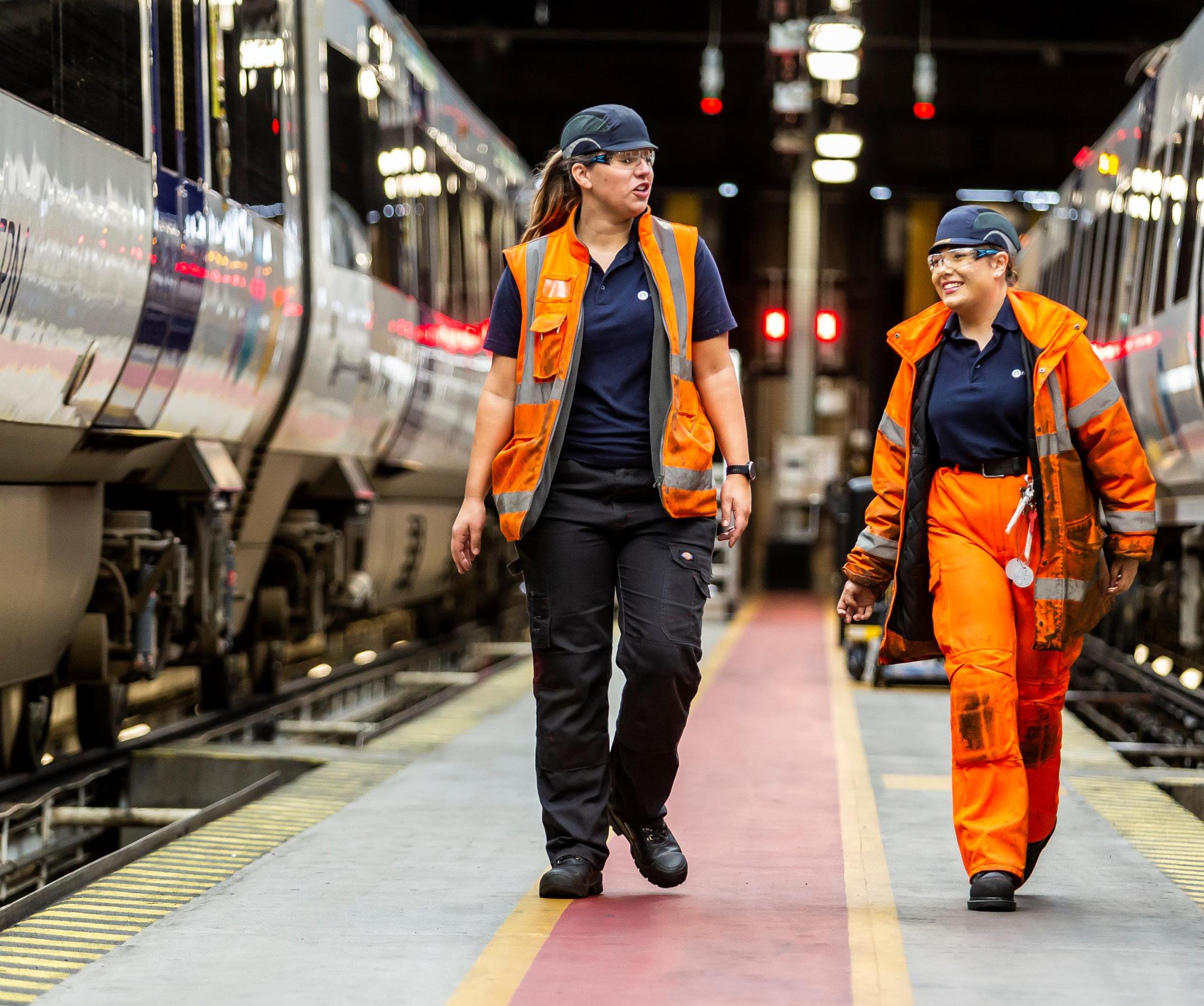
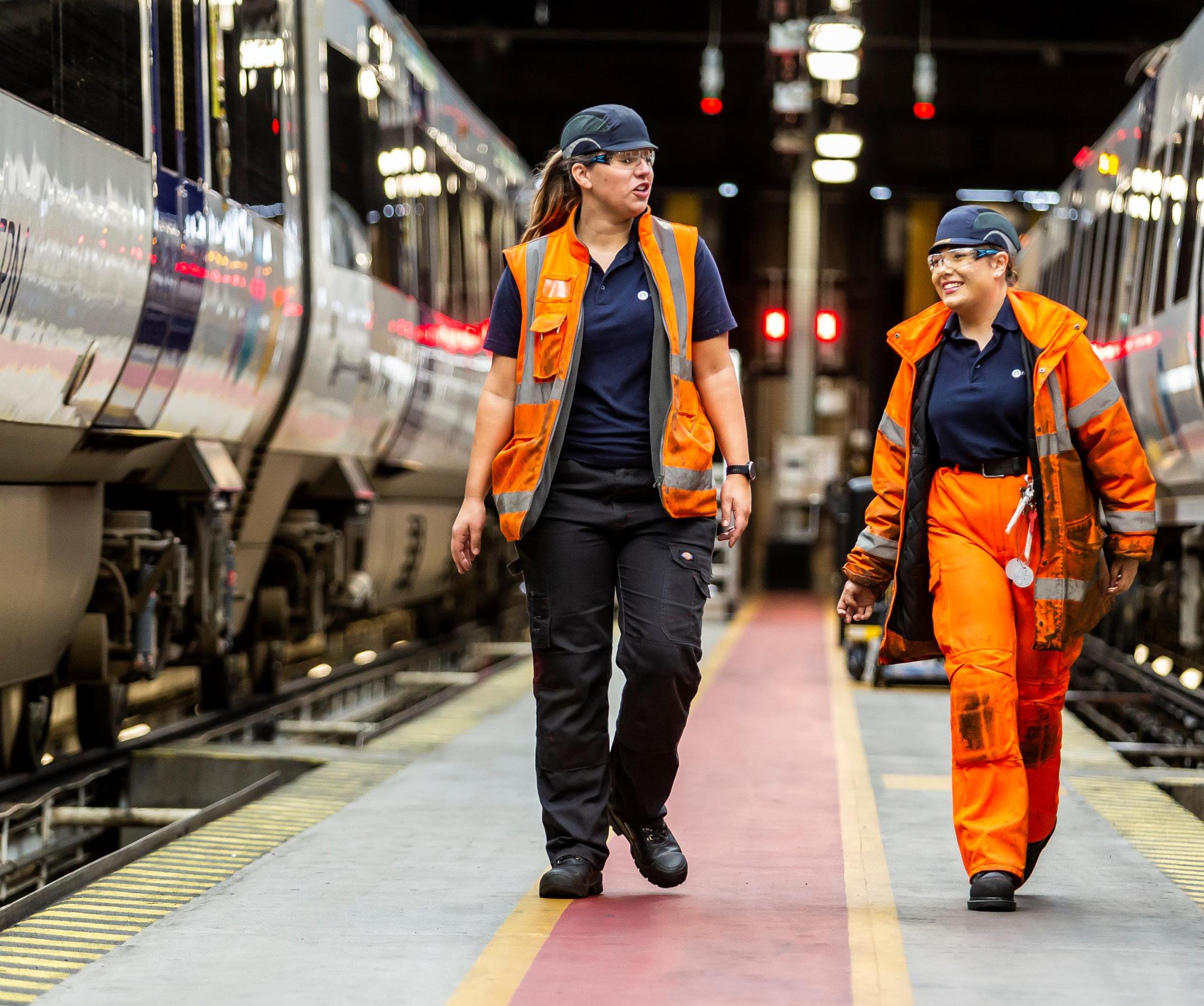
Looking for your future rail leaders?
When recruiting for a team manager, it can be a real dilemma whether or not a front-line employee has the capability to make the jump from being a team member to a motivational, skilled leader. Undertaking a front-line role can be very different to moving into a supervisory position, managing a team. Some employees may already demonstrate management skills that could help them excel in a leadership role. But how can we judge whether someone has the potential to become a good manager?
The Leadership Potential Indicator (LPI) could help you find out.
It’s a new, online, untimed, situational judgement test (SJT) that can help identify an employee’s leadership potential, by measuring the following five key managerial competencies:
• Leading others to deliver results;
• People skills that build positive relationships and successful teams;
• Thinking skills e.g. effective decision making, problem solving and planning;
• Strong customer focus with external and internal customers; and
• Driving improvements in themselves and others.
The LPI can also be used as a development tool with existing supervisors and front-line managers to identify strengths and areas for development.


Email our friendly team at admin@theopc.co.uk or visit www.theopc.co.uk to start using the new LPI assessment tool.
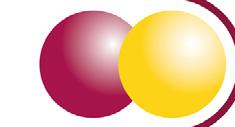



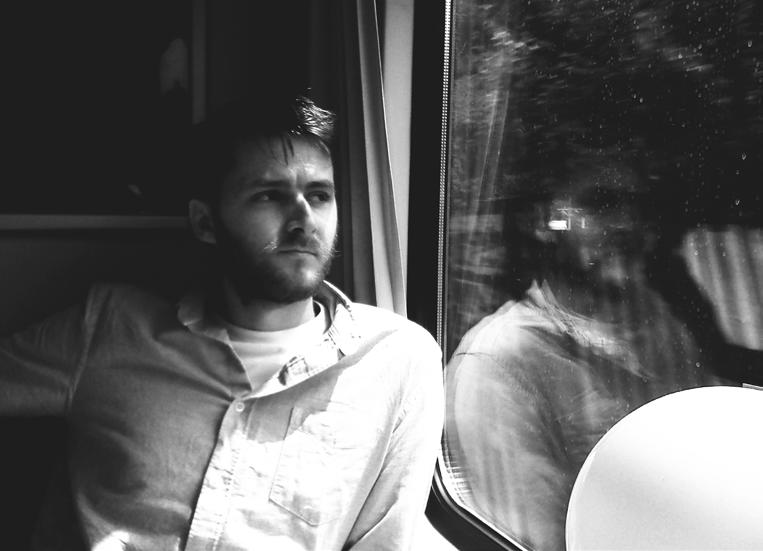
As I’m writing this the Government just published the responses to its consultation on The Plan for Rail. A few respondents raised the impacts on the wider supply chain and suggested this be incorporated into the impact assessments, as the current private sector focus is on operators rather than other businesses. The Government response was that the main operating company of Great British Railways will be a non-departmental public body and will be obliged to act in the public interest. The response also stated that Great British Railways' governance framework will be structured to ensure that Great British Railways acts fairly when overseeing the specification of the customer offer and managing decision-making about retail strategy.
As far as events go, we have two major events taking place this month, starting off in March with Transport Ticketing Global, taking place on Tuesday 5 and Wednesday 6 March 2024 at Olympia, London. Celebrating its fifteenth year, the event will be the world’s largest public transport forum for smart ticketing and mobility professionals. With a host of new speakers, interactive formats and new exhibitors, the event will showcase the very latest in smart ticketing, mobility solutions and passenger experience.
Mobility and ticketing professionals from more than 65 countries will once again be in London to discover a vast range of insightful and original content, highlighting new projects from across the globe.
Later this month the award-winning RIA Innovation Conference 2024 takes place at the ICC Wales on 26-27 March with the theme ‘Inspired by Innovation’. The conference and exhibition bring together rail innovators, clients and stakeholders and share ideas and create new partnerships. It attracts over 300 railway professionals, innovators, media representatives and investors. The event’s strategic partners are the UK Rail Research and Innovation Network (UKRRIN), Network Rail’s RD&I Portfolio and Transport for Wales.
In this issue we are focussing on stations with a look at the renovated Gatwick Airport Station and the work being done at Aldridge Railway Station as well as commentary from Jools Townsend Chief Executive of Community Rail Network.
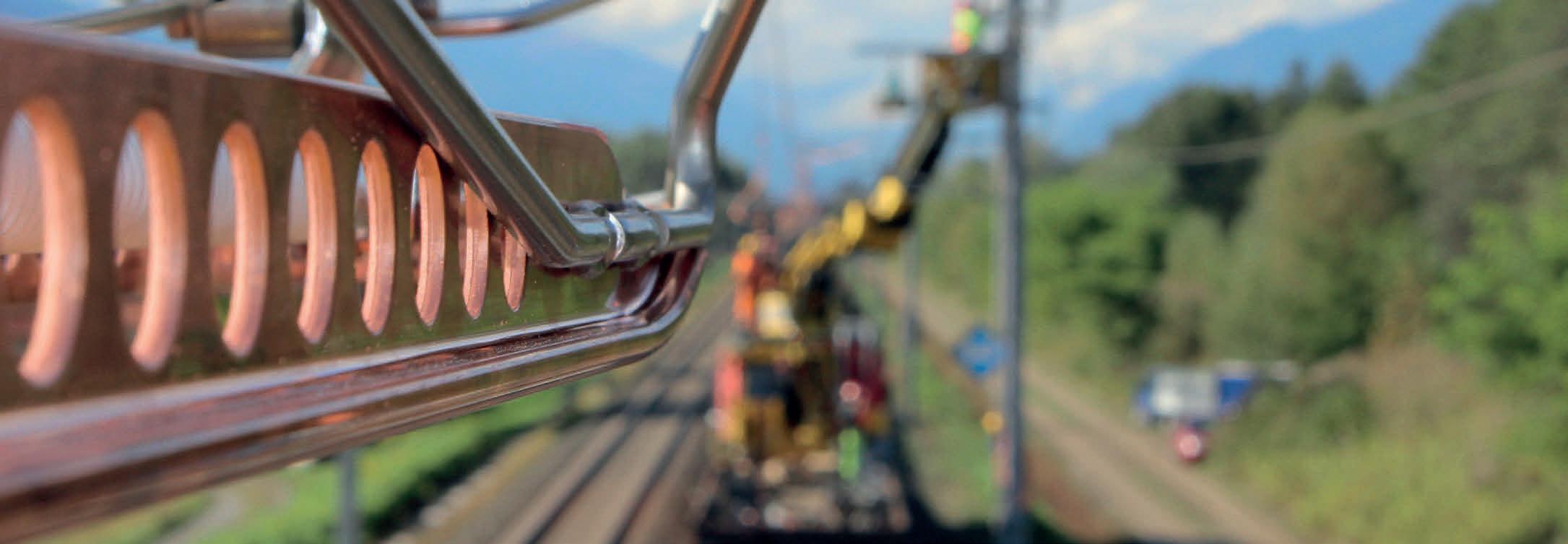
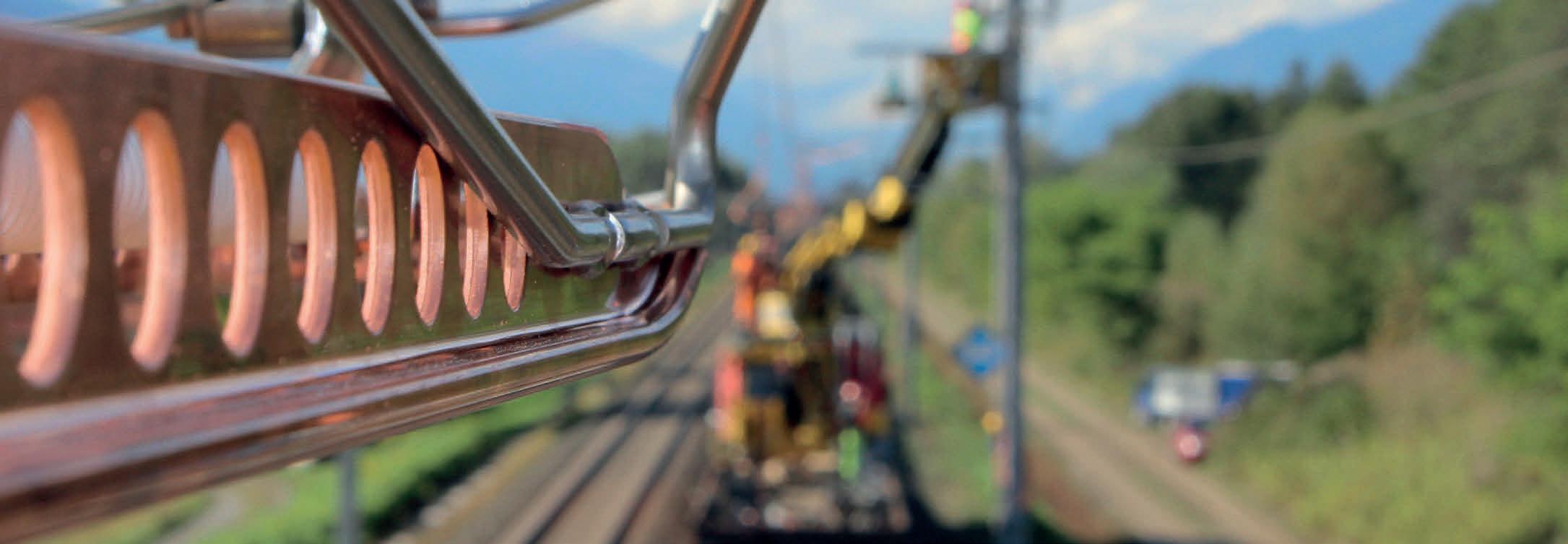


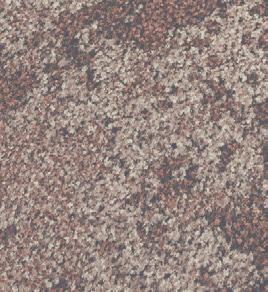

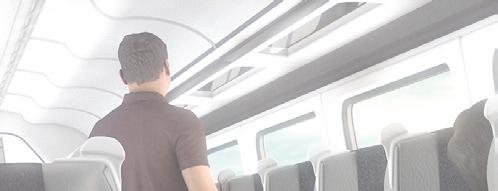
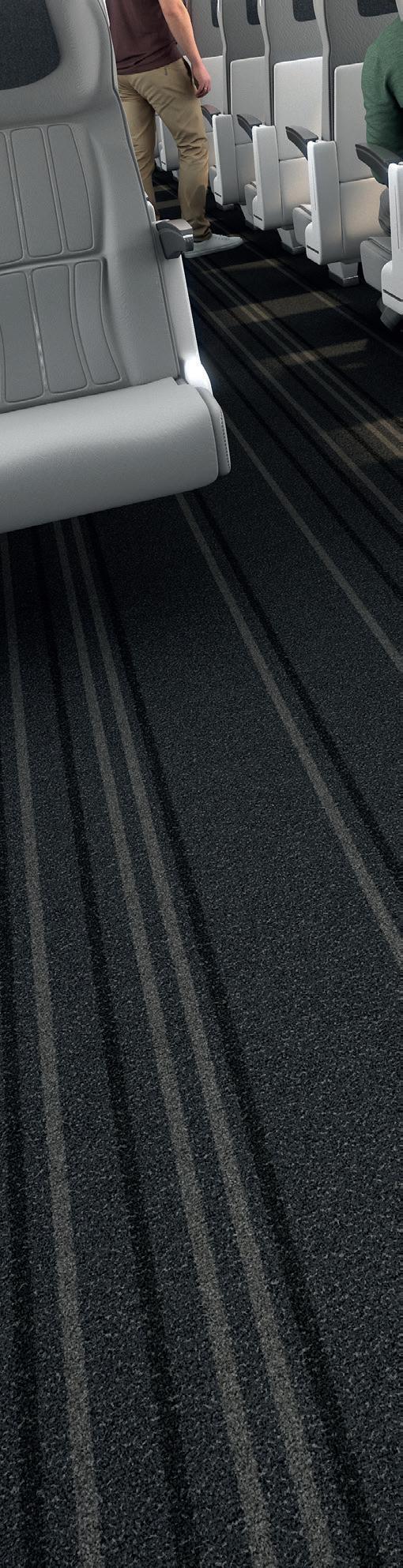
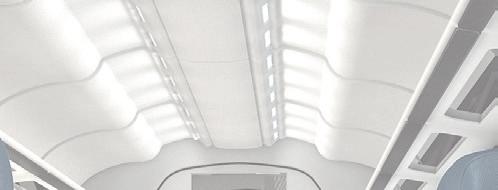
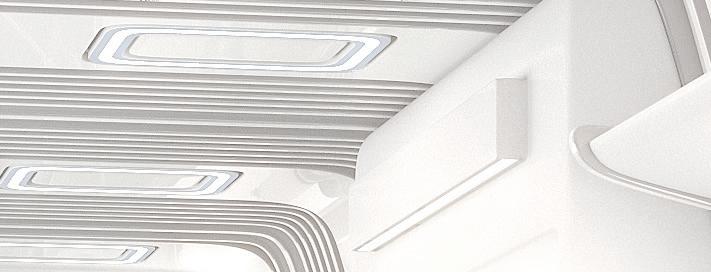
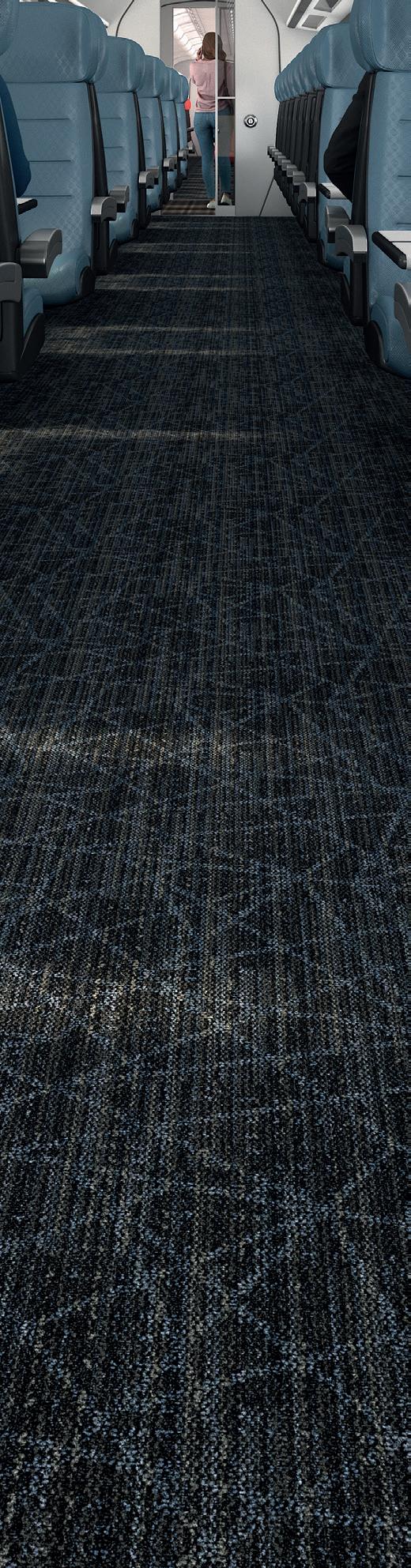
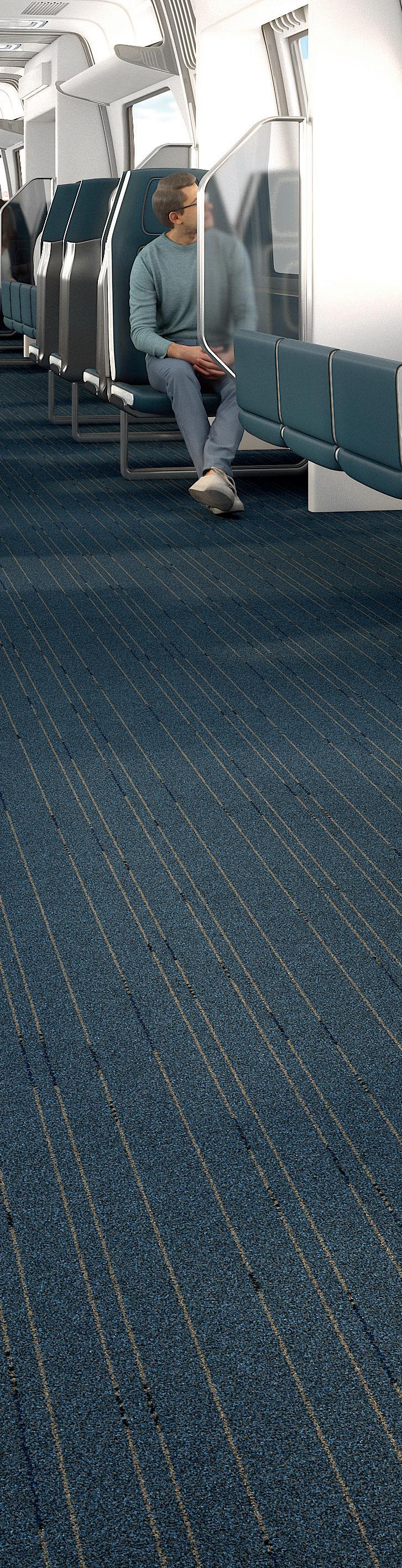
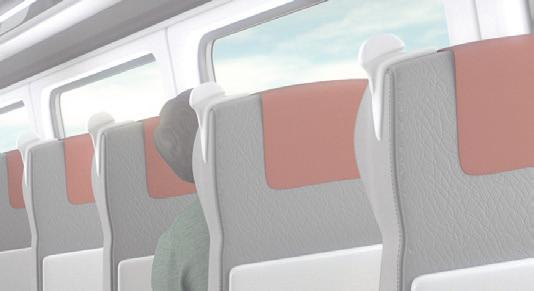


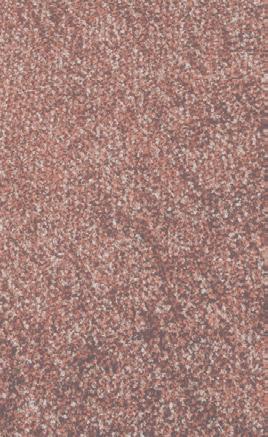

East Midlands Railway, Great Western Railway, RIA, HS2, University of Birmingham, Transport for Wales, Railway Mission, Southeastern and more

With
Graeme Craig, Director & Chief Executive of Places for London explains how TfL’s land is being used to make the capital a better place
Alan
Howard


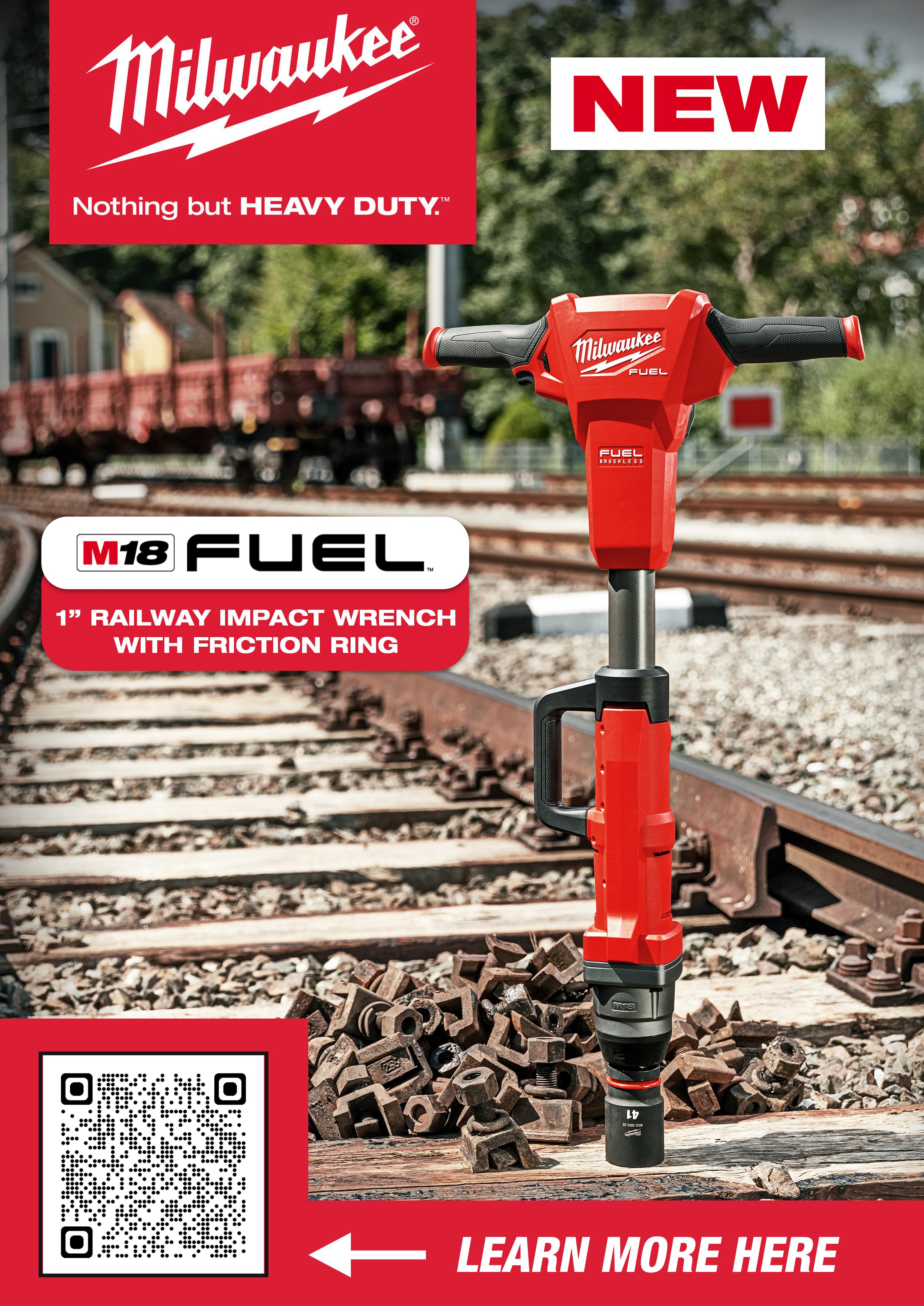
59
SPECIALIST SKILLS
New region-wide College Rail Training Academy
60 IN CONVERSATION
Mo Al-Akayshee, Power Applications Engineer at Fortec Technology UK
62 IN CONVERSATION
Steve Jasper, Operations Director at Pre Metro
65 TICKETING
Transport Ticketing Global 2024
66 STATIONS
In conversation with Simeon Evtimov RSD Marketing & Communication at Industrial & Rail Equipment Dpt Atco Trade Eood, Bulgaria
69 STATIONS
Work underway at new Aldridge Railway Station
70 IN CONVERSATION
Windhoff Bahn- und Anlagentechnik GmbH
72 STATIONS
Brent Cross West to Transform Area
74 STATION REFURBISHMENT
Open heart surgery at Gatwick Airport Station
79 STATIONS
Jools Townsend, Chief Executive of Community Rail Network, explains how the grassroots network connecting people with their local railways is putting stations at the heart of communities via an increasingly diverse range of projects and activities
83 SPECIALIST SKILLS
Neil Franklin, Workforce Planning at NSAR on NSAR’s Annual survey of the rail workforce which shows 75,000 could leave the industry by 2030
86 SKILLS
Skills in focus in 2024
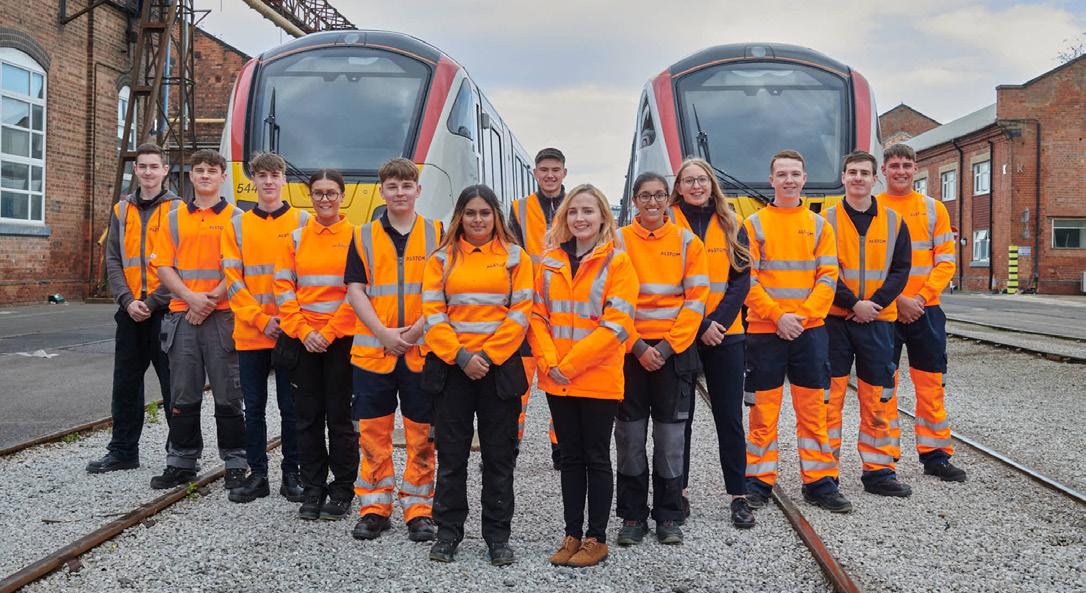
94 BUSINESS PROFILE
Forbo Flooring

97 RAIL CARRIAGE REFURBISHMENT
J-Flex offers an extensive range of unique elastomer materials for Surface, Sub-Surface, Tunnel and Rolling Stock applications
101 INNOVATION & NEW PRODUCTS
New Leadership Potential Indicator (LPI) Manager Narrative Report
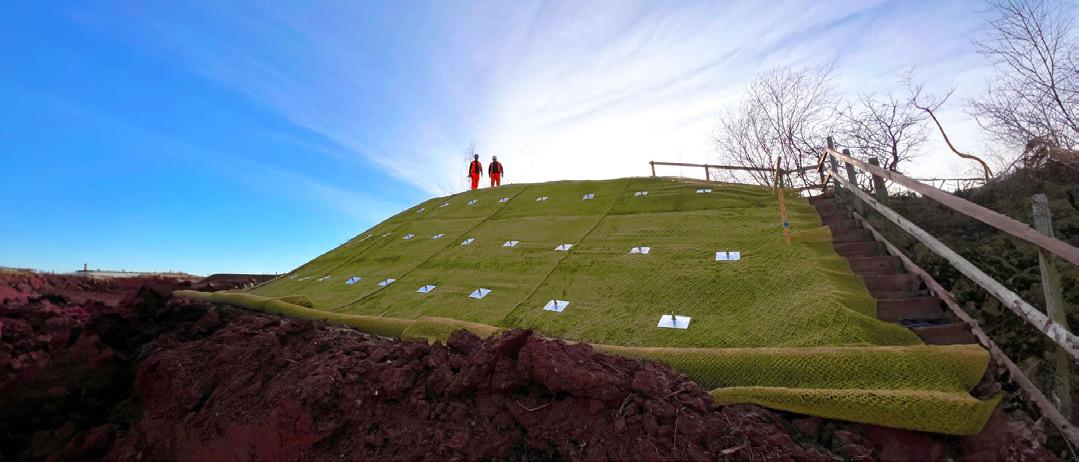
110 PEOPLE

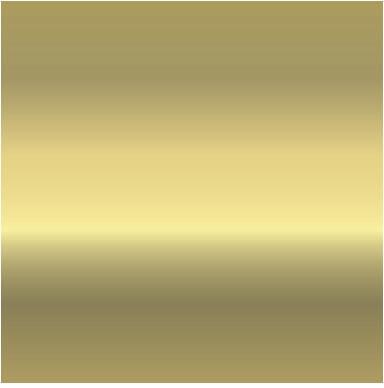
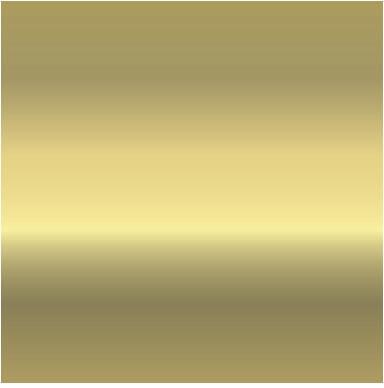
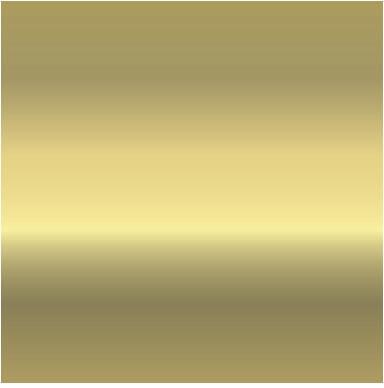
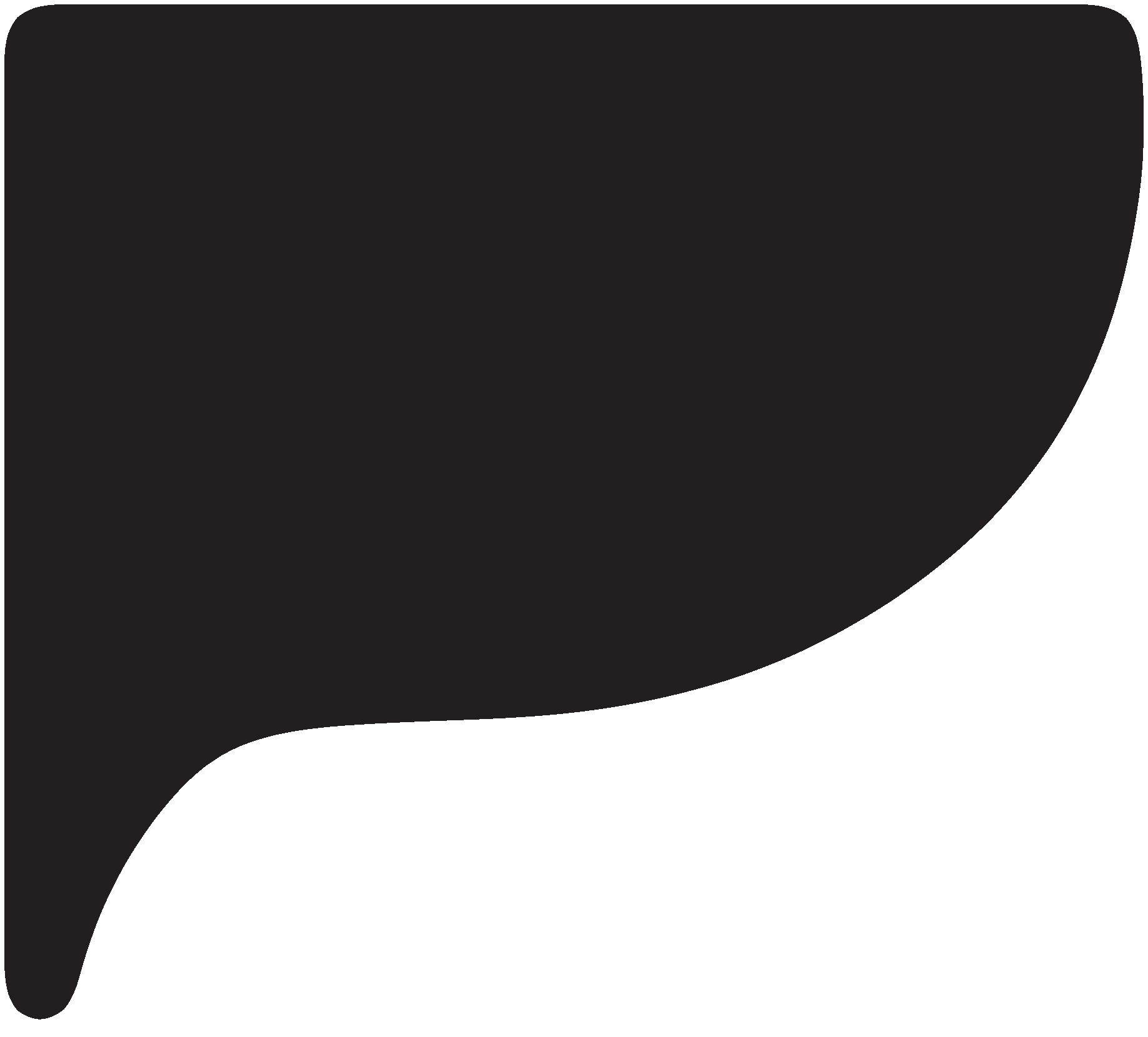
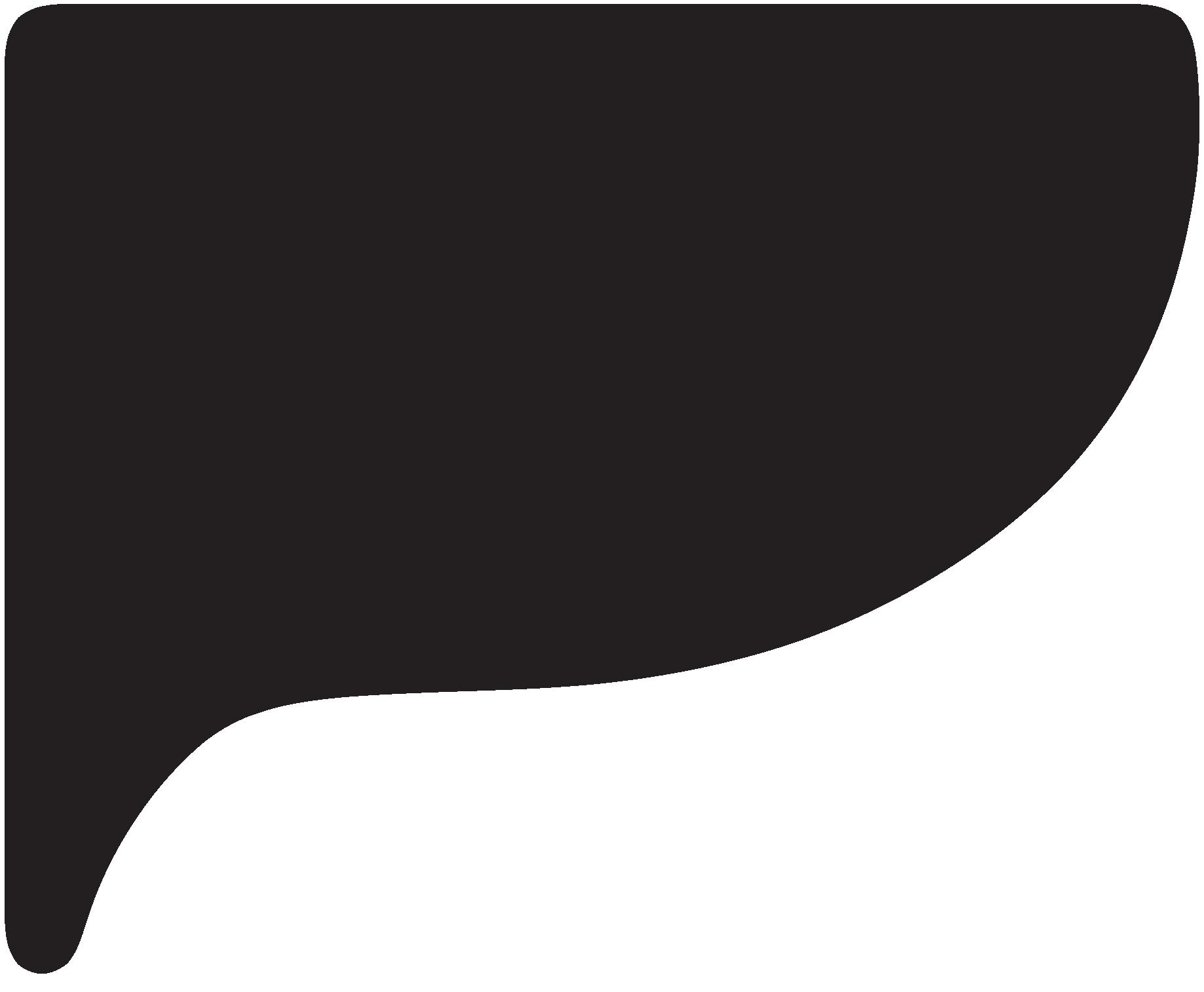
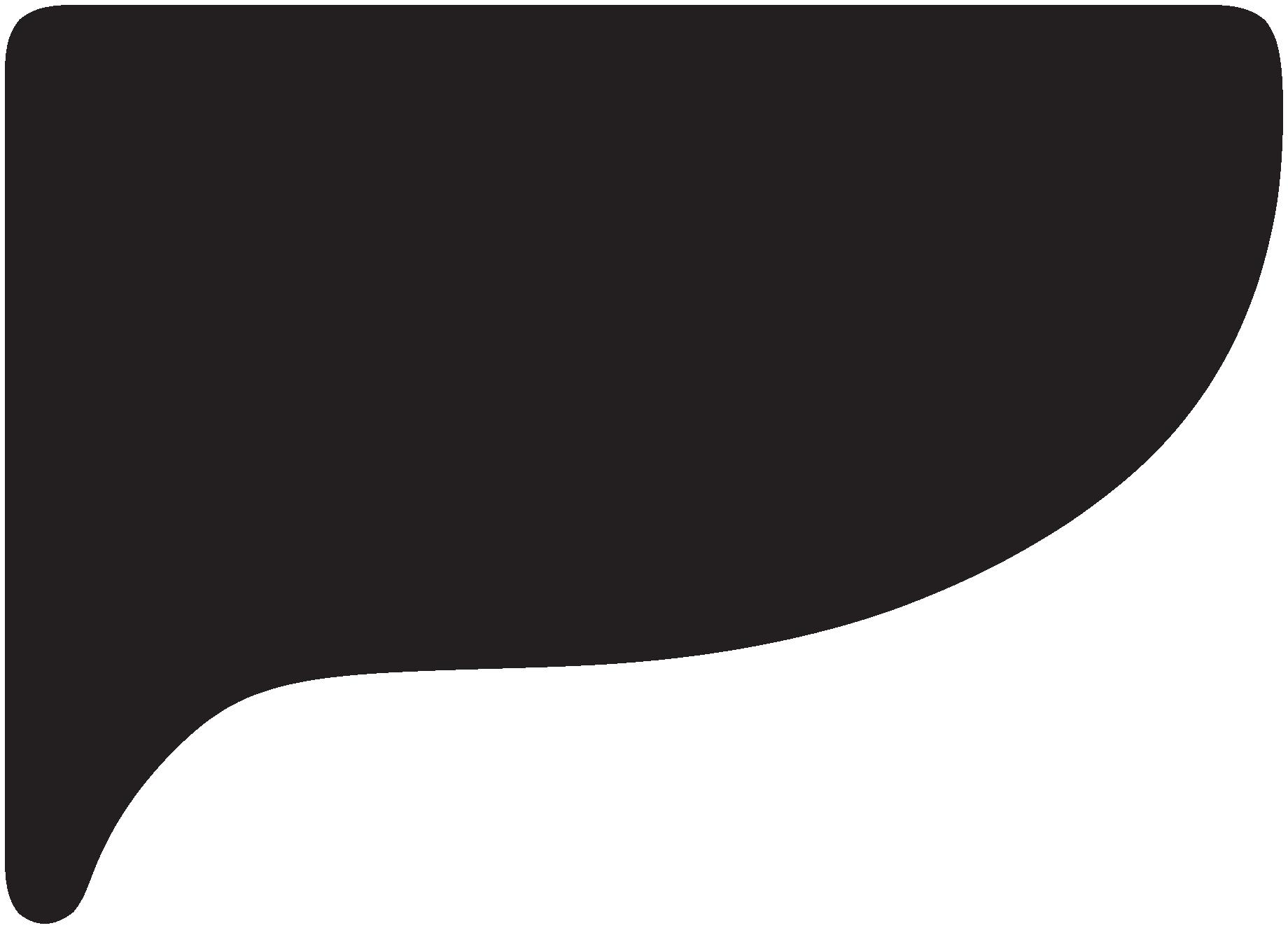

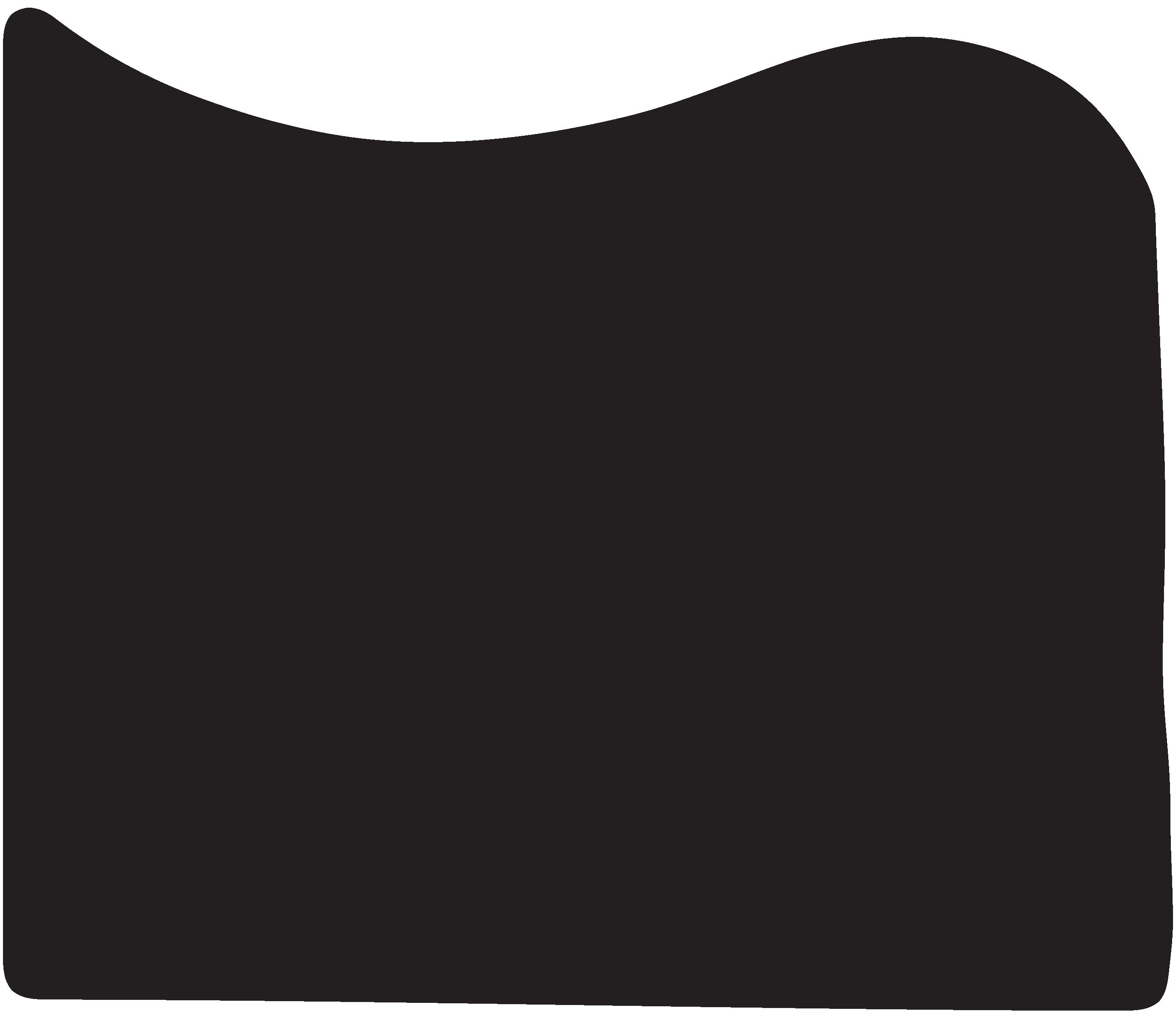
The ceremony will take place at RIA’s fifth Annual Dinner on 27 June 2024 at the Landmark, London.
Deadline for nominations is 19 April 2024
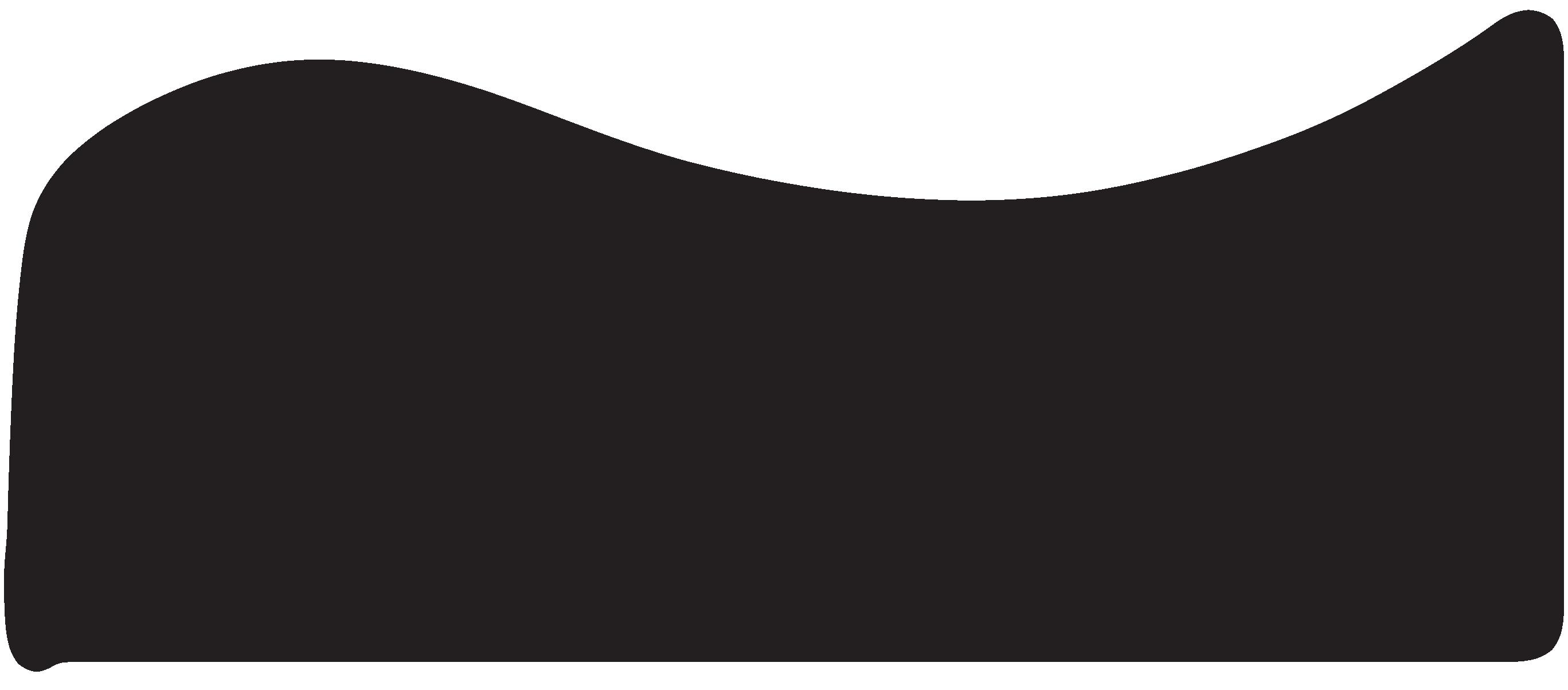
Innovations to Cut Rail Electrification Costs and Carbon Emissions
The UK government has awarded Furrer+Frey GB, the British arm of the Swiss railway engineering company, £1 million to build prototypes as part of the Global Centre of Rail Excellence (GCRE) in South Wales. The funding will deliver a railway test track demonstrator aiming to reduce costly bridge works and further develop low-carbon electrification equipment.
The first Furrer+Frey project aims to cut electrification costs by optimising the incline of electrification lines on either end of bridges, platforms and level crossings. At these points, trains often have to slow down to maintain good contact between their pantograph (the arm that reaches up to collect power from wires above) and the electrification equipment. Bridges over lines are also typically raised up to fit electrification equipment in underneath. Marginal changes in these situations could produce large benefits for the railway network as a whole.
The Cost-Reducing Dynamic Electrification System (CODES) will help determine the most efficient incline designs, aiming to save construction costs and speedup existing lines. The company’s second project to receive funding will develop an innovative cantilever for rail electrification made of composite materials.
A prototype mast by Furrer+Frey produced just three-quarters of the embodied carbon of traditional masts but still achieved similar strength and durability properties. With the new funding, they will extend these benefits to the cantilevers that hold wires above the railway. The composite cantilever would further reduce the weight, embodied carbon and cost of the vital piece of equipment. This project is being developed in conjunction with the National Composites Centre.
Both projects are funded by the Department for Business and Trade through the competition ‘GCRE: Railway
Construction Innovation Phase 2’ delivered by InnovateUK in collaboration with the GCRE. Noel Dolphin, Head of UK Projects for Furrer+Frey, said: ‘We’re delighted to be working with the GCRE to accelerate our innovations. It gives us the platform and opportunity to develop practical solutions to boost rail electrification across the UK. The kind of testing and development we will do at the GCRE could help us decarbonise more of our railways for less. And speed up existing lines.’
Construction of both prototypes will be completed by Spring 2025. The second phase of the ‘Railway Construction Innovation’ competition awarded £7.4 million to 15 projects to demonstrate their ideas at the GCRE facility.
A typical electrified railway will have 20 galvanised steel masts per kilometre. Each will weigh around 750kg requiring deep pilings. Reducing the weight provides whole lifecycle carbon and cost benefits.
First Reveal of Aurora's Interiors
EMR's new Intercity fleet of 33 fivecarriage trains, capable of running on electricity and diesel, is being built by Hitachi Rail in County Durham and financed by Rock Rail East Midlands. They are due to be in operation in early 2025, with the full fleet of trains in service during the year. The seats have been designed in close collaboration with Derby-based design firm DGDESIGN.
EMR has taken the proven product of the FISA Lean seat and refined it to offer enhanced comfort and support. It has also improved the appearance to match what they believe customers expect from an Intercity service seat. The seat rework has included enlarging the size of cushions, headrests, and armrests and ensuring that high-quality durable materials are used throughout, such as wool-rich moquette and leather.
The trains will also include features that customers have said they want to see, including air conditioning, free Wi-Fi throughout, better mobile phone signal access, more luggage space, plug sockets, and better passenger information screens.
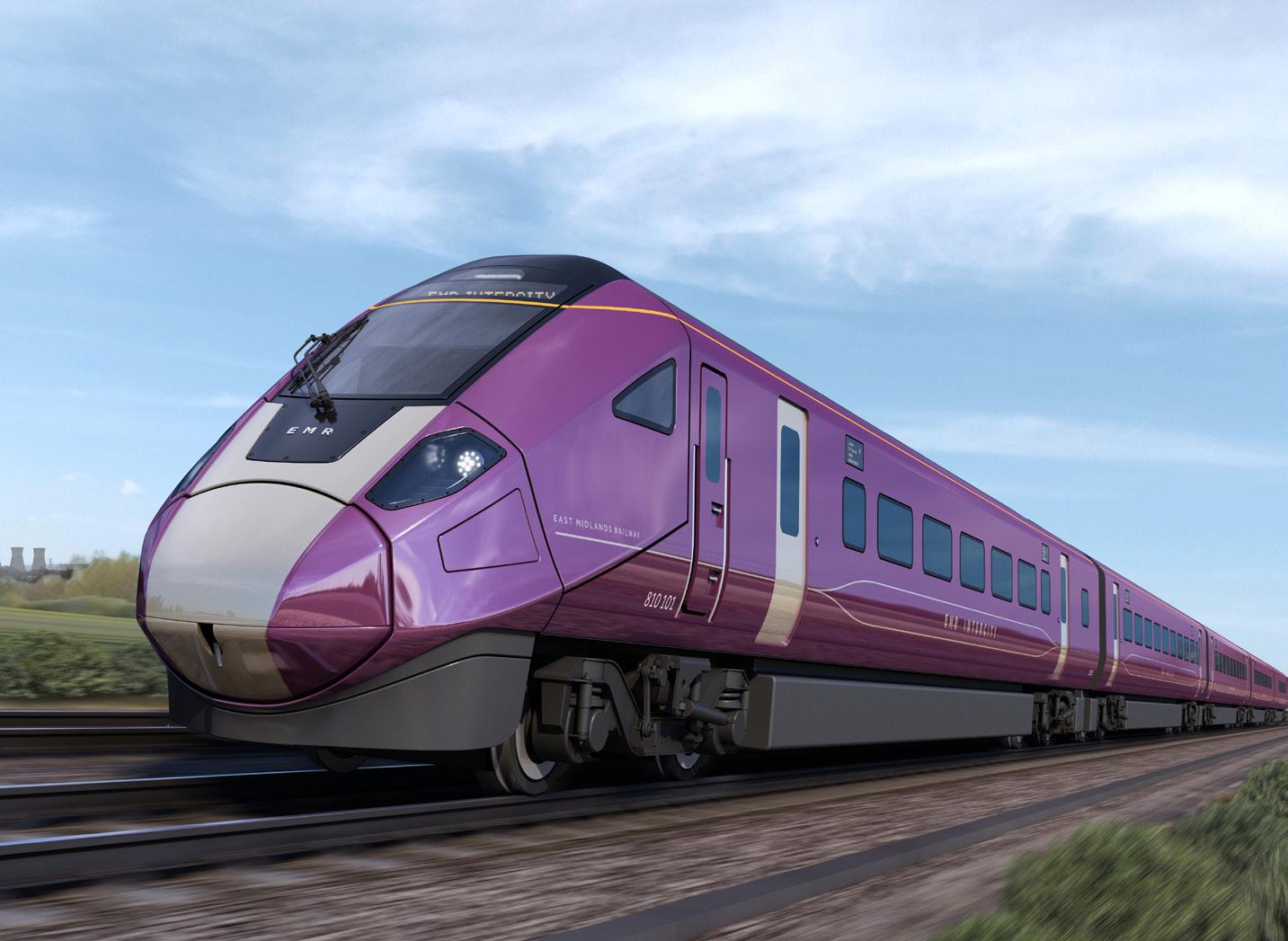
Devon and Cornwall Signalling Upgrade in Final Phase
Network Rail’s final phase of work to modernise signals in Devon and Cornwall and improve the resilience of the railway in the South West will be taking place throughout March. Signals that have reached the end of their working life will be replaced with a new digital system. The system will improve the reliability and safety of the railway and new digital technology will allow for real-time information to be provided to passengers.
The work is the third stage of a major programme to transform how trains run in the region. Over the past few months, Network Rail’s contractor Siemens has installed new equipment and signals and laid new cabling over a combined 66 miles of railway. In this final phase of work, the new system will be brought into use and control moved to the regional signalling centre at Exeter, for Cornwall, and the Devon section to Plymouth.
New signals in Cornwall are due to come into use on Monday 11 March, with Devon following on Friday 22 March.
Part of the project is one of the largest programmes of track work ever completed in Cornwall. A team of more than 100 people will work across a 50-mile site to install new equipment that will ease congestion at Truro, remove redundant equipment, and lay new track, sleepers and ballast.
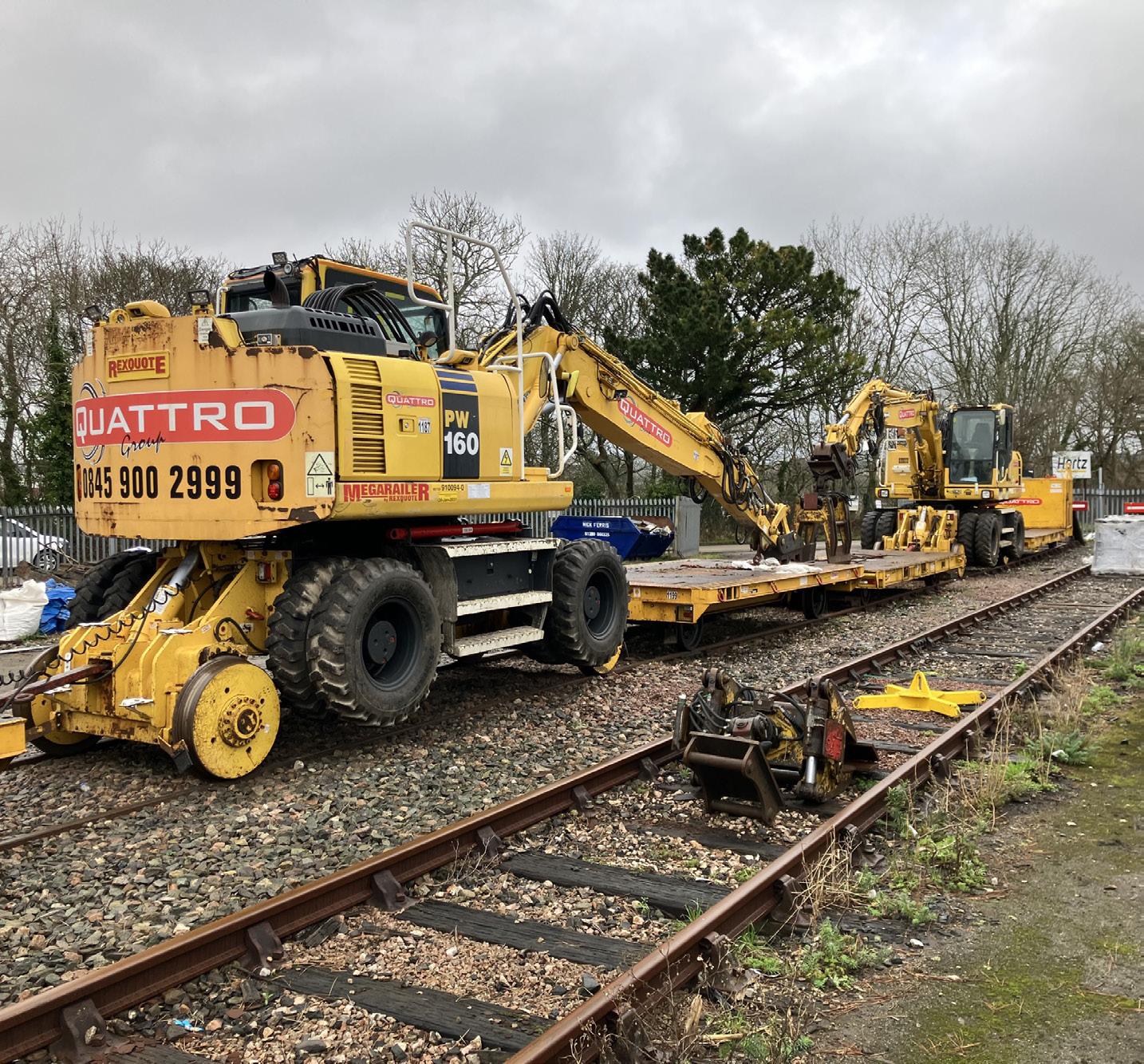
Great Western Railway’s Battery Train Sets New Distance Record
Great Western Railway’s innovative FastCharge battery trial has achieved another significant step – just days after laying claim to a battery train UK distance record without recharging. The train demonstrated its capability on Wednesday by travelling a UK record of 86 miles on battery power alone and without recharging. Today the Class 230 battery train completed a 70-mile move from Long Marston to Reading Train Care Depot – using just 45 per cent of its battery capacity. GWR’s team of specialist engineers on board the train claim it could have travelled more than 120 miles on a single charge.
The train exceeded the 84 miles recorded by a Stadler Class 777 under test conditions in 2022 – believed to have been the greatest distance travelled by a battery train designed for the UK. GWR’s FastCharge technology has been designed to solve the problem of delivering reliable, battery-only trains capable of fulfilling timetable services on branch lines, eliminating the use of diesel traction and
helping to meet the Government and wider rail industry’s target to reach net-zero carbon emissions by 2050.
The use of batteries for extended operation has typically been constrained by their range and meant widespread implementation has, until now, not been possible. It also negates the need for overhead electric lines which are expensive, time consuming to install and impact the landscape.
At West Ealing, where the technology will be trialled in a realworld environment for the first time this spring, the train will charge for just three-and-a-half minutes before restarting its journey on the Greenford branch line. GWR has already carried out simulations on other branch lines in the Thames Valley to explore how it could be rolled out even further in the future. This could reduce GWR emissions alone by over 1,700 tons of CO2e per year. It is hoped the technology could one day see battery-powered trains in operation across the UK’s approximately 2,000 miles of 80-plus branch lines.
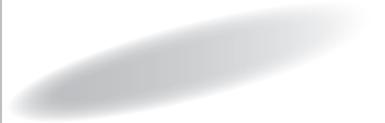
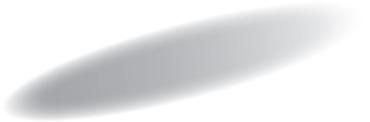
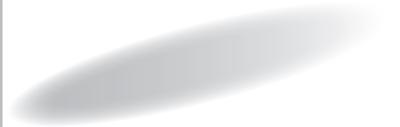
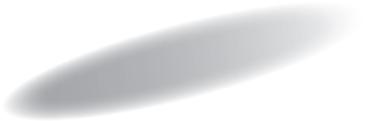
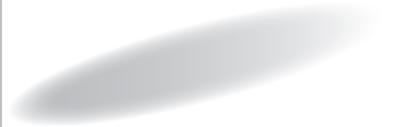


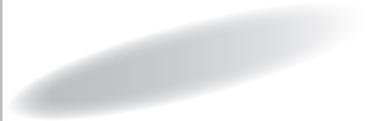
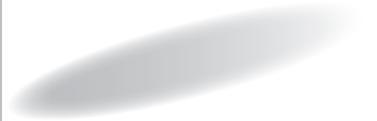
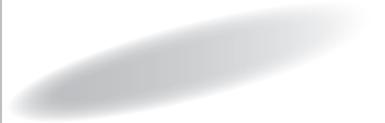
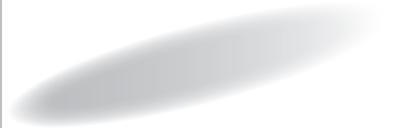
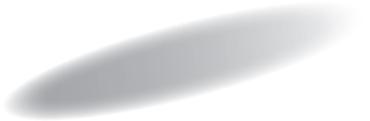
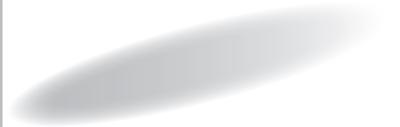

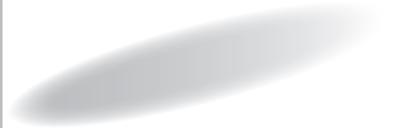
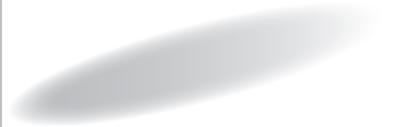


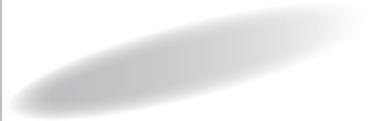

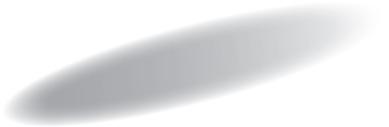
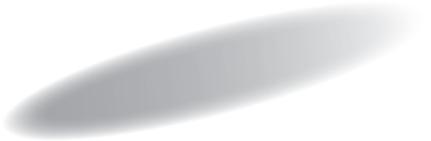

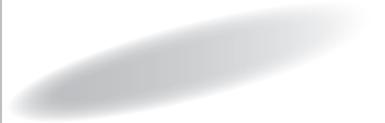
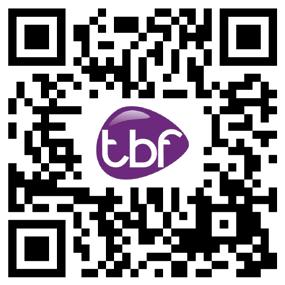
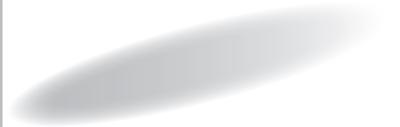
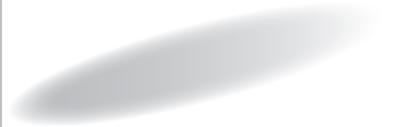
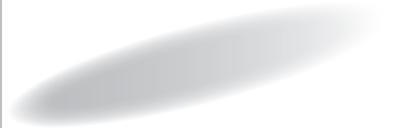
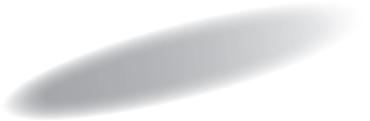

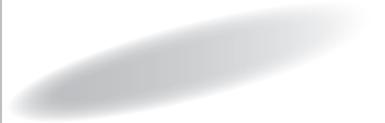
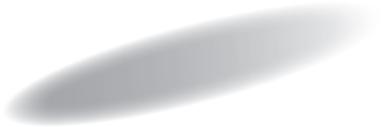
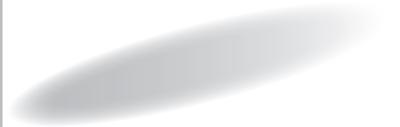
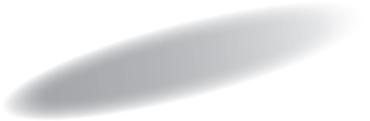
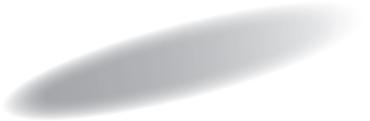
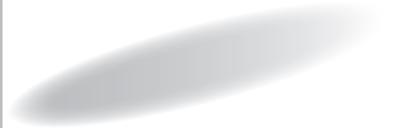



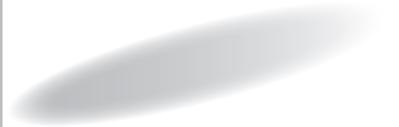
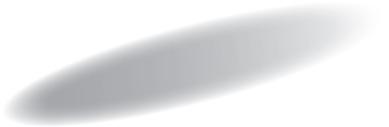

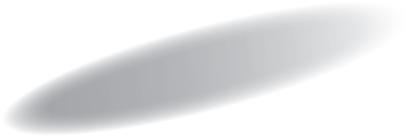
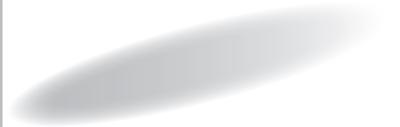
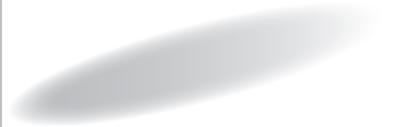
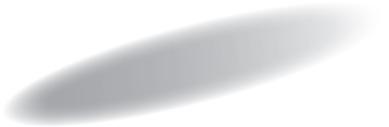
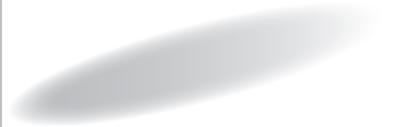


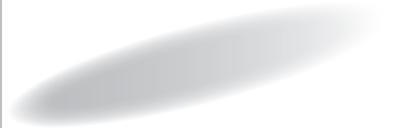

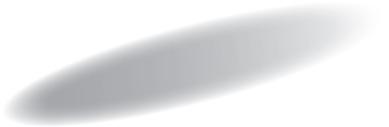
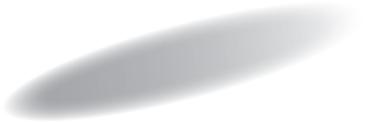
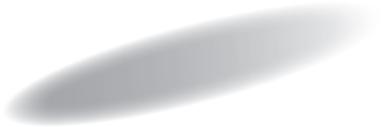

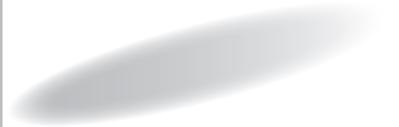
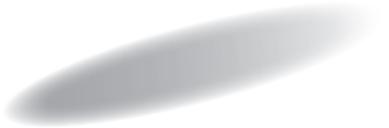

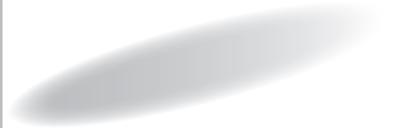
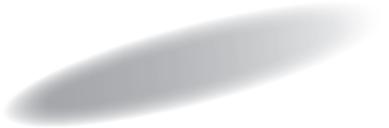
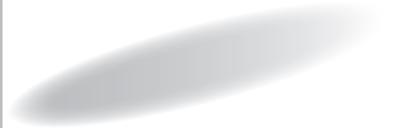
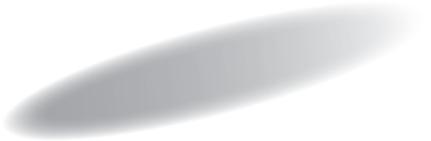

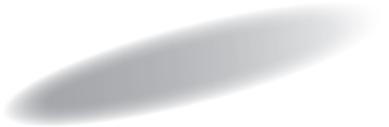
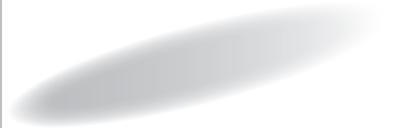

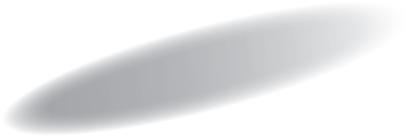
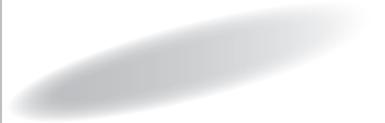
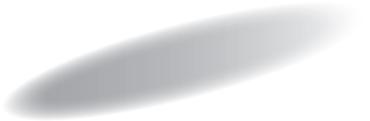
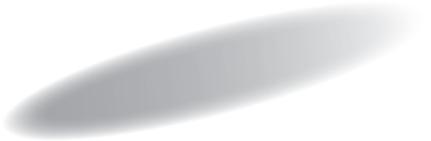






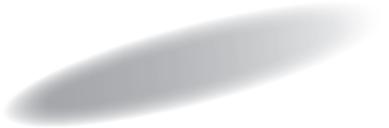
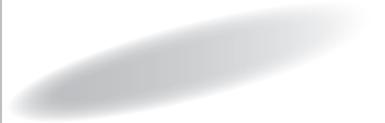
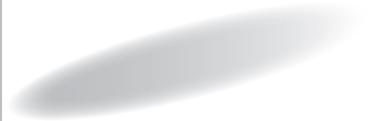
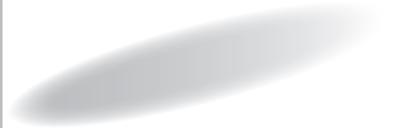
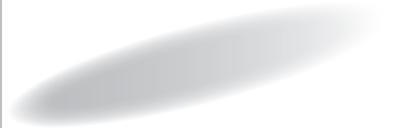
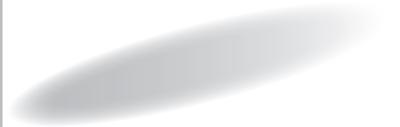
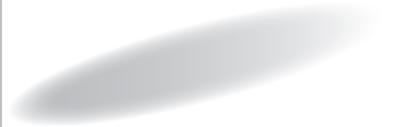
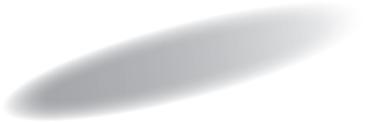
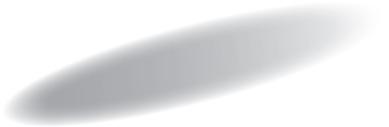
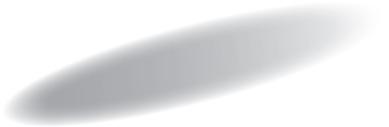

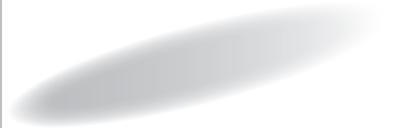
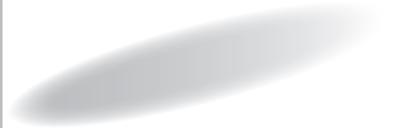

Telent in Innovation Partnership with RIA
Telent is delighted to announce that it has joined Rail Industry Association’s (RIA) acclaimed Unlocking Innovation programme as a Strategic Partner. RIA’s Unlocking Innovation programme promotes and highlights the many innovations and developments happening across UK rail and helps businesses identify new opportunities to innovate. Working closely with RIA, Network Rail and the UK Rail Research and Innovation Network (UKRRIN), Telent will have an active role in the development of the Unlocking Innovation programme and in delivering its strategic objectives.
RIA Innovation Director Milda Manomaityte said: ‘We are delighted to welcome Telent as the third Strategic Partner of the Unlocking Innovation programme, strengthening the collaboration and bringing new ideas. This year we are planning a series of Unlocking Innovation events across the UK’s nations and regions to connect with local stakeholders, suppliers and researchers. Unlocking Innovation ‘on tour’ aims to work closely with Network Rail’s routes, regions, and capital delivery teams as well as regional transport bodies to
bring together the innovation community and local railway stakeholders for a showcase of market-ready innovations, R&D work, funding and accelerator programmes, as well as testing capabilities.’
The Unlocking Innovation programme is aimed at promoting innovations and new developments within the sector. Through a series of events, articles, thought leadership reports and industry surveys, the programme seeks to understand the challenges innovators face, provide clarity for routes to market and connect individuals with ideas and the ability to make changes.
‘UK rail is facing many challenges –ageing infrastructure, obsolete systems, climate change – which all lead to operational uncertainty and although wellfunded, UK Rail is not funded sufficiently to address these issues without doing things differently’ said Kevin Bonanno, Director of Rail at Telent. ‘Innovative technology solutions are key to addressing these challenges. Telent has a proud history of innovation and of transforming legacy analogue infrastructures into future proofed digital environments. Being part
of RIA’s acclaimed Unlocking Innovation programme will allow us to support SMEs and innovators in bringing and deploying their solutions to Britain’s railways.’
Unlocking Innovation events are the centrepiece of the programme, bringing railway clients and suppliers together to share the latest innovations in the market and engage with academic institutions. This allows for a better understanding of research and development pipelines and provides an opportunity to learn about funding and accelerator opportunities to bring innovations into the market.
Telent will be on-hand at each event and support the programme to help make positive connections with UK rail stakeholders, suppliers (current and potential) and developers of innovative technologies that seek to address the challenges faced by the rail industry. Telent will play an important role in bridging the gap between innovators and national railway priorities, by working with and supporting Small and Medium Enterprises (SMEs) to bring their products and solutions to the rail sector.
HS2 Moves First Huge Delta Junction Viaduct Section over M42/M6 Link Road
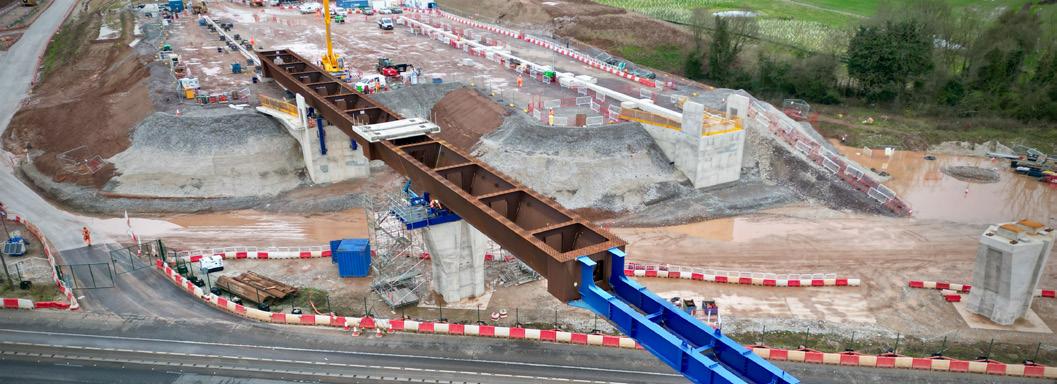
HS2 has moved the first huge viaduct section into place over the motorway network in North Warwickshire, marking a milestone for the project’s Delta Junction as HS2 reaches peak construction in the region. Contractors working for HS2 have used a specialist push-pull technique to move the 84 metre, 300 tonne steel viaduct section into place over the westbound link road between the M6 and M42 near Coleshill.
This is the first of two moves to install the deck for HS2’s ‘East Link Viaduct’, which is part of the triangular Delta Junction. The second operation in April will create the full 158-metre-long composite deck over both westbound and eastbound motorway link roads. Further work, including in-situ concrete deck works and parapets installation will be undertaken to complete the structure.
It was delivered by specialist steelwork company Victor Buyck Steel Construction (VBSC), working on behalf of HS2’s main works contractor Balfour Beatty VINCI (BBV). Using a push-pull jacking system which gives greater flexibility during the launch operation, it was the first time VBSC have used their specially designed technique in the UK.
The team completed the move ahead of schedule in a total of 11.5 hours during a weekend closure of the motorway link roads. Working in close collaboration with National Highways, the roads were reopened at 2.35am on Sunday morning.
Before the end of this year, a similar two-stage operation will move the identical ‘West Link Viaduct’ which runs parallel to the East Link Viaduct. This section of the triangular Delta Junction enables high speed trains to travel between London, Interchange Station in Solihull and Birmingham Curzon Street Station.
The first launch takes the viaduct section to its halfway position over the westbound link road. Following completion of the first launch, three further steel girders will be welded to the back of the first structure, and 40 precast slabs will be installed on top of the girders. In April, this entire structure, weighing 1,100 tonnes will then be moved to its final position over both westbound and eastbound motorway link roads.
The Delta Junction is made up of embankments, cuttings and a total of 13 viaducts taking high speed tracks over motorways, local roads, existing rail lines, rivers and floodplains. The viaducts include six precast segmental viaducts, four composite viaducts and three low viaducts.
The layout of the Delta Junction triangle means the railway from London curves west on a spur towards Birmingham Curzon Street Station. As trains come out of Birmingham, the line heads north to meet the main HS2 line, which will then connect to the West Coast Main Line to Manchester. The third side of the triangle allows trains to run between London and Manchester without stopping at Birmingham.
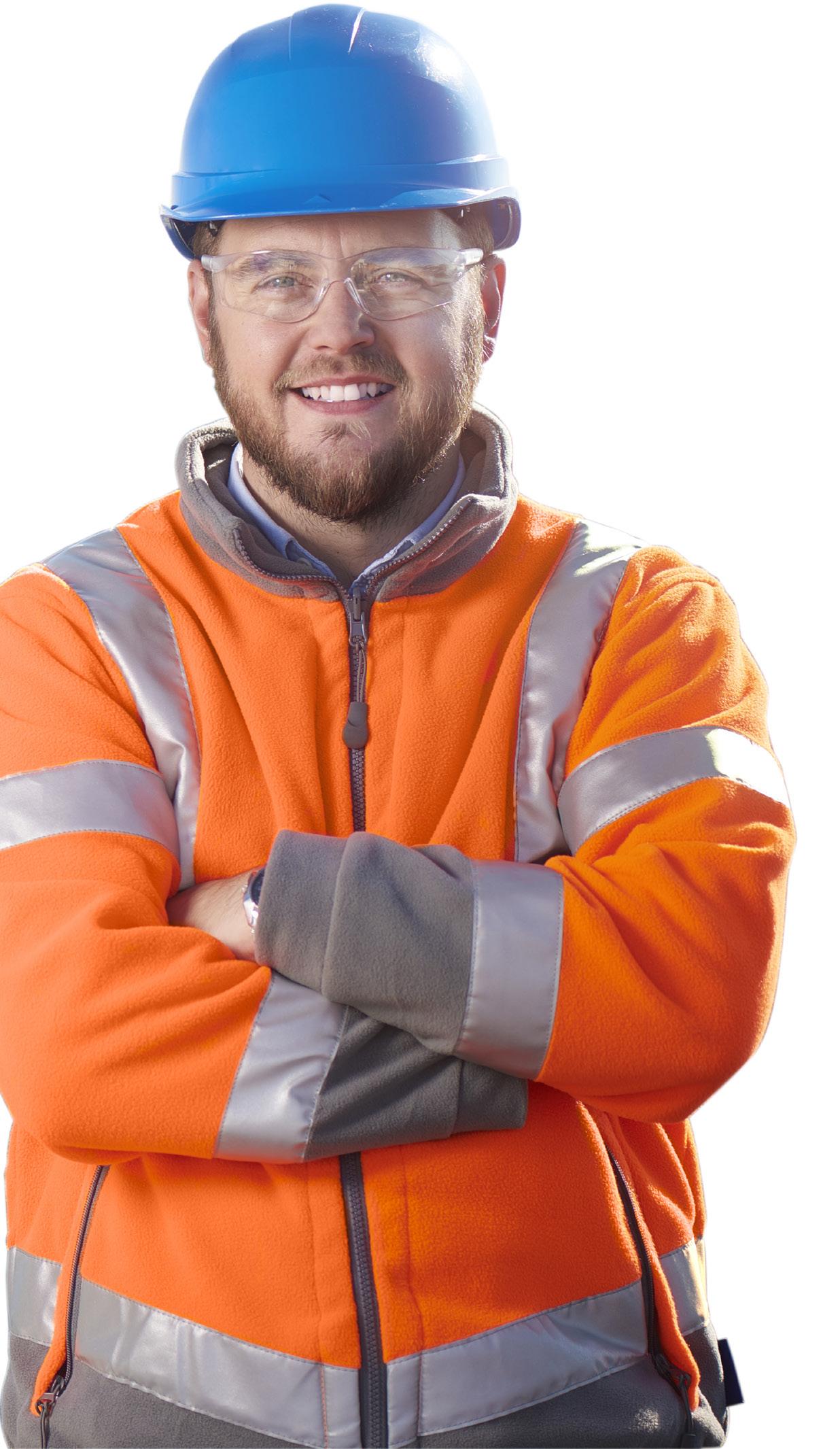
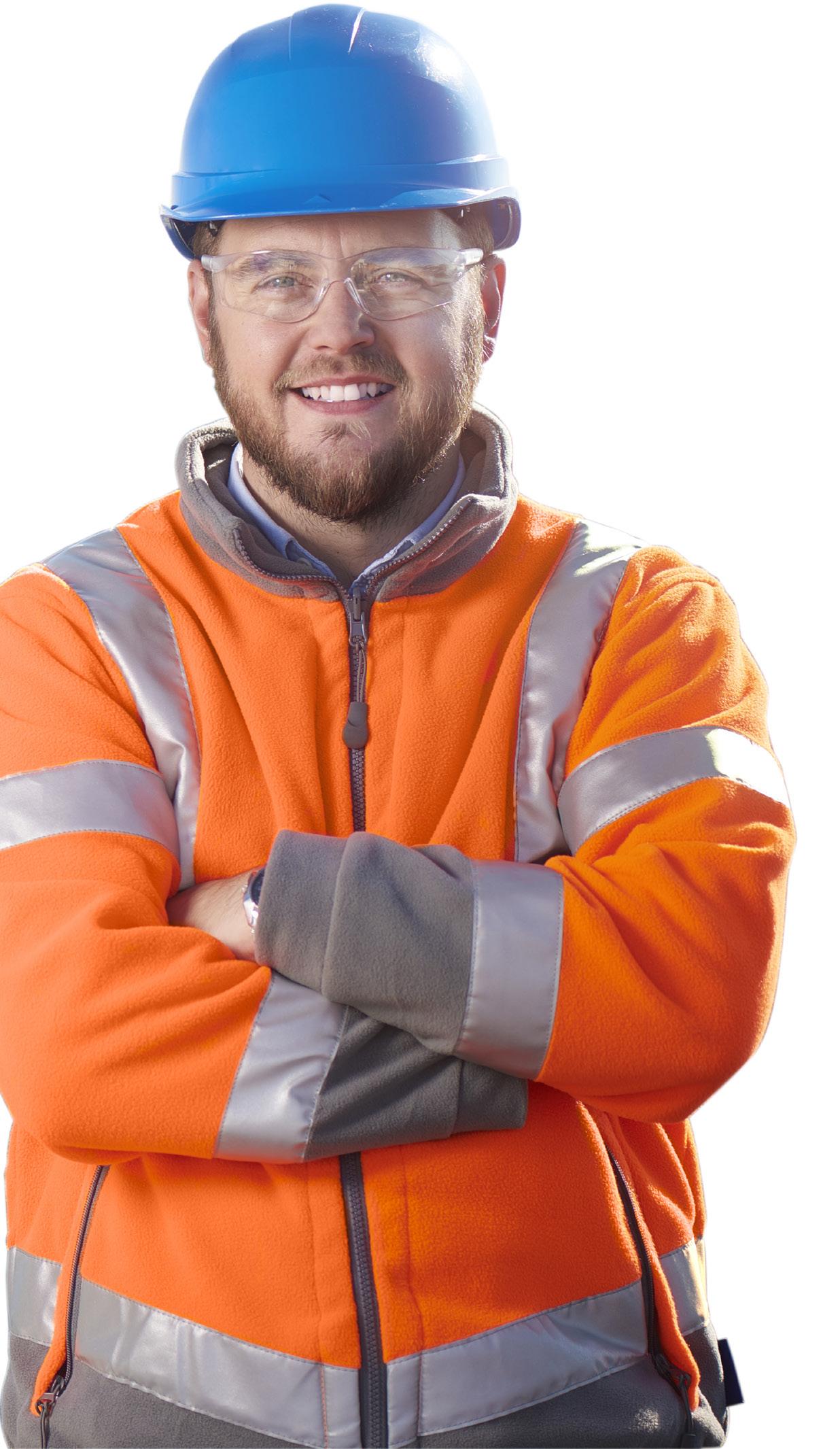

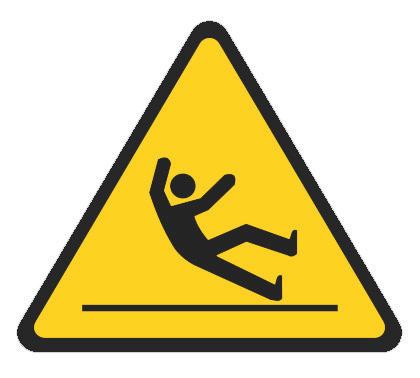
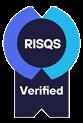
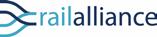
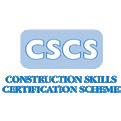



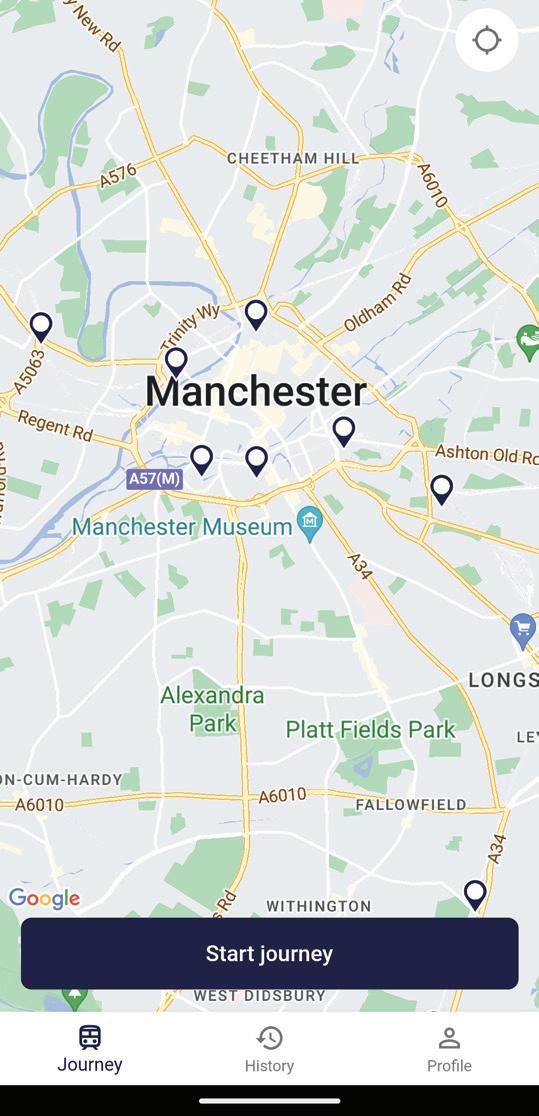
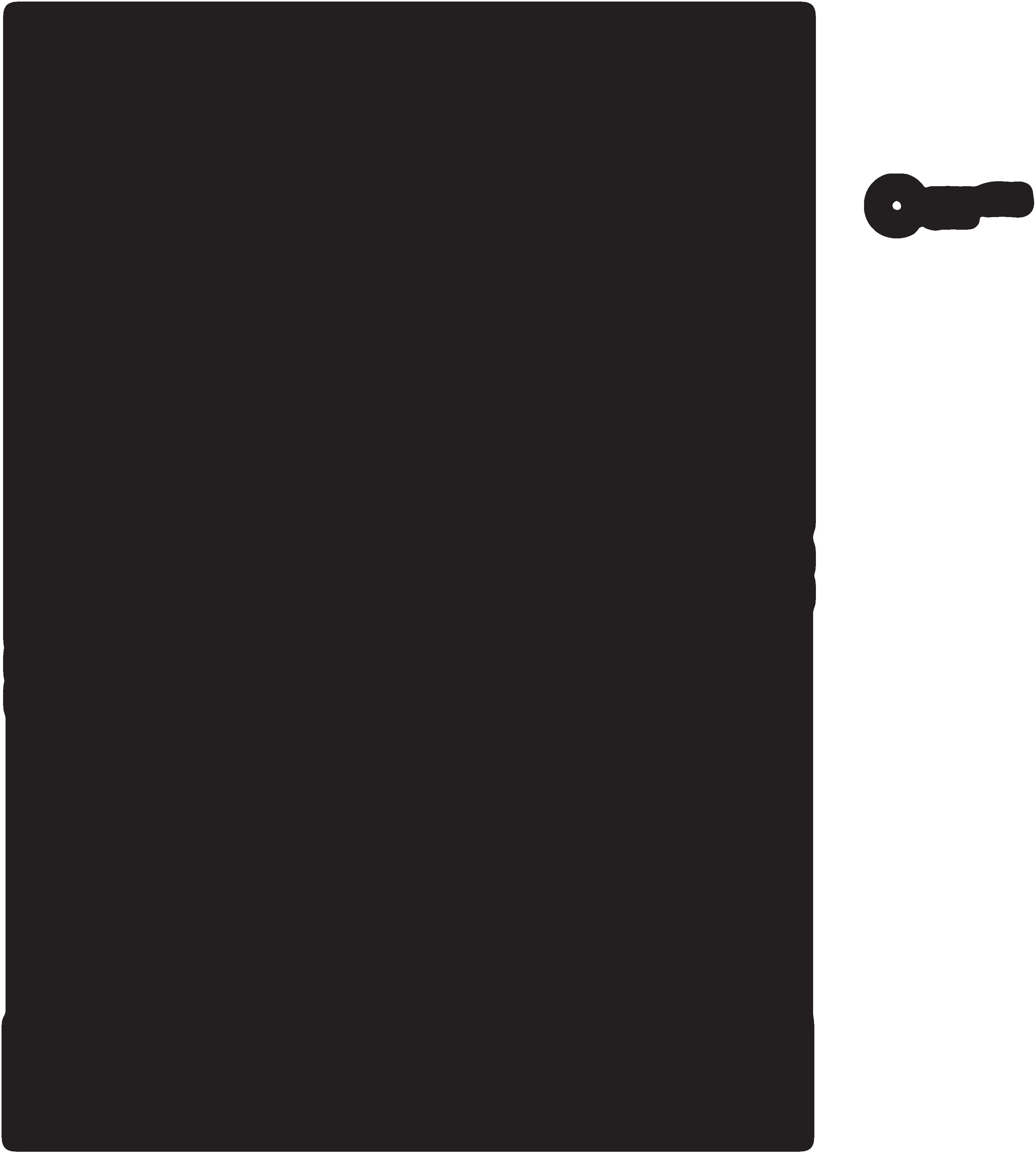
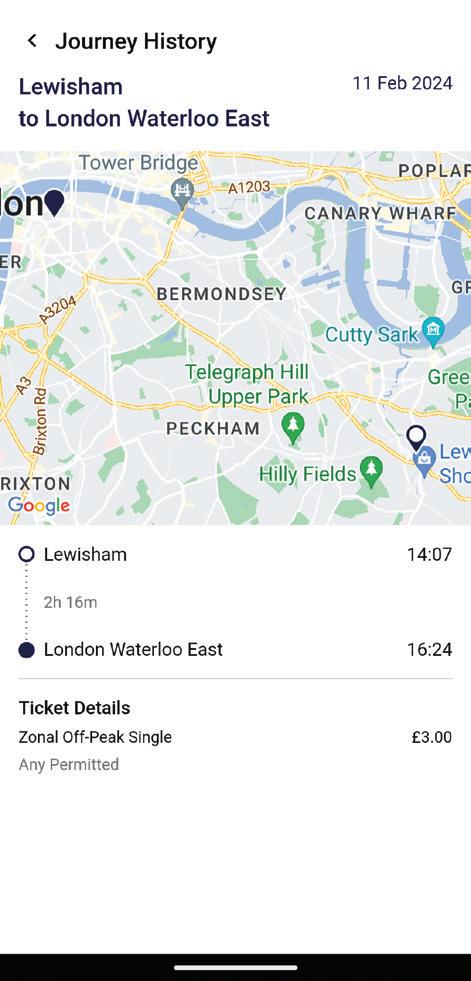
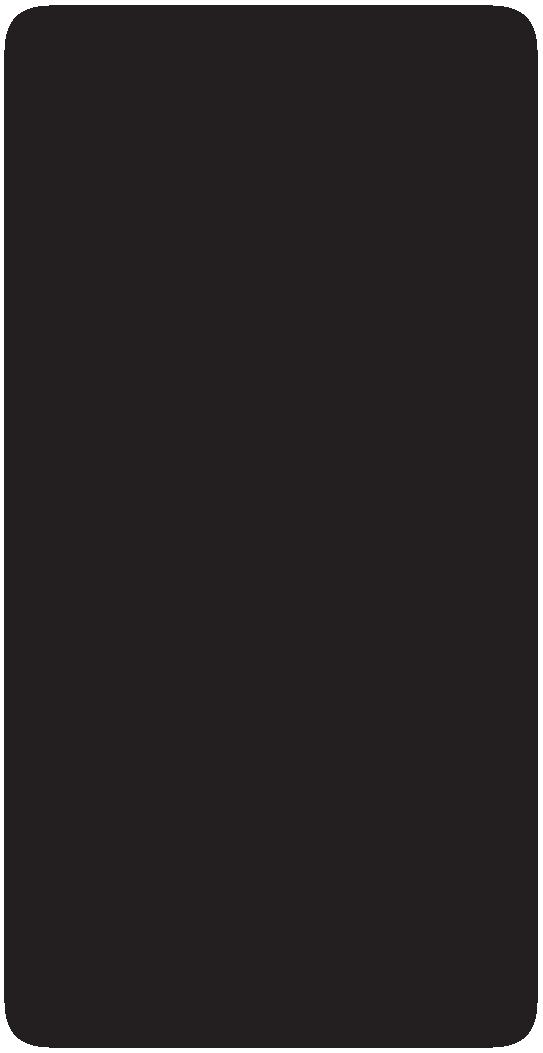
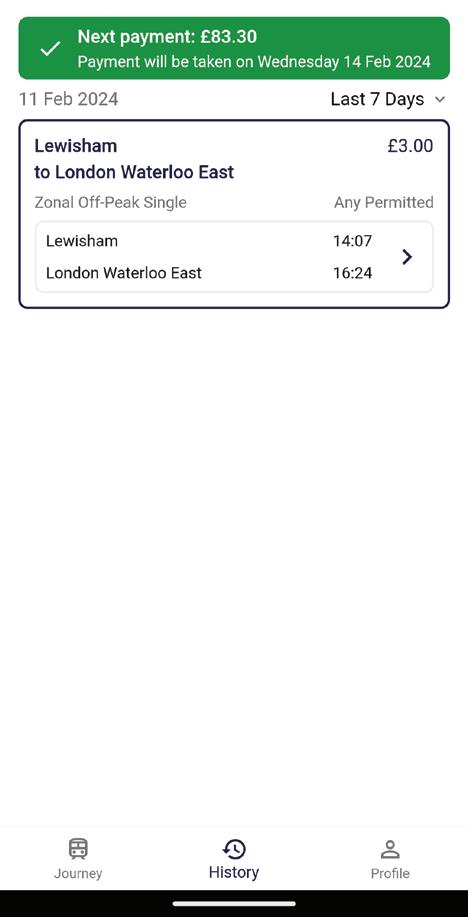

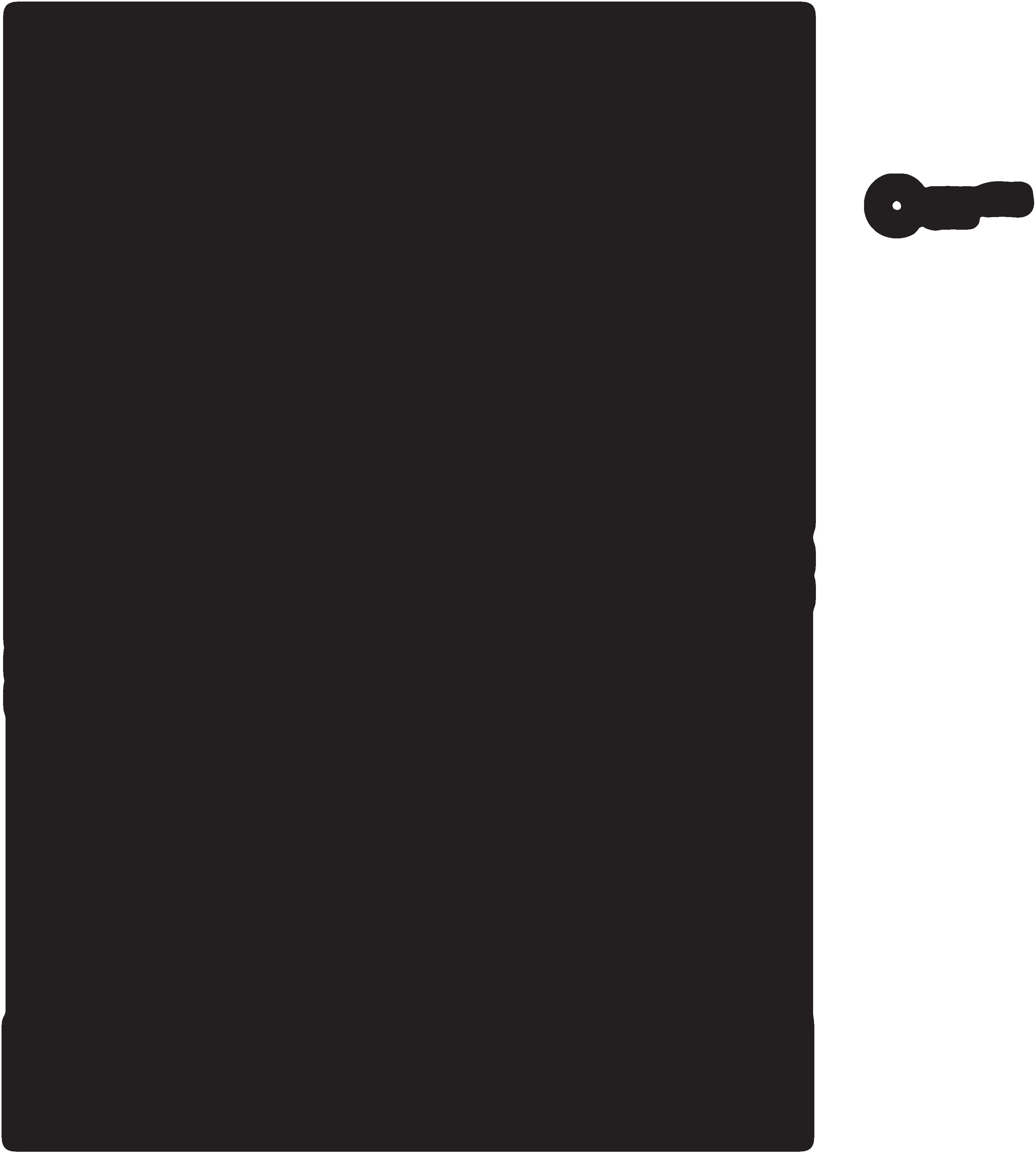
Brand New Trains on the Maesteg Line
People living in the Maesteg valley are set to benefit from brand new trains. Assembled in Wales, the Class 197 fleet have been cleared to operate on the Maesteg line down into Bridgend and across to Cheltenham Spa via Cardiff, Newport and Chepstow. The trains are part of an £800 million investment by Transport for Wales to upgrade rolling stock.
The Class 197 fleet began it’s roll out last year, with 77 ordered via Spanish manufacturer CAF, who have set up a factory in Newport to assemble their UK trains. They will become the backbone of the mainline fleet and can run in formations between two and six carriages. Following the introduction to Maesteg and Cheltenham, we expect the trains to be launched on the Ebbw Vale line and the Pembroke Dock line in time for the summer and on the Cambrian line in 2025.
As more arrive they will continue to replace the older trains, but customers may see both operating as our transition continues.

University of Birmingham on Track with Japan Trail Partnership
Railways experts at the University of Birmingham are joining forces with East Japan Railway Company (Japan Railway East) to create innovative rail technology and new ways of staffing Japan’s railways. University of Birmingham Provost Professor Stephen Jarvis and Japan Railway East Senior Executive Officer, Shunzo Miyake signed a Memorandum of Understanding (MoU) in a special ceremony at the University’s UK campus.
Japan Railway East experts will join their counterparts in the Rail Innovation Cluster at the Birmingham Centre for Railway Research and Education (BCRRE) - working with start-up companies in the UK and Europe and conducting demonstration experiments in various technical areas.
The partnership will also establish an innovation hub at Takanawa Gateway City, which opens to the public later this year. There will also be an educational programme for railway personnel and joint research into railway-related fields, such as digital transformation (DX) and decarbonisation.
Provost Professor Stephen Jarvis from University of Birmingham commented: ‘The University of Birmingham is honoured to be signing a Memorandum of Understanding with Japan Railway East. Working with leading international partners opens several opportunities for academia and industry to work together and showcase the impact of applied R&D, we look forward doing this with East Japan Railways.’
Shunzo Miyake, Senior Executive Officer, Director General of International Affairs Headquarters, Japan Railway East, commented: ‘We are honoured to take this first step in collaborating with the University of Birmingham, which has a British heritage as
the birthplace of railways and the prestigious railway research institution BCRRE.
‘British inter-city rail to London began with the LondonBirmingham Railway, and Japanese railways began with the intercity between Tokyo and Yokohama, where we currently operate, passing through Takanawa Gateway City. We hope this partnership would develop railway technology and generate innovation that will change the future of the rail industry and beyond.’
Professor Paul Plummer, Director of the Birmingham Centre for Railway Research and Education, University of Birmingham commented: ‘It is great to build on strong international relationships through agreements that will improve our railways and the railway workforce. We are therefore delighted to be collaborating with Japan Railway East to develop and demonstrate technological advances. Education and upskilling are important to us, and we look forward to working with Japan Railway East to enable sustainable economic growth and wellbeing.’
The Rail Innovation Cluster encourages startup companies in the UK and Europe to innovate in the railway field - fostering innovation in railway technology by leveraging the University of Birmingham’s research and development capabilities railways and providing support through BCRRE’s international network.
BCRRE is one of the largest railway research and education institutions in Europe, located within the University of Birmingham. It is a leading partner of the UK Railway Research and Innovation Network (UKRRIN), which works with the rail industry in the UK to deliver world-class research, education, and innovation to the world.
Taking Safe Decisions
Safety Management Intelligence System
Annual Health and Safety Report
Safety Risk Model
Precursor Indicator Model
PRIMA – proportionate risk response
Bowtie Hub
Generic Hazard List
Rail Risk Toolkit
Risk and Safety Intelligence:
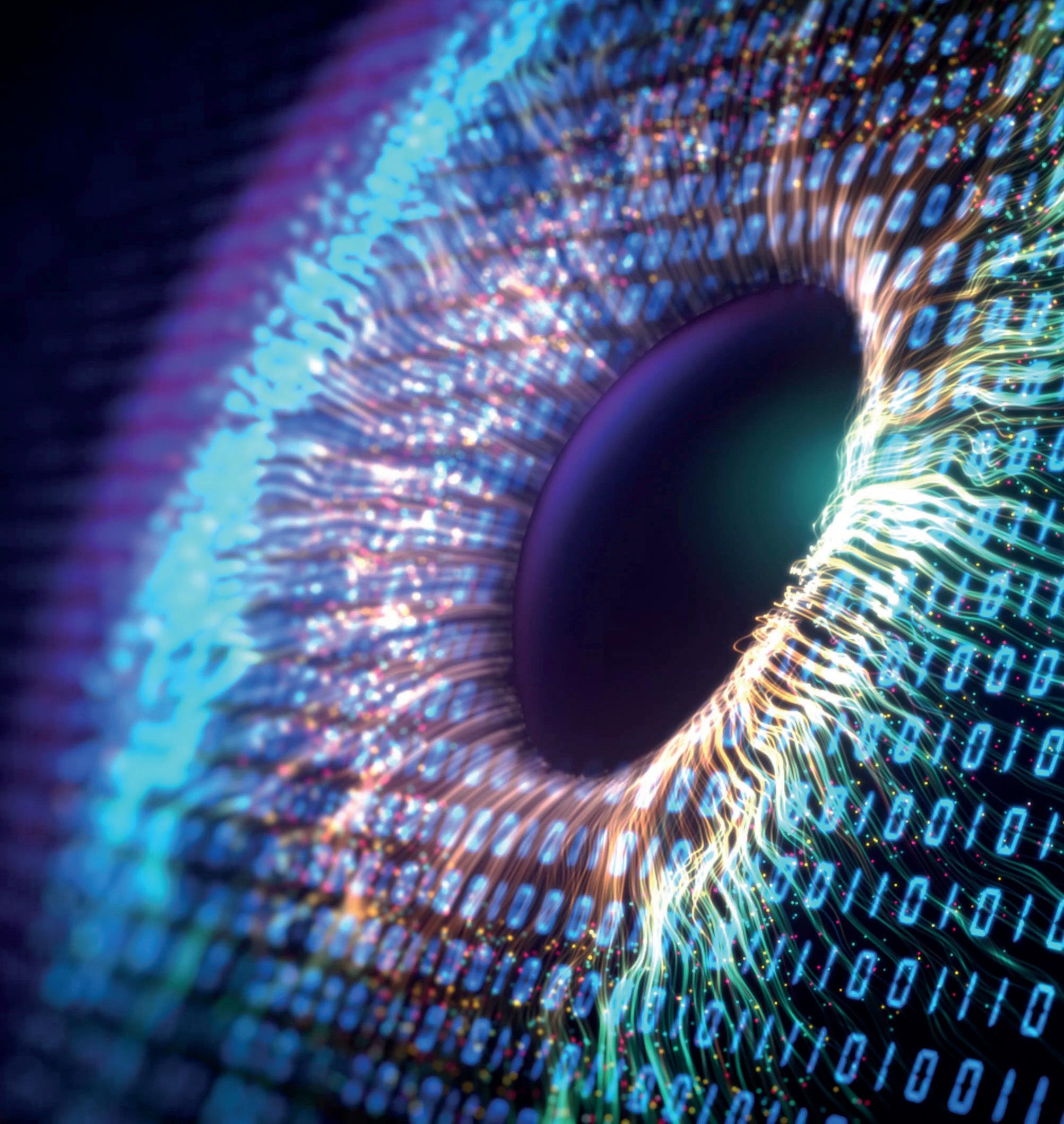
We’re with you every step of the way
Shared intelligence: the foundation of safety
Safety data is at the heart of our efforts to keep making rail safer. Decades of safety event data come from sources like the Safety Management Intelligence System (SMIS). All recorded and shared across the industry, and analysed by RSSB.
This shared intelligence is central to the creation of tools like the Safety Risk Model, which quantifies risk across the rail network.
Our independent, whole-system view helps keep Britain moving –with safer, smarter rail.
For more on rail risk & safety intelligence: www.rssb.co.uk/sharedintelligence
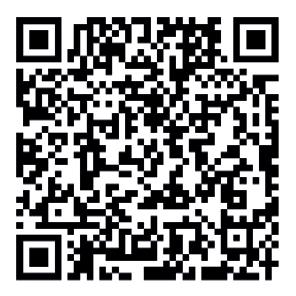
Southeastern’s Work to Provide a Safe Railway Formally Recognised
Southeastern’s efforts to provide a safe railway for customers and colleagues has been formally recognised by the British Transport Police (BTP). The Safeguarding on Rail Scheme (SRS) Accreditation recognises rail sector organisations for their work to protect vulnerable children and adults at risk on the railway. Southeastern’s audit took place in January and saw the operator surpass the required 92.5 per cent standard – one of only three passenger train operators to do so in the country.
The accreditation follows major investment and focus from Southeastern in
recent months to enhance the protections it puts in place across the network as it seeks to build a better, more reliable and sustainable railway.
This includes the introduction of a new Safeguarding Team, which comprises a number of new roles and includes people with a vast experience in safeguarding, all of whom will continue to drive the safeguarding message across the Southeastern network.
Mark Sutton, Safeguarding Manager at Southeastern, said: ‘Everyone involved with achieving the Safeguarding on Rail Scheme
Accreditation is absolutely thrilled to be recognised by the British Transport Police (BTP). Safety is at the heart of everything we do on the railway, whether it is customer facing or behind the scenes but this accreditation recognises our extra efforts to protect those who are vulnerable and who need our support and care more than others. We look forward to working with the BTP and other partners in the future as we strive to make our railway even safer and more supportive of everyone who travels with us.’
Project Promises Revolution in Light Rail Training
The management of training and development on UK tramways is set to be transformed with the launch of an ambitious sector-wide initiative. Led by the Light Rail Safety and Standards Board, the project aims to revolutionise learning across the sector and includes the development of an online resource that networks can use to plan and maintain their own training programmes. The centralised learning platform will monitor employee competencies, keep track of required certifications, and help identify the most appropriate training courses. It will also provide a hub for best practice, delivering consistency across the sector while driving even higher standards in all aspects of light rail training.
Carl Williams, LRSSB Chief Executive, explained: ‘By listening to colleagues and key stakeholders, we’ve identified a clear need for a comprehensive Learning Management System that embraces the current and future needs of UK tramways. As a vital next step, we’re currently planning a series of workshops to ensure the support of HR and training professionals from across the sector.’
Porterbrook Takes Stake in Brodie Engineering
On 20 February 2024, the UK’s leading rolling stock financier and asset management company Porterbrook agreed a deal to take a 49 per cent stake in Brodie Engineering. The Kilmarnock based company is the only active rail engineering business in Scotland, specialising in heavy maintenance, refurbishment and overhauls for passenger and freight vehicles. The company began operating in 1996 and works
To help manage the project, which has the backing of the Office of Rail and Road, the LRSSB has expanded its expert team to include Edinburgh Trams Training Manager, Marlene Pearson.
Having successfully delivered a similar system at a network level, Marlene is working with the organisation to help develop a scaled-up platform for the entire sector while on a part-time secondment to the LRSSB.
‘I am excited to be part of this initiative and fully appreciate how this can support the sector as we continue to advance and explore the use of technology within light rail. I believe that, with the help of the sector, the LRSSB is perfectly placed to achieve this’ Marlene said.
Carl Williams added: ‘Marlene’s skills, knowledge and experience are already proving invaluable as we work towards the delivery of what promises to be an essential tool for standardising competences across key roles within light rail, identifying any skills gaps, and providing another major boost for sector safety.’
across two sites based either side of the Kilmarnock rail track; the Bonnyton Works, and the Caledonia Works which the business acquired in 2020. Today’s deal further underpins Porterbrook’s ability to provide a full turnkey solution for its customers and fleets, alongside continued investment to upgrade facilities across the 135-acre Long Marston Rail Innovation Centre in Warwickshire.

New Partnership between RIA and the Railway Benefit Fund for 2024
The Railway Industry Association (RIA) has announced the Railway Benefit Fund (RBF) as its Charity of The Year for 2024. The RBF provides assistance, advice, and support to current, former, and retired railway staff and their dependents across the UK. Established in 1858, the charity offers a range of services including financial grants, confidential advice, and a legal helpline among others.
The RBF’s overarching mission is to deliver customised support to railway people and their families, improving the lives of current and former workers, wherever they are in rail.
Over the past five years, demand for their services has more than tripled. In 2023:
• An existing or former railway employee approached RBF every four minutes.
• RBF supported over 1,000 railway families with direct financial support.
• 65 per cent of grants awarded were for those who currently work in rail.
• Nearly 70 per cent of applicants are under 50 years old, with an increased prevalence of those in their 20s.
• RIA will be taking part in the ‘Station to Station’ challenge as part of RBF’s Railway Family Week. This involves taking on a step challenge which equates to a 2000-mile route around Great Britain, calling at 23 stations, over three weeks.
Jo Kaye, Chief Executive of the Railway Benefit Fund (RBF), said:
‘We are delighted that RIA have chosen the Railway Benefit Fund as their Charity of the Year for 2024. Their support will be crucial to us as a small charity, enabling us to meet the rising demand for our services, and raising awareness of the work we do within the rail supply community. We look forward to attending RIA’s events throughout the year and networking with their members.’
Darren Caplan, Chief Executive of the Railway Industry Association (RIA), said: ‘The Railway Benefit Fund plays a hugely important role in supporting current, former and retired railway people and their families across the UK. The Railway Industry Association is proud that the RBF is our Charity of the Year for 2024 and we look forward to working with Jo and her team in promoting the charity and its work among RIA members.’
Covid Plaque Unveiled by Network Rail Chair and Railway Mission Chaplain
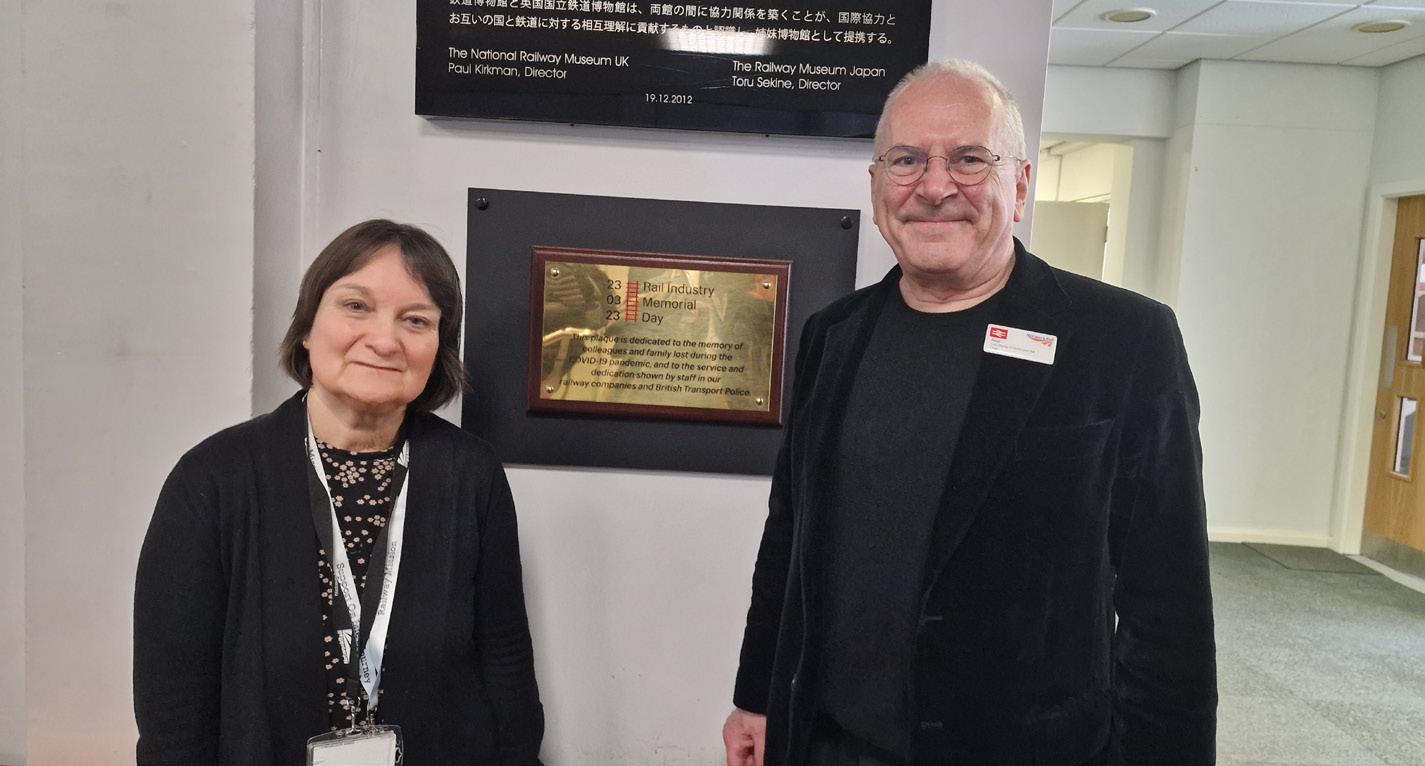
A commemorative brass plaque has been unveiled at the National Railway Museum by Network Rail Chair Lord Peter Hendy of Richmond Hill and Angela Levitt-Harwood, Railway Mission's York region chaplain. Ahead of Reflection Day on 3 March, Lord Hendy of Richmond Hill revisited the York Museum where he had previously unveiled a temporary version of the plaque at the Railway Mission-organised
Rail Industry Covid Memorial Day service held on 23 March last year, three years after the first Covid-19 lockdown.
The plaque is dedicated to the memory of railway employees and family members who died during the pandemic and commemorates the service and dedication shown by staff and British Transport Police.
‘It is absolutely right that we commemorate the loss, and suffering of
railway people during the pandemic, and also dedication of the railway in delivering essential passenger and freight services to transport key workers, and goods, during the pandemic’ Lord Hendy commented.
‘Railway Mission supported people during the pandemic and continues to do so’ added Angela. ‘My prayer is that this permanent memorial can be visited by those for whom the pandemic has left a lasting sense of loss.’
The 2023 Rail Industry Covid Memorial Day service was led by Railway Mission's Executive Director Liam Johnston who, with British Transport Police Director of People and Culture Rachael Etebar, devised the idea of holding a commemorative service. The live-streamed service was attended by hundreds of employees who helped to keep key workers and essential goods moving throughout the pandemic.
The service concluded with Lord Hendy unveiling the temporary plaque, which will now be housed at Locomotion in Shildon. Further services, led by Railway Mission chaplains, were held at stations and the Railway Benefit Fund's Crewe headquarters, with a minute's silence observed at midday at stations, offices and depots across the rail network.
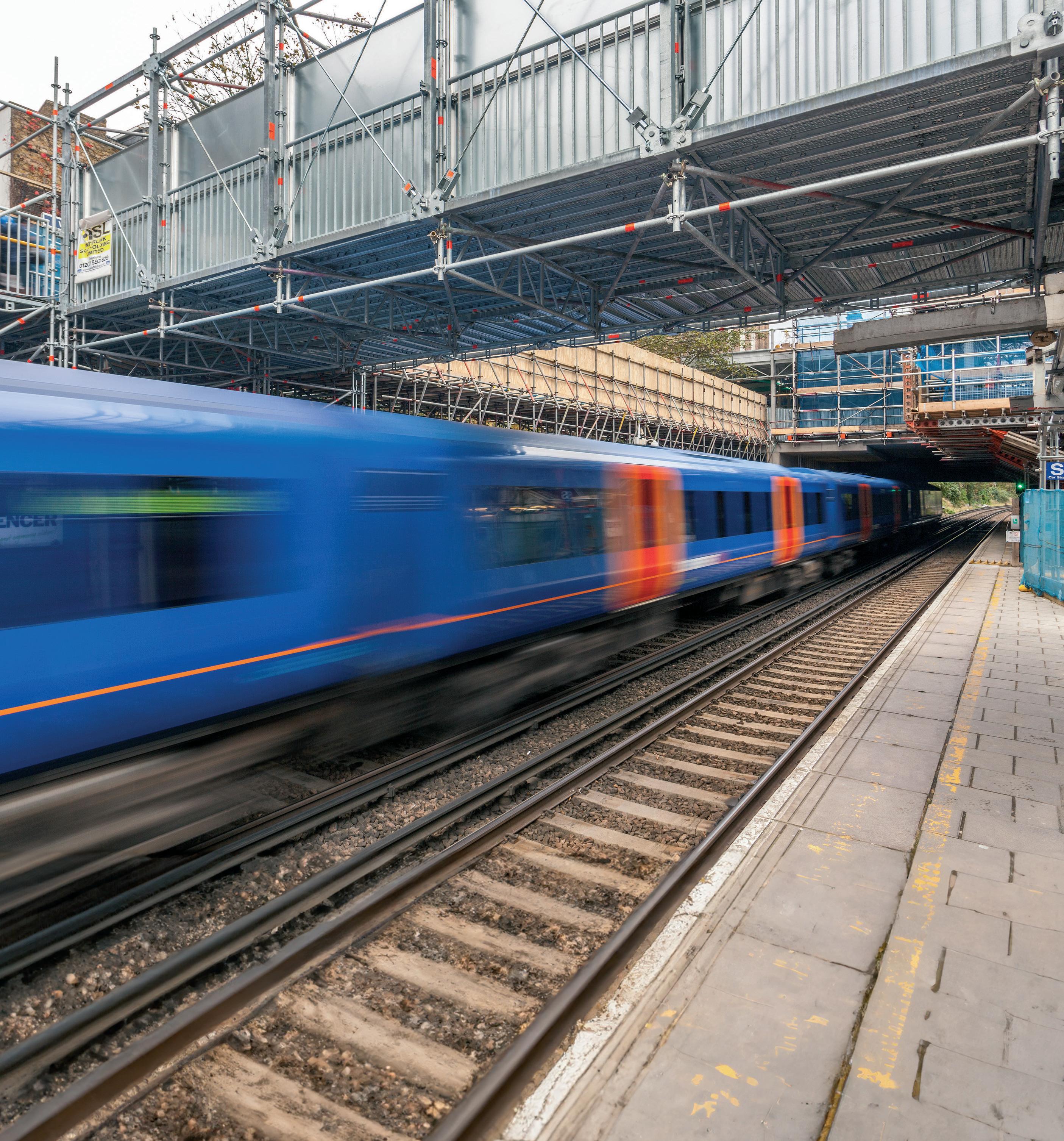
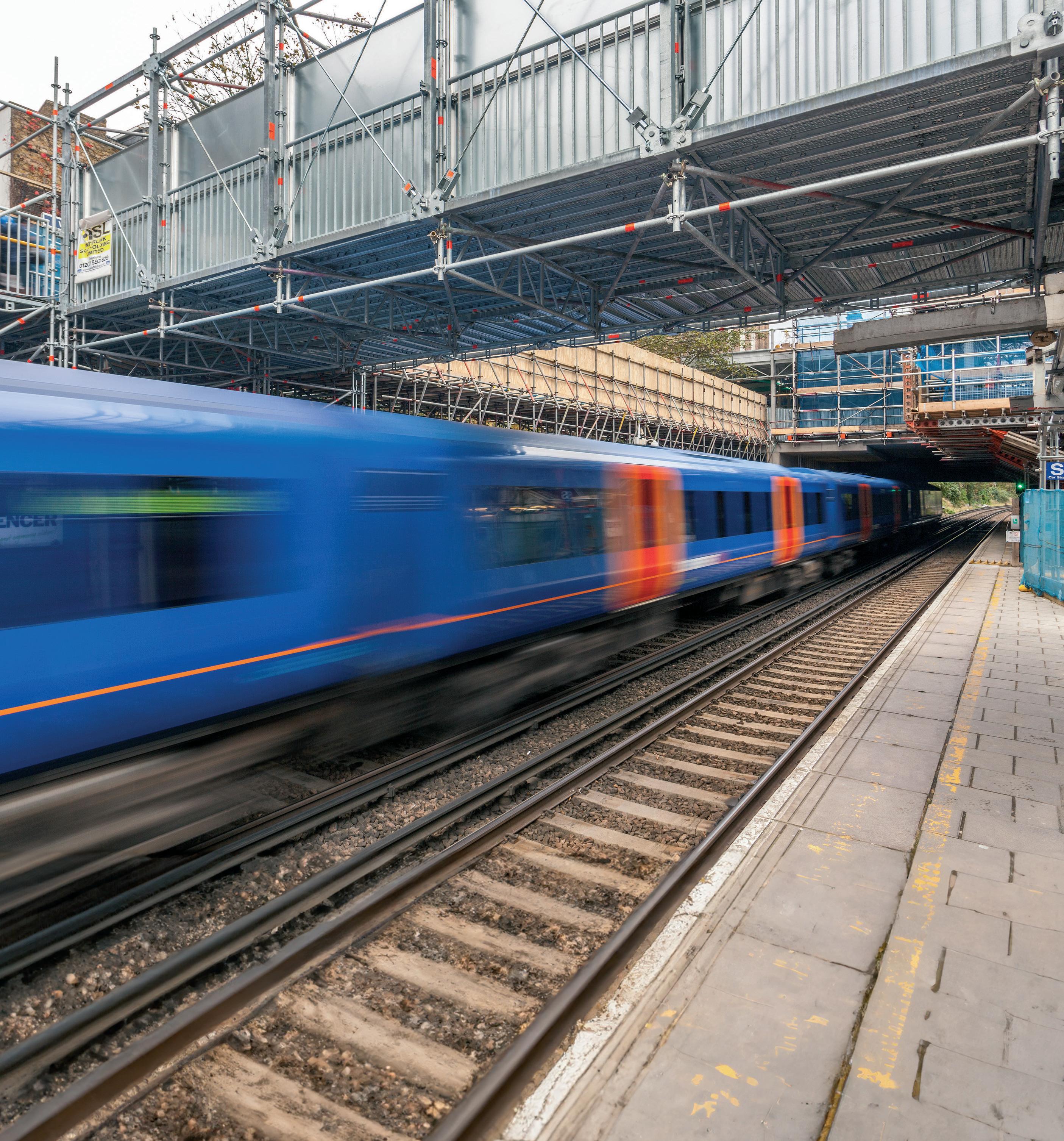
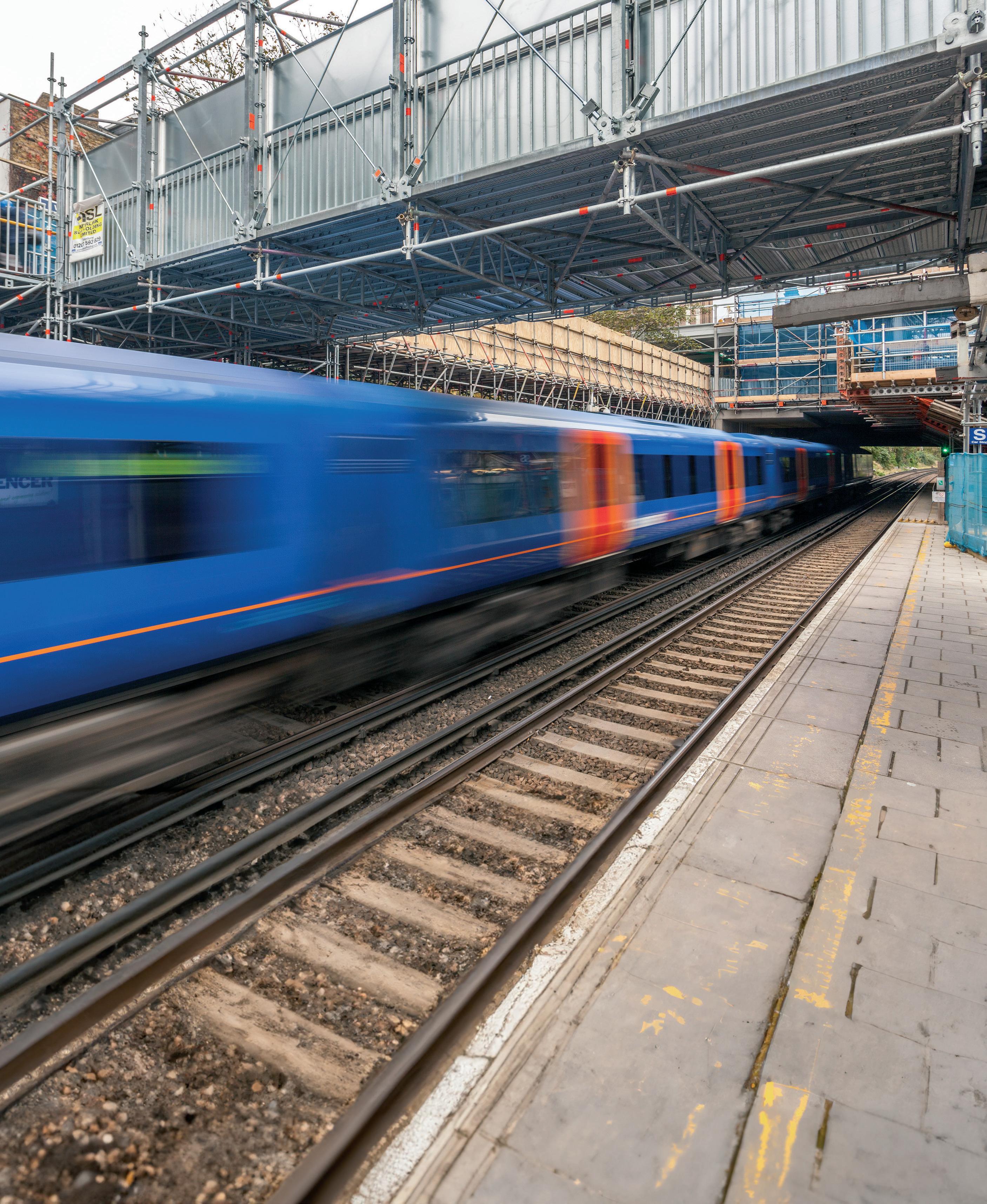
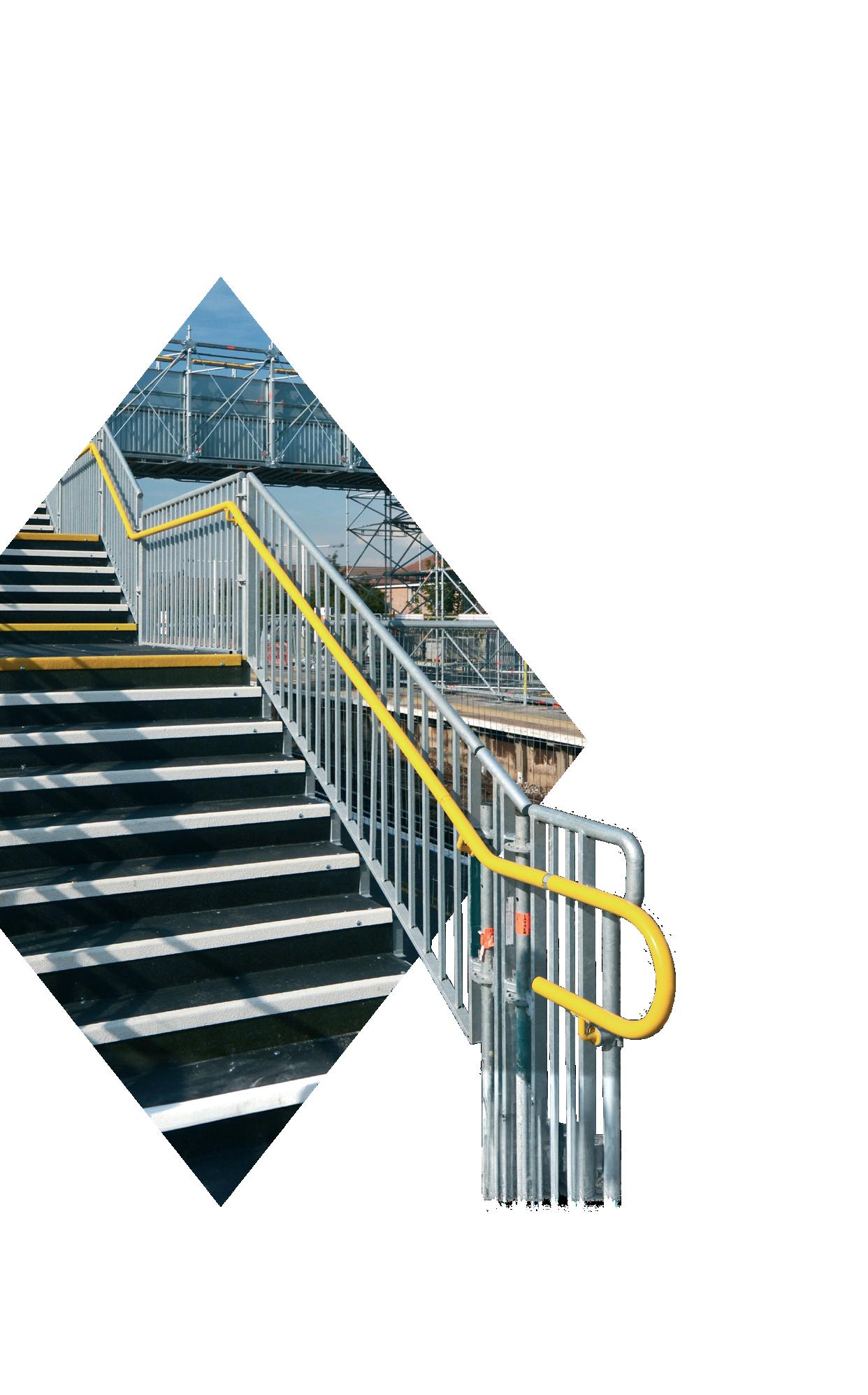

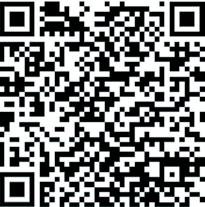

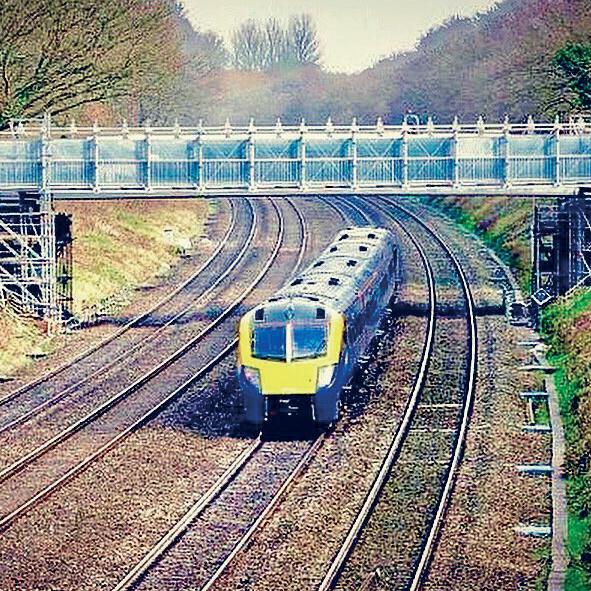
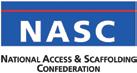
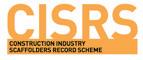

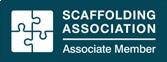
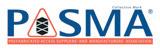
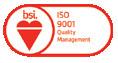


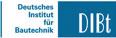



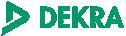




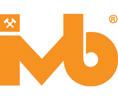
JAMES WOOD
SALES DIRECTOR AT ARMORDUCT
James Wood is the Sales Director at Armorduct. Having started his career as an Electrical Engineer, James is able to bring hands-on design and installation experience to the world of cable containment, by partnering with customers to deliver project success no matter what the technical or commercial challenge.
How did you get started in the industry?
I started in 2009 as an apprentice Electrical Eng in the Building Management Systems (BMS) sector. I worked on control systems for steel manufacturers, installing and maintaining automation and control equipment for the steel production process, so I’ve actually worked in all the major UK sheet steel manufacturing companies. I stayed in that business for 10 years, but started looking at other roles in associated industries. I moved into selling bespoke enclosures for Motor Control switchboards which I felt was a good combination of my knowledge and experience but it was a big adjustment for me to shift into a sales role.
As I adapted and began to think about new challenges I met the team at Armorduct and decided to jump into a newly created internal sales role. That was in 2016 and it’s been an amazing journey since then!
Tell us about Armorduct.
Armorduct are part of the Hudson Cable Management Group, together with our sister companies RMS and Milton. We’re one of the last remaining independent cable management manufacturers in the UK, producing trunking, tray, basket and underfloor cable containment solutions. We supply to the industry through our network of local and national electrical wholesalers, but we liaise directly with M&E contractors and consultants in terms of the specification and design elements for a project.
What is your role within Armorduct?
I became UK Sales Director for Armorduct in September 2023. Prior to that I was the National Accounts Manager, having spent a few years as Area Sales Manager for the East Midlands, but I started with an internal sales role back in 2016.
How long has your company been in business?
Armorduct were founded in 1998 and so we’ve been trading for 26 years this year – we started off making specialist steel trunking solutions, but our product range has expanded hugely since then on the back of projects with our customers.
What is your Unique Selling Point?
Our USP is really how we deal with the more challenging requirements that inevitably crop up with every project installation. I guess you’d call them ‘specials’ as they’re certainly not your typical ‘pick-from-acatalogue’ products, and they’re something we’ve got lots of experience with. They can range from a simple modification on a standard product to a completely new bespoke design to cater for difficult routing or security issues.
When it comes to working with our customers on projects, we don’t shy away from problems, as helping to solve them has benefits all round. Firstly, we gain closer working relationships with our customers by delivering successful projects. This helps secure future business and also builds our reputation in the industry. Secondly, many of the special products developed become part of our portfolio which helps showcase our experience and expertise as a solutions provider. Of course, none of this can happen without our UK-based design team who interact directly with customers during the product design process.
What types of products and services do you offer?
Armorduct manufacture a portfolio of cable management solutions for the rail industry. We have product ranges for cable basket, cable tray and cable trunking, as well as underfloor solutions, available in all the standard industry sizes and materials. Where we differ from most of our competitors is that we also offer almost everything in-between. Special shapes, sizes, fixings, compartments, converters, couplers and materials. All that comes from our legacy of working on projects with customers who need fast and flexible solutions to the problems they encounter on a job. Our engineering team can turn a sketch into a physical sample in 24 hours and we can supply certified, manufactured parts in high volumes within days. We can offer solutions for every environment – be that highly corrosion resistant materials (Stainless Steel, GRP, Magnelis), or highly secured, tamper-proof installations in public spaces.
What are some standout projects you’ve been involved in over the years?
We’ve supported a huge variety of projects in the rail industry. Crossrail has probably

seen our single biggest involvement, where we’ve supplied cable management solutions for numerous London Underground (LUL, now TfL) and Network Rail installations as part of the extensive overall project. We also supported the Northern Line Extension, supplying some of our most innovative and technically complex cable trunking products. We’ve worked on DLR projects and we’re now in the midst of design and development work where we’ve been specified for HS2 on a number of jobs.
When a client comes to you with a particular problem, what’s your process for coming up with a solution, and how closely do you work with clients throughout the projects?
This is where things get exciting for us! When we get a call from a client about a problem, instead of just trying to palm them off with another part from the catalogue, we see it as an opportunity for Armorduct to get involved and share the success of fixing things… Working together to sort out a problem builds trust, friendships, reputation, new products and long-lasting relationships – everything you need for
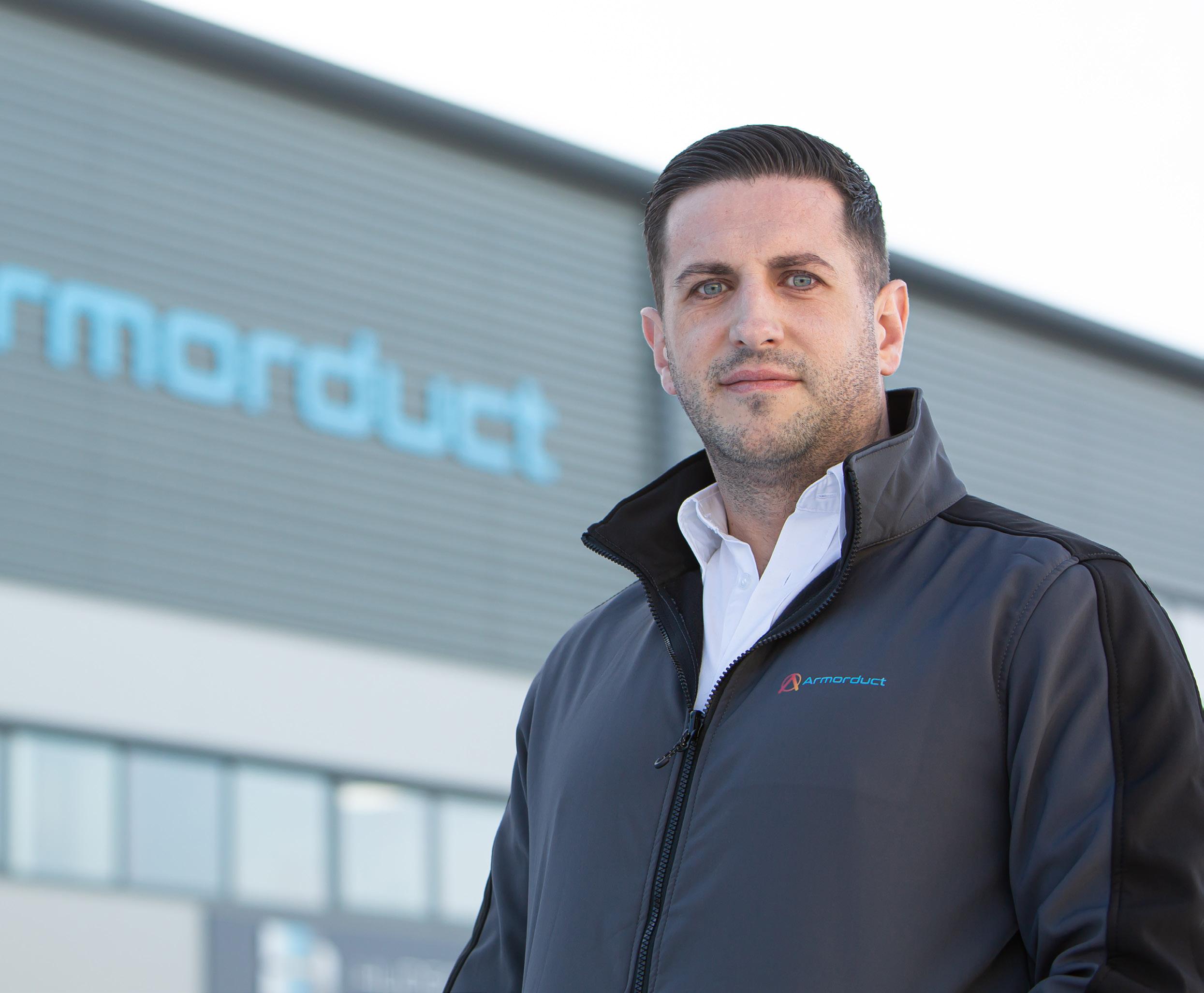
mutual success! This usually means site visits and getting our technical teams connected for some creative thinking to get a practical solution fast. It’s where we excel for UK projects as we can be on-site and onhand the same day if necessary.
Every problem tends to be different, but being blessed with the luxury of having a full turn-key product development team at our disposal usually means we can deal with anything. Challenge accepted!
How do you work with the supply chain within this sector?
Meeting the required specifications for rail industry projects is essential. This is really where our supply chain work starts in this sector, which means we will liaise with the authorities responsible for overall system design to understand all the necessary regulations. Once we have this information, we will then engage with the contractors tendering for the project to discuss options designed to meet the dictated specifications.
As with every project, we work with the contractors to arrive at a solution which meets the spec, at the right cost. And when I say cost, I mean cost in terms of labour
resource, finance budget, installation longevity and, to a much greater extent now, improved sustainability. Every supply chain everywhere is being tasked to deliver in a more planet-friendly way, and it’s why we’re switching over to greener steel, more sustainable finishes and coatings, and running more of our manufacturing facilities on renewable energy. We’re also being asked more frequently to provide embodied carbon equivalents for our products and processes to demonstrate our green credentials.
In many ways, sustainability regulations are now becoming another ticket to the game, in much the same way as compliance to electrical standards, and it’s something we have embraced throughout the business. The supply of our products to the end user is handled through our electrical wholesaler partnerships.
We work with contractors through an agreed, nominated wholesale partner to provide end-to-end customer service in terms of stock and deliveries, as well as technical support. As we mentioned previously, the vast majority of jobs encounter unexpected issues at some point, and so site visits by our team help to deliver solutions for a successful project.

ARMORDUCT
Since 1998, Armorduct has been a high volume UK manufacturer of cable management components and systems. Based in the Midlands, it supplies cable trunking, cable tray and cable basket, plus lighting, flooring and perimeter cable containment solutions for UK and European projects..
Want to know more about Armorduct?
Tel: 01384 233445
Visit: www.armorduct.com
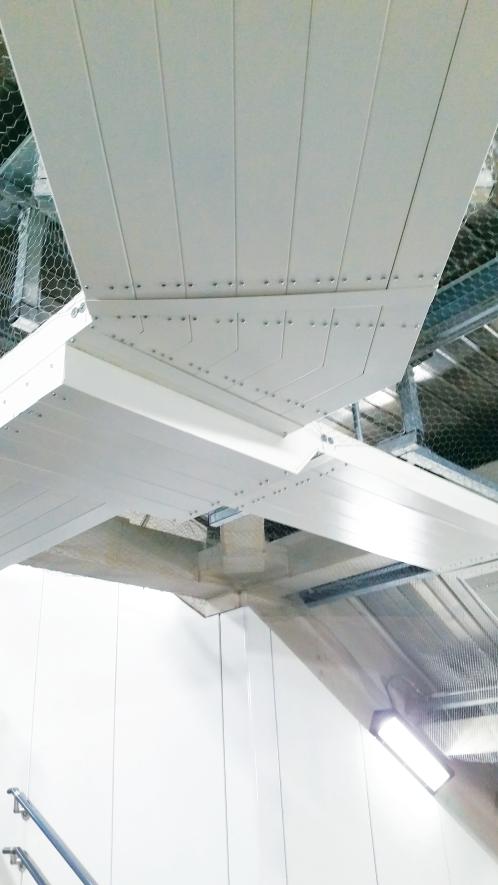

RAIL APPROVED TRUNKING SOLUTIONS FOR EVERY INSTALLATION Cable
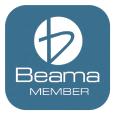
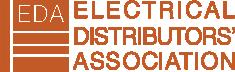
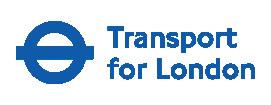
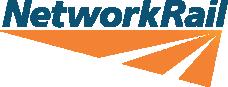

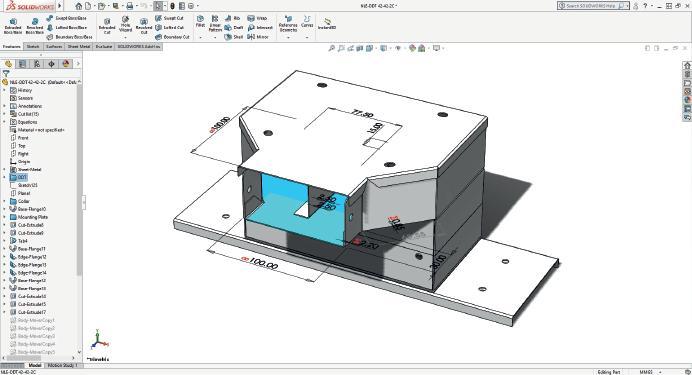
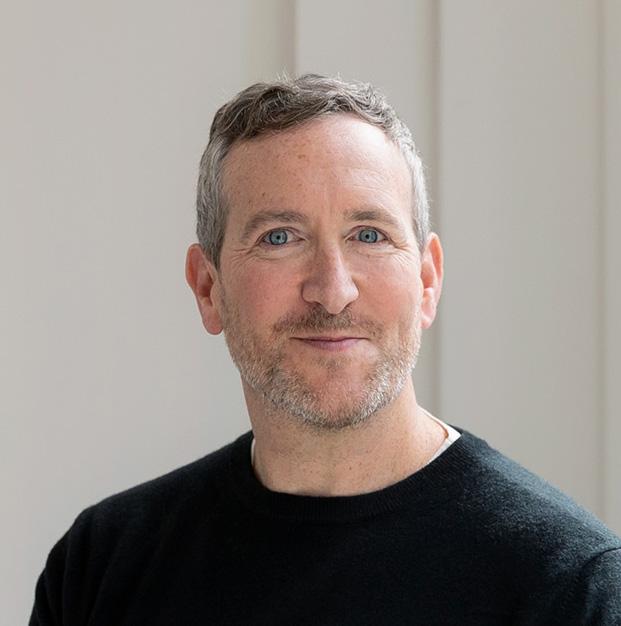
James Sellar is Chief Executive Officer at Sellar. Under James’ leadership, Sellar has become renowned for delivering some of the boldest and most complex mixed-use schemes, often at major transport hubs across central London.
A Living Station: A Vision for Liverpool Street Station’s Future
In the heart of London, Great Britain’s busiest station stands on the verge of a transformative journey. A journey that will ensure it is as relevant to the travelling public of the 21st century as it was revolutionary for the travellers of the Victorian era
Celebrating its 150th anniversary this year, Liverpool Street station has been a witness to the ever-evolving landscape of rail travel. From its earliest days, its sunken platforms and concourse served as a gateway to London and billions of passengers have passed under its historic roofs, beginning and ending all manner of journeys.
Its notable history includes the provision of one of the most direct routes between London and the continent, via the Harwich ferry terminal, a route which poignantly played a major role in the Kindertransport, the evacuation of Jewish children from Nazioccupied territories in the 1930s.
Fast forward to the present day, Liverpool Street has evolved into a major interchange, still serving the eastern regions and the rest of the world through its connections to Norwich, Ipswich, Heathrow and Stansted.
Yet whilst it has seen its use rebound following the pandemic, with passenger numbers now 16 per cent higher than in 2019, demonstrating its resilience in the face of changing working patterns, this is not a station which can rest on its laurels.
Serving communities for 150 years
Its opening in 1874, during the great age of rail expansion, was part of a revolutionary shift in transportation that reshaped the fabric of society and commerce. For
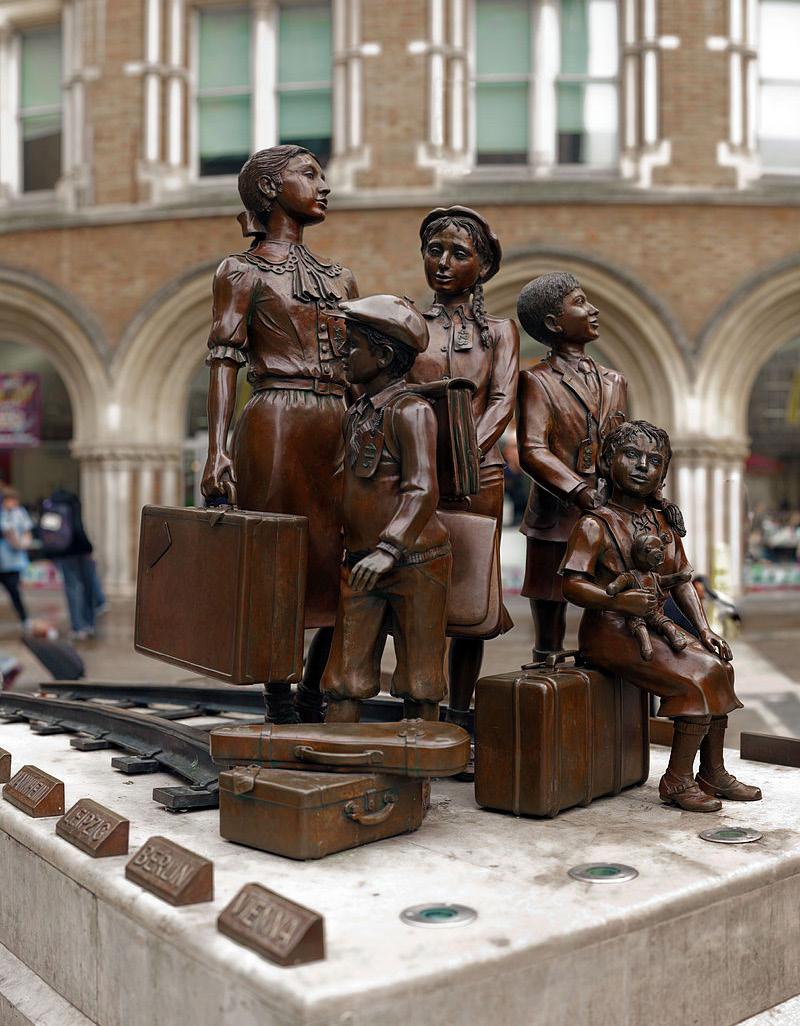
About the Network Rail, MTR and Sellar partnership
MTR and Sellar are working with Network Rail to transform Liverpool Street station. All three bring extensive experience of creating world class interchange destinations.
Sellar is known for the Shard Quarter regeneration around London Bridge Station and the ongoing Paddington Square office and retail development, which includes a new tube station entrance at Paddington Station.
MTR is a world-class operator of sustainable rail transport, with extensive experience in connecting communities across its network through the integration of rail, commercial and property development.
Network Rail own, operate and develop Britain’s railway infrastructure. Over the last ten years they have transformed a range of major stations, including Kings Cross and London Bridge.
nineteenth century communities, the introduction of railways brought about unprecedented connectivity, connectivity that today, we take for granted. Liverpool Street station emerged as a vital hub in this railway revolution, serving as a gateway to the expanding network that linked London with the far reaches of the Great Eastern Railway.
The railway played a vital role in the economic development of the regions it served by providing a reliable and efficient means of transporting goods to consumers in London and other urban areas. The fertile lands of East Anglia produced a variety of crops such as grains, vegetables, and fruits which could be transported quickly and economically to the markets in the capital.
The efficiency and speed of rail travel not only facilitated the movement of goods. These ‘iron arteries’ increasingly played a pivotal role in the movement of passengers, allowing individuals to commute into London for work, whilst enjoying the benefits of spacious living beyond the city's crowded neighbourhoods.
Over the years, this historic terminus has seamlessly transitioned from being a carrier of produce to a bustling hub that now accommodates over 100 million station users annually.
The changing faces of Liverpool Street station
The station we know today is, in some ways, very different to that of 150 years ago.
Costing over £2 million and built over land that had been previously occupied by Bethlem Royal Hospital, the original ‘Bedlam’, its construction was initially controversial, with over 3,000 residents displaced to make way for its Gothic architecture and vaulted glass roofs.
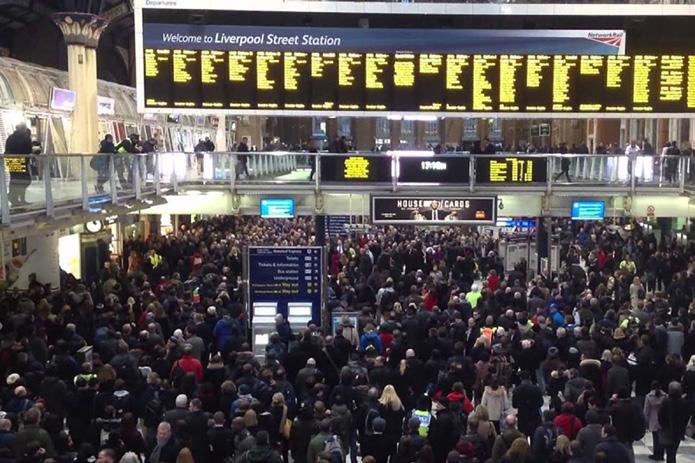

Extensive excavations took place to allow it to connect with the sub-surface Metropolitan Railway, but this was short lived. Further change came in the 1880s, with the addition of a railway hotel, now the Andaz, operated by Hyatt, with a great ballroom, and two masonic temples. At the turn of the century, it was operating at capacity, as one of the busiest stations in the world, and its continued success led to a number of upgrades and redevelopments throughout the twentieth century, including electrification of its suburban services in the 1940s and the completion of a major upgrade in the early 1990s.
Its constant evolution belies the fact that London’s great termini could not stand still if they were to continue to successfully serve the travelling public. As passenger numbers fluctuated, engines and rolling stock came in and out of service, and the needs of the travelling public evolved, Liverpool Street station adapted too.
The last upgrade, completed in 1991, responded to an anticipated decline in passenger numbers, and saw the sale of the adjacent Broad Street station, with the public funds raised used to finance the demolition of large parts of the Victorian station offices and train shed, to be replaced by the replica development we know today.
The station today
In its current iteration, Liverpool Street station stands as Great Britain’s busiest transport hub, with its dedicated staff smoothly managing over 135 million station users annually. However, success
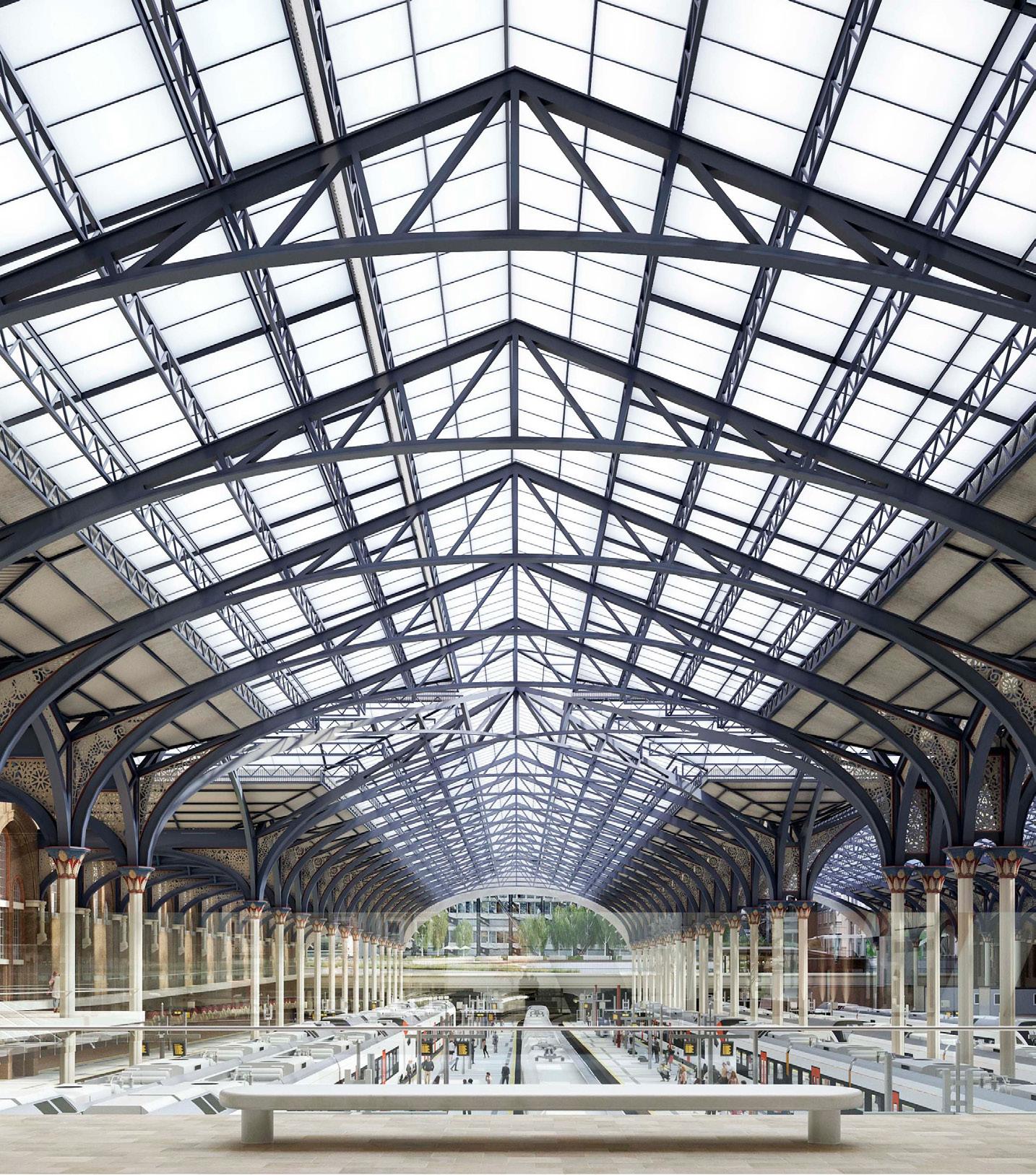
has brought challenges, with the station grappling with capacity issues, and a lack of accessibility infrastructure, and its bustling environment, posing difficulties for passengers, especially those with mobility issues. This is not acceptable for a London terminal station.
It is evident that the station today is at a crossroads, requiring a thoughtful and comprehensive approach to meet the needs of its diverse users.
Preparing to meet the challenges of the future
Looking towards the future, Liverpool Street station is poised for a transformative journey. A new vision, spearheaded by a unique public-private partnership that brings together MTR, the operators of the Elizabeth line, Sellar, the developer who transformed London Bridge, and Network Rail, this will secure a sustainable future for Liverpool Street station for the benefit of the public, crucially at no cost to the passenger or taxpayer.
The latest vision for the station will not only meet but exceed the challenges of the modern era. These plans include significant investment into vital station infrastructure
upgrades including more escalators and lifts, as well as new concourse spaces, addressing the overcapacity issue and ensuring seamless accessibility for all passengers. The station environment will be supplemented through the introduction of new public green spaces, with leisure and convenient retail offerings serving a range of needs. The glory of the station’s heritage will be recaptured, through the removal of 1980s infill development which blocks views of the trains, and by reconnecting the station hotel to the station by opening new entrances that utilise the fine Victorian spaces on the ground floor.
This forward-thinking approach reflects a commitment to creating a worldclass station that will serve as a model for sustainable, efficient, and inclusive transport, securing the legacy of Liverpool Street for generations to come by ensuring it continues to meet the needs of station users for decades.
We are excited to see Liverpool Street station become the gateway that a forwardlooking, thriving, and accessible transport system needs, standing apart as one of the great stations of the world, fit for the 21st century traveller. For more information, visit www.upgradelss.com.
Noise reduction and eradication
Wheel
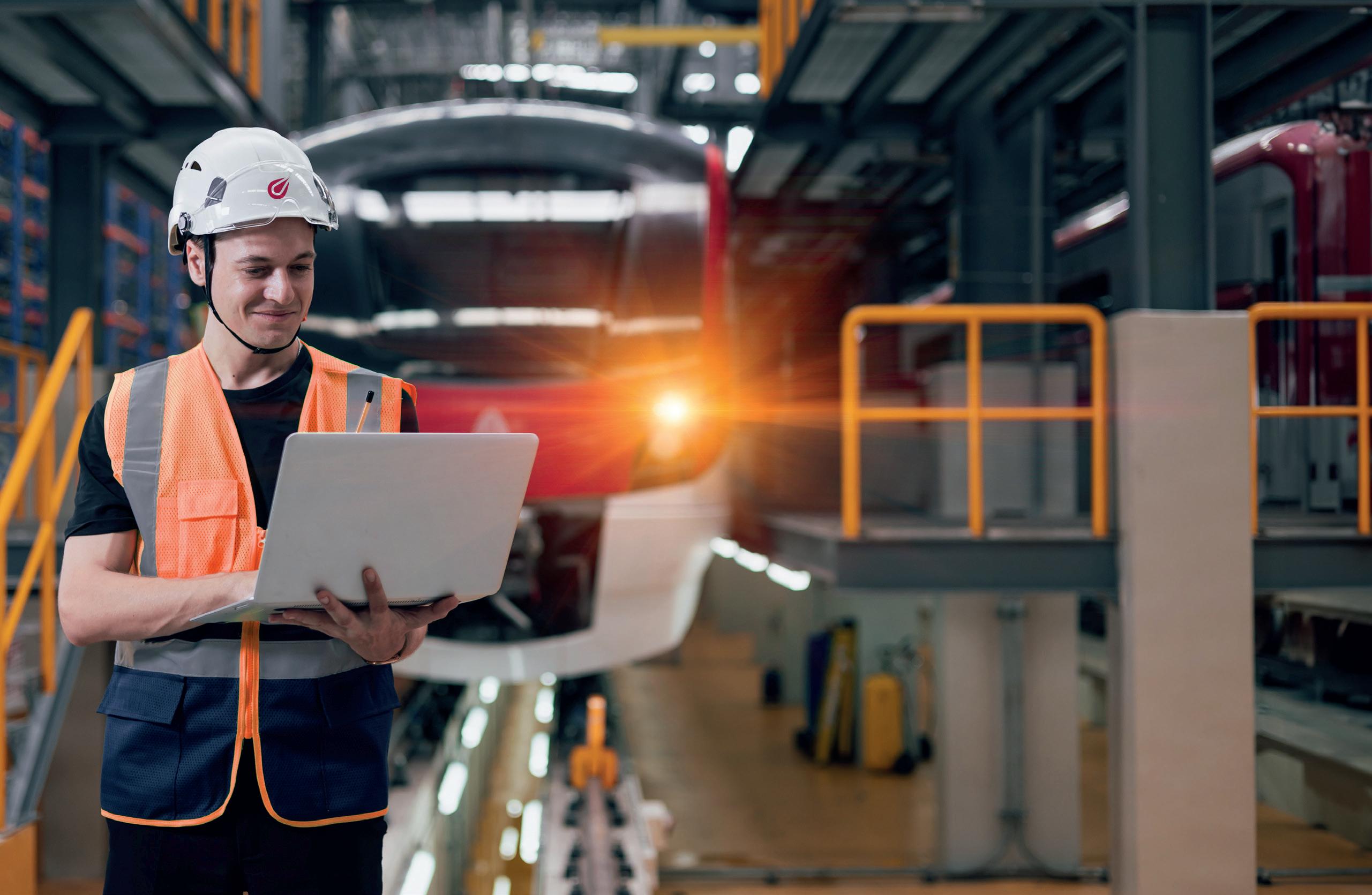
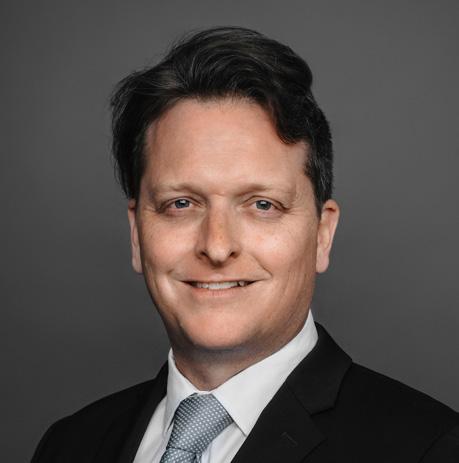
As CEO of BAI Canada, Ken Ranger oversaw the deployment of wireless network connectivity, including public Wi-Fi, cellular and fare payment card connectivity across Toronto's subway system. In 2019, Ken relocated to London to take up a new role as COO of Boldyn Networks UK & Ireland (formerly BAI Communications). Ken has built and managed wireless and wireline networks in Canada, the United States and South America, and has twenty years' experience in the telecommunications industry. Visit: https://www.boldyn.com/uk-ie
Connecting Underground
Ken Ranger, COO at Boldyn Networks UK & Ireland explains how they’re bringing ultra-fast connectivity to the world’s oldest underground network
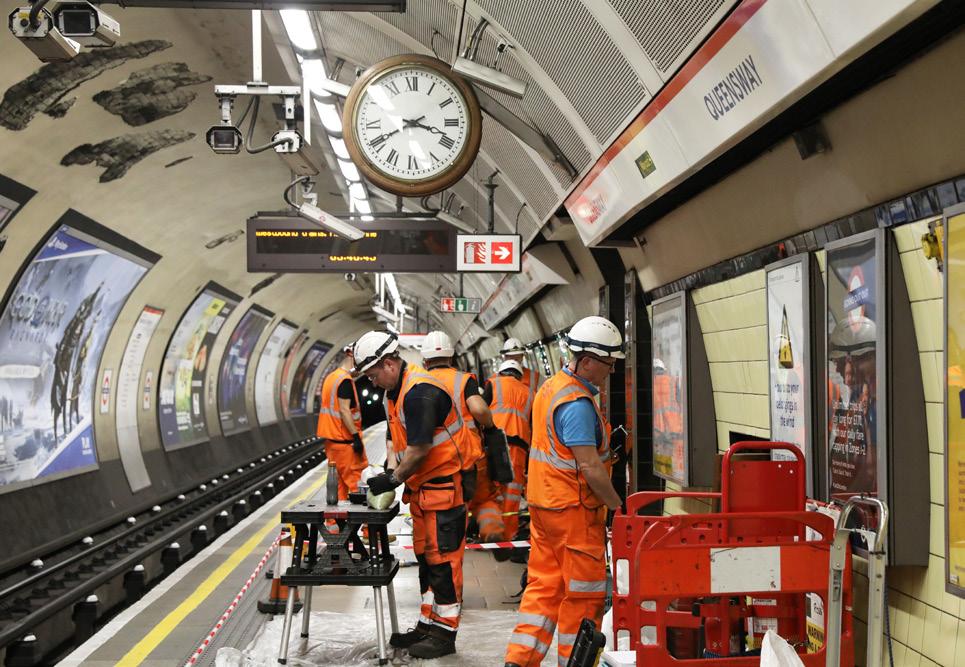
As the London Underground sleeps between the hours of 1am and 5am, more than 500 workers descend into the tunnels to conduct the complex task of bringing mobile connectivity to the 160-year-old network. The Underground, which has some of the oldest and smallest metro tunnels in the world, has remained one of the biggest ‘not-spots’ falling behind many city subways including New York, Hong Kong and Toronto. With demands for 24/7 connectivity and the Mayor of London’s project to deliver 4G and 5G across the capital’s transport network, Boldyn Networks in partnership with Transport for London (TfL), are delivering a new communications network to provide ‘alwayson’ mobile connectivity across the entire network, from ticket halls to platforms and tunnels, for the first time.
Engineering challenges
The London Underground is vastly different in comparison to other metro networks across the globe and delivering this next generation connectivity infrastructure has
meant working closely with TfL’s engineers to find new ways to work in such a unique environment.
The historical importance of some TfL stations also means that maintaining the conditions and aesthetics is a key part of the project. There is no such thing as a standard underground station and the heritage stations in particular, such as Covent Garden, Piccadilly Circus and Kings Cross, have to be treated with great care.
The age of the network means very limited space is available for additional communications equipment. This has led to the adoption of a ‘neutral host’ model. The model makes available services from each of the UK’s four mobile network operators but with only one set of infrastructure that is shared by all of the operators.
Another challenge is that high temperatures can be reached in some sections of the network during the summer, so the equipment needs to be designed to ensure it does not add extra and unwelcome heat and can also work in a range of temperatures.
Innovative solutions
The project, which began in 2021, requires new and innovative technological solutions to deliver 4G and 5G coverage for the world’s oldest underground network. From assessing the structural loads imposed by the equipment to ensure the structure can hold the weight, to finding out where best to fit the equipment with a few inches to spare, the project presents a number of challenges that need to be overcome.
This has required the creation of bespoke solutions and working practices to cater for the cramped and complex environments of the 19th century tunnels. The unique conditions mean tools such as 3D visualisation and remote equipment monitoring have been deployed to build and maintain the project, whilst specialist apparatus such as flatter profile radio equipment has been designed to carry out the works. The limited space at stations also means our ten specialist data centres across London are needed off site, to house the equipment required to interconnect with the mobile operator’s networks.
The project requires fibre and radio service deployment across the Underground, using the latest technology and design techniques to overcome the operational challenges including installing new equipment within the restricted space.
With a four-hour window each night, to ensure no service disruption for commuters and tourists, hundreds of workers carry cables and specialist machinery down into the tunnels to install the technology within the hot, cramped environment. To provide reliable, high-speed mobile coverage, engineers are installing cables known as ‘leaky feeders’ along the walls of the tunnels that connect to high-power radios, located every 500 metres. Once complete, over 2,000 kilometres of cabling will have been installed within 137 stations and 400 kilometres of tunnel pairs, as well as nearly 9,000 radios in the tunnels and stations. All this will allow millions of commuters to catch up on work, access online shopping, send emails, stream content and access social media while travelling.
Benefits of the project
When the project is completed, customers will have access to uninterrupted mobile connectivity across all networks throughout their journey, from the station entrances to the platforms, all the way through the tunnels and back up to the street, to transform the customer experience and keep the capital connected.
Passengers are already enjoying mobile coverage along sections of the Jubilee, Northern, Central and Elizabeth lines, with some of the capital’s busiest stations having access to high-speed connectivity, with rapid progress continuing in 2024 as more stations and tunnels go online for the first time.
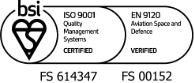


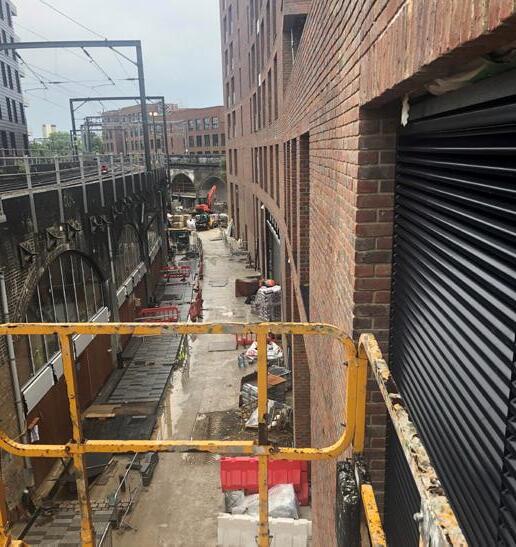
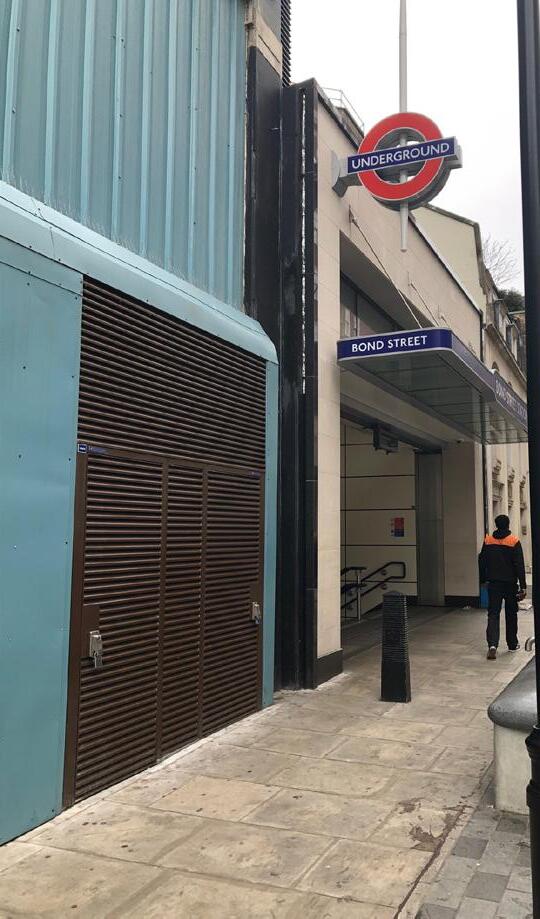
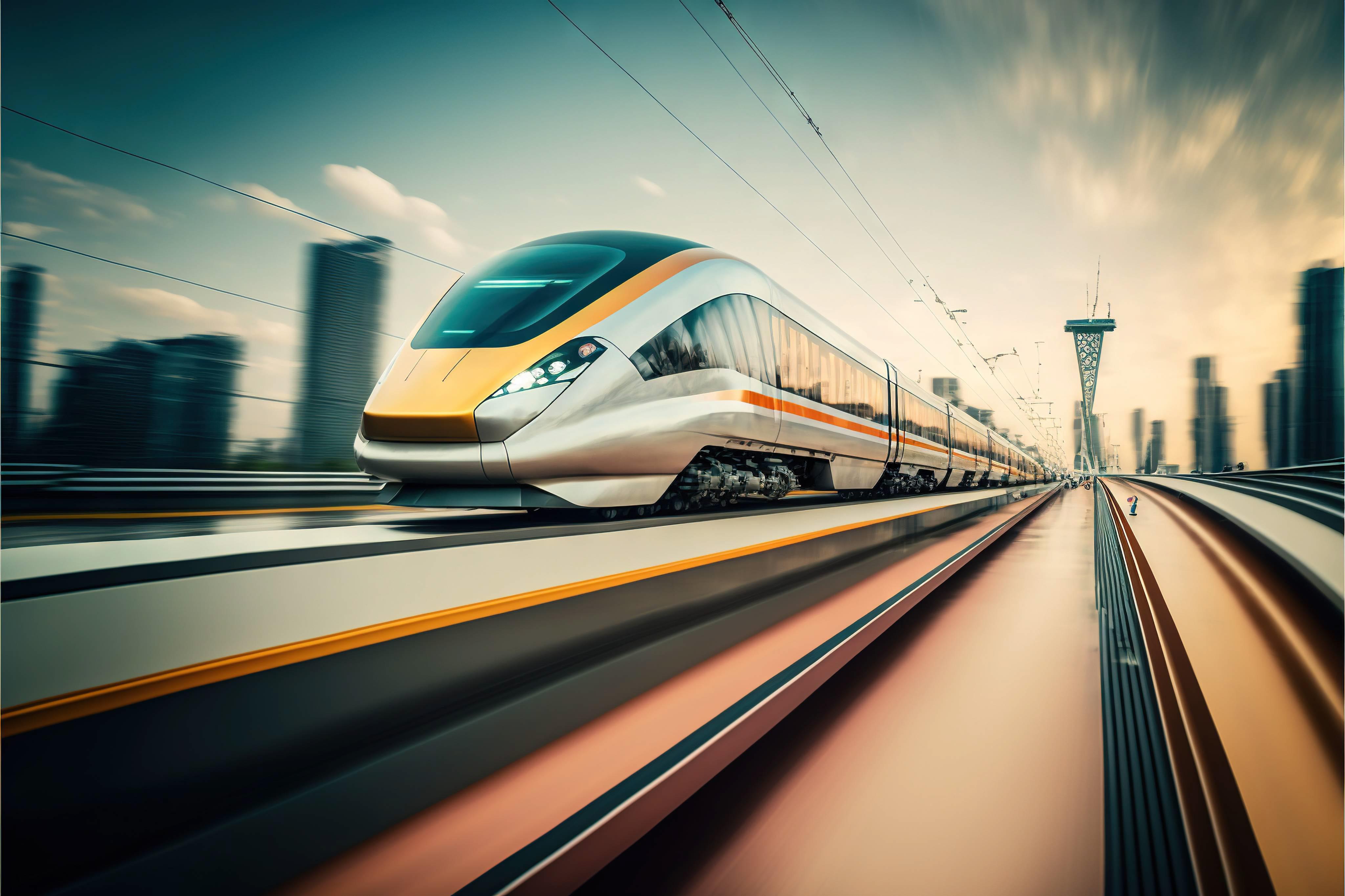

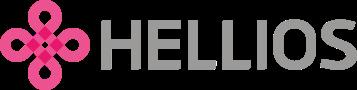
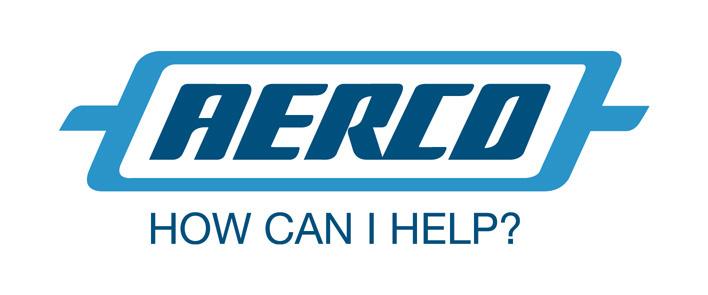

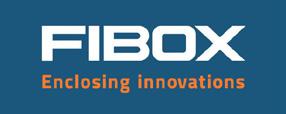

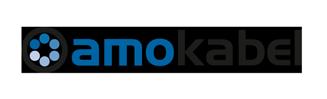
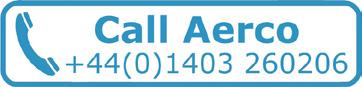
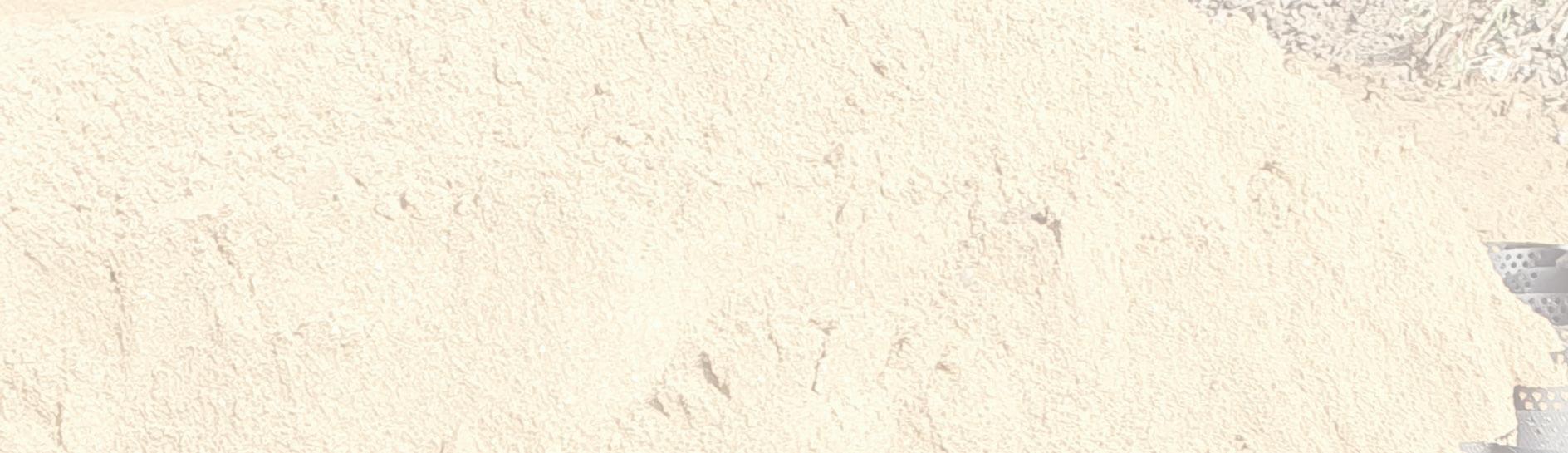

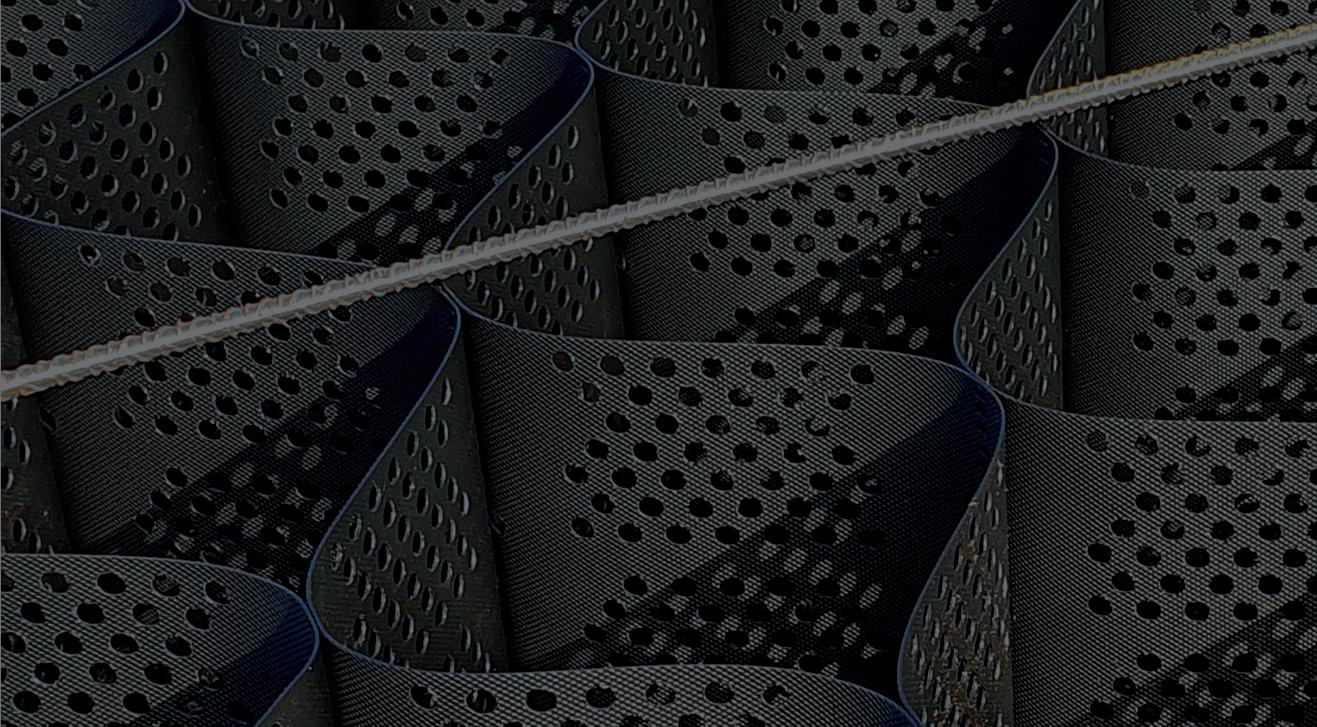
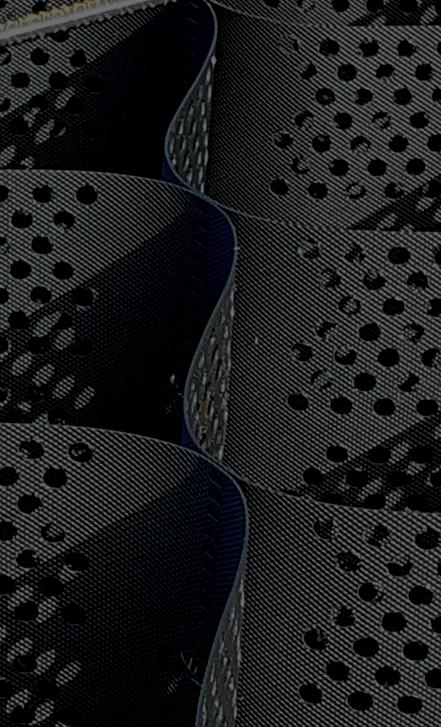
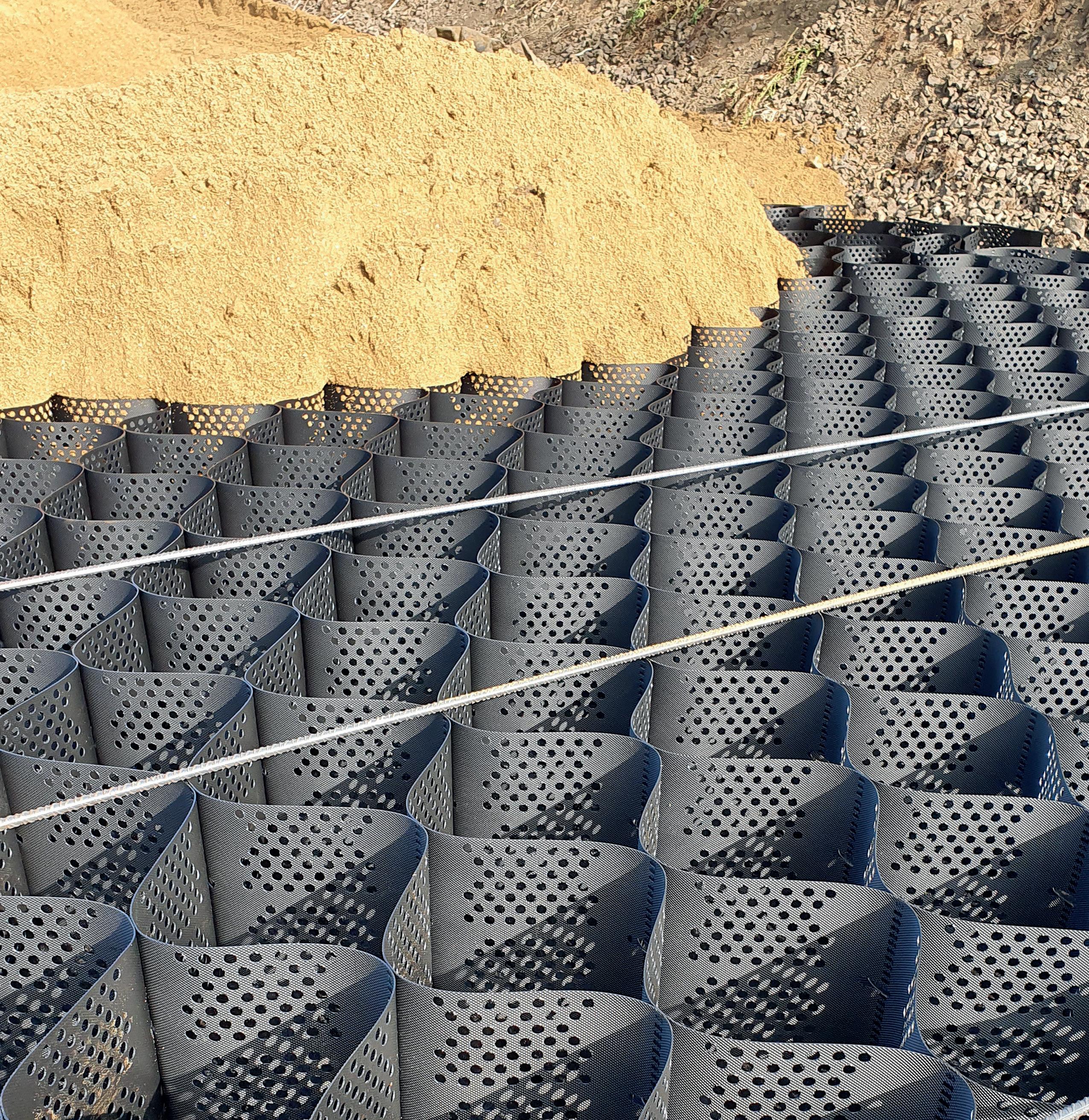

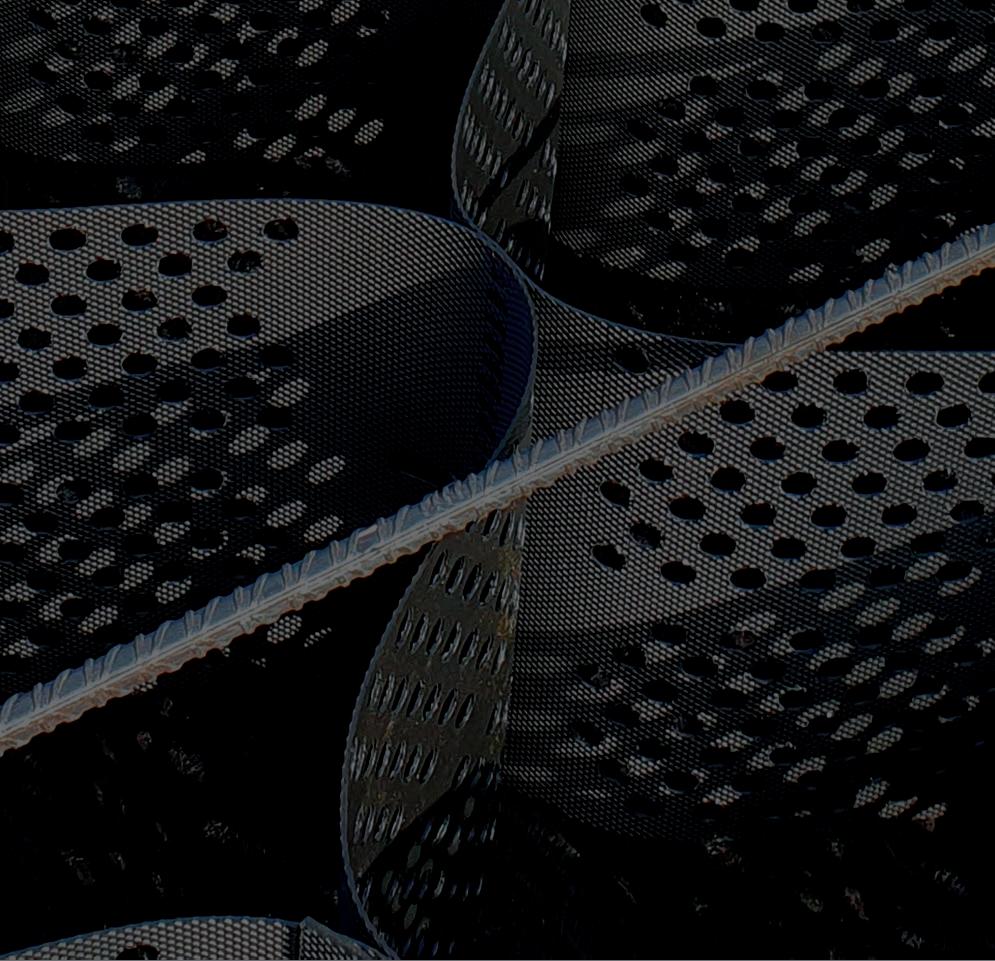
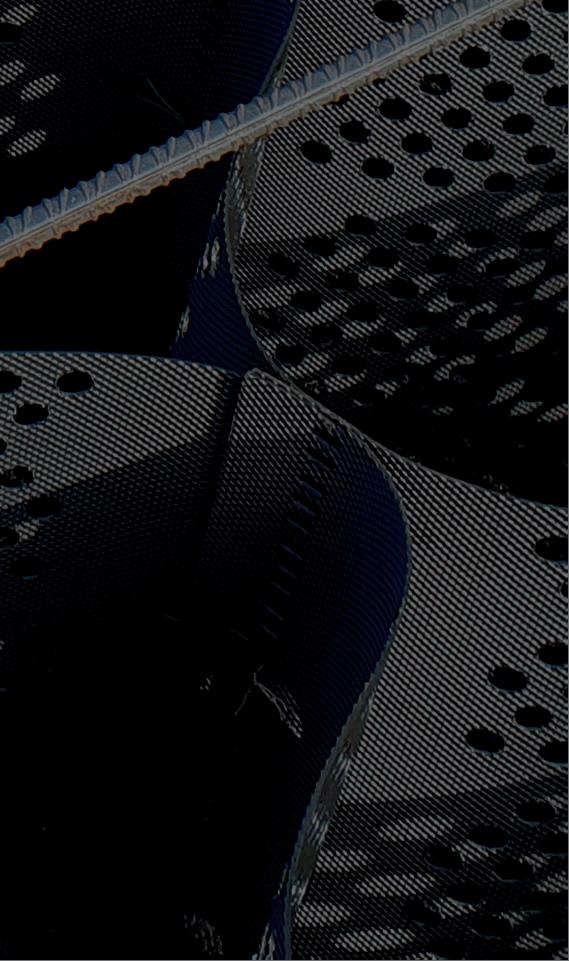
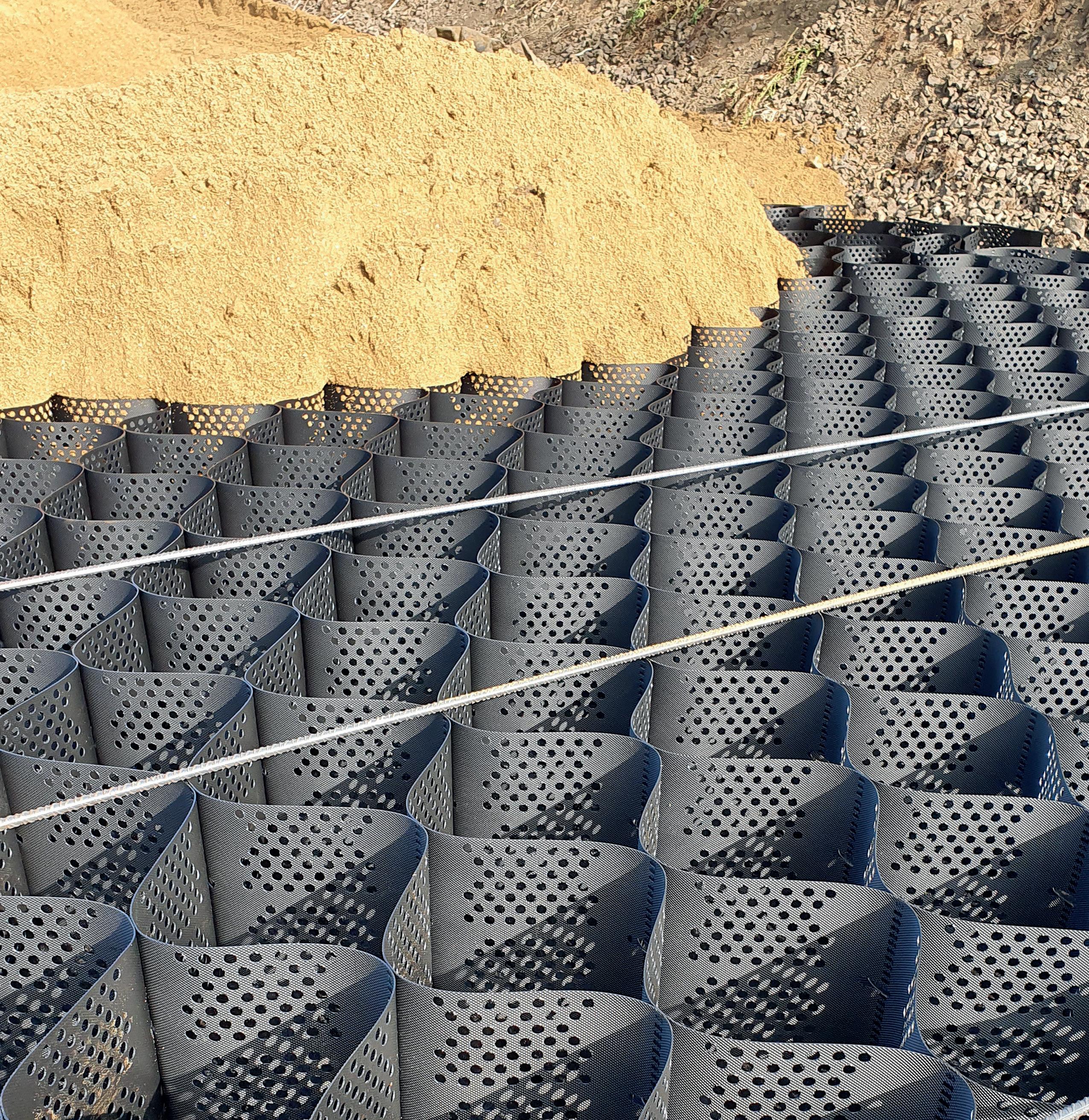
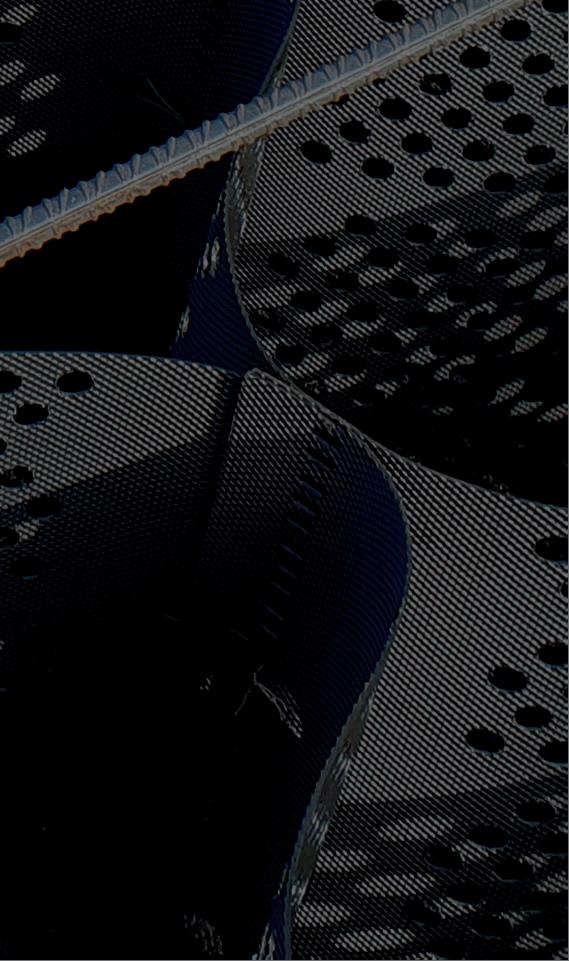
Raising the Bar on Hygiene Post-pandemic
Crowded train stations must be ready to combat the latest viral outbreaks in close indoor settings, which can rapidly spread among potentially hundreds or even thousands of customers, employees, and the general public
Whether due to influenza or other respiratory viruses, winter is often a time of viral spread and commonly touched items become a source of infection. Simply putting out hand sanitizer at a minimum is insufficient to prevent potential outbreaks.
So, proactive facility managers are looking to technology partners to help protect their customers, staff, and the public more comprehensively. One promising development is a new tool that can help facility managers safeguard public health in a manner that goes far beyond handwashing, which is insufficient when frequently handled items are contaminated. Today, portable UV disinfection stations can protect everyone at entrances and communal areas to quickly disinfect any handled items, which otherwise can spread viruses to hands, noses, mouths, and others in a viral manner.
According to various studies, individuals check their phones approximately 150 times each day, but the number of times they touch their phone is estimated to be in the thousands. If cell phones are presumed to be relatively clean compared to your hands, consider that scientists at the University of Arizona found cell phones carry ten times more bacteria than most toilet seats.
In fact, we handle our mobile devices so often they should be considered an extension of our own hands. If the items are dirty, so are our hands – and vice versa. So, when published health advice recommends cleaning smart devices ‘at least once a day’ it seems woefully insufficient. In addition, wipes, sprays, and cleaning solutions that are abrasive or contain bleach can damage phones, cases, and protective coatings.
Other personal items we regularly handle with our hands include face masks, ID badges, baseball caps, sunglasses, keys, wallets, and jewellery. Many of these items pass through other people’s hands as well, including credit cards, business cards, pens, bills, and coins. Public transportation employees are increasingly using shared tablets, workstations, and Personal Protective Equipment (PPE) like safety glasses and gloves.
Given the risks, disinfecting our personal items and accessories should be an ongoing health mandate. For those that feel the COVID19 pandemic is over, what if there is a resurgence? A new more transmissible variant? Some other new viruses? What about the other pathogens we already know about? What about protecting those already at-risk prior to the pandemic due to preexisting conditions?
One solution that warrants closer scrutiny is the use of ultraviolet (UV) light devices. These devices utilize shortwavelength ultraviolet C (UV-C) light to inactivate pathogens including viruses (such as SARS-CoV-2), bacteria, mould spores, and yeast.
UV-C light works by interfering with the nucleic acids of bacteria and other microbes to prevent reproduction and effectively destroy them. UV light has the advantages of being effective, low cost, chemical-free, and in most cases presents no risk to the items being disinfected.
UV-C light irradiation is already a proven technology, verified in many studies and utilized prior to the pandemic in both commercial and residential settings. In large hospital settings, UV light air purifiers are installed to decontaminate surgical equipment/tools and reduce the transmission of pathogens. Hospital-grade UV light machines are also widely used to disinfect patient rooms and operating areas.
To be clear, there are already many UV light devices on the market. However, the main barrier to adoption and perhaps the primary reason these devices are not as ubiquitous as hand sanitizer stations are inherent limitations in design.
Many require direct contact and manipulation to operate the appliance, and there can be questions about the intensity and contact time of the applied UV light. If the item is treated in a static manner, for example placed in an enclosure without being rotated or moved, it is like tanning on the beach on only one side. The UV-C light may not reach all the relevant surfaces.
‘Simply adding a UV lamp to a product and expecting it to destroy pathogens does not mean it will be effective’ says Robert
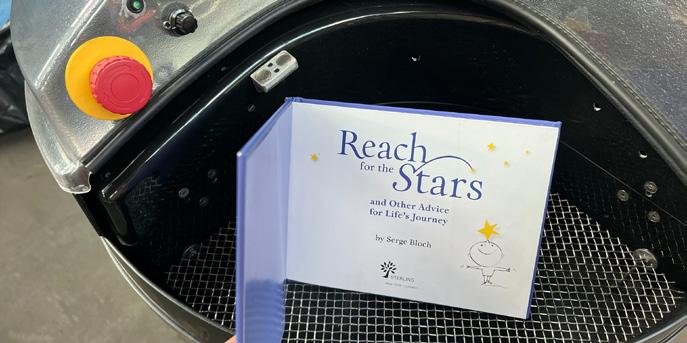
Tegel, founder, and CEO of Tebots, Inc., a design-build company with experience designing everything from consumer devices to products and automation systems for the textile, automotive, and other processing industries.
‘UV light sources can vary in intensity and output, and there can be line-of-sight issues as well. You have to make sure the UV light is directed at the items from many angles with uniform intensity, and all this requires a high level of engineering’ explains Tegel.
Many UV disinfection appliances are also essentially designed like microwave ovens. To disinfect an object, the door must be opened, the item added, the door closed, and push buttons used to initiate the cleaning process. The door then must be reopened to remove the item.
‘When you are opening and closing the door it can be detrimental to how effective the appliance will be’ says Tegel. ‘One reason is the UV lamps do not instantly reach their maximum power and there is a long warmup time. So, if you turn it off to open the door, you either have to wait until the lamp reaches full power or live with a less efficient and less well determined exposure time.’
Based on this observation, Tegel and his two partners, Herm Adams and Turan Erdogan, a former research professor at the University of Rochester's Institute of Optics, decided to design a better mousetrap that would address many of these limitations. Tebots excels at prototyping and production and has a long history of solving industrial problems by arriving at creative solutions.
The patent-pending UV disinfection appliance the trio designed runs continuously without a door to open or close. The appliance resembles a small, portable charcoal grill. Tablet sized, or smaller items are placed on a rotating platform and then move in a 360-degree arc through the chamber where they are bombarded from all angles by UV-C light for approximately ten seconds.
Tegel envisions the self-service disinfection stations being installed in front of public transportation facility entries/exits, bathrooms, and shared spaces. This includes ticket purchasing, waiting, and rest areas, offices, restaurants and vending machines – to name a few common areas where viral spread is likely. Facility managers could install the POZ to protect the entire community as part of an important public health and safety initiative.
For more information, visit www.tebots.com or contact Robert Tegel on +1 847 66 6876.
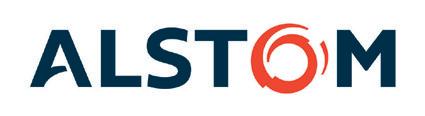
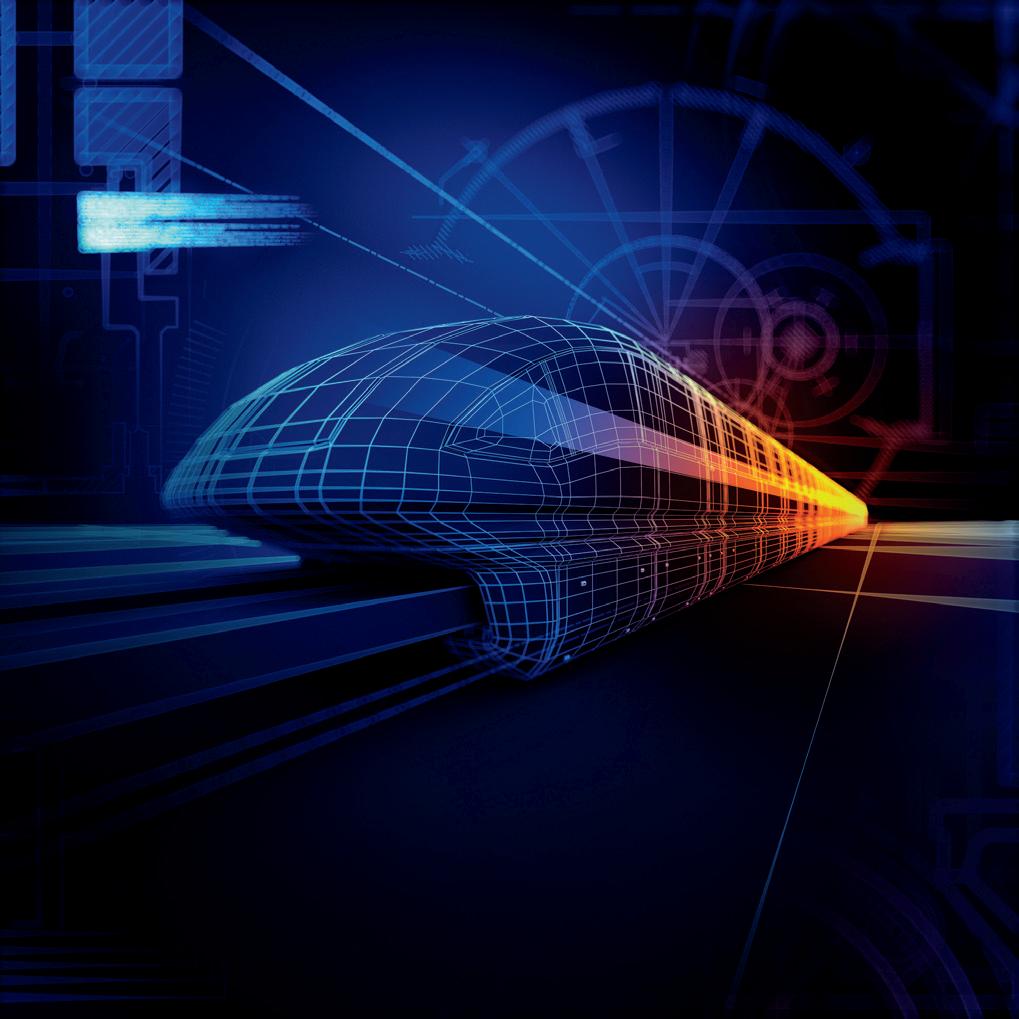
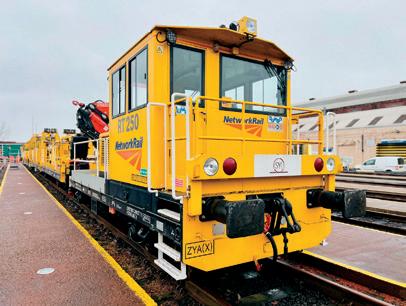
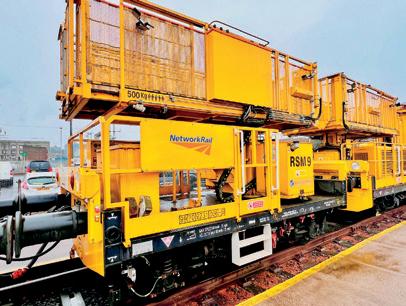
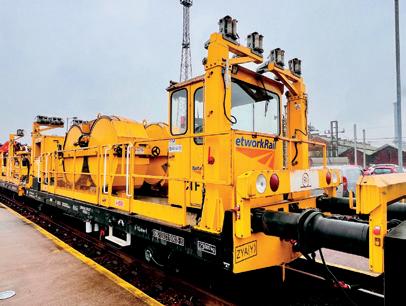
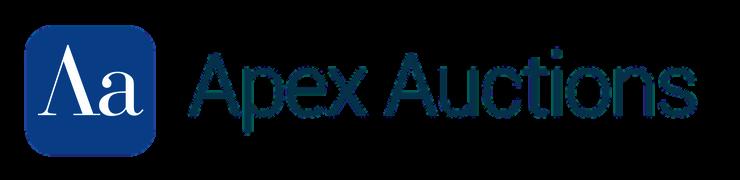
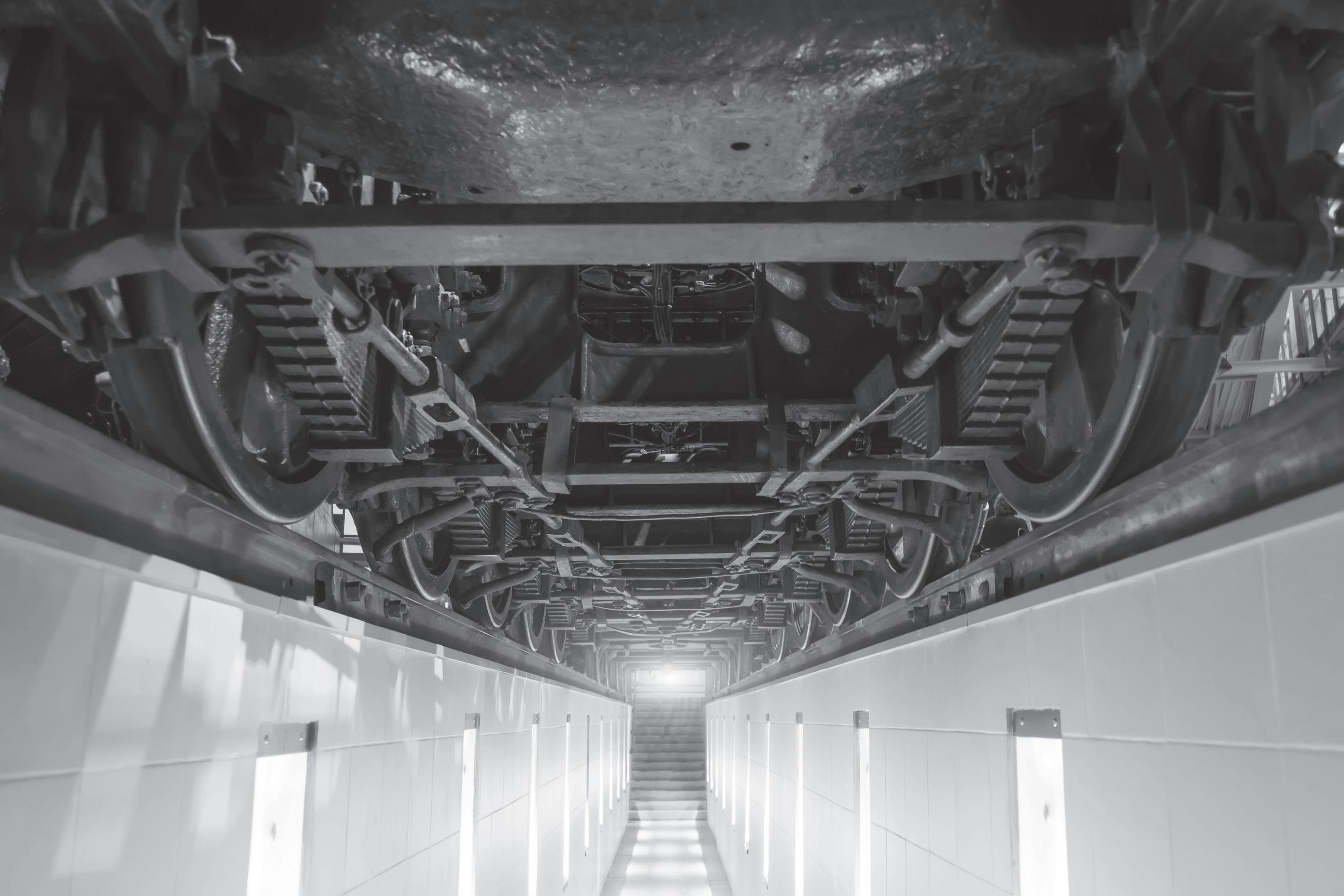
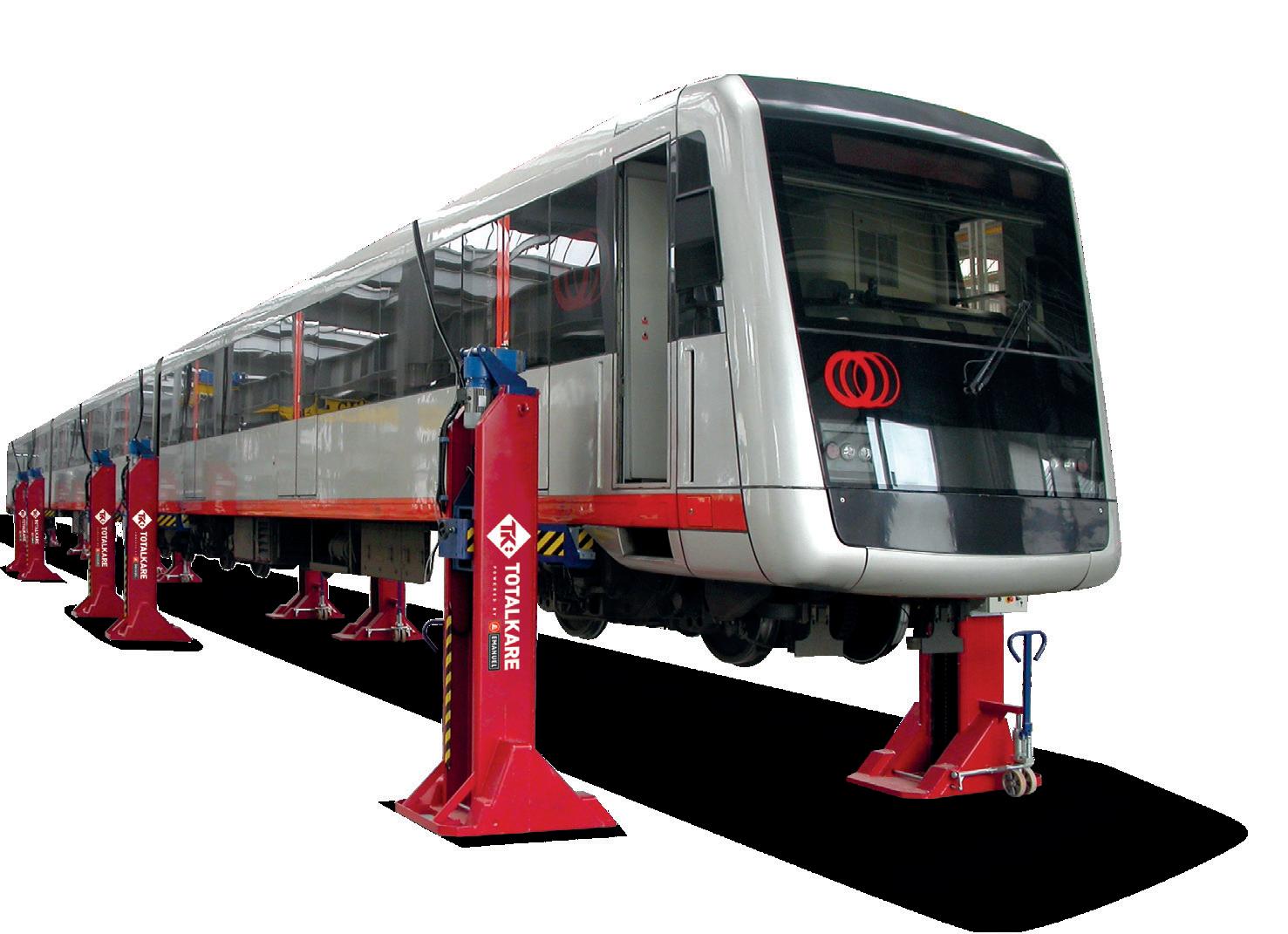
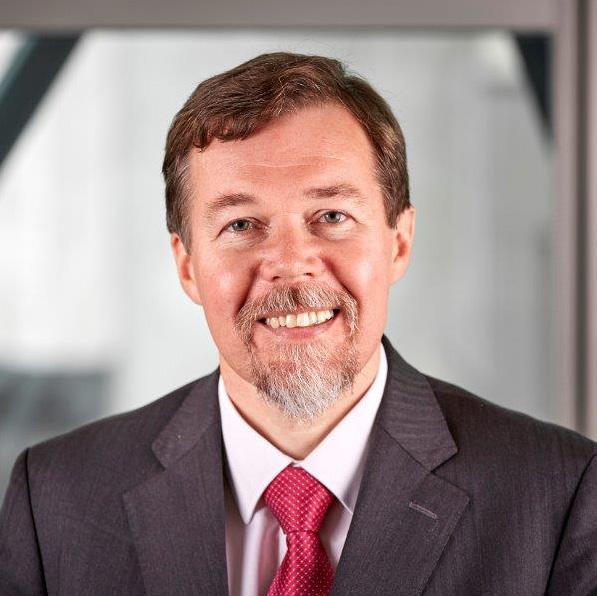
LAYING DOWN THE LAW
by Martin FleetwoodObtaining the Benefit of a Well-run Procurement
Managing procurements is a common task within the rail sector - either as a public body running a procurement or as a private sector party responding to such requests
When speed is of the essence, there is the temptation to cut a few corners in the procurement process. However, given that procurement challenges against the manner in which the procurement was handled are now more common, running the procurement well is becoming even more important as a recent decision of the Court of Appeal has shown. While the case of Braceurself Ltd v NHS England concerned an NHS's procurement of a seven-year contract for the provision of orthodontic services, the decision is equally applicable to procurements in the rail sector.
The original dispute
In this case, a supply contract was coming to an end and the incumbent, Braceurself Ltd (Braceurself), was bidding for the replacement contract. However, it lost the procurement competition to the only other bidder for the contract by a very narrow margin. Braceurself's bid scored 80.25 per cent and the successful bidder scored 82.5 per cent. Due to the marking system used, simply by increasing its score on one question by one mark Braceurself could overcome the gap of 2.25 per cent. Braceurself subsequently made several claims before the High Court that its scores should be increased and the successful bidder's decreased.
While most of Braceurself's claims were dismissed, the High Court decided that for one of its claims the score awarded for a question reflected a ‘manifest error’ in the evaluation by NHS England (NHS). The Court found that the NHS had
misunderstood Braceurself's proposal and scored it lower than it would have been had the NHS not misunderstood the proposal.
As this was a ‘manifest error’, rather than the result of a mere difference of opinion between the challenger and the evaluators, the High Court re-scored Braceurself's answer to the question from three to four, with the consequence that Braceurself's score should have been 2.5 per cent higher; and, consequently, it should have been the successful bidder. As the contract had already been awarded, Braceurself brought a claim for damages against the NHS for its breach of the procurement procedures.
Claiming damages for the error
At the subsequent damages hearing, the High Court decided that the breach was not sufficiently serious to warrant an award of damages. In considering the seriousness of the breach, the court was required to apply the eight factors identified in the leading case of R. v Secretary of State for Transport Ex p. Factortame Ltd (No. 5).
Those factors included:
• The importance of the principle which had been breached.
• The degree of excusability of an error of law.
• The state of mind of the infringer.
• The persons affected by the breach.
Braceurself had argued that as an individual breach had altered the outcome of the competition, it was in and of itself a sufficiently serious breach on the facts of the case. The High Court disagreed and noted that the phrase ‘sufficiently serious’ indicates that a fairly high threshold must
Martin Fleetwood is a Consultant at Addleshaw Goddard’s Transport practice. The Rail Team has over 30 lawyers who advise clients in both the private and public sectors across a wide range of legal areas. As well as contractual issues, the team advises on operational matters, franchises, concessions, finance, regulatory, property, employment, environmental and procurement issues.
Disclaimer: This article is for informational purposes only and does not constitute legal advice. It is recommended that specific professional advice is sought before acting on any of the information given.
‘The phrase ‘sufficiently serious’ indicates that a fairly high threshold must be passed.’
be passed. Having regard to all the factors, the judge decided that the breach did not meet this threshold and Braceurself was not entitled to damages.
In the judge's view:
• There had been a single breach in a very close competition.
• The evaluators' errors on the relevant question were at the excusable end of the spectrum and were minor.
• The breach was inadvertent and not deliberate.
• The procurement itself was carefully planned and well organized.
However, as the decision covered some important points of law the judge allow Braceurself to appeal his decision to the Court of Appeal.
The outcome of the appeal
On 30 January 2024 the Court of Appeal upheld the High Court's decision that an (apparent) manifest error in the scoring of a single question was not ‘sufficiently serious’ to warrant damages being awarded, despite it resulting in Braceurself not being awarded the contract.
This is a significant decision as it is the first time that the ‘sufficiently serious’
test has been applied at Court of Appeal level. The Court of Appeal described the case as ‘unique’ due to the low culpability of the contracting authority and the ‘extreme consequences’ of the (apparent) marking error.
On the face of it, this decision appears to be surprising and unfair to Braceurself. Had the NHS scored the question correctly (according to the first instance judge), then Braceurself should have been awarded the contract. However, the test when determining whether a breach is ‘sufficiently serious’ concerns the nature of the breach itself, and not the consequences that flow from it.
As a result of this decision, a single breach in an otherwise well-run procurement is apparently unlikely to tip the scale in favour of a tenderer who would have won the contract, but for the breach. The importance of the procurement being wellrun was re-emphasised in the decision and the overarching legal principles of openness and fairness of process were the main focus in reaching the court's conclusion. The Court of Appeal went on to suggest that an award to a different bidder as a result of an error of the contracting authority would be a ‘relevant consideration’, but not the deciding factor.
In the Court of Appeal hearing Braceurself had argued that it had been denied an effective remedy because:
• In lifting the automatic suspension of the contract award, the first instance judge held that damages were an adequate remedy.
• It was later held that there was a manifest error that led to the contract not being awarded to Braceurself.
• It was then held that the error was not of sufficient seriousness to warrant an award of damages.
The Court of Appeal quickly dismissed this argument. They felt that this fundamentally misunderstood the principle of ‘effectiveness’ of a remedy - there being a proper remedial process to be followed. It did not provide a guarantee of entitlement to damages. Aggrieved bidders should note the lack of a guarantee of damages, while procuring authorities should consider the weight placed on a carefully planned and well-organized procurement as an influence on whether a damages claim would be successful. Given the cost of procurement litigation, ensuring that procurement advice is obtained, and clear systems followed, could end up being a very good investment after all.
NEWS IN BRIEF
NORTHERN USING AI TO TRIAL BRITISH SIGN LANGUAGE ANNOUNCEMENTS ON TRAINS
Northern customers travelling between Manchester and Leeds as well as Leeds to York will be able to see some of the train operator’s announcements in British Sign Language (BSL) thanks to a trial involving AI. The train operator has been working with software experts InfoTec and Signapse on the scheme, which ‘knits together’ individual words signed by a BSL interpreter and displays the complete sentences on customer information screens onboard. Census data in 2021 showed that in addition to spoken languages, BSL was the main language of 22,000 people. after customer feedback.
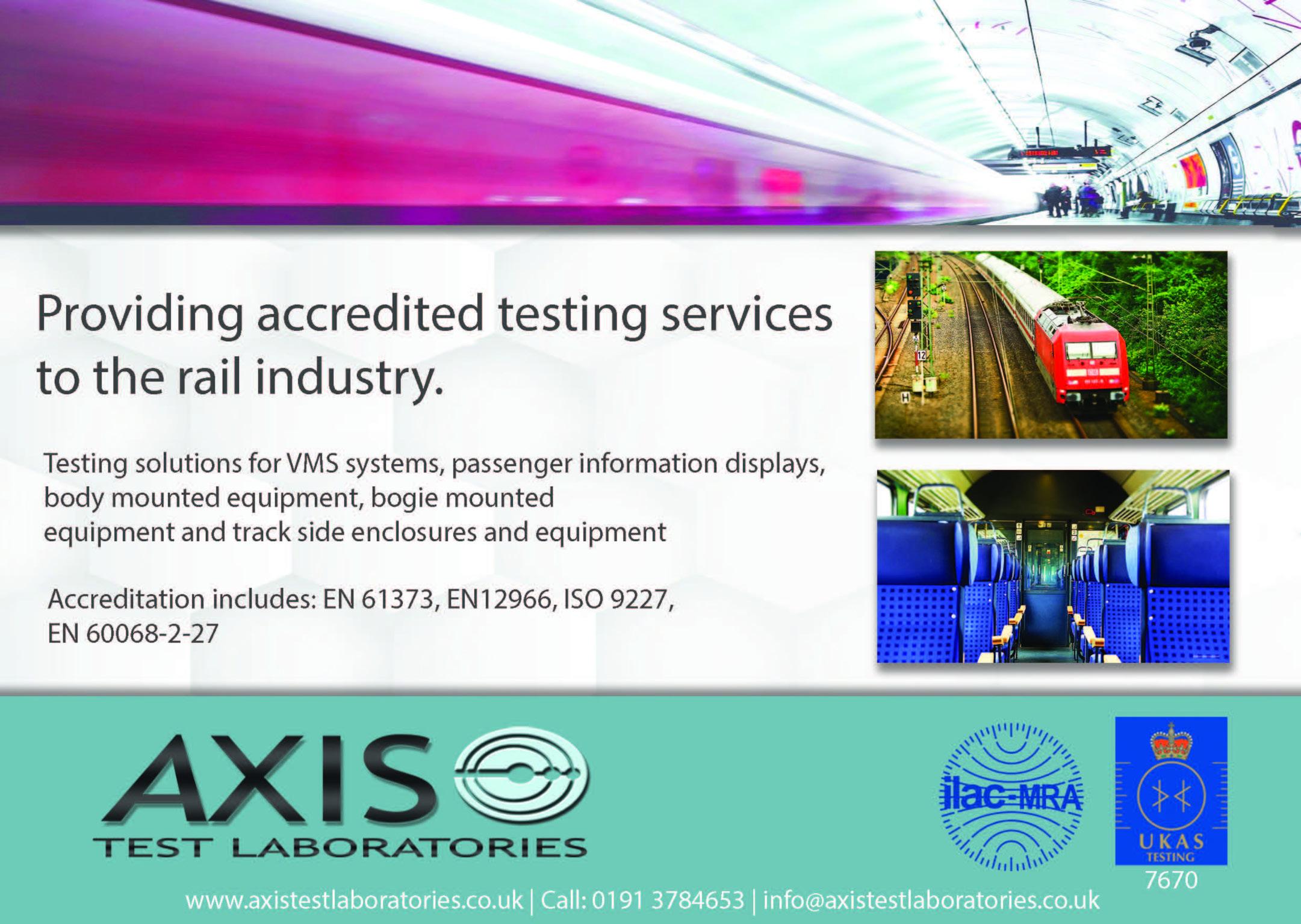
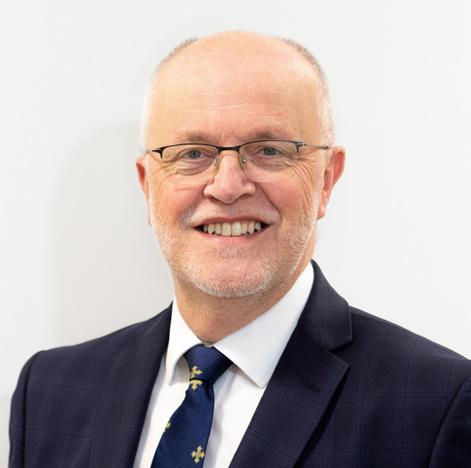
DELIVERING THE GOODS
by David WellsAppointing a Minister for Logistics and Supply Chain
David Wells OBE, CEO of Logistics UK, explains why such an appointment is so vital to the UK’s future growth
Finally, we know that a General Election will be held this year. And with logistics established at the heart of all economic activity in the UK, we are urging the next government to prioritise the appointment of a Minister for Logistics and Supply Chain.
Every part of our economy relies upon logistics to provide all the goods needed to generate and support business, from construction to retail, banking to infrastructure.
However, decisions are often taken without input from our industry. Our members recognise that focusing on investment and growth in our sector will bring dividends for the UK’s whole economy. The appointment of a Minister for Logistics and Supply Chain, with the interests of our sector at heart, will ensure that the needs of our industry are considered as part of any decision-making process, rather than as an afterthought, which can add complexity and cost to any project.
Logistics activity is at the heart of the economy, creating opportunities and delivering for everyone, everywhere, every day. In fact, logistics activity contributes a staggering £163 billion in GDP each year, representing twelve per cent of the country’s non-financial economy. 2.7 million people are employed in logistics roles – 8.2 per cent of the UK’s workforce – and there are 230,000 logistics businesses across the UK involved in making, selling and moving goods.
Recent research conducted by Oxford Economics found that reversing the decline in the UK’s productivity, caused to a large
extent by deteriorating infrastructure quality and increased border friction, would have a significant impact on the UK’s productivity. In fact, it could deliver a £3.9 billion to £7.9 billion boost to GDP through productivity gains by 2030.
One of the biggest ways that the incoming government could assist in improving productivity is through investing in a national logistics network, as well as in planning reforms and innovation funding to enable goods to be moved in the optimum productive, strategic and green manner. The UK’s logistics sector is becoming increasingly integrated, between modes, sites and businesses, as well as working smarter and more innovatively. This integration needs to continue, and investment in infrastructure needs to be prioritised if integration, and the resulting productivity benefits, are to be realised.
Top of our asks for the incoming government is the establishment of a national logistics network. The government’s 2022 Future of Freight plan committed them to creating such a network and making this a reality. Speeding up the planning process is also vital to deliver efficiencies and economies right across the country. Increasing the use of rail freight is key to the success of this ambition, not only reducing congestion and lowering carbon emissions, but also boosting trade through improved connectivity with ports and airports. A switch of mode also adds further resilience to the supply chain as a whole, which benefits the entire economy.
The UK’s transport infrastructure is increasingly constrained by congestion and

Logistics UK is one of the UK’s leading business groups, representing logistics businesses which are vital to keeping the UK trading, and more than seven million people directly employed in the making, selling and moving of goods. With Covid-19, Brexit, new technology and other disruptive forces driving change in the way goods move across borders and through the supply chain, logistics has never been more important to UK plc. Logistics UK supports, shapes and stands up for safe and efficient logistics, and is the only business group which represents the whole industry, with members from the road, rail, sea and air industries, as well as the buyers of freight services such as retailers and manufacturers whose businesses depend on the efficient movement of goods. For more information about the organisation and its work, including its ground-breaking research into the impacts of Covid-19 on the whole supply chain, please visit logistics.org.uk.
lack of maintenance – traffic congestion cost the UK economy in £9.5 billion in 2022 alone. Journey planning has become difficult to predict, leading to increased business costs. This is where shifting loads from road to rail could benefit the whole UK, providing the infrastructure investment necessary to enable such a move can be guaranteed. And it is also vital that government invests to ease congestion at existing hotspots across the rail network to ensure the smooth passage of goods as well as passenger trains.
As an industry, logistics has always led the way with technological and other advancements aimed at improving efficiencies and reducing transit times. For some time, logistics businesses have led the way in the use of AI and robotics, implementing clever solutions to support modal shirt and adopting new technologies to reduce carbon emissions. Our manifesto challenges government to think about the whole supply chain to enable broader investment and encourage further innovations to be created and implemented. The incoming administration needs to work with investors, SME innovators and the sector as a whole, to develop new solutions that will benefit all those charged with moving the goods the economy needs.
To establish such a national network will require reforms to planning regulations and alignment between national, regional and local plans. Infrastructure needs to be planned holistically, with a longer term,
30-year strategy to run alongside a five year delivery plan.
Our industry has committed to a Net Zero future but now needs support to ensure a smooth transition to a greener economy. Our members are committed to playing their part in helping the UK to achieve net zero but need a greater say in plans to deliver a fair transition and unlock private investment.
Any new plans must protect the current supply chain and the demands of its customers: developing plans for rail electrification and calling for investment in its implementation can only be successful if ongoing business relationships are maintained. Our sector is already making key decisions on the road to net zero, while operating on narrow margins, so must invest carefully in order to cut emissions while avoiding inflationary impacts for households, businesses and public services. There is also some risk that the energy infrastructure needed will not be delivered at the pace our sector requires – something that government must pay close attention to in order to enable modal shift to happen efficiently and at pace.
Unlocking the necessary private sector investment in decarbonisation will require the new government to work in partnership
with industry and be committed to developing clear plans and policies. Logistics UK is clear that the industry must have a seat at the table as plans progress, to ensure that strategic decisions about energy supply move from a ‘first come, first served’ approach to prioritisation by industry and community needs, and are based on realistic timescales and available technologies. All this should help our members to continue to move goods efficiently without increasing costs for households, businesses and public services.
Underpinning all this activity is the need to maintain and grow the workforce of the future, so that logistics benefits from the best and brightest talents to shape the sector. The Generation Logistics campaign has already made progress in changing the way young people think about careers in the industry, and is now expanding its activity to include working with educators and other professionals that advise young people on their future opportunities.
There is still much to be done, but with the continuing support of the industry, logistics should become a career spoken of in the same breath as accountancy, medicine, retail or leisure – our manifesto urges the next government to continue the existing funding model to continue and expand the
campaign’s work. To find out more, please visit www.generationlogistics.org
While the sector continues to raise awareness to attract the next generation of workers, it is clear that the Apprenticeship Levy needs urgent reform to enable employers to draw down the necessary funds. There is a lack of colleges offering the apprenticeships the sector needs, and more flexibility is required to support training for roles that do not necessitate a year-long apprenticeship. In the experience of our members, the lifetime skills guarantee is currently inflexible and barriers to entry are too high.
The development of innovative, integrated infrastructure backed by a national logistics network will deliver efficiencies and opportunities that can benefit us all. Giving logistics a voice at the heart of government would ensure that the needs of industry and business are heard, and that our sector can work with government to drive up the country’s productivity.
To find out more about the asks of the logistics sector, the full Logistics UK 2024 Manifesto can be found at https://logistics. org.uk/research-hub/policies/logistics-uk-2024manifesto. Follow us on X (formerly Twitter) @LogisticsUKNews and find us on Facebook, Instagram, LinkedIn and YouTube.


WOMEN IN RAIL
Rajinder PryorThe Women in Rail Mentoring Programme
Rajinder Pryor MBE, Womenin Rail Board Trustee and Lead Delivery Manager (Customer) at Network Rail on over a decade of transformation
As we proudly move towards over ten years of Women in Rail, one of its most notable achievements is the Women in Rail mentoring programme which sits at the heart of our purpose to attract retain and develop women in the rail industry. This initiative has played a crucial role in empowering women, breaking down biases and challenging prejudices within the rail industry, one mentoring pair at a time.
The programme's ethos revolves around human connection, recognising that mentoring is all about building relationships and supporting others through the sharing of knowledge and experiences. These connections enable individuals to achieve their goals, both personally and professionally. The power of mentoring is something I hold dear, as someone who found herself stuck in her career in 2017.
It was through attending a deeply impactful mentoring workshop session that I discovered the magic ingredient that propelled me forward – and I’ve been an advocate for the power of mentoring and this incredible programme ever since.
Launched in 2014, the programme started with a commitment to matching female mentees with mentors from different organisations within the rail industry for a nine-month development journey. Over the years, the initiative has grown significantly, evolving from twelve mentoring pairs in its first year to an impressive 452 mentees and mentors from 24 organisations in 2023. In 2019 Women in Rail partnered with the expert team at Moving Ahead, specialists in structured, cross-company mentoring, which marked a pivotal moment for the programme's expansion and inclusivity.
An additional significant shift came in 2020 when the participant criteria was broadened to include both female and male mentees. While women's development and career progression remain a priority, the programme recognised the importance of fostering more inclusive workplace cultures by actively involving male allies as mentors and mentees.
As Women in Rail continues into the next decade, the mentoring programme stands out as a beacon of positive change within the rail industry. The diverse lineup
‘The purpose of the programme is to provide people working in the rail industry with a platform to receive support for their professional development and growth while at the same time encouraging diverse thinking and crossfertilization of ideas.’
Adeline Ginn, MBE, Founder of Women in Rail

‘Mentoring has the potential to shape professional development and equip colleagues with the right skills to achieve their career goals. I have seen firsthand the benefits of good mentoring and the ability to broaden perspectives and empower inclusive thinking throughout the workplace.’
Andrew Haines, Chief Executive, Network Rail
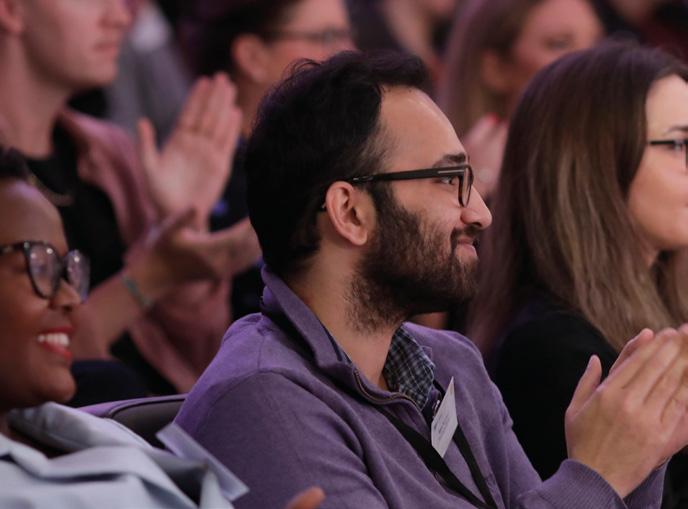
of inspirational speakers, including Dr Kate Goodger, Former Olympic Performance Psychologist and Mindset Expert and Kirk Vallis, Google’s Global Head of Capability Development, demonstrates the programme's commitment to continuous development.
The success of the mentoring programme is testament to the dedication of both mentors and mentees, as well as the ongoing support of organisations involved. Marie Daly, Women in Rail Chair and Chief Customer and Culture Officer, Transport For Wales said: ‘This programme continues to support our collective efforts to make change at scale in the rail industry, driving successes of the joint Women in Rail and
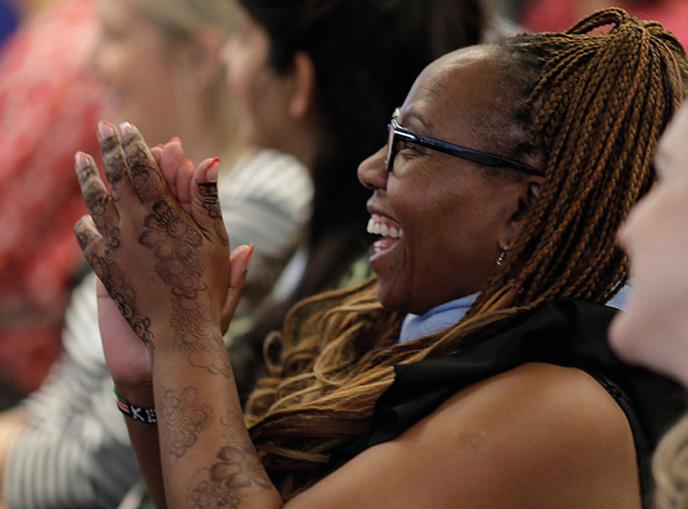
Railway Industry Association (RIA) ‘Equality, Diversity & Inclusion (EDI) Charter.’ The Charter underpins a commitment to work together, to develop a more balanced higher performing sector and has over 220 organisation signatories.’
Significant progress has been made, but this programme is needed now more than ever. Whilst the proportion of women in rail had been gradually increasing, it dropped to 14.6 per cent in 2022 – and the proportion of women in C-Suite roles in the rail industry was at just one per cent in 2021.
The Women in Rail mentoring programme is not only transforming individual careers but has also contributed significantly to promoting diversity, equality,
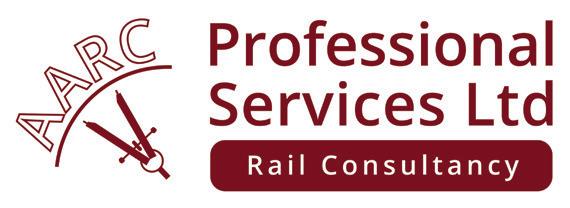
of
to the industry.
We are a railway consultancy bringing together likeminded rail professionals with a common aim to deliver outstanding outcomes by..
• Helping clients achieve their goals...
• Through strategic and technical expert advice...
• Across a range of disciplines...
• From the frontline through to the boardroom
Whether you’re looking for high level advice & guidance or direct project support, we’re here to help you deliver excellent outcomes.
To get in touch, please visit www.aarcps.co.uk
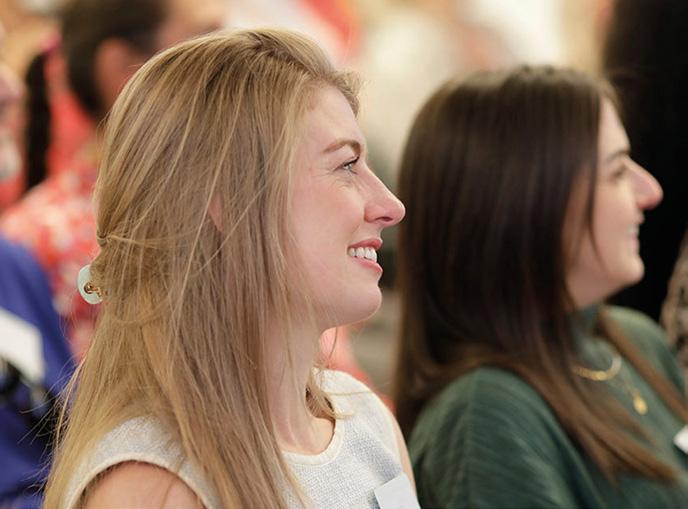
and inclusion within the rail sector. As the programme continues to evolve, it remains a powerful force shaping the industry's future leaders. I want to extend a huge thank you and congratulate all the organisations that have supported Women in Rail and its work, laying the foundation for a more inclusive and dynamic rail industry.
For those interested in learning more about the mentoring programme, which launches again in April 2024, and how to get involved, please reach out by email wr@ womeninrail.org or WRMentoringTeam@ moving-ahead.org. We would love to welcome you into this amazing community of changemakers.
Run by railway people, for railway people


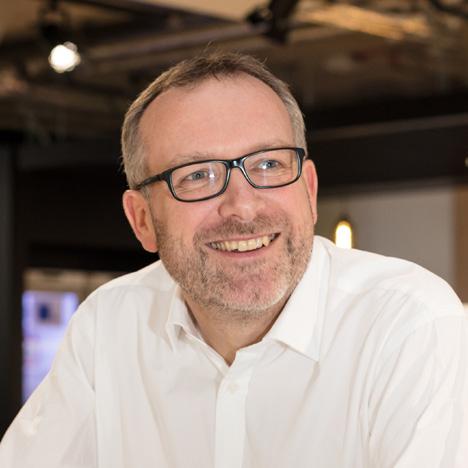
Graeme Craig is the Director & Chief Executive of Places for London, the company responsible for Transport for London’s (TfL’s) commercial property estate. Places for London is wholly owned by TfL but financially independent – taking no funding from TfL and delivering a dividend to be reinvested into the transport network.
Building on the Right Track
Graeme Craig, Director & Chief Executive of Places for London explains how TfL’s land is being used to make the capital a better place
People are sometimes surprised to hear that Transport for London (TfL) has its own dedicated property company. They wonder why TfL would have anything
to do with building new homes. And yet, more than one hundred years ago, the Metropolitan Railway – the precursor of London Underground – set up a subsidiary company, ‘Metropolitan Railway Country
Estates Limited’, to buy and develop land on what was then called ‘Metro-land’.
From Metro-land and the Jubilee Line and Northern Line Extensions to, most recently, the Elizabeth line, we have seen time and again how investment in transport infrastructure has reshaped the city. Decades of evidence shows us that transport and property development are inextricably linked. That is why TfL has established a dedicated property company, now called Places for London. We use our expertise and our land to unlock property development and those developments provide homes – including significant levels of affordable housing – for the people who then drive ridership and income, unlocking further investment.
Our estate – which ranges from railway arches to brownfield land and car parks – is filled with exciting opportunities, whether that is providing a first workspace for a fledgling business or giving a Londoner the keys to their first home. Places for London remains part of TfL, but is financially separate – meaning that we do not take any investment away from public transport, while all Places for London’s operating profits are returned to TfL as a dividend to reinvest into the transport network.
Places for London is not a small-scale operation. We are already a major landlord with 1,500 tenants, 95 per cent of whom are small and medium enterprises. Our assets are found in and around London’s

stations, on London’s High Streets and in railways arches across the capital. In addition, we have a programme to start on 20,000 homes across the capital, and a target for 50 per cent affordable housing. We will also be building some of the most sustainable commercial offices yet seen in London, working with Helical, starting at Bank station.
We are increasingly taking advantage of land acquired for major construction projects to provide housing. Working in joint venture with Grainger plc, the UK's largest listed residential landlord, we are bringing forward 479 new rental homes and commercial space at Nine Elms – something that was possible only because the new station was designed with development in mind. Again with Grainger, we are building 460 new rental homes on a former Elizabeth line worksite in Southall. Both schemes will also be bringing forward 40 per cent affordable housing.
Development can, of course, deliver improvements to the transport network. Working with another joint venture partner, Native Land, our scheme includes providing much-needed step-free access from street level to the ticket hall at South Kensington station, as well as completing the delivery of step-free access to trains on the Circle and District line platforms. Anyone who
has used the station will know how many people travelling with young children to the Natural History Museum, Science Museum or any one of the other nearby institutions currently struggle with the lack of step-free access at South Kensington.
We work hard to understand the unique context of every site, which ensures our approach to developing a place reflects the needs of the local community. Most of our developments are immediately adjacent to one of our stations, many of which have their own rich history. As an example, on our scheme next to the Grade II listed Arnos Grove station, we worked hard to make sure it was a heritage-led scheme to reflect the architectural value of the station. The scheme will enhance the station’s surroundings, including delivering a new public square to make it easier and safer for people to walk and cycle, encouraging active travel in the area.
We are not the only transport organisation taking this approach. A year ago, we announced an innovative collaboration agreement with Network Rail. This collaboration will see Places for London and Network Rail working together to deliver thousands of new homes, including a significant proportion of affordable housing, over the next decade.
Work is well underway between us and Network Rail. A full professional team has been procured, and dozens of sites are now being assessed. Our two organisations are among the largest landowners in Greater London, with more than 600 stations in addition to extensive retail, office and operational portfolios. Collectively, we own almost 14,000 acres of land across the capital and, while a significant proportion of this is operational, there are also brownfield opportunities across London boroughs and surrounding counties that both organisations are keen to unlock.
Working together will not only provide greater flexibility and opportunity, it will also enable both companies to learn from each other and allow us to make a stronger contribution to housing delivery as well as supporting the wider economic growth of the capital. Critically, we will look to fund and deliver transport and wider public realm improvements as part of every scheme.
Housing and transport are both transformative industries. I am excited to see where we will be able to take London in the coming years. With the experience we’ve already gained and with a strong partnership with Network Rail, we will build a better future for everyone.
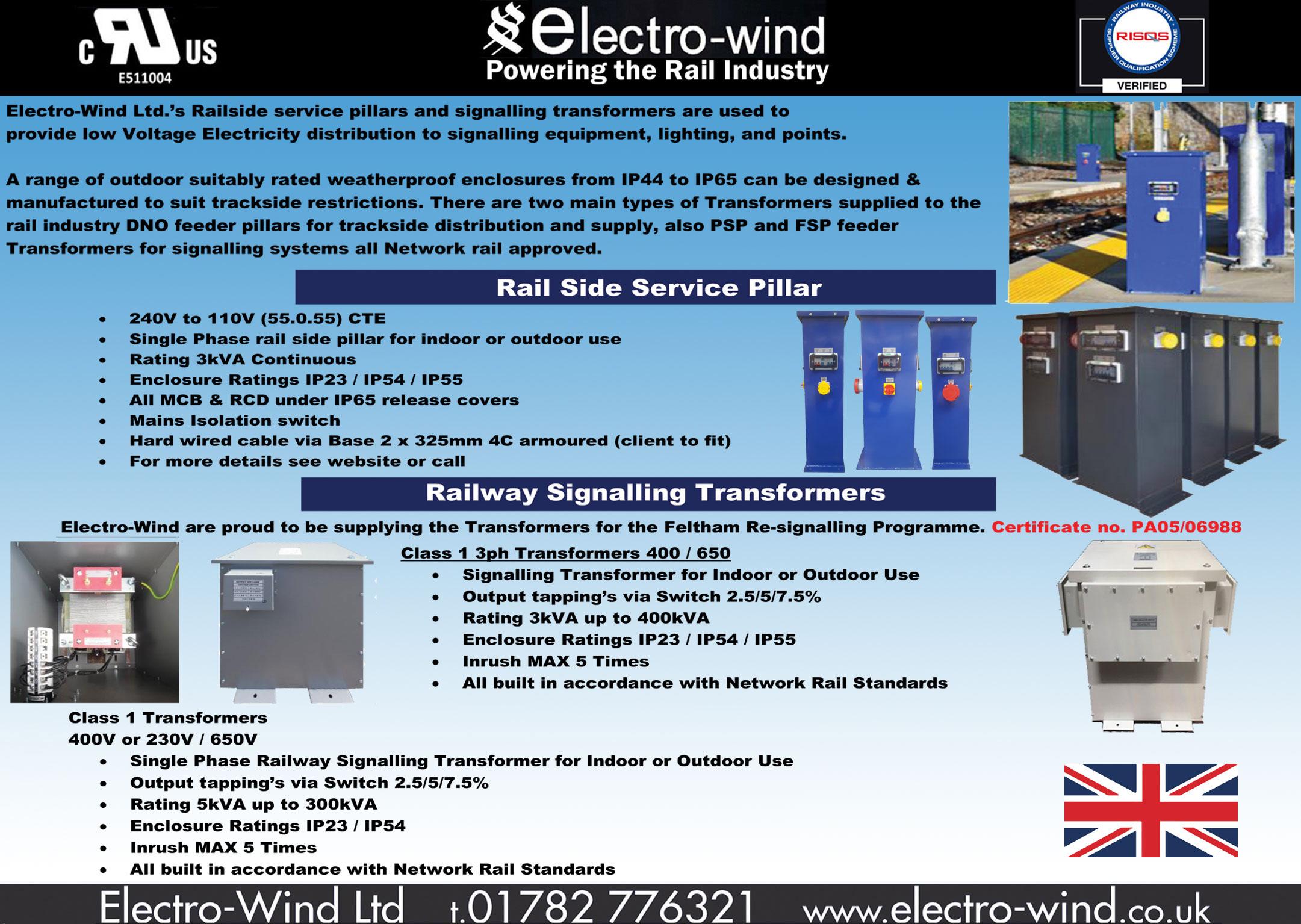
The Maintenance Jigsaw
Maintenance, Repair and Overhaul (MRO) conversations typically focus on the physical aspects of the job such as drive trains, moving components, inspection and test
This article looks at the complexity of modern maintenance operations and how Environmental, Social Governance (ESG) is impacting decision making for today's engineering in the rail and rolling stocks MRO sectors.
Specified components and installed parts rely on high-quality maintenance chemicals to deliver on performance targets and inservice reliability and, as corporate ESG requirements are written into standard operating procedures (SOP), so the entire maintenance jigsaw should be considered, and trusted brands selected that can deliver on maintaining service levels whilst implementing ESG commitments.
Putting ESG into the mix
A typical repair operation involves many components, each equally as important as the others to ensure a reliable, productive, and efficient planned maintenance-cycle. Whether it is ‘invisibles’ such as:
• Training.
• Schedules/planning.
• Service agreements.
Or Physical Ones:
• Tools.
• Components and parts.
• Chemicals.
Should one piece be missing, sub-standard, or overlooked, then it is often the case that the trinity of ‘reliability, efficiency, productivity’ is compromised resulting in increased risk of unscheduled maintenance being required. In the case of documented environmental performance, such as through the EcoVadis ESG audit (ecovadis. com); a change in maintenance products from traditional to ‘green’ can improve the scorecard, yet the reverse is also true if unauthorised supply sources are made, or reverted to. Making a commitment to ESG stick on the frontline of maintenance is challenging, especially across multiple sites.
Cleaning and inspection vital before lubrication
Lubrication is often the focus when talking about the ‘chemicals’ aspect of a maintenance process, and often a squirt of grease or top-up of oil is all that is required
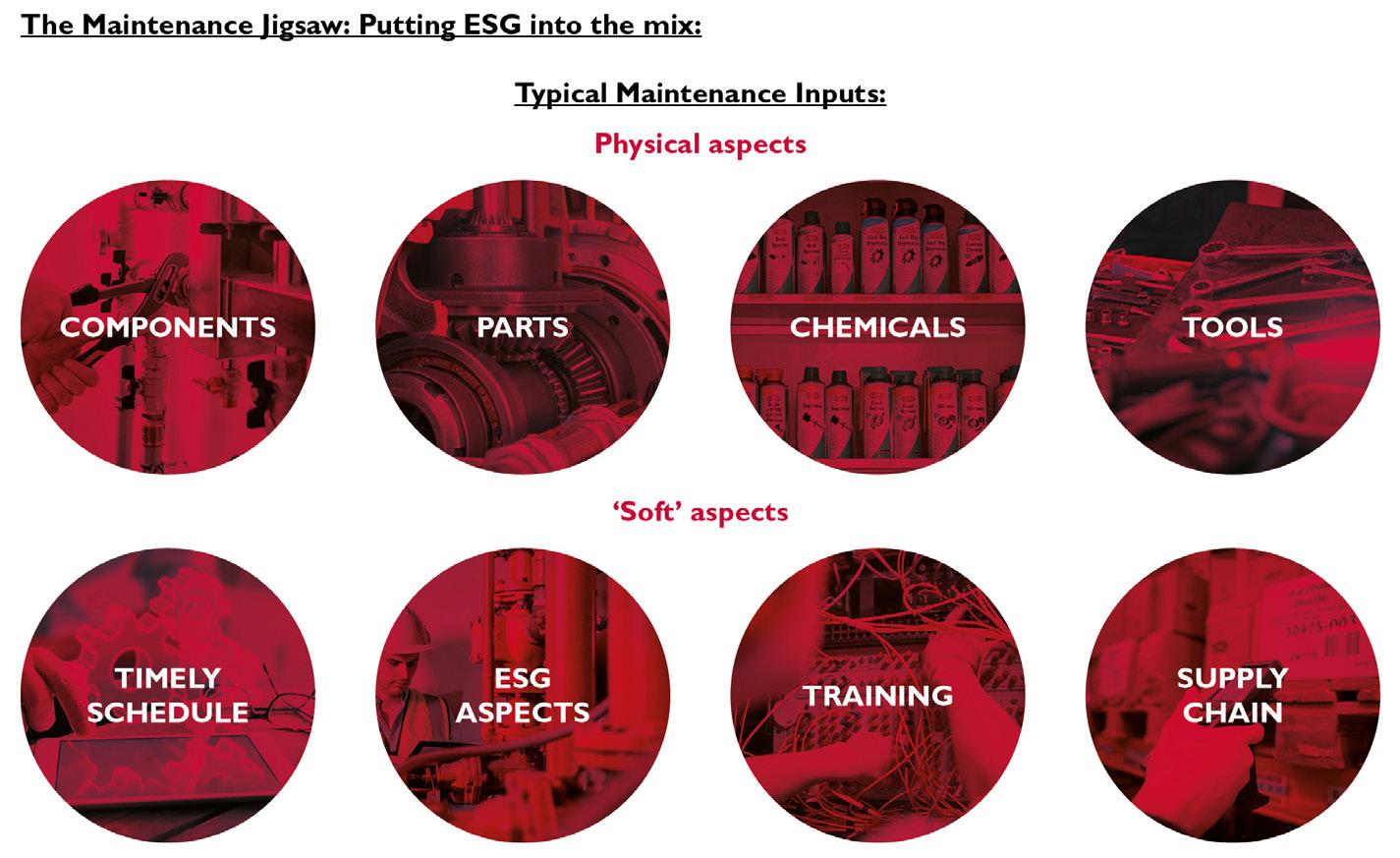

to complete the works order. However, should more extensive servicing be called for, it will require some component or part of equipment to be taken apart, inspected, and replaced to identify if it is the cause of (or likely to cause) problems.
This is where the maintenance chemical options expand, revealing the true extent of the choice: cleaners/degreasers, lubricants, anti-corrosion, metal cutting, welding, wipes and more. Cleaners and degreasers are designed as a critical first stage of the servicing process, ensuring that all old lubricant or contamination is removed allowing the clean surfaces to be inspected for wear and preventing recontamination during re-lubrication and assembly.
The technology behind cleaning chemicals is complex: through the expert blending of raw materials, cleaning properties can be displayed: fast evaporation, foaming action, grease removal, dry deposit removal, material compatibility, and so on.
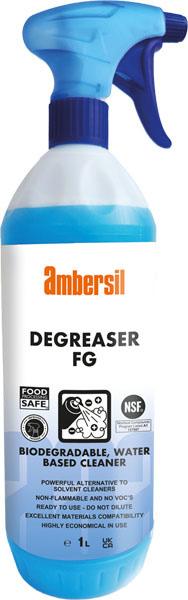
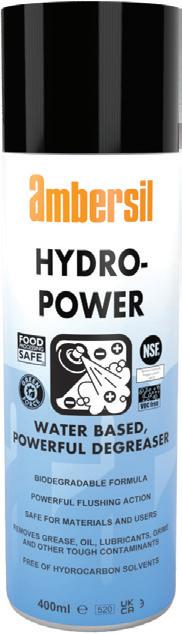
For decades, the only true options for grease and grime removal have been solvent degreasers and their associated VOCs (volatile organic compounds). Similarly for lubrication, hydro-carbon oils and base stock have been the normal solution, along with their environmental impact. These days, chemical technology and blending is catching up to user demand, allowing some companies to bring new solutions to market that meet performance criteria and improved user safety and reduced environmental impact.
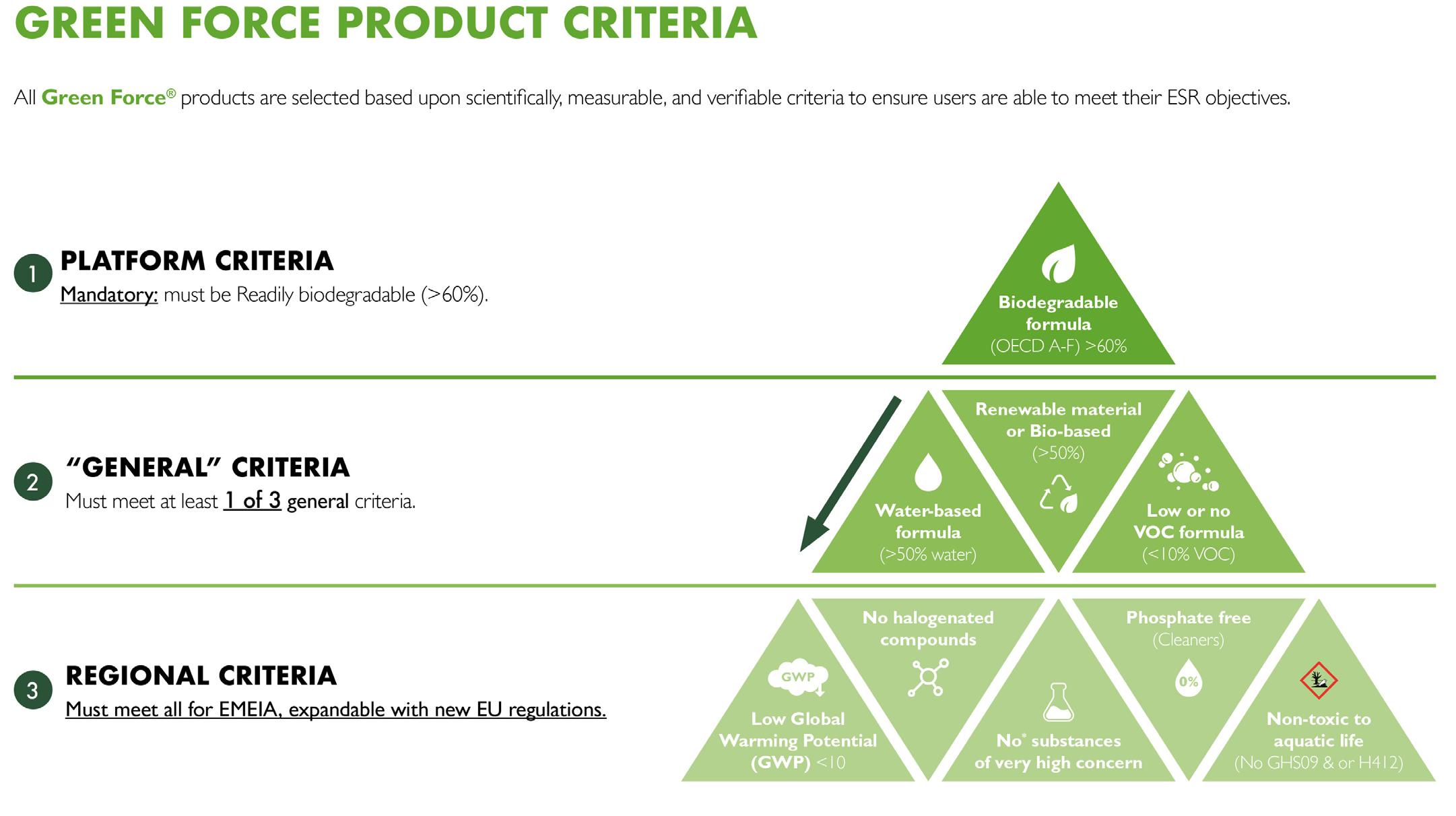
‘Environmental’ product portfolios such as ‘GREEN FORCE’ from Ambersil, seek to deliver user-focussed solutions that do not compromise on product performance, yet also meet the safety and environmental impact minimisation aims. In this case, a science-led product evaluation has been implemented that scores products against eight criteria: six mandatory ‘pass’ and two desirable. To date, the range includes degreasers, lubricants, weld anti-spatters, with coming through the development pipeline.
Other environmental and user safety products are also available to maintenance professionals. Bioremediation parts washers are rapidly replacing traditional solvent parts washers in many sites. The move away from the strong-odour, flammability, and cost of maintaining a solvent station has convinced budget-conscious managers to take a look at non-contract bioremediation, such as that offered by CRC industries and their SmartWasher machines and fluids. These machines have been trialled by a number of depots and it is reported that multi-site rollout is underway (UK & Europe).
Company profile
CRC Industries is a worldwide supplier of professional chemical products for multiple market segments: industrial, professional, trade, and consumer. As specialist manufacturers, CRC has seven-global production sites, 19 offices and warehouses, and over 3000 employees. Established in 1958, CRC has evolved over the years into a worldwide leader in the production of maintenance, repair, and overhaul (MRO) solutions. CRC Industries Europe is ISO
9001 certified, with the UK site also holding ISO 14001. CRC products are sold through the world via a network of distribution partners.
For more information about CRC Industries, the ‘Green Force’ platform, SmartWasher, and to discuss chemical consolidation with improved audit compliance get in touch via the contact information below.
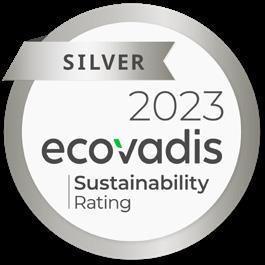
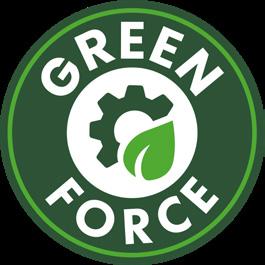

Tel: 01278 72727
Visit: www.ambersil.com
LinkedIn: crc-industries-emeia
Address: Ambersil House, Wylds Road, Bridgwater Somerset, TA6 4DD
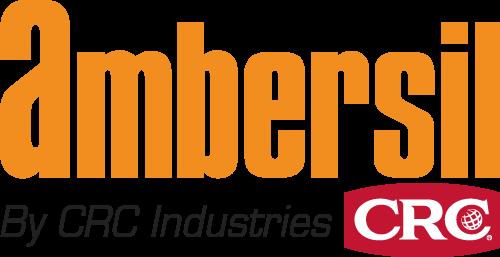
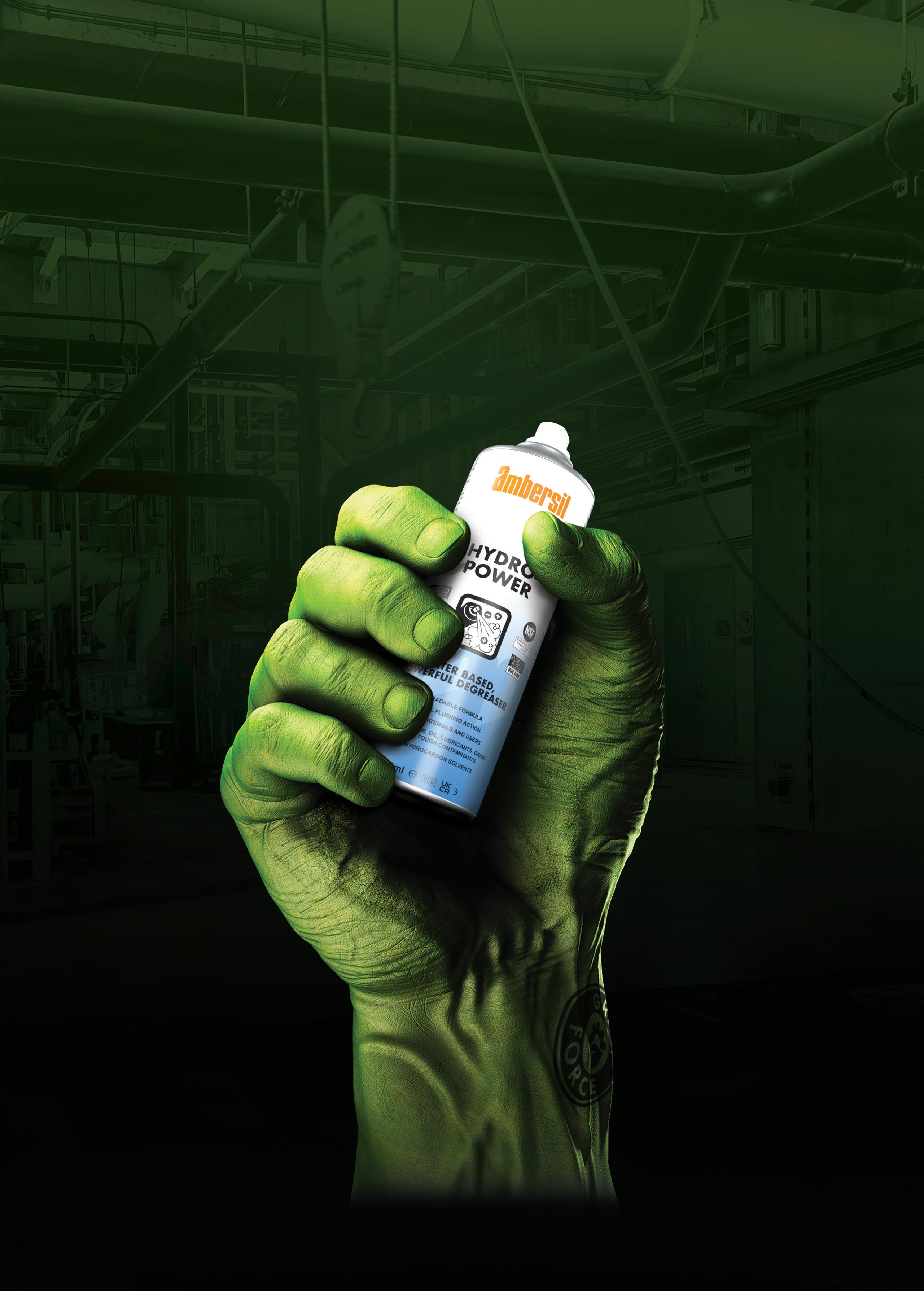
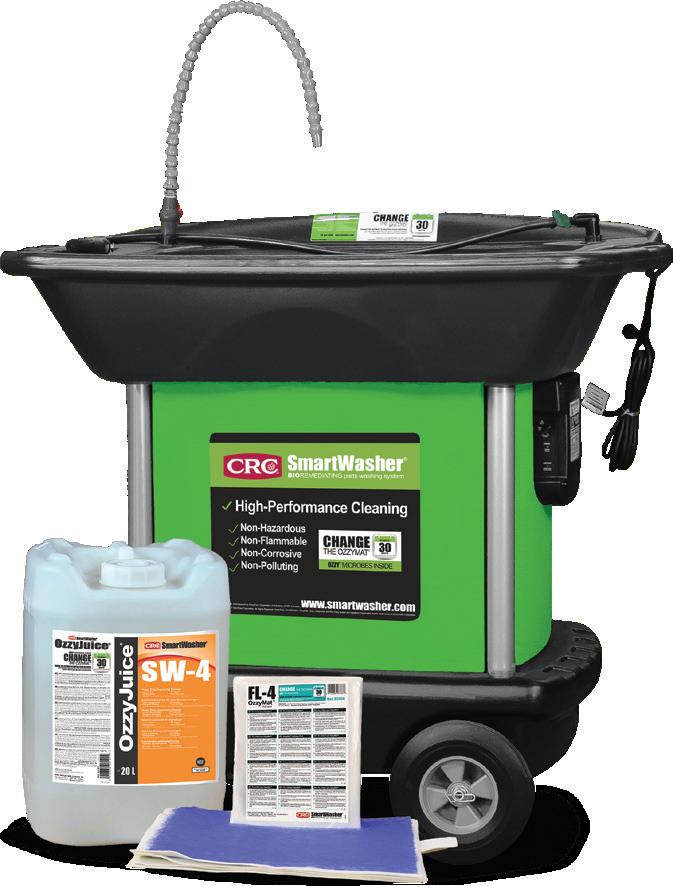
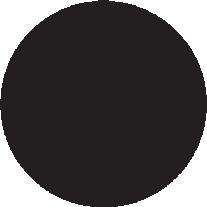
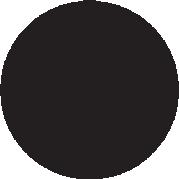

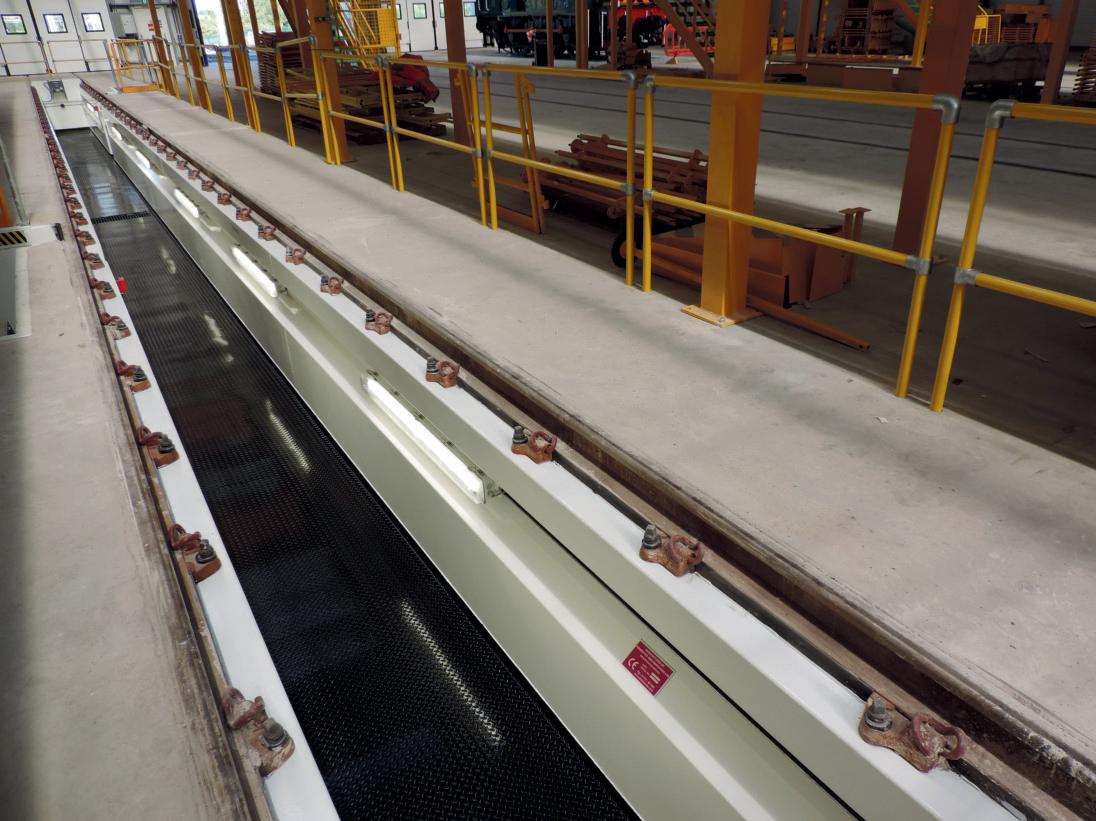
Improve
the efficiency of your workshop with our range of pre-f

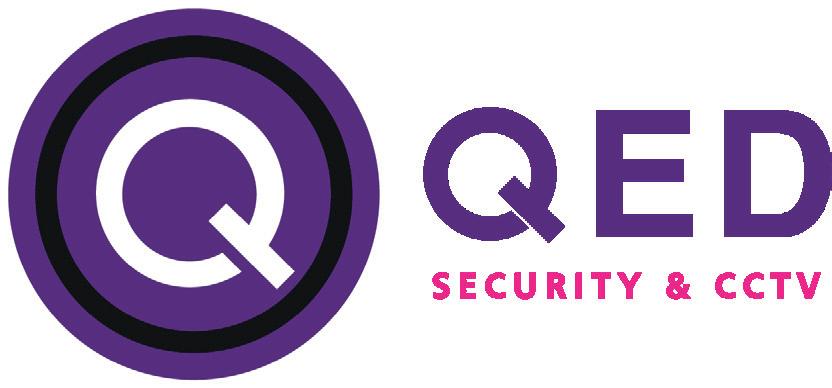
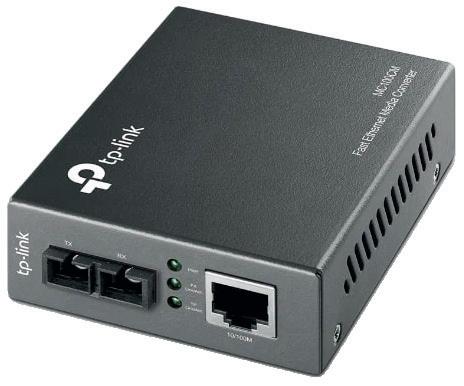
Premier Rail Pits offer the following benefits:
• Welded construction to ensure a water tight finish
• Quicker installation time compared to precast concrete
• High quality finish
• All internal service ducts fitted prior to installatio
• Easy to clean
• Rail attachments fitted prior to installation
• Full or part installations are available
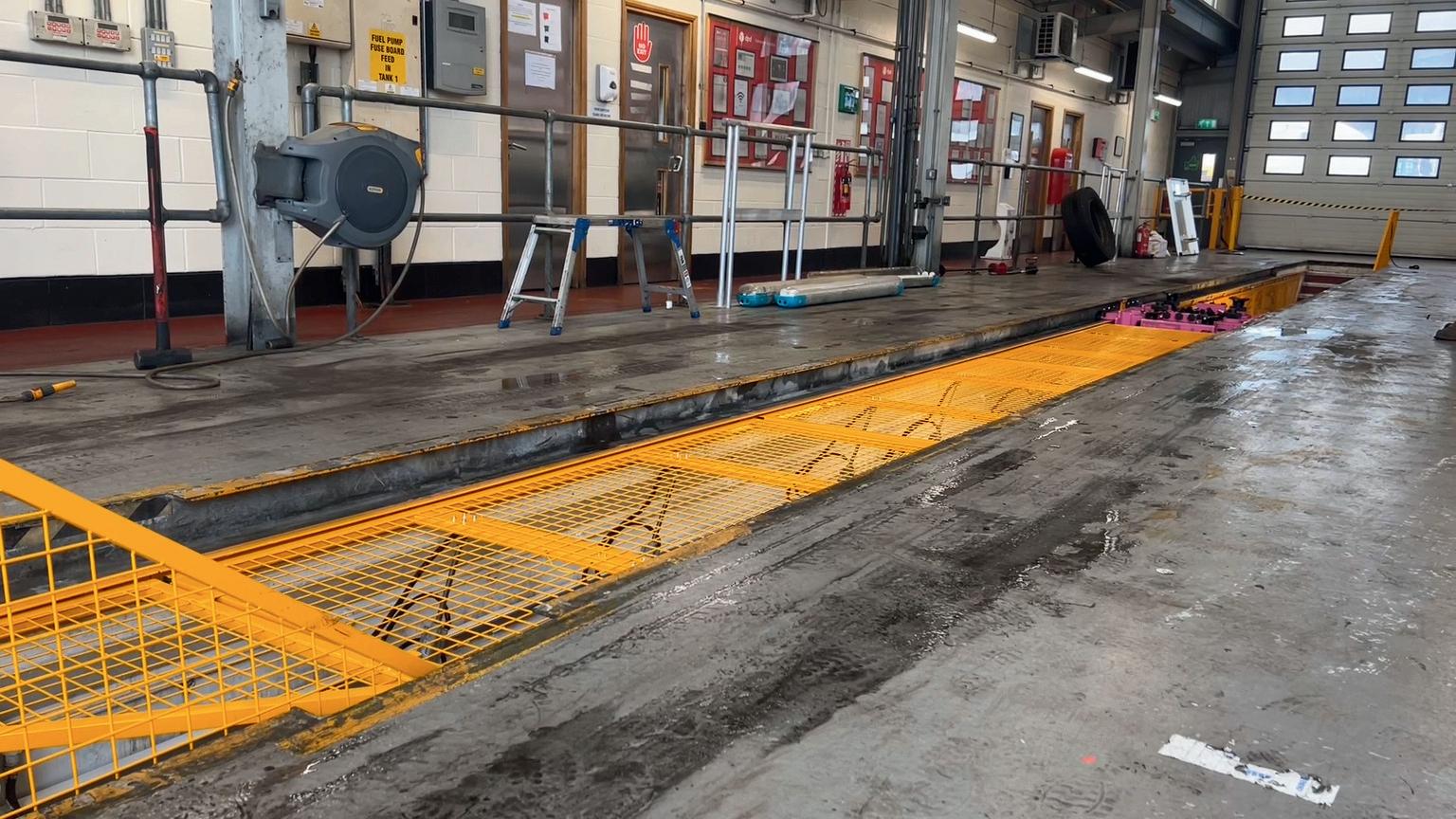
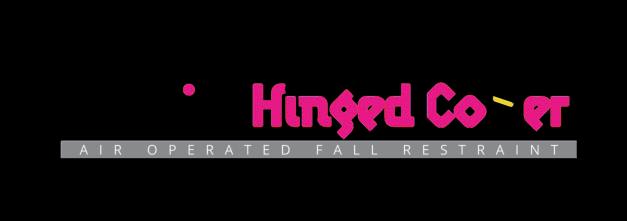
Tel:






Easily retrofitted to any pit with a light recess
No civils work required
Minimal working space lost
Air operated
Quick & easy operation

The Premier Hinged Cover (patent No. E2—886-747-B1) is an air operated fall restraint made up of 2.5m steel mesh panels. The panels are operated by pneumatic cylinders connected to a central control box for an easy one person operation. The stairs of the pit are covered by individual sections which are manually lifted, and have the additional benefit of acting as a hand rail for ingress and egress.
The Premier Hinged Cover enables clients to protect their staff with minimal disruption whilst keeping the maximum working space, and can be installed on existing steel, concrete or block pits.

CONTACT US 01772 336111 www.qedgroup.co.uk sales@qedgroup.co.uk
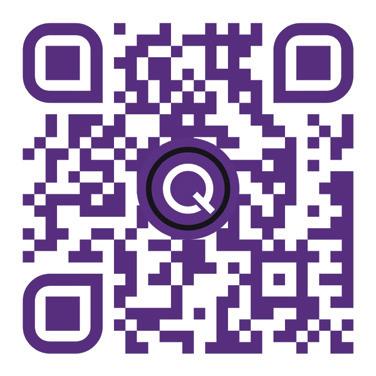
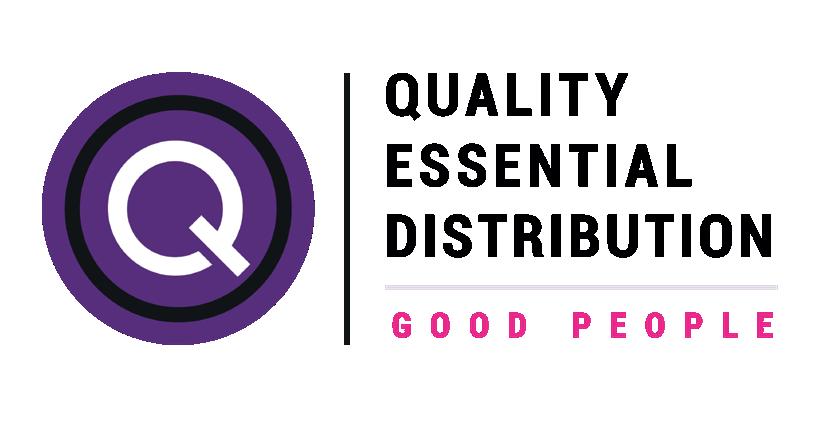
Partnership Transforming Rail Security
In the ever-evolving landscape of rail transport, security remains a top priority
Recognizing the critical need for advanced surveillance solutions, Quality Essential Distribution (QED) has strategically partnered with LILIN UK, a renowned provider of IP video solutions. This collaboration aims to revolutionize rail security, offering cutting-edge technology, unmatched expertise, and tailored solutions for the unique challenges faced by the industry.
Quality Essential Distribution has carved a niche for itself as a leading distributor of security and audio-visual products. With a commitment to delivering excellence, QED has become a trusted partner for integrators and installers seeking reliable solutions in the security and AV sector. The company's extensive portfolio includes products from industry-leading manufacturers, ensuring that customers have access to the latest and most innovative technologies.
LILIN UK is synonymous with highquality IP video solutions, recognized globally for its commitment to innovation and reliability. Specializing in surveillance solutions for diverse industries, including transportation, retail, and hospitality, LILIN has consistently set the standard for advanced video technology. The partnership with QED signifies LILIN's dedication to enhancing security within the rail sector through the deployment of state-of-the-art solutions.
The rail industry faces unique security challenges, ranging from the protection of critical infrastructure to ensuring passenger safety. With the increasing complexity of these challenges, the partnership between QED and LILIN comes at a crucial time. By combining QED's distribution expertise with LILIN's advanced IP video solutions, the collaboration aims to address the specific needs of the rail sector comprehensively.
Key Aspects of the QED and LILIN Partnership:
• Expanded Product Portfolio – the partnership enables QED to extend its product offerings to include LILIN's comprehensive range of IP video solutions specifically designed for the rail industry. This includes high-resolution
cameras, intelligent analytics, and scalable video management systems.
• Tailored Solutions for Rail Security – QED and LILIN recognize the need for customized security solutions in the rail sector. By leveraging LILIN's expertise and QED's understanding of the industry, the collaboration promises tailored solutions that address the unique security challenges faced by rail operators.
• Integration Capabilities – the partnership emphasizes seamless integration capabilities, allowing rail operators to integrate LILIN's IP video solutions with existing security infrastructure. This ensures a smooth transition to advanced surveillance without disrupting current operations.
• Training and Support Programs – QED and LILIN are committed to empowering rail integrators and installers with the knowledge and skills needed to deploy, maintain, and optimize security systems effectively. Training programs and ongoing support initiatives are integral to the partnership.
• Scalability and Future-Proofing –recognizing the dynamic nature of the rail industry, the collaboration focuses on providing scalable solutions that can adapt to evolving security requirements. Future-proofing rail security is a key consideration in the development and deployment of LILIN's IP video solutions.
As part of their collaborative efforts, QED and LILIN will be showcasing their innovative solutions at the upcoming The Security Event (TSE) 2024. This event provides a platform for industry leaders, operators, and stakeholders to explore the latest advancements in rail technology and security.
Attendees can expect live demonstrations of LILIN's IP video solutions tailored for the multiple sectors, highlighting features such as intelligent video analytics, highresolution imaging, and seamless integration capabilities. QED representatives will be on hand to discuss how its distribution expertise enhances the accessibility of
these solutions to rail operators, ensuring a streamlined and efficient adoption process.
The partnership between Quality Essential Distributions and LILIN UK is poised to transform the landscape of rail security. With a shared commitment to excellence, innovation, and customer satisfaction, QED and LILIN are wellpositioned to address the unique challenges faced by the rail industry. As the collaboration unfolds, the rail sector can anticipate a new era of security solutions that not only meet current demands but also adapt to the dynamic and evolving nature of rail transport.
The partnership being showcased at The Security Event at the end of April is a testament to the dedication of QED and LILIN to shaping the future of rail security through advanced technology and strategic collaboration.
LILIN UK CEO Steve Liddiard is thrilled by the appointment: ‘I’m excited to be working with Andy and his team, their initial enthusiastic response and their approach to training has been wonderful to see and I believe that this new partnership will firmly re-establish LILIN’s position in the security market. The current demand for non-Chinese, NDAA-compliant products is at a high, and we’re looking to give installers more value by putting profit back into the security sector.’
QED CEO Andy Barker is similarly enthusiastic: ‘We at QED are very excited to be working alongside a worldwide leading CCTV Security manufacturer like LILIN, offering quality CCTV products which comply with the UK government guidelines and putting profitability back into the installer’s pockets.’
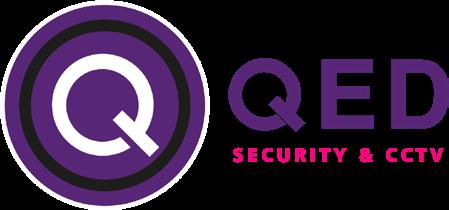
Tel: 01772 336111
Email: sales@qedgroup.co.uk
Visit: www.qedgroup.co.uk
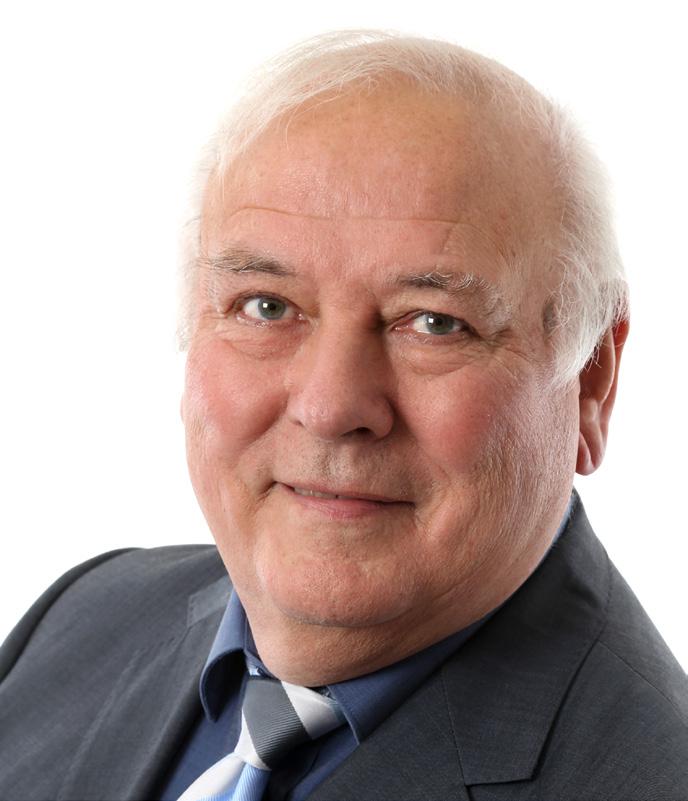
ALAN BARROW MRICS, FINSTCES, FOUNDER & MANAGING DIRECTOR OF ABA SURVEYING LTD
Past President of The Chartered Institution of Civil Engineering Surveyors, and a lifelong surveyor since leaving college where he passed the RICS examination specialising in Land and Engineering Surveying, Alan has consistently been at the surveying forefront, with his contribution being recognised by the University of East London conferring on him an Honorary Doctorate in Science.
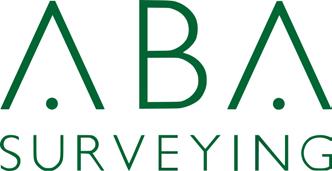
ABA SURVEYING LTD
Formed in 1990, ABA Surveying is a UK based survey company providing high precision dimensional surveying services throughout the UK and Europe.
How did you get started in the industry?
My first experience of surveying started in the railway sector when the Channel Tunnel was being constructed. Balfour Beatty were contracted to install and set the OCS (overhead line equipment) before any track was in place. Having no track meant the heights and staggers schedules supplied by the designers could not be used.
The OCS was supported by two-part Halfen brackets with the channel part bolted into four locating holes cast into the tunnel segments. The second part of this bracket was the registration arm which could be slid up and down in the channel section.
This was 1990 remember, and OCS engineers knew very little about coordinates at this time. Fortunately, ABA Surveying did and, being a software writer myself, I was employed to devise the system and write the software linking together the asbuilt surveyed coordinates of the bracket mounting holes, the tunnel soffit at that point, the track design alignments and then applying the planned heights and staggers to finally produce a printout for each bracket location. The printout listed the distance up the Halfen bracket channel to set the second part of the bracket, the distance along the registration arm to set the registration point and finally a dimension down from the tunnel soffit to the contact wire.
‘Can do’ then became the byword which has underpinned ABA Surveying’s reputation and is still in evidence today.
What was the inspiration behind starting ABA Surveying?
I had been Chief Surveyor with two international survey companies and had become frustrated by my inability to act quickly and take advantage of fast emerging technologies. With these big companies, business cases, can we afford it, we’ve never done it this way before all became sources of frustration and inhibited the progress that I wanted and considered would become inevitable at some time.
ABA Surveying was started expressly to provide our clients with a professional surveying service, secure in the knowledge that the service they were getting was truly the best service possible considering both the techniques and the technology available. This philosophy continues and we have purposely kept to a small company, so that we can continue to be in charge of our own destiny.
How has technology developed since you started in the industry?
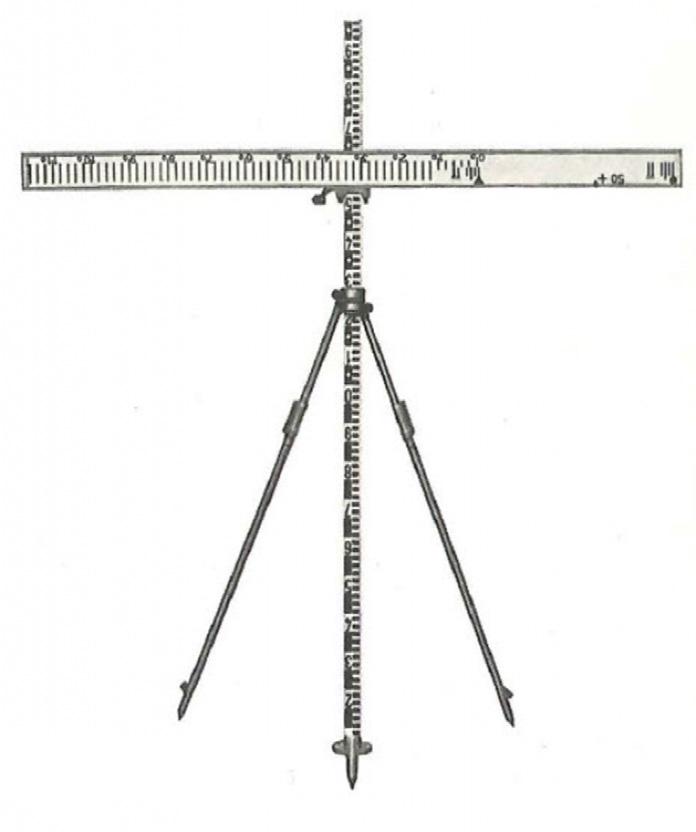
using Peters trigonometric tables and a mechanical calculating machine, either a Brunsviga or Facit. The observed detail points were then plotted by hand back in the office by a draughtsperson using a manual polar plotter.
Only the key detail points were surveyed in this way and a revisit to site was needed to infill the rest of the detail by taping it in.
In this way, on a good day the survey team together with the draughtsperson would achieve a progress of 150 detail points plotted each day at a cost then of around a £1 per point. In the last sixty years the contribution that electronics have made to the surveying profession has been phenomenal and continues to develop exponentially.
We now have EDM (electro-magneticdistance-measurement), total stations (now with contactless laser measurement), GPS (now called GNSS – Global Navigation Satellite Systems), UAVs (unmanned aerial vehicles or drones), USVs (unmanned surface vessels), multibeam side-scan sonar, 3D scanners and automatic reading levels in our armoury.
With a press of a button we now know our absolute 3D position in the world to an accuracy of 25mm or better in a second or two. We can also measure, code and record a point with a total station to an accuracy of 1mm or so in just a few seconds and use a 3D scanner to record a site with 400 million points to an accuracy of 1-2mm in just three minutes. If only we were paid the same rate per point now as when I first started surveying!
Want to know more about ABA Surveying?
Tel: 01483-797111
Email: alan@abasurveying.co.uk
Visit: www.abasurveying.co.uk
When I started surveying, state of the art data collection was done by a survey team of two using a horizontal bar tacheometer. Booking the point number, horizontal angle, vertical angle, distance and target height was all done by hand together with a field sketch. The control traverse was calculated
The process times involved have completely changed around. Whereas it used to be 85 per cent fieldwork and 15 per cent office work it is now 15 per cent fieldwork and 85 per cent office work. Our focus now is on reducing the office time and we do this by continually streamlining our processes and writing bespoke software to support this.
Since the coming of 3D scanning in late 1999, we can often capture the whole site
in just a day and now process it to the final deliverables back in the office where we are in controlled conditions and not exposed to the vagaries of the weather.
What is your USP (Unique Selling Point)?
We are easy to talk to and we listen. Our reputation for motivation and accuracy, coupled with our experience, brings solutions to our client’s problems.
When a client comes to you with a particular problem, what’s your process for coming up with a solution, and how closely do you work with clients throughout the projects?
We listen to them very carefully to understand their requirement for the survey data, the accuracy they are needing to satisfy their design purpose, their timescale for the requirement and, of course, their budget. These are all factors which will influence the proposal we put to them. We have all the survey technology in house to be able to present to clients a solution which best satisfies their requirements, particularly as surveying techniques have moved so fast that many designers remain unaware of the surveying possibilities that are available.
What are some standout projects you’ve been involved in over the years?
We have been involved in so many major projects like West Coast Mainline upgrade, Euston re-modelling, Thameslink, Crossrail, HS2 and many more that it is difficult to choose between them.
I guess the Thameslink Programme was a gamechanger where, in 2002, we introduced the Thameslink team to 3D scanning in both static tripod mounted form and in kinematic form in 2003 with our TMDs (Track Measuring Devices).
We used the original datasets throughout the life of the project from 2002 to 2018, updating them as the construction progressed – BIM in action even before it was conceived.!
A more recent and rather unique project involved Hammersmith Bridge over the Thames which has been closed since 2020 following the identification of microfractures in the 136-year-old structure. The proposed solution involved reinforcement to the structure at sixteen locations. The reinforcements were to be milled from 1.4m x 0.85m x0.85m thick steel blocks and had to fit precisely to the contours of the original castings to an accuracy of 0.1mm.
We proposed the system, scanned the original castings, modelled the surfaces and produced the digital STEP files for the company who were to do the milling. In approving our proposal, the consultants first checked the early datasets against the original castings using a straightedge and feeler gauges and found nothing exceeding 0.1mm.
What are your plans going forward to ensure ABA Surveying services are still around for years to come?
You could say that those plans were laid some fifty years ago with the birth of my two sons.
Both sons have joined me in the business and my eldest grandson joined us two years ago.
With three generations in the business I think we have the succession plan sorted, at least from my point of view.
On a more serious note, it is often said that inter-operability doesn’t exist between software companies, and we would add that it doesn’t exist between clients either.
Our clients have all developed their own versions of BIM with different specifications, detail content, coding structures, layer names, presentation details and a host of other differences.
As a company we cannot possibly accommodate so much variation at the data capture and production levels, to do so would only cause confusion and increase the likelihood of mistakes.
We have therefore developed our own procedures which enable us to capture all data and extract and structure the deliverables to our client’s requirements through our own translation software. This is a continual development for us and will see us well into the future.
What new developments/strategies do you have?
We have always been at the leading edge of survey developments since our use of kinematic scanning for data capture on the railway in 2003 followed by our mobile scanning rig for the road in 2009.
Our goal now is making these systems smaller, more portable and with more functionality. The mobile scanning rig is now complete and has been used very successfully for capturing railway corridor detail to 1-2mm accuracy but at a walking speed of 3kph+. We are thrilled with the resolution of the resulting pointcloud which is even better than our standard method of static scanning everything and five times faster. The portability of the rig means that we can now use it on road, rail and water.
We are, even now, developing our own software to extract detail automatically from this dataset.
We do have a further hardware development in its advanced stages, but I can’t say more about it just now. Maybe in six months – watch this space.
What would you say is the most exciting technology in the industry?
The most exciting technology has been the developments in 3D scanners and will remain so for the foreseeable future. We recognised the potential for 3D scanning and were the first company to buy a
3D scanner for survey purposes as far back as 1999.
The point cloud has completely replaced the field book for the surveyor in that it captures the complete scene and all detail, whether you want it or not, in just a few minutes and to an accuracy of millimetres.
It brings a highly detailed digital twin of the real world into the office thus allowing the data extraction to be done under controlled conditions, 24/7 if necessary, and at no risk from the weather or time constraints. It is truly the least risk method of surveying.
• It is non-intrusive and non-contact.
• It captures everything in view.
• It can be done from a place of safety.
• It works equally well in the dark as in the daylight.
• It means less boots on the ground and for significantly less time.
What are some of the biggest challenges this sector currently faces?
In my opinion there are two challenges, lack of staff and the procurement system. The first is that the profession is seriously undervalued which has contributed to the current lack of properly trained and qualified surveyors. This is being offset to some degree by the adoption of automated data collection which has become a push button exercise and can be done with little training.
But – and it is a big but – we still need the fully trained staff to take possession of the captured datasets and process them through to deliverables for our clients. At the moment this training is having to be done by the companies themselves with varying results and more needs to be done by academia to increase the supply of trained surveyors.
This will only happen if the profile and status of surveying is raised, maybe by regulation but certainly by remuneration, such that more students are attracted to surveying as a worthwhile career and start to populate the academic route.
Geospatial data is of increasing importance to the management of our environment and the assets within it so I believe UK The Geospatial Commission could itself be much more pro-active.
The second big challenge is, I believe, the procurement route which, in its current form, does nothing but lead to a race to the bottom. There can be a lack of understanding by our clients about the possibly different surveying solutions offered and this is evident in the way they procure their surveying services.
For transparency reasons, most large procurements are done by open tender, managed by the ‘buying department’ with a PQQ (prequalification questionnaire) and a price. The PQQ is generally a series of tick boxes more directed towards rectifying perceived social inequality than for evaluating the competency of the bidder. The client’s assumption being that any risk
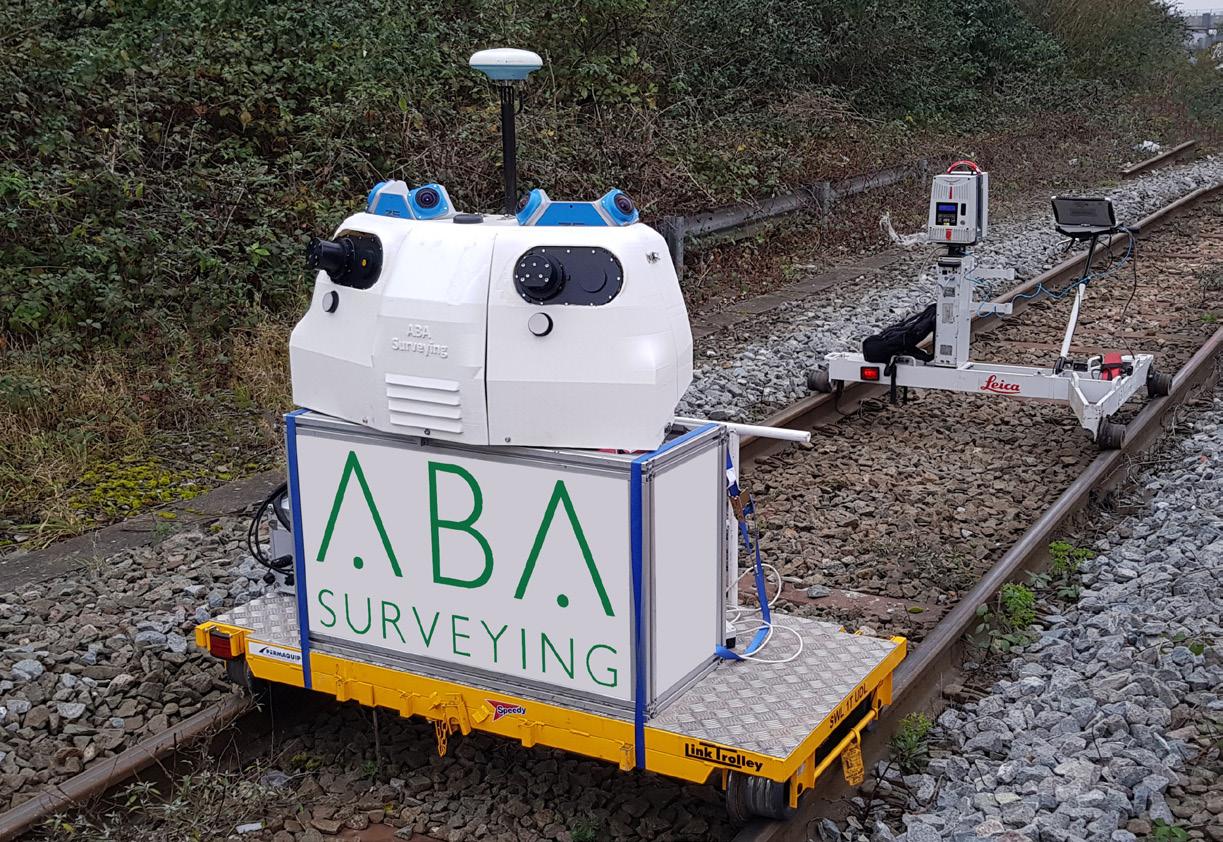
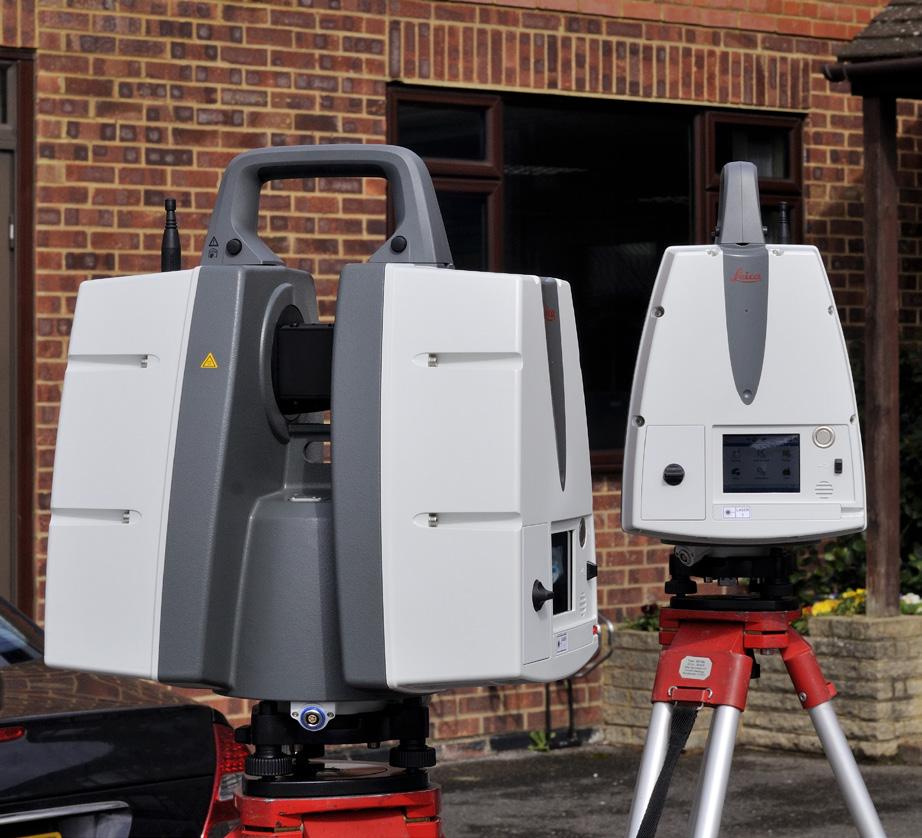
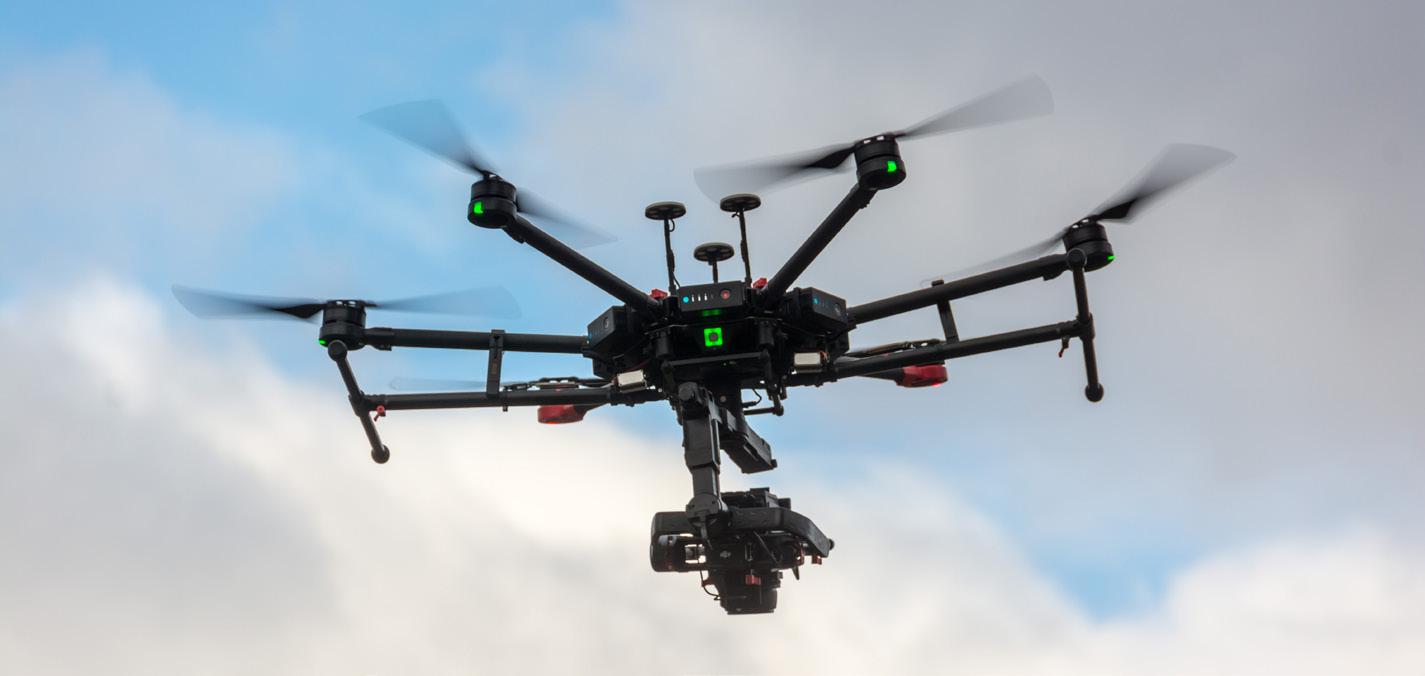
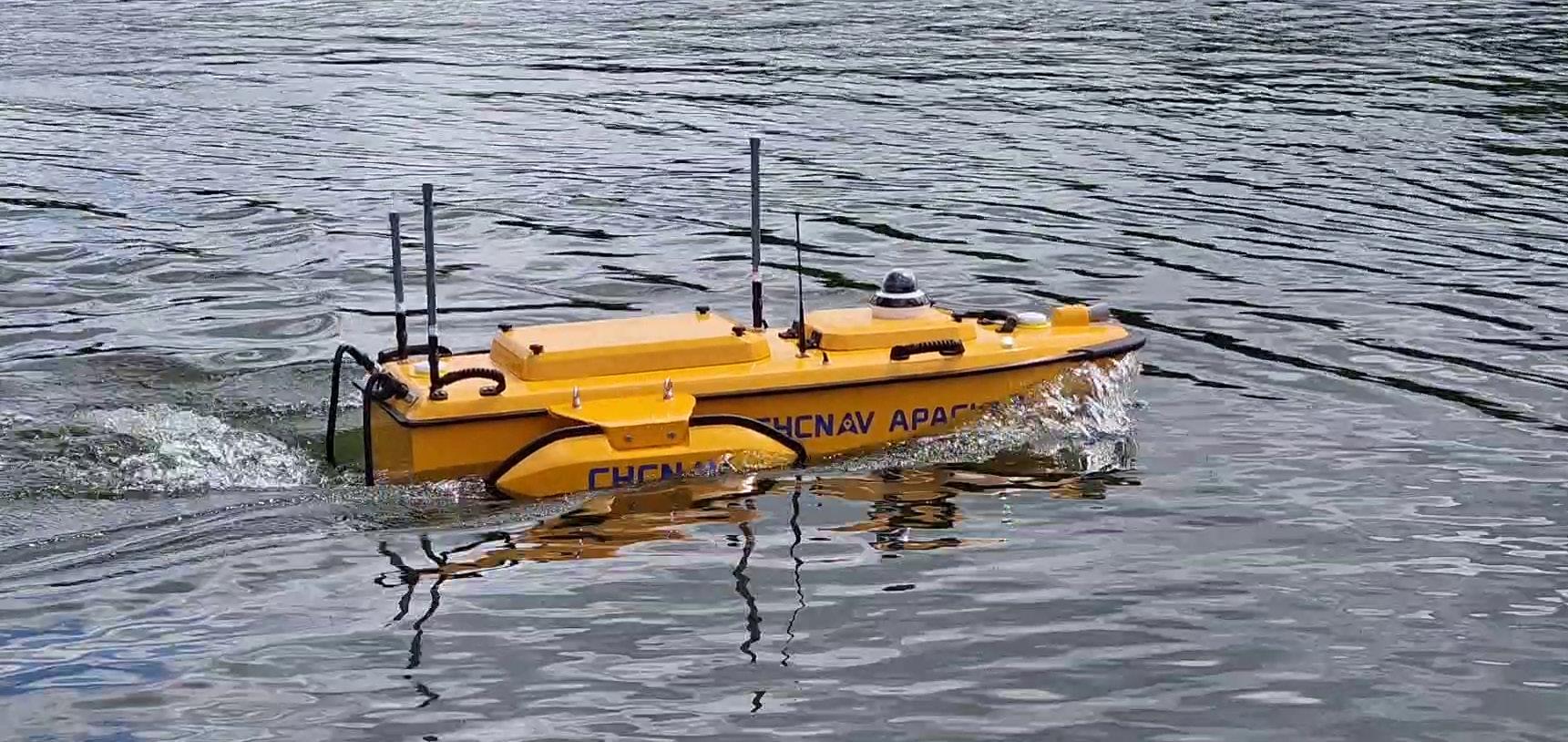
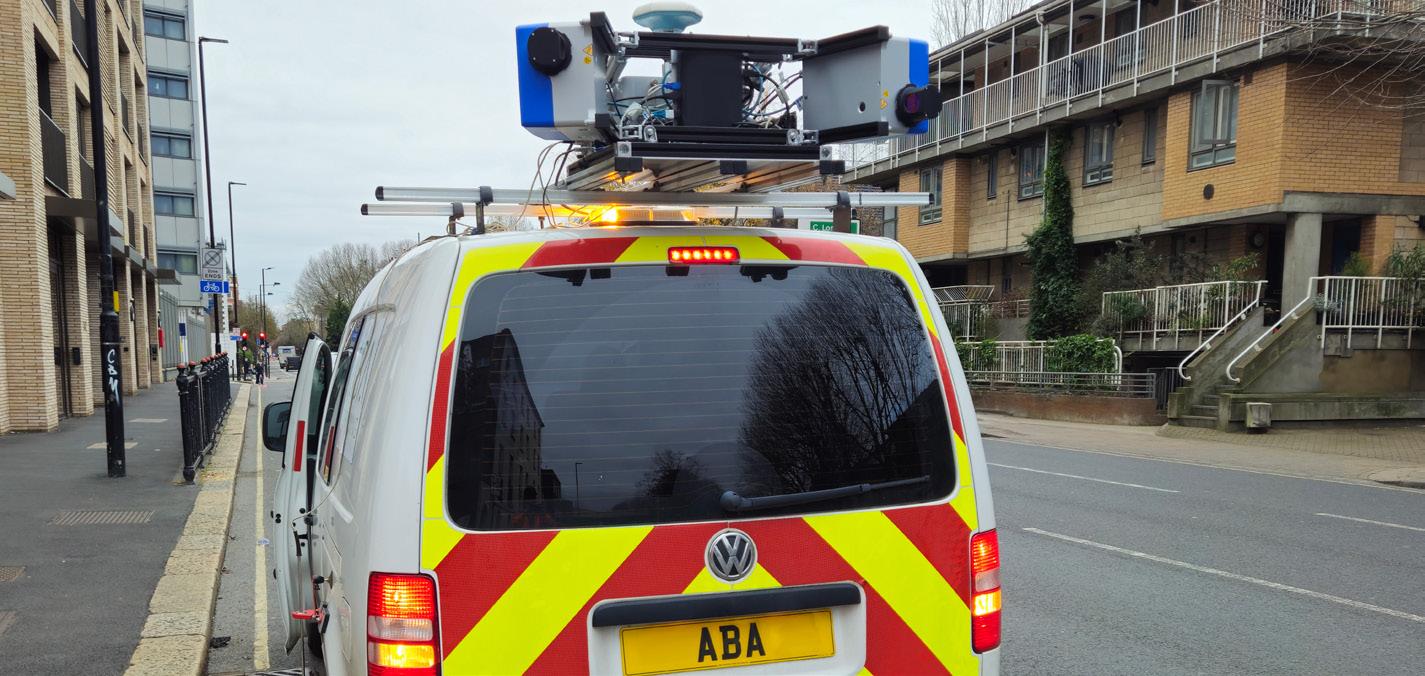
to them is covered within the fixed price. Tick all the boxes, lowest price, get the job. No consideration is given to the risk to the contract through weather, access, performance, results or simply in delay to the project and in my opinion the method of survey can have a significant impact on all these risk factors.
Too many clients can be hoodwinked by marketing ploys, drone surveys being a typical example of this over recent years. When a survey goes wrong, the buyer will blame the company and hold the opinion ‘we tried that, and it didn’t work’ for many years to come. In reality, it is usually the buyer who is at fault by not researching the proposed method and company experience in more detail. Nobody objects to competition but, please can we have a level playing field?
My suggestion would be for potential clients to get their survey managers to approve a select list of survey providers based on proven capabilities, and for the work to be let on a mini-tender basis among these approved providers.
What are your views on collaborative working?
Collaborative working is a very important concept and very often provides the best solution for the client. Our company has the equipment to carry out static scanning, mobile scanning for road and rail, UAV surveys and bathymetric surveying, but our investment in equipment is over £2 million which many smaller companies could not afford.
Admittedly they could hire in the equipment, but that doesn’t come with our experience to use it efficiently and properly, and collaboration might well be a better solution.
We collaborate with other survey companies where our expertise fills a gap in their capability.
We do the same when we have a gap in our own capability or, more usually, when additional resource is required.


HOWARD LEACH MANAGING DIRECTOR AT ENGPRO SOLUTIONS
Howard is an accomplished advisor, business coach and consultant, having been a Managing Partner of Danburykline, Head of Operations at Baines Simmons and Senior Production Manager at British Airways. He brings significant expertise in operations, maintenance, planning, and safety management in both aviation and rail. Howard has helped several clients achieve improved maintenance performance.
How did you get started in the industry?
My background is in aviation, where I served in the Royal Air Force then joined British Airways working as a licenced engineer before moving into management and executive grades. Interestingly about 25 per cent of the rail industry have some form of aviation roots. My first introduction into the rail industry was through High Speed 1 looking into asset management and renewal challenges. I followed that by going on to work with Greater Anglia, and then East Coast Trains (as they were then known).
Why did you start EngPro Solutions?
In my first few years in the rail industry, I saw many competent people who were not reaching their potential in lots of cases. The rail industry, in my opinion, has more than its fair share of talented young people, although in engineering disciplines we are not great at supporting these people to their fullest potential. I saw some fantastic development programmes with significant resources that weren’t quite connecting to the engineering community.
I reflected on my time in aviation and recognised a similar pattern. The word professional kept coming back to me; we needed to nurture our great people to start becoming professional engineers and managers. I set up EngPro to hopefully provide some of the steps that I felt were missing to help people develop. The company name, EngPro, was an abbreviated version of Engineering Professional Solutions.
What does EngPro specialise in?
ENGPRO SOLUTIONS
EngPro is a boutique consultancy and training organisation specialising in maintenance professionalism and efficiency improvements. As well as training incident/near miss Investigations to RSSB standard, maintenance efficiency programmes, and managing change in the maintenance world.
Want to know more about EngPro Solutions?
Tel: 07841029276
Email: howard@engpro.co.uk
Visit: www.engpro.co.uk
Having been in the corporate world I wanted to develop an agile business which could offer a tailored approach to clients. As with any business having the ability to be entrepreneurial and adaptable is key however, keeping the focus on improving maintenance performance through our people has always been at the forefront of my mind. The bulk of our assignments have been around introducing and building strong planning and maintenance management capability. This in itself is quite varied and typically has us helping increase planning skill, competence, and capability. Building longterm load and capacity models and helping embed stronger management metrics and performance management have also been an important part of our offering. But I guess the bedrock of our services has always been professional standard training – for maintainers.
Tell us more about the training you do.
We developed the Management Excellence PathwayTM approach. The idea of this is that it takes the advancing technician who is looking for promotion and provides all the tools and techniques they need to manage effectively as a Team Leader.
We have core skills courses that are designed as an entry-level course for newly promoted junior managers (team leaders).
All our training is baselined around the UK Engineering Council UKSPEC framework and in doing so gently moves the delegates towards a more professional direction. As a Chartered Engineer myself I know the value such registered professionals can bring to an organisation and how much more personally fulfilling the engineering management roles are when you have a professional support. That is exactly what the CS08 course sets out to deliver.
Finally, there are growth skills courses that teach engineering managers how to be professional in their role. Most people I meet in rail are engaged and energetic; our courses help layer on professionalism.
This CS08 course sounds very exciting, tell us more.
The Moderner Production Supervisor (CS08) came about following a discussion in a TOC headquarters a little while ago. I had for a long time felt there was a gap in the education and training of supervisors. They have three strands to their competence map – technical, leadership, and management (or supervision). Technical training being regulated through ROGS is covered well, and most companies run good leadership development programmes (managing people).
The missing element was supervision, it wasn’t trained, it was passed from Fred to Chris to Simon, to Joe…. Each stage getting slightly diluted, there wasn’t a standard approach. Whilst I was having this discussion a mature manager mentioned ‘that sounds similar to the NEBSS course we did in BR days!’ He still had his notes from those days and looking through them, I realised this was a very good course –and probably why the notes were valued sufficiently to be kept for 30 years.
So, what is specifically in the CS08 course?
There is a full specification sheet that lists all the learning outcomes that can be downloaded off our website. But to contextualise for you here, we wanted the course to have the same standing and importance as the British Rail NEBSS course had, so we have invested a lot of time and energy in developing it. For me personally it had to match my professional aspirations, it had to raise the professional bar for our team leaders.
We have produced an EAL-assured, five-day intensive course that covers topics such as how to hold effective morning briefings, email comms, the importance of handover, planning and scheduling, with an introduction to materials management, managing your team competence, mapping, and development. Essentially all the supervision skills a junior manager needs in and around a rail depot. It has a 60-question
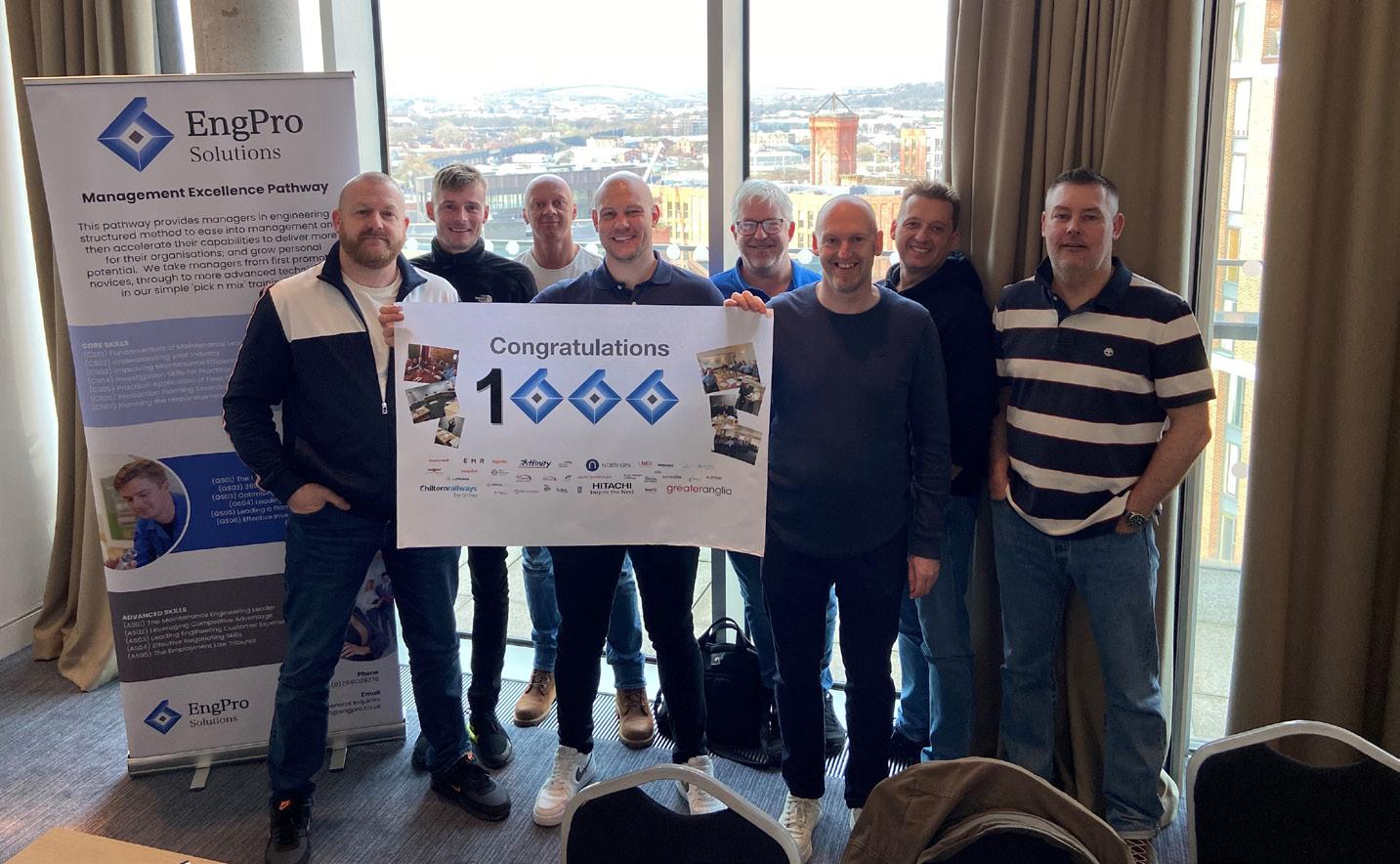
exam at the end and all students undertake a work-based assignment. I’d be happy to chat more specifically to anyone interested.
Why EAL assured?
Quite simply I felt it was important for the course to offer a recognised qualification.
Having an organisation with the pedigree of EAL ensuring the course is of a professional calibre and meets the specification standards was important to me. It has meant EngPro has had to sharpen our processes to become an approved training centre, but that is all good news I feel. Even though it was a lot of hard work!!
Has CS08 been received well?
Still early days but the initial signs are very good. We have run several courses now for both TOC and OEM and the feedback shows all have been impressed. The standard of the work-based assignments has been high and illustrates the latent potential many organisations have. I do believe this is a course that can help unlock some of that. We have delivered for four rail companies so far, and many others are talking to us about it. Yes, I feel it has been received well – On a personal level, I am pleased it is doing the ‘professional’ bit I was so keen to emulate.
What’s next for EngPro?
Well right now my focus is firmly on a skiing holiday with my family, but after that we have plans to take two more of our courses through the EAL-Assured route; CS04 – error investigation training, and CS06 – planning essentials. I feel both areas if given the professional brush could provide so much more value to organisations and the people undertaking those roles.
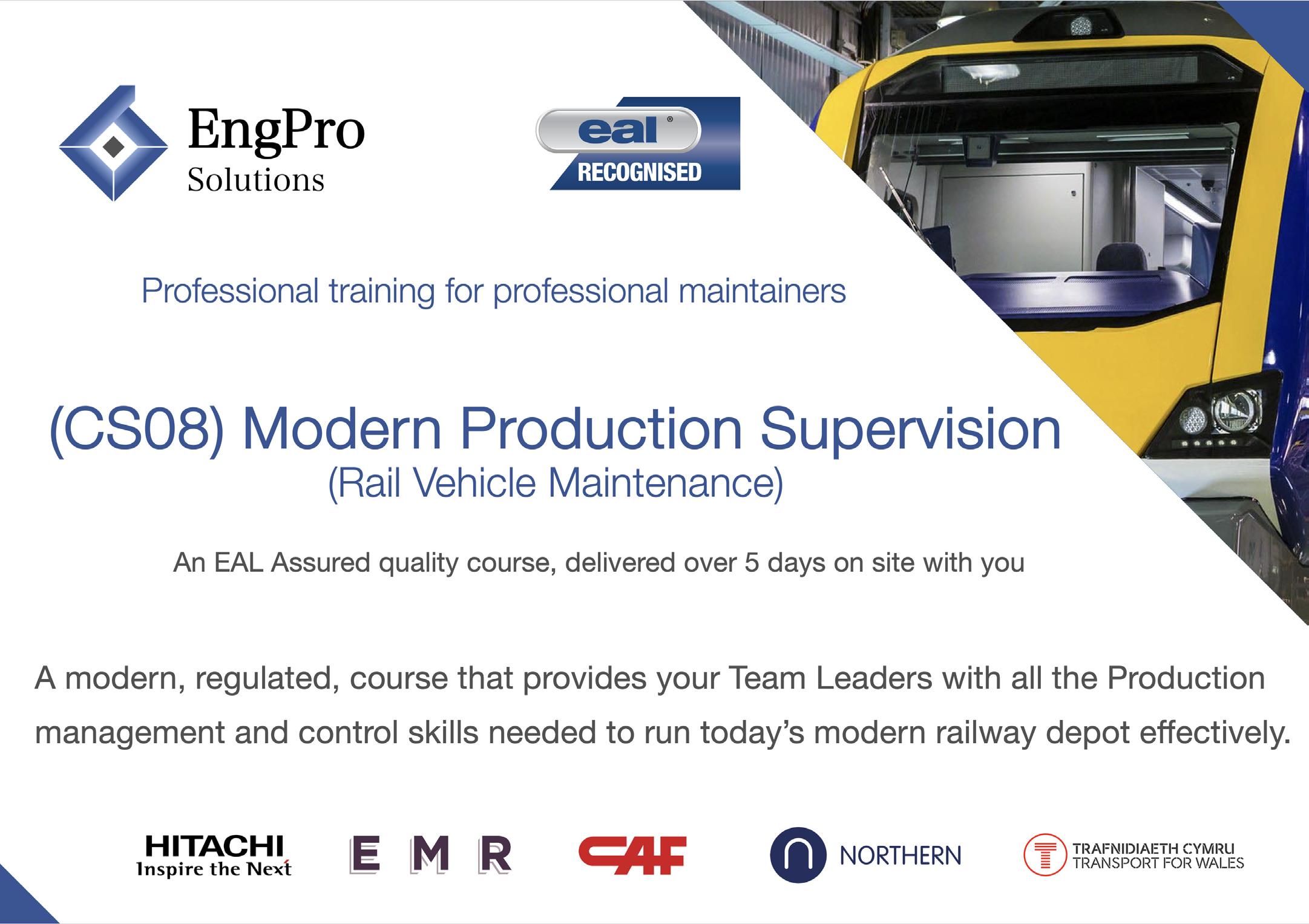

How did you get started in the industry?
I was working for a tool and plant hire company in the late 1980’s when portable toilets first came to the uk market from the United States and that company was one of the first to invest.
When did you first start the company?
I left a company called Toilet Hire UK who were a division of Speedy Hire in 2004 and started this business with my current business partner.
What challenges have you faced in the industry?
Pre-Covid, the biggest challenges came from smaller companies, who had less overheads from training, investment etc, undercutting us on hire rates. Since Covid, the importance of a higher standard of service, equipment and training as become more apparent and our level of service and value for money is appreciated more by customers.
What success have you experienced in the last twelve months and how do you measure success?
We measure our success by retained customers. We don’t advertise a great deal and our main objective is always to receive repeat orders by providing a good service and then gaining additional business through recommendations.
Solar and battery power is the only real development effecting our product range in the last five years. Prior to this we saw a big rise in the use of self contained toilet units run by their own generator, but this is now rapidly being phased out.
A1 Loo Hire Rail Division has been providing eco-friendly welfare facilities for the rail industry for over ten years. Covering the whole of Great Britain and Northern Ireland, the Rail Division operates 24 hours a day, seven days a week – offering servicing, delivery and collection or welfare and tool facilities wherever and whenever you need it.
What is your Unique Selling Point?
With climate change a constant concern for public sector services, we have designed and manufactured our own bespoke range of eco solar powered units which we are continuing to expand to meet the high demand. From our eco-vehicles, to eco-welfare units, everything we use on the rail industry has the environment in mind.
CLIVE OWEN DIRECTOR AT A1 LOO HIRE
Clive Owen, director of A1 Loo Hire, seen it’s launch in 2004. Under his leadership, the company has expanded with seven depots across the UK, including South Wales, Wokingham, Oxford, Coventry, Portsmouth, Essex, and Taunton, solidifying its position as the UK's leading portable hire company for construction and events.
A1 LOO HIRE
A1 Loo Hire Rail Division provides ecofriendly welfare facilities for the rail industry.
Want to know more about
A1 Loo Hire?
Tel: 0118 989 4652
Email: loohire@a1groupuk.com
Visit: www.a1groupuk.com
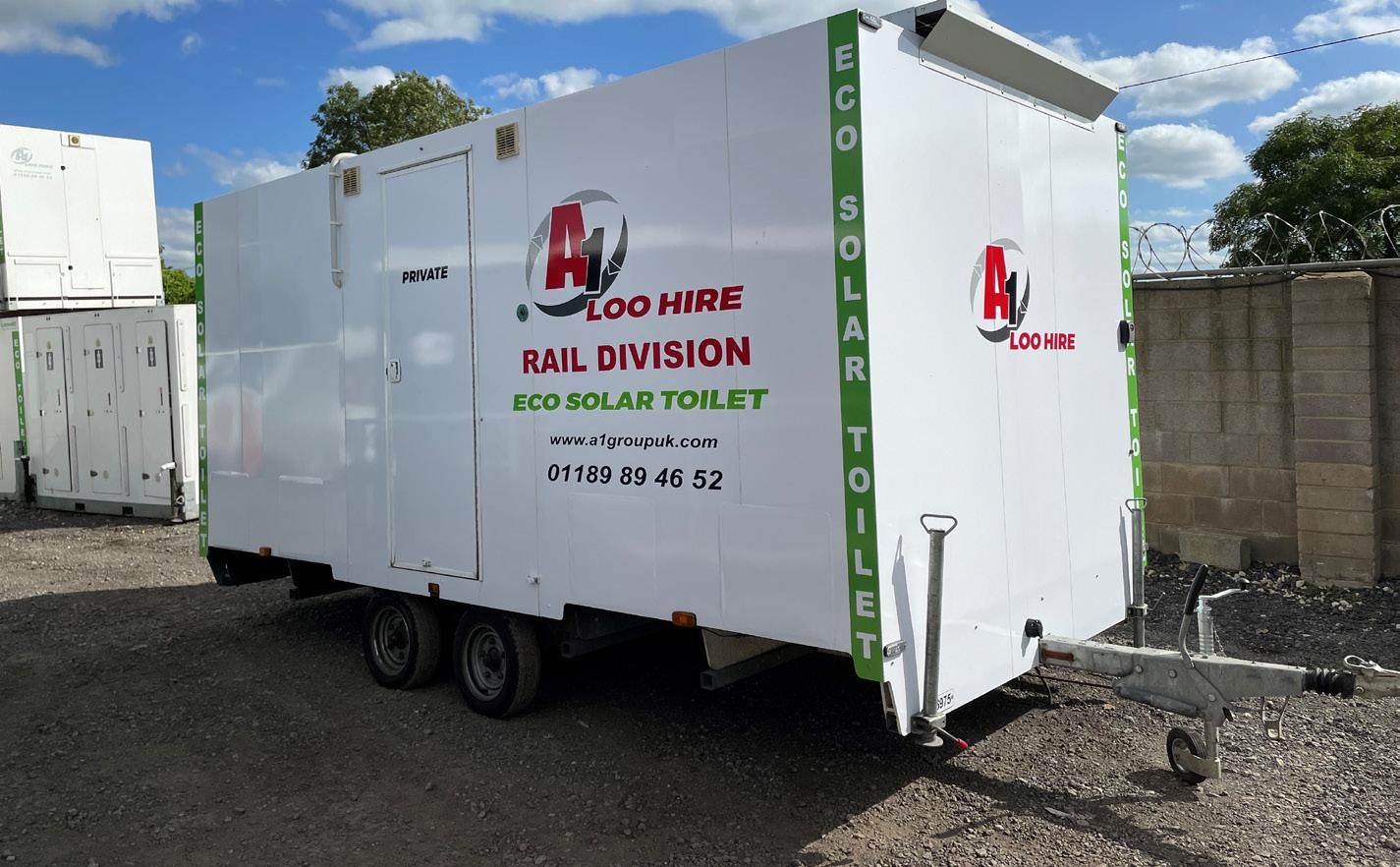




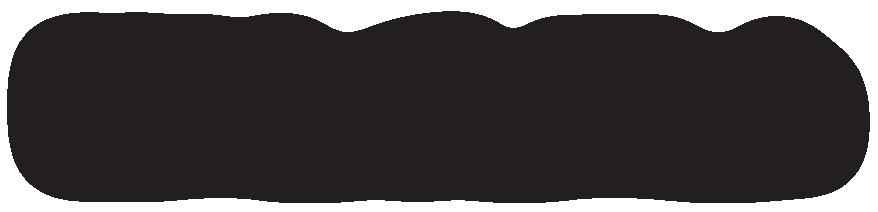

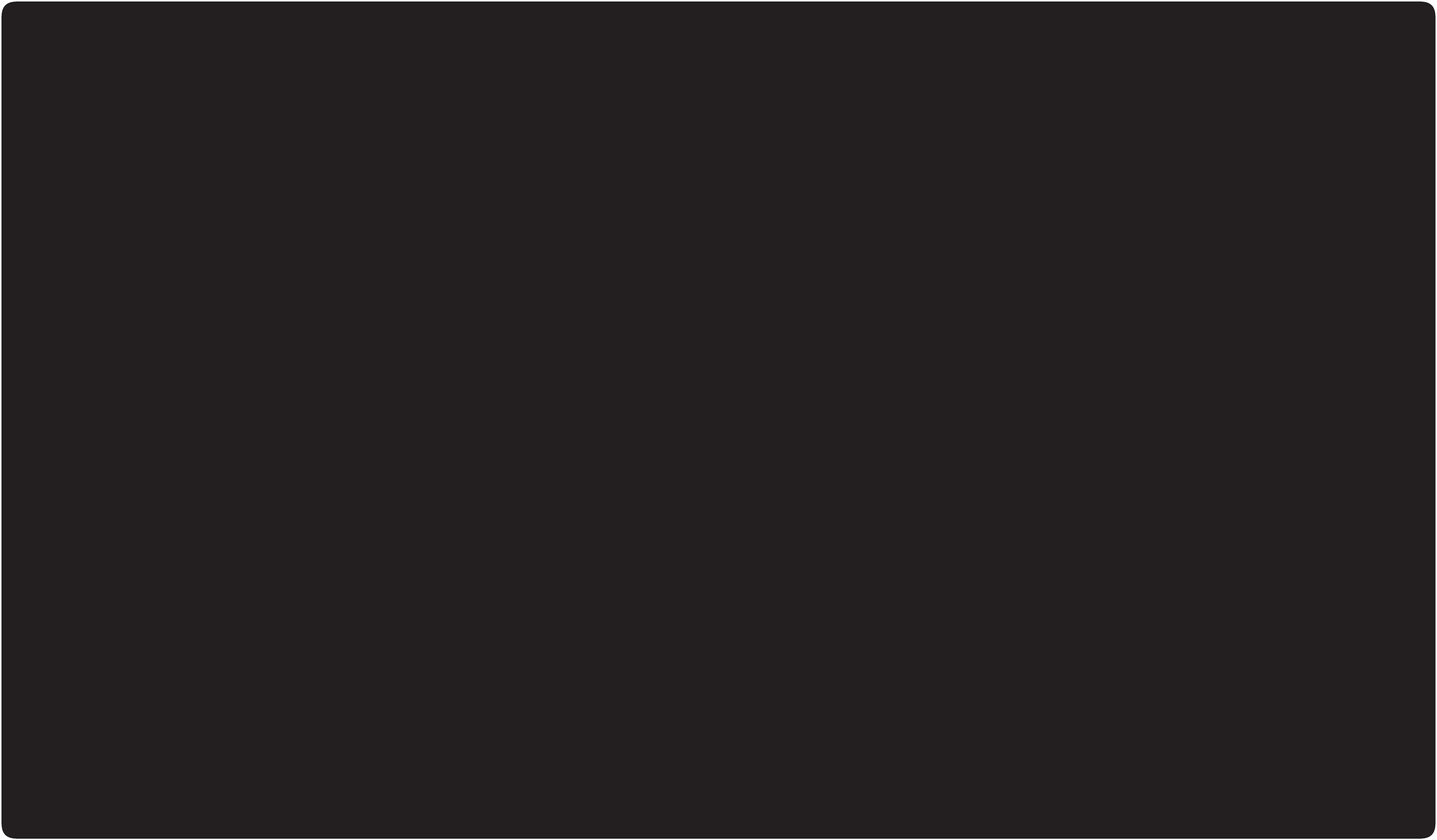
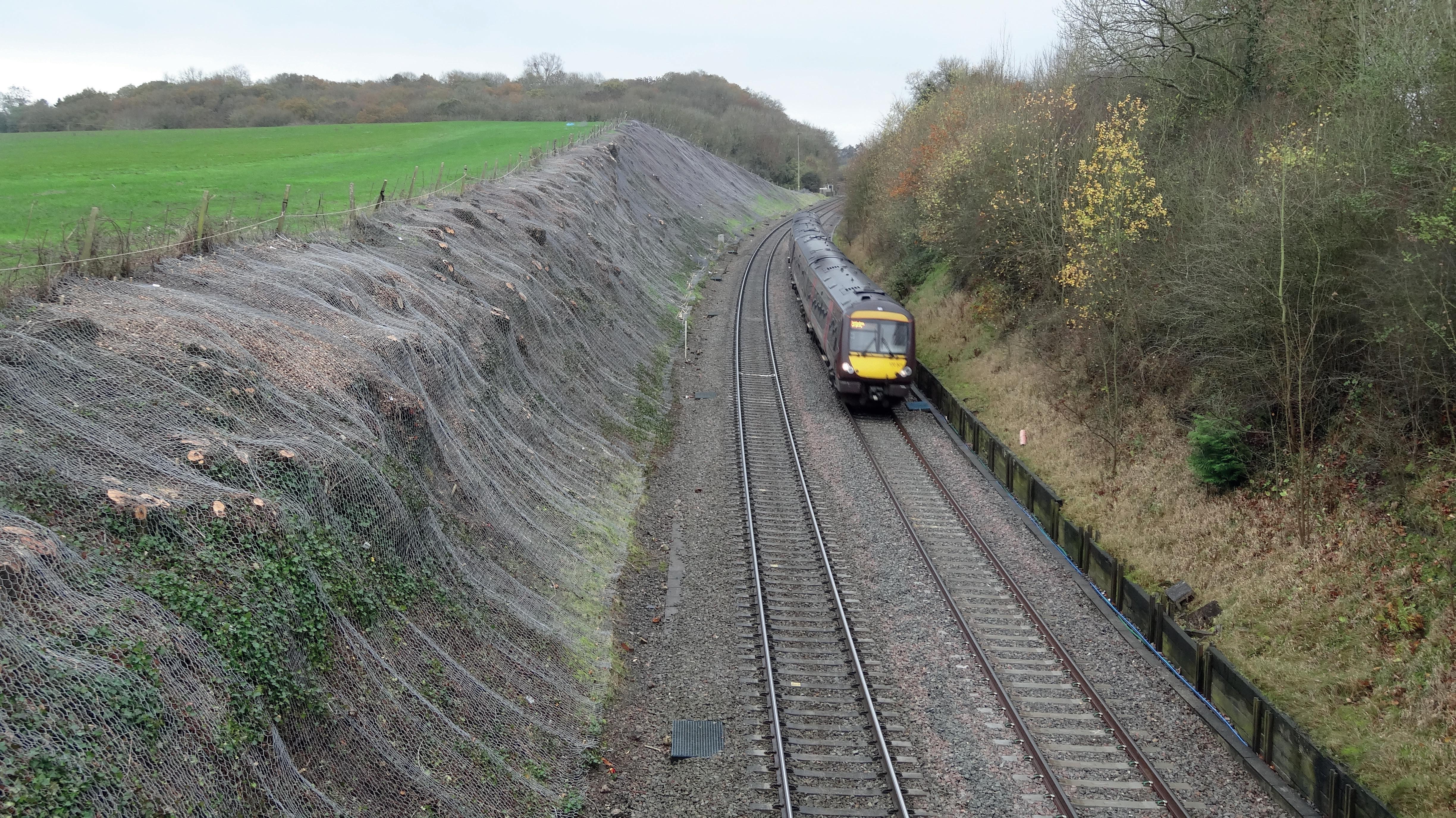
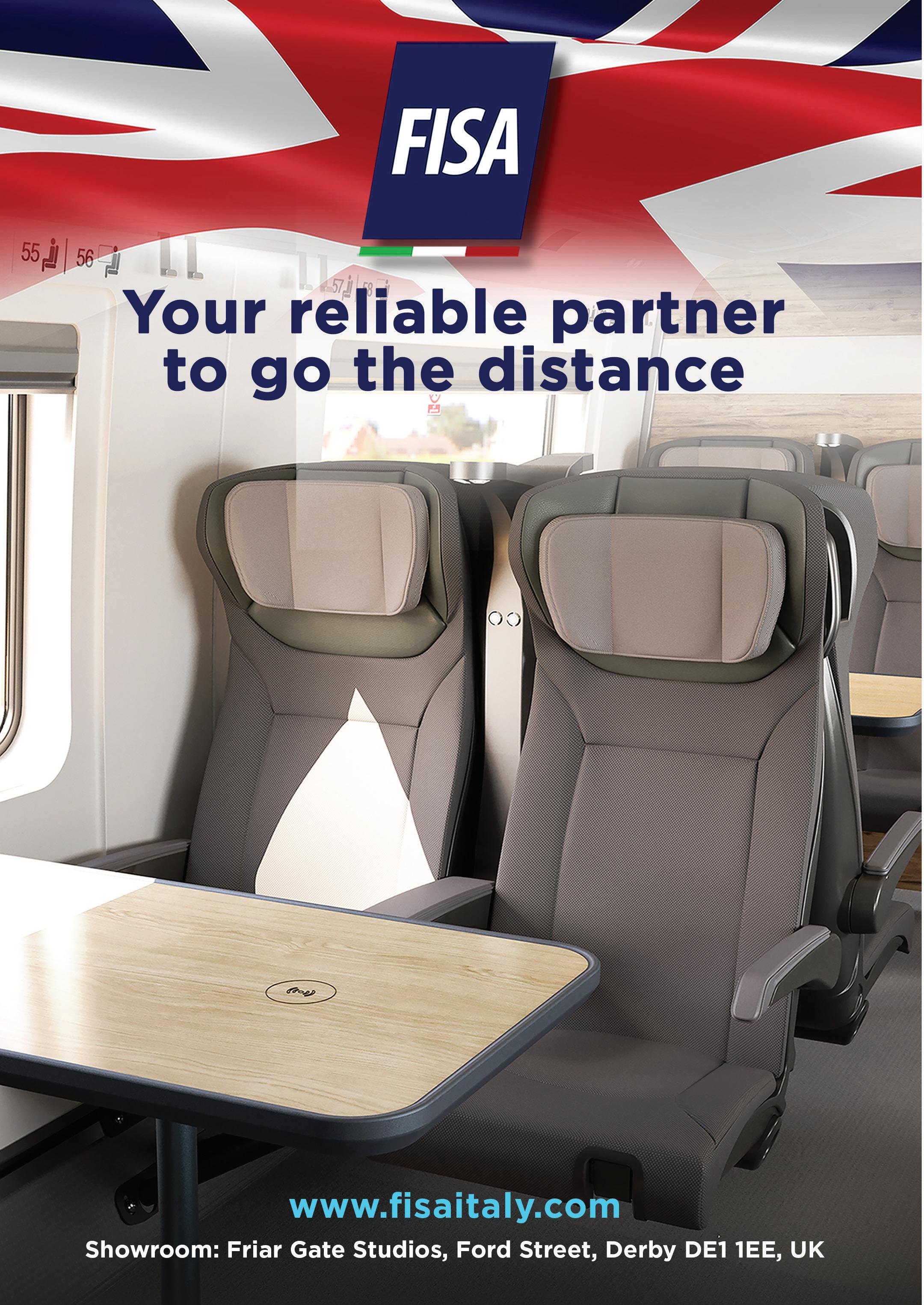
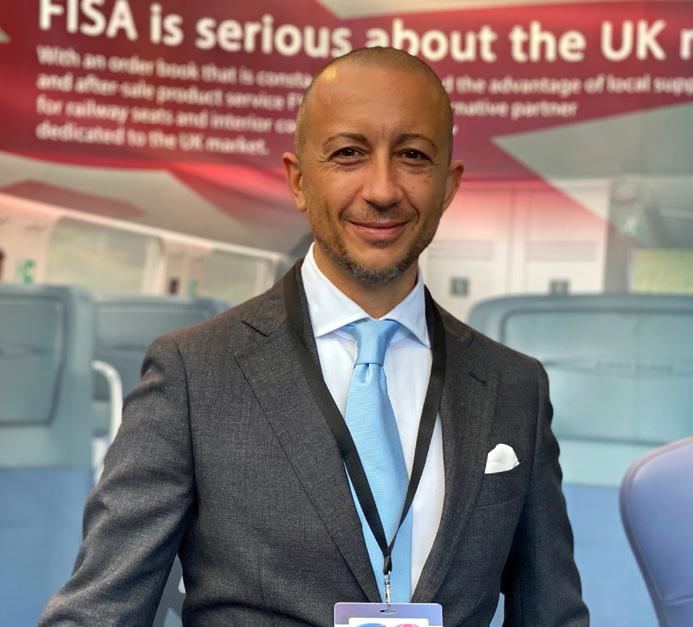
LUCA GIANTIN SALES & MARKETING DIRECTOR AT F.I.S.A. FABBRICA ITALIANA
SEDILI AUTOFERROVIARI SRL
Luca Giantin is the Sales & Marketing Director at FISA from Italy. He has worked for the company for over 17 years and has an extensive experience of the railway market in Europe, UK and Australasia.
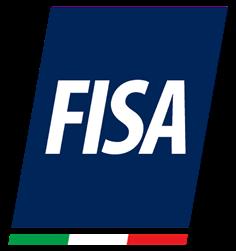
F.I.S.A. FABBRICA ITALIANA
SEDILI AUTOFERROVIARI SRL
FISA is an Italian company specialized in the design and manufacturing of railway passenger seats and interiors.
Want to know more about FISA?
F.I.S.A. Fabbrica Italiana Sedili
Autoferroviari Srl
Address:
Via G. De Simon, 6
Zona Industriale Rivoli 33010 Osoppo (UD) – Italy
Ph: +39 0432 986 071
Email: info@fisaitaly.com
Visit: www.fisaitaly.com
UK Showroom:
Friar Gate Studios, Ford Street Derby, DE1 1EE UK
Tell us about FISA.
We are an Italian company specializing in the design and manufacturing of railway passenger seats and interiors. FISA is a solid and trustworthy family-owned company founded in 1960 and based in Osoppo in the northeast of Italy. We are now led by a third generation of entrepreneurs who are still directly involved right here in Osoppo. This allows the company to be reactive and effective in every decision process because the issue and opportunities are approached immediately without needing to wait for feedback from an external source.
I believe the second aspect that distinguishes us is that we strongly believe that it’s all about people: our constant and significant growth in particular this past decade has been accompanied by an investment in people, employing a vertical approach we have transformed our organisation into an horizontal one where the involvement of people matters and is present, in this way people spreads the wings of their skills and attitudes.
Over the years and in particular in the last decade, thanks to cutting-edge products and a constant commercial effort, FISA has managed to establish itself not only in the domestic market but also in Europe and globally. This international vision has allowed FISA a constant consolidation and growth that has robustly kept us at the front of the leading global rolling stock manufacturers.
This international attitude paired with a continuous commitment to shape ourselves to the needs of the railway market has helped us with continuous evolution. Following on from this vision, in 2020 FISA started the acquisition of IMET that now is part of FISA group. IMET has been a leading manufacturer of railway seats and interior components, such as bay-tables, couchettes, partition walls and interiors item in general.
Further to the significant increase of its production capability gained from the acquisition, FISA can now offer the customers a wider package of products in addition to the seats, such as couchettes and a very wide range of bay tables, also in compliance with GM/RT2100 crashworthiness standard.
We can support our customers with a comprehensive interior proposal combining the passenger seats and driver seats with
bay tables, couchettes and items typical of a train interior: this simplifies the approval and delivery processes.
How did you start at FISA?
I started at FISA as the Purchasing Manager. Then, after some years, the company was in a position to expand commercially –particularly in foreign markets where at that time we were either outsiders or even unknown. This created the necessity for a new role and new opportunities in the sales department. I was offered to ‘turn’ to the other side of the desk and switch to sales.
My attitude is to always see any change as an opportunity and this, combined with the huge perspective and growth potential that I was feeling the company could have, was more than enough for me to embrace the opportunity of the new job.
Anyone who works for a manufacturing company should take this path, it has given me a deep and robust understanding of the product, the processes and everything related to the manufacturing side of the business.
What is your role within FISA?
I feel that in order to be a part of a fantastic team of people, at any level, awareness is essential and something I consider in my daily work and in every action I take. I see a collective of people in a company the same way you would see a film crew; you can be the leading actor in front of the camera, but without good people to prepare the set, or a good film producer, or a talented makeup artist, you will likely be a mediocre actor.
As Sales & Marketing Director at FISA, my responsibility is to advance our company’s presence and to grow it in the rail industry, I lead our dedicated sales team made of an internal back-office, agents and partners in the local markets, defining our sales strategy to meet our targets.
To seek new opportunities and collaborations is of course a significant part of my job and probably the most stimulating and challenging at the same time, since it requires a constant focus on the market players and trends.
I personally believe that in a business world made up of excel matrixes, boxes to be ticked and agendas full of e-meets, the human side continues to be paramount and
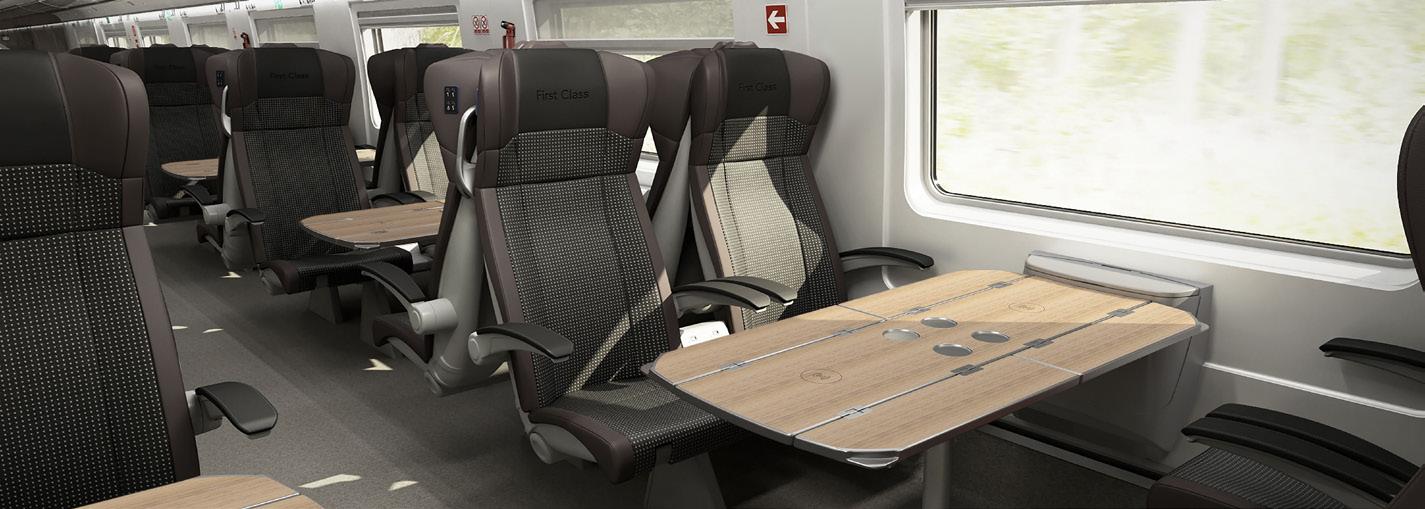
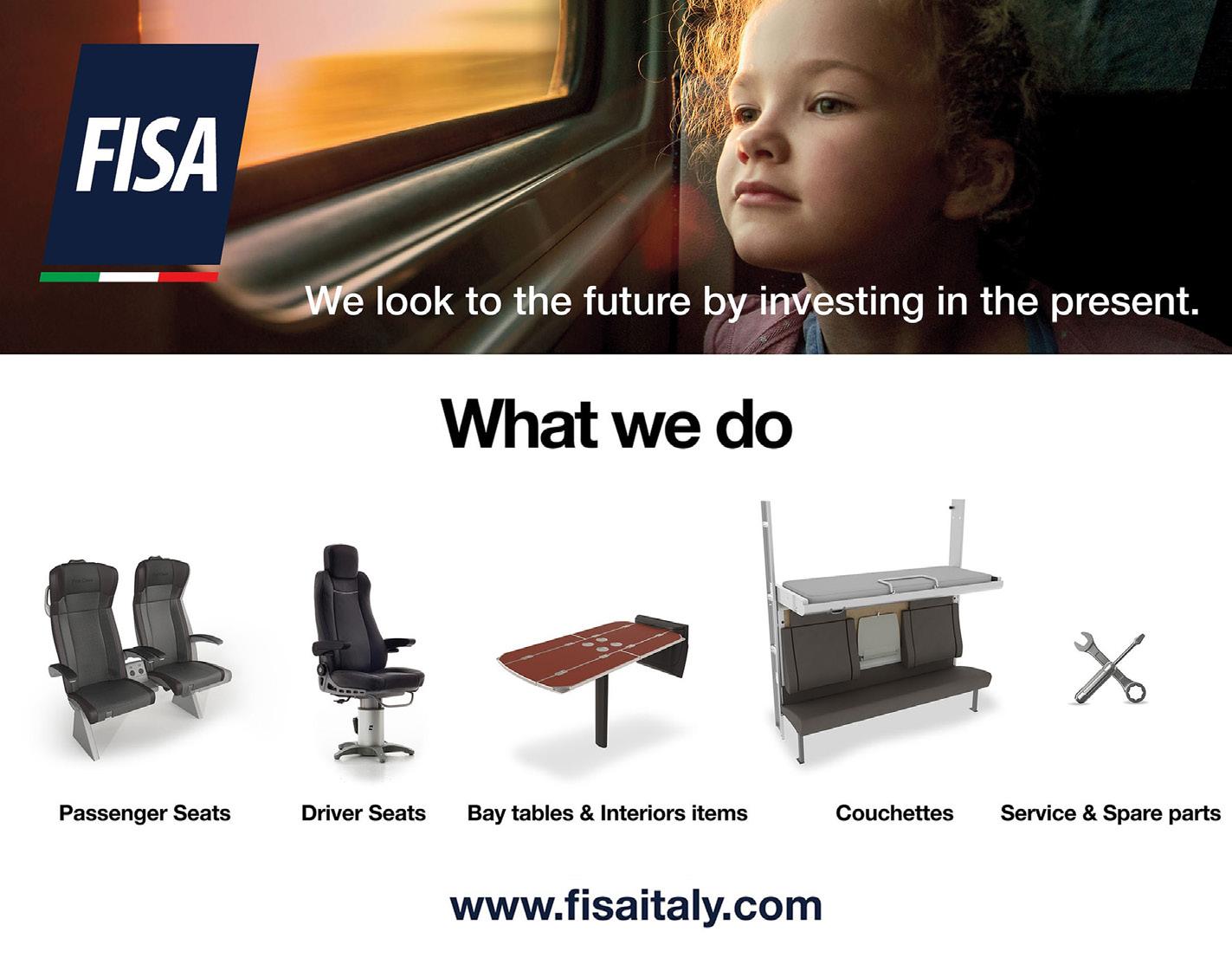
will remain the only way to generate trust between organisations.
This is not just a motivational concept but the way I live.
What are your views of collaborative working?
There are two ways in my opinion to answer to this question that are complementary to one another since they are based on the same belief.
The first one I already mentioned, is the value FISA places on its people and how we strongly believe that a place of work based on collaboration, respect and supportive behaviours can make a huge difference. We are facing this daily, and often this becomes a reason to say that one plus one makes three, meaning that collaboration is a booster to reach better results than what could be achieved going solo.
The second regards collaborative working with our customers, in recent years we have worked on projects where our customer has become the leader of a group of parties (FISA as supplier, the designer, the final customer or train operator) who established phases of collaborative work from the beginning of the project.
I can mention the new Aurora fleet for EMR, but also other projects, where this kind of modern and smart approach has created a value stream throughout the project phases, with the final result satisfying all parties.
Collaboration makes the difference, collaboration is all, we and our customers strictly cooperate at any level and at FISA we are strongly committed to promoting to pursuing this.
What is FISA working on in the UK market?
I am thrilled to answer this question because our presence in the UK market is built around a business case which we are very proud of. As I mentioned before, in the past 10/12 years we expanded our presence in the global rail market with a constant and capillary penetration made of commercial presence, substantial products and quality, all combined and sustained by company growth.
In 2016 we performed and in-depth analysis of the potential of the UK market and I remember knocking on the door of Litchurch Lane (at that time it was still branded as Bombardier) and a senior engineer spoke to me as he would to a student who failed the exam: ‘Young man, once you have a proven compliant product feel free to come again, that’s all for the moment.’
So being driven by this and despite not having any project in hand, we decided to voluntarily perform indicative testing against GM/RT2100 of our LEAN passenger seat (that to be honest was not designed under those requirements) and preliminary results were brilliant, this was an incentive to start putting our foot into the market by opening a show room in Derby. This was the start of a long learning curve about the UK market due to its complexity and peculiarity in respect to any other railway market. Due not only to specific compliance standards but also the intricate network of stakeholders such as TOCs, ROSCOs, manufacturers compared to elsewhere.
The challenge wasn’t just to learn (and how many ale pints that costed!) but to
create relationships and a reputation as we knew the responsibility of being a new player in such an important market.
In the meantime, one of our major customers and manufacturer of rolling stock awarded us a big project for Greater Anglia’s new fleet.
At the same time our mission was not only to be a supplier, but the kind local player which could be trusted by this market. When we opened the show room in Derby we also established cooperation with high level technical and commercial consultants and searched for a local partner to better serve our customers with reactiveness and effectiveness.
Today we can say that there are going to be more than 100,000 FISA seat places across UK, making it one of our leading markets, on which we will continue to strongly focus and to invest our resources in.
It’s because of this conclusion and for all these reasons that I began by stating that the UK market is for us a brilliant business case we are very proud of, based on an accurate long-term work made by listening to the market and its peculiarities and to act consequently.
What are some specific challenges you face?
There is of course a wide range of challenges we face and most of them go hand-in-hand with the complexity of our major customers: in parallel to the booming railway market we have witnessed in recent years to an increasing level of demand in terms of project management that has required and is continuously requiring a reshaping of our organization to bear the new challenge.
Furthermore, we are facing a major issue of recruitment and retention of skilled personnel, this is happening across all positions and is due to basically two reasons, one is the high level of demand in employment, and second is the recruitment of people with specialised skills as rail technicians and skilled engineers who are in high demand. This makes it extremely challenging to look for and retain qualified staff, and can lead to less skilled people requiring longer in-work training.
The advent of Great British Railway –without entering a favourable opinion or not – has undoubtedly created a limbo situation in the market by capturing the attention and distracting from the decisional processes about rolling stock life extension or new fleet introduction. Despite all this we appreciate that the wheels are starting to move again in fact after quite a long time spent in extensive discussions several business opportunities have become more concrete.
The last one is a very good point to conclude, we have a sort of recipe in the markets where we play and that is in our company DNA: perseverance, patience and attitude, these are characteristics which are just some of the main ingredients that inform our actions and results.
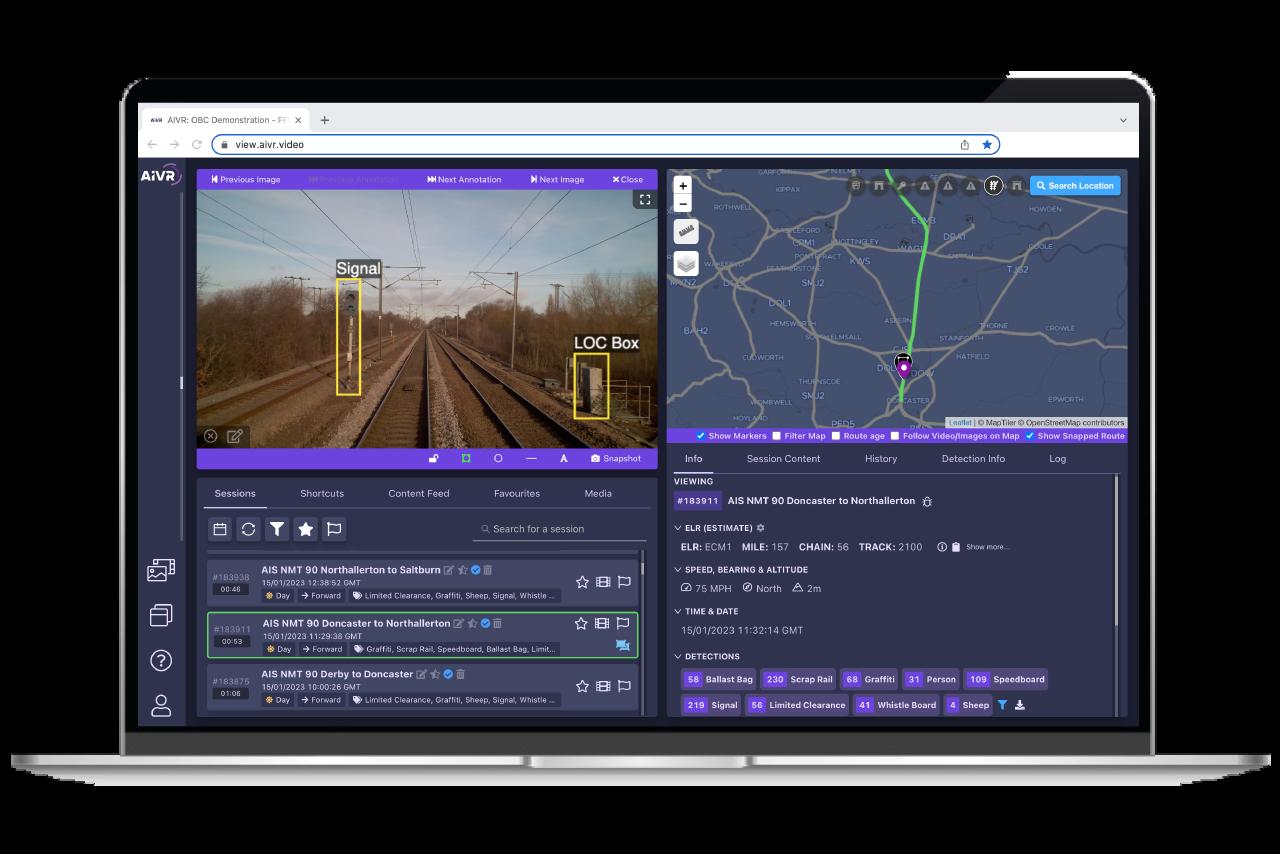
The multi-award-winning AIVR system provides digital inspection capability and more, enabling experts from any rail discipline to monitor the lineside environment remotely and safely.
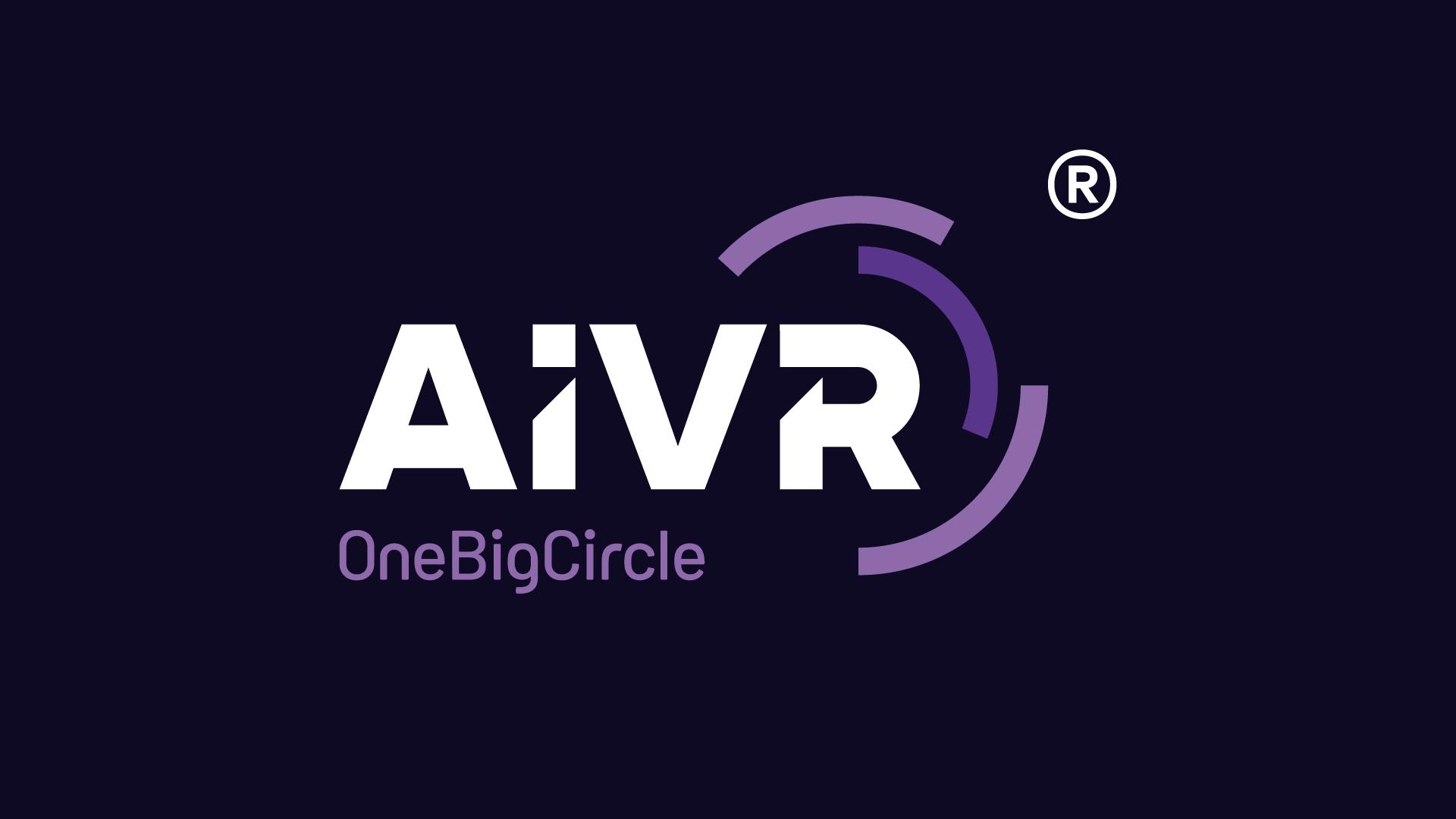
Track & Maintenance
Electrical & Power Plant Signaling Telecoms Planning
....and
AIVR captures and transmits a range of data - from Forward Facing Video, Thermal, to Overhead and Line Scanning. Data can be integrated with a range of fault detection systems, and have Machine Learning applied to automatically detect assets and anomalies.
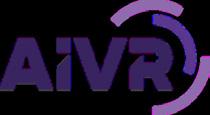
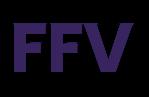
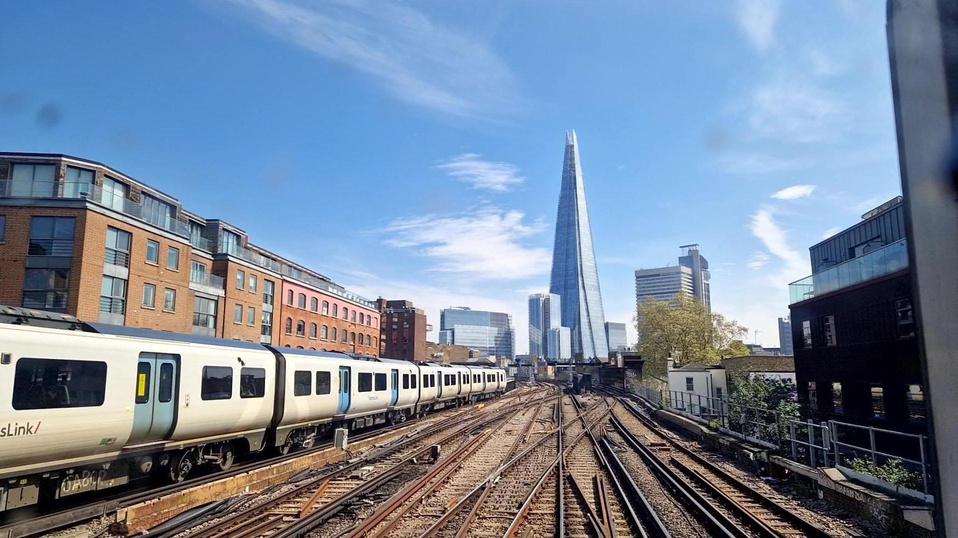
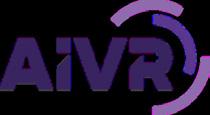


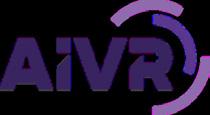

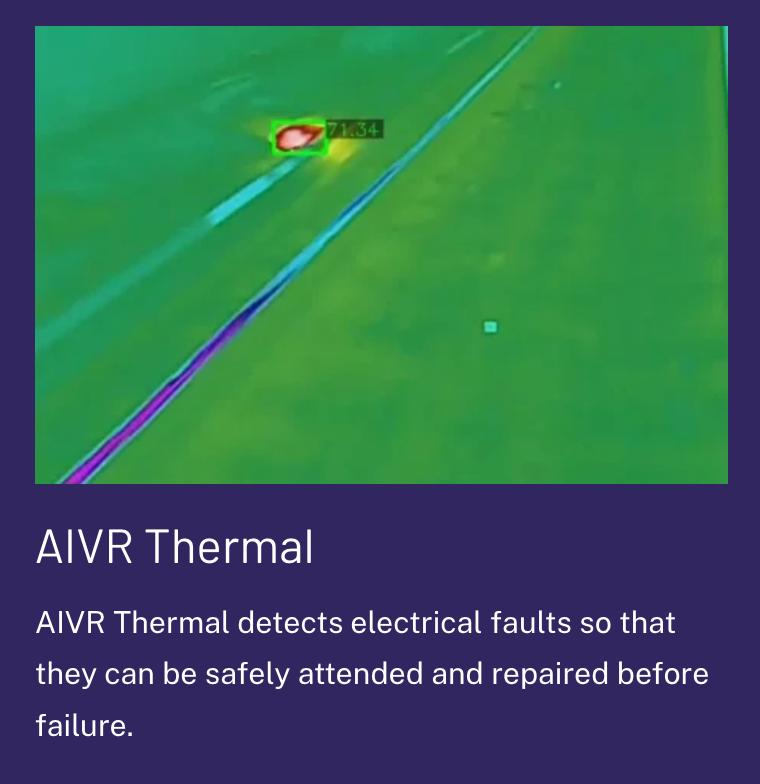


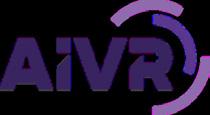
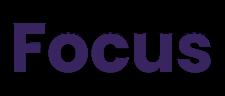
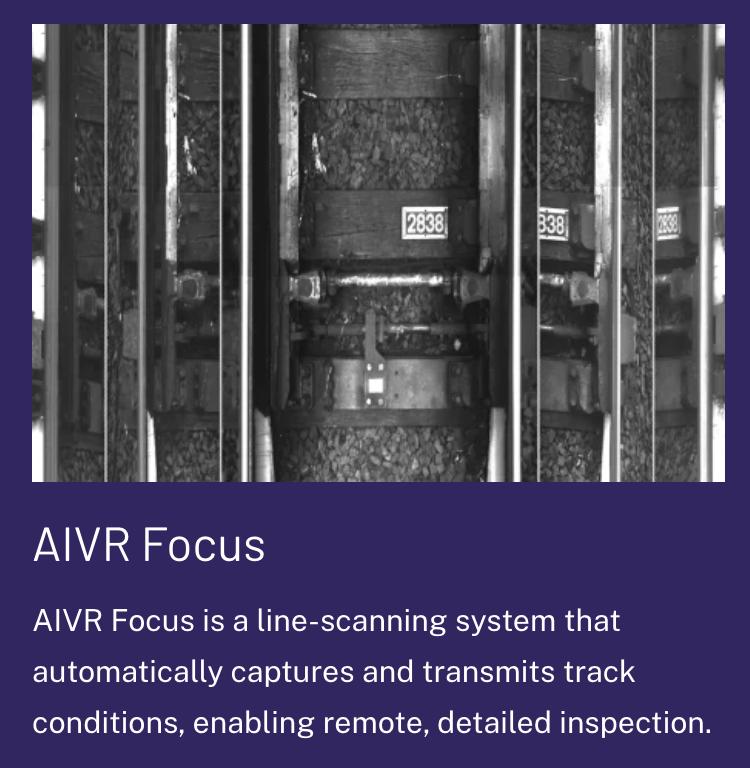
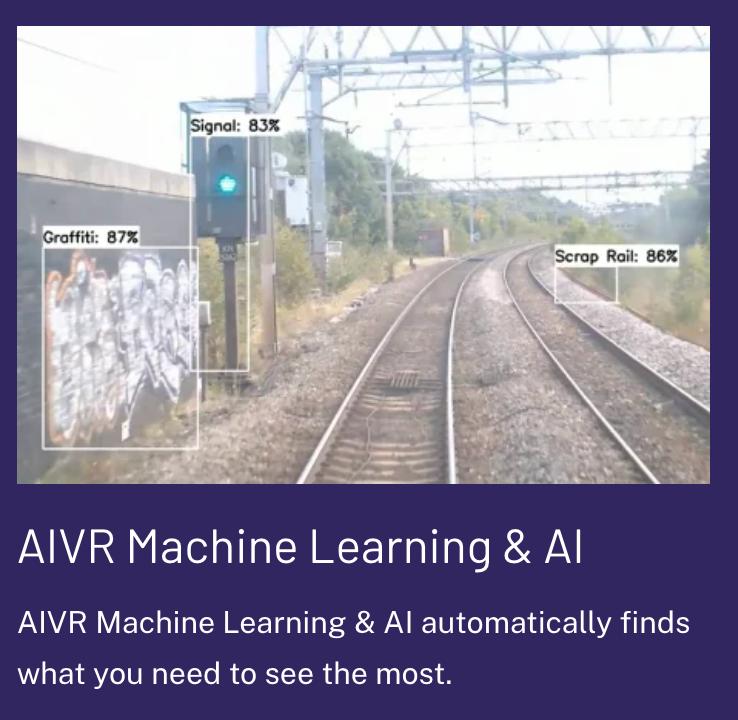

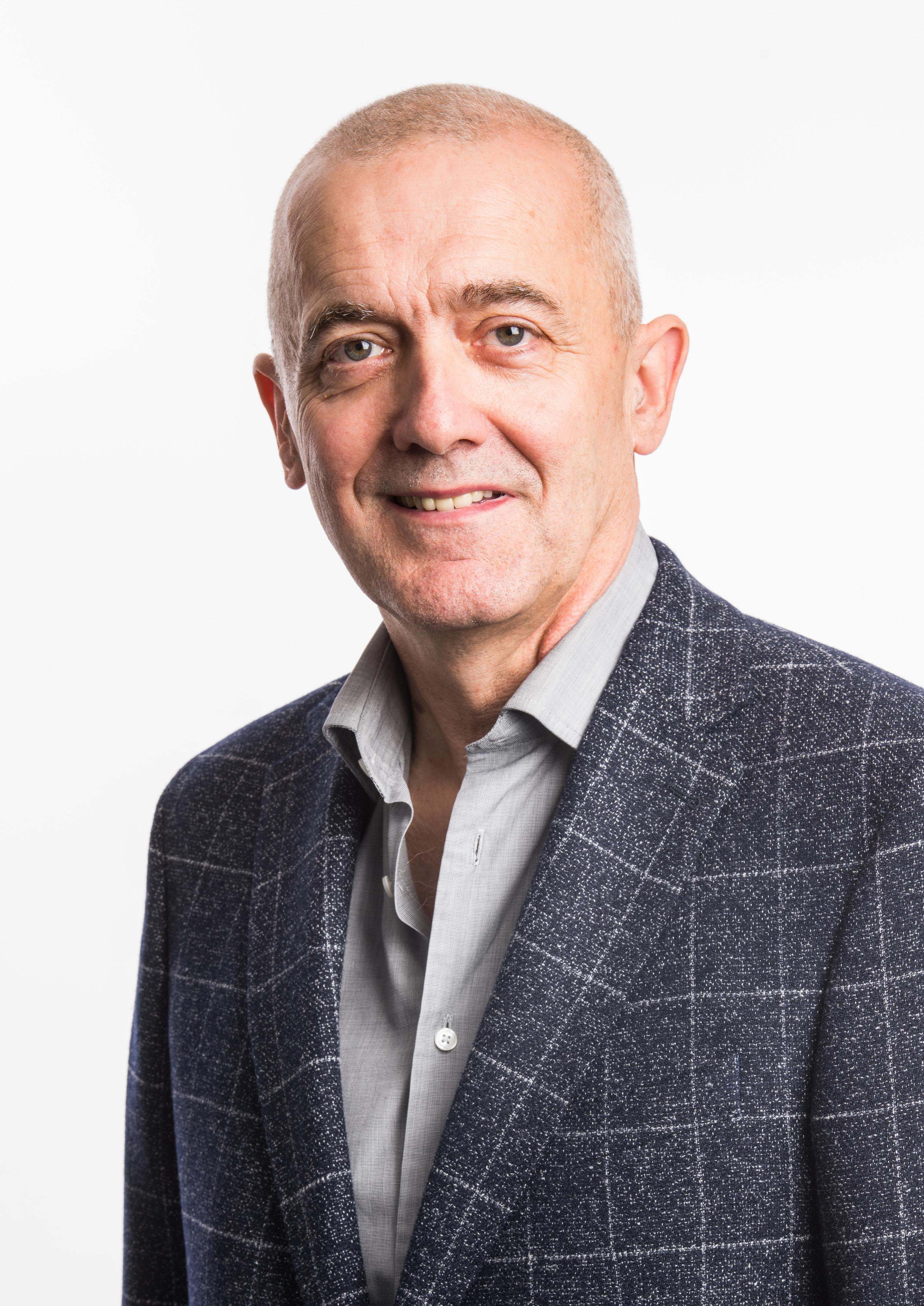
KEITH TILLEY
CEO OF INTOWARE LTD
Keith has been CEO of Intoware since 2019, a SaaS company delivering digital workflow software on mobile and wearable devices. During the prior 30 years he held executive positions in a $1.4 billion Tech Services Company. He also has NED and Advisory positions with a small number of IT services and software companies.
How did you get started in the industry?
A long time ago!! I had an early interest in technology that led me into starting out in computer operations for an automotive company. From there I moved into a business development role, where using the latest technology to help companies to improve their business outcome was key to success.
This has allowed me to see how different technology best practices can be transferred between industries. This is particularly true in the rail industry where it has such a wide use, from ‘front of house’ with travellers to behind the scenes track inspections, maintenance work and ensuring health and safety, and compliance.
How has technology developed since you started in the industry?
The rail industry has been transformed by technology in various ways and has played a crucial role in helping to make it safer, more efficient, and more environmentally sustainable. It has also, despite some headlines to the contrary, greatly enhanced the passenger experience.
Technology has driven improvements to the infrastructure, as well as the trains themselves, thanks to a wide range of areas such as Digitalisation, Automation, Communication, Information Systems and Safety. These developments have helped to develop predictive maintenance algorithms, advanced communication systems (including Wi-Fi on trains), realtime monitoring systems, and safety enhancements.
Tell us about Intoware.
Intoware is a Nottingham based SaaS company specialising in the development of mobile workforce management solutions. Our flag ship product, WorkfloPlus, is key to help companies start on their digital transformation journey.
Our aim is to partner with our customers to ensure successful delivery and deployment of a project, so they get the maximum return from their investment as soon as possible, which we do this through a simple Engage – Design – Deploy methodology to ensure the desired business driven outcomes are achieved.
What types of products and services do you offer?
Our digital work instruction platform, WorkfloPlus, streamlines operations, improves productivity, and enhances worker safety by digitalising procedures and optimising processes. It can either make use of the mobile technology that workers are familiar with or run on the latest wearable technology to make use of innovative features such as AR/AI if hands free working is needed. It maximises the
efficiency and safety of the workforce and adapts to the demands of modern industrial environments to drive operational excellence.
How have the products and services you offer developed over the years?
Intoware was born in 2015 and since then we have developed and enhanced WorkfloPlus to meet the changing needs of our customers and the market.
As well as running on iOS, Android, Windows and wearable devices, we’ve also ensured it can be integrated into existing ERP systems to generate a one hundred per cent real-time accurate view of your frontline operations.
The instant digital reports remove the time previously wasted by inputting information from paperwork. It also eliminates any data-lag which means repairs can be scheduled quicker than ever before.
Have you changed your approach to work at all since Covid?
Since Covid Intoware has moved towards a more hybrid and flexible way of working. We still have our headquarters in Nottingham, but by moving to a hybrid and remote model of working we’ve been able attract and retain the right staff to enhance our product and services from further afield too.
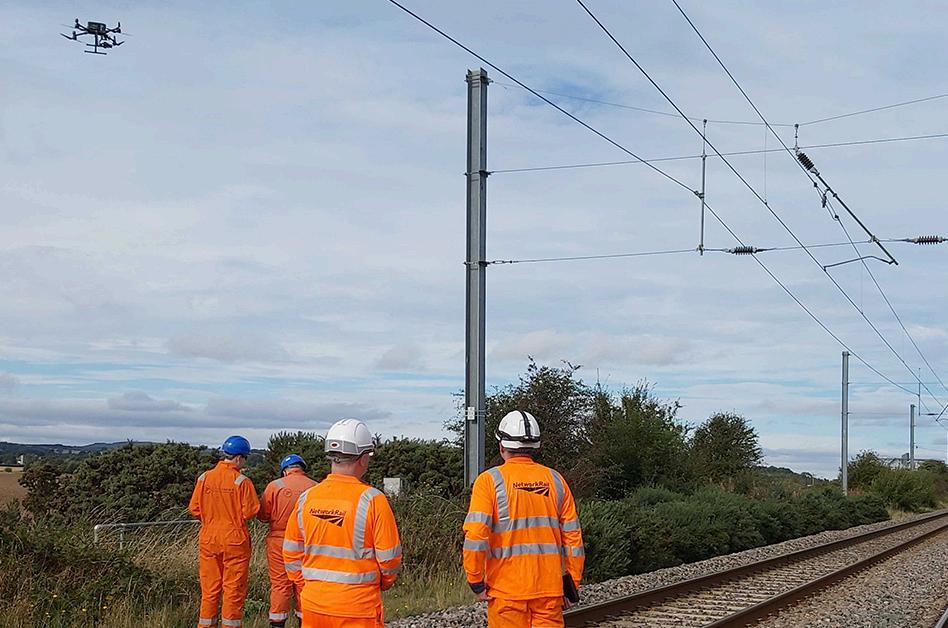
In terms of technology, how do you anticipate things might change in the next five to ten years?
We have also enhanced WorkfloPlus’ team management capabilities so larger jobs can be split into individual tasks and assigned to the most qualified person to compete that process. However, there’s also the possibility of connecting to a remote expert if a more experienced workers input is needed to complete the task at any point, rather than having to reschedule the whole job.
The increased use of technology has definitely accelerated over years. We have even incorporated digital workflows into the use of drone technology, so workers could keep their feet on the track rather than increase the safety risk by working at height when carrying out maintenance inspections.
How can the industry tackle its skills shortage and how do you recruit/retain/ train your staff?
WorkfloPlus is a key tool to help tackle the current skills shortage crisis through its training and upskilling capabilities. By digitalising the knowledge from experienced workers it’s possible to retain and store their best practices for future generations.
This means workflows can be designed and enhanced that can educate and train the next generate, which really helps to enable a new workforce to quickly come up to speed. Combined with the remote expert communication, you can provide over the shoulder support to maximise the use of the experience staff in assisting trainees.
Technology changes very rapidly, no sooner do you think you know it then it changes again. This is why it is exciting to work in the industry and to see how it can future benefit business and individuals.
Clearly over the next five to ten years, AI (Artificial Intelligence) and AR (Augmented Reality) are likely to have profound effects across various industries, driving significant changes in the way we work, interact with technology, and experience the world. Whether this be: enhanced Productivity and Efficiency, Personalised Experiences, Improved Communications, AI and AR will likely empower the connected worker.
AI and AR hold tremendous potential to transform the rail industry further and help with its digital transformation journey.
What are the key benefits of the products and services you offer to the Rail Industry?
The key benefits of WorkfloPlus from Intoware are:
• Efficiency – WorkfloPlus can streamline workflows and processes within the rail industry, reducing manual tasks and administrative overhead. This efficiency improvement leads to faster turnaround times, optimised resource allocation, and ultimately cost savings.
• Compliance Management – WorkfloPlus helps ensure compliance with industry regulations and safety standards by providing tools for tracking and
managing regulatory requirements, certifications, and inspections. This reduces the risk of non-compliance penalties and improves overall safety and reliability.
• Asset Management – the platform enables comprehensive asset management, allowing rail companies to track the status, maintenance history, and performance of their infrastructure, rolling stock, and equipment. This proactive approach to asset management minimises downtime, extends asset lifespan, and enhances operational reliability.
• Resource Planning – WorkfloPlus facilitates effective resource planning by providing insights into workforce availability, skills, and schedules. This enables rail operators to allocate resources efficiently, minimise idle time, and optimise workforce productivity.
• Data Analytics – the platform offers advanced analytics capabilities, allowing rail companies to analyse operational data, identify trends, and make data-driven decisions. This insight enables continuous improvement initiatives, enhances operational efficiency, and supports strategic planning.
• Collaboration and Communication – WorkfloPlus fosters collaboration and communication among various stakeholders within the rail industry, including maintenance crews, dispatchers, and management teams. This improves coordination, reduces misunderstandings, and enhances overall organisational effectiveness.
• Mobile Accessibility – WorkfloPlus is accessible via mobile devices, enabling field workers to access critical information, submit reports, and communicate in real-time while on the go. This mobility improves responsiveness, enables faster decision-making, and enhances operational agility. Scalability and Customisation – the platform is scalable and customisable to meet the specific needs and requirements of different rail operators. Whether managing a small rail network or a large-scale transportation system, WorkfloPlus can be tailored to accommodate varying levels of complexity
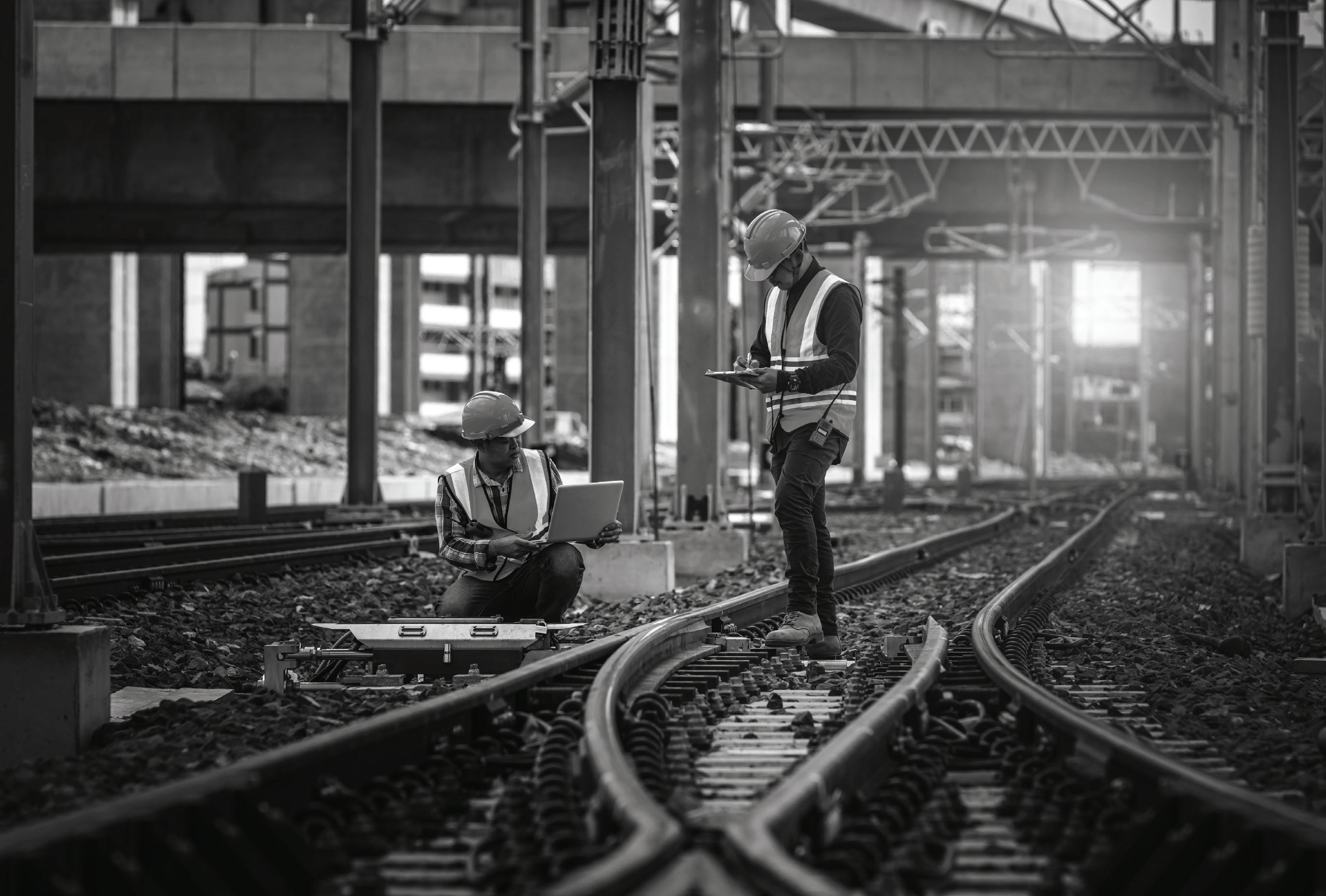
improving safety and compliance, and driving efficiency gains
WorkfloPlus empowers the connected worker to save time and reduce costs.
WorkfloPlus creates standardised, consistent digital work instructions accessed via mobile, tablets and wearables.
It eliminates the need for time consuming paperwork, ensuring the correct data is collected and automatically distributes reports as soon as a job is completed.
improvement that empowers their workforce operations.
New Region-wide College Rail Training Academy
A new rail training academy opened in February to support hundreds of new training and employment opportunities for local people in the sector.
The Transport, Rail and Infrastructure Academy (TRIA), which has been developed by the City of Wolverhampton College and National Infrastructure Solutions (NIS), will give individuals entry and advanced skills required to gain sustainable jobs, whilst also meeting the demand for skilled operatives to work in the construction and maintenance of train lines, tram routes and stations.
The launch took place at TRIA's new site at the Black Country Innovative Manufacturing Organisation (BCIMO)'s Very Light Rail National Innovation Centre in Dudley, where the Mayor also cut the ribbon on a state-of-the-art new Signalling Academy.
To support residents into good jobs in rail, the WMCA is investing £1.1 million to create 432 training places at the Dudley site. Andy Street, Mayor of the West Midlands and Chair of West Midlands Combined Authority (WMCA) said: ‘Hundreds of millions of pounds are being invested right now into the region’s train and tram network, with new rail lines and stations being built and new Metro routes under construction.
‘That’s great news for the travelling public but we also need to make sure this unprecedented investment benefits local people in terms of new jobs and careers. That’s why the WMCA is helping to fund this state-of-the-art training academy and matching skills courses to the needs of our regional economy.
‘I can’t wait to see local people land good quality jobs in the rail industry as a direct result of this latest investment, further cementing the role of the West Midlands as the training hub of the UK.’
TRIA is an extension of a fiveyear partnership between the City of Wolverhampton College and National Infrastructure Solutions (NIS), the latter a leading provider of training in the rail, civil engineering, and utilities industries.
The Dudley site boasts more than 2,000 metres of conventional rail track, including two split-level platforms, an 870-metre tunnel and signalling components to give students hands-on training in multiple disciplines across the industry and enhance their learning experience by working with the same equipment as used on rail construction sites.
This latest development has seen the two organisations leverage considerable investment from the private sector as employers rush to back the training model and the new Signalling Academy highlights even further how training courses are being developed to meet a real need in the industry.
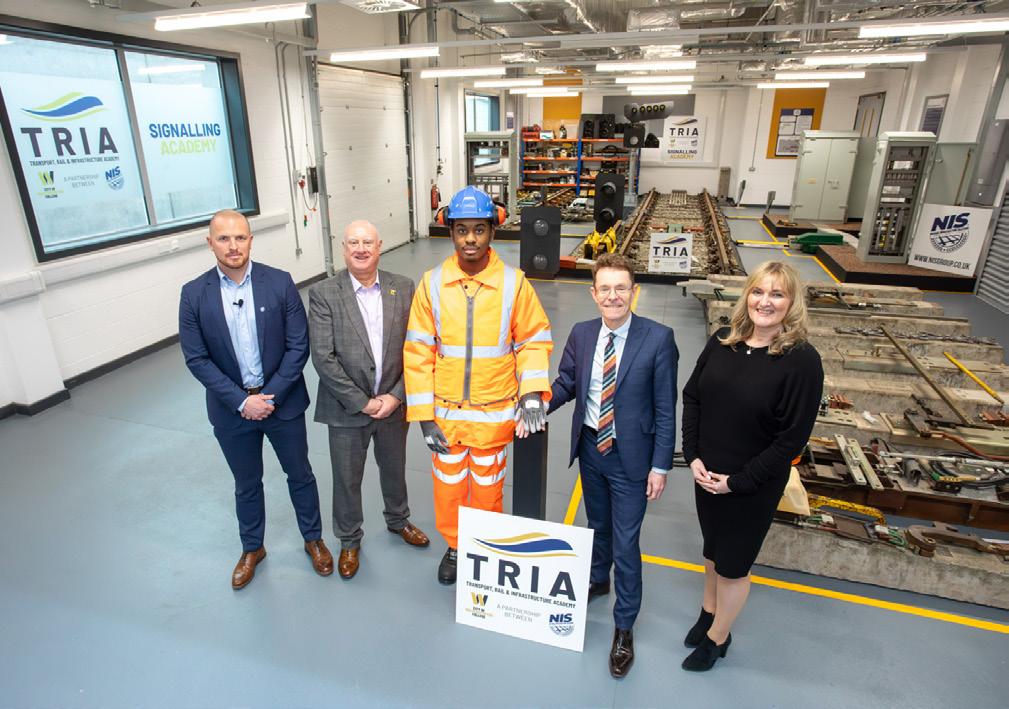
trained already. This is just the start.’
Davie Carns, Managing Director of National Infrastructure Solutions, continued: ‘Our partnership with City of Wolverhampton College and the WMCA is now in its fifth year and, by working together, we have delivered training that has created sustainable employment for more than 2,000 people.
‘TRIA is the next step in the relationship and will give us the framework to provide specialist courses across multiple locations in the West Midlands, encouraging greater employer engagement and the potential for more jobs.
‘The Black Country Signalling Academy at BCIMO is another example of how we are listening to businesses and developing training for more technical roles that are currently in high demand.
‘Our first six months in Dudley have been a resounding success with 500 students
Malcolm Cowgill, Principal of City of Wolverhampton College, added his support: The economic climate at the moment means we need to support local people into jobs. Working in partnership with our training provider NIS, the academy will offer employer-led training to address skills gaps in specific areas, focussing on getting entry-level candidates into work, upskilling existing operatives and ensuring that the workforce is equipped with the latest industry-recognised qualifications and accreditations to ensure sustainable skilled employment now and in the future.’
TRIA already has an industry-standard rail training site at the college's Wellington Road campus, in Bilston – which features more than 40 metres of railway track and was the first in the UK to offer training on slab track technology which is used in the construction of high-speed rail lines – with plans to open an additional site in Aston, Birmingham, later in the year. For further information, please visit www.wmca.org.uk or www.nisgroup.co.uk.
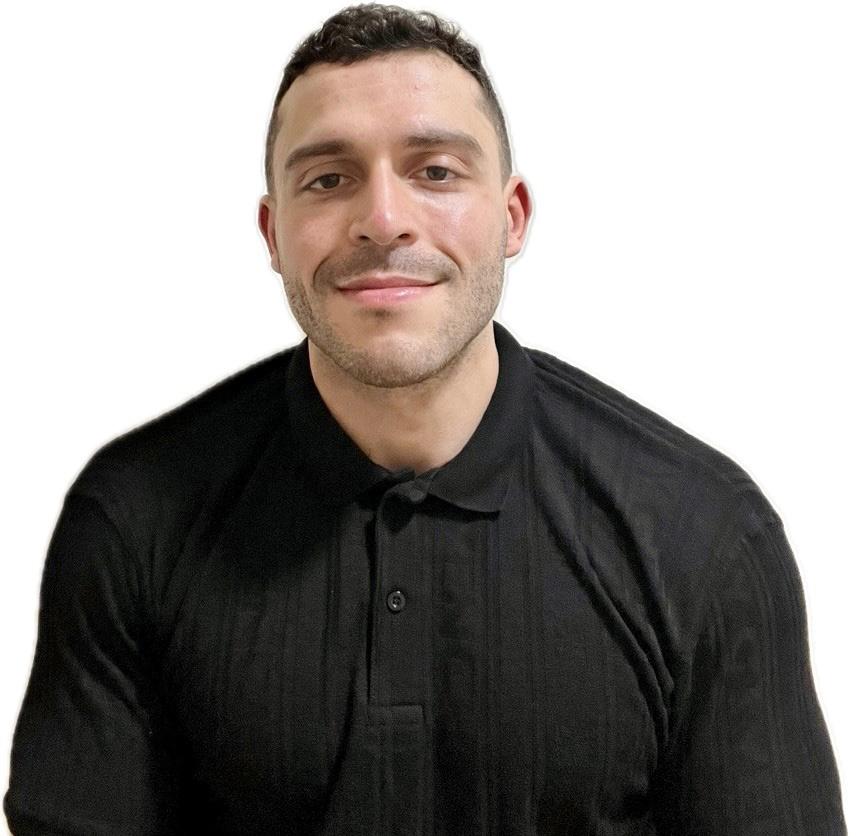
MO AL-AKAYSHEE POWER APPLICATIONS ENGINEER AT FORTEC TECHNOLOGY UK
Mo joined Fortec Technology UK (previously known as Display Technology) back in 2022, as an Applications Engineer. He has held roles in the semiconductor and power electronics design fields, working on innovative projects in refurbishment and research. He has been involved in traction, onboard-systems, and other areas outside of rail.
What is your role within Fortec Technology UK?
My role within Fortec Technology UK is primarily as a Power Applications Engineer, as the name suggests I specialise in Power. Specifically AC-DC and DC-DC Power Supplies, for use in several industries mainly rail. There are some projects where the requirements are already defined, and it’s a matter of selecting a power supply from our portfolio that matches the requirements in a COTS (commercial off the shelf) solution. However, the most interesting projects are the ones where the requirements evolve as the project develops. These projects require consistent communication with engineering teams, on both the client and manufacturers sides.
One of my main responsibilities is to work with the client’s engineering teams to define requirements in detail and ensure we get them right the first time in terms of what our partners capabilities are. This is particularly important when working on custom-mod or fully custom solutions, as going back to the drawing board takes up valuable development time.
Depending on the application and solution put forward, I also get involved in the design of the auxiliary circuitry around the power supply. For example, sometimes we need to design in transient protection or EMC filtering. The EMC filtering is interesting, sometimes we’re able to make mechanical changes to the system that improves EMC performance or it may involve adding an external filter, or a combination of both.
Tell us about Fortec Technology UK. We’re a bunch of technology enthusiasts, specialising in a few key areas. With inhouse R&D, and manufacture for power supplies designed for the rail industry and TFT displays assemblies. We’re also partnered with several external manufacturers, which has broadened our portfolio and allows us to provide the most appropriate solution for the application.
FORTEC TECHNOLOGY UK
Fortec United Kingdom is at the forefront of introducing cutting-edge technical advancements in the realms of displays, monitors, embedded computing, power supplies, and wound components across the UK and Ireland.
Want to know more about
Fortec United Kingdom?
Tel: 01480 411600
Email: info@fortec.uk
Visit: www.fortec.uk
Fortec Technology UK is what we are known as now, this is to reflect our affiliation to the Fortec Group which was established in 1984. Up until January 2024 we were known as Display Technology, which was established in 2001.
Our strategic setup and being part of the group allows us to share technical knowledge and expertise, pool stock, access a global inventory, and build strong relationships with suppliers for increased quantities and favourable pricing.
As we've grown and adapted, our dedication to top-notch customer service hasn't changed a bit. We're not just about transactions; we're in the business of building lasting relationships with our clients built on technical knowledge, commercial awareness and flexibility. Picture us as the friendly neighbour who seamlessly
fits into your design, procurement, and manufacturing processes – we're not just partners; we're the glue that holds it all together.
Our group's vision is clear – we aim to be the first choice for the development of innovative systems and solutions. The mission is straightforward: with sustainable and innovative approaches, we work to enhance the competitiveness of our customers in the ever-evolving technology market.
What is your USP (Unique Selling Point)?
Our unique selling point for the rail industry is having an in-house manufacturer which specialises in power supplies for the rail market. We are uniquely placed to work on complex requirements, where a standard solution is too much of a compromise.
We often work with our customers from the concept phase, and design a power supply that is specific to their application. Sometimes the requirements are challenging from a thermal, mechanical, or electrical perspective. Often it’s all 3!
We also offer commercial off the shelf solutions for specific industries, including the rail industry. Our USP here, is that we are a value-add specialist offering design and supply chain support and enjoy working with our clients to influence our partners to develop future solutions that are tailored to the industry and specific applications.
What are some standout projects you’ve been working on?
There have been a few standout projects, one was for an air filter onboard trains. This required a custom solution for the client, and the requirements were very difficult. An 8kV output which constantly shorted, with stringent EMC and mechanical requirements.
We had a project that looked deceptively easy to meet the requirements for from a technical perspective, it was for a box PC power supply used in rail applications. After an initial meeting with the client where we nailed down the requirements in more detail, it became clear that we could not offer an off the shelf solution.
Therefore, we introduced our in-house power supply manufacturer to look at designing a solution. We were heavily involved in the development of the solution having multiple meetings throughout each week the project was active. As a result of the progress the client made on their side of the project, we would often have to make changes to accommodate the updated requirements.
It was particularly interesting as there were many EMC critical components located near the power supply we had to account for, such as the processors and 5G modules.
Another standout project was a data recording application, where the client required operation down to -50°C. The
project had a few easier requirements such as multiple outputs and a wide input range, the challenge here was the space constraint and thermal considerations. This ended up being another custom project with our inhouse manufacturer.
When a client comes to you with a particular problem, what’s your process for coming up with a solution, and how closely do you work with clients throughout the projects?
It really depends at what stage of the project the client engages with us and the application, a lot of the time the power supply is an afterthought and we have to work around what has been designed already.
We set up an initial meeting with the engineers to nail down the requirements in more detail, and to explain how we can support them with integrating the power supply into their application. It’s useful to have project managers in these meetings to keep expectations realistic, in terms of project timelines and if any changes can be made to system design. We then engage with a few of our partners who have suitable products in their portfolio and aim to provide a range of solutions for our customers to choose from.
Some projects have complex power supply requirements, for these projects we have to work with our clients closely. Partly because defining the requirements is more difficult, but more so because they evolve as the project develops. We often replicate the client’s system in our test labs to test the performance of the power supply, or if possible obtain a spare system from them to carry out the testing. This happens with both standard, and custom power supplies.
drivers capable of dimming while meeting rail safety standards, such as EN50155.
Another exciting technological advancement is the integration of intelligent power management systems. These systems integrate with the trains existing infrastructure and are designed to enhance the power utilisation onboard, which would improve efficiency without compromising on the comfort or passenger experience.
The development of advanced climate control systems, which can be integrated into the intelligent power management system contribute significantly to passenger comfort. These systems optimise the distribution of power to heating, ventilation and air conditioning (HVAC), ensuring a consistent and comfortable interior environment.
to attract and retain a skilled workforce essential for implementing and maintaining new technologies such as driverless trains. This challenge will need collaborative efforts between industry, stakeholders, governments, and technological innovators.
In terms of technology, how do you anticipate things might change in the next five to ten years?

What are some of the biggest challenges this sector currently faces?
What would you say is the most exciting technology in the industry?
Ambient lighting is an exciting topic, there has been a lot of work done recently around the topic of circadian rhythm LED lighting. This is a dynamic lighting solution which is synchronised with the time of day and specific travel conditions, the idea is to improve well-being by minimising the impact of electric light on the human circadian rhythm. I see this technology being rolled out onto trains once official guidelines are in place for residential and commercial applications. It will need LED
Legislation and approvals are very important to ensure safety and traceability, but it’s also a barrier to getting new technology into the industry. One of the biggest challenges is the aging infrastructure, the modernisation of tracks, bridge and signalling systems require substantial investments and strategic planning to keep up with evolving technological standards.
The talent gap is a tricky challenge, most industries, including our own are contending with an aging workforce and a need for specialised skills in emerging technologies. Pre-industry education, and training programs in tandem while working in the rail industry is a good solution
Over the next five to ten years I think the rail industry will change drastically due to the technological advancements and requirement to replace aging infrastructure. AI and machine learning is talked about a lot, these technologies will play a pivotal role in enhancing predictive maintenance, optimising schedules, and improving overall system efficiency. These systems will require complex electronics to implement, in certain cases high speed electronics and radar systems will be required. These high speed systems will require a power distribution architectures that do not compromise the performance of the application, point of load (PoL) converters would be a great candidate here. Power consumption onboard trains will increase, we’re starting to see a lot of devices switch to USB-C which provides up to 240W. A lot of trains already have USB-A sockets which provide around 10W, so it’s going to be a challenge to manage the higher power demand and current flowing through the carriage. We’re going to see some innovative solutions being implemented to overcome this, and provide an improved passenger experience where we can all charge our devices simultaneously. Battery backup systems are one solution that comes to mind, perhaps charging during the breaking process (regenerative breaking) or while stopped at a station to reduce the peak load on the power network.
In essence, the next five to ten years looks bright for rail and there are a lot of technological advances that will make the industry more attractive as the go to method of transport.
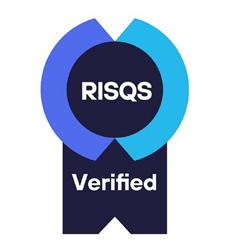
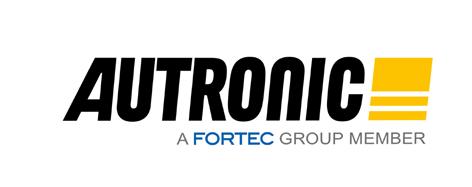

STEVE JASPER OPERATIONS DIRECTOR AT PRE METRO
Steve Jasper is the Operations Director at Pre Metro, the train operating company behind the successful Stourbridge Shuttle. Steve actively collaborates with industry colleagues, local authorities and the private sector. He has been heavily involved in the public transport industry since 1979 across both the bus and railway industries.

PRE METRO OPERATIONS (PMOL)
Pre Metro Operations (PMOL) was founded in 1999 as an independent train operation company with the aim to establish innovative and low cost light rail transit services on branch lines across the UK.
Want to know more about Pre Metro?
Tel: 01384 441325
Email: info@premetro.org
Visit: www.premetro.co.uk
How did you get started in the Public Transport industry?
I qualified as an accountant while working in Local Authorities before joining the transport industry – the West Midlands Passenger Transport Executive – in 1979. I worked extensively on financial planning for the deregulation of the bus industry in the 1980s and remained in the ‘private’ sector except for a brief return to the West Midlands Passenger Transport Executive.
I had several roles ranging from Finance Director to Customer Services Director as well as managing the bus operations in Wolverhampton and Coventry. The roles involved extensive liaison with Local Authorities, Chambers of Commerce, Trade Bodies, and Politicians – local Councillors and MPs.
When did you join Pre Metro?
I joined Pre Metro just before it commenced operation in 2009, initially as Company Secretary and later with the added responsibility of Operations Director.
What is your role within Pre Metro?
As Operations Director I have responsibility for day-to-day aspects of service provision on the Stourbridge Shuttle. As a Director I sit on the board and share responsibility for the overall activities of the company and the strategic direction that we wish to take. The role also involves collaborative/partnership working with West Midlands Trains, local authorities and private sector organisations.
I have always tried to be a hands-on manager so when I joined the company I insisted on being trained as a driver and have only recently finished providing cover for holidays, sickness etc.
What are the core principles of your company?
At the heart of our company lies a steadfast commitment to operational excellence, innovation, and community engagement. Our operational approach focuses on reliability, efficiency, and customer satisfaction, exemplified by our Stourbridge Shuttle. This service, boasting an impressive 99.6 per cent annual reliability rating, reflects our dedication to offering frequent, dependable, and environmentally friendly transport.
Innovation also forms another key pillar of our ethos. We enthusiastically adopt advanced technologies and sustainable practices, redefining the potential within the light rail sector. The Shuttle has been a trailblazer for Very Light Rail (VLR), and our ventures into new VLR systems demonstrate our commitment to revolutionizing underutilized branch lines into essential transport links. Our efforts go beyond mere technological advancements; they are about shaping a future where public
transport is more accessible, efficient, and environmentally conscious.
Our dedication to community involvement is equally vital. We view rail as a powerful tool for connecting and enhancing communities. Our board consists of local people who want to make sure the Stourbridge service is more than a transportation solution; and so, it’s become a vital element of the community we serve. By engaging with local stakeholders and supporting charitable causes and events, like the Side By Side Theatre group and the Annual Military Vehicle Parade, we aim to enrich the social and economic well-being of the Stourbridge area.
What do you have planned for the year ahead?
This year is set to be transformative for us, as we strive to exceed in service excellence, deepen community engagement, and lead in sustainable Very Light Rail advancements.
A primary focus for us is to enhance our community engagement. We are set to launch several initiatives that deepen our bonds with residents, businesses, and organisations, including partnerships with local charities, community events, and active participation in shaping public transport's future.
Operationally, we're preparing for extensive testing of the latest VLR vehicles further afield, ensuring they meet our stringent standards of safety, efficiency, and reliability. The results from these tests are critical in shaping our future services and aiding manufacturers in integrating VLR on heavy rail infrastructure effectively.
The key highlight to look out for this year is the launch of our 'Stourbridge Dasher' proposal document, or ‘Stourbridge’s Bigger Picture’. This is a strategic initiative to broaden our service provider across Stourbridge and Dudley. The 'Dasher' is designed to provide faster, more frequent, and eco-friendly transport to connect Stourbridge Junction with Brierley Hill, embodying our dedication to innovation and sustainable public transport.
What types of companies do you collaborate on projects with?
Pre Metro collaborates with various organisations to enhance its rail services and community impact. Key partners include local and national government bodies like the DfT and WMRE for regulatory alignment and proposal funding; national operator West Midland Trains who sub-contract us to operate the Stourbridge Shuttle and contribute to their PPM; industry peers such as Network Rail for infrastructure optimisation and the Revolution Consortium (Eversholt Rail and Transport Design International) for vehicle testing capability and support; research firms like Oakham Research for public consultation and service improvement; local
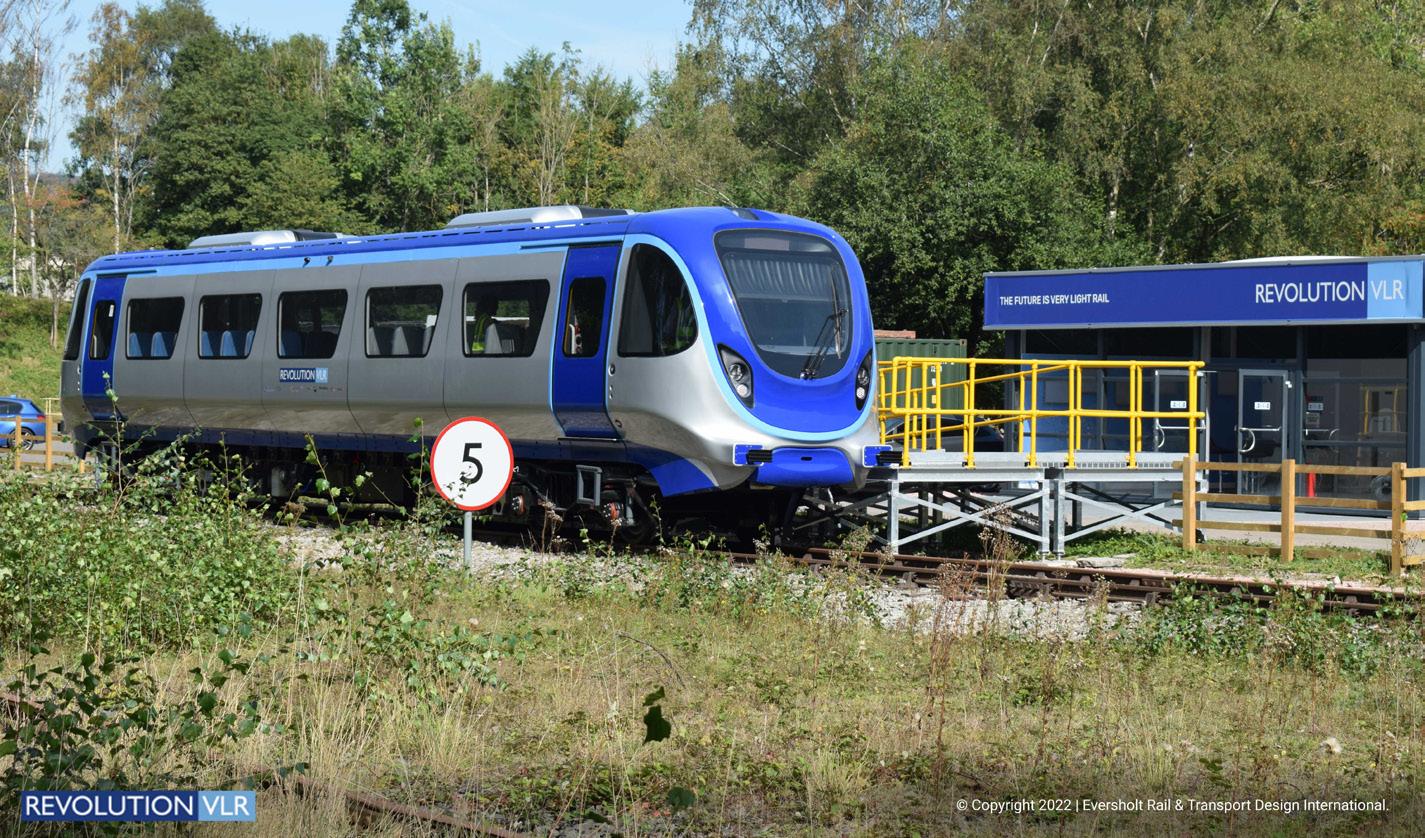
businesses and charities for community engagement and support; and a repertoire of technology and engineering companies that can support our in-house maintenance of the Class 139 fleet. We believe these collaborations are essential for supporting and extending our current service providing, as well as for integrating innovative technologies, ensuring service excellence, and fostering strong community ties.
What are some of the biggest challenges this sector currently faces?
A significant challenge is the ageing infrastructure of many rail systems. Keeping up with the maintenance and modernisation of tracks, stations, and associated facilities is not only costly but also essential to ensure safety, efficiency, and reliability. We were fortunate to have the Branch Line renovated in 2019, but there is plenty more work to be done.
As urban areas grow, there's also a pressing need to expand the railway network to meet increasing demand. Finding sustainable solutions that minimize carbon footprints while expanding services is a complex task, involving careful planning and investment in green technologies.
Of course, financial constraints remain a perennial challenge. Securing funding for new projects, maintenance, and upgrades in an economic landscape that is often uncertain is a formidable task. This issue is particularly acute in the light rail sector, where initial investments can be significant (particularly in the UK).
The rail sector must cater to a wide range of users with different needs, from daily commuters to tourists. Ensuring accessibility, convenience, and affordability for all users is a complex balancing act, requiring continuous innovation in service design and delivery.
As such, we believe that the Stourbridge Shuttle model provides a template for exactly how some small and medium-sized towns and cities can utilise their existing
infrastructure to develop economically and environmentally sustainable services. Such services can become an integral lynchpin between various modes of public transportation; adapting to and integrating VLR technologies is essential for establishing patronage and public confidence within the industry.
A massive challenge is encouraging the whole industry to adopt a “can do” attitude particularly when it comes to cost-effective, simple-to-implement projects – less expensive, consultant-led studies, more delivery!
What are some potential solutions to these issues?
Three pillars – consultation, collaboration, and investment – are essential for advancing the rail industry and ensuring its resilience and relevance in the future. Pre Metro's Stourbridge Shuttle, renowned as the ‘Most Reliable Railway Service in the UK’ with a 99.6 per cent service reliability rate over five years, exemplifies the benefits of consultation, collaboration, and investment in the rail sector. Despite its success, there's a noticeable lack of engagement from other operators and stakeholders in understanding and emulating these achievements.
Active engagement with operators, communities, and stakeholders in the early stages of rail projects can lead to more effective, reliable, and widely supported solutions. Adapting to post-pandemic commuter patterns necessitates flexible service models, like dynamic scheduling and integrated multimodal ticketing, to boost patronage.
Investment in modernising rail infrastructure and innovations is also crucial, encompassing track and signal upgrades and station or branch line renovations to enhance safety and efficiency. Embracing innovation through research and development is key, with a focus on new propulsion technologies, lightweight
‘With the current generation of projects, rising costs –particularly in light rail – come close to 300 per cent more than the current worldwide average. Why? No one seems to know.’
vehicle designs, and smart urban transport integration for long-term sustainability.
The late John Parry MBE – who pioneered VLR technology with the Parry People Movers – is the perfect example of this. Although his companies are being wound up, the impact of his ideas and contributions to the field of transportation cannot be overstated. It’s a poignant reminder of the need for greater support and investment in entrepreneurs who bring forward innovative solutions, as their success often hinges on the willingness of others to take risks and invest in their visions.
In terms of technology, how do you anticipate things might change in the next five to ten years?
Well, the evolution of Very Light Rail and its application across the UK will certainly be something that the industry can look forward to, with both the Coventry and Revolution Very Light Rail projects progressing steadily and offering the potential to provide a more affordable mode for tram systems and railway restoration projects.
Following the success and outpour of support for the ‘Restoring Your Railway’ scheme established by the government, it is also clear that there is a path to pursue schemes which were deemed ‘fiscally unviable’. We hope that these new next-gen VLR models demonstrate their potential and become available rolling stock.
However, this can only be achieved if there is a strategic plan for how the UK’s railway and tramway network will be expanded and projects efficiently financed. There have been many pitfalls with the current generation of projects, rising costs –particularly in light rail – come close to 300 per cent more than the current worldwide average. Why? No one seems to know.
This lack of financial control or accountability is not something we can ignore should we want to revolutionise our public transport network, and we must ask and keep asking the question; how can we support patronage growth more affordably and effectively?
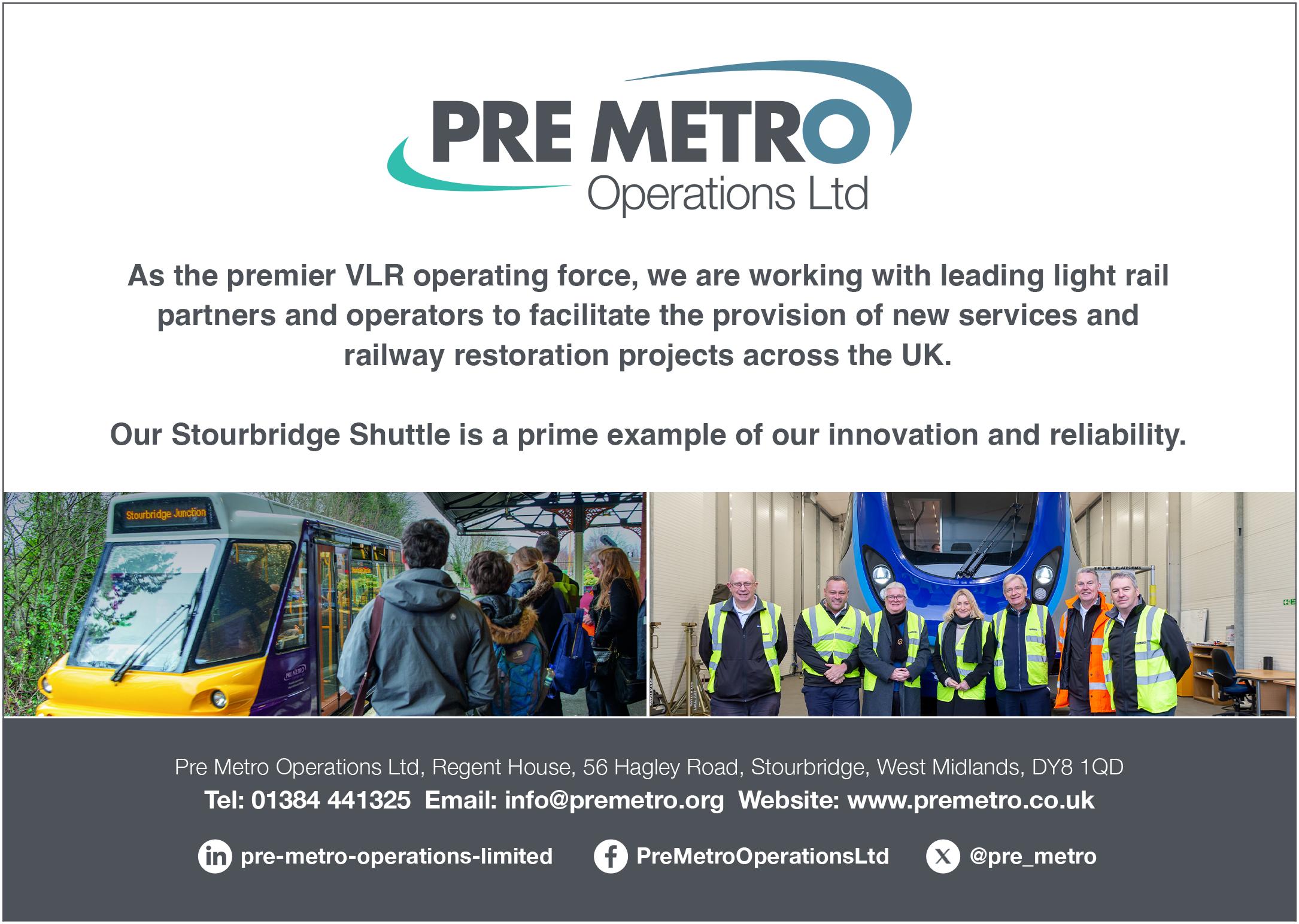


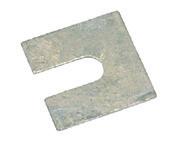


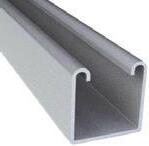

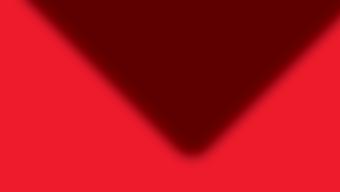
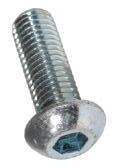
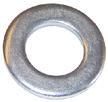


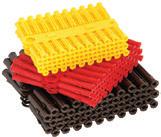



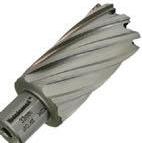

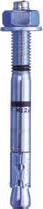


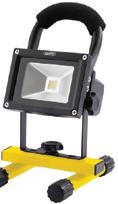

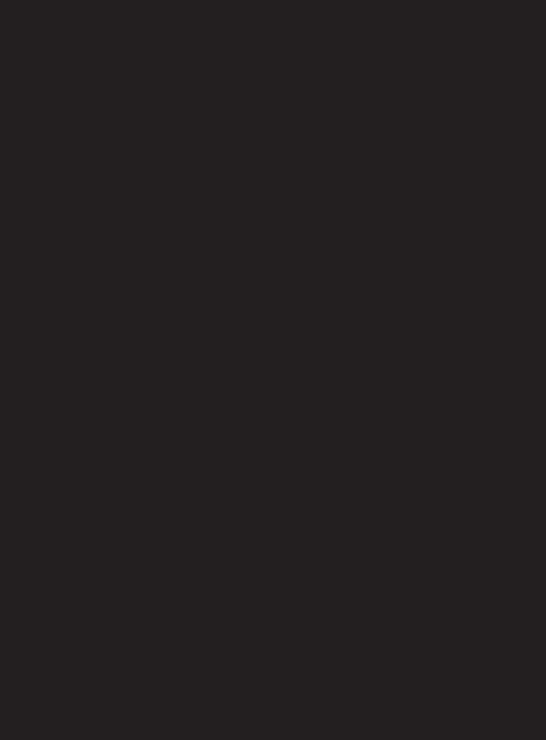
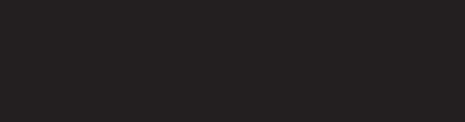
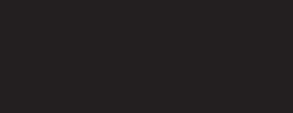
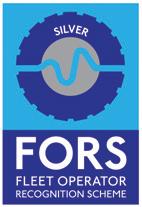
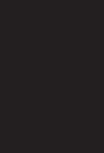
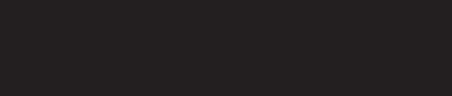
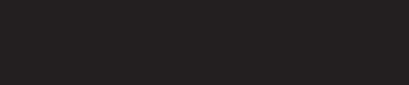
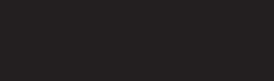

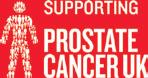
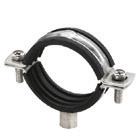
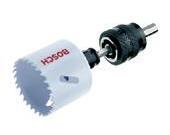

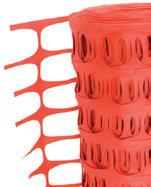
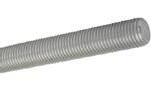

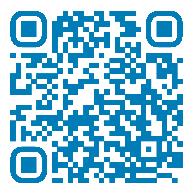

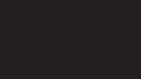

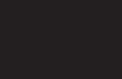

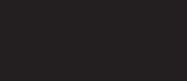


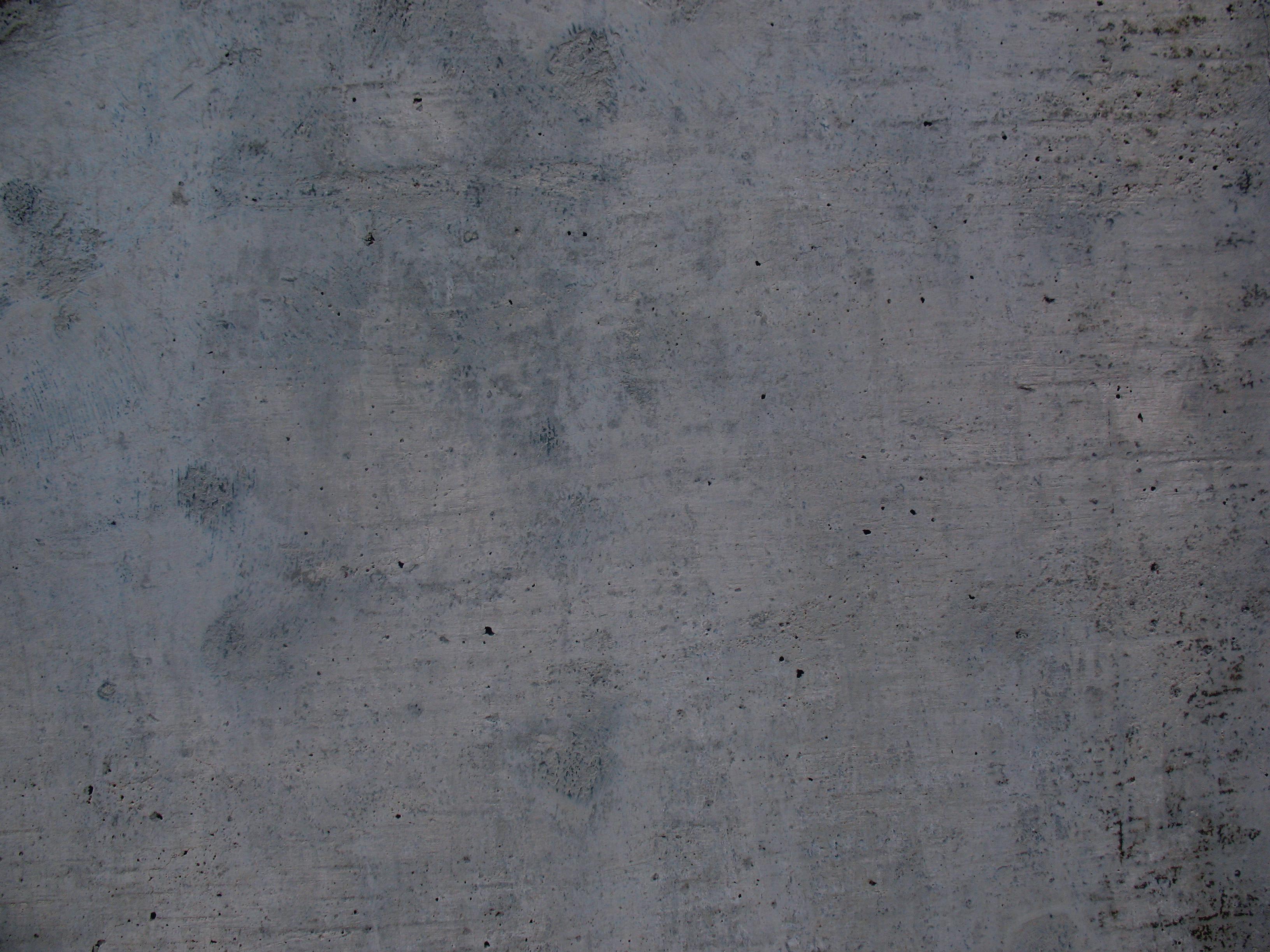
Transport Ticketing Global 2024
Celebrating its fifteenth year, Transport Ticketing Global 2024 will be the world’s largest public transport forum for smart ticketing and mobility professionals
Taking place on Tuesday 5 and Wednesday 6 March 2024 at Olympia, London and with a host of new speakers, interactive formats and new exhibitors, the event will showcase the very latest in smart ticketing, mobility solutions and passenger experience.
Event Manager Andrew Earle said: ‘We can sense the excitement and anticipation in the industry when we speak to exhibitors and delegates. Everyone is looking forward to meeting industry colleagues from around the world and catching up on what’s new and what’s moving forward. With many new speakers, new sponsors, new products and services, we’re building up to another superb event.’
Mobility and ticketing professionals from more than 65 countries will once again be in London to discover a vast range of insightful and original content, highlighting new projects from across the globe.
Expert speakers
During the two-day conference programme set in the three theatres, more than 120 expert speakers from the Americas, Europe, Africa and Asia will present in-depth case studies and engaging presentations and speak in panel discussions on the key issues now and innovations coming in the near future.
Among the topics that will be covered in detail will be the impact of AI on ticketing and public transport, open payments, ABT, revenue protection, card virtualisation, improving the customer experience, distribution systems for rail operators and more.
Notable speakers will include Michael Wooldridge, Professor of Computer Science, Director of Foundational AI research – University of Oxford, The Alan Turing Institute – who will be discussing the development of AI tools and the implications for the ticketing and public transport. The C-Level keynote panel will feature Shashi Verma, CTO of Transport for London alongside Nick Mackie from
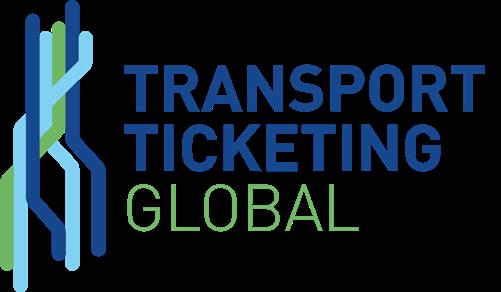
Visa and C-level executives from Metrolinx (Toronto, Canada), Express Rail Link (Malaysia) and Rejsekort & Rejseplan A/S (Denmark).
This year’s show also features a raft of new exhibitors joining the event’s regular supporters. With a substantial number of product launches planned, the 80 plus organisations on show will highlight the technical innovation driving the industry forward.
For information please visit www.transport-ticketing.com
SPONSORS
Sponsors include: Vix Technology, Mastercard, Visa, Worldline, Conduent Transportation, Cubic, Thales RCS, Ticketer, Almaviva, American Express, Indra, INIT, littlepay, NXP, Scheidt & Bachmann, Accenture, Elavon Masabi, Thales Banking & Payment Services, Tmoney, Discover Global Network and Flowbird.
Among the event partners are Calypso Network Associates, Consult Hyperion, First Partner, ITS (UK), ITSO, MaaS Scotland, Smart Application Management (SAM), Smart Ticketing Alliance (STA), Transport for London, VDV eTicket Service and Women in Transport.
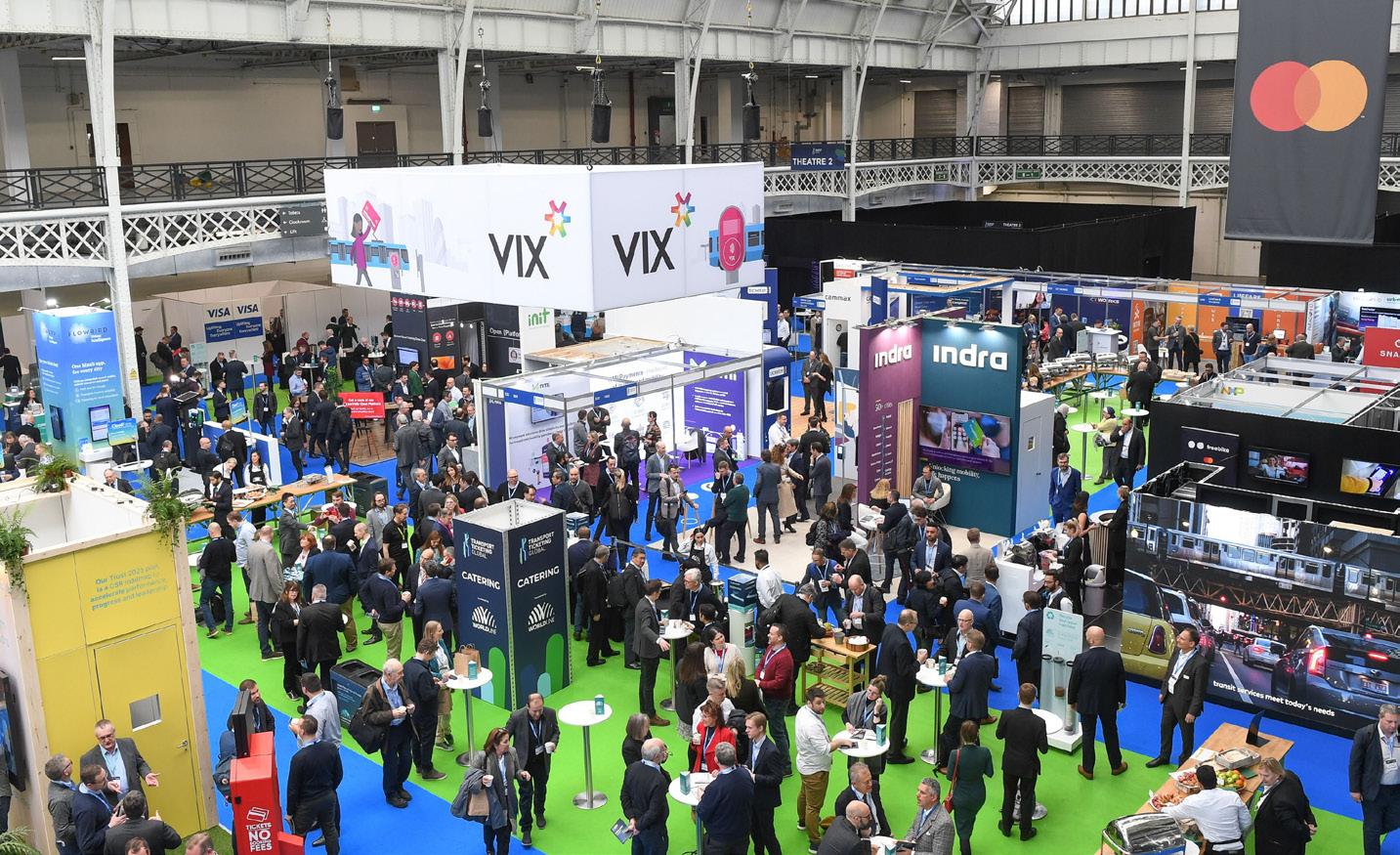
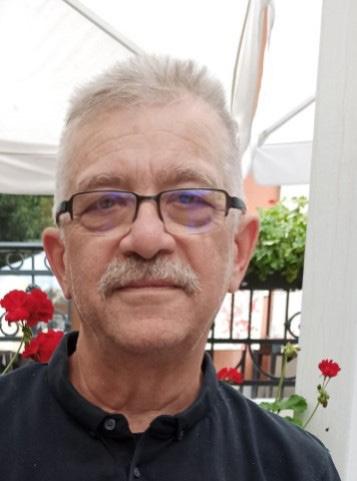
SIMEON EVTIMOV RSD MARKETING & COMMUNICATION AT INDUSTRIAL & RAIL EQUIPMENT DPT ATCO TRADE EOOD, BULGARIA
Simeon is an expert in engineering and foreign trade matters at the Bulgarian private company ATCO TRADE. More than 20 years in the system of Bulgarian State Railways. From 1998 to 2013 free-lance consultant to transport and infrastructure projects management. CEO of the Austrian-Bulgarian company voestalpine VAE Sofia, before retirement.

ATCO TRADE EOOD
Founded in 1999, ATCO TRADE EOOD is commercial and engineering system solutions provider delivering technology equipment, spare parts and specific consumables.
When did you join ATCO TRADE and what is your role within the company?
I joined ATCO TRADE in September 2017 following my retirement from voestalpine VAE Sofia. My role is to consult on the company’s engineering and foreign trade activities. My responsibilities include strategic analyses and coordination of design, manufacturing, sales, supply, installation, commissioning and postsales service of equipment under various rail projects in the field of public electric transport.
Recently, I have been paying more specific attention and time to marketing and communication of the Rope-type Platform Screen Doors system focussing on registration of a protected RSD brand mark (logo and text), participation in international exhibitions and fora, as well as showcasing the valuable resources and benefits that UITP membership provides.
How did you start at ATCO TRADE?
My start as an ATCO TRADE employee was in fact a continuation of the good partnerships which voestalpine established within the supply chain under various railway and public transport projects. Delivery of products and services to the satisfaction of railway sector customers required mutual trust and understanding of specific railway market aspects. Developing these kinds of relationships allowed for a seamless transition as a retiree to ATCO TRADE. My railway professional qualifications and fluent knowledge of the Russian language contributed to the company’s stable position in the market.
Tell us about your career before you joined ATCO TRADE?
Sweden, Germany, Belgium, USA and Austria. I have more than 60 publications and have participated in 26 international conferences.
Tell us about ATCO TRADE?
ATCO TRADE EOOD was founded in 1999, by engineers with proven professional qualifications and experience in foreign trade. The company is certified under ISO 9001:2015 and is a registered member of BCCI (Bulgarian Chamber of Commerce and Industry), CRIB (Confederation of Employers and Industrials in Bulgaria) and BMGK (Bulgarian Chamber of Mining and Geology). As of May 2023, ATCO TRADE is a regular member of UITP and is contributing to the improvement of the public transport passenger experience in line with the UITP supported urban mobility standards. Our activities cover commercial and engineering system solutions with delivery of technology equipment, spare parts and specific consumables.
What is your Unique Selling Point?
Our company’s USP is the competence of our highly qualified engineers. This allows ATCO TRADE to guarantee specific features and advantages of equipment by strict control at every step from design and installation to commissioning and service in operation, in order for customers to be satisfied by the service provided, while manufacturers have additional warranty for the reliability of their products.
Want to know more about ATCO TRADE EOOD?
Tel: +359 2 978 5575 +359 2 978 9008
Email: atcotradebox@gmail.com
Visit: www.atcotrade.com www.rsd.bg
Address: 72, Andrey Lyapchev Blvd. 1799 Sofia, Bulgaria, P.O.Box 10
I am a civil engineer (MSc.) and graduated in 1979 from the Leningrad Institute for Railway Transport Engineers (today St. Petersburg University of Railway Engineers) in Russia. For 20 years I have worked in the system of Bulgarian State Railways (BDZ) with active involvement in strategic investment projects for railway sector restructuring. From 1998 to 2013 I was actively involved as a freelance consultant for various transport and infrastructure projects management. For four years before my retirement, I was the CEO of the Austrian-Bulgarian company voestalpine VAE Sofia producing and delivering railway track turnouts with the relevant operation and maintenance services. The peak of my professional career I consider my appointment in year 2000 as the Head of the Project Implementation and Management Unit for the notable construction project of the New Bulgaria-Romania Road and Rail Bridge over the Danube River at Vidin – Calafat. I have attended training courses, seminars and specializations in Bulgaria, Russia, Greece, Japan, Italy, UK, France,
In terms of our marketing strategy, our USP is the Rope Screen Door System, which we have registered under the brand RSD. This is an intelligent passenger safety system for preventing platform accidents and non-authorized track access based on the concept of automated vertical movement of large span lightweight rope panels, in combination with area control sensors. ATCO TRADE was the leader of a BulgarianKorean Consortium, which designed and installed the RSD System technology in the Sofia Metro to successfully resolve a specific safety problem. RSD platform safety system’s world premiere was at InnoTrans 2022 in Berlin.
What are some major projects you’re currently working on?
The first priority now is the Sofia Metro Extension Project where our company is either a contractor, or a sub-contractor, providing engineering services related to new line sections track equipment installation; new trains delivery and commissioning; and train maintenance depot equipment. Another major project we’re involved in relates to the industrial rail sector where we are providing engineering services to a copper metallurgy plant under a contract for upgrading the technology for liquid slag transportation by rail.
Of course, our continuous major project is our customers’ satisfaction. We are allocating qualified engineering staff to post warranty services for maintaining operability of the equipment delivered by ATCO TRADE, in a way that our customers feel like partnership.
What types of companies do you collaborate on projects with?
ATCO TRADE is a service-oriented company and we have developed a relationship of mutual trust with our customers. As a result, we are usually involved in projects that represent an engineering challenge. Therefore, we can only afford collaboration with companies that have a solid presence in the international market applying an innovative approach in resolving engineering problems without taking unreasonable commercial risks. Our company is an authorised representative for Bulgaria of companies producing rail lubrication systems, train maintenance depot equipment, such as lifting jacks, wheelsets diagnostic and processing systems, and rolling stock washing systems. We are also partnering with design and railway safety consultants.
When a client comes to you with a particular problem, what’s your process for coming up with a solution, and how closely do you work with clients throughout the projects?
In partnership with our customers, we have implemented a number of projects, which have become a solid base for long-term cooperation. We know very well the specific operational conditions of our customers and are close to them on a weekly basis at the service operation level. In such a way, we jointly identify specific problems at an early phase, before starting the process of an engineering solution finding. That is why, in any equipment supply contract, we are involved from the design phase, as an authorised representative of our customer to the manufacturer. Under the project implementation contract, we play the role of a system integrator and usually execute final installation and commissioning providing training with solid guarantees to the customer. This is how we are able to maintain a relationship of mutual trust and continuity. In a couple of rolling stock depot projects with the Sofia Metro we have proved our capacity to coordinate more than 100 suppliers, and to successfully commission all rail structures, standard and special machines, tools, appliances and repair stands.
What new developments/strategies do you have?
The engineering services business of ATCO TRADE is an integral part of the global supply chain markets and is therefore, dependent on international trends and fluctuations, sometimes influenced by political changes. We maintain stable business contacts with partners from Austria, Belarus, Czechia, Germany, Hungary, Italy, Israel, Kazakhstan, Latvia, Poland, Romania, Russia, South Korea, Spain, Switzerland, Turkey, UK, Ukraine and other countries in line with the preferences and interests of our customers. We consider that our most prestigious project is the Bulgarian-Korean partnership for execution of design, prototype testing, manufacturing, delivery, installation, commissioning and warranty services of 24 RSD passenger platform safety systems in the Sofia Metro. The success of the Sofia Metro project added value to our experience and
Rope Screen Door Rope Safety Device www.rsd.bg
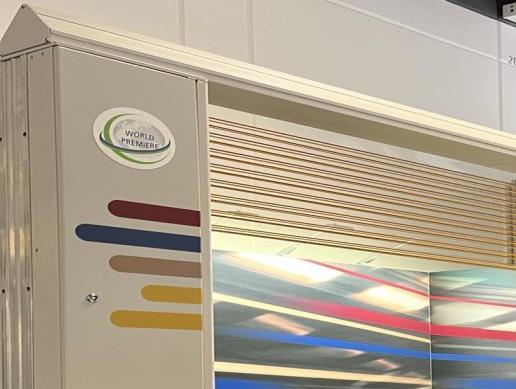

An innovative concept of platform safety using high strength steel rope elastic barriers with large span vertical opening. Fast installation without interfering train operation schedules. Taylor made robust solutions with low power consumption. Unrivaled efficiency at mixed traffic of various train length and door configurations. Applicable in conventional rail and metro lines, high speed or light railways, or any other locations of people’s traffic requiring additional safety measures
Meets the requirements of SIL 4.
Aesthetic integration in any architectural environment
Applicable with both automated and non-automated train operations.
Maximum use of natural lighting and ventilation
Allows for transit passing of high speed trains
The RSD System is installable on any type of passenger platform to prevent accidents and unauthorized access to rail track Highest possible (99.99%) RAMS indicator proven in operation. Improves passenger experience and makes the choice of public and rail transport easy and attractive in favour of the green mobility.
engineering competence. Our marketing strategy is focussed on Europe for capitalizing the RSD System operational safety advantages and its innovative technology potential.
What would you say is the most exciting technology in the industry?
My choice is high-speed rail. This technology doesn’t just change the industry, it changes society by giving new dimensions to time and space management, to mobility as a quality of everyday life, and to connectivity of people, territories and nations. High speed railways, being safe, green and energy efficient technology, play the role of a universal competitor to water, air and road transport improving the efficiency of the entire transport sector. The most exciting effect of this technology is the transformation of railways into an attractive, intelligent and accessible service to become the transport medium of the future.
Where do you think the industry will be in the next 10-15 years?
I believe that in the next 10-15 years high-speed technology is likely to have a significant impact on the rail
industry’s development as an integrated system – infrastructure, trainsets, telecommunications, signalling, operation safety and security equipment. Within this period I expect to see significant expansion across the continent of an interoperable rail network connecting major cities. Trains will become the preferred mode of transport and many ‘stations of the future’ designed today will become lively hubs in the urban environment, where accessibility, safety and security will complement customer assistance from the threshold crossing, through the ticket offices, to the platform/ train interface.
What are your views on collaborative working?
When your company is in the engineering services business collaborative working has no alternative. Since the very start of ATCO TRADE the company has kept to this principle and that was the way of growing in the market by gradually expanding fields of activity in collaboration with other companies. As our company strategy is now focussed on project export, collaborative working with local engineering service companies has become a key factor, especially for exploring the potential of the
UK high-speed rail or urban mobility market. We appreciated the opportunity to exhibit at Railtex 2023 where, thanks to RIA, we established valuable contacts with a number of companies interested in collaborative working.
How can a company achieve the necessary creativity to innovate without compromising their existing business?
The shortest possible answer is: by investing in people in such a way that veteran innovative experience can motivate inventive enthusiasm in young engineers to catch sustainable business opportunities.
Why is RSD your strategy for sustainable development of the company?
We see big potential for growing the demand for RSD System due to its incomparable advantages of structural flexibility and robustness, quick installation without interfering with the regular train schedule, and high reliability. This makes it a very attractive engineering solution for stations retrofitting projects, which would allow raising of platform safety to the level of automated traffic management systems in the ‘stations of the future’.
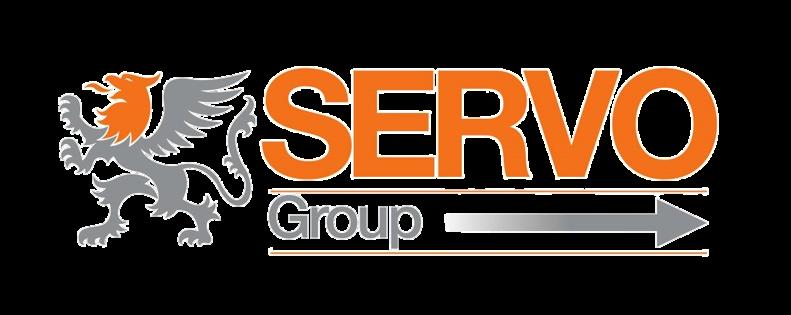
Work Underway at New Aldridge Railway Station
Aldridge Railway Station’s future site is being secured and cleared to pave the way for the start of construction
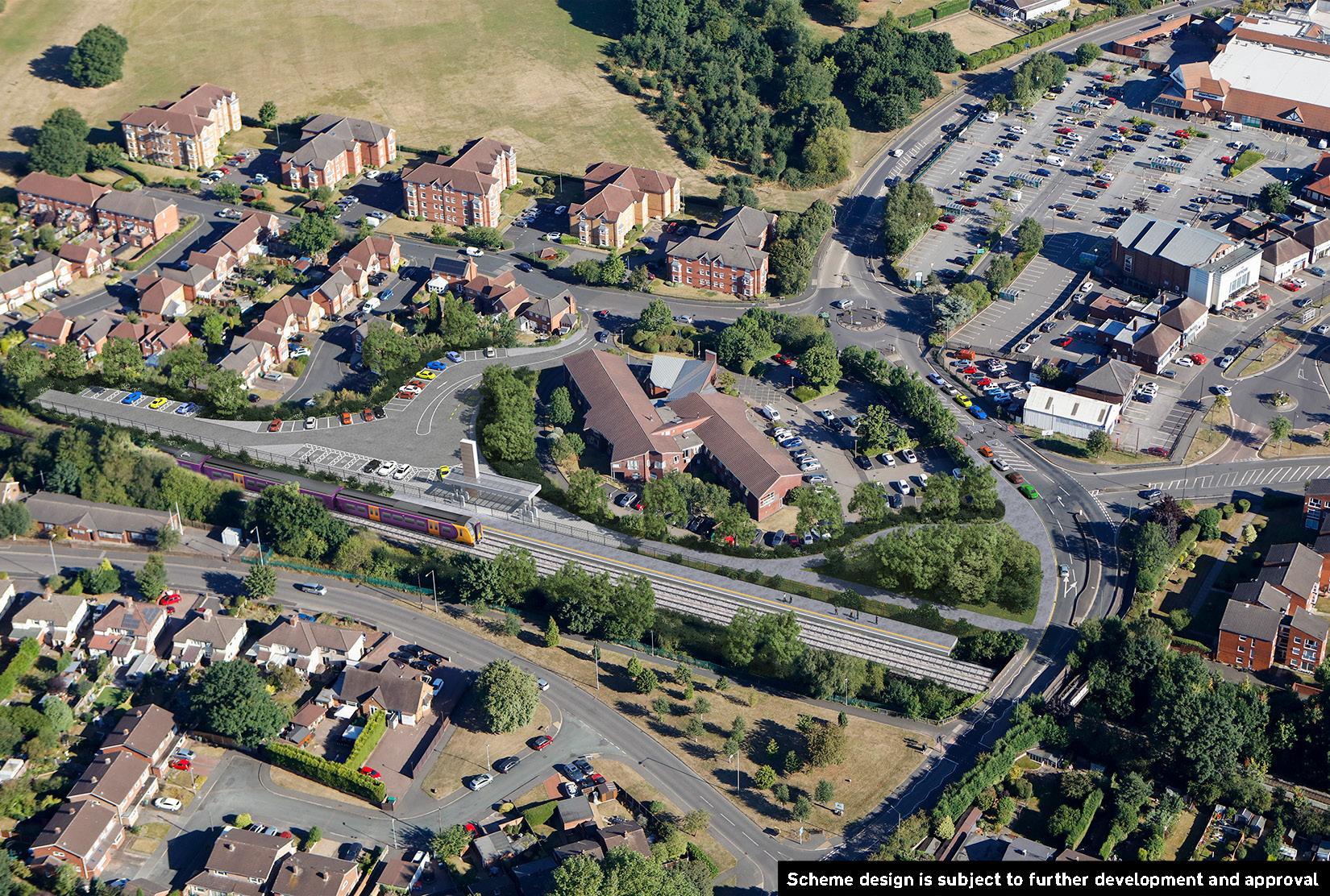
The £30 million project will see a single platform station built with a 40 space car park and road access from Westfield Drive. Transport for West Midlands (TfWM) and the West Midlands Rail Executive (WMRE) are working with Network Rail to get the station built and open – restoring passenger rail services to the town for the first time in 60 years.
Planned to open during 2027, Aldridge Station will initially offer a half-hourly service to Walsall town centre where passengers will be offered an easy interchange with services to Birmingham as well as the opportunity to connect to wider regional and national services.
Longer term plans could see both the line electrified offering direct services to Birmingham and beyond, and the station upgraded as part of the wider reopening of the Sutton Park Line to passenger services.
The new Wrexham, Shropshire and Midlands Railway Company (WSMR) has recently announced plans to run services
from north Wales and Shropshire to London Euston via the Sutton Park Line and opportunities for the service to stop at Aldridge are being explored.
Reopening railway stations and reconnecting communities to the rail network as an alternative to private car use contributes to the #wm2041 target for a net-zero carbon region within two decades.
The £30 million has been allocated from the City Regional Sustainable Transport Settlement (CRSTS) funding awarded to TfWM, which is part of the West Midlands Combined Authority (WMCA) by the Department for Transport.
Funding for the £1.7 billion Midlands Rail Hub, the scheme to improve rail capacity and links across the East and West Midlands, has recently been confirmed by Government. By providing increased capacity for train services into Birmingham city centre it will offer the opportunity to reopen the Sutton Park Line in full.
Andy Street, Mayor of the West Midlands and chair of the WMCA, said: ‘It’s
astonishing to think that despite being on an active railway line no passenger trains have stopped at Aldridge since 1965.
‘That’s why we are making this investment and working with Network Rail to get this station open for the people of Aldridge – starting with a shuttle service to Walsall from Spring 2027. This will finally start to give Aldridge the railway services it so badly needs – offering residents a convenient alternative to the car.
‘But we are not resting there, we are actively seeking further opportunities to improve and increase services at Aldridge. This includes working with the Wrexham, Shropshire and Midland Railway Company on plans to give Aldridge a direct train service to London.
‘We will continue to work with partners in the months and years ahead to realise this and our longer term ambition to reopen the Sutton Park Line in full, something which is now a step nearer thanks to the funding we have secured for the Midlands Rail Hub.’
Rob McIntosh, managing director for Network Rail's North West and Central region said: ‘We are delighted to work in partnership with the WMCA to build a better connected, more prosperous, fairer and greener region.
‘Aldridge station is one of a number of new stations being funded by TfWM and WMRE across the West Midlands. These exciting transport hubs will not only support economic growth by improving connectivity for passengers, but also provide multiple benefits for local communities.’
Cllr Mike Bird, WMCA portfolio holder for transport and leader of Walsall Council said: ‘This is an exciting time for rail in the region with work now underway on delivering six new stations, including at Willenhall and Darlaston, and plans for more in the pipeline.
‘New stations offering convenient rail links not only open up new work and leisure opportunities for residents and the communities they serve, but by making it easier for visitors and works can act as a catalyst for future investment in our towns.’

WINDHOFF BAHN- UND ANLAGENTECHNIK GMBH
WINDHOFF Bahn- und Anlagentechnik GmbH, headquartered in Rheine, operates within the realm of the rail vehicle industry, boasting a distinct presence in the sector.
Want to know more about WINDHOFF?
Tel: +49 (0)5971 580
Email: info@windhoff.de
Visit: www.windhoff.de
Address: WINDHOFF GmbH
Hovestrasse 10
48431 Rheine Germany
Which sectors do you work in?
WINDHOFF Bahn- und Anlagentechnik GmbH strategically divides its operations into two pivotal Business Units: Rail Vehicle Technology and Railway Technology. Within the Rail Vehicle Technology domain, the focus lies on auxiliary vehicles, commonly referred to as the ‘yellow fleet,’ dedicated to construction and maintenance endeavours in the realms of tracks and overhead line systems. This unit plays a crucial role in facilitating seamless operations within the railway infrastructure, ensuring the efficacy of maintenance initiatives.
Concurrently, the Railway Technology Business Unit specializes in depot equipment, including but not limited to lifting jacks, platforms, and similar apparatus crucial for the meticulous upkeep of rail vehicles. The product portfolio extends further to encompass shunting vehicles and attachments, showcasing the company's comprehensive and diverse offerings.
WINDHOFF's commitment to innovation and multifaceted solutions is evident in its expansive product range, demonstrating a steadfast dedication to addressing the intricate needs of the rail industry. Through the convergence of Rail Vehicle Technology and Railway Technology, WINDHOFF establishes itself as a prominent player in the intricate landscape of rail and facility management technologies.
What challenges have you faced in the industry?
The contemporary landscape of the rail vehicle industry in Europe is marked by a myriad of challenges, necessitating a nuanced approach to address the intricacies of diverse rail networks. One prominent challenge lies in the existence of varying track gauges across different regions, complicating the standardization of rolling stock. The coexistence of multiple gauges poses a substantial hurdle for manufacturers, demanding adaptable solutions to cater to the heterogeneous rail infrastructure prevalent throughout the continent.
Furthermore, the divergent train control and safety systems employed across European rail networks contribute to the industry's complexity. Harmonizing these systems to ensure seamless interoperability remains a persistent challenge, requiring concerted efforts from stakeholders to establish standardized protocols and enhance overall rail safety.
Additionally, the demand for rail equipment tailored to specific operational needs further compounds the challenges faced by the industry. Customers, including railway operators and maintenance entities, exhibit diverse requirements for working tools and machinery, necessitating versatile and customizable solutions. The ability to deliver equipment that aligns with varied operational demands is imperative for manufacturers aiming to thrive in this dynamic and demanding sector.
In essence, the contemporary European rail vehicle industry grapples with the harmonization of diverse track gauges, the integration of disparate safety systems, and the provision of versatile equipment tailored to multifaceted operational requirements. Addressing these challenges requires a collaborative and innovative approach to ensure the sustained efficiency and advancement of rail transport across the continent.
What are some potential solutions?
In the dynamic landscape of rail vehicle manufacturing, customer expectations hinge on the delivery of proven solutions that not only meet stringent quality standards but are also economically viable. Striking a delicate balance between diverse customer requirements and the cost-effective application of established technologies poses a significant challenge.
WINDHOFF, in addressing the varied demands of its clientele while employing proven technologies for smaller production volumes, has strategically embraced a solution-oriented approach: modularity.
Modularity stands as a key paradigm in WINDHOFF's methodology for rail vehicles, allowing the company to provide tailored solutions without compromising on the reliability and effectiveness of proven technologies. By structuring
components and systems in a modular fashion, WINDHOFF achieves a harmonious synthesis of versatility and efficiency.
This approach not only makes it easier to perform the required functions based on the modules but also ensures the costeffectiveness of the solutions offered.
WINDHOFF's commitment to modularity reflects a strategic alignment with the evolving demands of the rail industry. This method underscores the company's dedication to delivering solutions that seamlessly blend quality, adaptability, and economic feasibility. In essence, modularity emerges as a cornerstone in WINDHOFF's pursuit of providing cutting-edge solutions within the realm of rail vehicle manufacturing.
What is your Unique Selling Point?
In our latest generation of Mainline MultiPurpose Vehicles, the ‘MPV® VentuS®,’ a pioneering approach to design is evident. Both the drive components and working equipment are ingeniously organized into modular units. Each module is meticulously defined by a pre-established space and corresponding interfaces, ensuring a standardized and efficient integration process. This modular design not only enhances versatility but also streamlines maintenance and support, embodying a sophisticated engineering solution for the evolving demands of the railway industry. The ‘MPV® VentuS®’ exemplifies our commitment to cutting-edge technology and modular innovation in the realm of rail vehicle development.
How passionate are you about sustainability in the rail sector?
The conceptual approach of modularity significantly influences the sustainability of our vehicles. The interchangeability and expandability of drive modules allow for adaptable vehicle concepts over their lifecycle. In response to new regulations or technological leaps, the vehicle configuration can be easily adjusted. While the future of propulsion technology remains uncertain, modularity ensures that our vehicles will stay aligned with cutting-edge technology. This forward-thinking design not only extends the longevity of our products but also underscores our commitment to staying at the forefront of technological advancements, thus future-proofing our vehicles in a dynamic and evolving landscape.
How has technology developed since the last years?
In recent years, the technical requirements within the field of rail vehicle technology, particularly in the realm of propulsion, have undergone heightened stringency. Noteworthy developments include the imposition of stringent limits on exhaust
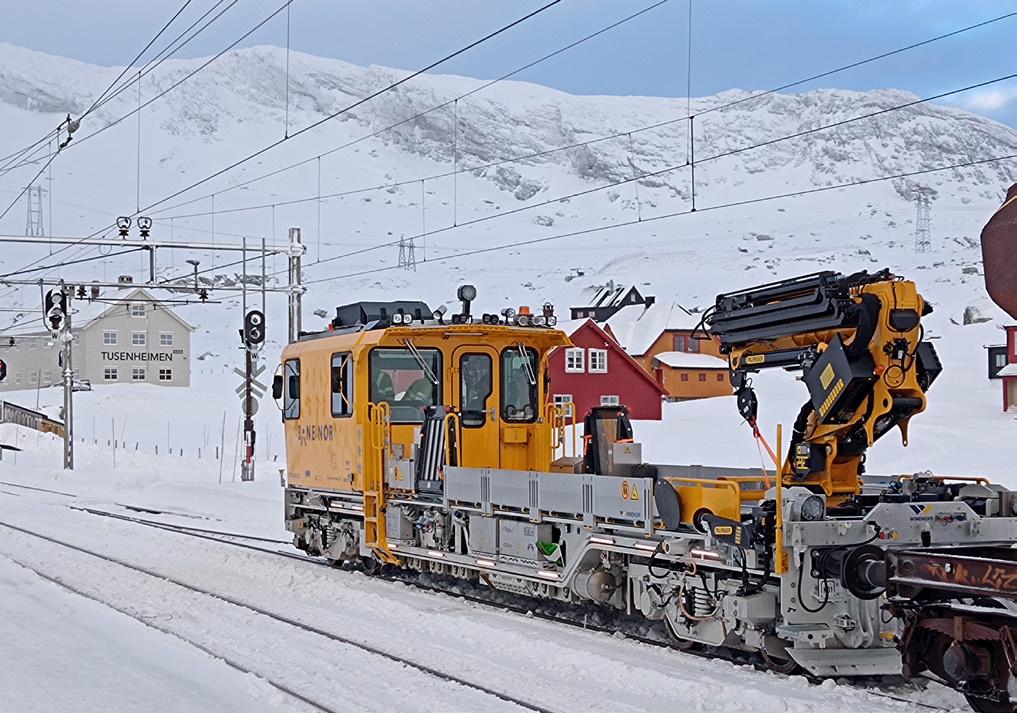
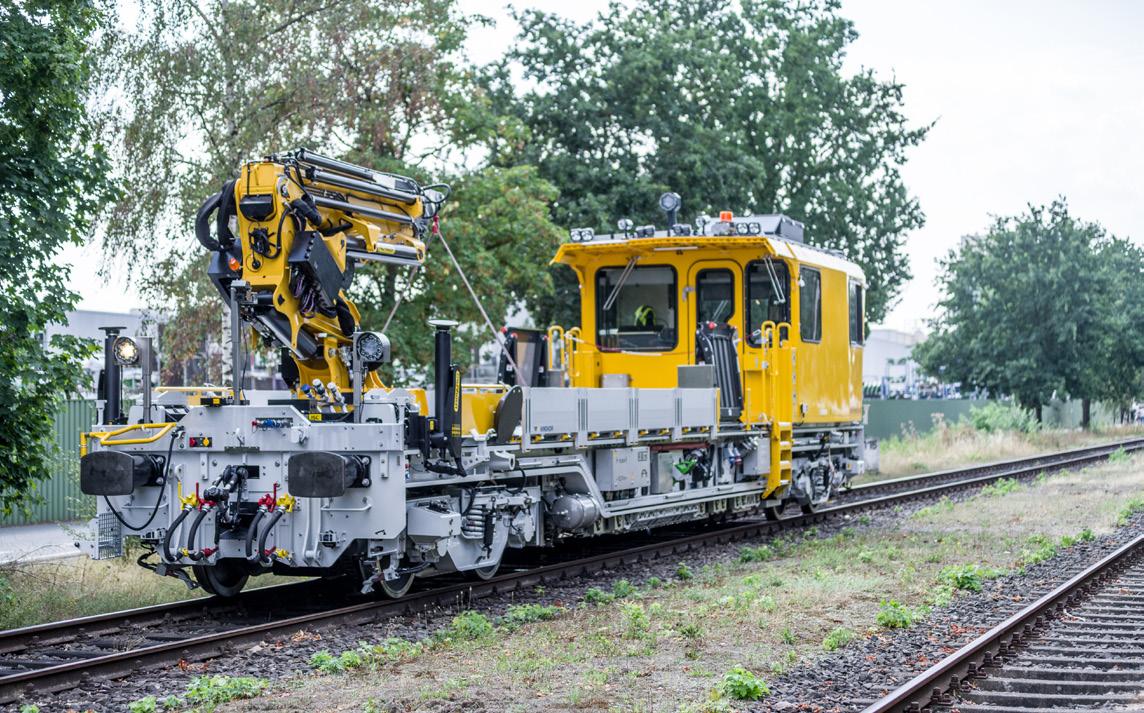
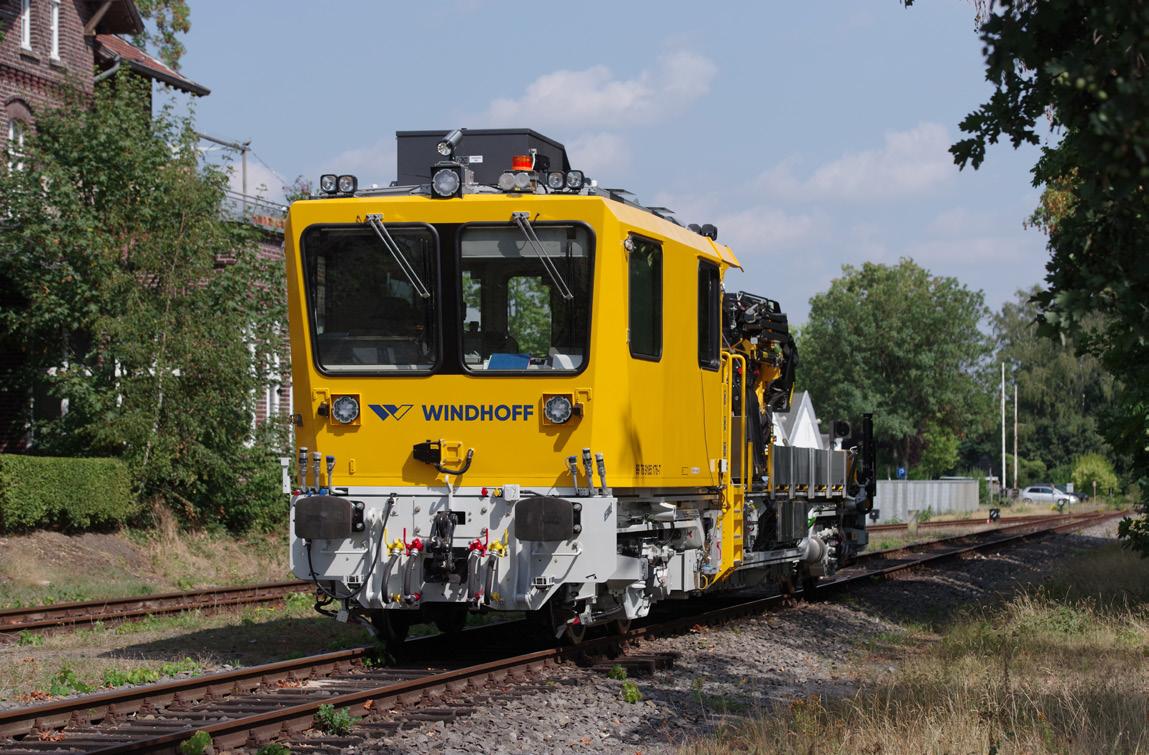
emissions, a concerted effort to diminish noise emissions at construction sites, and an overarching commitment from vehicle operators to achieve emission-free operation for both commuting and on-site work. These evolving standards underscore the industry's dedication to environmental sustainability and reflect a collective endeavor to advance rail vehicle technology in alignment with contemporary environmental and operational imperatives.
When a client comes to you with a particular problem, what’s your process for coming up with a solution, and how closely do you work with clients throughout the projects?
We firmly believe in the pivotal role of collaboration between the client and the manufacturer for the success of a development project involving the creation and production of auxiliary vehicles. Continuous client involvement in the product development process ensures accurate comprehension of requirements by the manufacturer and precise formulation by the client, establishing a shared understanding. To facilitate this, we have integrated joint quality gates within our development and manufacturing processes, aiming for maximum transparency with the client. This approach fosters a
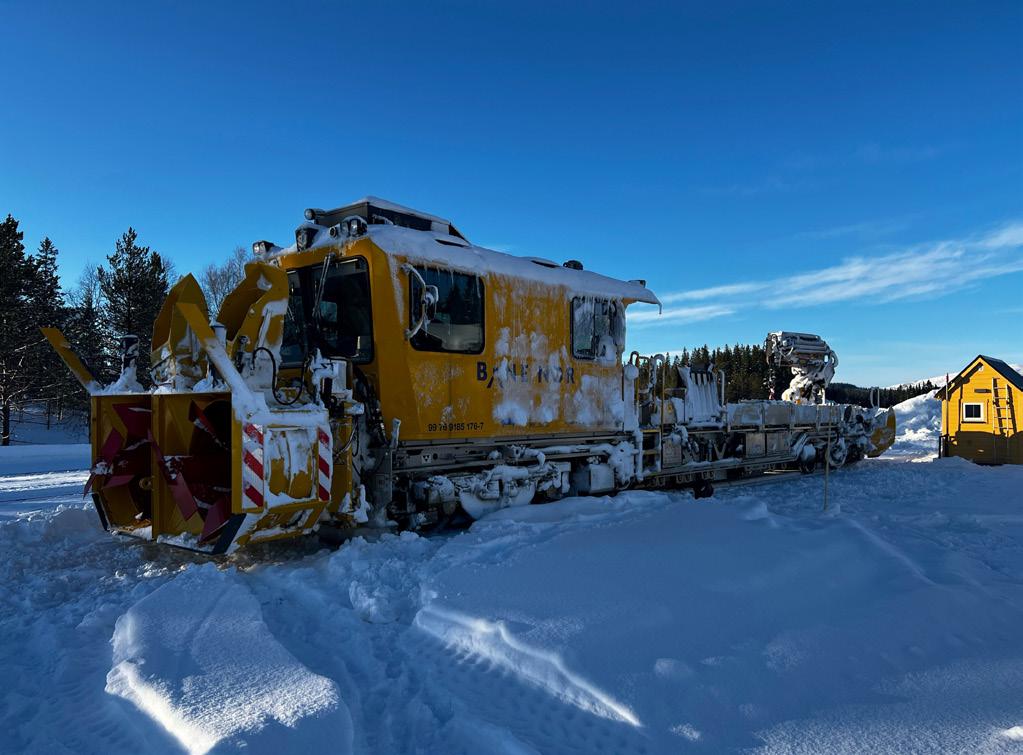
synergistic partnership, promoting effective communication, and enhancing the likelihood of a development project's success through shared insights and collaborative decision-making.
What are some major projects you’re currently working on?
Our modular system, the ‘MPV® VentuS®,’ has been available in the market for approximately four years, yielding diverse projects. Notably, we are currently engaged in a collaborative venture with the Norwegian State Railways, Bane NOR, involving the development of twelve vehicles. Additionally, we have partnered with the German State Railways on a separate project. The cumulative result of these endeavours underscores the success of our modular strategy, with a total of 30 MPV® VentuS® units ordered over the past four years. This substantiates the efficacy and acceptance of our modular approach within the industry.
What are some of the biggest challenges this sector currently faces?
Among the most significant challenges facing the rail vehicle sector are political constraints. Financial planning uncertainties and extensive bureaucratic hurdles, particularly concerning vehicle
approvals, pose considerable obstacles. Consequently, these challenges significantly impact delivery times and economics, despite the essential role that construction and maintenance vehicles play in fostering a robust rail infrastructure. Navigating these political intricacies requires industry stakeholders to implement strategic measures, ensuring timely and costeffective solutions that contribute to the sustained health and development of rail transportation networks.
How can we make the rail industry a place people want to work in?
The rail sector is already a popular working environment for various reasons. Firstly, it provides a sense of contributing to critical infrastructure, offering professionals a fulfilling and impactful role. The industry also boasts job stability, a key attraction for many seeking reliable career paths. To further enhance its appeal, the rail sector could focus on promoting innovation and adopting sustainable practices, aligning with evolving societal expectations. Investing in professional development programs and fostering a collaborative and inclusive workplace culture would also contribute to making the rail sector an even more desirable and sought-after working environment.
Brent Cross West to Transform Area
On Sunday 10 December 2023, Brent Cross West, London’s new mainline railway station welcomed its first passengers

The new Thameslink station is the first to be built in London in over a decade and led by Barnet Council, is one of only a handful of new railway stations to be delivered by a local authority. It is a massive achievement for us and our partners.
The station is a huge 7,000 square ft and 16 metres tall with four platforms. Architecturally the steelwork and feature canopies are a unique design feature, and in the station’s eastern entrance sustainability has been a key focus with strong timber frames that are a long-lasting natural alternative to steel and concrete.
With an estimated 5000 people visiting the station on opening day alone the feedback has been resoundingly positive, and it was a joy to see visitors including many local people enjoying the activities alongside the official celebrations, which were led by Mayor of London Sadiq Khan.
But the Brent Cross West programme has been about more than just the physical station.
Over £100 million has been invested in new sidings and rail systems needed to accommodate the new station. We also worked hard to ensure passive provision for the proposed West London Orbital was
incorporated into Brent Cross West’s design now rather than in the future.
A new overbridge gives pedestrians the ability to cross this part of the Midland Main Line for the first time since it was built more than 150 years ago, linking communities on both sides of the station, making it much easier to get around the area. Thameslink trains connect the area to central London in as little as twelve minutes, with up to eight trains an hour at peak times, and direct connections to Luton Airport and Elizabeth Line services. New planned TfL bus services along with improved walking and cycling routes all help encourage sustainable travel.
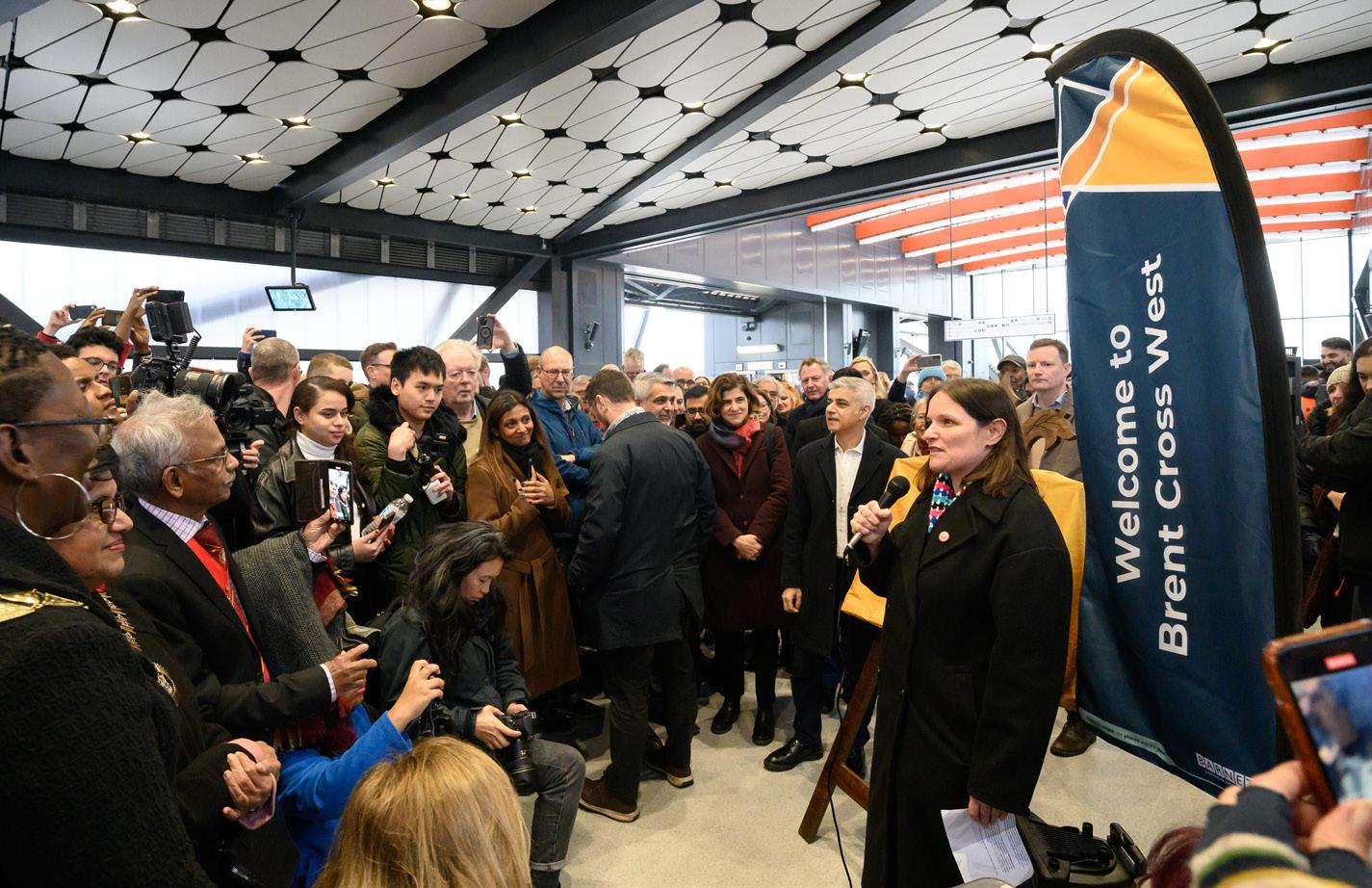
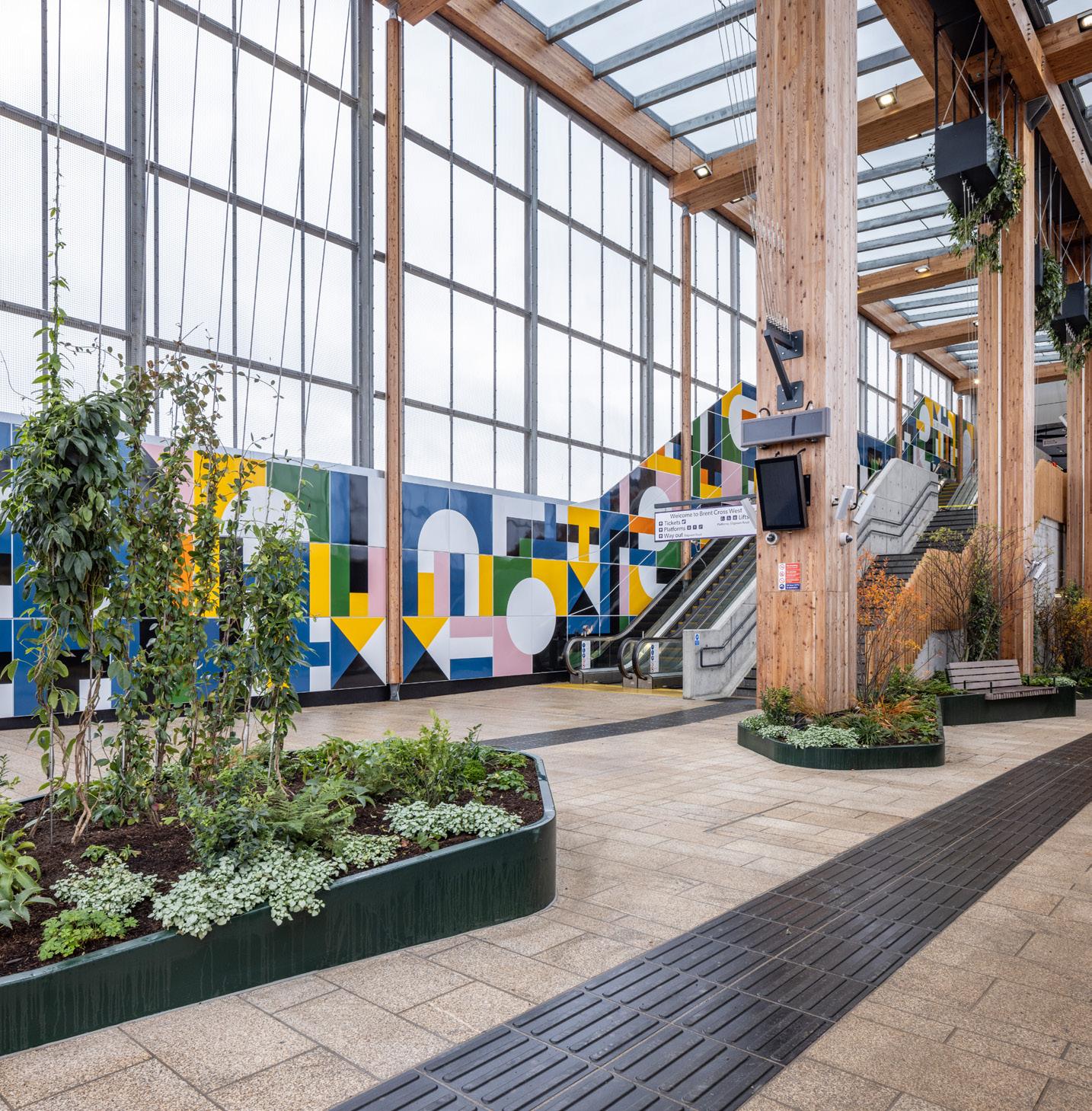
And, importantly, Brent Cross West is also the catalyst to deliver much needed housing and investment into this part of the Borough. It is the gateway to Brent Cross Town the 180-acre, £8 billion net zero park town that is being delivered in partnership between Barnet Council and Related Argent. In future the new neighbourhood will provide 6,700 new homes, create 25,000 jobs, and provide all the necessary retail, leisure and community facilities
residents need all within the footprint of predominantly underused industrial area.
Anyone visiting the area will already get a taste of things to come as the regeneration programme, one of the biggest in Europe, continues at pace. New parks, public art, and locally run businesses have already been delivered, and the first residential blocks are well underway, offering affordable homes, market sale and build to rent apartments, and student accommodation.
Space is cleared right next to the station to start building the first office block, home to Sheffield Hallam University’s new London campus.
Brent Cross West makes Brent Cross Town possible and was one of the key drivers for Barnet Council to step in and ensure the new station was built when the original developers deferred their commitments to delivering the relevant infrastructure to make the whole scheme viable. Not only did we step in but we also rephased the planning consent to bring forward the completion of the station early in the development. This not only increases desirability for prospective investment partners and occupiers, but ensures existing communities benefit from the transformation of the area early on.
As a local authority spearheading the programme, we also set ambitious social value targets, with over 100 Barnet residents helping to build Brent Cross West and over 20 per cent of the local workforce from Barnet and neighbouring boroughs Brent and Camden.
We wanted to provide more training and opportunities to local people, from a range of backgrounds and through a range of routes. Five young people were recruited as part of the government’s Kickstart Scheme as well as apprentices, and more were given the opportunity to learn about careers in construction through tours given by teams working on site. We also worked hard to encourage more women to get involved in different roles on the project, including through work placements.
We employed local businesses where possible including family-owned social enterprise Tarem Services for cleaning, and local business owner Emma Blackman who ran the staff canteen.
Of course, building the new station wasn’t without its challenges and our teams have learned a lot. Thanks must go to Mace, who project managed the programme on our behalf, VolkerFitzpatrick who built the station, Govia Thameslink Railway, and Network Rail who has been a key programme partner.
Brent Cross West and associated rail works have been funded as part of a £419 million government funding agreement which Barnet Council has secured through close collaboration with Central Government partners from the Department for Levelling Up, Housing and Communities, HM Treasury and the Greater London Authority.
Find out more about Brent Cross West at transformingbx.co.uk
Councillor Alan Schneiderman is Cabinet Member for Environment and Climate Change at Barnet Council. Barnet Council led the programme to build Brent Cross West, it is one of the first local authorities in England to deliver a rail infrastructure project.
Open Heart Surgery at Gatwick Airport Station
Gatwick Airport Station has undergone a huge upgrade in capacity and accessibility – all while remaining operational 24-7
Any UK rail expert or enthusiast travelling through Gatwick Airport Station will notice something different about it, compared to every other Network Rail station. Rather than the standard blue-and-white or black-and-white signage, Gatwick’s signs match those at the airport: yellow lettering or pictograms on a black background.
It may be a small detail. But it’s also a visible illustration of how the various stakeholders in this landmark station upgrade project have been willing to compromise, with the ultimate, shared goal being to improve the end-to-end passenger journey.
‘This was the most collaborative project I have worked on, and I’m not the only one to have said that’ says Jordan Gill, principal architect at SYSTRA, which was lead designer for design-and-build contractor Costain. In practical terms this meant that all the stakeholders involved – Network Rail, Gatwick Airport and train operator GTR – had to give and take when it came to achieving their aspirations.
The result is a station with more than double the circulation space, improved accessibility and a sleek new look befitting of a major gateway into the UK. The upgrade has added a new concourse to the station with a striking vaulted roof; widened platforms 5 and 6; remodelled the existing
concourse; added eight escalators and five lifts; and built a new two-storey staff accommodation and back-of-house building on an adjacent piece of land purchased from Gatwick Airport by Network Rail.
And, since this is the UK’s second busiest airport, trains had to keep running throughout the construction period, 24 hours a day, seven days a week. Gatwick Airport Station has seven platforms for services from Gatwick Express, Thameslink and Southern and Great Western Railways. The only concession to the construction works was that the number of trains was reduced to 16 trains per hour rather than the usual 18, with normal service now resumed.

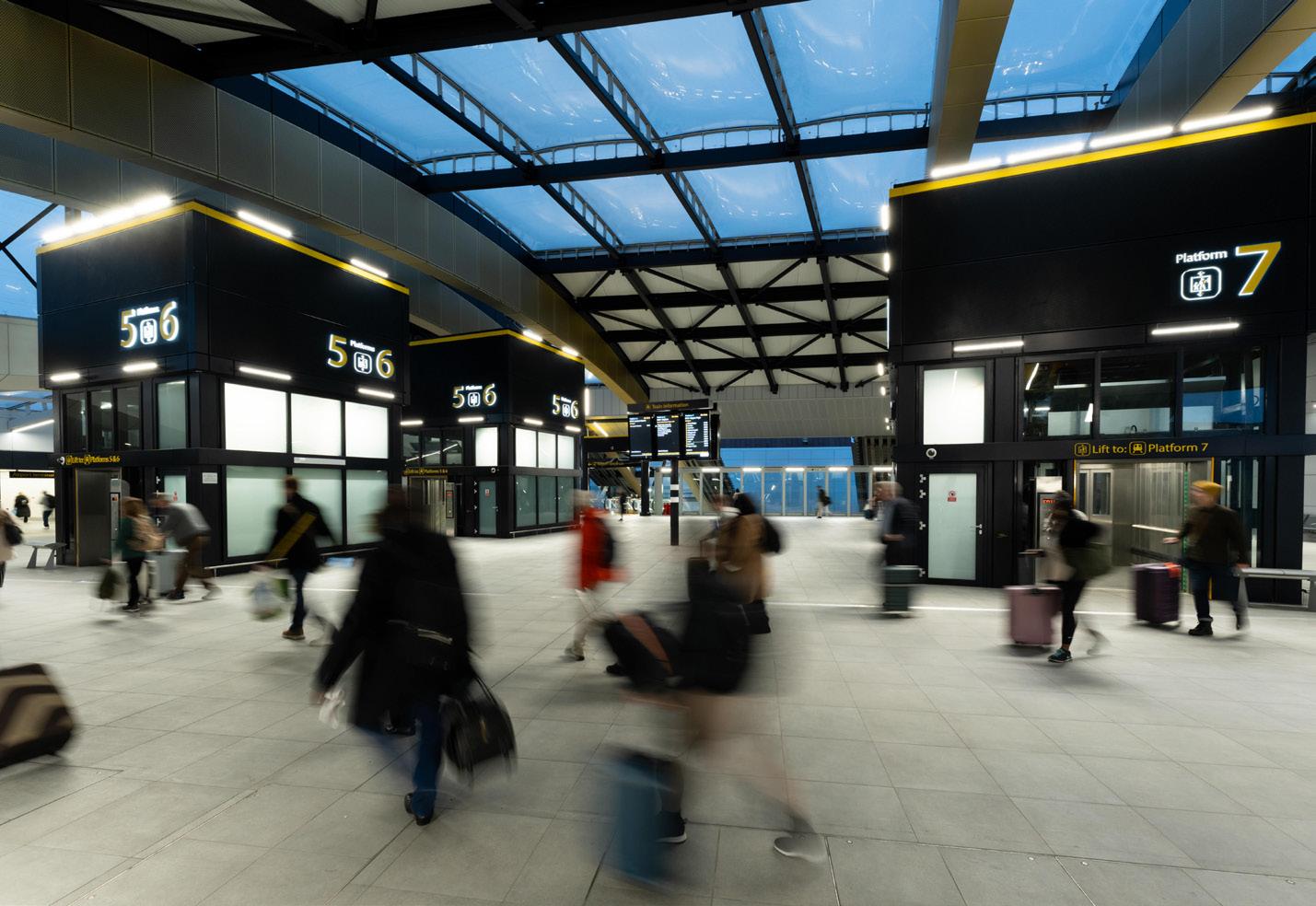
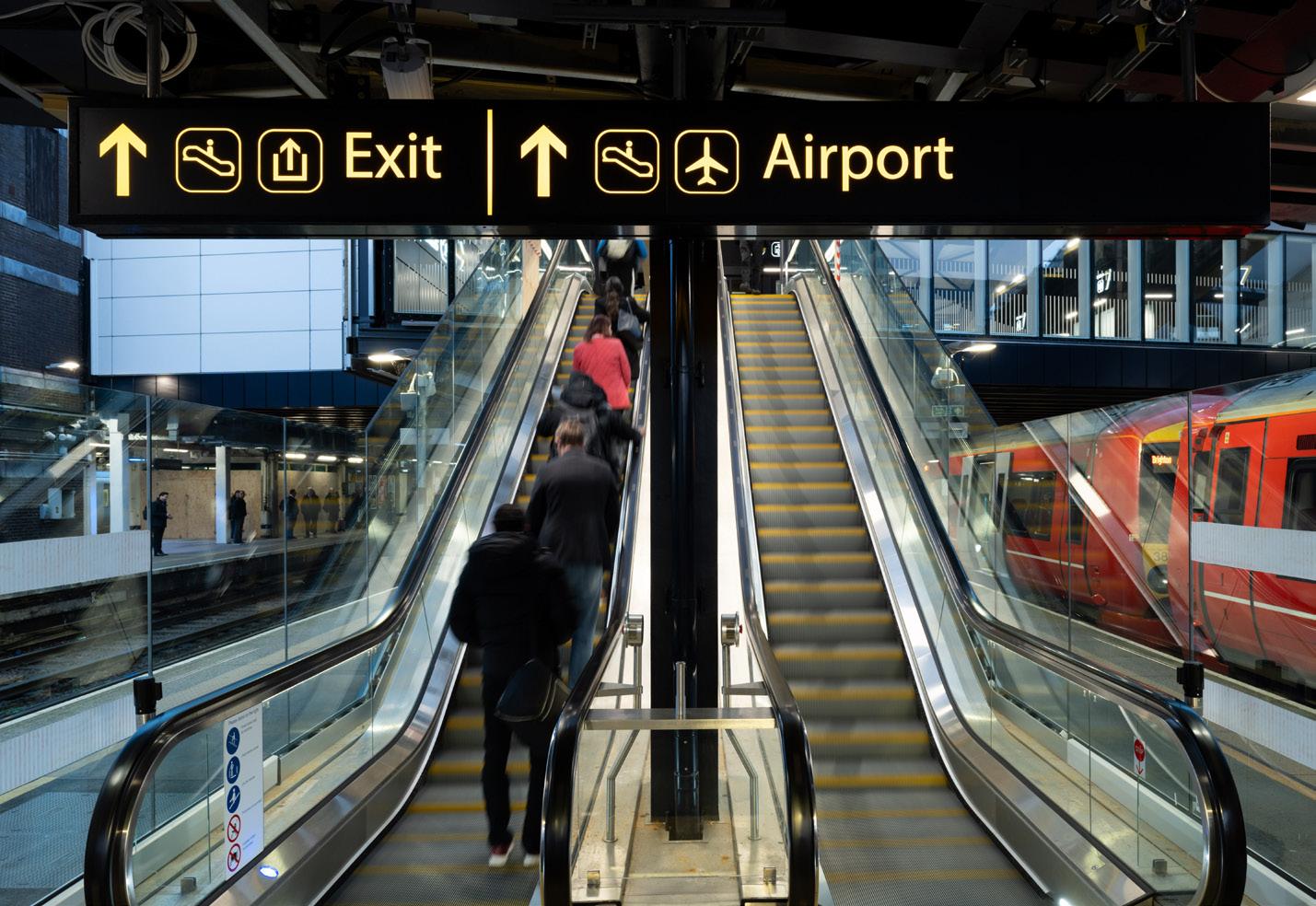
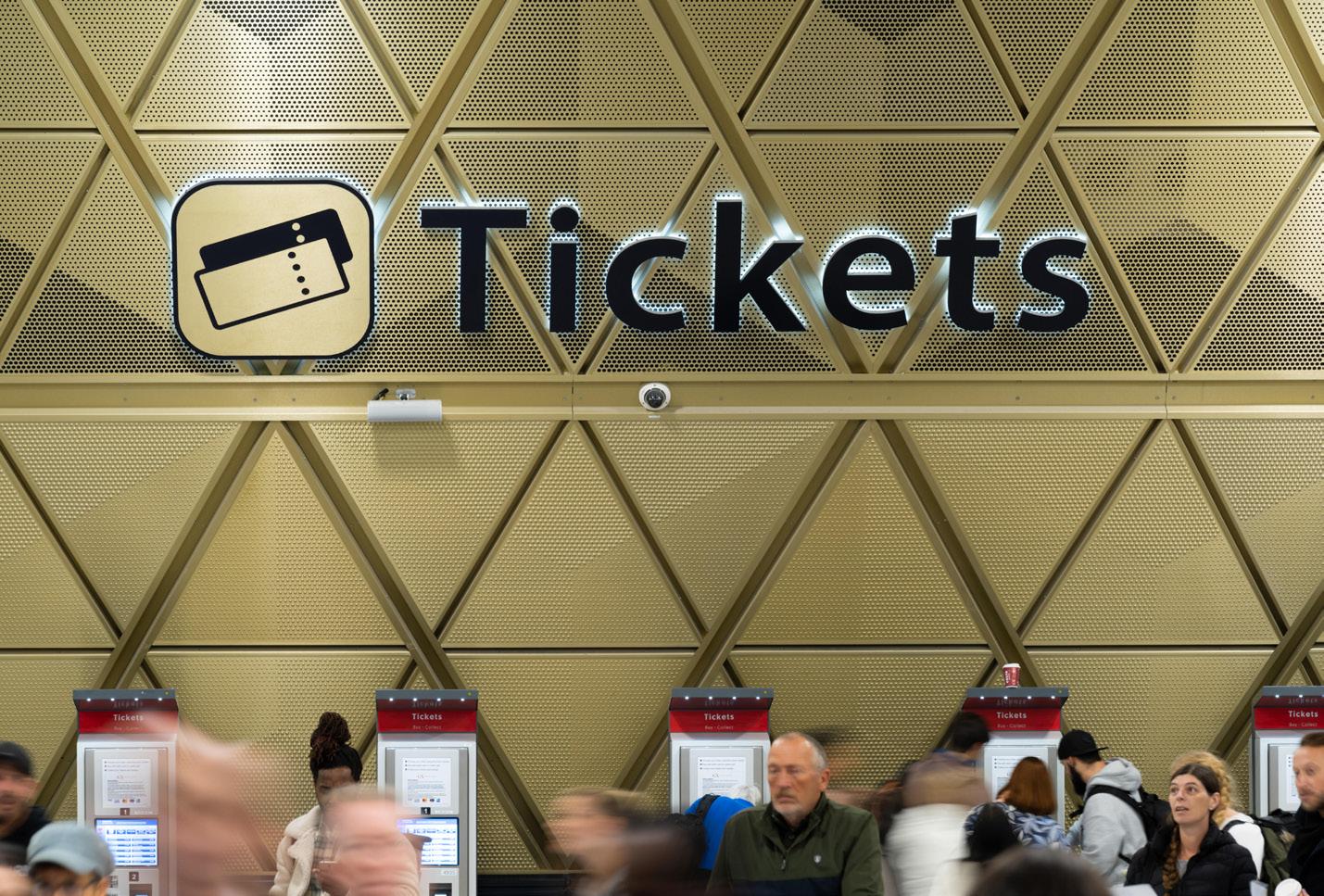
Congestion relief
Opened in May 1958, the station at Gatwick was designed for a capacity of between five million and ten million passengers each year. The airport grew around the station, and so did the number of passengers using it. In 2019, over 21 million people a year passed through it.
The old station layout saw everyone leaving and arriving via a concourse suspended over the seven tracks that pass through the station. That concourse was often crowded. There had been ad hoc additions over the years, eating away at space until only 21 per cent of its floor area was available for circulation.
The result was congestion and overcrowding, delayed journeys, frustrated passengers and increased safety risks. Without intervention, things would only have got worse. The airport expects to see 67 million passengers a year by 2028 and has ambitions to increase the proportion of people arriving by train from 42 per cent currently to 50 per cent by 2040.
Network Rail commissioned Costain, with SYSTRA, in 2016 to deliver planning and design and then to carry out the construction phase which began in June 2019. ‘We were involved very early, which is quite rare’ says Jordan.
Although Costain’s contract covered only the station, the project team thought through passenger journeys beyond the station in designing the upgrade. So, for instance, Gatwick Airport made changes to the way that passengers flow to and from the station in the South Terminal. And GTR made changes at Victoria to ensure that passengers arriving on the Gatwick Express were spread out down its length rather than concentrated in fewer carriages.
‘The whole design was led by a focus on the passengers’ says Gill. ‘We looked at the passenger journey from train to plain and plain to train.’
Modelling of passenger flows took into account the fact that passengers could be transporting luggage or moving with children. ‘We had to think about people who did not have English as their first language or who were restricted because of baggage or children and we made spaces bigger to account for that’ says Gill. ‘An airport can be a stressful environment and we wanted to reduce the potential for stress as far as possible.’
There were multiple other accessibility improvements included in the upgrade such as tactile signage, including braille and hearing loops at key points along the routes in and out of the station. A special assistance point, which is operational 24-7, means that passengers who need help can be transferred smoothly from airport to station operator, and vice versa.
Competing priorities
Like many infrastructure projects, one of the early hurdles the project team had to clear was budgetary constraints against a
backdrop of competing priorities for the three main stakeholders. ‘Network Rail were most concerned about safety and capacity. GTR were focused on station operations and were keen on investment prioritised in the existing concourse and Gatwick Airport wanted investment in the new concourse because that is the element that welcomes passengers to Gatwick’ says Gill.
There were difficult conversations at times, says Gill, but issues were resolved with a ‘project first’ perspective. So, for instance, plans to refresh the existing overbridges above the tracks were pared back to a basic refurbishment so that funds could be used elsewhere. Revamping platforms 1 to 4 were not in the project scope.
Solutions other than constructing additional concourse space were initially on the table. One option was extending the existing concourse; this was rejected since adding to a 1950s structure was deemed too complex and inefficient. Another possibility was building a much bigger new concourse while converting the existing one to staff accommodation.
The chosen plan, however, was to demolish footbridges over platforms 5 and 6 and 7 and replace them with a new concourse which would be dedicated to passengers arriving at the station. Meanwhile, the existing concourse would be repurposed for passengers travelling away from Gatwick Airport. Circulation space on the existing concourse was won back by removing the ticket office, the Station Control Room, staff accommodation and other clutter that had accumulated over the years.
The scheme moved the track on platform 6 towards platform 7 to allow the widening of platforms 5 and 6. Network Rail also took the opportunity to remodel the track in the Gatwick area to speed up journeys for passengers on the Brighton Main Line, aiming to shave five minutes off the journey times for each of the 30 trains which pass through the station every day.
From a technical perspective, the big ask was working out how to execute all the work, while the station remained operational 24-7. Costain’s construction and logistics knowhow fed into design decisions with early involvement from some of the key specialist contractors, such as the lift and escalator suppliers Express and Kone, the steelwork contractor Kilnbridge, building envelope specialist Prater and the mechanical and electrical contractor Emico.
‘The position of the toes of the escalators set out the layout for the whole building’ explains Gill. ‘The size and width of the escalators decided how far we had to move platforms 5 and 6 to get the minimum widths of 2.5 metres. If we had waited for that information until later, or a different supplier had come with a wider escalator, the platform would have had to move and then so would the track which, in turn, would influence the tracks to the North and South for miles.’
Input from Kilnbridge was vitally importing in designing the assembly method for the steel roof trusses over the new concourse. Gill describes the project as a ‘letterbox site’, with train lines below it, planes above and a 24-7 airport on all sides which limited the size of crane that could be used. The four steel trusses for the new arched roof had to be delivered in smaller units and assembled on site with ETFE ‘pillows’ rather than glass, installed between the trusses to bring in light – and allow views of the planes and the sky.
Long-term view
The station upgrade also had to be designed with longevity in mind, from the colour scheme selected to costs of maintaining and running it. Both the new concourse – and the old one – feature neutral greys and ochres, with gold detailing, aimed to stand the test of time. Lighting has been installed at low level, or on lift shafts, so that maintenance team will not have to work at height.
Operational carbon emissions were also considered carefully in the upgrade. Various interventions add up to savings of 143.6 tonnes of carbon and £58,700 a year, according to Network Rail.
The lighting is LED throughout, which saves emissions when compared to halogen bulbs, while the station’s new escalators have an energy-saving feature which means that they run slowly when empty, speeding up when passengers walk onto them. The new two-storey back-of-house building employs a hybrid heating and cooling system to cut emissions and instant water heaters use less energy than a traditional water heating system would have done.
Significant carbon savings were made during construction due to the use of low carbon concrete which saw 70 per cent of its Portland cement content replaced with ground granulated blastfurnace slag (GGBS). This saved over 500 tonnes of carbon. Additionally, any left-over concrete from pours was turned into concrete planters, which were then donated to hospitals and schools, rather than it going to waste.
With construction works having started in June 2019, the upgraded station works were fully complete by November 2023. The long project period reflected the complexity of the operation, and all the additional temporary works needed to keep people moving through the station. But now passengers should enjoy safer, faster and easier journeys – for many years to come.
Another detail that Gill is keen to point out is a small plaque on the new station concourse commemorating the 35-year-old construction worker who sadly died on 22 July 2022 during a lifting operation on the project. A service took place when the plaque was erected involving the project team and leaders.
SYSTRA’s architecture team have worked on several railway station redesign and refurbishment projects throughout the
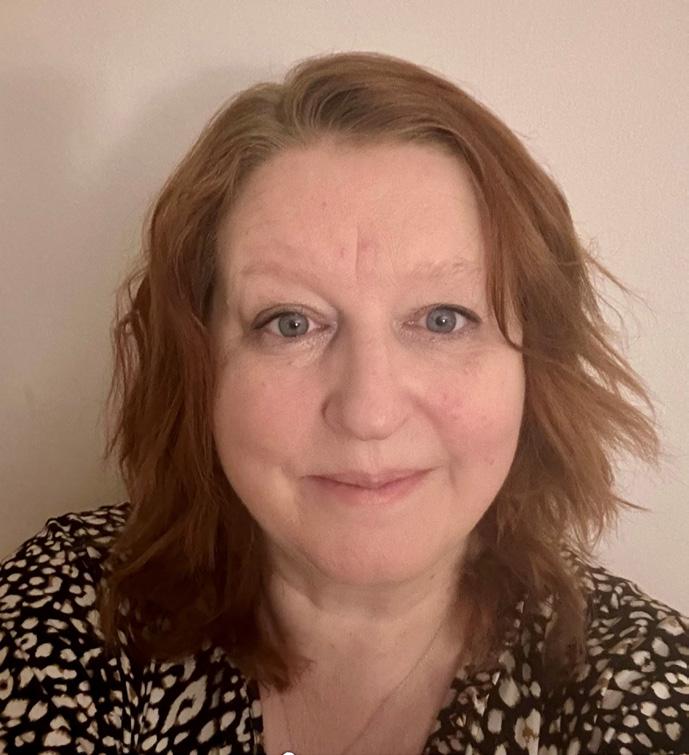
‘Around three million passengers have used the station since the new concourse opened at the end of November. The station is operating exactly as designed with platforms clearing quickly as the new lifts and escalators take people up to the new concourse and into the airport terminals in under a minute.
‘Passenger experience at the station has been transformed and the reduced platform dwell times, along with track upgrades delivered by the project, are improving reliability and journey times from the south coast to the capital and as far as away as Milton Keynes and Cambridge.
‘Delivering the Gatwick station project certainly had its challenges, including working through a global pandemic, over the 24/7 Brighton Main Line and next to the busiest single runway in Europe. These challenges were overcome through close collaboration between all parties involved in delivering the project and I’m delighted that we now have a station that is a fitting gateway to the UK for passengers arriving into or leaving from London Gatwick Airport.’
Louiza Provins, Senior Project Manager at Network RailUK including Leeds and Reading stations. SYSTRA is currently working on the design of HS2’s Old Oak Common station and is working on several new stations for the Grand Paris metro project.
Shaping the Future of Mobility
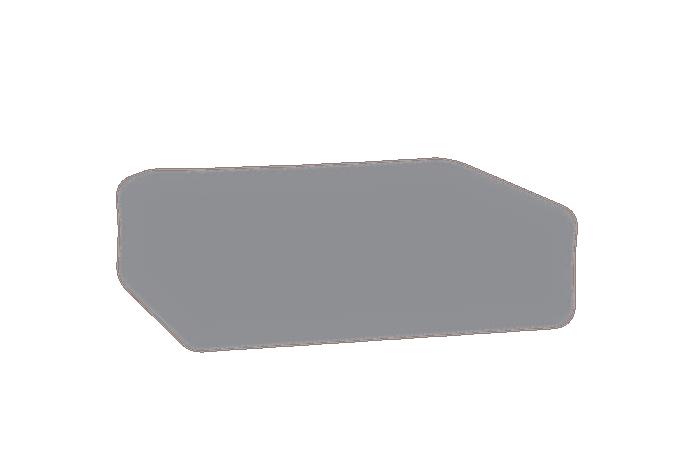
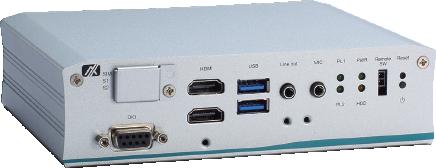
for Transportation Gateway
Fanless Embedded System with Intel Atom® Processor E3940 for Vehicle PC
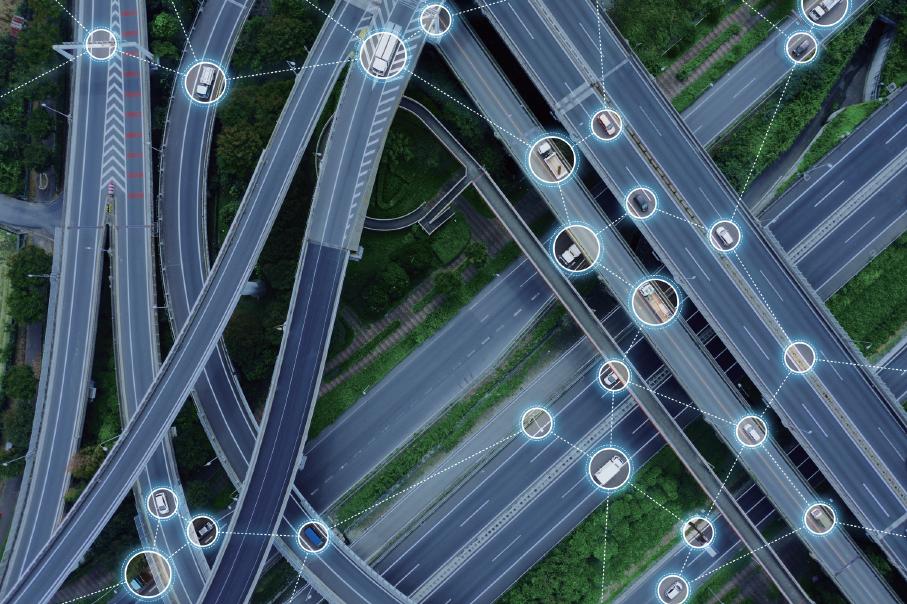
Key Features
CE and FCC certified and ISO 7637-2 compliant
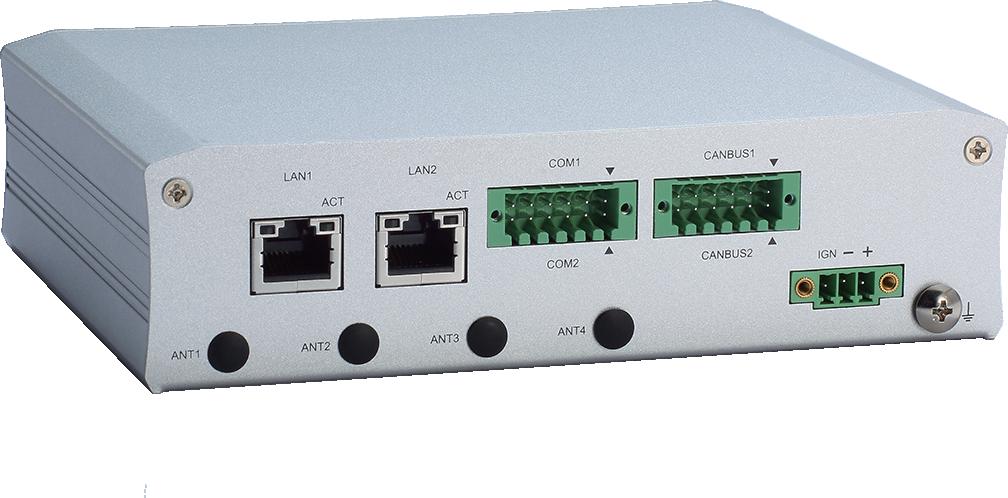
Intel Atom® processor E3940
Supports 9 to 36 VDC and 12/24 VDC typical in-vehicle power input
Smart Ignition for power on/off schedule, vehicle battery protection, and different power modes

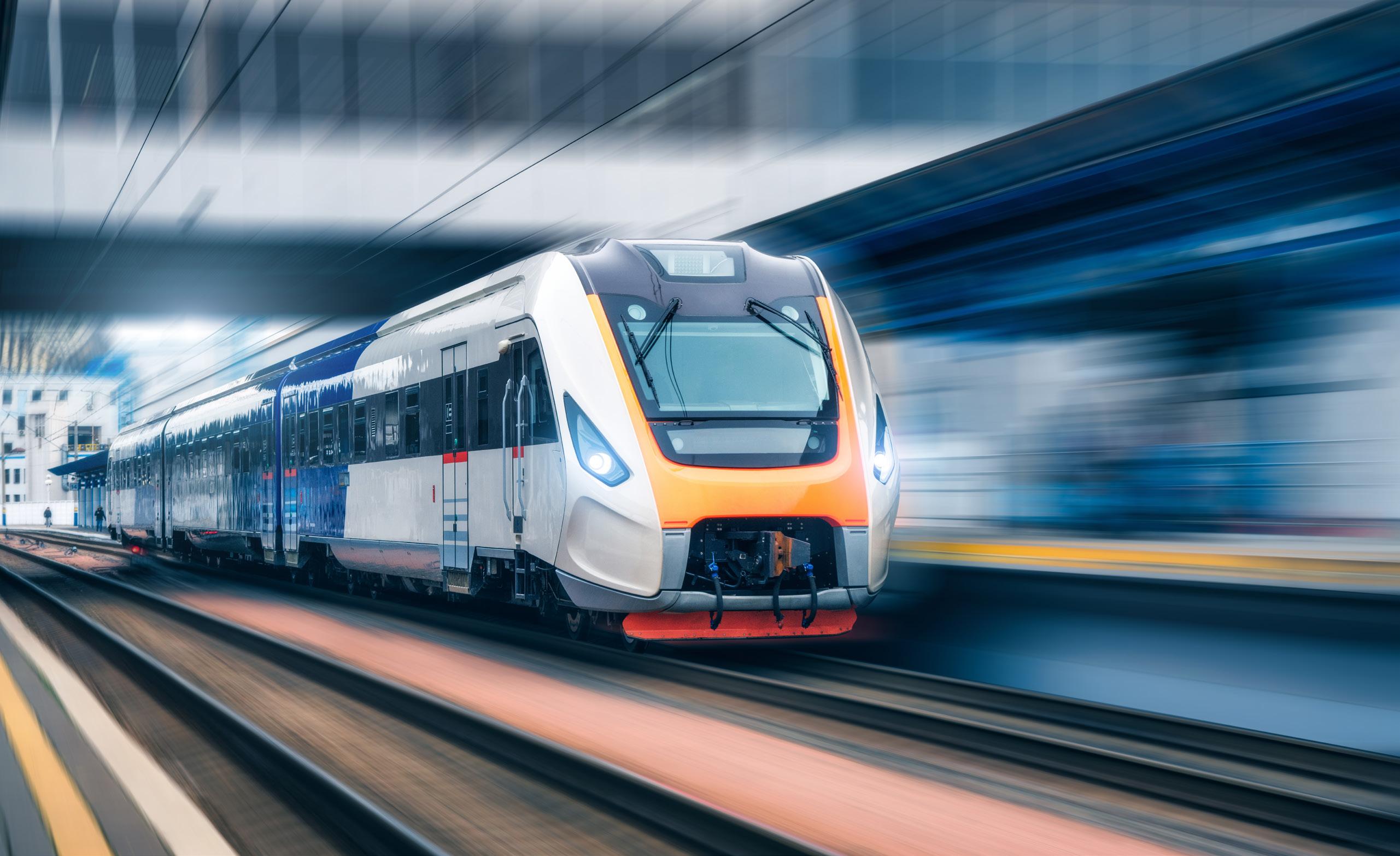
Norbar is a UK manufacturer of battery, electric, pneumatic and manually operated torque multipliers, wrenches, torque measurement equipment and bespoke torque control solutions specially developed for the rail industry
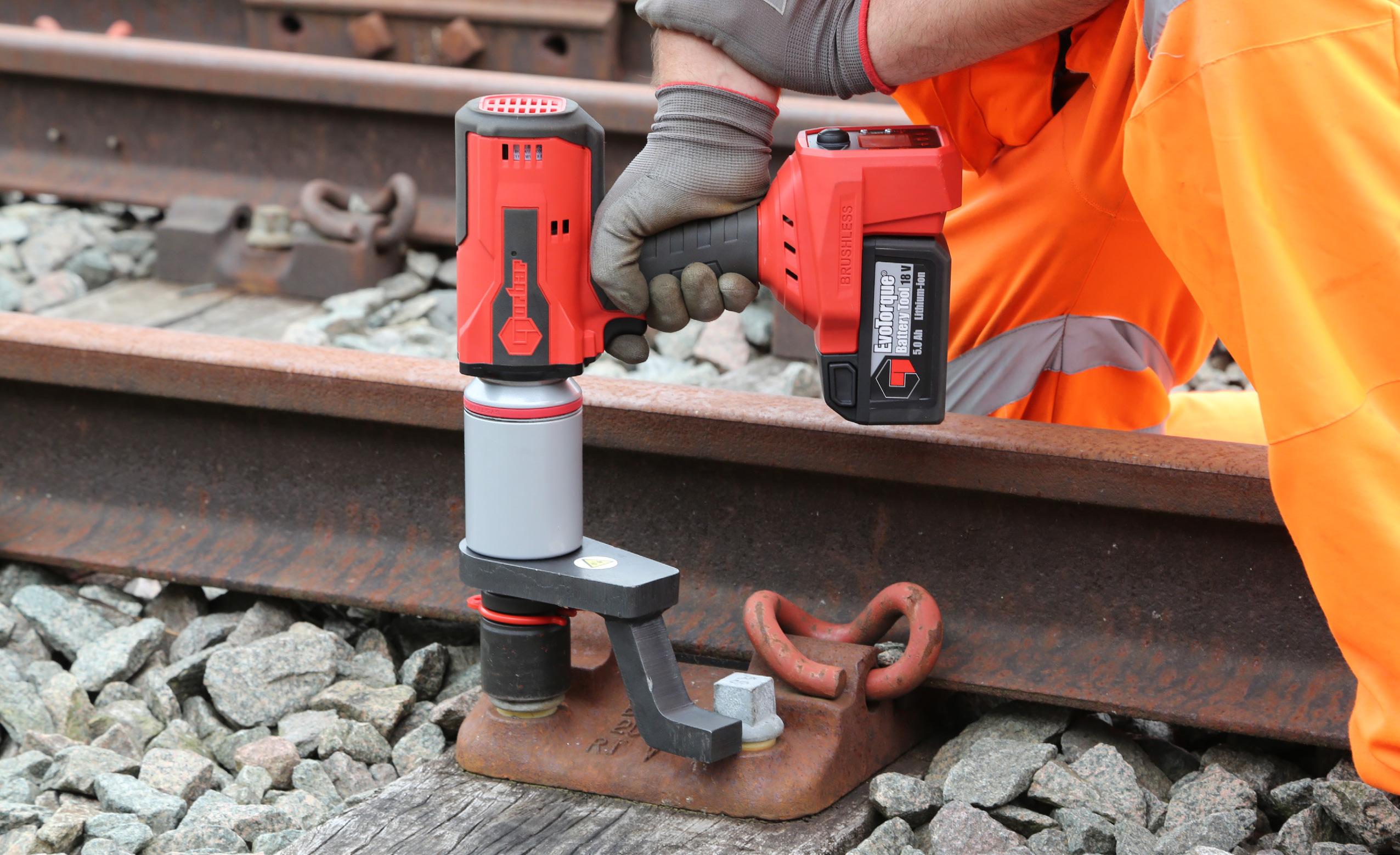
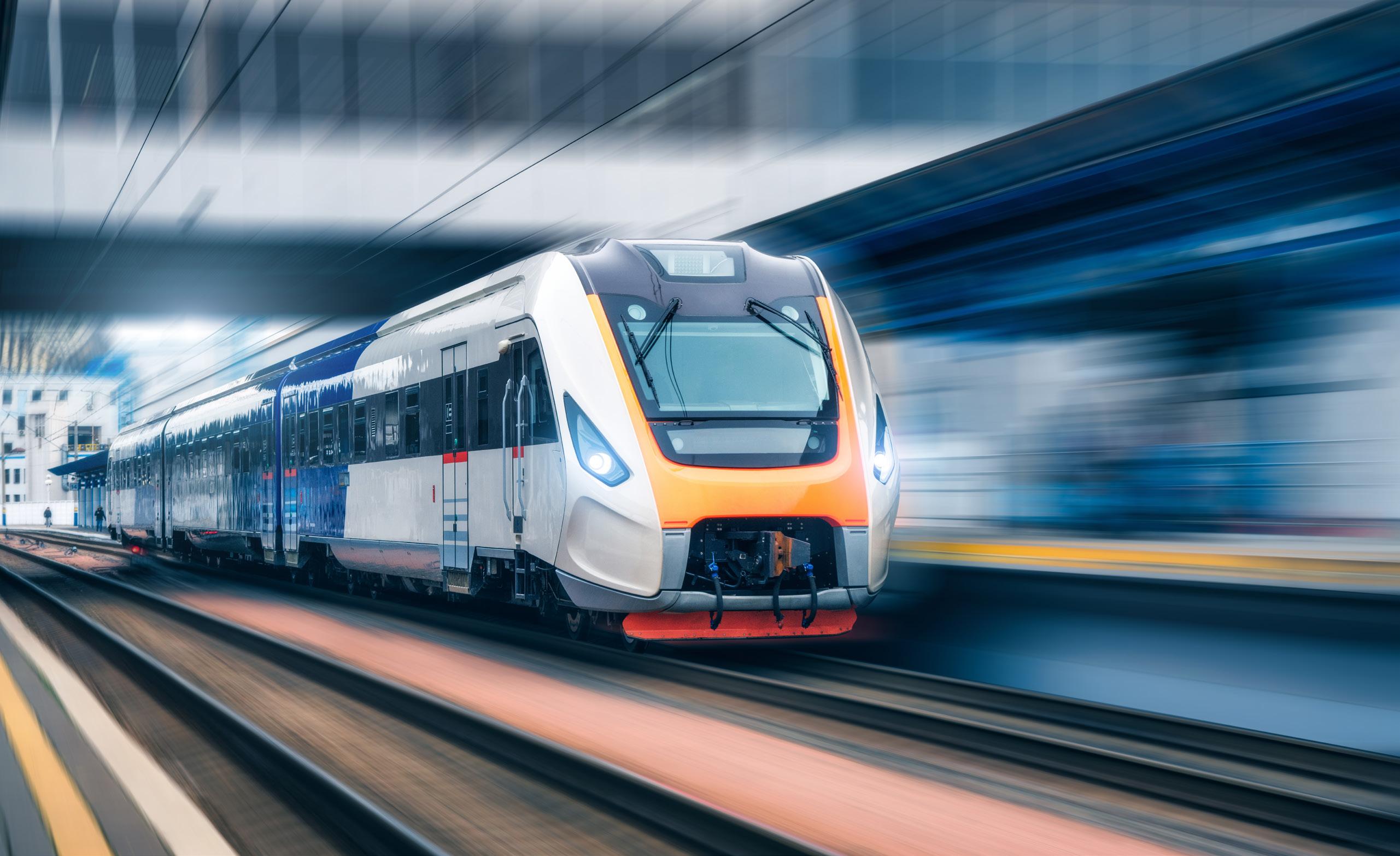
Making Stations Integral to Community Life
Jools Townsend, Chief Executive of Community Rail Network, explains how the grassroots network connecting people with their local railways is putting stations at the heart of communities via an increasingly diverse range of projects and activities
Stations are a critical part of community rail's growing momentum and impact. Station ‘adoption’, in which stations are nurtured and developed by the communities they serve, has been one of the many successes of the community rail movement, and now covers almost half of the stations on Britain’s rail network.
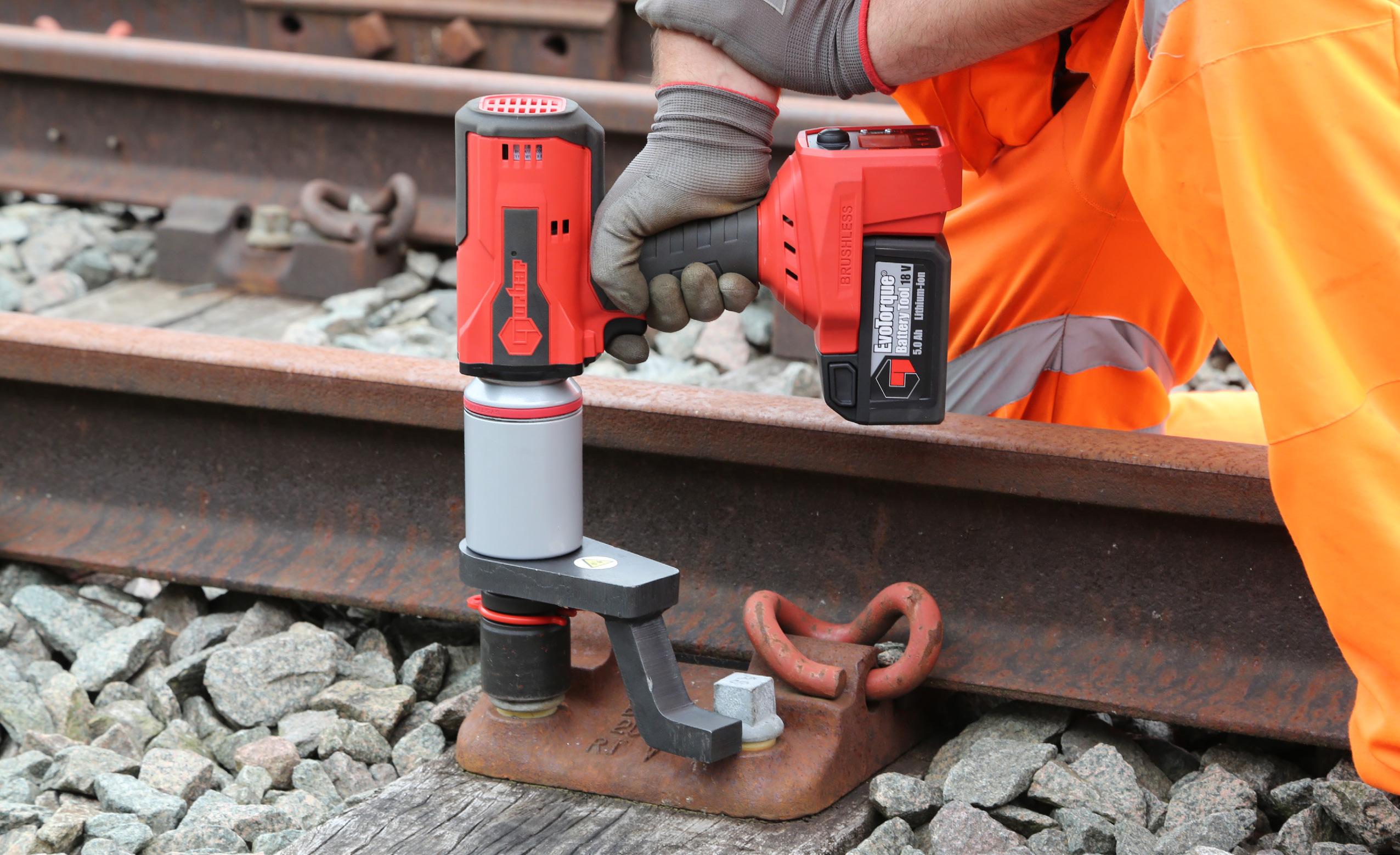
In times gone by, volunteers would assist the rail industry by reporting faults or issues and helping with basic station upkeep, but this model has now developed into something much more. There are now at least 1,200 station groups, mainly ‘Friends of’ groups, in existence – up 140 per cent from an estimated 500 in 2015 – all bringing communities together with the station as a focal point.

We work with our station group members to develop and increase their impact locally, enabling and encouraging collaboration with the rail industry and wider partners. These groups play a critical role in making their stations safe, welcoming, pleasant and attractive places, and thriving and celebratory gateways and hubs. They appreciate, and seek to promote, the notion that as well as somewhere to catch a train, and perhaps link to other modes of transport, stations can be vital local centres of social, economic, and environmental activity, integral to community life.
We are now seeing work that reaches well beyond station boundaries, and many stations are being adopted not only by volunteers interested in the station itself, but also by schools, colleges, support groups, and charities or social enterprises, who see the benefits of working in a rail environment, and opportunities for making a tangible difference to their locality.
For example, the work of one small station friends’ group can provide healthy, outdoor volunteering and food growing opportunities that give many people enjoyment, boosting health, wellbeing, cohesion, and skills. They may also promote their town, village or line for leisure and tourism, providing maps and information. They might engage local young people in creative projects, creating a sense of familiarity and ownership of the station. They might spearhead station buildings being brought back to life in a way that celebrates local identity, creating a community asset from a wasted space. The list, and the ideas that our members continue to come up with, and develop, goes on.
Promoting sustainability
Community rail is playing a vital role in enhancing environmental sustainability via biodiversity, gardening, and wildlife projects, developing stations as green spaces offering multiple benefits to communities and ecosystems. Many station groups continue to focus much of their efforts on
community gardening but are becoming increasingly aware of tailoring activities to deliver biodiversity gains, helped by us championing this work to, and encouraging links with, rail industry partners.
Groups create station and community gardens, nurture and enhance wildlife habitats, and deliver a host of awareness-raising activities such as educational programmes and food growing schemes. This type of work can have a wider impact on biodiversity and the environment by supporting community efforts to protect certain species and raising awareness among local people about everyday steps to support wildlife. For example, various station friends’ groups in Derbyshire’s High Peak area are involved in the ‘Buzzing Stations’ project, which aims to ensure that station gardens are bee-friendly habitats. As well as installing planters filled with moorland plants designed to nurture and feed bees all year round, the groups also lead bumblebee safaris in their local areas, encouraging people to appreciate the wildlife on their doorstep and get involved in protecting local bee populations.
Station groups are also crucial in encouraging more sustainable transport behaviours, and we have recently been stepping up our support for members on modal integration initiatives. They undertake walking and cycling audits to improve first and last mile connections and active travel access to and from stations, run events and workshops to promote sustainable travel, and spearhead infrastructure improvements like wayfinding, footpaths, cycle storage or waiting shelters.
Recent projects in this area include installation of a new integrated travel map
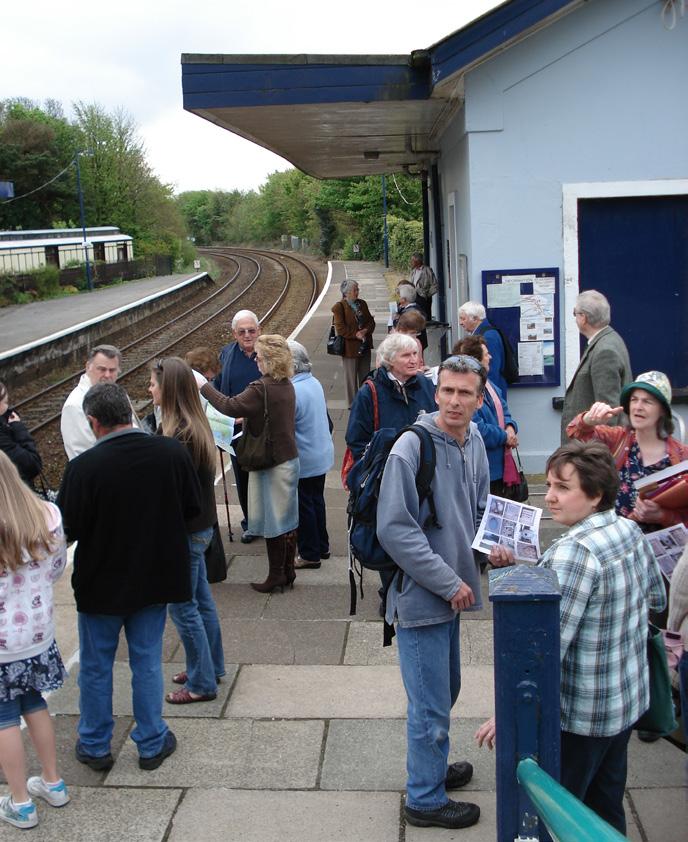
at Seaford signposting walking, wheeling, cycling and bus routes accessible from the station, and the St Germans & Area Public Transport Group in Cornwall devising and conducting a survey to examine local travel patterns and promote the case for better integration across local transport modes.
Embracing creativity and identity
Every station has its own story to tell, and station groups are constantly devising different ways to use stations to demonstrate what people love about their communities and promote local pride and a sense of place. Friends’ groups often use participatory, creative, community-led approaches, drawing on local ideas and involvement to put the community and its identity centre-stage.
This can manifest itself through artwork or poetry, heritage and history boards, celebrations of well-loved people or places, and exhibitions that portray what the station and the place it serves means to local people. One such example is the ‘talking benches’ now installed at stations across Essex including Manningtee, Braintree, and Alresford. The solar-powered benches feature a button which, when pressed, tells the story of the area using the voices of local people and/or station staff. The benches not only add to the character of stations and offer a window into the communities they serve, but also provide a place for people to connect and chat and feel connected with the area.
Taking a creative approach also sees many station groups working with young people or people who may be marginalised from rail in some way to embrace their ideas and encourage the notion that rail and rail travel is for them. Working with schools or colleges on station-based projects such as artwork or storytelling often provides a first taste of rail travel for young people, and this exposure can help to create familiarity, which in turn gets more people using stations and creates positive perceptions and relationships.
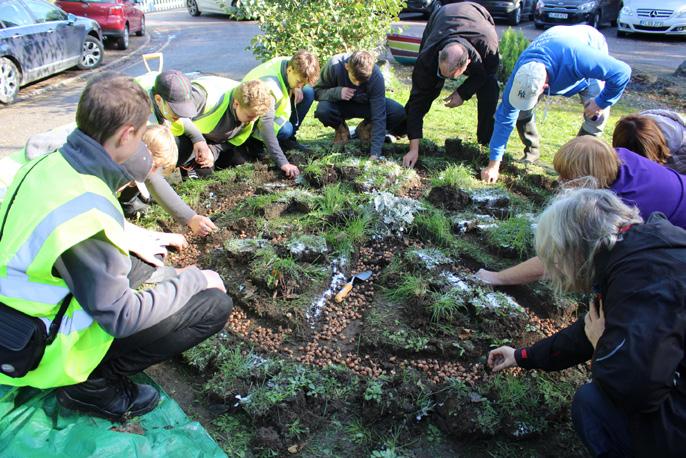
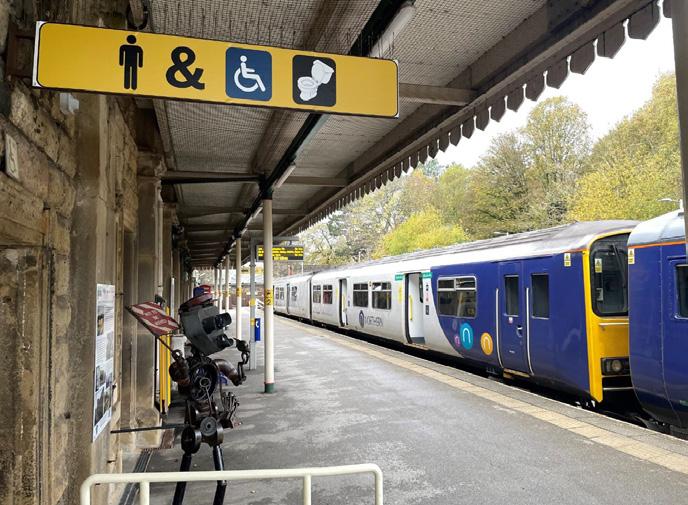
Some stations become adopted by groups who have been directly engaged in activities at stations, such as Flimby in Cumbria, which is adopted by the local village primary school, and stations on the Swale Rail Line in Kent, which are adopted by Sheppey College and provide a huge range of opportunities for students to deliver community projects, from creating promotional videos, posters and PopArt, to building and installing new station benches, planters, and birdboxes.
Developing stations as community assets
We have seen scores of projects in recent years where stations have been rejuvenated into community hubs through communityled projects supported by the railway and ourselves, with activities as varied as hospital radio stations, free food shops, community bike hires, community meeting and events spaces, art galleries, community cafes, museums and more. While common barriers to station buildings projects remain, we are continuing to work with partners including Network Rail and the Great British Railways Transition Team to help more of these schemes come to fruition.
The phase ‘bringing stations into the heart of communities’ is one we use a lot in community rail, as it sums up how community-driven activities create an improved relationship with the railway and derive greater benefit from rail assets. This not only applies to rejuvenating station buildings for community good, as we have seen recently in projects including the new community hub at Bishopstone and the community café at Shawford, but also to stations more generally.
Making a station somewhere a community can feel proud of and ownership towards in turn may widen access to rail travel by encouraging people to see rail as a part of their lives. We are seeing a
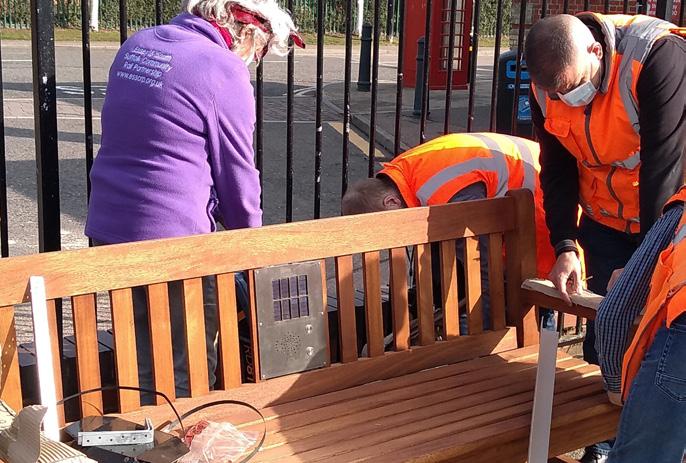
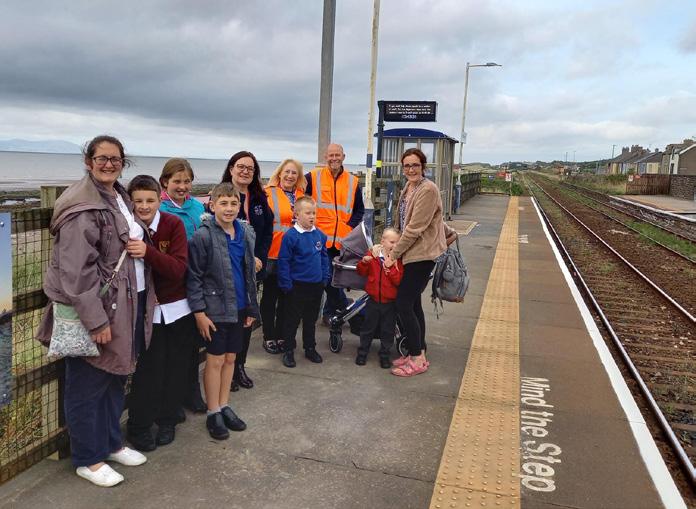
commitment to making stations welcoming and inclusive in the work of station groups via the addition of features including accessible station displays, e.g. BSL artwork, and spaces such as sensory gardens.
We are also seeing station groups like the Friends of Buxton Station widen community access by trialling dementia-friendly station signage, and charities working with marginalised groups using stations as sites to expand and diversify their work and deliver social value, such as the Newcastle branch of the St Vincent de Paul Society at Manors Station, where migrants, former homeless people, students, deaf people, and other members of the community are being supported to develop creative and sustainability-related projects.
The value of volunteers
So, who is doing all this work? Well, the driving force behind station adoption groups and projects remains an army of volunteers helping to shape community rail’s contribution to railways and society. There are more than 10,000 volunteers giving 470,000 hours of their time per year to community rail, worth £39.9 million in social value to the volunteers and their communities.
The tangibility and visibility of their efforts, and positive feedback they get, further bolsters their passion and pride, and with our ongoing support, they continue to be a huge part of the success of community rail. As the station adoption movement continues to grow and evolve, we would encourage rail industry partners to work with us to ensure their contribution cements the place of stations at the heart of communities and helps us move towards a greener, more inclusive transport future.
For more information on station adoption and community rail, visit communityrail.org.uk.
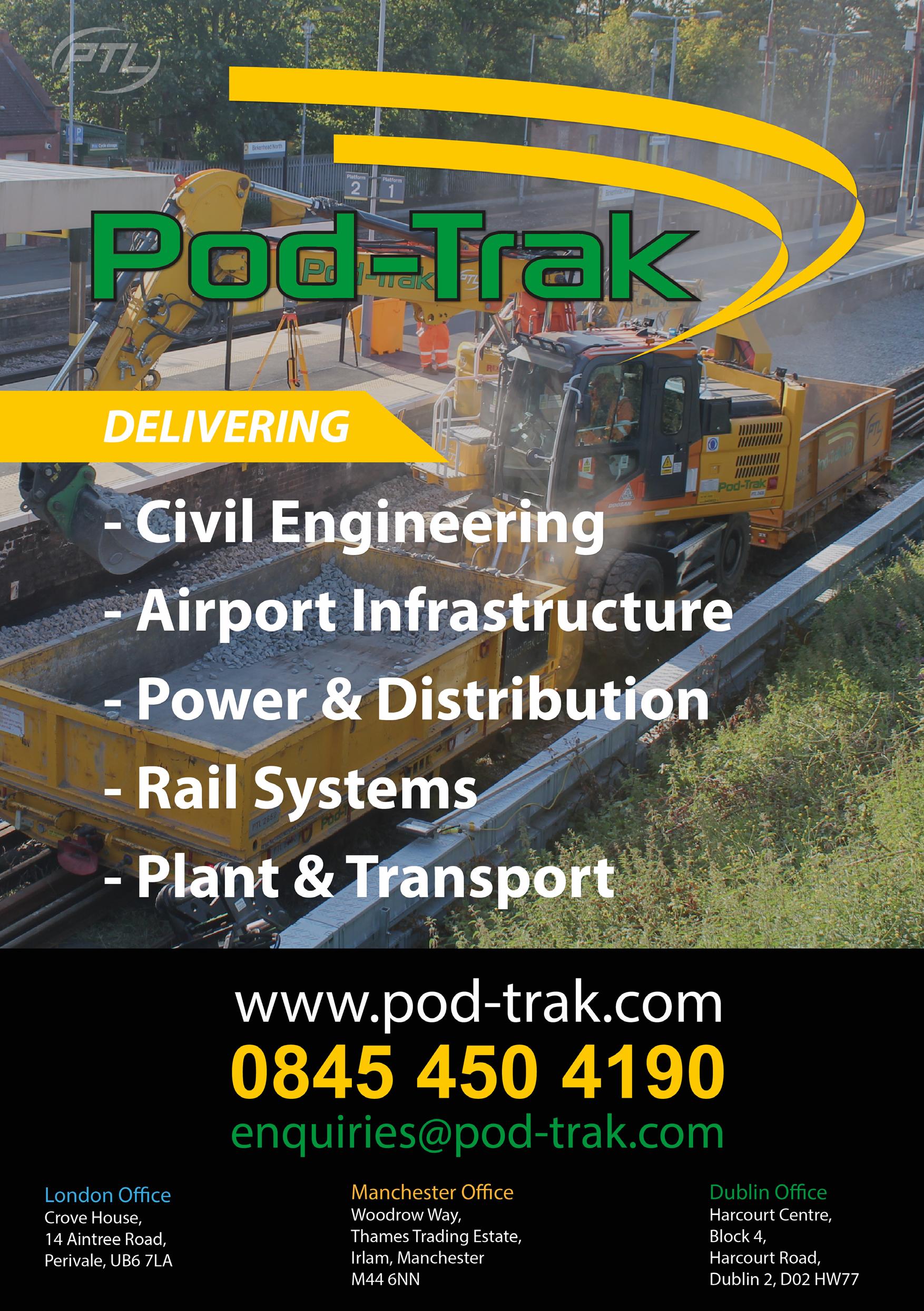
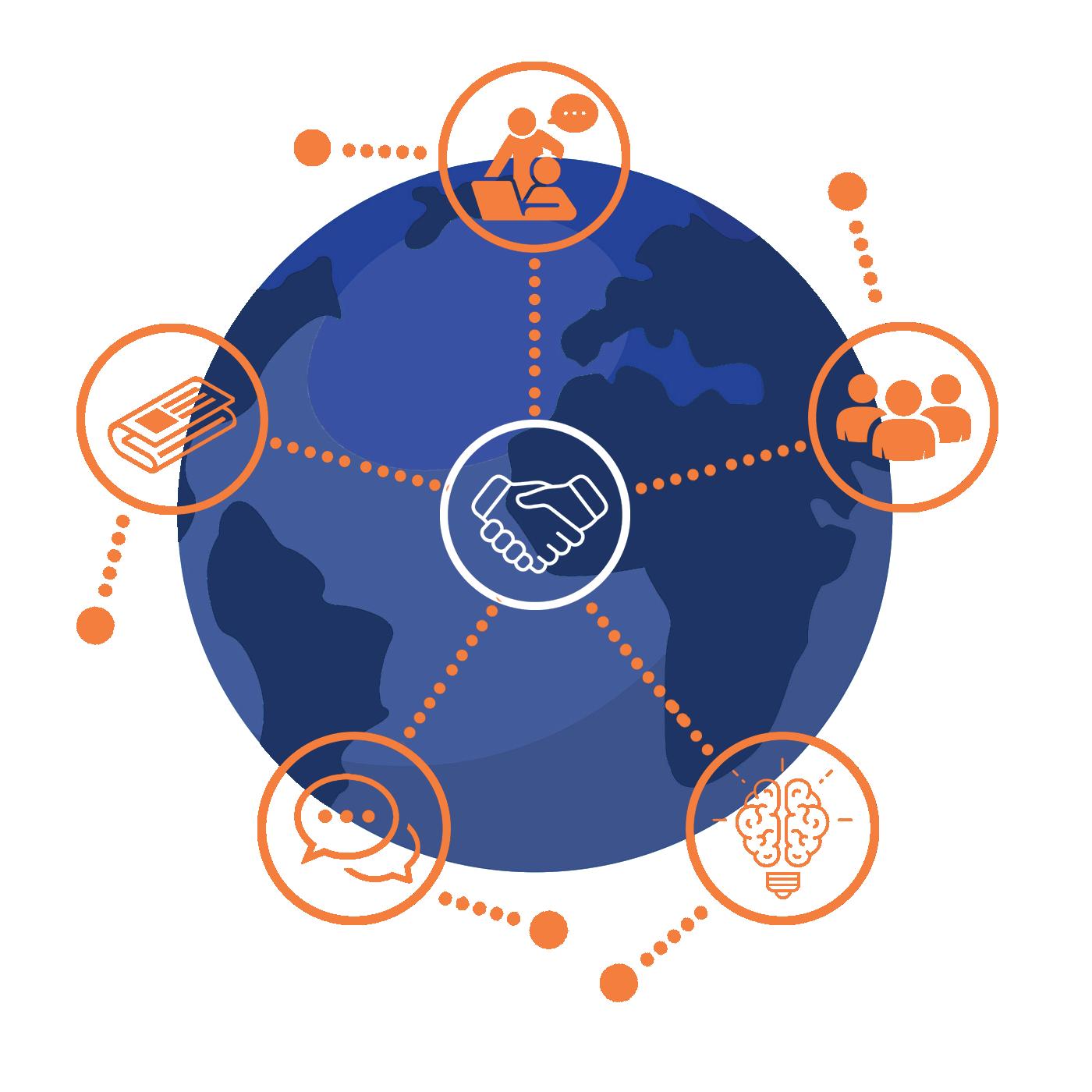


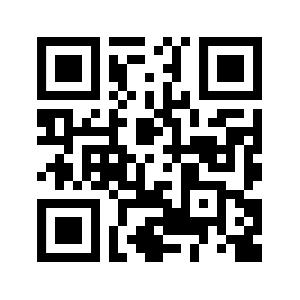
Rail Workforce Survey
Neil Franklin, WorkforcePlanning at NSAR on NSAR’s Annual survey of the rail workforce which shows 75,000 could leave the industry by 2030
TNEWS IN BRIEF
ALPHA TRAINS AND STADLER SIGN FULL-SERVICE AGREEMENT
Alpha Trains has signed a Full-Service maintenance agreement with Stadler. The contract covers the complete maintenance of all EURO9000 locomotives recently ordered by Alpha Trains for a minimum period of ten years as from delivery of the locomotives. The scope of service includes preventive, corrective and heavy maintenance to guarantee the highest service standards to Alpha Trains’ customers across Europe.
This milestone agreement further strengthens the collaborative efforts of both companies to enhance sustainable and efficient transportation solutions across Europe. In 2023
Alpha Trains announced its first order for the purchase of twelve of this latest generation of six-axle hybrid multi-system locomotives. Delivery is scheduled for 2025 and 2026.
The strategic collaboration between Alpha Trains and Stadler underscores their longstanding and successful partnership and at the same time emphasizes their commitment to providing customers with a reliable and efficient fleet of EURO9000 locomotives across Europe.
Alpha Trains provides attractive leasing products and state-of-the-art locomotives which contribute to enable and increase the modal shift of freight from road to rail. This cooperation with Stadler is an example of the common vision of both companies to contribute to a more sustainable and efficient future for European transport.
he National Skills Academy for Rail (NSAR) published the findings of its annual Rail Workforce Survey at the end of 2023. It reveals that skills shortages continue to be a major issue for the rail sector, affecting the industry’s productivity and ability to deliver on its required objectives.
The Rail Workforce Survey is an annual survey of the rail industry’s workforce. Each year, organisations across the industry contribute by submitting their workforce data on demographics, job roles and work locations. The survey helps NSAR build the most complete and accurate representation of the UK rail workforce, allowing it to report back to the sector on changes to skills and workforce numbers over time.
2023 has seen the highest level of data from employers since collection started in Autumn 2016. NSAR has collated the information received directly from employers, in addition to data from the Sentinel database and from the Office of Rail and Road (ORR) to produce a workforce profile covering 243,387 individuals –approximately 95 per cent coverage across
the sector, including the supply chain.
NSAR has issued a report on the key findings of the survey – Navigating the Skills Shortage: an in-depth look at the UK rail workforce. The findings show that skills shortages continue to be a major issue for the rail industry.
The rail workforce is ageing year-on-year. The average age of the workforce has risen from 43 years old in 2018 to 45 years old in 2023. A third of the workforce is aged 50 or over. In addition, there are fewer younger people – the proportion of people under the age of 30 has decreased from 16 per cent in 2018 to ten per cent currently.
This means the rail industry is facing a critical loss of experience and knowledge in the next seven years. The number of people leaving through retirement and other forms of attrition could be 75,000 workers by 2030. 40 per cent of all active trainers will reach retirement age by 2030.
In addition rail also remains a maledominated industry, with women making up just 16 per cent of employees. This percentage, across the whole industry, has remained stubbornly between 15 per cent and 20 per cent over the last eight years.
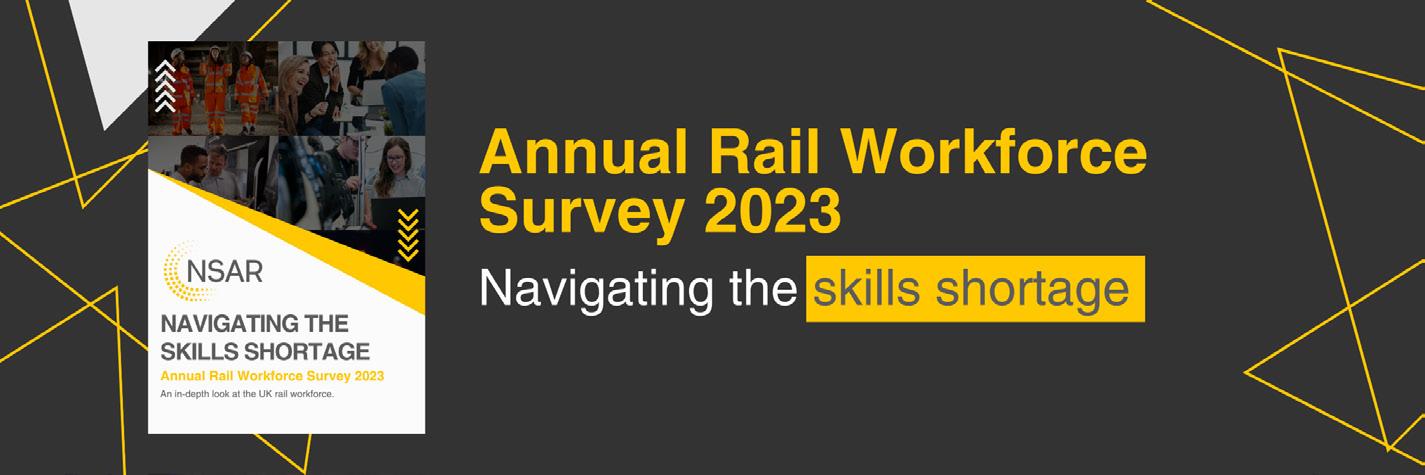
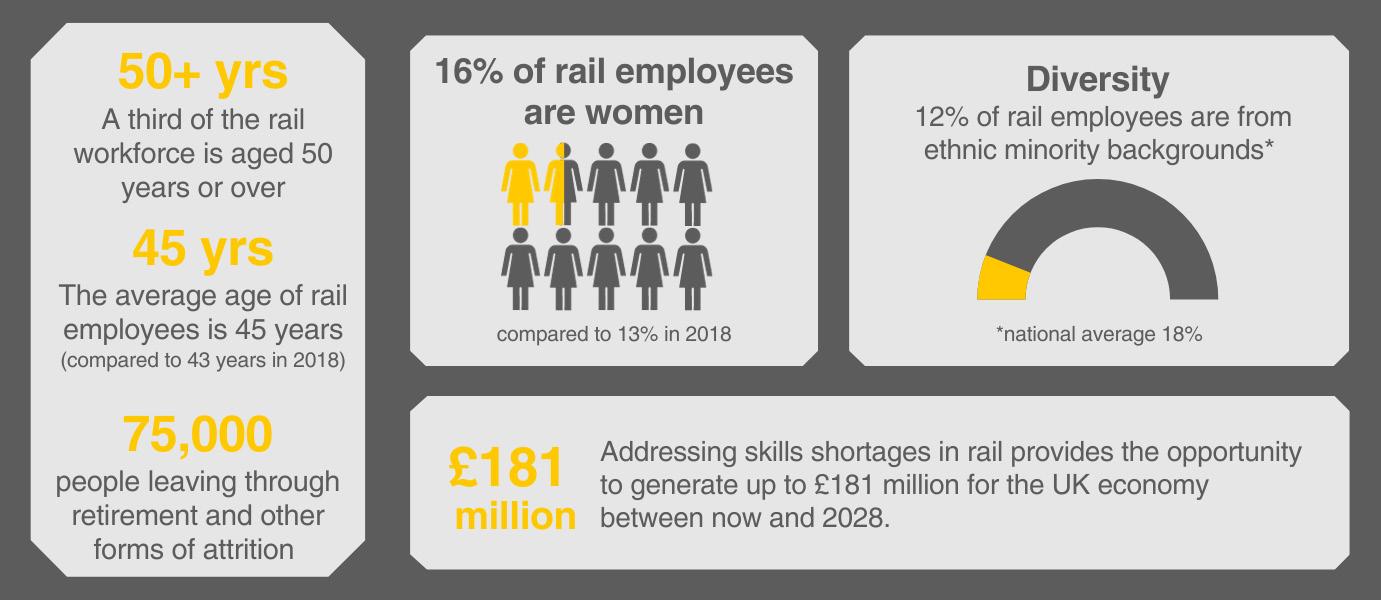
There are pockets of the rail workforce that reach a much higher proportion of women, but they remain anomalies rather than an overall trend.
The combination of higher average age, high predicted levels of people leaving the industry and low numbers of new, younger entrants highlights an issue with the attractiveness of the industry and a lack of investment in the next generation of workers – and indicates the likelihood of significant skills shortages in the coming years.
The survey data reveals clear and key areas where consistent workforce deficits already exist, which include Signalling & Telecoms, Systems Engineering and Electrification & Plant, where the gaps typically range between 1,000 and 2,000 people per annum. These deficits are creating wage premiums for skills – for Electrification twelve per cent and for Signalling ten per cent, evidenced by increased salary demands.
The benefits of addressing skills shortages in rail are immense. There is the opportunity to generate between £128 and £181 million for the UK economy between now and 2028. And, using the assumption that 20 per cent of roles are filled by economically inactive people
‘The average age of the workforce has risen from 43 years old in 2018 to 45 years old in 2023. A third of the workforce is aged 50 or over. In addition, there are fewer younger people – the proportion of people under the age of 30 has decreased from 16 per cent in 2018 to ten per cent currently.’
from a disadvantaged background, the rail sector could produce £412 million in social value by 2028.
In providing a clear picture of the rail industry workforce and predicting future
shortages and opportunities, NSAR’s Rail Workforce Survey 2023 can be used by rail employers to help plan their workforce recruitment strategy, set priorities for training and help an industry-wide reduction in wage inflation that is driving up rail project costs.
The survey findings are available to download via the NSAR website. www.nsar.co.uk/wp-content/ uploads/2023/10/Rail-Workforce-Survey2023-FINAL-VERSION-compressed.pdf
Neil Franklin is Strategic Workforce Planning Advisor at the National Skills Academy for Rail. Current projects include Skills Forecasting for the next 10 years for Traction & Rolling Stock resource, curriculum development for the new National Training Academy for Rail at Northampton and developing the Client Specification for the new High Speed Rail College for HS2.

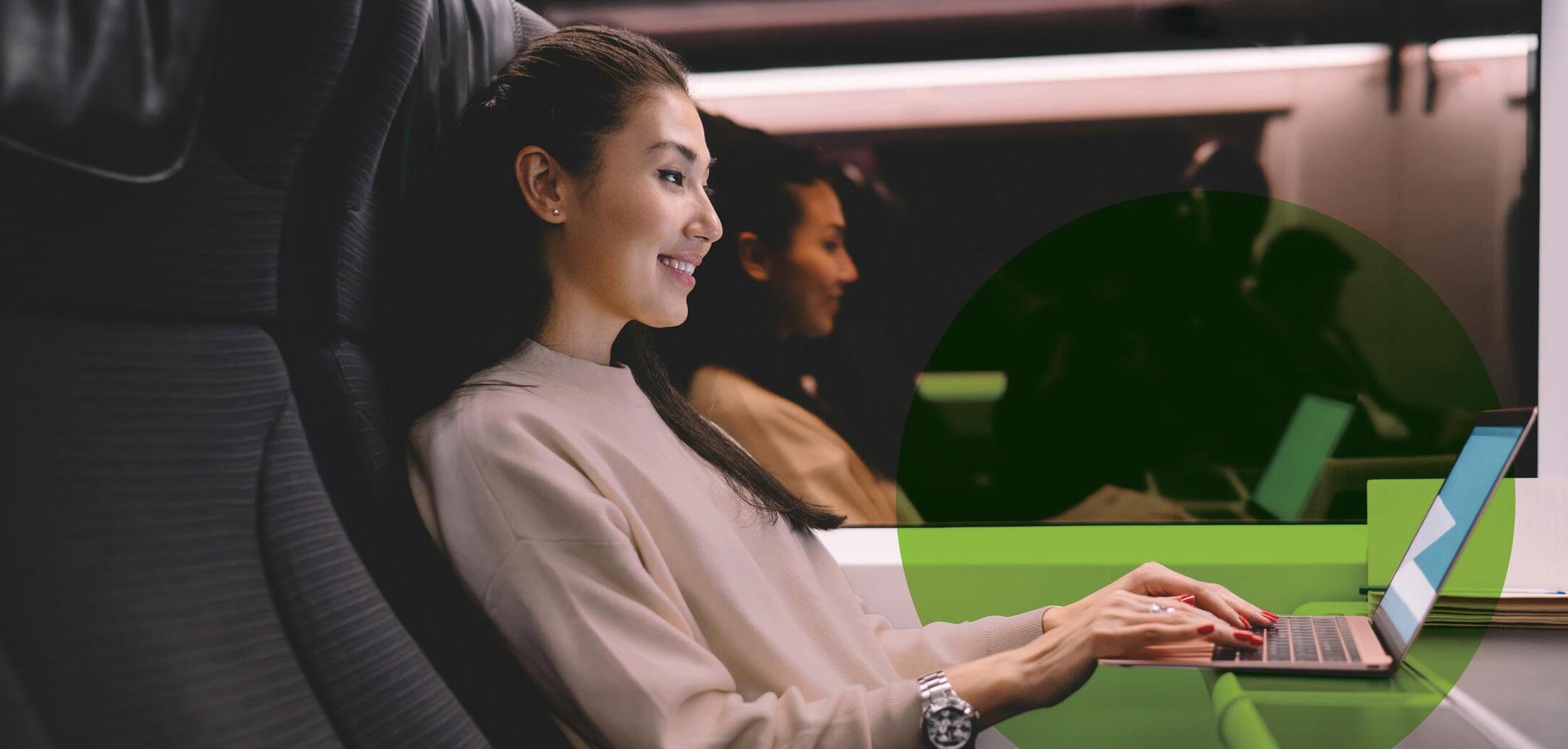
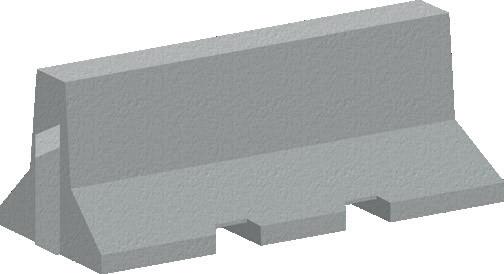


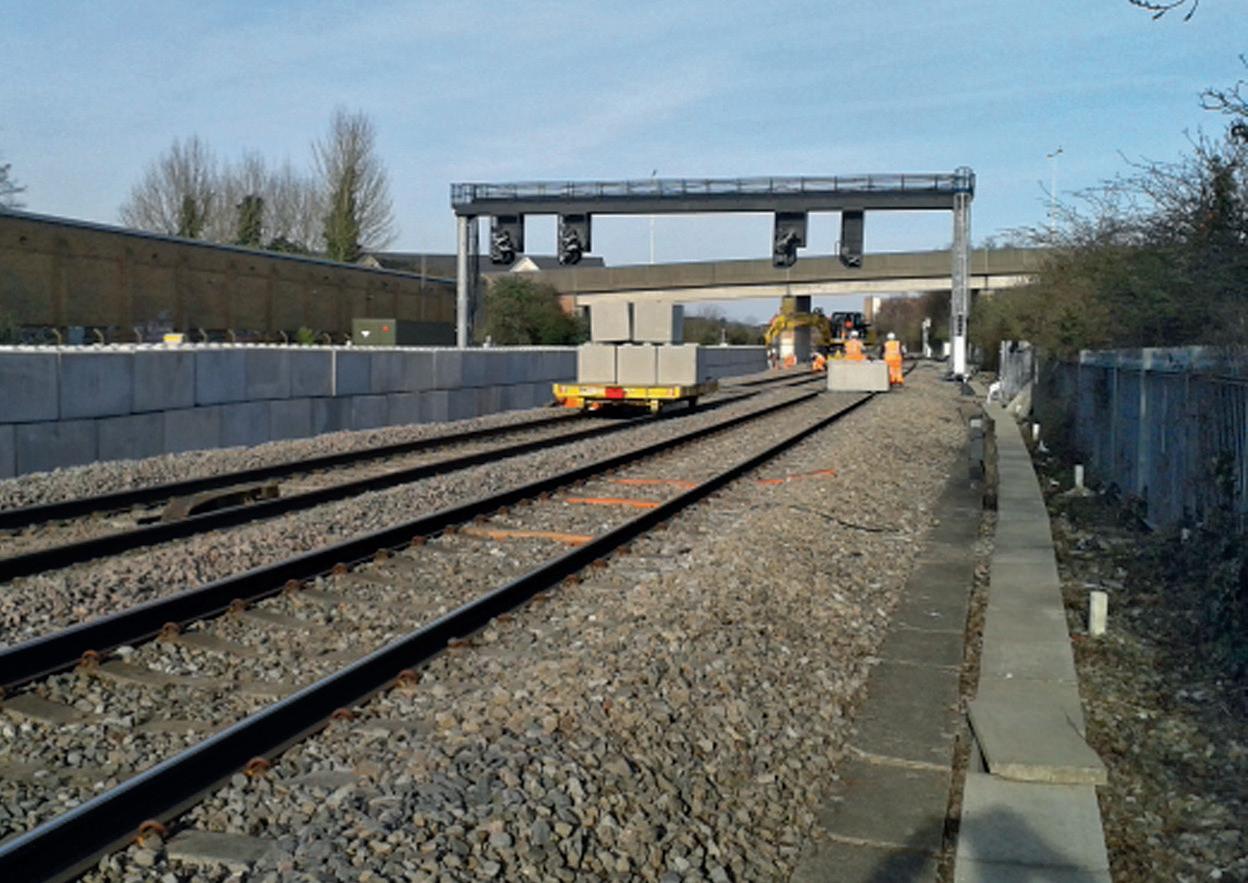
Workforce protection barriers avoiding all line closures with adjacent line open
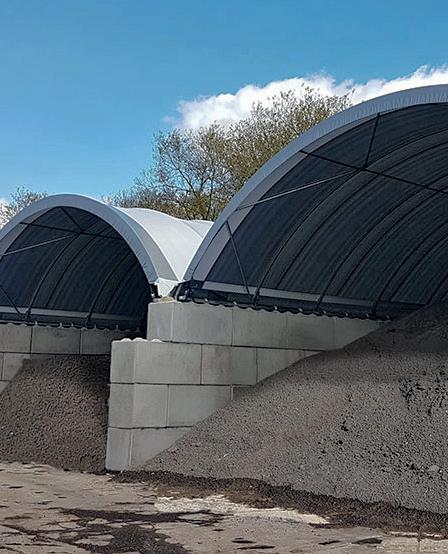
Rockfall prevention with our multi-purpose Jersey barriers
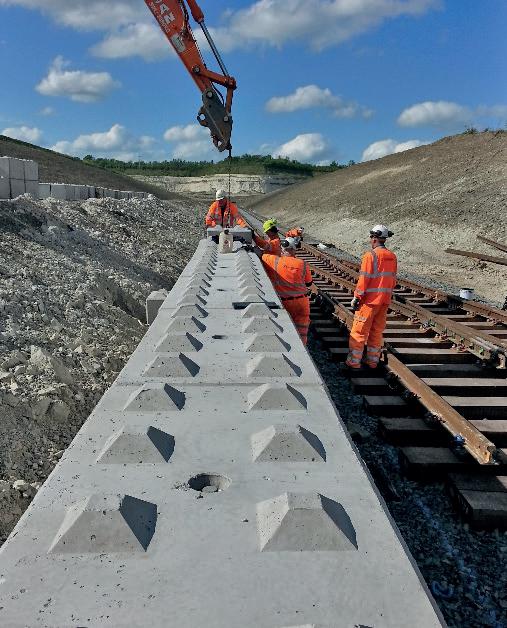
Large
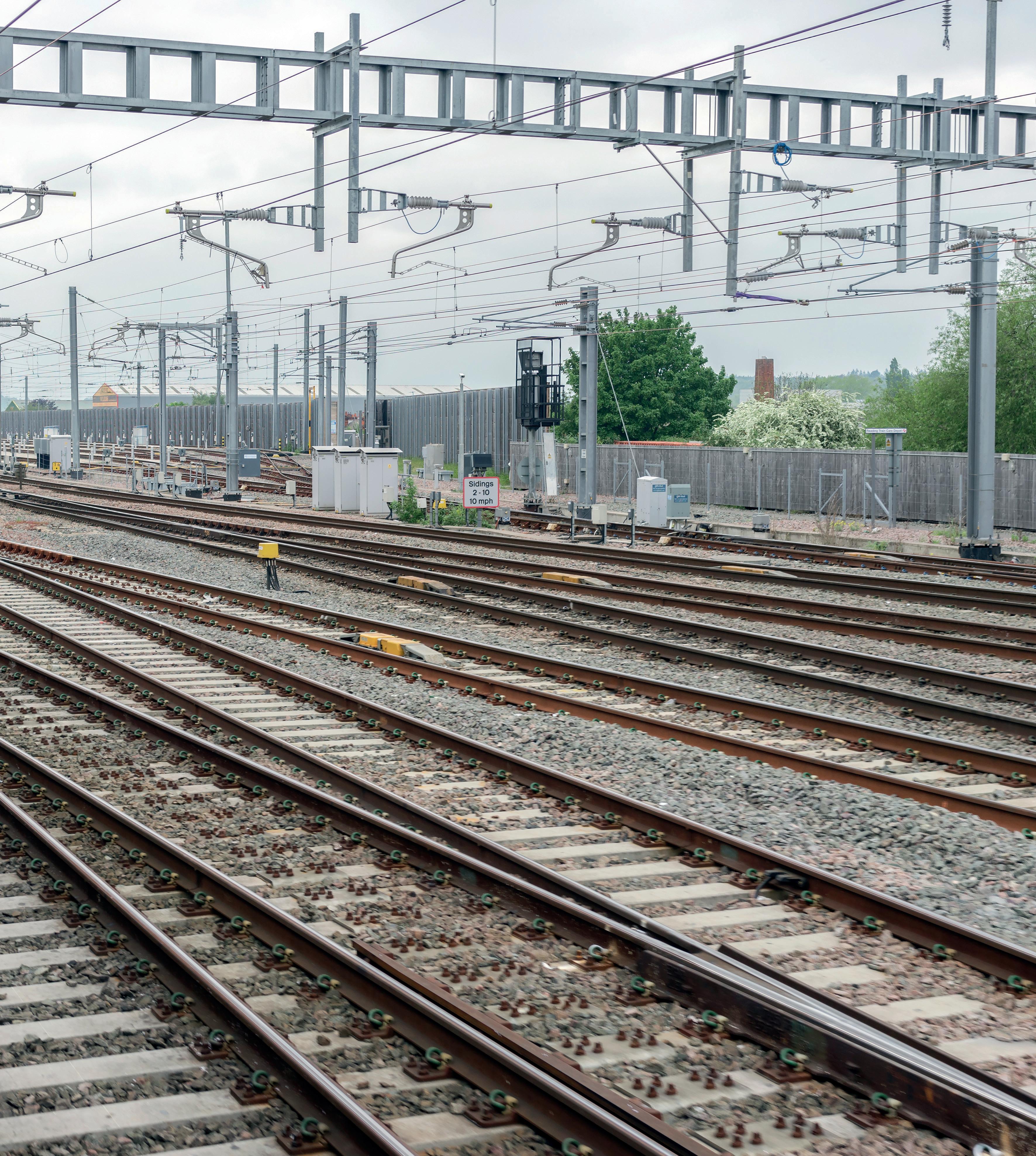
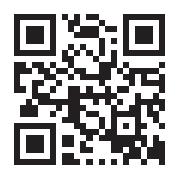
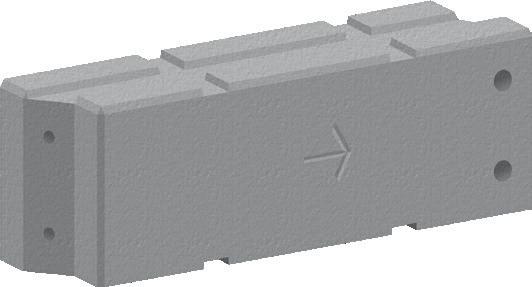
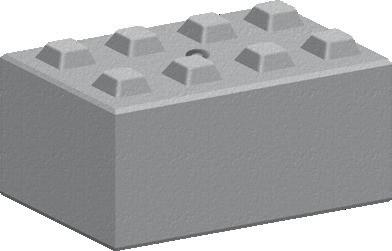

Hoarding stabilisation utilising Elite Duo interlocking blocks
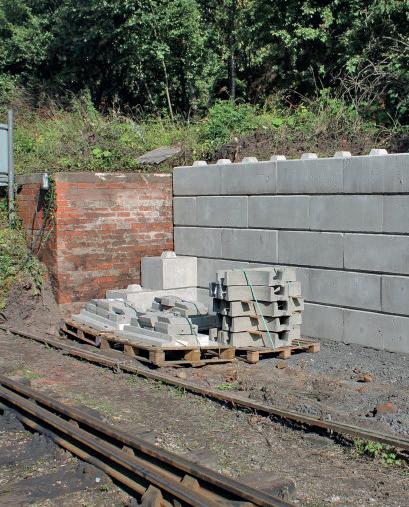
Workforce safety refuges built from Elite Duo blocks
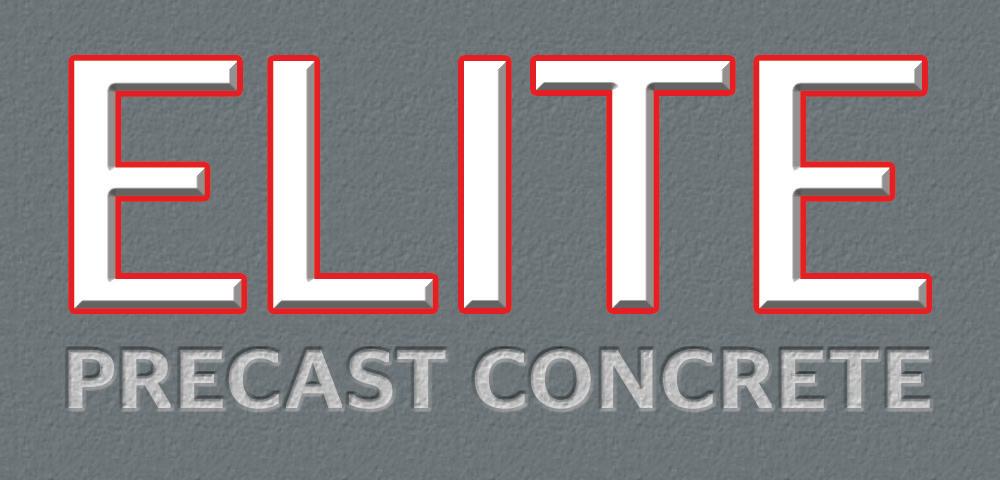
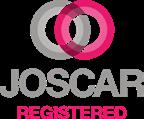

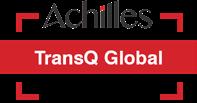
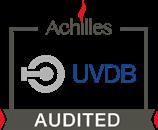
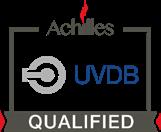
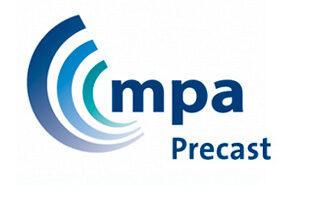
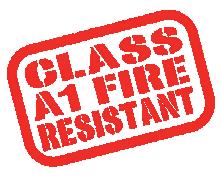
Skills in Focus in 2024
A common lament amongst senior figures in the rail industry focusses on the knowledge and skills that we stand to lose in the coming decades
Latest research by the National Skills Academy for Rail in its Annual Rail Workforce Survey 2023 indicates that a third of the railway workforce is aged 50 or over, and the industry is at risk of losing significant experience and skills through retirement and other forms of attrition, with an estimated figure of 75,000 leavers by 2030. Rail Forum hopes that the lessons will inspire young people to consider careers in rail and help to both address skills shortages and improve diversity in the industry.
Rail Forum has launched a suite of rail themed lessons aimed at Key Stage 3 students. Developed to reach students all across the UK, iRail aims to raise awareness of the vast array of careers available and inspire the next generation of rail professionals. The lessons are freely available to schools to download from Rail Forum’s website. They have been designed so that teachers can deliver the material independently in the school environment, however, where industry volunteers are available to go into school and support teachers, this is encouraged.
The initial suite of five lessons are linked to the national curriculum and include lesson plans, PowerPoint presentations, videos and all supporting activity resources. Subjects include problem solving, manufacturing, accessibility, sustainability, and engineering tolerance. Each lesson is stand alone with teachers able to mix and match to suit their needs. The lessons are further enhanced with a comprehensive project, comprising five further sessions, which involve students selecting the location for and designing a new main line railway station.
Elaine Clark, CEO of Rail Forum said: ‘We encourage rail supply chain companies and in fact any employees within the rail industry who have relationships with their local schools to make them aware of these free rail themed lessons. Those who wish to play a part in inspiring the next generation of rail talent may also wish to volunteer to support the delivery of the materials in their local school.’
Mike Noakes, Head of Rail at the Department for Business and Trade said: ‘The rail industry is facing a critical skills shortage and recent analysis demonstrates the scale of this challenge. We need to use as
‘PlanBEE Rail is a fantastic opportunity to develop a really rewarding career while supporting the rail industry, which offers an array of roles to work in. All of us at TRU fully support the initiative which reflects our commitment to nurturing a skilled workforce that can meet the evolving challenges of the sector.’Neil Holm, Managing Director of the Transpennine Route Upgrade
many opportunities as possible to encourage more young people to consider rail as a career and we need more employers to then take action and commit to recruiting and training apprentices and graduates. These lessons from Rail Forum are a fantastic additional resource available to employers, and the schools local to them, to support the development of a future talent pipeline.’
The materials have been developed with support from Rail Forum members’ AtkinsRéalis, Alstom, Porterbrook, Morson Group, Bridgeway Consulting, Story Limited and Resonate. We would like to thank these organisations for helping to make the suite of lessons a reality.
Rail Forum has long supported the need for a future talent pipeline through its iRail activities, as well as supporting Primary Engineer and being an active member of the Routes into Rail Board. Rail Forum hopes to reinstate the iRail Challenge Days next academic year. Originally launched some 14 years ago these were paused during the pandemic. The day involves bringing a number of schools together to see the industry in action followed by participation in a STEM challenge activity.
Originally established by the Derby Railway Engineering Society some 15 years ago and adopted by Rail Forum in 2016, iRail began as a STEM Challenge Day for schools in and around the East Midlands. Over the years it expanded to include inschool days across the country (subject to funding) but was paused during the Covid
pandemic. Aimed at 13 to 14 year olds, iRail aims to inspire the next generation of rail professionals raising awareness of and interest in the vast array of carers available.
Green apprenticeships
Businesses in England are making a difference in this country by designing all government-funded apprenticeships, with support from the Institute for Apprenticeships and Technical Education (IfATE).
Jennifer Coupland, Chief Executive of IfATE, said: ‘Apprenticeships and skills training are key to helping us reach net zero. We have prioritised our work with employers on this to ensure people can be trained to do their jobs in the most sustainable way and have now reached a crucial milestone with over 200 apprenticeships deemed supportive of England’s drive to net zero emissions by 2050.’
Inaugural Leicester College Apprenticeship Awards
At the end of 2023 Adey Steel was named an Apprenticeship Partnership Winner at the inaugural Leicester College Apprenticeship Awards. The steel fabrication infrastructure, which specialises in the rail, highways and energy sector, was singled out for an Employer Partnership Award by Leicester College for supporting its intermediate apprenticeship programme in recent years. Adey Steel currently has six members of staff completing their three-year apprenticeship programmes at its’ 100,000 square foot purpose-built facility on the outskirts of Loughborough.
Robert Hall, Operations Director at the Adey Steel Group said: ‘Training the next generation in engineering, fabrication and welding is critical to the long-term future of both the Adey Steel Group and the wider UK steel fabrication industry. As our workforce ages and the recruitment of experienced employees becomes harder, we will increasingly need our apprentices to help us deliver the critical infrastructure projects we work on across the rail, highways and energy sectors.’
Leicester College is the largest apprenticeship training delivery organisation in Leicester, helping apprentices learn new skills and gain experience to succeed in their chosen career.
‘Apprenticeships are fast becoming the norm for people who want to fast-track their careers.’Lisa Leighton, People Director at Northern
HS2 apprentice took centre stage at STEM LIVE
HS2 civil engineering apprentice, Nusayba Abaas, was selected to play a lead role at STEM LIVE, which took place at the Science Museum in London on 28 November 2023. 22-year-old Nusayba from North London is one of three guest speakers chosen by the museum and event organisers NST to lead today’s event. She will help to inspire an audience of young people from across the UK to follow STEM career pathways.
Nusayba joined HS2’s construction partner, Balfour Beatty VINCI SYSTRA (BBVS), as a civil engineering apprentice in 2021. She’s part of the engineering team building HS2’s new ‘super-hub’ station at Old Oak Common in West London, the largest new station to be built in the UK.
Now, two years into her five-year apprenticeship, which is fully funded by her employer, Nusayba combines work and study, while earning a wage. The work experience element of her degree enables her to rotate between different departments every six months, so she gains experience in all aspects of civil engineering.
Safety-critical rail training
NSAR has developed a new mentoring programme dedicated to improving the quality of training and assessment for safety-critical rail roles. NSAR developed the three-week long programme in collaboration with training provider Bridgeway. The programme took place in 2023 and has proved so successful with Bridgeway’s trainers that the company want to roll out the programme to all its newly assured personnel.
The new mentoring programme will have a dramatic impact on the quality of training and assessment and is set to pave the way for a new industry-wide accreditation process for safety-critical rail training.
The programme has three distinct weeklong sections. Firstly, classroom-based learning on safety critical compliance, procedures and standards involving the Rail Training Accreditation Scheme (RTAS) rules. Secondly, live ‘trackside walkouts’ at two different sites allowing trainers to embed the technical criteria involved in the RTAS approved material. Thirdly, back to the classroom to test, develop and refine the trainer’s delivery skills using pragmatic scenario-based case studies. The programme concludes with an adjudication panel consisting of leading industry coaching and compliance experts from NSAR and Network Rail. Given that 40 per cent of all active rail trainers will reach retirement age by 2030,
the industry needs modern and responsive initiatives to attract, encourage and retain new trainers. NSAR’s programme will drive improvements in the quality of mentoring standards therefore improving the quality of training delivered across the industry. It will also support career paths into this important and essential professional sector.
PlanBEE Rail to drive talent development in the rail sector
A pioneering apprenticeship has been launched to address skills shortages and give people the chance to launch their careers in the rail industry. Network Rail and their supply chain partners have joined forces with Gateshead College to launch PlanBEE Rail, a bespoke apprenticeship programme which aims to develop a new generation of multidisciplinary project managers, specifically trained to meet the changing needs of the rail sector.
Apprentices will complete a Level 4 higher apprenticeship in associate project management, gaining hands-on experience on some of the UK’s most significant infrastructure projects, including the Transpennine Route Upgrade programme, the Digital Railway programme and Northern Powerhouse Rail.
Successful candidates will be based in York, Leeds, Doncaster, and Huddersfield and will be employed to learn on the job, with a starting salary of more than £22,000. During the two-year programme, they’ll undertake four six-month placements working for leading employers in the rail sector including Alstom, AmcoGiffen, Amey, Balfour Beatty, BAM, Keltbray, Morgan Sindall, Network Rail, Systra, Transpennine Express, and Volker Rail.
Tim Craddock, HR Director at Network Rail Eastern Region, said: ‘PlanBEE Rail is a fabulous opportunity to start a dynamic career in rail - it is not just a standard apprenticeship programme; it's a strategic initiative to bring talent into the rail industry by working collaboratively with our supply chain partners.
‘This approach ensures that our apprentices will not only gain a valuable qualification but will get the opportunity to work with a range of employers across the sector. In doing so, they will be able to develop the skills and understanding, necessary to become fully qualified project management professionals, with all the potential and opportunity that brings for the future. I am proud and excited to be part of such a fantastic programme.’
The programme offers a viable alternative to traditional university routes with tuition fees covered. Apprentices will spend one day a week learning and developing their industry knowledge with Gateshead College.
Neil Holm, Managing Director of the Transpennine Route Upgrade, said: ‘PlanBEE Rail is a fantastic opportunity to develop a really rewarding career while supporting the rail industry, which offers an array of roles to work in. All of us at TRU fully support the
initiative which reflects our commitment to nurturing a skilled workforce that can meet the evolving challenges of the sector.’
The apprenticeship is based on a similar, highly successful apprenticeship in the built environment sector – PlanBEE – which was developed by Gateshead College in partnership with architecture and design company Ryder. Launched in 2016, the award-winning PlanBEE has been highly successful in developing talent in the built environment industry with 98 per cent of PlanBEE graduates progressing to permanent jobs within the sector.
The programme has been rolled out nationally across the UK, in the North East, Manchester and London. It’s also been implemented internationally in Canada through a partnership with the British Columbia Institute of Technology (BCIT) in Vancouver.
Chris Toon, Deputy Principal at Gateshead College, said: ‘We are very proud to be launching PlanBEE Rail which will offer the same life-changing, career opportunities for those looking to pursue a career in project management within the rail sector. The PlanBEE programme has been a massive success story in the North East with 98 per cent of our graduates securing roles in the built environment sector.
‘PlanBEE is a truly innovative programme which has the flexibility to be adapted to different markets and geographical areas. It brings together businesses to provide each apprentice with a flexible range of skills to meet the needs of a sector. The kind of opportunities PlanBEE offers can’t be found on any other apprenticeship anywhere else in the country.’
Greater Anglia celebrates National Apprenticeship Week 2024
Greater Anglia offers fully funded apprenticeships to all of its staff, regardless of their age or the stage of their career, giving them the chance to develop and improve their skills to reach their full potential. There are currently almost 200 Greater Anglia staff undertaking qualifications.
Greater Anglia’s apprentices sit in all areas of the company from administration, engineering, and customer service, to onboard roles such as conductor and train driver. The scheme offers fully funded apprenticeships in levels two to five, starting at an intermediate level up to a higher apprenticeship level, the equivalent of a foundation degree.
The programme gives tutor-led training but also provides crucial on-the-job development, allowing the apprentice to improve and gain skills from communication and teamwork to problem-solving, leadership and even learning about other areas of the business and industry.
Support and mentorship are provided on an ongoing basis by the learners’ managers, training provider-allocated coaches and skills tutors. It means that anyone
‘The rail industry is facing a critical skills shortage and recent analysis demonstrates the scale of this challenge. We need to use as many opportunities as possible to encourage more young people to consider rail as a career and we need more employers to then take action and commit to recruiting and training apprentices and graduates. These lessons from Rail Forum are a fantastic additional resource available to employers, and the schools local to them, to support the development of a future talent pipeline.’
Mike Noakes, Head of Rail at the Department for Business and Tradewho completes it will gain a nationally recognised qualification, along with useful transferable skills.
Viktorija Novikova, Greater Anglia’s Early Careers and Apprenticeship Manager, said: ‘We are really pleased to be celebrating National Apprenticeship Week and to be able to champion the incredible successes of our current and former apprentices. Since it was set up in 2017, our apprenticeship scheme has trained over 265 of our colleagues from all areas of the business including operations, customer service, and officebased roles. Apprenticeships allow everyone to develop skills that all ultimately improve the experience provided to our passengers every single day.’
John Smith, a former apprentice who currently works as a Lead Driver Manager at Greater Anglia, said: ‘There is a false perception that apprenticeships are only accessible to those fresh out of school, but that is simply not the case – apprenticeships are open to anyone and provide a wealth of new skills, all the while being given support and guidance so that staff can reach their full potential.
‘Initially I was apprehensive as to what the benefits of the apprenticeship would be. As it went on, I found that the course was excellent for my professional development and it has equipped me with skills and knowledge to excel within my role.
‘I would recommend anyone wishing the challenge or develop themselves to take any opportunity for an apprenticeship scheme.’
In July 2023, The Transport UK Group, which owns Greater Anglia along with East Midlands Railway, West Midlands Trains, and Merseyrail was placed within
the Top 100 Apprenticeship Employers. The employer rankings celebrate England’s outstanding apprenticeship employers, recognising their commitment to creating new apprenticeships, the diversity of their apprentices, and the number of apprentices who successfully achieve their apprenticeships. The Transport UK Group was placed 56th in the rankings.
Skills for Life
To mark the start of this year’s National Apprenticeship Week, HS2 confirmed more apprenticeship jobs will be created. Over 1,400 people, of all ages and backgrounds, have already secured an HS2 apprenticeship and are on track to boost their career. Today, recruitment opens for 19 new roles with HS2 Ltd, with more apprenticeships set to be created in the weeks and months ahead with HS2’s stations and civils construction partners. The first round of jobs to be advertised include Level 3 and Level 4 opportunities with HS2 Ltd’s project management, cyber security, customer service and quality practitioner teams.
Southeastern’s biggest-ever intake
Throughout 2024, Southeastern expects to recruit 412 apprentices to a range of roles; from train drivers to conductors and from engineers to data analysts and head office management opportunities – including the opportunity to progress up to a Masters in Business Administration.
Southeastern is one of only three organisations in the UK which has achieved ‘Gold’ standard in all three aspects of Investors in People; People, Wellbeing and Apprentices. It’s also helped nearly 550 people complete their apprenticeship programme since 2018.
Southeastern is also:
• Winners of the Male Apprentice of the Year Award (2022).
• The first operator in the country to have completions in Level 2 and Level 3 Train Drivers.
• Made the Top 100 for Apprentice Employers three years in a row.
• Gold Award holder for the ‘5 per cent Club’ for two years in a row – meaning Southeastern has had more than five per cent of its workforce on an apprenticeship in the last two years.
Northern seeks the engineers of the future
Northern Trains has launched a recruitment campaign to attract the engineers of the future. Engineering apprentices are being sought at five locations across the north of England to learn as they earn while working on and maintaining Northern’s nearly 400 strong fleet of trains. These rare and exciting opportunities are likely to attract thousands of interested applicants and Northern is looking for candidates that have a ‘can do’ attitude, are great at problem solving, have a questioning mind and enjoy working in supportive team environments.
The 18 Rail Engineering Apprentice roles will be spread across maintenance depots in Liverpool, Manchester, Leeds, Hull and Heaton in Newcastle. The successful applicants while undertake a four-year training programme and will achieve a Level 3 qualification, in Rail Engineering Technician on Traction and Rolling Stock.
The apprenticeship scheme has been developed in partnership with the National Training Academy for Rail and Myerscough College in Preston.
For the first two years of the course, apprentices will spend three half terms living and studying in Myerscough College which offers a space to study, mix with your fellow apprentices but also a place for to relax and unwind with onsite facilities, a local shop and public transport to local Market Town and Preston City Centre.
When not at college apprentices will be at their home depots gaining practical experience as part of a guided learning programme.
Jack Commandeur, Engineering Director for Northern commented on the apprenticeship opportunities: ‘A regular in-take of apprentices is important to help nurture the next generation of railway engineers and engineering leaders. In these roles, the apprentices can develop their skills and experience in an environment that speaks to their passion for science and technology.’
Northern currently has more than 660 colleagues on apprenticeship programmes across its driving, conducting, engineering and business support operations and this year is planning on enrolling a further 467 onto an apprentice qualification.
First ever all-female apprentice event
The High Speed Rail Group (HSRG) and West Coast Partnership Development are delighted to have hosted our first ever allfemale apprentice event to coincide with this year’s National Apprenticeship Week. Taking place at Alstom’s Crewe factory earlier this week, the event focussed around equipping the next generation of women in rail with skills for life.
The event was formed based on a suggestion from female apprentices in the High Speed Rail Apprentice Network as a way of bringing together women from across the rail and construction industry to share expertise and personal experiences. The Network is run by the HSRG as a way of connecting apprentices and graduates from across HS2 and its contractors, and the wider HSR industry – and provide members of the network with opportunities for networking, meeting other apprentices and sharing experiences and best practice.
Those present were able to hear from Susan Evans, Board Director, High Speed Rail Group; Shamit Gaiger, Managing Director, West Coast Partnership Development ; Anne-Marie Rotter, HS2 VSHT Project Director at Alstom and Natalie Penrose, Head of Legacy at HS2 Ltd on the

‘Apprenticeships and skills training are key to helping us reach net zero. We have prioritised our work with employers on this to ensure people can be trained to do their jobs in the most sustainable way and have now reached a crucial milestone with over 200 apprenticeships deemed supportive of England’s drive to net zero emissions by 2050.’
Jennifer Coupland, Chief Executive of Institute for Apprenticeships and Technical Education (IfATE)came together to demonstrate there are women leaders in the sector who are actively supporting future generations. We do not underestimate the importance of everyone working together to support these young women who will one day do the same.’
TPE celebrates inspiring stories of skills for life
TransPennine Express (TPE) celebrated National Apprenticeship Week by profiling four dedicated colleagues who started out as apprentices and have seamlessly integrated the skills acquired during their apprenticeships throughout their careers.
After identifying the skills shortage and rising demand, the TSA fostered working relationships with organisations across the region. This includes Birmingham City Council, Wolverhampton City Council, Black Country Transport, Midland Metro Alliance and West Midlands Combined Authority –all of which have embraced and supported transport-related apprenticeships.
challenges women face in the rail industry, and how women in the industry can support each other’s development.
In addition to several keynote speeches, the event featured an interactive mentoring session, where senior women in the industry shared their insights and knowledge of how they have progressed into senior leadership roles, as a way of helping the apprentices to develop leadership skills.
Women remain a minority in the rail industry, representing just 23 per cent of the workforce last year according to the Office of Rail and Road. HS2 Ltd has implemented processes like blind sifting CVs to reduce hiring bias, and has made strong progress, increasing female representation to 39 per cent of internal staff and 30 per cent of supply chain staff. Yet clearly more progress is needed across the industry, both in encouraging new women into the industry and supporting them once they join.
Commenting on the event, Shamit Gaiger, Managing Director of West Coast Partnership Development said: ‘Events like this are a great opportunity to bring together women from across all levels in the industry to champion each other’s successes in a positive way. Diversity is an important passion of mine and it was fantastic to be part of an event that recognises all the contributions made by female apprentices. They are the next generation of talent and leaders, and it is our role, as senior women in rail, to continually inspire them and support their development.’
Susan Evans, Board Director, High Speed Rail Group said: ‘I was delighted to see such a strong turnout from women at all levels in their career at the High Speed Rail Group’s first ever dedicated event to female apprentices this week. Whilst there is still more to do to continue to increase diversity in the rail sector, this week our members
Paul Staples, Fleet, Safety and Service Delivery Director, who began his apprenticeship in 1989, said: ‘My apprenticeship gave me a valuable start, offering an overview of the entire company. It taught me skills such as resilience, perseverance, and problem-solving, which I continue to use. Above all, it taught me not to be afraid to ask for help, acknowledging that none of us know everything. I joined the rail industry in 2003 and have carried those initial skills throughout a variety of roles, including my more recent position of Director.’
Caitlin Gent, Assistant Commercial Engineer, said: ‘Moving around different areas of the business at TransPennine Express during my two apprenticeships allowed me to experience several different departments. This helped me to understand how each area interacts, providing a holistic perspective that’s invaluable in my current role.’
Leeanne Matuszczyk, Fleet Maintenance Planner, who had an unconventional journey to rail, said: ‘I started my apprenticeship in 2003 in the Royal Air Force. This slightly different route allowed me to learn military training alongside my engineering apprenticeship, providing valuable on-thejob experience in an operationally tough environment. It gave me confidence, people skills, and excellent time management – things I wouldn’t have learned in a traditional classroom setting.’
David Walker, Head of Fleet Commercial, said: ‘A good apprenticeship takes you to areas of the business you never get to see, allowing you to form your development path and experience aspects of the business you may not know you want to be involved in.’
Transport Skills Academy
The Transport Skills Academy (TSA) is encouraging local people in the West Midlands to consider a career in transport. By 2035, the West Midlands will need to fill nearly 60,000 new jobs in the sector to help operate its growing rail, road, bus and tram networks. To help meet this demand, the TSA – founded by Transport for West Midlands (TfWM) – was launched in 2022 to provide a one-stop destination, inspiring the future workforce to choose a career in transport while upskilling its existing workforce.
After working in retail for five years, Birmingham resident Keya Allen wanted a career that offered job security and opportunities. She joined an eightweek junior software development skills bootcamp, and on completion, secured a job at TfWM.
Keya is now doing a higher apprenticeship in DevOps, learning a wide range of skills from upgrading databases to looking after the road traffic collisions data downloader. Her enthusiasm and thirst for learning was recognised just last month, with Keya named as West Midlands Combined Authority (WMCA) Apprentice of the Year.
Transport for West Midlands colleagues are currently receiving transport-related training and are encouraged to learn at all stages of their career journey. Catherine Rooney, project officer at TfWM, undertook an associate project management apprenticeship to strengthen her skillset and experience. Following completion of her apprenticeship, Catherine had the opportunity to lead a project creating an Active Travel Centre of Excellence, supporting the TSA’s work, inspiring new entrants into a career in active travel.
In the last year, Birmingham City Council offered two level six transport planning degree apprenticeships and successfully filled both roles. The transport planning team has hugely benefitted from bringing young people into their team to share their learnings and ideas from their degree courses and are helping to shape the future of the sector.
When asked why he decided to start an apprenticeship, apprentice transport planner in the city centre team at Birmingham City Council, Ben Butler, said: ‘I believe that an apprenticeship is an ideal way to establish a solid foundation within a career. The structured nature of apprenticeships allows for ample opportunities for continuous development and learning, which helps to facilitate the transition into professional working without overwhelming pressure.’
Wolverhampton City Council found similar experiences when employing apprentices with Black Country Transport, who offer two positions annually alongside two graduate placements. Employers found that the individuals coming through apprenticeship schemes were able to improve the overall skill base of the transport team over time, and they are looking to expand on this in future years.
Emily Cooper, transport planner degree apprentice at Black Country Transport,
added: ‘This apprenticeship is a great opportunity to gain skills in design and writing, communicating, negotiating, project management, taking the lead on smaller tasks within a wider project and working for the best outcome for everybody. You can progress to many jobs using the skills and experience gained here.’ Emily splits her time working between Wolverhampton, Sandwell, and Birmingham.
The Midland Metro Alliance, who consists of the WMCA and a joint venture consortium of construction and design partners, has also been working with TfWM since 2016 to deliver apprenticeships in a range of roles and at varying levels, including leading a group which created the first apprenticeship in the country sharing the skills and knowledge required to deliver light rail projects.
Rose Rees, Head of Engagement and Skills, Midland Metro Alliance, commented: ‘We’ve got some fantastic people retiring but they’re taking with them their skills, knowledge and experience, so we need to encourage new people to come into our sector, young people as well, particularly, to bring their innovation, their fresh ideas, and learn from the people that are currently in the sector. In addition to a variety of interesting roles at site, at Midland Metro Alliance, we have welcomed numerous apprentices in our offices ranging from level two customer service technicians, through to Level Two and Three business admin, marketing, to Level Six-degree apprentices who are working as quantity surveyors out of our site in Dudley.’
On the successes of the TSA to date, Michele Roberts, Head of Transport Skills at TfWM, said: ‘At the Transport Skills Academy, we are on a mission to challenge perceptions of the transport sector, and inspire people – no matter their age or background – into a career in the sector. Apprenticeships are a valuable gateway for anyone looking to develop their skills and learn on the job. Through working collaboratively with our partners and providing people with resources and guidance, we’re able to connect them with the right opportunities to support their career development – both within TfWM and across the region. We encourage you to get in touch with us if you’re interested in pursuing an apprenticeship or furthering your career.’
To find out more about the Transport Skills Academy, visit: www.tfwm.org.uk/whowe-are/what-we-do/transport-skills-academy.
The Prince’s Trust employability programme
Trenitalia c2c has announced that seven participants from its recent work experience programme, delivered in partnership with The Prince’s Trust, have been appointed to full and part-time roles with the company. The programme, ‘Get into Customer Service’, developed by The Prince’s Trust and delivered by c2c, has been designed to give young
people (aged 18-30), who are struggling to find work, the opportunity to learn and develop employability skills required to help them secure a job and establish a career in the rail industry.
One of the course attendees, John-Paul Uzowuru, started in his new role as interim Data Analyst with c2c back in January, and the six other colleagues took up their posts in train dispatch and on gatelines, at c2c’s London stations, earlier this week.
c2c’s Resourcing Manager, Michelle Burningham, who delivered the employability programme, said: ‘c2c truly believes that everyone, regardless of educational background or employment history, should have the opportunity to embark on a rewarding career in the railway, and I am delighted to be welcoming seven new recruits to the business.
‘Working with The Prince’s Trust has allowed us to offer this group of young people, some of whom come from disadvantaged communities, the chance to learn and develop practical, everyday workplace skills – relationship building, staff engagement, timekeeping, personal conduct – building the confidence and motivation required to enter employment within the rail industry.’
The 18-30-year-olds selected for the Get into Customer Service programme joined for three week-long training courses which were held at c2c’s head office in London, on the route and at its training centre in Southend during November and December 2023.
Alstom apprentices celebrated as applications open
Alstom held its inaugural Apprenticeship Awards. The awards are designed to recognise the exceptional impact of apprentices at Alstom in the UK working across a range of railway-related fields, including engineering, manufacture, design, maintenance, digital and integrated systems, procurement and logistics.
Five winners across the country were honoured at a virtual ceremony on Wednesday 7 February, with 21-year-old Billy Gamov from York named overall Apprentice of the Year. As an Engineering Product Delivery Apprentice, he has been supporting the delivery of signalling projects around the UK from Alstom’s York office.
The judges praised Billy for his work in delivering a state-of-the-art, first of its type level crossing simulator, while a digital support system he helped develop has driven significant efficiencies across Alstom’s signalling business. His extracurricular role as a science, technology, engineering and maths (STEM) ambassador was also highlighted, which has seen him attend an event at the National Railway Museum to talk to students about careers in rail and beyond.
Alongside his work, Billy is studying for an engineering degree apprenticeship at Aston University and is expected to graduate later this year.
‘Apprenticeships are vital for the long-term future of Nexus. We are committed to developing early career paths, providing solid succession planning for critical roles. Apprenticeships are an ideal route both for us and the apprentice. They learn bespoke skills and competencies and we gain skilled and engaged employees who see real career development. And Nexus apprentices have a high chance of getting a job at the end, with nine out of ten previous apprentices going on to have a long term career in our organisation.’
Head of Learning at Nexus, Heather
BlevinsAlstom’s commitment to creating ‘Skills for Life’ – the theme for this year’s National Apprenticeship Week – was further reinforced as it confirmed 36 more apprenticeship roles will be created across the UK in areas such as engineering, project management and supply chain. Apprenticeships at Alstom offers trainees the chance to earn while they learn. Alongside their day job, apprentices will spend at least 20 per cent of their working hours undergoing learning at university or college, additional training and studying. The new cohort is expected to start working at the company from September.
CrossCountry welcomes new cohort of eight train driver apprentices
CrossCountry has welcomed a new cohort of eight apprentice train drivers to their headquarters in Birmingham. CrossCountry has offered a range of apprenticeships to employees across the country since October 2020. Now in their third year, the 16 schemes cover a range of different business areas and are offered to new and existing colleagues as part of the business’ learning and development programme.
So far, 141 colleagues have already fully passed out on their schemes, with another 144 coming ‘down the line’ – totalling almost 300 new apprentices moving through the business over the last three years. Last year CrossCountry was awarded Top 100 Apprenticeship Employer status and was recognised as a Gold member of The 5% Club – a charity committed to increasing the numbers of ‘earn and learn’ positions offered by UK employers.
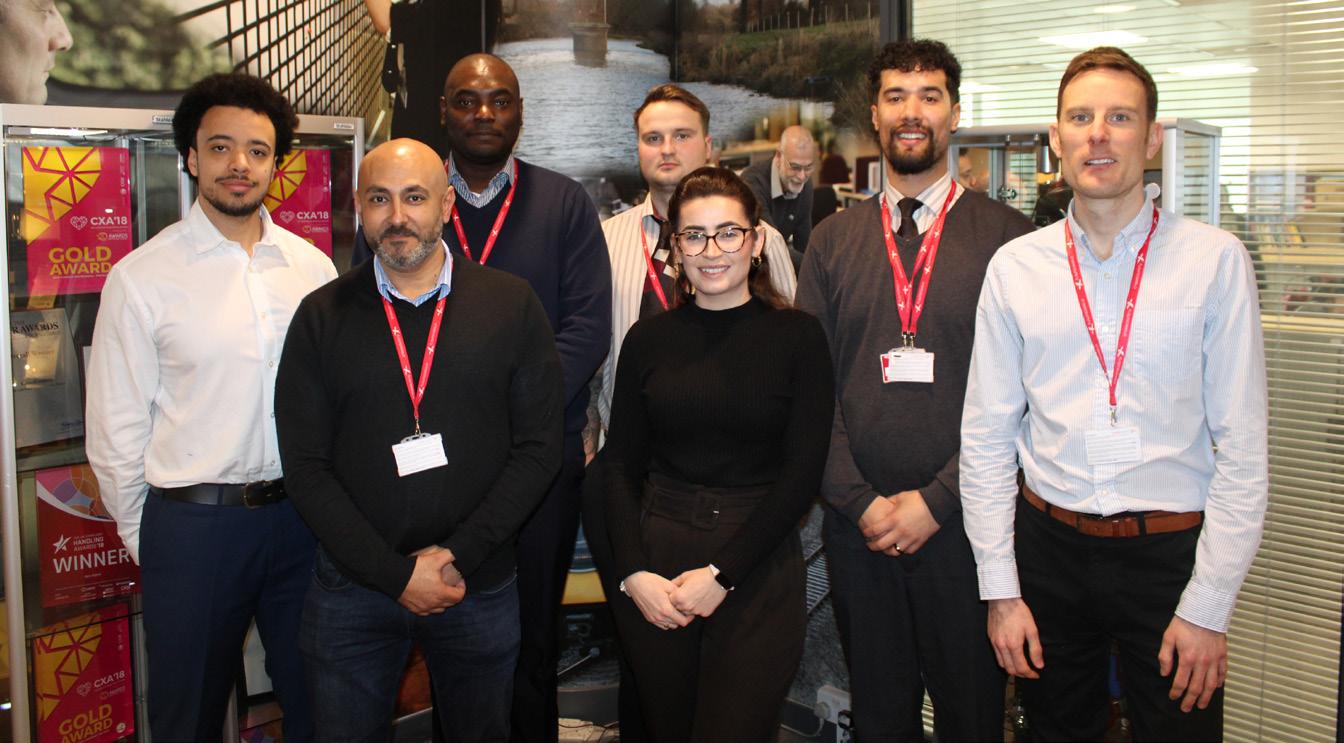
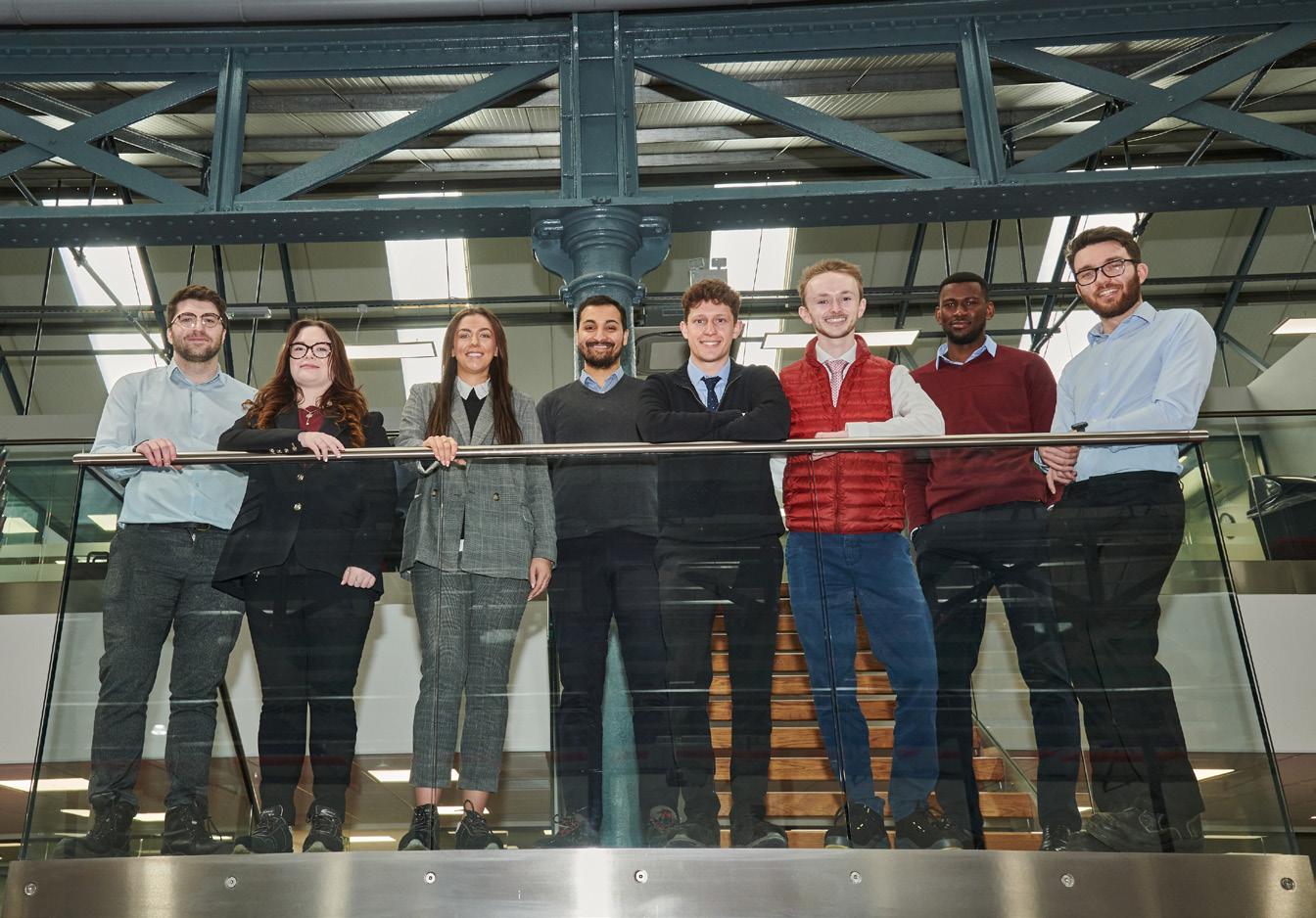


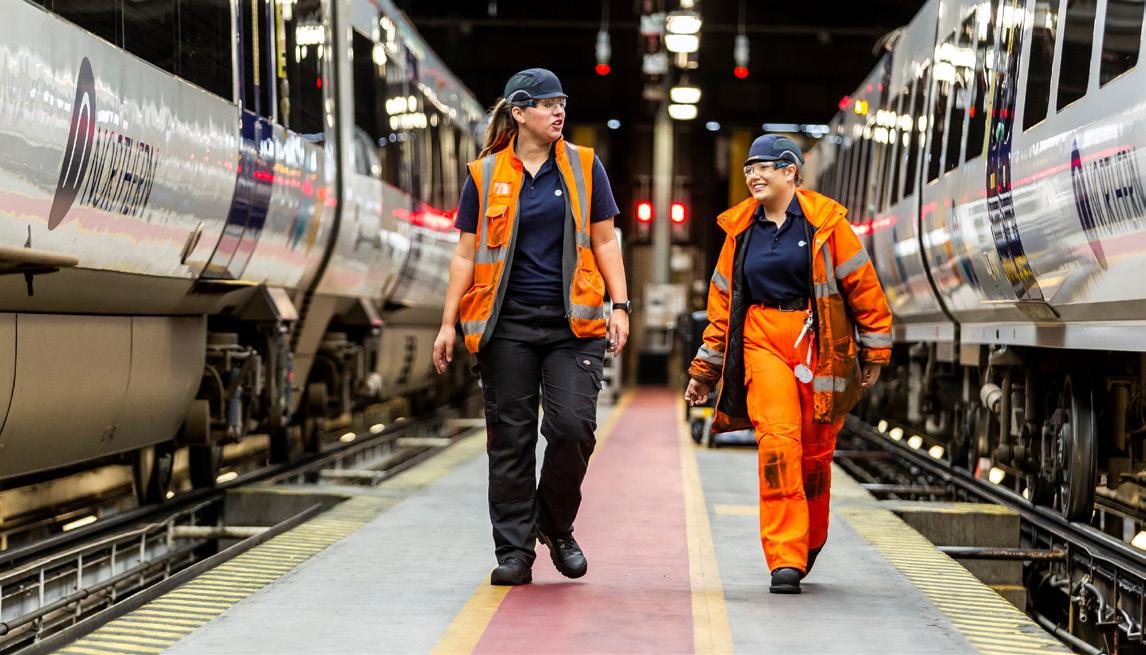
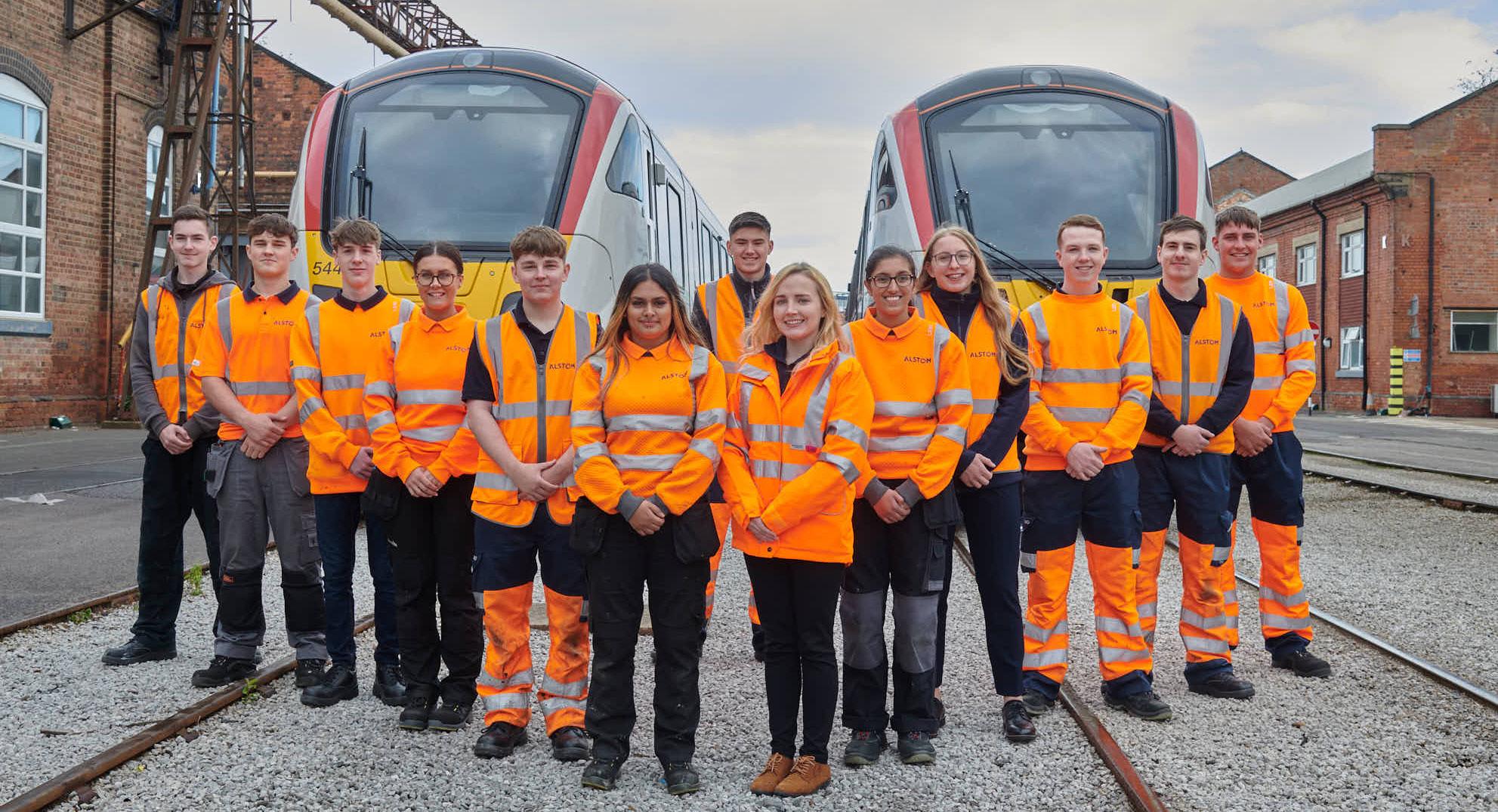

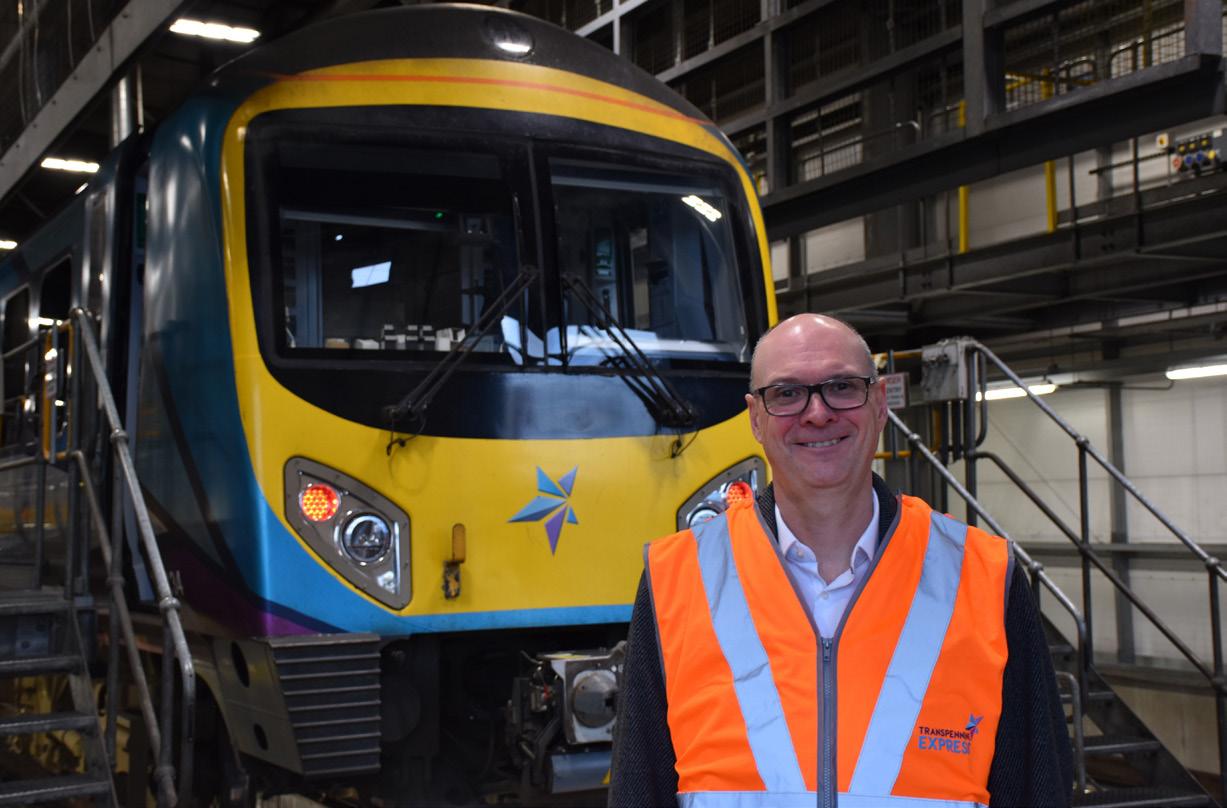

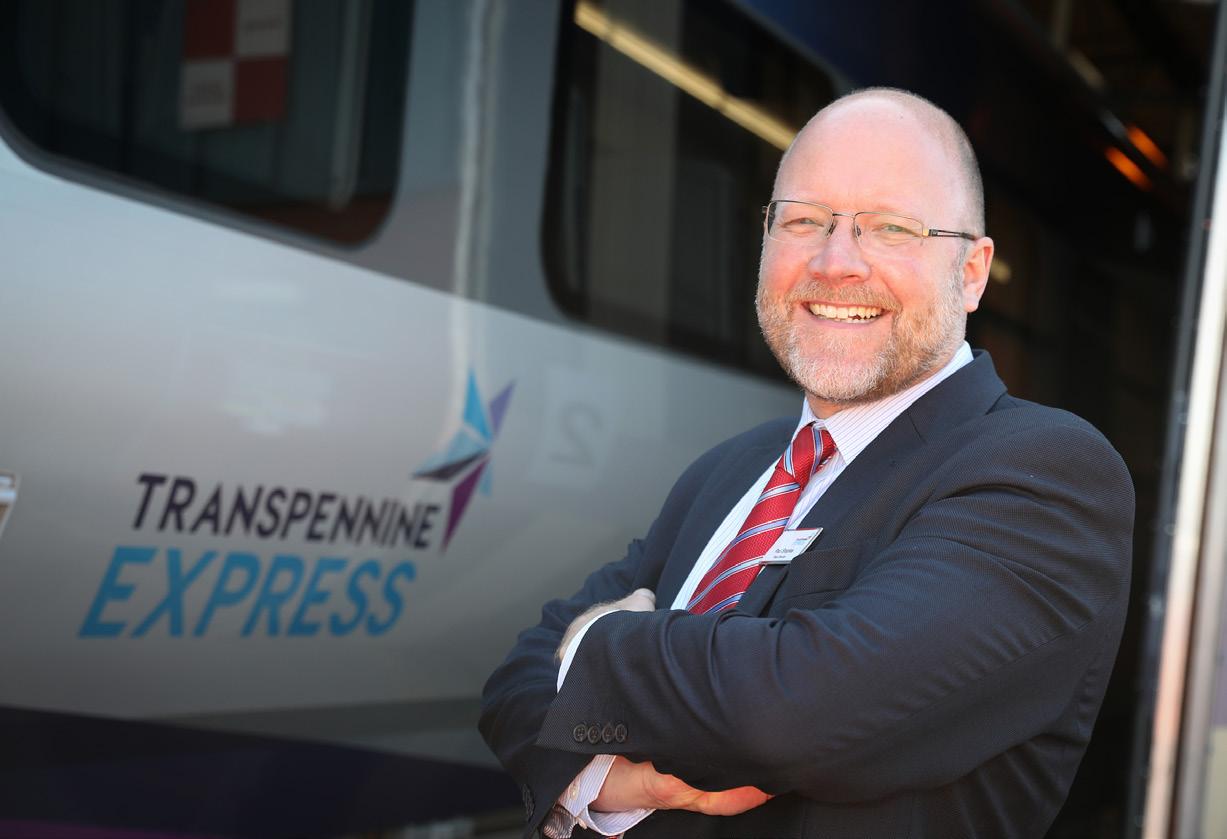
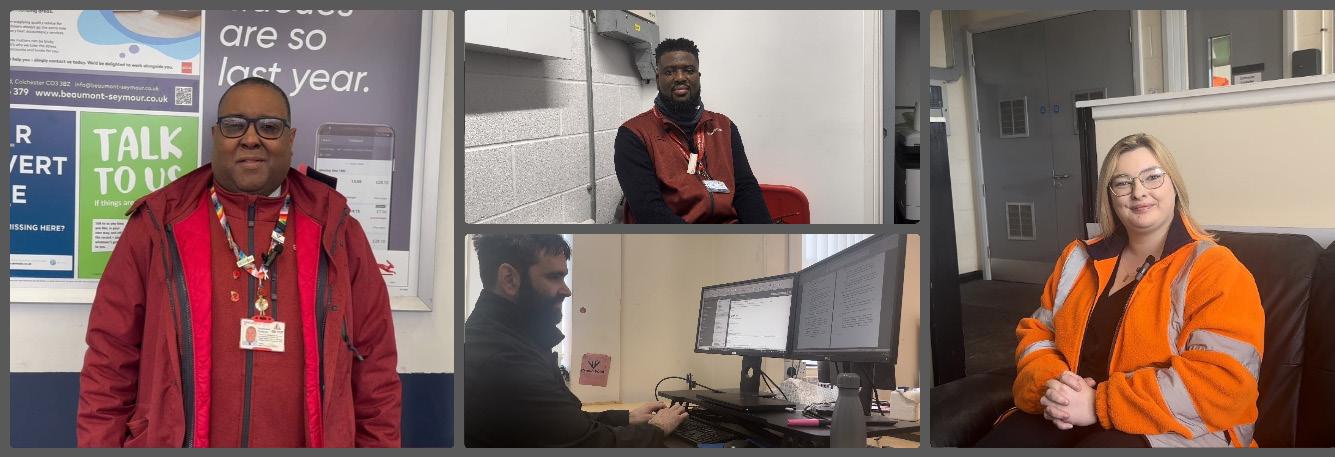
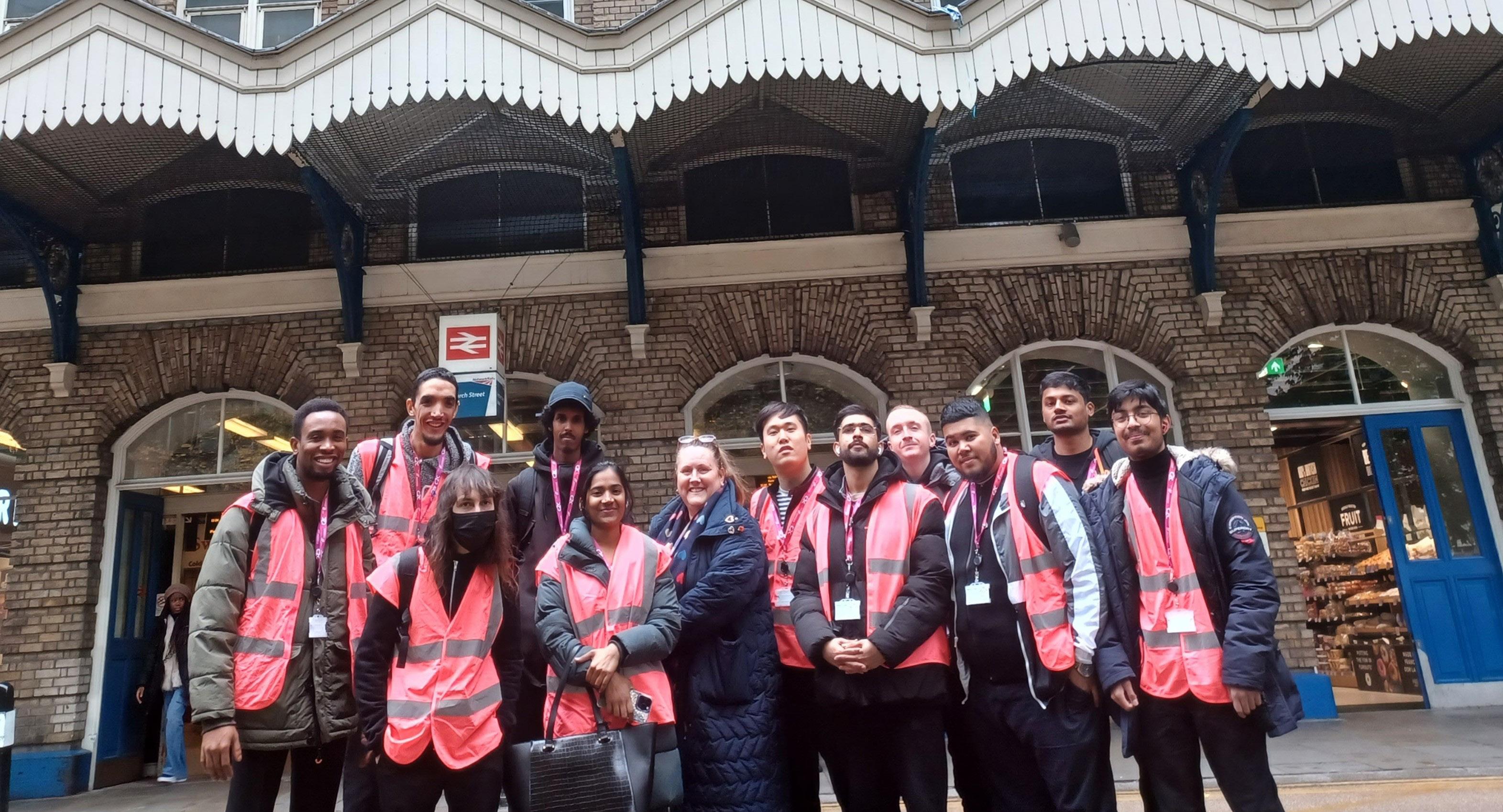
Discover the New Coral Move Vision FR Collection
Designed specifically for rail vehicle interiors, Coral Move Vision FR is an exceptionally versatile, premium cut pile carpet solution offering extensive design possibilities and colourways to complement a wide range of design schemes
Coral Move Vision FR is a luxurious made-to-order floor covering, manufactured from one hundred per cent regenerated Econyl yarn, that offers the aesthetic styling, durability and lost lasting appearance retention required for heavily trafficked carriage interiors. The carpet pile density also delivers slip resistance and outstanding acoustic properties.
This carpet also meets all of the fire and smoke requirements for rail vehicles with regards to EN45545-2: HL2, as well as a host of other product benefits:
• Durability thanks to a one hundred per cent nylon yarn construction.
• Reaction to fire EN 45545-2: HL2.
• High-definition digital printing allows for extensive customisation possibilities and bespoke design.
• Natural latex backing from rapidly renewable source.
• Ease of maintenance thanks to open cut pile construction.
• Available in a lightweight option at approximately 1.9kg/m2
Coral Move Vision FR uses a digital printing process which allows for customisation in terms of design and colour. The digital printing process makes non-linear type designs possible and is perfect for more complicated designs and when there are many different colourways within a design.
There are five different designs within the Coral Move Vision FR collection: Lines, Pinstripe, Plexus, Landscape and Terrain. Design styles ranging from distinct linear to random all over type patterns to semi plains.
If you don’t find what you are looking for within the collection, then please note that Coral Move Vision FR carpets can be made to a bespoke specification. If you are looking for design ideas, re-colouration or rescaling of existing designs or help with the development of a unique design that works

perfectly with your rail design scheme, then we have the resource to help. The dedicated design team will work with you on a projectby-project basis.
Innovative Installation Systems
As an alternative to fully adhering the floor covering to the subfloor, Coral Move Vision FR can also be supplied with different backing options designed to improve efficiencies in time, cost and operation throughout the life of the rail vehicle. The `Pro-Fit` hook and loop solution for example has numerous advantages over traditional
fully bonded adhesive systems thanks to:
• Quicker and easier installation and replacement.
• No need to wait for the adhesive to dry.
• No waiting time before the carpet can be walked on.
• Immediate use of the train after installation.
The optional backing solutions cannot be added to the latex backed material after production, so the required backing type must be clearly specified sat the time of ordering.
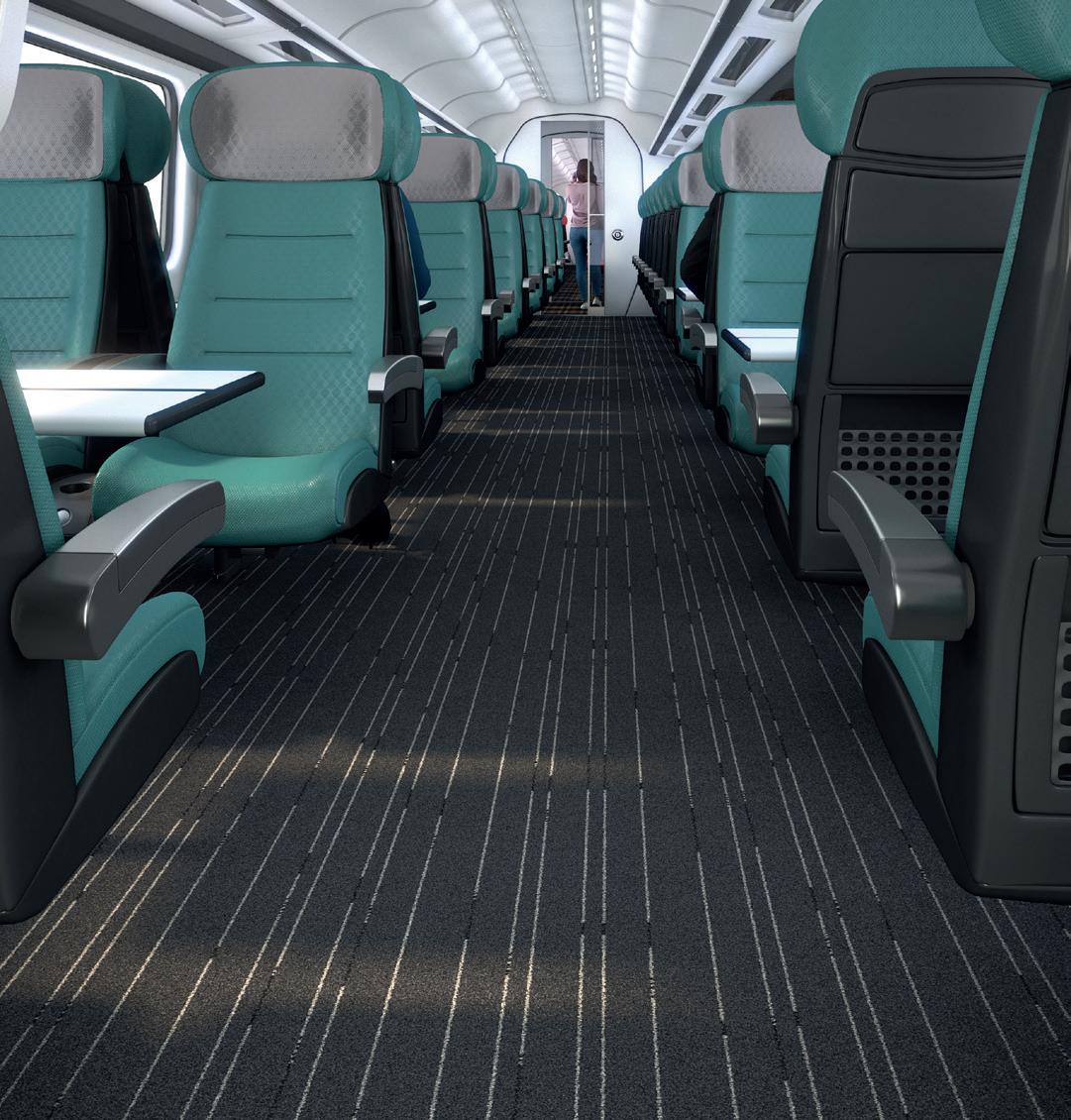
Coral Move Vision FR and the environment
From how they're made to how they perform, Forbo Flooring Systems makes outstanding floor covering products that are truly sustainable.
One hundred per cent green electricity from renewable sources
Of all the electricity we buy, one hundred per cent comes from renewable sources. This means the Coral Move Vision FR production site is part of an effective environmental management system and has achieved ISO 14001 certification.
Zero landfill
Virtually zero landfill is achieved by the Coral Move Vision FR manufacturing plant.
Reuse waste
All the waste yarn from the Coral Move Vision FR production is re-used by the yarn supplier. Forbo's search for new ways to reduce its environmental impact has led it to work very closely with forward thinking suppliers who are able to incorporate ever higher levels of recycled content in their materials.
Econyl® yarn
Coral Move Vision FR floorcoverings use Econyl® yarn which is made from used and abandoned fishing nets. Using Econyl® is a way to reduce existing waste, avoid additional manufacturing-related pollution, and keep the consumption of natural resources and energy to a minimum.
To view the full range of Coral Move Vision FR designs and colourways, visit www.forbo-flooring.com/rail or click on the QR code.
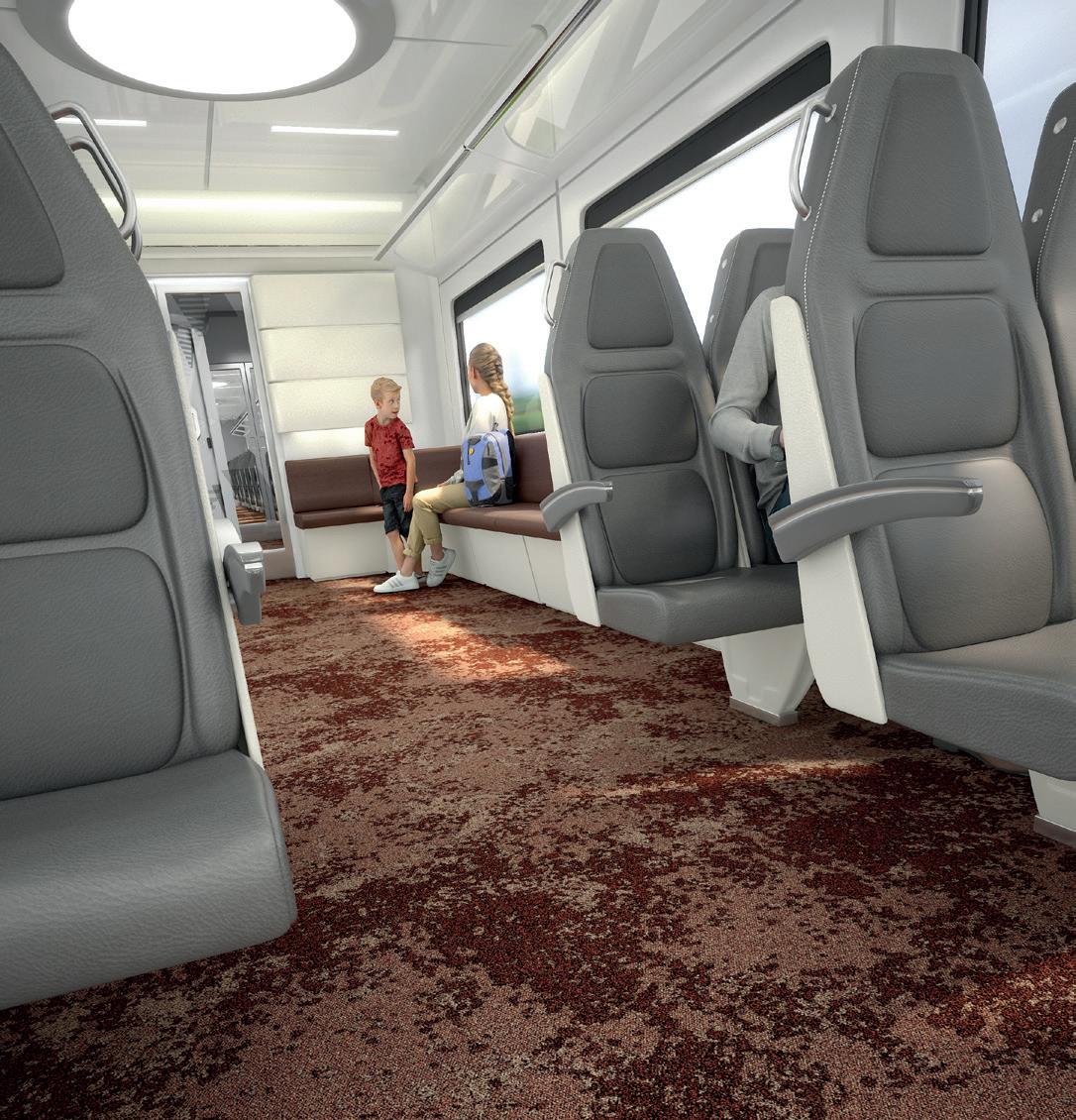
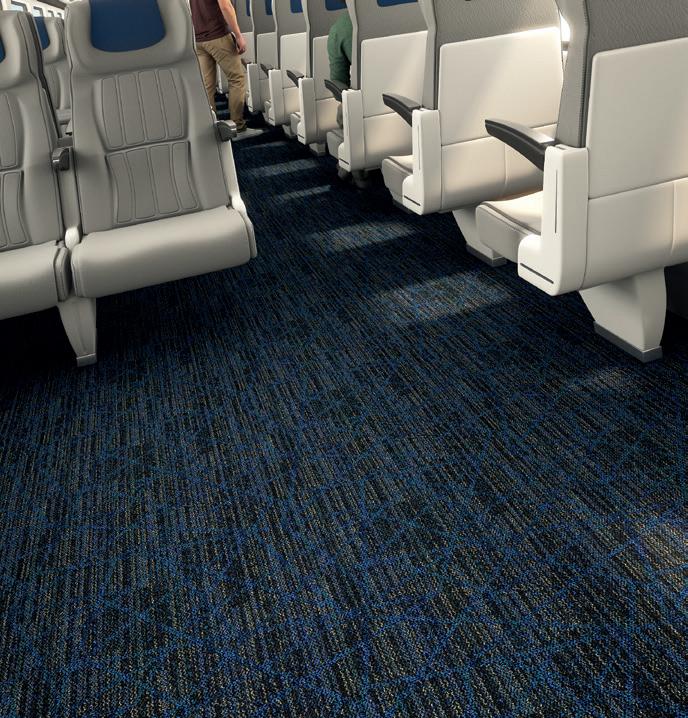

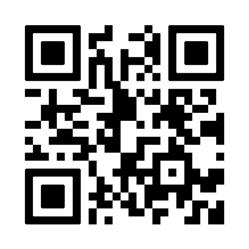
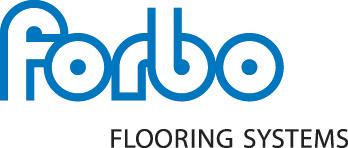
Tel: 01773 744121
Email: transport@forbo.com
Visit: www.forbo-flooring.com/rail
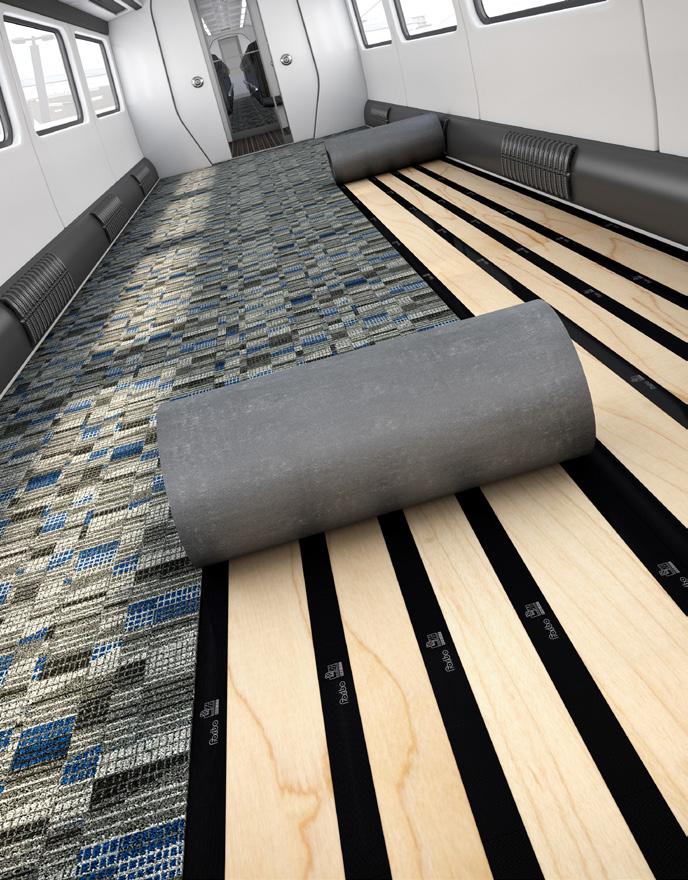
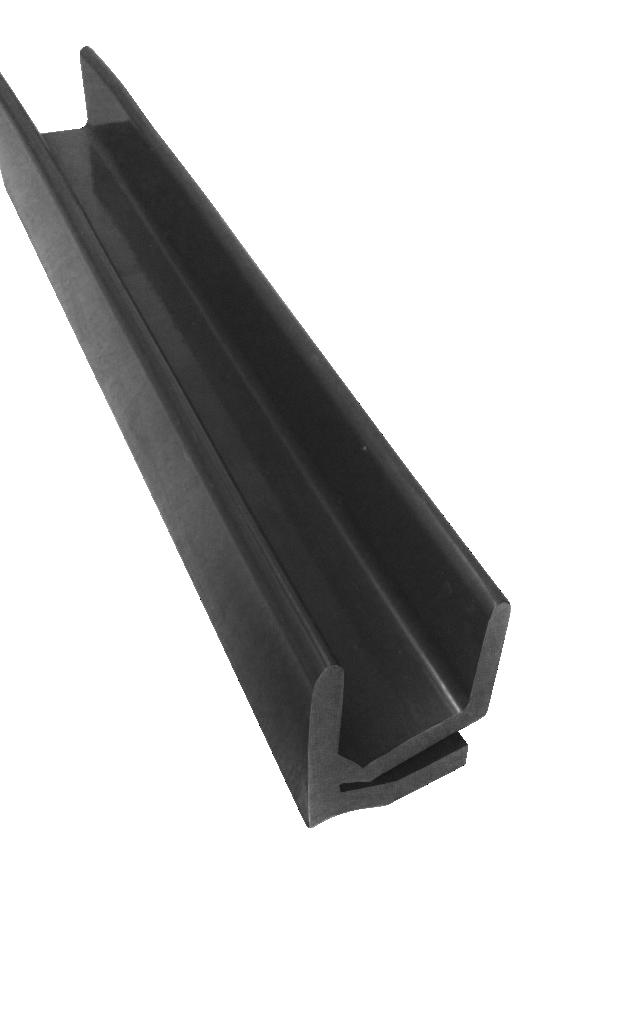
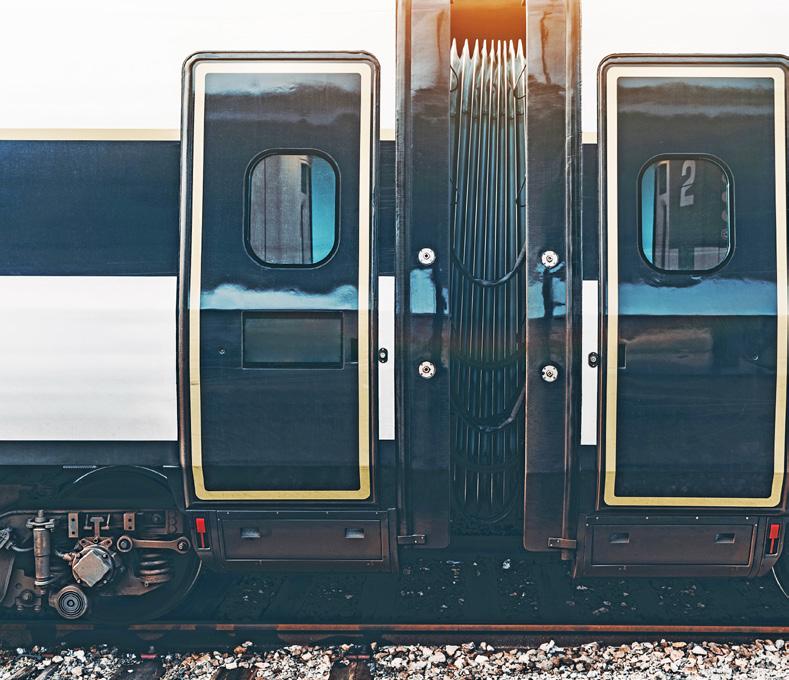
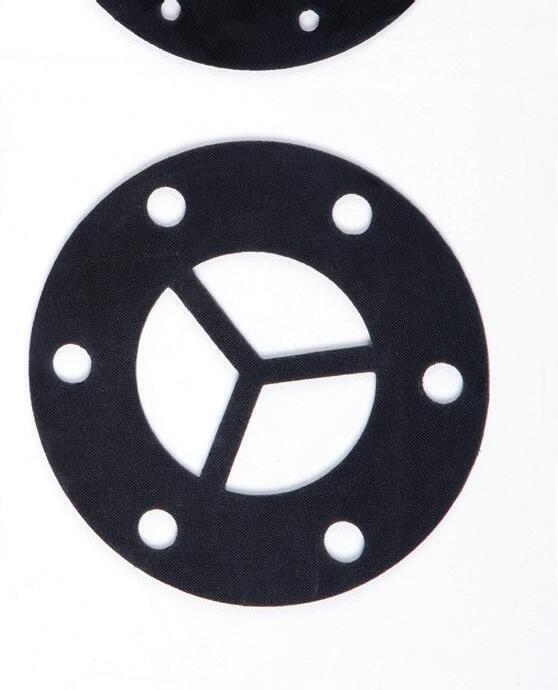
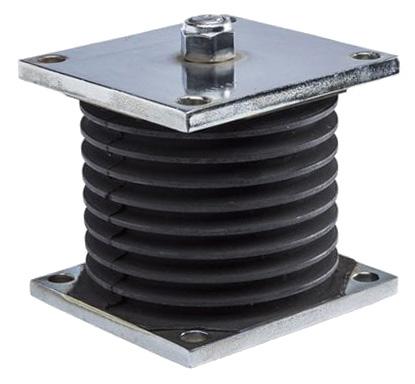
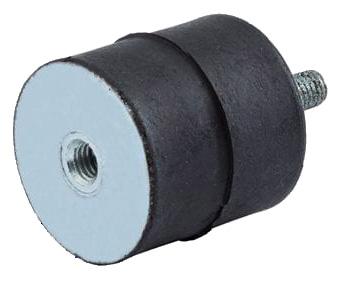
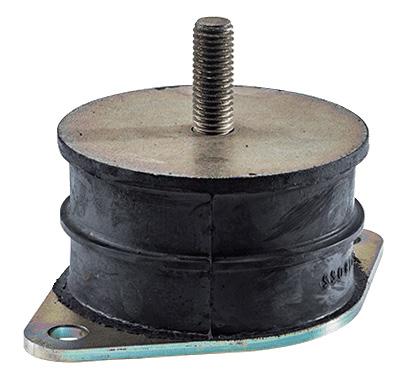
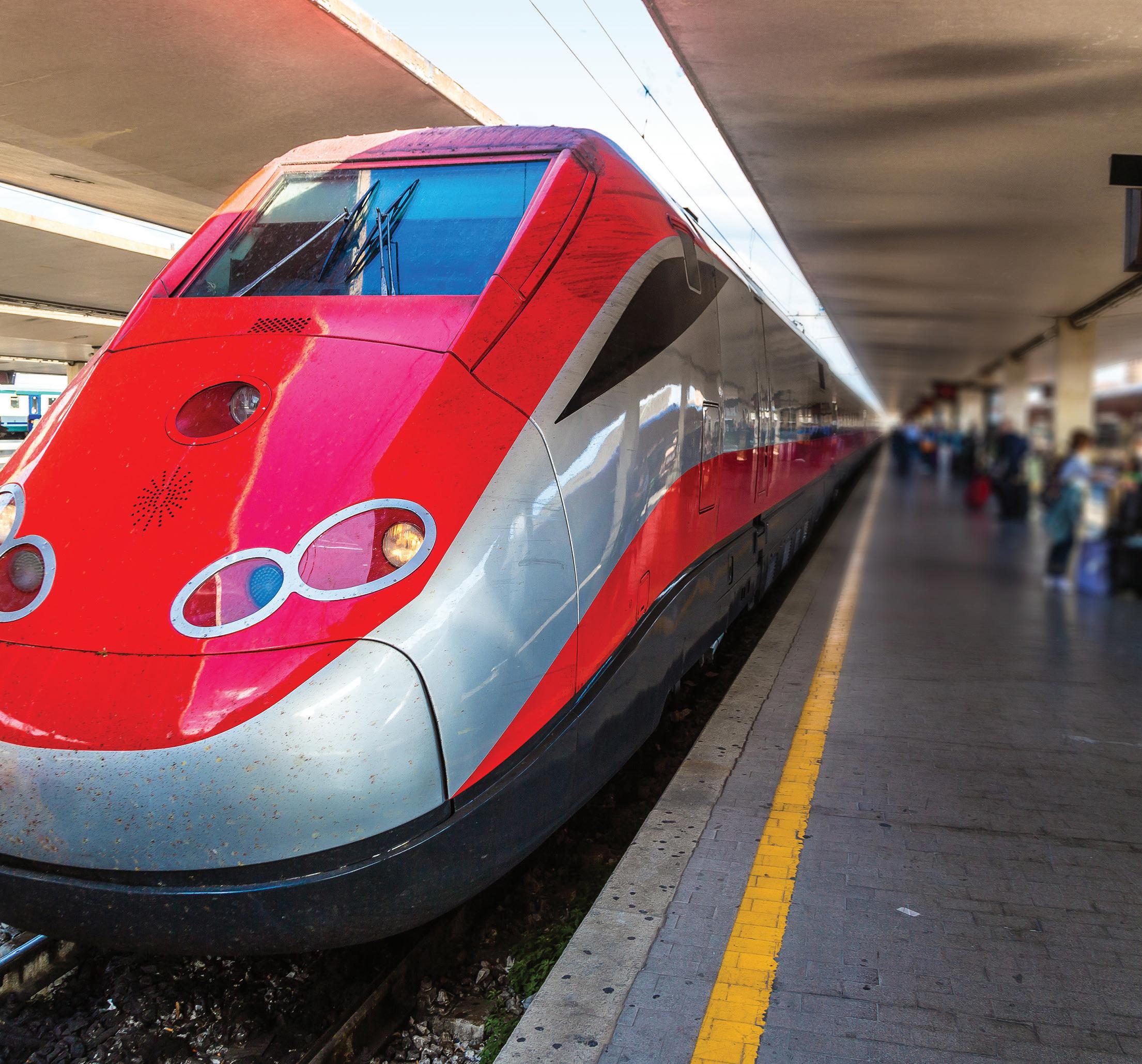
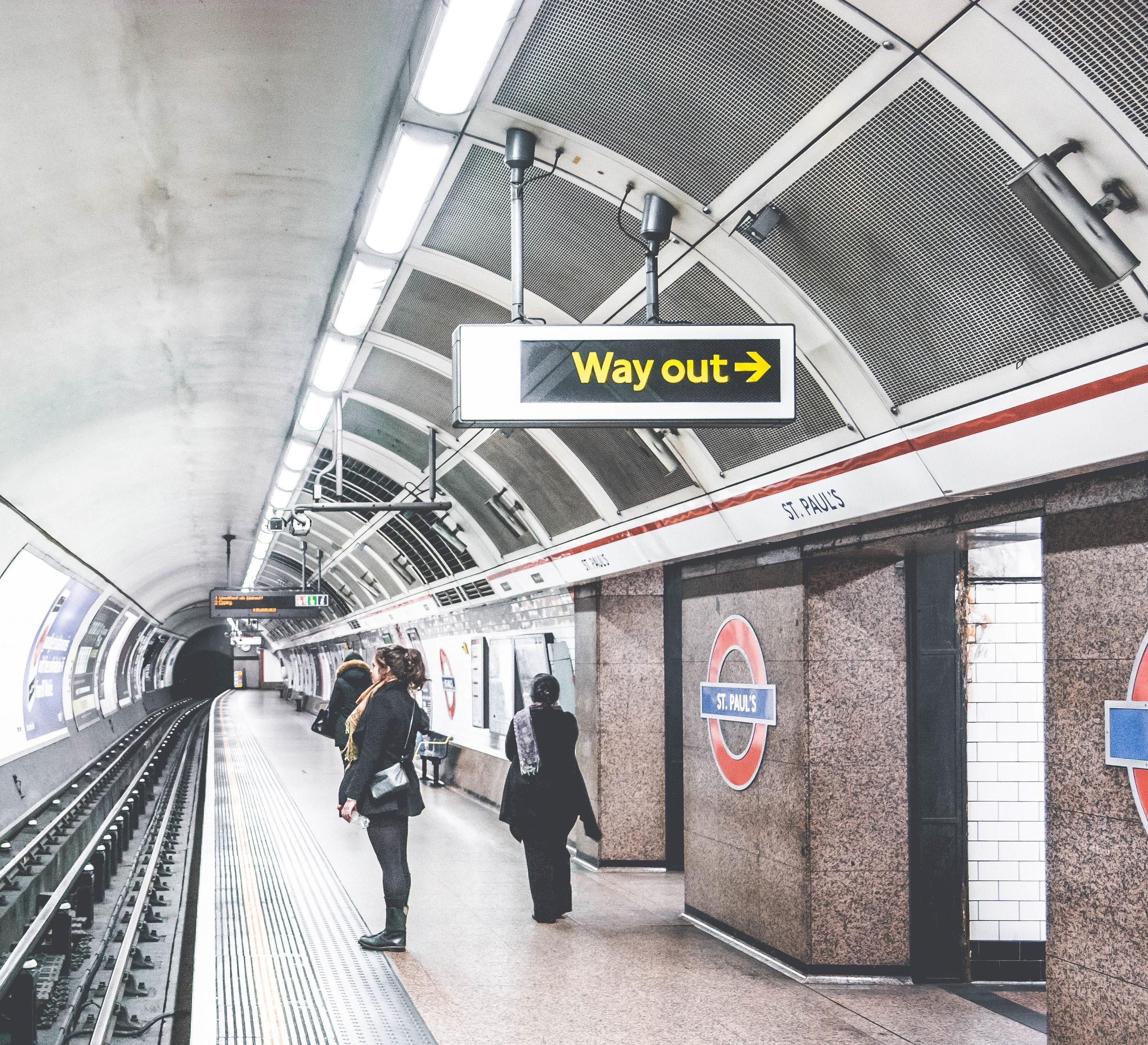
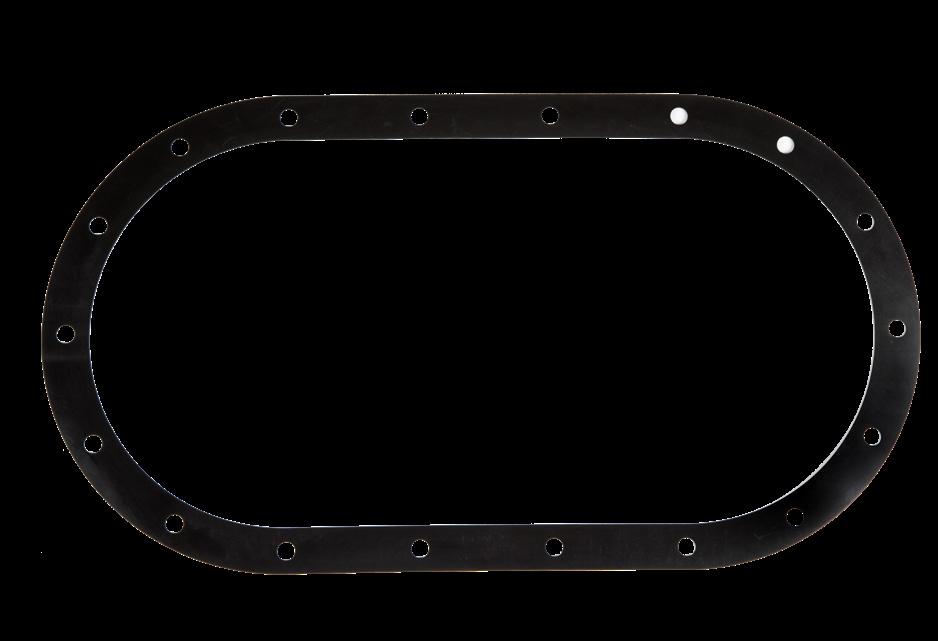




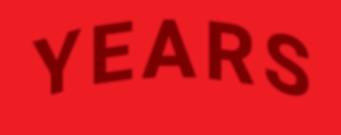




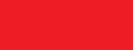
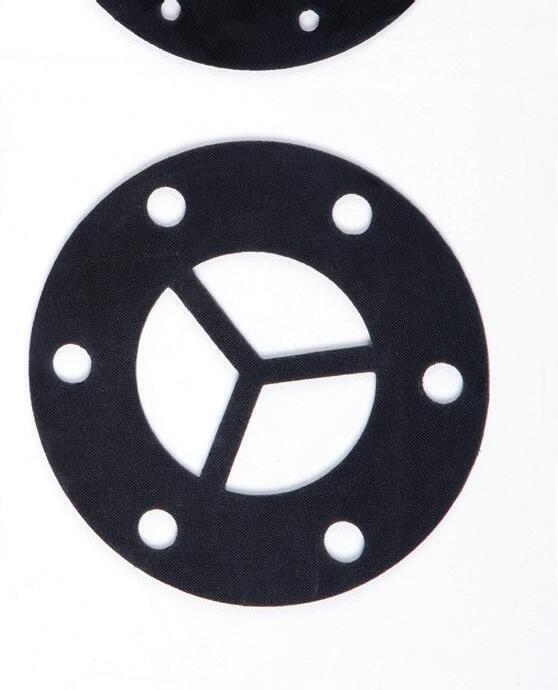
Rubber Products for Rail Refurbishment Projects
J-Flex offers an extensive range of unique elastomer materials for Surface, Sub-Surface, Tunnel and Rolling Stock applications
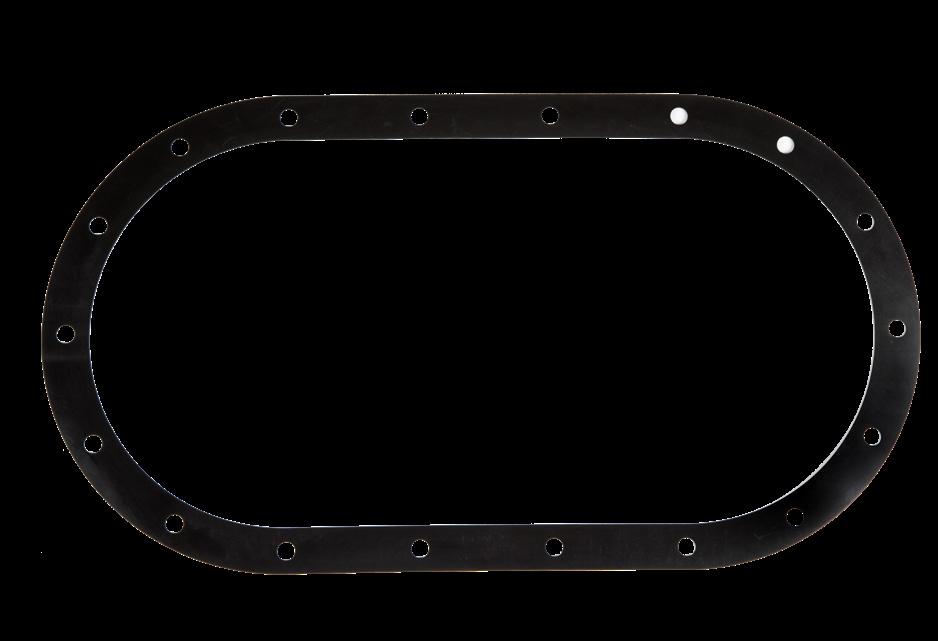
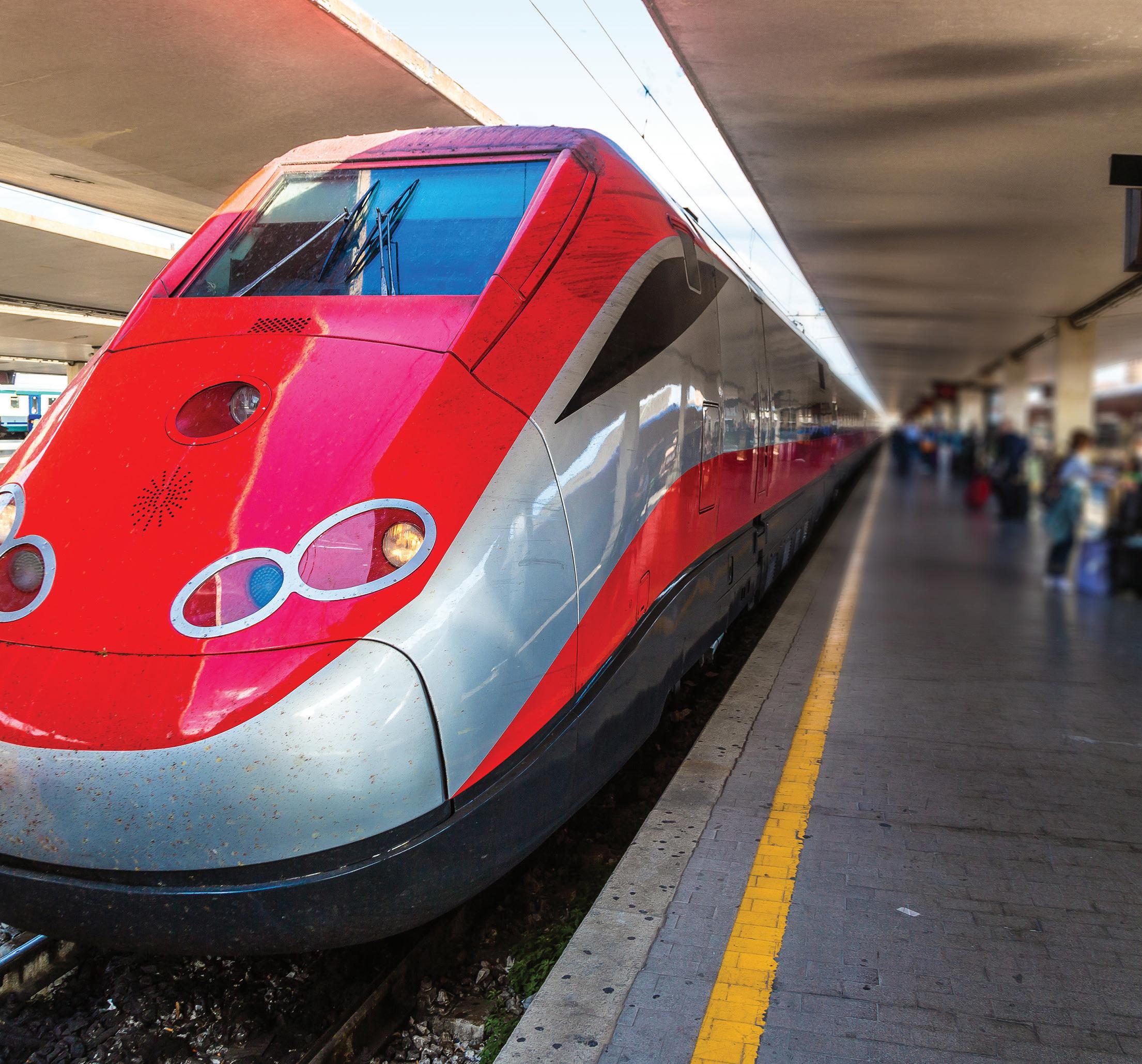
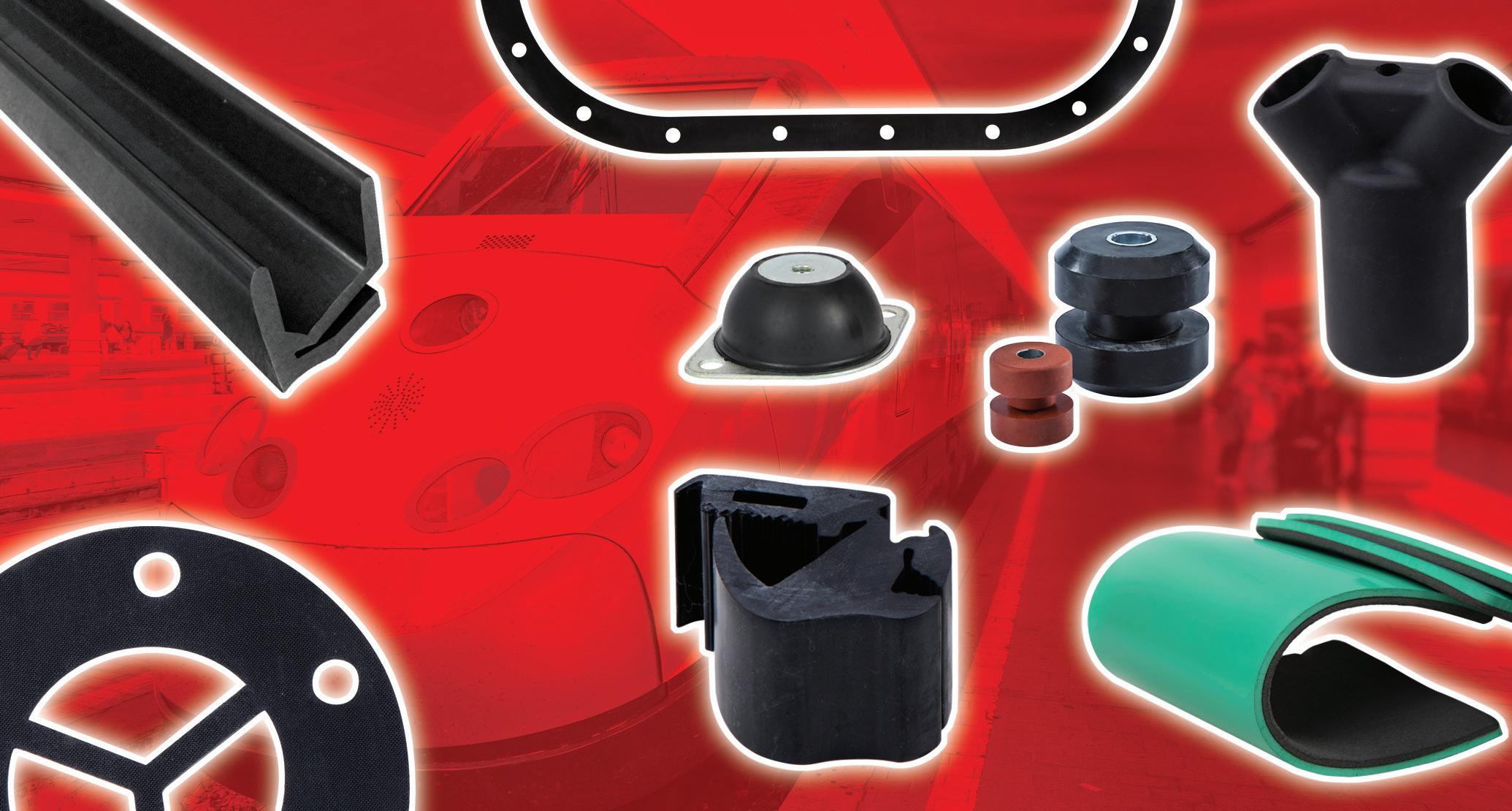
J-Flex EPDM, Silicone and Neoprene and Vamac® materials are tested and approved to EN45545-2 and many other certifications, including LUL S1085 compliance and are designed specifically for low smoke low toxicity requirements, particularly with regards to enclosed space applications.
This makes them ideal for all safety critical applications in rail, mass transit, marine vessels, oil & gas, public transport and heavy goods vehicles. With resistance to corrosion, moisture, salt and light fuels, they offer outstanding flexibility, strength and durability. This includes environmental resistance – withstanding Ozone, U.V., rain and frost – meaning outdoor applications such as lighting systems and enclosures are kept water and dust tight.
Vamac® for example has excellent abrasion resistance, so is ideal where
wear is a concern – one notable use being protection of cables laying on ballast trackside. Gaskets and seals for enclosures such as lighting fixtures, battery boxes/ covers and the like will prevent the ingress of environmental factors.
Extruded seals are perfect for glazing partitions, door portals and floor covings. Anti-vibration gaskets and mouldings come into play for seating mounts and floor vibration dampening. As you can imagine, our various elastomers can perform many functional and critical roles within Surface, Sub-Surface, Tunnel and Rolling Stock applications. With various degrees of hardnesses being available, and gaskets, seals and mouldings being achievable in virtually any required dimensions, the possibilities are endless.
The following page should gives some food for thought but with so many
possibilities, maybe there’s something you have in mind that isn’t shown? Get in touch, we love a challenge and providing solutions!
Materials that can be supplied:
• EPDM
• Silicone
• Vamac®
• Silicone Sponge
• Neoprene Sponge
• Natural Rubber
Which can be supplied as:
• Calendered Sheet Rubber.
• Cut Gaskets; Joints and Strips.
• Precision Moulded Components.
• Extruded Profiles and Sections.
• Vulcanised Joined Profile Frames.
• Laminated Composites (rubber and sponge).
• Sponge/Foam Sheets or cut parts.
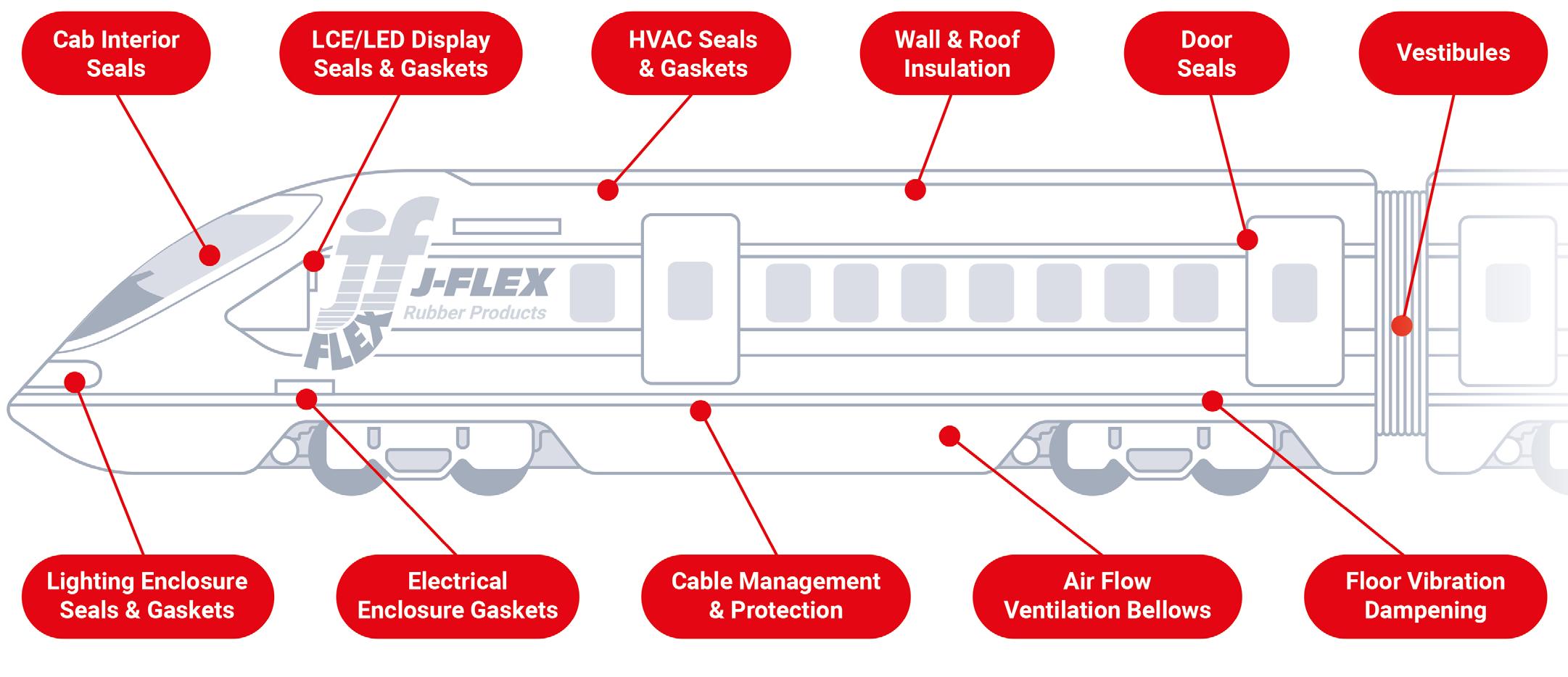

• Machined Plastics and sheets.
• Seals.
J-Flex’s extensive range of unique elastomer materials are tested and approved to EN45545-2 and many other certifications, including LUL S1085 compliance. J-Flex can also cross reference international standards, providing the best solutions – matching or alternative – that meet or exceed your specifications. The company’s extensive knowledge of the worldwide rubber market means it can usually source any specific material requirements you have.
About J-Flex
Established in 1984, J-Flex is a privately owned company involved in the manufacturing & distribution of high
performance rubber products. Over this time they have gained an enviable reputation for high quality manufactured rubber components, elastomer sheetings and vacuum forming consumables, backed up with excellent customer service.
Trackside applications include:
• Cable Jacketing.
• Signal Cable Hose.
• Cable Ductings.
Material data sheets, test reports and samples are available upon request.
Datasheets and A Guide to Flame Retardant, Low Smoke, Low Toxic Rubber Materials can be downloaded at www.j-flex.com/productmarket/rail-and-mass-transit
7548





Tel: 01777 712400
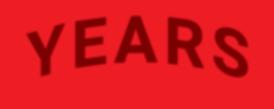



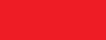

Email: sales@j-flex.com
Visit: www.j-flex.com
Address: J-Flex Rubber Products
Units 1 & 2 London Road Business Park
Retford, Nottinghamshire, DN22 6HG
LinkedIn: j-flex-rubber-products
Facebook: JFlexRubber
Twitter: JFlexRubber
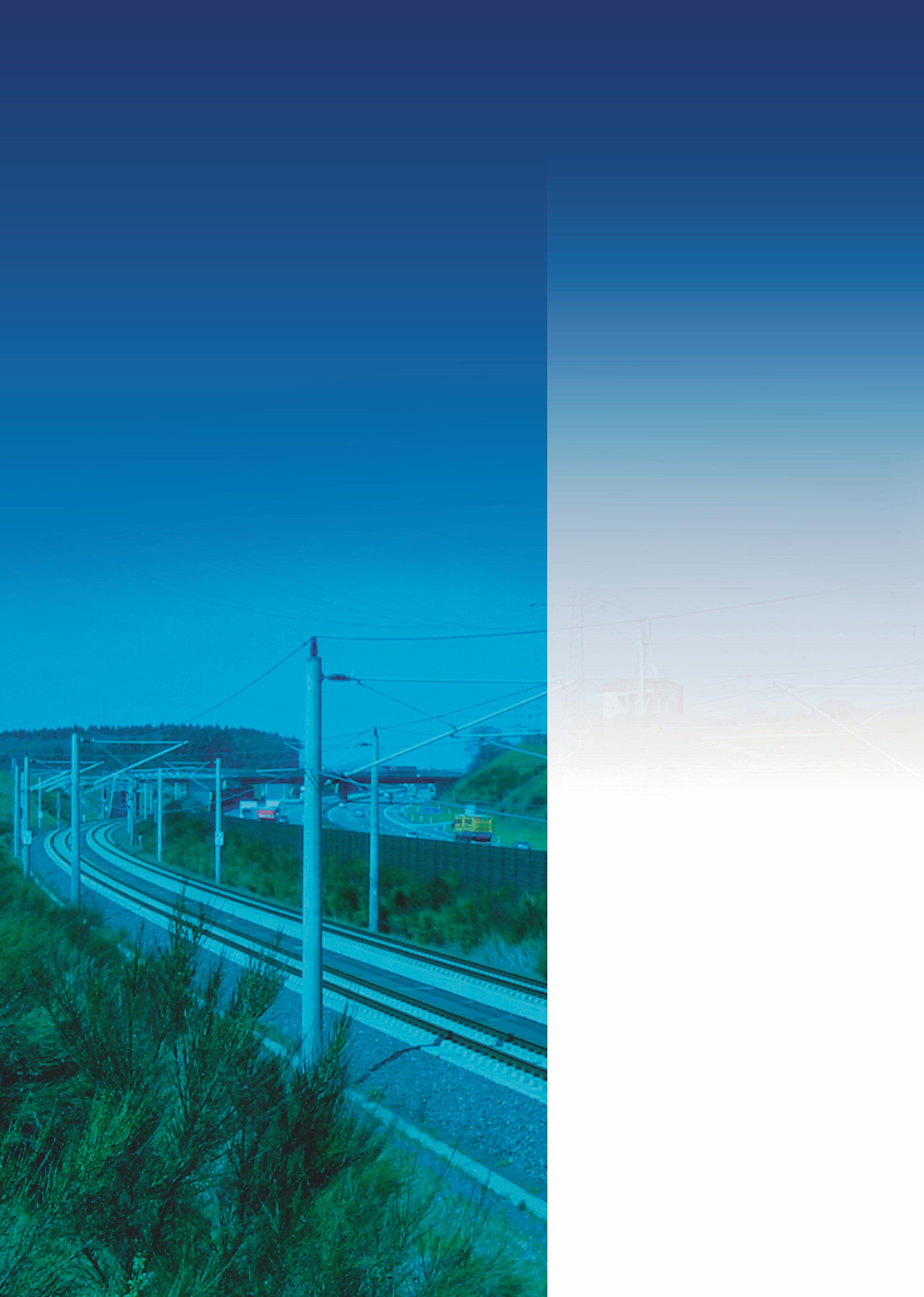
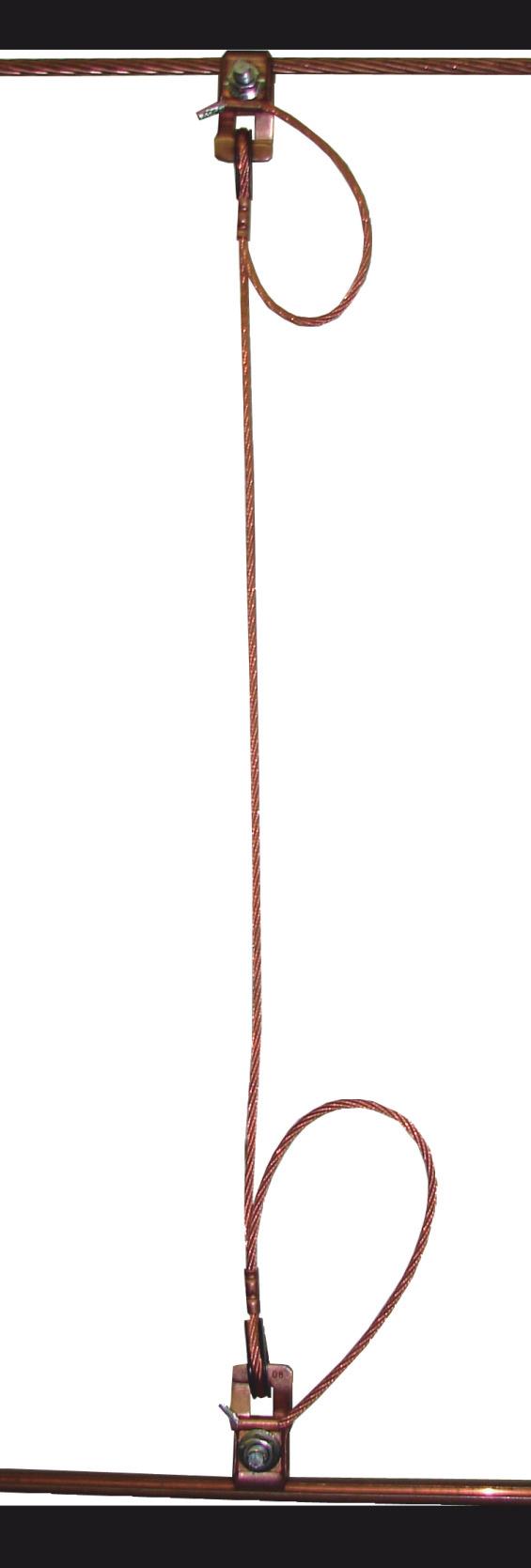
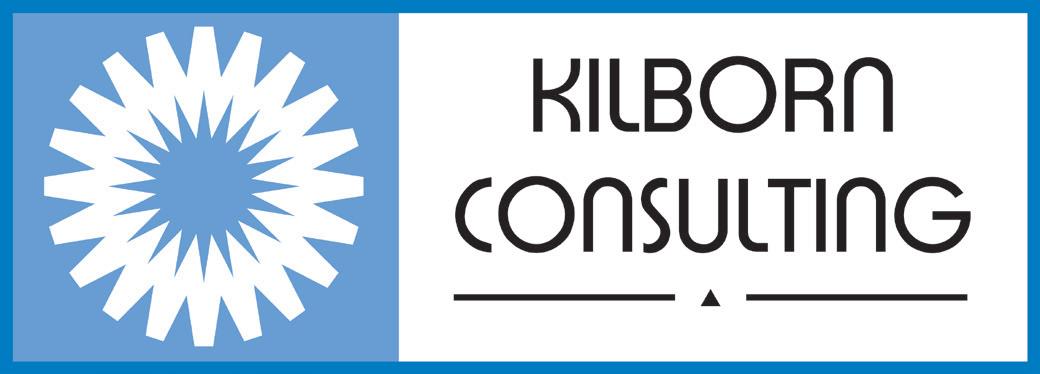
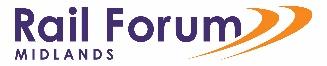
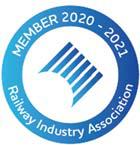
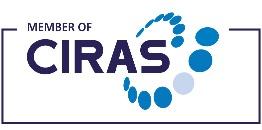
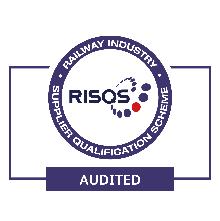
Kilborn Consulting Limited is an independent railway engineering consultancy and design business, with over 21 years of railway experience.
We specialise in the design of new and altered railway Signalling & Telecoms systems for the UK railway infrastructure.
Our areas of specialism are:
•Signalling and Telecoms Consultancy, including technical advice & support;
•Asset Condition Assessments, Correlation and Surveys;
•Signalling & Level Crossing Risk Assessments;
•Feasibility and Optioneering Studies;
•Concept and Outline Signalling Design;
• Telecoms Option Selection Reports (including AiP), Reference System Design and Detailed Design;
•Detailed Signalling Design;
•Competency Management & Assessments;
•Signal Sighting assessments, covering the full Signal Sighting Committee process with a competent Chair.
The new office which is located in the heart of Wellingborough can accommodate all staff and visitors alike and offer widespread views across Wellingborough and the surrounding green spaces
We would be delighted to welcome you to our office to discuss your requirements and how we can support you to achieve those.
Kilborn Consulting Limited 6th Floor, South Suite, 12 Sheep Street Wellingborough, Northamptonshire NN8 1BL
Email: pmcsharry@kilbornconsulting.co.uk
Phone: 01933 279909 www.kilbornconsulting.co.uk
New LPI Manager Narrative Report
Introducing a new reporting tool to enhance leadership decision-making and employee development in the rail industry

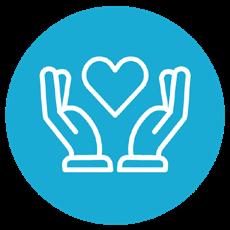
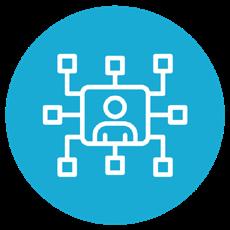
In the realm of talent acquisition, promoting frontline employees into a leadership role can be a daunting task, especially from technically biased or lone-working roles prevalent in the rail industry. Leadership roles often demand oversight, planning, organization, and positive people management skills, which may not have previously been demonstrated by entry-level employees.
In a comprehensive move to support leadership recruitment, OPC Assessment proudly introduces the new LPI Manager Narrative Report, enhancing the effectiveness of its recently launched Leadership Potential Indicator (LPI) tool.
The LPI, is an online situational judgment test, that identifies five crucial managerial competencies:
• Being interpersonally skilled.
• Thinking skills such as effective decision making.
• Strong customer focus prioritizing external and internal customer needs.
• Driving performance. Achieving excellence in oneself and others.
• Leading others to deliver results.
Introducing the New LPI Manager Narrative Report
The new narrative report complements the LPI and the automatically generated profile report from Candela by providing a detailed 'portrait' of a candidate. Organized around the five LPI managerial competencies, it delves into specific competencies, highlighting areas of excellence, potential development needs, and behavioural responses in some typical work scenarios. The report assigns a candidate’s relative performance on a five-point scale and provides a written narrative in support.
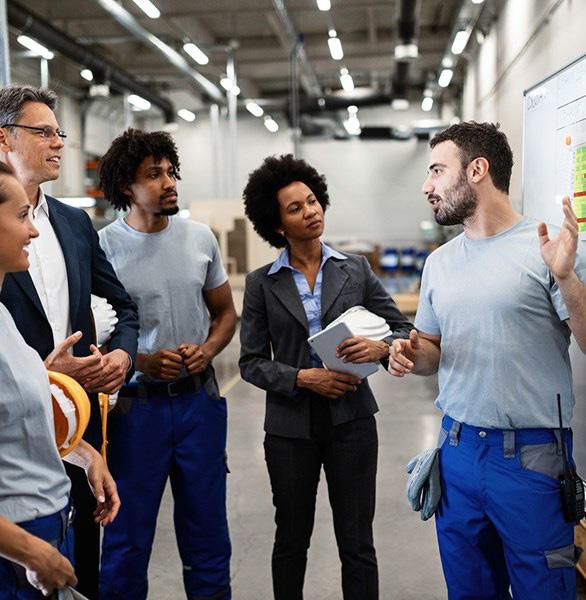
For example, in the competency ‘Driving performance’ a high score might suggest a confident manager capable of consistent decision-making under pressure. Conversely, the report may highlight an area for improvement, such as ‘Interpersonal Skills’, by maybe suggesting that a candidate could face challenges in providing appropriate direction to team members.
Benefits for a recruiting manager
This innovative LPI Manager Narrative Report is invaluable for decision-making, particularly with external candidates, or those who don’t have any previous managerial experience. It provides a nuanced understanding of a candidate's potential to be a leader and their supervisory skills. Additionally, the LPI and the Narrative Report for Managers can also serve as a developmental tool, identifying strengths and training needs for existing first line managers with leadership potential, helping create a more targeted Leadership Development Plan.
Developed by skilled OPC Assessment Psychologists through meticulous job analysis, industry research, and collaboration with senior rail managers, the LPI and its Manager Narrative Report reflect a deep understanding of managerial
‘The new LPI Narrative Report offers valuable insights and reassurance about a candidate's strengths and areas for development before promotion.’
competencies. This expertise positions the new report as a reliable resource for effective decision-making in talent acquisition and leadership development.
Emily Wong, Business Psychologist at OPC Assessment said: "As psychologists, we emphasise the need to base recruitment decisions on tangible competency evidence when recruiting for leadership roles or any position. The new LPI Manager Narrative Report provides valuable insights into a candidate's strengths and areas for development before promotion, essential for individual success, team harmony and organizational performance.”
Get in touch with the friendly OPC Assessment team if you’d like to hear more about the New LPI Manager Narrative Report or the Leadership Potential Indicator (LPI) tool.

Tel: 01923 234 646
Email: admin@theopc.co.uk
Visit: www.theopc.co.uk
Embankment Stabilisation
In a bid to modernise their Tamworth, Staffordshire site, Forterra embarked on a £27 million investment project, aiming to revamp their facility
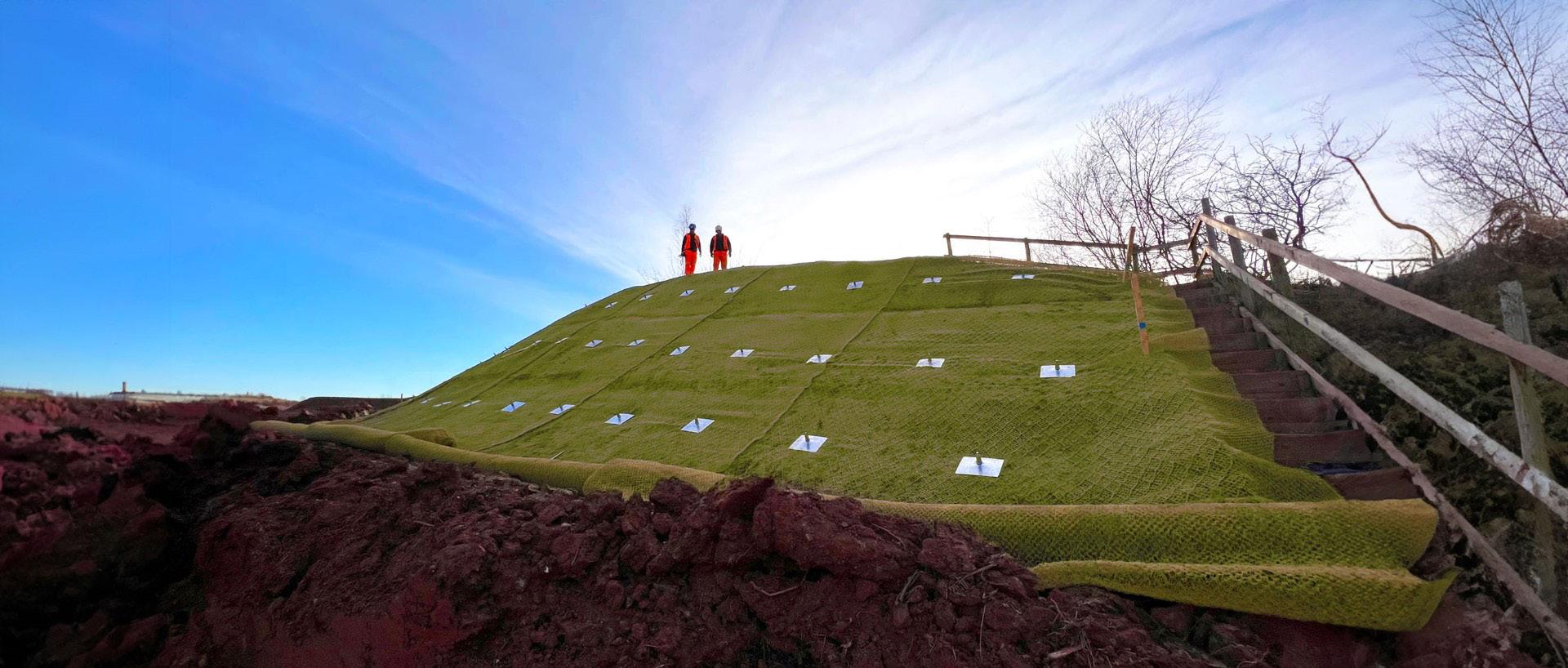
Among the myriad of enhancements, addressing slope instability stood as a crucial challenge. The upgrade scheme included the installation of a box feeder adjacent to an existing bund, spanning approximately 150 metres, which had a history of slope instability.
Forterra entrusted Anchor Systems (International) Ltd to tackle the slope instability and erosion issues. Collaborating with Key GS for slope stabilisation/ remediation design, a comprehensive solution was devised for the eastern slope of the bund. The recommendation from Key GS's global stability analysis led to the installation of the AS-50 Vulcan Earth Anchor System at 1.5-metre centres across the slope face section, reaching a minimum depth of four metres. Anchors were installed at a 20° angle from the horizontal, achieving a minimum hold capacity of 35kN. Additionally, Greenax meshing was employed to prevent localised erosion.
Hartmann Construction took charge of the reprofiling works, ensuring the slope adhered to the specified parameters – a
maximum height of 5.8 metres with a slope angle of 34° (1v:1.5h). Over a three-week period, a team of four operatives installed 330 AS-50 Vulcan Earth Anchors across the 150-metre by eleven-metre bund, adhering to the recommended 1.5-metre spacing and utilizing the pre-laid Greenax meshing. Testing confirmed the anchors' 35kN hold capacity. The installation equipment included a 12T excavator with a breaker attachment, T38 x 5m drive rod kit, and handheld hydraulic loading equipment.
The deployment of the Vulcan Anchor System and Greenax meshing proved instrumental in stabilising the reprofiled bund, effectively mitigating further erosion or slope instability. This solution, in alignment with Key GS's recommendations, not only achieved the desired outcome but also offered a cost-effective and efficient approach, perfectly aligning with Forterra's modernisation and sustainability goals. The project's timely completion within budget underscores the successful collaboration between Forterra, Anchor Systems, Key GS, and Hartmann Construction.
This project exemplifies the synergy
between innovative engineering solutions and collaborative partnerships in addressing complex infrastructure challenges, ultimately paving the way for sustainable modernisation in the railway sector.
Forterra's commitment to modernisation goes hand in hand with their dedication to environmental sustainability. By opting for the Vulcan Anchor System and Greenax meshing, Forterra minimised the environmental footprint of the project. Traditional stabilisation methods often involve the use of wet trades such as grouts, which can have detrimental effects on the surrounding ecosystem and groundwater. In contrast, the non-invasive nature of the Vulcan Anchor System not only reduces disruption to the environment during installation but also ensures longterm sustainability by avoiding potential contamination risks associated with cementbased solutions. This environmentally conscious approach aligns with Forterra's broader sustainability objectives.
The success of the Wilnecote Brickworks Embankment Stabilisation project underscores the pivotal role of technological

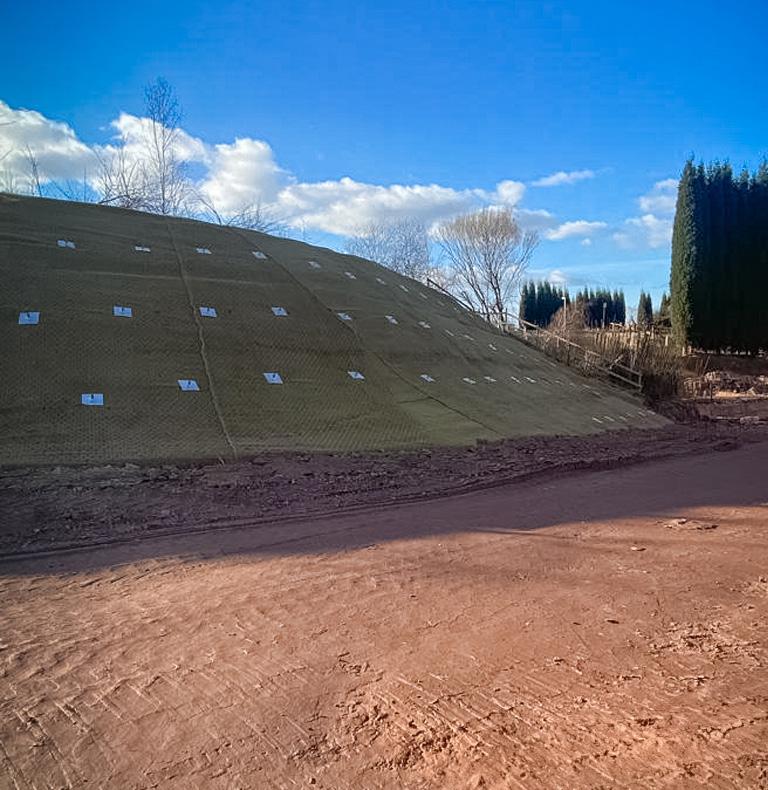
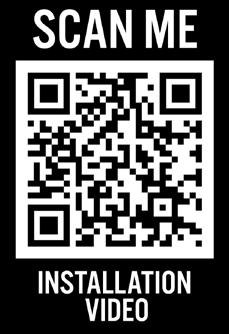
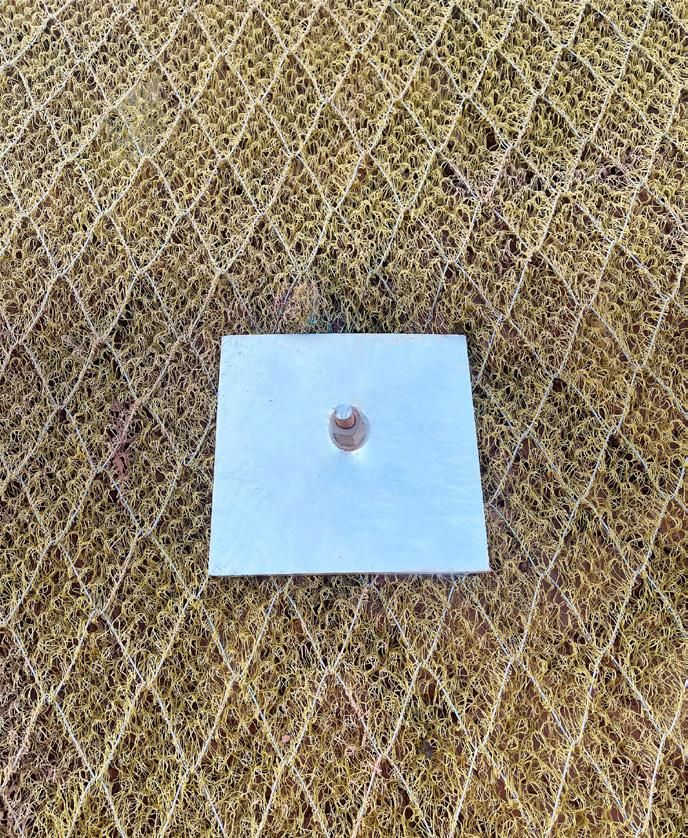
advancements in addressing infrastructure challenges. The utilisation of hydraulic equipment and precision-engineered anchor systems exemplifies the fusion of innovation and practicality in modern engineering solutions. Looking ahead, this project serves as a testament to the potential of advanced anchoring technologies in railway infrastructure projects worldwide. As the industry continues to evolve, embracing solutions like the Vulcan Anchor System paves the way for enhanced efficiency, costeffectiveness, and sustainability in future railway development initiatives.
Advantages of geotextiles and geosynthetics:
• Promotes vegetation growth for a sustainable result.
• Wet trades such as grout are not required with the system, providing a more environmentally friendly operation.
• Reduced labour and associated cost savings compared to hard armour installation.
• Reduces heavy traffic and installation plant necessary for hard armour/concrete processes.
• Aesthetically appealing and discreet, allows vegetation to take root providing a natural finish as opposed to unattractive traditional concrete methods.
• Recessed system
• Reduces groundwork and maximises use of space.
• Resilient and durable, our anchors are made from corrosion-resistant materials and work with the majority of geofabrics available.
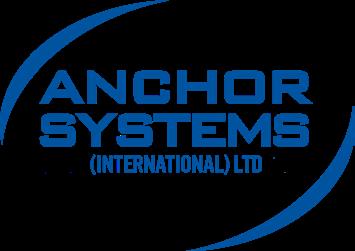
Tel: 01342 719 362
Email: info@anchorsystems.co.uk
Visit: www.anchorsystems.co.uk
Supporting the efficient, greener movement of freight
Utilising over 7 years of historical data, PathPlanner seeks out unused paths across the network to unlock capacity and generate new opportunities for the freight sector to transport more goods seamlessly and sustainably.
Make. Change. Work.

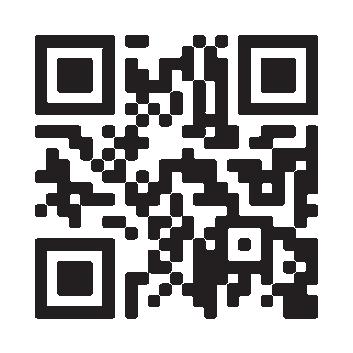
Innovative Digital Solutions
The Office of Rail and Road (ORR) outlined its final decision on Network Rail’s £43.1 billion five-year plans back in October 2023, to deliver a safe and customer-centric railway
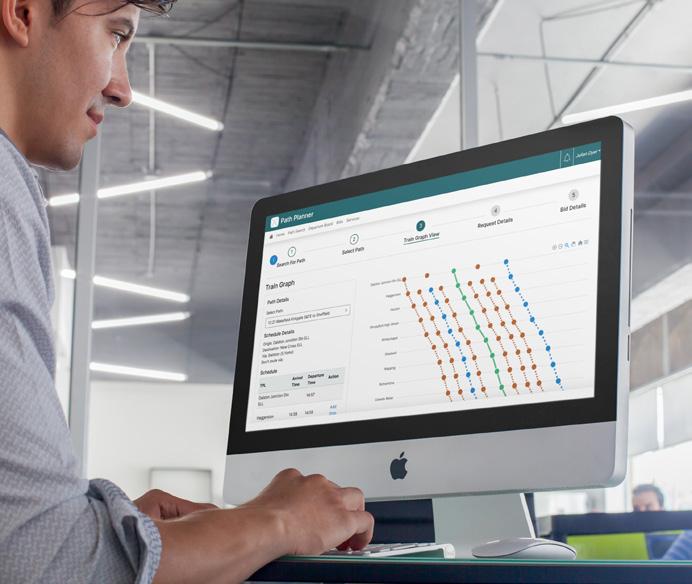
The plans will see a staggering £38.5 billion invested in England and Wales and £4.6 billion invested in Scotland. This is a promising step forward, and with the right support and backing from across the rail industry, is sure to bring about positive change. However, what does this mean for the freight sector and what processes are currently in place to ensure there is a solid foundation for these plans to build upon?
Developing technological solutions to meet precise needs
Through extensive collaboration with freight operators and the industry, 3Squared has developed solutions customised to meet the exact needs of the freight sector. The PathPlanner tool has been specifically designed to assist freight customers in more effective planning, with the overarching goal of minimising cancellations.
The system aims to assist Freight and Passenger Train Operators to better manage their Very Short-Term Planning (VSTP). As it stands, VSTP currently operates under Control Conditions – i.e., additional trains do not follow the same planning principles as trains bid into the Long-Term timetable, however, they are entered directly into operational systems by control staff.
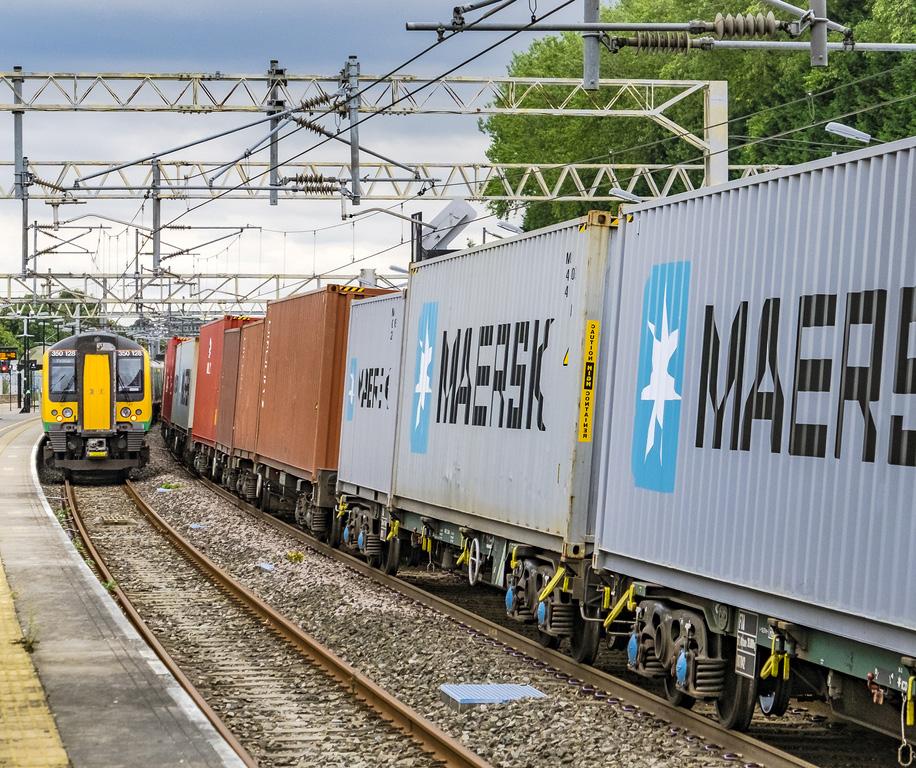
PathPlanner is designed with freight operators in mind, as it unlocks ‘hidden’ paths on the network, finding grey space in the timetable to add schedules at short notice. This maximises freight movement, productivity, and asset optimisation, whilst improving fuel efficiencies and reducing idling.
PathPlanner also streamlines the booking process so that customers can efficiently transport their cargo using existing trains. For example, if a customer urgently needs to transport a shipment last minute, PathPlanner can identify suitable providers, estimate costs, and leverage historical train data and machine learning technology to propose paths that may not have otherwise been clearly visible.
Adoption of the tool across the industry has to date been significant, with ample opportunities ahead as 3Squared outlined in a whitepaper published early last year. The company looks forward to seeing PathPlanner’s wider expansion this year, to support the industry wide plans to deliver a safe and customer-centric railway.
Tackling complex challenges through innovation
The BulkSmart solution is also revolutionising logistics operations, particularly at HS2. 3Squared's range of
digital RailSmart solutions assist major freight operators in saving time, reducing costs, and delivering digitally enhanced operating practices.
Such initiatives have the potential to overhaul complex processes and contribute to the expansion of rail freight by making the space easier to operate within. Simplifying operations to ensure a seamless customer journey can make the switch from road freight to rail freight more appealing to potential customers, who are looking for dependable and increasingly greener modes of transport to deliver their goods.
Each individual RailSmart product has been designed to support a low emission railway. As digital solutions, they can help freight stakeholders reduce energy consumption by increasing efficiencies through digital means.
As remotely accessible solutions, they remove the need for rail workers to travel up and down the country to complete tasks. When combined, this provides a wealth of operational and sustainable benefits to everyone involved with the rail network, from operators to passengers and beyond.
Looking
ahead to a greener future
The rail industry of the future must be able to adapt to a diverse range of needs and demands to meet its growth targets and deliver a safe and customer-centric railway. It is hard to undermine the rich benefits that freight transport provides this wider goal with and when supported by innovative tools such as PathPlanner and BulkSmart, the opportunities for growth are endless.
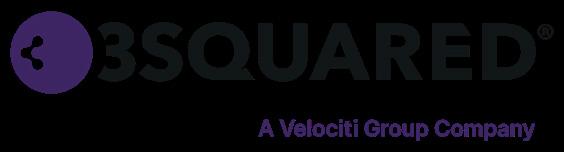
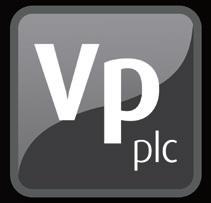
Supporting Network Rail for over 40 years
Torrent Trackside is the UK's only specialist rail plant hire company We have been supplying portable tools and equipment to Network Rail and its associated contractors for over 40 years. The company has always been at the forefront of innovation and development to provide the best equipment to ensure rail projects and maintenance is carried out quickly, safely and efficiently Our customers benefit from:
l 9 depots providing a full UK wide coverage
l Professional service from dedicated rail professionals
l Continuous investment in the latest emission free, low vibration, lightweight battery tools, lighting and equipment
l The most compliant and safety focussed business in the sector
l Near 100% reliability record
l A determination to fully support Network Rail through the next Control Period and beyond.
For more information visit our website, phone our helpline or scan the QR code below:
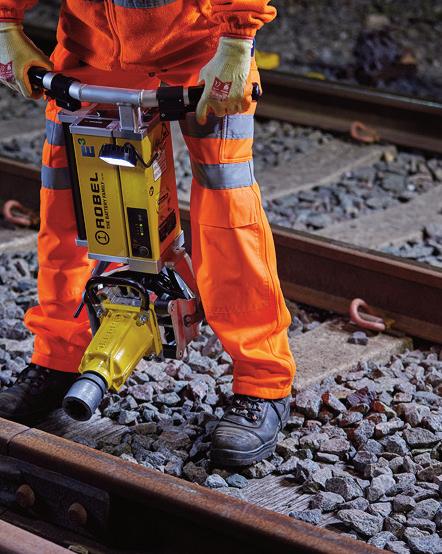
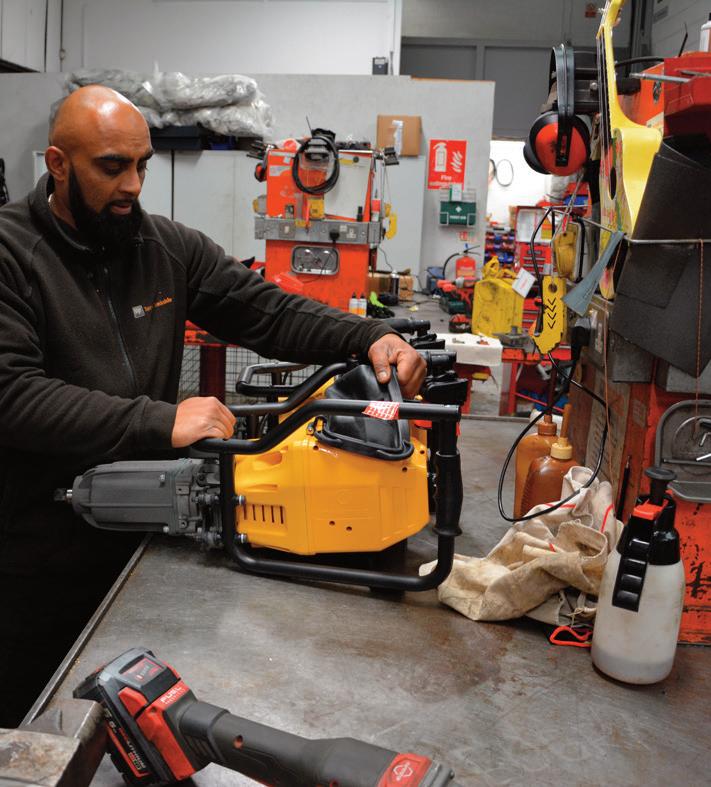
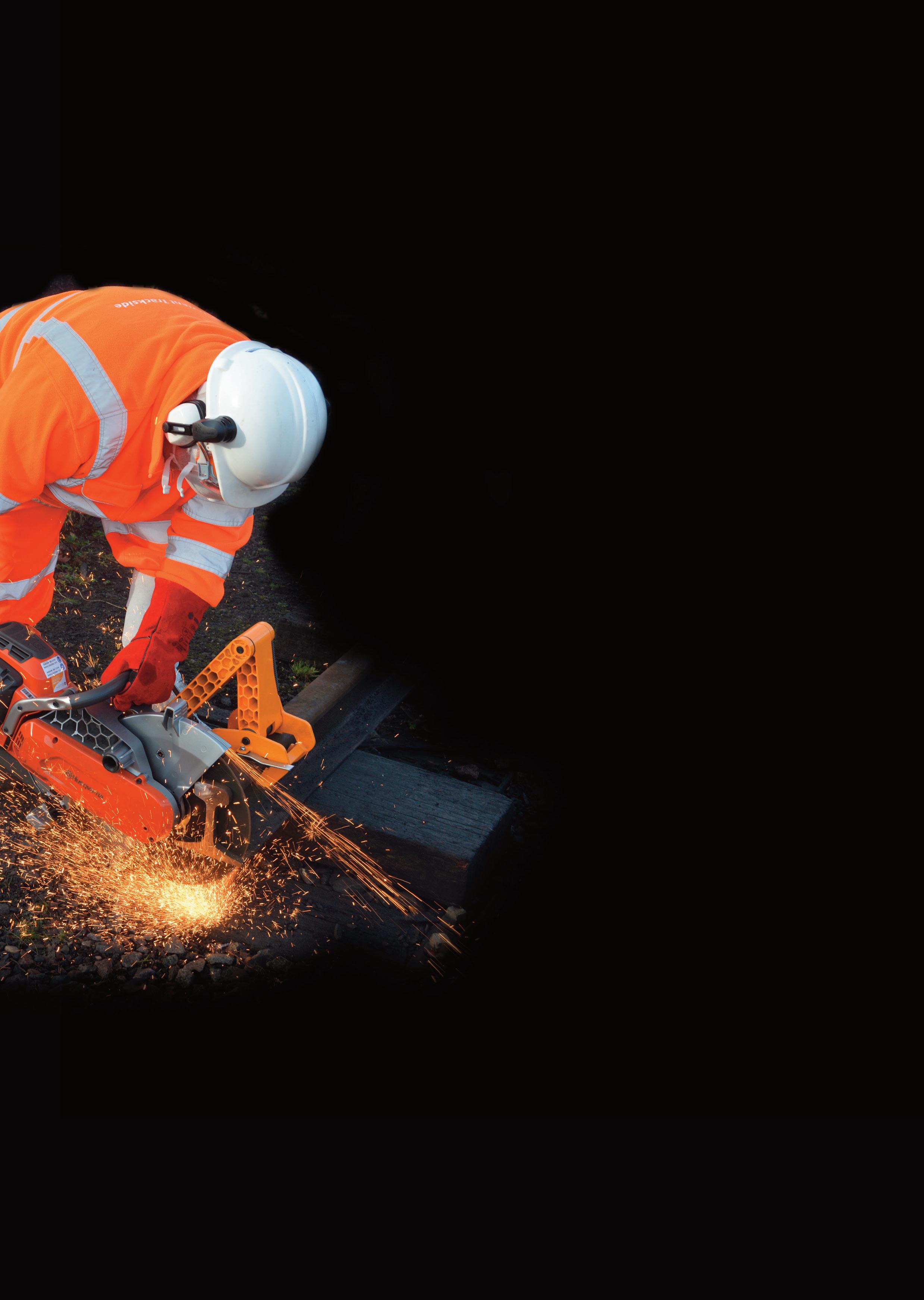
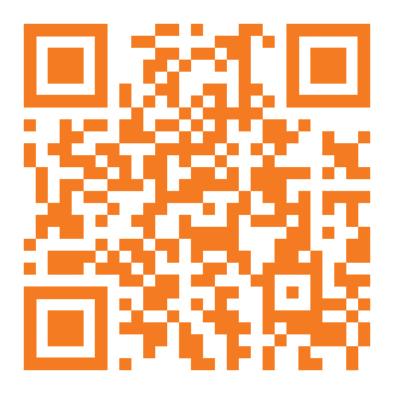
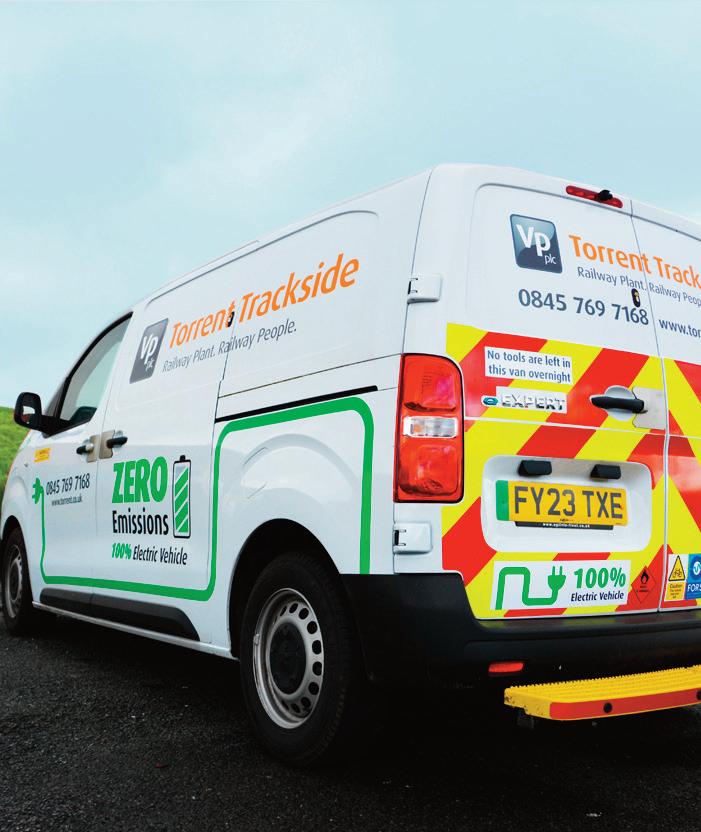


www.torrent

Electro-Wind Ltd’s 45th Anniversary
In January of this year, Electro-Wind Ltd celebrated its 45th anniversary

Whilst the first generation started and developed the business for 20 years, the next generation, our current Directors have been committed to leading the company’s growth for the last 25 years.
The company has evolved and grown, widening its product range in size and diversity gaining expertise and capability along the way. The advancing product range offers bespoke transformers from 10VA up to 2MVA in addition to AC reactors, DC rectifiers and chokes. Supported by an extensive range of associated products including site electrical accessories.
Electro-Wind has outgrown three different premises and with the new addition in 2024 of a further production unit to house the significant machinery investments the momentum of company shows no sign of slowing down.
People are integral to any business success and the strength and enthusiasm of its determined team is key in driving the organisation to a greater success.
Electro-Wind is committed to continued growth for the next generation. The company would like to thank all of its staff, suppliers, and customers for their continued support and is looking forward to the next exciting stage in Electro-Wind’s journey.
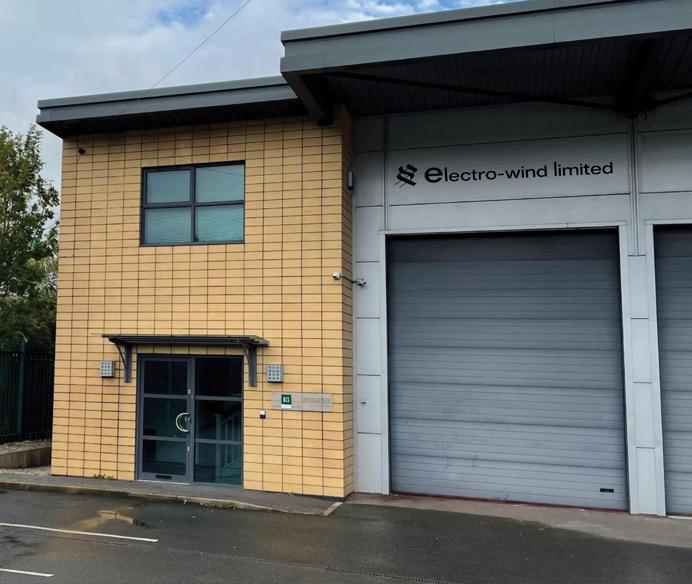
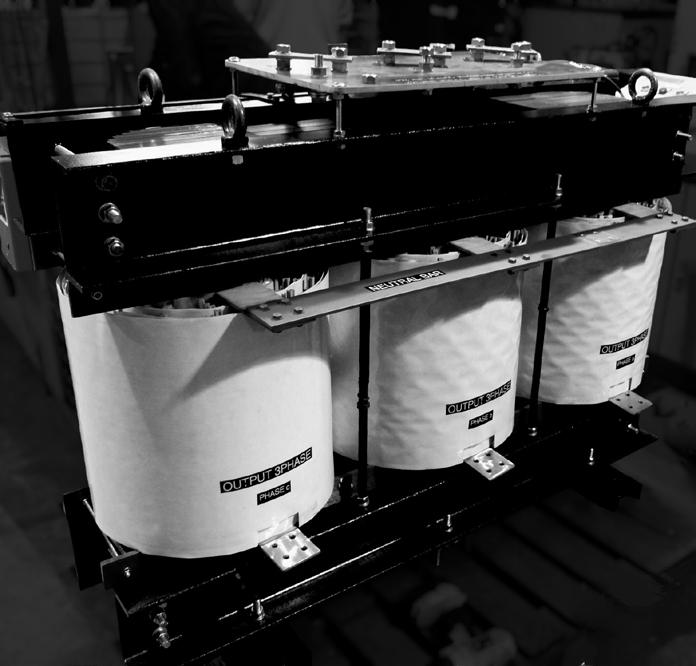
Tel: 01782 776 321
Email: sales@electro-wind.co.uk
Visit: www.electro-wind.co.uk
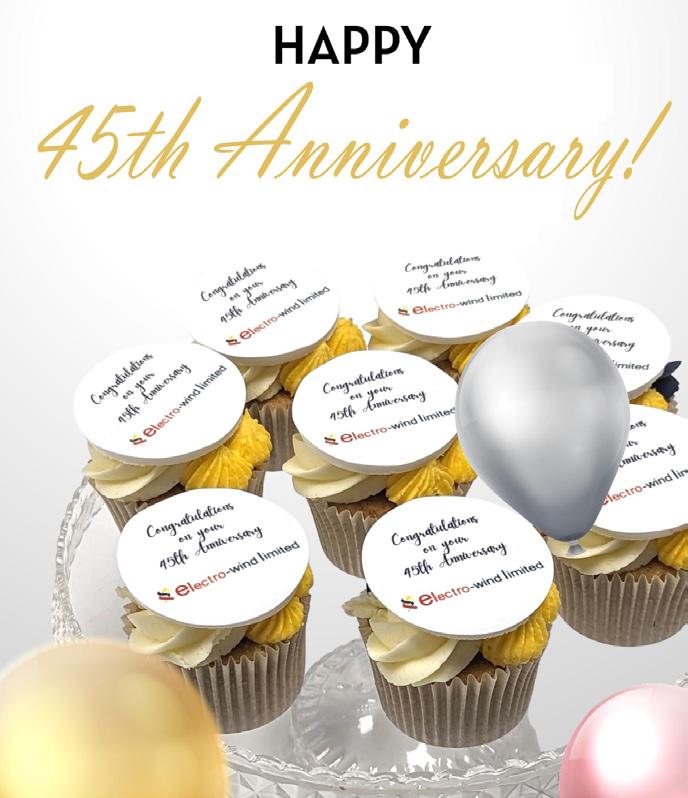
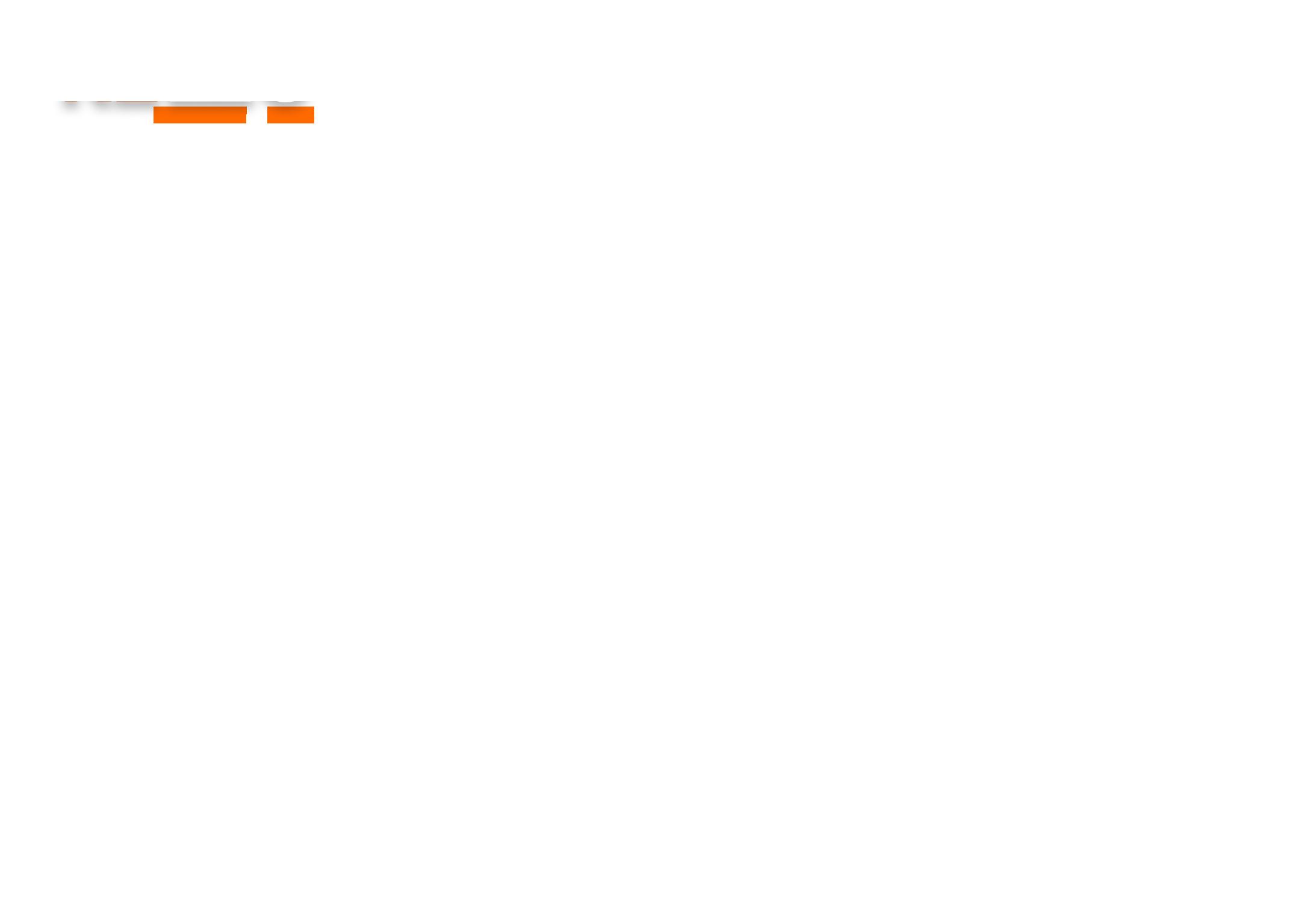
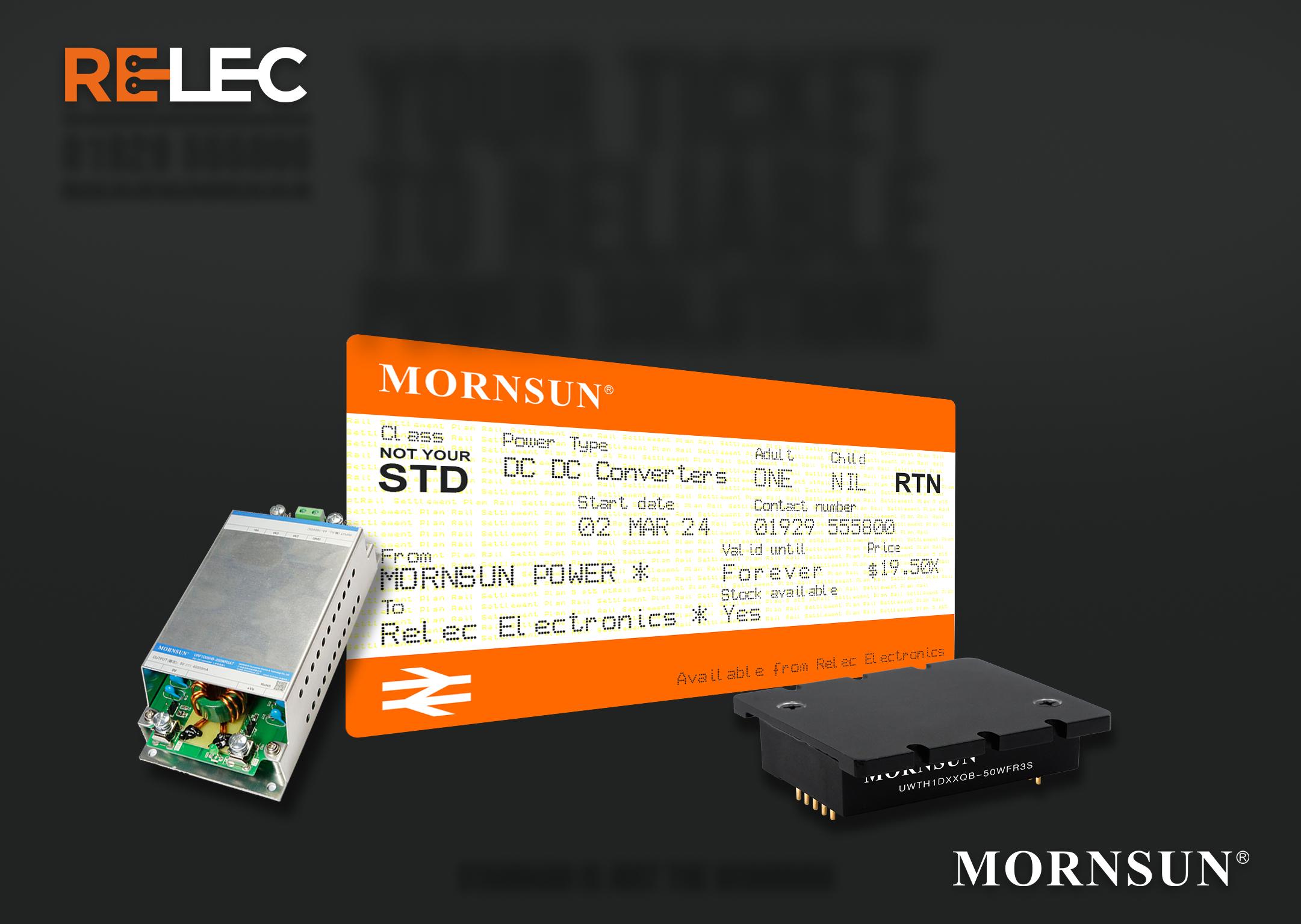
Approved Hydraulics have been supplying some of
largest
build and maintenance firms for over 10 years. Now considered some of the best in the world!
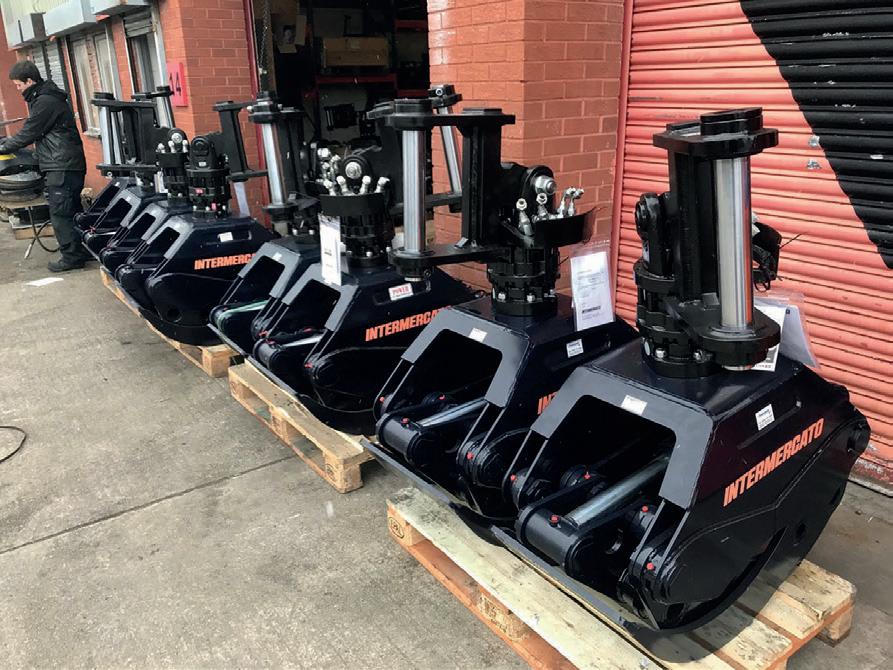
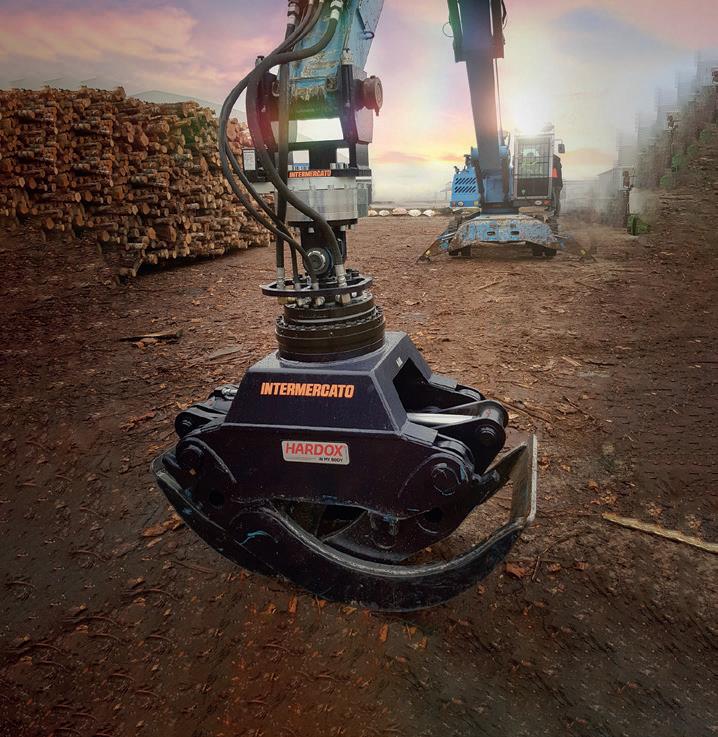
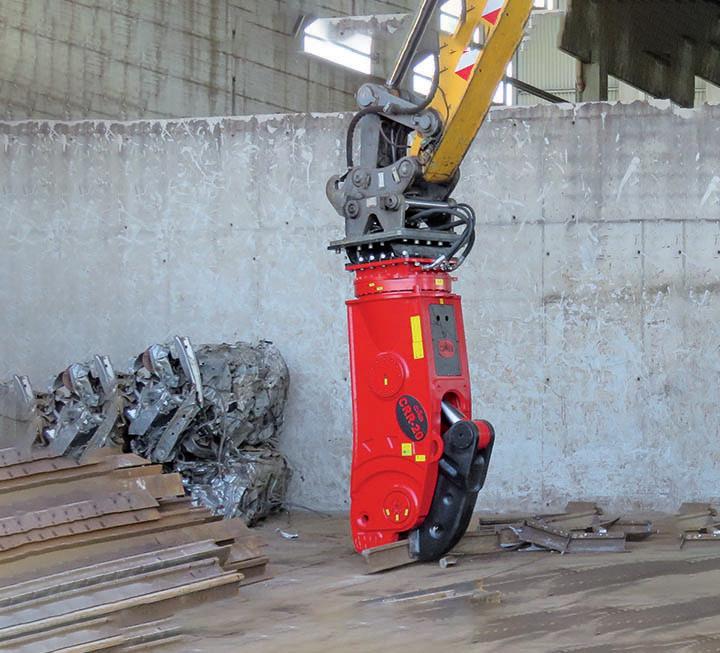
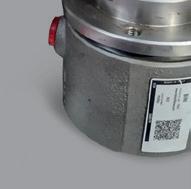
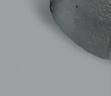
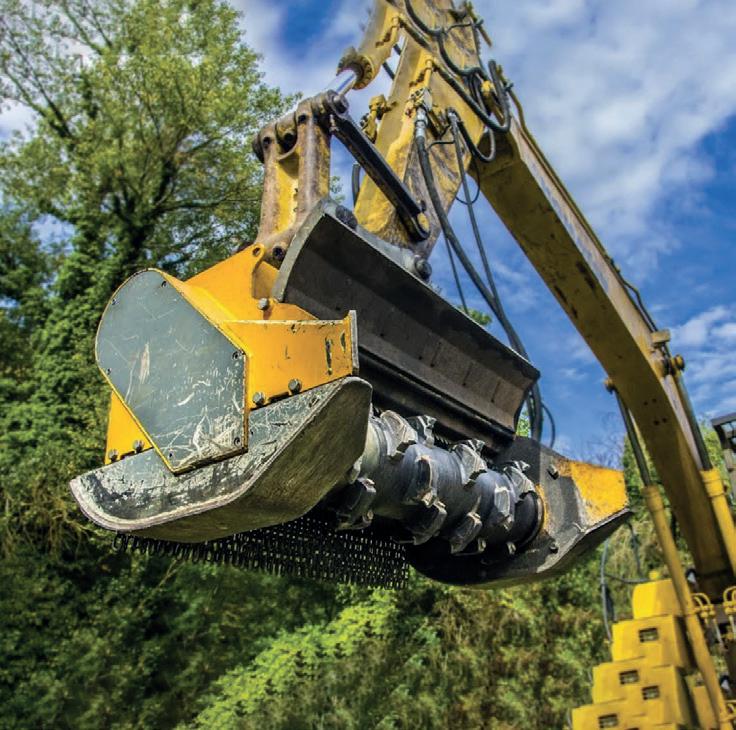
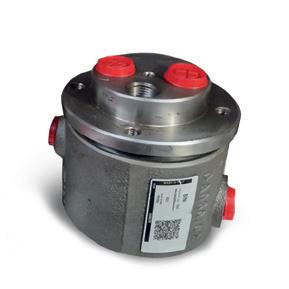


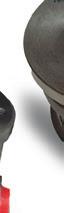
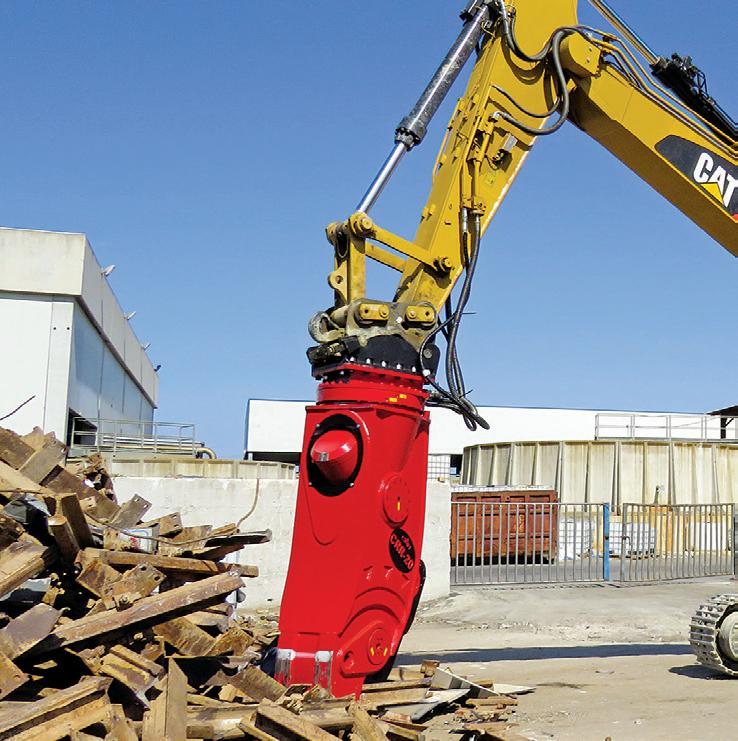






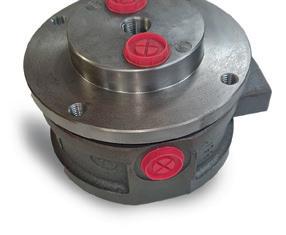




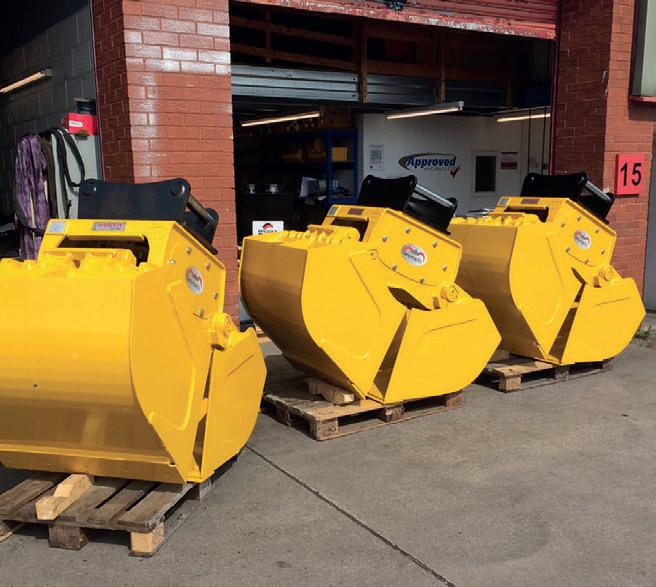

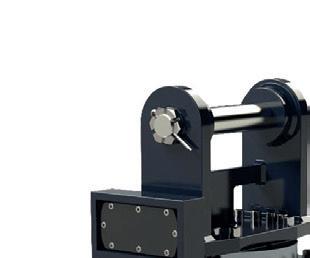
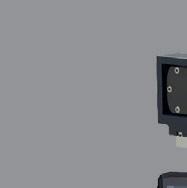
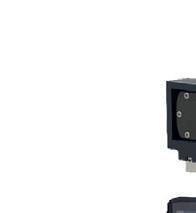








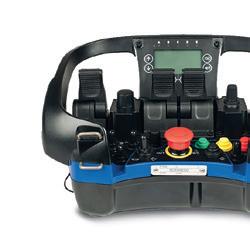


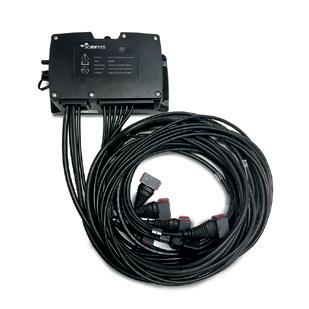
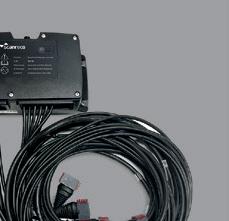

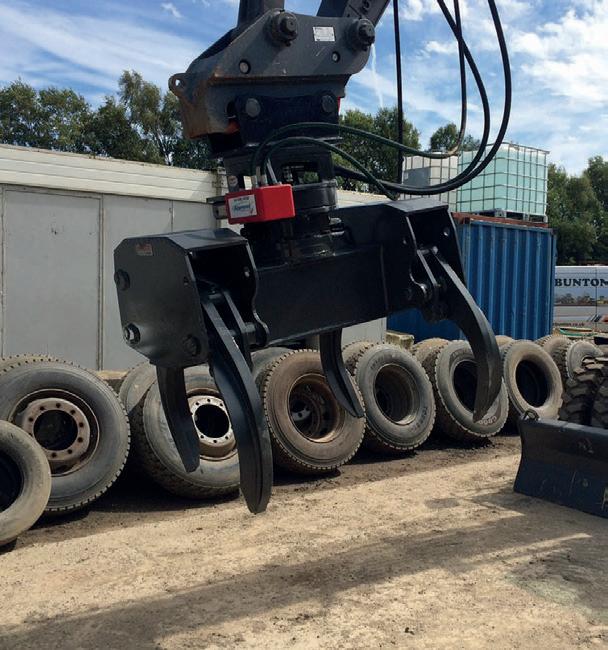



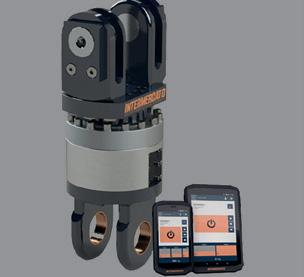
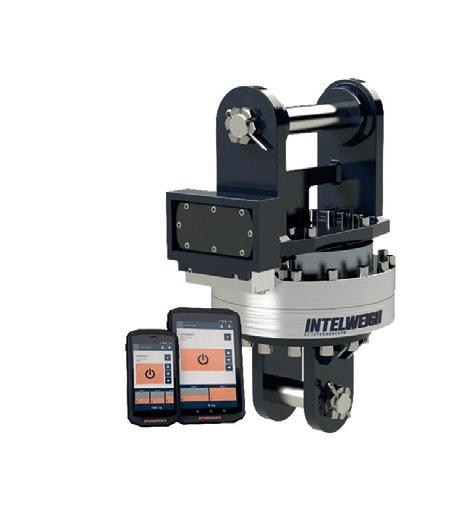
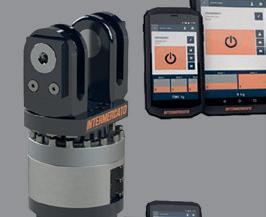

Cutting-Edge Power Supply Solutions
In the dynamic world of rail transportation, the demand for reliable and efficient electronic systems is paramount
Trains, subways, and trams are not just modes of transport; they are moving ecosystems requiring sophisticated electronic support. Mornsun Power, a leading name in industrial power supply solutions, and represented in the UK by Relec Electronics, stands at the forefront of this technological evolution.
The backbone of railway electronics
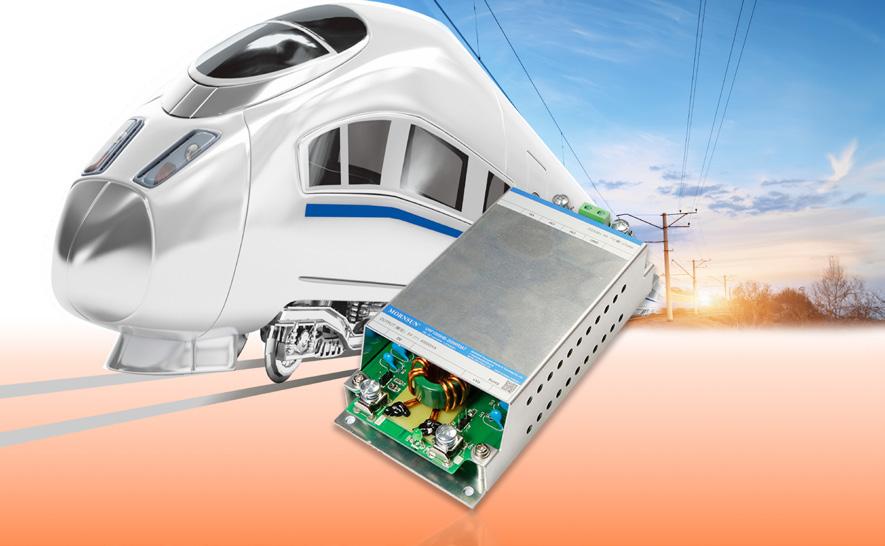
The railway industry is a complex network of systems – from Passenger Information Systems (PIS) to emergency communication and operation monitoring. Products for each of these systems demands a power supply that is not only efficient but exceptionally reliable. Mornsun Power, understanding these needs, has developed a comprehensive range of converters from six watts to 400 watts. These products are designed to cater to all international traction voltage systems, including 24V, 36V, 52V, 72V, and 110V DC, ensuring global applicability and compliance.
Adherence to EN50155 Standards
Mornsun's commitment to quality and safety is evident in its strict adherence to the EN50155 standards. These standards are critical for electronic equipment used in railway vehicles, focusing on aspects like input voltage range, safety, and overall power supply requirements. Mornsun's latest power supplies boast an ultrawide input voltage range of 14-160VDC, accommodating all the diverse needs of the global railway system.
Safety and reliability
In an industry where safety cannot be compromised, Mornsun's power supplies excel with reinforced insulation, achieving input-output isolation of 3,000VAC and input-shell isolation of 2500VAC. This design is particularly beneficial for high-altitude and cold area applications,
surpassing the standard 1,500VAC insulation voltage requirements.
Innovative design for enhanced performance
Mornsun's UWTH1DxxQB-xxWR3 series, a highlight in its railway power supply range, is a prime example of its level of innovation. They feature active hold-up time protection technology, ensuring 10ms hold-up time with a simple peripheral circuit and using as little as 470uF/100V capacitors across the entire input range.
The UWTH1DxxQB-xxWR3 series is designed to operate efficiently across a wide temperature range of -40°C to +105°C, with low no-load consumption and compliance with EN62368, EN50155, and EN45545 standards.
One-stop power solutions
Mornsun's 6-400W Railway Power Supply series is a testament to its commitment to providing comprehensive solutions. These products meet the rigorous EN50155 certification standard and are equipped with features like wide voltage input and reinforced insulation. They are ideal for various applications, including PIS systems, HVAC control systems, and communication systems. Mornsun through its partners at Relec electronics, also offers customisation services to meet specific needs, simplifying the challenges of electronic systems in railway applications.
A legacy of innovation
Mornsun Power, headquartered in China, has established itself as a leader in industrial power supply manufacturing over the past 25 years. With a focus on magnetic isolation technology and product research, Mornsun has developed a range of high-quality products, including AC/ DC converters, DC/DC converters, and more. Its commitment to innovation is evident in its 1,700+ patents for inventions. With subsidiaries in America and Germany and a distribution network in over 40 countries, Mornsun is a global powerhouse in power supply solutions.
The UK gateway to Mornsun's excellence
In the UK, Relec Electronics proudly represents Mornsun Power, bringing their cutting-edge power supply solutions to the British railway industry. Relec's expertise in the field, combined with Mornsun's innovative products, ensures that the UK railway systems have access to some of the most reliable and efficient power supplies in the market.
Mornsun Power, through its comprehensive range of power supply products and its partnership with Relec Electronics in the UK, is setting new standards in the railway industry. Their commitment to safety, reliability, and innovation makes them an indispensable ally in the ever-evolving world of rail transportation.

Tel: 01929 555700
Email: sales@relec.co.uk
Visit: www.relec.co.uk
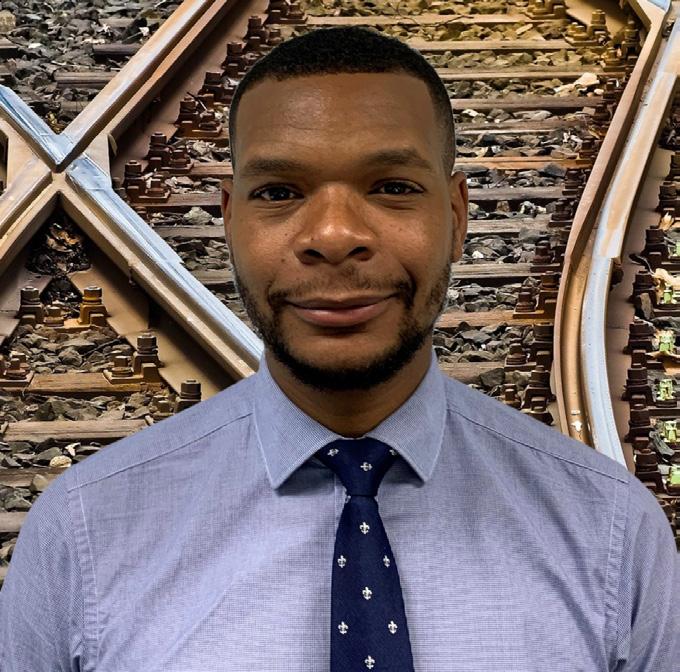
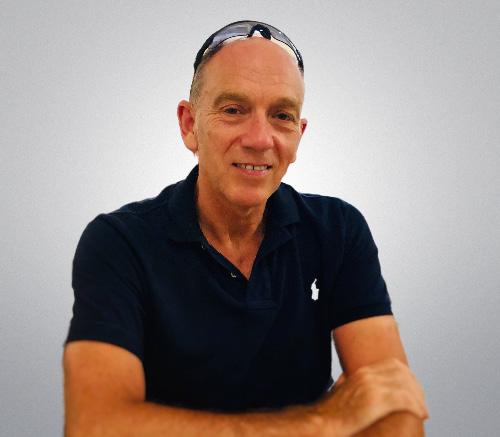
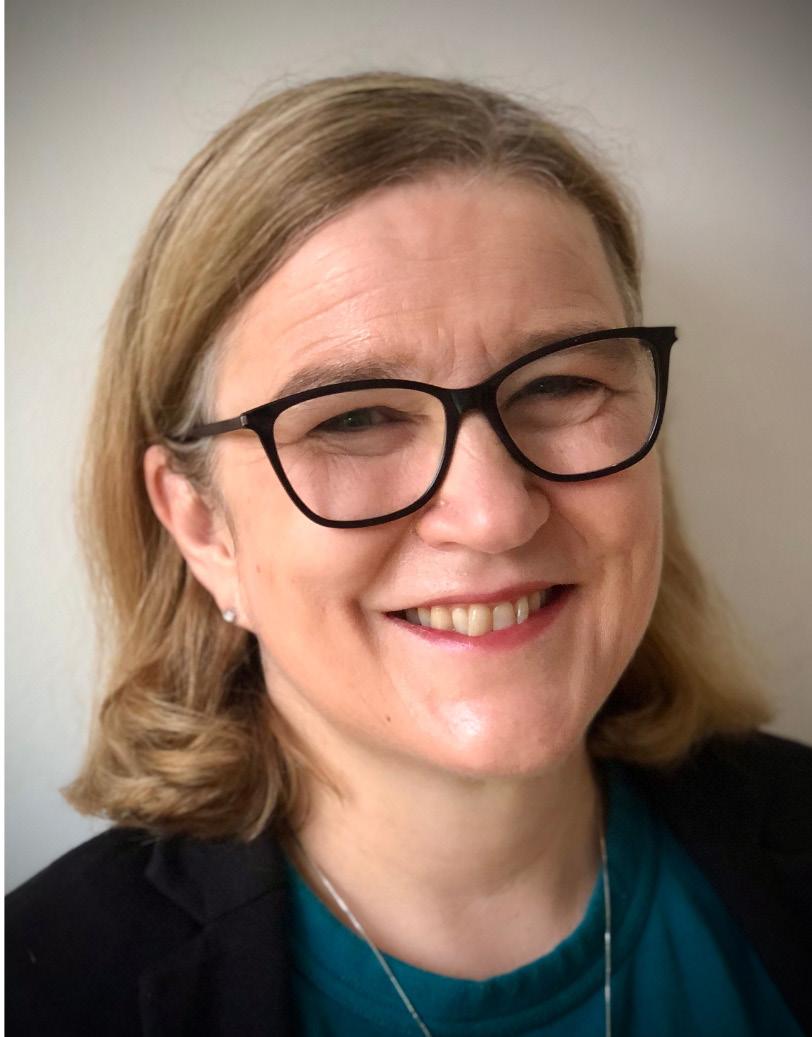
London Transport Museum appoints new Enterprise Director
London Transport Museum has announced Sarah Fellingham-Adkin as its new Enterprise Director.
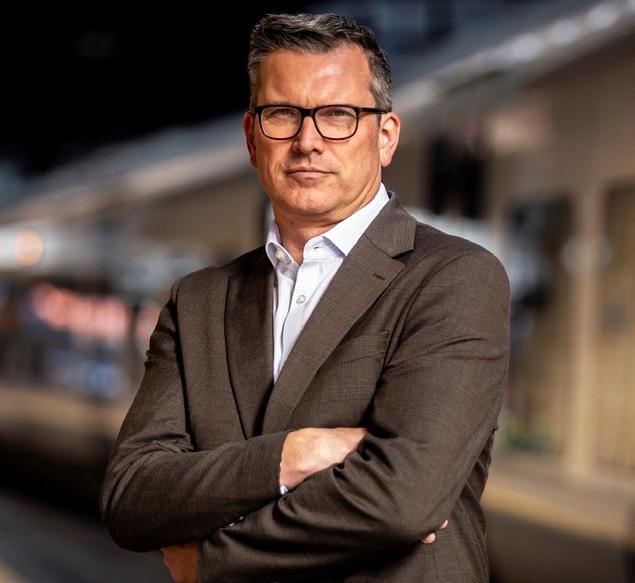
Regional Director for Northern in the North East appointed Northern has appointed Jason Wade as its new regional director for the North East.
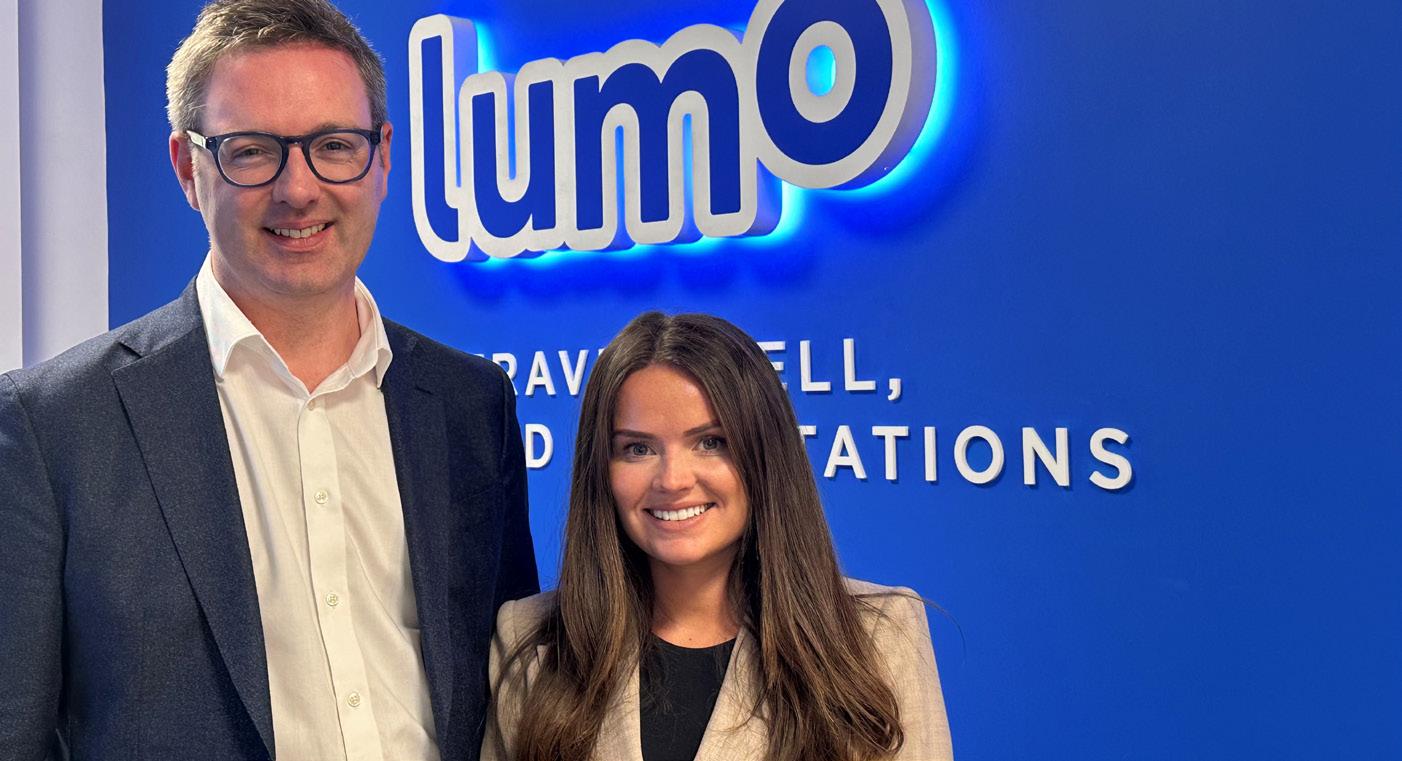
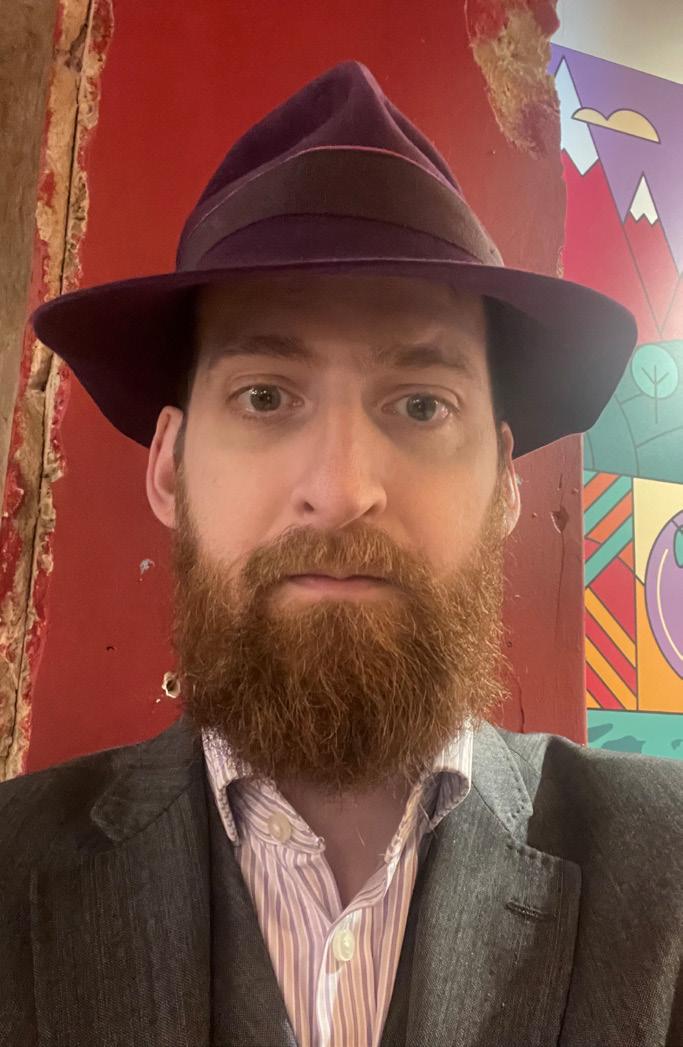
Northern appoints new
for accessibility user group Northern has appointed Mark Cutter as accessibility campaigner to chair its independent user group which focuses on empowering people to use public transport – no matter their circumstances.
High Speed Rail Group appoints ex-HS1 Chief as Chair
The High Speed Rail Group (HSRG) has announced that Dyan Perry has recently been appointed as the Group’s new Chair.

New Interim Managing Director for South Western Railway
Stuart Meek will become Interim Managing Director at South Western Railway from 19 March. He takes over from Claire Mann, who will be leaving SWR to take up the position of Chief Operating Officer at Transport for London.
Premier global manufacturer of components and kits for railway applications

In addition to supplying individual components, the global companies of STAUFF and their authorised system partners use the STAUFF Line approach to support Original Equipment Manufacturers with the supply of custom-designed and ready-to-install fluid power lines from connection to connection and also provide supplemental services that create added value: · Components · Systems · Services · Contact
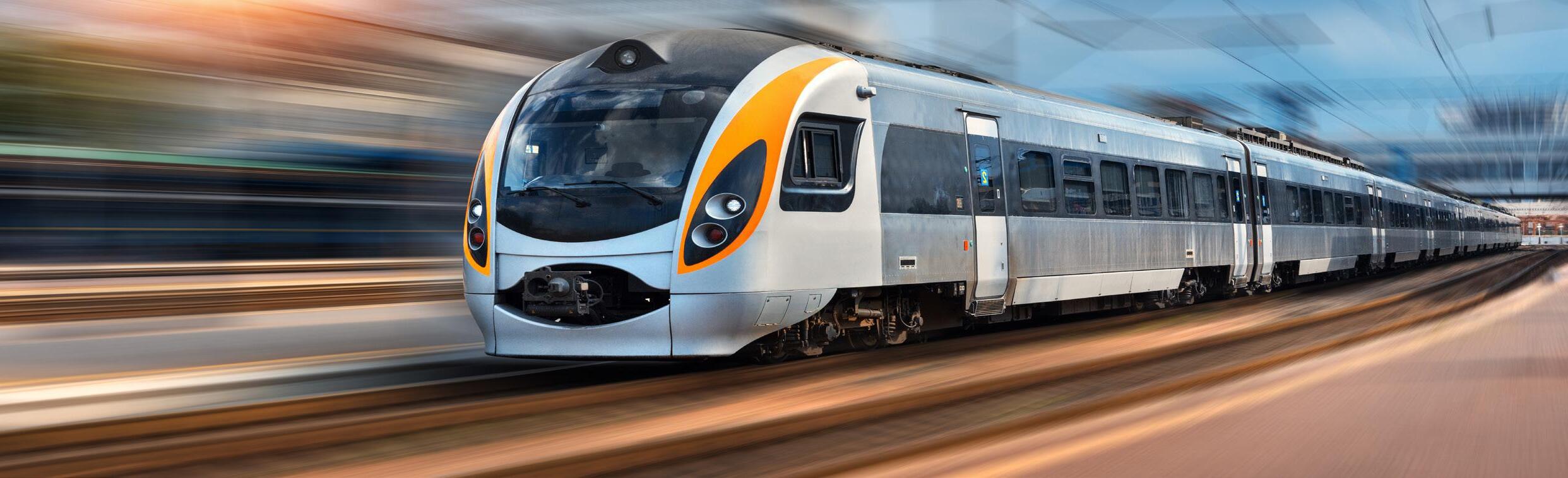
Sheffield Tel: 0114 251 8518
Email: sales@stauff.co.uk
Aberdeen Tel: 01224 786166
Email: sales@stauffscotland.co.uk
Ireland Tel: 02892 606900
Email: sales@stauffireland.com
Southampton Tel: 023 8069 8700
Email: sales@stauffsouthampton.co.uk
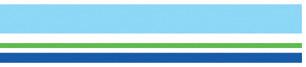

Inspired thinking to deliver a better future
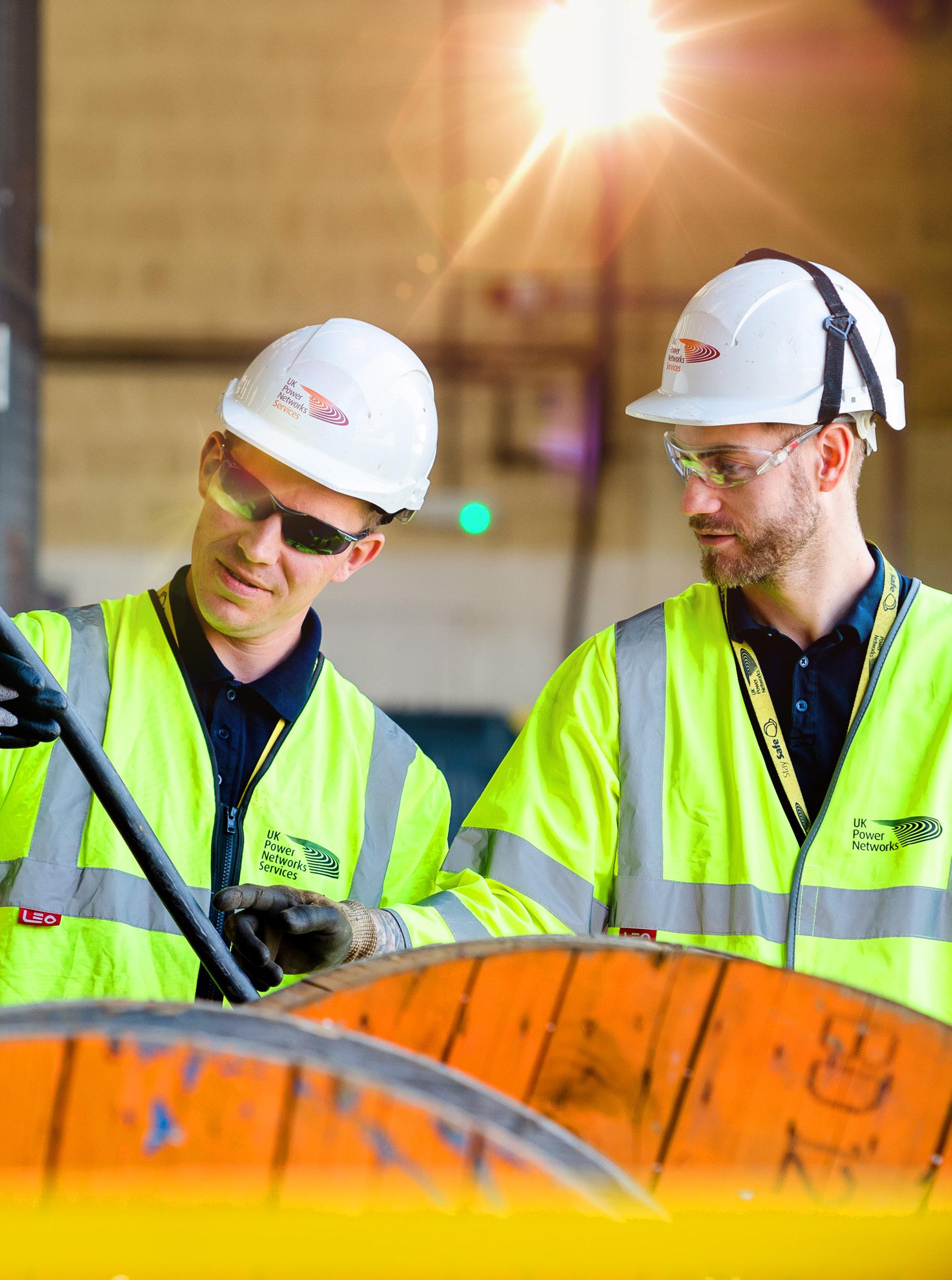
We are at the forefront of providing innovative technical solutions which enables our clients to meet their sustainability objectives. Our inspired thinking approach allows us to utilise our long-term expertise to work in partnership with our clients to deliver resilient, bespoke and cost efficient solutions.
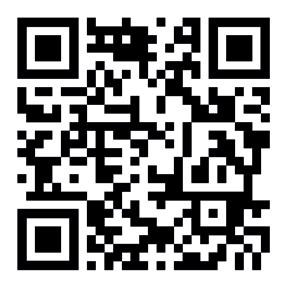