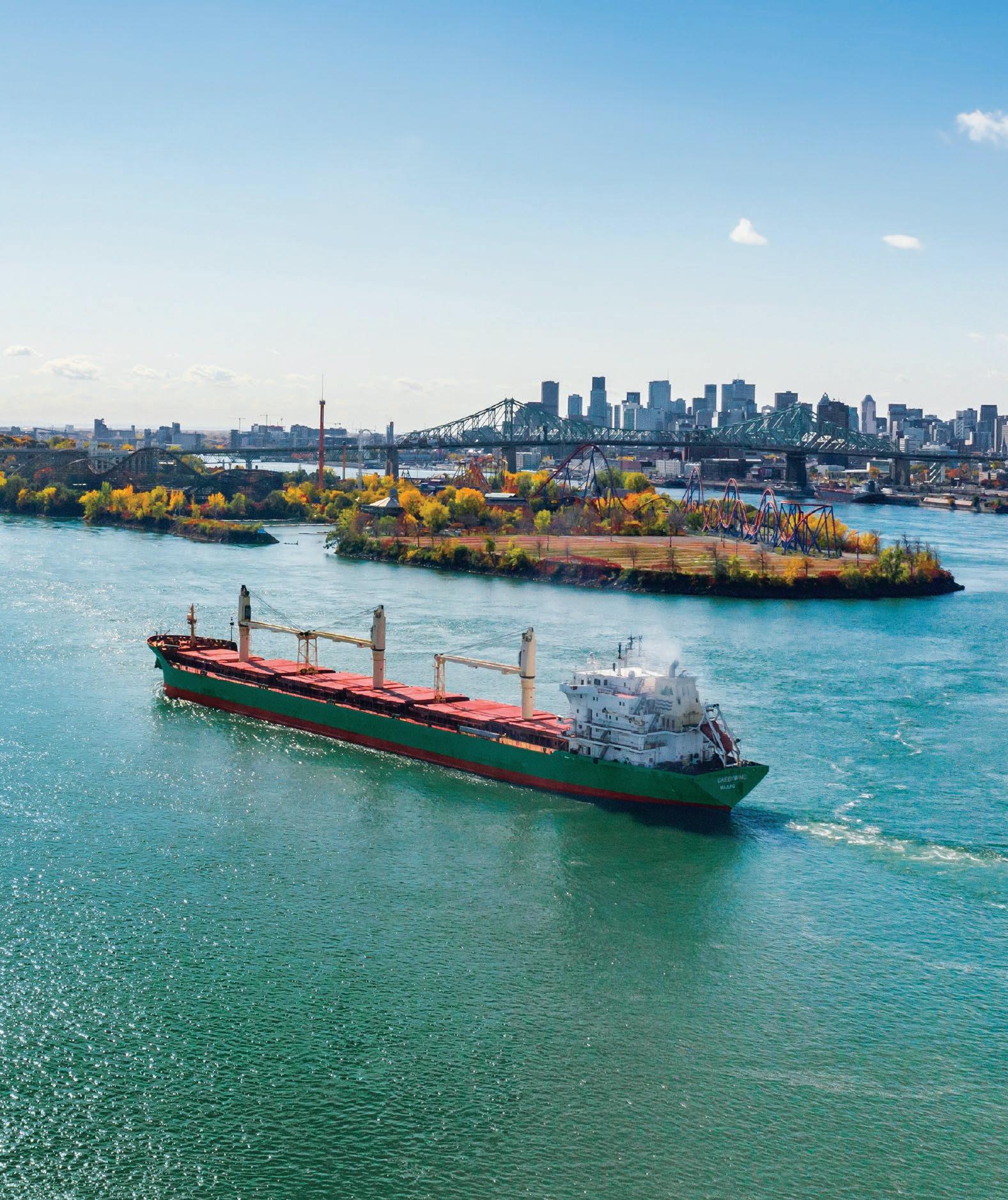
NOR-SHIPPING
Q&A with Director Sidsel Norvik Inside this issue:
Singapore Maritime Week
Review of this international event
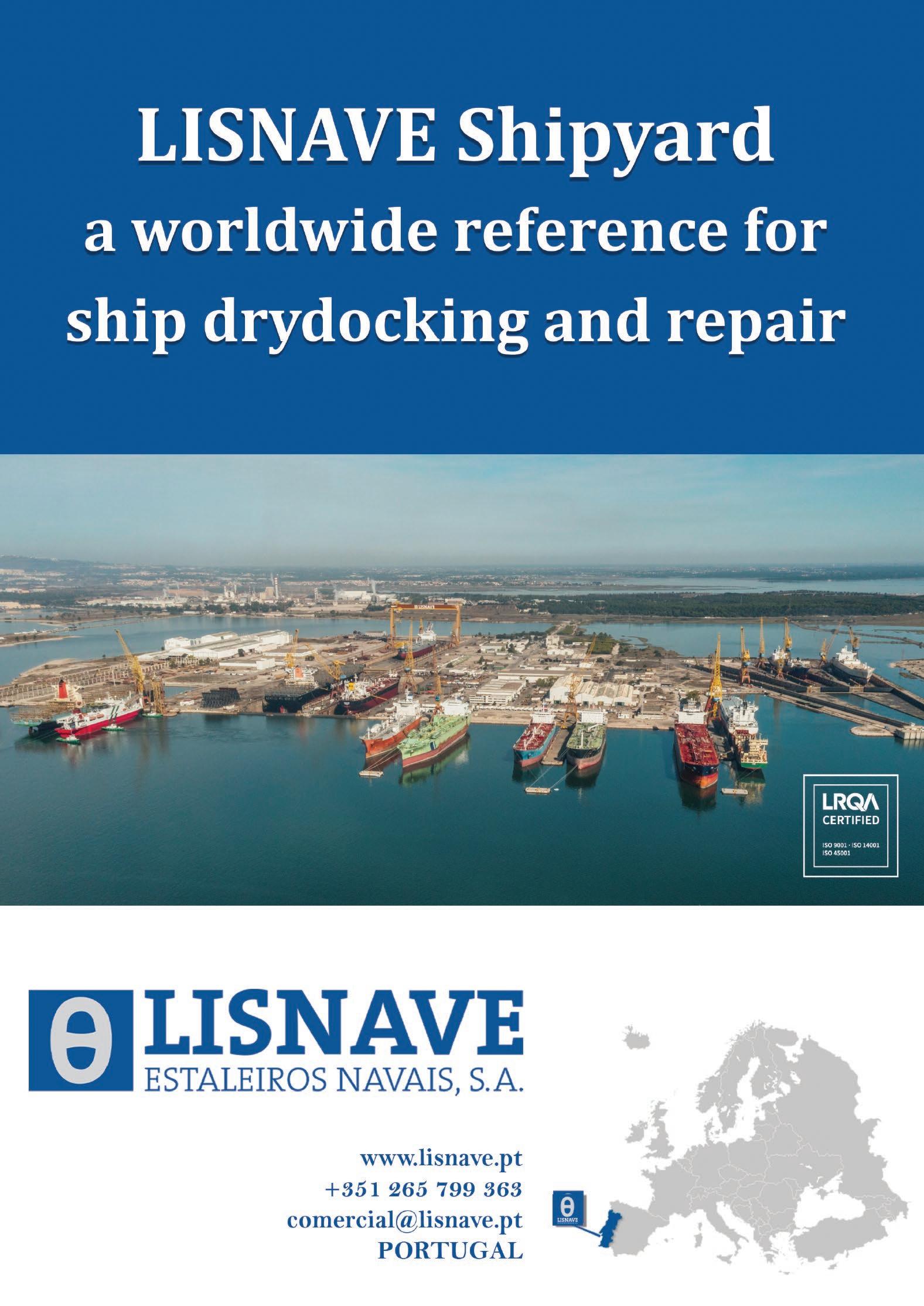


NOR-SHIPPING
Q&A with Director Sidsel Norvik Inside this issue:
Singapore Maritime Week
Review of this international event
– Phil Nicholls Editor –
Editor Phil Nicholls presents a selection of maritime wisdom from across the seven seas.
Hello, and welcome to the latest edition of Inside Marine. Preparing the assorted articles for this issue made me realise just how much the wisdom of the sea is all around us.
As an island nation, it is no surprise that naval idiom has woven its way into the language. Instead of being ‘all at sea’, or even ‘sailing close to the wind,’ it is clear that many sailors simply ‘know the ropes.’
One clear example of this wisdom can be found in the pages that follow, as we share another selection of business advice from some of our recent interviews. These personal insights into the character and experience of the people we interview are always a highlight and perfectly illustrate the cut of their jib.
Yet, a deep, cultural interest in maritime knowledge is not exclusive to the UK. In the
Edo period, Japanese artist Katsushika Hokusai created a woodblock print series known as Oceans of Wisdom. This series was roughly contemporaneous with his classic The Great Wave off Kanagawa. Almost 200 years old, these images from another island nation capture the changing nature of our oceans.
As part of our event coverage, the interview with Director Sidsel Norvik highlights the latest changes at Nor-Shipping, with similar evolutions occurring at Singapore Maritime Week. Indeed, the overall message from the collected wisdom gathered together in this issue is how the first-rate maritime sector is in the energy transition for the long haul.
I trust that as you sail through the remainder of this edition, you will find an enlightening selection from the oceans of wisdom within the maritime community. n
To open a magazine featuring the usual breadth of maritime companies, here is a visual review of the varied nature of the marine business world. There are so many
Managing Director
John White
Editor
Phil Nicholls
Feature Writers
Imogen Ward
Hannah Barnett
Antonia Cole
Finance Director
Filomena Nardi-Smith
Accounts
Chloe Frosdick
Angel Esherwood
Business
Development Manager
Darren Foiret
Research Editors
Mark Simmonds
Judi Wheaton-Mars
Ginelle Lorenzo
Tony Ingrouille
Kristel Hitter
Natalie Martin
Becky Scrivens
Tarjinder Kaur
Matt Spalding
Sales Director
Richard Brightmore
Sales Manager
Helen Leisi
Project Managers
Kym Hamilton
Chris Renicar
David Earl
Dennis Morales
Greg Churchill
Josh Hyland
Taylor Green
Studio Manager
Philip White
Webmaster
Michael Stamp
Designers
Sarah Jones
Sam Moyse
Operations Manager
Gavin Bellward
Marketing Manager
Adam White
Administration Manager
Joanna Wartacz
Latest developments from the Australian industry
Energy and marine consultancy ABL has been appointed as marine warranty surveyor (MWS) for the marine transportation of modules to Perdaman Chemicals and Fertilisers Pty Ltd’s new urea plant on the Burrup Peninsula, Western Australia.
The facility on the Burrup Peninsula is located approximately 20km north-west of Karratha, Western Australia. Once the construction of the plant is completed, it will be the largest urea plant in Australia and one of the largest in the world.
Urea is a vital component of the agricultural fertiliser market with increasing demand as more efficient and intensive global food production is required to meet the needs of a growing world population.
The construction of the Perdaman urea plant will be modular, whereby the modules for the plant are built in India and shipped to Australia. In support of the construction, over 50 long-lead cargos will also be transported internationally. ABL will conduct module transport document reviews, site attendance in India and Australia related to load-out, marine transportation, discharge and road transport to the plant site, plus conduct vessel surveys. In total, 113 modules will be transported on a minimum of 15 RoRo transports and 7 LoLo
transports. ABL will deliver its MWS scope as a subcontractor to Saipem-Clough JV. Equally shared joint venture reached the development and EPC contract with Perdaman Industries in 2022.
“This is a substantial marine transportation project that involves a number of modules, ports and vessels,” said Kervin Yeow, ABL’s Regional Director for Energy Services in Asia Pacific. “Our extensive marine warranty surveyor team is set up to manage such logistical challenges to ensure the safe transportation and delivery of all equipment.”
ABL will manage the project out of its office in Perth, Western Australia, supported by the company’s office in Mumbai, India. n
To have your company’s latest news included online or in our Inside Marine magazine, contact us today. media@insidepublication.com
Latest developments from the Japanese industry
Seatrium Limited has been awarded a contract by Japan-based Penta-Ocean Construction (POC) to carry out the engineering, procurement and construction for a 5,000 ton fully-revolving Heavy Lift Vessel project for the Japanese offshore wind market.
The new vessel will be the fifth and largest vessel to be added to POC’s fleet, enabling the company to undertake larger wind turbine projects in offshore wind construction.
POC is Japan’s leading marine contractor with a keen interest to expand its business in the offshore wind sector. POC owns a range of self-propelling trailing suction hopper and cutter suction dredgers for marine construction works, as well as two turbine installation vessels equipped with an 800 ton and a 1,600 ton lifting capacity crane respectively.
“We are proud to confirm the contract with Seatrium for the development of an advanced heavy lift vessel featuring a 5,000 ton fully revolving crane,” said Tetsunori Ohshimo, Senior Managing Executive Officer, Head of the Offshore Wind Construction Business Divisions Group, POC. “We are confident that this
vessel will make a significant contribution to the development of offshore wind in Japan, enhancing our efforts towards a sustainable energy future.”
In Singapore, POC is a main contractor in various marine and land civil engineering, and building projects, including the development of Pasir Panjang Terminal Phase 3 and 4, Tuas Mega Port, LTA projects and ION Orchard.
“We are excited to announce our first heavy lift vessel project with Penta-Ocean Construction and are fully committed to delivering this to our customer,” said William Gu, Executive Vice President of Seatrium Energy (International). “This project is significant to us on various fronts, as it marks our maiden collaboration with Penta-Ocean and our foray into the Japanese offshore wind market. We are deeply honoured to develop this heavy lift vessel, adding onto our track record of innovative and cost-effective solutions that accelerate the energy transition.” n
Latest developments from the Scottish industry
Forth Ports, the UK’s third largest port operator, has announced a £50 million private investment in infrastructure at the Port of Leith having secured its largest ever offshore wind contract, the delivery of the 1.1GW Inch Cape Offshore Wind Farm.
This latest investment in infrastructure at the Port of Leith will enhance the port’s marine access, infrastructure and vessel assets. It will also create up to 50 new and upskilled green energy jobs to support the project.
Forth Ports’ agreement with Inch Cape, to be sited off the Angus coast, will utilise the port operator’s bespoke facilities and expertise at newly created renewable energy hubs at both the Port of Leith and Port of Dundee.
Upon visiting the Port of Leith, Deputy First Minister Kate Forbes, said: “Investment in key sectors such as Scotland’s ports can reap rewards. This is why the Scottish Budget commits £150 million to the offshore wind infrastructure and supply – to attract private investment such as this announcement from Forth Ports.”
The Leith announcement follows a decade of private investment, during which time Forth Ports has created the land, quayside
and skills capacity, which has not previously existed in Scotland, to deliver very large offshore wind contracts.
“Inch Cape represents a very significant milestone for Forth Ports, as it is the largest offshore wind contract ever to be awarded to our business,” said Stuart Wallace, Chief Executive Officer, Forth Ports. “When it goes live, Inch Cape will have a significant impact on Scotland’s energy transition as the country drives to achieve net zero carbon emissions.”
“This announcement is a gamechanger for Forth Ports and the Scottish offshore wind market,” explained David Webster, Commercial Director at Forth Ports. “We have created world class renewables hubs in Dundee and Leith and solved the challenge of local content by locating at ports near the construction sites, creating high-quality local green jobs and local supply chains, while securing work for future generations.” n
Latest developments from the Spanish industry
United European Car Carriers (UECC) has performed the first-ever ship refuelling operation in Spain with a truck-borne shipment of liquefied biomethane (LBM) to widen access to supplies of the sustainable fuel and bolster the country’s circular economy.
INthe landmark event at the Port of Vigo, overseen by the president of the port, LBM supplied by green energy developer Naturgy was pumped directly from a tanker truck into the tanks of UECC’s multi-fuel LNG battery hybrid Pure Car and Truck Carrier, Auto Advance.
“This is an important step it is the first time LBM has been delivered by truck to ship in the whole of Spain,” said UECC’s Energy & Sustainability Manager Daniel Gent. “We view Spain as a promising market for biomethane production, and so it’s great to get this first delivery over the line.”
The delivery allows the leading sustainable carrier in the European shortsea RoRo trade to diversify its regional sources of supply for LBM beyond its main hub of Zeebrugge, where it has a long-term supply agreement in place with Titan Clean
Fuels. Another aspect of this diversification is that it also represents the first physical molecule delivery of the fuel – instead of mass balanced – as UECC explores multiple alternative delivery pathways to broaden its LBM portfolio.
UECC is boosting uptake of the fuel, also known as bioLNG, in line with expansion of its Sail for Change sustainability initiative launched last summer. LBM is being bunkered on the company’s five dual- and multi-fuel LNG PCTCs for several major vehicle manufacturers to cut their Scope 3 emissions.
“Securing additional sources of renewable fuel contributes to our decarbonisation pathway, a key element of our corporate long-term sustainability strategy to hit net zero by 2040,” Mr Gent added, in conclusion. “We hope the LBM truck delivery in Spain will be the first of many.” n
seven seas, five oceans, one voice
A selection of future events, followed by a review of Singapore Maritime Week and a preview of Nor-Shipping.
Bringing together over 11,000 attendees, Breakbulk Europe provides the ultimate networking platform to grow connections, generate new business and strengthen key existing relationships. Join the industry decision makers in Rotterdam to drive the connections and innovations that support the completion of global projects.
click here for weblink
Held at the Dubai World Trade Center, Seatrade Maritime Logistics Middle East is the must-attend event for maritime and logistics professionals in the Middle East.
Join over 7,500 attendees from more than 90 countries at this global hub for maritime logistics.
click here for weblink
Nor-Shipping across the knowledge, showcase relationships necessary of sustainable success. the ocean comes
click here
Following on from the successful 2024 turns to The Empire Riverside Hotel. for purchasing professionals who are committed and efficiency in their supply chain. With a line-up event promises to be an unparallelled opportunity.
click here for weblink
Nor-Shipping
Nor-Shipping gathers industry leaders from the world to debate pathways, share showcase innovation and help build the necessary to navigate towards a future success. This is where the business of comes to life.
for weblink
2024 event, IMPA Hamburg reHotel. This event is specifically tailored committed to achieving sustainability line-up of esteemed speakers, this opportunity.
GreenTech is the not-to-be-missed event of the year for anyone interested in the maritime industry, green technologies and innovation in sustainable maritime transportation. The programme includes renowned speakers, the exhibit hall showcases state-of-the-art exhibitors, and the event is full of networking opportunities.
click here for weblink
Why not give your event exclusive coverage to thousands of readers and connections globally? Contact us: events@insidepublication.com
An overview of Singapore Maritime Week.
Singapore for
Singapore Maritime Week was held from the 24th to the 28th March, 2025, at the Suntec Singapore Convention and Exhibition Centre. Organised by the Maritime Port Authority of Singapore, the event brought together the international maritime community to explore the future of the industry.
Every year, Singapore Maritime Week (SMW) brings together maritime leaders and industry professionals from across the globe to facilitate conversations on the sector’s issues, trends and opportunities. The 2025 event attempted to accelerate the evolution of the maritime industry, promoting areas such as decarbonisation, digitalisation and green shipping corridors.
SMW enabled attendees to connect with experts, exploring the latest developments in maritime research and development. Showcasing the technologies transforming the industry, the event gave visitors access to advancements in cybersecurity, robotics, AI and more.
Conferences were held on key maritime issues, allowing visitors to engage in conversations that pushed progress and discussed the future of the industry. SMW also featured a range of networking receptions and a trade exhibition, allowing visitors to create new partnerships and diversify connections.
Event highlights
In the face of unprecedented challenges posed by climate change and the urgent need for sustainable practices, the maritime industry is at the forefront of transformative change. This 3-day conference assembled visionaries, thought leaders, innovators, policy makers, researchers and industry experts to explore the intersection of digitalisation, decarbonisation and how services such as insurance and financing must evolve to support the needs of the sector.
With a sharp focus on the convergence of digitalisation, cybersecurity, AI, big data, green finance and decarbonisation technologies, the conference offered profound insights for navigating the dynamic changes ahead.
SMW also offered visitors a selection of site tours, including an exclusive look at PSA Singapore – the world’s busiest container transhipment hub. Highlights of the guided visit included the highly-auto-
Singapore Maritime Week more information: www.smw.sg
mated Pasir Panjang Terminal 5 & 6 and the PSA Innovation Centre – an experiential, multimedia showcase of PSA’s next-generation port and wider supply chain ecosystem.
A key location
Singapore holds a strategic position along major shipping routes, as well as being a hub for a diverse range of maritime services. These include ship management, agency, finance, insurance, surveying, technology and more. With over 5,000 maritime establishments and businesses, Singapore is a key location for business in the maritime sector.
SMW allowed attendees to explore the industry’s transformative developments in a region where the latest technologies are
being implemented. For example, the Maritime Port Authority of Singapore is building the world’s first fully automated terminal. The event gathered together leaders, experts and enthusiasts from all over the world to discover and engage with the innovations of the future. With conferences, displays, networking opportunities and more, SMW continued to push the maritime sector forward and facilitate the connections that transform the industry. n
Director Sidsel Norvik explained what the show will include.
Running from 2nd to 6th of June, Nor-Shipping 2025 will gather industry leaders from across the world to debate pathways, share knowledge, showcase innovation and help build the relationships necessary to navigate towards a future of sustainable success. Inside Marine spoke with Director Sidsel Norvik to learn what visitors can expect. on 2-6 June, 2025 more information visit: www.nor-shipping.com
2025 marks 60 years of Nor-Shipping. In what ways does the event keep evolving and adapting?
Nor-Shipping 2025 is reaching further than ever before, welcoming more international pavilions, visitors and exhibitors, while enhancing content to cater for emerging opportunities and areas of interest. Our conference programme showcases that ambition.
For the first time we will offer a dedicated LNG event, Ocean Invest (focusing on finance) and one of the industry’s first seabed minerals conferences. Of course, this is in addition to firm favourites such as the Ocean Leadership Conference, the Blue Talks, The International Ship Autonomy & Sustainability Conference, and much more.
Our growing global influence can be seen with the arrival of major pavilions from China and India (another first for Nor-Shipping), while we’re also working to open up access to new talent and opportunity through initiatives such as Career Port. This will help build connections
between students, the next generation of industry talent, and established businesses. It is part of Nor-Shipping’s DNA to always evolve and look to the future – as demonstrated by our main theme this year, #Future-Proof – but we must also acknowledge our proud history at such an important milestone. With that in mind, everyone will have a chance to celebrate with a grand 60th anniversary party on the final night.
The exhibition floor features a range of national pavilions. What do you see as the benefits to visitors of these geographical groupings of exhibitors?
There are several attractions to this format. Exhibition feedback tells us that visitors from those nations really appreciate having ‘a home away from home’, where they can connect and network with companies within their national cluster.
Plus, as a marketing platform, they provide interactive hubs where visitors find themselves
Director Sidsel Norvik explained what the show will include.
face-to-face with the innovations, products and services defining key markets – getting a taste of the latest developments and building international connections and opportunities.
This is a global industry, bringing nations together to empower trade and economic development. These national pavilions bring that to life on the exhibition floor.
Another key feature of Nor-Shipping is the Startup Area. How important is it to promote innovation within the industry?
The Startup Area is absolutely vital –a dynamic hub where emerging companies, even those working with smaller budgets, can showcase breakthrough ideas to audiences from around the world.
Often, big innovations emerge from small businesses, and it’s vital that these companies have a platform to demonstrate their potential. Innovation drives this industry forward and, from a sustainability perspective (both environmental and commercial), new technologies, business models and approaches are more important than even before.
I advise all our participants to spend time in the Startup Area. The next big thing might just be waiting for them.
Join us for more www.
Nor-Shipping is also looking to the future with the Ocean Campus area. Please explain what visitors can expect from this feature of the show.
Ocean Campus is a window into the future of maritime talent. Led by the World Maritime University, together with a consortium of key maritime schools and universities, this area focuses on the development of the next generation of our industry colleagues.
Every day, visitors can learn from a series of presentations, while building understanding of the latest innovative training programmes.
We believe Ocean Campus demonstrates how education can keep pace with, and help enable, further industry change.
Returning for another year are the Nor-Shipping awards. Please outline how innovation is taking centre stage at the 2025 awards.
Innovation has always been centre stage at Nor-Shipping. The awards provide a tangible recognition of that fact, with each initiative tailored to showcase and celebrate the people and projects driving ocean business forward.
The Next Generation Ship award highlights newbuilds, retrofits and conversions that set
Director Sidsel Norvik explained what the show will include.
new standards, while the Ocean Solutions award turns the spotlight on innovations from exhibitors that address pressing challenges and opportunities.
In addition, our partnership with YoungShip recognises emerging talent with the Young Entrepreneur Award and the 10 Women to Watch Award. These accolades not only celebrate innovation but also inspire fresh talent that helps set the course for the future of ocean and maritime business.
Nor-Shipping also offers visitors a strong conference and seminar programme. At this early stage, do you have any previews to share with our readers?
Our programme is as vast as it is exciting, running throughout the entire week.
Join us for more www.
We kick things off on Tuesday with the Ocean Leadership Conference, giving key international decision makers the chance to gain insights from a unique line-up of worldclass speakers. Topics will span disciplines ranging from politics and economics through to regulations, investment, technology and much, much more.
It is a packed first day, with attention turning to finance for Ocean Invest and then Offshore Aquaculture, another key growth area. Wednesday gives visitors an array of options, with regional events focusing on Singapore, India and Brazil, alongside the first Deepsea
“ “
on 2-6 June, 2025
more information visit: www.nor-shipping.com
Minerals conference, and dedicated Offshore Wind and LNG conferences.
Thursday shifts our gaze to the horizon with sessions on autonomy, AI and Hydrogen. We wrap up the week on the final day with special sessions on Startups and Career Port on the Blue Talk stage. Plus, the inspiring Blue Talks schedule running alongside the main conference programme through the week.
We really do believe we have something for everyone!
Are there any other notable aspects of Nor-Shipping you would like included in the article?
Absolutely! This year, we are bringing together a broader range of industry segments and a more diverse international community than ever before.
That is great for business, but also great for fun. With that in mind, we have a social and networking calendar as full as the conference and knowledge sharing schedule, giving everyone, we hope, a Nor-Shipping to remember!
What do you consider to be the main industry challenges within the maritime sector?
Our industry is navigating a complex mix of challenges – from stringent regulations and financial issues to geopolitical uncertainty and the growing pressure to decarbonise shipping. These challenges cannot be addressed in isolation.
As such, Nor-Shipping has a vital role to play in gathering together the experts, innovators and global business leaders needed to plot an optimal pathway forward.
This is a collaborative, engaging and inspiring arena, one where key stakeholders can work as one to share insights and work on practical, profitable and sustainable solutions. Nor-Shipping 2025, and events like it, are absolutely instrumental for industry progress.
What is most exciting for you about Nor-Shipping, on a personal level?
For me, it is the sheer scale and significance of Nor-Shipping.
The event has grown over the last six decades, from a regional shipping show into one of the world’s most important maritime and ocean business meeting places.
I’m proud to play a part in its ongoing development and delighted to see its growing influence and impact.
I can’t wait for June to roll around!. n
seven seas, five oceans, one voice
This edition of Inside Marine includes a special feature profiling the sustainable and innovative shipping services offered by Canfornav.
planet, the company is also adjusting to new technologies. Knud Jensen, President and CEO, explained more to Hannah Barnett.
From its HQ in Montréal, Canfornav’s team of 40 skilled employees proudly provide a world-class service to customers, developing long-lasting relationships. The company’s main focus is the Atlantic
handysize market, linking the Great Lakes and the St Lawrence River to ports around the world. As a relatively small player in a fairly niche sector, Canfornav prides itself on precision and quality of service.
“We have an open book policy with all our clients,” explained Knud Jensen, President and CEO. “We also encourage the idea that if there is a problem, to let us know. Actually, we behave the same way. If a charter client somehow misbehaves, we will let them know that it’s not fair game. Does it always work?
No, but the open book policy, I think, works. It doesn’t mean we get more money for our work, but we get a good look at all relevant business information.”
Canfornav is focused on innovation and is proud to provide a reliable service; its vessels carry approximately eight million tonnes of
various types of cargo annually. This includes grain, agricultural products, fertilisers, steel, concentrates and more.
Since 2019, the company has been expanding its fleet with a series of Japanese bulk carriers on long-term charters. M/V Woody, the first vessel, was delivered at the
2024, totalling 14 vessels of 40,000 tonnes. Canfornav has further concluded business for an additional 10 vessels of 40,000 tonnes to be delivered between 2025 and 2028.
Canfornav has also ordered two 40,000 tonnes Ice Class 1C from Onomichi shipyard for delivery 2028.
Significantly, Canfornav now owns a fleet of 24 30,000 to 37,000DWT lakes-suitable
irecto sident and CEO, KnudJe completes around 450-500 fixtures a year. Much of the company’s success it owes to a skilled team, according to Mr Jensen.
April 2025. It will be run by one of Canfornav’s most experienced employees, Christoph Held, a chartering broker who has been with the company for 15 years.
“We know from experience that being
President,
Chri
“Of course, we already do a fair amount of business in Japan, Korea, Southeast Asia and utive Vice
“The time difference kills it. So, we decided that we will be moving into Hong Kong for chartering reasons.
It will be kind of a one-man-service for the moment. It’s not going to be anything big, but good enough to support our clients in in the Pacific region.”
Strong relationships with suppliers are one of the sources of Canfornav’s longevity. Clear communication is therefore vital too; as the company has evolved and
developed over the years, so too have the business relationships.
In April 2026, the company will celebrate its 50th birthday, an undeniably significant milestone. The company plans to mark the occasion accordingly, with cele brations in multiple locations on the shipping map. For Mr Jensen, who has been in the game since 1968.
“If I had to start again, I would still go into shipping,” he concluded. “It has to be a hobby.” n
seven seas, five oceans, one voice
An introduction to ship operators, with advice and innovations, followed by company profiles.
Inside Marine asks the experts about their personal experience in the industry
What is the best single piece of business advice you have ever received?
One of the main things I was told at a young age, that really benefited me, was to do hard and difficult things that other people don’t want to do. That really stuck with me. I’ve always worked in the marine industry, but I’ve still tried to put myself into new positions that are slightly uncomfortable. They say: ‘if you’re the smartest person in a room, get out of the room and go into a different one.’ Not to say I was ever the smartest one. But as soon as something got a bit boring and a bit comfortable, I always felt that it was maybe a good time to try something else.
Taylor Lawson, Business Development Manager,, Hostmost Group
Look after your staff, and they’ll look after your customers, and ultimately the customers pay the bills. I don’t know where I heard it from, but I really think if you look after your staff, everything else will fall into place.
Steve Evans, General Manager, Mainprize Offshore
Always remain open-minded and humble.
Victoire
Boudet, Deputy CEO, Geogas Group
Be as transparent and honest as possible and trust your colleagues to deliver. In my experience, this openness not only builds a foundation of trust, but also cultivates an environment where independent, reliable and dedicated professionals can thrive.
Sidsel Norvik, Director, Nor-Shipping
You are always becoming, there is always a next level to reach. We are always changing, growing and striving to achieve more. There’s always room to be better than we were.
Brendan Williams, Special Assistant to President, Interasia Lines
Somebody once told me to focus on solving the real problem. At their core, successful businesses are built around addressing genuine needs or points in the market. When you focus on truly understanding the problem you’re trying to solve and create value for customers, then everything else, whether it’s marketing, funding or scaling, becomes much easier. This advice reminds me that it’s all about keeping priorities customer-centric, ensuring long term sustainability and success by delivering real value to the customer.
John MacLellan, Operations Director, Subsea Testing and Evaluation
I was told to never make assumptions. This has served me well in my line of work where I am dealing with many different types of people from different cultures.
Jehad Abbas, Sales and Business Development Manager, Al Mutawa Marine Works
In the context of negotiating, when they go fast, you go slow, and when they go slow, you go fast.
Jennifer Cleversey-Moffitt, Chief Administrative Officer & General Counsel, Port of Belledune
Just focus on one thing at a time. If you stay focused, then you will continue to improve every day.
Jeff Lo, Executive Vice President, Interasia Lines
Stay focused. I think that’s essential.
Gerhard Drenth, Business Development Manager,, Royal Bodewes
Get Involved
Why not share your advice with our readers and get involved. Please send to: media@insidepublication.com
Latest innovations from the marine industry
With effect from 27th February 2025, Susesea Bulk Pte Ltd has been renamed as YK Bulkers Pte Ltd.
INaccordance with the Companies Act 1967, any rights or obligations of the company are not affected by this switch to a new name.
“This change reflects our growth and commitment to exceptional service while aligning with our evolving vision,” explained Yahya Karahasan, Managing Director.
“Rest assured that this is solely a name change. Our ownership, management team, service quality, physical and registered address, company UEN, and bank information remained unchanged, apart from the company name.”
All existing agreements, contracts and legal obligations with Susesea Bulk Pte. Ltd. will remain valid under the new name.
Alongside the new company name, there is now a new website at www[dot] ykbulkers[dot]com and the company email addresses now end with @ykbulkers.com.
All other information remains unchanged, including the company address in Eon Shenton, Singapore, and the contact telephone number.
Under its new name, YK Bulkers has invited all partners to update their records to reflect the new name and contact details. The YK Bulkers team stand ready to provide additional information on request.
“We would like to take this opportunity to thank all our partners for their unwavering support over the years,” Mr Karahasan said. “We look forward to strengthening our partnership as we move forward under our new name.” n
To have your company’s latest innovation included in our Inside Marine magazine, contact us today.
Please send to: media@insidepublication.com
Swiss marine power company WinGD’s first methanol-fuelled engine is to be delivered to the shipyard after passing factory and type approval tests. The ten-cylinder, 92-bore X-DF-M engine is destined for a 16,000TEU container ship and is the biggest methanol-fuelled engine built to date.
There are 56 X-DF-M engines on order across bore sizes ranging from 52 to 92, in similar cylinder configurations and engine rating fields as diesel-fuelled X-Engines.
The addition of methanol capability to WinGD’s engine line-up further extends the decarbonisation options available to deep-sea ship operators, which include the long-established X-DF LNG-fuelled engine platform and a new ammonia-fuelled X-DF-A platform.
“Production of sustainable, renewable fuels of all types continues to advance, but longterm availability and cost remain uncertain,” said Dominik Schneiter, CEO, WinGD. “Ship operators can place their trust in WinGD to deliver reliable, efficient engine designs that enable decarbonisation across all candidate fuels. As interest in methanol and regulatory clarity increases, we anticipate the X-DF-M platform will become a key contributor to reducing greenhouse gas emissions from global shipping.”
The milestone was marked by a delivery ceremony held at engine builder CMD in
Shanghai, attended by senior executives from WinGD, CMD and China State Shipbuilding Corporation, as well as local government officials and global customers and partners.
“It is a big responsibility to build the first engine of any type, especially one for an emerging fuel with the potential of methanol,” said a spokesperson for CMD. “Our debut methanol-fuelled engine performed as expected across all tests and we are looking forward to offering the X-DF-M platform as a new option for shipbuilders.” n
PascoGas is committed to delivering reliable and sustainable shipping services, General Manager Zehra Yiğit said:
“A pivotal moment was the decision to reduce our GHG emission intensity gradually by 2035 and to achieve net zero for the entire group by 2050.
“Despite all the cyclical difficulties and uncertainties of world trade, we are dedicated to our environmental strategy. This is a core principle that guides every decision we make, ensuring our vessels and operations reflect the highest standards of sustainability.”
PascoGas provides sustainable solutions to the shipping industry. With vessels built to the latest specifications, the company maintains a fleet of modern and efficient ships. General Manager Zehra Yiğit discussed new investments and environmental targets. Report by Hannah Barnett and Antonia Cole.
The company’s origins date to 2010 when it operated medium-sized gas carriers.
Building upon this experience, PascoGas was established in 2019, becoming a global LPG shipping owner, focusing on the development of an environmentally-friendly fleet. Now the
company employs 365 people who deliver high-quality services.
“As General Manager, I’ve always focused on staying ahead of the curve, balancing technical innovation with environmental responsibility from the very beginning of working for this company in 2015,” Ms Yiğit explained. “My management style is centred on precision and determination, with a collaborative,
forward-thinking approach that empowers our team to deliver exceptional results.
“I believe in making critical decisions with a long-term vision, which is why we’ve consistently pursued cutting-edge technology and quality, even when faced with market uncertainties. This mindset allows us to stay resilient during tough times and lead the way in a rapidly evolving industry.”
PascoGas’ management office is based in Istanbul, Turkey, with a site management office for newbuilds in South Korea. The company has become a leading ship owner with a sustainable fleet, having ordered nine dual-fuel gas carriers and already taken the delivery of three. In April 2025, PascoGas expects the delivery of the fourth, with all vessels to be delivered by 2027.
“These are highly-sophisticated ships, equipped with LPG dual fuel and full ammonia-ready, cutting-edge technology,” added Ms Yiğit. “They will be delivered to Hyundai Mipo Drydock in South Korea, one of the world’s leading shipyards. Two of the vessels
are VLACs, which have been ordered to Hyundai Heavy Industries in Korea. It is clear that we are pioneers of our industry.”
PascoGas operates a state-of-the-art, energy-efficient fleet. With a transportation capacity of 424,000CBM and an average age of three years, this fleet is positioned to become one of the world’s youngest and largest dual-fuel mid-size gas carriers.
“Only three of our twelve fully-refrigerated gas carriers are conventional-type ships,” explained Ms Yiğit. “This already puts us in an impressive place in terms of the ratio of conventional ships in the fleet to new generation environmentally-friendly ones. We aim to continue evolving the fleet with modern sustainable vessels that drive environmental action and create new value.”
Creating a fleet focused on environmentally-friendly vessels is essential in building longterm relationships with clients. This approach enables the client to deliver their trade in the quickest and most efficient way possible, supporting their operations and environmental goals. It is important for PascoGas to facilitate sustainable travel in order to meet the requirements of the market and protect the planet.
The company also completes all managerial tasks in-house. With a knowledgeable team of technical experts, PascoGas works closely with traders and adapt services to satisfy individual needs. The majority of the company’s business comes through chartering, so it is essential that this aspect of operations is run efficiently. Providing a streamlined service drives profitability and customer satisfaction.
“For us, it is not only about having the most environmentally-friendly ships, but also about having skilled technical, commercial and operational teams to make the process easy and efficient,” continued Ms Yiğit. “The ships cannot operate by themselves; it takes a talented crew with the right expertise to guarantee
an effective service. Our professional and driven team are committed to delivering high-quality services for our clients.”
Until recently, the transportation sector has significantly contributed to the world’s greenhouse gas emissions. With the development of sustainable technologies and the adoption of dual-fuel
systems, companies like PascoGas are now taking positive action in the transition towards more environmentally-conscious operations. These solutions reduce harmful impacts whilst also enhancing efficiency and cost-effectiveness.
PascoGas’ newbuilds feature a two-stroke, dual-fuel MAN B&W
ME-LGIP engine. This is designed to run LPG, but it can also run on ammonia once applicable. When run with LPG, the engine offers up to an 18% reduction in CO2 emissions, as well as a 90% reduction in particulate matter.
“LPG, as a fuel, is easier to access, store and handle than cryogenic gaseous fuels,” commented Ms Yiğit. “Furthermore, LPG is cheaper yet delivers the same performance and efficiency. The ability to use LPG cargo as a supplemental fuel
source provides significant cost savings for owners and charterers, including reduced time and fees for fuel bunkering.”
With regulations, such as the EU ETS, being implemented to reduce the environmental impact of international shipping, it is vital that shipping companies take steps to limit greenhouse gas emissions. Additionally, 2025 will see the introduction of the FuelEU Maritime Regulation. This will greatly impact the industry as a whole, pushing sustainability to the forefront of shipping requirements.
“Considering the additional taxes that these rules and regulations will directly and indirectly impose on shipowners and charterers, it is clear to see the advantage that our state-ofthe-art, efficient ships will offer,” added Ms Yiğit. “The specifications of our newbuilds meet maximum efficiency and performance criteria. Our ships are designed
to be highly sophisticated with automation, voyage optimisation, software, hardware and AI-supported tools to easily meet the needs of our crew, shipowners, charterers and all stakeholders in the supply chain.”
PascoGas has worked closely with its partners to continuously develop its fleet for a more sustainable future. Offering high-quality and environmentally-friendly services, the company aims to be an honest and reliable shipping operator. Building close relationships with shipyards has enabled collaborative and efficient operations, driving PascoGas forward.
“International shipping accounts for around 90% of the world’s trade,” said Ms Yiğit. “It is important for us to have a system that considers all international and local rules, and progresses as standards evolve. The responsibility to actively satisfy all key stakeholders is a great challenge, but something that offers me personal excitement.”
Moving forward, the company will welcome the delivery of its remaining dual-fuel ships. However, in the effort to achieve the overall goal of net zero emissions, PascoGas is investigating the role of alternative fuels in the shipping industry. This includes both ammonia- and hydrogen-fuelled vessels.
“We are working with clients to explore the best fuel options for the future,” explained Ms Yiğit, in conclusion. “This industry is constantly evolving, so it is essential that we have these conversations now in preparation. The key milestones in our journey – from setting bold sustainability goals to making critical investments in our fleet – have been shaped by a clear, consistent vision.
“I’m proud of how far we’ve come, and I’m confident that our approach will continue to lead PascoGas to new heights in the years ahead.” n
Ashley Group is renowned within the marine industry, having specialised in steel shipping and carved out its own distinct niche. Now, after several years of success, the company is undergoing some important changes. CEO Peter Allan explained more, during an in-depth interview with Inside Marine. Report by Imogen Ward.
Over the years, Ashley Group has worked hard to establish itself as a versatile, reliable and multifaceted company operating within the remit of ocean freight logistics. Although this mission has been achieved, the company continues to adapt and evolve its offering in order to maintain a strong, market-leading presence. Its most recent focus? A comprehensive fleet renewal.
“As a group, fleet renewal has always been at the forefront of our minds,” explained CEO Peter Allan. “Of course, it’s the standard cycle of shipping, when buying ships there is always an understanding that they will not last forever and that technology will continue to advance.”
A welcome refresh
Initially, back in 2019, the group was focused on purchasing aged vessels that were built in the early noughts. Since, then the company has been naturally transitioning to a younger, more efficient fleet.
“We wanted to do this in an organic manner to avoid overextending ourselves too much,” continued Mr Allan. “So, every move we make is very much targeted towards what we want to do and how it supports our group and our growth.
In 2024, the company signed a deal that saw four new vessels join the Ashley Group fleet. Initially presented the opportunity
by one of its partners, Ashley Group was onboard with the idea of a deal. After eight months of back-and-forth, the two companies came to an agreement, which resulted in Ashley Group being equipped with three near-new Kamsarmaxes and one Ultramax.
“The collaboration was a perfect match for our growth plans,” said Mr Allan. “It enabled us to expand our fleet without overextending ourselves. Following completion of the deal, we received four vessels, three which were built in 2020 and one in 2019. This was a great success for us and as whole really fit well into our business strategy mould.”
With this deal a roaring success, Ashley Group went on to add another new vessel to its ranks just a few months later. This ship
came in the form of a 184m chemical tanker called Carole M. Built in 2016, not only did the new vessel help increase Ashley Group’s fleet numbers, but it also opened new doors within the chemical sector.
“We have been operating Medium Range (MR) vessels for several years, owning four or five in recent times,” explained Mr Allan.
“Recognising an opportunity to expand into the Handysize segment, we saw strong similarities in the fundamentals of both sizes, making it a logical and promising move.
“Additionally, our experience in the MR sector revealed growing demand for parcelling in the Atlantic Basin. This insight drove our decision to acquire Carole M, a 37,000dwt chemical tanker.”
Just as Ashley Group’s fleet is undergoing its own metamorphosis, the company felt it was time to implement another important update. This one focused on its website. After sitting dormant for several years, following a renewal in 2019, the company’s website was in need of a refresh to reflect who we are.
“Since our last website refresh, we have evolved into a very different company,” commented Mr Allan. “Of course, our principles remain the same, but we had to evolve and modernise, and our previous website no longer reflected who we are.
“We hope our customers feel the new website is a better reflection of Ashley Group’s journey, which still puts across our values and what we bring to the industry as a whole.”
Although Mr Allan is very proud of the new website, he was also quick to point out that a strong digital presence is important, but not as important as proving what the company is capable of.
“At the end of the day, it’s all about how you perform, how you report to shareholders and whether you actually execute what you are saying online,” added Mr Allan.
Of course, as a company, Ashley Group has been showcasing that commitment
from the beginning, and the results speak for themselves. Since 2021, the company has increased its ship count, cargo book and its employee numbers – with 22 highly-experienced members now positioned within the UK and across the globe.
As part of this continuous growth, as well as Ashley Group’s broader evolution, the company has also seen a shift in focus when it comes to the commodities it is transporting.
“Historically, we have always focused on products related to the steel industry,” said Mr Allan, “Now, however, we have begun to pivot, and we are diversifying into commodities related to renewables.
“We can see where the industry is headed, and we want to be a part of that transition: adding value wherever possible.”
Determined to make its mark on the green energy transition, Ashley Group is currently
looking to invest in battery-powered ships.
With this infrastructure in place, the company will be better positioned to become a prominent member of the renewables supply chain.
In line with this, the company has also recently implemented a new in-house management team, which is following set KPIs, one of which is focused on ensuring the efficiency of Ashley Group’s vessels.
As the transition continues to progress, Ashley Group believes this will become a more prominent focus of the business.
“We are a young company when it comes to length of operation, but the values that we are implementing come from 100 years of experience,” said Mr Allan, in conclusion.
“There’s a longevity in what we do, which is why we are investing in our employees and in the future of the marine industry.
“We believe Ashley Group will be here for a long time to come and we are ready to help make a difference.”
For 90 years, Anbros Maritime has delivered praise-worthy ship management and dry bulk transportation for customers worldwide. Now in its third generation of leadership, the Company continues to honour its rich legacy as it moves forward with innovation and its expertise at the helm. Directors George and Diamantis Angelakis discussed the Company’s journey, during an in-depth interview with Inside Marine. Report by Imogen Ward.
Anbros Maritime stands as a testament to the dedication and vision of three generations. Since its founding in 1934, the Company has operated successfully for 90 years, with each generation contributing to its development.
“Each generation has built upon the achievements of the previous one, driving Anbros towards its vision of continued success, while staying committed to its core values of quality, integrity and customer -focused service,” shared Director George Angelakis. “The first generation, brothers Georgios J. Angelakis and Nikolaos J. Angelakis, laid the Company’s foundation. They established a reliable and efficient business with a primary focus on quality and customer satisfaction. This became the essence of Anbros’ reputation.”
Georgios’ son John G Angelakis joined the Company in 1975, bringing with him a new era of development. It was at this point that Anbros’ vision began to broaden, and the Company extended its presence further afield. This was achieved with Anbros’ swift entrance into the larger bulk carrier market.
“Our global presence cultivated robust partnerships with leading charterers and trading houses worldwide, ensuring it remained competitive in an ever-evolving international marketplace,” continued George. “Under our father’s leadership, Anbros was an early adopter of technological advancements and one of the first Greek family-owned companies to have its accounts externally audited by one of the ‘big four’ auditing firms.”
It was this long-lasting legacy that inspired the third generation’s vision – one that is still materialising today.
In 2002, the third generation entered the family business, starting with John’s son, George, followed gradually by his siblings - Katerina, Diamantis, and Anastasia - after all had completed their studies at UK universities.
Not only are they honouring the foundations laid by their father and grandfather, but they are also propelling the Company forward in line with the objectives of modern shipping.
“We are continuing to acknowledge the Company’s rich legacy and values, while integrating sustainable practices and innovation into the Company’s strategy to meet the demands of the eco-conscious modern era,” explained Director Diamantis Angelakis.
Over the past 90 years, Anbros has owned and managed a fleet of more than 70 vessels (equalling a combined carrying capacity exceeding 1.3 million deadweight tonnes), to collectively transporting and delivering an estimated total of more than 60 million tonnes of cargo across the globe.
This notable figure includes grain, which is historically Anbros’ most frequently transported commodity – accounting for 35% of all its cargo.
As a testament of the quality of its management performance, the Company consistently achieves an average fleet utilisation rate of around 98%.
The sense of responsibility and respect to those achievements, helps Anbros remain
focused and dedicated on building upon them and keep evolving alongside the rapidly changing market.
“Fleet expansion and renewal have remained an integral part of our growth and continuity strategy throughout our 90-year history,” remarked Diamantis. “Our primary focus today is on modern, eco-friendly vessels, ranging from Handysize to Kamsarmaxes. These vessels provide a competitive edge over older, non-eco fleets, especially in view of all the new environmental regulations impacting our industry. In light of this, we see fleet renewal as a natural next step for our business and are working to
determine the optimal timing to grow the fleet to a sustainable and optimal size. Through this approach, our goal is to improve our operational efficiency and address the growing demands of our customers.”
Although fleet renewal is expected to play a prominent part in steering Anbros towards a greener future, it is just one component in a much larger strategy.
“As a Company with nine decades of experience in the shipping industry, we recognise that our long-term success is closely tied to our ability to operate
responsibly and sustainably,” explained George. “That is why sustainability remains a central consideration as we navigate the evolving challenges of the maritime industry. We acknowledge the environmental responsibilities that come with shipping, particularly in areas such as fuel consumption, emissions and waste management.”
The Company fosters a culture of environmental awareness among both crew members and office staff, actively implements optimised voyage planning to reduce fuel consumption and emissions, promotes the use of greener fuels, and supports the transition to alternative energy sources whenever feasible.
When it comes to enhancing its footprint, the Company is also inspired by past accomplishments. Over a decade ago, back in 2011, Anbros partnered with its longterm charterer Cargill as part of its pioneering Green Era Initiatives. The partnership saw Anbros install a SkySails kite system onboard its Handysize vessel AGHIA MARINA. Despite the challenges faced during this project due to the operational limitations of the kite, Anbros remains committed to embracing innovation and collaboration.
In addition to its environmental initiatives, Anbros places a strong emphasis on the wellbeing of its employees. This commitment is reflected in the impressive average employee retention rate of approximately 30 years, highlighting the Company’s success in fostering a supportive and loyal workplace culture.
The Company relies on a number of long-term, mutually-beneficial partnerships that have been developed on the basis of transparency, open communication and collaboration. These relationships have been pivotal in ensuring Anbros’ continued success and sit at the heart of its business philosophy.
“Our primary focus remains on continuing our shipowning legacy, which has been built on decades of dedication and expertise,” said George. “At the same time, we value the strong collaborations we have cultivated and are open to embracing new partnerships that align with our vision. This ensures we remain competitive, drive growth, and continue delivering excellence in the services we provide. By collaborating with investors or managing vessels from third parties, we adopt a flexible model that builds on our foundation, while embracing innovation and adaptability. This strategy enables us to navigate changing market demands, strengthen our position as a trusted partner in the global shipping iindustry, and ensure long-term sustainability and competitiveness.” n
Alpha Gas, Pantheon Tankers Management and Alpha Bulkers are sister companies committed to providing high-quality shipping services. The first specialises in LNG vessel management, the second in tanker services and the last in dry-cargo vessel management. Antonia Cole explored the companies’ fleets and future plans, in a report for Inside Marine.
ASa group, Alpha Gas, Pantheon Tankers Management and Alpha Bulkers combine to operate an impressive fleet and deliver exceptional shipping services. With the mission to exceed customer expectations in every project, the group conducts operations according to strict safety and environmental regulations. Each company regularly invests in innovative technologies and skilled crew members to ensure the smooth-running of each project.
The group strives to be the preferred choice of major charterers, with advanced and high-performing eco-ships, as well as services that protect humans, the environment and shipping property. Operating under a long-term vision to be a leader of the shipping industry, the group ensures to maintain high standards throughout all undertakings and takes progressive action to grow within the sector.
Headquartered in Athens, the group has expanded to have an additional three affiliated offices around the world. These are in London, Singapore and Manila. With a global network, including approximately
230 shore-side personnel and access to 3,000 seafarers, the group is well-equipped to offer fast and reliable services to a diverse range of clients.
Alpha Gas, Pantheon Tankers and Alpha Bulkers combine to offer the group’s clients a comprehensive fleet. Overall, the group manages eight LNG carriers, 39 crude oil and product tankers, and 36 bulk carriers. With an average fleet age of nine years, the group is committed to continuous development.
Each company invests in its individual fleet, advancing technological capabilities and preparing for the future.
2024 saw the expansion of the groups’ fleet with its building programme introducing a selection of new vessels. In the first quarter of the year, two LNG carriers were delivered whilst four dual-fuel VLGC/VLAC ships were put on order. The additions of the LNG Energy Endurance and the LNG Energy Fortitude increased the group’s offering of sustainably-focused vessels. With the landscape of shipping evolving to meet environmental
regulations, it is essential that the group adapts its fleet to suit customer demands.
Later that year, the M/V Alpha Force was taken under Alpha Bulkers management in China. The group has another four product tankers and two ultramax bulk carriers
currently on order in China with a scheduled delivery from 2025 to early 2026.
“We usually keep our vessels to operate ourselves, and we usually do not sell until they reach three quarters of their lifetime,” said the Director in a previous interview with Inside Marine. “That is one of many aspects that differentiates us from some organisations. We like to build our vessels; a big portion of our fleet was constructed directly through our organisation. This means we ordered the ships and negotiated the specifications with the shipyards. Of course, we also have second-hand ships, but the majority are newbuilds.”
When Alpha Gas, Pantheon Tankers or Alpha Bulkers introduce a new vessel to their fleets, it is a long-term investment where they retain the ship for the majority of its lifetime. This approach focuses on maintaining the vessels, ensuring operations are safe and controlled. The group’s fleet renewal programme is introducing a range of vessels equipped for the future, which will replace some of the older vessels.
“I think one of the main characteristics that makes us stand out is our long-term vision,” explained the Director in a previous interview. “We see various players in this market entering shipping with a short to medium term horizon, in order to gain financial benefit but not necessarily to remain in the industry for long. We don’t have an exit strategy, we are here to stay, and to grow further.”
In operations, the group is committed to safety and environmental protection. Whether
ashore or on-board, the group takes the necessary precautions to support its workforce. Employing highly qualified people, encouraging teamwork and open dialogue, and sponsoring continuous professional development through training opportunities are some of the ways the group guarantees effective operations.
Each company aims to provide high-quality services to its clients by minimising risks and encouraging innovation. Maintaining these values has driven the group forward to become a leader of the sector.
Since its establishment, the group has completed many significant projects. This includes multiple series of tankers in Korea and eight Capesize vessels in China. Between 2021 and 2022, the group took the delivery of seven tanker and two bulker vessels, as well as acquiring eight
second-hand product tankers and three LNG resale vessels.
The group intends to continue growing its fleets, following this previous success. As older vessels reach their end-of-life, each company plans to replace them with more modern vessels that improve efficiency and environmental impacts. Additionally, the group is currently investigating the implementation of new sustainable technologies and fuels. Exploring the possibilities of dualfuel ships will prepare the group to serve the developing industry.
As well as adapting to new environmental regulations, the group
makes sure to develop its workforce, the Director said previously: “Finding the right seafarers, and also training and educating them, is a very big challenge. We have opened a training centre in Athens. We’ve felt the need to do that because we strongly believe in the importance of improving training and education in the sector.”
Despite these challenges, each company within the group is committed to continuous improvement. With a wealth of knowledge and a skilled team, the group looks forward to facing the future of the sector.
“The market sentiment can change quickly in shipping and volatility is a key theme these days, but that is one of the aspects that makes shipping interesting,” added the Director previously, in conclusion. “It means that ship owners and operators need to be able to adapt very fast to a changing environment. I think that working out how to respond is what excites me most about my job.”
n
As a first-class sustainable aggregate provider, Mibau Stema Group dedicates every waking moment to shaping the future of the construction industry. With innovation, excellence and sustainability at the helm, the company works tirelessly to supply its customers with the finest quality aggregate – a task that would not be possible without the deployment of its fleet of self-discharging vessels. Executive Director of Logistics & Planning Jens Madsen divulged more on the pivotal role these ships play, during an in-depth interview with Inside Marine. Report by Imogen Ward.
Mibau Stema Group has carved out a solid home for itself within the construction industry thanks to three fruitful quarries, a fleet of seven impressive vessels and a 40-terminal strong distribution network. All of these elements have gradually nurtured the group to fruition over the last 50 years.
“Our journey has been a really long and intensive one, filled with development, growth and success,” said Executive Director of Logistics & Planning Jens Madsen. “But it is a fantastic story to be a part of, one which has evolved considerably in the last few years.”
From its founding in 1975 (when it was focused on raw material trade between
Norway and Sweden), to the company’s current leading position as the largest supplier of aggregates in Northern and Central Europe, Mibau Stema has experi enced a lot of change over the years. This includes its recent decision to bring all its subsidiaries under one umbrella.
“As a collective, Mibau Stema was growing bigger and bigger,” explained Mr Madsen. “And ensuring everyone was headed in the same direction became paramount. It was well and truly time to tear down the metaphorical walls and make sure there were no barriers within our business.”
By implementing this change, Mibau Stema aims to strengthen its identity and provide greater transparency to its customers, which it has worked hard to establish a strong level of trust with over the years.
Everyone at Mibau Stema is especially looking forward to celebrating the company’s 50th anniversary later this year as one entity.
of which is loaded from its three quarries onto the company’s specialised fleet and third-party tonnage in all sizes.
Although not an easy task, the company operates its quarries with sustainability at the forefront. All three ofMibau Stema’s quarries are powered by hydroelectricity and have been since the early 1980s. The company has also worked hard to reduce its CO2 emissions by 20% per produced tonne in the last ten years.
“We always aspire to operate a sustainable and smooth-running business,” said
Mr Madsen. “And of course, we would not be able to do that without the governmental support we have received over the years. Especially in the Stavanger area where we are allowed to run our quarries.”
Another sustainable element of the business is Mibau Stema’s strategic choice of transportation. To effectively transport its aggregate to its distribution network and beyond, the company relies on a fleet of seven unloading vessels and one barge.
Each of Mibau Stema’s unloading vessels is equipped with a specialised belt system that enables it to reach 75 metres ashore from shipside. With this impressive system, Mibau Stema can successfully offload up to 5,500 tonnes of aggregate each hour, without the crew even having to leave the vessel.
“These vessels are a hugely important part of Mibau Stema’s success, and if it weren’t for our owner pushing to specialise in belt vessels
from the get-go, then we would not be where we are today,” said Mr Madsen.
One of the reasons that Mibau Stema Group is so successful in its independent approach in and out of ports, is the discharging equipment onboard its specialised fleet that reaches the second-row area in ports. Furthermore, powerful engines and thrusters
allow the fleet to operate in many ports without the assistance of tugs.
The combination of highly technical vessels and highly skilled crew is a large part of the group’s success. Last, but not least, the fleet is also a benefit towards achieving Mibau Stema’s target to reduce the company’s carbon emission target.
This is an aspect that is greatly appreciated by Mibau Stema’s robust network of 35 to 40 terminals, which the company regularly relies on to distribute its aggregate all over the world.
“We need a lot of terminals to help distribute our aggregate, because each year there are millions of tonnes worth to deliver,” explained Mr Madsen. “The number of terminals that we work with often rises and falls, depending on whether we are employing project-specific terminals in addition to those we work with on a regular basis.”
According to Mr Madsen, these terminals are a major aspect of Mibau Stema’s business, and they are all run efficiently by a team of highly-skilled individuals.
Although Mibau Stema Group relies on its 40+ Terminal network and skilled sales personnel to distribute it aggregates, the company also gets
hands-on with several major projects. One such example is a long-term, ongoing project that is called the Fehmarn Belt Tunnel.
The Fehmarn Belt Tunnel project is set to be a major game changer for those looking to hop between Denmark and Germany.
Designed to connect Lolland with Fehmarn, the 11-mile-long crossing will run along the seabed and is expected to cut travel time by about one hour.
“We have been involved with the Fehmarn project since the beginning,” revealed Mr Madsen. “And we regularly deliver our aggregate to a large newly-built project port near the future tunnel location, so that the aggregate can be utilised to produce specialised concrete for the tunnel.”
This project is just one of many that Mibau Stema has been involved with over the years.
“Being a part of major industrial projects is in our DNA, and being able to deliver large amounts of aggregate within such a short time is what we excel at,” said Mr Madsen, in conclusion. “We will continue doing that to the best of our ability as we look to retain our position as the leading European supplier of sustainable aggregate.
“Of course, being a part of such a dynamic industry, one that is undergoing a significant transition, means we do not know what next year will bring. It is, however, a truly exciting time to be a part of the industry, and I can’t wait to see where the future will take Mibau Stema Group and shipping in general.” n
Marcap stands tall in the marine world through its unwavering reliability and client-centric service, with a fully-fledged fleet and a commitment to serving MEA’s top national and international oil and construction companies. Eager to expand in advance of its 30th anniversary, the company is investing in several new areas of interest. President & CEO Samer Qiblawi explained more to Imogen Ward.
Marcap is synonymous with reliability. Having dedicated the last 29 years to developing the perfect fleet, the company is now exploring new areas to further enhance its offering.
“When the company was established, it operated primarily as a vessel owner and manager; that all changed when we expanded our capabilities over the last few years,” explained President & CEO Samer Qiblawi.
When it comes to market expansion, Marcap has all the necessary experience. The company established itself in the UAE in 1996, serving customers within the Arabian Gulf, Arabian Sea and the Red Sea. From there, Marcap ventured into the Saudi market
“We started with one office in Dammam, serving Saudi Aramco,” revealed Mr Qiblawi.
“Before long, we expanded our network of clients and became an approved contractor for KGO and many other highly esteemed companies. In 2025, we have 3 offices in Saudi Arabia, celebrate 15 Years in the Kingdom and reap the benefits of that risky decision.”
Today, the company manages a fleet of 30+ vessels after the successful fleet expansion over the last two years. Marcap began management of seven towing tugs and an SSRV, which was fully enhanced to meet stringent UAE regulations, to improve Marcap’s ADNOC L&S offshore projects.
The three 40-tonne towing vessels were mobilised outside the UAE in mid-2024 and have been in operation ever since. The SSRV was brought all the way from Malaysia and upgraded with A-Frame Davit and a fast rescue boat, as per tender requirements.
now developing new relationships and implementing new services to suit the needs of this market.”
Expanding the portfolio
Keen to stay ahead of the curve, last year, Marcap introduced new verticals, in response to the evolving needs of customers, especially those coming to the MEA market from abroad and not familiar with the local requirements.
The success of these new additions has encouraged Marcap to continue its expansion plans into 2025, with several LCT building contracts underway.
With so much success in complex projects under its belt, Marcap felt confident in stretching its geographic presence, specifically in the Mediterranean, South America and East Africa.
“We launched several new service packages in order to better cover a client’s demands,” explained Mr Qiblawi. “These include ship management from A to Z, tailored crew supply, get home safely ship delivery service, logistic project management and end-to end solution, vessels cross chartering, and becoming the classic OSV vessel provider and operator. These packages are already being utilised in several key regions, including UAE, Malaysia and Latin America.”
So far, these new services have been received positively, with customers appreciating Marcap’s ability to tailor its approach to each project.
“We recently began operating in Chile and Mozambique, both outside of our traditional geographical area,” revealed Mr Qiblawi. “We are proud to say that we performed well, and we are now mobilising another vessel from Paraguay to Mozambique.”
This tender is not the first time that Marcap has experienced Mozambique waters.
The company already has two vessels from Noatum Marine (ex-Safeen) under its management in the area, so it is well-positioned to execute this new project.
“The success of our latest contract has really increased our curiosity for the region,” said Mr Qiblawi. “For that reason, we are
“There was a signficant gap in the market for comprehensive services, and we felt our experience would be crucial to helping meet that need,” said Mr Qiblawi. “By leveraging our expertise and global reach, we have been able to provide customised solutions that not only enhance efficiency but also operational effectiveness and crew safety.”
In line with its mission to be recognised as the first-choice supplier, providing the highest level of marine offshore services with absolute
regard to safety, Marcap continues to prioritise crew welfare.
which we are going above and beyond on a daily basis.”
In 2019, Marcap introduced ‘Happiness Programme’ – a moral booster and extra motivation for people. It is an indirect message from the management saying: “Everybody is important and valuable.” For example, Marcap has a dedicated coach who regularly visits the office and vessels to keep people in a good physical shape.
Last year saw the company implement a brand-new campaign focused on crew happiness. ‘One Big Family’ focused on bringing together people in the offices and offshore to strengthen the bond between every member of the team. Designed with each employee in mind, the campaign aimed to ensure no one felt alone, to provide everyone with easy access to support when needed and to build a stronger sense of community throughout the entire company.
“We are always eager to find new ways to further enhance crew safety and wellbeing,” continued Mr Qiblawi. “The ‘One Big Family’ campaign allowed us to really bring the spirit of our people together and make sure they have access to hotlines designed to help them in their time of need.
“When you have so many crew members, it can be difficult to ensure they all feel seen and heard, that is why we are determined to get the word out there.”
Mr Qiblawi was especially proud of Marcap’s success in its contracts with ADNOC. There is minimal overstay during crew changeovers and the company works hard to stay ahead of changeover times.
Alongside its dedication to social sustainability, Marcap also always prioritises its environmental impact.
Eager to provide crew members with many different avenues for communication, Marcap is also utilising ShipArc software, to gain valuable insight from onboard its vessels. It is hoped that communication and safety levels will increase with the adoption of this app.
“Implementing ShipArc was an important step in our HSE development programme, because it is designed to help reduce incidents, increase safety of crew members and improve our service offering,” shared Mr Qiblawi. “We have also been honoured to attend many of our clients’ HSE events, where we take the opportunity to talk about our own practices and the different ways in
“Sustainability is a very important subject across the entire industry,” said Mr Qiblawi. “And it is one that touches our company too. From small changes like implementing plastic collection in the office to examples that have a much greater impact, such as operating efficient vessels that create minimum pollution. This, in addition to many other detailed programmes, ensures we continue to prioritise sustainability wherever possible.”
With its 30th anniversary fast approaching, Marcap intends to maintain this crucial commitment to crew safety and environmental protection as it continues to grow.
“We want to keep expanding and developing,” remarked Mr Qiblawi, in conclusion. “Whether that be our internal systems or our geographical reach, we are determined to enhance our offering to provide customers with the very best, sustainable and socially responsible service on the market.” n
Anglo-Eastern Leisure Management and Anglo-Eastern Cruise Management represent the passenger ship division of Anglo-Eastern, a global provider of independent ship management services with over 50 years’ experience. Covering all aspects of cruise and leisure operations, the company aims to deliver memorable onboard experiences. Report by Antonia Cole.
Headquartered in Miami, Florida, Anglo-Eastern Leisure Management (AELM) and Anglo-Eastern Cruise Management (AECMI) were established through Anglo-Eastern’s acquisition of Cruise Management International (CMI). Anglo-Eastern is an expert provider of vessel management solutions. Already well-established in the industry, the company decided to enter the cruise and leisure market in 2023 and expand its ship management footprint.
“This sector was the last notch missing from our belt,” said the COO of Anglo-Eastern in a previous interview with Inside Marine.
“Over the years, we had discussed entering
the cruise sector from scratch, but there are lots of challenges involved with that. When the opportunity to purchase CMI first surfaced, it was a golden moment. The two companies were experts at what they do, and for that reason, we were confident that they could successfully guide us into the industry, and we could build from there.”
Anglo-Eastern has over 750 vessels under technical management and managed a deadweight tonnage of 68 million in 2024, which equates to 2.9% of the world’s total. The skills and experience gained from the company’s ship and crew management projects have transferred into its cruise and
leisure divisions, enabling AELM and AECMI to become leaders of the industry.
Safety, performance and crew wellbeing are key factors that remain essential in the company’s operations. Both AELM and AECMI are committed to maintaining these high standards whilst also delivering a personalised service that covers both technical and hospitality services.
With capacities ranging from 50 to over 2,000, AELM and AECMI manage a wide range of vessels. The global fleet consists of 12 expedition vessels and three cruise ships, operating in the expedition, arctic operations, luxury adventure and educational cruising markets.
AELM and AECMI manage all aspects of a ship’s operation, ensuring every voyage runs smoothly and any issues are resolved quickly. The ships are regularly inspected for performance, with necessary maintenance
being conducted. Additionally, the company takes the time to understand the clients’ individual needs so it can deliver specialised solutions. With access to a large number of skilled officers and crew, the company is able to select the right people for each job.
“The cruise industry is in the business of creating experiences for passengers,” explained AECMI’s President & CEO in a previous interview. “We lead with that knowledge. It’s all about creating that experience, from the quality of the carpets and the food to the ambience and air conditioning.
Anglo-Eastern brings scale and scope to the table. The company has immense resources, including very talented people who have successfully delivered excellent products in various other sectors. There’s no reason why they can’t take that and apply it to the cruise industry as well.”
The company is committed to delivering exceptional hospitality services, offering
unique guest experiences. This includes culinary options, spa services, shore-side experiences and more. AELM and AECMI have strong supplier relationships, enabling the company to offer high-quality services for a cost-effective price.
In all its services, the company adheres to high standards of safety. The wellbeing of crew is of great importance and there are regular training opportunities for employees, as well as investments into modern safety equipment.
In both AELM and AECMI, there is a commitment to protecting and supporting people and the planet. Onboard vessels, the company has implemented various initiatives to promote an active culture of safety, encouraging crewmember wellbeing. The majority of the company’s ship management units have received a 5/5 RightShip DOC safety score. AELM and AECMI also promote diversity and
inclusion, ensuring operations are supportive of all demographics.
Anglo-Eastern was a founding member of the Getting to Zero Coalition, an alliance committed to supporting the development of zero-emission vessels in the maritime industry. The company was also the first leading ship manager to be certified as carbon neutral, having had the accreditation since 2019.
“When it comes to sustainability, AngloEastern always goes above and beyond compliance,” said AELM’s President & CEO in a previous interview. “That’s really important to us, because we want to sustain these destinations for everyone’s sake. These
places are our home away from home, and we want to protect that.”
The company operates with strong values of integrity. All divisions of Anglo-Eastern are passionate about human rights, health and safety, equal opportunities, training and development, sustainability, and supply chain management. The company always complies with relevant bodies, laws and agreements, as well as continuously reinvesting into its workforce.
With strong connections to a variety of luxury hospitality companies, AELM and AECMI are able to offer guests premium products and services. From high-quality wine to relaxing
spa treatments, the company works with its partners to deliver the best onboard experiences. Partners and memberships include Adventure Travel Association, United States Sommelier Association, International Luxury Hotel Association, Marine Hotel Association and The Association for Cruise Development of Taiwan.
Recently, the company also announced its partnership with Four Seasons Yachts. AELM and AECMI will be managing Four Seasons I, an ultra-luxury yacht that is scheduled to begin commercial operations in 2026.
“This landmark collaboration marks a significant step in our growth as a premier provider of ship management services, now spanning into the luxury yachting
category,” explained COO of Anglo-Eastern Carsten Ostenfeldt. “By uniting leaders in hospitality and ship management, we’re creating a one-of-a-kind experience at sea. Anglo-Eastern will leverage its deep expertise in the maritime sector and the Group’s global resources to meet the exacting standards of Four Seasons Yachts.”
Reinforcing this growth, the company relocated its Miami office to Blue Lagoon and Singapore office to Labrador Tower. These relocations aim to enhance collaboration, drive innovation, and strengthen company culture, facilitating future progress.
AELM and AECMI will rely on supplier relationships to make these endeavours successful, in a previous interview AELM’s
President & CEO said: “Knowledge is number one, and you’ve got to know and trust who you’re dealing with. We are lucky enough to have amazing suppliers that we can trust, who really help us deliver these special and unique experiences.” n
Neptune Lines’ mission is to be the finished vehicle logistics partner of choice. Offering sustainable transportation and shipping solutions to the automotive industry, the company is committed to high-quality service. Antonia Cole explored Neptune Lines’ projects and services, in a report for Inside Marine.
Celebrating its 50th anniversary this year, Neptune Lines has grown into a major industry player. In a previous interview with Inside Marine, the Chief Operating Officer said: “This was due to the foresight and hard work of its founder, Nikos Travlos. ‘All you need is a vision and the willpower to make it happen,’ he used to say. Mr Travlos put all the different market parameters together and the result was an agile, very customer-centric, focused company that never deviated from its course.”
Founded as a cargo and ship handling services company, Neptune Lines evolved into a ship owner and operator with the purchase of its first vessel, Melina. Over the years the company’s fleet size increased to 20, offering a more diverse range of capabilities. Neptune Lines’ global reach also expanded from its headquarters in Greece. The company now
operates across 50 ports in 27 countries in Europe, the Mediterranean, the Black Sea, North America and the Far East.
With over 500 employees, Neptune Lines is able to offer efficient and comprehensive short sea transportation solutions for cars, plus high and heavy vehicles. Some of the world’s largest automobile manufacturers utilise the company’s services due to its reliability and capabilities. Neptune Lines has an aggregate capacity of 75,000 units. The company completes over 1.5 million sea miles and transports more than 1.3 million cars per year.
The shipping industry represents 3% of global carbon dioxide emissions. Although ocean transportation emits the lowest amount of carbon dioxide per
vehicle-transported kilometre compared to any other form of vehicle transportation, Neptune Lines still takes the responsibility of environmental management seriously.
Currently, the company is investigating alter native fuels, as well as emission capture and storage systems to find innovative sustainable solutions. By developing technologies, ship designs and monitoring systems, Neptune Lines hopes to create a more environmentally-friendly future for the sector.
“We have an exigent responsibility to positively impact emissions in our sector while improving governance and societal aspects related to our business,” explained the Chief Operating Officer in a previous interview. “We hope our sustainable projects can feature in the next generation of new vessel orders, when that time comes.”
The company continuously invests in modernising its fleet for efficiency, as well as into its emissions reduction and energy efficiency programme. Each of the company’s vessels is measured for environmental
performance. This keeps Neptune Lines on track to meet environmental targets. The company has reduced carbon dioxide emissions by more than 7% and decreased energy use by over 13%.
Various operational measures are in place to limit the impact of the company’s journeys. From speed and trim optimisation to weather routing and advanced itinerary planning, Neptune Lines ensures it maximises the efficiency of its modern vessels. Neptune Lines is also incorporating digitalisation into its operations to optimise efficiency and minimise energy use.
Finished vehicles are transported by Neptune Lines through its extensive transportation network. From Europe to the Far East to the US, high and heavy vehicles, construction and agricultural equipment, oversized machinery and static cargo can be moved all around the world.
Utilising roll-on/roll-off technology, the company is able to efficiently and safely transport a broad range of products. Neptune Lines has its own fleet of roll trailers, as well as cargo-handling equipment to provide individual solutions for each client. The company is dedicated to offering comprehensive solutions tailored to specific client needs. Combining flexibility, market knowledge and innovation, Neptune Lines
strives to offer exceptional customer service. With a team of skilled and experienced professionals, the company is able to address complex customer needs and challenges. Neptune Lines has access to more than 20 PCTC vessels, offering flexibility that allows the company to cater to the demands of a wide range of clients. The three main categories of the fleet are feeder, mid-size and deep-sea vessels. Depending on the specific cargo, the company chooses the vessel best suited to the client to deliver efficient and effective operations. Creating unique and efficient routing options, Neptune Lines effectively connects its customers to destinations and markets across the world.
As a shipping company, Neptune Lines is heavily affected by disruptions to the global supply chain. Fluctuations in worldwide markets mean that the company has to
constantly adapt to changing circumstances. This creates pressure on Neptune Lines’ capacity planning and causes inefficiencies.
However, by maintaining open and consistent communication, the company is able to combat these issues. In a previous interview, the Chief Operating Officer said: “We are in good dialogue with our customers to adjust trading conditions together and ensure we not only perform in the short to mid-term but are also able to invest in a new and more environmentally efficient capacity
Moving forward, the company aims to keep improving its capabilities to meet the needs of the growing automotive industry. Through innovation, customer service and determination, Neptune Lines strives to be the leading logistics partner in the market.
In a previous interview, the Chief Operating Officer explained: “The world’s population has a rising middle class, societies are developing at a fast pace, and prosperity is increasing like we have never seen. Mobility, and therefore vehicles, being a key feature in
seven seas, five oceans, one voice
An introduction to the engineering and services sectors, with news and a photo feature, followed by company profiles.
Anew training programme that aims to promote and sustain crew wellbeing on board has been launched by maritime welfare charity Sailors’ Society. This revolutionary Sea Mate initiative sees the new role of wellbeing officer created on board ships, with comprehensive training provided by the charity’s global team.
Sailors’ Society offers 24/7 practical support and wellness training to the world’s 1.9 million seafarers and their families, providing a unique circle of care that begins at cadetship and that helps crews and companies thrive.
With funding from Trinity House, Sea Mate aims to equip wellbeing officers with the skills to roll out wellbeing initiatives on board ship, offering basic counselling and guidance to fellow crew members facing personal or professional challenges and acting as a crisis responder to assist during emergencies.
Sea Mates will advise the crew of all the services Sailors’ Society offers, including training, resources and helplines. The aim is to create safer and more harmonious operations on board ships.
“As crews spend less time in port and more time at sea, it is vital that seafarers get the support they need whenever and wherever they need it,” said Sailors’ Society CEO Sara Baade. “As part of our mission to offer 24/7
support to as many of the world’s 1.9 million seafarers as possible, this role will help maintain crew wellbeing on board and offer that first and vital triage support when seafarers are in distress.”
The Sea Mate pilot took place in February 2025 with seafarers from companies, including Seaspan, Seaarland Shipping Management Services, Uniteam Marine, Sanmar Group, MT shipping and Songa Shipmanagement, trialling the three-day online course.
Sea Mate is part of Sailors’ Society’s gold standard Wellness at Sea programme for the maritime industry, which provides a circle of care for seafarers and their families. n
To have your company’s latest news included online or in our Inside Marine magazine, contact us today. Send
Global leader in pump and flow solutions across the marine, defense, aquaculture and industry sectors, DESMI, is proud to announce the acquisition of Nordan Marine.
Nordan Marine is a trusted partner in the maritime sector and provider of comprehensive service and repair solutions for cargo and fuel handling systems, including those used for LPG and LEG carriers, as well as LNG and alternative fuel-capable vessels.
This acquisition strengthens DESMI’s commitment to deliver top-tier flow solutions and services, with a particular focus on the maritime industry, while continuing to support a variety of other sectors.
While DESMI continues the process of expanding its market presence, the company is also enhancing its portfolio of gas cargo- and fuel-pump solutions, which now includes advanced technologies for emerging fuel types.
“As part of our growth strategy, we aim to provide the products and solutions that shipowners and shipyards need, especially in supporting the transition to green fuels,” said Rasmus Folsø, Head of New Green Solutions at DESMI. “A global service network is key to ensuring these new solutions are successfully implemented.”
Nordan Marine brings extensive expertise and a strong presence in the gas carrier market, making it a perfect fit for DESMI’s growth plans.
“We are thrilled to welcome Nordan Marine to the DESMI family,” said Humphrey Lau, Group CEO of DESMI. “Nordan Marine’s expertise will complement our service offerings and strengthen our promise to support the green fuel transition.”
This acquisition aligns with DESMI’s longterm promise of ‘Making Life Flow’ through sustainable and efficient solutions. Over time, Nordan Marine and DESMI have built a strong collaboration, and both recognise the significant advantages and potential of joining forces to drive future growth and innovation. n
Felixstowe has a proud record of innovation, being the first port in the UK to embrace containerisation in the 1960s. It also developed the world’s first Port Community System in the 70s and 80s.
More recently, the Port of Felixstowe was the site of the UK’s first mega-vessel berths in the 2010s and the deployment of Autonomous Trucks in the 2020s.
www.portoffelixstowe.co.uk
Rem Offshore has grown significantly by acquiring and constructing advanced vessels equipped with low- and zero-emission technology. Today, the company operates a modern fleet of 18 vessels, with three more under construction, and employs over 700 dedicated staff. Newlyappointed CCO Trond Skodjevåg Bø spoke to Hannah Barnett about the company’s next moves.
Thanks to innovation, reliability and strong partnerships, Rem Offshore has established itself as a leading marine services provider in oil and gas, renewable energy, and subsea operations. Now, with its environmentally friendly vessels under construction, the company is set to enter a new era.
“Rem is the ship owner of the future; we are willing to invest into environmentally-friendly technology and keeping our people up to date,” said Trond Skodjevåg Bø CCO. “For our clients, the important thing to know is that Rem is a company they can trust. We will be
at the forefront of the challenges that come with the reduction of emissions and help clients achieve their goals.”
Although Mr Skodjevåg Bø has not been directly involved until recently, it has been a busy eighteen months at Rem. “It’s been remarkable,” he said. “There are many highlights. For an offshore ship owner, the most important thing is safety, so our reduction in incident statistics is worth celebrating.
We’re also very proud of achieving a vessel
utilisation for our fleet of 94 per cent last year, which was a good contribution to a revenue growth of 40 per cent from the year before and EBITDA margin of 63 per cent. 2024 was a good year for us.”
In April 2024, the company took delivery of Rem Wind, a new CSOV, designed and built by Vard to provide support to offshore wind farms. The vessel was the second of two ordered after Rem Power was delivered in 2023 and is currently working for Siemens Gamesa servicing the Global Tech 1 Wind Farm in Germany. Later same year Rem also ordered a third vessel of the VARD 419 design, to be delivered from Vard’s Vung Tau yard in late 2026, bringing the fleet of custom-built CSOVs to a total of four vessels.
Marking a new era for the company, Rem signed a newbuilding contract for Rem Pioneer, the clearest demonstration of the
company’s commitment to sustainability yet. The highly advanced ESCV (Energy Subsea Construction Vessel), designed by Ålesund-based ship designer Skipsteknisk, is powered by green methanol, which reduces emissions dramatically and, as the name suggests, will be a pioneer in the offshore energy industry. It is due to be delivered from Myklebust Shipyard in 2026.
Furthermore, a second vessel of the same ST-245 design was signed after the recently secured contract with DeepOcean. Worth nearly six billion Krone (£428 million), the eight-year charter agreement includes additional extension options and the construction of Rem Ocean, also to be built at Myklebust, due for delivery in 2027.
Described as the next generation subsea vessel, Rem Ocean will be deployed by DeepOcean for subsea operations such
as inspection, maintenance and repair on Equinor installations on the Norwegian Continental Shelf. The vessel should not only set new benchmarks for environmental sustainability and operational efficiency but also strengthen Norway’s maritime industry.
“The eight-year contract is obviously very significant for us,” said Mr Skodjevåg Bø. “We are thrilled by the trust placed in us by DeepOcean and Equinor, and very much look forward to delivering services
accordingly. Including the IMR-contract signed in 2024 with DOF, to utilize our Rem Inspector for three years plus options, we have positioned ourselves well as a trusted supplier for IMR-duties on the Norwegian Continental Shelf.”
The type of contracts and newbuildings clearly showcase Rem’s goal to play a key part in the development of zero emission
vessels. By choosing to back the development of methanol vessels, the company has set a standard for the direction it is heading.
“For all ship owners ordering new vessels, it’s a big challenge to decide what kind of technology to go for, because it’s not a decision that can be made alone,” explained Mr Skodjevåg Bø. “We need clients that are willing to participate in this development. If you can get it, methanol produced by renewable energy is greenest fuel going at the moment, and also the most efficient.
“Clients like Equinor have also stated that this is something that they would like to work on together with us, to use as much methanol as possible in future operations,
because it will help them reach their environmental targets. So that’s why we do it.”
Of course, making low-emissions fuels a cost-efficient option will likely be the main challenge facing sustainable shipping for some time to come. To add to that, recruiting the right people also remains a challenge at Rem, as it is a challenge across the wider marine industry. Growth, however, will be the key driver in the company’s strategy for the future.
“Not growing for growth itself, but growing into, the right kind of assets, the right kind of clients, and the right kind of projects for our new vessels,” Mr Skodjevåg Bø explained. “We are serious about being
a strong partner and developing alongside our clients. Going forward, we need to have a fleet that is technologically driven. The standard for reducing emissions is important for us and important for our clients.”
People focused Rem is clearly doing very well when it comes to securing long-term contracts and staying ahead with the latest developments in technology. But it is the company’s skilled staff that complete the package. “It’s people that makes the vessels perform every day,” said Mr Skodjevåg Bø. “I think that’s our strongest asset, and also the reason why our clients come back time after time.
“Ultimately, our goal is to be a ship owner with a state-of-the-art fleet. There are lot of challenges for ship owners in this business, but we have the right people on board at the moment, people who are stepping up and wanting to achieve something.
I think that that’s a key factor to make this happen.”
For Mr Skodjevåg Bø, having joined the company in January from services provider Island Offshore, Rem’s history and achievements are part of what made it an appealing move. Having initially operated since the 1970s, Rem was re-established in 2016, by Åge Remøy and his partners, and has grown healthily ever since. According to Mr Skodjevåg Bø, this success story was impossible to ignore.
“Before I joined Rem, I was watching Rem from the outside, both as a supplier and a competitor,” Mr Skodjevåg Bø concluded. “It’s really impressive what Åge and his family and partners have achieved. Restarting Rem and turning it into a huge contributor to the offshore industry was extremely forward-thinking, and that is one of the reasons why I wanted to join the company.” n
Following the news of its recent acquisition, CRE Marine has continued to provide a high-quality and flexible approach to underwater connectivity, while supporting customers. Staying loyal to its roots has not stopped the business from implementing important changes. Business Development Director Paul Morrison and General Manager Paddy Mair explained more. Report by Imogen Ward.
Underwater connectivity expert CRE Marine has been delivering excellence to a wide range of industries since it was established in 2002. Initially operating as a third-party OEM cable moulding shop, the company continued to expand its capabilities, all while enhancing its own position within the market.
“Although we were predominantly focused on cable moulding and subsea cable assemblies for the offshore market, the company grew swiftly thanks to its can-do attitude and exceptionally fast turnaround,” explained Business
Development Director Paul Morrison. “Thanks to this rapid growth, CRE Marine has been able to expand into renewables, aquaculture, ocean science and even defence.”
CRE Marine stepped into the world of subsea connectors in 2011, with the development of its own line of metal shell dual seal subseaconnectors. By bringing the subsea connector manufacturing in-house, CRE Marine hoped to enhance quality control, reduce lead times and drive innovation from within. Not only did this move help meet increasing customer demands, but it also positioned the company
as a leading provider of reliable, high-performance subsea connectivity solutions.
The business transformed once more in 2018, when Mr Morrison and Mr Mair were brought on board. The two men were mentored by the legacy Directors in hopes that they would become the next generation of management and input their own vision into the company. This venture proved highly successful, allowing the company to grow steadily until its acquisition by Trexon in 2024.
In the six years between hiring the next generation of management and Trexon’s acquisition, CRE successfully doubled its workforce – a true testament to the company’s growth trajectory and the success of its expansion efforts.
As a multinational portfolio company specialising in highly engineered connector solutions, Trexon saw CRE Marine as a natural fit for its expanding portfolio.
Today, CRE provides a diverse range of connectors, each custom-designed to meet the unique requirements of its clients. This
Subsea Supplies values the strong, longlasting relationship with CRE, a consistent partner throughout our 25-year journey. Since 2002, our collaboration has only grown, reflecting a shared vision. We thank CRE for its support and look forward to our continued collaboration.
tailored approach has made connectors a cornerstone of the company’s operations, accounting for greater than 50% of its output. Many of these connectors were designed in collaboration with customers, including the renowned CS-MS.
After receiving a request from a worldrenowned engineering and technology solutions company with its own line of ROVs, CRE set to work developing a new connector purpose-built for these unmanned vehicles. Today, these connectors are known as CS-MS, named after developer Craig Simpson, and are aluminium shell connectors specifically designed for the needs of the customer.
Most commonly used for ROVs, recreational submersibles, stress monitoring and downhole applications, the CRE connector
range have been supplied for solutions from splash zone, down to full ocean depth and can be designed bespoke at no extra cost to the customer.
Innovation at CRE often stems from customer requests, though not all projects end up where they were originally intended.
In 2018, the company developed its first miniature connector in response to a client’s request for a compact solution that could fit within extremely tight spaces. Although the client ultimately chose not to proceed with the project, CRE recognised its potential and introduced the design to a company in the aquaculture sector. The connector proved to be a perfect fit for the company’s small net cleaning vehicle.
Within a year of its debut, CRE’s miniature connector quickly rose to prominence as one of the company’s best-selling products. Its success served as a clear testament to the strength of the idea behind its development.
The company also offers a range of fibre optic connectors, which are designed to withstand increasing water depths and bandwidth requirements. Having already
had great success in this area of expertise, CRE has recently expanded the range.
“Historically, we have only ever manufactured expandable beam fibre optics,” explained Mr Mair. “However, when a client asked if we could turn our expertise to a point-to-point fibre-optic connection, we felt ready to explore this new opportunity.”
CRE has dedicated the last two years to developing this new range of connectors and is extremely happy with the results.
The company’s impressive portfolio has been utilised across a diverse range of projects over the years. From camera installations that aid the aquaculture industry to multiple large submersible projects, CRE has eagerly taken up the challenge of each and every one.
According to Mr Mair, the company has experienced a significant increase in demand for cabling used in semi-permanent
With its growth goals firmly underway, CRE Marine has also been developing a high voltage connector range. To ensure the success of this project, the company recently invested in new testing equipment and has upped its game when it comes to training.
camera systems in aquaculture pens worldwide. To carry out these specific projects, CRE utilises custom-manufactured Vectran braided cable alongside the CRE range of stain-terminated connectors to ensure the weight of the camera system can be supported, while ensuring the critical power and data requirements of the camera system are not compromised.
“We are also seeing an increasing number of ROV-, AUV- and UUV-based projects, as the
drive for these continues to skyrocket within multiple subsea sectors,” said Mr Morrison. “These vehicles are becoming larger and more advanced to respond to the growing demands for enhanced exploration, safety and efficiency.
“As the underwater vehicles become more sophisticated, the need for reliable, high-performance power and data solutions have never been greater. Our expertise perfectly positions us to support this expansion.”
Naturally, the development of such complex products, means CRE needs to trust in its employees’ capabilities. In order to enhance its workforce, the company has developed its own grassroots training programme. Designed to help people enter the industry, this programme targets a wide range of sectors, with applicants regularly needing to have no previous experience within the industry, providing them with the knowledge and experience needed to become a subsea cable technician.
“The grassroots training programme has been incredibly successful, with candidates completing the course and moving up into crucial positions within the company,” revealed Mr Mair. “We have really enjoyed giving people the opportunity and the time to develop into great technicians.”
Ensuring its employees are highly competent is an important element in the top-quality service that CRE provides. Another critical piece of the puzzle is its longstanding suppliers and partners.
“A lot of our suppliers have been with us for many years and are an integral part of our business,” shared Mr Mair. “They understand what we do, they have diversified with us in order to continue to meet
the needs of our customers, and they are always quick to help.”
Having developed these relationships over a number of years, CRE intends to continue working with these trustworthy suppliers while also growing the chain. This growth will be important as the company seeks to globalise its business.
“In the near future, CRE aims to establish a stronger physical presence across the globe,” explained Mr Morrison. “Our primary focus will be on placing CRE employees into markets within the US and Asia. Once we have a physical presence in these key regions, we plan to broaden our product portfolio to better serve the growing market demands.” n
Dutch energy technology business EST-Floattech develops and supplies battery energy storage solutions for maritime applications. With hundreds of successful projects, the company is one of the strongest suppliers of maritime battery systems worldwide. CEO Mark Witjens, CTO Diederick Stam and CFO/CBDO Joep Gorgels spoke to Hannah Barnet.
Thanks to EST-Floattech’s innovative technology, 68 million litres of diesel have been saved and almost 250 million kg of CO2 emissions avoided. The company serves clients around the world from an HQ in the Netherlands and has a simple goal: to create a sustainable future via zero-emission shipping.
The milestones
EST-Floattech is a merger of two previous companies. Floattech was founded back in 2005, by current CTO Diederick Stam
and a Co-Founder, as a system integration company for superyachts. In 2009, Mr Stam and a Co-Founder created ESTechnologies, for the design and supply of maritime battery management systems.
In 2015, the companies merged, their strong application and integration knowledge paving the way for EST-Floattech to become one of the world’s strongest suppliers of maritime Energy Storage Systems. “From that day on, we said goodbye to system integration and focused on manufacturing and installing batteries in the field,” said Mr Stam.
In 2018, EST-Floattech was one of the first companies to obtain DNV certification for the second generation of its battery system. Today, the latest version of the system also has approval from Bureau Veritas, Lloyd’s Register and RINA.
The next milestone was launching the Octopus platform in 2023. The system showed how the company has continued to leverage its experience to optimally serve clients. Consequently, EST-Floattech is now the world’s second largest maritime battery supplier.
“We have delivered battery systems on over 300 projects, of which more than 250 are onboard ships,” said Mark Witjens, CEO. “Our production capacity is 50 megawatt hours. This can easily be extended to 100 megawatt hours per year.”
The company’s first flagship product was called Green Orca, with lithium-ion polymer pouch cells. This was followed by the
Octopus series, the next-generation maritime advanced Battery Management System (BMS). The BMS was developed to configure a variety of batteries and provide a userfriendly interface that connects the systems, with current modules based on Durapowers cell technology and developments for new modules and chemistries on the way.
“The Octopus system was built with the customer in mind,” Mr Stam explained. “It offers one platform to the customer, but we can integrate all kinds of battery types throughout. We developed everything in-house to make the system capable of handling all different kinds of properties of cell technology.”
“Plus, there’s a single interface for the client, so they can use whatever system they need and the interface stays the same,” Mr Witjens added. “That’s different from our competition.”
The system offers improved cooling, remote access and a more sophisticated safety and cyber security offering than the previous Orca
iterations. This created a system which can be remotely maintained.
“Before, we always had to send an engineer on board if something went wrong,” Mr Stam said. “It was one of our main problems. Now, we can easily diagnose the issue remotely, if necessary. It’s a big improvement.”
With over 300 to choose from, the range of impressive projects the company has been involved in is vast. One excellent example is a recent contract for KOTUG International, the leading international towage and maritime company. EST-Floattech was tasked with developing a containerised energy storage solution for the E-Pusher 1, the world’s first fully electric pusher boat.
The design revolutionised the way energy is stored and distributed in the maritime industry. All components were designed in house, making it easier for the company to accommodate specific requests from customers and to work fast.
“In about six months, we managed to design and deliver this system,” Mr Stam explained. “During this period, we developed the complete containerised solution and delivered the batteries. This is a good example of what we are capable of in a very short time. Thanks to the strength of our in-house R&D team we can design and deliver these sorts of bespoke solutions quickly.”
Working at speed and under pressure is certainly something the company is particularly good at. Even the first Octopus series was designed with a tight delivery deadline.
As EST Floattech’s strategic partner for battery cell technology, Durapower’s solutions enable critical applications with high performance, long life and safe operation. Leveraging its portfolio of products and services, Durapower enjoys a significant track record of delivering value in mobility applications like buses, trucks and mining vehicles, plus energy storage systems. With its added remote digital monitoring platform like DP Pulse, Durapower contributes to customer use cases by improving battery health visibility and supporting predictive maintenance, guaranteeing a higher uptime and peace of mind.
Ask what our battery solutions can do for you today, for a greener tomorrow.
This means when the company is approached by customers using a different system, it is able to make the modifications quickly.
“We help those clients and deliver in a short time,” Mr Witjens explained. “That’s our advantage. We are a flexible company, not too big, but also not too small. We can pick something up, give it priority, and get it done as soon as possible.”
“Most projects that we do are ferries,” Joep Gorgels, CFO, said, “and ferries need to be charged regularly and quickly. They also move at a relatively high speed, so they discharge a lot of energy. Because of these
Reederei Norden-Frisia and the Orbit Clipper for Uber Boat by Thames Clippers built by Wight Shipyards, both equipped with Octopus Series.
In order to maintain its reputation for innovations, the company has been working closely with specific suppliers for some time. Main components like battery stacks housing, PCBAs (electronic boards) and racking are constantly improved alongside supply partners like Durapower, TTI and Bruinekool.
“Most big suppliers are also relatively small,” Mr Gorgels said. “It’s simple; if we are successful, they are as well. Most components are specifically made for us.”
“It’s not like a supplier; it’s more like a partnership,” Mr Stam added. “We involve them during the development and also ask for their input for solutions.”
EST-Floattech has several clear goals for the future. One is to simply reduce the cost of the lithium-ion batteries. For inland vessels, the company is focused on expanding in the greater Rotterdam and Amsterdam area, where there is already the infrastructure in place for recharging. As the size of the product increases, the company must also address a common concern with lithium-ion batteries: safety.
“There’s a trend for the average system to get bigger,” Mr Witjens explained. “But of course, safety also must be guaranteed. We’re developing systems for that all the time. For instance, we will introduce a new development in June that will reduce short circuit currents.”
In order to usher in the energy transition, huge changes are clearly on the horizon, and it is an exciting time to be part of the industry. “Every day is a new challenge, which I like,” said Mr Gorgels.
“It’s super interesting.”
“We are very passionate about what we are doing,” concluded Mr Stam. “This is influenced by our early period when we were system integrators. It has meant that not only do we make batteries for the maritime industry, but we also understand what’s needed to have a successful energy storage system on board a vessel. We use all this knowledge to work with customers and make their story successful. Because in the end, that’s what counts.” n
MKN made its name specialising in professional thermal cooking equipment. The German company is known for classical cooking equipment combined with innovative multifunctional appliances. Regional Vice President Global Marine Stephan Kammel explained more to Hannah Barnett.
From Berlin to Dubai, and Paris to Manila, MKN equipment is powering first-class cuisine. This includes usage in top-class hotels, restaurants, corporate canteens and luxury cruise liners around the world.
In order to succeed at this high level, MKN has established a reputation for extremely innovative cooking technology. Perhaps the company’s most significant technological breakthrough has been the development of the flagship MKN FlexiCombi® steamer.
“This appliance set new benchmarks in terms of speed, efficiency and digital technology by revolutionising flexibility and performance in professional kitchens,” said Stephan Kammel, Regional Vice President Global Marine. “We are also known for SpaceClean®, the first and only fully automatic cleaning system for skillet pans.”
Then there is FlexiChef®, a multifunctional powerhouse that takes modern day kitchen routines to a new level. Users can cook and grill
at high speed or deep fry all in one appliance in the smallest of spaces.
The company keeps expanding. In 2019, MKN opened a new production site in Wolfenbüttel, Lower Saxony, to meet increasing demands.
Just four years later, a state-of-the-art welding centre was opened. MKN’s entire manufacturing site now covers an impressive 80,000 square metres.
“A further milestone is the MKN Campus,” Mr Kammel added. “This includes new offices, state-of-the-art meeting rooms, a culinary lounge and a co-working space to foster both innovation and team collaboration.”
This is supported by the impressive increase in company turnover, which has grown approximately fivefold in the last 23 years. The number of employees has also increased to around 600.
“We used to be a nationally oriented medium-sized company – now, we are a premium brand worldwide and a hidden
champion,” said Mr Kammel. “We have earned an excellent position in new segments and markets, and our export share has expanded to over 65 per cent.”
A portion of the company’s expertise is focused on producing innovative cooking technology for the marine industry. The equipment builds upon solutions that have already proven a success in the land-based market. The safety of the galley crew and compliance, along with the highest standards of hygiene for the guests, are particular focuses. But that is not all.
“Reliability, durability and quality of our appliances are equally important to us,” Mr Kammel
explained. “To meet these high requirements, we strictly adhere to the specifications of the USPH compliance standards. We attain this level thanks to close collaboration and joint development between our R&D department and the culinary expertise of our in-house application consultants.”
Sustainability is also firmly anchored in MKN’s culture. The company already buys green electricity and uses its own photovoltaic system to produce renewable energy. Now, it is finding further ways to improve.
“The future is our focus,” Mr Kammel explained. “This means starting with the development of new ideas for our professional cooking technology and extending over the entire production cycle to the utilisation of
renewable energy. We aim to achieve groundbreaking advancements by focusing on durable, energy-efficient products, sustainable packaging and numerous other measures to reduce our environmental footprint.”
Additionally, in 2024 the company began offering customers MKN SteelPlus. This low-carbon option means MKN commits to processing low CO2 equivalent stainless steel in its production in accordance with the customer’s order. This does not mean that the ordered equipment is directly manufactured using low CO2 equivalent stainless steel. However, on selecting this option, the percentage share of low CO2 equivalent stainless steel used in MKN’s entire production increases by the acquired share.
The launch of MKN SteelPlus enables the company to reduce its carbon footprint in professional kitchens considerably. MKN is the first and only company in the market to offer this option, setting the standard for the industry. An orientation towards sustainability also means the business is increasing its own operational efficiency as well as that of its customers. Of course, using fewer resources also reduces costs and therefore, for ecological and economic reasons, MKN appliances are always designed to save electricity and water.
Alongside the products, MKN consistently invests in developing its manufacturing lines. In recent years, the focus has been on digitalisation and sustainability. Latest innovations centre on the famous FlexiCombi steamers.
“A new lighting concept combined with a fast operating system revolutionise cooking processes and increase productivity,”
Mr Kammel said. “Our FlexiRack® offers an incomparable increase in capacity of up to 50 per cent. Even the FlexiChef, with the first and only fully automatic cleaning system for professional cooking pans so far, demonstrates the high level of innovation in MKN’s premium technology.”
The company approaches each project separately. One of its latest high-profile projects in the maritime market has been with Virgin Voyages, a well-known cruise
line, with a capacity of approximately 2,700 passengers per ship.
“Every project and customer is unique,” explained Mr Kammel. “With Virgin Voyages, the objective was to increase the efficiency of kitchen processes and, at the same time, ensure a perfect on-board dining experience for a large number of guests. Our kitchen equipment solutions were the key to successful implementation of these requirements.”
It is clear that MKN has several key strengths. These include innovative technology, bespoke solutions, durability and sustainability, all of which have helped the company cement its reputation in the sector. “It is the combination
of these factors that allow us to stand out from many of our competitors, as a leading provider of professional kitchen equipment,” as Mr Kammel put it.
In order to be so successful, MKN also relies on robust inter-business relationships. Indeed, collaboration and personal partnership is crucial to the company’s success.
“We attach great importance to longterm and intensive relationships with all of our authorised galley contractors,” said Mr Kammel. “In addition, direct contact to the shipping lines and shipyards is crucial. Personal contact plays a decisive role and for us, particularly, has a special significance.”
A strong supply chain will prove a vital tool at a time when many companies are facing political and economic challenges around
the globe, including deglobalisation and increasingly complex export regulations.
As an independent family business, those at the top of MKN remain confident it will act on a long-term basis to secure prosperity for the business, employees, customers and partners.
“Our vision is to calmly build trust and increase confidence throughout the entire company with a clear focus,” concluded Mr Kammel. “Every change brings uncertainty, but it also brings opportunity – whether it be innovative product development, entering a new market or adjustment of production processes. We are patiently and persistently driving sustainability forward. Planned investments in our company location and digital innovations underline this path.
“What I enjoy most about my job is the variety and the collaboration with people from different countries around the world. It’s fantastic to be able to represent a premium product and accompany exciting, large-scale projects. I’m involved from the initial kick-off meeting up until the ship is put to sea – and it fascinates me every time.” n
PowerCon’s mission is to design, build and implement innovative and scalable shore power solutions. The company has become the go-to partner for ports and customers worldwide and intends to keep it that way.
Peter C. Knudsen, Partner & CFO, told Hannah Barnett how PowerCon has secured its leading market position and is working to achieve its goals.
With a vision to push technical boundaries and develop the shore power solutions of the future, PowerCon plays a key role in maritime decarbonisation today. The company has built its reputation on being specialised, reliable and committed to long-term success. But expert knowledge and practical experience with shore power is not enough for the company.
“We don’t see ourselves as just a supplier in the industry,” said Peter C. Knudsen, Partner & CFO. “With each customer, we are looking to establish long-term partnerships where we guide, inform and educate them.
To many ports, shore power is something new. We hold a lot of expertise and practical knowledge in this area, so we feel obliged to help them as much as possible so they can make the best, long-term decision for their specific port.
“Many ports are becoming energy hubs, but the development is still in its infancy. We have the knowledge that they need on not just what a shore power system is, but what the technology can be and the potential for scaling it over time.”
Today, PowerCon plays a crucial role in the development of maritime electrical infrastructure. Its origins as a supplier to wind turbine OEMs like Vestas and Siemens Gamesa have allowed the company to certify the reliability of its core technology in tough environments around the world, often offshore.
Similar to offshore wind turbines, shore power solutions are implemented in harsh environments, reflecting the requirements that these solutions have to live up to. “We have done installations at the border of the Arctic, all the way to some of the hottest and most humid climates in the world,” said Mr Knudsen.
Today, PowerCon numbers about 250 employees with the majority based at a purpose-built new facility in Hobro, Denmark. With 2,500 square metres of office space, and an additional 3,500 square metres for production, assembly and warehousing, the site is well-equipped to test the full range of products before they are shipped to customers around the world.
The new facility has not only given PowerCon the ability to serve the market as it is, but also to keep expanding. This means adapting to shore power being implemented on an increasingly larger and more complex scale.
PowerCon’s team is largely made up of highly skilled hardware and software developers, engineers and electrical system designers. The company also collaborates with a range of experienced sub-contractors, ensuring that only the best materials and components are used.
The port of Kristiansand in Norway was the first to trial PowerCon’s shore power design, allowing the company to demonstrate that its technology could work effectively in a real port environment. “It was important for
us to get that first milestone and to show a tangible example of these systems in action,” said Mr Knudsen. “We now play a significant role in the shore power industry, which is something that we are very proud of.”
Shore power products must be of a high quality to stand the test of time in port environments. PowerCon has found an innovative way to guarantee durability. Each shore power system consists of standard shipping containers into which the company integrates the main electrical components, creating a building block design approach that is flexible, yet highly effective and reliable.
“We are able to be flexible to our customer’s requirements,” Mr Knudsen explained, “but we do that with standard components produced in our factory, ensuring an easier installation onsite. Using 20-foot shipping containers to encapsulate the equipment has been a significant part of our success and is something that really sets us apart from the rest of the market.”
The containerised solution not only improves the efficiency of shore power systems, but it also allows the manufacturing to happen inside a factory, instead of onsite.
This ensures a controlled environment, without bad weather or interruptions from port operations, and “improves the quality significantly” according to Mr Knudsen.
The other benefit of modulization is that the company can use the same types of containers, configured in different ways, to serve a variety of vessels. Ports often demand complete solutions for different ships, but each system type can be
scaled over time, as more ships connect to shore power.
“We convert and transform the electrical supply from the grid to meet the requirements of the ships”, explained Mr Knudsen.
“There is a tendency to look at shore power as an extension of the grid. What sets us apart is that we do not make a prototype system every time and we do not try to extend the grid. We look at shore power
as a product, and we utilise scalable modules to configure a solution that meets every demand.”
PowerCon is currently working on a significant project at the Port of Bremerhaven, Germany. This project requires designated shore power solutions for two container vessels, one RoRo ship and one cruise ship, with all systems prepared for future expansion. In order to pull off a project of this complexity, the company relies on strong relationships with sub-suppliers. Cable management suppliers in particular are essential, according to Mr Knudsen.
“We don’t have exclusivity contracts with any of our suppliers,” he added. “We have transparent communication, and we develop these relationships to benefit each other, as well as ports and the industry in general. It’s all about adding value to the supply chain.”
As a business focused on standardisation, PowerCon is able to offer very competitive lead times; a desirable attribute for ports needing to swiftly comply with regulations or looking for a partner exclusively focused on shore power.
“By having a scalable platform tailor-made for shore power, and a focused approach solely on shore power solutions, we can be more competitive than some of the large multi-nationals,” said Mr Knudsen. “Shore power is a niche market, and we have specialised in it for years, which is why we have won a lot of projects. We are world champions within this area.”
Looking ahead, the industry anticipates the demand to keep increasing for shore power solutions. This is partly due to regulatory requirements such as the ‘Fit for 55’ directive in the EU or the CARB regulations in California. For PowerCon, this means ensuring that the company continues to be able to serve a rapidly expanding market.
“What we’re seeing now is only the tip of the iceberg when it comes to the electrification of the maritime industry,” said Mr Knudsen. “As a technology at the forefront of the energy transition, it’s clearly a dynamic moment for shore power.”
PowerCon is currently installing Europe’s largest shore power installation in Copenhagen and finalising the world’s largest installation in Miami. At the same time, the company is preparing to start the first shore power installation in the Southern Hemisphere in Sydney.
Such demand is the main reason why PowerCon has invested so proactively. The company aims to service the market for many years to come and hopefully “break another record soon,” concluded Mr Knudsen, with a smile. n
Netherlands-based RanMarine Technology is on a mission to clean up the world’s waters with its innovative autonomous surface vessels (ASVs) and collaborative ventures. Founder and CEO Richard Hardiman shared the company’s progress during an in-depth interview with Inside Marine.
RanMarine’s ASVs are paving the way for a cleaner, more sustainable future for our waterways. “RanMarine was established in 2016 with a clear mission to rid our waters of plastic,” explained Founder and CEO Richard Hardiman. “While we began with a focused goal, our technology has since evolved, allowing us to address broader aquatic environmental challenges.”
basket’s netting is customisable, allowing operators to target specific floating pollutants, from waterlogged debris to smaller items like duckweed algae, ensuring efficient and tailored cleanup.
“By prioritising agility and compactness, we designed the WasteShark to access hard-to-reach areas, while ensuring it could handle moving waters,” noted Mr Hardiman.
Guided by this broader vision, RanMarine launched its first ASV, the WasteShark. This lightweight, autonomous vessel resembles a small catamaran – roughly the size of a mid-sized dining table – with a basket between its hulls to collect waste. The
The WasteShark can be operated via a handheld remote control or autonomously, utilising advanced GPS, precise positioning through T-Mobile, sensors, cameras and AI. Despite its compact design, the vessel offers impressive storage capacity, enabling it to collect substantial amounts of waste before needing to offload.
RanMarine’s partnerships have been instrumental to its success. Collaborators include Aquavision for its high-precision Eureka sensors and RimDrive, which enhanced the vessel’s thrusters to reduce blockages. Unlike traditional propeller systems, RimDrive’s design eliminates shafts, ensuring smoother operation even in debris-laden waters.
While the WasteShark is easy to deploy and highly agile, RanMarine recognised the need for a larger solution to tackle bigger challenges. This led to the development of the MegaShark, a high-capacity ASV launched in August last year.
“We always envisioned a larger vessel to complement the WasteShark,” shared Mr Hardiman. “The WasteShark
excels in efficiency, but the MegaShark delivers the scale and capacity needed for tougher tasks.” With proper maintenance, RanMarine’s ASVs operate reliably for 12-15 years, ensuring sustainable, long-term water management solutions.
Designed to resemble a conventional catamaran-workboat, the MegaShark offers familiar functionality. Operators can helm it on board or remotely, making it highly versatile. Fully electrified, it operates emission-free with Cleantron batteries powering eight or more hours of continuous use.
The MegaShark’s enhanced capacity and robust aluminium design enable it to tackle rougher waters whilst efficiently cleaning large waterways, ports, and harbours – all while staying true to RanMarine’s sustainability principles.
Both the WasteShark and MegaShark utilise RanMarine’s proprietary software to enable full autonomy. Designed to target floating waste, algae and biomass on the water’s surface, the ASVs capture debris efficiently while also mapping water quality metrics. The integrated data portal aggregates and geo-codes this information, providing operators with actionable insights to better understand and manage their environments.
“Today, we remove waste, clear algae and map water quality with precision,” said Mr Hardiman. “Our technology is capable of transforming water systems in ways we never initially imagined, which is hugely exciting.”
RanMarine’s software development has expanded the company’s mission far beyond clearing plastic and simple algae from the world’s waters.
“Every year since our founding, we’ve been asked about tackling Blue-Green algae,” said Mr Hardiman. “Removing it from the surface can be done, but the real challenge lies in handling it post-removal and preventing future blooms. To achieve these goals, we needed a partner with a chemical-free solution.”
Cyanobacteria, also known as Blue-Green algae, can pose severe hazards to aquatic ecosystems, humans and animals. These algae release toxins that contaminate water supplies, harm wildlife and create dead zones by depleting oxygen levels. Addressing this issue requires both innovative removal and sustainable treatment methods.
Enter Eget Liber, a specialist in chemicalfree water solutions. While the company had developed a system to neutralise Blue-Green algae by breaking it down and restoring oxygen to the water, Eget Liber needed an autonomous platform to deploy it effectively.
“Eget Liber approached us two years ago with its solution, which involves driving over algae and killing off the live bacteria, and at the same time mitigating further potential blooms,” explained Mr Hardiman. “We helped automate the process to enhance data collection and system control. This collaboration has been highly rewarding.”
The partnership has now expanded to include Clear Water Systems, a biotechnology leader, for a pilot project in Lough Neagh, Northern Ireland. Backed by a portion of a shared £450,000 grant, the initiative aims to test an integrated system that combines RanMarine’s ASV technology
with Eget Liber’s algae treatment and Clear Water Systems’ expertise in biotechnology.
“We’ll know more after testing, but I’m confident this could revolutionise the industry,” said Mr Hardiman. “Toxic algae blooms are a recurring problem in many European lakes. If we can address this effectively, then it would be transformative. Long-term, we hope to see this technology used proactively to prevent blooms before they occur.”
With its sights set on the future, RanMarine is pushing the boundaries of ocean cleanup with several new developments, including the highly anticipated OilShark.
After maritime logistics provider HEBO Maritiemservice sought a quick solution for minor oil spills, RanMarine began designing the OilShark.
“The goal was to create a first-response ASV for minor fuel leaks and oil spills in ports,” explained Mr Hardiman. “Initially, we developed a small oil collection unit for the WasteShark, but it quickly became clear that it wasn’t suited for larger commercial jobs. As we were preparing to launch the MegaShark, adapting it for this purpose made sense.”
This collaboration has been a gamechanger for RanMarine, enabling it to enter the hydrocarbon cleanup market while leveraging HEBO’s expertise as an oil spill response company. The partnership also freed resources for reconsidering other innovations, such as the SharkPod.
Set for completion this year, SharkPods are docking stations for RanMarine’s ASVs,
RanMarine also produces an innovative ASV called TenderShark, which stemmed from a Mediterranean moment of insight – when a friend’s yacht ran short of basic supplies, requiring a costly and environmentally insensitive shore-to-ship delivery. This inspired Mr Hardiman to adapt WasteShark’s proven technology into an emission-free autonomous vessel for waterbody deliveries, streamlining harbour logistics.
designed to charge batteries, discard collected waste and enable continuous 24/7 operations. Available in multiple sizes to meet varying customer needs, the SharkPods will further streamline ASV deployment.
“The SharkPods are a perfect addition to our roadmap because they offer universal benefits to our customers,” said Mr Hardiman. “This has been a long-standing project, and I’m excited to see it implemented.”
RanMarine’s dedication to research and development remains a cornerstone of its success, but the company is now shifting focus towards global commercial operations.
“R&D will always be critical to what we do, but we’re also focusing on scaling commercially to ensure long-term success for our clients and the business,” added Mr Hardiman. “This includes enhancing our production capacity to meet growing demand, ensuring we can deliver solutions at scale and with consistent quality.”
In addition to expanding production, RanMarine is strengthening its customer support and training programmes, which have become key pillars of the business. n
Inglasco International provides the marine industry with exceptional safety and supply packages. Working with reputable marine contractors, the business offers high-quality tailored services around the globe. MD Chris Giljam and Business Development Director Andrea Gerali explained more to Hannah Barnett.
Inglasco International was founded by Chris Giljam in 2020, together with the VIVAR GROUP, with a simple approach to distinguish itself from the large players in the market.
“Those companies are big and slow,” Mr Giljam, MD, said. “Clients with issues are sent from representative to representative. We wanted to offer the same package and global network, but with a different, more personal, approach. They can call us anytime and we will find somebody to assist them.”
As a one-stop shop for safety and services, Inglasco International is the facilitator between ship management companies and service suppliers. Its network of trusted, hand-selected, local partners allows for global coverage. For a small operation of six employees, the company has an impressive turnover of €4.5 million, a testament to its high demand.
“We ensure that everything runs smoothly,” said Andrea Gerali, Business Development Director. “We take care of problems before they arise. We’re available 24/7, so WhatsApp is our best friend.”
One of Inglasco International’s leading capabilities is understanding what is required and when it is needed. In recognition of the fact that all shipping companies work in different ways, the company offers a suite of tailored services.
“Sometimes, the technical superintendents are making the orders,” Mrs Gerali explained. “In other cases, it’s the purchasers. Some superintendents want to make the order
and forget about it. Others need to know exactly what is happening the whole way through. We are tailored because we examine exactly what the customer needs and respond accordingly.
“We see it as customer care, not selling services. Services are mandatory, we don’t need to sell them. What we do sell is peace of mind.”
Alongside working with clients, the other key to Inglasco International’s success is ensuring local partners feel valued. This has the added bonus of developing loyalty between the two parties – particularly beneficial when things go wrong.
“They will go the extra mile for us,” Mrs Gerali explained. “We’ve been working with most of our local partners for many years, because Chris and I were in the same line of work before this business was founded. It’s not just about ‘do what we say, because the customer is always right.’ We try to strike a balance between keeping customers and
partners happy. Ultimately, if we don’t have our local partners, we don’t have a business.”
The company has a policy of trying to avoid flying in contractors to do a job.Not only are locally-based partners less logistically complicated when it comes to solving last-minute problems, but focusing on quality of service, rather than price, is key to Inglasco International’s company philosophy.
“Most of our local partners are our friends too,” said Mr Giljam. “Most of our clients are friends also. It’s the personal touch; not every client is a good fit for us, because of the way we work, while some companies only look at the lowest price. Our team is a mixture of experience with youth and enthusiasm. I’m not young anymore but I’m still enthusiastic. Combining this team with the global network of skilled local partners is how we deliver world class service.”
As part of the Vivar Group, Inglasco International exists in a sweet spot whereby the company can offer tailored services and
act quickly but also has access to the same resources as the big companies. “A complete legal or compliance department is only a phone call away, but we only use it when we need to,” Mr Giljam explained. “For the day-to-day, we can be the boutique shop we want to be. It’s the best of both worlds.”
This year, Inglasco International has already signed two new large fleet agreements and is due to sign more. The ultimate goal is to turn the €4.5 million turnover into €10 million in the next three or four years. Finding the right people to support this growth remains an ongoing challenge.
“Nowadays, people want fast and easy money,” said Mrs Gerali. “Fast and easy money is not possible when it comes
to shipping. Plus, it’s a very stressful job, because it’s 24/7 and 90 per cent of things happen last minute. We’ve been really lucky with the people we’ve found this far, but growing further, while maintaining the quality of service is always a challenge, but we will manage.”
Mr Giljam shared his philosophy for crafting a successful business: “Our first and second objectives are making the client and local partners happy,” he explained. “The third objective is to make money. If the first two are achieved, and the third one is not, then it’s fine, because we will have a repeat order at some point, so the money will come. More important is that we make sure that we hit objectives one and two.” n
Short installation times and significant fuel savings make air lubrication systems and Exhaust Gas Cleaning System (EGCS) attractive investments for shipowners. Report by Clean Marine.
Shipowners are facing an unprecedented challenge to reduce the carbon footprint of their fleets. With the pressure to cut carbon growing, the question of how to achieve cleaner operations is more urgent than ever.
Fuel-related emissions remain a primary concern for shipowners, but the current marine fuels landscape is riddled with uncertainty. Many of the alternative fuel options on the market are prohibitively expensive, complex to implement, or require new engine technologies that shipping companies are not ready to adopt overnight. Green hydrogen and green ammonia, while promising, are not yet available at scale. As a result, many owners are seeking solutions that can be applied to their existing ships immediately –solutions that are cost-effective and do not necessitate major structural changes.
Clean Marine, a long-standing manufacturer of marine technologies, has been helping the maritime industry navigate emission reduction challenges for over two decades. Initially known for its exhaust gas cleaning systems (EGCS), Clean Marine has expanded its product portfolio in recent years, staying ahead of the curve in response to industry demands and the evolving regulatory framework.
Since 2004, Clean Marine has been at the forefront of EGCS technology, providing shipowners with an immediate solution to comply with International Maritime Organization (IMO) regulations on sulphur emissions.
Today, the company has installed more than 300 EGCS, designed to remove 99.9%
of sulphur from ship exhaust gases. These systems ensure compliance with the IMO’s 0.1% sulphur cap in Emission Control Areas (ECAs), which will expand in May 2025 with the inclusion of the Mediterranean Sea as a new ECA.
European gasoil-fuel oil forward price spreads are wider for the third quarter, according to Freight Investor Services. The ICE Gasoil-VLSFO forward spread has gone up to $191/mt, and the ICE Gasoil-HSFO spread to $256/mt. This is a clear indication that the market expects LSMGO to become costlier relative to VLSFO and HSFO after the Mediterranean ECA has been implemented. By installing EGCS, ships sailing in the Mediterranean ECA can avoid these extra fuel costs by continuing to consume HSFO instead of switching to costlier LSMGO.
HSFO-fuelled ships in operation today already use Clean Marine’s exhaust gas cleaning systems to filter the sulphur oxide levels in their exhaust gas down below the compliant 0.10% limit in ECAs.
“We have always pushed ourselves to meet or exceed regulatory standards, preparing for future challenges as much as addressing current ones,” said Nicholas Macleod of Clean Marine.
One of Clean Marine’s key innovations was transitioning from super duplex steel to 254 SMO grade steel for its EGCS in 2018, improving both the durability and environmental footprint of its systems. As a result, the company now offers a fiveyear structural warranty on all installations, giving shipowners added confidence in their investments.
While EGCS remain a cornerstone of Clean Marine’s product line, the company has significantly broadened its portfolio. Recognising the growing need for decarbonisation solutions that don’t rely solely on fuels, Clean Marine has developed an Air Lubrication System (ALS) – technology aimed at reducing frictional drag between a vessel’s hull and the water.
Air lubrication has long been considered a promising way to improve fuel efficiency, and Clean Marine’s system stands out because, unlike other ALSs on the market, it can be adapted. In partnership with Pascal Technologies, a specialist in hydrodynamics, naval architecture and control systems engineering, the Clean
Marine ALS is designed to dynamically adjust to a vessel’s operating conditions – such as wind, current, and draught – to optimise the system's effectiveness and maximise energy savings.
“The adaptive ALS we have developed can be applied across different ship types, from tankers, bulkers, cruise ships and containerships, and can fine-tune itself in real-time,” says Macleod, ensuring notable KW savings.
These savings are more than theoretical.
Six ALS systems have already been installed on vessels operated by Navig8, one of the world’s leading ship management companies, demonstrating the growing trust shipowners are placing in this technology.
Charterers increasingly consider ships with lower fuel costs and lighter carbon footprints more attractive prospects, so installing ALS will make ships stand out positively in the global fleet. ALS can also improve Carbon Intensity Indicator ratings, which measure CO2 emitted per cargo tonne mile and are becoming stricter every year. Feasibility calculations on expected net KW gain for any ship type can be completed by Clean Marine upon request.
“Installation can be completed within ten days, meaning minimal downtime for ship operators,” Macleod added.
Clean Marine continues to innovate by actively developing a range of additional solutions to help shipowners reduce emissions. Among these is its rotor sail technology, which relies
on wind propulsion to provide an alternative source of thrust. With the technology currently undergoing extensive land-based testing, the company’s rotor sails are one step closer to going to market.
Additionally, the research and development team is working on a carbon capture system. Although still in its nascent phase, this technology represents a key part of Clean Marine’s future strategy.
“Our aim is to offer a full suite of solutions, enabling our customers to meet not only current regulations, but also future CO2 reduction targets,” said Macleod.
The European Union’s Emissions Trading System (EU ETS) provides commercial incentives for ALS, onboard carbon capture and rotor sails by allowing shipowners to reduce their CO2 emission liabilities. Under the EU ETS, shipping companies must purchase
allowances for their emissions, and carbon capture can help lower the amount of CO2 released, reducing the number of allowances a ship needs to buy. This creates a direct cost-saving mechanism for shipowners who invest in ALS, carbon capture and rotor sail technologies, as capturing CO2 means fewer emissions to account for.
Throughout its expansion, Clean Marine has remained a trusted partner for shipowners around the world. With certifications from all major class societies and an extensive global service network, the company is well-positioned to support its customers in this new era of decarbonisation.
Unlike many of its competitors, Clean Marine can provide in-house servicing, reducing costs and turnaround times for its clients.
“Other companies might need to outsource servicing, but we have the global reach and capability to offer a seamless service experience,” Macleod pointed out.
This is particularly valuable as downtime becomes increasingly expensive for shipowners.
Looking ahead, the company is keen to be recognised not just as an EGCS provider, but as a leading player in marine technology.
“We’ve come a long way from just being a EGCS company,” said Macleod. “Our goal
is to be seen as a world-class marine tech company with a comprehensive range of solutions that can help shipowners meet their decarbonisation goals.
“The shipping industry is facing significant change, and we are determined to be part of that transformation.”
As the maritime sector braces for stricter environmental regulations, Clean Marine’s combination of proven technology and forward-thinking innovation offers shipowners a practical, scalable way to navigate these challenges. n
For more information email post@cleanmarine.no or visit cleanmarine.no
40,000sqm state-of-the-art facility in Batam, Indonesia
125 strong manufacturing workforce
90% of global aftersales repairs carried out on the spot
300+ EGCS in operation
6 ALS on the water