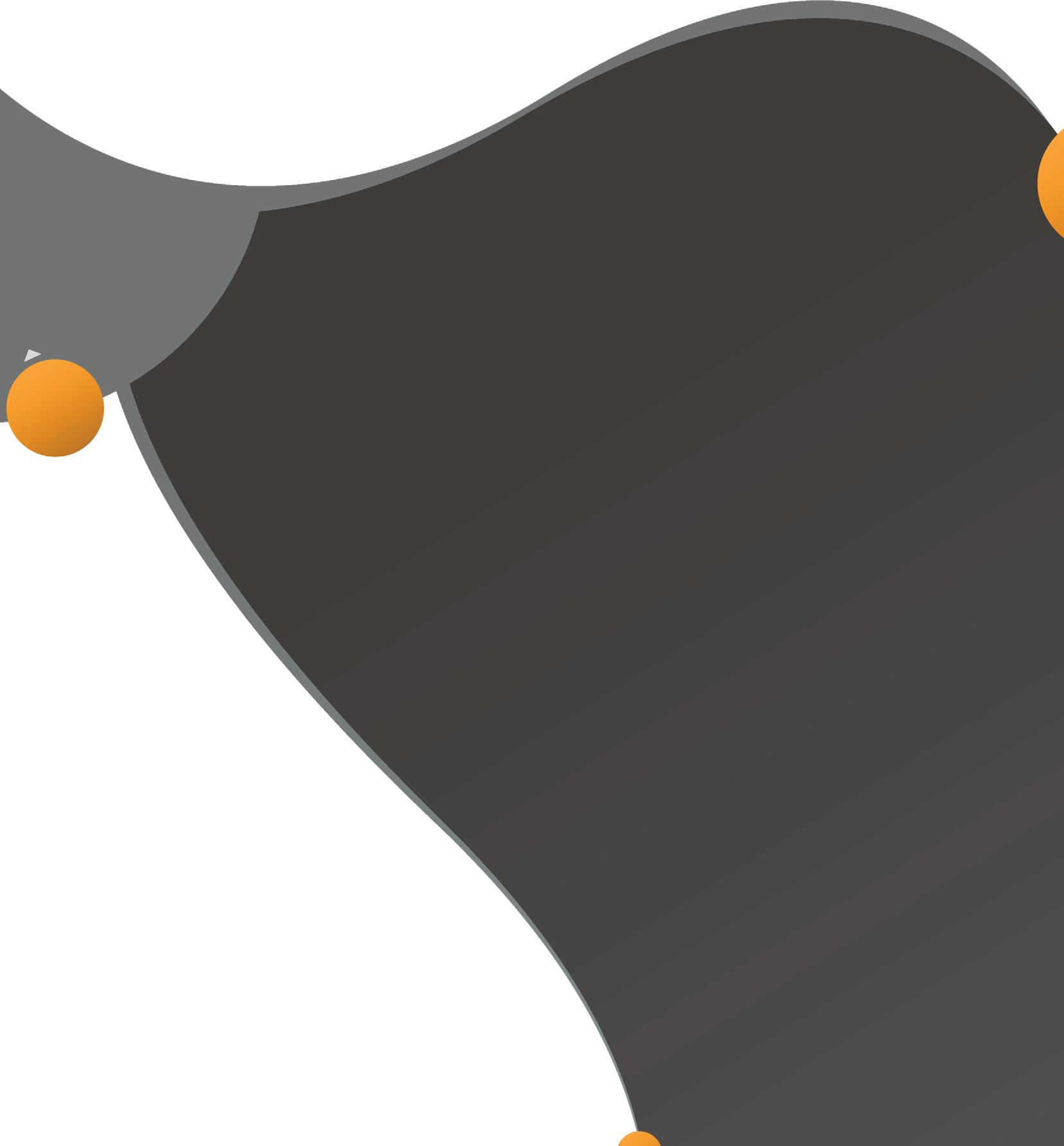
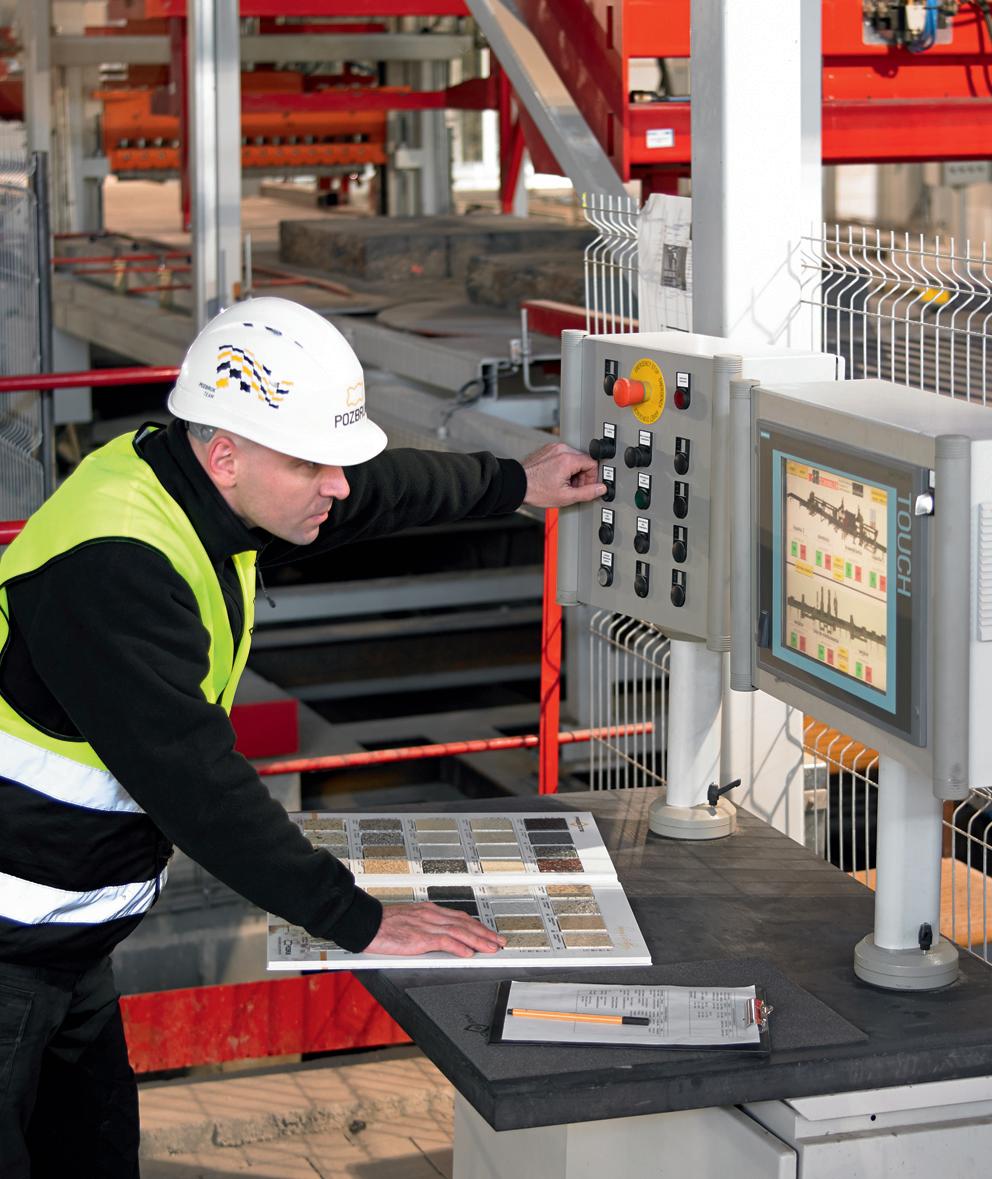
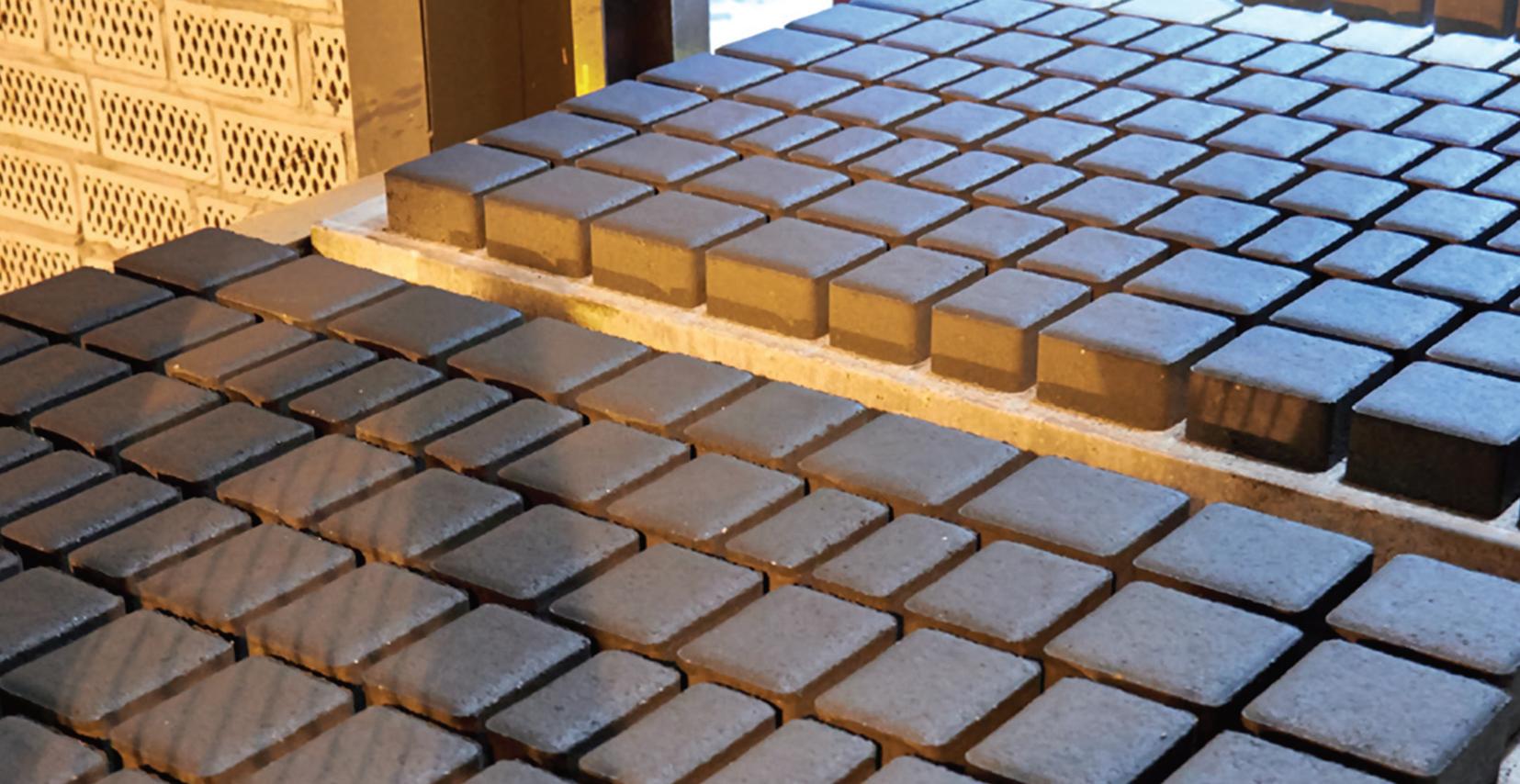

Advanced technologies and continuous production optimisation have been driving POZBRUK for nearly four decades, making the company one of Poland’s leading manufacturers and innovators of concrete products. “Every day, we provide modern solutions for individual clients, as well as for large construction projects,” emphasised Sales Director Bartosz Nowicki.
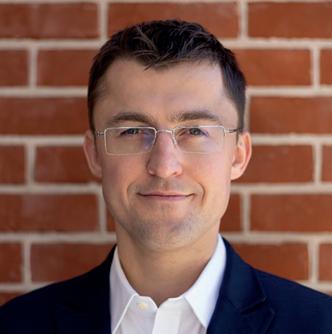
POZBRUK, headquartered near Poznan in central Poland, is not just a concrete slab manufacturer: today, the POZBRUK Group has a network of plants producing prefabricated concrete elements in addition to its own aggregate mines, rail transport and specialised equipment facilities, as well as its own laboratory.
reports.
“These assets, combined with state-of-the-art production lines and a qualified staff of 600 people, provide our customers with a wide range of top-quality products,” said Sales Director Bartosz Nowicki. “Our technologically advanced and extensive machinery makes us unique in Poland.”
POZBRUK’s portfolio includes decorative pavements, terrace solutions, stairs, fences, structural landscape elements, floor slabs and much more. The company also offers products designed for public facilities, such as industrial pavements and noise barriers, and pre-stressed concrete lintels and a system for the construction of prefabricated halls.
Growing into a national leader
POZBRUK was founded in 1985 as a family business, and over the years the business grew and diversified, reaching a significant milestone in 2008 with the acquisition
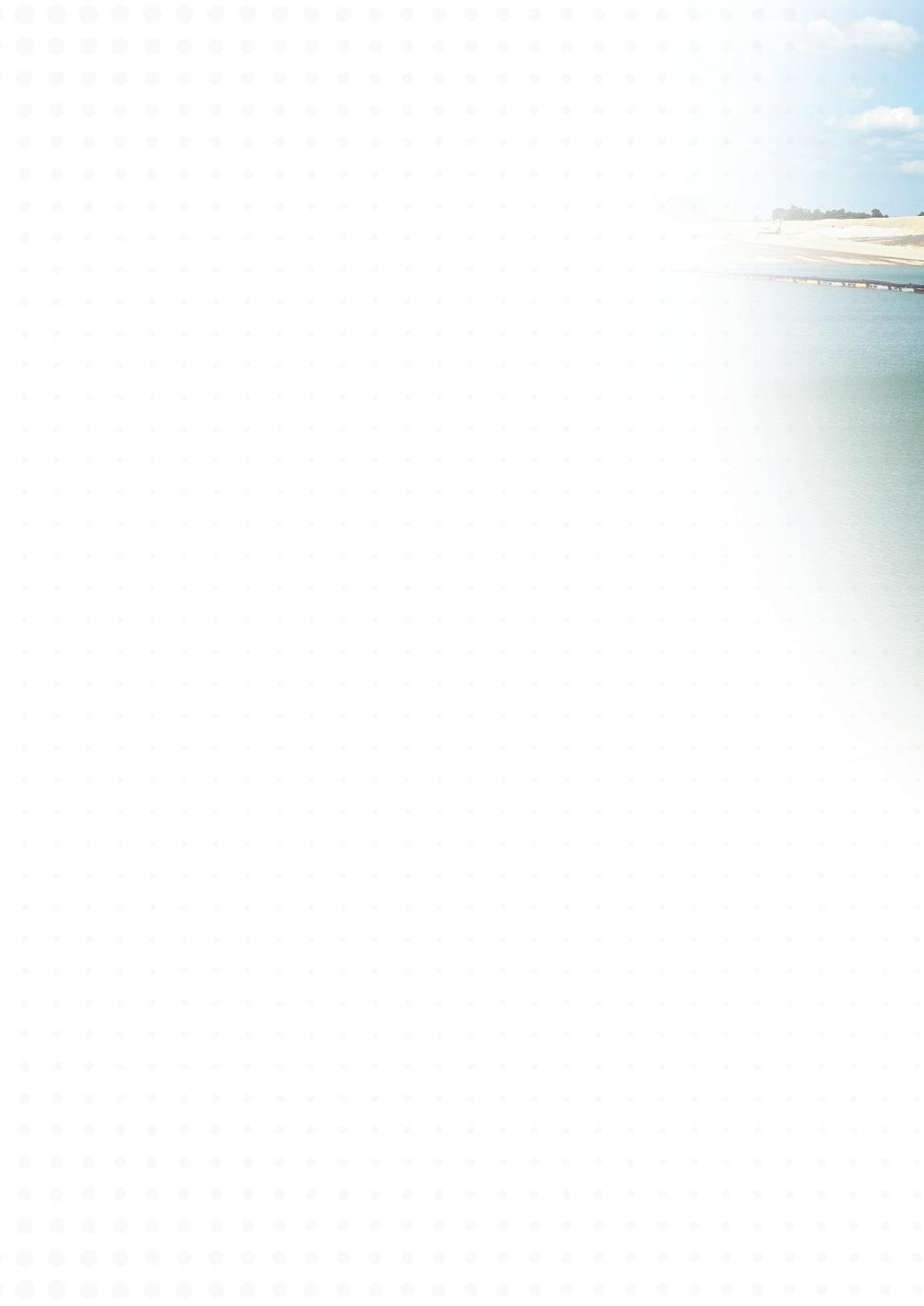
of two Polish mines, making the company independent of aggregate suppliers. Further expansion and diversification followed. In 2016, POZBRUK acquired a technological line for the production of reinforced and prestressed concrete prefabricated elements, dedicated primarily to the construction of industrial buildings.
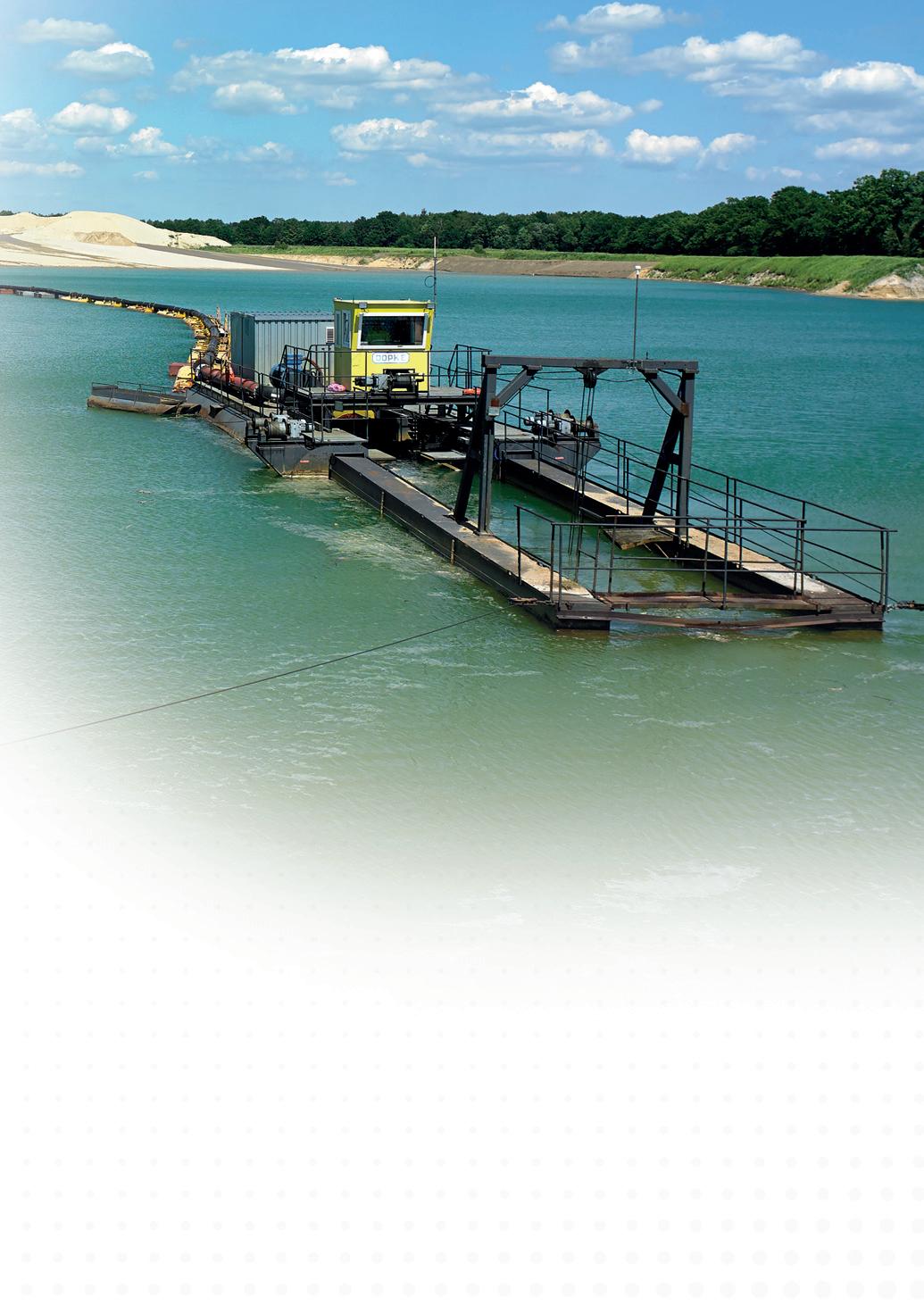
Two years later, the company launched the production of modern large fibre-concrete panels with digital overprint, for façades, internal walls and floors. In 2019, a modern plant was built for precast composite walls
and semi-precast floors, used for module building. These latest developments resulted in the company significantly increasing its product range and, ultimately, expanding into foreign markets.
“The highest quality and continuous growth – these words simply sum up the decades of POZBRUK’s development,” said Mr Nowicki. “They have become the basis of everything about the business – from choosing the right people and creating modern technological facilities, through to professional customer service.
“Quality, combined with innovation, has made POZBRUK one of Poland’s leading manufacturers in the prefabrication industry, as a strong brand that has won customers’ trust.”
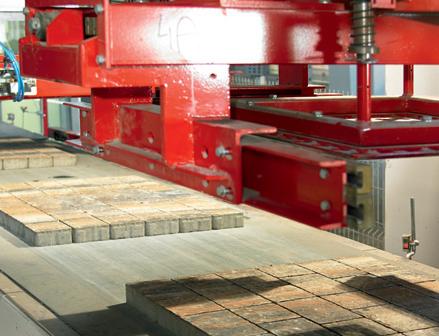
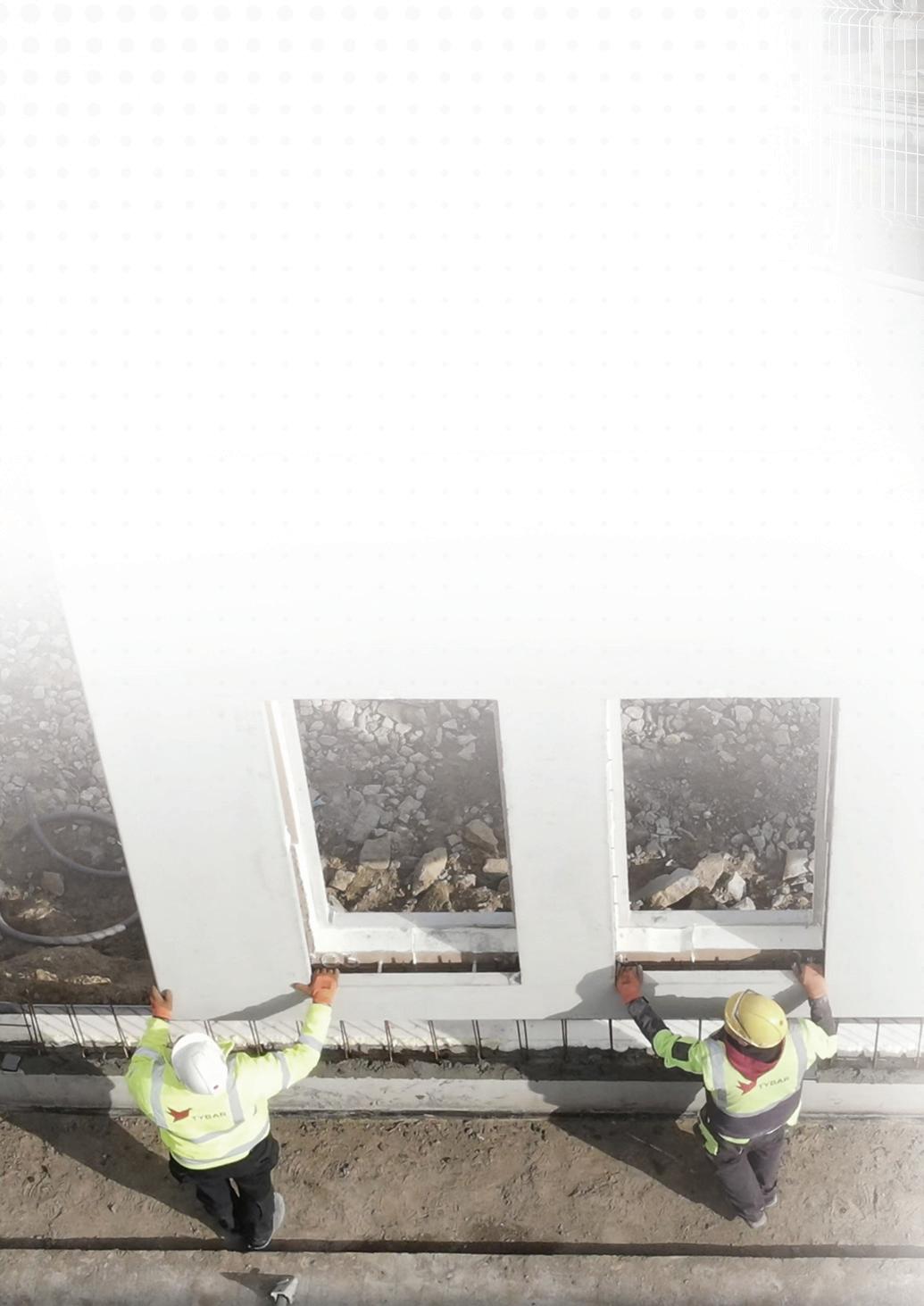
Proud achievements
Speaking about the company’s wide portfolio, Mr Nowicki reflected that each of the products is extremely important to the business. However; one product group, the company’s latest offering, specifically stands out, creating previously unknown opportunities – prefabricated facade walls. The elements can be delivered directly to the site, which reduces the construction process by up to 40%.
“A great example is the façade of the ‘Bałtyk’ tower in Poznań, which is made up of around 4,000 precast concrete components, and which made the building a new icon of the city of Poznań,” stated Mr Nowicki.
“The priority was to achieve an effect of non-homogeneous colours, which would accentuate the irregular form of the building. The surface of the facade was expected to shimmer in the sun and change its hue depending on the angle of the light falling on it. The desired effect was achieved through the use of mica, which lends the facade a shimmering texture.”
The building received numerous prestigious local awards and was also nominated for the EU Prize for Contemporary Architecture – the Mies van der Rohe Award.
“Another project that fills us with pride is the B10 hotel and office complex in Wrocław,” said Mr Nowicki. “For the 6-storey office building, we provided prefabricated three-layer walls with a finished polished façade, prefabricated pillars and precast prestressed beams, HC floors and double walls.”
The strong, thermally insulated external partitions with windows included were delivered to the construction site as prefabricated components: no scaffolding
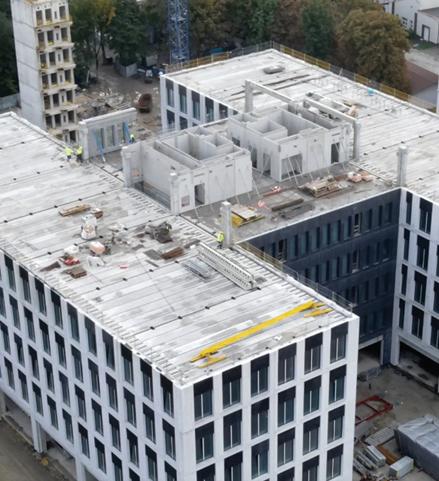
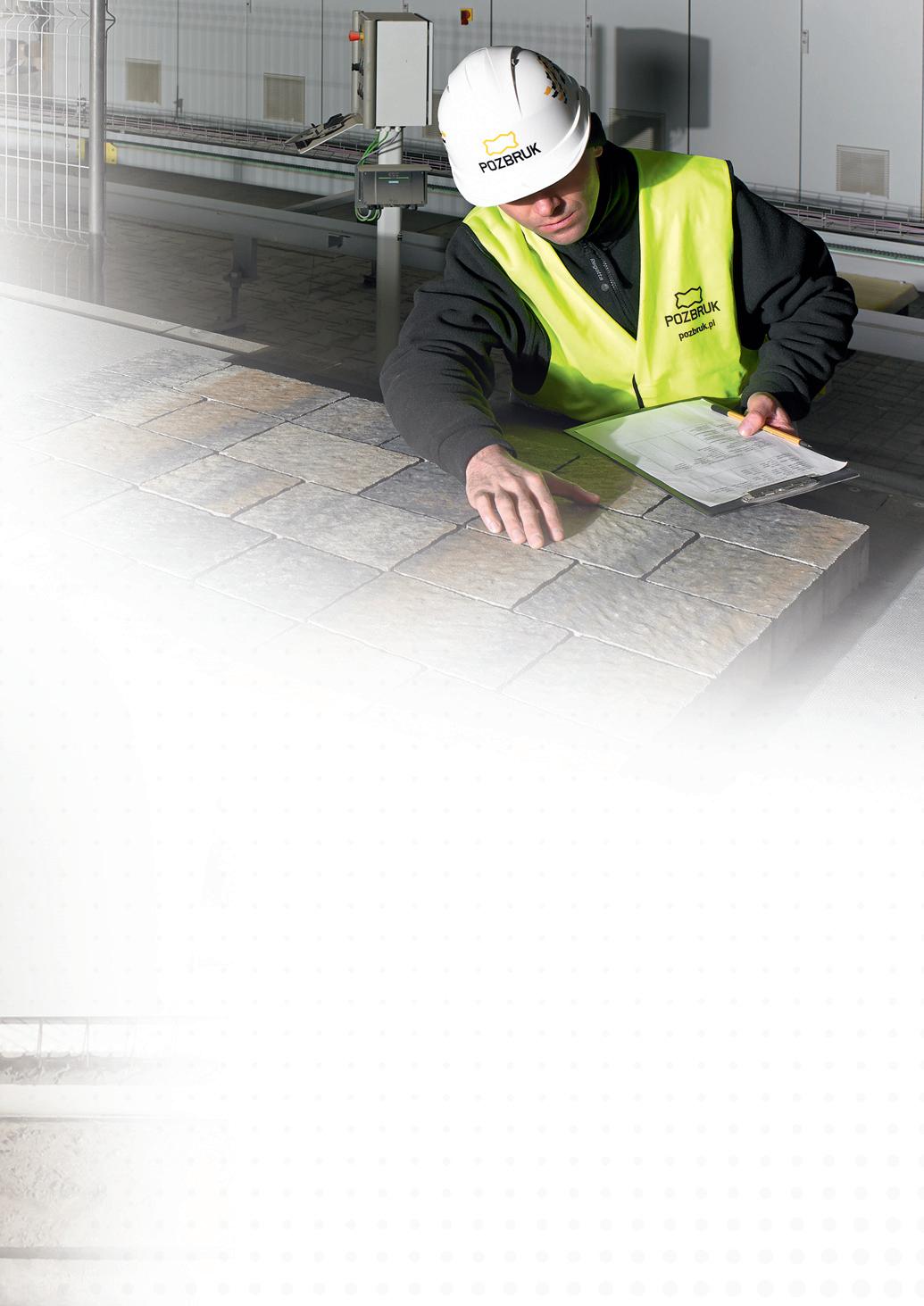
and formwork was needed, and no additional finishing was required, so construction time was significantly reduced.
Environmental harmony
While POZBRUK continues to grow and expand, environmental aspects are an integral part of its development. The company has integrated environmentally sustainable practices into the design, production and distribution of its products: according to Mr Nowicki: “Our teams of technologists and laboratory employees strive to come up with solutions that reduce the amount of cement used in production.
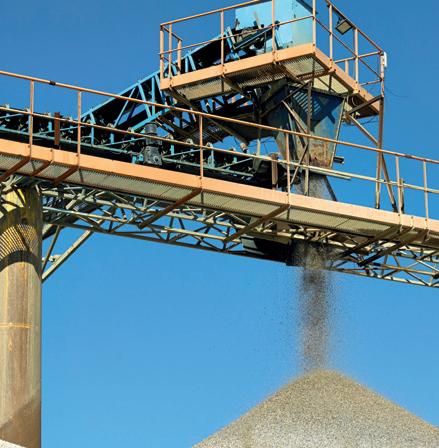
“Production optimisation is an on-going process. We use electric rail transport to move crystals from our mines and we hope to build a siding on our premises to enable direct unloading of raw materials onto the conveyor belt, in order to eliminate the use of motor vehicles. We also plan to invest in solar power in our factories.”
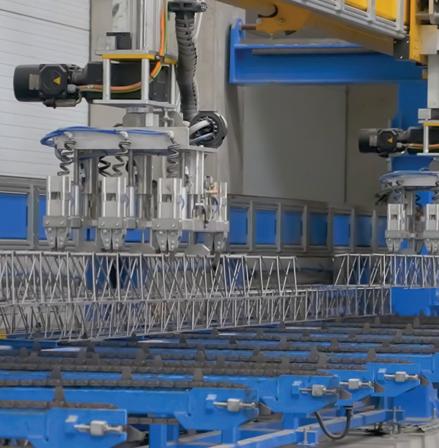
He affirmed that efforts to optimise the products themselves are also ongoing:
“We offer an increasingly wide range of ecological surfaces. An example is cement enriched with nanoparticle titanium dioxide (TiO2), referred to as ‘self-cleaning concrete’.
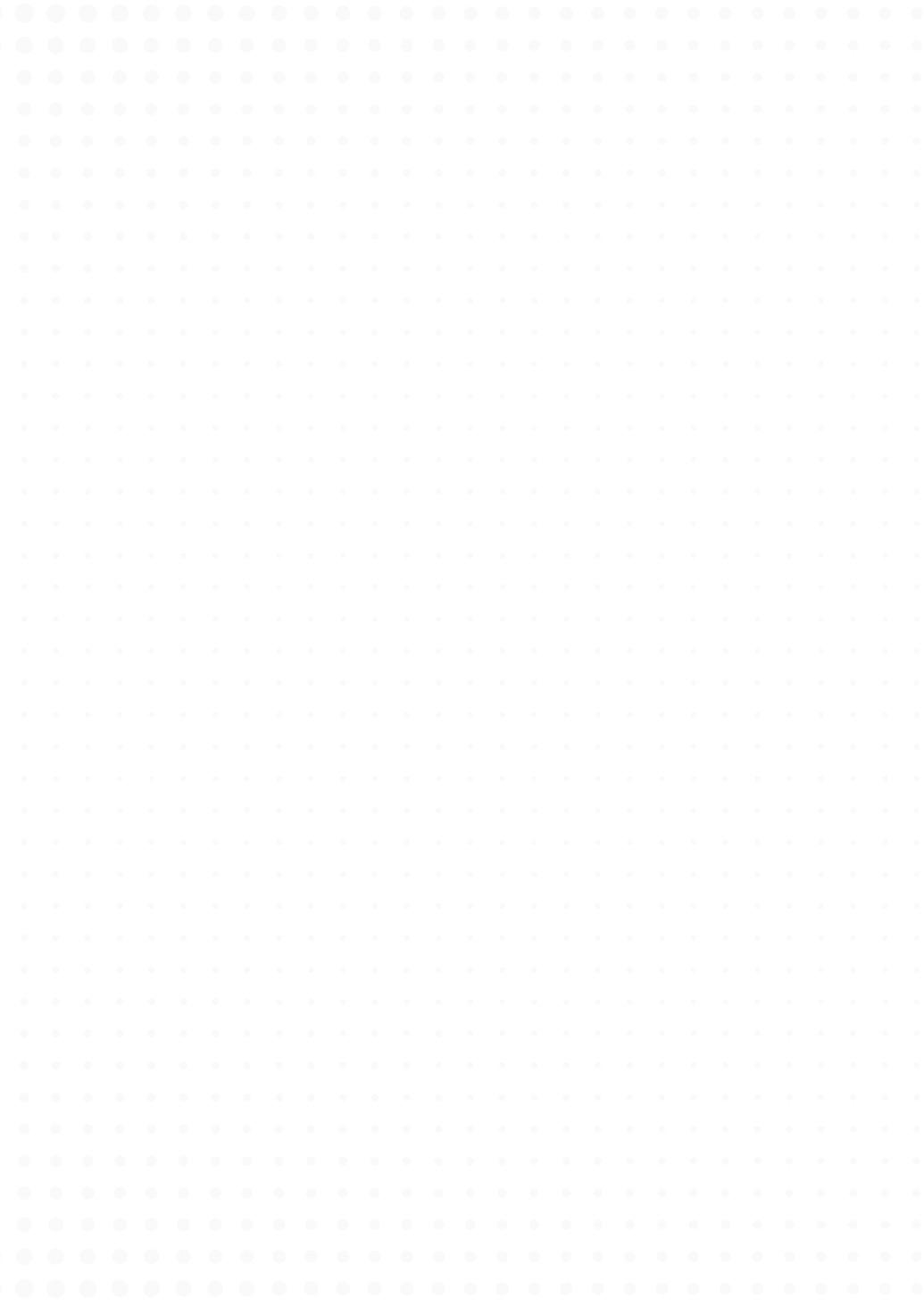
“TiO2 is a photocatalyst. In sunlight, it accelerates oxidation reactions from polluted air, turning harmful nitrogen oxides to harmless nitrate ions. These are easily washed away by rain, which reduces harmful nitrogen and the sulphur oxides emitted by vehicle engines and industrial devices. By using paving stones with TiO2 added, the quantity of impurities can be reduced by up to 25 per cent.”
Mr Nowicki further explained that the prefabricated buildings that have become popular in recent years generate a lower carbon footprint as a result of the increased speed of production, as well as greater energy efficiency: “The better insulation materials reduce heating costs, resulting in lower CO2 emissions during the life of the building. The amount of construction waste during the implementation of a prefabricated building is immeasurably smaller
than that of traditional construction. The savings in formwork timber, polystyrene and packaging are up to 80 per cent.”
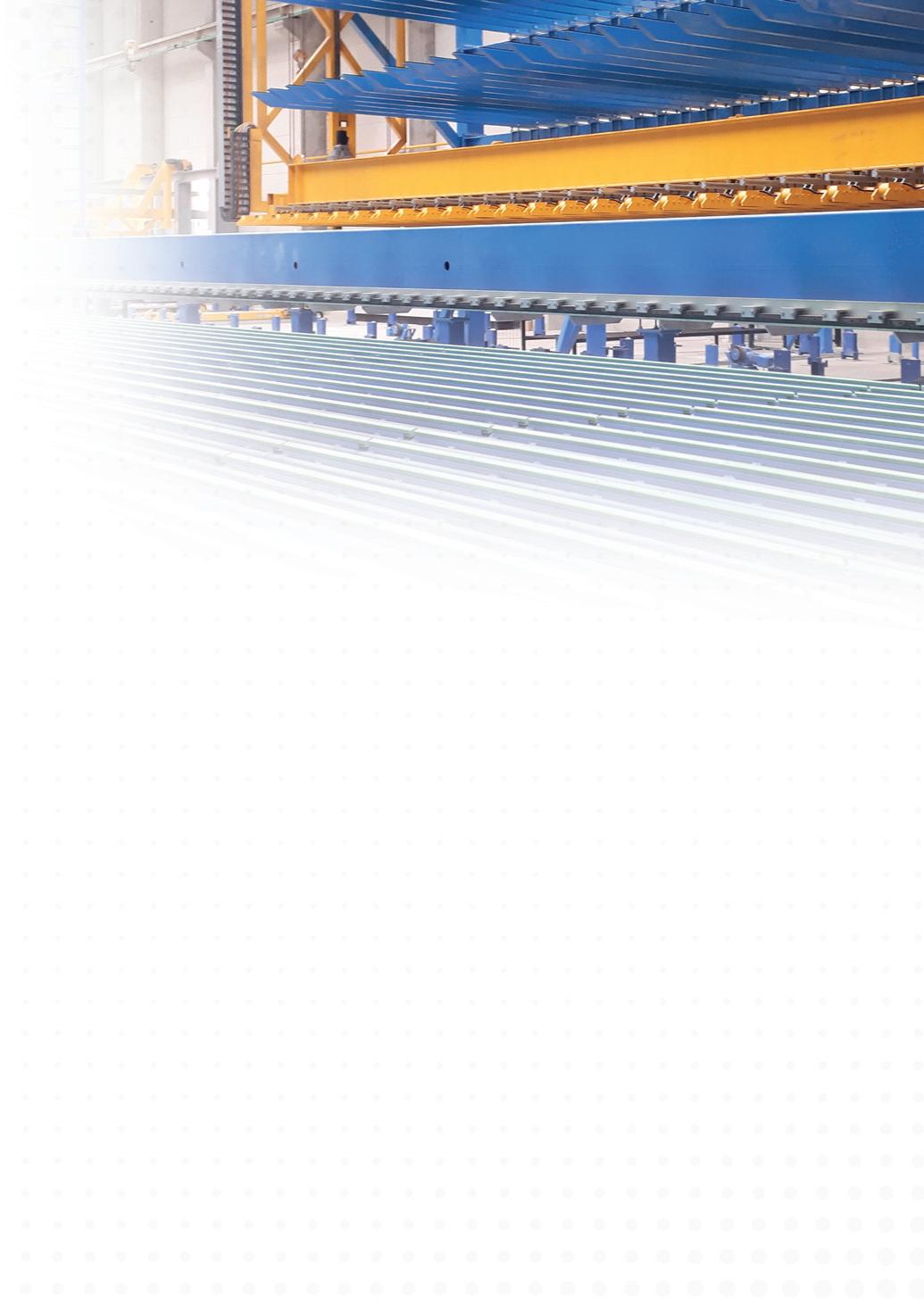
Future plans
Sustainability is also an important factor when choosing suppliers, agreed Mr Nowicki: “We select only certified suppliers that promote environmentally friendly practices, and we strive to build mutual trust through good cooperation: resolving problems quickly and being supportive in challenging situations fosters true partnerships, so that we can work together toward our sustainable goals.”
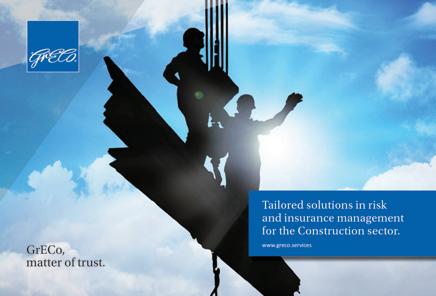
Speaking about future development against a background of market turbulence and geopolitical challenges, he noted that POZBRUK strives to see change as an opportunity: “POZBRUK has so far focused on the domestic market, but we are now pursuing a number of expansion activities to the west and north. We are also ready in the front rank to support our neighbours and to help rebuild Ukraine when the time comes.”
Back on home soil, current projects are numerous and include, for example,
a waste incinerator facade. POZBRUK has also just been contracted to deliver a facade for the court building in Wrocław and a building structure with facade for a museum warehouse project.
“In the coming years, we will continue to invest in automation and are continuously implementing AI solutions to increase efficiency and production process control, ” Mr Nowicki concluded. “My personal goal is to create effective, winning teams. With the right people on board, creating new technologies and implementing difficult projects is a pleasure.
“Strong, creative, close-knit teams are the foundation of the POZBRUK Group’s future development and success.” n
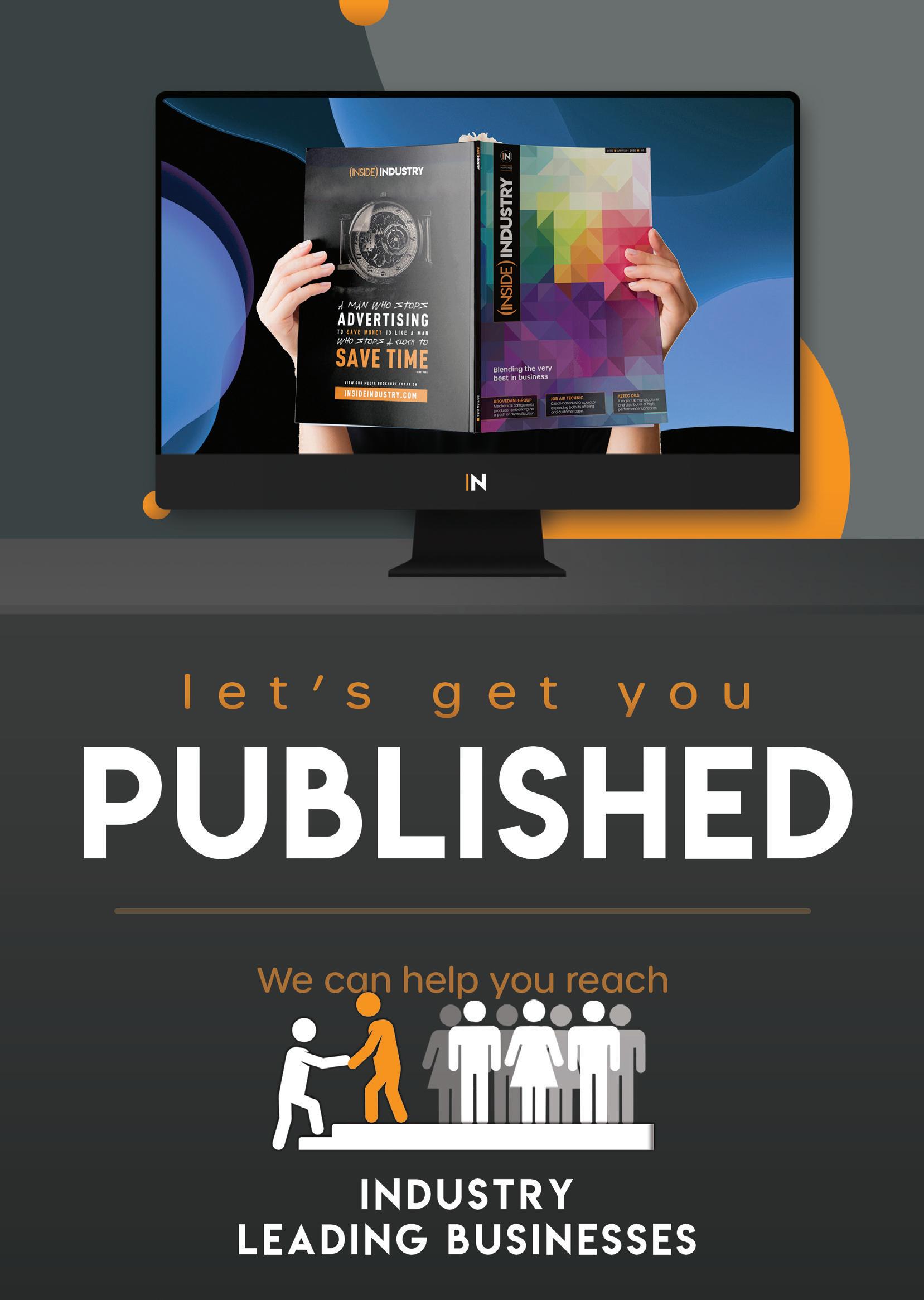
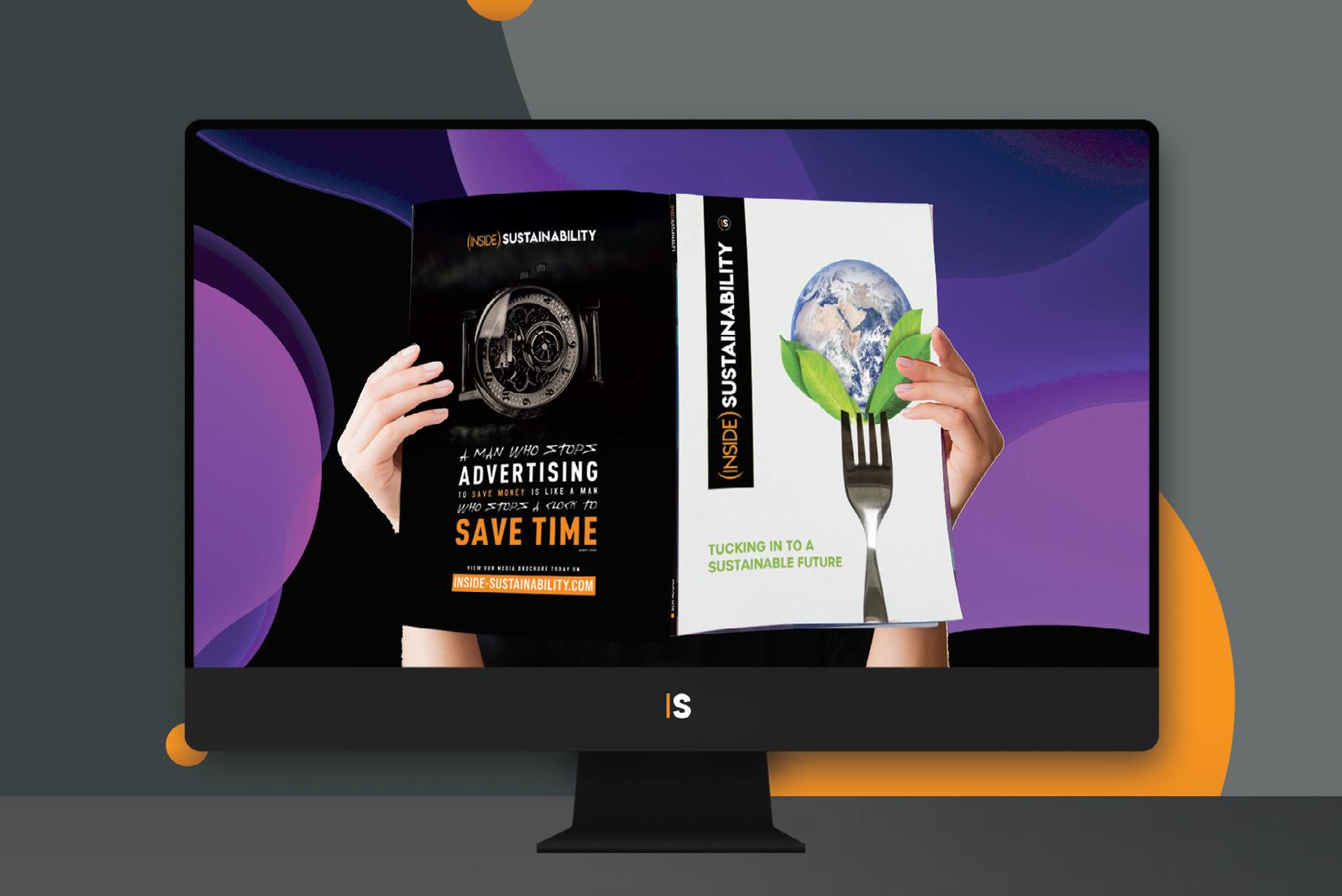