
8 minute read
Steel’s seriously green credentials
DECARBONIZATION
The ever-expanding application scope of steel and its increasingly integral role in the decarbonization of heavy industries brings the alloy to the fore as a crucial engineering material, says Global Market Insights
FOR years, nearly every aspect of life, from buildings to cars and beyond, has been infl uenced by steel in some capacity. As a critical material in construction, automotive, natural gas pipelines, electricity networks, military weapons, and other industrial sectors, the use-cases of steel are vast and continue to expand. In fact, according to a Global Market Insights report, the steel market for automotive and aerospace applications is expected to surpass $175 billion by 2027.
One of the main reasons for the popularity of steel over the years is its versatility. According to estimates from the World Steel Association, more than 3,500 grades of steel are in existence, building a foundation for the modern world. Steel is also renowned for its recyclability, and as a result, has secured an important position in the circular economy.
Considered one of the basic engineering materials, steel has also been critical in the development of novel sustainable technologies and is coming to be a major driving force behind the decarbonization of heavy industries.
Escalating use of steel in additive manufacturing for aerospace applications
With the rise of the digital era, technologies like 3D printing or additive manufacturing have started to make their mark in various high-performance sectors, particularly aerospace and defense. Aerospace engineers are constantly on the look-out for solutions to make their products stronger, faster, and lighter, which has thrust 3D printing into the limelight as an ideal technology for the production of important structural parts like forgings and castings, in satellites and military aircraft.
The coronavirus pandemic has also been a contributor to the growing adoption of additive manufacturing in the aerospace sector. Given the massive halts of global passenger air traffi c during the peak of the crisis in 2020, aircraft manufacturers have had to face several challenges and detriments over the past few years. In order to ready themselves for recovery, many of these manufacturers have started to embrace digital technologies like additive manufacturing, to enhance fuel effi ciencies, cut down lead times, and improve the sustainability of air travel in general.
Metal 3D printing, especially, has triggered signifi cant evolution in aircraft production over the past few years.
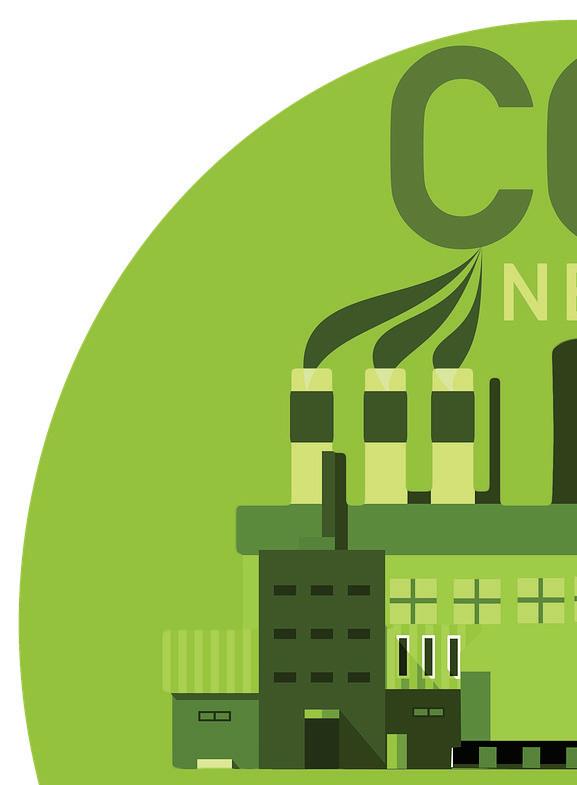
DECARBONIZATION

Several aerospace fi rms and OEMs are ramping up their investment in large-scale metal AM equipment and projects to develop high-performance, mission-critical metal parts designed to accommodate the stringent requirements of modern aircraft.
To illustrate, in March 2021, global engineering fi rm Renishaw was awarded funding worth £26.4 million by the UK government and industry, via the ATI (Aerospace Technology Institute) programme, designed to revolutionize the production of aerospace products in the UK. The LAMDA (Large Scale Additive Manufacturing for Defence and Aerospace) project, spearheaded by Renishaw, was geared towards creating a novel metal 3D printing system, both to mass-produce smaller aircraft parts as well as to fabricate large aircraft parts as well as to fabricate large aerospace components aerospace components at accelerated at accelerated production production rates rates and lower costs.
The objective behind the project was to facilitate the production of lighter, smaller aircraft components that would eventually play a major role in helping the aviation sector achieve its net-zero targets.
Materialise made similar efforts in October 2021, partnering with Proponent, an aircraft part distributor, to study how 3D printing could benefi t aerospace OEMs. Through the collaboration, the entities envisioned a digital supply chain facilitating on-demand production by integrating additive manufacturing into procurement and making 3D printed parts easily available to MROs.
While polymeric materials have long been the preferred choice for the development of 3D printed products, of late, material focus is gradually shifting towards metallic materials like steel in additive manufacturing. 3D printed metals are rapidly gaining a stronghold across industries that require highperformance, durable, and lightweight metal components. Use-cases are growing tremendously within sectors like aerospace, which is set to emerge as a prominent segment of the steel industry and will exhibit a nearly 3.5% CAGR through 2027, as per GMI projections. This is being supported by various efforts from fi rms like Desktop Metal, which announced the qualifi cation of Grade 420 stainless steel, a heat-treatable, martensitic stainless steel for high-volume additive manufacturing in October 2021. Known for its hardness, strength, and corrosion resistance to foods, freshwater, mild acids, and atmospheric elements in a fully hardened state, the 420 SS was designed for use on the Single Pass Jetting (SPJ) technology-based production system platform.
By achieving faster build speeds in metal 3D printing, this announcement was received well by manufacturers looking to mass-produce high-strength 420 SS-based end-use components for high-performance industrial applications like aerospace, defense, and medical, among others.
Similarly, in September 2021, 3D Systems introduced two novel high-strength alloys for metal additive manufacturing on its 3D printing systems. The alloys, including a hardened stainless steel certifi ed M789 (A), were designed for use in various application sectors from automotive to energy to aerospace and more. The certifi cation of M789 for the DMP platform was achieved via 3D Systems’ collaboration with GF Machining Solutions, a machine-tool builder, to accommodate the burgeoning demand for corrosion-resistant, hard tooling steel.
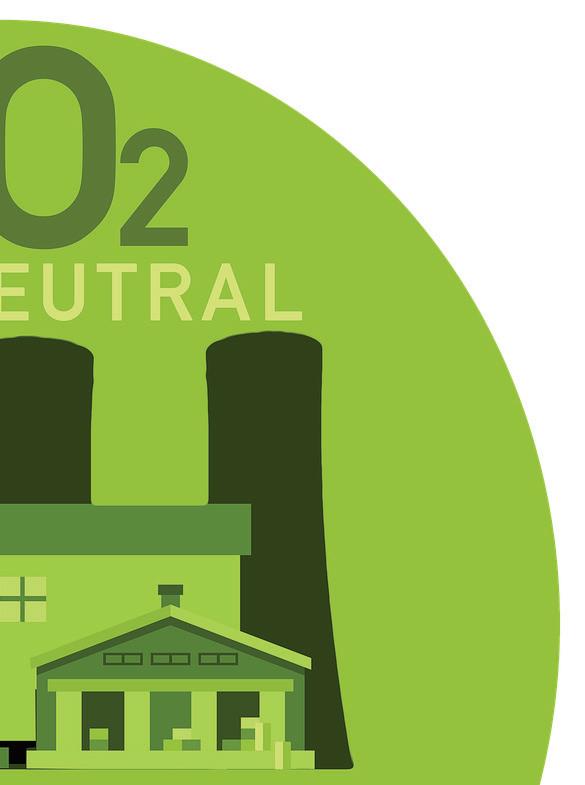
Major global initiatives promoting steel as a building block for decarbonization
Steel is a building block of the modern economic landscape, featuring in nearly everything from transport infrastructure, buildings, heavy equipment, and consumer goods, among others. More recently, this applicability has expanded to green technologies like public transit, electric vehicles, and wind turbines, which rely heavily on steel-based components and structures.
On the downside, steel is among the most prominent carbon emitters, accounting for almost 7% of GHG (greenhouse gas) emissions worldwide. The conventional process of iron ore-based steel production is the primary source of these emissions, given the use of blast furnaces that require the use of metallurgical coal.
Considering the monumental burden of the steel industry on environmental health,
DECARBONIZATION
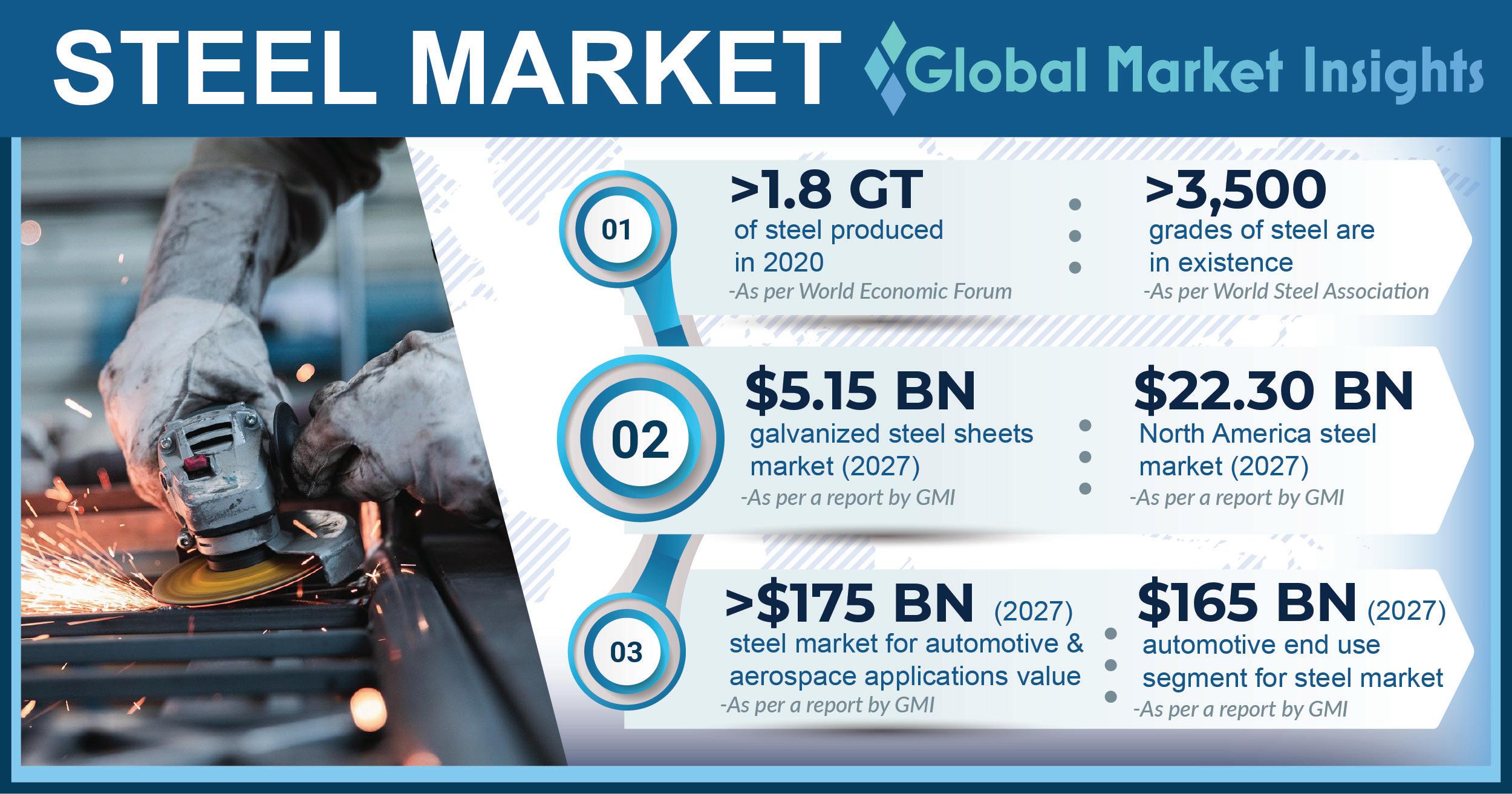
governments and regulatory authorities are making targeted efforts to decarbonize the industry and alleviate its impact. These efforts seem to be paying off; over the past few years, a new solution has been emerging in the form of green steel, which is made from hydrogen instead of coal, creating significant opportunities for the steel market.
According to research from the World Steel Association, the successful implementation of green steel technology could potentially reduce indirect and direct emissions by nearly 20% and 50% as compared to average ore-based steelmaking and scrap-based steelmaking sites respectively. Statistics such as these indicate a massive change in the steel production landscape, with Green Steel Tracker estimates suggesting that seven out of 10 of the world’s largest steel-producing countries have introduced at least one green steel initiative.
In June 2021, for instance, The European Commission and ESTEP (European Steel Technology Platform) introduced the Clean Steel Partnership and e-signed a memorandum of understanding, to pilot and explore groundbreaking technologies capable of reducing CO2 emissions from EU steel production. In alignment with the targets of the European Green Deal, the Clean Steel Partnership was developed to extend support for EU leadership in its efforts to turn the steel industry into a carbon-neutral sector and act as a catalyst for other strategic industries as well.
In November 2021, numerous countries including India, Canada, Germany, the UAE, and the UK signed a pledge under CEM’s Industrial Deep Decarbonization Initiative (IDDI), which was introduced in June the same year. As part of the initiative, which was designed to facilitate global collaboration for the decarbonization of heavy industries, the countries pledged to enhance the adoption of green steel alongside other green procurement principles, and collectively develop a set of targets for 2030.
Major players in the global steel industry and other associated sectors are also blazing the trail for technical innovation and green steel adoption, through a flurry of research efforts and massive investments to support them.
Prominent automotive entities like BMW and Mercedes-Benz, for instance, have committed to integrating the use of green steel in their vehicles from 2025, as part of their numerous efforts to achieve carbon neutrality. This transition to CO2-free steel has been facilitated by the firms’ collaboration with H2 Green Steel (H2GS), an up-and-coming steel producer focused on the decarbonization of industry using sustainable resources like green hydrogen.
Steel companies HKM and Thyssenkrupp Steel also inked a partnership with the Dutch port of Rotterdam in May 2021, to examine the import of renewable hydrogen or the production of green steel. Rotterdam is also set to establish a carbon dioxide transport and storage system, which will help store CO2 captured from natural gas-derived hydrogen production, as part of the “H2morrow steel” project, which has Thyssenkrupp Steel as a partner.
All-in-all, steel is by far the most versatile, multi-functional, and integral of engineering materials in the modern industrial world. The steel industry has long been the backbone of the developed economy and will continue to serve as a strong and steadfast foundation as the world navigates towards a more sustainable industrial ecosystem in the years to come. �
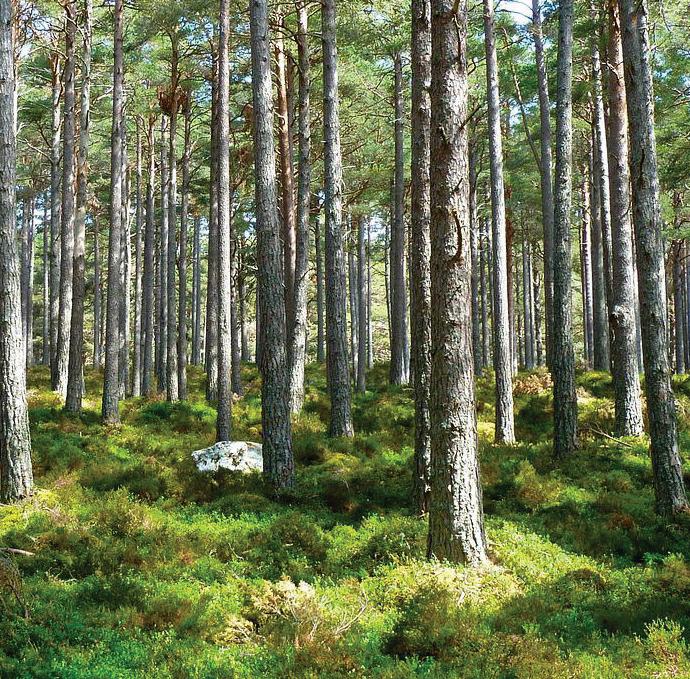
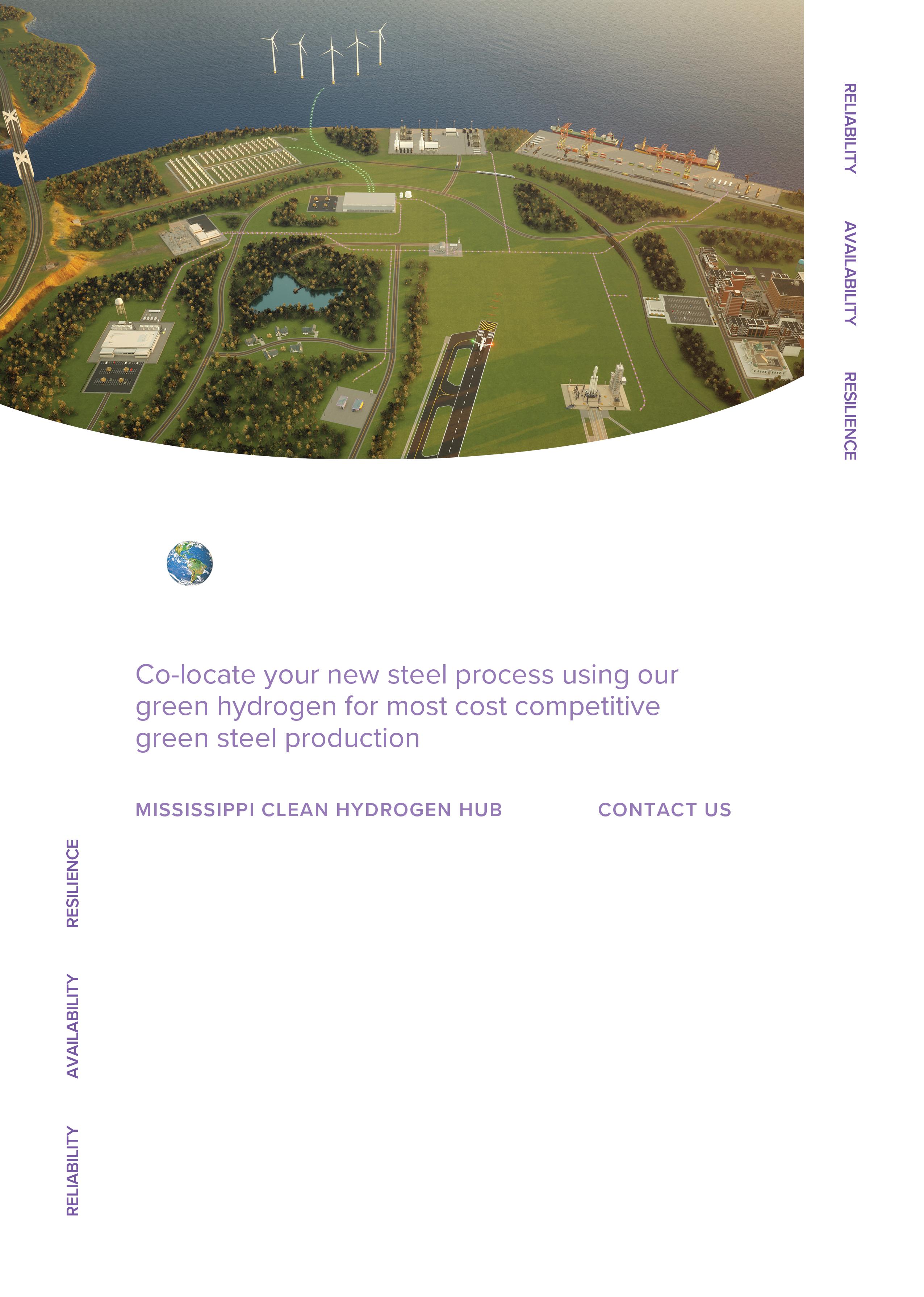
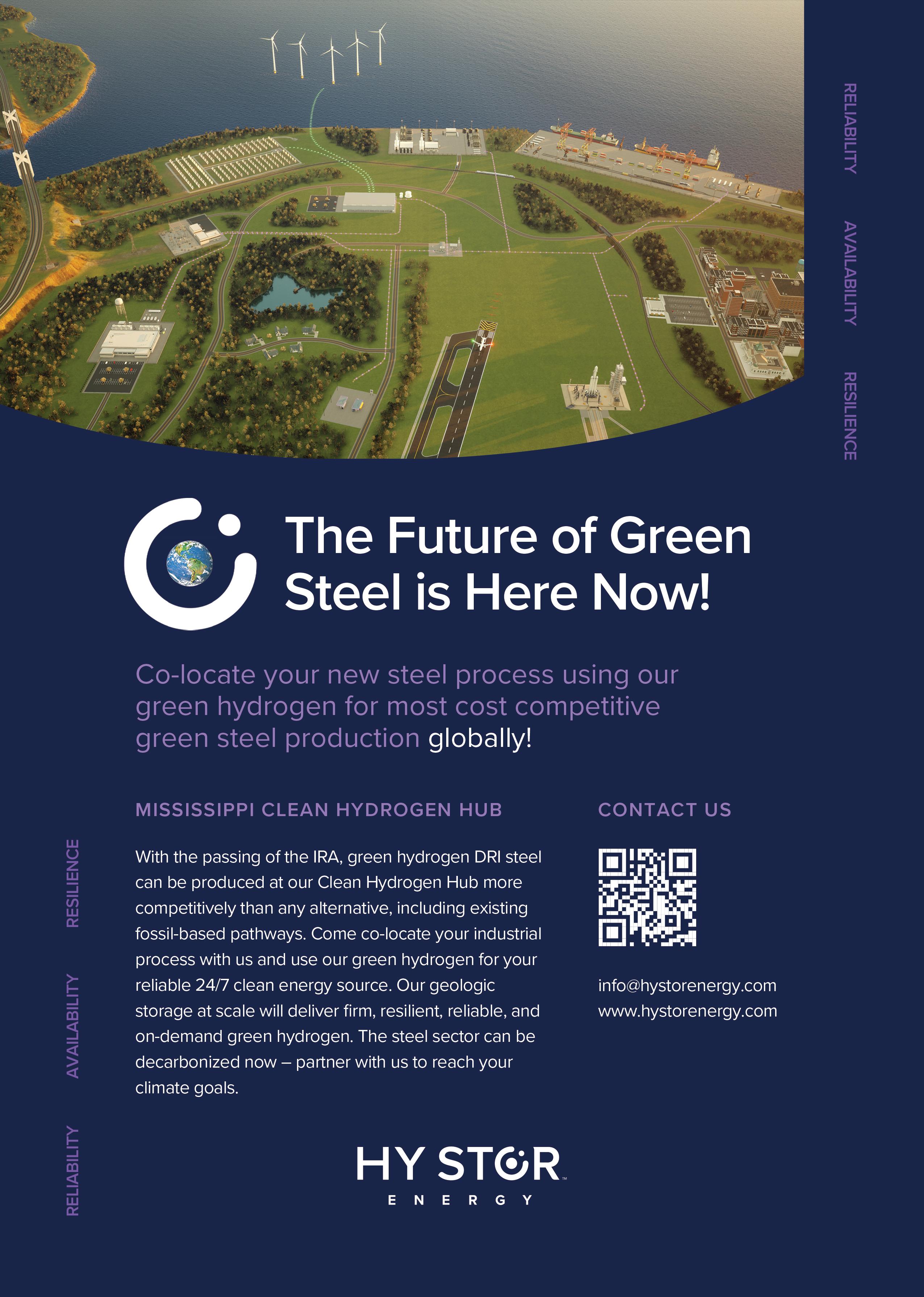
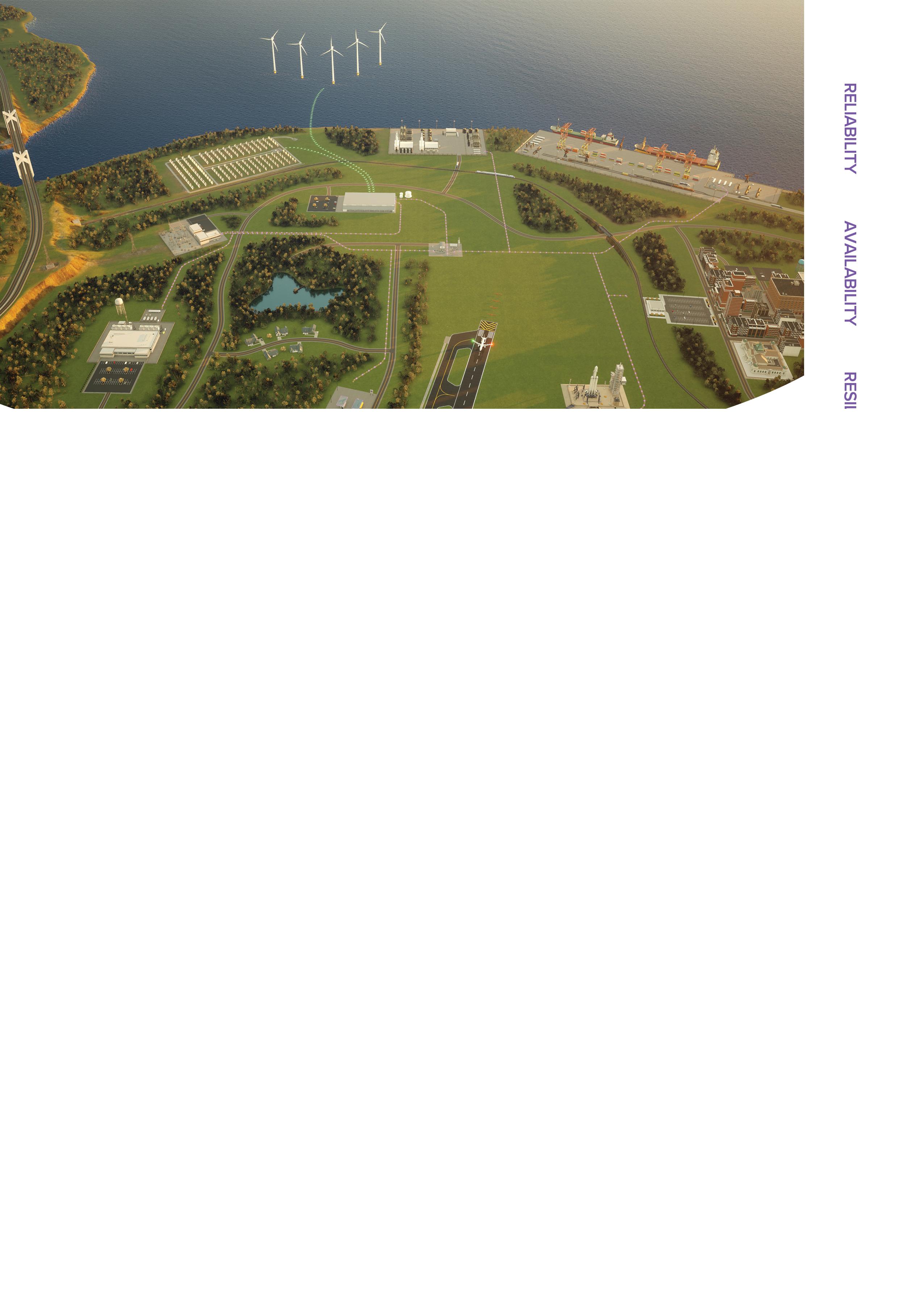
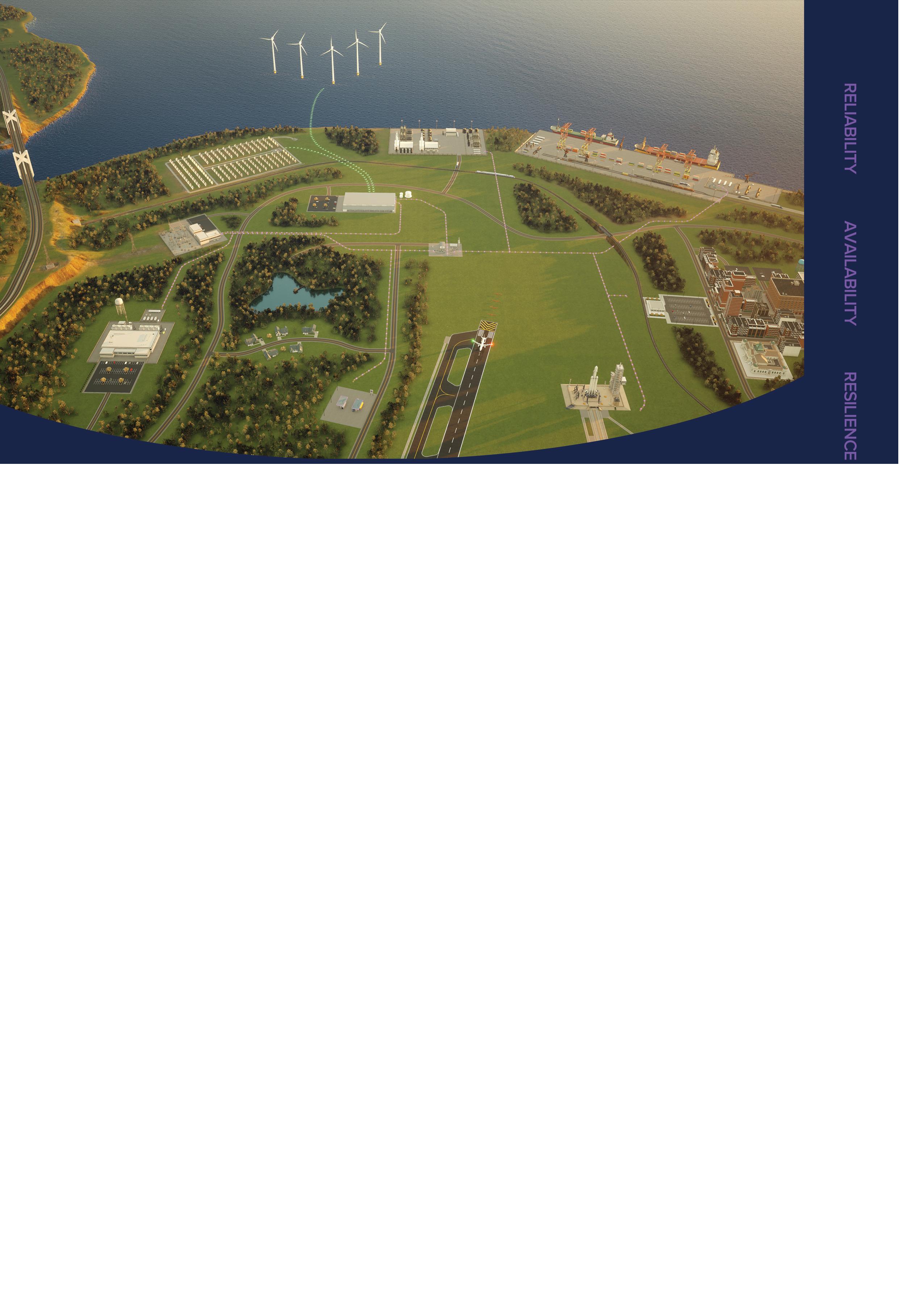
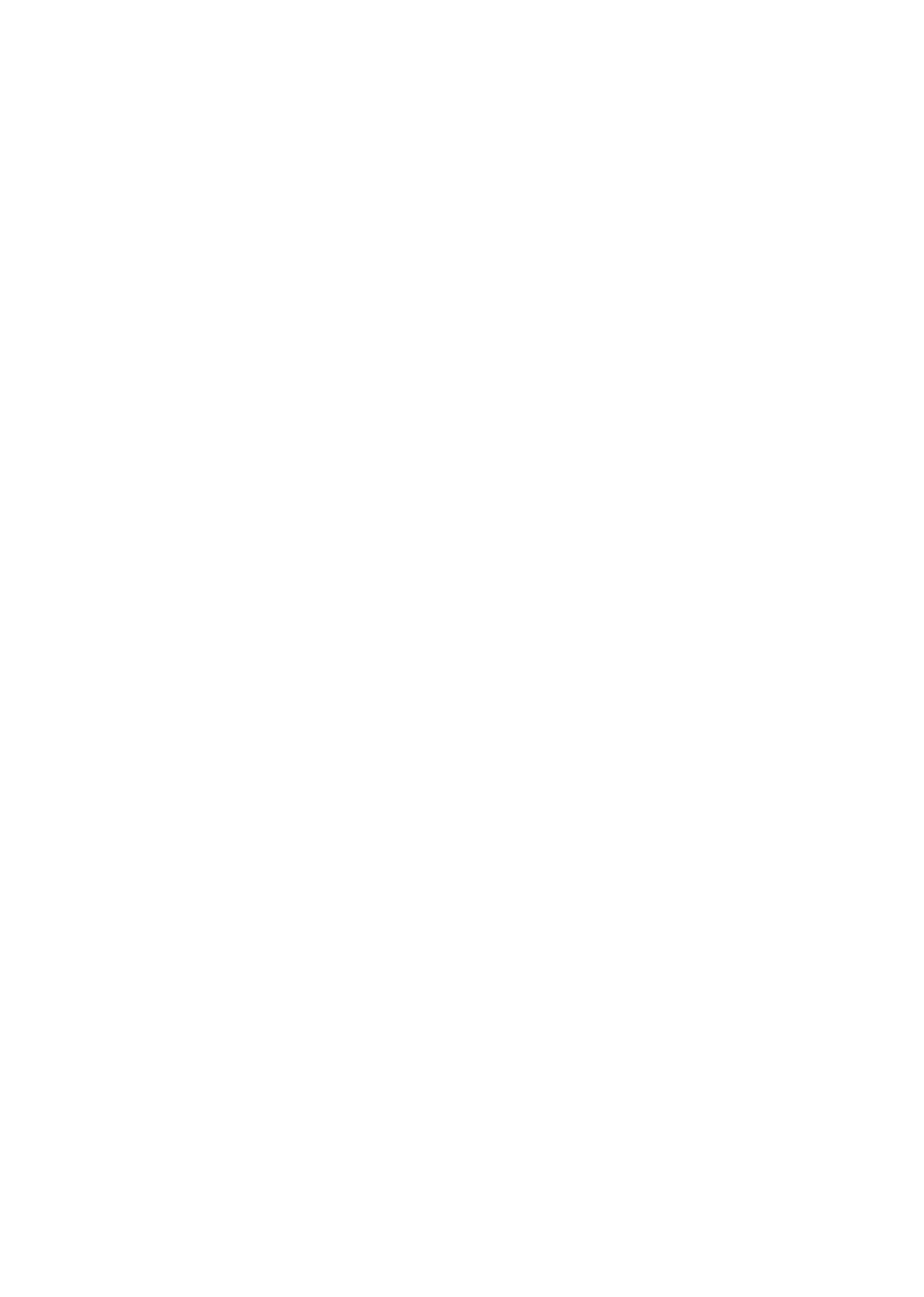