
8 minute read
3600 approach to sustainable steel production
SOFTWARE SOLUTIONS
Steelmaking is a huge part of the global market and economy, but its large contribution to carbon emissions has put it under a great deal of pressure to decarbonize quickly and effectively. A way of achieving this, according to Heinz-Josef Ponten*, and Gunter Schober**, is to utilize digitization throughout the production process – which not only lowers emissions, but also costs, making it an efficient way to save money and the environment.
*Product manager, liquid and energy, PSI Metals Non-Ferrous GmbH, hjponten@psi.de ** Sales manager, PSI Metals Non-Ferrous GmbH, gschober@psi.de
SOFTWARE SOLUTIONS
360º approach to sustainable steel production
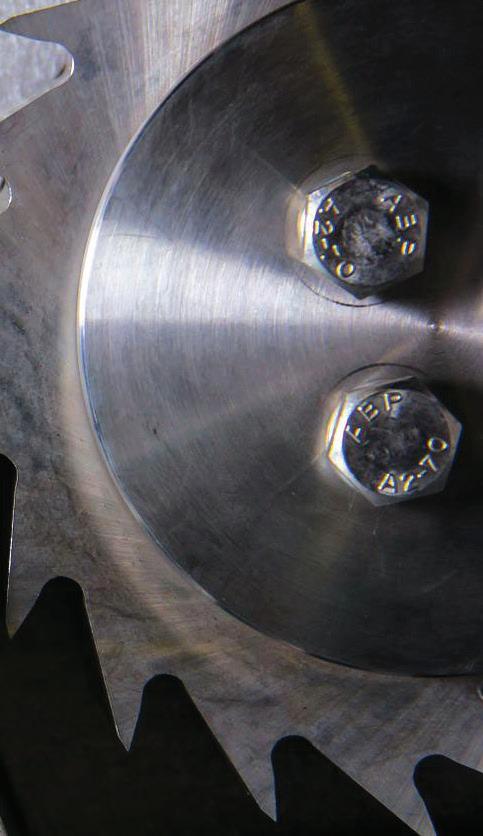
STEEL is one of the most important engineering materials due to its multifunctional qualities. While steel is one of the most recycled materials, steel production is highly energy consuming and emits huge amounts of CO2. For every metric ton of steel produced in a conventional blast furnace (BF) or basic oxygen furnace (BOF), over 1.6 metric tons of CO2 are emitted, contributing to 7-10% of the world’s global carbon emissions.
In recent decades, steel producers have had to cope with pressure to decarbonize the steel making process. Recent studies reveal that 14% of steel companies’ potential value is at risk if serious measures are not taken to significantly reduce the carbon footprint of steel production.
Although planting trees to offset CO2 emissions is popular, using this method alone is not ideal as it is expensive, time consuming, and tedious – and will require massive land space to achieve a significant difference. Steel makers will need to implement drastic measures to achieve the United Nations’ 2050 net-zero target.
The 360º view on sustainable production management
The steelmaking process is complex as all production steps are partially interdependent, and impossible to isolate. While many companies have digitalized some stages of their steel production, the problem remains that some of these automated processes are still treated in isolation, which results in breakdowns during production. This makes it a challenging endeavour to keep the production highly efficient, while complying with changing markets demands.
With its 360º strategic approach to sustainable steel production management, PSI Metals offers a pathway using smart software solutions to support energy savings and reduce the carbon footprint through all the stages of steel production. Software services optimize scrap usage for the best quality at the lowest costs. Online heat scheduling and other planning tools increase the overall equipment effectiveness and material usage. Reactive deviation management allows quality prediction for an increased ‘firsttime-right’ rate. An integrated production management system provides necessary flexibility while minimizing CO2 emissions.
Reduce waste and energy consumption
Production planning is one of the biggest challenges of the steel making process. Not only is it more complex than a game of chess, it is also affected systematically by unpredictable events. Therefore, steel plant managers require agile planning that is adaptable to external constraints, and tailored to suit both companies’ business priorities and changes in market demands. In most plants today, responding to production disruptions is a human decision which is often unreliable and can cause production downtime and additional material and production costs. Supportive KPI-driven planning systems help steel makers define their KPIs in a more user- friendly way, allowing clients to visualise existing interactions and conflicts and make simulations where constraints arise. The result is a more sustainable steel production
SOFTWARE SOLUTIONS
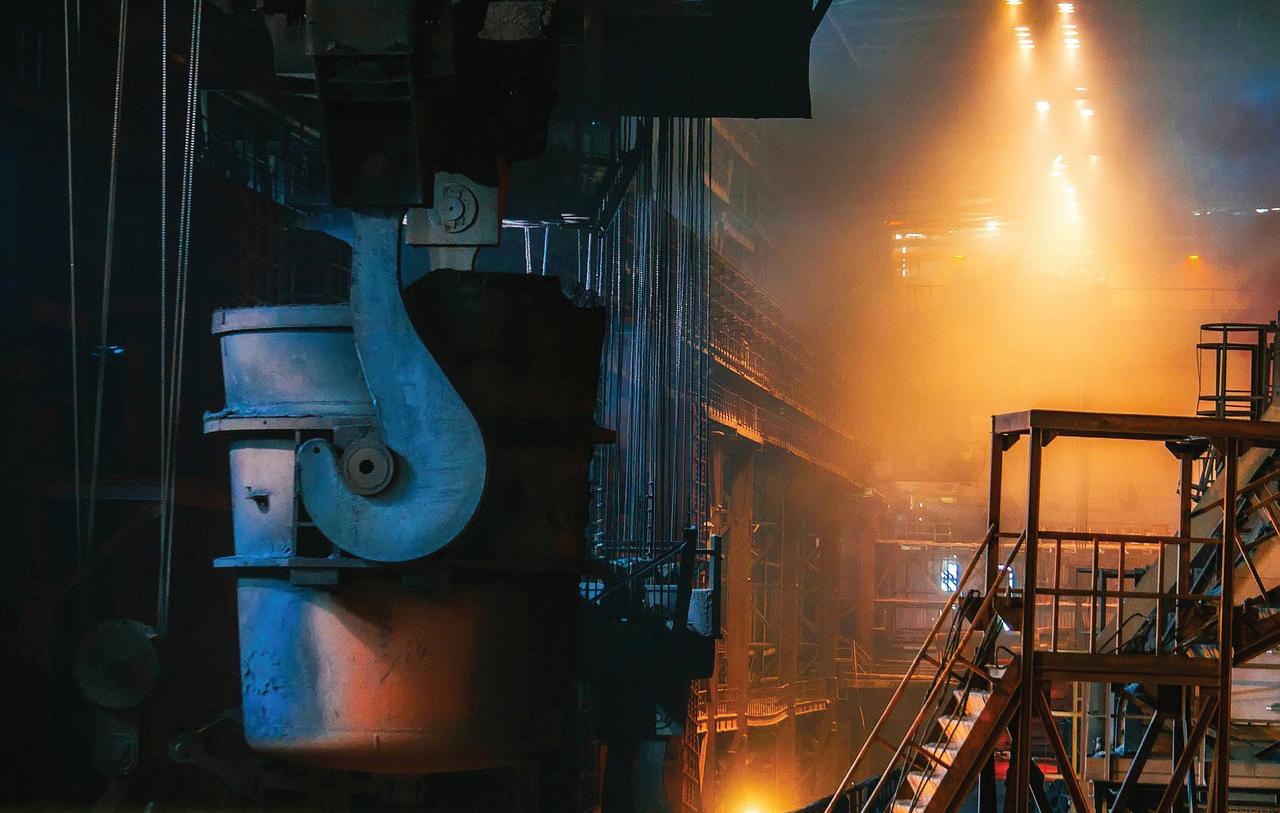
approach with less downtime, reduced energy consumption and CO2 emissions, and increased plant efficiency.
Ensuring production excellence
Customer product demands are quite diverse and, therefore, require a smart solution that is flexible and not vulnerable to errors. PSI Metals’ Order Dressing Solution defines all the details necessary for each single production step and helps optimize production and waste reduction. Using Bills of Material (BoMs) to represent the complexity of process production, as many steel producers do, is complex to create and maintain, and it is a process prone to errors which does not allow the necessary flexibility in production. However, optimizing material usage requires dynamic order dressing that is rule and characteristic-based and always calculates the optimal route and material demand depending on actual customer requirements. Within seconds you have a production order with all the details on qualitative and quantitative material requirements, tests, process and sampling instructions, including time demand for planning and costs. You can also calculate the carbon footprint for each production step and compare it later with the actual result. It gives you all the details you need, and even more.
Scrap and alloy optimization
An important software solution for the melting and casting process is alloy and charge optimization. The system must know all the available inputs, alloying materials, and their corresponding costs. Occasionally, plant managers may want to support the use of a particular material that has been sitting in the yard for some time. You can reduce the cost and hold a scrap sale. You may want to restrict the popular material to prevent customers from cherry picking. You can set an upper or lower limit for the use of a particular ingredient.
You set the parameter accordingly and together with the recipe, the system suggests the optimal mix for the alloy. You specify the target, and the system finds a way to get there – just like a GPS. In addition, liquid material and sump can be treated like any other material. Process scrap can be prioritized over external scrap and liquid material comes first. The goal should always be to save costs, but you can also significantly reduce your carbon footprint.
Green KPI-Driven melt shop optimization
Line breakdowns or production delays typically occur when unexpected and least needed. The effect of a breakdown is that the current heat treatment at the affected line is suspended and only resumes after fixing the breakdown.
PSI Metals’ Online Heat Scheduler (OHS) derives a detailed work plan for all planned heats which consists of all required treatment and transport steps, their durations, and production lines or facilities where these treatments can be performed. OHS manages the interferences during production in order to secure the delivery of the heats to the caster at the required time. PSI Metals’ OHS supports the customer to optimize a green KPI-driven melt shop. With OHS for a green-driven melt shop, you can optimize the tapping temperature and buffer time, prevent heating or cooling through transparent time management, prioritize heat or sequences in order to increase the hot connect rate, forecast energy consumption, and provide forecasts to Energy Management Systems (EMS) and power providers.
The results of steel plant optimization are not only savings in production and material
SOFTWARE SOLUTIONS
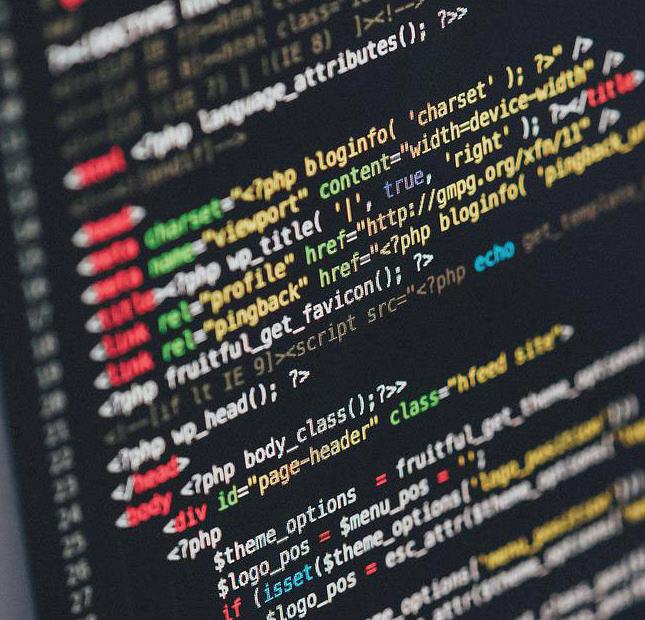
amounts of energy and produces process related CO2 emissions. With an intelligent software solution, you can optimize energy consumption and further bring the power supplier closer to the consuming process. Smart software can predict the power
consumption of all its consumers and combine this information with forecasts of power supply depending on renewable energy such as wind, hydro or solar power. Smart software can optimize the grid and significantly reduce CO2 emissions.
Software can further suggest the best time to exchange the anodes and manage the crucibles in an optimized way. In addition, when it comes to tapping, smart software solutions will make the ideal tapping decisions.
It’s all about sustainable steel production
Software will not change the steel manufacturing process. However, intelligent software solutions can support steel makers toward sustainable steel production. To achieve these results, all production units within the steel plant’s production chain need to be harmonized in a 360° approach so that there is smart communication at every stage. Each unit thus contributes towards a sustainable steel production.
Software services that are orchestrated by a central platform such as PSI Metals’ Service Platform, will provide benefits on a new level. If you optimize production at the highest quality level; you minimize production and material costs, and our environment will thank you for less carbon emissions. �
costs, but the ability to support the future decarbonization goals of steel production. Some global steelmakers have successfully integrated OHS in their steel plants. These newly integrated features make it even more beneficial to steel producers, including those who are transforming from BOF to EAF and DRI/HBI routes.
Automatic corrections with tracking and deviation management
In metals production, up to 4% of the metal needs to be scrapped due to quality issues. This is partly because these quality issues cannot be detected and corrected in advance. Intelligent software can predict the defects and automatically suggest solutions to avoid them. The software will not only predict the errors, but it will help to find the root cause using various methods. We are talking about a 2% reduction of scrapped material and with that, a 2% reduction of CO2 emissions.
Using PSI Metals’ solutions saves costs and increases quality. It improves the rate of first-time success, and reduces energy consumption, which also translates to reduced CO2 emissions.
Better to organize than to search
A digitalized yard turns an unorganised plant yard into a well-optimized one. Countless material movements consuming lots of energy and human resources belong to the past. By digitalizing the yard, the customer can find the ideal location based on the subsequent production steps, and control can be maintained by having full transparency of the yard within reach.
If the material is needed in the next schedule, a location near the next line would be ideal. In the same way, if the material is needed at a much later time in the schedule, the perfect location for the material would be further away in the yard. Digitalized yard management keeps track of all movements and knows the exact location of each material at a given time, including its position within a stack.
By digitalizing yard management, the software plans rather than reacts. When it harmonizes with a digitalized planning solution, it results in an optimized and sustainable steel production.
Optimizing energy consumption with energy forecasts
The smelting process consumes vast
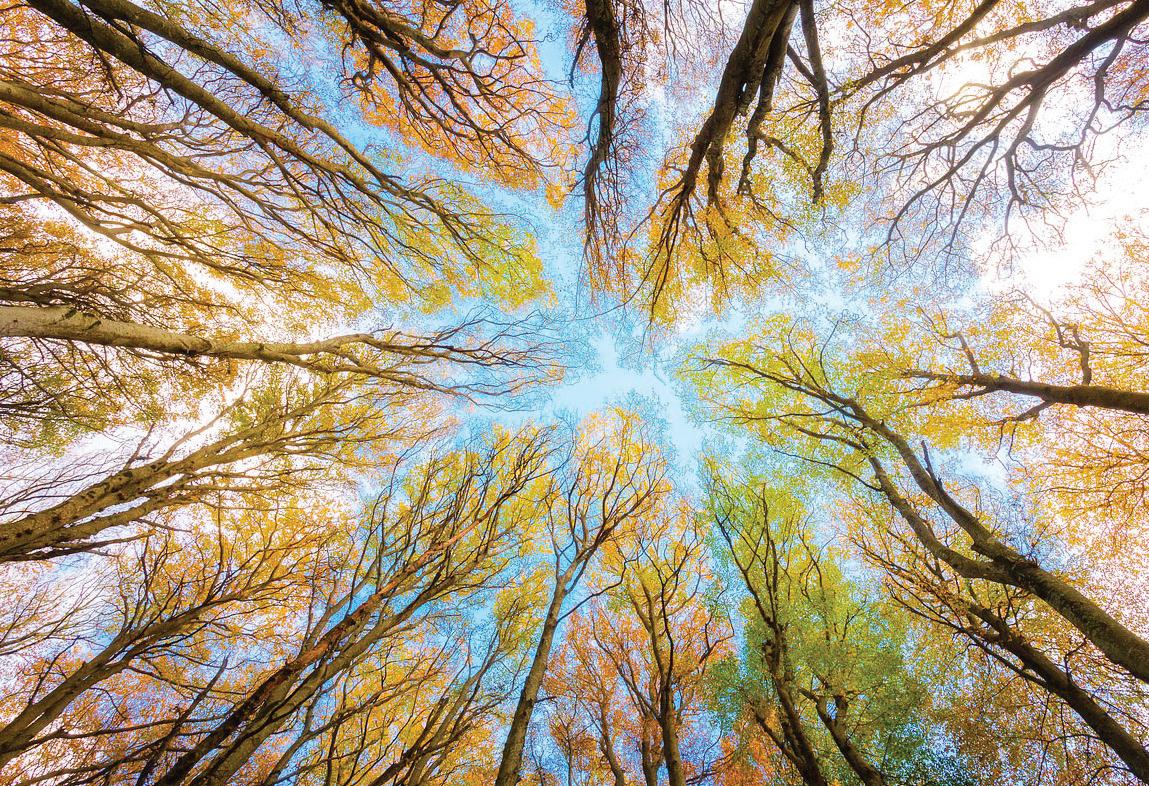