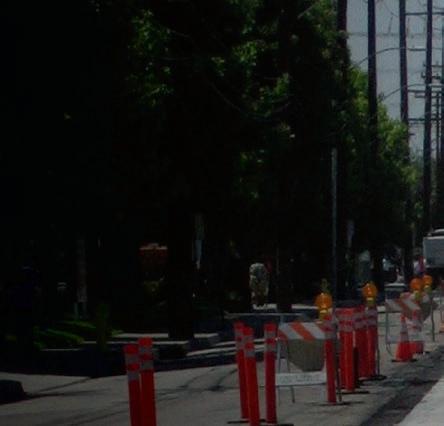
6 minute read
KEEPING IT SMOOTH
Maintaining
By Jennifer McLawhorn, Managing Editor
Imagine you are in a vehicle travelling down a road. e trees on either side of you begin to clear out, and you see a familiar sight – railroad tracks. A freight train is in the distance. A bell starts to ring and the crossing gate in front of you starts to come down. While you watch the train go by, there are several elements of the grade crossing that work together to ensure the safe passing of the train as well as the smooth transition of your vehicle over the tracks once the train has passed and the gate has gone back up.
With over 200,000 grade crossings in the United States alone, ensuring private vehicles can safely cross without causing damage to either the vehicle or the railroad is very important. Investing money into and developing crossing materials is an evolving business. From mid-nineteenth century rail workers who relied on a simple system of ags to communicate, to the wood crossings of the rst half of the twentieth century, to the highly sophisticated technology of present-day, grade crossing surfaces are a feature of the railway infrastructure that deserves a closer look.
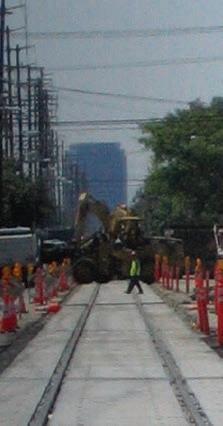
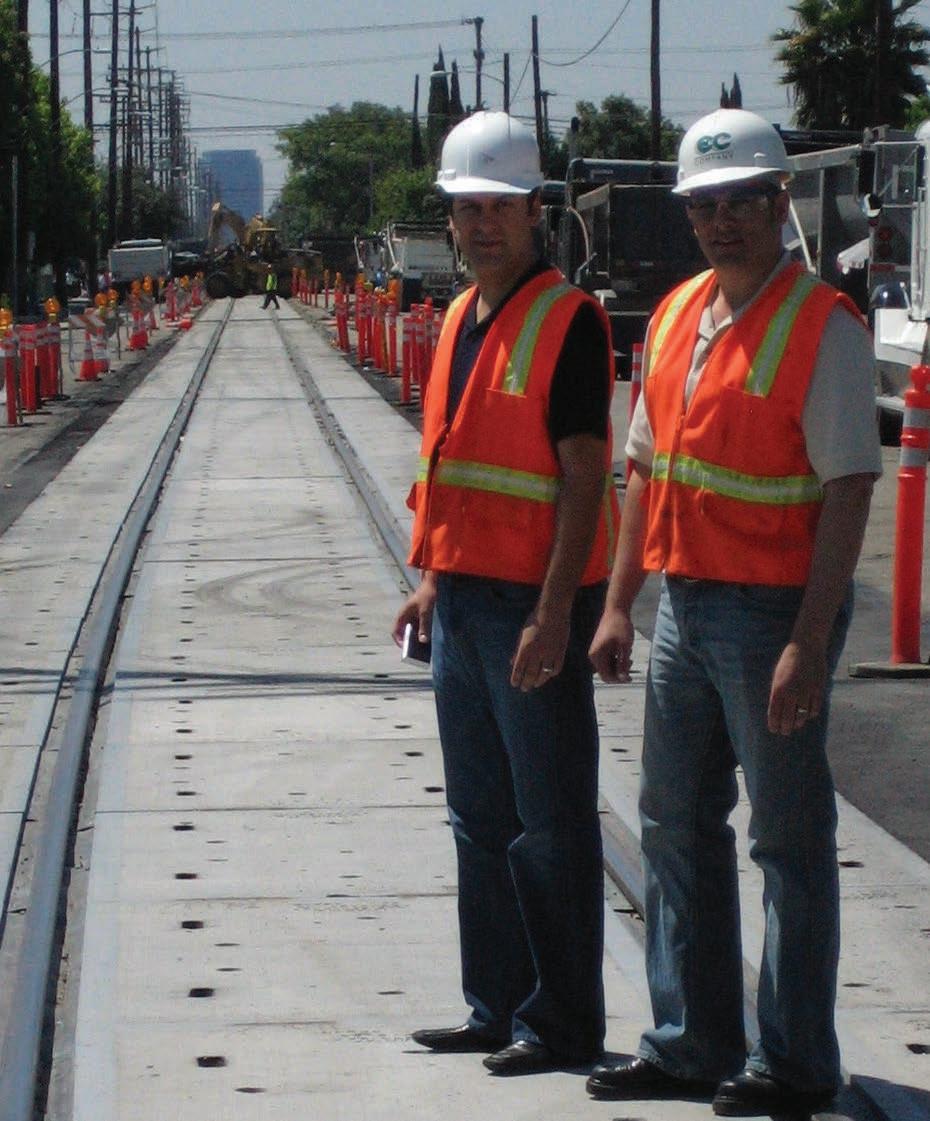
One such element Hitachi Rail o ers is a digital audio frequency track circuit called DGTRACK. It’s a sophisticated audiofrequency track circuit that can simultaneously distinguish an oncoming train and transmit cab speed command signals to the train. Not long ago, DGTRACK was approved for use on a major passenger rail operator, so it may catch your eye the next time you board a passenger train.
While centrally located in Texas, Kansas, and Nebraska, American Concrete Products can ship their grade crossing products to either U.S. coast. Having provided concrete products for almost eight decades,
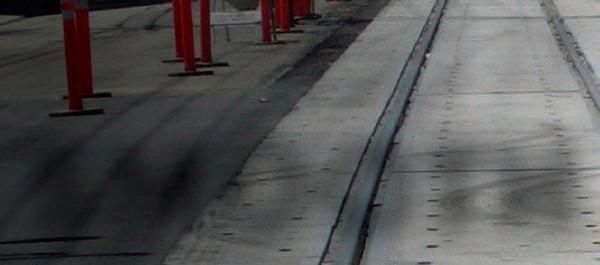
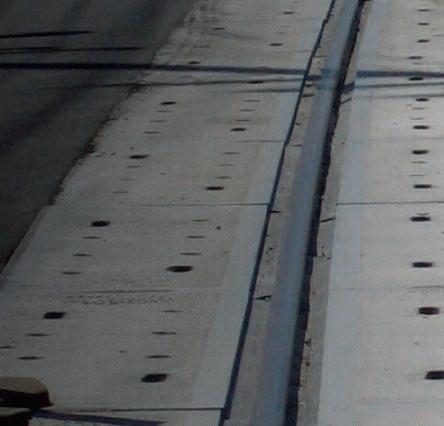
American Concrete Products has a full range of concrete grade crossings, girders, and railroad bridge substructures, to name a few. e panels conform to Union Paci c/ BNSF standards as well as adhering to speci cations for other Class Is and short lines. American Concrete Products utilizes certied welders to produce its all-steel cast-in frames. e company also o ers ADAcompliant crossings for transit railroads, industry sidings, and pedestrian crossings.
Omni Products has been building rail industry products for years and has designed a unique Improved Concrete that utilizes its own manufactured virgin rubber alongside the ECR concrete panel. Several Omni grade crossing products are designed to last under all climate conditions. For example, its TraCast 1 concrete tub module along with the TraCast 2 design, consist of a heavy-duty bolt-down gauge and eld rubber. Another product, their VRA Railguard is made with all virgin heavy-duty rubber. ese rubber products combined with steel reinforced rubber for crossings, absorb impact and distribute it, e ectively preventing the rail itself from the stresses of automotive tra c. O ering a six-year warranty to its tearresistant and load-bearing rubber grade crossing products, Omni also manufactures custom panels that t speci c applications based on customers’ needs. e panels themselves are installed around xed objects. Sheen Fong, Director of Technical Sales told RT&S that since their introduction, “initial acceptance has been among passenger rail systems with several transit agencies installing ATPs on various sites along their lines. Interest has also been growing among NA transits and state DOTs.”

L.B. Foster o ers two grade crossing safety products – LiDAR Obstacle Detection and Anti-Trespass Panels. Sold throughout North America since 2017, L.B. Foster’s Anti-Trespass Panels are conically shaped panels that are installed trackside. ey are made of recycled rubber and are an environmentally friendly option to deter trespassers.
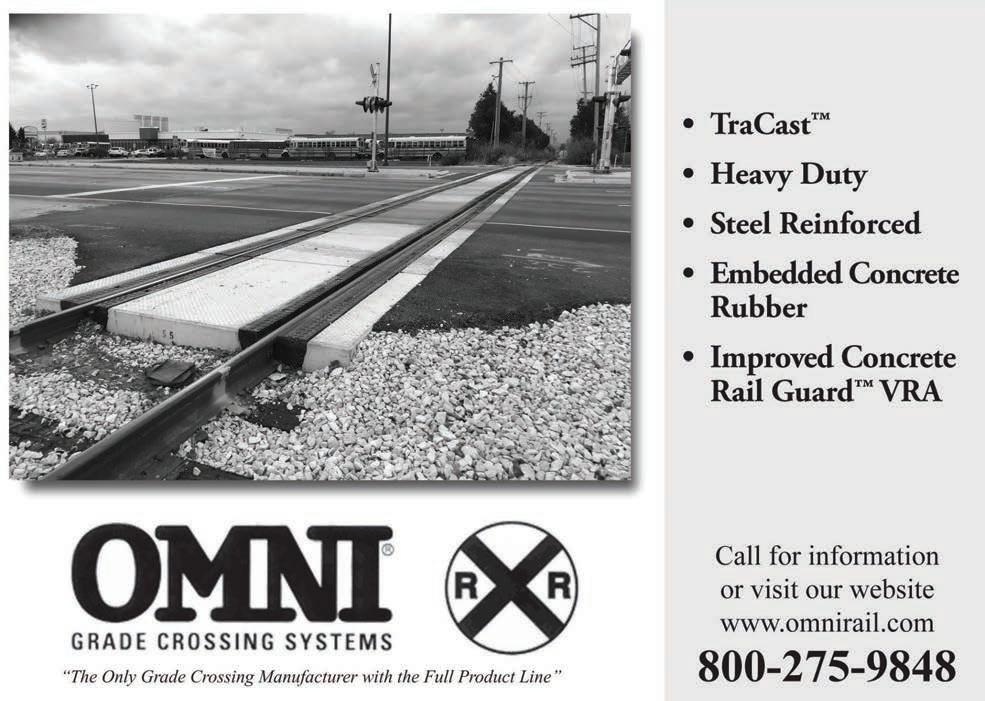
Indeed, a er a study was conducted by the Federal Railroad Administration (FRA) a few years ago, it concluded that L.B. Foster’s AntiTrespass Panels reduced pedestrian trespassers by 38%. Made entirely from recycled rubber, these Anti-Trespass Panels also come with a 15-year warranty.


L.B. Foster also o ers LiDAR to detect obstacles that may be in the area. Housed by steel, LiDAR devices monitor and record any violations that occur on or around a crossing. Once a barrier lowers due to the presence of an oncoming train, LiDAR scans the area and can alert trains of any potential obstacle.
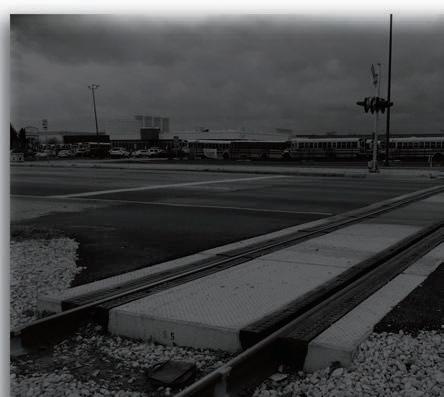
Regarding safety integrity levels, Michael O’Connell, Manager of Product and Business

Development commented that “our unique Insight LiDAR system complies to SIL3 level, the highest safety integrity level that is economically feasible for most industrial operations. With this, it delivers improved reliability of detection in all weather conditions, improved accuracy of obstacle detection down to the inch, reduced maintenance routines, and the exibility in utilizing intelligent algorithms such as velocity and direction.”
HiRail has had requests for more specialized products to t various rail fastening systems and track con gurations. Jim Overfelt, Director of Sales and Marketing, told RT&S, “ e market remains strong for grade crossings and we are cautiously optimistic that this will continue for the forseeable future.” Indeed, HiRail provides products for new transit start-ups and those extending their current systems. e HiRail Rail Seal is a rubber product that works with concrete crossings or asphalt. It ts most timber or concrete ties using any type of rail fastener. HiRail’s PedeRail is a speci c crossing surface manufactured with a raised diamond surface designed with pedestrians in mind. It meets Americans with Disabilities Act (ADA) requirements. eir namesake HiRail full-depth rubber crossing systems come in lagged and lagless designs, with lagless lessening crosstie degradation over time and allowing for installation on both concrete and steel ties. ese HiRail products can also be recycled.


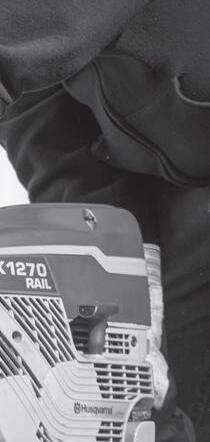

In addition, the company o ers a line of rubber grade crossing surfaces. Among these are its HiRail, PedeRail, and HiRail Rail Seal.
Manufacturing over 120,000 track feet of precast crossing panels each year, Omega Industries has a product line that includes lag-down panels that adhere to BNSF/UP standards as well as panels that are Canadian standard. Moreover, it o ers non-lag panels for use on concrete ties, curved panels, custom turnout panels, DF Track crossing panels, and ADA approved pedestrian panels, along with narrow gauge panels, and steel switch point covers. Using steel, rubber, and concrete products made in the USA, Omega serves many Class Is, short lines, and port authorities. Furthermore, Omega Industries has begun to see growth in public transit, thereby increasing demand for light rail and commuter rail crossing panels. ese include but are not limited to Amtrak, DART, Tri-Met, LA Metro, Southwest Light Rail, and Sound Transit.
Omega Industries has seen a high demand from Class I and short line railroads regrading concrete crossings. Mark Mottola, National Sales Manager for Omega Industries, told RT&S, “As a result, we have experienced record sales in the rst quarter of 2023.” To meet the need for increased production, the company is adding more casting boxes to its current manufacturing locations. Omega Industries told RT&S that its goal is to “increase production capacity to 200,000 track feet by the end of this year,” despite the concrete cure time limiting pour to one set of panels per casting box each day. One way Omega Industries works to meet the demand is by using a poly ber reinforcement in its panels to improve impact and abrasion resistance, reduce water migration and plastic shrinkage, and provide strength and durability. Omega Industries believes this enhancement to their current product should increase the life of the panels by up to 10%.

For pedestrian crossings, Omega Industries has engineered a panel that adheres to ADA requirements and incorporates a replacement rubber angeway ller and a non-slip concrete surface. erefore, even when the surface is wet, it should provide
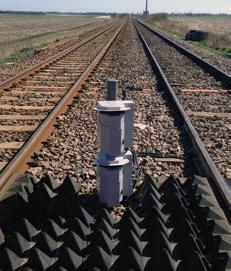
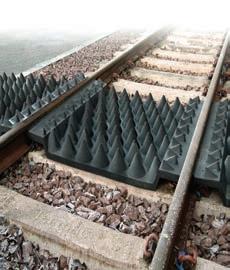
Grade Crossing Safety
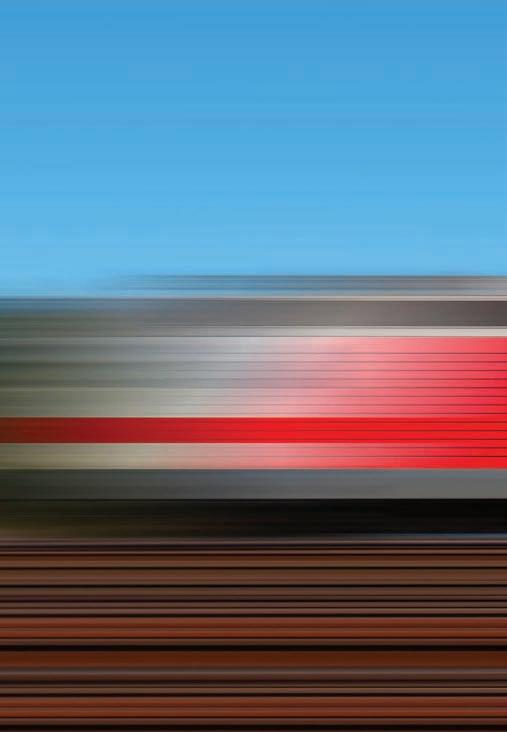
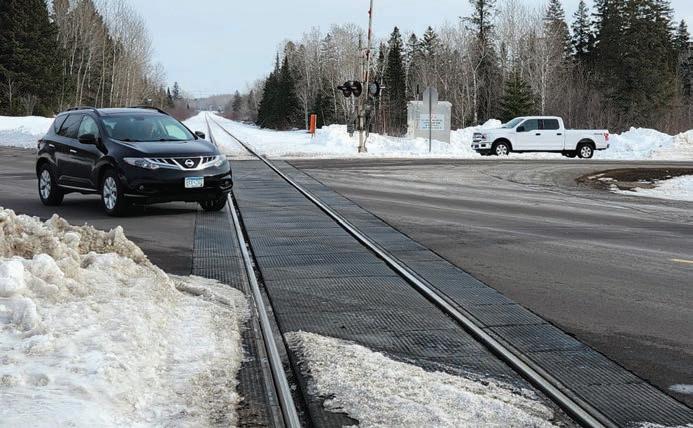
traction for crossing pedestrians.
Industry Railway Suppliers, or IRS, has distributed AREMA track tools, battery tools, abrasives, heavy railroad equipment, work equipment, and mechanical shop tools to railroads and transit systems across North


Railway Supplier has also supported distressed crossing surfaces. Its grade crossing product comes in the form of its exclusive FastPatch Railroad Distressed Pavement Repair kit, or DPR. Manufactured along with Willamette Valley Company, the kit is an easy-to-install designed to be adhesive and freeze-thaw resistant whilst also absorbing impact to thoroughly repair broken down concrete or asphalt grade crossings along bridges or roadways. Industry Railway Supplier’s DPR kit requires little site prep and includes everything needed for repair. e product is made from recycled materials and is odorless and completely VOC free, eliminating the need for outdoor-only installation. DPR is quick to cure, with normal tra c able to resume just outside of an hour. Ensuring an adherence to ADA compliance, the DPR kit is manufactured to work quickly and e ciently.
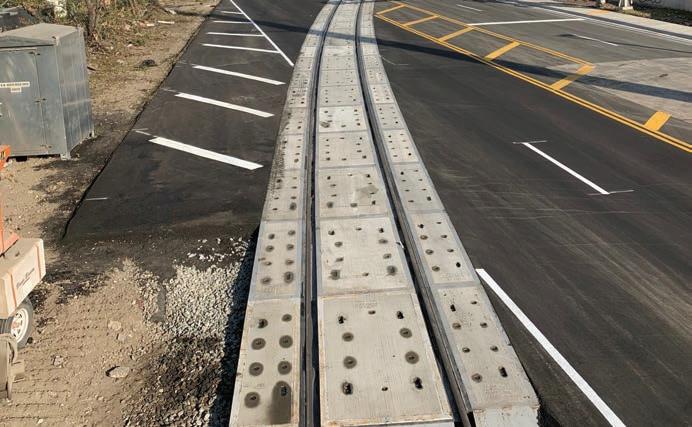
Looking closely at the current grade crossing surface product selection, it is apparent that the rail industry has come a long way since the ag system from close to two hundred years ago. Rail technology continues to improve to produce stronger, safer, and more environmentally friendly grade crossing products each year. A er the train passes in front of your vehicle and the crossing gate comes up, keep in mind this sampling of grade crossing surface products that work to ensure a safe and smooth crossing for your trains and your vehicle.