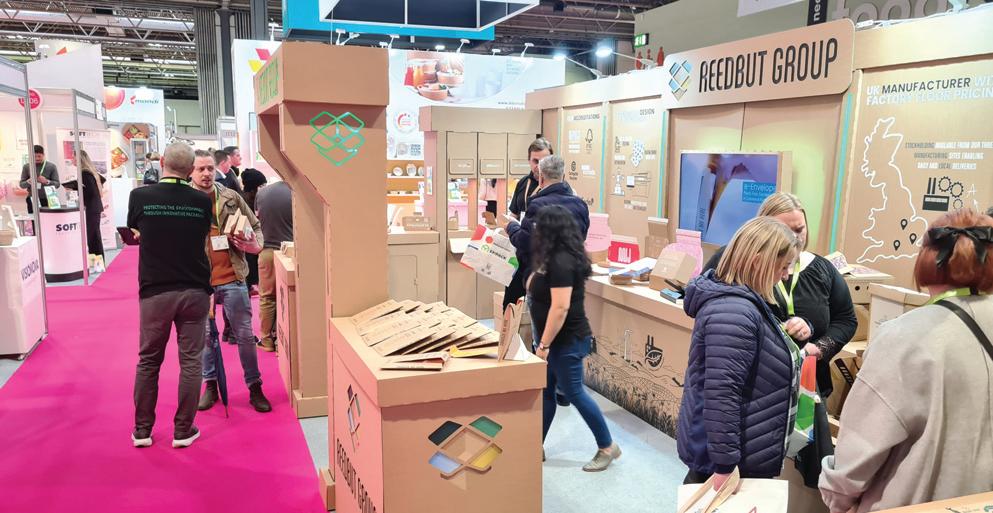
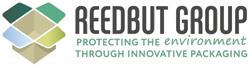


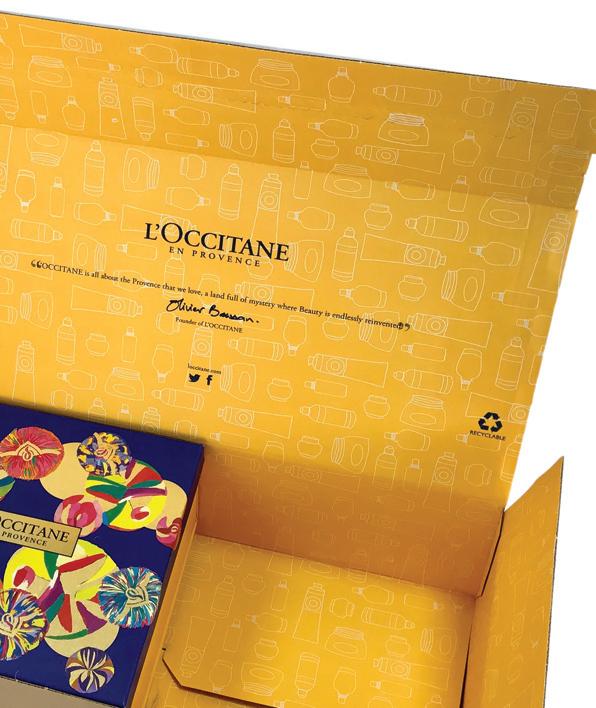
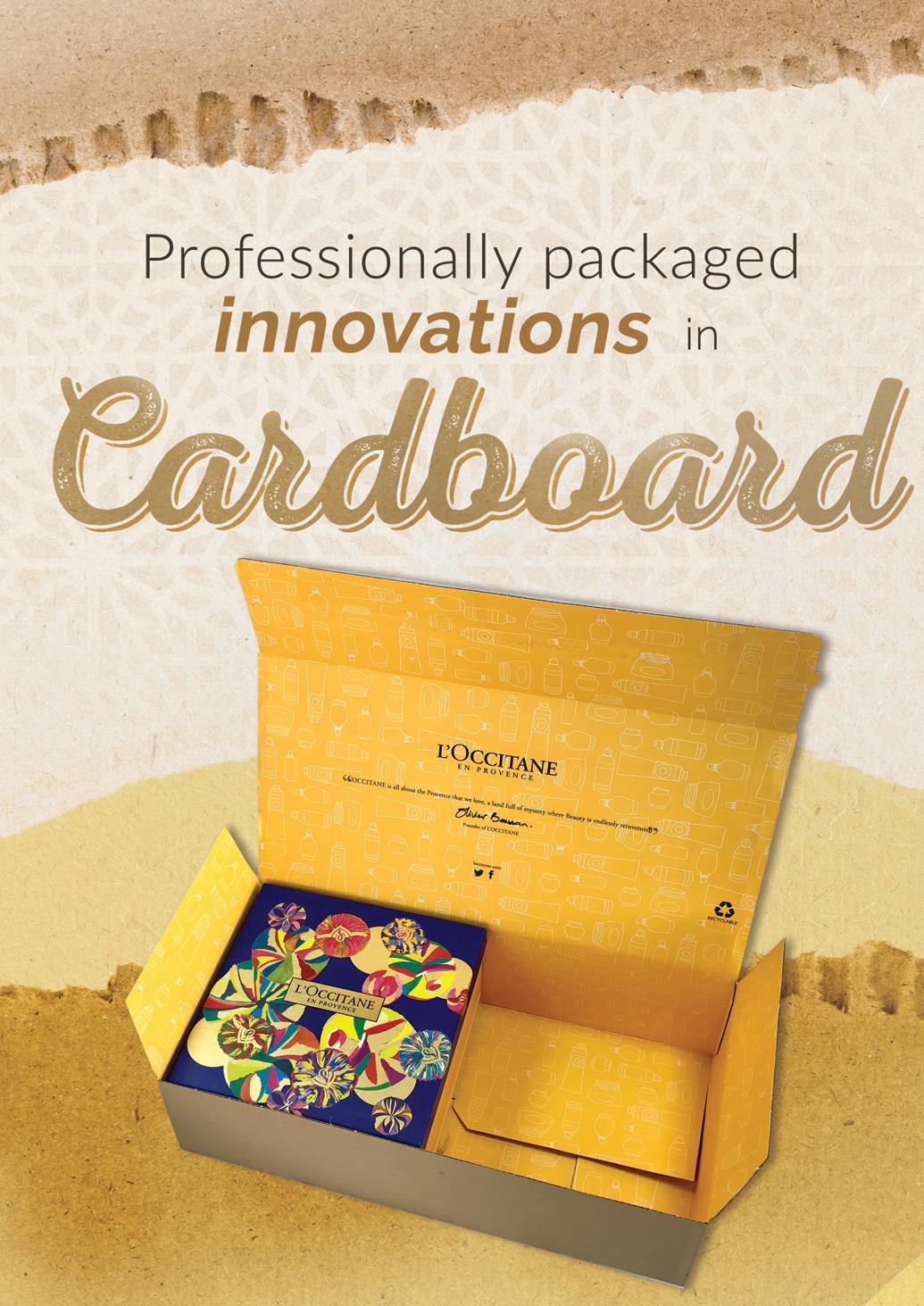
From a small family business established in the late 1970s, the Reedbut Group has grown into a packaging powerhouse serving customers in multiple industries, with an annual turnover exceeding £19 million. Customer Experience Director Stuart Deaton told Richard Hagan how the company is leveraging its capabilities and expertise to bring extremely innovative, sustainable packaging products to the market, changing customer perceptions and unlocking value.
When Reedbut Group attended Packaging Innovations in Birmingham and London, they manufactured its entire exhibition stand using cardboard, and all of it was built inhouse on Reedbut Group’s own machinery. This achievement was different, exciting and typical of Reedbut Group’s ability to think outside the proverbial box.
“We always try to show our customers what we can do for them, so we design our stand to
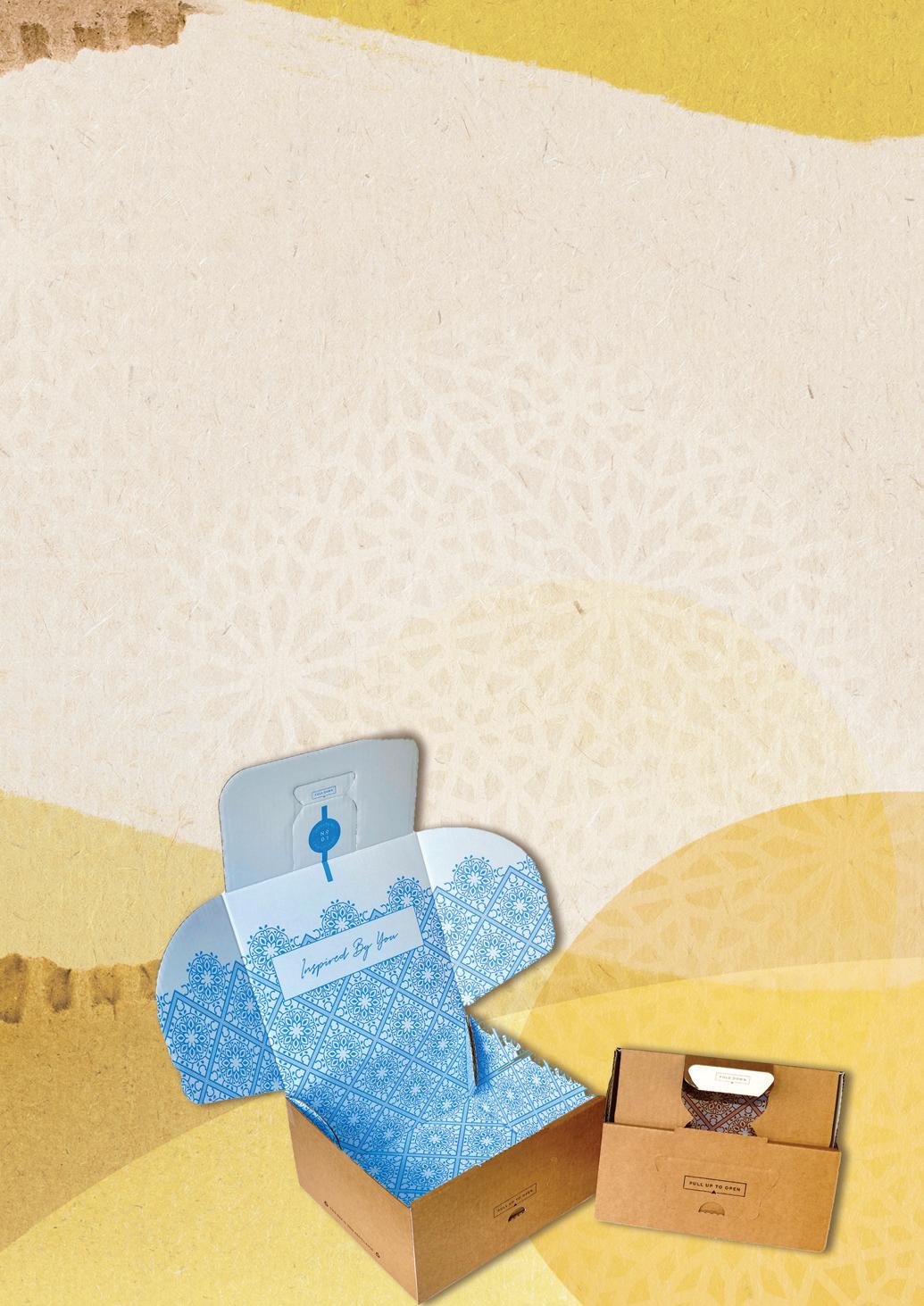
look like a museum of innovation, full of our most innovative products,” explained Customer Experience Director Stuart Deaton. “We always have at least one brand new product in place for people to view.”
The company was rewarded with the Innovation Award for the eReturn at the London Packaging Week, in September 2023, and the eLetterbox in 2022 as well Both of these products are tape-free solutions enhancing Reedbut Group’s aspirations to move forwards with improving its sustainability strategy.
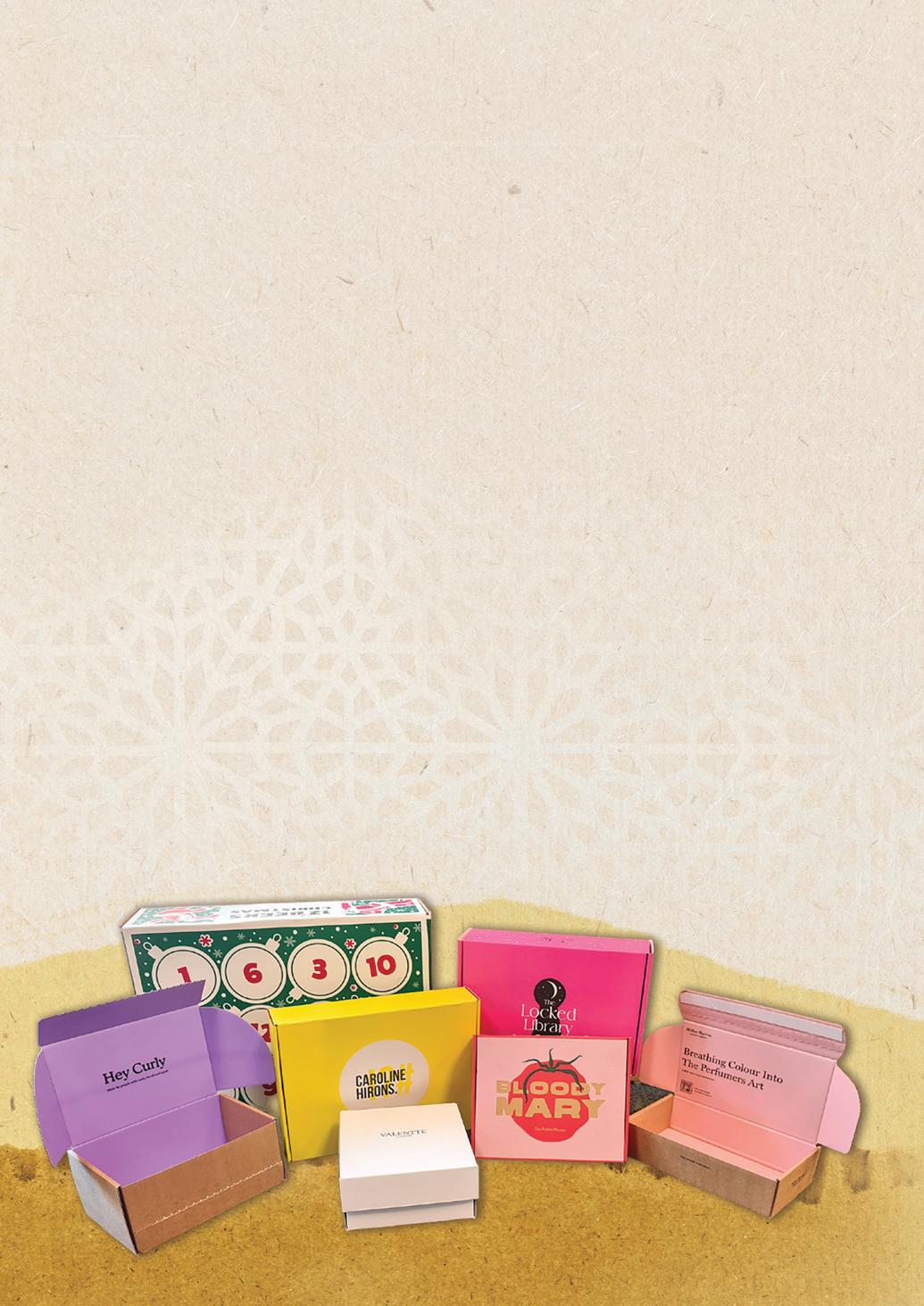
Tidying up the airline sector
In May 2024, Reedbut Group will also attend the World Travel Catering & Onboard Services Expo in Hamburg. The company will be presenting the revolutionary skytidy ® airline bin. This bin is designed for onboard trash compactors, serving as a receptacle into which refuse is placed and which is itself then placed into the trash compactor for processing.
skytidy’s sturdy, sustainable cardboard construction has made it a top seller for Reedbut Group. “We sell hundreds of thousands of them directly to the airlines each year, with a value of around £1.2 million,” Mr Deaton confirmed. “It’s a very niche market but it’s one of our largest volume products.”
To keep up with the high volumes required to meet the market’s demand, Reedbut Group’s skytidy production has been completely automated with robots. The line, which previously required a large human workforce, is now extremely lean and efficient, with complete quality control.
Complete cardboard capability
Reedbut Group is exclusively a corrugated cardboard packaging manufacturer. Based in the UK, the company began life in 1977 as a small family-run packaging business owned by Len Harris. In the early 2000s, Reedbut Group’s current MD, Trevor Green, bought Mr Harris’ business and immediately began scaling up the company’s operations.
The company’s single site subsequently scaled up to the three that it currently owns, with facilities in Milton Keynes, Andover and Strood. Across the three sites with 100 employees in total, Reedbut Group produces and offers a comprehensive variety of cardboard packaging targeting the industrial, aviation, shelf-ready, retail, storage and eCommerce markets.
In keeping with international trends, Reedbut Group’s eCommerce market is thriving. Mr Deaton was eager to highlight the company’s specialised capabilities that drive its success in the eCommerce sector: “We have the machinery to print
on both sides of the board in a single pass, on cardboard grades ranging from E Flute to Double Wall BC Flute, which is very challenging under normal circumstances. Where other manufacturers typically have to print twice to print on both sides of a board, we’re able to do both prints at once.”
At Reedbut Group’s Milton Keynes facility, it is able to produce window cuts for products such as cake boxes, for which its machinery also installs the clear window section. Since this facility’s products must interface with food, the factory is BRC (Brand Recognition through Compliance) Food Safety certified. BRC is a UK trade organisation recognised across
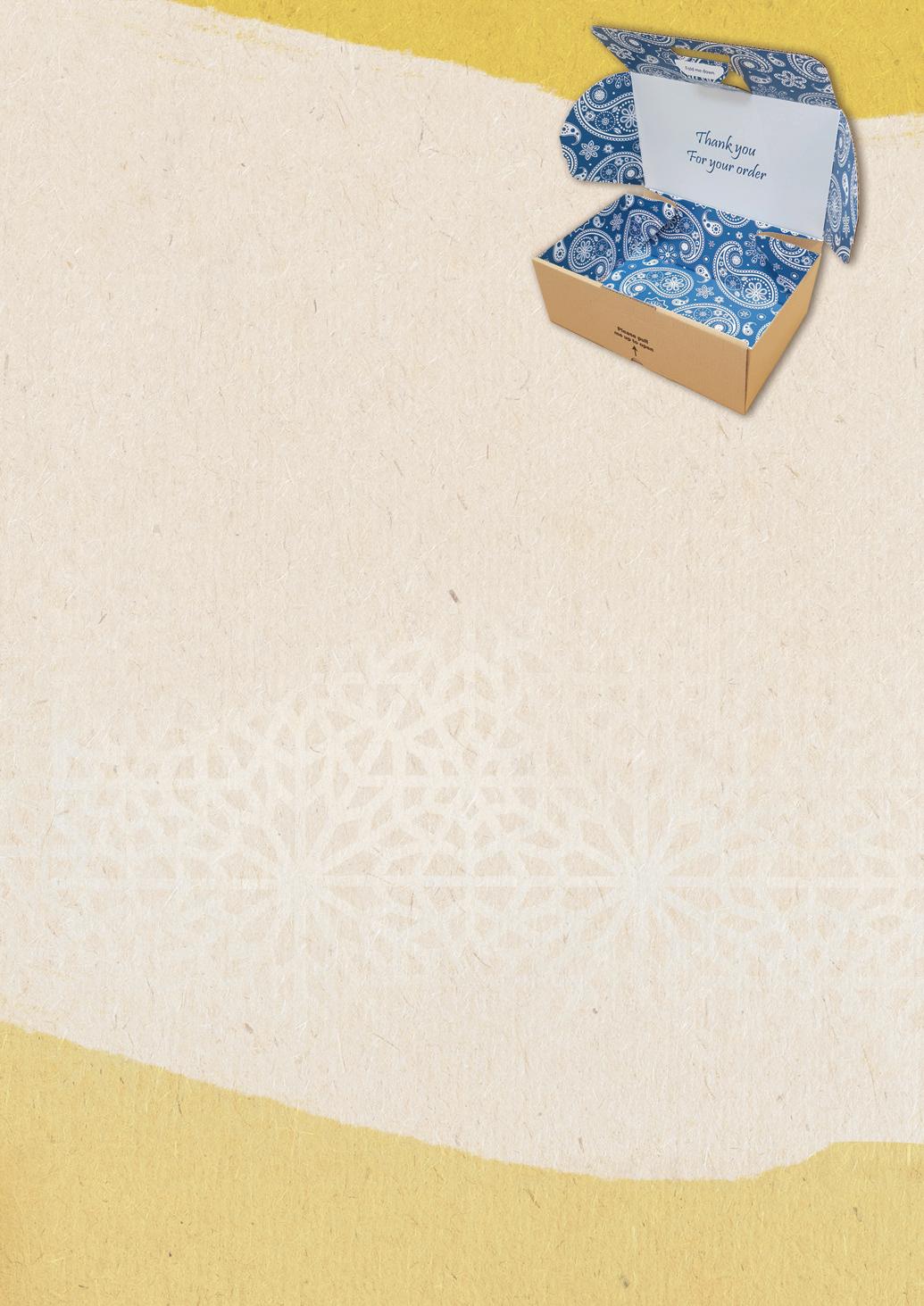
the world, which works with compa nies to help them comply with UK and EU food safety legislation.
The refurbishment market
Meanwhile, Reedbut Group is developing an exciting new range of cardboard packaging products aimed at the
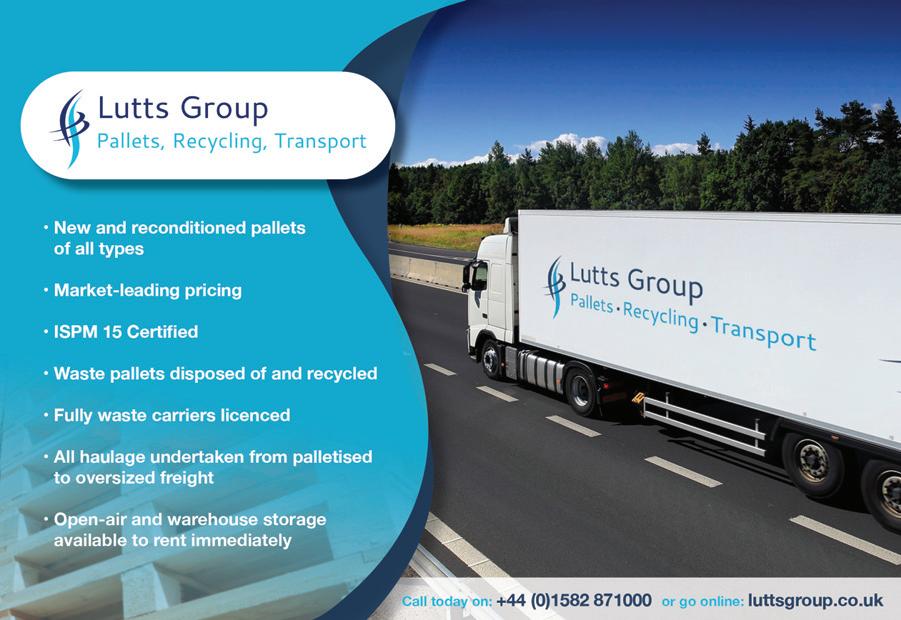
refurbished consumer electronics market. The new boxes are purposedesigned and built to perfectly fit PlayStations, Xboxes, Nintendo Switch consoles and a range of popular mobile phones. “The customer experience is usually overlooked by that market, so it’s something we’re really pushing now, to give them proper packaging,” Mr Deaton explained.
Innovations such as this one, and all of Reedbut Group’s other projects, are powered by its close relationships with suppliers. One example is Progroup AG, the company’s main supplier of corrugated products. “Out of all of our suppliers, our relationship with Progroup is the strongest,” confirmed Mr Deaton.
“Also, we have purchased pallets from the Lutts Group since 2022,” he

continued. “I cannot fault Lutts’ excellent customer service and quality. Sam and his team react to all of our needs, and I could not rate them any higher as a supplier. We have been approached by various other suppliers in relation to pallets. However, Lutts’ strong performance means we would not even contemplate entering into a conversation on this matter.”
Tape-free sustainability
Reedbut Group takes sustainability seriously and has demonstrated so with the latest tape-free product lines, as Mr Deaton explained: “A lot of people talk about sustainability, but we’re actually trying to act on it.
“We have started with our own products, from which we’re removing glue and tape lines to make the product fully recyclable, without the user having to
take additional steps of pulling off tape. We’ve had lots of success with that project and our eLok tape-free box is already selling close to about 1.5 million units a year.”
Reedbut Group is also encouraging customers to become more sustainable by offering packaging designs that eliminate the need for filler products such as air sacs and paper filler, so that the box carries the product perfectly. Additionally, Reedbut Group has been using the InkSave system on its printing machines for the last two years. This system is highly efficient, using only the ink required for a particular printing run, with zero waste or excess ink.
The company’s customers have reacted favourably to these new developments. “There was initially some caution about moving to new packaging, but as our customers – particularly bigger corporate brands – become
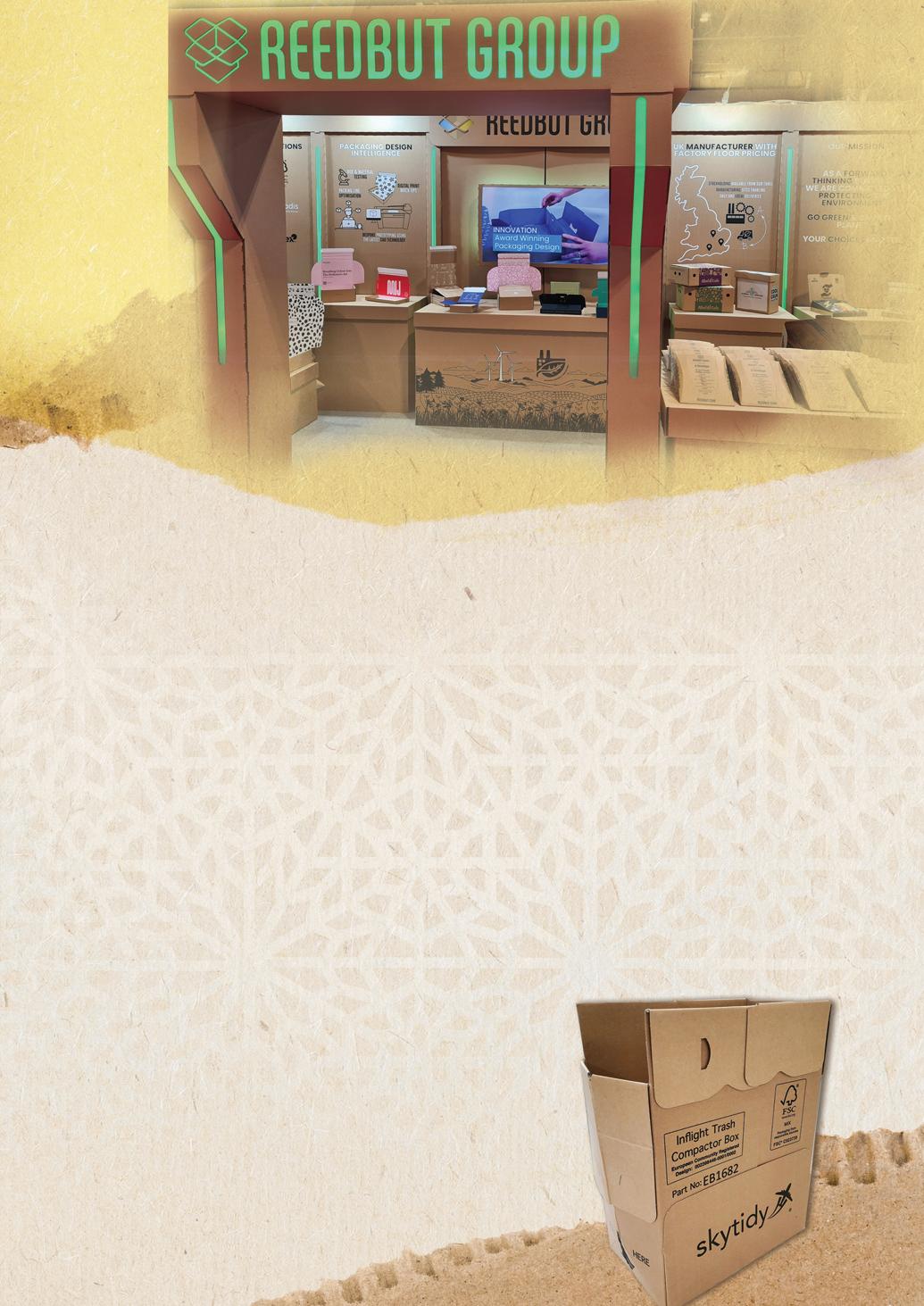
more aware of the need for sustainability, they are choosing to move to tape-free boxes and it has worked very well,” said Mr Deaton, in conclusion. “There is definitely a change in people’s mindsets now.
“In the future, we are looking forward to continuing to work with businesses to understand their objectives and where we can assist them with our technical knowledge.” n
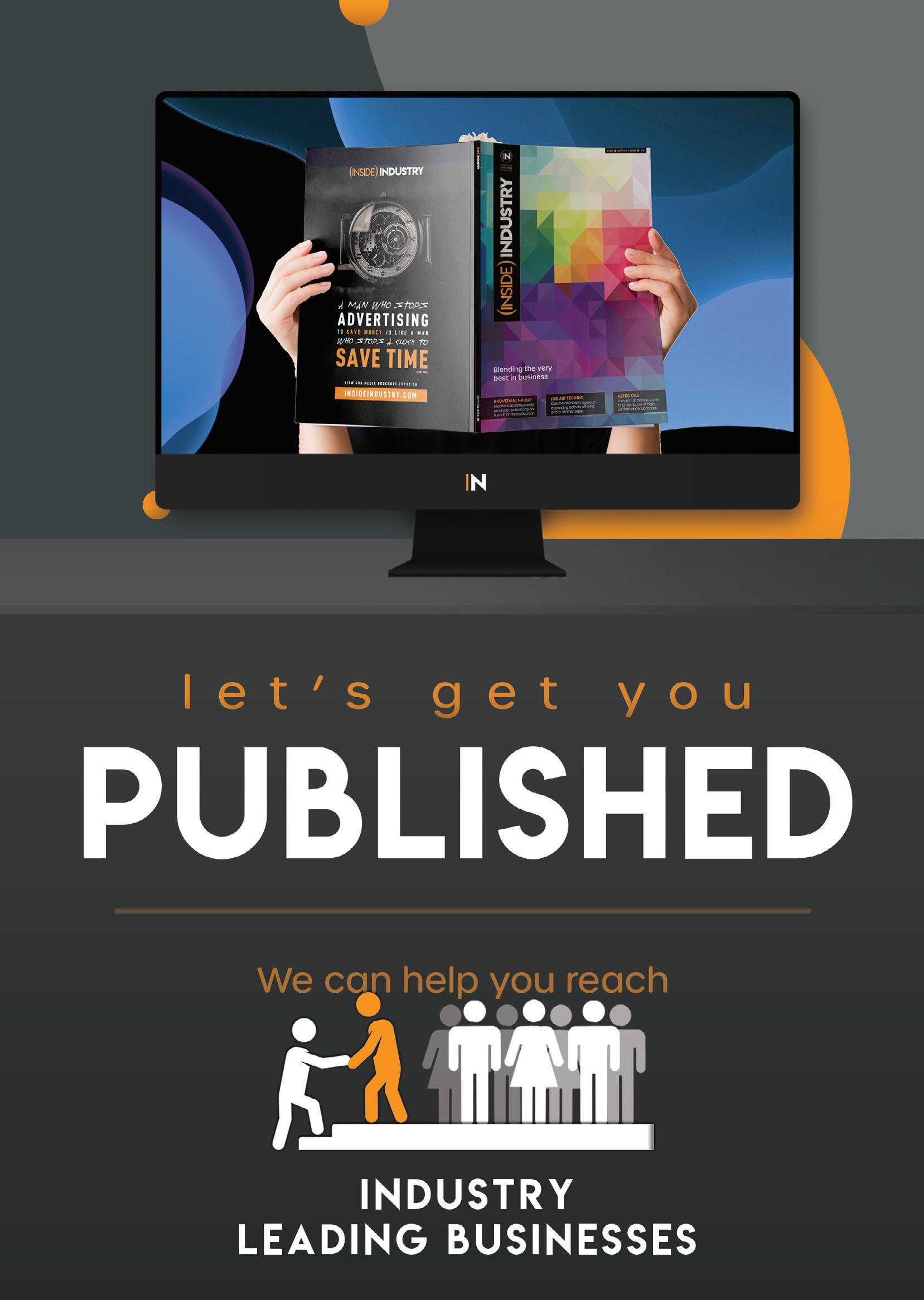
