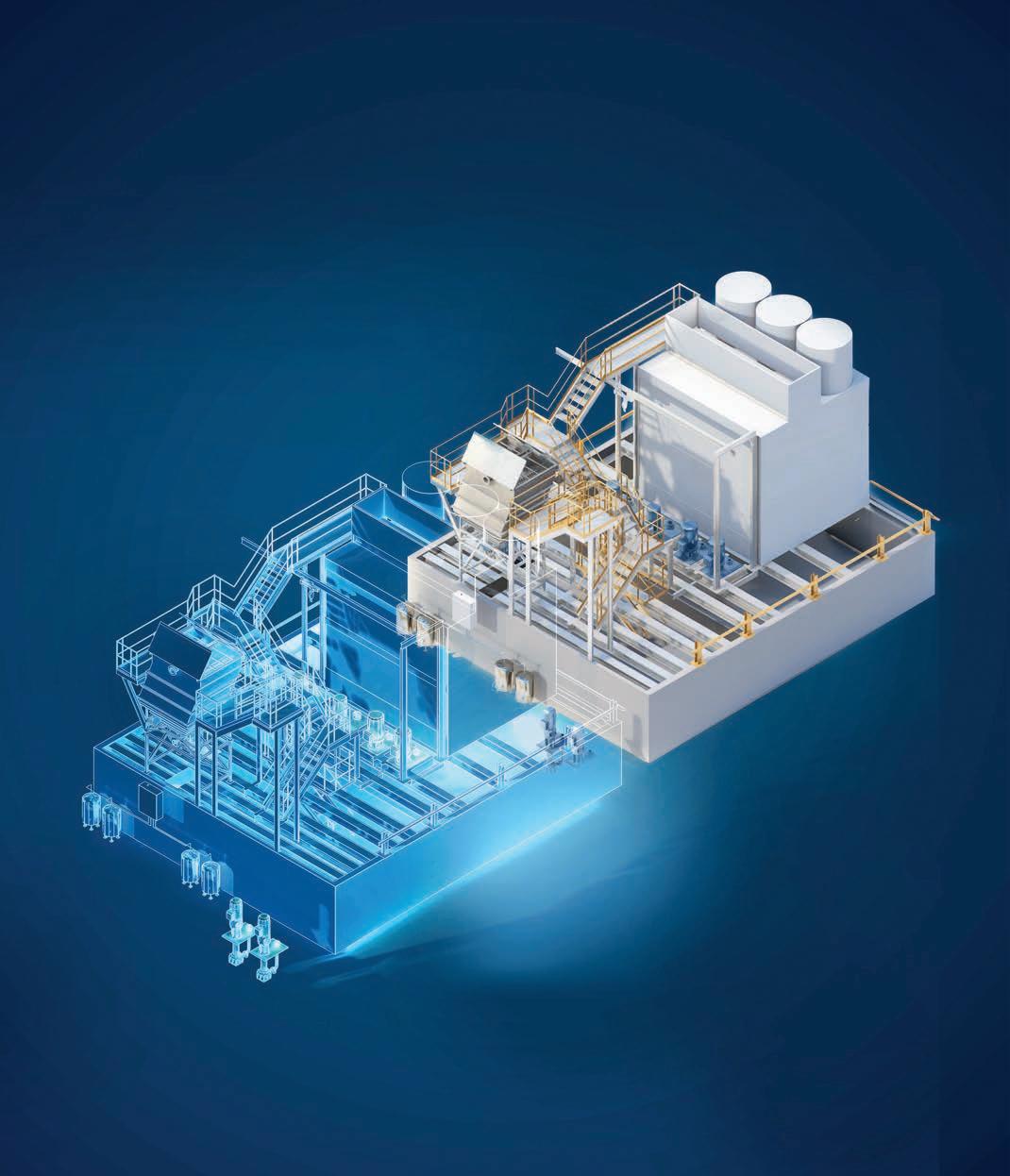
3 minute read
Digital glassmaking: PVAG
Digital twin in water saving and treatment systems
Will an investment project deliver the required value? This major question is asked by each company when new equipment, repairs, or capacity extensions become necessary, reports Markus Franz*.
To be able to answer this simple question, complex modelling must be carried out, which is costly financially and in time. To evaluate upfront the functionality and efficiency of a project, Industry 4.0 comes with several tools. Industry 4.0 is the current state of the art, and the technical revolution keeps advancing.
New techniques enable mirroring the physical system with a digital version and to simulate infinite possible scenarios upfront without any impact on production. This visualisation of a system is the so-called ‘digital twin’.
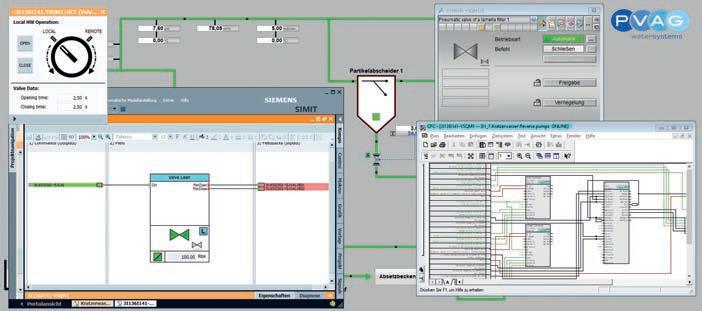
Digital twin
The concept is based on the idea that existing processes or systems are used to implement a digital version. This provides a substantial benefi t since the model can be optimised, by accessing a substantial database on how the system will react based on multiple variables.
During sensitivity analysis, the model will fi rst be used to verify that the set-up is correct, and in a second stage to vary all parameters which can have an impact.
In addition to varying input parameters like pressure or temperature, also complete equipment can be changed in the model to simulate the impact of the respective changes.
Important to note for a completely new process design, the digital twin cannot substitute the engineering process, but is complementary. The digital model in addition to the detail engineering shows the behavior of the process for different inputs, allowing the detail engineering planning to be adjusted or verifi ed.
PVAG water systems has been working with Siemens to develop and promote the introduction of the digital twin to the glass industry.
For projects where current systems are to be optimised or for new designs of a cooling or water treatment system the digital twin is used to simulate the full potential of a system and to make the right engineering decisions for the processes.
After a common understanding of what the system should look like and after basic engineering, a 3D model is set up to support the process planning. All necessary information like pump curves, equipment, valve data sheets, pipe routings, and specifi cations are included in the digital model.
Simulation tool
The simulation tool SIMIT incorporates these data and is used to simulate the system’s different operating scenarios. The evaluation of the simulation is not only used to refi ne the detail engineering, however, also to improve customised programming solutions for each customer. Finally, after determining the most promising parameters to change with the model, they are used to change and optimise the physical model.
Before implementing major changes to a current system, the operating team needs to be informed and trained on the new solution. Here the digital twin is also used, providing the operators with a virtual environment with real process visualisation and process behaviours to get familiarised with the changes.
Different scenarios like emergency cases can be trained for upfront, ensuring the operator knows better to react and feel confi dently prepared for such incidents. Equipment damage and downtime can be reduced with this approach.
To expand the implementation of the digital twin, PVAG water systems and Siemens will continue to work together.
Especially inside the glass industry, there are substantial benefi ts to implementing this tool for improvements and reliability. Based on a distributed control system the digital twin can support predictive maintenance measures, improvements in logistics, and optimisation of process control.
This advanced technology will enhance future investment projects. �

* Business Unit Director, PVAG water systems GmbH, Julich, Germany https://pvag-watersystems.de/en/
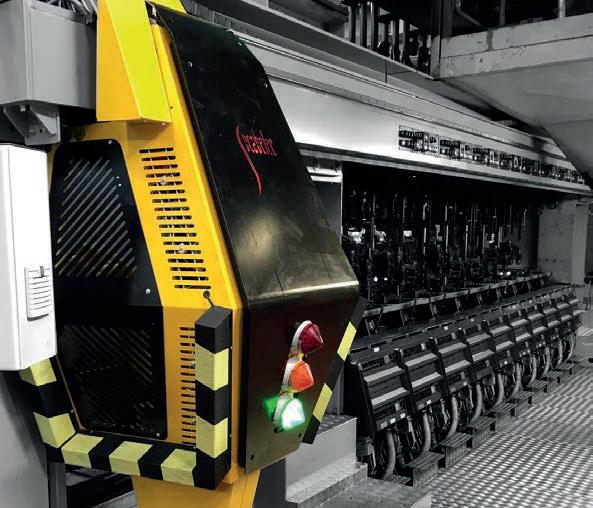


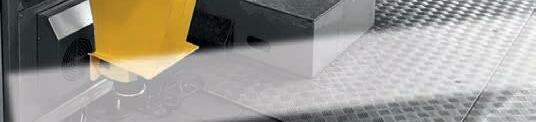




