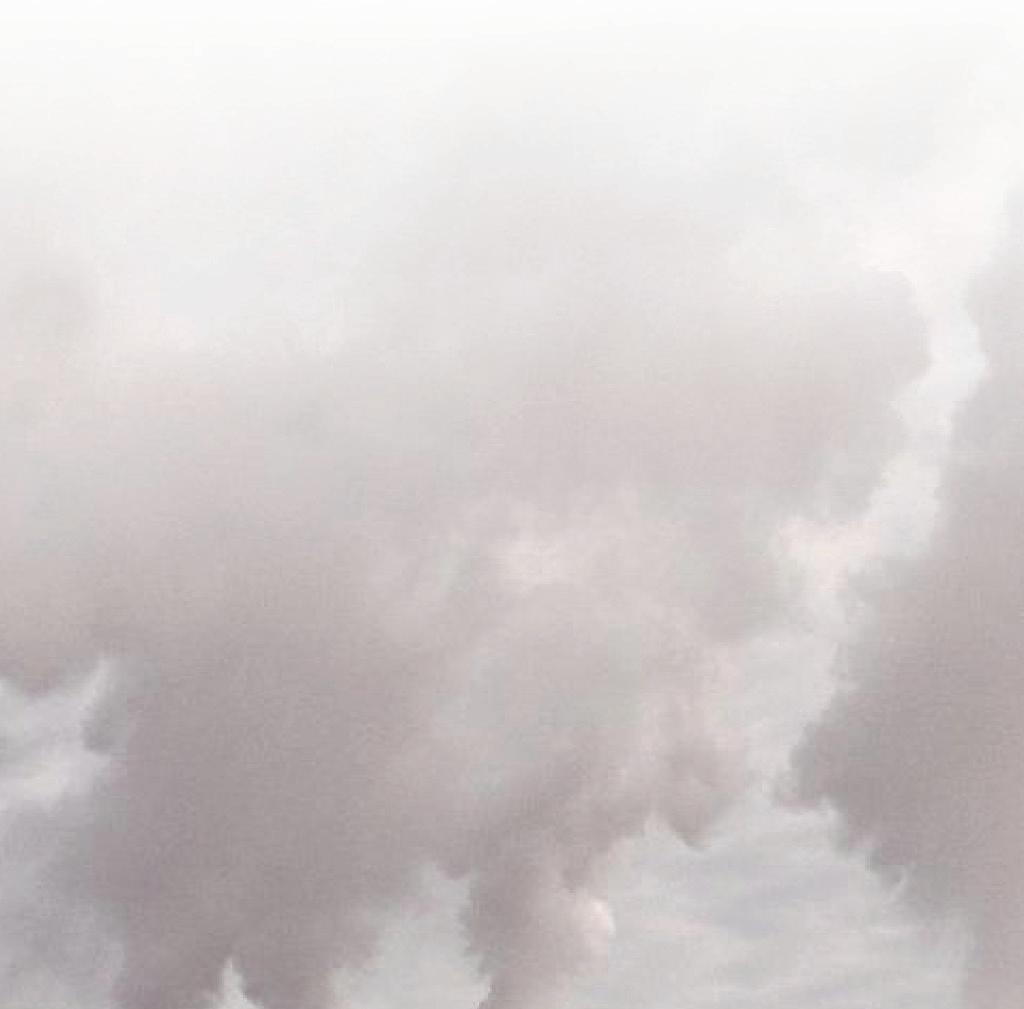
7 minute read
Low CO2 in blast furnace ironmaking
IRONMAKING
Low CO2 in blast furnace ironmaking
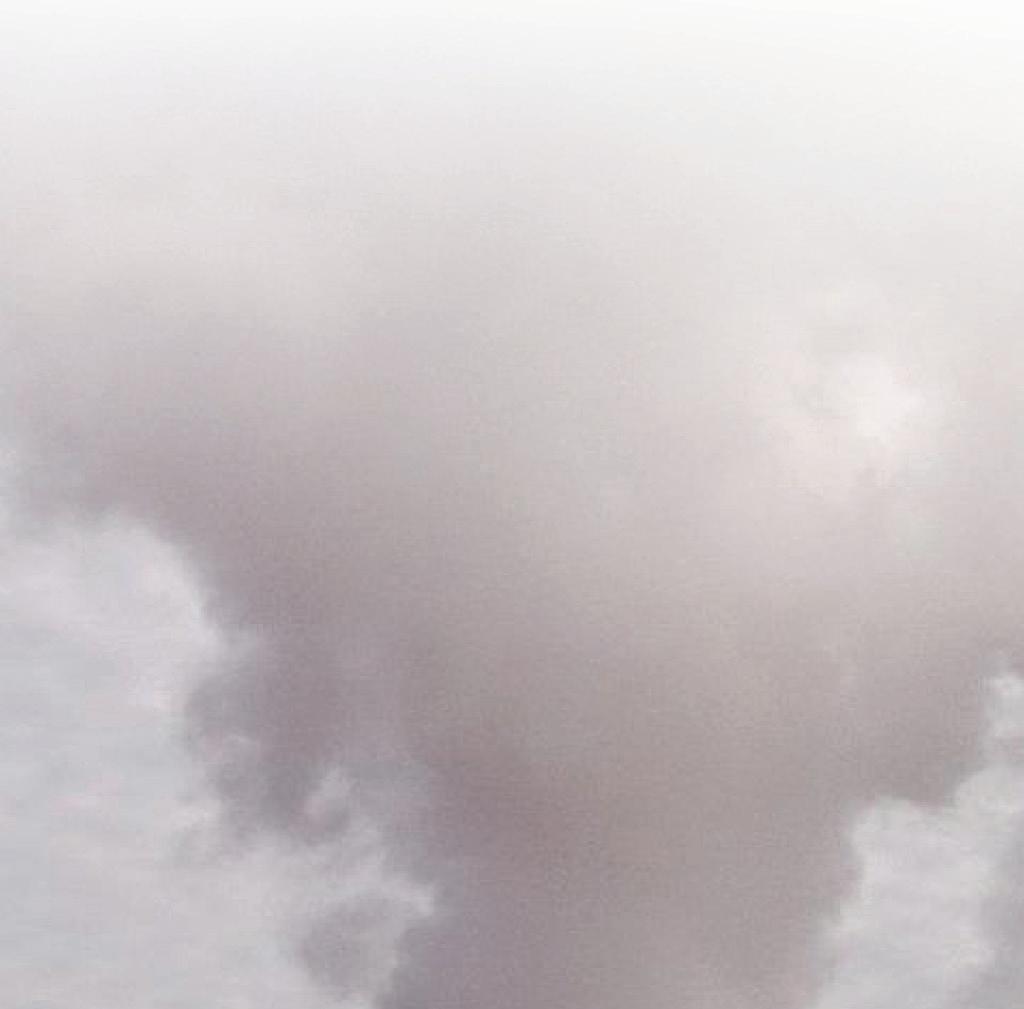
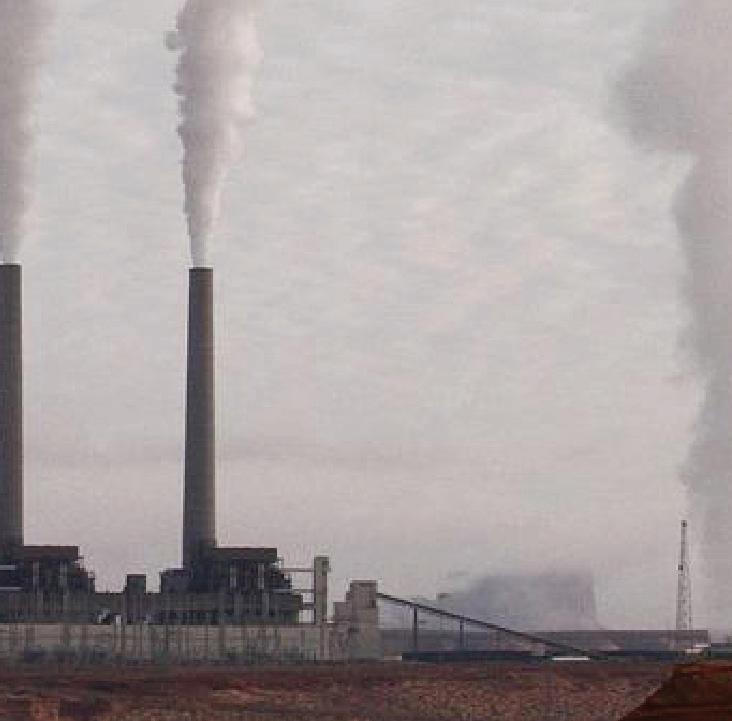
Kobe Steel announces the launch of ‘Kobenable Steel’, Japan’s fi rst low CO2 blast furnace steel, and discusses key strategies for lowering emissions, and developing clean technologies
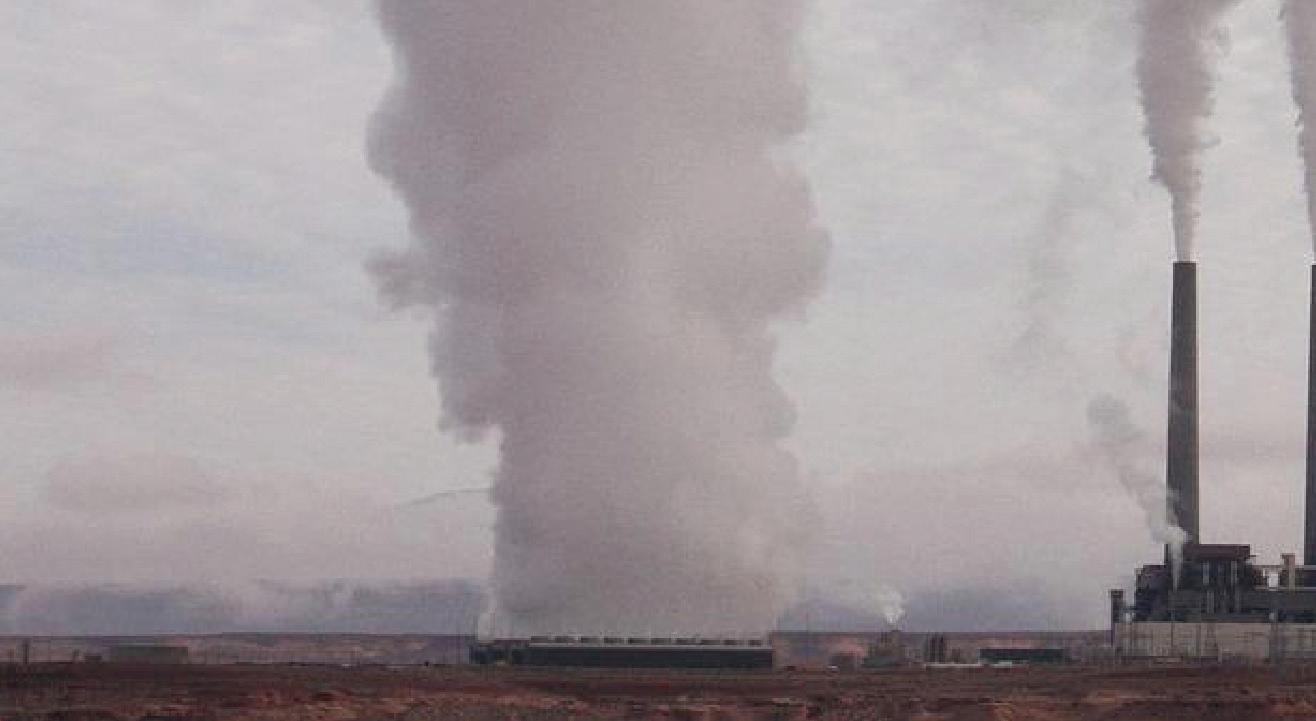
KOBELCO Group CO2 Emission Reduction Targets
The Kobe Steel Group (also known as the KOBELCO Group) is one of the few companies in the world that operates a diverse range of businesses, based on three core business areas: the materials businesses consisting of steel, aluminium, advanced materials and welding; the machinery businesses consisting of industrial machinery, engineering and construction machinery; and the electric power business. Kobe Steel aims to reduce CO2 emissions in its production processes by 30–40% in 2030 (compared
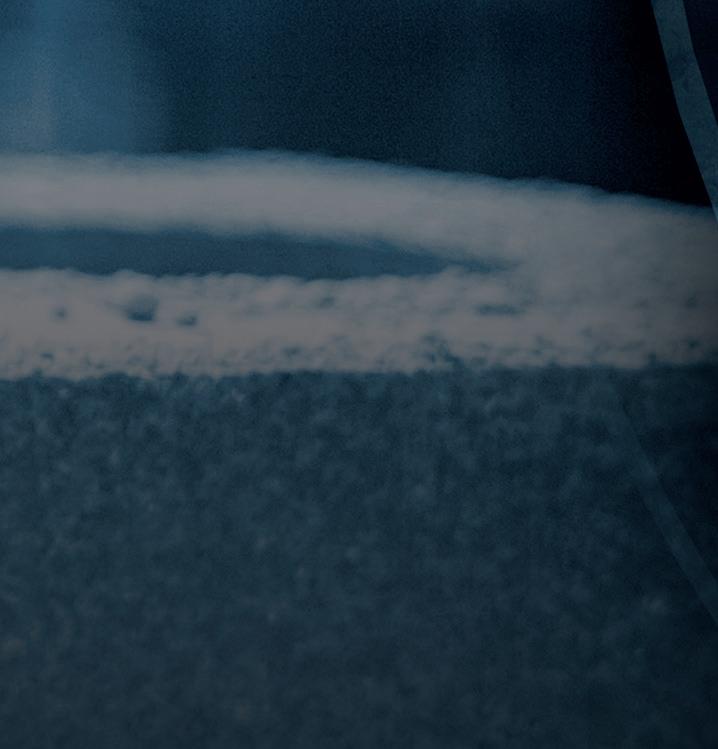
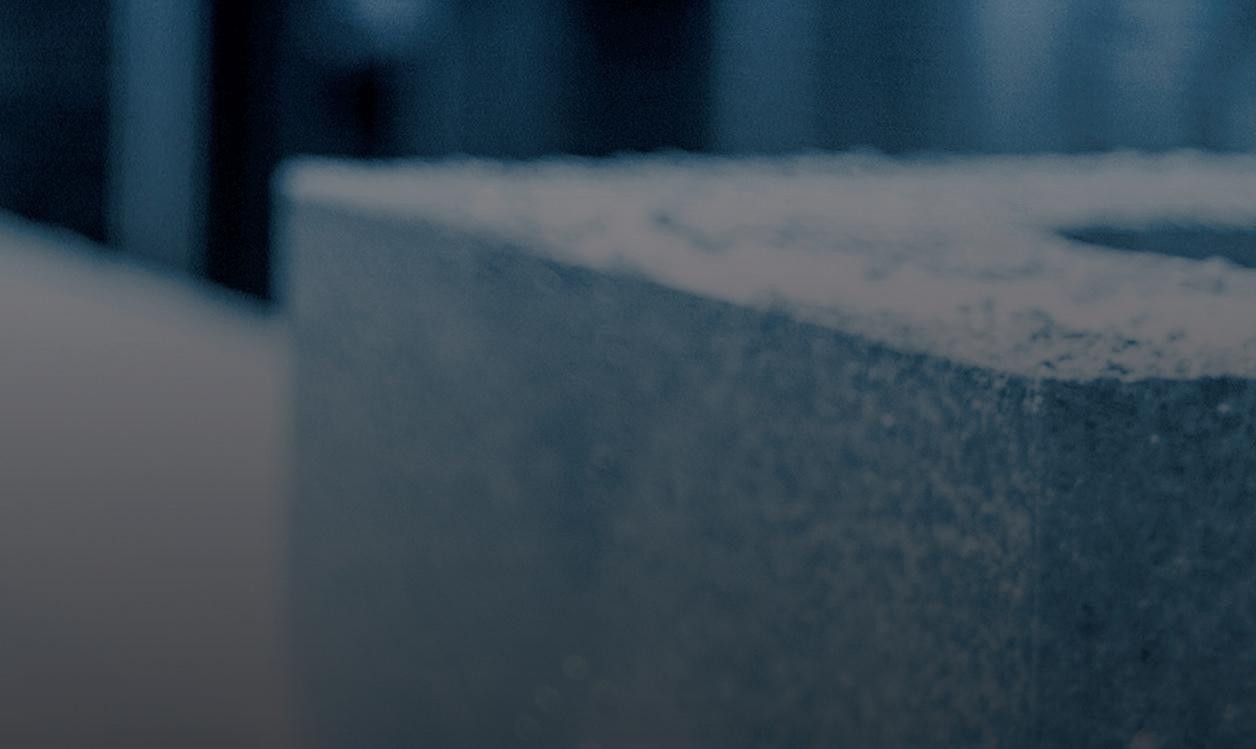
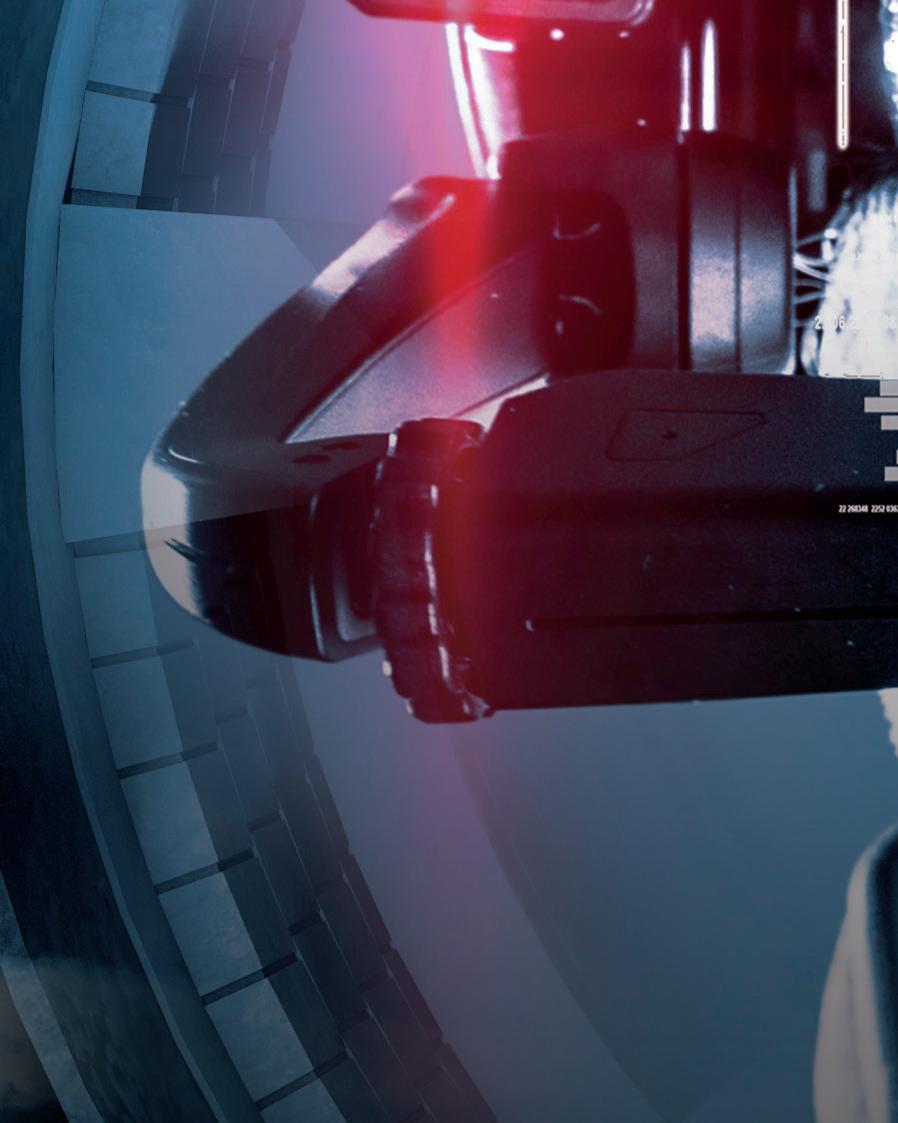
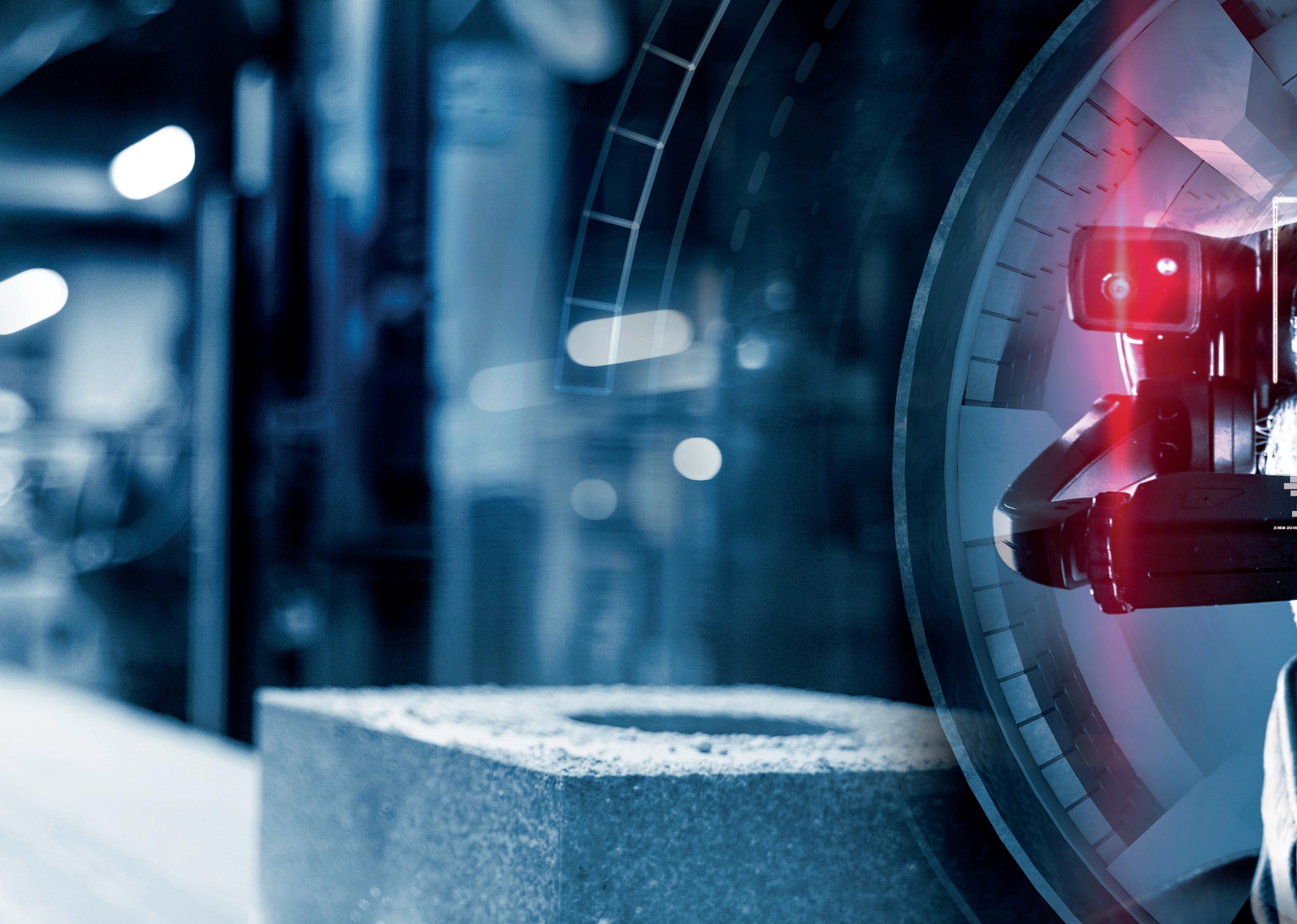
20 years of experience and over 40 installed plants make Steuler the Refractory Technology Partner
for tomorrows DRI Processes.
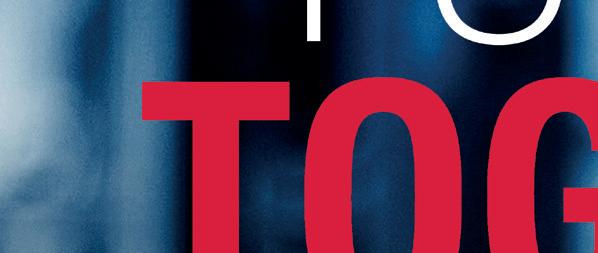
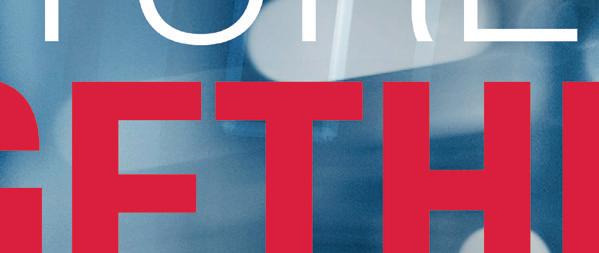
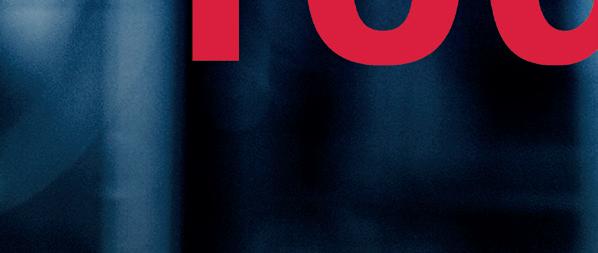
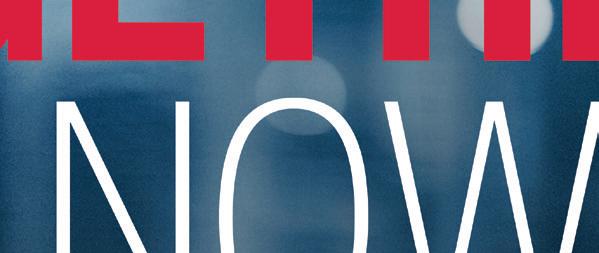
IRONMAKING
to fiscal 2013 levels) and to achieve carbon neutrality in 2050. The company is also working to realize a carbon-neutral society by achieving its fiscal 2030 target of reducing CO2 emissions through its unique technologies, products and services by 61Mt or more.
Low CO2 blast furnace steel –Kobenable Steel
Kobe Steel is working to reduce CO2 emissions by leveraging its strengths as a company with diverse businesses, technologies, and human resources. One of the achievements of the company’s efforts was the launch of Kobenable Steel, a low CO2 blast furnace steel product with significantly reduced CO2 emissions during the blast furnace ironmaking process as the first manufacturer of such products in Japan (according to the company’s survey as of 17 May 2022). Kobenable Steel is based on the KOBELCO Group’s CO2 reduction solution for blast furnace ironmaking announced on 16 February 2021. This technology is a fusion of the Midrex technology of the engineering business and the blast furnace operation technology of the steel business, leveraging Kobe Steel’s strengths.
Technology of Midrex (MIDREX® Process)
The MIDREX® Process is a direct reduction ironmaking technology developed by Kobe Steel’s wholly owned subsidiary Midrex Technologies, Inc. in the United States. It is the world’s leading direct reduced iron (DRI) making process, which produces approximately 80% of the world’s DRI produced with natural gas (approximately 60% of the world’s DRI at large). This process uses hydrogen-rich gas reformed from natural gas as a reductant, and pellets processed from powdered ore as the iron source to produce DRI in the shaft furnace. Compared to the blast furnace route (using the blast furnace and the basic oxygen furnace), this process (using DRI and the electric arc furnace) can reduce CO2 emissions in the ironmaking process by 20–40%. Over 80 MIDREX modules are in operation worldwide.
An effective solution
In addition, this technology has the advantage that if economical and large-scale hydrogen use becomes possible, it will be an effective solution to carbon neutrality without major equipment modification. With the transition to carbon neutrality quickly becoming a global trend, the company is ready to provide CO2 reduction solutions to achieve carbon neutrality in the global steel industry.
Blast furnace operation technology
By charging a large amount of hot briquetted iron (HBI) produced using the MIDREX® Process into the blast furnace and thereby reducing the amount of coke used, CO2 emissions from the blast furnace can be significantly reduced. In a demonstration test at Kobe Steel’s Kakogawa Works in 2020, it was confirmed that CO2 emissions from
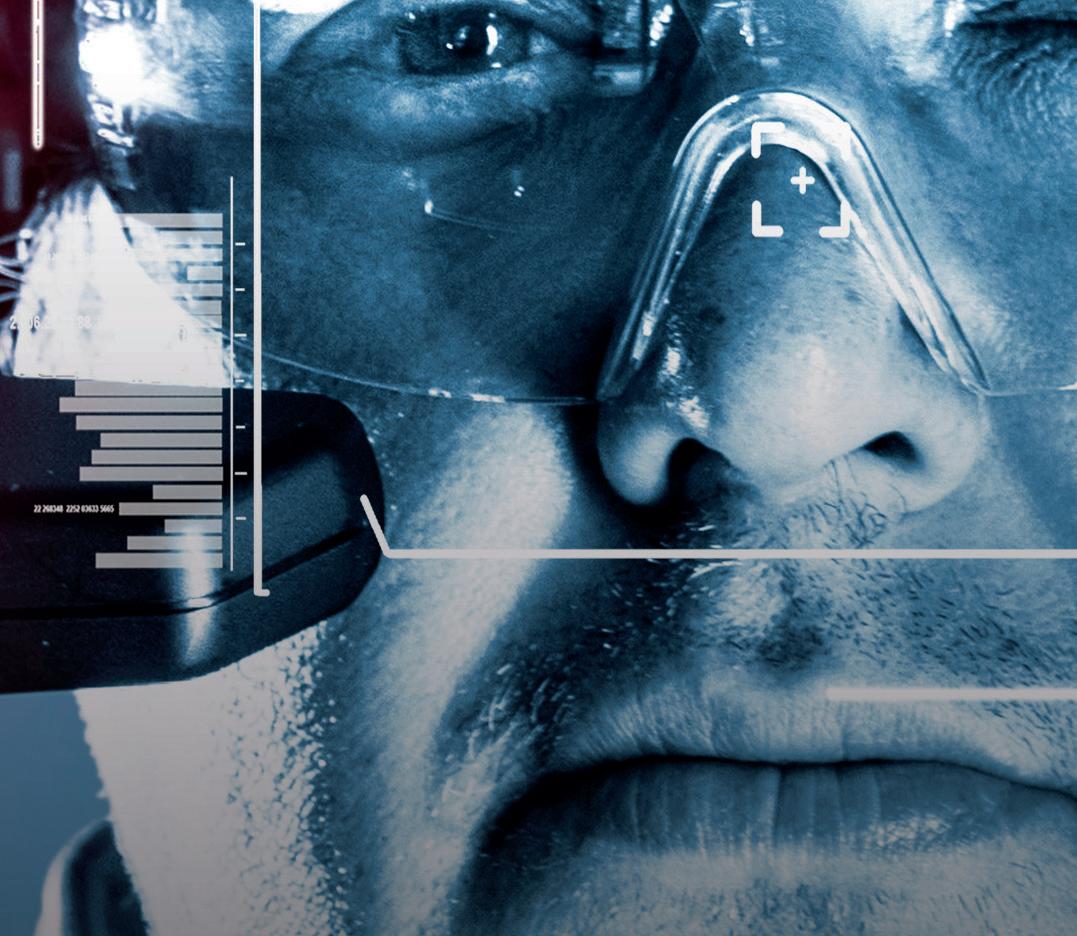

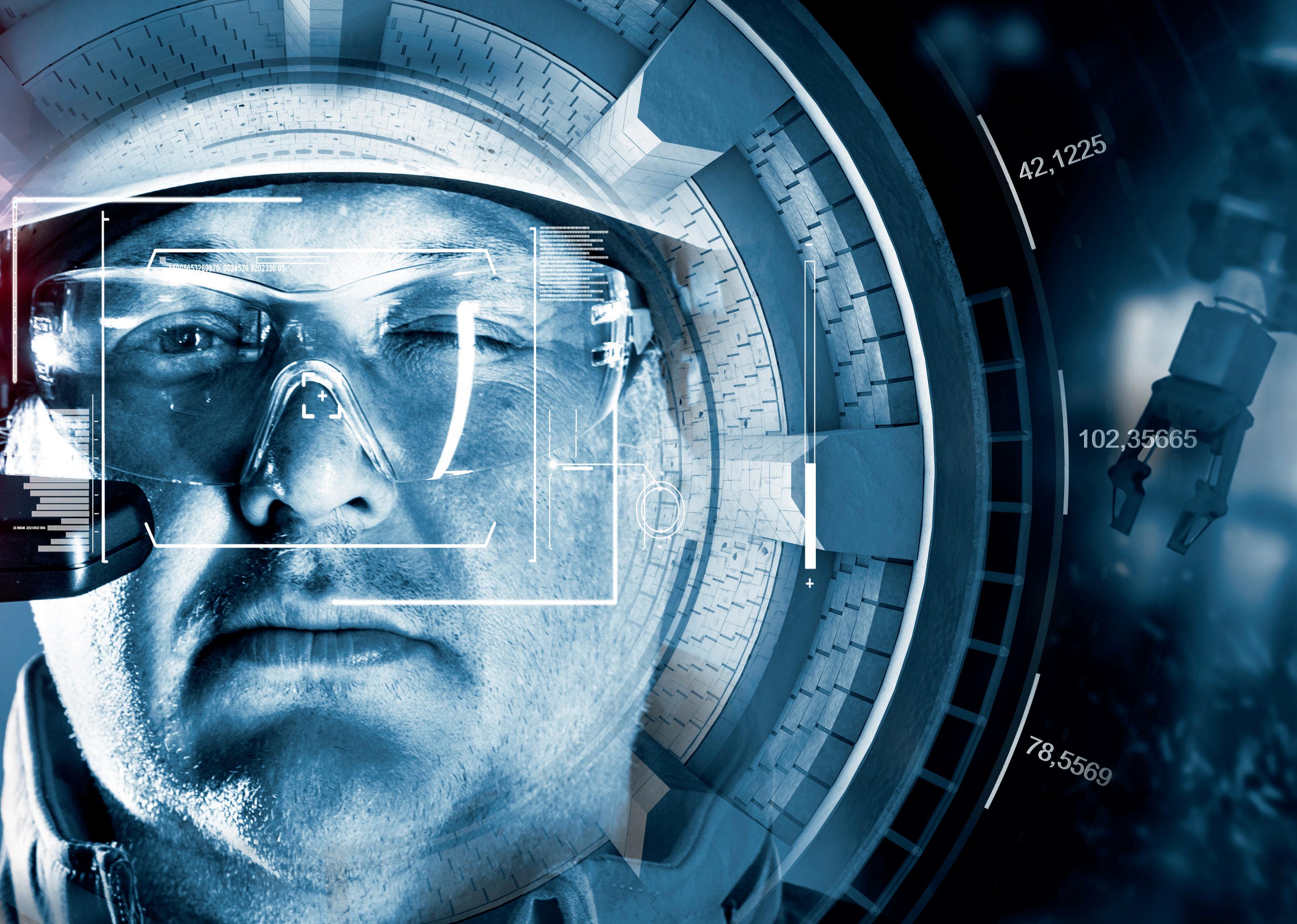
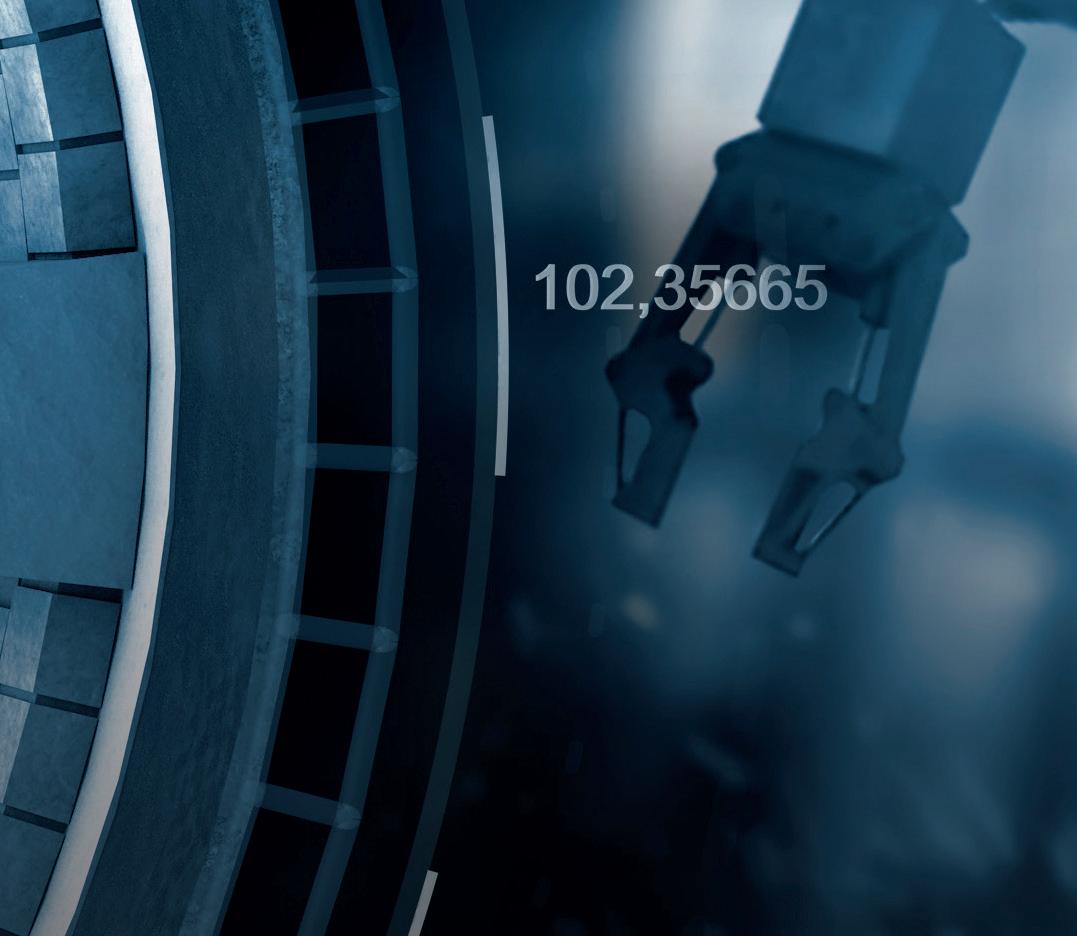
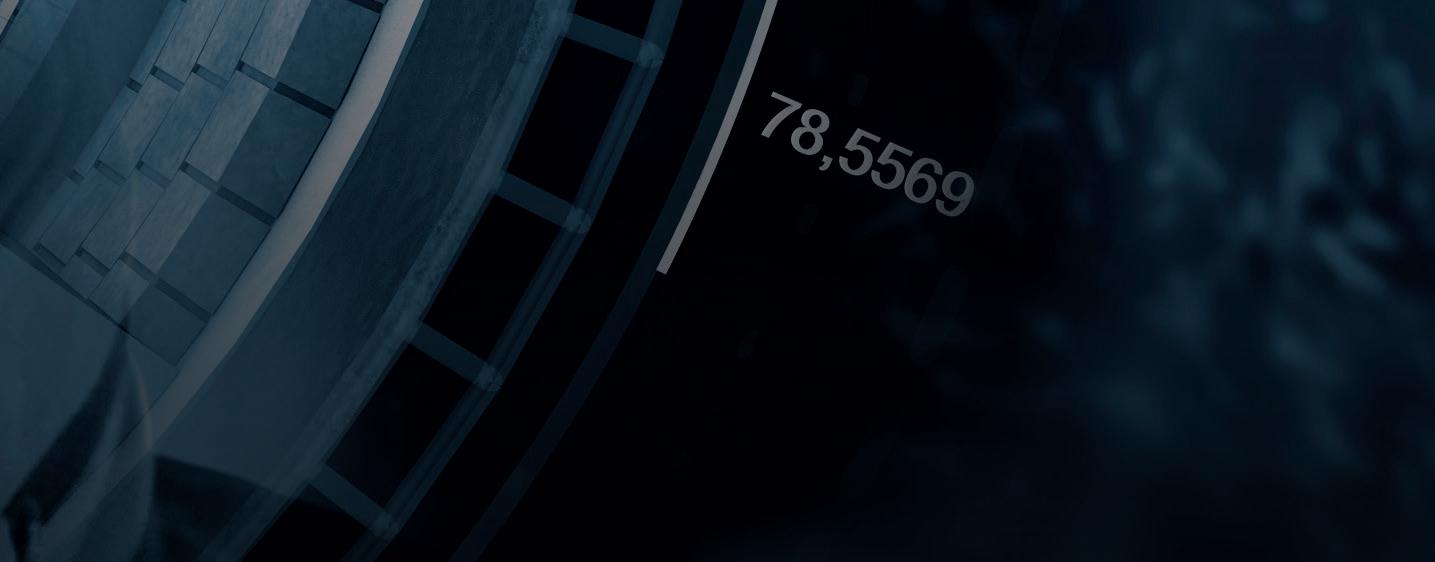
STEULER-KCH GmbH | 56427 Siershahn | GERMANY Phone: +49 2623 600-216 | E-Mail: info@steuler-kch.de
www.steuler-linings.com
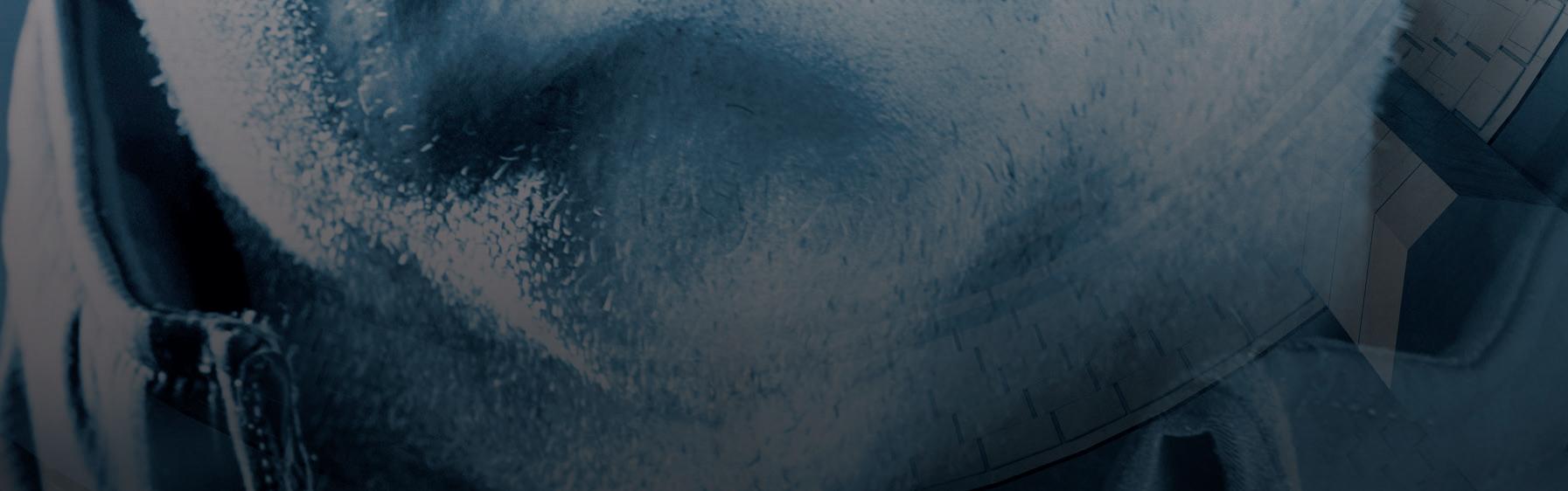
IRONMAKING
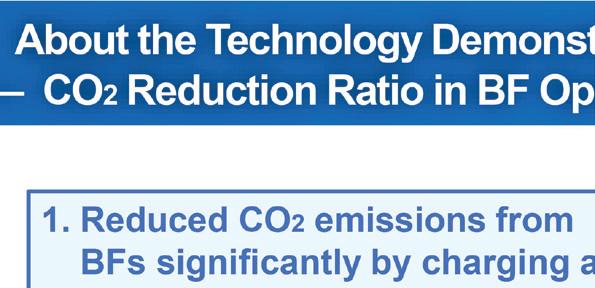

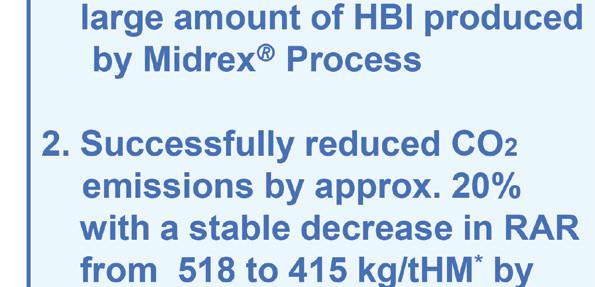

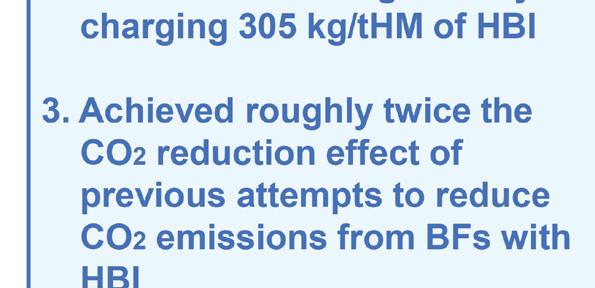
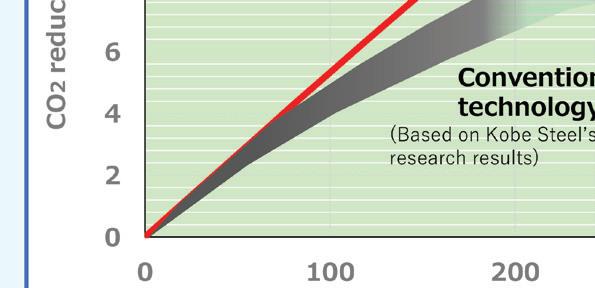
the blast furnace process could be reduced by approximately 20% compared to fi scal 2013 levels. In order to reduce the amount of coke by charging a large amount of HBI, there are various technical challenges to overcome such as the destabilization of blast furnaces. The company made a breakthrough and signifi cantly reduced CO2 emissions from the blast furnace by combining Midrex’s HBI manufacturing technology with its blast furnace operation system which includes HBI charging, AI-based blast furnace operation systems, and advanced pellet production.
CO2 reduction effects calculated by mass balance methodology
This year, Kobe Steel will start selling low CO2 blast furnace steel in two product categories: Kobenable Premier with 100% reduction rate of CO2 emissions per ton, and Kobenable Half with 50% (compared to fi scal 2018 levels). For the calculation of these CO2 reduction effects, the company has adopted the mass balance methodology by which CO2 reduction effects are allocated to specifi c steel products.
Methodology
The methodology is to allocate specifi c characteristics to a certain portion of products according to the input amount of raw materials with the characteristics when there is a mix of raw materials with no such characteristics (e.g., low CO2) in the manufacturing process. This approach has been used for products such as recycled plastics, bioplastics, electricity generated from renewable energy sources, and certifi ed food products like cocoa and palm oil, for which separation of product properties are diffi cult due to the characteristics of the manufacturing process or the supply chain. In the ironmaking process, it becomes possible to reduce the amount of coke used and thereby reduce CO2 emissions by replacing a portion of iron ore with HBI, a raw material for steel that has already been reduced. Using the mass balance methodology, the company allocates the reduction effects to specifi c low CO2 steel products and adds environmental value.
Features of Kobenable Steel
Kobenable Steel, manufactured in the same process as the conventional blast furnace method, has the following two features. First, it is available for all types of steel products (sheet, plate, wire rod and bar products) manufactured at Kakogawa Works and the Kobe Wire Rod & Bar Plant. Second, it maintains the same level of high quality as conventional products. It enables customers to continue to use blast furnace steel products that require high quality, such as special steel wire rods and ultra-high-tensile strength steel, which are the company’s strengths.
Certifi ed by a third-party
For commercialization, reduction rates of CO2 emissions are calculated in accordance with ISO 20915. The calculation method and results are certifi ed by the DNV Business Assurance services UK Ltd., a third-party certifi cation body in the United Kingdom. At the time of the sale of the products, Kobe Steel will provide the customer with a third-party certifi cate issued by DNV and a low-CO2 steel product certifi cate issued by the company.
Sales Volume
Kobe Steel achieved a CO2 reduction of approximately 20Kt through the demonstration test of HBI charging conducted in 2020. With this amount of reduction, the sales volume of Kobenable Steel is estimated to be approximately 8Kt on the condition that all the amount of low CO2 steel secured this time is sold as Kobenable Premier.
In this manner, sales volume changes according to the actual amount of CO2 reduction. The company will continue to further develop its HBI charging technology for blast furnaces and conduct the study of equipment for mass production.
Emissions reduction intensifi ed
In 2030, the company anticipates that the CO2 reduction effects will be increased by a technology that continuously charges HBI into its two blast furnaces, as well as other CO2 reduction and energy saving technologies. If all of these are realized, the company will be able to sell Kobenable Steel at a scale of 1 Mt/yr (calculated with Kobenable Premier).
Expansion based on demand
The company will consider the pace of expansion of the product by 2030 based on demand. The company will contribute to a green society by leveraging its comprehensive strengths as a corporate group that operates various businesses and provides Kobenable Steel, the fi rst low CO2 blast furnace steel product commercialized in Japan, to a wide range of fi elds. The group will strive to provide solutions to the needs of society through making the best use of its diverse businesses, technologies, and human resources, in order to continue to be indispensable to stakeholders. �