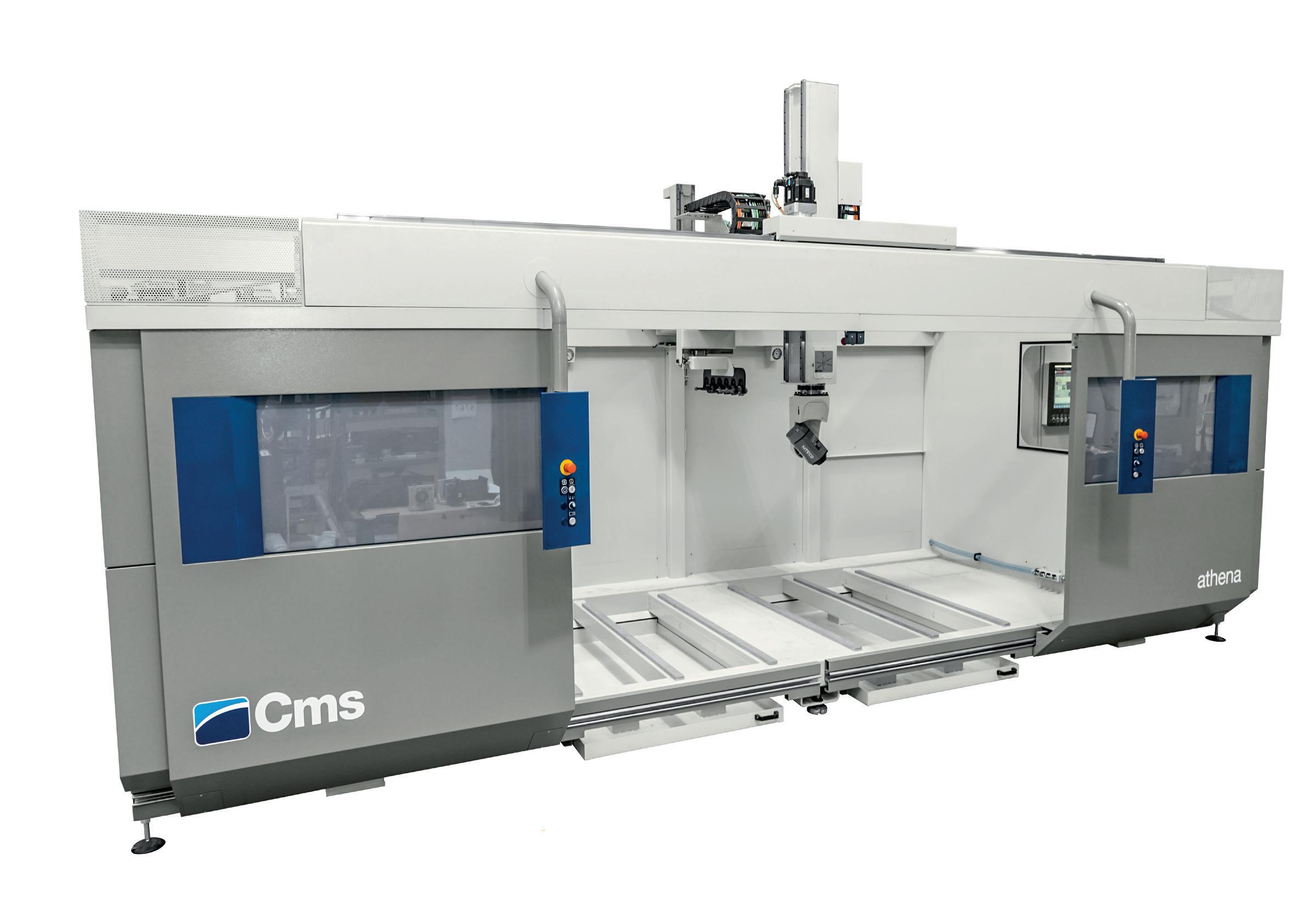
88 minute read
MACCHINE & ATTREZZATURE
from MacPlas 383
by PROMAPLAST
SVILUPPI E INVESTIMENTI IN CASA CMS
L’EVOLUZIONE DEL CENTRO DI LAVORO
L’AZIENDA CMS DI ZOGNO (BERGAMO) STA VIVENDO UN MOMENTO DI INTENSA ATTIVITÀ, NONOSTANTE I TEMPI DIFFICILI. ALLA RICERCA E ALLO SVILUPPO TECNOLOGICO AFFIANCA IMPORTANTI INVESTIMENTI, CHE A LORO VOLTA ALIMENTANO I PRIMI PER CONSOLIDARE E RAFFORZARE LA PROPRIA POSIZIONE DI MERCATO NEL SETTORE DI RIFERIMENTO
Con la nuova macchina athena di CMS la rifinitura di termoformati in materiale plastico diventa ancora più semplice, flessibile, veloce e accurata. Athena è un centro di lavoro a portale mobile progettato espressamente per lavorazioni ad alta velocità di materiali plastici, in grado di offrire un’eccellente dinamica di movimento e tradursi in un’elevata produttività. La progettazione strutturale avanzata garantisce la riduzione delle vibrazioni generate dalla lavorazione e un’ottima qualità della finitura.
LE CARATTERISTICHE PRINCIPALI
La massima libertà produttiva è assicurata da aree di lavoro di grandi dimensioni e ampiamente configurabili (zona unica o pendolare). Il design compatto favorisce la movimentazione e il trasporto senza la rimozione di alcun organo meccanico, a tutto vantaggio di tempi di messa in servizio ridotti. Dedicato alla generazione ottimizzata del percorso di rifilatura e basato su software interattivo e tastiera portatile con joystick e touch screen per la gestione di tutte le funzioni del CNC, il sistema di programmazione Smart4Cut permette la creazione del programma di taglio partendo dal modello 3D o direttamente dal pezzo campione montato in macchina, eliminando in automatico tutti i movimenti inutili e riducendo al minimo il tempo di ciclo. La macchina è disponibile anche con tavole rotanti
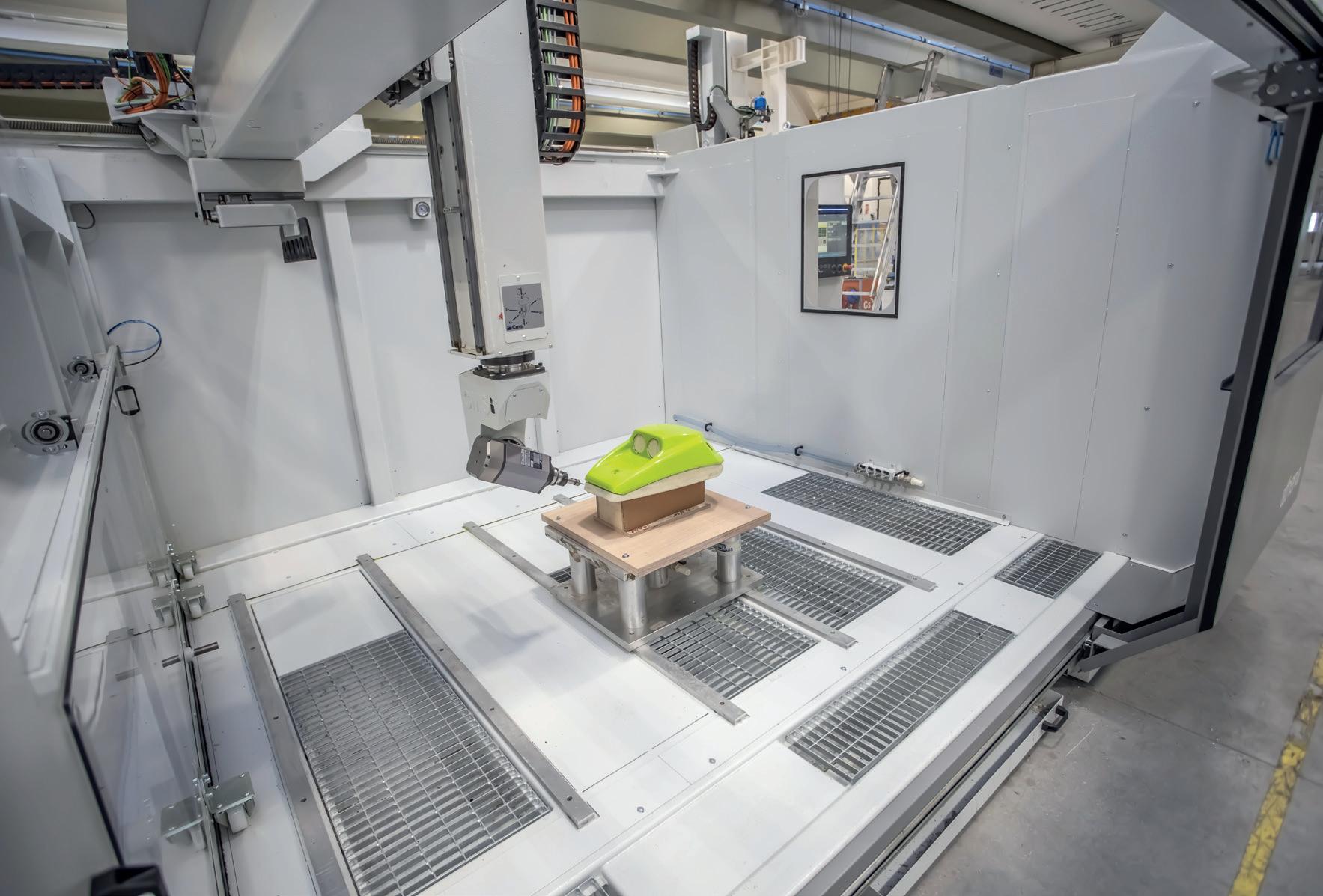
Operatività all’interno del centro di lavoro athena
(TR) e con tavole estraibili APC (Automatic Pallet Change). La gamma prende origine dai precedenti modelli di CMS per il taglio dei materiali plastici, di cui rimangono invariati tutti i vantaggi, inclusa l’unità operatrice CX5 e il sistema per la raccolta degli sfridi integrato nel basamento, così che l’area di lavoro sia sempre pulita e facilmente accessibile, ma si arricchisce dell’estensione dell’asse Y fino a 2500 mm. Le capacità dinamiche degli assi sono state portate a un livello più elevato, così da sfruttare meglio, anche in spazi ridotti, tutte le prestazioni di movimento della macchina. Qualità e precisione dei movimenti e della lavorazione risultano ulteriormente potenziate grazie all’utilizzo del nuovo sistema di programmazione Smart4Cut e all’unità operatrice CX5: il primo consente di generare in modo automatico percorsi di rifilatura ottimizzati, mentre la seconda si mantiene sempre alla minima distanza dal pezzo da lavorare, in modo da ottenere il miglior tempo di taglio nel rispetto della qualità richiesta. Ne conseguono riduzioni del 15% dei tempi di taglio e programmazione (con sistema Smart4Cut) dei cicli di scontornatura, del 13% dei tempi complessivi di lavorazione, grazie all’ottimizzazione delle dinamiche di movimento assi, e del 15% dei tempi di pulizia della tavola, grazie al sistema di raccolta dei trucioli integrato nel basamento, e, per tutte le versioni, il massimo sfruttamento dello spazio nel reparto produttivo in rapporto al cubo lavorabile.

COMPATTO E POLIEDRICO
Altro centro di lavoro che si distingue per compattezza e poliedricità nella gamma di CMS, time 100 presenta uno tra i migliori rapporti prezzo/prestazioni. In particolare, la macchina ha un design compatto che ne riduce al minimo l’impronta a terra e l’ingombro, rendendola accessibile da tutti i lati per la movimentazione di pannelli o piccoli componenti. Questo centro di lavoro, infatti, rispetto alle soluzioni tradizionali, occupa il 17% in meno di spazio, consente un risparmio medio del 25% sull’attrezzaggio e sul cambio formato e non pone limiti alle geometrie dei pezzi da lavorare, anche quando molto complesse. Le prestazioni rendono time 100 la soluzione ideale per soddisfare tutte le esigenze di “nesting” e di lavorazione degli articoli tecnici da lastra. Inoltre, grazie a dispositivi dedicati, è in grado di adattarsi alle più svariate necessità dei settori

Il centro di lavoro time 100
della grafica e della cartellonistica. La configurazione della versione cella è studiata appositamente per garantire la massima automazione e la conseguente ottimizzazione del ciclo produttivo. La consolle multi-touch Eye-M di ultima generazione rende il lavoro dell’operatore intuitivo e quindi immediato, mentre lo schermo semplice ma elegante è reso ancora più luminoso dalla tecnologia LED.
A Zogno Nuovo reparto dedicato alla costruzione delle macchine più grandi
Gli investimenti non si fermano in casa CMS, che ha appena realizzato una nuova area produttiva. Lo stabilimento produttivo di Zogno (Bergamo) dispone adesso di una nuova struttura all’avanguardia sotto tutti i punti di vista. Un’intera area di 85 mila metri cubi è stata realizzata, nel pieno rispetto dell’ambiente e del paesaggio circostante, specificamente per la costruzione delle macchine più grandi dell’azienda, che verranno movimentate tramite otto carroponti dalla portata di 15 tonnellate ciascuno. La superficie totale coperta è di 7740 metri quadri, l’altezza utile interna del fabbricato arriva fino a 12 metri, l’illuminazione delle aree di produzione avviene per mezzo di 200 proiettori LED, che garantiscono una luce mediamente superiore a 350 lux, e durante la realizzazione degli impianti sono stati posati circa 10 mila metri di cavi elettrici. Le facciate e l’impatto paesaggistico del capannone sono stati studiati con la collaborazione dell’architetto Cinzia Robbiati della soprintendenza archeologica belle arti e paesaggio per le provincie di Bergamo e Brescia. La certificazione energetica lo colloca in Classe A1, mentre sulla copertura è installato un impianto fotovoltaico composto da 504 moduli solari policristallini con una potenza complessiva di picco di 150 kW. Il solaio di pavimento, dello spessore di 48 cm, è in grado di sopportare carichi dinamici fino a 3500 kg, con un cedimento differenziale inferiore a 2 centesimi di mm, così da permettere di eseguire i collaudi direttamente sul posto, comprese le prove più impegnative e severe, assicurando risultati precisi e affidabili.
Una panoramica dell’interno del nuovo capannone realizzato da CMS a Zogno per la costruzione delle sue macchine più grandi
INSIDE SPRING DI BIESSE GROUP
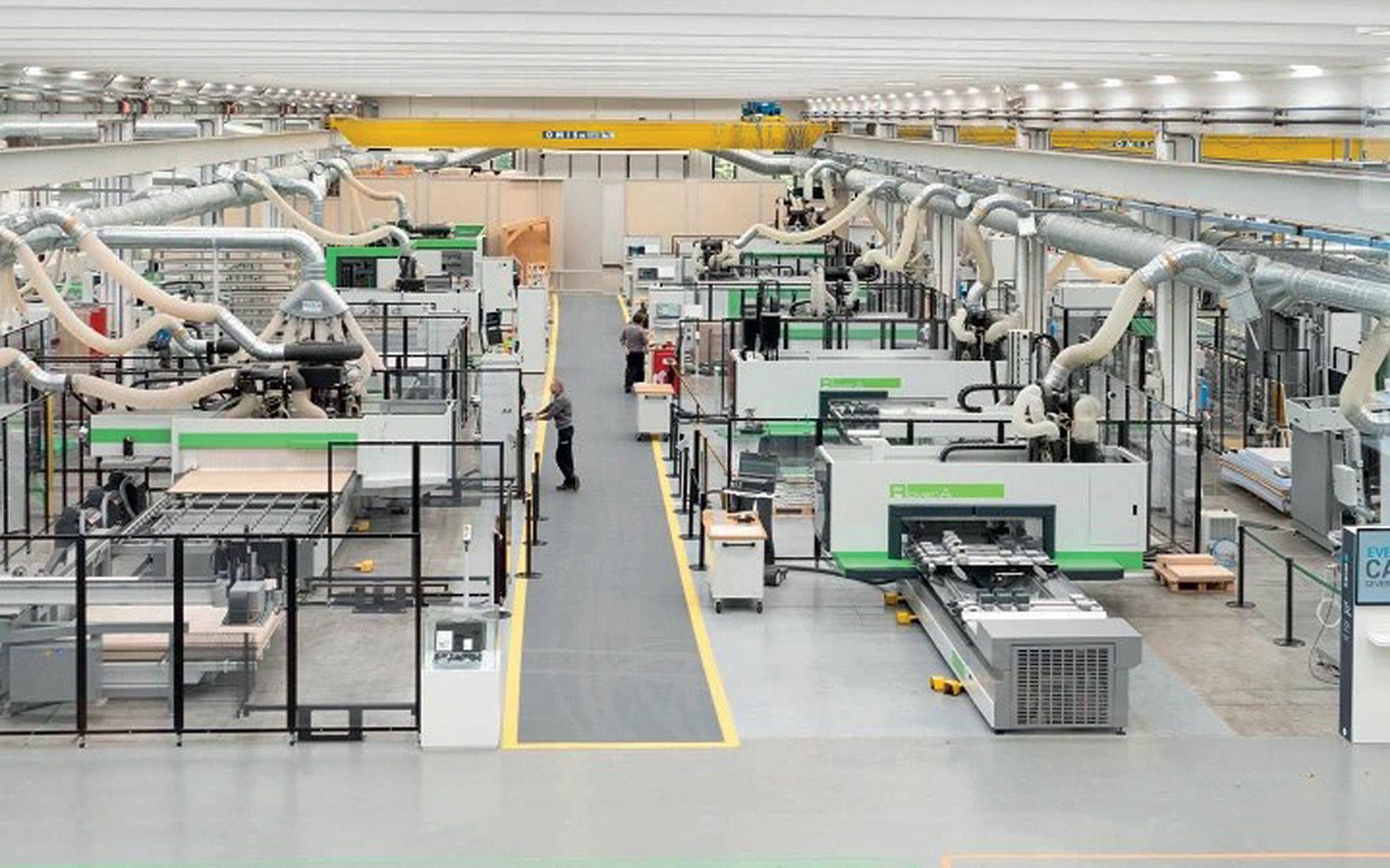
EDIZIONE STRAORDINARIA DI UN EVENTO SENZA CONFINI
UN EVENTO GLOBALE E COMUNE A TUTTE LE DIVISIONI, CON UN’EDIZIONE STRAORDINARIA CHE HA UNITO REALE E VIRTUALE: INSIDE È TORNATO IN SCENA IN UNA NUOVA VERSIONE PRIMAVERILE, PER UN’ESPERIENZA COMPLETA E IRRINUNCIABILE, CHE VEDE DA SEMPRE PROTAGONISTE LE TECNOLOGIE BIESSE, INTERMAC E DIAMUT
Edizione speciale primaverile, Inside Spring è andato in scena presso il Campus di Biesse a Pesaro, dal 10 al 28 maggio, con dimostrazioni fisiche in showroom e visite guidate nei reparti produttivi, rispettando i protocolli di salute e sicurezza, ma anche con webinar tecnologici e approfondimenti in linea diretta con gli esperti dell’azienda. Con questo evento, di cui sono state protagoniste assolute le ultime soluzioni per la lavorazione dei materiali tecnologici, così come di legno, vetro e pietra, Biesse Group conferma l’esclusivo format “on-life”, lanciato lo scorso autunno con Inside in Action. Un format che comprende due versioni: “offline” e “online”.
AL CAMPUS DI PESARO E ONLINE
Le showroom di Biesse e Intermac a Pesaro hanno aperto le porte con oltre 60 macchine, prodotti e servizi digitali da scoprire, in totale sicurezza e nel completo rispetto dei protocolli di tutela della salute di visitatori e dipendenti, così come degli ambienti di lavoro. Grazie a un sistema di prenotazione online dedicato all’evento, i visitatori hanno potuto prenotare autonomamente visite e dimostrazioni tecniche in base alla disponibilità giornaliera. A tale scopo sono state predisposte 20 business lounge dedicate esclusivamente a ospitare i visitatori, per illustrare le soluzioni Biesse e Intermac garantendo la salubrità degli spazi. I “visitatori virtuali”, tramite un’unica registrazione, hanno avuto invece a disposizione un ricco palinsesto, la cui protagonista era l’innovazione tecnologica, con novità di prodotto e di processo. L’evento Inside Spring, nella sua versione online, ha preso forma grazie ai “Technology in Action”, approfondimenti premium dai contenuti esclusivi, streaming di video sulle tecnologie all’avanguardia, tradotti in otto lingue e disponibili per i diversi fusi orari del mondo: America, Europa e Apac. Durante le proiezioni dei video, è stato possibile interagire con gli esperti dell’azienda grazie alla chat sempre attiva, comunicando nella lingua locale e attivando eventualmente anche l’opzione di videochiamata per meeting “one-to-one”.
UN FORMAT DI APPROFONDIMENTI
Per l’occasione è proseguita anche la serie “Make & Talk”, il format fatto di approfondimenti e storie di successo volto a delineare fin da ora le sfide che ci attendono nel futuro. Due sono stati i nuovi appuntamenti nella location di Casa Lago a Milano, in programma il primo e l’ultimo giorno dell’evento, che hanno potuto contare sulla presenza di due ospiti d’eccezione: il 10 maggio, nella rubrica “Next Comes First”, è andato in onda il talk “Sostenibilità e competitività”, con la partecipazione di Rossella Sobrero, presidente di Ferpi, la federazione italiana di relazioni pubbliche che da anni organizza il salone CSR-Corporate Social Responsability. Il 28 maggio, invece, è stato il turno della rubrica “Fu-
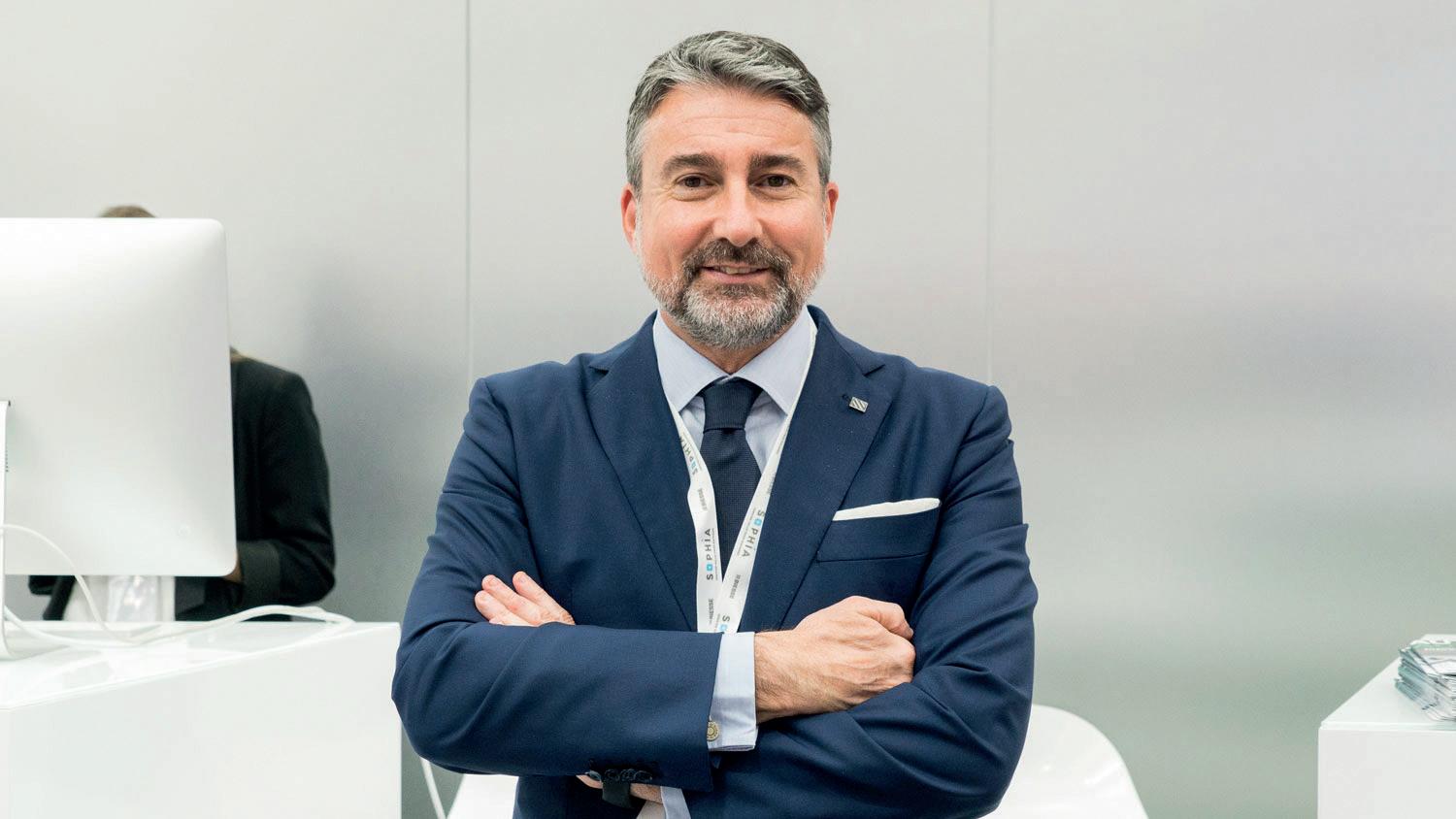
turing”, che ha ospitato la conversazione “Che il design trasformi la società” con Daniele Lago, CEO e head of design della società Lago. Tutti i video sono stati poi resi disponibili a richiesta in streaming sulla piattaforma interattiva digitalarena.biessegroup.com.
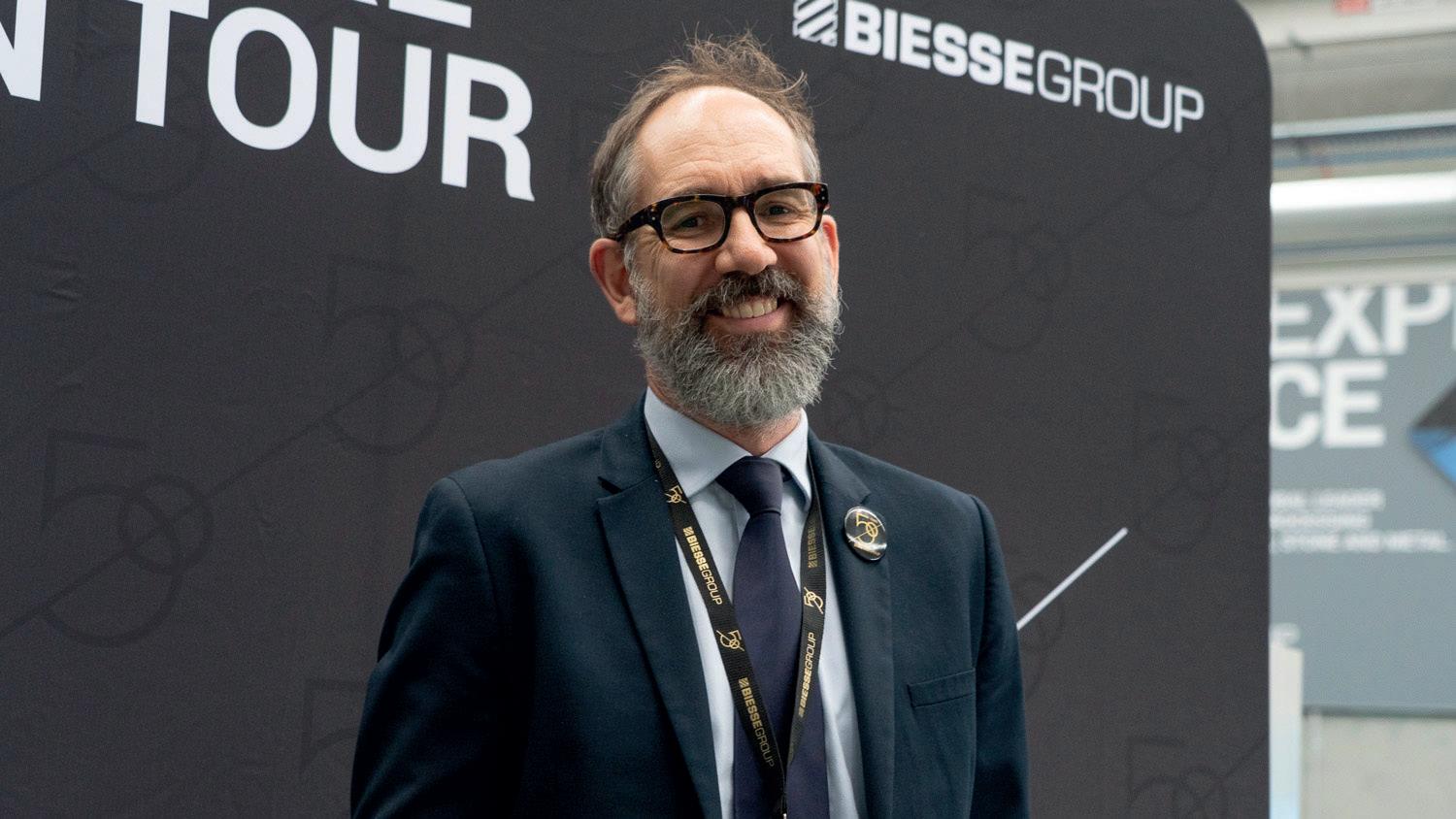
Gli approfondimenti tecnologici e le innovazioni, disponibili in showroom o in versione digitale, sono stati guidati da Automaction e Smartaction, le due chiavi di lettura della trasformazione digitale che Biesse offre ai propri clienti, per accogliere le esigenze di grandi impianti industrializzati che desiderano rafforzare e incrementare le prestazioni produttive, nel primo caso, e soddisfare le esigenze di piccole e medie aziende, nel secondo, presentando tutti i vantaggi della digitalizzazione. “Un evento di gruppo senza confini: un’occasione imperdibile per i nostri clienti, trasversale a tutte le tecnologie prodotte da Biesse, Intermac e Diamut, e internazionale. Abbiamo offerto ai clienti di tutto il mondo e di tutte le divisioni una formula completa in tutte le sue forme, che ha integrato la presenza fisica con quella digitale, per consentire, anche a chi non ha potuto essere presente fisicamente a Pesaro, di poter partecipare, tramite demo in streaming e videochiamate con la nostra forza vendita locale, a un evento veramente internazionale. La collaborazione con le nostre sedi nel mondo ha rappresentato la vera chiave di volta di un evento che è durato realmente 24 ore su 24, in ogni parte del mondo, superando limiti temporali e fisici. L’evento ha confermato infatti la volontà dell’intero gruppo di rafforzare la presenza internazionale, la vicinanza territoriale, l’ampia capillarità, fonte di arricchimento culturale e da sempre opportunità di sviluppo professionale e di attrattività dei migliori talenti”, ha dichiarato Federico Broccoli, Chief Commercial & Markets Officer di Biesse Group. “Abbiamo aperto le porte delle nostre showroom in primavera, anticipando l’evento Inside e confermando di fatto la formula ibrida dello scorso ottobre, che si è rivelata vincente da diversi punti di vista: abbiamo garantito infatti ai nostri clienti interazione, condivisione e partecipazione, fisica nei nostri showroom o digitale sulla piattaforma Digital Arena. Abbiamo investito grandi risorse per ampliare il nostro ecosistema digitale, sia per quanto riguarda le innovazioni tecnologiche, dai prodotti ai servizi, sia per quanto riguarda il nostro modo di relazionarci con i clienti di tutto il mondo. I canali digitali rappresentano oggi un nuovo modo per essere in contatto con loro, dando la possibilità a tutti di partecipare a ciò che accade nelle nostre showroom, pur non essendo fisicamente a Pesaro. I nostri clienti non sono stati semplici spettatori, ma veri interlocutori con i nostri esperti in tempo reale (durante le demo virtuali in showroom o nel corso dei documentari tecnologici su Digital Arena), rendendo sempre più labile il confine tra la modalità fisica e quella digitale e intensificando il valore della relazione e della partecipazione all’evento”, ha aggiunto Raphaël Prati, Chief Marketing & Communications Officer di Biesse Group.
Federico Broccoli, Chief Commercial & Markets Officer di Biesse Group
Raphaël Prati, Chief Marketing & Communications Officer di Biesse Group
Biesse Group si espande all’estero Nuove sedi in Israele, Giappone e Brasile
Con l’apertura di nuove sedi in Israele, Giappone e Brasile, Biesse Group espande la propria presenza internazionale e si rafforza in mercati considerati strategici. Il gruppo ritiene che lo sviluppo della dimensione internazionale, insieme a investimenti tecnologici e organizzativi e a opportunità di crescita inorganica siano elementi indispensabili per il raggiungimento degli obiettivi futuri. Guarda da sempre a Israele con grande interesse, come dimo-
Dalla fine degli Anni Ottanta, con l’apertura della prima sede negli Stati Uniti, a oggi, il processo di internazionalizzazione rappresenta uno dei cardini principali della strategia del Gruppo Biesse, presente con 39 sedi in Europa, Nord America, America Latina, Medio ed Estremo Oriente, Asia e Oceania stra la collaborazione avviata lo scorso anno con il progetto Open-I, il laboratorio di “open innovation” di gruppo che in Israele viene sviluppato attraverso la partnership con AdlerInlight Technology Observatory, osservatorio nato per unire industria e innovazione sul territorio italiano. La nuova sede, oltre a dare ulteriore stimolo a questa iniziativa, permetterà di sviluppare il potenziale commerciale del gruppo. L’espansione in Giappone rappresenta invece la volontà di investire in un paese dall’ottimo potenziale. La nuova sede permetterà, attraverso l’unione di competenze manageriali locali e di gruppo, di sviluppare in Giappone l’attività già avviata grazie alla partnership che Biesse aveva con il partner Shinx. In Brasile, infine, il gruppo allarga la propria presenza, che permetterà inoltre di valutare più da vicino le opportunità di altri paesi del Sud America. All’interno del programma di espansione internazionale, rientra poi il rafforzamento della rete del gruppo, grazie all’accordo con un nuovo partner in Lituania. Previsto inoltre l’ampliamento della sede negli Stati Uniti, attraverso la realizzazione di un nuovo capannone all’interno del Campus di Charlotte (North Carolina), grazie al quale le sedi in Nord America raggiungeranno complessivamente una dimensione superiore ai 15 mila metri quadri.

INTERVISTA A FABRIZIO POLI, AD DI FAP
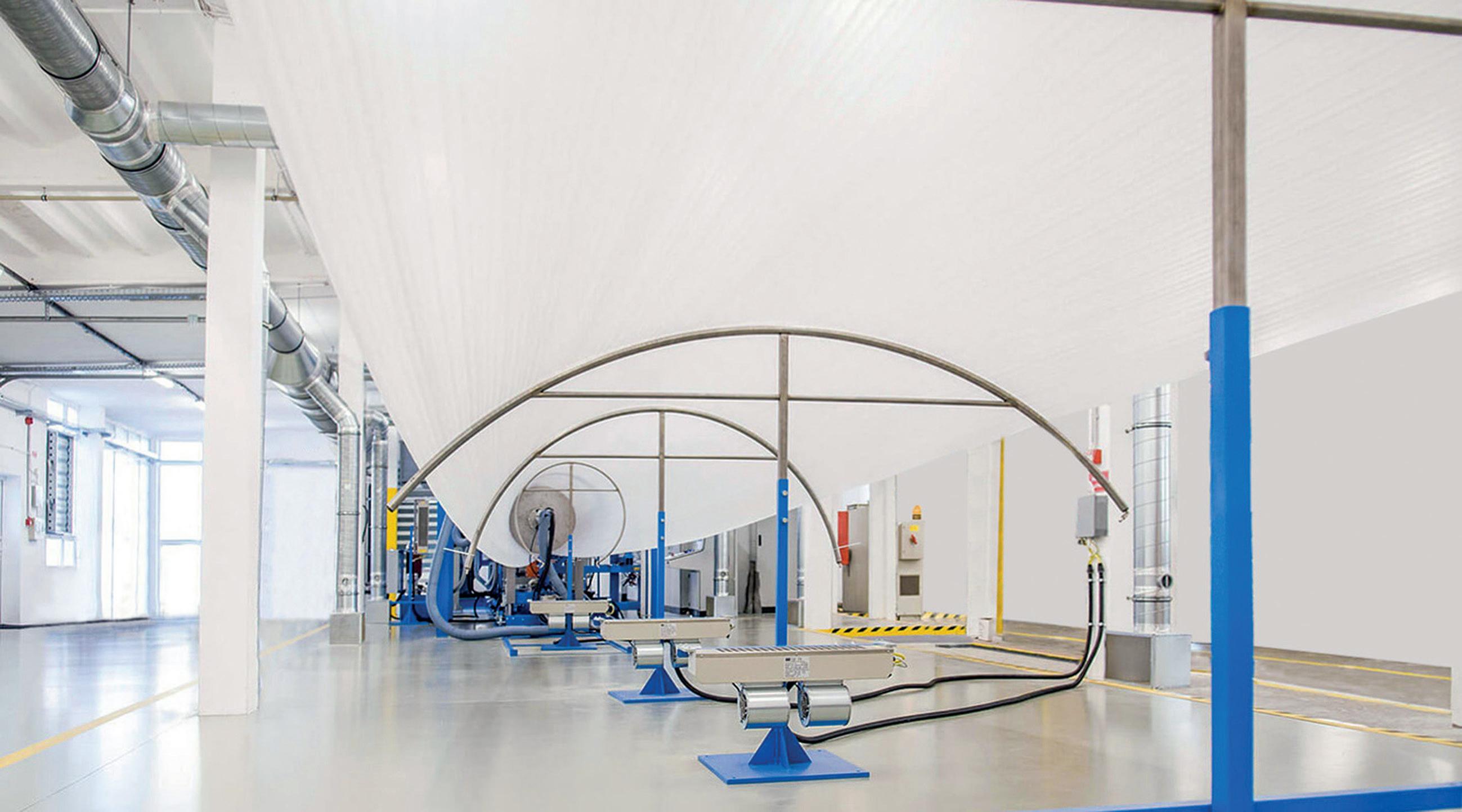
AFFRONTARE IL NOSTRO TEMPO CON L’OTTIMISMO CHE DERIVA DALL’ESPERIENZA
UN’INTERVISTA A 360° CON FABRIZIO POLI, AMMINISTRATORE DELEGATO DI FAP, CHE INSIEME AL FRATELLO FRANCESCO POLI, DIRETTORE VENDITE, DIRIGE L’AZIENDA DI FAMIGLIA, DA OLTRE TRENT’ANNI ATTIVA NELLA COSTRUZIONE DI IMPIANTI D’ESTRUSIONE PER LA PRODUZIONE E LA LAVORAZIONE DI MATERIALI ESPANSI
DI LUCA MEI
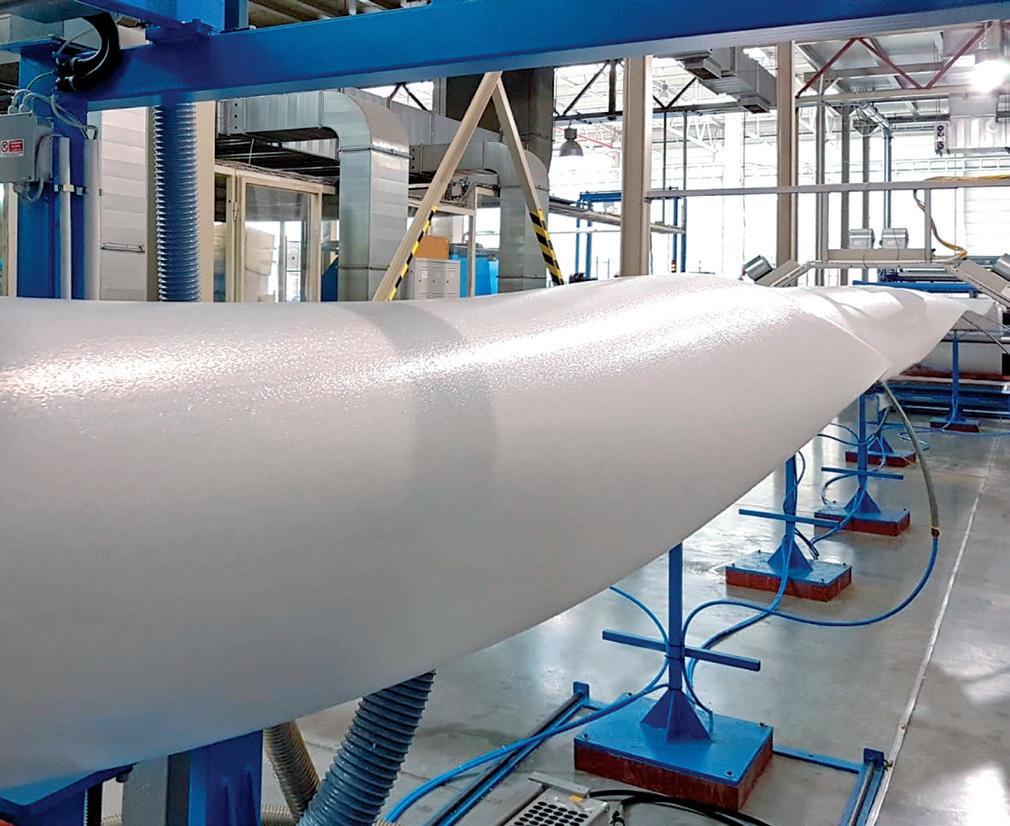
“L a miglior pubblicità per FAP è sempre stata il macchinario innovativo di qualità, con cui il cliente costruisce il successo della propria impresa”. Sono, queste, le parole di Luigi Poli, fondatore nel 1987 di FAP, azienda con sede a Besana in Brianza che costruisce impianti per l’estrusione, specializzata soprattutto in quelli per la produzione di film in materiali espansi, e guidata oggi dai figli Fabrizio e Francesco Poli, amministratore delegato il primo, direttore vendite il secondo. Parole che riassumono bene la filosofia data fin dall’inizio all’azienda dall’imprinting tipico dello spirito brianzolo, ben noto a livello nazionale e internazionale, ossia quello di persone dedite al proprio lavoro, anche quando questo si fa duro, e che considerano i prodotti che ne sono il frutto come la migliore referenza per sé e per la propria attività. Alla guida di FAP dal 2020, i fratelli Poli sono entrati entrambi nell’azienda di famiglia quando erano ancora giovanissimi, così che il vantaggio di un lungo tirocinio svoltosi tra i vari reparti e le diverse funzioni aziendali li rende oggi imprenditori di esperienza nonostante l’ancora giovane età. I due titolari sono attualmente impegnati non solo nella guida dell’azienda, bensì anche in una spinta in avanti a tutto tondo della sua attività, con importanti investimenti che, soprattutto in tempi difficili come quelli che stiamo vivendo, richiedono una buona dose di coraggio e di competenza allo stesso tempo. Di cui, evidentemente, Fabrizio e Francesco non difettano. Per farci raccontare tutto questo con le sue parole, abbiamo intervistato Fabrizio Poli, le cui risposte proponiamo nelle colonne seguenti, non prima però di averlo ringraziato per la disponibilità.
PARTIAMO DAL VOSTRO CAMPO DI SPECIALIZZAZIONE, QUELLO DELLA COSTRUZIONE DI LINEE PER L’ESTRUSIONE DI MATERIALI ESPANSI. QUAL È LO STATO DELL’ARTE IN QUESTO CAMPO E QUALI SONO I VOSTRI PIÙ RECENTI SVILUPPI TECNOLOGICI PER QUESTO PARTICOLARE TIPO DI LAVORAZIONE?
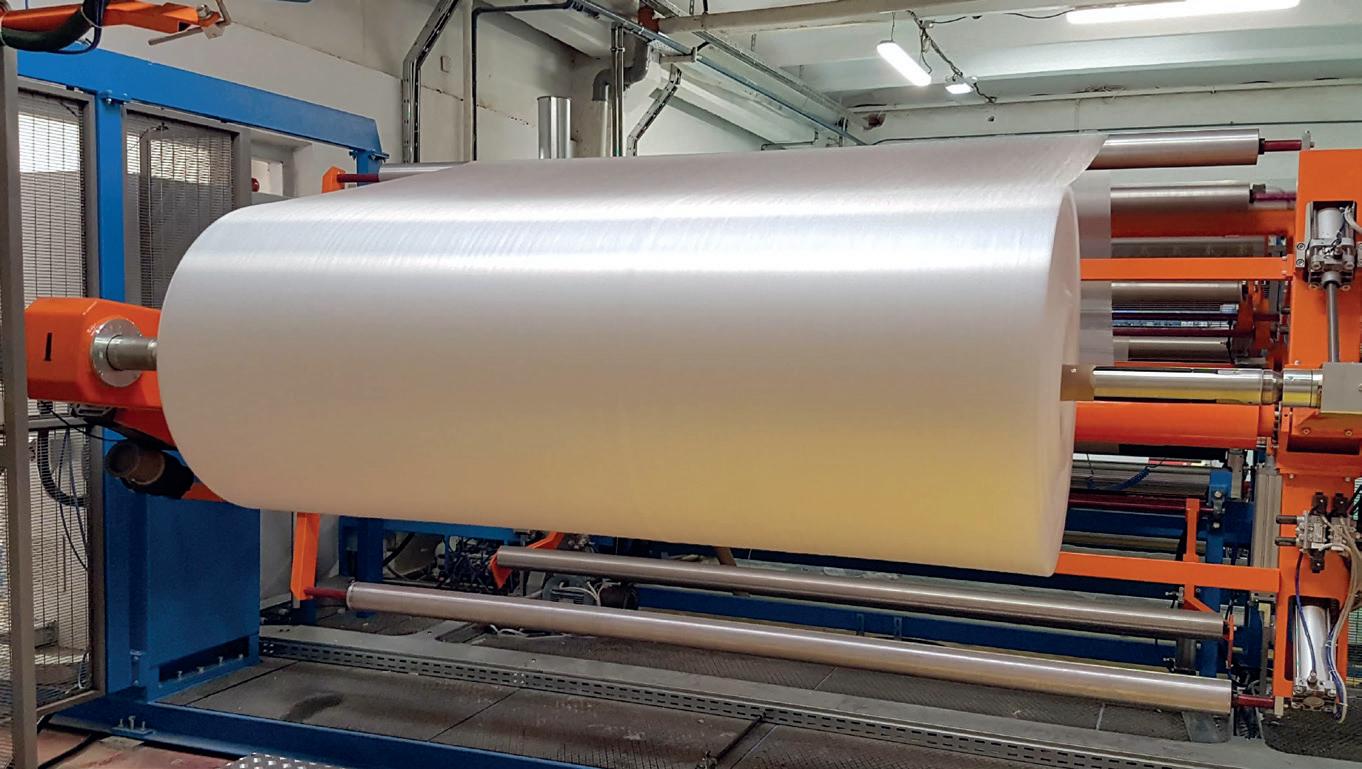
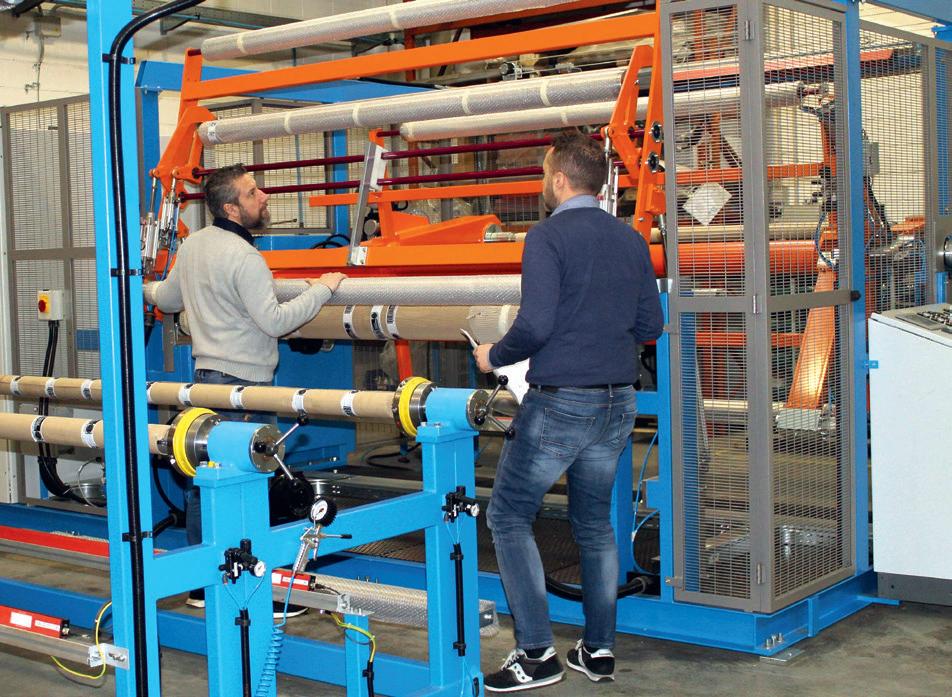
“FAP vanta un’esperienza di oltre trent’anni nel settore dei film in materiale espanso e grazie al nostro laboratorio di ricerca e sviluppo in Francia siamo in grado di studiare le novità applicative offerte dai materiali non ancora presenti sul mercato, rendendo la nostra tecnologia adeguata alla loro lavorazione. In questi termini, cerchiamo sempre di anticipare le esigenze dei produttori e del mercato per farci trovare pronti”.
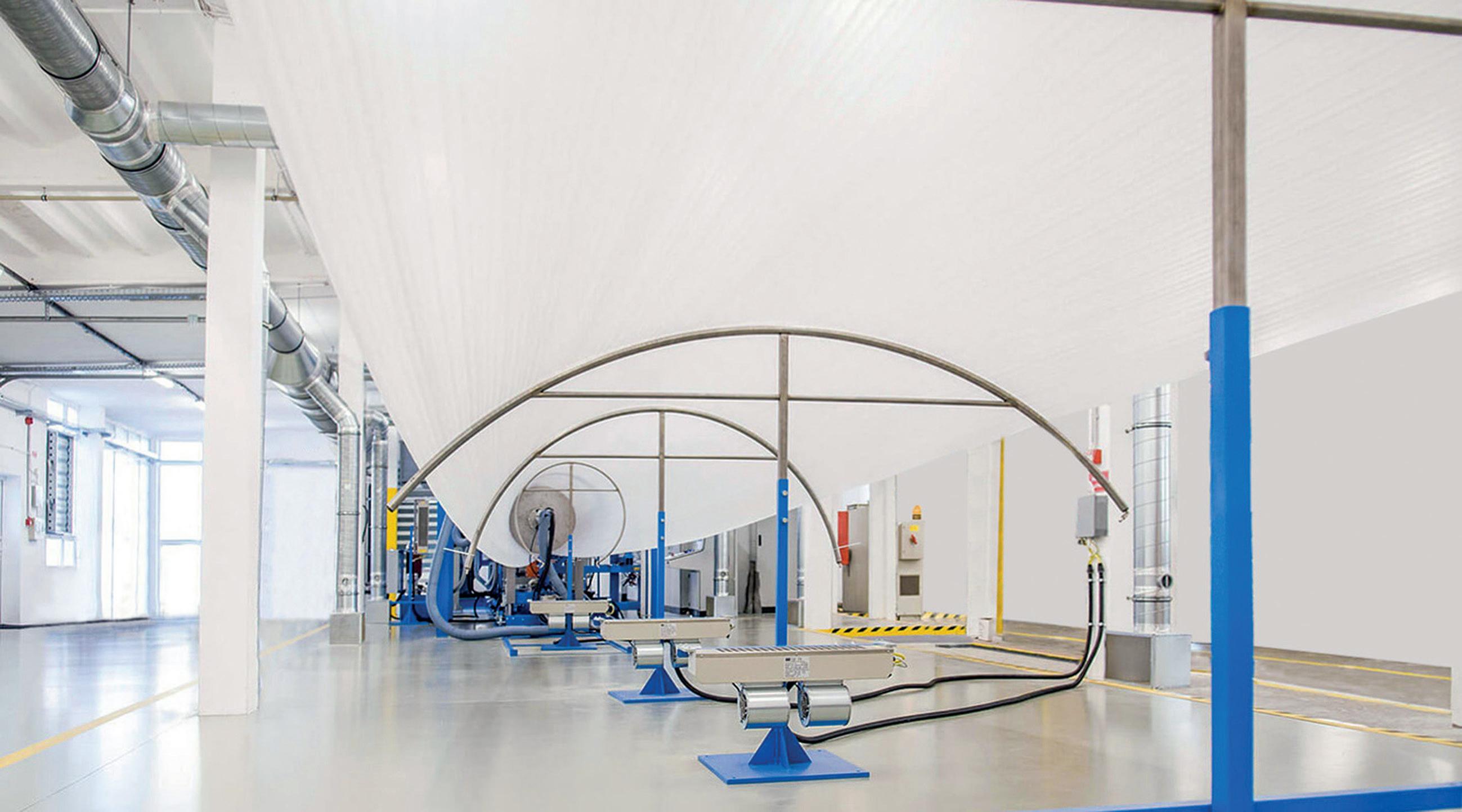
L’INDUSTRIA 4.0 HA CAMBIATO GLI IMPIANTI CHE COSTRUITE E I PROCESSI INTERNI ALLA VOSTRA AZIENDA? SE SÌ, IN QUALE MODO?
“Ormai da anni il settore della produzione è sottoposto a un processo di trasformazione senza precedenti, grazie a tecnologie come la robotica, l’intelligenza artificiale e la realtà aumentata. FAP ha investito molto nell’Industria 4.0, migliorando l’accesso ai dati e la gestione del processo di estrusione, per offrire ai nostri clienti una maggiore competitività, in particolare in termini di efficienza, precisione e abbattimento dei costi di produzione”.
COME STA ANDANDO IL VOSTRO MERCATO DI RIFERIMENTO IN QUESTO PERIODO COSÌ DIFFICILE?
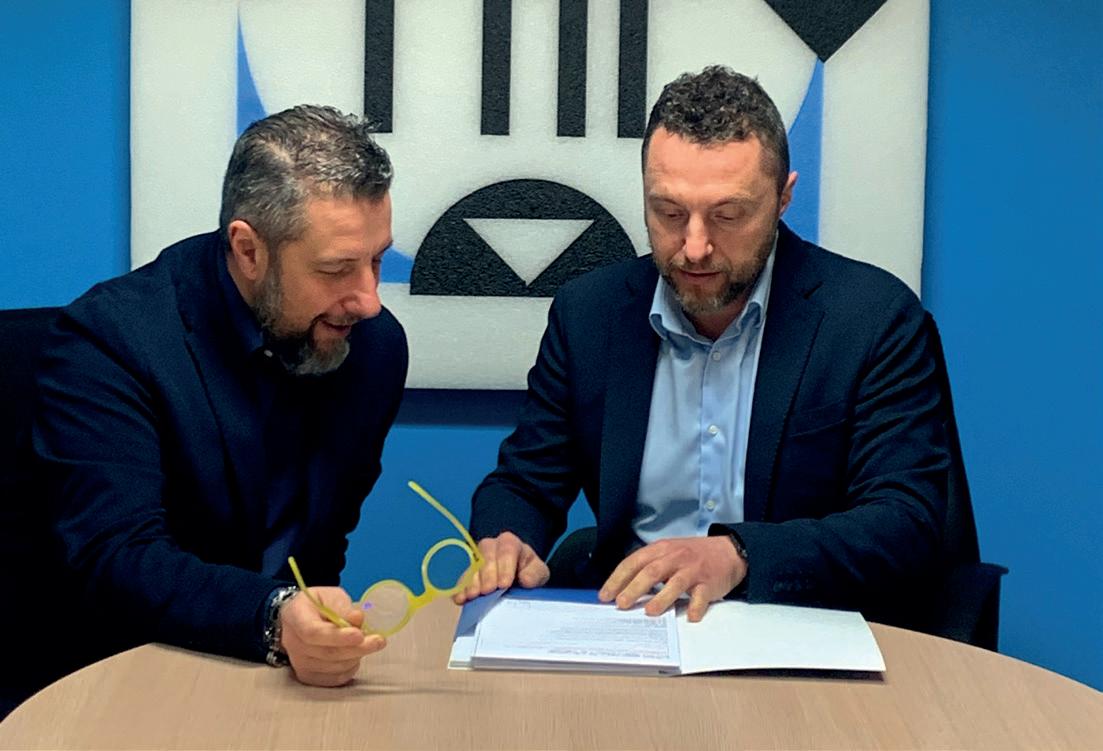
“Nel marzo del 2020 abbiamo registrato un rallentamento, sebbene la ripresa sia stata quasi immediata. Nonostante tutti i comparti abbiano risentito della crisi causata dal Covid-19, la nostra clientela è fortunatamente costituita da aziende che operano in differenti settori e che quindi hanno subito meno gli effetti della difficile situazione. Grazie a prestazioni tecniche elevate, i film in materiali espansi sono ampiamente utilizzati in molti ambiti industriali, come l’imballaggio, l’edilizia e l’automobile. Inoltre, a causa delle imminenti restrizioni alla commercializzazione e all’uso di contenitori per alimenti in polistirene espanso, stiamo rilevando, da parte delle aziende operanti nel settore alimentare che saranno obbligate ad adattarsi a questo cambiamento, un aumento della domanda di soluzioni per sostituire i loro prodotti con quelli in polipropilene espanso riciclabile al 100%. A questo proposito, stiamo eseguendo parecchi test nel nostro laboratorio per poter offrire le migliori soluzioni che permettano ai clienti tale passaggio. Secondo le nostre stime, nel 2021 metteremo a segno un’ulteriore crescita del fatturato rispetto agli anni precedenti”.
Al termine della produzione, il film in materiale espanso viene raccolto in bobine con avvolgitori costruiti dalla stessa azienda
I fratelli Fabrizio e Francesco Poli al lavoro nei reparti di produzione dell’azienda
A PROPOSITO DI COVID-19 DA LEI CITATO, QUALI RIPERCUSSIONI AVETE SUBITO DALLA PANDEMIA E COME AVETE AFFRONTATO L’EMERGENZA SANITARIA DA UN PUNTO DI VISTA LAVORATIVO? AVETE DOVUTO CHIUDERE O RIORGANIZZARE LA PRODUZIONE?
“Abbiamo chiuso l’azienda nell’aprile del 2020, quando la paura era tanta, quando i dispositivi di protezione individuale ancora scarseggiavano e quando c’era ancora poca chiarezza su come organizzarsi nei posti di lavoro. Come tutte le aziende abbiamo dovuto riorganizzarci, mettendo al primo posto la salute dei nostri dipendenti e collaboratori, ridistribuire gli spazi di lavoro, sanificare le aree comuni, rendere disponibili a tutti DPI e gel sanificanti e organizzare corsi di formazione sui comportamenti da assumere in azienda”.
CI PUÒ PARLARE DEGLI INVESTIMENTI PER IL RINNOVAMENTO E L’AMPLIAMENTO DEL VOSTRO STABILIMENTO? A CHE PUNTO SIETE E QUALI INTERVENTI COMPORTERANNO?
“Inizieremo i lavori per il nostro nuovo sito produttivo all’inizio del secondo quadrimestre del 2021. La nuova sede sarà situata sempre a Besana in Brianza e il progetto prevede l’ampliamento dell’area produttiva, divenuta insufficiente per gestire il sempre crescente numero di commesse. Inoltre, porteremo in Italia il laboratorio di ricerca e sviluppo, attualmente in Francia, ampliando il polo di ricerca in abito internazionale”.
RECENTEMENTE AVETE ANCHE RINNOVATO SIA LA VOSTRA IMMAGINE CHE IL MODO DI COMUNICARE. DOVE E COME SIETE INTERVENUTI A QUESTO SCOPO?
“Il nostro impegno, la nostra dedizione verso i clienti e i traguardi raggiunti parlano per noi, ma volevamo raccontare la nostra storia anche a chi ancora non ci conosce. Si sa che da sempre il logo di un’azienda è un elemento essenziale nella definizione della sua immagine; ecco perché abbiamo fatto il restyling del nostro e rinnovato anche il sito internet, rendendolo più moderno e semplice. Siamo molto orgogliosi del risultato e crediamo che il nostro nuovo logo corrisponda al meglio a ciò che siamo oggi: un’azienda dinamica a conduzione familiare, con una lunga storia di successi, una grande esperienza internazionale alle spalle e in crescita costante”.
GRAZIE AI NUOVI INVESTIMENTI, SEMBREREBBE CHE STIATE IMPRIMENDO UNA SPINTA IN AVANTI ALLA VOSTRA ATTIVITÀ. QUESTO VI PORTERÀ ANCHE AD ASSUMERE NUOVE FIGURE TECNICHE E COMMERCIALI?
“Abbiamo già avviato la ricerca di nuove figure da inserire in ambito ricerca e sviluppo e nell’ufficio tecnico. Ci siamo mossi in anticipo perché diamo molta importanza e poniamo molta attenzione alla ricerca del personale. Sono i nostri collaboratori che costruiscono giorno per giorno il successo di FAP”.
Il CEO Fabrizio Poli (a sinistra nella foto), con il fratello Francesco Poli, direttore vendite di FAP
I QUARANT’ANNI DI TECNODINAMICA
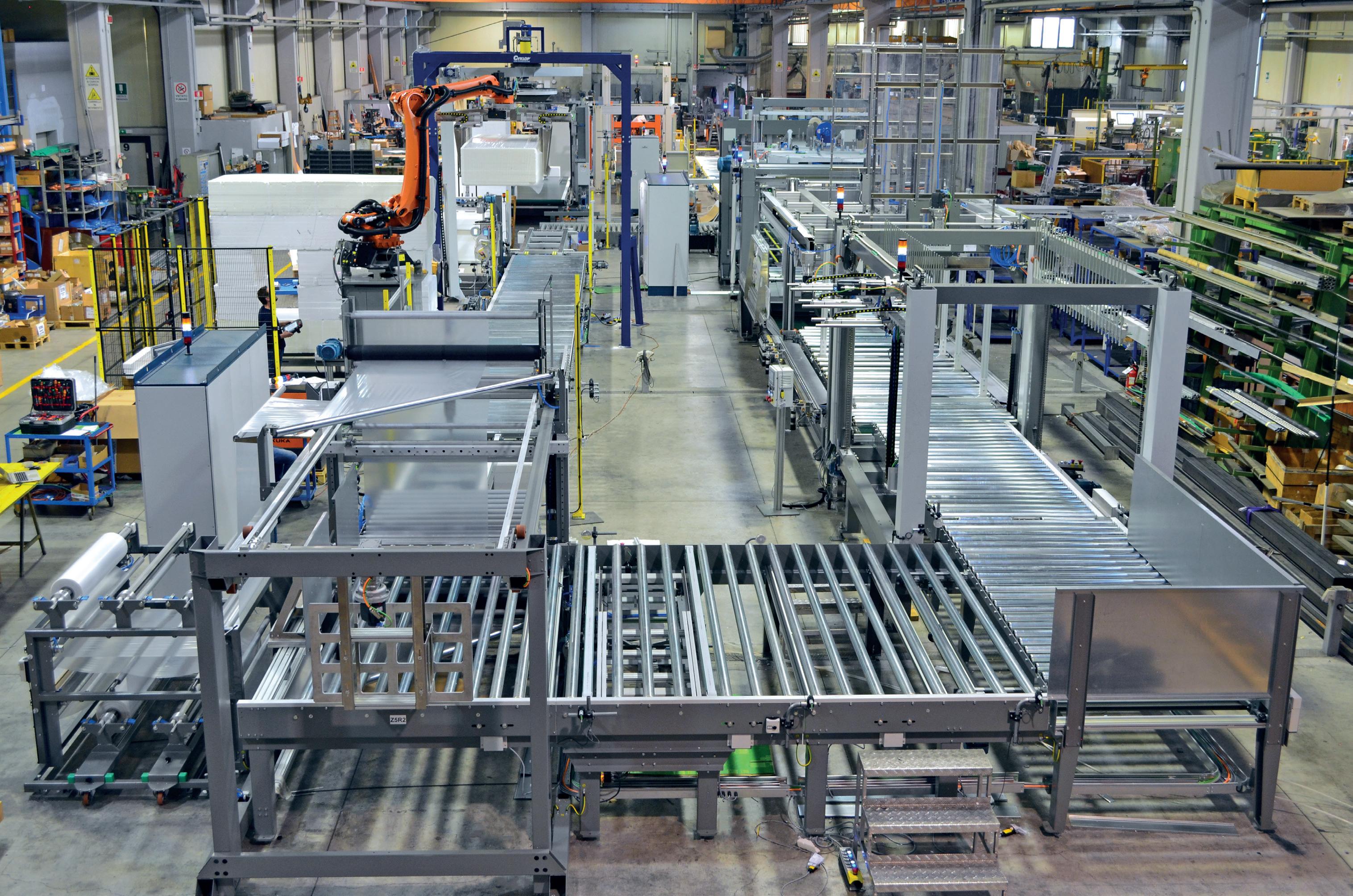
DAL PASSATO AL FUTURO DELLE TECNOLOGIE PER EPS
QUATTRO CHIACCHIERE CON ADRIANO DE ROSSO E GRAZIANO FREGOLENT, SOCI FONDATORI DELL’AZIENDA TREVIGIANA TECNODINAMICA, CHE NEL 2021 CELEBRA QUARANT’ANNI DI ATTIVITÀ, PROPONENDOSI COME VERO E PROPRIO TRAIT D’UNION IDEALE NELLA STORIA DELLE TECNOLOGIE PER LA LAVORAZIONE DELL’EPS
C’ è un legame indissolubile che unisce il mondo dell’EPS e Tecnodinamica, l’azienda fondata nel 1981 in provincia di Treviso, tra le meravigliose colline del Prosecco, di recente nominate patrimonio dell’umanità da parte dell’Unesco. Componenti per l’isolamento termico e acustico e per la protezione dagli urti, ma anche elementi scenografici e di arredo sono prodotti in tutto il mondo ormai da quarant’anni grazie a tecnologie e know-how sviluppati all’interno di questa “boutique tecnologica”, come la definiscono Adriano De Rosso e Graziano Fregolent, i soci fondatori di Tecnodinamica. Ed è questo che i due titolari hanno raccontato alla redazione di MacPlas. “Abbiamo iniziato con semplici macchine per il taglio a filo caldo destinate principalmente al mercato italiano e da lì siamo andati avanti assecondando le esigenze dei nostri clienti, ma anche la nostra curiosità e voglia di innovare. Di recente abbiamo integrato la nostra offerta con una nuova gamma di tecnologie per il packaging, ossia imballatrici tira-film, orbitali e fardellatrici che, come tutte le nostre macchine, sono interamente progettate e realizzate presso i nostri stabilimenti”.
Graziano Fregolent (a sinistra) e Antonio De Rosso
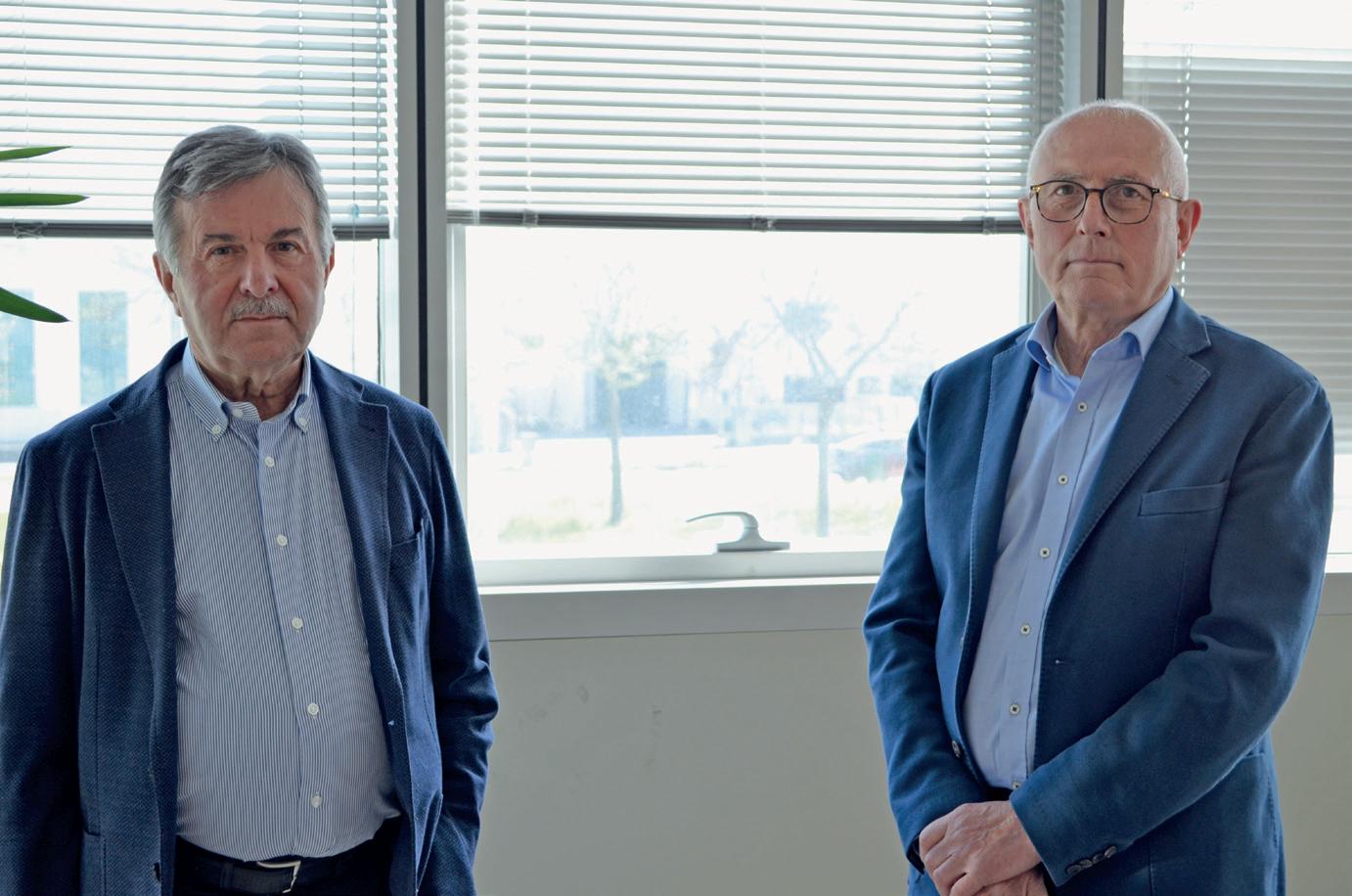
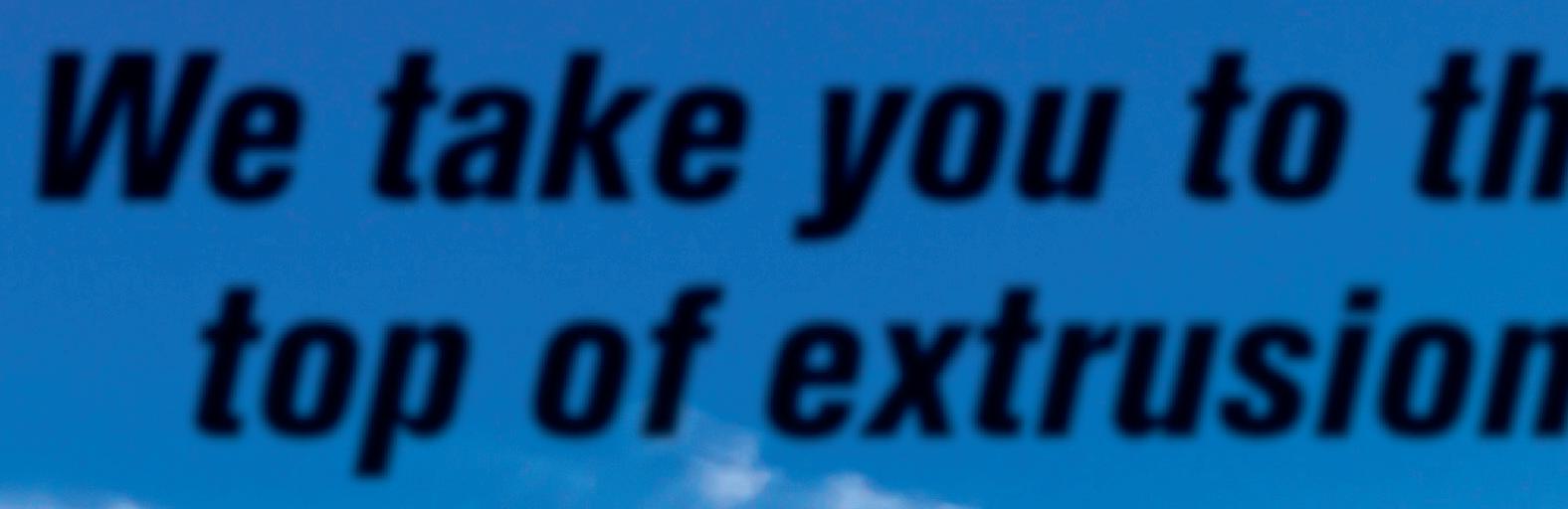

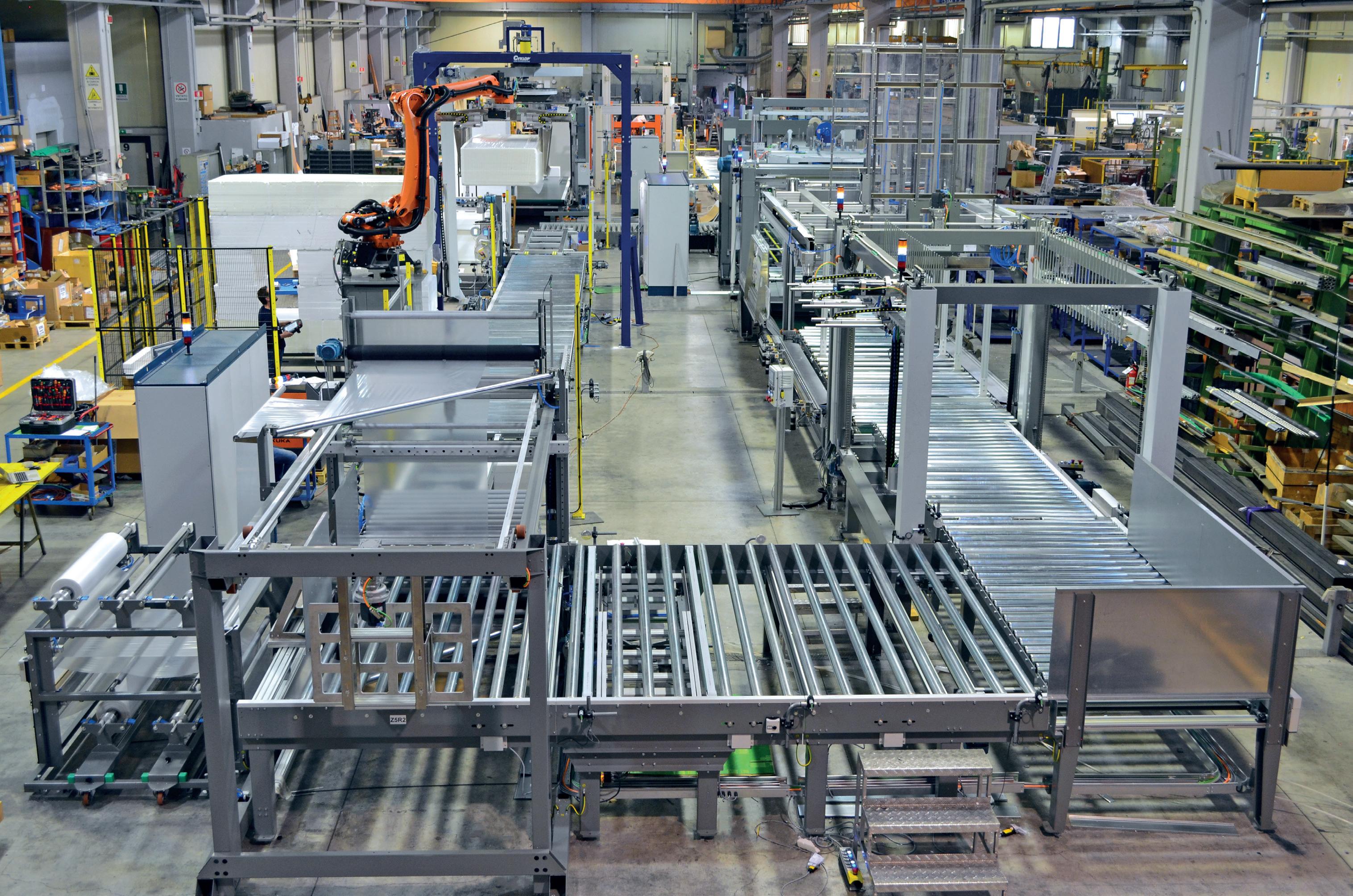
Un esempio di impianto per la produzione di blocchi in EPS realizzato da Tecnodinamica
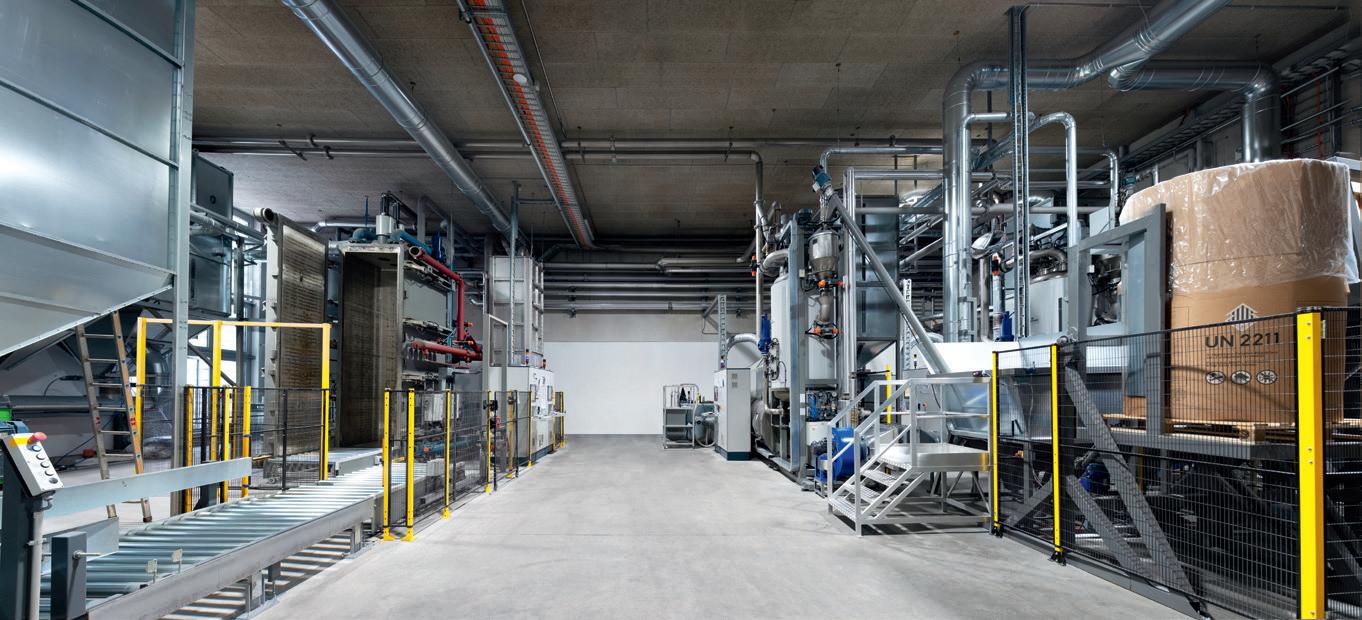
QUALI SONO GLI ELEMENTI DISTINTIVI CHE HANNO PERMESSO A TECNODINAMICA DI GIOCARE UN RUOLO RILEVANTE NEL MERCATO GLOBALE?
“Ce ne sarebbero molti da citare: pensiamo all’attenzione nei confronti del cliente, all’affidabilità impiantistica, alla ricerca e al miglioramento continuo. Sicuramente molto importante è la capacità di personalizzazione dei prodotti e dei servizi. I nostri clienti sanno di trovare in Tecnodinamica un partner tecnologico con il quale poter progettare e innovare i propri processi. Il ventaglio di soluzioni attraverso cui questo può avvenire è estremamente ampio e include macchine a catalogo, personalizzazioni più o meno spinte ma anche soluzioni speciali interamente progettate e realizzate ad hoc per le specifiche applicazioni. Questo approccio orientato al cliente è possibile grazie a una struttura completa e organizzata, che nel tempo ha mantenuto e sviluppato al suo interno tutte le competenze necessarie, dalla progettazione meccanica, elettrica e software alla costruzione, fino all’assistenza post vendita”. PER QUANTO RIGUARDA IL PROSSIMO FUTURO, COSA POTETE ANTICIPARE? “Nei prossimi anni ci aspettano molteplici sfide, poiché i mercati si stanno evolvendo in modo sempre più dinamico e imprevedibile. Da un punto di vista organizzativo e di mentalità sarà fondamentale mantenere flessibilità e reattività verso questi cambiamenti. Per quanto riguarda l’aspetto tecnologico, continuiamo a investire in ricerca e sviluppo: nuove macchine, nuovi servizi e un forte orientamento alla digitalizzazione dei processi”.
MACCHI_ADV_ISTIT_MACPLAS ITALIA 172X125mm IT 60.ai 1 10/03/21 10:22 POTETE FARE QUALCHE ESEMPIO?
“I visori e le tecnologie per la realtà aumentata e mista si sono rivelati fondamentali per il supporto a distanza di clienti e operatori in una situazione di lockdown generalizzato. Da qui siamo partiti con il progetto “Service 4.0”, che ci porterà in qualche mese a digitalizzare completamente l’infrastruttura dedicata ai servizi e ad aggiungere a quelli già in uso, come la teleassistenza, nuovi e migliori strumenti per i nostri clienti. Un’altra importante area di sviluppo riguarda le interfacce operatore. Da circa un anno abbiamo avviato un importante progetto che rivoluzionerà l’esperienza d’uso delle nostre macchine. I prototipi realizzati hanno dato un riscontro molto positivo e presto anche i nostri clienti potranno toccare con mano questa importante novità”.
We take you to the top of extrusion
Macchi S.p.A. Via Papa Paolo VI, 5 21040 Venegono I. (VA) Italy
Tel. +39 0331 827 717 E-mail: macchi@macchi.it www.macchi.it
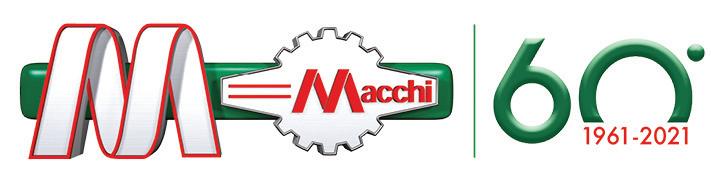
MACCHI SCEGLIE GEFRAN ESTRUSORI SEMPRE PIÙ “GREEN” E PRODUTTIVI

IL COSTRUTTORE DI LINEE D’ESTRUSIONE MACCHI SI È AFFIDATO AL PRODUTTORE DI SISTEMI D’AUTOMAZIONE GEFRAN QUALE PARTNER DI FIDUCIA PER MIGLIORARE L’INTERO PROCESSO DEI SUOI IMPIANTI IN OTTICA 4.0. ALLA BASE DI UNA COLLABORAZIONE A 360 GRADI, DALLA FORNITURA DI COMPONENTI ALLA CONSULENZA, VI È LA CONDIVISIONE DEI RISPETTIVI KNOW-HOW
Per potenziare l’efficienza produttiva dei suoi estrusori, Macchi si è recentemente affidata a Gefran quale partner di fiducia, in virtù di un pacchetto completo di soluzioni, tra le quali spiccano i sensori di pressione per il melt (fuso) con uscita digitale IO-Link. Questi ultimi sono in grado di contribuire all’ottimizzazione dell’intero processo di estrusione, anche in ottica 4.0. La rilevazione precisa della pressione del fuso, pure a elevate temperature, è fondamentale per mantenere costante la qualità del prodotto finito. In aggiunta, l’interfaccia IO-Link permette di acquisire una serie di dati sostanziali per la manutenzione predittiva. Informazioni come i valori dei picchi
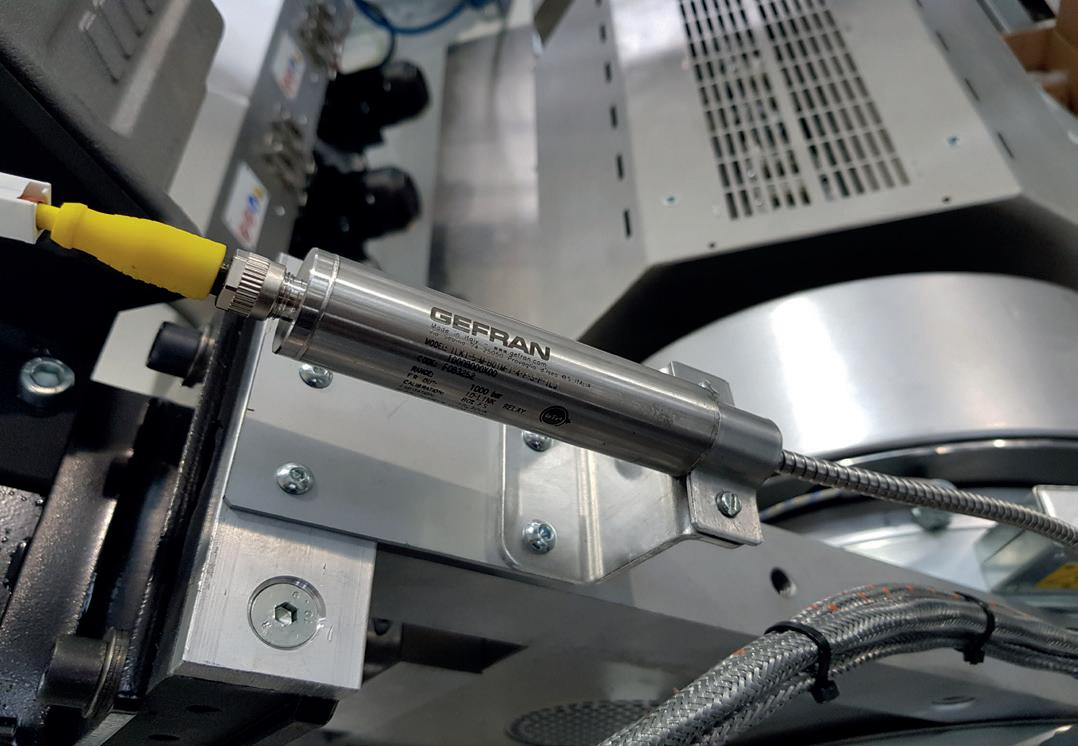
Il passaggio dal riempimento al mercurio a quello con miscela di sodio e potassio (come nei dispositivi ILK) rende Macchi uno dei primi costruttori di impianti per l’estrusione ad aver optato per soluzioni più “green” massimi di pressione e temperatura registrati, così come le ore totali di funzionamento del sensore in pressione e gli scostamenti delle soglie di calibrazione, consentono di sviluppare algoritmi in grado di assicurare una migliore efficacia sulla produttività, garantendo, al contempo, un ciclo di vita più longevo dell’estrusore.
SONDE A IMPATTO ZERO
Macchi è stata una delle prime aziende a optare per soluzioni più “green”, sostituendo le sonde con tecnologia di riempimento a mercurio con quelle a impatto zero dal punto di vista ambientale. La scelta è ricaduta sulle serie ILI, con l’innovativa tecnologia “Impact” senza fluido di riempimento, con spessore della membrana 15 volte superiore rispetto alle versioni standard, e ILK, con riempimento a miscela di sodio
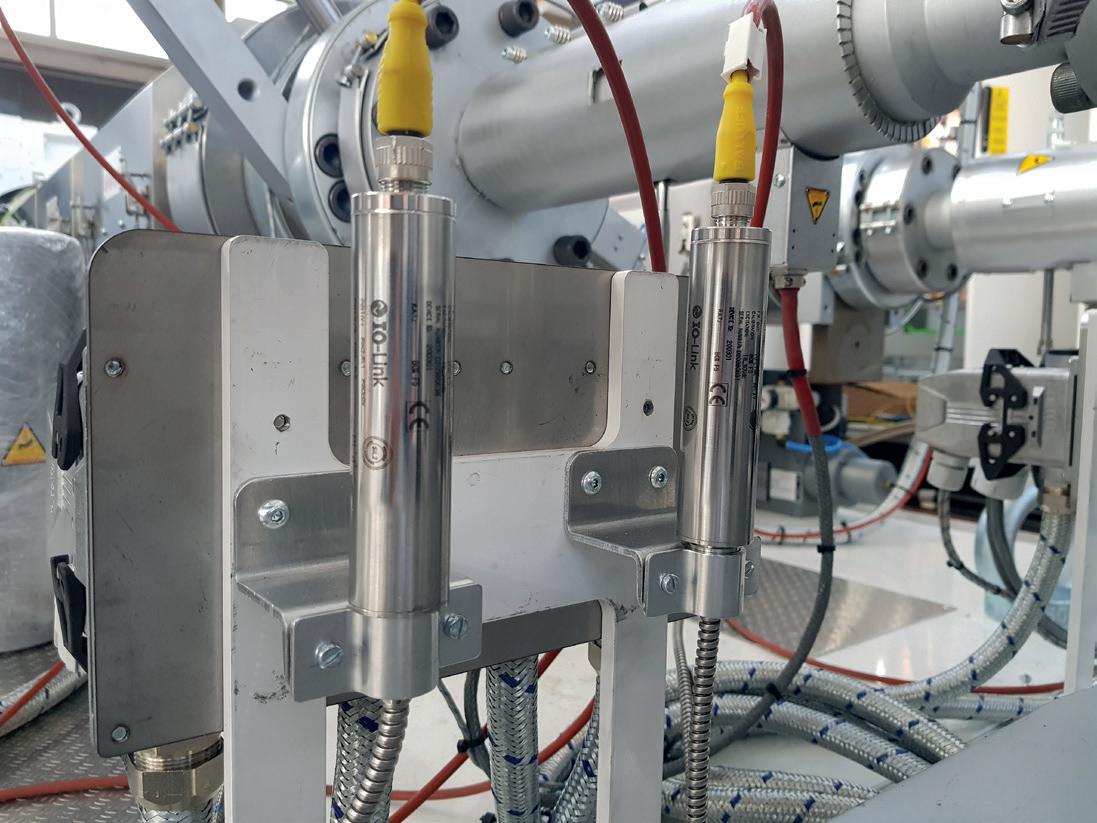
e potassio. Una gamma completa di sensori, certificati PLd e SIL2, in grado di operare in processi critici con temperature superiori anche ai 500°C. La trasformazione digitale della sensoristica installata sugli impianti Macchi si completa con i trasduttori di posizione serie WPL di Gefran. Dotati di tecnologia magnetostrittiva Hyperwave e con uscita digitale IO-Link, questi sensori sono in grado di registrare contemporaneamente un elevato numero di parametri in chiave 4.0, garantendo al contempo un’assoluta precisione lineare anche in presenza di shock, vibrazioni e disturbi elettromagnetici.
FORNITURA E CONSULENZA
Infine, l’integrazione di tutti i sistemi che compongono l’estrusore è garantita da Gefran Soluzioni, che completa la fornitura di componentistica con un servizio di consulenza per la progettazione, lo sviluppo e la realizzazione dei quadri elettrici. A questo si aggiunge il costante affiancamento alla divisione ricerca e sviluppo di Macchi nella realizzazione di software ad hoc, multipiattaforma, per la gestione delle linee in un costante
L’uscita digitale IO-Link dei sensori di pressione consente di ottimizzare il processo di estrusione anche in ottica 4.0
processo evolutivo della logica di gestione e dell’automazione di processo. Tra le linee coinvolte in questa sinergia spicca Recotrim, un sistema di pellettizzazione unico, progettato per consentire il riciclo in linea dei rifili prodotti durante l’estrusione di film. A tal proposito, Cristiano Procopio, direttore ricerca e sviluppo di Macchi ha commentato: “L’unione e la condivisione dei know-how di ricerca e sviluppo di Macchi e di Gefran stanno portando sempre più gli impianti a un livello elevato di performance”. “Oltre all’estrema affidabilità, in termini di qualità dei prodotti e lead-time ridotto, l’aspetto consulenziale è per noi il vero plus della collaborazione con Gefran. In tal senso, dalla sensoristica alle piattaforme di automazione, fino alla costante assistenza, anche da remoto, Gefran è per noi un partner qualificato, in grado di proporre soluzioni innovative e di supportarci sia nello sviluppo di nuove linee che nel revamping di impianti esistenti, con grande flessibilità e professionalità. Un risultato che affonda le sue radici in una sinergia basata sulla stima reciproca quale presupposto condiviso da entrambe le realtà, all’insegna dell’eccellenza”, ha dichiarato Matteo Spinola, direttore vendite e marketing di Macchi. “Macchi e Gefran sono due leader tecnologici nei rispettivi settori, che fanno della qualità un valore essenziale per una continua innovazione. Ringraziamo, pertanto, l’azienda Macchi per la costante fiducia che ripone nei nostri confronti”, ha concluso Renzo Privitera, direttore vendite Italia per i sensori e i componenti di Gefran.
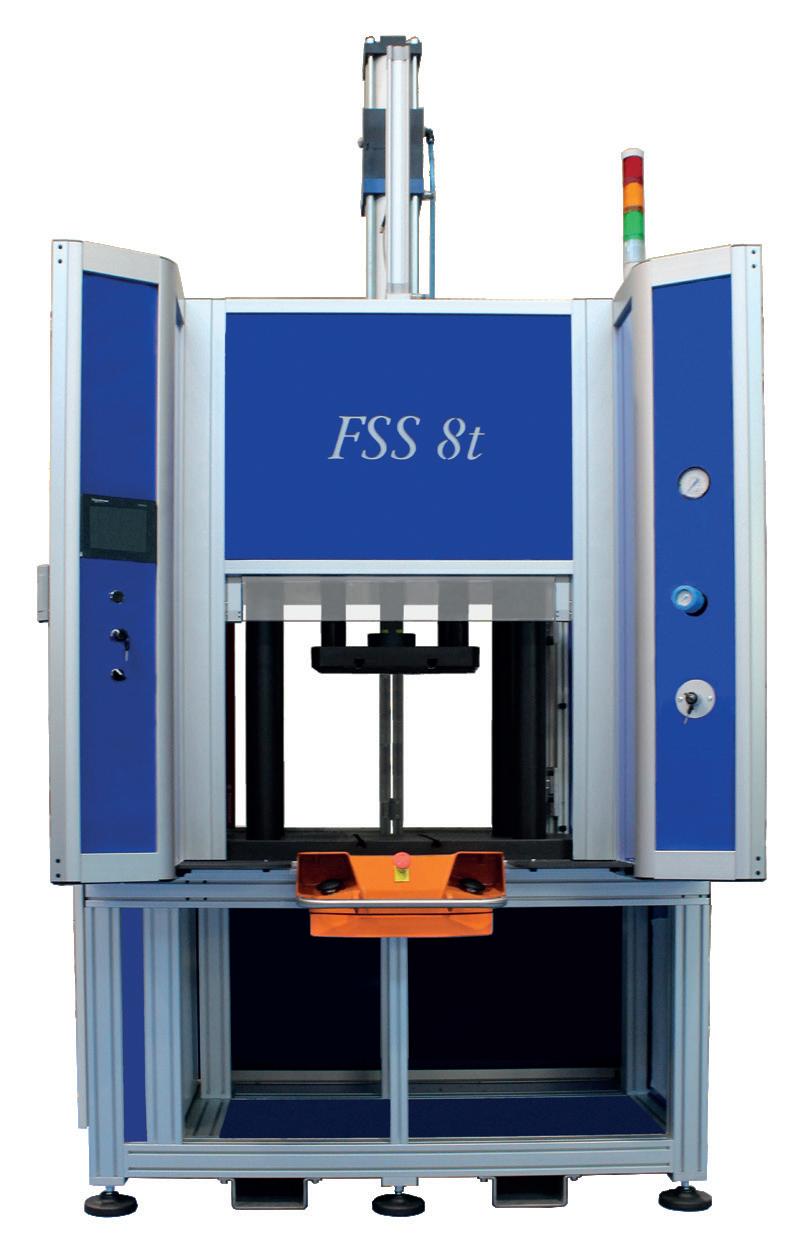
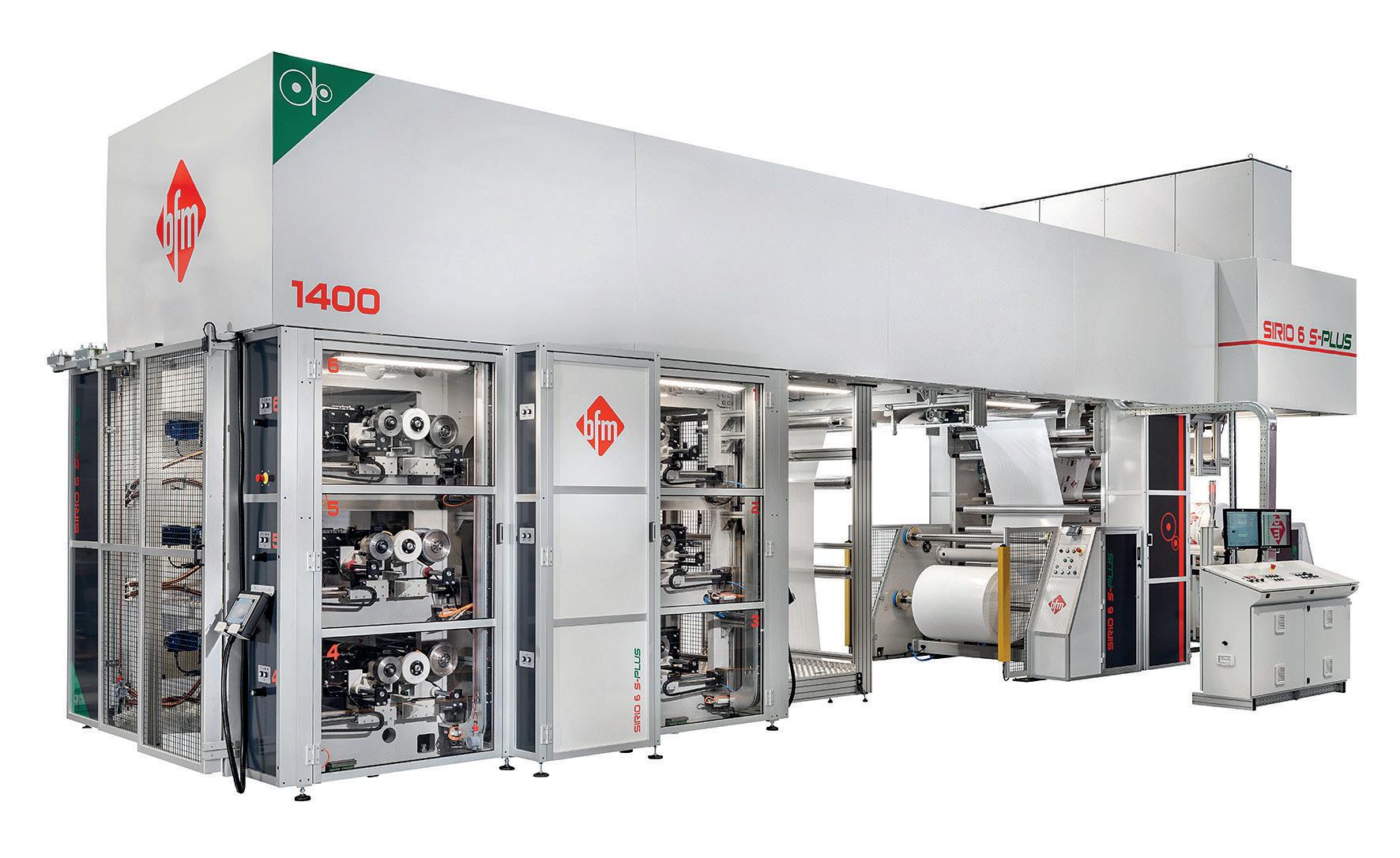
La Stack Sirius S Plus in versione 6 colori
BFM PRESENTA LA NUOVA STACK SIRIUS S PLUS
COMPATTA E FLESSIBILE PER LA STAMPA A SEI O A OTTO COLORI
SUL MERCATO DAL 1975, BFM RAPPRESENTA OGGI UN PUNTO DI RIFERIMENTO INTERNAZIONALE NELLA COSTRUZIONE DI MACCHINE PER LA LAVORAZIONE DELLE MATERIE PLASTICHE, DAI TRAINI E DAGLI AVVOLGITORI AUTOMATICI PER LE LINEE D’ESTRUSIONE IN BOLLA ALLE MACCHINE PER LA STAMPA FLESSOGRAFICA A TAMBURO CENTRALE FINO A 10 COLORI E A QUELLE DI TIPO “STACK” A 2, 4, 6 E 8 COLORI, COME LA SUA ULTIMA CREATURA
L’ 8 luglio BFM presenta in streaming la nuova macchina da stampa Stack Sirius S Plus, illustrando caratteristiche come: elevata qualità di stampa, efficienza di processo e produttività, risultanti da cambi di lavoro agevoli e precisi; flessibilità di impiego, grazie alla capacità di lavorare materiali di diverso tipo, anche di origine biologica; compattezza e design moderno. Come ormai tutte le macchine di BFM, anche questa è idonea alla connessione alla rete aziendale in chiave di Industria 4.0, potendo così usufruire dei benefici e delle risorse stanziate dal piano nazionale per la trasformazione digitale delle aziende. Macchina di tipo “Stack” a 6/8 colori, il nuovo modello è progettato per la stampa su diversi materiali plastici destinati al settore dell’imballaggio e può essere impiegato sia in linea con gli impianti d’estrusione sia per la lavorazione da bobina a bobina, con uno sviluppo di stampa da 350 a 1200 mm su larghezze da 800 a 1600 mm. La macchina è composta da uno svolgitore, che può essere fisso, senza albero (shaftless) o a revolver, e da un gruppo di stampa a 6/8 colori, con asse di controstampa motorizzato indipendente e inchiostrazione pneumatica. Completano la linea: il gruppo di asciugatura, dotato di cappa con riscaldamento elettrico o a gas, e l’avvolgitore con diversi tipi di funzionamento. L’impianto, inoltre, è munito di una piattaforma d’automazione progettata in collaborazione con Bosch Rexroth.
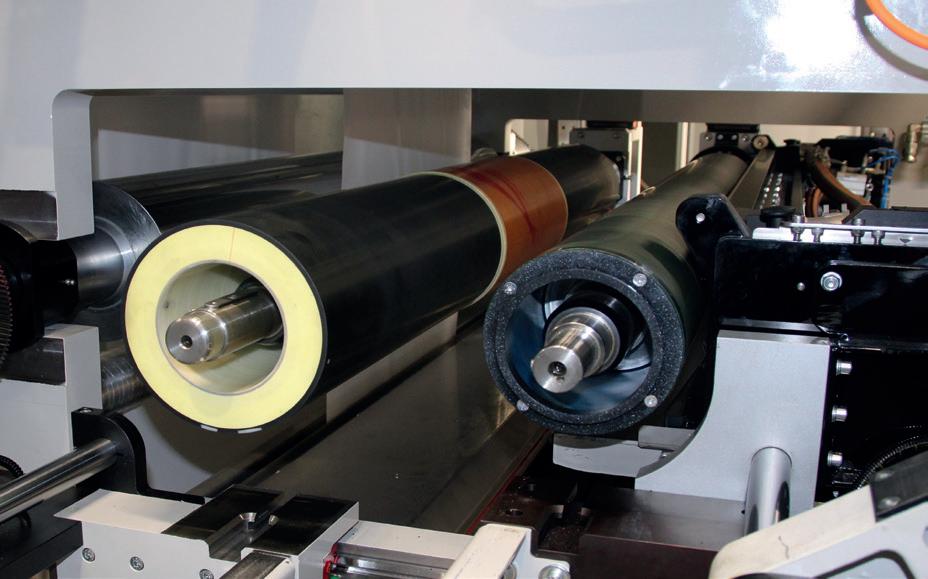
LE MIGLIORI SOLUZIONI TECNICHE PER UN IDEALE COMPROMESSO
L’ultima nata in casa BFM viene proposta come ideale compromesso tra costi e prestazioni, cui contribuiscono anche i motori torque IndraDyn
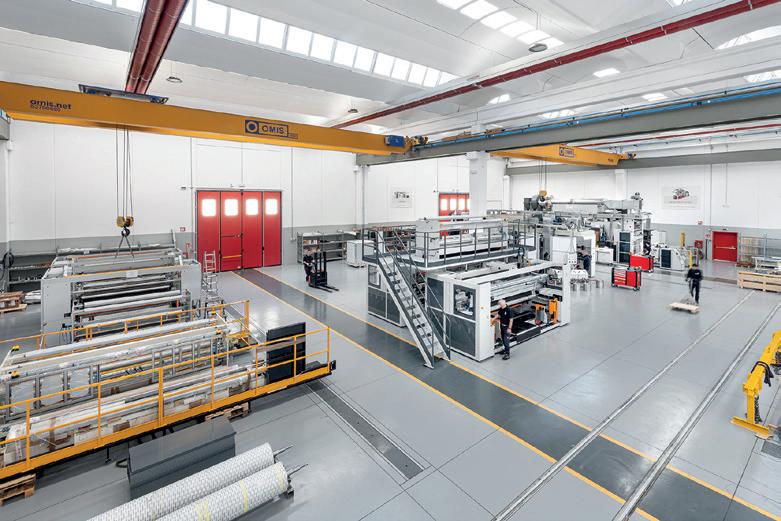
La consolle di controllo per la gestione delle funzionalità della macchina
MBT di Bosch Rexroth per la movimentazione dell’unità colore, composta da gruppo controstampa-cliché-anilox, favorendo compattezza dimensionale e precisione di stampa. L’utilizzo di azionamenti digitali IndraDrive M garantisce la costante sincronia di posizione tra i diversi elementi di stampa, con il conseguente mantenimento del registro, sia alle velocità più elevate sia in fase di accelerazione e decelerazione. La messa a registro iniziale risulta rapida e può essere effettuata anche a macchina ferma, riducendo gli sprechi energetici e lo scarto di materiale. Ogni gruppo colore può essere movimentato in senso longitudinale in modo completamente indipendente, grazie all’adozione di servoassi Indradrive Cs e motori MSM dotati di encoder assoluto multigiro, a beneficio di una messa a punto più accurata, di tempi di riconfigurazione ridotti e di una migliore gestione e memorizzazione delle ricette. I motori torque MBT, abbinati ai doppi servoazionamenti HMD e al sistema di controllo del moto MLC, garantiscono anche una perfetta sincronizzazione del materiale in macchina, un miglior controllo della tensione e l’utilizzo flessibile delle unità colore secondo le combinazioni 3+3, 4+2 e 5+1, nel caso dei 6 colori, e 4+4, 3+5 e 2+6, nel caso degli 8 colori. Insieme alle soluzioni tecniche adottate, il sistema “cantilever” per il cambio delle maniche “sleeves”, sia anilox sia porta-cliché, ha permesso di ridurre notevolmente i tempi richiesti dai cambi di lavorazione. Infine, tra le novità della macchina Stack Sirius S Plus rientra anche l’interfaccia grafica da 22 pollici, semplice e intuitiva ma allo stesso tempo completa, per assicurare una gestione ottimale di tutte le funzionalità della macchina.
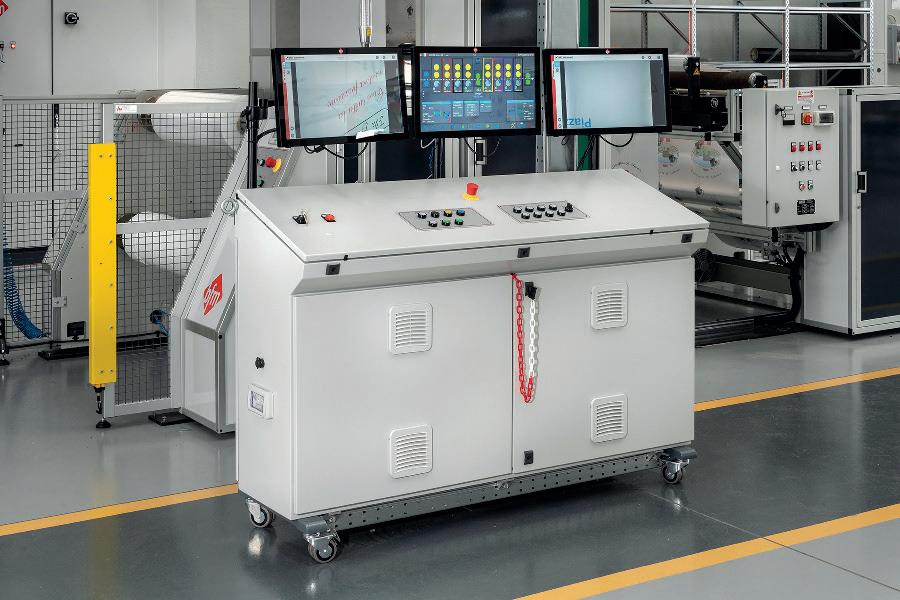
Ampliamento Un nuovo capannone per i 45 anni
In occasione dei suoi 45 anni di attività, BFM ha recentemente ampliato la propria sede di Solbiate Olona (Varese) con un nuovo capannone, realizzato accanto a quello esistente. La nuova struttura ha aggiunto 1500 metri quadri ai 3000 precedenti, dove hanno trovato spazio il montaggio e l’esposizione degli impianti, così come le attività di ricerca e sviluppo. L’investimento si è reso necessario per rispondere alla crescita aziendale, trainata, nonostante le difficoltà del momento, dall’aggiornamento tecnologico che sta interessando tutta la gamma di BFM e che si inquadra in una più ampia serie di investimenti volti a potenziare tecnologie e risorse.
Una veduta interna del nuovo capannone

L’ESPERIENZA DI PREVIERO
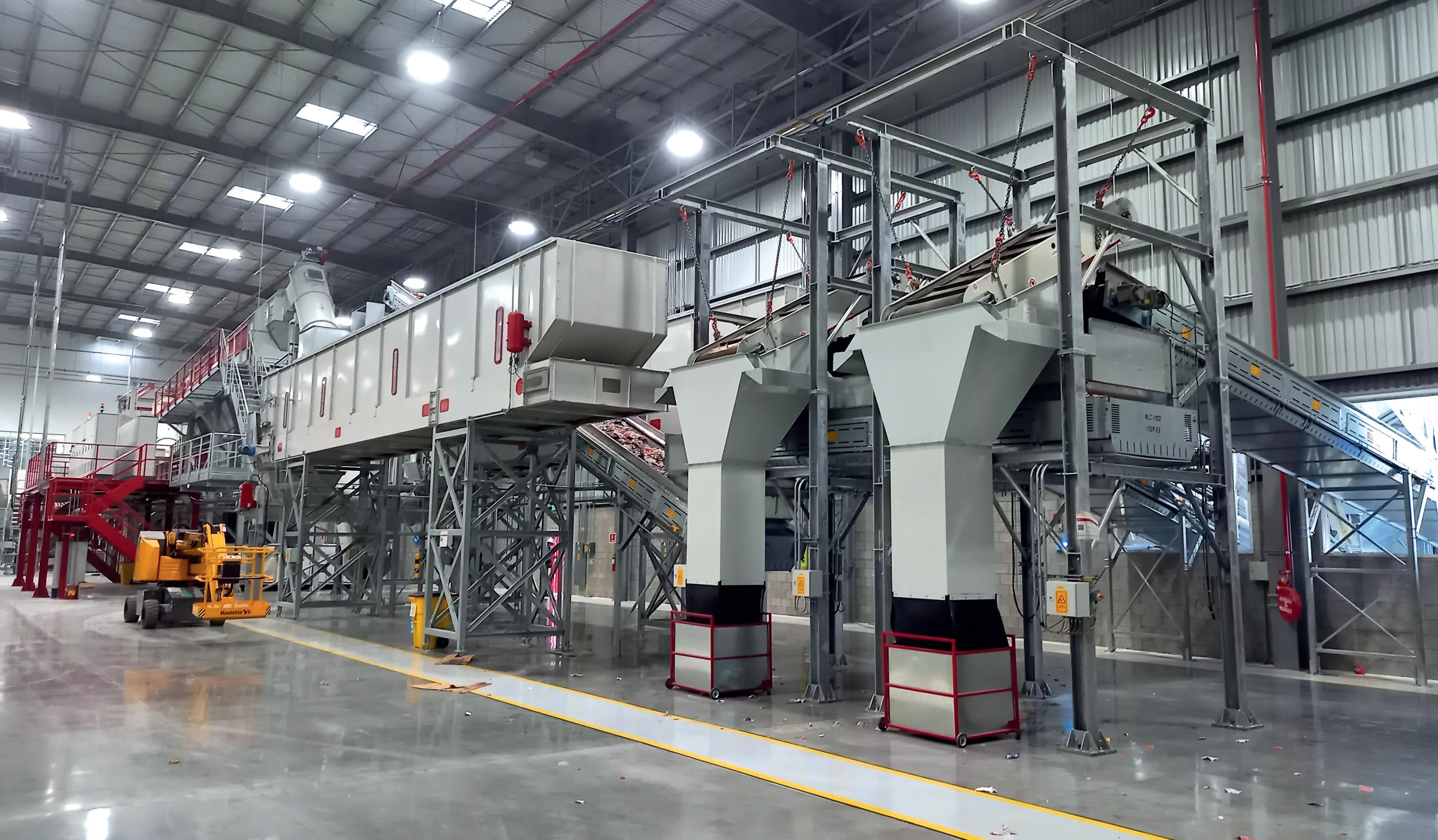
IL “BOTTLE TO BOTTLE” IN PANDEMIA: TRASFORMARE UNA DIFFICOLTÀ IN OPPORTUNITÀ
SPECIALIZZATA NELLA COSTRUZIONE DI IMPIANTI PER IL RICICLO, LA SOCIETÀ PREVIERO HA RECENTEMENTE PORTATO A TERMINE ALCUNE IMPORTANTI COMMESSE. E LE MODALITÀ CON CUI CIÒ È AVVENUTO IN QUESTI MESI DIFFICILI DI PANDEMIA SONO STATE CONSIDERATE UN’OPPORTUNITÀ PER FISSARE NUOVI STANDARD DI LAVORO CHE POSSANO ESSERE VALORIZZATI E APPLICATI ANCHE IN FUTURO
Alcuni impianti “chiavi in mano” per il riciclo di bottiglie in PET post consumo provenienti dalla raccolta municipale, con produzioni orarie da 2000 a 9000 kg di scaglie lavate e rigranulate, sono stati recentemente forniti da Previero-Sorema in America Latina. Tali impianti comprendono sezioni di: alimentazione automatica, prelavaggio, rimozione delle etichette, macinazione a umido, lavaggio a caldo, risciacquo con flottazione e asciugatura. Nelle linee sono inclusi anche rilevatori di bottiglie e scaglie, in base a materiale e colore, gestiti da un unico sistema di supervisione Scada di Sorema, per un efficiente controllo locale e remoto. L’azienda è in grado anche di integrare in linea impianti di depurazione delle acque, composti da sezioni di filtraggio, trattamento chimico e biologico, disidratazione dei fanghi e super filtrazione (mediante filtri in quarzite o a carboni attivi, trattamenti con ozono e a osmosi inversa ecc.), in modo da ottenere elevati livelli di efficienza del processo e di qualità del prodotto, riducendo al minimo i problemi legati alla gestione dell’impianto.
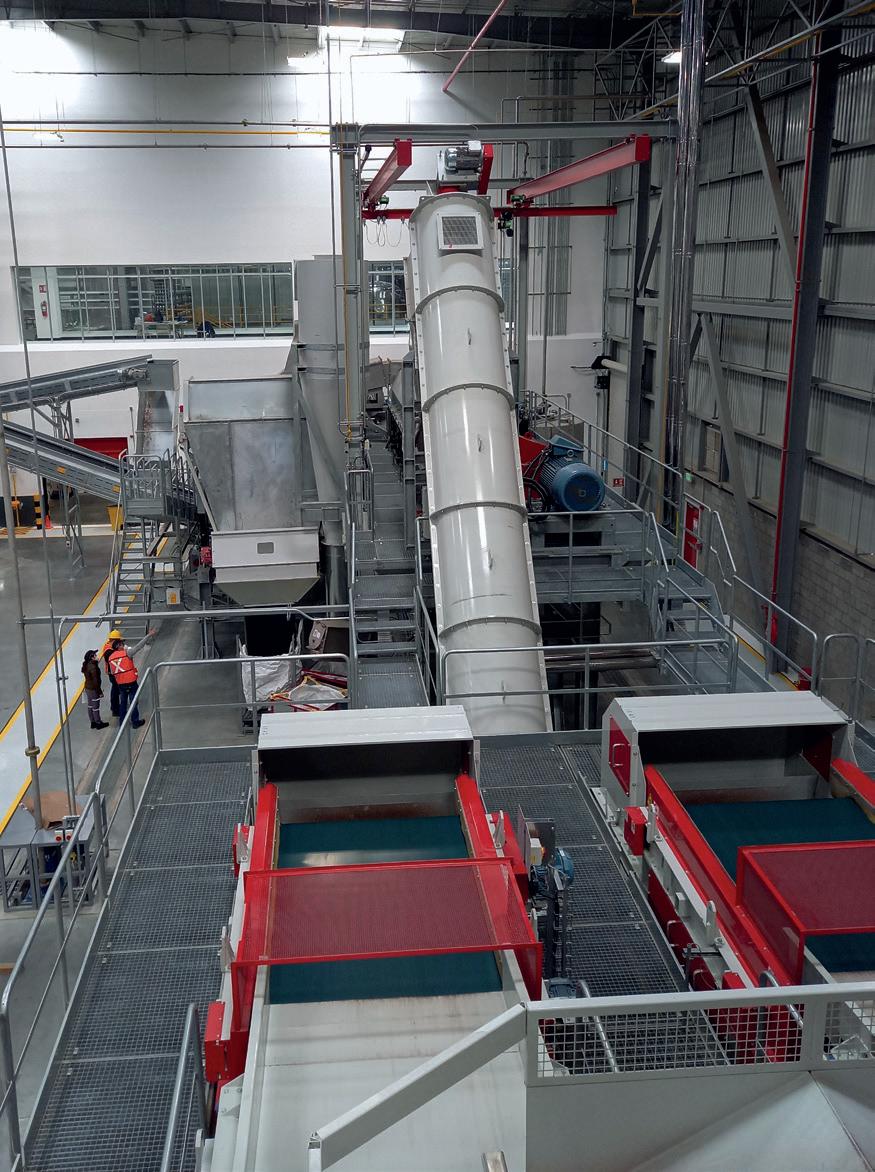
TEAM E PROGRAMMA DI LAVORO “AD HOC”
L’azienda, per superare le restrizioni ai viaggi imposte dalla pandemia, che non le hanno consentito d’inviare i propri tecnici presso i committenti per l’installazione e l’avviamento degli impianti, ha costituito un apposito team composto di personale specializzato ed esperto, che ha sviluppato un programma di lavoro dedicato al controllo da remoto di tutte le fasi d’installazione dei macchinati spediti e della connessione alle utenze presso i siti di installazione, in seguito alle quali tutti i componenti dell’impianto sono risultati accessibili da computer e dispositivi mobili. Per il costruttore comasco la sfida era molto impegnativa, poiché le difficoltà non riguarda-
Un dettaglio dell’impianto per il riiclo “bottle to bottle”
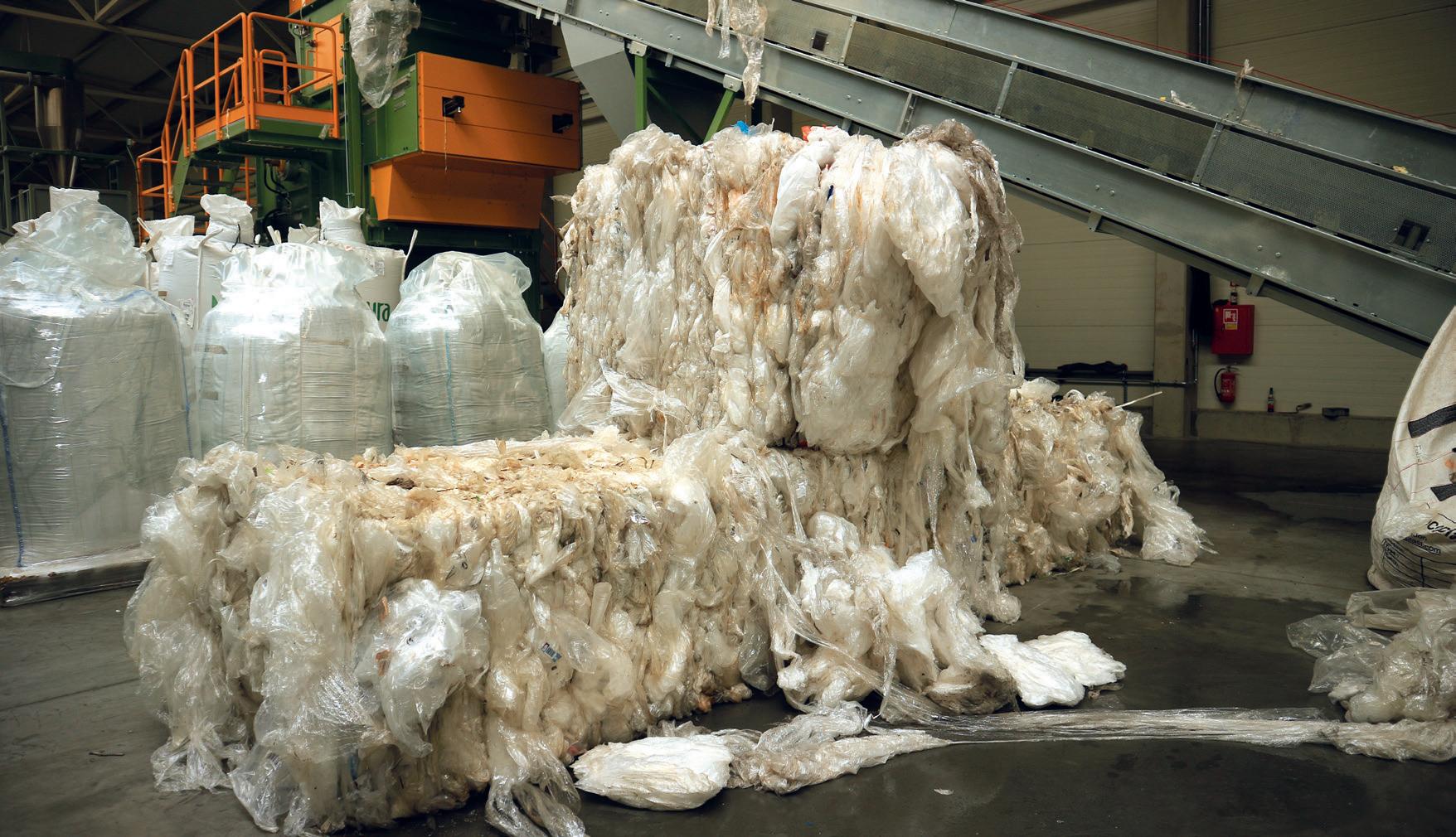
vano una singola macchina, ma l’intera linea per il riciclo di bottiglie in PET post consumo, che coinvolge molte macchine e relative tecnologie, sensori, valvole, tubi, pompe, essiccatori ecc., che devono operare correttamente tutti insieme. Grazie all’elevata qualità degli standard di Previero nella costruzione dei macchinari, con particolare riferimento al test di preaccettazione in fabbrica, che comprende l’assemblaggio completo della linea prima della spedizione e una prova a vuoto per la maggior parte delle attrezzature, la divisione Sorema è riuscita a superare la criticità di questa situazione. Dopo un lavoro propedeutico, i committenti sono riusciti a montare e mettere in funzione gli impianti di lavaggio, per la prima volta senza la presenza sul posto di tecnici Sorema, con il supporto quotidiano di teleassistenza, videoconferenze, telefonate ed e-mail da parte del team tecnico dedicato di Previero-Sorema. Gli impianti per il lavaggio e il riciclo “bottle to bottle” di PET sono stati quindi avviati senza problemi. Le linee sono riuscite a raggiungere gli obiettivi prefissati di qualità e di quantità del materiale riciclato, con piena soddisfazione dei committenti in termini sia impiantistici sia di partnership in tempi così difficili. L’azienda ritiene che questo rappresenti l’esempio concreto di come una soluzione nata in una situazione di emergenza possa diventare una procedura standard per la messa in servizio dei suoi futuri impianti di lavaggio, proprio per l’esito positivo dell’esperienza e l’assenza di particolari inconvenienti. Questo nuovo approccio si traduce in un’apprezzabile riduzione dei costi per il committente, a fronte di un lieve aumento del tempo necessario per completare il lavoro. Un nuovo approccio che non influisce sulla copertura della garanzia da parte di Sorema né sull’assistenza post vendita.
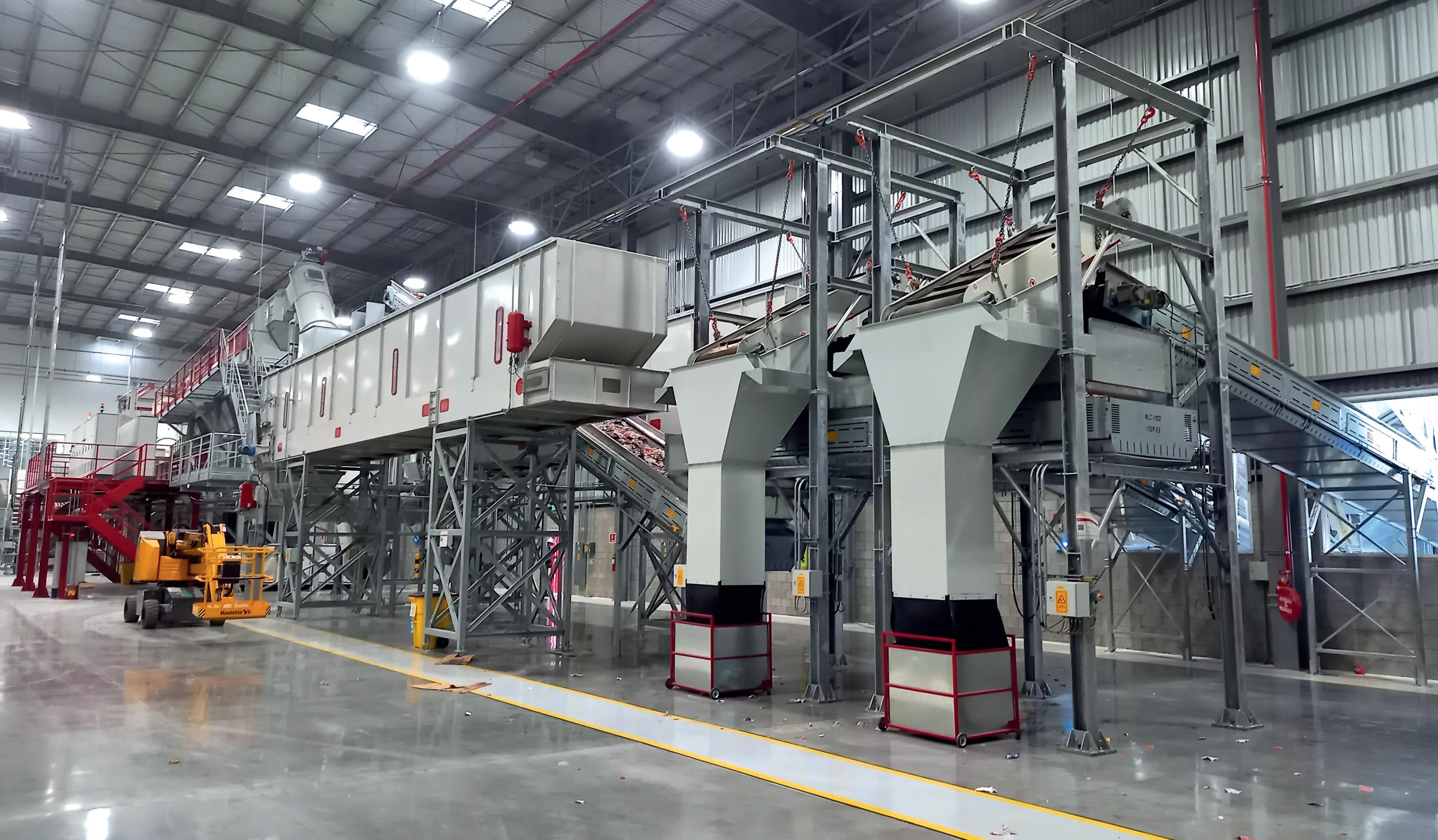
RICICLO “FILM TO FILM”
I film in polietilene sono sempre più utilizzati e svolgono un ruolo essenziale per una corretta e sicura consegna, conservazione e protezione degli alimenti e delle merci lungo l’intera catena di approvvigionamento, ma una volta svolta la loro funzione e diventati rifiuti devono essere riciclati. Di conseguenza, la quota di film da riciclare in Europa sta crescendo e in Polonia la società Anna Recykling, con sede a Celestynów, vicino a Varsavia, ha scelto a questo scopo un impianto di riciclo di Sorema. L’azienda polacca, fondata nel 1995, è da sempre tra i principali produttori di granuli in polietilene provenienti da scarti industriali. Negli ultimi anni, tuttavia, la crescente domanda di materiale di alta qualità ottenuto da scarti post consumo e la visione orientata al futuro del suo management, hanno portato Anna Recykling a cercare un partner di qualità con cui collaborare allo sviluppo del riciclo di film post consumo in polietilene. Sorema è stata scelta a questo scopo già nel 2019, grazie alla sua linea di lavaggio flessibile appositamente studiata per il riciclatore e in grado di garantire il rispetto dei parametri richiesti per la produzione di materiale di alta qualità proveniente da scarti post consumo, quali film estensibili e industriali, così come da film agricoli, rafia e sacchi jumbo.
Balle di film pronte per il riciclo
La linea per il riciclo “film to film” comprende le soluzioni tecniche modulari più avanzate di Sorema, come il trituratore idraulico a bassa velocità e a coppia elevata, appositamente progettato da Previero, il sistema di prelavaggio super flessibile ad alto modulo di attrito e la centrifuga di prelavaggio per processare un’ampia gamma di materiali contaminati. A fine linea è presente un deposito di fluff per alimentare un estrusore con materiale deumidificato. Grazie alla linea Sorema, la produttività di Anna Recykling è cresciuta oltre le aspettative, raggiungendo i 1000 kg all’ora di materiale perfettamente decontaminato e granulato a un rapporto qualità/prezzo competitivo. Il materiale ottenuto è quindi idoneo per l’estrusione su linee per film in bolla sia in Polonia che all’estero. Tra i trasformatori che utilizzano tale materiale rientra Bogucki Folie, che produce l’innovativo film B-ECO in polietilene, con struttura a tre strati a base di materiale al 100% riciclato ottenuto da scarti post consumo e rifiuti post industriali, chiudendo così il ciclo dell’economia circolare.
Teknodepurazioni Aquae, Nuova divisione di Previero per il trattamento delle acque
Recentemente Previero ha acquisito, attraverso la neocostituita società Teknodepurazioni Aquae, il ramo di azienda di Teknodepurazioni, con sede a Rivarolo Canavese (Torino). Attiva da più di trent’anni nel settore ambientale, Teknodepurazioni ha maturato una larga esperienza nello studio, nella progettazione e nella realizzazione di impianti per il trattamento delle acque e delle tecnologie applicate a questi impianti. Forte del continuo successo nella realizzazione di progetti nei settori: civile, alimentare, autolavaggi, lavanderie e concerie, derivante dall’attività della società acquisita, Teknodepurazioni Aquae si concentrerà sulla realizzazione di impianti per il trattamento delle acque usate per il lavaggio di materiale plastico negli impianti di riciclo in genere e, più specificamente, in quelli per film e imballaggi in PET, PP e HDPE. In tale ambito Sorema, divisione di Previero, potrà proporre un’offerta completa e unica nel mondo del riciclo della plastica, fornendo progetti completi “chiavi in mano” e una gestione integrata e omogenea. Teknodepurazioni Aquae intende garantire continuità e risposte all’avanguardia ai clienti che necessitano di un trattamento acque efficiente e affidabile, realizzato con l’impiego delle migliori tecnologie presenti sul mercato.
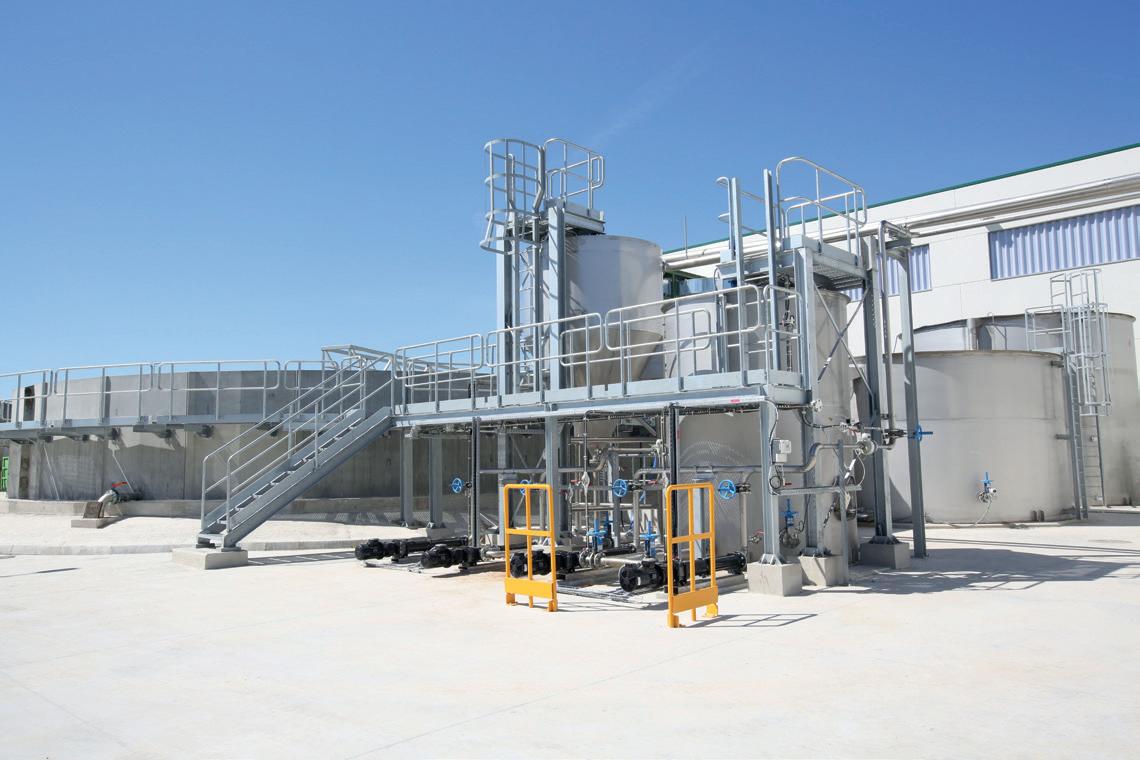
Un impianto per il trattamento delle acque di Teknodepurazioni
RICICLO ALL’AVANGUARDIA
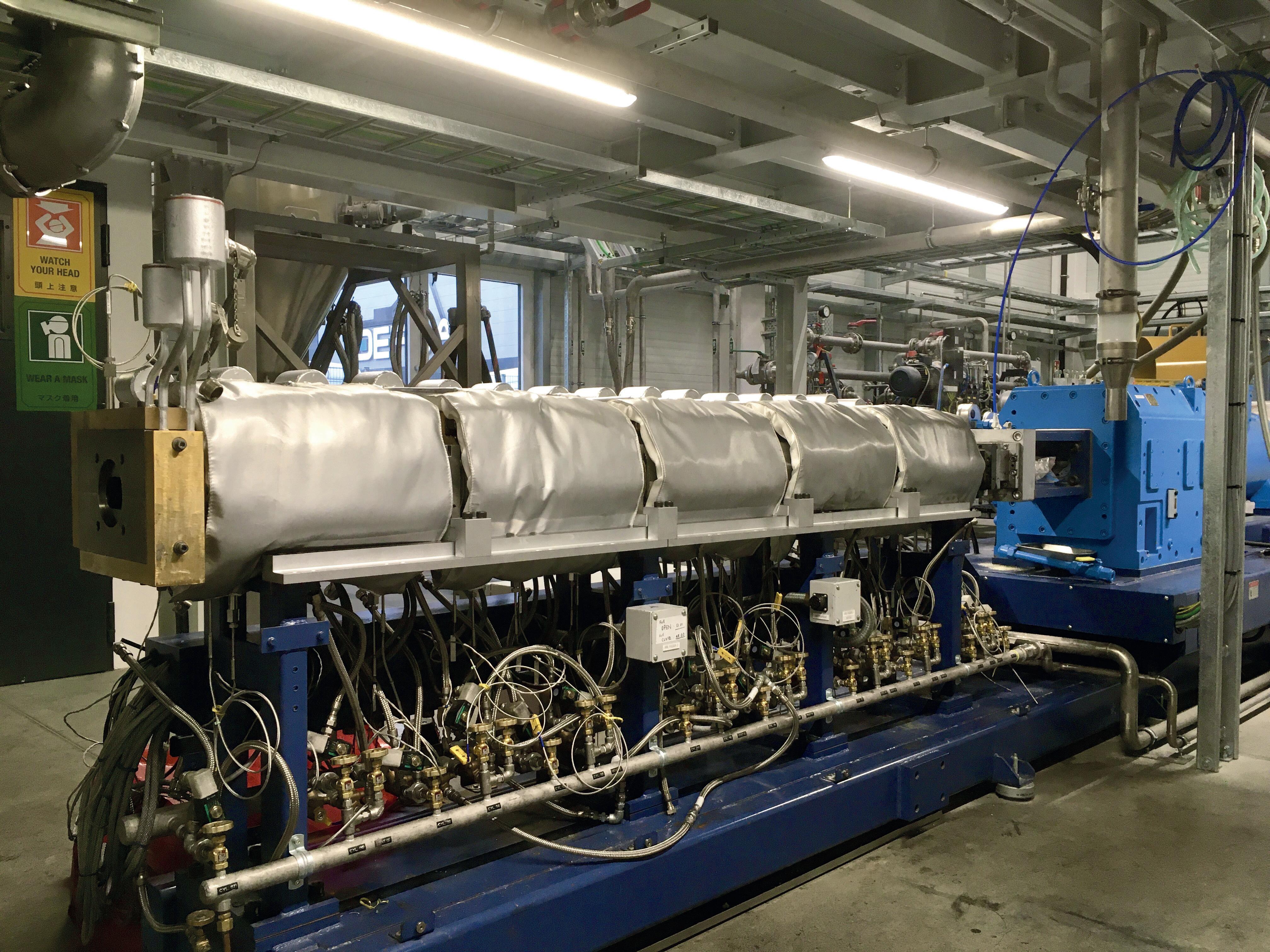
DEPOLIMERIZZAZIONE DI PMMA: VERSO L’INDUSTRIALIZZAZIONE DEL PROCESSO
UN PROGETTO FINANZIATO NELL’AMBITO DEL PROGRAMMA HORIZON 2020 E CONDOTTO DA UN CONSORZIO DI 13 AZIENDE EUROPEE SFRUTTA LA TECNOLOGIA FORNITA DA JSW EUROPE PER RICICLARE SCARTI DI POLIMETILMETACRILATO IN MODO SOSTENIBILE E REDDITIZIO, OTTENENDO COSÌ MATERIA PRIMA SECONDA DI ELEVATA QUALITÀ, UTILIZZABILE IN VARI AMBITI APPLICATIVI.
La depolimerizzazione degli scarti a base di PMMA non è solo un “bel gesto” a beneficio dell’ambiente, ma rappresenta soprattutto una risorsa e un capitale enorme che a tutt’oggi non è ancora stato sfruttato su scala industriale. Il consorzio MMAtwo sta affrontando con metodo la soluzione economica di questo problema ambientale e a tal fine 13 aziende europee hanno unito le loro forze e si stanno muovendo nell’ambito del programma Horizon 2020 dell’Unione Europea. L’attenzione dei tecnici si concentra sull’Extrusion Technical Center di JSW Europe, dotato di un estrusore bivite modificato TEX44 III (nella foto di apertura), utilizzato per realizzare diverse serie di test di depolimerizzazione del PMMA. LA CONOSCENZA
“Non è facile riciclare vari tipi e miscele di scarti a base di PMMA. Tuttavia, testiamo un processo che pone nuovi accenti su quest’argomento in termini sia ecologici che economici”, dichiara Makoto Tojo, direttore tecnico di JSW Europe, con sede a Düsseldorf (Germania). Il suo collega Hayato Hobo, responsabile vendite, spiega le condizioni generali: “Normalmente, la maggior parte della plastica - non soltanto PMMA - viene riciclata meccanicamente. In questo processo, la qualità del materiale plastico diventa sempre più bassa ogni volta che il materiale viene sottoposto al riciclo. La rigenerazione mediante depolimerizzazione può portare invece alla conversione del polimero in monomero. E il PMMA può essere ricondotto allo stato di monomero mediante depolimerizzazione termica. Però, non possiamo dire che la depolimerizzazione termica può essere applicata a tutte le materie plastiche. Per esempio, il policarbonato (uno dei concorrenti del PMMA dal punto di vista delle proprietà ottiche) non può essere depolimerizzato. Anche il polistirene può essere riciclato nello stesso modo, ma il rendimento è più basso. In Asia, il processo di distillazione a secco è spesso utilizzato per la depolimerizzazione del PMMA. La tecnologia presenta un basso costo, ma la purezza del monomero recuperato è solitamente bassa e al disotto delle aspettative
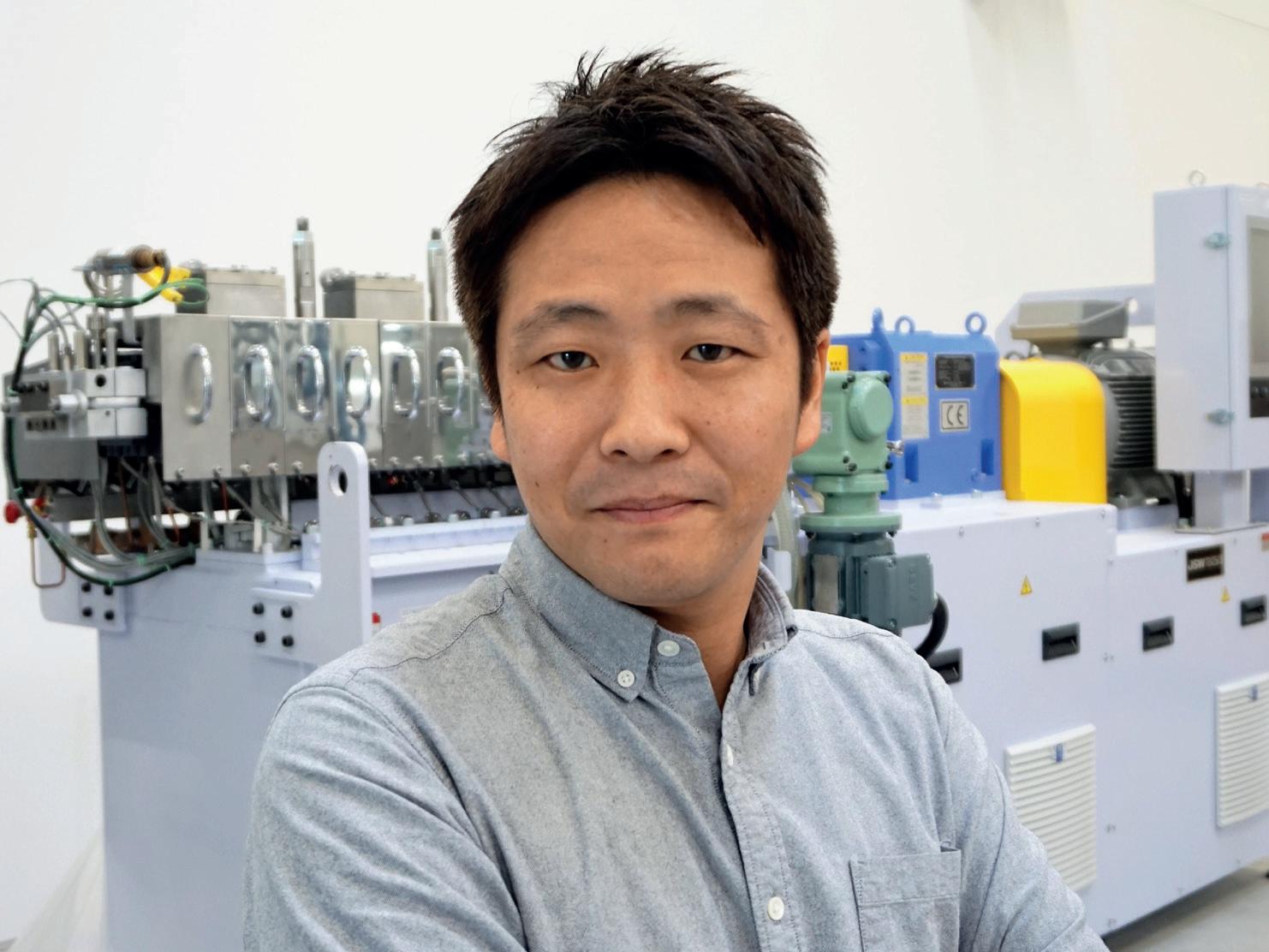
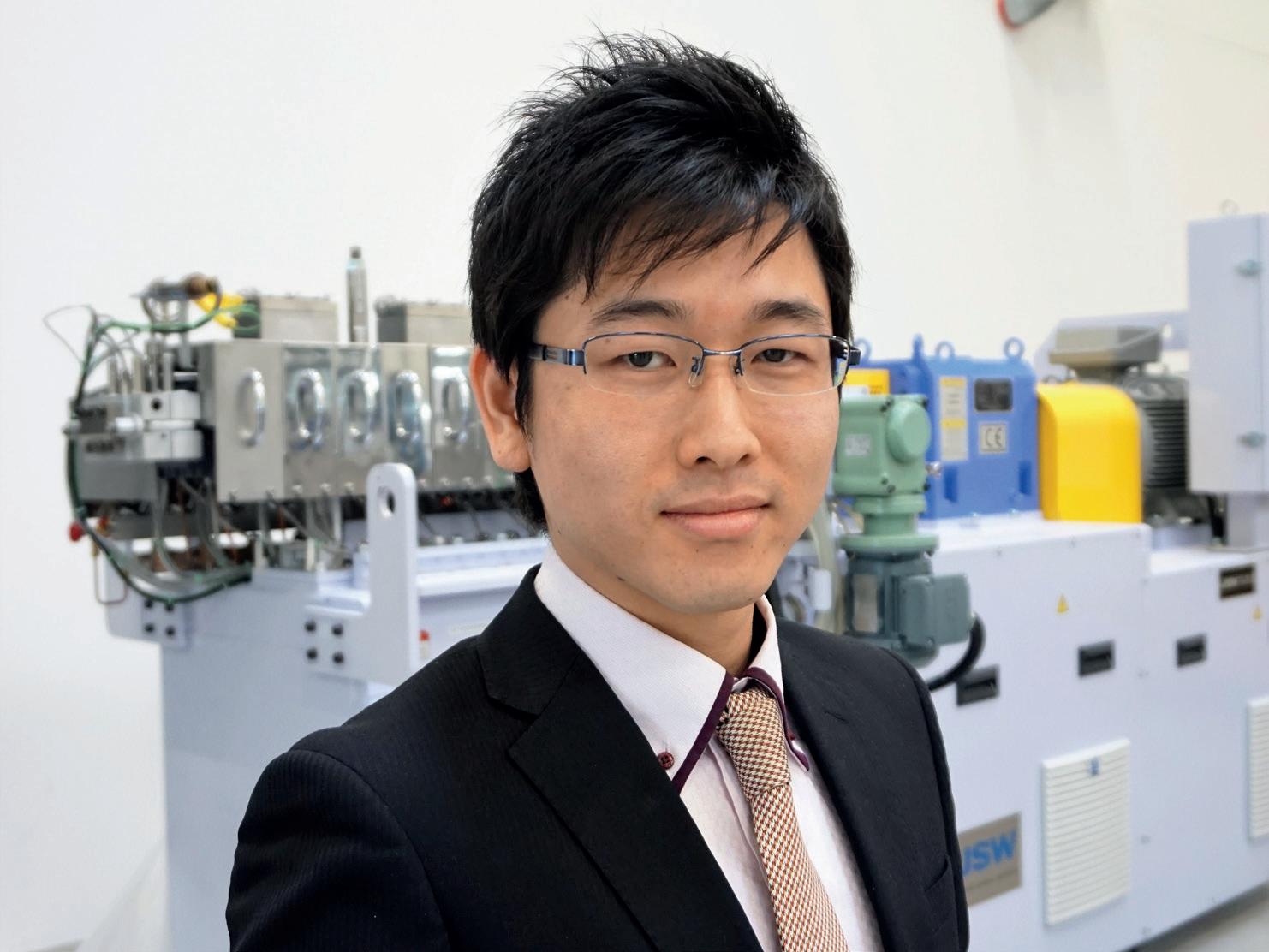
del mercato UE. Inoltre, non è molto efficiente dal punto di vista energetico. In più, la gamma di gradi di PMMA che possono essere trattati è limitata. In Europa, la depolimerizzazione del PMMA viene ottenuta mediante bagno di piombo fuso e solo i rifiuti di PMMA di alta qualità, come i residui post industriali, possono essere riciclati con questo processo. Tuttavia, il processo di depolimerizzazione con il nostro estrusore bivite TEX può trattare un’ampia gamma di rifiuti a base di PMMA, compresi gli scarti contenenti impurità inorganiche, e ottenere un rendimento elevato. Il successo del progetto MMAtwo significa che una grande quantità di rifiuti, che normalmente verrebbero conferiti in discarica, inceneriti o esportati, può essere riciclata più volte e riutilizzata”.
I FATTI E LE CIFRE
Il PMMA ha eccellenti proprietà ottiche e fisiche. Viene usato, ad esempio, per: vetrature di camper e roulotte, facciate di edifici, gruppi ottici di autoveicoli, mobili, schermi piatti, insegne pubblicitarie, decorazioni e articoli di gioielleria. Tale materiale è utilizzato dalle industrie informatiche, aerospaziali, medicali e farmaceutiche. Con un valore di mercato intorno a un miliardo di euro, circa 300 mila tonnellate di questo materiale vengono attualmente prodotte ogni anno solo in Europa e solo il 10% di tale quantità viene raccolto e riciclato alla fine del ciclo di vita del prodotto. Il resto viene esportato, conferito in discarica o incenerito. Hayato Hobo spiega il punto di partenza e lo sviluppo del progetto MMAtwo: “Arkema ci ha contattato per la prima volta nel giugno del 2017. Così siamo andati a Parigi e abbiamo parlato del brevetto di JSW del 1997 sul riciclo chimico del PMMA. A quel tempo non conoscevamo la pianificazione del progetto. Nel novembre del 2017 abbiamo avuto un ulteriore incontro con Arkema e Heathland, che ci hanno invitato a entrare a far parte del consorzio come fornitori di tecnologia per la depolimerizzazione. Il consorzio MMAtwo ha preparato la proposta e l’ha presentata alla Commissione Europea, che ha poi approvato il progetto ed erogato il relativo budget. MMAtwo ha preso il via nell’ottobre del 2018 e durerà quattro anni, terminando nel settembre del 2022”. Il compito è quindi quello di sviluppare un processo innovativo per trasformare i rifiuti post industriali e inutilizzabili di PMMA in materia prima MMA di “seconda generazione” - ossia rMMA - e di dare il via a una seconda filiera per questo materiale. Tredici aziende di sei paesi dell’UE sono coinvolte nel progetto MMAtwo coordinato dalla francese Arkema e dall’olandese Heathland: Quantis ha il compito di preparare il bilancio ecologico per le diverse possibilità di realizzazione della filiera di MMAtwo; PDC sviluppa il design del processo ed esegue le valutazioni tecnico-economiche; Certech esegue le analisi delle emissioni e degli odori, nonché la standardizzazione delle analisi per i rifiuti di PMMA; l’Università di Gand è incaricata di capire la cinetica della depolimerizzazione e di convalidare i valori dei test; Ecologic, Arkema, Delta Glass e Heathland forniscono i rifiuti; Heathland e Comet Traitements sono responsabili della separazione e del pretrattamento del materiale; JSW Europe è responsabile di tutta la tecnologia di estrusione; Speichim si occupa della pulizia finale dell’MMA grezzo; Delta Glass, Arkema e Plados Telma sono gli utenti finali del materiale recuperato dal consorzio; ultimo, ma non meno importante, Ayming offre il proprio aiuto nella gestione del progetto. Il progetto viene finanziato con 6,6 milioni di euro dal programma di ricerca e innovazione Horizon 2020 dell’Unione Europea.
Hayato Hobo, responsabile vendite di JSW Europe Makoto Tojo, direttore tecnico di JSW Europe
LE PRIME FASI
Il primo setup di prova era pronto nel giugno del 2020 presso il centro tecnico di JSW a Düsseldorf. “La base era il nostro estrusore bivite corotante TEX44 III. In precedenza abbiamo dovuto adattarlo per la depolimerizzazione ad alta temperatura dei rifiuti di PMMA post industriali e a fine vita. Il nostro stabilimento in Giappone ha progettato e costruito i componenti necessari - secondo i nostri dati tecnici e le nostre specifiche - e ha implementato i programmi di simulazione al computer”, spiega Makoto Tojo. In una prima fase sono stati trattati rifiuti di PMMA relativamente puri, mentre nelle due prove successive del 2020 l’attenzione si è concentrata sul PMMA di scarto contaminato. “Si trattava chiaramente di rifiuti difficili da rigenerare, con vari gradi di contaminazione, colore e altre influenze negative, ma alla fine siamo riusciti a convertire questa miscela di scarti in rMMA di alta qualità”, aggiunge il direttore tecnico. Il processo di depolimerizzazione viene effettuato fondendo il materiale nella zona a monte dello speciale estrusore bivite TEX44 III, con successivo riscaldamento della massa fusa alla temperatura di depolimerizzazione e conversione in materia gassosa nella zona a valle dell’estrusore. Il prodotto lique-
fatto è assorbito nel successivo serbatoio di condensazione. JSW ha raggiunto la purezza desiderata dell’rMMA. La materia prima seconda di alta qualità ottenuta è stata fornita a Speichim e Arkema per ulteriori lavorazioni e applicazioni. Nel novembre del 2020, un’intera settimana di prove di depolimerizzazione su scala ridotta (corrispondente a una capacità di circa 1000 tonnellate all’anno) è stata condotta a Düsseldorf utilizzando vari rifiuti di PMMA come materia prima per la produzione di rMMA di alta qualità. Tra i rifiuti, tutti lavorati con la tecnologia del consorzio MMAtwo, c’erano scarti di PMMA provenienti da attrezzature elettriche ed elettroniche e materiali compositi, che hanno fornito eccellenti rendimenti di MMA grezzo rigenerato.
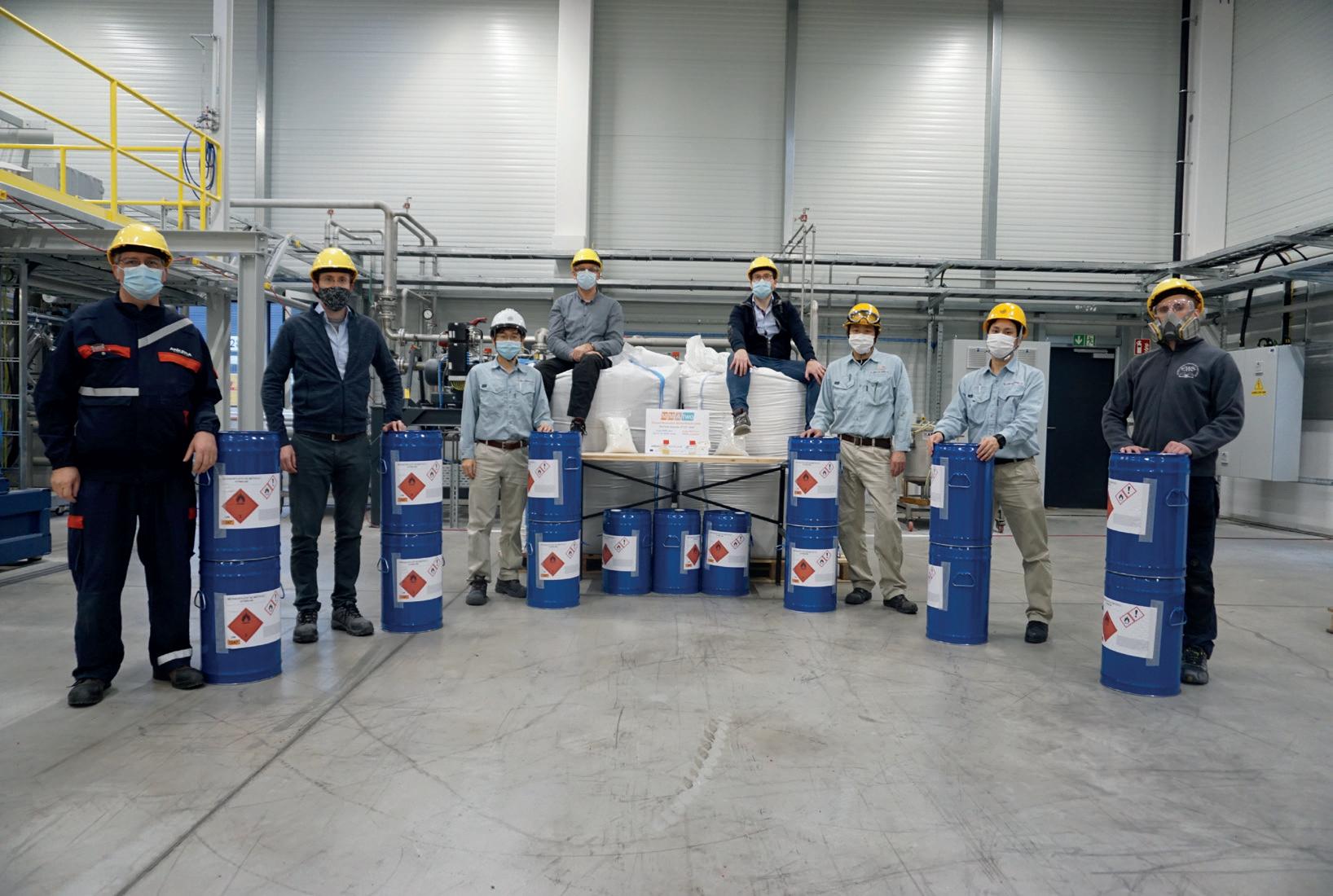
LE FASI SUCCESSIVE
La quarta fase di test è stata programmata per questi primi mesi del 2021. “Siamo sempre più vicini alla realizzazione industriale, economicamente molto interessante, del nostro progetto di depolimerizzazione del PMMA. Il fabbisogno di manodopera è significativamente più basso rispetto al processo convenzionale concorrente. Il vantaggio ecologico, la sostenibilità e la sicurezza degli utenti sono fuori discussione”, riassume Makoto Tojo. Altre due o tre serie di test sperimentali sono previste nel corso del 2021. Il contributo di JSW Europe - lo sviluppo di una soluzione tecnica per la monomerizzazione di vari scarti a base di PMMA - sta per essere completato. Poco dopo la fine del progetto sarà messo in funzione il primo impianto su scala industriale.
Il team di progetto durante i test condotti nel novembre del 2020
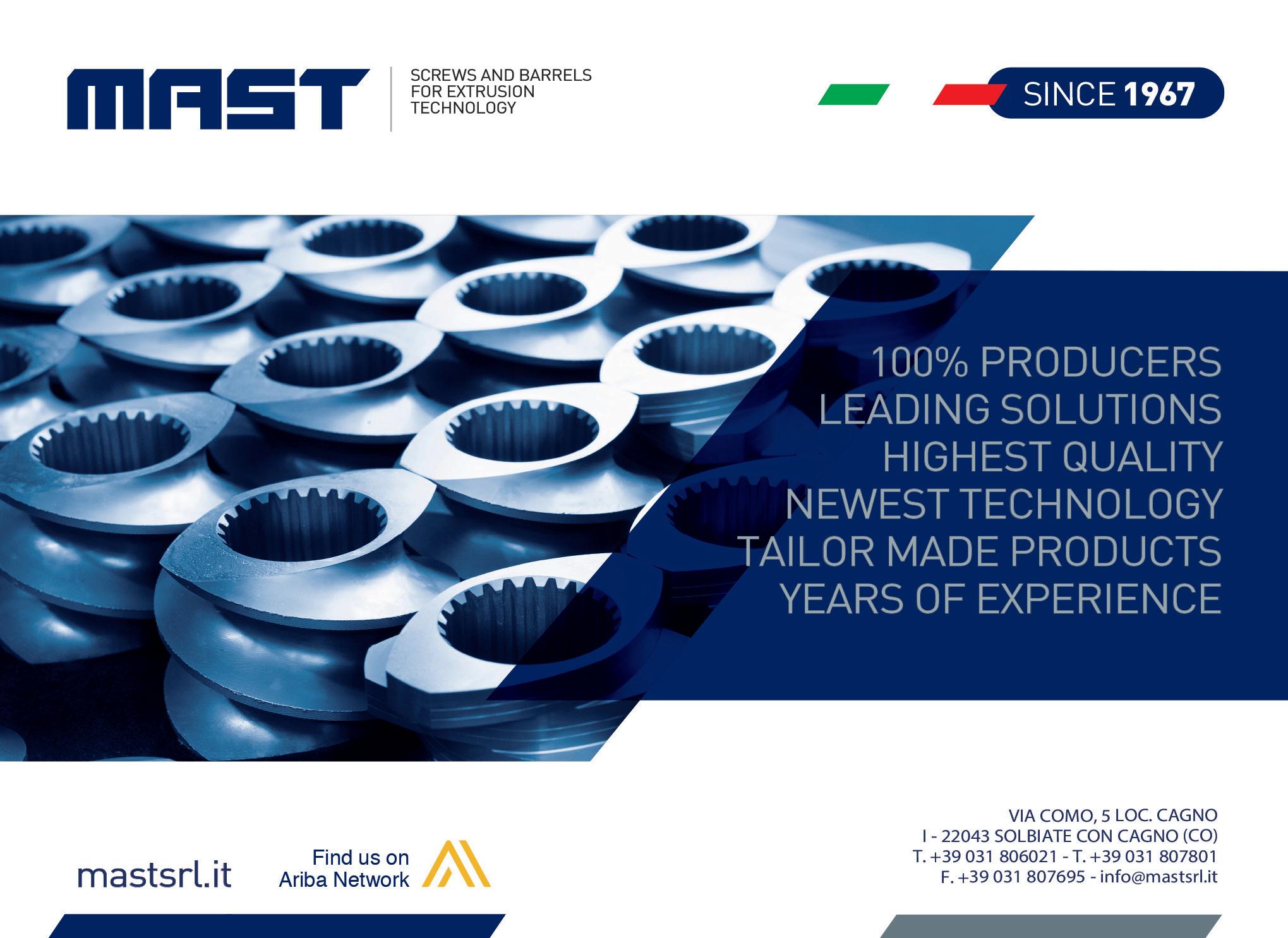
NEWS
Meaf e Promix insieme
LINEA PER LA PRODUZIONE DI PANNELLI
Costi di investimento ridotti e meno interventi di manutenzione. Sono questi i punti di forza della linea di schiumatura discontinua Panelfoamer di Hennecke-OMS, la cui principale innovazione consiste nel sistema di schiumatura a stampo aperto: per mezzo di una condotta di distribuzione, la formazione della schiuma avviene direttamente sul piano della pressa durante il suo ingresso all’interno di quest’ultima. Hennecke-OMS è uno dei principali costruttori al mondo di sistemi discontinui completi con sezione umida (schiumatrice) e sezione asciutta (presse multipiano con vasche movibili) per la produzione di pannelli mediante tecnologia di schiumatura di PUR e PIR. L’evoluzione degli impianti discontinui ha consentito di rendere le linee di produzione molto più flessibili e di adattarle alle esigenze dei trasformatori, per ampliare la gamma di dimensioni, spessori, densità e geometrie dei pannelli ottenibili. Il sistema di schiumatura a stampo aperto offre vari vantaggi: distribuzione ottimale e uniforme su tutta la sezione del pannello, senza vuoti all’interno del pannello stesso; densità ridotta e omogenea; possibilità di realizzare pannelli lunghi, spessi e larghi con un’unica iniezione, in modo che siano privi di giunzioni; schiumatura completamente automatica, senza alcun intervento dell’operatore; per l’iniezione del pannello non sono necessari tubi o prolunghe, così da evitare la formazione di bolle d’aria nell’espanso; adattabilità a qualsiasi tipo di formulazione della schiuma e agente espandente; l’utilizzo di pentano come agente espandente non richiede alcuna inertizzazione come nel caso dell’azoto.
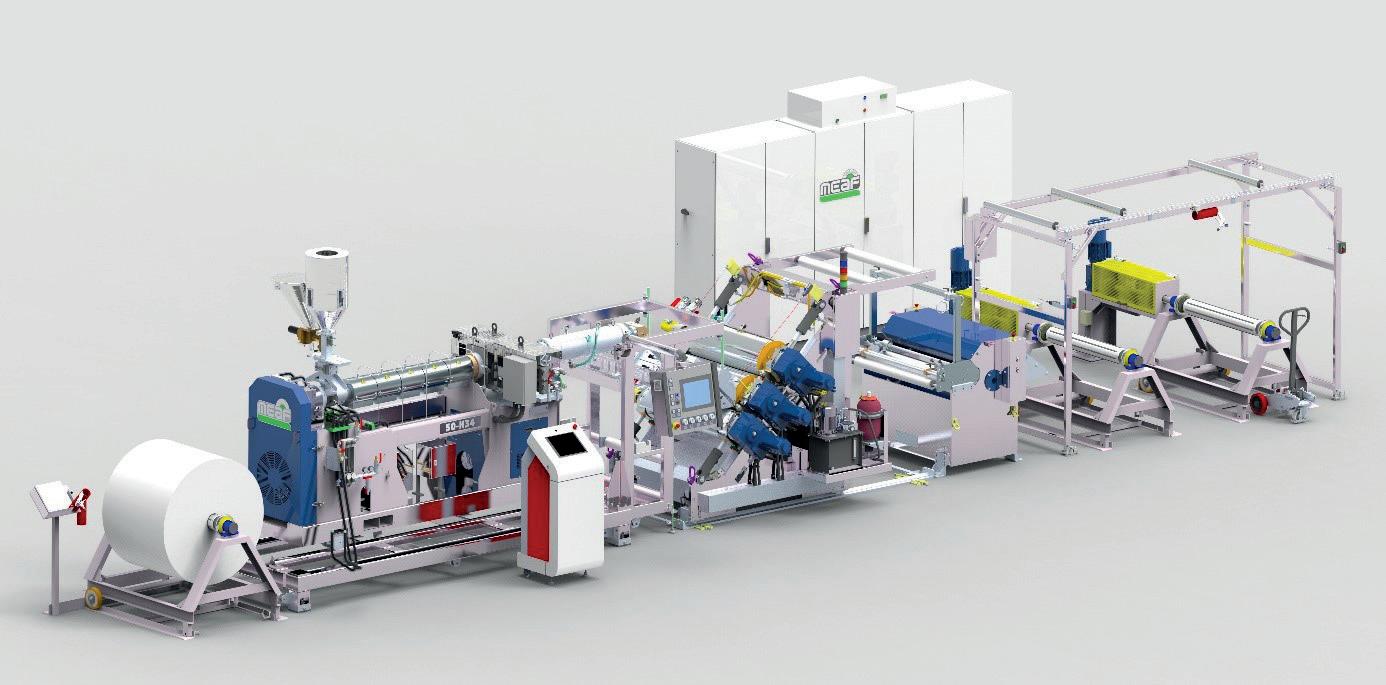
Meaf Machines ha aggiunto l’unità di Promix alla sua linea per permettere ai clienti di effettuare prove con i propri materiali e acquisire esperienza con il processo di espansione, al fine di risparmiare materiale
Veduta della linea Hennecke-OMS per la produzione di pannelli mediante schiumatura a stampo aperto Un sistema di Promix per l’espansione fisica è stato aggiunto da Meaf Machines alla sua linea interna per l’estrusione, così da consentire ai clienti di effettuare prove di produzione con i loro materiali. “L’espansione fisica offre un notevole potenziale di risparmio di materiale. Promix sta fissando nuovi standard nella produzione di espansi microcellulari con una struttura molto omogenea e una stabilità del processo senza precedenti, utilizzando agenti espandenti ecocompatibili come CO2 e azoto. A seconda dell’applicazione, è possibile ottenere riduzioni di densità dal 5% a oltre il 30%. Il conseguente risparmio di materiale non va solo a vantaggio dei trasformatori, ma anche dei loro clienti e dell’ambiente”, ha spiegato Roald de Bruijne, direttore vendite presso Meaf. Nell’estrusione di foglie e film, i maggiori costi di produzione dipendono dalle materie prime, che spesso superano il 70% del costo totale. Un approccio per ridurre i costi legati alle materie prime consiste nell’aumentare la quantità di materiale riciclato, rimacinare gli scheletri di produzione o impiegare scaglie di bottiglia nel caso dell’estrusione di film in PET, oppure utilizzare riempitivi come il CaCO3. “Per ridurre ulteriormente i costi complessivi delle materie prime, è necessario fare ancora di più. È qui che entra in gioco la linea di estrusione Meaf in combinazione con l’unità di schiumatura di Promix. Non solo riduce il costo del materiale plastico del 20% rispetto agli imballaggi convenzionali, ma la riduzione del peso complessiva dal 10% al 30% porta ulteriori benefici, poiché alcuni paesi lo prendono come base per la tassazione degli imballaggi. Inoltre, gli imballaggi possono essere resi riciclabili al 100%, consentendo pure l’utilizzo di materia prima riciclata, anche schiumata”, ha aggiunto Roald de Bruijne. Il processo di microschiumatura offre eccellente rigidità, isolamento e resistenza ai graffi e si traduce nel più basso consumo di energia per kg di materiale lavorato. Inoltre, consente la lavorazione di più tipi di materiali in un unico estrusore, come PP, PS, PET, PE, GPPS e PLA, e la stessa linea permette di produrre foglie espanse e non, anche multistrato A/B/A, con lo strato centrale in espanso.
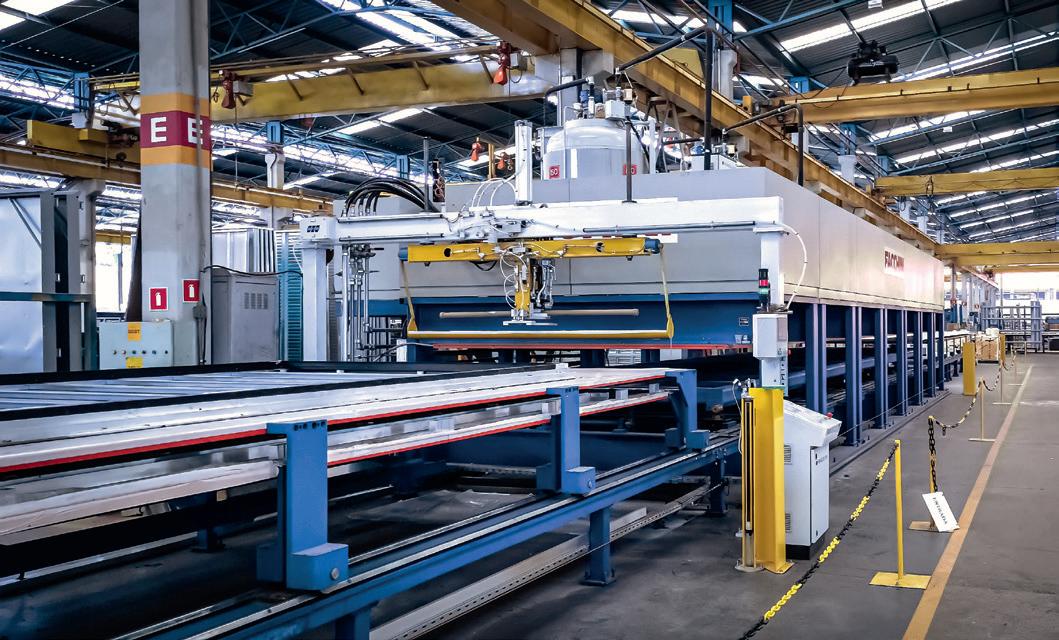

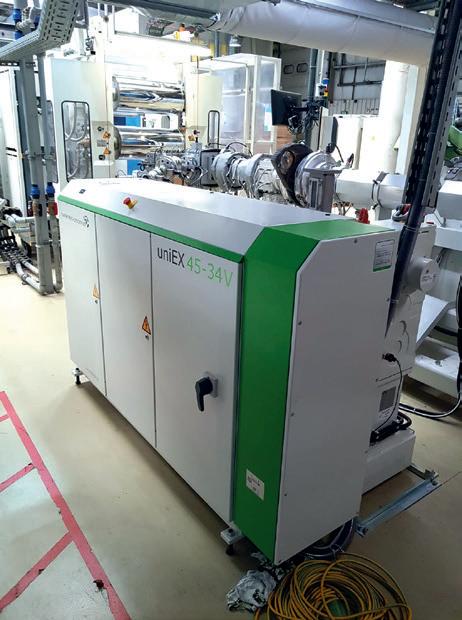

La maschera Fastback permette il cambio automatico dei modelli per la produzione di refrigeratori sia industriali che domestici
Negli ultimi mesi il Gruppo Pozzi Industries ha sviluppato una nuova soluzione integrata per la produzione di frigoriferi industriali impiegati nel settore medicale per lo stoccaggio e il trasporto a bassa temperatura dei vaccini anti-Covid, e in particolare del vaccino Pfizer, che va conservato a una temperatura di -80° C. La soluzione offerta dal Gruppo Pozzi Industries viene ottenuta con la combinazione del dispositivo di schiumatura universale di nuova concezione Fastback Foaming Fixture, di Saip, e di una serie di innovativi sistemi poliuretanici di Pozzi-Arosio che, insieme, garantiscono prestazioni ottimali. Fastback Foaming Fixture utilizza una tecnologia versatile in cui il cambio degli stampi avviene in modo rapido e semplice per l’operatore, alternando automaticamente gli stampi di schiumatura durante la produzione. Il cambio degli stampi, infatti, avviene senza interruzioni della produzione, evitando i tempi morti solitamente richiesti per la regolazione o il cambio degli stampi e risparmiando di conseguenza tempo ed energia. Il sistema Fastback Foaming Fixture può essere utilizzato per frigoriferi sia industriali che domestici. In dettaglio, il dispositivo di schiumatura, con una forma “a cappello”, ospita due stampi: uno opera nella parte inferiore, mentre l’altro è in posizione di attesa sulla parte superiore. Una piattaforma superiore consente all’operatore di immagazzinare il numero desiderato di stampi mentre un sistema a gru integrata consente agli stampi di spostarsi nella posizione di traslazione. Il cambio stampo avviene con la rotazione del “cappello” in circa 20 secondi. Le pareti laterali del dispositivo di schiumatura possono essere configurate dal pannello operatore e adattarsi alle dimensioni impostate, funzione particolarmente importante nel caso di isolamenti ad alto spessore. Il dispositivo di miscelazione prende in considerazione le caratteristiche dei più comuni sistemi poliuretanici ed è finalizzato a migliorarne le prestazioni. La posizione di ciascun ugello all’interno della testa di schiumatura garantisce la massima omogeneità e la testa è configurata per ospitare anche un terzo flusso.
Ampliato il campo di applicazione della serie uniEX Estrusori polivalenti ora anche per foglie e lastre
La gamma uniEX di estrusori monovite di battenfeld-cincinnati è adesso disponibile anche per l’estrusione di foglie e lastre. A prescindere dal fatto che il trasformatore desideri realizzare foglie speciali multistrato, monostrato con rivestimento legL’estrusore germente modificato oppure strutture con monovite strato intermedio in materiale rimacinato, uniEX 45-34V la coestrusione si conferma la soluzione più giusta. Gli estrusori uniEX consentono configurazioni estremamente compatte, poiché, grazie al loro design a “U”, possono essere installati in spazi molto ristretti, garantendo non solo un ingombro inferiore, ma anche la presenza di canali di adduzione più corti, con un effetto positivo sui tempi di pulizia e sui consumi di materiale. In seguito all’estensione delle opzioni di processo, la gamma è ora disponibile per l’estrusione di foglie e lastre nei modelli da 35, 45 e 60 mm, che vanno a sostituire tutte le serie precedenti. La velocità di produzione varia da 50 a 500 kg/h, in base al materiale lavorato. Il design modulare degli estrusori consente di eseguire praticamente ogni tipo di processo speciale e la vasta gamma di gruppi di plastificazione disponibile consente di coprire ogni esigenza applicativa. I gruppi di plastificazione possono essere equipaggiati con un’ampia scelta di zone di alimentazione, scanalate o lisce. Anche l’installazione di un’unità di degassaggio negli estrusori non presenta problemi.
Centro di lavoro a 5 assi LaborShape Produttività, precisione e qualità tutto in uno
Centro di lavoro a 5 assi, interamente progettato e costruito da Comi (divisione Techmill), LaborShape è sempre più apprezzato nella lavorazione di parti in materiali compositi, oltre che nella realizzazione di stampi e prototipi in alluminio. In questi ambiti, rappresenta la soluzione ideale laddove si richiedano elevata produttività, precisione e qualità di finitura. Questo centro di lavoro è dotato di testa operatrice con doppi motori su ogni asse A e C e doppi binari lineari per aumentare la rigidità della macchina. La RAM è equipaggiata con due guide lineari contrapposte, per garantire la migliore linearità di movimento dell’asse verticale (Z). Diverse configurazioni sono disponibili per i tavoli di lavoro (ghisa, acciaio, alluminio ecc.), così come per i cambiautensili automatici ATC (a cremagliera, rotante o a catena). Vasta la possibilità di personalizzazione, con la lavorazione sia a secco (con cappa aspirante elettrica o pneumatica, sistema di aspirazione, chiusura totale ecc.) sia a umido (con refrigerante a bassa e ad alta pressione, sistema di convogliamento per l’asportazione truciolo ecc). I mandrini, da 22 a 42 kW, arrivano fino a 24 mila giri al minuto.
LaborShape è disponibile con varie combinazioni di configurazioni, per adattarsi alle diverse esigenze nella lavorazione di materiali compositi, nella costruzione di stampi e nella realizzazione di prototipi
Come ben spiegato da Guido Ahlfeld, direttore vendite Automation di Wittmann Battenfeld Germany (in foto), gli alloggiamenti Easy Cell sono progettati soprattutto per equipaggiare in retrofit presse a iniezione già installate e collocate a distanza ridotta l’una dall’altra
CONFERENZA STAMPA IN STREAMING PER WITTMANN GROUP

GRAZIE ALLA PIATTAFORMA DIGITALE “WITTMANN INTERACTIVE” E A UNA SERIE DI WEBCAM, I GIORNALISTI CHE HANNO PARTECIPATO ALLA CONFERENZA STAMPA ONLINE DEL 19 MAGGIO 2021 HANNO POTUTO ENTRARE VIRTUALMENTE NELLE SHOWROOM EUROPEE DEL GRUPPO WITTMANN E OSSERVARE DA VICINO LE NUOVE ATTREZZATURE PROPOSTE A PARTIRE DAL GIUGNO DI QUEST’ANNO
DI RICCARDO AMPOLLINI
Nel primo pomeriggio di mercoledì 19 maggio Wittmann ha tenuto una conferenza stampa in streaming per fare il punto sulla situazione economica del gruppo e presentare dal vivo alcune delle sue più recenti innovazioni. In collegamento dal Technical Center di Kottingbrunn, in Austria, c’erano Michael Wittmann, general manager del Gruppo Wittmann, e Rainer Weingraber, managing director e CEO di Wittmann Battenfeld. Nell’illustrare l’attuale situazione economica del gruppo, che conta attualmente circa 2200 dipendenti, Michael Wittmann ha dichiarato che c’è stato un forte recupero in termini di ordinativi già a partire dalla seconda metà del 2020, per raggiungere addirittura picchi record nel primo trimestre dell’anno in corso. Tale crescita ha caratterizzato un po’ tutti i settori applicativi e le aree geografiche. Nonostante questo, la carenza di materiali in quasi tutti i settori industriali e presso i trasformatori di materie plastiche sta tuttora causando il “congelamento” della situazione a un livello standard. “Per fortuna, facciamo produrre in Cina solo pochi componenti elettronici e microchip e sono perlopiù quelli a creare problemi di ritardo nelle consegne, insieme naturalmente ai blocchi alle frontiere verificatisi durante l’ultimo anno”, ha commentato Wittmann, “In sintesi, se è vero che c’è stata una crescita, si sarebbe potuto fare sicuramente di più in condizioni
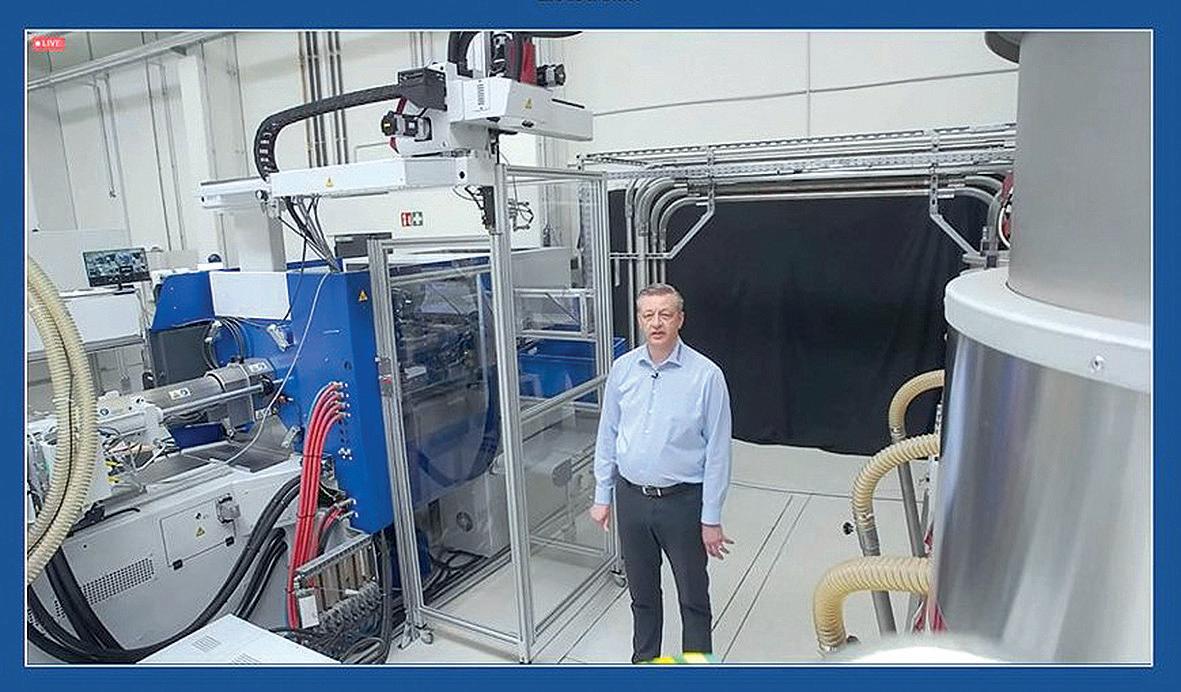

normali”. Il fatturato previsto per il 2021 dovrebbe comunque attestarsi intorno ai 350400 milioni di euro. La disponibilità di materiali/componenti, che rimane critica, farà la differenza. Dal canto suo, Rainer Weingraber ha posto l’accento sugli investimenti per l’aggiornamento del Technical Center e per l’incremento della capacità produttiva. Nel primo caso si parla dell’espansione dell’area dedicata alla formazione, agli eventi e al training di clienti e personale interno, oltre che dell’integrazione del servizio “Wittmann Interactive”; i lavori dovrebbero essere completati entro la prima metà dell’anno. Per aumentare invece la capacità produttiva dello stabilimento di Kottingbrunn, entro il 2022 verrà aggiunta un’ulteriore area per l’assemblaggio delle macchine verticali e di grandi dimensioni, sarà approntata una nuova officina elettrica e sarà rivisto il centro logistico, dotandolo di circa 1500 zone di magazzinaggio dei pallet, di maggiore automazione e di aree separate di prelievo e stoccaggio. Michael Wittmann ha quindi ripreso la parola, descrivendo gli investimenti previsti per le nuove tecnologie e per le filiali in Cina e in Bulgaria, che entro il 2022 verranno ampliate sia in termini di nuovi uffici, magazzini e aree showroom sia a livello di servizi offerti. Verrà inoltre fondata una nuova filiale per il mercato della Cina Meridionale. L’espansione riguarderà anche l’impianto austriaco numero 2 e i dipartimenti di Meccatronica e Sviluppo software, a cui si aggiungeranno 1050 m2 di uffici e area test.


Si è passati quindi ai collegamenti dal vivo con gli altri stabilimenti europei del gruppo, sfruttando la modalità “Wittmann Interactive”, la quale, grazie a videocamere mobili (head cam o dome cam, controllabili anche via App sul proprio smartphone), consente solitamente al tecnico Wittmann di mostrare in dettaglio al cliente parti della macchina da riparare o manutenere. Collegati sempre da Kottingbrunn, Valentina Faloci (direttore vendite di Wittmann Battenfeld) e Wolfgang Roth (responsabile Applications Engineering e gestione fiere/eventi di Wittmann Battenfeld) hanno quindi permesso ai partecipanti di effettuare un tour all’interno del rinnovato Technical Center e di una prima showroom per le prove dei clienti, dov’era installata una macchina a iniezione SmartPower 240 configurata per lo stampaggio multicomponente.
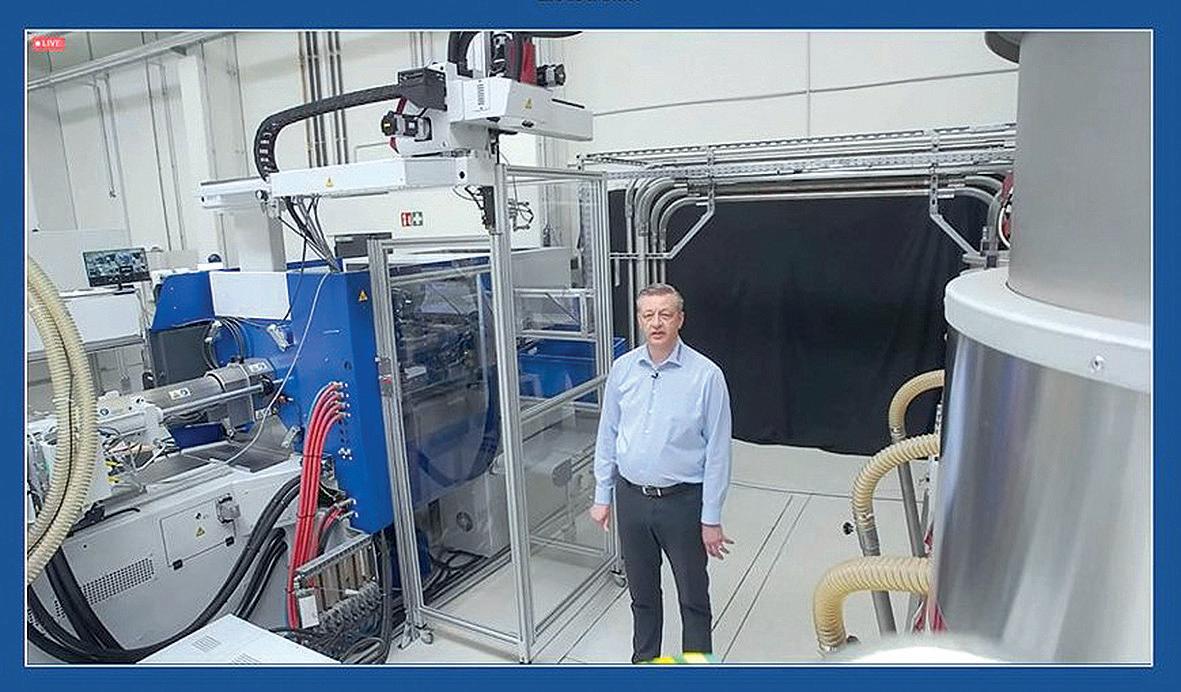
Michael Wittmann, general manager del Gruppo Wittmann (a sinistra), e Rainer Weingraber, managing director e CEO di Wittmann Battenfeld, introducono la conferenza in streaming del 19 maggio e rispondono alle domande finali dei giornalisti
In una seconda showroom, solitamente dedicata al training e ai corsi di formazione, una SmartPower 60/210 Ingrinder stampava clip per lavanderia. Grazie alla videocamera mobile è stato possibile osservare da vicino, come se si fosse sul posto, i dettagli della macchina, dello stampo montato e anche di un articolo prodotto. In collegamento dal Competence Center di Meinerzhagen (Germania), Andreas Hollweg (direttore vendite di Wittmann Battenfeld Deutschland per la tecnologia di stampaggio a iniezione) ha illustrato il processo Airmould (stampaggio a iniezione assistito da gas: generalmente azoto), implementato di recente con la versione Next, su una SmartPower 120. Il vantaggio principale di questo processo è la riduzione dei tempi di ciclo e del materiale utilizzato, grazie al vuoto creato all’interno del pezzo; il che porta a una riduzione dei costi totali di stampaggio. EASY CELL: ALLOGGIAMENTO PROTETTIVO PER SPAZI ESTREMAMENTE RISTRETTI
Dal Technical and Training Center Wittmann di Norimberga, Guido Ahlfeld (direttore vendite Automation di Wittmann Battenfeld Germany) ha invece mostrato un’isola di lavoro per lo stampaggio a iniezione di portasalviette, dotata d’automazione inserita nel nuovo alloggiamento Easy Cell. Sempre grazie a una webcam portatile, è stato possibile “entrare” in Easy Cell per osservarne le caratteristiche principali, tra cui: la semplicità, l’economicità e il ridotto ingombro in stabilimento, anche con l’integrazione di robot. Quando vi è la necessità di potenziare con sistemi d’automazione aggiuntivi le presse a iniezione già installate in reparto, gli spazi disponibili risultano spesso insufficienti per il montaggio di alloggiamenti protettivi fissi
Sempre collegati in streaming, Valentina Faloci (direttore vendite di Wittmann Battenfeld) e Wolfgang Roth (responsabile Applications Engineering e gestione fiere/eventi di Wittmann Battenfeld) hanno permesso ai partecipanti alla conferenza di fare un tour all’interno del rinnovato Technical Center di Kottingbrunn
con barriere di sicurezza. Gli alloggiamenti Easy Cell non necessitano invece di barriere di sicurezza e quindi occupano uno spazio minimo a lato della pressa. Per esempio, la larghezza totale necessaria per il montaggio di un trasportatore d’uscita di 600 mm non supera gli 850 mm. Gli Easy Cell sono montati su ruote girevoli e possono essere spostati in base alle esigenze, ad esempio per l’accesso durante il cambio stampo sul lato macchina non utilizzato dall’operatore. Nonostante il loro design compatto, sono dotati di tutte le funzioni di sicurezza necessarie secondo gli standard CE e sono disponibili in sei diverse versioni, adattabili alle necessità degli stampatori ed estendibili con accessori opzionali come pinze, pacchetto di messa in servizio rapido o installazione CE completa.
GRANULATORE S-MAX 3 CON ALBERO D’ALIMENTAZIONE AGGIUNTIVO
Dalla grande showroom dello stabilimento di Wolkersdorf, Domenik Nikollaj (direttore vendite di Wittmann per i sistemi ausiliari) e altri suoi colleghi hanno illustrato le novità del gruppo e i loro vantaggi nel campo dei granulatori (nuovi modelli delle serie G-Max ed S-Max), dei termoregolatori (come il nuovo Tempro plus D L120, in grado di mantenere una temperatura costante in ogni condizione operativa; vedi box a pag. 51), dei dryer mobili, dei caricatori/dosatori e dei sistemi di trasporto centralizzati per i materiali plastici, citando in particolare il pannello di controllo M8 per la loro gestione. Rispetto ai granulatori a lame convenzionali, i nuovi granulatori senza filtro S-Max 3 offrono una serie di vantaggi come l’efficienza energetica, la rumorosità ridotta e un granulato pulito e uniforme seppur ottenuto da plastiche dure e fragili come PC, ABS, PA o plastiche rinforzate. I motori dei granulatori erogano una coppia elevata, funzionano senza bloccarsi anche a basse velocità (27 giri/min a 50 Hz) e sono adatti al taglio di materozze e scarti più spessi del normale, trasformandoli in pellet di 4-10 mm. Un albero di alimentazione aggiuntivo, offerto come optional, mantiene in movimento i grandi pezzi di scarto effettuando un taglio preliminare e riducendone già le dimensioni, al fine di evitare accumuli in zone morte o la formazione di ponti, specialmente in presenza di materozze lunghe e parti piatte. L’albero addizionale aiuta anche a evitare i tempi morti causati da eventuali ritorni di materiale, o da cariche eccessive, e a mantenere più “fluido” il processo produttivo. È dotato di comando indipendente e presenta ganci allungati per consentire di effettuare il pretaglio degli scarti e di spingerli verso la camera di taglio, dove viene eseguita la granulazione vera e propria. Il taglio preliminare opzionale può consentire anche d’impiegare un granulatore di dimensioni più compatte, con un possibile risparmio sui costi d’acquisto.
NUOVE OPZIONI D’AUTOMAZIONE PER PRESSE DI MEDIO TONNELLAGGIO
È stata quindi la volta del collegamento da uno dei più importanti Development & Production Center per l’automazione del Gruppo Wittmann, quello di Vienna, da dove è stato mostrato in funzione il nuovo robot WX153, recentemente aggiornato e installabile su tutte le macchine a iniezione con forza di chiusura medio-alta, da 500 a 1300 t. La sua struttura ad assi cartesiani è caratterizzata da un asse X mobile con funzioni d’estrazione dei pezzi dallo stampo e una corsa che può raggiungere i 1400 mm, con uno sbraccio massimo di circa 1790 mm. Quest’ultimo rappresenta un parametro essenziale per il layout del robot e indica la distanza massima tra l’asse orizzontale e la piastra di montaggio dell’asse rotativo, misurata all’estremità inferiore dell’asse verticale. La corsa orizzontale può arrivare fino a 18 m e quella verticale fino a 2,6 m. I condotti interni e/o i cablaggi nel tubo verticale a Y, i punti di lubrificazione facilmente accessibili e l’armadio comandi integrato nella parte posteriore del supporto orizzontale fanno parte dell’equipaggiamento standard del robot WX153. L’armadio mantiene le dimensioni originarie indipendentemente dal numero di assi aggiuntivi collegati. Per manovrare la pinza d’estrazione è possibile montare tre assi rotativi aggiuntivi servocomandati (A, B e C) sull’estremità dell’asse verticale del robot, come nel caso del modello presentato il 19 maggio. Tale configurazione consente di programmare movimenti sincronizzati fino a 6 assi tramite il controllore R9 di Wittmann. Varie ottimizzazioni consentono inoltre al WX153 di funzionare con una pinza di peso superiore a 20 kg (+30% rispetto alla versione precedente) anche in


Aprendo la tramoggia di carico del granulatore S-Max 3 è possibile dare un’occhiata dal basso all’albero di alimentazione addizionale
Il robot WX153 con assi rotativi servocomandati montati sull’asse verticale; a destra, lo schema di funzionamento di tali assi addizionali
presenza dei tre assi aggiuntivi. Inoltre, Wittmann è in grado di fornire robot in configurazione tandem (due unità che traslano insieme sulla medesima guida), per la quale è possibile fare a meno del secondo armadio comandi, risparmiando così spazio accanto alla pressa.
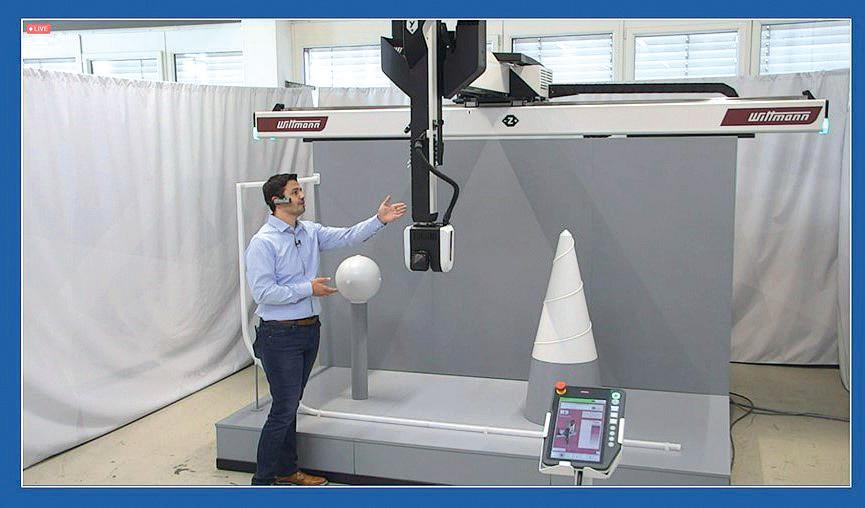
Nell’ultima parte della conferenza stampa, rispondendo alle domande dei giornalisti, Michael Wittmann ha dichiarato: “Nel 2019 gli ordini provenienti dal settore automotive avevano toccato il fondo, ma sono lentamente risaliti nel corso del 2020, con un leggero miglioramento pure rispetto al 2019. Anche il settore imballaggio sta fornendo eccellenti risultati”. “Le applicazioni nel campo dei termoindurenti continueranno inoltre ad avere un ottimo futuro in Wittmann”, ha proseguito Rainer Weingraber. “Oltre ad Airmould, i processi più richiesti in questo momento sono Combimold, microstampaggio e produzione di packaging. Gli ordini di macchine elettriche e idrauliche si equivalgono, 50:50, nonostante le note caratteristiche che le distinguono”. Parlando invece dei prossimi eventi di settore, il general manager del Gruppo Wittmann ha affermato: “Come membro dell’Advisory Board di Fakuma, posso confermare sin d’ora che la prossima edizione della fiera si dovrà svolgere con regolamenti particolari e restrizioni per rendere l’evento più sicuro… però restiamo convinti di organizzare comunque l’esposizione a Friedrichshafen, dal 12 al 16 ottobre”. “Posso già anticipare che il nostro stand sarà collegato direttamente via web con gli stabilimenti Wittmann, un po’ com’è avvenuto per l’odierna conferenza stampa”, ha aggiunto Weingraber. “Siamo ottimisti e riteniamo che il trend positivo degli ultimi mesi proseguirà anche nel 2022”, ha quindi concluso Michael Wittmann.

Termoregolatore Tempro plus D L120 L’ultimo e potente “pacchetto” Wittmann per il controllo della temperatura
Lo stampaggio a iniezione con stampi grandi e massicci richiede un’elevata capacità di riscaldamento, ma anche canali di raffreddamento con portate adeguatamente elevate. In questo caso, il nuovo termoregolatore Wittmann Tempro plus D L120 si propone come la soluzione ideale. Si caratterizza innanzitutto per una capacità di riscaldamento massima di 36 kW, che garantisce tempi di riscaldamento ottimali per lo stampo dal punto di vista sia tecnico che economico, ma anche una notevole rapidità d’innalzamento della temperatura, utile per esempio dopo un cambio stampo. Il calore accumulato nell’acciaio riscaldato dello stampo, a cui si aggiunge quello del polimero fuso, deve essere asportato il più velocemente possibile e in maniera omogenea attraverso i canali di raffreddamento. Per creare le condizioni ideali di questo processo, Tempro plus D L120 può essere dotato della nuova pompa a frequenza variabile SpeedDrive, con una potenza di 4 kW e in grado di gestire portate fino a 300 l/min alla pressione massima di 5 bar. Grazie a questa pompa, gli utenti sono in grado d’impostare valori corretti anche di altri parametri, quali: giri motore, portata del circuito, pressione della pompa e temperatura differenziale.
Un approccio che contribuisce in modo sostanziale alla stabilità del processo. La regolazione automatica delle impostazioni entro un certo margine di tolleranza ottimizza pure i tempi attivi della macchina. L’utilizzo di SpeedDrive è sinonimo d’elevata efficienza energetica, poiché, per rispettare in generale le impostazioni dei parametri selezionati, è sufficiente azionare la pompa a regime parziale. La funzione di raffreddamento diretto di Tempro plus L’elevata potenza di D L120 è invece assicurata da un sistema ad acqua raffreddamento di Tempro plus D L120, che raggiunge i 175 kW, a elevata efficienza. In questo caso, l’uso di valvole a solenoide convenzionali comporterebbe alcuni rischi, consente per esempio di poiché la sequenza temporizzata di raffreddamento gestire una temperatura causerebbe inevitabilmente picchi di pressione, oltre a differenziale di 60°C tra fluttuazioni di temperatura e pressione che potrebbero acqua dello stampo e acqua di raffreddamento perfino causare fenomeni di cavitazione nella pompa. Per eliminare tali problemi alla radice, il termoregolatore è stato dotato di una valvola di raffreddamento proporzionale da ¾ di pollice, con una portata di 100 l/min, comandata da un motore passo-passo che apre o chiude la valvola in modo graduale, al fine di mantenere un controllo costante della temperatura ed escludere ogni possibile malfunzionamento. Grazie allo speciale design, questa valvola è inoltre completamente esente da manutenzione.
RIGRANULATRICI EXACT LA SEMPLICITÀ È LA CARTA VINCENTE NEL RECUPERO DI RIFILI
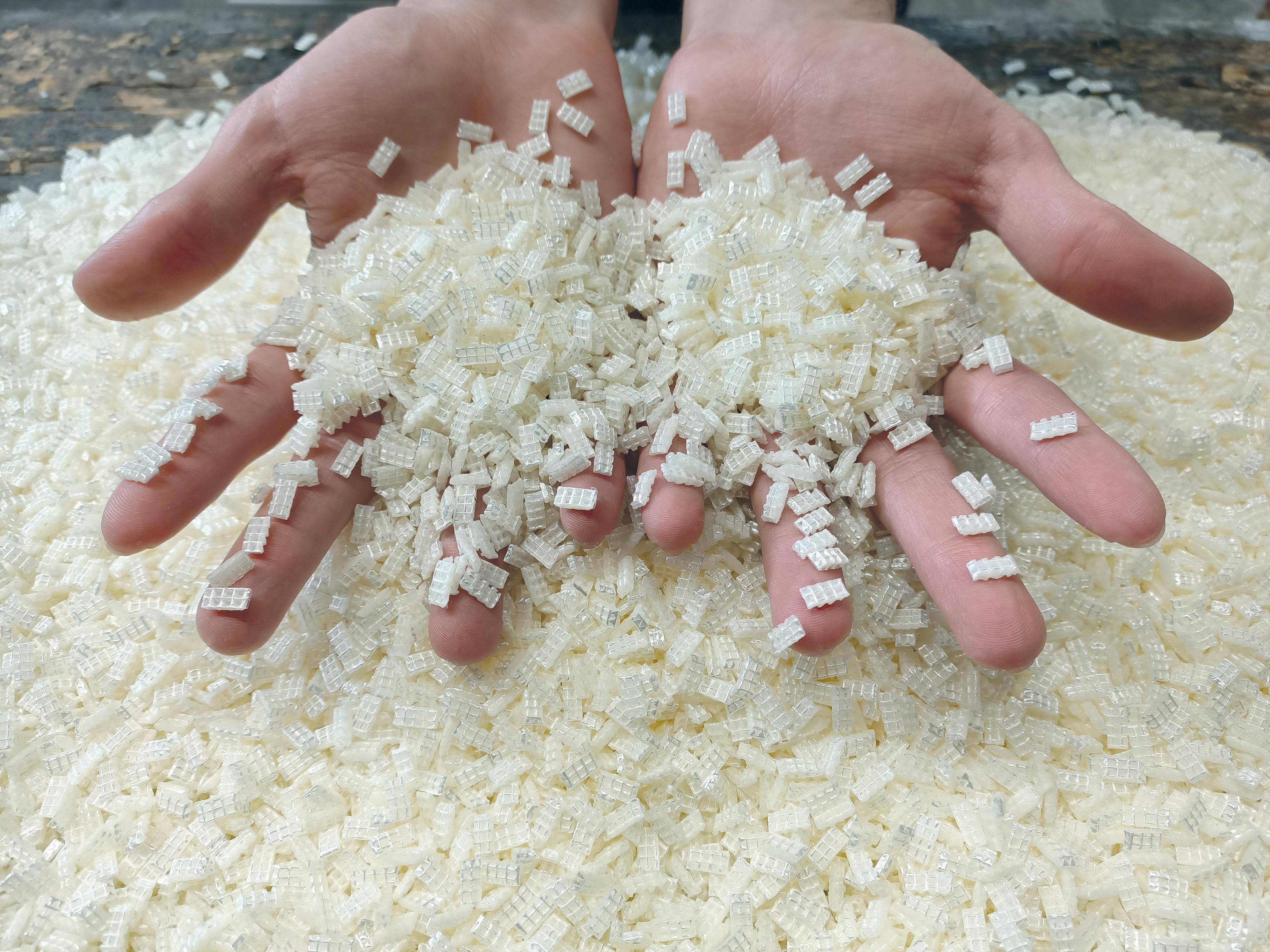
LE RIGRANULATRICI DEL COSTRUTTORE DI ZINGONIA (BERGAMO) SONO OGGI MACCHINE MODERNE E AL PASSO CON I TEMPI, MA AFFONDANO LE LORO RADICI NEI PRIMI ANNI DI ATTIVITÀ DI EXACT E NEL LAVORO E NELL’INVENTIVA DEL SUO FONDATORE, ILARIO MAZZOLENI. FRUTTO DI QUASI MEZZO SECOLO DI SVILUPPO E MIGLIORAMENTI, OGGI HANNO OTTENUTO LA CERTIFICAZIONE “INDUSTRY 4.0-READY”

Da quasi 50 anni Exact produce macchinari ausiliari per l’industria delle materie plastiche, il cui fiore all’occhiello è rappresentato dalle rigranulatrici utilizzate per il recupero di film termoplastici mono e multistrato, biodegradabili, a bolle d’aria, spunbond, in tessuto non tessuto ecc. Il funzionamento di tali macchinari è semplice: l’estruso viene compattato da speciali bussole di compressione e la fettuccia semirigida che ne risulta viene tagliata fino a ottenere piccoli pellet dall’alto peso specifico, pronti per essere nuovamente estrusi, permettendo così di lavorare - per esempio, nel caso del recupero di rifili - a ciclo chiuso con l’impianto di estrusione, senza nessuna contaminazione del materiale. L’alto peso specifico dei pellet così ottenuti differenzia le rigranulatrici Exact dai mulini, il cui prodotto finale è costituito dal cosiddetto “fluff”, un materiale leggero e voluminoso. Motivo, questo, per cui Exact considera le sue rigranulatrici come l’anello di congiunzione tra i mulini, appunto, e gli estrusori.
IL RECUPERO “A FREDDO” RECUPERA TERRENO
Queste macchine, che sono il frutto del lavoro e dell’inventiva dello scomparso fondatore di Exact, Ilario Mazzoleni, sono state sempre più perfezionate nel corso degli anni, per rispondere alle necessità di un mercato che dal 1974 - anno in cui l’azien-
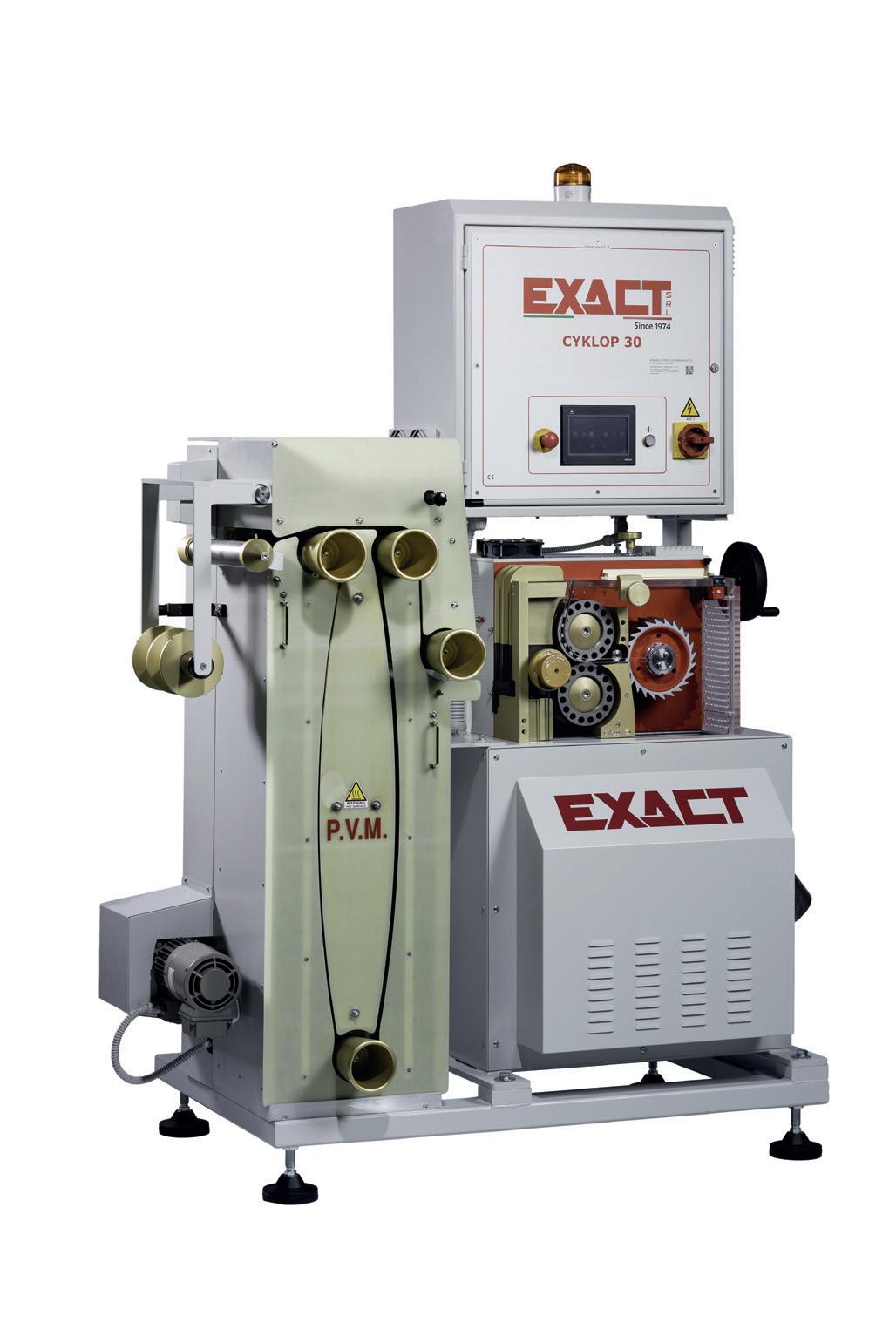
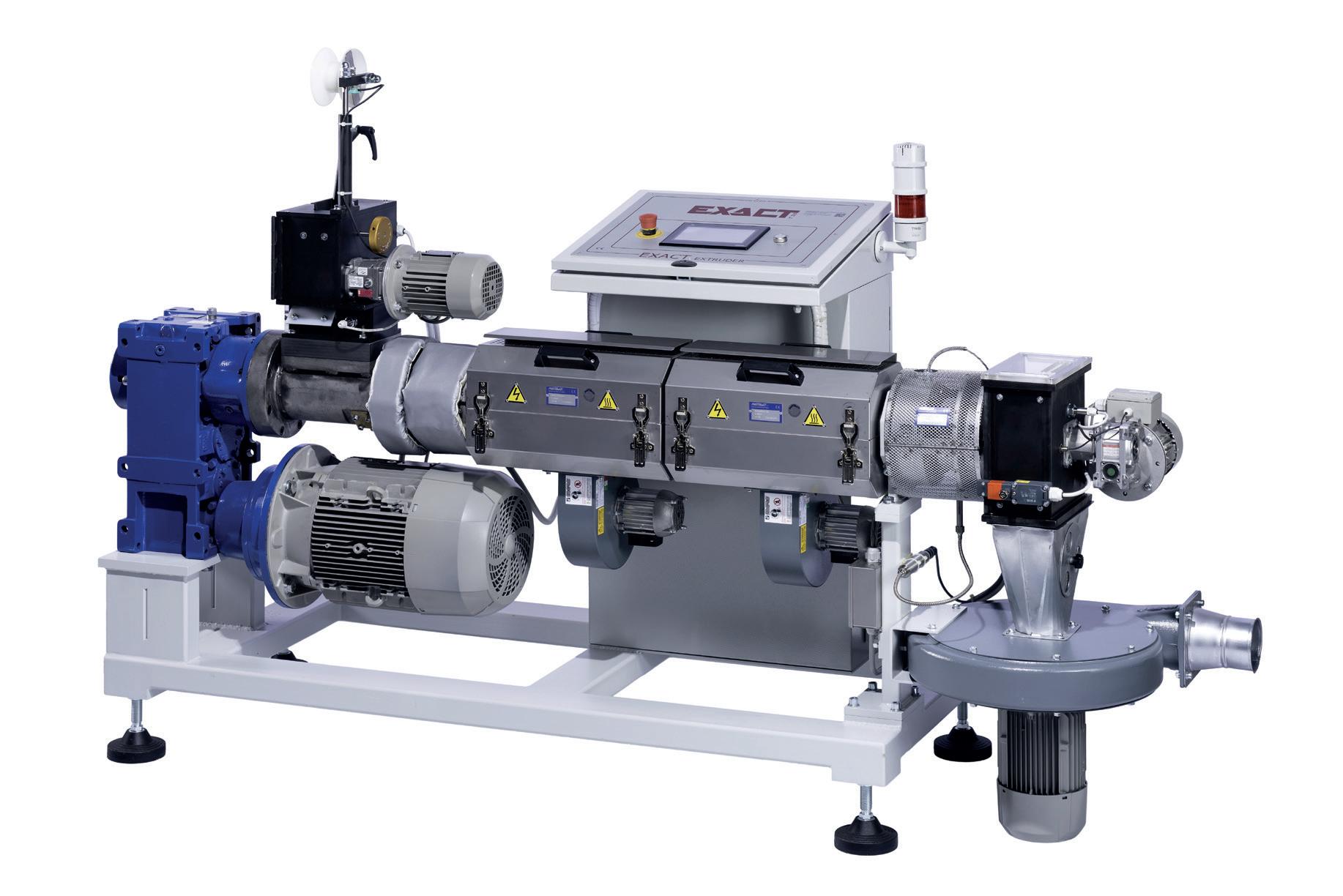
da ha iniziato la propria attività - si è ampliato e trasformato significativamente. Sebbene l’azienda produca anche estrusori per il recupero di rifili “a caldo”, la soluzione “a freddo” sta registrando un netto recupero di terreno nei loro confronti. A confermarlo, oltre ai numeri, è Noris Mazzoleni, CEO di Exact, che spiega così il fenomeno: “Per nostra esperienza, il mercato della produzione di film plastici si sta muovendo lungo tre direttrici principali: produzione di materiali altamente tecnici, ripresa decisa della produzione di tessuto non tessuto e continua crescita della domanda di prodotti biodegradabili. La prima è conseguenza del procedere dei tempi, la seconda della perdurante pandemia, con conseguente aumento produttivo di dispositivi per la protezione individuale (DPI), e la terza è figlia di un cambio di sensibilità nei confronti della sostenibilità ambientale”. “Rispondere a tendenze così differenti non è cosa banale; ancora meno farlo con un solo prodotto. Fortunatamente le nostre rigranulatrici rispondono a questa sfida con naturalezza e semplicità, forse proprio perché scevre di quelle complicazioni che, se sommate alle complicazioni stesse dei prodotti, portano tendenzialmente al solo caos. E, in tempi travagliati come quelli che stiamo attualmente vivendo, le persone desiderano solo semplicità e risultati”, aggiunge Noris Mazzoleni. Adattabilità a diversi materiali, semplicità di utilizzo e solidità storica del marchio diventano quindi un’ancora di sicurezza per i produttori di film che, in tempi incerti caratterizzati da ripresa dei prezzi delle materie prime e corse sfrenate per riadattare i processi produttivi a seguito di mutazioni della domanda finale, cercano soluzioni concrete per la gestione dei propri scarti di produzione. Le rigranulatrici possono poi essere personalizzate in base alle esigenze degli utilizzatori finali, in seguito a test effettuati con i loro materiali o in base alle singole applicazioni di destinazione.
INDUSTRY 4.0-READY
Le rigranulatrici di Exact hanno recentemente ottenuto da Amaplast (l’associazione nazionale dei costruttori di macchine e attrezzature per materie plastiche e gomma) l’attestazione di conformità ai requisiti previsti per definire i macchinari “Industry 4.0-Ready”. L’ufficio tecnico dell’associazione ha infatti analizzato le caratteristiche tecniche di tre modelli di rigranulatrici Exact
Attualmente sono in corso di ultimazione le attività di verifica per concedere anche ad altre macchine di Exact l’attestazione di conformità ai requisiti previsti per i macchinari “Industry 4.0-Ready”
Il modello Cyclop 30 è uno di quelli dichiarati funzionali alla trasformazione tecnologica e digitale delle imprese e che hanno ottenuto la certificazione “Industry 4.0-Ready” da Amaplast
e ne ha certificato la rispondenza ai requisiti indicati nell’allegato A della legge n. 232 dell’11 dicembre 2016, per l’ammissibilità al credito d’imposta previsto dalle misure del “Piano di Transizione 4.0”, che per il 2021 sale al 50% del valore del bene. Si tratta di una modalità importante per comunicare al mercato la possibilità di usufruire del credito d’imposta 4.0, a patto ovviamente che l’acquirente assolva ai suoi obblighi specifici (interconnessione del bene al sistema informativo aziendale ecc.). Le rigranulatrici Evolution 10, Cyclop 20 e Cyklop 30, in particolare, sono state dichiarate funzionali alla trasformazione tecnologica e digitale delle imprese secondo il modello Industria 4.0, ovvero beni strumentali il cui funzionamento è controllato da sistemi computerizzati o gestito tramite opportuni sensori e azionamenti. Sono in corso di ultimazione le attività di verifica anche per altre macchine costruite da Exact: le rigranulatrici a caldo E60 ed E120 e quelle a freddo R6 Jumbo e Gold, per il recupero di film termoplastico. La valutazione è stata svolta dagli esperti di Amaplast con l’analisi della documentazione tecnica e progettuale dei macchinari, accompagnata da un confronto con i referenti tecnici del costruttore e dei suoi fornitori e da una verifica diretta delle attrezzature, con vari sopralluoghi in azienda. Il rapporto di conformità rilasciato descrive le caratteristiche tecniche dei beni e ne illustra il sistema di controllo e l’interconnessione ai sistemi informatici e logistici di fabbrica, prendendo in considerazione vari elementi: efficace interfaccia uomomacchina; rispondenza ai più recenti criteri di sicurezza; predisposizione per i sistemi di telemanutenzione, telediagnosi e controllo in remoto; possibilità di monitoraggio continuo delle condizioni e dei parametri di processo; sussistenza di un sistema cyberfisico.
MAST VA VELOCE
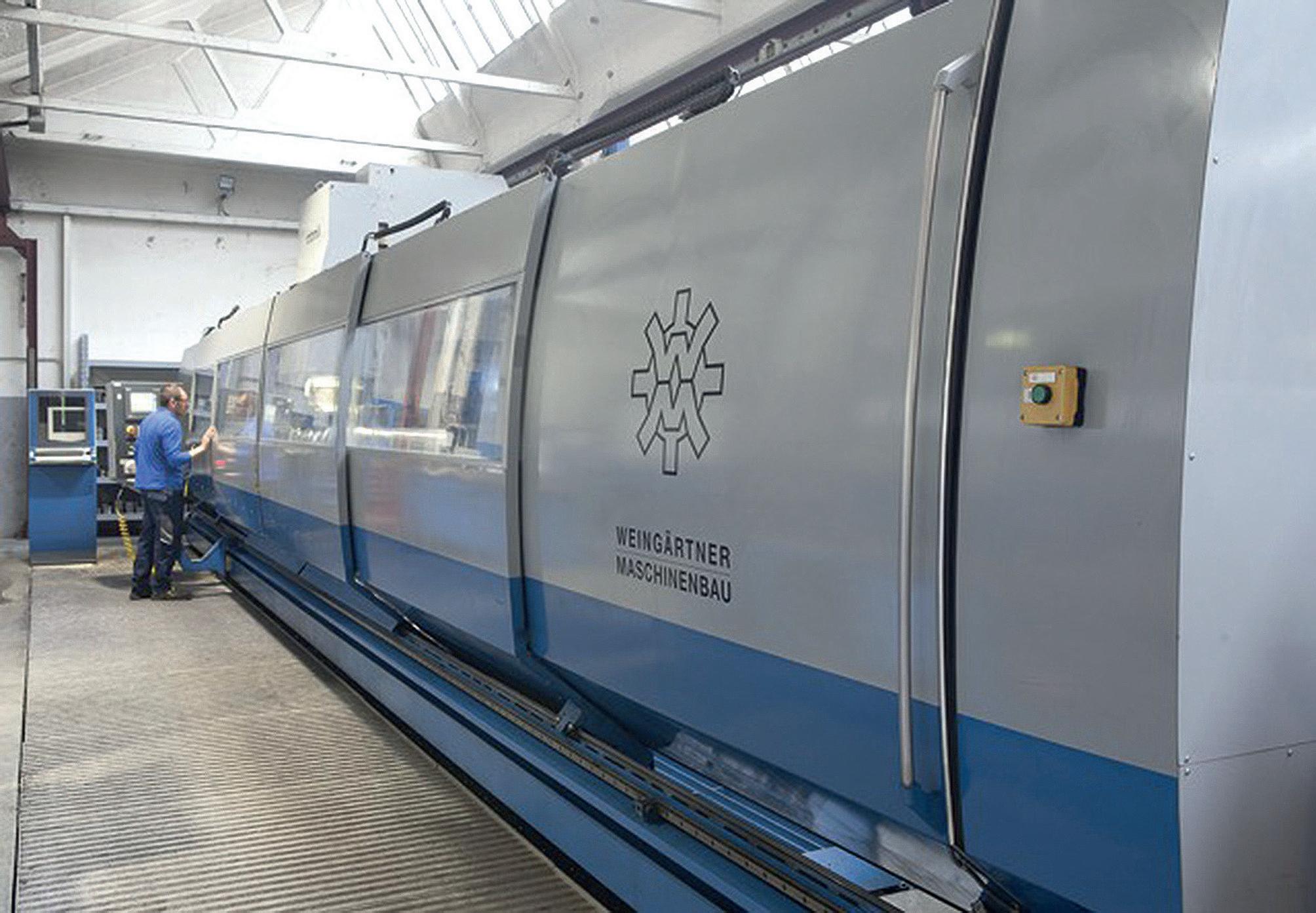
CAMBIARE, PUR RIMANENDO SÉ STESSI
IN POCHI MESI IL MONDO È CAMBIATO TANTISSIMO E RAPIDI CAMBIAMENTI DI QUESTO TIPO SEMBRANO ESSERE QUELLO A CUI CI DOVREMO ABITUARE ANCHE IN FUTURO. E ALLORA BISOGNA ESSERE DISPOSTI A CAMBIARE INSIEME AL MONDO CHE CI CIRCONDA E A FARLO ALTRETTANTO VELOCEMENTE. COME MAST, CHE, NON NEGANDO LE DIFFICOLTÀ, AFFRONTA QUESTO PERIODO SENZA RASSEGNAZIONE E CON SPIRITO D’INIZIATIVA
DI LUCA MEI
Con più di cinquant’anni di attività alle spalle, traguardo tagliato nel 2017, Mast rappresenta oggi al meglio le piccole-medie imprese che costituiscono la forza del tessuto industriale e produttivo italiano: quelle a conduzione familiare (nella fattispecie, alla guida di Mast vi sono Carlo e Marco Arioli, fratelli e figli del fondatore Marino Arioli) e terziste, ossia che lavorano per lo più per altre grandi aziende e che, per questo, devono possedere un know-how ampio e approfondito dei prodotti che escono dai loro reparti. In poche parole, non per sminuire il significato di quello che stiamo scrivendo, bensì per specificarlo ulteriormente e renderlo meglio comprensibile, aziende che per tradizione e tipo di attività sanno fare le cose e le sanno fare bene. Proprio come avviene in Mast, e non potrebbe essere altrimenti, visto che i suoi prodotti sono viti e cilindri che vengono installati prevalentemente sulle linee di estrusione e, in quanto tali, richiedono inderogabilmente una fattura accurata e un’estrema precisione. Di cui, infatti, non difettano. Ma l’azienda sta assumendo anche quella caratteristica che è sempre più importante per essere competitiva nell’era 4.0 e che in molti casi è trasversale alla più classica categorizzazione in piccola, media e grande impresa, ossia sta diventando anche veloce, come sempre più vuole il mercato odierno. Veloce nell’adattarsi a nuove abitudini, e tutti sanno quanto queste siano cambiate negli ultimi mesi; veloce nel capire le esigenze sempre più stringenti dei clienti; veloce
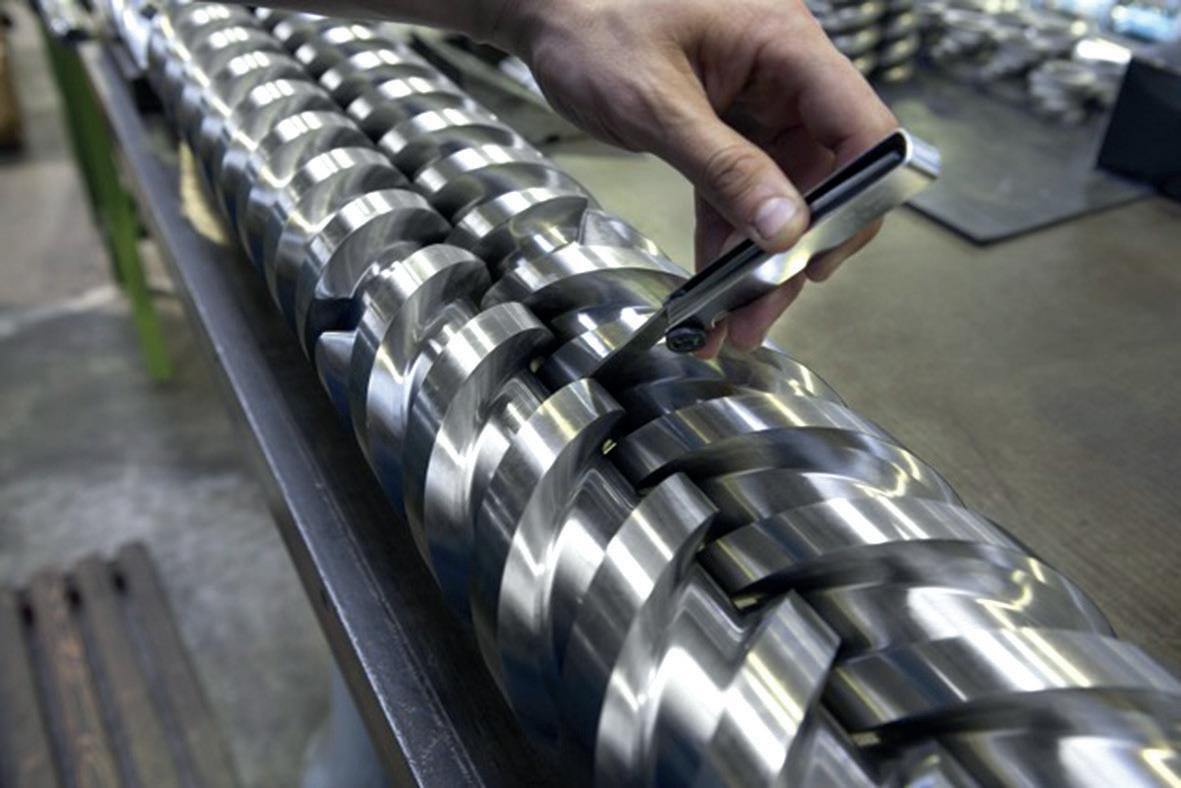
Un’elevata precisione deve essere posta nella realizzazione di ogni componente meccanico destinato a macchine e impianti industriali, ma nel caso di viti e cilindri diventa essenziale
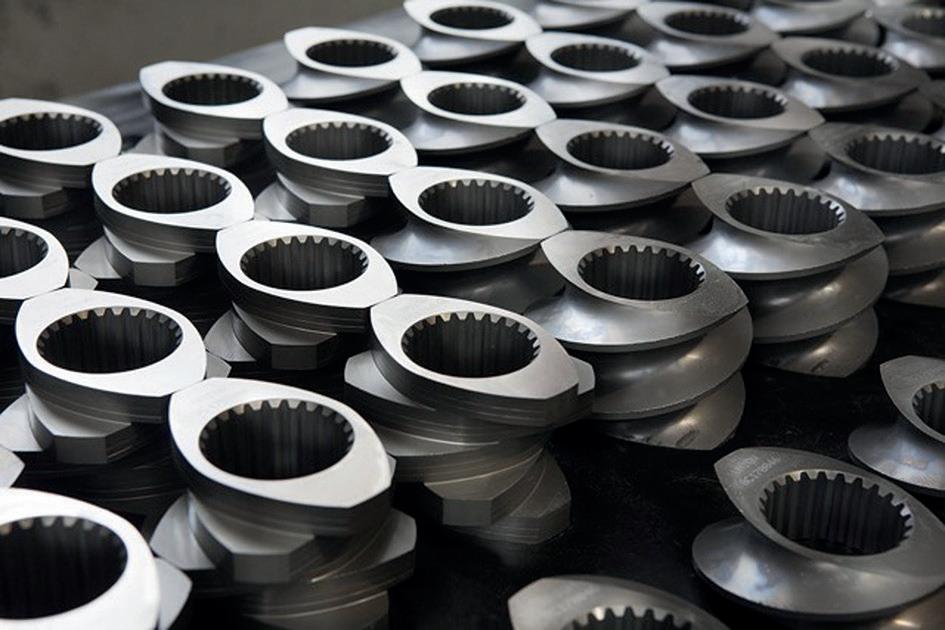
nell’anticipare gli sviluppi tecnologici e tradurli in innovazione. Insomma, capace di adattarsi al cambiamento ma senza snaturarsi, il che vuol dire guardare indietro a quello che si è fatto e avanti verso dove si vuole andare. Ed è quello che sta accadendo in Mast, come emerge dal racconto di Carlo Arioli, che ringraziamo per aver risposto ad alcune nostre domande.
LA VOSTRA AZIENDA PUÒ ESSERE IDENTIFICATA COME IL TIPICO TERZISTA DEL TESSUTO INDUSTRIALE ITALIANO, CHE NEL VOSTRO CASO SIGNIFICA COSTRUIRE VITI E CILINDRI PER GLI IMPIANTI DI ESTRUSIONE DEI PIÙ GRANDI COSTRUTTORI. IN QUEST’OTTICA, QUALI SONO GLI SVILUPPI TECNOLOGICI IN ATTO CHE MAGGIORMENTE EMERGONO DALLE RICHIESTE DEI VOSTRI CLIENTI?
“Effettivamente Mast è un’azienda che ben rappresenta il cosiddetto terziario avanzato e in questa veste dobbiamo essere sempre pronti a soddisfare ogni nuova richiesta da parte dei clienti. E se questi ci forniscono le specifiche tecniche per realizzare i loro prodotti, sta a noi essere bravi a sviluppare i processi produttivi più idonei per arrivare a fornire viti e cilindri che assicurino, per esempio, le tolleranze e i gradi di finitura richiesti: caratteristiche sempre più stringenti. Tutto ciò, inoltre, utilizzando spesso nuovi tipi di acciaio, come quelli ottenuti per sinterizzazione delle polveri, i cosiddetti “HIP”, i quali, oltre che essere particolarmente costosi, richiedono utensili e processi di lavorazione specifici”. DI PARI PASSO CON LO SVILUPPO TECNOLOGICO, RECENTEMENTE AVETE AVVIATO UN PIANO DI INVESTIMENTI PER AMMODERNARE LA VOSTRA ATTIVITÀ E IL VOSTRO STABILIMENTO. QUALI NUOVI MACCHINARI AVETE ACQUISTATO E A CHE PUNTO È LA REALIZZAZIONE DELLA NUOVA SEDE?
“Gli investimenti per noi sono un processo continuo, che non si ferma mai. Alcune volte vengono fatti “passi” un po’ più importanti, come nel caso dell’acquisto della nuova macchina per la rettifica tangenziale o del nuovo centro di lavoro per i cilindri, altre volte “passi” un poco meno impegnativi dal punto di vista economico, ma molto significativi per l’efficientamento, come la completa ristrutturazione della nostra foratrice per cilindri. In tutto questo, non va taciuto il continuo aggiornamento degli strumenti di misura, dei vari utensili o dei sistemi CAD-CAM in uso nei nostri reparti. Nel contempo sta proseguendo il progetto del nostro nuovo sito produttivo, anche se l’emergenza Covid-19, unita ad alcune lungaggini burocratiche, non ci ha certo aiutato negli ultimi 12-18 mesi”.
QUEST’ULTIMO ACCENNO ALL’EMERGENZA COVID-19 CI OFFRE LO SPUNTO PER UNA DOMANDA, QUASI D’OBBLIGO DI QUESTI TEMPI, LEGATA ALLA PANDEMIA. QUALI SONO GLI EFFETTI DELL’ULTIMO DIFFICILE ANNO DI EMERGENZA SANITARIA SUL VOSTRO MERCATO DI RIFERIMENTO E QUALI SONO LE RIPERCUSSIONI SULLA VOSTRA ATTIVITÀ?
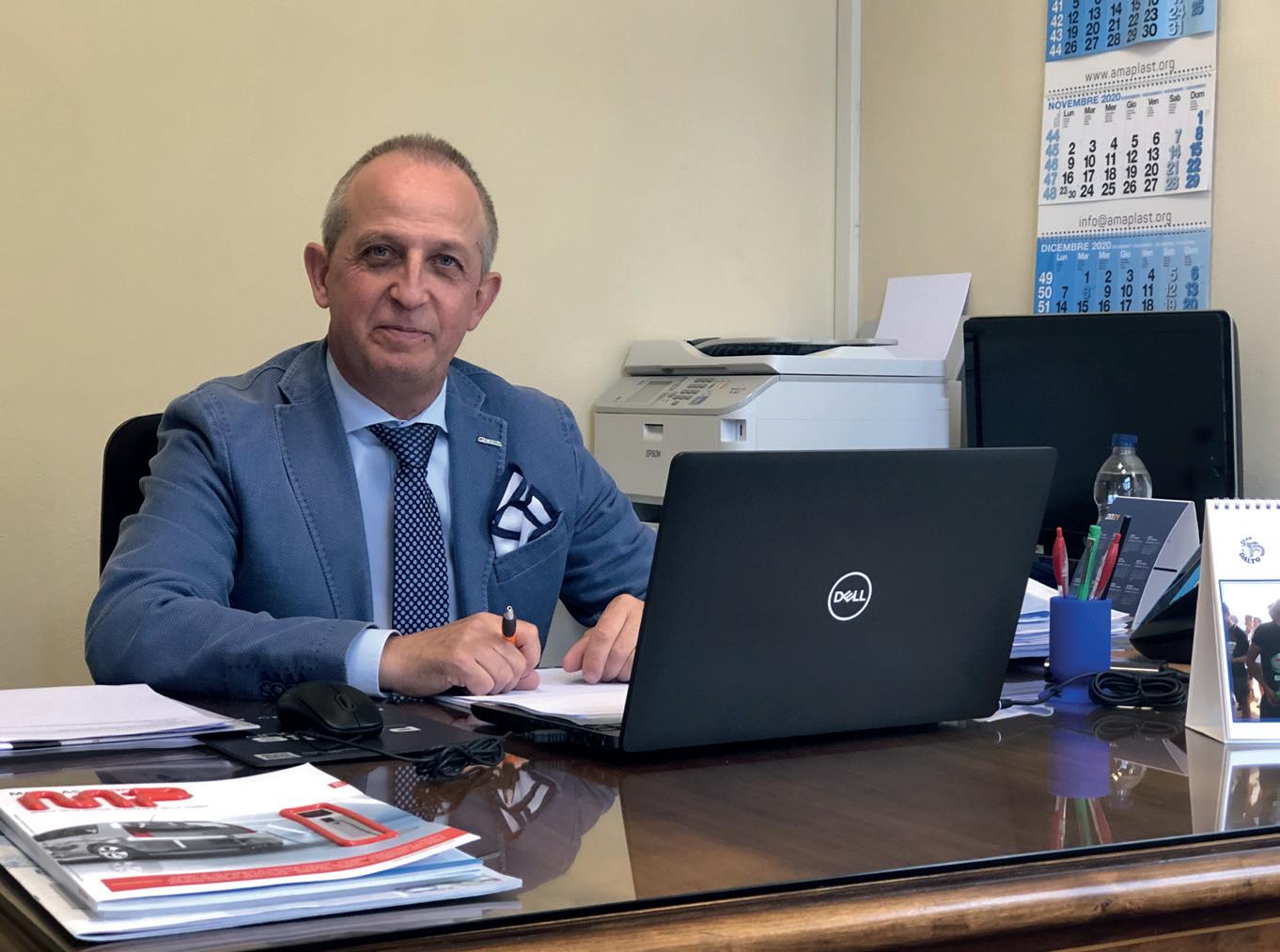
Le sezioni vite sono una delle parti base delle viti corotanti, che, insieme ai cilindri, costituiscono i prodotti realizzati da Mast
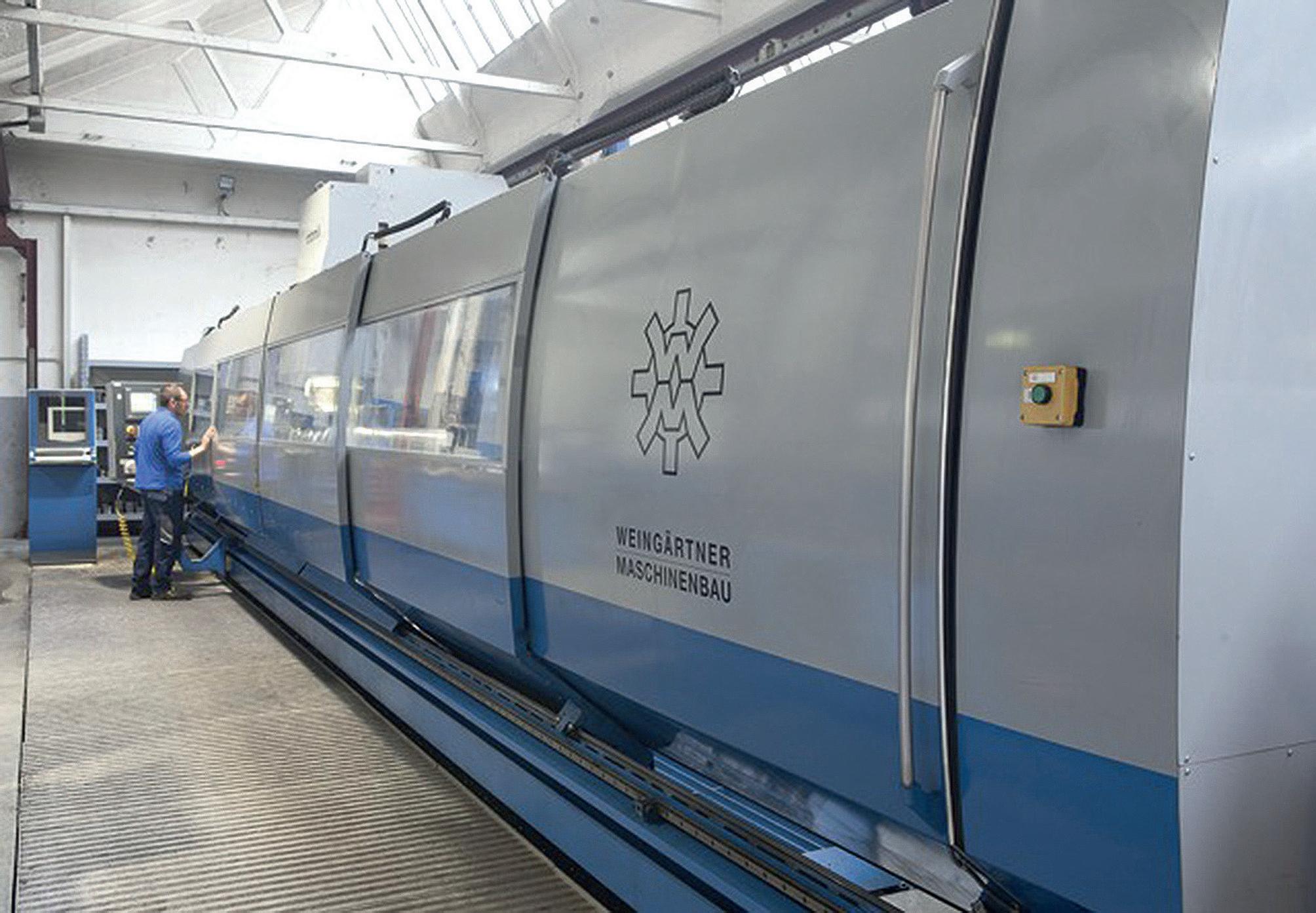
“La pandemia ci ha colpito su vari fronti. Il bilancio 2020 non si è chiuso in passivo, ma certamente con un forte calo del fatturato dal mercato sia interno sia estero. In questo momento i segnali che riceviamo sul fronte della domanda sono molto positivi e stiamo velocemente tornando ai numeri, per così dire, “pre-Covid”... anche se la mancanza di materie prime, che di questi tempi affligge un po’ tutta la nostra filiera e di cui l’aumento dei prezzi è una conseguenza, ci sta preoccupando”.
SULLA SCORTA DI QUESTE CONSIDERAZIONI, AVETE SFRUTTATO, E COME, LA TECNOLOGIA PER ORGANIZZARE INCONTRI A DISTANZA CON FORNITORI E CLIENTI, IN MODO DA MANTENERE VIVE LE RELAZIONI COMMERCIALI NONOSTANTE LE LIMITAZIONI AGLI SPOSTAMENTI DI QUESTI MESI?
“Oltre all’adeguamento delle norme igienico-sanitarie nei luoghi di lavoro, la pandemia ci ha costretto a modificare le abitudini commerciali, con una drastica riduzione delle trasferte per far visita ai clienti, ma anche con l’azzeramento delle partecipazioni alle manifestazioni fieristiche. Non sempre è stato possibile compensare tutto questo utilizzando le tecnologie di comunicazione di cui oggi disponiamo. Queste ci consentono di supplire in qualche modo alla riduzione degli spostamenti, anche se, purtroppo, non tutte le relazioni commerciali e i rapporti di lavoro si riescono a risolvere facendo ricorso allo smart working. Inoltre, probabilmente questo cambio di abitudini si cristallizzerà in parte anche quando l’emergenza sanitaria finirà e si potrà tornare a muoversi e a incontrarsi come un tempo”.
Tra le applicazioni delle teste di estrusione di EDI rientrano foglie e laminati per la produzione di dispositivi di protezione personale che hanno offerto un grande contributo nella lotta al Covid-19 degli ultimi mesi
NORDSON MIGLIORA LA GAMMA EPC DI EDI
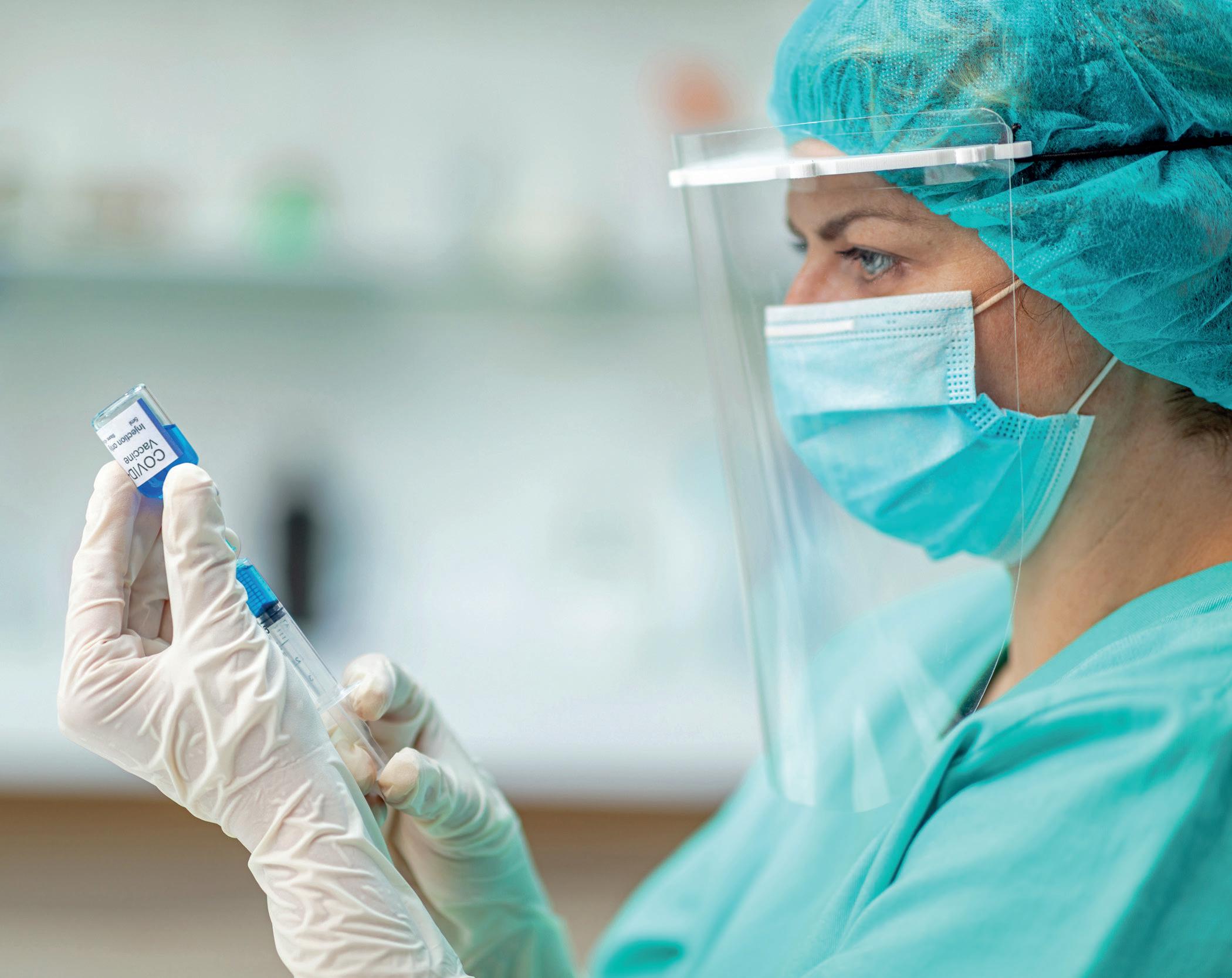
TESTE DI ESTRUSIONE PIÙ FACILI DA USARE E PIÙ PRODUTTIVE: QUESTIONE DI PARZIALIZZATORI
DAL 2012 NORDSON CORPORATION RAGGRUPPA LE ATTIVITÀ DI NORDSON, EDI E BKG E OGGI OPERA COME UNO DEI PRINCIPALI FORNITORI GLOBALI DI LINEE E ATTREZZATURE AUSILIARIE PER L’ESTRUSIONE E LA GRANULAZIONE, CON UNA STRUTTURA MODERNA E PRODOTTI IN CONTINUO AGGIORNAMENTO
Il sistema di parzializzazione delle teste di estrusione EPC di EDI, per la laminazione e il rivestimento, è stato migliorato per rendere più semplice il controllo dei bordi laterali e ridurre i tempi di fermo macchina legati alle operazioni di variazione della larghezza degli estrusi, così come di pulizia delle attrezzature. Le teste di estrusione EPC sono dotate di un sistema di regolazione interno per controllare l’ingrossamento dei bordi laterali, che consente di ridurre i costi legati al consumo di resina e agli scarti di rifilatura, e di uno esterno, per regolare la larghezza dell’estruso. Le migliorie progettuali apportate si traducono in vantaggi quali: - maggiore facilità di controllo dei bordi laterali: per la regolazione separata dei singoli componenti del regolatore della larghezza, un ingranaggio a pignone e cremagliera è stato sostituito con un perno filettato, che facilita la regolazione di precisione dei bordi laterali, riducendo la quantità delle rifilature necessarie e gli sprechi di materiale; - maggiore facilità di regolazione manuale della larghezza del parzializzatore: un riduttore utilizzato per la regolazione della larghezza complessiva di parzializzazione è stato sostituito inserendo un dado sull’asta di regolazione, riducendo in tal modo la larghezza e il peso del
sistema di parzializzazione e migliorando l’accesso per gli operatori; - costruzione più robusta e maggiore facilità di controllo: la regolazione del parzializzatore risulta semplificata grazie a una nuova guida di supporto dell’asta; - maggiore facilità di accesso per le operazio-

I tre rami d’azienda di Nordson Corporation sono stati accorpati in un nuovo grande stabilimento a Chippewa Falls, negli Stati Uniti, a poca distanza dalla sede originaria di EDI
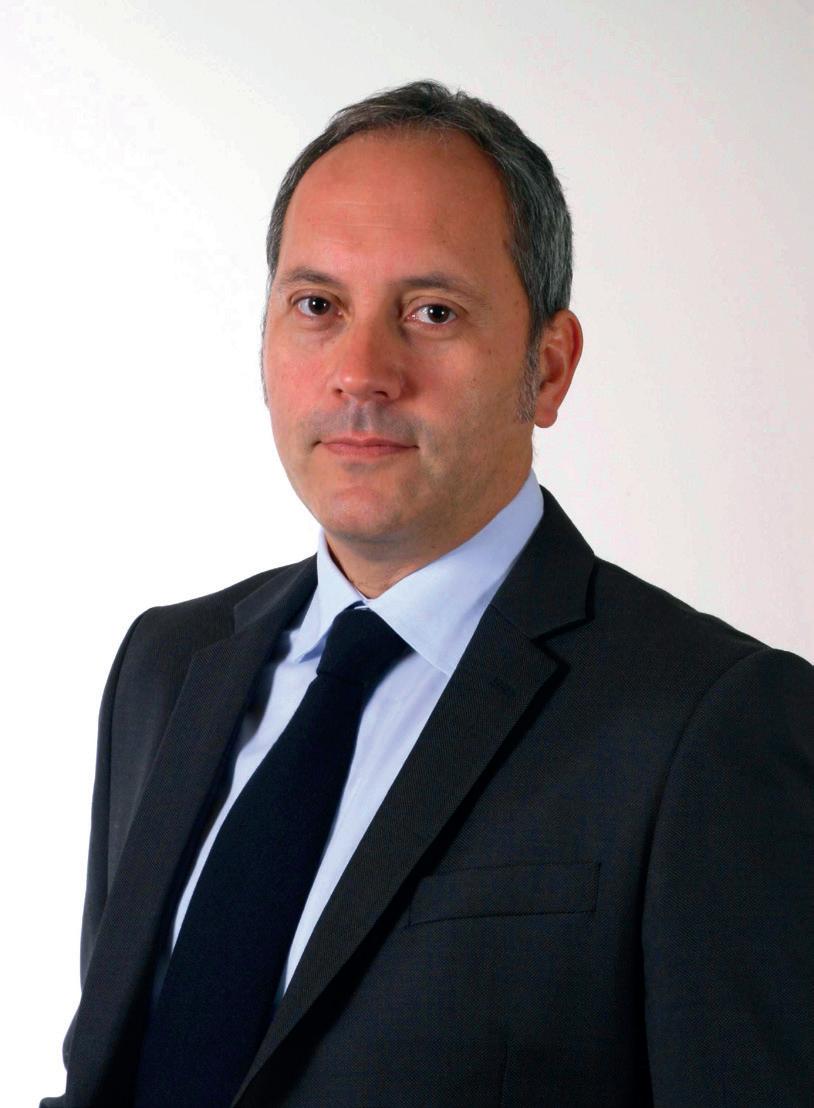
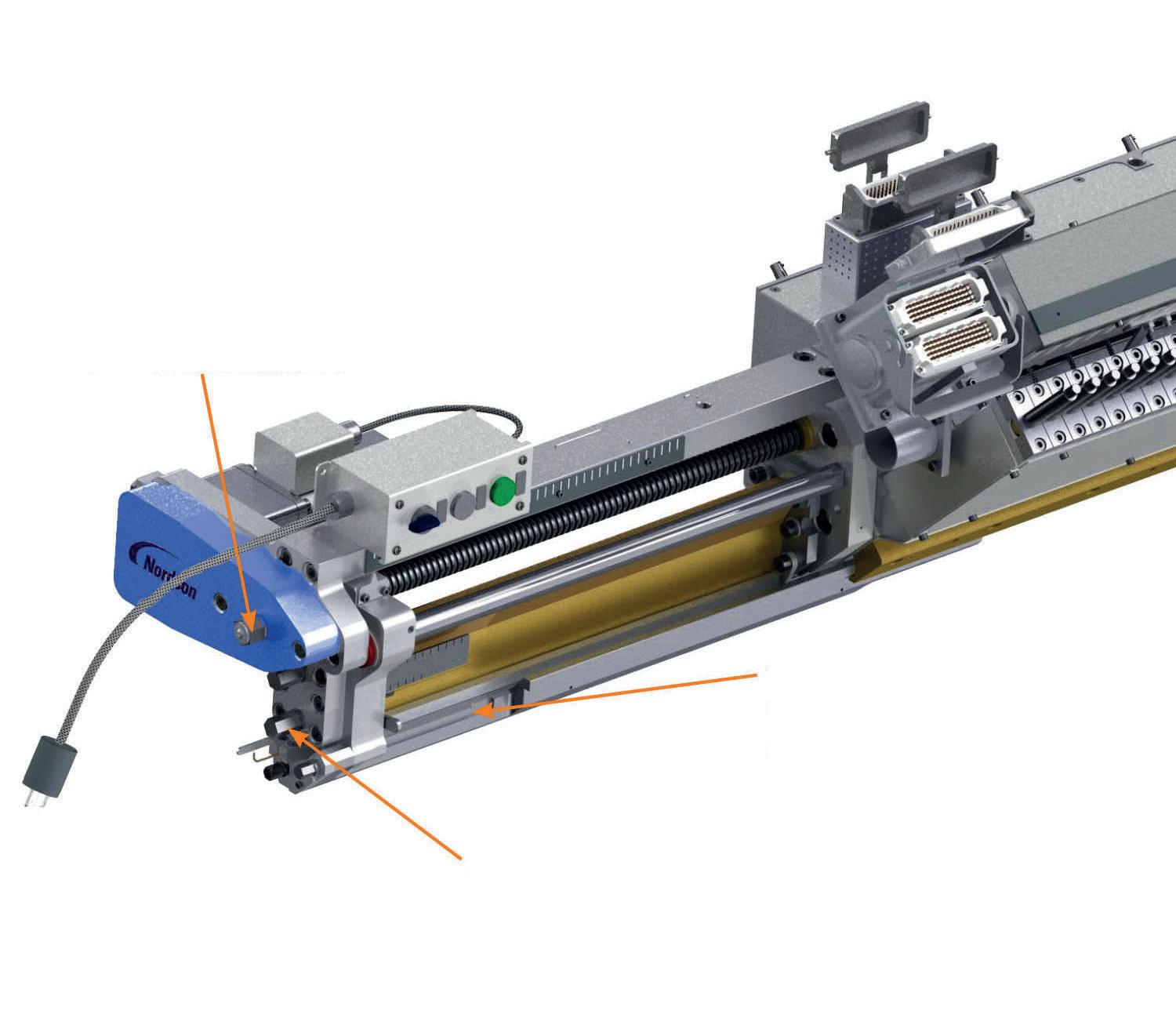
Le principali funzioni del sistema di parzializzazione delle teste EPC
Il dado dell’asta di regolazione regola la larghezza complessiva del parzializzatore
Il supporto della barra del parzializzatore ne limita la flessione
Il sistema a perno filettato regola i singoli componenti del parzializzatore
ni di pulizia e manutenzione: il regolatore di larghezza esterno a basso profilo può essere smontato come unico componente o può essere sfilato per installare un raschia-labbri senza dover smontare l’intero gruppo parzializzatore; analogamente, i componenti del regolatore interno possono essere smontati rimuovendo sei perni presenti all’estremità del parzializzatore, senza dover disassemblare l’intero gruppo. “Le migliorie apportate da Nordson alla progettazione del sistema EPC risolvono i problemi evidenziati dalle aziende di trasformazione, soprattutto per quanto riguarda la spinta competitiva ad aumentare la produttività. Le nostre teste di estrusione di nuova progettazione sono più semplici da usare e da mantenere, consentendo lo stesso efficace controllo dei bordi laterali: il fiore all’occhiello del sistema EPC”, ha dichiarato Patrick Meinen, direttore globale delle linee di prodotto per le teste EDI. Il sistema interno di parzializzazione delle teste EPC consente la regolazione di precisione del profilo d’uscita del rivestimento. Nelle teste sprovviste del sistema di regolazione della larghezza EPC, il polimero fuso evidenzia un flusso trasversale, che crea un ingrossamento più esteso dei bordi laterali dovuto al “necking” all’uscita della testa. Nel sistema EPC, i componenti del parzializzatore interno per la regolazione del profilo dei bordi laterali sono sistemati a valle del collettore principale, uno nella sezione precedente i labbri di uscita e l’altro nel collettore secondario. Regolando le posizioni reciproche di questi componenti è possibile ridurre il flusso di polimero alle estremità del rivestimento, riducendo così al minimo l’ingrossamento dei bordi laterali.
CINQUANT’ANNI DI TESTE DI ESTRUSIONE
Lo scorso 15 febbraio EDI ha tagliato il traguardo dei cinquant’anni di presenza nel mercato. La piccola attività avviata nel 1971 con un organico di cinque persone, nella cittadina di Chippewa Falls (USA), oggi è parte di Nordson Corporation ed è conosciuta a livello globale come uno dei principali costruttori di teste piane per l’estrusione di film, foglie e rivestimenti in diversi materiali polimerici. Nata come Extrusion Dies Incorporated, l’azienda è stata acquisita da Nordson nel 2012, che lo scorso anno ha accorpato i suoi tre rami d’azienda proprio a Chippewa Falls in un nuovo grande stabilimento, dove adesso si trova anche la sede centrale del marchio EDI, a poca distanza da quella originaria. Attualmente il marchio può contare su diversi stabilimenti di produzione negli Stati Uniti, in Germania, in Giappone e in Cina e su personale di vendita e di assistenza che opera in altri paesi, con un organico che a livello globale conta 350 persone. “Fondamentali per il successo del marchio EDI sono stati la competenza e l’impegno di progettisti, tecnici, meccanici e addetti al servizio clienti che lavorano alle nostre dipendenze in ogni parte del mondo. Si tratta di persone che hanno costruito la nostra reputazione di azienda affidabile e di qualità e che hanno prodotto numerose innovazioni, dal sistema automatico di controllo dello spessore, introdotto negli Anni Settanta, a diversi avanzamenti nel campo delle teste di estrusione per foglie, film e rivestimenti, introdotti dopo l’acquisizione da parte di Nordson”, ha dichiarato Scott Smith, responsabile del ramo d’azienda EDI di Nordson. “Il nuovo hub globale del marchio EDI è la riprova della fiducia che nutriamo in un futuro di crescita e innovazione costanti. Questi primi cinquant’anni non sono stati che un inizio”, ha aggiunto Smith.
Nordson nel nostro Paese La filiale italiana venderà direttamente i prodotti BKG
Le vendite e il servizio di assistenza in Italia dell’intera gamma di prodotti a marchio BKG di Nordson Corporation verranno gestiti direttamente dalla filiale nel nostro Paese. La responsabilità dell’assistenza di tutti i clienti italiani sarà affidata ad Alberto Bondavalli, che assumerà la direzione del team italiano di BKG dedicato principalmente a sistemi di pellettizzazione, pompe volumetriche e sistemi di filtrazione per l’industria dei polimeri. “Alberto Bondavalli segue i nostri clienti dal 2013 e prima di approdare alla nostra azienda ha maturato un’esperienza decennale in Italia, nella vendita di beni strumentali nei settori della plastica e degli imballaggi, per cui già conosce la nostra clientela italiana e ha le carte in regola per poter lavorare direttamente con le aziende interessate e per coordinare le attività fondamentali di supporto alle applicazioni e di assistenza tecnica con i responsabili della zona Emea”, ha dichiarato il responsabile vendite Andreas Trouvain. “Per 17 anni Gupa è stata una partner capace e affidabile della nostra azienda e, ora che entrambe le società si stanno preparando a una svolta, desidero ringraziare tutto il team Gupa per essere riuscito a introdurre e consolidare i nostri prodotti sul mercato italiano e gli auguro di avere successo in quelli che saranno gli sviluppi futuri della sua attività”, ha dichiarato Alberto Bondavalli.
Alberto Bondavalli
NEWS
SISTEMI PER TRASPORTO PNEUMATICO
Componenti altamente resistenti all’usura
È in continua espansione la gamma di componenti altamente resistenti all’usura di HS Umformtechnik, tra cui la famiglia HVA Niro di raccordi a gomito per tubi in acciaio inossidabile, i raccordi a “Y”, i riduttori e le stazioni di montaggio. I raccordi a gomito in acciaio inossidabile HVA Niro sono stati sviluppati appositamente per il trasporto di granuli in plastica rinforzata con fibre di vetro e, grazie alla loro lunga durata, riducono al minimo i cicli di cambio dei raccordi. Sono disponibili in acciaio Aisi 304/Aisi 304 L con diametro da 38 a 139,7 mm e spessore di parete da 1,5 a 5 mm, nei raggi 75, 150, 250, 300, 500, 800 e 1000 mm. Un punto di forza di questi raccordi è rappresentato dalla semplicità di installazione e dalla facilità di gestione, in quanto non sono richiesti attacchi speciali. Tra i prodotti di HS Umformtechnik altamente resistenti all’usura rientrano anche i raccordi DWR a doppia parete. La doppia parete forma un’intercapedine che consente di ridurre l’usura e aumentare la durata utile anche in presenza di sollecitazioni molto elevate. Inoltre, per alcuni materiali movimentati è consigliabile versare nell’intercapedine del cemento ad alta resistenza. I raccordi a gomito e a “Y” in vetro, le spie di livello anch’esse in vetro e le stazioni di montaggio dei componenti in vetro completano la gamma ad alta resistenza all’usura del costruttore tedesco. I componenti in vetro borosilicato 3.3 hanno una durata 10-20 volte superiore a quella dei prodotti standard in acciaio inossidabile. Sono disponibili raccordi a gomito in vetro a 90° e 45°, con diametro di 47, 56 e 66 mm e raggio di 250 e 500 mm. Per collegare componenti in vetro e in acciaio inossidabile sono a disposizione gli attacchi a tubo DVK 6 di vario diametro.
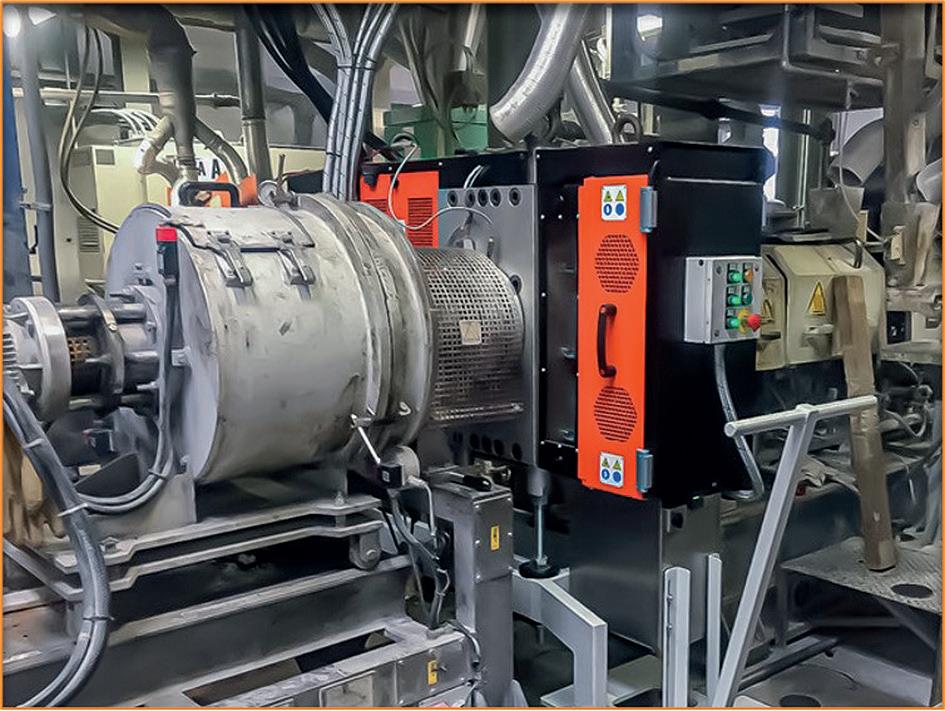
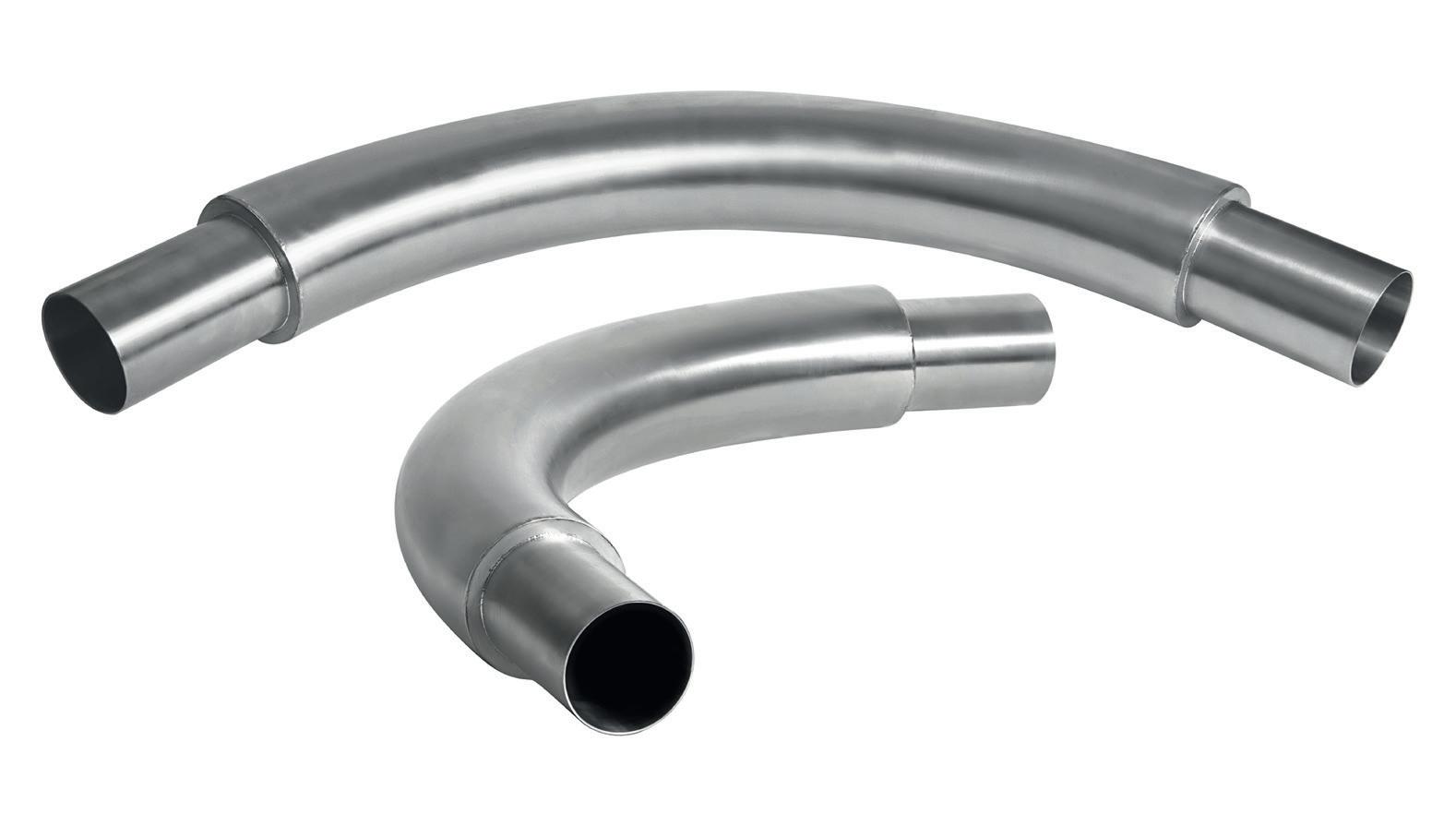
Alcuni raccordi della serie DWR a doppia parete
Mepol sceglie BD Plast Cambiafiltri compatto, ma innovativo e performante
Il cambiafiltri BDOx3 BF 140 di BD Plast è in funzione presso Mepol
Dalla fine di giugno 2020 il cambiafiltri autopulente BDOx3 BF 140 di BD Plast opera con soddisfazione a Riese Pio X (Treviso), presso la società Mepol, che dal 1996 produce compound termoplastici ed ecosostenibili certificati. Mepol fa di capacità produttiva, competenza e know-how i suoi punti di forza per fornire supporto tecnico per la creazione di prodotti su misura e un’assistenza efficiente. Dal 1986 BD Plast è invece specializzata nella costruzione di cambiafiltri e sistemi per l’estrusione dei polimeri, sfruttando flessibilità e capacità di personalizzazione dei prodotti al fine di soddisfare anche le esigenze più particolari. Grazie alla collaborazione tra le due aziende durante la fase di progettazione e costruzione, BD Plast ha realizzato un prodotto compatto con caratteristiche innovative, riuscendo ad assecondare le aspettative di Mepol, che ha così incrementato l’efficienza di una linea destinata alla filtrazione e alla granulazione di polipropilene caricato con carbonato di calcio. Il cambiafiltri autopulente BDOx3 BF si rivela la soluzione ideale anche per il retrofit di linee esistenti, in quanto non richiede spazi aggiuntivi rilevanti, che spesso non sono disponibili. Uno dei punti di forza del sistema BDOx3 BF consiste nella capacità di svolgere il ciclo di autopulizia con contropressioni particolarmente basse. A questo si unisce il fatto che si tratta di un cambiafiltri a flusso continuo in cui, a differenza di altre tipologie di cambiafiltri, la sostituzione degli elementi filtranti avviene senza fermare l’impianto, quindi senza lo spreco di tempo e gli scarti di materiali tipici delle fasi di arresto e riavviamento della linea. Nel cambiafiltri autopulente di BD Plast, inoltre, la sostituzione delle reti avviene con l’espulsione automatica della piastra rompitrice (breaker plate), consentendo l’agevole sostituzione dell’elemento filtrante e un ulteriore risparmio di tempo. La capacità di autopulizia a bassa contropressione, l’espulsione automatica della breaker plate e i ridotti tempi di spurgo sono gli elementi chiave che consentono di arrivare fino a 200 cicli di autopulizia prima che si renda necessario il cambio reti.
Servopompa Piisma Un investimento che si ripaga in un anno
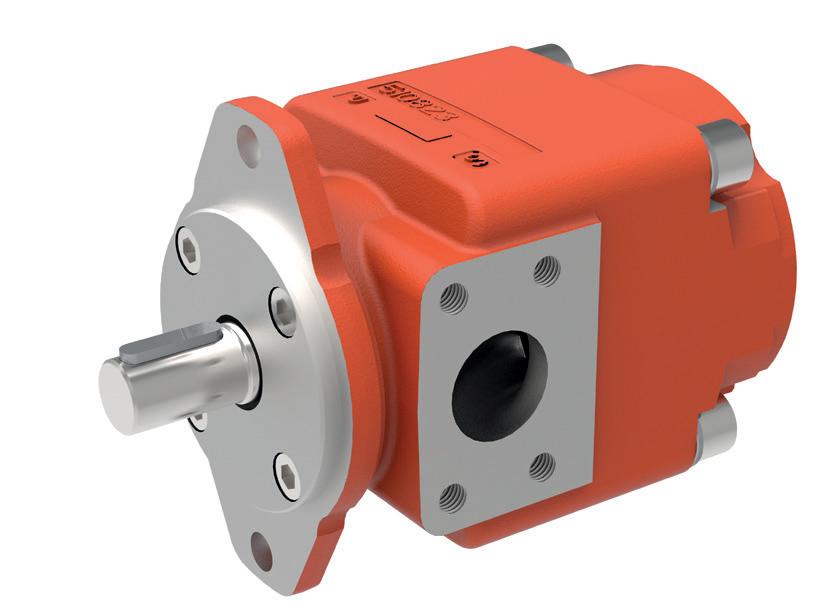
Secondo quanto si legge nel Green Deal europeo, sono necessari 25 anni per permettere a un settore industriale di trasformarsi. Si stima quindi che i prossimi quattro anni siano d’importanza chiave per le aziende, al fine di definire le azioni da intraprendere per raggiungere l’obiettivo della neutralità climatica nel 2050. Con l’obiettivo di agevolare questo processo, l’Europa ha messo a disposizione delle aziende il Fondo per una transizione giusta (JTF), per sostenerle nel percorso verso tecnologie a basse emissioni di CO2 e incentivare i processi di ricerca e innovazione. In questo contesto si collocano le nuove tecnologie sviluppate per l’oleodinamica, come il sistema a giri variabili comunemente definito “servopompa”. Spesso, infatti, gli impianti oleodinamici sono sovradimensionati e sprecano molta dell’energia erogata. Grazie alle servopompe, oggi è possibile raggiungere un risparmio energetico fino all’80% semplicemente sfruttando in maniera intelligente i tempi di inattività della macchina. Questa tecnologia, in particolare, presenta un grande potenziale di crescita nel settore delle presse a iniezione, portando a una riduzione della rumorosità fino a 20 dB durante l’attività della macchina e del 100% nei tempi d’inattività. Ciò vale sia nel caso in cui si costruisca un nuovo impianto sia nel caso di interventi di revamping. Per questo, la società Interfluid ha sviluppato Piisma, un sistema modulare con servopompa installabile su qualsiasi pressa esistente, sia di piccolo che di grande tonnellaggio, sia con circuito dotato di pompa tradizio-

Pompa a ingranaggi interni Bucher della serie QXEHX
I vantaggi di Piisma
● Risparmio energetico fino all’80%. ● Regolazione del numero di giri e della pressione in funzione del singolo momento del processo produttivo e della reale necessità di funzionamento. ● Semplificazione dell’impianto idraulico attraverso, per esempio, l’eliminazione delle valvole proporzionali. ● Riduzione della rumorosità fino a 20 dB durante il ciclo macchina e del 100% durante la pausa del ciclo. ● Massima ripetibilità dei parametri di portata e pressione. ● Maggiore rendimento del sistema. ● Minore riscaldamento dell’olio e dell’ambiente circostante.
nale che con circuito ad accumulatori oleopneumatici. Il sistema è controllato da un inverter accoppiato a una pompa a ingranaggi interni Bucher serie QXEHX, la cui potenza può essere adattata di volta in volta ai requisiti necessari, in modo da eliminare quasi del tutto le perdite a macchina inattiva.
Quando la macchina a iniezione non sta eseguendo alcun movimento, si ferma anche il motore della pompa. Gli stampatori che hanno avuto modo di testare Piisma con le pompe di Bucher, con cui Interfluid collabora da circa tre anni, hanno notato un livello di rumorosità ancora più basso di quello ottenuto con le precedenti tecnologie, con un notevole miglioramento della qualità del lavoro degli operatori. Interfluid supporta il cliente in ogni fase del progetto, dall’ideazione del sistema, studiato per risolvere specifiche necessità produttive, al set-up iniziale della macchina. Le esperienze condotte finora hanno dimostrato che il risparmio ottenuto grazie a Piisma permette di ripagare l’investimento in un anno.
NEWS
Maag a Chinaplas Nuove generazioni alla ribalta
Uno dei prodotti a marchio Ettlinger esposti dal Gruppo Maag a Shenzhen
Il fornitore globale di soluzioni per sistemi di pompaggio, filtrazione, granulazione, polverizzazione, riciclo e digitalizzazione per il settore dei polimeri, Gruppo Maag, ha esposto le sue ultime innovazioni alla fiera Chinaplas 2021, svoltasi a Shenzhen (Cina) dal 13 al 16 aprile. In evidenza: il filtro ERF350 ad alte prestazioni per la filtrazione di polimeri fusi fortemente contaminati. Di tipo autopulente e a tamburo rotante perforato, attraverso il quale scorre un flusso continuo del fuso dall’esterno verso l’interno, il filtro è dotato di una lama che rimuove i contaminanti trattenuti sulla superficie e li convoglia al sistema di scarico. Ciò consente al filtro di funzionare automaticamente, senza interruzioni per lunghi periodi e senza dover sostituire l’elemento filtrante. Ne derivano perdite minime di materiale e ottima miscelazione e omogeneizzazione del fuso. Altro prodotto in mostra: il sistema di taglio immerso Pearlo per la produzione efficiente e flessibile di granuli sferici, con velocità di produzione fino a 36 mila kg all’ora. Compatto e modulare, dall’ingombro ridotto, il sistema si basa sulla tecnologia EAC a controllo elettronico, che garantisce una pressione precisa dei coltelli durante il funzionamento, consentendo così lunghi tempi attivi senza interruzioni e una qualità elevata del granulato. Nello stesso campo, è stato presentato il sistema di taglio a secco di terza generazione Baoli-3 per la lavorazione di materiali sia duri che morbidi. Come nelle precedenti generazioni, il sistema di bloccaggio automatico della camera di taglio consente una movimentazione rapida, garantendo al contempo la sicurezza dell’operatore. A Chinaplas, Maag ha presentato anche la pompa a ingranaggi Extrex in versione x6, di cui sono stati completamente riprogettati e ridisegnati i componenti, dagli alberi ai cuscinetti e alle guarnizioni, ottimizzandone l’interazione. I denti degli ingranaggi a bassa compressione, sviluppati specificamente per questa versione, consentono di ottenere pressioni molto elevate con basse velocità di taglio. Il risultato è un ulteriore aumento della qualità del prodotto, dell’efficienza volumetrica, nonché della ripetibilità e della sicurezza della produzione.
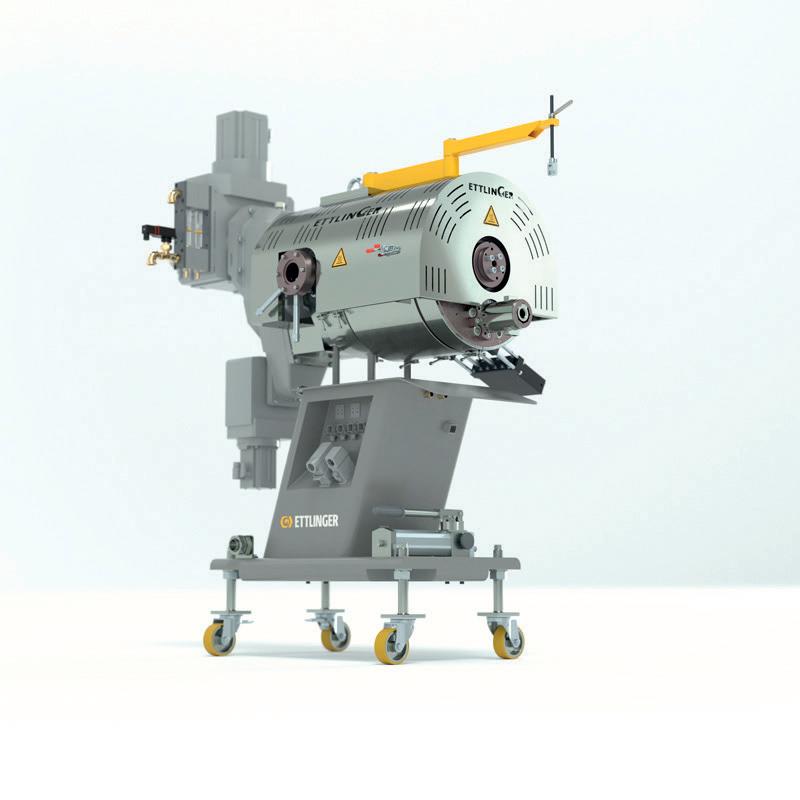
Con il misuratore di livello a ultrasuoni PCE-ULM 10 di PCE Instruments è possibile sapere in ogni momento se i silos di stoccaggio continuano a essere sufficientemente pieni. Dispositivo in grado di determinare il livello di riempimento di un silo, questo misuratore di livello a ultrasuoni trova applicazione in molti settori industriali e, più in generale, in tutti i campi che prevedono lo stoccaggio di prodotti di vario tipo. Il metodo di misurazione a ultrasuoni rappresenta una so-
Rilevazione della quantità di materiale all’interno di un silo di stoccaggio e indicazione della temperatura ambientale sono le funzioni svolte in contemporanea dal rilevatore di livello a ultrasuoni PCE-ULM 10 Misuratore a ultrasuoni
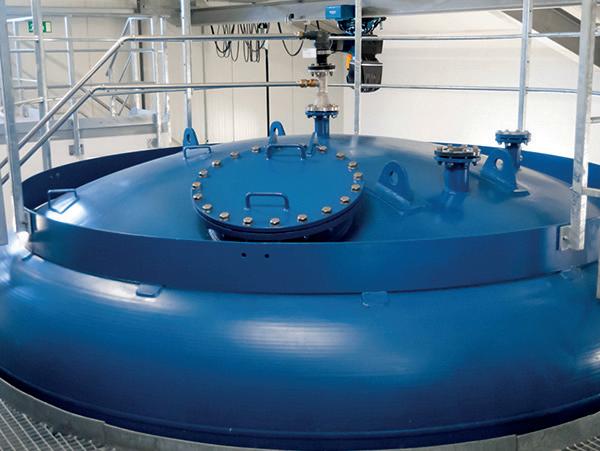
Livello nei silos sotto controllo
luzione consolidata ed economica per la misura di livello in liquidi e solidi sfusi. Il principio di funzionamento è semplice: il sensore di livello emette gli impulsi a ultrasuoni, la superficie del fluido o del prodotto contenuto nel silo riflette il segnale e il sensore lo rileva nuovamente. Il “tempo di volo” del segnale a ultrasuoni riflesso è direttamente proporzionale alla distanza percorsa e, conoscendo la geometria del serbatoio, è così possibile calcolare il livello del prodotto contenuto nel silo. Con la misurazione di livello a ultrasuoni, le proprietà fisiche e chimiche del prodotto contenuto nel silo non influiscono sui risultati della misurazione. È quindi possibile effettuare misurazioni attendibili in presenza di sostanze aggressive, abrasive, viscose e adesive. La misurazione del livello nei serbatoi avviene dall’alto, senza che vi sia contatto con il liquido. Gli impulsi ultrasonici emessi dal trasmettitore vengono riflessi e inviati a un display con microprocessore, che li elabora proporzionalmente alla loro frequenza, rilevando costantemente l’altezza della colonna. Il misuratore di livello PCE-ULM 10, grazie al segnale d’uscita da 4-20 mA, può essere collegato a un PLC o da altri apparati di controllo o di regolazione. La profondità di misura di 10 m consente di utilizzare questo dispositivo per il controllo di silos anche di grandi dimensioni. In base al tipo di applicazione, il misuratore di livello a ultrasuoni può indicare come valore di misura il livello o la distanza tra il contenuto e il sensore. Oltre a sapere in ogni momento se il silo continua a essere sufficientemente pieno, questo dispositivo rileva allo stesso tempo la temperatura ambientale. L’alto grado di protezione IP del misuratore garantisce la protezione dei componenti elettronici in caso di possibile perdita d’acqua.