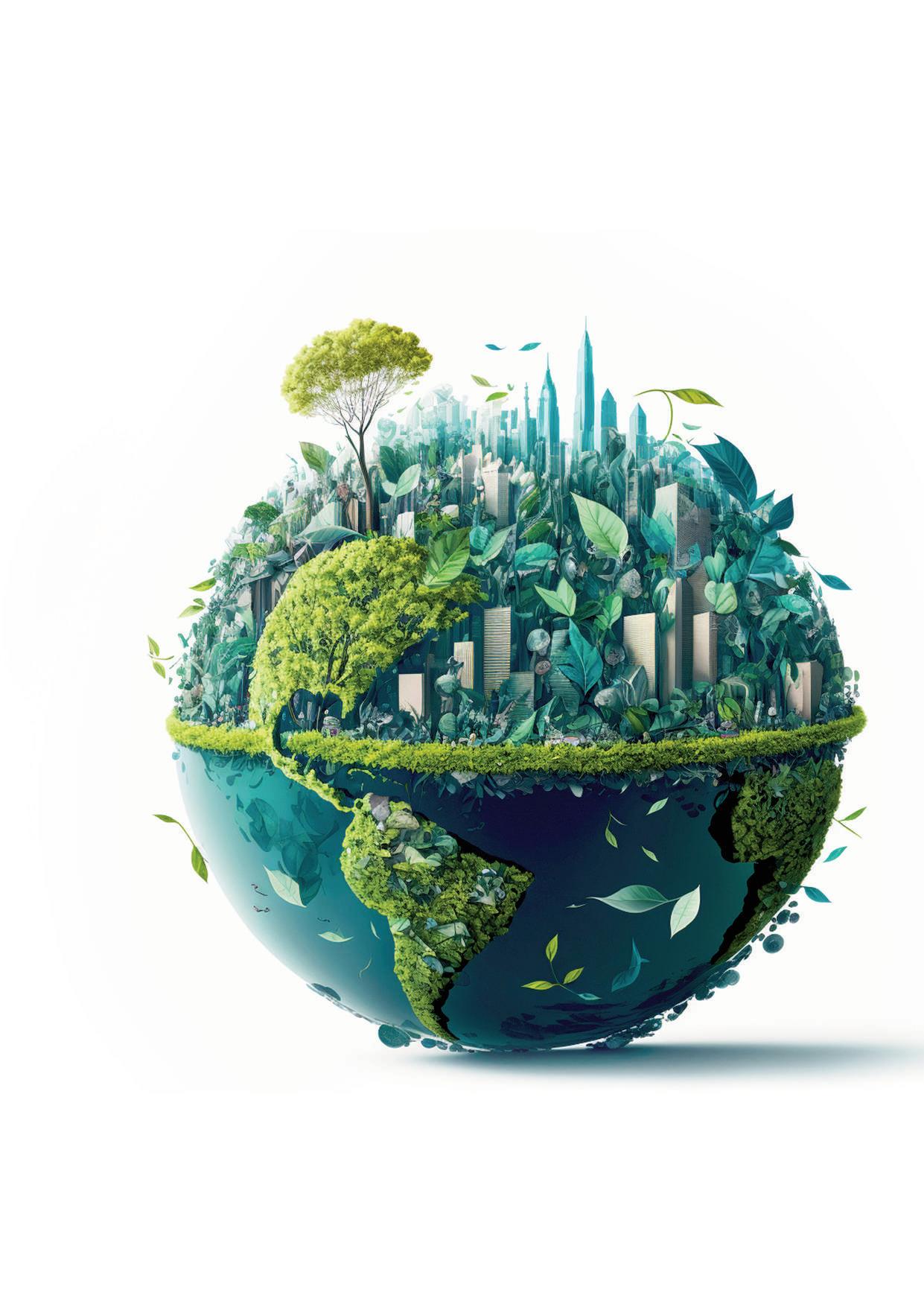
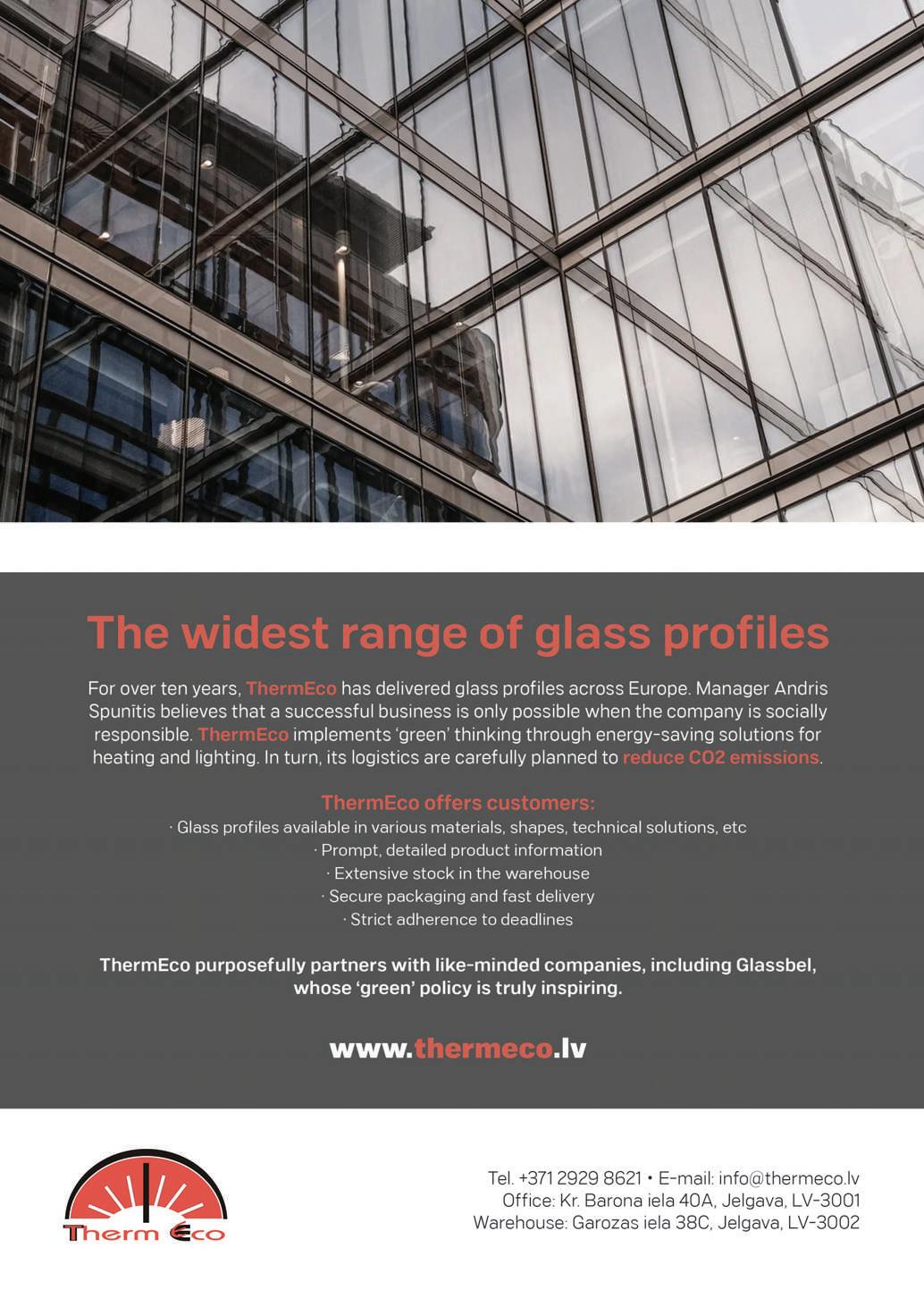
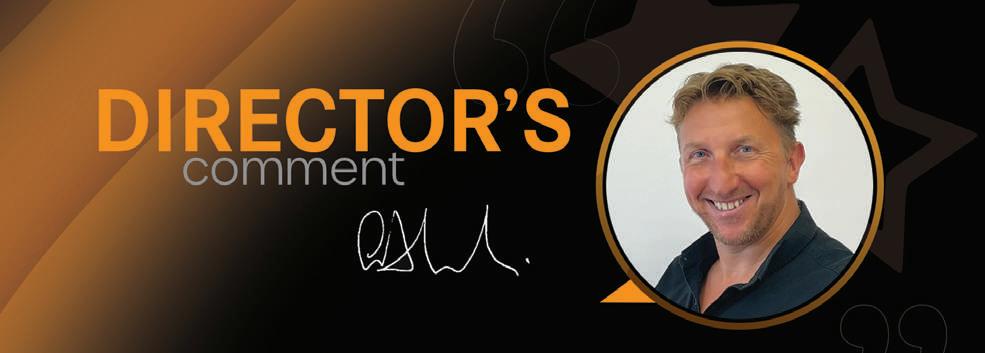
John White Managing Director
John White Managing Director
Welcome, Dear Reader, to your latest edition of Inside Sustainability. As many of you know from my ramblings within the last edition, such is the popularity of this magazine now that we publish it roughly every five weeks, rather than every ten.
This seems to keep our readers happy, but the same is not necessarily so for yours truly. It means I must think of something inspirational and informative to write twice as often throughout the year. Some of you will doubtless be snorting and saying, ‘Well, you didn’t write anything inspirational before, so no loss.’
Anyway, your cheeky remarks aside, I’ll endeavour to do my best. Those of you that also follow our regular social media posts, will have seen the recent video about the journey of sustainability in terms of recycling. This made me think back to my childhood, growing up in the ‘70s and ‘80s, when sustainability was not a word that was part of our everyday life.
I grew up in a mostly throw-away culture. It was not until my time in the armed forces in the late ‘80s and ‘90s, whilst at sea, that I practised any form of sustainability. You
couldn’t really pop to the shop to purchase a new uniform, so it was needle and thread time and a tactical repair.
My time at sea was sustainable out of necessity, though. Whereas now, we are, or should be, practicing it for the common good. As a popular quote says, ‘Do something today that your future self will thank you for.’
And really, that’s the journey we should all be on. If not for ourselves, then, more importantly, for future generations. A proverb I am fond of, paraphrasing Cicero, seems appropriate to sign off with:
“A society grows great when old men plant trees in whose shade they shall never sit.” n
The range and variety of company profiles in this issue make it clear that we are all on a path towards sustainable operation. Proactive Publications is with you on this journey as we progress into a more sustainable future.
Managing Director
John White
Finance Director
Filomena Nardi-Smith
Accounts
Chloe Frosdick
Angel Esherwood
Editor
Phil Nicholls
Editorial Assistants
Imogen Ward
Hannah Barnett
Antonia Cole
Feature Writers
Andy Probert
Richard Hagan
Colin Chinery
Business Development Manager
Darren Foiret
Research Editors
Jeff Johnson
Mark Simmonds
Judi Wheaton-Mars
Ginelle Lorenzo
Natalie Martin
Dane Coady
Becky Scrivens
Amy Lawrence
Sales Director
Richard Brightmore
Sales Manager
Helen Leisi
Project Managers
Alexander Paterson
Tony Ingrouille
Chris Renicar
David Earl
Lisa Smith
Will Tottie
Bobby Godfrey
Loretta Smith
Mika Warner-Wright
Sam Ransome
Studio Manager
Philip White
Webmaster
Michael Stamp
Designers
Sarah Jones
Georgina Maclead
Sam Moyse
Events Manager
Jasmine Lodge
Marketing Manager
Adam White
Administration & IT
Summer Clover
Gavin Bellward
T: +44 (0)1493 445121 +44 (0)1502 566216
E: media@insidepublication.com
W: www.inside-sustainability.com
Gamuda is taking the next step in its Australian growth plans by targeting the energy sector with the long-term goal of being a leading end-to-end developer-builder-owner of assets to accelerate Australia’s clean energy future.
Since establishing itself in Australia in 2019 as a fully owned local subsidiary of regional engineering, property and infrastructure company Gamuda Berhad, Gamuda has focused on its core infrastructure business and secured three major road and rail projects with a combined value of $4.5 billion. Australia is now its largest construction market, with $2.5 billion in revenue forecasted for FY24 following the acquisition of DT Infrastructure from Downer Group.
To continue its growth, the company is now focusing its efforts on the Australian $328 billion clean energy and renewables infrastructure market. Gamuda’s strategy will go beyond the construction of renewable projects to invest up to 40% equity in solar and wind assets to build a 1-2GW portfolio within five years.
Gamuda will also continue to selectively bid for major contracts in solar, wind, pumped hydro and transmission network upgrades and expansion,
fuelled by electricity demand and the transition to renewables.
Ewan Yee, Gamuda's Chief Executive Officer, outlined how the company was ready to take the next step to diversify and grow its business in Australia. The target is to achieve a sustainable $2 billion revenue in the next five years from energy projects alone.
“Our vision is to become a leading sustainable energy contractor and a key equity partner for the long term with a particular focus on solar, wind, pumped hydro and transmission,” he said. “This vision builds upon our ongoing success in the Australia infrastructure market and is informed by our energy and water infrastructure experience across a number of projects globally.
“We also see our demonstrated key strengths in completing complex largescale linear construction, tunnelling, hydro and geotech in Australia as highly suited to now transition to energy projects.” n
EWE and H2eart for Europe have announced their new partnership and are joining forces to support the development of Underground Hydrogen Storage (UHS) technologies across Europe.
The collaboration between EWE and H2eart for Europe comes at a critical moment: European Member States are faced with an increasingly urgent network flexibility challenge caused by important decarbonisation efforts and the integration of variably produced Renewable Energy Sources.
EWE and H2eart for Europe commit to leveraging UHS technologies to provide network stability for the European energy system, and to ensure green energy is available on demand. Moreover, both players recognise that there is a significant gap between identified flexibility needs and the current project pipeline for 2030, requiring urgent action.
EWE is a leading player in UHS technologies and investing up to €800 million into the development of a series of promising large-scale hydrogen projects. The energy company brings a wealth of expertise along the entire hydrogen value chain to the alliance. As stated by EWE, hydrogen storage systems play a crucial role
in ensuring security of supply and grid stability in a future hydrogen system.
The first large-scale project in Huntorf (Lower Saxony) is part of the Important Project of Common Interest ‘Clean Hydrogen Coastline’, with which EWE aims to combine the production, storage, transport and use of green hydrogen.
The hydrogen storage facility is set to commission in 2028, boasting an impressive storage size of 70GWh in a salt cavern –depending on the national pending funding decision and the final investment decision of the EWE committees. By providing a stable supply of on-demand green energy, this transformative project will serve as a catalyst eg for carbon-neutral steel production, chemical industry applications and power generation. It is paving the way for a cleaner, more resilient energy future in Europe.
Furthermore, EWE is currently testing the operation of a small cavern in Rüdersdorf, Brandenburg. This R&D project marks a significant milestone to provide the basis for large-scale hydrogen storage projects in the future.
Latest developments from the USA industry
The US. Environmental Protection Agency has recognised 32 clean water and drinking water infrastructure projects for excellence and innovation. These projects were funded in part by the Clean Water State Revolving Fund and Drinking Water State Revolving Fund programmes.
EPA’s AQUARIUS and PISCES national recognition programmes highlight exemplary water infrastructure projects. They showcase improvements in water quality and public health protection as a result of strong partnerships at the federal, state and local level.
“Communities across the country are tackling water infrastructure challenges ranging from removing lead pipes to improving infrastructure resilience to climate change and addressing emerging contaminants,” said EPA Acting Assistant Administrator for Water Bruno Pigott. “I am thrilled to recognise innovative infrastructure projects that are delivering cleaner, safer water for communities while providing insights that can be replicated across the country.
“I look forward to seeing more projects break ground as we continue to invest $50 billion through President Biden’s Bipartisan Infrastructure Law.”
EPA’s AQUARIUS programme celebrates Drinking Water State Revolving Fund projects that are innovative, sustainable and protect public health. 12 projects by state or local governments and drinking water utilities were recognised by the 2023 AQUARIUS programme.
The PISCES programme celebrates innovative CWSRF projects implemented by assistance recipients. 20 projects by state or local governments, public utilities and private entities were recognised by the 2023 PISCES programme.
The SRFs are an EPA-state partnerships that provide communities with a permanent, independent source of low-cost financing for a wide range of water quality and water infrastructure projects. EPA’s SRFs have provided over $229 billion in financial assistance to over 48,000 water quality infrastructure projects and over 19,000 drinking water projects across the country.n
A study from sustainable waste management company Biffa has revealed that the UK’s manufacturing sector is leading the charge on sustainability. This sector is more aware of, and engaged with, the circular economy than its contemporaries in construction, retail and hospitality.
The survey revealed that almost three-in-four (74%) manufacturers view the circular economy as important, especially those in large organisations (81%). The survey of over 1,000 UK business decision makers (of which 136 were from the manufacturing industry) conducted by the YouGov analysis institute, explored attitudes towards, and engagements with, the circular economy.
Over two-thirds (69%) agreed that they participate in the circular economy – rising to over three-in-four (76%) for bigger manufacturers. Moreover, manufacturing decision-makers led the way, with over three-quarters (78%) adopting a sustainable strategy, surpassing counterparts in construction, retail, and hospitality sectors. The main areas of support needed by manufacturing businesses to be more sustainable include financial incentive (38%), access to technology (35%), and challenges in data and reporting (26%).
More than three-quarters (79%) of manufacturing decision makers surveyed
recognise the vital role that waste management and recycling play in preventing climate change. Manufacturing SMEs surveyed overwhelmingly view waste management as critical to being a sustainable business. ‘Reductions in general waste’ (47%) and ‘volume of resources used’ (49%) were the preferred methods of measurement.
“We’re encouraged to see a critical UK industry with such a comprehensive grasp of the significance of the circular economy, and how sustainable waste management enables the circular economy,” said Iain Hollington, Biffa’s Chartered Resource Waste Manager MCRWM, CRWM. “Biffa is committed to delivering a solution that supports business of all sizes’ goals
“Conscious decisions made in the manufacturing process have an enormous impact on the reusability and recoverability of materials introduced to the UK market, in line with policy asks and carbon hierarchy adoption recommended in our Blueprint for Waste Net Zero.” n
click to sections: ENGINEERING &
SERVICES & TECHNOLOGY BACK TO CONTENTS
one planet – one chance – one voice
A selection of future events, followed by a preview of WindEnergy.
24-27 September 2024
WindEnergy Hamburg
WindEnergy Hamburg is one of the world’s biggest and most important wind business platforms for exchanging news and views, building networks and closing major deals. The event is run in partnership with national and international wind industry associations.
[click here] for weblink
24-26 September 2024
FACHPACK
FACHPACK is a European trade fair for packaging, technology and processes, and is therefore an important guide for the packaging industry and its customers. Solution-oriented thinkers meet at FACHPACK to exhibit their innovative packaging solutions.
[click here] for weblink
26-29 August
ONS
Every other year, ONS welcom of exhibitors, delegates and energy industry. The two ma are the ONS Venue at Stavanger Foru and social arena downtown.
e largest community of senior hydrogen ofessionals will convene in Copenhagen a week of knowledge-sharing, innovation king with the ultimate goal of achieving economy. The week also includes the 5th d Hydrogen Congress. here] for weblink
UK Construction Week Birmingham has grown to become the UK's largest built environment event. UKCW is a catalyst for change in the sector, gathering the top speakers to panel the many seminar theatres to discuss and debate the issues affecting construction
[click here] for weblink
t 2024
mes to Stavanger thousands people interested in the in locations of the event um and ONS+, the debate
Why not give your event exclusive coverage to thousands of readers and connections globally? Contact us: events@insidepublication.com
A short preview of WindEnergy Hamburg.
©Hamburg Messe und Congress/Nicolas Maack
Running from 24th to 27th September, WindEnergy Hamburg is one of the world’s biggest and most important wind business platforms for exchanging news and views, building networks and closing major deals. National and international wind industry associations cooperate with WindEnergy Hamburg and encourage their members to attend.
Every two years, one of the most fascinating industries meets at WindEnergy Hamburg for the leading global networking event for the sector. Around 1,500 companies from 40 countries will present their innovations and solutions in ten exhibition
halls, seen by up to 40,000 visitors from 100 different nations.
Covering 73,500m² across the exhibition campus, equipment manufacturers and suppliers representing all stages of the onshore and offshore wind energy
value chain provide a comprehensive overview of the market. The trade fair is accompanied by conference sessions where top-ranking experts address the industry's current key topics.
ambition
The goal is set: by 2030, the EU wants to have 425 gigawatts of wind energy generation capacity in place, with two thirds contributed by onshore units. To date, however, Europe has installed no more than 272 gigawatts (79 per cent of which are onshore turbines).
So, to achieve the 2030 goal, it will be necessary to install an average of 33 gigawatts every year. “We can only reach this by maximising our expansion efforts.
One key means to that end is repowering – replacing wind turbines that have reached the end of their lifespan with more powerful models,” explained Claus Ulrich Selbach, Business Unit Director Maritime and Technology Fairs & Exhibitions at Hamburg Messe und Congress.
A joint EU directive facilitating wind energy projects has improved the conditions for the construction of additional high-output wind farms.
At WindEnergy Hamburg in September, decision-makers will be able to meet the right partners for implementing repowering projects. One of them is the Norwegian wind energy company Statkraft, which intends to modernise 35 older wind farms it has acquired in Germany.
A short preview of WindEnergy Hamburg.
“A major portion of the energy transition onshore will be accomplished through repowering projects,” said Stefan-Jörg Göbel, Statkraft Country
Manager in Germany. A wind turbine erected 15 years ago typically has a capacity of two to three megawatts. By comparison, the latest-generation turbines designed for onshore use have a capacity of six to seven megawatts.
These state-of-the-art units are more powerful, but also significantly larger than their predecessors. Over the past 30 years, the hub height has tripled. And while in 1980 a typical rotor had a diameter of 15 metres, this dimension is expected to increase
to 250 metres by 2035. At WindEnergy Hamburg, experienced logistics companies and heavy-lift specialists such as Eager.one, Liebherr, Schmidbauer and GRUBER Logistics will showcase solutions for safely handling these oversized items.
Repowered wind turbines not only come with logistical challenges. The higher energy output also requires smart grid feed-in management, as well as innovative, high-performance energy storage tech -
nologies. For exhibitors addressing this field of expertise, WindEnergy Hamburg will lay out a dedicated Storage Tour.
“The Storage Tour will allow visitors and exhibitors to locate all companies dedicated to this complex topic at a glance, and speak with them directly,” said Andreas Arnheim, Director WindEnergy Hamburg.
Exhibitors will include Avacon, GP JOULE, OAT and many others. n
one planet – one chance – one voice
An introduction to the engineering and manufacturing sectors, with innovations and a special report exploring premium brands, followed by company profiles.
Design Director Rachael Edwards from Born Ugly explores brand sustainability.
can’t be
While the desire for luxury and premium products remains, consumers are actively seeking brands that prioritise sustainability. Rachael Edwards, Design Director at brand transformation consultancy Born Ugly, outlines to Inside Sustainability how a brand can be both premium and sustainable.
WElive in a world where individuals are increasingly mindful of their consumption habits. In fact, 76% of consumers say they expect brands to ‘do their part’, 57% say their perception of a brand is influenced by its sustainability practices, and 30% are compelled to action by a brand’s sustainability practices, either by switching away from or advocating on behalf of a brand.
Investors are also scrutinising companies based on environmental, social and governance criteria. They want to invest in compa-
nies that not only generate profits, but those that have a positive impact on the planet.
This leads us to the crucial question: How can you develop a premium brand with sustainability at its core?
One of the easiest ways for designers to ‘premiumise’ a product used to be putting it into a fancy box. However, with ‘premium finishes’ like foiling and complex laminates being difficult to recycle, and with overpackaging being wasteful and unsustainable, we must get more creative and look further afield to premiumise.
Over time, the definition of a premium brand has also evolved. Contemporary consumers often look beyond traditional markers such as packaging aesthetic, brand heritage, exclusivity, pricing and superior materials. In today’s landscape, where more and more brands lay claim to premium status, brands can no longer rely on just their name, price, or a fancy box to get by. Consumers demand more.
Premiumisation has evolved
Similarly, merely asserting a commitment to sustainability is insufficient for brands. There is no tolerance for greenwashing. With the introduction of more legal restrictions and shifts in customer priorities, premium brands must prioritise sustainability. It has become a necessity, rather than a luxury.
The myth that premiumisation and sus tainability are not compatible simply is not true. By employing thoughtful creativity and finding solutions that satisfy both environmental concerns and customer expectations without compromising the premium experience, brands can have the best of both worlds.
The essence and appeal of premium brands is significantly shaped by the experiences they offer. Beyond the
tangible qualities of a product or service, premium brands understand the importance of creating distinctive and unforgettable experiences for their clients.
These experiences transcend the transactional nature of business to create emotional connections that resonate long after the purchase is made. More and more premium brands are recognising this.
Louis Vuitton hosts its ‘Time Capsule’ exhibitions in various cities across the world, to provide an immersive and educational journey through the label’s rich history and heritage. This is not just an excuse to be fancy for the sake of it. The brand is being present to create special, memorable moments between itself and its customers that feel worth more than a simple purchase.
Similarly, Johnnie Walker’s ‘Journey of Flavour’ experience leverages AI to customise drink recommendations for customers, choosing from over 1,000 combinations to pick a drink perfect for their palette. This provides a unique experience for each customer, and generates an opportunity to create memories, shared experiences and social connection.
This all stems from a change in consumer mindset in recent years – that moments mean more than material
things. Consequently, the key for brands is to be at the heart of these moments to create long lasting emotional connections with their consumers.
Mercedes-Benz taps into this mindset by offering the public a chance to engage in a unique and memorable way through driving experiences. Often held in scenic or exclusive locations with professional driving instructors, these events provide attendees the opportunity to experience the performance capabilities of the latest models – an experience which feels special and unique, and therefore premium. Such events, coupled with a commitment to eco-friendly practices like electric and hybrid technology in the case of MercedesBenz, contribute to an authentic and responsible brand image.
In essence, premiumisation goes beyond a flashy exterior. It is about creating
distinctive and memorable experiences for each customer, recognising that premium is about the journey, not just the product.
Experiences play a pivotal role in sharing your brand’s story. The tale behind the brand’s inception and ethos acts as a bridge, allowing your customers to align their values with a chosen product. By sharing the journey of creating a premium sustainable brand, a deeper narrative of purpose and responsibility is created.
At Born Ugly, we incorporated this thinking into our work with health tech company MitoQ. As part of a complete brand overhaul, we helped shift MitoQ into a more emotional territory that aligned a deep human truth and with the product’s high price point, supported with a premiumised visual identity that communicates luxury, black tech and science.
Rolex does this extremely well. It uses its Perpetual Planet Initiative to allow customers to explore the brand’s heritage, innovation and commitment to precision watchmaking. This provides an opportunity for customers to appreciate the craftmanship and history behind the iconic timepieces, in addition to high -
lighting Rolex’s vision of a sustainable future.
In this way, storytelling is central to shaping a sustainable and premium brand. When customers buy into the narrative of a brand, provenance and sustainability go hand in hand. The brand’s story becomes an intrinsic part of the product, fostering loyalty by offering consumers more than just a product – an immersive narrative reflecting shared values and a collective vision for a more sustainable and responsible future.
What is fascinating about these wellestablished premium, luxury brands is that even they are having to move beyond what might have worked for them in the past.
So, while your company might not be at the same level as Louis Vuitton or Rolex, you can learn something about the future of premiumisation by looking at brands with an established reputation and their need to be innovative, creative and forward-thinking.
Consumers no longer buy brands just because of how they look. Consumers remember experiences and how a brand makes them feel, and they need a story
behind the brand that resonates to establish a genuine connection.
By embracing the transformative potential of storytelling, brands embark on a journey where every purchase becomes a testament to a collective commitment; a commitment to premium experiences, sustainable practices and a future built on authenticity and purpose. n
To learn more about the work of Born Ugly, please visit: https://www.born-ugly.com/
Latest innovations from the engineering and manufacturing industry
ABLIC, a group company of MinebeaMitsumi Inc, has launched the S-19990/9 Series of automotive step-up switching regulator controllers.
With the increasing electrification of vehicles recently, ECU and sensors are being incorporated in most applications. Most ECU operate using 12V auxiliary batteries as their main power supply. However, if a vehicle is subject to a severe impact, such as from a traffic accident or collision, and the power is lost, then these ECU will stop operating.
As electrification continues to progress, there has also been an accompanying increase in safety requirements. To ensure the safety of vehicle passengers, backup power supplies can be installed for ECU in, for example, electric door latches and E-Call, in order to maintain operation for a set period of time even after an accident. Backup power supplies are generally composed of capacitors/batteries and a step-up circuit, and when they use low voltage capacitors/batteries in order to achieve downsizing and reduced costs, a step-up circuit is required to boost this low voltage to 12V backup power.
The new S-19990/9 Series products are 36V step-up switching regulator controllers which can secure operating voltage from the industry's lowest 3V, making this an ideal IC for constructing backup power supply step-up circuits. The S-19990/9 Series is available with an oscillation frequency of 400kHz or 2.2MHz.
These ICs are also equipped with a spread spectrum clock generation circuit which enables reduction of the conduction noise and emission noise emitted by the step-up circuit. These IC can also continue operation at a low consumption current of 60 µ A typ. during switching off, while still maintaining excellent response characteristics. These features allow these products to support ever increasing safety requirements while continuing to decrease the voltage of backup capacitors/batteries, and achieving downsizing, lower costs, lower noise, lower standby current and high-speed response. n
Viritech, the leading hydrogen powertrain solutions provider, has launched its 60KW VPT60N readyto-run vehicle powertrain. Part of the Viritech powertrain family and the culmination of a number of years of research and development, the VPT60N powertrain combines the array of Viritech powertrain products and enabling technologies into a complete powertrain solution for OEMs, Tier-1s and research bodies allowing for the rapid deployment of hydrogen fuel cell electric vehicles.
The powertrain includes a 60kW fuel cell with balance of plant and boost DC/DC power converter. It also has a 16kWh 400V battery energy store with battery management system and cooling components.
Customers can also benefit from the full function Vehicle Control Unit with Tri-Volt™ energy management, which manages all aspects of the powertrain, including HVIL and related safety systems.
Both the battery energy store and hydrogen storage are available in bespoke form to aid integration in a vehicle, with a standardised option for both available to minimise lead-times. The powertrain is delivered with all systems integration between powertrain components completed and the VCU preconfigured for system start-up within the vehicle.
The powertrain is offered in a nonhomologated form for prototype and development vehicle use, with Viritech’s engineering division able to support vehicle integration and development (including HMI and functional safety case) to achieve a fully homologated end vehicle.
With the launch of the fuel cell powertrain, Viritech is again reinforcing its commitment to enabling the production of fuel cell vehicles and assisting OEMs and Tier-1s to meet zero-emission vehicle targets without vehicle performance compromises. n
2022 Earthshot Prize winner and industry disruptor Notpla has continued to scale up its seaweed-based packaging. While commercial success and innovation have advanced the company’s story, a pivotal decision by the Dutch government to declare its material ‘truly plastic-free’ is poised to open more doors. Andy Probert spoke to Hoa Doan, Head of Impact & Sustainability, to find out more.
solutions for packaging foods, drinks, care products and many other everyday items. While some are edible, some compostable and some dissolve in water - they all disappear back into nature without any harmful traces.”
Having created a family of regenerative packaging materials made from seaweed and plants, Notpla is tackling environmental issues on two fronts: denting the 6 billion tons of plastic waste dumped in our seas and promoting sustainable seaweed aquaculture.
ASour seas have become dumping grounds for plastic packaging, so Notpla has sought a solution from the sea. Notpla’s seaweed-based packaging is nature’s answer to a man-made problem. Notpla, which stands for ‘Not Plastic’, has revolutionised the single-use packaging space since Founders Pierre Paslier and Rodrigo Garcia Gonzalez created its first product, the Ooho, a seaweed-based, edible water sachet.
“Our mission is to make packaging disappear,” Head of Impact & Sustainability Hoa Doan said. “Notpla provides true
Based in London, its 60-strong interdisciplinary team includes experts in material science, engineering, biology and bio-design. Notpla is supported by impact-driven investors and advisors, as well as being embedded in a larger ecosystem of sustainability-minded companies, climate initiatives and caring consumers.
From kitchen to global star
Pierre and Rodrigo studied Innovation Design Engineering and graduated with MScs from Imperial College, London. The germ of an idea began to form when they looked into using natural materials as packaging to replace the small plastic bottles that litter the world.
They discovered seaweed in its raw form could create a membrane that
would make bubbles for water. Prototypes were developed in their kitchens and the innovation culminated in the Founders receiving grant funding from Imperial College Incubator. This helped them create their first Ooho, an edible sachet for drinks and condiments. While initially making the bubbles by hand, they then focused on designing the first industrial Ooho machine.
Notpla went on to partner with Lucozade to replace single-use plastic cups and bottles with nearly 40,000 edible capsules containing liquid for runners at the 2019 London Marathon.
The Founders secured £10m in Series A funding to accelerate the scale-up of its portfolio. They launched Notpla Takeaway boxes with partner Just Eat Takeaway. com, to replace plastic at the 2022 UEFA Women’s EURO Final.
Notpla created a seaweed coating for cardboard food containers as an alternative to plastic-coated boxes. To date, Notpla has replaced over 9 million plastic-coated
containers with its seaweed-coated boxes in Europe.
All these initiatives led Notpla to become one of the winners of the 2022 Earthshot Prize to ‘Build a Waste-Free World’. Founded by Prince William and The Royal Foundation, it is the world’s most prestigious and ambitious environmental prize, with each winner awarded £1m. “The prize was a major milestone for Notpla and validation of how our products will be a game-changer for the packaging industry,” Ms Doan said.
2023 proved an exciting year, with Notpla doubling sales and production to four million seaweed-coated takeaway boxes.
The company now has a portfolio of six packaging products, including food containers, energy gel pods, pipettes, sachets, rigid packaging and seaweed paper.
Notpla has continued to set the pace on the commercial front. The company distributes to clients across Europe and has expanded into the USA. “We now supply independent restaurants, catering companies, big stadiums and events across Europe,” Ms Doan explained. “We hope to continue expanding in the UK, Europe and the US.”
Notpla has also been a packaging provider to major events, including the BRIT Awards and COP28. In other developments, Notpla was awarded a €1.3m grant to work with a partner to transform seaweed extracts into flexible film packaging. As an alternative replacement to plastic film,
Notpla has, in collaboration with Mack, launched an industry first – a sustainable clothes detergent sachet. Additionally, Notpla was awarded a £1m grant by Innovate UK to scale up production of the seaweed material for takeaway cutlery.
Available in pellet form, the material can be shaped into a variety of products, offering versatility in manufacturing. Ms Doan described how the company’s Rigid material is “an exciting addition to Notpla’s portfolio and offers a sustainable solution to support the global initiative to reduce plastic waste.”
The awards came shortly after October 2023, when the UK banned single-use plastics and amidst the staggering statistic that over 40 billion units of
plastic cutlery are annually produced. Notpla is ideally positioned to meet that gap in the market and respond to demand for alternative materials.
“We have ambitions to double our impact and replace eight million singleuse plastic items in 2024,” added Ms Doan. “Notpla’s impact is at the heart of what we do: raising awareness about the
problem we are solving, which is plastic pollution in packaging and educating stakeholders about the benefits of our products.”
Another boost came from the Dutch government’s environmental body, which after wide-scale testing of thousands of material solutions, declared Notpla’s seaweed-based packaging as the first material to be recognised as truly plasticfree. “This was a hugely pivotal moment for us,” Ms Doan said. “This sets Notpla apart and for the first time, a government has intervened to assess packaging materials to verify plastic-free claims in the market.”
However, the policy landscape remains complex and the need to raise awareness of the benefits of seaweed packaging as a new material category in the industry is ongoing.
“Notpla’s main aim is to continue working with brands that consider how they can replace plastic-based packaging with more sustainable materials, such as ours, which have a more positive environmental impact compared to plastics” Ms Doan reflected.
To that end, Notpla has initiated the Natural Polymers Group, a global consortium of biomaterial companies in the pack
aging industry to push for shared sustainability standards and legislation of harmful materials. The aim is to inspire businesses to adopt sustainable alternatives and advocate change.
“Notpla has demonstrated that its products are commercially viable and all its partnerships in the supply chain are aligned on shared values and ethics,”
Ms Doan said, in conclusion. “While 2023 was an amazing year, 2024 could be even more exciting for Notpla in driving the movement to replace plastics and see the industry adopt our sustainable packaging. Seaweed is truly the solution.” n
On the cusp of its 30th anniversary, Finland’s Earthpac Oy is contemplating new horizons as it seeks to expand its wooden packaging business. A leader and specialist in wooden pallet and package creation and distribution, the company’s commitment to quality and environmental responsibility remains undimmed. CEO Timo Nieminen explained more in a report by Andy Probert.
Demonstrating sustainability in the field of wood is a natural fit for Earthpac Oy, Finland’s leading manufacturer of wooden packaging for industrial clients across the nation.
So much so that external partner
Reforest Finland calculated Earthpac’s CO2 levels and found its scope 1 and 2 emissions had reduced by over 70% since 2018. Earthpac now intends to deepen that commitment by working with its suppliers, Finland’s sawmills, to reduce scope 3 emissions.
“At Earthpac, we have always focused on quality and customer satisfaction while being totally committed to delivering highquality, sustainable packaging solutions,” said CEO Timo Nieminen.
Reliable source
Earthpac, founded in 1995, manufactures about three million wooden packages annually across six production facilities in Äänekoski, Lieksa, Kruunupyy, Kouvola, Hämeenlinna and Kotka, all in Finland.
While manufacturing wooden pallets and packages, its product portfolio includes other packaging materials such as EUR pallets, pallet collars, plywood, cardboard and plastics. Clients come from various industries, including carton and paper, industrial equipment manufacturing and subcontracting, chemicals, plastics, building materials manufacturing, and food processing.
It also provides a host of services, from packaging design to its highly respected ePac logistics services, which encompass logistics, storage, packaging and goods delivery to help clients support their core business, find solutions to maintain supply chain efficiency and reduce costs.
“Our ePac services have been provided to demanding international companies for years,” Mr Nieminen added, “At the heart of what we do is our motto ‘It’s easy to do business with us.’ This deeply resonates with customers who want a reliable industrial packaging manufacturer.
“We have high customer satisfaction, retention and experience levels; these have been central goals and guided the company’s operations since its early days. We continue to monitor these efforts annually, and our performances remain consistent and strong.”
Mr Nieminen explained how Earthpac currently operates in the Nordic markets, with its export business accounting for over 15% of revenue. However, the company, which is employee-owned and has a workforce of 150 people, is contemplating expanding its operations.
In late 2023, the company acquired Hoky Lavarakenne Oy, helping to strengthen Earthpac’s presence near Kotka, Finland, according to Mr Nieminen: “Hoky Lavarakenne fits our growth strategy well and excellently com -
plements our production structure.
“We are also investigating other acquisition opportunities to strengthen our growth further and will invest heavily in the technological development and efficiency of these companies.”
As part of this strategy, Earthpac is conducting an investigation of the Swedish market, partially funded by the EU. It aims to gain valuable insights into customer needs and market potential while positively looking for the best ways to impact the industrial packaging landscape in Sweden and beyond.
Earthpac has also deepened its cooperation with Mitra, which operates in Troms County, Norway. Earthpac has been Mitra’s main supplier of timber for years. Mitra mainly uses timber in its pallet production.
Mitra AS, owned by the municipalities of Senja and Sørreisa, is one of Norway’s social enterprises and offers people with different needs the opportunity to return to working life. The Senja region is Norway’s capital of fish processing and Mitra has been operating as a local pallet manufacturer to the fish industry for 25 years.
More recently, large industrial investments have been made in Northern Norway, and the use of pallets has been growing significantly. Mitra wanted to meet the growing demand, so it turned to Earthpac, which was delighted to share its technological expertise.
“The new line, opened in late 2022, fully meets Mitra’s
wishes, and target production efficiency was quickly achieved. We are very happy to help Mitra AS in Norway. This kind of cooperation, with social responsibility aspects, makes us even a bit proud.” said Mr Nieminen.
Earthpac’s facilities hold ISO 9001 and 14001 certifications, ensuring it remains dedicated to quality and environmental management excellence. This is reflected in many ways from converting its forklifts to electric, introducing LED lighting, implementing comprehensive collection and
recycling procedures and organising a plastic collection.
It has also acquired emission-free electricity for its production sites, installed a solar system for one of its factories and optimised logistical routes.
Mr Nieminen noted how all wood sourced from suppliers is Programme for the Endorsement of Forest Certification or Forest Stewardship Council-certified. “We ensure the sustainable use of forest resources is a priority, and we constantly improve our methods towards a more sustainable future,” he said.
In March 2024, Earthpac renewed its EcoVadis silver rating and was also CSR-audited by a major customer.
While the dual effects of sluggish global industrial performance and rising inflation rates are cause for concern,
Earthpac continues to propel itself forward with a growth strategy and investment in its facilities.
“We have been investing lately in production technology in our different production locations, with the aim to increase automation,” Mr Nieminen explained. “Naturally, we want our industrial customers to expand their businesses in the EU and Finland. This will have a positive effect on the packaging industry. Without industrial growth, the B2B packaging industry will not significantly grow.
Mr Nieminen highlighted that the company’s performance was primarily based on selecting the best sawmills in Finland as its support base, while its employees were highly attuned to delivering the best in customer service.
“We have many customers who have been with us since the company first started out,” he said, in conclusion. “Their continued support shows how easy it is to do business with us as we head into our 30th year of operation. It is not only a source of pride, but our strength from within that has made us what we are today: a leader of the industry.” n
Lovepac is a market leader in the customised protective packaging industry. The company aligns quality custom corrugated box and foam solutions with the latest design innovations, manufacturing strategies, and customer care. Vice President Sophie Pepin explained more to Hannah Barnett.
Lovepac is shaping the way North American businesses package their goods and materials. Since it was founded in 2002, the company has excelled in the design and manufacture of bespoke industrial packaging made from corrugated boxes, wooden pallets, and protective foam.
The company operates in the aeronautical, pharmaceutical, medical, food, and high-tech sectors and is known for innovative, sustainable materials.
“Our conscientiousness towards sustainability sets us apart,” said Sophie Pepin, Vice President. “If a customer is looking for that, they are coming to the right company. Plus, we are a manufacturer. We transform foam, corrugated, and wood. We’re the only ones in the whole province of Quebec that work with all three products.”
A testament to hard work and commitment, Lovepac began life in the garage of its now President and CEO, Robert Sibthorpe. “He was just a distributor at the time,” Ms. Pepin explained. “Over the years, he bought one machine, and then another, and started producing: first in foam and then in corrugated. Then later we added wood.”
The company has around 70 employees across several sites in Montréal, Beauce, and a manufacturing plant in Guadalajara, Mexico, which opened in 2018. In July 2023, Lovepac was acquired by Antalis, a group specialised in the distribution of papers, packaging and visual communication products and services with activities in Europe and Latin America. Antalis is in turn a wholly-owned subsidiary of KPP Group Holdings Co., Ltd., a publicly-listed company
on the Tokyo Stock Exchange. According to Ms. Pepin, so far this relatively new integration is running smoothly.
“Antalis have the same culture and phil osophy as us, so we are very well aligned,” she explained. “It is obvious the Antalis management cares about its employees, and at Lovepac we have an acronym that our culture is one that CARES, which fits in well. It’s so important in a company buyout that the culture blends. I think Antalis did its homework and saw what kind of company we are.”
Antalis is similarly conscientious about the environment and published an ESG report in December 2023, with an updated one to be published every year. The information will also be available to Lovepac’s customers and suppliers.
Lovepac concentrates on small to medium runs, manufacturing specialty packaging for, sometimes very heavy or fragile, products to ship around the world.
The company offers turnkey manufacturing of custom corrugate, crating, and low- and high-density foam packaging to ensure a customer’s solution is professionally designed and manufactured to the highest standards.
“Our sales staff are out on the road, they scour the territory and bring back projects from our customers,” Ms. Pepin explained. “We have four designers, three in Montréal and one in Mexico, who design the specific packaging for each product.
“The material we use largely depends on the size, weight, and destination of the
product. We make a sample and there’s usually a lot of back and forth with the customer, but once they approve the packaging, they’ll place a P.O., and we start production.”
As part of its full turnkey service, Lovepac also offers assembly of foam into the boxes.
“Often, all a customer has to do is open the box, take the top foam off, put their product inside, place the top foam back in, and close the box,” Ms. Pepin said.
Around 14 years ago, the company began incorporating recycled foam into its process, in response to a market that was, at the time, dominated by white virgin polyethylene foam.
“Everyone was just putting white foam in the garbage,” Ms. Pepin explained.
“Robert (Sibthorpe, President and CEO) started pushing our suppliers to recycle their foam and we began to reuse all our
The company’s value system is based on the following tenets of packaging success: Continuous improvement Attitude Respect Excellence Sustainability
scrap foam from production, working with our customers to approve and test it. The process took two years, but we finally came up with something that pleased everybody and met with the requirements of the poundage.
“At first, they were mixing different colours together, so the foam was multicoloured, but customers didn’t like that. So, we had to work to make it look prettier. Now it’s all
black – and that’s how the black recycled foam came into the market.”
As a result, the company has also decreased its specific foam offering from 20 types to around seven. To promote circularity, Lovepac also melts foam in a densifier and sends it to another company that makes the substance into pellets, before it is sold on to plastic companies manufacturing products with reused content.
“Customers sometimes will call me and say they have a lot of foam from a shipment they received, and they don’t know what to do with it,” Ms. Pepin said. “If it’s a P-foam that we can melt, then I’ll take it from them just to make sure that it doesn’t go in the garbage.”
Customers are clearly a highly valued element in the Lovepac formula.
“We take care of our customers from A to Z,” agreed Ms. Pepin. “We follow through after sales, making sure they received deliveries and they like the product and that sort of thing. This takes place through the whole process, from the moment that we get the project in, all the way till the customers are happy and ready to ship their product.”
Additionally, the company also values strong trustworthy relationships with its supply chain. Lovepac uses many of the same regular, local suppliers. Foam suppliers, for example, are located just 15 minutes away.
“Recently, we calculated our corporate carbon footprint (scopes 1 and 2), and I sent letters to our suppliers asking them what sustainable actions they are putting in place,” Ms. Pepin said. “I’m still waiting for answers from some. Keeping track of everything is difficult, which I understand. But from a supplier’s perspective, we are very easy to work with because everything in corrugated is made from recycled anyway.”
It is this combination of environmental forward thinking and versatility which makes Lovepac stand out. The company now shares a goal with Antalis to
grow in North America, perhaps by the acquisition of a packaging distribution business.
For Ms. Pepin, who joined the company back in 2011 and achieved an Executive MBA in 2015, life at Lovepac is a gift that keeps on giving. “I love what I do, otherwise I wouldn’t be doing it,” she concluded. “I used to be in sales and what really drove me wasn’t getting paid my commission at the end of the month, it was getting the customers to come on board with us.
“Now, my satisfaction is derived from my team. I challenge them every day, I coach them and help them improve themselves and grow as people and as employees. That’s what really motivates me; if my team is happy, then I am happy.”
Armultra Ltd has been providing engineering solutions for the offshore industry since 1985. The company is highly adaptable; continuing to serve the oil and gas industry while also responding to the needs of the emerging energy transition sector. Director Tom Beales explained more to Hannah Barnett
IThas been a successful, if sometimes challenging, year at Armultra.
The company, along with much of the industry, has been impacted by the fluctuating price of oil and gas. This i s alongside some renewable projects being put on hold, though others are progressing quickly, with the push to net zero.
“It’s been an up and down year, from a work point of view,” reflected Tom Beales, Director. “But overall, with how the last few years have been, up and down is the new normal. So, we’ve adapted and overcome the challenges and we’re out the other side. We’ve got a full order book for the next year and are trying to take on more people in all areas to cope with demand. I think that this proves more than anything how well we’ve coped with conditions out of our control. As a team, we’ve all stuck together and got through it, and now we’re seeing the benefits.”
Armultra’s facility in Great Yarmouth occupies 160,000 square feet with dedicated carbon steel and exotic metal workshops,
including goods inwards and pressure testing areas. The company also has a 12-metre tower for rope access, working at height and GWO training. This is supported by one of the largest archives of Welding Procedure Qualification Records in the UK. The company employs around 150 staff in its workshops, offshore and onsite and is projecting a turnover of £14 million for the 2024 financial year. “It’s looking good, though of course we never know what’s around the corner,” said Mr Beales. “But, as a business, we can only deal with what’s in front of us.”
One of Armultra’s clear strengths is its multi-skilled workforce, who are adept at moving between the renewables sector and projects for oil and gas companies.
The company is keen to encourage new blood into the industry. It currently has 10 apprentices and is training them in different levels of fabrication engineering, to equip the workforce of the future with
the skills necessary to facilitate the energy transitio n.
“We’ve also got six individuals in an internal improver programme,” Mr Beales added. “We’re trying to develop and bring in all age groups; people that want to change career paths and come into engineering and fabrication, as well as school and college leavers.”
Armultra is looking to contribute to the energy transition by exploring the potential
of solutions such as carbon capture and hydrogen. The company is a member of the East of England Energy Group (EEEGR), where Mr Beales is also a Director.
“EEEGR is heavily involved in discussions with various hydrogen and carbon capture teams,” Mr Beales explained. “From a fabrication point of view, at Armultra we are one of the last pieces of the puzzle and most of these projects are in the early stages of development, so we haven’t received any orders yet, but we’ve been in discussions and helping with the upfront work of such projects.”
The company now has projects in the pipeline with a variety of different sectors, including renewables, oil and gas, nuclear, and petrochemical.
In the last year, the company has also been going through a transition of its own, with old staff retiring and new employees
hired to replace them. “That’s been a key milestone,” said Mr Beales. “We had three people retire who had been in the business for 30 odd years, so we lost a lot of experience and knowledge, but the new people have settled in well and hit the ground running.”
One of Armultra’s flagship projects has seen the company fabricating refrigeration packages for Hinkley Point nuclear power station. The contract has been running for
two years, with another year to go, and was Armultra’s first big project in the nuclear power industry.
For the Hinckley client, Armultra builds units from the ground up at its Great Yarmouth workshop. This includes fabrication of oil separators, pressure vessels, shell and tube heat exchangers, liquid receivers, and surge drums. The base frames and support steel are also manufactured at the workshop. Once the painting and electrical work is done, the products are shipped to the client for final installation at Hinkley.
“Winning this work has been a big feather in our cap,” explained Mr Beales. “And with the potential of Sizewell, and other nuclear power plants being built around the country, it is a great opportunity for us.
“There is such a great project team here, along with our Responsible Welding Coordinator. We can do the design, the fabrication and the installation. We can obviously just do parts of that, if needed. We can offer our clients the complete package from start to finish, keeping to the quality, timeframe and price set out at the offset.”
To maintain this strong relationship with clients, Armultra relies on its supply chain, using local suppliers wherever possible to ensure successful delivery of the final product.
“We wouldn’t be here without a successful supply chain,” Mr Beales agreed. “Everyone, from local suppliers to those in the wider parts of the country, does a great job for us.
Communication with our suppliers is something that we especially pride ourselves on.
If we need something in hurry, then we can get it from speaking to the right person. But if there is a delay in a part, then we can work with the supplier to expedite it too.
It’s all about keeping those communication lines open.
“There are local companies we have used since when we started in 1985, and there are companies out there that we’ve just started using in the last year. They’re all just as important to us and critical for the strength of our supply chain.”
It comes as little surprise to learn that Armultra plans to continue the same successful path and upward trajectory. This means remaining both resilient and flexible.
“We are still on our five-year plan to keep growing the business via headcount and turnover, and we want to keep making the most of the opportunities out there,” said Mr Beales. “Working with our clients and supply chain is how we maintain our
success. We’ve been in the business close to 40 years and are a well-established, well-known, world-class fabrication engineering company. We just need to keep building on that reputation by always improving.”
For Mr Beales, on a personal level, it is the variety of work that keeps the job exciting.
“Every day is different,” he concluded. “ I enjoy working with people and getting to know how they operate. We take on a diverse range of jobs, which means I am always interacting with different people and different suppliers. I love working in this industry. It’s truly the variety and the clients that we deal with that keeps me going every day.”
in 1912, The Fine Bedding Company is a fourth-generation busirovides premium bedding through sustainable manufacturing. Director Claire Watkin and Head of Marketing and Ecommerce discussed the company’s passion for sustainability and in conversation with Antonia Cole.
Throughout its long history, The Fine Bedding Company has continuously adapted to the evolving market by staying flexible and proactively taking advantage of new opportunities. As gaps in the market opened, the company developed new machinery and technology, inserting itself as an industry-leading innovator in bedding.
Constantly improving its product range with new innovations, The Fine Bedding Company utilises technology to increase the efficiency of products. The cuttingedge fibre technology Smartfil has the same thermal efficiency as a premium down duvet with a lighter and more breathable feel. Also, the company’s sonic seam technology uses ultrasonic waves to neatly seal fabric edges, reducing waste by up to 5%.
The company employs around 170 people and generated £28 million in
turnover last year. Its eco-factory produces approximately 55,000 duvets and 100,000 pillows per month and there are plans to increase these figures by evolving current software and machinery.
Thinking into the future has always been at the core of The Fine Bedding Company’s operations. The company accomplished a world-first with a duvet made entirely out of recycled PET bottles in 2018 and is continuing to push the boundaries of sustainable bedding, working with partners to stay at the front of the market and making new innovations accessible to customers.
“We’re always developing new technology and finding ways to increase the efficiency of our operation,” said Managing Director Claire Watkin. “We have two new projects coming out next year that we’re very excited about.”
The Fine Bedding Company’s eco-factory is based in Tallinn, Estonia, a country with a substantial environmental focus. With over 2,200m2 of manufacturing space, 3,000m2 of warehousing space and connections to cargo routes, the company is well-equipped to develop and manu facture bespoke products that promote sustainability.
At its factory, the company uses 100% renewable energy and has 42 energy monitors to observe usage and effectiveness of machine upgrades in terms of efficiency. It also recycles 100% of the waste produced.
There are many innovative ways in which the company recycles waste material from production. One of which being that excess fabric is sent to a company in Lithuania that re-purposes it to make cuddly toys. Calibrated scales are also used to measure materials throughout the production process and recycled raw materials are utilised in new designs to limit waste.
All of the cotton used in the factory comes from the Better Cotton Initiative, a group promoting improved cotton farming standards across the globe. The Fine Bedding Company also uses post-consumer plastic waste and transforms it into fibres to be used in bedding. Recycling procedures at the factory are Global Recycle Standard approved and certified, attesting to high levels of environmental sustainability within the company.
“As well as establishing environmental policies within our operations, it is also important for us to integrate sustainability into our workforce,” explained Ms Watkin. “We have green teams, in both the UK and Estonia, that create employee-led environmental initiatives.
“There’s a lot of passion for sustainability throughout every level of the company and so, we are using the TIMWOODS framework to identify and limit waste across the business.”
The company also helps customers to be more sustainable by creating environmentally conscious products. Through the use of premium materials, technologically advanced production techniques and informed designs, The Fine Bedding Company is able to create long-lasting and high-quality bedding.
This reduces waste as it means that customers can keep their bedding for longer, minimising the amount of bedding that ends up in landfill. The company is also working on an initiative educating consumers on how they can recycle bedding to limit their environmental impact.
“There are some incredible people down the supply chain that really want to make a difference and we are working with them to make developments in materials, fabrics and fibres,” said Head of Marketing and Ecommerce Laura Keay. “170 tonnes of bedding get disposed of as general waste every day in the UK, which is a huge amount.
“This is mainly low-quality bedding that only lasts a couple of months before it has to be replaced, which is damaging to the environment. We are changing this standard and promoting the use of long-lasting premium bedding.”
The Fine Bedding Company has created sustainable options that improve sleep quality. There are multiple products that help solve typical sleep problems including allergies, temperature and breathability, but the most popular product is the Night Lark Coverless Duvet.
This duvet has no cover, and so there is no duvet cover replacement struggle. The entire duvet can be put in the washing machine, allowing for convenience and accessibility, whilst still retaining quality and durability.
HeiQ, a global leader in material innovation, developed a four-in-one allergy treatment that The Fine Bedding Company uses in bedding to create products targeted at those with allergies It is
not chemical based and targets the four most common allergens, making it an effective and sustainable solution.
As a certified B Corporation, the company is constantly striving to improve sustainability. It has spoken in B Corp panel talks, participated in volunteering opportunities and connected with charities to improve environmental awareness.
The Fine Bedding Company has been working with Montcalm hotels to provide sustainable bedding, giving the hospitality sector better access to environmentally friendly options.
“As a B Corp, it is our job to educate and communicate about sustainability,” explained Ms Keay. “We’re holding ourselves publicly accountable. With the accreditation comes a lot of work, as we must constantly improve. We choose to provide impact reports because were confident in what we’re doing and want to be fully transparent.”
All of the company’s suppliers have been audited for social compliance and environmental targets using the Higg Index. Through site visits and open communication, The Fine Bedding Company is able to work with suppliers to build relationships founded on the common goal of sustainability.
“Our fibre supplier Huvis is doing great work in terms of sustainability, it has a low carbon footprint and is very forward-thinking,” said Ms Watkin.
“By choosing suppliers whose values align with our own, we are able to build long-standing relationships and can work together to improve the industry.”
The company has lots of new innovations that it is working to bring to the market including more efficient technology, recyclable materials and waste reduction techniques.
“Going forward, our biggest impact will be through the companies we’re working with,” concluded Ms Watkin. “We are altering the course of some major companies through education and access to our sustainable products, leading to a more environmentally conscious world.” n
Ulster Carpets was founded in 1938 in Portadown, Northern Ireland, by George Walter Wilson and remains privately owned by the same family. The company is the premier supplier of Axminster and Wilton carpets to the residential, hospitality, marine and casino sectors across the world. Sustainability and Product Engineer Carol Howson told Hannah Barnett some of the secrets of the company’s success.
The story of Ulster Carpets is one defined by innovation. The company has combined its family-owned values with a pioneering, global approach to business. The result is a technologically advanced, service-driven company with flair, flexibility and a dedication to quality.
“Looking back through our history,” said Carol Howson, Sustainability and Product Engineer, “it is clear that forward-thinking is at the heart of everything we do. We continue to pioneer innovative, marketleading technology that focuses on manufacturing the highest quality carpets in the most efficient way.”
Innovation woven in Ulster Carpets has continuously led in its sector. The company introduced the first 15-foot Axminster loom in 1962, installed electronic Jacquard looms in 1987 and later became the first carpet manufacturer to offer 5-metre-wide woven Wilton carpets.
In 1999, Ulster Carpets launched a patented weaving technology and in 2022, this was taken a step further with
the introduction of the new generation of PSYLO TM looms. This technology has revolutionised the colour and designs the company offers, while also significantly increasing efficiencies.
The company is now well established with offices around the world, including London, Berlin, Paris. In the US, the company operates a main office in Marietta, Georgia, and has sales and design teams across North America working with the leading hotel brands and all the major casinos.
“Having expert teams working directly with our customers helps to turn interior
design visions into reality,” said Ms Howson. “We take a collaborative approach to every project and work closely with customers to develop design ideas. It is this partnership approach that makes all the difference to our customers and why we have such high levels of repeat business.”
Every week, Ulster Carpets weaves the equivalent of four football pitches of Axminster carpet and the company buys around 2.5 million kilos of wool a year – the equivalent to 1.47 million fleeces.
As an innovative operation, Ulster Carpets has been actively looking at its environmental impact and carbon footprint for at least 20 years. In 2008, it was the first company in Northern Ireland, and the first textile manufacturer in the UK, to be awarded the Carbon Trust Standard after cutting carbon emissions by over half.
The company has now taken a holistic approach to its sustainability strategy,
which means looking at all areas of business to drive improvement.
“As the world’s largest Axminster weaving site, efficiency in production is one of our top priorities,” Ms Howson explained.
“In 2021, we conducted a robust review to assess our environmental standards.
The findings showed that we have made a great start, with strong foundations in place which have been used as a springboard to grow our sustainability strategy.”
In April 2023, the company published its first sustainability report. The report outlines how Ulster Carpets has made changes over the last few years to reduce its impact and sets out sustainability targets to achieve by 2025. These include a 50% reduction in carbon emissions, reduction of water consumption by 5% and a 20% reduction of waste.
On the crest of a wave
Ulster Carpets recently completed its largest ever cruise ship project and the illustrious Icon of the Seas set sail for the first time in January 2024.
The game-changing cruise ship from Royal Caribbean International is 365 metres long, weighs 250,800 gross tonnes and has a capacity for 5,610 guests and 2,500 crew. It also features over 55,000 square metres of bespoke carpet designed and manufactured by Ulster Carpets.
“Projects like this demonstrate that there is still an appetite for wool-rich carpets in the hospitality sector, particularly the envi -
ronmentally conscious cruise industry,” Ms Howson reflected. “It was certainly a project that put us to the test. We created over 75 different designs for Icon – a huge increase on the 20 different designs for an average project.”
The Icon of the Seas project also allowed the company to showcase its ability to create unique designs, with the team in Portadown and the design studio
in London producing flooring works of art to match the distinctive design and style of each area on the ship.
“Like every project we work on, we had to make sure we met strict deadlines to keep the project on track – which put our weaving and finishing teams under pressure,” Ms Howson said. “However, while Icon of the Seas was a larger project than most, we have vast experience of working on hospitality projects that have high demands in terms of design and quality.”
An Ulster Carpets product contains a high percentage of wool, a rapidly renewable raw material, sourced primarily from the British Isles. As a fully integrated manufacturer, the company enjoys full control over its processes. Wool is sourced and spun at its own mill and all Axminster and Wilton products are designed and manufactured in the UK. Additionally, all process waste is used to produce a luxury triple layer underlay called Axfelt.
“From sourcing the highest quality wool, spinning and dyeing the yarn, through to the bespoke design, weaving and delivery of luxury carpets and rugs, we control every aspect of the manufacturing process,” Ms Howson explained. “This is different to most carpet manufacturers, who will outsource different elements to other companies.”
As a result of this fully integrated status, the company also enjoys control over a large part of its supply chain. The materials that are sourced externally, are largely done so as locally as possible. “We choose suppliers who can deliver goods and services that align with our sustainability ethos and support us in achieving our own targets,” said Ms Howson.
Looking ahead, Ulster Carpets plans to continue to innovate and lead in every aspect of its business. Like many manufacturers in the UK, the company faces cost pressures compared to the competition based in lower cost economies, so intends to find innovative solutions to offset that disadvantage.
“Our focus is on reinforcing our position as a premium quality producer by adding as much value as possible to our product offering,” said Ms Howson. “That will be achieved through skilled people, use of technology, R&D and investment in machinery. We are always looking for ways to improve and will continue to provide excellent products and service to our customers.”
Ms Howson’s position of Sustainability and Product Engineer was created just
last year, demonstrating Ulster Carpets’ ongoing commitment to becoming a more sustainable brand.
“I feel very privileged to be given the opportunity to make positive changes for the future of the company, as well as on the overarching path to Net Zero,” she concluded. We all have a role to play as individuals, but it is very rewarding being able to make a positive contribution on a larger scale.”
n
A leading supplier of food-safe panelling systems and coldstores, HBCL Coldstores supplies full-package hygienic and temperture-controlled environment solutions to the food manufacturing, storage and distri bution industries, plus other specialist end-users. Managing Director Craig Lovett discussed the company’s efforts to improve sustainability and its commitment to customer satisfaction. Report by Imogen Ward and Antonia Cole.
Established 22 years ago, HBCL C oldstores has grown and developed through years of experience and working in diverse settings. As specialists in design, manufacture and installation, the company is able to deliver effective solutions to satisfy a range of client needs.
Through the provision of chiller and freezer coldstores, food processing facilities, temperature-controlled environments, firewall systems and partitioning, HBCL Coldstores has developed an expansive and varied customer-base including leading retailing groups, food processors and manufacturers, plus pharmaceutical and construction clients. The company currently has a contract supplying coldstores to new ALDI stores across the north of England.
Operating from a 20,000ft2 factory and storage facility in Bradford, West Yorkshire , the company has a fleet of vehicles and an experienced team of directly employed fitters, which enables it to efficiently deliver service.
HBCL has a subsidiary company, RCL Doors, operating from a 10,000ft2 factory. RCL make bespoke hinged and sliding coldroom doors, hygienic insulated personnel doors, and all types of freezer doors. RCL also provides a range of high-speed doors. RCL is a huge asset in helping HBCL by manufacturing doors as often work is scheduled at short notice, so RCL allows for flexible timescales.
“We’ve been taking on increasingly larger projects as the company has grown,” said Managing Director Craig Lovett. “Our ability to understand our clients’ needs means that we are able to adapt our services to fit each individual project. We learn how our clients operate and are flexible in our operations to suit their practices.
“Having this concern for our clients allows us to build stronger relationships and deliver greater results. We see the importance of listening to our clients and enjoy providing a service that really benefits their operation.”
A client that HBCL Coldstores has worked and built a relationship with is FareShare UK, the largest food redistribution charity in the UK. FareShare works with leading retailers and manufacturers to enable the collection, storage and distribution of food to Community Food Members.
In partnership with ASDA, FareShare has been working on the Fight Hunger Create Change campaign, which redistributes
good quality surplus food to disadvantaged communities facing food poverty. Through school breakfast clubs, elderly lunch clubs, homeless shelters and community cafés, food that would have otherwise been wasted is able to reach people who need it.
HBCL Coldstores has supported FareShare’s mission by installing freezers and cold rooms, as well as using refurbished panels, doors and ancillary items at a reduced margin. The cold rooms have been designed specifically for the facility, meaning foods can be stored and distributed more efficiently, whilst also limiting energy consumption.
“Every week, FareShare provides almost a million meals for vulnerable people, so it’s really great to be able to support a charity doing such impactful work,” explained Mr Lovett. “We’re always looking for ways that we can save them money and help expand their operation.”
As well as supporting UK charities, HBCL Coldstores is dedicated to decreasing its carbon footprint. In the last few years, it has incorporated electric vehicles into the fleet. To further reduce environmental impact, the company uses British-made materials, meaning that fewer carbon emissions and other pollutants are pro duced through the transportation of goods.
One of HBCL Coldstores’ UK suppliers is Hemsec Manufacturing, which manufactures insulated panels. Hemsec’s products meet CE standards and have advanced insulative properties that support end-users in operating more sustainably. By utilising effective insulation, less energy is required to maintain set temperatures, and thus fewer harmful emissions are produced.
The company is also actively working to reduce waste on projects and at its facility. I f there are surplus materials such as panels or doors on a project, then HBCL Coldstores will reuse them on a different job instead of disposing of them.
With an experienced and professional team, HBCL Coldstores offers clients knowledgeable design and installation recommendations. After taking into consideration client requirements, the company’s in-house CAD designers produce detailed drawings for client approval, taking into account functionality and efficiency, plus health and safety.
Currently, HBCL Coldstores provides in-house and external training to its team, to ensure that elevated levels of quality are met throughout the company. This involves the continuous development of employees and supporting trainees working on site.
“We are always monitoring quality and training levels within the company,” said Mr Lovett. “By enforcing open communi -
cation between the installation team and contract managers, we are able to create effective plans for staff development.”
The company is currently advocating for NVQ qualifications to be reinstated within the industry as a form of external training.
As a member of the Controlled Environment Building Association (CEBA), HBCL Coldstores is working with others in the industry to achieve this goal.
“I’m hopeful that CEBA will be successful in making this NVQ available again,” explained Mr Lovett. “Better access to training will benefit the whole industry and will help workers to develop their skills with the necessary support.”
As well as working within the industry to improve training opportunities, HBCL Coldstores is always aiming to develop relationships with partners and suppliers. The industry innovations of suppliers allow
HBCL Coldstores to advance its own services and are essential to the success and evolution of the company.
Working with suppliers like Fermod UK, a leading supplier of door furniture, is beneficial as it shares the same value for premium-quality products and services. By integrating high standards throughout the supply chain, HBCL Coldstores can be confident in the services it is providing.
“Our relationships with Hemsec and Fermod UK have lasted over 40 years,” said Mr Lovett. “My late father worked for Hemsec, so some of my connections there have been lifelong, and we are proud to be one of its leading customers.
“The relationships that we have built with all our partners are so important to us. There is a sense of mutual respect where we know we can rely on them and they can rely on us too. They help us to grow, and we aim to do the same for them. It is very rewarding to see the progress we have all made together over time.”
As HBCL Coldstores continues to develop, it wants to continue upgrading
machinery in order to achieve improved efficiency, in terms of time and energy, for itself and clients. The company will also keep advancing the training measures for employees to ensure that high standards of quality and customer service are maintained.
“One of the elements that sets the company apart is the level of customer service,” concluded Mr Lovett. “We work to deliver a service that keeps clients coming back. A lot of our projects come from referrals, where people have been so impressed with us that they have recommended us to someone else. This level of customer satisfaction is something that we are striving to uphold now and into the future.”
Kadant PAAL’s primary products are horizontal balers and conveyors. These are used to process recyclable materials including paper and plastic, as well as various non-recyclable materials like RDF, waste and agricultural products. Based in Georgsmarienhutte, near Osnabruck in Germany, the company was founded in 1854. President Craig Heley explained more to Hannah Barnett.
The PAAL Group of Companies was formed in 2002 as a combination of Spanish, German, French and British baler manufac turers, establishing a firm European footprint. In 2016, the Group was acquired by Kadant Inc, a NYSE listed company. The Group now employs around 230 personnel and operates across five sites, with the main production facility in Germany, boasting a production capacity of around four balers a week and a smaller manufacturing unit in the UK.
“We have a standard product design with lots of options,” said Craig Heley, President. “Our balers will satisfy 99 per cent of customer applications and from a production point of view, it means we can plan with a much higher degree of certainty. We have a very simple, structured and highly effective production process for customers; we give a delivery date, and we stick to it.”
Kadant PAAL Ltd also designs and manufactures its own range of vertical balers and waste compactors in the UK, as well as distributing the full range of auto-tie balers and conveyors built in Germany.
All of the Kadant PAAL units have mobile engineers strategically located throughout their respective countries, offering comprehensive preventative maintenance cover, as well as a rapid response to any unexpected machine downtime.
Kadant PAAL is dedicated to the efficient compacting of a range of materials for recycling, thereby enabling the sustainable benefits of a circular economy.
“Where waste can be reused, it needs to be efficiently handled, stored and transported,” Mr Heley said “Our job is to make the material as dense as possible so that fewer operations per volume of material are needed and transport costs can be minimised. It makes the whole process more efficient, more cost-effective and therefore, more sustainable.”
Baling plastics for recycling tends to be a more challenging process than baling a material like cardboard, because it has an inherently slippery nature, and it retains its material memory so wants to re-expand after being compressed.
“To overcome this, we have increased the power of the pantograph and extended the length of the channel,” explained Mr Heley. “Also the varying material characteristics when baling need to be considered because there are numerous parameters that are automatically adjusted in the baler to optimise performance for each specific material grade. We refer to these as ‘recipes.’ With plastics, we are trying to get the memory out of the plastic, so the recipe must be a lot more sophisticated than with carboard.”
Bales of recycled material are typically secured in place with wire. Roughly two kilos of steel wire are used per bale, but
with sustainability in mind, the company is striving to reduce that number.
“For an operation producing 50,000 bales a year, customers may consume around 100,000 kilos of wire,” said Mr Heley. “So even a 10 per cent increase in bale density saves 10,000 kilos of steel wire, as well as meaning that more material is sent on a transport load, thereby reducing the number of loads and, as a result, the level of emissions.”
The company has also developed highefficiency motors and axial piston pumps as part of its machinery design. Compared with the previous design, Kadant PAAL now offers the same speed of operation with a 55kW motor that previously needed a 75kW motor, thus saving energy while maintaining the throughput.
Kadant PAAL recently worked on a significant project for a US customer which involved baling pulp for export.
“We’ve developed a baling process that forms a homogenous block of fibre pulp, without the need to tie or secure the bale,” Mr Heley explained. “It’s been quite a challenging process, but I think the most interesting bit is that it was a very international project for us.
“The customer is in the US, the machines are made in Germany, the tests were run in France, we used Spanish engineers, and the final commissioning process was
managed by a UK engineer. It covered all aspects of our Group.”
Mr Heley also explained about a further interesting project involving the automatic application of bale labels, including RFID chips: “Although designed in Germany, this has been project-managed in France and the system is currently being trialled at a major French customer,” he said. “Such a system could revolutionise the circular processing function because, for the first time, there will be genuine material traceability at the level of each individual bale.”
To accomplish such logistically complex projects and maintain the company’s guarantee of delivery within ten weeks, strong long-term relationships across the supply chain are crucial. Kadant PAAL favours a single source of supply and has frame contracts in place with its core suppliers.
“We give them a commitment in terms of what we will use over the course of the year and the maximum that we will
demand weekly for each specification, so they’re able to plan,” said Mr Heley. “This means they supply us in a very timely way f or things like cylinders, motors, panels and so on. We have a very structured approach to the whole procurement and production planning process. When we get a customer order for a baler, we place the order on our suppliers and know that they will be able to deliver to us within a four-week period, because we have a long-term historical working relationship with them, and they have the security of the frame contract. Our suppliers’ performance enables us, in turn, to be a reliable, market-leading supplier to our customers.”
Having already established a strong presence across Europe, where Kadant PAAL is known for its outstanding localised service, the Group’s next steps are set to continue on the path of international expansion.
“The US market is still relatively untapped,” said Mr Heley. “We’ve had some success but there are still significant challenges to overcome, and we need to provide our potential customers with new ideas because we are confident we can provide them with more efficient ways of doing what they’re currently doing.”
Kadant PAAL is ultimately a business dedicated to helping processes run more efficiently and sustainably. It is also, according to Mr Heley, a highly meritocratic organisation.
“Working here is all about dealing with smart and committed people,” he concluded. “Personally, I have a great sense of the talent at all levels within the company. So, I love seeing a person taking on responsibility and developing as an employee. There are lots of exam -
ples of people who have moved up significantly within the organisation. We are small enough to be able to enable people to push themselves forward and to give them opportunities. This also benefits our customers because these employees have a depth of knowledge and experience that is impossible to match.” n
Desert Board is an exciting new company revolutionising the construction and living sectors with the world’s first engineered carbon-neutral wooden board, crafted from upcycled palm fronds. After making an impression at COP28, the UN Climate Change Conference, Director Kamal Farah explained how the UAE company is determined to showcase how sustainability can flourish by tapping into the heart of the desert. Report by Andy Probert.
Sheikh Zayed bin Sultan Al Nahyan, the late President of the United Arab Emirates and Ruler of the Emirate of Abu Dhabi, was a champion of conservation and safeguarding the environment for future generations.
While the national leader and visionary died in 2004, his inspiration and legacy live on in Desert Board, a young UAE company. It is determined to uproot traditional thinking by taking the lead
in empowering the decarbonisation efforts of the construction industry and transforming the built environment.
Desert Board has developed innovative, engineered, locally manufactured biobased Palm Strand Boards (PSB) from upcycled palm fronds. They are free of formaldehyde, a noted carcinogenic, and can be safely used indoors.
“Our PSB is the future of construction, it can be recycled up to 40 times,” said
Director Kamal Farah. “It is the equivalent of a standard Oriented Strand Board (OSB), but the key difference is that we don’t have to cut down trees to make them.”
PSB ® is an authentic nature-based construction material derived from the abundant palm biomass of date palm trees across the UAE. Desert Board sources the waste from municipalities and farming communities. At a state-ofthe-art factory in Kezad, Abu Dhabi, it utilises a patented manufacturing process to create durable and eco-friendly building materials.
“Our patented technology allows us to establish a circular economy,” Mr Farah explained, “meeting our goal to support environmental preservation efforts, uphold
global sustainability agreements to protect our planet and facilitate healthier structures.”
The board, which can be fashioned in thickness from 9mm to 44mm, has a high mechanical strength equivalent to a traditional OSB. “You can build high beams and structures, including prefabricated h ousing units to fire prevention door cores , shuttering and construction boards,” Mr Farah said.
The concept was derived from Mr Farah’s father, Hatem, Chairman of ECC Group, a family-owned parent group renowned in the Middle East construction industry. The first PSB ® was created on December 14, 2021.
In a video created by The Climate Tribe, a UAE-based NGO championing sustainable businesses, Mr Hatem Farah explained:
“The palm tree has a lot of culture and history, and the people of the UAE were building houses and fences from that resource. As I am from construction, I never considered utilising this material.”
The Farah family was concerned on a number of fronts: palm waste was being thrown away, burnt or buried, polluting the atmosphere; spiralling importation costs, and the rise in carbon emissions, with construction accounting for up to 40% of global emissions.
“Around 11 per cent of emissions are from building materials, so Desert Board was born with the aim of replacing plywood for forming concrete,” continued Mr Kemal Farah. “After a long R&D period,
the board emanates from the desert environment. Because we are only utilising the palm fronds that are cut down, we are allowing the tree to continue living and capturing carbon.
“Our ancestors used to be sustainable and environmentally friendly because they used to take these palm leaves and build barasti houses and fences. Now we are crafting buildings from this board.” Desert Board produces around 110,000 cubic metres annually, or 340m3 daily.
The patented technology allows it to establish a circular economy meeting the goals to support environmental preservation efforts and uphold global sustainability agreements to help protect our planet for future generations while facili tating healthier structures.
Kamal Farah Director
“We have calculated internally that for every tonne of PSB® used, it is equivalent to capturing 400 tonnes of carbon,” said Mr Farah. “Key to that is how the board can be recycled and repurposed as part of the circular economy.”
PSB ® can be used to create fire-rated door cores that meet British standards for 60 and 90 minutes. It is being used as shuttering boards for casting concrete, as well as hoardings and scaffolding.
Desert Board is going further to use PSB ® to make furniture, such as kitchens,
wardrobes and doors, and even built 25 homes for the Red Crescent to accommodate refugees. “We have built one and two-storey homes in our factory, created acoustic wall panelling for events , exhibitions and stands, and for prefabricated volumetric construction for projects in Saudi Arabia,” Mr Farah explained.
One significant step to raise awareness around PSBs was Desert Board’s invitation to provide products as part of a showcase for COP28, the UN Climate Change Conference, hosted in Dubai
from November 30 to December 12, 2023. The Climate COP meets in a different city yearly to demonstrate the importance of collaboration between nations to fight climate change.
The company also makes door core frames that are better than solid wood door frames and PSB® has excellent screw-holding capacities. PSBs are fully utilised by the UAE-based Abanos Interior Fit-Out & Joinery, one of several related companies under the ECC Group umbrella.
Desert Board also conforms to the Al Sa’fat Green Building System, which ensures PSBs contribute to environmentally friendly construction practices.
While the aim is to scale up production capacity, Mr Farah noted that the com -
pany had eyes on enabling the boards to be used more for timber structures due to its inherent mechanical properties.
“There is enormous potential to build timber structures,” Mr Farah continued.
“We are also aided by a strong R&D team and the eight companies within the ECC Group. We are already using PSB shuttering boards for casting concrete and adding veneer to give it a wood look for furniture. It has also been used for raised flooring, and we intend to look at using it for floorboards.
“The challenge is to get traction and for the wider market to buy into what is a nature-based solution that can aid decarbonisation in the construction industry. It will take time, but we are on the right track.”
For over 30 years, Coral Windows has improved homes in and around Yorkshire. The company specialises in producing and installing windows, doors and conservatories, with a service that centres upon satisfying the customers’ needs. Operations Manager Brendan Cowey discussed the company’s sustainability goals and latest innovations, in conversation with Imogen Ward and Antonia Cole.
Coral Windows has five showrooms spread across Yorkshire, with outlets in Bradford, Wakefield, Leeds, Huddersfield and Sheffield. The company is proud of its Yorkshire heritage and strives to provide exceptional products and service to the local community.
As a family-run business, Coral Windows extends these values to clients, resulting in it winning the Feefo Gold Trusted Service Award. This award recognises exceptional customer experiences, rated by real customers. Alongside being a Which Trusted Trader, which is not common in the windows industry, Coral prides itself on its reputation.
“We provide a beginning to end service for our customers,” said Operations Manager Brendan Cowey. “From the initial enquiry, to servicing the product 10 to 15 years later, we make sure our customers are supported every step of the way and are left with high-quality
home improvements that better their daily lives.”
Last year, despite a decline of approximately 20% in the window market, Coral Windows saw a 20% increase in window sales and a 40% increase in conservatory sales.
With a yearly turnover of around £20 million and the production of around 450 frames a week, the company is predicting continuous growth and success in the coming years.
Coral Windows undertakes regular reviews of its supply base to certify that the practices of suppliers align with the views and ethics of the company. It scores suppliers based on several criteria, with sustain ability being a key factor. The company looks at whether raw materials
have been ethically sourced and if suppliers are recycling and reducing waste in operations.
“We have long-standing relationships with our suppliers, which allows us more involvement in their processes,” explained Mr Cowey. “One of our suppliers, Deceuninck, is a leader in PVCu recycling and prevents up to three million doors and windows from going to landfill annually. We’ve been working with the company for over a decade as it provides high-quality products and is willing to support us in making operations more sustainable.”
Coral Windows also reduces its carbon footprint by producing its own glass. This limits transportation emissions and ensures that the full production process aligns with the company’s vision of sustainability.
As well as this, Coral Windows has a strategy in place to minimise waste in operations by maximising the use of materials and being resourceful in the production process. The company has begun separating waste to recycle more and is utilising IT to transform into a paperless system, further reducing environmental impact.
Coral Windows is developing its use of technology to increase automation in facilities.
The company is aiming to automate 70% of its factory. This will make production more efficient in terms
of both time and energy, as well as limiting waste products produced.
This will all contribute to a more environmentally friendly system within the company. Coral Windows is hoping to introduce these new IT systems by mid2024 and integrate them into practice within the following months.
There is also a new system that minimises the number of miles contractors have to travel. The system chooses the closest qualified person to the project and provides the shortest route to limit engine emissions. It also reduces wear on a vehicle, making it more efficient and increasing longevity.
Coral Windows has recently released a new product, the Coral SmartFrame. This is a smart sensor which is fitted to all windows and doors at no extra cost, providing security and protection.
The sensor pairs with a smart hub through the Coral Smart Home App to send instant alerts when a window or door has been interacted with and will warn of any unusual behaviour. The sensor will send reminders to close open windows or doors when the homeowner leaves the property and can be controlled via smartphone.
Ideal for more vulnerable homeowners, the sensor provides an extra layer of protection to Coral Windows’ already secure doors and windows. This product will revolutionise the industry and provide peace of mind to homeowners. The sensor will help people to reduce their
energy use, minimising heat loss and improving the efficiency of the home.
Coral Windows’ products are highly energy efficient and use designs that limits heat loss in the home. As well as double glazing, the company offers triple glazing to increase the insulative properties of windows, doors and conservatories.
The A+ energy rated windows use Low E glass, argon gas within the units and thermally efficient warm edge spacers separating the glass. These factors will contribute to a more environmentally conscious home. With improved insulation, there is less necessity for heating and thus, less carbon emissions in the atmosphere.
The windows are also incredibly durable, meaning they have improved security and resistance to weather impacts. Excess materials and energy required to produce replacements will not be needed as often, so the impact on the future environment is reduced.
“We are able to advise people on what energy efficient solution is right for their home,” said Mr Cowey. “It is important to us that our customers
have access to sustainable windows so that they can reduce energy use and save on costs.”
“Most of our suppliers have been working with us for over five years,” said Mr Cowey. “We build these lasting relationships for a variety of reasons whether that be unique products and services that they offer, or their willingness to work and grow alongside us.
“By developing our partnerships with suppliers, we are able to collaborate and create new products that have the potential to alter the market, like we have done with Era on the Coral Smart Range. Our partners know that we will remain loyal to them, despite factors such as price increases, because of how much we value these relationships.”
Being a family business, Coral Windows has strong ethical values and ensures that it is a reliable and trustworthy company for both suppliers and customers. The owner is directly
involved in the running of operations, so if a customer has an issue, he will directly attend to the problem and provide a personalised solution.
The company’s salespeople are also instructed not to hard-sell products. They are directed to provide the customer with the right solution for their individual needs and manage expectations within that solution. This means that clients will receive an honest and trustworthy service
when enquiring with Coral Windows. The company does not take up-front deposits or survey fees; it will only take money for a completed project that the customer is satisfied with.
“I love that Coral Windows is continually innovating,” concluded Mr Cowey. “The company is eager to be ahead of the market, so we don’t just make sales on price, but on the quality and value of our products and services.” n
The portfolio at RETOS VARNSDO covering new machines, overha tancy services, plus the deliver accompanying documentation. a milestone anniversary and his important to his family. Report b
ORF is focused on horizontal boring mills, auls, partial or medium repairs and consulry of spare parts, accessories and the . Managing Director Jan Müller discussed s goals for this business which is so by Phil Nicholls.
IN2023, RETOS VARNSDORF celebrated its 30th anniversary. Throughout its existence, the company has maintained a strong family atmosphere.
“Working at RETOS is about creating something with real value: not money, but products, a brand,” explained Managing Director Jan Müller.
“We are keeping alive the family tradition. My grandfather designed horizontal boring mills for his whole professional life at TOS VARNSDORF. My father was a fitter and later th e
founder of RETOS, and CEO for twenty years. Today, even my children work for RETOS during their holidays.”
The original retrofitting department of TOS VARNSDORF was split off in 1993 and founded as RETOS still focusing on repairing horizontal boring mills. Over t ime, the company steadily invested in new technology and gradually presented itself as a producer, instead of only bein g a repair company. The major change came in 2016, at the point of release of the brand-new product line RET10XP, the company rebranded. This resulted in a new logo, company colours, machine designs and commercial product names
Last year’s big anniversary was a wonderful opportunity to reflect on the company’s achievements. “We simply let people know that we are here,” said Mr Müller. “We had a garden party for ou r staff and local partners, which was fun. At the International Engineering Fair in Brno, we gave an illustrated presentatio n about our history.”
The company continues to use the original facilities at Varnsdorf in the Czech Republic. RETOS has two photovoltaic power stations installed on the roof, with a total power of 25kW, plus a new installation adding a further 150kW to the tota l generation capacity. The company has about 85 employees, plus another ten external co-workers.
RETOS has a strong focus on the Western Europe market, where the company produces, overhauls or sells approximately 35 machines a year. This delivers an average turnover of about €8 million.
The team at RETOS produces a range of high-quality machines in its distinctive branding of green, white and grey. This portfolio is in addition to an extensive range of spares and accessories. The experienced engineers at RETOS also offer after-sales services for RETOS machines, both in the Czech Republic and abroad.
“My goal, every single day I go to work, is to help build an even better version of RETOS”
Even with such a diverse portfolio, the company continues to juggle the competing market demands, according to Mr Müller: “The market wants the impossible combination of German quality for Chinese prices.
“What sets us apart is that we cover all the design, production, sales and service activities, including spare parts even long after the warranty period. No matter if it is a new, overhauled or used machine, our customers have all they
need in one place and can rely on us to deliver satisfaction.”
The availability of an extensive selection of spares at RETOS is a huge step towards helping customers achieve sustainable operation through the overhaul of their machines. Notably, the manual production of gears at RETOS is quite a rarity. This is more than necessary, considering how many of them are needed for just one headstock of the conventional W100A boring mill.
“To repair, in comparison to producing new heavy machines, is very environmentally friendly,” Mr Müller explained.
“Regarding the range of new machines, the only way of reducing the carbon footprint is to optimise the design, the energy intensity and technological management – so as not to waste energy, tools or coolant liquid.
“We supply machines for long-term service. It is common for our machines to serve the customer for 20 years, and then, after an overhaul, last for a further 20 years.”
The recent anniversary was also an opportunity for RETOS to acknowledge the support of suppliers as part of its 30-year history.
“The challenging market means that we are all in the same boat,” said Mr Müller. “Suppliers should support RETOS, just as the producer should support the customer. Certainly, suppliers are very important for our success. For example, some of the specialised mechanical parts are things we are not able to produce alone.”
Mr Müller acknowledged that the biggest challenge for RETOS involves finding the right product for the future. Even though there is a large degree of innovation in the company’s product line, the core product is still a machine tool.
“The competition with the Asian market is growing more intense, year by year,” he continued. “We have also been affected
by supply issues, especially regarding electronic components. At RETOS, we will continue to produce as much as we can using our own knowledge, resources and facilities.
“This distinct combination of traits helps us to be more resilient to the ongoing market fluctuations.”
Looking towards the next 30 years, Mr Müller was clear about his goals: “My personal dream as Managing Director is stability for RETOS. Our broad target is to maintain growth in correlation to that of the general economy.
“At the 30 years party, there were three generations of my family in attendance,” he said, in conclusion. “Yet, my family is not the only one with a tradition of working in this company. It is fulfilling to see how knowledge and traditions are preserved at RETOS.
“Every generation also brings new ideas as it struggles to keep pace with an ever-changing world and makes its own contribution to progress. Sometimes, this creates pressure. My goal, every single day I go to work, is to help build an even better version of RETOS.” n
Founded in 1973, RIFIL is a leading yarn manufacturer in Europe. The company has a focus on creating Italian-quality acrylic yarns mixed with wool for indoor, outdoor and automotive furniture, plus knitwear, fabrics and more. RIFIL’s management team discussed its product selection, including the new Infinity range. Report by Antonia Cole.
With an annual turnover of €67 million, RIFIL has established itself as a key player in the international export of yarns. The company has 450 employees and five key values that contribute to its success: service, quality, ethics, health and sustain ability.
The company ensures that all employees are protected and supported throughout operations, making the process of creating high-quality Italian yarns not only safe, but rewarding. RIFIL views its community as a big family and aims to integrate those values into practices.
In the Romanian NEAMT region, the company has six factories, in which highly skilled and experienced employees produce premium yarns. 14,000,000 kg of yarn is made annually, which is then
used in textiles for a variety of industries. The durability of the fabric and resistance to weathering makes it ideal for not only clothing, but also outdoor furniture and specialised uniforms.
RIFIL has 50 years of experience in the industry and has progressed to become
the largest yarn producer in Eastern Europe. The company’s experienced team of professionals work to innovate the sector and evolve the properties of products to suit customer needs.
More than 10% of RIFIL’s annual turnover is reinvested into industrial innovation, research and development. Through this, the company is continuously evolving aspects such as quality, style and performance in products. RIFIL’s new Infinity range of yarn is a result of this commitment and investment into improvement.
“RIFIL was the first public-private company established in the Soviet bloc,” said the Commercial Director. “We have always been leaders in this respect, but we are
now also focusing on driving the change to more sustainable operations. At RIFIL, we comply with the highest certifications, in respect of the environment and health of future generations. We hope to inspire other companies to do the same.”
From over 300,000 m2 of production facilities, with more than 50 spinning, doubling and twisting lines, RIFIL has produced around one billion kg of 100% Italian-quality yarn over the past 50
years. The company’s acrylic and wool blend yarns come in a variety of forms, from chenille to knitting yarn balls. RIFIL’s broad portfolio means that it can fulfil various customer requirements.
The company’s range of knitting yarn is high-quality, stylish and versatile. From jumpers to socks, the yarn can be used by end consumers for a variety of purposes. This durable, yet soft, yarn is available in a wide selection of colours and can be ordered in any size batch, according to the customers’ needs.
RIFIL also creates resilient acrylic yarns to be used in the production of outdoor furniture, such as chairs or parasols. The company’s spinning, dyeing and finishing techniques contribute to the completion of strong and modern fabrics. The material is specially dyed according to the customer’s requirements, resulting in a personalised product, specifically designed for the customer.
“Our industrial dyeing plant utilises the most advanced techniques in Europe,” explained the Commercial Director.
“We pride ourselves on being able to develop products that are not only functional but are high-quality and stylish too. Most of all, we work to satisfy the customer through our adaptability and specialised services.”
These processes can also be applied to yarns for the automotive industry. RIFIL’s materials maintain their colour, quality and durability over time, making them ideal for vehicle interiors. The yarns can be used in cars, as well as in various modes of public transport.
Another sector of RIFIL’s product range is indoor furniture, which also benefits from the longevity delivered through the fabrics high quality. Offering a broad portfolio of solid colours and patterns, the company’s products are able to meet many differing needs across the industry.
Finally, combining these features, RIFIL serves the technical uniform industry. The company’s yarns are featured in uniforms for police officers, health professionals, football teams, transport workers, security guards and others. RIFIL recognises a uniform as an important symbol of membership, which is why it has a dedicated range of yarns, focused on style and durability, for this purpose.
In the creation of all the company’s materials, RIFIL has a strong environmental focus. The company has been actively working to reduce carbon emissions in operations through increased efficiency and environmental awareness. Sites are equipped with renewable energy sources, such as solar panels, to minimise the company’s reliance on unsustainable forms of energy like fossil fuels. This will limit carbon emissions and the depletion of raw materials.
Additionally, RIFIL carefully selects all components, dyes and additives used in processes with their environmental impact in mind. They are all ISO 9001, GRS,
RWS and OEKO TEX certified, promoting the sustainable and ethical sourcing of ingredients.
The company’s dedication to sustainability and innovation has resulted in the production of a new environmentally friendly range: the Infinity line. This yarn is made from a recycled acrylic fibre called Regel. Incorporating this yarn into the company’s portfolio allows RIFIL to minimise environmental impacts and excess waste, whilst maintaining a high-quality feel and colour vibrancy.
Regel is GRS certified and uses a chemical recycling process to limit the unnecessary use of raw materials. As well as this, it is antibacterial and hypoallergenic. Therefore, it can be utilised for a variety of specialised purposes, including in baby clothing.
“I am very proud to be a part of the launch of our Infinity range,” said the Commercial
Director. “This is a huge step towards a more circular economy, where we are able to conserve natural resources without compromising on quality. This is a great achievement for both RIFIL and the planet.”
The Infinity range was made in collaboration with TAF, one of the world’s top five acrylic fibre producers. RIFIL actively makes connections across the industry in order to drive innovation and positive action for the environment. Working with TAF has allowed RIFIL to spin this new recycled fibre and make new sustainable options available for both clients and end-consumers.
“We at RIFIL are very excited about the results of this collaboration,” explained the Commercial Director, in conclusion. “TAF’s new technology, combined with our expertise, has allowed us to create a premium yarn that also drives positive change for the environment. All of our partners and suppliers are very important to us. It is by working together that we will be able to see real developments within the industry.”
RIFIL is committed to producing highquality Italian yarns and will continue to advance product ranges in terms of colour, function and durability. Looking into the future, the company is also planning to implement more sustainability measures and innovations.
The company has found success thus far through building connections and collaborating across the industry. RIFIL hopes to continue meeting like-minded companies and working with them to create a more sustainable future. n
Renowned worldwide for cutting-edge biochemistry and all-natural raw materials, Omega Ingredients delivers exquisitely sourced flavour projects. Product Manager Martyn Warner explained to Hannah Barnett how the company made its name with a focus on high-quality, provenance-driven, natural flavours and extracts (kiiNotes®).
Omega Ingredients fuses a portfolio of processing knowledge with sophisticated manufacturing capabilities. The company harvests, extracts, analyses and composes botanicals from around the world to create top-of-the-range flavours for the food and drink industry.
“Unlike many of our competitors, we are unapologetically all about natural taste, and do not compromise on that,” said Martyn Warner, Product Manager. “We
often create bespoke flavours specific to requirements, rather than offering them from a library. This enables our customers to develop a food or beverage product customised to a market where the consumer is ever more demanding about naturally sourced items.”
Omega Ingredients was founded in 2001, with the intent to supply natural, innovative and sustainable ingredients. “At the time, the industry was dominated by synthetic ingredients for flavouring,” said Mr Warner. “Our founder and CEO, Steve Pearce, travelled the world meeting farmers and producers and building
strong partnerships. We are still working with many of them today.”
As the business grew, Omega shifted its focus from ingredients to the creation of flavourings. The company now boasts a vast portfolio of natural flavours, scents and ingredients. This, combined with the team’s expertise and creativity, allows Omega to provide cutting-edge solutions that are truly like no others available in the market. In 2022, Omega joined the Robertet Group. The latter has an extensive and illustrious history in the sector: founded in 1850, it is based in the home of perfumery in Grasse, on the French Riviera. Robertet remains the world leader in 100% natural and sustainable ingredients for the flavour, fragrance and beauty industries. The acquisition was
therefore a match made in a perfumed heaven for both Omega and Robertet, with the company’s site in Ipswich specialising in the manufacture of liquid natural flavourings and extracts for the beverage, dairy and culinary sectors.
With quality at the heart of all Omega does, the company goes to great lengths to ensure that everything it produces meets the highest standards. Therefore, investing in the latest equipment and expertise is a given. As Mr Warner put it: “We are spoilt for choice when it comes to our specialist production and extraction facilities.”
The company’s capabilities include both traditional techniques for
distillations and infusions, and cuttingedge methods such as supercritical CO 2 extraction, a spinning cone column and molecular distillation.
Omega opened a Culinary Science Suite in 2023, as a creative space for customers to taste, smell and experience the company’s flavours. All samples are prepared by the Head Development Chef, who was previously employed by high-end London restaurants. The suite allows customers to work with the flavourists and applications team on-site, accelerating the development process.
“It’s not just a competitive advantage for us,” said Mr Warner. “We sell our flavours to other food manufacturers and retailers across different sectors. So, we pass on the advantage to our customers, meaning they can sell more products.”
Omega sources all its ingredients sustainably and ethically, while striving to reduce its impact on the environment. The company has made several commitments to sustainability, including reducing waste through effective planning, re-using where possible and recycling what is generated from its business operations.
“Because we work with natural ingredients, we pay extra attention to our impact
on the environment and the natural world,” Mr Warner said. “Being eco-conscious is one of our values. For the last five years, we’ve been raising money for environmental charities like Surfer’s Against Sewage, organising and participating in beach cleans along the Suffolk Coast and countryside, as well an annual ‘Climb & Clean’ challenge for the whole team to go up a mountain and litter pick en route.”
The company is also researching the possibilities of natural ingredients produced from surplus food. A recent development has investigated creating extracts from fruit and vegetable peels.
“We take surplus product, extract, analyse and compose flavourings and ingredients to put back into the food supply chain,” Mr Warner explained. “It’s a great example of upcycling and the circular economy. Moreover, the taste and
technological attributes of the extracts offer our customers a unique competitive advantage over conventional extracts.”
With global support within the group, the company can spot trends from around the world and bring them to the UK market before any competitors.
“Our diverse portfolio of botanicals and extraction techniques, combined with our innovative team who think outside of the box, has enabled Omega to be at forefront of the Lo&No alcoholic spirits sector,” said Mr Warner. “We worked with the company that developed the first non-alcoholic spirit. That was a really special project. We have since helped our customers to produce some of the most successful Lo&No alcoholic spirits ever launched by creative entrepreneurs.”
To remain ahead of the curve, the company works closely with its suppliers and partners around the world. “It’s the breadth of our suppliers that really contributes to our success,” said Mr Warner.
“We work directly with the growers and manufacturers wherever possible, each one specialising in their product. This ensures we are selecting the very best ingredients to create our flavours, rather than going to a single supplier that can offer it all.”
Not content with the state-of-the-art site it already has, Omega is also building a brand-new production facility next door. It will be dedicated to the liquid manufacture and blending of natural flavourings, increasing capacity and efficiencies to serve the UK and European markets. The facility will feature eco-conscious initiatives such as solar panels and rainwater harvesting, as well as being built from sustainably sourced materials wherever possible.
In addition to building its team and expertise, the new site will facilitate
Omega’s ambitious growth plans: it i ntends to double the size of the company in the next five years.
“The flavouring industry is such an interesting business to be a part of,”
Mr Warner concluded. “It can be little understood by consumers, despite being used so widely. It’s fantastic to explain to our customers how natural flavours and extracts are made and the advantages they offer.journey is very satisfying.”
“As an agile organisation, we are always developing something new. To see a project through, from the early concept and development stages, to being able to purchase a product containing our natural flavouring solutions in the supermarket is brilliant. We believe in building strong relationships with our customers, so supporting them on their journey is very satisfying – for Omega, our customers and ultimately, the end consumer.” n
one planet – one chance – one voice
An introduction to the technology and services sectors, with news and a special report reviewing B Corp, followed by company profiles.
The latest company and industry related developments from the services and technology world
The BIG LEAP project just started its 42-month journey. This project aims to achieve the next generation of Battery Management Systems (BMS) to improve the interoperability between battery chemistries and architectures, enhancing the operation reliability of second life batteries, thus extending adaptability.
Batteries are identified as a key technology in guiding the clean-energy transition, especially in automotive and energy storage. The BIG LEAP project addresses challenges such as the lack of interoperability or the non-standardised processes, by developing solutions for Second-Life Battery Energy Storage Systems. The technological breakthroughs planned for the Battery Management Systems include a three-layer architecture to ensure interoperability, safety, and reliability.
This will be complemented by an adaptable Energy Storage System design, facilitating BMS integration and expanding SLB's potential applications.
Moreover, the project aims to optimise the battery refurbishment process by making it cost-effective, faster and standardised.
The development methodology involves collecting data from Electric Vehicles (EV), maritime E-Vessels and Energy Storage System batteries. The testing will take place at three demonstration locations. The aim is to validate the effectiveness and compatibility of the innovative BMS and ESS, facilitating their upscale in the market.
Under the leadership of Brussels Research and Innovation Centre for Green Technologies (BRING), BIG LEAP brings together a consortium of 16 partners from 10 EU Member States, with two countries associated with Horizon Europe and two international partners.
The BIG LEAP project aims to boost EU technological competitiveness by enhancing Battery Management System (BMS) interoperability and improving the reli ability of Second-Life Battery Energy Storage Systems (SL-BESS). n
Gregory Group, a leading UK logistics company, has pledged to be fully net zero by 2038.
Gregory Group has been focused on its sustainability agenda for a number of years, taking a proactive approach to the impact the industry has on the environment.
“The transport sector is the highest contributor to UK greenhouse gas emissions, accounting for 26%, with both heavy and light goods vehicles alone contributing to over 10% of the total,” said Group Legal, Fleet and Sustainability Director Paul Jefferson. “We firmly believe that it is our responsibility to lead the way in changing this statistic.
“Many of our customers have set net zero targets for 2040 so, by setting our target two years prior, we will be in a solid position to be able to help our customers deliver on their ambitions.
“At the end of 2038, the Group will be entering its 120th anniversary, so it feels like a poignant line to draw. From our origins transporting coal by horse
and cart, we have grown to deliver a huge array of goods for well-known brands across the UK. At any given time, we have over 1,200 Gregory Group trucks on the UK roads.”
Gregory Group has set a target to be net zero by 2038 across scopes 1, 2 and 3. The company’s near-term ambitions to reduce its carbon emissions by over 40% by 2030 are supported by a commitment to the Science Based Targets initiative, a global body that helps businesses set ambitious emissions reduction targets. n
B Corp Certification is a designation showing that a business is meeting high standards of verified performance, accountability and transparency. The process reviews factors from employee benefits and charitable giving to supply chain practices and input materials. Report by Hannah Barnett.
INorder to achieve certification from B Corp, a company must demonstrate a number of features.
First, it must demonstrate high social and environmental performance by achieving a B Impact Assessment score of 80 or above and passing a risk review. Multinational co r porations must also meet baseline requirement standards.
A company must also make a legal commitment by changing its corporate governance structure to be accountable to all stakeholders, not just shareholders, and achieve benefit corporation status if available in its jurisdiction.
Transparency must be exhibited by allowing information about a company’s performance to be measured against B Lab’s standards and be publicly available on its B Corp profile on the B Lab website.
As leaders in the movement for economic systems change, companies with B Corp verification reap remarkable benefits.
The companies with the certification build trust with consumers, communities and suppliers; attract and retain employees; and draw mission-aligned investors. As they are required to undergo the verification process every three years in order to recertify, verified companies are by definition also focused on continuous improvement, leading to their long-term resiliency.
B Corp Certification is holistic, not exclusively focused on a single social or environmental issue. The To
process to achieve and maintain certification is rigorous and requires engaging teams and departments across a company.
Taking an organisation’s size and profile into account, verification involves documentation of a company’s business model and information about operations, structure and various work processes, as well as a review of potential public complaints and possible site visits.
Recertification confirms these standards continue to be met on an ongoing basis.
The B Corp team may recommend a different pathway for each individual business once the process has begun. Revenue and company size are the typical criteria used to guide companies in their approach to certification. In some cases, companies might undergo a different method based on factors such as sector, industry, scoring and ownership structure.
If a company generates less than $5M USD in annual revenue and employs fewer than 50 full time employees, the B Corp website offers a Small Enterprise Guide to download more about how B Lab certifies small businesses. It offers a sim -
ilar guide for small-medium, medium and large companies.
Companies with more than $5B USD in annual revenue can participate in a B Movement Builders programme. All subsidiaries must also follow the large enterprise approach, regardless of size.
While the certification process varies depending on a company’s size and complexity, all companies must take the same multi-step process to become a B Corp. It begins with registering for a free and confidential B Impact Assessment. Several steps later, it ends with meeting a verified 80-point threshold, when a company will enter the post-verification stage and sign the B Corp Agreement.
In order to meet the transparency requirement for B Corp Certification, a company needs to publish its public profile in the B Corp Directory, including the company’s score and impact report.
The final step in a B Corp journey lasts the longest. A company must prepare for recertification every three years and use the B Impact Assessment and the certification process as a tool for continuous improvement. n
For more information on B Corp, visit: https://www.bcorporation.net/en-us/
C.A.T. Group, an acronym for Contracting and Trading, is a pioneering Middle East engineering and contracting firm, renowned for its unwavering commitment to excellence. Hannah Barnett spoke to the KSA Area Managing Director Ricardos Najm to learn what makes this innovative company purr.
Like its feline namesake, C.A.T. Group is smart and agile, assisting clients through multiple construction and engineering-oriented skillsets across the world.
“Our distinct advantage lies in our blend of historical depth, commitment to progress, focus on sustainability, empowerment of our people and unwavering dedication to the success of our clients,” said Ricardos Najm, KSA Area Managing Director. “This comprehensive approach sets us apart, making us a trusted partner.”
Founded in 1937 by Emile Bustani, an MIT graduate in civil engineering, C.A.T. began with a modest yet significant project: installing a bathroom for the General Manager of the Iraq Petroleum Co. The task was financed by the sale of a gold ring gifted by Mr Bustani’s
mother, symbolising the dedication and sacrifice at the core of C.A.T. Group.
Initially, C.A.T. secured contracts with the British forces and several foreign oil companies, notably IPC. During this period, Shukri Shammas and Abdallah El Khoury , who had significant experience with IPC in contracting and trading respectively, laid the foundation for their future collaboration. This partnership, formalised in 1941, enhanced C.A.T. Group's capability to address diverse demands.
Over the decades, C.A.T. has contributed to the monumental growth of the energy industry and infrastructure in the Middle East, becoming synonymous with high-quality and timely project delivery. The company constantly ranks in the top 5 for pipeline construction in the ENR Global Sourcebook.
“One major milestone was the establishment of corporate governance in
1994,” explained Mr Najm, “which was considered an avant-garde step for a family-owned business in the Middle East at the time.”
C.A.T. has now completed over 2,000 projects and installed over 25,000km of pipeline. The company boasts 18,000 employees and over 4,700 pieces of equipment and machinery, spread across the Middle East and West Africa. Annual turnover is around $800 million. “However, we focus on outcome and not on volume; we are very selective of clients and projects,” Mr Najm added.
Indeed, the company has been involved in many impressive large-scale projects, including the Master Gas System Phase II for Saudi Aramco. Locations were scattered over a wide geographical area, meaning covering long distances to supply construction and support materials for a $75 million – $250 million project.
Serving the energy transition
Energy is at the core of C.A.T. Group, and the company is supporting the energy transition in several ways. For instance, C.A.T. has increasingly
focused on the gas subsector, especially on the midstream and light processing side, as well as the development of green hydrogen.
C.A.T. is actively supporting clients in carbon capture and sequestration too, typically via pipelines transporting captured CO2 to injection sites.
“We are trying to find feasible solutions on the capture side,” Mr Najm explained. “By aiding clients find economical technologies for carbon capture, we contribute to the energy transition and the push for decarbonisation.”
Clearly, C.A.T. will play a large role in the future energy mix, whatever direction the industry takes.
“The transition to new energy sources is not always obvious because of the lack of econometric drivers, while the technologies and regulations still need to develop,” Mr Najm
explained. “The solar PV sector is a good example of how accelerated growth occurred as the technology matured, making it cheaper to produce power from solar compared to conventional plants.
“The industry has been disrupted with new opportunities such as distributed production, virtual plants, microgrid management and power wheeling. We are prepared for the next big thing in the energy industry.”
The recent establishment of an official C.A.T. sustainability department underlines the company’s commitment to leading the way in sustainable business practices.
“Our approach to sustainability is rooted in the belief that building a resilient and responsible business
is essential for enduring success,” said Mr Najm. “From the very beginning, our mission has been a vision of lasting impact. This philosophy has driven us to implement sustainable practices that not only enhance our operational efficiency and reduce our environmental footprint, but also solidify our foundation for a future where our business continues to thrive.”
The department has developed a comprehensive strategy that aligns with the company’s vision of being a sustainable contractor of choice, setting ambitious targets that reflect a dedication to environmental stewardship and social responsibility.
“At the core of the department is the environmental aspect; over a decade ago, there wasn’t that focus,” said Mr Najm. “Now, we are measuring the company’s carbon footprint which is the first step towards improving it. If we can’t measure it, then we can’t improve it.”
Carbon footprint has already been reduced at C.A.T. by incorporating hybrid vehicles into the company fleet, embracing renewable energy
sources to power operations and conserving water through advanced treatment technologies.
It is clear that C.A.T. Group’s dedication to sustainability and green initiatives reflects a deep-seated commitment to the future. This means that as well as reducing its environmental impact, the company also fosters a culture of responsibility and innovation within its team. C.A.T. is therefore always striving to empower its workforce and was the first company in the Middle East region to have a female team member receive prestigious industry certification.
C.A.T. also promotes a client-centric approach, ensuring that the unique needs of each project are met by delivering
tailored solutions. A reputation for reliability and quality, combined with the ability to consistently complete challenging projects ahead of schedule, solidifies the com pany’s position as a preferred contractor.
“As we look at our clients and their willingness to pay for our services, balancing the value captured between ourselves and our suppliers is key,” said Mr Najm. “We emphasise fairness, which relies on a deep understanding of the supply chain and the market’s dynamics.
“Suppliers end up wanting to work with C.A.T. Group. They don’t see us as a risky client and, as such, we get better payment terms with them. This takes years of nurturing and a centralised procurement
network, whereby we keep track of the performance of our suppliers and their workloads. This helps us chose the most suitable suppliers for our projects and our clients.”
It is clear that whether working with suppliers, clients or its own staff, C.A.T. is guided by the uniting force of its company values, reflected by its family-owned status.
“Family values are deeply rooted in the company and its culture,” Mr Najm concluded. “We are here to stay, and our existence depends on the strong relationships we have formed with our clients, employees and communities.
“The nature of our work is very demanding and stressful. Many of us work in remote locations for long hours, away from our home countries and families. However, the reward comes when we see a project completed and realise that we have contributed to a country’s vision and growth. We want everyone that works for us to reach home safely, so we stress on having safety encrypted in the DNA of every C.A.T. person.” n
Argent Energy is a European biodiesel company that turns waste fats and oils into renewable fuel, contributing to significant reductions in CO2 emissions. It has a vision to decarbonise transport worldwide by using only certified waste materials in the production of fuels and constantly searches for new forms of waste to be transformed into higher value products. CEO Dr Louise Calviou discussed the company’s recent developments and goals to promote a more circular economy, in conversation with Hannah Barnett and Antonia Cole.
The key objective of the company is to take degraded waste fats and oils that cannot be used for anything else and turn them into a useful product: biodiesel. Replacing fossil fuels with wastebased biodiesel leads to an approximately 90% reduction in carbon emissions.
Argent Energy was founded in 2001, with the company producing 45,000 tonnes of biodiesel a year, which grew to 140,000 tonnes in 2016. It has now grown to produce over 195,000 tonnes per year across sites in the UK and Netherlands, employing around 350 workers.
“The company was bought by John Swire and Sons (Green Investments) Ltd in 2013 as it was looking for projects that could benefit its sustainability agenda,” said CEO Louise Calviou. “Since then, we’ve continued to expand and invest in our business, making us the leading European specialist in production of waste-based biodiesel.”
Argent Energy’s new glycerine refinery will begin production later this year in the Port of Amsterdam and is set to produce 50,000 tonnes of refined glycerine annually. The company will transform a by-product of the biodiesel process to create a technical-grade product for the chemical industry, aligning with its mission to explore innovative ways to transform waste into high-value products.
“In our production of biodiesel, we currently produce the co-product of a low-grade glycerine, which is mainly used for anaerobic digestion” explained Dr Calviou. “With the investment into our glycerine refinery, we will turn a waste product into a useful chemical.
“We’re set to triple our biodiesel capacity at Amsterdam by 2026, with the potential to expand even further. We’re focusing our investments on our
Amsterdam site due to its proximity to the port and the access that allows to the marine sector. As a company, we are trying to decarbonise transport, which includes the marine industries, and this expansion allows us to contribute further to road and Heavy Goods Vehicle decarbonisation but also to offer sustainable alternatives to ship owners.”
Last year, Argent Energy successfully trialled the use of 100% FAME with FincoEnergies and VT Group, showing how biodiesel can be used to progress marine decarbonisation. The MTS Vlissingen was fuelled with 100% FAME, a sustainable option that does not require engine modification, making it cost effective and environmentally sustainable.
“We manufacture 100 per cent FAME that easily meets marine grade specifications,” said Dr Calviou. “Our biodiesel supplied to FincoEnergies towards this
trial achieved a reduction of around 85 per cent in C0 2 emissions.”
Argent Energy’s waste-based biodiesel provides a highly cost-effective solution to a range of industries whose customers seek to reduce their carbon footprint. This versatile fuel is supplied directly as an effective drop-in replacement for fossil fuel diesel to road transport operators, including bus, coach and HGV fleets. The company has been supplying this industry with High Blend Biodiesel Fuel solutions since 2008. Argent’s biodiesel is also used to power furnaces in energy intensive industries, showcasing its adaptability across various applications as a sustainable alternative to traditional fossil fuels.
Argent Energy aims to decarbonise a variety of industries by promoting the use of biodiesel over fossil fuels. It is looking to find applications where it can apply 100% biodiesel and progress the industry into a more circular economy.
Functional reliability is crucial for our customers which is why we use smart blending” explained Dr Calviou. “We adjust the blend of our biodiesel to take account of conditions so there aren’t any operational issues, and we plan to keep offering higher grade biofuel to power industries in the future.”
Argent Energy exclusively uses waste products that have reached the end of their life cycle to produce biodiesel,
making it a sustainable source of fuel in comparison to fossil fuels. The end product limits carbon emissions to the atmosphere and provides a solution that decarbonises transport industries.
The company is also managing wastewater in its operations. Argent Energy’s Stanlow site has an Eco Clarity Waste Conversion Hub, which filters out beneficial oil residues to be reused instead of discarded.
Fats, oils and greases are separated from wastewater to become a sustainable raw material that can be used in the production of second-generation biodiesel. The cleaned water is then reused or returned to the waste stream, enhancing Argent Energy’s operations as sustainable and reducing harmful waste
in water systems. Argent Energy also has two operational Wastewater Membrane BioReactors, a system that ensures effective cleaning and recycling of the water used in its biodiesel production, enabling the reuse and safe return of the water to the environment.
“We’re looking at everything we do and that includes limiting water waste,”
said Dr Calviou. “Our aim is to take waste that could otherwise harm the environment and transform it into useful materials.
“As a company we are also looking at our energy sources to decarbonise those too. We have a steam turbine that we use to generate electricity from our biomass boiler so that we can be more
sustainable and have less of an impact on the environment in our operations.”
“We find partners who share our vision and values so that we can work together to reduce the use of fossil fuels,”
Dr Calviou continued. “With sustainability at the heart of Argent Energy’s operation, it is important for us to partner with likeminded people so that we can make sustainability goals a reality.
“As a company, we are looking for solu tions. We want to find issues and create innovative solutions with our partners playing a significant role. We collaborate with our partners to find sustainable solutions that fit their needs and simultaneously promote a more circular economy.”
Argent Energy wants to challenge the way things are done and make a difference in the industry. It constantly invests in new R&D as well as encouraging employees to generate and submit their own ideas for progression.
“We want to be a global player, not just a European player,” explained Dr Calviou. “We want to continue to expand our footprint and the range of products we make. Our objective is to take waste that has no other use and turn it into a useful product on a global
scale. We’re not short of ideas on how to achieve this.”
It is important to Argent Energy for people to understand that biodiesel is part of the environmental solution and that utilising waste products in transport industries will lead to a more sustainable future.
“At Argent Energy, we are helping to shape the future,” said Dr Calviou, in conclusion. “I think it’s exciting. I have the opportunity to be part of something that is growing, contributing to decarbonisation and really making a difference.”
n
Morro Partnerships is a leading partnerships developer with a purpose. Providing high-quality, sustainable and affordable housing within the Midlands region, Morro works with local authorities, Homes England and registered providers, to drive regeneration in under-invested areas and disused brownfield sites. The company also operates an effective recycling and segregation scheme on all developments to minimise the impact they have on the environment.
CEO Matthew Moore explained more, in an exclusive interview with Inside Sustainability. Report by Imogen Ward.
Morro Partnerships underwent a rebrand in late 2023, after being named Jessup Partnerships for more than 30 years. Created on the solid foundations of its new purpose to be better tomorrow makers, the company is proactive in driving regeneration, and introducing new technologies to build efficient developments that are sustainable, modern, accessible and affordable, whilst utilising the highest-quality materials.
“We embarked on the process of creating a new name and a new brand, and with that came a new purpose: we are helping to make tomorrow better than it is today,” explained CEO Matthew Moore. “We are providing people that need it most with a roof over their heads, whilst also working hard to better ourselves and the industry. That’s where the name Morro Partnerships evolved from.”
With a current pipeline of 2,500 plots, Morro will help to meet the growing demand for affordable housing in the Midlands region. The company is developing a mix of one-, two-, three- and four- bedroom properties across two- and three- storeys, as well as apartment blocks and care homes, which will contribute hugely to the housing shortage that the nation now faces.
Morro is always searching for new ways to improve the experience of future homeowners. With its client base ranging from tenants and user groups to wider
communities, the company ensures that everyone is equipped with the right tools.
“There is pressure on our clients to provide optimal tenant management, whilst remaining environmentally conscious,” explained Mr Moore. “We are committed to helping them accomplish that.”
As a demonstration of this, Morro has developed a new initiative that highlights its conscientious efforts to minimise paper waste and be a better environment maker. All of Morro’s clients are given access to an exclusive QR code which they can share with their customers. By simply scanning the QR code, users gain access to a short, convenient, virtual home user guide, which explains every aspect of their new home from operating appliances to maximising energy effi ciency.
“The QR code is great because it gives homeowners access to visual, step-by-step guides for different aspects of the house,”
Mr Moore continued. “This removes the need for printed manuals – which, from an ESG perspective is great – but it has also had a positive impact on our clients as well. There has been a 20 per cent decrease in defect calls since we first implemented these digital guides.”
Not only is Morro Partnerships striving towards a more sustainable future, but it has also underlined a commitment to social value and early careers across the region, by appointing Abdul Mozzamdar as Head of Social Value, bringing over 20 years of experience to Morro.
Working with several clients and key stakeholder partners, Morro has
devel oped strategic social responsibility targets and is delivering meaningful employment and training opportunities including apprenticeships, staff volunteering, mentoring and so much more.
Now, more than ever, there is a large focus on environmentalism and carbon reduction.
In addition to building a sustainable future for future generations, Morro Partnerships is focused on the overall environmental impact of the construction industry and how it can help reduce carbon emissions and recycling effectively on all its sites.
“We were inspired to test ourselves both in terms of construction methods, but also ESG credentials,” said Mr Moore. “Most of our work involves brownfield sites in need of regeneration, and we aim to deliver all our homes with 100 per cent timber frames.”
The company has also implemented zeroto-landfill and site segregation policies to encourage recycling within the workplace. In partnership with a Midlands-based environmental solutions provider, Morro has dedicated waste streams at its construction sites where all waste is correctly sorted, ready for recycling.
Keen to get as involved as possible, Morro recently held a ‘Meeting Morro’ event for its supply chain, providing the companies with an opportunity to get to know Morro better and understand what it stands for. As part of this event, ESG was a hot topic of discussion.
The team is equally as passionate about improving the environment and reducing waste, with several team members proactively exploring different initiatives they can implement on their sites, and others within the region.
“We fully believe in giving our teams a voice and allowing them to have a say in what we do, especially when it comes to improving our environmental commitments,” explained Mr Moore. “Following on from the implementation of our green policies, one of our site managers was inspired to start the Greenkeeper’s Guide. We now have dedicated Greenkeepers stationed at each site who assist in locating new and creative ways to manage waste.”
One recent idea saw Morro create planters out of old pallets, giving the
wood a new lease of life and preventing it from being thrown away. The company also releases monthly internal reports which highlight how many different waste streams a site has utilised, how much waste they have recycled and whether they are on target.
In an exciting development, Morro recently embarked on a collaboration project with Birmingham City Council that could affect the future of council-developed properties in the area.
“We just recently completed a 36-unit project for Birmingham City Council as part of the council’s greener energy pilot scheme,” explained Mr Moore. “All of the units were constructed with different
heating technologies, including air source, ground source, electric, infrared and solar. The council is now going to monitor these occupied properties over a 12-month period to assess the viability of each energy source. From there, the council will start looking at their future build designs and adapting them accordingly.
“We have been able to support them during the initial design process, and we even brought consultants on board to ensure everything ran smoothly. This has been a great project to be involved with, because it is quite rare to have a client willing to try multiple different technologies on one site to locate the most economic and environmentally friendly solution.”
With Morro set on a path of innovation, the company recently brought David Thacker on board as Head of Innovation. Taking a holistic approach to the company’s operations, Mr Thacker intends to drive
innovation in every aspect of the business whilst continuing to push the envelope of what it means to be better tomorrow makers.
“We believe that Mr Thacker is a fantastic addition to what is already a very dynamic team,” Mr Moore said. “The addition of this ne w role is fitting for what is a very fresh yet well-established business, and it is great to have an additional team member on board who really gets involved with making a positive impact in the industry.”
“Our job isn’t just about the homes, it’s about the community and the people within our business,” added Mr Moore, in conclusion. “We got deeply involved, and we love making a difference. As we head into tomorrow, we will continue placing ourselves at the forefront of the market whilst also providing affordable housing solutions that make a positive difference to people’s lives.” n
Oxalis Logistics Group was born from an investment sale in February of this year. Having previously acted under the Hoyer Group, Oxalis is now stretching its wings under new ownership as a market leader in the transportation and distribution of bulk fuels and gases. CEO Allan Davison and HR Director Nichola Blenkinsop explained more, in an exclusive interview with Inside Sustainability. Report by Imogen Ward.
Oxalis Logistics Group stepped back into the limelight earlier this year, following a pivotal acquisition and a rebranding.
“In February 2024, Hoyer Group sold part of its portfolio to an investor; from this development the Oxalis brand was born,” said CEO Allan Davison. “We are the market leader in the distribution of bulk fuels and gases in the UK, Germany, Ireland and the Czech Republic, with 1,900 trucks and tank trailers, and more than 2,700 colleagues.
“This includes the entire management team that came with the business, so all experience and expertise in these specialised products is retained within Oxalis.”
With the company successfully retaining its experience from Hoyer Group, it has
also maintained relationships with more than 100 customers, providing 800,000 deliveries annually, which equate to an impressive 22.5 million tonnes of product.
“We have a totally unrivalled operational network in our core markets,” said Mr Davison. “With nearly 100 operating locations and over 2,300 drivers, we provide unmatched operational coverage. This means we can provide flexible and costeffective logistics solutions for all products and services under one company.”
Following on from the successful acquisition, Oxalis intends to maintain its industry-leading status with the help of its ‘people first’ approach. The company
regularly engages with its workforce and even went as far as incorporating their input into the rebranding process.
“Our colleagues helped us decide what our values would be going forward,” commented HR Director Nichola Blenkinsop.
“This inclusive approach was really important to us as these values would become the framework of behaviours which we adhere to, to meet the challenges of the industry.”
“The ability to work and interact with so many different people, from so many different backgrounds and cultures is amazing,” added Mr Davison. “We value the input of each and every employee.”
The company relies on a mix of innovation, responsibility, agility and respect to provide a stellar customer experience.
“Of course, safe and ethical behaviour is our number one priority,” said Ms Blenkinsop.
“Our safety culture is second-to-none, whilst our state-of-the-art driver training programmes (developed in-house) far exceed any legal requirements for guidelines.
“We have a responsibility towards our people, the environment, the communities in which we operate, as well as our valued customers. We also make sure to treat all stakeholders in a way that we would expect to be treated ourselves, embracing diversity, respecting different opinions and ensuring everyone feels heard.”
“Our values are also reflected in our vision, which is very clear: we want to be recognised as the innovative logistic partner that drives positive change and creates a sustainable future,” continued Mr Davison. “The world in which we live, and the industry in which we operate, is ever-changing. But this change gives us an opportunity to innovate with intention
– delivering our strategic objectives whilst providing service excellence to our customers.
“In this context, a sustainable future means providing sustainability for our business and all our colleagues as we move to a more diversified product portfolio. Whilst fuels remain a core element of our business, we will be at the forefront of the logistics industry in the move towards transporting, and using, more environmentally friendly products.”
Supporting sustainability
Oxalis is expanding the business with a more diverse portfolio as it focuses its efforts on industry-wide decarbonisation. Although the company intends to continue investing in logistics solutions for every kind of bulk petroleum-based product, emerging markets and organisations are of increasing interest.
“We are already involved in green hydrogen, bio-CNG, bio-CO2, bio-LPG, biofuels and carbon capture projects, with high levels of product and technical expertise in all these areas,” said Mr Davison. “This is in addition to our offerings on a wide range of other gas products.”
With innovation at the heart of its business, Oxalis intends to continue trialling new equipment and technologies to ensure its operations remain as efficient as possible during this period of sustainable development.
“Positive change is driven by an intense focus on the responsibility we have to our people, the environment, our communities and our customers,” said Mr Davison. “Challenging the norm can be difficult, but it is necessary in order to grow a successful and sustainable organisation.”
Of course, these achievements would not be possible without the strategic partnerships Oxalis developed in its previous form. According to Mr Davison, the company is dedicated to fostering an
open dialogue with all its suppliers and seeks long-term partnerships that work for all involved parties.
As it focuses on meeting its targets, Oxalis retains a realistic outlook on what the future will entail. From strategic growth to improved profitability, the company is optimising its process flows and identifying operational efficiencies to help make its goals a reality.
“We also want to reduce our number of main safety incidents by 25 per cent from 2023 to 2030 and cut our CO2 emissions in half by the end of the decade, when compared to our 2019 measurements – an aggressive target that is almost unheard of for a company of our scale in this industry,” explained Mr Davison. “We are aware, however, that our goals will come with their own sets of challenges.
“The past three or four years perfectly exemplify that, with a multitude of events that no one could have predicted. From Covid to the driver shortage crisis, and with ongoing geo-political turbulence across the world, it has been very difficult to predict what will happen next.
“Over time, the volumes and activity associated with some of our petroleum
products will also reduce – but that presents an opportunity for growth and development in other markets. We already have the necessary skills, expertise and infrastructure to grow in these emerging markets, and by sticking to our vision and values, we are putting ourselves in a great position to succeed.” n
For the past 10 ye with its turnover achieved, in an e
ears, Sorensen Civil Engineering has experienced a consistent growth trajectory, growing twentyfold. Managing Director John Wallace explained how this was exclusive interview with Inside Sustainability. Report by Imogen Ward.
Between 2014 and 2024, Irelandbased Sorensen Civil Engineering successfully built its turnover up from a respectable €3 million to an awe-inspiring €65 million.
“As a company, we are extremely proud of the consistent and controlled growth we have accomplished over the last 10 years,” said Managing Director John Wallace. “We
achieved this whilst protecting our excellent safety record of having no major accidents or incidents on our projects, and with the help of the calibre of people that we have retained over the years.”
Established by Olaf Sorensen in 1977, Sorensen began its journey as a subcontractor before it quickly developed into a mid-sized main contractor with the help
of Mr Sorensen’s brother David Sorensen. With a focus on public works contracts for local authorities, Sorensen has built up an exceptional portfolio over the years.
“We run on a self-delivery model, which is quite rare for our industry,” said Mr Wallace. “We own our plant and directly employ trained and skilled people to deliver all our projects in-house. This model has afforded us greater control over resources and better management of the programme.”
In 2014, with only one client on the books, Sorensen made the decision to diversify its services, targeting mid-size road safety schemes, as well as public realm and urban renewal projects. This move helped to develop the company in a balanced and complementary way, and in 2020, Sorensen diversified once more, establishing its own marine division With projects dotted across Ireland and Northern Ireland, including the
Castletownbere Harbour extension, this has been an incredibly successful endeavour.
Alongside its continual diversification, Sorensen developed its own Waste Hierarchy management system, which it employs on all its projects. After witnessing first-hand the issue with inert waste disposal on construction projects in Ireland – and a lack of licensed waste facilities – Sorensen decided to take matters into its own hands.
“We identified the issue in 2017, and since then have operated a number of licensed waste facilities in the Munster region that have enabled us to dispose of excess site won material in an efficient and sustainable manner,” Mr Wallace explained. “We also have ‘Take-Back Policy’ agreements with our suppliers, so where possible, no delivery will leave
Supporting the next generation:
Sorensen is an Engineers Ireland Accredited Employer who has worked closely with EI to create an undergraduate placement programme for civil engineers. This has led to partnerships with the UL, UCC, MTU and TUS.
The company is also an approved National Apprenticeship Employer for the Generation Apprenticeship Programme for Civil Engineering.
site without taking associated waste and packaging with it.”
The company has also commenced measuring its Embodied Carbon Emissions, to provide a better picture of what areas of the business can be improved.
“We are currently implementing measures to trial a HVO conversion on part of our 200 strong fleet of heavy machinery,” said Mr Wallace. “We hope to begin this before the end of this year. We are also assessing the viability of solar PV panels for our site offices and have joined the Supply Chain Sustainability School Ireland.
“Being a member enables us to collaborate with peers, partners and clients on issues surrounding sustainability and the environment. Achieving carbon reduction is no longer a choice or an impossibility, it is a necessity in the fight to combat climate change.”
Amongst the long list of Sorensen’s successes are several standout projects that are distinct in their ability to be both innovative and sustainable.
In 2021, the company successfully completed the Youghal Eco Boardwalk. This 1.9km elevated boardwalk was a finalist
in the 2021 Irish Construction Excellence Awards and had a huge impact on the surrounding community.
“The social impact of this build was immeasurable, and it came at such a crucial time as the community battled through the global pandemic,” commented Mr Wallace. “We really enjoyed working on this project and its surroundings inspired us to take a more sustainable approach. We proposed an alternative wood material for the substructure and decking called Ekki, which came from an FSC certified, sustainable forest in Cameroon.”
The company is also currently involved in the €1.6 billion Celtic Interconnector project. Once complete, this cable route between Ireland and France will facilitate the exchange of 700MW of electricity. Playing its role in this major development, Sorensen signed a €45 million contract last year, that will see the contractor deliver a section of the large high voltage grid line.
“We have partnered with large cable manufacturer Nexans on the project, who will manufacture and commission 575km of subsea cable for the client CIDAC,” said Mr Wallace. “To meet our contractual obligations, we will install 44km of ducting and cables from Youghal beach to Knockraha, County Cork. This project is a key step in Ireland’s journey to a greener energy future, and we are so proud of our contribution towards that.”
Project completion is targeted for 2026 and will result in enough electricity to supply 450,000 homes, once finished. So far, this project has proven to be an exceptional opportunity for Sorensen, opening the doors to a new market. With its feet now firmly planted in the energy sector, the company intends to develop its presence even further.
The success of each project can be attributed to a team effort, from the hardworking employees of Sorensen to
the dependable supply chain, which it has built up over the last 46 years.
“We have some very talented and innovative project managers, quantity surveyors, engineers and general foremen working across all our projects,” said Mr Wallace.
“The quality and experience of our current group of professionals would give any of Ireland’s Tier One contractors a run for their money. They truly go above and beyond when it comes to their job.”
Mr Wallace recalled a prime example of the team’s commitment. Currently delivering the Glashaboy Flood Relief Scheme in Glanmire for Cork County Council and OPW, the team was present during the tragic floods brought on by Storm Babet, last year.
“I was extremely proud of the Sorensen site team as they went shoulder-toshoulder with the Glanmire community to battle the effects of the floods,” explained Mr Wallace. “They diverted flows, unblocked culverts and assisted the local community to reduce the
damage caused by the flooding. Their efforts prevented dozens of businesses and houses from being flooded.”
As Sorensen closes the chapter on the last decade and looks ahead to the next 10 years, it is clear that the company’s journey of development is far from over. Having just created a new executive committee with four new Directors in January this year, the company is confident that this is the first step of many in its journey to the next level.
“In the coming years, we intend to grow our geographical footprint throughout Ireland whilst diversifying into new sectors,” said Mr Wallace. “We will complete this with caution due to the current shortage of construction professionals and will happily recruit skilled workers from other countries to overcome this challenge.
“With our new executive committee in place, and a hardworking culture, I am confident that the future will be bright and sustainable for Sorensen Civil Engineering.” n
United Terra Enterprises provides sustainable and pioneering solutions within the energy sector. Through three distinct segments – Oil & Gas, Wind & Solar and Hydrogen – the company remains steadfast in its mission to foster an environmentally conscious and prosperous future. Hannah Barnett spoke to Founder & CEO Peter Krempin, CFO Bill Cummins, Vice Chairman of the Board of Directors Patrick Allman-Ward and Group COO Bayne Assmus to learn more.
United Terra Enterprises is a multifaceted energy business, based in Liechtenstein, with a focus on the oil and gas sector. Various initiatives in renewable energy are also currently under evaluation in order to develop a balanced energy portfolio within the next three years.
“Oil and gas is much more than energy for trucks,” said Peter Krempin, Founder & CEO. “Without it, there would not be many of the products that keep the world turning. What many people don’t understand is that the farming industry, chemical industry and a lot of other industries rely on hydrocarbons. The reality is, for at least the next 50 years, without oil and gas companies the world will not turn.”
“All anyone has to do is look out the window to see the use of hydrocarbons,” agreed Bill Cummins, CFO. “Not even out of a window, look at a window; an immense amount of energy is used to melt down sand to make the glass. We see glass towers being built all over the world - we wouldn’t have them without hydrocarbons, because we can’t produce enough electricity to power those sort of furnaces.”
As the company is keen to point out, even electric vehicles and solar panels require hydrocarbons to produce them in the first place. As a result, the United Terra
Enterprises’ ethos is to emphasise that a multifaceted approach is needed to the energy transition; it cannot be rushed.
“We need more time, that’s our job as an oil and gas principal leader,” Mr Krempin added.
“The energy transition is difficult. We all know solar, wind and hydrogen are good proposals, but green hydrogen doesn’t yet make money. So, we say: why not go to blue hydrogen first to start to change something? It’s a process. We are a small company, but we want to do our best to help the world get better.”
The corporate vision of United Terra Enterprises emphasises the necessity of a dual-track approach, embracing renewable energy in recognition of a world that is evolving. As a result, the company currently welcomes hydrogen as a future-visioned business, once the infrastructure has developed and matured.
“The energy transition is real, climate change is real, no one is denying that,” said Patrick Allman-Ward, Vice Chairman of the Board of Directors. “We must decarbonise the energy system. But the idea that we
can flip a switch and change something that has taken nearly 300 years to build in just 25, is crazy.
“Whilst we need renewable energies, society still runs on hydrocarbons, not just for fuel. Imagine what the world would be like if we didn’t have pharmaceuticals made from petroleum products and we didn’t have all of the kit currently used in modern health care, we would be back in the 19th century. So, this is not a simple solution. There is no silver bullet. The global energy system is highly complex and it’s going to take time to evolve.”
As part of this multifaceted approach, United Terra Enterprises is also committed to solar as an affordable, efficient and environmentally friendly way to pro duce energy. The company’s goal is to develop solar and wind farms of up to 200MW, including up to 50MWh storage capacity, in the Mediterranean region.
Focusing on areas with good sun exposure and shortages of energy supply, the company plans to enhance the Mediterranean’s economic prosperity as part of a €200 million investment.
“We also need to commit to decarbonising our existing production where possible,” said Mr Allman-Ward. “This means to keep doing what we are doing, but with less energy and less waste, certainly when it comes to the gas industry.”
One of the potential avenues the company may explore in the renewable space involves carbon capture and storage. The blue hydrogen production process, for
example, requires that the CO2 produced is sequestered underground, an action that can be controversial.
“I’m a geologist and frankly, there’s an awful lot of nonsense about carbon sequestration and how unproven it is,”
Mr Allman-Ward said. “Most hydrocarbon resources have been in the ground for tens or hundreds of millions of years. So, to say that putting the CO2 back where the hydrocarbons came from in the first place means it’s all going to leak out again, is rubbish.
“Clearly, there are some technical challenges, but conceptually, these fields are perfectly capable of retaining CO2 for the same period - millions of years. So, this is a real growth area, because as the sector matures, we have even more depleted fields that we can use as a place to store the CO2. That’s a very exciting opportunity for our industry.”
United Terra Enterprises is also a uniquely positioned onshore Albanian oil producer, having operated in the country since 2012. Over this period, it has successfully produced over 1.3 million barrels of oil. But the inherent potential of such projects is not limited to the oil and gas sector.
“We have an opportunity to put together an interesting investment package with several different aspects, whether it be solar, hydrogen or traditional oil and gas,” said Bayne Assmus, Group COO. “And it’s not just Albania, there are a few other entry points as well.”
Contracting the right people has proven crucial in developing the most efficient solar solutions, without skimping on cost.
“It is important to have a very skilled tech nical advisor, to make a thorough analysis of the weather at the location over the years,” Mr Krempin explained. “We are looking into hybrid solar parks too, with some battery storage. What we are thinking of doing at some farms in the north of Albania, is to position the panels high up so they can follow the sun. The farmers working the fields can still have their business and come poor weather the panels can even be used as a roof to protect crops.”
United Terra Enterprises is clearly an innovative company with plenty of moving parts. Indeed, this is by design, rather than accident.
“The entrepreneurial spirit is really key to our business development,” said Bill Cummins, CFO. “We’re pretty lean. So, we can decide if something’s worth pursuing quickly. Then it’s about trying to go down the path of due diligence with negotiations to determine whether we can get a deal done.”
“We have a combination of the ability to make quick decisions, and a fundamental cadre of expertise,” added Mr Allman-Ward. “We are staffed by people who have been in the industry for a very long time. This means we have the expertise to make that due diligence process happen very quickly.”
As the CEO of a private company operating in the oil and gas sector, Mr Krempin is well aware of the difficulties of remaining stable and financially sound. Following several turbulent periods in the market over the last decade, the survival of United Terra
Enterprises is something he attributes to hard work and resilience.
“Standing behind your own ideas, I believe, is a key factor in our success,” he said. “The reason we have survived is by always working together to identify the next step. I love working in a team with professionals. And we are now ready to execute our ideas.”
“We’ve all been through the trenches during the worst of the down periods in the sector,” Mr Cummins agreed. “We fought, and we survived. And now we are restructuring the company, with some Board and personnel additions. We’re in a place that should be attractive to all sorts of different investors, employees and other stakeholders.”
For Mr Allman-Ward, who joined in November 2023 and boasts an illustrious CV stretching from Shell to small independents, it is the start-up attitude at United Terra Enterprises that makes it such a dynamic workplace. “It’s very exciting,” he said. “There’s huge growth potential and opportunity to start with something small and to develop it to become successful.”
“My motivation is the opportunity to engage in that start-up aspect too,” Mr Assmus concluded. “It means there’s the opportunity to be involved in day-to-day decisions to implement growth. I’ve been with bigger companies, smaller companies and other start-ups over the years and start-ups are always the most interesting. They give the greatest satisfaction at the end of the day because there’s the incentive to cultivate something from nothing. I guess that’s the gardener in me.” n
IN2006, three budding engineers set out on a quest to evaluate the commercial viability of wave energy.
“Martin and Kristian had worked together on other projects, and they were inspired to develop a system that would have positive impact on the planet,” said CEO Michael Henriksen. “They decided wave energy had a very large, unexploited potential. I came onboard in 2013 after they have worked out of the garage in parallel with their day jobs for the first years to prove the Wavepiston concept they had developed.”
Wavepiston was officially founded in 2014. An intensive period of fund raising started, for both equity and public cofunding, and then finally in February 2015 after years of bootstrapping the first salary could be paid. From there, the company implemented stringent development and testing on its system.
“Wave power is a large, unexploited renewable energy source,” Mr Henriksen explained. “There have been several companies that have tried and failed in the past, but we feel now, with the transition
Over the last 18 years, the experts b have been working tirelessly to mar as a competitive option in the race Now, with its first full-size demonstra well underway, the company is gear commercialisation. CEO Michael Hen explained more, in an exclusive inter Inside Sustainability. Report by Imog
to greener energies, it is the perfect time to bring this technology to market.
“Experts say the theoretical potential of wave energy equates to the entire world’s current electricity consumption. To play our part in developing this segment, we are following three tracks for development: technology, projects, and testing and demonstration.”
The Wavepiston system consists of a series of non-intrusive energy collectors attached to the Wavepiston WEC (the supporting line). These collectors are perfectly positioned to use the oscillating horizontal motion of waves and the subsequent mechanical energy to create a palpable source of usable energy.
Having previously run several small-scale trials, Wavepiston elected to run a fullscale demonstration project at the PLOCAN test site, Gran Canaria, to test the effectiveness of its system for power generation and seawater desalination.
ehind Wavepiston rket wave energy to greener energy. ation project ring up for nriksen rview with gen Ward.
The Competitive Wave Energy on Islands (CWEI) project consists of a supporting line of up to 20 energy collectors and a turbine generator. All going to plan, this project could be a critical step towards providing isolated islands with a consistent supply of clean power and water, with CWEI expected to produce 547,000kWh per year.
“Before we start offering this technology on a global scale, we really want to focus our efforts on creating a positive impact locally, by reducing energy prices and ensuring access to clean water.”
Mr Henriksen explained. “At the same time, we seek to protect these islands from the volatility of energy prices –taking fossil fuels out of the equation.”
With the first energy collector having been tested in the water and six more to come, Wavepiston intends to run data collection throughout 2024, before implementing any system upgrades in 2025 and 2026.
“The results we get from 2024 will be a really good indicator for what improvements we need to make, before we take the system commercial in 2027,” said Mr Henriksen. “The results so far have been positive and have really helped us to understand the dos and don’ts of installation and data collection.”
To successfully market the Wavepiston system as a commercially viable product, several changes need to be implemented to make it cheaper, lighter and more robust. Currently, the system’s wave energy collectors are the most expensive element of the build. To overcome this cost, Wavepiston is running a project on Composites, Hybrid Testing, and Simulations for a Disruptive Wave Energy Collector (COHSI-WEC).
This project, which was awarded a grant of DKK15.6 million from the Energy Technology Development and Demonstration Programme (EUDP), will see Wavepiston replace key steel components with lighter fibre-reinforced polymer alternatives. If successful, these new components will make production costs much lower, making scalability a more likely scenario.
“To successfully meet our 2027 commercialisation target, we are currently implementing a project in collaboration with DTU and Aalborg University, focused on adapting our energy collectors,” said Mr Henriksen. “We developed our protypes using steel components, which worked well to demonstrate the technology, but it is not an ideal material for the final product.
“We started developing the new polymer components last year, and they are now going through wave tank testing. The completed energy collectors should be ready for full-scale offshore testing next year.”
Wavepiston is also running a second project in parallel to COHSI-WEC, which will help advance the system’s journey to commercialisation. The SHY project is set to advance wave energy through the development of key components for a seawater hydraulic power-take-off system. The company will also establish an advanced control strategy at the same time to help reduce energy costs and minimise environmental impacts.
This project has just received €4 million in funding from Horizon Europe and is supported by partners Maynooth University,
DTU, FibronPipe GesmbH, LESER GmbH & Co Kg, Julia F. Chozas, Applied Renewables Research, Marine Systems Modelling, and Plataforma Oceánica de Canarias.
Whilst these projects are underway, Wavepiston is also focused on several other pursuits to progress to the next stage of commercialisation.
“We are also placing the foundations for future project development, by establishing collaboration agreements with project developers and partners,” said Mr Henriksen. “We must do this in parallel with our current projects because there is no time to just sit and wait. Project development, permissions and agreements can take up to five years to implement.”
None of Wavepiston’s work would be possible without the help of key suppliers and partners. The industry innovator is grateful for the contribution of every single company, including mooring expert Delmar, which has been a prominent player in ensuring the mooring of the Wavepiston system.
Another key partner for Wavepiston has been TCDL Steel; it has been involved since 2021.
TCDL Steel is also a trusted supplier of components to the Wavepiston wave energy system and an important partner in giving input to the optimisation of its piping system. TCDL Steel has supplied the drill-pipes and the specialised subs that are the backbone of the Wavepiston Wave Energy Converter string. They are a highly professional supplier and deliver high-quality items at a competitive price.
Wavepiston has also enjoyed creating new relationships, especially when it comes to the SHY project, where is has been able to work alongside Austrian safety valve manufacturer LESER for the first time.
“We also recently collaborated with major energy conglomerate Shell,”
Mr Henriksen explained. “The company was interested in witnessing the potential of wave energy.
“Wave energy is beginning to garner the attention of these larger players, and it is an area of the market that could become very interesting in the mid- to long-term.”
As Mr Henriksen looked to the future, he made it clear that the road ahead was not going to be smooth: “Although there is an increasing amount of investment going into wave energy, there is still push back.
If we stay on the track for renewables, we will get there, but the sector requires significant support to successfully commercialise these different technologies.
Advancement doesn’t just happen by itself; it requires a lot of active involvement and funding before it can go global.
“I love being a part of a company that is having such a positive impact on small communities, and I can’t wait to witness this evolve into a global enterprise that has a major impact everywhere.” n
Showcase Interiors is an award-winning independent furniture dealer, providing consultancy, procurement and installation services to all market sectors and businesses of various shapes and sizes. Hannah Barnett spoke to Group Sustainability Specialist Harry Hill and Group CEO Nigel Boreham to learn more.
Since it was founded in 2007, Showcase has made its name delivering inspiring, design-led workspaces that transform the way businesses work. The company has always taken sustainability seriously – and for a furniture dealer, this largely involves working with the right suppliers.
“As part of a wider sustainability strategy, we’re putting the onus back into the supply chain,” said Harry Hill, Group Sustainability Specialist. “By stitching sustainability into all business activities, rather than trying to build
it from scratch as its own ‘pillar’, we’re setting the precedent for intrinsic working. We are slowly trickling sustainable ideas into the mix and incrementally raising the bar –taking the suppliers on the journey with us.”
A history of sustainability Showcase began operating in the niche luxury retail market, taking on projects for illustrious clients like Porsche and Mercedes Benz. In 2010, the company moved into the commercial sector and started dealing in higher volumes.
Certifications followed - ISO9001 first, then ISO14001 in 2013 - and this marked the start of the gradual transformation of the business.
“I started to think about where we could make a difference,” explained Group CEO Nigel Boreham. “We started to question whether suppliers were committed to using FSC timber and the equivalents. We began to use manufacturers that were ISO14001 certified, or better, themselves. Every year, we shifted the objectives up as we saw our supply chain becoming more aligned with us.”
Showcase’s turnover for the last financial year was around £60 million, large growth from £20 million in 2021. Among the company’s 145 employees, Mr Hill’s Group Sustainability Specialist position is a relatively new addition, demonstrating the company’s evolving commitment to sustainability.
In 2021, Showcase began working alongside noted accreditation body and consultancy Planet Mark. The company started to comprehensively measure across all scopes and, in 2022, became Carbon Neutral through offsetting. The next rung on the ladder will be a tangible move towards carbon net zero.
“Planet Mark gave us a starting point for our strategy,” Mr Hill explained. “But we must still be proactive. This means looking into issues as granular as where the tea and coffee comes from, up to the treatment of workers within the supply chain.
“Certifications can’t just be a logo on a website, they need to provide direction and hold meaning. There has been a lot of focus in the industry on B Corp, but we are waiting to see if the standards currently set by B Lab increase; you currently
achieve B Corp with just 40%. I, personally, do not feel that this is high enough for those holding B Corp to be considered an ‘industry leader’ in sustainability. If B Corp becomes an industry standard, then we will have to reassess.”
To ensure that the information Showcase is putting into the public realm is accurate and transparent, the company submits its granular data to inhouse analysts at Planet Mark.
“Having ISO14001 is no longer enough,” said Mr Boreham. “That’s why we’ve developed our carbon reduction plan. The big volume manufacturers that we work with have got every accreditation under the sun, which is great. But we’re also keen to work with smaller, innovative manufacturers who offer different solutions.”
For a service-driven business like Showcase, carbon impact from scopes
1 and 2 is limited, totalling around 5% of total emissions. Managing scope 3 emissions has therefore proven vital for the company.
“That’s the key take away of being a furniture dealer, compared to being a factory making the furniture,” Mr Hill reflected. “But it doesn’t mean that we haven’t got an influence on environmental impact. On the contrary, the work passes through us from our suppliers’ factories, then onwards to our clients.”
There have been real, sustainable changes both at Showcase and through the wider industry. “Planet Mark has helped us to get everybody thinking about impact,” said Mr Boreham. “We saw a seismic shift in perspective. The business will continue to invest in staff engagement on key
environmental topics, but we’ve also seen a massive change from a client point of view. Every project now has a much larger percentage target for reused items.
“In fact, we’re currently working on a project with a 90 per cent reused furniture target. That’s a truly ambitious goal, given that the client’s current offices and furniture are nearly 20 years old. So, that’s really testing our internal resources and creativity. But, although a percentage that high is uncommon, the intent no longer is.”
Showcase has also introduced a series of quarterly business reviews with some of its key strategic suppliers, working to achieve take back and refurbishment initiatives collaboratively.
“Part of our role is to help the manufacturers be accountable for
the products they bring to market,”
Mr Boreham explained. “Some of them have got their heads around it; they’ve worked out how to monetise circularity in their factories, and they’re aligned to that aspiration. Others just aren’t there yet.”
Several years ago, Showcase ran a project for law firm Freshfields that had an SKA Gold standard on the furniture used, meaning a very narrow selection process. The prequalifying questionaries sent to manufacturers had revealing results.
“250 prequalifying questionnaires went out to meet the SKA Gold standard,” Mr Hill explained, “and around 10 per cent hit the brief, which indicates where the industry was at in terms of sustainability.
“That said, most manufacturers have invested in a best-in-class product as part of the culture shift towards embracing more recycled and reused materials. The circularity aspects just need to be baked into more products from the beginning.”
The company is also developing a best-in-class league table, tentatively called The Green League. “What we’re doing is only on the surface, but it’s trying to look past the fog of greenwashing which is rife,” said Mr Hill. “Not just in this industry, it’s rife everywhere.”
While the sustainable frontier of the furniture dealing business remains broad, Showcase is seizing the advantage of the relative lack of targets or legislation in the field.
“It doesn’t give us much to aim for, but it allows us to be creative,”
explained Mr Hill “We achieved carbon neutrality via offsets, but from this year we will be trying to mirror our impacts from the offsets across as many UN SDGs as possible. The first year Showcase did this, we hit four goals. Last year, it was seven and this year, we’re on course to hit 11 or 12.”
For Mr Boreham, Showcase’s progress is testament to the values the company was originally founded on.
“My wife and I started the business as response to working for other people and becoming disillusioned by not being able to do the things we wanted to do,” he concluded. “Now, we have been able to grow and bring something different to our clients and it feels like we can influence change in our marketplace. It’s a really exciting place to be.”
n