemen in bestehenden Anwendungen bewährt.
Wir helfen Ihnen, Ihren Maschinenpark am Laufen zu halten.
KONTAKTIEREN SIE UNS BITTE ÜBER DIE UNTENSTEHENDEN ADRESSEN, DAMIT WIR SIE MIT IHREM ÖRTLICHEN HÄNDLER IN KONTAKT BRINGEN KÖNNEN.
WWW.ROTACHOCK.COM +31 (0) 10 268 8018
Dokumentation
Videos
Download Center 2D/3D-Zeichnungen
INFO@ROTACHOCK.COM
RotaChock®Auswahltool WhatsAppUnterstützung
Zugelassene Händler
info@rotachock.com www.rotachock.com
® RotaChock ist eine eingetragene Marke von Chock Design B.V. ©Chock Design B.V. 2024
Der Inhalt dieser Publikation unterliegt dem Urheberrecht des Herausgebers und darf ohne vorherige schriftliche Genehmigung nicht (auch nicht auszugsweise) vervielfältigt werden. Die Richtigkeit der Angaben in dieser Publikation wurde mit größter Sorgfalt geprüft. Dennoch kann keine Haftung für direkte, indirekte oder Folgeschäden übernommen werden, die sich aus der Verwendung der hierin enthaltenen Informationen ergeben.
Publikation RotaChock® Informationsbroschüre Ausgabe 08/2024