
12 minute read
Personality profile: Tiama
The hot end specialist
Michel Carpentier was recently appointed head of Tiama’s Hot End business unit. He reveals his plans for the unit and how it can help glass manufacturers as well as describing his 25-year career in the glass industry.
1. HOW CAN TIAMA’S HOT END UNIT HELP A GLASS COMPANY’S HOT END OPERATIONS?
For more than 15 years now, Tiama has gradually invested in the development of process sensors dedicated to the hot end. Tiama’s Hot End business unit, which is now well structured and strengthened by a doubled developer staff, is 100% focused on supporting the hot end operators in the factories.
Our historical ‘vision’ know-how, coupled with our growing hot end expertise, enables the company to provide real technological responses to our customers’ needs, and to evolve these responses to the constant and changing challenges of the factories.
The quest for performance and quality is at stake for all glassmakers, especially today in the global context of inflation and the environmental challenges.
We are, and will be, more and more present to develop the appropriate tools to help our customers to better understand their process, but also to better anticipate drifts and thus improve their performance. This is the heart of our ambition.
Finally, everything we do now and tomorrow in terms of products developments within the hot end business unit fits perfectly into our Tiama ecosystem strategy and allows our customers to complement their overview of their production, already fuelled by all cold end and laboratory equipment data. The correlations thus possible, the cross-alerts are all key means made possible by what we do and want to do within the hot end business unit.
2. HOW HAVE TIAMA’S HOT END SYSTEMS EVOLVED SINCE THEIR ORIGINAL LAUNCH?
Hot end systems were launched 15 years ago to meet a glass industry need to monitor productions directly at the output of the IS machine, rather than waiting for the cold end information. An infrared analysis of the articles was an obvious response in the process monitoring, so Tiama launched the I-CARE system, which became well known to the glass industry. Quickly, it became clear that we had to go back up the process and come up with a gob monitoring solution, where everything starts. Thus, after the acquisition of the company Gedevelop, our product range expanded to include our Hot Mass, based on a two-dimensional acquisition of the images of the gobs. This was, for Tiama and what was going to become the business unit hot end, a major breakthrough in the conquest of the hot end process.
Then things got faster. After the development of the I-CARE and the feedback of our customers, we understood that a more modular approach to the monitoring of the IS machine output process was a real need. Moreover, with our cold end expertise, the logic of integrating a ‘vision’ machine into the hot end has emerged as a great opportunity to create a hybrid solution, combining the best of both worlds, with infrared analysis and visible light analysis, and at the same time allowing us to differentiate ourselves from our competitors, based solely on infrared technology. This is how our dual system, Hot Eye/Hot Form, was born, supplemented by our Hot Move solution for tracking the alignment of articles on the IS conveyor.
Today, we are in a dynamic of intense development: we will officially present at glasstec 2022 our new gobs monitoring system, the Hot Mass II, based on a 3D analysis of the gobs, with extreme precision and stability of measurements. We are integrating the evolution of the technologies available at the core of our equipment, both in the soft and the hardware side, with increasingly powerful systems and HD cameras. Tools available today such as artificial intelligence, machine learning, big data are opportunities to increase the performance of our products, to meet the still existing and numerous field expectations.
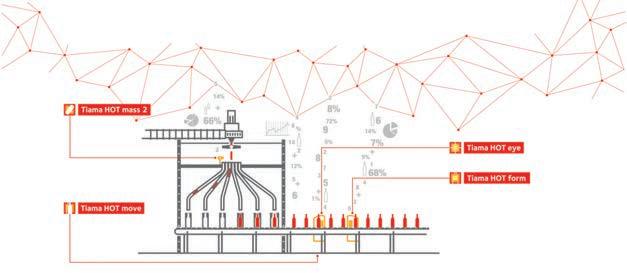
3. HOW WILL THE GLASSFORM.AI SOFTWARE BE USED IN THE HOT END UNIT?
First of all, a few words about GlassFORM.ai: This company was born at the end of 2021 from a common and convergent view of both Tiama and Bottero on the future of the hot end. The conviction was, and remains, that this future depends on data management and automation for many reasons. GlassFORM.ai is now operational and about to release its fi rst product, the GOBexpert, and will soon start the development of the FORMexpert product.
These software programmes will operate on the same principle: collect real-time data from everything that is accessible on the production lines (feeder, IS machine, hot end sensors, cold end machine inspection systems, etc.), build a dynamic database that will be used by the GlassFORM.ai platform, which will implement artifi cial intelligence, machine learning modules to refi ne pre-established models that will fi nally enable regulation models to interfere with the feeder mechanism, on the IS machine, tomorrow on the feeder and more.
GlassFORM.ai software will be standalone solutions, connected to a data collection architecture implemented on each production line, and connected to production systems, to help our customers improve their performance and quality, through a more stable and controlled process.
4. HOW ELSE WILL THE HOT END SYSTEMS DEVELOP/USE INDUSTRY 4.0?
There are two answers to this question.
On the one hand, we consider hot end products to be stage 1 of industry 4.0. Indeed, all our sensors, connected to a data structure through our Tiama ECO-system solution, provides in real time bulk information that will be collected, analysed and correlated as with our Tiama DataMine tool to bring back relevant and delayed information to the teams on the production lines, and/or will be used in the GlassFORM.ai tools to bring a true ‘loop’ to the heart of the glass process.
On the other hand, our hot end sensors are capable of providing a huge amount of crucial information which can be treated with artifi cial intelligence to become even more useful to the hot end teams, such as the recognition and monitoring of critical defects directly at the output of the machines. This is already a major contribution that is totally linked to what we call industry 4.0.
5. CAN THE HOT END UNIT HELP WITH A COMPANY’S SUSTAINABILITY PLANS?
Our major ambition within the Business Unit Hot End is to provide our customers with systems which will give them real-time information, or even top-level regulation. All this contributes to improve performance and overall stability of the lines, with undeniably increased responsiveness and accuracy in the corrective actions implemented.
Each bottle, each small container thus saved by this improved performance, is in fact an economy made in terms of carbon footprint and thus contributes directly to the sustainability of the glass industry. Since the global average glass yield is around 85% of PTM, the margin for progress of this carbon footprint is enormous and we are with our customers’ sides to contribute actively to it.
6. ARE YOU ABLE TO INDICATE ANY FURTHER PLANS TO DEVELOP THE UNIT?
The hot end business unit is in a strategic development cycle. On the one hand, we are strengthening our internal skills so that we can better meet our ambitions, and on the other hand, we are working to make our organisations evolve to be more reactive. Our goal is to improve our time to market. Finally, we want to develop our business by relying fi rst on some strong mature products, which provide a solid ground to ensure our capacity to develop new products. The ambition is strong and the means to achieve it are being implemented! The challenges facing our customers are opportunities for us to support them and develop ourselves.
7. WHAT DO YOU ENJOY ABOUT WORKING IN THE INDUSTRY?
In a nutshell, I had the chance to discover the world of industrial glass as part of my engineering training. Since day one, I have been fascinated by this industry, which is little known but so complex What I fi nd extremely attractive and fascinating in this industry is that, on the one hand, it is impossible to go around it, you learn about it every day from morning to evening until the end of your career, and, on the other hand, you are confronted to all the techniques and technologies of the industry, and they evolve very quickly.
To finish on the process side, each time I see a gob falling remains for me a pleasure that all the glassmakers know well. It is the magic of glass!
On another side, and this is the main one, this job is hard! You do not count your hours, but the teamwork with women and men who have the same passion is so rewarding, that you end up forgetting your diffi culties. The successes are won together. In short, the world of glass is a ‘small family’ in which it is a good place to live, and that is what driven me since day one!
8. HOW HAS THE INDUSTRY EVOLVED IN THIS TIME?
Since I began my career in the glass world in 1997, I have witnessed several profound transformations at the heart of the factories. First of all, although the glass process has remained unchanged for many years, the production tools have been thoroughly modernised. The digital age has come, and the machines have gradually integrated servo-drives, offering unrivalled setting and control possibilities. Quality control tools at the cold end have also undergone a major change with the age of digital and camera vision control.
In addition, production supervision tools have also been completely reviewed with an impressive amount of real-time information that can now be obtained.
Overall, the control of the process has been considerably strengthened, in order to meet the quality requirements of bottler customers who have nothing to do with what they had even 10 years ago, or 20 years ago. The procedures, the control of materials, moulds, equipment, etc. all contribute to a major structural change in the glass world: We have moved from a time when glass was ‘magic’, when empiricism was the standard to a much more scientific, more Cartesian approach, to fact-based, data-driven approaches which are now the daily work of factories, even though much remains to be done! In conclusion, I would like to highlight one last point which has become a growing problem for the glass world. Indeed, over the past two decades, it is undeniable that a loss of skills has occurred in factories as a result of the retirement of experienced glassmakers, as it is increasingly difficult to recruit and retain good profiles. Thus, a race against the clock has begun between this challenge of competence in factories and the technological development which must now and in the future compensate, with increasingly intelligent sensors, with regulation systems based on artificial intelligence. It is clear that man will remain at the heart of the glass equation, but the tools must be at his side, adapted to the challenges of tomorrow.
9. HOW HAS YOUR EXPERIENCE OF THE INDUSTRY INFLUENCED YOUR NEW ROLE?
The answer to that question is obvious to me.
Having spent 21 years in the glass industry, 100% in the factory, when I was contacted by Tiama to take the lead of the Hot End business unit, I immediately saw the logic and coherence for me to take up this challenge. Indeed, what is more important for the development of this activity, with a young learning team, than knowing the world of glass from the inside, so that we can share on a daily basis what is important and what is not, and to be able to guide the solutions to be implemented in the future in order to meet a single objective: help the glassmakers to improve their lives with improving performance. All my experience today, with all the hot end team, helps me to be particularly careful not to develop only “Nice to have Products”, but “Must have products” that really meet factory expectations that I faced myself in the past. Coming from this industry also allows me to enhance the understanding of our customers, speaking the same language, so that we can go straight to the goal and move faster.
There is still a lot to do in our business unit and being a former glassmaker from training and from the heart is an asset I will use to make the most of my new position!
10. WHAT DO YOU BELIEVE TO BE THE MAIN CHALLENGES IN THE GLASS PACKAGING INDUSTRY?
In short, I would like to mention the following four major challenges, which are completely interrelated:
Technical performance, economic performance, environmental performance around a key issue related to people knowhow... In a context in which the quality of production has been considerably improved and can still be improved, it is clear that these four subjects are at the heart of the glass world’s attention. The current global context and the succession of crisis we face only reinforce the weight of these challenges, and that is where Tiama, with its HE Business unit, can and must help its customers in the coming years. Tiama, Saint-Genis-Laval, France www.tiama.com
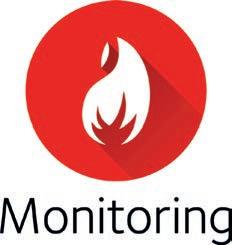
11. HOW WILL TIAMA’S NEW HOT END UNIT HELP CUSTOMERS FACE THESE CHALLENGES?
To follow on the previous question, through our tools, our ability to stand by the plants, our ability to innovate, our ability to adapt and build the appropriate dynamics, as with GlassFORM.ai. We are fully aware of these challenges and are fully committed to addressing them. These are in fact challenges that concern all of us, whether you are a glass producer or a supplier of technology such as Tiama.