
85 minute read
MACCHINE & ATTREZZATURE
“LA SECONDA VITA DEL PET” SECONDO COSTRUZIONI MECCANICHE LUIGI BANDERA
PRODURRE E RIUTILIZZARE VASCHETTE FOOD GRADE MONOMATERIALE
LO SCORSO 9 NOVEMBRE SI È TENUTO, IN LINGUA ITALIANA, IL PRIMO DI UNA SERIE DI WEBINAR ORGANIZZATI DA PROMAPLAST IN VISTA DELLA FIERA GREENPLAST 2022, SEGUITO POI IL 10 NOVEMBRE DA UNA DIRETTA STREAMING IN LINGUA INGLESE, SEMPRE SUI MEDESIMI ARGOMENTI. TOMRA, PREVIERO/SOREMA E BANDERA SONO LE AZIENDE CHE HANNO INAUGURATO QUESTE SESSIONI EDUCATIVE DA REMOTO. DI SEGUITO IL FOCUS SULLA TECNOLOGIA REVOTECH DI BANDERA E SUI PROCESSI “TRAY-TO-TRAY”
DI ERMANNO PEDROTTI E RICCARDO AMPOLLINI
Se l’obiettivo perseguito da Promaplast era lampante, e cioè fornire aggiornamenti sulle tecnologie che contribuiscono a rendere più sostenibili le materie plastiche, pure la formula comunicativa scelta dall’ente organizzatore delle fiere Plast e Greenplast s’è mostrata impeccabile: incontri webinar con partecipazione da remoto, tramite connessione Internet. Conformemente a tali stringenti premesse, Alessandro Granziera (direttore commerciale di Tomra Sorting), Andrea Villa (sales area manager presso Previero/Sorema) e Pietro Zanotto (sales area manager della divisione Film soffiato e testa piana di Bandera) hanno inaugurato, in preciso ordine d’apparizione, la prima di una serie di dirette streaming concepite ad hoc da Promaplast in vista della mostra-convegno Greenplast, evento che si terrà in Fiera Milano dal 3 al 6 maggio 2022. Il titolo di questa prima sessione, che ha avuto luogo il 9 novembre scorso, era “La seconda vita del PET” e, attraverso la descrizione di loro recenti impianti, i tre relatori hanno tracciato complice la non banale complementarietà delle tecnologie Tomra, Previero e Bandera - un esaustivo stato dell’arte sull’intero processo di riciclo dei rifiuti plastici in polietilentereftalato (PET). Di fatto, si sta parlando di una catena produttiva

Pietro Zanotto, sales area manager della divisione Film soffiato e testa piana di Bandera
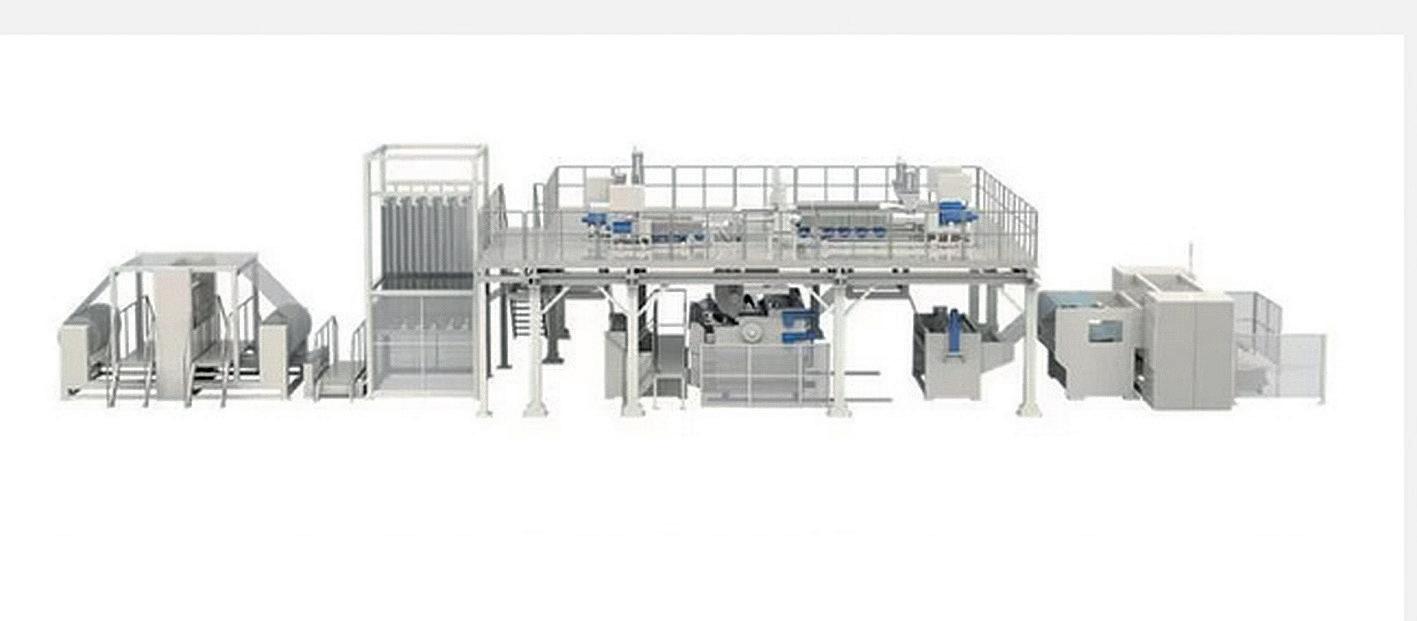
basata principalmente sulle fasi di: lavaggio, trattamento dell’acqua, selezione ed estrusione. Non è quindi un caso se il primo relatore, Alessandro Granziera, ha parlato del ruolo della tecnologia di selezione ottica messa a punto dalla norvegese Tomra Recycling nei processi di riciclo “bottle to bottle”. Seguito da Andrea Villa, il quale ha fornito nozioni sul processo di riciclo del PET, estendendo poi il concetto ad altri materiali, come l’HDPE, e ad alcuni tipi di film, oltre a dare pure spazio al progetto DE_inking (ndr: sistema di lavaggio che prevede la rimozione dell’inchiostro legato alle etichette), che è in corso d’opera presso Sorema. Il terzo relatore, Pietro Zanotto, ha poi dato particolare enfasi alla tecnica di riciclo denominata Revotech, marchio registrato di Bandera, ma anche divisione specializzata nello sviluppo dei processi di recupero di poliolefine e PET da materiale di scarto post consumo o post industriale, per la produzione di materia prima seconda in forma di granulo. L’obiettivo della tecnologia Bandera Revotech è quello di fornire un granulo riciclato con qualità e caratteristiche paragonabili al vergine, con la possibilità di includere anche cariche minerali e/o fibre. Un processo particolare e una casistica degna di nota sono offerti dalle soluzioni Bandera “trayto-tray” (in italiano: “da vaschetta a vaschetta”). Queste ultime consentono di realizzare prodotti food grade in PET monomateriale, requisito fondamentale per un vero e proprio riciclo delle vaschette post consumo, che di molto differisce da quello attualmente in uso per le soluzioni accoppiate PET+PE+strato barriera. Incuriositi dalla tecnica Revotech di Bandera e col fine di seguire il piano editoriale della rivista MacPlas, come redazione s’è arbitrariamente deciso di dedicare questo primo focus dal webinar del 9 novembre proprio a quest’approccio verso l’economia circolare, frutto - come si vedrà di seguito - della combinazione di innovative tecnologie d’estrusione, converting e riciclo.
TECNOLOGIA, RICERCA E INNOVAZIONE “MADE IN BUSTO ARSIZIO”
Costruzioni Meccaniche Luigi Bandera è oggi sinonimo di sistemi d’estrusione all’avanguardia, di produzione d’imballaggi innovativi, di soluzioni ecologiche e redditizie da materiali riciclati e biodegradabili, di servizi d’ingegneria personalizzati e d’efficienza globale post vendita. Dato però che “pensare al passato è fondamentale per capire il presente”, saggiamente Pietro Zanotto ha esordito citando, seppur brevemente, le date cruciali che hanno fatto la storia dell’azienda: 1947 - Nasce ufficialmente Costruzioni Meccaniche Luigi Bandera che, seppur a livello artigianale, s’occupa fin da subito d’estrusione; 1950 - Da artigianale, l’attività nel comparto dell’estrusione viene ampliata su scala industriale; 1960-1970 - L’azienda conosce una notevole espansione, offrendo una più vasta e diversificata gamma di prodotti per l’estrusione; 1980-1990 - In Italia e nel mondo, Bandera diviene sinonimo d’estrusione di film in bolla (o film soffiato) e testa piana; 2015-2016 - Viene inaugurata “The House Of Extrusion” (THOE, la “casa dell’estrusione”), un’area di 6000 m2 con linee complete di produzione, servizi di progettazione personalizzati e una rete globale per il post vendita. “Dal 1947 a oggi l’azienda si è sempre spesa nel mercato dell’estrusione”, ha quindi puntualizzato Zanotto, “muovendosi, di fatto, su quattro pilastri fondamentali: gli impianti per film in bolla, le linee a testa piana, i sistemi speciali per l’estrusione e le tecnologie dedicate al riciclo. Ed è proprio nel campo del riciclo che si colloca il concetto Revotech… che, di fatto, costituisce una vera e propria divisione di Bandera, più che un semplice concetto”. Pietro Zanotto ha poi spiegato che Bandera si occupa di riciclo da almeno due decenni: “È del 1999 il nostro primo brevetto relativo a un estrusore bivite corotante HVTSE (marchio registrato di Bandera), ad alto vuoto, per la lavorazione con PET riciclato fino al 100%”, ha detto Zanotto, citando poi una sequenza di date cruciali in materia, questa volta, di riciclo: 2009 - La tecnologia corotante HVTSE riceve la FDA No Objection Letter; 2015 - Inizia la campagna “Lighter Packaging” con tecniche di espansione fisica; 2017 - La tecnologia PURe (marchio registrato di Bandera), che serve per la decontaminazione delle scaglie da bottiglia (flakes), riceve anch’essa la FDA No Objection Letter; 2019 - Bandera crea i primi vassoi monomateriale in PET. Venendo poi al nocciolo del suo intervento, Pietro Zanotto ha dichiarato che: “Negli ultimi 25 anni abbiamo visto, in pratica, tutte le tendenze nel campo del riciclo. Ed ecco che, seguendo il trend relativo agli articoli monomateriale, nell’ottica di provare a supportare il più possibile i nostri clienti con innovazioni e con sviluppi che permettano loro di essere più competitivi nei propri mercati e, al contempo, del tutto rispondenti a quelle che sono le esigenze ambientali e le esigenze produttive, siamo riusciti a sviluppare un processo “tray-to-tray” in grado di produrre - e successivamente di riutilizzare - vaschette monomateriale adatte al contatto alimentare (food grade)”.

Vista dall’alto della “The House Of Extrusion” (THOE), la “casa dell’estrusione” che si trova presso lo stabilimento principale di Bandera a Busto Arsizio (Varese)
IDENTIKIT DEL PROCESSO REVOTECH
È possibile affermare che Bandera Revotech, combinando le più innovative tecnologie d’e-
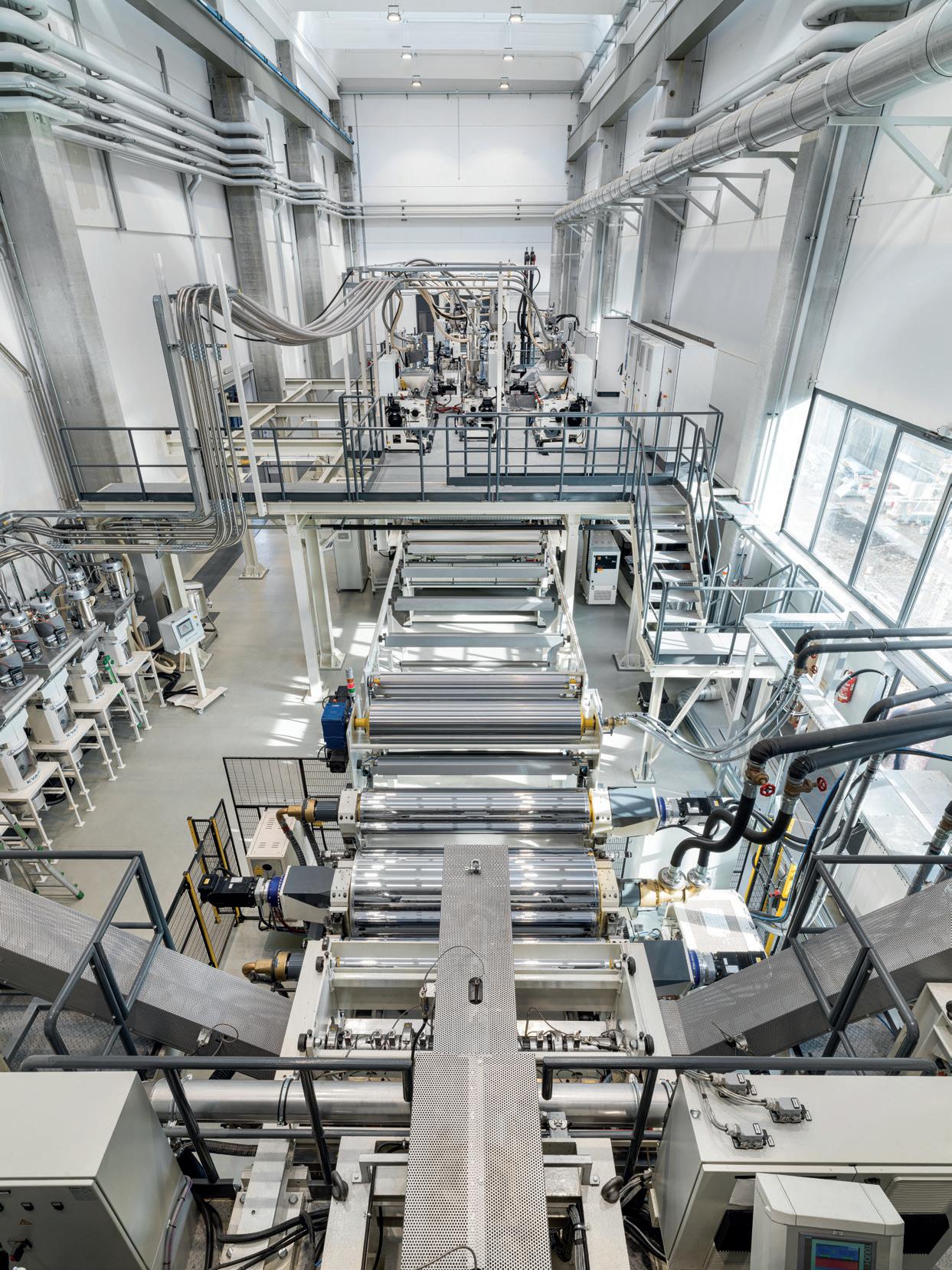
strusione, di converting e di riciclo, rappresenta lo stato dell’arte nell’approccio alla circular economy e al packaging sostenibile. Sempre Zanotto ha infatti detto che Revotech comprende anche le fasi di pre e di post trattamento del materiale (con i sistemi PURe e VOC & Odor Removal), grazie a un mix di tecnologie brevettate che garantiscono risultati e prestazioni superiori. Riportiamo qui alcuni moduli dei quali si è parlato nel webinar: HVTSE - Una citazione a sé merita l’estrusore bivite corotante che, grazie a condizioni quali alto vuoto, minimo shear stress, ampia superficie esposta al degassaggio, ridotti tempi di residenza, produce materiale di elevata qualità, utilizzando fino al 100% di rimacinato; inoltre, non necessitando di un processo di deumidificazione a monte (dry-less), i consumi energetici risultano contenuti. PURe - Si tratta di un processo brevettato che permette la purificazione/decontaminazione delle scaglie di PET post consumo, garantendo materiale in uscita pienamente conforme ai requisiti di decontaminazione FDA/EFSA per il contatto alimentare, da impiegare (anche in-line) in qualunque processo di estrusione. VOC & Odor Removal - Un innovativo componente brevettato che consente di soddisfare la crescente richiesta del mercato del riciclo delle poliolefine di rimuovere odori e VOC, con tempi e consumi estremamente ridotti. Condor Line e Revotech costituiscono un insieme di tecnologie e competenze a disposizione delle imprese che vogliono innovarsi nel settore del packaging e del converting e, in generale, sviluppare nuove idee nel mercato della granulazione, del riciclo, della testa piana e del film in bolla. Uno degli obiettivi fondamentali dei progetti in essere è testare una nuova generazione di materie prime riciclate e riciclabili. Presso la THOE, in collaborazione con Bandera, le imprese possono gestire nuovi progetti, valutarne i progressi e il workflow attraverso l’esecuzione di test. Per esempio, il filmato mostrato da Bandera durante il webinar illustra alcune peculiarità del processo e la composizione della Condor Line (anch’essa a marchio registrato Bandera). Aspetti fondamentali del processo sono: la possibilità di potenziare l’effetto barriera e di prolungare la durata dei prodotti confezionati, con materiali standard o innovativi; la possibilità di migliorare le proprietà fisiche e meccaniche attraverso la combinazione di strati rigidi e flessibili, sia attraverso la laminazione sia mediante il coating. Con la tecnologia “Revotech tray-to-tray” Bandera propone l’utilizzo di sistemi d’extrusion coating con formulazioni personalizzabili per la produzione di vassoi in “PET monomateriale” e con caratteristiche equivalenti a quelle delle soluzioni composite “multimateriale” attualmente presenti sul mercato. Più in generale, per poter ottenere un’impostazione industriale universalmente riconosciuta e applicabile, tutti i vassoi in PET destinati al mercato FFS (Form-Fill-Seal) non devono includere altri polimeri che possono generare contaminazione, come resine barriera specifiche e film di laminazione. Anche nel processo “tray-to-tray” sono quindi garantite sia la capacità di tenuta sia la barriera ai gas (ove necessario) e, in aggiunta a tutto questo, sono pure evidenti una maggiore trasparenza e migliori caratteristiche meccaniche. Il tutto si traduce - per punti - nelle seguenti performance: • da 100% riciclato a 100% riciclabile; • proprietà barriera assicurate; • saldabilità con film “top lid” garantita; • trasparenza riproducibile; • confermata sostenibilità industriale.

Un dettaglio degli estrusori della Condor Line
Siamo quindi oggettivamente in presenza di una soluzione che non risponde solo alle richieste di sostenibilità, ma anche a quelle di: profittabilità, grazie a tempi di lavorazione in alcuni casi dimezzati; risparmio energetico; bassa frequenza di manutenzione degli impianti e dei componenti; tecnologia dalle performance superiori. Anche in questa fase transitoria con tray di PET, o misti PET e poliolefine, la tecnologia Bandera è comunque in grado di ottenere prodotti food grade dal 100% di riciclato. “Revotech ci consente di posizionare il PET in seno alla circular economy, potendo contare su materia prima seconda di qualità anche sotto forma di film rigido per termoformatura o per uso industriale, sia esso di grado alimentare o non, e sempre con qualità ottiche e meccaniche superiori”, ha chiosato infine Zanotto.
NOTA OPERATIVA FINALE
Ultimo in ordine d’esposizione, ma non d’importanza, l’accenno al fatto che nella sede di Bandera, a Busto Arsizio (Varese), il processo Revotech s’è materializzato nella già citata linea ad altissima efficienza “Condor Line”. Si tratta di un impianto in grado di processare due tonnellate all’ora di PET e che è ubicato nella già nota “casa dell’estrusione” di Bandera. Sempre in quell’ambito, il costruttore varesino dà la possibilità ai propri clienti di testare dal vivo i materiali più disparati: dal polipropilene “tal quale” al PET, dal polipropilene modificato al già citato materiale per il “tray-to-tray”. “Un asset per certo di notevole interesse, ha quindi concluso Pietro Zanotto, “e non tanto per la possibilità di tentare una certa prova, ma per l’opportunità di definire con i clienti i parametri di un loro nuovo prodotto da immettere sul mercato”.
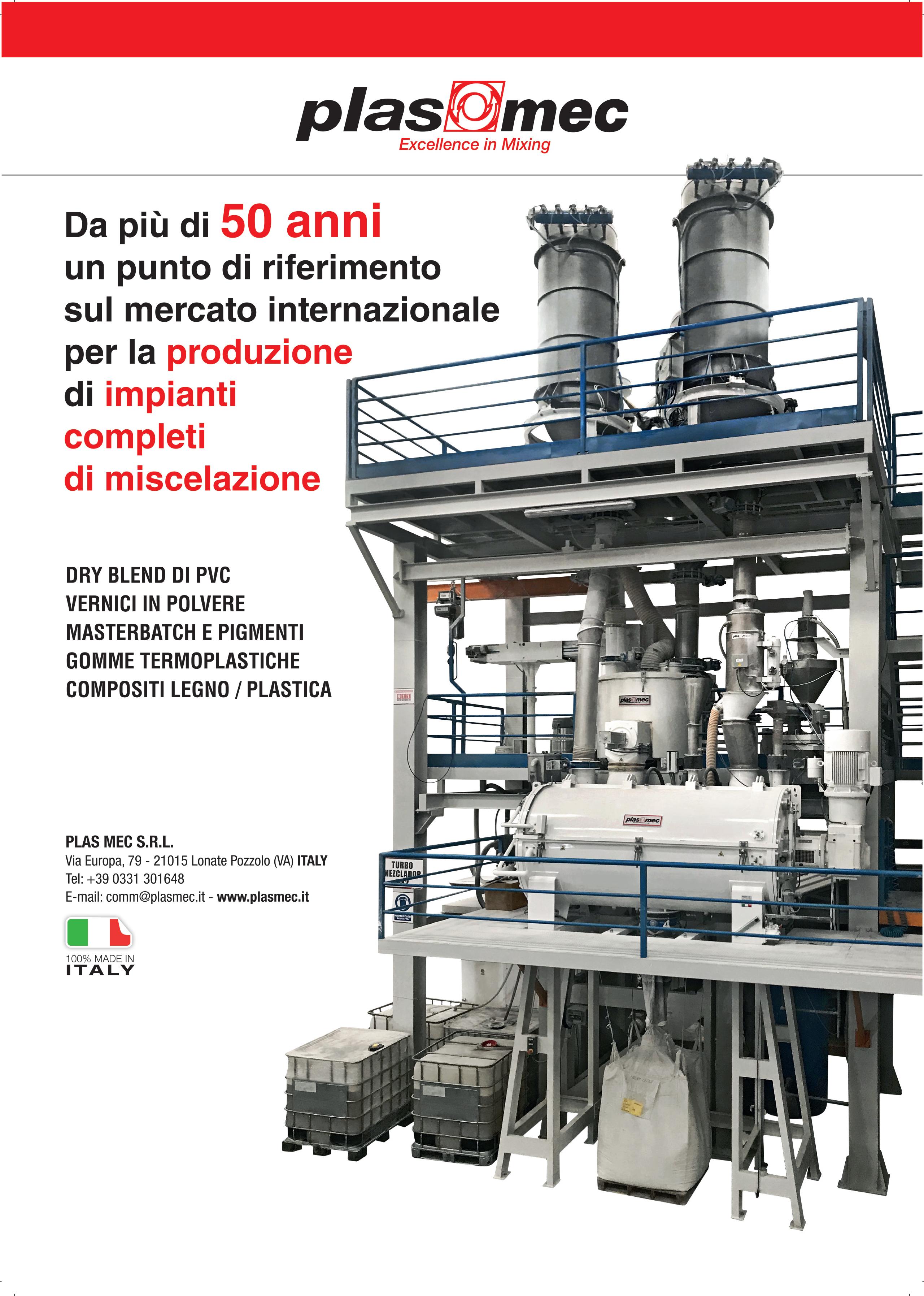
ATTIVITÀ INTENSA IN CASA COLINES NEGLI ULTIMI MESI

UN AUTUNNO CALDO CON TANTA CARNE AL FUOCO
LA SOCIETÀ PIEMONTESE COSTRUTTRICE DI LINEE PER L’ESTRUSIONE VALICA IL PASSAGGIO AL NUOVO ANNO SULLA SPINTA DI TANTI RECENTI SVILUPPI. CON UNA NOVITÀ IMPORTANTE: DALLA COSTRUZIONE DI IMPIANTI A TESTA PIANA, SI LANCIA NELLA REALIZZAZIONE DI QUELLI PER FILM IN BOLLA
Lo scorso autunno, per Colines, è stato ricco di lanci di prodotto, collaborazioni ed eventi che hanno visto l’azienda di Nibbia (Novara) protagonista su più fronti. Tra le novità più importanti presentate dal costruttore rientra la nuova serie Polyblown di impianti per la produzione di film in bolla, disponibili in configurazione da 3 a 11 strati. Tradizionalmente attiva nel campo delle linee per l’estrusione a testa piana e solo occasionalmente, in base a richieste specifiche di clienti selezionati, in quello degli impianti per film in bolla, negli ultimi 24 mesi Colines ha investito molto in questo ambito, anche assumendo tecnici di elevato livello e prolungata esperienza nella messa a punto di tale tecnologia. Ne è nata la nuova famiglia d’impianti per l’estrusione in bolla che è stata presentata ufficialmente con un’open house di tre giorni, dal 23 al 25 novembre, presso la sede di Marano Ticino (Novara). In open house è stata presentata la linea Polyblown multiuso a 7 strati da 2600 mm, che ha dato dimostrazione di tre differenti produzioni nell’arco dei tre giorni di evento. “Lavoriamo a questo progetto da due anni e abbiamo deciso di lanciare le nostre nuove linee con uno speciale evento in presenza. Sappiamo bene che il mercato del film in bolla è altamente competitivo ed esigente. Tuttavia, come squadra, siamo estremamente fiduciosi delle tecnologie che abbiamo sviluppato e ingegnerizzato. Siamo tornati a pieno regime in questo mercato”, ha anticipato Anthony Michael Caprioli, CEO di Colines. Positivo il riscontro raccolto dall’azienda durante i tre giorni di evento, con la presenza di oltre 60 clienti e circa 100 incontri online con coloro che non hanno potuto partecipare a causa delle restrizioni imposte dalla pandemia agli spostamenti. “Siamo molto contenti del successo dell’evento. Abbiamo potuto dimostrare l’estrema versatilità e flessibilità delle nostre linee Polyblown, realizzando, nell’arco di tre giorni, tre diversi prodotti che sono stati molto apprezzati”, ha dichiarato il direttore marketing e comunicazione e sales area manager di Colines, Gabriele Peccetti. D’altron-

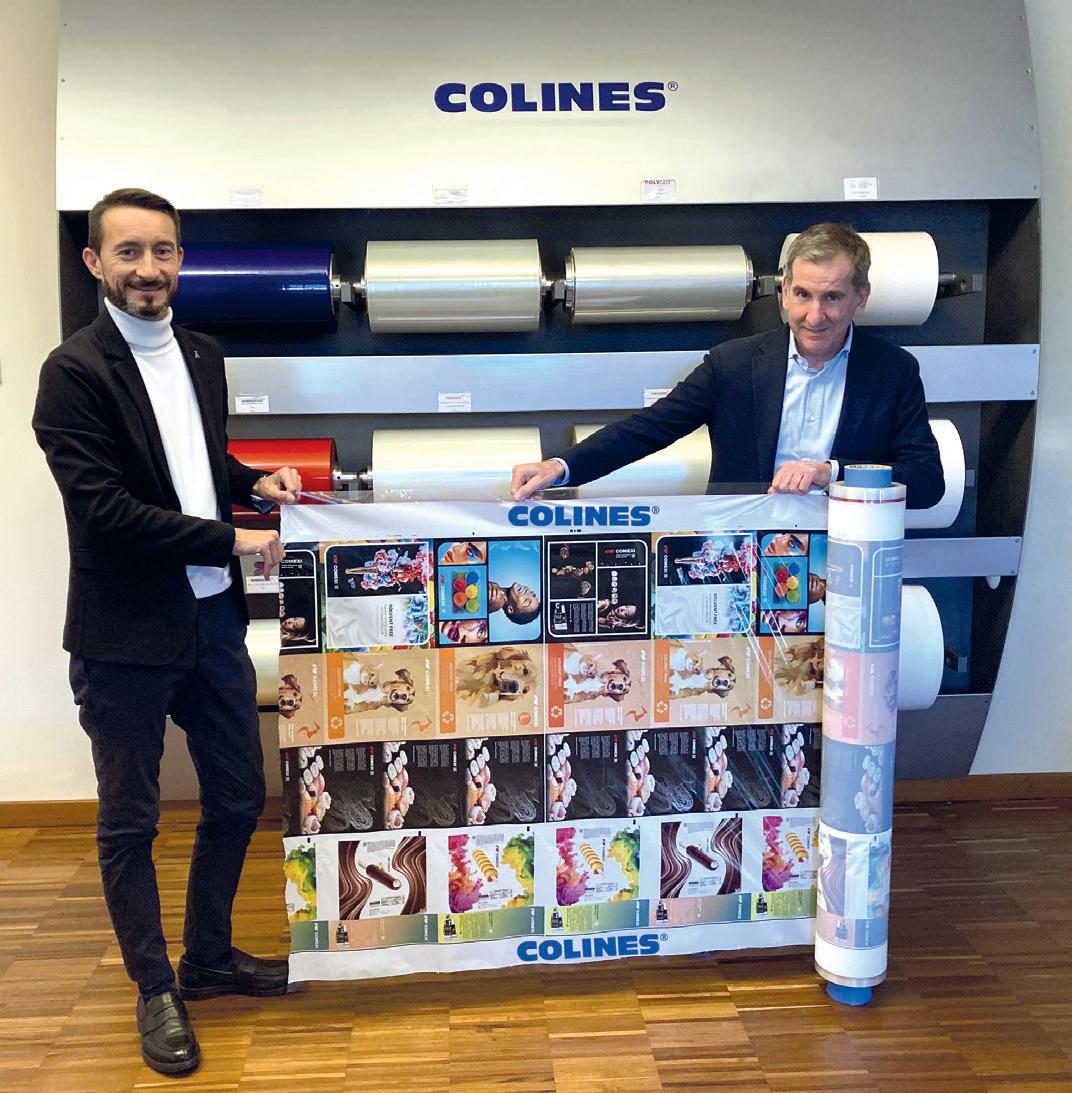
de, la flessibilità è uno degli assoluti punti di forza della nuova famiglia di impianti.
UN CLASSICO SEMPRE SULLA BRECCIA
Grandi protagoniste degli ultimi mesi in casa Colines anche le linee ALLrollEX. Per aggiornare il proprio parco macchine, il gruppo Manupackaging, attivo nel mercato del film estensibile in Europa e America Latina, si è rivolto all’azienda novarese per la fornitura di due linee di tale gamma - una 1500 mm e una 3000 mm - per la produzione di film estensibile con tecnologia a testa piana; linee installate nel suo stabilimento a Schkopau (Germania). “Siamo soddisfatti di aver scelto Colines come partner tecnologico per questo investimento e crediamo che questa collaborazione possa essere ulteriormente sviluppata in futuro con investimenti in nuovi progetti per prodotti più sostenibili e performanti. La qualità del prodotto è sempre stata per noi un punto cruciale e riscontriamo in Colines la stessa attenzione”, ha dichiarato Pierfranco Di Gioia, CEO di M Stretch, holding di Manupackaging. “Alla base della scelta di Manupackaging c’è l’elevata qualità del film realizzato dalle nostre linee e questa per noi è una valutazione importante. Abbiamo migliorato molto la nostra attività di ricerca e sviluppo e i risultati possono essere sperimentati direttamente dai clienti, grazie agli elevati standard produttivi e alla flessibilità delle nostre linee”, ha affermato Eraldo Peccetti, presidente esecutivo di Colines. Altre due linee ALLrollEX da 3000 mm sono state fornite da Colines a Grupo Reyma, rafforzando così una collaborazione avviata dalle due aziende un paio di anni fa. Attivo dal 1970, Grupo Reyma vanta sette stabilimenti in Messico che producono semilavorati e prodotti finiti, un centro di distribuzione a Phoenix (Stati Uniti) e un canale per le attività di marketing nei Caraibi e in America Latina. “Abbiamo una partnership salda e consolidata con Reyma e ne siamo orgogliosi. Dopo aver inizialmente investito nelle linee per film estensibile ALLrollEX, hanno deciso di espandere la loro “flotta” Colines con altre due linee”, ha spiegato Anthony Michael Caprioli.
COLLABORAZIONE A TRE
Ultima ma non ultima, Colines è stata protagonista anche di una recente collaborazione a tre insieme a Dow e Comexi, da cui è nata la produzione di film in PE monoorientato (MOPE) con spessore di 30 micron e specifiche caratteristiche meccaniche e ottiche ottenute mediante tecnologia a testa piana. Questo film è stato realizzato con resine Dow a base PE, estruso con una linea Polycast di ultima generazione di Colines, dotata di sistema brevettato MDO, e successivamente stampato con una macchina CI per la stampa offset di Comexi, senza l’utilizzo di solventi. “I film in PE monoorientato vengono solitamente prodotti con tecnologia in bolla, ma presentano dei limiti, come, per esempio, cattiva lucentezza e opacità, che invece possono essere superati con la tecnologia a testa piana. Quest’ultima, inoltre, consente di ottenere un estruso con un lato con buona saldabilità. Queste caratteristiche aprono ai film in PE monoorientati molti mercati, anche in sostituzione di prodotti esistenti come i film BOPET (Bi-Oriented PET), garantendo una riduzione degli spessori e una maggiore riciclabilità”, ha spiegato Nicola Lombardini, direttore ricerca e sviluppo in casa Colines. “Abbiamo realizzato qualcosa di estremamente innovativo e presto faremo ulteriori passi avanti grazie alla nostra nuova linea Polycast per ricerca e sviluppo, perfettamente ottimizzata anche per la lavorazione di PE e dotata della nostra ultima unità MDO. Abbiamo programmato ulteriori test con Dow e Comexi e siamo disponibili anche per l’esecuzione di prove con i nostri clienti, per portarli al “livello successivo” della produzione di film in PE monoorientato”, ha aggiunto il CEO di Colines, Anthony Michael Caprioli. “Dow è impegnata a sviluppare e fornire soluzioni per consentire e accelerare il passaggio a imballaggi sostenibili basati su strutture monomateriale, a tutto vantaggio di un’economia circolare della plastica. Siamo molto soddisfatti del risultato raggiunto insieme a Colines e Comexi sulla tecnologia a testa piana per film MOPE e i risultati dimostrano che abbiamo intrapreso la strada giusta con le nostre resine ad alte prestazioni”, ha affermato Jaroslaw Jelinek, alla guida del marketing globale delle tecnologie per polietilene orientato presso Dow Packaging & Specialty Plastics. “La tecnologia offset CI è sostenibile e priva di solventi e fornisce la massima qualità di stampa con un rapido “time to market” e costi competitivi. Questa tecnologia utilizza inchiostri e rivestimenti polimerizzanti ElectronBeam, consuma meno inchiostro ed energia, non usa solventi ed è in grado di stampare un’ampia gamma di substrati. La polimerizzazione EB fornisce la migliore soluzione per gli imballaggi riciclabili: il processo di reticolazione parziale aumenta la resistenza termica dello strato esterno dell’imballaggio durante la stampa dello strato interno e fornisce un’elevata protezione superficiale durante la stampa”, ha dichiarato Felip Ferrer, direttore dello sviluppo di attività e marchio presso la divisione stampa offset di Comexi.
Le linee a testa piana della serie ALLrollEX sono tra ii prodotti di punta di Colines e continuano a essere richiestissime in tutto il mondo Anthony Michael Caprioli (a destra) e Gabriele Peccetti mostrano il risultato della collaborazione a tre con Dow e Comexi
EIDOS SI CANDIDA A STANDARD DEL SETTORE

DARE FORMA ALLA TERMOFORMATURA
NUOVA MACCHINA IN CASA CMS, PER FORNIRE ELEVATE PRESTAZIONI CON LO SGUARDO RIVOLTO ALLA SOSTENIBILITÀ DELLA PRODUZIONE. PER TRACCIARE UN NUOVO CORSO NON SOLO AL PROPRIO INTERNO, BENSÌ IN TUTTO IL SETTORE DI RIFERIMENTO. NE ABBIAMO PARLATO CON FABIO GAIAZZI, PRODUCT MANAGER PER LA TERMOFORMATURA DELL’AZIENDA DI ZOGNO
DI LUCA MEI
Società con sede a Zogno (Bergamo), in tempi recenti CMS si è dimostrata molto attiva sul fronte degli investimenti, intesi come strada maestra in grado di portare sia allo sviluppo delle proprie attività e tecnologie sia all’acquisizione di nuove quote di mercato, e quindi di ripagare al meglio e velocemente gli sforzi economici richiesti. Rientra nel primo novero la costruzione, proprio a Zogno, di un nuovo stabilimento produttivo all’avanguardia sotto tutti i punti di vista. Un’intera struttura di 85 mila metri cubi, realizzata nel pieno rispetto dell’ambiente e del paesaggio circostante, è stata infatti destinata specificamente alla costruzione delle macchine più grandi dell’azienda, che verranno movimentate tramite otto carroponti con portata di 15 tonnellate ciascuno. La superficie totale coperta è pari a 7740 metri quadri, l’altezza utile interna del fabbricato arriva fino a 12 metri, l’illuminazione delle aree di produzione avviene per mezzo di 200 proiettori LED, che garantiscono una luce mediamente superiore a 350 lux, e durante la realizzazione degli impianti sono stati posati circa 10 mila metri di cavi elettrici. Le facciate del capannone, così come il suo impatto paesaggistico, sono state studiate con la collaborazione dell’architetto Cinzia Robbiati della Soprintendenza archeologica, belle arti e paesaggio per le province di Bergamo e Brescia, mentre la certificazione energetica lo colloca in Classe A1 e sulla copertura è installato un impianto fotovoltaico composto da 504 moduli solari policristallini, con una potenza complessiva di picco di 150 kW. Inoltre, il solaio di pavimento, dello spessore di 48 cm, è in grado di sopportare carichi dinamici fino a 3500 kg, con un cedimento differenziale inferiore a due centesimi di millimetro, così da permettere di eseguire i collaudi direttamente sul posto, comprese le prove più impegnative e severe, assicurando risultati precisi e affidabili. Nel secondo ambito, invece, trova la propria ragione d’essere lo sviluppo della nuova termoformatrice Eidos, macchina concepita per coniugare senza compromessi prestazioni e stile, assecondando così i più attuali e pregnan-

ti canoni che guidano la produzione industriale moderna. In questa chiave, la nuova Eidos racchiude soluzioni meccaniche raffinate, per garantire la massima prestazione in termini assoluti, e software innovativi, per fruire della tecnologia che ne è alla base con immediata semplicità. Per farci raccontare tutto questo e molto altro ancora, la redazione di MacPlas si è rivolta a Fabio Gaiazzi, che, nel suo ruolo di product manager per la termoformatura in CMS, è in grado di sviscerare le peculiarità più intime della macchina e di proporle in tutta la loro chiarezza e valenza innovativa.

PER COMINCIARE, POTREBBE ILLUSTRARE, DA UN PUNTO DI VISTA TECNOLOGICO, LA NUOVA TERMOFORMATRICE EIDOS, CHE AVETE ESPOSTO PER LA PRIMA VOLTA A FAKUMA 2021? QUALI SONO LE PRINCIPALI DIFFERENZE RISPETTO ALLO STATO DELL’ARTE DELLE TERMOFORMATRICI DELLO STESSO TIPO OGGI DISPONIBILI SUL MERCATO?
“Si tratta di un prodotto nuovissimo, che è il risultato di quasi due anni di sviluppo. La prima presentazione è avvenuta nel novembre del 2020, nell’ambito di un evento online organizzato dal nostro nuovo Technology Center nella sede di Zogno. Fakuma 2021, invece, ha rappresentato il primo lancio “in presenza” e difatti ha offerto la possibilità di toccare con mano il prodotto, che al momento proponiamo come un riferimento nel settore delle termoformatrici monostazione da lastra. Già da un primo sguardo ci si accorge di essere di fronte a un prodotto di elevata fattura, compatto e con contenuti tecnologici d’avanguardia. Le soluzioni meccaniche adottate ci hanno permesso di realizzare una macchina estremamente compatta, nonostante l’immancabile flessibilità in termini di altezza stampo e dimensioni lastre. La componentistica di cui Eidos è equipaggiata rappresenta il meglio attualmente disponibile sul mercato. Con questi presupposti è chiaro che il nuovo prodotto di CMS non può che ambire a essere leader del settore. Ma non è tutto. Abbiamo deciso di utilizzare Eidos come piattaforma per integrare nuove funzionalità mai viste su queste macchine. Anche la scelta del nome non è da meno e punta in questa direzione. Infatti, abbiamo cercato di trovare un nome significativo dell’idea che sta dietro a questo prodotto. Ecco che Eidos, dal greco “forma”, ci è sembrato quello migliore per definire un prodotto che darà forma appunto ai progetti dei nostri clienti”.
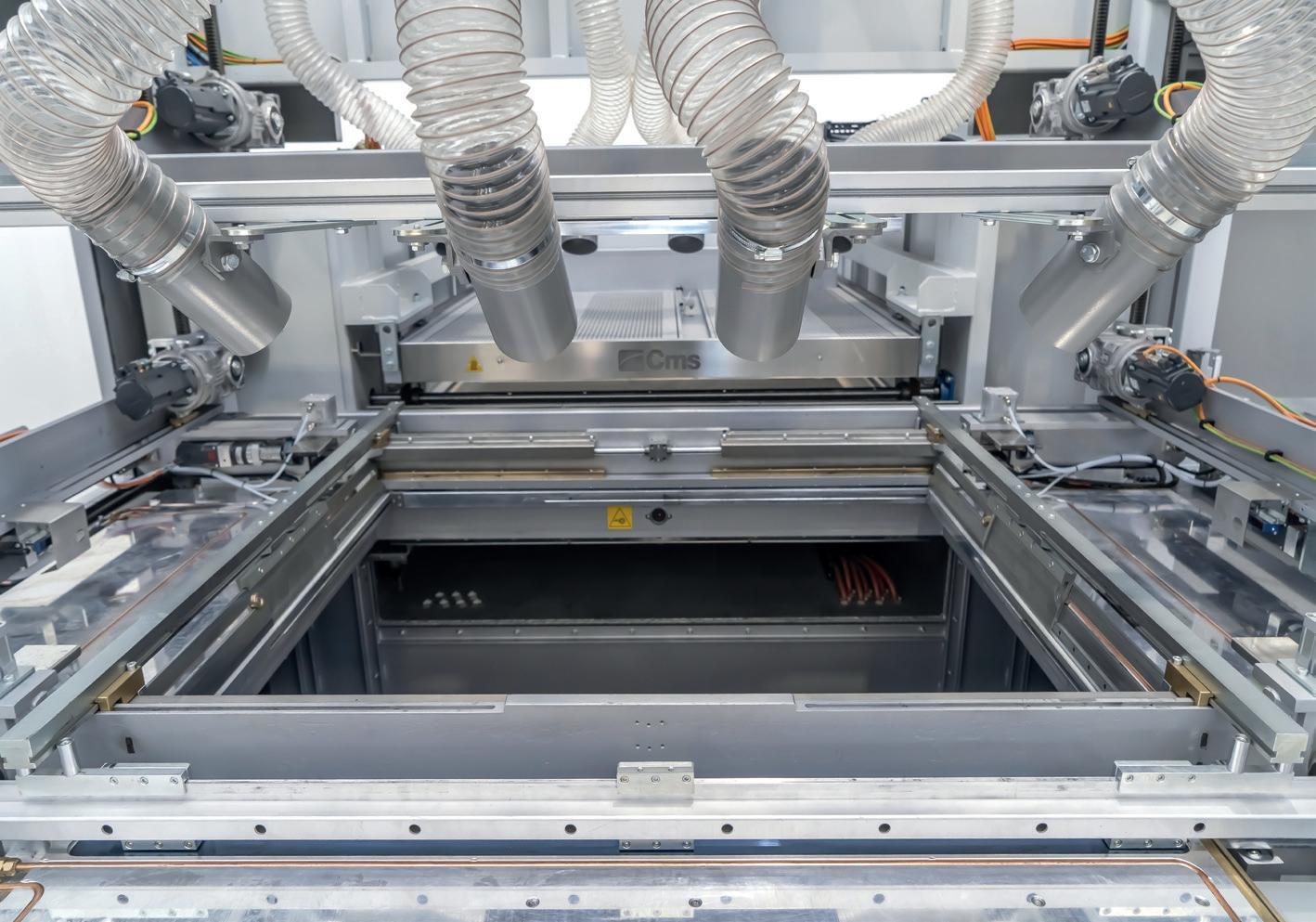
QUALI SONO I SUOI PRINCIPALI PUNTI DI FORZA TECNOLOGICI E DI PROCESSO?
trostampo e cornice si basa sul concetto di semplificazione estrema. Abbiamo quindi deciso di eliminare catene e alberi di trasmissione a favore di assi in configurazione gantry. Questa soluzione riduce al minimo la manutenzione della macchina e garantisce una perfetta distribuzione delle forze, unitamente a una precisa dinamica di movimento. Anche la stazione di carico e scarico automatici è stata rinnovata, consolidando la nostra storica soluzione con sistemi sempre finalizzati a ridurre la manutenzione e a migliorare le prestazioni. Per la parte di automazione si è deciso di migrare a un’architettura Siemens S7-1500 e a un’interfaccia completamente rinnovata, basata su un’applicazione HTML5. Si tratta del nuovo software CMS ThermoActive, che rappresenta il nuovo standard per la gestione delle termoformatrici CMS. È un software specificamente pensato per il processo di termoformatura profonda (heavy-gauge). L’utilizzo è semplificato dall’impiego della nuova consolle con touchscreen capacitivo. Tutti i parametri di processo sono facilmente comprensibili, in quanto organizzati in un sistema totalmente visuale. L’interfaccia utente, quindi, non è più solo una consolle per interfacciarsi con la macchina, ma diventa un vero e proprio strumento con cui sviluppare il proprio progetto di termoformatura, rendendo così l’esperienza di utilizzo parte integrante del successo del prodotto. Sempre in tema di CMS ThermoActive, troviamo la nuova implementazione dell’ormai collaudato sistema ThermoProphet, per la programmazione automatica delle resistenze tramite visione termografica. Soluzione già vista sul modello precedente, ma oggi ulteriormente sviluppata e migliorata. Questo è il sistema con cui riusciamo a sgravare l’operatore dal compito di adattare il programma di produzione al variare delle condizioni ambientali. A questo si aggiunge una nuova opzione chiamata 3D-Ranger. Tramite l’impiego di una telecamera di profondità siamo in grado di rilevare la forma tridimensionale, sia dello stampo sia del pallone, durante la fase di prestiramento del materiale, in modo da rilevare difetti nel processo di formatura e da adattare il comportamento della macchina alla produzione specifica. Oltre a tutte queste implementazioni, l’adozione della nuova piattaforma CMS Active anche sulle termoformatrici ha aperto le porte del mondo CMS Connect anche a questo prodotto, rendendo ora possibile accedere a tutti i servizi cloud di CMS: supervisione della produzione, comunicazione remota, raccolta e analisi dati, gestione autonoma dei ticket per l’assistenza, manutenzione predittiva, insieme a una serie di servizi specifici per la termoformatura. Ovviamente, sono tutte caratteristiche che ci rendono assolutamente adeguati alle specifiche dettate dall’Industria 4.0”.
Una vista generale della nuova Eidos, che unisce soluzioni meccaniche raffinate a software innovativi, per disporre di una tecnologia avanzata e poterne fruire in maniera semplice e intuitiva, senza rinunciare a prestazioni elevate
Specificamente pensato per il processo di termoformatura profonda, il software ThermoActive rappresenta il nuovo standard per la gestione delle termoformatrici CMS
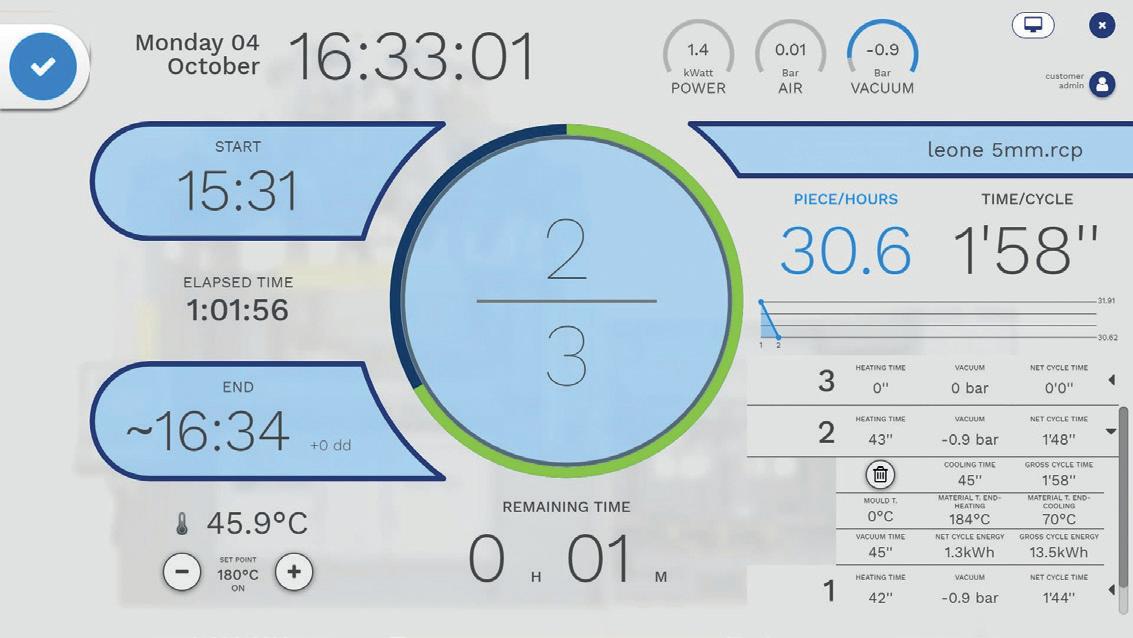
QUALI RISCONTRI AVETE AVUTO DA FAKUMA 2021, DOVE, PER LA PRIMA VOLTA DALL’INIZIO DELLA PANDEMIA, ESPONEVATE UNA MACCHINA? SI PUÒ PARLARE DAVVERO DI RIPARTENZA, NONOSTANTE LE TANTE DIFFICOLTÀ ECONOMICHE E SANITARIE A CUI SI DEVE ANCORA FAR FRONTE?
“Fakuma per noi, come sempre, si è riconfermato un appuntamento di riferimento. Nonostante le numerosissime visite al nostro stand, l’organizzazione è stata impeccabile e la cosiddetta emergenza sanitaria non è stata di intralcio allo svolgimento delle nostre attività. Abbiamo deciso di optare per uno stand al quale poteva accedere solo un numero limitato di visitatori contemporaneamente, in modo da essere in grado di gestire al meglio ogni situazione potenzialmente pericolosa. Molti clienti hanno prenotato la propria visita riservandosi uno slot libero. In questo modo siamo stati in grado di mostrare la nuova Eidos mentre produceva un articolo accattivante, dando anche la possibilità agli interessati di esplorare i dettagli più tecnici.
Fabio Gaiazzi, product manager per la termoformatura di CMS Oltre alla macchina, abbiamo allestito anche un corner per le soluzioni software e un’area per una fantastica esperienza virtuale dei nostri prodotti, tramite l’impiego di un visore a 360° che permetteva una vera e propria navigazione all’interno delle macchine. Dal nostro punto di vista si è trattato di una vera e propria ripresa in grande stile, che ci ha permesso di chiudere il 2021 come l’anno record in assoluto per la Business Unit Plastica”.
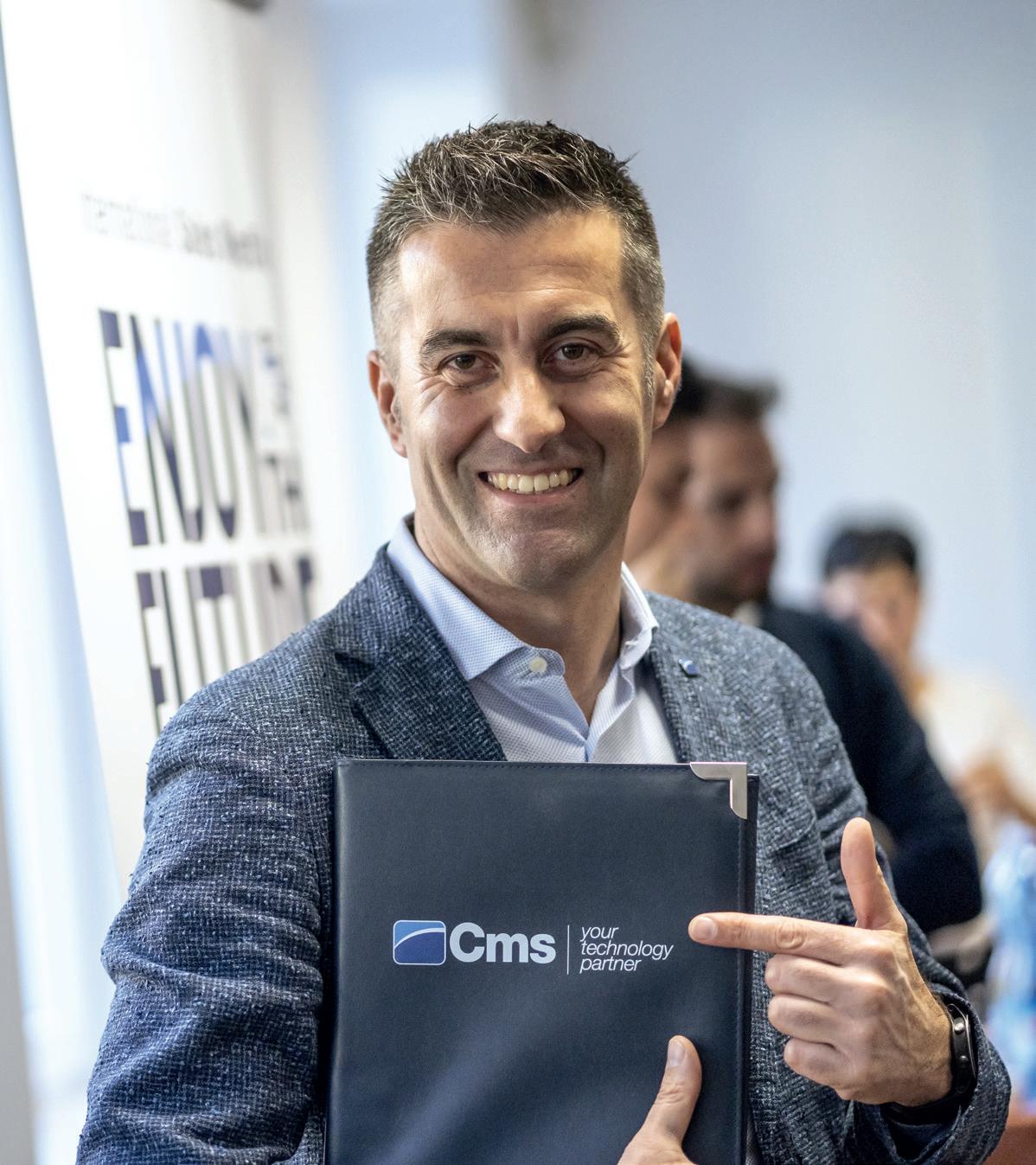
COSA PUÒ DIRCI SULL’ANDAMENTO E SULLA POSSIBILE EVOLUZIONE DEL MERCATO DELLA TERMOFORMATURA SUL FRONTE SIA DELLE TECNOLOGIE SIA DELLA TRASFORMAZIONE?
“In linea generale, ritengo che il mercato della termoformatura sia tutt’altro che saturo. I nostri clienti sono assolutamente sensibili ai temi relativi all’innovazione e all’ambiente. In questo senso, il mercato sta deviando verso quei produttori di macchinari green in grado però di offrire sempre un livello prestazionale massimo. Questo messaggio è stato recepito da CMS ormai da parecchio tempo. Per questo, a ogni occasione ci presentiamo con nuovi sviluppi e nuove tecnologie non ancora esplorati. Abbiamo un vasto elenco di soluzioni coperte da brevetti internazionali e altrettante domande di brevetto in fase di deposito. Il livello tecnologico di questo settore si è quindi innalzato parecchio negli ultimi dieci anni, ma credo che questo trend sia tutt’altro che esaurito. Anche il mondo dei materiali termoplastici è in continua evoluzione, sempre teso allo sviluppo di nuove soluzioni sostenibili e riciclabili. Lo sviluppo delle macchine in grado di trasformare tali materiali non può essere da meno. Per questo, nel nostro Technology Center sono in funzione le macchine che regolarmente utilizziamo per testare soluzioni e materiali nuovi. Questo per poter essere sempre il partner ideale anche in previsione delle evoluzioni future del mercato e delle applicazioni da parte dei trasformatori”.
QUALI SONO I PROGRAMMI DI CMS A BREVE-MEDIO TERMINE PER QUANTO RIGUARDA L’ATTIVITÀ AZIENDALE E LO SVILUPPO TECNOLOGICO, IN PARTICOLARE NEL SETTORE DELLA TERMOFORMATURA DI SUA COMPETENZA?
“Azienda storicamente focalizzata sul mercato dei materiali compositi e dell’alluminio, CMS crede sempre più nei materiali termoplastici. Per questo motivo, oggi, la nostra Business Unit Plastica è una delle più attive in azienda. Da lungo tempo abbiamo a catalogo macchine CNC per la lavorazione degli stampi e per la rifinitura (trimming) della plastica. Più recentemente abbiamo introdotto una gamma completa di macchinari per l’articolo tecnico (CNC con assi Z bassi e macchine per la lavorazione dei pannelli). Oltre, ovviamente, alla gamma completa di termoformatrici, che spazia dalla nuova Eidos fino a quelle specifiche per il “TwinSheet”, gli articoli sanitari, gli interni auto ecc. Ricordo che la nostra esperienza risale agli Anni Settanta grazie all’acquisizione dello storico marchio Villa, che ha determinato lo sviluppo e la diffusione di questa tecnologia in Italia”.
COME SI STA MUOVENDO CMS A PROPOSITO DI TRANSIZIONE ECOLOGICA ED ECONOMIA CIRCOLARE? QUALI SONO LE AZIONI CONCRETE CHE STATE METTENDO IN ATTO IN QUESTI AMBITI?
“CMS è da sempre molto attenta alle tematiche “green”. Negli ultimi due anni abbiamo investito in un nuovo sito produttivo chiamato “Plant Z”, che è andato ad aggiungersi allo storico “Plant A”. Nella costruzione, o meglio, ristrutturazione di un’antica e ormai fatiscente manifattura, sono stati integrati sistemi moderni per il contenimento dello spreco energetico grazie all’impiego di illuminazioni LED e ambienti produttivi coibentati. Sul tetto di questo imponente nuovo sito produttivo è stato installato un potente impianto fotovoltaico in grado di fornire buona parte dell’energia necessaria per la produzione delle macchine. Sono state poi attuate politiche legate alla riduzione degli spostamenti non necessari, grazie all’introduzione dello smart working e delle videoconferenze, impiegate non solo a uso interno per le riunioni fra colleghi, ma anche per dimostrazioni e presentazioni dei prodotti ai clienti. Anche il parco auto aziendale si è rinnovato, ricorrendo principalmente all’impiego di auto a trazione ibrida. Ritengo che il contributo maggiore che siamo in grado di dare all’ambiente sia quello di fornire alle aziende che si affidano ai nostri prodotti macchinari moderni in grado di operare con la massima efficienza in termini sia di consumo energetico che di produttività. Riducendo al minimo gli sprechi e azzerando gli scarti dovuti a difetti. In questo modo possiamo garantire una produzione sostenibile grazie all’elevata qualità che ci contraddistingue”.
COLLABORAZIONE TRA COMI E WENGLOR
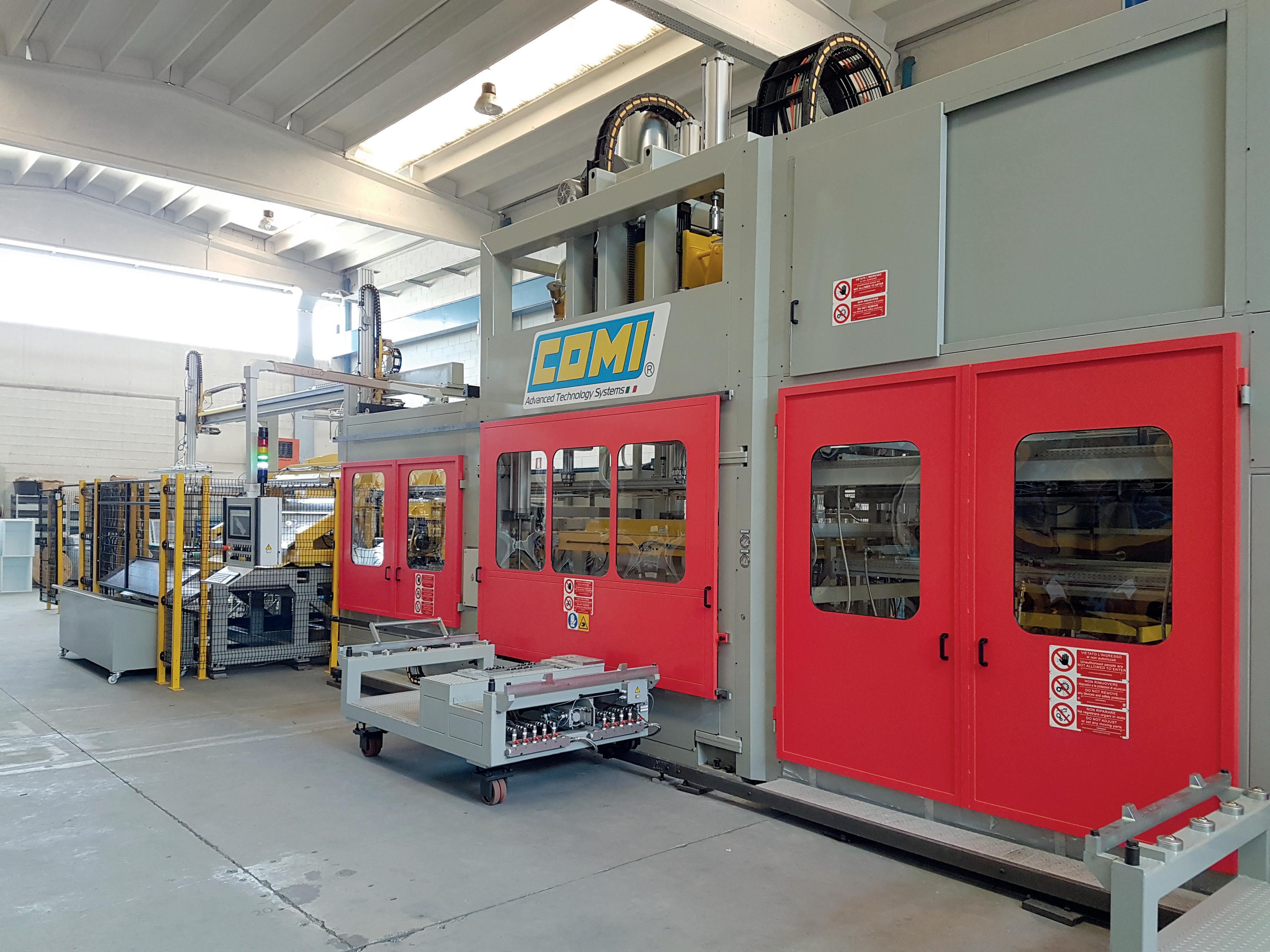
IL SENSORE GIUSTO PER OGNI ESIGENZA DI TERMOFORMATURA
PER LE SUE TERMOFORMATRICI, COMI HA SCELTO I SENSORI WENGLOR, TUTTI DOTATI DI PROTOCOLLO DI COMUNICAZIONE IO-LINK E CAPACI DI GARANTIRE AFFIDABILITÀ ANCHE NEI PUNTI DI INSTALLAZIONE PIÙ CRITICI. A QUESTO SI AGGIUNGE UNA VASTA SCELTA DI SENSORI, CHE PERMETTE DI TROVARE SEMPRE LA SOLUZIONE PIÙ ADEGUATA ALLE SPECIFICHE NECESSITÀ
Le migliaia di macchine che in quasi cinquant’anni sono state costruite e messe in funzione da Comi, in svariati settori industriali, ne fanno una delle eccellenze della meccanica strumentale italiana. Questo con particolare riferimento al settore della termoformatura, tecnologia per la quale l’azienda è un vero e proprio punto di riferimento internazionale grazie agli oltre 1300 impianti installati nel mondo, dagli Stati Uniti al Brasile, dall’India al Giappone, dalla Cina al Medio Oriente fino, ovviamente, all’Europa. La missione di Comi è quella di assicurare ai trasformatori le soluzioni produttive non solo più adeguate alle loro esigenze, ma anche capaci di garantire il più elevato rendimento in ogni condizione di lavoro. “Le nostre macchine sono tutto fuorché standard: in base alle necessità del cliente, disegniamo sempre una soluzione su misura. La gran parte degli impianti di termoformatura che produciamo è dedicata al settore degli elettrodomestici bianchi e, in particolare, alla produzione delle celle e delle controporte dei frigoriferi”, spiega Marco Cattaneo, responsabile della produzione presso il sito produttivo di Comi a Ciserano (Bergamo). Spesso gli impianti si configurano quali vere e proprie linee di produzione complete, poiché alla macchina per la termoformatura sono abbinati moduli aggiuntivi, soprattutto a valle, per il completamento automatizzato delle operazioni di taglio e finitura: manipolatori, ghigliottine, presse punzonatrici per la foratura delle celle e delle controporte, sistemi di scarico ecc. Un ruolo molto importante nella gestio-

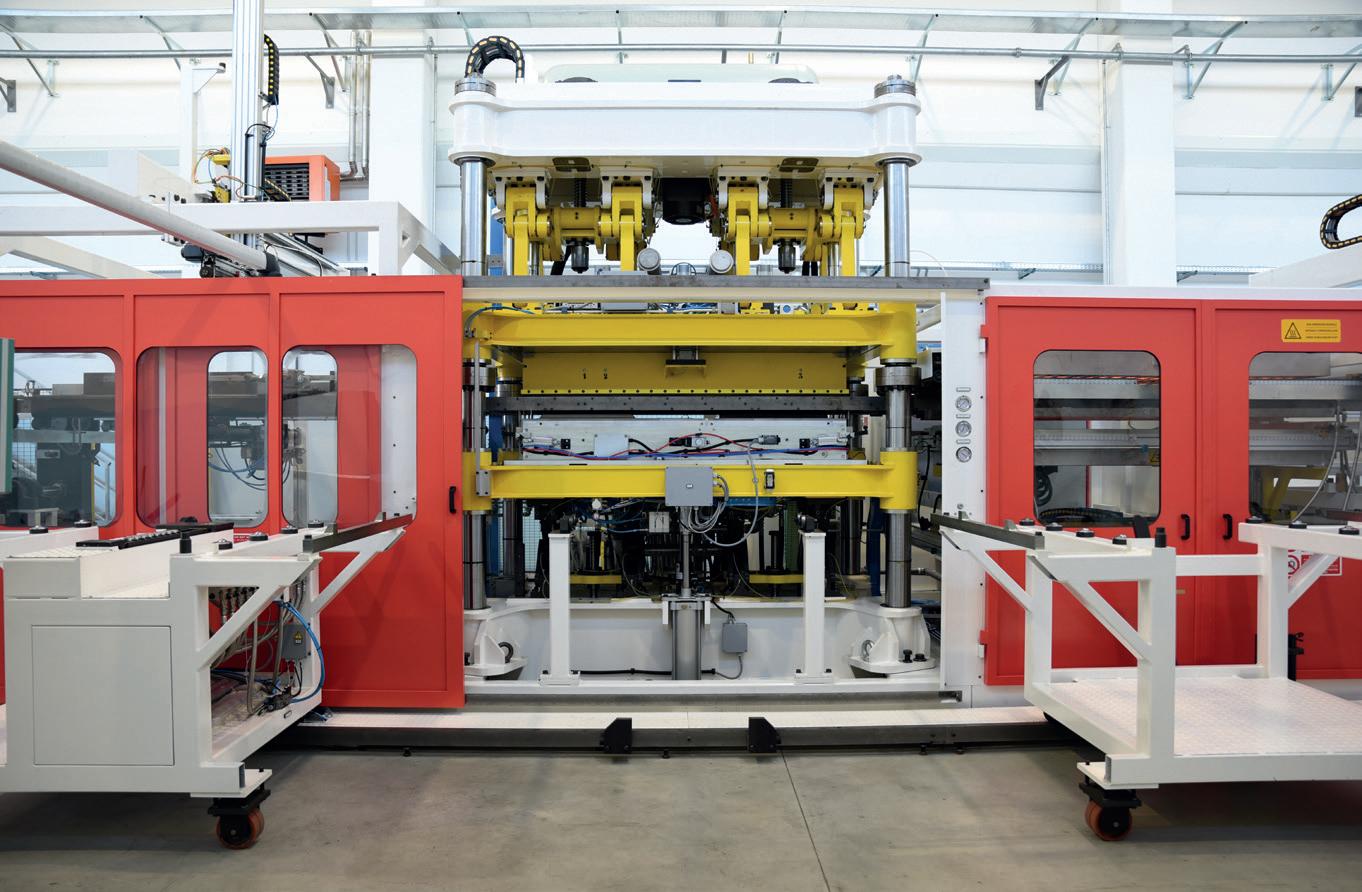
ne delle linee prodotte da Comi, che nelle versioni più evolute possono raggiungere uno sviluppo anche di parecchie decine di metri di lunghezza, viene svolto dai sensori. Se ne trovano installati di numerosi tipi, per svolgere i compiti più disparati: oltre ai più classici dispositivi optoelettronici a fotocellula, sulle linee sono montati sensori di prossimità, di sicurezza e ottici per il rilevamento dei profili, così come flussostati e pressostati. Comi ha scelto di collaborare con Wenglor Sensoric non solo per l’ampiezza della sua gamma di prodotti e per l’affidabilità che i suoi dispositivi offrono, ma anche per il livello di supporto su cui può sempre contare, inclusi i tempi di consegna, sempre rapidi e puntuali.
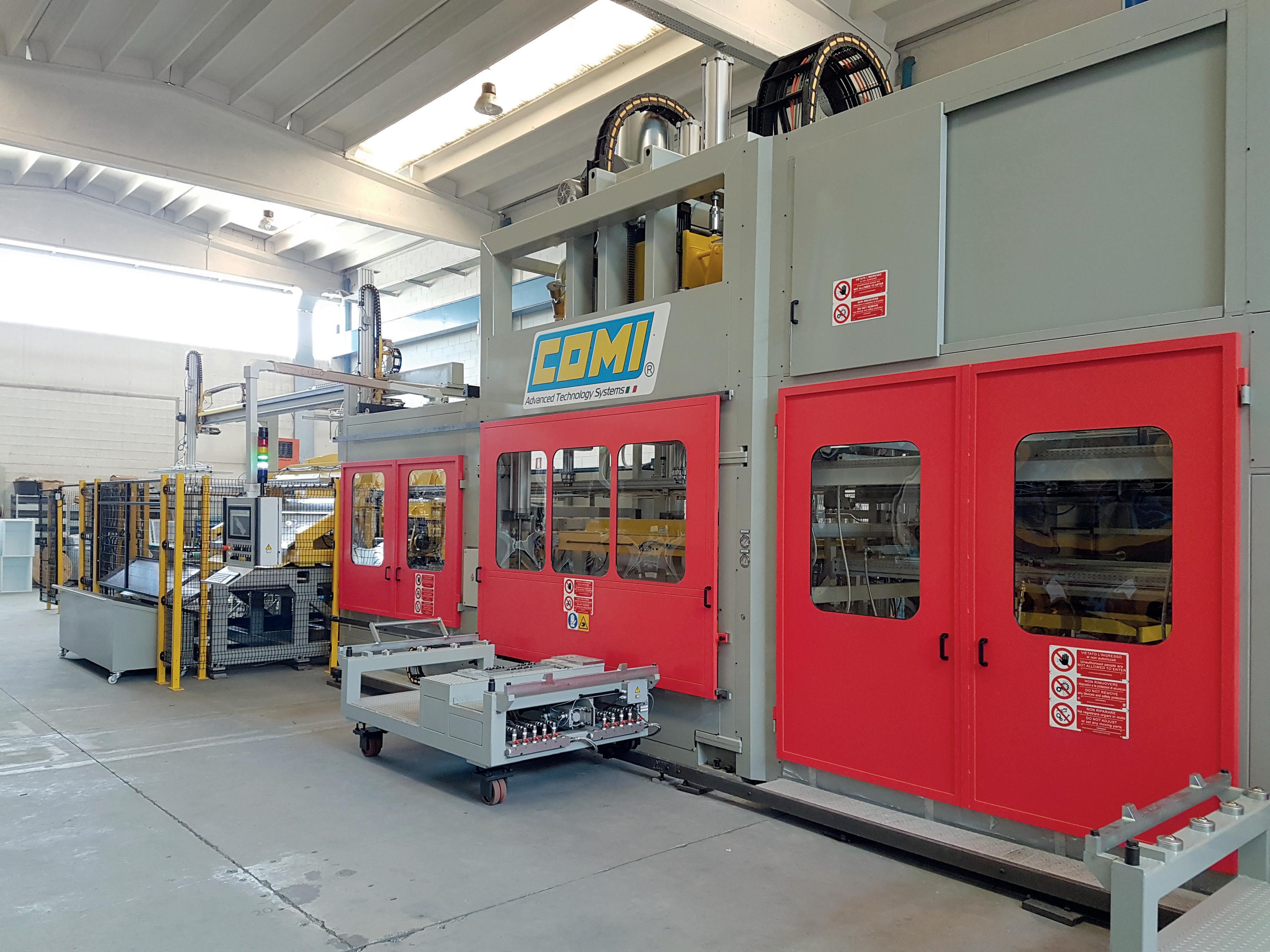
AFFIDABILITÀ, ANCHE NEI PUNTI PIÙ CRITICI
“Collaboriamo con Wenglor da alcuni anni e siamo molto soddisfatti. La gamma delle sue soluzioni è molto ampia e ci ha permesso di trovare sempre la soluzione più adeguata alle nostre necessità, nonché di disporre di sensori affidabili anche nei punti di installazione più critici dei nostri impianti, come per esempio quelli che si trovano in prossimità delle zone di riscaldo”, sottolinea Marco Cattaneo. All’interno di un impianto per la termoformatura la zona di riscaldo è quella che presenta la maggiore criticità in termini di sicurezza, in quanto il contatto accidentale di una lastra con gli elementi riscaldanti (ceramica IR, quarzo o flash back) potrebbe provocare un incendio, con seri rischi non solo per l’integrità del macchinario, ma anche per gli operatori di linea. A tale scopo Comi utilizza, sia nel modulo di preriscaldo che nella stazione di riscaldo, sensori optoelettronici in configurazione emettitore-trasmettitore. La loro funzione è quella di intercettare l’eventuale “spanciamento” fuori norma delle lastre, ovvero di controllare che la deflessione della lastra riscaldata sia tale da non entrare pericolosamente in contatto con gli elementi riscaldanti, nel qual caso comunicando al controllo della linea di effettuare una fermata di emergenza. Lo stesso tipo di fotocellule, in particolare l’emettitore SW983 e il ricevitore EW 98PC3, si trova montato anche nella zona di taglio, a valle del modulo di formatura, con il compito di controllare che la lama di rifilatura delle bave non si azioni nel caso in cui il carro si venga a trovare in traiettoria di collisione.
I sensori weFlux2 sono utilizzati da Comi per controllare pressione e portata dell’acqua nelle condutture del sistema di raffreddamento della zona di riscaldo e dell’acqua di riscaldamento dello stampo In una termoformatrice, la zona di riscaldo presenta le criticità maggiori in termini di sicurezza; qui si trovano installati i sensori Wenglor in configurazione emettitore-ricevitore

DAL CARICO DELLE LASTRE AL CONTROLLO DIMENSIONALE, IL DISPOSITIVO PIÙ ADATTO
Anche la zona di carico delle lastre, situata a monte dell’impianto di formatura, è opportunamente sensorizzata, per consentire alla linea di operare in costante continuità di esercizio. Vi si trovano montati alcuni sensori optoelettronici con catarifrangente del tipo LM89PA2, il cui compito è quello di controllare il sopraggiunto fine pacco delle lastre che, una volta prelevate, devono essere inviate al riscaldo. Le termoformatrici di Comi sono dotate di un doppio sistema di caricamento, che lavora in maniera alternata: ciò consente di garantire la massima produttività. Nel momento in cui il sensore determina il fine pacco lastre all’interno del caricatore, il sistema commuta automaticamente, avviando il prelievo delle lastre dalla seconda “baia” di carico. Nel frattempo, l’operatore viene allertato per effettuare la ricarica del carrello vuoto: la macchina continua così a operare senza interruzioni. Su richiesta del trasformatore, le linee di termoformatura possono essere equipaggiate con stazioni adibite al controllo dimensionale dei manufatti prodotti. Il rilievo delle quote viene effettuato in due punti ben precisi: il cielo e la canalina perimetrale. Per il cielo si utilizza una coppia di sensori di distanza, che provvedono a misurare quota e spessore del manufatto, al fine di assicurare che la profondità e la consistenza delle celle siano corrette. Le caratteristiche geometriche della canalina perimetrale vengono invece rilevate da una coppia di sensori ottici di profilo MLWL132, al fine di garantire che le tolleranze siano conformi al corretto assemblaggio del termoformato all’interno del frigorifero.
VALORE AGGIUNTO ANCHE IN TERMINI DI SERVIZIO
Come detto, la gran parte delle linee per la termoformatura di Comi si trova installata un po’ ovunque nel mondo, progettata
e realizzata per tutti i più grandi nomi internazionali che operano nel settore degli elettrodomestici bianchi: Haier, Hisense, Arcelik, Electrolux, Bosch, Whirlpool ecc. Per aziende di questo calibro, l’affidabilità dei sistemi produttivi è un fattore determinante: un fermo impianto può provocare perdite rilevanti per chi lo utilizza, nonché un impatto non indifferente nel caso in cui si rendesse necessario un intervento da parte dell’assistenza tecnica. “Negli anni Comi ha consolidato le sue competenze facendo della continua innovazione un caposaldo. In questo senso, la collaborazione con fornitori che, come Wenglor, sanno proporre soluzioni non solo performanti e affidabili, ma anche all’avanguardia, è un plus notevole, che aggiunge valore ai nostri progetti”, afferma Marco Cattaneo. Vi sono inoltre altri fattori da tenere in considerazione, che per Comi sono estremamente importanti: tra questi vi sono le tempistiche di fornitura e il livello di assistenza tecnica. “Con Wenglor abbiamo instaurato un ottimo rapporto di collaborazione, che si esplica in un servizio di assistenza molto competente, capace di supportarci sempre nella scelta della migliore soluzione. Inoltre, Wenglor ci garantisce tempistiche di fornitura molto rapide: un aspetto che per noi è determinante, poiché ci consente di fronteggiare efficacemente gli eventuali imprevisti che, nel caso dei progetti di una certa rilevanza, sono sempre in agguato, per esempio in termini di varianti o nuove richieste da parte del cliente”, conclude il responsabile produzione di Comi.
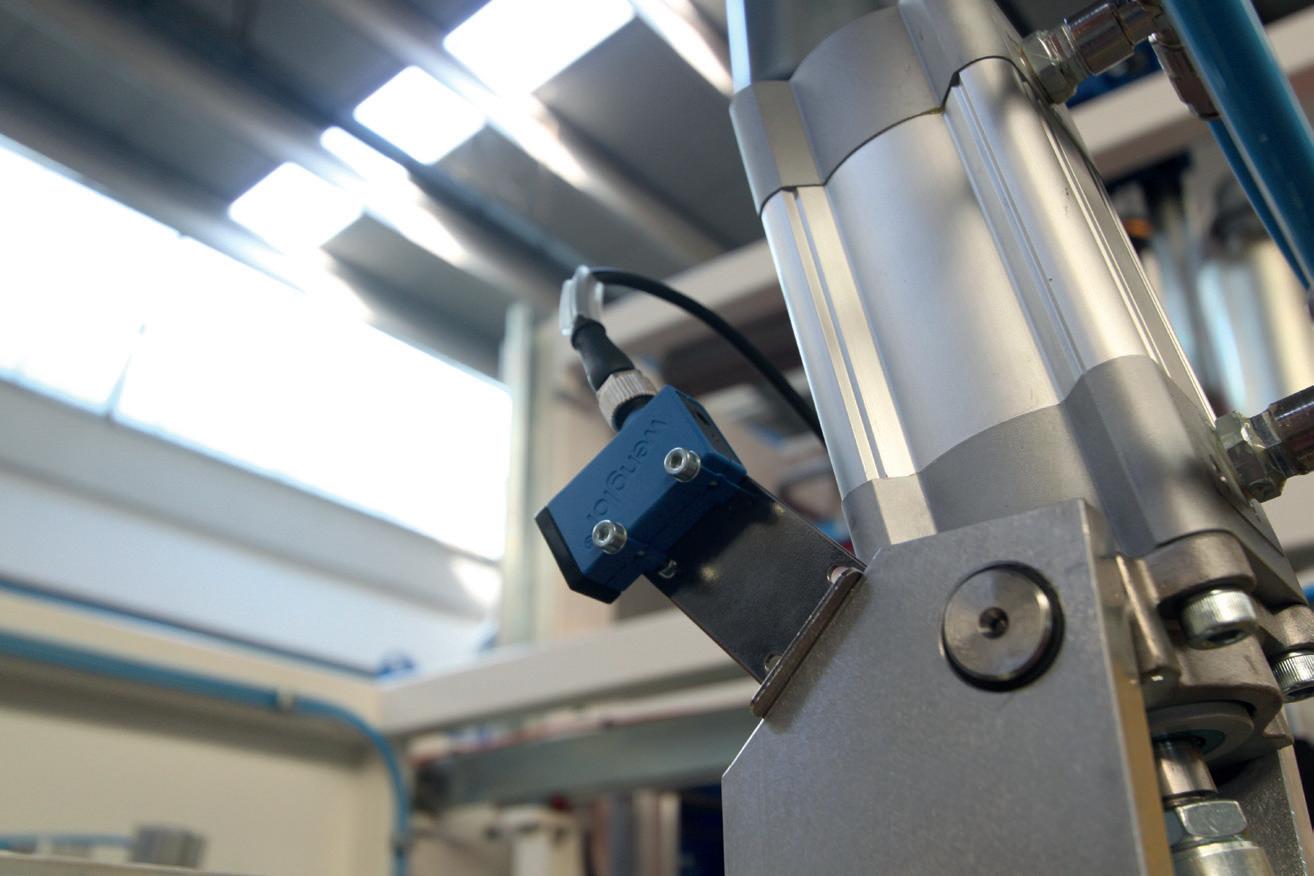
“La gamma delle soluzioni Wenglor è molto ampia e ci ha permesso di trovare le soluzioni più adeguate alle nostre necessità anche per i punti di installazione più critici dei nostri impianti”, affermano in Comi I SENSORI PIÙ UTILIZZATI DA COMI A BORDO DELLE SUE TERMOFORMATRICI

Sono diversi i sensori che Comi impiega a bordo delle sue macchine per la termoformatura: optoelettronici, ottici, di flusso, di pressione e di temperatura. La caratteristica che li accomuna è la dotazione di protocollo IO-Link, che consente - qualora il trasformatore ne faccia richiesta - di offrire specifiche funzionalità di comunicazione per effettuare controlli di stato avanzati, anche in ottica di manutenzione predittiva.
Sensori combinati di pressione, flusso e temperatura Controllano pressione e portata dell’acqua nelle condutture del sistema di raffreddamento che percorre le stazioni di riscaldo, per mitigare le temperature generate dagli elementi agli infrarossi. Sono utilizzati anche per controllare pressione e portata dell’acqua di riscaldamento dello stampo di formatura. I sensori FX5P202 e FXFFF003 restituiscono a video i valori in tempo reale; il sensore FFAF001 agisce da sentinella, innescando un allarme al superamento della soglia preimpostata. Il sensore FFAF001 (in alternativa, l’FXFF102) rileva flusso e temperatura.
Fotocellule con catarifrangente I dispositivi LM89PA2 sono utilizzati per controllare il fine pacco lastre nella zona di carico. Quando il sensore segnala l’esaurimento delle lastre, il sistema avvia il prelievo dal secondo caricatore, avvisando l’operatore della necessità di ricaricare le lastre sul carrello vuoto.
Barriere fotoelettriche Forniscono protezione all’operatore durante il caricamento manuale delle lastre, evitando l’accidentale intromissione delle mani in zone pericolose. Le SEFG413 sono utilizzate anche nella zona di scarico, con un campo di lettura maggiore e set di muting Z2MG002.
Sensori di profilo Utilizzati per misurare la forma, l’angolo e l’altezza della canalina perimetrale di un manufatto, i sensori di profilo MLWL132 possono essere impiegati in combinata con i sensori di distanza PNBC003, per misurare lo spessore di un termoformato.
Fotocellula emettitore-fotocellula ricevitore Il set di sensori M18 in acciaio viene utilizzato nella zona di riscaldo per controllare la deflessione della lastra (al fine di prevenire eventuali incendi innescati dal contatto con gli elementi riscaldanti) e nella zona di taglio per inibire l’operazione nel caso in cui il carro sia in traiettoria di collisione con la lama.
Le barriere fotoelettriche proteggono l’operatore durante il caricamento manuale delle lastre, evitando l’accidentale intromissione delle mani in zone pericolose
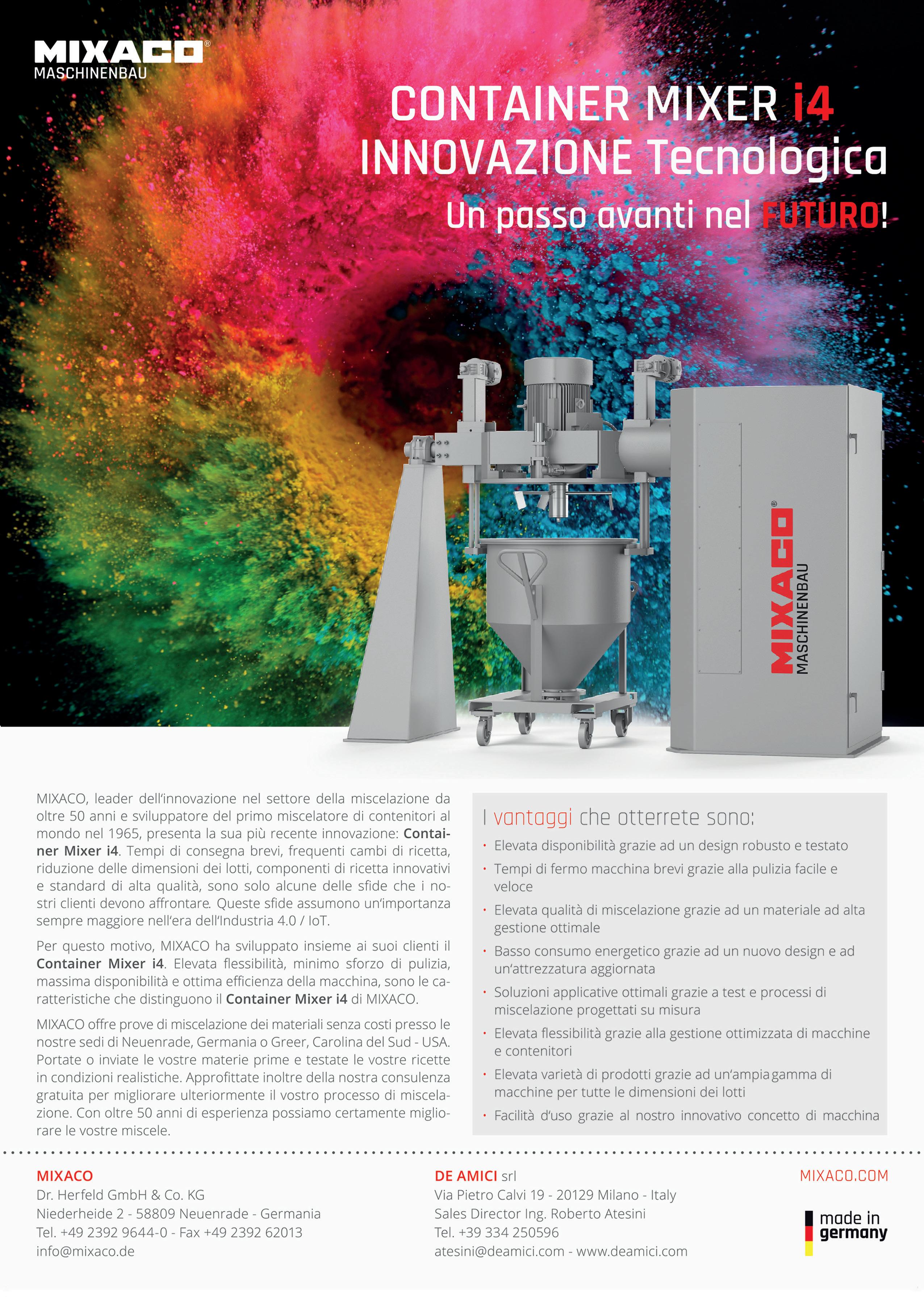
NEWS
Anniversario per WM Thermoforming Machine Tra passato e futuro della termoformatura
Il 2021 è stato un anno importante per WM Thermoforming Machines, nel quale l’azienda ha raggiunto l’importante traguardo dei quarant’anni di attività, celebrati con diverse iniziative, come la serie di eventi “Synergizing Technologies”. Si tratta di una serie di appuntamenti tenuti dall’azienda in diretta streaming, ognuno della durata di circa un’ora e mezza e caratterizzati dalla presenza di ospiti quali stampisti, produttori di linee di estrusione, termoformatori e così via. Tali eventi hanno offerto l’occasione di ascoltare direttamente dalla voce degli addetti ai lavori dell’industria delle materie plastiche gli sviluppi presenti e futuri e le tendenze del mercato e di porre domande agli esperti della termoformatura specializzati, in particolare, nelle applicazioni dell’imballaggio alimentare. “Da quando abbiamo iniziato i “Synergizing Technologies”, abbiamo visto un grande aumento di attenzione, grazie agli interessanti contributi da parte di aziende partner, come Bandera, KGL, Kiefer, Marbach, e clienti, nonché ai molti argomenti specifici intorno alla macchina di termoformatura stessa proposti da WM appositamente per questi eventi. I partecipanti da tutto il mondo sono intervenuti attivamente agli appuntamenti, con domande interessanti o approfondimenti”, ha sottolineato Jörg Huth, sales area manager. Il 40° anniversario è stato anche l’occasione per riconoscere l’importanza delle persone che lavorano in WM, che sono state ritratte in 12 immagini e raccolte nel “Calendario WM 2022”. In questo modo WM ha voluto mo-
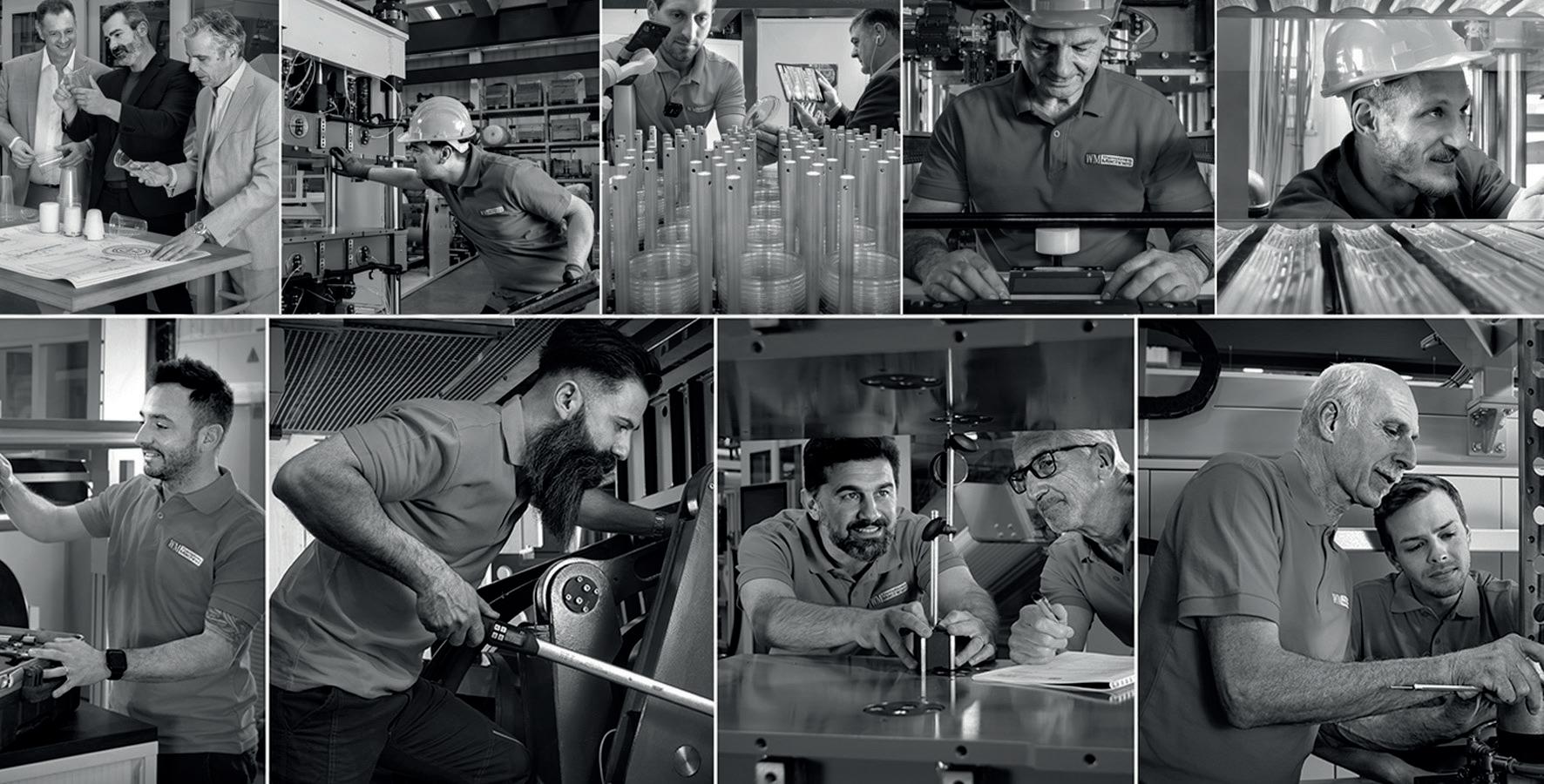
Una serie di immagini del personale di WM Thermoforming Machines che appare nel suo colendario 2022
strare i volti, anche quelli meno noti, delle persone che lavorano dietro alle quinte per garantire sempre il massimo della qualità. Il 2022 di WM Thermoforming Machines è iniziato subito con la partecipazione a due fiere internazionali: Plastex, al Cairo dal 9 al 12 gennaio, e Interplastica, a Mosca dal 25 al 28 gennaio. Queste due fiere sono molto importanti per i mercati in Medio Oriente, Nord Africa e Russia e l’azienda vi ha partecipato attraverso gli agenti locali, rispettivamente Acis e Plastmash, con la presenza degli area manager Ottavio Tonon e Jörg Huth.
Attività recente di GAP Linee per l’estrusione in bolla e centro ricerche
Un dettaglio di una delle nuove linee per l’estrusione di film in bolla Presso il suo stabilimento a Mezzomerico (Novara), GAP ha recentemente collaudato quattro linee per l’estrusione di film in bolla a tre strati con struttura A-B-A. Gli impianti sono composti da due estrusori, due teste da 100 mm, dispositivo IBC e anello ad aria esterno con labbro flessibile regolabile manualmente. Completano la configurazione delle linee: traino oscillante, macchina per la stampa flessografica in linea, dispositivo taglia e salda, saldatrici in linea per cuscini d’aria e avvolgitore con cambio automatico dei cartoni. Le linee sono concepite per la produzione di nove milioni di cuscini d’aria al giorno, saldati e stampati in linea, senza ulteriori passaggi e partendo sia da LLDPE sia da materiali biodegradabili. Nei mesi scorsi, l’azienda novarese ha anche inaugurato il suo nuovo centro di ricerca e sviluppo con un evento di alcuni giorni svoltosi in parte in presenza e in parte in forma virtuale. In tale occasione si sono tenuti anche tre interventi per illustrare un’altra nuova linea sviluppata per produrre film in bolla fino a ben 27 strati. Tale linea si basa sulla tecnologia per microstrati che, adattata alla testa circolare, permette di sovrapporre materiali diversi per incrementare le prestazioni del film mantenendone ridotto lo spessore. L’impianto include nove estrusori, testa con diametro di 400 mm e vari blocchi di alimentazione, anello di regolazione automatica dello spessore, tavola oscillante, trattamento corona e doppio avvolgitore da 1600 mm.

Termosaldatrici Mobert Versatilità: una risposta universale
Per rispondere alle richieste di quei trasformatori che non si accontentano di soluzioni standard, da sempre Mobert fa della versatilità un punto di forza delle sue termosaldatrici. Tra i vari modelli concepiti con tale criterio dalla società di Castellanza (Varese), la linea Roller SHP 6M, realizzata nelle versioni 110 e 130 (con larghezza utile di saldatura di 1100 e 1300 mm) per la produzione di sacchi in rotolo, garantisce con i suoi tre brevetti: rapidi cambi di produzione, riduzione degli scarti e costante controllo della qualità della produzione. L’esclusivo sistema di fustellatura a taglio passante dei sacchetti non necessita di alcuna registrazione della lama, garantendo un taglio estremamente accurato anche nella lavorazione di film biodegradabili e una durata della lama di gran lunga superiore alla media. Il sistema di visione per controllare e correggere automaticamente la fustellatura dei manici dei sacchetti elabora le immagini inviate da una telecamera ad alta risoluzione posta sulla stazione di fustellatura stessa attraverso un algoritmo proprietario, verificando la corretta larghezza dei manici fustellati e la corretta asportazione dello sfrido, correggendo la posizione di ogni singola pista di lavorazione quando necessario. L’esclusivo sistema di arrotolamento con pinze, denominato “a linguetta mobile”, consente, anche lavorando su tre o quattro piste, di passare rapidamente dalla produzione di rotoli con anima di cartone a quella di rotoli senza anima. La linea, dunque, è in grado di produrre: su due piste sacchetti con e senza anima di cartone per i reparti ortofrutticoli, su tre piste sacchetti per la raccolta domestica dei rifiuti, su quattro piste sacchetti a bocca con e senza anima di cartone e su tre piste sacchetti con fondo anti-goccia. Completano le caratteristiche della linea: robustezza e affidabilità, ottenute con componenti elettronici, elettrici e pneumatici tra i più affidabili sul mercato. La Roller SHP 6M è controllata da un PC industriale di ultima generazione, che consente di monitorare da remoto il processo ed evidenziare eventuali problemi che possano insorgere durante la lavorazione.
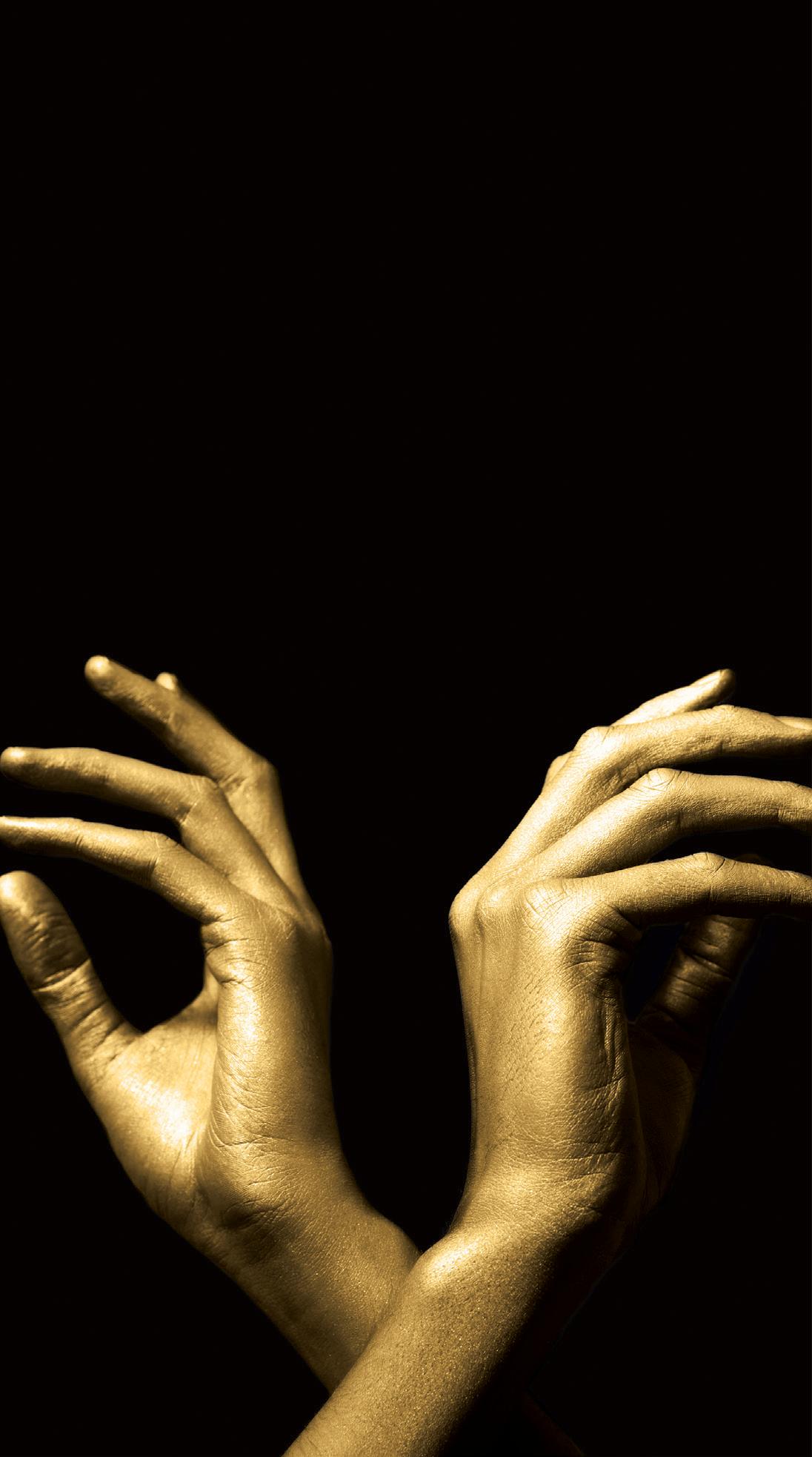
La versione 110 della termosaldatrice Roller SHP 6M

INNOVATION IN EXCELLENCE
END OF ARM TOOLING, CUSTOM AUTOMATION

NEWS Saldatrice per guanti in PE Quando un’opportunità diventa valore
Focalizzarsi sulle opportunità e non sui problemi. È questa la “filosofia” alla base di un recente sviluppo di Saldoflex. Durante il primo lungo lockdown, infatti, era diventato difficoltoso approvvigionarsi di guanti monouso in PE, normalmente utilizzati nei reparti ortofrutticoli dei supermercati. In quel periodo, la domanda di questo prodotto è arrivata a essere fino a dieci volte superiore all’offerta, dopo che, storicamente, da almeno un decennio veniva sodUn dettaglio della saldatrice disfatta con l’importazione da pa- a quattro piste per la produzione esi dell’Estremo Oriente. di guanti in PE Il risultato finale ottenuto da Saldoflex è frutto dell’opportunità colta e perseguita: una saldatrice elettronica automatica in grado di affiancare alla classica produzione ad alta velocità di sacchetti quella di guanti monouso in PE, goffrati e non. Le linee guida del nuovo progetto hanno portato l’azienda a costruire una macchina ad alte prestazioni in grado di realizzare differenti quantità di prodotto finito, tenendo presenti le peculiarità che da sempre caratterizzano le sue linee: affidabilità, flessibilità e velocità. Per la produzione di guanti in PE, la saldatrice è stata configurata con un doppio svolgitore sovrapposto (in grado di processare bobine con diametro massimo di 1100 mm), un’unità di goffratura in linea e un modulo di fustellatura ad alta velocità (fino a 200 cicli al minuto). A regime di lavoro, con la linea di produzione distribuita su 4 piste, l’impianto garantisce una capacità produttiva di 48 mila guanti all’ora.
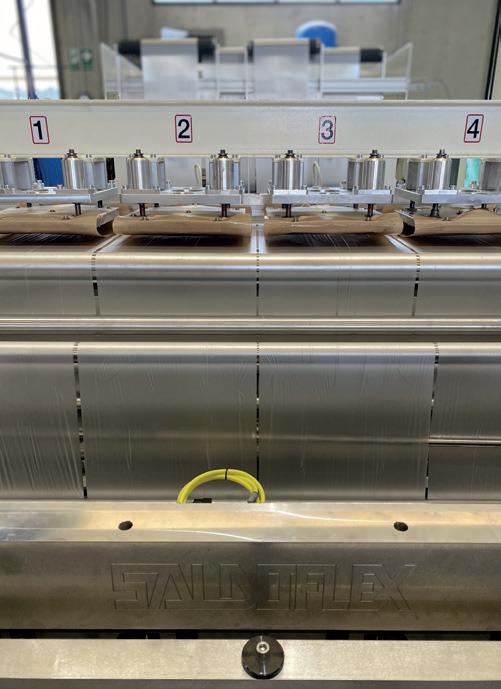
Plastisavio fa il bis con Union Con il riciclato come con il vergine
Il produttore di laminati plastici Plastisavio ha recentemente commissionato a Union una seconda linea con capacità di 1500 kg all’ora per la produzione di foglie per termoformatura partendo dal 100% di materiale post consumo. Il trasformatore utilizza già da alcuni anni un’altra linea simile, fornita sempre dal costruttore di San Vittore Olona (Milano), e la commessa per questo nuovo impianto destinato al suo stabilimento di Mercato Saraceno (Forlì Cesena) rientra in un piano di investimenti programmato per il 2022. Il processo di pulizia del materiale avviene mediante filtrazione meccanica e degassaggio, a garanzia dell’elevata qualità del prodotto, che risulta pari a quella dei prodotti ottenuti con materie prime vergini. L’estruso ha
Una parte della linea Amut installata presso lo stabilimento produttivo di Bitumat a Dammam (Arabia Saudita)
Amut e Bitumat C’è anche l’Italia nel nuovo Biecc in Bahrain
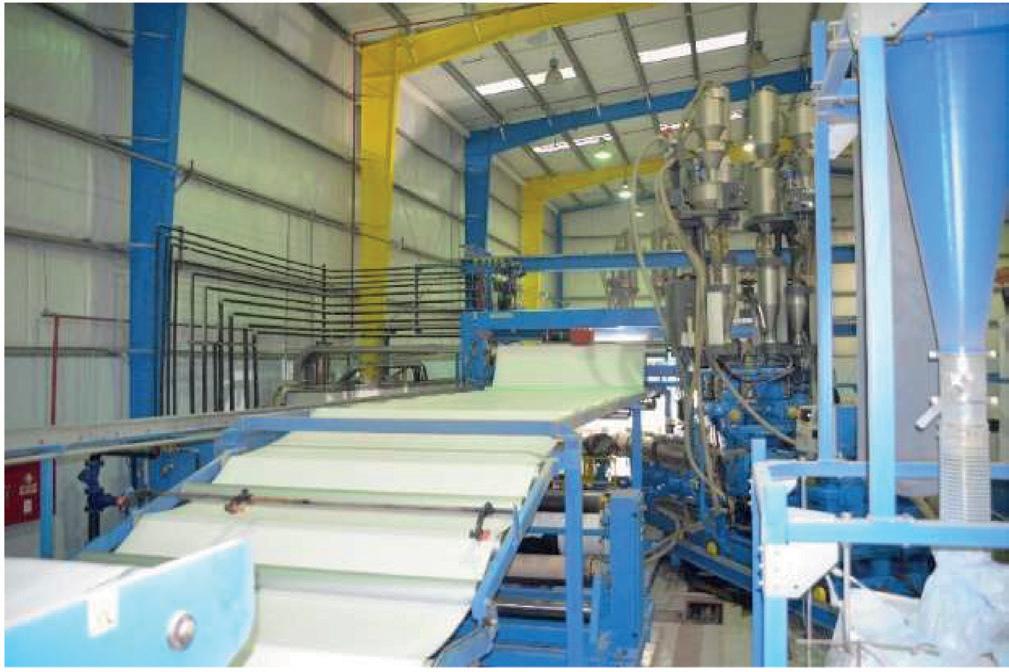
L’azienda saudita Bitumat ha contribuito all’impermeabilizzazione del nuovo Bahrain International Exhibition and Convention Centre (BIECC), i cui lavori prevedevano due interventi d’impermeabilizzazione: quella del seminterrato, completata nel 2020, e quella del tetto, iniziata a giugno 2021. Nel primo caso sono state utilizzate membrane Bitumat Premierflex 2000 e Bituprotect, entrambe da 4 mm di spessore, su superfici rispettivamente di 230 mila e 30 mila metri quadri; nel secondo caso è stata impiegata la membrana in PVC Bitumat Polymet Roof UV-R 2.0 FB su una superficie di 150 mila metri quadri. Bitumat produce una vasta gamma di membrane tecniche che si adattano a diverse applicazioni e garantiscono protezione nel lungo termine. Dal 2010 utilizza linee di estrusione di Amut, che ha fornito diverse macchine all’azienda, l’ultima delle quali è una linea completa per l’estrusione di membrana impermeabilizzante a tre strati in PVC e TPO, installata nel com-
spessori particolarmente sottili ed elevata stabilità, in modo tale da combinare proprietà fisiche ed estetiche per assecondare le esigenze di mercato attuali e future. Tra le sue possibili applicazioni rientrano componenti auto, imballaggi ortofrutticoli e florovivaistici e pannelli per edilizia. Il riutilizzo di plastiche post consumo permette di realizzare un prodotto economicamente vantaggioso ed efficiente, così come di ridurre le emissioni di CO2 derivanti dall’intera catena produttiva, consentendo alla linea di contribuire alla realizzazione di un’economia circolare. plesso produttivo di Dammam. Le linee del costruttore novarese per l’estrusione di membrane impermeabilizzanti sono in grado di lavorare diversi materiali termoplastici (PVC, TPO, TPE) conferendo al prodotto le caratteristiche fisiche e tecniche necessarie ad assecondare gli standard internazionali del settore civile. La flessibilità della tecnologia sviluppata da Amut per queste applicazioni consente, oltre che lavorare più materiali con la stessa linea, anche di realizzare in un’unica fase produttiva membrane impermeabilizzanti multistrato, con o senza rinforzo, e laminate con una base di supporto.
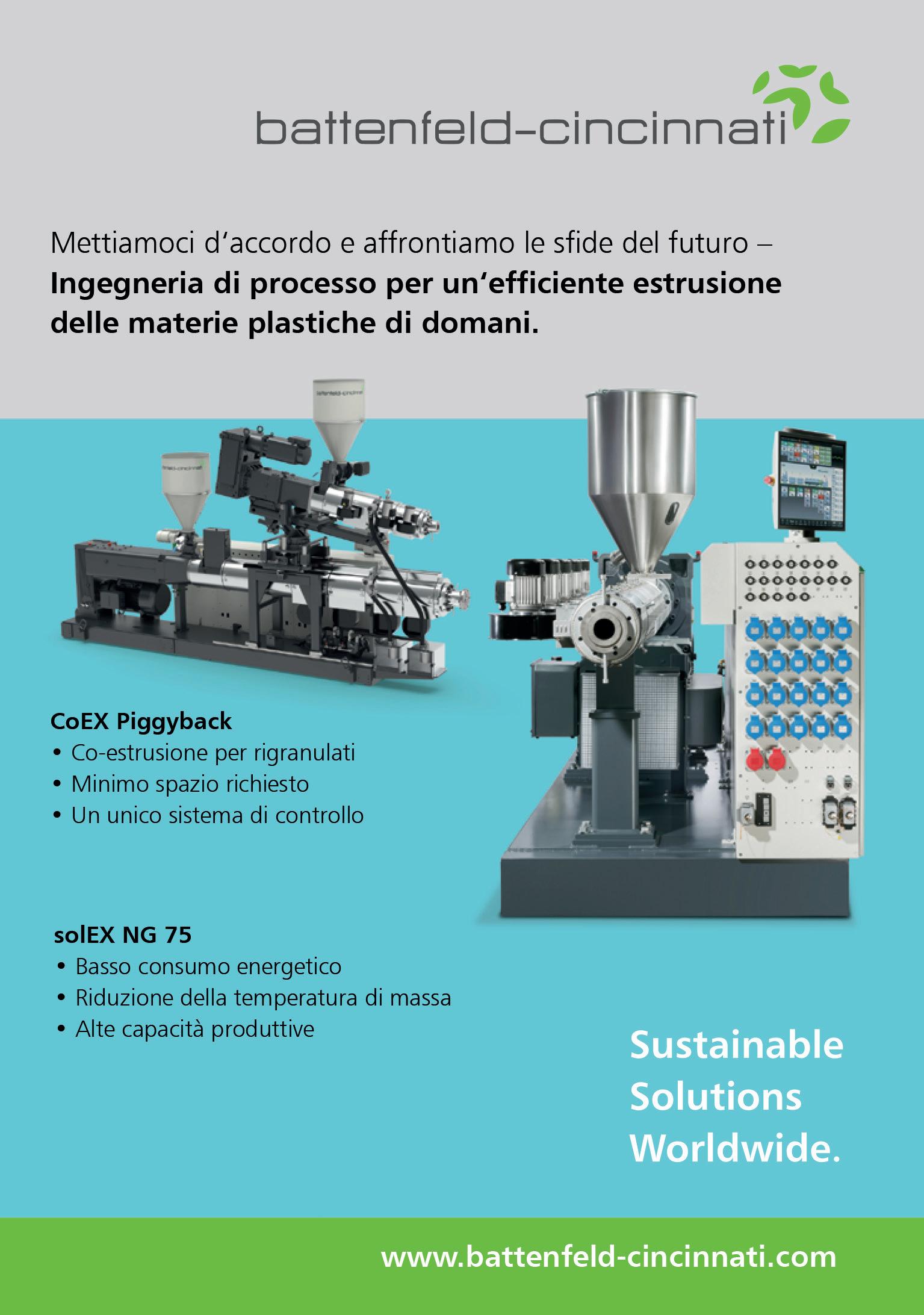
KOCH TECHNIK A FAKUMA 2021
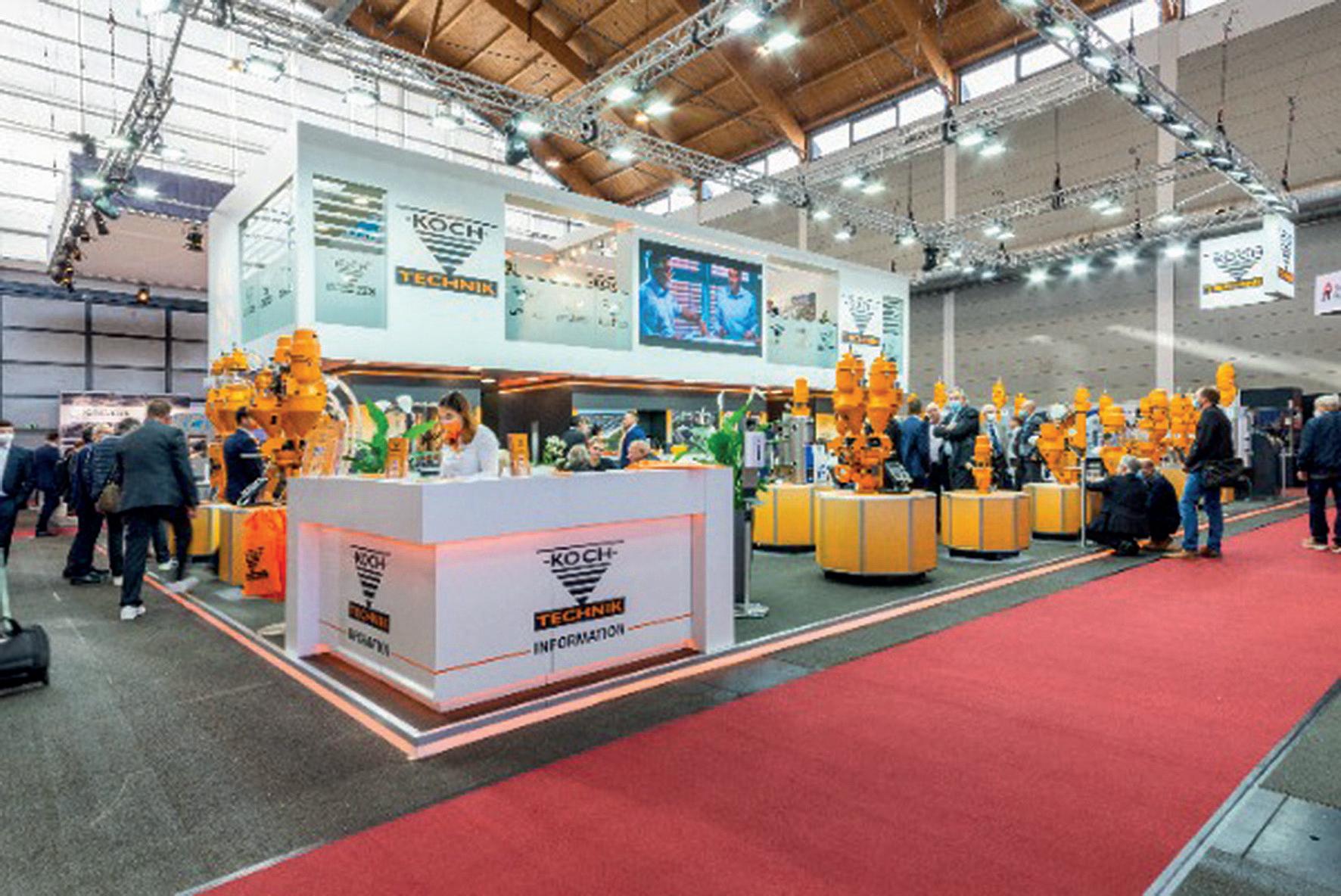
POSITIVA RIPARTENZA SUL LAGO DI COSTANZA
TANTA VOGLIO DI TORNARE A PROPORSI IN PRESENZA È STATO IL LEITMOTIV DELL’ULTIMA EDIZIONE DELLA FIERA DI FRIEDRICHSHAFEN, CHE NON HA LASCIATO IMMUNE NEMMENO KOCH TECHNIK. L’AZIENDA TEDESCA SI È PRESENTATA IN GRANDE SPOLVERO, CON UNO SPAZIO ESPOSITIVO PIÙ CHE RADDOPPIATO RISPETTO ALL’EDIZIONE DEL 2018 E ALCUNI NUOVI PRODOTTI
Il nuovo e sempre più efficiente deumidificatore EKO-N ad aria secca. Nella foto: il modello EKO-N 200F con due recipienti di deumidificazione da 150 e da 60 litri D opo la cancellazione dell’edizione 2020 a causa della pandemia, Fakuma è stata la prima fiera di settore in Germania a svolgersi in presenza nel 2021. In uno stand ampliato rispetto a quello della precedente edizione del 2018, Koch-Technik ha messo in mostra un portafoglio completo di miscelatori, deumidificatori, dosatori e sistemi di trasporto centralizzati, distribuiti nel nostro Paese da Nickerson Italia. Fiore della sua presenza alla mostra sulle rive del Lago di Costanza sono stati i nuovi deumidificatori ad aria secca EKO-N e la gamma di unità di controllo MC7, concepita per la gestione dei miscelatori gravimetrici Graviko e dei deumidificatori ad aria secca carrellati della serie KKT. “Mentre ci preparavamo a partecipare a
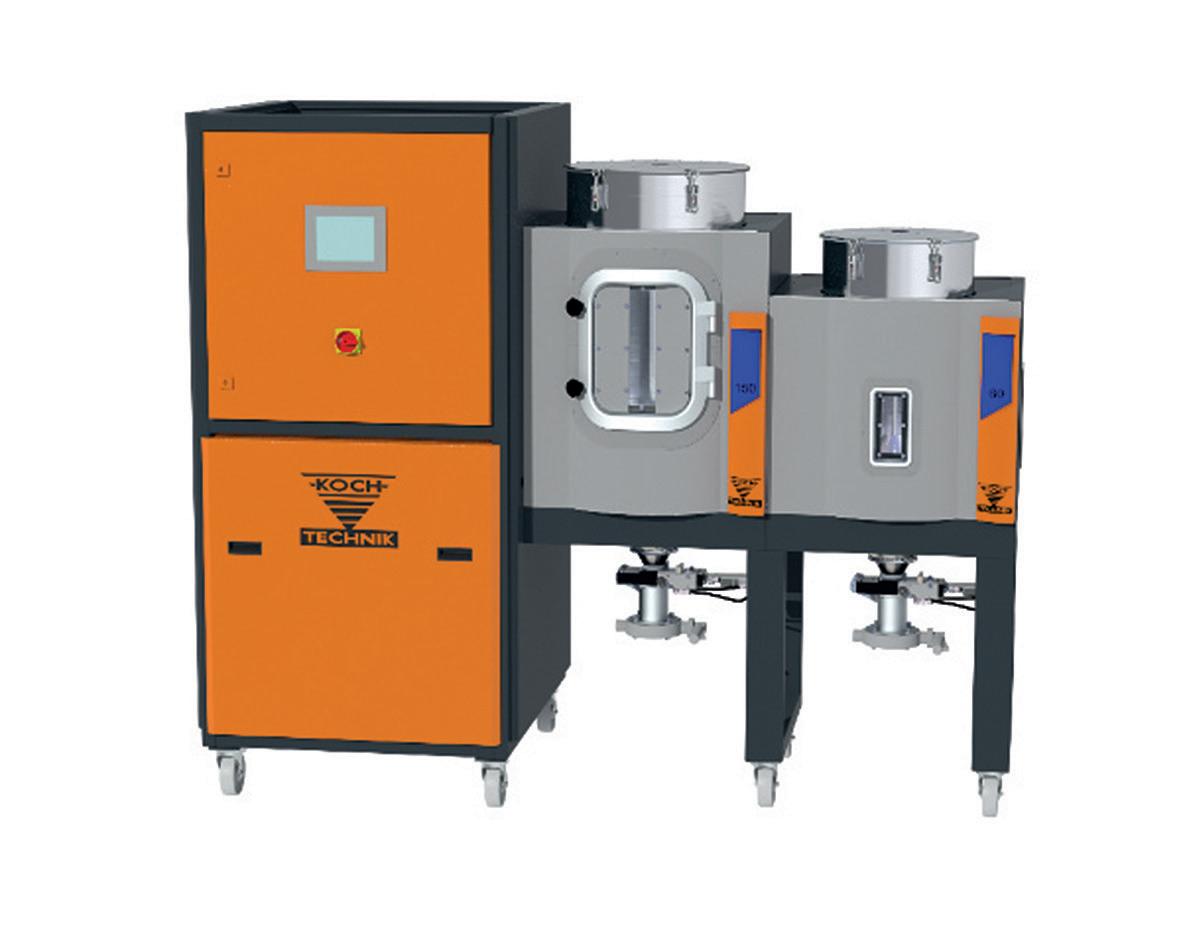
Fakuma 2021, non sapevamo quanti visitatori si sarebbero fatti vedere in fiera. Nonostante un’affluenza ridotta rispetto alle edizioni passate, l’evento si è comunque rivelato un successo, in particolare per il dialogo in prima persona con i professionisti presenti e per la qualità dei colloqui. Inoltre, si avvertiva un cauto ottimismo, specialmente dal settore automobilistico, riguardo alle difficoltà di approvvigionamento. Particolarmente soddisfacente, per noi, è stata la percezione estremamente positiva, da parte del pubblico, del nostro stand in fiera, interamente rinnovato, dopo la pausa indesiderata dello scorso anno”, ha commentato Carsten Koch, CEO dell’azienda.
PIÙ SPAZIO E TANTE NOVITÀ
A Fakuma 2021, Koch-Technik ha presentato un ampio portafoglio di prodotti dedicati a miscelazione, dosaggio, trasporto e deumidificazione, oltre a un’ampia varietà di soluzioni sostenibili per le applicazioni in svariati settori tra i quali, per esempio, l’automotive, i beni di consumo e il sanitario. L’azienda tedesca ha accolto i visitatori in uno stand più ampio, la cui superficie è stata ampliata dai 100 metri quadri dell’edizione precedente a 270 metri quadri. Lo stand era aperto su quattro lati e offriva, nel rispetto anche delle norme igienico-sanitarie e di sicurezza adottate dal quartiere fieristico di Friedrichshafen, tutto lo spazio necessario per esporre l’intera gamma di miscelatori, deumidificatori, sistemi di trasporto e dispositivi di dosaggio proposti. Più in dettaglio, in fiera ha fatto il suo debutto la versione definitiva del nuovo deumidificatore ad aria secca EKO-N, già presentato in anteprima in occasione della fiera K 2019. Il deumidificatore è stato perfezionato in termini di efficienza energetica: in combinazione con il sistema brevettato Öko per il controllo dei consumi energetici, il nuovo modello è in grado di abbattere i consumi fino a dimezzarli. Un’altra novità era rappresentata dai deumidificatori carrellati KKT, proposti con un nuovo pannello di controllo tattile. I nuovi schermi a colori sono più grandi rispetto ai modelli precedenti, oltre a offrire una serie di vantaggi quali: un utilizzo semplice e intuitivo del sistema di controllo, l’integrazione del sistema di movimentazione centralizzato (compatibile con i principi dell’Industria 4.0 grazie allo standard di comunicazione OPC UA) e la possibilità di un’integrazione completa nel software di visualizzazione Koch. Un’ulteriore novità presentata in fiera consisteva nell’unità di controllo MCGT per i miscelatori gravimetrici Graviko. Affiancate ai modelli installati sui premiscelatori gravimetrici e sui deumidificatori carrellati KKT, le nuove unità di controllo si sono presentate in una livrea uniforme e moderna. L’interfaccia di comunicazione OPC-UA consente la totale e agevole integrazione dei sistemi Graviko nei processi produttivi del cliente. Tra i numerosi vantaggi spiccano, inoltre, la grafica chiara e il facile inserimento dei parametri di processo attraverso il pannello touchscreen. L’unità di controllo, infine, è in grado di calcolare automaticamente i parametri di processo necessari, in modo tale da garantire un dosaggio costante e continuo.
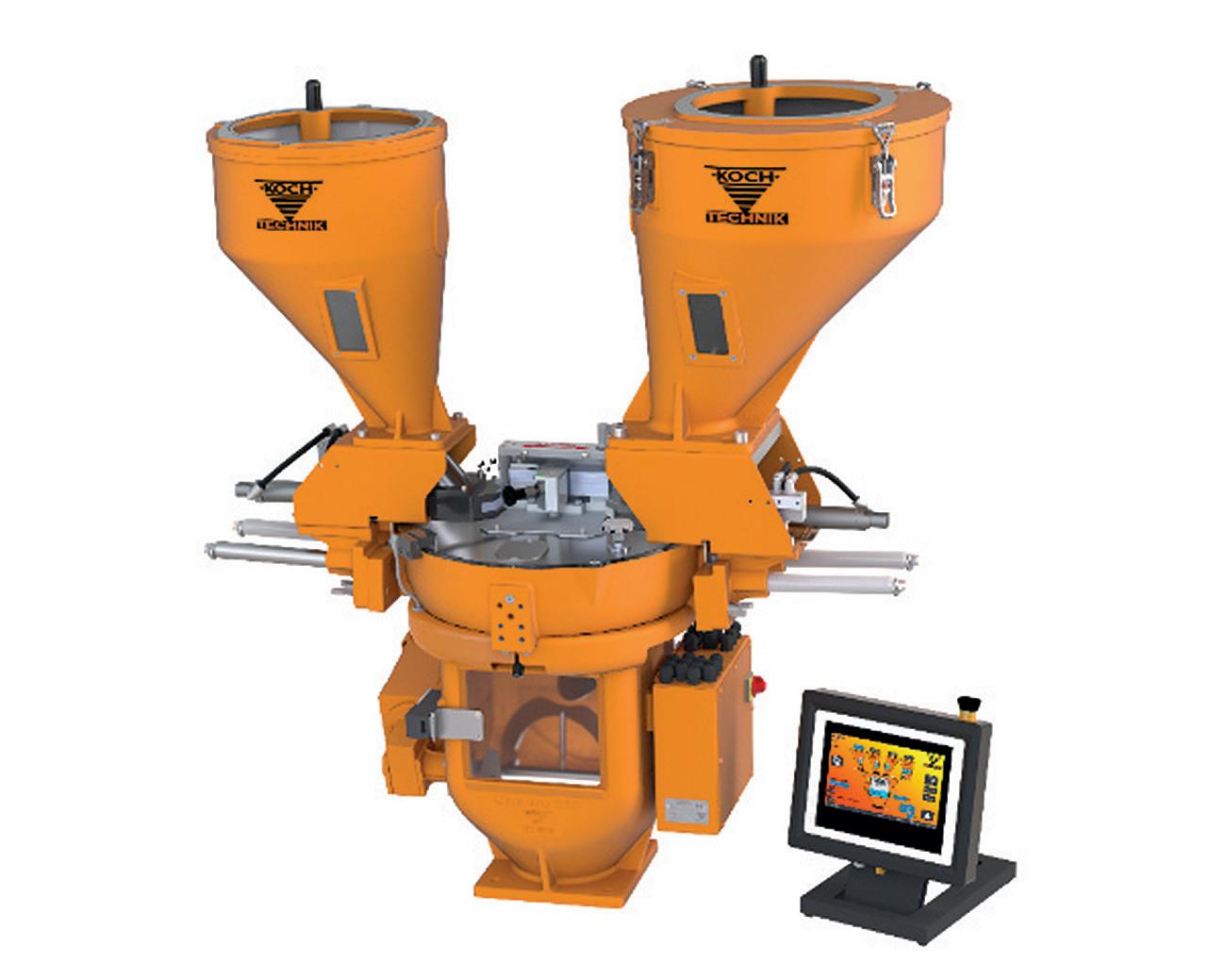
Grazie al nuovo pannello tattile, non solo l’operatività dei deumidificatori KKT ad aria secca è stata aumentata: i dispositivi sono adesso anche pronti per l’Industria 4.0
La nuova unità di controllo MCGT è in grado di gestire fino a quattro unità di dosaggio e un miscelatore gravimetrico Graviko
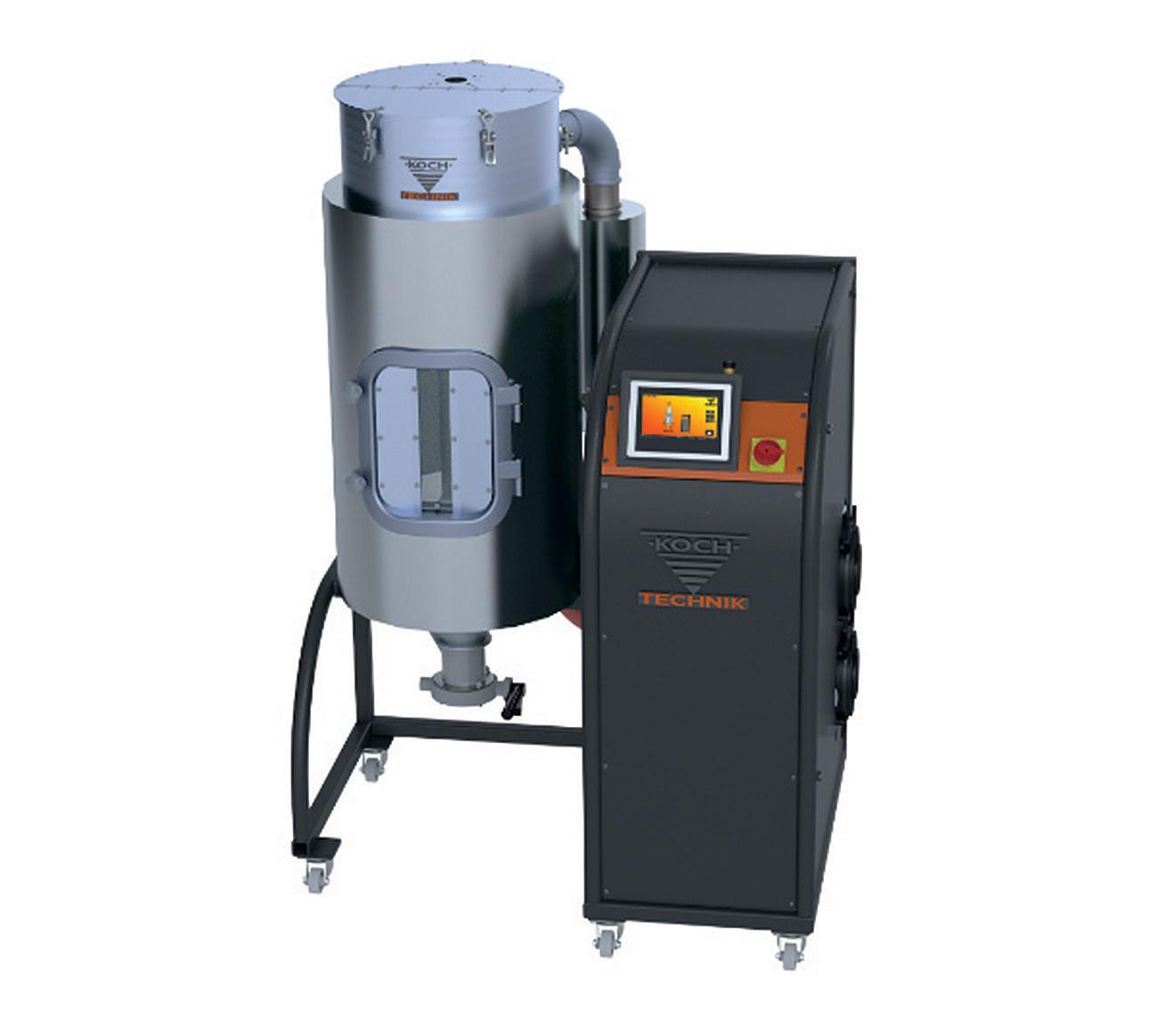
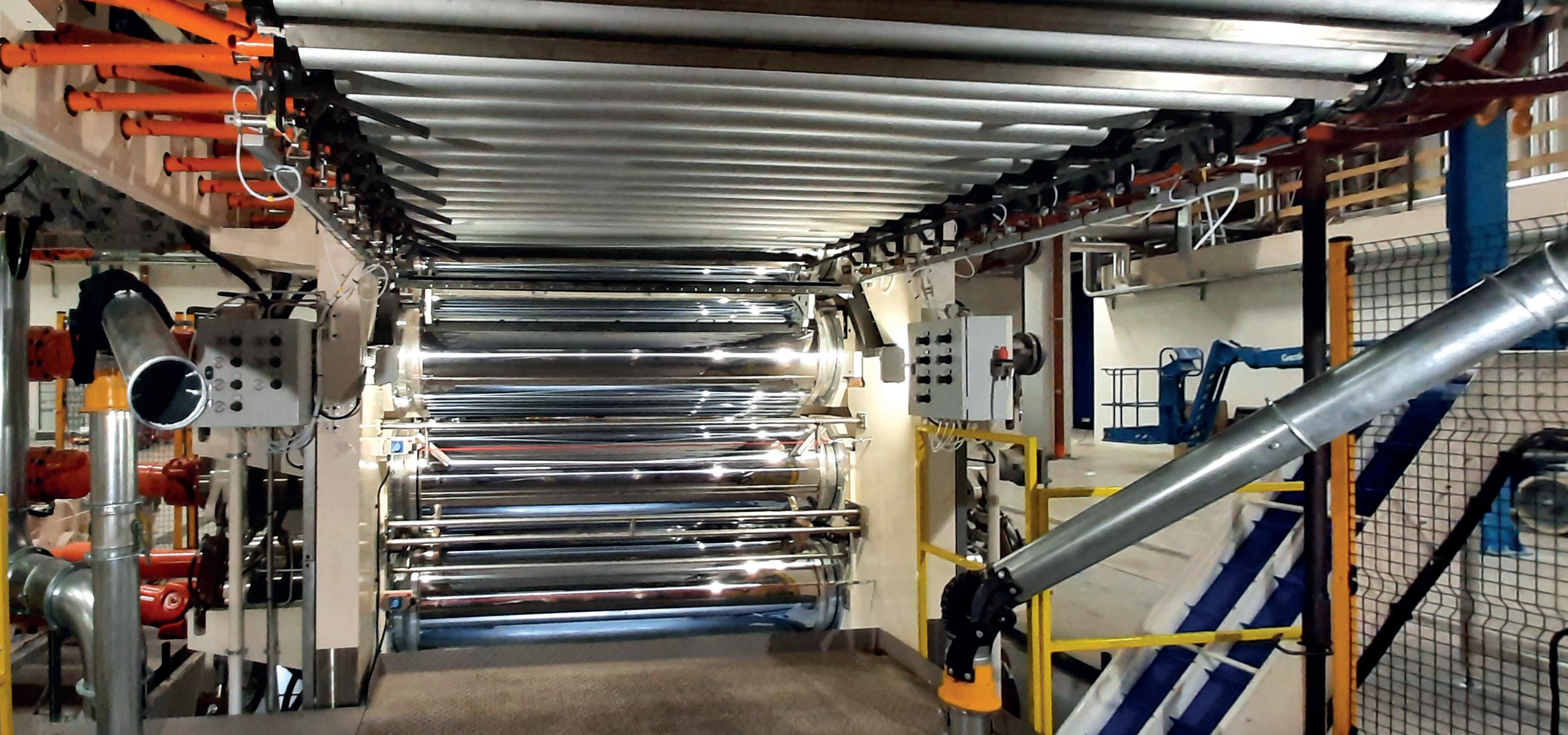
UNA CALANDRA PER DUE
DUE AZIENDE LOMBARDE CON UNA LUNGA STORIA ALLE SPALLE HANNO SAPUTO METTERE A FRUTTO LE RISPETTIVE ESPERIENZE PER USCIRE INSIEME RAPIDAMENTE DA UNA DIFFICILE SITUAZIONE ANCHE IN UN PERIODO COMPLICATO COME QUELLO DELLA PANDEMIA. HA GIOVATO IL CONOSCERSI A FONDO DA MOLTO TEMPO

Con la fornitura di una nuova linea di calandratura ad alte prestazioni da parte di Rodolfo Comerio a Tekni-Plex Gallazzi continua e si rinsalda la collaborazione tra le due aziende lombarde. Nel marzo del 2020, in piena emergenza sanitaria e con il lockdown in atto, Tekni-Plex Gallazzi era stata colpita da un incendio che aveva danneggiato le tre linee di calandratura di Rodolfo Comerio in funzione presso i suoi reparti produttivi di Gallarate (Varese) e aveva reso necessario l’intervento del costruttore per il recupero e il completo ricondizionamento di una di esse presso il proprio stabilimento di Solbiate Olona (Varese), prima di riavviarla all’inizio dell’estate del 2020. Tale linea di calandratura, dalle considerevoli dimensioni, è alta 5 metri, larga 4 e lunga oltre 5 e pesa 80 mila kg. Dotata di 5 cilindri da 610 mm di diametro, consente di produrre foglie in PVC con larghezza pari a 2,5 metri ed è stata trasportata premontata fino allo stabilimento di Tekni-Plex Gallazzi con un mezzo per il trasporto eccezionale.
UN INCONTRO FRUTTIFERO DI ESPERIENZE
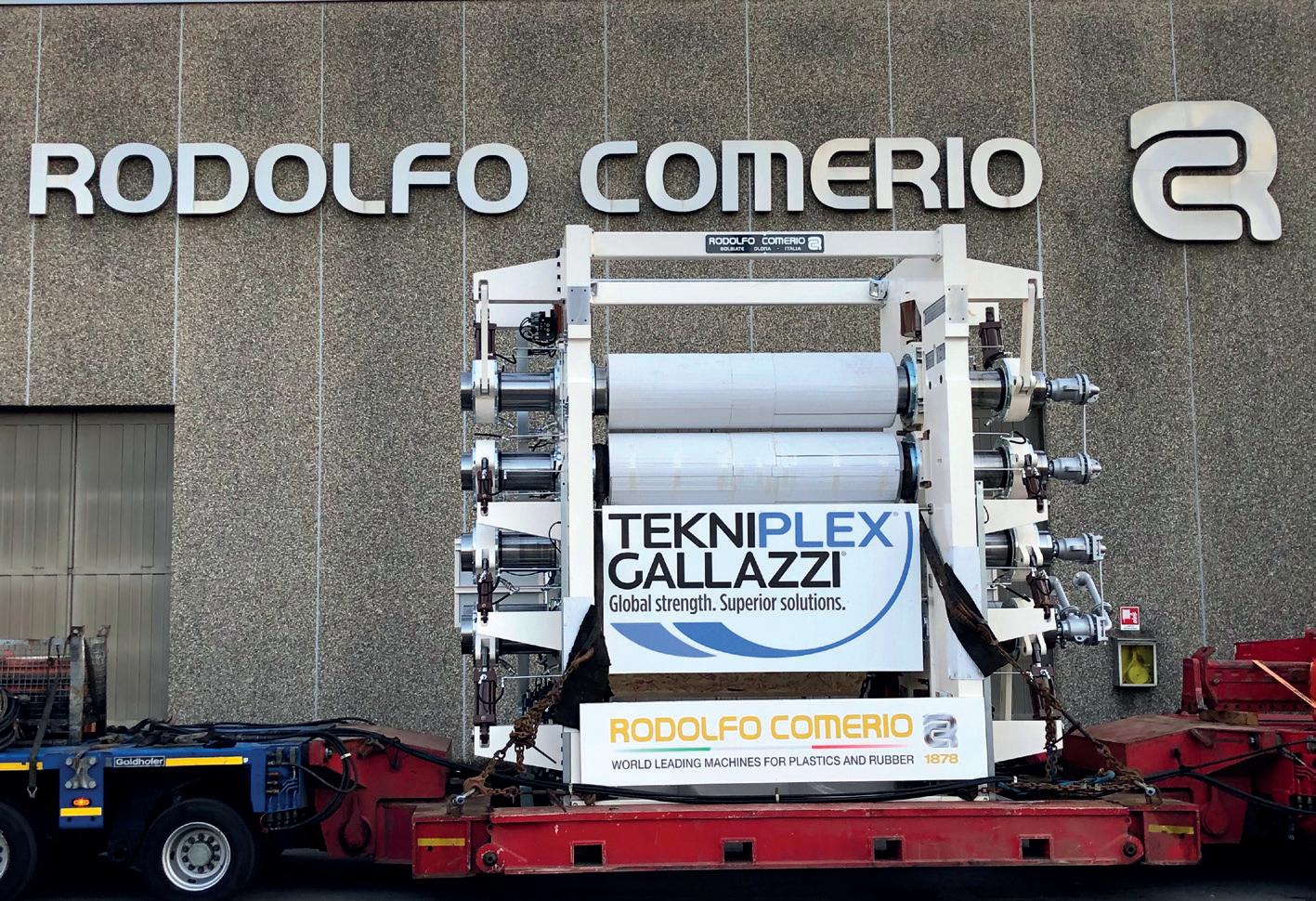

A poco più di un anno dalla rimessa in funzione della linea di calandratura ricondizionata, recentemente Rodolfo Comerio ne ha fornita una nuova di dimensioni ancora maggiori e dotata delle sue soluzioni tecnologiche più innovative e performanti, frutto della propria continua attività di ricerca e sviluppo. Si tratta di un traguardo importante raggiunto in tempi così ristretti e, soprattutto, contraddistinti dalle difficoltà determinate su molti fronti dalla pandemia e superate proprio grazie alla prolungata collaborazione che lega le due aziende, che hanno messo in campo le rispettive migliori risorse e competenze. Fondata nel 1878, Rodolfo Comerio opera a livello mondiale nella progettazione e nella costruzione di impianti per la calandratura di materie plastiche e gomma. Guidata dai membri della famiglia Comerio discendenti del fondatore Rodolfo Comerio, di cui ancora porta il nome, da oltre 140 anni l’azienda fa di qualità, innovazione e tecnologia i cardini su cui ruota la sua attività e i punti di forza che trasferisce nei suoi prodotti. Tekni-Plex Gallazzi è invece un’azienda
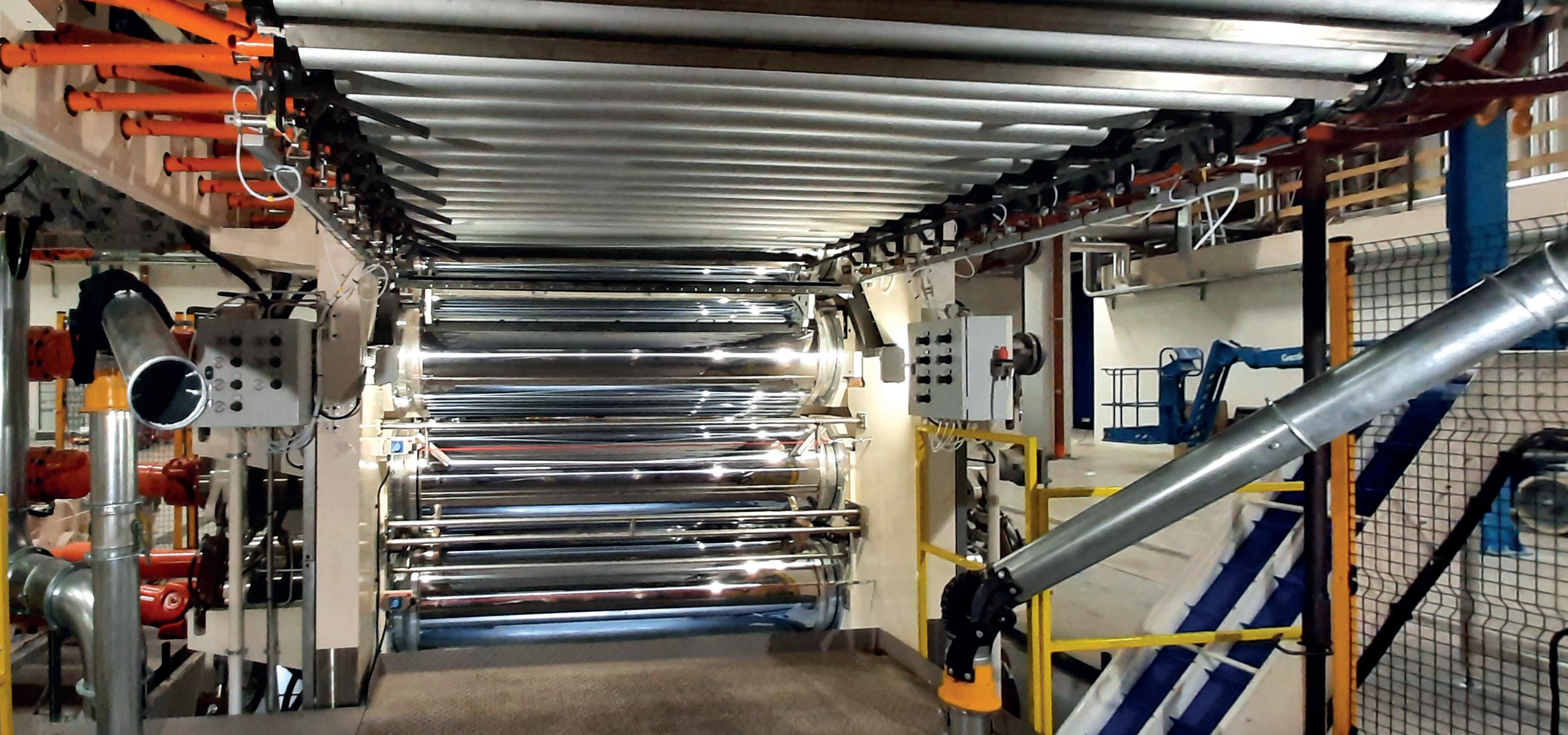
La movimentazione dei sistemi di calandratura di Rodolfo Comerio dagli stabilimenti di costruzione a quelli di installazione richiede spesso, come nel caso di quelli destinati a Tekni-Plex Gallazzi, il ricorso a mezzi per il trasporto eccezionale
fondata nel 1973 che produce film e foglie in PVC per applicazioni farmaceutiche e substrati per nastri adesivi, distribuiti in tutto il mondo. Parte del gruppo statunitense Tekni-Plex, vanta due siti produttivi in Italia, con una capacità produttiva totale di 50 mila tonnellate all’anno di film in PVC, che vengono esportati in 53 paesi. Nei suoi due stabilimenti italiani, di Gallarate e di Tradate (Varese), sono in funzione diverse linee di calandratura, tutte fornite da Rodolfo Comerio, oltre a impianti di spalmatura, accoppiamento e taglio.
Carlo Comerio (a sinistra), amministratore delegato di Rodolfo Comerio e conosciuto a livello internazionale come “Mr. Calender” per la sua pluriennale esperienza nel mondo della calandratura di materie plastiche e gomma, insieme ad Antonino Crisafulli, amministratore delegato di Tekni-Plex Gallazzi


www.star-europe.com
NOVITÀ E ANNIVERSARIO IN CASA HERRMANN ULTRASCHALL
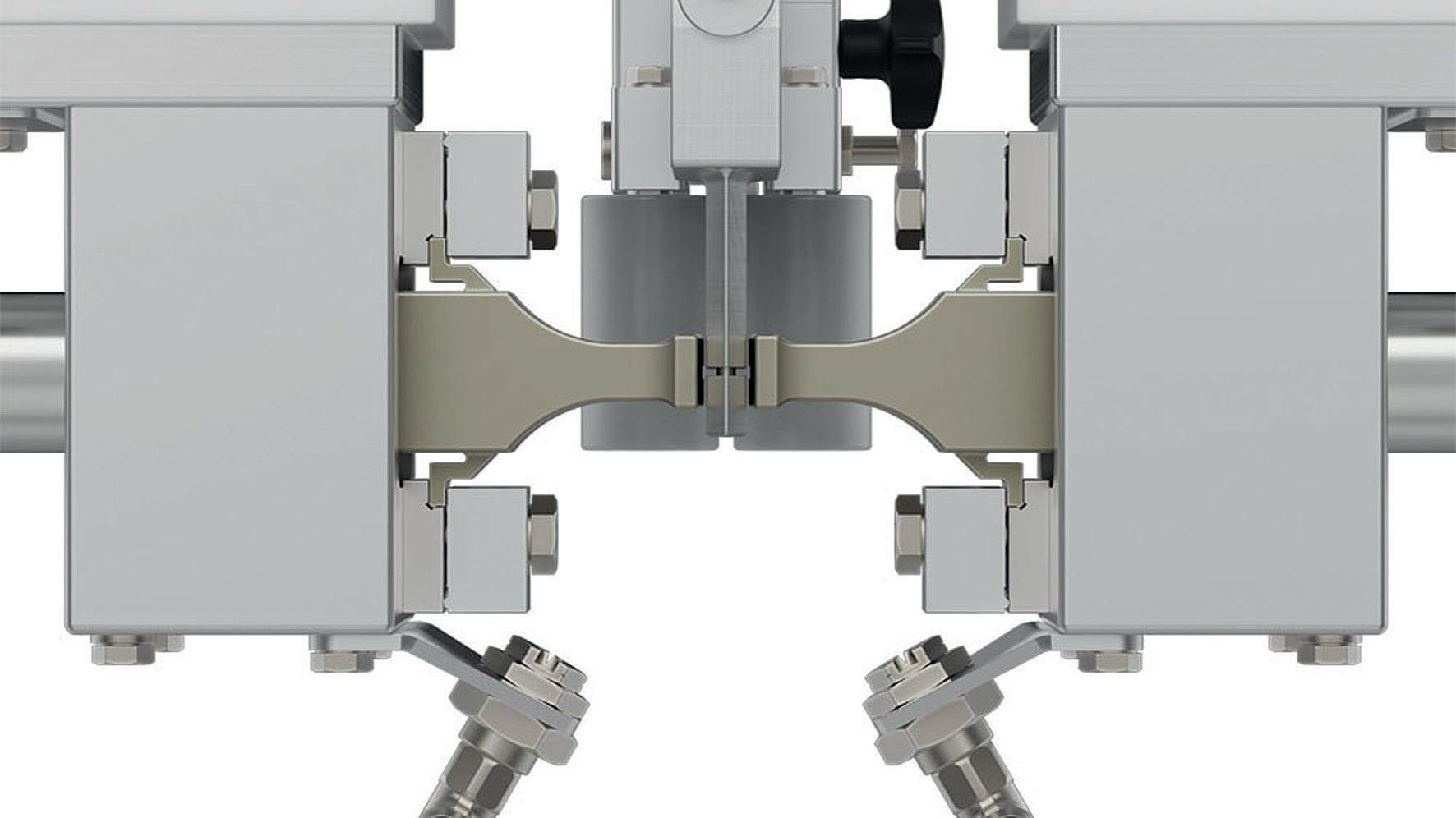
PIONIERI DELLA SALDATURA A ULTRASUONI
LE RECENTI INNOVAZIONI E LA CELEBRAZIONE DEI SESSANT’ANNI DELL’AZIENDA HANNO CONTRADDISTINTO L’ANNO CHE SI È APPENA CONCLUSO PER IL COSTRUTTORE TEDESCO DI SALDATRICI, I CUI SISTEMI OTTENGONO RISCONTRI POSITIVI E PREMI INTERNAZIONALI

Il nuovo sistema modulare Zipper Seal Module (ZSM, nella foto di apertura), sviluppato da Herrmann Ultraschall, consente di saldare in continuo le zip dei sacchetti in plastica, comprese quelle realizzate in monomateriale facilmente riciclabile. Le confezioni richiudibili, in particolare quelle realizzate con materiali sostenibili, stanno diventando sempre più diffuse e Herrmann Ultraschall ha sviluppato un sistema che rende i vantaggi della saldatura a ultrasuoni utilizzabili con le confezioni stand-up e tubolari mono e multimateriale con zip integrata. Il modulo ZSM occupa poco spazio, è igienico e offre risultati di tenuta eccellenti, anche a velocità di processo variabile. Ciò è reso possibile dalla combinazione ottimizzata di un generatore di ultrasuoni e del sistema ZSM stesso. In particolare, il generatore Ultrapack utilizzato è specificamente progettato per realizzare applicazioni di confezionamento ad alta velocità e consente il controllo riproducibile del processo di saldatura. Questo significa che il dispositivo può essere adattato in pochi secondi alle proprietà dei diversi materiali. Il sistema ZSM consente un processo di saldatura continuo con due sonotrodi disposti l’uno di fronte all’altro. Il materiale da saldare passa tra i due sonotrodi, che lo riscaldano e lo fondono. Il materiale non aderisce ai sonotrodi durante il processo di saldatura e, di conseguenza, a differenza di altri processi, il sistema non necessita di pulizia. Tuttavia, per soddisfare anche gli standard igienici più elevati, ZSM consente un facile accesso alle sue parti per la pulizia. Il dispositivo è compatto e può anche essere integrato in impianti già esistenti. Quando necessario è possibile effettuare l’arresto e il riavvio del siste-
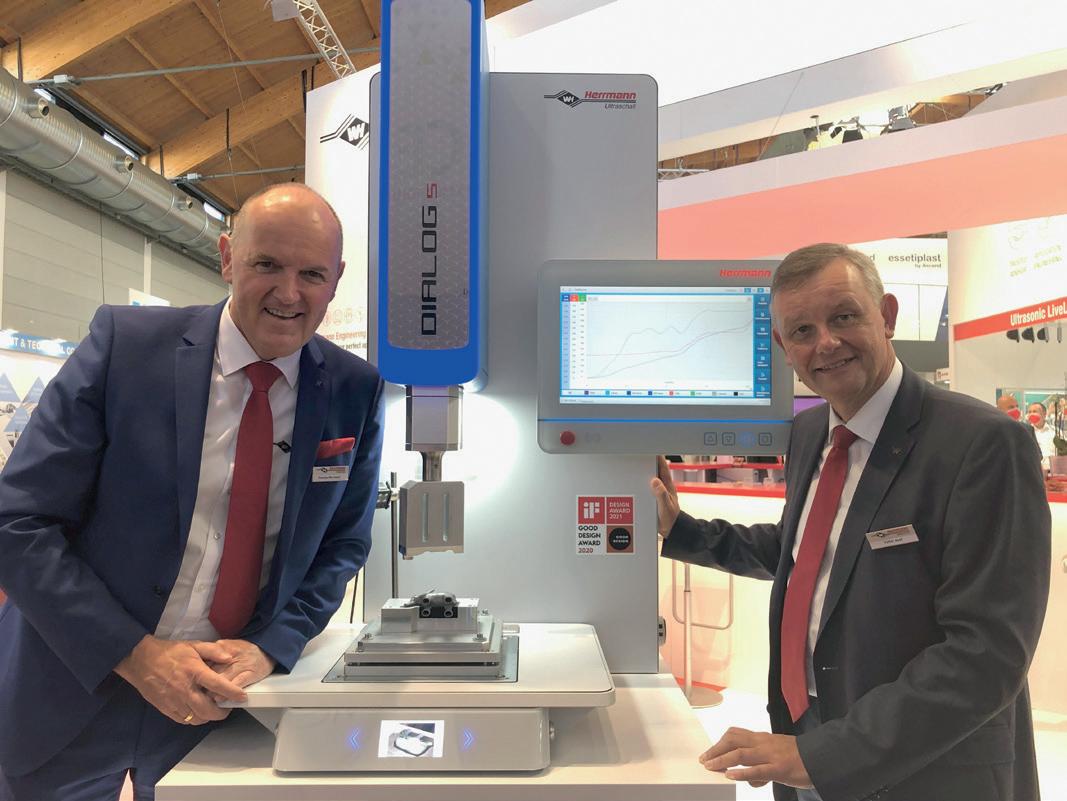

Il momento delle sei donazioni da 10 mila euro ciascuna durante la celebrazione dei sessant’anni dell’azienda
ma, che funziona anche a velocità variabile, aumentando così la flessibilità di produzione. Poiché il calore viene generato direttamente sulla saldatura, il processo è particolarmente delicato sul materiale di imballaggio e consente la saldatura continua delle zip sulle confezioni realizzate in mono o multimateriale. Tra le ultime innovazioni messe a punto da Herrmann Ultraschall troviamo anche il nuovo sistema ThermoControl, che monitora in modo estremamente preciso la temperatura del materiale durante la saldatura e la regola in modo tale da rimanere all’interno della finestra di processo impostata. In particolare, con ThermoControl la lavorazione di materiali sensibili alla temperatura nei processi di saldatura longitudinale diventa ancora più controllabile e quindi più facile ed efficiente. Di conseguenza, i materiali riciclabili possono essere utilizzati in modo ancora più versatile nelle applicazioni di imballaggio.
SESSANT’ANNI DI ATTIVITÀ
Il costruttore tedesco ha recentemente celebrato sessant’anni di attività con un evento durante il quale sono state ripercorse le tappe principali della lunga storia dell’azienda. “L’anniversario è un’ottima occasione per ringraziare. Costruire saldi legami con le persone con cui veniamo in contatto è diventata nel tempo la nostra missione”, ha voluto inoltre sottolineare Thomas Herrmann, CEO di Herrmann Ultraschall, in tale occasione. All’evento è stato ricordato come il fondatore dell’azienda, Walter Herrmann, industrializzò la tecnologia per la saldatura a ultrasuoni su tre basi: un generatore di ultrasuoni robusto e affidabile; uno schermo per rendere visibile e controllabile il processo; un isolamento acustico per abbattere i rumori generati dal processo. Da allora, Herrmann Ultraschall è cresciuta incessantemente e oggi conta 500 dipendenti, 600 a livello mondiale, ed è presente in 20 paesi. Se Walter Herrmann è stato il pioniere della tecnologia della saldatura a ultrasuoni, il figlio Thomas ha capito subito la necessità di espandere e internazionalizzare la società, obiettivi entrambi raggiunti. Dal 2007, quando ha assunto la guida dell’azienda, dipendenti e vendite sono quadruplicati e recentemente il CEO ha ricevuto da Ernst & Young il premio di “Imprenditore dell’anno” nella categoria “Innovazione” per i progressi tecnologici e per una gestione aziendale e delle risorse umane innovativa e orientata al valore. Durante la celebrazione per i sessant’anni, la società di Karlsbad (Germania) ha anche effettuato sei donazioni da 10 mila euro ciascuna destinate ad altrettante organizzazioni locali. L’attività filantropica di Herrmann Ultraschall comprende anche la ricerca di un donatore di cellule staminali, anche tra i propri dipendenti, per un paziente del luogo affetto da leucemia. Sistema funzionale Doppio premio
La nuova generazione di saldatrici a ultrasuoni HiQ Dialog di Herrmann Ultraschall ha ricevuto l’IF Design Award 2021 e il Good Design Award 2020: le giurie di entrambi i premi sono state convinte dall’interazione ottimale tra uomo e macchina in termini di funzionalità. Il design del nuovo dispositivo è interamente orientato verso un funzionamento facile e sicuro. Il sistema di controllo comunica con l’operatore tramite un’interfaccia utente personalizzabile a diversi livelli. Frecce di indicazione illuminate e schermo secondario alla base della macchina forniscono informazioni su conteggio dei pezzi lavorati, stato della macchina o dati di processo, mentre la visualizzazione di funzioni e accessori può essere integrata nella nuova piattaforma di controllo tramite widget. Una procedura guidata, visualizzata sullo schermo, assiste l’operatore nel cambio degli utensili e il sistema è in grado di selezionare automaticamente il programma di saldatura in base all’utilizzo; la macchina verifica tramite RFID se attrezzatura, strumento di saldatura e programma di saldatura selezionati corrispondono tra loro. Grazie al design lineare, sono stati eliminati spigoli e sprechi di spazio, favorendo anche la facile movimentazione del dispositivo. L’integrazione della piastra di bloccaggio delle attrezzature nella base della macchina riduce l’altezza complessiva di quest’ultima e consente un’installazione più ergonomica delle attrezzature stesse. La base, inoltre, offre spazio per riporre utensili e accessori e può essere utilizzata come superficie di montaggio per unità aggiuntive.
La pluripremiata saldatrice a ultrasuoni HiQ Dialog tra Thomas Herrmann (a sinistra), CEO di Herrmann Ultraschall, e Volker Aust, esperto di ingegneria e design di prodotto
WERKCAM SCEGLIE LEISTER LASER PLASTIC WELDING
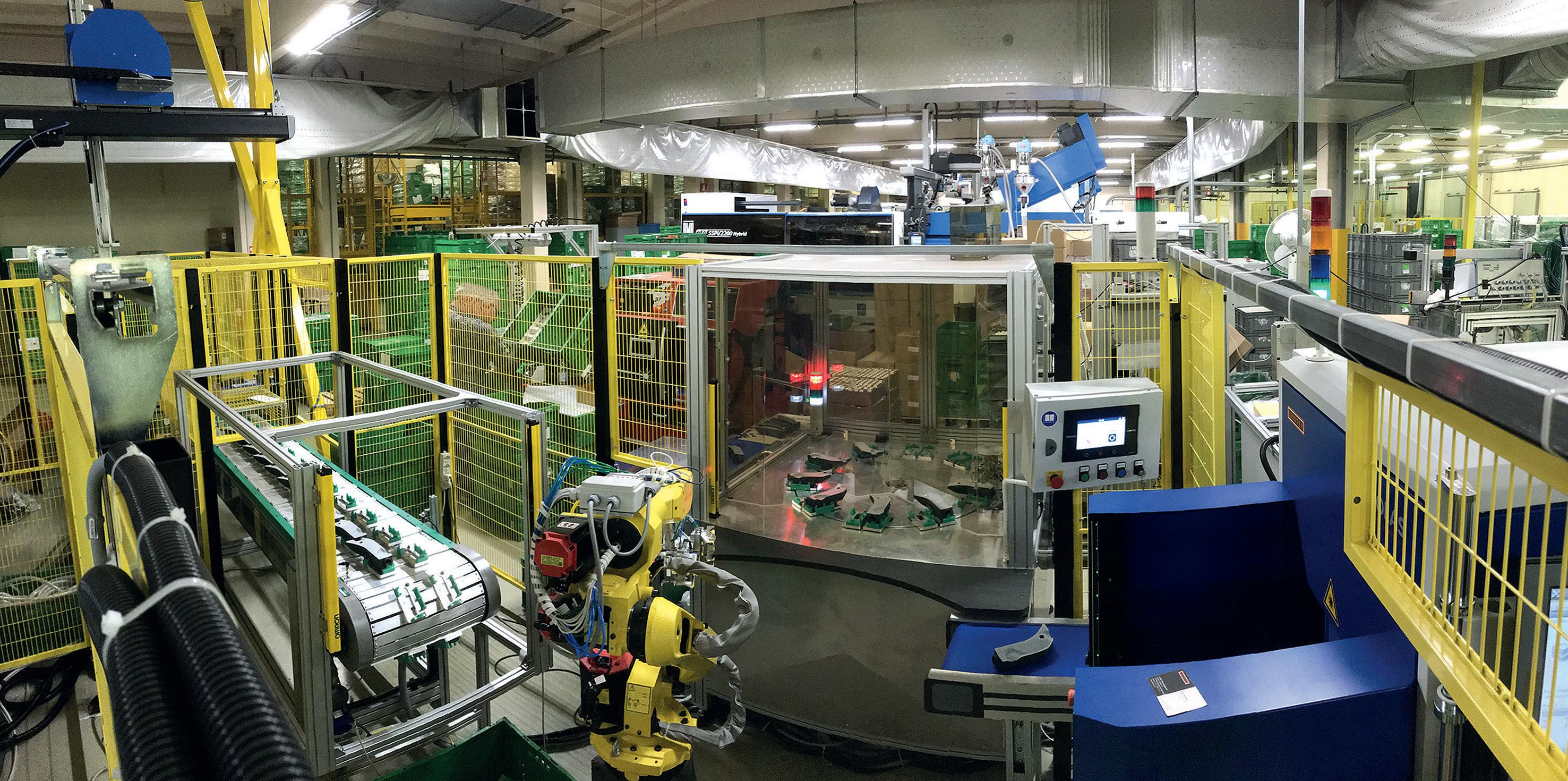
TENUTA STAGNA ED ESTETICA ASSICURATE GRAZIE ALLA SALDATURA LASER
LA NECESSITÀ DI REALIZZARE UN COMPONENTE A VISTA CHE GARANTISSE NON SOLO ELEVATE PRESTAZIONI MA ANCHE UN’ESTETICA ATTRAENTE E UNA PERFETTA INTEGRAZIONE NELL’ELETTRODOMESTICO HA PORTATO ALLA COLLABORAZIONE TRA LE AZIENDE WERKCAM E LEISTER E ALL’UTILIZZO DI UNA SALDATRICE RIVELATASI IDEALE PER QUESTO TIPO D’APPLICAZIONE
Azienda del gruppo Think Plastic e realtà all’avanguardia nel settore della trasformazione delle materie plastiche, Werkcam, con sede ad Arcore (Monza Brianza), è nata per produrre componenti per gli aspirapolvere Vorwerk Folletto e nel corso del tempo si è evoluta fino a diventare un’azienda con oltre 70 dipendenti e uno stabilimento di 5000 metri quadri, ponendosi tra i principali operatori nell’industria degli elettrodomestici. Dal materiale plastico al prodotto finito, Werk- cam segue tutte le fasi che portano alla realizzazione dei suoi manufatti: progettazione, prototipazione, collaudo e produzione in serie, controllando ogni aspetto con estrema attenzione. Lo stabilimento ospita infatti linee di assemblaggio, laboratori, uffici e magazzino. Il risultato finale è una gamma di prodotti finiti che uniscono prestazioni e aspetto estetico eccellenti, caratteristiche imprescindibili nel mercato degli elettrodomestici di alta gamma.
UNA SFIDA SU PIÙ FRONTI
Proprio la necessità di ottenere elementi in grado di garantire il perfetto funzionamento dell’elettrodomestico e allo stesso tempo un aspetto gradevole ha spinto Werkcam a ricercare una soluzione innovativa per la realizzazione di un serbatoio di acqua e detersivo realizzato per una macchina lavapavimenti. Il serbatoio, una volta inserito sulla lavapavimenti, risulta a vista, il che spiega l’importanza dell’aspetto estetico; la struttura del prodotto impone inoltre una perfetta tenuta delle saldature per evitare perdite che potrebbero compromettere non solo la qualità dei risultati ottenuti in termini di pulizia delle superfici, ma anche il funzionamento dell’intera macchina. In pratica, Werkcam si è trovata a ricercare
una soluzione che garantisse la stessa perfetta tenuta e la totale assenza di sbavature di un prodotto realizzato in un unico blocco, sebbene le caratteristiche progettuali imponessero la realizzazione del serbatoio mediante l’unione di due mezzi gusci.
ALLA RICERCA DELLA TECNOLOGIA IDEALE
Il primo approccio di Werkcam, anche su indicazione del cliente finale Vorwerk, ha preso in esame la tecnologia più collaudata per unire i due mezzi gusci, ovvero la saldatura a lama calda, ma già dalle prime prove quest’ultima non è risultata idonea a soddisfare i requisiti di progetto in termini di tenuta nel lungo periodo e di aspetto estetico finale, visti gli elevati standard richiesti per questa applicazione. Lo staff tecnico di Werkcam ha quindi preso in esame tecnologie alternative; dopo averne scartate alcune come la saldatura a ultrasuoni, rivelatasi non idonea per il tipo di materiale impiegato, è stata presa in considerazione la saldatura laser, che ha attirato l’attenzione dei tecnici per gli eccellenti risultati ottenuti in altri campi, come l’automobile e il medicale. Sono stati quindi messi a confronto diversi fornitori di sistemi per la saldatura laser di componenti in plastica. Dopo un attento esame, la realtà più vicina alle esigenze del trasformatore è risultata Leister Laser Plastic Welding, che si occupa esclusivamente di tecnologia laser ed è una divisione della multinazionale svizzera Leister, costruttrice di sistemi per la saldatura e la lavorazione della plastica.
Una fase del processo di saldatura dei due mezzi gusci per ottenere il serbatoio a vista della lavapavimenti
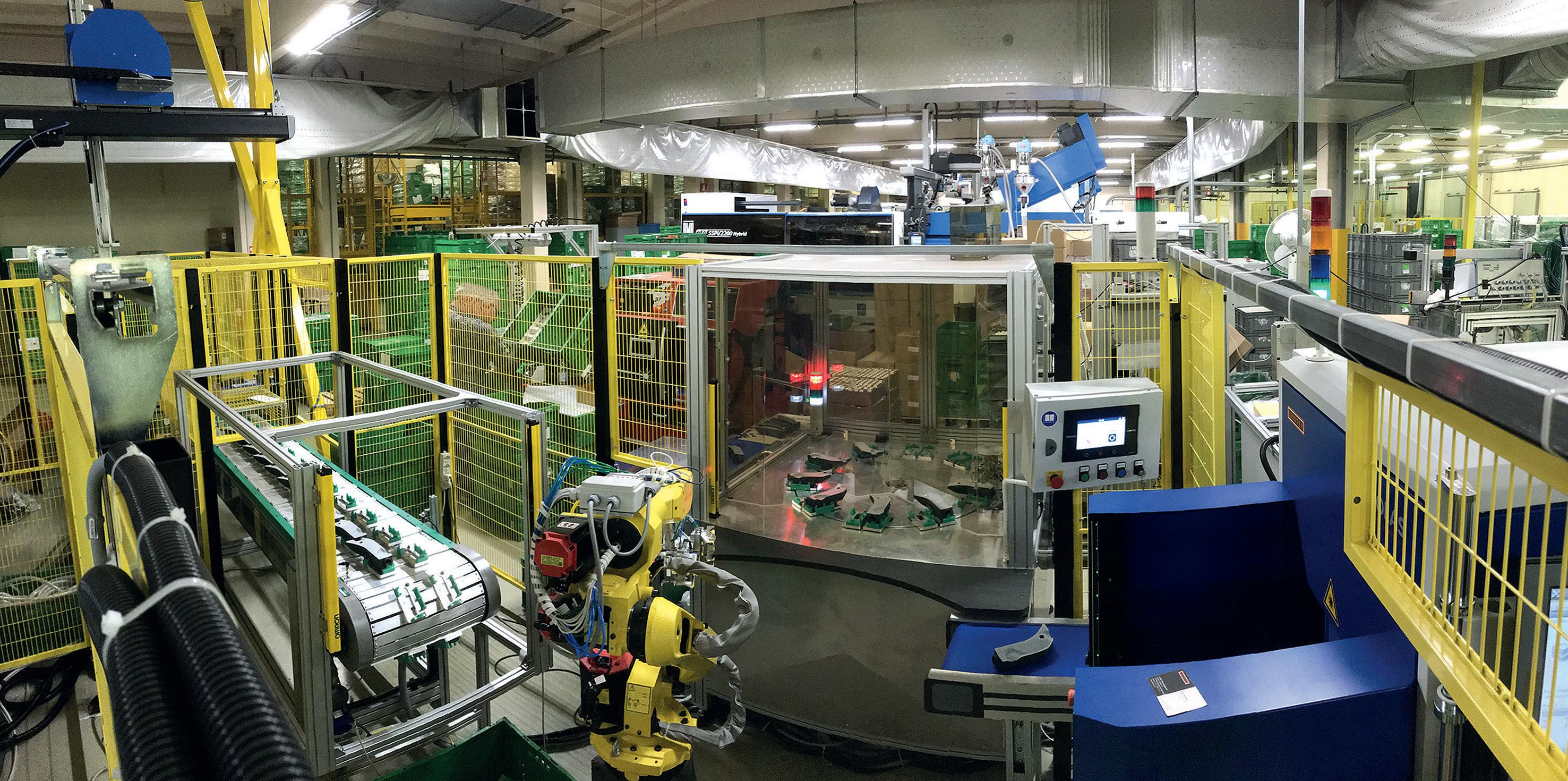
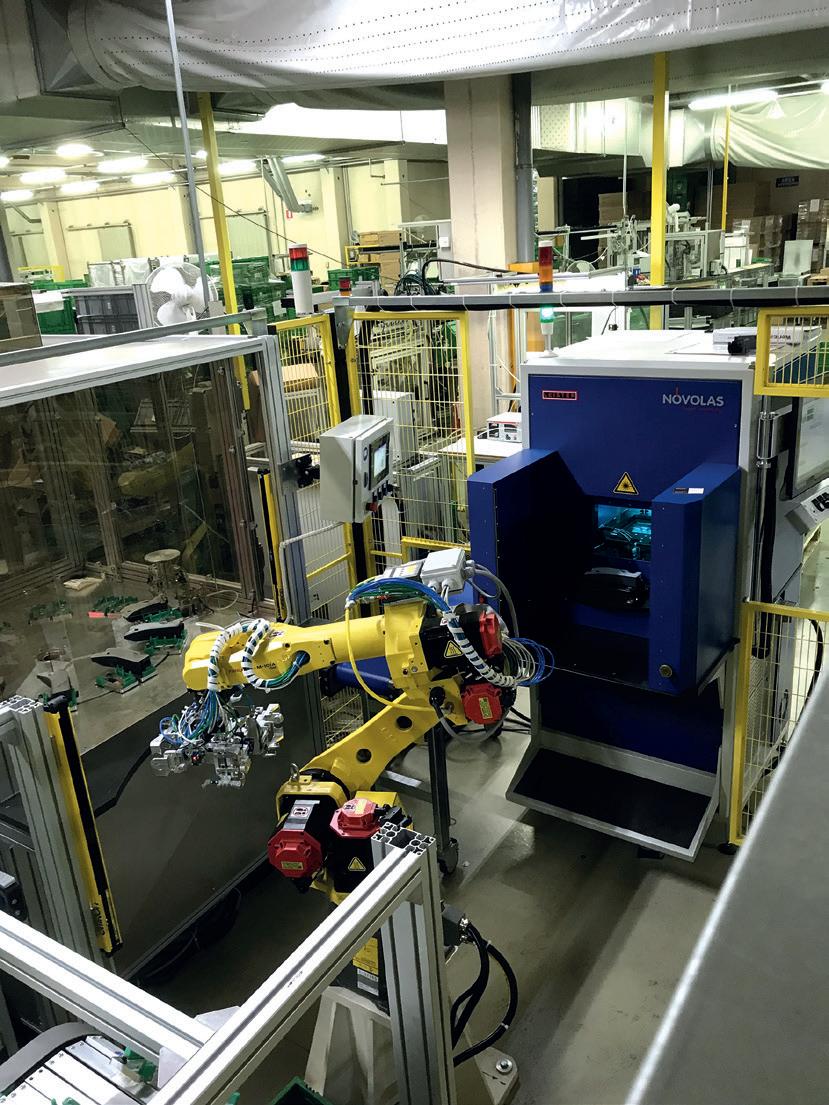
Grazie alla precisione della saldatura laser, le parti non vengono riscaldate più del dovuto, permettendo a un robot antropomorfo di spostare il serbatoio verso la stazione di raffreddamento, una volta saldato UNA COLLABORAZIONE EFFICIENTE

La messa a punto dell’impianto che salda i mezzi gusci per realizzare i serbatoi ha richiesto diversi passaggi: Leister ha messo la propria professionalità a disposizione del trasformatore aiutandolo nello svolgimento delle prove, nella prototipazione, nel collaudo e nella valutazione delle campionature. Ne è scaturita la realizzazione di una cella robotizzata (nella foto di apertura) nella quale i due mezzi gusci in polipropilene vengono saldati grazie a un processo perfetto nella sua semplicità. Il primo mezzo guscio, trasparente, è attraversato dal laser che viene “fermato” dall’altro mezzo guscio, realizzato con uno speciale additivo in modo da assorbire l’energia del raggio.
ENERGIA LASER E PRECISIONE
Il perfetto apporto d’energia reso possibile dall’apparecchiatura di Leister permette di fondere l’esatta quantità di materiale plastico necessaria a creare una saldatura resistente, a tenuta stagna, senza alcuna sbavatura e in tempi rapidissimi. Un robot antropomorfo sposta il serbatoio saldato verso la stazione di raffreddamento, che avviene molto rapidamente: grazie alla precisione della tecnologia laser, le parti non si riscaldano più del dovuto durante la saldatura. Segue il collaudo della tenuta, al termine del quale il pezzo è sottoposto a marcatura laser per consentire una perfetta tracciabilità di ogni componente del prodotto finito.
UNA SCELTA ACCURATA
Fra i numerosi sistemi per la saldatura laser offerti da Leister, la scelta è caduta su Novolas WS-AT, soluzione chiavi in mano molto facile da integrare nei processi produttivi. Modulare e versatile, tale sistema è disponibile con espansioni e accessori collegabili con facilità, come una tavola rotante per l’indicizzazione e un nastro trasportatore. I numerosi accessori disponibili hanno permesso a Werkcam di adattare perfettamente il sistema alle esigenze di questa particolare applicazione. Il software di controllo di Novolas WS-AT permette di variare con estrema facilità i parametri di saldatura, velocizzando le operazioni di sintonia fine per il raggiungimento della saldatura perfetta. Il software comprende la funzione di monitoraggio in linea per identificare immediatamente eventuali anomalie durante la lavorazione. Novolas WS-AT è ideale per saldare materiali plastici, specialmente nell’applicazione realizzata da Werkcam. La velocità del sistema permette di ottenere un’elevata produttività, contribuendo a contenere tempi e costi di produzione.
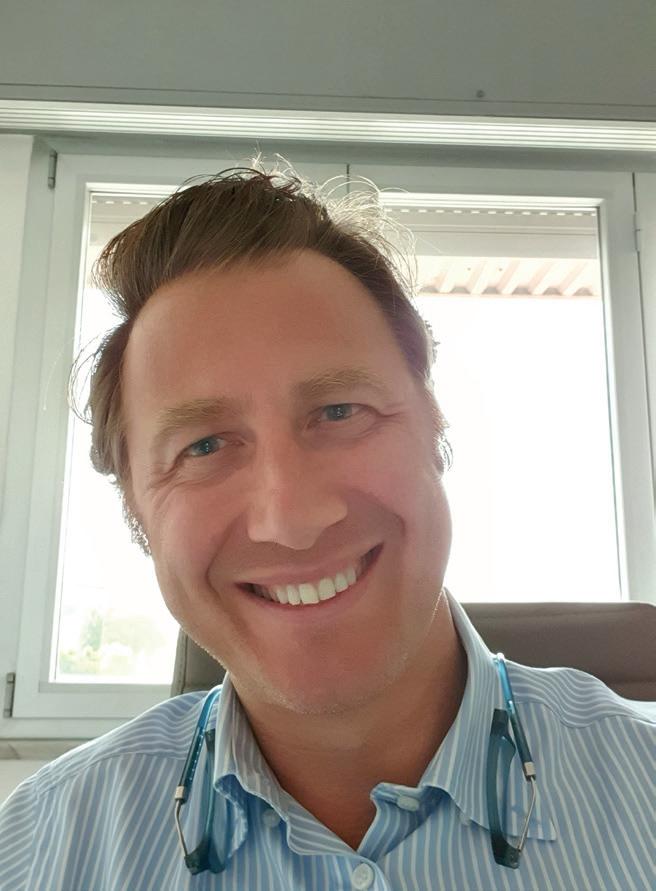
Aldo Caminada, CEO di Think Plastic, la casa madre di Werkcam
UNA PARTNERSHIP DI SUCCESSO
“La collaborazione con Leister Laser Plastic Welding ha dato ottimi risultati e ha posto le basi per l’utilizzo di quest’innovativa tecnologia anche in altre nostre applicazioni“, ha spiegato Aldo Caminada, CEO di Think Plastic. Le due aziende hanno infatti numerosi aspetti in comune. “La ricerca di prestazioni elevate e l’attenzione all’estetica che ci contraddistinguono hanno trovato un’ottima rispondenza nell’offerta di Leister, della quale abbiamo apprezzato anche la grande attenzione alle nostre esigenze e, non meno importante, la presenza di personale che parla italiano nell’area Supporto, che ha reso tutto più facile per i nostri tecnici”, ha concluso Caminada.
IL TRATTAMENTO CORONA SECONDO ME.RO
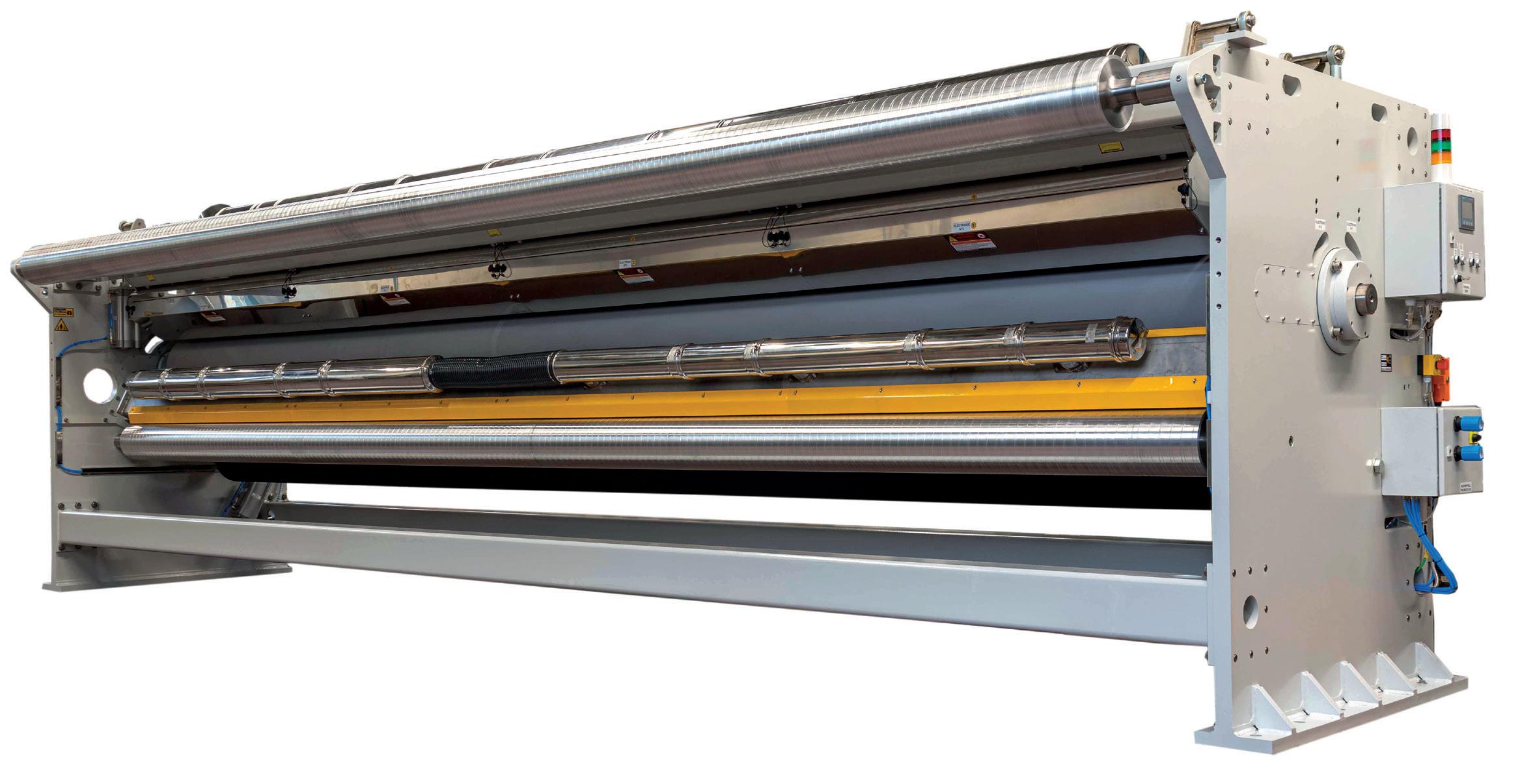
INNOVAZIONE E PERSONALIZZAZIONE: LE CHIAVI DEL SUCCESSO
CON UN’OFFERTA AMPIA E ARTICOLATA, ME.RO SI POSIZIONA TRA LE PRINCIPALI AZIENDE INTERNAZIONALI NEL CAMPO DEI SISTEMI PER IL TRATTAMENTO CORONA. ALLA BASE DI QUESTO RISULTATO C’È UNA GRANDE ATTENZIONE ALL’ATTIVITÀ DI RICERCA E SVILUPPO E AL RUOLO DEI SERVIZI POST VENDITA, ATTRAVERSO CUI I CLIENTI VENGONO SEGUITI E FIDELIZZATI
Uno dei costruttori di sistemi per il trattamento corona di riferimento a livello internazionale, Me.Ro, azienda toscana di proprietà della famiglia Mennucci, ha saputo costruirsi nel tempo una solida reputazione in tale ambito specializzandosi nella costruzione di macchine capaci di adattarsi a svariate applicazioni e rifornendo costruttori d’impianti del calibro della tedesca Brückner. Il trattamento corona viene eseguito per aumentare la tensione superficiale dei film plastici, migliorando l’adesione su questi ultimi di inchiostri, rivestimenti e adesivi. Il suo ruolo fondamentale in specifici ambiti produttivi richiede quindi sistemi capaci di garantire un livello di affidabilità tale da non compromettere per nessuna ragione il funzionamento della linea di produzione. Robustezza, resistenza, affidabilità e massima integrazione con quest’ultima risultano quindi caratteristiche che Me.Ro considera imprescindibili per i propri sistemi, insieme a un’elevata personalizzazione per assecondare esigenze di volta in volta mutevoli a seconda dell’utilizzatore e dell’applicazione. L’ampio spettro di potenze dei generatori e di tipologie di stazioni di scarica consentono, infatti, di realizzare un trattamento corona perfettamente calibrato per ogni applicazione specifica, al quale si unisce una costante attenzione all’innovazione, che porta a una continua evoluzione dei prodotti. Me.Ro, infatti, non propone un catalogo “statico”, con un determinato numero di modelli, ma integra e aggiorna costantemente la propria offerta con novità e innovazioni tecnologiche per seguire in tempo reale l’andamento e le evoluzioni del mercato.
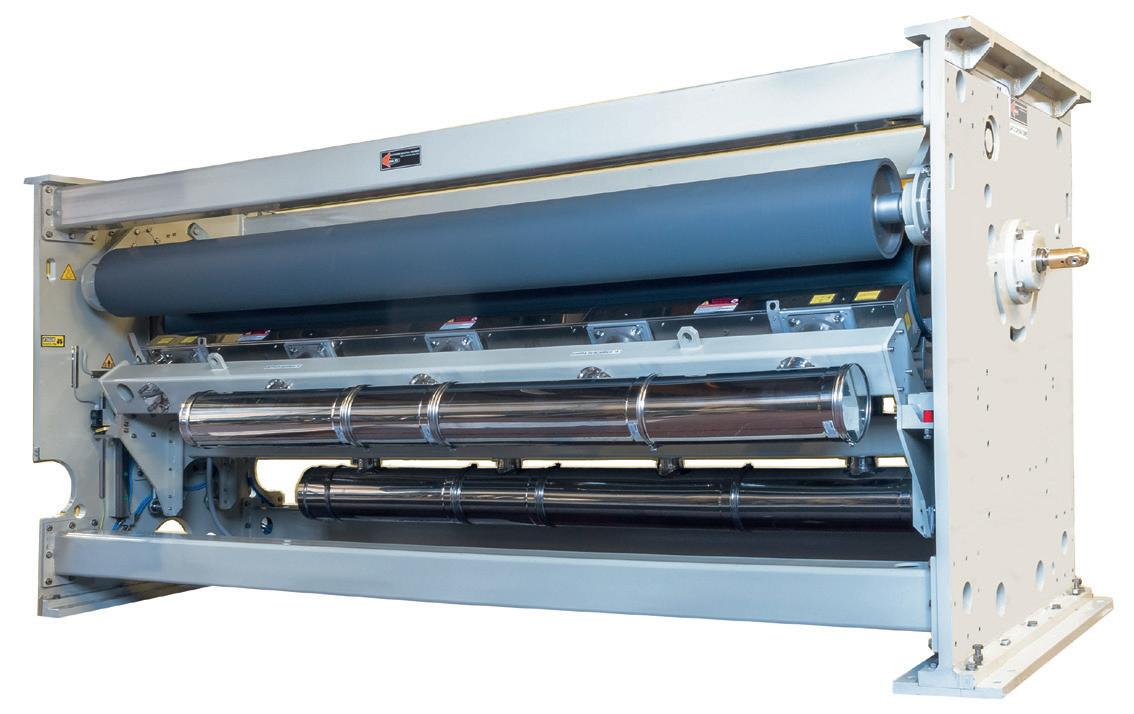

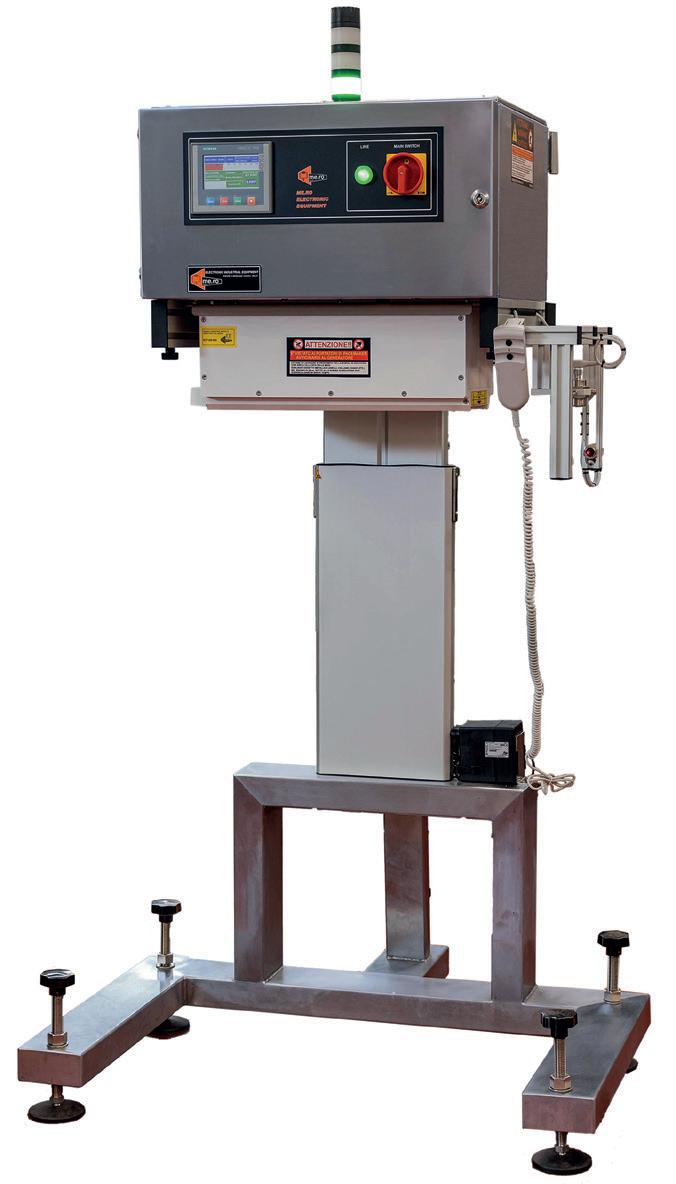
APPLICAZIONI
Uno dei settori su cui Me.Ro ha puntato di più e dove è presente dagli Anni Ottanta è quello delle linee per film biorientato in polipropilene, polietilene, poliestere e poliammide. L’azienda collabora ormai da oltre trent’anni con Brückner, costruttore tedesco di linee per film biorientato, cui fornisce i propri sistemi per il trattamento corona. Nel caso di clienti “storici”, di aggiornamenti degli impianti o di richieste specifiche, Me.Ro si rivolge anche direttamente alle aziende utilizzatrici dei suoi sistemi per individuare e fornire la soluzione più adatta. Al “core business” del film biorientato si affianca il settore del converting, con applicazioni su macchine per la stampa, accoppiatrici, laminatrici e spalmatrici. Un settore, quello del converting, che fino a una ventina di anni fa era secondario per l’azienda, ma che negli ultimi anni è cresciuto molto, spinto da richieste qualitative sempre più elevate. Altro settore storico per Me.Ro, seppure ancora in fase di espansione, è quello dell’estrusione con tecnologia a testa piana, in particolare di film in polipropilene, dove l’azienda vanta una competenza riconosciuta dai principali costruttori europei. Ultime ma non ultime, tra le destinazioni delle macchine del costruttore toscano rientrano le linee per l’estrusione di film in bolla. Oltre al trattamento corona, l’offerta di Me.Ro comprende anche sistemi per il trattamento al plasma sottovuoto e a pressione atmosferica. Quest’ultimo, di fatto, rappresenta una variante del trattamento corona e permette di ottenere risultati migliori su determinate tipologie di film, garantendo una maggiore durata della tensione superficiale e, quindi, una migliore adesione di inchiostri, colle ecc. I sistemi di trattamento al plasma sottovuoto operano invece in condizioni di alto vuoto e il trattamento superficiale viene eseguito tra lo svolgimento e la metallizzazione. Tale trattamento consente di ottenere una migliore adesione del metallo - o di altri rivestimenti realizzati con ossidi di alluminio o di silicio - e più elevate proprietà barriera. Il metallo, infatti, va a distendersi in maniera più uniforme, senza imperfezioni responsabili del passaggio di ossigeno e vapore acqueo attraverso la superficie metallizzata. Soprattutto nel settore dell’imballaggio alimentare, si sta assistendo alla tendenza a realizzare un rivestimento trasparente, in alternativa a quello con alluminio (il rivestimento per eccellenza per ottenere la barriera), utilizzando ossidi di alluminio o di silicio per ottenere appunto barriere trasparenti. Infine, Me.Ro è oggi uno tra i pochi costruttori italiani di macchine per la sigillatura a induzione, utilizzate per apporre un sigillo, appunto, nella parte interna dei tappi di flaconi per prodotti alimentari e bevande, farmaceutici, cosmetici, agricoli o industriali, e ottenere una barriera che impedisca sversamenti del contenuto. AGGIORNAMENTO COSTANTE
Il costruttore ha scelto un approccio basato sul costante aggiornamento della sua offerta, applicando alla propria produzione novità e innovazioni a livello di componentistica ed elettronica. Nel trattamento corona gli sforzi dell’azienda si sono da sempre concentrati nell’assicurare qualità, affidabilità e robustezza di generatori e stazioni di scarica. “Aziende che lavorano con impianti da 10 metri e mezzo di larghezza e con una produzione di 50 mila tonnellate annue di film non possono permettersi di fermare il processo per un malfunzionamento o una rottura del sistema per il trattamento corona. Per noi è quindi fondamentale assicurare la più totale affidabilità e robustezza a livello sia meccanico sia elettronico. Le nostre stazioni di scarica sono costruite con criteri di assoluta robustezza: nel caso di rottura del film su impianti da 650 metri al minuto, infatti, nella stazione di scarica entrerebbe una coda di film impressionante e con un impatto che, se l’elettrodo e la struttura della stazione non sono concepiti con determinate caratteristiche, danneggerebbe sicuramente l’intero dispositivo, con conseguenti problemi di uniformità di trattamento. Il nostro compito, quindi, è quello di assicurare il massimo della robustezza e dell’affidabilità e le scelte costruttive derivate dal settore del film biorientato vengono poi trasferite anche alle altre applicazioni”, spiega Armando Mennucci, direttore generale di Me.Ro. Un ulteriore punto di forza dell’azienda è rappresentato dall’ampia gamma disponibile di potenze dei generatori, da 1 a 125 kW (oltre 25 taglie),
Sistema di sigillatura a induzione
Sistema largo 10,5 metri per il trattamento corona di film BOPP
insieme alla possibilità di scegliere tra oltre 40 differenti stazioni di scarica a seconda dell’applicazione. Combinando le diverse taglie di generatori con la stazione di scarica più adatta è dunque possibile offrire una soluzione personalizzata e “ritagliata” sulla specifica applicazione. “Offrire una scelta così vasta è certamente oneroso, ma è il punto di forza che ci distingue. Le variabili in gioco sono infatti numerose: tipo, larghezza e velocità del film, solo per citarne alcune; noi siamo in grado di offrire il trattamento che meglio risponde alle specifiche caratteristiche dell’applicazione in questione. Questo, fino a qualche tempo fa, ci ha posto su una fascia di prezzo superiore rispetto a certi concorrenti, ma ultimamente siamo riusciti a ridurre significativamente la differenza di prezzo, adottando una politica commerciale più “battagliera”, pur mantenendo inalterata la qualità. Non abbiamo infatti nessuna intenzione di creare linee “low cost”, che si rivelerebbero un boomerang; al contrario, sfruttiamo tutto ciò che c’è di nuovo sul mercato per proporre macchine sempre più affidabili e performanti”, aggiunge Mennucci. L’azienda ha sempre spinto anche sulla gestione elettronica. Me.Ro è stata infatti la prima a integrare su macchine a rotocalco e accoppiatrici il sistema di gestione del trattamento corona a ricetta, evitando, quindi, di regolare di volta in volta i vari parametri in base al film e al trattamento richiesto: soluzione particolarmente utile nel converting. A questo si aggiunge la flessibilità di Me.Ro nell’adattare la configurazione dei propri dispositivi al layout esistente della macchina.
SERVIZI
Anche i servizi giocano un ruolo sempre più strategico e per questo Me.Ro dispone di uno staff di dieci tecnici pronti a muoversi in ogni momento per raggiungere sul posto gli utilizzatori delle sue macchine. Nel 2005 l’azienda ha aperto un proprio ufficio anche in Cina, così da seguire più da vicino il mercato asiatico, dove il numero di installazioni e impianti è sempre più consistente. Proprio il mercato asiatico, insieme a quello sudamericano ed europeo, traina le esportazioni, che continuano a rappresentare lo sbocco principale dei prodotti del costruttore: attualmente il 95% delle sue installazioni avviene sui mercati esteri.
NEWS
VITI E CILINDRI RESISTENTI
CONTRO LA CORROSIONE DEI FLUOROPOLIMERI
I gruppi vite e cilindro di Xaloy sono progettati per resistere agli effetti corrosivi dei fluoropolimeri nell’estrusione per l’isolamento di cavi e fili, soddisfacendo al tempo stesso i requisiti di lavorazione di materiali quali FEP e PVDF. I fluoropolimeri sono fra i materiali più corrosivi nell’estrusione standard e i nuovi gruppi vite e cilindro utilizzano materiali a elevata resistenza alla corrosione per tutti i componenti, oltre a includere viti progettate su misura per soddisfare la lavorazione a diverse temperature di FEP e PVDF e per specifiche singole esigenze di miscelazione. Nel caso delle viti resistenti alla corrosione del FEP vengono utilizzate leghe di nichelcromo Inconel per quanto riguarda l’acciaio base e leghe Colmonoy a base di nichel per la saldatura delle creste, ossia i filetti esposti all’usura. Per quelle resistenti alla corrosione di PVDF, il metallo base è costituito da acciaio legato o inossidabile 4140 HT con rivestimento in cromo. Per entrambe le viti, il costruttore propone un cilindro rivestito in Xaloy X-800, una lega a base di nichel a elevata resistenza alla corrosione e all’abrasione, con carburo di tungsteno, mentre le flange e la bocca di alimentazione sono realizzate in Inconel. I due fluoropolimeri hanno diversa temperatura di fusione: da 230 a 290°C il PVDF, da 360 a 380°C il FEP. Si tratta di un parametro decisivo per la progettazione della vite usata per applicazioni che richiedono la miscelazione con additivi, modificanti e coloranti. Per il FEP viene proposta una vite con miscelatore Xaloy Stratablend II, che effettua una miscelazione distributiva e dispersiva con una bassa deformazione. Un mixer è invece raccomandato per la miscelazione del PVDF, ma con l’aggiunta del profilo barriera Xaloy Efficient. Grazie alla sua concezione, la vite barriera separa la resina già fusa da quella ancora da fondere, evitando la sovradeformazione del PVDF già fuso e mantenendo bassa la temperatura di fusione dell’estruso nel suo complesso. Altre caratteristiche progettuali delle viti per la lavorazione di questi fluoropolimeri riguardano la lunghezza delle sezioni di alimentazione e di trasporto e il rapporto di compressione.
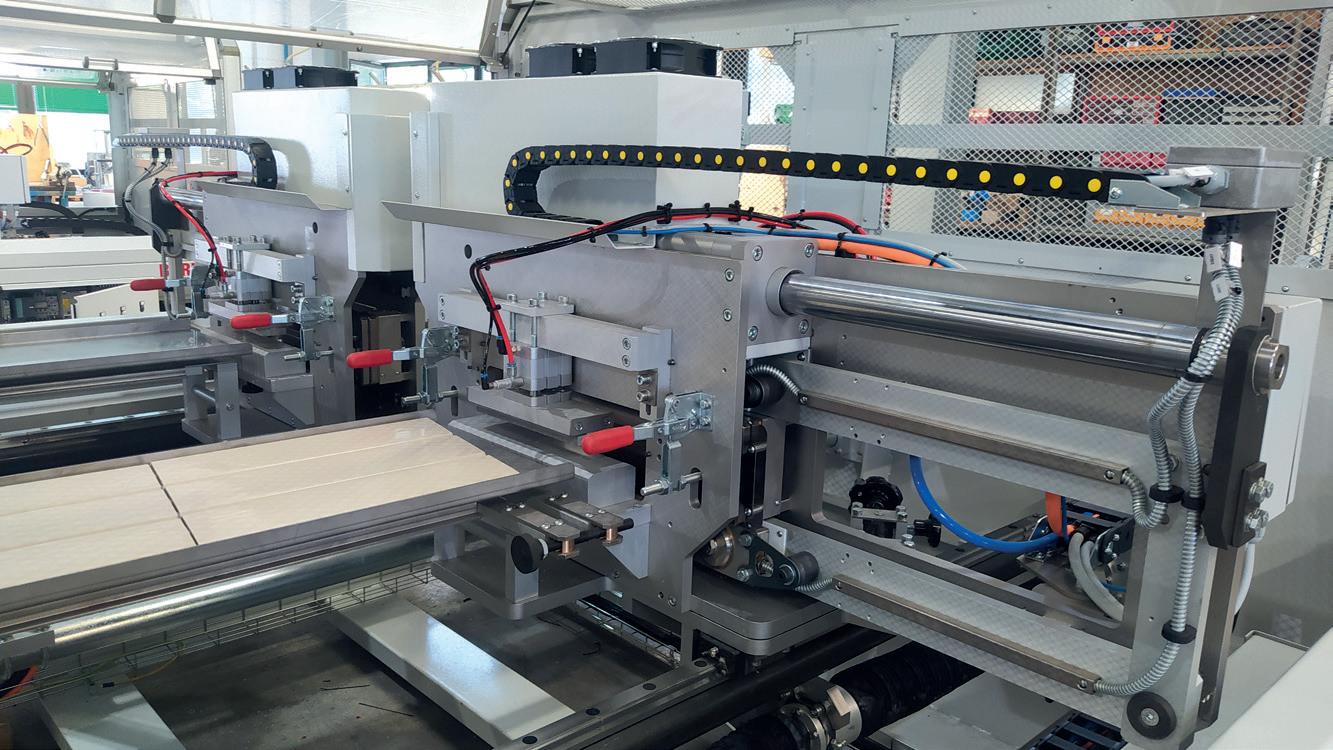
Vite con miscelatore Stratablend II per la lavorazione di FEP Sviluppi in casa Baruffaldi Fine linea evoluto

Un dettaglio delle due ghigliottine doppie
Tra i più recenti sviluppi in casa Baruffaldi Plastic Technology troviamo due nuove ghigliottine doppie a lama calda di taglie diverse, ognuna dedicata a profili in plastica provenienti da altrettante linee di estrusione affiancate. Le ghigliottine servoassistite possono eseguire anche tagli inclinati, grazie alla rotazione del gruppo di taglio, montato su un’apposita piastra metallica. Le ghigliottine doppie sono disponibili in taglie diverse a seconda delle dimensioni dei profili da tagliare: la sezione di taglio misura 100 x 200 mm e 200 x 300 mm rispettivamente nella versione più piccola e in quella più grande. La due unità, inoltre, possono essere personalizzate in base alle specifiche esigenze dell’utilizzatore. A marchio Primac l’azienda ha invece messo a punto il sistema iCut per il taglio di tubi, che si differenzia dai sistemi tradizionali per l’assenza della lama planetaria. Le dimensioni ridotte migliorano la dinamica e consentono di tagliare tubi molto corti a elevata velocità senza asportazione di materiale, evitando così la produzione di polvere. Questo sistema si contraddistingue anche per un consumo energetico molto basso e un taglio rapido, che garantisce un prodotto finale senza bave o sfridi, esaltando la qualità della superficie. Tra i vantaggi di questa unità rientra il ridotto numero di parti mobili, che si traduce in una minore manutenzione, nonché in una maggiore precisione e flessibilità applicativa. Tra i nuovi progetti di Baruffaldi rientra una nuova versione di punzonatrice pneumatica ad alta velocità, che, parte di un sistema di assemblaggio per avvolgibili in alluminio, è stata implementata anche per le linee per l’estrusione di profili in plastica. Mentre questa unità è destinata a profili di spessore ridotto, per quelli più spessi Baruffaldi ha messo a punto la punzonatrice idraulica rinforzata POVI 3000, con due teste di punzonatura. Per la punzonatura e la coniatura, in linea e non, di canaline elettriche, invece, il costruttore ha sviluppato un pallettizzatore automatico dotato di manipolatore con due pinze rotanti che si muovono verticalmente e orizzontalmente, prelevano le canalette e le ruotano di 180° per depositarle in maniera ordinata. La macchina può accoppiare ordinatamente le canaline per facilitare l’inscatolamento manuale da parte dell’operatore.
NEWS
Mast tra tradizione e modernità Al passo con i tempi da cinquant’anni
Con oltre cinquant’anni di attività alle spalle - il traguardo del mezzo secolo è stato tagliato nel 2017 - Mast rappresenta al meglio le piccole-medie imprese che costituiscono la forza del tessuto industriale e produttivo italiano: quelle a conduzione familiare (nella fattispecie, alla guida di Mast vi sono Carlo e Marco Arioli, figli del fondatore Marino Arioli) e terziste, ossia che lavorano per lo più, ma non esclusivamente, per altre grandi aziende e che, per questo, devono possedere un know-how ampio e approfondito dei prodotti che escono dai propri reparti. In poche parole, aziende che per tradizione e tipo di attività sanno fare le cose e le sanno fare bene. Appunto come avviene in Mast, e non potrebbe essere altrimenti, visto che i suoi prodotti sono viti e cilindri installati prevalentemente sulle linee di estrusione e, in quanto tali, richiedono inderogabilmente una fattura accurata e un’estrema precisione. Di cui, infatti, non difettano. Ma l’azienda sta assumendo anche quella caratteristica che è sempre più importante per essere competitiva nell’era dell’Industria 4.0 e che in molti casi è trasversale alla più classica categorizzazione in piccola, media e grande impresa, ossia sta diventando anche veloce, come sempre più vuole il mercato odierno. Veloce nell’adattarsi a nuove abitudini, e tutti sanno quanto queste siano cambiate negli ultimi mesi; veloce nel capire le esigenze sempre più stringenti dei clienti; veloce nell’anticipare gli sviluppi tecnologici e tradurli in innovazione. Insomma, capace di adattarsi al cambiamento ma senza snaturarsi, il che vuol dire guardare indietro a quello che si è fatto e avanti verso dove si vuole andare. Ed è quello che sta accadendo in Mast. Effettivamente si tratta di un’azienda che ben rappresenta il cosiddetto terziario avanzato e in questa veste deve essere sempre pronta ad assecondare ogni nuova esigenza, raccogliendo le specifiche tecniche dei committenti per soddisfare le loro richieste, e in grado di sviluppare i processi produttivi più idonei per arrivare a fornire viti e cilindri che assicurino, per esempio, le tolleranze e i gradi di finitura richiesti: caratteristiche sempre più stringenti. Tutto

Vite rigenerata con riporto antiusura
ciò, inoltre, utilizzando spesso nuovi tipi di acciaio, come quelli ottenuti per sinterizzazione delle polveri, i cosiddetti “HIP”, i quali, oltre a essere particolarmente costosi, richiedono utensili e processi di lavorazione specifici. Per tutto questo risultano funzionali investimenti continui, compiendo “passi” alcune volte un po’ più lunghi ed economicamente impegnativi, come nel caso dei recenti acquisti di una nuova macchina per la rettifica tangenziale o di un nuovo centro di lavoro per i cilindri, altre un po’ più corti, ma sempre significativi per l’efficientamento, come l’altrettanto recente ristrutturazione di una foratrice per cilindri. Senza dimenticare il continuo aggiornamento degli strumenti di misura, dei vari utensili o dei sistemi CAD-CAM in uso nei reparti dell’azienda. Nel contempo, prosegue il progetto per realizzare il nuovo sito produttivo, anche se l’emergenza Covid-19 tuttora in corso non sta rendendo facili le cose.
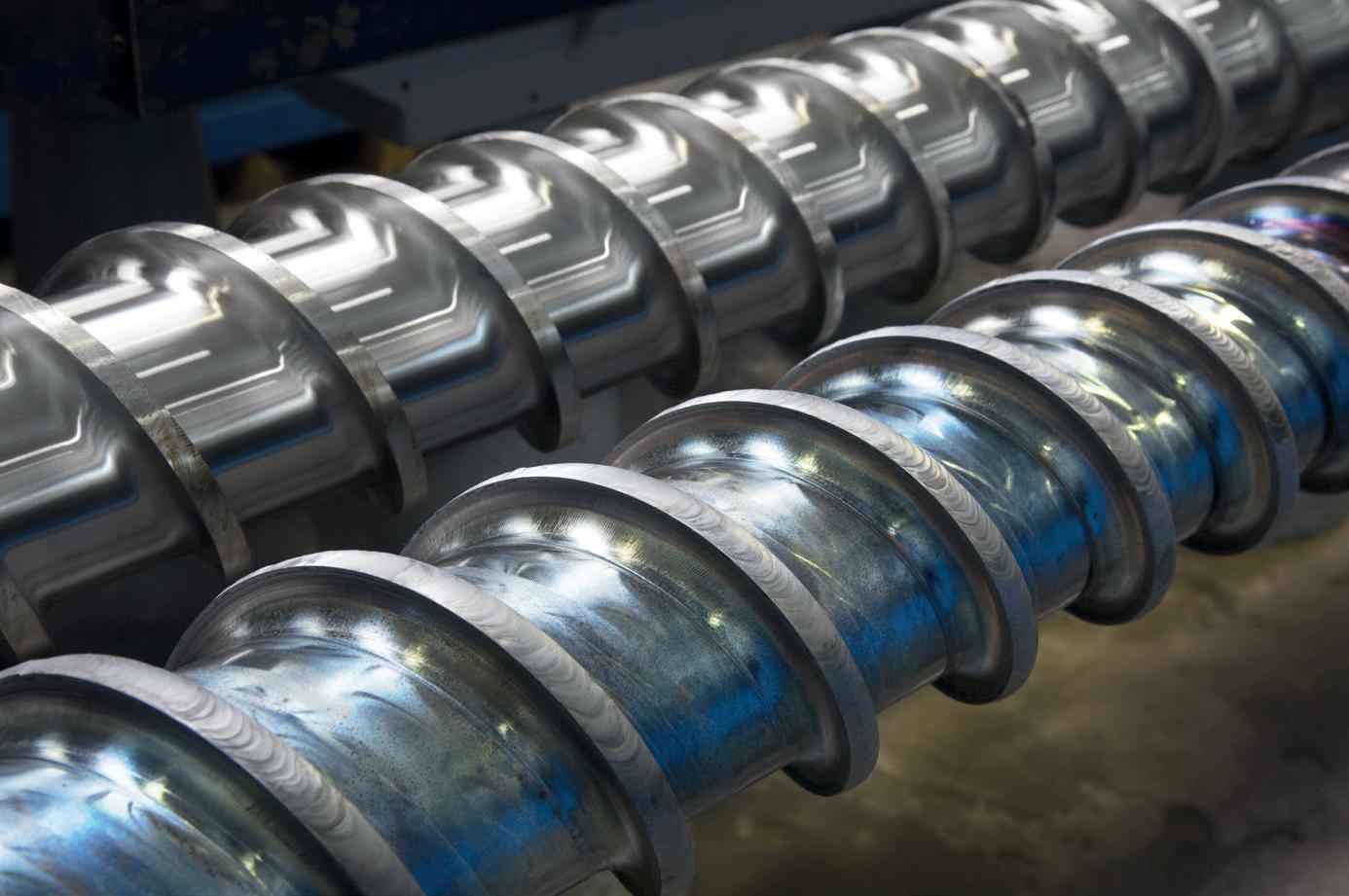

AQW di Evosys Saldatura quasi simultanea
La nuova tecnologia AQW (Advanced Quasi-Simultaneous Welding) per la saldatura quasi simultanea lanciata da Evosys Laser consente di aumentare l’efficienza e ridurre i costi di processo. Già nella sua forma abituale, la saldatura laser delle materie plastiche rappresenta un processo estremamente economico ed è oggi utilizzata in quasi tutti i settori industriali. Con il nuovo processo AQW è stato inoltre raggiunto l’obiettivo di implementare l’efficienza e l’affidabilità per alcune materie plastiche selezionate. Il nuovo processo sfrutta le proprietà di assorbimento delle materie plastiche e combina due diverse lunghezze d’onda che vengono alternativamente guidate nella zona di saldatura in maniera controllata. Le prove effettuate con la saldatura AQW evidenziano un miglioramento dei tempi di processo rispetto alle tecniche standard con una sola sorgente laser. Il nuovo processo può essere applicato a materiali come il PC, ma anche altre plastiche comuni potrebbero rivelarsi idonee in futuro. Parallelamente al processo di concessione del brevetto, è, stata sviluppata e ottimizzata per l’uso in serie anche la tecnologia di sistema necessaria per il processo AQW. “I nostri clienti possono testare il processo nel nostro centro tecnico in qualsiasi momento, per utilizzarlo in futuro nelle loro produzioni di serie”, ha spiegato Frank Brunnecker, managing partner di Evosys Laser.
I componenti automobilistici come la fanaleria posteriore sono tra le applicazioni possibili del nuovo processo di saldatura AQW
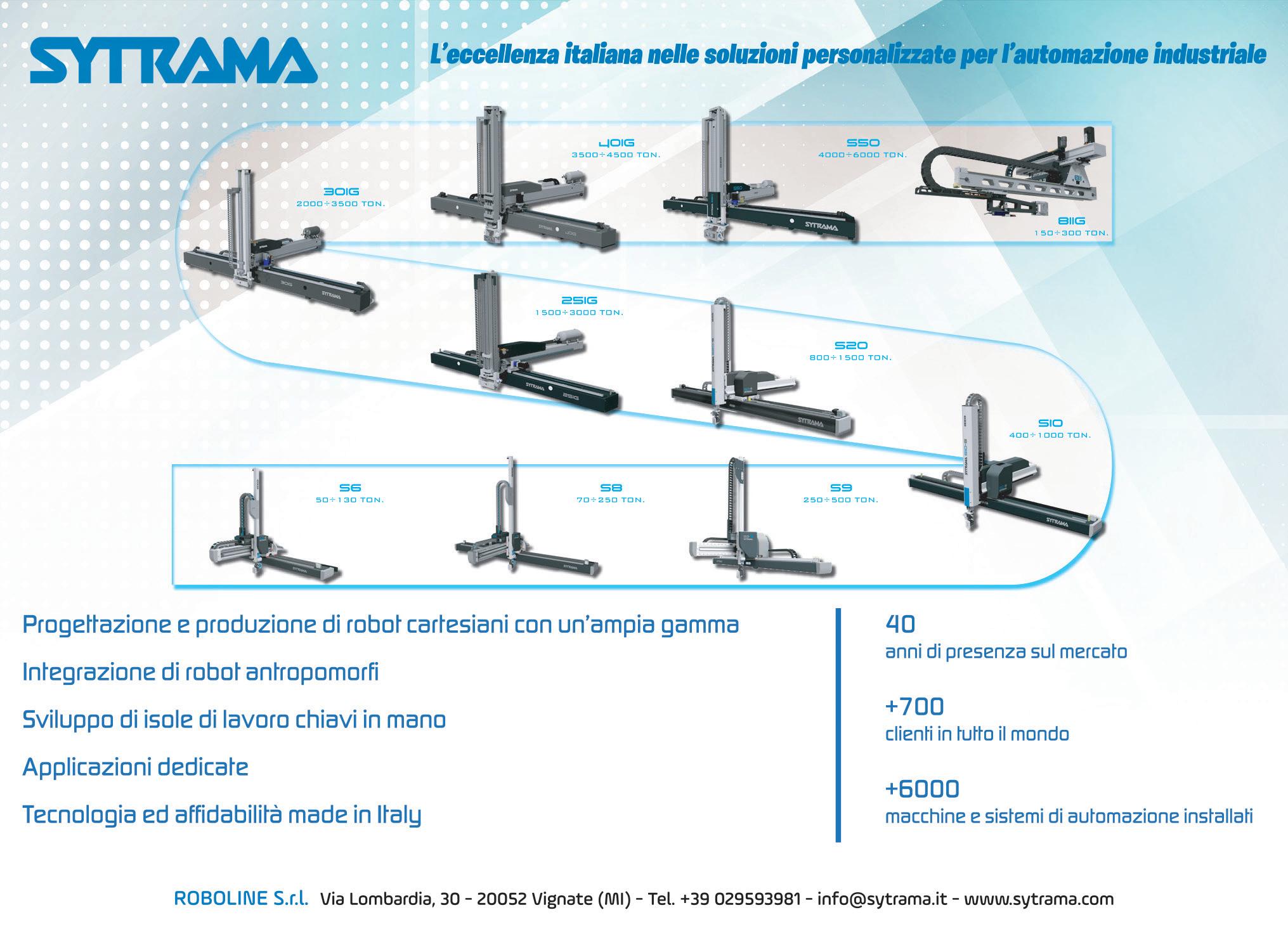
INTERVISTA A TOMRA SORTING RECYCLING
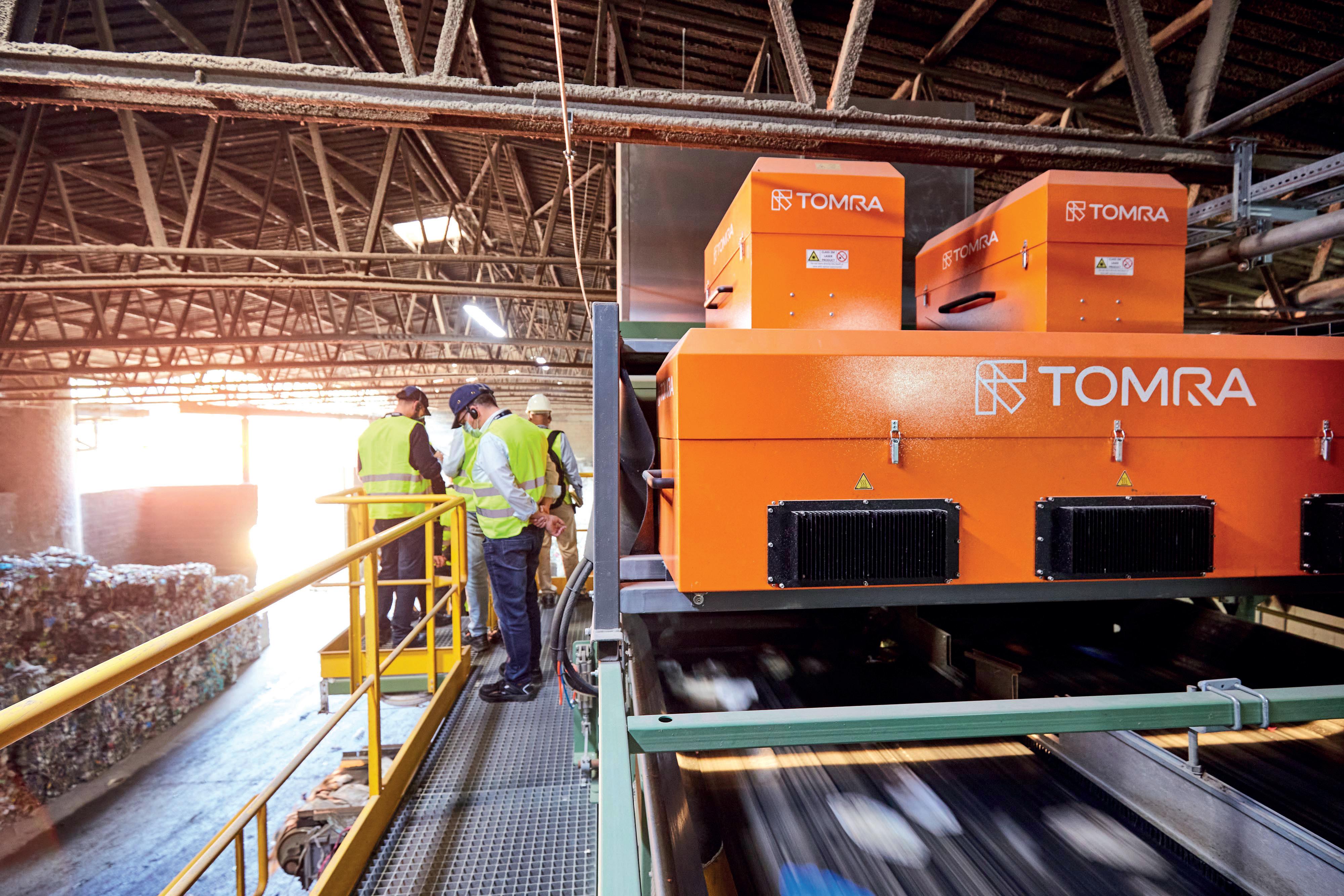
SELEZIONE SENZA FRONTIERE DI RIFIUTI PLASTICI
TOMRA SORTING RECYCLING È UNA MULTINAZIONALE COSTRUTTRICE DI IMPIANTI DESTINATI A PIÙ SETTORI, TRA I QUALI LA SELEZIONE PER IL RICICLO DI MATERIE PLASTICHE. IN QUALITÀ DI PIONIERE IN QUESTO SETTORE, DISPONE OGGI DI UNA TECNOLOGIA AVANZATA DI SELEZIONE A SENSORI CHE NE FA UN PUNTO DI RIFERIMENTO A LIVELLO MONDIALE
DI GIAMPIERO ZAZZARO, LUCA MEI ED ERMANNO PEDROTTI
Migliorare la gestione e il riutilizzo dei rifiuti in plastica è diventata la vera sfida dei nostri tempi, che impegna senza sosta mondo della politica, amministrazioni centrali e locali, collettività e industria di settore. Oggi, ogni attore è chiamato direttamente in causa a fare la propria parte allo scopo di instaurare un flusso virtuoso lungo il quale si parta da una risorsa e si ritorni a una risorsa in un ciclo chiuso. In questo ambito, materiali avanzati, manufatti con essi prodotti e tecnologie per il loro recupero e riutilizzo giocano tutti un ruolo primario per protrarre quanto più possibile, e tendenzialmente all’infinito, la riciclabilità dei beni per dar vita a un sistema in grado di autoalimentarsi, riducendo, se non azzerando, l’utilizzo di nuove risorse: in poche parole, per realizzare quella che viene definita economia circolare. Tra i protagonisti di tale scenario troviamo Tomra Sorting Recycling, multinazionale che costruisce impianti per il riciclo con selezione a sensori. Questa tecnologia è capace di garantire rese elevate con un’ampia varietà di flussi di materiali grazie a una spiccata flessibilità applicativa, che si traduce in elevate efficienza e qualità di prodotto. Recentemente l’azienda ha avviato a Parma un nuovo centro prove per la selezione e lo smistamento di scaglie riciclate, che si è andato ad aggiungere a quelli già attivi in Cina, in Corea del Sud, in Germania, in Giappone e negli Stati Uniti. A questo proposito abbiamo incontrato Alessandro Granziera, responsabile commerciale per l’Italia, che ha risposto ad alcune nostre domande sulla nuova struttura, ma anche sul mercato di riferimento in Italia e nel mondo e sulle strategie dell’azienda, in particolare nel nostro Paese. Lasciamo quindi la parola a lui, ringraziandolo per la disponibilità.
IL NUOVO CENTRO INAUGURATO A PARMA SI INQUADRA NELL’AMBITO DEL PROGRAMMA DI TOMRA PER LO SVILUPPO DI SOLUZIONI PER LA SELEZIONE DEI MATERIALI DA RICICLARE. CI PUÒ ILLUSTRARE A QUALI ATTIVITÀ
SPECIFICHE VERRÀ DESTINATA QUESTA STRUTTURA?

“La scelta di inaugurare la nuova struttura presso la nostra filiale italiana a Parma rappresenta un tipico modus operandi di Tomra Recycling, ossia quello di investire e di farlo in maniera crescente nel settore della plastica, ovvero nella selezione delle scaglie. In particolare, abbiamo ritenuto necessario ampliare le possibilità per i nostri clienti di effettuare test, incrementando il numero di centri di riferimento in Europa, il principale dei quali si trova a Langenfeld, presso la sede tedesca di Tomra. Per questo, quindi, a Parma abbiamo deciso di installare anche alcune unità per la selezione delle scaglie”.
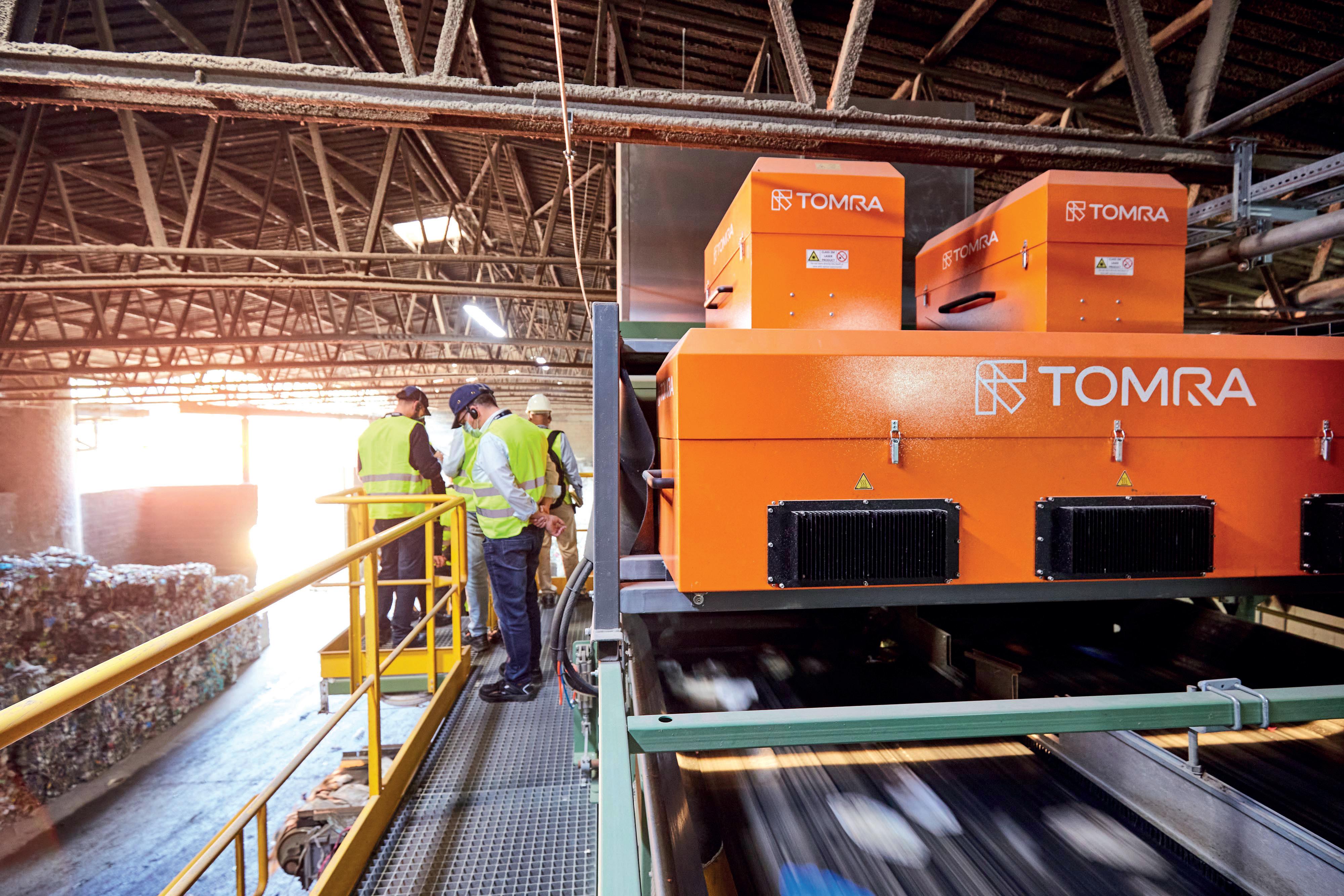
A PROPOSITO DEGLI IMPIANTI DEDICATI ALLA SELEZIONE DELLE SCAGLIE, A PARMA SONO STATI INSTALLATI I VOSTRI SISTEMI INNOSORT FLAKE E AUTOSORT FLAKE. QUALI SONO LE LORO CARATTERISTICHE TECNOLOGICHE DI PUNTA, ANCHE IN RELAZIONE AI MATERIALI DA TRATTARE?
“Autosort Flake e Innosort Flake sono due piattaforme dotate di tutti gli optional disponibili sul mercato, in maniera tale da poter effettuare test di qualsiasi tipologia. Di fatto, dal punto di vista dei polimeri, è possibile trattare PET, poliolefine (quindi PE e PP), ma anche PS e PVC. Questi due impianti permettono di lavorare sulle contaminazioni dei materiali in base a polimero, colore e metallo, singolarmente o su tutti questi aspetti contemporaneamente, e, allo stesso tempo, sono in grado di lavorare secondo processi che prevedono anche più di un passaggio. Alcune lavorazioni, infatti, possono richiedere un passaggio in una prima macchina di sgrossatura e una lavorazione successiva in un’altra apparecchiatura, in modo da garantire che la qualità finale del materiale sia in linea con le esigenze del cliente. A questo riguardo, inoltre, tengo a precisare che è anche possibile partire da contaminazioni molto elevate del materiale”.
Alessandro Granziera mentre risponde alle domande poste dalla redazione di MacPlas
CI PUÒ ILLUSTRARE LO STATO DI SALUTE DEL MERCATO DEL RICICLO IN ITALIA E NEL MONDO? IL SETTORE STA RISENTENDO DELLA CARENZA DI MATERIE PRIME E IL RICICLO PUÒ RAPPRESENTARE UNA SOLUZIONE A QUESTO PROBLEMA?
“In questo periodo, lo stato di salute del mercato della selezione e del riciclo, in generale, è decisamente buono. Naturalmente ci sono diversi fattori trainanti, legati alcuni ai costi del materiale, altri a diverse disposizioni legislative, in Italia come nel resto del mondo. In particolare, da circa un anno c’è anche una forte pressione da parte della società civile, che è sempre più attenta alla tutela dell’ambiente e ad aspetti con un forte impatto emotivo, come, per esempio, la presenza della plastica negli oceani. Questi temi piuttosto scottanti suscitano molto interesse verso tutte le tecnologie dedicate al recupero e alla valorizzazione dei materia-
La nuova struttura di Parma Un centro prove per essere sempre più glocal
Nell’ambito del proprio programma di sviluppo di soluzioni per la selezione dei materiali da riciclo, Tomra ha inaugurato a Parma il nuovo centro prove dedicato allo smistamento delle scaglie nel processo di recupero dei materiali plastici, per ampliare i suoi servizi e le applicazioni dei materiali riciclati. Situato in una delle aree industriali e produttive più importanti d’Europa, il nuovo centro prove offre vari servizi. A seconda dell’applicazione, è possibile testare PO, PET e PVC in scaglie sui sistemi Innosort Flake e Autosort Flake di Tomra, per determinare le configurazioni dei sensori di smistamento e, di conseguenza, la soluzione impiantistica più adatta a ciascuna esigenza. Utilizzato in precedenza principalmente per il PET, il sistema Innosort Flake è oggi dotato di un sensore specifico per scaglie di poliolefine con pezzatura fino a 2 mm, per la selezione anche in flussi di rifiuti altamente contaminati. Questa miglioria non mira solo a incrementare i tassi di recupero e i rendimenti dei processi di riciclo di materie plastiche, ma anche ad aumentare la purezza dei riciclati, massimizzare l’efficienza operativa degli impianti e ridurre al minimo fermo macchina e costi. “La domanda di materiali plastici riciclati di alta qualità è elevata, ma i bassi tassi di riciclo lasciano ancora aperte opportunità non sfruttate. Con il nostro nuovo centro prove non solo puntiamo a soddisfare la crescente domanda di test sullo smistamento delle scaglie, ma offriamo adesso una struttura in cui sviluppare nuove applicazioni, al servizio delle tendenze di mercato attuali e future”, ha commentato Alberto Piovesan, direttore del segmento plastica dell’azienda per le aree Emea e America. “Uno dei motivi per cui abbiamo investito nel nuovo centro prove di Parma è quello di servire i nostri clienti locali e internazionali in modo più flessibile ed esteso. Inoltre, fa parte della nostra strategia quinquennale nell’ambito delle materie plastiche, che prevede una forte attenzione alla ricerca e allo sviluppo e all’aumento del nostro personale specializzato”, ha aggiunto Fabrizio Radice, vicepresidente e direttore vendite e marketing a livello globale di Tomra.
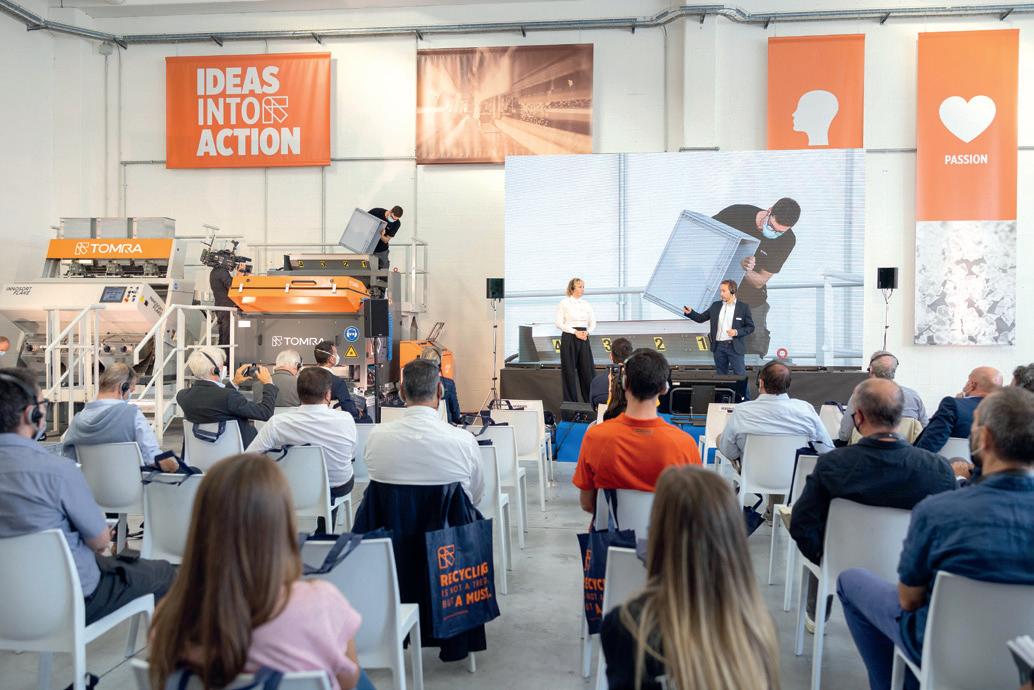
Un momento dell’inaugurazione del centro prove di Parma
li. A tale proposito, vorrei sottolineare che una pressione come questa da parte della società civile non si era mai vista prima. La questione sociale fa sì che i titolari di importanti marchi, quindi i grandi consumatori di plastica, così come di carta e di metallo, comincino a investire sempre di più nelle tecnologie per il riciclo, anche per poter appunto garantire che i propri prodotti finiti contengano una quantità di materiale riciclato sempre maggiore. A questo riguardo ci sono diverse spinte, in particolare legislative, che obbligano i produttori di imballaggi a recuperare una parte sempre più elevata del materiale utilizzato per il prodotto finito. Inoltre, va considerato che, in futuro, una certa pressione dal punto di vista sociale potrà comportare l’ingresso di nuovi attori nel mercato della selezione e del riciclo”.
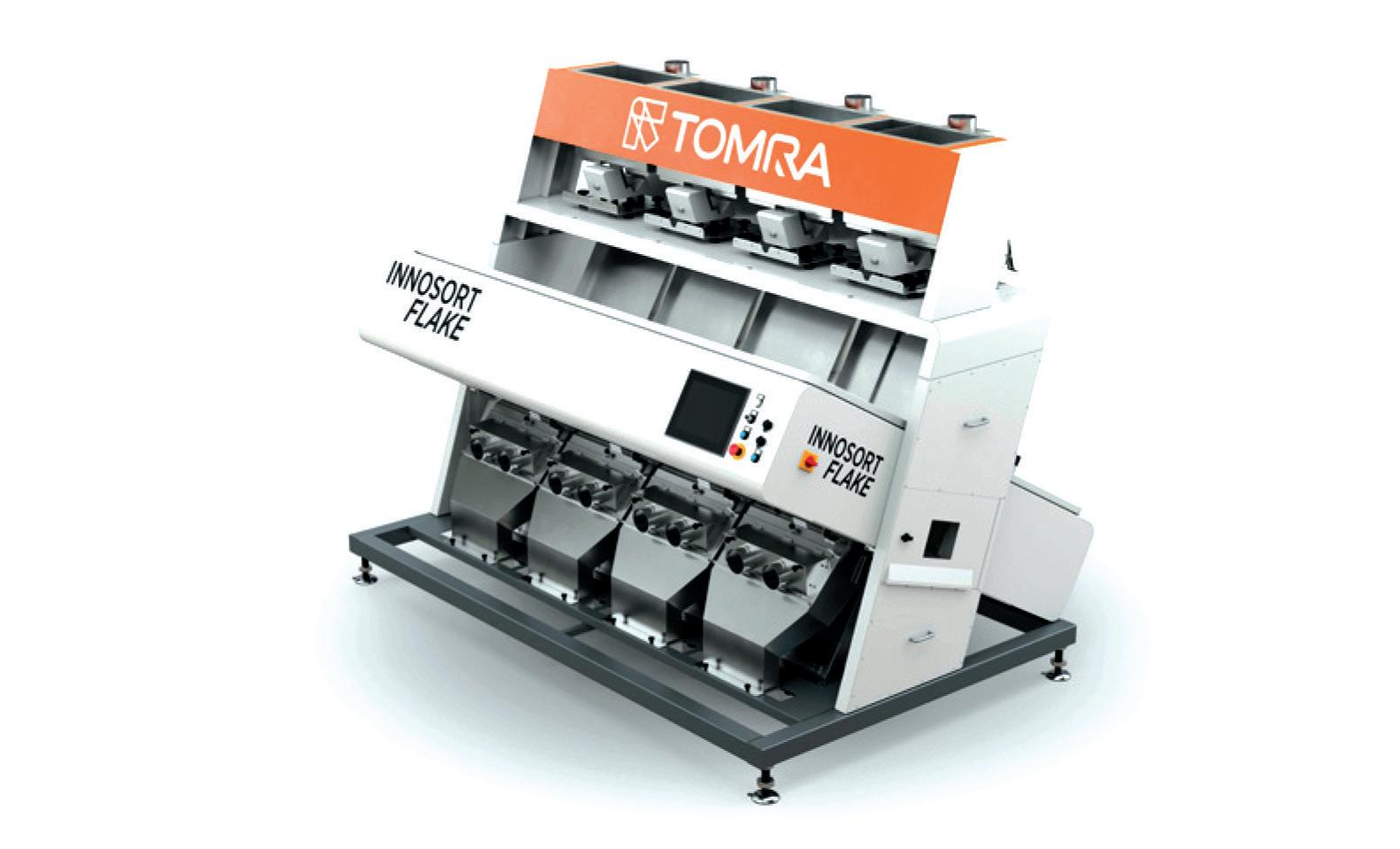
DAL 3 AL 6 MAGGIO PROSSIMI SI SVOLGERÀ A FIERA MILANO LA PRIMA EDIZIONE DI GREENPLAST, FIERA DEDICATA AL MONDO DEL RICICLO A TUTTO TONDO. CI PUÒ DIRE SE VI SIETE GIÀ ISCRITTI ALL’EVENTO E, SECONDO LEI, CHE CONTRIBUTO POSSONO OFFRIRE ALLA TRANSIZIONE ECOLOGICA LE TECNOLOGIE PER LA LAVORAZIONE DI MATERIE PLASTICHE E GOMMA E, IN PARTICOLARE, QUELLE PER IL RICICLO?
Le due macchine installate nel centro prove di Parma: Innosort Flake (a sinistra) e Autosort Flake
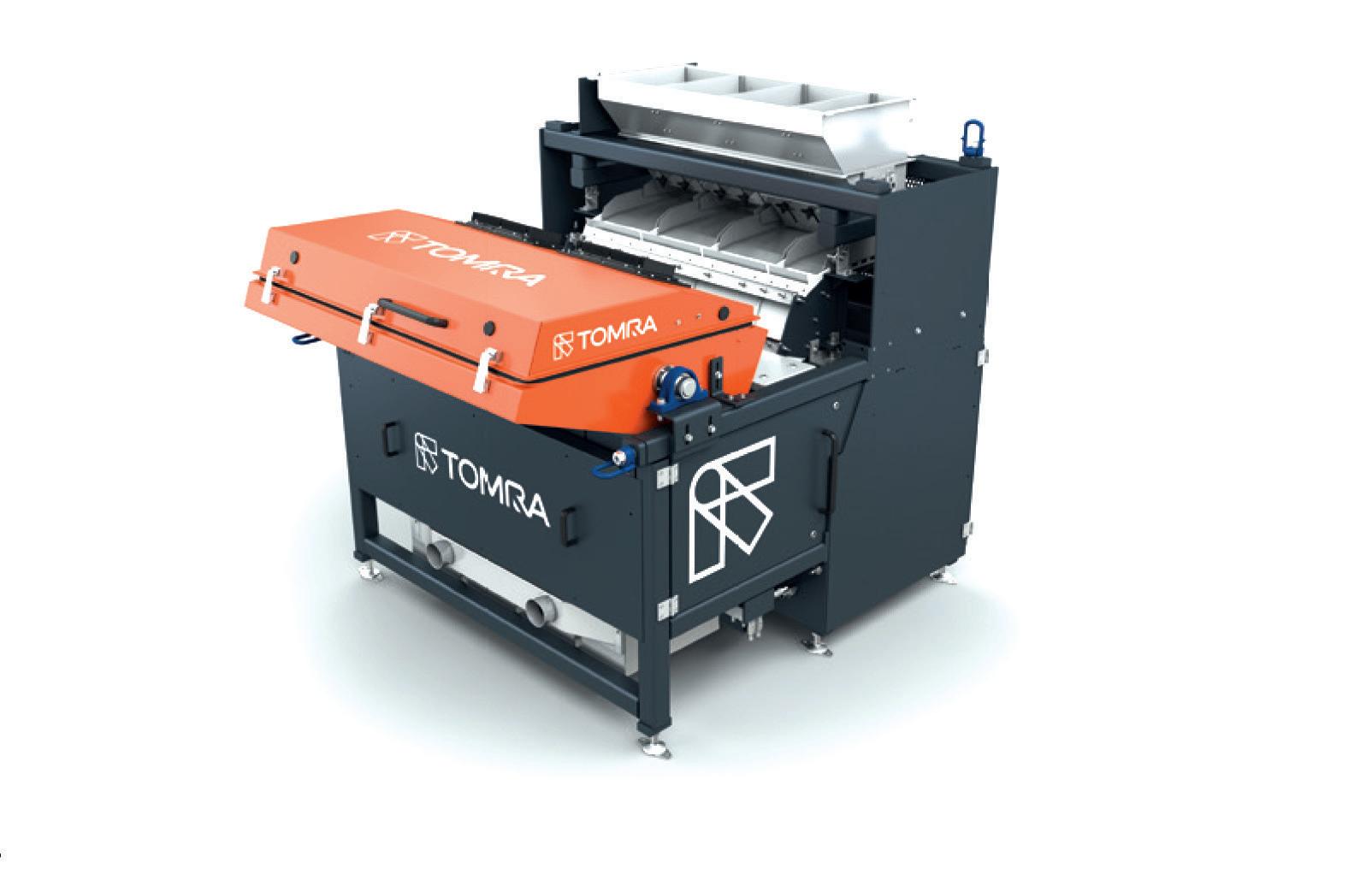
“A Greenplast parteciperemo attivamente. Come ogni appuntamento fieristico, anche questo nuovo evento sarà per noi importante per incontrare i clienti, discutere progetti, presentare innovazioni tecnologiche e ampliare la rete dei nostri contatti. Per ciò che concerne la transizione ecologica, la tecnologia di Tomra rappresenta il “cervello” degli impianti, nell’ambito sia della selezione sia del riciclo. In entrambi i casi, le soluzioni della nostra azienda prevedono il coinvolgimento di un gran numero di apparecchiature, ognuna con la sua specifica funzione. Per quanto riguarda l’identificazione dei diversi componenti del rifiuto e la purificazione del materiale, la selezione ottica è stata, è e sarà una delle tecnologie principali nell’ambito della selezione dei materiali e del riciclo”.

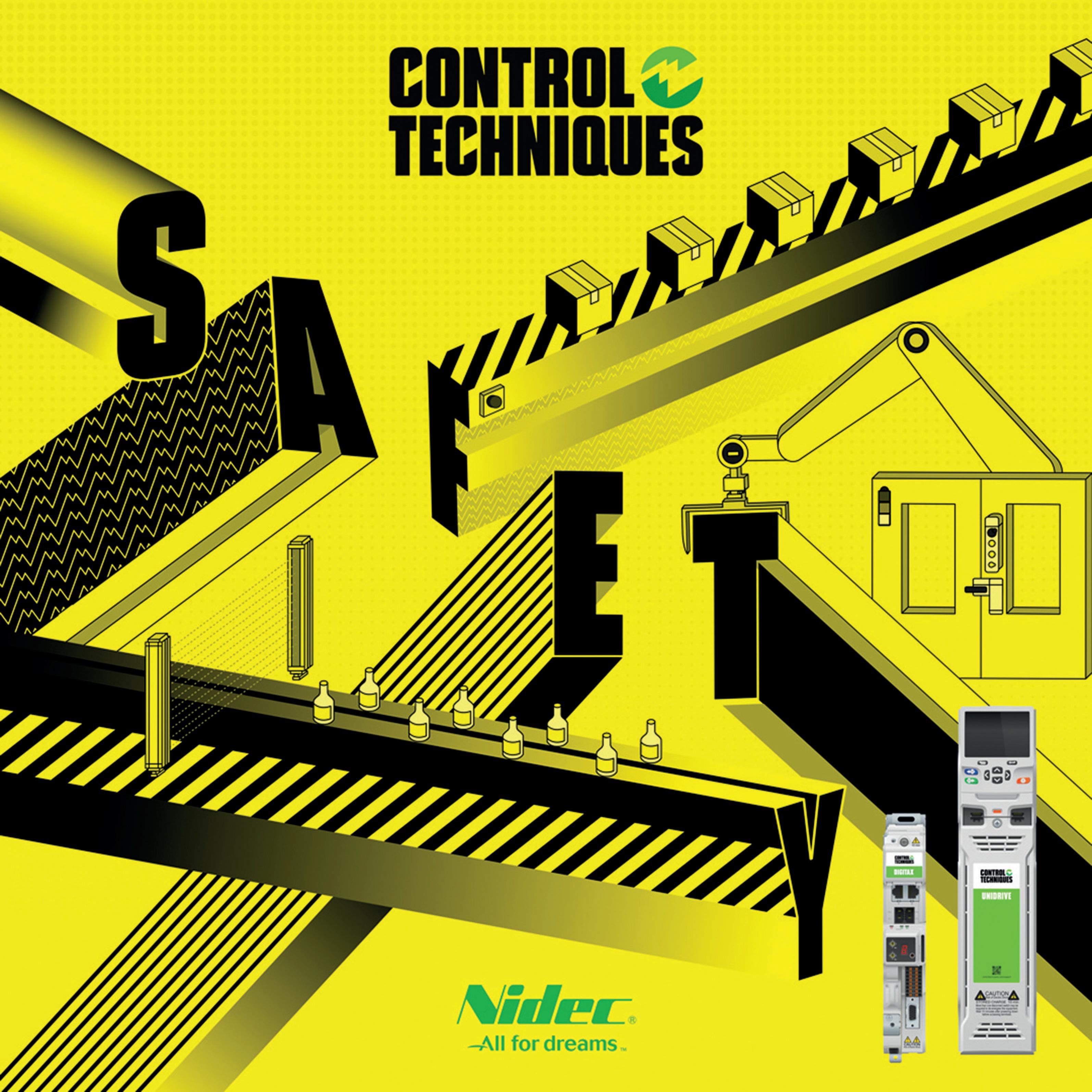
NEWS
I dispositivi Unidrive e Digitax Soluzioni di Control Techniques Sicurezza integrata
I moderni processi industriali si trovano ad affrontare la richiesta costante di una maggiore capacità produttiva e di una riduzione dei guasti delle macchine, garantendo al contempo salute e sicurezza degli operatori. Ecco allora che la sicurezza integrata diventa il nuovo paradigma dei sistemi di produzione e modernizzare la progettazione di questi ultimi è il nuovo standard per aumentare efficienza e disponibilità d’uso in tutti i settori. Le soluzioni proposte da Control Techniques (azienda di Nidec) sono sviluppate per garantire la massima flessibilità nella progettazione funzionale e nella scelta di componenti e protocolli da integrare. Unidrive e Digitax offrono ingressi integrati Safe Torque Off (STO) doppi, conformi a SIL3 / PLe, che consentono una soluzione più elegante e affidabile rispetto ai tradizionali contattori del motore. I moduli opzionali MiS210 ed MiS250 estendono la funzione integrata STO con la capacità di monitorare e/o limitare il campo del motion. La sicurezza integrata supporta la decentralizzazione delle funzioni di sicurezza del motion di una macchina, offrendo vari vantaggi: riduce complessità e tempo di progettazione e posa del cablaggio, facilita la messa in servizio e interviene rapidamente, riducendo anche i costi complessivi da sostenere. Un ingresso STO integrato disinserisce la coppia al motore in modo sicuro, senza la necessità di contattori esterni. L’aggiunta di un modulo opzionale Safety MiS2x0 consente un monitoraggio sofisticato del motion direttamente nell’azionamento, attraverso l’encoder esistente del motore. MiS210 ed MiS250 supportano vari protocolli encoder e fino a quattro diversi canali collegabili all’azionamento, così come tutti i principali standard industriali per la facile integrazione in qualsiasi architettura di automazione. Il supporto del protocollo Safe EnDat riduce ulteriormente i costi grazie ai minori cablaggi e all’assenza di dispositivi di retroazione aggiuntivi, non più necessari.
Plastlab a Samuplast Offerta ampliata
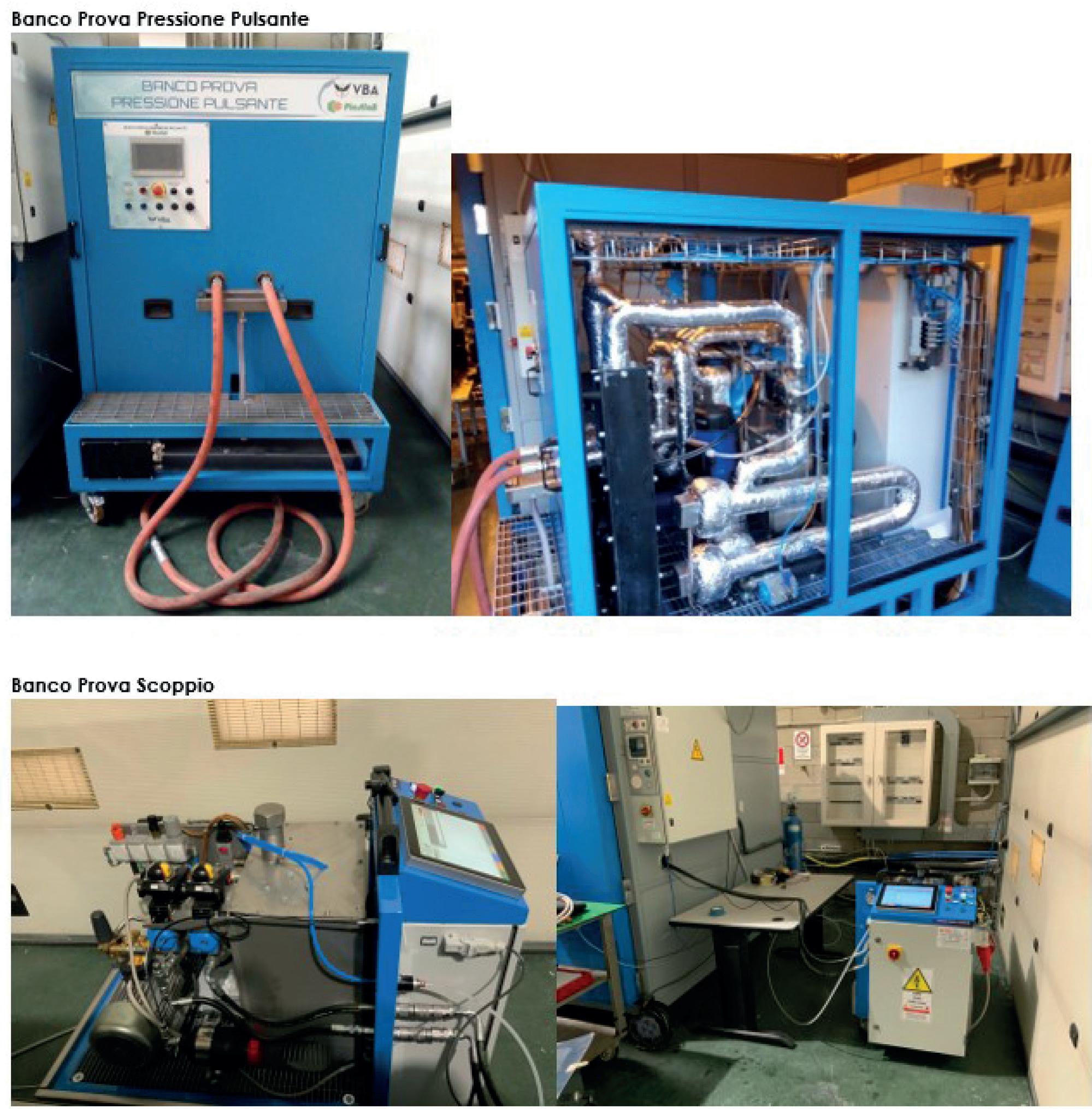
Alla fiera Samuplast (Pordenone, 31 marzo-2 aprile), Plastlab presenterà le nuove attrezzature installate presso la sua sede di Orbassano (Torino). Si tratta di un banco per prove di pressione pulsante, di uno per prove di scoppio su tubi ad aria e glicole e di una cella multifunzione da 1200 litri dotata di shaker per test di vibrazione. L’investimento di circa 500 mila euro, completato nel 2021, rientra nella strategia di sviluppo della struttura piemontese, che ha avviato un piano di interventi per dotarsi di nuovi macchinari e attrezzature al fine di allargare i servizi offerti legati alle prove.
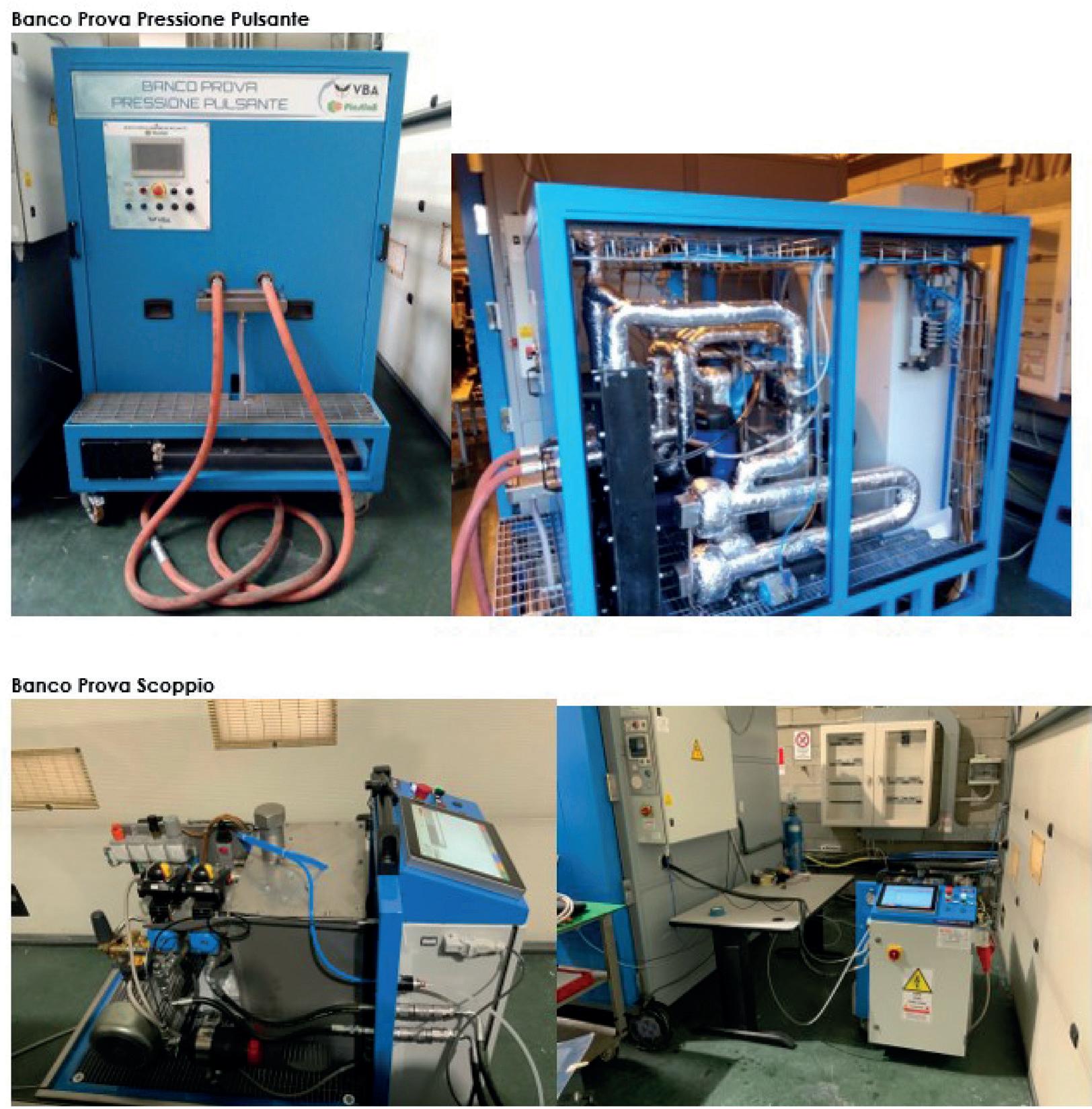
Una delle attrezzature di cui è dotato Plastlab a Orbassano
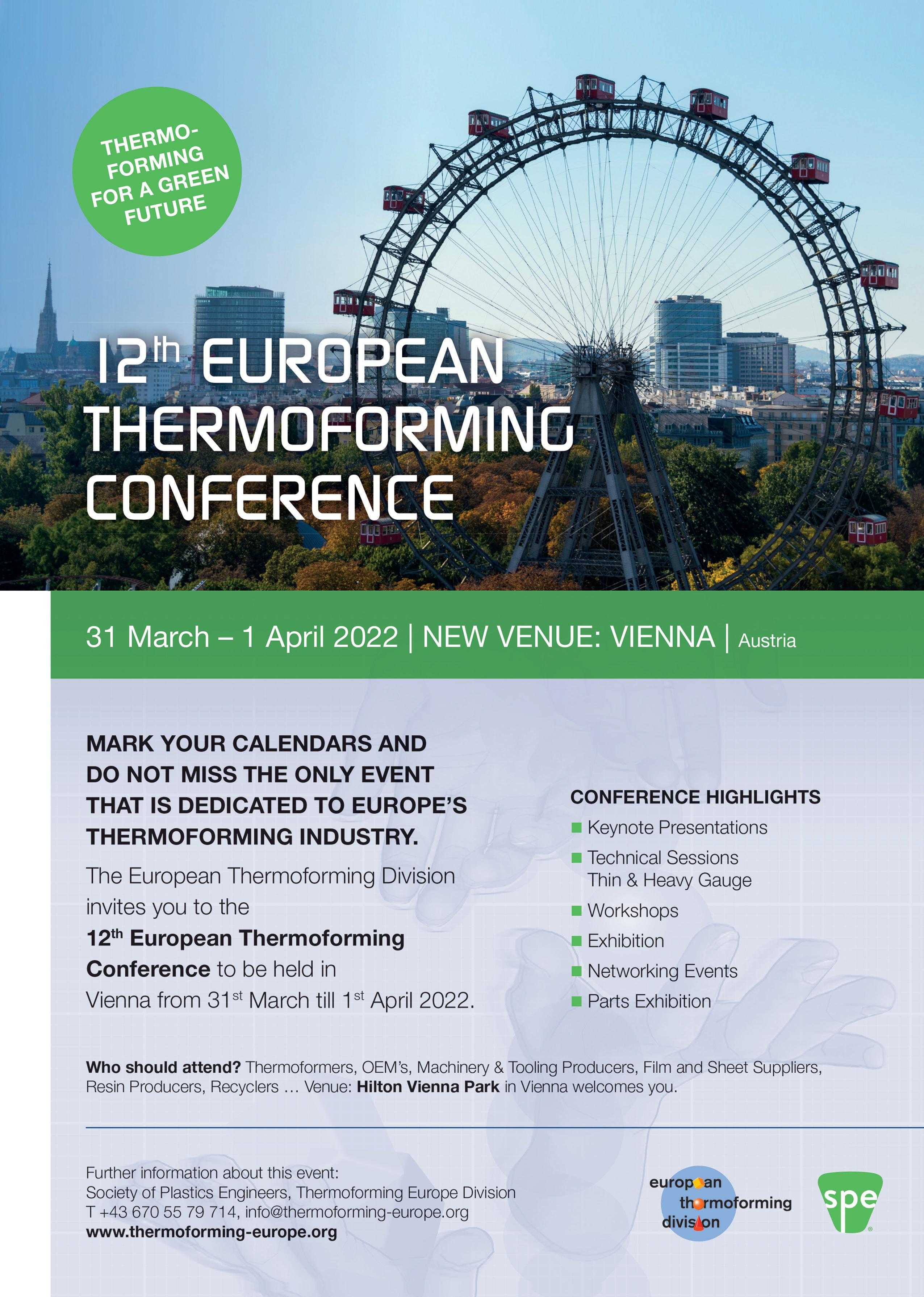