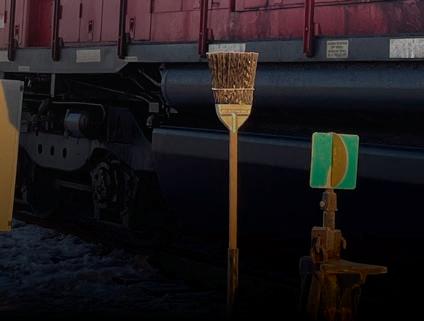
20 minute read
GET DONE HOW THINGS
Project Work is the Key to Building and Maintaining Rail Infrastructure
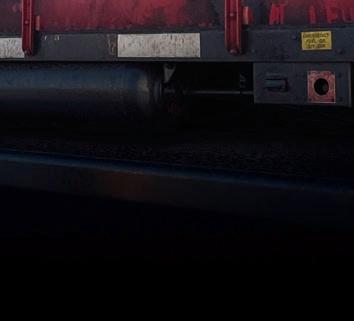
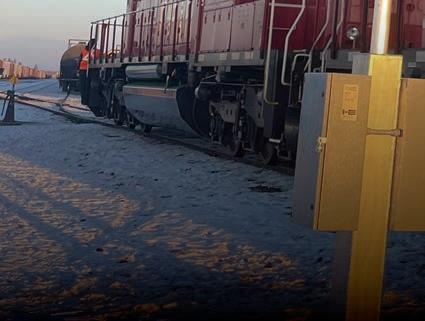
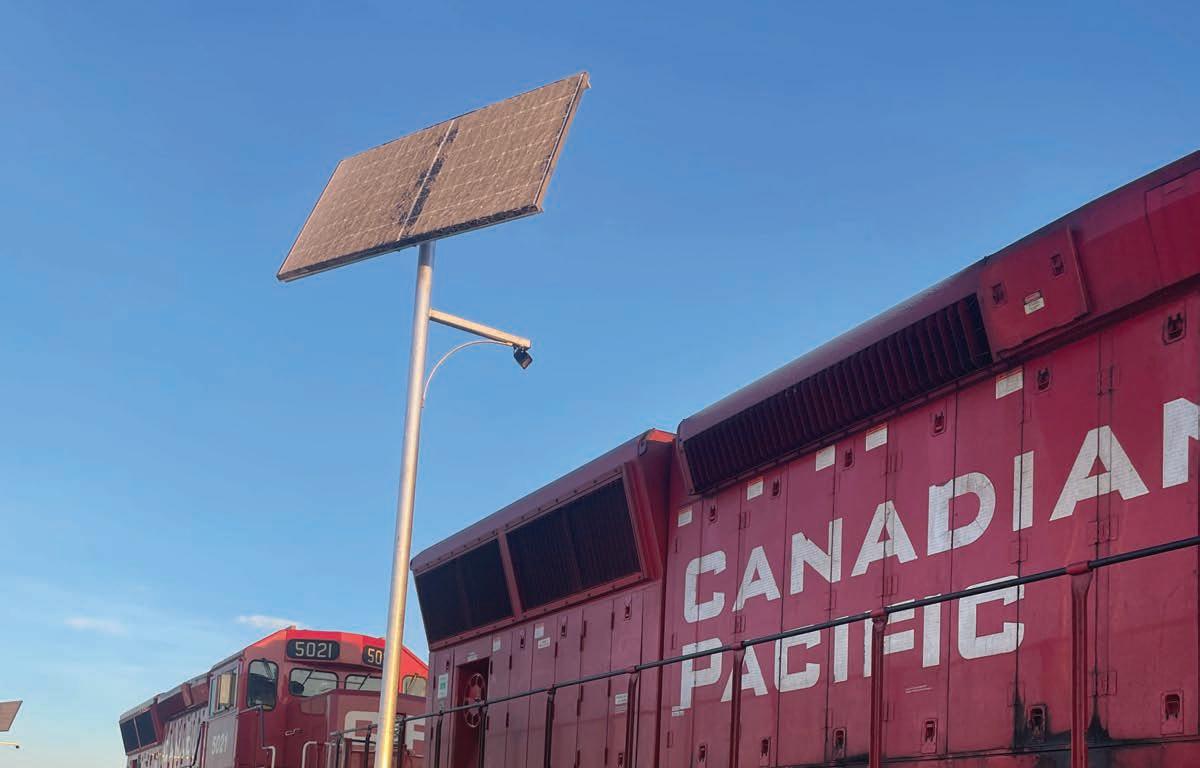
The term “project” can mean many things. You could say that your plan to clean out your garage this weekend is a project. Remodeling your bathroom is a project. And, if you haven’t done it in a while, balancing your checkbook could be considered a project.
Maintaining the nation’s railroad infrastructure is usually a cooperative e ort between engineers, construction rms, and rail carriers. While the railroads typically own their entire infrastructure, and perform regular maintenance on it, the involvement of engineering design rms and contractors to execute major projects is critical. e level of professionalism among the parties executing
By David C. Lester, Editor-in-Chief
the project must be very high, the project must stay within budget unless something unforeseen crops up, and the work between development of the project plan to opening the new infrastructure for rail service must be managed with great care and focus. Lack of attention to detail or carelessness of any sort will likely result in problems down the road. And as they say in engineering schools, “you don’t get partial credit if the bridge falls down.” is year, we’re pro ling nine projects that stood out from the other submissions. While we would like to have pro led every project, available space would not allow it. While we only feature what we consider to be top projects, we tip our hats to all the projects that were submitted for consideration of this honor, as well as those that were not submitted. Despite industry challenges of the past few months, the North American railroad infrastructure is among the strongest and best maintained in the world. All of this is accomplished through well-managed projects. Please join us as we review our top picks for 2023.
CLASS I: NEW CONSTRUCTION (BRIDGES)
NS Pearl River Truss Replacement
Pearl River, La.
• Prime Contractor: PCL Civil Constructors, Inc.
• Prime Designer: G&A Consulting Engineers
• Owner: Norfolk Southern e project team for the Norfolk Southern bridge crossing the East Pearl River in Louisiana faced several challenges throughout the on-line replacement of the nearly 120-yearold existing truss span while allowing the safe passage of trains across the river. e success of the 22-month Pearl River project was achieved with minimal disruption to the rail tra c that utilizes the line. In addition, the constant ow of local vehicular and pedestrian tra c underneath the bridge had to be maintained throughout the construction process. e Pearl River project also endured a major hurricane, several seasonal ood events from record rainfall and material delays due to the COVID-19 Pandemic. e project began in January 2021 with the temporary falsework / access trestle utilized to perform the main span change, followed by the installation of the structure’s new drilled sha /cast-in-place concrete cap foundation and substructure. ere were six seasonal ood events that halted work during these activities, resulting in a cumulative 15 days of delays, followed by Hurricane Ida, which hit Louisiana in late August 2021, causing another 10-day delay due to high winds, power outages, and additional jobsite ooding. In August 2021, PCL was noti ed of a supply chain delay of the raw steel material used to fabricate the new through plate girder spans. e original span swap date was scheduled for February 2022, but due to the signi cant delays caused stemming from the COVID19 Pandemic the span swap was successfully completed in July 2022. roughout the delays, PCL worked with Norfolk Southern to minimize the potential for additional lost time on site by completing all substructure and falsework installation by e project team was also a steward of nature while working on this project. Located within the Honey Island Swamp and Bogue Chitto Wildlife Area, PCL took great care to minimize the environmental impacts on the project. Items such as turbidity curtain, silt fence, 110% containment, etc. were utilized to avoid impact to any wildlife or environmental areas along the Pearl River. is project also dismantled the existing truss span, which contained lead paint on its members. PCL took great care to follow all regulatory requirements to perform the demolition of the existing span safely and successfully. e project team worked to prevent a signi cant carbon footprint and reduce risks of leaks and spills from equipment by only utilizing the bare minimum. In addition, all hydraulic oils used on the project were environmentally friendly biodegradable oils. In addition, PCL was able to donate a portion of some used construction materials at the end of the project, that we used to improve property roadways and access to previously saturated areas. is project resulted in reduced maintenance costs for Norfolk Southern and allows a crucial transport line to be intact for years to come. PCL achieved nal completion on October 4, 2022, to the satisfaction of Norfolk Southern.
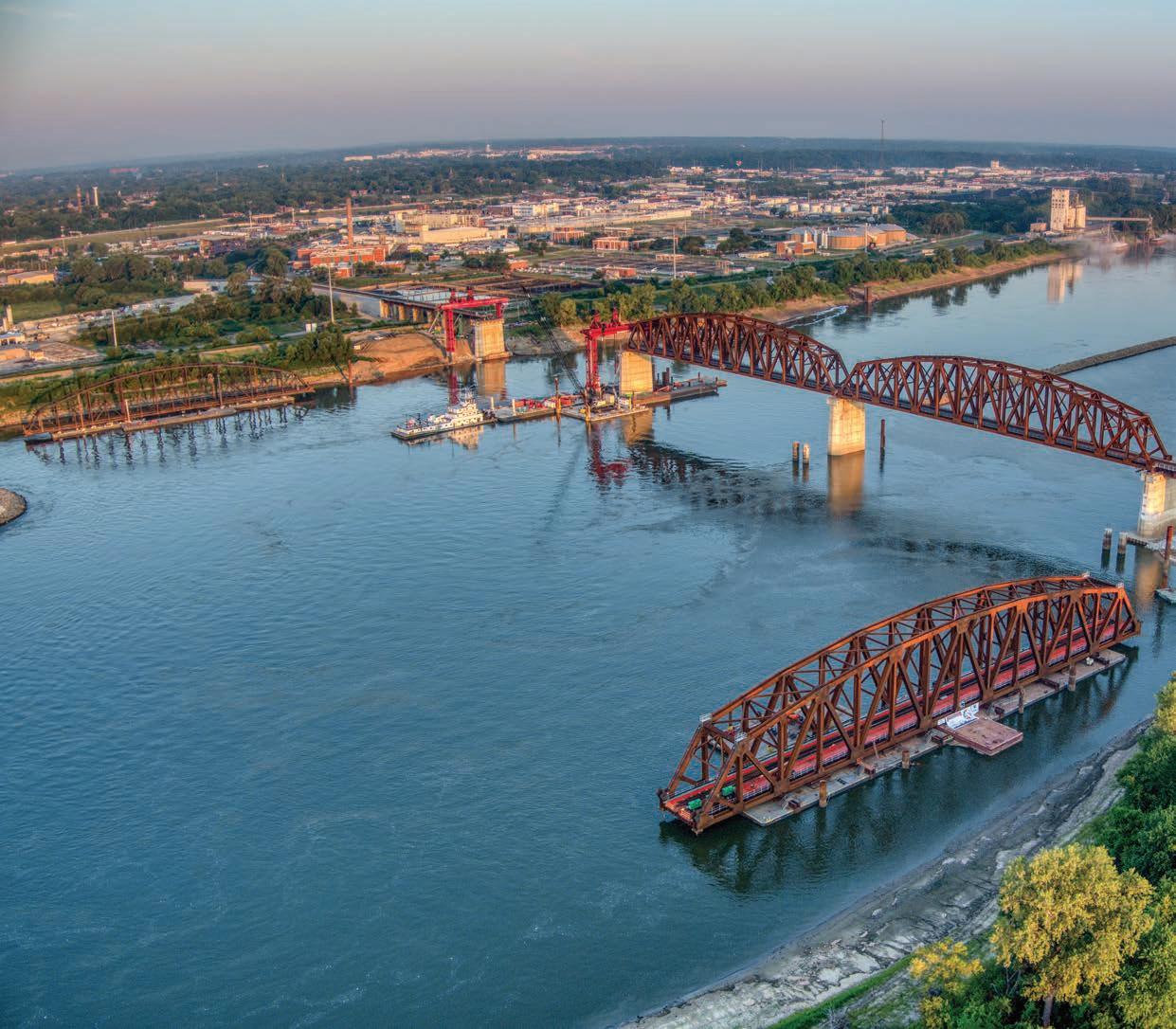
February 2022, as scheduled. Upon the delivery of the steel, PCL accelerated and modied its steel erection schedule to deliver the completed project as soon as possible. Some of the innovations that were used on this project included the slide system designed by PCL’s construction engineer, McNary Bergeron & Johannesen, along with a spin on accelerated bridge construction. To minimize delays to the rail tra c above, PCL/McNary designed a slide system o a temporary trestle on either side of the existing truss span. Each trestle provided access for construction materials & equipment to successfully install all foundation and substructure elements without disruption. In addition, these trestles also provided support for falsework beams to be placed beneath both new and existing spans. ese “slide beams” provided a straight track for each “cart” supporting each span. e carts were pulled via a hydraulic jacking system. is jacking system allowed the spans to move e ciently during the 16-hour change outage and not cause any delays once complete.
PASSENGER/TRANSIT: NEW CONSTRUCTION (RAIL)
EastBound Re-Route Construction for the East Side Access Project
East Side Access, New York, N.Y.
• Prime Contractor: Railroad–Michels,
Joint Venture
• Prime Designer: Gannett Fleming
• Owner: MTACC e Railroad-Michels Joint Venture, LLC continues to complete the MTA Construction & Development design/build Eastbound Re-Route Project, contract CH058B, within Harold Interlocking, the largest railroad junction in New York City and the busiest in the United States. e improvements will re-route track carrying Metro-North, Long Island Rail Road and Amtrak trains, improving the daily travels of thousands of commuters and providing congestion relief for trains traveling along the Northeast corridor. e project’s scope of work includes the design and construction of a new 2,100 LF cut and cover tunnel, modi cation and re-support of the existing Honeywell St. Bridge, demolition and new track work, and overhead catenary systems, all of which is being conducted in an active railroad environment, requiring close coordination with ongoing train operations.
Existing track and catenary systems were removed which initiated the start of a longterm outage allowing the construction of the East-Bound Re-Route structure. Following completion of the structural work, track installation including two #20 turnouts, insulated joints, compromise joints and transition rails as well as third rail systems will be installed in conjunction with new catenary structures and wires to support the movement of Amtrak train consists through the interlocking. Additional work includes traction and facility power, signals, communication systems and improvements to the storm sewer system.
PASSENGER/TRANSIT: NEW CONSTRUCTION (BRIDGES)
Massachusetts Bridge Bundle
Massachusetts
• Prime Contractor: Barletta Heavy Division
• Prime Designer: VHB
• Owner: Massachusetts Bay Transportation Authority e design team needs to provide innovative solutions to solve the varied challenges. To do this, ve of the six bridges are being built using precast concrete substructure components installed behind the existing abutments, leveraging consistent details to simplify design, fabrication, and construction.
A key goal of this project is to minimize impacts to riders. e contract allows only nine total weekend rail line shutdowns to fully replace all six structures and each bridge has its own set of needs and circumstances.
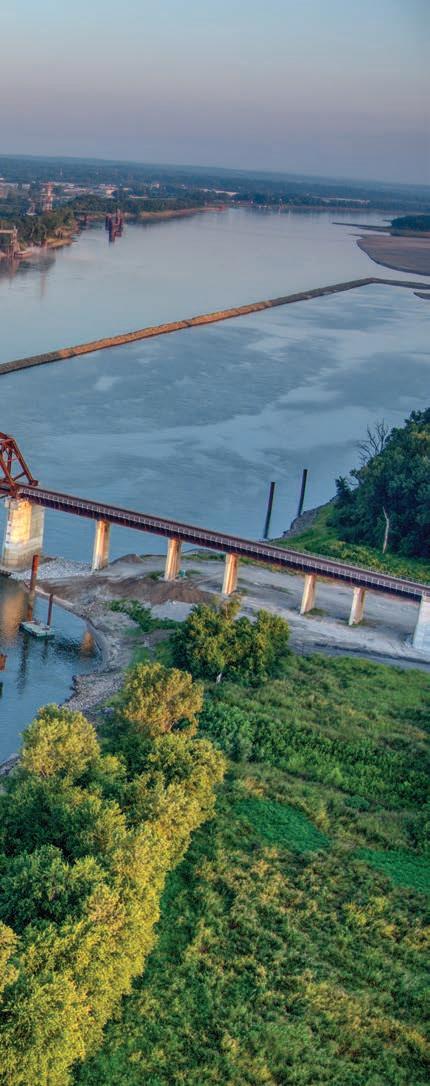
Most of the bridges are being replaced using Accelerated Bridge Construction (ABC) techniques, including self-propelled modular transporters (SPMTs) to move the superstructures into place. Work on two of the bridges needs to be conducted simultaneously. Two of the bridges, one at Bacon Street and one at Intervale Road, are located within just one mile of each other on the same line. Due to their proximity, work on the bridges had to progress simultaneously during each weekend outage. Although challenging to coordinate double crews and equipment needed, the bridges were designed with common details and nearly identical construction sequences to simplify the process, reduce risk, and minimize impacts to the traveling public.
SHORT LINE MAINTENANCE (RAIL)
Johnson County Railroad 286K Rehabilitation
New Century Commerce Center, New Century, Kan.
• Prime Contractor: TL Wallace
• Prime Designer: In House
• Owner: Johnson County Airport Commission e greatest challenge of rehabilitating an active, predominantly single-track short line railroad was maintaining the highest level of service to time sensitive customers on short notice. is has been accomplished with the highest level of safety and service with the cooperation and exibility of the contractor, along with JCAX’s rail employees. Each rail customer fully understood that the key benets of upgrading rail and turnouts from 90 lbs. (aged at nearly 100 years old) to 136 lbs. are to increase safety and prevent obsolescence.
Cooperation from all stakeholders has been key in making the entire project a success. Another challenge to the process is determining what rail components must be replaced now, and what can wait until more funding is available to upgrade the entire system. Material cost increases have greatly reduced the trackage that can currently be upgraded to 286K standards. Adjustments have been made to redirect mainline tra c onto the heavier relayed rail wherever possible. Despite the increase in cost, the JCAX has been able to rerail 56% of the total system, or 9,500 track feet of the 17,000 total system trackage.
Also very notable, 11 of 25 system turnouts, which are potential points of failure, have been replaced as well. Because of the activity of the work being performed and the overall improvements to the system, an existing food producing lessee located next to the railroad is taking notice. In the past, this national customer utilized rail delivery and stopped. Because of the and upgrades made to the system, they have approached the JCAX with the intention of beginning rail service once again.
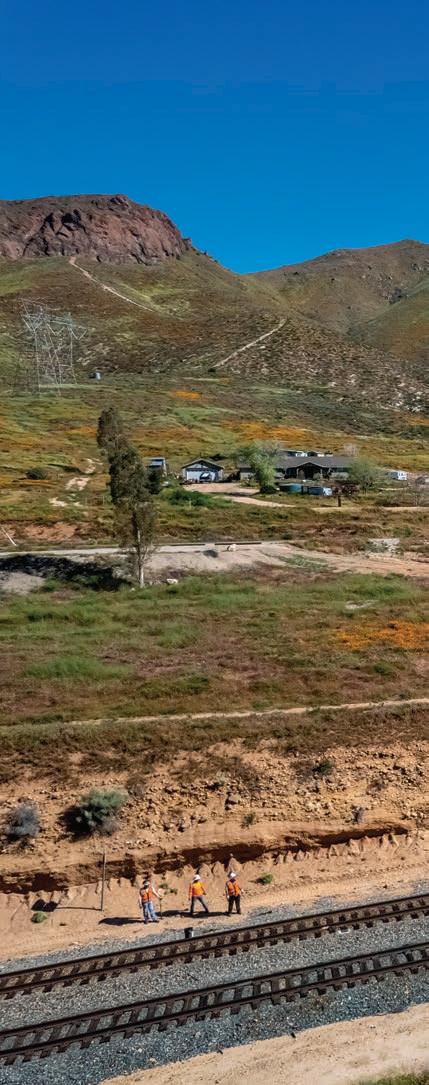
CLASS I: NEW CONSTRUCTION (BRIDGES)
BNSF Bridge 81.4
Washington state
• Prime Contractor: Hamilton Construction
• Prime Designer: HNTB
• Owner: BNSF Railway e bridge’s extremely remote location made it di cult to secure substructure and geotechnical information. Virtually the only access is via rail, and it was not possible to drill a boring in the river without suitable access. e team, therefore, had to make assumptions in its foundation design for the piers in the river and get borings when construction started and a temporary work bridge was installed. To accomplish this, the team built on information available from drilled sha s along the banks of the river. However, once the team had site access, they found that the basalt rock layer was higher than expected. It presented a dramatic elevation change –deep on one end of the bridge and almost at the surface on the other. e team rapidly made foundation design changes in coordination with Hamilton Construction, including placing rock sockets into the basalt rock layer. In addition to the basalt rock layer challenges, boulders were rampant at the site, making it di cult to drive H piles as planned because the piles would not have remained straight. To mitigate this issue, the design and contracting teams elected to drill sockets for the H piles. e design changes were completed without impacts to the schedule. Construction was successfully completed in March 2023.
Project development and design of BNSF Bridge 81.4 across the Cowlitz River in Washington state began in 2013 requiring signicant stakeholder coordination and regulatory approval. e existing bridge consisted of 101’-8” long deck plate girders and a 250’-0” long pin-connected truss. e 100+ year old bridge had reached the end of its service life and needed to be replaced to ensure reliable service.
HNTB evaluated a range of replacement options which included re-using the existing substructure, using an on-line alignment and o -line alignment to fully replace the bridge. e project was initially designed and went out to bid as an online replacement bridge with a truss span. BNSF ultimately decided on an o ine alignment due to high train tra c. Working closely with Hamilton Construction, BNSF changed the delivery method from design-bid-build to Construction Manager/General Contractor. By moving into the construction phase with Hamilton, the project team was able to streamline construction and reduce project costs. e nal bridge consisted of 143’-4” and 207’-6” long deck plate girders supported on large diameter drilled sha s with rock sockets and box beam approach spans supported on H-piles.
Construction commenced in 2020 due to the challenge of coordinating various stakeholder interests. To address this challenge, HNTB’s design team coordinated closely with local permitting agencies as well as with the local Cowlitz and Chehalis Confederated tribes, whose tribal lands would be a ected by the project. Early and o en in the process, the team met with tribal representatives to understand the potential impacts on the tribes’ land, shing access and historical or cultural resources.
PASSENGER/TRANSIT: MAINTENANCE (RAIL)
Metrolink Track and Signal Infrastructure Maintenance and Support Services
Los Angeles
• Prime Contractor: Herzog Contracting Corp.
• Prime Designer: N/A
• Owner: Metrolink
As the Southern California Regional Railroad Authority (SCCR) Metrolink Commuter Rail Maintenance-of-Way provider, Herzog Contracting Corp. (Herzog) is responsible for maintaining a network of 419 Metrolink route miles spanning over 33,000 square miles in the Los Angeles basin. is includes maintaining – come rain or shine –all track, signal, bridge, and drainage structure infrastructure within the Metrolink right-of-way to ensure safe and reliable commuter rail operations. roughout these recent severe weather events, Herzog collaborated closely and proactively with SCRRA to keep the Metrolink commuter rail system open and operational for commuters. Herzog strategically staged resources, materials, and heavy equipment across the Metrolink network to be well-positioned to respond to weather-caused right-ofway service disruption.

From December 2022 through January 2023, Southern California experienced unprecedented rainfall – 400-600 percent above average – resulting in major ooding, rockslides, and mudslides across LA County, which caused major impacts and damage to the SCRRA Metrolink right-of-way.
Metrolink’s rail infrastructure was signicantly impacted by track washouts and track obstructions caused by tree, rock, and mudslide debris. Rainfall was so severe in January that Union Station ooded. ese weather events resulted in Metrolink systemwide service disruptions such as slow orders, delays, dark signals, and other service impacts that had the potential to compromise the safety of Metrolink operations.
Additionally, Herzog communicated closely with Metrolink and with the community to address ooding and mudslide issues as they arose - and before they became unmanageable. Herzog maintenance-of-way crews worked around the clock repairing rail infrastructure, clearing debris from the track, and xing drainage problems to keep Metrolink trains moving, never ignoring or refusing an issue because it was or wasn’t their job.
Speci c to this year and a direct result of the ooding was the development of sinkholes in and around the Metrolink mainline tracks. To combat this hazard, Herzog personnel worked tirelessly to inspect each sinkhole, check for utility obstructions, and ll the holes with ballast to keep the trains running. Additionally, they worked continuously to keep the track operational during constant rock slides in the Santa Clarita area, where the train runs through rock-covered hills. is required continual monitoring and clearing of the track using backhoes and loaders.
Herzog’s e orts in the midst of these challenges did not go unnoticed. At the
January 2023 SCRRA Metrolink board meeting, Herzog was recognized for its success in tackling these challenges by the Metrolink Board of Directors and CEO, Darren Kettle.
SHORT LINE: NEW CONSTRUCTION (BRIDGES)
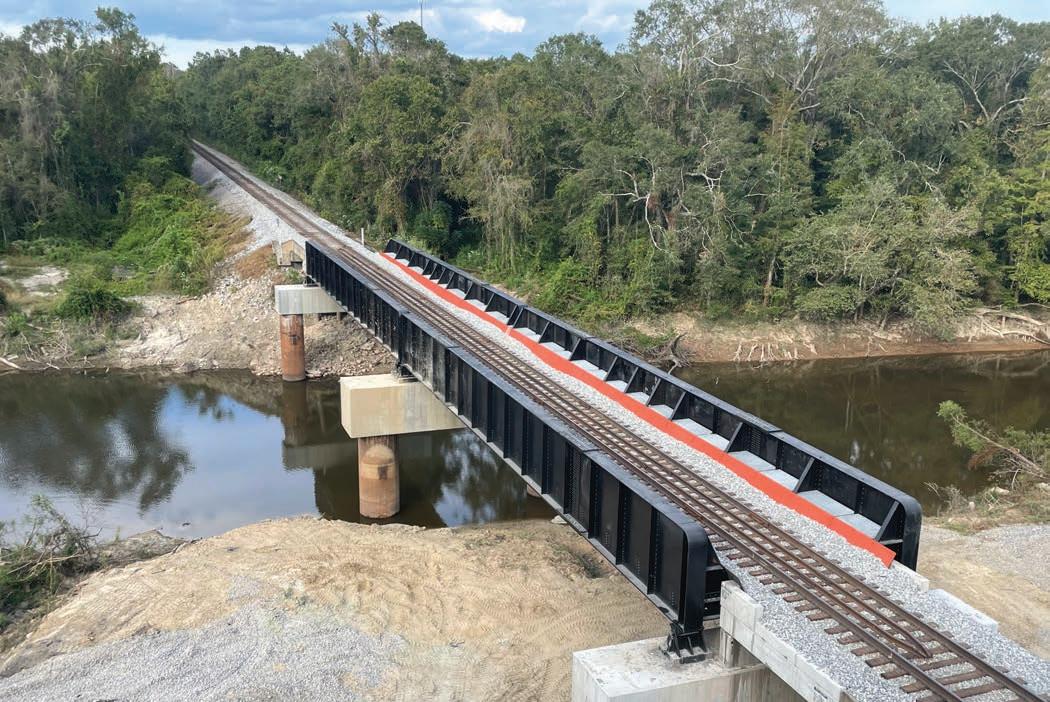
Merchants Bridge Main Span Trusses & East Approach Replacement
St. Louis, Mo.
• Prime Contractor: Walsh Group
• Prime Designer: TranSystems Corporation
• Owner: Terminal Railroad of St. Louis (TRRA)
Reconstructing a historic bridge of this magnitude involved a number of construction-related challenges.
Pre-construction environmental clearance and permitting was complex involving multiple federal lead agencies and the bi-state coordination necessitated by this major Mississippi River crossing involving Missouri and Illinois state agencies as well as municipalities. Because this was a federal action with federal permits, NEPA documentation was required to evaluate the potential impacts to the human and natural environment. e historic signi cance of the bridge necessitated additional coordination culminating in a Memorandum of Agreement amongst the US Coast Guard (USCG-lead agency), both State Historic Preservation O ces (MO & IL), Federal Railroad Administration (FRApotential funding entity) and the owner, TRRA. In total, the project’s environmental clearance required approval of three NEPA documents: Categorical Exclusion (USCG & FRA), subsequent Re-examination (USCG), and an Environmental Assessment for the US Army Corps of Engineers (USACE). A er the bids were received the permitting processes could be facilitated on behalf of TRRA by collaborating with the selected contractor. Permits included USCG Section 9; USACE Sections 10/404/408 Permits; ILEPA/MDNR Section 401 Water Quality Permits; Floodplain Permits (MO & IL); Land Disturbance (Section 402) Permit and Stormwater Pollution Prevention Plan (SWPPP). In addition to the lead federal agencies (USCG, FRA, USACE), project agency coordination involved but was not limited to US Fish and Wildlife Service (USFWS), Illinois Environmental Protection Agency (ILEPA), Missouri and Illinois Departments of Natural Resources (MDNR & IDNR), Metropolitan Sewer District of St. Louis (MSD), Metro East Sewer District (MESD), the cities of St. Louis (MO) and Venice (IL), Madison County Transit and Great Rivers Greenway. Maintaining NEPA and permit compliance demanded continued coordination with many of these state and federal agencies through and beyond construction completion. e heavy li gantry system was designed and fabricated by Mammoet. e east approach is within the levee limits on the Illinois side of the river thus maintaining ow during high water events was required. In contrast to the previously encased west approach, cast-in-place concrete culverts were designed with a supporting foundation system to allow ow to pass through. Lightweight cellular concrete ll was designed to minimize pressure and settlement on the existing and proposed foundation systems. is ll also was able to ow in and around the existing steel towers and girders eliminating the need for costly steel demolition and interruptions to rail operations.

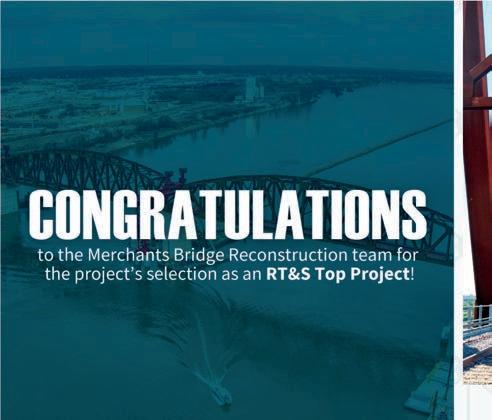
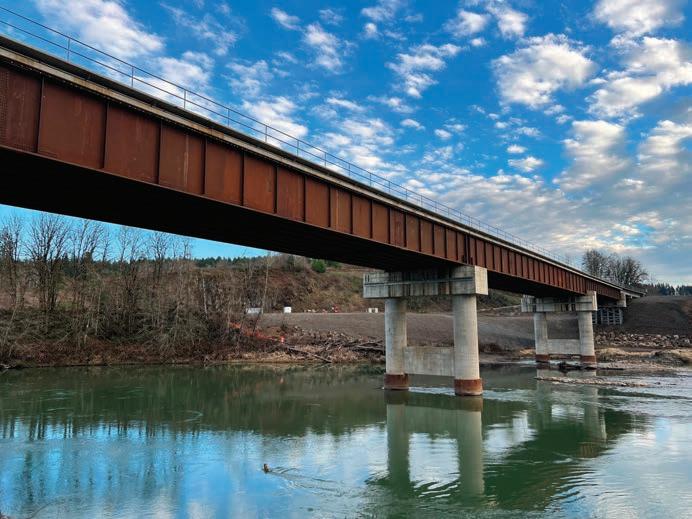
Replacing the three 523’ main river truss spans, complete with a gantry system with strand jacks to li and slide the old and new truss spans, also required precise on-site coordination. Removing the existing truss weighing 3,900,000 pounds and installing the proposed truss weighing 9,000,000 pounds proved to be the most challenging aspect of the project. Coordination and collaboration between all parties was key for success. e erection and demolition engineering, barge stability analysis and gantry tower foundation design was performed by Genesis Structures.
Working on a live rail line was another challenge that required coordinated track outages. Twin lines were reduced to a single track with a scheduled 5-hour daily track outage to accommodate construction. A planned 10-day rail outage took place for each of the three truss span replacements, as did two 24-hour river channel outages so workers could remove the old river truss spans and install the new ones. Coordinating daily river tra c in the primary and secondary river channels required tight logistics and constant monitoring of the river levels.
Building within the footprint of the existing Merchants Bridge also lent a layer of complexity to the job.
PASSENGER/TRANSIT: MAINTENANCE (BRIDGES)
Cherry Valley Avenue Design-Build Bridge Replacement Project
Garden City, N.Y.
• Prime Contractor: Railroad
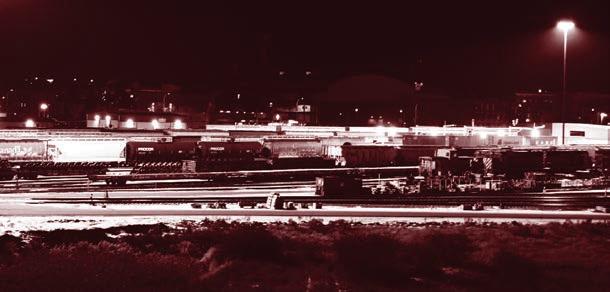
Construction Company, Inc.
• Prime Designer: KSE Engineers
• Owner: Long Island Rail Road e existing bridge’s low clearance triggered numerous safety issues with box trucks and tractor trailers striking the bridge, causing tra c back-ups and train delays. e two biggest challenges with this project were: 1. Performing the work without interfering with weekday commuter trains. 2. Moving the new bridge, a large pre-assembled structure, into location, in one piece. e new bridge installation was accomplished without impeding weekday commuter trains by the following steps:
Project Scope: is Design/Build project replaced the existing bridge, built in 1871, with a new bridge and increased vertical clearance from 11 . to surpass the minimum state DOT standard of 13 . 6 in to 14 . 6 in.
1. Reinforce the existing abutments and footings by adding additional concrete encasement. Under an approved tra c pattern, RCC performed the work during the day by exposing the existing footing, drill and
Railway Facilities Electrical Specialists
•Complete Electrical Services
•Yard & Building Lighting:
• Office Lighting
• High-Mast Towers
• Solar Lighting Solutions

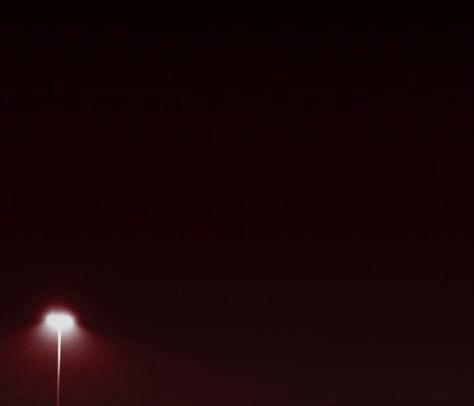
• Turn-key wood & metal pole installation
•Electrical Distribution Service & Upgrades
•Excavation Services:
• Trenching
• Hydrovac
• Horizontal Drilling
• Helical Piles grout dowels to both footings and abutments and then set formwork, place concrete and strip. e new encasement secured the structure ensuring its strength to safely carry the new bridge. e time to travel approximately 1,000 . for both the old bridge, and new bridge was one hour in each direction.
2. A er the abutments and footings were structurally encased, RCC would then jack the existing bridge to provide the additional 42” of clearance for the new bridge. is required three weekends of Jacking, one weekend to re-construct a nearby roadway crossing, and nally, one weekend to remove the existing bridge, and “Roll-In” the new bridge into its nal location. We had to jack the existing bridge over multiple weekends due to the subsequential work of having to then re-align the existing track on both sides of the existing bridge to meet the new height. Had we simply removed the old bridge and installed the new one at an additional 42” in vertical height –there would never have been enough time to re-open the track to the traveling public by 5 a.m., Monday(s). Each weekend outage typically supplied enough time to jack 12” of vertical li . Once the bridge was jacked, steel bolsters were installed to hold it in place until the following weekend, when it could be jacked once more.
3. When the existing bridge reached its nal vertical clearance, the nal weekend closure occurred to rst remove the old bridge, second, Install the Precast Bridge Seats, third, install the New Bearings and fourth Install the New Bridge.
We proceeded to burn out the bolsters and move the Self-Propelled Modular Transport trailer (SPMT) underneath the old bridge. is machine had shoring towers with integral jacks which allowed an approximate stroke of 11 in. to “pick” up the old bridge, and transport it away to a nearby lay-down yard. is bridge (and the new bridge too) weighed over 300,000 lbs.
A er the old bridge was removed, we installed four precast bridge seats. ese seats made up the vertical clearance needed and weighed 30 tons each. ese precast seats were then grouted to the underlying newly encased bridge previously constructed.
Following installation came the bearings. Each bearing weighed approximately 1,500 lbs.
Finally, once again utilizing the SelfPropelled Modular Transport trailer (SPMT) the new bridge was moved into position.
Once the new bridge was in place, crews proceeded with the nal track work, and 3rd rail connections. RCC installed the ballast utilizing a telescoping conveyor belt (telebelt) set up on the roadway. Ballast was installed up to the underside of the tie elevations, then new 40 . pre-assembled tie/track units were own in using a Liebehr LTM 1250 (300-ton capacity) crane. is Design-Build project also demonstrated that with careful planning, a bridge can be replaced by only working weekends – ve (5) all together, with minimum disturbance to the environment and public. is project achieved Substantial Completion on April 3rd, nearly 7 months in advance of the Contract required date.
Track work on this project above the ballast setting was performed by the Long Island Railroad. RCC provided crane, and trucking support to the LIRR for the pre-assembled track sections.

Impact to the industry: is project vastly improved and corrected an on-going safety hazard (bridge hits). With an adjacent school, and Adelphi University nearby – many pedestrians walk under this bridge each day making the existing structure particularly dangerous. With the new clearance, this is no longer a concern.
CLASS I: BEST USE OF TECHNOLOGY ON A PROJECT Yard Switch Solar Lights
Western Canada
• Prime Contractor: Electrical Solutions, Inc.
• Prime Designer: Electrical Solutions, Inc.
• Owner: CPKC e conventional procedures for this are to trench through the rail yard to the nearest utility power source and install a wood pole or steel pole with a concrete base. is procedure can be very costly due to the size of the rail yards. CP requested Electrical Solutions, Inc. to source a solar option while keeping in mind all the industry light level policies and safe clearance policies. e many hours spent sourcing the required device turned up empty. Absolutely nothing on the market met the stringent minimum requirements needed for the rail industry. e most signi cant challenge was practicality. Could a solar option be manufactured and installed to industry standards and still be more cost e cient than the conventional utility powered method? Secondly, keeping in mind our diverse country, can a light operated by batteries that are charged by a solar panel be designed for reliability during our harsh, dark Canadian winters? How do we keep the batteries warm in low temperatures without consuming too much of the produced wattage? e battery enclosures would have to be well insulated and as small as possible since every square inch would have to be heated. It would become a rail safety issue if these lights only performed intermittently. ere is no room for error; they must perform awlessly on the coldest, windiest, cloudiest, and shortest day of the long winter.
Electrical Solutions, Inc. has been an electrical contractor for Canadian Paci c for over twenty years. One of the main tasks we have asked them to perform throughout western Canada is to provide lighting for rail switches.
Electrical Solutions, with their many years of experience with rail lighting took it upon themselves to research, design and test a switch speci c solar option for the rail industry. is came with many challenges.
Other challenges included logistics. How high should the light be installed? How far from the track should it be mounted? When illuminating the area for a switchman, where does he need the light speci cally to safely perform his task? ese were all challenges that Electrical Solutions faced when sourcing the perfect xture.
Without jeopardizing light levels and watts per lumen output, they wanted to meet or exceed the minimum requirements without using excessive wattage as to suit the solar component.
With their experience in lighting rail switches, Electrical Solutions knew that not all switches are installed in prime or accessible locations for large equipment. How do we service this light and panel without the use of an aerial li platform? To solve this problem, they designed the light with the capacity to be lowered to the ground for maintenance.
Every unit can be dropped away from the switch and serviced without the use of li ing equipment. Because of this, they can be installed in the worst possible locations and ground conditions. How do we mount the unit to a secure base since installing concrete piles beside a rail bed in remote locations would be too costly? ey designed the unit to mount to a single 4.5-meter helical pile and since not all switch locations are alike, these units are designed to accommodate a le side lowering pole or a right side lowering pole. To top it all
Our Employees are the Secret to Our Success
Hamilton has been building bridges, highways, dams, and critical infrastructure as a heavy civil contractor since 1939. Our crews consistently perform above and beyond requirements to complete complex projects. They preserve history, respond to natural disasters, and develop innovative construction techniques to solve unique challenges. We are proud of their award-winning work in safely building and maintaining our nation’s infrastructure.
o , the speed of unit installation from start to nish is remarkably fast. Gone are the days of waiting for concrete to set and trenching hundreds of meters to get to the utility power.
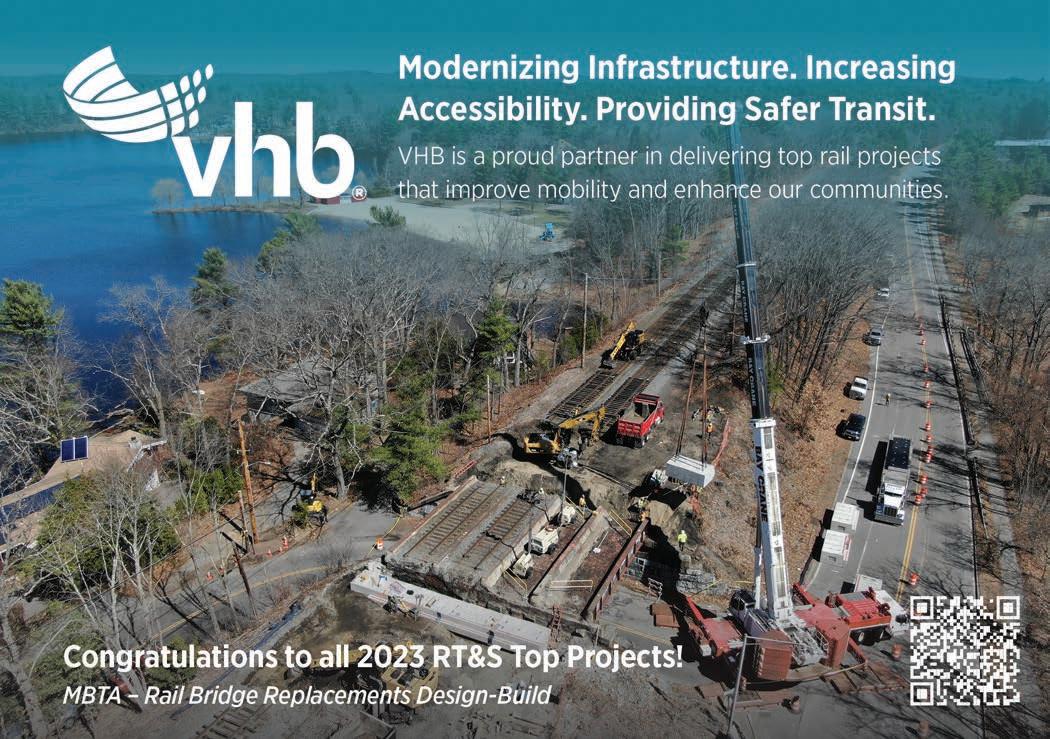
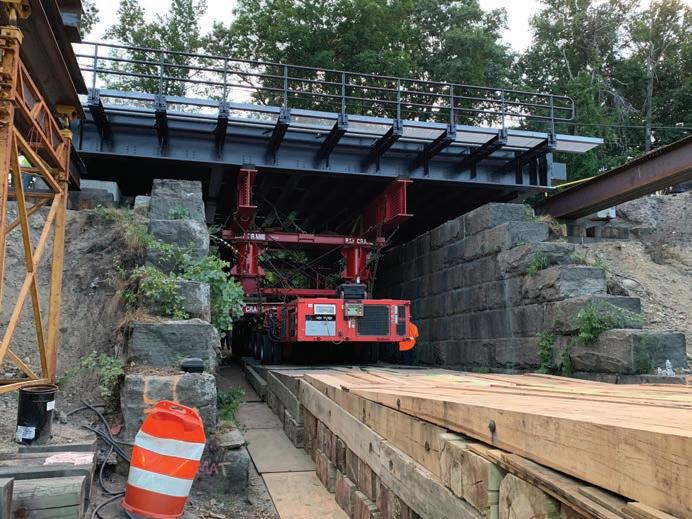
On top of all the design challenges, Electrical Solutions knew the importance of reliability and safety and wanted to provide a way for us to monitor the e ciency and status of the new lights. How do we ensure this safety and e ciency beyond the extensive research and carefully engineered design? ey installed a charge controller that can log performance of the equipment 24 hours a day, 365 days a year so we can always have peace of mind.
is innovative light designed by Electrical Solutions Inc. not only gives us the option to illuminate rail switches in challenging places throughout our network but it is cost e ective enough to install in rail yards where utility is available. To add to the list of reasons why these lights are such a great t for Canadian Paci c, the design meets our company’s green initiative as well. Carbon footprint is on the mind of all companies as we strive to nd more ways to do our part to reduce our impact on the planet. Electrical contribute