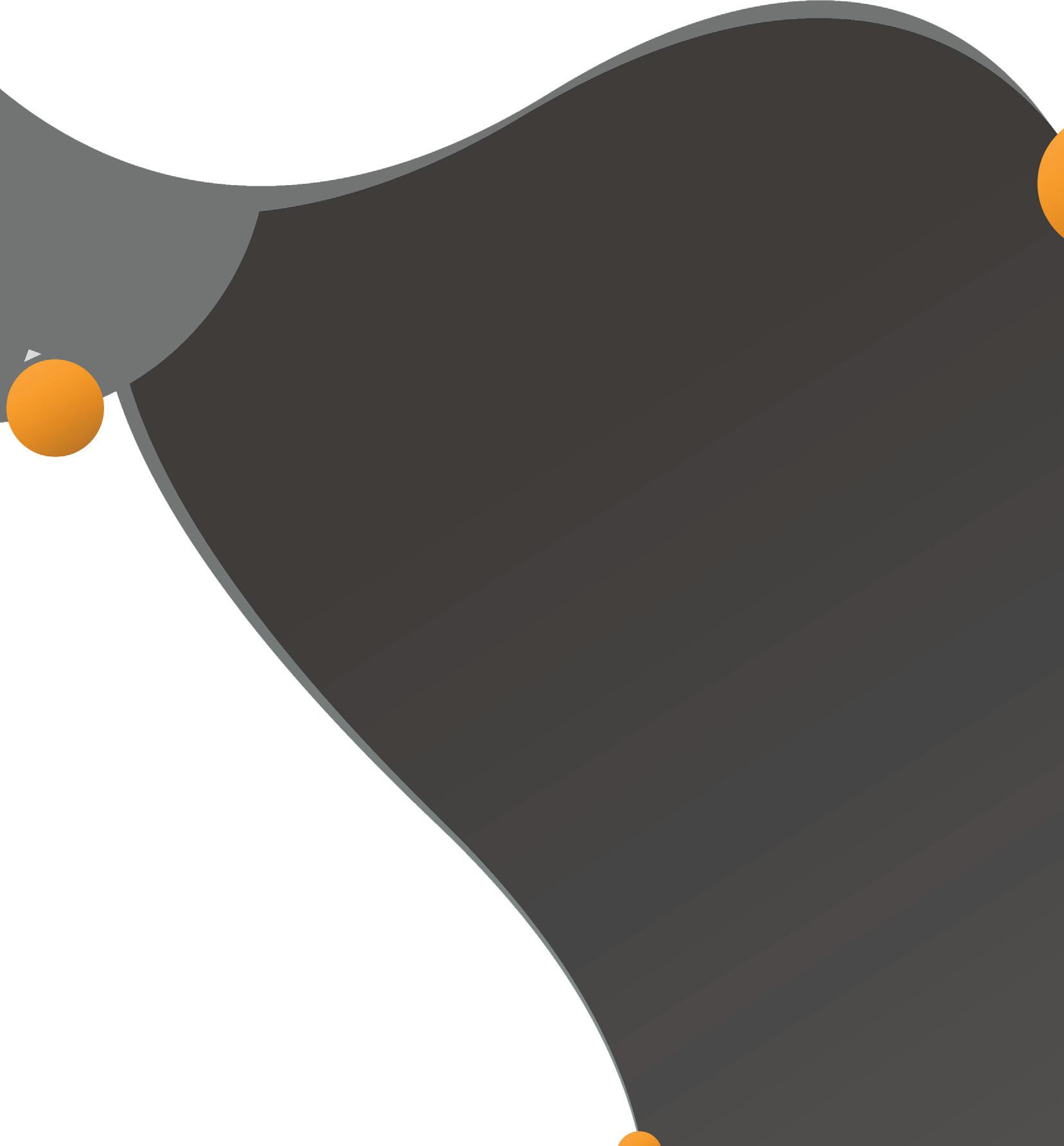



LISI AEROSPACE is one of the world’s leading players in the aerospace industry, manufacturing and designing a wide range of assembly systems and structural components with high added value. Having successfully weathered the industry’s challenges during Covid, LISI AEROSPACE is gearing up to meet the technical challenges of producing next-generation aircraft. Richard Hagan spoke with Mark Capell, General Manager of its Rugby factory, about the company’s history of innovation and its new Smart Factory concept.
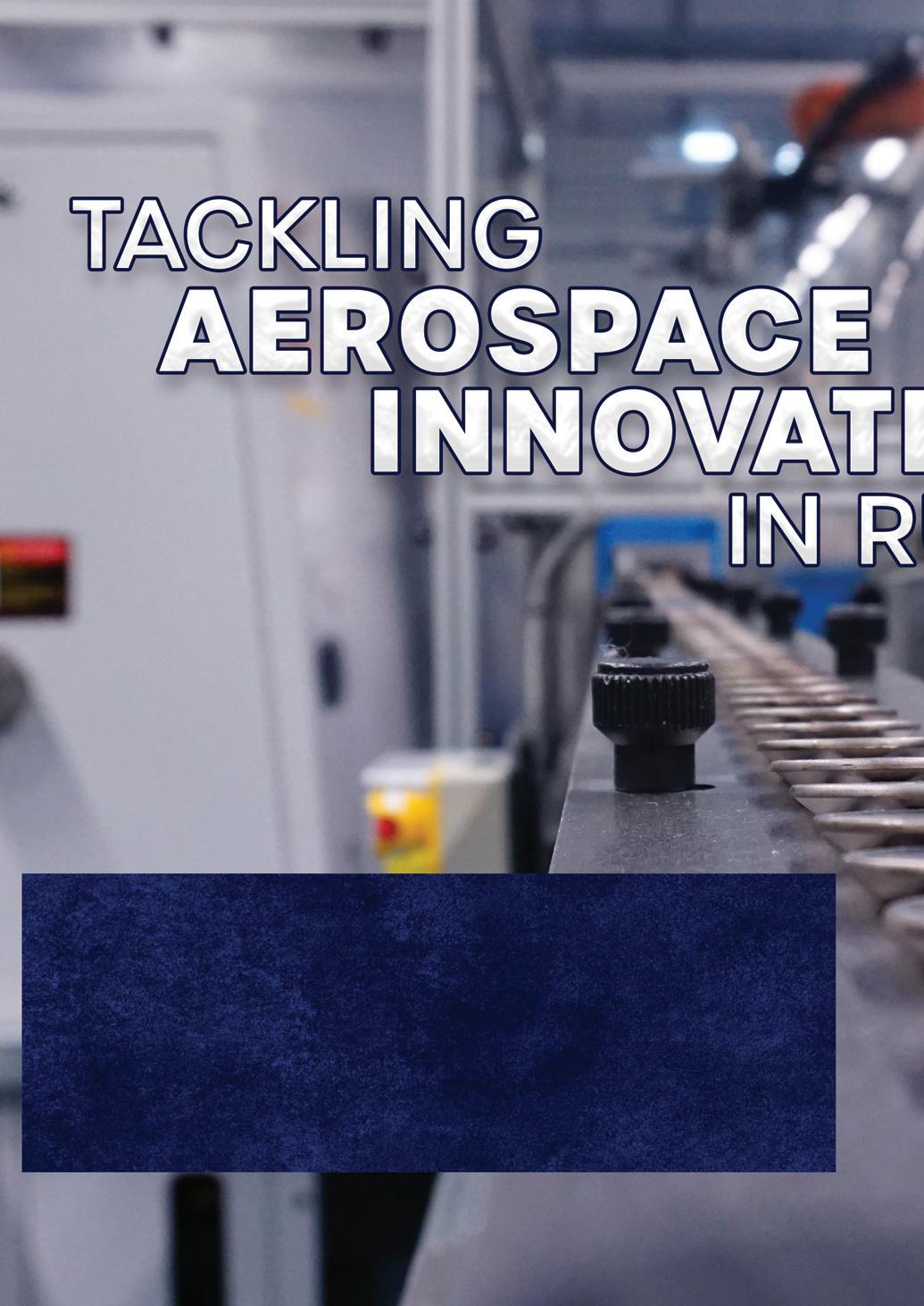
LISI AEROSPACE is a world-class leading manufacturer of assembly solutions and high-value-added components for the aerospace industry. These include fasteners, structure assemblies and components, equipment and engine components, as well as componentry for the defence and space industries. The company also assists the main aircraft manufacturers and aircraft systems manufacturers in the development of major innovation programmes towards building the aircraft of tomorrow, which will be safer and more environmentally friendly.
Strength in numbers
In 2000, the Rugby factory became part of the LISI Group, a global industrial group with manufacturing interests in the aerospace, automotive and medical sectors. In 2022, LISI AEROSPACE reported an impressive €717 million in turnover, making up 50% of the LISI Group’s total sales.
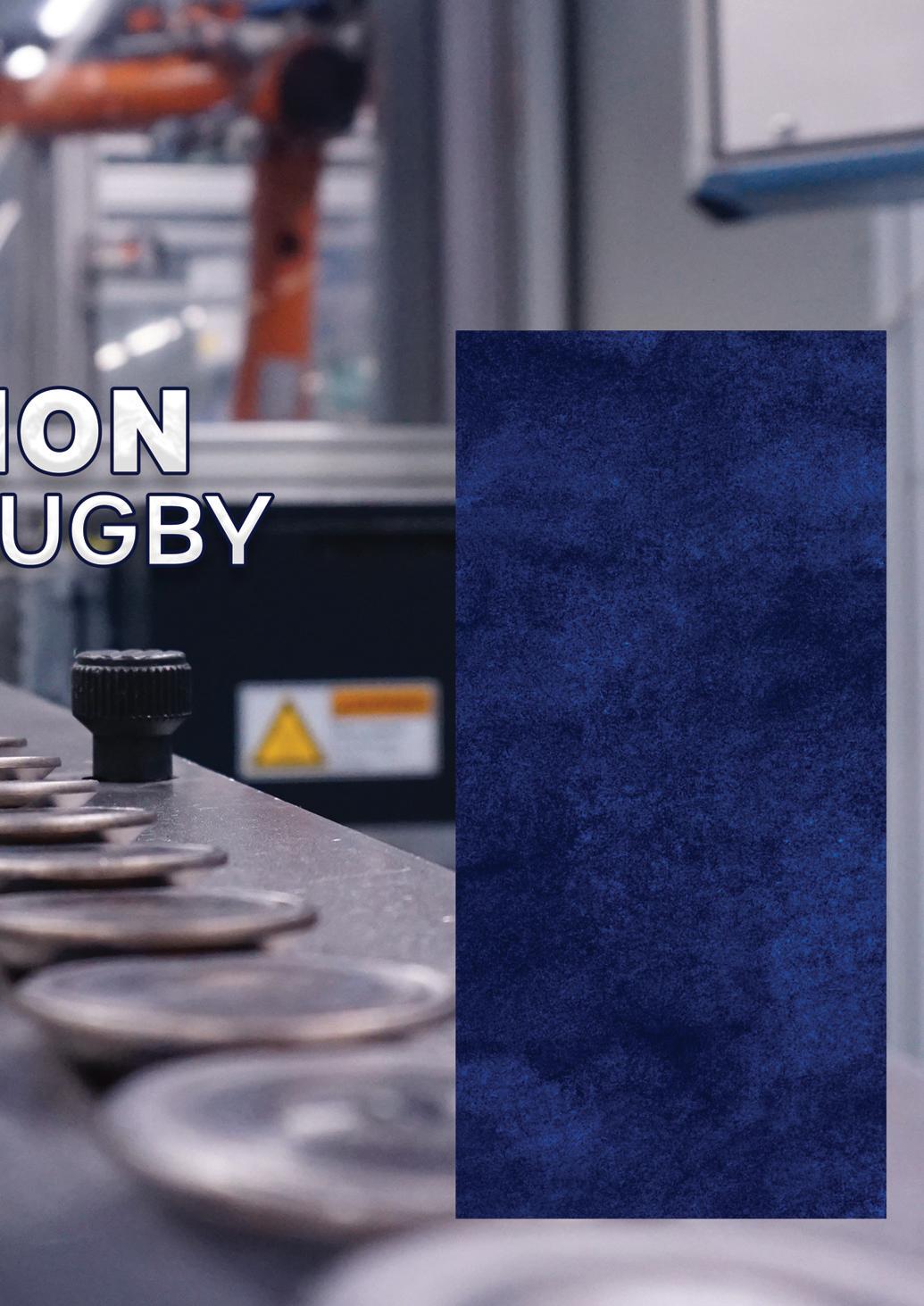
LISI Group has more than 9,600 employees in 13 countries across four continents. Of those, LISI AEROSPACE in particular involves more than 5,500 highly skilled employees in 17 facilities in seven countries.
LISI AEROSPACE’s only UK-based facility is located in Rugby, Warwickshire. The 16,000sqm site combines three production facilities known internally as Rug 1

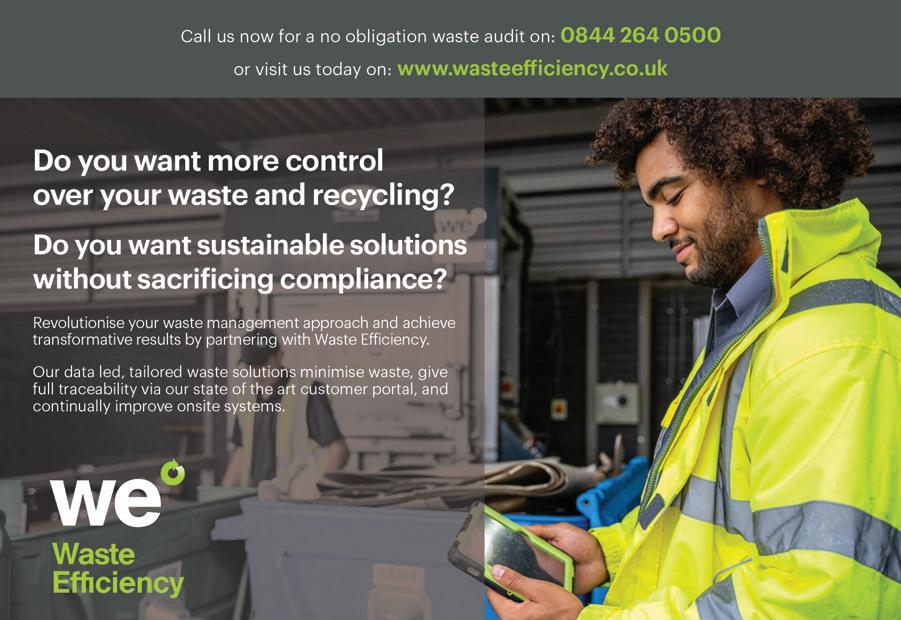

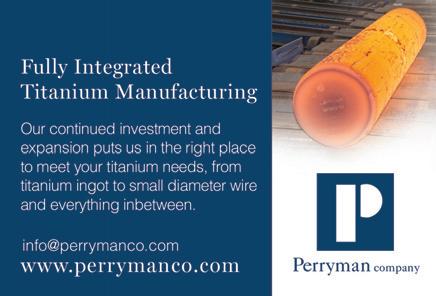

(10,000sqm), Rug 2 (4,000sqm) and Rug 3 (2,000sqm). 285 employees are permanently based here.
A Smart decision
In 2020, LISI AEROSPACE embarked on a production modernisation programme called Smart Factory. The programme came about in 2017 when the company set out to develop a new, highly advanced production line concept, according to General Manager Mark Capell: “We wanted to bring our factory up to a level that was genuinely in line with Industry 4.0 standards, incorporating artificial intelligence, machine learning and augmented reality. However, this kind of technology simply didn’t exist for our applications, so we set out to create it.”
The programme has been partially funded via a £1 million grant from the UK government’s Innovate UK fund. LISI AEROSPACE’s teams are collaborating with the University of Sheffield’s Advanced Manufacturing Research Centre (AMRC) to develop the software that will run the company’s new machinery - all of which must also
be developed from the ground up. “The University team is helping us develop the machine learning algorithms to allow our machines to make basic decisions, mostly relating to quality control without human intervention,” said Mr Capell.
Quality control, he added, is especially important in the aerospace industry, where

tolerances are less than half the width of a human hair and a single aircraft can require up to 3 million fasteners spanning 10,000 different types.
“Aerospace is heavily regulated - there are lots of standards with which our components must comply,” Mr Capell explained. “Normally, our production line

would produce the part and then our employees would physically measure the part – often with a non-contact device. Our new automatic process will now monitor and control the outputs itself. Sensors and accelerometers will measure the manufacturing process and based on that data, the system will predict whether or not a part is good - meets quality control standards - or not.”
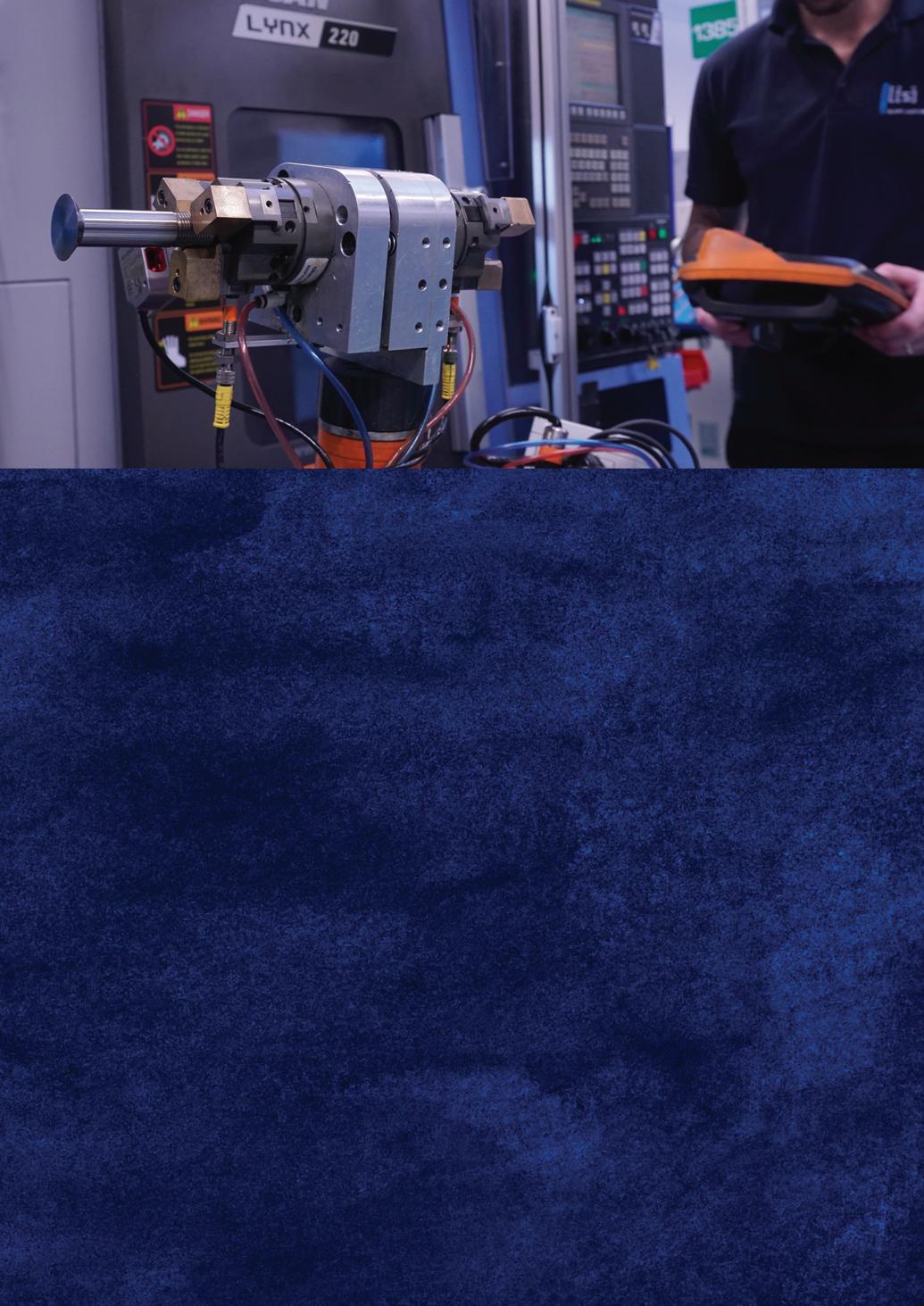
The new energy-efficient machinery on which Smart Factory will run is also being developed from the ground up. “There are five new machines that we’re developing with three different suppliers,” said Mr Capell. “One partner – Earlsdon Technology – is located nearby in Coventry, with the other two in western Europe.”
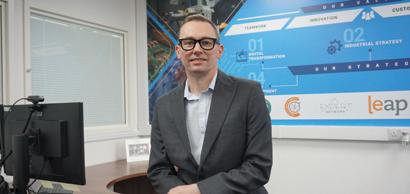
Collaboration in innovation
Whilst the Smart Factory production line is in development, plans are well underway to ensure that the required employees are available to operate this advanced new equipment. “It was clear to me from the start that the people operating the Smart Factory
were as important, if not more important, than the technology itself. For that reason, we immediately began a process of identifying the best people within our organisation to run that line. We looked for people with the right mindset and attitude for the job and upskilled them via additional training and a range of new, professional qualifications,” said Mr Capell.
In the fast-moving aerospace industry, LISI AEROSPACE stays ahead thanks to its relentless focus on innovation and, according to Mr Capell, the company is already looking ahead to servicing the next generation of aircraft: “We currently produce parts for all of the current generation of aircraft, some of which have
been around for 50 years already. Meanwhile, we’re expecting the next generation of aircraft to reach the skies in 2035.
“Airbus, for example, have a high-profile project called The Wing of Tomorrow that we’re collaborating on. To ensure that we’re ready for that next generation, we’re focused on innovating our products and developing new products that will be used by that next generation. We’re already involved with qualifications for our next generation of fasteners.”
Within these efforts, LISI AEROSPACE has partnered with leading scientific and engineering minds to turbocharge its research and development initiatives. These efforts extend to its employees, too: the company has developed a unique programme called the Culture and Communication Project in collaboration with the University of Birmingham.
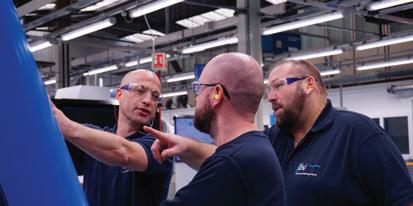
“We have a unique culture,” Mr Capell said, “and this programme aims to leverage that culture to make this factory one of the best places to work in the area. I believe it will really set us apart from any other organisation.”
Sustainability
Amidst all of this activity, LISI AEROSPACE Rugby has found time to implement a robust environmental sustainability programme as well, in line with the LISI Group's sustainable development strategy structured around three entry points called the 3Ps: PEOPLE, PLANET, PROFIT. The company has replaced its compressors with more energy-efficient ones and installed 60,000 square cubic metres of rainwater cisterns which fill process tanks and supply the factory’s bathrooms.
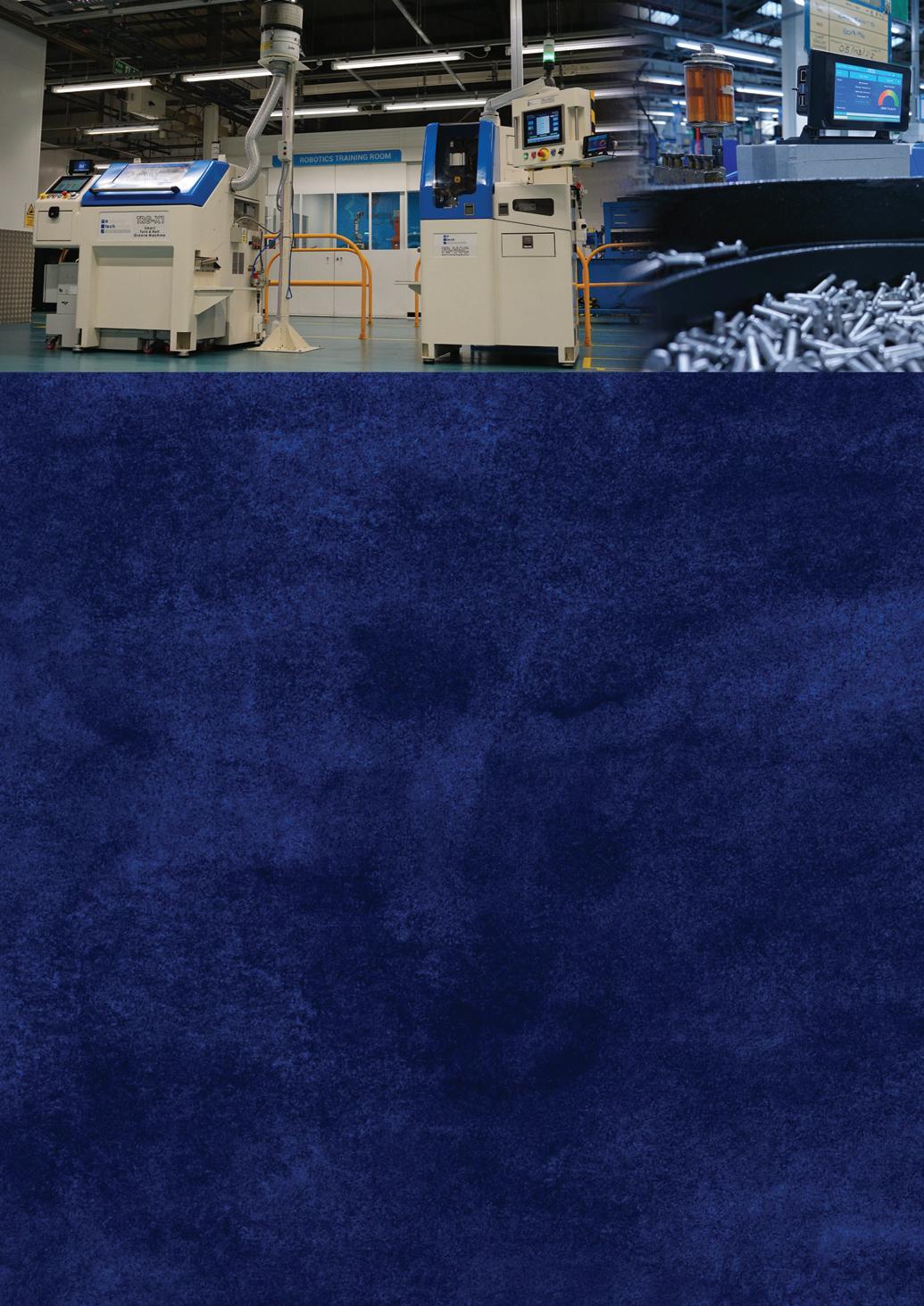
The company has also fitted electric car charging points around the site, which are

powered by 5,600sqm of rooftop solar PV panels that are installed on two of the factory roofs by the buildings’ landlords, with panels supplied by JRP Electrical Services.
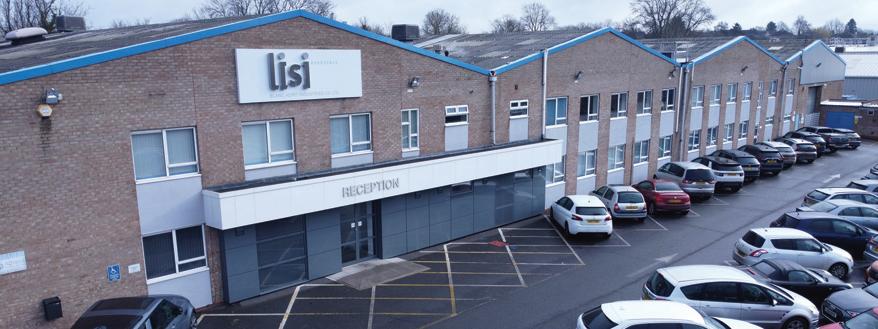
LISI AEROSPACE’s Rugby factory employees now can charge their electric vehicles for free at these charging points, using solar energy generated on-site. And finally, the company has made a substantial effort to reduce its physical waste, with exactly zero waste being sent to landfills from its factory in 2022. This process is managed by Waste Efficiency, a one-stop solution involving a full audit of the business.
“We use the Waste Efficiency online portal for all of our waste transfer notes and certificates,” explained Mr Capell. “This is so
beneficial for when we are audited by external parties for our ISO 14001 certification. The auditors even commented that it’s one of the best systems they have seen.
“Waste Efficiency are very proactive –by suggesting improvements in how we deal with our waste and also getting us the best rebates for our metal wastes. The whole of our waste management system is now run efficiently, and it’s a pleasure to work with such a great team at Waste Efficiency.
“We achieved all of this sustainability through our passion for teamwork,” concluded Mr Capell. “I love the people and the innovation within our organisation, and we love achieving things as a group.” n
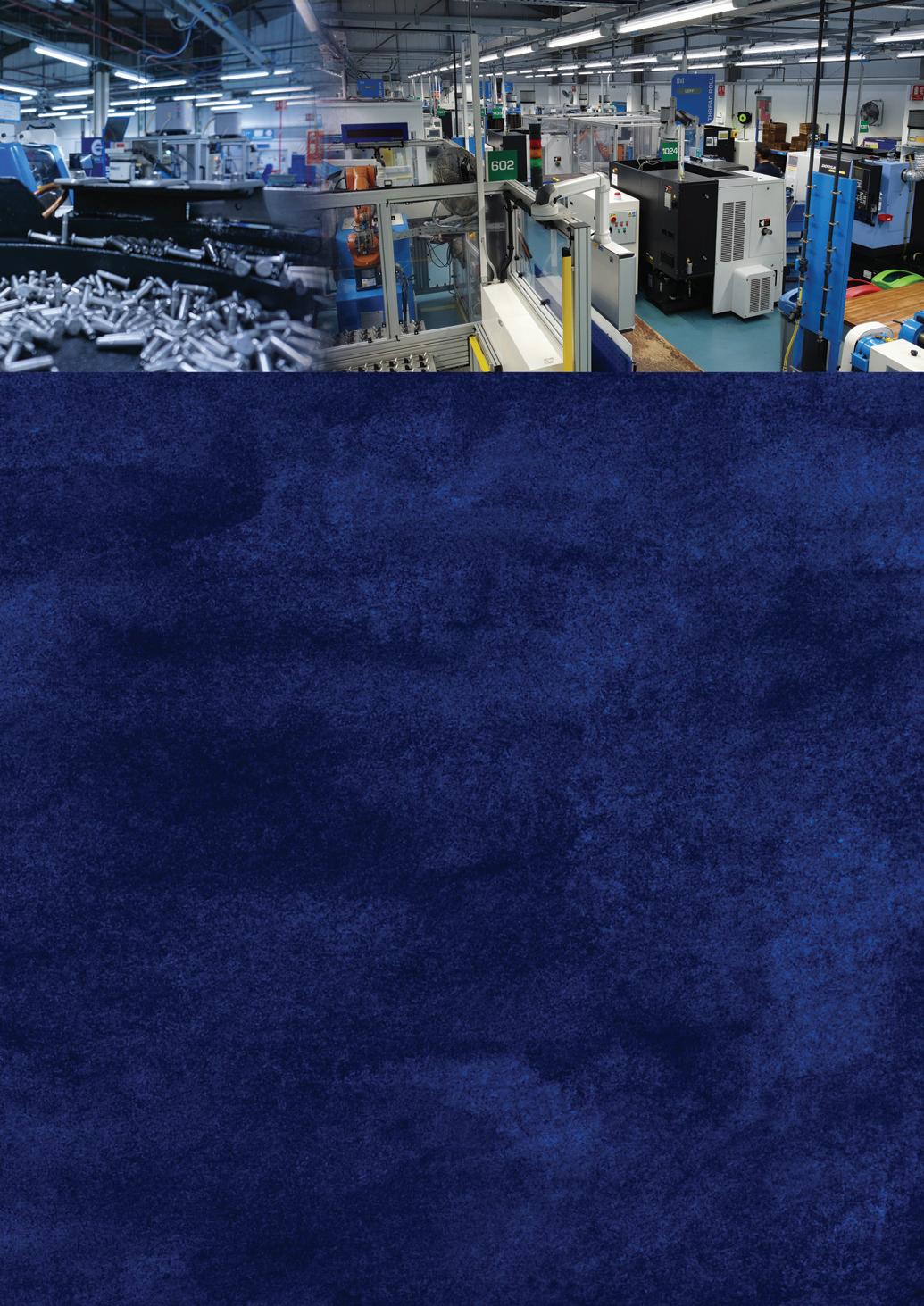
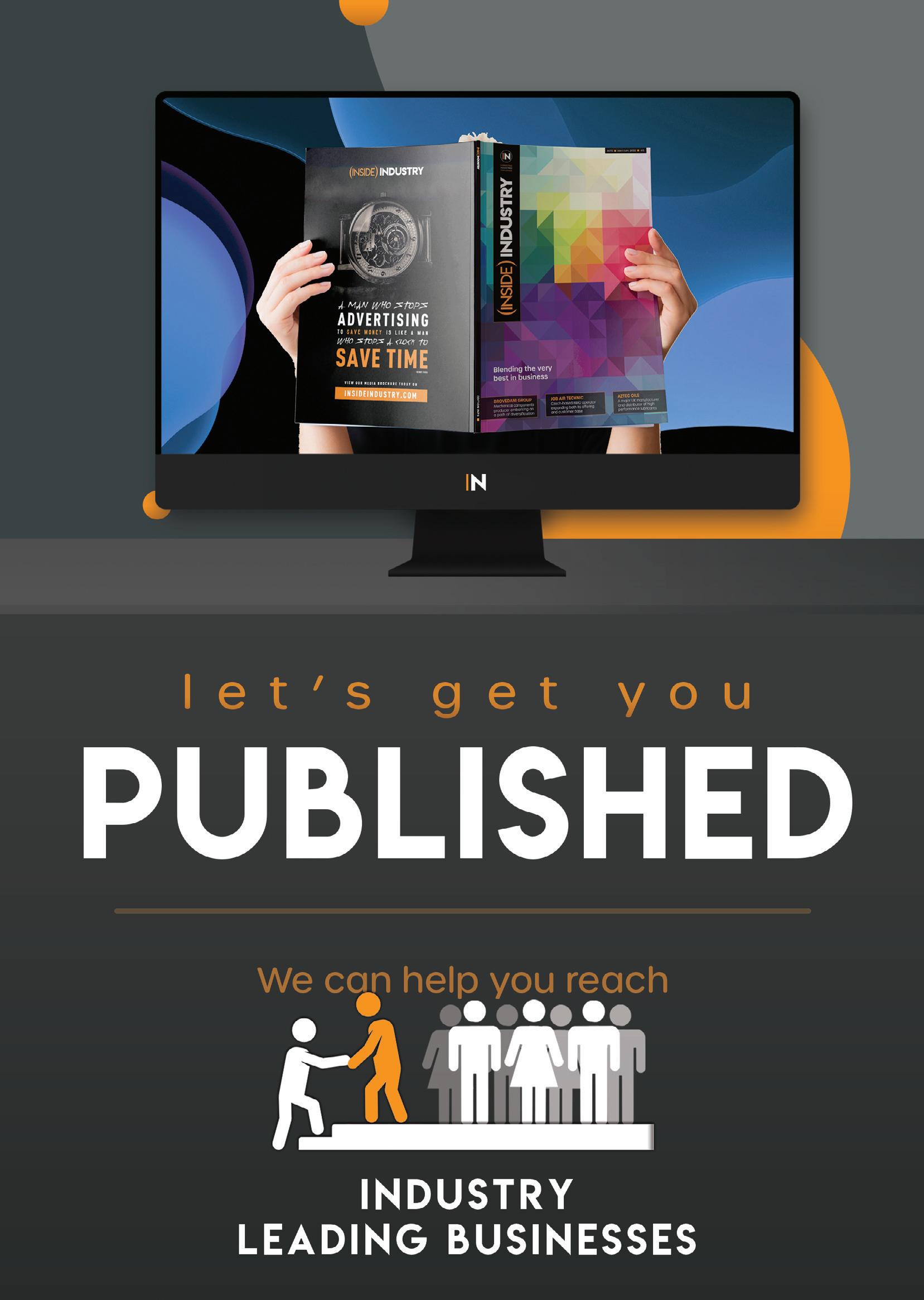
