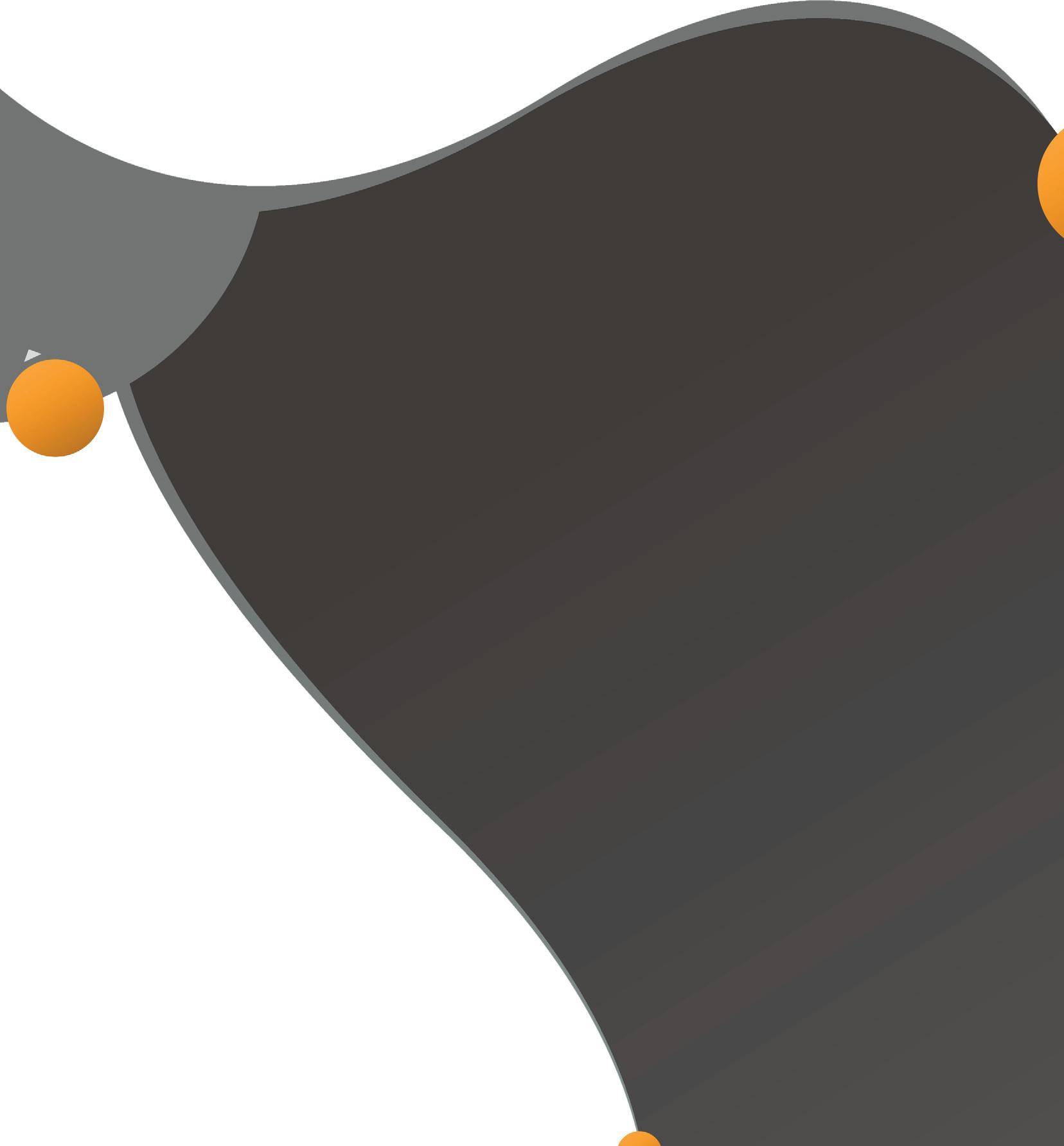
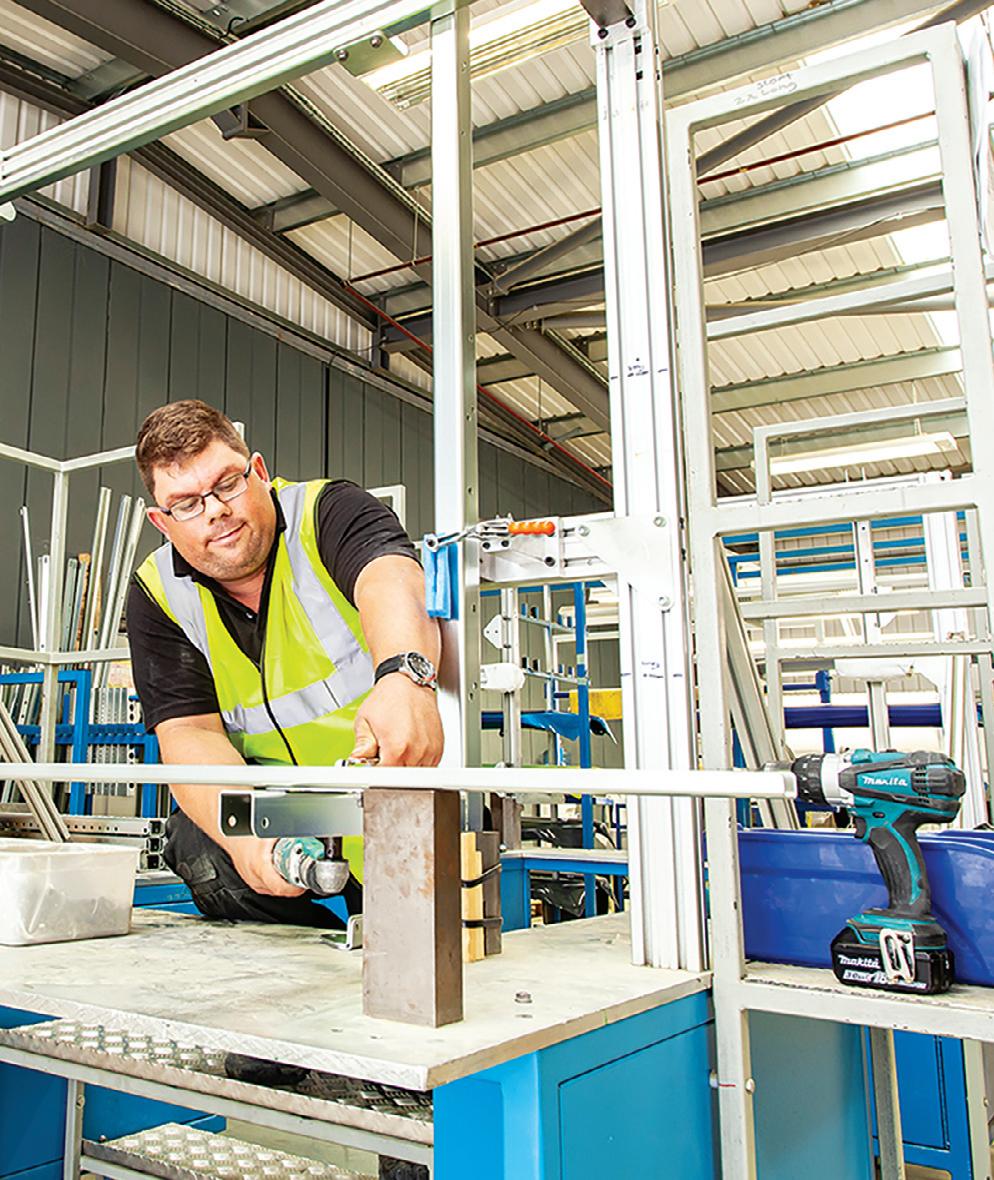
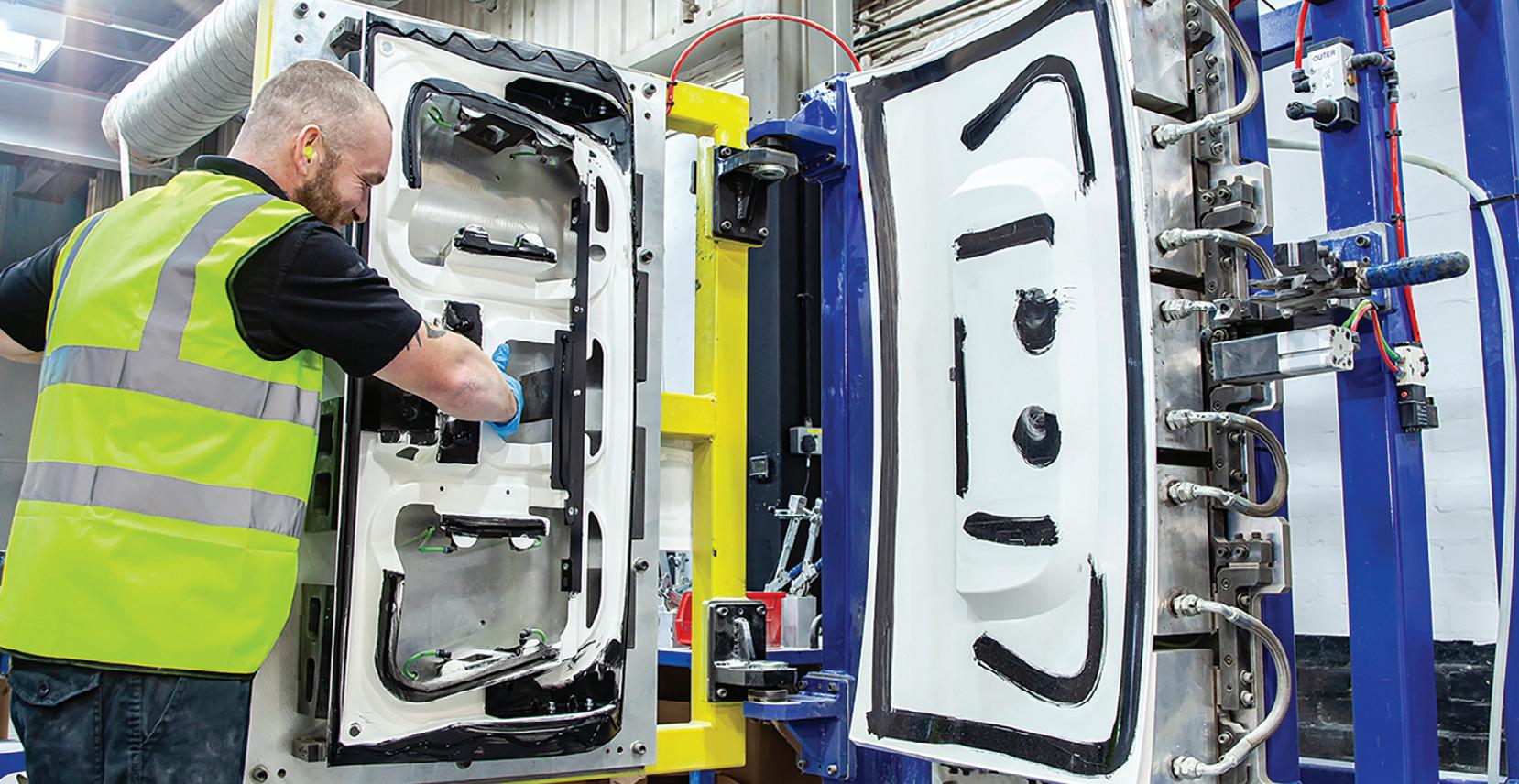

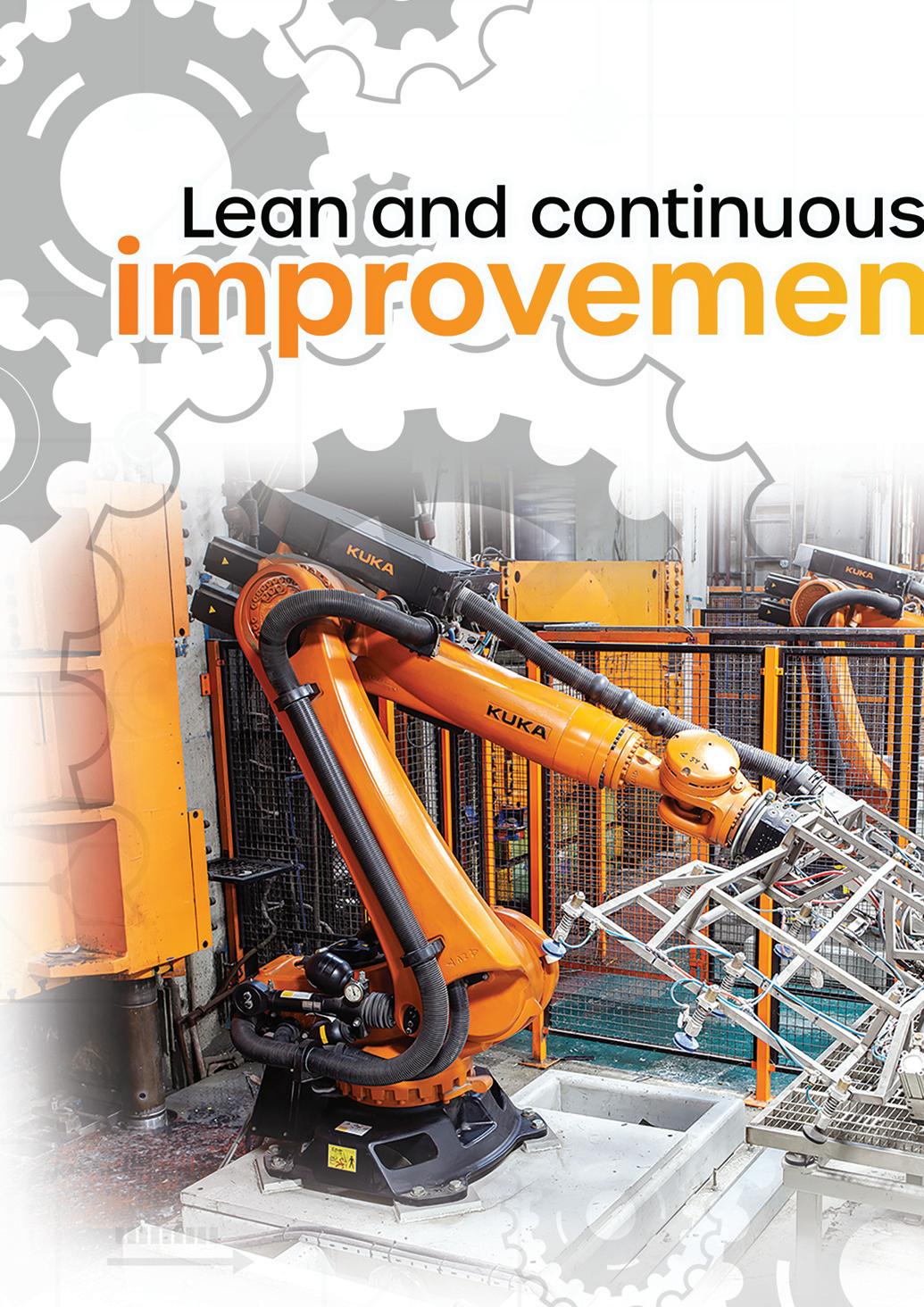
Based in the north-west of England, Mitras Automotive offers a complete service for the design, development and supply of composite components. The company is enjoying a period of healthy growth, while continuing to invest in infrastructure. Luke Robinson, Head of Sales, told Hannah Barnett how Mitras is going from strength to strength.
Mitras Automotive is flourishing. Despite the impact of Covid across all industries, the company is doing better than ever.
The company specialises in compression and reaction injection moulding. Mitras is a leading supplier of SMC (compression moulding) and DCPD (reaction injection moulding) components to the automotive, off-road, lorry, rail and industrial markets.
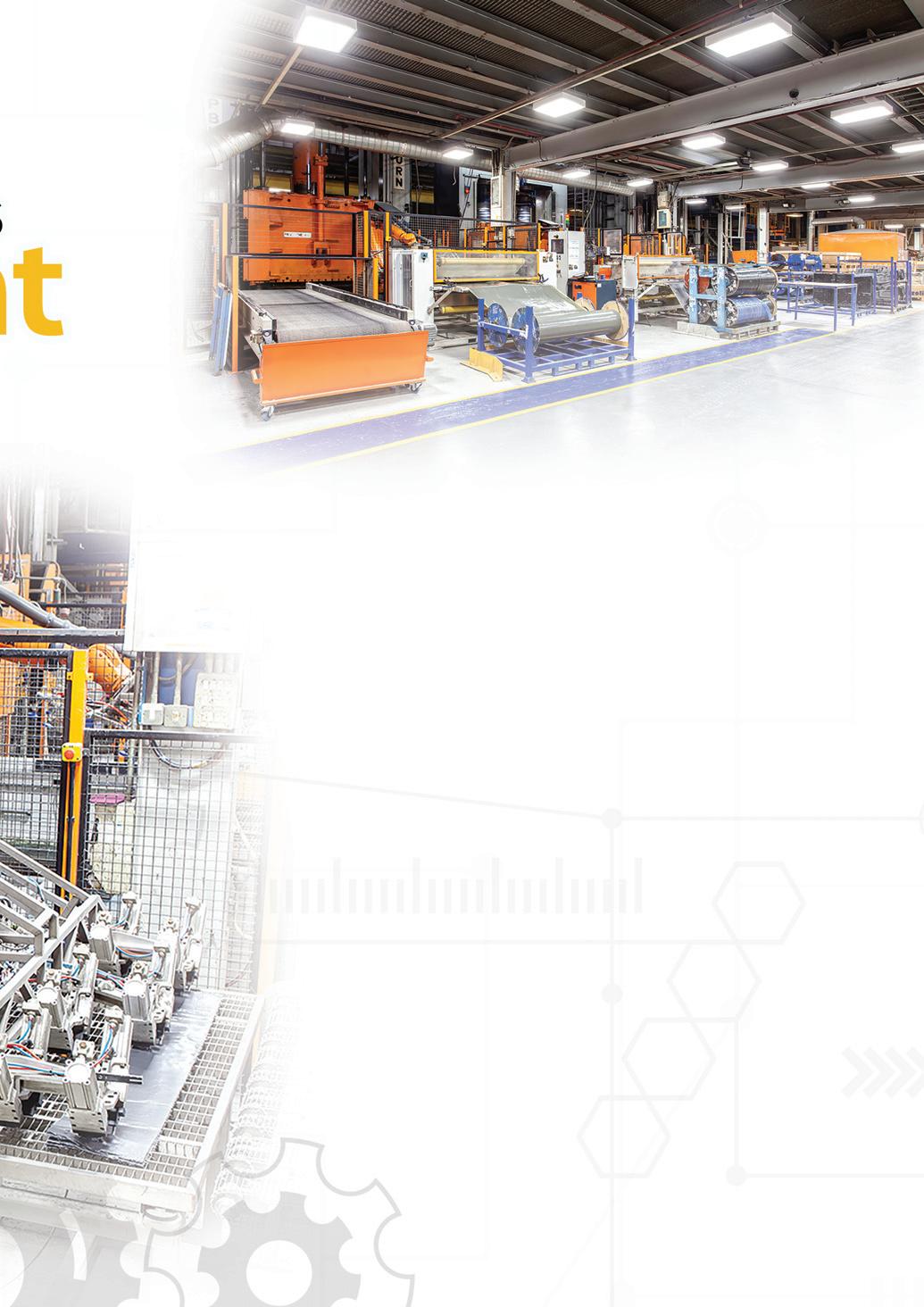
“In 2021, our sales returned to pre-Covid levels,” explained Head of Sales Luke Robinson. “Since then, we've secured various new pieces of businesses during and whilst emerging from the pandemic. Now that the tooling and NPI programs have been delivered, we are seeing the benefit in terms of additional turnover, particularly in 2022 and going forward.
“2022 was a record year for sales revenue, due to a combination of new business wins, natural sales growth from existing
clients and products, plus rising costs. We’re anticipating this year to exceed that level, and for this level of sales to continue for the foreseeable future; we are able to meet the ever-increasing customer demand and expectations, plus achieve such record levels of sales, due to the efforts and ingenuity of our people who always strive for continuous improvement.”
Facilities and figures
The numbers show that the company is on an upward trajectory. Mitras recorded sales of £27.7 million for 2022. A considerable rate of growth from the £21.7 million it generated in 2021 and £21.6 million in 2019, the year before the Covid pandemic severely hampered industry production.
This growth is partially made possible by the fact that the company is one of 13 businesses in the German-owned group, Senata. “The group is very supportive. Most of the profit we have made in recent years has been reinvested back into the business, through upgrading the existing plant and equipment, new machinery, and investment in people,” said Mr Robinson.
Operations are split across two sites, just under one mile apart. The first, Mitras 1, houses the press shop, made up of an impressive range of SMC and DCPD presses, CNC machinery, robotic capability and several standalone paint booths. The other facility, Mitras Paint Operations, functions primarily as home to the state-of-the-art automotive standard robotic paint plant.
This sort of robust and extensive infrastructure helps to set Mitras apart. “We have the largest range of SMC presses in the UK,” said Mr Robinson, “with multiple presses capable of generating up to 3,000 tonnes of moulding pressure and platen sizes of up to threeand- a-half metres squared, so we have the capability to produce some very large components. With SMC, typically it is the press bed size which is the limiting factor, so we are well equipped to meet existing and potential customer requirements.”
Value-added
There is little doubt the company is well equipped. But what it does with this equipment makes it really stand out.
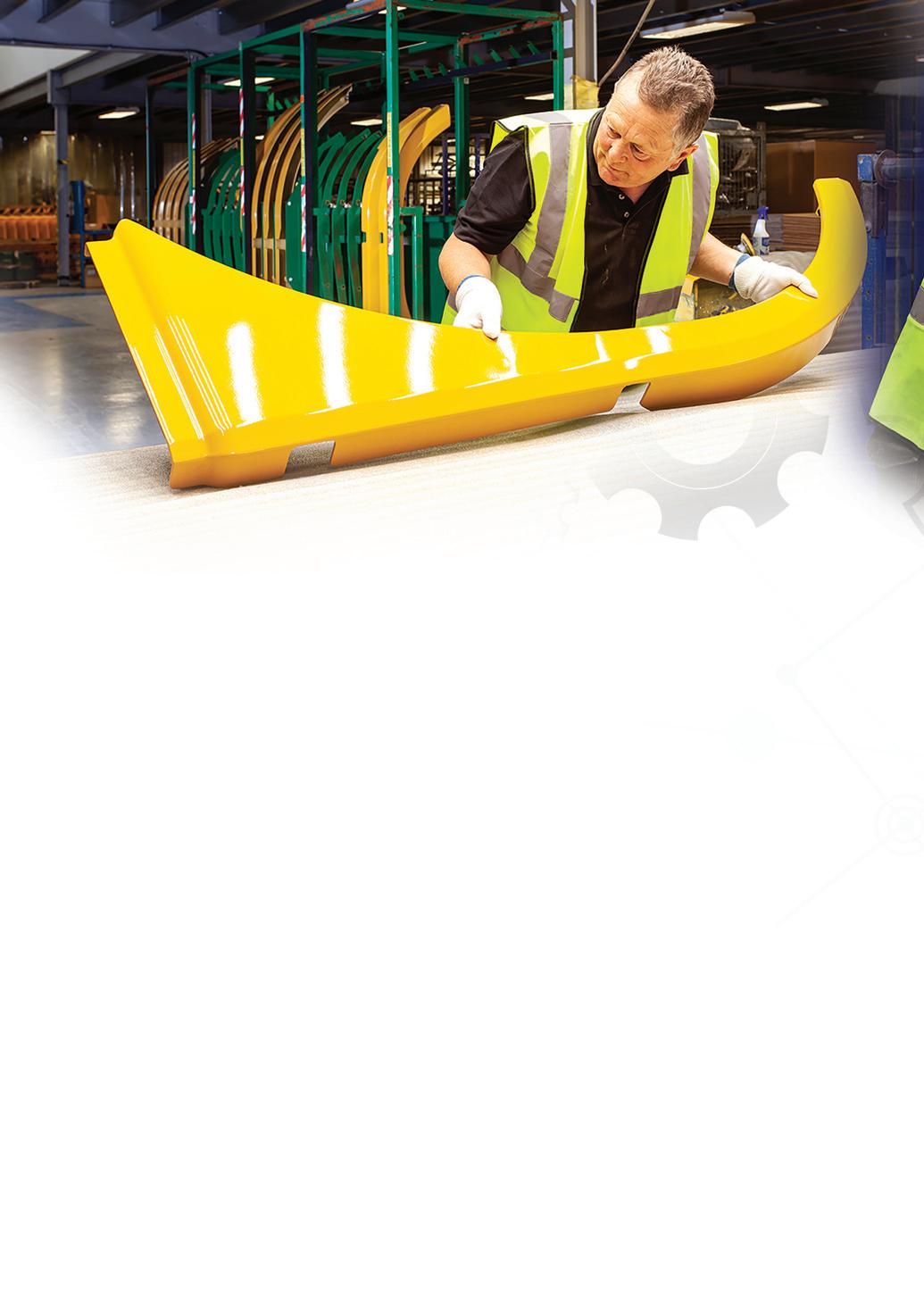
“We offer our customers a value-engineered product,” said Mr Robinson. “CNC and robotic machining, painting, bonding, final assembly. It's not just about supplying a product; it's about looking at the customer’s process to see how we can make it more efficient or cost effective. We also examine their product specifically to understand how to make the component as high-quality, lightweight and cost-effective as possible, whilst ensuring that the manufacture process is established and controlled to ensure that this high level of quality and manufacturability will be maintained over time.
“For example, we supply an SMC bonnet assembly which is moulded, machined, painted, and has a steel grille and framework bonded to it. We also fit several auxiliary components (locks, latches, hinges etc.) to the bonnet assembly, before loading it into a bespoke customer delivery stillage for transportation.
“On arrival at the customer site, this is taken directly to their production line for
assembly onto the machine. The added value and assembly work also reduces complexity within our customers’ supply chain, as we manage and order materials from several businesses which become Tier 2 suppliers to the OEM.”
Mitras helps to keep the manufacturing process lean by minimising the work its customers have to do.
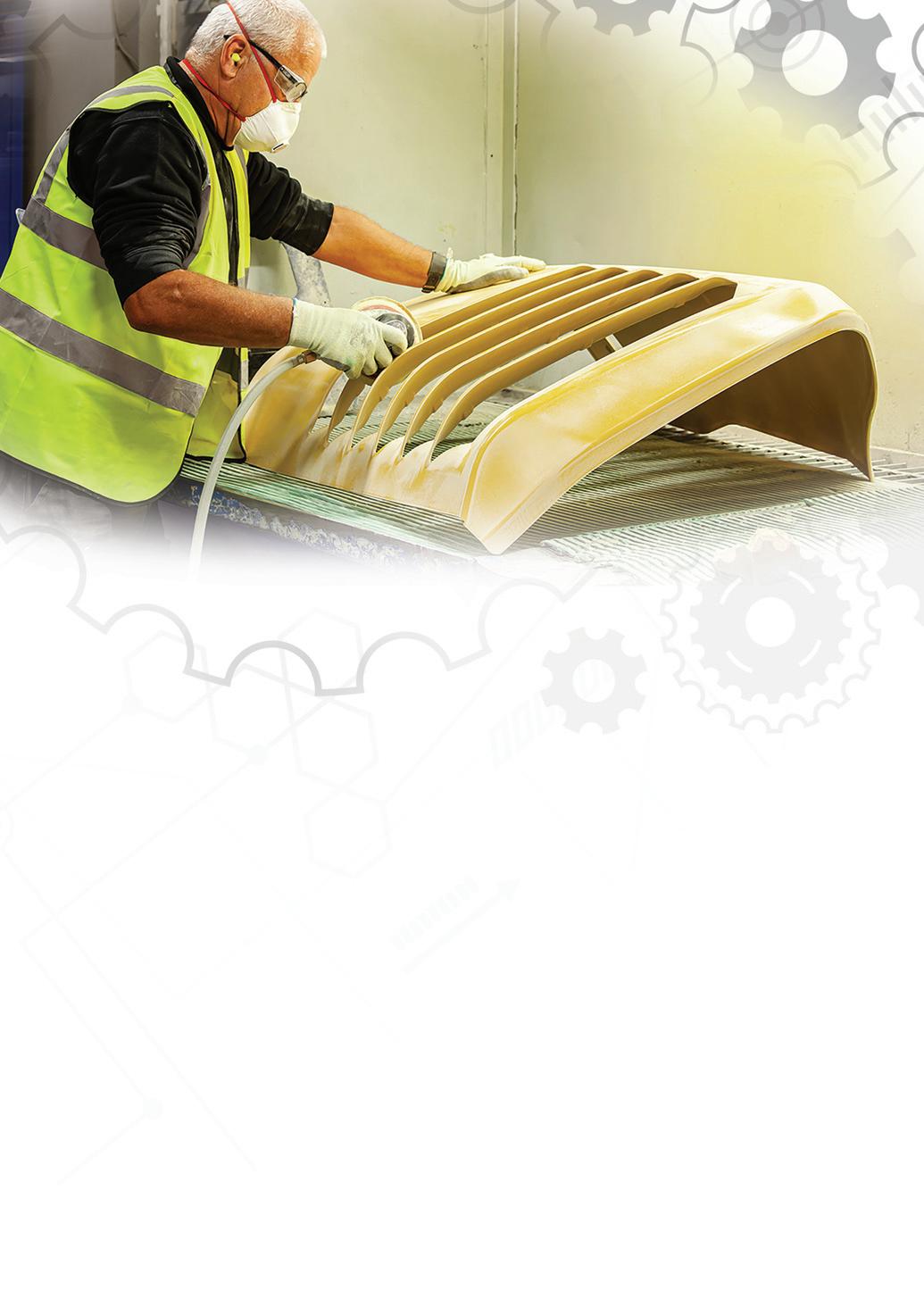
DCPD sustainability
DCPD is a useful material for various reasons. It boasts a low carbon footprint, as the primary raw ingredient is effectively a biproduct of the crude oil cracking process. The moulding process requires relatively low pressure and temperature, meaning rela tively little energy is used.
“It is also very lightweight,” explained Mr Robinson. “The specific gravity of DCPD is 1.03. As a comparison, steel is in the region of 7.8. Switching from a steel panel to DCPD typically provides a significant weight reduction, which is critical for our
clients in terms of increasing potential payloads and also reducing CO2 emissions. These are some of the biggest advantages for our customers.”
DCPD is frequently used in the construction industry due to its superb impact resistance, design flexibility and relatively low initial tooling costs. When panels are designed accordingly, it can comfortably withstand drop testing.
Further green measures
There are other ways Mitras is seeking to improve its sustainable credentials. One is by investing in solar panels for the Mitras 1 facility, its largest site. Additionally, all company cars are electric or hybrid.
Further sustainability is achieved through investing over £500k in a new, state-ofthe-art CNC machine, amongst the most efficient machinery available in the market. This investment provides significant benefits for the company in the long term.
“If we can achieve the anticipated increase in throughput from this most modern machinery with better capability, accuracy, efficiency and speed,”
Mr Robinson said, “this will lead to a reduction in energy consumption and greater longevity of ancillary equipment. This also unlocks additional capacity which can potentially be utilised to generate additional revenue.”
Another crucial cog in the Mitras machine is the company’s objective to build long term, sustainable relationships with its supply chain.
“Although cost competitiveness and commitment to continuous improvement are key considerations in what is a cost sensitive market, we don't want to be changing suppliers every two minutes just to save a few pennies here or there,” explained Mr Robinson. “Our ethos is about developing relationships with strategic partners who meet our needs and are aligned to our KPIs.”
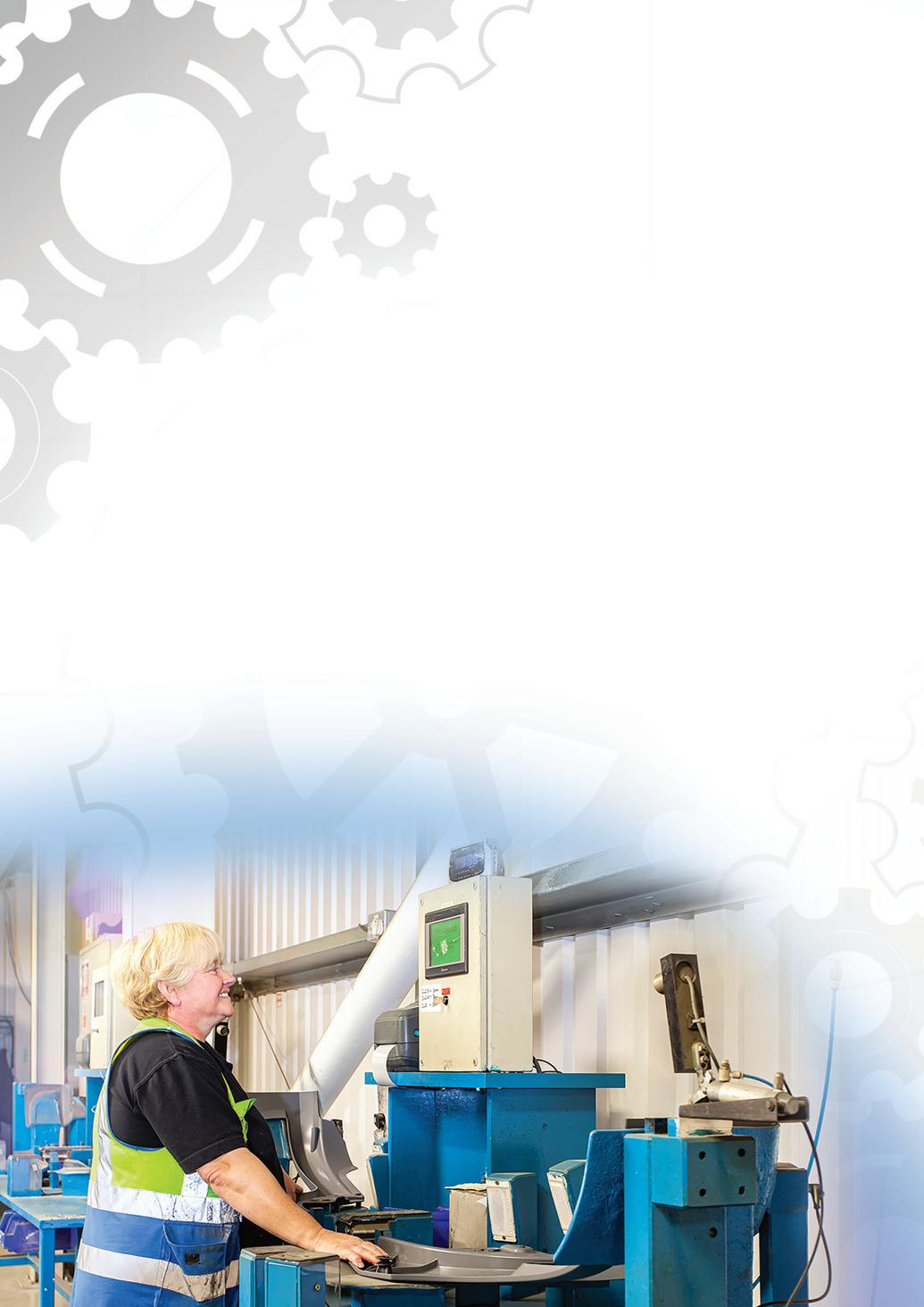
As Mr Robinson explained, parent group Senata is fully backing the company’s vision for sustainably focused growth.
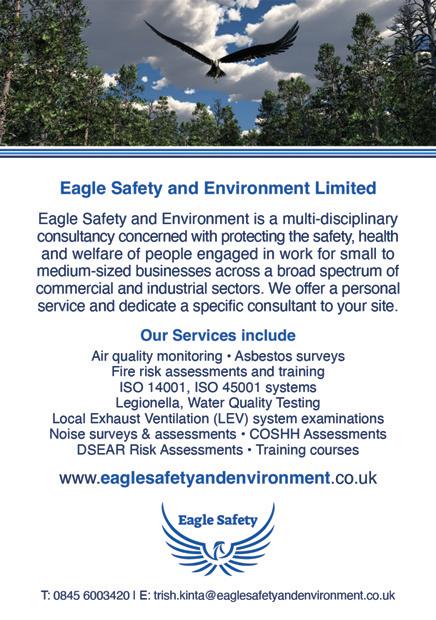
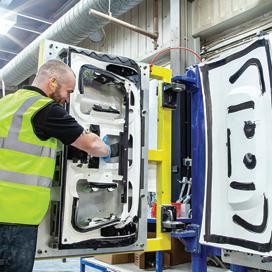
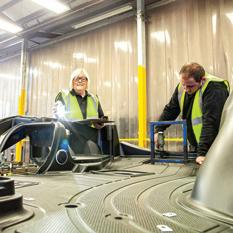
“We want to move the business forward and become more sustainable by doing so,” he said. “Senata is committed to investing in the business. Part of the CapEx sign off process involves asking us to consider energy usage and consumption, to ensure we’re doing things in the right way. We must also ensure that all our suppliers are compliant with Senata’s code of conduct, which sets out our expectations in terms of responsible use of resources and energy, waste han dling, etc.”
It is clear that Mitras is not about to stand still. There is considerable opportunity for Mitras to continue growing, and the company is investing to support these ambitions. For instance, as Mr Robinson pointed out, it is impossible to ignore the electrification revolution happening in the automotive industry.
“The EV market is growing and creating potential opportunities for us,” he reflected. “SMC is a natural electrical insulator, and it is already being used to produce components for electric vehicles, so it is a proven technology for such applications. And with
DCPD being very lightweight, it can offer a potential solution as OEMs look to offset the additional weight of the powertrain in electric vehicles. There are strong, exciting opportunities for us within the expanding EV market.”
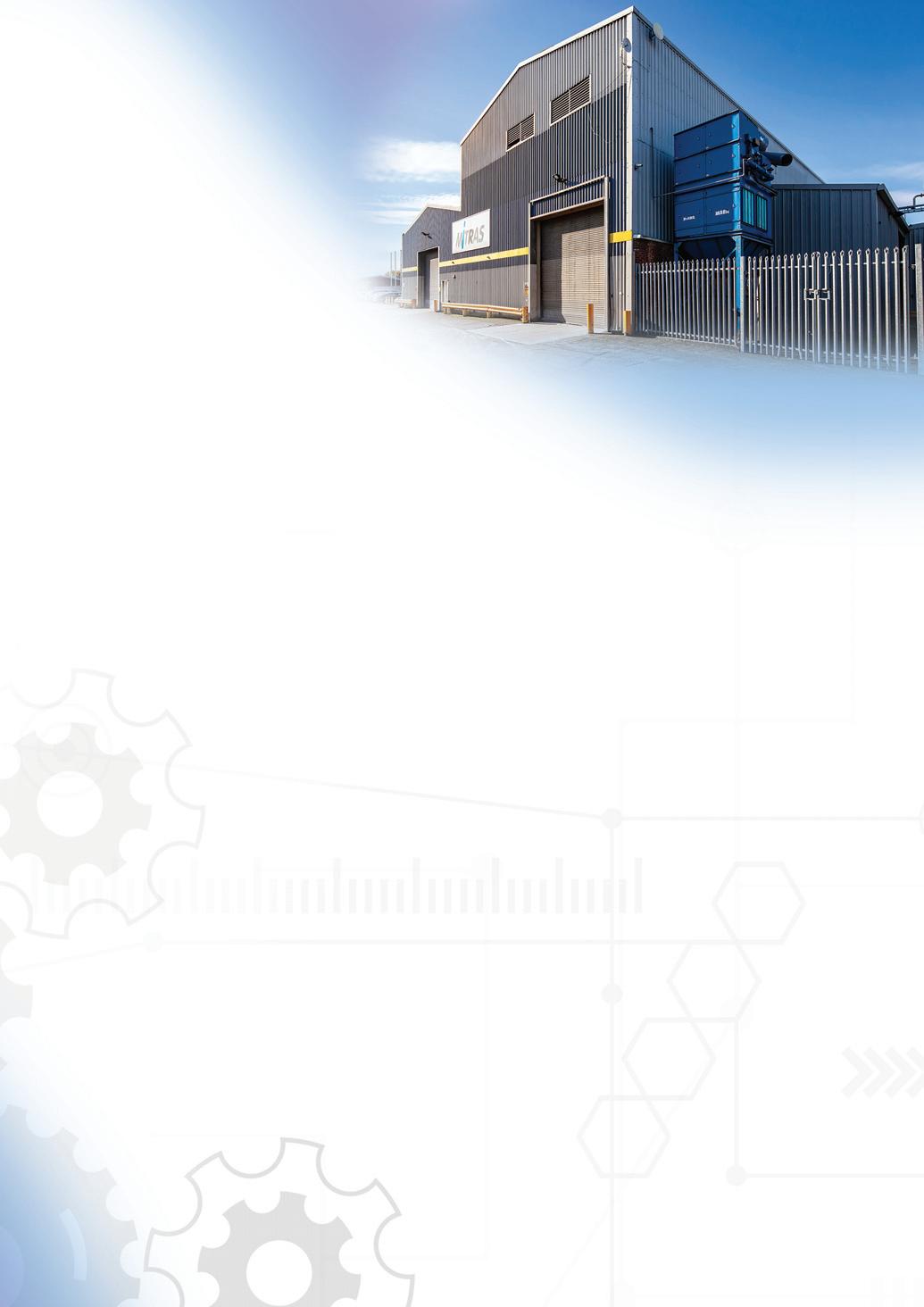

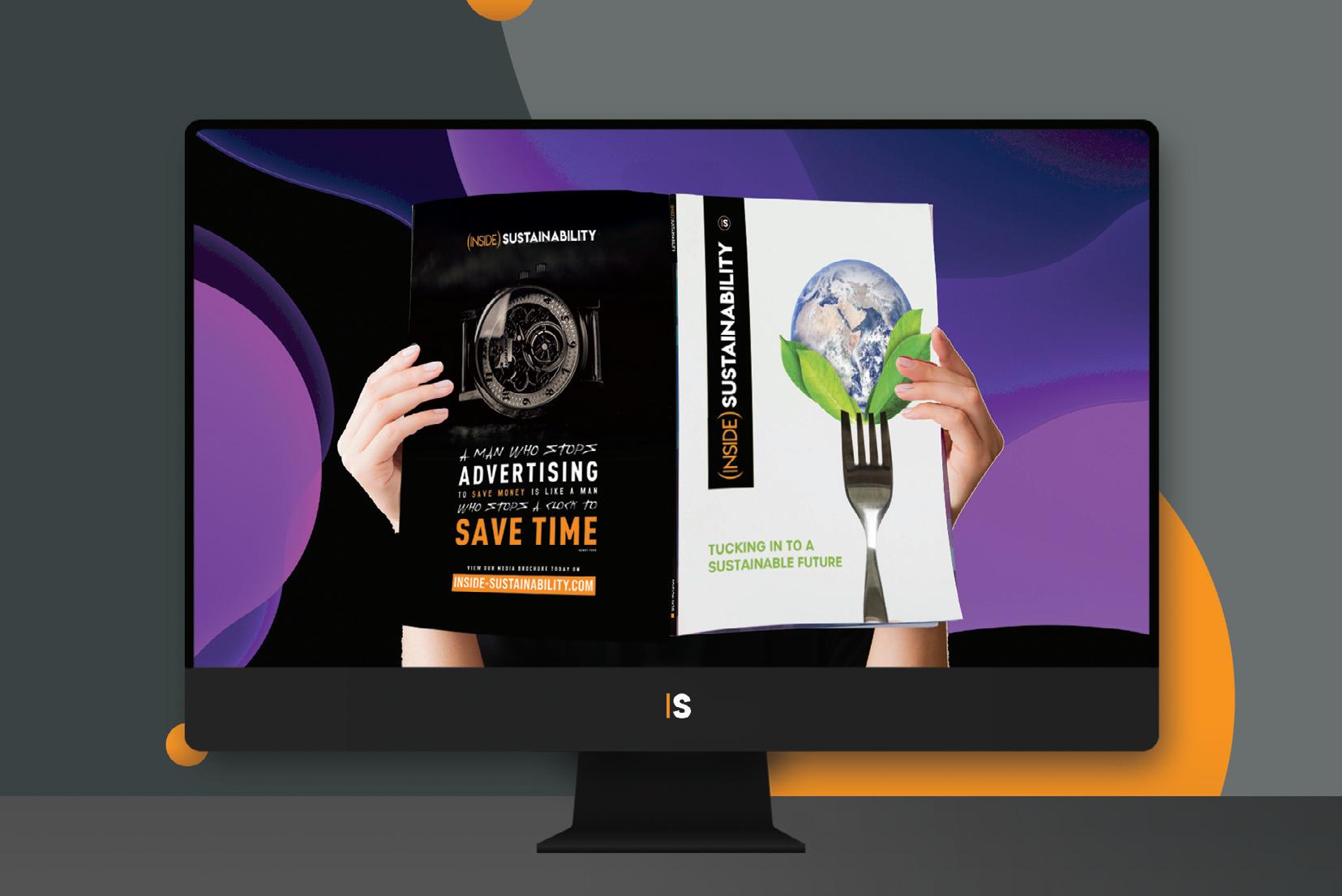