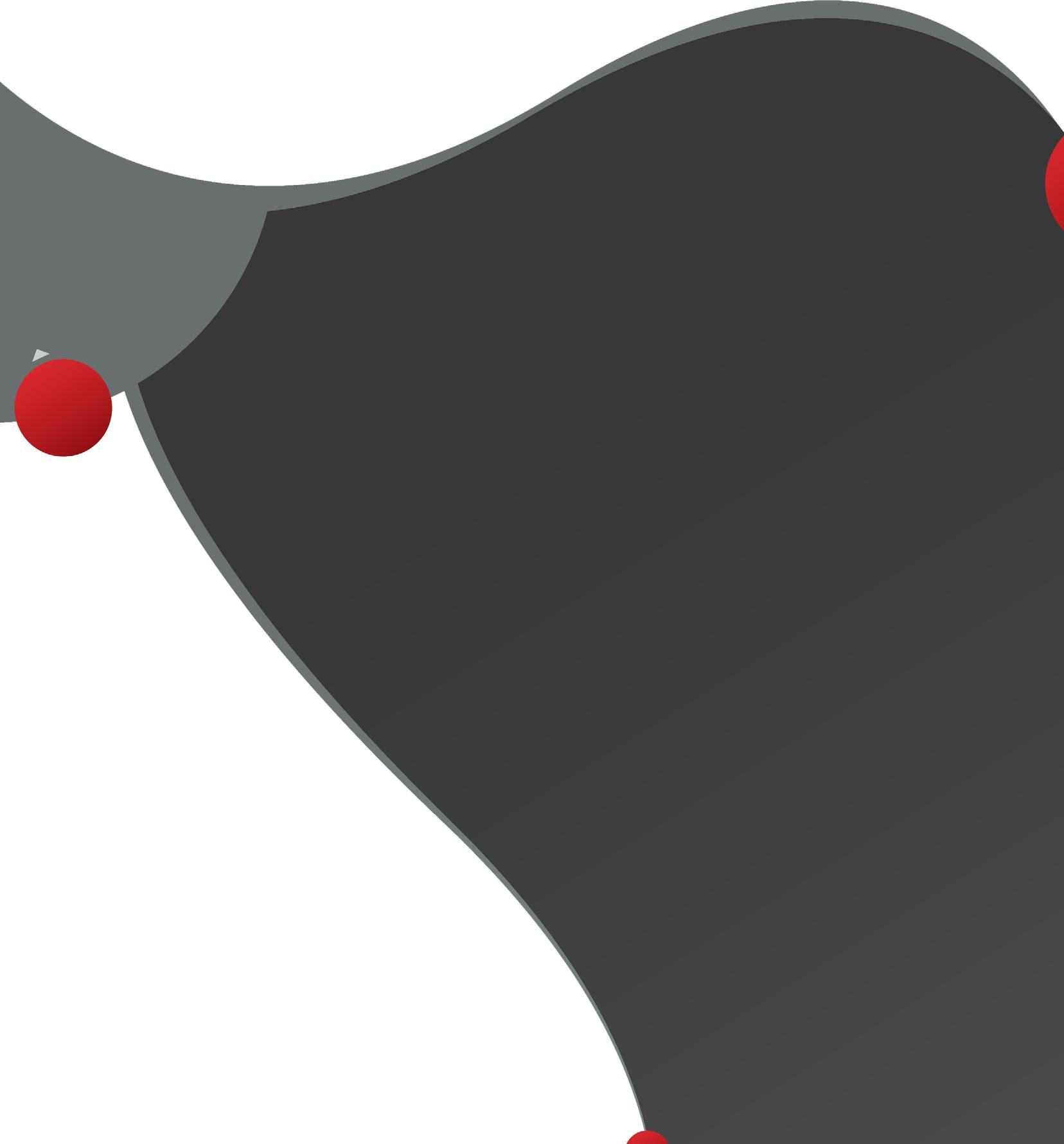
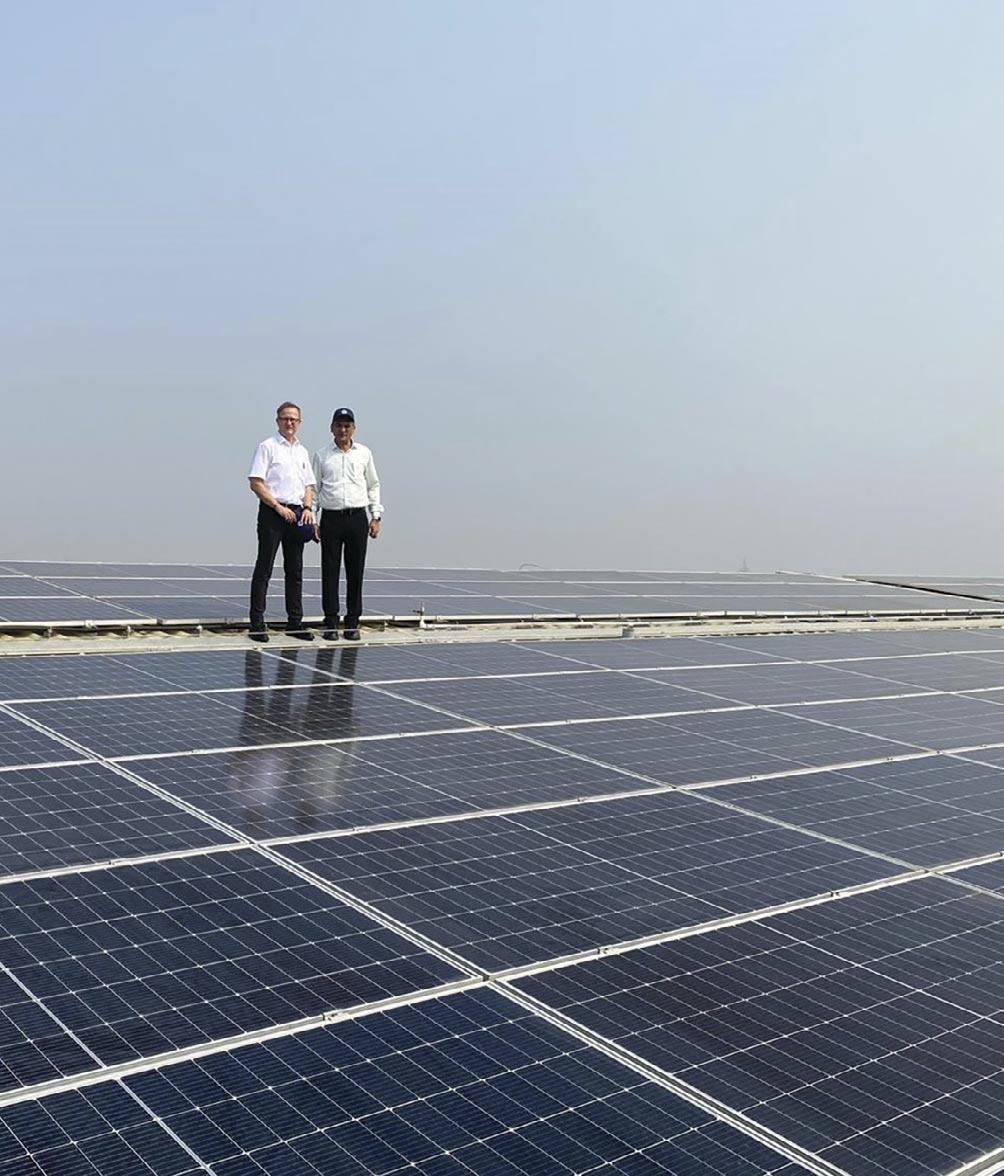
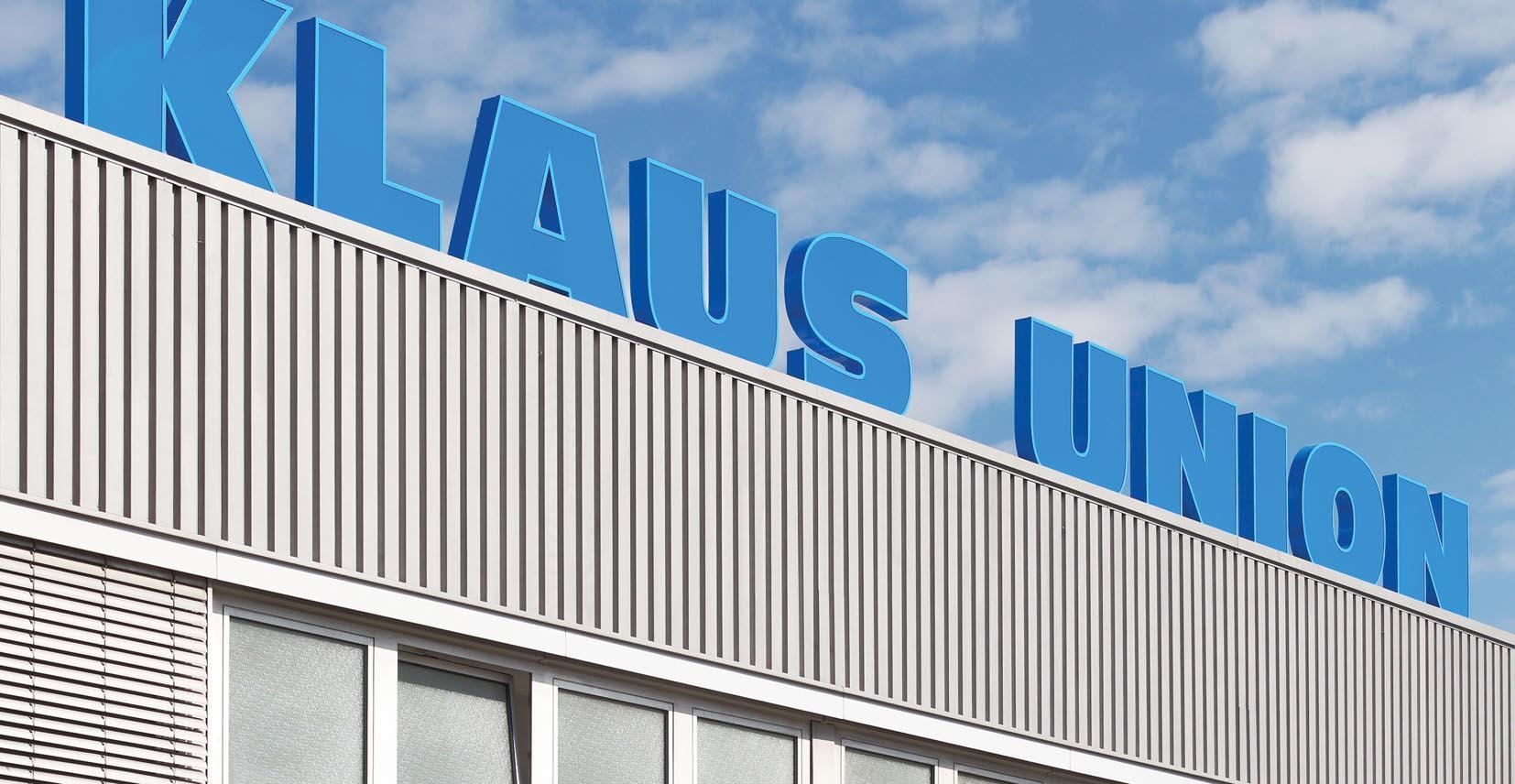

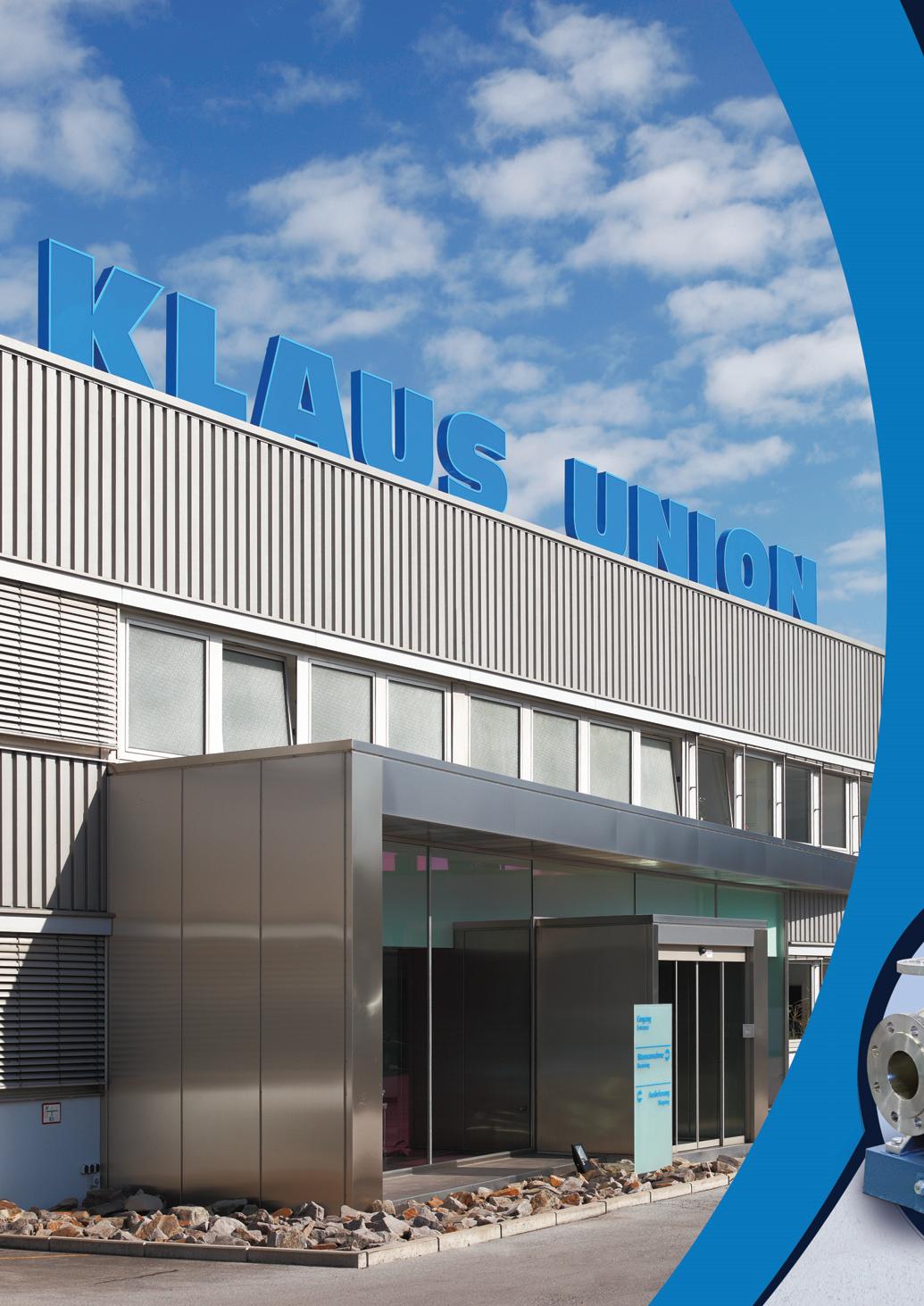
Klaus Union, a global leader in the manufacture and supply of pump and valve solutions, is one business that does not just go with the flow: with multiple patents and continuous research and development, the company is well-placed to support clients as the energy transition away from fossil fuels gathers pace. Alexander Enghardt, Managing Director, Sales & Marketing, spoke to Andy Probert about its ambitions to expand the business footprint internationally while reducing its carbon emissions impact.
When choosing pumps, pumping systems and valves, Klaus Union’s name is usually at the top of the list of choices for clients. Since the early 1950s, the company has been a market leader in producing and supplying these solutions to the chemical, oil and gas, petrochemical, and, latterly, the renewables industries.
Based in Bochum, Germany, the familyowned company offers a comprehensive portfolio of centrifugal pumps and screw pumps, with a focus on seal-less magnet drive technology. Following norms such as ISO, ASME/ANSI and API, the Klaus Union standards are considered to be one of the highest available on the market.
Since many of the global operators of Klaus Union products emanate from the oil and gas, petrochemical and chemical
sectors, exceptional requirements in technology and quality are Klaus Union’s daily business.
“ When handling critical liquids, there is zero room for error when it comes to pump and valve solutions, and ours always meet exacting standards,” said Alexander Enghardt, Managing Director, Sales & Marketing. “Transport of aggressive, toxic, explosive, hot or valuable fluids does not allow any compromise on quality, service life and safety. Our failure-free products guarantee the most reliable operation and protection of people and the environment.”
Shortly after inception, Mr Franz Klaus, the founder of the company, developed the world’s first seal-less magnet drive centrifugal pump, introducing it to industries at the world-famous ACHEMA exhibition in Frankfurt in 1955.
German chemical companies picked up this idea and spurred Klaus Union's rapid growth. Further developments included the first titanium pump manufactured in Europe and new, more powerful magnet systems providing power transmission of nearly 1MW and managing temperatures up to 450°C.
Klaus Union was one of the first companies to reach ISO 9001 certification.
Since 1999, when the first API685 was published, the oil and gas industry relies more and more on seal-less magnet drive technology. With the launch of the DSP twin screw pump series (single/double volute, timed/untimed, sealed/seal-less) in 2012, Klaus Union established a very good name in the displacement pump sector.
Today, with around €80 million-turnover, the company employs 300 people at its two plants in Bochum, plus the sales and service offices in Europe, Asia and North America. “We are also engaged in the global energy transition from fossil fuels to renewable energies,” Mr Enghardt said. “Our specially designed seal-less centrifugal pumps are ideal solutions to perfectly match many applications.”
One of Klaus Union's key concepts in the development of magnetic drive pumps was the introduction of non-metallic containment shells. By using them instead of the conventional metallic ones, Klaus Union has eliminated eddy current losses and significantly increased the efficiency of magnetic drive pumps.
This technical innovation has led to the concept of leakage-free magnetic drives becoming even more prevalent in the chemical, oil and gas, and petrochemical industries.
Over many years, Klaus Union relied on non-metallic technical ceramics for a wide variety of applications, primarily because of their high resistance to chemical corrosion and wear. Until now, the range of applications has been limited due to the specific material properties.
However, pump applications increasingly require higher operating pressures, temperatures and flow rates while maintaining maximum efficiency. Klaus Union now offers an expanded application range of these non-metallic shells up to 914 psi (63 bar) pressure and for temperature ranges from minus 200°C (-328°F) to +450°C (+842°F).
The company has also developed solutions of double containment shells, used for most critical applications, having one metallic and one non-metallic shell – called hybrid double containment shells – where eddy current losses are significantly reduced as well.
Klaus Union’s non-metallic shells are made of zirconium oxide, which is electrically non-conductive. “Because of this property, no eddy current losses affect pump performance,” Mr Enghardt explained, “and no heat is added to the pumped fluid.”
This concept brought other significant advantages, such as enabling dry-run capable executions (RTZ-design) and executions without continuous flush flow (OTZ-design). It enables applications with high gas content, pumping solid loaded liquids and liquids close to boiling point.
Instrumentation to monitor the containment shell temperature is not required as eddy current losses are eliminated.
Further advantages include higher mechanical strength, vacuum-tight up to 0 bar absolute, enhanced energy efficiency and high corrosion and erosion resistance, enabling zirconium oxide to be used in a nearly unlimited application range, primarily when related to acids.
Ceramic containment shells are a fundamental part of Klaus Union's modular pump system. Due to the universal casing cover, containment shells can be easily mounted or replaced.
“The operator saves on stock capacities and service costs,” Mr Enghardt continued. “There is no heat input into the pumped liquid; this significantly increases the process's reliability. Consequently, no temperature monitoring is required.”
Additional advantages include lowered energy consumption as there are no performance-impairing eddy currents. “The consumed power can be reduced by an average of 10 to 15 per cent, compared to metallic containment shells. And with reduced shaft power demand, smaller electric motors and cables can be installed.”
With these continuous advances in its product range, Klaus Union is poised for major growth. “The company intends to move beyond traditional markets into new regions such as South America and Africa,” Mr Enghardt said. “One focus is to be an even bigger player in renewable energy, carbon capture or recycling, in addition to its current applications.”
Klaus Union, which was awarded the ECOVADIS Silver Medal, is continuing on its path toward sustainability and is focusing on reducing its carbon footprint, Mr Enghardt said, “We are already operating the facilities with a high percentage of green energy, producing 2,000kW of solar energy or using an energy mix with a high percentage of green energy. Our employees are even using this energy to charge their cars at various e-charging stations around our factory.”
One of the challenges for the company is attracting qualified personnel. “This is a general problem that many industries in Germany have,” Mr Enghardt said. “Hopefully, with the help of the government, the problem will be lessened, but
for a medium-sized company like Klaus Union, this problem is likely to remain a constant headache.”
Although German-made products are not always the lowest in CAPEX, a strong emphasis on product excellence and customer service has helped raise Klaus Union’s profile.
“Customers and operators rely on the good name of Klaus Union, which stands for experience, responsibility and progress,” concluded Mr Enghardt. “Through our network of subsidiaries and representatives, we offer comprehensive services such as expert advice, after-sales and detailed assistance in solving individual pump problems.
“The quality of its products and the exchange of experience with its partners in various industries have made Klaus Union one of the world market leaders. The motto 'Our quality is your success' is at the heart of everything we offer customers.”