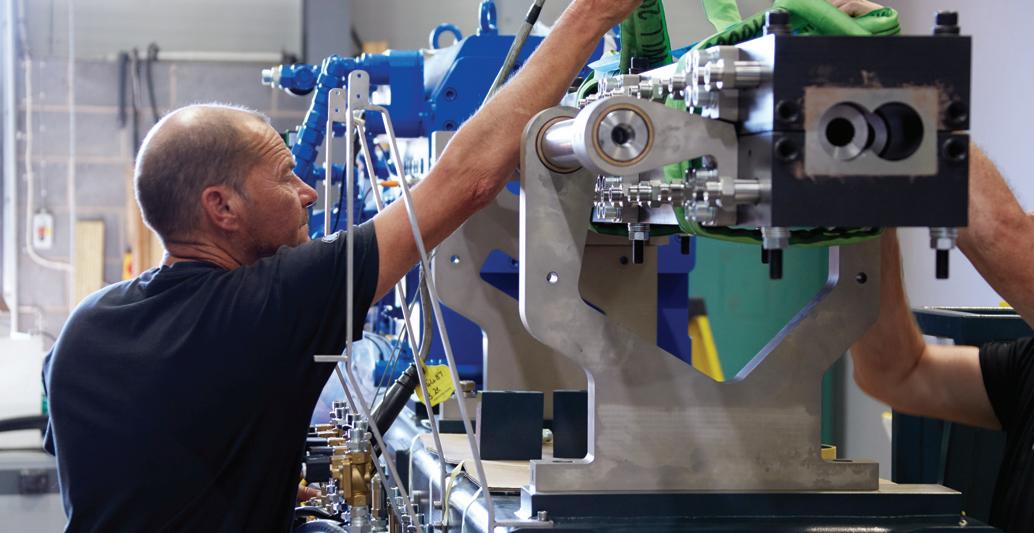


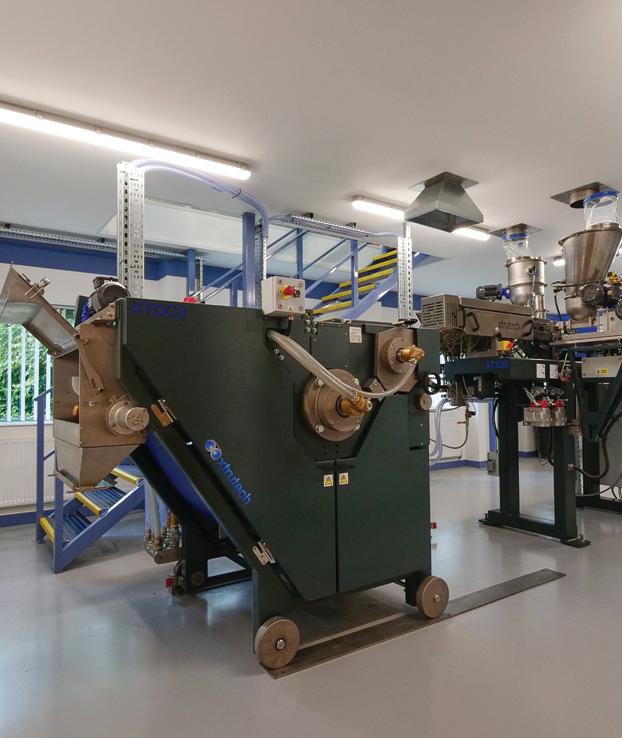
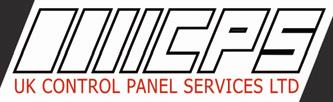
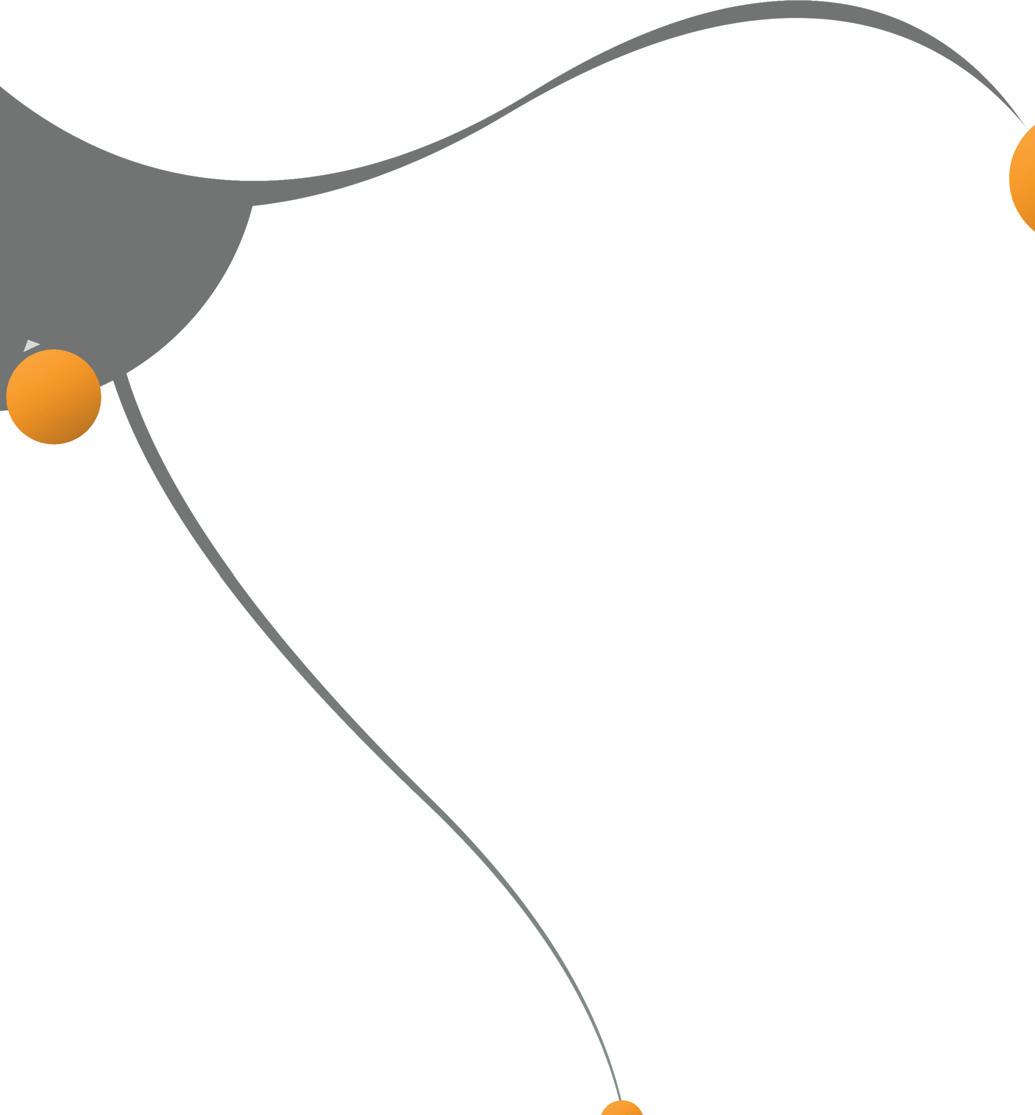
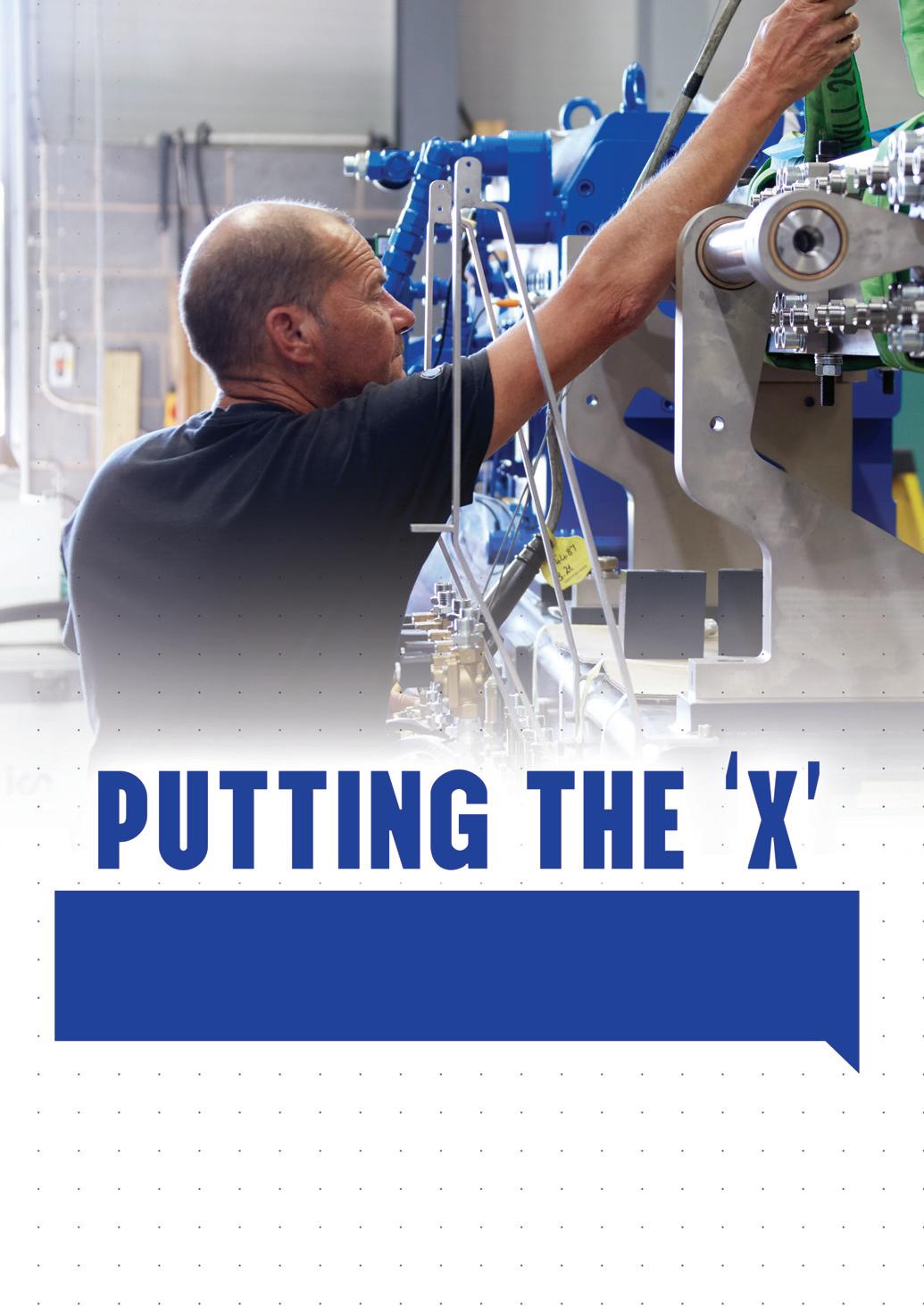
Stoke-on-Trent-based Xtrutech is known for the design and manufacture of the XTS Twin-Screw Extruders, as well as for being the leading independent supplier of spare parts and services for twin screw extrusion. Managing Director Ryan Moore explained the secrets of the company’s success to Hannah Barnett.
Since it was founded in 2002, Xtrutech has established a presence in a diverse range of sectors including powder coatings, thermoplastics, biopolymers and pharmaceuticals.
Ryan Moore joined the company in 2020 as MD and part-owner, with a vision to help Xtrutech better promote itself on the global stage. “We found that a lot of the big players worldwide didn’t take us seriously because they thought we were a small business,” he explained. “I wanted to project a larger image and reach, while internally keeping our family-business values.”
As a result, Xtrutech Inc opened in Philadelphia in 2021, firmly establishing the company’s footprint in the American and South American markets. “The American
market continues to grow,” said Mr Moore. “Since then, we’ve built a presence in Southeast Asia and India as well.”
The figures speak for themselves. Over the last three years, the business has doubled in size, increasing turnover from £6.5 million to last year’s £14 million. Additionally, employee numbers have increased from 35 to 48.
“The key was to have a local presence worldwide, to better support our customers,” Mr Moore reflected. “Big companies take us seriously now. We invested in a new Innovation Centre, workshops and people, enabling us to fulfil the growth in orders, whilst continuing to offer an excellent service.”
Alongside its global growth strategy, the second prong to Xtrutech’s success is heavy investment in innovation.
In the summer of 2023, the company opened an Innovation Centre for process trials, housing a range of different machines, including a number of extrusion lines. The facility provides an environment where creative ideas flourish and groundbreaking solutions take shape.
“We have a recycling unit there as well,” Mr Moore explained. “Our extruders are often used for producing powder coatings, and often, factories produce around five per cent waste in that process, which traditionally gets sent to landfill. We’ve developed a machine that recycles that waste to support our customers sustainability drive.”
The machine in question, known as the XTS Fines Compactor, was developed alongside
a large European paints and performance coatings multinational. Xtrutech sells the equipment many powder coating producers world wide. “We’re doing well with those units, as the companies all have strong sustainability targets themselves,” Mr Moore said.
Xtrutech runs demo days to test the compactor at the Innovation Centre, inviting customers to see waste products run through the machine, either in person or via video. The material is then returned for analysis, while the customer often follows up by placing an order.
“The innovation centre is great because we can prove the product works well,” Mr Moore explained. “It means the customer is not just hearing the sales guys telling them what a machine can do; they can see for themselves.
“And it’s also beneficial when the customers do come in and look at the new technologies we are working on. We’re constantly developing something at the centre; we’ve got an R&D team working there permanently.”
The company takes sustainability seriously and is striving to make improvements all the time. This includes looking into introducing an electric vehicle fleet for its sales team and upgrading the lighting and heating systems at its sites. As a result of these improvements, Xtrutech was recently awarded EcoVadis certification.
Even more significantly, the company’s bricks-and-mortar presence overseas has allowed it to reduce air travel, too.
“I’d say that’s the biggest saving we’ve made,” said Mr Moore. “85 per cent of what we do is export, but now we are replicating our UK capabilities in the US, and have a solid presence in Asia, so we are not flying our engineers around the world all the time. That’s good for the company, financially, as well as for the environment.”
Of course, innovation has long gone handin-hand with sustainability for the company. For instance, Xtrutech has developed a PET polymer recycling machine, reusing the waste derived from blow moulding, for a bottle packaging business in the US. “The machine granulates the waste and puts it through the extruder,” Mr Moore explained. “It is then placed under UV light at the right temperature and speed. This re-crystallises
the polymer, so it’s as good as the virgin polymer.”
The company is also keeping up with the emerging EV sector, where battery materials are now produced with an extruder. “It’s a big market for us currently,” according to Mr Moore.
Partnerships to last
Xtrutech has suppliers across the Staffordshire area and, true to its familybusi ness values, places great emphasis on maintaining the integrity of that network.
“Suppliers are crucial,” said Mr Moore. “We do some machining here ourselves, but the majority is purchased from items we design and pass on to local engineering shops to fabricate and manufacture the parts. It’s extremely important to us to have a close relationship.
“So, it’s no good if we’re driving them on price all the time. We are UK-based, we’re not going to compete with Chinese or Indian machines on cost. To survive in the market, we need innovations to set us apart and keep us a step ahead. And, to do that, we need quality suppliers. It’s about working together because suppliers have a lot of input on our innovations. We are always asking: ‘What does the customer need?’ That’s vital.”
Internally, the company also emphasises the benefits of regular training to support the growth and development of employees.
“To me, a successful business is all about the people,” said Mr Moore. “I had a lot of help from my bosses in the past, and I want to pass that on. So, we are supported by local universities and there’s several people here doing degrees and apprenticeships. We really value them, and we
want these guys to work here for a long time, because it takes a while to build up the knowledge and skills.”
Looking ahead, it is clear Mr Moore is not about to let Xtrutech stand still. While the company’s extensive capabilities in machinery are evident, there are areas that need strengthening, too.
“The digital transformation of the business is something I want to take a step forward with,” he concluded. “We can talk about innovations in mechanical design, but we've got to think about innovations digitally too. That might mean looking
at AI a bit more, to keep ahead when it comes to software and processes on site areas. I think we could be more efficient and offer a better service to customers that way.
“Overall, I’m really interested in the innovation side. I started out as an engineer, and I do like to see the way everything works. The whole process is exciting, not to mention the developments we’ve got, and the offers we provide to the market. It is vital to keep moving and to have the right people, as we do here, to go forward with.”
n