TOP PROJECTS FOR 2023
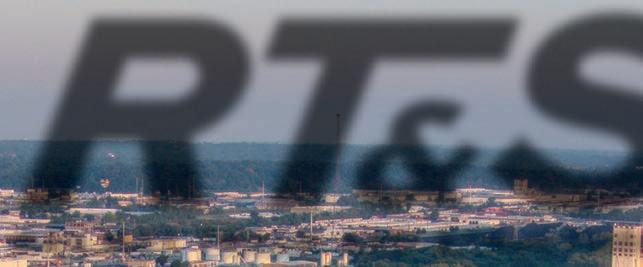
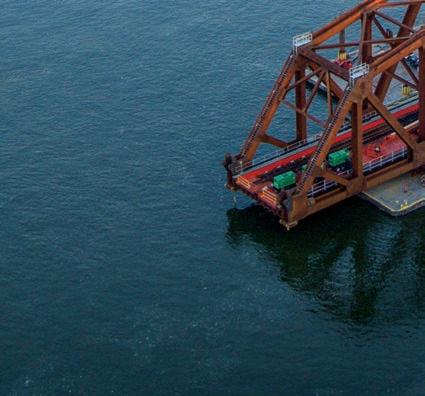
BUILDING AND MAINTAINING NORTH AMERICA’S RAIL INFRASTRUCTURE
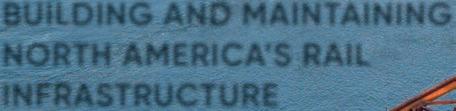

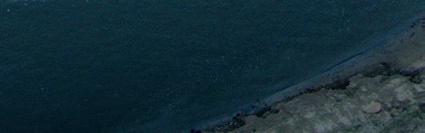

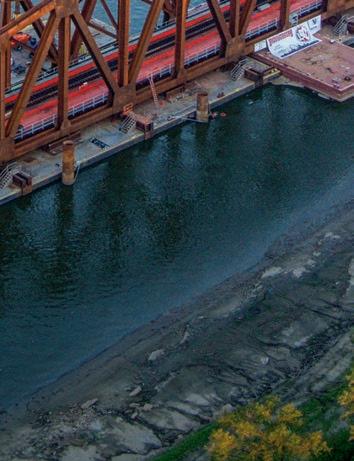
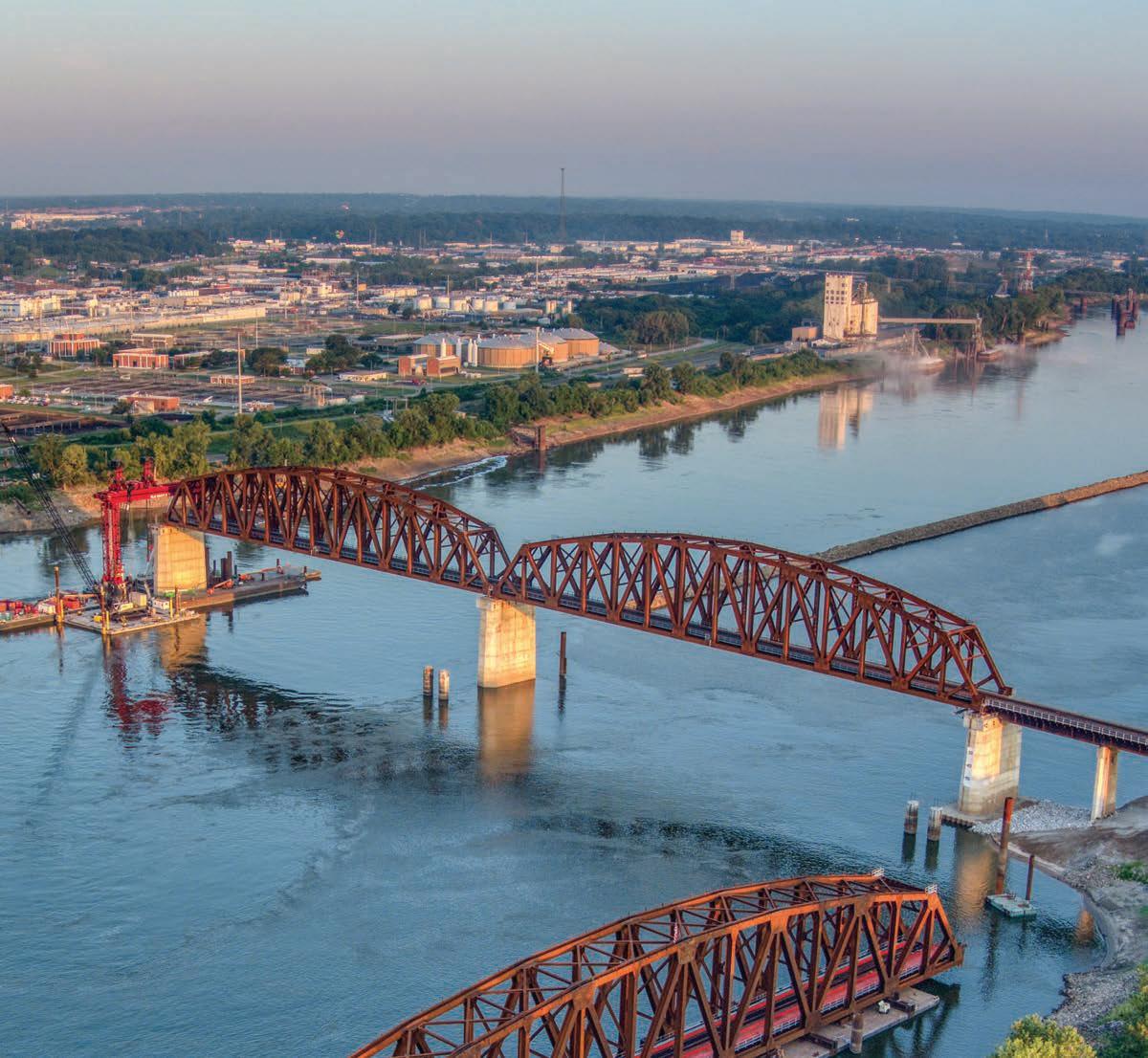
ALSO:
EXTREME WEATHER GRADE CROSSING SURFACES DERAILMENT
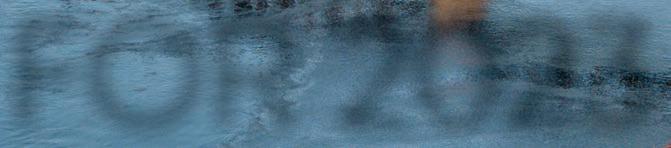








BUILDING AND MAINTAINING NORTH AMERICA’S RAIL INFRASTRUCTURE
ALSO:
EXTREME WEATHER GRADE CROSSING SURFACES DERAILMENT
When a puzzle switch at the Port of Beaumont in Texas was identi ed as aged and unreliable, Progress Rail was contracted by Trans-Global Solutions Inc. (TGS) to supply a switch with optimized ef ciency and reliability.
We designed a new, custom puzzle switch – consisting of a double crossover containing two #6 turnouts and two double slips with a crossing diamond in the center.
Creating new solutions for dated infrastructure is one more way Progress keeps our customers rolling.
We keep you rolling.
The engineering, fabrication, and installation of the Port of Beaumont’s New Replacement Puzzle Switch was completed in August 2022.Vol. 119, No. 6
Print ISSN # 0033-9016, Digital ISSN # 2160-2514
EDITORIAL OFFICES
1025 Rose Creek Drive Suite 620-121 Woodstock, GA 30189 Telephone (470) 865-0933
Website www.rtands.com
DAVID C. LESTER Editor-in-Chief dlester@sbpub.com
JENNIFER M c LAWHORN Managing Editor jmclawhorn@sbpub.com
CORPORATE OFFICES
1809 Capitol Avenue Omaha, NE 68102 Telephone (212) 620-7200
Fax (212) 633-1165
ARTHUR J. MCGINNIS, JR. President and Chairman
JONATHAN CHALON Publisher
MARY CONYERS
Production Director
NICOLE D’ANTONA Art Director
HILLARY COLEMAN
Graphic Designer
JO ANN BINZ Circulation Director
MICHELLE ZOLKOS Conference Director
CUSTOMER SERVICE: 402-346-4740
Reprints: PARS International Corp.
253 West 35th Street 7th Floor New York, NY 10001
212-221-9595; fax 212-221-9195
curt.ciesinski@parsintl.com
This is the seventh issue of Railway Track & Structures produced since I became editor in November 2022. For most of these issues, I enjoyed the support of former Managing Editor, Kyra Senese, who returned to RT&S part-time to help, mainly focusing on daily news and a few print articles. For all these issues, I’ve enjoyed the support of everyone whose name appears on the masthead to the immediate le . In addition, regular and periodic contributors have supplied excellent material important to those involved in building and maintaining railroad infrastructure. e phrase “it takes a village” certainly applies to the magazine business.
During these past few months, the Railway Age team, particularly Editor-in-Chief Bill Vantuono, has provided tremendous support and guidance to the edgling editor of RT&S While I’ve been writing about railroads for a long time, assuming the editorship of and responsibility for a monthly magazine is a di erent animal. I’ve enjoyed Bill’s unwavering support, advice, and counsel these past few months. Also, I would be remiss in failing to mention the tremendous help Railway Age’s Executive Editor Marybeth Luczak and Senior Editor Carolina Worrell provided.
ey’ve come to my aid many times when the press of business le little time for writing news stories and posted many timely and insightful reports. Railway Age and editor Vantuono are fortunate to have such capable professionals on the team.
Michelle Kolkos is the company’s Conference Director who keeps us all on our toes regarding virtual conferences and podcasts. I didn’t realize how many nuances were involved in these productions until I had a couple under my belt. Our production department, led by Mary Conyers, joined by Art Director Nicole D’Antona and Graphic Designer Hillary Coleman, is intimately involved in the production of each issue, and their design skills are phenomenal. Erica Hayes, Leia Sills, Carol Franklin, Peter Fine, and Jo Ann Binz serve in various capacities to keep things on track. Our publisher, Jon Chalon, is a publishing expert, and I’m very
grateful to him for the opportunity to edit this great magazine. Moreover, our Chairman and President, Arthur J. McGinnis, Jr., oversees a strong publishing group reporting on railroads since the 1800s.
I’m pleased to announce that RT&S has a new Managing Editor – Jennifer McLawhorn. At this writing, Jennifer has been with us for almost a month, and she’s spent time enduring my brie ngs and hitting the books to learn about the railroad industry. Jennifer holds bachelor’s and master’s degrees from Old Dominion University and makes her home in the Norfolk area. During graduate school and as an academic, she focused on interdisciplinary research in lm studies and feminist theory. While she is new to railroading, Norfolk Southern’s main line is within a stone’s throw from her house, so that she can combine eld observation with her learning. When asked about her study of the rail industry, Jennifer responds, “this is interesting,” and o en explains why she nds a particular aspect of the industry fascinating. Jennifer is a quick study and has already learned much about our industry. Yet, no one knows better than she does that there is a tremendous amount yet to learn, and she looks forward to maintaining the study she’s doing and meeting people in the industry. I’m pleased to report that her rst work for the magazine appears in this issue, our Vendor/Product spotlight on grade crossing surfaces. Please join me in welcoming Jennifer to the industry and our team.
A retired railroad CEO recently told several of us that “this is an interesting time to cover the railroad industry,” and he is correct. Over the past decade, this grand industry has faced tremendous challenges and celebrated many victories, particularly in the area of technology. e next decade promises to be even more exciting.
So, please stay with us for the ride!
DAVID C. LESTER Editor-in-ChiefATLANTA – We are pleased to announce that Railway Track & Structures has a new Managing Editor, Jennifer McLawhorn.
Jennifer is an East Coast native and recent graduate from Old Dominion University with a master’s degree in Humanities and a bachelor’s degree in
English Literature. Her earlier work dealt with interdisciplinary research across the fields of film studies and feminist theory. Having spent time in academia, she has developed her writing and editorial skills to bring with her to the publishing industry.
Jennifer is in the process of learning
about the railroad industry and railroad journalism, a process that will continue for another thirty days. You will see Jennifer’s work in the this issue (p.22) and her reports on the daily news feed will follow. We are very glad to have Jennifer in the Simmons-Boardman family.
WASHINGTON – Amtrak’s Office of Inspector General released a report outlining fraud risks Amtrak could face as it leverages significant federal investments for major acquisitions and capital projects.
According to the report, historic levels of federal funding from the Infrastructure Investment and Jobs Act will, in part, advance the company’s long-term, large-scale infrastructure goals and significantly expand its traditional passenger rail operations mission to now include a major capital delivery mission. The sheer size and nature of this expansion will, however, increase the company’s fraud risk, the report said.
The report identified four high-risk fraud areas the company faces: contracts and procurements, health care, employee wrongdoing, and cybercrime. It includes examples of
how such fraud manifests, and potential fraud mitigations for consideration. For example, the OIG’s prior work exposed contract steering and bid rigging schemes, overcharging by contractors, schemes in which employees conspired with doctors to bill Amtrak’s health care plan, employee theft, and cybercrimes involving Amtrak’s e-voucher program.
Amtrak OIG pointed out in another news release that “If history is any indicator, funding from the Infrastructure Investment and Jobs Act—like other large spending bills—will be targeted by criminals through a variety of unlawful fraudulent schemes.”
To develop the report, the OIG leveraged its experience from 99 fraud-related investigations and 22 audits conducted since 2017, as well as industry research on fraud schemes and best practices to prevent and detect fraud.
The OIG credits Amtrak for establishing its Integrated Risk and Compliance Program (IRCP) to monitor fraud risks and establish capabilities to proactively identify fraudulent activity. The report notes that the IRCP could bolster Amtrak’s enterprise-wide fraud defenses, a culture of integrity, and employee awareness of fraud schemes and indicators.
MxV Rail (formerly TTCI) tested the ballast compaction ability of a truck-based Dynamic Track Stabilizer (DTS) against accumulated tonnage under speed restriction in a heavy axle load (HAL) environment. Two tie types and DTS down-pressures were evaluated both in terms of lateral tie resistance and track settlement.
The loosening of ballast particles during tamping and other ballast maintenance activities can reduce the ballast particle interlock strength, thereby reducing lateral track strength. Reduced lateral strength increases the risk of track buckling in continuously welded rail (CWR) track, and trains are typically put under a speed restriction (also
known as slow order tonnage) until the ballast compacts. Ballast compaction can occur in one of two ways: through train tonnage—typically the first 0.1 million gross tons (MGT)—or through vibratory compaction using a DTS. If a DTS is used following surfacing, the number of trains requiring speed restrictions is significantly reduced from the number required
to accumulate ~0.1 MGT (~6 to 10 trains or more) to one train.
In the 1990s and 2000s, multiple DTS tests were performed using heavier DTS machines.(1) Recent tests were performed to ensure a similar benefit would be observed with lighter DTS systems that could be moved by truck from one location to another and were more versatile than
their heavier counterparts. Additionally, it was important to understand the effect of different tie types and DTS down-pressures. This article presents the results of a DTS test that occurred at the Transportation Technology Center, (TTC) in Pueblo, CO, in fall 2021.
The DTS was tested on three different tangent track zones. Zone 1 consisted of wood ties, while Zones 2 and 3 consisted of concrete ties. The DTS (Figure 1)
applied a down-pressure of 40 Bar (580 psi) in Zones 1 and 2 and a heavier downpressure of 60 Bar (870 psi) in Zone 3. Down-pressures of 80 to 90 Bar (1,160 to 1,305 psi) were tested with the heavier DTS in the past.
A similar test, but with HAL slow order tonnage, occurred in Zone 1 and Zone 2 in fall 2020 and was used for comparison. (2) The ballast in all three sections was clean, but the wood tie section ballast may have had less texture, and therefore, less interlock.(2) The ballast shoulder
and crib height varied between and within the test zones, but these parameter variations were accounted for in the lateral tie resistance results using historical equations that have been shown to represent the change in ballast shoulder width and crib height.(3)
To assess ballast compaction, the lateral tie resistance and track settlement were measured. Lateral tie resistance was measured by performing single tie push
tests (STPTs) immediately after tamping and after stabilization. STPTs measure the lateral resistance of a single tie. The test is conducted by removing the fastening system, lifting the rail, and pushing the tie with an actuator. The peak force within 0.25-inch of lateral tie displacement is used as the output. Unloaded track settlement was measured using top-of-rail (TOR) survey elevations immediately after tamping and then after stabilization or accumulation of 0.1 MGT.
The lateral tie resistance increase from compaction, either by slow order tonnage (2020 test) or DTS (2021 test), was calculated by taking the increase percentage from the post-tamping state. Figure 2 compares the increase percentage from the recent test for the three test sections with slow order tonnage in blue and DTS in red. The 0.1 MGT test was not performed for Zone 3. The results, which agree with historical measurements, show a slightly greater lateral tie resistance from the DTS (4 to 11 percent). These test results also suggest that tracks with concrete ties have a greater relative compaction from the DTS (22 to 32 percent) than tracks with wood ties (16 percent). For DTS only, Zone 2 (concrete ties, 40 Bar) provided a greater increase in lateral resistance than Zone 3 (Concrete Ties, 60 Bar), suggesting the lower down-pressure provided a greater lateral strength. The reason for this difference is unclear.
To add historical context, Table 1 and Figure 3 show the compiled results of all testing mentioned in the available literature.1 The tests are separated by tie type (wood and concrete), and the down-pressure, if known, is shown in the legend. Other factors, e.g., ballast condition, tie texture, etc., may play a role, but these factors are not consistently documented in previous tests so they cannot be compared.
While these test results show a wide variation in lateral resistance increases, general patterns can be observed. First, the DTS consistently produces a similar or greater increase in lateral tie resistance than slow order tonnage for all tie types and downpressures. This observation is important as it demonstrates the effectiveness of DTS systems while indicating their impact on a railroad’s average train velocity. The shaded regions in Figure 3 show the general range of lateral resistance increases with slow order tonnage ranging from 10 to 20 percent while the DTS increases ~15 to 35 percent.
Second, concrete ties generally show a slightly greater lateral resistance than wood ties. Third, when viewing all datasets, there is no recognizable down-pressure pattern. Based on the available test results, it is currently unclear if there is an optimal down-pressure, but it appears all tested down-pressures were shown to be effective.
Track settlement is a more direct method of assessing ballast compaction, but it is not a direct measure of lateral tie resistance. For the 2021 test, TOR survey elevations were measured at multiple intervals, including: pre-tamp, post-tamp, and poststabilization. The tamp lift height can be calculated from the difference between the pre- and post-tamp states. The initial settlement from DTS is calculated from the difference between post-tamp and post-stabilization.
Figure 4 shows the settlement from each scenario normalizing for a 1.0-inch lift height. The initial settlement shown
in Figure 4 indicates the DTS generally provides greater or equal settlement when compared to tonnage. This settlement agrees with the lateral tie resistance measurements: more ballast settlement
should produce greater ballast particle interlock strength, and therefore, greater lateral track strength. For the DTS, the concrete tie sections did seem to have greater settlement than the wood tie
section, again agreeing with lateral tie resistance values. However, the previous studies did not measure settlement, so it is unclear if this amount of settlement is consistent with historic values.
The authors would like to thank BNSF Railway and Russell Wood from Plasser for DTS support and the MxV Rail Instrumentation and Track Teams for their efforts.
1. Wilk. S. (2021). “Literature Review of Lateral Track Resistance Testing.” Technology Digest TD21-004. AAR/ TTCI. Pueblo, CO.
2. Wilk, S.T. (2021). “Ballast Parameters Influencing Lateral Track Resistance.” Technology Digest TD21-030. AAR/TTCI, Pueblo, CO
3. Kish, A. and G. Samavedam. (2013). “Track Buckling Prevention Theory, Safety Concepts, and Applications.” DOT/FRA/ORDE-13/16. Washington DC.
The term “project” can mean many things. You could say that your plan to clean out your garage this weekend is a project. Remodeling your bathroom is a project. And, if you haven’t done it in a while, balancing your checkbook could be considered a project.
Maintaining the nation’s railroad infrastructure is usually a cooperative e ort between engineers, construction rms, and rail carriers. While the railroads typically own their entire infrastructure, and perform regular maintenance on it, the involvement of engineering design rms and contractors to execute major projects is critical. e level of professionalism among the parties executing
By David C. Lester, Editor-in-Chiefthe project must be very high, the project must stay within budget unless something unforeseen crops up, and the work between development of the project plan to opening the new infrastructure for rail service must be managed with great care and focus. Lack of attention to detail or carelessness of any sort will likely result in problems down the road. And as they say in engineering schools, “you don’t get partial credit if the bridge falls down.”
is year, we’re pro ling nine projects that stood out from the other submissions. While we would like to have pro led every project, available space would not allow it. While we only feature what we consider to be top
projects, we tip our hats to all the projects that were submitted for consideration of this honor, as well as those that were not submitted. Despite industry challenges of the past few months, the North American railroad infrastructure is among the strongest and best maintained in the world. All of this is accomplished through well-managed projects. Please join us as we review our top picks for 2023.
CLASS I: NEW CONSTRUCTION (BRIDGES)
NS Pearl River Truss Replacement
Pearl River, La.
• Prime Contractor: PCL Civil Constructors, Inc.
• Prime Designer: G&A Consulting Engineers
• Owner: Norfolk Southern
e project team for the Norfolk Southern bridge crossing the East Pearl River in Louisiana faced several challenges throughout the on-line replacement of the nearly 120-yearold existing truss span while allowing the safe passage of trains across the river. e success of the 22-month Pearl River project
was achieved with minimal disruption to the rail tra c that utilizes the line. In addition, the constant ow of local vehicular and pedestrian tra c underneath the bridge had to be maintained throughout the construction process. e Pearl River project also endured a major hurricane, several seasonal ood events from record rainfall and material delays due to the COVID-19 Pandemic.
e project began in January 2021 with the temporary falsework / access trestle utilized
to perform the main span change, followed by the installation of the structure’s new drilled sha /cast-in-place concrete cap foundation and substructure. ere were six seasonal ood events that halted work during these activities, resulting in a cumulative 15 days of delays, followed by Hurricane Ida, which hit Louisiana in late August 2021, causing another 10-day delay due to high winds, power outages, and additional jobsite ooding. In August 2021, PCL was noti ed of a supply
chain delay of the raw steel material used to fabricate the new through plate girder spans.
e original span swap date was scheduled for February 2022, but due to the signi cant delays caused stemming from the COVID19 Pandemic the span swap was successfully completed in July 2022.
roughout the delays, PCL worked with Norfolk Southern to minimize the potential for additional lost time on site by completing all substructure and falsework installation by
February 2022, as scheduled. Upon the delivery of the steel, PCL accelerated and modied its steel erection schedule to deliver the completed project as soon as possible. Some of the innovations that were used on this project included the slide system designed by PCL’s construction engineer, McNary Bergeron & Johannesen, along with a spin on accelerated bridge construction. To minimize delays to the rail tra c above, PCL/McNary designed a slide system o a temporary trestle on either side of the existing truss span. Each trestle provided access for construction materials & equipment to successfully install all foundation and substructure elements without disruption. In addition, these trestles also provided support for falsework beams to be placed beneath both new and existing spans. ese “slide beams” provided a straight track for each “cart” supporting each span. e carts were pulled via a hydraulic jacking system. is jacking system allowed the spans to move e ciently during the 16-hour change outage and not cause any delays once complete.
e project team was also a steward of nature while working on this project. Located within the Honey Island Swamp and Bogue Chitto Wildlife Area, PCL took great care to minimize the environmental impacts on the project. Items such as turbidity curtain, silt fence, 110% containment, etc. were utilized to avoid impact to any wildlife or environmental areas along the Pearl River. is project also dismantled the existing truss span, which contained lead paint on its members. PCL took great care to follow all regulatory requirements to perform the demolition of the existing span safely and successfully. e project team worked to prevent a signi cant carbon footprint and reduce risks of leaks and spills from equipment by only utilizing the bare minimum. In addition, all hydraulic oils used on the project were environmentally friendly biodegradable oils. In addition, PCL was able to donate a portion of some used construction materials at the end of the project, that we used to improve property roadways and access to previously saturated areas. is project resulted in reduced maintenance costs for Norfolk Southern and allows a crucial transport line to be intact for years to come. PCL achieved nal completion on October 4, 2022, to the satisfaction of Norfolk Southern.
EastBound Re-Route Construction for the East Side Access Project
East Side Access, New York, N.Y.
• Prime Contractor: Railroad–Michels,
Joint Venture
• Prime Designer: Gannett Fleming
• Owner: MTACC
e Railroad-Michels Joint Venture, LLC continues to complete the MTA Construction & Development design/build Eastbound Re-Route Project, contract CH058B, within Harold Interlocking, the largest railroad junction in New York City and the busiest in the United States. e improvements will re-route track carrying Metro-North, Long Island Rail Road and Amtrak trains, improving the daily travels of thousands of commuters and providing congestion relief for trains traveling along the Northeast corridor. e project’s scope of work includes the design and construction of a new 2,100 LF cut and cover tunnel, modi cation and re-support of the existing Honeywell St. Bridge, demolition and new track work, and overhead catenary systems, all of which is being conducted in an active railroad environment, requiring close coordination with ongoing train operations.
Existing track and catenary systems were removed which initiated the start of a longterm outage allowing the construction of the East-Bound Re-Route structure. Following completion of the structural work, track installation including two #20 turnouts, insulated joints, compromise joints and transition rails as well as third rail systems will be installed in conjunction with new catenary structures and wires to support the movement of Amtrak train consists through the interlocking. Additional work includes traction and facility power, signals, communication systems and improvements to the storm sewer system.
Massachusetts Bridge Bundle
Massachusetts
• Prime Contractor: Barletta Heavy Division
• Prime Designer: VHB
• Owner: Massachusetts Bay Transportation Authority
A key goal of this project is to minimize impacts to riders. e contract allows only nine total weekend rail line shutdowns to fully replace all six structures and each bridge has its own set of needs and circumstances.
e design team needs to provide innovative solutions to solve the varied challenges. To do this, ve of the six bridges are being built using precast concrete substructure components installed behind the existing abutments,
leveraging consistent details to simplify design, fabrication, and construction.
Most of the bridges are being replaced using Accelerated Bridge Construction (ABC) techniques, including self-propelled modular transporters (SPMTs) to move the superstructures into place. Work on two of the bridges needs to be conducted simultaneously. Two of the bridges, one at Bacon Street and one at Intervale Road, are located within just one mile of each other on the same line. Due to their proximity, work on the bridges had to progress simultaneously during each weekend outage. Although challenging to coordinate double crews and equipment needed, the bridges were designed with common details and nearly identical construction sequences to simplify the process, reduce risk, and minimize impacts to the traveling public.
Johnson County Railroad 286K Rehabilitation
New Century Commerce Center, New Century, Kan.
• Prime Contractor: TL Wallace
• Prime Designer: In House
• Owner: Johnson County Airport Commission
e greatest challenge of rehabilitating an active, predominantly single-track short line railroad was maintaining the highest level of service to time sensitive customers on short notice. is has been accomplished with the highest level of safety and service with the cooperation and exibility of the contractor, along with JCAX’s rail employees. Each rail customer fully understood that the key benets of upgrading rail and turnouts from 90 lbs. (aged at nearly 100 years old) to 136 lbs. are to increase safety and prevent obsolescence.
Cooperation from all stakeholders has been key in making the entire project a success. Another challenge to the process is determining what rail components must be replaced now, and what can wait until more funding is available to upgrade the entire system. Material cost increases have greatly reduced the trackage that can currently be upgraded to 286K standards. Adjustments have been made to redirect mainline tra c onto the heavier relayed rail wherever possible. Despite the increase in cost, the JCAX has been able to rerail 56% of the total system, or 9,500 track feet of the 17,000 total system trackage.
Also very notable, 11 of 25 system turnouts, which are potential points of failure, have been replaced as well. Because of the activity of the work being performed and
the overall improvements to the system, an existing food producing lessee located next to the railroad is taking notice. In the past, this national customer utilized rail delivery and stopped. Because of the and upgrades made to the system, they have approached the JCAX with the intention of beginning rail service once again.
BNSF Bridge 81.4
Washington state
• Prime Contractor: Hamilton Construction
• Prime Designer: HNTB
• Owner: BNSF Railway
Project development and design of BNSF Bridge 81.4 across the Cowlitz River in Washington state began in 2013 requiring signicant stakeholder coordination and regulatory approval. e existing bridge consisted of 101’-8” long deck plate girders and a 250’-0” long pin-connected truss. e 100+ year old bridge had reached the end of its service life and needed to be replaced to ensure reliable service.
HNTB evaluated a range of replacement options which included re-using the existing substructure, using an on-line alignment and o -line alignment to fully replace the bridge. e project was initially designed and went out to bid as an online replacement bridge with a truss span. BNSF ultimately decided on an o ine alignment due to high train tra c. Working closely with Hamilton Construction, BNSF changed the delivery method from design-bid-build to Construction Manager/General Contractor. By moving into the construction phase with Hamilton, the project team was able to streamline construction and reduce project costs. e nal bridge consisted of 143’-4” and 207’-6” long deck plate girders supported on large diameter drilled sha s with rock sockets and box beam approach spans supported on H-piles.
Construction commenced in 2020 due to the challenge of coordinating various stakeholder interests. To address this challenge, HNTB’s design team coordinated closely with local permitting agencies as well as with the local Cowlitz and Chehalis Confederated tribes, whose tribal lands would be a ected by the project. Early and o en in the process, the team met with tribal representatives to understand the potential impacts on the tribes’ land, shing access and historical or cultural resources.
e bridge’s extremely remote location made it di cult to secure substructure and
geotechnical information. Virtually the only access is via rail, and it was not possible to drill a boring in the river without suitable access.
e team, therefore, had to make assumptions in its foundation design for the piers in the river and get borings when construction started and a temporary work bridge was installed. To accomplish this, the team built on information available from drilled sha s along the banks of the river. However, once the team had site access, they found that the
basalt rock layer was higher than expected. It presented a dramatic elevation change –deep on one end of the bridge and almost at the surface on the other. e team rapidly made foundation design changes in coordination with Hamilton Construction, including placing rock sockets into the basalt rock layer. In addition to the basalt rock layer challenges, boulders were rampant at the site, making it di cult to drive H piles as planned because the piles would not have remained straight. To
mitigate this issue, the design and contracting teams elected to drill sockets for the H piles. e design changes were completed without impacts to the schedule. Construction was successfully completed in March 2023.
Metrolink Track and Signal Infrastructure Maintenance and Support Services
Los Angeles
• Prime Contractor: Herzog Contracting Corp.
• Prime Designer: N/A
• Owner: Metrolink
As the Southern California Regional Railroad Authority (SCCR) Metrolink Commuter Rail Maintenance-of-Way provider, Herzog Contracting Corp. (Herzog) is responsible for maintaining a network of 419 Metrolink route miles spanning over 33,000 square miles in
the Los Angeles basin. is includes maintaining – come rain or shine –all track, signal, bridge, and drainage structure infrastructure within the Metrolink right-of-way to ensure safe and reliable commuter rail operations.
From December 2022 through January 2023, Southern California experienced unprecedented rainfall – 400-600 percent above average – resulting in major ooding, rockslides, and mudslides across LA County, which caused major impacts and damage to the SCRRA Metrolink right-of-way.
Metrolink’s rail infrastructure was signicantly impacted by track washouts and track obstructions caused by tree, rock, and mudslide debris. Rainfall was so severe in January that Union Station ooded. ese weather events resulted in Metrolink systemwide service disruptions such as slow orders, delays, dark signals, and other service impacts that had the potential to compromise the safety of Metrolink operations.
roughout these recent severe weather events, Herzog collaborated closely and proactively with SCRRA to keep the Metrolink commuter rail system open and operational for commuters. Herzog strategically staged resources, materials, and heavy equipment
across the Metrolink network to be well-positioned to respond to weather-caused right-ofway service disruption.
Additionally, Herzog communicated closely with Metrolink and with the community to address ooding and mudslide issues as they arose - and before they became unmanageable. Herzog maintenance-of-way crews worked around the clock repairing rail infrastructure, clearing debris from the track, and xing drainage problems to keep Metrolink trains moving, never ignoring or refusing an issue because it was or wasn’t their job.
Speci c to this year and a direct result of the ooding was the development of sinkholes in and around the Metrolink mainline tracks. To combat this hazard, Herzog personnel worked tirelessly to inspect each sinkhole, check for utility obstructions, and ll the holes with ballast to keep the trains running. Additionally, they worked continuously to keep the track operational during constant rock slides in the Santa Clarita area, where the train runs through rock-covered hills. is required continual monitoring and clearing of the track using backhoes and loaders.
Herzog’s e orts in the midst of these challenges did not go unnoticed. At the
January 2023 SCRRA Metrolink board meeting, Herzog was recognized for its success in tackling these challenges by the Metrolink Board of Directors and CEO, Darren Kettle.
Merchants Bridge Main Span Trusses & East Approach Replacement
St. Louis, Mo.
• Prime Contractor: Walsh Group
• Prime Designer: TranSystems Corporation
• Owner: Terminal Railroad of St. Louis (TRRA)
Reconstructing a historic bridge of this magnitude involved a number of construction-related challenges.
Pre-construction environmental clearance and permitting was complex involving multiple federal lead agencies and the bi-state coordination necessitated by this major Mississippi River crossing involving Missouri and Illinois state agencies as well as municipalities. Because this was a federal action with federal permits, NEPA documentation was required to evaluate the potential impacts to the human and natural environment. e
historic signi cance of the bridge necessitated additional coordination culminating in a Memorandum of Agreement amongst the US Coast Guard (USCG-lead agency), both State Historic Preservation O ces (MO & IL), Federal Railroad Administration (FRApotential funding entity) and the owner, TRRA. In total, the project’s environmental clearance required approval of three NEPA documents: Categorical Exclusion (USCG & FRA), subsequent Re-examination (USCG), and an Environmental Assessment for the US Army Corps of Engineers (USACE). A er the bids were received the permitting processes could be facilitated on behalf of TRRA by collaborating with the selected contractor. Permits included USCG Section 9; USACE Sections 10/404/408 Permits; ILEPA/MDNR Section 401 Water Quality Permits; Floodplain Permits (MO & IL); Land Disturbance (Section 402) Permit and Stormwater Pollution Prevention Plan (SWPPP). In addition to the lead federal agencies (USCG, FRA, USACE), project agency coordination involved but was not limited to US Fish and Wildlife Service (USFWS), Illinois Environmental Protection Agency (ILEPA), Missouri and Illinois Departments of Natural Resources (MDNR & IDNR), Metropolitan Sewer District of St. Louis (MSD), Metro East Sewer District (MESD), the cities of St. Louis (MO) and Venice (IL), Madison County Transit and Great Rivers Greenway. Maintaining NEPA and permit compliance demanded continued coordination with many of these state and federal agencies through and beyond construction completion.
Replacing the three 523’ main river truss spans, complete with a gantry system with strand jacks to li and slide the old and new truss spans, also required precise on-site coordination. Removing the existing truss weighing 3,900,000 pounds and installing the proposed truss weighing 9,000,000 pounds proved to be the most challenging aspect of the project. Coordination and collaboration between all parties was key for success. e erection and demolition engineering, barge stability analysis and gantry tower foundation design was performed by Genesis Structures.
e heavy li gantry system was designed and fabricated by Mammoet.
e east approach is within the levee limits on the Illinois side of the river thus maintaining ow during high water events was required. In contrast to the previously encased west approach, cast-in-place concrete culverts were designed with a supporting foundation system to allow ow to pass through. Lightweight cellular concrete ll was designed to minimize pressure and settlement on the existing and proposed foundation systems. is ll also was able
to ow in and around the existing steel towers and girders eliminating the need for costly steel demolition and interruptions to rail operations.
Working on a live rail line was another challenge that required coordinated track outages. Twin lines were reduced to a single track with a scheduled 5-hour daily track outage to accommodate construction. A planned 10-day rail outage took place for each of the three truss span replacements, as did two 24-hour river channel outages so workers could remove the old river truss spans and install the new ones. Coordinating daily river tra c in the primary and secondary river channels required tight logistics and constant monitoring of the river levels.
Building within the footprint of the existing Merchants Bridge also lent a layer of complexity to the job.
Cherry Valley Avenue Design-Build Bridge Replacement Project
Garden City, N.Y.
• Prime Contractor: Railroad
Construction Company, Inc.
• Prime Designer: KSE Engineers
• Owner: Long Island Rail Road
Project Scope: is Design/Build project replaced the existing bridge, built in 1871, with a new bridge and increased vertical clearance from 11 . to surpass the minimum state DOT standard of 13 . 6 in to 14 . 6 in.
e existing bridge’s low clearance triggered numerous safety issues with box trucks and tractor trailers striking the bridge, causing tra c back-ups and train delays.
e two biggest challenges with this project were: 1. Performing the work without interfering with weekday commuter trains. 2. Moving the new bridge, a large pre-assembled structure, into location, in one piece.
e new bridge installation was accomplished without impeding weekday commuter trains by the following steps:
1. Reinforce the existing abutments and footings by adding additional concrete encasement. Under an approved tra c pattern, RCC performed the work during the day by exposing the existing footing, drill and
•Complete Electrical Services
•Yard & Building Lighting:
• Office Lighting
• High-Mast Towers
• Solar Lighting Solutions
• Turn-key wood & metal pole installation
•Electrical Distribution Service & Upgrades
•Excavation Services:
• Trenching
• Hydrovac
• Horizontal Drilling
• Helical Piles
grout dowels to both footings and abutments and then set formwork, place concrete and strip. e new encasement secured the structure ensuring its strength to safely carry the new bridge.
2. A er the abutments and footings were structurally encased, RCC would then jack the existing bridge to provide the additional 42” of clearance for the new bridge. is required three weekends of Jacking, one weekend to re-construct a nearby roadway crossing, and nally, one weekend to remove the existing bridge, and “Roll-In” the new bridge into its nal location. We had to jack the existing bridge over multiple weekends due to the subsequential work of having to then re-align the existing track on both sides of the existing bridge to meet the new height. Had we simply removed the old bridge and installed the new one at an additional 42” in vertical height –there would never have been enough time to re-open the track to the traveling public by 5 a.m., Monday(s). Each weekend outage typically supplied enough time to jack 12” of vertical li . Once the bridge was jacked, steel bolsters were installed to hold it in place until the following weekend, when it could be jacked once more.
3. When the existing bridge reached its nal vertical clearance, the nal weekend closure occurred to rst remove the old bridge, second, Install the Precast Bridge Seats, third, install the New Bearings and fourth Install the New Bridge.
We proceeded to burn out the bolsters and move the Self-Propelled Modular Transport trailer (SPMT) underneath the old bridge. is machine had shoring towers with integral jacks which allowed an approximate stroke of 11 in. to “pick” up the old bridge, and transport it away to a nearby lay-down yard. is bridge (and the new bridge too) weighed over 300,000 lbs.
A er the old bridge was removed, we installed four precast bridge seats. ese seats made up the vertical clearance needed and weighed 30 tons each. ese precast seats were then grouted to the underlying newly encased bridge previously constructed.
Following installation came the bearings. Each bearing weighed approximately 1,500 lbs.
Finally, once again utilizing the SelfPropelled Modular Transport trailer (SPMT) the new bridge was moved into position.
e time to travel approximately 1,000 . for both the old bridge, and new bridge was one hour in each direction.
Once the new bridge was in place, crews proceeded with the nal track work, and 3rd rail connections. RCC installed the ballast
utilizing a telescoping conveyor belt (telebelt) set up on the roadway. Ballast was installed up to the underside of the tie elevations, then new 40 . pre-assembled tie/track units were own in using a Liebehr LTM 1250 (300-ton capacity) crane.
Track work on this project above the ballast setting was performed by the Long Island Railroad. RCC provided crane, and trucking support to the LIRR for the pre-assembled track sections.
Impact to the industry: is project vastly improved and corrected an on-going safety hazard (bridge hits). With an adjacent school, and Adelphi University nearby – many pedestrians walk under this bridge each day making the existing structure particularly dangerous. With the new clearance, this is no longer a concern.
is Design-Build project also demonstrated that with careful planning, a bridge can be replaced by only working weekends – ve (5) all together, with minimum disturbance to the environment and public.
is project achieved Substantial Completion on April 3rd, nearly 7 months in advance of the Contract required date.
Western Canada
• Prime Contractor: Electrical Solutions, Inc.
• Prime Designer: Electrical Solutions, Inc.
• Owner: CPKC
Electrical Solutions, Inc. has been an electrical contractor for Canadian Paci c for over twenty years. One of the main tasks we have asked them to perform throughout western Canada is to provide lighting for rail switches.
e conventional procedures for this are to trench through the rail yard to the nearest utility power source and install a wood pole or steel pole with a concrete base. is procedure can be very costly due to the size of the rail yards. CP requested Electrical Solutions, Inc. to source a solar option while keeping in mind all the industry light level policies and safe clearance policies. e many hours spent sourcing the required device turned up empty. Absolutely nothing on the market met the stringent minimum requirements needed for the rail industry.
Electrical Solutions, with their many years of experience with rail lighting took it upon themselves to research, design and test a switch speci c solar option for the rail industry. is came with many challenges.
e most signi cant challenge was practicality. Could a solar option be manufactured and installed to industry standards and still be more cost e cient than the conventional utility powered method? Secondly, keeping in mind our diverse country, can a light operated by batteries that are charged by a solar panel be designed for reliability during our harsh, dark Canadian winters? How do we keep the batteries warm in low temperatures without consuming too much of the produced wattage? e battery enclosures would have to be well insulated and as small as possible since every square inch would have to be heated. It would become a rail safety issue if these lights only performed intermittently. ere is no room for error; they must perform awlessly on the coldest, windiest, cloudiest, and shortest day of the long winter.
Other challenges included logistics. How high should the light be installed? How far from the track should it be mounted? When illuminating the area for a switchman, where does he need the light speci cally to safely perform his task? ese were all challenges that Electrical Solutions faced when sourcing
the perfect xture.
Without jeopardizing light levels and watts per lumen output, they wanted to meet or exceed the minimum requirements without using excessive wattage as to suit the solar component.
With their experience in lighting rail switches, Electrical Solutions knew that not all switches are installed in prime or accessible locations for large equipment. How do we service this light and panel without the use of an aerial li platform? To solve this problem, they designed the light with the capacity to be lowered to the ground for maintenance.
Every unit can be dropped away from the switch and serviced without the use of li ing equipment. Because of this, they can be installed in the worst possible locations and ground conditions. How do we mount the unit to a secure base since installing concrete piles beside a rail bed in remote locations would be too costly? ey designed the unit to mount to a single 4.5-meter helical pile and since not all switch locations are alike, these units are designed to accommodate a le side lowering pole or a right side lowering pole. To top it all
Hamilton has been building bridges, highways, dams, and critical infrastructure as a heavy civil contractor since 1939. Our crews consistently perform above and beyond requirements to complete complex projects. They preserve history, respond to natural disasters, and develop innovative construction techniques to solve unique challenges. We are proud of their award-winning work in safely building and maintaining our nation’s infrastructure.
o , the speed of unit installation from start to nish is remarkably fast. Gone are the days of waiting for concrete to set and trenching hundreds of meters to get to the utility power.
On top of all the design challenges, Electrical Solutions knew the importance of reliability and safety and wanted to provide a way for us to monitor the e ciency and status of the new lights. How do we ensure this safety and e ciency beyond the extensive research and carefully engineered design? ey installed a charge controller that can log performance of the equipment 24 hours a day, 365 days a year so we can always have peace of mind.
is innovative light designed by Electrical Solutions Inc. not only gives us the option to illuminate rail switches in challenging places throughout our network but it is cost e ective enough to install in rail yards where utility is available. To add to the list of reasons why these lights are such a great t for Canadian Paci c, the design meets our company’s green initiative as well. Carbon footprint is on the mind of all companies as we strive to nd more ways to do our part to reduce our impact on the planet. Electrical
contribute
Amajor challenge for the railroad industry is that it operates outside. Railroads build, own, and maintain their infrastructure, and when bad weather hits, it’s up to them to plan for and deal with it using their personnel and money. Railroads that regularly face a particular type of weather, such as heavy snow, may own equipment to deal with the a ermath, or they will lease the equipment necessary to do the job.
RT&S recently spoke with Dwayne Gibson, AVP – Maintenance of Way & Structures at Norfolk Southern, about how the Class I road handles extreme weather events. From an overall engineering project perspective, Gibson said that “Norfolk Southern’s focus is on planning, preparation, and execution (PPE) [not to be confused with personal protection equipment] – this has been the key to engineering success on our railroad. We do this to get the job done e ectively,
on time, and on budget and to ensure we don’t have any incidents or injuries.” Gibson also said, “Every weather event deserves a custom response. Whether it’s fast-moving or slow-moving, if high winds are involved, and what threat the storm poses to trees, are just a few of the things we consider. We also must ensure our response covers the particular hazards workers will face when they arrive on site.” For example, Gibson points out that if a heavy cold front moves into the southeast,
bringing heavy rain, it’s essential to know how fast it’s moving. If the storm parks over a particular territory for several days, he and his team know they’ll be dealing with ooding, potential washouts, and drainage problems. Storms parked over mountainous areas of the system are particularly challenging. If a storm is moving fast, it’s likely accompanied by high winds that will bring down trees, potentially blocking the right-of-way, so the plan and equipment for the latter event di ers from one needed for the former.
Gibson adds that “Location is huge on our system. We must protect 22 states across the NS system, and location will also dictate our strategy. Sometimes we have a hurricane that pushes through the southeast. When dealing with one of these, we may curtail tra c along the coast, pull our people back away out of the eye of the storm until it passes, and then we start coming in to make the inspections and restoring service.” Making inspections is one of the most important parts of the process. A er a hurricane, we must inspect inland parts of the line along with the
coastal. e ultimate goal is to protect the operation and, from an engineering perspective, nd the trouble before the trains nd the trout.
When bad weather strikes, railroaders must prepare and plan for, endure, then address the a ermath of a storm. Preparation, planning, and clean-up are done before and a er the storm, but what is done during the storm? For the most part, the storm must be endured. When it comes to storms with high winds, tornadoes, and hurricanes, crews can only hunker down and wait for the fury to pass.
However, rain events o er opportunities to begin work during the storm, provided the crews can stay ahead of the water ow. For example, if water is not draining from the ballast and roadbed fast enough, crews can, in some cases, create additional channels through which the water can ow to help it run o more quickly rather than sink into the sub-ballast. Yet, before work can start in these situations, railroads have crews out on the track monitoring conditions. It may be that if conditions are reasonable, trains can continue to run if
their path ahead is inspected thoroughly. If the railroad must stop running trains, crews will continue to monitor potential ooding and take whatever corrective action they can before the storm is over.
Dealing with snowstorms has its unique challenges. Roads ensure their switches and other special trackwork do not freeze and become immobile. Switch heaters take care of much of this. If the switches are working, the next step is to remove as much snow from the tracks as possible, usually with various sizes of blowers. If it’s a light accumulation, teams may use brooms to sweep away the snow. Other tools that help ght snow and ice include propane torches when ice accumulation is heavy, and special chemicals for brushing on track and switches to prevent them from freezing. Snow plows attached to the locomotive pilot are also helpful.
e road does everything it can to keep trains moving during snow and ice events because if snow and ice accumulate and crust over each other, it’s much more di cult to clear the line.
Gibson pointed out that NS partners
with Accuweather to obtain storm alerts and monitor rail territory conditions. “For example, the Accuweather system alerts us if total snowfall in an area is six inches or greater or has occurred in 12 hours or less, and we also have another warning that prompts our people if we have rainfall totals greater than eight inches within 24 hours, or if either of these events is forecasted to occur in the next 24 hours.
When crews deploy to address a weather event, the railroad tries to keep a given group within a radius of 30 to 50 miles. Local hotels are o en available with food and lodging, but if one is not nearby, the railroad will use trailers with beds and a bathroom and contract with a local foodservice provider to provide meals to the crew.
Rock and mudslides can happen due to things other than weather, but where there is the potential for these along NS lines, slide fences are erected to alert the railroad if a slide occurs. Gibson points out that weather can, indeed, cause slides. Extremely heavy rain can cause mud to ow down a hill, hit the slide fence, and spill onto the tracks. Rocks can fall in the spring when frozen water starts to thaw out, causing rocks to pop o the side of a hill and down to the fence.
While railroad operations pose various challenges, some variables can be controlled to minimize difficulty. Weather issues, obviously, cannot be controlled. The only recourse a railroad has is to plan, prepare, and execute (PPE, as Gibson said) when bad weather hits. While recovery from most storms can be managed in days or weeks, Norfolk Southern faced a considerable challenge when Hurricane Katrina hit in 2005. Katrina hit in late August, wiping out much of the railroad along the Gulf Coast, but NS fully restored service to New Orleans in early October. Indeed, the railroad restored the Lake Pontchartrain trestle in just sixteen days by setting up a bank of cranes to lift the track blown off the trestle during the storm. In addition, crews cleared approximately 5,000 trees from the right-of-way, beginning in Birmingham and working south toward New Orleans. Gibson was part of the crew that dealt with the aftermath of this vast, damaging storm. He said, “That was a heck of a storm, no doubt about it. That was very abnormal, and you hope you don’t have very many of them in your career, that’s for sure.”
Imagine you are in a vehicle travelling down a road. e trees on either side of you begin to clear out, and you see a familiar sight – railroad tracks. A freight train is in the distance. A bell starts to ring and the crossing gate in front of you starts to come down. While you watch the train go by, there are several elements of the grade crossing that work together to ensure the safe passing of the train as well as the smooth transition of your vehicle over the tracks once the train has passed and the gate has gone back up.
With over 200,000 grade crossings in the United States alone, ensuring private vehicles can safely cross without causing damage to either the vehicle or the railroad is very important. Investing money into and developing crossing materials is an evolving business. From mid-nineteenth century rail workers who relied on a simple system of ags to
communicate, to the wood crossings of the rst half of the twentieth century, to the highly sophisticated technology of present-day, grade crossing surfaces are a feature of the railway infrastructure that deserves a closer look.
One such element Hitachi Rail o ers is a digital audio frequency track circuit called DGTRACK. It’s a sophisticated audiofrequency track circuit that can simultaneously distinguish an oncoming train and transmit cab speed command signals to the train. Not long ago, DGTRACK was approved for use on a major passenger rail operator, so it may catch your eye the next time you board a passenger train.
While centrally located in Texas, Kansas, and Nebraska, American Concrete Products can ship their grade crossing products to either U.S. coast. Having provided concrete products for almost eight decades,
American Concrete Products has a full range of concrete grade crossings, girders, and railroad bridge substructures, to name a few. e panels conform to Union Paci c/ BNSF standards as well as adhering to speci cations for other Class Is and short lines. American Concrete Products utilizes certied welders to produce its all-steel cast-in frames. e company also o ers ADAcompliant crossings for transit railroads, industry sidings, and pedestrian crossings.
Omni Products has been building rail industry products for years and has designed a unique Improved Concrete that utilizes its own manufactured virgin rubber alongside the ECR concrete panel. Several Omni grade crossing products are designed to last under all climate conditions. For example, its TraCast 1 concrete tub module along with the TraCast 2 design, consist of a heavy-duty bolt-down gauge and
smooth grade crossings is good for the railroad and the neighborsWorkers survey recently completed crossing surface.
eld rubber. Another product, their VRA Railguard is made with all virgin heavy-duty rubber. ese rubber products combined with steel reinforced rubber for crossings, absorb impact and distribute it, e ectively preventing the rail itself from the stresses of automotive tra c. O ering a six-year warranty to its tearresistant and load-bearing rubber grade crossing products, Omni also manufactures custom panels that t speci c applications based on customers’ needs.
L.B. Foster o ers two grade crossing safety products – LiDAR Obstacle Detection and Anti-Trespass Panels. Sold throughout North America since 2017, L.B. Foster’s Anti-Trespass Panels are conically shaped panels that are installed trackside. ey are made of recycled rubber and are an environmentally friendly option to deter trespassers.
e panels themselves are installed around xed objects. Sheen Fong, Director of Technical Sales told RT&S that since their introduction, “initial acceptance has been among passenger rail systems with several transit agencies installing ATPs on various sites along their lines. Interest has also been growing among NA transits and state DOTs.”
Indeed, a er a study was conducted by the Federal Railroad Administration (FRA) a few years ago, it concluded that L.B. Foster’s AntiTrespass Panels reduced pedestrian trespassers by 38%. Made entirely from recycled rubber, these Anti-Trespass Panels also come with a 15-year warranty.
L.B. Foster also o ers LiDAR to detect
obstacles that may be in the area. Housed by steel, LiDAR devices monitor and record any violations that occur on or around a crossing. Once a barrier lowers due to the presence of an oncoming train, LiDAR scans the area and can alert trains of any potential obstacle.
Regarding safety integrity levels, Michael O’Connell, Manager of Product and Business
Development commented that “our unique Insight LiDAR system complies to SIL3 level, the highest safety integrity level that is economically feasible for most industrial operations. With this, it delivers improved reliability of detection in all weather conditions, improved accuracy of obstacle detection down to the
inch, reduced maintenance routines, and the exibility in utilizing intelligent algorithms such as velocity and direction.”
HiRail has had requests for more specialized products to t various rail fastening systems and track con gurations. Jim Overfelt, Director of Sales and Marketing, told RT&S, “ e market
remains strong for grade crossings and we are cautiously optimistic that this will continue for the forseeable future.” Indeed, HiRail provides products for new transit start-ups and those extending their current systems.
In addition, the company o ers a line of rubber grade crossing surfaces. Among these are its HiRail, PedeRail, and HiRail Rail Seal.
e HiRail Rail Seal is a rubber product that works with concrete crossings or asphalt. It ts most timber or concrete ties using any type of rail fastener. HiRail’s PedeRail is a speci c crossing surface manufactured with a raised diamond surface designed with pedestrians in mind. It meets Americans with Disabilities Act (ADA) requirements. eir namesake HiRail full-depth rubber crossing systems come in lagged and lagless designs, with lagless lessening crosstie degradation over time and allowing for installation on both concrete and steel ties. ese HiRail products can also be recycled.
Manufacturing over 120,000 track feet of precast crossing panels each year, Omega Industries has a product line that includes lag-down panels that adhere to BNSF/UP standards as well as panels that are Canadian standard. Moreover, it o ers non-lag panels
for use on concrete ties, curved panels, custom turnout panels, DF Track crossing panels, and ADA approved pedestrian panels, along with narrow gauge panels, and steel switch point covers. Using steel, rubber, and concrete products made in the USA, Omega serves many Class Is, short lines, and port authorities. Furthermore, Omega Industries has begun to see growth in public transit, thereby increasing demand for light rail and commuter rail crossing panels. ese include but are not limited to Amtrak, DART, Tri-Met, LA Metro, Southwest Light Rail, and Sound Transit.
Omega Industries has seen a high demand from Class I and short line railroads regrading concrete crossings. Mark Mottola, National Sales Manager for Omega Industries, told RT&S, “As a result, we have experienced record sales in the rst quarter of 2023.” To meet the need for increased production, the company is adding more casting boxes to its current manufacturing locations. Omega Industries told RT&S that its goal is to “increase production capacity to 200,000 track feet by the end of this year,” despite the concrete cure time limiting pour to one set of panels per casting box each day. One way Omega Industries
works to meet the demand is by using a poly ber reinforcement in its panels to improve impact and abrasion resistance, reduce water migration and plastic shrinkage, and provide strength and durability. Omega Industries believes this enhancement to their current product should increase the life of the panels by
up to 10%.
For pedestrian crossings, Omega Industries has engineered a panel that adheres to ADA requirements and incorporates a replacement rubber angeway ller and a non-slip concrete surface. erefore, even when the surface is wet, it should provide
traction for crossing pedestrians.
Industry Railway Suppliers, or IRS, has distributed AREMA track tools, battery tools, abrasives, heavy railroad equipment, work equipment, and mechanical shop tools to railroads and transit systems across North
Railway Supplier has also supported distressed crossing surfaces. Its grade crossing product comes in the form of its exclusive FastPatch Railroad Distressed Pavement Repair kit, or DPR. Manufactured along with Willamette Valley Company, the kit is an easy-to-install
designed to be adhesive and freeze-thaw resistant whilst also absorbing impact to thoroughly repair broken down concrete or asphalt grade crossings along bridges or roadways. Industry Railway Supplier’s DPR kit requires little site prep and includes everything needed for repair. e product is made from recycled materials and is odorless and completely VOC free, eliminating the need for outdoor-only installation. DPR is quick to cure, with normal tra c able to resume just outside of an hour. Ensuring an adherence to ADA compliance, the DPR kit is manufactured to work quickly and e ciently.
Looking closely at the current grade crossing surface product selection, it is apparent that the rail industry has come a long way since the ag system from close to two hundred years ago. Rail technology continues to improve to produce stronger, safer, and more environmentally friendly grade crossing products each year. A er the train passes in front of your vehicle and the crossing gate comes up, keep in mind this sampling of grade crossing surface products that work to ensure a safe and smooth crossing for your trains and your vehicle.
Derailments are never a good thing. But when they occur, as they have on every railroad over the years, they open a window into vehicle / track interaction, albeit poor interaction in these cases. In the a ermath, investigators comb through the wreckage and operating and maintenance records, to identify the cause or causes. And under the right light, the ndings yield lessons that can lead to operating, maintenance, or even regulatory changes. For a look into
some of the lessons learned, Mike Roney, of Iron Mustache Consulting, examined two decades of derailment investigations by the Transportation Safety Board of Canada.
Roney, a former General Manager of Track and Structures, and Chief Engineer at CP Rail, who in 2019 was inducted into the International Heavy Haul Association’s Heavy Haul of Fame for his “lifetime vision and dedication to the advancement of heavy haul railroad technology, engineering and operations,” examined derailment incidents through the
lens of the TSB investigators and through the corrective action plans that were provided in response to the TSB’s ndings.
“Twenty years of derailment investigations by the Transportation Safety Board of Canada is a story about how knowledge is advancing and how we are making it work for us,” Roney told delegates at the 2022 Wheel/Rail Interaction conference. “It’s also a story about how there has been collaboration between railways and the regulators to make things better.”
e Transportation Safety Board of
Canada (TSB), like the National Transportation Safety Board (NTSB) in the U.S., is an independent federal agency that is there to advance transportation safety by investigating occurrences in air, marine pipeline, and rail. e TSB selects and investigates derailments to determine the cause of incidents that might indicate a trend or indicate a risk to the public. e TSB reports identify the factors that caused or contributed to the occurrence, and the safety de ciencies that need to be addressed. While the TSB does not have a mandate or authority to implement corrective actions, it monitors recommendations and actions of Transport Canada and the railways for mitigating actions that eliminate or reduce the so-called safety de ciencies found in these investigations.
Overall, the TSB investigated 327 derailments between 2000 and 2020; 90 derailments re ecting 28% of the total derailment costs identi ed a track issue as a primary cause; 100 derailments re ecting 31% of the costs were attributed to human factors; 58
derailments re ecting 16% of the costs were attributed to a mechanical-related cause.
e majority of the track-related derailments (49%) were attributed to three causes: broken rails, broken joint bars, and broken welds. e remainder were attributed to wide gauge (17%), track buckles (12%) wheel
climb and rail rollover (10%), geotechnicalrelated (7%) and geometry defects, other than wide gauge (5%). “ at’s actually a very good result for the track geometry departments,” Roney said.
irty ve derailments in this sample identi ed broken rail as a primary cause; 21 of the derailments, the majority of which were prior to 2015, resulted from undetected internal aws. e four major derailments that were investigated in 2002, for example, had defects that TSB determined should have been detected by a rail aw detector car if it had the right instrumentation, if it had been run frequently enough, and if rail surface conditions such as rolling contact fatigue had not blocked or interfered with the ultrasonic signal.
“A lot of the early broken-rail derailments were characterized as detectable,” Roney said. In 2015, two out of the three should have been detected. In 2019, one of four should have been detectable. e positive trend, particularly since 2015, indicates that railroads have done a better job of ferreting out defects that are detectable with ultrasonic inspection.
A TSB study showed that mainline derailments as a whole decreased by a factor of three between 1980 and 1988 (although the downward trend attened out between 1988 and 1993). e TSB attributed the reduction in derailments between 1980 and 1988 to improved installation and repair of CWR and increased use of automated rail defect detection and track geometry measurement technology. “I would add that replacement of older rail steels with cleaner steels rolled in 1985 or later also had a positive impact,” Roney said.
Rail grinding, particularly the conversion from corrective to rail pro le grinding, was another important part. Joint elimination and the movement away from standard carbon rails to intermediate grade rail steels in tangents and light curves, and premium head-hardened rail in sharp curves were also important, he said. “Improved steelmaking has reduced the indications of tensile residual stresses in the rail web, and there is less clustering of transverse defects than in the past. And when they occur, rail breaks have tended to be cleaner breaks, which are picked up by the signal system before a train nds them.
“Advancements in internal rail defect detection and more frequent ultrasonic testing –moving from 25 million gross tons (MGT) to 5 MGT testing intervals , in particular, has been a big factor in reducing the number of broken rails,” he said.
e TSB identi ed wide gauge as a primary cause in 13 derailments over those
THE TRANSPORTATION SAFETY BOARD OF CANADA INVESTIGATED 327 DERAILMENTS BETWEEN 2000 AND 2020.Mike Roney addresses the 2022 Wheel/Rail Interaction Conference Photo Credit: Wheel/Rail Seminars
20 years. ey also indicated that in ve of those derailments, poor inspection practices missed things that should have been seen. “Granted, some of them were wintertime inspections during which inspection was di cult and there was no visible indication in the snow that the rail was spreading,” Roney said. “Nonetheless, the circumstances led us into corrective actions, such as use of gaugerestraint-measurement systems, which are very e ective at nding hidden and dynamic instances of wide gauge.” e data shows that 85% of the wide-gauge derailments that were investigated occurred in 2012 or earlier. ere were no major derailments between 2013 and 2016; only one in 2018 and one in 2020 — a dramatic improvement in preventing widegauge derailments, he said.
A revision to the track safety rules by Transport Canada in 2012 increased the requirements for track geometry testing, and spurred railways to increase light geometry testing on lighter used lines and some yard tracks. e problematic gauge areas identi ed as a result has also likely had an impact on the reduction in wide-gauge derailments.
During the 20-year period in question, there were 11 track buckle derailments. “Not surprisingly, track work had been performed at the time of or just prior to the derailment in seven of these cases. It’s likely that the rail had not been properly de-stressed before a tie gang moved in and disturbed the track,” Roney said. Four of the derailments noted insu cient or inadequate anchors and poor tie condition as primary factors. “ e good news is that there was only one investigation (in 2019) of a major track buckle derailment.”
e TSB issued a safety recommendation in February 2003 concerning the need to de-stress continuous welded rail. Work done by the TTCI (now MxV Rail) in Pueblo showed how track reacts before and a er tamping, and how neutral temperature tends to drop over time as track is disturbed. ey also provided very good information on how long a rail needs to be unclipped to do a proper destressing, he said.
With a push from the Federal Railroad Administration, railroads developed common standards for CWR management, which included measuring rail temperature, measuring the gap or bypass every time rail was cut, guarding areas that were particularly at risk of track buckling, and de-stressing the rail before doing major programs or before the weather got hot. With signi cant portions of their networks in the U.S., Canadian National and Canadian Paci c adopted the collaborative CWR standard.
Six of the derailments that the TSB investigated cited rail rollover as a primary cause. Also identi ed were: poor tie condition; train handling was noted in three derailments; high l/v ratios in two derailments; and a binding truck in one derailment. Also noted was the e ect of the b/h ratio in rail rollover; that the location of the primary contact band of the rail is an important factor; and that wheel/rail conditions such as at rail heads with hollow-worn wheel treads coupled with wide gauge reduce the b/h ratio and move the contact beyond the base of the rail and start the rail rollover.
CN and CP have installed truck performance detectors to detect higher l/vs from bad actor cars as part of their corrective action plans. Both railways established programs to identify locations where the design superelevation in curves didn’t match the current operating speeds of longer, heavy trains.
“We all know that the rails speak to you,” Roney said. “When the gauge face of the high rail is wearing rapidly and the plates are cutting on the eld side, the curve is under elevated. And if the low rail shows heavy, mushrooming RCF, it’s likely over-elevated. A good understanding has been developed on how to balance those.”
e TSB expressly states that it’s not its function to assign fault, so they don’t address the faults of an individual inspector’s ability. “But in looking at some of these incidents in which the issues are pretty obvious, you have to scratch your head and say, ‘what was he thinking?’ at was pretty obvious.” Roney said. (See Understanding the Role of Human Factors in Railway Inspection, published in the May issue of RT&S.)
e TSB indicated that poor training was a root cause of 12 of the 90 track-caused derailments it identi ed.
“A er going through these derailments and looking at the training intervals versus a given derailment, we found little relationship between risk and manual inspection frequency: Roney said “But we did think there was something relating to training aptitude versus competency assurance. If we rely on a sole inspector in a critical territory to make all the right decisions, is that the right thing? Or do we need management oversight? Do we need competency assurance by having prociency tests on that inspector?” he asked. He noted that CP had instituted a ‘ride with the inspector program,’ several years ago in which managers were required to go out with the inspectors to “see if their eyes saw the same
things.” Another initiative was to establish electronic record keeping so managers could look in on inspectors to see what they were and what they were not nding.
Opportunities for improvement include the ability to:
• better identify disturbed track risks in advance of track work
• target rail neutral temperatures to strike the right balance between the frequency and consequences of track buckles vs. broken rails
• improve understanding of geotechnical and water management hazards to better anticipate extreme weather hazards
• employ mentoring and quality control of manual visual inspections, which is more e ective than training
• increase inspection frequency when tonnage rapidly increases on jointed track
• better de ne combination track geometry defects
• better identify the risk of rolling contact fatigue
Some opportunities for improvement have been incorporated into Transport Canada’s latest rules respecting track safety. ese include a new maximum time intervals between rail for detection tests that are de ned by tonnage and track class. Track geometry test cycles are now de ned for light and heavy geometry inspection vehicles. Quality assurance of track inspection and maintenance activities is now required, and a professional engineer must sign o on CWR management and rail wear management plans, Roney said.
“In the future, we’re going to have better integration of automated inspections and manual validation follow up. ere’s an opportunity to get away from biweekly manual / visual inspections and replace them with more e ective frequent automated inspections. e inspection regime could be better tailored to the risk pro le, the combination of track condition inspection capabilities and tra c mix,” Roney said. “We’ll need to continue working on lowering the vehicle/track interaction stress state. And we’ll need an escalation of what we do for maintenance and renewal action, based on predictive algorithms.”
Bob Tuzik is Publisher and Editor-inChief of Interface Journal (www.interfacejournal.com)
This article is based on a presentation made at Wheel/Rail Seminars’ 2022 Wheel/Rail Interaction conference.
What about the “M” in AREMA? e Maintenance team of railway engineering departments is by far the largest part of their organization. How does AREMA support this important group in our industry and how can we improve what we o er them? First, I will provide some background about the “M” and discuss how we have been striving to better support the maintenance teams.
AREMA was formed in 1997, as the result of a merger of three associations - the American Railway Bridge and Building Association (B&B), the American Railway Engineering Association (AREA) and the Roadmaster’s and Maintenance of Way Association (Roadmaster’s), along with functions of the Communications and Signals Division of the Association of American Railroads. e Roadmaster’s Association was the oldest of these associations dating back to 1883 and its purpose was very similar to the B&B Association. ey were a group of track maintenance professionals from many railroads who met to discuss common problems and share solutions for the betterment of the railway industry. Annually, they published the discussions and recommended practices on the topics they addressed, which were focused on practical eld applications.
AREMA operates similar to how AREA did. Most areas of the new association ourished, however some of the maintenance areas, particularly track, struggled. To address this and make a commitment to support this important group the Maintenance Functional Group was created in 2005. Within it, “Teams” were established
to focus on providing practical guidance and training materials. e Teams were Engineering Safety, Track Maintenance, Bridge Maintenance, and Signal Maintenance. is helped to provide some momentum, but more was needed to strengthen AREMA’s maintenance expertise. In 2016 the Functional Group Board of Directors (BOD) elevated the Teams to full Committee status to allow for the development of technical material and provide emphasis on not just design of infrastructure, but maintenance of it as well. e following year the BOD, with direction from the Board of Governors, realigned a few Committees within the Functional Groups and renamed the Maintenance Functional Group the Maintenanceof-Way Functional Group. is resulted in the MOW FG Committees we have today that focus primarily on track maintenance:
• 2 - Track Measurement and Assessment Systems
• 27 - Maintenance of Way Work Equipment
• 40 - Engineering Safety
• 41 - Track Maintenance
Committee 42 - Bridge Maintenance was merged with Committee 10 - Structures Maintenance & Construction which is part of the Structures FG. Committee 43 - Signal Maintenance was moved to the Communications, Signals & Information Technology FG.
e MOW FG is currently led by FG Vice President Mathew R. Porto (Sr. Director Workforce Planning and Analytics, Amtrak) and produces various educational and reference materials as listed below:
• 15 presentations are scheduled at the 2023 Annual Conference in conjunction with Railway Interchange this October in Indianapolis. Providing informative presentations on track maintenance has been a long-term strength of this FG.
• Committee 2 has two webinars that are available On Demand on the AREMA website for purchase - Critical Geometry Defects and Ground Penetrating Radar (GPR) for Track Bed Inspection. Committee 41 is working on a future Track Inspection Procedures webinar.
• Committee 2 is reorganizing their chapter this year for the 2024 Manual of Railway Engineering (MRE) publication. Both Committees 2 and 27 are actively updating their respective
MRE chapters.
• Committees 40 and 41 do not have a corresponding chapter in the MRE, but instead develop and maintain Best Practices for practical eld applications, intentionally similar to the objectives of the former Roadmaster’s. Committee 41 published ve Best Practices in 2022 exclusively as a member bene t –Installation of Switch Points and Stock Rails; Renew and Repair Road Crossings; Correct Gage Repair on CWR; Jointed Track, and Turnouts, Installation of Frogs; and Proper and Safe Spot Tie Replacement. ese can be found on the AREMA website under Member Home and then “Track Maintenance Best Practice.”
• Committee 40 is taking over the bridge worker and track safety subjects from other committees outside of the MOW FG and is working on e ective safety brie ng material.
Class I employee memberships have re ected the slow downsizing of Class I engineering sta s in recent years. is has particularly impacted the MOW FG. Committees 40 - Engineering Safety and 41 – Track Maintenance have the greatest need for members from railways. Because of their very small rosters it has been di cult for these committees to progress their work. Class I employee memberships are essential to how AREMA operates and to ensure the materials produced are aligned with the needs of the industry.
How can AREMA better position the MOW FG to add more value and to be more relevant to the track maintenance community? What changes should be made? e current organization of the MOW FG and the methods of material delivery were speci cally intended to align best with the needs of the maintenance community. Have we achieved that goal, or do we have more to do?
I have spoken with several of my maintenance peers in recent months to understand what they think would improve AREMA’s value. Here are a few things I heard:
• Provide good material for safety meeting discussions.
• Provide practical advice and actionable materials that can be applied by the eld for day-to-day business.
• Hold training events geared toward
eld supervisors and those with less experience. Provide “back to the basics” topics.
• Format material and events that accommodate eld supervisors’ limited time.
• Seek to attract the new, younger generations. e support of the Class I’s, Transits and Shortlines is imperative when seeking younger generations. ese companies must support their involvement and encourage participation in AREMA Technical Committees.
• O er maintenance symposiums to share common concerns and solutions, much like the former Roadmaster’s did. ey are less intimidating due to the smaller group, require less of a time commitment, and are tailored to more speci c interests.
• Consider using a local/regional maintenance group meeting format that limits the need for travel and time commitments by the maintenance personnel
JUNE 9-10
Committee 24 - Education & Training
Baltimore, MD
SEPTEMBER 30 -
OCTOBER 1
Committee 24 - Education & Training
OCTOBER 1
Committee 33 - Electric Energy Utilization
OCTOBER 1
Committees 11 and 17 Joint Meeting
yet provides networking opportunities. AREMA will look at this helpful feedback to see how it can be incorporated. What additional recommendations do you have? Please consider how you might bene t by joining a MOW FG committee and what you may have to o er to support the railway maintenance community. Your knowledge, experiences, and perspectives are important to AREMA and the next generation of railway professionals. Pass this article to colleagues in your organization who may not be familiar with AREMA. Expose them to this opportunity and encourage involvement. To learn more about what the MOW FG committees are involved with or to contact a committee chair go to the AREMA website under About Us and then “Technical Committees.”
Enjoy your journey until next month.
TRENT M. HUDAK AREMA President 2022-2023Register now for the AREMA 2023 Annual Conference in conjunction with Railway Interchange. Railway Interchange is back after four years October 1-4 at the Indiana Convention Center. For the latest information about Keynote Speakers, Technical Presentations, Sponsorship, and more, visit www.conference.arema.org
Is your Library up to date? Order the new 2023 Communications & Signals Manual today. With over 35 new, revised, reaffirmed, or extended Manual Parts, including over 500 pages of updates, get your copy of the 2023 Manual. Order online now at www.arema.org
NOT AN AREMA MEMBER?
JOIN TODAY AT WWW.AREMA.ORG
CONNECT WITH AREMA ON SOCIAL MEDIA:
JUNE 15-16
Committee 8 - Concrete Structures & Foundations Washington, DC
OCTOBER 1
Committee 5 - Track
OCTOBER 1
Committee 16 - Economics of Railway Engineering & Operations
OCTOBER 1
Committee 14 - Yards & Terminals
JUNE 21
Committee 16 - Economics of Railway Engineering & Operations Virtual
OCTOBER 1
Committee 10 – Structures Maintenance & Construction
OCTOBER 1
Committee 17 - High Speed Rail Systems
OCTOBER 1
Committee 40 - Engineering Safety
*Indianapolis, IN in conjunction with the AREMA 2023 Annual Conference
OCTOBER 1
Committee 12 - Rail Transit
OCTOBER 1
Committee 11 - Commuter & Intercity Rail Systems
OCTOBER 2
Committee 13 - Environmental
Joining a technical committee is the starting point for involvement in the Association and an opportunity for lifelong growth in the industry. AREMA has 30 technical committees covering a broad spectrum of railway engineering specialties. Build your network of contacts, sharpen your leadership skills, learn from other members and maximize your membership investment. If you’re interested in joining a technical committee or sitting in on a meeting as a guest, please contact Alayne Bell at abell@arema.org.
For a complete list of all committee meetings, visit www.arema.org.
1. Why did you decide to choose a career in railway engineering?
Growing up in Pittsburgh, I was always fascinated by the intricate bridges that spanned the city. is sparked my interest in engineering, particularly in the eld of structures. As I delved deeper into my studies, I realized that the railway industry presented a unique and exciting challenge. e combination of engineering principles, the dynamic nature of rail operations, and the opportunity to contribute to the transportation infrastructure motivated me to pursue a career in railway engineering.
2. How did you get started?
A er completing my engineering degree, I joined Norfolk Southern in their Bridges and Structures department. is was an excellent starting point for me to apply my knowledge and gain practical experience in the railway industry. Working on various bridge projects and collaborating with a team of experienced professionals provided me with valuable insights into the complexities and nuances of railway engineering.
3. How did you get involved in AREMA and your committee?
My involvement with AREMA began a er receiving encouragement from our then Chief Engineer, Jim Carter. Recognizing
the importance of professional development and industry collaboration, he suggested that I join AREMA and become actively engaged in one of its committees. I followed his advice and joined Committee 10 - Structures, Maintenance and Construction. is involvement allowed me to contribute to the advancement of the industry, network with like-minded professionals, and stay abreast of the latest developments and best practices in railway engineering.
4. Outside of your job and the hard work you put into AREMA, what are your hobbies?
When I’m not working or dedicating time
to AREMA, I cherish spending quality time with my family. I have a 5-year-old and a 20-month-old, and being a parent has been a profoundly rewarding experience. Watching my children grow and learn brings me immense joy.
5. Tell us about your family!
My family is incredibly important to me. I am blessed with a loving spouse and two amazing children. ey bring so much happiness and ful llment to my life. Being a parent has taught me valuable lessons about patience, resilience, and the importance of nurturing relationships. My family is my support system, and their unwavering support enables me to pursue my career and actively contribute to the railway industry.
6. If you could share one interesting fact about yourself with the readers of RT&S, what would it be?
I enjoy most outdoor activities which allow me to unwind and appreciate the beauty of nature. I particularly enjoy soccer, hiking, and biking.
7. What is your biggest achievement?
While I have achieved several professional milestones throughout my career, my biggest achievement is undoubtedly my family. Being a parent and seeing my children grow and thrive brings me immense pride and ful llment. eir happiness and well-being are my top priorities, and I consider the love and bond we share as my greatest accomplishment.
8. What advice would you give to someone who is trying to pursue a career in the railway industry?
To someone pursuing a career in the railway industry, my advice would be to soak it all in. e rail industry is a unique eld that o ers a wide range of opportunities and experiences. Embrace the chance to learn about the various operational disciplines and technologies involved. Stay curious, be open to new challenges, and actively seek out mentors who can guide you along your career path. Additionally, networking and involvement in professional organizations like AREMA can provide valuable connections and insights.
The Governance Nominating Committee, Chaired by Past President Michael P. Freeman, PE has completed its task and the following nominee has been o cially elected: Mr. Brent L. Laing, P.Eng. – Board of Governors. He will begin his Board of Governors position at the conclusion of the AREMA 2023 Annual Conference which is being held in Indianapolis, Indiana, October 1-4, 2023.
Brent Laing is a professional engineer with extensive Class I heavy haul freight railway technical and management experience. Brent was Vice President Engineering, and Chief Engineer of Canadian Pacific Railway, with overall responsibility for engineering issues in Canada and the US. He has led corporate environmental teams as Director Environmental Affairs, locomotive and freight car repair teams as General Manager Mechanical Operations, technical staff as General Manager Structures and Projects and as General Manager Track Maintenance. He retired from CP in 2015 and started up his own consulting business.
Brent was appointed to VP Engineering
at Canadian National Railway in June 2022 and has system responsibility for all engineering functions at CN.
Brent is a long-time member of AREMA and a professional engineer for over 37 years
Elected as Governor (2023 – 2026)
Name Brent L. Laing, P.Eng.
Title
Vice President Engineering
Organization/Company
CN
Rail A Caterpillar Co
MAIN OFFICE
JONATHAN CHALON Publisher (212) 620-7224 jchalon@sbpub.com
AL, KY, TN, CHINA
JONATHAN CHALON (212) 620-7224 jchalon@sbpub.com
CT, DE, DC, FL, GA, ME,MD, MA, NH, NJ, NY, NC, OH, PA,RI, SC, VT, VA, WV, CANADA: QUEBEC AND EAST, ONTARIO
JEROME MARULLO (212) 620-7260
jmarullo@sbpub.com
AR, AK, AZ, CA, CO, IA, ID, IL, IN, KS, LA, MI, MN, MO, MS, MT, NE, NM, ND, NV, OK, OR, SD, TX, UT, WA, WI, WY, CANADA: ALBERTA, BRITISH COLUMBIA, MANITOBA, SASKATCHEWAN HEATHER DISABATO (CHICAGO OFFICE) (312) 683-5026 hdisabato@sbpub.com
AMERICAS, EUROPE, ASIA, AFRICA, AUSTRAL ASIA NORTH AMERICA - CT, DE, DC, FL, GA, ME, MD, MA, NH, NJ, NY, NC, OH, PA, RI, SC, VT, VA, WV, AND EASTERN CANADA. EUROPE EXCEPT GERMANY, AUSTRIA, GERMAN SPEAKING SWITZERLAND, EASTERN EUROPE, ITALY, AND ITALIAN-SPEAKING SWITZERLAND. ASIA EXCEPT JAPAN AND CHINA. JEROME MARULLO (212) 620-7260 jmarullo@sbpub.com
GERMANY, AUSTRIA, GERMAN-SPEAKING SWITZERLAND, LATVIA, LITHUANIA, ESTONIA, POLAND, CZECH REPUBLIC, SLOVAKIA, HUNGARY, SLOVENIA, CROATIA AND SERBIA SIMONE AND SIMON FAHR
Breitenbergstr. 17
Füssen 87629
Germany
Tel: +49 8362 5074996 sfahr@railjournal.com
ITALY, ITALIAN-SPEAKING
SWITZERLAND
DR. FABIO POTESTA
Media Point & Communications SRL
Corte Lambruschini
Corso Buenos Aires 8 V Piano, Genoa, Italy 16129
+39-10-570-4948
Fax: +39-10-553-0088
info@mediapointsrl.it
JAPAN
KATSUHIRO ISHII
Ace Media Service, Inc.
12-6 4-Chome, Nishiiko, Adachi-Ku
Tokyo 121-0824
Japan
+81-3-5691-3335
Fax: +81-3-5691-3336
amkatsu@dream.com
IRJ PRO AND CLASSIFIED ADVERTISING SALES
JEROME MARULLO
(212) 620-7260
jmarullo@sbpub.com
Reader Referral Service
This section has been created solely for the convenience of our readers to facilitate immediate contact with the RAILWAY TRACK & STRUCTURES advertisers in this issue. The Advertisers Index is an editorial feature maintained for the convenience of readers. It is not part of the advertiser contract and RTS assumes no responsibility for the correctness.
When I began studying railroads, I quickly became a fan of Southern Railway and its then-president, W. Graham Claytor, Jr. It didn’t take long to realize that Claytor spent considerable time on the road riding freight trains, visiting crews, and meeting employees at various facilities around the system. While Claytor was a self-avowed rail enthusiast, the goal of his time on the railroad was much more than pursuing his passion. Claytor knew that e ective CEOs, particularly rail CEOs, must be visible and known to as many of the hard-working people in the eld as possible. e CEO must appreciate and understand the eld jobs, not simply from a textbook or job description. It’s hard for a job description to convey the feeling of blowing snow and wind in your face while switching a plant. You must be out there. You must feel it.
While one might expect this attitude from a former operating railroader who has been there and done it, Claytor’s background was law. Indeed, he joined the company as Vice President – Law several years before he became CEO. e time he spent on railroads before he came to Southern was likely as a passenger on a passenger train. Yet, he appreciated and respected the job done by railroaders in the eld, and he made a point of letting them know it.
I don’t know how much time the current rail CEOs spend in the eld. For all I know, Keith Creel, Lance Fritz, Katie Farmer, and Tracy Robinson are in the eld frequently. I hope they are. I do know that the two CEOs missing from this list spend a lot of time in the eld meeting and talking with employees – Alan Shaw of Norfolk Southern and Joe Hinrichs of CSX. Both chief executives seem to naturally know that it’s essential to be on the ground frequently with those who run the railroad daily.
Shaw has, understandably, been especially visible since the East Palestine derailment. However, he began spending time with employees in the eld as soon as he became CEO on May 1, 2022. Moreover, Shaw spent time in an operations position with NS earlier in his tenure, giving him rst-hand experience with work in the eld. He has
continued to visit places around the system even a er East Palestine, which speaks to his commitment to the railroad’s culture and employees. In my view, the time Shaw has spent in and working on East Palestine has been very e ective, and he is living up to his commitment to “make it right.” Did NS get a slow start out of the gate in addressing what happened in Ohio? Perhaps. Not to take anything away from the challenges to and su ering of the residents of East Palestine, I believe NS has more than made up for a slow start with what it has done and promised to do. I think it’s fair to say that while other CEOs would do what Shaw has done regarding remediation in Ohio, it’s fortunate for the rail industry and NS that Shaw was in the chair when this happened. Having the wrong CEO or the wrong response to this tragedy would have spelled disaster for the company and the industry.
Joe Hinrichs’s time on the ground has also been well spent. As the former president of Ford Motor Company’s automotive division, he understands people’s importance. Despite the in ux of robotics into automobile manufacturing facilities, people are as important in that industry as ever. Hinrichs brought this understanding of people to CSX and appears to have begun mending the company’s employee relations that were su ering badly from the brief tenure of Hunter Harrison and precision scheduled railroading run amuck.
Hinrichs has also held events bringing employees and their families together, promoting goodwill and a sense that the company cares about workers and their loved ones. While I’m sure other railroads do this to some extent, it seems this has been a priority for Hinrichs since he became CEO.
Future CEOs should study the careers of people like Claytor, Shaw, and Hinrichs. Again, I don’t know how much time the other “big six” CEOs spend in the eld. Given the recent issues with labormanagement agreements, customer service concerns, and other challenges, I imagine they spend a respectable amount. To repeat what I said earlier, CEOs need to be out there. ey need to feel it. ey need to show their employees that they give a damn.
TheAREMA2023AnnualConferenceinconjunctionwith RailwayInterchangeisbackafterfouryears.Joinusto network,expandyourknowledgefromthenearly80Technical Presentations,findsolutionsintheExhibitHallfeaturingover 700companies,andmuchmore.