VESTDAVIT: High-quality davits tailored to meet customer needs EEKELS TECHNOLOGY: Electrical, technical & mechanical specialists
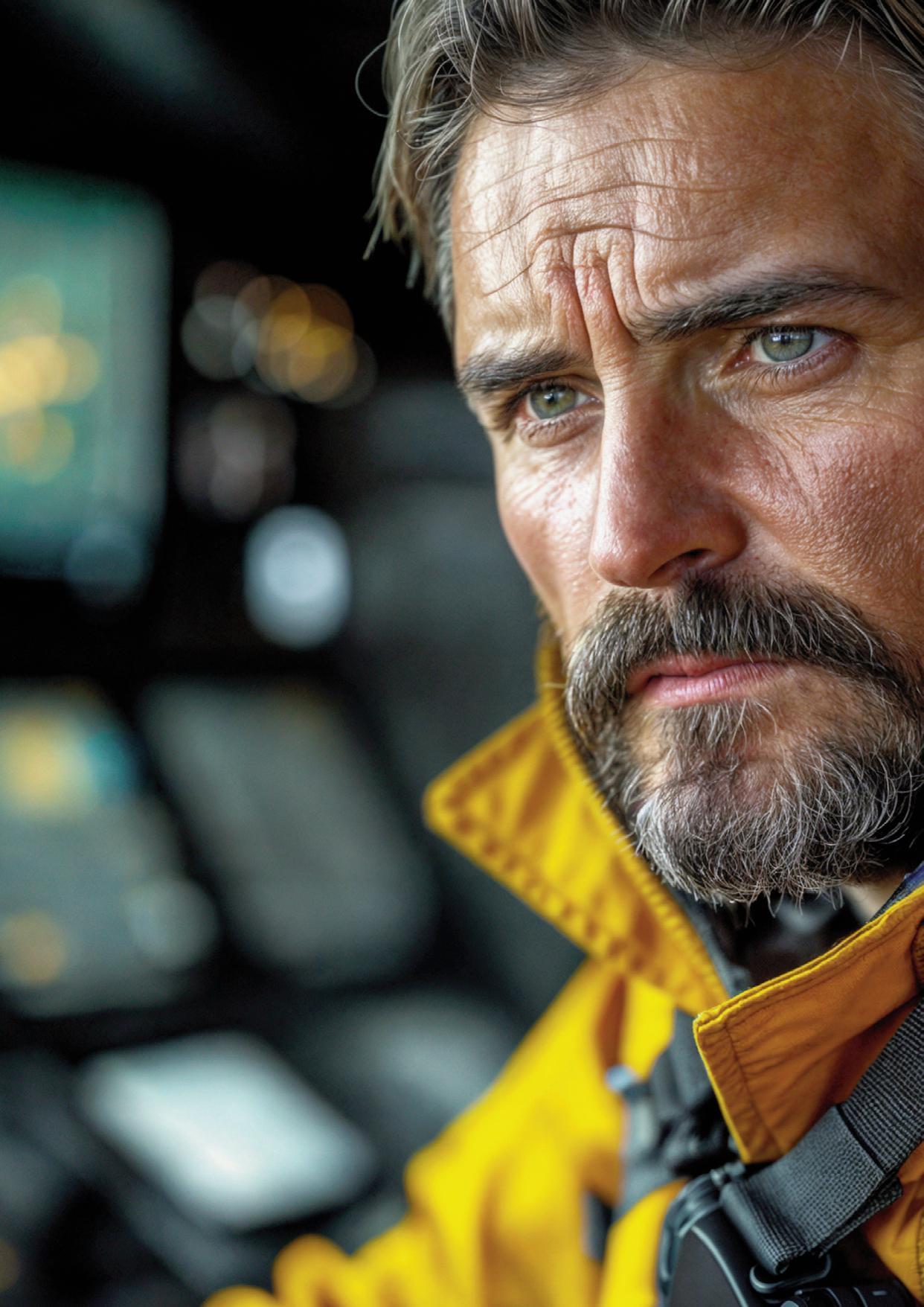
SWAN SHIPPING CORP: First-class ship & technical management
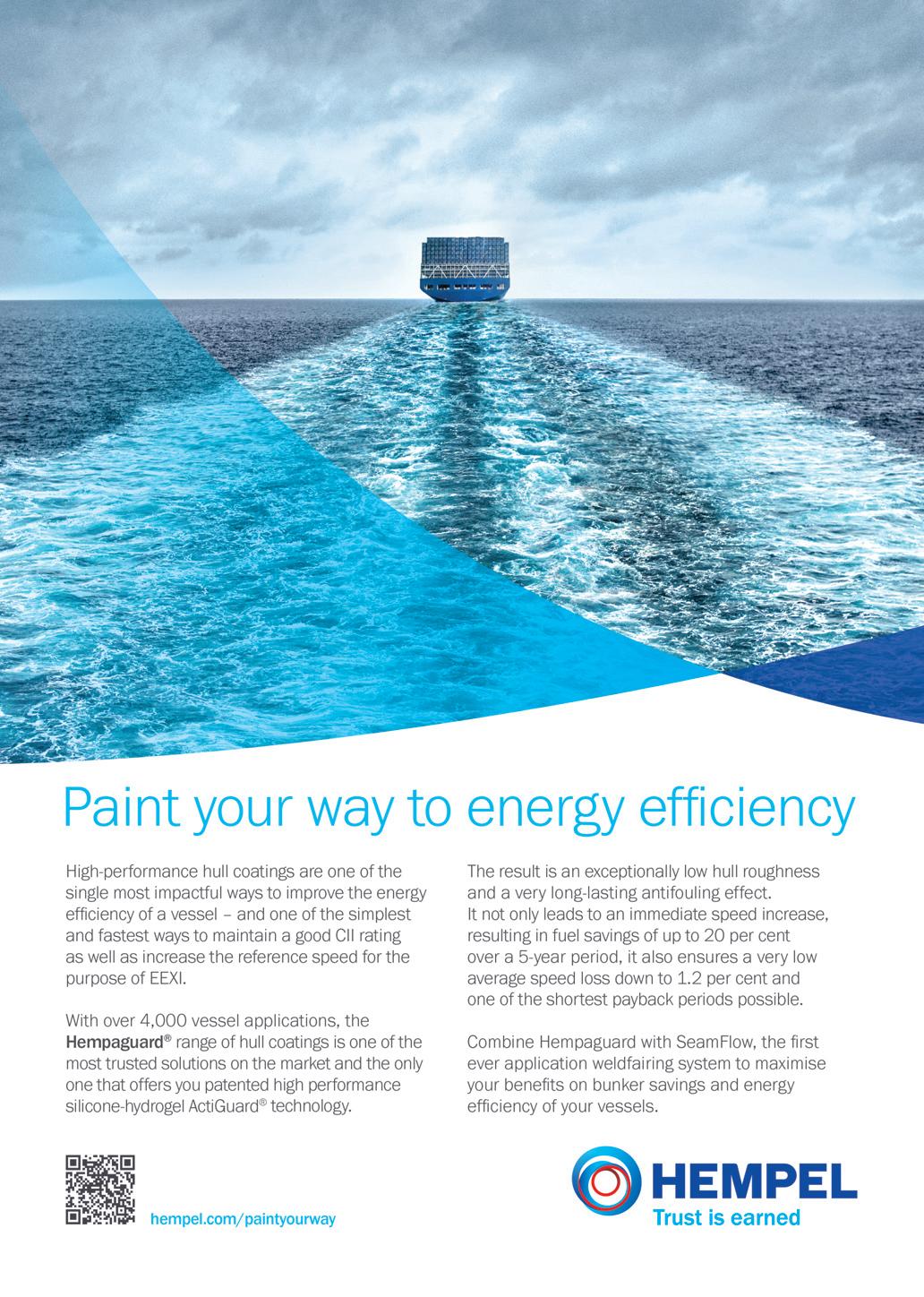

John White Managing Director
VESTDAVIT: High-quality davits tailored to meet customer needs EEKELS TECHNOLOGY: Electrical, technical & mechanical specialists
SWAN SHIPPING CORP: First-class ship & technical management
John White Managing Director
Managing Director John White dedicates a lap of honour to the equipment industry.
Welcome, Dear Reader, to your latest edition of Inside Marine. This issue is being produced during a rare warm spell here on the East coast of England. An almost Mediterraneanlooking North Sea is just a short walk away from our office.
Situated as we are, between the ports of Lowestoft and Great Yarmouth, my team and I regularly see a wealth of freight arriving at, and leaving, the ports. Much of this cargo is the vast array of equipment needed to support the maritime industry, some of which is manufactured locally. Indeed, several of our neighbours on the business park are involved in this exact sector.
It is easy to picture a vessel at sea, often for weeks on end, self-sufficient and weathering all that the waves can throw at it. However, what we seldom appreciate, is the small army of companies and industries required to get the vessel to sea in the first instance, help to keep it there safely and then supply the necessary maintenance when the ship returns to port.
For those who enjoy watching Formula One racing, we might liken this to an F1 team. Most of our focus is on the small car, with its one driver, racing around the track. Yet, when the car returns to the pits at the end of the race, a huge support team with masses of equipment will descend on it to prepare for the next race.
The amount of equipment needed to support any sea-going vessel is arguably even more vast than an F1 team. This is far too numerous for me to list here. Therefore, might I suggest further, and more enlightened, reading in the pages that follow. Here you will enjoy hearing from those teams of companies involved in the all-important maritime equipment sectors. n
Marine equipment
Cranes and harbour equipment are such important components for keeping the shipping industry running smoothly. In this issue, Inside Marine takes a closer look at this vital sector, from the smallest deck winch to the largest harbour crane.
Managing Director
John White
Finance Director
Filomena Nardi-Smith
Accounts
Chloe Frosdick
Angel Esherwood
Editor
Phil Nicholls
Editorial Assistants
Imogen Ward
Hannah Barnett
Antonia Cole
Feature Writers
Andy Probert
Richard Hagan
Colin Chinery
Business Development Manager
Darren Foiret
T: +44 (0)1493 445121 +44 (0)1502 566216
E: media@insidepublication.com W: www.insidemarine.com
Research Editors
Jeff Johnson
Judi Wheaton-Mars
Ginelle Lorenzo
Tony Ingrouille
Natalie Martin
Dane Coady
Becky Scrivens
Amy Lawrence
Sales Director
Richard Brightmore
Sales Manager
Helen Leisi
Project Managers
Alexander Paterson
Chris Renicar
Mark Simmonds
David Earl
Lisa Smith
Will Tottie
Bobby Godfrey
Loretta Smith
Mika Warner-Wright
Sam Ransome
Studio Manager
Philip White
Webmaster
Michael Stamp
Designers
Sarah Jones
Georgina Harris
Sam Moyse
Events & Operations Manager
Gavin Bellward
Marketing Manager
Adam White
Administration
Summer Clover
Latest developments from the Egyptian industry
Höegh LNG Holdings Ltd. (Höegh LNG) has announced an agreement for the deployment of the Floating Storage and Regasification Unit (FSRU) Hoegh Galleon.
The aim of the agreement between Höegh LNG, Australian Industrial Energy Pty Ltd (AIE) and Egyptian Natural Gas Holding Company (EGAS) is to support energy security in Egypt. Hoegh Galleon will be located in Ain Sokhna, Egypt, for a likely period of 19-20 months, after which it is expected to be deployed to AIE’s LNG terminal currently under con struction at Port Kembla, Australia.
“Together with AIE and EGAS, we are pleased to provide Egypt with flexible infrastructure in support of energy security,” said Erik Nyheim, President & CEO of Höegh LNG.
“Höegh LNG is the industry leader in the rapid deployment of FSRUs, and we are pleased that we can provide this solution for EGAS together with AIE while continuing to develop our strong partnership.”
Höegh LNG and AIE announced a 15-year FSRU charter agreement for Hoegh Galleon in June 2022. The agreement with EGAS is for an interim period of June 2024 to February 2026.
Höegh LNG is a pioneer within maritime energy infrastructure, providing countries
and energy consumers with rapid, flexible and cost-efficient access to the global LNG market. The company is a leading innovator, owner and operator of Floating Storage and Regasification Units (FSRUs) and LNG carriers (LNGCs). In addition to providing energy security, the company’s vessels support the transition to renewables by providing reliable access to lower carbon natural gas and a flexible infrastructure solution for delivering carbon-free energy. For over 50 years, Höegh LNG has provided safe and reliable access to critical and costcompetitive LNG infrastructure. Its global organisation consists of approximately 900 employees at sea and onshore, with half of its capacity deployed in Europe. n
To have your company’s latest product, technology or concept included in Inside Marine, contact us today.
Latest developments from the European industry
31 participants have successfully completed EMSA’s Common Core Curriculum.
Working together, 25 participants from 17 EU Member States, Iceland and Norway, plus six participants from four beneficiary countries to the IPA/ENP projects, have successfully completed the Common Core Curriculum for Sulphur Inspectors developed by EMSA within the context of the EMSA Academy.
The Curriculum is organised in three phases with eight units, covering a wide spectrum of learning areas such as general legal and technical requirements, pre-boarding information analysis, on-board fuel-based methods and abatement methods, sampling process, tools and equipment, reporting and logging, data management, and health and safety requirements.
It was delivered in a blended mode from 15 February to 28 April 2024. Participants followed an asynchronous part covering the above-mentioned areas with three live sessions and the use of the Virtual Reality Environment for Ship Inspections (VRESI) for ship familiarisation purposes. The content of the course also included a three day
in-person session at EMSA’s premises in Lisbon. During the three days, participants had the opportunity to go through specific case studies, reporting exercise into THETIS-EU database and collective work into groups.
This curriculum is designed to develop the necessary individual competencies for carrying out duties associated with the inspection of ships for compliance with the international and EU instruments regarding the limits of sulphur in marine fuels (MARPOL Annex VI and the EU Sulphur Directive). It aims to provide learners with the opportunity to increase the knowledge, skills and attributes required to carry out inspections professionally, efficiently, effectively and to the required standards established by law and benchmarked industry practice.
It is an ISO 29993:2017 certified learning service outside formal education developed by the EMSA Academy and it is delivered on the Maritime Knowledge Centre (MaKCs), the eLearning Platform of the Agency. n
The Global Centre for Maritime Decarbonisation (GCMD) has partnered with NYK Line to launch Project LOTUS. This six-month project will trial the continuous use of a biofuels blend comprising of 24% Fatty Acid Methyl Esters (FAME) and very low sulphur fuel oil (VLSFO) onboard a short-sea vehicle carrier that will call at multiple ports.
FAME, a readily available biofuel derived from second-generation feedstocks, presents a promising fuel alternative for immediate GHG emission reduction in the shipping industry.
The past decade has seen trials of various biofuels onboard vessels; these have primarily focused on their combustion characteristics and the extent of emissions abatement. Data on the impact of long-term and continuous use of biofuels on engine performance and fuel delivery system operations remain limited.
Project LOTUS aims to address this knowledge gap by establishing industry guidelines for monitoring engine and equipment performance when using biofuels. This pilot will also evaluate the total cost of ownership of using
biofuels, covering the cost of fuel and additional maintenance costs associated with its use. Additionally, it will identify potential challenges such as the corrosion of engine systems and valve failures related to continuous biofuels use, and then recommend mitigation strategies.
The quantitative findings from Project LOTUS offer an opportunity to contribute complementary real-world data to the upcoming revision of ISO 8217:2024, which includes specification of standards for a wider range of FAME-based blends up to B100.
Furthermore, these learnings will be crucial for shipowners and operators who are considering biofuels use to meet vessel compliance with regulations, like Carbon Intensity Indicator (CII) and the FuelEU Maritime Standards. n
Latest developments from the UK industry
Sustainable technology firm, Recycl8, has completed its first commercial project with Port of Aberdeen.
The Aberdeenshire-based company Recycl8, in conjunction with Inverurie Pre-Cast, was responsible for manufacturing concrete blocks for defence at the South Breakwater of the North Harbour as well as slipway repairs for Port of Aberdeen.
The firm was chosen for the project due to its strong commitment to environmental sustainability – a key priority for Port of Aberdeen as it strives to be the UK’s first net zero port by 2040.
Recycl8 partnered with construction materials specialists, Breedon Group, to supply its patented solution of sustainable, lower carbon R8 Mix concrete for the project, which is the latest in a series of successful pours carried out this year by Recycl8 across a number of sectors.
Working with Port of Aberdeen marks another significant achievement for Recycl8; gaining a new client affirms the growing recognition within the marketplace of the necessity for sustainable concrete solutions.
“We are thrilled to have carried out our first small-scale marine project with Port of Aberdeen and to be able to offer a solution which contributes to the port’s environmental sustainability goals,” Mark Gillespie, CEO of Recycl8, said. “We believe that our R8 Mix is the future of sustainable construction.
“It is fantastic for Recycl8 to be involved in such an important infrastructure development in Aberdeen, and we look forward to continuing our relationship with Port of Aberdeen and supporting them in future marine projects.”
“Our vision is to become the UK’s first net zero port by 2040 and that requires new and innovative ways of working,” added Head of Engineering at Port of Aberdeen, John Wilson. “We are investing heavily in becoming a leading exemplar in environmental stewardship and sustainability, and Recycl8’s slipway repair work supports that ambition.”
n
The world’s leading manufacturer of electric and hybrid drives for the marine market, Torqeedo GmbH, is taking the next step toward cleaner waterways and a more sustainable marine industry by diverting and integrating ocean-bound plastics into its emission-free boating products.
Every year, an estimated 14 million tonnes of used plastics end up in the world’s waterways and oceans. These plastics entangle wildlife and break down into hard-to-remove microplastics, plus they litter our human and natural environments.
Torqeedo GmbH has established a new Advanced Engineering Team that, among other tasks, explores alternative materials to further minimise the environmental impact of its recreational and commercial marine products. The Team is testing recycled ocean-bound PET and PP plastic pellets, which are estimated to reduce the source material’s CO2 impact by more than 80% and are very close in quality to virgin plastic due to strict processes and advanced recycling equipment.
“The typical way to integrate new materials is to start with a small percentage –maybe with just 10 or 20 per cent recycled content. However, we decided to aim
higher,” said Florian Deger, project lead & Engineer of Advanced Materials & Technologies. “We made our prototype propellers from 100 per cent recycled ocean plastics. We’re thrilled to report that they surpassed all benchmarks in the first round of environmental and stress testing.
“After some slight adjustments, we will produce the next prototypes in Torqeedo orange. These will be very similar to the propellers that are in use today. It feels good to hold one of the prototypes in my hands and know we are keeping plastic bottles and pollution out of the waters we all love to explore on our boats.” n
Wescom Group has released new first aid kits targeted towards the marine industry, all of which have Lloyd’s Register Approvals.
Wescom Group’s new ANP
Pharma branded products are the culmination of internal investment expanding Wescom Group’s UK pharmaceutical distribution facilities in Basildon, UK, to enable the development of SOLAS and Category C first aid kits for the marine sector. These first aid kits are Lloyd’s Register Type Approval certified.
Approval of the new range of first aid kits provides Wescom Group’s exten sive global distribution network with the economic benefits of a single source partner that offers trusted large volume manufacturing, with logistical expertise in handling time sensitive and highly regulated products such as pharmaceuticals.
The new kits offer a range of medical sup plies for specific mandated requirements.
SOLAS Kits are specifically designed to cater to the medical needs of life rafts and lifeboats, and are approved for use on ships registered outside the EU. These kits have a minimum 30-month shelf life and are drop tested to 36 metres to ensure
they are robust enough to withstand harsh marine conditions.
The Category C Kits are intended for vessels operating within a range of less than 60 miles from a port, including lifeboats and commercial life rafts, this medical kit is
ATthis year’s Smart City Summit and Expo, Taiwan International Ports Corporation (TIPC) successfully ran a Smart Port Vision Pavilion which reflected the exhibition’s ‘Digital and Green’ transformation theme.
Among other things, the pavilion shared the results of the Trans-SMART 2.0 Plan, introduced the joint TIPC-Chunghwa Telecom 5G AIoT-based 24/7 Smart Harbor & Coastal Surveillance System Verification Project. It also demonstrated a 24/7 IoTbased oil pollution surveillance system, plus an autonomous surface vehicle designed to collect and dispose of waste floating in harbor waters. These innovations are designed to help to raise the effectiveness of port water area management and infuse new vitality into port city sustainability.
As part of the event, organisers invited TIPC Executive Vice President Chin-jung Wang to join a host of prestigious names at the Smart Harbors Forum. Seminars included topics addressing digital net zero, sustainable development and smart applications in the context of port cities.
In his presentation, VP Wang discussed the important role that smart application and system integration is playing in enhancing TIPC port competitiveness.
VP Wang emphasised how new and innovative digital solutions have been steadily introduced and integrated in the four critical areas of work safety, operational efficiency, service quality and sustainable development. He also discussed the results of Port of Kaohsiung’s transformation over the past few years, as well as how the port has addressed the brisk pace of smart technology development. He also updated forum attendees on the company’s progress with installing intelligent berth status e-billboards, the Port-168 system, the 3D smart operations map base and a KPCT operations management platform.
Looking ahead, smart port efforts at TIPC will focus on leveraging ‘Digital Twin’ functionality and installing IoT-connected sensing equipment to collect real-time dynamic data to raise operational efficiency. n
Dutch emission-reducing tech enterprise, Value Maritime (VM) and Japanese shipping company Mitsui
O.S.K. Lines, Ltd. (MOL) have inked a contract for VM to supply an Exhaust Gas Cleaning System (EGCS) and Carbon Capture feature for an LR1 Product Tanker.
VM will provide a 15MW next generation EGCS Filtree with its additional Carbon Capture unit set to capture 10% CO2 onboard MOL’s LR1 product tanker Nexus Victoria.
With a deadweight (DWT) of 75,000, this is the largest vessel, in terms of DWT, and the first LR1 tanker that will sail with a Value Maritime Filtree and Carbon Capture unit. Installation is expected to take place before the end of the year.
MOL has established the ‘MOL Group Environmental Vision 2.2’ as a roadmap to achieve net zero greenhouse gas (GHG) emissions by 2050 and promote the sustainable development of people, society and the Earth. MOL positions the environmental strategy as one of the main strategies in its management plan, ‘BLUE ACTION 2035.’
The Filtree system is based on innovative technology that filters sulphur, CO2
and 99% of ultra-fine particulate matter from the tankers’ exhaust stream. The plug and play Filtree system installed on the MOL product tanker will be outfitted with a CO2 capture and storage system to help reduce emissions further. With this, CO2 is captured from the vessel’s exhaust and stored in tanks onboard. This is then discharged onshore where it can be used, for example, in the sustainable cultivation of greenhouse crops, methanol plants and even the food industry.
With this signed deal, Value Maritime plans to collaborate further with other product tanker companies in the Asian market and further expand its carbon logistics services onshore. n
seven seas, five oceans, one voice
A selection of forthcoming events, followed by a review of Posidonia and a preview of SMM.
10-15 September 2024
Cannes Yachting Festival
Cannes Yachting Festival brings together key players from the yachting industry to exhibit new products and innovations. With the launch of a new space dedicated to showcasing eight to 12 metre motorboats, the festival will present an exciting range of vessels.
[click here] for weblink
10-11 September 2024
IMPA London
IMPA London, a premier maritime event, will feature a vibrant exhibition area, a comprehensive conference programme and various side events. From prominent ship-owners and operators to maritime suppliers and manufacturers, the event will bring together influential decision makers from over 60 countries.
[click here] for weblink
03-06 Septembe
SMM
As the world's leading trade fair and maritime industry, SMM 2024 will br participants from over 120 countries platform for business, the exchange of ideas
[click here] for weblink
orld Offshore Week is a leading meeting ace for the offshore oil, energy and maritime ctors. The event features exciting programs y thought leadership sessions, as well as n hall where companies can showcase a targeted audience.
here] for weblink
The award-winning AntwerpXL event provides a platform for the breakbulk, RoRo, heavy lift and project cargo industries. Encouraging the formation of meaningful relationships across the sector, this event promotes the development of more efficient practices, valuable connections and unforgettable experiences.
[click here] for weblink
er 2024
d conference event for the ring together about 40,000 s and serve as a unique s and cooperation.
Why not give your event exclusive coverage to thousands of readers and connections globally? Contact us: events@insidepublication.com
Having run from the 3rd to 7th of June, Posidonia 2024 provided the perfect platform for professionals to meet and discuss the latest ideas and developments from the maritime community, and with over 2,000 exhibitors and 40,000+ visitors, it is safe to say Posidonia retained its position as the flagship event for all things shipping.
Posidonia has been a hotly anticipated date in the calendar since its first exhibition back in 1969. With the biennial event estimated to bring in more than €70 million to its home in Athens, Greece, it is clear that Posidonia has a crucial impact on the Greek economy and the world of shipping.
From the Posidonia Sea Tourism Forum (which quickly became the leading platform for professionals within the global cruising and yachting sectors) to the prestigious seminars that highlight current trends worthy of address – over the years, Posidonia has established an esteemed reputation as an event not to be missed.
Posidonia 2024 was no different. Centred around the theme of ‘powering ahead’, this year’s event hosted over 2,000 exhibitors, more than 40,000 visitors, and thanks to Posidonia TV and TradeWinds Content Studio, the entire conference was available to more people than ever before. With a global audience of 300,000 plus monthly unique visitors, Posidonia TV provided live access to the
www.posidonia-events.com
bustling exhibition floor, exclusive interviews and behind-the-scenes previews that made at-home viewers feel as though they were experiencing the event first-hand.
Having successfully housed more than 65 inspiring seminars and conferences, including the ever-popular TradeWinds
Shipowners Forum and the Greener Shipping Summit 2024, it is no wonder why so many people are singing the praises of this year’s international shipping exhibition.
Just like at previous Posidonia exhibits, the TradeWinds Shipowners Forum provided the perfect opportunity to dive into hard-hitting and pertinent topics. On this year’s agenda was the role that shipowners, charterers, financiers and regulators could play in fostering a new paradigm against a backdrop of geopolitical turmoil, economic flux and climate crisis considerations.
Visitors enjoyed enigmatic and lively talks from industry experts, including Katerina Bodouroglou and Leon Patitas, with technological advancements, innovation and eco-friendly fuels all crucial topics as we seek to ‘power ahead’ in a new climate.
Also on the cards for those who were looking to get inspired was the Greener Shipping Summit 2024. This prestigious summit lasted an entire day and hosted panel discussions focused on the next generation of ships, education for the
future of shipping, as well as green shipping technology. It comes as no surprise that this summit, with the underlying theme of ‘New Technologies and Education’ also stimulated the discussion of more general topics, including job security, digitalisation, carbon capture and the energy transition.
Having inspired another cohort of industry experts to drive forth a more sustainable sector, this event was incredibly successful thanks to the exceptional organisation of Newsfront/Naftiliaki and
w.posidonia-events.com
the support of MARTECMA (Marine Technical Managers Association).
The 2024 exhibit also shone a spotlight on crew management at the Crew Insights @ Posidonia 2024 conference and provided a platform for the Polish Embassy to discuss the Polish seaports, renewable energy, shipbuilding and maritime logistics at POLAND – Thinking out of the box about the maritime industry.
There is no doubt that across five days, Posidonia 2024 offered entertainment, insight and education: it was the perfect place to stimulate unconventional thinking and inspire minds to ‘power ahead’ with implementing a greener future in a world filled with opportunities. n
Scheduled for the 3rd to 6th September, SMM 2024 is set to draw the attention of the maritime industry, with an estimated 2,000 international exhibitors from 70 nations expected to attend. With the event scheduled to address the needs of the industry in a vastly evolving digital age, SMM 2024 will be one to watch this September.
With roots dating back to the mid-50s, SMM as we know it today held its first exhibition in 1963 to discuss the development of a diverse range of maritime sectors. This theme has remained prevalent throughout the exhibit’s history.
SMM 2024 is set to draw on this legacy with insight from the cruise industry, the world of AI and marine recruitment to name a few.
For four days, SMM will bring together decision-makers, leaders and industry professionals from across the globe,
024, Hamburg Germany, ww.smm-hamburg.com
under the theme of ‘driving the maritime transition’, in the hopes of inspiring dialogue and expanding relationships that could impact the future of the marine industry as we know it.
With an estimated 2,000 international exhibitors and 40,000 visitors expected to attend, SMM 2024 will bring together experts from the worlds of large-scale industrial shipping, shipyard engineering, outfitting, cargo handling, offshore engineering, marine services and many more.
The fair will cover the entire value chain of the maritime industry from 12 exhibition
halls and will feature an awe-inspiring conference programme, which will take place on open stages for the first time – ensuring the latest news and developments are accessible to all fair visitors, without charge.
But what can we actually expect from this leading international trade fair?
Those who travel to the Hamburgbased exhibit in September will be met with a whole host of inspiring seminars and conferences.
The worlds of AI and shipping will collide at this year’s AI CENTER (Hall B6). Visitors should expect great things as start-up companies are set to take centre stage to discuss the importance of AI and the opportunities it could bring.
The topic of carbon-neutral shipping will also be prevalent at the Green Stage (Hall A4) on the second day of events. Here, visitors will get to witness this year’s Global Maritime Environmental Congress: where experts will discuss the pros and cons of different alternative fuels. With greener fuels predicted to be the future of the industry, for the first time ever, SMM will also have a dedicated exhibi -
tion area for hydrogen in the Future Fuels Arena (Hall A2).
Following the theme of change, the importance of sustainability in recruiting will be addressed in both the Maritime Career Market and the Career Forum –both of which will be in Hall B2 across two days of the fair. As excellent opportunities for young, aspiring minds to connect with potential employers, these two events will highlight why the maritime industry is the place to be for sustainably minded, passionate young jobseekers.
With the cruise industry estimated to be worth around $20 billion, it plays a crucial role in the current and continued success
024, Hamburg Germany, ww.smm-hamburg.com
of the maritime industry. To pay homage to this magnificent market, SMM 2024 will host MARINE INTERIORS @SMM in Hall B5, where 130 exhibiting companies specialising in ship interior design will gather to share their latest products, innovations and services.
For the first time ever, SMM’s official partner Cruise Lines International Association, will also be represented on the Cruise & Ferry Stage. With a focus on sustainable cruising, this conference is not one to be missed.
As the fair fast approaches, tickets are available now for those looking to take part in what is set to be an event to remember. n
seven seas, five oceans, one voice
An introduction to marine equipment, with a special report on winches and a selection of news stories and innovations, followed by company profiles for: one marine services vestdavit
Mikael Holmberg from ABB explores the next step for marine winches.
The maritime industry is embarking on a transformation, steering away from traditional hydraulic winch mechanisms in favour of advanced electrically operated systems. Mikael Holmberg, Segment Sales Manager, Cranes and Marine Winches, ABB, explains more to Inside Marine.
The use of variable speed drives (VSDs), also known as variable frequency drives (VFDs) or, simply, drives, paired with high-efficiency electric motors is redefining all kinds of marine winch, including spooling winches, with a focus on energy efficiency, operational precision and reliability.
The ABB ACS880 industrial drive is setting a new standard in management of special application solutions for different marine winch machinery needs. Those include solutions for reliable and efficient anchoring, mooring, offshore AHC and tug operations.
As a special solution, the ACS880 drives can also handle the management of the rope guiding that is crucial for offshore and mooring vessels around the globe.
Mechanical spooling winches contend with a number of operational challenges. Mechanical and hydraulic power transmission systems face inherent inefficiencies, including wear and tear on the rotating parts that require synchronisation. The physical bulk and complex nature of their mechanical transmission makes these systems difficult to maintain and keep in sync.
ABB’s solution replaces the mechanical power shaft transmission with an integrated electronic synchro shaft functionality, similar to an electronic gear rather than mechanical gearing. This is made possible via the software built inside the ACS880 industrial drive that controls the motors of the main winch and spooler device. This approach allows for the electrical spooling device or motor to remain mechanically independent from the main winch, while maintaining precise synchronisation through the spooling software embedded in the drive.
The result is streamlined and the management of the ropes on offshore and mooring vessels is safe thanks to the integrated drive-to-drive communication capability that coordinates movement accurately between the main winch and spooler device.
The traditional mechanical transmission spooling devices offer raw strength, but lack the precision needed to adequately control the rope’s tension and position. This limitation can result in ‘bird nesting’, where ropes tangle and overlap, potentially damaging both the ropes and the winch. Thereby risking the safety of equipment and crew, especially with deep sea winches that have a long rope on the drum in multilayers.
In addition, these systems, which involve chains, belts and wheels, are large and cumbersome, requiring a lot of space. The wear and tear from their use can lead to uncontrolled spooling operations. These systems also present challenges in extreme weather conditions.
Transitioning to electric winches powered by motors and drives has the potential to revolutionise maritime deck operations. The precise control afforded by drives directly mitigates the risk of improper spooling. The
drive’s ability to control the speed of the motor allows for careful management of winch speed and torque, ensuring smooth operation and protecting the ropes from undue stress and wear.
Electric winch systems react quickly and precisely to operational commands, providing a big improvement on the slower response times that traditional mechanical transmission systems have. By using drives, electric winch systems can match energy consumption to actual demands. This not only prevents excessive energy use, but also promotes long-term operational cost savings and a marked reduction in the associated emissions.
ABB has introduced a ready-made, innovative solution to address the challenges posed by traditional marine winch systems. With an expanded offering for the marine winch market, ABB’s marine drive family, the ACS880, includes dedicated software designed to enhance spooling and rope guiding functions.
The key feature of this solution is a ready-made AC drive application tailored for synchronised operations between the main winch drive and the spooler device. This application facilitates direction
Mikael Holmberg from ABB explores the next step for marine winches.
For further information: https://new.abb.com/drives/segments/winches
changes effortlessly, filling one layer completely before advancing to the next, all while maintaining the desired fleet angle –essential for orderly and safe spooling.
The drive-based spooling control software provides a user-friendly interface, ready for configuration via a PC tool that simplifies parameter adjustments. Its diverse features and functionalities meet the varying needs of marine winch operations, including manual and automatic modes. In manual mode, the operator controls the movement of the spooler servicing and inspection. When in automatic mode, the system directs the spooler left and right in synchronisation with the rotation and speed of the main drum.
The software also features direction change logic: in automatic mode, the system can seamlessly switch the spooler’s direction from left to right using discrete input sensors and or actual position feedback from sensors. Additional benefits of the software include end-limit logic for both left and right sides, fleet angle support, options for referencing the main drum or the line reference with various inputs, such as encoders or external PLC function blocks. Thanks to this integrated software and the versatile functionality of the ACS880 marine drive, operators can expect significantly improved spooling accuracy and
efficiency. The system’s ability to adapt to different operational modes, coupled with the support for extreme temperatures, translates to more reliable and safer marine winch operations, effectively mitigating common issues such as tangling and bird nesting.
The collaboration between dedicated drive software and option of combining also PLCs is key to delivering advanced winch operations. This level of automation allows for sophisticated control strategies and real-time adjustments, ensuring operations are executed with accuracy and coordination.
For example, the ACS880 drive software can regulate the layering of rope on the drum to prevent tangles and overlaps, while drives or PLCs can synchronise multiple winch drums for balanced load distribution,
Mikael Holmberg, Segment Sales Manager, Cranes and Marine Winches, ABB
which is vital for complex lifting operations. ACS880 winch drives can also support do synchronisation and load sharing between drives without the need of a PLC.
The drive software also facilitates adaptive programming, helping to customise operations to accommodate the unique demands of the vessel and the sea conditions. Through integrated diagnostics and monitoring, PLCs can also provide critical operational data as feedback, including load tension, motor speed, system temperature and electrical current values. This allows for the analysis of the winch’s performance and condition in real-time.
This information is essential, as it enables the anticipation of potential maintenance needs based on actual usage and wear patterns, rather than on a predetermined schedule. This proactive approach better maintains the winch system’s reliability, cost-effectiveness and lifespan.
Maritime operators also benefit from the user-friendly nature of electric winches with drives. The common hardware and software platforms standardise setup procedures, making troubleshooting and maintenance much more straightforward. Instead of having different parts and unique software for each type of winch, manufacturers can design a range of winches that use the same core components such as motors,
drives, control units and the software interfaces that operate them. This means that operators can use similar procedures to install, program and repair multiple winch systems across their fleet.
Standardisation reduces the need for specialised setup and training, resulting in reduced engineering time and lower overall operational costs. Electric winching systems with reduced mechanical components also have fewer potential failure points, leading to lower maintenance requirements and better reliability. The added convenience of removable memory units for software simplifies the management of updates, further streamlining the setup and maintenance processes.
The integration of motor-drive systems and PLCs in marine spooling winch operations is ushering in a significant advance in maritime technology, enhancing precision, efficiency and adaptability.
Through optimised energy consumption, refined operational control and vastly improved safety, electric winch systems are now an asset for the modern maritime industry. The adoption of these advanced electric winches with ABB ACS880 drives signals a commitment to innovation, sustainability and progress. n
Vestdavit’s Dutch subsidiary boosted revenue by 50% last year. The regional business is growing through increased aftersales and davit commissioning work on newbuilds.
Vestdavit BV, led by regional Managing Director Magnar Bøyum, saw turnover rise by 25% in the first quarter of this year. This mirrors a similar trend for the overall group that has recorded huge sales growth, amid a significant rise in offshore wind orders.
The Vianen (Utrecht)-based sales and service centre is situated on an important European shipping route for vessels passing through ports in Germany, the Netherlands, Belgium and France, giving clients direct access to Vestdavit’s service expertise. This results in reduced time for inspections, maintenance and spare parts delivery carried out during port stays.
The company supports davit deliveries by assisting with system integration in the design phase, as well as during installation. It also performs commis -
sioning work on mainly naval and offshore wind vessel newbuilds at regional yards, including Damen Shipyard in the Netherlands and French shipbuilding facilities.
Furthermore, the regional unit provides davit support for seismic vessels and assists with service requirements for German and Belgian pilotage vessels.
In line with business growth, the local subsidiary has recently moved into a larger office premises and is looking to bring onboard an additional service engineer in the Dutch team as it targets multi-vessel service contracts for naval and other clients.
Vestdavit has gained a prominent market reputation as a leading supplier of robust and reliable davit systems through more than 2,000 deliveries over the past 40 years. The company utilises constant product development and innovation to provide high-specification boat-handling equipment tailored to the needs of clients. n
The first production system of Kongsberg Discovery’s revolutionary long-range Autonomous Underwater Vehicle (AUV) HUGIN Endurance has completed factory acceptance testing.
Sea trials for the first production unit began in September 2023, with the Kongsberg Discovery Uncrewed Platforms team since working to verify and refine all system capabilities. Sea trials culminated in March 2024 with a successful demonstration of the AUV capabilities.
The system can be equipped with a wide array of standard sensors. This includes a wide-swath high-resolution synthetic aperture sonar (HISAS 1032 Dual RX), multibeam echo sounder (EM 2040 MkII), sub-bottom profiling system, colour camera, laser profiler, magnetometer and environmental sensors collecting data such as conductivity, temperature, sound speed, methane, plus CO2 and O2 concentration.
In addition, the vehicle includes a large configurable volume that can be used to carry a mixture of batteries and custom payloads as needed. The system is designed to
allow autonomous operations directly from shore, and with a full complement of batteries, it can spend up to 15 days at sea, traveling up to 2,200km.
While the new AUV incorporates many of the industry-leading capabilities found in previous HUGIN vehicles, to enable long-term unsupported missions, new advancements had to be made. This includes greater redundancy, a new autonomous mission management system, greater situational awareness and the ability to deal with a wide range of varying water densities. n
Latest innovations from the marine industry
Cathelco, part of Evac Group, is launching patented ultrasonic protection technology which protects against hull biofouling.
Cathelco’s new Ultrasonic Protection (USP) DragGone reduces drag and improves fuel efficiency, reducing fuel consumption and associated emissions by up to 13%.
Biofouling is the accumulation of various aquatic organisms that gather on any part of a vessel that is exposed to sea water. This increases the drag as a vessel moves through the water, increasing the load on the engines, which in turn increases fuel costs and carbon emissions. Effective
biofouling management prevents these accumulations, reducing friction and thereby reducing fuel consumption and associated GHG emissions.
Ultrasonic protection is a proactive solution, complementary to anti-fouling paint, which ensures the hull remains clean from day one for a newbuild, or as soon as it has been cleaned for existing vessels. With DragGone, transducers are attached to the inside of the hull and emit ultrasonic waves which disrupt any kind of a biological attachment to a hull surface. This also mitigates the risk of the translocation of invasive aquatic species, which has a significant ecological impact.
DragGone combines two key technical differentiators from other ultrasonic antifouling systems; guided wave and heterodyning technology – two existing and established principles, applied to biofouling management for the first time.
With guided wave technology, DragGone enables the waves to travel over longer distances than traditional ultrasonic fouling solutions, which means fewer cable runs, fewer control panels, and up to 60% fewer transducers. This makes it easier to install, easier to maintain and reduces service costs.
Cathelco’s antifouling systems are already installed on over 25,000 vessels worldwide. These marine growth prevention systems (MGPSs) are volume treatment systems for the protection of sea chests, internal pipework and box coolers.
DragGone joins Cathelco’s full suite of products for vessel protection from biofouling, with MGPS, impressed current cathodic protection (ICCP) technology –which reduces maintenance costs by preventing corrosion on ship hulls and offshore structures – and now ultrasonic antifouling. n
To have your company’s latest product, technology or concept included in Inside Marine, contact us today. Send us your innovation: media@insidepublication.com
The test rig replicates real-world conditions to ensure the reliability and safety of winches.
Technidrive, a bespoke integrated automation systems provider, has introduced an advanced testing rig designed to help its customers rigorously assess the performance and reliability of winch systems. The state-of-the-art rig offers precise and comprehensive testing capabilities and is designed to redefine winch performance standards across a range of industries and applications — including offshore drilling critical marine environments and more.
Technidrive has designed its in-house testing rig to enhance reliability, efficiency and safety in lifting applications. Standing at ten metres tall, and equipped with builtin concrete weights of varying sizes, the rig conducts meticulous manual, load cell and speed tests to evaluate winch capabilities under diverse conditions.
A key feature of Technidrive's rig is its advanced load cell mechanism, which enables the application of forces
exceeding those exerted by concrete blocks. This makes it possible to perform rigorous static and dynamic load tests, in order to confirm the winch’s ability to securely hold weights under extreme conditions.
The testing rig incorporates a range of sophisticated technologies, including advanced load cells, encoders, programmable logic controllers (PLCs), data logging equipment and power meters. Furthermore, the rig integrates power meters on the winches, enabling real-time monitoring of voltage, speed, current and power factor during lifting operations.
The rig's versatility is highlighted by its generator system, which caters to specific voltage requirements for various applications including the offshore drilling, marine and industrial sectors. For example, the standard voltage requirements for cruise ships of 690V. The system is driven by an IP55 rated W22 Motor, CFW11 variable speed drive (VSD) and an AG line alternator to ensure a reliable power supply in the same voltage and frequency as the winches’ final destination. This results in enhanced efficiency and reduces operational costs.
Monte Carlo-based One Marine Services is a multifaceted maritime enterprise supplying systems and equipment for communication, navigation, entertainment and safety, plus effective and integrated management for these systems. Managing Director Simone Gori discussed the company’s growth and services. Report by Antonia Cole.
ASa subsidiary of Fameline Holding Group, One Marine Services has access to a network of skilled and experienced people, plus resources, to deliver effective marine solutions. The company also works with its sister companies, One Tech and One Net Groups, to deliver high-quality, specialised equipment and services to clients.
One Marine Services offers clients a full package, including installation services and the provision of spares, as well as project management services for vessel upgrades and refits. The company works within the commercial, cruise, ferry and yacht sectors to deliver inte grated solutions that streamline management, prevent issues and provide technical assistance.
The company also offers mobile communications equipment, services and solutions, including maritime VSAT, plus others. This helps ships to improve communication, navigation and safety measures in operations. One Marine Services allows for the successful integration of this equipment, minimising risks, delays and costs for clients.
“Our main goal is to satisfy and exceed our clients’ needs,” said Managing Director Simone Gori. “Since 2021, we have seen a growth of 35 per cent in our internal revenue. This is due to our ability to work with, and support, our clients by offering individual and customised solutions.”
The company separates services into three main categories: navigation, communications and IT services. These combine to offer clients a complete, high-quality service that lowers risks, delays and costs. One Marine Services continuously integrates market developments into services to consistently offer the best possible options to clients.
“We provide installation and maintenance services worldwide,” explained Mr Gori. “Our professional and talented team work to provide the best solutions, tailored to each individual client.”
Due to One Marine Services’ position as part of a group, the company has access to a greater variety of specialised equipment at more competitive prices. In terms of navigation, this means that the company can offer the latest and most advanced equipment within the industry.
As well as utilising the sectors latest innovations, One Marine Services provides clients with a full maintenance and repair support contract on an annual fixed-price basis, plus drydock surveys and services.
Having a broad portfolio of tools, in combination with a global and knowledgeable service, means that clients are offered optimised navigation solutions quickly and efficiently.
In terms of connectivity, One Marine is aiming at ICT independence by deploying an Interoperable, Scalable and Modular infrastructure. This means that at a fleet level, the customer will not only be more flexible regarding vendors and contracts, but
also will get the most out of the technology available. This solution enables a future-proof infrastructure that is interoperable with different ISP’s, is scalable and modular.
In fact, One Marine enables different technologies to failover or aggregate seamlessly, improving online availability close to 100%.
One primary goal of One Marine is to provide real-time data insights to clients. By standardising the fleet's ICT, One Marine can collect and analyse vast amounts of data from each vessel. This data enables the company to offer predictive maintenance solutions, proactively addressing potential issues before they become critical. Clients benefit from increased vessel uptime and reduced operational costs.
Furthermore, this system enhances the user experience for the crew by implementing advanced management and welfare procedures, streamlining administrative tasks such as payroll management and certification tracking. Additionally, AI-powered chatbots provide instant support to crew members on common queries or concerns.
For shore staff, One Marine has a centralised digital platform that integrates all relevant information from various sources. This platform provides real-time updates on vessel status, crew
welfare reports, cyber security management and other critical data. By having access to comprehensive information at their fingertips, shore staff can make informed decisions quickly and efficiently.
Finally, the company’s IT services encompass software maintenance and cybersecurity. Maritime cyber risk management services safeguard vessels from cyber threats and vulnerabilities, in line with IMO recommendations.
One Marine Services uses advanced knowledge and expertise to guide ship owners through the adoption of a stalwart cyber risk management scheme, as well as providing IT solutions and services to maintain vessel cyber-safety.
“We try and avoid the traditional working relationship with clients,” said Mr Gori. “In our work, we try to break down boundaries and really establish a partnership, as opposed to a transactional relationship.”
To achieve this, One Marine Services assigns a member of the company to each client to act as their point of contact. This means that the client can build a relationship with the representative and that service can be more personalised.
The company has also upgraded the software within the office to monitor client services, to proactively attend to client needs. One Marine Services can identify any expired services, then approach the client with a suitable solution.
“Our clients are very busy,” explained Mr Gori. “This is why we have these systems in place to save them time. Our clients
know they can rely on us, not just to provide exceptional services initially, but to consistently look out for them and build a relationship founded on trust and transparency.”
Every three months, One Marine Services arranges phone calls with clients to discuss any new requirements and evaluate the effectiveness of existing services. This is so the company can fully understand the client’s operation and how One Marine Services is working within it. The company aims to fully satisfy the needs of the client and this process allows for a more complete service.
As well as building relationships with clients, it is essential to One Marine Services to maintain relationships with suppliers, such as Alphatron Marine. Through suppliers, the company gains access to the latest innovative technology and industry developments.
“We maintain direct contact with our suppliers and partners,” said Mr Gori. “Where possible, we like to meet in person and really develop those relationships. When exhibitions are taking place, we always take advantage of the opportunity to meet and discuss our ideas for improvement.”
One Marine Services will be attending SMM, the world-leading trade fair for the maritime industry. With over 2,000 exhibitors and 40,000 visitors from all over the world, SMM will be a significant opportunity for the company to connect with people from across the industry.
“SMM will be great for us,” concluded Mr Gori. “We are looking to invest more into the German market and this will allow us to develop our relationships with people from around the world. I am excited to see lots of new and old faces. There are so many talented people within the sector and I’m looking forward to sharing ideas with them.”
Through these connections, One Marine Services hopes to grow in Asia, plus build
even stronger foundations in Europe. Going forward, the company views environmental measures as increasingly important for the future of the industry. Currently, One Marine Services is implementing a paperless system through the increased digitalisation of operations, greatly reducing waste. The company plans to improve environmental measures further in the future. n
Founded in 1982, Vestdavit provides davits tailored to meet customer needs. The company mainly serves two customer segments, the navy and coastguard, plus offshore energy industries. The company offers a specialised service that protects both vessels and people. Managing Director Rolf Andreas Wigand discussed Vestdavit’s expansion and commitment to high-quality service, in conversation with Antonia Cole.
Headquartered in Norway, Vestdavit works to provide safe boat handling through high-quality davits and service. With offices in the US and the Netherlands, as well as a factory in Poland, the company has a global service network prepared to undertake inspections and deliver spare parts quickly and efficiently.
Vestdavit’s boat-handling systems are sophisticated solutions, equipped with wave-compensating winches, shock absorbers and other technologies. The systems are designed for high-performance and frequent use over a long lifespan, often in harsh conditions with high sea states, compared with lower-spec systems that are typically used less frequently in more benign marine environments.
In the late ‘90s, the company secured a contract with the US Navy, retrofitting davits
to the Ticonderoga class of guided-missile cruisers, which started the international expansion of Vestdavit to the successful global operation that is run today. Through expansion into international markets, the company has increased its customer base and is now focusing on major NATO countries.
Four years ago, Vestdavit invested in a production facility in Poland. This allows the company to control and manage the entire value chain, from design and engineering to procurement and commissioning. The company has the ability to customise and specialise its products to fit client requirements more closely, thus providing better service.
Starting with nine employees, Vestdavit has gradually and
organically grown to now employ 120 people. With rapid expansion of the global offshore wind industry, naval market and the oil & gas sector, the com pany attained an all-time high order of €50 million and a revenue of €25 million in 2023.
The global naval and energy sector remains the biggest market for Vestdavit. The company specialises in delivering davits and support systems that can withstand harsh weather conditions and are tailor-made to meet a customer’s needs.
“Here at Vestdavit, we have always been driven to provide the most innovative and the best lifesaving equipment to those at sea,” said Managing Director Rolf Andreas Wigand. “With our wealth of experience and continuous innovative expertise, Vestdavit is equipped to offer unique boat handling solutions across the shipping and maritime industries.”
Vestdavit offers a range of launch and recovery systems, as well as mission bay handling systems. The company’s portfolio of launch and recovery systems consists of deck mounted and deck head davits. The company also provides a range of Telescopic davits with a capacity range between 2,000kg to 25,000kg in single point mode. The TDB type are of a high degree of redundancy which provides an advantage in the prevailing market place.
The company’s FRC and MOB davits are equipped with advanced functionalities to meet a customer’s specific requirements. The reliable machinery supports the launch and recovery process in conditions up to Sea State 6.
As well as this, Vestdavit offers dual point workboat davits designed to handle even the largest of work boats and daughter crafts of up to 60 tonnes. Computer augmentation and dual fall technology work to assist the operator in the safe launch and recovery of vessels in harsh weather conditions.
The Mission Bay Handling System from Vestdavit can lift a wide range of boats and equipment, enabling ships to store and deploy a variety of assets either side of the vessel safely. This system can stow,
launch and retrieve multiple RIBS, daughter boats and USVs from within a protected hangar.
Over time, the company has been increasing the performance and safety of products through tools such as shock absorbers, self-tension systems, wire pillars, painter booms, guiding arms, PLC control and other innovative technologies.
“Our focus is only on davits,” explained Mr Wigand. “This means that we are able to invest all our energy into developing the best quality davits on the market. To maintain our position within the industry, we have had to be innovative and produce new solutions to our customers’ challenges. Everything is made to satisfy unique specifications, which is what keeps us at the forefront of the market.”
One of the company’s individualised solutions was for a Danish wind service operator. A long-term customer of Vestdavit, the wind service operator already had 15 davits for its daughter craft. These davits had very high specifications for safety and operational windows, which Vestdavit was able to provide.
The wind service operator is now building even bigger ships and in collaboration with the customer, Vestdavit developed a special dual point davit system. This system can lift a 25 tonne daughter craft or service boat, alternatively it can lift a standard 15 tonne boat on a single point lift.
“This project succeeded through collaboration and communication,” said Mr Wigand. “We make sure to fully understand the needs of our clients and develop a solution that suits them. We adjust our designs until the customer is completely satisfied with the result and
this level of service is what encourages customer loyalty.”
In 2023, Vestdavit saw order intake increase by 76%, due to high-quality davits and personalised customer service. The company has also expanded its position within the offshore wind market
with 30% of sales now coming from the sector. Vestdavit is entering new markets with a significant sale in Italy, as well as securing a contract in Canada. Whilst also maintaining its presence in the UK, US, Australia, Germany, France and Spain.
As a result of Vestdavit’s success, it is expanding its facility in Poland. The capacity of the factory will be increased by 35% to meet growing demand. The company is building a new assembly and test facility to improve the site.
Also, to be closer to customers in continental Europe, Vestdavit has set up a subsidiary in the Netherlands. This allows the company to be within the vicinity of large European ports, such as the Port of Rotterdam.
Vestdavit has over 40 years of experience, which allows it to better serve and advise customers. The company knows what type of davit systems or features would best fit a client’s needs and is able to deliver this efficiently.
It is vital to ensure that davits and boat handling systems are constantly safe and fully operational. Vestdavit has a dedicated after-sales support system that supplies all genuine davit spare parts in accordance with the original build specifications, from installation through to operational phase.
The company has ISO 9001 and ISO 14001 certifications, which assures quality, as well as environmentally conscious procedures. Vestdavit’s focus is on serving customers and as more request environmentally friendly oils in hydraulic systems, the company has been researching bio-oils and how to integrate them into products.
Vestdavit is specialised in building davits from the highest possible quality components so that they can last for the lifetime of the ship, up to 30 years. The company uses non-corrosive parts to provide a high level of protection and longevity.
Moving into the future, Vestdavit foresees great progress in the naval and offshore energy sectors that it is currently serving. With the green shift, there is a lot of potential for growth in these industries, plus the ability to expand into new markets.
“I’ve been leading this company for 18 years,” concluded Mr Wigand. “The progress we have made so far has been fantastic and I am looking forward to the future. At Vestdavit, we are a team and we work towards a common goal, which is really rewarding. The enthusiasm within the company is what will keep us succeeding.” n
seven seas, five oceans, one voice
eekels technology junma services all american marine pure superyacht refit asenav catana group jbj techniques terem-shipyard flotski arsenal - varna
Eekels is an electrical, technical and mechanical specialist for the marine and offshore sector. The company has over a century of expertise offering state-of-the-art solutions on an international stage and is now fully committed to developing and delivering zero emission technology. Manager Sales & Business Development Ulco Hoekstra explained more to Hannah Barnett.
SApart of Dutch technology giant TBI, Eekels has successfully delivered projects on more than 2,400 vessels, including over 300 superyachts. Expertise is not limited to newbuilds, however, as the company also offers an impressive portfolio of small- and large-scale refits, conversions, environmental upgrades and life-time extensions.
“As a one-stop shop and product partner with high-quality specialised knowledge, we excel in developing, delivering and managing standardised and customer-specific solutions for electrotechnical issues,” said Manager Sales & Business Development Ulco Hoekstra. “Sustainability, energy-efficiency, reduction of operational costs and future flexibility for the shipowner are paramount. Eekels achieves these goals by providing integrated solutions and applying innovations that add value for the client –both shipyard and shipowner – and, in a broader sense, for society.”
The company is headquartered in Kolham, the Netherlands, and extends
its global presence with offices in China, Germany, Romania, Spain and Vietnam, along with a network of international partners. Eekels records an annual turnover of more than €100 million.
Eekels has strategically located itself across Asia with offices in both China and Vietnam, in recognition of the continent’s key importance to the marine sector.
The company has been collaborating with SaierNico, a Chinese company, for twenty years and continues to do so to build strong partnerships in the region.
In India, Eekels has seized the initiative to form robust relationships with shipyards and local entities. This effort aims to unburden both national and international customers, demonstrating the company’s dedication to providing comprehensive services.
“And we don’t stop at services; we have also achieved success by delivering substantial complete electrical packages in Asia,” said Mr Hoekstra. “This underscores
our capability to meet the diverse needs of the market.”
Recently, Eekels was awarded an order by Damen Shipyards Gorinchem, for the electrical installations on seven Commissioning Service Operation Vessels (CSOVs) to be built in Ha Long, Vietnam, for customers Windcat/CMB.Tech, TSSM and Purus. The CSOVs will be equipped with hybrid battery technology and for Windcat/CMB.Tech prepared for conversion to hydrogen as an energy source. The order comprises the engineering, production, supervision and commissioning of the electrical installations, among which: switchboards, lighting installations, vessel
automation system, and semi 24 pulse DP2 propulsion drive systems, based on a closed bus-tie solution.
The company strengthened its collaboration with Danfoss Drives by signing an indefinite Framework Agreement in November 2023.
“This development aligns with a series of successful maritime projects in which we operated as a pioneer, playing a cen tral role in transforming the new iC7 drives platform into a complete system,” said Mr Hoekstra. “Innovation and expertise are the driving forces in the relationship. We prioritise collaborative and long-term relationships with our suppliers and partners, such as Danfoss, recognising their vital role in our success.
“Battery suppliers also play a crucial role in advancing our sustainable solutions. Our partnerships extend to naval archi -
tects, such as Groot Ship Design, where mutual understanding and effective communication ensure successful project outcomes. The support from companies affiliated with TBI also reinforces our capabilities. These collaborative efforts underscore our commitment to building enduring relationships within the marine and offshore market.”
Eekels is extending its emphasis to include crew training, remote support, and remote monitoring. As part of this commitment, Eekels delivers project-specific training on the systems it provides; on board the vessel, at the Eekels HQ or the client’s office.
The company also offers a fully integrated power and automation system that facilitates comprehensive remote support. This incorporates advanced features for remote assistance such
as diagnostics for swift issue resolution, software maintenance and assistance to enhance on-site troubleshooting.
“These elements are central to our approach to service support, guaranteeing the highest levels of efficiency, reliability, and proactive maintenance for our clients,” said Mr Hoekstra. “These dashboards in our Vessel Performance System make Smart Shipping possible for fleet managers, operators and superintendents.”
The ability of Eekels to produce bespoke products in-house is a distinctive factor that sets the company apart from competitors. Eekels offers, amongst others, the construction of standard or fully customised consoles and panels, utilising state-of-the-art CNC machines. Eekels is a market leader in Shore Power Converters (SPCs) offering compact and lightweight designs and a front runner in cutting-edge power conversion technology. For these
highly sophisticated products, Eekels can rely on its own trademark: Marpower.
“Having our multi-redundant automation system fully designed in-house positions us as a comprehensive and independent system integrator,” explained Mr Hoekstra. “The capacity to create the latest technology internally, from concept to manufacturing, showcases our commitment to innovation and self-sufficiency.
“This not only ensures that we remain at the forefront of technological advancements but also allows us to tailor solutions to meet the unique needs of clients.”
Eekels is fully committed to sustainability. New, environmentally friendly technologies, digitalisation, AI, the Cyber Resilience Act, GHG protocol, circularity and energy efficiency are high on the company’s agenda.
“We contribute to sustainability by providing integrated solutions,” said Mr Hoekstra. “This involves a multidisciplinary approach to the design and realisation of projects, including the technical installations and maintenance of the entire system.”
Eekels focuses on minimising emissions and maximising the use of smart energy solutions. As every project is unique, there
is no one-size-fits-all solution; this requires an integrated approach early in the design phase. Eekels offers solutions for reducing lifetime energy demand, while also increasing the share of energy from alternative sources.
The company has also developed an innovative, future-proof Modular Propulsion Platform (MPP), which allows ships to sail electrically. To generate electricity on board, various green sources and fuels can be linked to the MPP. Those sources include clean generators, heat recovery, solar panels, wind power, shore connection and electrical storage systems such as batteries. Green fuels like hydrogen, methanol and ammonia are necessary for operating with reduced or zero emissions.
“The core and uniqueness of the MPP is our breakthrough technology to make these different energy sources work together and integrate both AC and DC systems, along with all other applications on one platform,”
Mr Hoekstra explained. “The first ships with the Eekels’ MPP are now in service and the results exceed all expectations.
“With more than 30 year’s active experience in the maritime industry, I am driven by overcoming climate challenges and creating electrical power and propulsion solutions for vessels with zero emissions,” concluded Mr Hoekstra. “It is tremendously exciting to make an impact while also working closely with ship owners, fleet managers, naval architects and shipyards.” n
Singapore-based Junma Services is a leading name in marine engine services and a front-runner in shipping eco-solutions. Managing Director Ma Yulin divulged the latest company news, in an exclusive interview with Inside Marine. Report by Imogen Ward and Colin Chinery.
ASthe world’s biggest maritime hub with state-of-the-art infrastructure, Singapore is a major player in the growing ship repair and maintenance services market.
With vessels becoming larger and more sophisticated, the need for specialised repair services is intensifying. 18 years of
expansion saw Singapore-based Junma Services become a leading name in marine engine services.
Delivering some of the most comprehensive two- and four-stroke marine engine repair and automation services available, Junma’s premier portfolio includes engine docking and repair, genuine spares,
troubleshooting, consultancy, decarbonisation solutions-based innovations, CII and Rightship rating improvement.
With expertise comparable to that of engine makers, Junma’s engineers analyse, repair and monitor complex engine defects, a core team part of a worldwide warehouse and service network including China, Middle East, India, Europe, the USA and Brazil.
“We are dedicated to meeting the needs of our customers, delivering reliable and efficient services, and high-quality technical support,” Managing Director Ma Yulin said.
And with turnover doubling in the last two years, Mr Ma attributes the company’s focus on establishing long-term relationships with clients as key to its continued success.
Junma had been authorised as a marine engine repairer and sales agent by engine makers such as HHM, CSIC Diesel Engine Co, which combined Dalian Marine Diesel, Yichang Marine Diesel Engine, and Qingdao
Haixi Marine Diesel for MAN engines, as well as WinGD and J-Engines. In addition, Junma was also an authorised service and spares provider of Shaanxi Diesel Engine Heavy Industry for its MAN, MTU, SEMT Pielstick and Daihatsu until CSIC and CSSC regrouped.
“We serve a broad range of clients catering from normal maintenance to highly complex troubleshooting, mainly for dry dock projects and emergencies,” said Mr Ma. “These customers – among the elite of ship owners and ship managers – include AET, Anglo-Eastern, OSMThome, BergeBulk, CMA CGM, Evergreen and many more.”
With the shipping industry’s race to ecocompliance, Junma’s technical expertise is honed to the demands for a greener industry. After a big success in launching EEXI-EPL service package and completed around 700 vessels installation – it is now offering customers more decarbonisation options that reduce carbon emissions though optimised engine performance and reduced fuel oil consumption: a key issue at Posidonia 2024.
Here, decarbonisation will be on the radar more intensely than ever, with the industry debating ways of achieving targets in the race to comply with sustainability directives.
With new technologies showcased and fuel options analysed, Junma will be at the forefront, providing clients with engine de-rating and eVIT solutions, enabling fuel savings and improving CII/Rightship rating.
“While we were providing EEXI-EPL solution to clients, we noticed that many vessels suffered from huge load restriction due to regulations that engine must work in the un-optimised load,” said Mr Ma. “The result of this is although overall carbon emission reduced, the specific fuel consumption (fuel needed per kWh) increased significantly. We began the De-Rating project in 2023, first showcased at the Hamburg Maritime Forum in April 2023.
“To de-rate the overpowered vessels the fuel saving can be huge. We calculate for large container vessels, annual savings of 4-5 million USD can be expected directly from fuel costs. If other add-on solutions (shaft generator and high efficiency propeller) are considered, then the saving can be 6-7 million.”
Another simplified solution achieves 2-4 g/kWh fuel saving through VIT optimisation on the main engine. This solution applies to all MC and ME.
Junma has many options to help customers reduce carbon emissions, according to Mr Ma: “We have now become the authorised agent for CM Technologies, a leading global provider
of condition monitoring and testing technology solutions, machinery condition monitoring and fuel and lube oil analysis.
“We need those tools to help our customers secure the best engine performance – the only way to achieve lower fuel consumption.”
The CM-Junma partnership is already paying off. “Last October our joint two teams visited many customers here in Singapore and gained an understanding of their requirements and we are already getting orders,” said Mr Ma. “The demand for CM products is huge and the potential is great.
“For customers interested in their end performance, we can assess their data
online, get real-time data and advise them on the issues they are facing or how they can reduce their consumption or improve their engine performance.”
Other ongoing developments include investment in engine cylinder liner reconditioning. “Most of the costs of
maintenance is in the cylinder unit, with the piston rings and liners needing to be changed,” Mr Ma said.
Often made of around 10 tonnes of steel, these components wear out within 10 years and result in major costs not only for the client, but also for the environment.
“We have completed two phases of the project and are now looking for customers to trial it on their ships,” Mr Ma continued. “We expect this methodology will be certified in the next five to six years.
“We are also working to help reduce our customers’ cylinder oil consumption, having co-developed specially coated piston rings. We now have several interested parties for this, including a major player within the market.”
Junma is also benefiting from a brand-new workshop in joint venture with IMC-SY Shipyard, which began operation in December last year. According to Mr Ma, this workshop has provided an excellent opportunity to collaborate: “The workshop
was developed to advance our ability to provide high-end engine services.
“The entire workshop is shared amongst several parties and will support the needs of our neighbouring shipyards in the Zhoushan area. As the main partner in this workshop, we are incredibly excited about this development.”
“We continue to focus on our service quality and our level of expertise, while continuing to develop new capabilities and products to better serve our customers and their vessel fleets,” Mr Ma said.
A highly experienced marine engineer, Mr Ma has a strong decades-long background in shipbuilding, operations and inspection, with expertise in maintenance and repair, and international shipping.
“I have never worked without an engine, and my driving force is to achieve progress, improve performance, collaborating with our clients to help them make things better. And I will never stop doing so,” said Mr Ma, in conclusion. “Junma is a trustworthy brand with growth ambitions.
“We strive to be more than just a service provider, we aim to be a solution provider, delivering innovative and effective solutions to our customers, helping them achieve their business goals.”
Strong vibrant partnerships – a key factor in Junma’s success – have evolved into an immensely strong global network. “We collaborate with many workshops around the world – in Europe, USA, Brazil, Africa, India and Australia – each supporting one another,” Mr Ma added. “This has helped us a lot. You could fly an engineering team to Panama or somewhere, of course, but that’s very costly and not a very good solution. But now, since we have these localised networks, we are benefiting greatly.”
n
All American Marine, founded in 1987, is known for craftmanship and expertly manufacturing aluminum vessels at a fair price. These include traditionally powered propeller and waterjet boats, plus hybrid and zero emission vessels. The company builds cutting edge catamaran designs and holds a principal role in the emerging hybrid and zero emissions vessel market. President and COO Ron Wille told Hannah Barnett more about All American Marine.
ITis firmly ingrained in the All American Marine DNA to be innovative. In 1999, All American Marine attained exclusive North American building rights with one of the world’s top naval architects and designers, Nic de Waal of Teknicraft Design, based in Auckland, New Zealand.
“ Integrating developments in a meaningful way is extremely important,” said Ron Wille, President and COO. “We’re all about s ustainable innovation and continuous improvement. Through the partnership with Teknicraft we have shown that we’re willing to take risks; when they’re well thought out and skillfully executed. ”
The 25-year partnership with Teknicraft has allowed All American Marine to build innovative, adjustable, foil assisted hulls. The unique design incorporates the use of a cutting-edge hull shape and an optiona l hydrofoil system to create lift and enhance vessel performance. The vessels are fully customizable depending on the intended application.
The shipyard, based in Bellingham, Washington, prides itself on the scope and scale of its capabilities. “One feature that’s unique about All American Marine is that we do nearly everything in house,”
said Mr. Wille. “Raw aluminum comes in one side of our facility, and a finished boat comes out the other.”
The company moved to its state-of-the-art 57,000 square foot facility in 2017. The yard includes two large production bays with space in the middle for welding, fabrication, and an electrical systems shop.
“We also have a large, elevated carpentry loft,” Mr. Wille added. “Once we build boats on the floor, on our laser leveled jig, we roll them to the outfitting section adjacent to our carpentry loft. This elevated loft provides our crew with safer access to the vessels and enables efficient operation.”
The company’s skilled and growing workforce numbers around 65-70, making it an agile operation. Staff welfare and longevity are crucial.
“We rely on our crew to see a vessel through from start to finish,” said Mr. Wille
“We keep them busy, and we don’t let them go when projects finish. The attention to detail and the quality that our team produces sets us apart.”
Thanks to the long-term partnership with Teknicraft, each All American Marine customer enjoys a single point of contact within the team. This mitigates the need for the customer to interact with the naval architect and a builder separately, as they may have conflicting interests.
“We’re one unified team, with a focus from stem to the stern, analyzing every square inch of the vessel to get optimal results,” said Mr. Wille. “This has allowed us to be innovative, resulting in some of the most fuel efficient and lowest wake wash catamarans in their class. Doing that with Teknicraft helps mitigate risk when it comes to building.”
To see the work that our team puts in, and be a part of that, is rewarding in so many ways
Each vessel is custom designed for a specific mission, meaning communication between the designer and builder is crucial. All American Marine has constructed over 75 Teknicraft vessels, more than 40 being high speed hydrofoil boats. Ensuring its hydrofoil assisted high performance vessels run efficiently has positioned All American Marine for the rise of hybrid boats.
“We’re able to segue into the hybrid and zero emissions boat market because we already excel at building efficient boats,” Mr. Wille said. “Hybrid vessels generally operate at slower speeds, but the same principles apply. For instance, we have leveraged Teknicraft’s work utilizing computational fluid dynamics to measur e resistance to hulls on fast boats. We are applying these principles to slower boats , ensuring that the electric systems are energy efficient.
“For alternative propulsion, there’s no ‘one size fits all’ solution. It depends on the operating profile of the boat. Once we know that, then we work with the boat owner, or operator, as a designer and builder team, to create the most efficient and effective vessel.”
All American Marine has so far constructed three hybrid and zero emissions vessels: Enhydra, Waterman and Sea Change. It has several more hybrid projects in the pipeline, including a parallel hybrid and a serial hybrid project.
The parallel hybrid project is an agreement with All American Marine's longtime partner, Harbor Breeze Cruises, to design and build a new state-of-the-art 108’ hybrid passenger vessel, for deployment in the Ports of Los Angeles and Long Beach, CA. This innovative vessel will provide harbor tours, whale watch cruises and dinner events. The vessel design will be developed by Nic de Waal and will exceed US EPA Tier 4 requirements. It will include a DPF system, plus an optional hybrid battery propulsion package that exceeds
the most rigorous emissions guidelines in North America.
This new vessel will set a benchmark in maritime innovation. The multi-purpose monohull will operate as a USCG Subchapter K passenger vessel, with systems and equipment installed to meet the USCG requirements. It will operate on a ‘Limited Coastwise’ route, in a parallel hybrid configuration and with advanced data collection capabilities.
The vessel will be powered by a combination of lithium-ion batteries and twin MAN D2862 EPA Tier 4 Engines, driving fixed pitch propellers, and will serve as a valuable asset for the Harbor Breeze fleet. Tier 4 standards typically involve the implementation of advanced technologies, such as selective catalytic reduction, but this vessel will be enhanced by incorporating diesel particulate filters, achieving further reductions
in exhaust emissions. These technologies will enable the vessel to exceed stringent California emission standards while maintaining performance and fuel efficiency.
Going forward, All American Marine is responding to the growth of the offshore wind industry.
“We have already built very successful boats for hydrographic survey work in the offshore wind market, such as the 73’ Shackleford for NV5/GeoDynamics, so our future in that sector is bright,” said Mr. Wille. “Ultimately, our niche is building boats from 50 to 150 feet, which is ideal for offshore wind.”
The company values strong relationships with its supply chain, sourcing items with care and consideration. According to Mr. Wille, this gives customers an easy after-sales experience.
“We focus on the larger, established suppliers in the market that provide high levels of competence for us, and ultimately, for our customers,” he explained. “We’ve been successful using products from BAE Systems in three different hybrid or alternative propulsion vessels. BAE has supplied hybrid equipment and supported applications
around the world, so we felt confident supplying its equipment, knowing our customers will get the support and service they need.”
All American Marine is equally confident in the strength of its relationships with customers. “Past performance is especially important,” said Mr. Wille. “If someone is interested in a project with us, I tell them check our references; look at the different boats that we’ve built and reach out to those folks independently.
“We have customers that return repeatedly. When they have concerns about warranty, or even non-warranty items, then we are there to answer the phone. We are focused on the long-term support of our customers.”
Despite the unprecedented challenges of Covid, the company delivered on time and on budget contracted vessels that were under construction, including two boats for Major Marine Tours in Alaska.
“I spent much of my career in the marine industry on the operational side,” Mr. Wille concluded. “I really enjoy interacting with our clients, because I’ve been in their shoes, so I understand their challenges. We also have a fantastic group of hard working, knowledgeable employees. To be a part of this team is rewarding in so many ways.” n
Based in Palma de Mallorca, PURE Superyacht Refit provides professional and specialist superyacht refit management services, tailored to fit clients’ needs. Owner Nic Clarke discussed PURE’s services and innovative business model, in conversation with Hannah Barnett and Antonia Cole.
With over 20 years of experience in professional yacht racing as a team manager, boat captain and sailor, Owner of PURE Superyacht Refit Nic Clarke has an extensive knowledge of the marine industry. Mr Clarke saw the increasing demand for specialist refit services and used his expertise to found PURE in 2007, a leader in the service of superyachts.
The company is based within the open Servicios Técnicos Portuarios (STP) facility in Palma de Mallorca. This means that PURE is able to offer clients a range of highly skilled contractors to fit individual project needs.
STP consists of 102,000m2 of hard standing area for 80 hauled vessels up to 67m & 1000 tonnes and 60,000m2 of berthing area for 60 vessels to a maximum of 110m LOA. There are six travel lifts ranging from 30 to 1000 tonne maximums and seven keel pits accommodating deep-draft sailing yachts of up to 67m.
Despite being a small company with three permanent staff members, PURE accounts for a high percentage of Mallorca’s superyacht refit business. Palma de Mallorca has many skilled nautical professionals and sub-contractors from around the world, giving PURE the ability to provide a high-performance
service, regardless of language barriers or weekly working hour constraints.
Pure also offers refit accounting services, providing detailed status reporting of the refit as it progresses. Thus, allowing captains, owners, management companies etc. to be completely informed.
“One of the benefits of working with PURE is that we don’t take every project that comes along,” said Mr Clarke. “We take on projects that are challenging and require the advanced involvement and expertise that we are able to offer.”
PURE determines the scope of work required and establishes a realistic timeframe. The company then organises designs, berthing or haul-out options, suitable skilled contractors, plus work lists and budgeting to meet client and project requirements.
The company’s first project in 2007 took a 52m 650 tonne motor yacht out of the water, before cutting 2m square openings into either side of the hull/engine room, then removing and replacing generators, exhausts and engine management systems. A 1.3m swim platform hull extension was constructed and the project was completed with teak deck replacement and full, four colour paint re-finish, making it a nearly €5 million project.
“Projects like these, that exceed expectations, are what have put us on the map,” explained Mr Clarke. “Our ability and determination to achieve the incredible is what makes our clients confident that PURE will meet and deliver their needs.
“We have no problem cutting holes into the bottom or sides of vessels if required, as it is often more efficient and less intrusive. We go that extra mile to deliver exceptional services as efficiently as possible. Our standards are high and we meet them with every project.”
As a qualified engineer and professional skipper with experience in shipyards world-wide, Mr Clarke has the knowledge to interpret client requirements to a greater degree. This expertise allows PURE to complete all projects to the level of quality that the customer envisions.
“I’ve got very high standards for our work,” said Mr Clarke. “I am confident in the fact that if I accept something, then the client will accept it too. We don’t waste our clients’ time, so we make sure to get it right.”
PURE begins project management around three to six months before the vessel arrives, in a process it calls ‘pre-fitting’. This means that preparations are made so when the vessel does arrive, the company can begin work immediately and clients receive their services quickly and efficiently.
“The initial three weeks after the vessel arrives are critical to the successful completion of works in the allotted time period,” explained Mr Clarke. “Through preparation and access to skilled crews and
sub-contractors, we are able to deliver refit services that are guaranteed to satisfy our clients.
The company operates out of the STP boatyard, a unique public facility that allows independent contractors to deliver works, whilst STP provides berthing, hauling and occupation services. There are no contactor relations through STP, so there are no surcharges for choosing subcontractors as there would be in a private shipyard.
This business model allows clients the freedom to choose contractors that mee t their individual needs without excess charges. Based within STP, PURE is able to provide clients with the best possible contractor options, tailored to suit skill requirements and price points.
“Whether it’s someone from across the world or someone local, our clients have the opportunity to use whichever
contractor they want,” said Mr Clarke. “For example, a lot of our clients have systems in their properties that they want to replicate in their vessel, such as audio-visual set-ups. We can assist in access into STP for the specific company, providing they submit the required documentation, to come and carry out the desired works without any additional surcharges.
“This model means that we can meet specific requirements for our clients and can bring in the specialised skills from a range of industries to develop the vessel into the client’s vision.”
With Palma de Mallorca as PURE’s main location, the company has access to large numbers of highly skilled craftsmen across all superyacht services and trades. With access to a large workforce, PURE is able to complete projects quickly and deliver significant upgrades that exceed expectations. Over the last 17 years, the company has managed painting over 30 vessels.
One of PURE’s recent projects involved transforming an 82m industrial vessel into a leisure vessel/toy carrier with a helicopter pad, a basketball court, a golf simulator room, a bar and more, all within three weeks. This highlights PURE’s capabilities as a company to achieve the almost unachievable.
PURE has built long-standing relationships with partners across the industry, so that it can trust that projects are being completed to a high standard and on time.
“We work with some really good companies,” explained Mr Clarke. “They understand how we work and allow us to succeed. We all see the importance of going out and getting the work done as soon as possible. With our distinctive handson approach, we are well positioned to anticipate client and contractor needs and plan well in advance. Being proactive
instead of reactive allows for a smoothrunning operation.”
PURE often finishes projects ahead of schedule, meaning that clients have the ability to have more works or services added to the project within the original allotted time frame. The company’s focus on efficiency means added convenience for the client, as well as more business for partners and suppliers.
Going forward, PURE hopes to maintain this management system, but to expand into other facilities. The company will be able to create teams and work on vessels in different areas, increasing PURE’s project capacity.
“I like to succeed,” concluded Mr Clarke. “Taking what seems like an impossible project and turning it into a reality is rewarding. I am passionate about the industry and what we do, which shows in the projects that we deliver.” n
ASENAV, a world leader in shipbuilding, is currently celebrating its 50th anniversary with several exceptional projects on the table. Business Development Director Germán Schacht divulged more details in an exclusive interview with Inside Marine. Report by Imogen Ward.
The Chilean shipbuilding company ASENAV broke records and implemented innovative designs during 2023, ending the year with ongoing contracts worth 150 million dollars, making this period one of the shipyard's most successful years.
“Last year was a source of pride for ASENAV,” explained Germán Schacht, Business Development Director. “We have signed some really exciting projects, and we are looking forward to what the rest of 2024 will bring.”
ASENAV has achieved a lot during its 50 years of operations, and with 192 projects completed (and lots more underway), the shipbuilder is on track to reach 200.
In recognition of this special anniversary, the company is planning a whole host of surprises for its collaborators,
stakeholders and ship owners, all of whom have been instrumental in ASENAV's continued success.
“We have built up many important rela tionships through years of hard work,” said Mr Schacht. “To complete a project, both parties must fulfill their commitments, which is why we are especially grateful to each of our partners, as they are part of our history and helped to build trust in our work.
“We have many exciting celebrations planned to thank all our partners, stakeholders and the community that surrounds us; however, the details of our plans are still very much under wraps , as we want to make each of the activities as successful as possible.”
Earlier this year, ASENAV successfully completed its first ever oceanographic and fisheries research vessel.
Constructed for the Chilean Fisheries Development Institute, Dr Barbieri received an investment of USD $14.5 million from the Undersecretariat of Fisheries and Aquaculture. This vessel was also particularly special, as it was the first of its kind in Chilean history to be designed by Chilean engineers, built by a Chilean shipyard and operated by the Chilean government.
“This project was truly special, not only for us, but also for the country of Chile,” Mr Schacht explained.
ASENAV Project 191, Dr Barbieri, encouraged the development of Chilean engineering solutions that reduced the amount of noise radiation released into the sea so as not to disturb marine species. It also incorporated technology capable of capturing species in shallow water areas for observation.
This exceptional example of ASENAV craftsmanship was delivered two months ahead of schedule and well within budget.
Continuing the path of record-breaking achievements, 2023 also saw ASENAV deliver the largest live fish transporter ever built in the Americas. This 3,000 cubic metre vessel was designed entirely by ASENAV for the Chilean aquaculture industry and featured diesel-electric propulsion to ensure lower emissions. This carrier also provided a great opportunity for ASENAV to expand its expertise in Live Fish Carrier vessels.
“This project was a standout achievement for us,” said Mr Schacht. “It helped
position Chile as a country with innovative equipment for aquaculture and fishing activities, but it was also a great feat of ingenuity because the boat relies on a 'dry' loading and unloading method: after collecting the fish from the cages in the sea, they are separated into storage wells containing seawater in ideal conditions for safe transportation.”
ASENAV has always respected the environment within which it works, and with its builds entering the world’s oceans, the company is committed to constructing vessels that have a positive influence on their surroundings.
One such example is the company’s 193rd build. The Sign project will see ASENAV builda hybrid cruise ship, powered by diesel-electric propulsion
and batteries. Once completed, this const-ruction is expected to transform the tourism landscape.
“With the construction of project 193 we are raising the standard of the sustainable tourism industry,” commented Mr Schacht. “The vessel will have a maximum capacity of 96 passengers and 67 crew members, providing space for a total of 163 people.
“The ship will also stand out for its luxu rious facilities, including a gym and sauna with panoramic views, spacious cabins with balconies and a range of recreational areas sure to entertain.”
Designed for Antarctica21, this ship will support excursions to the southernmost territory of Antarctica and is expected to position ASENAV as an alternative for tourism companies governed by European standards.
“Aside from reducing CO2 emissions thanks to its diesel-electric propulsion and batteries, the ship will also feature a heat recovery system that utilises the heat generated in the ship's engines and exhaust gases for other areas of the ship,” Mr Schacht added. “On top of this, the heating in public areas and cabins uses exchangers to collect warmed air before it is expelled outside, harnessing up to 30 per cent of the air that would typically be lost through ventilation.”
The vessel will also feature elevators with regenerative braking systems capable of capturing the energy generated from braking, before converting it into electricity ready to recharge the ship's batteries. Having already started construction on this interesting project, ASENAV is on schedule for the vessel’s estimated delivery date of October 2026
Each of ASENAV's builds reflects the needs of the owner. ASENAV has the capacity to develop ships to the exact specifications of each client and is open to building propulsion designs with new energies, including green hydrogen and ammonia.
As it looks to the future, ASENAV intends to maintain its position as the most important private shipyard on the Pacific Coast and across the Caribbean.
“Today we are a strategic partner in the advancement of any type of vessel that our shipowners require,” said Mr Schacht, in conclusion. “We intend to retain our strong position in the market whilst also situating ourselves as a key player for the industrialisation of Chile, and we seek to consolidate ourselves as a preferred option for countries such as Argentina, Peru, Paraguay, Ecuador and Colombia.
“The needs of the Southern Cone of Latin America are currently being met by long-distance providers, where it is difficult or expensive to supervise the work. We invite these companies to learn about ASENAV's solutions, since we are sure that we will be able to meet all the requirements and challenges that arise. Over the last 50 years, we have demonstrated how valuable we can be, not just to the Government of Chile, but to the whole of the Americas.”
n
As it celebrates its 40th anniversary, the Catana Group simultaneously celebrates the opening of its newest factory. Designed to help the Catana Group cope with surging demand for its hugely popular catamarans, the new facility represents the latest milestone for the company in this highly competitive market. Group Sales & Marketing Director Boris Compagnon, spoke with Richard Hagan about the challenge and the excitement of delivering dreams to customers worldwide.
Headquartered in France, the Catana Group consists of three iconic brands: Bali Catamarans, Catana Catamarans and YOT Power Catamarans. Each brand delivers a unique portfolio of products designed to meet the specific needs of particular markets and customers.
The Group’s biggest brand in terms of volume is Bali Catamarans, which supplies high-quality, robust catamarans designed to be enjoyed by a large spectrum of customers with a variety of needs and skills. Catana Catamarans, meanwhile, is the company’s oldest brand, manufacturing each year a low number of bespoke high-performance, high-specification catamarans for some of the world’s most demanding clients. The Catana Group’s newest brand is YOT. YOT specialises in building beautiful, luxurious power catamarans which are sold through a dynamic new distribution
network that is generally separate from the Group’s other brands.
Each brand is individually set up to serve unique buyers in unique markets, but all three brands benefit from the Catana Group’s industrial expertise, manufacturing prowess and industry reach.
Catana Catamarans was established in 1984. Almost immediately, it became the world’s top manufacturer of fast, high-performance cruising catamarans, producing five to seven hulls a year over the decades that followed.
In 2003, amidst strong emerging growth in global demand for catamarans, sailing enthusiast Olivier Poncin bought Catana Catamarans and quickly set about expanding the company. Catana Catamarans attracted – and continues to attract - a dedicated following of
highly demanding sailors who are drawn to the bluewater capabilities and highperformance characteristics of Catana Catamarans, amongst other aspects. But the company soon found that the same qualities that made Catana Catamarans attractive to its target market, also made them unsuitable for a wider, more casual sailing audience, particularly that of the massive charter market.
Consequently, in 2014 Olivier made a bold decision to launch a completely new brand aimed squarely at the charter market.
“He decided to design a brand new, very ambitious product that would break all the rules of catamaran design,” explained Boris Compagnon, Sales & Marketing Director for the Catana Group.
Given that Bali Yachts were conceptualised to meet the needs of charter clients,
the first Bali yacht would offer design and engineering elements specifically aimed at more casual sailors. According to Mr Compagnon, these included “more space, more value, more ventilation and a solid foredeck.”
The yacht’s uniquely solid, integrated foredeck (instead of the trampolines typically found on catamarans at the time), flowed into a large common space between the saloon and the aft cockpit, closed off with a tilting garage-style door for accessing that area.
The design saw almost overnight success with the charter market. “We started producing fifteen boats a year, and today we’re producing between 300 and 350,” said Mr Compagnon. “The Bali yacht was the perfect solution for the mass and charter markets. These markets typically use the boat for 25 miles a day, sailing
from one bay to another. The guests want to chill. They are not doing 100 or 250 miles per day.”
Since its launch in 2014, Bali Yachts has enjoyed annual growth of between 30% and 50%, which brings its own unique set of industrial challenges. “The growth has been a huge challenge for the entire team, at every level and every department, from Human Resources to R & D, supply, production and sales,” Mr Compagnon noted. Mr Compagnon credited the Catana Group’s corporate structure with Bali’s ability to move fast enough to keep up with its growth: “Our major strength is our flexibility. As a family-owned company, with a board of only eight people, we can make decisions within minutes. That’s our flexibility; that’s our strength.”
Indeed, after Olivier Poncin sadly passed away in 2023, his son Aurelien proudly took over the reins, leading the Catana Group’s 1,400 employees to continued success in this fast-moving market.
Today, 50% of Bali’s production is credited to the charter market, while the remainder of its production is purchased by private owners. “We have noticed that once people have tried a Bali yacht on a charter, they often want to privately own a boat like that, too,” said Mr Compagnon. “So, while Bali was originally a charter boat, today, at least 50 per cent of our orders come from private owners from our distribution network.”
In the meantime, Catana Catamarans continues to draw dedicated sailors seeking a boutique sales experience and the world-class customer service for which Catana Catamarans is famous. Building twelve yachts a year, Catana
Catamarans works directly with each owner to tailor the yacht specifically for that owner’s individual needs.
While the Catana Group celebrates its 40th anniversary, Bali Yachts is celebrating its 10th anniversary with the launch of its latest model: the Bali 5.8.
Within its 18-metre length and 9-metre beam, the Bali 5.8 is the company’s new flagship and offers 20% more interior space than traditional catamarans of the same size. In addition to its spacious accommodation, the Bali 5.8 offers a variety of spaces and features designed to maximise onboard relaxation, comfort and ease of use. This exciting new model will be on display for the first time at the 2024 Cannes Yachting Festival.
In late April 2024, the Group opened its brand new 20,000sqm factory in Portugal. This high-tech new facility has been developed specifically to build its YOT brand products. “Within less than ten years, we expect YOT to produce the
same turnover that we achieve with our combined sailing yacht products,” Mr Compagnon said. “The new factory is a huge investment for us, but we believe in the market and ultimately, we want to be the global catamaran specialists.”
Concluding, Mr Compagnon reflected on his passion for the fast-moving catamaran market: “I love trying to read what the market will look like tomorrow. What is the next big thing? How will boats be used?
I love the fact that the trend in charter is to make the sea, and the pleasure of being at sea, accessible to most people.” n
With more than 300 years of embedded engineering experience among its staff, jbj Techniques offers exceptional mechanical and fluid power expertise to a diverse client base across many industries. “Flexibility and adaptability are keys to the success of the company’s longevity,” said Sales Manager Paul Coidan. Report by Andy Probert.
ASa company, jbj Techniques is a reliable partner to customers worldwide. One look at its extensive portfolio – 60 product lines, thousands of different units – sums up the company’s tenacity to remain strong in its 50th year of trading.
The engineering company, based in Redhill, Surrey, UK, has established itself as a manufacturer and comprehensive supplier of components for mechanical and hydraulic power transmission systems.
“Our wide-ranging product portfolio has opened doors to all aspects of engineering in a vast array of industries from agriculture and aviation to energy, maritime, offshore, renewables and subsea,” said Sales Manager Paul Coidan. “We have products that cover a wide range of applications that require mechanical and hydraulic power.”
jbj Techniques’ machine shop is constantly manufacturing and integrating diverse components to assist clients’ bespoke systems and projects. The
company is as much at home providing for a drivetrain as it is deriving component combinations, such as couplings, bell housing and pump combinations or mechanical drives for subsea wave energy, steel works crucible handling equipment or marine winch drives.
“We stock couplings in a pilot bore configuration, that is, not machine-finished,”
Mr Coidan continued. “However, at our
machine shop, we will machine-finish the couplings to the client’s specification, while also creating our product range.
“Our specialism is being able to look at a customer’s application and their specific requirements, then turn it into a finish product. In addition, our technical sales team has the expertise to supply a package of products that are specified, machined and shipped to fulfil customer’s requirements.”
jbj Techniques also supplies various products to the shipbuilding and maintenance industry, including plate heat exchangers, power take-off gearboxes, planetary gearboxes, electromagnetic clutches and brakes, pneumatic motors, pneumatic starters, hydraulic gear pumps, hydraulic screw pumps, hydraulic gear motors, and more.
The company fields a UK-wide team of technical sales engineers to ensure the business is close to its customers. jbj Techniques enjoys excellent associations
with European and North American manufacturers, often acting as sole UK and European distributors.
Mr Coidan outlined how over the years, following the move in 1984 to its current location, the company has significantly developed and augmented the products and services it provides to a growing number of customers, approximately 80% located in the UK with a growing global customer base.
With second-generation owners, the company employs 23 staff, including a team of external and internal sales and support engineers. “jbj has a long history of continuing investment in new machinery, staff and equipment,” said Mr Coidan.
jbj Techniques recently developed its own ATEX-certified wet mount bell housing in conjunction with an industry partner. This is a valued addition to jbj’s comprehensive range of bell housings, with product ranges that conform to metric standards as well as VDMA and NEMA.
A different wet mount bell housing style including remote coupling monitoring was developed for exhibition at the 2023 SPE Offshore Europe event in Aberdeen.
These are tailored to suit each individual drive, this system can connect electric motors with frame sizes from D56 to D400L to any given pump type without misalignment. Available in aluminium for general industrial power transmission applications, an additional range of noise reduction equipment exists for noise and vibrationsensitive applications.
The company also has a complete range of equipment to connect diesel, petrol and air motors to any driven component.
“Our business plan is one of progression and growth,” said Mr Coidan. “We are always looking to improve our staffing
levels, manufacturing capabilities and stock levels to meet expected client demand.”
jbj is also adjusting its processes to ensure a more environmentally friendly approach to meet government aims to achieve Net Zero and minimise its carbon footprint.
“Business challenges range from changes in government legislation, continuous improvements in ISO9001 and 45001 standards, and the lingering impacts of Brexit and Covid,” Mr Coidan explained.
jbj has further strengthened its networks with the exclusive UK partnership agreement for the extensive range of the German-manufactured Flender range of couplings.
jbj Techniques is also the official UK distributor for Marzocchi Pompe of Italy. In a relationship that it has enjoyed for over 40 years,. jbj supplies hydraulic gear pumps and gear motors for many industrial sectors, including marine, offshore and even Formula 1. In addition, and in partnership with Marzocchi Pompe, jbj has developed bespoke pumps to suit customer requirements.
The company also stocks a large inventory of Concentric (formerly Haldex) hydraulic components for the UK and European Market. This range includes hydraulic gear pumps, motors, flow dividers and mini power packs.
jbj is also the exclusive distributor of Hayes power transmission products from
the USA and has a long-standing relationship with R & L Hydraulics of over 40 years.
“There are many other product ranges available from jbj Techniques, but our unique selling point is to specify a package of products that fits the application requirements,” said Mr Coidan. “This can be for new machinery build projects or existing machinery breakdowns that require quick turn arounds with minimum downtime.”
jbj has been instrumental in supplying several large projects, from shipbuilders and repairs for clients involved in oil spill disasters. It is also a partner in green energy propulsion turbines, presently being developed for vessels.
“We pride ourselves on having long-term partnerships with localised suppliers as
they offer quality and reliability,” continued Mr Coidan, in conclusion. “We are highly flexible and adaptable to meet client demands on projects. If we can, we will meet their needs on the same day, due to our technical expertise.”
Enjoying the 50th year in business, celebrating the anniversary in September 2024, jbj Techniques remains well positioned for the future, because of a strong network of blue-chip suppliers, their innovation and technical capabilities. n
Bulgaria’s FLOTSKI ARSENAL – VARNA LTD is an originator of its nation’s ship repair industry and a current global key innovator for clients. Having remained at total capacity throughout the Covid years, the Black Sea yard is looking ahead confidently. “We offer more than repairs to clients; we guarantee reliability,” emphasised Commercial & Marketing Director Radoslav Kostadinov in a conversation with Andy Probert.
The Covid era proved exceptionally strong for TEREM-SHIPYARD FLOTSKI ARSENAL – VARNA , with a 40% boom in business through to 2021 and smaller but significant increments to the end of 2023.
While some shipyards wilted, TEREM SHIPYARDcontinued to tick over and came through the worst relatively unscathed.
At its heart, according to Commercial & Marketing Director Radoslav Kostadinov, is a cautious approach to business. However, TEREM-SHIPYARD leans heavily on its highly-skilled Bulgarian workforce to be as reliable as the ship projects it turns around. 2024 is set to be another good year for the yard. Among the new projects is a four-year deal to repair and maintain Bulgaria’s naval assets, while negotiations on building its first floating dock for a Croatian client are inching ever closer.
“We are not fazed by a new project,” Mr Kostadinov added. “It offers a new
challenge, a new opportunity to learn and to move on into the next one more enlightened than last time.”
Situated on the shores of Varna Lake, 20km from Varna, the largest city on the Black Sea coast, TEREM-SHIPYARD was founded in 1897 as a port of special purpose to focus on maintaining the ships of the newly-established Bulgarian Navy.
127 years later, the 100% state-owned Ministry of Defense shipyard, which operates on a totally self-supporting basis, remains a staunch partner in the maintenance of military vessels. However, it has increasingly widened
its mission to repair commercial ships, due to expanding foreign partnerships.
Across 617,000sqm, the yard has two floating docks, four quays, a lifting capacity of 2,200 tonnes and four floating quays along a 1,300m length of coastline. It has three 135m long rail slipways, serviced by a 45-tonne auto crane, and equipped with electrically-driven rail trucks, a 16 tonne/20m portal crane and a 6 tonne/30m tower crane. The slipways, which are supplied with electricity, acetylene, oxygen, fresh water and compressed air, are used for repair, conversion and new build projects.
Vessels up to a maximum of 14,000DWT and 200m in length can be accommodated,
with vessels up to 165m in the bigger of the two floating docks.
Given its modern and well-equipped workshops and employing 400 people, with a pool of 200 subcontractors, TEREM-SHIPYARD is geared to handling high-quality complex ship repairs at short notice.
Mr Kostadinov noted how the past five years had been one of continual growth for the yard as more clients, particularly with strong links to the Black Sea, had turned to Flotski Arsenal.
Projects have ranged from complex repairs to conversion and modernisation of ships, steelwork, spectral analysis of metals and materials, and repairs of radar systems, armaments and electronic equipment. The work scope has encompassed bulkers, general cargo vessels, tankers and dredgers, plus mega-yachts.
Mr Kostadinov acknowledged that the yard had embarked on a new investment to build a new pipe workshop, which the EU is partly subsidising: “This will enable us to continue evolving our work scope for clients and building our experiences in that area.” The yard will also look to replace one of its cranes in the next two years.
Having constructed an 80m target vessel, which took six months to complete for the Bulgarian Navy, and the conversion of a landing craft into a mine-laying vessel, TEREM-SHIPYARD recently sealed a four-
year repair and maintenance contract for Bulgarian naval assets. This will encompass dock repairs of Bulgaria’s three Drazki-class frigates, its single ex-Soviet frigate, a missile corvette, two anti-submarine warfare corvettes and three Tripartite-class mine countermeasure vessels.
While averaging around 70 ship repairs per annum, the shipyard is poised to build a new 86m x 16m floating dock for a client
in Croatia. “This is an exciting upcoming project and a first for the shipyard,” said Mr Kostadinov. “If all goes well, then we may well see more companies coming forward for similar floating docks building. It could open a whole new chapter for us.”
TEREM-SHIPYARD successfully handled major repairs on the MV Vera Su (now MV SAFINA) cargo vessel after it collided with rocks near Varna. “We restored the vessel’s
entire bottom, the engine room, the auxiliary engines and electrics,” Mr Kostadinov explained. “It was a big job, but we completed it within eight months.”
These projects have been supplemented by the installation of ballast water treatment systems for various vessels throughout 2023.
Maintaining a reputation
“Due to the outbreak of the RussianUkraine war, we stopped working with Russian fleet owners,” said Mr Kostadinov. “However, we have begun working with many Ukrainian clients because they cannot accomplish ship repairs in their nation’s shipyards. We have established excellent relationships and look to move these connections forward this year.
“The shipyard has continued to pursue more digitisation innovations to enable us to conduct repairs without the need for clients to visit. We are looking to develop an app to help increase communications between our workshops. This will provide a better overview of a project and improve efficiency.”
Recruiting specialised workers, such as welders, pipefitters and machine operators, has become a challenge in Bulgaria and across the global ship repair field.
“No one wants to work in these professions anymore,” Mr Kostadinov continued. “No one is coming from the schools or specialised academies, even though we are increasing wages. Most young people want to be in IT, so recruitment is a struggle. In the near future, we may have to consider employing other nationalities.”
The success of TEREM-SHIPYARD is aligned with using local suppliers, according to Mr Kostadinov: “We work with those that are fast, affordable and offer the highest quality of work that will enable us to complete projects on time for clients.
“Our mission is to maintain our worldwide quality reputation, because we are highly adaptable at handling a stream of diversified projects,” he said, in conclusion. “I believe TEREM-SHIPYARD FLOTSKI ARSENAL – VARNA LTD. is entering new and exciting years ahead, and we are looking forward to it with confidence.” n
seven seas, five oceans, one voice
rotterdam shortsea terminals port gdański eksploatacja montserrat port authority brestport s5 agency world
The largest dedicated shortsea shipping hub in Europe, Rotterdam Shortsea Terminals offers container handling and storage, as well as additional services, to solve demanding logistical challenges. CEO Arno Storm discussed the company’s improved sustainability measures and future investments. Report by Antonia Cole.
Established in 1977, Rotterdam
Shortsea Terminals (RST) operates on 64 hectares of terrain with 2,850 metres of quayside, suitable for ships with draughts up to 13.65 metres. It employs 310 highly trained people, who utilise their skills and experience to provide efficient and safe services.
Located in the heart of Rotterdam, the terminal is positioned to offer ideal accessibility through roads, waterways and railways, all connecting to the site. This makes operations more streamlined and convenient for all parties involved.
The terminal handles an average of 50 shortsea vessels per week, equating to 2,500 vessel calls annually. Through the terminal’s size, advanced equipment and
expertise in container handling, RST is able to effectively serve as a hub for many shipping lines.
“At RST, we are committed to excellence,” said CEO Arno Storm. “There are very high standards instilled within the company. We aim to anticipate the evolving needs of clients and exceed requirements efficiently and effectively. Through our dedication to continuous improvement, we are adapting the company to promote improved sustainability measures.”
Sustainability is a focus for RST, with it improving environmental targets to have reduced carbon emissions by 95%, for scope one and two, by 2025. In 2022,
RST minimised emissions by 26% and then, a further 20% in 2023. The company is already making significant progress towards its goals and is trying to maximise the positive impact of the terminal.
Approximately half of the company’s electricity usage is currently powered through green energy. There is a plan set in place to increase RST’s reliance on green energy to 100% by 2025. This will help to set a new standard of sustainability within the industry.
RST has also purchased six new hybrid straddle carriers for its fleet. These carriers will move RST forward towards achieving
environmental targets as they have improved efficiency and use 50% less diesel than a standard carrier. When fully electric carriers become available, RST hopes to invest in these too.
These carriers will be run on HVO 100 diesel, a fossil-free fuel made from 100% renewable sources. This diesel is a more environmentally friendly option, with up to 90% carbon reduction. By utilising more sustainable fuel sources, the company is minimising the emission of greenhouse gases.
“It is vital to our, and our community’s, future that we actively pursue an operation that
benefits people and the planet,” explained Mr Storm. “We aspire to transform RST into a truly sustainable container terminal and are working with others across the industry to achieve this.”
In collaboration with the Port of Rotterdam and Samskip, RST has launched its Green Shore Power Initiative. As the first sea-terminal in the Netherlands with shore power connection, RST is working to be a leader in the transition to sustainable energy sources. This project will greatly reduce harmful emissions and promote environmentally conscious operations.
As well as this investment into shore power, RST has installed 700 solar panels on buildings. This has allowed two of the company’s buildings to become carbon neutral and has greatly limited the overall environmental impact of operations.
RST has also been investing into the efficiency and quality of operations. The company has refurbished one of its older cranes, which will allow for a more reliable and structured service that better accommodates clients. RST is also in the process of acquiring a new gantry crane, as well as two ship-to-shore cranes.
“Previously, shortsea markets used smaller vessels, of up to 850TEU,” said Mr Storm. “Now, customer shipping lines are sizing up vessels to a 2,000TEU maximum. Due to the change in market circumstances, we have to adapt and expand the capacity of our operation to meet client requirements. We are further investing into ship-to-shore operations so that we can maintain our successful position within the market.”
In the next three years, RST is planning to invest between €35 and €40 million into the expansion and improvement of operations. This will not only make the facility more sustainable through improved efficiency, but it will advance RST’s ability to serve clients’ evolving needs.
The company has recently been collaborating with two software partners in the development of an automated storage planning software. Through the use of AI technology, the system will digitalise the vessel planning process at RST, making operations more efficient, reliable and effective.
As well as this, RST has collaborated with several parties in the development of a hydrogen-fuelled ReachStacker. Hyster, a manufacturing company, and the Port of Rotterdam have worked
with RST to create a pilot version of the ReachStacker, which will limit greenhouse gas emissions in operations.
In addition to equipment, RST has also been investing in staff. The company’s already skilled and experienced staff have been given training to further maximise the effectiveness of RST’s operation.
“Staff are the heart of RST,” explained Mr Storm. “It is important that we support them and work together to create the best outcomes. We have been working with our staff to limit waste in operations and enhance productivity.”
RST also works with partners to enable more efficient operations. To make the interchanging of containers from the rail terminal to RST more streamlined, the
company has been collaborating with Samskip to define 14 work streams that will minimise transit times.
“Our partners and suppliers are very important,” said Mr Storm. “We are all working together to deliver the best possible service to the client. Companies like Seamark, which provides reef monitoring services, allow us to attain the high standards that have made us so successful. At RST, we believe in collaboration and cooperation. By building up these relationships, we can achieve more.”
As RST continues to develop, it plans to work with partners across the industry
to improve the quality and capabilities of services. The company aims to consistently meet and exceed client expectations through innovation and technological developments, as well as by limiting environmental impacts and implementing more sustainable practices.
“We know what society is asking from us as a company,” concluded Mr Storm. “RST is demonstrating that it is serious about sustainability and is dedicated to becoming more environmentally friendly. It is important to us to be a responsible player within Rotterdam and that we work to make a positive impact on the environment.”
n
Port Gdanski Eksploatacja SA is one of the largest port operators in Poland. With 30 years’ experience backing it, the operator is in a prime position to support expansion plans at its home base of the Port of Gdańsk. Mariusz Wdowczyk, CEO of Port of Gdański Eksploatacja, explained more in conversation with Hannah Barnett and Imogen Ward.
Port of Gdański Eksploatacja (PGE SA) can be found on the southern coast of Gdańsk Bay in Poland. As one of the largest transshipment operators across the Polish seaports, PGE’s operations are supporting the continued growth of its base at the Port of Gdańsk.
“Here at PGE SA, we employ almost 400 people,” said Mariusz Wdowczyk, CEO of Port of Gdański Eksploatacja. “Each one is part of a strong and well-coordinated team. Through hard work and determination our team is supporting the continuous expansion that is occurring at the Port of Gdańsk.”
The Port of Gdańsk
Situated in Poland, The Port of Gdańsk is built up of three parts: the inner port, the outer port and the northern port. The
outer port handles the largest vessels, w hilst the inner port handles a large variety of cargo. Most recently, this has included a large portion of agricultural goods and liquid fuels, which successfully contributed to the port’s latest annual
cargo handling milestone of more than 80 million tonnes. This is an increase of more than 12.7 million tonnes in comparison to the previous year.
As the port serving a population of one million civilians, and a rotating population of up to 70 million seafarers, it is no wonder that it maintains a heavy focus on growth. Currently in its 10th year of record growth, t he port is reliant on its operators to ensure this vision becomes a reality.
With 30 years of experience behind it, PGE SA is the largest operator at the Port of Gdańsk. The company operates with the support of two main divisions: Goods and Services, and Waterfront.
Under its Waterfront operations, PGE SA has eight quays, spanning the length of 5km. Each one is pivotal to the operator’s ability to aid the Port of Gdańsk’s recordbreaking growth.
The quays of the Górniczy Basin are hugely effective at reloading dry bulk goods, liquid bulk goods and other unitised general cargo. With three quays in situ, the basin consists of Węglowe Quay, operating with a length of 780m, Rudowe (695m) and Administracyjne (125m).
The Szczecińskie Quay is adept at handling unitised general cargo, as well as steel products and structures. With a total operating length of 365m, the quay is home to 4,800 sqm of warehouses and two storage yards totalling 48,500 sqm.
The company’s two WOC quays are also geared up to handle the reloading of steel structures and products, as well as cars and more general cargo. With a combined length of 1,066m these quays come equipped with a Ro-Ro ramp and 60,000 sqm of storage yards.
Finally, the Oliwskie Quay, which is 600m in length and features around 31,200 sqm of storage, and the Vistula
“We have an excellent team onboard, that never fails to give it their all. This is what motivates me every single day”
Quay (the largest of them all at an impressive 1,160m) are both capable of handling steel products, unitised general cargo and dry bulk cargo.
“We also have convenient access to the A1 motorway, and two railway stations enable us to easily and efficiently reload goods by rail,” Mr Wdowczyk explained.
When it comes to offloading goods, PGE SA is the perfect partner. With 640,000 sqm of storage space and the capacity to load 6.9
million tonnes, PGE SA is an unstoppable force at the Port of Gdańsk. The company currently has three cranes located at the port, also each with a maximum lift of 120 DWT. Two of these cranes are recent additions, following a strategic acquisition last year.
Both cranes were supplied with grabbers for coal and ore – the operator’s main source of business – as well as a spreader. It was hoped that with these purchases, PGE SA would be able to improve its overall operational efficiencies.
With this in mind, the company also made several other investments in the same year, including a new RIMO SL1400/M conveyor belt. Acquired in May last year, the new equipment was added to PGE SA’s portfolio to improve truck-to-ship loading times. So far, the equipment has been a positive investment, working to reload grain and other goods at the port.
“The bulk of our goods covers coal, coke and grain, but we also discharge dangerous goods and steel profiles,” said Mr Wdowczyk. “At the moment, the
coke, coal and grain attribute to the largest portion of our daily activities.”
The port operator also handles fertilisers and structures weighing up to 150 tonnes. It also has all the equipment needed to carry out Ro-Ro reloading.
With teamwork a prominent element of PGE SA’s operations, the company likes to align itself with other organisations that reciprocate this ethos. Also one to partake in community-led events and CSR initiatives, last year PGE SA partnered with
Torus Wybrzeże Gdańsk, a local handball club based in Pomerania. Having signed a cooperation agreement with the club, PGE intends to support the sports group for the foreseeable future, providing them with better opportunities to create memories and add to a long-standing legacy of handball within Gdańsk.
With another successful year on the cards, PGE SA journeys through 2024 with a new President of the Management Board. Having been elected into the role at the end of Q2 last year, Mr Wdowczyk joined the role with over 20 years’ experience in similar roles. With expertise in building strategies, security departments and investment management, Mr Wdowczyk is the perfect person for the role as the operator continues to support the port’s mission for growth.
When discussing his time at PGE SA, Mr Wdowczyk also highlighted teamwork as a crucial element in the company’s daily operations.
“Every day is new, and no two hours are the same,” said Mr Toda, in conclusion. “As the largest operator in the port, we have to be prepared to react quickly to these changes, sometimes that can be very challenging, but I enjoy a challenge, and so does our team. We have an excellent team onboard, that never fails to give it their all. This is what motivates me every single day.
“I have worked here for 27 years, and as one of PGE SA’s longest-standing employees, I am in the unique position of witnessing the evolution of both the port and PGE simultaneously over the years. It’s an incredibly exciting position to be in.” n
The Montserrat Port Authority works to provide a safe multi-use port facility and service. It is improving and expanding the Little Bay Port through superstructure, infrastructure and human resource development, in keeping with international maritime standards. Port Manager Joseph O’Garro spoke on the development of Little Bay Port and how the Authority fulfils maritime responsibilities. Report by Imogen Ward and Antonia Cole.
Established in 1978, the Montserrat Port Authority manages and operates Port Little Bay and Port Plymouth on a 24-hour basis, accepting container vessels (RoRo & LoLo), breakbulk vessels, tugs and barges, fuel vessels in addition to facilitating anchorage for cruise ships and pleasure yachts.
The Authority regulates the safe use of port facilities and controls navigation. The Government of Montserrat is investing in a substantial development of port Little Bay to provide a new, deeper draught pier.
On the Caribbean island of Montserrat, the Authority has endured multiple natural disasters. This includes the 1989, category four, hurricane Hugo and the 1995 eruption of the Soufrière Hills volcano
that saw the tragic destruction of substantial portions of the island.
Since these disasters, the island has been working to rebuild with the Montserrat Port Authority contributing to the recovery of the island. The port of Little Bay, Montserrat, is set to see huge developments in infrastructure to improve access to the island.
After encountering challenges and delays, the Government of Montserrat plans to invest US$26 million into the development of the port has now been increased to US$46 million.
The project is being financed with US$36.8 million in grant funding from UK aid through the United Kingdom
Caribbean Infrastructure Fund (UKCIF) which is administered by the Caribbean Development Bank, and US$9.2 million from the government of Montserrat.
“We’ve updated our design specifications recently to closely correlate with the current and future goals and objectives of the port,” said Port Manager Joseph O’Garro. “We are quite pleased that the funding has been secured for the construction.”
The new facility will comprise of a 130m pier with an 8m draught. The pier will have a mooring dolphin 40m from the end, making the effective usable length a total of 170m, and have a deck width of 20m. A 23m wide RoRo ramp will be an integral part of the pier, to further enhance the usability of the pier.
The Meridian Construction Company Limited, based in the British Virgin Islands (BVI), is responsible for the delivery of the development and is estimated to have progressed 30% of the way through the project.
“The Environmental and Social Impact Assessment required the relocation of corals to protect the islands marine biodiversity and the monitoring of a protected bat habitat near the development project,” said Mr O’Garro.
The assessment ensures that strict international standards are met and that the project will not degrade or damage the natural environment.
“Significant amounts of the required dredging have already been completed by the Trailing Suction Hopper Dredger (TSHD) vessel, Elbe,” explained Mr O’Garro. “About 75 per cent of the
dredging is now completed, with the remainder to be potentially undertaken using a long-reach excavator that is able to access the areas which were not suitable for dredging by the Elbe.”
Construction has already begun on the concrete caissons, and reclamation and shoreline protection works are ongoing. The project is progressing efficiently, ensuring that the port of Little Bay will become a safe, secure and modern port for Montserrat, delivering critical access to the island and enabling further economic development. The Authority has been advised a January 2025 project completion and ready-for-service (RFS) date by the Government of Montserrat Project Coordinator.
The Montserrat Port Authority is also working to refurbish the fenders and bollards at existing facilities, which includes the previously damaged port of Plymouth. Port Plymouth is primarily used for aggregate exports, which is a significant revenue stream for the Authority and an important economic sector for Montserrat.
“It is in our best interest to ensure that Port Plymouth remains not only accessible, but that we continually make improvements in order to safely accept larger barges/tugs and cargo ships,” said Mr O’Garro, “which are currently transporting Montserrat aggregate as far as Suriname in the south and Haiti in the north.
“The ongoing fender and bollard replacement project is estimated to cost
just over half a million US dollars. This includes ancillary works, such as highvisibility life ladders and pier deck maintenance. We are investing approximately one million US dollars total across both of our existing piers at Port Little Bay and Port Plymouth.”
The Authority is also upgrading and modernising its cargo handling equipment,
investing in two electric, two diesel forklifts and a telehandler to improve cargo handling capabilities. The Authority also expects to further invest in a modern reach stacker within the next two years.
“This is to support the expected increase in cargo volumes as we attract new business activity at the new pier,” explained Mr O’Garro.
“We are investing approximately one million US dollars total across both of our existing piers at Port Little Bay and Port Plymouth”
The Montserrat Port Authority has had to work closely with the contractor to ensure that Port Little Bay was able to operate without interruption by the ongoing construction. Weekly meetings, to efficiently coordinate normal vessel traffic and the delivery of construction materials to the port, are an essential part of the project plan.
“The Meridian Construction Company is a crucial partner for us, making this development project an affordable reality,” explained Mr O’Garro, “We recognise and value the company’s contribution to this project.”
In future, The Montserrat Port Authority plans to increase marketing efforts to encourage more niche tourist vessels (max. 800 passengers) and small yachts to visit the island.
It currently manages approximately 400 yacht calls a year and is hoping to increase that number by 25%. This increase in tourism will help the island and its people to economically recover from a difficult past. n
BrestPort was set up in 2021 to handle operations at the commercial Port of Brest with a 40-year concession. The longevity of the contract is a revolutionary step, never-before-seen in France, and represents a strong commitment to the development of the Port of Brest and the surrounding area. It will also enable the Port to embrace the energy transition. CEO Christophe Chabert explained more to Hannah Barnett.
The Port of Brest has historic roots, stretching back to 1631 when it was built as a military port. The Port continued to evolve over the ensuing centuries and its latest chapter, under new management by BrestPort, reflects a shared vision for the future. A total of €900m will be invested over a 40-year period, including an initial injection of €500m for the first 10 years.
The change of management marked a significant step which accelerated the path to investment. Owner and concessioning authority, Région Bretagne, gave the green light, following approval by the Port’s other shareholders, Brest Métropole and the Chamber of Commerce and Industry.
“We had to have a long-term approach,” explained Christophe Chabert, CEO. “We needed to bring together investments for infrastructure and for equipment. The region and owner created an external company, BrestPort, to operate everything
“We succeed today because we have this new company, we have the confidence of our shareholders and of the owner. We now have a solid chunk of investment to guide us into the next 40 years on a decarbonisation path. The
climate change challenge is not in opposition with industry developments. In fact, it gives us the opportunity to create new, sustainable energy solutions. I think Brest, France and Europe have all the conditions necessary to succeed.”
Following the recent windfall investment, the Port of Brest will expand its traditional activities, centred on logistics and cargo handling, by diversifying the business sectors it manages. This major step means the Port will contribute to the development of offshore renewable energies, as well as establishing public-private partnerships and incubating maritime businesses. The company is therefore investing heavily in infrastructure.
“At the harbour we will create a new space of 40 hectares and a new MRE
(Marine Renewable Energies) quay of 400 metres, alongside the 200 hectares of concessions we already have,” said Mr Chabert. “This will allow us to be ready for offshore wind development in France, specifically floating offshore wind. So, we are going through geographical change with the new harbour, and an organisational change, with the establishment of BrestPort, the new company to manage it.”
BrestPort is also investing in new logistics terminals, which will be ready in 2025 and 2026. “We want to develop our logistics area to have one place for trains, ships and lorries,” Mr Chabert explained. “We will therefore be ready
for the future with more logistics via train and less via the road.”
2.8 million tonnes of goods with 700 port of calls pass through the Port of Brest each year and the company has increased turnover by 4% over the last year to an impressive €22 million. BrestPort currently employs 90 persons, that generates around 2,500 jobs in the closest area, with the goal to increase it to 6,000 to meet the expansion of infrastructure.
“We have an engineering team in place to respond to this new work and are expanding the team to be ready for the future,” said Mr Chabert. “But we also must reinforce our strong industrial capability.”
To help improve said industrial capability, port services, anchored around the dry dock and the boat lift, will soon be able to handle up to 650 tonnes in weight. Working alongside the Lorient and Concarneau shipyards along the coast, BrestPort will offer additional berthing capacity on pontoons for medium-sized vessels and sea access for key industrial and logistics players.
“We need the capability to repair small Navy vessels, as we are located close to the Navy base, as well as the offshore wind farm service vessels,” explained Mr Chabert. “Yacht and cruise ships are increasing in numbers in Brittany, so we want to service them too. We want the capacity in our harbour to repair anything from the biggest ships in the world to the smallest.”
Like any successful port operator, the company must work closely with partners and suppliers to ensure success, especially when it come to the number and scale of the developments scheduled for the next few years.
“The Port cannot operate alone,” Mr Chabert explained. “We must work in cooperation with others. For example, with offshore wind, it wouldn’t be possible to manage all the logistics on our own. That means we will work together to propose the best solution and put in place a real capability with which to enter the renewables market.”
As a result, BrestPort is set to modernise its ship repair facility to be more environmentally friendly. It will have tanks specifically for the transfer of low carbon fuels like LNG and hydrogen, along with offering electrical onshore connections for ships.
The company also has its own sustainability targets, namely to reduce its carbon footprint by 66% by 2040, as well as ensuring employment across the Port.
“It is also important that the new activity will support the agriculture and export side of the Port,” Mr Chabert added. “The
Brittany region exports a lot of foods like chicken, potatoes and grains. BrestPort will also invest in ship repair and be one of the leaders for the development of offshore wind. We will combine all this to be ready for the future.”
decades and more
With so much going on at the Port of Brest, there are also plenty of obstacles to overcome.
“Yes, there are a lot of challenges,” said Mr Chabert. “I think what will be very important is to ensure that the industry will be able to incorporate green solutions. We need to move fast to be ready. It’s a challenge for new markets, but there are a lot of offshore wind projects today in Western Europe. We need to upgrade to serve this market for the long-term and to find a balance, while also accommodating and accounting for the historical traffic in the port.
“Our geographical position is a benefit because we are at the northwestern edge of France, very near the Celtic Sea wind developments. I think our location will be advantageous specifically in development of renewable energy.”
BrestPort may exist to oversee ships and harbours, but for Mr Chabert, it is the human element that makes his job so enjoyable.
“My work is about the management of people,” he concluded. “No company can succeed without the people that make it up. It is our main asset, far more than a quay or a crane or anything like that. People are the most important element in any successful company.” n
S5 Agency World is the fastest growing international port agency in the world. The company’s expansion in this competitive marketplace has been built on reputation and the ability to tailor its process-driven products to meet the specific and evolving requirements of its clients. Global Sales Manager Captain George Tsouris explained more to Hannah Barnett.
Based in London, S5 Agency World is a port agency provider. It was formed in 2004, but has origins rooted as far back as the 18th century. As a result, the company offers more than 250 years of industry experience.
“Through close cooperation with our existing client base, our approach has always been to look for new ways to create value in our services, which sets us apart from other providers,” said Captain George Tsouris, Global Sales Manager. “We have invested heavily in a robust global hub structure to ensure first-rate service, delivery, continuity and a 24/7 operation through one common IT platform.
“As a testimony to the success of our management structure, we are proud to continuously exceeded the expectations of our client’s by regularly surpassing our agreed KPI targets.”
S5 has a large regional presence in the Americas, Europe, the Middle East and Asia. “Our integrated
structure combines the benefits of an internationally partnered management team with unsurpassed local operational control, diligence and experience,” Captain Tsouris said.
The company has grown to serve more than 85,000 port calls and 87,000 crew changes per year, seamlessly delivered from over 360 owned port offices. At the same time, the team has also increased to more than 2,700 personnel.
S5 is focused on delivering five key areas of value: internal efficiency, improved voyage return, improved cash flow, real business intelligence and integration.
Internal efficiency is achieved through simplified processes tailored to a client’s specific needs. Voyage expenses are reduced by a tactical approach to cost management; S5 has created a Strategic Vendor Management team in order to translate local knowledge into international delivery.
Improved cash-flow involves consolidated funding and billing in a single currency via the S5 Global Financial Hub. This results in a
dramatic reduction in the number of financial transactions required and makes final reconciliation smoother and easier.
Business intelligence refers to a fast web-based tool, which gives the ability to use the S5 database to retrieve management information and facilitate tactical, as well as strategic, decision making. It provides a window into operational and financial data and clients have found it particularly helpful in preparing cost management programs.
Alongside its business targets and strategies, S5 is keen to ensure a high level of focus is placed on the human element of shipping. This includes cultivating a close partnership with shore-based staff to develop customised solutions which support the day-to-day activities of the company.
“Working with the crew starts with the smooth coordination of services while the vessel is in port,” said Captain Tsouris. “We cooperate with the senior crew, as well as with the local authorities and terminals.
This ensures the safe transfer of personnel during crew changes and medical visits. These include, but are not limited to, any additional personal needs which may arise for a crew member while in port. Everything we do is in close liaison with the master of the vessel.”
The business is ISO-certified, part of which means it provides centralised processes, including an account management model focused on client needs. The system combines localised port expertise with standardised, worldwide oversight and knowledge. S5 also offers single points of contact, available 24/7.
This high level of service is further supported by forward-thinking digital solutions, such as the company’s stateof-the-art operation system Simply5.
An industry-leading piece of software, Simply5 streamlines communications to achieve transparent information on operations and financial activities.
“Simply5 provides value by giving clients real-time information,” Captain Tsouris explained. “We also integrate
S5’s systems to ensure we minimise manual entry and allow the clients to focus on their key responsibilities. We can also provide monthly reporting and data analytics, which allows our clients to make more informed decisions.”
Alongside integrity, service and innovation, sustainability is one of S5’s four core values. As part of the maritime sector, the
company is well aware of its responsibility to play a part in the decarbonisation of the industry. S5 is aiming to reach net zero by 2050.
The company maintains a two-way environmental strategy, encompassing both its own footprint reduction and supporting clients and suppliers in reaching their sustainability goals.
S5 has identified the most important ESG factors to demonstrate its commitment to
making improvements in these areas wherever possible. For example, the company is involved in GHG emissions data collection across all its locations, encompassing scopes 1, 2 and 3.
“S5’s focus has always been on how we can reduce our footprint on the world and help our clients to achieve the same,”
Captain Tsouris explained. “This started with a reduction in single-use plastics and packaging, as well as ensuring that we partner with like-minded port vendors to reduce emissions where possible.”
The company further supports clients to ensure the smoothest coordination of services when they arrive to a port. “This starts with just-in-time arrival, when possible, to optimise vessel speed and allow our clients to slow steam, saving fuel and emissions,” said Captain Tsouris. “It is also important to optimise the turnaround time in port and reduce unnecessary transport.”
In addition, S5 has been at the forefront of working with clients on alternative fuel sources and the company is actively involved in areas such as LPG, LNG and
methanol bunkering. The company is also working on carbon capture projects to return stored carbon back to the wells from which it was originally drilled.
“S5’s partnerships are rooted in our sustainable ethos and reflected across our solutions,” said Captain Tsouris. “We collaborate exclusively with like-minded partners that share our commitment to ecological stewardship, social welfare and ethics. The values of integrity, service, innovation and sustainability shape trusted, transparent and reliable long-term supplier relationships.”
Though not directly employing seafarers, S5 works hand-in-hand with leading crew managers globally to elevate crew safety, welfare and efficient movement through solutions tailored to manager and seafarer needs.
“As a key player in the shipping industry worldwide, we consider it a duty to provide the highest standards of services to all existing and potential clients,” Captain Tsouris concluded. “The work we do is always based on the principals of the past fulfilling the needs of the present and looking forward to the trends of the future.” n
seven seas, five oceans, one voice
polarquest contships management chemship öl shipping group swan shipping corporation sealink navigation
PolarQuest has been operating small ship expedition cruises to polar destinations since 1999. With five different destinations, the company offers a tailored and unique experience to those looking to explore the wilderness. CEO Marie Lannborn discussed PolarQuest’s new journeys and memorable experiences, in conversation with Antonia Cole.
Photo: Ulrich Kühn
Celebrating 25 years in business, PolarQuest has grown into a worldleading provider of small ship expedition cruises and is now operating fully-booked vessels across the polar regions. The company used six vessels that deliver journeys to the most remote corners of the world.
The MS Quest carries 50 passengers, whilst the MS Stockholm and MS Sjøveien both carry 12 passengers on expeditions to Svalbard. The MS Stockholm is also used for journeys to the Norwegian coast and Lofoten Islands.
PolarQuest uses three more ships, Ocean Nova (78 passengers), the MS Balto (12 passengers) and the Coral II (19 passengers) that travel to Antarctica, Greenland and the Galápagos Islands, respectively. These smaller ships can reach remote areas and venture into narrow fjords, delivering unique and immersive experiences to guests. The limited number of passengers allows for more personal and
intimate journeys, with once-in-a-lifetime encounters in the wild.
Travelling in small groups results a more relaxed atmosphere, maximising time ashore and creating opportunities for memorable moments and sights. Zodiac boats allow guests to safely navigate through icebergs and land ashore, feeling close to the natural wonders the polar region has to offer.
“With small groups, we can focus on providing high-quality experiences,” said CEO Marie Lannborn. “People who travel with us know that they are getting a journey like no other. With our variety of destinations, including our newest trips to Greenland, we offer life-changing expeditions.”
As a company built on the appreciation of nature, sustainability has always been at the heart of PolarQuest’s operations. Through measuring and reducing emissions, investing in environmental projects and managing tourism, the company minimises environmental impact.
“We calculate everything,” explained Ms Lannborn. “From the lightbulbs in our office to the journeys of the ships, we measure our carbon impact and we work to compensate for it.”
PolarQuest is one of eight founders of the Association of Arctic Expeditions Cruise Operators (AECO). This organisation strives to conduct responsible and sustainable expeditions, respecting the natural environment of the Arctic.
Tourism in the polar regions is closely monitored. PolarQuest’s educated and
experienced Expedition Leaders and guides observe and record wildlife sightings for research and record any changes to the natural environment in order to prevent environmental deterioration.
“We strive to create awareness and want to educate ambassadors,” said Ms Lannborn. “Our presence in the polar regions creates ambassadors solely through the environment’s beauty, but also through education.
“At PolarQuest, we aim to provide our guests with a deeper understanding of these environments and how climate change is impacting them. Our hope is that after their trip, guests will spread the word about these vulnerable areas
and create a broader interest in environmental conservation.”
The company also has a giving back programme, in which it donates to sustainability researchers spots on the trips or projects that create awareness. Last year a study was conducted through this programme, investigating how the mentality of guests evolves throughout the trip regarding environmental conservation. This study produced very positive results, supporting the company’s ambassador theory.
PolarQuest encourages travellers to collect waste during expeditions through project Clean Up Svalbard, a coastal cleanup programme supervised by the Governor of Svalbard, in coordination with AECO. The company is also working to reduce the use of single-use plastics on vessels as a preventative measure.
As well as these compensation measures, PolarQuest is actively trying to reduce its carbon footprint by planning itineraries in advance to minimise fuel consumption and investing in technical upgrades to improve efficiency.
PolarQuest’s newest vessel, the MS Balto, delivers travellers to the remarkable wilderness of Greenland. Able to travel through remote fjord systems and visit isolated Inuit set tlements, the MS Balto shows travellers majestic peaks and wildlife such as whales, arctic foxes, seals
“Adding Greenland to our portfolio has been an important step for us,” explained Ms Lannborn. “As we use a 12-passenger vessel, we are able to visit small communities without them feeling invaded and we can see some of the most beautiful sites the world has to offer.”
The trip from Disko Bay to Uummannaq offers a diverse landscape with unique geological formations. Whilst the trip from Narsarsuaq to Tasiilaq offers rich history and Innuit culture, as well as views of the Prince Christian Sound mountains. PolarQuest’s true expeditions mean that each trip is different and has a new natural wonder to discover.
The company also invites specialist speakers onto trips, such as BBC filmmaker Doug Allen and photographer Rick Tomlinson, to deliver informative and inspiring talks. This not only adds value to the trips but encourages the environmental awareness of guests and creates more ambassadors.
On an upcoming journey through Svalbard, PolarQuest will not only show guests the magnificent polar scenery, but will attempt to reach Kvitøya, the historical site where Salomon August Andrée, Knut Frænkel and Nils Strindberg were found 33 years after their fateful North Pole expedition with the hydrogen balloon Örnen. Special lecturer, polar historian Håkan Jorikson, will teach guests the story of Kvitøya, providing an interesting and immersive experience in Svalbard.
“Svalbard has always been our primary destination,” said Ms Lannborn. “It is the Arctic Pearl, and we have an in-depth knowledge of the area, which is our strength in providing high-quality, memorable expeditions.
“For me, being able to experience these natural wonders up close is a really incredible adventure. Having seals pop-up next to you with the beautiful views of icebergs, glaciers and mountains is a
memory like no other. It’s that closeness to nature that we want our guests to be able to experience too.”
After 25 years in business, PolarQuest has built an expansive knowledge of Svalbard and the polar regions, as well as building long-standing and valuable partnerships. Starting with the original owner of the MS Stockholm, the company has formed relationships with people across the industry to create unique polar expeditions.
“Our suppliers are fantastic,” explained Ms Lannborn. “We work with the best people out there. People who are detailoriented, know what customers want and how to create those experiences, as well as having the same vision as PolarQuest. Our partners value environmental conservation, just like we do, and we are working together with the aim of eventually decarbonising the industry.”
Going forward, the company hopes to continue improving sustainability and spreading the word about ambassadorship for the environment, whilst offering the best nature experiences in the area.
“The most rewarding part of working for PolarQuest is not only being out on the trips myself, but talking to our guests about their incredible adventures,” concluded Ms Lannborn. “Hearing their stories about spotting whales and being by the pack ice is what really drives me.
“Having this community of people with a passion for the natural world and environmental conservation is amazing and I feel honoured to be a part of it.” n
N. D. Pateras’ latest venture, Contships, the largest independent container feeder ship provider globally, has successfully navigated the commercial waters thanks to resilience and vision. While the Greek concern focuses on expanding its fleet and improving the value chain, it is also vocal on the pressing topics affecting the industry. George Pateras, Deputy Chairman of Contships Management, spoke with Andy Probert.
Contships Management is an invaluable component in the start of the global supply logistics chain and a lifeline in the final delivery of cargo to remote communities. Its feeder fleet, with capacities between 900 and 1,500 TEU, works like a well-oiled machine, providing uninterrupted and reliable services.
At the heart of its operations is a dedicated team with a long track record in shipping, ensuring continued success in this niche. Contships is led by Nikolas and his cousin George Pateras, the fifth and sixth generations of a Greek family
whose ties to shipping date back to the 1800s, demonstrating its strong roots and resilience.
“As the world’s largest independent supplier of feeders, we are immensely proud to be playing an active and prominent role in the Greek and worldwide shipping industry,” Deputy Chairman George Pateras said.
The Pateras family’s shipping history began by investing in sailing vessels in 1870 before buying its first steel sail-assisted vessel in 1902. The family expanded into triple-expansion steamships and owned general cargo ships and bulk carriers before later generations moved into the feeder vessel segment.
Contships, established in 2015, has acquired 58 container ships and currently runs 47 vessels that cover the first- and last-mile of the supply chain within the hub-and-spoke system. Its fleet now calls at 4,800 ports and carries a 1.7m TEU annually, while employing 1,000 seafarers and 125 shore staff.
“Our vessels take cargo from ‘spoke’ ports to larger ‘hub’ ports,” Mr Pateras explained. “Motherships take the cargo from hub to another hub, and from there, our feeders take them to remote ‘spoke’ ports. Feeder containerships are a vital link as they are the backbone of the supply logistics chain.”
Contships has an established record with the world’s leading container feeder charterers, such as MSC, Maersk Line,
CMA-CGM, Cosco and ONE. Contships’ feeders presently operate in the Caribbean, the Far East, Australasia, West and East Africa, Northern Europe, and the Mediterranean.
“Our reputation is that we don’t like challenging our business partners,” said Mr Pateras. “If an issue arises, we find a solution. We provide a reliable service and enjoy repeat business.
“Our company is loyal to Greek suppliers because we want to support our economy in any way we can. But we expect consistent quality and need our suppliers to be available 24/7, because shipping never sleeps.”
Looking ahead, Mr Pateras summarised Contships’ goals: “For us, expansion of our fleet is always on the table as we don’t like sitting idle. But sustainability is at the
top of our agenda: how we can burn less fuel and reduce carbon emissions. Our mentality is to be more efficient with the vessels we currently trade.
“Sustainability also involves a cultural transition. We are training crews to be proactive and encouraging them to come forward with their innovations. We are heavily invested in ensuring that sustainability becomes second nature on board.”
Contships is considering potential avenues of new builds and conversions.
“Our fleet has an average age of around 14 years, but over 50% of the global fleet in our sector is over 20 years old,” Mr Pateras continued. “So, sustainability must eliminate the older vessels that are uneconomical to transform and make way for younger ones. At least 180 feeders (1000 -1500 TEU) are over 20 years old and must be scrapped immediately.
“We need science to prevail on sustainability, not a politically correct, votewinning decision. We must consider the well-to-wake element in shipping terms, similar to the cradle-to-grave lifecycle.
“However, we are not into these whimsical ideas on alternative fuels that are either unreliable, unsafe or untested. We must be honest with our charterers and safe for our crews. We can’t afford to get it wrong on fuel because we are getting too near the critical stage of climate change.”
Despite the talk around methane, hydrogen and ammonia, Mr Pateras favoured nuclear energy and carbon capture as long-term solutions.
Contships is also adapting to many issues: sustainability, geo-political issues, sanctions and market disruptions. One topic close to Contships’ heart is the long-
term investment in quality officers and shipping personnel.
As President of the Hellenic Chamber of Shipping, Mr Pateras is leading a campaign to recruit more young people into the industry. The Chamber, which represents thousands of stakeholders in shipping, is the official advisor to the government on all shipping matters and works closely with the Ministry of Merchant Marine.
“We have to persuade the youth to com e back to the sea, because if we don’t have good and qualified seamen, then we will not have future personnel for our offices, ”
Mr Pateras explained. “We want to give school leavers a chance; otherwise, they will never get ahead.”
Contships is also concerned about EU regulations imposed on shipping, such as the tax on fuel and the uneven application of the IMO’s Carbon Intensity Indicator (CII), according to Mr Pateras: “The IMO’s carbon intensity rules put container feeder ships at a disadvantage as almost all the voyages are less than 3 days, together with long ports stays compared to the larger container ships that perform the long haul voyages with comparatively short port stays. The CII rating assesses work done whilst sailing and not whilst idle in port.”
The IMO regulation, which entered into force on 1 January 2023, lists ‘heavy-load carriers’ in a catalogue of special vessels to which the CII does not apply. Yet there are concerns that carrying containers on heavy-lift vessels might be environmentally counterproductive, as
they require higher-consumption engines for propulsion.
“92 per cent of our voyages are under three days,” said Mr Pateras. “It makes it very difficult to get a good CII rating, especially when sailing to a port where we may face external delays before discharge.
As you can appreciate, calling at 4,800 ports annually seriously affects our CII rating.
“Contships goes to remote islands and small inaccessible ports whose
economies rely on us. Our feeder services are the lifeblood of communities. We are doing a service, but potentially destroying our CII credit due to the short voyages. So, change is seriously needed.”
Such a hot issue is bound to dominate discussion at Posidonia 2024, the world’s most prestigious shipping exhibition. Contships and thousands of global exhibitors are expected to converge on Athens for the June 3-7 event.
The Hellenic Chamber of Shipping will contribute with a stand in the Shipping Square, a focal meeting point for stakeholders.
“Posidonia supports the shipping community and can bring it closer together in a friendly, non-business atmosphere,” Mr Pateras continued. “It is an excellent networking event to meet people, thank them for the work we have done together and get to see innovative ideas emerging in the industry.”
Enthused about Contships’ future, Mr Pateras said, in conclusion: “Contships has dedicated, high-quality staff and
a fleet which is maintained to a high standard. We are at a perfect point to take advantage of any market upturns, adapt to new regulations and respond to environmental concerns.” n
Where traditional chemical tankers carry a full load of a single product, Chemship has established itself as a leader in parcelling. Now, Chemship has unveiled its latest innovation with a groundbreaking installation of high-tech Ventofoils on one of its vessels. Operations Director Michiel Marelis told Richard Hagan all about this exciting project.
Chemship is a tanker operator and ship owner active in the chemical sector on a trade route between northwest Europe and the eastern Mediterranean, and one running from the United States’ east coast to the Mediterranean.
From its headquarters on the outskirts of Rotterdam in the Netherlands, Chemship’s 21-strong team directs and manages the company’s uniquely sophisticated fleet of fifteen chemical parcel tankers. Through its fleet’s ability to carry multiple different products on board in a single trip, Chemship’s parcelling service sets it apart in a traditionally inflexible market.
Out of the world’s fleet of commercial vessels, very few are chemical tankers. Of those, fewer still boast full stainless steel cargo tanks as Chemship’s fleet does. Stainless steel, being the highest standard for the chemical industry, means Chemship can transport all of the most high-end chemical parcels. Consequently, the company’s client portfolio includes
high-profile companies such as all of the oil majors and multinational petrochemical manufacturers. Indeed, in an average year, Chemship serves more than 100 different customers.
Chemship’s fleet - all in the 12,000 to 16,000DWT range - is focused on parcelling, meaning that each vessel carries several cargoes from multiple clients, jointly on a single ship. Chemship’s vessels typically boast around twenty cargo tanks, across which as many as fifteen different products might be carried.
“We have many different parcels onboard at a time, ranging generally from 200 tonnes to 2,000 tonnes, and occasionally even a vessel full of a single product,” explained
Operations Director Michiel Marelis, who estimated that within Chemship’s specific m arket niche, there are only approximately eight to ten competitors. That number is set to decrease.
According to Chemship’s forecasts for the industry, the global fleet of chemical tankers, across all sizes, is rapidly ageing out and is not being replaced in sufficient
numbers. Consequently, Chemship expects the globally available fleet capacity to shrink considerably in the coming years, creating an opportunity for those remaining to capture an even greater volume of market share.
This adds further impetus to Chemship’s ongoing effort to maintain a fleet of modern, newer, efficient vessels.
“We’re in a comfortable position with our young fleet and it’s a position that we actively maintain,” said Mr Marelis. “In our fleet, which has an average age of seven years, we prioritise onboard innovations using the latest and best technologies to ensure that our vessels are efficient, well maintained and constantly in line with the latest emissions caps.”
In keeping with its focus on innovation and efficiency, Chemships is excited to announce that in February 2024, it is fitting
four high-tech VentoFoil sails to Chemical Challenger – one of its latest vessels – in a groundbreaking new sustainability project for the company. VentoFoils, which resemble aircraft wings, are foldable, autonomous, rigid structures fitted to the deck of a ship. These structures create high propelling forces, maximising thrust and substantially reducing the vessel’s fuel consumption.
The VentoFoil project has been in development for two years, having begun early in 2022 and having received final sign off in January 2024from Mr Marelis – the project’s lead. “It’s something special and we are very excited about it,” he revealed. “We have calculated that the fuel savings from the VentoFoils should be at least 10 per cent, but in optimum conditions, they could theoretically reach 20 per cent.
“However, our main focus is emissions reduction. Since wind offers non-polluting propulsion, it’s an easy choice for us. On that basis, we expect an annual reduction in our carbon emissions of about 1,000
tonnes of CO2; or the equivalent of about 500 average passenger cars per year.”
Each VentoFoil, which is sixteen metres tall, is equipped with a smart suction s ystem that uses internal fans to optimise airflow across the sail, maximising thrust g eneration and fuel consumption reduction. The VentoFoils are manufactured using aluminium, and their light weight of only seven tonnes each means that structural modifications were not required to fit them to Chemical Challenger.
Furthermore, the VentoFoils are able to fold down, allowing Chemical Challenger to maintain full visibility around the ship when entering or leaving ports, or to safely clear navigation hazards.
Chemical shipping is subject to a constantly evolving raft of legislative, regulatory and institutional rules, with the oil industry being particularly demanding, and there are good reasons for all of that. “Safety is the biggest priority at all times, not only to protect human health and welfare, but also to safeguard the environment, for example to avoid oil spills,” Mr Marelis said.
It comes as no surprise, that Chemship devotes substantial human resources to safety compliance.
Chemship’s ability to dedicate such a large amount of resources is thanks, in large part, to its long-term relationship with Fleet Management Limited, a Hong Kongbased ship management service provider.
Established in 1994, Fleet Management Limited began working with Chemship only a few years later in 1998 and the relationship has continued to bear fruit ever since.
“They’re a big company with which we have a long tradition,” Mr Marelis proudly noted. “We were the first chemical transport company to join Fleet Management Limited and the relationship is now so close that
their team has almost become like an in-house department for us.”
Fleet Management Limited takes care of Chemship’s technical and crewing management, freeing Chemship’s staff up to focus on the day-to-day running of its ships, compliance issues and client relationships.
Concluding, Mr Marelis reflected on his enthusiasm for chemical shipping. “I’m especially excited by the day-to-day challenge of finding the perfect combinations of cargo for the most efficient voyages, all while minimising emissions. And all of this while we’re working on keeping the fleet sustainable and experimenting to see what will work best for us into the future.” n
Österreichischer Lloyd Shipping (ÖL Shipping Group) has an extensive history stretching back almost two centuries. Over this time, the bespoke shipping service has remained committed to quality and working closely with partners. COO & Partner Sunil Kapoor and Chairman, CEO & Partner Captain Eberhard Koch explained this process to Hannah Barnett.
ATthe start of 2024, ÖL Shipping Group took a significant step forward with the appointment of Sunil Kapoor as Partner & Chief Operating Officer. He joined forces with Captain Eberhard Koch, Chairman, CEO & Partner, elevating the group’s potential.
“I retired from my last company in September 2023,” Mr Kapoor explained. “And I was intending to think more about what to do next, but Captain Koch made me an offer. It was clear we would make a great team to take ÖL Shipping in a new direction. So, all my retirement plans were cast aside.”
Captain Koch also noted that the age difference between the two individuals will guarantee the continuation of the company’s legacy for many more years.
The new managing force intends to develop ÖL Shipping and return to the bulk carrier market, purchasing ships as well as expanding its third-party ship management services and securing a shipping fund. Mr Kapoor is convinced that the company’s hands-on approach makes it stand out from the pack.
“We are a boutique ship management company,” he said. “We have a great pro fessional team based at our office in Limassol, Cyprus. Captain Koch has a lot of experience in shipowning and commercial banking and mine is in third-party ship management and operations. So, together we have formulated some strategies.
“There is a demand for hands-on firms offering services to owners based
on value and quality. We are focusing on the niche market because most ship management companies are huge. For small owners or small fund managers, that size does not justify doing business. They are looking for quality and ways that expenses can be minimised, while at same time, being run by skilled and experienced management.”
ÖL Shipping consists of a team of 12 onshore staff and an exclusive pool of 150 seafarers, many of whom have been working for 25 years or more alongside Captain Koch. The personal touch remains vital.
“I want our superintendents to treat third-party vessels the same as an owner would,” said Captain Koch. “That’s why we don’t want to have 50 ships, we want
to be a small, first-class ship owner and manager. Sunil and I can talk to owners on a daily basis, if so wished, which the big ship managers don’t have time for. We make the time.”
“We ensure that our operations remain simple yet efficient,” Mr Kapoor added. “Honesty and integrity are fundamental to our ethos. Every fund allocated for the operation and maintenance of our vessels is meticulously spent solely on the ships’ necessities. We diligently negotiate to secure the best prices for any stores and spares required for the vessel.
“Plus, we want to extend the life of those ships for many years, so we ensure predictability in terms of maintenance and reliability in operations.”
ÖL Shipping currently owns and operates three ships on long-term charter and one Kamsarmax bulker on third-party management. The company follows all EU and IMO guidelines regarding environmental measures, though in an uncertain and undeveloped market, is also keen not to waste money on untried technology.
“During dry docking, we take care of everything we can to reduce fuel con sumption and improve efficiency,” said Mr Kapoor. “However, we also have a ‘wait and watch’ attitude, unless new
regulations come in which require us to act. But, as of now, our approach is to see how things develop.”
ÖL Shipping works closely with suppliers, owing a portion of its success to corporate relationships that stretch back for decades. At the same time, it is part of the company ethos to conduct business in a considered manner.
“Even if we have a main supplier, we will still tender three different companies, taking our time to compare quality and price, then the best quality for the best price will get the order,” Captain Koch explained. “We have suppliers in Cyprus, Singapore and China that we have worked with for 25 years. They know exactly what our standards are.”
Indeed, to uphold such principles, ÖL Shipping only uses genuine spare parts from recognised suppliers.
“We don’t cut corners,” said Mr Kapoor. “We use first-class spares and pay for them on the dot so there is no question of a dispute later. That has been our forte, even during turbulent times in the market, and we have been able to maintain good relationships that way.”
This focus on quality suppliers is reflected in the company’s relationship with its customers, too. Namely, the price a customer pays guarantees the standards the company will deliver.
“We set our budget on this basis,” said Captain Koch, “and it is down to the ship owner to decide whether to go for a company with 500 ships or us, a small boutique. We will deliver quality and attendance 24/7, 365 days a year, while treating the vessels like our own. But the owner must accept, possibly, a slightly higher price than they will get from a large third-party management company.”
As ÖL Shipping has a relatively small number of ships to look after, its superintendents can focus on delivering a superior
service. The company’s crew retention rates are high, meaning those employed are skilled and familiar with the operation of the vessels.
The company also has its own riding teams based around Europe. Whenever necessary, they will go on board a ship to carry out maintenance, contributing to ÖL Shipping’s focus on crew safety and security.
“Our mobile phones are not switched off overnight,” said Captain Koch. “If the captain or chief engineer of a vessel needs support or advice, we tell them not to hesitate to call us, anytime.
We are a team, and it is the team that is successful.”
The company has a goal to increase its fleet to 12 ships within the next few years, as well as creating a fund to invest in more vessels. With these plans firmly in motion, and ever more possibilities offered by technology, digitalisation and AI, will ÖL Shipping ever lose its hands-on approach?
“A ship cannot be run by sitting ashore and giving instructions to the crew,” Mr Kapoor concluded. “Yes, technology is required to improve efficiency, but at the end of the day, we need to support the ship staff who are actually onboard. So, we embrace the technology that is out there, but that does not mean that our ships will ever be operated solely that way.
“ I’ve been in shipping all my life. There’s no better career because every day is different. It keeps us excited. We work hard and take problems in our stride. Though we may not carry the weight of industry giants, our strength lies in our unwavering commitment to delivering tailored excellence, ensuring every interaction reflects the core principles of the requirements that define us.”
n
SWAN Shipping Corporation is a prominent player in the Philippines – providing first-class ship and technical management, plus newbuild supervision. With almost 30 years in the business, and a flourishing fleet, the operator is getting ready to welcome new growth. President Bong Salas explained more, in an exclusive interview with Inside Marine. Report by Imogen Ward.
Despite its small size, SWAN Shipping Corporation has successfully maintained a strong global presence since it began operating in 1995.
“Our fleet operates worldwide,” said President Bong Salas. “In terms of trade breakdown, we have ten vessels trading in the region of Southeast Asia (including one Philippine domestic); six in West Africa (with occasional calls at European, Caribbean and US ports); one in Australia/South Pacific; two in the Mediterranean; and two in South Asia/Middle East. We are running a truly global operation.”
Time and time again, SWAN has proven its position as a market leader, becoming the first Filipino ship management company to receive a document of compliance from ABS (before it became a mandatory requirement).
“We are now 100 per cent Filipino owned, and as one of the first companies to hold
that status within the petroleum sector, we have been recognised internationally as a leading ship manager within this expertise,” continued Mr Salas.
This prestigious status has placed SWAN in high regard with major energy conglomerate Shell, who the company has maintained approved contracts with for many years.
Currently, SWAN manages a fleet of 21 LPG carriers, which range from 3,500CBM to 15,000CBM (the 15,000CBM gas carriers
are the largest Type 2PG gas carriers ever built). These LPG carriers are commercially operated, mostly by gas traders, including one of the biggest operators in Europe. 17 of these carriers belong to Japanese shipowners; three to a Greece-based client; and one to a Filipino client. The fleet has an average age of seven years, with the newest vessel just a few months old.
“Collectively, the management at SWAN has over 100 years of experience in ship management,” explained Mr Salas. “It is our main area of business and offers our shipowners full technical management
services from crewing and maintenance to drydocking.”
SWAN provides a comprehensive planned maintenance system as part of its technical management service and arranges the supply of stores, spare parts and lubricating oils. The company also provides an in-depth inventory system and arranges servicing and safety inspections on lifesaving equipment.
“Most importantly, we arrange oil major inspection, which is a standard requirement in the petroleum industry,” Mr Salas added. “We inspect our ships twice yearly, and we handle all drydocking work as well.”
The company also has a team of engineers dedicated to newbuild supervision and has successfully overseen the construction of eight LPG carriers (six of which joined the SWAN fleet).
“We make sure our team is always abreast of new requirements to maintain customer satisfaction,” explained Mr Salas. “The shipping industry is very dynamic, and regulations often change. We provide con -
tinuous training, keep in touch with industry partners and adopt new technologies to stay ahead of the curve.”
Keen to advance its position in the global maritime market, SWAN recently implemented a strategic growth plan focused on its fleet.
“Every ship management company has a desire to grow its fleet, and we are no exception,” commented Mr Salas. “This is our core business, and we are committed to developing it in a way that does not jeopardise the safety of our operations. We plan to add a further two vessels to our fleet before the end of this year. Between the years of 2025 and 2027, we intend to increase this by another five vessels.”
With completion targeted for 2027, the company is well on its way to achieve its ambitious objective. Of course, when new vessels are added to the roster, an increased number of crew members are
needed to provide the quality and safety assurance that SWAN is renowned for.
“Fleet expansion requires an increase in manpower, both offshore and onshore,” added Mr Salas. “To account for this development, we have leased an additional office space. We believe this will be a real benefit for our employees.”
SWAN has also implemented an internal development programme, which allows it to identify what training each employee needs to perform the job properly.
“Above all, investing in our people and their personal growth is the most important thing we can do,” Mr Salas explained. “We always ensure the necessary training is provided, so that each crew member can perform their daily duties. Not just that, but we really like to see them advance in the company as well.
“This has been a huge success, because each worker is encouraged and motivated,
knowing that management is looking after their future and helping them progress to the next level.”
The company also assists its manning agent, a sister company, in running its cadetship programme, which key people in the office have benefited from. This has been in place for many years and is something that SWAN is incredibly proud of.
“From General Manager Captain Luis Laurente to our Marine and Technical managers, they are all a product of our cadet programme,” said Mr Salas. “Right now, our group has around 353 cadets (209 onboard / 144 on vacation) on the programme. Fifteen of those cadets are currently assigned to SWAN, while the rest will go to other principals in order to help sustain manning needs of the industry.”
In line with its commitment to its people, HSSE has always been a number one priority for SWAN, and the company is continuously
looking for areas in which it can improve. The company recently hired a third-party auditor to carry out an inspection on its safety management system.
“In March, we flew in an industry expert from Singapore to carry out an audit of our company,” Mr Salas explained. “We really wanted to identify the gaps in our existing safety management system. Of course, we work with it every day, so there is always a risk in becoming blind to the imperfections, and we don’t want that to happen.
“The expert brought a fresh set of eyes to the process and, using gap analysis and comparative investigation, he was able to highlight areas that could be adjusted to improve our system.”
As it travels this path of positive improvement, SWAN intends to continue growing to position itself on the cutting-edge of the industry.
“Our ultimate objective is to be recognised as one of the biggest management companies in the world, whilst providing an efficient, cost-effective and environmentally friendly shipping operation,” Mr Salas said, in conclusion. “We are incredibly proud of all that we have achieved over our almost 30year history, and we can’t wait to see what the future brings.” n
Sealink Navigation was founded in 2011 by a team of shipping professionals with a long history in the industry, most notably in the Asia-Pacific and Europe. The company has headquarters in Singapore and Greece, where it operates a fleet of modern Japanese-built vessels equipped with the latest eco-technology. Hannah Barnett spoke to Nicholas Kosmatos, President & Co-Founder, to learn more.
Since 2011, Sealink Navigation has been transporting dry bulk cargo and working with renowned charterers worldwide. The company’s business plan, both then and now, focuses on quality Japanese tonnage.
“I was born in Japan,” said President & Co-Founder Nicholas Kosmatos. “Though I have no actual Japanese blood, I have a long history with the country, the culture and the people. So, when we started the
company, it was natural to want to do a lot of Japanese business.”
Sealink Navigation began operations with the purchase of a 28,500DWT ship built by Imabari Shipbuilding, Japan’s l argest shipbuilder in terms of tonnage and revenue. True to the international flavour of the company’s operations, this initial
J apanese ship was bought with a loan from a German bank and fixed to a Norwegian chartering company in Singapore.
“A few years later we signed an order for two Namura handysize vessels, a traditional Japanese yard known for its quality products,” said Mr Kosmatos. “This was very important for Sealink Navigation because it was our first newbuilding contract. It was also a very proud milestone because it was Japanese-built and therefore very important for us in terms of quality and company reputation.”
Between 2013 and 2021, Sealink Navigation was strategically focused on expanding its fleet. The company purchased eight ships in that time (six of them being new buildings from Imabari), as well as selling several more. That period officially ended with the delivery of an Imabari 63,600DWT eco-Ultramax in December 2023.
“That phase was a very serious ongoing project and a hugely capital intensive
one which took away most of our time and money,” Mr Kosmatos explained. “It was effectively about building the company from scratch, while running a new business plan at the same time.
“Now, we are holding our firepower, as prices are quite firm. But there are always plans to expand and at some point, we will go back into the newbuilding process to update our fleet to the latest technology at that time.”
Indeed, investing in newbuild ships has so far allowed Sealink Navigation to keep up to date with innovative ecofriendly designs that correspond with the shifting and developing landscape of regulations.
“Eco-regulations are an ever-changing topic,” Mr Kosmatos added. “We try to adhere to all the regulations available. Luckily, when we buy a good Japanese ship from a yard known for its quality,
all these standards are a given. It means we don’t have to try and reinvent the wheel all the time.”
As a company with a clear focus on high standards, a strong relationship with partners and suppliers is inevitable. But what is the secret to ensuring a loyal partnership?
“It’s really easy, we just pay on time,” said Mr Kosmatos. “We are quite surprised that many people haven’t figured it out yet. In return, we expect a lot from our suppliers and are very firm on what we want in terms of service and quality.
“We have quality suppliers; we do not cut any corners in terms of quality.
“I think the quality and tender loving care that Japanese shipyards offer fits with our company ethos very well”
As well as paying on time, we build long-term relationships by making sure that we meet all the obligations that we
have as a buyer. And for our spares, we use strictly original Japanese parts.”
Challenges, of course, remain across the shipping industry, including the struggle to keep up with ever-changing regulations. Another ongoing task is encouraging new seafarers into the industry and training them to the high standards expected from a company like Sealink Navigation.
“Human resources are going to be a big part of the future, especially with the growth of AI,” Mr Kosmatos reflected. “I think it’s going to be a much more difficult challenge than regulations thrown about by governments. Plus, the human element is much more important - how do we convince somebody in India or the Philippines to go to sea?”
Due to the importance placed on hiring the right people, the company has an ongoing close relationship with AngloEastern Ship Management in Hong Kong, which provides all its crews.
“We’ve been doing business with Anglo-Eastern since we started in 2011, when it was called Univan,” said Mr K osmatos. “And we are very satisfied with their performance. They are a key partner for us. We haven’t had any problems with recruitment all these years, because we slowly built up a very strong roster of people and we like to think that we are very professional in how we meet our obligations towards our staff.”
The company has training facilities in India and Manila and conducts regular meetings and visits to make sure that the best education possible is provided for the up-and-coming seafarers.
“It’s Anglo-Eastern’s job to source our crew, but it’s our job to make sure that the people who come to us are the best people available and then to provide them with the best facilities possible to use,” said Mr Kosmatos. “Our operations department likes to maintain personal relationships with captains, engineers
and chief officers: all the key personnel on ships. We make sure that we have the personal touch. I also make a point of meeting as many of the crew as I can, because they’re the most important people in our business.”
In a corporate industry, one of Sealink Navigation’s main goals is to show the benefits of the personal touch, including the flexibility that a smaller company can offer clients.
“I think there’s a lot of value to be had as a small company,” said Mr Kosmatos. “We find that our clients like that as well, because they can talk directly to owners and the people who matter, rather than deal with faceless corporations.”
Indeed, this person-centred approach correlates closely with the company’s
focus on Japanese design and the associated culture. It is part of what makes working at Sealink Navigation so special.
“I’m biased because I’m very pro-Japan, but I think the quality and tender loving care that Japanese shipyards offer fits with our company ethos very well,” Mr Kosmatos concluded. “These are ships that the shipyards are proud to build. It’s similar to the traditional Greek family shipping company; taking pride in the job and working with efficiency and skill, while remaining flexible. I think this is a complementary ethos.
“Tradition is very important for us. It is reflected in the quality of all the products we use; whether they are financial, or whether they are assets, like ships. Tradition is what makes the shipping industry beautiful. We don’t believe in disruption for disruption’s sake.” n
seven seas, five oceans, one voice
privatsea aderco international hays hydraulics & ca engineering geoquip marine mekiro bv
Yachting management specialist PrivatSea operates a network of global facilities strategically positioned to optimise service. Chairman Stavros Xenakis outlined the core features of the company and the importance of attention to details. Report by Phil Nicholls.
Greece-based PrivatSea is the complete yacht management company. A pioneer in the yachting world, PrivatSea offers full-service management packages, supporting private and corporate super yacht owners.
“What makes us unique is not just the variety of services we offer, but also our dedication to delivering excellent, individualised care,” explained Mr Xenakis. “We don't just handle tasks; we take a thorough approach that revolves around tailoring solutions to match each client's specific requirements.”
PrivatSea is part of the Latsis Group, which was founded in the 1940s by the late John S Latsis, with early entrepreneurial ventures focused on trade and shipping. The group quickly expanded to include diverse business interests such as commercial shipping, energy and real estate. The Latsis Group moved into yacht management in 1977, following the acquisition of Henriette, a 53-metre yacht built in 1949.
Expansion of this involvement in yacht management came with Sete Yacht Management established in 1998, followed by PrivatSea in 2004. Building on this extensive experience, PrivatSea today manages some of the world’s most famous mega yachts. The team works hard to provide a transparent, professional service that accounts for every detail.
“Our esteemed team consists of highly skilled professionals meticulously trained to handle all facets of yacht ownership, with close attention and utmost diligence,”
said Mr Xenakis. “Our notable growth over time serves as evidence of our clients' confidence in our expertise and reliability.”
With offices in prominent locations in Athens, Monaco, London, Geneva, Jeddah and Bahrain, PrivatSea is always close to its clients.
The focus of PrivatSea encompasses a broad spectrum of projects, from routine maintenance to complex refits and newbuilds. At present, the company is involved in various projects including regular upkeep, intricate renovations and the management of new vessels.
Also within the Latsis Group is the Talos Shipyards, one of the largest shipyards
in the Eastern Mediterranean, with 1,500m of docks and piers, plus 88,000sqm of land. This facility handles large vessels up to 300m, with a maximum draft capacity of 20m.
From 2006, the shipyard was transformed to accommodate vessels for permanent or seasonal berthing, maintenance, refits and conversions. Services available at Talos Shipyards include power, telecommunications, water, waste removal, fuel, storage, office space, 24-hour security and CCTV. The company is licensed by the Greek Authorities for building of vessels, conversions, repairs and maintenance.
In partnership with PrivatSea, Talos Shipyards is committed to providing the highest standards for services at competitive rates. Talos is the shipyard of choice for yacht refits, refurbishments and maintenance for vessels under PrivatSea’s management.
“One notable project was our recent completion of a major renovation for a 62m Amels yacht,” continued Mr Xenakis. “This accomplishment showcased our strong interior design team and technical abilities with meticulous attention to even the smallest details,
further solidifying our standing in the industry as a leading management firm.”
C ore to the appeal of PrivatSea is the ability to deliver a bespoke package of capabilities to discerning clients. This package encompasses a wide range of yacht management services, covering technical, operational and financial aspects, all of which are precisely tailored to meet the specific needs of each client.
“It is this mindset that allows us to form strong, lasting bonds based on trust and dependability, setting us apart in a crowded market,” Mr Xenakis explained. “Furthermore, our Shipyard and Project Management Team contribute significantly to this commitment, ensuring that every aspect of our clients' projects is handled with the same level of attention to detail and quality.”
To maintain these high standards, PrivatSea continues to evolve. Active participation in prominent events underlines PrivatSea’s dedication to propelling the global yachting sector forward. The company encourages industry-wide cooperation and pioneering advancements, according to Mr Xenakis:
“An exemplary demonstration of this commitment is our engagement at the Monaco Yacht Show. Here, we showcased our latest innovations and forged key alliances to drive global progress and innovation within the industry.”
The Monaco Yacht Show is a truly spectacular showcase for the industry, set against the glamorous backdrop of M onte Carlo. PrivatSea is able to welcome VIP visitors to its offices just across the
road from MYS, a location which boasts a terrace with a bird’s eye view of the entire bay. The show is always a great opportunity to have a 360 ⁰ view of the sector, reconnect with associates and discover the latest trends in the world of super-yachts.
Alongside discussing bespoke services face-to-face with clients and prospective clients, the 2023 MYS also saw interest in PrivatSea’s two vessels for sale: MV Minerva and the exquisite MY Lady Sarya. MV Minerva is a boutique cruise vessel, tastefully decorated, that can accommodate 300 guests on six decks. A legendary 76m yacht, Lady Sarya can accommodate 11 guests in six cabins with en-suite bathrooms and up to 36 crew. Refurbished in 2020, the yacht is
the ultimate combination of vintage ambience and classic luxury.
Delivering high standards of service requires close partnership with a network of suppliers. The underlying philosophy at PrivatSea is to foster long-term relationships with suppliers and partners through open communication, mutual understanding and a commitment to shared goals.
“ Our approach emphasizes transparency, reliability and responsiveness, ensuring that collaborations are based on trust and respect,” concluded Mr Xenakis. “We greatly value the contributions of all our partners, as every collaboration is instrumental in our success, collectively contributing to our operational excellence and helping to deliver client satisfaction.” n
Aderco International is globally renowned for its innovative and cutting-edge fuel treatment solutions. With the journey towards net zero a global priority, Aderco is implementing solutions for the future. CEO Olivier Baiwir, COO Philippe Lecloux and CAO Charlotte Baiwir explained more, in an exclusive interview. Report by Imogen Ward.
When it was first established in 1981, Aderco Ioperated with a desire to improve fuel efficiency and operational reliability. Throughout its evolution and adaptation over the years, the company has remained deeply connected to its original purpose.
“Today, Aderco is very much a forwardthinking company, consistently driving innovation to enhance the performance of energy transition,” explained CEO Olivier Baiwir. “Our products are perfectly designed to treat and solve fuel issues for almost all types of vessels, while also minimising their environmental impact.”
Aderco started more than 40 years ago in Montreal, Canada.
“At the time, Aderco was conducting research to improve the fuel efficiency, operational reliability and environmental
impact of the Canadian Coastguard’s icebreaking fleet,” said Mr Baiwir.
With support from the Government of Quebec, Aderco developed its first surfactant formula into a product that could be industrialised for the marine industry. “The product became a great candidate for those looking for a non-solvent-based solution,” continued Mr Baiwir.
In 2007, following an industry wide crudeoil shock, the business was tasked with researching a vegetal-based alternative to its famed solution, in the hopes that it would greatly improve product performance and be better for the environment.
“It took almost two years just to identify the product, from there we had to test its stability, quality and performance,” explained Mr Baiwir. “Following a full validation of the new formula in 2013, we decided to implement it everywhere. ”We are proud to have a fuel additive from the 21st century.”
In March 2014, a change in company ownership served as the true catalyst for the company's transformation and growth. “Since then, our company has been the first to design and formulate green and sustainable organic surfactant technology,” said Mr Baiwir. “Through extensive research and development, we have effectively addressed fuel-related issues with great success, as well as developing environmentally friendly products for the most diverse applications involving combustion engines.”
One of the most significant milestones in the company’s 40-year history, particularly in terms of enhancing its reputation, has been the implementation of the new IMO low sulphur regulations, which took effect on January 1, 2020.
Leading up to the deadline for low sulphu r fuels, the entire Aderco technical team played a pivotal role in advising ship owners and managers with clear and concise facts, emphasising the necessity of tank cleaning prior to the introduction of new fuel and highlighting the critical importance of fuel treatments for the ongoing maintenance and operation of marine engines.
The company is proud to offer sustainable products that continue to improve efficiency, solving fuels issues and making a positive impact by minimising fuel consumption and reducing CO 2 emissions.
Today, Aderco operates with a full line of plant-based solutions – each one designed to provide crucial improvements in the fuel economy of its clients while also prioritising environmental suitability.
According to COO Philippe Lecloux, when it comes to its customers, Aderco serves three separate categories: “There are the customers that religiously use Aderco’s additives, these individuals are proactive in ensuring vessel maintenance. If these customers ever have a problem, it is minimal and can be easily solved.
“We also serve companies that use our additives when there is a problem because they help clean engine components, filters and separators. The third category involves the companies that have tried several other products, and they haven’t worked. These are often the most complex cases,
because by this point the fuel is a hybrid mixture of lots of different chemicals. It is difficult to decipher whether the fuel was actually poor quality or whether it is the cocktail of additives that is negatively affecting the vessel’s efficiency.
“No matter the category, we are happy to help, because we are experts in our field, and we have confidence in our products. If Aderco cannot solve the problem, then others certainly cannot.”
When it comes to the shipping industry, Aderco currently offers two separate solutions. The 2055G is the perfect solution for those looking for power generation and fuel conditioning. As the company’s most concentrated surfactant, the 2055G homogenises fuel, works to clean and protect components, and improves energy efficiency whilst reducing carbon emissions.
The L1050 is also a perfect solution for generating power. The perfect partner for low and ultra-low sulphur fuels, this solution solves lubricity loss, and thus protects a vessel’s fuel pump and injection system.
Also on offer are two products that were developed with inland sectors in mind. The V35 and V25 are both hybrid combustion and lubricity improvers perfect for road and rail transportation. The company also has a surfactant/dispersant dedicated to road users who consume a smaller amount of fuel.
With the increased popularity of its products, in 2017, Aderco made the strategic decision to expand its physical presence, by opening a new branch in Singapore: Aderco Pte.
“We assessed the market to see what fuel treatment solutions were available,” explained Mr Lecloux. “The products ranged broadly from sophisticated solutions to snake oil, and we realised that there weren’t many competitors at our level of specialism. So, we took the opportunity and introduced our solutions to the Asian market. This was an incredibly exciting time that brought with it several challenges.”
Aderco strongly believes that the next generation should be able to live in a sustainable world that has embraced an efficient energy transition. With this in mind, and with the shipping industry heavily focused on lowering emissions, Aderco is looking at different ways to apply its own knowledge.
“Now more than ever, there is a huge amount of talk surrounding the potential of biofuels, and we are ready to help provide solutions,” said Mr Lecloux. “As a member of the Singapore Shipping Association’s fuel and biofuel committees, every day, we witness the ways in which Singapore is looking to push the boundaries of fuel supply in order to develop a huge business for biofuels in Asia.
“We have developed lots of tests with industrial partners to place ourselves on the cutting edge of this new market, including corrosion prevention which has provided some very promising results. We are ready to face the challenge of biofuel.”
This is just one of the many ways that Aderco is working to progress carbon reduction in the marine industry. The company
remains committed to innovation through its research and development, in addition to conducting various studies on its current portfolio to accurately assess the products’ capabilities when it comes to carbon reduction.
Aderco also involves itself in a lot of CSR initiatives, following the implementation of its CSR indicators in 2021. According to CAO Charlotte Baiwir, this is incredibly important: “When we give our support to a project or initiative, we don’t believe in just giving financial support. We take pride in our hands-on approach and the collective achievements of our team.
“In February 2024, I was in Sierra Leone supporting Mercy Ships, an international humanitarian NGO, focused on enhancing healthcare accessibility in African
countries by providing treatment onboard their ships. We take pride in our collaboration with Mercy Ships, offering s upport through various means, including product donations.
“Every Aderco branch actively participates in CSR initiatives, even though we are a small company, we continuously seek new avenues to support those in need.”
“ We are constantly driven to act for the climate, and we work hard to implement effective R&D for tomorrow’s fuels,” Mr Baiwir said, in conclusion. “Our ability to be innovative has helped develop Aderco into a responsive company that is treating a huge volume of fuel annually to improve our customers’ efficiencies and help combat climate change.”
n
Hays Hydraulics and CA Engineering are a match made in heaven. The two companies operate side-by-side, having carved out their niche within a diverse range of sectors. Director Cameron Steel explained more, in an exclusive interview. Report by Imogen Ward.
Business partners Cameron Steel and Andrew Milne were both employees of Aberdeen-based Hays Hydraulics when they became inspired to set up their own business. Determined to make their dream a reality, the two coworkers established CA Engineering in 2012.
“I had been at Hays for three years when we decided to take the plunge and set up CA Engineering,” Director Cameron Steel explained. “We really wanted to give it a go with a business that was both similar and different to Hays. CA was definitely focused more on plant construction, and we successfully built it up as the years progressed.”
Following seven years of successful growth, CA acquired Hays. Now, both com -
panies are operating with a close-knit team, Hays with 12 employees and CA with 11.
“We worked tirelessly to build CA from the ground up and have really enjoyed diversifying the company’s presence in various sectors,” Mr Steel continued. “We began the company with a focus on plant work and eventually diversified into marine, alongside oil and gas. This transition aligned perfectly with Hays’ expertise, and an acquisition felt like the perfect step forward.”
Today, CA also offers fleet support, HGV diagnostics, repairs and recoveries, whilst also providing its services for thirdparty businesses as well. The company has a large fleet of onsite mobile hose
manufac ture vans; six at CA and a further six at Hays. It also maintains three lorries and one recovery wrecker at CA.businesses as well.
“We work anywhere that requires hydraulic which covers many different types of industries,” said Mr Steel. “We recently started doing work in the renewables sector, which is an area that Hays is exploring as well.”
Positioned two minutes from the Aberdeen Harbour, Hays operates from a purpose-built facility, supplying a diverse range of hydraulic components and lubricants to both the marine and the oil and gas sectors. More recently, the company has been making a name for itself within renewables.
A path to renewables
Determined to make waves in the renewables market, Hays recently entered a significant contract with North Star Renewables. Having worked with North
Star previously on several successful oil and gas projects, Hays was confident that this partnership would continue to bloom in new waters.
“The contract with North Star Renewables has just been extended,” Mr Steel explained. “Originally, the company contracted us to design two cargo lifts for its new vessels; we are now under contract to manufacture six. This has been an incredibly successful project, and we now have several other clients enquiring about the same equipment for various applications.
“We are really enjoying growing this side of the business, having previously focused on repairs. It has taken us out of our comfort zone and been a huge learning curve, but we are incredibly proud of what we have achieved.
“Having worked with North Star since the inception of Hays, it has been great to con-
tinue our relationship with that company in a way that has enabled us both to flourish and grow.”
The new cargo lifts will help to speed up North Star’s operations considerably, whilst also working to improve safety at port and save the company money.
Renewables is a sector that has witnessed rapid expansion over the last decade, and now with the world transitioning to greener energy, it is an area within which both companies are hoping to branch out further.
“In our line of business, everything is much the same,” said Mr Steel. “That’s why, for us, the transition from traditional energy to renewables was fairly straightforward. Of course, the equipment is a bit more advanced, but we are confident we can keep up.
“We have even had several companies requesting our skills to help them break into the renewables market here in
Aberdeen. More than anything, breaking into the market is the biggest challenge. So far, we have experienced quite a simple transition.”
Hays also works closely with Dales Marine, which is a dry dock specialist with multiple facilities located across Scotland.
“We travel to the Dales Marine dry docks frequently,” Mr Steel added. “This is where we complete all the hydraulics works for the vessels that come into dock. We carry out inspections and repairs to various types of cranes and davits.”
Hays and CA also share a davit system, which is available for hire throughout the year. This is great for launching lifeboats and fast-recovery craft.
Teamwork is a crucial element of both Hays and CA. The two companies regularly work together when opportunity arises.
“If one company is significantly busier than the other, then we are able to share the workload to ensure the job gets com -
pleted on time,” said Mr Steel.
“This collaboration also helps when location comes into play. If Hays is working on a job and CA needs to respond to a breakdown in the same area, we can pool our workforce and remove unnecessary traveling by sending our Hays engineers to both sites.”
This teamwork really helps to provide the best customer service, whilst also keeping their combined carbon footprint to a minimum. This is reinforced by the locality of the two companies, with them both situated within a mere 15 miles of one another.
Staff are also an important element of this collaboration, with both companies utilising a solid team of hardworking individuals. Included in this are several apprentices. With CA housing two and Hays supporting another, the sister com-panies really value the importance of bringing fresh faces into the industry, whilst providing them the knowledge and support needed to succeed.
This sentiment is also extended to the wider workforce with regular training sessions provided from an in-house training room. Most recently, employees were recertified for ABS accreditation, allowing them to carry out annual and five-yearly inspections on life saving equipment.
The two businesses also rely on a chain of reliable suppliers to complete each project to a high standard.
“We couldn’t do it without our suppliers,” Mr Steel explained. “In our line of business, everyone wants everything yesterday. When it comes to boat repair especially, there is only a short period of time where repair work can be carried out, so we rely on our suppliers to be able to source parts quickly and at a reasonable cost.”
With more than 30 years’ experience combined, Hays Hydraulics and CA Engineering have built a solid base of reliability, quality and ingenuity. As far as the future is concerned, the two companies intend to continue this journey of success with new growth opportunities.
“We really want to concentrate our efforts t owards growth,” Mr Steel said, in conclusion. “However, we also want to take the opportunity to streamline our businesses to make them better for our customers.
“When we set up CA Engineering 12 years ago, we never visualised that it would take off in the way that it has,and we can’t wait to see what the future brings for both CA Engineering and Hays Hydraulics.” n
Geoquip Marine is a leading player in offshore geotechnical data acquisition, specializing in safely delivering reliable data. In recent years, bolstered by a team of key individuals, the company has explored several new markets. Head of Technical & Business Development Hans Hanse explained more to Imogen Ward.
ASfrontrunners in the acquisition of offshore technical data, Swiss-based Geoquip Marine is expanding its presence within the offshore renewables sector.
“Over the last few years, we have experienced massive growth,” said Head of Technical & Business Development Hans Hanse. “Back in 2018, we were a relatively small company of around 130 people, and now we have more than 600 employees. This expansion was mainly triggered by the energy transition, which enabled us to sell our expertise to a new market.
“We are now one of the main players in supplying offshore geotechnical data, and
more than 95 percent of our work comes from offshore wind projects.”
The remainder of Geoquip Marine’s work is dedicated to supporting scientific research, as well as oil and gas.
“We also aid investigation work for gas hydrates, which we have done mainly in Southeast Asia, and we work with many ports and harbors to facilitate large port expansions,” Mr. Hanse revealed.
Since 2011, Geoquip Marine has developed a strong reputation within the offshore sectors. Today, the company uses i ts fleet of six geotechnical drilling vessels to deliver a reliable and efficient service across the globe.
With business booming in the offshore wind sector, Geoquip Marine has taken the opportunity to explore business within America.
“Over the years, we have completed quite a few projects in the United States, it is a market with a lot of potential,” said Mr. Hanse. “In 2019, we conducted site investigation for what will be the biggest wind farm in the States, if not the world. Being awarded this project was a major milestone for us. In fact, one of the main
reasons we were granted the job was our scalability: we had enough vessels to provide a reasonable turnaround time.”
The project took two years to complete and relied on half of Geoquip Marine’s fleet. In that time, the company covered 220 sites. Since then, Geoquip Marine has remained active in America, particularly on the East Coast.
Geoquip Marine is currently conducting an ongoing campaign for Vineyard Wind, offshore from New York and Massachusetts. According to Mr. Hanse, the project will utilize two of its vessels for a considerable amount of time.
“We actually completed the initial site investigation work for Vineyard Wind, last year,” said Mr. Hanse. “Now, we have successfully negotiated a separate contract for two more programs, which are about to begin.”
With innovation at its core, Geoquip Marine spends its time on the cutting edge. Most recently, the company has developed a new site investigation deep push seabed CPT machine.
The new equipment is expected to hit the market early in 2025 and is anticipated to really enhance the company’s offering.
Geoquip Marine has plenty of experience in the development of CPT machines, having already developed the 200kN seabed CPT unit, which can conduct tests whilst a vessel is stationary. All the data from these tests is captured in real time, ready for processing.
The Geoquip Elena (a DP2 integrated geotechnical survey vessel) is equipped with a 20 tonne seabed CPT unit
All this data is collated by Geoquip Marine’s engineering team, which is an element of the business that Mr. Hanse is incredibly proud of.
“We are becoming a force to be reckoned with when it comes to engineering,” explained Mr. Hanse. “We are developing
our own software to analyze data, which is crucial in today’s market. Back in the day, we would be working on one big platform at a time, now we are completing projects in America with over 200 sites. The amount of data we now process has increased substantially , and we are developing smarter ways to deal with it.”
The company has also been advancing its Environmental, Social and Governance initiatives, to help safeguard the environment within which it works. With a strong presence in the development of renew able energy, Geoquip Marine has worked hard to implement measures to reduce the use of fossil fuels.
“We have assessed several different methods that will be useful in reducing
our fuel consumption, from the reuse of power to the reduction of energy used; we are considering all angles to ensure our footprint is minimal,” Mr. Hanse explained.
The company has also implemented policies to reduce waste, particularly aiming to minimize the use of single use plastics offshore. More recently, volunteers from Geoquip Marine’s UK-based office partook in an annual beach cleanup operation at Sand Bay in North Somerset, to help preserve the natural surroundings.
Today, Geoquip Marine is a sizeable company with plenty of experience. Despite its size, the company has maintained a unique structure.
“Our ability to remain quite a flat organization is what really sets us apart in the market,” commented Mr. Hanse. “We are incredibly accessible, with an aversion to red tape, which makes us more approachable. Our clients also appreciate our commitment to the project – typically, the people who they negotiate the contract with are also involved during the execution of the work. This creates a positive rapport and makes our clients more comfortable with us.”
This particular dedication to clients has afforded Geoquip Marine many successes over the years, and the company hopes it will be a continuous aid as it approaches new marketplaces and expands its presence in current markets.
“We successfully operated a geotechnical vessel in Taiwan over the past three y ears, where we also have an office, so the Asia-Pacific region is one that we are following with great interest,” explained Mr.
Hanse. “We intend to develop our presence within Australia and Vietnam as well.
“Of course, the Australian wind industry is still very much in its infancy, so we are waiting eagerly for these projects to be at a point where they need our help. We are probably still two years away from that point.”
The company is also looking into the possibility of using its vessels to aid the installation of structural anchors within the floating offshore wind sector.
“We can use our vessels to drill holes where the anchors are going to be located,” Mr. Hanse added. “This would be a great opportunity for us to diversify from geotechnical site investigation works.”
Geoquip Marine is currently in discussions with several developers regarding the
possibility of implementing the required technology. All going well, the geotechnical expert intends to begin trialing projects early next year.
“We will actually be looking to adapt our larger drill rigs, originally designed to support offshore projects in ultra deep water, to drill these anchor pile holes,” said Mr. Hanse. “It is great to see vessels which were traditionally designed to serve oil and gas being repurposed for floating offshore wind.
“I am really looking forward to what the future holds, and it’s so refreshing and exciting to be part of a successful company that everyone contributes to. All of us here in Geoquip enjoy the freedom to make decisions which will take the company in the right direction.” n
Mekiro BV is renowned for being a premier distributor of speciality chemicals. The company offers a firstclass service that is swiftly expanding. Sales Director Anthony Hughes explained more, in an exclusive interview. Report by Imogen Ward.
For chemical distributor Mekiro, 2020 sparked a journey of growth, as it sought to enter previously unexplored markets.
“When I joined the Mekiro team in 2019, I stepped into my role with the ambition to broaden our offerings,” said Sales Director Anthony Hughes. “It was essential to ensure the wider stability of our operations, rather than being solely focused on one main area.”
Established in 2009, Mekiro is a fully owned subsidiary of Meade-King, Robinson & Co, a key partner to the world’s largest chemical companies since 1867.
“Mekiro was actually launched to expand the group’s activities on European soil, whilst also taking selected product groups into new markets,” Mr Hughes explained. “Soon after that, Mekiro became the official distributor for Koreanbased Kukdo Chemicals – a company dedicated to the manufacture of epoxy resins, curing agents and diluents – within the Benelux region.”
Having been represented by MeadeKing, Robinson & Co in the UK and Ireland since 2006, Kukdo’s evolving needs were a perfect match for Mekiro’s ambitions.
From there, Mekiro continued to expand its offering of epoxy-based products in a range of sectors, including industrial flooring, marine and several other highend composite segments.
“We lay foundations with stock holdings in key areas of the Benelux region, and we also have footholds to stock in Rotterdam and Antwerp,” Mr Hughes continued. “Mekiro also remains active in the
supply of both packed goods and bulk materials across Benelux.”
In 2020, having already diversified its portfolio, Mekiro made the decision to explore more growth opportunities in the region.
“Following the lead of our parent company, we placed an emphasis on the distribution of new products which would not only complement our existing activities, but also aid our desire to enter, explore and embrace new markets,” said Mr Hughes.
It was at this point that the company introduced a range of technical vegetable oils , including castor, linseed and rapeseed, which are regularly used within the
coatings sector. This line was very successful for Mekiro and encouraged it to continue with its plans for expansion.
Now, three years on from the implementation of its new growth strategy, Mekiro is in a stronger position than ever. With a continued presence in a diverse range of sectors, the company can readily divert focus depending on market conditions.
“Our diverse positioning in the market, provides us with a big advantage,” Mr Hughes explained. “As long as we continue to listen to our customers, their
knowledge allows us to remain pre-emptive when it comes to cross-industry changes. Listening to our customers also allows us to strengthen our own abilities to help companies that are further afield.
“Covid also had a significant effect on our strategic development. With the state of the market being so uncertain, it led to some really challenging times. We are proud to have been able to address the challenges head on, whilst remaining robust as a business.”
So far, 2024 has proven to have great potential. With the business introducing several fresh ranges into the European market, Mekiro expects it to be a year filled with traction and promise.
“We are bringing to the market a new range of polyols, polishing compounds, speciality amines, defoamers and tall oil derivatives,” said Mr Hughes. “With support from our key manufacturing partners,
we are already gaining approvals and fulfilling orders, which has been a very promising start. We really must take the opportunities as they arise, and show our customers – both new and current – that we are building a bright future.”
Each new line is at a different stage of progression, some of which is influenced by seasonal levels. The company has already received several orders for the exciting natural bio-based polyol ranges for the polyurethane flooring and coating markets as well as the new polishing compounds for the automotive sector.
Despite having such a broad focus, Mekiro still maintains a strong presence within the sectors of marine and offshore. From various epoxy resins and flame retardants to specialised antifouling components, Mekiro has full access to the top manufacturers within the industry
“We are really focused on the coatings aspect within these two sectors,” Mr Hughes explained. “We also have plans to expand our product offering in these markets, with emphasis on bio-derived materials from our epoxy range.”
According to Mr Hughes, the company intends to continue advancing its presence within the marine and offshore sectors: with the aid of its partners, the company is confident that this will be a successful feat.
“The Kukdo range fills us with confidence,” Mr Hughes added. “Kukdo really excels in product development, so we are always looking for new opportunities and angles that will offer our customers
a wider portfolio of products that will provide solutions to the challenges they face.”
A collaborative effort
Every success achieved by Mekiro has been gained with the support of a reliable supply chain. As a distributor, Mekiro relies on the innovation and quality of each company.
“We work very closely with all our partners on a technical level to bring the very best options to the market,” said Mr Hughes. “This also helps to expand our partners’ ranges.”
With the world focused on the journey towards net zero, Mekiro only works with companies that share its own environmental
values. As a distribution company, Mekiro’s main emissions come from the storage and movement of goods. Mekiro works with warehousing and transportation partners who maintain a strong approach to responsible operations.
“We always make sure that our partners make positive choices when it comes to their environmental impacts,” Mr Hughes explained. “The warehouses that we partner with share our vision. They operate by using solar panels and even wind turbines, providing them with increased self-sufficiency. Our transportation partners also have plans to transition to all-electric fleets in the future.”
Mekiro is also currently working with industry innovators who are developing new and exciting bio-based options to meet the current and future demands of its customers.
“We are always looking to introduce materials that can take customers’ products in new directions: this is especially the case when it comes to bio credentials,” Mr Hughes continued. “The chemical industry is in a constant state of development and adaptation – through new legislations, restrictions and general dayto-day changes. We always endeavour to be in-tune with those developments and work hard to strike a balance between
new product development, new opportunities and customer satisfaction.
“We are continuously looking for new options that are sustainable and can now offer anywhere between 28 and 100 per cent bio-based content in some of our materials, which is incredible. These advancements are proof of our commitment to innovation. After all, if you aren’t at the forefront, you’re at a disadvantage. n