OFFSITE
SUSTAINABILITY IN STEEL LIGHT GAUGE FRAMING OPTIONS AND REDUCING ENVIRONMENTAL
A
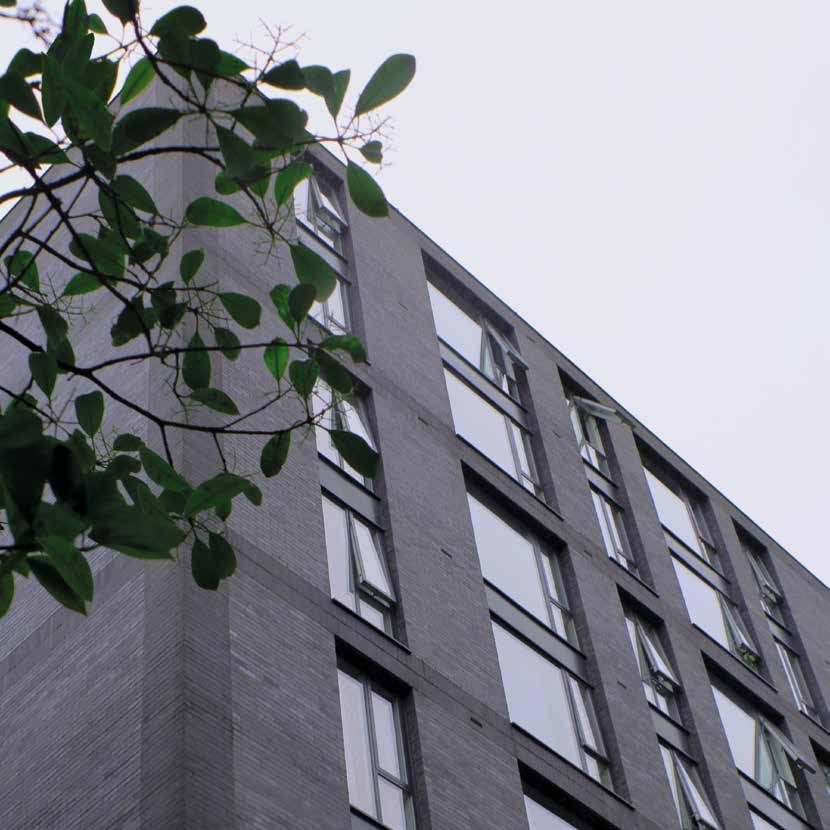
A
Developers before we became manufacturers, we’re committed to protecting choice in the design process and to offering hybrid solutions that combine traditional with modern methods of construction.
There are just two things we’re not flexible on. Precision manufacturing to your exact specifications and our “fabric first” approach, that radically reduces energy use in the construction of buildings and in their operation.
UNisystem panels, walls and floors are suitable for much more than simply house, mid-rise and high rise apartments blocks. They are readily adaptable for student accommodation, education, healthcare and commercial projects, of all sizes.
Designers and developers have complete control over architectural features and have the option to manufacture basic or “fully dressed” panels for internal and external walls and floors. The light gauge steel at the core of UNisystem is dressed with board, insulation, fire stopping and external cladding to your exact design specifications.
Champions of precision, born to build 137,000 sq ft second factory open for business
Our hybrid solutions bring traditional and modern methods of construction together, in alignment with your individual ambitions and needs. We’re here to support you at every stage of your transition to offsite, from as early as pre-planning, with land optimisation and logistics consultancy, as well as pre-planning design.
Our precision manufacturing and fabric first approach to construction save energy by making sure it isn’t needed in the first place. We manufacture panels that create air tight, highly insulated buildings that use less energy in operation.
Our UNipanel significantly outperforms the requirements of current Building Regulations (ADL2021), and UNiSystem is expected to outstrip the requirements of the Future Homes Standard which comes into operation in 2025.
So let’s start the conversation about your project, using the flexible UNisytem product range that’s leading the way on build quality and energy efficiency standards.
FRONT COVER
voestalpine Metsec
PRINTED ON:
FSC Mix paper by Buxton Press
PUBLISHER:
Offsite Magazine is produced and published by Offsite Media Ltd
101 Longden Road, Shrewsbury, Shropshire, SY3 9PS
T: 01743 290001 www.offsitemagazine.co.uk
©Offsite Media Ltd.
SUBSCRIBE TO RECEIVE OFFSITE:
This magazine is a bimonthly publication and the annual subscription fee for UK postage is £29.70 plus VAT for all six issues (£4.95 per copy). Visit www.offsitemagazine.co.uk
ADVERTISING ENQUIRIES PLEASE CONTACT:
Julie Williams // T: 01743 290001
E: julie.williams@offsitemagazine.co.uk
SEND US YOUR NEWS:
Gary Ramsay // T: 01743 290001
E: gary.ramsay@offsitemagazine.co.uk
BACK ISSUES VISIT: www.offsitemagazine.co.uk
FOR OFFSITE ENQUIRIES PLEASE CONTACT:
E: info@offsitemagazine.co.uk
DISCLAIMER: The content of Offsite Magazine does not necessarily reflect the views of the editor or publishers and are the views of its contributors and advertisers. The digital edition may include hyperlinks to third-party content, advertising, or websites, provided for the sake of convenience and interest. The publishers accept no legal responsibility for loss arising from information in this publication and do not endorse any advertising or products available from external sources. The publisher does not accept any liability of any loss arising from the late appearance or non-publication of any advertisement. Content including images and illustrations supplied by third parties are accepted in good faith and the publishers expect third parties to have obtained appropriate permissions, consents, licences or otherwise. The publisher does not accept any liability or any loss arising in the absence of these permissions for material used in both physical and digital editions. No part of this publication may be reproduced or stored in a retrieval system without the written consent of the publishers. All rights reserved.
KEEP
Welcome to the new edition of Offsite Magazine and as befitting the one that will be distributed at Offsite Expo, it is a bumper one full of companies and comment on what is making the industry tick right now.
When Offsite Expo comes around it tends to be a landmark for various reasons. Not only is it the premier show for all those working in and around the offsite/MMC arena plus the opportunity to meet, network, socialise and do business. But it acts as something of a milestone and pause for thought. One year on from the last show and what has changed – which individuals have moved on, what new products are on the market and does the industry still have the same allure, the same impetus?
The last 12 months has seen some notable exits from the offsite sector that don’t need detailing here – each organisation had their own specific issues compounded by wider economic and business problems –suffice to say, that many suffered from the illusion that entry into the world of factory manufacture was going to be relatively straightforward, depending on how much investment money was
available. The general gist of what I hear from industry insiders is: you design and create a special product then build a factory to manufacture it. Not build a lovely big factory then try and figure out what you are going to fill it with. A simplification I know, but it highlights a universal truth that many ignore.
Enough from me. Amongst the many highlights to read inside are three particular ones. Firstly, Trina Chakravarti from Building Better, heads up a team that is making a compelling case for MMC in the world of social housing and told me why demystifying the process for clients is key. Secondly, a roundtable discussion hosted by VOLUMETRIC™ had much to say about supply chain collaboration and why sharing knowledge and data can make your project a smoother process. Thirdly, the MPBA’s Richard Hipkiss offers a refreshing view of the merits of Pre-Manufactured Value and how you measure it.
Thanks to all our contributors, advertisers and supporters for their help this issue. I hope to see many of you in Coventry at Offsite Expo and the Offsite Awards!
Gary Ramsay Consultant EditorEmail: gary.ramsay@offsitemagazine.co.uk
•
•
•
•
•
A central hub for heating, ventilation, water management, communications and electrical services.
Arrives on site fully assembled, rigorously tested and certified, ready for simple ‘plug and play’ installation. WWW.VOLUMETRIC.CO.UK/MEP-PODS
With the built environment being responsible for a significant proportion of global greenhouse emissions, the construction industry needs to adopt practices which minimise carbon emissions and promote sustainability. Deciding whether to adopt such processes may not be entirely voluntary either, as central government and local authorities are already putting policies in place to encourage a greener approach – a trend which seems likely to continue in the future.
Net zero carbon forms part of the government’s procurement policy, with the Cabinet Office’s Action Note PPN06/21 stipulating how government departments need to take account of suppliers’ Net Zero Carbon Reduction Plans when procuring for major government contracts.
Together with other environmental initiatives, such as the London Plan 2021 requiring medium- and
large-scale construction projects in London to have an Environmental Product Declaration (EPD) and carbon footprint statements as part of the planning application, these policies place increased pressure on architects to design buildings which can be constructed using sustainable materials and methods.
The green credentials of Light Gauge Steel Framing (LGSF) are recognised throughout the industry and include:
• Reduction in a structure’s embodied carbon by using less steel
• Less embodied carbon than traditional construction methods
• Zero waste in manufacturing and on-site
• Reduced weight reduces concrete in foundations or podium structures
• Fewer, and lighter deliveries to site
• High recyclability/reuse.
Leading the way towards a more sustainable future in the steel framing arena is voestalpine Metsec plc. As part of the multi-national steel and technology group, voestalpine AG, the company is committed to the group’s target of achieving net zero carbon emissions throughout its Metal Forming Division by 2035, placing sustainability at the core of the company’s operations and providing designers with absolute confidence that Metsec systems, and their efficient installation, are as environmentally responsible as possible.
“The construction industry will come under increasing pressure to meet environmental targets,” says Chris Holleron, Sales Director for voestalpine Metsec’s Framing Division. “Which encompass the entire design, construction and ultimate demolition of a building, including reuse of the materials from which it has been constructed.
“The sustainability credentials of steel framing systems and relatively low environmental impact achieved through the efficiency of their installation by modern methods of construction (MMC) are well documented, with Metsec systems delivering at all levels. We believe that our net zero carbon initiative sets new standards in the industry by committing us to verifiable targets which will have real benefits for the environment and provide designers with total assurance of the sustainability credentials of our construction systems.”
Achieving this industry-leading target requires a focused effort within voestalpine Metsec together with the co-operation of suppliers and others in the value chain. The company has
With all parts of the economy under increasing pressure to become more sustainable in their operations in the international push towards net zero carbon, the use of light gauge steel framing (LGSF) can provide many answers.
created its own ‘Roadmap to Net Zero’, which establishes targets and strategies for achieving net zero carbon across all its operations in the UK. The multi-faceted approach includes investigating areas where energy can be saved and processes optimised, as well as exploring ways to source green electricity and even generate its own renewable energy.
Green electricity
To date, this initiative has seen voestalpine Metsec move its electricity requirements to 100% renewable sources, resulting in a 67% reduction in its carbon footprint, from 1500 tonnes of CO2 to 500 tonnes of CO2 per year. Further measures include the installation of solar panels on the roofs of the company’s manufacturing facilities. Arrays totalling more than 4600 photovoltaic panels and covering some 9300sq m of roof space will generate up to 1.4MWh of electricity per annum.
In total, the solar panels are expected to provide 40% of voestalpine Metsec’s total electricity requirements. They will not only reduce the company’s reliance on electricity from the National Grid but will also return unused electricity to the Grid at times when the facilities are not in operation, such as evenings, weekends and bank holidays.
More energy-saving
Further measures aimed at reducing the company’s impact on the environment and achieving net zero carbon include a host of energy-saving schemes throughout its operations. These include, replacing company
cars with hybrid and electric vehicles, the introduction of fully electric fleet vehicles, installing charging points across the company site, reducing gas consumption and investment in sophisticated, state-of-the-art energy management systems.
Green steel
At the core of the voestalpine business, an investment of around €1.5billion is being made into constructing electric arc furnaces at each of the group’s two steel production sites in Austria. As part of its ‘greentec steel’ plan, construction will start in 2024, and commissioning of the two units will take place in 2027. This will allow the voestalpine group to reduce its CO2 emissions by up to 30% from 2027.
Supporting these industry-leading initiatives, and underlining voestalpine Metsec’s commitment to providing designers and specifiers with unequivocal information on which they can base their design and specification decisions with confidence, is the company’s publication of an Environmental Product Declaration (EPD) for its purlins and framing systems.
The EPD encapsulates the quantifiable environmental impacts of a product’s lifecycle, from manufacture and transport to end of life, in a single, comprehensive report. It includes a lifecycle assessment and environmental impact data comprising core environmental impact indicators, use of natural resources and end of life information.
“As construction industry regulations increasingly incorporate requirements for sustainability,” adds Chris. “Building design together with the materials and processes used in construction will need to meet ever more rigorous standards. Along with other parties invested in the project, materials manufacturers will need to state and prove the environmental credentials of their products and systems.
“As the UK’s largest designer and manufacturer of constructional steel systems, we have always been at the forefront when it comes to setting, adopting, maintaining and verifying the most rigorous standards across all of our operations. Our net zero carbon initiative, together with EPDs and other environmentally responsible measures puts sustainability at the very heart of our operations, assuring designers and specifiers can be confident in the green credentials of voestalpine Metsec products and systems.”
For more information visit: www.metsec.com
Images: 01-04. The road to net zero carbon is one that every business is travelling including voestalpine Metsec which has a range of green initiatives including the installation of solar panels on the roof of the company’s manufacturing facilities
The Hill Group has formed an Investment Partnership with Gravesham Borough Council to accelerate the delivery of affordable homes for local people in Gravesend and the surrounding area. The Gravesham Community Investment Partnership (GCIP) will identify locations and develop suitable sites for new councilowned homes, in a bid to help reduce the number of households on the borough’s Housing Register, which currently stands at more than 1,000.
Cllr John Burden, Leader of Gravesham Borough Council, said “We have long-held ambitions to build hundreds of new council homes, in order to provide real social housing for those with demonstrable roots in Gravesham, thus reducing the number of people on our Housing Register.
“However, we are a local council, and while we have succeeded in directly developing 200 new council-owned homes in the past four years, we recognise our limitations and the fact that bringing a specialist private sector housebuilder with investment, commercial, and financial expertise on board will greatly accelerate the progress we want to achieve.”
Andy Hill, Group Chief Executive of The Hill Group, said: “We are proud to have formed an Investment Partnership with Gravesham Borough Council and are looking forward to working closely together to expand the delivery of affordable homes for local communities in the area. Work now begins to identify suitable sites where we can apply our significant experience and expertise for the swift delivery of much-needed new homes for Gravesham.”
Recognising the need to tackle homelessness in the borough, Hill is donating eight purpose-built SoloHaus homes to the Council. Created to provide safe, secure, and quality accommodation for the most vulnerable people in society, these modular homes will be donated as a part of Hill’s Foundation 200 initiative. Launched to mark Hill’s 20th anniversary, Foundation 200 is a £15million pledge to design and donate 200 modular homes to local authorities and homelessness charities by 2025.
“We are so grateful to Hill for their generous offer to donate these modular homes that will help prevent people from becoming homeless,” said Cllr
JennyFollowing an extensive overhaul, the Offsite Hub is being relaunched during Offsite Expo at Coventry Building Society Arena on 19-20 September 2023. Offering an invaluable source of information on the offsite sector, the new website will have a sleeker design with easy navigation, plus up-to-date news and views.
The Offsite Hub aims to create a singular online destination for professionals and experts, as well as clients, developers and specifiers wanting to explore the sector in more depth, including the analysis of industry challenges and acknowledge the successful achievements of offsite construction. Users can expect to see new and emerging technologies, informative articles and opinion pieces from leading industry figures. The Offsite Hub will showcase awardwinning projects and businesses and will bring a new
Wallace, Gravesham Borough Council’s Cabinet Member for Housing Services. “We are currently identifying suitable council-owned land where we can install them and are working to have them in use as quickly as we possibly can.”
Andy Hill added: “We are also delighted to further the partnership by donating the first purposebuilt modular homes in Gravesham, reflecting our commitment toward making a positive social impact in the areas in which we work. We designed SoloHaus to aid vulnerable individuals with nowhere to call home, and I am confident that once this scheme has been delivered, these innovative modular homes will have an incredibly positive impact on the lives of the most vulnerable people in the area, for many years to come.”
Gravesham Borough Council is now working to identify suitable Council-owned land within the Borough to situate the SoloHaus homes.
Source: www.solohaus.co.uk
dimension to how offsite information is published and perceived.
Registration is completely free and gives users access to a supplier directory listing, a comprehensive library of resources and downloads, and exclusive content from Offsite Magazine, the Offsite Awards and Offsite Expo. The Offsite Hub offers a highly visual platform for businesses keen to demonstrate their innovation, cutting-edge products and projects. There will be multiple opportunities to contribute articles or news to the Offsite Hub, putting your business in front of a wider audience of offsite specialists. The team behind the revamp will be revealing further features and added benefits of the Offsite Hub during Offsite Expo.
You can register for free access to the Offsite Hub at: www.offsitehub.co.uk
Modular specialist Elements Europe have been awarded a central Birmingham build-to-rent (BTR) residential contract. Acting as both the main contractor and offsite manufacturer, Elements Europe will deliver a full turnkey solution to the scheme. The four-acre island site will be transformed into a residential destination, branded Smith’s Garden, with 550 spacious one, two and three-bedroom apartments in six separate blocks centred around one acre of private garden, the tallest block being 26-storey.
The design and procurement teams at Elements Europe will work closely with the client, Goodstone Living, a leading UK real estate investment manager in the rental sector and architects – Darling Associates. This project represents a significant milestone in the construction sector, incorporating innovative techniques and technologies to enhance efficiency, sustainability and affordability.
The majority of the superstructure will be constructed by offsite manufactured room modules, minimising environmental effects and disruption thanks to fewer site deliveries, reducing noise and pollution. The 1143 modules needed for the project will be manufactured in Telford between November 2023 and January 2025. Construction activities started on the Birmingham site in July 2023 and phased handover of the six blocks will be between September 2024 and January 2026.
With its exceptional design and attention to detail, this residential community sets a new standard for modern living in Birmingham. The scheme will be sustainably built with +50% reduction in operational carbon and a +30% in embodied carbon (vs. current UK building regulations).
“Elements Europe is dedicated to innovation and excellence. With a commitment to sustainable practices and cutting-edge technology, we strive to transform the construction industry and create lasting, impactful structures,” said David Jones, CEO for Elements Europe. Martin Bellinger, Principal at Goodstone Living, added: “Smith’s Garden is one of the largest and most exciting Build to Rent residential projects in the UK and is testament to the evolution of this sector over the past 15 years.”
Transitioning from a merchant to a manufacturer of steel systems and components was said to have been a ‘stroke of genius’ and instrumental in the growth of the Frameclad business. After 15 years and driven by customer demand, Frameclad now design, manufacture and supply a complete range of steel frames for the construction industry across the UK.
Founder Mark Munns knows that success is built by people and is on a mission to attract ‘premier league’ talent to the Frameclad team. “Our customers are ‘king’ and we believe they deserve the best,” says Mark. “I’m therefore chuffed to announce that Dan Payne will be joining us as Regional Sales Manager for the South. With his ‘can do’ attitude and vast experience, this is a top signing for the Frameclad team. This industry is in his DNA – he knows his stuff and I can’t wait to introduce Dan to the wider team and our much-valued customers in the south of the country.”
Elements Europe are majority owned by GS E&C who took a controlling interest in 2020. As an international company with headquarters in Korea, GS E&C are a $9.5billion a year organisation that is supporting both this project and Elements Europe’s growth as one of the main offsite manufacturers and turnkey modular main contractors in the UK.
Source: www.elements-europe.com
Frameclad operate as a close-knit community, but it is their customers that are at the heart of the operation. “We are known for versatility and agility, but we have learnt this business from the ground up and we understand the market,” added Mark. “We strive to meet our customers’ demands – asking the right questions, listening and reacting. We don’t take a one system fits all approach – we meet our customer’s requirements – they don’t have to meet ours. From ‘off the shelf’ standard infill systems to bespoke developments such as Concord Street, a nine-storey apartment block in central Leeds – projects large and small get the same high-quality products, attention to detail and dedicated services.”
Source: www.frameclad.com
Following the success of previous years’ partnerships, the Structural Timber Association (STA) is proud to once again be an Industry Partner with Offsite Expo, taking place on the 19-20 September at the Coventry Building Society Arena. Playing host to leading offsite manufacturers and suppliers over a two-day event, Offsite Expo is focused on supporting those that are driving change in the construction sector.
As the largest UK trade association within the structural timber sector, the STA will be exhibiting on stand F10 to highlight its mission to promote the use of structural timber in construction, as timber presents the best opportunity for meeting the UK’s net zero commitments by 2050. As such, the quality and standards of timber construction must be to the highest degree; making accreditation crucial to providing investors and insurers with evidence that companies are held to high standards.
At the event, the STA will explain how its STA Assure scheme provides solid reassurances to the construction community that members meet or exceed current legislation and regulatory requirements. Recognised by warranty providers, as well as other key stakeholders including insurers, STA Assure ensures that we remain on top of the
NG Bailey has announced a raft of contract wins worth over £150million for its engineering business, in the last quarter, as it continues to build on its industry-leading expertise in the mechanical, engineering and plumbing (MEP) sector. The series of wins spans sectors including healthcare, education, film and television and rail. This includes a £68million project for the University of Bristol’s Temple Quarter Enterprise Campus, a two-year contract which will see NG Bailey act as the MEP supply chain partner for the project.
The campus, which will sit at the heart of the city’s vibrant new Temple Quarter, will offer a new academic and scientific research hub, featuring six floors of teaching areas, learning zones, academic offices, research and computer labs, and innovation spaces. NG Bailey will be providing a range of MEP installations on the project, including water source heat pumps, heat recovery units, PV panels and LED lighting as well as connecting the building to the Bristol City district heating network.
Other recent project wins include a £8.5million project with Transport for London to provide complete
constantly evolving changes to quality and standards. The team will also be there to discuss how structural timber systems and offsite construction combined can support carbon neutral goals.
The Offsite Expo is also host to the Offsite Awards, which take place in the same venue on the 19h September; with the STA’s Andrew Orriss again on the judging panel. Additionally, the STA are also sponsoring the ‘Best Use of Timber Technology Award’ for this year’s event. The awards celebrate companies and projects that are at the forefront of the industry in terms of innovation and expertise.
Andrew Orriss, from the STA, said: “It’s always an honour to be part of this event and I’m very pleased to have been invited to return to the judging panel for the 2023 Offsite Awards. The standard of entries
has been exceptionally high this year and it’s very encouraging to see the progress and achievements that are being made across the industry. Awards like this are an excellent way of ensuring this innovative thinking is recognised and replicated.”
STA Chief Executive, Andrew Carpenter, will be leading a Q&A Session as part of the Masterclass seminar programme. Held in Seminar Theatre 1, at 10.30 am on the 19 September, Andrew will be on hand to answer any questions about integrating structural timber into offsite construction projects.
Source: www.structuraltimber.co.uk
You can also visit the STA at Offsite Expo on Stand F10
MEP and communications services to a new maintenance facility building at Beckton Depot, which will service TfL’s new fleet of trains. The business has also been awarded two projects with Shinfield Studios, a new UK film, TV studio and production hub in Reading which will encompass over 1million sq ft of purpose-built sound stages, workshops, contemporary offices and post-production facilities, with NG Bailey delivering all MEP services.
Paul Aulton, Managing Director Regions at NG Bailey said: “These recent contract wins demonstrate the continued demand for our engineering expertise, and
fully support our growth across strategic sectors. As a business we have a long track record of delivering offsite manufacture and installation of complex mechanical and electrical solutions. We are looking forward to working together with both new and existing partners to continue delivering outstanding work for some of the UK’s most exciting projects in infrastructure and the built environment.”
Source: www.ngbailey.com
Mid Devon District Council received the prestigious Client of the Year award in the South West’s Constructing Excellence Awards, whilst being shortlisted for further regional accolades. The standout projects that led to this recognition were the zero carbon developments, being built in partnership with innovative, modular house contractor ZED PODS.
Set to be installed on council-owned sites in St Andrews Estate, Cullompton and Shapland Place, Tiverton, both developments are set to be zero operational carbon, making this one of the first social housing projects of this type within the district. The judges were extremely impressed by the Council’s approach to meeting their requirements whilst adopting a framework to support Modern Methods of Construction (MMC). The Council was also recognised for embracing the future and inviting neighbouring authorities to share their experiences.
Councillor Simon Clist, Deputy Leader and Cabinet Member for Housing & Property Services said: “This recognition is a testament to the hard work and dedication of our team, who consistently strive for excellence. We take great pride in our work, and this award reaffirms our commitment to delivering sustainable housing for our community.”
Tom Northway, Chairman of ZED PODS, added: “The council’s team have been focused on delivering exemplar net zero projects. Together, we overcame numerous barriers – from demystifying perceptions of modular housing to unlocking brownfield sites for development including a scheme in a Flood Zone –one of the first in the UK.”
The awards were run by Constructing Excellence South West which forms part of the Constructing Excellence Regional Partnership (CERP) and exists to improve industry performance in order to produce a better built environment. With this win, the Council automatically becomes a finalist in the same category at the National Constructing Excellence Awards Programme, to be held on 23 November 2023 in London.
Both sites will be completed with triple glazing and solar panels, have their own private communal green space as well as separate storage for residents’ bins and bicycles – with plans for new homes to be built on land previously occupied by garages and car parking. “As identified within our Housing Strategy,” added Simon Clist. “There is a need for more social rented housing within the district. These ready to move homes and our long-term programme of housing look to positively address this – these new zero carbon, energy-efficient homes are a way forward and will help towards the Council’s net zero ambitions.”
Source: www.zedpods.com
www.middevon.gov.uk
Connect Modular and Cunninghame Housing Association (CHA) were delighted to host Scottish Government Minister for Housing, Paul McLennan MSP along with Provost Jim Todd to welcome CHA’s first residents to their first volumetric modular, affordable housing development at Shortlees, Kilmarnock.
The properties are manufactured offsite by Connect Modular and the Minister began his day with a tour of their manufacturing facility in Cumnock, East Ayrshire, where he met some of the team responsible for designing and manufacturing the housing modules and to see firsthand the benefits that volumetric-modular construction provides. The tour provided insight into the efficient manufacturing process and rigorous inspection routines delivered by Connect Modular in the production of these new homes to exceptional quality for Cunninghame Housing Association. This process delivers particularly significant improvements in waste reduction, environmental outcomes, and programme certainty.
Connect Modular has returned employment to the former carpet factory, creating and sustaining jobs within the local, East Ayrshire economy. Following the tour of the manufacturing facility, the Minister travelled the short distance to the Shortlees site where he was joined by Provost, Jim Todd, and the
first
Linda Anderson, Acting Chief Executive Officer at Cunninghame Housing Association, said “The Association is committed to delivering high quality homes for rent and it’s been exciting to see this fantastic modular housing development take shape. The handover of these first completed houses to the new tenants is an important milestone in the delivery of 101 new homes in an area where demand for housing is much needed. We’re excited to continue our successful partnership with Connect Modular through to Summer 2024 when the site will be fully complete.”
The collaboration between Connect Modular and Cunninghame Housing Association represents a shared commitment to addressing the pressing need to deliver affordable housing quickly and efficiently. The completion of the first houses is just the beginning of a wider initiative that will ultimately deliver 101 purpose-built modular homes, positively impacting the lives of many individuals and families. Housing Minister Paul McLennan said: “The partnership between Connect Modular and Cunninghame Housing Association, supported by £10.5million of Scottish Government funding, will
deliver 101 affordable new homes at Shortlees. This means that more households will live in a home that meets their needs. Partnerships like this will help us to deliver at least 110,000 affordable homes across Scotland by 2032. At least 70% of these will be for social rent and 10% will be in remote, rural and island communities.”
Connect Modular has a strong pipeline of affordable housing projects, including a second phase of homes with Cunninghame Housing Association and is delighted to bring innovation to support the Scottish Government’s target of delivering 110,000 new homes by 2032.
Richard Reid, Acting Chief Executive Officer at Connect Modular, said: “We are absolutely thrilled to see the completion and handover of the first homes in this 101 modular housing development. This project demonstrates our dedication to delivering innovative, sustainable, and affordable housing solutions for our local communities. We’re delighted to be working with Cunninghame Housing Association on this development and look forward to the continuous handovers of our homes over the next year.”
Source: www.theweehousecompany.co.uk
Just landed! Our NEW pre-painted OSB is a blank canvas, perfect for applying marketing messages and graphics. With all the inherent properties of our popular OSB3, SterlingOSB Zero PrimedPlus has a primed textured finish, and is designed for hoardings, screening, exhibition stands and walkways etc, inside or out. SterlingOSBZero.com
Leading modular and offsite building solutions brand Algeco has introduced a new post-handover electrical testing service for its full range of site accommodation. Alongside this is an extended choice on Algeco 360 turnkey climate control and site Wi-Fi. The new electrical testing element of Algeco 360 turnkey service provides customers with peace of mind that the site accommodation meets all requirements post-handover and includes an NSI certificate just five days after testing.
Under the Health & Safety Act 1974 (HSWA) and the Electricity at Work Regulation (EAWR), employers have a legal duty to ensure the workplace is a safe environment. Algeco electrical testing service provides customers with an electrical installation condition report for all its site accommodation solutions. The condition report is carried out in compliance with BS7671 2018 IET Regulations for Electrical Installations and IET (Institute of Engineering and Technology) Guidance Note 3 Inspection and Testing.
Electrical testing on-site is important because once site accommodation is delivered, customers will connect to a local/generator electrical source. These new connections require re-testing to ensure
everything is safe for use. Algeco units, as is all site accommodation modules, are only tested for delivery and not after on-site installation or on obligatory annual service.
The climate control offering means Algeco customers can reduce energy consumption within their site accommodation by up to 65% – potentially saving hundreds of pounds or more each year – as wells as CO2 emissions. Functionality is extended on climate control to user needs as well as providing yearround climate control, heating, air conditioning and dehumidifier, all in one unit. Being more responsive means that Algeco climate control heats and cools workplaces quicker, whilst reducing electrical load. This means it can be used as an on- or off-grid set up. Remote control and optional Wi-Fi allow temperature to be managed to a fine degree.
The Wi-Fi element of the extended Algeco 360 turnkey service allows customers to stay connected on construction sites with new 5G broadband and large antenna added to the range. These blend the latest technology with expert support to create a bonded cellular connection with the UK’s leading carriers.
Customers can continue to choose either Plug ‘n Play or professionally installed and managed Wi-Fi service. Algeco has link up with a professional installation partner that can install and remotely manage the system wherever the site is located. Algeco Wi-Fi products can be securely connected to corporate networks, enabling site teams to access cloud applications securely. Both ‘plug-and-play' and professionally installed Wi-Fi packages have access to tech support over the telephone between the hours of 09:00 and 17:00 (Monday – Friday).
Chris Coxon, Head of Marketing at Algeco, said: “Our new and extended 360 turnkey services have been welcomed by busy contractors on-site that are tired of managing multiple suppliers, purchase orders and communications. Now, with just one point of contact, our 360 turnkey services does all this for them. And with the extended options on climate control and Wi-Fi, plus new electrical testing, it really couldn’t be easier – a full turnkey solution, including social enterprise options, providing you with everything you need from just one supplier.”
Source: www.algeco.co.uk
Steel fabricators are facing a challenging market, with price rises, increased client demand and a renewed focus on sustainability. With this in mind, Trimble has released a new eBook with the aim of demonstrating how digital technologies can help relieve some of the pressures faced by those in the industry.
Material shortages, fluctuating prices and increased client demand have combined to create a complex landscape for steel fabricators to navigate, who are not only looking to protect their all-important profit margin and continue providing customers with highquality work, but to also meet key sustainability aims. This has, understandably, left many in the industry feeling overwhelmed as to how they can overcome these challenges, whilst remaining profitable, productive and efficient.
Trimble’s latest eBook: ‘A Guide to MIS for Steel Fabricators’ aims to help those in the steel industry to streamline their workflows. Available to download for free online, the eBook covers each individual stage within the steel fabrication workflow (from estimation and procurement through to fabrication, reporting and delivery) and explores the value that a digital management information system (MIS) can bring to businesses, along with cloud-based collaboration tools and a 3D modelling workflow – meaning there is something for everyone.
Providing specific examples of how digital technology can help streamline the fabrication workflow, such as the ability to create more accurate tenders, deliver a traceable flow of up-to-date and accurate data and co-ordinate deliveries to meet with on-site construction schedules (to name just a few). The guide also features a range of customer testimonials and case study examples, to better illustrate the effect digital technology has had for other steel fabricator companies.
Chris Gatehouse, Detailing & Manufacturing Specialist at Trimble, says: “We recognise that the steel industry is a challenging one to work in currently, with a highly volatile landscape to navigate. However, we want steel fabricators and detailers to know that there are many digital tools and technologies available to them, which
can help to streamline their workflow and make their businesses more efficient, profitable and productive. It is our hope that this eBook will truly bring the power to steel detailers and fabricators, allowing them to arm themselves with the knowledge of what digital technologies can do for them and how they can get more from their software, guiding them through this challenging period.”
With cloud-based connectivity and model-driven workflows covering every section of fabrication and construction, Trimble offers interconnected solutions that unite the digital and physical worlds, helping you to build faster, cheaper, greener, and safer.
Source: www.tekla.com/uk
Shaun brings 35 years of experience in the construction industry and an outstanding track record in project delivery. He joins from international construction firm Mace, where he spent 17 years as a Director and was the driving force behind launching and running a business unit focused on maximising offsite pre-manufacture value and assembly.
During his long career, Shaun has led major construction projects across residential, commercial, education, biopharmaceutical, and medical facilities, and many more sectors. He thrives on complex construction schemes and has been central to delivering challenging, award-winning, technical solutions. At Reds10, Shaun’s expertise will be instrumental to setting the foundation for the next phase of the company’s growth trajectory. This includes building on its successful platform approach, harnessing more production and delivery methodologies, bringing innovative solutions to a wider client base, and driving operational efficiencies and social value.
Together, we will continue to challenge and push what the construction industry can and should be, with MMC and technology at its core.”
Shaun Tate (pictured) COO of Reds10, added: “I genuinely believe that our industry is at a crossroads, and we have a unique opportunity to redefine how the built environment is delivered. Offsite construction methods offer an opportunity to drive more intelligent solutions that will enable clients to benefit from a far more predictable and controlled construction delivery experience. Our clients deserve far better from our industry and Reds10 offers the repeatable, predictable consistent outcomes that enable them to achieve higher performing buildings with full confidence in delivery every time.
Vertically integrated offsite construction specialist Reds10 has welcomed Shaun Tate as Chief Operating Officer (COO), to support and accelerate its ambition to become the leader in a new breed of Tier 1 contractors. The appointment follows the third consecutive year of turnover and profit growth for the company, which recently reported an annual 32% revenue and 17% profit increase, attributed to Reds10’s continuing commitment to investing in its products and people.
Portakabin has added three new leaders to its executive team as the company bolsters its dominant position in the offsite industry. With the recent acquisition of healthcare specialist Darwin Group, Portakabin is making serious inroads in asserting pressure on other players in the modular market. With 283,900sq m of manufacturing space across three sites, and over 80 customer locations across Europe, it remains the largest supplier of modular buildings in the UK alone.
Dan Ibbetson, CEO comments: “There are many elements required to not only make a business successful but to also make it a great place to work; a clearly defined strategy, excellent governance and amazing people certainly helps. Gavin, Simon and Kim are the final pieces in the puzzle for us and I’m incredibly excited to see where they’re going to take us.”
Kim Panton joined in August 2022 as People and Culture Director from Rolls-Royce where she has spent the past 20+ years working with one of the world’s most reputable brands. Her strategic HR skillset has ranged across the group’s business units and brings considerable experience in people and organisational development. Kim said: “Portakabin is a fantastic business with brilliant people and
Matt Bennion, CEO of Reds10, said: “We are delighted that Shaun has joined the Reds10 team. Like us, Shaun is passionate about changing our industry and is a real innovator in the delivery of high-quality offsite construction. His major project experience and drive will help us to accelerate our ambition to become the leader in a new breed of Tier 1 contractors, so that clients have a viable and sustainable alternative to traditional delivery.
“Reds10’s platform approach, focus on product innovations that meet client needs and vertically integrated model are unique in our industry and mean that we control every step of the production process and our own destiny when it comes to delivery, by driving a production mindset and deploying the right technology through ever more powerful digital platforms. To be part of a team with a shared vision of a better future and an insatiable desire to drive our industry and lead a revolutionary change for the better, is something that genuinely excites me, and I can’t wait to get started.”
Source: www.reds10.com
represents an exciting new challenge for me. I’m delighted to have joined the team and I’m looking forward to supporting the organisation as it grows and develops.”
Simon Thomson joined in January 2023 as Company Secretary and General Counsel from Aggreko and has quickly become a strategic partner to stakeholders both within the legal function and throughout the wider organisation. Simon comments: “I’m incredibly proud to be part of this organisation; it has a fantastic heritage, and our people strike the right balance between being commercially minded and customer focused. I’m looking forward to realising the outstanding potential for future growth and success with Portakabin.”
Gavin Urwin joined in March 2023 as Chief Financial Officer from Smart Metering Systems PLC (SMS) and brings considerable experience of working within both PLC and family-owned businesses along with his ability to manage multiple stakeholder groups. “There’s never been a better time to join a market leading brand name such as Portakabin,” said Gavin. “It’s a growing and ambitious business, both in the UK and Europe, has fantastic people working for it and I’m delighted to be part of its future.”
L-R Gavin Urwin, Kim Panton and Simon Thomson
Source: www.portakabin.com
THROUGH OUR MODERN METHODS OF CONSTRUCTION NEW HOMES (NH3) FRAMEWORK
Our frameworks are procured in accordance with The Public Contracts Regulations 2015 and are free to use. They provide public sector organisations with easy access to procure works, products and services for the construction, refurbishment and maintenance of social housing, schools and public buildings.
LHC Procurement Group strives for excellence in the services provided to their clients and aims to deliver the best solution to suit every project’s individual needs.
Our dedicated Client Support and Project Support teams are on-hand to assist throughout the life of the project.
For more information on how our frameworks can work for you, get in touch.
www.lhcprocure.org.uk
HELPING YOU TO BE MMC READY
A 32-bed short-stay ward for Northwick Park Hospital London is being created above the existing A&E department by MTX in one of the most complex build programmes ever undertaken by the company. More than 50 structural steel modules manufactured offsite will be used to construct the new ward on a steel deck installed on existing concrete stub columns that were part of the original A&E department build.
The challenging location amid the busy hospital site requires the use of the UK’s largest crane to lift the modules into place and MTX is currently constructing additional site infrastructure including high strength concrete foundations and piling to support the crane.
MTX has huge experience working on hospital sites and the team pride themselves on being able to deliver contracts with minimum disruption to the vital services provided by the medical staff. At Northwick Park this means maintaining safe access to the A&E Department for both pedestrians and ambulances throughout the build programme. They also prioritise the safety of their own staff and contractors which in this case entails building a pedestrian bridge over a busy road on-site to enable access to the build location.
Modular building specialist Integra Buildings has announced a £1million programme of investment at its East Yorkshire site to reduce the carbon footprint of its operations. Integra is driving down emissions at its headquarters in Paull, East Yorkshire, with an ambition to become a carbon neutral business by 2038.
Key sustainability projects on-site include the installation of more than 70 rooftop solar panels on Integra’s office building, with a further 150 panels fitted to one of the factory units. Integra has also reduced the volume of waste leaving its site by almost 20%, thanks to a compactor which cuts the number of lorry trips to the processing facility and saves on carbon emissions. The business has also secured ISO 14001 Environmental Management accreditation as it sets out a roadmap to carbon neutrality.
Integra CEO Gary Parker said: “We’ve done a huge amount of work to firstly understand our carbon footprint and then identify the priority areas and key actions we can take to become more sustainable.
The programme includes designing and installing mechanical modules pre-manufactured offsite to control the ventilation and the environment of the wards, with a dedicated integrated plant facility provided within the new building as part of the M&E specification. The new first floor construction will link to the existing hospital buildings via a 20m-long suspended connecting corridor. It will also link to two existing stairwells to provide access for staff and visitors.
Northwick Park Hospital is situated on the outskirts of Harrow in North West London and managed by the London North West University Healthcare NHS Trust. The new £20million state-of-the-art short-stay ward is designed to enhance the quality of care provided to patients at Northwick Park, and is part of an NHS
England initiative to meet the growing demands for general and acute beds across the country.
MTX Managing Director David Hartley explains: “We have worked with the Trust on previous projects, and we are immensely proud to have been awarded this contract to deliver the new facility. Our team at MTX recognises that these new beds are urgently needed at Northwick Park, and we are working closely with the Trust to progress the build programme as swiftly and safely as possible. With such a major development within the busy hospital site there will inevitably be some disruption to existing access and traffic management arrangements but our close collaboration with the Trust team aims to ensure it is kept to a minimum and mitigate any impact on patients and staff.”
Source: www.mtxcontracts.co.uk
Construction companies like us face significant challenges in reducing their emissions and becoming carbon neutral, but we’ve taken significant steps forward and we’re committed to working with our suppliers, clients and partners to share ideas and help each other on the decarbonisation pathway.”
The first phase of Integra’s solar installation saw 72 panels on the roof of the office building expected to reduce annual energy bills by over £80,000. Since then, an additional 150 panels have been fitted to the roof of one of Integra’s factory units. The two installations combined will generate close to 200,000 KW of clean electricity every year. All the modular buildings Integra manufacture are 100 per cent re-usable and can be relocated. Should the building ever be disassembled, timber and steel products can be easily recycled.
Simon McGeachy, SHEQ (Safety, Health, Environment and Quality) Manager at Integra, added: “Our sustainability work also extends into the local community. We’ve been supporting the Humber Wood Recycling Project for a number of years, donating our surplus wood which is used to create outdoor furniture for Dove House Hospice.”
Integra is carrying out further work to understand its scope two and three emissions, including those produced throughout its supply chain and operations offsite. Integra’s environmental approach is to only consider carbon offsetting as a last option where there is no possible outcome of achieving net zero.
Source: www.integrabuildings.co.uk
Smartroof has successfully completed a groundbreaking project at Claremont Garden Centre in Essex. The Claremont Garden Centre project in Woodham Mortimer marked an exciting milestone for Smartroof, as it was their first venture into the commercial sector and the first time the company has installed its panelised roofing system to a steel portal frame instead of masonry.
Overcoming unique challenges posed by the project's size and requirements, Smartroof's offsite ‘room in roof’ system has been employed to create a new cafe, office, staff room, and greenhouse. Partnering with architectural firm Acanthus and client English Auberge, Smartroof demonstrated their expertise and adaptability, providing an exceptional roofing solution for this new multi-use garden centre building.
Drawing on their expertise and recommendations, Smartroof collaboratively enhanced the designs, incorporating their ‘room in roof’ system seamlessly into the architectural vision. The project’s scale presented a remarkable feat for Smartroof, leading them to manufacture their largest panelised roof panels to date – each an impressive 13m long. Rigorous planning and precision during the design and manufacturing stages ensured a smooth process for both the factory and logistics, ultimately resulting in a flawless installation.
The Smartroof system offers a complete roofing solution for builders and developers seeking to unlock a building’s full potential by creating functional spaces within the roof space. Comprising a series of factory-produced panels, including insulated roof panels, spandrel wall panels as well as dormers, roof windows, decorative chimneys, soffit, and fascia where required the system is expertly delivered and craned into place on-site. Smartroof’s offsite fabrication facility in Derbyshire provides a controlled environment that enables the technical team to achieve the architect's vision with millimetre precision in both cutting and fabrication.
In an era demanding faster construction methods and heightened energy efficiency, the offsite fabrication of roofs at Claremont Garden Centre delivered substantial benefits to all stakeholders. From improved health and safety to accelerated construction speed,
and exceptional quality control, Smartroof's innovative solution was tailored to this bespoke design and resulted in estimated savings of up to three weeks when compared to traditional on-site methods of roof construction.
Ian Dean, Operations Director at Smartroof said: “We take immense pride in delivering cutting-edge roofing solutions that are custom-tailored to meet the unique requirements of each project. Our collaboration, along with our vast design and fabrication experience, played a pivotal role in the success of the Claremont Garden Centre project. With a genuine passion for efficiency and an unwavering pursuit of perfection, we are the ideal partner when it comes to the creation of superior quality buildings.”
Source: www.smartroof.co.uk
Theory, practice, experimental campaigns: putting it all together on screws takes years of lectures, workshops and construction sites. We make it available to you in 70 pages that are extra catalogue. Because our experience is in your hands.
O’Keefe is carrying out the second phase of groundworks and infrastructure works for a new residential development by modular offsite specialist TopHat. The project is part of a larger scheme that will see TopHat deliver almost 300 new volumetric modular homes over three phases on the 4.8-acre Kitchener Barracks site.
O’Keefe is the groundworks contractor on the current second phase, which started with enabling works in January 2022 followed by the main works package in March 2022. The company was principal contractor on the first phase of the scheme, completed in early 2021. The site knowledge gained by the team on that phase has assisted greatly when dealing with the construction element of the phase two works.
The Kitchener Barracks project involves the construction of three four-storey blocks of modular apartments which will comprise 96 oneand two-bedroom homes. On this phase, some 240 modular sections were assembled on-site, and cassette corridor sections were then installed at the upper levels between the rows of apartments.
O’Keefe’s role includes part-construction of foundations, drainage and services for the modular apartments, plus access roads and external finishings. Although the apartment modules are manufactured
offsite, they still require foundations and services to be built in-situ. The foundations are mass concrete strip footings bedded a minimum 200mm into the underlying chalk strata. One of the biggest challenges for O’Keefe has been to ensure the on-site works perfectly align with the factory-built modules. Working to exacting tolerances, O’Keefe has formed upstands to receive the prefabricated modular units.
“Co-ordination is vital when offsite manufacturing and site build foundations are carried out,” says Project Manager Daniel Gough. “It is essential that precise as-built surveys are carried out to ensure that the position and levels are within the specified tolerance and any drainage pipes are located correctly.”
O’Keefe formed the drainage connections prior to the modular sections being installed. Service entries were taken into the plantrooms situated in the two stair cores and then distributed to the modular units. Reinforced concrete upstands and slabs were constructed within the two cores and the end escape stairs and a reinforced concrete in-situ lift core constructed to each of the cores, with a steel framework installed prior to installation of the modules. O’Keefe’s contract has also involved construction of a reinforced concrete (RC) frame extension off the back of the existing Khartoum Building, dating from the 1930s.
“The complex design has been a continuous, coordinated process assisted by O’Keefe, the consultant engineers, architects and TopHat, to ensure that further survey work was carried out to slabs, roofs, cavities and foundations for the structural frame to have its final design,” added Daniel. “Underpinning was carried out on the building in the early stages of the project and then the installation and cutting back completed after the concrete had cured. TopHat and O’Keefe have worked together throughout the RC frame element of the works to monitor progress and provide live survey data to the consultant engineers and architects to assist with overcoming any issues encountered during the RC frame build.”
Andrew Shepherd, Managing Director of TopHat added: “TopHat have worked closely with O’Keefe on this complex and groundbreaking project. It was essential that we had a partner that was able to address a number of different challenges from foundations for an innovative modular project through to a concrete frame that would tie into an existing heritage building. This ongoing relationship has been formed on a process of innovation and continuous improvement, which underpins our joint approach to future projects.”
Source: www.okeefe.co.uk
www.tophat.io
Fusion Steel Framing has been brought on board as a contractor for 5-star housebuilder The Hill Group and L&Q’s large-scale redevelopment of the former Citroen garage, Kew Bridge Rise, in West London.
Fusion will be fabricating 13,720sq m of its innovative TraxTM product to form the steel frame system infill across five buildings of up to 18 storeys on the development. Kew Bridge Rise, located within the heart of the Brentford regeneration area, will deliver 441 new homes, of which 50% will be affordable. Construction of the steel frame system has already begun on-site, with the development expected to complete in 2026.
Since its foundation in 2000, Fusion has delivered more light steel residential structures than any other European producer and worked with some of the largest contractors and developers in the UK construction industry. In 2022 Fusion was acquired by Hill to advance Hill’s progress in MMC and more efficiently integrate light gauge steel frames on developments such as Kew Bridge Rise.
Mike Fairey, Managing Director at Fusion Steel Framing, said: “We are delighted to be providing our industry-leading TraxTM product on this significant residential scheme, and to support our partners at Hill and L&Q in bringing their vision for the project to life. TraxTM’s custom design, high-precision engineering, and exceptional thermal and acoustic insulation mean our product aligns perfectly with their ambition to deliver high-quality residential units across the development.”
TraxTM is a highly economical non-load bearing infill system which helps to create rapid dry building envelopes on a range of building types using steel
framing. The works at Kew Bridge Rise will involve Fusion forming the openings, applying RCM DensGlas external board, Kingspan K-Roc insulation and fitting of brick tie channels. Fusion expects to be working on-site for around 12 months.
Fusion will manufacture TraxTM at the company’s high-grade 80,000sq ft manufacturing facility in Northampton, which has the capacity to deliver over 30,000sq m of light steel each year. The company’s expert engineers will then deliver and install the TraxTM system at the Kew Bridge Rise site. The development will have a concrete frame structure and TraxTM will be used for the infill between floors, sitting on the floor slab up to the ceiling. In addition, Fusion will create the window apertures, providing a complete solution for the project.
Cain Peters, Regional Director at The Hill Group added: “The key advantage of using Fusions’ trail-blazing TraxTM system is the ability to rapidly accelerate construction projects while de-risking the process of installing a structural framework system. The system also reduces fire risk which is always at the forefront of our construction design. This extensive redevelopment project will be an impressive example of the capabilities of delivering prefabricated steel frame systems at scale.”
Hill and L&Q began on-site in Brentford in September 2022. The project also includes a new public square, alongside significant investment in local infrastructure improvements. The joint venture partnership will also provide a range of social benefits for the local area during construction, including investment in significant employment, training and community focussed opportunities.
Source: www.fusionsteelframing.co.uk
Approval has been granted by Charnwood Borough Council for the creation of a new Space4 timber frame factory – believed to be the biggest in the UK – on the edge of Loughborough. The stateof-the-art facility will bring up to 120 new jobs to Loughborough and the surrounding areas, whilst also utilising the latest automation technology as part of the manufacturing process.
The factory will produce timber frame units for up to 7,000 homes a year and is set to be in full operation towards the end of 2025. Utilising modern methods of construction (MMC) systems within Space4’s products places sustainability at the core of its build practices. Utilising timber over other materials enables the homes to be more environmentally friendly – all the timber used is from sustainable forestry sources. The factory-assembled nature of the product will also help to improve the speed and consistency in quality of the homes built, with timber frame homes being around 20% more efficient to build than other methods.
Gareth Wicks, Managing Director Designate at Space4, said: “We’re delighted to have received approval for our new Space4 facility and I want to thank Charnwood Borough Council for their support. Not only will the development deliver up to 120 new jobs, it will also further our goal to place sustainable practices at the very heart of our developments. We’re committed to creating vibrant, successful communities with the environment in mind. We’ll continue to work in partnership with the Council and other stakeholders to ensure our new Space4 factory delivers real benefits for local industry and the wider Loughborough community.”
The new Space4 facility will be placed on the Garendon Park Sustainable Urban Extension (SUE), a community of over 3,000 homes on the Garendon Park estate. Dan Endersby, Managing Director of Persimmon Homes North Midlands, added: “Garendon Park will be one of Persimmon’s flagship communities, with over 3,000 homes, employment and leisure facilities, and a range of preserved historic monuments around the site.”
Source: www.persimmonhomes.com
M-AR Offsite has partnered with Biffa, the UK’s leading sustainable waste management company, to ensure all waste generated through its manufacturing and construction operations is reused or recycled.
Through the partnership M-AR is refreshing its current waste management programme with the aim of diverting 100% of its waste from landfill. The new Biffa skips in place around M-AR’s factory have clear signage as well as being colour coded to help visually identify what waste goes in which skip. It also creates a clear central focal point for waste management in the factory, which along with M-AR’s newly appointed ‘Waste Champions’, is designed to maximise take-up among staff.
Tom Malcom and Jamie Leckenby, who are both part of M-AR’s internal logistics team, nominated themselves to be M-AR’s first ‘Waste Champions’. The role involves educating the team and communicating policy changes to the whole production team. They will both receive specialist training and support from Biffa to appreciate the benefits of segregating waste effectively.
Biffa and M-AR will collaborate on future waste reduction initiatives to implement within the business. M-AR will also be able to accurately report on waste
volumes and disposals to track ongoing progress and understand where changes may need to be made to the process through its own online Biffa portal. The signage boards placed around the factory, as well as acting as prominent reminders about segregation of waste materials, will be used to provide feedback to the factory from the data collated from the Biffa portal.
Dan Lowther, Head of Procurement and Supply Chain at M-AR said: “While this first phase covers waste management specifically relating to our manufacturing facility in Hull, our ultimate aim is to roll the programme out to all our live construction sites across the UK. This step marks a significant improvement in the reduction of waste generated on construction sites which are typically harder to regulate than a controlled factory setting and will mean that we’re able to divert all waste material from
landfill whether that’s generated in the factory or on-site. Reducing our waste materials to zero is a key part of our ongoing commitment to achieving net zero status as a company and reducing the embedded carbon of the modules we manufacture and install.”
Shaun Williams from Biffa's commercial team in Humberside, added: “We know recycling and sustainable waste management is extremely important to companies of all sizes, so we're delighted to be working with the team at M-AR to bring our knowledge and skills to drive sustainability at their factory. Small steps can make a big difference and recycling more waste means there's less consumption of raw materials and fewer carbon emissions, which all contributes to the UK's effort to achieve net zero.”
Source: www.m-ar.co.uk
HENCO PRO-FIT
• 100% Visual jointing control
•
•
•
• Secure non demountable function
• Ergonomic design
HENCO PK FITTING
• Chemically resistant
PVDF and stainless
steel construction
• Leak Before Press technology
• 100% recyclable
and share best practice to provide high quality new facilities, drive down carbon emissions and deliver social value to the prison community. Alliance members will also collaborate on how to support and work most efficiently with supply chain partners across the sites.
The prison places will be in new houseblocks with a standardised design and construction approach maximising quality, efficiency and sustainable outcomes through modern methods of construction (MMC). Each houseblock will include 60 singleoccupancy rooms and be supported by larger kitchen spaces and other relevant ancillaries.
A number of the sites will contain educational areas for study and light industrial units where prisoners can take professional courses such as bricklaying. All three contractors will also provide training and employment opportunities for prison leavers to support rehabilitation.
A spokesperson for the Alliance said: “This vital project will deliver much-needed prison places while also providing valuable training and employment opportunities to those leaving prison. Working in partnership together and using standardised designs, modern methods of construction, and a shared strategic supply chain enables us to drive efficiency and deliver significant value across multiple concurrent projects.
We welcome this pioneering approach from the Ministry of Justice and look forward to working with them on this programme that will see the delivery further safe, modern, sustainable, and fit-for-purpose accommodation for the Justice system.”
Kier, Laing O’Rourke and Wates have been appointed by the Ministry of Justice (MoJ) to provide up to 1,200 new prison places across the UK with a focus on safety, security and rehabilitation and will be using offsite methods.
Building on the success of the MoJ’s pioneering Alliance model, all three contractors will collaborate
This approach is fully aligned with the government’s Construction Playbook and recognises the significant benefits of Tier 1 contractors working together to drive innovation, maximise social value outcomes and create a contemporary prison estate that will deliver on the UK’s 2050 net zero carbon targets. This programme builds on the success of the Ministry of Justice’s pathfinder projects at HMP Five Wells, HMP Fosse Way, and HMP Millsike.
In addition to this programme, Kier, Laing O’Rourke and Wates are working with ISG and the MoJ in the separate Alliance 4 New Prisons (A4NP) which will deliver an additional 6,000 new prison spaces. Kier and Wates are also working as an Alliance to provide up to 2,200 places through the MoJ’s Accelerated Houseblock Delivery Programme.
The three teams will immediately commence an intensive preconstruction period. Construction work is anticipated to begin in 2024, with the houseblocks set to be operationally ready from 2025.
Source: www.wates.co.uk
With a product range specifically developed to improve the operational energy efficiency of buildings, leading manufacturer Glidevale Protect has launched several initiatives to reduce the environmental impact of its business operations.
Glidevale Protect is at the forefront of designing ‘hidden protectors’ such as specialist roofing and construction membranes and ventilation solutions, that help to improve a building’s overall thermal efficiency and airtightness, whilst reducing the risk of condensation. The manufacturer is working to improve the sustainability and operational efficiency of its business, with key projects underway including the creation of Environmental Product Declarations (EPDs), progressing towards accreditation to the ISO 50001 energy management standard and tracking recycling levels and
energy consumption across its UK based manufacturing facilities. The business is also investing in closed loop recycling of its product waste and is looking at other ways to improve the environmental footprint of its packaging.
The company has established a dedicated Group Sustainability Board and has gained a silver accreditation from the Supply Chain Sustainability School, which highlights its commitment to employee engagement and training.
John Mellor, sustainability lead for Glidevale Protect says: “Our current activities are being implemented from the front line with both internal and external customer drivers and we are not paying lip service or greenwashing with regards to reducing our environmental impact across our factory sites. Our key stakeholders within the business engage in monthly meetings to help push through positive changes and where necessary
we are consulting with industry experts who can assist us in our sustainability roadmap.”
Glidevale Protect is a UK producer and a subsidiary of Building Product Design Ltd – one the UK’s leading forces in the development of building ventilation solutions and specialist building products.
www.glidevaleprotect.com
Images:
01. L-R: Glidevale Protect’s commercial director Ben Gerry, sustainability lead John Mellor and quality technician Dean Horner holding granulated ABS, made from waste offcuts from its tile vent production line. This is then compounded, moulded, and recycled back into products.
Trina Chakravarti, Director at Building Better, took some valuable time out to speak to us about the organisation’s role and why MMC is integral to the improvement of the social housing sector.
Q: Building Better is an alliance of housing associations and local authorities committed to using more offsite manufacture in social housing – can you a say a little about its background and mission?
Trina Chakravarti (TC): Building Better was set up by social housing providers, for social housing providers. Everything we do centres around our social purpose – to provide homes that help people lead healthy, happy lives. I think that’s a real strength for us as an alliance. It’s in our gift to do something that impacts both our residents and the environment they live in and MMC supports both areas. Our mission is also to focus on sustainability in its broadest sense and the more we save by harnessing demand from other social housing organisations (we now have 32 members), the more we can all build and benefit both the climate and residents.
Q: The quality of housing generally in the UK is under a constant critical spotlight – perhaps more so in the social housing sector. Where are the main pinch points in social housing supply and how can offsite improve building at scale and give registered landlords best value for money?
TC: There’s no silver bullet here. We’re not for a second suggesting offsite alone can make up for the chronic undersupply over a generation –but it must be part of the solution. The labour crisis means there aren’t enough skilled tradespeople to build homes traditionally and layers of subcontracting encourages the passing down of risk and a lack of ownership.
Offsite and the assembly-led manufacturing process improves quality because employees (and their work) can be checked more easily –reducing downstream operational and
maintenance costs. It’s also a more attractive environment to work in – one location, safer, not exposed to the elements and appealing to a more diverse workforce. A development director recently described traditional construction as “building the retrofit of the future” and this highlights another way scaled offsite construction can give housing providers value for money. Our members are thinking about how the homes they build now will stand the test of time in terms of environmental and energy performance as well as customer comfort and affordability.
Q: How easy – or difficult – is it to convince clients that MMC is a viable route to better housing for their portfolios and residents? What objections do you often come across?
TC: We’re finding that sharing experiences, case studies and data is critical to engaging clients and
showing them that MMC is viable and will help them provide safer, higher quality homes for their residents, but also homes that will need less maintenance and retrofit down the line. Hearing first hand from other housing associations and local authorities helps to break down the fear factor around risk in the market, but also where to begin and what type of MMC is right for their homes.
Objections include cost and cost certainty. We’ve designed our procurement framework and dynamic purchasing system to provide clarity on cost. With our procurement partner, Procurement for Housing (PfH), we’ve created an MMC cost modeller that members can use to quickly find out prices by choosing from a range of housing archetypes, confirming the number of units and their location. This provides an estimated cost per square metre for a fully completed site with the opportunity to get an uplift price for net zero.
Q: Procurement, planning and pipeline are three Ps associated with many frustrations surrounding the wider growth of offsite manufacture – is that fair to say from your experience? What are the barriers to wider adoption?
TC: I’d agree on those, but I’d add a fourth: Price! MMC has got an image problem when it comes to price, with people often (wrongly) assuming it will cost more than traditional. Building Better has been tackling this head on by creating streamlined, accessible ways to procure MMC at affordable prices but also by gathering cost data from housing providers using MMC
at scale. We’ve worked with several housing providers, each delivering MMC homes, to gather their figures which you can read about on our website. This data shows that MMC costs are on a par with traditional homes when you compare like for like on specification. If there is a slight increase for MMC then it’s offset by savings from offsite where homes need less maintenance and retrofit down the line.
Q: Are any preferences being shown by the membership for MMC Categories and what level of understanding is there amongst housing associations and local authorities of the various methods and benefits behind these?
TC: We’ve seen a lot of interest in both Category 1 and Category 2 and there is some knowledge about the different processes and advantages but equally, housing organisations are really appreciative of the webinars, factory tours, workshops, case studies and other content we create that clearly explains what MMC is, the different categories and the difference within those categories.
We get a lot of feedback from members saying that they want to take people from across the whole organisation on the MMC journey –from asset management and sales, through to comms and finance teams. That means ditching the jargon and laying out the benefits to different stakeholders plainly. It also means painting a rich picture of what MMC is all about, different experiences, different schemes, different techniques so everyone gets on board.
Interestingly, there’s also demand from our members to unpick the term ‘net zero’. It’s almost meaningless because it’s so overused and that’s why we’re launching a sustainability campaign.
Q: Factory-design and offsite manufacture can solve many issues surrounding ‘net zero’ housing and reduce the construction sector’s carbon footprint – how are you instilling sustainability into your client conversations?
TC: Offsite manufacturers are much clearer on how they get from their current product to net zero than traditional builders – it’s definitely a bigger leap for traditional. For the MMC industry, sustainability has always been a key selling point and it’s threaded through their processes and products.
We’ve just launched an MMC sustainability campaign to provide information, ideas and evidence so housing associations and local authorities can identify key sustainability standards, pick the outcomes they want to achieve and understand the actions they need to take around MMC. There’s still work to do in terms of communicating the link between MMC and improved environmental standards. People know there is a connection, but they’re often hazy on the standards and terminology – a bit like with offsite. We want to support housing providers by outlining the sustainability benefits of MMC for customers and the climate.
Q: At the heart of Building Better is the aggregation of demand for offsite housing delivery and streamlined procurement routes – what are the benefits of this approach and wider collaboration within the membership?
TC: A member said to me recently that when you have a relatively new approach like offsite, some housing providers must be the torch bearers. MMC requires enough of these torch bearers to step into the arena and work with manufacturers to realise economies of scale. That’s starting to happen. We’re harnessing demand in the sector by giving housing associations and councils confidence they are going down the right route, in the right way.
Another thing members tell us is that the procurement routes we’ve developed with PfH – a MMC Category 1 framework and a MMC Category 2 dynamic purchasing system – remove the hassle factor. Historically, MMC procurement has always been seen as complex – it can slow a project down and add on cost. We wanted to remove the procurement headache for housing providers and offer them a ready-made, compliant route to market that allowed early engagement with the supply chain. Procurement for Housing really know their stuff in this area and the support they give to our members is invaluable.
Q: You have a key role working with the Department of Levelling Up, Housing and Communities (DLUHC) on research into standardisation and a ‘kit of parts’ approach – how can these platform approaches and repeatable components deliver building improvements?
TC: I’ve been borrowing a transport analogy to describe the huge variation in offsite. Its seven different categories vary as much as a scooter does from a double-decker bus. For a relatively young industry like this one, a lack of commonality, not just between categories but within them, can get in the way of large-scale adoption.
DLUHC have launched research to develop specifications for standardised MMC components that can be used in housebuilding. Partners are engaging the sector to create a digital kit of parts and I’m chairing a strategic advisory board to guide the research. This open access approach will use a common language that encourages all housing organisations and manufacturers to describe offsite performance and compliance requirements in the same way. It will also tackle the fragmentation of data in MMC which is blocking collaboration. If we get this right, then the benefits include being able to offer more choice through increased interoperability of components and techniques. We’re also hoping to improve resilience and steadiness in the industry and lower risks levels.
Q: What plans has Building Better in place for 2024 and how do you see the offsite sector developing generally over the next 18 months?
TC: There are a number of trends we see developing across offsite including business models becoming clearer, the turnkey offer maturing, and as confidence grows, a move away from an all or nothing approach to MMC. Clients are prepared to take more of a mix and match approach to categories, based on the outcomes they want to achieve.
As an alliance, we have three priorities over the next 18 months. The first is building demand-side capability. The key to moving the dial on delivery through offsite methods is to build confidence and capability within social housing providers’ development teams. We’re doing this by providing hands on, practical support through one-to-one training and workshops.
We’re also developing supply-side resilience. There’s been well-publicised volatility in Category 1, as well as across housebuilding more generally, and that’s something we’re tackling through greater collaboration between traditional and offsite. The first step
is to develop a procurement route to traditional contractors who have experience in MMC. The third aim is all about evidencing benefits. Our members have developed a high-level post-occupancy evaluation dashboard of metrics and a feedback loop. We’re collecting data on quality and customer experience of all Building Better homes to prove the benefits of offsite and improve design and delivery of future homes.
For more information on the work of Building Better visit: www.buildingbetter.org.uk Images:
Offsite and BIM technologies are two aspects of construction frequently proclaimed as holding the key to the industry’s more efficient, sustainable and digital future – but what happens when the two come together? Craig Johnson, Business Development Manager at Trimble, explains.
“You get to construct it twice: once in the digital environment and once on-site. From accuracy at the detailing phase through to on-site coordination, Tekla software comes into play at every stage and feeds into our Virtual Design and Construction (VDC) processes.” – Sigmat
In many ways, BIM and offsite are perfect partners. With a BIM workflow, the value and benefits of offsite that we are already seeing can now be leveraged and pushed even further, helping contractors to deliver offsite projects to an even higher standard and produce a new generation of sustainable and impressive buildings.
Perhaps the main value of offsite construction is the enhanced level of control it offers clients and contractors – invaluable as we consider a construction industry that has an increasingly fragmented workforce, material price rises, stringent building regulations and a push on sustainability. A key enabler of this control is having and leveraging data correctly, with a streamlined flow of constructible data running from the beginning to the very end of a project, and BIM software and other digital technology at its heart.
“Quality is key within MMC – it’s all about bringing factory quality products and components into the construction site setting. And modelling tools and model-based software are a key part of achieving this.” –
Design & ConsultancyWith BIM software, such as Tekla’s constructible modelling solutions,
manufacturers, detailers and contractors can have confidence in the accuracy and reliability of their data. The 3D environment offers enhanced visibility, in turn ensuring high levels of precision and exact coordination, enabling contractors and fabricators to meet the tight tolerances required.
“The benefit of BIM on offsite projects is huge, with the ability to easily check, verify and compare information to ensure it is correct, before you progress to fabrication. When you know the data you are using is correct and constructible, the overall project delivery is a lot simpler and more straightforward. It makes you more confident in your design, with the ability to see instantly if there’s any discrepancies or issues and be able to resolve those effectively.” - Frameclad
In many ways, Tekla can also provide a digital rehearsal of the works, with teams able to consider not just the structural design but also the logistics of the transportation, installation and assembly. The focus goes beyond just detailing the components to also include consideration of the fabrication and on-site erection, ensuring the structure is being designed in a way that is best for everyone – in other words, taking a Design for Manufacture & Assembly Approach (DfMA).
Another value of BIM for offsite is the interoperability of software and technology. Done correctly with an openBIM approach, data from the 3D model can be fed into the factory machinery for a truly automated and streamlined fabrication workflow. Looking towards the future and the rise of smart machinery presents the potential for fully automated manufacturing lines, with minimal manual input required following the sign-off of the model and significant productivity gains as a result.
“When it comes to fabrication, we’re able to upload the CNC files from the Tekla Structures model directly into the factory and use this data to programme our machinery. When processing stud and track profiles, for example, the machines will use the model data to correctly profile it, cut it to specification, drill the holes, etc. Fully automated, this enables our steel frame fabrications to be carried out to extremely high levels of accuracy – to within 2mm.” – Sigmat
For more information visit: www.tekla.com/uk/resources/ modular-manufacturer or see Trimble at Offsite Expo Stand D07
Delivering more light steel residential structures than any other European producer
At Fusion, we are leaders in light steel framing solutions, a modern method of construction that brings huge benefits to our clients. Our light steel solutions and accompanying products offer outstanding precision, efficiency, adaptability, sustainability and performance. Using digitally enabled processes, we work closely with our clients across a range of schemes to help them achieve exceptional results.
Whatever your project, speak to us today to find out how we can assist you.
Can the offsite industry better embrace and foster a culture of ideas and knowledge sharing through improved supply chain integration? A recent roundtable event hosted by VOLUMETRIC™ explored how.
property (IP). Nothing is interoperable. Companies see each other as pure competitors and do not see the benefit of interoperability between systems. That is where I see a significant barrier to collaborative R&D.”
When we utilise the knowledge and skills of others, we find opportunities to enhance the R&D process and maximise lean manufacturing opportunities and as often discussed – early supply chain engagement can bring new ideas, improved products and better solutions. Early integration and collaboration offer up a wealth of opportunities, tapping into the experience and skills available throughout the supply chain to create better synergy to deliver products more valuable than the sum of individual parts.
Early collaboration also leads to greater efficiency, improved productivity and cost savings. In a survey of over 100 organisations in multiple industries conducted by global consulting firm McKinsey,
companies that regularly collaborated with suppliers demonstrated higher growth, lower operating costs, and greater profitability than their industry peers. Yet consensus amongst supply-chain experts is that these opportunities are not being used to their full advantage. So, what is stopping the industry from adopting a more co-operative R&D strategy –and how can we implement a more collaborative culture?
Trevor Richards, Operations Director at VOLUMETRIC™ thinks that when it comes to development, the answer lies in moving from individualism to a more universal approach to standardisation. “I think the problem – especially with modular – is that everybody is protective of their intellectual
“It feels very individualistic. Nobody wants to come together and say this is the standard –that is a standard wall system that meets the industry criteria and is compliant,” adds Ian Quinton, Managing Director for RCM/Benx who would like to see better engagement when it comes to product testing, and better access to test facilities for product collaborators. “There are more and more manufacturers, and they are all doing testing individually rather than bringing it all together.”
One of the key benefits of early engagement and collaboration is the opportunity to prototype new products and work cohesively to explore product range options. Clients, developers and architects want the flexibility to create unique designs and structures. However, what is desirable and what is realistically achievable, whilst being compliant and meeting required standards, may not be the same. This is where getting people around the table, working together to design, test and iron out any complexities as soon as possible, can make all the difference. Adopting a culture of collaboration allows the supply chain to work out what is possible.
Simon Buckmaster, Technical and Sales Service Manager for Fermacell/ James Hardie explained how their approach helps to find opportunities and reduce risk, adopting a mindset of early engagement to pinpoint and solve potential production challenges. “Early engagement gets everyone around the table, talking and finding out what is needed,” says Simon. “What is the end goal and how can we maximise our products to meet those requirements? It also gets people thinking about potential obstructions and production delays. The problem is that it is easy to sit around a table with a piece of paper and sketch things out. But when you have a whole production line stopped and everyone screaming at you suddenly it becomes a more tense situation. Having these conversations at the start is going to flag any problems before they start gaining momentum and affecting the upward chain.”
Following a year of major changes to building regulations, and with compliance and safety becoming ever more prevalent in construction conversations, Ian Pearson, Project Sales Manager for Hansgrohe – a global leader in bathroom and kitchen component manufacturing – sees better collaboration as a way to improve not only standardisation but compliance too. “I think there needs to be more collaboration between the whole supply chain regarding
compliance and conformity,” says Ian. “That's going to help ensure everyone is meeting the quality standards required. We need to look at how compliance is policed and ensure everyone is on the same page about safety, standards and performance –creating a more cohesive way to get everyone to a place where any product that comes into your business meets those requirements right from the outset.”
When it comes to production, sudden unanticipated changes to requirements or a lack of first-phase communication are often responsible for delayed delivery or manufacturing bottlenecks. Repetitive ‘back and forth’ between manufacturers, suppliers and clients means increased lead times and higher costs, particularly when products are being adapted to fit a particular project. Collaborative R&D accelerates the product development cycle. Early collaboration leads to customisation of products that work on every level, achieving maximum results from performance, design and delivery.
Martin Rowlands, Managing Director of Pipekit, has extensive experience in the pipe manufacturing sector and has seen great success working with supply partners and clients to improve their product offerings to meet specific sector needs. “Collaboration is a
two-way street,” says Martin. “A prime example is the utility cupboards with the Heat Interface Units (HIU). We are working with another manufacturer with a different approach. We are looking at how they can better suit the modular sector because the HIU has a first-fix bracket with all the connections the M&E contractor puts in. Then the second fix comes along, sticks it on the wall and connects it to the rest of the utility cupboard. But if you can have a one-piece unit that just screws to the wall, you’re improving efficiency even further. It is getting the manufacturer to buy into the idea that we can make these changes.”
Paul Millington, Key Account Manager for Morland, explained how this type of collaboration around product development has worked for the fire door industry. “We carry standard product ranges. We have customers buying a lot of doorsets every week, but then we can take that product and change it slightly for a lower quantity but increase the margins, so we have a nice mix of high-volume low-margin products and vice versa. Everything we are talking about – standardisation, for example – we have done for years in the leisure industry. A prefinished product, cut to size and delivered to line with returnable stillages – it is a collaborative process end to end.”
Getting buy-in from the rest of the industry is key to effective supply chain integration and frequent communication from the start is vital. One thing that all parties at the roundtable discussion agreed on was that the information and resources needed to foster an environment of collaboration already exist. The industry holds a wealth of experience and knowledge – but there needs to be more of an outward-looking approach to using that information. The challenge is not whether the resources exist but how to ensure people know where to find them.
Jason Bennett is a National Business Development Manager for Zehnder Group, which provides indoor climate solutions for commercial and residential spaces. He has seen the benefits of improved communications and information sharing – particularly in helping clients find the balance between meeting regulations and retaining design flexibility. “We see it all the time,” says Jason. “There is difficulty in co-ordination between an architect and a consultant because they want a building to look unique, but you have restrictions because of compliance or requirements.
“If we go back a decade, ventilation systems were almost an afterthought. Builds are tighter now, so indoor air quality is more of a priority. The
ventilation system is at the core of the design. I was recently asked by a client if it was possible to use a cooling system off a ventilation system with a standard unit they currently use. The answer is no, so if we had not looked at that detail at the concept stage, the design of the utility cupboard would have been wrong. That initial conversation let us share our understanding and knowledge, so the client knows what is feasible and what isn’t. We used to come in at RIBA stage 4. Now we are seeing a difference in the market, we are coming in at RIBA stage 2 or 3.”
Information sharing helps to establish trust and well-balanced supplier/ manufacturer relationships. Also, when it comes to data and product information, a certain degree of transparency is something Andrew Fawcett, Materials Manager at VOLUMETRIC™ wants to encourage. “There needs to be commercial knowledge that is equitable. The problem is there needs to be a high level of trust for that. There is information that would be useful for us to know. If we look at one product – but you are moving 100 more of a similar product – are you informing us of that? Is there a parallel product that we should be adopting? It is also helpful to know – and this is a more delicate issue – what the feedback and quality issues from other customers
are. What has got the highest feedback and what has got the lowest? Quality improvement is a two-way thing, but we don’t tend to focus on that. We need to get it all on the table in a collaborative way.”
Delivering a common goal
As the traditional construction industry faces a shortage of skilled workers, supply chain collaboration and engagement are also key to developing the future of the offsite industry and bringing more MMC into the mainstream.
Michael Rowell, Engineering Manager for Fusion, believes skills and knowledge sharing between the industry and educational facilities could help bridge gaps in awareness and understanding of offsite technology. “If you look at the universities, the architects and engineers spend three to five years learning traditional construction methods – steel, concrete, timber, etc. There is no focused element on MMC. The only way we will get that is through the Engineering Council or RIBA because they set the standards for qualifying degrees. If we could say there is a requirement that MMC should be taught, that is when you start educating people. Then you start changing the industry – not for now but for ten or twenty years in the future.”
It is clear that everyone working in the offsite industry share one common goal – creating market growth and increasing the uptake of offsite technology and manufacturing. Bringing together the skills and knowledge available to make this happen benefits all those working in the industry. Whether it is globally established organisations such as James Hardie/Fermacell and Hansgrohe – who can offer unparalleled market experience – or in specific products and niches such as Morland. Or even new businesses bringing innovation and fresh ideas, everyone has something to offer in achieving collective common objectives.
But high-level collaboration should mean more than sitting around a table and talking. There is a lot to learn from getting out there and visiting manufacturers, seeing how different processes work and taking lessons from what others – both in and outside the offsite industry – are doing.
Simon Buckmaster is keen to encourage in-person site visits to demonstrate more effective ways of working. “You can sometimes have situations where people are doing something and when you get down to the manufacturing or assembly facility and see how they are processing or
assembling the products – that you realise the different ways you could adopt to improve your own systems and make things safer or more efficient for your business.
“We need to make more effort to get out there and look at what people do and how they do it. We need to come and see how the product is produced, cut or whatever it ends up being, because that then enables us to ask better questions rather than making assumptions. Part of collaboration around the R&D is making the effort to have a look, not just at the design stage but for the guys doing the real nuts and bolts bits. It comes down to creating value through shared experience.”
Trevor Richards from host company VOLUMETRIC™ agrees with this, citing the importance of building the supplier/manufacturer relationship and improving retention. “What makes a supplier arrangement work is the service and the relationship,” says Trevor. “It is about building partnerships – and that means having those in-person interactions where possible. You want to reduce any
potential changes because the risk you take when you change your supply chain is that you get worse customer service. When we have a problem, we need to know it will be responded to. Let’s have a conversation and see what we can do. This is where it all starts.”
RCM/Benx’s Managing Director, Ian Quinton, also agrees on having an honest conversation, saying: “What would be ideal is a forum for the offsite manufacturers to connect with developers and architects, for example, to show how offsite technology can be applied to projects. The information and knowledge are there. But it is about ensuring people use the right products and interfaces and understand how they work. I think expectations of what can be delivered and what is realistic are often different – those complexities slow delivery when not addressed at the first stages. It is all about changing the mindset and developing that culture.”
While there is a desire for improved collaboration from many within the industry, the offsite sector has work to do in developing a culture that sees this sort of R&D activity as ‘the norm’. However, as identified by those in attendance at the roundtable, the path is laden with opportunities that will lead to better products, stronger business relationships and a more cohesive industry. Perhaps it is time for
a new approach and to ask, how can we better work together?
The idea of a dedicated Supply Chain Innovation Group or forum is something that VOLUMETRIC™ is keen to pursue. Plans are currently being put in place to engage with the sector through regular meetings and roundtable events as well as via dedicated online knowledge sharing spaces.
Expanding Knowledge – we need to foster a better understanding of offsite methods and technologies through information sharing with suppliers, designers, architects and students/trainees entering the industry.
Growing Relationships – building collaborative relationships with suppliers and manufacturers offers exciting prospects for product development, best practise and innovation.
Evolving Culture – the general mindset of the industry needs to evolve when it comes to sharing data, conducting testing collaboratively and finding solutions to obstacles.
Setting Expectations – expectations and limitations need to be identified and communicated earlier through collaborative R&D to improve delivery and negate delays to production.
VOLUMETRIC™ encourages anyone who is interested in hosting or attending a supply chain innovation event to get in touch to discuss opportunities.
If you would like to learn more or would like to participate in a supply chain innovation forum, please contact VOLUMETRIC™ on: info@volumetric. co.uk
Many thanks to VOLUMETRIC™ for hosting the roundtable event and thanks to all participants for their time and contributions to the lively discussion.
For more information on VOLUMETRIC™ visit: www.volumetric.co.uk
Buildoffsite (BOS) recently launched ‘Offsite construction: concept design and delivery’. Here they explain what this comprehensive new publication provides for those working in the offsite arena.
Focusing particularly on offsite methods and high pre-manufactured value (PMV), this free guide offers a strategic yet pragmatic approach to integrating modern methods of construction (MMC) across various projects. It provides insights into the different facets and implications of this transformative shift and presents a comprehensive roadmap to effectively harness the advantages of MMC.
The new BOS guide commences by underscoring the strategic significance of applying MMC across portfolios and programmes. Addressing the call for heightened productivity, cost reduction, and sustainability
objectives, it demonstrates how MMC can play a pivotal role in realising these goals. It acknowledges the critical importance of combatting climate change and attaining net zero carbon outcomes, showcasing how offsite methods can significantly contribute to these endeavours.
Expanding horizons
Unlike prevailing MMC categories that often focus solely on residential projects, the guide’s scope extends to both infrastructure and buildings. This expansion acknowledges the adoption of MMC across diverse sectors. It delves into the intricacies of various MMC categories and offers insights
into how they can be effectively specified.
With the industry's growing emphasis on holistic evaluation, the importance of considering whole-life cost assessment and carbon evaluation is underscored. It elucidates how offsite solutions can not only reduce project duration and cost but also facilitate the development of more resilient and performance-driven designs for long-term operation.
The BOS guide also issues a caution against inadvertently constraining MMC adoption due to design and specification choices. It advocates for early engagement with specialists to comprehend the opportunities and limitations of MMC. The need for flexibility in requirements and designs to foster the co-existence of both traditional and MMC approaches is emphasised.
The guide delves into the unique considerations associated with incorporating offsite components, covering integration, co-ordination, factory lead times, and the concept of design freeze and offers insights into the differences in cost planning, cash flow, and risk profiles inherent in MMC projects.
In the dynamic landscape of evolving innovations, light is shed on the management of intellectual property and the fostering of new breakthroughs. It introduces the Buildoffsite Property Assurance Scheme (BOPAS) and other assurance processes, designed to facilitate market acceptance, and ensure the industry's transition to a more efficient, safe, and low-carbon sector.
This project was steered by an advisory group including funding representatives from the Environment Agency, National Highways, Thames Water, Anglian Water, Transport for London Property, Sir Robert McAlpine, Costain, Ferrovial Construction, Arup, C-Probe, Autodesk and Bentley. Under the guidance of lead author Nigel Fraser, Buildoffsite worked with a team of authors including Ahmad Alrifai, Rutland, Cartz, Coates, Fraser, Hacking, Kelly, Kyle, Martins, Rolf.
“Buildoffsite is delighted with the publication which was put together by an expert group of authors with many years of experience in delivering good practice in offsite construction,” says Dirk Vennix, Buildoffsite Executive Director and Chief Executive Officer, CIRIA. “We are also indebted to our advisory group which includes key funders and stakeholders. Without them, CIRIA and Buildoffsite would not have been able to make this free guide
happen, and we highly recommend practitioners in the industry use it.”
In a groundbreaking stride towards enhancing productivity, quality, safety, and sustainability, the construction industry is placing offsite solutions at the epicenter of its transformation. A surge of reports and initiatives has converged to underscore the pivotal role offsite methodologies play at this juncture. Recent publications like the Construction Playbook for both public and private sectors, alongside BOS reports explain the quantifiable advantages of offsite practices and substantiate this paradigm shift. Notably, these advances manifest in various benefits, tightly entwined with accelerated project timelines and their ensuing rewards.
While embarking on this trailblazing journey, certain challenges demand attention and action. At times, excessive design specifications necessitate offsite suppliers to reengineer plans for tender submissions. A proactive remedy is in the offing, as BOS prepares to unveil ‘Performance-Centric Specification’. This new guide starts with a workshop programme in the autumn and anyone who is interested in participating can contact Buildoffsite on info@buildoffsite.com.
Ambiguity looms over the alignment of offsite solutions with Building Regulations, compounded by inconsistent interpretations across geographical locales. Of particular concern are issues regarding fire performance validation and intermodule fire stopping.
It is important that we strike a balance between product testing and validation requirements while fostering parity between conventional and offsite methodologies.
The capital-intensive nature of offsite manufacturing facilities necessitates sustained high utilisation rates to unlock their cost-efficiency potential. Overcoming the challenge of demanddriven operations, catering to multiple clients becomes instrumental in maintaining factory performance.
The sector must pioneer a unified approach to product assurance to elevate industry standards collectively and bridge the information gap for specifiers and designers regarding cost dynamics. Introducing novel products to a traditionally conservative construction landscape also poses
challenges, albeit the imperative of the ‘climate emergency’ is nudging transformation across diverse offsite systems, fostering their optimal exploitation.
It is crucial that these perceived risks are addressed from financial and insurance perspectives, wherein the BOPAS framework takes centre stage. At the core of these advancements lies the infusion of digitised design and manufacturing processes, empowering seamless automation deployment and the creation of digital twins.
New look for Buildoffsite
Set up in 2004 as a trusted independent voice of the construction industry with respect to offsite and pre-manufacturing, BOS has been working hard with our members and government to facilitate offsite solutions and deliver guidance, resulting in tangible change. Dirk Vennix said “Our new brand image represents our community of buyers and supply chain members collaborating to deliver standardisation and greater adoption of offsite. Our actions and decisions today will shape the way we will be living and building in the future.”
“It has also been a time for a change to Buildoffsite’s brand,” adds Dirk Vennix. “Our new image reflects who we are today and where we are aiming to be in the future. This change represents our community of clients and supply chain members collaborating to deliver standardisation and greater adoption of offsite.”
You can download your free copy of ‘Offsite construction – concept design and delivery at:
https://www.ciria.org/ItemDetail?iProductCode=X538F&Category=FREEPUBS
For more information visit: www.buildoffsite.com
Images:
01. The Ivy, Manchester
02. COVID-19 Test Centre, Havant. Courtesy Premier Modular
03. Desborough Road. Courtesy Premier Modular
04. Offsite delivery is helping boost social housing numbers. Courtesy Building Better/ Partnerships for Homes
05. Formed in 2004, BOS recently rebranded and unveiled a new logo
The SmartSpace range brings all our precision and expertise together in a high-performing, efficient modular fleet for rental and sale Sustainable, adaptable, and futureproofed, SmartSpace offers endless configurations and applications.
Features & Benefits
• Available for rental and sale
• Stackable configuration of up to three storeys
• Boasts enhanced superior thermal performance
• Superior air tightness and U values that exceed current performance requirements
• 90-minute plus fire rating floor to floor
• 60-minute plus fire rating inside to outside
A2 non-combustible cladding, insulation, and roofing
• For added design versatility and re-usability they come in three compatible and interchangeable module sizes
• Ceiling heights ranging from 2.7m to 3m
SUPPORTS YOUR PROJECTS HELICAL PILES FOUNDATIONS
TECHNO METAL POST HELICAL PILES ARE ENGINEERED AND GUARANTEED
Andy Higson, Business Director for Intrastack, discusses how offsite manufacture can help boost the affordable housing market and help supplement traditional construction to bridge the gap between supply and demand.
Offsite construction has been proven to be an effective solution to housebuilding, offering speed, certainty and lower on-site costs. And as demand for low carbon and sustainable construction continues to pick up pace, they often produce less waste and use less energy. Witnessing high-profile manufacturers of offsite builds struggle to operate a profitable business creates a misguided hesitation over its effectiveness as a viable alternative to traditional methods of construction, which I absolutely believe it is. But what role does volumetric modular construction play in the housebuilding sector, what challenges does it face, and how do they impact its future in residential housing?
Speed vs cost
There is a balance that needs to be identified between the speed and the cost of the solution, and it’s vital that the decision makers understand what solutions are available and how they best suit the needs of the project they’re working on.
Volumetric modular systems may be fast to produce, but it has added costs associated with it. Some, such as Housing Associations, may be happy to swallow this cost in exchange for providing a large quantity of affordable housing quickly. However, others, such as national house builders, may build a large volume of housing, but they're not necessarily looking to construct them as quickly, so the added costs are unnecessary.
The reason for the extra cost of volumetric housing is that it's essentially a fully finished volumetric box. Elements such as the carpets, the kitchen and the bathroom are all fitted in the manufacturing stage before the final modular structure is shipped to site. But to do this, they need to be engineered in such a way that they can be safely lifted and transported without incurring any damage. This means they are inherently over engineered for the final use, and the additional material used to create that temporary structural stability will result in added cost.
If you compare this to other methods of construction, such as traditional bricks and mortar or a panelised system where more work is done onsite, it only needs to have the strength to withstand the final building design. This is why volumetric providers are often constrained by very tight, if any, internal margins and are increasingly under pressure to remain competitive, especially for customers that value cost over speed.
From a volumetric perspective, there are limitations in tailoring buildings to meet the specific needs of end users. Typically, volumetric modular houses, regardless of whether they have two or five bedrooms, tend to have long and narrow floor plans. This constraint arises from the need to fit the modules onto vehicles for transportation and lifting into their final positions using cranes.
Volumetric providers also face challenges when it comes to
attaching roofs to their factory-built structures. Considerations, such as tunnel clearance height along motorways, often require shallower roofs with minimal pitch, which is a common characteristic of volumetric houses. These factors can influence the aesthetics and architectural variety of volumetric constructions. Consequently, if a more intricate design is desired, modular boxes may not offer the same flexibility as a panelised system.
And when it comes to low-rise housing, whether for national housebuilders or housing associations, the focus is on placemaking. It's not just about maximising the number of units on a site – it's about creating a residential environment that feels complete and caters to the needs of the residents. Incorporating diverse designs and orientations can greatly enhance the street scene, resulting in visually captivating neighbourhoods.
One of the advantages of modular housing is the ability to standardise the design, which is particularly beneficial for organisations like housing associations or other largescale affordable housing projects. However, achieving standardisation becomes challenging when it comes to the finished house due to the vast number of variations in elements such as kitchen types, brick finishes, roof
finishes, and windows. The potential combinations of these elements can reach thousands, requiring the factory to maintain stock levels of numerous products to provide flexibility. Adequate stock levels are essential to prevent delays caused by running out of fixings, as a halt in the production process can occur until the items are replenished.
Some of the longer standing volumetric providers did some earlystage exploration of the low-rise housing market, but quickly backed away once manufacturing costs were set against unit sale rates. As a result, they have continued to focus on more profitable commercial markets, leaving the newer volumetric entrants to learn the larger, more expensive lessons.
When evaluating offsite construction, it is crucial to consider the total commercial package. If the goal is to accelerate construction speed, improve building performance, and ensure programme and cost certainty, then offsite methods are indeed the right approach. However, it is essential to fully comprehend the advantages and disadvantages of different offsite delivery methods and work with contractors who can guide clients through the decision-making process. This prevents uninformed or incomplete decisions regarding the most suitable approach. The
commitment and support for offsite manufacturing in the affordable housing market is evident in the initiatives led by Homes England and the industry's focus. And while progress is being made, there is still a long way to go if we are to offer affordable homes to those that need it.
Looking ahead, a combination of construction methods is envisioned. Traditional construction will still play a role, whether through superstructures like reinforced concrete frames with light gauge steel infill or the continued use of timber for its natural and aesthetic appeal. However, there may be a shift toward elemental masonry solutions, employing large elemental sections instead of traditional breeze blocks. Light gauge steel frames are expected to gain traction due to their ability to address challenges such as fire risk and production speed while maintaining flexibility and commercial viability. Panelised construction is particularly well-suited for low-rise housing as it enables the pre-manufacturing and storage of houses tailored to various customer requirements and house types. This approach ensures that houses are readily available and can be promptly sent to the site when needed.
There is ample market demand for various construction methods, but the commercial model will ultimately determine their viability, especially in the affordable housing sector where affordability is paramount. If the cost of construction becomes too high, someone within the supply chain, whether the volumetric provider, developer, or client, will bear the burden. It is crucial for stakeholders to explore the full range of options beyond volumetric construction and engage in meaningful discussions with the supply chain to understand what can be accomplished. Collaboration and expertise are key factors in ensuring successful outcomes.
For more information visit: www.intrastack.co.uk
Mark Rooney, Rental Divisional Director at Premier Modular, explores the opportunities that modular construction offers to the education sector and how it can help universities grow responsibly and at speed.
Faced with a rising intake, universities will need to extend existing facilities whilst ensuring new buildings support their sustainability targets. Offsite construction methods, such as modular construction, are an ideal solution to this pressing situation, ensuring higher education institutions can boost capacity in line with ESG commitments.
Growing sustainably
Interest in STEM subjects has increased exponentially over the past few years with three million people predicted to occupy STEM jobs by 2026. As such, universities are under pressure to maintain high quality facilities with topof-the-range technology to reinforce student education. The government’s £490million investment in worldclass facilities will go some way to supporting this and can be used by universities to secure exceptional learning environments without significantly contributing to carbon emissions.
Investing in modular construction is one way for universities to pursue this, a sustainable type of building that enables capacity expansion in a short amount of time. This is crucial for higher education institutions given the increasing pressure from the government and public for net zero targets to be met. However, despite more than 100 institutions declaring their intentions to divest fossil fuels, in the academic year 2022/23, many universities in the UK were behind on their carbon neutral commitments.
With the UK’s student population growing year on year, the higher education sector is under pressure to expand quickly and in a way that embraces their environmental, social and governance (ESG) responsibilities.
Annual applications for university places are expected to reach one
million by the end of the decade, prompting calls for adaptation and expansion in the higher education sector. The growing popularity of STEM and technology-based subjects have been attributed as driving factors of this increase with computing now ranked as the seventh most popular university course in the country.
Maximising energy efficiency and curbing emissions where possible, modular construction poses a significant opportunity for universities. The building method employs precision manufacturing to create modules, meaning components are cut to the exact size and shape required, limiting waste to landfill.
This technique was used for the Data Science, AI and Modelling (DAIM) Centre that modular specialist, Premier Modular, delivered for the University of Hull. Coupled with the implementation of green technologies such as solar panels and LED lighting, the use of modular construction in this project minimised the building’s embodied and operational carbon, contributing to the building's EPC ‘A’ rating.
When expanding facilities, universities have to consider the impact construction work will have upon students and communities in the vicinity, and whether this is in line with their ESG commitments. Choosing modular buildings is beneficial in this regard – pre-manufacturing modules inside a factory significantly reduces the disruption and pollution caused by construction sites, equating to a fast installation of modules on-site.
The modular units that formed the facility the University of Hull commissioned Premier Modular to complete took five days to install, enabling the internal fit out of the building to be delivered in just 20 weeks. This was the case despite the challenging logistical management, a procedure that necessitated the modules be lifted over a bridge and into a tight space.
The limited interaction between the public and the risks associated with a construction site is equally an advantage of modular construction. Prolonged exposure to hazards like moving vehicles and waste materials is a serious downside of traditional construction and something universities should aim to limit as part of their duty of care to society. Choosing modular solutions will not only help to achieve this but support universities in contributing to circularity by implementing a reusable, sustainable building solution.
If the higher education sector is to continue growing sustainably and responsibly, it is essential that modular solutions are considered in decisionmaking. Doing so is an important facet of proactive governance and will ensure institutions invest in highquality learning environments and the circular economy.
Providing flexibility and cost certainty, modular solutions will help universities to expand in a way that suits their budgets and does not hinder student learning. Available to be leased over short or long-term rental periods, or purchased for permanent use, modular solutions can be acquired via several means.
To ensure nothing goes to waste, modules can even be reconfigured after installation to reduce or extend the building. If required, additional units or floors can be added, allowing universities to modify their buildings to accommodate fluctuations in demand. This is furthered by the fact that modules can also be recycled, supporting universities to acquire facilities with the knowledge that they will not be wasted after use.
Such flexibility is an enormous benefit to the higher education sector, which is juggling priorities to grow, embrace sustainability and give back to local communities.
With demand for university courses changing and the need for highperforming learning environments surging, higher education institutions are increasingly turning to the modular opportunity before them.
For more information visit: www.premiermodular.co.uk
Images:
01. Mark Rooney, Rental Divisional Director, Premier Modular
02-04. The University of Hull’s DAIM Centre. Students will benefit from the state-of the-art facilities modular solutions provide at the University of Hull's DIAM Centre.
• BDA Agrement
BAW-20-154-P-A-UK
• A1 (Non-Combustible) reaction to fire in accordance with EN 13501-1
• CE & UKCA assessed to EN 12467:2012 + A2:2018
• Highly moisture tolerant
• Helps improve the air tightness of façades
• Relative high density for excellent acoustic performance
• BDA Agrément
BAW-19-093-P-A-UK
• A2-s1,d0 reaction to fire in accordance with EN 13501-1
• CE & UKCA assessed to EN 13986:2004 + A1:2015
• Offers exceptional mechanical performance
• Highly moisture tolerant
• Helps improve the air tightness of façades
• Relative high density for excellent acoustic performance
BAW-19-093-P-A-UK
BAW-20-154-P-A-UKEuroform Product’s Versaroc® MPA1 sheathing board has been used in the construction of Europe’s largest living wall at Eden, Salford, which is set to be one of the UK’s most sustainable office buildings.
Read the case study on our website for more information.
A1 non-combustible fibre cement board
• Lightweight, score & snap
• Exterior grade with mesh reinforcing facings
• Highly moisture tolerant
• Ideal exterior sheathing board to SFS walling
• Inorganic making it dimensionally stable compared with traditional wood based boards
• UKCA marked according to BS EN 12467:2012+A2:2018 “Fibrecement flat sheets”
• Can be used for internal wall & floor tiling applications
ModuleCo Healthcare (MCH) has successfully handed over a new state-of-the-art facility for Neath Port Talbot Hospital that is set to become the centre of excellence for orthopaedic and spinal surgery in the region.
This three-storey theatre complex provides the Hospital with three brandnew, state-of-the-art operating theatre suites, five pre-assessment rooms, clinical staff changing rooms, rest areas and a seminar room.
It will provide capacity for up to 3,000 additional procedures to take place every year. The surgical facility will also form part of Neath Port Talbot Hospital’s development as the Centre of Excellence for orthopaedic and spinal care, urology, diagnostics, rehabilitation and rheumatology.
After a highly competitive tender process, MCH was awarded the project through the Shared Business Service framework (SBS) via a 10-year managed services agreement. Swansea Bay University Health Board required a new facility to help address the backlog
in elective orthopaedic procedures reducing waiting times for their patients. Once the backlog has been addressed, the additional capacity also helps the Health Board futureproof for sudden changes in demand giving them increased stability.
With waiting lists for elective orthopaedic surgeries already an issue for the Health Board before COVID-19, the impact of the pandemic only heightened the backlog with over half of patients waiting over two years for surgery. This led the health board to act using their ‘changing for the future’ programme in which the new facility provided by MCH plays a key part in delivering the objectives set out.
The unique and flexible hire solutions MCH provides allowed the Health Board to address its mounting backlogs and grant them access to a state-of-the-art facility that will become the centre of excellence for the region without the need to find the significant upfront capital required through traditional funding routes.
The installation of the facility was completed over seven days which came in ahead of an already tight schedule reducing the impact on the
live hospital site. The Health Board plan to offer a ring-fenced elective service to address the backlog as quickly as possible and from then on remain on top of all orthopaedic elective surgeries across the region moving forward.
“The three new theatres have been built quickly and efficiently to meet the exacting standards of modernday orthopaedic and spinal surgery,” said Paul Williams, Orthopaedic Consultant Surgeon and clinical adviser to the project. “They provide a substantial increase in the size of the theatre footprint which should enable more complex spinal and revision arthroplasty to be performed in a dedicated elective surgical hub.”
MCH Managing Director Alan Wilson added: “We have worked in close partnership with Swansea Bay University Health Board and have built up a strong relationship with them over the course of the project. To be able to deliver a state-of-the-art modular centre of excellence which is set to
cover the region is a testament to the strides the NHS has made towards adopting alternative procurement routes in recent years.
“This additional capacity will allow the Health Board to address their backlogs in elective orthopaedic and spinal surgeries much quicker for their patients some of whom have been waiting several years. We’re very proud of this facility and the pivotal role it’s set to play in the region for many years to come.”
It took only a week for the operating theatre facility to be installed in mid-December 2023 following the offsite manufacturing phase which saw nearly 90% off the construction process take place away from site. ModuleCo provided a turnkey project delivery service to the Health Board,
3 4
owning the design, manufacturing, installation and commissioning of the modular healthcare facility, as well as the required enabling and foundation works on-site. The facility was officially opened on 15 June 2023 by the Minister for Health and Social Services, Eluned Morgan.
Images:
01-04. The NHS is benefiting from offsite construction with modular a central method of delivery
ModuleCo is the healthcare division of BRG Technologies and has been building specialist facilities for the healthcare sector for over two decades. BRG Technologies has successfully delivered over 300 mission-critical projects across Europe, USA, Australia and Africa, providing the highest-quality healthcare facilities to the NHS, the UK and US Armed Forces and NATO.
For more information visit: www.moduleco.com
Ewelina Woźniak-Szpakiewicz, Chief Executive Officer of DMDmodular, is a familiar face on the international offsite scene and outlines a recent energy -efficient volumetric modular project undertaken in Poland.
Being the fourth-largest CO2 emitter in 2019, after China, the United States, and India, the EU is leading the transition towards becoming the first carbon-neutral continent by 2050. To achieve this goal, member states are deeply committed to reducing greenhouse gas emissions originated by their economies and particularly the ones generated by the construction sector.
In this context, DMDmodular has recently achieved a significant milestone by successfully completing a relevant energy-efficient housing project, fully financed by EU funds, that tackles the industry's most pressing challenges. This energy-efficient multi-family building, emerged as a response to an initiative led by the Polish National Center for Research and Development, titled: ‘Energy and Process-Efficient Modular Construction’ and was designed and built using a volumetric modular system. It was developed by DMDmodular in collaboration with researchers, architects, and technologists.
The project comprises 29 apartments ranging in size from 45 to 70sq m, and it were delivered through 56 fully finished and furnished modules. These modules – manufactured at DMDmodular's facility near Kraków –were transported and assembled in Mysłowice, Poland during July 2023.
The showcased multi-family building integrates innovative solutions that enable a positive energy balance, resulting in surplus energy generation. It incorporates cutting-edge air handling units with 95% air recovery efficiency, moisture recovery systems, ceiling-based heating and cooling through capillary mats, thermal energy storage, and thermal energy recovery from sewage tanks. The building solely relies on renewable energy sources for its energy needs and integrates measures to minimise water consumption and the overall carbon footprint.
This building stands as a technology demonstrator, offering an invaluable scalable and global solution for both local governments and private
investors developing projects across the countries. Energy efficient modular technology can effectively address the housing shortage and energy crisis, as well as rising construction costs associated with traditional methods.
The project is defined by its superior quality finishing, energy efficiency, and remarkably rapid construction timeline of just four months. This high quality, energy efficient and quick delivery method not only can help alleviate housing shortages and the immediate need of building solutions to rebuild Ukraine (only 250km from the Ukrainian border), but also significantly enhances returns on investment in the build-to-rent sector, encompassing hospitality, PRS ventures, co-living initiatives and student accommodations, compared to conventional construction techniques.
The experience gained by DMDmodular has facilitated the establishment of a seamlessly integrated supply chain which
for investors translates to a more stable project execution and cost predictability, which highlight the advantages of DMDmodular technology over traditional methods.
Poland offers a sustainable and efficient supply chain which is a perfect environment for DMDmodular, focused on turnkey modular units. The country has become one of the hottest manufacturing clusters in Europe as the economy continues to perform strongly being among the
Our AluSpace Interior Screening System is designed to divide or delineate both residential and commercial spaces, while at the same time providing an effective acoustic barrier.
Choose from hinged single, double doors, pivot or sliding doors to accompany our stylish fixed glazed screen. This flexible and versatile system provides almost limitless design options whilst requiring minimal maintenance. AluSpace will provide many years of assured, reliable and robust performance.
For more information visit smartsystems.co.uk/aluspace
E sales@smartsystems.co.uk
three fastest-growing economies in the EU. Poland is a major producer and supplier to the automotive industry and a leading manufacturing position in the windows industry in the EU. And it holds the fourth position in the world as an exporter, and sixth place as a producer in the furniture industry. Thanks to the stable and credible local supply chain, DMD claims to be the attractive and reliable business partner for the UK construction market.
DMDmodular is an award-winning company focusing on the housing and hospitality industries, delivering unique volumetric modular solutions to international markets. Noteworthy recent developments are PBSA schemes in Scotland, Denmark, and Switzerland and numerous houses for recreational parks in the Benelux region. The company is presently engaged in several hotel projects, encompassing establishments in the UK and Belgium. DMD earned international recognition by securing an award in the Green Building Category for its innovative co-living modular solution implemented in Paris.
For more information visit: www.dmdmodular.com
Images: 01. Ewelina Woźniak-Szpakiewicz, Chief Executive Officer, DMDmodular 02-04. Poland is a key global centre for the developoment of offsite systems
Proud members of
MODULAR MATTERS Conference & Exhibition features the latest developments, innovations, and investments in the volumetric modular sector.
Taking place on 19 & 20 March 2024, MODULAR MATTERS is moving for the first time since inception in 2018, to the Coventry Building Society Arena.
Modular technology is ever evolving and to help keep pace with this fast-moving sector, MODULAR MATTERS demonstrates how to tackle industry challenges through a range of project case studies, panel discussions, innovative architecture and building design together with net zero and future transformation. Presenting an insight into the future of construction, this event represents a great opportunity to gain industry intelligence and network with those who are at the forefront of the volumetric modular sector.
If you would like to be considered to present at Modular Matters 2024, please email your name, company and proposed presentation title and description to ellie.guest@radar-communications.co.uk
To enhance your presence at MODULAR MATTERS book an Exhibitor or Sponsor package.
For more information on the promotional opportunities available call 01743 290042 or email julie.williams@radar-communications.co.uk
Previous Exhibitors & Sponsors Include:
To find out more and book your place at this essential fast-track construction conference and exhibition go to: www.modularmatters.co.uk
Richard Hipkiss, Development Director for the MPBA, believes Pre-Manufactured Value has some failings and the government is missing a trick by measuring value only in terms of a financial calculation.
Pre-Manufactured Value (PMV) is a driving force in the specification of volumetric technology in public sector projects – particularly in healthcare and education. Without doubt PMV is a step in the right direction, as the government drives to boost the uptake of modern methods of construction (MMC) through the broader Offsite Construction Solutions framework which encompasses volumetric and panelised building solutions.
As the name suggests, PMV is the financial proportion of a project’s gross construction cost derived through pre-manufacturing. It is a core metric for measuring the level of MMC in a project and is central to the UK government’s procurement programme. Contractors are required to show that pre-manufacturing will account for at least 70% of all
construction costs. This essentially plays to the strengths of a volumetric modular approach – so you might ask why I am questioning this?
Defining PMV
It is widely acknowledged that we do not have an industry wide definition of PMV that stands up. It has yet to be comprehensively defined and applied. As constructors move to respond, the accuracy of PMV calculations, particularly for the purposes of tendering – is something that must be addressed. Not only does it have to be precisely and consistently calculated but also it should be monitored to ensure fairness in the public sector procurement process.
PMV as it stands is a starting point. But a barrier to progress is the need to rethink the scope and calculation
of pre-manufactured value used in project procurement. Currently metrics fail to account for the complexity and range of jobs that fall within the 70% PMV remit. MMC has its origins in small scale residential housing, but is now used on major projects, from hospitals to infrastructure. The scale, diversity and complexity of projects also adds to the uncertainty about PMV’s accuracy and confusion opens doors for misinterpretation.
It would be good to see a standard calculation tool that can be regulated and legislated. We need greater education and clarity around PMV across the wider construction industry and standardisation of how it is calculated.
When you read the Construction Leadership Council’s definition of PMV,
it appears to have been written by a quantity surveyor. It is a commercial metric and rightly so as the government must demonstrate best value, but PMV could be much more than this. One of the major benefits of pre-manufacturing and volumetric construction is reducing embodied carbon – which leads me to my second point.
I accept this is very much in its infancy and there is more work to be done, but the government has an opportunity here to align construction costs with net zero targets to demonstrate economic and environmental best value.
The government has set stretching net zero targets by 2050, so why is PMV’s calculated ‘value’ just in monetary terms. Of course, demonstrating value
for taxpayers is critically important, particularly in these times of financial hardship, but as we all strive to reduce carbon in construction, is there not an opportunity here to include economic and environmental benefits within the PMV procurement scope?
As an industry association, it is one of our objectives to demonstrate how the route to 2050 could follow many different paths. It is now established that volumetric modular approaches reduce build times by an impressive 50-60% whilst increasing quality, productivity and safety. But what is not so widely understood, is that compared to traditionally built projects it is easier to control energy use in factory settings than in an open construction site. On average 67% less energy is required to produce a volumetric manufactured building and up to 50% less time is spent on-site,
The Modular and Portable Building Association (MPBA) plays a key role in supporting all sections of the industry. Leading best practice principles, the association is represented on many committees for the benefit of members. Importantly, the MPBA ensure evolving government policies and decisions are not made on behalf of the construction industry without due consideration for the impact they may have on the volumetric modular sector. Regardless of the size and type of your business, becoming an MPBA member will open doors to valuable business development, training and collaboration opportunities.
For more information visit: www.mpba.biz
resulting in up to 90% fewer vehicle movements which is less disruptive and reduces carbon emissions. Not only is the actual construction of the building ‘greener’ but volumetric manufactured buildings are more energy efficient – reducing primary energy requirements and in-use operational emissions during the lifetime of the building.
Carbon calculators are now widely used throughout the offsite construction sector, and these could potentially form the basis for a PMV calculation tool. I accept we have to get the financial calculations right first, but by aligning financial and sustainability goals, public sector projects could expand the ‘value’ criteria.
Greenford Quay is a large-scale Build to Rent (BTR) development in Ealing, London, showcasing the best in volumetric modular technology and another exemplar project from offsite specialists Tide and Vision.
Building on many successful and award-winning volumetric modular schemes, Greenford Quay further demonstrates the companies’ successful partnership in delivering innovative factory-led design and construction alongside developers Greystar and investor Ivanhoé Cambridge.
As one of the largest purpose-built rental communities in London, this 27-acre site was derelict for over a decade before Greystar and Ivanhoé Cambridge stepped in to pave the way for a huge regeneration project. The mixed-use waterfront neighbourhood will include 2,118 new homes in seven main buildings on derelict industrial land, breathing new life into a previously inaccessible stretch of the Grand Union Canal.
The land was acquired by Greystar in 2015 whom secured planning with Tide appointed as main contractor and starting work on-site at 379-home Tillerman’s Court in 2018, followed by 251-home Lyon’s Dock. Further phases of development are on-going, comprising 354 homes at Block 8 and 390 homes at Block 7. At the heart of the new neighbourhood is a a central square, a canal bridge and walkaway and an amphitheatre, together with shops, cafes, a vet, creche and even a brewery, creating an
attractive community space, delivering local employment and amenities, with material from the demolished factory buildings used to create new landscaped areas.
Tillermans Court contains 379 apartments in a range of designs and sizes, as well as a gym, rooftop terraces, meeting rooms, a cinema and residents’ lounges. The building was originally designed traditionally but adapted to a volumetric modular approach which increased the net area without altering the architectural vision of the varying layouts and high-end finishes. Tide and Vision are helping deliver 2,400,000sq ft of residential accommodation combined with 190,000sq ft of additional commercial and retail accommodation across the entire development with improved public realm.
Adopting an offsite construction path offers a cutting-edge, strategic solution to many of the UK’s housing needs and Ealing Council saw the benefits of volumetric modular to provide a range of living spaces quickly, sustainably and efficiently – all key benefits for any local authority wishing to create muchneeded new communities.
The volumetric approach is more streamlined and provides a cleaner construction timeline – with 80% of the logistics on-site reduced, minimising disruption for surrounding businesses and homeowners. The offsite approach also helps reduce embodied carbon across the scheme. On Tillerman’s Court, detailed analysis conducted by Heriot Watt University to compare the volumetric approach with the original construction strategy, showed
savings of 26,000 tonnes of embodied carbon – a reduction of 44% compared to traditional construction and a 10% improvement on RIBA 2025 and & LETI Band C benchmarks.
Being a factory-led precision process, the creation of the volumetric homes is executed with a high degree of manufacturing discipline employing constant, stringent quality control throughout the entire process from module creation to final installation. The significant investment in research, development and testing refines and enhances the system. As a fullyaccredited system, the schemes are fundable motgageable and insurable.
Tide and Vision are responsible for delivering seven of the world’s ten tallest modular buildings, including the world’s tallest at Ten Degrees, Croydon. Working within a wellunderstood and vertically integrated procurement model, they offer a full turnkey offsite solution and are committed to driving forward the modernisation and decarbonisation of the built environment. The work at Greenford Quay is acting as a blueprint in combining modern living with contemporary design and showing how BTR projects can be delivered efficiently, sustainably and costeffectively.
For more information visit: www.tideconstruction.co.uk www.visionmodular.com
Images: 01-03. Greenford Quay is breathing new life into a neglected part of London and creating a thriving new community with volumetric modular design at its centre
Howick is a pioneer in the technology of precision light steel rollforming machines. For over 40 years, our commitment to innovation in Cold Formed Steel (also known as Light Gauge Steel), precision manufacturing, uncompromising quality and exemplary customer service has defined the Howick way. This commitment underpins the competitive advantage enjoyed by our customers.
We are trusted partners and suppliers to developers, builders and offsite construction companies in over 75 countries. Our machines offer high-precision manufacturing direct from coil steel for all your cold formed steel framing, flooring and roofing needs.
Using CAD technology, our machines produce cold formed steel components ready to assemble for walls, floors and trusses for a total steel building solution. Custom-made to your specifications, you will enjoy proven reliability, rapid build speeds, improved accuracy and dramatically reduced wastage.
So, whether you are looking to create framing systems for residential new builds, low-rise commercial or even bathroom pods, our machines make framing up fast and incredibly efficient.
To make the switch to steel, or simply lift your steel framing game, start with a conversation with us today.
There is a major problem globally with the cost of housing, so the construction industry is striving for better, smarter ways of doing things. At Howick, we see ourselves as part of the solution. If we get it right, we will help create a better place for everyone.
For a more in-depth look at why you should choose Howick for all your LGS requirements, download our Machine Buyer Guide today. Alternatively, you can contact us via our website at www.howickltd.com, or get in touch with our Head of Global Sales, Deon Anderson, on deon@howickltd.com
Unique in our sector, our roll-forming systems are 100% manufactured at our Auckland plant, using locally manufactured componentry of the highest standard, ensuring complete quality control.
Unlike competing machines, with a Howick system there are no meterage fees, so you can run as much steel as you need, and you pay zero in toll fees. What is more our machines receive data from any partnered CAD framing package. You are free to pair your machine with an existing CAD system, or switch as required.
Features like our unique end-bearing stud details enable the construction of load-bearing frames for multi-storeyed structures, making Howick technology the most advanced framing systems available.
We take every care to reduce the environmental impact of our machines during manufacture. With drive motors that surpass European and international standards and auto-off switches, they also come with energy efficiency built in, further reducing their carbon footprint.
Adam Salt, Business Development Manager at A. Proctor Group, has seen the benefits of modular construction thrive with a key example being at the Northampton School for Boys Multi-Academy Trust.
1 2
Modular and offsite construction is revolutionising the way we build. These modern methods of construction are rapidly gaining popularity in the industry for projects of all sizes, and for good reason. The country has seen numerous successful projects utilising this innovative building technique, including high-rise modular buildings. These pioneering building techniques offer numerous benefits over traditional construction methods, including faster construction times, improved quality control, and reduced waste.
One of the key advantages of modular and offsite construction is speed. This is particularly important in the UK, where construction timescales are often critical due to weather conditions and other factors. Modular construction allows for much of the construction work to be done offsite, which greatly reduces the time needed on-site. This can lead to faster project
completion times and reduced disruption to the surrounding area.
One notable success in the UK has been the use of modular construction to deliver high-rise buildings. Wembley, London is home to the impressive Apex House project. This 29-storey tower was built using modular construction and was completed in just 12 months. The building includes 560 student apartments and is one of the tallest modular buildings in the world. Another notable modular construction project in the UK is the Mount Pleasant project in London. This development includes 136 affordable homes that were built using modular construction. The homes were also completed in just 12 months, which is significantly faster than traditional building methods. The modular construction process also allowed for a high level of customisation, with each module being tailored to the specific needs of the development.
Algeco UK Ltd has secured a Department for Education (DfE) funded project for the offsite construction of Northampton School for Boys Multi-Academy Trust. The project was secured via the MMC1 Lot 1 modular framework (*DfE published contract value is £27.6million). Algeco, acting as Principal Design & Build Contractor and working with Watson Batty Architects, is providing a full turnkey solution. A total of 210 modules will be supplied by Algeco using the innovative Seismic technology, plus a hybrid structure for the halls, to create the 1200 place new secondary school, including sixth form provision. The first modules, which will be manufactured by Algeco in its Carnaby facility in East Yorkshire. Handover of the completed school is scheduled to take place in 2024. Utilising Seismic technology for the Northampton school modules
will deliver important benefits; it is 75% faster and achieves a 47% improvement in value compared to traditional construction techniques; it even offers a 33% improvement in speed when compared with standard modular construction. In terms of sustainability, Seismic delivers significant reductions in both operational and embodied carbon of up to 70%. This is achieved through factors including design efficiency, materials selection and manufacturing effectiveness, leading to limited wastage.
There are many benefits to modular and offsite construction including improved quality control, reduced waste and the potential to be more sustainable than traditional construction methods. Improved quality control is due to the modules being constructed in a controlled environment, where the quality of the materials and workmanship can be closely monitored and controlled. This can help reduce the risk of errors or defects in the final product, leading to a higher quality finished building.
This optimised construction method also assists waste reduction with the efficient use of materials.
Modular revolution
Modular construction is considered more sustainable for several other reasons. One of those reasons is because modular can reduce the carbon footprint of a building project during the construction period. Manufacturing, transportation and the use of large machines and equipment on traditional construction sites all contribute to carbon emissions, something which modular and offsite manufacturing greatly reduces by the very nature of the process taking place in a factory environment. Less disruption to the surrounding area of the construction site itself can help preserve natural habitats and reduce the impact of development on the local ecosystem.
At A. Proctor Group Ltd, we are proud to be a part of the modular construction revolution. Our range of building solutions, including insulation and membranes, are designed to support the unique needs of
modular construction projects. We are committed to providing our clients with the highest level of technical support and expertise to help them achieve their goals. If you’re interested in learning more about modular construction and how our products can support your project, please do not hesitate to get in touch.
The UK has seen numerous successes with modular construction in recent years which have been noticed all over the world. The speed, efficiency, and customisation offered by this building technique have made it an attractive option for a wide range of complex projects, including high-rise buildings. As the construction industry continues to evolve, it is likely that modular construction will continue to play an important role in shaping the future of building in the UK.
For more information visit: www.proctorgroup.com
affordable housing markets,” says NHBC CEO Steve Wood. “The Government’s renewed focus on housing policy is welcomed, however a more favourable environment will be reliant on a fall in inflation, easing of mortgage rates and action to address the key supply side constraints of planning and nutrient neutrality.
“It is hardly surprising that consumer demand for new homes began easing in the second quarter. With mortgage rates at a 15-year high, volumes of homes built for private sales have weakened, although this is partly offset by bulk sales into affordable housing markets. The Government’s renewed focus on housing policy is welcomed, however a more favourable environment will be reliant on a fall in inflation, easing of mortgage rates and action to address the key supply side constraints of planning and nutrient neutrality.”
There were 24,783 private sector registrations in Q2 2023, down -51% on Q2 2022. The rental sector saw a shallower decline, with 13,261 registrations in Q2 2023, down -14% on Q2 2022.
New figures released by NHBC, the UK’s largest provider of new home warranties and insurance, show that the number of new home registrations fell by 42% in Q2 2023 compared to the same period last year, with completions falling by 11%.
A total of 38,044 new homes were registered in the months of April, May and June, compared to 65,645 in Q2 2022. The reduction is largely due to
the accelerated registration volumes in Q2 2022 caused by changes to building regulations in relation to energy conservation. Completions also fell in the quarter, mainly due to some dampening of demand caused by rises in mortgage rates.
“With mortgage rates at a 15-year high, volumes of homes built for private sales have weakened, although this is partly offset by bulk sales into
It was a mixed picture for registrations across the UK. London and Wales saw increases in Q2 of 9% and 1% respectively compared to the same period last year, while the North West (-67%), North East (-60%) and Eastern (-56%) regions saw the largest falls in registrations. The rise in London registrations may reflect a greater focus from builders on the alternative residential markets such as build to rent.
New home completions saw a lesser decline overall, down 11% on Q2 2022 to 35,936 in Q2 2023. New home completions in the private sector were down -18% in Q2 2023 to 24,746 and in the rental sector were up 8% compared to Q2 2022.
According to new figures from NHBC, new home volumes are being weakened by challenging economic conditions.
“While new home registrations are down in Q2 2023, activity on-site continues at a steady pace with builders focused on completing homes already in the pipeline. The increase in completions in the rental sector may signal a renewed focus on affordable housing, helping to address some of the underlying demand for new homes among those impacted by higher mortgage rates.
For more information visit: www.nhbc.co.uk
Images: 01-02. With mortgage rates at a 15-year high, volumes of homes built for private sales have weakened
In its August 2023 Review, Glenigan, one of the construction industry’s leading insight experts, focused on the three months to the end of July 2023, covering all underlying projects with a total value of £100million or less (unless otherwise indicated, with all figures seasonally adjusted).
The central finding of the August Review is that construction-starts remained weak throughout the three months to the end of July, with main contracts awards also slumping as the sector continues to be weighed-down by a stalled economy. Sustained external pressures continue to be the root cause of this disappointing performance. Rising interest rates and inflated material, fuel, and labour costs have shown no signs of easing in the short-term, further weakening investor and consumer confidence.
Yet again, project-starts dropped, this time by 10% against the preceding period, to stand 33% lower than the same time a year ago. These disappointing figures were echoed throughout the construction pipeline, with main contracts awards also falling back against the preceding three months (-24%) to finish 33% behind the year before.
However, a couple of bright spots appear amidst the gloom. While detailed planning approvals fell 26% against the preceding three months, the value increased by 37% against the previous year. Further, major project planning approvals were up a massive 167% on 2022 levels. This is indicative of recovery on the horizon, buoyed by upcoming planned major works which will provide a muchneeded boost to the industry.
Commenting on the findings in the August Review, Glenigan’s Economic Director, Allan Wilen, says “Starts on-site are softening and, as global and national disruption continues, we’ll likely see clients continue to adopt a cautious approach, pushing back start dates until the economic landscape looks less hostile. Short term, changing Government priorities in the run-up to the General Election are also likely to slow investment in major infrastructure projects, halting activity further. Despite this, residential construction offers a glimmer of hope, with increases in private housing starts helping to offset sluggish activity in this sector vertical.”
Sector Analysis – residential
Residential construction experienced an uptick, rising by a fifth (+21%) during the Review period, but remained 26% lower than a year ago. Private housing starts increased 40% during the three months to the end of July but fell back 26% on 2022 levels. Social housing starts were down 25% on the preceding three months and 21% on the year before.
Sector Analysis – non-residential
Non-residential performance was weak. However, the health sector showed some signs of life, growing 23% against the preceding three months but remaining 25% lower than 2022.
Posting one of the worst performances, office project-starts suffered a 35% fall during the three months to July, with levels declining 50% against last year. Similarly, industrial starts also fared poorly with their value slashed 24% against the preceding three months and 51% compared to the same period in 2022.
Hotel & Leisure starts declined 22% against the preceding three months and 41% compared to last year. Retail followed a similar trajectory, remaining flat against the preceding three months and standing 40% down on the year before. Education and Community & Amenity also crashed, dropping 34% and 36% against the preceding three months, to stand 7% and 40% down on the previous year, respectively.
For more information visit: www.glenigan.com
Across Europe and worldwide, BeA’s fastening technology, tools and consumables are the trusted choice for some of the biggest and best known names in timber frame and offsite construction.
BeA manufacture an extensive range of market leading fasteners, nails, staples and tools. We offer customers:
• An unrivalled range of manual and semi-automatic fastening solutions combined with a fully automated range in Autotec.
• Using industry leading quality controls, BeA meet or exceed standards such as Eurocode 5.
Reliable products, competitive prices and the kind of service and delivery you can depend on from BeA.
01482 889 911 sales@uk.bea-group.com visit our website www.bea-group.uk
THE POWER OF FASTENING
MAX PowerLite tools are extremely powerful yet their size is 40% smaller and tool weight is 30% lighter than conventional regular pneumatic tools with a wide variety of fasteners. HN120
The MAX HN120 is a top of the line professional grade pneumatic concrete/steel powered by MAX’s Powerlite compressor.
No Powder, No Gas, Just Air.
Following the national launch of the new Remagin brand, Scott Bibby, Country Manager for UK and Ireland at Etex New Ways, discusses how this move can drive significant sustainability benefits.
These businesses have been established in the sector for a considerable time and have developed
leading positions in their respective markets. Each has individual strengths and specialisms and by combining this array of skills, we are creating an offsite focused brand with impressive sustainability credentials. The overarching objective is to enhance our light steel frame solutions portfolio for our valued customers.
As the industry addresses the challenges inherent to building a more sustainable future, offsite construction and light steel frame can have an important role to play. There is growing pressure on the construction industry to reduce waste and to achieve this we have to move towards resource efficiency.
The circular economy is rising up the political and construction agenda. At its simplest, it prioritises the reuse of materials, preventing the overextraction of natural resources and the amount of usable construction components that end up in landfill. Steel has excellent circular construction credentials, both as a material which is strong and durable and as a structural framing system which is lightweight, adaptable, recyclable and reusable.
Steel is responsible for technological advancements across the globe and continues to drive innovation today. Topping the list for the most recycled material by weight, steel can be continuously recycled without any damage or degradation to its properties. Our steel sourcing currently comprises around 60% recycled content and is 100% recyclable.
Construction can be a complex business but as we evolve with more advanced offsite technologies, Remagin can help developers reduce risk and operate with more certainty and confidence.
Sustainability is a key driving force in our strategy. We want to inspire developers to construct buildings that are inherently safe and highly sustainable – supporting net zero objectives. As the world moves towards circular construction protocols, Remagin will be leading
the charge in enhancing the environmental credentials of light steel framed buildings.
For more information visit: www.remagin.world
Images:
01.The David Attenborough Building, Conservation Campus, University of Cambridge
02. Light steel frame has excellent circular construction credentials
03. Remagin – supporting net zero objectives
As the construction industry continues to prioritise green building solutions, light steel frame has become increasingly attractive as a low environmental impact option. As a material which is strong and durable and as a structural framing system which is lightweight, adaptable, recyclable and reusable.
Greater Recycled Content – our steel currently comprises around 60% recycled content and is 100% recyclable
Enhancing Materials and Efficiency – through our DfMA protocols and digital engineering, we eliminate waste and optimise material use
Best Strength to Weight Ratio – of all construction materials, our light steel framing systems create a lightweight loadbearing frame, meaning resource extraction and consumption is minimised, whilst still maintaining a robust structure
Reducing Foundation Requirements – according to the Steel Construction Institute (SCI), concrete foundation requirements are reduced by up to 70%, as light steel structures are substantially lighter than masonry, concrete or timber
Reduced Production Waste – steel wastage is minimised by the efficient use of materials. All steel factory off-cuts and drill swarf are sent for recycling back into new steel components
Reduced Transportation – as Remagin solutions often consolidate several components into a single system, vehicle movements to and from site are reduced and emissions minimised
Virtually No Onsite Waste – using pre-engineered and prefabricated light steel framing systems eliminates onsite waste and costly disposal charges
Energy/Thermal performance – U-values of less than 0.15 W/m2K and high levels of airtightness can be achieved using boarding and insulation within our light steel framing systems
Lowering Carbon Emissions – by achieving a highly airtight building envelope, the use of light steel frame reduces emissions and energy consumption throughout the lifecycle of the building
Greater Adaptability – our structures are extremely versatile and adaptable, offering ease of modification across the lifetime of the building
Offering End-of-Life Options – as the most recycled construction material, light steel framing systems offer refurbishment, dismantling for re-use or recycling alternatives.
Etex Group has 160 sites operating in 45 countries. In 2022 the group reported revenues of €3.7billion. The trend towards greater offsite production has prompted Etex Group to leverage its existing offsite construction companies to create a comprehensive, full-service business, from design to installation, to meet customer demand and drive performance. The new brand, Remagin – brings together the collective capabilities of three existing businesses, Leeds-based Sigmat, County Durham-based EOS and Horizon, operating from Ireland. These businesses have been established in the sector for a considerable time and have developed leading positions in their respective markets in their own right.
Through sharing information and sector knowledge, the Light Steel Frame Association (LSFA) is on a mission to highlight the sustainability credentials of steel – so how is the industry decarbonising the production process and creating green steel?
In the UK, Morgan Sindall Construction is to design and build a £20million R&D facility in Neath Port Talbot to help steel and metal industries decarbonise. The net zero facility is the brainchild of Neath Port Talbot Council in partnership with Swansea University. To be known as SWITCH – South Wales Industrial Transition from Carbon Hub – Harbourside it will be located close to Tata Steel’s Port Talbot plant and is expected to take 18 months to complete.
In recent years ‘green steel’ has for the most part been used to refer to steel production using carbon-neutral methods – but with recycling and the reuse of steel components, this is also a meaningful method of ‘greening’ steel production throughout the material’s lifespan and beyond.
‘Green steel’ refers to steel production using more environmentally sustainable methods. This usually involves energy produced from renewable sources to vastly reduce carbon emissions in the manufacturing process. One of the methods of producing green steel that is showing the most potential, is using renewable hydrogen in the place of the fossil fuel coal. When burned, hydrogen primarily produces water as a byproduct. Therefore, if steel is produced using only renewable electricity, it can be considered sustainable and play a role in circular production. When using an Electric Arc Furnace, hydrogen can be used to produce the same chemical reaction which occurs in traditional steel making but with reduced emissions.
In 2004 a group of steel companies with the support of the European Union (EU), started the ULCOS (UltraLow CO2 Steelmaking) project. The objective was to identify technologies that will reduce CO2 emissions per tonne of steel by 50% by 2050.
Steelmaking has been viewed as a carbon intensive activity, but with the first ‘green steel’ plants coming on line in 2025, things are changing. The EU increased the number of planned green steel projects to 38 in 2023, up from 23 in 2021. Additionally, Germany alone has invested €8.5billion into the decarbonisation of its steel industry, clear steps towards a more environmentally responsible form of production.
Steel is the world's most recycled material with more than 500 million tonnes recycled every year – the equivalent of 180 Eiffel Towers every day. Once produced, steel is a valuable asset that can be reused or recycled infinitely with little or no reprocessing – vastly reducing embodied carbon emissions in steel production. This unique characteristic gives steel a high value at all stages of its lifecycle.
Light steel is created through a process known as cold forming. This involves passing thin sheets of steel through rollers and presses while at room temperature, to create various shapes such as U, C, Z, or S-sections. Light steel framing contains a minimum of 25% recycled steel, making it a more environmentally friendly option than traditional methods of construction. Now many LSFA manufacturing members have as much as 40%-60%
recycled content in the light steel they use, and this is set to increase.
The UK leads the world in steel construction commercially, technically and in terms of quality. The industry has made dramatic improvements in technological advances and improving its productivity and efficiency. According to research carried out by independent consultants Construction Markets – steel continues to be the overwhelming structural framing material of choice, with their survey showing that steel now has a 72.5% share of the multi-storey office market
and a 60.9% share in the ‘other multistorey buildings’ which includes retail, education, leisure and healthcare sectors.
Robust, reusable, recyclable and adaptable – steel has excellent and well-understood construction credentials. As a material it is strong and durable and as a structural framing system it is lightweight and cost efficient. These properties make steel a hugely sustainable construction material both in terms of its longevity, material properties and enhanced safety credentials.
• 99% of steelwork and 96% of steel construction products are reused or recycled
• Steel can be recycled or reused endlessly without detriment to its properties
• Steel components can be reused with very little or no reprocessing
• Steel has the best strength to weight ratio of all construction materials
• Steel construction is lightweight reducing material consumption and concrete foundation requirements by 70% when compared to blockwork construction.
The LSFA works to drive engagement, champion change, and spread the word about the cost, productivity, performance and sustainability benefits of contemporary light steel systems. Trusted and widely specified by the UK construction industry –highly innovative and digitally savvy, the light steel sector has developed panelised and modular solutions that deliver high quality buildings on fast-track construction programmes. Bringing together a wealth of experience and technical know-how, the LSFA membership represents manufacturers, installers, industry supply chains, architects, engineers, consultants and clients operating in the light steel sector.
For more information visit: www.lsf-association.co.uk
SCI operates a certification system which covers product certification and the design of complete buildings which utilise those products. These complementary schemes provide reassurance to specifiers, end clients and other interested parties that the certified building products meet specified requirements and that the building design follows appropriate procedures.
SCI have applied to UKAS for an extension to scope to cover steel panels used as wall, floors and ceilings.
The SCI is committed to helping members meet their design, manufacture, construction and commercial objectives.
SCI have gained UKAS accreditation to ISO/IEC 17065:2012 to provide product conformity certification. SCI’s current accreditation covers self-supporting modular building units (modules) comprising walls, floors and ceilings
10414
certification@steel-sci.com
www.scicerts.com
Further to this collaboration, MiTek's Posi-Joist found a remarkable application in the construction of the Black Chapel Pavilion at the Serpentine Gallery in London’s Kensington Gardens. Integrating seamlessly into designer Theaster Gates’ vision, the Posi-Joists facilitated a quicker installation while echoing principles of sustainability.
MiTek is here to help and with a long history of steering advancements in building for nearly seven decades, its well placed to help the sector on its journey to net zero.
Founded in 1955, MiTek changed residential construction with the invention of the Gang-Nail plate, providing an affordable and scalable way to manufacture wood trusses. Today, MiTek serves residential and commercial customers delivering software, services, engineered products, and automated solutions that optimise a more integrated Design-Make-Build™ approach to construction.
By enabling upfront collaboration across the value chain, including architects, engineers, builders, component manufacturers and more, we create a single source of truth that guides each design decision and unlocks the power of offsite construction. A Berkshire Hathaway company since 2001, MiTek is backed by a team of over 6,000 professionals globally. The business enables the delivery of exceptionally streamlined builds, offering higher quality, increased speed, less waste, more value, and in turn, transforming how the world builds.
As MiTek makes its debut at the Offsite Expo, visitors to our stand can
see firsthand how our products and solutions are helping to shape the future of construction.
We will be showcasing our offsite manufactured Posi-Joist, which is helping the industry to meet new building regulations, housing targets, improved efficiency and quality. With tens of thousands of low-carbon homes projected to be built in the UK, Posi-Joist will play an integral role, offering the housing industry the ability to meet new building regulations, and support the UK energy transition.
Our Posi-Joist and Connector Plates are all verified with Environmental Product Declarations (EPD) in the UK. This endorsement allows industry stakeholders to assess the environmental footprint of MiTek's offerings, promising not only quality but sustainability across the lifecycle of the building.
These factors no doubt helped in the selection of Posi-Joist being used in the eHome2 project. This project is a collaboration with Saint Gobain, Barratt Developments and the University of Salford. Situated within the University’s innovative Energy House 2.0 research lab, it explores the boundaries of sustainable housing, incorporating technologies that surpass the current regulations, to see what is possible.
MiTek are proud to sponsor the ‘Client of the Year’ category at the 2023 Offsite Awards, a ceremony that recognises excellence and innovation in the sector. As we await the award ceremony, MiTek extends its best wishes to the remarkable finalists whose groundbreaking projects are all helping to pave the way for a more sustainable and innovative housebuilding sector.
We invite everyone to explore the future of construction with MiTek at Offsite Expo. First and foremost, we want to hear from you, come and tell us about your projects, products, services and any challenges you have. We can tell you about our Posi-Joist offsite manufactured floor system, the Design Optimisation service for housebuilders, and show you how our ‘Design-Make-Build’ methodology that is steering the industry towards a promising future.
MiTek will be exhibiting at Offsite Expo, showcasing its Design-Make-Build™ solutions on Stand E10.
For more information visit: www.mitek.co.uk
Today sustainability is not a buzzword it’s a necessity, and the transition to modern methods of construction (MMC) is now an integral part of solving the issue of climate change.
and whilst we’re incredibly proud of our roots, we’re also incredibly excited about the future and the rebrand reflects the business we’ve become.
“We continue to invest to support the sector having recently spent over £1million in additional door manufacturing machinery to increase capacity. We have also invested heavily in our people this year. On top of our excellent sales and admin functions, we have developed and recruited a wider team of estimators, project coordinators and specialists. We offer our customers a full support and technical service from initial enquiry, right through to product delivery on every project.
Historically known across the leisure industry, Morland have developed their technical and manufacturing excellence and ‘just in time’ production skills to become a trusted supplier to the offsite and modular industry. This year they have successfully worked across multiple sectors from education, healthcare, retail, residential, MoD and MoJ projects.
As the offsite and modular industry continues to grow and play a bigger role in building better, so does the
need for manufacturing partners such as Morland. Recognising this, Morland has evolved and from its dedicated door and doorset production facility in Welshpool, now offers a range of thirdparty certified fire doorsets.
Richard Allen Morland UK, Sales & Marketing Director says: “We’re incredibly proud of the strategic growth of our business and the role we play in supporting the offsite and modular industry. The rebrand reflects our evolution and growth as a business
The Welshpool-based business is a third generation, privately owned and operated organisation, employing over 130 people and is part of the Inter Products Group (IPG). As a member of the British Woodworking Federation (BWF) Morland offer a range of fully encapsulated, certified FD30 and FD60 fire doors and doorsets. Under the Certifier scheme they offer both completed doorsets and component materials. They will be exhibiting their fire doorset range and their new logo at Offsite Expo on Stand D18.
For more information visit: www.morlanduk.com
“MMC continues to play a pivotal role in UK construction and as a business we’re developing solutions to support it. Over the last five years we have increased our manufacturing capability and introduced several products as a result. From prefinished plasterboard, MDF skirting and architrave, along with Partition Kits which are all fully finished and ready for on-site installation. From our dedicated warehousing facility, we are able to offer a stocked range available within 48 hours of order. We’ll also be launching some new products in Q4 and in 2024 which will offer our customers an even wider choice of fully finished solutions. Morland UK will continue to develop innovative products and manufacturing processes to the support the offsite construction industry and we’re proud to be a trusted partner.”
Images:
A collaborative approach from Joe Jack Williams, Partner and Andrew Abraham, Architect at FCBStudios plus Alex Lynes, Associate Director at Webb Yates, collaborated to design out the complexities in the timber structure of Paradise – and in turn helped it on its zero carbon journey.
Timber is a key material for our current era of construction, providing not only a low carbon option for the structure of a building, but also bringing a warmth and delight to a space that other materials often miss. However, creating a timber structure is not a simple swap out for the more conventional steel or concrete, it requires a collaborative design philosophy that embraces the unique properties of timber. Exposing the timber is a benefit to the occupants, but needs input from the architect, structural engineer, fire consultant and full design team – not to mention support from the client – to enable the true benefits of timber to be realised.
At Paradise, a new workplace development by Bywater, the client and design team arrived at a vision for the building early on, putting wellbeing and sustainability at the forefront of the design. Throughout the design process the team has sought a ‘less is more’ approach, through simplifying details and interfaces. It has been a client ambition from the outset of the project to expose timber internally and celebrate these crafted details to enhance the internal environments for end users. With this preference made early on, a great deal of focus was put on devising a scheme that not only worked with the material but played to its strengths
and used it in the most effective way when considering all the building’s requirements together.
Exploring mass timber was an obvious choice, partly due to its ability to sequester carbon and partly due to its simplicity of form and construction. Timber locks away CO2 from the atmosphere during its growth, helping to balance the emissions elsewhere. Keeping it locked away is a key strategy against the action of climate change.
To realise the impact of this carbon storage though, a circular economy
approach to construction must be taken, thinking of component life from cradle to cradle and ensuring the sequestered carbon is kept locked away for longer than the life of the building. To achieve this for a mass timber building, we have designed with deconstruction in mind as well as construction. Each component is screwed or bolted together with reversible connections. At the end of its life, the Paradise building can be used for the creation of a new building, built from its timber components. To make this a reality, each connection needs additional consideration, moving away from traditional grouts, glues, and screeds.
To achieve this, we were faced with several challenges relative to the detailing of interfaces between different materials. One such example being where steel columns interface with CLT floor slabs. Conventionally, firestopping is handled through cementitious grout in these conditions, but noting that this would impact the potential disassembly of the building in future, the team worked through options that explored alternatives to grouts, preferring stone wool and sealants. For fixings to CLT, details have been developed using mechanical fixings over the use of adhesives to allow for future flexibility. This principle of future flexibility is key to the project brief, and as a result, the team sought to design this into the project as much as possible, such as designing ‘future cut out zones’ into the floor plates where they can be accommodated without adding additional structure.
Testing and research played a major role in the design process, the proposals for the Paradise building do not rely on cementitious screeds on CLT slabs to meet acoustic and fire performance. Instead, the team researched a number of methods of achieving these technical requirements and arrived at a fibre-board solution that is more lightweight, has a smaller carbon footprint and allows for disassembly much more easily than a screed.
The journey does not end with the design team, however. Bringing the various statutory and legislative bodies along in the process has been key in the development of the project. This has relied on strong inter-disciplinary
relationships and communication of the design principles and details early on in the project. Critical issues were identified and a pathway to compliance agreed at the start. This led to the creation of a full-scale mock up to interrogate the details being proposed for the building and assess them in relation to buildability as well as fire performance.
It was always the aspiration to celebrate the timber internally and so it was important that close attention was paid to the co-ordination of exposed services, structural junctions and finishes. Given the range of suppliers of mass timber, it was important to work closely with the supply chain to ensure that visual consistency was achieved across the different timber element types proposed for the building. This was primarily examined through developing an understanding of the materials and through a sampling process whereby different washes and fire-retardant coatings were applied to different grades and types of mass timber proposed.
Collaboration is as much about problem solving as it is about identifying opportunities. Keeping an open dialogue between the whole design team enables changes to be considered holistically. Constant communication and engagement throughout all stages between the consultant team was crucial to the
development of key details in a bid to keep things simple and rational, in line with the original concept of the design. This relied on iteratively developing details, testing them, and often adapting them when required.
During Stage 3, it was identified that increasing the thickness of the CLT in some areas would resolve acoustic issues and as a result, we spotted an opportunity to reduce the number of steel beams by utilising the thicker CLT to change some of the spans. This would typically be deemed a somewhat drastic change late on in the design process, however through swift collaboration, this was achieved, resulting in a more rational design. This change meant using less carbon – through the omission of steel – simplification of the services routes and a better overall appearance internally, through more timber being visually exposed.
Similarly, when undertaking the Stage 4 detailing of some difficult connections, it was recognised that moving a column to allow for a symmetrical steel junction into the timber would greatly simplify the detail. This resulted in a structural redesign of some junctions which in turn meant that connection plates became smaller and required significantly fewer bolts, again simplifying the design.
Designing and building with timber requires an awareness of complexity. The comparative newness of engineered timber and the relatively limited number of buildings that use it translates into a lack of standard details that can be adopted. At the early stages, any complex junctions
will require consideration – do they justify the additional work required to deliver them in practice? By giving them the time to be evaluated early on, we provide the opportunity to design them out, and for those that are necessary, flag for additional input as the project progresses.
Having a consultant and subcontractor team that have an awareness and experience of the complexities associated with mass timber has been crucial in developing the project effectively. It was important from the outset that everyone was on the same page and understood the design aspirations of the project. This allowed each team member’s expertise to feed into developing the design and produce a beautifully simple final building.
For more information visit: www.fcbstudios.com www.webbyates.com
Images: 01-03. Innovative detailing, interfaces and connections used on Paradise means the building can potentially be deconstructed and reformatted in the future
NMITE (New Model Institute for Technology & Engineering) will again open its doors to Built Environment Professionals for its Timber Technology Engineering Design 1 course, which starts on 18 September. Delivered in partnership with Timber Development UK and Edinburgh Napier University.
The TED courses are led by Assistant Professor Steve Bertasso, who recently joined NMITE and will also teach on NMITE’s BSc (Hons) Sustainable Built Environment. Steve graduated from Brigham Young University with a Bachelor of Science in Engineering, bringing a wealth of experience to the classroom. Throughout his 25 years in the industry, he focused on process improvement, strategy implementation, research, development, and training. His resume includes project management, purchasing, quantity surveying, and managerial experience in all aspects of the built environment with companies large and small across many markets and regions.
Steve comments: “I started work in the built environment when most work was completed by hand on worksites. Advancements in technology and process improvements open the industry to a diverse and inclusive workforce. This change helps retain talent with diminishing physical abilities and employs new talent with different perspectives and talents. Our industry has historically not been the most inclusive environment, but that’s starting to change, and it’s a change for the better.”
The TED1 course explores how to improve construction productivity using offsite manufacturing techniques with renewable natural capital rather than carbon-intensive material of concrete and steel, which accelerate the climate crisis. Participants explore ways to develop design work and construction that increases productivity and reduces the opportunities for error and re-work.
As part of the course, participants attend on-campus residentials at NMITE in Hereford, within the Centre for Advanced Timber Technology (CATT). This is a purpose built 2,500sq m ‘Living Lab’ hybrid structure which demonstrates advanced timber technologies and acts as an exemplar in the region, aspiring to net zero carbon targets. Those who have completed the TED course have come away feeling confident in their understanding of sustainable building and the use of timber as a building material. They have been keen to take that knowledge back to their workplace.
For more information visit: www.nmite.ac.uk
Cambridge-based architects MCW have completed work on a new cluster of social spaces at the heart of St John’s College, Cambridge, transforming a 500-year-old tradition of community dining with some contemporary timber prefabrication.
1
Alongside a new bar and a completely rebuilt buttery dining room is a café – a first for the college since its foundation in 1511. The new social spaces aim to fuse the contemporary need for an airy and vibrant social hub and eatery for students and academics alike, using modern construction methods and contemporary material choices, with the need to preserve a sense of history and character.
A comprehensive Masterplan Strategy had set out a series of aspirational objectives in 2017, underpinned by the notion of strengthening the College community. This project represents the first major step in response to a recognised need to provide an inclusive, supportive and energising social space at the centre of the campus.
The most significant element of the scheme is the new glulam oak superstructure of the buttery dining room, chosen because of its inherent warmth and tactile quality- reflecting the original oak columns and beams within the bar and cafe, as well as its low carbon credentials and potential to be assembled as a kit of parts.
This brief was met by a creative and thoughtful team of architects and planners, led by MCW with Purcell, Turley Planning Consultants, Tobit Curteis Associates and KJ Tait. The project has been an ongoing collaboration with Historic England and the Cambridge City Council Planning and Conservation group. Turner & Townsend project managed the scheme from design stage to completion, with Barnes Construction as the main contractor.
2
“The dramatic curved, trapezoidal timber structure, formed of prefabricated components, was brought on-site across what is reputed to be the second oldest bridge over the Cam.”
The new structure, a collaboration with Swiss timber specialists Blumer Lehmann and local structural engineers Smith and Wallwork, is ‘freestanding’ with only minimal, delicate stainless-steel ties back to the original brickwork, replaces a 1970’s steelframed roof that had been brutally built into the 16th century brickwork of both the Second Court building and the boundary wall to Trinity College.
The dramatic curved, trapezoidal timber structure, formed of
prefabricated components, was brought on-site across what is reputed to be the second oldest bridge over the Cam – designed by Christopher Wren and executed by Robert Grumbold – who also built the pair of Grade I listed, eagle-topped gate piers which had to be completely dismantled and carefully relocated as part of the project. Gaining approval to dismantle and rebuild Grade I listed fabric was one of the many challenges that the design team overcame.
The MCW team worked hard to preserve a character authentic to St John’s, taking a fabric-first approach to construction, which protects the integrity, stability and condition of historic fabric, whilst also boosting energy efficiency and carbon reduction. This meant retaining the building’s signature red brick and centuries-old wood panelling – whilst also incorporating elements that promote energy efficiency and health and wellbeing, including a ‘green wall’ watered by collected rainwater from the carefully detailed pre-patinated copper roof.
Paula Mejia-Wright, Project Lead for MCW, explains: “The application of contemporary retrofitting into historic settings is going to be crucial for colleges to thrive beyond the
21st Century. With collaborative design work, we have been able to re-energise an important part of the College, creating a sustainable and elegant meeting place for the whole college community.”
The social spaces sit within a site that includes the Grade I listed Second Court which has been continuously used as part of College accommodation since it was constructed in 1599. The surrounding park and gardens are Grade II* listed. Therefore, a comprehensive heritage impact assessment was critical to unlocking the potential for change to enable the site to continue to evolve, bringing relevance for a new era without harming the historic integrity of the building.
Purcell worked as Conservation Architect for the existing building, upgrading the environmental performance and repairing the fabric as well as working collaboratively with MCW on the interface between old and new to develop a solution that would touch the historic fabric as lightly as possible, outlining areas where change was possible without causing unnecessary harm.
A trophy cabinet has been made within a historic window that was discovered behind 18th century panelling during
the works. Original window seats have been carefully reconstructed incorporating power-points for laptops. Improving inclusivity and accessibility was a primary component of the brief. A careful re-grading within Second Court has created a level access where stone steps used to be and a new ramp alongside the terrace does the same for people approaching from the ‘Backs’, on Queen's Road.
Heather Hancock, Master of St John’s, said: “We have gained bright, warm and welcoming space for our day-today lives in College. We are privileged to learn, live and meet in such a beautiful and inspiring environment, and this latest development is a worthy addition to the fabric of the College.” Despite the challenges of preserving historic detail and meeting the complex demands of development within and around a Grade I listed building, the project achieved a BREEAM Excellent rating.
For more information visit: www.mcwarchitects.com
www.turnerandtownsend.com
Images: 01-05. The new offsite glulam structure blends in effortlessly with the historic college building. Courtesy MCW Architects/Richard Fraser
wedi Systems (UK) Ltd
PHONE: 0161 864 2336
BROWSE: www.wedi.net
EMAIL: enquiries@wedi.co.uk
with integrated, fully sealed Hansgrohe iBox & waterpipes
√ to suit over 200 thermostatic mixer designs
√ use as a fixed wall or as a free-standing partition
√ directly tileable, 100% waterproof and adjustable on site
√ in 900mm or 1200mm width and 80mm or 100mm thickness
√ individualisation options to meet customer specific needs (i.e. niche)
√ reinforcement plates for shower head attachments at selectable heights
Sustainability is becoming a compulsory requirement within the design brief, as the construction sector accelerates towards Net Zero 2050, says Stuart
Devoil, Group Head of Marketing at James Latham.This is certainly the case in the offsite sector where developers are constantly looking for ways in which to achieve a circular approach as possible to the design, manufacturing, and assembly of their systems and components. This means using fewer materials and thinking smarter about the products specified, particularly for structural elements, which usually carry the highest carbon cost.
The past decade has seen the emergence of a greener, lighterweight, cost-effective, and highperformance alternative in structural
plywood, specifically created to meet the demands of a range of applications including walls, flooring, roofing, framework, and joinery. One of the market leaders in the category is Finnish manufacturer UPM’s WISA®Spruce.
Manufactured using their own, proprietary adhesive, WISA® BioBond replaces at least 50% of standard glue’s fossil-based phenol with lignin, timber’s inherent bonding agent. Obtained as a by-product of the Kraft Process, this partial-substitution reduces the carbon footprint of WISASpruce by approximately 10%, without compromising technical performance or visual appeal.
Ranging from slender 3-ply to 13ply panels, WISA®-Spruce is carbon neutral, produced from timber from sustainable, certified forests, and manufactured in a low-emission facility.
modelling and detailing services as one holistic team. The approach, which takes clients from concept stage, right through to construction and manufacture, sets a new benchmark for industry excellence, with its own delivery framework – a step-by-step process, that overlays the RIBA Stages of Work.
Following a transformative rebrand earlier this year, which saw Design4Structures (D4S) and the former TDS combine as a single business, the company has been propelled to the forefront of offsite engineering.
Offsite project delivery is seeing more predictable, efficient, and sustainable outcomes, thanks to the approach of growing engineering consultancy D4S. Uniquely, D4S brings together engineering and construction
The methodology has gained vast recognition, from contractors and manufacturers, across industry. During the past 12 months, the business has both formed and strengthened a range of design partnerships including: M-AR, the JRL Group, British Offsite, the Darwin Group, Crown House Technologies, and the Berkeley Group.
Delivery ranges from bespoke LGSF homes, modular education, and healthcare facilities, through to, highrise modular builds, that seamlessly incorporate RC detailing as part of the optimal solution. The function is further
WISA®-Spruce engineered panels are high- quality and robust. Panels come in a variety of dimensions and are easy to CNC to the exact dimension required, keeping waste to a minimum with all offcuts with re-useable or recyclable, further encouraging circularity within the design and construction phase.
Available from James Latham, WISA®-Spruce is stocked nationwide throughout our 14 depots.
For more information visit: www.lathamtimber.co.uk
Images:
01. WISA®-Spruce is available in a variety of dimensions
enhanced by an in-house team of civil and infrastructure engineers.
Specialist Team
The offsite team at D4S is made up of sector and service specialists, who collaborate to enable clients to access an innovative set of solutions, tailored to their desired project outcomes, whether that is sustainability, manufacturing at scale, new product development or reducing project timescales without compromising quality:
Marc Ricks, Associate and Sector Lead for Low to Midrise Volumetric Modular
Adam Harkin, Senior Structural Engineer and Sector Lead for Mid to Highrise Volumetric Modular
Alex Kearney, Senior Structural Engineer and Sector Lead for LGSF
John Breeze, Associate and Sector Lead for Offsite Construction Modelling.
For more information visit: www.design4structures.com
Modular construction relies on a smooth, fast process that remains consistent.
A factory-produced brick cladding panelised system, the Gebrik Modular system allows for fast-track construction, providing you with a solution that is quick and easy to use and allows you the creativity and flexibility needed to get the finish and details that you want from your brick façade.
• Different house types available
• Choose from 700 brick finishes
• Supplied in kit form
• Quick and easy to install
• Free training provided
To find out more, contact us on: (0)808 223 9080
info@aquariancladding.co.uk www.aquariancladding.co.uk
assessment of U-values ensures optimal thermal comfort for occupants, minimises heat loss and gain, and reinforces commitment to creating environmentally responsible structures that promote long-term sustainability and reduce carbon footprints.
Inaccuracy issues remain, however, with U-values used in Building Regulations submissions. This has a negative impact on energy compliance, puts homeowners in difficult positions and increases CO2 emissions. To combat this, it’s a requirement to discuss stipulated U-value outcomes for domestic new-build projects with an energy consultant. Advisors are able to offer professional guidance based on the Standard Assessment Procedure (SAP).
For commercial properties, Simplified Building Energy Modelling (SBEM) is the approved national calculation methodology used to highlight their energy efficiency. With SBEM, a property’s overall U-value compliance is determined by the thermal outcomes of individual elements such as walls, floors, pitched and flat roofs. A calculation also takes into account a property’s size, location, model, shape and construction.
A correct outcome will ensure a building meets regulation levels of thermal performance. However, such is the prevalence of errant practice in relation to U-value calculations, it’s become something of an industry issue. If buildings are to meet required levels of energy efficiency, an accurate interpretation of heat transfer through building materials – which determines a U-value – is essential.
U-values feed into a building’s overall performance alongside Psi-values and renewable technologies such as heat pumps and solar panels. The lower a U-value is, the more thermally efficient the build-up is – meaning the more cost-effective homes are to heat.
Accurate U-value calculations hold paramount importance, as they allow informed decisions to be made regarding material selection, building envelope design and overall energy efficiency strategies. A meticulous
With SAP methodology, the thermal ratings of walls, floors, roofs, junction details and any renewable technologies are put into a metaphorical mix. The overall must correspond with or exceed the required regulations for the building. Elements can be changed, as long as the property achieves the required dwelling performance.
Working on the notional dwelling specification, which has to be followed as a minimum to achieve a pass, is an alternative to the SAP assessment. However, solely working to backstop values will result in failure.
SAP is a fairly complex assessment, as it allows for a compensatory approach to the elements involved. For example, if a roof’s height is preventing a U-value target from being achieved, the performance deficit can be madeup by installing additional insulation in wall and floor areas. With new-builds, therefore, adjustments to U-value outcomes can tip the balance in favour of achieving the required performance targets.
Ensuring a property’s thermal envelope has been specified correctly is prerequisite to achieving a property’s as-designed performance. The calculations involved in meeting this outcome should be performed by a professional using methodology outlined in BS EN ISO 6946:2017. In 1997, the guidance was expanded to include how tapered insulation should be calculated. This is now known as ‘Annex E’ calculations.
Incorrect U-value calculations will compromise a roof, and the overall building’s, thermal performance. Ultimately, this will have a negative impact on the environment, with the increase in CO2 potentially thwarting the UK government’s ambition to achieve net zero emissions by 2050. Thus – purveyors of best practice in respect of building design should put a high price on true U-values.
For more information visit: www.recticelinsulation.com
Images:
01. Ensuring a property’s thermal envelope has been specified correctly is a prerequisite to achieving as-designed performance and securing the correct U-value calculation. Courtesy Taylor Lane Timber Frame
The importance of accurate U-value calculations should not be underestimated. Simon Blackham, Senior Technical Manager at Recticel, illustrates why getting the calculation correct is so important.
Are you ready to take your offsite builds to new heights?
Unmatched Expertise: With over 80 years of industry experience, our team brings a wealth of knowledge and expertise to every project.
Quality and Durability:
Our commitment to delivering top-quality precast components guarantees long-lasting performance, providing a solid foundation for your offsite builds
Tailored Solutions:
Our advanced offsite manufacturing process allows for efficient production, reducing construction timeframes and minimising on-site disruptions
Sustainability Focus:
Embrace eco-friendly construction with our lowcarbon concrete solutions O'Reilly Precast is dedicated to minimising environmental impact and creating a greener future
AMS objective, with clear benefits to the client due to increased capacity, as a result of shorter cycle times, often implying a more detailed design and engineering input ensuring what is designed, is delivered.
AMS is setting new standards in efficiency, quality, and sustainability with its revolutionary approach to offsite construction. Multi-millionpound contracts have been secured with clients operating across traditional offsite-oriented sectors, including healthcare, education, defence, plus the more challenging residential sector, indicating a clear endorsement of the value of AMS’ services.
The new business was developed to target the needs of the MMC environment with the aim of reducing TAKT time within client facilities, increasing productivity and improving quality and output. The AMS approach reduces TAKT time by 50% on average, leveraging Pre-Manufactured Value (PMV) and helping to reduce embodied carbon impacts, whilst maintaining a cost neutral position compared to conventional installation methods.
Understanding the client’s requirements is one of the core values of AMS. Outlining how they engage clients, managing director Darren Charlton, says: ‘’Members of our team have attended numerous manufacturing facilities to gain a better understanding of how the offsite market currently operates and to discuss the future needs and aspirations of the MMC industry.
The key messages typically derived from these meetings were, time, consistency, quality, and cost.”
Across most sectors, the average module turnaround time is six weeks, of which four were for the services fitout. The initial driver for AMS was to reduce this four-week period to two weeks, resulting in increased client productivity. The starting approach with any new client is largely based on conventional installation methods rather than the full embracing of offsite techniques, inevitably reducing PMV in the short term. The knock-on effect being more work is left to do on-site, but as client confidence grows and the parties better understand each other, AMS seeks to introduce increased PMV at the factory facilities to reduce the programme time further.
In all locations, projects were being delivered to different stages of prefabrication, dictated by the current M&E installation teams. Each project had a different design and approach to providing a semi-offsite solution. The service’s design was not truly a Design for Manufacture & Assembly (DfMA) design and was simply being made to work by the site teams. The drive to deliver PMV to a minimum of 80% on all projects over time is a key
With client teams facing numerous installation challenges, it was difficult to drive quality into the build and achieve consistent outcomes due to the different installation approaches of each contractor. By utilising factory manufactured and tested subassemblies, AMS’ aim is to eliminate snagging and deliver top quality to ensuring both efficiency and productivity on-site.
Thanks to the solutions offered by AMS, saving time, means saving money. Not only is cost driven out, but value is driven in, measured by the increase in output achieved thanks to more work being done offsite with a corresponding reduction in overall project cost. Consistency in design, quality and installation are all a key component of AMS installation, providing huge gains for the client in environmental and project certainty. The benefits to the client of adopting the AMS delivery method for M&E services are quantifiable and increase with time.
Formed by two North East modular construction businesses, Apex Modular Solutions is based at CDE’s Stockton HQ with manufacturing carried out at Apex’s Durham plant, maximising the strengths of both companies within manufacture and installation.
For more information visit: www.apexwiringsolutions.co.uk
Images: 01-02. By utilising factory manufactured and tested sub-assemblies, the aim is to eliminate snagging and ensure efficiency and productivity on-site
Since launching Apex Modular Systems (AMS), a business specifically formed to supply and install pre-manufactured M&E services to the offsite construction sector, the business has seen orders soar.
Concrete and precast elements are well understood and widely seen in the built environment, but what are their benefits and how is the process changing the way we build?
There are clear advantages offered by offsite construction. Whether it is the digital streamlining of manufacture including repeatable elements and design for manufacture and assembly (DfMA) or programme efficiencies, including just-in-time delivery and the speed and safety of installation. Concrete MMC also offers unique sustainability and safety benefits. Recent examples demonstrate how a concrete offsite approach is changing the way we build in the UK.
The increased demand for housing and accommodation in the UK is becoming an acute issue and speed of construction is an important factor when considering solutions. Nowhere is this more evident than where universities are looking at innovative ways of delivering planned accommodation ahead of schedule.
In 2021, The University of York was committed to build a set of 18 three
and four-storey accommodation blocks, which would provide 1,480 student rooms, the £130million Campus East Gateway. Wanting to deliver a portion of that accommodation quickly, the university turned to an MMC solution using precast concrete. Precast specialist FP McCann delivered the panels which formed the crosswall construction system on a ‘just-in-time’ basis.
Small installation teams and mobile cranes meant work could take place on more than one accommodation block at a time. The build was so fast that the team completed the enclosure of each room in an average of 1.9 hours. The resulting programme saving enabled the delivery of 300 rooms a full two terms ahead of schedule. The accommodation block facades are made from insulated 465mmthick sandwich panels, while slimmer 160-180mm panels form the internal walls. Each room is completed with a 175mm-thick precast slab which
cantilevers beyond the room perimeter to form half the ceiling for the internal corridor.
The concrete structure means that every room performs very well acoustically and exceeds the requirements for fire performance. Indeed, as an inherently noncombustible material with the highest fire safety rating of class A1, concrete is the best way to provide peace of mind to occupants.
The HS2 rail network is the UK’s largest ongoing infrastructure project, which includes new tunnels to help reduce the impact of the project on local communities. Where appropriate HS2 is deploying an innovative cut-andcover method of construction with precast concrete tunnel sections manufactured offsite and installed quickly and efficiently at the surface. These tunnels are then recovered and planted on top with trees and shrubs,
giving rise to their ‘green tunnels’ name. In total Sateba Stanton Precast will produce more than 13,290 tunnel segments to form the three green tunnels.
Four miles worth of tunnels will be built at Stanton Precast’s Ilkeston factory and assembled at three locations in rural Buckinghamshire and Northamptonshire. The first green tunnel will stretch for oneand-a-half miles (2.5km) past the village of Chipping Warden in Northamptonshire. This tunnel comprises of more than 5,020 individual tunnel segments and is being produced by Stanton as part of the contract awarded by HS2’s works contractor, EKFB – a team made up of Eiffage, Kier, Ferrovial and BAM Nuttall. They are working with specialist engineers Matière who have been appointed to install the tunnel segments on-site.
Designed as a double arch, the tunnel has two separate halves for southbound and northbound trains. Five different concrete precast segments are slotted together to achieve the double arch – one central pier, two side walls and two roof slabs. The UK concrete industry is rapidly decarbonising, however construction is a source of carbon emissions. The lighter-weight modular approach used here is expected to more than halve the amount of carbon embedded in the structure.
For more information visit: www.thisisconcrete.co.uk
Images:
Due to the many advantages associated with MMC, precast concrete can offer highly cost-effective solutions for bespoke concrete projects. Here are five ways where concrete MMC can deliver benefits for construction.
MMC can significantly cut down on-site construction time since precast concrete products prepared offsite can simply be brought to site, ready to be installed. All required elements from a fully digital construction model can be planned into production schedules, meaning that suppliers can meet demands for large projects on a ‘just-in-time’ basis. With fewer workers required for assembling materials onsite, the entire construction programme becomes much more efficient.
The precast technology used in concrete MMC leads to considerable cost savings, thanks to both reduced labour and shorter construction times. The quality control procedures and robust, sophisticated manufacturing involved in MMC mean that snagging costs are also reduced.
From a health and safety perspective, construction workers can be better protected on MMC projects as its techniques reduce both the amount and scope of traditional on-site construction activities. The installation of precast concrete has recently seen new innovations, including the use of air-inflated crash bags and nets to ensure that workers operate in the safest environment when fitting the precast elements.
Designers and architects are increasingly looking towards creating long-life resilient buildings. Concrete MMC can contribute to the circular economy by creating longerlife, low carbon assets that can be designed for change of use, disassembly and element reuse. Through its durability and resilience, precast helps to protect people and property not only from fires but also water damage and the effects of climate change.
Although MMC has typically been associated with the installation of lightweight materials, the production of precast concrete panels for both floor and wall units has been tried and tested over many years, with concrete MMC delivering significant advantages. Concrete is an inherently non-combustible material with the highest fire safety rating of class A1, reducing risk and providing more reliable construction and greater confidence to customers.
Concrete plays a central part in many construction projects and the continuing development of low carbon concrete with supporting EPD information is fundamental in the transition to a cleaner and healthier built environment.
Concrete is a critical construction material due to its durability, versatility, and affordability. However, its production, particularly cement, is a significant source of carbon emissions, accounting for around 8% of global greenhouse gases. Despite this, concrete is irreplaceable due to its unique advantages.
Low carbon concrete is a promising alternative to traditional concrete, and Environmental Product Declarations (EPDs) are helping to ensure its adoption. EPDs are documents that transparently communicate the environmental performance of a product over its lifetime. This information can help stakeholders to make more sustainable choices and drive industry-wide change. Therefore, EPDs for low carbon concrete can be valuable in transitioning to a sustainable construction industry.
What is low carbon concrete?
Low carbon concrete is a type of concrete that has a lower embodied carbon footprint than traditional concrete. However, there is no universally agreed-upon definition of ‘low carbon’ concrete. Some local initiatives, such as Germany's Concrete Sustainability Council and Norway's Lavkarbonbetong standard, have attempted to define low carbon concrete, but there is no global standard. The UK has its own voluntary Low Carbon Concrete Code. Low carbon concrete is typically made by substituting cement with alternative materials, such as fly ash or ground granulated blast furnace slag (GGBS). However, there are other potential solutions, and innovation is key to developing more low carbon concrete.
EPDs: the key to a greener concrete industry
1• EPDs play a crucial role in quantifying and communicating the benefits of adopting low carbon concrete. Specifically, EPDs can:
• Provide a comprehensive assessment of the environmental impacts of low carbon concrete, including its carbon footprint
• Compare the environmental impacts of low carbon concrete to other types of concrete
• Help to identify and quantify opportunities for further improvement
• Communicate the environmental benefits of low carbon concrete to decision-makers.
Transparency in EPDs for low carbon concrete is essential for empowering stakeholders to make informed choices about using it. By providing clear and accurate information about the environmental impacts of low carbon concrete, EPDs can help stakeholders to select the most sustainable option for their project.
EPDs can be used to compare the environmental performance of different materials, including concrete. This information can be used by builders and designers to make informed decisions about the materials they use in their projects and prioritise materials that minimise ecological impact without compromising structural integrity.
As governments worldwide implement stricter environmental regulations and incentivise sustainable practices, EPDs provide a valuable means of ensuring compliance. Low carbon concrete producers who provide EPDs for their products are better positioned to navigate evolving regulatory landscapes and demonstrate adherence to environmental standards. In addition to ensuring regulatory compliance, EPDs can help low carbon concrete producers differentiate their products in a competitive market. EPDs can also help low carbon concrete producers to appeal to environmentally conscious consumers and businesses.
The integration of EPDs for low carbon concrete stimulates innovation across the construction sector. For example, manufacturers may be able to reduce the environmental impact of low carbon concrete by exploring novel
production techniques, optimising material formulations, or adopting renewable energy sources.
EPDs can help reduce construction materials’ environmental impact by providing information about their environmental performance throughout their lifecycle. However, the cost and complexity of creating EPDs can hinder their adoption. One Click LCA, a leading construction LCA platform, has developed a pre-verified EPD generator that can significantly reduce the time and cost of creating an EPD.
This tool automates many steps involved in creating an EPD, such as data collection, calculation, and reporting. It also eliminates the need for third-party verification, which can be a time-consuming and expensive process. The pre-verified EPD generator is a comprehensive solution that can be used by manufacturers of all sizes, regardless of their experience with EPDs. It makes EPDs more accessible and affordable, which can help to accelerate the adoption of this important tool for sustainability.
One Click LCA's innovative Concrete EPD Generator streamlines EPD publishing, facilitating rapid and adaptable creation of project-specific or tender-based EPDs. The One Click LCA Concrete EPD Generator empowers manufacturers to showcase
decarbonisation potential effortlessly, meeting market demands with a simple click.
Low carbon concrete helps reduce carbon emissions in the construction industry. EPDs help to make this happen by providing transparency, informed choices, compliance, and market differentiation for sustainable construction. As global climate commitments become more important, EPDs for low carbon concrete show us a hopeful path to a more sustainable future.
For more information visit: www.oneclicklca.com/pre-verifiedepd-generator
Images:
01. Precast concrete is one of the leading offsite construction products 02. Composition of concrete 03-06. Lifecycle analysis and the use of EPDs are essential to understanding and specifying sustainable materials
Mechanical, electrical and plumbing (MEP) are key elements to all buildings and modular units are providing a new dimension to offsite designed structures.
MEP services can represent more than a third of the cost of constructing a building, as they provide the heart and lungs that turn it from a shell into a safe, comfortable and fully functioning environment. The value of building services goes way beyond construction, as the provision of water, sanitation, heat, light and ventilation make an impact on a building’s occupants across its lifetime.
Consultants and contractors as well as clients and facilities managers are looking to ensure that quality and performance is designed in at the start of a project and delivered and maintained throughout the building’s
usage. In a world with increasing demands on health, safety, wellbeing, efficiency and sustainability, this could feel like an impossible task, but a new generation of platform solutions is bringing fresh thinking to how MEP services are delivered and sustained.
MEP platforms such as modular risers, bathroom wall panels, corridor cassettes and prefabricated utility cupboards can be designed in from the early stage of a project, and then built using a Design for Manufacture & Assembly (DfMA) approach and delivered direct to site. Not only does this reduce time and effort in the installation process, but it also ensures that the finished services are fitted to the highest standards and match exactly with the building’s specifications, supported by a full warranty and maintenance package to simplify facilities management.
MEP platform solutions are providing better quality solutions on projects from apartments and care homes to hospitals and schools – they are changing the way that building services perform for the benefits of constructors and occupants alike.
For more information visit: www.aliaxis.com
Images:
01. MEP platforms such as modular risers, bathroom wall panels, corridor cassettes and utility cupboards can be designed in from the early stage of a project
new products developed with the offsite market in mind.
perfect package. Knauf Airless is a quick and easily applied alternative to traditional gypsum plasters. GIFA Flooring is a high-density screed panel provided in a tongue-andgroove interlocking flooring system. Both systems reduce installation time and water usage, with Knauf Airless retaining its flexibility once dry whilst Knauf GIFA retains its structural integrity.
The evolving range of products and solutions provided by Knauf UK & Ireland provide the perfect starting point with a combination of longestablished technology with innovative
Exterior products such as the Knauf ThroughWall system provide a unique, BBA-approved solution. Comprising steel framing components (SFS), internal insulation, plasterboard and external sheathing insulation, the ThroughWall system allows for a range of external finishes such as rainscreen cladding or brickwork to be added in the factory or on site.
Driving efficiency for interiors, Airless Spray Finish and GIFA Flooring combine speed and quality into the
As a manufacturer that doesn’t need to enter the debate about whether offsite or traditional building methods provide the best solution, Knauf UK & Ireland provides a range of lightweight solutions that are equally appropriate for fast, high-quality construction whatever route is chosen.
See us at Offsite Expo on Stand D08. For more information visit: www.knauf.co.uk
Images: 01-02. Knauf products offer many innovative ways to improve the construction process
Fundamental to the principle of volumetric modular construction is the need for easy transportation and assembly of the finished modules. Products must therefore be light and flexible as well as suitable for installation in a factory environment.
SEE THE KNAUF EXPLODED MODULAR UNIT HIGHLIGHTING WHERE KNAUF PRODUCTS AND SYSTEMS CAN BE USED WITHIN YOUR BUILDS
TO SEE THE LATEST OFFSITE, MMC SOLUTIONS, VISIT US ON STAND D08
Since the nineties, Sto has been partnering with modular and offsite housing companies and developers across Europe. Its expertise in developing façade and application solutions for the prefabrication industry has seen their dedicated industry team – created in 2001 –continue to grow, to focus on meeting the needs of offsite specialists, with local support available throughout Europe, the UK and Ireland.
Specialist product range
Sto’s external wall insulation systems can be factory applied to a wide range of modular panels, including timber and steel framed structures. StoSilco render or brick-slips which offer a variety of design, colour and texture options, can then be used to finish the panels prior to them being transported to site for installation.
Thanks to the skills of more than 170 R&D experts in a wide range of laboratories, Sto has also developed unique products designed to further speed up the productivity for offsite specialists. These include an adhesive and base coat which can dry faster than standard products used on-site. A further benefit is that products can be delivered to factories in large quantities using 180-litre barrels or alternatively, in silos – machines which enable up to 1,000kg of base coat and adhesive to be directly sprayed onto the modular panels.
When creating an offsite panel, sourcing the components from a single supplier like Sto is more important than ever before. This approach ensures the components will work together as a system and perform as expected to meet UK building regulations. To help prefabrication housing companies and developers achieve this aim, Sto also manufacture their own StoVentec carrier board which is significantly lighter than traditional third-party cement boards.
With more than 20 years’ experience gained across Europe, Sto’s prefabrication expertise extends beyond products. Its dedicated team offers technical guidance and support and testing throughout the production process, to provide faster cycle times, higher degree of automation, consistent layer thicknesses and triedand-tested production sequences.
Sto’s expertise also includes best practice advice on the most suitable products, eliminating the need for offsite specialists to spend time experimenting with different types of components. Bespoke method statements can be developed too, ensuring the most effective process is put in place for aligning and connecting the panels once on-site.
As the need to reduce carbon emissions during construction intensifies, Sto is supporting its modular partners with environmentally friendly products and processes. The StoVentec board for example is made from 96% recycled content and the company’s German headquarters is completely CO2-neutral, with solar panels installed, runs on hydroelectric power, and 100% of the electricity they purchase is certified green electricity.
With the potential to deliver a significant proportion of new homes, especially in the social housing sector, offsite manufacturing will continue to grow. With a proven track record, Sto is ideally placed to respond, providing tried and tested façade solutions that can meet any demand.
For more information visit: www.sto.co.uk
Images:
01. Factory installed Sto external wall insulation with a StoCleyer B mineral brick slip façade finish
02. Sto has developed unique products designed to further speed up the productivity for offsite specialists, including an adhesive and base coat which dries in just 24 hours, and can be supplied in silos
03. Sto’s dedicated team offers technical guidance, support and testing throughout the production process to provide faster cycle times and tried-and-tested production sequences.
With more than 20 years’ experience, Sto is enabling the prefabrication industry to create faster, simpler, and more efficient production processes.
MODULAR BUILDING AUTOMATION DESIGN AND MANUFACTURE INNOVATIVE MACHINERY FOR THE OFF-SITE CONSTRUCTION SECTOR, FOR BOTH TIMBER FRAME AND STEEL FRAME. WITH OUR INDUSTRY LEADING MACHINERY SOLUTIONS AND EXPERTISE, OUR TEAM CAN HELP YOU FIND THE RIGHT SOLUTIONS FOR YOUR PRODUCTION NEEDS!
If you are interested in learning more about offsite construction and the associated manufacturing processes then the following industry events may be of interest:
04 October Structural Timber Awards NCC, Birmingham
Timber continues to stand at the core of success across so many sustainable construction projects. This, combined with enhanced speed and performance benefits, are just some of the reasons for the abundance of exceptional projects. The Structural Timber Awards provide one of the most effective platforms to promote brands or companies alongside the best of the best. To join the sponsors, judges and finalists as they celebrate the 2023 Winners & Highly Commended at the National Conference Centre, please book online.
12 October British Offsite Factory Tour Essex
2023 marks the opening of British Offsite’s brand-new 180,000sq. ft. Horizon Factory in Braintree. To celebrate the occasion, British Offsite are opening their doors to a select group of construction professionals interested in exploring their state-of-the-art, light gauge steel panel semiautonomous assembly line purpose-built to manufacture up to 11,000Lm of UNisystem by 2025. To register your interest to attend, please contact Jessica Holland (Jessica.holland@radar-communications.co.uk).
15 March Tall Buildings Awards Entry Deadline Online
Tall buildings present unique challenges in terms of both design and construction. Their sheer scale demands that particular attention is paid simultaneously to strategic and detailed issues. The Tall Buildings Awards celebrate those that are developing unique design and engineering solutions to maximise space in city centres where demand is high whilst creating a legacy of iconic superstructures that are transforming the UK's built environment.
19 & 20 March Modular Matters Coventry Building Society Arena
Modular technology is ever evolving and to help keep pace with this fast-moving sector. Presenting an insight into the future of construction, this event represents a great opportunity to gain industry intelligence and network with those who are at the forefront of the volumetric modular sector.
16 April Structural Timber Conference ThinkTank, Birmingham www.structuraltimberconference.co.uk
The groundswell of interest in engineered timber is driven by both technological advances and concern for the environment and sustainable construction practices. Experts from the structural timber sector will come together to address timber’s use in the construction industry as a versatile and natural material undergoing a contemporary design resurgence.
14 May Focus on Framing ThinkTank, Birmingham
The only specialist event of its kind, Focus on Framing provides a solution for light steel frame professionals looking to gain a greater understanding of the latest advances and best practise principles from sector experts. Through informative speakers and case study presentations the seminar will focus on the fast-track non-combustible solutions that are having a significant impact delivering outstanding buildings across all construction sectors.
31 May Offsite Awards Entry Deadline Online
www.offsiteawards.co.uk
Returning for its tenth year, there will be 25 categories that cover every aspect of the industry from hybrid and modular technology to engineering and installation, ensuring that all aspects of the offsite building process is celebrated - recognising the design and technology that makes these inspiring projects possible.
21 June Structural Timber Awards Entry Deadline Online
Featuring compelling examples of what can be achieved using the most natural and sustainable of materials, the 2024 Structural Timber Awards will be a celebration of not only outstanding projects and inspiring individuals, but the coming together of an industry.
17 & 18
September Offsite Awards - 10 YEAR ANNIVERSARY
Taking centre stage at Offsite Expo, the Offsite Awards will be a major coming together of the industry where over 500 guests will gather to celebrate ground-breaking achievements and the pioneers who are developing radical new offsite technologies, innovative product developments and landmark projects using factory-based methods.
Timber continues to stand at the core of success across so many sustainable construction projects. This, combined with enhanced speed and performance benefits, are just some of the reasons for the abundance of exceptional projects. The Structural Timber Awards provide one of the most effective platforms to promote brands or companies alongside the best of the best.
ACROSS OUR VALUE CHAIN WE’RE REDUCING THE AMOUNT OF ENERGY THAT’S NEEDED AND MAKING RESPONSIBLE CHOICES ABOUT THE RESOURCES USED.
Because the best way to save energy is to make sure it isn’t needed in the first place.
QUICKER TO BUILD, AIRTIGHT AND ENERGY EFFICIENT BUILDINGS
UNipanel significantly outperforms the requirements of current Building Regulations (adl2021), and UNisytem is expected to outstrip the requirements of the future home standard when it comes into operation in 2025.
THAT MEANS LOWER ENERGY USE AND BILLS.
U-VALUES THAT VALUE PEOPLE AND PLANET
120 DAYS 60 MINUTES 20%
We can convert a traditional construction project to a hybrid manufacturing and construction project and deliver to site in as little as 120 days.
We have the capacity to create a complete set of panels for one apartment every 60 minutes.
The time between first fork in the ground to first handover of keys can be reduced by up to 20%.
PRECISION, EFFICIENCY AND CONTROL – FROM END-TO-END OF OUR VALUE CHAIN
Designed with Randek UK, Horizon utilises state-of-the-art machinery with energy control features built in. Renewable energy is self-generated from solar panels on the roof.
Responsibly sourced steel for UNisystem core contains 38% recycled steel. An insulation layer on UNipanel is made from recycled bottles.
We follow a just-in-time manufacturing process focused on precision and efficiency, to optimise the use of raw materials and radically reduce waste.
Our just-in-time manufacturing methods ensure fewer site deliveries reducing road miles and energy consumption.
Exterior panels come with 200mm of interior insulation and 100mm on the outside. Pre-installed glazed windows offer exceptional air tightness, increasing insulation further.
With UNisystem the work of up to five trades can be combined into one panel. Fewer trades are needed on site and build time is reduced, cutting road miles and energy consumption.
DISCOVER HORIZON
ONE OF THE MOST AUTOMATED LIGHT GAUGE STEEL PANEL ASSEMBLY LINES IN EUROPE AND THE LARGEST SINGLE PRODUCTION LINE IN THE UK TO DATE.
137,000 SQ FT SIZE
£40 MILLION INVESTMENT 4X PRODUCTION CAPACITY
British Offsite Head Office Horizon, 1 Rontgen Place Horizon Boulevard, Braintree Essex CM77 7AX
01371 707270
info@britishoffsite.com britishoffsite.com
Looking for a superior building membrane that can keep up with the unique demands of modular construction? Look no further than Wraptite! Our innovative and versatile, self-adhesive membrane conforms to the shape and size of your modular buildings, ensuring an airtight seal, while allowing for easy installation and protection during transportation. Don’t settle for traditional building membranes that may fail under the pressures of modular construction – choose Wraptite for a reliable, highperformance solution that delivers results.
01250 872 261