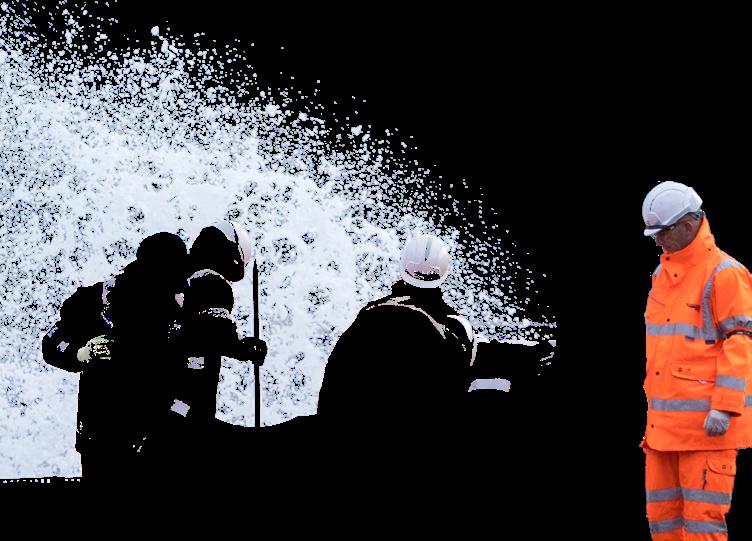
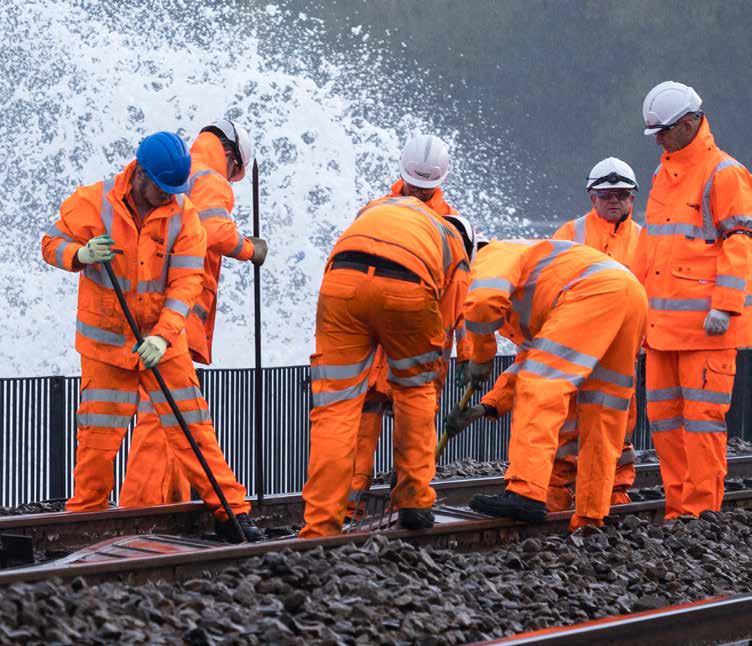
Synthetic Sleeper
Simply working & sustainable

Simply working & sustainable
SEKISUI CHEMICAL GROUP : Enhancing Lives, Preserving the Planet.
we’re dedicated to advancing the quality of life worldwide while championing the protection of our planet.
Better possession protection
David Shirres discusses a new possessions initiative with Craig Milne, Network Rail Scotland’s planning and logistics director.
Do rules keep track workers safe?
The rules around work in possessions can be confusing and don’t always address the practicalities of engineering work.
Siemens S60+ barrier boom development
Siemens has produced a revised barrier design to address the issues around climate change and safely managing level crossings.
Signalling the future
Paul Darlington reports on this impressive event which brought experts together from across the globe.
FRMCS: A touch of reality
GSM-R’s obsolescence is a reality, and a future radio network can no longer be considered as ‘nice to have’.
Artificial Intelligence and people in rail
The rail industry has an opportunity to harness the power of rapidly evolving
Fletcher Moorland: the supplier you didn’t know you needed
Rail Engineer visited Stoke-on-Trent to chat with Matt Fletcher, managing director of this multi-faceted engineering firm.
NCB Rail Assurance: Collaborative, reliable, and expanding its services
NCB discusses its rebranding, its new range of services, and how it differs from its competitors.
HS2’s Delta Junction
With embankments, cuttings, and 13 viaducts, Delta Junction will take tracks over motorways, existing rail lines, rivers, and floodplains.
A boost for bridges across the regions
Rail Engineer examines the work carried out on bridges and viaducts in the first few months of 2025.
An update on East West Rail
David Fenner discusses EWR’s third non-statutory consultation on the proposed new route between Oxford and Cambridge.
72|
Railway 200: Signalling
As we celebrate the 200th anniversary of the railway, Rail Engineer looks at early developments in signalling.
Railway 200: Telecoms
Telecoms and railways evolved at the same time, with railways pioneering telegraph communication. Paul Darlington explains all.
Vehicle Track Interface Seminar 2025
Malcolm Dobell reports extensively on this annual seminar held in York in early March.
Adhesion Research Seminar 2025
This year’s seminar covered original research and kicked off studies into techniques for improving freight adhesion.
A Chippenham groundbreaking
With signalling technology moving into the digital age, Siemens Mobility has broken ground on a brand-new premises.
The myth of net-zero aviation
There are various estimates of how the UK will achieve netzero aviation by 2050, but are they really feasible?
DAVID SHIRRES
DAVID SHIRRES
RAIL ENGINEER EDITOR
“Having spent over two decades in the UK railway industry, I’ve never seen a situation this dire. Slow CP7 spending is hitting suppliers which forces layoffs. The industry is losing skilled professionals at an alarming rate, with engineers, site managers, and experienced rail workers moving to other sectors due to job insecurity.”
This is just one of many such comments to be found on LinkedIn. In a survey of 52 companies at the end of 2024, the Railway Industry Association (RIA) found that 39 were experiencing a significant hiatus in work and 22 were considering redundancies. The 2024 rail workforce study published by the National Skills Academy for Rail showed that the rail workforce declined by 9.4%, predominantly in the supply chain.
One reason for the slow start to CP7 is the wait for this summer’s spending review. It is hoped that this will set out a plan for visible and smooth volumes
of work. The current ‘boom and bust’ cycle, results in skill shortages which, if unaddressed, will increase future costs for both the rail industry and the taxpayer.
With no immediate prospect of an electrification rolling programme, OLE design and construction personnel are particularly at risk. Yet there are various ‘no regrets’ cases for electrification. These include lines to the London Gateway and Flexistowe ports which would retrospectively require six and 26 route km of electrification. This would offer significant WCML capacity benefits by making it possible for freight trains to have electric traction throughout their locomotives throughout their journey.
Four years ago, the Williams Shapps report promised a whole industry strategic plan which never appeared and is not mentioned in current Great British Railways (GBR) proposals. Instead, the only government priority relating to GBR’s engineering is the formation of
the GBRX organisation to accelerate the adoption of emerging technologies such as artificial intelligence (AI).
While this is a worthy ambition, it is also important to acknowledge that engineering the railway to best meet customer needs requires an appropriate mix of emerging and current technologies.
While AI offers significant benefits it also presents significant risks. These issues were explored in a seminar organised by the IMechE and IRSE which focused on decision making, failure prevention, and infrastructure monitoring. This seminar considered AI’s significant benefits though it recommended that AI should not be used for any safety function above Safety Integrity Level (SIL) 1. For comparison, signalling controls require a SIL 4 system. Applications using emerging technologies will require significantly increased data and voice transmission to and from trains. Currently, such transmissions are handled by the 2G
GSM-R system that was developed in the late 1990s and will soon be obsolete. Hence, as Clive Kessell describes, GSM-R needs to be replaced by the 5G Future Railway Mobile Communication System (FRMCS).
The implementation of FRMCS was covered by the ‘Signalling the Future’ conference on which Paul Darlington reports. This considered projects and issues from a wide range of countries from which common themes emerged. These included the need for standardisation, simplification, proactive obsolescence management, and less customisation, as well as efficiencies and economies of scale to reduce costs.
From signalling’s future to its past, we have Railway200 features describing the early development of railway signalling and telecoms. For example, telegraphs and mechanical interlocking which were respectively introduced in 1838 and 1843. The huge technical developments in signalling and telecoms over the past 200 years still follow many of the principles established in the railway’s early years.
An impressive recent development in Scotland is the Initiate system which integrates the engineering access planning into the signalling system. This enables complex possession limits to be preprogrammed so that when the possession is taken protecting signals are simultaneously placed at danger. As we describe, this system eliminates the risks associated with placing detonators and speeds up the time required to set up the possession to provide, typically, an extra 30-minutes productive time per possession.
The article “Do rules keep track workers safe?” is the result of my experiences of 20 years ago, when I found possession rules did not address the practicalities of engineering work and were confusing. Having been advised that little has changed since then, it is hoped that this feature will stimulate discussion, particularly about the process for producing possession rules.
The Vehicle/Track System Interface Committee (V/T SIC) and ADHERE (ADHEsion REsearch challenge) research programme managed by RSSB undertake essential work across the track train interface. Their work was recently presented at a conference on which Malcolm Dobell reports. This included ADHERE reports on conductive sand and sticky leaves, as well as V/T SIC initiatives on infrastructure monitoring and the modelling of rail defects.
Editor David Shirres editor@railengineer.co.uk
Production Editor Matt Atkins matt@rail-media.com
Production and design
Lauren Palin lauren@rail-media.com
Adam O’Connor adam@rail-media.com
Engineering writers
The first part of the East West Rail project to provide a rail link between Oxford and Cambridge opens later this year to provide a train service between Oxford and Milton Keynes. Yet, with the EWR route between Bedford and Cambridge requiring a new railway on a yet-to-be confirmed route, services from Oxford to Cambridge are not expected to start until at least 2034. Planning a new rail route is a complex matter as David Fenner describes in his feature on the EWR route consultation. Planning HS2’s route was also problematic. Outside Birmingham its route requires a Delta junction. As Bob Wright describes, this is the most complex section of HS2, featuring embankments, cuttings, and 13 viaducts carrying tracks over motorways, local roads, existing rail lines, and rivers. Bob’s report describes the complicated construction methodology and innovative design of these striking structures.
Finally, we have an aviation feature which explains why net-zero aviation is a myth.
In its Net Zero report, the Committee for Climate Change calls for the demand for flights to be restricted and for modal shift from planes to high-speed rail. Government has rejected this advice and has instead decided to build a third runway at Heathrow while claiming that aviation has green credentials.
In 1975, British Rail ran an advertising campaign pointing out that other forms of transport are costing the earth. In this year of Railway200, it would be good to see the industry similarly debunking false net-zero aviation claims and explaining why trains are engineered to be particularly energy efficient and therefore carbon friendly. This should be both stressed and celebrated. PHOTO:
bob.hazell@railengineer.co.uk bob.wright@railengineer.co.uk clive.kessell@railengineer.co.uk david.fenner@railengineer.co.uk graeme.bickerdike@railengineer.co.uk malcolm.dobell@railengineer.co.uk mark.phillips@railengineer.co.uk paul.darlington@railengineer.co.uk peter.stanton@railengineer.co.uk
Advertising Craig Smith craig@rail-media.com
Rail Engineer
Rail Media House, Samson Road, Coalville Leicestershire, LE67 3FP, UK. Switchboard: 01530 816 444 Website: www.railengineer.co.uk
Rail Engineer Videos http://rail.media/REYouTube
Editorial copy to Email: news@rail-media.com
Free controlled circulation Email: subscribe@rail-media.com
The small print
Rail Engineer is published by RailStaff Publications Limited and printed by PCP Ltd.
© All rights reserved. No part of this magazine may be reproduced in any form without the prior written permission of the copyright owners.
Part of:
www.rail-media.com
what’s the plan for
In February, Rail Minister Lord Peter Hendy described how GBRX has been established to deliver one of the five priorities that Secretary of State for Transport Heidi Alexander has set for the Shadow GBR (Great British Railways) organisation which are:
1. Integration between operators and Network Rail to ‘rip out duplication’ and ‘simplify the management of track and train’.
2. Drive up operational performance.
3. Reform the fares structure and ticketing processes.
4. Fostering innovation, including partnering with ‘world leading innovators, particularly around AI’ to ‘create a better passenger experience and greater efficiency’.
5. Be ‘a force for positive change beyond the tracks’.
Priority 4 is to be delivered by GBRX which Hendy advised “will break the pattern of slow adoption that has historically held our railways back due to fragmentation, contractual complexities, and the way our system operates particularly across the track / train interface.”
GBRX’s managing director, Toufic Machnouk recently advised the Railway Industry Association (RIA)’s innovation conference how his new organisation will help modernise the railway faster and embrace new technology more effectively. To do so it will bring together industry and academia and enable different parts of the railway to collaborate more efficiently.
These statements raise two questions: is the industry slow in adopting new technology and what can GBRX offer in addition to the existing industry bodies that promote innovation?
As shown in Issue 211 (Nov/Dec 2024), in 1987, the development of 125mph track renewals handbacks was only possible as British Rail’s Inter City profit centre saw the benefits of the required investment. Hendy is right to point out that misaligned incentives on today’s railway can be a significant barrier to progress, especially if those who spend significant sums do not get significant benefits.
Yet it is GBR, rather than GBRX, that will provide an industry structure that aligns incentives. Furthermore, Rail Engineer has reported on various successful initiatives across the track / train interface including the ADHERE and VTSIC features in this issue. Another example, reported in Issue 204 (Sept/Oct 2023), was the use of train operators’ passenger train to collect gauging data for Network Rail. This was done by a train-mounted gauging unit which gauged 14,987 structures over a six-week period. Eight years previously, such data was collected by Network Rail’s structures gauging train.
This is just one example of a train operator’s train being used to provide Network Rail with worthwhile infrastructure data.
This year, RIA’s innovation conference had numerous examples of the adoption of new technologies.
Furthermore, with 7,500 vehicles being ordered since 2012, the average age of the UK passenger fleet is now 17 years. As a result, most trains are state-of-the-art as they are digitally enabled with hundreds of sensors. The recognition of the importance of sharing open data has resulted in the creation of a rail data marketplace. This enables data app developers or tech firms to use it for various applications including infrastructure monitoring and customer innovation.
It is certainly true that rail’s adoption of new technologies is sometimes slow and ineffective. This was illustrated by our report in issue 201 (Mar/April 2023) about the ORR’s 2023 report on Network Rail’s technology adoption. Yet, with many examples of new technologies adopted in recent years, we feel it is unreasonable to portray the industry as slow to adopt new technologies.
initiatives between different parts of the railway. In essence, they are already working in many of the ways that GBRX says it will.
Yet the roles of these various innovation bodies and how they work together can be confusing, especially to those new to the industry who wish to offer their innovations. GBRX is to be a strategic innovation body and so may well provide a better focus for innovation. As it has been created to deliver a government priority, it may also be better placed to remove some of the barriers to the adoption of new technologies.
However, the scope of its activities in relation to other rail innovation bodies has yet to be clarified.
GBRX has also yet to define the key problem areas that it expects emerging technologies to address. It will be interesting to see how these differ from problems that are already being addressed.
As readers may recall, GBR was first mentioned in the Williams Shapps report which was published in 2021. A key commitment in this report was the production of a 30year Whole Industry Strategic Plan (WISP), the first version of which was to be produced in 2022. This plan never appeared.
Organisations that currently promote rail innovation include Innovate UK; Connected Places Catapult; UKKRIN (a partnership between industry and academia); RSSB; RIA; Network Rail and individual train operators. These organisations have formed partnerships, brought together industry and academia and have led collaborative
The professional engineering institutions who contributed to the WISP consultation exercise all stressed the need for the railway to be engineered as a whole system. As there is no one organisation with the financial, technical, and operational authority to oversee the design, investment, and management of the whole railway system, fleet, infrastructure and timetable strategies are not aligned.
Integrating these strategies in a WISP would specify the optimum engineering solutions for the railway to deliver customer requirements by providing sufficient capacity, performance, and facilities in a sustainable, safe, and cost-effective manner. This would also support strategic Government objectives such as decarbonisation and economic growth.
Hence the lack of a WISP is a significant omission from the Government’s plans for GBR which only appears to consider railway engineering in respect of the introduction of new technology. Yet new technology should not be considered in isolation as much of the railway currently operates in a sub-optimal fashion as full advantage is not being taken of existing railway technologies.
Having reported on emerging technologies such as AI and robotics, Rail Engineer understands their potential benefits. Yet such technologies are not a panacea, and some problems can only be resolved with better use of conventional technologies.
As an example, a 1,600 tonne intermodal train hauled by a 2.4 MW Class 66 diesel locomotive can only average 45mph up to the gentle 1 in 300 gradient from Willesden to Tring summit. After climbing the 1 in 75 gradient up Shap fell, such trains typically crest its summit at 19mph. Mixing such slow freight trains with 125mph passenger trains eats capacity. This loss of capacity can only be addressed by freight locomotives having the power that only electric traction can provide, for example the 3.7MW Class 90 locomotive.
This is one of the many reasons why almost all rail freight on the European continent is electrically hauled, which compares with about 5% having electric traction in the UK. It is to be hoped that the
creation of GBR may enable a whole life view to be taken of the costs and benefits of electrification. In the absence of the promised WISP, the RIA report ‘Delivering a Lower Cost, Higher Performing Net Zero Railway by 2050’ is an excellent example of such a railway engineering strategy document. This report has also been endorsed by the Committee on Climate Change.
Another strategic rail engineering requirement is the need to replace the GSM-R network and its obsolete 2G technology. As we describe in this issue, the proposed Future Railway Mobile Communication System (FRMCS) offers 5G technology. This will provide a significant increase in bandwidth and data handling capability which will be necessary for large-scale ETCS deployment and future train communications to meet future passenger and business needs which will no doubt be required by the technologies that GBRX wishes to see adopted. However, there is nothing in the public domain to show that it has been accepted that GSM-R needs to be replaced.
Government pronouncements about GBR quite rightly stress the importance of improving the passenger experience by bringing track and train together to unify the railway network. From an engineering perspective, this should provide a technical authority to oversee the whole system though it is not clear how such a body will function. Nor has anything been said about the need for the whole systems plan mentioned in the Williams Shapps report.
Instead, the only government priority for Shadow GBR relating to engineering is creating GBRX to introduce new technology. Rail Engineer supports this aim and wishes GBRX well in its goal to accelerate technology adoption. But this is not enough as GBR also needs to make best use of existing technology. This needs engineering leadership which ensures that the customer requirements are delivered by the most appropriate mix of new and existing technologies.
Sir Andrew Haines, chief executive of Network Rail, has announced he will retire from the company in October 2025.
“It has been a privilege to lead Network Rail through a time of such change and transformation for Britain’s railways, and I am proud of the progress that we have made on performance, safety, reliability and customer service,” he said.
“After seven years as chief executive, as Great British Railways starts to progress through legislation and into implementation, I have decided it is the right time for me to retire.
“I am a passionate supporter of the principles behind Great British Railways and the once-in-a-generation opportunity it presents to create an integrated railway that delivers a better service and experience for passengers, stakeholders and colleagues. It has been a privilege to lead this transformational journey to date.”
Sir Andrew’s career in transport began as a holiday job in the left luggage office at Victoria Station, before he became one of the youngest leaders in rail at South West Trains, transforming its declining performance and significantly improving punctuality.
As head of the Civil Aviation Authority, his fresh thinking and vision were crucial in implementing passenger-focused reforms. He did this while building on the UK’s excellent record in aviation safety and security. He also led the sector through the process of reopening the airways following the Icelandic volcanic eruption in 2010 and transformed the CAA into an emergency airline for what was the largest peace time repatriation of British citizens following the collapse of Monarch Airlines.
Sir Andrew joined Network Rail in August 2018 and, during his seven years as chief executive, has maintained a relentless focus on making the organisation a more customerfacing organisation and drive improved performance.
He led the company through the challenges of the Covid-19 pandemic, ensuring that the railways ran safely and efficiently for key workers and critical goods. His commitment to maintaining open communication and supporting the supply chain was widely acknowledged, earning him a special award from the Railway Industry Association in 2020 for outstanding leadership.
Connecting the UK rail industry for over 28 years.
Sir Andrew has helped to turn around Network Rail’s performance on major projects and infrastructure delivery, driving a new focus on costcontrol and efficiency, such as the £10 billion Transpennine Route Upgrade and outperforming its regulatory efficiency targets. The company has achieved best-ever levels of safety under his leadership.
A passionate advocate for professional development, Sir Andrew championed structured training and continuous learning to cultivate the next generation of railway leaders. He stressed that “we cannot afford to see operational expertise as a given – we must invest in it, nurture it, and ensure that the skills of our people evolve alongside the industry.”
Recently, he has been a coinstigator and sponsor of a new social mobility network across the rail sector reflecting his passion to create opportunities for everyone who strives to succeed and make a difference.
He received his Knighthood in the 2025 Honours list.
Since the news of his retirement was broken, tributes have poured in from colleagues, industry bodies, and politicians alike.
Network Rail Acting Chair Mike Putnam said: “Andrew has been an exceptional leader for Network Rail at a critical time in the history of Britain’s railways. He has secured reforms that will lead to a more reliable railway, while maintaining a continual focus on safety and performance.
“His vision, leadership and ambition for an integrated, simpler railway that will deliver a significantly better experience for passengers has been at the heart of the creation of Great British Railways.
“I’d like to thank Andrew for his unwavering dedication and leadership of Network Rail over the last seven years.”
Ben Plowden, chief executive of Campaign for Better Transport, commented: “Sir Andrew has been a passionate advocate of the railways, and has helped create the framework for the generational change, Great British Railways, that passengers and the industry need. We thank Sir Andrew for his service and wish him well.”
The Chartered Institution of Railway Operators (CIRO) also extended its gratitude for his exceptional leadership and unwavering commitment to operational excellence. “Throughout
his time with Network Rail, Sir Andrew has been a staunch advocate for the rail operations profession and a strong supporter of CIRO’s mission to advance excellence in railway operations,” the organisation said in a statement.
CIRO CEO Phil Sherratt added: “Sir Andrew has been the most dedicated public servant, navigating our industry through immense challenge and change. On behalf of the operating community, I thank him for his invaluable contributions – not only to the wider railway but specifically to promoting operations as a profession.”
Transport secretary Heidi Alexander said “I’d like to thank Andrew for the commitment and leadership he’s shown
over the past seven years. He provided stability during the most challenging of periods and ensured the railway kept running throughout the pandemic and through national industrial action.
“His vision and support has been vital as we establish Great British Railways – one of this government’s biggest reforms. His work has been a key part of our efforts to deliver a simpler, more efficient railway, with passengers at its heart.”
The process of choosing a successor will begin shortly, Network Rail has said, led by the Nomination & Remuneration Committee of the Network Rail Board, and subject to Secretary of State approval.
In 1841 Edward Alfred Cowper, a founder member of the IMechE, devised a warning signal for trains on foggy days. This had a detonating compound packed into a small circular container and was fastened to the rails by lead clips. By 1844 such fog signals were in widespread use and their use was enshrined into the Rule Books of the day. Over 180 years later, this is still the case.
Although the widespread introduction of the Automatic Warning Systems in the 1950s and 1960s removed the need for fog signals, millions of detonators are still in use. At the very least, six detonators are required to protect the 100,000 engineering possessions taken each year and each driving cab must carry 10 detonators to protect the line in the event of a train accident. Detonators have been used to protect engineering work for over 100 years as specified in the 1950 British Rail Rule Book which required three detonators to be placed 10 yards apart for this purpose. The theory is that detonators will stop irregular moves of engineering trains out of possessions, and of service trains into possessions, as well as providing a warning to track workers of such unauthorised train moves.
notice (WON) to the signaller. When the signaller then placed reminder appliances for the possession, he omitted to place one on signal WM494 which protected Line A where the PSW was placing protection. This was the last of a nine-line item in the WON for the possession extension.
The RAIB report into this incident considers why the signaller omitted to place a reminder appliance and concludes that this was associated with processes and methods for managing and communicating information regarding engineering work in modern, multi-panel signalling centres.
The report considered that another underlying factor was that the possession set up process requires people to be present on track and so exposes them to risk in the transition period before protection is fully implemented.
In 2015 the Rail Accident Investigation Branch (RAIB) undertook a class investigation into protection arrangements during engineering work. This found that in a two-year period up to April 2013 the number of protection irregularities were:
» 144 – protection incorrectly placed.
» 39 – protection set up whilst the line is open to traffic.
» 52 – working outside protected area.
» 52 – trains signalling into the protected area.
At Camden South Junction in 2017, a train was signalled over a line on which a possession support worker (PSW) was placing possession as authorised by the person in charge of possession (PICOP).
The PICOP had taken a possession at 2300 and, immediately prior to the incident had extended the possession at 0100 to include additional lines. Whilst doing so, the PICOP had spent one minute 19 seconds reading the list of the possession limits from the weekly operating
This recommendation would have been well received by those who, for many years, have considered that there must be safer way of protecting possessions than placing detonators. Yet this was not the conclusion of the RSSB reports that have investigated this issue. In 2005, a review on the continued use of detonators (report T507) concluded that detonators should not be replaced in T3 possessions but did show how three countries (Spain, Austria, and Italy) were able to protect engineering work without the use of detonators.
In 2019, the effectiveness of detonator and possession limit board protection (report T1167) was assessed by practical tests on the audibility of detonators. These concluded that they are not a reliable method of altering drivers of a possession and of alerting track workers of the presence of an approaching train. Yet, in 2020, a quantified risk assessment on the use of detonators and alternatives (report T1115) proposed that no changes should be made to T3 possession rules.
Nevertheless, these reports did show how other countries protect their railway engineering work without the use of detonators and that the effectiveness of detonators is questionable. Indeed, on the basis of the T1167 report, the risk assessment in report T1115 considered that detonators are only 50% effective.
In this respect the report recommended that it required Network Rail review its possession management process to reduce the need for staff to be on the track for possession protection and that this review should consider newly developed technologies.
A recommendation from RAIB’s Camden Junction report is for a review of the need for staff to be on track for the purpose of taking and giving back a possession.
Network Rail’s Track Worker Safe Access Strategy is addressing this recommendation with a possession
limit controls initiative which is considering how current and emerging technology could provide safer protection. This is assessing different possession protection methods such as signal disconnections (T3-D) and activation of equipment such as remotecontrol track circuit operating devices (T3-A). A derogation to the Rule Book was obtained to protect possession in this way in February 2024. Since then, the T3-D and T3-A protection has been successfully trialled in Tyneside and Selby.
A radical application of T3-A protection is being trialled in Scotland. This links the possession planning process directly to the signalling system to enable verified possessions to be preprogrammed into the system. This eliminates both the risk of a misunderstanding between PICOP and signaller at the time of the possession and of the signaller mistakenly signalling trains into the possession as happened in the Camden incident.
To learn more, Rail Engineer was glad of the opportunity to visit Edinburgh Signalling Centre to discuss this initiative with Craig Milne, Network Rail Scotland’s planning and logistics director.
The Edinburgh Signalling Centre is an integrated electronic control centre (IECC). These were developed in the late 1980s by British Rail Research and have VDU displays which replaced the switch and button panel control in earlier signalling centres. They also have an automatic route setting (ARS) system which makes automatic signalling control decisions based on the train timetable. After rail privatisation, British Rail Research was acquired by AEA Technology, the rail business of which was acquired by DeltaRail in 2006. In 2012, DeltaRail launched IECC Scalable so that IECCs can use modern hardware platforms and software architecture. DeltaRail became Resonate in 2016, which thus has the pedigree to support and maintain IECC systems.
Resonate’s traffic management system, Luminate, was introduced on Network Rail’s Western and Anglia routes in 2018 and 2021. It was introduced at the Edinburgh Signalling Centre early last year. Luminate can identify traffic conflicts, validate contingency plans and has a platform docker tool. Since its introduction in Scotland, the public performance measure (PPM) for trains managed through Luminate is 7% higher than those that were not. Luminate’s provision of the best platform docking options has also significantly reduced delays at Edinburgh Waverley and Glasgow Queen Street stations.
A recent development is Resonate’s Initiate infrastructure access planning system which links engineering access planning to the signalling system. Planners create possessions (or line blockages) in Initiate which must then be validated by an approver. Once the possession has been approved, its limits are fed to the Scalable system which controls the signalling interlocking. When the possession is taken, this locks signals to ensure trains cannot be signalled into the possession. Thus, it is a form of T3-D protection as the signaller has no control of the protecting signals during the possession.
Craig explains that much has been done during the past 12 months to enable Initiative to provide possession protection in this way. This includes the Systems Review Panel’s approval of the Initiate system, developing instructions for its use and the industry access board’s approval of a trial for its use as part of the possession limit controls programme. The personnel concerned and Trade Unions also had to be consulted.
As part of these approvals, a hazard study was undertaken which concluded that, in the protection hierarchy, Initiate was the highest form of protection. This validated the proposition that detonator protection was not required when possessions are taken by the Initiate system.
Training also had to be provided to planners, signallers, Persons in Charge (PIC), and others who use the Initiate system. As Initiate can be used to take both possessions and line blockages the individual who requests Initiate protection is known as the PIC. For wider use of the system, there is to be a full programme of internal and industry communications.
Initiate’s first possession
In a UK first, Edinburgh Signalling Centre authorised its first Initiate possession without detonators on 13 January. Craig explains that the process for this is:
1. Possessions are created, verified, and approved in Initiate in accordance with normal possession planning timescales.
2. Once approved, possession details are sent to Scalable and Luminate 72 hours before the possession start time.
3. Approved possession details are shown in Luminate 36 hours before possession start time.
4. Signallers can see the possessions displayed in Scalable six hours before the possession start time.
5. PICs can view the Initiate plan once they have been allocated to the possession/line blockage.
6. Normal PIC / signaller communications apply when requesting a protection with the additional requirement of the PIC advising the Signaller of a unique code.
7. Once signalling protection has been applied the signaller cannot change anything with the limits of the possession / line blockage until it is given up by the PIC advising the signaller of a unique removal code.
8. If there is a requirement to operate signalling equipment during the possession e.g. move points or for signal testing, the individual requiring this must get authority from the PIC who will issue the signaller with a temporary override code which is valid for two-minutes.
The first Initiate possessions were taken on the Cumbernauld workstation. Thereafter, as shown on the diagram, the system will be progressively rolled out until all nine Edinburgh Signalling Centre workstations will be taking Initiate possessions from July.
Craig is clearly enthusiastic about the introduction of Initiate and has every right to be so. Although almost all of the 14,000 possessions each year in Scotland are taken without incident, in
Control Period 6 there were an average 16 incidents per year involving protection or trains signalled towards a line blockade. This is an incident rate of 1 in 1,000 possessions.
Furthermore, the use of Initiate reduces the number of safety critical communications required to take and give up possessions from an average of 18 calls to three taking account of the need for the PICOP to communicate with those who place protection. This offers a significant safety benefit as safety critical communication failures are a significant incident causation factor. Another safety benefit is that there is no requirement for staff to be on track to place and remove protection before and after the possession is taken.
In its report into the fatal accident at Margam in 2019 that killed two track workers, an RAIB recommendation concerned the need to provide safe access to the track for routine maintenance. Although line blockages provide such safe access, their use is often not practicable due to the time to set them up between trains. Craig considers that Initiate has much to offer in this respect as he estimates that the slick, safe way that it offers protection will enable an additional 3,000 line blockages a year to be taken in the Edinburgh Signalling Centre area.
In addition to its safety benefits, the speed at which Initiate possessions can be taken and given up increases available track access time. Experience to date has shown that Initiate track access is granted in two to three minutes compared to the 20 minutes it normally takes with similar time savings at the end of the possession. With a normal overnight rules of route possession of typically six hours, this offers a 10% increase in productive access time.
A 2021 ORR report on possession efficiency noted that, typically, Network Rail’s supply chain undertakes 700,000 hours work within possessions with 100,000 possessions each year. This indicates the scale of the total efficiency savings from the network wide application of Initiate or a similar process. It should be noted that Initiate is only available alongside the Scalable system.
The use of Initiate to take possessions and line blockages improves a process that has long been prone to human error, however competent the individuals concerned may be. One issue identified in the RAIB report into the Camden Junction incident was “the processes and methods for managing and communicating information regarding engineering work in modern signalling centres”. The need for a PICOP to spend over a minute reading the details of a complex possession in the WON to a signaller is one such example.
The Initiate initiative effectively addresses this issue as well as the need to put people on track before the possession is taken. It has done so by considering the whole possession process, the provision of comprehensible information to those involved, and applying modern technology to deliver significant safety and efficiency benefits.
It is an impressive example of the dictum that good safety is good business.
The Initiate possession protection initiative is an excellent example of the need to consider an activity’s overall process to determine how it can best be managed both safely and efficiently.
Prior to retiring in 2009, I was involved with various possession management initiatives when it became apparent that work in possessions had not been considered in this way. As a result, some of the rules were confusing and did not address
the practicalities of engineering work. After I retired, the title of this article was the subject of a presentation that I gave to a conference of the Institution of Occupational Safety and Health (IOSH). Readers are invited to judge for themselves whether this title was unreasonably provocative.
Rules associated with the safety of railway engineering work are specified in Rule Book handbooks. Any work that requires the use of engineering trains or On Track Plant (OTP) requires a possession of the line to be taken under the control of the Person In Charge of the Possession (PICOP). The PICOP’s role is specified in Rule Book Handbook No 11 (HB11).
Essentially, this is to ensure that the possession is protected from train movements and that the open line is protected from movements leaving the possession. In addition, he/she must ensure the train and OTP movements outside of worksites within the possession. To enable work to take place, the PICOP authorises one or more Engineering Supervisors (ES) to set up a worksite(s) within the possession. The ES is not necessarily an engineer, nor a supervisor of work. As specified in HB12, the ES’s role is to control train/OTP movements and authorise Controllers of Site Safety (COSS) to set up their site(s) of work in the possession worksite as specified in HB9.
The COSS does not necessarily supervise the actual work. Their role may be limited to ensuring that the workgroup is protected from train movements and, if required, by isolation of Overhead Line Equipment (OLE). The Safe System of Work (SSOW) that they set up only relates to train/OTP movements and does not consider risk from the actual work. These are managed by a work supervisor who must have the required expertise. It is often not practical to provide such individuals with the full COSS competency.
When it is necessary to work under isolated overhead lines, the COSS must be in possession of an overhead line permit and brief the workgroup about its conditions before work can start. HB15 specifies how OTP movements are controlled by Machine Controllers (MC) who must get authority from the PICOP or ES for on or off tracking and movements in the areas under their control.
The site of work is where all engineering work is undertaken once protected by train/OTP movements by the SSOW set up by the COSS. This is not the same as the worksite which is the line(s) in the possession over which the ES has control of train movements. Lack of understanding of the distinction between the terms ‘site of work’ and ‘worksite’ has caused much confusion.
This is not helped by the Rule Book possession handbooks’ definition of a worksite which is “the portion of line within a possession of a running line where work will take place”. This is misleading as often work is only done in a small part of the worksite. For example, a typical worksite may be the length of track between an access point, where OTP is on-tracked, and the site of work. Given the distance between access points, it is not untypical for worksites to be a few kilometres long, while the site of work may be around 100 metres long.
As shown below, a more meaningful definition would be “the portion of the line in which sites of work are established”. Despite possession work being done within sites of work, this term is not defined in any of the Rule Book possession handbooks, nor are sites of work shown in any of the diagrams with the Rule Book handbooks.
HB12 requires the COSS and ES to agree the limits of the site of work. However, there is no guidance on how this should be done nor any requirement to demarcate it.
Within the site of work, OTP movements must generally be done at less than 5mph. Yet HB15 which concerns OTP movement does not mention sites of work. Moreover, HB15 does not give the COSS any authority to control OTP movements even though they are responsible for protecting their group from train movements. Instead, HB15 requires that, within a worksite, the ES must authorise all OTP movements. Often, the number of OTP movements are such that it is not possible to comply with this rule.
In January 2020, a Mobile Elevating Work Platform (MEWP) collided with another stationary MEWP within a possession at Rochford. The investigation by the Rail Accident Investigation Branch (RAIB) identified various causal factors, one of which was confusion among staff about who was in charge of the safe movement of ontrack plant.
In addition to the relevant Rule Book handbooks, the Mechanical and Electrical Engineers’ networking group has produced document M&EE - COP0001, a code of practice for the management of competence of plant operators. There is also a Network Rail standard NR/L2/RMVP/0200 ‘Infrastructure Plant Manual’. This defines the requirements and guidance for the use of OTP on Network Rail’s infrastructure.
Module P521 of this manual, the ‘Plant operations scheme’ includes the requirement for a Plant Operations Scheme (POS) representative to be on site. This is an additional role not mentioned in Rule Book possession handbooks. This illustrates how those on site must comply both with Rule Book Handbooks and the applicable Network Rail standards.
The RAIB report into the Rochford incident found that the COSS, who was also acting as MC, incorrectly believed that the POS was in charge of OTP movements. It concluded that due to the number of supervisory roles on site (COSS/MC, POS, and site supervisors) the COSS/MC and other staff were confused and lacked confidence in their role.
RAIB also asked RSSB about the impractical rule that only an ES can authorise an OTP movement within the work site (HB12 6.1 and HB 15 7.1). This was an issue mentioned in my 2010 presentation. The RSSB view was that this rule only applies to OTP movements to and from the site of work. Whilst this is a reasonable requirement, it is not what the rule states. Furthermore, ‘site of work’ is not mentioned in HB15 about OTP movements. Four years later, this rule has yet to be updated to reflect RSSB’s interpretation of it and so still includes a rule that cannot always be complied with.
RAIB’s Rochford report (08/2020) recommended that Network Rail review and clarify the roles and responsibilities of staff working in possessions and work sites to avoid duplication of responsibilities and confusion arising between roles. Although this recommendation was made in September 2020, RAIB’s website shows that it has yet to be closed out. It is difficult to see how Network Rail alone can close out this recommendation as changes to Rule Book handbooks are authorised by RSSB.
As well as the complexity of possession communications, my presentation to IOSH 15 years ago also considered the following issues:
Speed of movements in worksites. In 2009, it was generally considered that OTP could only move at walking pace in worksites although this was only required within the COSS’s site of work. Hence it was not unusual for an MC to walk with their OTP for the few kilometres between access point and site of work. Now the requirement is more realistic as HB15 allows movements at speeds of up to 25mph when authorised by the ES or PICOP.
Such movements are undertaken subject to defined send and receive arrangements or OTP being approved to carry the MC. HB15 specifies when movements are restricted to a maximum of 5mph. It implies, but does not mention, that this restriction is applicable to the site of work.
Need for an ‘all lines blocked’ COSS competency. Setting up an SSOW in an all-lines blocked worksite is relatively straightforward as this only requires the COSS to agree worksite limits with the ES and obtain his/her authority to start work. Yet the only person who can do this is a COSS who has attended a weeklong training course to learn how to set up different SSOWs on or adjacent to open lines as well as those within possession worksites.
As a result, it is not practicable for all those supervising the work to have a COSS competency. This, and the provision of an all-lines blocked COSS competency, would simplify communications by largely removing the need for a workgroup to have both a COSS and site supervisor.
COSSes losing open-line competencies. As many COSSes rarely work outside possessions there is a risk that they may lose their competence to set up a SSOW outside a possession should they be required to do so. This risk has increased as Network Rail has specified that, from 31 March, all MCs must have a COSS competency. Facilities for possession management. RAIB’s report into a serious possession irregularity at Balham in 2019 recommended that “Network Rail should review its requirements for locations in which PICOPs are permitted to carry out their duties, so that they have adequate facilities, information, and equipment to enable them to control train movements associated with possessions.”
Though this recommendation has yet to be closed out, there are many examples of good practice to manage complex possessions such as the use of magnetic white boards. The Transpennine Route Upgrade uses the eviFile digital possession management system as well as C&G checkpoint which enables an ES to simultaneously authorise all COSSes in the worksite to set up their SSOWs. Network Rail Wales and Western are using PodFlow to improve the safety and efficiency of communications between PICOPs, ESs, and COSSes.
Situational awareness. Fifteen years ago, personnel being in the wrong location was a frequent cause of possession irregularities. At the time, staff were given little information on how to get to the required access point. Much use is now made of Geographic Information Systems to find and visualise track locations. This includes the provision of an Access Point App for Apple and Google devices which enables users to easily find the location of Network Rail’s 18,000+ access points.
Network Rail is also keen to expand the use of geofencing technology from companies such as Onwave and Tended to ensure that track workers are where they should be. This also enables the ‘site of work’ to be virtually demarcated. Despite such innovations, I am advised that personnel being in the wrong location remains a significant issue and wonder whether there is adequate training on how personnel must use such new techniques to confirm their location.
The above shows that, although the process of managing possessions has improved, some issues remain and, as RAIB has identified, the roles and responsibilities of staff working in possessions need to be clarified.
In 2001, Lord Cullen’s report into the fatal Ladbroke Grove crash recommended that railway group standards should be produced by an independent body. This resulted in the creation of RSSB which manages the production of railway standards which include National Operating Publications (NOP) such as the Rule Book, the content of which is managed by RSSB’s
Traffic Operation and Management Standards Committee (TOMSC) which has 15 members of whom three are from Network Rail and two are infrastructure contractors.
The Railways and Other Guided Transport Systems (Safety) Regulations 2006 (ROGS) require train and infrastructure operators to have a safety management system (SMS) which includes procedures to comply national safety rules which include NOPs. However, as the ORR’s guidance to the ROGS regulations makes clear, the requirement for an SMS as specified by ROGS does not apply to work in engineering possessions.
Within an engineering possession all activities are done either by Network Rail personnel or those under contract to the company. Hence, unlike interworking on the open railway, Network Rail has the legal responsibity for everything done in possessions. It would thus seem reasonable for the company to have direct control over the rules for the work in possessions for which it is accountable.
Since British Rail days, possession rules have evolved over many years and been specified by operations rules committees. The basic framework for possession rules is the control of engineering trains by PICOP and ES for which the site of work need not be considered. However, from the 1990s there was increased use of road-rail OTP which entered the possession sideways by being on-tracked at an access point. Furthermore, much more work was being done in possessions from this time. This resulted in complex possessions with many sites of work and large numbers of OTP movements. The practicalities of managing such possessions are not fully addressed by the Rule Book handbooks.
Hence Network Rail produces its own standards in addition to the Rule Book requirements. For example, the requirement for a POS representative which is a role not mentioned in the Rule Book. This lack of a cohesive approach from having two different organisations producing possession rules and standards would seem to be the root cause of the confusion that RAIB has identified.
The perceived need to have possession rules to support Fundamental Operating Principles (FOPs) also has the potential to add complexity. For possessions, the most relevant are ‘Trains proceeding over any portion of line must not be obstructed in a way that threatens their safety’ (FOP3) and ‘People must be kept at a safe distance from moving trains’ (FOP8).
Yet work in possessions is pre-planned by competent personnel who understand the risks associated with these FOPs. RSSB defines rules as “direct instructions to railway staff” which implies real-time situations. It is thus not appropriate to apply such rules when planning complex work.
Little has changed
As it is over 15 years since I was on site as a Network Rail employee, I am conscious that my practical experience of possession management is dated. Hence, I sought feedback from those working for Network Rail and its suppliers before finalising this article.
The feedback I received was that this article is “spot on” and highlights very real issues. I was also advised that the introduction of additional roles such as the POS representative, and the “fleeting introduction of the Planning and Delivering Safe Work (PDSW) initiative which gave us the Safe Work Leader (SWL) competencies”, ultimately cause much more confusion.
Such feedback reinforces the conclusion of my 2009 presentation that Network Rail, as the responsible employer, should take ownership of track safety at director level to ensure a cohesive approach to rules and other risk controls. This requires Network Rail to have direct control of the possession safety rules.
In 2010, my presentation answered the question it posed as follows: “Yes, possession rules do control the risk to track workers. However, some are presented in a confusing manner, and some issues are not addressed. Furthermore, rules must not be considered in isolation from other risk control measures.”
This statement remains as true today as it was 15 years ago.
This feature was shared with RSSB prior to its publication. In response, RSSB wished to emphasise that Standards Committees are made up of members who represent a cross-section of industry stakeholders. Standards Committees decide whether to approve changes to rules and standards by consensus, and according to the decision criteria set out in the industry-agreed Railway Standards Code. RSSB then authorises the change, provided it is satisfied that due process has been followed.
RSSB also advised that there are several projects currently underway to update rules for track worker safety and possession management, based on ideas proposed by Network Rail. RSSB works closely with Network Rail, infrastructure contractors, and train operators to gather feedback on how the rules are working in practice, discuss proposals for change and take them forward.
Climate change and the increased risk of storm damage and high wind strength is just one of the challenging issues that Britain’s railways need to manage. Studies show a decline in days with minimal wind, indicating an increase in windy conditions. Research also suggests climate change will likely lead to more intense storms with stronger winds.
Another challenge for rail is to safely manage level crossings. Level crossing booms of 8.5 metres and above have, under excessive wind loading, displayed problems. This is not surprising given their height when the road crossing is open. The problems include lateral deflections, interference with the barrier closing time, barriers not fully closing the highway, and increased risk of barrier failures. The wind loading has even caused spurious trips of the level crossing obstacle detection system in some parts of the country. Siemens has therefore produced a revised S60 barrier design to address the identified issues. The new design is called S60+.
Great Britain’s level crossings are among the safest in Europe, but they still pose a significant safety risk to the public, and the law requires railway businesses to manage level crossing risk effectively. Therefore, level crossing asset management is one of the priorities of the Office of Rail and Road (ORR) safety regulator. The ORR’s
guidance on level crossings, ‘Principles for managing level crossing safety’, is focussed on continued improvement of level crossing risk management, and it emphasises that risk should be reduced through the design of a level crossing.
A study led by a team of Met Office climate scientists says that the North Atlantic Oscillation (NAO) could reach unprecedented magnitudes by the end of the century, leading to severe impacts in northern Europe. NAO is a largescale atmospheric pressure ‘see-saw’ in the North Atlantic and is a key driver of winter weather patterns in the UK. It is measured by the gradient between high pressure over the Azores and low pressure over Iceland, and controls the strength of the prevailing winds.
Network Rail expects it will become increasingly difficult to respond to extreme weather events and for railway assets to withstand extreme high winds. So, it will spend £2.8 billion on resiliency and planned maintenance activities during Control Period 7. There are over 1,000 level crossings with barriers on the mainline rail network and they all need to be managed safely and improved to reduce the safety risk to As Low As Reasonably Practicable (ALARP). This is increasingly important given the greater volumes of both road and rail traffic.
The S60 barrier machine is an established design which has gained a reputation as a rugged field proven unit with an excess of 11,000 worldwide installations. It has been used on Network Rail infrastructure since it gained approval in 2014 and over 88 installations have been provided around the GB network.
Power consumption is either 15A at 12V or 8A at 24V, which are relatively low voltage and currents enabling both cost and space savings on the cable core size and backup batteries. The machine uses electrical direct drive, which improves sustainability due to the lack of hydraulics, and it has simpler maintenance procedures as draining hydraulic fluid is not required.
While the machine is very reliable, it is designed so that maintenance access is at eye level with a swing down door. All vital components are mounted off the floor to reduce any damage from flooding and new motor brushes, when required, can be fitted in a few minutes.
The eye level access, plug coupled modules, absence of hydraulics, and on-board diagnostic LEDs, enable quick and easy installation and maintenance. The barrier machine is pre-assembled to the mounting post before delivery to site which makes it less time consuming to install. Additionally, the S60 is one of the lightest barrier machines on the GB railway, which leads to a lower cost and less labour-intensive installation. Network Rail says the S60 is one of the most reliable barrier machines on its network.
The boom lights are plug coupled and major bearings are sealed for life. Spare parts stock mainly consists of motor brushes, PCBs, and switches. Boom skirt service kits are available to replace any broken rods – reducing the need for complete boom replacement. With boom lengths without skirts of 2 to 12 metres,
and with skirts 2 to 8 metres, the S60 can be deployed on both manned and automatic crossings.
S60+
Siemens has produced the revised S60+ design that includes a stiffer boom aimed at addressing the wind loading and deflection issues. The imposing design of the larger diameter boom was chosen to make it sturdier and more robust, which is beneficial for deterring trespassers.
Golden High Hedges crossing near Donington, on the Lincoln to Peterborough line in Lincolnshire, was a crossing where data suggested some failures were due to the barrier being held up in high winds and exceeding the 10 second operating time. Golden High Hedges crossing was therefore chosen as the trial site for the improved S60+ design. This has now been in use and subject to intense monitoring for over a year and is shortly expected to receive full product approval.
Prior to the in-service trial, the S60+ barrier design was subject to extensive testing in the Siemens Chippenham factory. The testing involved a total of 616,915 cycles and, for a crossing such as the trial site at Golden High Hedges, many components had seen the equivalent of 56 years in service. The test machine was fitted with a 9.2 metre boom which is longer than the typical boom on the network (9.1 metres) and the longest boom at Golden High Hedges is 8.544 metres.
The Network Rail requirement was for a rigid construction, so that the gap between each boom should not exceed 30cm with a specified trespass force. The boom should also not be damaged by a wind speed of 50 m/s and not deflected more than one metre with wind speeds of up to 35 m/s.
These requirements have been met by the new design. The problem with high winds preventing the barrier from dropping to close the crossing is no more, as the barrier is now driven down 70 degrees, instead of just 30 degrees previously, which means it falls under gravity for the remaining distance. The stiffer, more rigid boom design also improves trespass management, making it far more difficult for anyone to force themselves through the barriers.
An additional counterbalance and a modified cage has also been designed, together with a different hand crank system to enable good access and a different wind catcher. A traditional BR843 barrier machine to S60 base conversion bracket is now also available. This will enable an easy ‘like for like’ replacement, if required, with no base change.
Network Rail says climate change is one of the biggest challenges facing the railway today and the weather over the past few years has seen unprecedented rainfall and storms. Climate change is projected to increase the frequency and severity of extreme weather, and Network Rail is planning how to keep passengers and services safe and moving. The Siemens S60+ barrier machine and its improved boom is just the sort of asset and initiative that the railway will need more of.
maximising the benefits and managing the risks
Artificial intelligence (AI) capabilities have rapidly accelerated in recent years. Historically, the rail industry has been slow to adopt new ways of working, but several railway companies have started to explore and implement AI for some activities. Today, all railway companies have the potential, and the opportunity, to harness the power of rapidly evolving AI technologies to improve the planning and delivery of services.
A recent seminar organised by the IMechE and IRSE explored the impacts that AI is having in the rail industry through the perspectives of human performance, design acceptance, and change management. The seminar focused on the potential benefits of using AI in decision making, failure prevention, and infrastructure monitoring, as well as the risks that need to be considered in rail’s highly regulated industry.
There are some who question if AI should be used in the rail industry and how the industry will adopt new intelligent technologies, such as AI and Machine Learning (ML). ML is a part of AI which uses algorithms to enable systems to learn from and make decisions based on data. Unlike traditional programming, where explicit instructions are given, ML allows the system to learn and make predictions from the data, without explicitly being programmed for each task.
The point was made early in the day that AI and ML
are already involved in many applications, and are being deployed in the industry. The next generation of engineers is also already working with the technology at university or college. Like it or not, it will be coming to the rail industry. Furthermore, it offers huge benefits but with risks that can be managed. This was demonstrated and discussed throughout the day.
Professor Rod Muttram, junior vice president and a Council member of the IRSE, presented the first session of the day by explaining the fundamentals of AI deployed in a safety function. Rod confirmed that AI and ML offer the rail sector significant benefits but, like all new technologies, there is a need to take a well-structured and disciplined approach to gain acceptance, and avoid reliability and safety problems. Rod explained the difference between automation and AI. Automation has been used for decades, using computers
and conventional engineering techniques with behaviours programmed and validated by human engineers. There is a need to define carefully what an AI system is, as some systems today referred to as being AI are actually ‘automation based’ with limited intelligence.
Alan Turing (1912 – 1954) introduced what has become known as the ‘Turing Test’ in his paper ‘Computing Machinery and Intelligence’. The Turing Test involves a human evaluator interacting with both a human and a machine without visual cues (i.e. using textual messages). If the evaluator cannot reliably distinguish between the two based on their responses, the machine is deemed to have passed the test.
The Turing Test still serves as a benchmark for assessing a machine’s intelligence. It gauges the machine’s capacity to emulate human-like cognitive abilities. True AI devices are machines that behave like a human brain, using multi-layer or deep neural networks, which are then taught or allowed to learn what to do. The environment and the learning programme for these systems are as important as the engineering.
AI and ML techniques are already being used in the road transport sector, for example,
and there have already been some high-profile incidents. The comparative safety ‘benchmark’ for roads is much less challenging than rail and the accident rate for human drivers on roads makes it relatively easy to make improvements.
However, the safety benchmark for rail is typically much higher compared to road, and even a single rail incident caused by AI would result in a public outcry. So, using AI / ML in any safety or operationally critical area will have to be very carefully considered, and is probably years away.
Another issue with very complex intelligent systems is the need for continual OEM support and ‘supplier lock-in’, which many railways want to escape from. Avoiding this may require the confinement of AI / ML to certain modules, rather than allowing extensive control. Rail suppliers are also unlikely to take on the longterm support liabilities required for intelligent systems without significant rewards. But could AI systems be made intelligent enough to design their own replacement?
Rod warned that a true advanced AI may develop human traits such as boredom and making errors. He also recommended that rail does not use AI when conventional technology will do. Where AI is used the following must be addressed:
» Transparency – especially for any safety function.
» Algorithmic bias – systematic and repeatable errors that create ‘unfair’ or unsafe outcomes different from the intended function of the algorithm.
» Traceability – important and essential for safety and reliability.
» Ethics – AI needs to learn ethically, which was a key part of the 2024 IEEE International Conference on Artificial Intelligence Circuits and Systems (AICAS).
Auto-reverse
Rod does not recommend using AI for any safety function above Safety Integrity Level (SIL) 1. For example an ‘auto reverse’ function is used at Westbourne Park on Crossrail, for turning the 14 trains per hour in the reversing sidings. The driver selects ‘auto reverse’ and walks back through the empty train.
By the time the train gets back to Paddington (about a mile away) the driver should be in the other cab ready to form the next eastbound departure. However, the signalling control is achieved using a conventional high safety integrity SIL 4 system, with AI providing surveillance of the track at the turnback to ensure no staff or trespassers are harmed by the moving train. This does not require more than SIL 1.
Other AI uses envisaged by Rod included identifying and highlighting incidents on platforms (for example) in real time from AI surveillance of many parallel video channels. High resolution CCTV is relatively inexpensive and extensive throughout rail, but human analysis of the video images is expensive, boring, and prone to errors. Using AI to search accurately and quickly through the video information, and ‘flag up’ incidents for human decision making and action could deliver huge benefits.
Dr Nick Reed, chief road safety advisor at National Highways and founder of Reed Mobility, gave a presentation titled ‘Trust in me? How emerging technologies might keep us safe and why they may not…’. Nick explained that many road incidents are caused by tired drivers who lose concentration. Surely an AI controlled road vehicle would not get tired and be safer?
Nick then discussed an incident where an AI controlled road vehicle hit a pedestrian who had already been knocked over by a ‘normal’ car. After hitting the pedestrian, the AI vehicle tried to continue its journey by reversing and going around the pedestrian, but this resulted in the pedestrian’s clothing getting caught by the vehicle and they were dragged up the road.
Incidents like this with AI vehicles could be corrected, but how could the behaviour of the AI vehicle be verified?
One solution suggested was by using a data version of a driver’s spoken thought commentary, which could be shared with the regulator.
AI road vehicles were discussed a number of times throughout the day with the observation that society accepts that human drivers will make some errors but is less likely to accept AI making any errors.
David Golightly, lecturer in human systems integration at Newcastle University, covered ‘A human-centric view on AI in railways’. He explained that AI needs to be looked on as a tool and examined how AI could help human perception, interpretation, decision making, and action taking?
If designed and implemented correctly, AI could help with the perception and interpretation of huge amounts of data, leaving the decision making and actioning to humans. The scale of data generated in modern systems far exceeds the human capacity to understand and analyse it, but AI algorithms can help process higher volumes of complex data, turning it into information which can be used more easily by decision makers.
To achieve this, AI must achieve the trust of humans and reduce the human workload. It must help not hinder. However, gaining confidence is not easy as it’s not possible to see how neural networks work.
Risk perception
Heather Taylor, of FraserNash Consultancy, presented on ‘Risk Perception and Management: how does AI change perception of risk?’ She explained that the key is finding the balance between human oversight and AI autonomy, to ensure that the
AI technology supports rather than replaces human decision making.
Regular checks and audits of any AI decisions will be required to ensure that risk management, safety and critical judgements are maintained as if they are made by a competent human. Training, collaboration and ethics must all be addressed, so that humans and AI are ‘teammates’.
To assure the safety of an AI enabled system-of-systems the key is to build trust in the system, and achieve ‘calibrated trust’, which is a balance of user trust and system trustworthiness. If it is not balanced, then there is either too much trust in the system, leading to ‘over trust’, or ‘under trust’, where the human does not believe the system.
Calibrated trust as a concept can apply to all system-ofsystems, including human centred ones. Frazer-Nash and University of Bristol have used a systems-engineering approach to design a set of ‘trustworthiness categories’, which can be prioritised for a system based on the concept of operations and risk analysis.
Applications of AI in rail
AI and autonomous ML intelligence systems are already being used in rail to deliver infrastructure management solutions.
Emily Kent, of One Big
Circle presented ‘Putting the AI in rAIl’ and explained how the company is assisting railway engineers by using AI to analyse huge amounts of infrastructure data, covering for example: video and heat monitoring of overhead lines, troughing routes, vegetation, IBJs, conductor rail, and switches and crossings. She emphasised the importance of identifying what information engineers actually need to harness the data and ‘power up’ intelligence with tailored AI. This involved talking to engineers for ‘hundreds of hours before designing the AI system.
Ansia Mamaniyat, director Chrome Angel Solutions and Jordon Langfield, fleet engineer at Angel trains, gave a talk titled ‘Train Engine Health Monitoring and Failure Prediction using AI’ which explained how ML techniques are being used to carry out deep analysis of Class 180 train data to predict engine health scores. Funded by Innovate UK, the scores are used to determine the priority of which trains to send into service, and tests have shown that 26% of Schedule 8 (unplanned service disruption) costs could be saved.
They emphasised that AI will not replace humans and jobs but will enable better targeted interventions to significantly reduce train cancellations, save costs, and deliver better reliability.
It’s important to gain user acceptability, collaboration, and trust in AI by addressing and providing:
» Transparency
» Privacy
» Safety assurance
» Unbiased outcomes
» Accountability
» Reliability
» Compliance
» Explainability
Rebecca Sellick, business development director UK and Europe, Cordel discussed “AI for railway infrastructure engineering monitoring – panacea for people and processes.” She said it was important to find out what the customer’s ‘pain points’ are when designing AI systems. For example, in Network Rail structure gauging is a pain!
Gauging is a complex issue involving the dynamic behaviour of a train and there are many limited clearance locations on the rail network. The lack of gauging information has caused problems with introducing new trains, and for example can prevent rail freight operators moving containers over a new route. Routes may be classified as not clear, but the reason and location why they are not clear may not be apparent.
It can take hours to manually gauge a structure, and even with accurate data the manual processing required is laborious
and takes too much time. The Cordel Workbench is an AIpowered automated survey data processor that can be mounted on in service trains, and analyse LiDAR (laser point clouds), track position and other data gathered from thirdparty sources and technologies. The data (110 Gbit per sensor, per day) is translated using AI into accurate and comprehensive high-quality, survey-grade gauge profiles for entry into the National Gauging Database.
Nick Kotsis, chief data scientist at Network Rail, explained ‘Network Rail’s vision for AI –what can railway engineers do with AI for us’, and covered Robotics, Automation and Artificial Intelligence (RAAI). This offers a potential step change in the way asset data is managed and how infrastructure inspection and maintenance activities are performed.
The vision is that autonomous systems will monitor the network, providing Al systems the data to analyse and develop trends of asset-risk. This will enable decision support tools to schedule the most effective inspection and maintenance regime with minimal disruption. It is also expected that robotics and automation could be one answer in enabling more productivity in possessions and reduce the number of staff working red zone and other workforce safety benefits.
The seminar provided a very comprehensive view of the benefits of AI in rail and the risks involved.
The main line rail industry is very complex and open, which will limit the use of AI, so operationally AI may be deployed easier and sooner in more closed metro systems.
Although as this article has shown AI and ML is already being deployed in UK rail.
A report by the International Union of Railways (UIC) and McKinsey titled ‘A journey to building AI-enabled railway companies’ identifies the AI use cases that have been deployed, or have potential to be deployed. The report says there are more than 100 potential AI use cases for rail. Use cases are at different stages of maturity, but the most mature use cases focus on shift planning and rolling stock predictive maintenance, while other uses cases include: energy efficiency; service scheduling; autonomous trains; real-time disruption management; predictive maintenance; capacity planning; realtime traffic management; inventory management; maintenance copilots; and network infrastructure digital twins.
The report says that AI could potentially unlock £10 billion to £16 billion a year, globally, for railway companies. However, as the IMechE / IRSE seminar demonstrated, good implementation is also key for realising the value that AI can offer to rail.
you didn’t know you needed
Fletcher Moorland has provided engineering services for nearly 80 years. With a wealth of experience in electrical and electro-mechanical engineering, the company works with major companies in the automotive, power generation, logistics, and manufacturing industries, and has worked in Rail for more than three decades.
Rail Engineer sat down with Managing Director Matt Fletcher to discuss the services the company offers, how it sets itself apart from its competitors, and the importance of its work for industry and our wider society.
Could you give us a brief history of Fletcher Moorland and an overview of the services you provide?
Fletcher Moorland is a multi-faceted engineering company with divisions in repair, sales, manufacturing, consultancy, and reliability. We’ve been providing engineering services to industry since my grandfather Sam Fletcher started the business in the mid-1940s.
Initially, the business focused on electric motor rewinds and that’s still something we’re heavily involved with. Today, life-cycle extension and maintenance are at the core of what we do.
We’ve been working with the rail industry for over 30 years. Our clients include most major rail transport authorities and operators across the UK, and we deal with everything from traction motors through to electronic controls for tram, passenger rail, and freight. We’re also specialists in tackling legacy equipment, and we’re currently repairing a great number of driver-call handsets, which keeps our 3D printing department busy.
The company encompasses repairs, sales, manufacturing, and reliability – and we fulfil all our customers needs from our workshop in Stoke-onTrent, which is open 24 hours a day, 365 days a year.
Fletcher Moorland is the go-to company for customers who have hit a brick wall – whether that’s because manufacturers refuse to repair their equipment, or other repair companies are unable to do so. We take on projects that others will not, and we respond quickly.
You’ve mentioned that manufacturers rarely offer repairs for their equipment. Why is that?
It’s simply a case of profitability. Manufacturers often claim that equipment is obsolete or too old to be repaired, but that’s not always correct. For example, we’re regularly repairing traction equipment from the 1960s, we come to the aid of steelworks which are using older equipment, and we even support Sellafield, which was designed in the 1950s.
Manufacturers might say that repairs aren’t as reliable as replacing equipment, or that specific software is required to complete specific jobs. This isn’t necessarily true, and we use the same equipment that many of the manufacturers use to make these repairs.
We’ll always support older equipment and, when our clients do decide to upgrade, they can do so through choice, rather than being forced to by the OEM.
Do many companies provide a similar service?
What makes Fletcher Moorland stand apart from the rest?
There are many companies which concentrate on motor rewinds, but that’s mainly for an industrial base. More specific skills are required when working with the rail industry and there are far fewer businesses providing a service quite like ours.
Our desire to solve problems is what stands us apart from our competitors. We’re the supplier that customers go to when everybody else has said ‘no’.
For example, a standout project that really launched our name and can-do approach in the rail industry was a refurbishment project for Class 90 freight locos. Their air blast circuit breakers (ACB) must have been from the 1980s. Nobody would touch the project, but we were eager to have a look. There were compressed air cylinders in there, all different contacts. We took the equipment into the workshop and reversed engineered it, manufacturing some of the parts we needed, including copper ball bearings for the swinging arm and copper contactors.
Once we’ve solved a problem like that, clients come back to us with further repairs that they once thought impossible. I truly believe we are one of the reasons that some locomotives can continue to operate without going through multi-million-pound upgrades.
Another differentiator is our speed of turnaround – very often, suppliers and manufacturers can take some time to repair equipment. Usually, the first time we’re called is when there is a breakdown situation and an urgent repair is needed. Having a true 24-hour manned workshop helps to speed the repair process and get equipment back to our customers quickly.
We’ve seen an instance where one supplier took nine months to deliver. At Fletcher Moorland we’re reducing that to two or three weeks. That’s critically important in an industry like rail where clients may be facing a shortage of equipment, or reduced availability of parts for maintenance.
Sustainability is a major concern these days. How does your work help to meet the needs of the rail industry without compromising on this goal?
Sustainability is nothing new, it’s the old idea of ‘make do and mend’ but rebranded. Eighty percent of our business is refurbishment or remanufacturing of components. Repairing, rather than
replacing is a sustainable practice and needs to be adopted on a wider scale. Our work has a positive effect on the planet as we’re actively preventing items from going to landfill.
Though it’s taken some time, it seems as though industry is now moving away from its throw-away model and, when we perform work for our customers, we provide a full report which gives them a breakdown of the waste they’ve saved as a result of the repair.
But we don’t just repair faults - what we do is to refurbish everything that comes into our workshops. Our policy is that everything is to be as good as it was when new, if not better, so that any future failures can be pushed further back.
The rail industry has had its ups and downs of late. What major challenges have you seen and how are you helping to overcome them?
The biggest challenge for us in recent times has been Covid. That said it also opened up a few opportunities. Prior to the pandemic we employed around 86 people and had a lot of business with the steel and car industries.
We remained open throughout the pandemic, supporting manufacturing and critical industries such as food and drink manufacturing, power generation,
transportation, and healthcare. Like many others, we were forced to furlough staff and had to make some very tough decisions.
At the same time, many of our customers were making redundancies and many engineers did not return to their old jobs –some had taken up alternative careers which may not have paid the same but were far less stressful. This trend only increased the need for our expertise. Additionally, the recession that followed Covid also brought benefits as companies increasingly opted to repair equipment, rather than replace it.
Recruitment is a problem across the industry, but we’re fortunate that we have no problem finding people. Since Covid, we have managed to increase our workforce to 120 people. Many of our staff come to us on recommendation from others working in the business. Four of our staff have been with us for over 50 years, and they wouldn’t stay if we weren’t serious about the work we do.
You’re also reaching out to the new generation of engineers – could you tell us more about that?
The skills gap is a problem for rail, but we’re doing what we can to close it as quickly as possible. Unfortunately, there are very few apprenticeships in motor re-wiring these days – they tend to focus on mechanical fitting. Electric motor repair hasn’t been seen as a required skill for some time in the UK as companies have focused on replacing rather than repairing and electric motors are relatively cheap these days.
We were recently approached by Stoke-on-Trent College to support 16 of their HNC General Engineering Apprentices by providing ‘Day in Industry’ workshops.
We welcomed the opportunity to support the college and tailored a split half-day workshop to provide real-world insight into electric motor maintenance, servo motor maintenance, and the application of reliability services in these fields.
We’ve decided that we’re going to do this for more apprentices going forward, putting some more structure behind it and giving more young people the opportunity to get some hands-on experience. This is a great industry and one in which you can have a job for life.
Finally, do you have any thoughts on the future direction of the industry? How do you see Fletcher Moorland fitting into that?
Clearly, electrification is the future of transport and we’re starting to see similar motors being used in trams systems, electric buses, and other modes, so there’s a crossover with the new technology there.
We’re also starting to see new equipment being repaired for the first time and beginning to discover why these items fail.
This is where our reliability services can help because we can begin to prevent equipment failing in the future. In an industry where there are penalties if something breaks down on the track, that is imperative.
That said, there’ll always be a need for repairs and we have very high standards here. Quality is key to everything we do. Our electro-mechanical workshop is EASA accredited and we are an IECEx certified service facility for Ex repairs. We also publish our repair standard which shows the materials we use are superior to a standard OEM product.
Luckily for us, our services will always be required as you’ll never get rid of friction, and equipment will always be prone to wear out. When that happens, we can confidently say you’ll be hard pushed to find another company that offers an equal range of services.
Operating as an independent subsidiary of Network Rail, NCB Rail Assurance is the UK railway’s leading infrastructure assessment and certification body. Rail Engineer has spoken to Managing Director Sam Brunker on a number of occasions. Here, he brings us up to date with the organisation’s subtle rebranding, its expanded range of services, and what sets it apart from its competitors.
Could you give us a brief history of NCB Rail Assurance and some insight into the services you offer?
NCB Rail Assurance was set up in 2012 to provide independent certification services to the rail industry, specifically as a Common Safety Method for Risk Evaluation and Assessment (CSM-RA) Assessment Body and an interoperability Notified Body (as it was called before Brexit). There are three main reasons that we were established. One was to grow competence in CSM-RA and interoperability because, back in 2012, there weren’t that many experts. Related to that was the need to increase competition in the marketplace. Network Rail also wanted a reliable ‘internal’
provider of these services. I say ‘internal’ because we’re a subsidiary of Network Rail. We are structured like that to satisfy independence requirements under our accreditation.
We’ve made really good progress on each of those objectives. The most obvious measure of this success is that we won the 10-year HS2 contract in competition back in 2018, which is now a large chunk of our work. We’ve also played a leading role in defining what ‘good’ looks like for railway infrastructure assessment and we have a reputation for being among the best, technically. In terms of being the internal provider, we do still have around 80% of the Network Rail market share, although what that means has changed in the last couple of years with the rollout of the various agile client models. In terms of our people, we have 40 highly experienced railway engineers covering all disciplines. They know the relevant standards inside out and they’re expert practitioners in the CSM-RA regulations, under which many projects need to appoint an assessment body.
We’ve learned a lot in the past 13 years. We now understand much more than we used to about how our clients
can get value from what we do. Clients are not just getting a certificate or an assessment report, although they are obviously the main deliverables. The process of getting to those deliverables provides them with assurance throughout the project that they are, and will be, compliant with the various standards and common safety methods regulations required of them. That enables any issues like emerging noncompliances to be addressed as early as possible before they become expensive to fix and cause delays.
We remain independent of our clients when we’re doing this work, but we do have shared objectives with them. That is that they want to be compliant, and we want them to be compliant. We all also want the project to be completed on time and to budget.
In the last couple of years we’ve expanded our competence management system, to promote ourselves in railway systems engineering competence, and also competence in IT. We’re utilising that skill set in our people to get into broader rail assurance work, including cyber security assurance and what we’re calling ‘safety management’. Clients don’t need to have a well-
defined problem. We will work with them to develop bespoke solutions to their assurance needs.
This journey has led us to recently make subtle changes to our name and logo, so that rather than just being Network Certification Body (NCB), we’re NCB Rail Assurance.
You mentioned cyber security, which is as a huge concern for the industry. Can you tell us more about your work in this area?
Cyber-attacks pose a significant threat to railway infrastructure and train operating companies, as many people know. A cyber-attack can disrupt essential services, compromising safety and damaging public trust. The rail network is increasingly reliant on interconnected digital systems for operations such as signalling, ticketing, and train control, so it is potentially vulnerable to malicious activities like ransomware, data breaches, and operational disruptions.
We’re giving our engineers training in this space and we always have experts in this area on hand. We also have people in our organisation who are involved in the work to set future global standards around cyber security assurance for rail. The synergy with our core services in terms of safety assurance and assessing compliance to applicable standards is strong. The combined experience we have in this space gives us a unique capability to assess our clients’ approach to cyber security and whether what they’re doing is likely to be best practice.
In what other ways is NCB Rail Assurance now helping organisations within the rail industry?
Providing safety management as a service is an example of one of the broader roles we can play using the same skill set required for independent assessment of certification. We have in place the internal mechanisms to manage any impartiality risks, meaning that we can provide a service to clients needing support with working through the CSMRA process. For example, we can compile system definition documents, we can manage hazard records, facilitate hazard identification sessions, and produce project authorisation strategies. We can either do that under the management of the client who may need an extra pair of hands, or we can provide more senior engineers who will manage the process for the client completely, including the interfaces with designers,
delivery teams, suppliers, and so on. Many of our clients consist of teams who do not do these things frequently, so it makes sense for them to seek support from our engineers, who are doing it all the time.
Looking ahead, what do you think is in store for your organisation in the next 12 months?
Although we’re broadening the services we’re providing, our core services of independent assessment certification still make up the bulk of what we do, and they, in turn, rely on there being a good pipeline of infrastructure enhancement work, which is currently quite uncertain.
HS2, Transpennine Route Upgrade (TRU), and East West Rail are the big projects. We’re involved in these as well as many others. However, there’s a lot of risk at the moment and that’s one of the reasons we’re diversifying our offering.
Finally, there are a few organisations offering similar services to NCB Rail Assurance. What sets you apart from the competition?
A lot of our core work – independent assessment and certification – is now done using our IT portal, which we rolled out a few years ago. This is a shared platform enabling clients to upload information to be assessed, such as drawings, hazard records, and so on. The system will notify our assessors when this information arrives, and then they will report their assessment directly into the system. If they have any technical queries or find any non-compliances, they raise those via the portal, enabling clients to respond quickly.
The system will manage communications to and from the client, with new evidence provided, and provide full traceability of the status of the findings. You can go onto the system and easily see what the status is of any particular assessment, and any assessment reports and certificates are produced by the system, having been populated as the assessment progresses. We’ve seen real efficiencies achieved and cost savings from the use of this system, leading to lower prices.
Another of our unique selling points is our relationship with Network Rail, our parent company. As mentioned, although we were set up as an independent legal entity and we’re not subsidised by it, our staff are Network Rail employees, working under the same terms and conditions. Most of them came into our
organisation from roles within Network Rail. They know Network Rail intimately and understand what our main client needs and how it works.
Something else to celebrate is our customer satisfaction scores. Our Net Promoter Score (NPS) in the yearto-date is 82 which means that our clients overwhelmingly feel that we’re supporting them to the point where they would promote working with NCB to their colleagues. Digging deeper into the details, another metric of which we’re very proud of is that 81% of our customers say they’re very satisfied with our responsiveness to the needs and requirements of their project.
This is a great achievement because as projects are getting more complex it shows we’re responding in a very positive way. If you would like to find out more about NCB Rail Assurance please contact ncbenquiries@networkrail.co.uk or visit www.net-cert.co.uk
Located north of Birmingham airport, HS2’s Delta Junction is a 1.5km triangular junction that will enable trains to travel between London and Birmingham, Birmingham and Manchester, as well as directly between London and Manchester.
After leaving Interchange station at Solihull, northbound trains will curve westwards on a spur into Birmingham’s Curzon Street Station. Any northbound trains that leave Birmingham will use the northern chord to head north to meet the main HS2 line, which will connect the West Coast Main Line to Manchester. The third side of the triangle will allow trains to run between London and Manchester without stopping at Birmingham.
This is the most complex section of HS2, featuring embankments, cuttings, and 13 viaducts carrying tracks over motorways, local roads, existing rail lines, rivers, and their floodplains. The viaducts have been designed by Mott MacDonald Systra DJV for the Balfour Beatty VINCI (BBV) contract, these comprise:
Six pre-cast segmental viaducts with standardised spans.
» River Tame East Viaduct.
» River Tame West Viaduct (one single track and one double track section).
» Water Orton 1 and 2 Viaducts.
» Coleshill East Viaduct (one single track section).
» Coleshill West Viaduct (one single track and two double track sections).
Seven composite viaducts with decks built on weathering steel boxes or beams.
» M42/M6 link East and West Viaducts.
» River Cole East and West Viaducts.
» Watton House Viaduct.
» M42 Coleshill North and South Viaducts.
The junction’s structures will be substantial, but landscape architects have developed plans for connected and accessible areas that will include tree planting and new wildlife habitats around the Delta Junction viaducts. These will tie the viaduct structures into the local landscape, with enhancements including improved connections through the junction area, with new paths and cycle routes set within a nature-rich corridor.
The M42/M6 link viaducts are two parallel structures that will carry trains westward into Curzon Street across these roads. These were the first to be installed in the Delta project.
These are both composite bridges with concrete decks formed on full-depth concrete precast slabs carried on weathering steel girders.
Construction across these strategic links between the M6 and M42 had the potential to be extremely disruptive for road users. HS2 Ltd, BBV, and National Highways collaborated to develop and deliver a methodology that would minimise disruption.
Working either side of the carriageways, two abutments and three piers were constructed for each viaduct. The new fabricated steelwork was fabricated and delivered to the north abutment.
This project used a push-pull jacking technique that ensured a safer and more accurate launch. A temporary concrete jacking reaction beam was formed along the approach formation, the jacks engaged in sockets in this and moved the bridge forward.
The first 300-tonne push of the East Link Viaduct in February 2024 took 84 metres of girders as far as the pier. Further steel girders were welded to the back of the first section to complete the 158-metre-long structure onto which precast concrete deck slabs were placed. By installing prior to launch, the number of subsequent highway closures required to complete the composite deck was significantly reduced.
In April 2024, the second, longer push completed the installation of all 1100 tonnes of steelwork, from abutment to abutment. The operation was completed during a weekend road closure in 13 hours – 10 hours ahead of schedule – enabling motorway link roads to be reopened early. The pier-top guide frames were then removed, the girders jacked down onto their bearings, and the remaining precast deck units installed on the spans. The precast parapet panels were installed during further road closures.
The Western Link Viaduct was erected in the same way during pushes in June and September 2024, and again both were completed earlier than planned, reducing disruption to road users.
Ahead of the preparation of the rail formation, this viaduct is currently in use as an internal haul road to move material from Bromford Tunnel into the Delta Junction, taking thousands of lorries off the local road network.
Panos Psathas, senior project manager at HS2 Ltd said that the viaduct pushes were an impressive achievement for the team, particularly as these were the first huge viaduct spans to be built in the Delta Junction.
The River Tame West Viaduct is a 472-metre precast segmental viaduct at the northern tip of the Delta Junction, crossing the River Tame near Water Orton. The project is being delivered by BBV and designed by MMSDJV.
In this complicated section, there will eventually be six tracks running alongside each other as they join the southern end of the Curdworth Box.
The River Tame West Viaduct will carry three tracks, the River Tame East Viaduct one track and the Water Orton Viaducts two tracks.
To the south, the 1,400-metre Water Orton viaducts curve towards the M42/ M6 link viaducts and on to Birmingham. The other four lines, on the River Tame Viaducts, will carry the mainline south to Interchange Station and on to London.
A total of 2,742 viaduct segments for Delta Junction structures are being made at HS2’s factory near Lea Marston using a ‘match-casting’ technique. This involves casting each segment against the following segment in a production line, with each segment fitting perfectly when assembled on site. The double track segments are 2.6 metres long, up to 13.2 metres wide, 3.5 metres high, and weigh 80 tonnes. The single-track ones are up to 84 tonnes.
Construction of the 20 piers and abutments to support the two River Tame Viaducts took place during 2023. The installation method for the viaduct as a whole requires the balancing of the cantilevered deck using cable stays anchored to the previous span. As a result, the first span of each structure was erected differently, by placing segments from the abutment end between two large 42-metre-long temporary truss girders and then moving these along on skidding trolleys.
The 16 segments were then combined into a single self-supporting 920-tonne structure by post-tensioning, before the trusses were removed and transferred to the adjacent abutment. This stage was completed in Spring 2024.
Following completion of the first spans of each viaduct, the 190 pre-cast concrete segments of River Tame West have been lifted into place using a specialist cantilever technique not used in the UK before. This patented progressive cantilever method, pioneered by VINCI, has been used on other major construction projects around the world, including the Tours-Bordeaux high speed rail project.
The temporary works give the viaduct the appearance of a cable-stayed bridge during its construction. A 22-metre-high mast is erected above the pier to support temporary tensioned cable stays and a 14-metre high, 81-tonne capacity swivel crane to erect the precast segments into final position. Four sets of masts and swivel cranes will be used across the Delta Junction site. These were designed and manufactured by Portuguese specialist, BERD.
The segments are stored in the adjacent lay down area and transported to site on a Self-Propelled Modular Transporter (SPMT). This passes beneath the mast, and
the swivel crane picks up the segment and places this at the nose of construction, where it is glued with epoxy resin and connected with temporary prestressing bars to the previous sections. Then, a pair of cable stays are attached to the segment connecting it to the mast and back to the anchor of the previous span. Both stays are then stressed simultaneously.
Once all 19 segments of the 45-metre span are placed up to the next pier, permanent post-tensioning tendons are installed, stressed, and grouted, allowing the destressing and removal of the temporary cable stays. Currently each span is taking five-and-a-half days to complete.
Ducted, grouted, post-tensioned bridges were banned by the Department of Transport in 1992 but National Highways has accepted a Departure from Standard for Water Orton 1 and 2 viaducts, following extensive trials and the use of modern materials to ensure full continuity and encapsulation of the tendons within their ducts.
After moving the mast forward to the next pier using the SPMT, the process is then repeated between each pier until
the far abutment is reached. The crane and mast will then be dismantled and moved on to the next viaduct.
Following the completion of the structure, precast parapets are installed, followed by walkways, cable troughing, and track formation.
The erection of the River Tame West Single Track Viaduct was completed in February 2025.
Nicolas Gallone, Pre-cast Segmental Viaducts Project Manager at Balfour Beatty VINCI said that:
“This is the first time in the UK we’ve used this innovative technique to build segmental viaducts. It’s an efficient and flexible process using cable stays from the cantilever structure to keep the viaduct in place, while a mast and swivel crane are used to place each segment in place. It’s a great achievement for the whole team and work now continues using this technique on the other eight pre-cast segmental viaducts in the Delta Junction.”
The construction of all Delta Junction precast segmental viaducts is expected to be completed by September 2026, and the completion of equipment installation and superstructures by summer 2027.
Class leading Natural Rubber wiper blade range (RWB) now available in sizes up to 1200mm
Robust 316 Stainless Steel Construction
Rail Safety Claws Prevent Screen Damage
Optimised Natural Rubber Profile For Rail
The class leading RWB range of glass safe stainless steel wiper blades has now been extended following investment in equipment and tooling technology. This advantage now enables us to extend the range previously capped at 1000mm up to 1200mm in length.
Our popular RWB heavy-duty blade has all the benefits of robust construction and corrosion resistance that you would expect from its 316 stainless steel build, combined with our unique polymer safety claws and moulded natural rubber wiping profile.
Although rare, rail wiper blades can be compromised in service by bird stikes and debris.
The RWB blades are not only stronger to resist damage whilst providing maximum water clearing performance, they remove the risk of damage to windscreens from metal claws and the huge cost and downtime of having to subsequently change screens.
Wabtec Faiveley Project Engineer
Network Rail is responsible for maintaining and improving thousands of bridges and viaducts across the UK rail network. Its work ensures they remain safe, operational, and resilient against environmental conditions, aging, and increasing train loads. Rail Engineer takes a whistle-stop tour of the work that took place to maintain, refurbish, and replace these structures during the first few months of 2025.
A 50-tonne footbridge was installed by Network Rail at Darlington station on the Tees Valley Line on 21 February. It marked a significant moment in the transformation of this transport hub.
The enclosed, step-free pedestrian bridge links the existing grade II-listed station with the new platforms 5 and 6 and eastern concourse building.
The bridge was fixed into place in two parts – one weighing 32 tonnes and measuring 31 metres in length, the other 18 tonnes and 16 metres. A hole had to be created in the Victorian station’s roof to allow the bridge to slide into place. A 750-tonne crane was purpose built for the lift onsite by a smaller crane.
Network Rail teams and partners are delivering £98 million of Department for Transport-funded rail enhancements as part of the wider £140 million scheme. The upgrades include the new platforms, footbridge and eastern concourse building, as well as upgraded track, points and signalling system. A target completion date of December 2025 has been set.
Luke Durston, Network Rail principal programme sponsor, said: “We’re at a crucial and exciting stage in this
transformational project, and the successful installation of this footbridge is a significant milestone.
“The site as a whole is really taking shape now, and the bridge provides a prominent visual marker of the progress being made.”
Also on the Tees Valley Line, over the weekend of 22-23 March, a 92-tonne bridge span was lifted into place at Eaglescliffe station. The steel structure was installed during a three-hour operation overlooked by 15 BAM staff.
The installation was part of the ongoing project to solve Eaglescliffe’s longstanding access issues and transform the station for passengers. When complete, the 56-metre-long bridge will feature three lifts to connect the existing car park – and a newly created car park – to Eaglescliffe’s island platform. The existing footbridge is being retained to ensure access to the station is maintained during the overhaul – while also providing a second emergency exit.
The project, which comes in at £14.5 million, has seen £9.2 million funded from the Combined Authority, £3.25 million from Network Rail and £2 million from the Department for Transport (DfT).
In the early hours of Sunday 23 February, seven railway workers abseiled down the side of the Grade II listed Stockport Viaduct as part of a £1.1 million revamp.
Overnight, the team used rope access equipment to go over the top of the viaduct’s piers and carry out important restoration work. Last year, Network Rail began a project to remove overgrowing vegetation, clean away graffiti, and carry out extensive repairs to the viaduct’s 11 million bricks.
All of the viaduct’s 26 spans have now received this much-needed treatment.
Michael Lally, Network Rail Works delivery manager, said: “The team have done a fantastic job carrying out important repairs to the viaduct arches that cross the M60 in Stockport.
“This is the final stage of the project, which started last year. The recent work means the overall appearance of the viaduct is much improved, but it also reduces the risk of damage caused by overgrown vegetation and graffiti.
“Managing plant growth on viaducts such as this is important in maintaining train performance as trees and shrubs can obscure signals and interfere with the overhead lines that power trains.”
Built in 1840, the viaduct carries almost 400 trains every day between the West Coast Main Line and Manchester Piccadilly.
On 31 March, work began on the £20 million bridge replacement project at the Greek Street road and roundabout in Edgeley, Stockport. The original bridge, constructed in 1958, has reached the end of its life and needs to be replaced.
The bridge, which takes vehicles and pedestrians in Stockport over the West Coast Main Line, is now closed to traffic to allow work to take place to prepare the railway for the bridge’s replacement this summer. From 2-23 August, the bridge, which is made of about 200 concrete beams, will be demolished and a new bridge installed.
Demolishing and rebuilding the 58-metre-wide bridge will be a complex process. Over Christmas 2024, engineers constructed a temporary bridge to reroute existing utility services such as water and electricity. With the road now closed, the road layout will be removed carefully in a way that does not damage the bridge structure while the railway is in operation.
The work is expected to be completed in Spring 2026.
Awe-inspiring refurbishment
Toward the end of February, Network Rail completed a £3.5 million project to refurbish Awe viaduct near Taynuilt on the Oban branch of the West Highland Line.
The three-span wrought iron viaduct, completed in 1879, carries the railway to Oban over the River Awe, south of Taynuilt. Work began in Summer 2024, with engineers replacing the existing timber deck which supports the track. The old paint was removed to allow repairs to the structure to be carried out. Once repairs were complete, the viaduct was repainted.
Owen Ferry, project manager, Network Rail, said: “We’re delighted to have completed this project on
Awe viaduct on time and on budget while causing as little disruption as possible.
“This significant investment not only improves the structure’s look but will help extend its life. Work on this scale won’t be required for at least 25 years.
“We know the viaduct sits in a much-loved part of the world and we thank our neighbours and visitors for their understanding while we completed this crucial project.”
The work was carried out by Network Rail and its contractor Story Contracting.
February also saw the completion a £3 million project to renew Rannoch Road bridge in Killiecrankie.
The six-month programme started in September 2024 and involved replacing the 128-years-old single span structure over the Highland Main Line.
Susan Menmuir, Network Rail scheme project manager, commented: “This vital work is part of a wider, rolling programme of improvements that are essential to running a safe and reliable railway for passengers and freight customers.
“The project wasn’t without its challenges, especially as much of the work was delivered throughout the winter and in the face of several storms. However, both Network Rail and our contractor AmcoGiffen has a wealth of experience of working under these conditions.
“Renewals such as this help to protect the lifespan of our assets, as we won’t need to do work on this scale again for about 120-years.
“We do appreciate the impact our works can have on communities and I want to thank the residents of Killiecrankie for the patience shown over the last six months. Also, the community council, who played an essential role in helping us keep the community informed as the work progressed.”
To maintain an all-vehicle access during delivery of the work, a temporary bridge was in place until the new bridge opened to traffic.
In the Southern Region, train services between Taunton and Weston-super-Mare returned to normal on 7 February, after five days of engineering work to carry out essential structural repairs to a number of bridges.
From Monday 3 February, engineers worked around the
clock during a temporary closure of the railway to repair four bridges in Somerset, ranging from fairly light-touch refurbishments to more extensive renovations.
A full replacement of the River Brue bridge deck took place alongside steel and masonry repairs, waterproofing and drainage work. The bridge was then repainted. While engineers carried out these repairs, another team replaced the track that runs over the top of the bridge.
Masonry repairs also took place on Middle Drove bridge, where the bridge span was fully replaced. New sections were lifted into place by crane, following the removal of the old span.
Somerset bridge was strengthened and repaired, while masonry and steel repairs were completed on Lympsham bridge, along with waterproofing.
Follow-up work will be taking place on the Middle Drove and River Brue bridges until 24 June. A full road closure will be in place on Accommodation Road until mid-June.
Scott Pillinger, Network Rail’s programme manager, said: “Our teams worked hard to complete these bridge repairs and reopen the line. We also used the opportunity to carry out track and drainage work while trains weren’t running – all of which is vital to ensure the continued safe and reliable running of the railway.
“Working over a solid week was the most efficient way to get this work completed and minimise disruption overall and I’d like to thank passengers and residents for their patience while this essential maintenance took place.”
Collaboration with contractors, local authorities, and communities has been key to ensuring the success of these engineering feats. While some works have caused temporary disruption, the long-term benefits far outweigh the short-term inconvenience. Rail Engineer salutes Network Rail’s continued work to bolster the nation’s rail infrastructure and keep the country moving.
Between 14 November 2024 and 24 January 2025, East West Rail (EWR) ran a third non-statutory consultation on the proposal for a new rail route between Oxford and Cambridge with a link to Milton Keynes.
EWR is a proposal to effectively re-establish a potentially strategic route between the two major university towns of Oxford and Cambridge. The old Varsity line, as it was known, was closed in 1966. Since then, significant redevelopment along the route has taken place, especially east of Bedford. The reintroduction is intended to support growth between the various ‘knowledge centres’ along the route and thus support growth in the economy as a whole.
The route is divided into a number of subsections which are currently at different stages of implementation. Coming east from Oxford the first section to Bicester is already in use as a two-track railway with services provided by trains between London Marylebone and Oxford. The second section from Bicester to Bletchley was a railway with some sections in use, for occasional freight, and others mothballed. This has been comprehensively rebuilt again as a two-track railway and should start providing a regular train service from Oxford to Milton Keynes later in 2025. It will also open up opportunities for freight services from the port of Southampton to inland distribution depots around Northampton.
The next section again upgrades an existing largely two-track railway - the Marston Vale line, between Bletchley and the southern edge of Bedford. The final section is a new railway through Bedford and across to Cambridge. When complete, the route is proposed to provide an approximately 95-minute journey time between Oxford and Cambridge at halfhourly intervals with other trains providing stops at intermediate stations.
The recent consultation precedes the statutory consultation which is due to take place later in 2025 or early 2026 with building to be complete to Bedford by 2030 and across to Cambridge by 2034, ready for the full proposed service to commence.
Previous consultations had several potential routes for the new railway, but this had been narrowed to a southern approach to Cambridge in an update published in 2023. The current consultation focuses on a single route apart from a short section near Tempsford, south of St. Neots, where two slightly different alignments are subject to optioneering.
The primary objectives of the project are to improve public transport connectivity on a broadly east-west alignment focussed on the two university cities of Oxford and Cambridge. In delivering that objective the aim is to increase the available labour market for businesses in the area and provide new housing opportunities thus helping growth in the economy. Indeed,
some of these opportunities were highlighted when the Chancellor of the Exchequer gave her speech on 29 January. East West Rail and the opportunities it offers was one of the themes. Provision of a route linking several north south lines will also maintain and expand rail freight opportunities.
The consultation extended to over 450 pages in the primary technical report with a significant number of supplementary documents and diagrams in support.
The primary aim of the project is to provide a new passenger train service on the route. The train service is expected to support greater communications between the major centres of Oxford, Milton Keynes, Bedford, and Cambridge. The plan also envisages opening up the labour market with opportunities to easily travel to the hubs mentioned from new housing either already planned or at least proposed.
The expectations are for a two-trains-perhour service from Oxford to Milton Keynes commencing later in 2025. Around 2030, once the Marston Vale line has been upgraded, it is intended to add one Oxford to Bedford service per hour and one Bletchley to Bedford service per hour. When the whole route is complete, planned for the mid 2030s, there would be two Oxford-toMilton Keynes and two Oxford-to-Cambridge services per hour plus one Stewartby to Cambridge and one Bletchley to either Bedford or Cambridge depending on station options on the Marston Vale line.
The Marston Vale line currently has 10 intermediate stations, several serving small communities with a few recording amongst the lowest annual entry and exits across the UK. As in previous consultations, one suggestion is to consolidate some of the stations thus reducing to five the number of intermediate calls. If the reduction is endorsed, the trains starting from Bletchley will run to Cambridge.
The aim of starting and terminating some trains at Stewartby is to provide an expanded service to Bedford St. Johns station, which is close to Bedford Hospital, and to reduce the requirement to terminate trains at Bedford Midland station. This part of the route also has a significant number of level crossings both for vehicles and non-vehicular traffic, that is pedestrians and bridleways. Several of these would be subject to closure proposals. Earlier plans suggested increasing the linespeed from 60mph to 100mph but this has now been reduced to 75mph with a consequent reduction in level crossing risk meaning fewer crossings need to be closed. Crossing closure is generally accompanied by a diversion route or by a bridge usually over the railway.
For the first time, the current consultation actively considers the role of the route as a freight carrier. No specific flows are identified but the consultation suggests locations for potential passing loops so that faster passenger trains can overtake freight traffic. It is proposed that passing loops would be a minimum of 850 metres long to accommodate a 775-metre freight train. The documents also address the potential future energy source to power the trains. In this case the proposal is for discontinuous electrification although this is unlikely to be suitable in the longer term should freight traffic become a reality and move to electric haulage.
Some of the consultation related to the west of Bedford, where further enhancements are suggested to meet potential capacity challenges and provisions for freight. In particular, the London Road level crossing in Bicester is proposed for closure with vehicle traffic diverted and options to facilitate pedestrians to cross the railway close to the current crossing. The other part of the consultation west of Bedford concerned the upgrades to the Marston Vale line already mentioned.
A substantial part of the consultation was, of course, focussed on the new railway through and east of Bedford. Unsurprisingly, this is the area with most contention. Starting just south of Bedford centre at Bedford St. Johns station, the proposal is to move the station and significantly enlarge it. The aim is to enable it to easily serve Bedford hospital which is adjacent to the proposed new location. The route would then run to Bedford Midland station on an amended alignment resulting in
the closure of Jowett Sidings where up to five Thameslink trains of 12 cars can be stored. These sidings would be relocated to an expanded Cauldwell depot.
Bedford Midland station would have two new platforms on the east side, largely using current car parking land between the station and Ashburnham Road and the current station buildings. This would reduce car parking space for which a new multi-storey car park immediately north of the station would be provided. Previous consultation had suggested three new platforms but the extension of services to Stewartby is credited with reducing this to two. Clearly, Bedford station is in for a major rebuild. It is perhaps notable that current considerations by Network Rail and East Midlands Railway to provide a platform on the up fast line are not mentioned.
Beyond Bedford the proposal is for two additional tracks alongside and east of the midland mainline for approximately one kilometre before diverging toward the village of Clapham which it passes to the south. This work requires the expanded railway to pass close to
existing housing known locally as The Poets area. Indeed, some houses would be demolished, and others would have their gardens reduced. Unsurprisingly this feature is causing significant local objection, including objections from Bedford Council.
Given that Thameslink traffic terminates at Bedford, the prime traffic on the slow lines north of Bedford is freight, often aggregate, traffic. The other current constraint is the Corby connect service which in the up direction has to cross to the slow line north of Bedford to serve the station. If the platform was established on the fast line this move could be removed making it more practicable to reliably run the service on the existing track and facilitating freight access to EWR with minimal point work. This would remove one source of significant objection.
Beyond Clapham the route runs through rolling countryside involving several cuttings and embankments, and intersects a number of roads and other nonvehicular crossing points. Replacement bridges will be provided in some cases with diversion of paths to link to the built crossing points. The proposed route then
passes north of Roxton before splitting into two options – one just north of the Black Cat roundabout where the A1, A428, and A421 currently meet, and one a little further south. Both then align with the currently under construction A428 dual carriageway.
Tempsford station would serve EWR and provide two platforms on the slow lines of the East Coast Main Line. There are two potential locations for this station depending on the final route option selected. If recent government statements are to be believed, a ‘new town’ is anticipated with the new station toward its northern end. The final route will be decided taking account of the consultation.
Beyond Tempsford the line follows the new A428 alignment to Cambourne where a second new station would be built, north of the A428, to serve a relatively new and substantial residential development and administrative centre for the county of Cambridge. The proposed route then enters the second area of significant dispute with local residents and politicians. The route heads south east to eventually join the existing Hitchin to Cambridge route at Harston.
Vociferous campaigning has advocated a northern approach to Cambridge which could serve another substantial new development at Northstowe between Cambridge and Waterbeach.
Leaving Cambourne, the railway would drop in to a cutting and then a cut and cover tunnel of approximately one mile beneath the A428 and the former Bourne airfield which is now part of another planned housing development. The cutting and tunnel are a response to the previous consultations which highlighted the visual impact of embankments and the negative effect on the planned housing. One long tunnel was the preferred option of the three studied.
The route would then pass the villages of Comberton, the Eversdens, and Harlton to reach the junction with the existing Hitchin to Shelford railway, passing under Chapel Hill in tunnel enroute. Again, tunnelling here is a response to previous consultations when the route would have been above ground. Harston to Shelford junction on the West Anglia route is a distance of about three miles. It is then a further three miles from Shelford to Cambridge, with Cambridge South station in between. The route proposes
a flying junction at Harston with the existing Hitchin line being diverted off the current route and going over the west bound EWR track. It is also proposed to quadruple the track between Shepreth Branch Junction and Cambridge where this is not already the case.
The extent to which the now-proposed route, with the significantly lower elevations, reduces the concerns of local people is currently unknown. A key objective of the project was to link the biomedical centre at Cambridge South and from a wider railway perspective arriving from the south opens many more opportunities than arrival from the north unless significantly more railway was built. So, the proposals made do have significant logic.
The plans then propose an additional platform at Cambridge and the need for a suitable turn back facility. The Cambridge station site is constrained and it would not be practicable to turn all the trains round within the platforms and deliver a reliable service. Hence the final part of the proposal suggests allowing terminating trains to proceed
to Coldham Lane junction and continue for a mile or so toward Newmarket to a turn back facility at Cherry Hinton just under two miles from Cambridge, this involves laying a length of double track, upgrading one level crossing and potential electrification.
The consultation documentation covers a significant number of areas including environmental impact, arrangements for any existing route diversions, and analysis of the local effects of construction and how those will be minimised.
The next stage in the re-establishment of a rail route between Oxford and Cambridge will be the statutory consultation followed by granting of permission to build by Government. Given recent statements about the need for economic growth, and the expectations for this to be partly driven by the Oxford-Cambridge corridor becoming the UK Silicon Valley, one anticipates this project will be a significant priority.
In late January, the Institution of Railway Signal Engineers (IRSE), the Signal and Electrical Engineers’ Technical Society (TechSoc London), and the Institution of Mechanical Engineers (IMechE) Greater London Region organised the ‘Signalling the Future’ conference in London. This was a very impressive event, with speakers and experts from around the world and some very insightful presentations and knowledge sharing.
The presenters shared their expertise covering: strategic needs, project and operational experience, and CommunicationsBased Train Control (CBTC) vs European Train Control Systems (ETCS) technology. CBTC is found in metro light railway and urban masstransit systems, while ETCS is used for heavy railway systems. ETCS was developed to
support interoperability of mainline railways, while CBTC systems are for automated operations on urban railways, and where interoperability is not required.
Andy Lord, commissioner at Transport for London (TfL) gave the opening address. Andy reports to the TfL Board and Mayor of London, with responsibility for delivering The Mayor’s Transport Strategy and the TfL strategy. He is also responsible for all of TfL’s operations across rail, strategic roads, river, bus, and cable car, transporting over 11 million passengers a day. He said the only engineering discipline missing is nuclear, but watch this space!
With a background in mechanical engineering, Andy worked for 26 years in the aviation industry before joining TfL and he said he very much respected signalling engineers and all they do. However, he said procuring metro railway signalling was so much more complex than buying the collision avoidance avionics system on an aircraft, for example. He said that rail industry clients from across the world must agree common requirements and use ‘off the shelf’ technology. Suppliers must also challenge clients and not say ‘yes’ to every bespoke requirement.
James Dzimba, chief control command and signalling engineer at Network Rail presented ‘Semaphores to DMIs, ETCS in Great Britain –Do we have a choice’. He explained the history of train protection systems on the GB main line network over the last 30 years, and that the original vision of the Train Protection Warning
System (TPWS) as an interim solution pending migration to ETCS has not yet happened. The success of TPWS has made the business case for ETCS difficult, but today the costs of conventional signalling renewals are unaffordable. So, future signalling must be affordable ETCS.
The East Coast Digital Programme is working towards ETCS on 100 miles of busy, mixed-traffic railway, with multiple fleets of trains, including freight, heritage, and on-track plant. Framework contracts are in place with four suppliers who are developing solutions for the West Coast Mainline north of Crewe, TransPennine, Brighton Mainline, Midland Mainline, and Great Western. So, things are finally starting to happen. ETCS will also deliver a better train protection system than TPWS. James said that there is no viable alternative to ETCS and that the pace of delivery must improve, and costs be driven down.
Gary Joynes, principal engineering leader, signalling strategy at TfL, began by saying that when he started his career in the mid1980s, all but one of London Underground lines had the same signalling system, using lineside signals and mechanical tripcocks. Over the last few decades new signalling and trains have transformed much of the network, and the asset base is now more diverse, with three main technologies: Hitachi CBTC, Siemens CBTC, and legacy equipment.
However, the obsolescence of the more ‘modern’ systems is a problem, together with the upgrade of the remaining legacy signalling. Computing and telecoms components can no longer be expected to last for 40 years and TfL is developing business plans to allow technology refresh. Systems need to be designed to reduce whole life costs and a long-term relationship with the suppliers is essential as the systems are so complex and soon become obsolete.
Jonathan Speak, head of engineering delivery with Hitachi UK, gave an excellent presentation from a supplier’s perspective. He said brownfield deployment is always going to be required with rail and signalling, and that there has to be genuine customer/ supplier collaboration.
In the future virtualised hardware agnostic architectures may reduce the impact of obsolescence, together with using COTS system from other industries. Suppliers are looking to use a common platform for their ETCS and CBTC solutions. So, there is evidence of a convergence between mainline and metro applications, and more use of open Long Term Evolution (LTE)/Future Railway Mobile Communication System (FRMCS) communication bearers. A number of FRMCS-ready 5G and LTE comms networks are already being deployed outside Europe, including Australia, South Korea, and India.
Products are also staring to appear using the EULYNX open interfaces between signalling system components, and Jonathan suggested that these may find deployment in metro and mainline signalling applications.
Gerrard Sheffran, the European Rail Traffic Management System (ERTMS) programme director for the Netherlands, said he was a “signalling novice”, but brought a managerial perspective and lessons learned from the deployment of CBTC and ETCS on the Amsterdam Metro and Dutch railways.
The learning points included that interface management is not enough to achieve integration and there was over-confidence in the added value of requirements management. He quoted the Prussian general Graf von Moltke who said, “No plan survives the first encounter with the enemy”, as the underestimation of the impact of digitalisation overlooked the need for collaboration and reputation management. He added that a focus on strict scope control endangers the delivery of added value.
The current phase of the Dutch ERTMS programme runs to 2031, involving the upgrade of 1300 trains and 700km of route to ETCS Level 2. The programme is divided into tranches of work using different approaches.
Steve Allday, an independent advisor to the National Transport Commission of Australia, presented ‘Achieving interoperability on the Eastern Seaboard of Australia’. He explained that in a country larger than Europe, railways in individual states developed in isolation. This resulted in different track gauges, signalling standards, and competency frameworks.
A recent review of the Inland Rail project, which is building a new route across state borders primarily for freight, recommended that the signalling system should be interoperable with state systems. This has resulted in an ‘Interoperability Action Plan’. Seven key principles have been identified to coordinate the consistent application of ETCS across state, federal, and private sector rail infrastructure managers and operators.
The operational requirements between urban, regional, and remote networks vary, but this needs to be addressed by configuring standard ETCS products from multiple suppliers, rather than by bespoke signalling customisation. A national governance body is to be established, and this may also include closer working with the EULYNX standardisation initiative in Europe.
Continuing with the project theme, Navneet Kaushik, director systems and operations for National Capital Region Transport Corporation in India, described the application of ETCS to a new regional rail network around Delhi. Population growth has prompted development of a Regional Rapid Transit System of eight routes radiating up to 100km from the city centre. The first three routes will be interoperable and ETCS has been selected as the standard signalling system.
A Level 2 system with virtual blocks subdividing the primary axle counter train detection sections will allow trains to operate at two-minute headways at 180km/hr. Automatic train operation (ATO) will be provided and platform screen doors are integrated using ETCS packet 44 messages between track side and train. LTE/4G has been selected as the radio system, using the 3GPP Release 15 standard which provides the necessary mission critical improvements over public mobile communications services. ETCS will only use 1% of the available capacity, so the same network can be used for video transmission from trains.
Clive Burrows, group engineering director at First Group UK, reminded everyone that ETCS is not the same as ERTMS and that both ETCS and Traffic Management is needed to ‘signal the future’. TPWS has also addressed many of the train protection risks, but not continuous speed supervision.
He described his experience on the Great Western route in UK, where Network Rail has introduced a Traffic Management System (TMS) to manage train movements through a dynamic train plan linked to automatic route setting. Great Western Railway trains are also equipped with a Driver Advisory System (DAS) to optimise train running for punctuality and energy consumption. These have now been linked with a Junction Scheduler that uses information from TMS to send revised target arrival times to DAS at three critical junctions on the route. This results in a Connected DAS (C-DAS) which smooths the flow of traffic.
Clive also said that a cross-industry robust Data Reporting, Analysis and Corrective Action System (DRACAS) is essential to ensure the reliability of ETCS is maintained and improved, and he suggested that a future ETCS Level 5 could include trains learning their own movement authority.
Ankit Dabral, head of business development for Stadler Rail presented ‘Innovation for Rail Signalling and COTS approach’. He outlined Stadler’s entry into the signalling market, initially as a train supplier providing an in-house supply for ETCS on-board equipment and developing through acquiring smaller companies with interlocking and lineside systems. Its strategy includes the use of commercial off the shelf (COTS) hardware, using multiple suppliers to support a robust obsolescence management strategy.
Stadler has developed a cost effective CBTC solution with minimal wayside for light rail and branch line applications as well as its traditional application on urban metros. Recent innovations include camera/lidar/radar sensors for positioning and object detection collision avoidance.
Hugh Rochford, modernisation strategy manager for Paris area, SNCF, described the ‘Modernisation and Roll out strategy in France’ and a prototype project applying the selected technologies on an international high density mainline in the south of France. This envisages using standardised elements and EULYNX interfaces. A standardised interlocking platform, ARGOS, has been developed and this will be deployed with ETCS Level 2 and FRMCS to a common baseline for existing and new lines,
managed from less centralised traffic control centres. ATO at Grade of Automation (GoA) 2 is also envisaged on high-speed lines. A national implementation plan has been developed for 5,700km of ETCS-equipped track by 2040.
Daniel Woodland, professional head of signalling (North America) for TÜV Rheinland UK, presented ‘Standards for CBTC and ERTMS’. He began with the basic signalling functions – Lock, Block, Interlock, Authority, Supervise, Unlock – and explained how these apply equally to Metro and Mainline railways, though different characteristics and levels of risk have led to historically diverse solutions.
He provided an excellent explanation of CBTC and ETCS. CBTC standards, principally IEEE 1474 and IEC 62290, are functional specifications defining expected end outcomes and features. There is no mandatory legal requirement for compliance, and railways and suppliers have wide-ranging freedom to specify and deliver solutions. ETCS however is specified within a European legal framework that mandates requirements for interoperability at the ‘air-gap’ between track and train, and requires detailed technical specifications defining the system architecture, interfaces, communication protocols, and reactions.
The first speaker of the final session was David Sherrin, TfL Elizabeth service reliability manager. He presented ‘Our journey so far, ETCS and CBTC in Passenger Service’. David started by covering the unique features of the Elizabeth Line which crosses London with its own dedicated tunnels in the city centre and runs on Network Rail tracks to the east and west. The line has been an outstanding success and on its busiest days now carries 800,000 passengers daily.
Elizabeth line trains work with three signalling systems, a Siemens CBTC system in the central metro section, AWS/TPWS, and ETCS. The on-board solution is integrated with a common IP backbone so that a single driver machine interface and data logger is shared by the systems. Between Shenfield and Reading, a train will encounter four transitions between signalling systems. It generally takes two years for a new system of this complexity to achieve an adequate level of reliability. This was the initial entry into service experience with ETCS from 2020-2022 and with CBTC from 2022-2024, and only recently has over 90% on-time performance been achieved consistently. The Wi-Fi solution used on the central section requires a large number of access points which can be difficult to maintain in tunnels, and using unregulated frequencies can be susceptible to third party interference in busy stations on the surface. Both ETCS and CBTC experienced major one-off system-wide failures in the initial period of operation and David said it is essential that complex projects prepare for similar things.
George Jackson (GTR), John Crossland (Network Rail), and Daniel Hill (Siemens) presented ‘Northern City Line ETCS –Lessons Learned’. This is the first deployment within the East Coast Digital Programme and covers the short section of railway from Moorgate in the City of London to Finsbury Park on the main line. This is operated by a dedicated fleet of trains that are already ETCS fitted, so it was an ideal first step in the overall programme.
The line was resignalled with lineside signals in 2022 and an ETCS Level 2 overlay added in 2023. All trains are now running ETCS and the lineside signals will be removed in May 2025. Dedicated teams were established for ETCS data analysis and fault finding, and the lessons are being shared industry wide, as the programme works towards the next major milestone of ETCS
Level 2 overlay running on the main line between Welwyn and Hitchin in December 2025.
The final presentation was ‘Deployment of ETCS in Belgium, Key challenges and solutions’ by Bavo Lens, ETCS projects design and test team leader with Infrabel. After serious train accidents, Belgium took a decision on the national roll-out of ETCS and, in 2010, railway undertakings were given 15 years notice to fit their rolling stock by 2025.
Since 2018, Infrabel has been working on a masterplan for deployment of ETCS on the tracks, and by 2024 79% of the network had been fitted with a mix of ETCS Level 2, Level1, and Level 1LS (Limited Supervision). The Level 1 applications are deployed on existing interlockings using Infrabel’s in-house design and installation resources, while Level 2 requires supplier involvement.
Despite the wide range of countries and railways represented, common themes emerged. Such as safety is the number one priority, the need for standardisation, simplification, proactive obsolescence management, and less customisation, as well as efficiencies and economies of scale to reduce costs. The event was well received by the international audience, who all gained a valuable learning and networking experience, and understanding of how global railways are tackling the challenges of modern-day signalling.
The take aways included that standardisation and simplicity are key to achieving the levels of interoperability needed to improve the efficiency and cost effectiveness of modern signalling; the provision of large scale ETCS/CBTC systems requires a greater level of cooperation between organisations; and that innovation and an ALARP approach is essential.
Signalling needs to make the most of commercially available communications technology and must also use off the shelf hardware and technology. The industry cannot afford to provide bespoke solutions to address every remote risk. Operational practice must also change to accommodate the signalling technology and not the other way around.
Many who attended said they greatly appreciated Jane Power, president of the IRSE, and the rest of the team for organising such a great event, which brought together knowledge from countries including the UK, Netherlands, Australia, India, Switzerland, France, USA, and Belgium. A special thanks was also made to the IRSE sponsors - Hitachi Rail and Stadler Rail (Gold), and RSSB and CPC Project Services (Bronze), who made the event possible.
FRMCS is slowly becoming a well-known acronym among people associated with the railway. It stands for Future Railway Mobile Communication System which, in broad terms, means Track to Train radio. The present system –GSM-R – has been around since the mid 1990s and has been a huge success.
As a former British Rail radio engineer, your writer can claim to have had a small part in selecting GSM as the technology standard for railway radio across Europe and beyond. In the UK, GSM-R replaced the former Cab Secure and National Radio Network systems and, in addition to providing voice communication between train crew and operating centres, it was adopted as the bearer for ETCS signalling in the few areas where that had been deployed.
The decision to design and implement GSM-R was made in the early 1990s after which it took Network Rail from 2007 to 2014 to deploy the full system.
So, what is the problem? By its very date of design, GSM-R is 2G technology. In other words - the mobile radio technology that replaced the former analogue phones and began the mobile revolution. Since then, the technology has advanced through
3G, 4G, into 5G, with even 6G in the feasibility stage.
All these advances have improved the availability of bandwidth, data handling capability, security protection from external interference, penetration of coverage, together with the reduction in phone size and access to the internet.
2G is an outdated technology but sticking with GSM-R has saved the railway considerable expense and system disruption
by not updating to the future generations of mobile network design along the way. However, there is however a limit to how far this can continue.
Your writer has been advocating for well over a decade that the railway needs to seriously consider GSM-R obsolescence, but there has been a reluctance to move forward at the required pace. Railway management, in particular, has a mindset that radio connectivity will always be there, much as water in the tap or power at the socket. The reality is very different, and a future radio network is needed to provide the safety and operational requirements to fulfil the vision of a ‘digital railway’.
Around 2015, it began to be recognised that GSM-R cannot go on for ever and that a new international standard for track to train radio must be developed. Various debates began to consider whether this should be 4G, which had by then started to deploy in the public mobile networks, or whether it should wait for the vision of 5G to emerge. After further lengthy deliberations, the latter was finally selected. This was sensible as 5G has, over time, become the new de facto standard.
Since then, development of the requirements has slowly taken place under the control of a group called European Radio Implementation Group (ERIG) that exists within the Union Internationale Chemins de Fer (UIC) which has its headquarters in Paris. The development of FRMCS will be European led, the net result being a common specification across Europe and for many other parts of the world.
Achieving all of this will be both a technical challenge and a logistics nightmare. The technical aspects will be to produce a specification that meets all foreseen demand. The logistics will be in changing over from GSM-R and maintaining a reliable operational service for all train fleets during the process.
Along with other countries, Britain needs FRMCS to offer many more services and applications than are available within GSM-R. In order of priority these are:
» A bearer for train control systems, principally ETCS, with sufficient capacity to allow multiple trains to be connected in dense traffic areas. The radio must also provide a secure speech path between signalling centres and train drivers including emergency calls, priority call provision and group calls to all trains in an area. This replicates what GSM-R already provides mainly through the adoption of packet switching but the present capability may be inadequate to connect all trains once ETCS is
The data handling requirement for ETCS is not great but it must be guaranteed continuous throughout a train’s journey.
» Communication for a train’s business and information needs. This will include updates to any onboard passenger information displays, connectivity to train crew for requests, rostering, unscheduled station stop or route changes, policing situations, train condition monitoring, and such like.
» Improved connectivity for passenger communication. The limitations of onboard WiFi are documented. It may be possible with OFCOM agreement to use FRMCS to enhance the service offering but this will also need bandwidth considerations. While some may question the need for this, it is a fact that people increasingly rely on data to communicate with one another.
With these requirements set out, the next step is to turn these into an operational and a technical specification. To achieve this, a series of preliminary trials under the banner name of MORANE 2 will take place over a 13-month period ending in September 2027 which, assuming a successful outcome, will result in Version 1 of the specification. Although the supply industry will be involved in the trials, design and manufacturing may not happen until after this date.
As has been noted, GSM-R is reaching the end of its life, and the present suppliers have stated they are only prepared to guarantee technical support and equipment supply until 2030. Readers will realise by now that it is going to take a lot longer than five years to deploy an FRMCS network. It is therefore essential that GSM-R remains operational for much longer than this date. The solution will be to pay the key suppliers sufficient sums of money to train and retain engineers with GSM-R expertise, and to ensure a supply of spare parts. Negotiations are already taking place for this to happen, with some countries looking to extend the date to 2035 but with others looking towards 2040. To put this into perspective, the UK and France have around 16,000 route kilometres, whereas Germany has 33,000. In Great Britain, the main infrastructure supplier is Kontron (formerly Kapsch). It cannot be emphasised more strongly that having a robust radio connection between track and train is vital to modern day train operation, so these negotiations have to succeed.
New radio spectrum
It took considerable negotiating over a period of time for GSM-R to obtain a 4MHZ chunk of bandwidth in both the uplink and downlink directions for railway use across Europe, namely 876-880MHz and 921-925MHz. Radio spectrum is valuable and considerable technical and economic arguments are necessary to convince the licensing authorities that a dedicated band of frequencies should be granted for specific customers.
For FRMCS, initial thoughts were that the new system could be superimposed on to the GSM-R allocation but, having looked more deeply at the requirements, this is deemed impractical and thus a new set of frequencies will be needed, especially as the dual operation of FRMCS and GSM-R will be required for several years.
Negotiations are well advanced for the use of spectrum in the 1900-1910MHz band to be made available across Europe. The GSM-R bands may be reused to enhance FRMCS services once GSM-R is finally switched off. In Great Britain, discussions with OFCOM are progressing and a positive view is emerging on using the 1,900MHz band.
Radio propagation
There are two fundamentals for radio networks: the higher the frequencies, the greater is the attenuation, and the higher the aerial, the better the coverage. Both present challenges for FRMCS and they are linked. Permitted development rules dating from the 1970s allowed British Rail to erect 100-foot aerial masts on railway land without the need for planning permission. This facility still exists although the 100 foot is now modified to 30 metres. However, erecting masts is always controversial and near neighbours can get very upset if a 30-metre mast suddenly appears close to their property. With this in mind, Network Rail is expected to limit new masts to a height of 15 metres, which will impact on the potential radio coverage from such sites.
Using the 1,900MHz band means higher attenuation, so the coverage from any aerial transmitter site will be reduced. Initial estimates indicate that an additional 3,000 masts will be required over and above the GSM-R masts that already exist, to provide FRMCS throughout Great Britain. In dense railway areas, this may be fortuitous since the 5G cells will be
smaller and thus more radio traffic can be handled. Out into the rural areas, the need for small cells is less obvious and one way to reduce the cost of FRMCS coverage will be to rent aerial space on masts / towers owned by third parties such as water, electricity, or mobile network operator companies. It will be very much a situation of ‘horses for courses’.
The current thinking is that FRMCS will be a private radio network wholly owned and operated by the Rail Infrastructure companies, which for Britain is Network Rail but soon to be Great British Railways (GBR). This is commensurate with GSM-R and previous radio networks that have provided track to train communication. There is a feel-good factor in this thinking in that it gives the railway full control over the network operation and its security. It does however come at a price and there will likely be pressure for the railway to share its future radio network either in full or in part with other industries that provide safety or security services within their radio operation.
In essence this would be by the provision of a Virtual Private Network (VPN) for which the railway would have full control but have to share much of the radio infrastructure with a third party. The Emergency Services (police, fire and ambulance) are a typical example. Their current AirWave networks will be requiring renewal and current plans are to move these to a 4G LTE operation, though 5G might yet emerge as an option. The thoughts of moving it all to a ‘cloud based’ operation have surfaced but any such ideas will need to be aligned to the requirements of the functional and technical specification.
A national network demands massive connectivity. As part of the GSM-R project, British Rail and then Network Rail had to invest in expanding its network of fibre optic cables and digital transmission. This had started as a roll out in the late 1980s and early 1990s to replace the co-ax cables and analogue systems established in the 1960s. The technology known as Synchronous Digital Hierarchy (SDH) enabled vital bandwidth to be made available to virtually all the radio sites as GSM-R was being built and commissioned. The transmission network branded as Fixed Telecom Network (FTN) was resilient in that, should a failure or cable cut happen, the radio control instructions and traffic could be routed another way. Since those days, both the radio and transmission technology have moved on and the current provider of the railway transmission network –previously known as Network Rail Telecoms but now renamed Digital Data & Technology (DDAT) – has introduced a new network known as FTNx which is based on Internet Protocol (IP) which permits improved accessibility to data systems and thus more flexibility of use. FRMCS will make use of this network and every radio infrastructure element will have an IP address.
In 2019, Rail Engineer reported on the contract to supply new V4 train mobile radios across the entire fleet of locomotive, multiple units, and yellow plant, a total of around 9,000 cabs. These had been designed by Siemens Mobility at its Poole premises and would be supplied over a five-year period. To ensure maximum return on the investment, each cab radio was fitted with an expansion card that provides increased functionality by adding GPS, 4G WiFi, and an accelerometer. This
also ensured that the train has a GSM-R cab radio that can enable the transition towards FRMCS. The radios are identical in terms of space envelope, screen display, power supply, and aerial connection to the preceding mobiles and thus changeover from old to new could be carried out at depots in the minimum of time. The project had a value of £55 million and is now complete. The performance of the sets has overcome the emerging difficulties with unwanted interference. The previous V3 radios were returned to Siemens for modification to the new design, thus saving considerable expenditure into the future.
Information received recently from Steve Parsons, the business development lead for Mobile Communications at Siemens Mobility, confirms that the 4G networking has been fully tested and has been deployed for train borne condition monitoring on the South West Railway infrastructure. This innovative solution, utilising the technology already deployed within the cab radio, links the GPS and vibration data which can be processed within the radio to identify any track degradation.
With FRMCS being capable of deployment across either a public or private network, Siemens is a key stakeholder within the Morane 2 project, which will test all associated equipment both in the laboratory and field environments, and in turn will impact on the final version 3 of the FRMCS specification. Information from
Siemens is that the V4 radio can be adapted to use the 1,900MHz band by changing out the 4G LTE module for whenever the FRMCS specification is finalised. This will require both software and hardware components to be designed but with the continuing capability of providing GSM-R operation in the 900MHz band while both radio networks have to work concurrently.
The hopeful news is that the existing cab radios will be replaced with new ones and then sent back to Siemens for the upgrade as much has already been achieved when upgrading from V3 to V4. A stock of radios can thus be created as the changeover to FRMCS is progressed.
Much will depend on the changeover strategy that is decided by Network Rail or GBR. It is expected that the means of changeover will be by having the trains able to operate on both FRMCS and GSM-R as the infrastructure is changed to FRMCS.
Clearly, the situation with providing train equipment with a FRMCS capability will be a major factor under the banner of Train On Board Equipment (TOBE), fitting is planned to start in 2029.
The predicted cost and timescale
This project is going to be huge. The amount of new infrastructure or modifications to the existing radio infrastructure will require considerable investment, and an initial estimate of at least £2 billion has
been calculated. A centralised radio planning, engineering, and implementation team, coupled with local resources to undertake the necessary connectivity, will be essential if the project is to proceed in the most efficient manner.
While the investment required will raise eyebrows, it will be spread out over a period of time. Establishing the principles and commencement of survey work has budget provision in Control Period 7 (CP7) but with the bulk of the implementation activities being spent in CP8 which begins in 2029. Paying to keep supplier support of GSM-R active into the 2030s, particularly the retention of people skills, could be significant.
The implications for the train borne equipment, as has been mentioned, affects not just the cab radios but also the train radio to support ETCS operation. This is an unknown but is likely to add to the overall cost burden.
This project is not one that can be regarded as ‘nice to have’ – it is absolutely essential as the radio connection is vital for so many applications. The Department for Transport is aware of the situation and knows that funding must be made available. The pressures will be on to keep this to a minimum which will demand the maximum pragmatism in both the architecture of the new network and the work of the implementation team.
We all await the emerging plans with a watchful eye.
As part of the 200-year anniversary of the opening of the Stockton & Darlington on 27 September 1825, this article looks at the early developments in signalling. At first there was generally no need as trains were slow and infrequent. But five years after the Stockton and Darlington Railway opened, the Liverpool & Manchester Railway ran its first train on 15 September in 1830, believed to be the first to use a true signalling system with the ‘time interval’ system to keep trains a distance apart.
From the mid-1830s, most railways in Britain were using the time interval system. ‘Policemen’ were stationed at intervals along the track and gave a hand signal to the driver of each passing train to indicate the state of the line ahead. If a second train approached immediately the previous one had passed, a ‘danger’ (stop) signal was shown to the second driver. After a specified period of time, typically five minutes, a ‘caution’ signal would be shown to a following train. After a further time interval, a ‘clear’ hand signal was given to any following train.
Bobby
The ‘policeman’ name for the operator of the signals is where the term ‘bobby’ originated from, and this remains in use to this day in the
UK when referring to a signaller. A lantern was provided for nighttime signalling with plain and coloured lenses. Most railway companies then provided similarly coloured flags for daytime use, in preference to hand signals. Fixed signals were subsequently developed and again the Liverpool & Manchester Railway is believed to have led the way, with a signal first used in 1834. A lamp for night use was provided, showing a red light for ‘danger’ or a white light for ‘clear’.
The railway companies introduced many variations of signals. These included revolving boards and balls raised and lowered on a post.
The Great Western Railway (GWR) company went on to introduce a ‘disc and crossbar’ signal, superseding its red ball and light signal. Incidentally ‘ball signals’ continued in use in North America and led to the expression ‘high ball’ for a train running at speed. These remained in use in America until 1960.
There were many types of fixed signals, but the semaphore arm adopted from Admiralty for telegraph use became the preferred version. The first appeared on the London and Croydon Railway in 1841, with danger and ‘stop’ (horizontal) and all clear (lowered). These were generally situated on stations, or on the roof of the signal boxes, once they were introduced. With increased speeds, an auxiliary or distance signal was introduced on the approach to warn drivers if the stop signal was at danger. This became known as the distant signal.
In terms of colours, for nighttime working, both white and green were used for clear, with white having a higher status than green (which was used for ‘proceed at caution’ for distant signals). In the UK, green finally became the standard for clear in 1898, but this took longer in other countries.
The signal mechanism was weighted to ensure the arm would return to danger if a breakage occurred and this ‘fail safe’ principle has been used in signalling engineering ever since. In early signalling, a signal only displayed ‘stop’ when a train, junction or other obstruction had to be protected. At other times they would be set to ‘clear’, and the slotted post signal was used, which enabled the semaphore arm to be dropped inside the post out of sight when at clear. However, a serious accident on the Great Northern Railway (GNR) at Abbots Ripton in 1876, with snow and ice holding the arm inside the post, led to the abolition of slotted post signals and leaving signals at clear.
Detonators, to warn drivers of restrictive signals on foggy days, were introduced in 1841. These consisted of a small circular container with a detonating compound inside which is fastened to the rails by lead clips. By 1844 such fog signals were in widespread use. It wasn’t until the introduction of powerful colour light signals in the 20th century that ‘fog men’ were no longer required.
The time interval system was based on simply allowing sufficient time for the preceding train to have left the section and giving permission for another train to enter the section, but without any knowledge of whether it had done so. So, trains failing in the section for any reason were not protected and accidents occurred. This required a safer way of controlling the movement of trains.
Electric telegraph
A solution was the electric telegraph. William Fothergill Cooke and Charles Wheatstone obtained a patent for their electric telegraph on 10 June 1837. In 1842, Cooke wrote the pamphlet ‘Telegraphic Railways’ recommending “block signalling” in which track was divided into blocks or sections into which only one train may enter, with their movement in and out of each block monitored electrically.
The introduction of the signal boxes enabled signals and points to be controlled from one place via wires and rodding. This removed the need for people walking about on the track to move points and operate signals. Centralisation of these activities was more efficient and safer, and it also facilitated the introduction of ‘interlocking’.
In 1843, Charles Gregory at Bricklayers Arms Junction created an embryonic interlocking so that conflicting signals could not be operated at the same time. John Saxby obtained the first patent
for what we recognise as interlocking and is often referred to as the ‘father of interlocking’ signals into a single locking arrangement, and is believed to be first to use the interlocking.
The early mechanical interlockings were designed to a defined set of principles, which many still apply today. There were many competing designs of mechanical interlockings, which while similar in principle the detailed designs varied and there were many patent infringement cases in the courts.
For signalling on single lines, space interval was initially used with only one train occupying the line between any two passing places. This was enhanced by providing a physical device (baton, staff, tablet, token) for each section of single line. Communications and the electric telegraph again provided a safer way of working and a solution to the problem of any imbalance of train movements in each direction. Instruments or token machines were provided and connected by electric wires, such that only one ‘device’ could be out of the instruments at any one time. After withdrawal of a token from one machine, a second could not be obtained from any other instrument until the one already drawn was returned to an instrument. The first such electric token system was invented by Edward Tyer and patented by him in 1878.
These were usually two storey buildings, with the signaller upstairs and the interlocking downstairs. The signaller would operate large levers, with separate ones for each signal and set of points. On the ground floor of the signal box, underneath the levers, was the interlocking arrangement of metal bars connected to the levers, with other bars at right-angles to the first. This was arranged to prevent the signaller from moving a lever, unless other levers were in the correct position. For instance, a signal lever could not be moved to allow a train to move, unless the relevant points levers were in the correct position.
Signalling engineers later introduced electro-mechanical locking in combination with the mechanical locking, to prevent a lever from being moved unless its electric lock was energised. This required other levers to be electrically proved to be in the correct position. Other controls were added to the lock circuits to improve safety, such as relevant ‘track circuits’ to be clear before a signal or set of points could be moved.
Safety features were also added to the block systems that controlled the movement of trains between signal boxes, to prevent a signaller from sending a train from the area they controlled to that of the next signal box unless it was safe to do so. Mechanically interlocked signal boxes are still in use and, for example, the Monks Sidings signal box interlocking and frame installed in 1875 near Warrington are still in use today, 150 years later.
The track circuit was invented by William Robinson in 1872, an American civil engineer. The principle is that the connection of the rails by the wheels and axles of trains makes an electrical circuit. This circuit is monitored, typically by relays, to detect the absence of trains in a fail-safe manner. However, any power or equipment failures ‘stop the job’ and are disruptive to railway operations.
It is believed that the first use of track circuits in the UK was in 1886 at St Paul’s station on the London, Chatham & Dover Railway. Like the block telegraph, track circuits were often only initially used at high-risk locations, however accidents caused by signaller error at Hawes Junction in 1910 and Quintinshill in 1915 (226 dead, 246 injured), led to the adoption of the track circuit as a safety device to help remind signallers that a train was present when out of sight.
The need for track circuits became even more important when the activation of the track relay was used to control electric locks on the relevant levers to prevent clearance of signals, or movement of points if a train was present.
Railway electrification caused a problem with the track circuit sharing the rails with the traction return current and the track circuit’s insulated joints creating a conflict with traction current. As early electrification schemes used Direct Current (DC) distribution it was not possible to use the simple DC track circuit.
A solution to the problem was the Alternating Current (AC) track circuit, with the first in America in 1903. DC traction current could not falsely energise an AC relay, so this method became the preferred method of track circuit operation after 1909. The ‘impedance bond’ was also developed, to provide a low resistance path for the DC traction current, but high impedance to the flow of the track circuit AC.
Throughout the last 200 years there have been huge technical developments in railway signalling, with improved safety, reliability, and performance. This article has only touched on some of them. The changes and improvements have often occurred as a consequence of accidents, inquiry recommendations, or through regulation. However, it is the ingenuity and dedication of engineers who have always adopted the latest technology to improve railway signalling.
Telecoms has always been an important engineering discipline for railways. Both telecoms and railways evolved at the same time in the 1800s and railways pioneered telegraph communication.
The Liverpool and Manchester Railway opened on the 15 September 1830. There was a steep incline outside the station and, because the gradient was too steep for the locomotives of the time, there was a ropehaulage engine at the top. A communication link was required from the station to the top of the incline and, in April 1837, William Fothergill Cooke proposed a simple electric telegraph system. However, the railway decided to use a pneumatic telegraph equipped with whistles, and the telegraph system was not used.
Cooke then went into partnership with Charles Wheatstone and they patented a five-wire system, and went on to demonstrate a four-wire telegraph system in July 1837 at Camden Town in North London for the London & Birmingham Railway. The system used a number of needles at the receiver, which could be moved by electromagnetic means to point to letters on a board. This made the system simple so users didn’t have to learn codes. However, the system could not transmit every letter.
The application was similar to the Liverpool project and to indicate to an engine house at Camden Town to start hauling carriages up the incline. Unfortunately, while there was initial enthusiasm by the railway for the system, the electric telegraph was eventually replaced by a pneumatic system with whistles.
Cooke and Wheatstone had their first commercial success in 1838 when a five-needle, six-wire, telegraph system was installed on the Great Western Railway over the 13 miles (21km) from Paddington station to West Drayton.
Interestingly, like today, the wires were originally installed underground, but instead of an insulated cable the wires were installed in a steel conduit using wooden insulators.
Cooke was an inventor and entrepreneur who wished to patent and commercially exploit his inventions, but Wheatstone was an academic with no interest in commercial ventures. They fell out and, at arbitration, Cooke was represented by no other than Isambard Brunel. Cooke eventually bought out Wheatstone’s interest in the telegraph system.
The line was extended to Slough in 1843, and a one-needle, two-wire system was installed. The buried steel conduit wooden insulated ‘cable’ was replaced with less expensive and easier to maintain suspending uninsulated wires on poles from ceramic insulators. Cooke patented this system, which went on to be the most common method of telegraph communication.
Commercial telecoms
Today many telecoms people new to the railways propose using the railway telecoms network for commercial purposes. This is not a new idea though. The telegraph extension to Slough in 1843 was completed at Cooke’s own expense, and the new agreement gave the railway free use of the system in exchange for Cooke establishing a public telegraph service. This was the very first public commercial telecoms system. The use of the electric telegraph started to grow as new railways were constructed in the mid-1800s. Robert Stephenson was one railway engineer who strongly supported the electric telegraph. In February 1845, an 88mile line from Nine Elms to Gosport was completed along the London and South Western Railway, far longer than any other system. The Admiralty paid half the capital cost and leased a private, two-needle telegraph to connect it to its base in Portsmouth.
Murderer arrested
On 1 January 1845 murder suspect John Tawell was arrested following the use of a railway needle telegraph message from Slough to Paddington. This is thought to be the first use of telecoms to catch a murderer. The message read:
“A MURDER HAS GUST BEEN COMMITTED AT SALT HILL AND THE SUSPECTED MURDERER WAS SEEN TO TAKE A FIRST CLASS TICKET TO LONDON BY THE TRAIN WHICH LEFT SLOUGH AT 742 PM HE IS IN THE GARB OF A KWAKER WITH A GREAT COAT ON WHICH REACHES NEARLY DOWN TO HIS FEET HE IS IN THE LAST COMPARTMENT OF THE SECOND CLASS COMPARTMENT”.
The Cooke and Wheatstone system did not support punctuation, lower case, or the letters J, Q, and Z. Hence the misspellings of ‘just’ and ‘Quaker’. The operator at Paddington repeatedly requested a resend after receiving K-W-A which he assumed was a mistake. However, the message got through and, after arriving in London, Tawell was arrested by a detective.
Another notable event was the use of the railway telegraph to communicate the birth of Alfred Ernest Albert, second son of Queen Victoria. The news was published in The Times 40 minutes after the announcement. Newspaper coverage of these incidents gave a great deal of publicity to the railway electric telegraph and its benefits. This led to its widespread use outside of the railway.
In September 1845, financier John Lewis Ricardo and Cooke formed the Electric Telegraph Company to establish the telegraph business. In 1869 the company was nationalised and became part of the General Post Office (GPO) which eventually became the BT of today. The one-needle telegraph proved highly successful on British railways, and 15,000 systems were in use at the end of the 20th century, with some still in service in the 1930s.
The telegraph needle system was adopted by signalling engineers to control the safe movement of trains via the block system. Railway telegraph (telecoms) engineers have always adopted the latest telecoms technology to support the railway, and today the railway telecoms network is at the heart of the digital railway.
Rail Engineer reported extensively on the Vehicle/Track Systems Interface Committee (V/TSIC) and Adhesion Research (ADHERE) seminar in 2024. The 2025 event, held in York in early March, provided the opportunity for over 100 delegates to hear presentations on a mix of original research, updates, and practical experience of applying learning. This article will cover the five V/TSIC presentations. Another article will cover ADHERE presentations.
of rails, overhead line (OLE), rail wear, ground penetrating radar (looking at ballast layers and fouling), and structural gauging, and the use of drones for site surveys for renewals/ enhancement and incident response.
Brian Whitney, Network Rail’s engineering expert for track and switches & crossings (S&C) is a regular speaker and, unusually, spoke about the process of monitoring track rather than his usual subject – the number and nature of track defects. He described the current Network Rail fleet of monitoring trains. Most of them are fitted with extremely high-tech equipment, some of it ‘cutting edge’, but there is an issue with the vehicles which are mostly life-expired with an average age of 54 years. Examples are the New Measurement Train, introduced in 2003, a 1970s High Speed Train (Class 43 locomotives and Mark 3 coaches), and the even older Structure Gauge coaches, based on 1950s Mark 1 coaches. While the aim is for all track to be covered by monitoring trains, there is still plenty of inspection provided by maintenance workers on the track. All S&C and some plain line is inspected this way. Road-rail vehicles, trolleys, or hand propelled ‘walking sticks’ are also sometimes used on sections of track not inspected by train. The aim is to replace ‘boots on ballast’ inspections with trainborne inspection of track geometry, ultrasonic testing
Brian added that three visits to a site are often required to inspect the track, scope the work after a defect has been identified, and then to carry out the repair. That said, wider aspects such as combination effects and root cause, such as track geometry, support conditions, and embankment conditions, are not always considered. This is a significant amount of activity given that 3,000 to 3,500 rail defects and around 2,000 new and 3,000 to 5,000 repeat track geometry faults are identified every month. In this context, Brian reported that the number of rail defects has increased slightly between 2024-2025 compared with the previous year whereas the rail break total is down a little. The ambition is to be able to gain accurate information about and the precise location of faults, with sufficient detail to allow the fix to be designed so that the only ‘boots on track’ activity is to carry out the repair.
Brian showed the progress being made with Network Rail’s Infrastructure Monitoring Programme in pursuing this ambition. For example, Machines with Vision’s RailLOC system has been fitted to an Ultrasonic Test Unit and the Class 153 Video Inspection Units to improve locational accuracy to within 30mm – a huge improvement. A Fault Navigator app has been developed for iPhones and iPads to guide verifiers directly to the suspect fault and Network Rail is working on a temporary variation to standards to enable this new way of working to be proved and adopted.
High quality video and machine learning developments are providing better reports of faults than manual methods leading to a review of the rail visual inspection standard.
As a result of the trials, validation reports are coming thick and fast, Brian said. For example, the first instance of removing a cyclic top speed restriction using Unattended Geometry Monitoring System (UGMS) data from a passenger train on Wales & West region was achieved in September 2024. Brian is now working with Network Rail’s Technical Authority on safety cases, together with process and standards changes to enable UGMS to be used as an alternative to attended measurements or dedicated track recordings using an infrastructure monitoring train.
All this has included vehicle trials and formal commissioning, trade union engagement, building ‘digital’ patrol route plans, training end users, and
making sure that video inspection paths are put in the Working Timetable. The first timetabled runs happened in early September 2024 to supplement manual S&C inspections and work towards the manual inspections being turned off.
“What’s next?”, Brian asked. In 2025-2026, further vehicles (e.g., more Class 153s) will be built and/ or commissioned so that trials can be rolled out as a national business-as-usual service, delivering the benefits of boots off ballast, improved identification of potential service impacting faults, accessible, exploitable data, and a foundation for further machine learning applications.
Geoff Watson from Southampton University described work on RSSB research project T1300 Heavy Axle Weight Assessment for Underline Bridges.
The maximum axle weight permitted on secondary routes in Great Britain can vary. Under certain circumstances, Network Rail issues a dispensation to operate wagons with a heavier axle weight, up to a maximum of 25.1 tonnes (RA 9) and 25.4 tonnes (RA10) on RA8 routes normally limited to 22.8 tonnes. Sometimes, there is a speed restriction imposed. The dispensation could be withdrawn at any time introducing uncertainty for freight operators and risks being unable to operate economically.
The aim of the project is to understand the impact of Heavier Axle Weights (HAW) on underline bridges and provide a tool to assess future route accessibility based on condition for two asset types – masonry and metal bridges –taking into account future HAW traffic. The work involved laboratory testing, field measurements, and modelling.
Geoff presented a case study of Briscoes Bridge near Reading on the Berks and Hants line. It is a brick-built flat arch originally designed by Brunel (who would never have imagined the loads it might be required to carry). It was reported in a 2019 report that its “arch barrel is very noticeably live under load of passing high speed and freight trains where the arch shows a ripple/wave effect in the direction of train travel … (estimated 10mm movement)”. It was upgraded in 2020 using the Masonry Arch Repair and Strengthening systems, but subsequent inspections reported significant movement post remediation. Unlike metallic structures, masonry is not really flexible.
Derailment mitigations modelled
Geoff’s team used a variety of sensors to measure deflections at different locations on the bridge as different types of train passed over. These were used as inputs to a finite element model and the effect of passing these loads across the bridge were demonstrated. Laboratory testing was carried out on typical masonry samples. The conclusion was that the bridge is responding well to the loads imposed on it and the remediation is performing very well.
Dr. David Griffin from RSSB and Dr. Julian Stow from University of Huddersfield described progress made on research project T1316 ‘Design features than can provide guidance to trains when derailed’ since the last presentation in March 2024.
Having developed a dynamic simulation model that could explore the behaviour of a derailed train interacting with ballast and sleepers, Julian described how it had been used to evaluate three methods of containment of a train following derailment: guard rails, a bogie mounted stopper, and duo block sleepers as shown in the diagram above.
Geoff also outlined laboratory tests carried out on ‘early steel’ from a very old bridge over a canal in Deptford and on wrought iron from a bridge in Audenshaw. Tests included accelerated corrosion and assessing the strength of sections that have either thinned or significantly pitted through corrosion.
The ongoing work is expected to create a framework for modelling other asset types, such as earthworks, in the future.
The simulation cases included high and low cant curves from 200-metre to 20,000-metre radius, and speeds from 25km/h to 200km/h.
The results from the simulations were then used as a basis for developing the risk model. Guard rails were found to be effective for derailment speeds up to 50mph, while bogie-mounted stoppers were only effective for derailment speeds up to 30mph and where the curve radius was more than 1,000 metres. Duo-block sleepers were also effective for derailment speeds up to 50mph with a curve radius more than 400 metres.
David then explained both how the risk model has developed over the last year and how the derailment containment solutions might be most effective in reducing risk. The complex multi-factor risk model aims to calculate for each 25-metre section of the GB rail network:
» How likely is it that the train might derail ‘here’? This takes about 40 independent causes of derailment, grouped into eight generic derailment types, into account and is dependent on the assets present at the location and train type.
» Where do the derailed vehicles end up? For each of the eight derailment types a derailment cone is calculated.
» This is the likely path of the derailed train for each derailment type – based on speed, curvature and switches and crossings. Derailment mitigation will impact the trajectory. Note the calculation does not consider the effect collision with structures, earthworks etc, has on the path of derailed train.
» Based on where the derailed vehicles end up, what possible escalations occur? The model calculates this based on 11 possible escalations. The probability of each escalation is based on: the assets that are present in the cone; the train type(s) involved; and the speed of the derailed train.
» For each escalation -what are the potential injuries/ loss? The model calculates the safety loss for the base derailment plus any escalations.
Derailment speed is often lower than line speed due to presence of stations, speed restrictions etc., and historic documents suggest that derailment typically occurs at about 75% of line speed and is consistent with a quadratic distribution. Thus, on a 100mph line, the probability that derailment speed is less than 50mph is 0.125, implying that guard rails would mitigate 12.5% of derailments. The conclusions for each of the three mitigations measures were:
Guard Rails: To fit guard rails, sleepers need to be replaced. Therefore, retrofitting guard rails at an existing location is expensive as it requires track replacement (nominally £2.3 million per km). If guard rails are fitted at the same time as a track renewal, the additional cost is about £600,000 per km. Exact cost would depend on the location and length of the guard rail section. Provisional results from the model suggest that there are some locations where guard rails could be reasonably practicable to fit during renewal. Duo-block sleepers: Duo-block sleepers are similar to guard rails at mitigating the consequences of derailment. They are unlikely to be viable as retro-fitment
(similar to guard rails). More work is needed to understand the wider advantages (e.g., reduced concrete - embedded carbon) and dis-advantages of duo-block sleepers (e.g., corrosion resistance) to enable cost-benefit analysis.
Bogie mounted stoppers: Bogie-mounted stoppers appear to be the least effective of the three derailment mitigations. Unlike guard rails and duo-block sleepers, they have general application and could potentially mitigate all derailment risk (i.e. not only installed at a particular high-risk location) but could be very costly. Design and approval are estimated at approximately £125,000 per bogie type (up to 50% more if the bogies need strengthening). Installation cost could be approximately £5,000 per bogie based on a simple attachment method (up to 100% more if the bogie needs strengthening). A rough Rail Engineer estimate suggests there would be little or no change out of £20 million for just the Thameslink Class 700 fleet. Retro-fitting to existing fleets may be difficult depending on bogie design.
Next steps include developing a policy on mitigation measures which might range from nothing to a blended approach of more than one solution. If measures are recommended then highlevel designs for the mitigation measures will be created, and an implementation plan developed.
Professor Mark Burstow, Network Rail’s principal vehicle track dynamics engineer, presented the V/T SIC Permanent Project Group (PPG) update. Mark described progress on managing hunting – a vehicle/track system issue where the latest work was covered in Issue 212, Jan/Feb 2025. He also described progress on understanding and hence treating rail surface damage including Rolling Contact Fatigue (RFC), squats, and studs. He presented the promising results of work to understand these faults better using data obtained from both train-borne ultrasonic inspection and eddy current testing. Four sites had been identified for detailed investigation of squats, all of which were on straight or shallow curved track and not near signals or station stops, allowing the elimination of traction/braking forces as a dominant factor.
AI Assisted Video Recording (AIVR) data had been used to augment site visit data. Eddy current measurements and vehicle dynamics simulations had all provided useful information, but it is still a work in progress.
Philomenah Holladay and Professor David Fletcher from the University of Sheffield presented a groundbreaking approach to modelling rail defects.
David said that a great deal of research has been carried out into the properties of premium steels, but their installed behaviour is sometimes different from that expected, something that only becomes apparent sometime after installation. He said that rail microstructure might be able to be optimised if it could be modelled to assess its response to load.
David briefed the group on the microstructure of most rail steel which takes the form of grains of pearlite. Pearlite consists of layers of soft ferrite (Fe) and hard cementite (Fe3C). Ferrite is ductile and tough, cementite is highly wear resistant. The spacing between these layers usually defines the rail steel’s wear resistance and response to load.
He outlined rail steel’s response to load where plastic flow causes strain hardening which increases wear resistance. However, plastic flow cannot continue indefinitely, hardness cannot rise infinitely, and wear debris and cracks form as the limit of ductility is reached. This process, known as microstructural damage, underpins most rail failures. Typically, it is assessed on rail sections or laboratory simulated samples using microscopy. More recently, a process called nanoindentation has provided better results. Modelling has, since the 1990s, used finite element analysis. This process struggles when trying to assess more than a few hundred wheel passages (stress cycles). An alternative hybrid approach was developed: the ‘brick models’ which combines stress analysis with experimentally determined material response. The properties of ‘bricks’ determined from experimental data is validated against wear rates based on incremental accumulation of permanent deformation to the rail steel with each wheel passage (ratchetting strain
accumulation). This was very promising but employed bespoke code that was hard to maintain and reuse.
Philomenah described a new approach – FLAME GPU accelerated computing.
The Computer Science team in Sheffield has developed a framework for parallel computing on PC graphics cards giving thousands of computing cores, whereas the classic microprocessor only has four or eight cores. This has allowed the ‘brick model’ to be re-implemented and validated against the old versions, delivering a modelling environment that is easier to handle. The faster computing is enabling deeper microstructural modelling with ‘bricks’ down to micron size. Multiple millions of bricks are possible, even on entry level hardware, allowing new ways to explore the mechanisms by which rail failure happens.
Animations showed modelled crack formation.
Philomenah explained how the technique is already modelling much experimental behaviour, though there are discrepancies at small wear depth/low contact cycles which she is now addressing through modelling an additional microstructural failure mechanism.
Future work includes modelling what happens when rail is ground; developing and assessing novel materials; and gaining a better understanding of the brittle white etched layer which can form on the rail surface due to wheel slide or grinding heat input.
The five presentations all showed how research and development is contributing to better and safer railways. It was fascinating to hear about original work modelling scenarios hitherto seen as impossible, and to hear from industry professionals who both support and sponsor such activity and then work hard to apply the results to their discipline.
With thanks to the presenters and RSSB’s Paul Gray for their assistance.
(Above) Test rig for demonstrating effect of adhesion enhancing products on
The collision between two trains at Talerddig, Powys, Wales on 21 October 2024 once again highlighted the issue of poor wheel rail adhesion, particularly in the autumn with ‘leaves on the line’. This continues to be a risk that can be realised despite the industry spending significant sums on mitigation and management.
Rail Engineer has frequently reported on the work carried out by the Adhesion Research Group. This year’s seminar included four topics including original research, experience with variable rate sanders, and kicking off studies into techniques for improving adhesion for freight trains.
During the 2024 Seminar, Dr Will Skipper from the University of Sheffield reported on the residual risk that applying sand to improve adhesion could cause trains not to be detected by track circuits (Issue 207, May/
June 2024). Summarising, approximately 5% of wrong side track circuit failures (WSTCF) have been attributed to sand or sandite. This led to the notion of ‘conductive sand’ and previous laboratory work had identified two promising materials. Further track trials led to just one remining: Product D, produced by LB Foster. Will described work to demonstrate that the conductive material improved track circuit detection compared to sand (known as braking sand or 10/18 sand), that it did not cause insulated block joints to become conductive, and that it was an effective adhesion enhancer.
Laboratory tests were carried out with a 10mm end post set up between two pieces of rail in full-scale rig. The objective was to demonstrate that the resistance between the two rails remained above the required 0.5 MΩ when the adhesion enhancers were applied. Measurements were taken when material was applied and after each subsequent wheel pass –three passes for each test.
Some interesting results were obtained. Neither GB ‘standard’ sand nor Product D created issues with end post insulation in dry conditions with material deposition rates up to 15g/m. Product D created issues when applied at 30g/m and above, far in excess of the application rate permitted. In wet conditions, Product D did not cause end post failure at 7.5g/m, but, curiously, GB sand did. Will suggested that this is because GB sand is less dense, has more particles, and displaced more water. Finally, the end post was lowered to simulate wear and no change in results were observed.
Track tests were carried out on the Great Central Railway on a low voltage DC track circuit using a Class 20 locomotive on sand laid at various application rates.
On the first pass, there were some isolating effects with GB sand present at all application rates. On the second pass, loss of train detection was less severe. Product D did not lose train detection on either pass.
Tests on leaf layers were carried out on the Wensleydale railway using a sander-equipped Class 142 unit and a similar track circuit. Leaf layers were created in two patches, so that the first two wheelsets were isolated upon entering the track circuit. The sand or Product D was applied via a calibrated sander set to 2kg/min, the first pass with the sander on and the second pass with the sander off. The tests showed that: (i) Product D could be applied from a typical sander set-up; (ii) an insulating layer using actual leaves could be created; (iii) GB sand exacerbated the effect of leaves; and (iv) Product D reduced voltage levels similar to clean contact.
Finally, braking tests were carried out at RIDC Tuxford using a Class 158 two-car unit at 50mph on wetted paper tape using sanders delivering 2kg/min flow. This test showed that Product D delivered stopping distances similar to those obtained with GB sand.
Summarising, Product D does everything that GB sand does without the risk of Wrong-Side Track Circuit Failures (WSTCF). The next step is a service trial which is planned to be carried out on a Northern Trains unit on a line with historic WSTCF issues.
Research continues into the fundamental issue of why leaves stick so firmly to rails and what are the influencing factors? Jordan Brant from the University of Huddersfield presented, building on work he reported at ADHERE 2023 (Issue 202, May/June 2023). This project covered: investigating the effect of different leaf species on adhesion levels and understand the bonding mechanisms related to leaf types; defining upper and lower bounds of wetting for low adhesion and correlating wetting conditions with rain rates; and quantifying persistence of leaf layers on wheels and rails and assessing its duration under varying running conditions.
Representative tests were selected using: wetting rates based on four rain rates from 0.5mm/hr to 2mm/hr; sycamore, oak, beech and horse chestnut leaf species - dried and powdered for easy application; and typical diesel multiple unit and typical inter-city train loads. Water and load parameters were adjusted to be appropriate to the University’s HAROLD test rig.
Conclusions included:
» Wetting rate is a critical factor in bonding strength and is the sole significant input on the resulting adhesion value.
» The leaf type does not affect the bonding strength, nor is there a statistical significance on the resulting adhesion.
» Leaf layer thickness is most affected by the interaction between wetting and leaf type. The thicker the leaf layer, the lower the bonding strength; thicker layers have also been shown to be made of several layers.
» A standardised method for measuring leaf layer bonding strength has been further developed.
» A further understanding of leaf layer durability has been established. In most cases, the leaf layer was still present after 24 brake tests.
» During the durability tests it was observed that the leaf layer primarily built on the wheel but subsequently transferred to the rail. Rail Engineer observes this suggests that, in the field, leaf layers could be spread further than might be assumed by the location of the leaves.
Rail Engineer has reported extensively on the development and trials of variable rate sanders, most recently in Issue 184, May/June 2020. Phil Gray from South Western Railway (SWR) and Rob Cummings from Northern talked about their experience on Class 158 and159 diesel, and Class 323 electric fleets respectively.
Following the collision in Fisherton Tunnel, Salisbury in 2021, all SWR’s Class 158 and 159 units have been fitted with Single Variable Rate Sanders (SVRS). These have been set up so that when two units are coupled, all sanders operate. Phil said that this was the first retrofit of a variable rate sand system to an ex-British Rail DMU as well as being fitted in-house within existing resources.
In spring 2022, SWR had secured £4 million from Network Rail’s Performance Innovation Fund. Following competitive tendering, Siemens Mobility was awarded the contract in December 2022. The First in Class was fitted in May 2023, with fleet fit between August 2023 and March 2024. The 39 units
went back into service with sanding rate fixed at 2kg/min. In March 2024, successful commissioning tests were carried out at RIDC Tuxford based on those defined in RSSB’s T1107 Report (Issue 158, November 2017). SVRS was enabled by a software update that was completed by September 2024.
Phil explained that there were issues to resolve as the system was rolled out but was pleased with the installation time: one day to fit and half a day to test – total 15 hours. One significant issue was that sand consumption increased by approximately 40%, something that was not experienced in the T1107 test programme. This was not an issue for the diesel trains as their time away from depot facilities is dictated by the need to refuel, but Phil said that this would be something to take into account when fitting SVRS or DVRS to electric units.
And the results? There had been three SPAD or Station Overrun incidents in 2022, four in 2023, but none in 2024.
Rob Cummings talked about Northern’s experience with DVRS on Class 323 units. He said that the Class 323 has demonstrated that retrofitting DVRS is feasible and practical, and DVRS is capable of delivering consistent braking that provides a more predictable and repeatable braking performance in very low adhesion conditions. He added that a minimum step 2 brake application (or equivalent –circa 6% g) is required to gain the braking benefits of DVRS in low adhesion. All 34 Northern Class 323 units were fitted with DVRS prior to the start of Autumn 2024 including 17 Class 323 units transferred from West Midlands Trains.
Rob said that the results were encouraging. Compared with 2020 to 2023 where there had been three, nine, four, and two station overruns respectively. There were no station overruns in 2024.
The results from encouraging drivers to take advantage of the system were mixed, and Rob suggested that it might take three seasons for drivers to develop confidence in the system through experience. This is partly because Northern’s Class 323 drivers also drive other diesel and electric units with different braking performance. That said, driver feedback has been extremely positive with the overwhelming majority believing that DVRS has had a positive impact on stopping distances. One driver reported: “Great improvement; I now feel the train will stop where I want it to.”
There were issues with brightness of lamps in the cab and, similar to SWR’s experience, sand consumption has been higher than expected. Rob reported that there was a significant number of failures in autumn 2024 which have been investigated. Plans are in hand to carry out modifications to reduce failures and to fit data loggers and labels to help monitor sand levels.
Tim Shakerley, an independent freight engineering expert, introduced a programme to improve freight train performance and safety, known as the Freight Safe Programme. It is jointly defined, resourced, and funded by freight Duty Holders, supported by RSSB, and endorsed by ORR. Its mission is “a collaborative health and safety plan designed to facilitate freight growth and to protect and enhance the reputation of the freight sector by tackling the network risks where a unified response is essential”.
The work includes several sector health, safety & wellbeing risks being managed by the National Freight Safety Group, as well as four priority projects managed by a Programme Management Office: Wagon Condition Programme, Freight Safe Insights, Horizon Scanning, and Climate Change.
Tim described the risk assessment work of the Wagon Condition project. This is the first detailed industry-wide review of whole system risks arising from the condition of rail freight vehicles. It will be used to quantify the risks and then prioritise actions to improve wagon condition.
While rail freight is inherently safe and the risks posed by wagon condition are low, there is a modest but important business case to do more. Tim added that, although Entities in Charge of Maintenance are discharging their fundamental duties, there is an opportunity for some to improve by applying best practice. He
Train length, vehicle types, and loads vary all the time
Interworking of different wagons with locomotives is a key business need
Apart from locomotive, vehicle control and monitoring equipment has been limited
Highly variable traffic density means wide range of encountered rail head conditions
Wagon tread brakes and mainly using sanders for traction are the norm
Standard lengths
Fleets are largely independent
Sophisticated and automated controls on all vehicles
Consistency of services - most on busy lines
Disc brakes and wheel slide protection systems are the norm
Significant changes in technology over last 20 years
added that perhaps the biggest opportunity to reduce risk is to improve understanding of brake drag and adhesion. The Wagon Condition Programme continues to pursue those opportunities. Paul Gray from RSSB took over and presented three projects being kicked off to explore freight train braking and low adhesion. There are some fundamental differences between freight and passenger train braking, see Table 1.
What seems at first sight to be an unusual research project is S386 - Knowledge Search on Freight Train Braking. Paul explained that the principles of freight train braking have not fundamentally changed for many years but are not documented in one place and rely on the knowledge of increasingly rare experts who are not getting any younger.
Train performance, especially accessing train paths is largely determined by train braking characteristics and, for freight growth (longer/heavier trains, product development, performance enhancement), understanding the principles and limitations of current systems is important as a baseline for improvement. This work will document operations, braking principles, braking performance, wheel/rail adhesion issues, and explore freight train future developments. It will also explain brake system architecture, describe single and two pipe systems including arrangements for both locomotives and wagons, and data captured by locomotive on-train data recorders and use of sanding. Some of the adhesion issues affecting freight trains are listed in Table 2.
Freight only routes and overnight services can mean challenging rail head conditions
Most wagons are not equipped with Wheel Slide Protection or equipment to detect Non-Rotating Axels
New systems being developed and introduced, for example VTG Rail and Knorr-Bremse iWagon
The importance of brake pipe overcharge to normalise response of all wagons’ brakes
Train brake system charging and brake continuity testing are key parts of train preparation. The time taken varies with train length. As an example, it can take around 10 minutes for the brake pipe pressure to rise from 0 bar to 5 bar on a 30 wagon train.
Modelling capability for freight train braking in low adhesion is limited
Tread brakes are the norm which can help with rail head/wheel cleaning
If a brake system overcharge is not fully executed and, if multiple INITIAL brake demands are made, brake cylinder pressures can be much higher than normal leading to wheels locking in low adhesion conditions
The second project is T1350 – Understanding and Preventing Wheel Flats in Freight. Two work packages have started. The first, WP1 is about understanding the factors that lead to wheel flats in freight trains. The aim is to develop a detailed understanding of the circumstances and mechanisms that lead to wheel flats, and to provide information to operators and maintainers that can be used to reduce the risk of them developing.
The expected benefits include providing a better understanding of the root causes of wheel flats on freight vehicles; determining flat length threshold values that might result in likely wheel locking for a range of speeds and adhesion
conditions; and assessing the potential/ likelihood of selfsustaining wheel flats occurring in practice (noting that these are exceptional events).
The second, WP2, covers modelling the factors that lead to wheel flats. It is aiming to determine the relative importance of the many factors that can result in the creation and growth of freight vehicle wheel flats and how they influence the level of adhesion required for rotation of a wheelset. The modelling is likely to explore the most significant factors that impede wheelset rotation; the influence of adhesion required for wheelset rotation; why some wheel flats “round out” and others continue to grow; and the viability of a “self-sustaining” wheel flat (see panel), and what conditions are required for this.
T1350 Work Package 1 and Work Package 2 are due to deliver in Summer 2025. A further work package is planned entitled Understanding Real World Freight Train Braking Through Static Testing and a potential fourth work package is Enhanced Investigation of Wheel Flats.
The third project is T1351 which will investigate the factors that affect freight braking in low adhesion conditions. It is planned that the project will explore the interactions between various influences, such as freight braking characteristics, environmental conditions, and freight driver policies and how these differ from braking behaviours in passenger trains. It will also review available freight air braking models and evaluate their ability to account for the interactions assessed within the project. The research will then assess the resources required to optimise the most suitable model(s) for GB freight operations. This project is due for delivery in early 2026.
The ADHERE Seminar 2025 covered a wide range of topics which will in time contribute to a safer railway. It was good to see practical experience of SVRS and DVRS being reported and that attention is now being paid to the issue of braking adhesion for freight trains.
With thanks to the presenters and RSSB’s Ben Altman for their assistance.
Self-sustaining wheel flats
Self-sustaining wheel flats is a term used by the RAIB in its report on the derailment at Petteril Bridge Junction on 19 October 2022. In its recommendation 1, RAIB stated:
“Network Rail and the freight operating companies should work in collaboration with RSSB to review the risks faced by freight wagons during normal brake applications in foreseeably low adhesion conditions. This work should include a detailed assessment of the risk of individual wheelsets sliding sufficiently so that they generate self-sustaining wheel flats that can ultimately lead to derailment. It should also identify what mitigations may be necessary to ensure that these risks are adequately controlled.”
From a subsequent V/T SIC paper:
“The mechanism which is postulated is that low adhesion under a normal brake application caused one wheelset to stop rotating and that, following the brake release, the wheel continued to slide. The presence of the wheel flat prevented the wheel from resuming rolling, and sliding of the wheel over the rail caused the wheel flat to continue to grow until the ‘false flange’ was too large to allow the wheel to pass through S&C, whereupon derailment occurred. The wheel flat was therefore ‘self-sustaining’.”
Just over a year ago in March 2024, Siemens Mobility announced to the press it would develop a brand-new premises in Chippenham and release the old site just to the north of the railway station. Siemens and its forbears (principally Westinghouse) had been on that site since 1897. With modern day signalling technology moving into the digital age, the old site was no longer fit for purpose, hence the decision to move to a green field location on the south side of the town.
One year on, another ceremony took place on 4 April to mark the beginning of the construction with the obligatory ‘silver spades’ being part of the action. The great and the good were duly assembled on a beautiful spring day.
A government presence
Rail Minister Lord Peter Hendy opened the formal proceedings explaining that £340 million was being invested in the UK as part of the rail reform agenda and acknowledging the £100 million that Siemens is investing in the Chippenham project.
The new premises will provide for 800 jobs with 47 apprentices, that being an expanding workforce for the area. It is calculated that around £80 million of benefit for the local economy will result.
In the bigger picture of things, the creation of Great British Railways (GBR) is now underway, after considerable debate and delay, and the rail industry in its entirety has been invited to take part in the consultation that will conclude on 15 April. GBR will provide a single guiding mind for rail, much needed to replace the disjointed thinking which exists today that does not yield the best service for passengers or freight.
Although much of the industry will come under government control, always remembering that Network Rail and several train operating companies are already in that state, private investment will remain vital for the outcome envisaged. Knowing that Siemens has a huge involvement in rail engineering, the message is that there will be no further investment in diesel-only trains so the development of electric and battery trains, including hybrid versions, will be all important.
The Trans Pennine Route Upgrade will create a 70-mile electrified railway where new trains and digital signalling will be at the forefront of technology. Siemens Mobility will be a significant part of this provision. Elsewhere, the East
Coast digital programme will fully introduce ETCS on the Finsbury Park to Moorgate section in May with lineside signals removed, a pre-runner to ETCS introduction on the Welwyn to Hitchin section that is under test at the moment and then onwards along the line as far as Grantham.
The Siemens perspective Rob Morris, Siemens Mobility’s joint managing director, emphasised that this was a major milestone for the company. It is considered a back drop for the change that is coming for the signalling industry in terms of its technology and implementation. It is to be hoped that rail investment will continue to permit programmes such as the East Coast ETCS to proceed northwards, the Midlands Hub project to begin, and the replacement of some very old trains on London Underground to go ahead despite the difficult times ahead for the national economy.
The company would wish for a constructive partnership with government to continue the transformative projects that have happened in recent times. Examples of these are the Elizabeth Line signalling, the newly opened line to Ashington in Northumberland, the use of modular signalling on the North Wales Coast, plus four contracts for HS2. The new Chippenham site will have a positive impact for job opportunities and especially the recruitment of apprentices within the local area. The investment represents a promise for the future.
Keeping it in the family Siemens is proud of the number of employees who have predecessors going back many years who also worked for the Chippenham company in its various guises. One of these, Alex Orledge is a fifth-generation member of staff and he especially remembered his grandmother Margaret (Miggie) Orledge. Alex is now a licensed tester, a very important role in the commissioning of signalling projects.
The new site
Although the ceremonial ‘spades in the ground’ was duly performed, this was symbolic rather than the real start of construction. Groundwork is already well underway, and the site is a hive of activity with lorries and earth moving equipment arriving and departing almost non-stop. Some of the steel framework is already erected and one gets a sense of urgency as to the progress being made.
Artist’s impressions of the finished building are there to be seen. The new premises will include research and development labs, project design and planning offices, and the all-important manufacturing capability of which around 50% of the floor space will be allocated for that. Keeping the industry supplied with spares for existing signalling systems remains an important element of the business plan, so the supply of relays, point machines, and such like will continue for as long as customers require them.
It is intended that the new site will become operational in 2026 which is not long given the building work and fitting out that has to happen.
Final thoughts on future signalling direction
It was good of Siemens to grant time for those of us from the railway media to have a few words with Lord Peter Hendy and Rob Morris. The UK roll out of ETCS seems to be proceeding at a very slow pace when considering that the Cambrian scheme was commissioned in 2010. In terms of logistics, that was relatively easy as it was a self-contained railway with primarily only a single type of train. Similarly, the Thameslink core is akin to a metro line with all trains being the same type with a standard stopping pattern.
The East Coast Main Line (ECML) is entirely different and, although the completion date of 2029 seems an awful long way off, this is the first real test for ETCS on a mixed traffic railway. The technology bit is relatively easy but the way the line will be operated is a major challenge. The training of drivers, other train borne crew, and control room staff takes on
a new dimension, let alone all the people involved with train planning and deployment.
The fitting of rolling stock with ETCS kit and the reluctance of operators to create captive fleets means that around 80% of all trains must be equipped before the removal of conventional signals on the ECML can happen. Hence the time needed for all this to happen is considerable, but it will bode well for the future of ETCS on the next set of routes earmarked for transformation.
Both gentlemen were aware of the radio upgrade from GSM-R to FRCMS which will need to go alongside the ETCS programme which is re-assuring and Siemens, both at its Chippenham and Poole sites, is well aware of the challenges this project will represent.
Siemens Mobility has to be thanked for opening up to the wider world what the new site will mean for the rail industry and the county of Wiltshire. Rail Engineer will monitor progress as the new site takes shape.
In 1896, Swedish scientist Svante Arrhenius predicted that changes in atmospheric carbon dioxide levels will create a greenhouse effect that increases average global temperatures. In 1967, a computer model confirmed this conclusion which, over the next two decades, became established scientific truth.
The increasing acceptance of the threat of climate change led to the Kyoto Protocol of 1997 which was the first international agreement committing states to reducing greenhouse gas emissions. It was signed by 192 countries.
Yet this threat was not universally accepted. As late as 2017, climate sceptic Nigel Lawson claimed in a BBC radio interview that average temperatures were falling. In response to scientists responding furiously to this claim, the BBC defended its decision to interview Lawson on the basis that “it had a duty to inform listeners about all sides of a debate.”
It is difficult to imagine that the BBC would take that stance today, given that the latest YouGov poll showed that 71% believe the climate is changing due to human activity. As a result, it is now a commercial imperative for businesses and Government to show they care for the environment and explain how they propose to reduce emissions.
Under the 2008 Climate Change Act, Government has a legal duty to take action to reduce greenhouse gas emissions (GHG) which are generally referred to as carbon emissions, though this is not wholly accurate. The Act originally mandated an 80% reduction in the 1990 baseline emissions by 2025. In 2019, this was amended to 100% i.e., net-zero carbon emissions by 2050.
The UK is seemingly well on its way to net-zero as, since 1990, total GHG emissions have been reduced by 49%. However domestic transport emissions excluding aviation have only deceased by 14% and aviation emissions are more than twice those of 1990 (214%). These figures do not take account of non-CO2 effects from aviation emissions that reflect sunlight which the Climate Change Committee (CCC) estimates may double the warming effect from CO2 emissions.
The Act required the formation of the CCC, an expert body to advise Government, report on progress made in reducing emissions, and make recommendations for five-yearly carbon budgets. In 2019 the CCC produced its report ‘Net Zero –
The UK’s contribution to stopping global warming’. This showed how it was technically possible for the UK to achieve net-zero emissions at a cost of 1-2% of GDP. It concluded that this could offer significant industrial opportunities and other benefits that could fully offset costs. However, it was recognised that some industries could suffer if policies were not in place for an effective transition. This report considered that aviation emissions could be reduced by a combination of technology, airspace and operations management, alternative fuels, and managing demand. With all these measures, the CCC report considered that, at best, this would only reduce aviation emissions to 83% of their 2017 levels.
A mode of transport that lifts passengers and goods over 10km into the air and propels them at 900 km/hr uses an enormous amount of energy. Hence a typical trans-Atlantic flight will use around 50 tonnes of jet fuel which is around 2,000 Megajoules (MJ) of energy. Trans-Atlantic aviation is only possible because of the jet fuel’s high energy density of 43 MJ/kg.
As with rail traction, the aviation industry is considering batteries and hydrogen as alternatives to jet fuel. Yet with a lithium battery having a typical specific energy of 0.7 MJ/kg, a transatlantic plane would require a battery weighing around 3,000 tonnes. Even with the most heroic assumptions about the development of battery technology, it is difficult to imagine that battery-powered transatlantic aviation will ever be feasible.
Yet a battery powered plane was certified for use in 2020. This is the Pipistrel Velis Electro which is a two-seater aircraft intended for pilot training. It offers 50 minutes of flight time with 20 minutes reserve and has a range of 185km. It is powered by a 58kW electric motor from a 70kg lithium battery.
Although it is claimed that this technology could eventually be scaled up to power domestic flights, the scaling factor must be considered.
In this respect the exponential scaling factor must be considered as objects are scaled up. For example, an Airbus A319 is five times the length of this battery plane but 95 times its weight. Thus, it is difficult to image that such flights could ever be battery powered.
Hydrogen, however, is a technically feasible option as Airbus has concluded from its ZEROe project. This has developed three concepts for hydrogen powered aircraft which can carry up to 200 passengers for over 3,500 km. Like the Saturn V moon rocket, these concept planes will be fuelled by liquid hydrogen which has an energy density of 8 MJ/kg which is 10 times greater than batteries, though still a fifth of jet fuel.
Airbus’s concept designs show that the hydrogen in these planes would occupy a third of the fuselage and so increase air fares by 50%. Furthermore, there would be the huge cost of installing liquid hydrogen fuelling and storage facilities at the world’s airports. The practicality of scaling up green hydrogen production also must be considered. A recent Royal Society report ‘Net zero aviation fuels: resource requirements and environmental impacts’ estimates that electricity required to produce enough hydrogen to replace UK aviation fuel consumption would require around 80% of the UK’s current electricity generation.
Thus, while technically feasible, practical and cost considerations would seem to make it unlikely that airlines will be using hydrogen-powered aircraft in the foreseeable future.
Organisations can compensate for their carbon emission by investing in projects that reduce emissions elsewhere. For aviation, such offsetting is encouraged by the UK Emissions Trading Scheme (ETS) and the Carbon Offsetting and Reduction Scheme for International Aviation (CORSIA).
Trading carbon reduction in this way is a key aspect of international climate change agreements. However, this is only effective if the offsetting investment creates emission reductions that are additional to those that were going to happen anyway. They must also be monitored and verified by independent third parties to verify the promised emission reductions.
A significant proposed investment in emission reductions outside the aviation industry is the £1 billion commitment in the previous Government’s Jet Zero strategy to develop Carbon Capture and Storage (CCS) clusters. Worldwide, there are currently relatively few such facilities almost all of which require Government support. There are plans to significantly increase CCS facilities including those with Direct Air Capture (DAC).
Outside of the petro-chemical industry, some environmental groups consider CCS to be an unproven, expensive technology that distracts from global decarbonisation efforts. Yet it would seem feasible to capture carbon as an integral part of an industrial process (e.g. producing green hydrogen from methane). However, it remains to be seen whether DAC is feasible at scale as the carbon dioxide it extracts only makes up 0.04% of the atmosphere.
The Jet Zero strategy estimates that, by 2050, 19 million tonnes of carbon (CO2E) will be abated outside the industry and that this will contribute 37% of aviation’s carbon reduction to achieve netzero in 2050. This is greenhouse gas removal by technologies such as DAC which various sources estimate will cost between £100 to £500 per tonne of carbon. If DAC CCS was used to achieve this 37% reduction, using the lowest estimate, the annual cost would be £2 billion per annum. It is not clear who will pay for this.
Within the aviation industry, ‘drop-in’ sustainable aviation fuels (SAF) are seen as the solution for net-zero aviation. There are three ways of producing SAF: biofuels from crops, biofuels from waste, and synthetic fuels.
Biofuels are deemed carbon free as, providing that they are grown in a sustainable manner, they absorb more carbon dioxide when they are grown than they release when they are burned. However, as with hydrogen, scaling up production to meeting demand is problematic. The CCC’s
net-zero report notes that “consideration should be given as to whether aviation is the most appropriate place to use biomass, given that it is likely to be a scarce resource with a range of alternative uses which may save more emissions.” As a result, it explains “a pragmatic planning assumption would be to aim for up to 10% biofuel use in aviation in 2050.”
The limitations of biofuel production are indicated in the Royal Society aviation’s fuel report. This concludes that over half the UK’s agricultural land would be needed to grow sufficient biofuel crops to replace the 12-million tonnes of aviation’s fuel consumed by the UK in 2019.
Biofuels are currently produced from waste include cooking oil. The Royal Society report considers that this fuel costs 50% more than jet fuel and could satisfy 0.3% to 0.6% of UK aviation fuel demand. It also notes that it may be possible to produce up to 10% of aviation fuel demand from municipal waste, though at a much higher price than fuel from cooking oil.
The production of carbon-neutral synthetic fuels is a process that has a low thermodynamic efficiency with multiple stages. Hence the energy required to produce such fuels can be far greater than their energy content. The Royal Society report estimates that between 468 and 660TWh of electricity would be needed to produce sufficient synthetic fuel to satisfy UK aviation demand. This is around five times the UK’s current electricity consumption. This report also shows that the cost of such synthetic fuels would be four times the cost of aviation fuel.
Given the importance of sustainable fuels for aviation decarbonisation, legislation has been enacted to mandate that aviation fuel suppliers blend a minimum percentage of SAF in their fuels. In 2025, 2030, and 2040 onwards this is respectively 2%, 10%, and 24%.
Much has been done to reduce aircraft fuel burn. For example, newer aircraft like the Boeing 787 Dreamliner and Airbus A350 are much more fuel efficient than previous generation aircraft. It has been estimated that halving fleet age by building more aircraft could reduce fuel burn by 11-14%.
Other measures to improve efficiency are designing aircraft to fly 15% slower to reduce fuel burn by 5-7% and ensuring aircraft are flown close to their design range which could lower fuel burn by 4-7%. There is also scope for increased efficiency in the management of airspace by giving aircraft the most direct routing and minimising level flight below an aircraft’s preferred cruising level.
Taking all these factors into account the CCC estimates that operational and air transport movement efficiencies could reduce the carbon intensity of flying by an average 1.3% per year between 2025 and 2050.
The CCC net-zero report proposes that the increase in aviation passenger demand should be limited to a 60% increase in passenger demand above 2005 levels by 2050. It notes that there could be policies to directly manage demand, and that demand may be lower in future if preferences or social norms change, especially as 80% of journeys are for leisure purposes.
This report shows the potential for modal shift from aviation to high-speed rail. However, it accepts that the potential for emissions saving from modal shift is limited to domestic flights which is a small percentage of air passenger km.
However, past and present governments have disregarded the CCC’s advice in this respect as they believe that the aviation sector can achieve net-zero without the need to limit aviation growth.
In January, the Government announced that it is “committed to ensuring that the economic benefits of airport expansions are delivered in a way that considers and addresses environmental responsibilities” and that there have been “great strides in transitioning to greener aviation”.
This statement was justified with reference to the SAF mandate which was claimed to be “one of the key measures required to reach net-zero emissions from aviation by 2050.”
Net-zero aviation?
There are various estimates of how the UK will achieve net-zero aviation by 2050. The Jet Zero strategy considers that by 2050 the UK aviation sector will have abated 52 million tonnes of carbon dioxide equivalent (MtCO2E) as follows:
» Offsetting - 14 Mt.
» Abatement elsewhere (DAC) - 19 Mt.
» Fuel efficiencies - 8 Mt.
» Zero carbon aircraft - 2 Mt.
» SAF - 9 Mt.
Hence the actual planned reduction in aircraft emissions by 2050 is 19 Mt which is about the same as that from the expected growth in air travel. This will leave UK-fuelled aircraft emitting 33 MtCOE by 2050. This is 74% more than aviation emissions in the 1990 baseline year. Readers can judge for themselves whether this constitutes net-zero aviation.
The extent to which the need for carbon reductions conflicts with the requirement for economic growth depends on the sector concerned. The impression cost reduction in renewable power generation provided an incentive to decarbonise. Railway electrification also offers decarbonisation and a more cost-effective railway, though at a high initial capital cost. Innovative lowcarbon technologies also provide significant business opportunities.
Yet innovation cannot change the laws of physics nor the properties of materials. Aircraft will always require large amounts of energy. Hence decarbonising aviation comes at a cost and is subject to resource constraints.
Air transport and aerospace makes a significant contribution to the UK economy by directly employing around 230,000 people and contributing around £20 billion to the nation’s GDP. This is a vital contribution to the UK economy and for many it is the only way to get to their destinations.
Hence it is clearly unrealistic to significantly reduce air travel. Yet the goal of net-zero by 2050 does require a transitional strategy which limits demand.
Although there is scope to reduce emissions by SAF and efficiencies, the Jet Zero strategy projections show that increasing air travel demand will cancel out any such savings. Therefore it is misleading to pretend that net-zero aviation is a possibility.
Minimising energy use should be a key aspect of the UK’s decarbonisation strategy. Between Glasgow and London, a 200-seat plane consumes four tonnes of jet fuel (176,000 MJ) while a 609-seat Class 390 Pendolino consumes 10MWh (36,000 MJ). Hence, the plane requires 15 times more energy per seat than a train.
In this year of Railway200, the fact that trains are engineered to be a particularly energy efficient and carbon friendly form of travel is something that should be both stressed and celebrated.
Salary is £36,610 plus £6,000 bonus (pro rata)
280 hours over an 8-week period with overtime opportunities
NVQ (Level 3) training offered to candidates
R e q u i r e m e n t s :
Must have current Charge of Site Safety (COSS) certification
Job Reference Number: 105362
Salary range £41,486 to £49,899 plus £6,000 bonus (pro rata)
No experience necessary - full bespoke training given and opportunity to train as a Train Driver
R e q u i r e m e n t s :
NVQ Level 3 in Mechanical or Electrical Engineering is desirable but in-house training is provided.
Job Reference Number: 105362
Salary £67,111
280 hours over an 8-week period with overtime opportunities
Company van, fuel card, iPad and mobile provided
Job Reference Number: 105872
Scan the QR code to view vacancies!
We are looking for skilled system technicians to work at our location in Leicester on the ground-breaking Class 99 locomotives, which will begin commercial operation this year. If you’re keen to pursue a career in an exciting, dynamic and international environment and be part of a team shaping the future of sustainable rail transport, scan the QR to learn more and to submit your application.
Stadler Rail Service UK provides service and maintenance to a growing number of clients in the UK. It offers tailored solutions to optimise availability and reliability for a range of rolling stock and is an international subsidiary of Stadler Rail AG.
stadlerrail.com
SIEMENS MOBILITY
Our UK-based, regional delivery teams understand that collaboration across the rail industry is crucial for reducing cost and driving transformation. siemens.co.uk/mobility