
Dear Customers:
Thank you for choosing our products, for your safety and benefit, please carefully read the manual and all the information before using. If you do not follow the manual and cause any personal injury, property or other losses, our company will not be liable.
Our company mainly produces and sells hot press, cold press, frame assembly machine, board-jointing machine, lifter, tenoner, circular saw and other woodworking machinery. We can also manufacture all kinds of machines according to customers’ requirements.
Our company always insists the quality policy of “consumers are supreme, quality assurance”, carries out the marketing principle of pre-sales assist planning, test-run demonstration and lifelong after-sales service. We welcome all the customers to consult and purchase.
PREFACE
★ Before you use the hydraulic cold press at the first time, please note the following tips:
● The operator should gothrough related technical training, or be guide by professional.
● This manual will help you understand the machineandguide you safe operation.
● This manual contains a lot of important tips for safety, economy and operation. If you follow these tips, not only can avoid the risk of accidents, lower maintenance costs, reduce parking maintenance time, but also can improve reliabilityand service life of the machine.
● The manual should be properly stored for convenient access.
★ It is recommended that every staff associated with the machine should read this manual, for example:
● Operators, including thestaff whofor assembly, troubleshooting, clean, machine maintenance and waste treating.
● Repair and debugging personnel.
● Transportation personnel.
1. Brief introduction
2. Operation cautions
3. The main components of hydraulic cold press
4. Storage
5. Description of components
6. Installation and operation
7. Faults and solutions
8. Maintenance
2. Operation cautions
1. Must read the manual in detail to understand the performance and correct operation methods before operating.
2. The machine must be connected to the reliable grounding device before connecting to power supply.
3. The machine power cord must be connected to the power supply with protective switch, check the power supplyvoltage and frequency.
4. Before operating the machine, please make sure the motor rotation direction is correct, otherwise, it needs to changethe wiring position of power supply phase lines.
5. Before operating the machine, check that all safety devices are working properly, the components are not loose and damaged, or you should adjust and change it promptly to ensure its normal function. And remember to remove all thetools.
6. When operating the machine, the operators are required to wear tight clothes, never wear loose clothes, neckties,watches, bracelets, etc., the long hair operators are required to wear working cap.
7. When machine is running, all securityguards are notallowed to remove or open.
8. When machine is running, the operator is prohibited to leave working post.
9. Strictly forbid to process the workpiece and accessories beyond the original design features of the machine.
10. Poor health or drunk is forbidden to operate the machine.
11. Make sure the main power is off before inspecting, maintaining andcleaning the machine.
12. Must cut off the main power after operating, and do not leave until the machine stops running completely.
3.The main components of hydraulic cold press
Themain components: oil hydraulic system, electricalcontrol system, press plate and machine body.
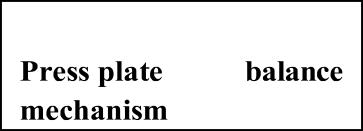
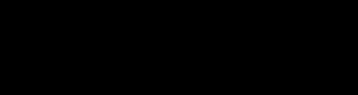



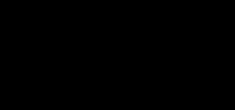
Oil hydraulic system: it consists of oil cylinder, fuel tank, oil pump, oil pump motor, control valves and pressure gauge.The fuel tank is filled with oil, it achieves oil pumping by electric drive pump, and transports the oil to oil cylinder by pipeline, so that the oil cylinder can work. The overflow valve can make the workpiece generate backpressure in pressing process and maintain steady. The electromagnetic valve ball is used to maintain the system setting pressure; the pressure gauge is used to show the pressure.
Electrical control system: it consists of main circuit and control circuit, the circuit uses automatic circuit breaker, fuse,AC contactor to carry out overload, short circuit and under voltage protection for press motor, solenoid valve, etc.
Press plate balance mechanism: it consists of balance lifting rack, lifting gear, rotation axis. The machine is equipped with fixed rotating bearing components, two balance racks (right and left). The both ends of rotating shafts are equipped with lifting gears and bearings, so that the rotation axis can rotate flexibly.
Press plate: it consists of the upper press plate and the lower press plate. Both press plates are welded by section barsand steel plates, the working plane is processed by large gantry milling machine to ensure it smooth. The upper press plate is connected with the cylinder rod, realizing press plate lifting by lifting cylinder. The lower press plate can be welded directly on the machine base, making the structure of machine fastened.
Machine body: it is welded by steel plate, the structure is compact and strength is good.
4.Storage
Toprolongthelife ofthe press, please do not: put in damp places, vibrate severely.
Machine transportation and load & unload

It is generally the overall transport, but if it needs to disassemble the oil cylinder to transport because of the height, you can remove the bolts on the flange, and pull the cylinder barrel down, then fix two oil cylinders with a batten or iron bar, which protects two oil cylinders from waggling during transportation to result in any damages. At last, pack the press well. It is forbidden to place inclining to one side when loading.
5.Description of components
Distribution box







A Thermalrelay, control oil pump motor, carryout overload protection of oil pump motor.
B Control circuit power transformer.
C AC contactor, control oil pump motor, carry outthe loss of pressure and zero- voltage protection of oil pump motor.
D Circuit breaker, short circuit or overload control.
E、F Intermediate relay, power supply and pressure maintaining time control.
G Fuse.




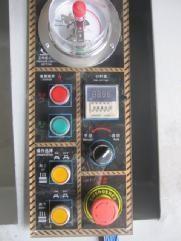




A Pressure gauge with electric contact. Red pointer is the working pressure setting pointer; green pointer is the pressuremaintaining setting pointer; black pointer is the pressure display pointer.
B Pressure maintaining time relay, there are three kinds of time setting modes to choose from: hour (h), minute (m), second (s). The maximum time for each mode can only be set to: 99.99.
C Automatic switch.
D Start.
E Press plate pressing switch, press downthe plate will decline, press it againto stop the plate declining.
F Press plateloosening switch, press down the plate will rise, press it again to stop the plate rising.
G Stop switch, stop workbench lifting.
H Emergencystopswitch, no matter what state the machine is, press the switch, all actions will stop.
6.Installation and operation
The placement ofmachine
(1) Place the machine on the flat and hard ground, and adjust the machine to horizontal position.
(2)Power distribution
Connect voltage, electric current and frequency-dependent power tothe head of the machine power outlet according tothe power distribution requirements on electric box.
(3)Confirm theoilcylinder motor turninginthe right direction. Press the power start button, and press the press plate pressing button, if the press plate is pressing down (if the cylinderis lowered, then the cylinder rises), then the turning direction of oil cylinder motor is correct. Otherwise, you should change over two lines of the three-phase power supply cord to get correct turning direction.
Oil cylinder reset
If the oil cylinder stops declining before transportation, then reset the oil cylinder and fixit after power distribution:A: Remove the batten and package fixing between two oil cylinders.
B: Turn the power on.
C: Press the dropping button, the oil cylinder will rise automatically; if the oil cylinder doesn’t work because of wrong power phase and motor reversal, when the oil cylinder flange rises to about 3mm from the roof, press the stop button to stop the oil cylinder rising, then tighten each flange and bolt.
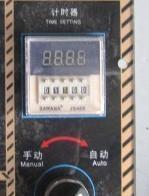
(4)Pressure retaining time setting
You can set the pressure retaining time according to actual demand.A: Choose the time mode: “hour (h), minute (M), second (S)”.
B:Settherequired number byfour digits"0-9":
If you choose the time mode is "h", the set value is: “9999”, the actual pressure retaining time is "99.99" hours; if the value is “0003”, the actual pressure retaining time is "0.03" hours; if the value is “0905”, the actual pressure retainingtime is "9.05" hours (If the time mode is set to " M" or " S", then the "hour" is changed to "minute" or "second").
C: The maximumtime value can be set to "99.99 hours".
D: After time up, the buzzer will ring, it is suggested that the workpiece hasbeen completed pressurizing.E: Prohibit setting the time to "0000".
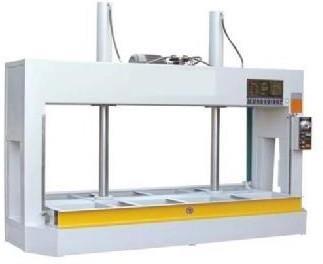
(5)The placement of workpiece
Before pressing the workpiece, it must be based on the actual size and height of the workpiece to select the correct placement, strictly prohibit pressurizing the workpiece inclining to one side or uneven. Before operating this machine, you should carry out a comprehensive and detailed examination to ensure safe operation:
(1) Check all safety guards are correct and reliable.
(2) Check the transmission components and connecting components.
(3) Check the pressure of hydraulic system.
(4) Checkifthe oil pump rotation direction is correct.
(5) Check ifthe lifting actionis flexible andreliable.
(6) Finally, operate theempty machine once, confirm whether the entire operation process is correct. Put the workpiece with correct method-------- →set the pressure according to the area of workpiece →set pressure retaining time by adjusting the time relay “B” →press the pressing button “E” →after compressing the workpiece and reaching the set pressure, the pressure retaining relay starts counting, the press plate will rise automatically when counting is completed - →remove the compressed workpiece, if you do not needthe pressure retaining time, then adjust time relay "H" to "9999" before pressing.
7.Faults and solutions
When checking out the faults listed in the following table, you can make a preliminary reference to the solutions, if still can not solve, you should ask manufacturer for technical support.
Faults Causes Solutions
The total power or controlpower is turned Turn on power switch. off.
Lack of one phase. Check and correct.
Circuit breaker is not closed.
The machine can not go up and
Open electrical box and close the circuit breaker. downwhen press the pressing switch or
Contactor is not working orthermal relay is off.
Check whether the circuit is open or overload, and repair. loosening switch.
The control solenoid Replace the solenoid valve. valveof hydraulic system is broken.
Poor contact of pressure Overhaul gauge contactor.
Intermediate relayis Replace the intermediate relay. broken.
The machine is loss of power and shutdown suddenly when working.
Short circuit or circuitbreaker tripped.
Check if the motor insulation is qualified, if the machine is installed with ground wire. Close the circuit breaker.
Overload results in circuit relay disconnecting. Check the circuit and reset thethermal relay.
Upper workbench is unbalanced.
The bearing bases at both ends of the balance rack are often broken.
Lifting gear and balance rack cause dislocation.
Adjust the gear and balance rack. The flange screw of oil cylinder is loose.
Fasten the flange screw.
Upper press plate is unbalanced.
Pipe joint leaks. Joint is loose.
Can not retain pressure.
Pressure retaining valve or electromagnetic ball valve is broken.
The oil leaks.
Adjust the lifting rack and lifting positioning roller to balance the press plate.
Re-wrap Teflon tape and tighten the joint.
Check and replace the corresponding valve.
Overhaul
Can not start the motor. Oil pump is broken. Replace the oil pump.
8. Maintenance
A. Dailymaintenance
(1) Keepthemachine clean, eachtransmissioncomponent andturning connection point should be kept lubricated.
(2) It is forbidden to pile up sundry on the machine.
(3) Checkthe screw fastening the oil cylinder flange andthe cylinder rod andpress plate flange every day, if loose, thentighten it in time.
(4) Check the oil line every day, repair it in time if leakage.
(5) Checkthe oil inthe fuel tank everyweek: replace the dirtyoil intime; and fill the fuel tank when lack of oil.
(6) Checkthe service condition of positioning roller andlifting pinion, rack ofpress plate every day.
B. Operating maintenance
(1) Operate the machine with correct method, it is forbidden to process the workpiece beyond the scope of the originaldesign.
(2) Put the workpiece with correct method, it is forbidden to pressurize in the situation of inclining to one side or uneven.
C. Overhaul period
(1) Each transmission component and safety device of the machine should be checked before processing. Check if the machine is flexible and reliable in every operation.
(2) Once overhaul a month, focus on the service condition of the components inside the electrical box and other stroke limit switches. Check the lubrication and wear of transmission components, the security situation of each safety protection assembly, adjust or replace.
(3) Check the using of oil cylinder, oil, hydraulic system, check if the oil must be replaced, if the oil line connectionleaks, if the system pressure is normal, etc.
D. Maintenance of storage
(1) Ifthe machine is not in use, it shouldbe kept clean, coat with lubricating oil to the transmission components and packit well.
(2) The machine should be placed in dry and ventilated room, avoid direct sunlight and rain.
E. Theselectionof hydraulic oil:
ISO-VG68#
MOBIL:DTE26 antiwear
hydraulicoil CALTEX:
HD68 antiwear hydraulic oil
Esso: NUTO H68 antiwear
hydraulic oil SHELL:
TELLUS OLL68
antiwear hydraulic oil
CALTEX:Meropa68,CALTEX:Multlfak Ep2
F.Theselection of balance gear bearing lubricating oil: calcium-based greaseor: CALTEX: Meropa68, CALTEX:Multlfak Ep2