New ad campaign under way

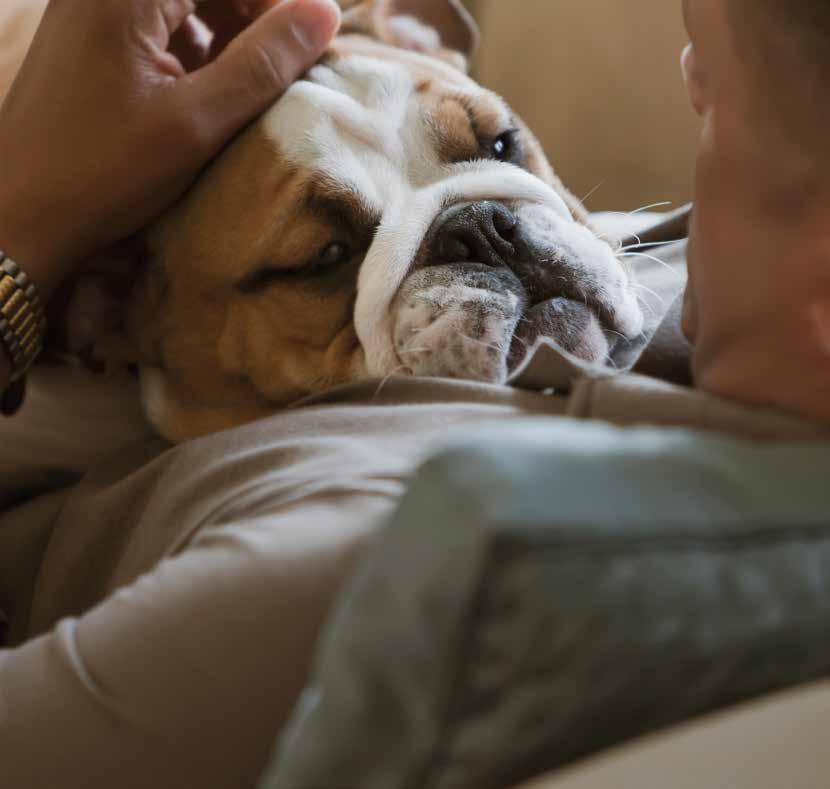
Technical
Industry Standard Update 124:
Gas supplies to mobile dwellings
LPG hoses: applications
Gas Safety Week
Spotlight on supporter activities during a week of unity and gas safety
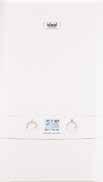
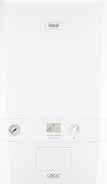
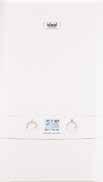
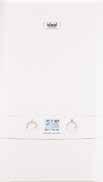
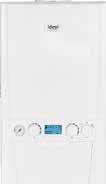
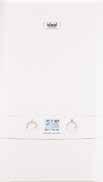
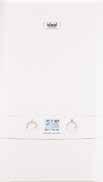
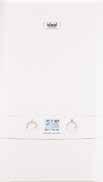
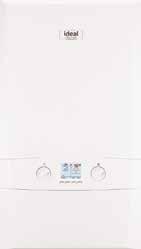
Technical
Industry Standard Update 124:
Gas supplies to mobile dwellings
LPG hoses: applications
Gas Safety Week
Spotlight on supporter activities during a week of unity and gas safety
Technical
Industry Standard Update 124:
Gas supplies to mobile dwellings
LPG hoses: applications
Gas Safety Week
Spotlight on supporter activities during a week of unity and gas safety
Did you take part in Gas Safety Week this year? For the 14th time, a huge variety of people and organisations signed up to help make a difference to gas safety in their own communities.
Whether it was sharing messages on social media or distributing leaflets and posters, this year’s theme of Checking, Every Check Counts struck a chord and was a simple but effective way to encourage people to check different aspects of their gas safety – whether it’s getting their gas appliances checked and serviced or making sure that their CO alarm is working.
Gas Safety Week helps to focus the nation’s minds on the importance of making sure their gas appliances are safe and working properly, especially ahead of the cold weather.
And the reminders continue with Gas Safe Register’s latest wide-ranging ad campaign, featuring a new set of memorable creative treatments, all with the same purpose: keeping people safe in their homes.
You can find out more about these important campaigns inside this issue, as well as the all latest technical updates and features.
Nicki Shearer, editor
Gas Safe Register, PO Box 631, DARLINGTON, DL1 9GD
Email: enquiries@gassaferegister.co.uk, register@gassaferegister. co.uk or technical@gassaferegister.co.uk
Managing editor: Sue Harker, sue.harker@gassaferegister.co.uk
Editor: Nicki Shearer, editorial@registeredgasengineer.co.uk
News: Jennie Ward, news@registeredgasengineer.co.uk
Publisher: Peter McCreary, publisher@registeredgasengineer.co.uk
Technical consultants: Rob Walkerdine, Carl Banister, Jonathan Palmer, Mike Cummings
Production: Mark Turpin
Advertising enquiries only: Ian Carter, ian@rgemagazine.co.uk
Additional print subscriptions £25 per year email: wgardiner@circdata.com, Tel 020 8149 9222
Registered Gas Engineer is written, designed and published by The Team on behalf of Gas Safe Register. 30 Park Street, London, SE1 9EQ
As the industry joined together to join in with Gas Safety Week 2024, we look at how Gas Safe Register supported this year’s theme of Checking, Every Check Counts, and the many ways that other organisations shared information with their own audiences
12
16
The views expressed in this magazine are not necessarily those of Gas Safe Register. The publishers will accept an advertisement or other inserted material only on the condition that the advertiser warrants that such advertisement does not in any way infringe copyright or contravene the provisions of the Trade Descriptions Act. All copy is subject to the approval of the publisher, who reserves the right to refuse, amend, withdraw or otherwise deal with advertisements submitted to it at its absolute discretion and without explanation. All advertisements must comply with the British Code of Advertising Practice. ABC membership approved 19 March, 2009.
18
Look out for Gas Safe Register’s new ads running through the winter PLUS Minor updates to Rules of Registration
Landlord and barber shop owner are brought to justice
Focus: CO exposure, exposed In support of Carbon Monoxide
Awareness week in November, we look at the work of organisations dedicated to reducing the number of incidents and helping households stay safe from CO
The good, the bad and the ugly
21 Letters
Changes to Approved Document J will come into effect in January 2025.
Some of the questions that gas engineers have asked Gas Safe Register’s Technical Team recently
Why and how a Safety Alert might be issued – and how you can stay up to date with the latest important information
From radiators to UFH to radiant heating, we look at some of the different ways we keep our homes warm
Top tips for helping customers with a smell disorder stay safe from the dangers of gas
The evolution of self-assessment and how HMRC can help you with your tax return PLUS A new online wellbeing tool can help you check in on your mental health
What’s holding back the clean heat transition? PLUS The role of heat batteries
The latest launches from around the
The 14th annual Gas Safety Week’s theme Checking, Every Check Counts had something for everyone in all corners of the industry.
At Gas Safety Week’s reception at the Houses of Parliament, Gas Safe Register’s chief executive Jonathan Samuel said: “Every year we set a simple, high-level theme that can be taken up by supporters and applied in multiple ways across their audiences.”
On this year’s Checking theme, he added: “That might be checking the ID card of somebody coming into your home to undertake gas work, checking for the signs of an unsafe gas appliance or simply checking that gas safety records are up to date.
“Or it could be something as simple as checking that the CO alarm is working correctly.”
The event included updates from the Gas Safe Charity on the vital work it’s been doing, including teaming up with Citizens Advice in Greater Manchester (see page 17), and from Cadent on its new Carbon Monoxide Partner Ecosystem (see page 15).
A highlight was hearing from gas engineer Kate Rose, who owns K2 Plumbing & Heating,
and who talked about how she became a gas engineer in 2012 after realising she had a terrible work/life balance in her career in logistics and distribution.
Kate, from Stoke on Trent, said: “My customers trust me to keep them warm and safe in their houses. They feel comfortable knowing I’m on the end of the telephone should they need me. I see my role as a Gas Safe engineer as really important in keeping my customers’ homes safe by servicing, checking and
Kate Rose (left) with Alanna Impey from CIPHE: “My customers trust me to keep them warm and safe.”
testing their gas appliances.
“I talk to them a lot about regular maintenance of their gas appliances: what signs to look out for that may mean their gas appliance isn’t working as it should do, and what to do if they suspect they’ve got an issue or if they smell gas.
“It’s great getting involved in Gas Safety Week as it helps me to promote gas safety even more. The resources available have been really good: I’ve got leaflets and posters, all sorts of things that I can hand out to my customers to spread the word even more.
“Educating people about gas safety is important now and will be for many years to come.”
A new film for Gas Safety Week voiced by well-known TV actor Will Mellor showed what can go wrong “when the gas goes” with comedic consequences.
The tongue-in-cheek public service announcement-style film shows ‘Silly Ali’, and what happened to him when he didn’t get his gas appliances safety checked every year. Shown in three different scenes, Ali was unable to shower ahead of an important job interview, couldn’t cook a romantic meal, and got left in the cold without heating after coming back from holiday – all because his gas ‘went’.
Actor Will is best known for his role in TV drama Mr Bates vs The Post Office, as well as Two Pints of Lager and Hollyoaks. He used his voice skills to help Gas Safe Register educate the nation about
gas safety in the home.
He said: “Why does it always feel like things go wrong at the worst moment? I’ve been caught out myself, coming back from a holiday to find out the boiler had packed in. It was bloomin’ Baltic!”
You can see the film on Gas Safe Register’s YouTube page.
‘Boilers seem to break down at the worst time’
Boiler breakdowns are one of the top inconveniences in life, according to new Gas Safe research for Gas Safety Week. Top were queue-pushers (44 per cent) and poor Wi-Fi (39 per cent), closely followed by a boiler breakdown (37 per cent).
In the poll of 2,000 UK adults, one in four said their boiler always seems to break down at the worst possible time. More than one in three people (40 per cent) said things seem to break at home at a time when they can’t afford to get them fixed, serviced or replaced.
More than two in three (67 per cent) agreed that being a little more organised can help avoid most inconveniences in life. Yet almost one in four (22 per cent) of homeowners had not had their gas appliances serviced in the past year.
As always, Gas Safe Register has been urging households to ensure their gas appliances are safety checked every year.
A huge variety of people and organisations from different sectors and across the country shared their messages during the week.
Energy and Utilities Alliance (EUA) used Gas Safety Week to call for mandatory annual servicing of all heating appliances in the home.
It pointed out that gas safety checks are carried out every year in rented homes but are not obligatory in owned properties. The trade body said a full annual service of all heating appliances – gas and oil boilers, fires and heat pumps – would also assess the efficiency of the heating system, potentially saving consumers cash, and highlight when an appliance is reaching the end of its life.
This would enable
NCASS shared important tips when it comes to the safe use of LPG appliances, as well as producing a free guide.
Clare Adamson MSP and IGEM’s Scottish Section hosted an event at the Scottish Parliament that focused on increasing awareness of gas safety, the risks of CO poisoning and essential steps for risk removal and control
consumers to better plan for replacing appliances, either as a straight swap for their existing product or to move to a newer technology.
CEO Mike Foster said: “The gas industry takes safety extremely seriously: Gas Safety Week, which is industry-led, is testimony to that. But we have a duty to go further in our desire to reduce risks to the bare minimum while also highlighting opportunities to help consumers with their bills too.
“Mandatory annual servicing of all heating systems can check their safety, absolutely, but they can also go further. Heating engineers can check that the system is running efficiently, helping consumers keep bills down.
“They can make recommendations to improve system efficiency, perhaps with
smart controls or lowering flow temperatures. More efficient systems cost less to run, reduce energy consumption and therefore help lower carbon emissions too.
“But an annual service can also do more. Anticipating when an appliance is near the end of life, not waiting for it to fail, is key to planning for change.
“Government could start with the rental sector. They already have an annual gas safety check; it wouldn’t take much to extend that to a full system service. Once that sector is up and running, then extending the requirement for a mandatory annual service for owner-occupiers would be that much easier.
“Gas Safety Week is a timely reminder, just ahead of the heating season, that we can always do more.”
Many supporters took advantage of the free Gas Safety Week toolkit to help make sure their audiences were in the the know, while others created their own informative campaigns. Here are just a few highlights that we spotted on social media.
Gas engineer Pete Brown reminded landlords of their legal duties
Homes
checks
Trade supplier BES ran special offers on a range of products
RoSPA encouraged consumers to get in the know about CO
South Wales Fire and Rescue used the toolkit’s Welsh language assets
Energy supplier Utilita highlighted the warning signs of faulty appliances
JTL illustrated how it’s training the next generation of gas engineers
Which? Trusted Traders shared the signs and symptoms of CO poisoning
With our newest revision of Vitodens boilers we’ve enhanced the commissioning flow across the 050-W and 100-W product ranges.
What’s new?
• More functionality
• Easy commissioning via the boiler panel
• Remote monitor and control with ViGuide app
10 year warranty as
12 year warranty as
As winter approaches and the cold months set in, Gas Safe Register’s newest campaign is under way.
The campaign is dedicated to raising awareness of Gas Safe Register and reminding consumers to only use a
HOW DO YOU AVOID UNEXPECTED COLD SHOWERS THIS WINTER?
legally qualified gas engineer to keep them, their family and home safe.
The Register is also warning people of the risks of carbon monoxide in homes across the nation. Winter brings increased gas usage, making it a crucial time to remind consumers of the importance of having regular safety checks on their gas appliances.
This year, the campaign has new, engaging images and messaging that
Episode 7 of Tech Talk focuses on how the Register tackles illegal gas work and includes an interview with one of its Regional Investigations Officers.
Tech Talk is a regular series that helps you stay up to date with the topics that matter to you and your work, and you can find them on Gas Safe Register’s YouTube playlists.
emphasise the importance of gas safety. You’ll see a wide variety of ads across TV and radio, in newspapers and magazines, and online. Look out for these messages in the coming weeks as the Register continues to raise awareness and promote gas safety through the winter.
Help keep your customers safe
Don’t forget you can order free leaflets and posters that you can leave with your customers to remind them how to stay gas safe this winter and throughout the year. Visit www.GasSafeRegister.co.uk/leaflets to order yours.
Minor updates have been made to Gas Safe Register’s Rules of Registration. Additional information has been added on the need for trainees and apprentices to carry out gas work only under supervision (Section 2).
Additionally, clarification is
provided on the requirements for reporting notifiable work (Section 9).
Important: Always make sure you refer to the most recent Rules of Registration, which you can download from your online account at: www.GasSafeRegister.co.uk
The method you use to renew your registration determines not only the cost but also the method of communication you have chosen.
When you renew your registration online you pay a reduced rate because you are choosing to receive all communications from Gas Safe Register electronically for the subsequent registration period.
When you renew by phone, you are choosing to receive all your registration communications as hard copies in the post. The higher fee you pay reflects the higher communication cost associated.
If you want to change your communication preferences from electronic to hard copy after you have renewed, you will need to pay the difference in fees, including VAT.
Important: You automatically receive a regular print copy of this magazine.
A landlord has been given a suspended prison sentence and electronically tagged after she put tenants’ lives at risk at a property in Kent.
Sevenoaks Magistrates Court heard that Dawn Holliday, 62, refused to undertake gas safety checks at a property in Eastchurch even after HSE had taken enforcement action by giving her an Improvement Notice.
Her tenants had what the court heard described as a very temperamental boiler that banged and often left them with no heating or hot water, as well as a condemned cooker.
Ms Holliday ignored the Improvement Notice to undertake gas safety checks, as well as other requests from HSE. She claimed to have no
money to carry out maintenance to the property. She said the tenants had moved out and had not been paying rent but the investigation found this claim to be untrue.
HSE found that Ms Holliday was receiving full rent from the tenant.
Dawn Holliday, from Minster on Sea, pleaded guilty to three charges under the Health and Safety at Work etc Act 1974, Section 21, and the Gas Safety (Installation & Use) Regulations 1998 36(2) and 36(3).
She was given a prison sentence of 26 weeks, suspended for 12 months. The judge imposed an electronically monitored curfew on Ms Holliday at her address between 8pm and 6am for four months and ordered her to pay
£750 in costs to HSE. A remediation order was made for her to undertake the gas safety inspection required of her.
Speaking after the hearing, HSE inspector Joanne Williams said: “We are dedicated to ensuring that landlords operate within the law and provide safe accommodation for tenants.
“We do not tolerate disregard for health and safety and consider the noncompliance of HSE enforcement notices as a serious offence.
“In this case, Ms Holliday chose to flagrantly ignore the support, guidance and warnings from HSE to assist her in compliance with the law and continued placing her tenants at serious risk of injury or even death.”
The owner of a Birmingham barber shop business, Hiwa Kadar, has been given suspended prison sentence after a large gas explosion forced the shop window to fall out on to a busy high street.
Birmingham Crown Court heard that the shop was open for business when the explosion took place in June 2022. Birmingham City Council environmental health officers, prosecuting, said there was significant damage to the fixtures and fittings and a large front window blew out into Holyhead Road, narrowly missing a pedestrian.
West Midlands Fire Service also found that a single-storey brick wall at the rear of the building collapsed because of the explosion, scattering bricks into a passageway used regularly by children of neighbouring residents.
The tenants of the flat above the barber’s shop were in their home and fortunately sustained no injuries. However, Mr Kadar suffered minor burns to his arm. Structural engineers from the council’s dangerous structures team arranged for contractors to make the building safe.
Investigations revealed that new gas pipes had been fitted to older pipes. Two open ends to the new pipework and tools
suggested that it had been extended recently. They also found equipment indicating a catering business was operating or that there were plans to install one.
Birmingham’s environmental health officers found that the barber shop had been let to Mr Kadar originally without a gas supply but the meter serving the tenants was located inside his barber shop business. The council said the newly installed fixtures and fittings had been removed shortly after the explosion.
A principal gas incident investigation engineer gave expert opinion that the cause of the explosion was gas escaping from the open ends of the newly installed pipework.
Installation of gas pipework installation should be subject to a Building Regulation Application but no application had been submitted for this work. Mr Kadar had not notified the managing agents or the landlords about the gas work. He did not provide details of the person responsible for extending the gas pipework.
The court heard that the time and effort involved in removing the catering equipment and illegal pipework suggested a deliberate effort to undermine any investigation. These were considered as
If you find gas work that you suspect has been carried out illegally, please report it to Gas Safe Register so that it can investigate. You can do this by signing into your online account, then choose Reporting Illegal Gas Work in the Resource Hub.
aggravating features at the sentencing hearing.
Hiwa Kadar, trading as Mardin Barbers on Holyhead Road, Birmingham, pleaded guilty to breaching the Health and Safety at Work etc Act 1974. He was given a 12-month prison sentence, suspended for 24 months. The court also ordered him to attend rehabilitation activities and provide details of his finances in order to pay towards the prosecution costs.
He is no longer the owner of the business trading from that address.
Councillor Sam Forsyth, chair of the licensing and public protection committee, said: “I am thankful that no one was seriously injured but this frightening incident could easily have been avoided by appointing a Gas Safe registered engineer. This council will take swift enforcement action against those who fall below the required standard.”
A new collaborative initiative to help report and understand the data around carbon monoxide incidents has found a much higher rate than previously thought.
Household exposure to carbon monoxide is being chronically under-reported, according to Cadent. In fact, the true figure is estimated to be up to seven times higher, data from an initiative aimed at reducing deaths and hospitalisations suggests.
Cadent has been working with more than 30 organisations to gather data about the silent killer and trial new solutions. The Carbon Monoxide Partner Ecosystem (COPE) brings together fire and rescue services, gas distribution networks, academia, trade associations, alarm manufacturers, research bodies and many more, to help prevent A&E attendances, hospital admissions and deaths
preliminary insights indicates that there were up to 19,500 household CO exposures in England in 20231 – more than seven times the figure currently reported2 – and that households with people living in vulnerable situations were more at risk.
The findings will help to mimimise the time that victims are exposed to CO and improve the rate of CO poisoning diagnosis.
Phil Burrows, head of vulnerability at Cadent, says: “There’s a big gap in what we know about carbon monoxide. People often don’t realise they’ve been exposed, and even emergency responders can’t always tell what’s happened.
“On top of this, different organisations like gas
“By pooling CO data and extracting insights, we hope to reduce the number of CO incidents each year.”
caused by the deadly gas.
A new CO Research & Analytics platform (CORA) collects data from these organisations across a range of areas – including true incident numbers, demographic differences, understanding of CO alarm sounds, who to call and hotspot CO exposure locations.
One of the surprising
distribution networks and fire and rescue services collect data in different ways from those who treat CO poisoning, like the NHS.
“All of this makes it hard to know the real number of cases in the country.
data and extracting insights, we hope to reduce the number of CO incidents each year and improve how the UK handles this issue.”
Following early trials of the CORA platform, insights have already revealed some important focus areas, including the need to standardise the CO alarm response process, as well as scaling up smart alarm use as an additional prevention method, to regular maintenance of appliances, like boilers and cookers, as the first line of defence against harmful exposure.
Isabella Myers, CO expert and indoor environment data maturity consultant, adds: “This new data platform is revolutionary as it’s the first time data is being captured that gives a national picture of the CO situation.
“Worryingly, it’s very common for people not to understand the sounds that their CO alarm makes, or to forget to regularly push the test button on their alarm. This means many households don’t realise that the alarm sensor or battery has reached the end of its life, potentially leaving them vulnerable to the risk of CO exposure.
1 There were 5,500 cases where CO was evident in the household in 2023 in England and a further 14,000 cases where CO was suspected. This is based on incident data recorded by the four gas distribution networks covering England and combined with the Home Office’s Fire & Rescue Services data (caveat: this excludes approximately 3 months of data for the Wales & West England area).
2 The Fire and Rescue services reported 2,647 carbon monoxide and carbon monoxide alarm-related incidents attended in 2022/23.
“Having this central hub of shared data will be invaluable in developing deeper understanding about our natioal and regional CO challenges and where we need to target efforts to tackle them.”
“Our new data platform is a crucial step to making a real impact, especially in vulnerable communities. By pooling CO >
In support of Carbon Monoxide Awareness Week this November, we’re looking at the work of several organisations dedicated to reducing the number of incidents and making sure that households stay safe from the dangers of CO.
Since its founding in 2005, the CO Research Trust has been at the forefront of protecting people from the dangers of CO poisoning,
says its CEO Adrian McConnell.
The registered charity’s mission is simple but crucial: to reduce the number of deaths and serious injuries caused by CO exposure.
CO poisoning is notoriously difficult for health professionals to diagnose. And although the immediate life-threatening impacts of high-level exposure are widely known, we are learning more about the potential dangers of lower-level exposure.
This under-reported issue could be the beginning of a much larger public health challenge: one that we believe needs urgent attention.
That is why the CO Research Trust is committed to understanding and addressing this problem. We focus on research because we believe
CORT’s 2024/25 grants call is open for applications until 4 December 2024 at: www.coresearchtrust. org/apply-for-funding
that is where the real change happens. By funding studies, gathering evidence and collaborating with various organisations, we aim to prevent CO exposure and improve diagnosis, treatment and outcomes for those affected.
Through our annual grants programme, which runs each autumn, we have awarded more than £1.5 million to support ground-breaking research. These grants help charities, social housing associations, academic institutions and others carry out essential work on CO safety.
We know the CO challenge is too big for any one organisation to tackle alone. That is why we are dedicated to fostering collaboration. Our conferences, lectures and training events bring together professionals who are passionate about CO safety.
As we head into our 20th year as a charity, we are planning even more activities. Together, we can create a safer future for everyone.
The All-Party Parliamentary Carbon Monoxide Group (APPCOG) fosters collaboration between parliamentarians, academics, healthcare professionals, industry bodies and other key stakeholders. Its aim is to improve public policy and awareness of CO.
The group has worked with a wide range of partners to identify gaps in policy and enforcement, and how the new government can ensure better safety in homes, even as funding for local authorities remains constrained.
APPCOG has long advocated for a coordinated, cross-sector approach to improving carbon monoxide safety. Its vital work continues through a new programme of political events, awareness-raising and advocacy in the new Parliament.
The Gas Safe Charity works with Gas Safe Register and selected organisations to help vulnerable people when they need it most and to promote CO safety. The charity is funded by the Register with extra support from HSE.
The Charity’s Hardship Fund works with Foundations
Independent Living Trust (FILT) and its network of local Home Improvement Agencies (HIAs) in most of the UK and Channel Islands. Gas engineers work with HIAs to ensure that elderly and disabled people are kept
works with Bath & Main Associates to run workshops for workers and volunteers who manage and work directly with people who go into the homes of those who are most at risk from CO and gives telephone and direct advice. Health workers, fire and rescue services, volunteers, social workers and others are trusted visitors and we make sure that they know how to recognise the signs and symptoms of CO poisoning and what to do if there might be a problem. There is a particular focus on
“The Gas Safe Charity has helped people in 11,000 vulnerable households.”
safe through safety checks and repair work, funded by small grants.
During the decade the programme has been running, it has spent more £2.4 million, helping people in 11,000 vulnerable households. The value of the charity’s grants is tripled by support from other organisations.
The programme also promotes gas safety messages, working with local partners and nationally with FILT.
The Think CO programme
the dangers of long-term, low-level CO poisoning.
Think CO runs free, hour-long online workshops every month and face-to-face workshops around the country, including cost-of-living crisis workshops in partnership with gas distribution networks, fire and rescue services, charities, councils, health professionals and others.
The team is working with the gas distribution networks to produce an app, which will be widely available as a reference
“Think CO makes sure people know how to recognise the signs of CO poisoning.”
guide about CO. The app is due to launch during CO Awareness Week.
All Think CO materials can be downloaded free from the Gas Safe Charity’s website.
The charity’s newest initiative, still in its final planning stage, will work with local Citizens Advice in parts of Greater Manchester. It will include a wide-reaching campaign using social media, websites, leaflets and radio as well as a programme of reaching out with messages about gas safety and carbon monoxide poisoning to local self-help groups in some of the most deprived communities.
Community advisers will visit schools to share critical CO safety advice so that information can reach parents and grandparents
The charity also works with Safety Centres, where groups of schoolchildren learn about safety issues, including a session on gas safety and CO poisoning. n
Registered Gas Engineer wants to see your pictures –whether you’ve come across some horrors or instances of really good work. Please email your stories and pictures to editorial@registeredgasengineer.co.uk
A roof tile had fallen and damaged the air intake to this boiler. Matt replaced the chimney/flue.
Peter was going to fit a boiler when he saw that the gas meter fitting was not soldered and the meter was not fixed into position. He re-soldered, secured and tested it, then fitted the boiler according to the manufacturer’s installation instructions.
FROM ADAM FOULSER
Adam attended a no heating or hot water call-out to find the builders had covered the chimney/flue and rendered over the top. He cut around the chimney/flue to give enough space for safe dispersal.
FROM SONG ZHOU
Song Zhou was servicing a boiler and found that the main heat exchanger had split. It has now been replaced.
Someone had fitted a two-inch waste pipe to the chimney/flue termination to disperse the products of combustion. Wayne corrected the situation by installing the correct plume management kit for the installation.
Jack was investigating a smell of gas in the kitchen. A tightness test revealed a drop, caused by two big holes in a steel pipe in concrete screed feeding the cooker. Jack made safe at the meter, then removed the pipe and replaced it with copper.
When Kyle removed this fire, he found scorch marks and a chimney full of twigs. The supply was capped off and the customer was advised to have the chimney swept. The fire was then re-fitted, serviced and tested.
This water heater had not been serviced for 12 years, so no one knew what was going on inside the case. Andy made the water heater safe and replaced it.
We may share some of your pictures on social media, so remember to include your contact details so we can tag you (or let us know if you’d rather we didn’t).
What's on your mind? Share your views with more than 80,000 readers
Name withheld
editorial@ registeredgas engineer.co.uk
I was interested in the article “What’s holding back heat pump installations?” in the Sep/Oct issue and in particular the emphasis on heat pump companies finding difficulty recruiting staff.
I have been in the plumbing and domestic gas industry, mostly as a sole trader, for over 30 years. In recent years, I have found my workload steadily diminishing in my local area and some of my contacts (builders/architects, etc) having also experienced a downturn in their workloads, which, in turn, has affected my business.
I decided to explore the possibility of dipping my toe into the world of employment. I considered that if I can get full-time employment with a company, it may provide me with some security while allowing me to keep working in the industry I love.
The process of seeking
employment in the current market is something I had no experience of, but it has left me feeling confused, disillusioned and also pretty worthless at times. I found that there are lots of job opportunities available, mostly through agencies, who I spent most of my day talking to but without any result. Perhaps my date of birth, salary requirements and other criteria presented me as a bad apple among their other job applicants.
I am interested in and have embraced the changes within our industry and participated in the necessary renewables training over the last few years. I enjoy keeping up to date with the “pioneers” out there who are beginning to install heat pumps and are sharing their journeys with us all via social media, etc.
With this in mind, I have made many applications to heat pump installation companies who are currently
advertising for staff but I am disappointed to say that I have not yet received a single response regarding an interview or even a brief chat. Weeks are now becoming months so I am assuming that I will not be hearing back from any of these employers, even if it’s only to say, “thanks but no thanks”.
I can only assume that this could be because I am now in my mid-50s and not hugely desirable to a prospective employer. Like many of your readers within my demographic, I like to think I am just as fit and active as at any time in my career. Also, perhaps more importantly, I have a wealth of knowledge acquired from working on domestic heating systems for over three decades.
So, with regard to the statement in the article, “finding staff is a major barrier in installing more heat pumps,” sorry, I have to disagree.
Martin Wright
You report that simple boiler controls will no longer be sold from 2026 in order to improve efficiency. This is a mistake because end users don’t
understand how smart controls work and are unable to use them effectively because they are too complicated.
As a result, virtually every smart heating controller I see is simply left on 24/7 or
manual. Simple timers that people understand are far more effective in improving efficiency. So-called industry experts need to look outside the bubble into the real world.
Extensive range of quality boilers and controls that give your customers reliable heating, at great value.
All backed by service and support you can count on, whenever you need it.
Plus, get even more through Club Energy! From extended guarantees and cashback to handy tools and training, we’ve got you covered.
Industry Standard Update 124
Date issued: 3 September 2024
This Industry Standard Update provides an overview of the key areas of change arising from the revision of IGEM/G/6 Gas supplies to mobile dwellings.
Introduction
In July 2024, IGEM/G/6 Edition 2(1) Gas supplies to mobile dwellings
Communication 1862 was released. The revised procedure supersedes IGEM/G/6(2) Gas supplies to mobile dwellings Communication 1728, which has been withdrawn. The revision to this standard comes into effect immediately.
The following is a brief overview of the amendments made in the update to IGEM/G/6.
Scope
It is now clarified that the nominal operation pressure for LPG installations downstream of any emergency control valve (ECV) is to be 37 mbar.
Legislation
The powers devolved to Scotland, Wales and Northern Ireland means that there may be variations to the legislation described in the document, and consideration of their requirements may be necessary.
Main document
Table 2 relating to the required competence for welding of steel pipes has been removed and replaced with guidance to refer to IGEM/UP/2(3) Installation Pipework in Industrial and
Commercial Premises for acceptance criteria.
The Note in Section 4.2.2 has added the consideration for possible flooding of the area around storage vessels.
Section 4.6.3 states that all cylinder installations with fixed pipework downstream of the cylinder hoses shall incorporate an OPSO device to prevent excess pressure from entering the property.
Temperature-compensated meters should be considered for all LPG installations, as now stated in Section 5.1.3.
The minimum distance given in Section 5.2.3 from a gas meter box to any electricity meter or electrical equipment shall be as follows:
• Supply pressure of 75 mbar or less shall be at least 150mm
• Supply pressure greater than 75 mbar shall be at least 330mm.
The minimum distance from a regulator relief vent tip to any electrical equipment shall be as follows:
• Natural gas meter box with a supply pressure greater than 75 mbar shall be at least 1550mm
• LPG meter box with a supply pressure greater than 75 mbar shall be at least 850mm.
Section 6.1.5 states that where movement is greater than 2m and a flotation device is fitted to a dwelling, longer hoses may be permitted, subject to adequate documented design and risk assessment, and only a single hose shall be used.
The option of a stainlesssteel hose manufactured to BS EN ISO 10380 has been added to the list of suitable hoses in the Note in Section 6.1.6 for flexible connection.
IGEM/G/6 Ed 2 is available at: www.igem.org.uk/ resource/igem-g-6-gassupplies-to-mobiledwellings.html
As previously stated, this Industry Standard Update is only a brief overview of the information contained in the amended standard. Registered businesses should be aware that they have a responsibility to ensure they are fully apprised of all the requirements of the whole published standard and their practical application.
Bibliography
(1) IGEM/G/6 Ed 2 Gas supplies to mobile dwellings (Communication 1862)
(2) IGEM/G/6 Gas supplies to mobile dwellings (Communication 1728)
(3) IGEM/UP/2 Ed 3 Installation Pipework in Industrial and Commercial Premises (Communication 1771)
Gas Safe Register’s Technical Team provide guidance on LPG hoses and tubing and their uses.
LPG hoses are used on a variety of installations to provide a flexible connection from cylinders and regulators. You can find examples of changeover valves mounted on upstands, residential park homes (RPH) and static holiday caravan connections, commercial mobile catering and transitioning to solid pipework, to name but a few.
When used downstream after a regulator, it is important that the hoses are sized correctly for the application to ensure that the gas supply is sufficient for the installation. Hoses should be of one continuous length but as short as practicable to allow for the flexibility that is needed. For static caravans/RPH connection, the hose should be a minimum of 300mm up to a maximum of 2 metres to allow for movement of the unit.
Hoses and tubing shall not be used where they could be subjected to ambient temperatures more than 50°C unless they have been designed specifically for that application/environment. Hoses should not pass through walls, floors or other voids.
By definition, a hose is of two-ply construction and designed to operate at higher pressures (BS EN 16436-1 Class 2 & 3/BS 3212 Type 2) whereas tubing is single-ply and designed to operate at lower pressures downstream
of a regulating device (BS EN 16436-1 Class 1/BS 3212 type 1).
Note: Any installation or commercial activity covered by the Gas Safety (Installation & Use) Regulations 1998 within the scope of BS 6891 requires only hoses of Class 2 or 3 to be used.
Type
LPG hoses and tubing and assemblies shall conform to:
• Stainless steel flexible hose to BS EN 1SO 10380. For working pressure up to 2 bar, these hoses do not require protective braiding
suitable for the application.
• BS EN 16436-1 Class 2, medium pressure (maximum 10 bar) hose used downstream of the regulator. It is recommended that these hoses are constructed with additional armoured protection.
• BS EN 16436-1 Class 3, high-pressure reinforced hose (maximum pressure 30 bar), commonly used where cylinders and hoses can be subjected to extreme summer temperatures. Typical use is a ‘pigtail’/ direct cylinder pressure connection.
“It is important that hoses are sized correctly for the application and that the gas supply is sufficient.”
or reinforcement. For more than 2 bar, the hose requires an outer braiding.
• BS EN 16436-1 Class 1, a low-pressure application tubing (maximum pressure 0.2 bar/200 mbar) typically used downstream of a low-pressure regulator. These are not suitable for outdoor installations except where used to connect to a portable appliance such as patio heaters/BBQs, where, after risk assessment, a Class 1 hose with rodent protection may be more
Liquid Gas UK Code of Practice 33 sets out that all hoses and tubing used outside shall conform to BS EN 16436-1 Class 2 and 3 shall be armoured against rodent attack unless used for portable appliances. Hoses installed directly to a cylinder and upstream of a regulator/changeover device shall be of a Class 3 type due to the higher operating pressures. If installed downstream of a regulator, a Class 2 hose should be sufficient.
Important: Hoses that provide rodent protection are not always the braided type. Certain brands have a rubber PVC outer layer and incorporate a metallic protection layer on the inside, which could provide adequate protection against rodent damage. If you are carrying out this type of work, you should consult with the manufacturer that they are of the correct type and suitable for the application required.
Hoses should be checked every time a cylinder is exchanged, and on any subsequent service/ maintenance visits.
Visual defects to check for include:
• Cracks
• Ruptures
• Blisters
• Stiffness
• Kinks/flattening
• General wear or damage. If any visual defects are apparent, the hoses should be replaced immediately.
Markings
You may come across LPG hoses manufactured to other British Standards such as BS 3212. Hoses should be marked to represent the British Standard to which they conform and with information about what application they are designed for, and an expiry date
or manufacturer date of hose.
Typically, a BS EN 164361 product should have BS number and date, class of hose with maximum working pressure, inside diameter of pipe, gas identification and an expiry date. These hoses should not be used after the expiry date and should be changed immediately.
For a hose conforming to BS 3212, this hose should show a date of manufacture. It is recommended that these are replaced after a maximum of 10 years of use.
If this information is not present on the hose, you should risk-assess each installation and assess the physical condition and use of the hose.
Rubber tubing to BS EN 16436-1 Class 1 fitted to cabinet heaters should be replaced after five years of service. This type of LPG tubing shall normally display an expiry date of five years from manufacture for engineers to visually identify when replacement is required.
All equipment, including hoses, cylinders, valves and piping, shall be checked regularly for leakage and any visual defects.
More info on hoses is given in Liquid Gas UK Consumer Guidance Sheet 05 and Liquid Gas UK Code of Practice 33. n
Bibliography
BS EN 16436 - Rubber and plastics hoses, tubing and assemblies for use with propane and butane and their mixture in the vapour phase
– Part 1 Rubber and plastics hoses, tubing and assemblies for use with propane and butane and their mixtures in the vapour phase. Hoses and tubings
– Part 2 Rubber and plastics hoses, tubing and assemblies for use with propane and butane and their mixture in the vapour phase.
Assemblies
– BS EN 16436-1 Class 3, for direct cylinder pressure connections
– Liquid Gas UK CoP 33: Use of LPG Cylinders
– Liquid Gas UK Consumer Guidance Sheet 05: LPG Hose and Tubing for use with Vapour Offtake Cylinders
BS 3212:1991 – Specification for flexible rubber tubing, rubber hose and rubber hose assemblies for use in LPG vapour phase and LPG/air installations
BS 6891:2015+A1:2019 –Specification for the installation and maintenance of low-pressure gas installation pipework of up to 35 mm (R11/4) on premises
BS EN ISO 10380 – Pipework. Corrugated metal hoses and hose assemblies
Ceda has published a Code of Practice for Safe Electrical Work in commercial foodservice facilities.
The Code of Practice clearly identifies the responsibilities of technicians and those of their client and other stakeholders, including qualified electricians. It clarifies the necessary competences of foodservice equipment technicians and the appendices include several examples of test procedures.
The CoP was published following the death of a foodservice equipment technician who was electrocuted while working in a commercial kitchen. The subsequent court case in 2023 highlighted several issues concerning the responsibilities of the parties involved in a commercial foodservice facility and indicated that there were some lessons to be learned.
Ceda, the trade body for commercial foodservice equipment specialists, regularly hears from foodservice equipment technicians that
many of their clients appear to believe that the “service engineer” is responsible for the whole electrical installation in a commercial kitchen. This is NOT the case.
To address these issues, Ceda’s Code of Practice identifies the competences and responsibilities of the foodservice equipment technician and those of the kitchen operator and other stakeholders in any venue.
The majority of foodservice equipment technicians are Gas Safe registered. Few are qualified electricians although they carry out limited electrical work, including safe isolation, earth continuity testing and insulation resistance testing to enable them to install electrical catering equipment safely.
Wherever possible, they will work “dead” – however, they often have to work safely on live equipment, particularly when fault-finding. n
“The Code of Practice identifies the competences and responsibilities of the foodservice equipment technician and those of the kitchen operator.”
The Electrical Work in Commercial Foodservice Facilities Code of Practice has been created by experienced foodservice equipment industry professionals alongside acknowledged electrical industry experts and in consultation with regulators.
As well as outlining a common regime of working practices for foodservice equipment service and installation technicians when working on electrical equipment, it also gives guidance on the level of electrical competence required by foodservice equipment technicians.
• www.ceda.co.uk
Updates are due to come into effect in Wales to Approved Document J (Combustion appliances and fuel storage systems) 2010 edition incorporating 2010 and 2024 amendments.
• Where a new or replacement fixed flued combustion appliance of any fuel (oil, gas –
including LPG – and solid fuel) type is installed in a dwelling (including fixed flued cookers), a carbon monoxide alarm should be provided.
• A CO alarm is required in the following:
– In every space (including connected spaces, for example, attached
garages and loft spaces) containing a fixed combustion appliance (including a fixed flued combustion appliance used for cooking), and – In high-risk accommodation, ie, a bedroom or principal habitable room such as a living room, where the flue serving a combustion appliance passes through these rooms.
Carbon monoxide alarms should comply with BS EN 50291-1:2018, include an integral sounder and be powered by a battery designed to operate for the working life of the alarm. The alarm should incorporate a warning device to alert users to the end of its working life.
The changes to Approved Document J come into effect on 6 January 2025. n
Gas Safe Register’s Technical Helpline receives around 5,000 calls every month. The team deal with a variety of queries from gas engineers about the gas regulations and relevant guidance documents. The following questions are just some of those that have been asked recently.
Q: Can I use a plume kit when the flue is too near a window?
A: You must confirm with each manufacturer whether they have an option to use such an accessory because not all of them allow one to be used for this purpose. Generally, a plume management kit is not to be used for overcoming termination issues. More guidance can be found in Technical Bulletin 016.
Q: Do I need any special/ extra qualifications to attend a CO alarm activation, such as CMDDA1?
A: Once confirmed that there has been no injury or illness associated with the CO alarm activation, you need only the relevant core and appliance qualifications to work on and check the appliance(s): no additional qualifications are required.
You can find guidance on responding to domestic CO alarm activations/reports of fumes after attendance by the emergency service provider or the LPG supplier in IGEM/G/11 Supplement 1.
Q: What can I do if my landlord refuses to issue me with the gas safety check paperwork?
A: The landlord is legally obliged to supply a copy of the paperwork within 28 days of the check being carried out or to any new tenants before they move into the property.
Q: Do I need to notify the relocation of a boiler?
A: New or relocated boilers MUST be notified for properties in England or Wales. Similar requirements exist in other parts of the UK.
Q: What are the requirements for extraction canopies on mobile catering vehicles?
A: The requirements depend on the individual appliances installed within the vehicle. Where forced mechanical extraction is in place, it must be interlocked so as to render the appliances inoperable if the extraction fails. You can find out more in UKLPG CoP 24 Part 3, Section 8.6.1.
Bibliography
Technical Bulletin 016: Room-sealed flue/chimney terminations
– Possible nuisance from fumes and the use of plume management kits
IGEM/G/11 Supplement 1 Responding to domestic CO alarm activations/reports of fumes after attendance by the emergency service provider or the Liquefied Petroleum Gas supplier
UKLPG CoP 24 Part 3: Use of LPG for Commercial Catering Events, Street Food and Mobile Catering
Why and how a Safety Alert might be issued, what goes into letting you know about a possible issue – and how you can make sure you stay in the know about the latest important information.
Before gas appliances enter the market, they undergo a testing procedure. Products must fulfil certain essential requirements to ensure their correct and safe functioning and subsequent CE marking.
However, there are occasions when, although the relevant tests have been carried out, it becomes evident over time that there may be a defect or simply a concern that needs to brought to the attention of the industry.
Some products will be removed from the market, others may require modification, and some just need to be inspected when a gas engineer encounters them on site.
Whatever the situation, it is the manufacturer’s responsibility to make the industry aware of the situation. This is often done by creating a Safety Alert, which is then made available to Gas Safe registered businesses as well as members of the public.
It will be available either on the manufacturer’s website, or sent via email or by mail to gas engineers, or through Gas Safe Register.
Are you worried about a gas appliance?
If you have a safety concern regarding a gas appliance, you can contact the manufacturer directly to relay your concerns. Alternatively, please let Gas Safe Register know by emailing technical@gassaferegister.co.uk and the Technical Team will contact the manufacturer for you, offering assistance and with a view to the potential creation of a Safety Alert.
Important: A Safety Alert can only be produced with the agreement of the manufacturer. All information included in the Safety Alert has to be agreed with the manufacturer.
When a manufacturer approaches Gas Safe Register regarding a possible safety issue, the Register will work with them to create a Safety Alert to highlight the issue to registered businesses and the public. Once the content of the Safety Alert has been agreed by both parties, Gas Safe Register will publish it and will also notify registered businesses via email.
Note: Please ensure that Gas Safe Register has your up-todate email address to make sure you receive these.
The Safety Alert will be published on Gas Safe Register’s website as well as that of this magazine.
The engineers’ section of Gas Safe Register’s website also hosts a great deal of important technical information, including Technical Bulletins, Industry Standard Updates and Safety Alerts, as well as important industry documents including IGEM/G/11, the Unsafe Situations Procedure.
When you have logged into your online account, you can find all Safety Alerts by choosing Technical Information and then Safety Alerts. There’s a full index of Safety Alerts and they are searchable.
And don’t forget to check out the Resource Hub for other useful information and tools.
To maintain safe working practices, it is important to stay up to date with changes, whether they are Safety Alerts, industry updates or changes to British Standards/IGEM documents, etc. The easiest way to do this is to check regularly for updates on Gas Safe Register’s website. n
Technical information is also published in the first available issue of this magazine. However, our production deadlines dictate that this may not be immediate and so Gas Safe strongly recommends that you check the Register’s website regularly to stay up to date with all relevant information.
Current and historic issues of Registered Gas Engineer magazine are available on Gas Safe’s website in the Resource Hub They are also on: www.registered gasengineer. co.uk
Radiators are still the main source of heat in well over 85% of homes. Despite some suggestions to the contrary, they work well with lower-temperature heating systems, writes Chris Harvey, head of Marketing at Stelrad Radiators.
Despite the rise of renewable heating systems, many people are choosing to replace their old boilers with new boilers rather than heading for heat pumps en masse.
Without the benefit of legislation to drive choice towards heat pumps, it’s quite natural that people will settle for something they recognise and understand – and feel better able to afford – and choose their heat source on price rather than the environmental considerations.
All heating systems need to benefit from adequate insulation and radiators need to be sized correctly for each room to deliver comfort heating around the home.
That may require larger radiators or radiators with a larger heating capacity – and this is where new K3 radiators
and larger vertical radiators come into their own.
K3s have three panels and three sets of fins, effectively offering 50% more heat than a standard K2 radiator – 50% more heat from the same radiator footprint. The radiator is a little wider and weighs more but will adequately supply heat from a heat pump around the home.
Vertical radiators have grown in popularity in recent years and many people prefer them in their rooms as they take up less horizontal space and will fit in nooks and crannies in older homes especially, ensuring sufficient heat while not taking up precious wall space.
All electric
Increasingly, we are seeing people opt for all-electric heating, particularly in off-grid areas, as well as new-build and self-build type properties. This is where electric radiators have a major role to play.
Electric radiators have been gaining popularity as a viable alternative to traditional heating options. With increasing concerns about energy efficiency and environmental impact, more homeowners are turning to these radiators to keep their spaces warm and comfortable.
When it comes to energy efficiency, electric radiators will excel as they convert all the consumed energy into heat output. Unlike some other heating options, no energy is
“Electric radiators have a major role to play as a viable alternative.”
wasted in the process, making them highly efficient. This means that the energy you pay for to run them is solely devoted to keeping the home nice and warm.
They produce zero carbon emissions during operation, contributing to a greener environment and they can be powered by renewable energy sources, such as solar or wind power, enhancing their ecofriendly profile even further.
Installing electric towel radiators is a breeze, especially compared with traditional heating systems. They don’t require complex pipe connections or a gas supply, simplifying the installation process.
Individual thermostats and programmable settings enable precise temperature regulation, ensuring optimal comfort. They can be zoned, heating different areas of the home at varying temperatures to match specific preferences and needs. They require minimal maintenance compared with traditional heating options, reducing long-term upkeep costs. n www.stelrad.com/trade
Stelrad, the UK’s No.1 radiator manufacturer have gone green with Tata Steel UK. Tata Steel are supplying UK made 90% Carbon Lite green steel, verified by DNV, to Stelrad so our customers can choose a Green Compactanother first from Stelrad.
Not just any rad. Stelrad.
ThermaSkirt is an energy efficient infrared radiant heating system that looks like a skirting board but can be controlled just like conventional radiators.
ThermaSkirt is a practical solution for people who would love to retrofit underfloor heating but are put off because of the work it would involve. It can be installed on the existing radiator pipework with very few plumbing alterations – the furniture can be moved to the middle of the room during installation.
Its flexibility means it can be installed on a room-by-room basis. When a heat pump is being fitted, installers can either replace radiators with ThermaSkirt or leave the radiators in place and use ThermaSkirt to make up any shortfall in total heat output. For new-build properties where underfloor heating is on the ground floor, it is an effective and energy efficient solution for heating the upper floors.
ThermaSkirt heats up quickly and provides a comfortable form of radiant heat. The quick response time means it can provide warmth soon after the heat pump starts operating, leading to a more comfortable living environment.
Integrating heating into the skirting boards frees up wall
space that otherwise would be occupied by radiators, including oversized radiators to compensate for the lower temperatures associated with heat pumps.
This enhances the aesthetic appeal of the room and gives more flexibility in furniture placement, which can be
particularly beneficial in smaller spaces or those with many windows.
ThermaSkirt distributes heat uniformly along the entire perimeter of the room at floor level, creating a consistent temperature without the cold spots often found with traditional radiators. n
ThermaSkirt manufacturer DiscreteHeat provides a comprehensive online training programme to give installers the opportunity to expand their businesses, provide energy efficient and cost-saving solutions for their customers and cater for the growing demand in heat pumps, without the need to install oversized radiators.
The training comprises three modules: Module One: This introductory module provides a detailed overview of ThermaSkirt and its components.
Module Two: The step-by-step process of installing a wet ThermaSkirt system.
Module Three: How to specify, design and quote for a ThermaSkirt system.
Upon completing all three modules, installers become eligible to become a Registered ThermaSkirt Installer and access the trade-only online portal and its benefits, including priority technical support. www.discreteheat.com/training/
Installers who focus on customer service and fitting quality, reliable products will always win more business, writes Chris Ingram, founder of Continal Underfloor Heating.
There are early signs that the green shoots of recovery could be on the horizon finally. So now is a good time to reassess your business and make sure you’re offering the products that customers want, alongside the very highest levels of service.
Wherever possible, choose a supplier who can offer you a full range of products from that sector. When that’s an UFH supplier, look for solid floor, suspended and overfloor systems, as well as a comprehensive range of controls and associated pipe and manifold products.
Check that your supplier can deliver quickly after you place
an order. The last thing you want is to win a job and then have to tell your customer that it’s going to take four to six weeks to get their product to you.
Another red flag is if you place an order with your supplier and they say they can only deliver part of the order now and the rest at a later date.
Fitting an UFH system must usually be completed from start to finish in one go (unless you’re waiting for a screed to dry): delays from the supplier risk causing knock-on delays to the rest of the project, potentially resulting in unhappy customers.
Watch how long it takes
your supplier to respond to your enquiries. Again, you want a company that is quick to respond to any questions, who can provide fast turnaround times for quotes, and who won’t keep you waiting ages for a response.
Product quality and reliability are usually the top requirements installers say they look for when choosing which suppliers to work with – even above price.
If the product you fit doesn’t live up to its hype, you’re bound to have returns, faults and unhappy customers to deal with. n
Continal Underfloor Heating is product-agnostic and offers every type of wet UFH system. Its technical advisors can provide unbiased advice, as well as full CAD designs and reliable support at every stage of the project. Its new OneBoard Plus structural UFH system provides increased performance and even faster response times. www.continal. co.uk
“Product quality and reliability are usually the top requirements.”
Registered Gas Engineer and CIPHE set out the risks of Legionella in hot water systems and how to avoid them.
In a well-plumbed domestic heating and hot water system, there’s usually little danger of Legionella bacteria forming. Day-to-day household routines ensure that stored hot water doesn’t stay stagnant for long and there’s little to no risk for those using combi boilers. But in bigger hot water systems and other environments, Legionella bacteria can multiply in temperatures of 20°C-45°C. Legionnaires’ disease is a severe pneumonia caused by the Legionella bacterium, and cases and outbreaks have been associated with a range of water systems and equipment. People become infected when they inhale
executive officer at CIPHE, adds: “While water supplies normally contain a range of microorganisms, if a system is not managed effectively, Legionella can grow and spread via infectious aerosols in water droplets, for example, from showers and flushing the toilet.”
The golden rule is “keep systems clean, flowing, the hot, hot and the cold, cold”
Because the bacteria are dormant below 20°C and are killed within seconds at 60°C, the traditional approach to control the risk from Legionella is via temperature control. The Health and Safety Executive
“Particular care should be taken when working in a property that hasn’t been used in a long time as stagnant water is a breeding ground for Legionella.”
airborne water droplets from a contaminated source.
These droplets can be created, for example, by hot and cold water outlets, atomisers, wet air conditioning plant and whirlpool or hydrotherapy baths. Cases and outbreaks have also been associated with a range of water systems and equipment, including humidifiers, jet washers and fountains (particularly those indoors).
Kevin Wellman, chief
(HSE) advises the following:
• Hot water storage cylinders should store water at 60°C or higher.
• Hot water should be distributed at least at 55°C so it reaches the outlet at 50°C (55°C in healthcare premises registered with CQC) within one minute of turning on the outlet.
• Cold water should be stored and distributed to reach the outlet at less than 20°C within two minutes of
turning on the outlet. In a well-plumbed system these target temperatures should be achievable in seconds. Where a risk assessment identifies there is a scalding risk and a need for thermostatic mixing valves these should need to be fitted as close as possible to outlets or within them.
Outlets such as those feeding baths and showers (where there is whole body immersion) should always have TMVs fitted.
When water is not drawn through the building’s water storage and distribution system or associated equipment over an extended period, the water will become stagnant, allowing biofilm microorganisms to grow to levels that can cause infection and be difficult to control. The levels of chemical contaminants from the materials used within the system may also increase (eg, lead).
It is therefore vital to ensure that water systems are safe to use after a prolonged shutdown.
Kevin says: “Anyone in control of premises has a responsibility to control the risk Particular care should be taken when working in a property that hasn’t been used in a long time as stagnant water is a breeding ground for Legionella. So it is essential to carry out a risk assessment and flush the system to the minimise risk.
“Whatever the circumstances, Legionella should always be included within the Water Safety Plan of a property and appropriate measures should be taken to protect both installers and end-users.” n
Testing or sampling for Legionella is not usually required for domestic hot and cold water systems, and only in very specific circumstances. Testing for Legionella should not be confused with temperature monitoring, which is a reliable method for confirming the water system is under control.
Health and safety law does NOT require landlords to obtain or produce a Legionella test certificate, nor does HSE recognise them. You can find out more in HSE’s document Legionnaires’ disease: Technical guidance (HSG274).
9 Connect
to
9 testo 300 Smart kit includes bluetooth pipe clamp probes and manometer
9 NEW testo 300 Smart heat pump kit includes testo 550i digital manifold
9 Enhanced sensors with 5 year lifespanreduced cost of ownership and increased range
Rinnai UK looks at the rise of continuous-flow water heating and what the future may hold.
Product developments have come fast in the past 10 years or so since the net-zero ethos took real hold of public and industry consciousness. Before then in the commercial sector, it was usually one of the following –domestic and/or commercial boilers ganged together to meet the demand and load, direct-fired cylinders and indirect cylinders supported by boilers or electric heating.
Product and system developments plodded along until the introduction of continuous-flow dedicated hot water heating units. Several manufacturers had variants of this type and style of product but they were slow to gain traction and the industry stayed with what was perceived as tried-and-trusted products and systems.
But change was coming. The big selling point of continuous flow was that they were much more economical, lighter, space-saving and with virtually non-stop flows of hot water that is temperatureaccurate. These gas-fired units
were dedicated just to heating and delivering hot water and the capital and operational cost was dramatically less than the stored equivalent.
Today, there are a variety of reputable manufacturers offering a wide range of commercial continuous-flow hot water heating units.
Do it faster
But the biggest change to hot water heating is the net-zero target. The consensus on energy efficiency appears to be that we must do what we are doing but do it faster. This appears to be happening in the UK, showing an inexorable move towards renewables gaining market share, with all points of the supply chain from end user through to component manufacturer.
But things don’t change overnight and gas will be used for many years yet. According to the Climate Change Committee, oil and gas will account for around half of all energy demand between 2020 and 2050. n
“The biggest
Why is it important to prioritise hot water delivery in your customer’s home? Navien UK technical director Sean Keleher has some answers.
The sheer size and scale of the range of boilers means that your customers see you as not just an installer but a consultant too. In the space of a couple of decades, the conversation has changed from the simple, “Can you fit my new boiler?” to “What kind of boiler is right for my home?”
enjoy better performance, less waiting for hot water and a significant reduction in water usage.
The average UK household uses 350 litres of water daily but using a hot water recirculation system can significantly reduce water waste and save on energy bills. Over half of the annual energy bill is due
“A hot water recirculation system can significantly save on energy bills.”
For larger domestic properties or the increasingly prevalent multi-occupancy homes, installers have traditionally favoured system boilers. This is because, historically, combi boilers servicing multiple bathrooms would have resulted in low flow rates and delays in delivering enough hot water to meet increased demand.
However, hot water recirculation systems can make combi boilers viable for these busier homes. Not only do they provide more comfort and convenience but they can also help save money.
Also known as secondary return systems, combi boilers with hot water recirculation create a hot water loop, providing near-instant hot water to every outlet.
A domestic hot water (DHW) recirculation system delivers significant benefits as soon as it is up and running. Homeowners
to heating water for various purposes. Recirculation reduces the amount of water that needs to be heated, benefiting both bills and the environment.
The homeowner benefits
from the fact that they take up a lot less space – and there’s no more waiting for the cylinder to re-heat after the hot water has been used.
This means boilers can deliver consistent hot water to larger homes with multiple bathrooms while giving precious space back to the property by eliminating the need for a bulky cylinder. n
The Navien NCB700 ON Combi Crossover comes with NaviCirc technology. This simple plumbing device is designed for installation at the furthest accessible hot water outlet away from the boiler. It uses a thermostatic valve to measure the temperature of the water flowing through the device.
Once the water has reached 35°C, the valve activates, essentially locking in the hot water to the outlet. Once all outlets have reached this point, the pump inside the boiler reacts by stopping the circulation of hot water until an outlet is used.
The result is a system that delivers hot water in a matter of seconds, from any outlet, as required and at consistent temperatures. The homeowner only pays to heat hot water when needed, reducing energy consumption and bills.
The console on the front of the boiler enables the installer to set specific times of day when homeowners are likely to benefit from hot water recirculation, which helps to reduce energy costs further.
As installers, you know the critical importance of accurate water performance measurements. Whether you’re diagnosing issues, specifying new products, or ensuring optimal system function, precise data on flow, pressure, temperature, and total dissolved solids (TDS) is essential. But let’s face it, juggling multiple tools for these measurements can be a hassle. That’s where Salamander Pumps’ AquaScan comes in, changing the game for installers.
This leap forward in technology is particularly significant in an industry where measuring mistakes can lead to significant delays, be costly and even damage reputation. When you select a measuring tool, do you consider these factors?
• Accuracy and reliability
• Ease of use and portability
• Versatility across different outlet types
• Speed of obtaining readings
• Durability in various work environments.
What is the best tool to measure domestic water performance?
AquaScan is a digital water multimeter designed to make water measuring easier and more efficient for professional installers. Here’s what sets it apart from traditional tools:
1. Comprehensive measurements: AquaScan measures flow rate, pressure, temperature and TDS (to give an indication of water hardness) – all in one tool.
2. Digital precision: Say goodbye to analogue guesswork. AquaScan provides clear, accurate digital readings.
3. Portability: Supplied in a hardwearing and robust case, AquaScan is easy to carry and protected from being accidentally damaged.
4. Versatility: AquaScan comes with 13 accessories to ensure it can be connected to various outlet types, making it suitable for a range of scenarios.
5. User-friendly interface: With a clear display and intuitive controls, it is easy to use, even in challenging work environments.
6. Quick results: You get instant readings, saving you time on every single job.
The guaranteed standards scheme (GSS) states that water companies must supply a minimum of 0.7 bar pressure water in the communication
outlet of the unit
3. Ensure all outlets in the property are closed during test
4. Record the ‘Pressure’ reading shown on the screen
5. Open the isolation valve to allow water to flow and then turn off the outlet
6. To take a dynamic pressure test or to find out more, visit www. salamanderpumps.co.uk/ customer-support/faqs/ how-do-i-check-the-waterpressure-with-aquascan/
pipe serving the premises.
If the flow rate is below 10 L/min, it is considered as low. However it is particularly important to check flow rates when installing a combi boiler/ unvented cylinder to ensure they operate efficiently. The performance of a mains fed hot system relies on an adequate flow rate – typically an unvented cylinder requires 20 L/min.
By following a few simple steps, installers can accurately check water flow:
1. Connect AquaScan to the outlet and open the outlet
2. Ensure the isolation valve on AquaScan is fully open
3. Take three measurements from the live ‘Flow’ reading
4. Calculate the average of the three measurements
5. Find out more by visiting www.salamanderpumps.co.uk/ about_aquascan/
For static pressure test, installers simply need to:
1. Connect AquaScan to the outlet
2. Allow flow through the unit and then close the isolation valve on the
For household hot water, the recommended temperature is typically between 60°C and 65°C. This range is hot enough to prevent the growth of harmful bacteria such as Legionella, which can thrive in lukewarm water. However, it’s also important to ensure that the water isn’t too hot, as temperatures above 65°C can pose a scalding risk, especially for the vulnerable like children and the elderly. Accurate check temperature using AquaScan:
1. Connect AquaScan to the outlet
2. Ensure the isolation valve on AquaScan is fully open
3. Fully open the outlet
4. Allow 30-60 seconds for the water temperature to settle
5. Take the measurement from the live ‘Temperature’ reading
6. Record the measurement in the AquaScan results notepad in the ‘Outlet 1 - temperature’ box.
For more information, to purchase an AquaScan tool, or to speak to an expert at Salamander, visit: www.salamanderpumps.co.uk
In buildings with high hot water demand, ensuring maximum energy efficiency while prioritising safety can seem daunting. Andy Green, head of Technical Solutions at Baxi, considers the options and the role of direct-fired water heaters.
Hot water provision is under scrutiny on the road to decarbonisation as well as heating. In older buildings, achieving more sustainable, energy-efficient hot water can present challenges because of the need to balance environmental goals with available budget while prioritising safe water. Where an all-electric approach is not considered feasible, the focus should be on reducing energy usage and increasing renewable energy supply where possible. Direct gas-fired water heaters can play an important role in this.
More energy-efficient system
In buildings where a central boiler plant and calorifier provide both heating and DHW, installing dedicated plant for each means that the chosen technology can be sized more accurately to meet the requirements efficiently. Many commercial buildings rely on water heaters for DHW generation due to their ability to meet sudden peaks in demand. Depending on where the building is in its net-zero journey, one early option might be to upgrade any non-condensing water heaters to more energy-efficient condensing models. With like-for-like replacement of non-condensing boilers ruled out under Building Regulations, switching to condensing models will ensure the hot water system is compliant, preparing
it for the future addition of renewable technologies. When carrying out an upgrade, re-assess the hot water demand as there may have been changes in building occupancy and demand. This might point to a smaller water heater being needed, reducing initial capital costs and longer-term running expenses. Consider relocating the plant to the roof or exterior in a packaged plant room as this may make better use of space in the building.
fired water heaters (DGFWH). Your chosen manufacturer should be able to offer training, schematics and design support.
From a design perspective, a hybrid solution involving DGFWHs brings several advantages as they have greatly reduced storage compared with indirect DHW systems (boiler calorifiers) and direct electric systems. This means less weight and fewer issues within roof top plant rooms. Energy usage is also reduced, along with
“Many commercial buildings rely on water heaters due to their ability to meet sudden peaks in demand.”
Flueing and condensate removal are two considerations associated with installing new condensing water heaters.
For the bigger task of replacing the hot water system, the lowcarbon credentials of air source heat pumps (ASHPs) are well established. However capital expenditure and operating costs may have an influence when dealing with older buildings.
A hybrid solution is often a fast, efficient and affordable solution to decarbonise hot water in these buildings. Where the natural gas supply is to be maintained, one option is for ASHPs to preheat direct gas-
associated emissions, as there is less water to maintain at temperature.
As some DGFWHs come with in-built anti-Legionella functions as standard, Legionella control is far more straightforward than with an all-electric approach. With smart return temperature sensor technology, they can provide further energy and emission savings by reducing the time required to complete the pasteurisation process.
As a final point, it is generally accepted that where a design includes renewable technology, such as heat pumps, project costs are higher. n
Peter Armstrong, CEO of Mixergy, looks at the differences between smart cylinders and existing ‘dumb’ products, and the benefits they can bring.
Smart hot water cylinders can connect to the internet, which opens up a raft of opportunities for the household and the environment. When you’re replacing a system or heat-only boiler, where there’s already a cylinder in place, they can help to future-proof the heating system. They have an important role to play as a way to reduce bills as energy providers introduce more flexible electricity tariffs for off-peak use. The cylinders can be scheduled to work only during the times when electricity is at its cheapest and cleanest levels.
Demand-side response
An increasing amount of electricity is generated by wind farms and solar panels, which is driving down the carbon intensity of our electricity supply. However, we can’t turn on the wind or the sun, so an increasing ratio of our energy is unpredictable and we need to have back-up ready. Conversely, the times when it is really sunny or windy don’t always align to when the demand is at its highest –usually between 4pm and 7pm. Demand-side response (DSR) is used by the National Grid to try and match demand to the available supply. When the frequency goes above 50Hz, this is an indicator that there is a surplus of demand with respect to supply, and devices like the Mixergy cylinder can be switched on remotely to help stabilise the power system and the homeowner can benefit from receiving the excess electricity. n
Most hot water cylinders work by heating the water using coils or a thermostat at the bottom of the cylinder, and then heating all the water in it like a big kettle, irrespective of how much hot water is actually needed.
Mixergy X cylinders are different because they use thermal stratification to make storing hot water more energy efficient. Thermal stratification is the result of heat rising; hot water floats on top of cooler water. The area between the hot and cold sections of water is known as the thermocline.
Mixergy X starts by heating a small volume of water at the top of the cylinder, either with an immersion heater or a coil at the top of the cylinder and then growing that volume of hot water downwards. A sensor in the cylinder lets the user know exactly how much hot water is available.
Only the required amount of water is heated, so heat losses are reduced and the water gets to a useful temperature quicker. This leaves room in the cylinder to take advantage of free electricity from solar PV if it’s installed or if the grid needs to ‘dump’ excess power (demand-side response).
The Mixergy app shows how much hot water is in the cylinder, its temperature, what it costs and how much space is left. The app can be used to boost the cylinder to provide 100% hot water and to change the temperature. A daily schedule can be set to ensure hot water is available when needed or it can be integrated with a smart tariff.
Cadent has some top tips for helping customers with a smell disorder stay safe from the dangers of gas.
More than one in three people with a smell disorder have had a gas scare at home in the past five years, according to research by Cadent’s partner charity Fifth Sense.*
This poses a big risk to those unable to detect gas, fumes or smoke. The condition, where someone has partial or full loss of smell, is known as anosmia and affects up to 5 per cent of the population. The numbers are rising due to illnesses such as Covid-19, medical conditions and ageing.
The most common single cause, either temporary or permanent, is illnesses that affect the nose or sinuses, such as polyps, fractured bones or cartilage, hayfever or tumours.
Head injuries and nervous system diseases like Parkinson’s or Alzheimer’s may also contribute by damaging the nerves responsible for detecting smells.
Cadent has been educating its engineers through a new e-learning training course to help customers suffering from anosmia to detect gas, to keep them safe at home.
Phil Burrows, head of Customer Vulnerability Social
Key customer advice from the course includes:
• Get your gas appliances serviced every year by a Gas Safe registered engineer.
• Fit a gas detector. These can detect dangerous and ignitable gas escaping and will sound an alarm to warn you of the danger. If your gas detector sounds, you could have a gas escape, so call the free National Gas Emergency number 0800 111 999 immediately.
• Sign up to the Priority Services Register and gain access to additional support. Cadent recognises sense loss as a condition and, in the event of a gas emergency, customers receive extra services tailored to meet their needs.
• Have a designated nose. Nominate a family member, friend or neighbour to call on if there might be a problem. It's also worth using tools like cooking timers as a reminder to attend to food and avoid burning that can’t be smelled.
Programmes, says: “This course will provide vital information for our engineers and others who are out and about in the community visiting customers in their homes.
“Safety is a priority for us. By raising awareness of the potential impact of not being able to smell a gas leak, we hope to decrease the likelihood of an incident.”
One Cadent engineer who has been using the advice is lead gas engineer C-Jay
“More than one in three people with a smell disorder have had a gas scare at home in the past five years.”
Fretwell. He says: “I recently came across a customer who couldn’t smell, and we had a chat about it because of the implications for detecting a gas leak.
“I shared tips from Fifth Sense to help the customer to find a new nose – whether that’s a friend or neighbour, a gas detector or even prevention measures to reduce the risk of gas escapes. We have a responsibility to help and I was happy I could do that.” n
*Survey with University of East Anglia, February 2024.
For more information on how smell can save lives see: cadentgas.com/sense-ofsmell
For information on smell and taste disorders visit: www.fifthsense.org.uk
For many self-employed workers, self-assessment has always been the way they declare their tax liabilities. But did you know it has only been around since 1996?
Self-assessment was created to streamline the tax collection process for those with any untaxed income who need to declare and pay tax on it. Back then, the online service we know today did not exist. So how did HMRC get from zero to 97 per cent of self-assessment filers submitting their tax returns online?
HMRC has faced the same challenge every year: how to get millions of people to file their return and pay any tax owed by 31 January. Simply, it created an online system that lets people self-serve to meet their tax obligations.
The self-assessment population is rising, with more than 12 million people expected to file a return every year. About 5-6 million of those leave it until January to file their return and this can cause delays.
The online service was launched in 2000 and that year 38,000 people submitted their self-assessment tax return online. Now more than 11 million people submit online:
in fact, nearly 68,000 people filed their 2023-24 tax return on 6 April 2024, the first day of this tax year.
The service has evolved since 2000 and any new services or enhancements are done with the customer in mind, through systematic customer research. HMRC wants you to navigate the service with ease, get your tax right first time and support you when you are stuck.
Some of the customerfocused changes to filing a self-assessment tax return on GOV.UK include:
• Using pre-populated forms to save time inputting your details
• Allowing you to tailor your tax return, so you only need to complete relevant parts
• Help functions with access to videos or guidance to support you every step of the way.
Self-assessment is a digital process on GOV.UK. You can set up your Government Gateway account, register for self-assessment, complete and submit the self-assessment forms, and set up a payment
“The self-assessment population is rising: more than 12 million people are expected to file a return every year.”
plan to pay any tax you owe.
HMRC provides a wide range of resources to help on GOV.UK and YouTube: during the most recent self-assessment peak, the website had 48 million page views, particularly to help users decide whether they needed to complete a tax return, and 1.4 million watched a range of YouTube videos.
In February 2024, HMRC launched an improved online appeal process for selfassessment, so that you can appeal against late filing or late payment penalties.
Millions of people use the HMRC app every year to manage and meet their tax obligations and the app was downloaded 3.6 million times in 2023-24. You can use the HMRC app to:
• Set reminders so you don’t forget to pay your tax bill
• Access the digital assistant
• Find your Unique Taxpayer Reference
• Claim a refund if you have paid too much tax
• Pay your tax bill.
As the self-assessment population evolves, HMRC will continuously adapt to make sure it can support you and help you get your tax right. n
If you need extra help, HMRC provides a specialist dedicated service to support you.
A new online wellbeing tool from engineering charity Foothold is designed to help gas engineers and their families access expert personalised mental health support.
The Mental Health Check-In tool is the latest addition to Foothold’s online support resources that are designed to empower people to take control of their mental, physical and financial wellbeing.
The digital tool has been developed in partnership with mental health experts Rightsteps. It provides a starting point to help gas engineers understand how they’re feeling right now, and offers personalised advice and suggestions on how they can make their mental health better.
It comes after a 2023 survey by Hays on the future of engineering revealed that 89 per cent of engineers experience some degree of stress from their job, while 40 per cent say they are struggling mentally due to the demands of their role.
Carly Snead, head of Support Services at Foothold, says: “We’re becoming more aware of our mental health as a society and now, more than ever, we need to remember to ‘check-in’ with ourselves and those around us when it comes to our wellbeing.
“We’re really pleased to launch Mental Health Check-In to help people understand how they’re feeling and what they can do to take more control over their day-to-day mental wellbeing.”
The tool works by asking a series of clinically validated questions about their experience of emotions such as worry, anxiety and low mood.
Foothold CEO Jane Petit says: “We are all becoming increasingly aware of how our mental health impacts us at work and home. By giving engineers and their family members access to a quick and easy-to-use tool to understand and improve their mental health, we aim to empower even more people to live well and thrive.”
The Mental Health Check-In joins the charity’s other free digital support services, including monthly webinar on a wellbeing or personal finance
“We’re all becoming aware of how our mental health impacts us at work and at home.”
Users are then given a personal mental health score based on their answers, alongside expert tailored recommendations and advice on where they can access relevant support.
They can download a copy of their report for future reference, or to use as a starting point for discussions with their GP.
Mental Health Check-In is free, quick, completely confidential (users won’t be asked to enter any identifying details) and available 24/7.
topic; the Wellbeing Hub which provides support on mental and physical health; the Differently Wired Hub, offering information and support for neurodiverse engineers, advice-filled blogs; and the Foothold app, for expert financial and legal advice. n
You can find out more about Mental Health Check-In and the charity's additional online support at: www.myfoothold.org
Baxi’s 2024 Installer Skills Survey shows heating engineers are held back from supporting the switch to low-carbon heating by a lack of practical training, complex government incentives and sluggish consumer demand.
The attitudes of heating engineers towards low-carbon heating are hard to shift, contributing to the slow growth in adopting heat pumps, according to Baxi’s 2024 Installers Skills Survey.
The survey, carried out with Gemserv, looks the appetite and confidence of more than 300 heating engineers to support households in their transition to clean heat technologies. It also shines a light on the future pace of change and their readiness to adopt and promote heat pumps in the context of evolving government policies and consumer demands.
This year’s survey reveals more positive sentiment towards heat pumps compared with the first edition in 2022, but it’s clear that many installers still lack the training, knowledge and incentive to help homeowners begin their transition away from gas boilers.
Just 9% of installers say they are fitting heat pumps. This is up from 3% in 2022 and 7% in 2023. Sentiment towards heat pump installation in the future looks weak, with half of installers saying they are “somewhat” or “extremely unlikely” to start fitting them
in the next three years. This compares to 46% in 2022 and even less confidence than in 2023.
There is more enthusiasm for hybrid systems, with 30% of installers showing interest.
Government schemes such as the Boiler Upgrade Scheme (BUS) are met with frustration in the survey, due to perceived complexity, excessive paperwork and lack of consumer awareness. Only 9% of installers rate government schemes as “good’’ or “excellent’’ and 42% say their customers never mention the BUS.
A lack of confidence to promote and install low-carbon heating technologies has been a feature of the Installer Skills Survey since it began in 2022. This year, there is a slight improvement, with 11% of installers saying they are “extremely confident” in discussing low-carbon technologies (up from 7% in 2023) and 35% are “moderately confident”.
Practical training is key to building confidence, with 34% of respondents indicating a preference for hands-on learning. The perceived high
“Half say they are unlikely to start fitting heat pumps in the next three years.”
“Just 3% of installers say customers always ask about low-carbon heating.”
cost of training, along with the complexities of MCS accreditation, are ongoing obstacles to learning.
The lack of consumer demand for heat pumps further contributes to installers’ low engagement. Without strong consumer interest, installers continue to be hesitant about making the transition to low-carbon heating, including investing in training. In the 2024 survey, just 3% of installers say customers always ask about low-carbon heating.
A recurring theme in all three surveys has been a generational divide, with those nearing retirement less inclined to invest in training. As more new installers enter the industry, it’s expected that more will be willing to embrace new technologies.
Ian Trott, Baxi’s head of UK training, says: “Many of the challenges highlighted by previous surveys, such as insufficient training, poor government support and low consumer demand, haven’t moved on. The transition to low-carbon heating will require more targeted interventions to support installers in overcoming these barriers.” n
Millions of UK homes could successfully switch to lowcarbon electrified heating using innovative heat battery technology, a trial has found.
The Neat Heat trial, led by UK Power Networks in partnership with OVO and Tepeo says it could ease pressure on the grid and help the UK to meet its 2050 net zero targets.
The Neat Heat trial ran for 18 months and involved installing Tepeo’s Zero Emission Boiler (ZEB), which uses heat battery technology, in customers’ homes in the South-east and East of England. The findings showed that heat batteries, an allelectric low-carbon alternative to fossil-fuel boilers, can provide grid flexibility by shifting peak energy demand for heating to off-peak times. Homes could be heated even in winter while providing substantial carbon savings compared to using gas boilers instead.
Using the ZEB’s thermal storage capability, homes could ‘charge’ their heating systems outside the most expensive hours of the day, with heat being released on demand when needed. At launch, the
project attracted more than 2,000 registrations of interest for the limited spaces available, evidencing a strong demand from customers for new alternatives to fossil-fuel heating.
The trial was built around OVO’s proposition called a ‘type of use’ add-on, giving customers access to a cheaper (than standard) rate to charge their ZEBs. They could also set their ZEBs to charge during the cheapest times of the day.
The Neat Heat trial showed 95 per cent of a trialist’s yearly heating demand could be moved outside peak hours, even during winter. The homes experienced no noticeable change to their heating.
Green solutions such as the ZEB are suitable for homes that lack the space for low-carbon solutions like heat pumps or where these solutions could prove difficult to retrofit.
Tepeo CEO Johan du Plessis said: “Heat batteries working in tandem with dynamic tariffs will enable millions of homes currently unable to switch to low-carbon solutions to join the green transition.”
‘Heat pumps emit 95% fewer emissions than gas boilers’
Heat pumps in a home setting emit almost 95 per cent fewer carbon emissions every year than a traditional gas boiler, according to a new study from Stiebel Eltron UK.
Its study took place over a 12-month period in a four-bedroom home. As well as showing significant carbon savings, the heat pump maintained a comfortable indoor temperature above 20°C all year round, with a co-efficient of performance (COP) consistently exceeding 4.2.
The heat pump cost £750 a year to run, some £250 less than a traditional boiler in the same setting.
Stiebel Eltron UK monitored performance using real-time reporting and data analytics via the company’s monitoring software.
Managing director Mark McManus says: “There is a growing onus being placed on technologies that will significantly reduce carbon emissions which come from homes and buildings. These results show that a heat pump does exactly that.”
•We can clean microbore, one pipe and plastic pipe systems.
•We offer zero risk “No fix No fee deals” If we can’t fix it, you don’t pay anything
•Earn £100 Commissions for completed client referrals
•We can fix blocked systems and blocked heat exchangers.
•No need to replace or re-run pipes.
Heating engineers in the East Midlands have a new Ideal Heating training hub on their doorstep.
The company’s Expert Academy training arm has opened the Pochin Ideal Renewables Training Centre in conjunction with Pochin P&H Supplies. The facility is in the heart of Leicester, providing easy access to training on gas boilers, heat pumps and other heating products.
Training director Andrew Johnson says: “Our new training base in Leicester will play an important role in
Mont Selas has opened a new training and ACS centre at its workshop facilities in Chadderton, Manchester. The company is celebrating 50 years in the gas engineering industry and provides a range of courses including a foundation diploma in commercial gas heating and commercial and LPG ACS. Its commercial package includes CODNCO1 or COCN1 with CORT1, CIGA1, CDGA1 and ICPN1. Individual courses cover CONGLP1 PD, TPCP1A, TPCP1 and BMP1
Mont Selas is a familyowned firm of industrial gas engineers who design and manufacture the Enviromont gas burner as well as providing nationwide service and installation of all types of gas equipment. www.montselas.com
helping more installers become low-carbon heating engineers, gaining the skills and expertise needed.”
The centre features a dedicated Ideal Heating room kitted out with the company’s products, including its domestic heat pump and boiler ranges.
David Pochin, executive chairman at Pochin P&H Supplies, says: “Pochin Renewable Heating Solutions has ambitious plans to develop the opportunities in the market for renewable technologies.”
Significant changes have been made to the Plumbing and Domestic Heating Technician apprenticeship standard. The revised standard caters to the evolving needs of the plumbing and heating sector, as well as tailored routes into industry for apprentices.
After completing the core plumbing programme, the revised standard provides individuals with three routes to professional development, so they can tailor their apprenticeship training:
• Gas: apprentices can hone their skills to join Gas Safe Register.
• Environmental technologies: this focuses on installing and maintaining solar thermal systems and air source heat pumps. Individuals can qualify for the Competent Persons Scheme and Microgeneration Certification Scheme, opening doors to the green energy sector.
• Non-domestic plumbing: this brand-new pathway caters to the specific requirements of non-domestic buildings such as schools, high-rise buildings, hospitals and health care settings. Apprentices will develop expertise in installing and maintaining plumbing systems, such as washrooms and extensive above-ground drainage systems.
The revised standard means apprentices can learn more about emerging technologies as well as the skills to maintain plumbing and heating systems. It aligns training with the industry trends and equips learners with the most in-demand skills.
Panasonic has a new partnership with three Scottish colleges to upskill the next generation of heating and plumbing installers in heat pumps.
Dumfries and Galloway College, UHI Inverness and Glasgow Clyde College provide BPEC-accredited heat pump courses, and Panasonic will provide additional productspecific air-to-water training for the trainers, apprentices and installers.
Product training will use the Panasonic Aquarea L Series outdoor unit, all-in-one indoor unit and Wiser controls.
Jim Brown, director at ESP, the college sector agency, says: “This will establish partner colleges as centres of excellence for upskilling industry and enhancing modern apprenticeship programmes.”
RWC product marketing manager Richard Bateman looks at how to use the latest technologies to futureproof heating and plumbing systems.
Leaky pipes might seem like a small problem in the grand scheme of efficiency and sustainability. However, when you consider that 3 billion litres of water are lost to leaks every day, addressing water wastage can make a crucial difference.
Each person uses around 140 litres of water every day and the government has set a target to reduce this to 110 litres by 2050. Technology will be key. Conventional plumbing can be enhanced through improved control, efficiency and comprehensive insights into water usage and management.
Manufacturers prioritise sustainability in their products, integrating advanced features such as real-time monitoring, automatic leak detection and remote control capabilities. These systems enhance efficiency, reduce water wastage and contribute to environmental sustainability by promoting responsible water management practices.
Installers will be familiar with the potential of installing pressure-reducing valves (PRVs) where water enters a property to achieve greater control over the system and stabilise the flow rate. This is a proven method of effectively managing
water usage and consumption throughout a home. But it is just the starting point.
PRVs can also be used in conjunction with leak detection systems to continuously monitor and measure the flow rate and pressure against pre-determined consumption levels, helping to accurately control water usage across the property.
The benefits of this integrated technology are far-reaching, delivering tangible improvements for homeowners as well as the planet. Greater control and reduced consumption can mean lower monthly bills while conserving water and reducing associated emissions.
Technology has a role to play when it comes to creating efficient, future-ready heating
“Systems can enhance efficiency, reduce water wastage and contribute to environmental sustainability.”
systems for homes. Underfloor heating is a viable, mainstream alternative with traditional radiator systems. And it’s no surprise why: UFH offers immediate energy savings of up to 15% compared to traditional radiator systems, especially when paired with a heat pump or solar thermal system.
Smart controls for UFH systems enable homeowners and building managers to regulate room temperatures precisely. They can manage individual rooms or zones independently, optimising comfort levels throughout the property while lowering energy consumption and costs.
As new technologies like smart controls, underfloor heating systems, and energy-efficient plumbing fixtures continue to evolve, knowledgeable installers can effectively guide homeowners towards solutions that minimise energy consumption, reduce operational costs and enhance overall efficiency. n RWC.com/uk
54 Heat, hot water and pure air with Daikin Multi+
54 Grant adds pre-plumbed smart cylinders
54 Baxi expands commercial heat pump offer
55 Heatrae Sadia unveils Supreme Evo hot water dispenser
55 Continal updates OneBoard UFH
55 Viessmann reveals Vitocrossal commercial boilers
Worcester Bosch has updated its Greenstar 8000 boilers with improved features and heating performance.
The 8000+ range is available in 32kW and 36kW combi variant outputs and improvements include:
• Superior heating output for bigger homes and highdemand environments
• New intuitive touchscreen user interface
• 12-year warranty.
Martyn Bridges, director of External Affairs, says: “The
Greenstar 8000+ is the next stage in the evolution of this tried-and-tested product. By concentrating on the higher-output variants, the 8000+ is suitable for the larger homes with heating outputs to suit, and hot water flow rates that meet the typical larger home requirements.
“With flow rates up to 18L/ min, a number of plug-in optional controls and the innovative auto-filling device, the 8000+ maintains its place as one of the most popular
Vokèra by Riello has added a Pinnacle boiler range, available in combi and system models. The A-rated boilers provide 94 per cent seasonal energy efficiency, adjusting output to match the heating demand and so reducing energy wastage and lowering running costs. The wide 1:13 modulation ratio minimises short cycling, fuel consumption and component wear.
Stay up to date at: www.registered gasengineer.co.uk
boilers on the market today.”
Every 8000 boiler registered until the end of 2024 could earn you a £75 Amazon gift card too.
www.worcester-bosch.co. uk/professional/8000-plus
The stainless-steel heat exchanger provides exceptional heat transfer and durability, says the company, while resisting corrosion and maintaining optimal performance. A digital modulation pump for precise flow regulation provides
optimal system water circulation and efficient heat distribution throughout the home.
The DHW plate heat exchanger guarantees domestic hot water performance with no temperature fluctuations for a consistent and comfortable hot water supply, even during peak demand. Smart functionality for DHW operation and weather compensation allow for bespoke adjustments to suit individual preferences
The Pinnacle is LPG “out-of-the-box”, which means it can be reconfigured to work with LPG through a simple parameter adjustment without the need for a conversion kit.
It comes with a 10-year warranty as standard. www.vokera.co.uk
Tado’s new X product range brings savings and simplicity to smart heating, says the company. The smart thermostats and sensors, smart radiator thermostats and heat pump Optimizer X predict savings of 19 per cent on average and control over heating bills.
Co-founder Christian Deilmann says: “Our latest generation of products is another step on Tado’s mission to make it simpler for millions of homes to decrease their energy consumption and bills without compromising on comfort.” www.tado.com
Daikin’s Multi+ system combines an air-to-air heat pump with a domestic hot water tank and air purification in one energysaving system.
It can be programmed to meet individual needs and features a weather-dependent setting, where the water temperature is determined automatically by the outside temperature. If the temperature falls or rises, the unit compensates automatically.
Where space cooling and hot water are required at the same time, the electric booster heater ensures that the water is at the right temperature. Space heating and hot water heating can be set to operate simultaneously.
The Multi+ requires minimal space and is a suitable replacement for domestic hot water (DHW) systems where air conditioning is also being installed. There are a variety of indoor units, including wall-mounted, floor-standing and concealed ceiling models.
Hamid Salimi, Daikin’s Residential product manager, says: “Not only is it quick and easy to install, but it gives the customer cooling, heating, air purification and hot water in one, simple-to-use system.
The outdoor unit size means that it is ideal for small outdoor spaces such balconies and terraces.”
G3 and F-Gas certification are required for installation.
https://shorturl.at/ LfJTT
Grant UK is adding to its renewables range with quick recovery smart pre-plumbed cylinders with heat pump controller kits and a new installation pack.
The pre-plumbed cylinders incorporate the Aerona smart controller, with the controller’s display, wiring centre and cylinder temperature sensor supplied fitted on the cylinder. The factory-fitted pre-wired controls and pipework can speed up installation, on-site set-up and commissioning.
The cylinders are available in 180L, 210L, 250L and 300L and are compatible with
Grant heat pumps.
The controller touchscreen display comes fitted but can be removed and located elsewhere. The wiring centre is also pre-wired and factoryfitted to the cylinder.
A new additional heat pump installation pack is designed specifically for use with the pre-plumbed cylinders. The pack is compatible with both the Aerona³ R32 heat pumps and Aerona 290 heat pumps, includes a flexi-foot kit, magnetic filter, 18L system kit and isolator, and is designed for use on S-Plan systems. www.grantuk.com
Baxi has added new Auriga medium temperature monobloc heat pumps, compatible cascade and hybrid controls, and a pre-contract design guidance service to its existing commercial offering.
The air-to-water Auriga air source heat pump (ASHP) series can achieve temperatures of up to 60°C. They come in single outputs of 20kW, 26kW, 33kW and 40kW, with cascade options up to 320kW to provide design flexibility.
A new series of compatible cascade and hybrid controls
maximise system efficiency. The Baxi Commercial HVAC Manager provides control of hybrid heating systems, with the option to cascade up to eight heat generators (either eight ASHPs or a combination of ASHPs and boilers).
The new Auriga indoor controller is designed for simple ASHP cascade system control, and the VM-T controller can be used as an extension to increase the number of secondary zones controlled.
Director of Building Solutions James Matthews says: “Our Baxi Auriga ASHP
has been designed with efficiency, occupant comfort and design flexibility in mind. Its excellent seasonal coefficient of performance (SCOP) of up to 4.83 at W35 is combined with quiet operation and sound power of less than 65 dBA.
“Our technical solutions team support customers with system design, sizing and simulation testing to assess solution suitability against the project requirements.
“By partnering with customers at the early stages, we can not only supply the required ASHP system
components, but precise, validated advice, backed with predicted energy and carbon savings and capital expenditure modelling.”
www.baxi.co.uk/lp/baxiauriga-air-source-heat-pump
Stay up to date at: www.registered gasengineer.co.uk
Heatrae Sadia has unveiled its Supreme Evo, an energyefficient instant hot water dispenser for use in highdemand commercial applications. It builds on the technology of the Heatrae Sadia Supreme and has a space-saving, filter-inside design, a one-touch digital dial and a new ‘learning’ thermostat.
Smart technology monitors usage patterns for energy management, ensuring water is brought on to boil to match user demand while intelligently reducing the temperature by 10°C after an hour of inactivity to optimise efficient energy usage. Alternatively, heating times can be preselected using the in-built seven-day programmer.
A built-in filter ensures potable drinking water while protecting against limescale and sediment build-up.
Users can choose different drinking water temperatures, including a coffee-specific setting.
The Supreme Evo comes in three capacities – 2.5 litres, 5 litres and 7.5 litres. www.heatraesadia.com
Continal Underfloor Heating’s
OneBoard Plus is an update of its OneBoard structural underfloor heating (UFH) system that gives increased performance and faster response times.
It comes with a full heat dissipation foil to ensure heat outputs of up to 72W/m2 right across the floor, directing heat from the UFH pipe and up into the room above faster than before. It can be laid directly on 400mm and 600mm joists and is suitable for both new-build and retrofit installations.
The inbuilt composite chipboard panel replaces the normal chipboard or plywood sub-layer. This helps to reduce floor build-up heights, creating an
extremely low-profile UFH system that can be fitted almost anywhere. The panel depth measures just 22mm to provide more flexibility when designing and fitting UFH systems. There are pre-routed 12mm pipe channels set at 150mm pipe centres to make it easier to lay the UFH pipes into the board. The pipe centres incorporate flexible underfloor heating pipe, which is kink-resistant and provides a bend radius of less than 100mm. www.continal.co.uk
Viessmann Climate Solutions
UK has a new range of high-efficiency, low-emission, commercial gas condensing boilers with the Vitocrossal 200 CI3.
With eight output sizes from 80kW to 640kW and integrated-control cascade operation up to 5,120kW (eight units), the Vitocrossal 200 CI3 is flexible and compact, making it suitable for modernisation projects or buildings where space is limited.
Each unit is 750mm wide and takes up 1.07m2 of floor space – 55 per cent less than
previous Vitocrossal 200 models.
Its single or dual-modulating MatriX cylinder burner with stainless steel heat exchanger, and automatic combustion controller make it easier to commission.
Performance is enhanced by the boiler’s large modulation range of 1:10, which gives greater efficiency at partial loads. It has two return connections as standard, so that there can be low and high-temperature circuits if desired, with a lower temperature return for better
condensation.
The Vitocrossal 200 CI3 is the first of Viessmann’s commercial boilers to be integrated into its One Base climate and energy management platform with built-in WiFi. One Base allows for simple, reliable and convenient operation of the entire energy system, as well as automatic optimisation of energy flows for maximum cost-effectiveness. www.viessmann.co.uk
OFTEC is one of the leading competent person registration schemes. It’s the name customers look for when selecting a technician, making registration with OFTEC the best way to demonstrate your competence and win new business. You can register for:
• Liquid fuel • Solid fuel • Solar thermal
• Heat pumps - air, ground and design
• Biomass • Non-operative • Electrical (Part P)
• PAS2030 • TrustMark • MCS
Our competent person registration includes a range of benefits:
• Searchable online listing of registered businesses.
• Self-certification of installation work*.
• Free technical support by phone or email.
• Access to exclusive 'technician hub'.
• Discounts with selected partners.
BTAAC offer a full range of Domestic and Commercial Gas training and assessments in a well-equipped training facility at very competitive prices.
· All ACS Domestic Gas – core + appliances ·All ACS Commercial Gas including CMDDA1 and BMP1
· Unvented Hot Water & Water Regs
· Highly knowledgeable trainers with years of experience
•
•
•
•
•
•
5 million Logics and counting!