
7 minute read
Furnaces: Ametek Land
Imaging camera provides essential insights for glass industry
A high-definition imaging camera I - - offers . million points of measurements. eil impson outlines the recent surveys conducted by the camera as well as its benefits over previous models.
Believed to be a unique service for the thermal optimisation of furnaces, in-furnace thermal glass surveys provide essential insights into the thermal processes within glass melt tanks.
As everyone in the industry is aware, glass melt tanks are enormously energyintensive, and experience the highest temperatures of the glass production process. Thermal monitoring of the tank ensures the efficiency of the melt process and maintains consistent glass quality.
Combining near-infrared borescope thermal imaging with portable multigas analysis, in-furnace surveys deliver accurate, real-time measurements to increase efficiency, productivity, and asset life in glass production.
The Near-Infrared Borescope (NIR-B) imaging camera was developed by Ametek Land in 2012. Since then, more than 100 NIR-Bs have been installed by a variety of companies and are still operating successfully after eight or more years.
Initial surveys
The initial glass surveys were simply demonstrations, where an NIR-B was initially installed in a peephole in the bridge wall, as close to a preferred CCTV camera location as possible. One major glass manufacturer suggested that it may be beneficial to look in other peepholes too. The resulting survey and cool-down of Allied G2 were reported in previous Glass Problems conferences.
It was only in 2019, when independent consultant Neil Simpson was struggling with flame optimisation for NOx in a float glass furnace, that the first full survey was performed by Ametek Land, this time including the regenerators.
The survey of the regenerators through the target wall revealed there was refractory damage to the regenerator checker pack. A lifting or heaving of the pack had created an internal by-pass flue which resulted in too much air going down the right-hand side of port 4.
The burner being used was a watercooled through-port burner which, typically, has the most adjustment, but with an in-balance of air the flame was deflected downwards. The survey was performed in 2019 using the original NIR-B-656 with 324,000 points of measurement.
In 2020 Ametek Land launched the new 2K (high-definition) model of the NIR-B, which now offers 2.9 million points of measurements. This is equivalent to 2.9 million of Ametek Land’s Industry Standard Cyclops portable pyrometers measuring continuously.
On a regenerative furnace, it is typical to take one optical measurement when the flame immediately goes out. If you were to take a Cyclops measurement every 20 minutes, you could take 72 point measurements in one day – so 36 on each side. It would take more than 24 years to get the image provided by one NIR-B-656, and 220 years to get the equivalent of a NIR-B-2K!
Float glass survey
In 2020, a float glass manufacturer attended one of Mr Simpson’s online training courses and saw the potential for a survey as part of its on-going asset protection plan.
During Covid-19 travel restrictions, it was not possible to travel to the customer, so the NIR-B survey camera was shipped to the furnace site and remote online training provided by Mark Briggs, Ametek Land’s Global Field Service Engineer for Glass. The customer then made the measurements themselves and transferred the data to Ametek Land for remote analysis. This example was the first float glass survey to utilise the highdefinition NIR-B-2K camera with Image Pro software.
The purpose of the survey is confidential however, previous reasons for such a survey include asset protection, quality/yield issues, energy reduction and environmental. The measured data can be used for validation of computational fluid dynamic (CFD) modelling, and it is often best to consider the analysis in a similar way to interpreting a CFD model.
On a float survey, it is typical to start at the waist and on the side closest to the control room, in order to know the time of the furnace reversal. If there is a skimming pocket, then this is the best initial position to check signals before moving to the bridge wall peep hole, which is typically at a slightly higher elevation.
The skimming pocket typically gives a good view of the walls and is the best location for measuring the glass temperature using Ametek Land’s patented reflection compensation method. With sufficient manpower, it is possible to survey the four corner locations in the furnace on the first day.
It is important to obtain the temperature when the flame immediately goes out. This is the highest temperature, since during the flame-out much of the temperature is lost. However, it is a calibrated temperature, since when the flame is present the emissivity is unknown.
The view from the waist is usually the best summary view, as this will show the suspended back or charging wall and whether it is symmetrical or closer to the firing or exhaust side. It should be possible to see all of the ports clearly on the opposite side and highlight which port is the hottest. With the NIR-B-2K and Image Pro Software, there is the potential to zoom in by 1600%, enabling refractory inspection for hot spots, cold
spots including holes, and areas at risk of NaOH attack.
The worst-case scenario is a hole which requires welding. The zoom function enables users to zoom in on an existing thermocouple block location and highlight it as a region of interest (ROI) to verify temperature.
Examples
Fig 1 shows a float furnace example of an in-furnace thermal survey. By way of a key, left and right are relative to the glass flow. With no flames, the temperatures are calibrated. The red cross highlights peak flame temperature at a relatively low 1578°C.
Fig 2 reveals the application of a simple isotherm below 1388°C is where there is a risk of NaOH condensation, which could cause corrosion to silica refractories.
When the burners are firing, the indicated temperatures are not real since we do not know the emissivity of the flames. The application of relative isotherms offers the ability to see which flames are typically hotter and give an indication of the flame length.
Generally, the higher the temperature the greater the risk of dissociating oxygen and forming thermal NOx, which is dominant in glass melting furnaces. While a flue gas analyser such as Ametek Land’s Lancom 4 can show which exhaust ports have the highest NOx, it may not indicate which of the burners is generating the most NOx.
By positioning the NIR-B survey camera in the target wall peep hole, there is the opportunity to look at the flames (not shown) from both the firing side and the exhaust side to see the cause and effect. Typically, the integrator function (not shown) is best to use, since it averages the frames to indicate the dominant flows. While this was zoomed in to look at the flames, the 100% view (not shown) would allow inspection of the regenerator to check that a blockage is not creating the imbalance.
Fig 3 shows the immediate frame following the flame-off. The temperatures are real. The 62-isotherm palette means that each colour is 4°.
enefits
Many large glass companies have invested in their own transportable NIR-B for their in-house survey teams. This offers the opportunity to have their technicians to send .erfx files to their refractory and combustion experts as well as validating in-house CFD models. Ametek Land also has some limited rental units available for hire. Typically, most customers start with a survey performed by Mr Briggs or one of Ametek Land’s survey team.
Philippe Kerbois, Ametek Land’s Global Industry Manager of Glass, said: “An infurnace thermal glass survey is a valuable supplement to traditional refractory inspections. It helps glass producers to identify ways to improve productivity
Fig F rnace from aist en of firing from left to right
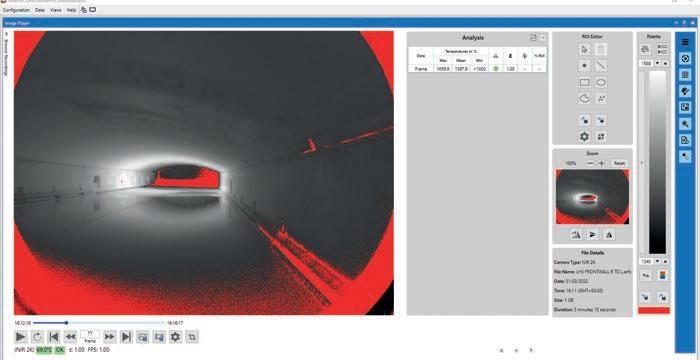
Fig F rnace from aist en of firing from left to right ith areas of a con ensation
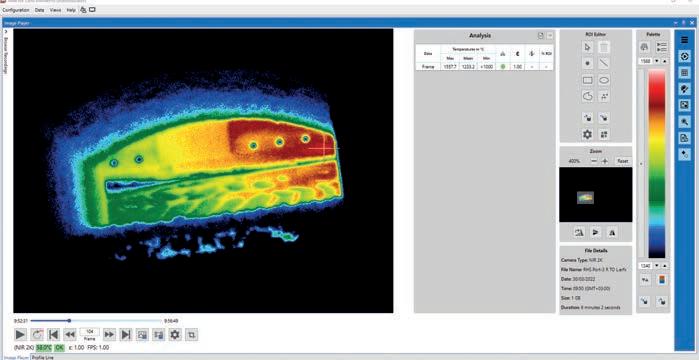
Fig F rnace ort en of firing from right left sotherms
with optimised pull rates, increase their thermal and combustion efficiency, extend campaign life, refractory asset protection, reduce energy consumption by optimising the flame pattern, and ensure emissions compliance.” �
*Independent Consultant - Combustion, Energy and Glass, Ametek Land, ro el , ite Ki o www.ametek-land.com

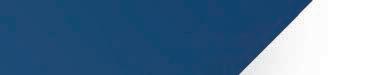
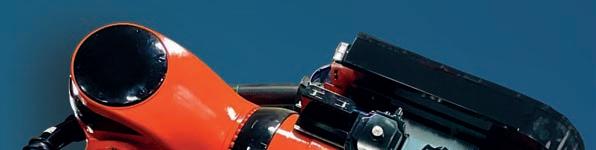
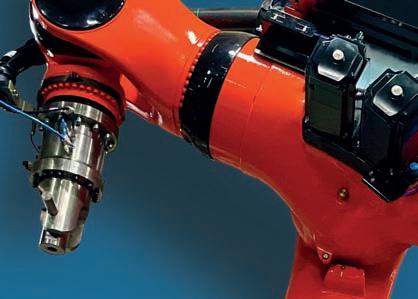
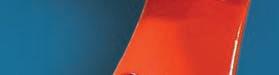

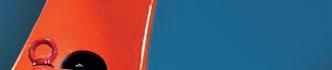
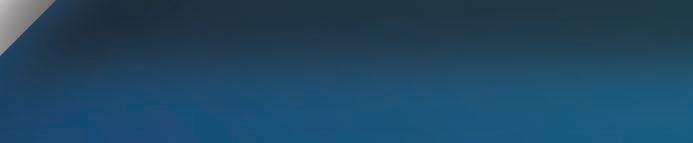
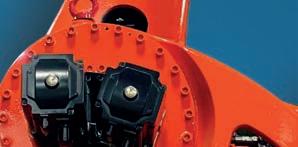
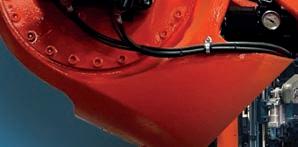


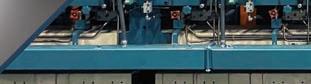