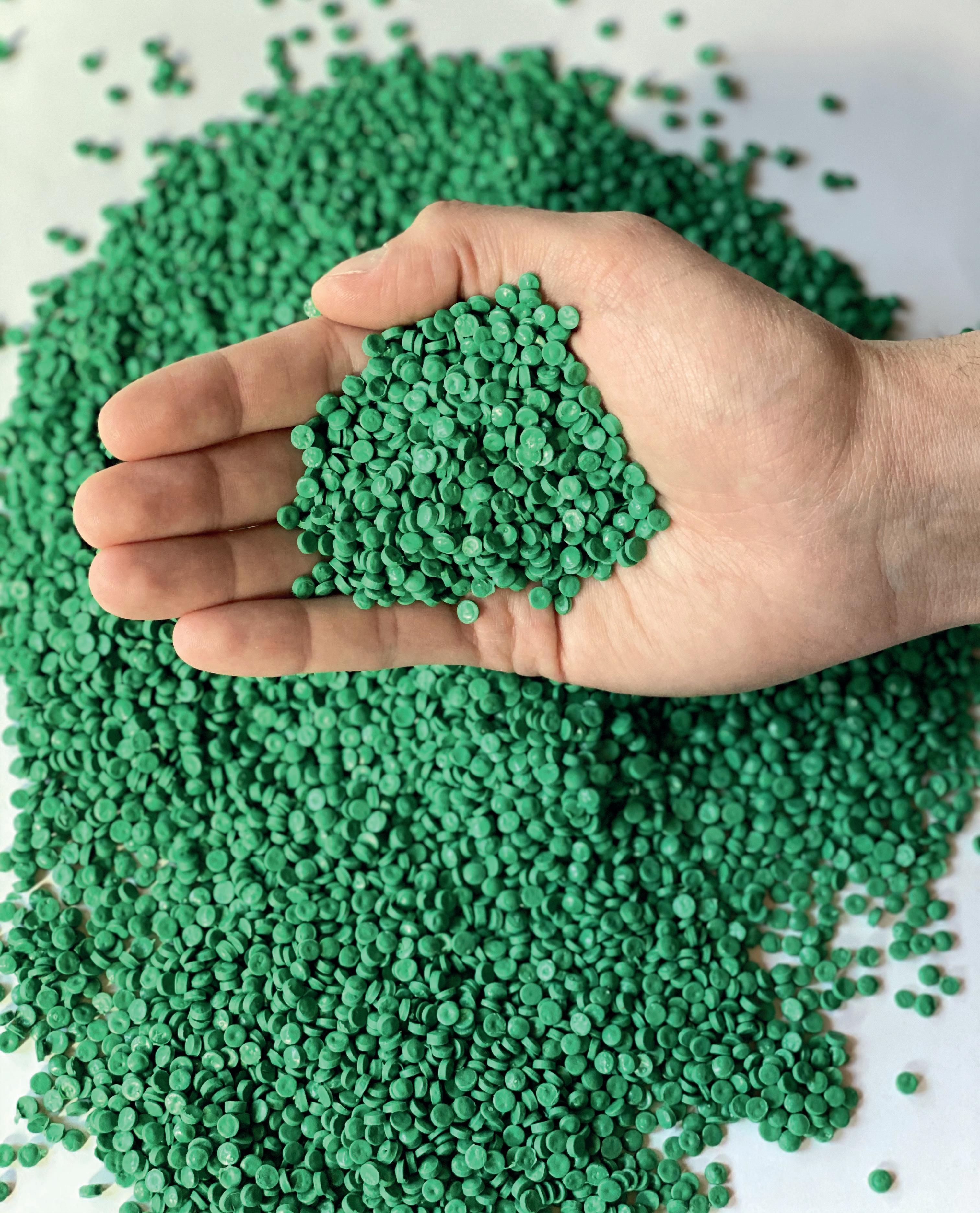
88 minute read
MATERIALI & APPLICAZIONI
L’APPROCCIO SOSTENIBILE DI SIRMAX GROUP
NOBILITARE LA PLASTICA RICICLATA PER RENDERLA UN BENE DUREVOLE
TELI BIODEGRADABILI PER PACCIAMATURA, CAPSULE DEL CAFFÈ COMPOSTABILI, SHOPPER, PRODOTTI ACCOPPIATI CARTA-PLASTICA. SIRMAX GROUP SI È PRESENTATO A FAKUMA E A ECOMONDO CON IL SUO BIOCOMPOUND INNOVATIVO DALLE ELEVATE PRESTAZIONI, CONTRIBUENDO ALLA RIDUZIONE DELLA CO2 IN ATMOSFERA
A CURA DI RICCARDO AMPOLLINI
Tecnologia, sostenibilità, nobilitazione. Alle ultime edizioni delle fiere Fakuma (Friedrichshafen, 12-16 ottobre) ed Ecomondo (Rimini, 26-29 ottobre) Sirmax Group ha proposto soluzioni sostenibili altamente tecnologiche e innovative. Specializzato nella produzione di compound di polipropilene, tecnopolimeri, compound circolari da raccolta post consumo e biocompound per molteplici settori d’applicazione, il gruppo di Cittadella (Padova) ha messo a punto famiglie di prodotti green dalle altissime performance. Forte di un decennale know how e dell’operato di cinque centri ricerca, il gruppo Sirmax, accanto alla tradizionale produzione “core”, è in grado di produrre biocompound biodegradabili e compostabili al 100%, ma anche plastica nobilitata proveniente dal riciclo meccanico di rifiuti post consumo e soluzioni di stampaggio che riducono l’utilizzo di polimero vergine. “Non ci siamo fermati nell’anno della pandemia, né negli investimenti, né nell’innovazione, né nella qualità del prodotto che offriamo”, spiega il presidente e amministratore delegato Massimo Pavin. “Abbiamo puntato moltissimo sulla sostenibilità, nel rispetto di tutti i criteri ESG e portando sul mercato prodotti innovativi. Abbiamo continuato a investire con prudenza, privilegiando la solidità patrimoniale e consolidando le competenze. Grazie a rapidità e affidabilità, abbiamo acquisito nuove quote di mercato. Siamo sempre stati vicini ai nostri clienti, con le nostre filiere regionalizzate e certificate e con la nostra tecnologia e organizzazione; in sintesi, con il nostro concetto di Proximity compounding”.
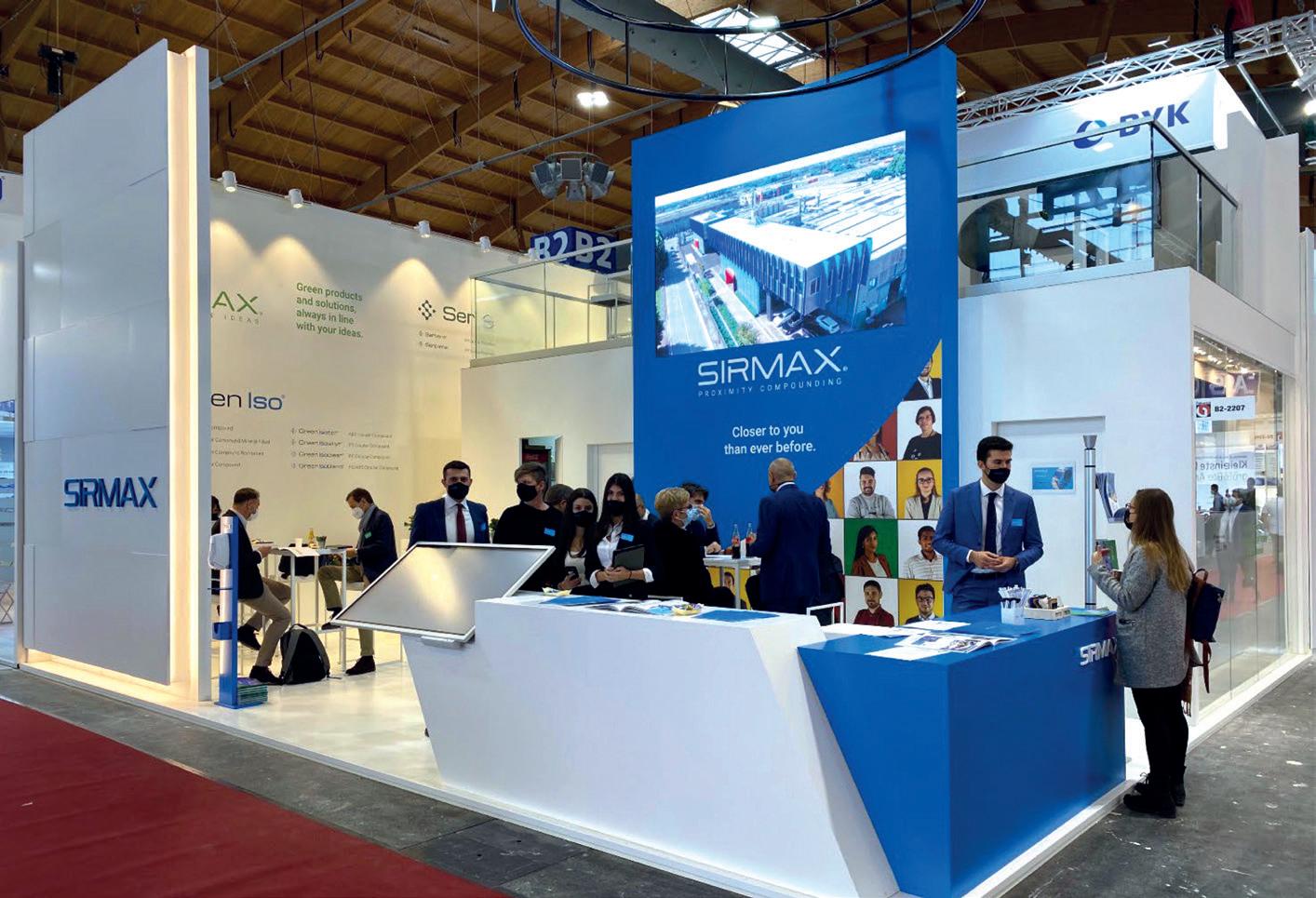
CIRCULAR ECONOMY, LA PLASTICA POST CONSUMO RIVIVE NOBILITATA

Per ciò che riguarda l’economia circolare, il Gruppo Sirmax nobilita la plastica da raccolta post consumo, dando vita a un prodotto che può essere utilizzato per la realizzazione di beni durevoli e componenti automobilistici dalle alte prestazioni. Il valore aggiunto di Sirmax risiede proprio nel processo di nobilitazione della plastica: il compound riciclato viene arricchito con capacità meccaniche e tecniche, grazie all’aggiunta di fibre di vetro, talco o altri additivi che rendono il materiale resistente, performante e affidabile come la plastica vergine. Questo piccolo “miracolo” accade grazie alla famiglia Green ISO, di cui fa parte, per esempio, Green Isofil: il compound a base di polipropilene che, a seconda dell’applicazione finale, può essere composto fino al 100% da resina post consumo; si distingue per la sua capacità di adattarsi anche ad applicazioni estetiche e di design. Vi sono poi: Green Isoglass, che condivide con Isofil il processo di nobilitazione, presentando però caratteristiche meccaniche più spinte, per realizzare, ad esempio, componenti strutturali automotive; Green Isoter, un tecnopolimero a base di ABS riciclato preconsumo, che viene utilizzato per applicazioni tecniche, anche estetiche, principalmente nel settore elettrico/elettronico (es.: placche elettriche da muro) e che viene realizzato in una particolare variante con finitura a effetto marmo, la quale richiama il suo contenuto di riciclato; Green Isoclear, tecnopolimero a base di policarbonato contenente sempre materiale preconsumo, che può essere prodotto anche in colorazione bianca per applicazioni tecniche elettrico/elettroniche. Le quattro fasi del processo Sirmax di nobilitazione della plastica (vedi figura 1), che portano a un compound green dalle prestazioni elevate e quindi adatto anche ad alcune applicazioni tecniche, sono le seguenti: 1. Plastic waste sorting. I rifiuti pre e post consumo vengono selezionati da un consorzio che ne certifica la tracciabilità in ogni fase. Internamente viene eseguita una prima selezione in base al polimero. 2. In-house production process. In questa fase avviene il processo produttivo, interno all’azienda, che lavora i polimeri circolari di SER, società del gruppo Sirmax. 3. Advanced circular compounds. Nella terza fase si giunge alla realizzazione di compound avanzati attraverso la formulazione messa a punto dai centri ricerca Sirmax. 4. Attività di co-design del prodotto. La fase conclusiva del processo di nobilitazione vede l’attività di progettazione assieme al cliente, in collaborazione con Smart Mold, che definisce le caratteristiche del manufatto da realizzare attraverso software di simulazione dedicati.
SOLUZIONI DI STAMPAGGIO INNOVATIVE
Grazie alla società d’ingegneria Smart Mold, spin-off dell’Università di Padova e di cui Sirmax ha rilevato il 50% nel 2020, il gruppo veneto è oggi in grado di completare l’offerta prodotto-servizio per merito di un particolare brevetto: un trattamento della superficie degli stampi utilizzati per iniettare la materia plastica, che permette di diminuire la pressione d’iniezione, rendendo più agevole il riempimento dello stampo e facilitando la lavorazione di materie plastiche riciclate. I materiali riciclati, infatti, per loro stessa natura, presentano una viscosità più elevata e variabile rispetto al materiale vergine e questo limita il loro utilizzo. Con il brevetto Smart Mold, invece, si aprono nuove possibilità per la plastica proveniente da raccolta post consumo, con la conseguenza di una riduzione dell’impatto ambientale e di un maggiore rispetto per l’ambiente.

“In un momento in cui il mercato dei polimeri continua a vivere una situazione di shortage”, spiega Massimo Pavin, presidente e amministratore delegato di Sirmax Group, “abbiamo potuto raccogliere i frutti di un posizionamento strategico corretto: una catena di approvvigionamento regionalizzata e fidelizzata che non ci ha fatto dipendere da un’unica area del mondo e che ci ha permesso di produrre a pieno ritmo senza mancare i nostri impegni con i clienti”.
In una sua seconda attività di business, Smart Mold si focalizza anche sulla riduzione del consumo di plastica all’interno di un manufatto, utilizzando materie prime con tecnologie all’avanguardia. Lo spin-off supporta le aziende partendo dalla progettazione ingegneristica del prodotto e studiandone le applicazioni (ad esempio, la struttura interna di un cruscotto per auto) e le caratteristiche meccaniche che deve avere (sopportazione di carichi e urti); utilizza software avanzati per simularne il comportamento meccanico e propone soluzioni progettuali per ridurne il peso e il consumo di plastica. Per ogni applicazione, grazie al suo know-how consolidato, Sirmax fornisce un materiale ottimizzato e accuratamente caratterizzato per la progettazione ingegneristica. Con l’utilizzo combinato dei materiali più performanti prodotti da Sirmax e dei trattamenti superficiali per stampi sviluppati da Smart Mold, è possibile ridurre significativamente lo spessore di molti componenti strutturali, diminuendo il peso del manufatto e, di conseguenza, il consumo di plastica vergine.
UN COMPOUND BIODEGRADABILE E COMPOSTABILE AL 100%
Il debutto di Sirmax Group a Ecomondo ha visto la presentazione del suo biocompound innovativo Biocomp, che contribuisce, tra l’altro, a ridurre le emissioni di CO2. Ottenuto da materie prime di origine sia rinnovabile che fossile, Biocomp viene prodotto in forma granulare da Microtec - l’azienda veneziana acquisita da Sirmax nel 2019 - tramite tecnologie di trasformazione delle materie plastiche già note, ma adattate secondo un know-how specifico per trattare polimeri biodegradabili e compostabili. I granuli così
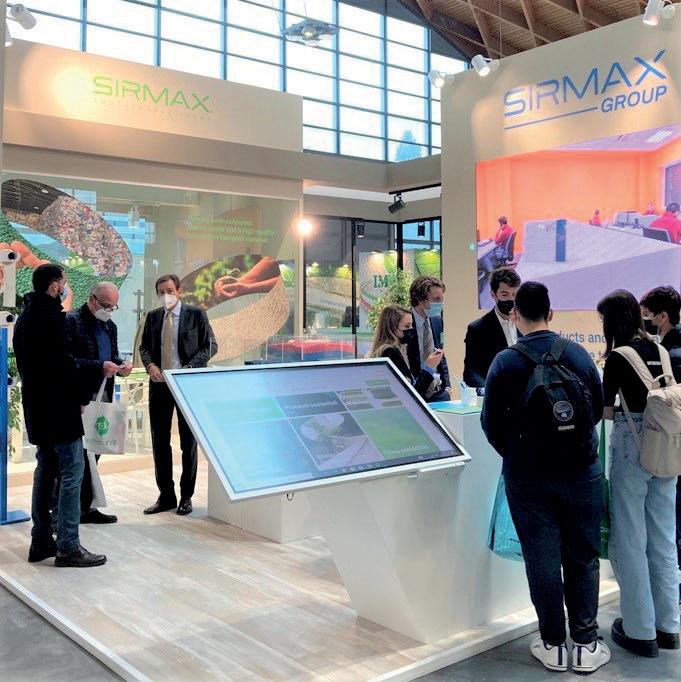
ottenuti possono essere utilizzati per realizzare prodotti con caratteristiche simili, o addirittura migliori, rispetto alle plastiche tradizionali, sebbene completamente biodegradabili e compostabili secondo la norma EN 13432. Molte delle applicazioni di Biocomp si possono trovare nell’ambito dell’imballaggio flessibile e rigido, dalla GDO al settore agro-alimentare, dalla ristorazione all’imballaggio a perdere. Non solo sacchetti da asporto, quindi, ma anche: imballaggi compostabili per alimenti solidi e liquidi, sacchetti per frigorifero e freezer, imballaggi accoppiati con carta per l’industria degli insaccati, imballaggi e accessori per il confezionamento di abiti e articoli di moda, produzione di piatti, bicchieri, vassoi e posaterie per il catering. Per il settore dell’agricoltura, sono in fase di sperimentazione sul campo teli per la pacciamatura sempre a marchio Biocomp, che Sirmax propone in sostituzione dei tradizionali teli in polietilene. Questo prodotto, a fine ciclo colturale, potrà essere fresato assieme ai residui di coltivazione, contribuendo alla fertilizzazione del terreno. “Oltre alla pacciamatura”, precisa Massimo Pavin, “stiamo lavorando anche su altri progetti, ad esempio per il settore delle capsule per il caffè, il cui consumo si è affermato in modo importante: durante la pandemia si è registrato un notevole aumento degli acquisti di macchine da caffè casalinghe. Oggi le capsule sono fatte in alluminio o in plastica tradizionale; Sirmax sta mettendo a punto una bioplastica compostabile che trasformi la capsula in fertilizzante. Un fertilizzante del tutto particolare, perché arricchito di residui di caffè: ottimo concime per le piante”. Non solo. “Il gruppo può contare sulla partecipazione in una cartiera di famiglia”, continua l’AD di Sirmax, “che vanta già importanti accordi per forniture di packaging alimentare e non. In questi mesi stiamo valutando l’ipotesi di aggiungere pure la carta all’offerta di prodotti a base di plastica tradizionale, plastica riciclata e biopolimeri. Impermeabilizzando la carta con biopolimero compostabile, gli accoppiati, oggi impopolari per la difficoltà di separare i materiali a fine vita, possono in realtà rappresentare, una soluzione ideale per prodotti come: bicchieri monouso, carte da salumeria e pescheria”.

Fig. 1 - Le quattro fasi del processo Sirmax per la nobilitazione delle materie plastiche da raccolta post consumo, che portano a un compound green dalle elevate performance, ideale anche per alcune applicazioni tecniche
Il debutto di Sirmax Group a Ecomondo ha visto la presentazione del suo biocompound innovativo Biocomp, biodegradabile e compostabile
I PRODOTTI SIRMAX CONTRIBUISCONO ALLA RIDUZIONE DI CO2
I compound prodotti da Sirmax Group contribuiscono alla riduzione delle emissioni di anidride carbonica. Lo dimostra uno studio commissionato a Spinlife, società dell’Università di Padova, il quale ha valutato il ciclo di vita (LCA) di due compound a base di polipropilene (PP) destinati ai settori automotive ed elettrodomestici: Isofil, prodotto a partire da polipropilene vergine, e Green Isofil, caratterizzato dal 33,8% di Serplene, materiale plastico riciclato prodotto da SER, società di Salsomaggiore Terme (PR), parte del gruppo e specializzata nel riciclo meccanico di plastica post consumo. Entrambi i prodotti sono stati additivati con cariche minerali, masterbatch coloranti e altri additivi in diverse percentuali. Sono state prese in esame diverse categorie di impatto: la protezione della salute umana e degli ecosistemi in correlazione all’estrazione di minerali e combustibili fossili; l’impatto potenziale delle sostanze acidificanti su suolo e aria; l’esaurimento dell’ozono stratosferico; il cambiamento climatico legato all’emissione di gas serra; l’impatto sull’ambiente da emissione di sostanze nutritive nell’aria (nitrificazione); la formazione foto-ossidante; la quantificazione del potenziale di deprivazione della risorsa idrica. I principali aspetti emersi dopo l’elaborazione dei dati hanno permesso innanzitutto di affermare che gli impatti più significativi su tutte le categorie ambientali avvengono in fase di produzione delle materie prime e, in misura inferiore ma comunque importante, sono determinati dai consumi energetici. È fondamentale notare che l’utilizzo di PP riciclato post consumo comporta una riduzione significativa degli impatti in quasi tutte le categorie prese in considerazione. Dall’analisi di alcune famiglie di Green Isofil emerge poi come la sostituzione di PP vergine con riciclato può comportare in molti casi il dimezzamento delle emissioni di anidride carbonica. Inoltre, le fasi di trasporto dei rifiuti non incidono in maniera significativa, confermando la bontà del modello scelto. “Oggi Sirmax è un gruppo sostenibile a tutto tondo”, conclude Massimo Pavin. “Gli investimenti effettuati negli ultimi due anni ci hanno permesso di raggiungere una capacità per trattare fino a 45000 t di polipropilene e polietilene provenienti da packaging post consumo, nobilitandoli in compound che l’industria dell’elettrodomestico e dell’auto trasformerà in componenti con un ciclo di vita di molti anni. Il nostro obiettivo è dar vita a cicli virtuosi attraverso un know-how interamente sviluppato in Sirmax e condiviso con i clienti finali. È la logica su cui, da sempre, si fondano le nostre scelte strategiche e che ha guidato l’acquisizione di SER e Microtec, così come il potenziamento dei reparti di ricerca e sviluppo e della business unit “opportunity to market”. Un percorso in linea con le direttive europee e con la visione dei nostri partner, ai quali non intendiamo solo trasmettere un messaggio di vicinanza al territorio e all’ambiente, ma anche di apporto di capacità per migliorare i loro processi e prodotti”.
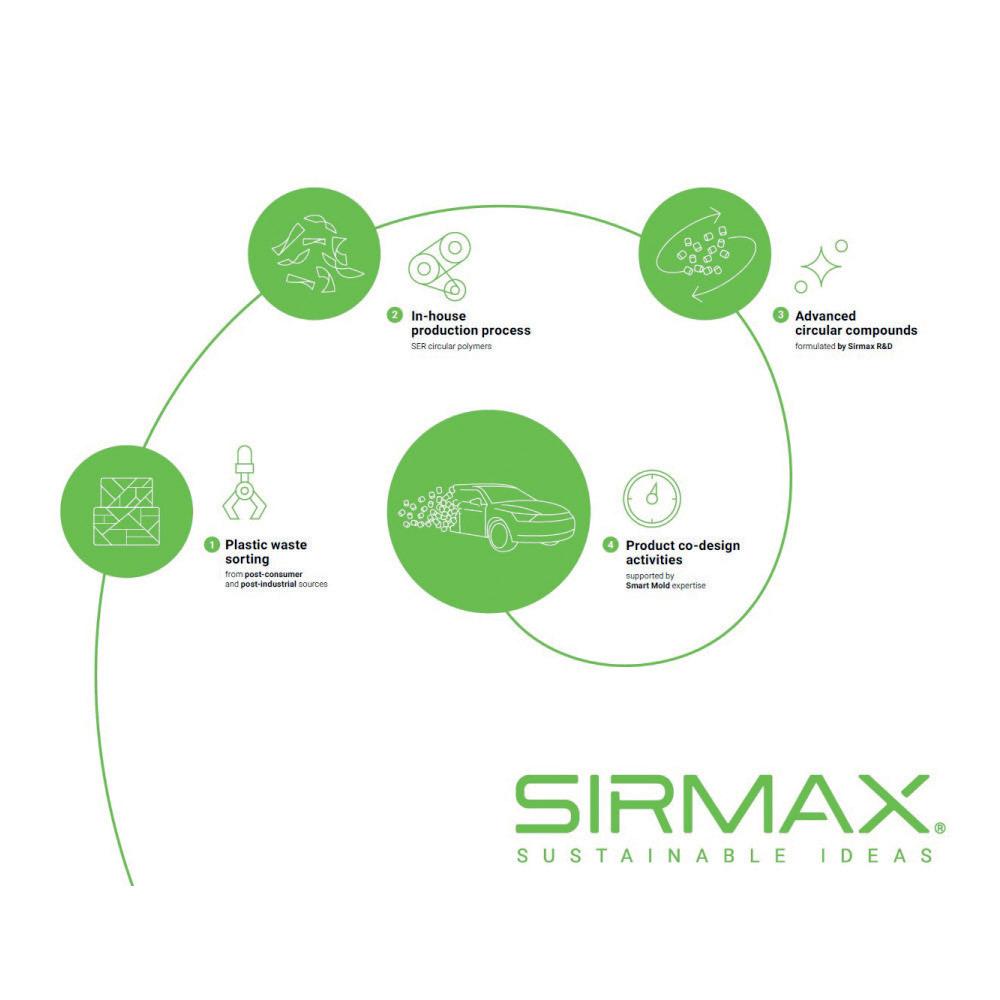
Gli atleti e gli allenatori dello Sci Club RadiciGroup, nato addirittura nel 1975, sono stati i primi a indossare la nuova tuta da sci in Renycle, diventando così gli “ambassador” ufficiali di un’iniziativa di concreta sostenibilità
ECODESIGN E RICICLABILITÀ, PUR MANTENENDO LE PRESTAZIONI TECNICHE UNA SOSTENIBILITÀ ALL’ALTEZZA DELLE NOSTRE MONTAGNE
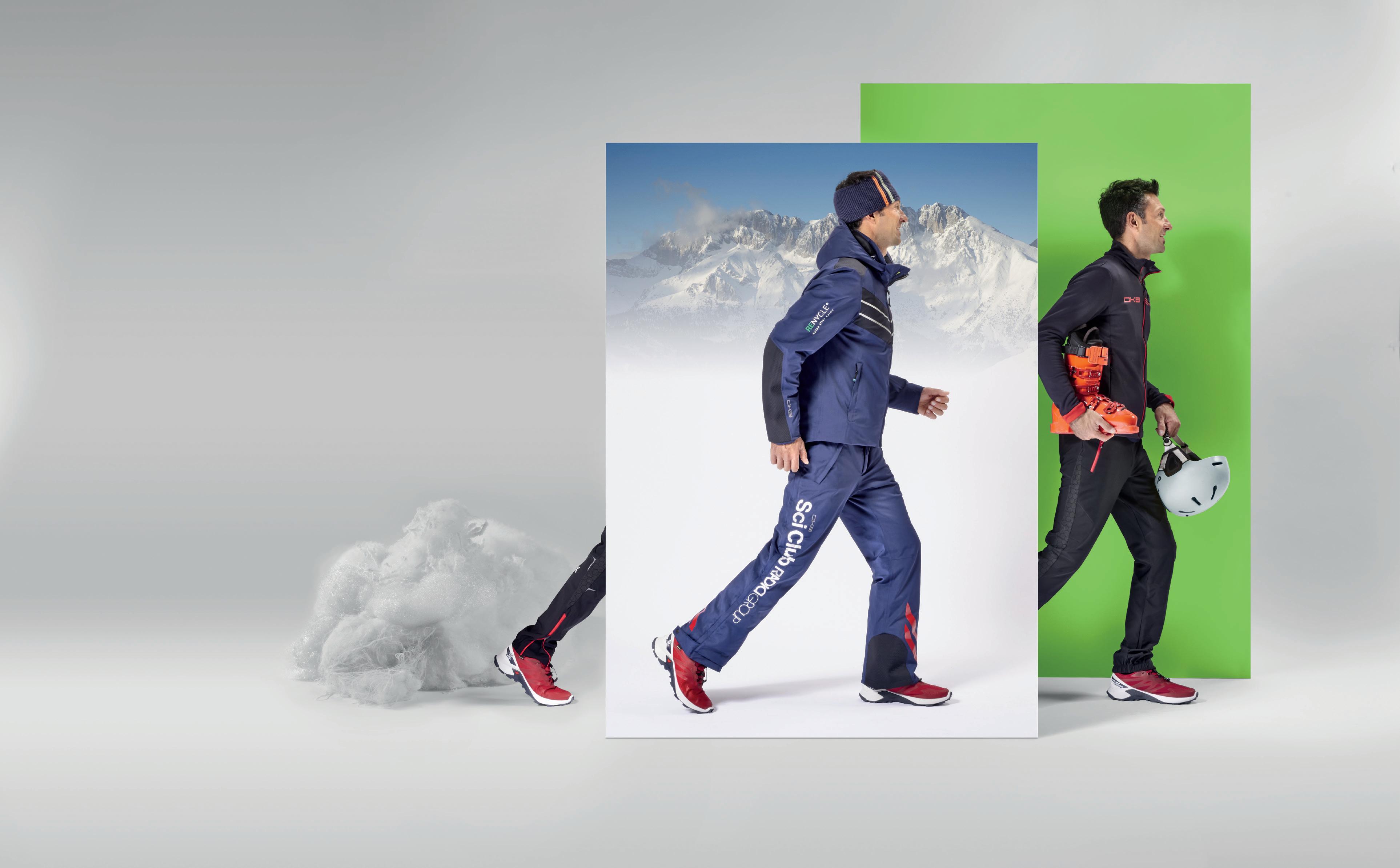
C’È UNA TUTA DA SCI “CIRCOLARE” TRA LE PRIME APPLICAZIONI DELLA NUOVA GAMMA RENYCLE DI TECNOPOLIMERI NATI DAL RICICLO PRE E POST CONSUMO. LE NOVITÀ PIÙ RECENTI DI RADICIGROUP VEDONO ANCHE FILAMENTI PER L’ADDITIVE MANUFACTURING E UNA LINEA DI DISPOSITIVI DI PROTEZIONE SVILUPPATA IN BASE ALL’ESPERIENZA VISSUTA DURANTE LA PANDEMIA
Quattro parole chiave - sicurezza, affidabilità, qualità e tracciabilità - sono alla base della nuova offerta sostenibile di RadiciGroup High Performance Polymers. Quest’ultima ha infatti lanciato alla fiera Fakuma (Friedrichshafen, 12-16 ottobre 2021) il nuovo brand Renycle di prodotti, su base PA6 e PA66, che includono percentuali variabili di polimeri riciclati sia d’origine post industriale che post consumo. “Da sempre, in RadiciGroup, ogni scarto di produzione diventa una nuova risorsa”, ha sottolineato Erico Spini, global marketing manager della business area RadiciGroup High Performance Polymers. “Abbiamo sviluppato un processo produttivo che monitora accuratamente la selezione e il trattamento delle materie prime in ingresso, al fine di ottimizzare le caratteristiche e la variabilità dei materiali. Inoltre, negli ultimi anni, abbiamo partecipato a progetti di economia circolare che ci hanno permesso di acquisire competenze anche nel mondo del riciclo post con-
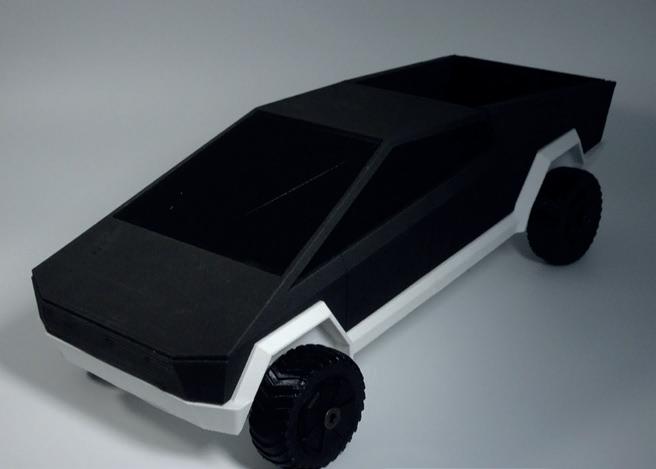
Nuovi gradi Radilon Adline a base di PA6 e da fonte rinnovabile sono attualmente in fase di sviluppo per la manifattura additiva sumo. Ecco perché a Fakuma abbiamo lanciato Renycle: il marchio con cui vogliamo firmare la nostra offerta di sostenibilità sia in riferimento alla caratterizzazione dei prodotti dal punto di vista delle proprietà richieste sia in riferimento alla riduzione dell’impatto ambientale”. Il marchio Renycle è già utilizzato dalla business area tessile per identificare i filati poliammidici provenienti da recupero, ma oltre a questo, ha concluso Spini: “I prodotti Renycle sono destinati ad applicazioni d’interesse per tutti i nostri mercati di riferimento: automotive, e-mobility, elettrico-elettronico, settore industriale e dei beni di consumo. Nella nuova gamma abbiamo inserito anche un prodotto rinforzato con fibre di vetro, con ritardante di fiamma ma senza alogenati e fosforo rosso, oltre a un materiale resi-
Alla fiera A+A RadiciGroup ha proposto la nuova linea di dispositivi di protezione Radipeople, realizzati con materiali tracciabili grazie a una filiera totalmente italiana e confezionati con un packaging concepito secondo le logiche dell’ecodesign
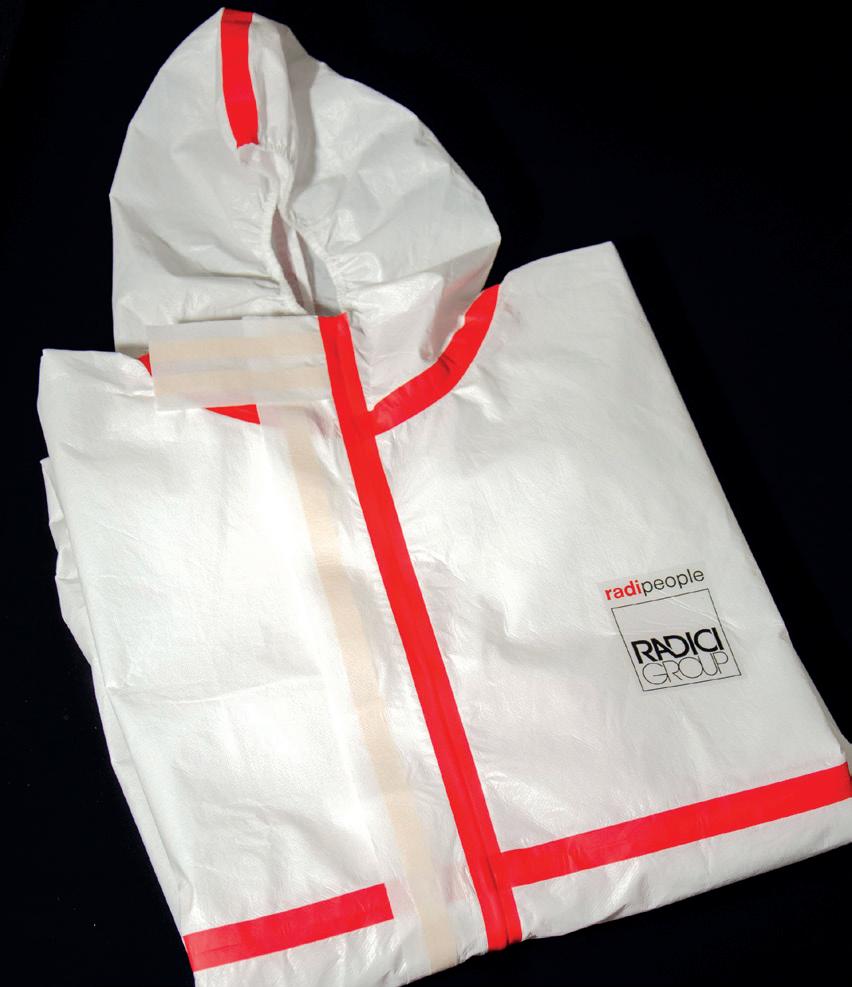
mente per rinforzare esternamente giacca e pantaloni e aumentare la resistenza all’abrasione, al taglio e alle basse temperature.
stente al contatto con i liquidi di raffreddamento motore per il settore auto”.
FILATI DAL RICICLO, SENZA RINUNCIARE A STILE E PRESTAZIONI

La prima tuta da sci concretamente sostenibile, con una forte attenzione allo stile e al design e con una progettazione a chilometro zero, è oggi realtà. Protagonisti nella realizzazione di questo capo sportivo altamente innovativo sono due eccellenze dell’area bergamasca: RadiciGroup e DKB, azienda specializzata in abbigliamento tecnico sportivo. Il completo, composto da giacca e pantaloni (vedi foto in apertura d’articolo, ndr), è caratterizzato da un tessuto realizzato in filato Renycle, che, come già accennato, è derivato dal riciclo meccanico della poliammide. Inoltre, anche l’imbottitura e i numerosi accessori della tuta, tra cui le zip, i velcri, i bottoni e il filo delle cuciture sono in poliammide. Un traguardo ottenuto grazie al grande lavoro di squadra di RadiciGroup e DKB per lo sviluppo di materiali tra loro chimicamente affini e utilizzabili in queste specifiche applicazioni, che richiedono prestazioni tecniche elevate. La composizione quasi monomateriale consente di facilitare in modo significativo il riciclo del capo a fine vita, attraverso la sua trasformazione in nuovo materiale polimerico utilizzato per produrre, ad esempio, componenti di scarponi e attacchi da sci, o che può trovare applicazione nell’automotive, nell’arredamento o in qualsiasi settore che preveda l’utilizzo di poliammidi ad alte prestazioni. La tuta realizzata da RadiciGroup rappresenta quindi un progetto di ecodesign e di economia circolare a tutto tondo applicato al mondo della moda e dell’abbigliamento, che concretizza il claim “Una sostenibilità all’altezza delle nostre montagne”, riportato all’interno della giacca. La composizione in poliammide permette anche di ottenere un peso significativamente inferiore rispetto a quello delle tute tradizionali e un ingombro estremamente ridotto, garantendo al contempo una resistenza agli urti e all’usura di gran lunga superiore rispetto a quella dei capi attualmente in commercio. Per coniugare le esigenze di comfort a quelle agonistiche, i tecnici di RadiciGroup e DKB hanno inoltre messo a punto inserti in tessuto poliammidico a esagoni neri studiati appositaPROTEZIONE SOSTENIBILE
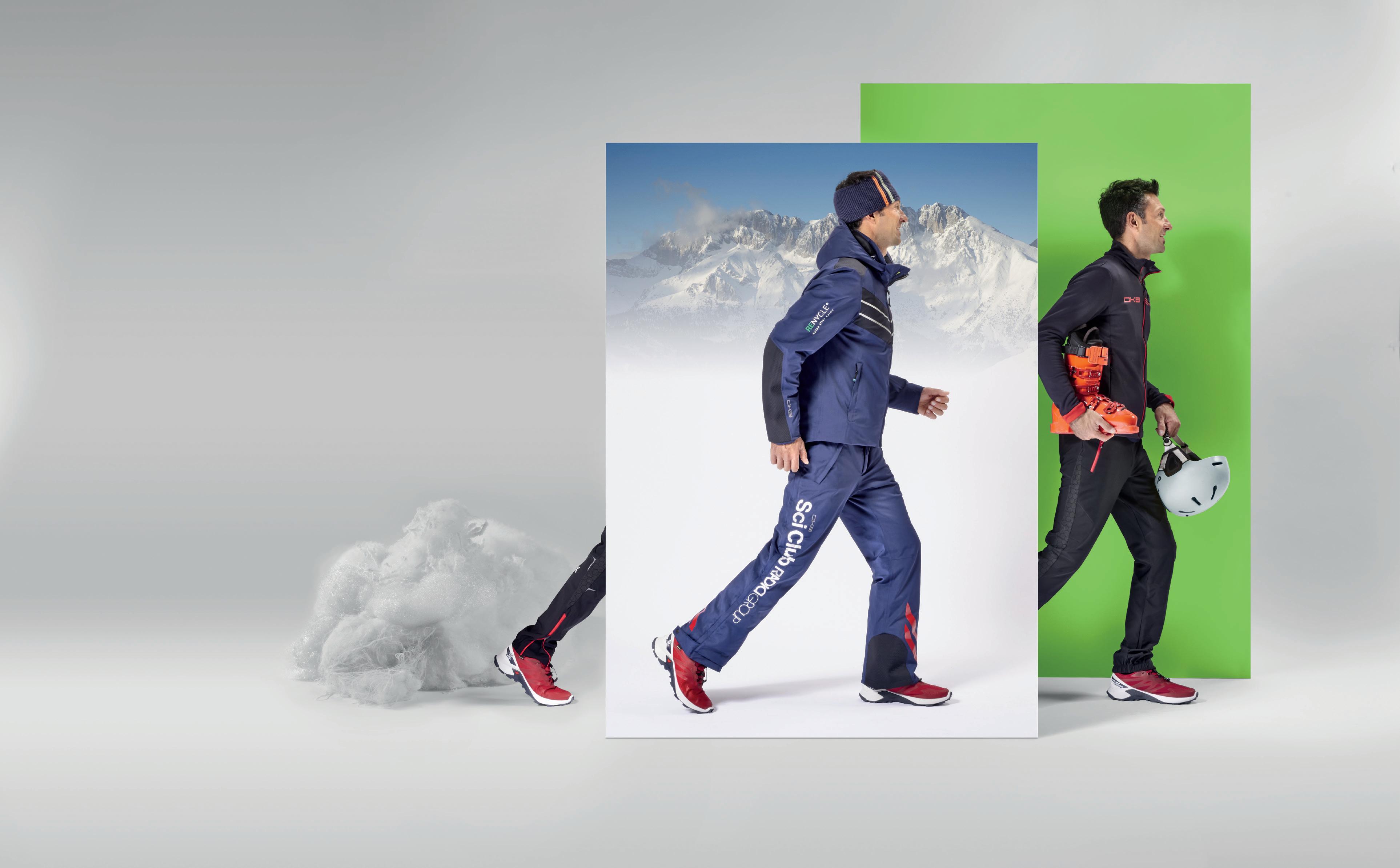
Il gruppo ha scelto A+A (Düsseldorf, 26-29 ottobre 2021), evento internazionale dedicato alle soluzioni per la sicurezza in ambito lavorativo, per presentare il nuovo marchio Radipeople dedicato ai dispositivi di protezione individuale, tra cui tute, camici, cuffie, copricapo, copriscarpa e calzari. L’attenzione alla salute e alla sicurezza delle persone si unisce così a un forte commitment per la tutela dell’ambiente. Ne è testimonianza Radipeople Eco: la prima tuta protettiva totalmente riciclabile a fine vita e realizzata al 100% in polipropilene. Tutte le sue parti, dal tessuto alla laminatura, dalla zip al filo utilizzato per le cuciture, sono prodotte a partire da un’unica tipologia di materiale. Inoltre, il gruppo propone capi realizzati con Respunsible: spunbond proveniente dal riciclo del polipropilene, o prodotto con materiali certificati secondo le linee guida ISCC Plus. “L’impegno di RadiciGroup nell’area dei dispositivi di protezione individuale”, ha ricordato il vicepresidente Maurizio Radici, “nasce nel marzo del 2020, nel pieno dell’emergenza pandemica: ci siamo messi in gioco per usare il nostro spunbond dylar come componente principale dei camici di protezione ad uso medico, avviando in tempo record una filiera locale per la produzione di questi dispostivi. Oggi siamo quindi in grado di produrre indumenti studiati per la protezione del corpo in numerosi ambiti industriali. Inoltre, a fine 2020, il gruppo ha investito 15 milioni di euro per l’acquisto di una nuova linea di produzione di meltblown, un altro tipo di TNT non presente sul mercato italiano, impiegato come intermedio nella produzione di mascherine protettive e DPI, ma anche ideale in numerose applicazioni legate alla filtrazione di aria e liquidi”. Per versatilità e caratteristiche tecniche, i dispositivi Radipeople si rivolgono a molteplici settori industriali e offrono un’eccellente difesa dagli agenti esterni (liquidi, particelle e spray), un’alta protezione dal rischio biologico ed elevata robustezza e leggerezza per ottimizzare protezione e comfort.
FILAMENTI PER LA PRODUZIONE ADDITIVA
Da una parte un mercato in rapida evoluzione, quello dell’additive manufacturing, dall’altra un’area di business come RadiciGroup High Performance Polymers con una lunga esperienza nel campo del compounding e una riconosciuta capacità di ottimizzare i materiali a seconda delle applicazioni: in questo contesto nasce Radilon Adline, la gamma di filamenti per la stampa 3D basata su speciali gradi di PA Radilon e presentata all’esposizione Formnext (Francoforte, 16-19 novembre 2021). I prodotti Radilon Adline si contraddistinguono per le alte prestazioni e sono adatti non solo per la prototipazione, ma anche per la produzione di parti funzionali. Sono stati inoltre testati con diversi sistemi di stampa 3D aperti per garantire facilità di lavorazione dei materiali. “La tecnologia additiva pone requisiti tecnici particolari, che non è così semplice soddisfare con i polimeri semicristallini”, ha spiegato Chiara Devasini, project leader Marketing & Development di RadiciGroup High Performance Polymers. “Per questo, la prima fase di sviluppo del progetto si è concentrata sull’individuazione delle poliammidi che rispondessero a tali requisiti tecnici. Nello specifico, abbiamo scelto di focalizzarci sui filamenti per FFF (Fused Filament Fabrication) e siamo giunti a sviluppare materiali ad alto contenuto tecnico basati su copoliammidi PA6/66, il cui basso punto di fusione, pari a 195°C, li rende adatti alla maggior parte delle stampanti”. Ad oggi, il portafoglio include Radilon Adline CS e Adline CS CF. Il primo è un copolimero PA6/66 caratterizzato da elevata facilità di stampa 3D e buon aspetto superficiale, in grado di garantire un’efficace adesione interstrato, insieme a un basso ritiro. La versione CS CF è invece rinforzata con fibre di carbonio per fornire, accanto alla facilità di stampa, ulteriori performance in termini di modulo, rigidezza e proprietà meccaniche. “L’Additive Manufacturing è un mercato in rapida evoluzione”, ha concluso Chiara Devasini, “pertanto a questi primi due gradi intendiamo far presto seguire nuovi materiali con performance tecniche elevate e anche attenti all’ambiente”.
Il brand Renycle rappresenta la volontà di RadiciGroup High Performance Polymers di rispondere alle nuove sfide legate alla sostenibilità, garantendo nello stesso tempo sicurezza e tracciabilità dei prodotti
BASF PRESENTA IRGACYCLE ED HEXAMOLL DINCH BMB
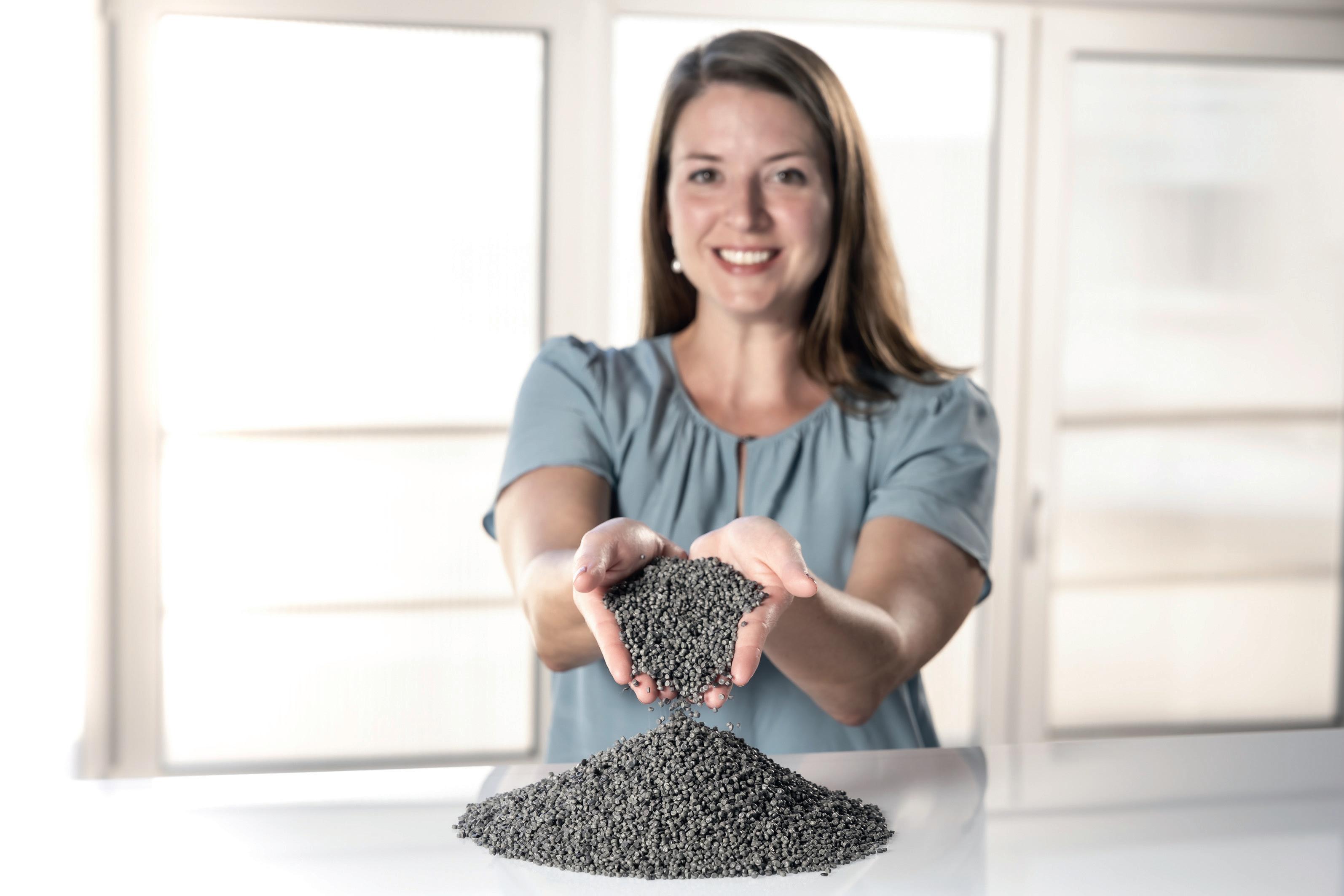
NUOVE FAMIGLIE DI ADDITIVI E PLASTIFICANTI PER UNA PLASTICA PIÙ SOSTENIBILE
ULTIMO NATO DELLA FAMIGLIA VALERAS, L’ADDITIVO IRGACYCLE DI BASF FAVORISCE IL RICICLO MECCANICO E MIGLIORA LE PROPRIETÀ DELLA PLASTICA RICICLATA IN DIVERSI SETTORI INDUSTRIALI. IL PLASTIFICANTE DA BIOMASSA HEXAMOLL DINCH BMB HA INVECE CONSENTITO A TECNOCAP DI PRODURRE GUARNIZIONI PER IMBALLAGGI ALIMENTARI RIDUCENDO L’USO DI RISORSE FOSSILI. TUTTO QUESTO È AVVENUTO MENTRE SI FESTEGGIAVANO IL 75° ANNIVERSARIO DI BASF IN ITALIA E L’AMPLIAMENTO DEL SUO STABILIMENTO DI PONTECCHIO MARCONI, SPECIALIZZATO PROPRIO IN ADDITIVI PER LE MATERIE PLASTICHE
A CURA DI RICCARDO AMPOLLINI
Lo scorso settembre il colosso della chimica Basf ha lanciato sul mercato IrgaCycle, una nuova gamma di additivi nata per rispondere alle crescenti esigenze in materia di riciclo delle materie plastiche. L’industria di settore, infatti, è sempre di più alla ricerca di soluzioni che permettano di incorporare nelle principali applicazioni finali un più elevato contenuto di materiale polimerico riciclato, rispondendo sia alle crescenti preoccupazioni dei consumatori riguardanti l’impatto ambientale della plastica sia ai sempre più stringenti requisiti normativi in materia di riduzione dei rifiuti plastici. In questo scenario, una delle principali sfide riguarda la minimizzazione delle carenze qualitative e prestazionali dei polimeri derivati dal processo di riciclo, imputabili solitamente allo stress termico e meccanico del processo stesso. La plastica riciclata, infatti, contiene spesso impurità e sostanze contaminanti che rischiano di accelerare la degradazione del polimero, modificando anche le proprietà del prodotto finale. Gli additivi che migliorano le proprietà delle plastiche riciclate possono quindi offrire una soluzione a questa sfida. “Grazie alle tecnologie disponibili e alla tendenza delle nuove normative, prevediamo che, da qui al 2030, i volumi di plastica prodotti dal riciclo meccanico possano quasi triplicare, crescendo di circa il +10% ogni anno”, ha commentato Thomas Kloster, presidente della divisione Performance Chemicals di Basf. “Con IrgaCycle, proseguiamo il graduale ampliamento del nostro portafoglio di prodotti e soluzioni a supporto di un’economia circolare delle materie plastiche”. La nuova gamma IrgaCycle include additivi che contribuiscono ad aumentare la percentuale di contenuto riciclato in diverse applicazioni finali, per settori quali: packaging, mobilità ed edilizia. Si tratta di soluzioni che eliminano difetti delle resine riciclate come: ridotta lavorabilità, scarsa stabilità termica sul lungo termine, insufficiente protezione dagli agenti atmosferici. I primi additivi di questa gamma, a cui presto si aggiungeranno nuove formulazioni, includono: • IrgaCycle PS 030 G, che migliora la stabilità termica a lungo termine in applicazioni rigide, principalmente per HDPE, poliolefine e polimeri misti riciclati; • IrgaCycle PS 031 G, che migliora la lavorazione e la stabilità termica a lungo termine di LDPE ed LLDPE riciclati, per l’incorporazione in film e rela-
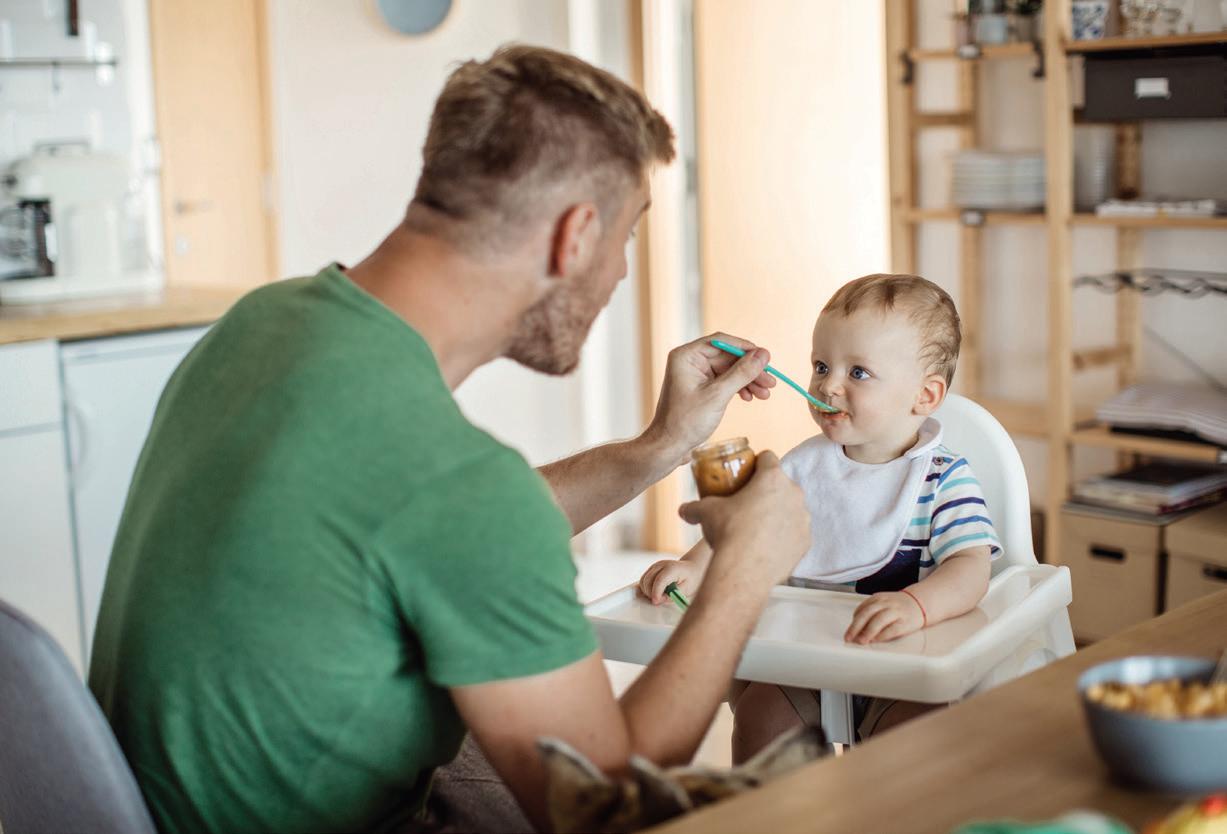
tive applicazioni destinate agli imballaggi flessibili; • IrgaCycle PS 032 G, che fornisce stabilità di lavorazione e protezione termica a lungo termine per PP e miscele di poliolefine riciclate contenenti impurità; • IrgaCycle UV 033 DD, che coniuga una maggiore resistenza agli agenti atmosferici e un’accresciuta stabilità termica e di lavorazione per miscele di HDPE e PP rigenerate destinate al riutilizzo in prodotti per esterni; • IrgaCycle XT 034 DD, che migliora la lavorazione, conferisce stabilità al calore a lungo termine e contribuisce a neutralizzare le impurità della “prima vita” della plastica, migliorando al contempo le proprietà meccaniche dei riciclati poliolefinici. Un vantaggio specifico di queste miscele consiste nel fatto di essere pronte all’uso e semplici da applicare durante le diverse fasi di riciclo. La forma in granulo consente un dosaggio facile e sicuro durante le fasi di compounding e trasformazione. La gamma IrgaCycle va ad accrescere il portafoglio di prodotti che Basf propone sotto il brand Valeras, un’ampia e crescente gamma di materiali e soluzioni lanciata il 30 giugno del 2021 e che contribuisce in maniera sensibile alla sostenibilità delle applicazioni plastiche, migliorando la durabilità, riducendo gli sprechi, facen-
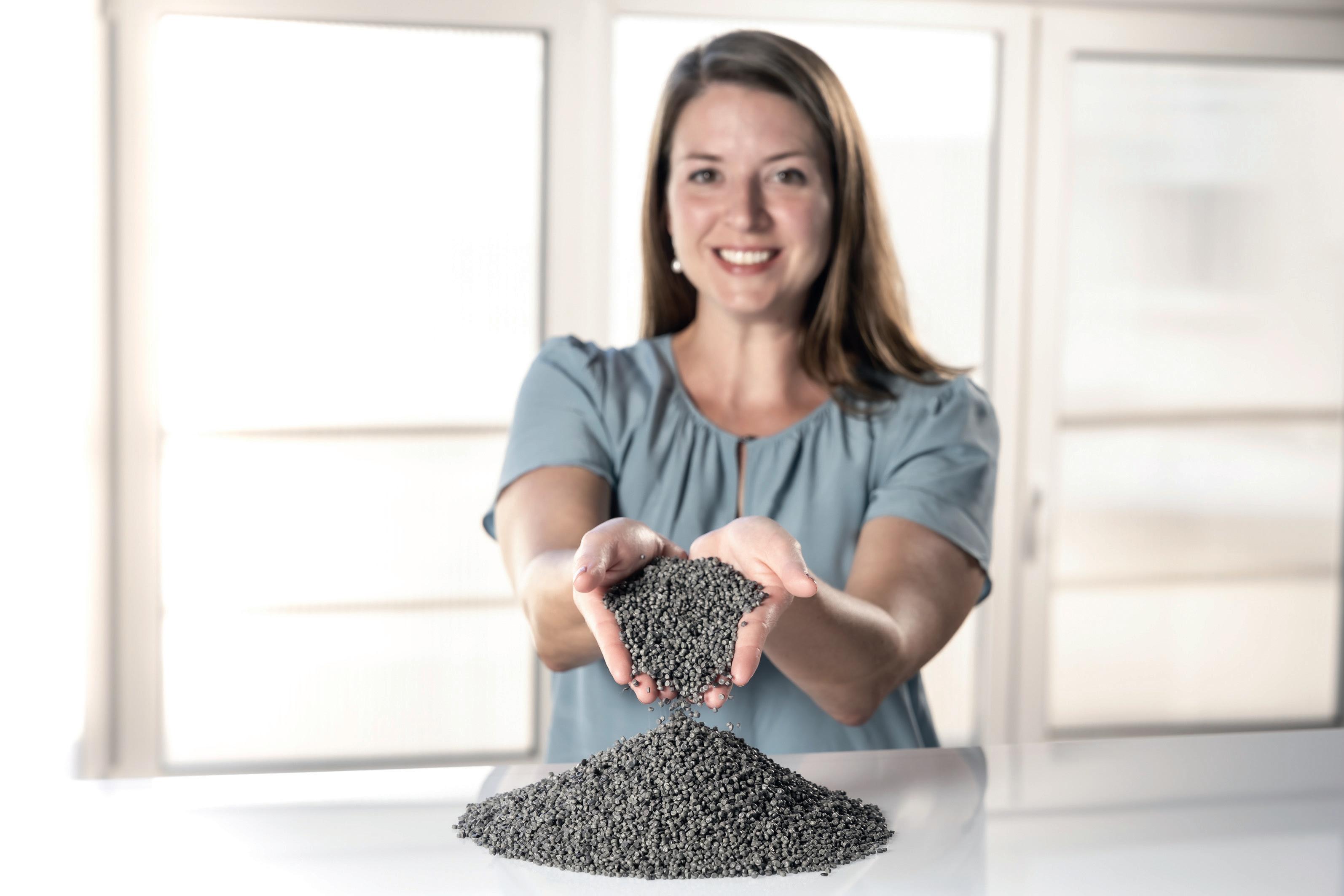
Burak Karadeniz, tecnico di laboratorio presso l’Application Center di Basf per gli additivi plastici a Kaisten, in Svizzera, controlla la superficie di un campione in ABS riciclato + additivo IrgaCycle, per verificare la presenza di eventuali difetti


Il nuovo reparto M del sito di Pontecchio Marconi (Bologna) produce stabilizzanti alla luce che consentono di realizzare teli da serra più duraturi e resistenti ai raggi UV e agli agenti atmosferici do risparmiare energia, riducendo le emissioni e promuovendo la biodiversità.
UN PLASTIFICANTE PER IMBALLAGGI OTTENUTO DA BIOMASSA
Terzo produttore mondiale di chiusure metalliche per alimenti, baby food e bevande, il Gruppo Tecnocap ha recentemente scelto d’impiegare il plastificante Hexamoll Dinch BMB di Basf per realizzare le guarnizioni sigillanti applicate all’interno delle sue capsule di sicurezza per il confezionamento sottovuoto di alimenti. La multinazionale italiana ha optato per questo plastificante da biomassa al fine di soddisfare le aspettative dei propri clienti in termini di trasparenza e sostenibilità. “Collaborare con partner strategici come Basf ci permette di migliorare costantemente la sostenibilità delle nostre soluzioni d’imballaggio in metallo. Grazie al Life Cycle Assessment e al conseguimento della Dichiarazione Ambientale di Prodotto (EPD), oggi possiamo misurare e ridurre l’impatto ambientale dei nostri prodotti in linea con il nostro Piano di Circular Innovability, che punta a una forte riduzione delle emissioni di CO2 entro il 2030”, ha commentato Michelangelo Morlicchio, CEO e presidente del Gruppo Tecnocap. Grazie a un’impronta di carbonio decisamente inferiore rispetto ai tradizionali plastificanti, Hexamoll Dinch BMB contribuisce al raggiungimento degli ambiziosi obiettivi di sostenibilità del Gruppo Tecnocap e consente di ridurre l’utilizzo di risorse fossili. Per produrlo, infatti, Basf impiega bionafta o biogas derivati da rifiuti organici, oppure da oli vegetali. Grazie a un efficiente processo produttivo, le materie prime rinnovabili affiancano quelle ottenute secondo l’approccio del bilanciamento della biomassa (BMB, Bio Mass Balance). Gli impatti sono certificati da revisori indipendenti secondo lo standard RedCert2. L’introduzione del plastificante BMB non ha causato alcuna variazione delle eccellenti qualità delle chiusure metalliche Tecnocap, alle quali, piuttosto, si sono aggiunte prestazioni di tenuta superiori e minore impatto certificato di CO2. “Basf condivide l’impegno di Tecnocap orientato alla sostenibilità e sta già implementando numerose misure per raggiungere la neutralità climatica entro il 2050. L’approccio del bilanciamento della biomassa è uno dei pilastri del nostro programma di misurazione e riduzione delle emissioni di CO2 e ha un impatto importante sul risparmio di risorse fossili”, ha spiegato infine Wolfgang Bien, vicepresidente Industrial Petrochemicals Europe di Basf.
75° COMPLEANNO E UN NUOVO REPARTO A PONTECCHIO MARCONI
Dal 1946 Basf Italia alimenta profondi legami con il mondo delle imprese, delle istituzioni e con le co-
Privo di ftalati, adatto al contatto con alimenti e prodotto a partire da materie prime rinnovabili, il plastificante Hexamoll Dinch BMB contribuisce a ridurre l’impiego di risorse fossili e le emissioni di CO2
iStock
munità dei territori in cui opera. Nel 2021 l’azienda ha celebrato i suoi primi 75 anni in Italia con una campagna di comunicazione ispirata allo slogan “La formula del futuro”, che ribadiva il contributo offerto dal gruppo per risolvere le sfide del nuovo millennio e difendere la competitività del Made in Italy. Tutto ciò per costruire, insieme a clienti e filiere produttive, un domani più sostenibile. Proprio nel 75° anniversario della sua attività in Italia, Basf ha inaugurato un nuovo reparto produttivo presso lo stabilimento di Pontecchio Marconi (Bologna), il più importante insediamento del gruppo nel nostro Paese. Il nuovo reparto M sta già producendo una gamma di stabilizzanti al calore e alla luce basati su una molecola sviluppata proprio dal team di ricerca e sviluppo di Pontecchio. Additivi che forniscono prestazioni meccaniche particolarmente elevate e una maggiore durata alle plastiche impiegate per coperture, serre, reti e macro o micro tunnel utilizzati in agricoltura, consentendo così agli agricoltori di aumentare la produzione, migliorare la qualità degli alimenti e ridurne l’impronta ecologica. La nuova struttura è stata costruita in soli 14 mesi di lavori, portati avanti con determinazione anche in piena pandemia, per un investimento complessivo di oltre 20 milioni di euro. La sua linea di produzione è totalmente automatizzata, in accordo con le logiche tipiche dell’Industria 4.0, proprio come dimostrato dall’avviamento da remoto della prima produzione, durante la cerimonia d’inaugurazione del primo febbraio 2021. “Con l’inaugurazione del nuovo reparto confermiamo l’impegno per far crescere la nostra presenza industriale in Italia. Pontecchio Marconi rappresenta per noi un punto d’eccellenza operativo, di ricerca e di innovazione, che continueremo a sostenere anche nei prossimi anni. Consideriamo quest’obiettivo beneaugurante in un momento in cui, tutti noi, siamo alla ricerca di notizie positive e di speranza”, ha commentato Lorenzo Bottinelli, amministratore delegato e vicepresidente di Basf Italia.
NEWS
Purging compound by Ultra System I benefici di una migliore pulizia dei macchinari
Nata dall’idea di due imprenditori che ha portato a realizzare un gruppo industriale che conta oggi sei unità di compounding in tutto il mondo, la società svizzera Ultra System è specializzata unicamente in purging compound e vanta un portafoglio di clienti che spazia in vari settori: dall’imballaggio all’elettrodomestico, dall’automotive ai giocattoli, sino al medicale e al farmaceutico. Tutto ciò è reso possibile anche grazie alle numerose certificazioni ottenute, tra cui: ISO, Food Contact, Reach, camera bianca. Il brand Ultra Plast, che comprende oltre 20 purging compound di quinta generazione, presenta caratteristiche che lo rendono quasi unico sul mercato: non contiene abrasivi (100% pulizia chimica) e quindi non danneggia le parti metalliche delle macchine di trasformazione; non necessita di tempo d’ammollo (procedura “sandwich”); non rilascia fumi od odori; infine, è rapido, semplice da usare, efficace e con un “costin-use” altamente competitivo. L’utilizzo di Ultra Plast è fondamentale per ridurre i tempi di cambio colore e/o materiale, per la rimozione dei depositi di colore precedenti, per l’eliminazione di punti neri e impurezze e per la ripartenza dopo un fermo macchina. È ormai ampiamente dimostrato che utilizzare polimeri (o, peggio ancora, detersivi) per la pulizia degli impianti di processo, genera costi maggiori, minore qualità, maggiori tempi di fermo macchina, maggiore impronta di carbonio, più scarti e costi energetici superiori… in poche parole, si tratta di un sistema più costoso rispetto all’utilizzo di un compound per la pulizia. E, nel 2022, non si possono più accettare non conformità come: impurezze, punti neri, ombre e rigature sul pezzo prodotto, soprattutto quando esiste una soluzione come Ultra Plast. Inoltre, l’utilizzo di materiale plastico per la pulizia dell’impianto implica un maggiore tempo di fermo macchina (a volte anche di alcune ore) ed è tutto tempo che non si sta dedicando alla produzione. Ancora oggi molti produttori considerano il compound per la pulizia come un costo supplementare, ma Ultra System e tutti gli altri produttori di purging compound hanno dimostrato che, al contrario, il purging professionale riduce i costi di produzione. A livello applicativo, per esempio, molti produttori di articoli stampati a iniezione non vogliono utilizzare i purging compound temendo che questi possano danneggiare il sistema a canali caldi dello stampo. Ultra System ha invece dimostrato che Ultra Plast si può utilizzare in completa e totale sicurezza poiché non contiene alcun componente abrasivo. E le preforme stampate in PET rappresentano l’esempio perfetto, come si può vedere dalla foto in questa pagina (dalla seconda preforma in poi è stato iniettato nello stampo anche il purging compound). Naturalmente Ultra Plast trova applicazione anche nell’estrusione, ad esempio per la produzione di film cast o in bolla.
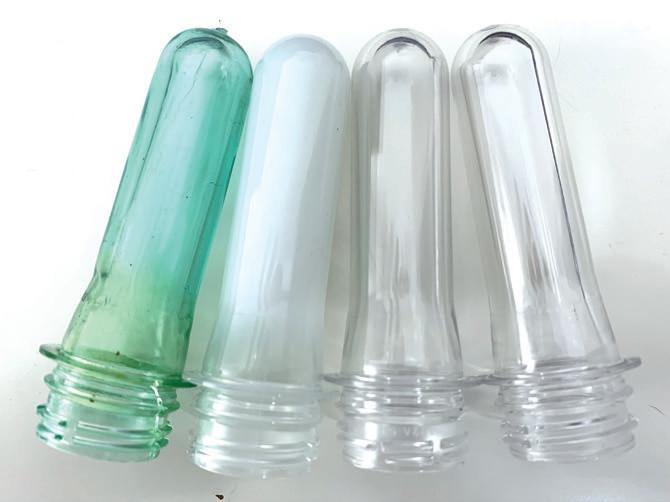
Il purging compound Ultra Plast può essere utilizzato in tutti i settori e su tutti i tipi di macchine durante il cambio colore e/o materiale a temperature fino a 420°C, senza generare sgradevoli fumi e odori
Additivi a base di carbonato di calcio Due nuovi materiali per contribuire all’economia circolare
Il 15 novembre 2021 la società svizzera Omya International, tra i principali produttori globali di minerali industriali derivati primariamente da carbonato di calcio, dolomite e perlite, ha annunciato ufficialmente il lancio sul mercato di Omyaloop: una nuova famiglia di prodotti a base di carbonato di calcio e dedicata alla transizione del settore dei polimeri dall’economia lineare a quella circolare. La nuova e ampia gamma di prodotti Omyaloop consente infatti di sostituire le cariche minerali attualmente utilizzate in numerosi prodotti estrusi, incrementandone la sostenibilità e il contenuto di materiale riciclato. Precursore in questo ambito, Omya utilizza per la gamma Omyaloop materiali accuratamente selezionati e recuperati da settori in cui sarebbero stati destinati a essere smaltiti come rifiuti. Nel maggio del 2021 la società aveva lanciato anche la gamma OmyaPET, a base di carbonato di calcio funzionalizzato e dedicata alle applicazioni del PET. Si tratta di una famiglia di opacizzanti altamente competitivi per la produzione di bottiglie in PET o di film in BOPET di colore bianco opaco. Consente inoltre di ridurre significativamente l’impatto ambientale di prodotti quali, per esempio, le bottiglie per il latte UHT, ottimizzando pure i costi di produzione senza compromettere le caratteristiche meccaniche, funzionali ed estetiche delle bottiglie. Inizialmente la gamma di opacizzanti OmyaPET sarà introdotta nel solo mercato europeo, per poi essere estesa gradualmente ad altre regioni. I prodotti Omyaloop e OmyaPET sono certificati da Bureau Veritas come materiali riciclati al 100% e, grazie alla loro elevata qualità, soddisfano i requisiti del regolamento UE n. 10/2011 per i materiali a contatto con alimenti.
Le nuove famiglie di prodotti Omyaloop e
OmyaPET riflettono l’impegno di Omya volto a offrire soluzioni sostenibili e innovative destinate ad aumentare la circolarità del settore dei polimeri
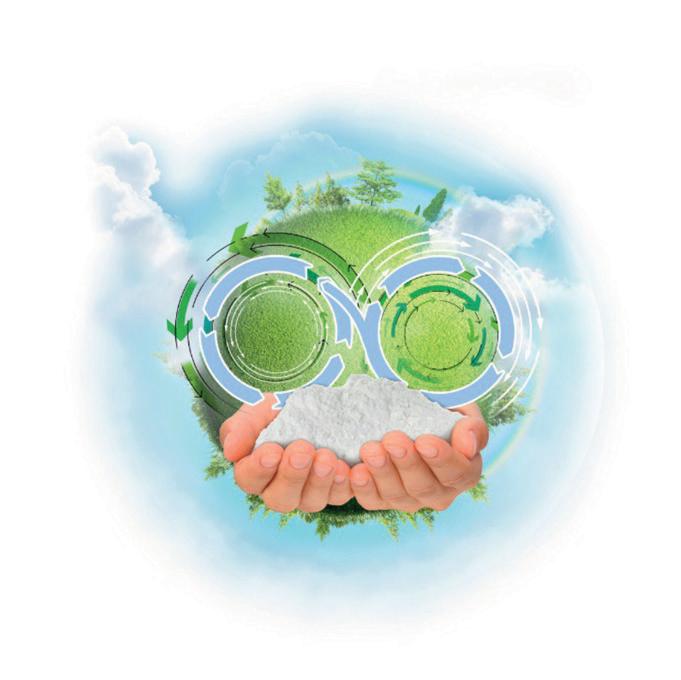

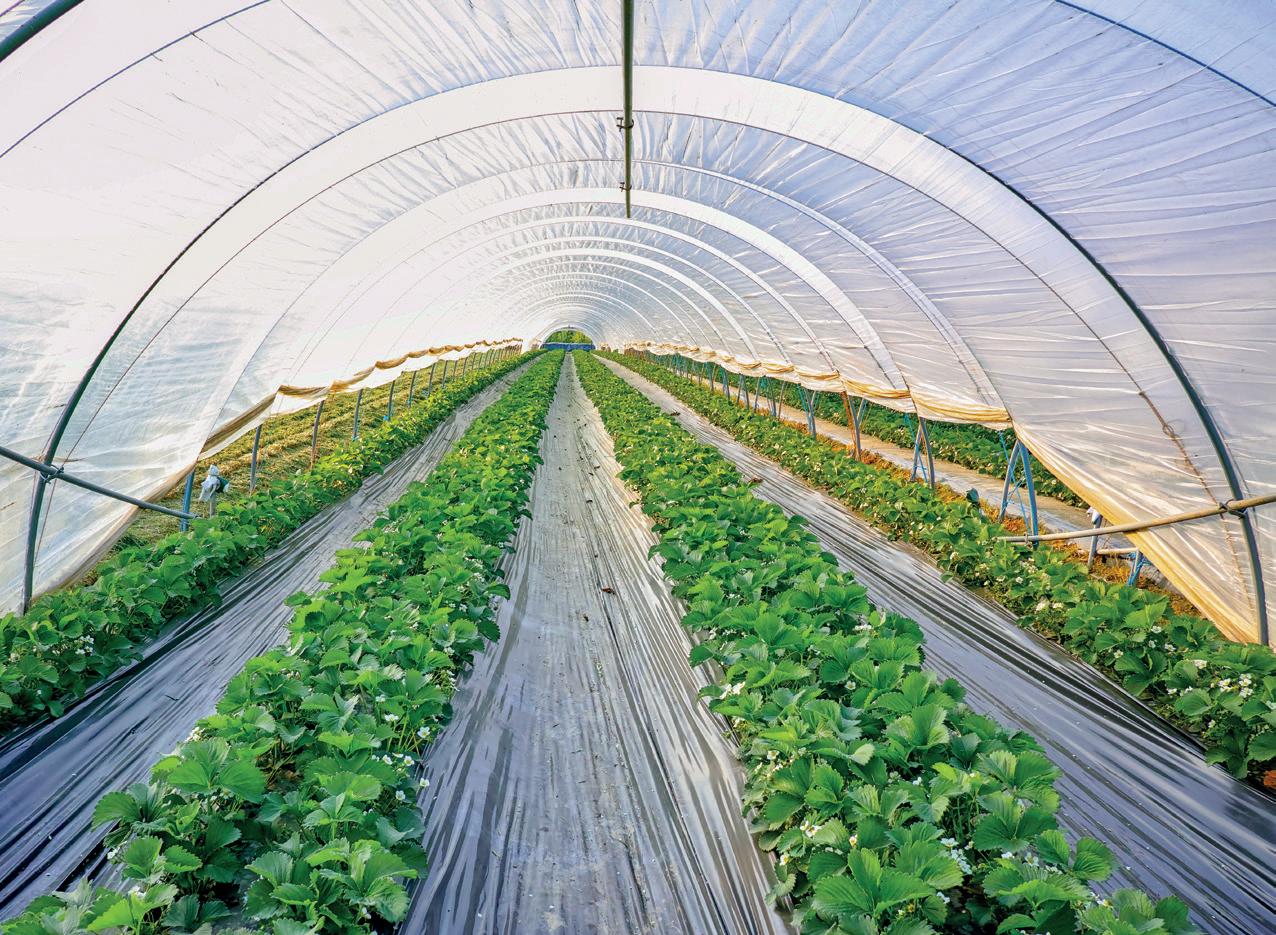
Stabilizzanti alla luce ad alte prestazioni Eccellenti proprietà antinvecchiamento nelle applicazioni delle poliolefine
UniteChem Group ha recentemente iniziato la produzione a pieno regime dei suoi stabilizzanti alla luce ad alte prestazioni LS2020 ed LS119
Con sede globale a Suqian City (Jiangsu, Cina), 1650 dipendenti e un fatturato di circa 300 milioni di euro, UniteChem Group si colloca tra i principali fornitori globali di stabilizzanti ad alte prestazioni per materie plastiche rivolti a una vasta gamma d’applicazioni industriali di fascia alta. Lo scorso novembre il gruppo ha annunciato di aver iniziato la produzione a pieno regime degli stabilizzanti ad alte prestazioni LS2020 ed LS119 presso i suoi impianti produttivi di recente avviamento. “UniteChem Group ha iniziato a produrre stabilizzanti alla luce secondo le specifiche del settore, come l’LS944, nel 1997 e da allora ha continuamente ampliato il suo portafoglio di additivi per polimeri”, ha dichiarato il CEO Junyi Lin. “Oggi, siamo orgogliosi di essere tra i più grandi fornitori al mondo di stabilizzanti alla luce e di altri additivi per materie plastiche, con un’offerta di oltre 40 mila tonnellate di prodotti finiti. La nostra completa integrazione a monte, con una capacità produttiva di oltre 80 mila tonnellate di intermedi, fornisce un’ampia flessibilità di produzione, alta affidabilità e massimo controllo della qualità. La produzione attuale, che si basa su due impianti all’avanguardia situati nella provincia di Jiangsu, sta per essere completata con due ulteriori grandi impianti nelle province di Jiangsu e Sichuan, il cui completamento è previsto per il 2022/2023”. UniteChem LS2020 è un moderno stabilizzante alla luce a base di ammine stericamente impedite (HALS), che offre eccellenti proprietà antinvecchiamento nelle applicazioni del polietilene reticolato e dei copolimeri delle olefine e di altri materiali polimerici. L’LS119 è invece particolarmente adatto per serre in polietilene, fibre di polipropilene, componenti automobilistici in TPO e altri polimeri come: EVA, EPDM, PA, PET e PMMA. “La produzione di UniteChem LS2020 ed LS119 viene incrementata costantemente con l’obiettivo di raggiungere rispettivamente una capacità di 1000 e 2000 t/anno per soddisfare la domanda globale”, ha aggiunto Junyi Lin. Il gruppo UniteChem destina regolarmente il 5% del suo fatturato alle diversificate attività di ricerca e sviluppo, operando con cinque laboratori indipendenti, compreso il moderno centro R&S di Shanghai, recentemente inaugurato. Gli sforzi attuali si concentrano sull’espansione della propria gamma con i richiestissimi assorbitori UV, gli stabilizzanti alla luce NOR-HALS e altri additivi fondamentali per l’industria dei materiali plastici.

NOTIZIARIO DEI COMPOSITI
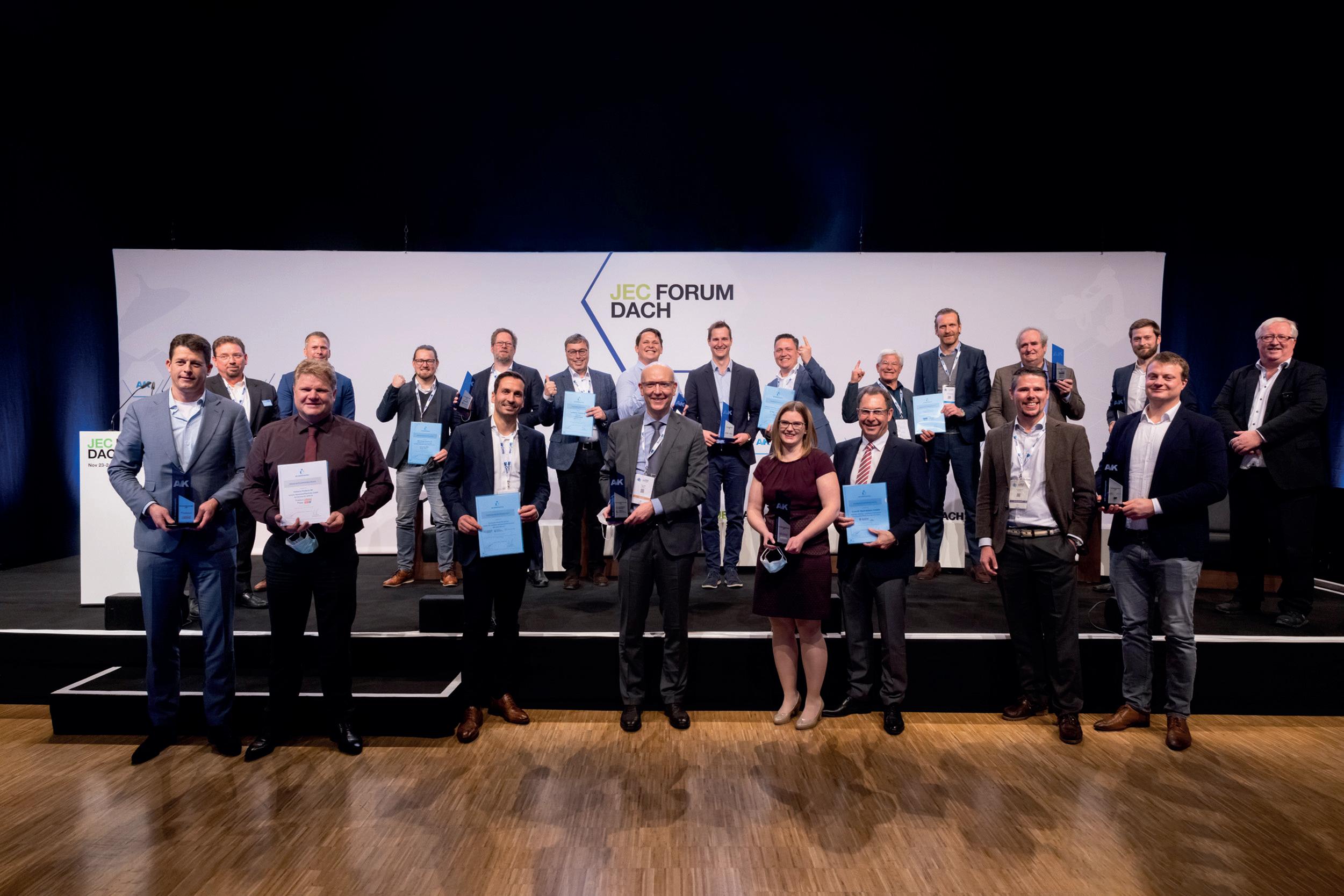
INNOVAZIONE E IMPRENDITORIALITÀ AL JEC FORUM DACH
Una nuova generazione di vincitori nel mondo dei compositi
DAL 23 AL 24 NOVEMBRE JEC FORUM DACH HA TRASFORMATO FRANCOFORTE NEL PRINCIPALE PUNTO D’INCONTRO PER L’INDUSTRIA DEI COMPOSITI DEI PAESI GERMANOFONI (GERMANIA, AUSTRIA E SVIZZERA). IL 24 NOVEMBRE I RIFLETTORI SONO STATI INOLTRE PUNTATI SUI VINCITORI DEI DUE CONCORSI AVK INNOVATION AWARDS E JEC COMPOSITES STARTUP BOOSTER, DEDICATI RISPETTIVAMENTE ALLE INNOVAZIONI E ALLE STARTUP
A CURA DI RICCARDO AMPOLLINI
In occasione dell’edizione 2021 dello JEC Forum DACH, tenutasi per la prima volta a Francoforte tra il 23 e il 24 novembre scorsi, AVK (la federazione tedesca che rappresenta l’industria delle materie plastiche rinforzate) ha consegnato i suoi prestigiosi Innovation Awards ad aziende, istituti e università, nonché ai rispettivi partner tecnologici, in ciascuna delle tre categorie del concorso: “Prodotti innovativi/Applicazioni innovative”, “Processi innovativi” e “Ricerca e scienza”. Il tema principale di quest’anno, in tutte le categorie, è stato quello della sostenibilità: un argomento chiave per il settore dei compositi, che si misura costantemente con lo sviluppo di prodotti e processi più rispettosi dell’ambiente. “Anche quest’anno, come di consueto, tra i candidati ai premi vi erano parecchi prodotti e processi molto interessanti e promettenti. Gli Innovation Awards evidenziano la straordinaria efficienza, economicità e sostenibilità delle materie plastiche fibrorinforzate, nonché delle aziende e degli istituti che operano nel nostro comparto”, ha commentato Elmar Witten, amministratore delegato di AVK. Una giuria composta dai maggiori esperti del settore ha premiato quest’anno nove imprese, in riconoscimento degli sforzi fatti per aprire nuovi orizzonti nel campo dei compositi.
PRODOTTI INNOVATIVI/APPLICAZIONI INNOVATIVE
Il primo premio in questa categoria è stato conquistato dai segnali stradali N-BMC, sviluppati da Nabasco Products e Lorenz Kunststofftechnik in collaborazione con i rispettivi partner Pol
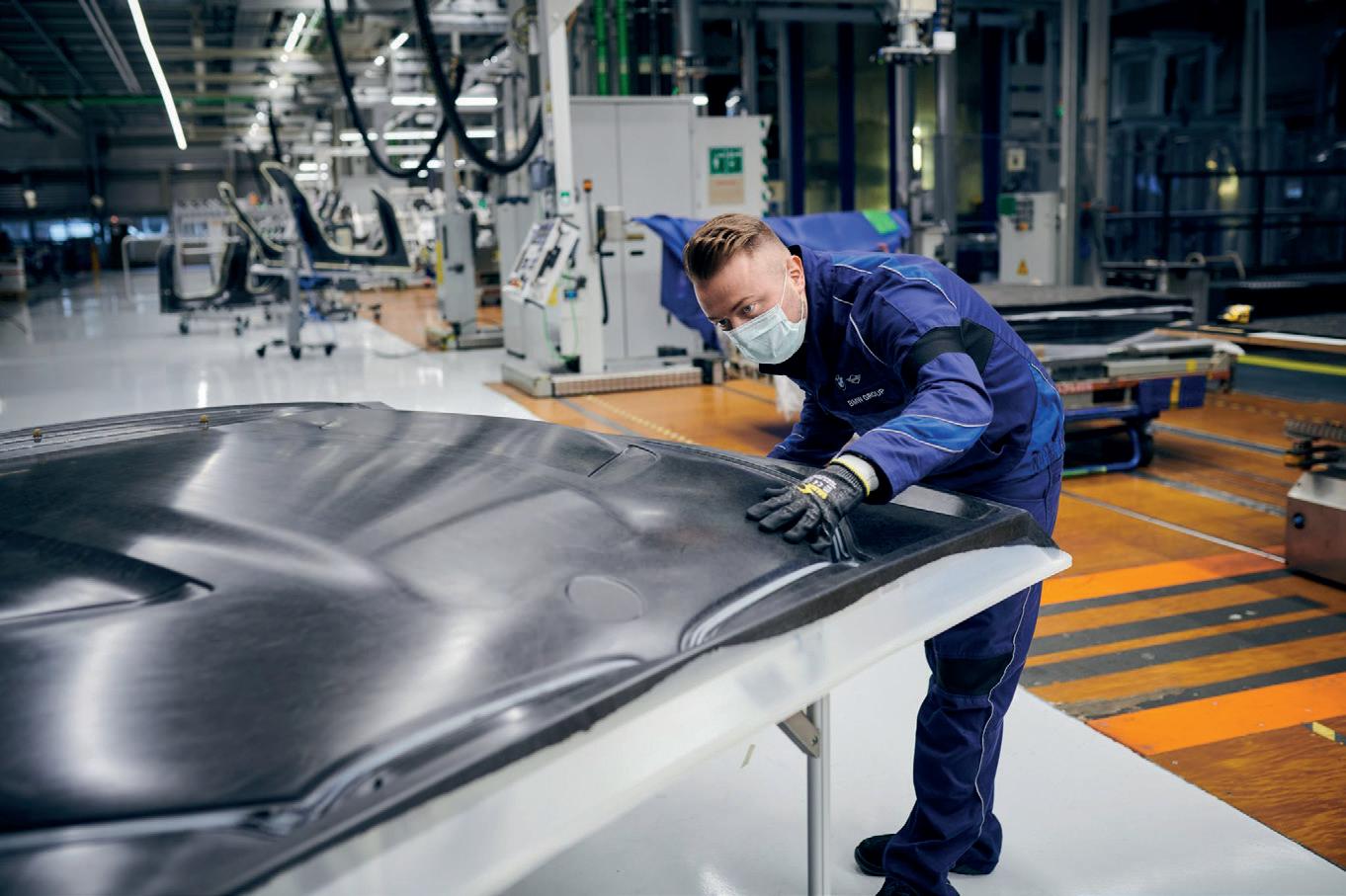
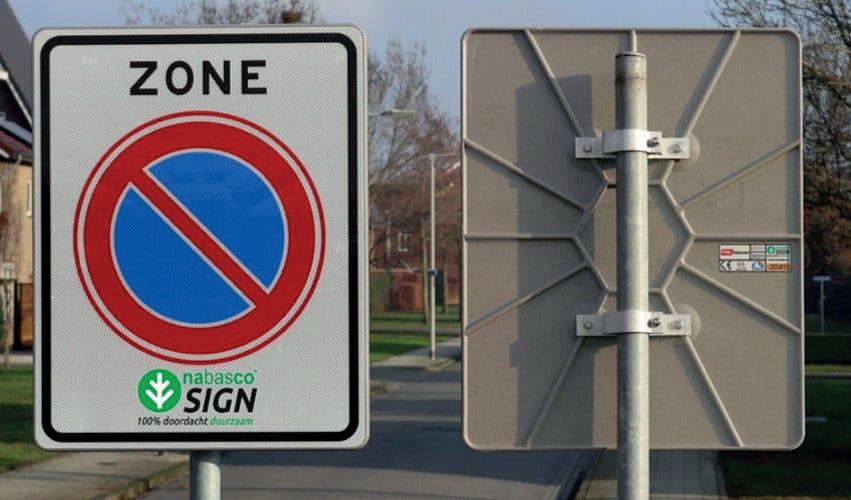
Heteren ed NPSP. I segnali sono stati realizzati in SMC (Sheet Moulding Compound), materiali più sostenibili rispetto al tradizionale alluminio, in quanto la loro lavorazione non comporta alcuno spreco di materiale. Inoltre, tutte le materie prime vengono acquistate in un raggio di 500 chilometri dal luogo di trasformazione. Questi segnali di nuova concezione hanno già ottenuto il certificato “Cradle-2-Cradle” per la sostenibilità (livello bronzo). Evonik Operations si è invece aggiudicata il secondo premio grazie a una nuova resina vinilestere ultratenace e adatta all’uso nella grande cantieristica marittima. Tale resina consente di costruire grandi scafi in plastica rinforzata con fibre di vetro in modo più rapido, più efficiente e più economico rispetto agli attuali materiali. Il miglioramento della resistenza a fatica della matrice polimerica ottimizza inoltre in modo significativo la durata dello scafo, con il risultato che sia i costruttori che gli operatori delle grandi navi possono sfruttare in modo ancora più efficace i vantaggi consentiti dai compositi in termini di sostenibilità. Infine, il terzo premio in questa categoria è andato a un alloggiamento multimateriale per aspiratore d’aria usato nelle turbine a gas, sviluppato da MAN Energy Solutions, Leichtbau-Zentrum Sachsen e Leichtbau-Systemtechnologien Korropol. L’idea centrale alla base dello sviluppo dell’alloggiamento è quella di separare le funzioni in due sezioni: una sezione ha funzioni portanti, mentre l’altra è soggetta quasi esclusivamente a sollecitazioni aerodinamiche. I deflettori dell’aria dell’alloggiamento, solitamente realizzati in pesante ghisa grigia, sono stati riprogettati come una classica struttura a guscio in vetroresina (GRP). L’innovativa progettazione di questo alloggiamento multimateriale non solo non comporta costi più elevati grazie alla riduzione del 60% della massa, ma consente anche di adattare rapidamente l’alloggiamento alle variazioni dei profili di flusso e offre un notevole potenziale per un’ulteriore riduzione dei costi.
PROCESSI INNOVATIVI
Il primo premio nella categoria “Processi innovativi” è stato assegnato al Gruppo BMW e al suo partner Renolit per il processo “in-mould wrapping” (avvolgimento nello stampo): un nuovo tipo di rivestimento dei componenti per uno strato esterno più sostenibile in composito fibrorinforzato. Questa tecnologia riduce i tempi, i materiali e i costi associati ai rivestimenti superficiali, grazie all’applicazione di un film nella fase di compressione. I processi convenzionali di preparazione e verniciatura delle superfici sono solitamente re-
Vincitori nella categoria “Processi innovativi” sono stati BMW e il partner Renolit per lo sviluppo del processo “in-mould wrapping”, in grado di produrre un rivestimento più sostenibile riducendo tempi, materiali ed emissioni di CO2
sponsabili della maggiore quantità d’emissioni di CO2 che si verificano durante la produzione di parti in plastica. Adatta a un’ampia varietà di processi di compressione delle resine termoindurenti, la nuova tecnologia utilizza invece film che possono essere formati sottovuoto senza ricorrere al riscaldamento. “In-mould wrapping” può ridurre le emissioni di CO2 fino al 93% rispetto alle tecniche di verniciatura standard. Il secondo premio è andato a Lufthansa Technik e al partner iSAM per aver messo a punto un sistema di riparazione automatizzato e adattivo di componenti strutturali in composito, destinato al settore aeronautico. Il sistema, che si basa su robot e che può raggiungere una precisione di ±0,06 mm, utilizza un software di pianificazione del percorso per eseguire riparazioni su diverse parti strutturali. Le aree in riparazione possono coprire vari metri quadrati e riguardare anche componenti con geometrie complesse. Questa nuova tecnologia riduce i tempi di lavorazione del 50-85% e i consumi di materiale fino al 50%, sollevando al contempo i lavoratori da compiti ripetitivi e non ergonomici. Consente inoltre di eseguire riparazioni che in precedenza non erano economicamente o tecnicamente possibili. La società tedesca CTC (Gruppo Airbus) si è piazzata al terzo posto con il suo pretrattamento superficiale automatizzato con lampade agli eccimeri VUV (vacuum ultraviolet: radiazioni ultraviolette con applicazione del vuoto). Il pretrattamento delle superfici in preparazione alla verniciatura dei componenti in plastica rinforzata con fibre di carbonio (CFRP) è un processo solitamente non ergonomico, che viene tradizionalmente suddiviso in più fasi e che richiede tempo e molta energia. Oggi questo difficile processo può essere automatizzato irradiando i componenti con UVC (radiazione ultravioletta con lunghezza d’onda corta: 100-280 nm), mediante una lampada VUV agli eccimeri. La lampada combina due funzioni chiave: pulizia e attivazione delle superfici. È importante sottolineare che questo sistema a robot mobile può essere posizionato autonomamente in cantiere ed eseguire trattamenti superficiali sul sito.
Il primo premio nella categoria “Prodotti innovativi/Applicazioni innovative” degli AVK Innovation Awards è stato conquistato dai segnali stradali N-BMC, sviluppati da Nabasco Products e Lorenz Kunststofftechnik
RICERCA E SCIENZA
Il primo premio in questa categoria è stato attribuito all’agenzia spaziale tedesca Deutsches zentrum für Luft- und Raumfahrt (DLR) per la sua Bondline Control Technology (BCT). Questo processo innovativo viene utilizzato per il controllo di qualità dell’incollaggio di diversi substrati. L’elemento centrale è rappresentato da un tessuto poroso che viene applicato su una superficie di giunzione mediante adesivo epossidico, o matrice polimerica. La rimozione di questo
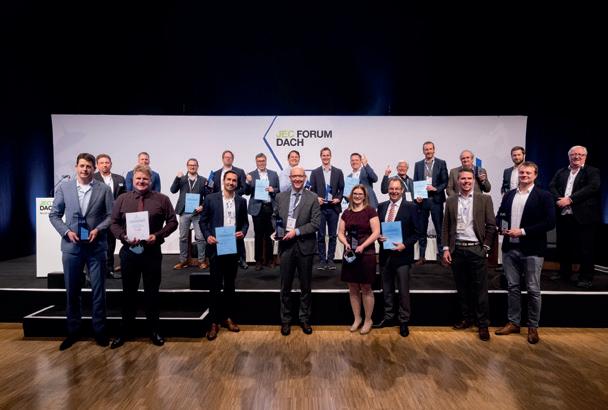
“strato pelabile” (peel ply) di tessuto crea una superficie a sottosquadro chimicamente reattiva, che può anche essere utilizzata per testare l’adesione al substrato. La tecnologia BCT ha il potenziale per adattarsi a un’ampia varietà di possibili applicazioni. Per esempio, un diverso strato pelabile può essere sostituito con il tessuto BCT per produrre componenti compositi con superficie di giunzione ottimizzata. L’economico peeling test BCT è poi adatto sia per test su provini sia per il controllo del processo. Inoltre, la combinazione di pretrattamento superficiale e test d’adesione può essere utilizzata per garantire la qualità delle riparazioni effettuate tramite incollaggio su strutture composite fibrorinforzate. In seconda posizione troviamo invece l’Istituto di tecnologie tessili (ITA) dell’Università RWTH di Aquisgrana e i suoi partner Aerovide, Altropol Kunststoff, Basamentwerke Böcke e TechnoCarbon Technologies GbR, che hanno presentato StoneBlade: una struttura leggera per l’industria eolica che fa uso di granito. Quest’innovazione consente ai produttori di ridurre la quantità di materiali non riciclabili utilizzati nella costruzione delle pale eoliche. Allo stesso tempo, riduce il peso di questi componenti e ne migliora le proprietà meccaniche che presiedono alla stabilità dei generatori eolici. L’approccio innovativo consiste nella sostituzione della vetroresina nei componenti delle pale con il granito, un materiale leggero naturale, economico e riciclabile. Le lastre di granito vengono tagliate e rettificate a uno spessore di pochi millimetri, e quindi incorporate in un laminato composito rinforzato con fibre di carbonio, che le stabilizza nel caso di carichi intermittenti. Il materiale precompresso nel composito è stabile alla pressione e può assorbire in continuo le forze di trazione in caso di carichi intermittenti, senza peraltro mostrare alcuna perdita di rigidità. Il terzo premio è andato all’Istituto per le tecnologie delle materie plastiche e per la costruzione leggera dell’Università di Dresda (ILK), il quale, insieme al partner Mercedes Benz, ha condotto uno studio interdisciplinare per sviluppare un modulo di ricarica induttiva altamente integrato, per veicoli elettrici. Tale modulo di ricarica, ultrasottile, è stato progettato per sfruttare al meglio lo spazio nel sottoscocca del veicolo senza ridurre l’altezza da terra. Lo studio interdisciplinare ha comportato la caratterizzazione elettrica, meccanica e di processo dei fili Litz ad alta frequenza, delle lamine ferromagnetiche e delle tele in filo metallico, nonché la creazione di un modello per le simulazioni. Il risultato è un prototipo dimostrativo di un sistema di ricarica con un’altezza strutturale di 15 mm e un peso totale di 8 kg, che raggiunge un’efficienza massima di trasmissione del 92% con una potenza nominale di 7,2 kW e con un raffreddamento ad aria attivo. La “parte hardware” del dimostratore è stata fabbricata mediante un processo in tre fasi, utilizzando le tecniche RTM (Resin Transfer Moulding) e VARI (Vacuum-Assisted Resin Infusion).
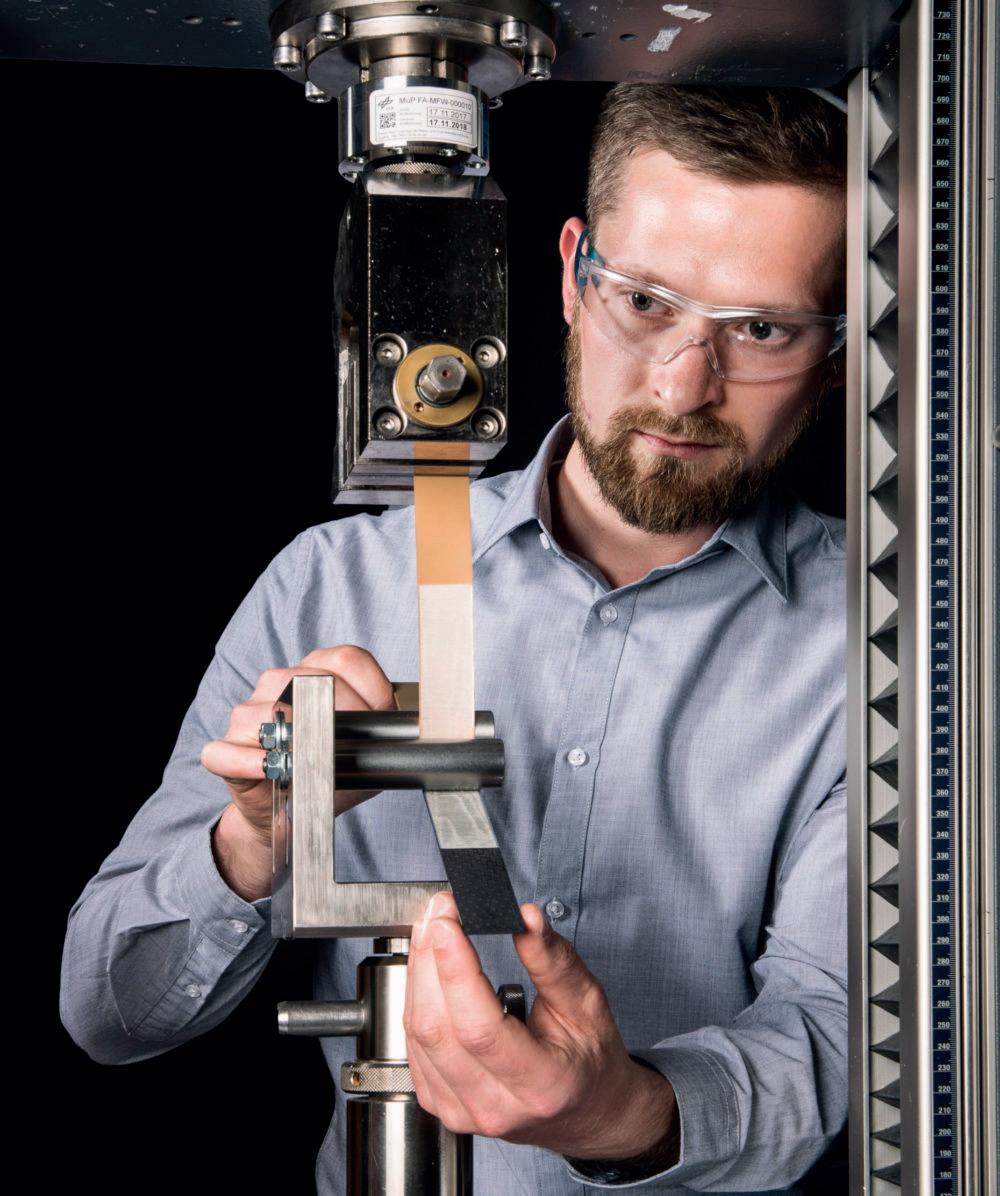
PREMIO STARTUP BOOSTER PER L’IMPRENDITORIALITÀ
Tecnologie, modelli di business, applicazioni... Le startup industriali sviluppano a getto continuo innovazioni d’avanguardia suscitando l’interesse dei produttori che desiderano entrare nei mercati di domani, i quali, in cambio, aiutano le stesse startup a crescere. Organizzato da JEC Group, il concorso Startup Booster ha inizialmente selezionato cinque startup come finaliste, garantendo ai loro progetti una notevole visibilità tra gli operatori europei del settore compositi. Nel pomeriggio del 24 novembre, in presenza a Francoforte e tramite piattaforma online, la giuria ha poi annunciato ufficialmente il nome del vincitore del concorso: l’azienda tedesca FibreCoat. Quest’ultima ha sviluppato un processo per il rivestimento diretto di materiali a base di fibre inorganiche, che consente l’utilizzo di materiali bicomponente a basso costo nella realizzazione di strutture leggere usate nel campo della schermatura elettromagnetica e della filtrazione industriale. La startup beneficerà di un programma di accelerazione dell’innovazione e avrà l’opportunità di avere un proprio stand a JEC World 2022, il principale evento del prossimo anno riservato al mondo dei compositi. Il concorso Startup Booster è stato sponsorizzato da RomagnaTech, società senza scopo di lucro che promuove, accelera e genera processi d’innovazione tecnologica. Oltre a essere un Organismo di ricerca e trasferimento tecnologico ai sensi del Regolamento CE n. 651/2014, RomagnaTech è accreditata come laboratorio di ricerca industriale e centro per l’innovazione e il trasferimento tecnologico nell’ambito della Rete Alta Tecnologia della Regione Emilia-Romagna.
I delegati dell’azienda tedesca FibreCoat ricevono il primo premio del concorso Startup Booster organizzato da JEC Group Il primo premio nella categoria “Ricerca e scienza” è andato all’agenzia spaziale tedesca Deutsches zentrum für Luft- und Raumfahrt (DLR) per la sua Bondline Control Technology (BCT), utilizzata per il controllo di qualità dell’incollaggio di diversi substrati
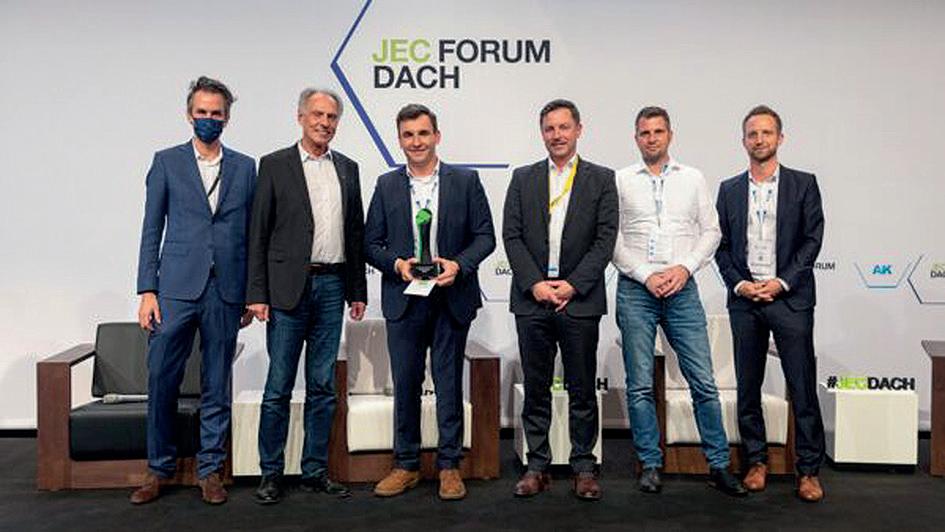
IN BREVE
Scegliere i materiali giusti Compositi per proteggere le forze armate
Per nascondere al nemico la propria presenza, la posizione e le intenzioni sul campo di battaglia, l’occultamento militare svolge un ruolo essenziale. Oggi i tubi telescopici in composito vengono scelti per sostenere le reti mimetiche al posto di quelli in materiali alternativi come l’alluminio per via di diversi vantaggi, come il peso inferiore e la velocità di montaggio. Data la “delicatezza” di quest’applicazione, occorre però considerare attentamente ogni fase della produzione, dalla scelta delle fibre di rinforzo al processo produttivo in sé. Ecco alcune considerazioni al riguardo di Patrick Loock, responsabile del segmento prodotti e applicazioni presso la società finlandese Exel Composites. Grazie alla sua eccellente resistenza alla trazione, che le consente di resistere a forze elevate meglio di alcuni metalli, per rinforzare i tubi telescopici viene generalmente scelta la fibra di vetro. Quest’ultima è inoltre un ottimo isolante, con un basso coefficiente di conduttività termica, pari a 0,3 W/m˚K. Quello dell’alluminio è invece molto più elevato: circa 200 W/m˚K. Sul campo di battaglia, dove le termocamere vengono spesso usate per individuare la posizione dell’avversario, la vetroresina risulta quindi praticamente non rilevabile. Anche l’allineamento delle fibre riveste un ruolo importante. Grazie al particolare allineamento elicoidale ottenibile, il miglior processo produttivo risulta in questo caso il pullwinding con una combinazione di fibre trasversali e unidirezionali. Si ottengono così pareti del tubo più sottili, nonché la forza e la rigidità necessarie per il supporto delle reti mimetiche. I tubi in alluminio sono dipinti con colori (di solito verde o sabbia Nato) che ne favoriscono l’occultamento. Tuttavia, la vernice si può staccare durante le manovre militari, riducendo l’occultabilità. Per proteggerne l’integrità, nel caso dei compositi, i coloranti vengono aggiunti direttamente alla resina utilizzata. Si ha così una pigmentazione uniforme su tutte le pareti del tubo e anche al suo interno, in modo che il colore rimanga lo stesso anche in caso di graffi profondi. La scelta delle resine di base è naturalmente fondamentale per garantire adeguate caratteristiche meccaniche e, di solito, vengono preferite quelle termoindurenti, in quanto mostrano una migliore resistenza chimica e consentono al composito di mantenere la propria forma per tutta la vita utile. I compositi per applicazioni militari devono essere notevolmente flessibili per far fronte a carichi di peso variabili e a temperature estreme, da -40°C a 80°C. Assorbono quindi meglio l’impatto ed è meno probabile che si frantumino sotto stress. Anche se perforata da un proiettile, la struttura permette al tubo di funzionare in modo adeguato. Inoltre, i compositi sono privi di ruggine, il che li rende resistenti all’acqua e ideali per l’uso in terreni umidi.

I pali telescopici in composito vengono oggi scelti per sostenere le reti mimetiche al posto dell’alluminio grazie a vantaggi quali leggerezza e velocità di montaggio
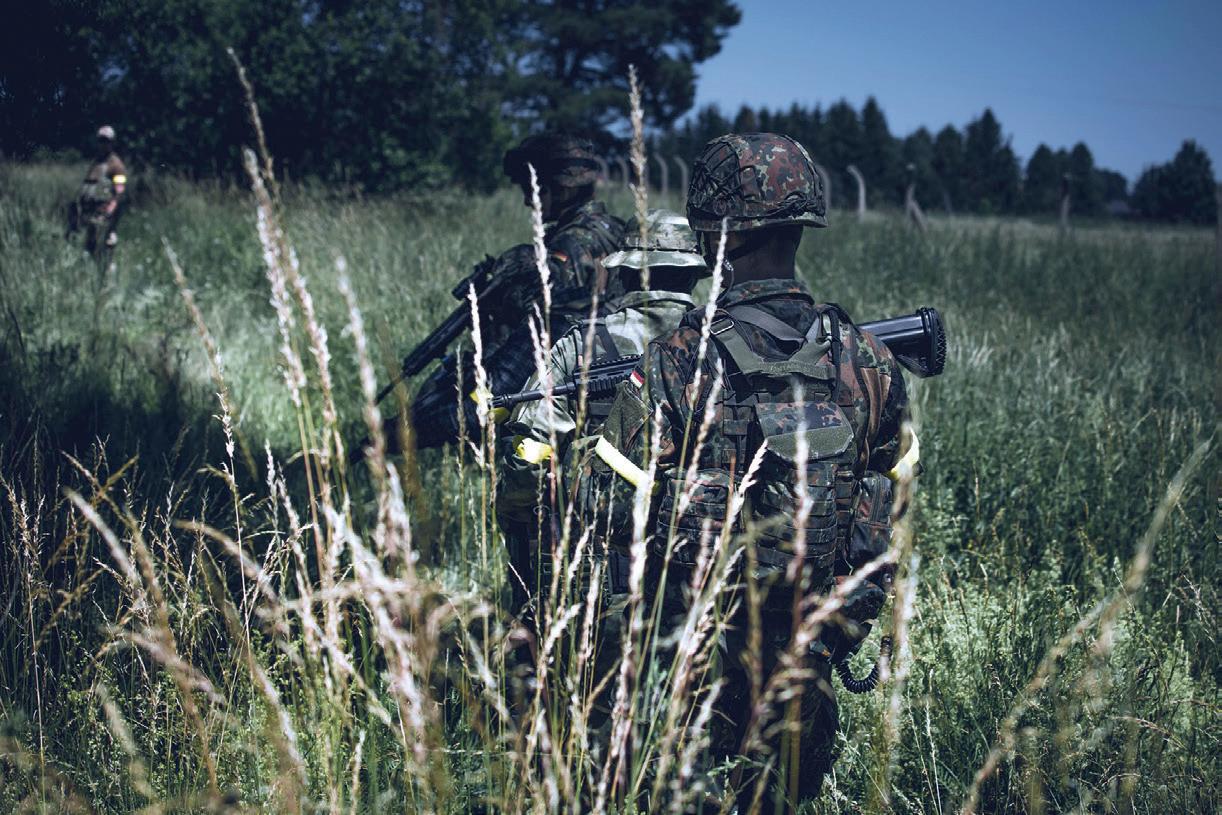
Tradizione e futuro degli yacht da competizione
Sviluppato da Schütz, il materiale per costruzione leggera Cormaster è un componente importante del nuovo yacht da competizione del velista Boris Herrmann
“A race we must win - Climate action now!” Questo slogan risalta in primo piano sull’imbarcazione “Seaexplorer” del velista di fama internazionale Boris Herrmann. Uno slogan che sta a rappresentare da un lato lo spirito sportivo e la passione per la competizione, dall’altro però anche l’urgente necessità di occuparsi, insieme, di una delle principali sfide del momento: la tutela del clima e dell’ambiente. Una missione che la società Schütz appoggia a diversi livelli e alla quale Boris Herrmann e il suo team Malizia si dedicano già da tempo. L’entusiasmo per la soluzione tecnicamente migliore e per il risparmio delle risorse naturali costituisce proprio la base della nuova partnership strategica tra il team Malizia e Schütz. In tutte e quattro le sue divisioni, Schütz offre prodotti e servizi che aiutano gli utenti a diventare più efficienti, a risparmiare materiale ed energia e a ridurre pertanto la propria impronta di carbonio. Sia come pioniere nell’economia circolare, con imballaggi che consentono di risparmiare risorse, sia come fornitore di sistemi che offrono una maggiore efficienza energetica e maggiore comfort in casa, oppure come pioniere nello sviluppo e nell’utilizzo di materiali all’avanguardia per costruzioni leggere. In particolare, nella propria divisione Composites, Schütz sviluppa e produce, con il marchio Cormaster, materiali per costruzione leggera che vengono utilizzati non solo nell’industria aerospaziale, ma anche nella costruzione di imbarcazioni e autoveicoli. Per esempio, i “Container”, gli yacht da competizione di Schütz coronati da recenti successi, sono stati costruiti essenzialmente con il materiale composito sviluppato e prodotto in casa. In quanto Official Technical Partner e Official Supplier del team Malizia, Schütz produce ora da questi blocchi a struttura alveolare importanti componenti strutturali per la nuova imbarcazione di Boris Herrmann. È con particolare orgoglio che l’azienda fa affluire oggi il proprio know-how, acquisito in decenni d’esperienza, anche nella fase di realizzazione del progetto tecnico e di costruzione del nuovo yacht da competizione. Schütz si occupa ad esempio della realizzazione dell’intera forma della coperta, ma l’esperienza e le soluzioni ingegneristiche del Westerwald affluiscono anche nel costante sviluppo e nella costruzione dei foil, che conferiscono all’imbarcazione la sua enorme velocità.
Laboratory Instruments for Rubber and Plastic Testing

LATI N° 182 Centro ACCREDIA per la Taratura di Durometri Shore e IRHD
Gibitre Instruments Srl
Via Dell’Industria 73 - 24126 Bergamo Tel.: +39 035 460146 - Fax: 035 460687 E-mail: info@gibitre.it - www.gibitre.it
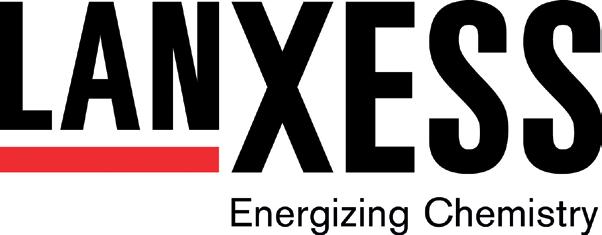
Business Units: RCH (Rhein Chemie), AII (Advanced Industrial Intermediates).
Prodotti e additivi speciali per l’industria della gomma
Lanxess Srl
Segreen Business Park - Palazzo Y Via San Bovio 1/3 - 20090 Segrate (Milano) Tel.: +39 02.3072.1 - Fax: +39 02.3072.2017 www.lanxess.com
3
5-8 SETTEMBRE 2023, MILANO IMG è un’azienda leader nella costruzione di presse per stampaggio. La lunga esperienza e la costante ricerca le permettono di proporre soluzioni che coprono l’intero settore dello stampaggio di elastomeri e materie plastiche.
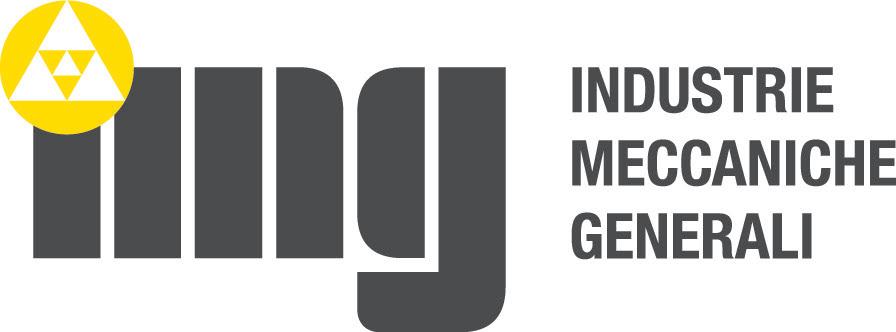
IMG Srl
Via Industriale 108 - 25020 Capriano del Colle (BS) Tel.: +39 030 31.46.45 - Fax: +39 030 31.26.64 E-mail: info@imgmacchine.it www.imgmacchine.it
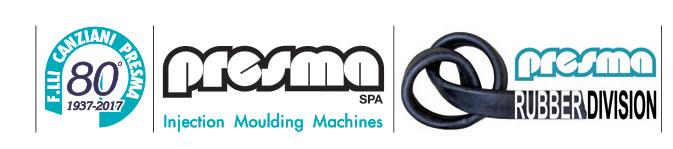
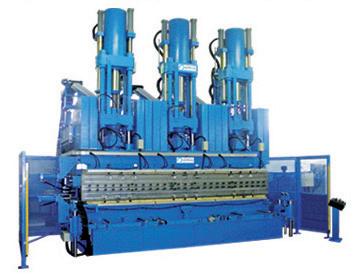

VENDITA , DISTRIBUZIONE E A SSISTENZ A TECNIC A PER GOMME SINTETICHE, L AT TICI SINTETICI E PRODOT TI CHIMICI PER L’INDUSTRIA DELL A GOMMA
ZEON EUROPE GmbH sede secondaria in Italia Piazza Quattro Novembre 7 - 20124 Milano Tel.: +39 02 67141701 - Fax: +39 02 36680124 ziinfo@zeon.eu www.zeon.eu
IL MONDO DELLA GOMMA
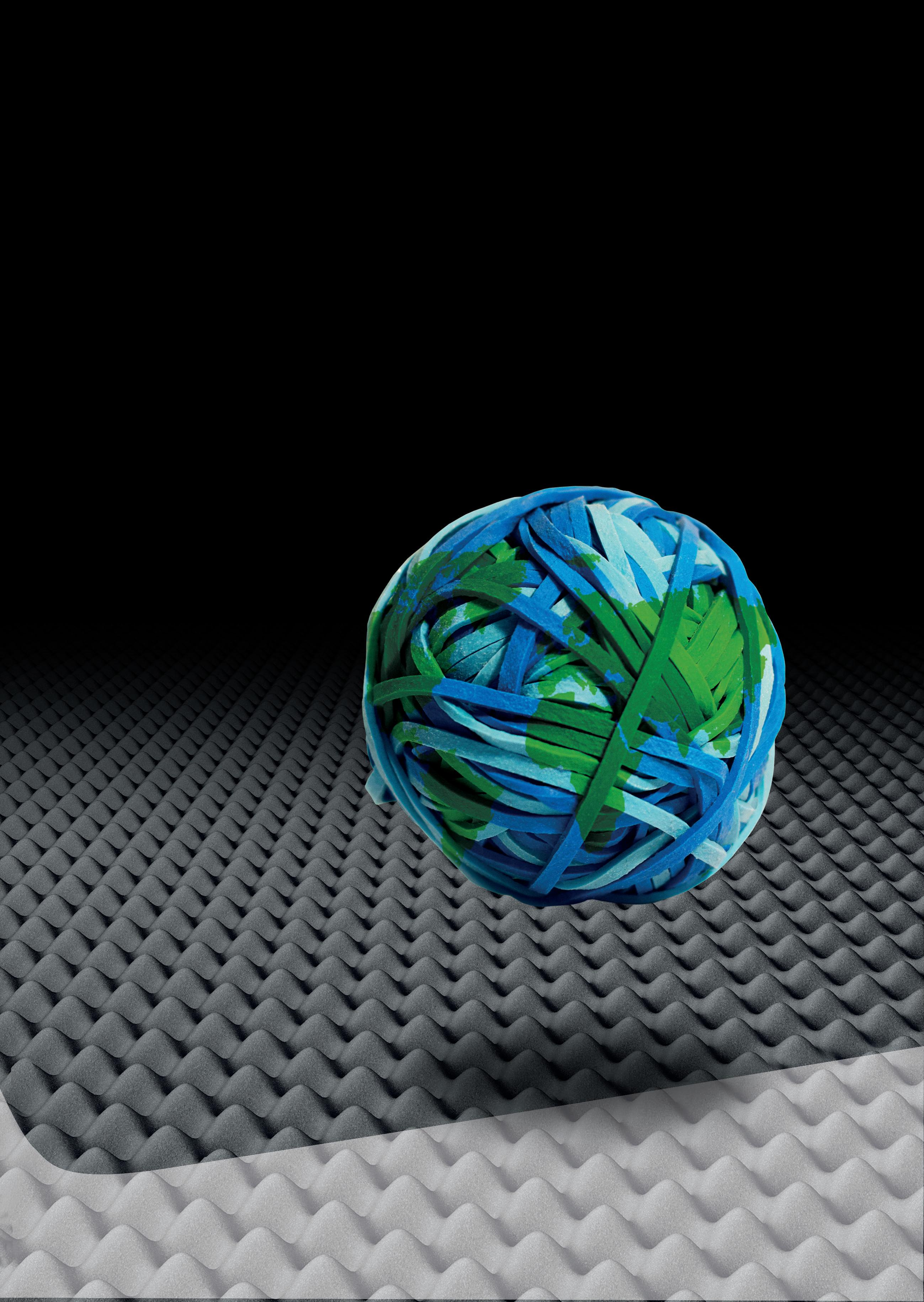
ECONOMIA CIRCOLARE DA “SCARTO = RIFIUTO” A “SCARTO = SOTTOPRODOTTO”
IL FUTURO DELLA GESTIONE DEGLI SCARTI DI LAVORAZIONE DELLA GOMMA PASSA DA QUESTA “TRASFORMAZIONE”, CON L’AIUTO DELLE NUOVE LINEE GUIDA DI ASSOGOMMA
La gestione degli scarti di lavorazione costituisce storicamente un problema critico per l’industria della gomma, che riscontra notevoli difficoltà a trovare sul mercato soluzioni per un loro recupero e persino per il loro smaltimento. Eppure, si tratta molto spesso di materiali potenzialmente interessanti per altre applicazioni, che, in linea di principio, potrebbero alimentare diversi processi industriali. In certi casi possono sussistere problemi di ordine tecnologico di non immediata soluzione, la cui ricerca può essere sfavorita dai volumi in gioco relativamente piccoli. La produzione di scarti in Italia si può infatti stimare in circa 40 mila tonnellate all’anno (pari a un decimo delle circa 380 mila t/anno di pneumatici a fine vita), che tuttavia non costituiscono un flusso omogeneo, ma un panorama complesso di materiali, distinti per tipologia di elastomero, stato fisico, grado di reticolazione (crudo/scottato/vulcanizzato), accoppiamento con altri materiali (tessili, metalli, adesivi ecc.) e così via. L’elevato potere calorifico rende la gomma un interessante candidato alla valorizzazione energetica, per esempio nei cementifici, ma ultimamente fattori di mercato stanno ostacolando questa strada, dominata da altri materiali (come la plastica), che risultano favoriti da volumi decisamente più elevati e dal sistema contributivo degli schemi di responsabilità estesa. Quanto sopra illustrato è tuttavia solo una parte del quadro: molto frequentemente scarti di lavorazione che sarebbero del tutto idonei ad alimentare altri processi industriali vengono smaltiti come rifiuti per ragioni del tutto svincolate da problemi tecnologici o di mercato, ma legate al panorama normativo. Infatti, la normativa sulla gestione dei rifiuti, di derivazione europea, prevede una fattispecie giuridica, il sottoprodotto, finalizzata proprio ad agevolare l’ulteriore utilizzo industriale di questi materiali (qualora sia soddisfatta una serie di condizioni), impedendo che diventino rifiuti. Tuttavia, l’interpretazione tradizionalmente restrittiva della normativa adottata dalle autorità del nostro Paese finisce molto spesso con lo scoraggiare le imprese dal procedere con lo sfruttamento di questa possibilità, inducendole a optare per la più sicura strada del rifiuto.
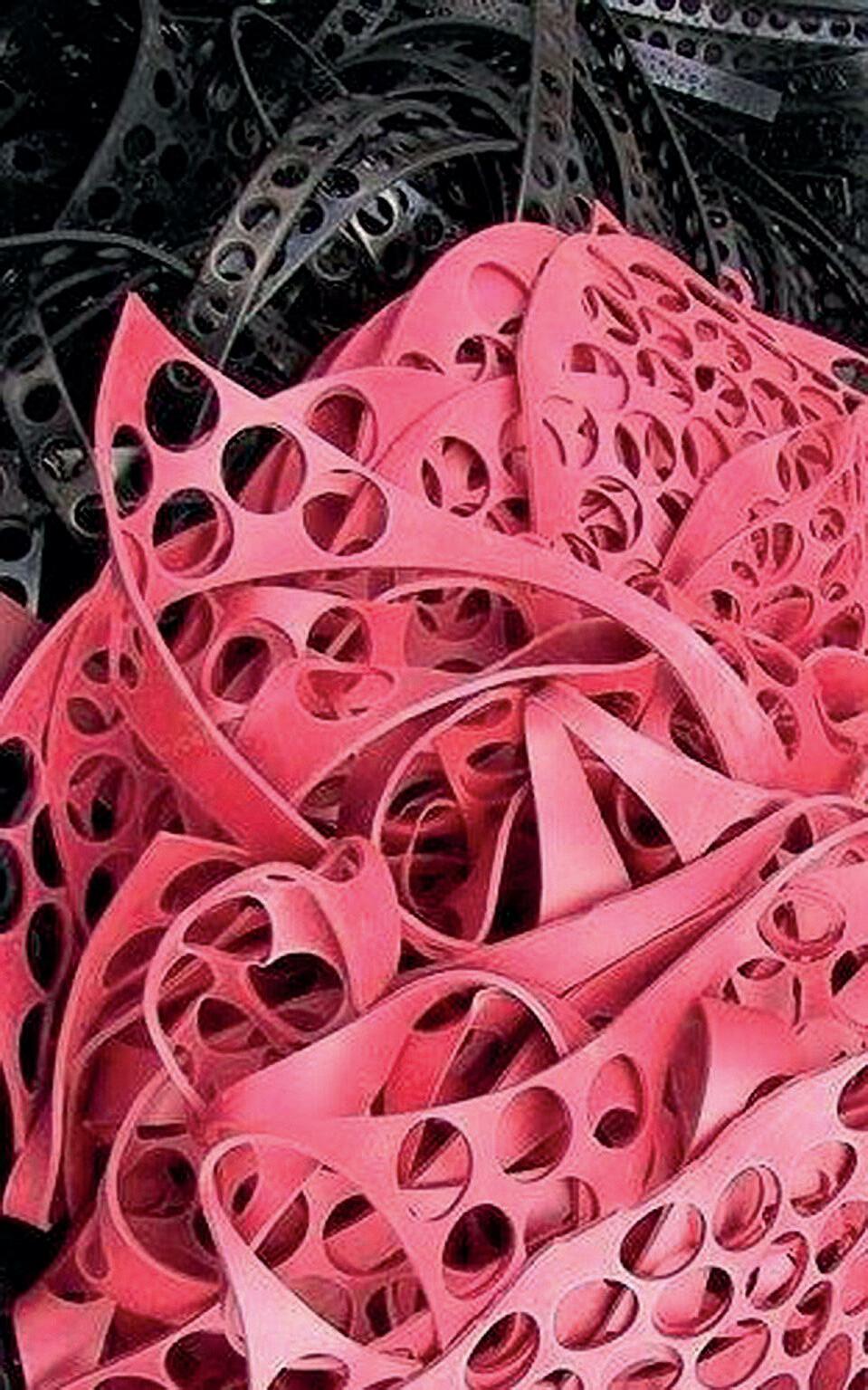
Inoltre, la mancanza di criteri specifici per la cessazione della qualifica di rifiuto (End of Waste, EoW) non agevola l’avvio di pratiche di recupero di questi materiali una volta divenuti rifiuti. I soli criteri EoW attualmente esistenti ed esplicitati in uno specifico decreto per la gomma riguardano i soli materiali provenienti da PFU (pneumatici fuori uso). Quest’inutile generazione di rifiuti è penalizzante sia sul piano ambientale sia su quello economico. Tutto ciò mal si concilia con il modello di economia circolare che le autorità europee stanno promuovendo con sempre maggiore determinazione; modello che rappresenta oggi anche l’opportunità di accedere a schemi di finanziamento da programmi comunitari, oltre che un importante driver del mercato. Assogomma ha pertanto ritenuto che i tempi per promuovere un cambio di rotta fossero maturi e, alla luce delle considerazioni sopra esposte, risulta evidente come la sfida non sia solo di natura tecnologica (un aspetto certamente fondamentale), ma richieda anche un cambiamento culturale.
LINEE GUIDA PER LA CLASSIFICAZIONE DEI RESIDUI DERIVANTI DALLA PRODUZIONE DI MANUFATTI IN GOMMA Purtroppo, sono sotto gli occhi di tutti i sempre più diffusi fenomeni di “green washing” e di dichiarazioni che nulla hanno a che vedere con solide basi tecnico-scientifiche, ma che si limitano a essere operazioni di marketing di bassa lega. Con tutto ciò in mente, Assogomma ha avviato un progetto con una duplice finalità: da una parte esplorare la possibilità d’adozione della fattispecie “sottoprodotto” nell’industria della gomma e dall’altra fornire alle imprese del settore gli strumenti per poter attuare questa possibilità in modo strutturato e solido sul piano normativo. Il progetto di Assogomma è stato condotto in collaborazione con TuttoAmbiente, una società di consulenza di riferimento in campo ambientale, che, dopo una fase istruttoria, ha elaborato un parere pro veritate declinato sulle specifiche caratteristiche del settore. La collaborazione ha permesso di mettere a fattor comune la conoscenza di dettaglio della normativa, nonché l’esperienza in diversi altri settori, con la conoscenza specifica del settore della gomma. Lo studio ha preso le mosse da una disamina delle tipologie di scarto di lavorazione tipicamente ricorrenti nell’industria della gomma, adottando per ovvie ragioni di sintesi un approccio schematico e rinunciando all’esaustività, ma tenendo parimenti conto delle caratteristiche fondamentali che si possono riscontrare, quali stato fisico (crudo/vulcanizzato), accoppiamento con altri materiali ecc., nonché delle principali tecnologie di trasformazione che li possono originare (mescolazione, stampaggio, estrusione ecc.). Sulla base delle tipologie di scarto individuate, sono state delineate le situazioni in cui la strada del sottoprodotto risulta in linea di principio percorribile. Tuttavia, occorre partire da un punto fermo: la valutazione va effettuata caso per caso, accertandosi che tutte le condizioni previste dalla normativa siano effettivamente verificate. Nel parere vengono quindi definiti tutti i passaggi necessari che l’azienda deve mettere in atto per poter operare in modo legalmente solido, nonché la documentazione probante necessaria. La naturale evoluzione del parere pro veritate è stata rappresentata dalla stesura di una linea guida associativa, pensata proprio per fornire uno strumento operativo per le imprese, che è stata presentata al settore e illustrata nel corso di uno specifico evento lo scorso 26 ottobre. Le imprese associate ad Assogomma dispongono quindi oggi di uno strumento di orientamento che consentirà loro di avviare un percorso, lungo il quale potranno continuare a contare sul supporto dell’associazione. Per un’attività formativa dettagliata è stato pianificato un programma di quattro giornate formative di approfondimento sul tema della gestione dei rifiuti e dei sottoprodotti in gomma, annunciato agli inizi di dicembre per le date del 25 gennaio e 1, 8 e 17 febbraio 2022. Infine, è stato siglato un accordo di collaborazione con TuttoAmbiente, autore del parere, che consentirà alle imprese associate ad Assogomma di accedere a servizi di consulenza personalizzata a condizioni riservate ed esclusive. Un pacchetto di servizi associativi sempre più completo e vicino ai bisogni delle imprese del settore della gomma.
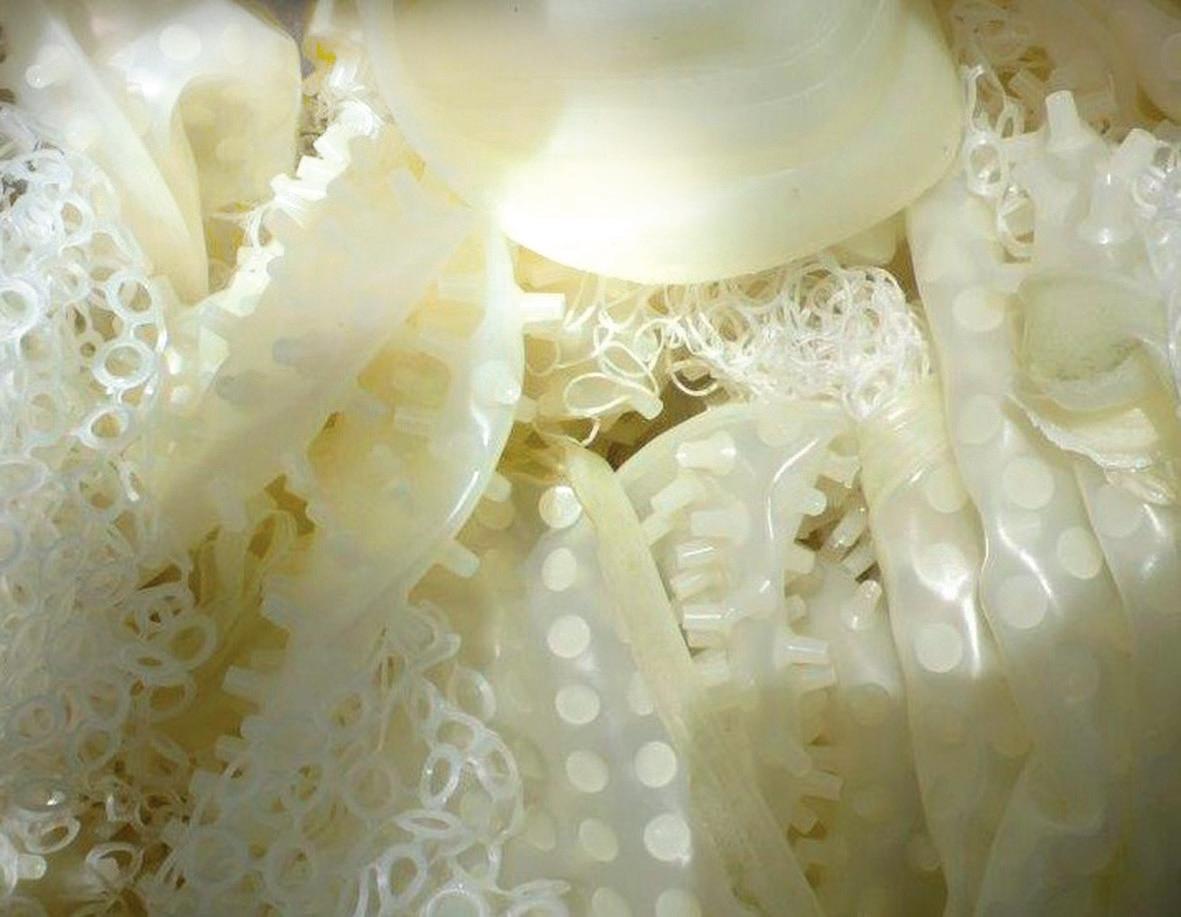
La normativa europea sulla gestione dei rifiuti prevede la fattispecie giuridica “sottoprodotto” per agevolare l’ulteriore utilizzo industriale di questo tipo di materiali
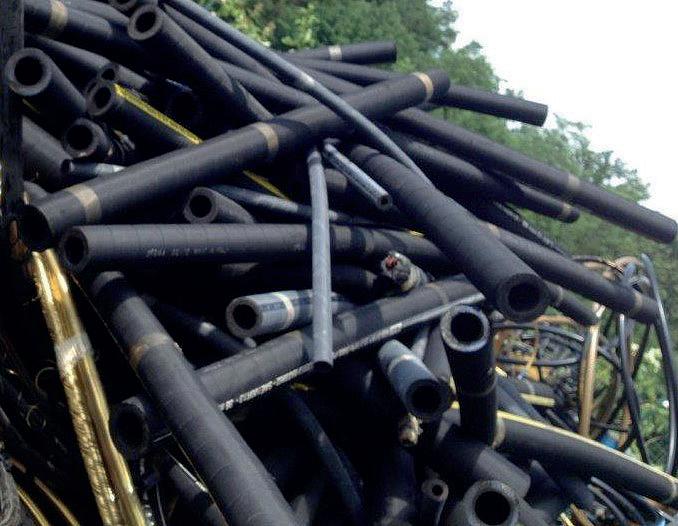
Applicazione del polverino da pneumatici fuori uso (PFU) La copertina del documento messo a punto da Assogomma e TuttoAmbiente con le linee guida per la classificazione dei residui derivanti dalla produzione di manufatti in gomma
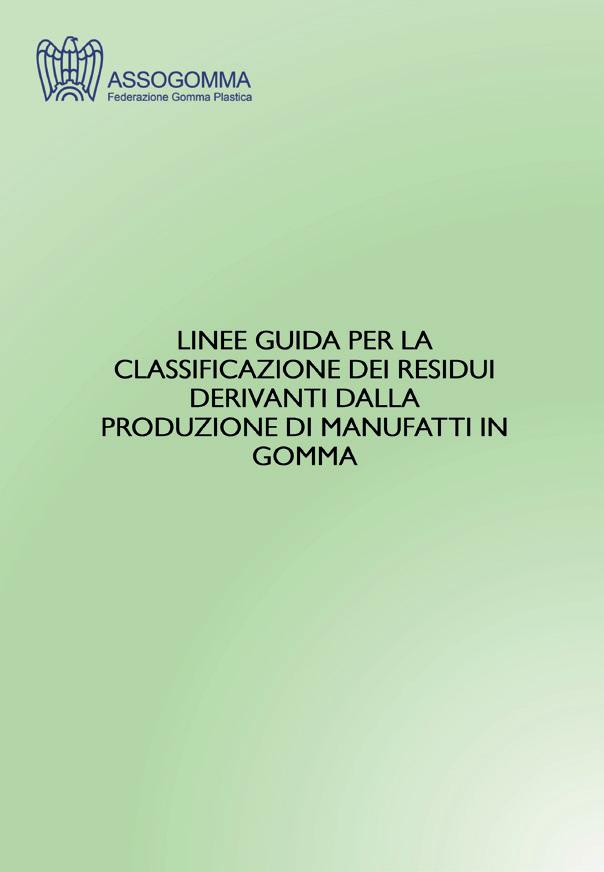
APPROFONDIMENTO DI CARATTERE TECNICO-SCIENTIFICO LE NOVITÀ EUROPEE PER LE GOMME DESTINATE AL CONTATTO CON ALIMENTI
LA RUBRICA “L’ESPERTO RISPONDE”, CHE HA ACCOMPAGNATO L’EDIZIONE DI ELASTICA SIN DALLA SUA RICOSTITUZIONE NEL 2018, CAMBIA NOME DA QUESTO NUMERO DIVENTANDO “CERISIE RISPONDE”, A TESTIMONIANZA DI UN APPROCCIO CORALE DA PARTE DELLO STAFF DEL LABORATORIO ITALIANO DELLA GOMMA: PARTENDO DAI PROBLEMI CHE LE AZIENDE DEL SETTORE INCONTRANO NEL LORO LAVORO QUOTIDIANO, IL LABORATORIO PUÒ FORNIRE SOLUZIONI, INDICAZIONI E INFORMAZIONI DI CARATTERE TECNICO-SCIENTIFICO CHE SIANO D’AIUTO ALLE IMPRESE PER MEGLIO INQUADRARE RISCHI E OPPORTUNITÀ
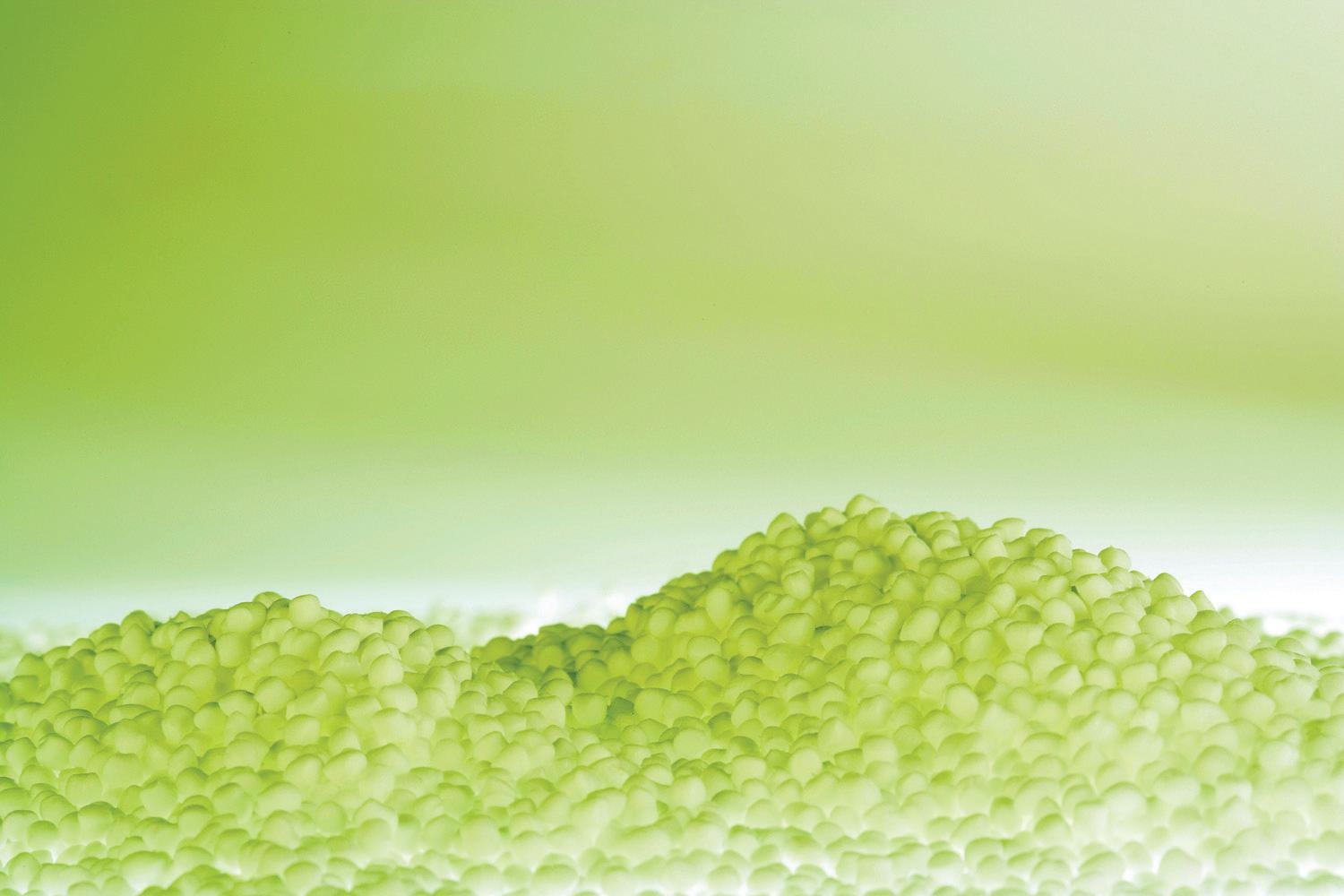
N
egli ultimi due anni le normative che disciplinano il settore delle applicazioni in gomma destinate al contatto con alimenti (MOCA) sono state caratterizzate da aggiornamenti importanti. Il laboratorio Cerisie, ben noto nel settore gomma per la propria esperienza decennale e per le competenze specifiche nell’ambito delle prove MOCA, ha immediatamente recepito tutte le recenti modifiche che riguardano le normative francesi e tedesche, con l’obiettivo di fornire ai propri clienti un servizio sempre aggiornato e d’eccellenza. Ecco, più in dettaglio, questi importanti cambiamenti.
1. ARRÊTÉ FRANCESE Nel 2020 l’Arrêté francese del 9 novembre 1994 è stato aggiornato inserendo alcune piccole ma sostanziali modifiche. La versione attualmente in vigore, Arrêté del 5 agosto 2020, introduce la migrazione specifica nei simulanti alimentari di metalli quali bario, rame, alluminio e zinco, oltre al limite di 1 mg/kg di impurezze presenti nel manufatto, intese come somma totale di elementi ritenuti nocivi per la salute, quali: piombo, cadmio, antimonio, mercurio e arsenico. Prevede inoltre la verifica della migrazione nei simulanti di esametilentetrammina (nota anche come metenamina: un’ammina utilizzata sia in campo medico, per il trattamento e la profilassi delle infezioni delle vie urinarie, sia come accelerante per la polimerizzazione della gomma), che deve essere valutata e quantificata insieme alla formaldeide. Quest’ultima rimane, in ogni caso, come migrazione specifica con un suo limite proprio.
2. BFR TEDESCO Un cambio di marcia sostanziale è stato introdotto dall’ente tedesco BfR (Bundesinstitut für Risikobewertung - Istituto federale per la valutazione dei rischi). Infatti, nel luglio del 2021 la norma BfR (capitolo XXI) “Articoli in gomma naturale e sintetica destinati al contatto con alimenti” è stata quasi completamente stravolta per allinearsi al Regolamento Europeo 10/2011, anche se quest’ul-
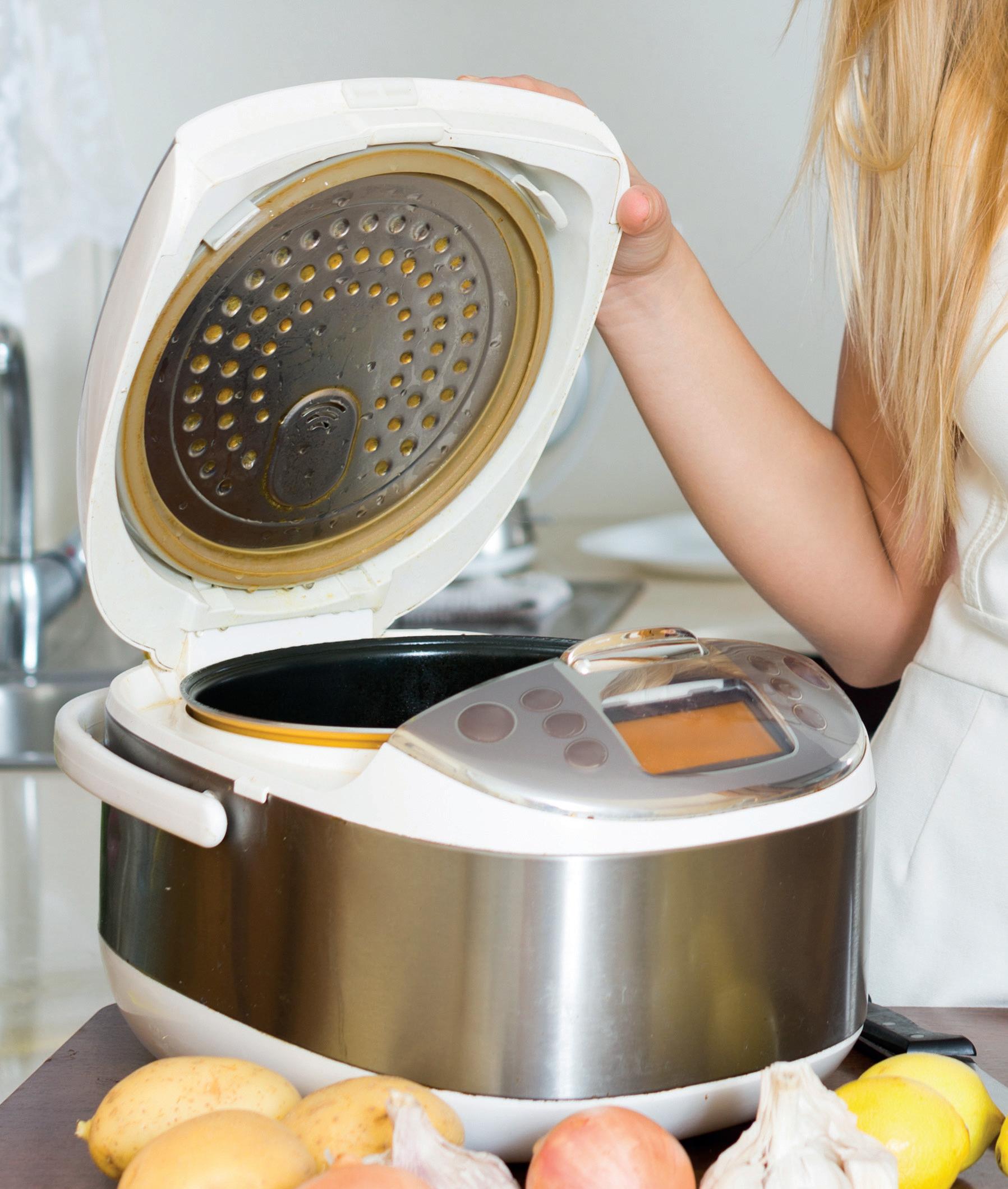
tima normativa riguarda esclusivamente le materie plastiche. Lasciando intatti i capisaldi della classificazione in categorie in virtù del tempo di contatto prevedibile fra l’alimento e il manufatto in gomma e la temperatura di prova uguale a 40°C, la Germania ha deciso di modificare completamente i simulanti degli alimenti, di introdurre nuove migrazioni specifiche e di modificare la lista positiva. La norma in questione è stata suddivisa in tre paragrafi differenti: XXI, XXI/1 e XXI/2.
3.a. BfR XXI E XXI/1
I paragrafi BfR XXI e XXI/1 suddividono i manufatti in categorie di prova, tengono conto dell’utilizzo del manufatto stesso e prevedono le seguenti classi: Categoria 1. Prova con durata di 10 giorni, destinata ai contatti prolungati (più di 24 ore fino a diversi mesi). Categoria 2. Prevede un contatto tra il manufatto e l’alimento di 24 ore, per i contatti della durata massima di 24 ore. Categoria 3. Per i contatti brevi, prevede una prova della durata di 10 minuti. Categoria 4. Per tutti i manufatti per cui non è previsto il contatto con l’alimento e, nel caso in cui tale contatto avvenga, sia o occasionale, oppure per tempi estremamente brevi o anche limitato a superfici molto piccole. Per ogni categoria vengono forniti esempi dei manufatti che rientrano nella classificazione:
Categoria Tipologia di prodotto
Contenitori per lo stoccaggio e rivestimenti, anelli e tappi di tenuta per lattine, barattoli, bottiglie e simili
Tubi per il trasporto di alimenti, anelli di tenuta per pentole a pressione, tubi flessibili per macchine da caffè, guarnizioni di coperchi (es. per contenitori del latte), sfere di valvole
Linee e tubi nei sistemi di mungitura, guarnizioni per macchine per la lavorazione del latte, membrane, pistoni, raccordi e simili, statori di pompe, nastri trasportatori per cibi grassi, guanti e grembiuli indossati durante la lavorazione dei prodotti alimentari
4 Nastri trasportatori e coperture di rulli per alimenti solidi, linee di aspirazione e mandata per alimenti solidi (es. per il riempimento e lo svuotamento di serbatoi di navi, carri e simili), guarnizioni per tubazioni, pompe, rubinetti e valvole a sede inclinata e simili per liquidi alimentari Esempio
È prevista solamente la temperatura di 40°C da utilizzare durante il contatto, in quanto si ritiene che tutte le applicazioni a temperatura superiore, come ad esempio sterilizzazione o breve riscaldamento, vengano comunque abbinate a una lunga permanenza a temperatura ambiente, e che le eventuali variazioni del valore di migrazione vengano compensate dalla lunga durata della prova. In precedenza, la normativa BfR, contrariamente alle altre norme europee (DM 21.03.73 e successivi aggiornamenti, e Arrêté francese del 5 agosto 2020), non prevedeva la possibilità di effettuare le prove d’idoneità sulla base degli alimenti effettivamente in contatto con i manufatti in gomma (come per esempio acido acetico al 3% per gli alimenti acidi, oppure etanolo per gli alimenti alcolici), ma si doveva considerare esclusivamente la conformità con tutte le tipologie di alimenti. In altre parole, il BfR prevedeva l’idoneità al contatto con tutti gli alimenti, oppure con nessuno. Nel 2021 il BfR ha invece introdotto tutti i simulanti alimentari previsti dal Regolamento 10/2011, quali: acido acetico 3%, etanolo 10%, etanolo 20%, etanolo 50%, olio vegetale, poli(2,6-difenil-p-fenilenossido), con in più l’aggiunta dell’acqua demineralizzata, prevedendo la possibilità di effettuare solo le prove di migrazione con l’alimento o gli alimenti effettivamente in contatto con il manufatto in gomma. La normativa BfR non prevede un elenco di alimenti con il relativo simulante da utilizzare, ma rimette tale scelta alla Tabella 2 dell’allegato III del Regolamento 10/2011; pertanto, la scelta dei simulanti per le prove di cessione dev’essere effettuata con le modalità previste dal Regolamento stesso. Mentre nel passato erano previste solo ed esclusivamente mi- ➤
➤ grazioni specifiche da effettuare a prescindere dalla composizione qualitativa del manufatto, la nuova versione della norma BfR ha introdotto il concetto di migrazione specifica dipendente direttamente dalla formulazione. Per poter ottenere la dichiarazione di conformità al contatto con alimenti è quindi necessario che il manufatto rispetti i limiti di cessione previsti per le prove di migrazione globale, migrazione di zinco, alluminio e piombo, migrazione di
N-nitrosammine e sostanze nitrosabili, migrazione di ammine aromatiche primarie ed N-alchil-arilammine secondarie, migrazione di ammine alifatiche secondarie e cicloalifatiche e migrazione di formaldeide. Oltre a tali requisiti, il manufatto deve sottostare ai limiti di migrazione specifica legati alla formulazione del manufatto.
Tutte le prove di migrazione globale e specifica devono essere effettuate su ogni simulante previsto dall’uso che verrà fatto del manufatto. Unica eccezione: il simulante poli(2,6-difenil-p-fenilenossido) designato per il contatto con alimenti secchi, che, essendo una polvere, non prevede la prova di migrazione globale ma solamente le migrazioni specifiche.

3.b. BfRXXI/2
Il paragrafo BfR XXI/2 si occupa esclusivamente della Categoria Speciale, riservata ai manufatti destinati al contatto con le mucose umane, come: articoli per puericultura, giocattoli e palloncini gonfiabili. Quest’ultima categoria ha prove di migrazione completamente differenti dalle altre, utilizza come simulanti degli alimenti: saliva artificiale, acqua e latte e le prove di migrazione devono essere condotte secondo quanto indicato nella Tabella 3 prevista dalla stessa normativa BfR. Le prove previste, tutte da effettuarsi sempre e comunque, sono: migrazione globale; migrazione di N-nitrosammine e sostanze nitrosabili; migrazione delle ammine aromatiche primarie; migrazione di zinco, alluminio e piombo; migrazione della formaldeide.
Non sono previste ulteriori prove di migrazioni specifiche dipendenti dalla formulazione, ma è necessario attenersi alle limitazioni d’uso previste per i singoli ingredienti. Rimane presente, anche se con alcune modifiche, la lista positiva. Contrariamente alla precedente versione, non esistono più le liste positive per ogni categoria di manufatto basate sulla logica delle “aggiunte”, che prevedeva una lista iniziale per la Categoria 1, alla quale venivano aggiunti ingredienti utilizzabili solo nelle categorie 2 e/o 3. Nella versione attuale del paragrafo BfR XXI è presente una lista di: monomeri utilizzabili per la produzione dei polimeri, cariche minerali, agenti, ritardanti e attivatori di vulcanizzazione, antiossidanti, coadiuvanti di processo, coloranti, oltre a un elenco degli ingredienti utilizzabili solo per i prodotti a base di lattice, tutti correlati del proprio valore limite, se previsto. Il BfR XXI/1 aggiunge nella Tabella 1 l’elenco dei polimeri utilizzabili con relative limitazioni e, nella Tabella 2, l’elenco degli acceleranti, indurenti, antiossidanti, coadiuvanti di processo, agenti lubrificanti, e ingredienti per prodotti a base di lattice. Tutti gli ingredienti presenti nella Tabella 2 sono in fase di valutazione, pertanto la tabella è destinata a rimpicciolirsi… fino a estinguersi. Ogni volta che viene completato il processo di valutazione di un

Genomatica
ingrediente, quest’ultimo viene spostato nella tabella presente nel BfR XXI se le verifiche hanno avuto esito positivo, altrimenti viene eliminato definitivamente dalla lista degli ingredienti utilizzabili nella produzione di manufatti destinati al contatto con alimenti.
Categoria Tipologia di prodotto Esempio
Speciale Giocattoli destinati a essere messi in bocca o destinati a bambini di età inferiore a 36 mesi, palloncini, tettarelle per biberon, ciucci, protezione per il seno, anelli da dentizione, paradenti
3.c. BfR E GOMME SILICONICHE
Le modifiche introdotte nel BfR XXI incidono, anche se in misura marginale, sulle prove previste dal Capitolo XV, “Siliconi”. Tale capitolo disciplina esclusivamente i manufatti realizzati in gomma siliconica, per i quali prevede una lista positiva completa di limitazioni d’uso e le prove alle quali devono essere sottoposti i manufatti in silicone per poter essere dichiarati idonei al contatto con alimenti. I requisiti previsti dal Capitolo XV per le gomme siliconiche sono: assenza di residui perossidici nel manufatto; sostanze volatili ed estraibili entro i limiti previsti. Le modifiche apportate al Capitolo XXI impattano anche sul Capitolo XV, in quanto le sostanze estraibili devono essere determinate utilizzando i simulanti degli alimenti previsti dalla nuova versione della normativa BfR XXI. Il Capitolo XV contempla anche gli oli siliconici e le resine siliconiche. Per tali categorie di prodotti è indicata solamente la lista positiva degli ingredienti utilizzabili per la produzione, ma non sono previste prove da eseguire sul manufatto.

Attend the leading event in the world dedicated to composite materials, technologies and production processes, and their applications sectors.
PIÙ DI DIECI RIVISTE ESAMINATE RASSEGNA INTERNAZIONALE DI SCIENZA E TECNOLOGIA
DICIASSETTESIMA PUNTATA DELLA RUBRICA DEDICATA AGLI ARTICOLI DI STAMPA ESTERA SELEZIONATI DAL COMITATO DI REDAZIONE DI ELASTICA, COMPOSTO DA: FABIO BACCHELLI, ALBERTO DAFARRA, RINO GILOTTA E FABIO NEGRONI, COORDINATI DA MAURIZIO GALIMBERTI
ADDITIVI SOSTENIBILI DERIVATI DALL’OLIO DI SOIA
Testata: Rubber World - Settembre 2021 Titolo originale: Targeting sustainable additives through derivatization of soybean oil Autori: Kelsey Cantwell e Joseph Kulig (Goodyear Tire & Rubber Company)
A CURA DI FABIO NEGRONI
Enoto che gli oli plastificanti utilizzati nella produzione di pneumatici sono ottenuti dalla lavorazione del petrolio greggio. Questi oli comprendono tre principali gradi commerciali: DAE (Distillate Aromatic Extract); TDAE (Treated Distillate Aromatic Extract); MES (Mild Extracted Solvate). A partire dal 2011, la divisione ricerca e sviluppo di Goodyear ha iniziato a provare l’olio di soia come alternativa all’impiego dei prodotti sopra elencati e, infine, a utilizzarlo nella produzione di un’ampia varietà di mescole a base di SSBR per battistrada e in combinazione con altri polimeri. La ricerca è continuata anche in questi anni per due motivi principali: l’olio di soia è un additivo in grado di migliorare sia la lavorabilità che le performance degli pneumatici; l’olio di soia risponde all’esigenza di sostituire gli additivi
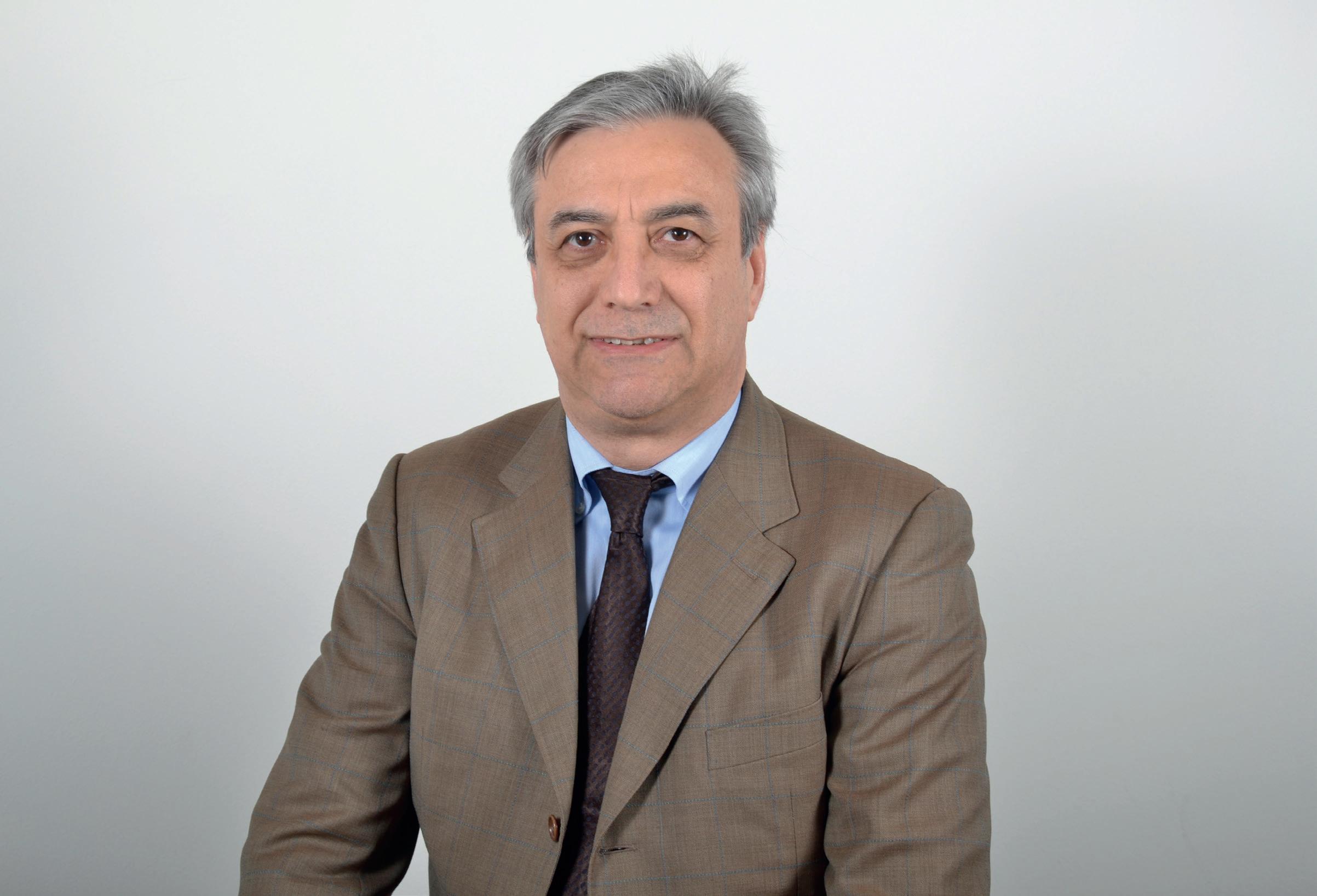
da fonti fossili con quelli da fonti rinnovabili. Nel 2020 tale ricerca ha portato a un aumento del 25% dell’impiego di olio di soia, con una pianificazione di completa sostituzione entro il 2040. Nell’articolo in questione viene descritto con dovizia di particolari il lavoro condotto sull’olio di soia secondo un secondo filone d’impiego: come additivo compatibilizzante della silice precipitata impiegata nei moderni pneumatici ad alta efficienza energetica. L’efficienza energetica degli pneumatici si misura infatti in termini di “resistenza al rotolamento” (Rolling Resistance) e si ottiene sostanzialmente impiegando diossido di silicio (o silice) e modificando chimicamente la superficie dei granuli di polvere, per migliorane la miscelazione con il resto dei materiali che compongono la mescola. Tale modifica superficiale prende il nome di “compatibilizzazione” ed è realizzata attraverso la reazione con additivi chimici denominati “silani”. Il metodo di Goodyear presentato nell’articolo consente, modificando la struttura molecolare dell’olio di soia, di ottenere la stessa funzionalità offerta dai silani. La modificazione chimica della struttura molecolare (o, per brevità, “derivatizzazione”) si ottiene tramite una reazione fotochimica, assistita cioè da radiazione luminosa nell’ultravioletto, e impiegando, oltre all’olio di soia, un fotoiniziatore della reazione e una sostanza (mercaptosilano) che rende l’olio capace di reagire con la silice. Le prove sperimentali con questo additivo sono state condotte sia su provini da laboratorio sia su prototipi di pneumatici. La reazione voluta di compatibilizzazione risulta confermata ed è più estesa rispetto a quella del silano preso come riferimento; ciò rende necessario miscelare l’olio di soia modificato con quello originale, per diluirne l’attività. Gli pneumatici prototipo danno quindi prestazioni equivalenti per quanto riguarda la resistenza al rotolamento e la tenuta su fondo bagnato, proprietà critica per la sicurezza degli pneumatici. Sfortunatamente, l’abradibilità è risultata eccessivamente alta e non consente, allo stato attuale, l’utilizzo di tale metodologia per la produzione di pneumatici secondo gli standard di qualità Goodyear.
Nel corso degli anni la progettazione dei componenti medicali è divenuta sempre più dipendente dalla capacità di realizzare simulazioni accurate agli elementi finiti (FEA). Queste simulazioni consentono di ottimizzare sistemi costituiti da più componenti in tempi rapidi e a costi inferiori, con l’ulteriore vantaggio di mettere a disposizione del progettista informazioni utili su come tali componenti interagiranno l’uno con l’altro durante la vita in esercizio. Come molte altre aziende del settore medicale, la società tedesca Starlim Spritzguss ha dovuto affrontare l’improvvisa crescita di richieste di nuovi dispositivi generata dall’emergenza Covid. Le simulazioni sono quindi risultate fondamentali anche per consentire ai progettisti di lavorare da remoto, limitando quindi la presenza in ufficio o nei reparti produttivi. L’obiettivo di ogni software di simulazione è quello di creare un modello che rappresenti dettagliatamente il funzionamento reale dei componenti installati. Tanto maggiore sarà la differenza tra i risultati del modello e quelli reali, tanto più grande sarà il rischio di errori che avranno effetto sui tempi finali di conclusione del progetto. Tutto ciò è ancora più rilevante nel caso dei componenti in gomma siliconica liquida (LSR), che sono intrinsecamente predisposti per fornire funzionalità critiche di tenuta, regolazione delle portate e regolazione dinamica delle pressioni nei dispositivi medicali. Queste sono le motivazioni che hanno indotto gli autori a sviluppare una procedura di laboratorio proprietaria (seppur non descritta nell’articolo) che, in base ai risultati mostrati, ha migliorato in modo decisivo l’accuratezza delle previsioni ottenute con i software di calcolo FEA. Si tratta di un tema ben noto anche al Cerisie (il laboratorio di Assogomma) e che può essere argomentato partendo dalla constatazione che la descrizione di come un materiale elastomerico reagisce a una deformazione, o a una forza applicata, dipende in ultima istanza dalla curva sforzo-deformazione che è stata fornita come input al software. Nella maggior parte dei casi, le curve disponibili nella libreria del software sono ottenute mediante prove di trazione, acquisite quindi sottoponendo il provino (forma a “osso di cane”, o a striscia) a un allungamento progressivo. Questa è la modalità standard con cui lavorano i dinamometri in laboratorio e, di conseguenza, tali curve sono facilmente ottenibili. Il problema dell’accuratezza della simulazione nasce dal fatto che questa modalità di allungamento (definita tensione uniassiale) è solo una delle possibili modalità di deformazione dei componenti reali e, anche dalle esperienze condotte al Cerisie, è emerso chiaramente che la simulazione produce un errore significativo se si basa esclusivamente su tali dati. Ne consegue, quindi, che i dati di input del software dovranno essere integrati da curve sforzo-deformazione ottenute, per esempio, applicando forze di taglio e nella cosiddetta modalità di tensione equi-biassiale, dove la tensione viene applicata simultaneamente in due direzioni, ortogonali fra di loro. Il lettore interessato può trovare una descrizione delle prove utili per la simulazione FEA nell’articolo pubblicato su Elastica di ottobre-novembre 2019 (pag. 94-95, MacPlas 373). Nell’articolo, vengono presentati i risultati della forza d’inserzione di una sonda che passa attraverso una guarnizione con due labbri distinti. La curva misurata sulla guarnizione mostra due picchi in corrispondenza della zona di contatto tra la sonda e i due labbri. Mentre la simulazione che include i dati multiassiali e quelli di taglio produce risultati accurati, quella che è stata condotta utilizzando esclusivamente i dati da libreria sovrastima il valore di forza necessario a 2,5 Newton, rispetto ai soli 1,3 Newton del modello migliorato.
SIMULARE IL COMPORTAMENTO DEI COMPONENTI IN LSR
Testata: Rubber World - Giugno 2021 Titolo originale: Part design simulations for silicone rubber components Autori: R. Hall, S. Baird e L. Püringer (Starlim Spritzguss)
A FAKUMA, TPE INNOVATIVI PER LE SFIDE DI OGGI Dalle strutture leggere all’economia circolare
“Con lo slogan “Discover Kraiburg TPE, Solutions with Thermoplastic Elastomers”, la nostra partecipazione alla fiera Fakuma 2021 si è concentrata sugli ultimi sviluppi volti a migliorare le caratteristiche tattili e il risparmio di peso e materiale, oltre che su soluzioni specifiche a favore dell’economia circolare”, ha dichiarato Franz Hinterecker, CEO di
Kraiburg TPE.
Ecco i principali TPE presentati in fiera: • TPE Smooth Touch. Grazie ai “nuovi standard tattili” e alle proprietà antiscivolo, questi compound dalla superficie morbida si adattano perfettamente ai settori del design e del packaging. La loro buona adesione alle poliolefine, li rende particolarmente adatti allo stampaggio a iniezione multicomponente; inoltre, soddisfano i requisiti imposti dagli standard internazionali per le applicazioni a contatto con gli alimenti e sono disponibili in colori personalizzati. Tra le attuali applicazioni vi sono i packaging per cosmetici, le parti bicomponente di sistemi elettronici e gli articoli per la casa. • Thermolast K con il 20-40% di materiale riciclato da risorse post industriali (PIR). Si tratta di compound che forniscono stabilità all'ozono e agli agenti atmosferici e resistenza al calore fino 90°C, per applicazioni esterne nell’automotive: rivestimenti di passaruota, guide antigoccia, guarnizioni dei finestrini ecc. I gradi RC/UV consentono un risparmio di peso fino al 25% rispetto ai TPE convenzionali. Sono disponibili con durezze Shore A da 50 a 90, evidenziano buona adesione al polipropilene e il loro contenuto di PIR contribuisce naturalmente all’economia circolare. • I TPE Supersoft di nuova generazione sono particolarmente morbidi, resilienti e durevoli. Si adattano alla crescente varietà d’applicazioni impegnative in stampaggio a iniezione e stampa 3D. Presentano una ridotta tendenza al trasudamento di olio e sono caratterizzati da un piacevole tocco, simile a quello della pelle. La conformità alle normative rende questi TPE adatti alla fabbricazione di dispositivi medicali e ortesi. Le prime applicazioni di successo nel settore degli articoli sportivi comprendono i gel pad per pantaloncini da ciclismo. • TPE elettricamente conduttivi pensati per il futuro mercato delle applicazioni intelligenti, che vanno dai sensori per veicoli all’abbigliamento sportivo, funzionale e di sicurezza. Questi compound combinano superfici sigillate e omogenee con un tocco non appiccicoso e forniscono un’eccellente adesione a vari termoplastici, tra cui le poliammidi. • TPE leggeri riempiti con microsfere di vetro 3M, per componenti estremamente leggeri e adatti, in particolare, per le costruzioni automobilistiche e di: aeromobili a pilotaggio remoto (APR, droni), utensili elettrici, tessuti e articoli sportivi e da esterni. A differenza dei materiali espansi, questi elastomeri leggeri consentono la produzione di parti stampate a parete molto sottile ma caratterizzate da un’elevata capacità di carico e da un’eccellente qualità superficiale. Oltre alla stabilità ai raggi UV, gradi specificamente sviluppati assicurano anche una compressione residua particolarmente bassa. Un’altra serie di questi materiali prodotti da Kraiburg TPE mira a eliminare la necessità di agenti leganti in parti multicomponente contenenti poliammide.

DISPOSITIVO PER I TUBI IN GOMMA Raggi X per una misurazione precisa dello spessore parete
I requisiti di qualità dei tubi flessibili in gomma per alte pressioni sono molto elevati. Inoltre, questi articoli sono soggetti a precise normative. Pertanto, dal 2007, quando ha iniziato la propria attività, l’azienda russa Svarog si è concentrata sulla produzione di tubi flessibili per alta pressione in conformità con la normativa europea DIN EN. Le elevate esigenze di qualità hanno anche portato alla collaborazione con Sikora, fornitore tedesco di tecnologie innovative di misurazione, controllo, ispezione e classificazione. Dal luglio 2021, infatti, il produttore russo utilizza il dispositivo X-Ray 6000 Pro di Sikora per la misurazione in linea dello spessore di parete, dell’eccentricità e del diametro dei tubi. È il primo dispositivo di questo tipo in tutta la Russia a essere installato su una linea per l’estrusione di tubi in gomma per alta pressione. La collaborazione tra le due aziende si basa sulla necessità di misurazioni precise e di un controllo automatico in linea al fine di garantire la massima qualità degli articoli prodotti e ottimizzare i processi di produzione. Prima di decidersi a installare il dispositivo a raggi X, il produttore di Novokuznetsk, in Siberia, misurava solo il diametro esterno, mentre oggi, grazie a X-Ray 6000 Pro, è anche in grado di misurare lo spessore parete dello strato esterno, posto dopo la treccia in filo metallico, e lo strato interno del tubo sul mandrino. I valori misurati in tempo reale forniscono al cliente le necessarie informazioni sul prodotto, al fine di soddisfare i requisiti tecnici. Per trarre il massimo vantaggio operativo, Svarog prevede d’integrare il dispositivo di Sikora nell’unità di controllo della linea d’estrusione, con l’obiettivo d’implementare il controllo automatico del processo produttivo. Ciò porterà a un’ulteriore ottimizzazione dell’efficienza dei processi, oltre a garantire la massima qualità del prodotto.
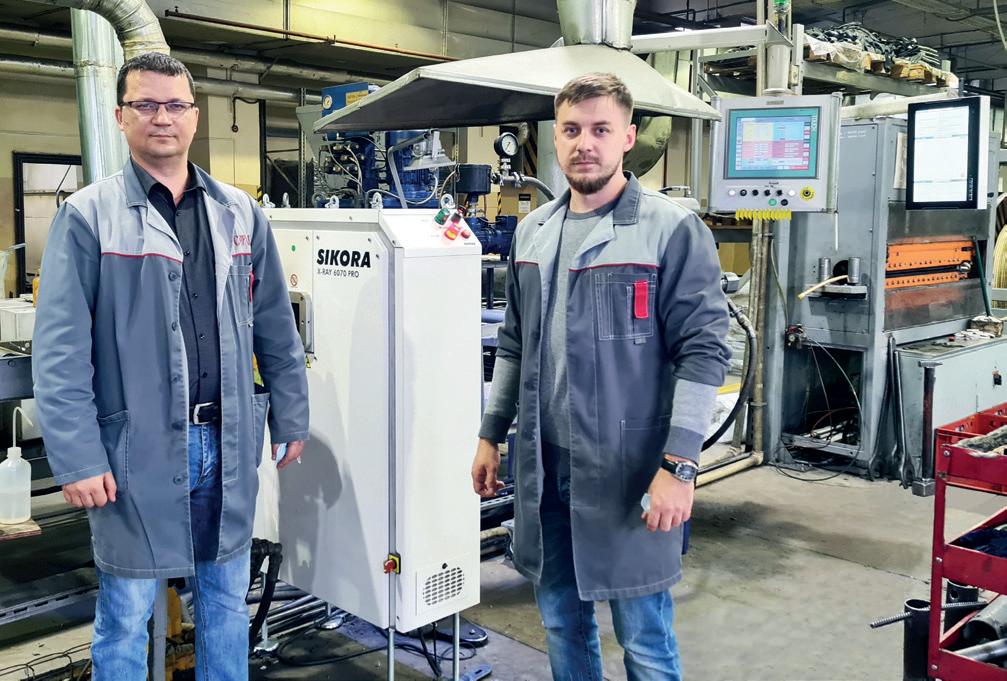
Vladimir Amelchenko e Konstantin Kozyrkov, rispettivamente direttore generale e capo tecnologo di Svarog, davanti al dispositivo X-Ray 6000 Pro di Sikora
Tra gli elastomeri termoplastici più innovativi esposti da Kraiburg TPE alla fiera Fakuma vi sono quelli elettricamente conduttivi, pensati per il futuro mercato delle applicazioni smart
CICLO D’INCONTRI FORMATIVI BY ASSOGOMMA Rifiuti, sottoprodotti ed End of Waste
Come preannunciato in occasione del seminario del 26 ottobre scorso, in cui è stata presentata la linea guida di Assogomma (vedi pag. 86-87), l’associazione sta organizzando un ciclo d’incontri formativi di approfondimento relativi alla gestione degli scarti di lavorazione gomma. L’iniziativa, intitolata “Rifiuti, Sottoprodotti, End of Waste: corretta gestione, classificazione e sanzioni”, si svolgerà su piattaforma web nelle mattinate del 25 gennaio e di 1, 8 e 17 febbraio 2022. L’obiettivo di questo articolato programma formativo è quello di proseguire il percorso d’approfondimento già avviato fornendo alle imprese di settore un’ulteriore occasione di aggiornamento riguardante la corretta gestione dei rifiuti, inclusi gli scarti di lavorazione gomma, andando dall’illustrazione del quadro normativo alla corretta classificazione, dalle qualifiche di sottoprodotto ed End of Waste fino agli aspetti sanzionatori di cui tenere conto. Il corso, che si rivolge principalmente ai responsabili in materia di ambiente, sicurezza, produzione (e, più in generale, a tutte quelle funzioni aziendali, direttive e non, interessate alla materia), è stato organizzato e articolato in quattro incontri che trattano temi distinti e separati, ma tra loro complementari. I partecipanti potranno quindi scegliere, in base alle proprie necessità d’approfondimento, di partecipare a tutti o solo ad alcuni degli incontri calendarizzati, con la possibilità di vedersi riconosciute particolari agevolazioni economiche in caso di adesione a più giornate. Tutte le informazioni sono reperibili presso la segreteria Assogomma (02/43928231 - www.federazionegommaplastica.it). 2021_NEW-DGTS_01_172x125-Btr.pdf 1 12/02/21 17:40 Tra le prossime iniziative di formazione Assogomma rientrano anche quelle seguenti, relative al primo semestre 2022: “Le Normative Reach in paesi diversi dall’UE” (febbraio). Questi corsi si propongono di fornire informazioni sulle normative Reach nei paesi extra-UE (Regno Unito, Turchia, Eurasia, Cina) verso i quali sono principalmente dirette le esportazioni italiane di settore, sia di prodotti finiti che di semilavorati. “La digitalizzazione nelle imprese della gomma” (marzo 2022). Le risorse economiche messe a disposizione dall’UE a favore della digitalizzazione meritano una riflessione riguardante le possibili opportunità per le imprese italiane produttrici di articoli in gomma. Partendo dall’analisi normativa, questo seminario fornirà elementi di valutazione per la digitalizzazione dei processi produttivi e la loro correlazione con le attrezzature finanziabili. “Lo stampaggio nelle industrie della gomma” (aprile/maggio): una giornata formativa con lo scopo d’illustrare i principi fondamentali della tecnologia di stampaggio e le diverse tecniche di processo, fornendo utili indicazioni operative anche in relazione alle differenti tipologie di prodotti da realizzare. “Attrezzature, macchine, strumentazioni per il recupero di materia” (maggio/giugno): una conferenza tecnica che si propone di presentare un aggiornamento dei macchinari per la rigenerazione, la devulcanizzazione e/o il recupero di sfridi, bave e scarti di lavorazione nell’industria della gomma.
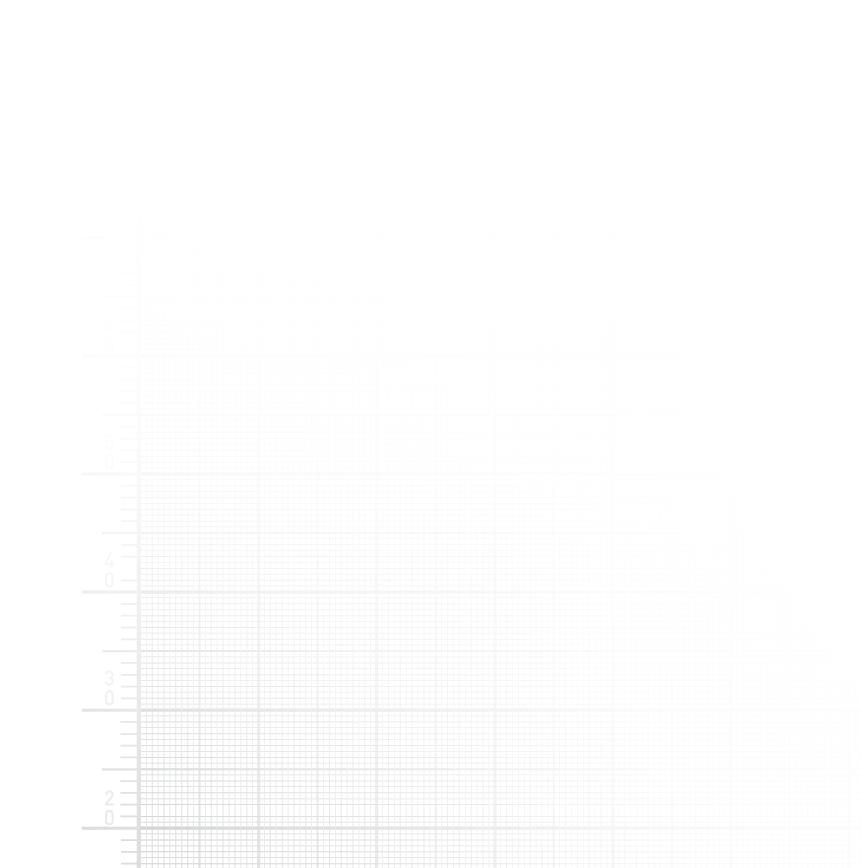
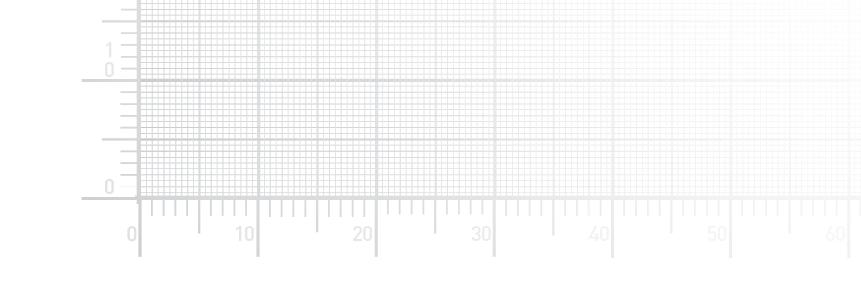
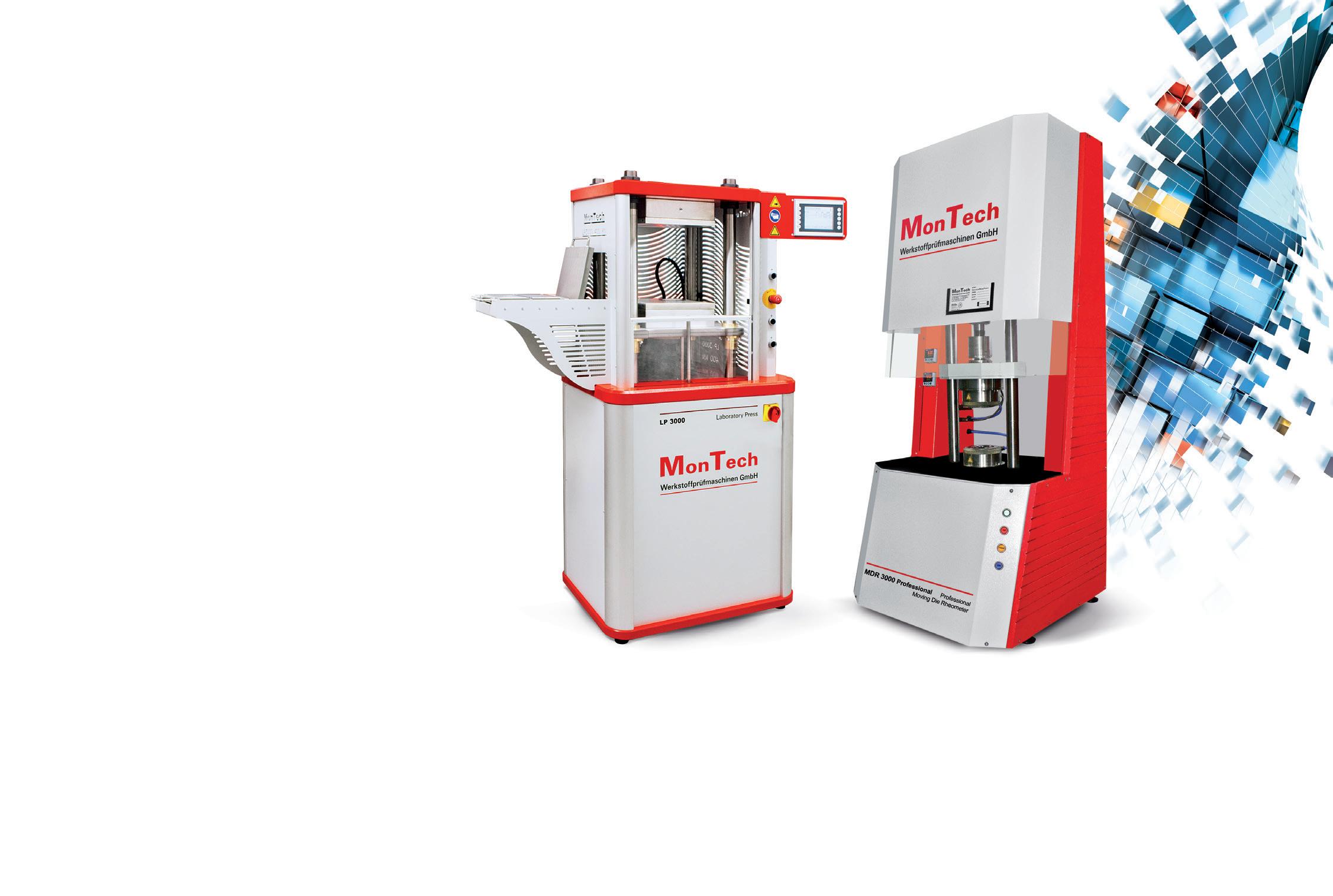
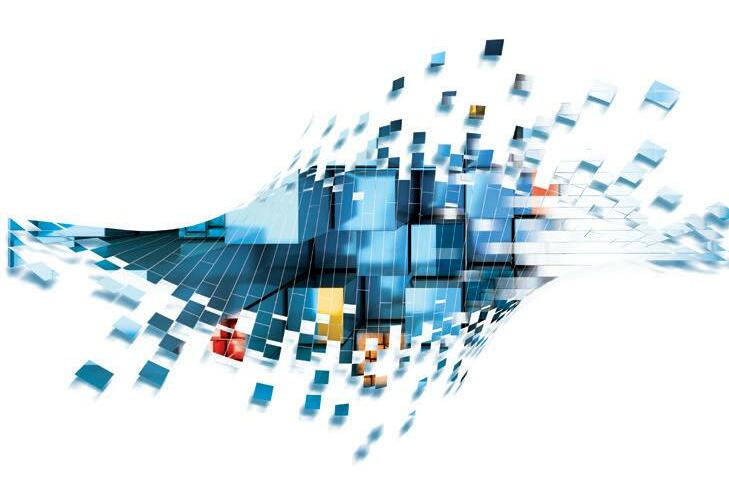
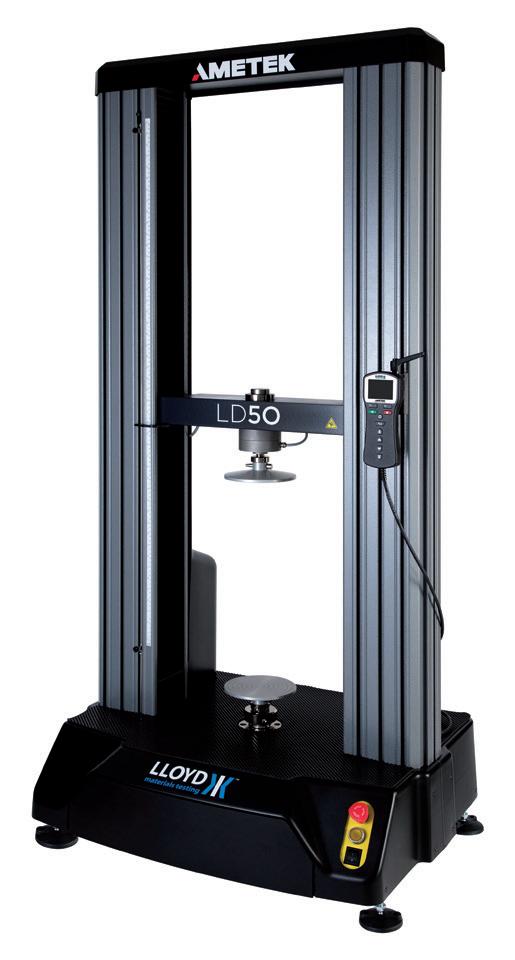
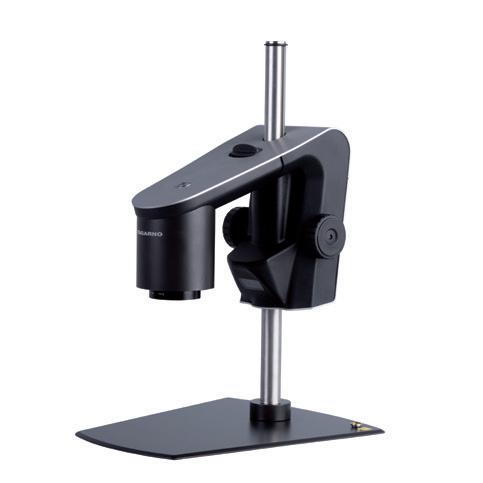
NOTIZIARIO UNIPLAST
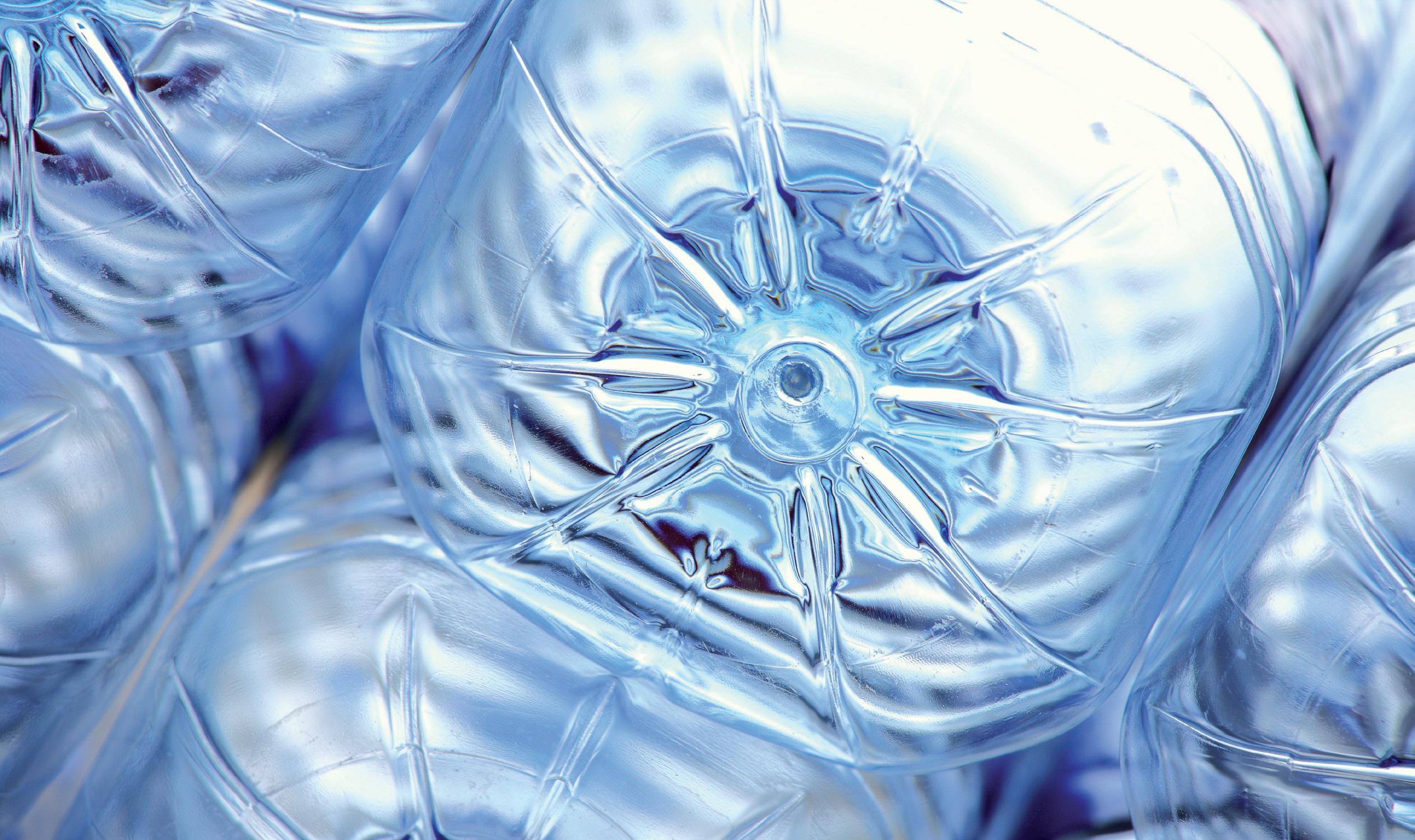
ENTE ITALIANO DI UNIFICAZIONE DELLE MATERIE PLASTICHE FEDERATO ALL’UNI
A CURA DI GIANLUIGI MORONI
LE RIUNIONI, TUTTE VIA WEB, DI NOVEMBRE Saldatura di termoplastici
Nella riunione del CEN/TC 249/WG16 del 2 novembre 2021 si è discusso della proposta tedesca di includere nella revisione della EN 2814-7:2002, proposta dal delegato del Regno Unito del BSI, la poliammide all’interno del prospetto per le velocità di prova, in accordo con la EN ISO 5271. Si è continuato quindi nella discussione della proposta per il nuovo lavoro “Qualification of Welding Procedures for Plastic Materials”, documento che spiega come una specifica di procedura di saldatura preliminare (pWPS) sia qualificata da prove per produrre una specifica di procedura di saldatura qualificata (WPS). La sua applicazione garantisce che la qualificazione della pWPS sia effettuata secondo procedure di prova uniformi.
TUBI E RACCORDI RINFORZATI
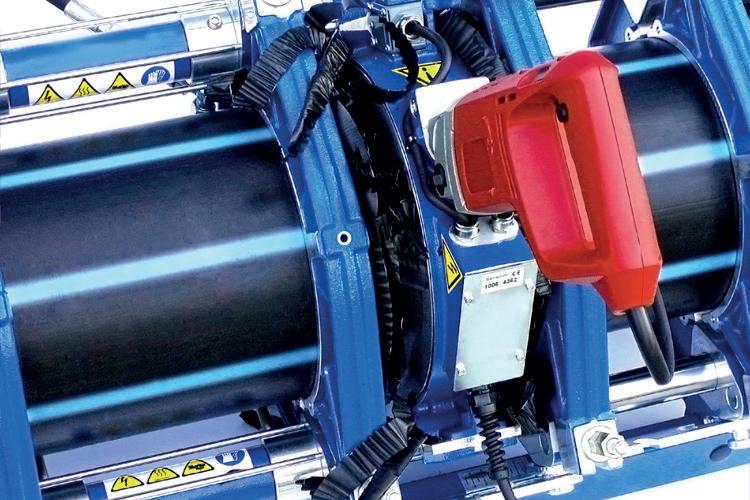
L’ISO/TC 138/SC6, riunitosi il 5 novembre, segue, attraverso i suoi esperti, le attività dell’ISO/ TC 67/SC6 per la revisione delle quattro parti in cui è articolata la ISO 14692: Part 1: Vocabulary, symbols, applications and materials; Part 2: Qualification and manufacture; Part 3: System design; Part 4: Fabrication, installation and operation. L’ISO/TC 138/SC6 ha attualmente attivi tre gruppi di lavoro (WG) e un task group (TG). Riguardo all’ISO/TC 138/SC 6/WG 1, si è deciso di iniziare le revisioni delle ISO 10468:2018, ISO 8639:2016 e ISO 8513:2016. Il WG3 sta lavorando sull’ISO/WD TS 20656-1, mentre il WG 5 ha allo studio un lavoro preliminare per il nuovo progetto ISO/TS 20656-2. Il TG1 sta invece lavorando sulla revisione del CEN/TS 14632 per la “Guidance for the assessment of conformity”. In collaborazione con il WG3 è allo studio la revisione della ISO 25780:2011 per individuare i parametri nel calcolo della rigidezza e modificare il fattore di sicurezza globale allineandone la terminologia con quella degli eurocodici.
RICICLO DI MATERIE PLASTICHE
Il 28 ottobre si era tenuta una riunione congiunta fra CEN/TC 249/WG11 e ISO/TC 61/SC14/ WG5 per discutere delle problematiche comuni e verificare l’instaurazione di collaborazioni per item di comune interesse. Come documento sperimentale, da portare avanti secondo il Vienna-Agreement, nella successiva riunione dell’8 novembre è stata scelta la revisione del CEN/TR 15353:2007. Sono stati resi noti i punti principali della riunione: l’accordo di collaborazione fra CEN (CEN/TC 249 e CEN/TC 411) e ASTM (ASTM D20.95 e D20.96) è stato rinnovato per altri due anni dal CEN/BT (decisione BT 023/2021 del 21/10/2021). Il progetto preliminare ISO/PWI è stato ritirato dall’ISO/TC 61/ SC11/WG5, mentre il progetto relativo al “chemical recycling” è stato inserito nella revisione della ISO 15270:2008, che sarà articolato in varie parti. Non sono state identificate problematiche con i documenti CEN per lo sviluppo dell’ISO/CD 5677. La proposta del delegato cinese dell’ISO/TC 61/SC9 per progetti di norma preliminari per il riciclo di alcuni polimeri (PC, PP, PA), sulla base della struttura già esistente per le norme dei polimeri vergini, ha sollevato numerose perplessità, anche per le disuniformità di impostazione che si verrebbero a creare con i vari lavori in corso in ambito CEN. La riunione è proseguita con l’analisi dei lavori in campo CEN. I prEN 15347 rev (WI=00249A44) e prEN 15348 rev (WI=00249A42) sono stati trasmessi al CEN/CCMC per l’inchiesta CEN. Il prEN 15346 rev è in completamento per l’inchiesta CEN. Sono in corso i contatti per la definizione della prima bozza di revisione della EN 5345:2007. È stata fermata la preparazione delle revisioni delle EN 15343:2007, poiché sono ancora da chiarire gli sviluppi delle discussioni fra la DG Grow e la DG Environment del-
Tecnodue
la EC per gli sviluppi della revisione della direttiva PPWD (Packaging and Packaging Waste Directive) e la “Standardisation Request on recycled plastics”, che avrà impatto sul CEN/TC 261 e sul CEN/TC 249. Il CEN TC 249/WG11 vorrebbe poter avere influenza su alcuni lavori del CEN/TC 261/SC4/WG3 e, in particolare, su quelli del PWI. Riguardo ai nove progetti preliminari “Plastics - Quality requirements for application of plastic recyclates in products”, presentati dai Paesi Bassi nel 2020, sono state evidenziate le difficoltà di finanziamento e le relazioni intercorse con i proponenti del progetto DIN SPEC: 91446. Per il progetto preliminare “Plastics - Quality requirements for application of plastic recyclates in products - Part 3: Polypropylene (PP)” sono stati messi in luce i nuovi proponimenti che si stanno delineando per avere specifiche di riciclati indirizzate alle richieste del cliente, creando non poche preoccupazioni a molti dei presenti per le problematiche relative alle fonti di approvvigionamento dei materiali da riciclare e ai requisiti richiesti.
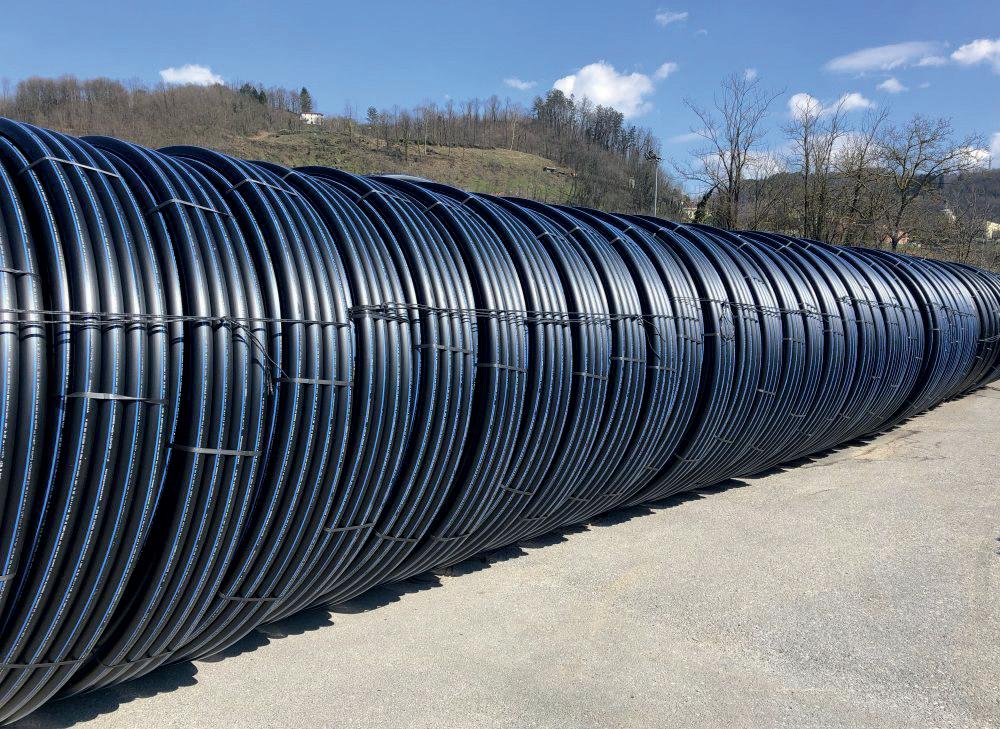
RESISTENZA ALLA FLESSIONE
Alla riunione del CEN/TC 155/WG32 del 12 novembre sono state riviste le modalità di prova e le procedure con cui si effettua la prova di resistenza alla flessione per le valvole, relativamente alla bozza di revisione della EN 12100:1997 (WI=00155462). Sono stati esaminati e reimpostati i paragrafi “Arrangements”, “Test procedure” e “Test report”.
TUBAZIONI NON IN PRESSIONE
Il 24 novembre si è riunito il gruppo di lavoro SC8/GS2, che ha continuato la discussione sulla redazione del progetto “Sistemi di tubazioni in lega di poli cloruro di vinile ad alta resistenza all’impatto (PVC-HI) per il trasporto di fluidi in pressione” dopo una prima analisi del progetto preliminare “PVC-HI water pressure pipes”, che è stato proposto all’ISO/TC 138/SC2/WG3 e che fa riferimento a norme della Corea del Sud (KS M 3401) e del Giappone (JIS K 6742) sulle tubazioni in HIVP (High Impact resistant PVC).
TUBI IN PE
L’SC8/AHG, riunitosi il 25 novembre, ha rivisto il testo del rapporto tecnico “Tubazioni di materia plastica - Linea guida per la definizione dei requisiti tecnico-funzionali delle tubazioni in polietilene (PE)” e, in particolare, le appendici. Il testo concordato in riunione, dopo un controllo redazionale, sarà inviato a inchiesta Uniplast per raccogliere gli ulteriori commenti. Alla riunione del 30 novembre dell’ISO/TC 138/ SC4/WG2 è terminata la discussione dei commenti che si sono avuti a seguito dell’inchiesta nella sottocommissione ISO/TC 138/SC4 del DTS per la revisione dell’ISO/TS 10839:2000. Il testo definitivo dell’ISO/TS 10839, che presenta molti paragrafi rivisti e ampliati rispetto all’edizione dell’anno 2000, sarà trasmesso all’ISO/ TC 138/SC4, che lo inoltrerà all’ISO/CS per l’inchiesta di approvazione.
Idrotherm 2000
UNIPLAST
Politecnico di Milano - Dipartimento di Chimica, Materiali e Ingegneria Chimica “Giulio Natta” Piazza Leonardo Da Vinci, 32 - 20133 Milano Tel.: +39 02 23996541 - Fax: +39 02 23996542 E-mail: segreteria@uniplast.info www.uniplast.info
Progetti di norma water supply, and for drainage and sewerage under pressure - Polyethylene (PE) - Part 2: Pipes - Amendment 1 Riportiamo qui di seguito l’elenco di parte dei progetti di norma ISO e CEN TC 249 (Plastics) CEN inviati in inchiesta pubblica nel mese di novembre 2021 per il settore Draft decision 806 on a NWIP for a TR Biodegradable plastics - Status of materie plastiche e gomma. Ulteriori informazioni possono essere standardization and new prospects richieste a Uniplast (tel.: 02 23996541; e-mail: segreteria@uniplast.info) Draft decision 807 on a NWIP for revision of EN 12814-7:2002 Testing of welded joints of thermoplastics semifinished products - Part 7: Tensile test ISO TC 61 (Plastics) with waisted test specimens ISO/TC 61/SC 14 - ISO/TC 38 DIS 4484-1 Textiles and textile products - prEN ISO 306 Plastics - Thermoplastic materials - Determination of Vicat Microplastics from textile sources - Part 1: Determination of material loss softening temperature (VST) (ISO/DIS 306:2021) from fabrics during washing FprEN ISO 489 Plastics - Determination of refractive index (ISO/FDIS DIS 306 Plastics - Thermoplastic materials - Determination of Vicat softe- 489:2021) ning temperature (VST) FprEN ISO 3915 Plastics - Measurement of resistivity of conductive plastics DIS 5412 Biodegradable plastic shopping bags for industrial composting (ISO/FDIS 3915:2021) DIS 5424 Industrial compostable drinking straws FprEN ISO 19712-3 Plastics - Decorative solid surfacing materials - Part 3: FDIS 871 Plastics - Determination of ignition temperature using a hot-air Determination of properties - Solid surface shapes furnace FDIS 489 Plastics - Determination of refractive index CEN TC 155 (Plastics piping systems and ducting systems) FDIS 3146 Plastics - Determination of melting behaviour of semi-crystalli- prEN 16903 Plastics piping systems - Environmental product declarations - ne polymers by capillary tube and polarizing-microscope methods Product Category Rules complementary to EN 15804, for buried plastics piping systems ISO TC 138 (Plastics piping systems and ducting systems) prEN 16904 Plastics piping systems - Environmental product declarations - NWIP 8233 Plastics piping systems - Environmental product declarations - Product Category rules complementary to EN 15804, for plastic piping Product Category rules complementary to EN 15804, for plastic piping sy- systems inside buildings stems inside buildings EN 17176-2 prA1 Plastics piping systems for water supply and for buriNWIP 16486-1 Plastics piping systems for the supply of gaseous fuels - ed and above ground drainage, sewerage and irrigation under pressure - Unplasticized polyamide (PA-U) piping systems with fusion jointing and me- Oriented unplasticized poly(vinyl chloride) (PVC-O) - Part 2: Pipes chanical jointing - Part 1: General FprEN 14541-1 Plastics pipes and fittings - Utilisation of thermoplastics ISO/TC 138/SC2 - ISO 4427-2:2019/DAmd1 Plastics piping systems for recyclates - Part 1: Vocabulary
CHINAPLAS 2022
Puntando a raggiungere la neutralità delle emissioni di carbonio entro il 2060, la Cina accelera in tutti i settori la transizione verso un’economia sostenibile. In programma a Shanghai dal 25 al 28 aprile 2022, l’esposizione Chinaplas vedrà oltre 4000 espositori presentare un gran numero d’innovazioni tecnologiche disposte su 360 mila metri quadri, proprio con l’obiettivo di affrontare le nuove sfide dell’economia circolare. I pareri del Consiglio di Stato cinese sulla riduzione delle emissioni di anidride carbonica entro il 2030 e sul raggiungimento della neutralità al 2060, unitamente al relativo piano d’azione varato nell’ottobre 2021, rappresentano le linee guida ufficiali per realizzare il cosiddetto “doppio obiettivo del carbonio”. Per far fronte ai sempre più rigorosi controlli sui consumi d’energia, da parte delle aziende manifatturiere vi è una forte richiesta di soluzioni produttive a basso consumo energetico e nello stesso tempo a elevate prestazioni. Viene inoltre promossa la domanda di materiali ecosostenibili, come bioplastiche e polimeri biodegradabili, di materiali riciclati, di resine facili da riciclare e di additivi sostenibili. Sono sempre più richiesti dal mercato anche i macchinari per lavorare tali materiali e le tecnologie di riciclo. Con la diffusione delle nuove fonti d’energia, settori emergenti come il fotovoltaico, l’eolico, lo stoccaggio d’energia, i veicoli elettrici e a idrogeno stanno prendendo slancio, incrementando la domanda di nuovi materiali. Grazie ai nuovi spazi dedicati alle tecnologie sostenibili e a basse emissioni, Chinaplas si appresta a presentare una quantità enorme e diversificata di soluzioni innovative per aiutare le aziende a esplorare le nuove tendenze. Le soluzioni green saranno presenti in tutti i padiglioni, ma in particolare nel 5.2, nella Bioplastics Zone e nella Recycled Plastics Zone. Lo sviluppo sostenibile nel settore plastica e gomma necessita urgentemente del sostegno delle tecnologie digitali. Intelligenza artificiale, IoT e big data possono rivelarsi molto utili sia nelle strategie di monitoraggio in tempo reale sia negli algoritmi d’interpretazione dei dati di consumo energetico. Lo sviluppo dell’automazione e delle tecnologie intelligenti e digitali ha subito un’accelerazione anche in risposta alla pandemia da Covid-19. Il monitoraggio e la gestione da remoto possono aiutare i tecnici a risolvere i problemi di produzione anche da migliaia di chilometri di distanza, mentre sofisticate attrezzature automatizzate e di precisione aiutano le imprese ad affrontare la carenza di manodopera e l’eventuale instabilità nelle caratteristiche qualitative dei prodotti.
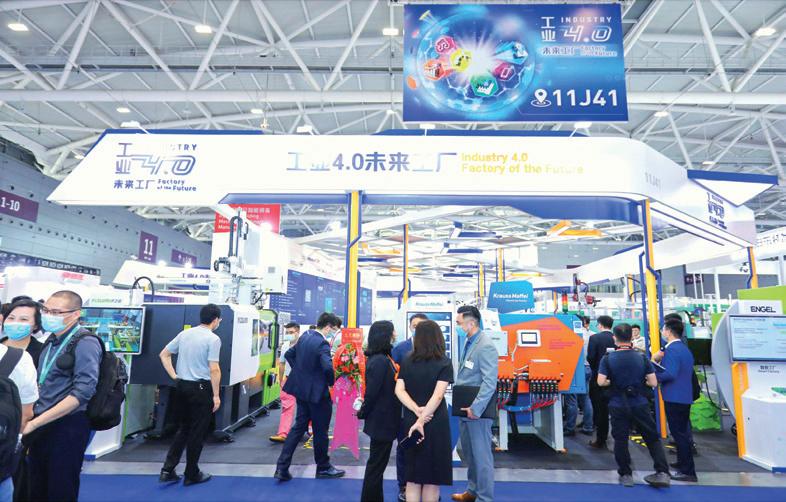
2022 ESPOSIZIONI E FIERE
25-27 gennaio - Oman Plast (Muscat, Oman) 25-28 gennaio - Interplastica (Mosca, Russia) 27-29 gennaio - PPP Expo Tanzania (Dar Es Salaam, Tanzania) 28-30 gennaio - Interplastpack Africa (Kampala, Uganda) 22-24 febbraio - Utech Middle East/Africa Foam & Polyurethane Expo (Dubai, Emirati Arabi Uniti) 4-6 marzo - Sino-Pack e PackInno (Guangzhou, Cina) 8-10 marzo - JEC World (Parigi, Francia) 8-11 marzo - Plastimagen (Città del Messico, Messico) 22-24 marzo - Plastprintpack Nigeria (Lagos, Nigeria) 23-25 marzo - PU Tech (Noida, India) 29-31 marzo - FiltXpo & Idea (Miami Beach, Florida, USA) 29-31 marzo - PTXpo, Plastics Technology Expo (Rosemont, Illinois, USA) 31 marzo-2 aprile - Samuplast (Pordenone, Italia) 5-8 aprile - FIP (Lione, Francia) 5-8 aprile - Interplast (Joinville, Brasile) 6-8 aprile - A&T (Torino, Italia) 14-15 aprile - Luxe Pack (Shanghai, Cina) 25-28 aprile - Chinaplas (Shanghai, Cina) 27-30 aprile - Die & Mould (Mumbai, India) 3-6 maggio - GreenPlast (Milano, Italia) 3-6 maggio - Ipack-Ima, Print4All, Pharmintech e Intralogistica (Milano, Italia) 11-14 maggio - Pack Show (Bucarest, Romania) 16-18 maggio - Plast Alger (Algeri, Algeria) 18-21 maggio - HanoiPlas (Hanoi, Vietnam) 20-22 maggio - Interplastpack Africa (Dar-es-Salaam, Tanzania) 24-26 maggio - SPS Italia (Parma, Italia) 24-26 maggio - Utech Las Americas (Città del Messico, Messico) 24-27 maggio - Hispack (Barcellona, Spagna) 24-27 maggio - Plastpol (Kielce, Polonia) 25-26 maggio - Injection Moulding and Design Expo (Detroit, Michigan, USA) 26-28 maggio - 3P, PlasPrintPack Pakistan (Lahore, Pakistan) 1-4 giugno - Plastexpo / Packexpo (Casablanca, Marocco) 6-9 giugno - Argenplas (Buenos Aires, Argentina) 6-9 giugno - Saudi Plastics & Petrochem (Riyadh, Arabia Saudita) 7-9 giugno - Rosmould/Rosplast (Mosca, Russia) 9-11 giugno - Mecspe (Bologna, Italia) 9-11 giugno - Plastprintpack Ethiopia (Addis Abeba, Etiopia) 10-13 giugno - Iplas (Chennai, India) 22-25 giugno - Interplas Thailand (Bangkok, Tailandia) 27-30 giugno - DKT IRC (Norimberga, Germania) 6-8 luglio - Plastics & Rubber Vietnam (Ho Chi Minh City, Vietnam) 3-5 agosto - Plastech, Rubber & Tyre, Rubber Tech Vietnam (Ho Chi Minh City, Vietnam) 16-18 agosto - Feiplar Composites & Feipur (San Paolo, Brasile) 24-26 agosto - Expo Poliplast (Monterrey, Messico) 24-27 agosto - Expoplast (Lima, Perù) 31 agosto - 3 settembre - Indoplas (Jakarta, Indonesia) 26-30 settembre - Colombiaplast (Bogotà, Colombia)
NOTA: Il calendario delle fiere qui riportate potrebbe subire variazioni a causa dell’attuale emergenza sanitaria dovuta al Covid-19. Vi invitiamo pertanto a consultare il sito web www.macplas.it per tutti gli aggiornamenti del caso.
CORSI E CONVEGNI
Austria
8-10 febbraio - Vienna: Pipeline Coating - AMI (www.ami.international/events)
Belgio
2-3 febbraio - Bruxelles: Petcore Annual Conference - Petcore (www.petcore-europe.org) 16 febbraio - Anversa: European Food & Beverage Plastic Packaging Summit - (www.wplgroup.com/aci/event/european-foodbeverage-plastic-packaging-summit)
Francia
3-4 marzo - Parigi: World Pultrusion Conference EPTA & ACMA (www.pultruders.com)
Germania
14-15 marzo - Berlino: Additive Manufacturing Forum - IPM, Institut für Produktionsmanagement (www.am-forum.eu) 14-16 marzo - Colonia: Cables - AMI (www.ami.international/events) 24 marzo - Webinar: Forum Plastic Recyclates - Fraunhofer Institute (www.kunststoffrezyklate.de)
Italia
1-2 febbraio (9.00-12.30) - Webinar/presenza: Materiali a contatto con alimenti - Cesap (www.cesap.com) 3-4 febbraio (9.00-13.00) - Webinar: Conoscere le tecnologie per l’imballaggio e le innovazioni del
bio!PAC 2022 Nuova edizione della conferenza dedicata agli imballaggi in bioplastica
In collaborazione con Green Serendipity, società di consulenza olandese la cui attività è focalizzata sulle materie plastiche rinnovabili, Bioplastics Magazine organizza la quarta edizione di bio!PAC, conferenza internazionale dedicata agli imballaggi realizzati con le bioplastiche, in programma dal 15 al 16 marzo 2022. Viste le restrizioni ancora in essere dovute alla recente evoluzione della pandemia da Sars-CoV-2, questo, come altri eventi, si terrà online. Tuttavia, se consentito dalle decisioni degli enti locali, la conferenza potrà svolgersi in presenza con un preavviso tempestivo da parte dell’organizzatore. Tra i vari materiali utilizzati per la realizzazione degli imballaggi alimentari, la plastica tradizionale, derivante dai combustibili fossili, è ancora oggi predominante. Tuttavia, le plastiche alternative, come quelle a base biologica e biodegradabile, stanno conquistando sempre più spazio nella produzione di packaging, rappresentando un’alternativa più sostenibile, sebbene il loro utilizzo possa comportare eventuali rischi da valutare con estrema attenzione. In questo contesto, la prossima edizione di bio!PAC si focalizzerà sugli imballaggi realizzati in materie prime a base biologica che porteranno a reali benefici ambientali in futuro. Il packaging realizzato con bioplastiche presenta caratteristiche estremamente competitive, tra cui: riciclabilità, biodegradabilità e compostabilità. Inoltre, questo prodotto innovativo può essere realizzato mediante risorse rinnovabili in grado di offrire particolari proprietà barriera, riducendo l’impatto ambientale e le emissioni di CO2. Il convegno bio!PAC 2022 sarà un’occasione d’incontro virtuale tra gli esperti provenienti dal mondo dell’imballaggio che utilizza le bioplastiche, dove potranno presentare le loro ultime novità, frutto di una costante attività di ricerca e sviluppo. La conferenza tratterà varie tematiche, tra cui anche le soluzioni possibili per gestire il fine vita di un prodotto e l’atteggiamento dei consumatori verso le plastiche tradizionali e le bioplastiche.
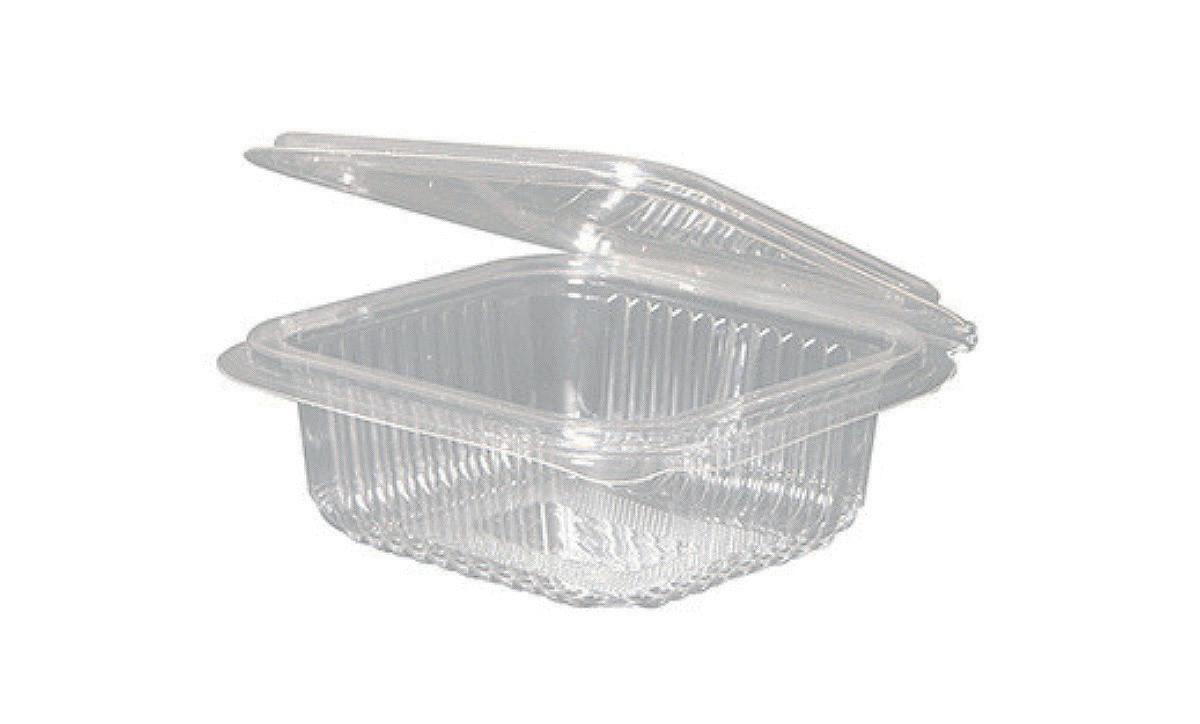
Vaschetta in bioplastica biodegradabile settore - SBS, Scuola Beni Strumentali (www.scuolabenistrumentali.it) 4 febbraio (9.00-12.30) - Webinar/presenza: Stampaggio a iniezione - La simulazione CAE - Cesap (www.cesap.com) 14-15 febbraio (9.00-17.00) - Webinar/presenza: Estrusione con bivite corotante - Cesap (www.cesap.com) 22-23 febbraio (9.00-13.00) - Webinar: La marcatura CE degli insiemi di macchine - SBS, Scuola Beni Strumentali (www.scuolabenistrumentali.it) 24 febbraio (9.00-13.00) - Webinar: La nuova norma EN 415-11 sul calcolo dell’efficienza e della disponibilità delle macchine per il packaging SBS, Scuola Beni Strumentali (www.scuolabenistrumentali.it) 3-6 maggio - Rho-Pero (Fiera di Milano): Packaging Speaks Green, Forum internazionale sull’imballaggio sostenibile - Ucima & Amaplast (www.packagingspeaksgreen.com)
Regno Unito
2-3 febbraio - Londra: - The European Biopolymer Summit - ACI (https://www.wplgroup. com/aci/event/european-biopolymer-summit) 15 febbraio - Webinar: Biobased Coatings - ACI (www.wplgroup.com/aci/event/biobasedcoatings-online-series)
Spagna
28-30 marzo - Barcellona: Agricultural Film Europe - AMI (www.ami.international/events)
Stati Uniti
1-3 febbraio - St. Augustine (Florida): Polyethylene Films - AMI (www.ami.international/events) 1-2 marzo - Clevelend (Ohio): PVC Formulation - AMI (www.ami.international/events)
Tailandia
8-9 febbraio / 5-6 aprile - Online MasterClass: EPDM Rubber Technology & Applications - KnowHow Webinars c/o TechnoBiz Communications (www.technobiz.org; www.knowhow-webinars.com)
NOTA: Il calendario dei convegni potrebbe subire variazioni a causa dell’attuale emergenza sanitaria dovuta al Covid-19. Vi invitiamo pertanto a consultare i siti web riportati in questa pagina e a visitare il sito www.macplas.it per tutti gli aggiornamenti del caso.
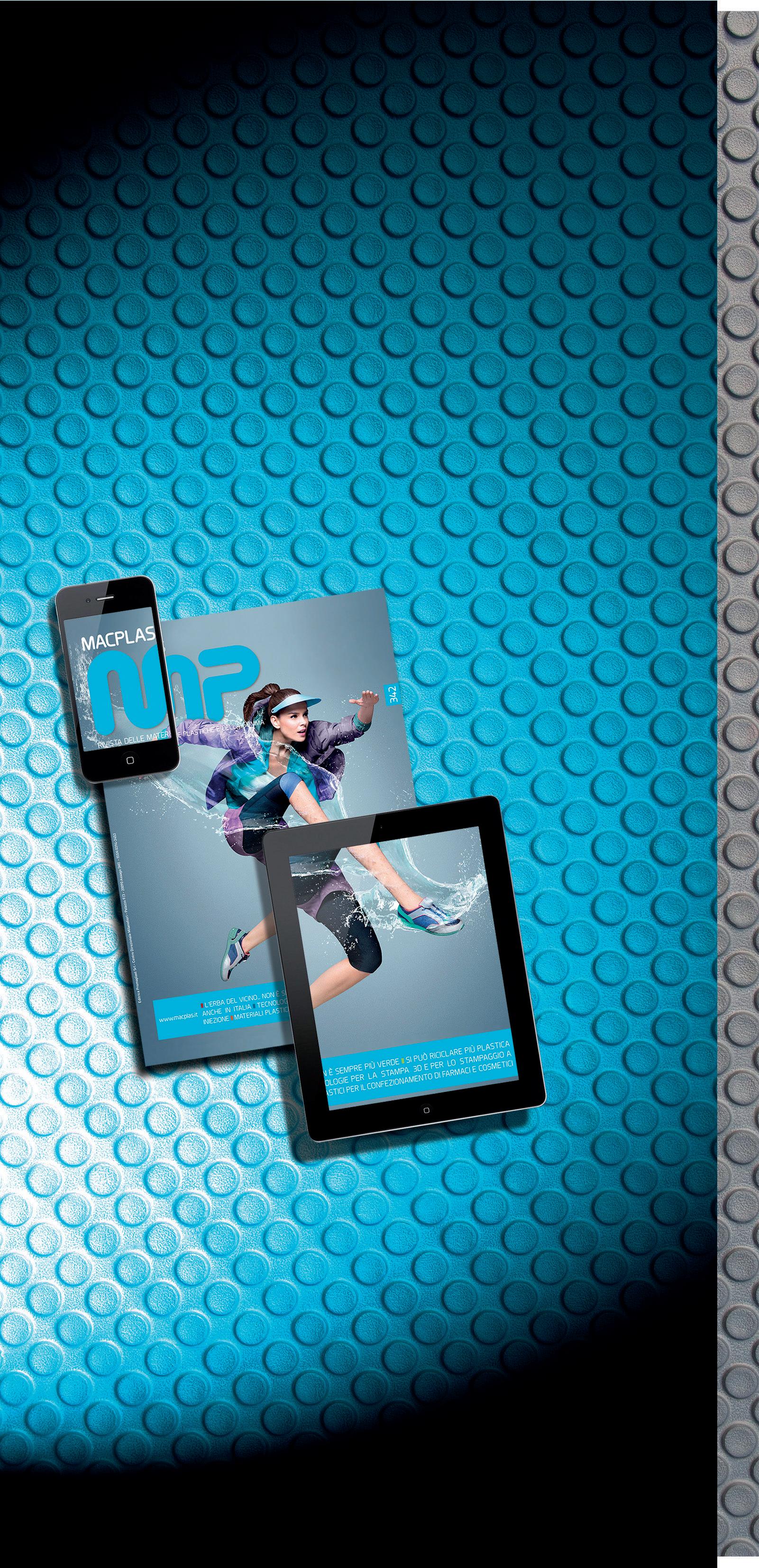
molto piu di un magazine
MACPLAS SI FA IN TRE: RIVISTA NEWSLETTER
SITO INTERNET.
MOLTA PIU VISIBILITA.À MOLTE PIU POSSIBILITAÀ DI CONTATTO.
MOLTE PIU OCCASIONI
DI BUSINESS.
SUL MERCATO DA OLTRE ANNI
Editore Promaplast Srl Centro Direzionale Milanof ori Palazzo F/3 - 20057 Assago (MI) tel. (+39) 02 82283775 - fax (+39) 02 57512490 macplas@macplas.it - www.macplas.it Per la pubblicita: r.pagan@macplas.it
IN QUESTO NUMERO SI PARLA DI:
AZIENDA/ASSOCIAZIONE/ENTE
AMAPLAST AMUT ASSOBIOPLASTICHE ASSOGOMMA ASSORIMAP AVK BANDERA BARUFFALDI PLASTIC TECHNOLOGY BASF BIO!PACK BITUMAT BMB CERESANA CERISIE CHINAPLAS CMS COLINES COMEXI COMI CONTROL TECHNIQUES DOW ECOMONDO EUBP - EUROPEAN BIOPLASTICS EVOSYS LASER EXEL COMPOSITES FEDERAZIONE GOMMA PLASTICA FONDAZIONE PER LO SVILUPPO SOSTENIBILE GAP GREENPLAST GSI (GLOBAL SERVICE INTERNATIONAL) HERRMANN ULTRASCHALL JEC GROUP KEY ENERGY KOCH-TECHNIK KRAIBURG TPE LEISTER MAST MECS ME.RO MOBERT MONTELLO MOOG NICKERSON ITALIA NIDEC NOVA-INSTITUTE OMYA INTERNATIONAL PET DAY 2021 PLASTICS RECYCLERS EUROPE (PRE) PLASTICS RECYCLING SHOW EUROPE (PRSE) PLASTISAVIO PLASTLAB PREVIERO PRIMAC RADICIGROUP RODOLFO COMERIO ROMAGNATECH SALDOFLEX SCHÜTZ SIKORA SIRMAX SMART MOLD SVAROG TEKNI-PLEX GALLAZZI TOMRA ULTRA SYSTEM UNITECHEM GROUP UNION UNIPLAST WENGLOR WERKCAM WM THERMOFORMING MACHINES XALOY
PAGINA
18 47 25 85-95 21 80 30 60 76 99 47 61 19 88 98 36 34 34 40 69 34 24 28 63 83 10 22; 24 44 26 14 54 80 24 49 94 56 62 18 58 45 29 61 49 69 28 78 14 28 28 46 69 18; 30 60 74 52 82 46 83 94 71 71 94 52 30; 64 78 79 46 96 40 56 44 60
#newlifetoplastic

1st EDITION
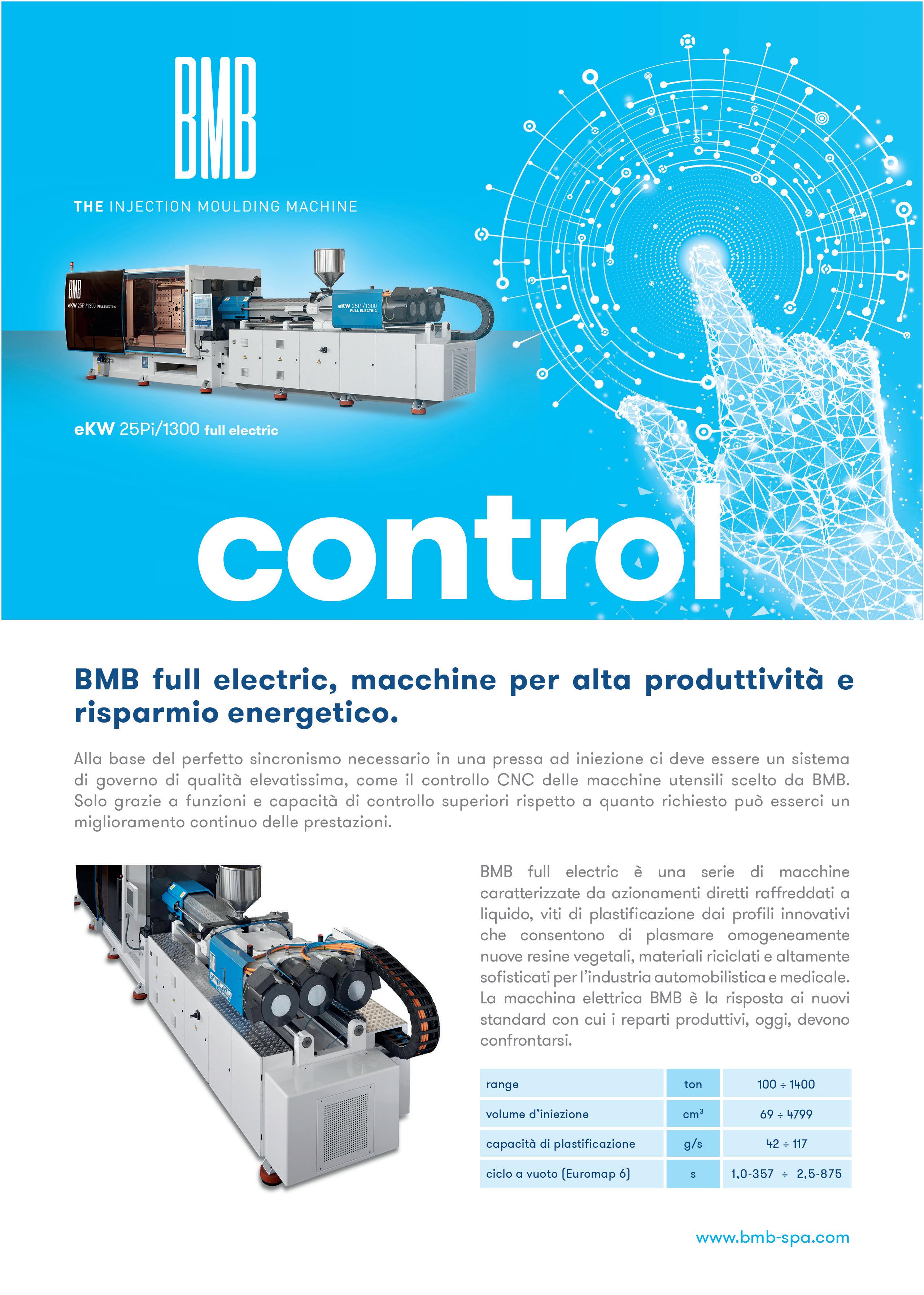