CORMAR CARPET COMPANY: Everything carpets
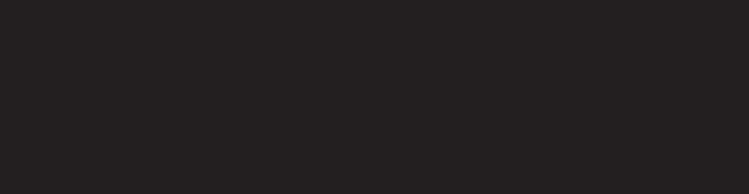
starts in the home
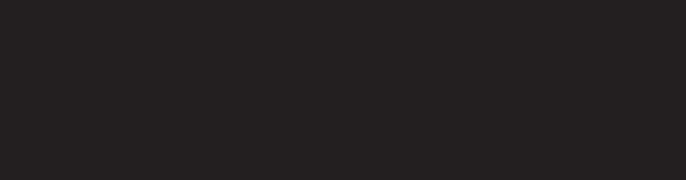
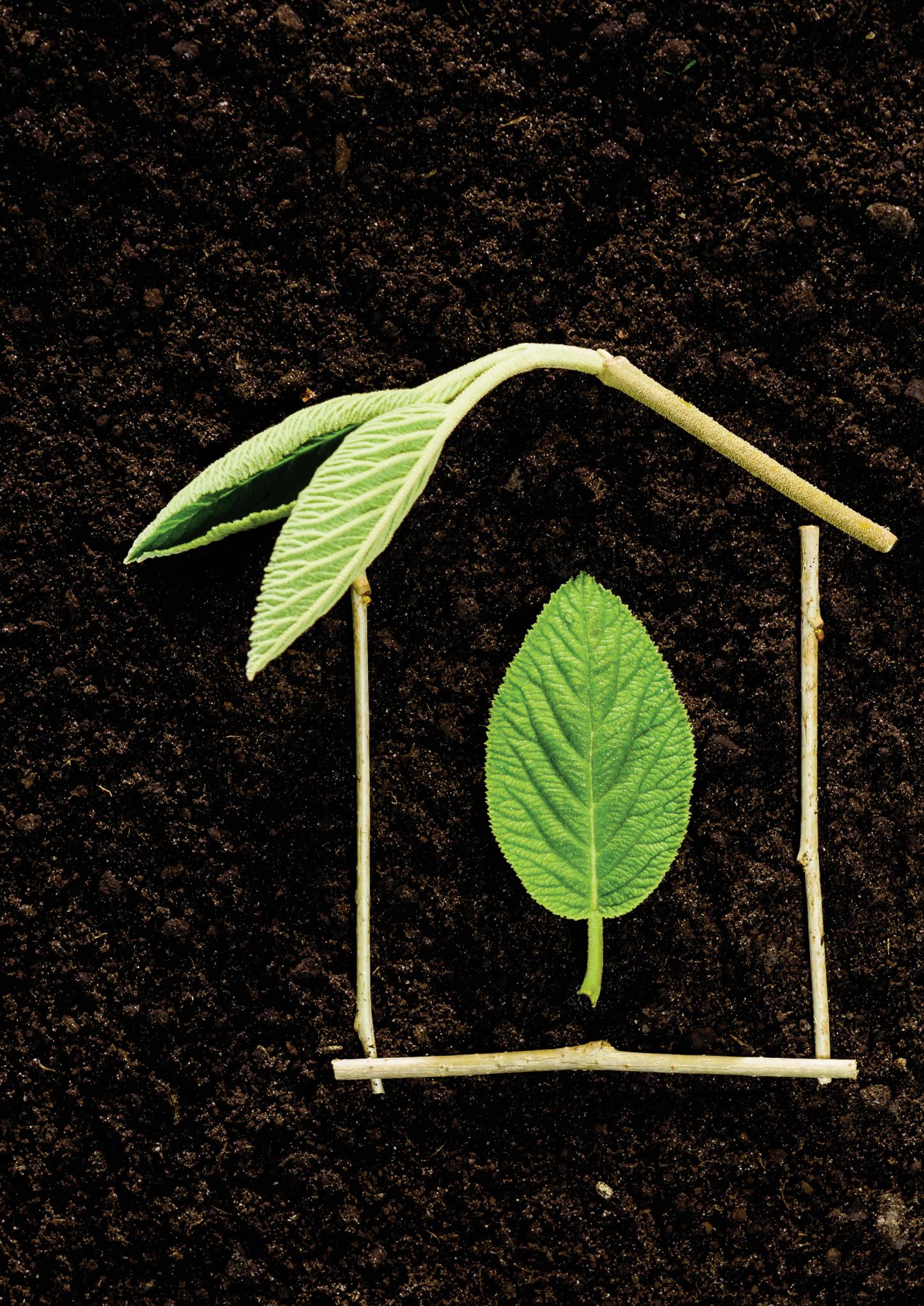
WHAT MORE UK: Manufacturer of bakeware, cookware and housewares
NATIONAL WINDSCREENS: Vehicle glass repair & replacement specialist

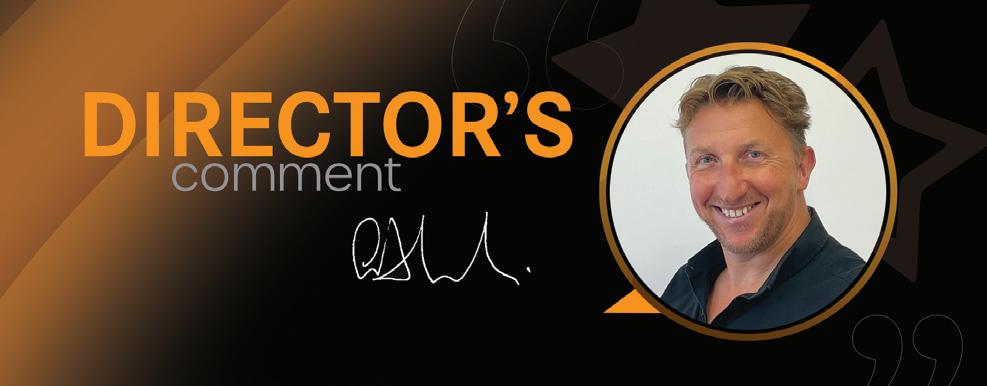
CORMAR CARPET COMPANY: Everything carpets
WHAT MORE UK: Manufacturer of bakeware, cookware and housewares
NATIONAL WINDSCREENS: Vehicle glass repair & replacement specialist
Welcome, Dear Reader, to your latest edition of Inside Sustainability and the first issue of 2024. Since launching this magazine 18 months ago, I am still impressed by the sheer volume of articles, advertisements, events and news items that scramble to appear within it.
I am naturally confident as to the benefits of this promotional platform for all your products and services. However, what impresses me further is the amount of innovation in all fields within this increasingly important aspect of business.
Just when we think we have seen it all, along comes another sector of industry with some great sustainability news to rightly shout about. This edition is no different, featuring many familiar sector focuses, plus one section that we have not seen in the magazine before.
A play on the English World Cup soccer chant of the 1990s springs to mind: ‘It’s coming home, it’s coming home, sustainability’s coming home-ware.’ Apologies for ruining that song, but please notice that
we now have a section dedicated to the homeware sector, with articles and advertisements linked to furniture, carpets and textiles, to name a few.
There is of course no market where we should not endeavour to make improvements and advancements to help businesses become more sustainable. Therefore, I am proud to be able to provide a platform for such developments and achievements.
Yes, our magazine, website and social media promotions help you all gain new customers and suppliers. However, increasingly it seems we also now operate as a network for sharing the best practices in the world of sustainability. What a truly lovely thing this is. Well done and thank you all. Keep up the great work! n
John White Managing Director Managing Director John White improves a famous football song.On the move with passion
ASSMAN produces furnishing solutions to create modern working environments where people feel good. The company supports customers and partners with extensive consultation and planning services ASSMAN is based at one of the most state-of-the-art office furniture production facilities in Europe with a strict sustainability strategy.
Managing Director
John White
Finance Director
Filomena Nardi-Smith
Editor
Phil Nicholls
Editorial Assistants
Imogen Ward
Hannah Barnett
Feature Writers
Andy Probert
Romana Moares
Richard Hagan
Colin Chinery
Business Development Manager
Darren Foiret
Research Editors
Jeff Johnson
Mark Simmonds
Judi Wheaton-Mars
Ginelle Lorenzo
Natalie Martin
Dane Coady
Becky Scrivens
Sales Director
Richard Brightmore
Sales Manager
Helen Leisi
Project Managers
Alexander Paterson
Tony Ingrouille
Kym Hamilton
Chris Renicar
David Earl
Lisa Smith
Will Tottie
Bobby Godfrey
Loretta Smith
Julien Carew
Sam Ransome
Studio Manager
Philip White
Webmaster
Michael Stamp
Designers
Sarah Jones
Georgina Harris
Events Manager
Jasmine Lodge
Marketing Manager
Adam White
Administration &
Summer Clover
20
22
30
58
66
72
42
78
50
86
Klöckner
Partnering with the Keep Sea Blue organisation, kp plays its part in closing the loop on plastic waste through the use of Recycled Coastal Plastics®, a certified post-consumer recycled raw material recovered from within 10km of the coastline in the Mediterranean basin.
In 2023, kp used more than 800 tonnes of recycled PET waste collected through this initiative to create new packaging. This is the equivalent of reusing 14 million PET bottles and underlines kp’s aim of promoting environmental stewardship and sustainably designed packaging solutions.
Keep Sea Blue's Blockchain platform, powered by Oracle technology, enables the team at kp to conduct rigorous quality checks, verifying the origin, date and location of plastic collection. The recycling process adheres to BRC, ISO 9001 and RecyClass certifications.
“What Keep Sea Blue does is ingenious, creating a closely monitored network to collect, sort and process plastics across
the Greek islands,” said Hendrik Bartels, Marketing Director, Rigid Films, at kp. “After processing through RecyClass-certified facilities, this raw material is then used to create the quality range of food packaging solutions that kp is known for. What sets this apart is the transparency of the system, which is essential in the food packaging industry.”
With over two decades of expertise in manufacturing high-quality products from post-consumer recycled PET, kp ensures the highest standards of food safety through the production of quality packaging solutions. Packaging using Recycled Coastal Plastics material is produced at multiple kp production sites across Europe and supplied to customers in Germany, Italy, Portugal, Turkey and the UK.
To drive greater consumer awareness, kp has also developed a dedicated logo that customers can use on the packaging to signify the use of Recycled Coastal Plastics. n
LG Chem and Enilive moved a further step forward to the final investment decision on the project of a new biorefinery in South Korea by signing the joint venture agreement. The agreement was signed in Rome by Eni CEO Claudio Descalzi and LG Chem CEO Shin Hak-Cheol.
Enilive (a company directly controlled by Eni, which holds 100% of its share capital) and LG Chem announced their partnership last September. The two companies were exploring the possibility to develop and operate a new biorefinery at existing LG Chem’s integrated petrochemical complex in Daesan, South Korea.
The project aims to complete the biorefinery by 2026 and to process approximately 400,000 tonnes of renewable bio-feedstocks annually using Eni's Ecofining™ technology. The site will also create multiple products including Sustainable Aviation Fuel, Hydrotreated Vegetable Oil and bio-naphtha. LG Chem and Eni will combine expertise in this initiative. The final investment decision is expected later in 2024.
“Biofuel production is one of the main pillars of our strategy to contribute to reach net zero emissions by 2050 also through the sale of increasingly decar -
bonised products to our clients,” said Eni CEO Claudio Descalzi. “The biorefinery project we are working on together with LG Chem is a key element to expand Enilive’s biorefining presence internationally, to raise its capacity from current 1.65 million tonnes/year to over 5 million tonnes/year by 2030 and to increase the optionality of SAF production to up to 2 million tonnes/year from 2030.”
“This agreement holds significant meaning as it represents the collaboration and joint effort of global leading companies towards the common goal of Net Zero,” LG Chem CEO Shin Hak-Cheol explained. “LG Chem will actively support the successful execution of this project and, moving forward, will solidify its position as a leading company in the eco-friendly plastic industry, achieving sustainable development and carbon neutrality as a true global entity.” n
Building on $180 million in joint energy-related research, EPB, based in Chattanooga, Tennessee, and Oak Ridge National Laboratory (ORNL) marked 10 years of collaboration with the announcement of the new Collaborative for Energy Resilience and Quantum Science (CERQS).
The new joint research effort will focus on utilising Chattanooga’s highly advanced and integrated energy and communications infrastructure to develop technologies and best practices for enhancing the resilience and security of the national power grid, while accelerating the commercialisation of quantum technologies.
US Representative Chuck Fleischmann (TN-03), Chairman of the House Appropriations Subcommittee on Energy and Water Development, who represents both Chattanooga and Oak Ridge, commented on this development.
“Since I came to Congress over 10 years ago, one of my highest priorities has been creating and strengthening the Chattanooga-Oak Ridge partnership that’s changed East Tennessee and the entire Southeastern region,” he said. “Because of the increased collaboration between outstanding entities in Chattanooga, such as
EPB, and organisations in Oak Ridge, like ORNL, major advancements are taking place in science, technology, research and moregenerating hundreds of millions of dollars in economic impact and making Tennessee and the entire Southeastern United States the world leader in emerging technologies.”
To date, EPB and ORNL have collaborated on nearly 30 funded projects. These efforts encompass a wide range of research, including the development of advanced energy models to optimise power distribution, the utilisation of predictive algorithms to identify likely energy equipment failures and the deployment of dynamic microgrids that can be rapidly scaled to meet changing energy needs.
Taken together, these projects reflect efforts to keep energy costs lower for customers while enhancing the reliability and resilience of their energy and communications services. n
Energy Systems Catapult has launched Net Zero Data, a range of new prepackaged datasets developed to streamline the design and delivery of local net zero projects.
The Catapult’s data bundles have been developed by drawing on 30 years of collective data modelling expertise provided to local authorities, network operators and renewable technology installers, delivering unparalleled insights that open data alone cannot provide.
These datasets have been applied, refined and tested in various real-world scenarios by the Catapult, such as understanding the baseline of a local energy system prior to full Local Area Energy Planning (LAEP), and are now available standalone.
The datasets are built to match the needs of different types of low carbon projects and support common use cases, such as identifying buildings suitable for net zero retrofit, buildings suitable for installing low-carbon heat or renewables, plus land with potential for renewables or electric vehicle infrastructure.
The datasets fill the gaps in common open data sources and enable the initial
feasibility assessments at the individual project level.
Covering GB-wide Local Authority regions, Net Zero Data offers low cost, ready-to-use, regularly updated information, minimising resource overheads. No more waiting for bespoke datasets to be built, or using data that is out of date when developing project feasibility studies.
Datasets and bundles from Net Zero Data can be visualised using any Geographic Information System (GIS) platform. However, for Local Authorities that do not have a GIS platform, the Catapult is able to offer costeffective access to the LAEP+ GIS platform powered by Advanced Infrastructure Technology Ltd (AITL). Using open and data sources such as ESC's Net Zero Data, AITL's LAEP+ platform uses digital twins to support decision making by local stakeholders and forecasts network capacity, building retrofits, heat networks and EV rollouts all in one platform. n
click to sections:
HOMEWARE
PACKAGING &
CONSTRUCTION
SERVICES & TECHNOLOGY
ENGINEERING & MANUFACTURING
one planet – one chance – one voice
A selection of opinions and future events, followed by previews of Hannover Messe and WindEurope.
HANNOVER MESSE
HANNOVER MESSE is the most important international platform and hot spot for industrial transformation – with excellent innovations and unusual products. The event brings the core industrial sectors together at one location –from drive engineering, automation, energy, R&D and industrial IT to subcontracting.
Hydrogen 2024
Hydrogen 2024 is the meeting place for the hydrogen and ammonia industry. Over 400 participants will benefit from the insights of 70+ C-Suite and executive speakers, addressing the pressing challenges faced by European, North African and Middle Eastern projects.
13-15
World Hyd The
WindEurope 2024
WindEurope is returning to S aspects of onshore and offs and operations. 10,000 visito three days, with over 400 compani all ready to showcase their latest pr
e landmark event in the industry’s lendar, World Hydrogen 2024 Summit Exhibition, is the largest and most senior rogen event. Part of the SEC World Series, the event features the largest ocused Exhibition in the world.
here] for weblink
Battery Cells & Systems Expo is an international showcase of manufacturers, users and the entire supply chain working to increase battery performance, cost and safety. The show will bring together automotive OEMs, electric utilities, battery cell manufacturers, system manufacturers and integrators.
[click here] for weblink
2024
pain in 2024, covering all shore turbine technology ors are expected over the es on the exhibition floor, roducts.
Why not give your event exclusive coverage to thousands of readers and connections globally?
Contact us: events@insidepublication.com
Question: What benefits do you see from attending industry events and conferences, either face-to-face or online?
“
The core benefit is networking, meeting new people as well as those you’ve known for years. Keeping on level with the latest developments in industry and tech is the biggest benefit for us.
“Michael Hadfield, Group Sales Director, Advanced Plastics Group
“
The benefit lies in talking to people and sharing what you know. No single person has all the answers for sustainability, but at these events, as an industry, we can work together to save the planet, and then the consumer benefits too.
Events are an opportunity to have those face-to-face meetings, talk to people and help each other out, rather than keeping your good ideas to yourself. We encourage our employees at different areas of respon sibility in the business to share best practices and find what works.
“Darren Marcangelo, Managing Director, Spinks
“
I think these events are becoming more and more important. If you look for any machinery on the internet, you’ll get three pages from Alibaba, IndiaMART, ChinaWay, etc. However, the real suppliers with the right, professional, reliable, quality machines are the ones you will meet at the conventions. If you want to find the actual industry leading suppliers of any product, they’re the ones you’ll find at the trade shows.
“Edwin Langbroek, Head of Sales, Tummers Food Processing
“
Attending industry events, whether in-person or online, provides invaluable networking and brand exposure opportunities. We find that attending industry events enables us to build rapport, make connections with decision makers and helps prospective clients understand how we can help solve loading problems.
“Gary Warner, Marketing Manager, Joloda Hydraroll“
People do business with people, and therefore you’ve got to build a network. Furthermore, decarbonisation and the whole net zero challenge is not one that any one business, company or country can achieve on its own. For all of those reasons, it requires a different way of managing a business. By being visible at events you can build those networks together. Attending events becomes fundamental to what we’re trying to achieve. These sorts of problems don’t get solved in isolation.
On the other hand, you could probably attend hydrogen events all day every day. It’s about ensuring you’re making the right connections and the right impacts in terms of what’s happening in the market going forwards.
“Mark Eldridge, Director of Hydrogen, Element Materials Technology
“
The benefits of attending trade fairs are to generate new clients, strengthen existing industrial relations and to see what our peers are developing in new products and techniques. By doing that, KZU can benchmark itself against the industry.
“
Raichin Antonov, Executive Director, KZU“They offer us an option to raise awareness across the insurance, fleet, rental and automotive glazing industries about what National Windscreens is striving to do. We can also network with industry peers and experts and find out the latest trends.
“Simon Hunt, Commercial & Services Director, National WindscreensWe would love to hear your answers, so send an email over to our Editor, Phil Nicholls. media@insidepublication.com
HANNOVER MESSE is the most important international platform and hot spot for industrial transformation – with excellent innovations and unusual products. Basilios Triantafillos, Global Director at HANNOVER MESSE, answered questions for Inside Sustainability.
How has HANNOVER MESSE evolved since the last show? What is new for this year?
Our lead theme for 2024 is ‘Industrial Transformation – Energizing a Sustainable Industry’. We know that innovative technologies can pave the way to a carbonneutral industry, but companies need guidance on how to use automation, artificial intelligence and renewable energies. We also know that bureaucracy and a shortage of skilled workers are reducing growth potential, so the event
also focuses on the contributions that industry needs to make as well as which roles politicians and younger generations should play.
How would you summarise what a visitor can expect from their trip to HANNOVER MESSE?
Visitors at HANNOVER MESSE can expect an in-depth look at the trends that are transforming industry – smart manufacturing, energy for industry, artificial intelligence,
www.hannovermesse.de
22 – 26th April 2024, Hannover, Germany
carbon-neutral production and green hydrogen. They will find the partners, prod ucts and solutions that will enable their companies to remain competitive.
What do you see as the benefits to companies exhibiting at the show?
Exhibitors have direct access to buyers and distributors from all over the world, which makes HANNOVER MESSE a great place to do business. Plus, it provides the perfect platform for networking, generating awareness in the media, and setting trends.
How does the extensive 2024 conference programme help companies improve their sustainable operation?
Our conference programme provides participants with the information they need to make good decisions for sustainability within their companies. For example, the Industrial Transformation Stage provides the big picture look at cross-technology and cross-industry solutions, whereas other stages deliver deeper dives into topics such as renewable energies, Industry 4.0 and technology transfer.
Another aspect of the conference programme deals with the hot topic of AI and industry. What can you share about this conference theme?
AI will be a topic at many of the conference stages, but the dedicated AI day is 23 April at the Industrial Transformation Stage in Hall 3.
HANNOVER MESSE includes an area dedicated to startups. How important is it for the show to support innovation and growth?
It is very important to support startups, because they develop new technologies and business models that help solve the challenges of our time. We offer a variety of turnkey packages that make it easy and affordable for young companies to present themselves and expand their networks at HANNOVER MESSE.
This year we have added new formats such as master classes, mentorship sessions and fireside chats. The pitches are an established highlight. A primary goal is to bring startups into face-to-face contact with big companies and SMEs.
Another distinct feature of HANNOVER MESSE is the Guided Tours. How popular are these tours?
Our guided tours are quite popular because they provide visitors with compact, targeted overviews of specific
www.hannovermesse.de
22 – 26th April 2024, Hannover, Germany
topics such as artificial intelligence, hydrogen and fuel cells, Manufacturing-X, and quantum technology.
What do you consider to be the main challenges to industry for the future? How far do events such as HANNOVER MESSE go in helping companies overcome such difficulties?
As I mentioned earlier, companies need guidance on how to apply technologies such as automation, artificial intelligence and energy systems. We also need to minimise bureaucracy and encourage young people to pursue careers in industry. HANNOVER MESSE promotes a mix of new technologies and
cross-industry collaboration as well as a clear political framework and young talent initiatives.
On a personal level, what aspect of HANNOVER MESSE are you most excited about?
One project I am excited about is the new conference ‘North Sea Energy Hub’. The first edition focuses on potential renewable-energy projects between partner countries Norway and Germany, but we are also considering including neighbouring countries. At the time of writing, we are still working out the details, but we plan to finalise the programme soon. n
WindEurope’s Deputy CEO Malgosia Bartosik outlines the focus topics for the show.
Malgosia Bartosik – Deputy CEO
https://windeurope.org/annual2024/
WindEurope 2024 is a three-day conference and exhibition held in Bilbao. Over 12,000 attendees will enjoy dozens of conference sessions, hundreds of speakers and more than 400 exhibitors from the whole wind industry value chain. Deputy CEO Malgosia Bartosik explores the event and the core issues facing the industry.
There will be over 40 conference sessions and more than 200 poster presentations, at the WindEurope annual event. How important is this aspect of the event?
Our event is a B2B show, meaning that WindEurope is entirely designed and financed by the industry. All the revenue returns to the sector, funding our work in the Secretariat in Brussels.
The conference schedule is developed by the Programme Committee, a group of experts drawn from our membership across the industry, academic and finance worlds.
Our broad programme gives delegates an overview of the latest political, technological, scientific and market developments.
Each session is carefully designed to be dynamic and engaging. We do not accept commercial presentations in the main programme, as these have dedicated side events.
WindEurope is the perfect platform for discussions between top business and policy people. We try to engage policy makers and market players on the European level, but also regionally. It is important that relationships are built where the legislation is made as well as where the projects are developed.
The event comes shortly before the European elections. Do you have any plans to make the connection between the key industry gathering and the key EU shift of powers?
The theme this year is: Our wind, Our value. We want to underline the value creation for the whole of Europe, appealing as widely as possible to Europeans, especially ahead of the elections in June. The word value has a double meaning – covering economic and physical benefits, but also the positive values that our industry stands for (climate action, labour standards, etc).
WindEurope’s Deputy CEO Malgosia Bartosik outlines the focus topics for the show.
WindEurope will discuss energy security, jobs, communities, growth and nature, along with the role of wind energy in all these areas. These topics are especially important to all EU citizens.
Alongside a floating wind partner, you also have a biodiversity partner. Could you please explain the importance of biodiversity to WindEurope?
Wind energy and biodiversity should go hand in hand. We supported the Nature Restoration Law and the European
Commission’s target to restore 30% of the EU’s degraded areas. The expansion of wind energy cannot go without nature restoration.
Climate change is the biggest threat to Europe’s biodiversity. Building more renewables is a critical aspect of biodiversity protection. For many years now, the wind industry has been mitigating its impact on nature and biodiversity. We avoid building wind farms during bird nesting seasons or along migratory routes. Same goes for noise pollution for marine life. We reduce noise by using air bubble curtains and hydro sound dampers.
BirdLife Europe & Central Asia is our biodiversity partner. It will share best practices to ensure wind energy remain nature-friendly and compatible with the energy transition principles. At the exhibition, participants can
https://windeurope.org/annual2024/
visit companies that deliver very innovative solutions helping to develop wind farms in the most sustainable way.
What challenges do you see facing the wind sector? How is WindEurope helping the industry to overcome these obstacles?
European manufacturing of wind turbines is indispensable for energy security and for competitive electricity prices. To reach the EU’s own targets we need bigger and more European factories. We need innovation, yes, but most crucially, we need more of the same.
We are working with European institutions and national Governments to set up legislation that will help to make it happen. A good example is the Net Zero Industry Act. This will encourage more production in Europe and support the European industry in those things it already does well, such as biodiversity protection and system integration, but also cybersecurity.
Permitting remains one of the biggest bottlenecks for deploying
wind energy at large scale in Europe, with about 80GW of wind power capacity stuck in permitting procedures. Developers can wait exceptionally long to receive permits –sometimes up to nine years. Although we have seen improvements in permitting at national levels, it remains a top issue.
Governments need to digitalise their procedures. WindEurope, Amazon Web Services and Accenture are working on a solution for this issue. We developed a tool called EasyPermits which gives Governments and local municipalities the instruments to digitalise permitting.
EasyPermits is a cloud-based, digital permitting platform, developed bottom up – with permitting agents in local municipalities. A successful test in Denmark demonstrated how the tool helps permitting agents to process three times more projects at the same time. The process also engages community in a transparent way.
Your website highlights the WindEurope membership experience. Please share with the readers of Inside Sustainability the benefits of this scheme.
We provide services to over 550 members (companies, academia, finance institutions and other organisations across the whole supply chain). We shape the future of renewable energy through our advocacy work and by creating meaningful connections between our members and partners.
Our members gain access to a network of industry stakeholders and opportunities for partnership and knowledge sharing. Membership of WindEurope also grants discounted access to events and supports project collaboration, facilitating innovation and progress. WindEurope empowers its members to drive sustainability, influence policy and stay competitive, working towards a cleaner energy future in Europe.
Spain is a leading player in the European wind industry, making Bilbao an ideal location for the event. How does the enthusiasm of the Basque Country for renewable energy help create the positive atmosphere at WindEurope?
20 – 22 March 2024, Bilbao, Spain
https://windeurope.org/annual2024/
We are delighted to return to Bilbao! This is the third time we are hosting our event in the Basque Country – THE shining example of the economic value of wind. Bilbao is home to Iberdrola and Siemens Gamesa: two of the leading companies in wind energy. that region plays a key role in the wind supply chain.
The sector boosts employment in the country by creating a total of 39,000 jobs. In addition, the wind industry provides 0.5% of Spain's GDP. Wind energy generation covers 24% of Spain's electricity demand making it Spain's leading source of electricity. Spain is now embarking on the development of offshore wind. the government is set to launch Spain’s first auctions for offshore wind in the coming years.
They want to install up to 3GW by 2030 and become a technology leader for floating offshore wind. Bilbao and the Basque Country will play a leading role in this process.
The Bilbao event also features an extensive social programme, further building up your community. Are there any further event highlights that you would like to share with our readers?
Together with Vestas HUB Ocean and Microsoft, we will host a wind hackathon Hack the Climate 2024. We are inviting designers, developers, data scientists to work with the biggest names in the industry to create use cases from three huge data sets: Vestas’ Climate Library, HUB Ocean’s Data Platform and Microsoft’s Planetary Computer. This is a unique opportunity to create game-changing solutions.
We are also looking forward to hosting students, to get them introduced to the wind sector by meeting companies and industry experts. We are organising a special student programme with an emphasis on knowledge and networking.
We hope to see many of Inside Sustainability readers in Bilbao at the end of March! n
click to sections:
PACKAGING &
CONSTRUCTION
SERVICES & TECHNOLOGY
ENGINEERING & MANUFACTURING
An introduction to the homeware and food sectors, with news and facts, followed by company profiles.
The latest company and industry related developments from the homeware and food world
The National Bed Federation (NBF) has launched a new website which aims to signpost consumers to the options for mattress recycling in their local town or city.
The website has been developed in response to the results of a new survey undertaken by the NBF using Freedom of Information requests, which sought to establish how councils across the UK deal with the estimated 6.4 million mattresses that are disposed of through their services every year.
“Not only has our comprehensive research given a clearer picture of what’s happening to those unwanted mattresses across the UK handled by local authorities, but it has also enabled us to create the first-ever dedicated mattress disposal portal,” Tom Williams, Sustainability and Circular Economy Lead for the NBF, said.
Replies to the NBF survey were received from all 385 waste authorities across the UK and revealed significant variations. Wales emerged as the front-runner in terms of recycling rather than just sending mattresses to landfill or incineration. All councils
report they divert mattresses from landfill, with components sent for recycling in over 86% of council areas.
Methods of disposal also differed within councils, depending on whether the mattress travelled via a household waste recycling centre or a bulky collection service.
As mattresses are classed as ‘difficult waste’ within the recycling industry, a number of councils have partnered with specialist bulky waste collection companies which are working to improve re-use/recycling processes, with the aim of creating viable and affordable solutions for the ever-increasing market.
With the new, free-to-use portal, consumers can search for and see what their local authority is currently doing with the mattresses they receive at household waste collection sites or through door-todoor bulky waste collections. There are also links to the NBF’s consumer information website, alternative collection services available to consumers if their local council is not recycling, and advice on mattress care. n
Pak has announced a collaboration with Absolicon, a Swedish solar thermal company, to offer a standardised solution for industrial equipment powered by renewable thermal energy.
Absolicon has designed a scalable solar thermal module that can be integrated with current and new UHT lines and enables a range of decarbonisation options.
Tetra Pak’s UHT processing line for high temperature sterilisation of dairy products is the first solution to be offered together with a scalable solar thermal supply, with the potential to reduce fossil fuel usage by up to 40%. The first module is forecasted to be installed during 2024, before scaling to a worldwide market.
“At Tetra Pak, we are committed to enabling our customers to improve their environmental footprint through optimising their operations and equipment,” said Nicole Uvenbeck, Director Factory Sustainable Solutions & OEM Components, Tetra Pak. “We recently launched a new
business solution called Factory Sustainable Solutions, helping customers opt i mise energy, water and CIP on a factory level.
“Absolicon’s solar thermal solutions are a good fit with this new Tetra Pak offering, as well as supporting our wider Net Zero Roadmap, where we have committed to reducing our value chain emissions and scaling decarbonisation solutions for our suppliers, customers and own operations.”
“By implementing clean thermal supply to its equipment, Tetra Pak is once again proving its reputation as a pioneer,” added Joakim Byström, CEO, Absolicon. “The company has global access to the world’s food and beverage companies and can become a change driver for the sector’s transition from fossil fuels to renewable heat. We are delighted to be part of this collaboration with Tetra Pak and to launch the first equipment line powered by Absolicon solar thermal, as part of our mission to reduce the world’s carbon emissions.” n
Interesting and unusual homeware and food facts from around the world
Water efficient fixtures can cut water use by 30%.
From 2013 to the end of 2022, around 3.7 million energy efficiency measures were installed in 2.6 million properties across the UK, through various government support schemes.
Globally, researchers estimate that the production and incineration of plastic will have pumped more than 2.8 billion tonnes of greenhouse gases into the atmosphere by 2050.
About half of household waste is reusable, but only 17% is recycled or composted.
Every problem is a gift we would not grow without problems
“ “
– Anthony Robbins –
Residential energy accounts for roughly 20% of annual greenhouse gas emissions in the US.
According to the US Environmental Protection Agency, a full bathtub requires about 70 gallons of water, while taking a five-minute shower only uses 10 to 25 gallons.
British households create over 6 million tonnes of waste each year, the weight of around 260 large cruise ships.
In 2021, 81% of the textile flooring waste produced in the UK was diverted from landfill. In 2007, this figure was only 2%.
Germany, Austria and South Korea remain world-leaders when it comes to recycling household waste, recycling 60 – 70%.
Washing clothes at 30 degrees rather than higher temperatures will save around 40% of the energy used each year.
When it comes to flooring, for many, carpet is the favoured choice. Available in a range of colours, textures and pile thickness, carpet has a lot of advantages over its competition. One downfall, however, is its reputation for being hard to recycle. Experienced in all things carpet, Cormar Carpet Company has been working to change that. Managing Director Ian Ford explained more, in an exclusive interview with Inside Sustainability. Report by Imogen Ward.
Carpet, thanks to its multipolymer structure, is renowned for being difficult when it comes to recycling. Cormar Carpet Company is determined to change this, one polymer at a time.
“Carpet is constructed using a number o f different fibres, including polypropylene, which is actually a plastic,” Managing Director Ian Ford explained. “These then must be separated and processed for recycling, which is often seen as more trouble than it’s worth.
“Cormar Carpets manufactures all its non-wool carpets to be mono-polymer.
Using just polypropylene in the manufacture of our yarn and backing makes the end-of-life process much easier.”
Cormar Carpets was born in 1956 from the roots of its predecessor Greenwood & Coope, when the company transitioned from the production of felts to carpets. With its head office, carpet finishing line and northern distribution centre all located in the original premises in Brookhouse Mill, Lancashire, the company now has two additional sites: Holme Mill where the tufting process is completed, and a southern distribution centre in Hemel Hempstead.
Green improvement:
Cormar Carpets recycles all its store carpet samples once the businesses are finished with them. The company also returns all its packaging waste to the supplier, so it can be reprocessed.
Sustainability has been a priority for Cormar Carpets for many years, and, as a founding member of Carpet Recycling UK (the only membership association dedicated to helping the UK carpet sector improve its sustainability), Cormar Carpets has been working hard to ensure that the entire industry makes a difference.
“As an industry, we don’t want to be disadvantaged by our lack of sustainability,” Mr Ford explained. “That’s why it is so impor-
tant that we are at the forefront of the latest developments in carpet recycling. It would be remiss to sit on the back burner and wait for change to happen to us.”
As the government looks to introduce an extended producer responsibility scheme that will affect the carpet industry, Cormar Carpets is collaborating with Carpet Recycling UK to protect the industry from potential penalisation.
“EPR schemes tend to come with an element of tax, and we want to make sure t hat doesn’t have any detrimental impacts on the carpet industry,” Mr Ford continued; “especially when other types of flooring are also manufactured using plastic. It would be unfair if those in the carpet industry were to lose trade to other flooring that is just as unsustainable.”
Cormar Carpets is also working closely with Innovate Recycle UK (developer of the clean, green and unique mechanical extraction process dedicated to waste carpets), to keep its post-industrial carpet from entering landfill.
Having opened the UK’s first true carpet recycling facility in the summer of 2023, Innovate Recycle has been busy implementing its patented process to extract polypropylene and calcium carbonate from Cormar Carpets’ waste product. The extracted polypropylene is turned into chips, which can then be re-melted and re-extruded to create injection moulded parts for the automotive industry.
“Although the process is not refined enough to reprocess the chips into carpet, Innovate Recycle is producing excellent non-carpet products,” said Mr Ford. “This is because different coloured carpets are processed together, resulting in a dark grey polypropylene chip every time. Virgin polypropylene is always white, making it susceptible to the addition of colour.”
Keen to find more ways to put its waste carpet to good use, Cormar Carpets has been looking into other landfill alternatives. So far, its carpets have been shredded for equine arenas, burned by the waste from the energy sector and used in the cement manufacturing process.
The company also maintains open communication with its yarn – primary backing and secondary backing suppliers to ensure these materials are made using the same polymer.
“We work hard to guarantee our raw materials are of higher quality, to make sure the end-of-life process will be as simple and pain-free as possible,” Mr Ford said.
Cormar Carpets has long preferred the use of single polymer because it produces a higher quality textile. By choosing quality over cost, the company has further benefited from the recent progression of single-polymer carpet recycling.
Also on offer at Cormar Carpets is woolbased carpet, which accounts for 30% of its overall carpet production. This product can be created as a mixed blend with up to 50% polypropylene, or entirely from wool. Although the inclusion of a mixed blend makes it more difficult to recycle, the product features significantly less plastic than the alternative non-wool options.
With the future of carpet recycling looking up, Mr Ford believes greater consumer awareness is needed to really promote positive progression: “At the moment, the only way to discover a carpet’s make up is by scanning the fibres. This is a real labour intensive ( and unnecessarily timely) process. As an industry, we should be labelling our carpets and communicating to customers what the labelling means. By doing this, it will make the entire end- of-life process more efficient.”
Until then, there is currently 480,000 tonnes of post-domestic carpet being pulled up every year, which needs repurposing. Cormar Carpets hopes that there will be a solution for this soon: in the meantime, the company is currently developing another more sustainable product that is expected to hit the market before the end of this year.
“It is possible to recycle plastic bottles into fibre that can be used to manufacture
carpet,” Mr Ford explained. “Of course, it is still early days and cannot currently be recycled again, but we intend to incorporate this recycled content into a new carpet, effectively extending the life of the plastic bottles.
“We are really looking forward to what the future holds for the carpet industry; and the fact that it is actively taking onboard the message of sustainability and recycling as an industry is incredibly exciting.” n
BekaertDeslee is the undisputed global leader in mattress textiles. With a large portfolio of products that prioritise consumer comfort and sustainability, the company has taken some major steps to maintain this commitment. Sustainability Manager Charles Christiaens explained more, in an exclusive interview with Inside Sustainability. Report by Imogen Ward.
From textile rolls to finalised mattress covers, BekaertDeslee manufactures top quality products that enhance hygiene and sleeping comfort.
“We offer various textiles for the mattress industry, including woven and knitted fabrics,” said Sustainability Manager Charles Christiaens. “Depending on the needs and requirements of the customers, we can produce a variety of options that are often finished to enhance hygiene and consumer comfort. Some of our products even offer anti-bacterial treatments, moisture and temperature control, and odourising treatments.”
BekaertDeslee is an amalgamation of two distinct and innovative companies: Bekaert Textiles (established in 1892) and Deslee (founded in 1928). Over the years, both companies witnessed steady growth,
and in 2015 – after being acquired by Haniel Holding (a German equity business) – the two merged, and BekaertDeslee was born.
“Since that point, we have remained the undisputed global leader in mattress textiles,” Mr Christiaens explained. “We have representatives on every continent and in every major market.”
With an ambition for growth, the company has made several acquisitions over the years. Most recently, in 2022, BekaertDeslee acquired Maxime Knitting, a Canadian leader in the manufacture of knitted fabrics for mattresses, pillows and foundations. This investment placed BekaertDeslee in prime position to become the leading mattress fabric suppliers in North America.
In 2023, the company set its sights on expansion once again; entering into a joint venture with Indian-based textile
manufacturer CMC Textiles. This agreement had been years in the making and marked a new era for BekaertDeslee, in one of the largest markets for mattress manufacturing.
Keen to retain its market-leading position, BekaertDeslee has a dedicated Innovation & Design team that is constantly working
on new developments and projects. In line with this, the team has been using emerging technologies to test the recyclability of its waste polyester: successful, this will be used to create sustainable yarn.
“Our Innovation & Design Center represents the big know-how of our company,” said Mr Christiaens. “The team is constantly working on new developments and complex R&D projects, with a continuous focus on circularity and sustainability.
“Currently, we are collecting our textile post-production waste, and using the polyester fragments to test recyclability. We are working to produce a new polyester yarn from our own waste, and our tests have been successful so far. In time, this will enable us to cover part of our resource needs in-house.”
Determined to take this one step further, BekaertDeslee is also considering investigating the waste of its customers and the end consumers.
According to Mr Christiaens, eco-design is gaining momentum steadily within the market. In response to this, the company is combining the results of its recycling trials and waste processing to create smarter designs.
“By incorporating fairly simple interventions, we can often overcome some big issues for recycling companies,” Mr Christiaens added. “The successful marketing of these concepts will become paramount in the coming years.”
With innovation always on the minds of those at BekaertDeslee, the company produced SmartSleeve Circular, a revolutionary mattress protector. Combining
BekaertDeslee’s Cairfull, Purotex and Adaptive technologies, the product enhances sleep, adapts to changes in temperature and reduces exposure to inanimate allergens. Manufactured using Seaqual yarn, a sustainable textile created using plastic waste recovered from the ocean, SmartSleeve aligns perfectly with BekaertDeslee’s commitment to sustainability. The product even won Interzum’s Best of the Best 2023 Award.
BekaertDeslee’s Innovation & Design team has also developed an innovative solution that seeks to provide customers with transparency regarding the circularity of this popular product. After several years of dedicated development, a digital
product passport is being piloted on SmartSleeve in various markets.
“We realised that the digital product passport is indispensable in a circular economy, and offers a lot of benefits for the recycling and end-of-life management of our products,” Mr Christiaens continued. “During the development of this, we spoke extensively with our stakeholders to decipher what information the passport should contain, and we are now trialling it through one of our subsidiaries in preparation of EU legislation.”
All of BekaertDeslee’s suppliers, partners and stakeholders are an essential element of its success – each one adhering to the company’s strict quality requirements.
“Quality and sustainability come as a package deal for us, because a decent product cannot be made in a bad environment,” said Mr Christiaens.
BekaertDeslee is able to ensure further product circularity from its initial product designs. For this reason, the company designs all its mattress covers to be easy
to disassemble at end of life. This decreases the risk of its products being sent to landfill and increases likelihood of recycling by the end user.
Thanks to a wave of high-quality competition, BekaertDeslee is always motivated to improve its quality and service. The company is able to meet the complex needs of the global market, whilst being actively challenged by new and exciting requests from its customers.
Not one to stand still, BekaertDeslee is now in search of new opportunities to accommodate its continued ambitions for growth:
“We are always targeting ambitious growth in all of our markets,” said Mr Christiaens. “We intend to accomplish this whilst continuing to offer the very best quality of service and retaining our leading market position; not only in size, but also in offering. If anything, we aim to enhance our position even further.”
When it comes to its products, BekaertDeslee always makes sure to do things the right way. It is this commitment that makes Mr Christiaens proud to work for the company: “I love knowing that we are contributing to society in a meaningful way. For me, the bigger picture is quite important; and working for a company that has integrity and is filled with fun, optimistic and committed colleagues certainly helps.” n
UK textile manufacturer Camira’s products are literally on the move. Each day, untold numbers of people interact with Camira’s textiles in locations ranging from mass transit systems such as buses and trains, to offices, hotels and educational establishments. Director of Marketing Ian Burn met with Richard Hagan to discuss how Camira is continuing its decades-long tradition for innovation, with several exciting new developments in its robust sustainability programme.
Each year, the textile sector is estimated to generate 92 million tonnes of waste, with less than 1% of all textiles being recycled into new products. Camira has set out on a journey to lead the industry into a new era of sustainability.
One of the ways in which Camira aims to achieve this is through its partnership with iinouiio. Founded by Dr John Parkinson, the name ‘iinouiio’ comes from the phrase ‘it is never over until it is over’. iinouiio specialises in textile reprocessing: converting high value raw materials from textile manufacturing waste, pre-loved wool and cashmere products, back into fibre which can then be re-spun into a yarn to make new fabric.
Camira acquired a majority shareholding in iinouiio in 2022 out of a desire to expand Camira’s capacity in textile circularity; using its own waste inputs to recycle, re-spin, reweave and breathe new life into discarded textiles.
“Our biggest challenge is transportation yarn waste, for which we use an 85 per cent wool, 15 per cent nylon mix,” said Ian Burn, Director of Marketing “We have since developed a fabric made from recycled transportation yarn waste. Named ‘Revolution’, we introduced the fabric at the Stockholm Furniture Fair in Sweden in February 2022. Revolution contains 31 per cent recycled material, consisting of 26 per cent recycled wool and 5 per cent recycled nylon from transport yarn. It was a successful proof of concept to see what we could do with our own waste.”
Camira’s partnership with iinouiio, however, is only the latest effort in the company’s decades-long commitment to sustainability.
Camira was originally founded in 1974 by David Hill as Camborne Fabrics in Huddersfield, West Yorkshire. Mr Hill had identified an opportunity to supply fabrics to the office furniture market, which, thanks to his relationship with local weavers, he was able to supply faster than the industry’s existing supply chains – and without the limitation of minimum order quantities.
Supplying his fabrics to customers across Lancashire out of the back of his car, Mr Hill’s ability to quickly supply customers ensured that his fledgling business soon flourished.
By the late 1980s, Camborne Fabrics had its own manufacturing facility and had begun exporting its wares
to customers worldwide, gaining market share not only in Europe but also in the Middle East, the Far East, North America and Australasia.
A number of buyouts and acquisitions followed, until in 2006, Camira was established. During the foregoing period, when the company was part of the global Interface flooring organisation, Camira developed substantial expertise in producing environmental fabrics. Consequently, by the time Camira was established, textile ecology had become part of the company’s core business philosophy.
Today, Camira is an illustrious textile designer and manufacturer operating in two broad market segments; specifically
commercial interiors (offices, hotels and education) and mass transit (trains and b uses). Camira is able to design and man ufacture various kinds of weaving and prints to furnish those kinds of interiors, all with specifications according to the customer’s precise needs.
“We are an environmental textile manufacturer seeking to be the natural choice for textile solutions globally,” said Mr Burn. “We bring colour, design, texture, comfort, safety and acoustic performance into all kinds of interiors.”
From its headquarters in Mirfield, West Yorkshire, Camira manages a substantial network of manufacturing sites across
the UK and abroad. Its head office hosts a centre for design, development and marketing, as well as support functions such as customer services, human resources and finance.
Altogether, the company employs 650 people spanning its headquarters and six manufacturing sites worldwide. A particular highlight in its portfolio is the large Huddersfield location which boasts over 100 looms, textile finishing, digital printing and a technical lab, as well as warehousing and distribution.
In addition to its large UK and European operations, Camira has a facility located in Grand Rapids, Michigan in the USA. As North America’s centre for office furniture manufacturing, it is strategically located close to the company’s key customers. Finally, the company also operates warehousing in Melbourne and in Shanghai.
It comes as no surprise that in 2008, in collaboration with a university in Leicestershire and other partners, Camira introduced a brand-new textile, Sting, made from wool and harvested nettles, grown on UK farmland. “Our competence in working with this type of material came about from a 1998 project called STING - Sustainable Technology in Nettle Growing,” explained Mr Burn.
“Progressing from nettles, we began exploring other types of plant-based materials with the same characteristics, including moving to grow hemp from cannabis plants with low THC properties. This culminated in us introducing a fabric made from wool and hemp.”
In addition to the sustainability benefits involved, wool blend fabrics made from plant fibres demonstrate inherent flame retardancy, making Camira’s bestselling wool-based fabrics Hemp, Main Line Flax and Main Line Twist especially popular in the commercial interiors market.
More recently, in 2020 Camira introduced Oceanic, followed by Quest; recycled polyester fabrics made from ocean waste plastic in partnership with the SEAQUAL INITIATIVE. The fabric’s yarn is created using plastic bottles taken from the land and the sea, highlighting the issue
of marine plastic pollution while supporting clean-up projects in the Mediterranean, the River Nile and the Caribbean.
In celebration of the company’s 50th anniversary in 2024, Camira will launch its next recycled wool fabric which will boast a further increased level of recycled content. Several other exciting product launches and events are planned to take place throughout 2024 as well, and readers are invited to follow the company on social media for more details. n
Each day, millions of people go to sleep on mattresses featuring microcoils manufactured by Spinks, one of the world’s most significant producers of pocketed microcoils for the bedding and furniture industries. Now, thanks to its uniquely bold sustainability vision, Spinks has developed several industry-leading innovations that continue to drive a greener path-not only for itself but for the industry as well. Managing Director Darren Marcangelo sprung into a discussion with Richard Hagan.
Spinks specialises in manufacturing unique low-height microcoils –essentially miniature pocket springs – for customers all over the world, the vast majority of which (95%) are mattress manufacturers, with the balance going to furniture manufacturers.
Thanks to its ability to compress and vacuum pack its products, Spinks costeffectively ships products to customers across the UK and Europe and as far afield as Australia and China.
Spinks’ microcoils act primarily as a comfort layer in mattress and furniture
construction. The company pioneered the microcoil concept in the early 2000s for use in its own products, before deciding to sell it to other mattress manufacturers. Its 2019 launch of Flexecore was a major milestone in this journey. Offering a full-height pocket spring, Flexecore is differentiated by its sustainably glued construction which contributed to its almost overnight success in the Australian and US markets. This sustainable glue technology is a major differentiator for Spinks microcoils and ensures that its mattresses can be fully recycled.
Spinks is a member of the larger Harrison Spinks Group; a mattress manufacturer with a history stretching back to 1840. Currently in its fifth generation of family ownership by the Spinks family, Harrison Spinks employs over
600 people and sells its range of beds under the Harrison Spinks brand as well as white-label mattresses for retailers including John Lewis and Dreams.
Of its 600+ staff, 100 are employed at Spinks across five sites, comprising two factories, its wire-drawing facility, an R&D facility and the company’s farm.
The Harrison Spinks Group is focused on sustainability. Consequently, each new mattress made by Harrison Spinks is foam-free, glue-free and FR chemical treatment-free.
Sustainability is similarly core to Spinks’ operation, and it starts in the design office. “We design every product with sustainability in mind,” said Managing Director Darren Marcangelo. “That process ensures
that the raw materials we’re using, all the way through to the end product, meet our sustainability credentials. But it also ensures that customers can recycle the product at the end of its life. That’s always at the forefront of the Spinks business model.”
It’s been like that since day one. In 2009 – the year that Spinks was formed: – its owner and founder, Simon Spinks, simultaneously bought a 300-acre farm. His vision was to grow natural fibres in the UK for use in mattresses.
“This was at a time in which the whole mattress industry was going the petrochemical
memory foam route,” Mr Marcangelo continued. “Back then, Simon already wanted to go the natural route, which demonstrates that we’ve been a sustainability thought leader in the industry since then.”
The farm produces natural fibres, including hemp and flax, as well as wool from sheep reared on the farm, both for sale to the industry and for use in its own mattresses. The farm is a key part of the Harrison Spinks Group’s commitment to sustainable bed making.
The group is also a member of the UN Global Compact and has committed itself to Science Based Targets, a global initiative to help businesses set out clear, realistic climate actions. By 2024, Harrison Spinks will send zero waste to either landfill or incineration, and by 2033 it plans to cut its carbon emissions by 95%. Additionally, the group has an advanced mattress circularity strategy, in terms of which it is working with its partners to ensure that Harrison Spinks mattresses never need to go to landfill, by repurposing all of the useful materials in every
used mattress and limiting its consumption of virgin materials.
Spinks’ efforts to address the circularity of its products were recognised in 2022 when its products were awarded Cradle to Cradle certification, with Spinks being the only pocket springs manufacturer in the world to receive this stringent certification.
Steel wire remains a key part of Spinks’ microcoils. Its main wiredrawing facility is in Scunthorpe, where it processes wire manufactured on-site by British Steel. While the production of steel has some remaining climate challenges, Mr Marcangelo highlighted how the company and British Steel are actively working to address those issues: “Steel is our biggest challenge because it makes up the biggest part of a coil and its manufacturing process is quite carbon intensive.
“Currently, all of the steel we buy is predominantly made in a blast furnace, which isn’t the most sustainable route. Over the next two years, however, British Steel will move from blast furnaces to electric arc furnaces, which require less energy and can use recycled steel that melts at a lower temperature.”
The new furnaces present a fresh manufacturing challenge for Spinks that the company is actively innovating to meet.
“We draw the finest wire in the industry because the resulting coils behave very softly and comfortably,” Mr Marcangelo explained. “This fine wire must be of a very high quality as we can have up to 5,000 coils in a single king-size mattress sheet, but if we use too much recycled steel content, then we find that the wire doesn’t meet our quality standards. So, the challenge we’re working to solve now
is how to sustainably incorporate enough high-quality raw material as possible.”
This kind of innovation is a significant part of Spinks’ DNA. In 2023, it was awarded two King’s Awards for Enterprise in Innovation and International Trade, bringing to seven the company’s total number of King’s and Queen's awards that it has won over the years.
Concluding, Mr Marcangelo commented: “Innovation is something that we pride ourselves on. I’m confident that we’ll find the solution to the wire challenge very soon.”n
What More UK is on a mission to become Europe’s biggest manufacturer of metal bakeware and cookware, plus plastic housewares. To make this dream a reality, the company has invested in itself and its people. Director Tony Grimshaw explained more, in an exclusive interview with Inside Sustainability. Report by Imogen Ward.
Wh at More UK has experienced a wealth of success in the UK market. Perhaps known most notably for its incredibly popular plastic storage boxes, Wham, the company is also a major player in the metal bakeware and cookware sectors. Holding the title as the third biggest manufacturer of plastic housewares in Europe, the company is going for gold. To achieve first place status, What More UK is on a journey of growth, business development and education.
“The demand for our products grows as quickly as our commitment,”Director Tony Grimshaw explained. “Because of this, we have an ongoing dedication to investment. We continue to invest in new products, our infrastructure, our customer and supplier relationships, and our people.”
In line with What More’s ambitions for growth, the company has made several key acquisitions in the last two years.
In a bid to have total control of the entire value chain, What More initially acquired Canteen Smithy, a mould manufacturer, in 2022.
“After starting our bakeware and cookware division in 2016, it became apparent that we needed to produce a whole new catalogue of products,” said Mr Grimshaw. “To allow for this, £1 million was invested in an onsite toolroom. Our product designers went berserk and soon outstripped the toolroom’s ability to manufacture the required moulds. So, when Canteen Smithy came up for sale, we purchased it without a second thought.”
Following the success of this acquisition, What More went on to purchase metal solutions manufacturer, Firsteel, i n 2023. According to Mr Grimshaw, this was a natural decision due to the company’s reputation as the best coil
coater of rolled steel and other metals. As one of only two businesses in the UK and five in Europe with this capability, it is no wonder that What More made the leap to invest.
“It made sense to complete the supply chain with the purchase of Firsteel,” Mr Grimshaw continued. “The acquisition of these two companies has afforded us complete control from the drawing board to the oven. We can now proudly say that not only are What More’s products made in Britain, but all our raw materials are too.”
With the company stretching vertically along the value chain, a decision was made to expand its manufacturing and distribution facility in East Lancashire, UK.
“We operate out of 500,000 square feet of real estate,” said Mr Grimshaw. “The surrounding land is currently being cleared, and foundations are being laid to increase this by another 100,000 square feet.”
All of What More’s growth has been accomplished strategically and responsibly with its environmental impact accounted for at every stage. This has been a consideration since the company first opened its doors 24 years ago.
“We have always recycled our owngenerated plastic waste,” Mr Grimshaw explained. “We designed a number of black item products that specifically enabled us to do this such as dustbins, seed trays and builders’ buckets. Over time, the demand for these products increased and very soon surpassed the waste levels that we produced internally. This required us to find another source for the waste, and with the increasing demand for recycling, our recycled ranges of storage products were born.”
The company’s RECYCLE range of storage solutions is made from recycled industrial waste and was launched in 2019, alongside What More’s other sustainably focused line, Upcycle, which
is manufactured from recycled single-use plastic waste.
“Both ranges received recognition at European level, they came in the top three at the European Recycling Industry Awards, and nationally in the UK Recycling Industry Awards,” Mr Grimshaw said.
In line with this commitment, What More has been spending a lot of time working with schools to encourage recycling across the board.
“It’s not just about plastic, recycling of all materials needs to be actively encouraged,” Mr Grimshaw explained. “We spend a lot of time opening our state-ofthe-art facility to schools and colleges to
spread this message. It also gives us the opportunity to show the difference between our products and single-use plastic.
“After all, single use plastic is drastic; What More plastic is fantastic.”
What More is always keen to work with students to help develop their passion for the industry. Eight years ago, the company took the next step and established its own apprenticeship scheme.
“We learnt the true value of apprentices when we first established our scheme all those years ago,” said Mr Grimshaw. “We now have a rolling cadre of apprentices
that join the workforce after their training . They take with them the knowledge gained from What More’s engineers and the valuable skills they pick up during their time at college. Each one of these apprentices has contributed and enabled our unprecedented growth. So, when we took over Firsteel, introducing a similar scheme was a no-brainer.”
Everyone at Firsteel has been very receptive to the newly initiated apprenticeship scheme. With a high staff retention rate and an average length of service of more than 30 years, What More felt the need to retain the valuable knowledge of the current workforce before they retired and took it with them. Currently, there are three apprentices working on their qualifications with Firsteel, with vacancies for a further two.
“What More is the UK brand and market leader,” said Mr Grimshaw. “We are continually developing our products, our relationships with customers and partners, but most importantly our staff. Without our staff, we are nothing. They help us stand out in the industry, providing the world with quality products made in Great Britain. Products that –through innovation, advanced manufac -
turing techniques and a workforce that cares – are world leading and affordable.”
Of course, staff are not the only people that What More relies upon when it comes to success. According to Mr Grimshaw, the company greatly depends on the r eliability of its suppliers: “Our ongoing aim is to work in harmony with our suppliers. Just like our staff, they are an imperative ingredient in our success. We depend on their innovation, ingenuity and ability to bring new ideas to the market.”
As What More looks to the future, it intends to explore more growth opportunities, which includes the international market. The company has already exported to 75 countries across the world and looks set to continue.
“Exports are always in our plan,” Mr Grimshaw concluded. “From design and product development to services, 18 per cent of our turnover comes from this market. So, we would love to develop this area further, whilst continuing to grow our presence in the UK market.
“It has been a pleasure to watch the entire company progress from its humbl e beginnings, with the backing of an amazing group of employees. Our mission to become number one is achievable because of this brilliant team.” n
Ingredient Solutions Ltd was established in 2000 to provide innovative cheese ingredients to the food industry. It is now a premier cheese supplier to large food manufacturers of ready meals, snack foods and foodservice companies in Ireland, the UK and across Europe. Hannah Barnett spoke to Sales Director Gary Davies, Technical Manager Suma Lakshmana and Logistics Supervisor Karina Souza to learn more.
One of the secrets to Ingredient Solutions success may be that it never stands still.
“We launch around five new product codes a month,” said Gary Davies, Sales Director. “These could be a new blend, pack, label, language, or something bespoke to deliver on a specific brief: melt, colour, flavour, nutritional requirement, format or price.
“We also send out over 100 samples a month to new and existing customers across the globe. We try to utilise current products in the range, but are flexible in terms of making something exactly as the customer requires it.”
The Irish company is a BRCGS-accredited, one-stop-shop for food producers looking for a quality cheese supplier. Since starting small, with just four employees working from one room at the turn of the millennium, Ingredient Solutions now exports cheese to over 30 countries and works with more than 200 customers.
The company has spent the last two and a half decades signing up several prestigious customers, including one that generated €8 million in turnover last year alone. Ingredient Solutions now has 85
employees, a turnover above €70 million and a production capacity of 14,000 tonnes.
In May 2022, Ingredient Solutions was acquired by Rupp, the largest familyowned company in the Austrian dairy industry which was founded in 1908. Rupp produces processed and natural specialty cheeses under the Rupp and Alma brands at four locations in Europe and Asia.
The following year was a successful one for Ingredients Solutions as it won 40 new customers. Alongside the acquisition, this accomplishment is also part in thanks to the efficiency and knowledge of the sales and new product development (NPD) team, working to streamline the NPD process, according to Mr Davies.
“Working as partners with our customers is key,” he said. “This means we offer a quick rate of response, as well as providing samples and interactive feedback, and establish a clear objective at the start of the process.”
Ingredient Solutions therefore remains at the cutting edge, and as a result, has built a cross-functional departmental team to drive AI and its potential.
Logistics Supervisor Karina Souza is leading the initiative and will oversee forward-thinking training budgeted for later this year.
Indeed, the company invests heavily in staff training and has managed to use the turbulence of the last few years to its advantage. “Covid gave us the opportunity to upskill the teams internally, with
cross-functional training across each sector,” said Mr Davies. “This gave my sales team the empathy, confidence and expertise to deliver not only what the customer requires, but what we, as a business, are experts at.”
Ingredient Solutions is committed to acting responsibly by integrating social and environmental concerns into business operations.
“Sustainability goes beyond regulatory compliance,” Suma Lakshmana, Technical Manager, explained. “We focus on economic, social and environmental impacts, as well as promoting waste reduction and cutting down on the use of packaging with the promotion of the circular economy.”
As a result, Ingredient Solutions is in the top 1% of companies rated by EcoVadis in the manufacture of dairy products industry. The company is also a verified member of the Origin Green sustainability programme, which covers the period 2023–2027.
Origin Green Sustainability Goals:
The seven pillars:
1. Raw materials and suppliers.
2. Product packaging.
3. Energy and emissions.
4. Reduce waste.
5. Save water.
6. Promote product health and nutrition.
7. Prioritise employee wellbeing.
“We have developed a total of nine goals within seven pillars, meeting Origin Green’s minimum Tier 2 member requirements,” said Ms Souza. “All our targets are regarded as SMART, and these seven pillars form the backbone of all that we do.”
The pillars include sustainable sourcing, which means a target of increasing the quantity of sustainably certified raw material purchases from 40% for the base year of 2022 up to 64% by 2027. There is also a commitment to reduce Scope 1 and 2 emissions by 30% and reduce the intensity of Scope 3 emissions by 50% by 2027.
Waste reduction is another key pillar, deeply anchored in Ingredient Solutions’ business strategy. The target is to reduce overall waste by 10.8%, measured in tonnes, by 2027.
“It is one of our biggest challenges, but we do have a series of initiatives to reduce waste in our process,” said Ms Lakshmana. “We are aiming to recycle our general discards as much as possible, by promoting the collection of food waste in the factory process for bio-generation.”
Beyond the immediate environmental impact, the company is similarly concerned with staff wellbeing: “Our goal is for our employees to be happier and healthier: and by investing in professional growth and keeping them motivated, we can increase productivity,” said Ms Lakshmana. “We want to create a positive working environment where individuals and organisations can thrive.”
Like any successful business, strong working relationships throughout the supply chain are vital. Indeed, many of Ingredient Solutions raw material and packaging suppliers have been with the company since its humble beginnings, so it is no surprise that these relationships are both flexible and trustworthy.
The company is also keen to maintain environmental principles in these partnerships, as using high-quality and sustainable suppliers can have significant benefits for the business. These benefits range from cost savings and improved reputation to longterm environmental and social impacts.
“We have approximately 20 top suppliers that all have sustainability targets and goals to reduce the impact of factors affecting the environment,” Mr Davies explained. “Ingredient Solutions follows a strict code of conduct that has also been sent to all suppliers to ensure we are all working to the same standard.”
Ingredient Solutions is a dynamic and exciting business to be part of, made all the more so by investment from the large r global group. The company intends to open a new state-of-the-art factory in 2025, thereby gaining a greater scope than ever.
“Every day is different and there is a whole new horizon out there now we are part of Rupp,” Mr Davies reflected. “I thrive on empowering the team to deliver; steering the culture of the business, and ensuring we are aligned in our mission.”
For Ms Lakshmana, the opportunities for personal growth are what drives her most of all: “One of my passions is selfimprovement and helping others grow, both personally and professionally. I knew best practices from my previous experience, so when I came in, I aligned with all the key members of the company and drew a formal road map. Transforming this into a reality is a large undertaking and I feel a deep sense of satisfaction knowing that I have made a difference.”
“The company is always growing,” Ms Souza concluded, “which can be challenging. Daily challenges require quick responses and actions, and this makes me increasingly exceed my potential to deal with problems, thereby becoming a better professional every day.” n
C.H. Guenther & Son is a leading food manufacturer that has delivered highquality products and ‘just baked from scratch’ flavours for over 170 years. With manufacturing locations worldwide – including Europe’s most advanced bakery – it is making significant strides in sustainability through energy and waste reduction, and progressive farming practices. Andy Probert discovered more in discussion with Rosalinda Sanquiche, Global Senior Manager, Sustainability & Communications, and Jean-Charles Philippon, Managing Director, Europe.
IN1851, C.H. Guenther & Son (CHG) began life as a humble flour mill near Fredericksburg, Texas. Its entrepreneurial visionary of the same name switched operations to neighbouring San Antonio, and CHG has been a powerhouse of production ever since.
Now employing 4,100 people across 29 manufacturing facilities in the U.S., Canada, and Western Europe, the company is a leading supplier of value-added grain-based and frozen food products for food service clients and select consumer markets.
CHG’s current portfolio focuses on ten areas ranging from artisan bread, buns, and English muffins to baking, griddle, batter, and breading mixes, biscuits, doughs, gravies, and dips. Its much- loved
retail brands, such as Pioneer, White Wings, Sunbird, and Cuisine Adventures, have been present at family meals for generations.
While CHG which is owned by Pritzker Private Capital is deeply committed to advancing food quality across its diverse operations, its dedication to sustainability is deeply embedded within its DNA.
These principles are best demonstrated at its latest high-tech operation at Coventry, in the UK. The £38M facility, which employs 90 people, can create 72,000 buns an hour or 1.1 million buns a day - one of the fastest bun production lines in Europe. The 106,000 sqft plant, designed and
built from scratch, is C. H. Guenther Bakeries in Europe’s third UK site.. Significantly, the facility is fully supported by McDonald’s as it will create fresh, quality buns exclu sively for the fastfood giant’s restaurants.
Jean-Charles Philippon, CHG’s Managing Director, Europe, said the facility underscored the company’s longstanding commitment to McDonald’s, which it has been supplying with fresh, quality buns since 2005.
Sited ideally in the West Midlands between major UK cities, the facility has been praised by senior McDonald’s management to help better serve their customers and is an excellent example of the work it is achieving with CHG.
The site is designed to BREEAM ‘Excellent’ specification and is targeting an EPC ‘A’ rating. Supporting CHG’s environmental commitments to reduce electricity, natural gas, and water intensity, and a zero waste
to landfill target, the building has installed solar PV, electric vehicle charging infrastructure, and a water recycling system.
“CHG is committed to high quality products, while sustainability and flexibility are key considerations with this latest facility,” said Mr Philippon. “We believe the development will become a key asset in C.H. Guenther Bakeries’ European growth plan.
“One of our core values is to offer bespoke production that exceeds customers’ expectations. Our customers are considered valued partners as we often collaborate with them to ensure we’re fully invested in their specific operations. Ensuring we never compromise on quality means their end users get the best products.”
Rosalinda Sanquiche, Global Senior Manager, Sustainability & Communications said CHG, backed by its parent company, is continuing to make significant strides in
sustainability activities on all its sites. This is through energy and waste reduction, advanced farming practices, and increased use of sustainable and recyclable sources for its product ingredients and packaging.
The company produced its first environmental, social, and governance report in 2022 and highlighted the many initiatives it is achieving, which are being shared with stakeholders, suppliers, and customers.
“Sustainability has become a firm focus for us. We are one of the few bakers in the industry to tackle Scope 1 and 2 carbon emissions, and we are now looking at Scope 3,” said Ms Sanquiche. “We began this initiative with our German plant, and it is now being rolled out across the company’s footprint.”
The report highlights a variety of sustainability measures undertaken. For
e ach metric tonne of product CHG creates, it is working to reduce the usage of electricity and natural gas, and waste generated to help lower its carbon footprint.
CHG supports farming practices and water efficient technologies that protect watersheds in communities at drought risk. Its facilities also meet all environmental compliance requirements, ensuring water released into community systems is contaminant free.
Most of the organic waste CHG plants produce is diverted from landfill and converted to animal feed. CHG also diverts waste through upcycling, turning organic materials into new product. Working towards zero waste to landfill has already been achieved at eight facilities.
A greater focus has also been placed on products made from sustainable ingredients, according to Ms Sanquiche:
“CHG requires all vendors to adhere to a Supplier Code of Conduct that tracks where ingredients are grown and harvested.”
CHG is also working closely with partners to develop packaging that is 100% reusable, recyclable, or industrially compostable by 2025 for retail markets.
“Our effort remains to reduce electricity, natural gas, and water intensity from
a 2022 baseline with SBTi-aligned goals and to target zero waste to landfill,” she explained. The corporate headquarters in San Antonio, Texas, is a LEED Silver building, using solar panels and an innovative HVAC system.
CHG’s R&D and culinary team is innovating with clients to provide options for healthy offerings: high protein, low sodium, whole grains, clean label, and more. It is also seeking out sustainably sourced or harvested ingredients, including RSPO certified palm oil.
“Having customers that share our beliefs and values, and backed by a parent company that is prepared to invest heavily, demonstrates how serious we
are in driving our sustainability goals further,” Mr Philippon agreed.
The company is also fully aligned with helping farmers look at new ways of innovating in growing wheat, maximizing yield while being mindful of best agricultural practices.
Both interviewees paid tribute to CHG’s global workforce in their commitment to maintaining best practices in performance, many geared towards the company’s sustainable goals.
The company is bestowed with many experienced workers who have served more than five, ten, and 20 years. “They are at the heart of what we do; they bring forward ideas for change and how we can evolve into a better company,” said Ms Sanquiche. “We ensure that the performance of the company and our sustainable goals are always interrelated.”
Additionally, CHG’s efforts to increase diversity and educate its workforce about diversity, equity, and inclusion (DEI) culminated in the company being named by Newsweek as one of America’s Greatest Workplaces for Diversity for 2023. CHG began its DEI journey in 2021 with a threeyear strategy to align diversity goals with its corporate business plan. The organization has spent the last two years implementing various programs and initiatives to help create a more diverse and inclusive corporate culture.
In conclusion, Mr Philippon said: “We never lose sight of what drives the consumer and how we work collaboratively with our partners to deliver on those trends and perceptions. CHG will never compromise on quality and will always strive for excellence. Those principles will always underpin our approach and growth.” n
Ugo Foods Group is a fourth-generation family business which prides itself on innovation and never compromising on quality. Hannah Barnett spoke to Charlie Ugo, Group Operations Director, and his brother Freddie, Head of Corporate Social Responsibility, to learn what makes this forward-thinking family firm tick.
There are businesses run by families and then there are family businesses.
Ugo Foods Group is the latter. A large measure of its enduring success is down to the company’s strong commitment to moral values and innovation, as passed down from its original founder.
“It’s not just about producing highquality food, we want to make a better impact on the planet,” said Head of Corporate Social Responsibility, Freddie Ugo. “That’s our philosophy. A lot of that comes from being a family business. It started with our great-grandad. He passed it down to our grandad, Leo, who passed it down to our father, Paul, who still works here as Chairman. And then there’s me and Charlie.”
Ugo Foods Group is infused with the values and vision of its founder, Luigi Ugo He emigrated to the UK from Italy in the
early 1920’s and began selling paper bags of homemade pasta, not a wellknown product in the country at the time.
In 1929, Luigi opened his first delicatessen on Gerrard Street, Soho, and began making fresh pasta in the window of his shop. Another man, who was trying – and failing –to source noodles for a Chinese restaurant, spotted this activity.
“Nobody was making noodles in the UK at the time,” Group Operations Director Charlie Ugo explained. “This man eventually ended up teaching my great grandfather how to make noodles and opened his Chinese restaurant next door. Gerrard Street is now the centre of Chinatown. So, we’re quite proud of our part in that history.”
As a result, Ugo Foods Group spent much o f the interwar period producing Chinese cuisine. There was a fundamental shift in focus following the Second World War, and the company began manufacturing dried and fresh pasta once more, supplying
high-quality shops like Selfridges, John Lewis and Harrods. Innovation and new cuisines fit for the UK palate followed in abundance.
“We brought gnocchi to the UK and developed the first gnocchi machine using fresh potatoes rather than dried,” said Charlie Ugo. “We also produced organic and wholewheat pasta for the first time in the UK in the ‘60s. We even created a gluten free solution in the early ‘90s. A lot of the period from the ‘60s onwards was about innovation and how we could create a bespoke, unique product offering for the UK. We started experimenting with lots of different fillings and flavour profiles.”
Ugo Foods Group now produces 500 million parcels of pasta a year from its HQ in Hertfordshire, accumulating a turnover of £25 million.
The company continues to innovate and its Cromer Crab and Crayfish raviolo
As seen on TV
Ugo Foods Group recently appeared on BBC TWO’s Inside the Factory. In the episode, Charlie Ugo showed Gregg Wallace an innovative machinery process that makes the company’s popular Cromer Crab and Crayfish raviolo so delicious, while Cherry Healey took a trip to Norfolk to meet the ingredients suppliers.
recently won a Gold Q Award; the ultimate accolade, bestowed on products which are truly outstanding.
Ugo Foods Group remains committed to using the highest quality ingredients in innovative ways, like a semolina-blend flour base for pasta dough.
“The semolina has a large grain size, is very yellow and high in protein, which allows us to create quite a unique dough,” explained Charlie Ugo. “This means we can reduce our egg content versus competitors, lowering our carbon footprint, while still having the texture and flavour expected.”
As a conscientious company run on family values, it is no surprise that Ugo Foods Group is keen to minimise both its environmental and social impact.
“Something that sets us apart is that we have a lot of charitable commitments that actually make a direct impact,” said Freddie Ugo. “We don’t just give a pot of money and say: ‘go ahead and use it,’ we like to be involved.”
This includes a partnership with the European Nature Trust, helping to preserve wildlife and ecosystems in Italy. A local hospice, Keech, for terminally ill
children, is supported with fundraising initiatives and by inviting residents to the factory to learn pasta making.
On the environmental side, Ugo Foods Group has almost eliminated scope 1 and 2 emissions by moving to renewable energy sources and replacing refrigerants. The company has also developed a semi-bespoke system for its triple-layered boiler to significantly increase efficiency and reuse waste heat as part of a reclamation system.
“We’re directly involved in the sustainable measures we go for,” Freddie Ugo explained. “We’re doing our due diligence, but we actually care about it. And that also comes across in the ingredients that we buy. There’s been multiple occasions where we’ve changed supplier because we realised there was either an ethical or an environmental issue with them .”
The company works closely with suppliers; sourcing ingredients as locally as possible and prioritising partners that are focused on carbon
reduction. In particular, Ugo Foods Group highlighted ethical flour millers, Wildfarmed.
Both Ugo brothers are particularly passionate about the eradication of waste where possible. As a result, company wastage has significantly reduced in recent years; but it cannot be entirely avoided due to vital quality control processes. Of course, Ugo Foods Group has multiple innovative solutions to mitigate this.
One partnership with a notable celebritychef-turned-farmer, involves feeding pigs uncontaminated scraps, thereby reducing food waste and the emissions usually derived from animal feed. Though successful it is not a consistently reliable solution to excess waste, due to variation in demand.
The next step involved even more innovation, when the novel idea of brewing beer from pasta was raised.
“We didn’t know whether it was even possible,” said Charlie Ugo. “We did
some early-stage trials with pots and pans in the kitchen to see if we could create fermentable sugars. This took maybe a year and a half to advance to a point where we had a good quality product. We have since patented that process throughout Europe and the UK, and we’ve launched applications globally.”
And with that, Beyond Belief Brewing Co. was born. The process involves using surplus fresh pasta as a base malt replacement, saving 2/3 of a litre of water and over 110 grams of CO 2 for every pint.
After nearly a century of innovation, Ugo Foods Group is not the kind of business to rest on its laurels. The company recently introduced fully recyclable packaging, investing hundreds of thousands into
converting its machines as a response to feedback from customers.
And there is plenty more to be done, according to Freddie Ugo: “We’re in the process of getting B Corp status. We’re signing up to the Science Based Targets Initiative to set a verifiable carbon emission reduction goal. We’re working with various consultancies to do lifecycle assessments of different products. Carbon accounting is a very collaborative thing, and we are trying to make it more accessible to smaller producers.”
This scope of innovation, as always, extends to the products themselves too.
“We are trying to do what we have always done: bring new things to the UK, just like our great-grandfather did,” Charlie Ugo concluded. “So, of course there is plenty coming up in the new product development pipeline.” n
click to sections:
HOMEWARE
CONSTRUCTION
SERVICES & TECHNOLOGY
ENGINEERING & MANUFACTURING
one planet – one chance – one voice
An introduction to the paper and packaging sectors, with innovations and a special report exploring recycling, followed by company profiles.
SereneP is the epitome of eco-friendly power generation, offering 80% CO2 emissions reduction with biomethanol and up to 100% reduction in CO2 emissions with eFuel use when compared to traditional fossil fuel power sources.
NOMOQ, the pioneer and leading provider of digitally printed cans in Europe, has announced the launch of blank (undecorated) aluminium beverage cans on its website, expanding its product offering beyond the core business of digitally printed cans.
Recognising the diverse needs of customers, NOMOQ is introducing ‘Blank Cans’ to cater to those who seek unprinted cans for their filling lines. This service allows cus-
tomers the flexibility to maintain labelled productions in combination with digitally decorated cans, both directly sourced from NOMOQ in the same transportation system.
The UK beverage industry was projected to reach over £8 billion in revenue at the end of 2023 with 22.2 million users by 2027 as Brits are set to become a nation of canned beverage consumers, due to changing drinking habits post-pandemic and a desire for fully recyclable packaging. This shows the demand for canned products will remain strong throughout 2024 and beyond.
NOMOQ’s growing portfolio of blank cans allows craft beverage businesses to consolidate their packaging supply chains whilst maintaining high quality and environmentally friendly solutions, as the demand for aluminium cans remains high.
Alongside each order, the experts at NOMOQ are also offering personalised business advice, providing information to ensure all transport, packaging and labelling is as environmentally friendly as it can be, and that the end result can be indefinitely recycled whilst not compromising on brand quality. n
reintroduced its holographic tear tape range
enable brands and their packaging suppliers
for a new age.
Whether looking to catch the eye through a kaleidoscope of rich colours or opting to pair holography with high-quality printing to achieve cost-effective brand protection, those accessing the Supastrip® Prism range of tear tapes also unlock the best-in-class easy opening that is synonymous with Filtrona Tapes.
Prism offers a range of unprinted or flood-printed decorative holographic films available from 1.6mm and Prism Plus utilises Filtrona’s design expertise to combine holographic films with print for maximum brand awareness.
Prism Ultra uses de-metallised or selectively metallised holographic effects to deliver a customised on-pack solution, whilst Prism Unique takes things to the next level by offering bespoke hologram designs and features for maximum security and brand protection.
The hologram design trend is a force to be reckoned with right now. As brands look for value-adding packaging solutions that offer increased differentiation, Prism creates a high impact in crowded marketplaces, combining holographic visuals with distinctive packaging that cannot easily be replicated.
Supastrip Prism, like its Supastrip® and Supastrip® PCR counterparts, can be applied to a range of products that use plastic or paper as the primary packaging across a wide range of FMCG applications, from pet food to personal care or food-to-go to frozen categories. Designed to tear through various flexible packaging types, providing quick and easy access to the product, pairing the Prism range with an application system and support should make deploying the new range seamless. n
Five years ago, the Ellen MacArthur Foundation and the UN Environment Programme launched the New Plastics Economy Global Commitment to create a circular economy for plastics and more than 500 signatories joined. Many global brands promised to drastically increase their use of post-consumer recycled (PCR) plastic instead of virgin plastic by 2025. Lee Metters, Group Business Development Director, Domino Printing Sciences, explores how business can help this recycling revolution.
Many brands have taken great strides in the right direction, but a problem remains – there is insufficient recycled plastic to meet demand. In its 2022 global report, the Ellen MacArthur Foundation announced that signatories had more than doubled their use of PCR since 2018 – from 4.8% to 10% – but remain a long way off the 2025 target. Moreover, virgin plastic use is back at 2018 levels after an initial drop.
The first step towards creating a circular economy for plastic waste is designing products for recyclability, but making products recyclable is only part of the solution. The world produces large volumes of recyclable waste daily, but the vast majority ends up in general waste collections. Indeed, a recent report by National Geographic found that 91% of
plastic waste is not sent to a recycling facility. Thus, there is a significant debate about how to improve materials recovery.
Multiple start-ups and businesses aim to improve product identification at materials recovery facilities (MRFs), with everything from artificial intelligence and machine vision applications emerging to identify waste better at the point of recycling.
However, focusing solely on recycling management overlooks the role of consumers – who have a significant impact on overall recycling rates. Consumers are vital stakeholders in the recycling process. One of the major obstacles to increasing plastic recycling rates is consumer confusion about what can be recycled, how it should be prepared and where to dispose of it.
In 2022, the Waste and Recycling Action Programme in the UK revealed that as many as 84% of households in the UK regularly contaminate recycling bins with so-called ‘wish cycling’ of non-recyclable products – including broken glass – which can affect the quality of collected material and, in extreme cases, lead to entire lorry loads of recycling being disposed of rather than recycled.
All this points to the need for more consumer awareness of correctly preparing and disposing of waste for recycling.
The consumer goods forum has a set of nine Golden Rules for designing packaging for recyclability, including using on-pack recycling instructions to help with consumer awareness. This idea is backed by research – with a 2023 report from the US-based Recycling Partnership finding that 78% of US consumers look for recycling information on product labels.
Using on-pack recycling labels not only makes things easier for consumers, but it can also add additional brand value. A recent study from McKinsey and NielsenIQ found a ‘clear and material link’ between sustainability claims and consumer spending.
For more information about Domino Printing Sciences, please visit: https://www.domino-printing.com/en-gb/home.aspx
Around the world, recycling labels are gaining traction, with many countries mandating compulsory end-of-life labelling requirements. In France, packaging must include the ‘Tri-man logo’, which shows how to dispose of each part of the packaging. Within the UK, producers must label all packaging types, except flexibles, with ‘recycle’ or ‘don’t recycle’ by March 2026, while the requirement for flexibles will follow in 2027.
The list is not exhaustive, with many other countries, including Spain, Portugal, Poland and Germany, expected to introduce compulsory regional labelling requirements in the coming years. In other regions, organisations have emerged to provide voluntary on-pack recycling labels for brands. For example, North America has the How2Recycle scheme.
There is clearly merit in adding on-pack recycling advice for consumers. However, having multiple regional labelling requirements can prove confusing and make it difficult for brands selling products internationally, especially where legislation and guidance are prone to change. There is work going on within the European Union to design a harmonised labelling system for waste across the EU. This is a significant undertaking and expected to be a long journey.
A potential solution could be to include recycling information within a scannable QR code. Indeed, the new French labelling laws already mandate that QR codes be added to specific packaging types to give consumers access to recycling information
The move by global standards agency GS1 is designed to see 2D barcodes at the point of sale by 2027. This also opens the door for the GS1 Digital Link – a phone-scannable QR code to be used at the point of sale, which can also take consumers to a brand-specific webpage for more information about the product. GS1 suggests that QR codes powered by the GS1 Digital Link standard could offer businesses an efficient and cost-effective solution for providing recycling information to consumers, while futureproofing their packaging in preparation for new legislative requirements.
With a GS1 Digital Link QR code, brand owners can link to any number of informa-
tion sources all from one symbol. This can include listing what materials make up the constituent parts of the packaging and tips on how to prepare an item for recycling. Specifically, the tips could include advice on separating packaging, whether to clean the product and if specific components (such as caps and pumps) need to be removed or left in place.
A QR code could also share tailored local information via geolocation, or postal code, to allow consumers to check any local recommendations, such as a link to the closest recycling facility. Finally, there would be the chance for additional consumer interaction, with incentives for recycling, advice on reuse or feedback and surveys.
The key advantages of using a GS1 Digital Link-enabled QR code lie in the geolocation functionality, allowing brands to provide different information, and different language formats, for different locations without changing the pack design. This is updateable, meaning that brands can adjust the information as required. By adding a GS1 Digital Link on product packaging today, brands can meet current consumer and business demands and tackle any future requirements as and when needed through a single, flexible and cost-effective solution. n
With over 40 years’ experience, FrontPac is Scandinavia’s leading manufacturer of offset-printed corrugated cardboard. Over the years, the company has continued to create high-quality products whilst respecting the planet. Managing Director Martin Enocson spoke exclusively to Inside Sustainability, providing insights into the company’s dedication to going green. Report by Imogen Ward.
Ever since its establishment in 1982, FrontPac has regarded sustainability as a huge element of its DNA.
“Although today, sustainability has become somewhat of a buzzword, it has always been a natural part of FrontPac’s operations,” said Managing Director
Martin Enocson. “We have been working with green electricity for 15 years now –not because the demand was there, but because we felt that it was the right thing to do.
“It is so frustrating seeing big companies shouting about their latest deals in greener
electricity when it has been available for so many years. It makes you wonder why they have waited so long to get involved.”
Over the past 40 years, FrontPac has worked hard to build a reputation for excellence, one that has afforded it a longstanding and loyal customer base, as well as an annual turnover of over €40 million.
“We are proud that we still have some customers who have been with us since the beginning,” said Mr Enocson. “Even as FrontPac has evolved, these companies have stuck by us. We have gone from being
a huge supplier to the mobile phone industry to packaging toys. Where we are today is very focused on supplying corrugated boxes for the wine sector.”
Sustaining the planet
The environment has always been an important factor when it comes to FrontPac’s decision making process.
“15 years ago, we replaced all our lighting with LEDs and have been using electric company cars since they were first introduced to the market,” Mr Enocson explained. “Sustainability is part of our DNA.
We even produced a sustainability report in 2019, which we weren’t obligated to do; but we felt it was important. Our carbon emissions are something that we work on day-to-day, and it really helps us when it comes to asking the right questions of our suppliers as well.”
These principles are reflected in every aspect of FrontPac’s operations. From design to investments, every element is carefully thought out to ensure it aligns with the company’s ethos.
“Manufacturing corrugated and cardboard packaging is what we do,”
said Mr Enocson. “Of course, we have the facilities here in-house to do that, but whenever we need to make investments or find new suppliers to help us, we always prioritise our vision of making appealing packaging that is low in carbon emissions.”
Over the years, these investments have come in various forms, with the most recent revolving around the company’s choice of handles. Originally working with plastic for most of its packaging handles, FrontPac
has invested in new ways to remove this plastic element.
“We have found some paper handles that are very strong, and have been introducing those to our customers’ packaging for some time now,” Mr Enocson continued. “All these small things add up, which is why it is so important to tackle them one by one to find better solutions. After all, Rome wasn’t built in a day.”
Working with one of its clients, FrontPac has also begun incorporating
fully recyclable tear tape made from paper. When it comes to new developments, FrontPac values the opinions of its customers and partners.
To ensure the continued efficiency of its operations (and to minimise risk of downtime), FrontPac has recently invested in a second printing press. The addition of this new machine means the company now has dual machinery for every aspect of its production process. This has also resulted in an increase in capacity.
“Dual machines allow us to secure contingency,” Mr Enocson explained. “If something were to happen to a machine, we always have a backup one that can run at the same time. Being able to offer
that reliability is very important for our customers. Of course, a new machine adds capacity as well, which will give us the opportunity to take new market shares.”
In a world where evolution is continual and the needs of many are changeable, FrontPac understands the importance of adaption. To further improve its production efficiency, the company is turning to technological advancements.
Since the Summer of 2023, FrontPac has relied on AI-based software to collate all its data on chemical safety regulations. The company has found this to be the most quick and efficient way to group important information. Additionally, this system can accurately locate and highlight the most relevant segments so that FrontPac’s engineers are always working safely.
“All the safety declarations need to be read and understood, so our AI system reads all of these documents and flags the most important parts so that management can inform staff in production,” Mr Enocson explained. “If accidents happen, then we need to make sure the right information is in place to help.”
Another exciting development planned for 2024 is a new Digital Buddy system that is designed to help newcomers with queries. The software will also ensure accuracy in work, eliminating any potential minor mistakes that occur as employees learn.
“We have been doing a lot of investigation on a Digital Buddy system,” Mr Enocson continued. “It’s a really interesting project,
because I think it will help make us better as a company. One of the main challenges involved in the integration of technology, though, is getting people to embrace it and see the possibilities. Nowadays, people are scared of AI, because they think they’ll lose their jobs: I don’t think that is the case at all. What we are doing is utilising AI to help the company improve.”
It is not just 2024 that is looking prosperous; FrontPac maintains a positive
outlook when it comes to the future in general.
“With the trend of transitioning from plastic to paper set to continue, we foresee a future of positive growth in our segment,” Mr Enocson concluded. “It’s a very exciting time, and I can’t wait to see where the future takes us. We are on a journey with an amazing team of people who are incredibly enthusiastic; their passion is a prominent part of our success.” n
RedpackPackagingMachineryhasexpertlymanufactured flow-wrapsystemsforthepast50years.Now,celebrating itsanniversary,thecompanyisbusierthaneverinvesting innewmachineryandexpandingitscustomerbase.General ManagerGaryHowardexplainedmore,inanexclusive interview.ReportbyImogenWard.
With a combined expertise of 756 years, the team at Redpack Packaging Machinery is renowned for designing and manufacturing reliable equipment with the help of its three pillars of strength:
“Our three pillars – quality, service and innovation – aid our strategic goals,” General Manager Gary Howard explained. “If a project doesn’t have all three elements, then we don’t do it. We dedicate a lot of time to our customers; not only listening to their needs but the needs of their customers as well. They are the ones that use the machines, so we have to pay attention to what they do and where improvements can be made.”
Founder Michael Briston established his precision engineering company in 1973, providing machined parts for companies in and around Norfolk, UK, one of which
was Redpack. In 1997, Mr Briston acquired the brand rights to Redpack, and the company evolved into what it is today.
50 years on from those humble beginnings, Redpack has continued developing a legacy of reliable machines that stand the test of time. As proof of this, the company is still servicing some of the original 100 models that were manufactured more than 40 years ago.
Since 2017, Schneider Electric has proudly collaborated with Redpack Packaging Machinery, pioneering innovative solutions in the food and beverage sector, with a focus on sustainability. Together, we are optimising production, integrating cutting-edge technology and deploying eco-friendly practices. This partnership reflects our shared dedication to environmental protection through innovation, ensuring a greener, more efficient future for industry.
We look forward to continuing our commitment to sustainability, demonstrating our shared vision for a more responsible and forward-thinking global community.
editorial mention
Over the years, Redpack has built a gleaming portfolio dedicated to the world of packaging. From produce to bakery, and snack to healthcare, the company manufactures the perfect solutions for a wide range of sectors. Currently, the most popular choice amongst Redpack’s customer-base is the NTS.
“The NTS is our most popular product because it was designed by our customers,” said Mr Howard. “They told us what features were needed, and we developed our design around those requests.”
With a solid presence in the fresh produce market, the company is aware of the extra requirements that come with packaging loose produce.
The NTS top seal flow-wrapper is renowned for its user-friendly command screen, easy configuration and its ability to process hardto-handle produce. It can be used with both flow and shrink wrap and is the ideal choice for customers looking to quickly and efficiently bag their trayless produce, making it perfect for the fresh market.
In celebration of its 50th anniversary, the company’s portfolio is set to grow once more with the addition of five new products, including several machines that will help make its customers’ operations more efficient.
“When developing a new product, it should always be designed to what your existing market needs and what potential new mar kets might require,” said Mr Howard.
“We looked at the packaging industry as a whole – at the current trends – and we realised that one machine that would really enhance it was a tray sealer.”
Armed with this knowledge, Redpack designed and developed a new machine capable of processing produce that relies on the stability of hard plastic trays and the security of a soft top seal.
All of Redpack’s machines go through rigorous testing before they go on sale, as the company wants to ensure the quality and longevity of each one. Throughout this stage of the process, the machines are exposed to safety, electrical and mechanical testing before being trialled with clients.
“Weight is another important factor within the fresh produce market, as our customers need to be able to provide accurate measurements on their packaging,” said Mr Howard. “Because of this, we have also developed checkweighers.”
The company is also keen to enter into quality control, with the addition of its new metal detectors and x-ray machines. These allow customers to test their produce to ensure metal and foreign objects have not made their way into the food.
Thanks to an increase in demand, and the news that more machines are on the way, Redpack made the strategic decision to redevelop its current floor space to further increase production capacity.
“We moved to our current facility around seven years ago, and it was four times the size of our previous premises,” Mr Howard explained. “However, we soon filled that space because of our everincreasing production rates. We currently have a large office space that is under -
utilised, so that will be divided into new production areas to make the most of our current square footage.”
Whilst Redpack’s facility undergoes a revamp, the company plans to improve the efficiency of the building with an upgrade to its BMS system.
“Our BMS system has been great, but it is getting quite old, so we are now looking into more efficient ways to heat and cool our facility,” said Mr Howard. “We want to make sure that this is completed at the most practical time, so we are allowing ourselves between 12 and 24 months to get it done.
“We are also looking at battery storage because we generate far more electricity than we need during the summer months. The hardware of our machines is also being upgraded, to make them more efficient and less wasteful. We have already implemented auto-standby features that
detect when there’s not enough product being processed, to ensure power is not being consumed unnecessarily and film is not being wasted.”
To further improve the footprint of its machines, Redpack has also been collaborating with customers and film suppliers to ensure its machines are compatible with paper, biodegradable and compostable films.
“We are always focused on improvement, because we truly believe that nothing is a finished article,” Mr Howard concluded. “That’s what drives everyone that works here; nothing is ever too much trouble, and everyone is so hands on. Once, our Managing Director fixed our floor cleaner because it was out of commission, and he had the skills to do so. Everyone mucks in, and the products benefit because of it.” n
Award-winning The Printed Image is one of Ireland’s top brand enhancers. It is also a world sector leader in eco strategies. “We are committed to helping reduce the environmental impacts of printing and protecting the environment we operate in,” said Managing Director Tom Moriarty. Imogen Ward and Colin Chinery report.
Brand domination and eco-sustainability – key for the successful specialist print sector in 2024 –see The Printed Image pre-eminent in Ireland.
“Delighting our clients is at the heart of what we do, and we have built a reputation for customer service, quality and reliability, unrivalled within our industry,” said Managing Director Tom Moriarty. “We start at the ideation and design stage, then carry that through the process right up to delivery and, in some cases, collection and disposal of a product.”
With multiple brands – big and small –like Amazon, BMW, Cadburys, Heinz, Lidl, Lindt, Tesco Bank and Zurich, the client portfolio is hugely impressive.
Formed 33 years ago as a conventional print business, the Dublin company has 50 staff and has evolved to become a large dynamic end-to-end service partner
to numerous brands. The Printed Image delivers creative, bespoke and costeffective marketing solutions in settings such as in-store, outdoor, at-home and online.
“Innovation is at the core of what we do,” continued Mr Moriarty. “We’re experts at design and converting agency and client ideas into captivating printed and promotional materials that stand out for all the right reasons.”
Sustainability is another standout: strategy that saw the company winning the prestigious Gold Standard from EcoVadis – an organisation that tracks 1.6 million companies across more than 175 countries. This places The Printed Image among the top 5% of companies globally for sustainability and Corporate Social Responsibility and in the top 2% of print companies worldwide.
“The Printed Image is committed to helping reduce the environmental impacts of printing and protecting the environment we operate in,” Mr Moriarty explained.
“We take environmental commitments seriously, and have gone to great lengths to measure andreduce our carbon footprint and minimise any potential wastage.
“We are proud to be FSC certified, ensuring our paper is sourced from FSC certified mills promoting good forest management. Alongside this, we recycle everything including waste paper, ink containers, LDPE, wooden pallets and plastic wraps. We are a 100% effluent and hazardous chemical free and zero PFAS site.”
The €10m turnover company’s continuous investment strategy maximises client delivery potential. “It’s very important for us to remain relevant to them, dedicated to their success and their brand promotion in the marketplace,” said Mr Moriarty. “With over 500 active customers who have dealt with us for many, many years and a live client base of over 2,500, we have a very loyal client base.”
Milestones in 33 years of consistent profitability include the move to full inhouse digitalisation in 2020, overseen by a management buy-out the same year: “a seamless transition of ownership of essen -
tially the same company,” according to Mr Moriarty. This was in addition to a move to spacious new premises; eco-friendly, with waste segregation, material recycling and solar-power installation in progress.
The Printed Image offers services ranging from signage display and promotional merchandise to marketing events and online portals. The company brands everything through the strategic use of branded promotional merchandise to increase brand loyalty, expand brand awareness and increase client top-line sales.
“One of the other areas we see a lot of growth in from our client demand is higher quality and longer lasting retail display,” Mr Moriarty continued. “So, again regarding sustainability, 20 years ago it was just cardboard, clipped together with plastic and glue on a shop floor and lasting a week. Today, clients and retailers are more interested in items that will stay in the store for longer and are of higher quality, more sustainable and better-looking.”
For graphic and structural design, the in-house creative team of three graphic and three structural designers works
closely with clients to understand their business and the message they want to deliver. Signage, display and vehicle graphics have seen the company working with some of the most forward-thinking brands, supporting them in creating the most powerful and appealing visual advertisement mediums.
“Our mission is to help grow a brand and increase sales through responsive connected marketing solutions, bespoke products and services, and meeting every advertising need – fitting corporate style with precision,” Mr Moriarty said.
Providing clients with an online portal streamlines the ordering process and manages brand and quality consistency. “In this digital age, we help join all the
dots, centralising solutions tailored to client needs,” Mr Moriarty explained. “From beautifully crafted websites to personalised ordering communication and logistics centres, we deliver efficient tools to support our client’s operations.
“Altogether, we have a continuous investment in the technology for our portals to make life easy for the client. If life is easy for the client, then they’re very happy with the service and the savings; plus they’re very likely to remain loyal to us.”
A showcase of typical testimonials shows why – ‘consistently exceeds my expectations… swift responses… outstanding value... above and beyond with valuable enhancements… great to work with… superb quality.’
Producing everything under one roof, in state-of-the-art facilities, allows the company to manage all project requirements promptly and efficiently. This ensures the highest ISO-9001 standards of quality and consistency, according to Mr Moriarty: “As part of our commitment to becoming a carbon-neutral company, we are keen to do all we can in-house, and also to support and partner with organisations who are consistently, tenaciously and successfully working globally for the benefit of all.”
The printing industry in general is responsible for a significant amount of environmental pollution. The production of paper requires a large amount of energy, water and chemicals, while the use of non-recyclable materials and disposal of printing waste in landfills also poses a significant environmental threat. Transportation of printed materials and the use of packaging materials also contribute to carbon emissions. Against this backdrop, The Printed Image took a decisive corporate step.
“When we carried out our MBO three years ago we decided that we would become the Home of Sustainability,” Mr Moriarty. explained. “Everything we do in the company is geared around ethical sourcing and ethical relationships with our suppliers and clients.
“Since we had a blank canvas, we totally redesigned our new premises fit for a full and proper segregation of all of our waste streams. Our industry has pretty high energy consumption, but by looking at new machinery we’ve succeeded in reducing our electricity consumption significantly, whilst working to achieve EcoVadis Gold Standard guidelines tracking of all our emissions.”
Investment in new machinery, technology and research to increase both efficiency and sustainability metrics is one priority
over the next two years. Another task is to grow across the whole island – Republic and Northern Ireland.
“And of course,” said Mr. Moriarty, in conclusion, “all these objectives and advances will be achieved as a company who are ‘The Home of Sustainability’: our tagline at The Printed Image.” n
Established in 1987, Skymark Packaging International has been at the forefront of delivering innovative, quality, packaging solutions on a ‘just-in-time’ basis across diverse markets. In September 2023, the company became part of the TOPPAN family, strengthening its commitments to sustainable packaging and putting the customer first. Hannah Barnett spoke to Sales and Marketing Director Dan Richards to find out more.
Throughout the industry, Skymark is renowned for exceptional product quality, rapid and flexible responses, and pioneering solutions. The company’s expansive manufacturing capabilities encompass recyclable cast and blown films, flexographic printing, solventless lamination, slitting, laser easy-open and scribing features, conversion, and an inhouse and medical, 8%: fully accredited recycling process.
Over the years, the company has focused on acquisition and growth, while putting its customers’ requirements before any thing else.
“The fundamental premise of what we’ve built has always been about inno -
vation and delivering what the customer needs,” said Sales and Marketing Director Dan Richards. “This allows us to remain a dynamic, developing and innovative privately held business.”
Skymark’s turnover is around £30 million. This is split into four key sectors in which personal care is the biggest, accounting for around 61%. Technical films make up about 26%, hygiene and medical, 8% and the company is growing within the food sector, which is currently 5% of overall turnover.
The company employs 175 people at its Scunthorpe facility, where it has the capacity to produce 12,000 tonnes of material a year. Customer loyalty is highly
valued, with 40% of current partners having worked alongside Skymark for over 15 years. “I think that speaks volumes in terms of our commitment to partnerships, long-term agreements and development alongside our customers,” said Mr Richards.
An important milestone in the growth of the company was reached in September 2023, when Skymark was acquired by global Japanese printing company TOPPAN, as part of the latter’s InterFlex Group subsidiary. It has already proved a productive alliance, with both sides bringing something to the table.
“Our two previous owners, John Turner and Mehrdad Toofanian, prioritised having a partnership that could continue Skymark’s growth, strategy and vision,”
said Mr Richards. “They weren’t interested in just selling, they wanted to ensure what they built survived. And TOPPAN shares the values of our mission statement regarding personalised collaboration and the drive towards sustainability.”
Indeed, Skymark has found plenty of alignments with TOPPAN’s approach. These include mitigation of the plastic tax and investment in the development of recycled films, material reduction and lightweighting. Skymark’s expertise in the field has even enabled TOPPAN subsidiary InterFlex to improve its sustainability agenda.
“Skymark has its own extrusion facilities,” Mr Richards explained. “We’re vertically integrated and so can now supply the InterFlex site with films. That creates a much better closed-loop recycling stream, because Skymark has a fully accredited
waste-processing facility. So, we can take our post-industrial scrap, and scrap from InterFlex, and reprocess it within our own four walls. That has a massive impact on carbon footprint, waste reduction and putting higher quality material back into our products.”
The synergy between the companies extends to wider decarbonisation measures, including studying granular level CO2 emissions. Skymark has installed monitors at its facilities to analyse energy consumption and is a member of the SME Climate Hub. This membership requires Skymark to calculate and report its carbon footprint.
As Mr Richards explained: “This means if a customer asks for information on a range of products, plus the carbon footprint against each one, then they can make not only a commercial or technical
decision, but a sustainable one. Working alongside TOPPAN, which is also committed to monitoring carbon emissions, we are able to deliver that.”
For its sustainability strategy, Skymark focuses on four key areas: reduce, regenerate, recycle and renew. “They’re the four pillars not too dissimilar to many in the industry,” said Mr Richards. “But we have very specific agendas.”
Around 55% of Skymark’s portfolio now contains 30% or more recycled content.
T he target is to reach 90% of products made with at least partially recycled content within the next few years.
“We’ve really invested in our extrusion capabilities and our reclaim unit, to be able to reprocess recycled content,” said Mr Richards. “But we are also looking at different avenues, such as ISCC accreditation, which InterFlex already has. That’s another synergy that will allow Skymark to use accredited polymer alternatives like bio-based resins.”
It is clear that Skymark values relationships with its customers that are personalised, flexible and reflect the constantly evolving market.
“If you look at how we approach Key Account Management, we really try and
embed ourselves with our customers at every level:” Mr Richards explained, “not just from an account management point of view, but with their technical team, the warehouse operators, machine technicians, their R&D department and their branding. This means we can create something that enables them to deliver the message they want to their consumers.
“When we started doing toilet tissue packaging it was 50 microns of film, and we’re now down to 25 microns at 50 per cent PCR. So, the innovation there is quite clear. And now, with the acquisition, and through the connections that we have across TOPPAN group, we can deliver that technology further throughout Europe and to North America.”
Skymark is keen to maintain similarly strong partnerships with its supply chain.
The company’s relationships with suppliers are based around fairness and integrity, making working with Skymark more than just a commercial decision.
“It’s easy enough go out to the marketplace and get the best price,” said Mr Richards, “but having security of supply and trusted partners is key to our success. Now, with InterFlex and TOPPAN our network is widened. There is a massive synergy, and we share common suppliers – meaning we can join forces and offer something even better.”
Skymark is set to continue its growth strategy focused on delivering to customers exactly what they want. Being sustainable in the modern market requires flexibility, and as Mr Richards reflected, there is no simple solution: “We did a project for one of our key customers where we ended up taking something like 400 tonnes of packaging out of their usage. As a packaging company, that is 400 tonnes in lost revenue for us. But we delivered what the customer asked for.
“Our commitment is to create sustainable packaging solutions. And there is no simple answer to the complicated question of what sustainable packaging really is. It depends on a wide spectrum. Brand owners and retailers might have individual objectives and they all want to have something slightly different from their competitor. No one is right or wrong, but of course, our objective remains being flexible and dynamic enough to meet those requirements.
“We always have to remember that our customer-centric approach is what got the company to where it is now.” n
As a leading manufacturer of protective packaging and insulation, Abriso Jiffy specialises in the extrusion of plastic polymers into technical foam solutions and air bubble products. Now, at one of its facilities, the company is fortifying a commitment to sustainability via the circular economy. Hannah Barnett spoke to Nicolas De Koker, Marketing Manager, and Dan Gavriliu, General Manager at the Piatra Neamț facility, to find out more.
The last few years have been a time of flux and growth at Abriso Jiffy. In 2019, Belgian film producer Abriso took over the Italian packaging company Jiffy, becoming a much larger group in the process and heralding an entire change of structure. This consolidation meant the
group significantly increased its annual turnover from roughly €100 million for each company to €350 million as a collective entity.
According to Marketing Manager Nicolas De Koker, the financial benefits of becoming a large group have not been the
only rewards: “It was our goal to project a European outlook. We have shown the benefits of small operations coming together to make one bigger, uniform company.
“We now have 17 factories across Europe. I think we are the only company in our industry with this European-wide coverage. We can serve more than 5,400 customers and have a big range of clients who all receive the same excellent quality and service.”
One of the 17 factories, Piatra Neamț in Romania, is an excellent case study, demonstrating how Abriso Jiffy is embracing change to become as sustainable as possible.
The company is focused on both postconsumer and post-industrial recycling at the facility. The former means collecting plastic waste from clients to be reused: the latter involves optimising every product process in the factory to recycle waste internally and reuse it.
At Piatra Neamț, the company is closing the circle on the circular economy in three ways: cutting down on waste, reducing the plastic content in products through decreasing their density and reusing the packaging it collects from consumers as raw material resin.
This all takes place at a state-of-the-art recycling workshop that opened in March
2023; a €1.5 million investment. The new site can produce the iconic Ocean Green® bubble film from between 50% to 90% recycled plastic resin. By putting the product back into the manufacturing process, its lifespan is significantly increased.
“Bubble wrap has sustainable properties when used and disposed of properly,” Dan Gavriliu, General Manager at the Piatra Neamț facility, explained. “Our Ocean Green® bubble film packaging is a special product that can be easily made from 100 per cent recycled low density polyethylene without compromising the quality or the features for which it was created.”
The company is also transforming waste from its manufacturing process into 100% recycled resin, without having to use any fossil fuel-based raw materials. This not only significantly minimises Abriso Jiffy’s carbon footprint, but it also prevents plastic getting into the ocean and other associated littering.
Abriso Jiffy maintains strong partnerships with successful companies like Lidl, as well as a significant automotive spare parts manufacturer, to collect plastic waste and reuse it as part of its postconsumer recycling programme. And the company is continuing to push the boundaries of innovation.
“We need significant investment in advanced technology to incorporate more recycled material in our products,” Mr Gavriliu explained “In 2023, we succeeded in using multicoloured recycled resin in a special product that we call break bubbles.
“This is mainly used in the building sector as reflective insulation; the product is called RoFlex ®. It’s a reflective insulation bubble field with an aluminium barrier that
is laminated on both sides to reduce heat transfer. It can be utilised in transportation of refrigerated products and to insulate the interior of vehicles.”
“Our advantage is that we have a wide range of product portfolios, designed for different industries,” Mr De Koker added.
“We have products for packaging, but also for building. So we can offer innovative and unique solutions that meet the specific needs of our clients.”
Building and maintaining long-term relationships with its supply chain is crucial for a company with the wide reach of Abriso Jiffy. “We have very open and transparent communication with suppliers, maintaining regular contact to discuss expectations and share feedback,” said Mr Gavriliu. “This gives us the opportunity to develop new technology and also implement better solutions for the circular economy in our organisation.”
Abriso Jiffy currently has the capability to use 100% recycled material to make bubble film, but is not yet capable of the same with foam packaging. This is therefore the company’s next challenge, and it is breaking ground already. Abriso Jiffy has been working with two big chemical factories to develop resin that can contain up to 40% post-consumer recycled content for foam packaging.
“This is a significant step forwards to achieving our main objective and reducing the fossil fuel-based raw material for plastic,” said Mr Gavriliu. “We want to get up to 70 per cent post-consumer recycled material in our foam, which will depend on regulation and the technological development of the coming years.”
The company is also working out how to recycle multi-layer plastic more efficiently, though this remains a challenge. The circular economy surrounding plastic extrusion is clearly a field with plenty of activity, but also one in need of more R&D.
“Transitioning to sustainable products requires a lot of investment in ecofriendly technology, new materials and processes,” Mr Gavriliu reflected. “The demand from the customer is uncertain and regulations vary from country-tocountry. When we have the same legislation everywhere, I believe we will have better opportunities to embrace more sustainable alternatives.”
Abriso Jiffy’s aim is to maintain a sustainable operation and achieve net zero by reducing its carbon footprint and offsetting any remaining emissions. In Piatra Neamț, the company utilises geothermal ground cooling systems instead of an electrical chiller, reducing water usage and electricity consumption by 15% across the whole factory.
“My personal objective is to create a healthy working environment here in Piatra Neamț to facilitate the teamwork that can improve people lives,” said Mr Gavriliu. “I want our employees to be happy because a happy employee leads to a happy customer: and happy customers create happy share holders. So I strongly
believe that my job is to take care of our team and create more value for the company.”
For Mr De Koker, investment is needed into changing mindsets more generally about the sustainable benefits of plastic. “We do a lot of investment in R&D,” he concluded. “But people can be sceptical and think plastic is always bad for the environment. If it is used in the correct way, it’s better for nature than alternatives like paper, which can only be reused seven times and for which the production process requires far more electricity and water than ours.
“Plastic is a valuable resource when it is used – and reused – properly.” n
INDUSTRIAUMBRA’s commitment to developing unique products follows its creation from the merger of two Italian paper industry heavyweights. Now, with a focus on developing sustainable solutions, the company has teamed up with Canadian-based Competitive Green Technologies. INDUSTRIAUMBRA’s Industrial Director Nicolò Fiorucci and Corporate Unit at Industriaumbra Dr Giulia Bendolini explained more, in an exclusive interview with Inside Sustainability. Report by Imogen Ward and Colin Chinery.
Working in partnership, INDUSTRIAUMBRA and Competitive Green Technologies have developed a new and exciting facility that is set to position the companies in a unique position within the market.
“Together, we have established a new company, the CGT Production Center srl, within the green core of Italy,” Corporate Unit at Industriaumbra Dr Giulia Bendolini explained. “This investment is set to position INDUSTRIAUMBRA as a natural sustainable industrial manufacturer that is unlike anything the market has seen before.”
“Having completed 2023 with a turnover of over €27 million, and so many exciting developments on the cards, we have a very busy year in front of us,” INDUSTRIAUMBRA’s Industrial Director Nicolò Fiorucci added, in support.
Four years ago, INDUSTRIAUMBRA was founded from the merger of two major Italian paper sector businesses, Brefiocart and fisadorelli.
Launched in 2003, Brefiocart had a long tradition in the production of paper products for office archiving and school sector material. A capacity to integrate production and commercial specialisation, along with a development strategy based on specific national market needs, rapidly established it as market leader.
Meanwhile, fisadorelli was founded in 2011 from a collaboration between Fisa, an historic paper converting company in Umbria, and entrepreneur Alessio Dorelli. This company grew to become an international award-winning European reference in the sector of material for points of sale.
With an inherited undisputed leadership in domestic and international markets, INDUSTRIAUMBRA launched in 2020 under a consolidated management, and enhanced industrial abilities aimed at uninterrupted innovation. Today, the company maintains a core emphasis on sustainability, which is fitting for a company based in Umbria, an inland region often called Italy’s Green Heart.
INDUSTRIAUMBRA has also gone on to gain an impressive award-winning status.
“INDUSTRIAUMBRA recently won the Best Supplier award from HH Global, the world leader in tech-enabled creative production,”
said Mr Fiorucci. “They look for suppliers that can provide first-class designing services and product development, and INDUSTRIAUMBRA ticked that box.
“We recently designed, developed and produced a beverage dispenser for Coca-Cola for the 2024 Paris Olympics. This machine is 100 per cent sustainable and every component is recyclable. This drink fountain is meant to impose the use of re-usable glasses, in order to eliminate the need for traditional single use beverage containers such as bottles or cans.
“Coca-Cola is so happy with these machines that it plans to re-install them in various places after the Olympic games are over.”
With its focus remaining on sustainability, INDUSTRIAUMBRA has developed a growing partnership with CGT.
Ranked among the ten best bio-composite resin manufacturers in the world, Ontario-headquartered Competitive Green Technologies’ founding vision is to popularise biomaterials in the quest for a greener planet. Today, it is the leading producer of bio-composite resins and biopolymers for a range of commercial products, including coffee pods, food packaging and lightweight automotive parts. This collaboration led to the creation of a new company – the CGT Production Center – focused on the production and commercialisation of bio-composite resin and biopolymers.
“The CGT Production Center’s objective is to create a European point of reference in the production and commercialisation of the innovative raw materials of Competitive Green Tehchnologies, based on a ten-year
exclusive licence,” said Dr Bendolini. “We work with the development team at the research University of Guelph BDDC in Ontario, which is our collaborator in implementing new technologies. One of my goals has been to collaborate with the Vice Presidents of Industriaumbra and CGT to invest in innovation, byproducts, and the circular economy in this new plant in Sigillo, Italy.”
With a twin-screw extruder in place, the CGT Production Center now has a
5,000-tonne per year production capacity, but an upgrade is expected in the near future.
“Our extruders allow us to make compostable products using bio-composite sourced from non-edible food waste and, until today, over thirty-five variants of biomass – none with an edible background – have already been sourced,” Dr Bendolini continued. “Our products do not create any microplastics, which makes the product much easier to dispose of at the end-of-life
s tage. This is our own unique way of contributing to the environment, and it is a great way of getting our customers to partake in a more circular economy.”
Meanwhile, INDUSTRIAUMBRA’s threestage corporate construction programme is nearing completion, according to Mr Fiorucci: “The first phase, completed two years ago, was about harmonising the processes, creating organisational efficiencies and a single and specific standard for the new organisation.
“The second phase, finished some three months ago, was a physical one; creating new physical processes using effectiveness and efficiencies for production. We also invested heavily in a new 35,000 square metre premises. We moved all machinery and production systems into this single unique plant, where we have invested in green technology for energy production. “
As part of this development, the company has also worked hard to eliminate plastic. INDUSTRIAUMBRA no longer uses PVC labels on its products: instead it has opted for
a paper-based alternative. The company is also experimenting with the use of bioplastics, which it hopes to implement in the near future.
“We are also focused on transitioning from animal-based glues to a plant-based alternative that will be much better for the environment,” Mr Fiorucci continued. “We are fully committed to ensuring our operations are sustainable, after all, we did start a new company with green in its name.”
The third and final stage of INDUSTRIAUMBRA’s corporate construction programme relates to the development of a harmonious corporate culture.
“We are determined to create a single corporate culture,” said Mr Fiorucci. “It’s going slowly and is very challenging and demanding, but we are confident that the process will be a success.
When discussing his time at INDUSTRIAUMBRA Mr Fiorucci was very reflective. “I take my role very seriously when it comes to the development of our people and their potential,” he said, in conclusion. “I am constantly thinking of ways to help our people grow, and I am determined to teach them the real meaning of improvement and enjoyment.” n
Tradeprint was established in 1997 and has grown into a full web-to-print business, acting as a partner for thousands of aspiring companies. Following its success in the print sector, the company is exploring the potential of sustainability in a myriad of ways. Hannah Barnett spoke to Sales & Customer Success Director - Sustainability Lead Anthony Rowell to learn more.
When it comes to improving its environmental footprint, Tradeprint has a lot going on. With a path to net zero by 2040 in mind, the company is investing in energy-reducing infrastructure and equipment, exploring lower emissions substrates, and seeking more sustainable shipping options.
“I look at sustainability as being the right thing to do, for the greater good,” said Anthony Rowell, Sales & Customer Success Director – Sustainability Lead. “So we collaborate with anybody, even competitors, on sustainability initiatives and work with industry groups like the British Printing Industries Federation, where I chair the environmental forum.”
Tradeprint has been measuring its environmental footprint for some time, with data stretching back roughly six years. “This has enabled us to look forward, set targets and develop a pathway to be more sustainable, said Mr Rowell. “Sustainability is at our core, and it doesn’t stop there; we
really value our people and have gone as far as hiring a Head of People & Culture to support our employee-centric goals.”
Nowadays, Tradeprint has 160 employees, is approaching a £20 million turnover and operates from a 40,000 square foot site in Dundee. The company remains dedicated to small but significant changes, like converting all its lighting to LEDs; but as the business grows, so too does its impact.
“We’ve got to work twice as hard to mitigate the impact of our expansion,” Mr Rowell explained. “We acquired a company out of liquidation in 2022 and doubled our footprint, going from 20,000 square feet to 40,000. That allowed us to install more LED lighting, invest in some additional state-of-the-art equipment and had the happy co-incidence of inheriting an HP Latex Wide Format printing kit that uses HP Latex Water Based Ink.”
The Tradeprint team are pioneers of mass customisation, leveraging
technology to optimise production flows and keep print costs at a competitive level. This has contributed to the international success of parent company Cimpress.
“When they acquired us in 2015, Cimpress recognised that we had a really good approach to commoditising print,” said Mr Rowell. “Mass customisation is all about collecting similar jobs, ganging them together and driving economies of scale. As well as mass customising leaflets, flyers, booklets, posters, letterheads and other small format products, we’ve applied our skills and leveraged our expertise by applying it to Wide Format Printing. Driving those economies of scale and bespoke manufacturing flows enables us to be very competitive in the signage and display space, especially on-line.”
The path to plastic-free I n 2020, Tradeprint committed to improving the profile of its plasticbased packaging, in line with targets set by the New Plastics Economy Global Commitment and EU Plastics Pact. This includes the elimination of problematic plastics.
“It’s exciting, because we’ve already introduced some PVC-free substrates,” said Mr Rowell. “We also focus on what’s recyclable: not all
plastic is bad at the end of the day. We sometimes have an opportunity to support our customers sustainability ambitions. For example, we collected corrugated plastic at the end of a recent campaign, had it chipped and it was subsequently recycled into some low-grade plastic that can be used for plant pots –a great circularity concept.”
Amongst a number of projects and initiatives, perhaps one of the most significant is Project Hulk, so-called “because its big and it’s green,” according to Mr Rowell. The project focuses on the transition from PVC to PVC-free materials. One of the challenges is that, due to being composed of multiple substrates, PVC-free materials can be harder to recycle. They also must meet the same printability and durability of PVC.
As this area of development is still in its early days, there are few reasonable alternatives on the market. Because of a lack of demand, PVC-frees are also traditionally more expensive. Tradeprint is striving to close that gap by leveraging
Tradeprint visits Number 10.
Anthony Rowell recently contributed to a roundtable discussion on Sustainability and Innovation at 10 Downing Street. Meeting with the PM’s Special Advisor on Manufacturing and Industry, Mr Rowell highlighted the huge contribution the printing and paper industry makes to the UK’s economy, while showcasing Tradeprint’s collaborative efforts to promote sustainability.
its group size, with a global tender to help drive the price to the point that can be accepted by customers.
Mr Rowell described recycling in the printing sector as “in a constant battle against greenwashing.”
He continued: “We are on a steep learning curve regarding sustainability, and it can be very complicated, so, making the right decisions is sometimes challenging. We want to be sure we can support any claims with evidence so we are not accused of greenwashing.
When we started printing on PVC-free, the material suppliers had claimed that the
material was recyclable. Technically, it is; but they couldn’t confirm where we could recycle it. After further investigation, we decided to re-think our strategy and we are looking forward to the result of the global supply tender so we can have confidence we are making the right choices.”
Tradeprint has an almost obsessive approach to waste. In 2021, Mr Rowell conducted a full cradle-to-grave analysis of the company’s waste streams. He discovered that Tradeprint sent less than half a percent of waste to landfill.
“Normally, printers would claim 100 per cent landfill avoidance if it was over 99 per cent,” he said. “But we don’t make that claim because we’ve still got work to do. We
have recently signed up to the FESPA-UK & Reconomy Sustainability Partnership, which supports the adoption of improved waste stream management to ensure we are pushing waste as high up the waste hierarchy as we can, whilst optimising the opportunity to increase revenue from our waste. Almost all waste has a value if managed in the correct way.”
Tradeprint is also a proud member of Two Sides, a not-for-profit which provides verifiable information about the sustainability of paper; encouraging forest certification schemes, the use of recycled fibres and the elimination of waste going to landfill.
“Two Sides helps to dispel myths and reduce greenwashing,” said Mr Rowell. “Print is a really sustainable industry because we recycle our waste paper and work only with paper suppliers that are involved in responsible forestry with environmental labels like FSC and PEFC.”
The company was recently honoured for its work with an Independent Printing Industries Association Sustainability Advocate Award. “Winning felt like recognition for what Tradeprint has been doing in the industry; an external endorsement on the internal action we have been taking,” said Mr Rowell.
Tradeprint is now focused on decreasing its Scope 3 emissions and is working closely with suppliers in order to do so. This involves collaboration, discussion and education. As t he company has been measuring its carbon footprint since 2016, it has the valuable resource of data, along with a centralised sustainability team to collate it.
“We recognise the importance of sharing knowledge, making sure our suppliers engage with us and understand our vision,” said Mr Rowell. It’s the right thing to do, because it helps them on that journey, too.”
Indeed, for Mr Rowell, life at Tradeprint has proved an inspiring and meaningful vocation.
“If anybody is looking for an exciting career, printing is a brilliant business to consider because of the sustainability: plus we’re really innovative,” he concluded. “More than 10 per cent of our workforce are software developers, for instance. The pace of change is fast, the technology’s amazing and we’re a really diverse employer, with colleagues all around the world. It’s great to be part of a global business and I get a lot of satisfaction out of knowing that we’re making a difference.” n
If you’d like to learn more about Tradeprint’s approach to Sustainability, contact Anthony Rowell: arowell@tradeprint.co.uk.
with a
Sonoco brings more to packaging than the physical wrapping. The company’s integrated solutions help define brand personalities, create unique customer experiences, and enhance the quality of products for people around the world. Hannah Barnett spoke to VP Global Environmental, Sustainability, & Technical Services Elizabeth Rhue and VP & General Manager, Paper & Fiber Supply, US/CAN, Palace Stepps to find out more.
Sonoco was established 125 years ago in Hartsville, South Carolina, with 12 employees and one vision.
“The company is rooted in small town USA,” Elizabeth Rhue, VP Global, Environmental, Sustainability, & Technical Services, said. “Our CEO, Howard Coker, is fifth generation to the founder, who, in 1899, wanted to build a company focused on innovation.
“Sustainability has always been at our core; we’ve been using recycled fiber in our paper based products for well over 100 years. We like to say we were sustainable before it was cool.”
Indeed, producing paper cones instead of wooden ones for the textile industry was a significant early innovation for the company. Sonoco later expanded outside of paper into plastics and flexible packaging. This is in addition to the industrial and healthcare ranges, plus
the Thermosafe division includes reusable packaging, giving the company recyclable and reusable offerings.
In 2022, the company further expanded its portfolio to include metal food and aerosol cans, an acquisition that increased annual revenue to $7.3 billion. Sonoco now employs 20,000 employees across 34 countries.
One of Sonoco’s most innovative recent projects has been a partnership with AMP Robotics, which uses AI to sort, identify, and recover recyclable items. The robots are programmed to identify different Sonoco products and ensure they are properly sorted.
“Essentially, any AMP robot in a Material Recovery Facility (MRF) across the globe could be programmed to recognize a particular packaging format,” said Ms. Rhue,
“so we can increase the likelihood that packaging is properly recycled. It’s been a great project for us, because it’s allowed us to open up the avenue of sortation for particular packaging formats.” Palace
Stepps, VP & General Manager, Paper & Fiber Supply, US/CAN, heads up the recycling teams “Generally, we focus on containers with the robots, things that may be valuable or a little bit different in terms of shape, size, or material,” he explained. “The robotic neural network is clever and can focus on specific products, even if they’re discolored or disfigured. The AMP robot is much better than other sorting equipment at identifying those materials.”
One of the main challenges comes when sorting packaging that is made of multiple materials. Education remains an important tool in the wider community when establishing what is recyclable, too. “Sometimes we have consumers who are well
meaning and want to maximize what they recycle, but don’t understand some of the difficulties,” said Mr. Stepps. “For instance, the plastic cord from Christmas tree lights; that can wrap around rotating equipment in our process, which can cause us to have to stop our production line.”
Sonoco has also recently increased its focus on paper based flexible packaging. This has meant developing a structure that maintains the appropriate shelf life and functionality of a product, but is made primarily out of paper, and can be recycled in a kerbside recycling stream.
“We also have several initiatives on the plastic side of our business,” Ms. Rhue added, “increasing the use of recycled content in our rigid plastic containers, minimizing the use of virgin plastics and ensuring that we’re
improving the sortability of containers at the MRF. For example, we are using NIR detectable black colorants in our rigid plastic trays.”
The company also has several worldwide initiatives to reduce emissions via solar projects at some of its facilities. In 2023, it broke ground on two PV installations; one in Texas, the other at corporate headquarters in South Carolina.
“We also continue to work on projects that drive energy efficiency in our facilities,” said Ms. Rhue. “We are looking at boilers across our network, making sure that they’re efficient and at ways to convert them to biogas or other lower emission fuels.” Sonoco
won an award through American Forest & Paper Association (AF&PA) in 2023 for Sonoco’s project to convert methane gas from its anaerobic digester into renewable natural gas.
Something that sets the company apart is that it is highly self-sufficient. Running its own recycling facilities, in the U.S. and around the world, has allowed Sonoco to become one of the largest recyclers in North America.
This provides a usefully thorough, and somewhat rare, cradle to grave awareness of sustainability. “We have a real understanding of how a packaging design can impact the ability of that package
• 25% reduction of Scope 1 and 2 emissions.
• Reduce Scope 3 emissions in line with 2° Absolute Contraction Approach.
• Reduce energy use by 8% at plants. Conduct water risk studies at sites by 2024.
• Implement Operation Clean Sweep by 2025.
to be recycled at end of life,” Ms. Rhue explained. “And I think that gives us a unique advantage that many of our competitors do not have.”
Like any effective global company, especially one operating on the scale that Sonoco does, a strong relationship with suppliers is crucial. As Ms. Rhue explained: “Our suppliers are a large part of our success. We ensure that they have a clear understanding of our goals, objectives, and expectations, and we hold them accountable for bringing solutions to us that correspond.”
The company has also sustained long term relationships with suppliers, navigating difficult periods, such as the Covid pandemic Though the company’s self-sufficiency comes into play again, too.
“One of the secrets to Sonoco’s success is that we own a lot of the supply chain,” Mr. Stepps added. “And we are vertically integrated, meaning the recycling side feeds fibers into our paper business. I’m also responsible for adhesives; we supply our own adhesives, as well as our own paper and a host of other things across the integrated supply chain. Managing the upstream materials means we can control the cost, and the availability to some extent, and run our operations much more efficiently, as a result.”
Looking ahead, Sonoco will continue to grow sustainably, though, according to Ms. Rhue that is not a proposition without its own challenges: “There are questions like: ‘How do we raise production and bring in new business without increasing our environmental footprint?’ And we know we are
a pretty energy intensive industry, in terms of paper making. In some cases, the technology doesn’t exist yet to help us drive the emissions to the level that we would want.”
Ms. Rhue, who started her career at Sonoco as an R&D engineer working on material development and design, has found the move into sustainability a fulfilling one, strengthened by her strong product knowledge. “The opportunity to mix business strategy with sustainability is that sweet spot for me,” she said. “Whether it’s a new package innovation, or a project at one of our facilities, anything that helps to drive
both a good business and environmental outcome is very fulfilling.”
Sonoco continues to stay ahead of the sustainable curve, growing and evolving, something the company has always done. “We continue to reinvent ourselves,” Mr. Stepps concluded. “That’s one of the things that attracted me to Sonoco from the start. As the demands of the consumers who use our packaging change, we keep innovating and growing into different packaging platforms. We are a large, but highly nimble, focused, and growing company.” n
Based in Abu Dhabi, Star Paper Mill Paper Industry LLC is one of the main manufacturers of tissue paper for facial, toilet and domestic use in the UAE region. Chairman Hussain Adam Ali and Managing Director Majid Rasheed highlighted the company’s sustainable journey. Report by Phil Nicholls.
Bu siness at Star Paper Mill Paper Industry LLC (SPML) is fuelled by innovation and sustainability.
“Our goal is to create a holistic approach to sustainability, where every aspect of our business – from production through distribution to customer engagement – is aligned with our commitment to environmental
stewardship and social responsibility,” explained Managing Director Majid Rasheed. “We strive to set new industry benchmarks and continuously raise the bar for sustainable practices within our sector.”
Founded in 2016, SPML began operation in 2019, with more than 100 employees, and a production capacity of 40,000 tonnes per year. The
company now supplies many worldclass brands.
SPML specialises in value added products such as low gsm facial tissue, ultra-soft and smooth tissue, lotionised tissue with satin finish, multicolour printable white napkin tissue, bonded napkin tissue and very tough wet-strength towels. The company manufactures ‘Prime Quality’ soft hygiene tissue paper in jumbo rolls from 100% virgin pulp in various grades
Thanks to the personalised and prompt service offered by the team, SPML is
considered a preferred supplier by customers. Keeping a flexible business margin, the company manufactures tissue paper according to each customer’s requirements
“We also offer a comprehensive after-sales service, such as following up with the clients to ensure the smooth operation of our tissue rolls on their machine,” continued Mr Rasheed. “We also inform our clients of any helpful new developments in the tissue market locally and internationally.”
In an exciting development, SPML is expanding its production capacities, having signed a lease agreement with KEZAD, Abu Dhabi. This collaboration will establish a new facility for manufacturing recycled Kraft Paper Jumbo reels, enabling the company to meet the growing demand for biodegradable packaging papers in the UAE. With an investment of AED 200 million, this partnership with RC Paper Machines will expand the existing capacities into a 59,000 sqm site.
“In line with the vision of the UAE’s leaders, we believe that to be successful and create long-term value in the future, being sustainable and adopting a circular system is vital,” said Chairman Hussain Adam Ali. “We are using this opportunity as a huge advantage for us to create products to achieve reduced carbon emissions and operate as a sustainable industry.”
Mr Rasheed agreed, emphasising the potential of the new facility: “The KEZAD economic zone has a unique eco-system, strategic location, world-class infrastructure and
integration with the region’s fastest growing port. The location gives SPML excellent global connectivity to our key consumer markets. We strongly believe this project will effectively make Star Paper Mill’s products a household n ame for global consumers.”
SPML’s new site will manufacture the paper used for producing corrugated cartons and highly sought-after, 100% eco-friendly biodegradable bag papers using recycled raw materials. This is part of the company’s unwavering commitment to a sustainable circular economy and the environment.
“Consumers and customers who use our products should feel secure that our products are manufactured and distributed in a sustainable and r esponsible way,” continued Mr Rasheed. “That is why we promote responsible business – both within the UAE and throughout our supply chain.”
Sustainability in supply chains requires three responsibilities: social, environmental, and financial. Examples at SPML include using raw materials that have a relatively favourable environmental footprint,
powering the company's operations with green energy sources and favouring suppliers that emphasise renewables.
SPML is dedicated to maintaining its certifications, such as ISO 14001 for environmental management and FSC COC (Chain of Custody) for responsible sourcing of raw materials. These certifications demonstrate a commitment to sustainable practices and provide assurance to customers and stakeholders.
Research and devel opment plays a crucial role in the company’s sustainability journey. The company regularly invests in R&D initiatives to explore new technolo -
gies, processes and materials that can further enhance its sustainability performance.
“We also recognise the value of data a nd analysis in driving informed decisionmaking for sustainable development,” said Mr Rasheed. “We leverage advanced
data analytics to gather insights from various aspects of our business, enabling us to identify opportunities for improvement, optimise our processes and minimise our environmental footprint.”
Suppliers play a vital role in the success of any business: helping to foster innovation, reduce costs, drive process improvements and deliver better lead times. SPML builds
understanding, trust and long-term relationships with business partners through on-time payments, streamlining agreements and investing in technologies.
“SPML understands that our suppliers and partners are essential stakeholders in our business ecosystem,” Mr Rasheed explained.
The company prioritises building strong relationships based on understanding, trust and collaboration. The contributions and support of business partners are vital to SPML’s ability to deliver value to customers and drive sustainable growth
L ike every company, SPML has faced multiple issues with the global supply chain. These disruptions led to shortages, delays and increased costs in the procurement of raw materials, transportation and logistics. “However; we took proactive measures to mitigate
these challenges,” Mr Rasheed continued. “One step we took was to increase our storage capacity for raw materials.
“This ensures that we have an adequate supply on hand to sustain our operations during periods of limited availability or increased lead times. SPML has maintained a continuous production flow, and met customer demands despite these supply chain challenges.”
SPML has a strong commitment to continuous improvement and sustainability. Its plans for the future revolve a round further enhancing the company’s sustainability efforts and aligning with global best practices.
“One of our key focuses is on improving energy efficiency and reducing our environmental footprint,” said Mr Rasheed. “We have set specific targets to reduce energy intensities, aiming for a ten per cent reduction in energy consumption. This aligns with the goals outlined in Abu Dhabi's Economic Vision 2030, which emphasises sustainable development.
“In conclusion, we are dedicated to embracing innovation, collaboration and data-driven decision-making to achieve our vision of becoming a leader in sustainable paper manufacturing. We believe that by working together with our stakeholders and leveraging cutting-edge solutions, we can make a significant positive impact on the environment, society and the future of the paper industry.” n
click to sections:
HOMEWARE & FOOD
PACKAGING & PAPER
SERVICES & TECHNOLOGY
ENGINEERING & MANUFACTURING
BACK TO CONTENTS
one planet – one chance – one voice
An introduction to the construction sector, with innovations and a special report exploring concrete, followed by company profiles.
SereneP is the epitome of eco-friendly power generation, offering 80% CO2 emissions reduction with biomethanol and up to 100% reduction in CO2 emissions with eFuel use when compared to traditional fossil fuel power sources.
SereneP outperforms battery-only systems charged from the grid in many countries and regions in terms of net emissions. The system’s load-following capabilities ensure optimal fuel efficiency while dynamically adjusting power output to match specific load requirements, reducing operational costs and environmental impact.
Engineered to withstand diverse environments, SereneP functions flawlessly in ambient temperatures ranging from -20°C to 50°C. Its reliance on liquid green fuels ensures simple and costeffective logistics.
Unlike traditional grid charging, SereneP’s fuel cell charges its batteries, enabling virtually limitless green power generation even during grid outages, dependent only on the availability of liquid green fuel. The Methanol Institute is tracking over 800 global projects
focused on renewable methanol, projecting an annual output of eMethanol and Biomethanol in excess of eight million metric tonnes by 2027.
In addition, Advent has established a global network of fuel suppliers, guaranteeing its clients a steady methanol supply for SereneP.
“We are confident that SereneP is well-positioned to efficiently replace diesel generators in construction and other global applications,” said Dr Vasilis Gregoriou, Advent’s Chairman and CEO. “Recognising a specific market need within the construction rental sector, where upcoming regulations are expected to prohibit diesel gensets, SereneP is ideally positioned as a valuable solution available today.
“We are meeting the evolving demand for clean and highly portable power across construction and beyond.” n
Leading construction materials supplier Aggregate Industries has successfully completed the trial of its new, innovative Foamix® product – a revolutionary lower carbon solution for pavement construction, repair and maintenance.
Manufactured by Aggregate Industries, this milestone marks a significant achievement in the pursuit of sustainable asphalt and ecofriendly infrastructure within the construction industry.
Trialled on the M65 slip road in Lancashire, the new Foamix solution is a cold recycled bitumen bound material, meticulously manufactured with negative carbon aggregates and biogenic bitumen throughout the process. The outcome is a cost-effective, high-quality solution that recycles the existing carriageway, offering a net zero solution production process and a highly sustainable option for asphalt construction projects.
Already well-established within the industry as a replacement for traditional asphalt and cementitious materials, Foamix has been widely recognised
for delivering a very low carbon footprint due to its cold process and recycled content. Making it an ideal choice for achieving a circular economy within construction.
After rigorous research and development processes, coupled with live manufacturing and installation trials in partnership with Lancashire County Council, the new carbon neutral Foamix is the most sustainable and lowest carbon asphalt construction material to date and represents a remarkably sustainable alternative compared to traditional methods.
The successful trial of the new carbon neutral Foamix marks a groundbreaking moment, as it not only provides a cuttingedge solution for construction projects but also represents the first potentially carbon-neutral asphalt solution within the construction industry. n
Experts from Tunley Environmental explore the environmental impact of concrete.
The team from Tunley Environmental explore the use of carbon sequestration in concrete as a method to mitigate the environmental impact of the construction industry. A report by Dr Gareth Davies PhD, Carbon Reduction Scientist, and Dr Luan Ho PhD, Senior Scientist.
Concrete, the most extensively used manmade material worldwide, carries a significant environ mental burden, contributing to 8% of anthropogenic GHG emissions. With a staggering 30Gt produced annually, the material consumption is over 3.5 tonnes of concrete per person annually. The majority of the emissions (88.5%)
emanate from cement production, the essential ingredient in concrete.
Carbon sequestration in concrete presents a promising avenue to offset these emissions. This process, often referred to as carbonation or mineralisation, essentially reverses the initial cement production steps, where carbon dioxide is detached from calcium carbonate
(limestone). Controlled carbonation of cementitious material, although first proposed in the 1970s, is recently garnering increased attention due to its substantial potential to mitigate against the colossal emissions from concrete production.
However, carbonation is not without its challenges. Uncontrolled, it can lead to the corrosion of steel in reinforced concrete and the formation of harmful compounds, jeopardising the structural integrity of buildings. Yet, advancements in controlled carbonation methodologies have demonstrated the potential to not only sequester
carbon dioxide but also enhance the prop erties of concrete.
One such method involves utilising accelerated carbonation chambers to carbonate pre-cast materials, offering control over essential parameters such as CO2 concentration, humidity and temperature. This impacts the rate and depth of carbonation, with the formation of calcium carbonate in the exterior pores blocking further carbonation.
Emerging techniques explore embedding CO2-rich materials within the concrete mixture. A notable investigation by MIT researchers examined incorporating sodium bicarbonate, which dissolves and
Dr Gareth Davies PhD, Carbon Reduction Scientistreleases CO2 during curing. This innovative method not only sequesters carbon but also addresses the detrimental impacts of latestage carbonation, such as shrinkage and crack formation.
Furthermore, the possibility of reusing carbonated Recycled Concrete Aggregate (RCA) from construction and demolition waste, which amounts to around 3 billion tonnes annually, offers an additional layer of environmental benefits. Although using RCA poses challenges such as increased costs and micro-cracking, controlled carbonation mitigates these issues and allows for a decrease in both water absorption and leaching instability.
These advances in carbonation technology could potentially sequester 2 Gt of CO2 annually if implemented at scale, significantly reducing the environmental footprint of concrete production. When combined with the predicted 50% reduction from electrification, emissions could be curtailed to just 32.7% of the current levels.
However, the journey towards sustainable concrete production is multifaceted and complex. As researchers and engineers continue to explore the potential of carbon sequestration in concrete, the combination of controlled carbonation and the incorporation of CO2-releasing materials represents a leap forward in our quest to mitigate the environmental impact of this ubiquitous material.
In conclusion, the path to mitigating the environmental challenges posed by concrete production lies in innovative solutions such as carbon sequestration. By acting as a carbon sink, concrete has the potential to offset a significant portion of the emissions generated during its manufacturing stage. The incorporation of carbonated end-of-life concrete as filler material further underscores the potential of this material to contribute to a more sustainable future. n
To learn more about Tunley Environmental, please visit: www.tunley-environmental.com
For more than 55 years, PP Control & Automation has provided award-winning outsourcing solutions to machinery builders across the globe. Now, the company is applying that experience and offering advice on the importance of ESG, to ensure everyone has the right information to support a more sustainable future. CEO Tony Hague explained more, in an exclusive interview with Inside Sustainability. Report by Imogen Ward.
Established in 1967, PP Control & Automation quickly became one of the largest suppliers of control and automation solutions in Europe. Having maintained a clear commitment to ESG, the company is perfectly poised to help others sift through the resources available.
“Everyone in manufacturing has a clear responsibility when it comes to an organisation’s impact on the wider environment and associated communities,” CEO Tony Hague explained. “When discussing ESG, many people can relate to the environmental aspects, but are less aware of the social and governance elements. Perhap s this is due to the tangibility of environmental actions and consequences; but these areas are of equal importance.
“After all, it is proven that high-performing businesses have higher than average employee engagement and a culture of learning and development: so investing in your people is guaranteed to create a competitive advantage within the marketplace.”
Although there are a lot of helpful resources when it comes to ESG support, there are also companies ready to take advantage.
“There are some excellent and genuine organisations out there that can support the development of ESG strategies, but companies also need to be aware of those who are out to make a quick buck,” Mr Hague continued. “These so-called ‘ESG experts’ are on the rise and are drawing people in with their ‘wares’
relating to ESG dashboards and compliance strategies.”
This is not the only risk involved in the development of ESG. If companies are going to be successful in creating clear ESG strategies, then PP C&A believes that innovation is the way forward.
Of course, a lack of commercialisation can be a major cause for concern when it comes to ensuring the development of ESG innovation. Mr Hague pointed out a historic resistance to fostering innovation within the UK market, which has often led to loss of overseas investment.
“We have to ensure that the right companies receive the appropriate backing,” Mr Hague explained. “For innovators, the opportunity for early collaboration and support is so important, and there is a definite concern when it comes to the initiatives currently available. We have acknowledged this problem and sought to develop PP Plus as a solution.”
PP Plus is an easy access support network designed to help create a more sustainable future. The network seeks to support the development of technological innovations within the UK. At the very centre
“From a sustainability perspective, the key factors are best use of internal resources, people, streamlined processes and automation”
sits an ecosystem of partners that are there to support and encourage the growth of innovation.
Operating by example, PP C&A has worked hard to explore its own ESG potential. To kick things into motion, the company gained its ISO 14001 accreditation and slowly developed from there.
“We have invested a significant amount of money into solar panels for our factory roof; these now generate a large portion of our energy requirements,” Mr Hague said.
The company has also collaborated with Warwick Manufacturing Group as part of its net zero programme. This led to the installation of an ecomax voltage optimisation device, designed and manufactured by GWE Group (renowned for its high-quality, cost-saving products that help reduce energy consumption).
When it comes to social development, PP C&A has been incredibly proactive, dedicating the last 20 years to the training and engagement of its employees.
“We founded our own internal training school in 2002, and now we have an online learning platform called Bright Sparks University, where we develop both technical and processing skills, ” said Mr Hague. “We also developed STEP (Success Through Excellence Programme), which was a huge success.
“Someone once asked me ‘What if you train people and they leave?’ Well, what
if you don’t train them and they stay? Training is an investment, not a cost.”
Working with schools on a regular basis, the company also promotes engineering and other STEM subjects to young people, highlighting the exciting opportunities that exist in today’s market.
In 2022, PP C&A also produced a CSR Policy, which it will continually
review. According to Mr Hague, this was a proactive step to show all stakeholders that the company’s intentions are clear and sincere. Following this, PP C&A intends to create a more cohesive ESG strategy, which will highlight clear metrics to measure the company’s success.
Tony Hague was recognised as ‘Industry Leader of the Year’ at the 2023 National Engineering and Manufacturing Awards, which he attributed to all the fabulous staff at PP C&A.
Originally an apprentice himself, Mr Hague was particularly proud of the company’s apprentice Sophie Young, who took home the ‘Rising Star Award’.
As an outsourcing specialist, PP C&A is eager to encourage businesses to look into the practicalities of subcontracting. The company has even designed its own guide to make this decision even easier.
“There are many factors to consider when looking for the right outsourcing partner, including size and location, markets and customers already served, and engineering and production capabilities,” Mr Hague continued. “To help companies better understand the benefits of outsourcing, we have developed our own ‘3D Guide’ which details the three key phases of discussion, decision and delivery.
“The step-by-step approach in the guide takes a closer look at the main considerations and should make an organisation much more confident when deciding whether to outsource.”
There are many elements to consider when it comes to formulating the perfect ESG strategy, and PP C&A believes that outsourcing is an increasingly important one to consider.
“From a sustainability perspective, the key factors are best use of internal resources, people, streamlined processes and automation,” Mr Hague explained. “So, outsourcing can help reduce the total cost of manufacture, ensure better use of space and resources, and help manage risk and waste within an organisation.”
Another trend that PP C&A has picked up on is the increasing demand for nearshoring. As companies across the globe focus more readily on what they can do to improve, localisation has become a clear option.
“The desire to seek outsourcing supply chain partners closer to home is an increasingly prevalent one,” said Mr Hague. “It ties back to the ability to support a wider ESG strategy – which isn’t possible if a supplier is on the other side of the world.
“In a post-pandemic world, many of us have seen supply chains severely impacted, with availability and lead times being hit hard, plus the rising cost of products and transport. All of this has led to companies requiring a stronger focus on total cost of acquisition and risk mitigation strategies within their supply chain plans.
“This can only be good for UK manufacturing, but investment is needed to ensure we have the skills, competency and capacity to meet the needs that exist, or opportunity will evaporate.”
With over two decades of experience working for PP Control & Automation, Mr Hague reflected back over the time positively: “I have been fortunate to work with some great people over the years. We have
successfully advanced from a small company of 22 staff and £2.5 million in sales to a whopping 230 incredibly supportive employees and an impressive £35 million revenue – so it’s been quite a journey.” n
Lithuania-based GLASSBEL produces highend architectural glass for iconic projects worldwide. CEO & Owner Dr Dmitri Sobolevski highlighted the innovative types of glass produced by the company, along with the supportive team culture driving its sustainable operations. Report by Phil Nicholls.
Established in 2001, GLASSBEL is a leading glass processing company focusing on high-end architectural and interior glass markets. As part of its impressive portfolio of services, GLASSBEL is also caring for the environment with innovative products.
“Recently, we have developed birdfriendly glass solutions featuring laser etching,” explained CEO & Owner Dr Dmitri Sobolevski. “GLASSBEL manufactures four types of bird-friendly glass in accordance with American Bird Conservancy requirements: glass which significantly reduces the risk of bird collisions. Our solutions aim to break the reflective surface of glass by adding laser marks that make it visible to birds.
“Alternatively, we put special digitally printed patterns on the glass or interlayers which also reduce collisions. We also process special UV-patterned glass, which is not visible to humans but can be seen by birds.”
The origins of GLASSBEL’s business philosophy go back to 1993, when the team ran a facade cladding business. Therefore, the company has a deep understanding of the facade business and its requirements, leading to the successful completion of architectural projects in 29 countries on four continents.
GLASSBEL operates from a 15,000 sqm production building, with additional 1,200 sqm dedicated to its laboratory –GLASSBEL LAB and offices. These facilities enable the production capacity of around 120,000 sqm of IGUs, plus 80,000 sqm of laminated glass for many different purposes. The glass can range in size up to 3.2 by 7 metres for the entire range of products (IGU, Laminated glass, fritted glass, etc).
“We have 187 employees from seven nations under one roof, united in peace,” said Dr Sobolevski. “I am proud to say that 55 per cent of the management team are women.”
A consolidated operation at GLASSBEL places all known architectural glass processing and products under one roof, with a focus on high-end architecture.
The package of services at GLASSBEL includes every step of the process, from support at the planning stage, through project management and quality assurance, all the way to a sophisticated logistics programme to ensure safe delivery of its bespoke glass products.
GLASSBEL LAB’s steadily expanding portfolio of innovations now includes electrochromic glass and IGUs. By adjusting solar control, these dynamic types of glass efficiently manage energy consumption, reducing the need for excessive cooling or heating. This can subsequently decrease a building’s CO 2 emissions by 20%. Along with these sustainability advantages, dynamic glass enhances the aesthetics of a building, reduces glare and improves privacy. Now, that glass can be produced with irregular shapes too.
“We have also developed laminated glass with SEFAR mesh, holes and cutouts,” explained Dr Sobolevski. “These
products represent new solutions for architectural ideas and a creative approach to sustainable construction.”
The development of customised products that meet the sophisticated needs of modern architecture is only part of the appeal of GLASSBEL, according to Dr Sobolevski: “Our unique competence is not only in glass processing, but also encompasses our focus on excellent client service, close cooperation with consultants and architects, plus an orientation on deep, long-term partnerships.”
It is this package of skills that enables the GLASSBEL team to deliver an impressive
array of iconic buildings from around the world. This portfolio includes offices for global businesses such as Facebook, Salesforce, Microsoft and Google.
Glass from GLASSBEL features in the Dubai Opera House in the UAE and in the King Abdullah Financial District in Riyadh. The stunning Bahai Temple in Santiago, Chile, is clad with digitally printed glass with a dot graded digital frit. GLASSBEL is very active in the US, with successful projects including the Buffalo AKG Art Museum in Buffalo, NY, plus 270 Park Avenue and SUMMIT One Vanderbilt – both in New York City – among many others.
“GLASSBEL is focused not on markets, but on projects,” said Dr Sobolevski. “We have established a decent niche in commercial buildings for global IT companies, culture, sport, transportation and high-end residential buildings.”
GLASSBEL has an emphasis on sustainable solutions, with the company running on 100% renewable energy. “Our thinking is always long-term,” continued Dr Sobolevski.
“Therefore, we emphasise the importance of finding sustainable solutions in our pro duction process and by fully utilising any by products.”
Thus, all glass culets are returned to the float producers for reuse. Likewise, any waste from GLASSBEL’s lamination foils cutouts is recycled. This is part of the pro gramme of recycling 100% of all by products, whether glass, foils or packaging. Sustainable operations are maintained with a system of efficient water consumption and recycling, including the filtering and utilisation of rainwater. Heating at the GLASSBEL premises is achieved by harvesting heat from the production process. The result of all these measures is a reduction of CO2 emissions by 2,856 tonnes a year.
The underlying philosophy at GLASSBEL is that reputation is the foundation of relationships, as Dr Sobolevski made clear: “We keep our promises and believe that integrity is crucial to cultivating authentic growth and maintaining successful relationships.”
In following these principles, the company believes that cooperation is better than competition. The team takes an individual approach to each relationship to properly meet each partners’ particular needs.
GLASSBEL intends to apply these concepts as part of its long-term strategy. “We plan to grow not only in production volume, but in our expertise,” explained Dr Sobolevski. “This will involve further education and team training, in combination with maintaining our focus on innovation and prioritising sustainability in all aspects of production.”
When discussing this growth strategy, the issue that concerned the CEO was the challenge of political instability around the world, which in turn can lead to economic turbulence.
Dr Sobolevski remains excited about the future of GLASSBEL, seeing endless opportunities for business growth. The company has a strong programme for the ongoing development of new products and technologies. These strategies run in parallel with the mentoring and continuous educational process for employees.
In conclusion, he emphasised the underlying corporate culture of the GLASSBEL
team: “We are curious and constantly learning. We are bright personalities, united to achieve success and personal growth, all dedicated to delivering excellence for world architecture.” n
Urban Design & Developments consists of three dedicated companies, each one focused on a different area within the development of features for external building facades. Managing Director of Urban Facades Dave Newton, Managing Director of Street Structures Tim Cowley and Managing Director of Urban Windows, Doors & Conservatories Billy Hawes, discussed the group’s latest developments with Inside Sustainability. Report by Imogen Ward.
SAa collective, Urban Design & Developments has achieved an impressive turnover of circa £10 million. This accomplishment is shared by its three subsidiaries: Urban Facades, Street Structures and Urban Windows, Doors & Conservatories.
“All three businesses work out of one industrial estate on 55,000 square feet of land,” said Managing Director of Urban Facades Dave Newton. “This really helps with manufacturing and resource sharing.”
“Each company can, and does, operate as its own entity, but we often work collectively as well, which is really beneficial, especially when one part of
the group is a lot busier than the rest,” added Managing Director of Street Structures Tim Cowley. “This also helps us maintain our edge in the market.”
The group originated from a failed company called Street Scenes in 1998, when the company’s subsidiary, Street Structures, was acquired and renamed Urban Design & Developments. From there Urban Design & Developments flourished and grew, establishing three limited companies along the way.
From the ingenuity of Street Structures’ architectural metalworks to Urban Facades’ creative curtain walling – and Urban Windows, Doors & Conservatories’ expertise in the residential market – each business brings its own strengths to the collective.
“We also fabricate everything in-house,” Managing Director of Urban Windows, Doors & Conservatories Billy Hawes explained. “This helps us stay ahead on lead times and means we can reassure our clients on quality.”
According to Mr Newton, this would not be possible without the support of the
group’s suppliers, who have been selected based on their quality, reliability and sustainability credentials: “Our suppliers are a massive element of our success. We choose to work with companies that operate responsibly. When it comes to our aluminium curtain walling, windows and doors, we rely on buying our aluminium profile from Seniors Architectural Systems and Metal Technology.
“Aluminium has infinite recyclability; so it is one of the most sustainable building products to use and is 100 per cent recyclable. Recycled aluminium meets almost 40 per cent of the demand where our
suppliers are close to 70 per cent in their production. This is nearly double: and those are the kind of standards our suppliers are setting.”
With a focus on going green, the three companies have completed many successful projects that help improve the energy efficiency and carbon footprint of buildings. This includes several collaborations that have gained BREEAM good and excellent status.
One particularly noteworthy project involved the largest Grade II listed building in Europe. Undertaken by Urban Facades, the curtain walling expert was honoured to partake in the £40 million Phase 2 refurbishment of Park Hill in Sheffield, providing subcontract works to a value of £2.3 million.
“The Park Hill flats had fallen into a state of disrepair, and we were very fortunate to supply the windows, doors,
balustrades and lift shaft curtain walling f or this redevelopment project,” Mr Newton explained. “We completed this project at the beginning of 2022, and it was a huge success.”
Street Structures has also been involved in its fair share of projects for high-profile customers. One such example is its work for Ascot Racecourse Ltd. Tasked to complete trackside glazing for the ‘Windy City’ concourse, the company set to work installing four full height laminated glazed screens alongside a new internal steel structure. In addition to this, the company was also asked to install four sets of double-glazed sliding doors measuring 2.8 metres in height and a further set of toughened clear glazed doors.
“The overall aim of the project was to reduce thermal wastage at the end of the concourse, whilst also creating a warm space for guests on race days,” Mr Cowley explained. “This also helped the company reduce heating costs, because the
space had previously been open, which allowed wind to travel through.”
Off the back of this successful £400,000 project, the company has been contracted to remove and re-install windbreaks pertaining to the concourse’s adjacent entrances to reduce heat loss over the winter period. This work will be completed i n two stages, the first of which will begin in May.
As the youngest of the three companies, Urban Windows, Doors & Conservatories has been busy building its portfolio, and recently completed a successful job for the Casey Group. Embarking on the Halton Bank Apartments in Salford, Urban Windows, Doors & Conservatories aided the building’s renovation with a first-class glazing package.
“We replaced the existing timber windows with our fully reinforced,
energy efficient, white uPVC Rustique Flush Casements,” said Mr Hawes. “As per the client’s specification, these were partially glazed in some areas with A2 S1 Fire Rates Aluminium panels that featured a powder coated soft silver finish.”
With 2024 set out to be another successful year, the group intends to continue delivering high quality projects, whilst growing organically. In particular, Urban Windows, Doors & Conservatories is anticipating a busy year ahead, thanks to its new accreditation.
To undertake Green Deal and ECO installations, a PAS 2030 accreditation is required. As an installer of Building Fabric Measures, Urban Windows, Doors & Conservatories has successfully gained its PAS 2030 certification.
“This enables us to retrofit energy efficient glazing into existing dwellings,” Mr Hawes explained. “We are really ahead of the game with this, because there aren’t a lot of window companies that hold this accreditation. It includes quite an involved application process, because a company needs to produce a lot of documentation to prove it has the underlying processes to achieve efficient installation.
“Now we have this, we hope to fill the rest of the year with jobs that really leverage the accreditation.”
Residential growth is also on the cards for the group despite the current market conditions.
“2024 is set to be a challenging year for the entire industry, because people are reluctant to invest in property development,” said Mr Newton. “Despite this, we are going to remain focused on developing the residential side of the business, whilst exploring our existing customer relationships further.
“We have set our sights inwards as well to improve the efficiency of our operations, which will really help us to provide the very best customer experience.
“Whilst working for Urban Design & Developments, I have had the opportunity to leave my mark on a lot of fantastic projects, and I love being able to point them out to my kids. The thought that these buildings will likely still be here in 100 years’ time, is also really pleasing.”
“All three businesses are really great at sharing resources as well, which helps us save costs and support one another,” Mr Cowley added, in conclusion. “Everyone at Urban Design & Developments work as a team, utilising our strengths to ensure that we maintain a strong presence in the market for years to come.” n
Over the past 37 years Balco Group has carved out a niche within the construction market, providing customers with innovative and climate-smart balcony solutions. Having just patented a groundbreaking new design, CEO Camilla Ekdahl sat down with Inside Sustainability to explain more. Report by Imogen Ward.
When it comes to designing the perfect balcony, Balco Group has it down to an art form. With a heavy focus on development, the company continues to produce new and exciting products that meet the needs and requirements of the marketplace.
“We are always working to develop our products, and we are actually one of the few companies exploring balcony glazing,” CEO Camilla Ekdahl explained. “Innovation is always on our mind, that’s why we have several brands in our portfolio and a long list of patents.”
Ever since its establishment in 1987, Swedish-based Balco has worked hard to progress from a local product-oriented supplier to a market-leading innovator. From renovations to new builds – and even out at sea – the company is a pioneer of smart and stylish balcony designs.
Now operating with seven companies and brands under its wing, the group successfully delivers a bold range of patented designs for all to enjoy.
When it comes to producing balconies, Balco’s main goal is to create products that help improve people’s welfare.
“A balcony is more than a piece of metal,” said Ms Ekdahl. “It contributes to a person’s living area and gives them an additional space to enjoy in their spare time. Being able to contribute to improving people’s living conditions is a core pillar of Balco’s ethos.
“That’s why we take the design of our products very seriously. Not only do they need to be practical, but they also need to look good and make people feel great.”
Balco’s impressive portfolio is wide and diverse. One of its most popular options is the glazed balcony. Acting as an additional room, this balcony provides customers with more than just extra floor space.
“The unique element of this balcony is that it can be enjoyed for most of the year,” said Ms Ekdahl. “No matter the weather, people can use this space and enjoy the views from it, whilst still being in the comfort and warmth of an indoor space.”
Focusing on the UK’s newbuild market, the company also developed Levitate in
2020. This pre-assembled open balcony is made to be robust and is available in aluminium and steel.
“Of course, if people were to look at the price of the product alone, it is not the cheapest option, but it is by far the most convenient and cost efficient from an installation point of view. Construction companies don’t want the hassle of having to store our balcony materials, or work around our installers as they build it. By constructing the balcony at our facility and delivering it in one piece, we are saving them time, space and money.
“We are working on getting more constructions companies in other countries to understand the huge benefits of using
our Levitate product versus the traditional way of making balconies in the new building sector.”
Always ready to shake up the market, Balco has recently developed a patent-pending design that cleverly integrates heat pump piping into its glazed balconies.
“We feel this new product will be immensely popular in the Norwegian market, because it works well with their heating systems,” Ms Ekdahl commented. “Norway relies heavily on electricity for warming up their apartments and using heat pumps is a good way to reduce the need. We are working with standard heat pumps to provide heating by integrating smooth, visually appealing piping into our glazed balconies. This removes the
need for intrusive heat pump systems running down people’s walls. One system is also capable of heating four apartments at once.
“As a bonus, the system doesn’t add unwanted noise to the balconies, meaning they retain their enjoyable and relaxing feel. This is a huge advantage of ours, and it took only eight months to develop.”
Following the release of this product, Balco has several projects underway that are incorporating the new design, including an agreement with a housing association in Norway.
In 2023, the company also took on its first total supply order in Sweden, which involved the installation of glazed units and solar panels.
Having dedicated the last 37 years to creating climate-smart balcony solutions, it should come as no surprise that sustainability is an important element of Balco’s decision-making process. With the company’s glazed balconies an ever-popular
option, these stylish additions not only look great, but they have a major green benefit as well. Thanks to its design, Balco’s glazed balcony offers customers an impressive energy saving of up to 30%.
The group has also been making important changes in-house to promote a more efficient operation. Aiming to become carbon neutral by 2045, the company has installed
solar panels on its production facility and worked hard to reduce its carbon footprint. So much so, that it has already reached its 2025 target of a 20% carbon reduction in comparison to the year 2019 (leading Balco to increase this target to a more challenging 38%, which was then also reached in 2023).
“The Covid pandemic was a really important period for us, as it allowed us to take the time to really explore our ESG work and set important and achievable targets,” Ms Ekdahl explained. “Wanting to have more of an impact, we also became a member of the UN Global Compact, the Swedish Green Building Council, and we were awarded the Nasdaq ESG Transparency certification. So, we have really put in the groundwork to bring forth positive change.”
With targets in mind, Balco is also determined to grow by an impressive 10% per financial year. One of the ways it intends on doing this, is by exploring new opportunities.
“Despite the current market climate, we are optimistic in our outlook and will strive to accomplish 10 per cent growth each year over a business cycle,” Ms Ekdahl continued. “We will achieve this organi -
cally, but also via acquisitions. As we carry on through 2024 and beyond, we also intend to explore new markets and expand in the regions we are currently in. We are very big in Sweden and Norway – especially since acquiring NMT (A balcony contractor in Sweden) in early 2023 – and although we have become a big player in Denmark, there is still room to grow.”
In January 2024, Balco Group acquired Riikku Group Oy, which works mainly with construction companies in Finland. The acquisition will give Balco Group a good platform in the Finnish market, although Rikku Group Oy products are also suitable for other Balco markets.
When discussing the job role, Ms Ekdahl expressed a lot of passion for the company and the positive effect it has on other people’s lives: “If we look at the overall picture and assess how Balco is contributing, it is clear that we are helping to improve people’s lives and giving them something extra that offers happiness.” n
modDsys is a pioneering force in modular construction. Utilising the latest developments in modern building methods to perfect its innovate process, the company ensures a continuous flowing value chain, from design to onsite assembly, at any scale imaginable. Managing Director Joshua Coetzee explained more to Hannah Barnett.
ASa leading innovator, modDsys operates a one-stop-shop for volumetric modular solutions capable of building durable, affordable and sustainable buildings. The modular
build trend is growing worldwide, having been successful in the USA and the UK for several years.
“We want to take the trend to the next level,” said Joshua Coetzee, Managing
Director. “And we’ve seen it growing in the Middle East, especially in Saudi Arabia, where there have been very aggressive timelines on the new giga developments we are working on. The only way to meet such deadlines is by doing a modular build. This is where the awareness that we have created about what we do is starting to pay off – not as a business, but as an industry.”
modDsys is a relatively new company, founded around three years ago, and has enjoyed impressive expansion ever since. In just two years, the company has grown from 30 staff to 8,000 highly skilled engineers and professionals. It manages a site of 45,000 square metres, of which 30,000 square metres are under roof.
“From the start, we were privileged to take on some key clients with projects like NEOM in Saudi Arabia,” said Mr Coetzee.
“So, it’s been a bit of a roller coaster ride. Looking back, I think we’ve achieved a lot. And we’re very excited for the future.”
The innovative process modDsys uses its volumetric modular solutions to complete up to 95% of a construction project offsite, in a climatecontrolled facility, reducing build time by up to 50%. The company procures construction materials of proven quality and durability that fit each clients’ requirements and constraints.
The production process is optimised by technology ranging from robotics, to industrialised processes for improving quality, speed, consistency and safety at each stage of manufacturing.
“We have a dedicated R&D department,” Mr Coetzee explained. “They are always looking at different materials and how to
use them in new ways, and they are always developing the fabrication process; adding automation or introducing more machinery and equipment. It all boils down to being more efficient, and at the same time, not jeopardising quality.”
Modular manufacturing, by its nature, generally ensures a superior product. At modDsys, this is enhanced by a stringent quality-control team and digital technology monitoring of the entire production line.
The process also allows for total traceability. The company is able to track each component as it makes its way through the production line, ensuring process accountability, adjustment of discrepancies and warranty management.
The advantages of modular building are numerous. The aforementioned closely controlled environment ensures both the highquality of the process and the end product, as well as providing a much quicker return on investment. The commercial impact to
the client is generally more up front with modular construction, rather than with conventional building, where paying as projects progress is more common.
“And with modular building, we can focus more on procurement of the materials needed to be more sustainable,” Mr Coetzee added. “We do not have the CO2 emissions that are usually found in a conventional construction domain. Also, the risks that come from work at a site are reduced, so, we can truly add value to a construction project.”
There are, of course, challenges that come with this sort of construction too. A lot of those challenges revolve around education
and the perception of modular construction. “In the Middle East region in particular, people still tend to think they are temporary buildings,” said Mr Coetzee. “So, we often have to explain that this is a permanent solution, that we lock in the design, do the whole fabrication and complete most of the building in a factory.”
Sustainable building modDsys keeps abreast of sustainable construction practices and regularly achieves strong U-value and R-value ratings for insulation on its builds. Ensuring that all constructions are airtight also adds value to the building itself
“The materials we use are all non-combustible,” Mr Coetzee explained, “and where we can, they are recyclable too. Obviously, the goals are dependent on the project itself. Completing 90 to 95 per cent of the building within the factory minimises site work, reduces waste and increases efficiency. This means a far
more sustainable product at the end of the day.
“There are thousands of other modular fabricators worldwide, but here in the Middle East, our competitors don’t focus on the sustainable side as much as we do. Nor are they looking at efficiency, quality and waste reduction as aggressively as we are. That is something that we are consistently revisiting and making sure that we stay on top of, as the leaders in the market.”
The other clear advantage to energy efficient designs is a carbon footprint that is reduced once the buildings are in use too, meaning added long-term value for the end user.
In order to be so successful, it is vital that modDsys maintains collaborative and trustworthy partnerships with all its supply chain, based on trust and respect. “We’re always ensuring our suppliers understand what our key objectives are and that we are all on the same page,” said Mr Coetzee.
modDsys looks set to forge ahead and continue to push the boundaries of what is possible in the construction space. However; a company is only as strong as its people.
“Of course, we want our clients to be happy,” Mr Coetzee concluded. “But ultimately, we can’t do anything without our own team. The team needs to be happy first, and then clients are happy almost automatically, because the quality of the work is so good.
“Modular construction is a very exciting industry to be in, it’s so fast moving. And now we want to reach different market sectors, like hospitality. So, there are a lot of things we are still looking at and plenty of goals we are planning to hit.” n
MXM Contractors is a dedicated provider of top-quality building and maintenance services. From building works to reactive repairs, and from bathroom updates to general maintenance, the company provides a comprehensive offering for clients across the UK. Managing Director Alfred Luca outlined the story of MXM and its driving philosophies. Report by Imogen Ward and Phil Nicholls.
SAa family-owned company, a key part of the philosophy at MXM Contractors is family values.
“We all have the same targets and look after each other,” said Managing Director Alfred Luca. “We have a strong sense of community and, although we are a big group, we are definitely family orientated.”
MXM was founded in 2016 by Mr Luca who already had 25 years’ experience in the building and contracting trade. He identified a gap in the market for a building and maintenance contractor that ‘self-delivers’,
meaning one that owns the entire project from start to finish.
The initial compact team focused on quick turn around and customer satisfaction. Demand for MXM’s services grew rapidly, and today, the team has around 40 operatives, including a dedicated management team based at the head office in East London.
“Most importantly, we put people at the heart of what we do,” continued Mr Luca.
“ Such as key members of the management team like Operations Director Leon Ettienne and Finance Manager Fiona Bain. Both of them have helped fundamentally to shape the company and our culture.”
This management team has led MXM to be incredibly successful over the past few years. The company has doubled its growth and finished this financial year with a turnover of £4.6 million.
The MXM portfolio consists of a broad package of construction services to business and residential clients, along with the affordable housing sector, covering housing associations and local authorities. This portfolio includes roofing and plumbing, plus the refurbishment and installation of kitchens, bathrooms and doors.
“We deliver these projects to a high standard of workmanship and customer service,” said Mr Luca. “Both aspects are equally important to achieve hassle-free projects for our clients. MXM offers the whole package, making us the perfect one-stop shop.”
All of these services are delivered with passion and a dedication to solving problems for clients in a safe and professional manner. This customer-focused approach is now being applied to the new MXM groundworks service. This will cover fencing, landscaping, boundary walls, tarmac, concrete paths, slabs and block paving.
“Although a fairly new division, we have had particular success with groundworks,” Mr Luca continued. “We plan to invest in this further over the next two years. We
are also dedicating time and resources to advancing the experience and training of our employees, as they are the core of our business.”
Deploying such a wide range of building services, MXM has completed over 250 successful projects. However; Mr Luca wanted to highlight MXM’s 2022
work in Walthamstow: “We renovated 27 apartments to be used to shelter the local homeless. This project ran smoothly, and we completed it within just three months.
“The positive client feedback was a highlight. Plus, of course, the feelgood factor of knowing that the end user came from one of the most vulnerable parts of the community.”
The core principles at MXM reflect the company’s family values, emphasising efficiency, passion, openness and unity.
“Each member of the team, from the Managing Director to the apprentices, understands that MXM stands for customer service and results,” explained Mr Luca.
“We have processes in place to ensure that our communication is clear, accurate, timely and transparent.”
This clear communication is also vital when dealing with suppliers and partners.
MXM relies on these companies to help ensure the success of every project, no matter how big or small.
“Strong relationships and teamwork are the foundations of our longevity,” continued Mr Luca. “It's critical that we maintain healthy relationships with our suppliers and partners. We do this simply by being transparent – and through communication. For example, this means being available at all times, replying promptly to emails and phone calls, providing regular updates, and always being held accountable. All of this builds trust.”
Keeping these values at the heart of everything, MXM has secured projects with an impressive range of clients, including United Living Group, Morgan Sindall and Southern Housing.
“We also work with various suppliers, proving that no man is an island,” said Mr Luca. “These include Travis Perkins, Selco Builders Warehouse, Nicholls & Clarke Group, Faithfull Floor coverings, Screwfix, City Plumbing, and Howdens.”
With such an importance on teamwork within MXM, it is no surprise that the company has a robust staff training programme, investing in the core of the business. This incorporates the exchange of knowledge between the experienced members of the team, as well as an active participation in apprenticeship schemes. MXM is keen to encourage young people into the industry, for both field work and management roles.
In parallel with this investment in the MXM family of workers, the company is also looking at growth strategies. The new groundwork operation is a good candidate for expansion, with Mr Luca looking to double that part of the company within the next year.
MXM is also looking to improve the general efficiency of its operation, according to Mr Luca: “Efficiency drives profits and avoids needless time wasting. One way we do this is by planning our workforce deployments. There is no need for all the fleet to be on the road and operators can travel together whenever possible.
“We also ensure that we dispose of waste in as eco-friendly way as possible, often repurposing these materials where it is safe to do so.”
This ongoing evolution at MXM is all part of responding to a market that is constantly changing. Thanks to its training programme, the team at MXM is able to respond to any new requirements or trends in the market. This agility will keep MXM in a good condition for the long term.
In addition, the company is mindful of general workplace trends around diversity and inclusion, as well as staff wellbeing and mental health. This is why the HR Manager at MXM ensures its policies and practices reflect these topics.
Working alongside the passionate MXM family, it is the satisfaction of a job well done that still motivates Mr Luca. “At the end of the day, what we do is provide complete projects to clients,” he said, in conclusion. “So, each construction job is actually an achievement that helps the customer, and that is really exciting.” n
Clancy is one of Ireland’s leading construction companies. With extensive experience in both public and private projects, in sectors ranging from commercial, residential, hospitality, education, healthcare and conservation, the company is known for its in-house expertise. Hannah Barnett spoke to Director Chris Chambers and Associate Director Tom O’Malley to learn more.
the competitive Irish construction market, Clancy delivers a high-quality main contracting service, focused on sustainable growth and brand integrity.
“It’s important for us to stay controlled, manage progress and deliver quality products,” said Chris Chambers, Director. “Reputation is critical. And we have built up a strong brand in a small industry, so it’s important that we maintain that. This is a family-started, (and remains a predominantly family-owned), business.
We are into the third generation now, so the plan is to make this as sustainable a business as possible.”
Clancy was founded in Tipperary in 1947 by the eponymous John Clancy. He, and later his sons, oversaw the business for many decades, until 2013 when several executive directors were brought in to run operations on the family’s behalf. Since then, the company has considerably expanded its footprint around Ireland.
“Over the last 10 years, there’s been significant growth, development and transformation of the company,” said Mr Chambers. “At the end of 2013, we documented the five core values of the business, to drive the culture and direction of Clancy.”
These core values include safety, quality and teamwork. In 2022, a sixth was added: sustainability. “We had been
working sustainably before that, but we thought it was important to fully document it as part of the overall core values,” Mr Chambers explained. “So, we developed a sustainability strategy, and launched it in November 2022. Since then, we have achieved a lot and have ambitious targets for 2030.”
With a turnover of €92 million in 2022, the company has a stated strategy to grow to €130 million by the end of 2025. It has 150 employees, primarily operating in management, supervision or on-site logistics.
People, planet & performance
Clancy’s sustainability strategy sets out to align with the with the UN Sustainable Development Goals (SDGs). This means taking in the full range of SDGs, rather than only the environmental side.
“We have approached three areas of sustainability: people, planet and performance,” Tom O’Malley, Associate Director: Construction, explained. “And from there,
we started putting together where we’re currently at. People, for example, are our main asset as a construction company.
So, we established a baseline in terms of good health, education and gender equality, then did the same for planet and performance. And then we sat down with the directors, and worked out where we want to be, and where focus on particular UN SDGs could bring us by 2030.”
The company also established a sustainability committee to monitor the goals and establish targets, which are sub-divided into energy, waste and supply chain management, and corporate governance.
Keeping an eye on these targets are the Clancy sustainability champions, located at each site. Their role is to measure areas like waste management and fuel usage and report back to Mr O’Malley. The company also received investment from Enterprise Ireland, an Irish state economic development agency, to fund the green energy and waste management improvements.
Every year, Clancy now produces a report to show the areas it is succeeding in, as well as the areas that need improvement.
“It is not just a greenwashed sustainability document that says we are doing great,” said Mr O’Malley. “Because we really want to know if we are we on the right road, and that we can achieve the goals we’ve set.
“Our 2023 report shows the number of EVs we have and the number of people we’re putting through education. It documents our areas of climate action in terms of kilogrammes of carbon that we’re putting into the atmosphere from our fleet and our work sites, and the equivalent carbon from the amount of electricity that we’re using. We are up to 92 per cent recycling at our Dublin site, while across the country 84 per cent of our waste is being recycled.”
The extra mile
It is clear that Clancy is a company willing to do what it takes to reduce waste and improve productivity. This includes embracing the innovative lean management Last Planner System, which originated from the Toyota manufacturing facilities in Japan.
The system promotes the creation of a predictable workflow in order to achieve reliable results.
“That’s gone very well for us,” Mr Chambers reflected. “It helps to coordinate and communicate between site teams, reduce the amount of waste and improve programme outcomes on projects. We’ve done a lot of lean management training over the last few years, and it’s
come to fruition. We now consider ourselves to be leaders in these innovative methods.”
Putting the principles into action, Clancy oversaw a fast-track project to build a hospital in Limerick in 14 weeks in 2020: and during the Covid pandemic, the company constructed a 554-bedroom student accommodation scheme in Cork.
“Despite all the stoppages, disruption and supply chain interruptions, we managed to deliver that project on schedule,” said Mr Chambers. “That was probably the only student accommodation built on time that year.”
Another significant initiative for the company’s sustainable credentials is
an investment in a battery pack to run site welfare and logistics, which will be charged and maintained using one generator, replacing the use of three on the pilot site.
“The three generators would have run two tower cranes and a large welfare setup,” Mr Chambers explained. “We have invested a significant amount of money – over €200,000 – in the battery. We predict it’s going to reduce our carbon by 340 tonnes across two years, a reduction of about 80 per cent.”
Clancy works with mainly local, Irish suppliers and has developed a supplier code of conduct which aligns the company’s core values and expectations with that of its supply chain. In 2024, it began running inspections, especially with suppliers of kit and equipment, to ensure that these commitments are being upheld.
“We want the relationships to be sustainable, so we’re very strong on paying people on time, creating that partnership
approach with them and being fair and reasonable,” said Mr O’Malley. “We’re not aggressive or overly contractual with our suppliers, or indeed our clients; but keeping the supply chain close is really important to us.”
Clancy aims to grow profitably over the next decade, while maintaining its domestic position and brand integrity. This will mean continuing to develop its sustainable potential, too.
“It is key for us to show our people that they can contribute, develop their careers and make a difference,” Mr Chambers concluded. “It’s a small enough company that the efforts of employees on a single site makes an impact on our success. Engagement with staff shows them that they’re making a difference: not just to Clancy as a business, but to our goals –and therefore to the planet as well.” n
click to sections:
HOMEWARE
PACKAGING & PAPER CONSTRUCTION
ENGINEERING & MANUFACTURING
BACK TO CONTENTS
one planet – one chance – one voice
An introduction to the technology and services sectors, with news and a photo feature, followed by company profiles.
The Mercedes-Benz EQE SUV next to its 132 components, with a total weight of 65.1 kilograms. All components are manufactured from resource-saving materials as part of trajectory to make MercedesBenz’s new car fleet net CO₂-neutral by 2039.
For more information please visit: https://group.mercedes-benz.com/en/
Have something interesting to show the business world?
We are always looking for beautiful and interesting visuals of new products, innovations, buildings and technology. Get in touch and start promoting your company to the global market. media@insidepublication.com
The latest company and industry related developments from the services and technology world
Tidal Transit, supplier of dedicated crew transfer vessels for the offshore wind industry, has begun the design and engineering phase of a groundbreaking project to deliver the world’s first retrofit electric crew transfer vessel (E-CTV).
The initiative benefits from £6.3m funding from the Zero Emissions Vessel and Infrastructure (ZEVI) competition, which opened in February 2023 as part of Innovate UK and the Department of Transport’s strategic plan to develop, deploy and operate clean maritime solutions. Just ten flagship UK projects were chosen to split more than £80m in funding, with the aim of unlocking an industry-led transition to net zero.
Over the next 15 months, Tidal Transit will retrofit a diesel-powered Mercurio 20m vessel, Ginny Louise, with over two megawatt-hours of battery capacity, electric motors and propulsion pods. The finished product, e-Ginny, will not only be 100% zero emissions in operation, but also boast
increased manoeuvrability while being near-silent for passengers and passers-by.
As existing shoreside charging capabilities are severely limited, the project will expand vessel charging infrastructure by installing both an onshore charging station from Artemis Technologies and an offshore wind turbine-based charger from MJR Power & Automation. This will allow for direct E-CTV charging on location, greatly increasing the time and range that electric vessels can stay in operation without returning to port.
“This project is a significant step forward in propelling the offshore transport industry into a new zero-carbon era,” said Leo Hambro, Commercial Director of Tidal Transit. “As a Norfolkbased company, we’re delighted to be working locally with our project partner Goodchild Marine and, alongside our other incredible design and engineering partners operating nationwide, continuing to lead the way in sustainable and decarbonised offshore transport.” n
Eatron Technologies and WMG, University of Warwick, have developed an innovative new approach to estimating accurately an electric vehicle battery’s remaining useful life. This helps to unlock additional performance, greater range and increased levels of safety.
Developed with funding from the Faraday Institution, the collaborative project (known as VIPER – Validated & Integrated Platform for battery Remaining useful life) has combined WMG’s advanced electrochemical models with Eatron’s cloud battery management and integration expertise to deliver Remaining Useful Life (RUL) estimates that are more than 90% accurate.
The condition and performance of a battery changes as the cells within it age over time. If this natural degradation is not monitored closely, then it can lead to cell failures with serious consequences. Traditional RUL estimates often rely on simple voltagebased analytics that may miss complex failure conditions, potentially risking the
safety of consumers, while others that err on the side of cau tion may result in perfectly healthy battery packs being unnecessarily rendered unusable.
By accurately predicting a battery’s RUL, it becomes possible to extract the maximum performance and longevity from it, without compromising safety.
The solution developed by Eatron and WMG can be embedded in an automotivegrade battery management system or deployed across a cloud-based platform, a concept that is particularly appealing for fleet applications.
“Unlocking the hidden capacity of a battery has the potential to increase an EV’s usable range and extend its lifetime,” said Dr Umut Genc, CEO of Eatron. “There are benefits for the used EV market, too; as a result of these highly accurate RUL estimates, buyers could have confidence in the condition of a vehicle’s battery and be reassured about its ability to perform for many years to come.” n
When it comes to solar PV, energy storage and charging systems, Segen is the UK’s leading distributor with an impressive portfolio. Keen to maintain its status in the world of clean energy, the company is dedicated to investing in its growth. UK Business Development Director Paul Gregory explained more, in an exclusive interview with Inside Sustainability. Report by Imogen Ward.
When it comes to supplying the renewables market, Segen provides installers with high-quality and reliable equipment.
“Segen’s main mission is to help bring a brighter future for the world by enabling clean technology for all,” UK Business Development Director Paul Gregory explained. “We continuously adapt to the latest market developments and changes to ensure that this is possible.”
Over the years, Segen has built up a vast portfolio of products perfect for the renewables market. Supplying solely on a business-to-business basis, the company can provide solar panels, inverters and storage, as well as charging and mounting solutions.
With two decades of experience under its belt – and a plethora of happy customers – Segen partnered with Tesla to become the only UK distributor of Tesla Powerwall. Designed to store energy, Tesla Powerwall can be used for power consumption and as a reliable backup during outages.
Segen also works in collaboration with a number of highly skilled manufacturers to offer the very best equipment.
With so many products available from its website, Segen invested in making the purchasing process as efficient as possible. In 2021, the company developed Kit Builder, which features all Segen’s current offering. This software enables users to efficiently and easily design an energy storage system that is compatible and complete. The Kit Builder is the quickest way for installers to receive
a quote and comes with the added assurance of a 30-day price-lock guarantee.
“When a business opens an account with us, it is then given exclusive access to the Segen Portal, which features all our products: it shows our stock availability and our prices as well,” said Mr Gregory. “This portal also features
our Designer tool and the Kit Builder tool, which allow the client to build a complete kit for its customer – this is especially helpful for installers who are less experienced.”
Also located in the portal is lots of training documentation, and technical masterclasses to ensure engineers have everything they need to provide a firstclass installation service.
As the company begins celebration of its 20th year of operation, Segen is busy implementing plans to centralise its distribution to a single location in the Southeast of England. With almost 80% of its customer base situated in this region, Segen feels this will be
a vital step towards improving the company’s carbon footprint and opera tional efficiency.
This 265,000 square foot centre in Kent will utilise state-of-the-art management systems, to provide an improved customer service experience and a more accurate stock count.
Keen to inspire the next generation of workers, and retain the skills of its current workforce, Segen’s new distribution centre will also be home to its new academy.
“We predict a need for around 20,000 additional installers over the next five years, and currently, there is a shortage of skilled labour across the industry,” Mr Gregory explained. “This scarcity creates stagnation in the market which is detrimental to our clients, and we want them to be able to grow without being constrained by the number of installers they have. Our new academy is the perfect solution.”
As part of its offering at the academy, Segen also intends to implement an apprenticeship programme. Complete with wiring booths and a training roof at ground level, the academy will provide the perfect environment for installers (first time and experienced) to flourish.
Alongside the new centre, Segen has been readily investing in other ways to improve its carbon footprint. One of
the most prominent is the company’s work on a carbon and energy calculator.
“At the moment, we are developing this to work out our carbon savings and how much energy we have provided over the last 20 years,” Mr Gregory explained. “Once this is ready, we are going to add it to our website, providing an updated figure every time we sell another product.”
In the past year, Segen has also invested in several philanthropic endeavours, most recently in Ukraine. Working with RePower Ukraine (a charity working tirelessly to provide emergency power to Ukrainians), Segen are about to adopt a hospital in Kyiv.
“RePower Ukraine works hard to provide hospitals and medical centres with energy,” said Mr Gregory. “There’s a real energy insecurity currently in Ukraine, so by adopting a hospital, we can completely fund all its equipment. More information on how to support this can be found at The RePower Ukraine Foundation website or by contacting their UK ambassador Nick Arnold at nick@repowerua.org.”
The company is also supporting schools in their decarbonisation across the UK. There is currently an ongoing initiative in place, called Solar for Schools, that guides a school through the journey from funding, design, installation and operation. More information can be found at the Solar for Schools website. However: there are a lot of underfunded schools that are
not eligible for this scheme, which is where Segen is stepping in.
“We are donating our products to the schools that don’t make the cut,” Mr Gregory explained. “We are even looking into schools that were not eligible but are part of groups that were – all angles are being considered to really ensure that those in need are not forgotten.”
As it journeys through 2024, these initiatives are not the only thing keeping Segen busy. The company has filled its diary with lots of exciting events, from Solar & Storage in April to the InstallerSHOW in June. Segen is excited to speak to customers old and new.
“We love having a presence at events because it gives us the opportunity to promote our brands and mix
with everyone in the industry,” said Mr Gregory. “At the InstallerSHOW, we will be located in the Innovation Zone, promoting our new academy. It’s an incredible time for us as we have lots of new and exciting opportunities arising in 2024. This includes our new finance option launching later in the year, which will allow installers to offer homeowners and customers a low-cost finance option that will only be available through our network.”
In conclusion, when discussing the industry as a whole, Mr Gregory said: “We are working in an industry that is very young and dynamic. When I first joined, somebody said ‘welcome to the solar coaster’, and that is exactly what it is. There are ups and downs, but it is a thrilling experience from start to finish.” n
Netherlands-based Baril Coatings is on a mission to become 100% renewable by 2030. The coatings expert intends to achieve this through product development and adaption. Owner Teun Duijghuisen and Technical Director Joost Broeders sat down with Inside Sustainability to explain more. Report by Imogen Ward.
After taking part in a local challenge 20 years ago, Baril Coatings was inspired to implement a greener way of thinking.
“The challenge was focused on corporate social responsibility,” said Technical Director Joost Broeders. “It really opened our eyes and made us realise that sustainability was the only way forward. We wanted to keep doing what we were doing, but in a more responsible way.”
For more than 40 years, Baril has delivered coatings that are durable, high in quality and cost-effective. With extended life span and fewer harmful substances, the
company’s portfolio is brimming with low-emission paint for every surface.
Currently, Baril has several brands within its portfolio: the industrial coatings brands DualCure, SteelKote, Aquaran and Bariline, plus the decorative coating brands Copperant and fairf; All of which are formulated and manufactured in its three production facilities located in the Netherlands and the US.
With the desire to minimise its impact on the environment, Baril invested in solar panels, electric cars and a myriad of energy saving measures, which have been implemented throughout each of its facilities.
However, armed with the knowledge that 90% of its carbon footprint is generated from its raw materials, the company switched focus to its supply chain.
With the intention of becoming 100% renewable by 2030, Baril has begun the long-winded process of adapting its portfolio to reduce its reliance on fossil-based materials. As it stands, the company has successfully replaced 50% of the fossil-based content from its decorative range and a further 25% from its construction paints.
“We use organic materials within all our formulations, but we still rely on fossil-based components,” Owner Teun Duijghuisen explained. “We are working to exchange these for bio-based ingredients; however, it’s going to take a lot of time and ingenuity. Currently, we still rely on minerals for our paint pigments, which cannot be easily replaced with organic material.
“To overcome this dilemma, we are actively exploring the possibility of recycled pigments.”
Due to the high environmental strain that sourcing its white pigment creates, Baril has been working alongside the construction industry to adapt the process. Currently, the pigment is extracted from mined ore –a process where 92% of the resulting material is waste. A high impact chemical process is also required for extraction, which generates a significant amount of carbon.
“We are attempting to use the waste material from the construction industry to create recycled pigment,” said Mr Broeders. “By introducing the recycled pigment into our formulations, we will considerably reduce the carbon footprint of the product.”
Although currently still in its pilot phase, the results are promising, and Baril anticipates a market release within the next two years.
The company is also collaborating with its supply chain to develop other greener alternatives to improve the sustainability of its products.
“We are working hard to co-develop all k inds of solutions with our partners,” Mr Broeders continued. “It is difficult to get a grip on the entire chain, but we have open communication with each supplier, and we are really encouraging them to operate with economic, social and environmental values in mind.”
Some of Baril’s more popular options include its DualCure coatings. Using patented technology these offer quick curing times, without using additional energy. Although currently relying on fossil-based activators, the company is developing several biobased alternatives for these products.
For Baril, 2023 was a year of successes. During this time, the company released two biobased coatings that are designed to meet the needs of the construction industry.
“We had to run pilot tests on the formulations and then introduce them to customers to decipher whether they were compatible with their requirements,”
Mr Broeders explained. “All together, this process took around two years to complete.”
All being well, Baril expects to transition its entire portfolio by 2030. With its first biobased polyurethane topcoats expected to hit the market in the coming months.
“The speed at which we transition our products really comes down to the availability of raw materials,” Mr Duijghuisen explained. “But we intend to transition them as swiftly as possible.”
To enhance its operations whilst inching closer to being 100% renewable, Baril is developing a new C5 system that will be ready for Q4 this year. This will contain at least 40% renewable content.
“The new system will include biowaste epoxy primer and a polyurethane topcoat,” Mr Duijghuisen added. “Joining our roster of C1, C2, C3 and C4 environment systems, the C5 allows us to supply a broader range of customers.”
For Baril, conferences are a key element of the industry. To facilitate industry-wide decarbonisation, the company believes everyone will have to come together to brainstorm solutions.
In line with this belief, the company is preparing to hold its own renewables conference later this year. The first of its kind, Baril will invite all raw materials suppliers and institutions to gather and promote sustainable development.
“We really want to show everyone what is already possible, by giving them the stage to showcase their developments,” Mr Duijghuisen explained. “This is a great
opportunity to bring the market together and encourage others to contribute towards the transition to renewability.”
L inked to the company’s desire to reach 100% renewability by 2030, the conference is just one of many things Baril has planned for this year. As part of its 2024 agenda, Baril will invest in students looking to enter the industry.
“We already have an internship scheme in place with local high schools and universities, which has been running for more than 30 years,” said Mr Broeders. “We believe in helping young people achieve their ambitions, and it gives us an opportunity to better understand the changing themes within society.”
“The creativity generated by these individuals is what it’s all about,” Mr Duijghuisen added, in conclusion. “We aspire to provide the perfect environment for our employees to thrive and excel. They are the backbone of Baril, and a huge factor in our success.” n
National Windscreens is one of the UK’s most recognised vehicle glass repair and replacement specialists, employing over 600 technicians across more than 100 locations. In a fast-evolving market, the company is powering ahead on its pioneering path to sustainability and evoking change in its industry. Andy Probert discovered more, in conversation with Commercial & Services Director Simon Hunt and Environmental, Social & Governance (ESG) Manager Craig Gibson.
The windscreen is a vital part of a car and represents 30% of a vehicle’s structural integrity. When they spot a chip or crack, National Windscreens’ technicians urge drivers to fix the problem before it spiderwebs into something more serious. The intricate technology plays a key role in the safety of modern vehicles.
Look closer, and National Windscreens is doing far more than just being a driver’s friend in their hour of need. The company is setting the standard on sustainability with a detailed plan for reducing its environmental impact.
Repairing whenever possible National Windscreens always aims to repair rather than replace a damaged windscreen according to the updated standards in the BSI code of practice.
“We are not just adapting to the demands ourselves, but are collaborating with motor insurers, drivers and suppliers on our sustainability journey,” said Commercial & Services Director Simon Hunt. “We are embracing the circular economy and embedding sustainability
so that it becomes an integral part of any decision-making.”
Having developed many partnerships with major insurers, National Windscreens is also positioned at the very front of the market for fleet support. With National Windscreens having Cary Group as an integral part of the organisation, the Swedish company’s presence in ten markets across Europe will bring significant advantages for the business.
“Given our commitments to sustainability targets, Cary Group has been instrumental in sharing global best practice to help drive forward that agenda and enable National Windscreens to grow its market share in the UK,” Mr Hunt acknowledged.
The company’s current sustainability strategy was launched in in 2022, assessing all aspects of its operations, to drive towards net zero through scopes 1, 2 and 3 in the supply chain. “We are working with our suppliers and recycling partners to drive towards a circular economy by aiming to recycle 100 per cent of the 3,300 tonnes of glass replaced yearly,” Mr Hunt said.
Both Mr Gibson and Mr Hunt agreed that the company is keen to focus on
sustainability in the glass sourcing and procurement from the supply chain, while remaining committed to setting the bar across the industry.
“We strive to recycle the glass in every screen that is replaced as we understand the environmental impact of glass production,” Craig Gibson, ESG Manager at National Windscreens, added. “We have embedded practices to recycle all damaged glass alongside a commitment to reduce our ecological footprint wherever possible.
“Every tonne of glass we recycle removes the need to extract that amount of sand, soda ash and limestone from the earth’s resources. Our repair-first policy ensures our technicians will avoid replacing the glass whenever possible, and assess windscreen damage according to BSI safety standards.”
“National Windscreens is geared to creating its own momentum,” said Mr Hunt: “We have committed to a SBTi near-term target to reduce emissions by up to 42 per cent for scopes Scopes 1, 2 and 3 by 2030, in line with the 1.5-degree Paris agreement. Also, we have compensated for all our calculated emissions in Scope 1, 2, and
3 in 2022, which we account for in our sustainability report.
“Scope 3 includes indirect emissions throughout the value chain, including glass manufacturing and movement, employee commuting and policyholder travel to the fitting centres. This information is valuable for our stakeholders to understand National Windscreens’ sustainability performance.”
Foundation stone
National Windscreens published its first Sustainability Report in 2023, reflecting its many achievements in setting the industry standard and outlining its progress and targets for the future.
“It is a key foundation of our desire to innovate and lead in our glass recycling efforts, driving towards a cleaner and more sustainable future,” added Mr Gibson.
The company also assures customers that sustainability is integrated in every step relating to vehicle glass; from initial customer contact when a stone chip is found, through damage assessment and the entire repair or replacement process until a solution is provided.
“National Windscreens completed over 450,000 repairs, replacements and calibrations in 2022. The sustainability aspect of our customer offering is therefore essential, both for reducing environmental impact and for educating and inspiring employees and customers,” Mr Gibson added.
Leaning on the Nordic experience of the wider organisation, National Windscreens has begun to transition to a fossil-free vehicle fleet across its UK network. Cary Group operates with a courtesy fleet with
a majority of electrical vehicles (EVs) and EV bikes.
“Our business model is based on simplicity, speed and convenience,” said Mr Gibson. “With digital tools such as AI damage assessment, digital signatures and the move to online payment, we ensure the business offering is as sustainable as possible.”
Replacing a windscreen releases direct emissions of approximately 44kg CO2e (carbon dioxide equivalents), including production, transport and fitting of used glass. For context, repairing a windscreen has a carbon footprint of less than 1kg CO2e.
“We are striving to find new ways to inform about the benefits of repairing in time to avoid replacement,” said Mr Hunt. “We monitor and report our repair rate to ensure that we repair windscreens rather than replace, whenever it is safe to do so.
“A big influence for us is understanding our footprint and the makeup of it. Around 15 per cent of our work was carried out inside our fitting centres in 2019, but that has risen to over 30 per cent in 2023 because of the advanced technology in cars.
“With cameras, HUDs (head-up displays) and the ability to watch a movie on a panoramic screen; the complexity of modern windscreens has created new challenges for our technicians. Glass manufacturing is highly energy intensive and requires higher temperatures than steel production, so it is an eye-opener on trying to meet the sustainable targets.”
“A significant proportion of our work comes from insurers, and we share a desire with our insurance partners to constantly drive towards a more sustainable solution for
customers, whilst carefully managing costs across all aspects of sourcing, supply and fitting,” said Mr Gibson.
“National Windscreens’ emission reduction strategy is centred on procurement, transport and energy,” Mr Hunt added. “We will also continue to improve the customer experience – digitally and through our service experience – while educating them on the environmental impact of their choices.
“We presently repair around a quarter of damaged windscreens, but that compares with about 40 per cent in the Nordics. We are working with insurers to encourage proactive engagement with their clients to opt for repairs rather than replacements and help minimise that carbon footprint further.”
National Windscreens works closely with its recycling partners, such as URM, and its insurance partners, plus fleet and rental partners across the markets. It has also engaged with suppliers, including Workwear Express, and glass suppliers, to get a deeper understanding of scope 3 emissions.
Indeed, National Windscreens has recently won the LV Award for Sustainability and is the winner of the Gold Prize at the Insurance
Times 2023 Awards for ‘Sustainability Initiative of the Year’, competing against some of the biggest companies operating in the insurance industry.
“From our perspective, it is all about education and awareness on sustainability,” said Mr Hunt. “For example; the van fleet and rental market has different challenges than the insurance market. We are now trying to be more proactive in the fleet space regarding the impact on their customers.”
“National Windscreens is positioning itself to be a leading sustainable supplier of choice, while engagement, awareness and collaboration will be our keys to positively influencing the industry,” Mr Gibson said.
Recently, a team of technicians from across Sweden travelled to the UK to work in London for two weeks in a landmark exchange between National Windscreens and Cary Group. The Swedish technicians worked in the Croydon, Crawley, Watford, Dartford and Romford centres: some of the fitting centres with the highest volume in the UK.
The two-week period gave an ideal opportunity for the technicians to speak with and work alongside their counterparts to exchange the best practices from different markets across Europe and compare them to those used in the UK.
There were valuable lessons regarding the different technologies, including ADAS calibration equipment used across the markets to build a sustainable business offering. The exchange helped to bolster the transfer of knowledge between the technicians from both countries.
“We were thrilled to welcome the technicians from Cary Group for this collaboration,”
said Andy Rae, Operations Director. “It was interesting to see how the practices of the technicians differed. Enhancing the skills of our team is at the forefront of everything that we do, so we embraced bringing over the technicians to compare the differing approaches of the UK and Swedish teams.
“By joining forces, we can leverage our respective strengths to enhance operational efficiency and streamline processes. Sharing innovations, skills and practices across our network is essential to continue to improve the service for our customers.”
Mr Hunt and Mr Gibson attended the book launch of ‘King Charles III: The Leadership and Vision of a Modern Monarch’ on The King’s 75th birthday at Claridge's in London.
The contribution to the book from National Windscreens focuses on the challenges and progress made regarding sustainability, the complexities of modern
automotive glazing, and how service is at the heart of success.
“It was an honour to attend the launch in Mayfair,” said Mr Hunt. “We spoke with some fascinating contributors to the book and with the dignitaries in attendance. Claridge’s was a perfect setting for the day.
“The focus of National Windscreens on embedding sustainability into every step of our work with vehicle glass is in total alignment with the environmental focus of King Charles.”
The book charts King Charles’ life from his celebrated birth and early years, through his role and responsibilities as the Prince of Wales, to his accession and coronation. It also considers how The King intends to shape a relevant and futurefacing monarchy for the world of today and tomorrow.
“The book launch in London was fantastic and was a pleasure talking with other people who are as passionate about the environment as I am,” Mr Gibson said, in conclusion. “The aim at National Windscreens is to provide the highest standards of quality, innovation, and service, all whilst preserving the planet’s primary resources.” n
Oilon is an international energy technology company specialising in burners and heat pumps. Hannah Barnett spoke to Tero Tulokas, CEO, and Sami Pekkola, Sales Director, to find out how the family business plans to achieve its sustainability goals.
Oilon is known for manufacturing high-quality heat pump solutions that are suitable for the most demanding industrial uses. It is also a pioneer in low-emission combustion technology, with decades of experience in the field. This combination gives the company a special niche in the market.
“We are forging the path from fossil fuels to renewables by offering both combustion technology and heat pumps in our product range,” said CEO Tero Tulokas. “That is something many of our competitors don’t do. We are privately-owned, internationally based and nimble. We can help our customers move to renewables as we already have the necessary connections and know-how.”
A global operation Oilon was founded in 1961 and began exporting products in 1963. It now has a turnover of €85 million and over 400 employees, two thirds of whom are
based in Finland, the rest scattered globally in countries including Brazil, China and the US.
The company first made its name in the burner sector, which still accounts for a significant portion of revenue. It has also manufactured residential and industrial heat pumps for several decades, which began as a business decision as much as an environmental one.
“In the 1990s, Oilon started to think seriously about climate change,” explained Mr Tulokas, “and to consider our future as a business. We didn’t want to be like Kodak and become obsolete. So, we started to build residential heat pumps in 2002.”
In the same year, Oilon also established its first factory in China. An acquisition by an industrial heat pump firm in 2011 aided the development of the industrial heat pump arm. In 2014, the company expanded to another significant location when it opened a factory in the US and
Oilon was recently approved to sell industrial heat pumps to the North American market.
Oilon is part of the UN Global Compact, the world’s largest corporate sustainability initiative. The company has pledged to align its strategies and operations with the ten principles on human rights, labour, environment and anti- corruption.
As a global business, Oilon is well- positioned to promote these principles through internal efforts and co-operation. The company offers a diverse workplace, upholding high ethical standards in its business operations. Occupational health and safety is regularly monitored and audited, and Oilon holds ISO 14001 certification.
“ISO 14001 was the starting point,” said Mr Tulokas. “We are also a member of
the ABB Energy Efficiency Movement and have been ranked at bronze level by the EcoVadis certification. We are aiming to reach silver in 2024 and are participating in different forums driving sustainability in the company. Our business is related heavily to sustainability, so it’s very important that we are keeping ahead in this field.”
The company were early adopters of science-based targets according to the Paris Climate Act. By 2030, Oilon intends to reduce its own direct and indirect greenhouse gas emissions by at least 46%. The primary means of reaching these targets include using ground source heating at production facilities, utilising solar power and investing in upgrades that reduce energy consumption at sites.
“The target is for 2030, but we are ahead of schedule and have almost reached that
now,” said Mr Tulokas. “We are continuing to explore Scope 3 emissions, because that’s the biggest share of the footprint that we have.”
“The science-based targets are a very significant step,” Sales Director Sami Pekkola added: “and it really makes a big difference – because we must not only report everything, but analyse a lot of data about where the carbon footprint of the company is coming from.”
The importance of innovation Research and Development plays an important role at Oilon, with about 6% of revenue re-invested into R&D. The company has launched some truly innovative products into the market, including patented technology to reduce emissions for its burners.
“With this equipment we can go below five milligrams per nominal cubic metre of
NOx,” Mr Tulokas explained. “Usually that level is only possible to reach by secondary means, but we can reach it by direct firing. NOx is harmful for the environment, so this achievement is very beneficial.”
Back in 2010, the company began selling low-NOx gas burners that reduced CO 2 emissions from a district heating system in Beijing, reducing CO2 emissions by around 50%.
“And in 2016, Beijing changed all its gas combustion to the low-NOx technology, and we were able to reduce emissions again,” said Mr Pekkola. “We are now providing reduced-emission heating for roughly 30 per cent of the 20 million-plus population there.”
The majority of heat pumps delivered by Oilon are IoT-enabled, giving customers the option to monitor and manage devices over a remote connection and generate reports
covering device utilisation, energy output and cost-savings. Corresponding systems for burners are currently under development.
Putting its breadth of knowledge into action, Oilon recently partnered up with Finland’s leading energy company, Fortum.
Microsoft is building a data centre complex in Helsinki, where Fortum will recover the waste heat and reuse it for district heating. This is set to be the biggest heatrecovery project of its kind in the world. Oilon will supply the industrial heat pumps; the largest delivery in the company’s history, valued at approximately €15 million.
“We are very proud of that project,” said Mr Tulokas. “District heating is very famous in Finland, and a growing trend in other countries, as a highly efficient way to connect large waste heat
streams. Finland is leading by example in this area.”
Forging a path into the future, Oilon is set to continue to maintain these strong relationships with customers and suppliers.
“We work closely on R&D with our suppliers,” said Mr Pekkola. “For example , with a famous German national technology conglomerate: when they want to develop their controls, they contact us, and we develop them together. This helps us too, and that way of working is really important in order to be able to employ the best products in the market.”
Oilon’s target is to double revenue over the next five years, as the heat pump market rapidly expands. That is also set to be a challenge, as the company will need to hire and train new staff across its international locations, while upholding its sustainable ethos.
Oilon has made a special commitment to 7/17 UN Sustainable Development Goals:
#7 Affordable and clean energy.
#8 Decent work and economic growth.
#9 Industry, innovation and infrastructure.
#11 Sustainable cities and communities.
#12 Responsible consumption and production.
#13 Climate action.
#17 Partnership for the goals.
For Mr Tulokas, though, running a global business and fighting climate change is all in a day’s work.
“I think it’s important to contribute to meaningful change,” he concluded. “That is certainly the biggest motivator for me. I’ve been in the energy industry for my whole career. The dynamic international community that we have at Oilon is very significant. There is so much going on; cooperation with different nationalities, travelling around the world, meeting our colleagues and peers in the industry. It’s very exciting.” n
The Element Materials Technology Group (Element) is driven by a clear purpose: making tomorrow safer than today. With a global presence spanning hundreds of locations in dozens of countries, Element’s expertise touches nearly every aspect of the daily operations of so many industries worldwide. Dr. Mark Eldridge, Director of Hydrogen at Element, spoke with Richard Hagan.
Since its establishment in 2010, Element has seen rapid growth thanks, in part, to approximately 50 acquisitions of testing, inspection, cer tification, and calibration companies worldwide. But while the Element brand itself is a little more than a decade old, its testing and scientific origins can be traced all the way back to the Victorian era.
Materials and product testing companies, such as Element, have historically helped give the world Ford’s Model T, helped put Concorde into the sky, and helped keep Venice afloat. And now, as industries grapple with net zero commitments, Element is also playing an increasingly pivotal role in facilitating the world’s transition to hydrogen energy.
Today, Element is organized around a clear purpose: To make tomorrow safer than today. Every day, the company’s 9,500 highly – trained staff members actively support Element’s clients in materials simu lation, modelling, engineering testing, product testing, and certification across a vast array of industries and product categories including aviation, construction, power generation/energy, pack -
aging, batteries, cellphones and tablets, computers, wearables, automotive, defence, maritime, rail, food, medical devices, pharmaceuticals, and many more.
For Element’s Director of Hydrogen, Dr. Mark Eldridge, the company’s purpose has personal significance. “I want to help change the world for the better,” he said. “I’m passionate about green credentials. I have two children and I want to create a better world for them to grow up in.
A crucial part of that is the energy transition to greener, more sustainable fuels – in particular hydrogen.”
A major focus within Element is about how it can support those clients that wish to adopt hydrogen as part of their energy transition strategy. “Our customers vary from major aerospace manufacturers and
oil and gas networks to new startups in the form of hydrogen production companies,” said Dr. Eldridge. “They span all parts of the hydrogen value chain, including supply, infrastructure, and demand.”
Elements’ customers’ needs in terms of their hydrogen transition vary as widely as the industries from which they hail. Dr. Eldridge and his team at Element translate each customer’s specific hydrogen related requirements into a bespoke package of services.
“We can then align the customer with our team of hydrogen specialists who will assist the customer with reaching their objectives as fast as possible,” Dr. Eldridge explained.
The relative newness of hydrogen as an energy vector means that for many, the specific certification journey is still challenging.
“We’ve routinely operated in saturated markets in the past, where clients and the marketplace usually know what they want and need,” continued Dr. Eldridge. “But the hydrogen market is in early development, so clients, specifiers, and regulators continue to wrestle with where, what, and how hydrogen will interface with the wider energy system in multiple contexts.
“There are many different Technology Readiness Levels (TRLs). Every part of the hydrogen value chain includes customers who have differing TRL needs, so there are many different packages that we ultimately support the market with.”
But there’s one commonality across all of the packages that Element offers, according to Dr. Eldridge: “Our focus is always on enabling: ‘Engineering Hydrogen Transitions – by simplifying them, improving them and assuring the process,’ ultimately supporting our wider corporate mission of ‘Making Tomorrow Safer than Today’. We’re essentially supporting what the energy system needs to look like with hydrogen, while making things safer by design.”
A typical H2 customer journey with Element may begin with a Research
and Development phase in which the company defines what the customer wishes to achieve. Next is proof of concept, followed by full production, and then finally, infield use, typically through the engineering V-V Cycle.
Element’s vast digital and physical testing capabilities substantially speed that process up, allowing the company to carry out any number of virtual tests, before moving to physical testing at a substantial array of sites worldwide with H2 capabilities.
“Once we start linking these capabilities together, it’s clear that we have a strong overall capacity that can follow our clients’ j ourneys all the way through to commercialization and beyond,” Dr. Eldridge explained. “This is especially important –given that the world has very little time to reach its net zero targets – and allows the more timely and cost effective route through product lifecycles.
“Consequently, we are constantly looking at new methods of testing the characterization of materials in order to allow our customers to develop their products faster; moving much quicker from a demonstrator level to full commercialization, at both our sites and client premises. That’s the real power of our combination of digital and physical services.”
In early November 2023, Element acquired Filton Systems Engineering, a highly distinguished aerospace engineering and testing services firm with notable hydrogen capabilities.
A few days later, Element announced a major $10 million investment into its hydrogen capabilities - the first investment of a series to come. The injection will see the introduction of new, cutting edge hydrogen testing across multiple sites and an expansion of its global hydrogen team.
These two major investments affirm Element’s commitment to continuing to support its customers as efficiently as possible in accelerating the adoption of hydrogen as a clean energy vector.
“We play a key supporting service with many of the largest, most recognizable companies in this space,” said Dr. Eldridge. “We are supporting the development of a variety of technologies with our clients, ranging from hydrogen tank designs, EMC response on H2 vehicles and planes, to the optimum design of a fuel cell for hydrogen, emissions testing of gases and non-metallic valves, seals and components that interact
with H2; to characterizing materials for global pipeline infrastructures based on potential susceptibility to hydrogen cracking; to optimize repurposing potential, to name only a few areas. This is all with safety at the heart of everything we do through bespoke consultancy.”
In closing, Dr. Eldridge had a message for readers: “What are the H2 challenges you are wrestling with? We want, essentially, to be your Chief Engineer. Let us solve those problems with or for you, using our large global portfolio of capabilities. Whether it’s material science, design, definition, testing, modelling, simulation, or validation, the whole of Element is ready to support you in your H2 transition journey.”
Element. Engineering Hydrogen Transitions – simplifying, improving, assuring. n
Autoflame Engineering is a global manufacturer of world-class commercial and industrial combustion control and monitoring solutions that empower customers to monitor and reduce their emissions, fuel and maintenance costs, as well as increase reliability in the boiler plant room. Report by Autoflame.
Autoflame is a trusted, familyowned, British manufacturer with a global footprint. Over the last 50 years, and as an ISO 9001:2015 and ISO 14001:2015 certified company with an £8 million turnover, it has grown into a multi-award-winning export champion. Made in Britain certified, the company manufactures 98% of its products inhouse in the HQ in Southeast London. A successful global partner network of over 100 Technology Centres installs and supports Autoflame products. Many of these partners have been working with the company for over 25 years and ensure that customers have effective local support.
Autoflame was the pioneer in using microprocessors to control the combustion process. In fact, the company had a patent for 20 years, which set it apart from competitors. That innovation has continued over the last 50 years, receiving a further 37 patents for the product range to date.
“We were able to sustain such a high level of innovation by securing strong relationships across our supply chain, localising our manufacturing and testing facilities, and investing heavily in our in-house R&D,” said Steve Kemp, Sales Director of Autoflame. During the pandemic, Autoflame expanded its R&D
capability by over 50% and it has not scaled back since. This has facilitated the launch of new products, including the highly anticipated Mini Mk9.
“Many of our innovations were conceptual inspirations by my father, Brendan Kemp, inventing over 38 patented ideas,” Mr Kemp highlighted. “But we are always spending time in the field with our Technology Centres to ensure we understand first-hand, not only the product’s journey once it leaves our warehouse, but also the endless applications - from biogas to biomass”.
Autoflame is fully immersed in honing the efficiency of boilers with precise, intelligent control of everything in the combustion process from the burner to the boiler, using just one controller.
In 2022, Autoflame was awarded the Queen’s Award for Enterprise in the Innovation category by the late Her Majesty Queen Elizabeth II, for its Exhaust Gas Analyser (EGA), the Mk8 EGA EVO. The EGA monitors exhaust gas emissions to comply with environmental regulations and improve the efficiency of combustion, reducing fuel usage and harmful emissions. With a controls
and burner upgrade, customers can see typical energy savings of 10-15%.
Autoflame has a proud association with the awards. This is the fourth award that the company has won, having previously been successful in 1996, 1997 and 2007, in the Export, Environmental and Innovation categories.
Autoflame delivers precise and sustainable combustion processes across six continents. As the world progresses closer towards net zero, with tighter controls on carbon and NOx emissions, Autoflame adopts a collaborative approach. The company has built longstanding, trusting relationships with many of its Technology Centres, growing and reducing plant emissions across the globe together.
“The Technology Centres understand their market, plus the local economic, environmental and geopolitical situation, ” explained Mr Kemp.
Products from Autoflame are trusted to meet environmental targets across the globe. Mk8 EGA EVOs are frequently and quickly installed in the UK to ensure
government mandated MCPD compliance, or to assist companies that are driving their own change and setting their own emission reduction goals.
“These days, when people in the industry talk about carbon footprint, they tend to measure the amount of fuel used, which isn’t completely accurate,” stated Mr Kemp. “The most accurate way of taking this measurement is by measuring how well you're burning that fuel. The EGA can input a fuel meter, providing data on how much fuel is being used, and how well you’re burning it. From this, customers can precisely calculate a site’s carbon footprint.”
Autoflame has worked with companies and sites worldwide on a variety of applications and fuel types – biogas, hydrogen and other alternative fuels. For example, the air pollution control programme, Coal-To-Gas, implemented by China in 2016. A huge increase was experienced in the uptake of the Mini Mk8 burner controller and Mk8 EGA EVO.
These controllers assisted sites in switching from coal to gas, burning the gas in the smallest quantities with
the highest performance and minimal emissions. At the press of a button, up to three years’ worth of data on burner and boiler performance is accessible in multiple language options – safely, securely and consistently .
Fuel has been a big concern for industry since 2022. With prices rising, companies are more aware of their fuel use. Many customers require fuel flexibility, which is a unique feature of the Mk8 MM. The controller enables a rapid changeover from one fuel to another, all whilst the burner is firing.
If fuel prices suddenly increase, sites can switch for a short period to an alternative fuel. This feature is utilised by one customer firing biogas at a wastewater treatment facility. When the supply of
biogas is down, the site quickly switches to gas – preventing unnecessary downtime and keeping the plant’s process in continuous operation. Precise, intelligent control Safety, accessibility and precision are paramount to Autoflame. Its products carry worldwide approvals in every country across the world and are tested and approved by the local safety body. These include UL, CE, AGA and ATEX.
These approvals, such as ATEX explosion proof, mean that Autoflame products can be securely used in hospital boiler rooms to petrochemical plants. Working closely with suppliers and their manufacturing teams, these products meet and exceed every safety
approval in the world at no additional cost to the customer.
Autoflame has recently launched the Mini Mk9, the latest generation of its pioneering burner controller. One of the main reasons for releasing the Mini Mk9, was the redundancy of many of the components which Autoflame currently uses in the Mini Mk8. Working with suppliers –many of whom Autoflame has worked with for decades – the company has almost halved the production time and ensured availability of components needed to manufacture the Mini Mk9. This increased the overall efficiency of the controller.
One of the most unique features of the Mini Mk9 is the ability to trim the combustion process by monitoring
the UV spectrum, making instantaneous changes to combustion to increase efficiency and overall safety of the plant.
“The pre-existing process had an inherent time lag,” said Mr Kemp. “With the new UV Flame Trim, a patented feature exclusive to Autoflame, combustion is trimmed within a second of it taking place, this means there is no time lag in feeding back data and correcting the combustion process, delivering safety, efficiency, performance with very little additional cost.”
There might not be an answer as to how to get to net zero tomorrow, but Autoflame provides a solution right now that delivers energy, emissions and cost savings, along with compliance and increased safety in modern boiler plant rooms. n
Demaco Holland offers expertise in cryogenic technology. The company builds infrastructures which facilitate the transportation and application of industrial gases at extremely low temperatures. Hannah Barnett spoke to Manager Sales & Marketing Maurice Dekker and BU Manager, Hydrogen, Richard Klos to learn more about this innovative, expanding industry.
SAa one-stop-shop for the design, development, construction and installation of bespoke vacuum insulated solutions, Demaco Holland is backed by years of experience and fuelled by passion. The company delivers advanced infrastructures for the cryogenic industry and has done so successfully for decades.
“Unlike most in the market, we have a vast amount of experience,” said Maurice Dekker, Manager Sales & Marketing. “We have been in cryogenics for over 35 years
and worked with liquid hydrogen for more than 25 years, so, we have a proven track record. Our focus has always been on the quality, the know-how and the added value we bring. A project can easily take between 12 and 36 months: so we become partners with the client during that time.”
Demaco was founded in 1960 as an agricultural machinery business, but in 1985 the company started to move into the cryogenic industry, distributing liquefied gases
at temperatures between -160 and -271°C. A full focus on cryogenics commenced in 1996.
With a turnover of roughly €24 million and 140 employees, the company now provides a full turnkey cryogenics service from its 10,000 square metre facility in The Netherlands. This means serving multiple sectors including automotive, electronics, pharmaceutical and food, as well as the space industry and the growing renewables sector.
As a pioneering part of the market, the company builds equipment to transport liquefied gases in a container which minimises heat loss. Liquefication is important for hydrogen in order to transport it safely
in small volumes, and at low pressures. One litre of liquid hydrogen is the equivalent of 800 litres of gaseous hydrogen.
“Once the liquefied gas is stored, it needs to be distributed to end users, so we have developed loading bays to put it into a trailer,” Mr Dekker explained, “and that trailer distributes the liquid to a nearby storage tank. We are one of few companies that have already built these types of loading bays. It’s not just a design, it’s something that we have put into practice.”
One significant project saw Demaco build a loading arm for a Norwegian ferry company that is using hydrogen to power the electric
motors of its vessels. “In this market, there are a lot of testing facilities, and small companies that have bright ideas and a lot of money, but they don’t have the knowledge we do,” said Mr Dekker. “So, they come to us: we think with them, and build prototypes.”
The company also builds the infrastructure for large-scale projects in the space industry. These projects are typically very complex and require knowledge, expertise and engineering at the highest level.
For example, Demaco played an active role in the development and manufacturing of cryogenic piping for a satellite carrier platform with ISRO in India. This included pipes for liquid hydrogen and oxygen at very high pressures, spanning a total network length of 1.3km.
More impressively still, Demaco completed the ISRO project over 20 years ago and the infrastructure is still in use, showing not only the durability and quality of the company’s work, but its firm position well ahead of the curve.
Recently, Demaco also built 13 loading bays for a South Korean automotive manufacturer. “The customer had invested heavily into hydrogen cars and bought 200,000 units,” Mr Dekker said. “We thought it was a smart move to be investing in that space, but there is a whole infrastructure that needs to develop; from fuelling stations, storage tanks, trailer trucks for distribution, loading bays and liquefaction plants. Demaco has been able to build 13 loading bays within the past two and a half years, so that is a huge milestone in our development.”
Working this close to the cutting-edge requires strong relationships with the other companies involved.
“For projects like the one in South Korea, especially when quantities get higher, we are looking not only to suppliers, but also partners for help,” said Richard Klos, BU Manager, Hydrogen. “Because in the
coming years, it’s expected there will be real growth in this market. And ultimately, we want to be able to serve it and we need partners to support us.
“We are specialists in cryogenics, but it r eally helps to have strong partners capable of undertaking certain parts of specialised projects, in close cooperation with us. We
have, luckily, a selection of those kinds of companies located relatively near to our own facility, and we can easily keep in contact and visit them if necessary.
“Along with the size of the company, and the experience we have in a wide range of cryogenics, we also have the production capacity to transfer that knowledge into
actual projects. There are a lot of companies focusing on the engineering and maybe a few have some manufacturing ability, but our combination of know-how and capacity for production is quite unique.”
In this developing market, the availability of liquid hydrogen (and qualified personnel to design and handle the gas) remains a challenge, alongside the stigma sometimes associated with it.
“In the past, hydrogen has been thought of as dangerous,” said Mr Dekker, “and linked to an exploding Zeppelin or the H-bomb, but that’s simply the energy depth that is available from the gas. Liquid hydrogen creates the force to put a rocket into orbit: it’s very powerful, but not dangerous if handled correctly.”
Always looking ahead, Demaco has already invested considerable time into setting up a strong team of engineers and project managers, as well as undertaking
multiple conceptual designs and field studies, ready for the inevitable expansion of the hydrogen market.
“Looking at market trends, there is the concept of a ‘hockey stick’ curve,” Mr Dekker reflected. “We believe that by 2025 to 2027 onwards, the sector will have a massive boost. This is also what we hear back from our clients, suppliers and the whole community. Demaco’s objective is to grow sustainably with the curve: that is something that we’re careful about, in terms of the projects that we invest in.”
For Mr Klos, cryogenics is a market he has watched evolve, and remains an exciting
and motivating one to be part of. “I’ve worked at Demaco for 19 years,” he concluded. “And like the markets we serve, the variety of customers is completely different. Obviously, the hydrogen market is becoming bigger and bigger: a large part of my job involves being part of this new growing market.
“Together we are building a greener world and learning new ways of working as a result. There is never a dull moment.” n
OneFifty has been providing specialist exterior surface cleaning for more than 10 years. Often operating at heights other companies do not dare reach, OneFifty offers reliable and cost-effective solutions that are perfectly tailored to each job. Directors Andy Morris and Max Morris explained more, in an exclusive interview with Inside Sustainability. Report by Imogen Ward.
Armed with more than 30 years’ experience within the cleaning industry, Director Andy Morris was inspired to establish OneFifty after witnessing an increasing demand for specialist external cleaning services.
“Whilst visiting the International Cleaning Show in Holland, we saw a steam jet washer,” Andy Morris explained. “I knew that there was a demand for this, because I had always struggled to find a subcontractor to complete the task during my time within the industry. So, we took the plunge and purchased the machine. From there, OneFifty was born.”
Initially established in 2013 to fill a gap within the industry, OneFifty soon expanded its capabilities, adding graffiti removal to its growing list of services.
“ Max did a lot of research on graffiti removal to gain a greater understanding of the methods needed to clean different building materials,” said Andy. “There is an art to the science of graffiti removal to ensure the job is done properly – and without any damage to the building.”
“It’s definitely not a one-size-fits-all process,” Director Max Morris continued. “In some cases, we have to tackle multiple surfaces in one job. There can be a mixture of paints used as well, so we have to assess each job as it comes.”
It soon became clear to OneFifty that there was a huge demand for cleaning at height. Keen to provide the very best service for its customers, the company became renowned for its capability to cover areas that others could not.
Having successfully carved out its niche in the market, OneFifty also offers cleaning services for facades, windows and gutters, utilising a variety of different cleaning systems, including jet washing, pressurised steam and media blasting.
The company also offers out its fleet of Multitel MZ250 cherry pickers on an operated-hire basis.
In the years since purchasing its first pressurised steam cleaning system, OneFifty has had to refit and adjust the
device several times. Following a successful redesign in 2018 that improved performance, OneFifty decided to take it further.
“We invested a lot of money into a new design for our jet washing and pressurised steam cleaning equipment ,” Andy Morris explained. “As a result, we have improved its technical specifications and made it more reliable. This bespoke design will be used for any new systems we purchase.”
At the end of 2023, confident with its position in the market, OneFifty invested in a second cherry picker. This has helped develop the company’s capabilities even further. It is now preparing to purchase an additional larger machine.
From motorway bridges to skyscrapers, no job is too big or too small:
“We have had to close entire motorways before, and these kinds of jobs are price and labour intensive,” Andy Morris explained. “They often involve large teams and several trucks just to lay out the cones and closure signs.”
OneFifty recently completed a complex project at Ashton Gate Stadium in Bristol: this involved cleaning the steel structures on the roof of the new south and west stands. The impressive white steel poles of the structure had become badly stained by algae which made them look dirty and gave a negative impression. OneFifty was asked to remove the algae and restore the poles to their original white colour.
Last year, the company also broke the record for its longest ever job, with the completion of a six-week project cleaning hospital roofs. Although it takes the prize for timespan, this was one of OneFifty’s more straightforward projects.
To ensure the success of each project, OneFifty relies on a dedicated workforce that is equipped with a high level of knowledge and experience.
“The entire workforce is competent in graffiti removal and working at height,” said Max Morris. “Whenever we take on inexperienced workers, we pair them with experienced members for several months to give them the time to settle in and gain an understanding of the role. Someone lacking in experience can cause a lot of damage during graffiti removal, so we do everything in our power to prevent that from happening.”
OneFifty also relies heavily on its supply chain. Made up of reliable companies, OneFifty’s supply chain
is always quick to provide highquality solutions.
“It takes a long time to track down the right people to work with, and I think we have been very successful in doing so,” said Andy Morris. “We are working with the best chemical supplier there is. We also rely on G&S Penrith to supply a lot of our equipment – and on a short turnaround as well – and several of our platforms are supplied by Summit Platforms. We can rely on them to fulfil our queries as soon as possible.”
Initially overwhelmed by the amount of empty plastic chemical containers that were stacking up in its warehouses, OneFifty came to an agreement with its chemical supplier to return all its containers for cleaning and reuse.
The company also plans to make its headquarters as sustainable as possible with the installation of solar panels and a new heating system featuring more efficient heat pumps. Currently using recycled crushed glass in its media blasting, OneFifty also reuses the material across its projects, and retains all its wastewater to avoid contaminating local waterways.
“Other companies would just let the chemicals wash off into local drainage systems and waterways, but we don’t agree with that mindset,” Max Morris added.
With an eye on the horizon, OneFifty plans to continue growing. This will be achieved gradually over the next few years.
“We are always looking to grow sustainably,” said Max. “We take our cashflow and the state of the market into careful consideration before making any significant investments, because of recent inflation.”
“We would also like to acquire a new business that will allow us to expand our capabilities whilst also cross – selling our services,” Andy Morris added, in conclusion. “We are just waiting for the right opportunity to come along.
“As a family, we have dedicated a lot of time to ensuring this business thrives, and we can’t wait to see what the future has in store for OneFifty.” n
Rioglass Solar is a global leader in designing and manufacturing optical concentrated solar power and concentrated photovoltaic components
Andy Probert spoke to Jeroen van Schijndel, Chief Sales & Marketing Officer, about the company’s business development and diversification into related service fields.
Within 15 years, Rioglass Solar has become an industry leader in developing key optical components across two market segments: CSP (Concentrated Solar Power) and CSH (Concentrated Solar Heat). The former means producing electricity with solar energy, while the latter involves supplying heat to industrial and other processes with solar energy through concentrated sunlight. This is also known as SHIP – Solar Heat for Industrial Processes.
Having completed its largest-ever contract for the world’s biggest CSP Plant in Dubai, supplying mirrors and receivers
for the 3x200MW Parabolic through Units of the Noor Energy 1,950MW CSP Hybrid Power Plant – Phase IV of the Mohammed bin Rashid Al Maktoum Solar Park, Rioglass Solar has become the torch-bearer for setting industry standards.
Now, from its HQ in Brussels and with operations across Spain, the company is diversifying its business. This means supporting customers’ smaller industrial applications for heat and light solutions and developing different types of technical and maintenance services for clients.
“Rioglass Solar thrives on innovation,” said Chief Sales & Marketing Officer
Jeroen van Schijndel. “Our expanded service offerings mean we can offer a 360-degree approach to clients.”
In CSP units, oil is heated to nearly 400 degrees and later converted into steam to drive a turbine. The oil heating decomposition process creates hydrogen in a vacuum of the receivers, which can be destroyed over time and become less efficient.
Rioglass Solar has developed an online and continuous measurement system to measure the dissolved hydrogen in the HTF oils used in CSP. The tool helps measure and monitor not only this value continuously and online, but also quantity preventive and predictive maintenance to reduce the values.
“We have implemented the solution at 14 CSP plants on three continents and it is being rolled out further as clients see the advantages of monitoring this value over time,” said Mr van Schijndel. “This value was never considered in the design process for a CSP plant, but operators now plan to build in this tool from the beginning.”
Patented technology has also been designed to inject a specific gas into the vacuum, which neutralises the hydrogen and enables the tube to operate for the rest of its lifetime without further problems and to increase the solar field efficiency. “That solution has since been implemented in over 40,000 products worldwide,” Mr van Schijndel said.
Other innovations have included increasing the reflectivity of mirrors by
improving coating and reducing glass thickness, plus developing new coatings and coating processes for the receiver tubes for next-generation CSP technologies.
“We have created higher precision glass bending processes to boost the intercept factor of our mirrors,” Mr van Schijndel continued. “This is as well as finding new technologies to bring overall costs down and introducing, for example, improved heliostat mirror mounting and canting methods to improve the optics of Central Tower plants.”
Rioglass Solar has also devised groundbreaking drone thermographic technology for inspections to monitor heat emissions to detect problems and deviations, and opto-mechanical aspects of collectors in the solar field.
“Our technology for drone inspections is more precise than anything on the market,” Mr van Schijndel explained. “We are expanding that for transmission lines and PV plants. In detecting early deviations in the field, we can immediately work on preventative and corrective maintenance as part of an integrated package which means more added value for customers.”
The company also supports solar field inspections looking for deviations in components that need to be repaired, corrected or replaced. Welding services to replace valves, pumps or ball joints have also been developed, as well as new technology to test the efficiency and durability of ball joints.
“Our dedication to innovation plays a key factor in the competitiveness, productivity,
and sustainability of Rioglass Solar,” said Mr van Schijndel. “These services are offered on many continents with various customers, but it is one of continual expansion. They now account for over half of our business.”
These services further complement and consolidate Rioglass Solar’s excellent reputation within its industry. Now employing 111 people, it has offices and factories in Europe, North and South America, South Africa and the Middle East.
Having supplied more than the equivalent of 4GWe of mirrors and more than 5
GWe of receivers delivered worldwide, Rioglass Solar is the world’s leading provider of CSP receiver tubes or heat collector elements (HCEs) and glass mirrors.
Its products are the best on the market: the tempered mirrors boast low breakage rates, the highest specifications for geometry and reflectivity, and the highest absorption rate available. Its receiver tubes for linear CSP applications are built and tested for extreme environmental conditions and comply with strict standards for power piping, plus boiler and pressure vessels.
Rioglass Solar’s experience came to the fore when it landed its largest contract for the DEWA CSP Plant in Dubai, which uses CSP and PV solar technologies. It supplied high-performing PTR 90-4G receiver tubes and 8.2 Parabolic Trough mirrors for all three parabolic trough CSP units; each with a capacity of 200MWe. The complex will provide clean energy to 320,000 homes in Dubai while reducing annual carbon emissions by 1.6 million tonnes.
The innovative tempered Parabolic Trough mirror technology from Rioglass Solar has been utilised by customers worldwide for its high performance optically and mechanical resistance, where it reduces cost from an O&M perspective. More than 4GWe of these mirrors are operational and have been adapted to different trough designs and other CSP technologies.
More and more CSH technology is now being used to replace fossil-fuel based industrial heat processes.
New CSH projects are coming to the fore due to the reliability of these solar power technologies over other emerging renewables.
“We have a clear advantage: other renewable technologies are cheaper but intermittent,” Mr van Schijndel explained. “CSH is more complex; but thanks to an integrated thermal storage technology it can supply electricity or heat 24/7 and avoids expensive backup systems for the evening and night hours and is more manageable. The challenge is to make customers more familiar with the CSH technology. But it is a proven technology and provides many solutions especially when the thermal storage is considered an integral part of the energy transition. It can also be easily hybridised with PV systems.
“There are many new complexities that the industry needs to consider when searching for renewable technologies. Each industry has different needs, from
food and beverage to concrete and steel, and there is never a one-size-fits-all solution. Sometimes hybrid solutions are the best option to transition to renewables.
“For CSP, Rioglass Solar is working hard to expand its range of solutions and services to meet clients’ requirements. One of our main R&D projects is to be able to work at higher-temperature processes. If the temperatures cycle is higher, then there are more efficiencies, making the technology cheaper.”
Transparency and trust remain fundamental pillars in maintaining Rioglass Solar’s long-term customer relations and have deepened further with its service offerings. “Working so closely together, you can profit from the engineering knowledge of both and develop new technologies,” Mr van Schijndel continued. “That was the case for the hydrogen measurement tool.
“On the CSH side, alternative energies are coming to the fore due to the increased volatility in fossil fuel costs and availability, and the business risks operators are exposed to. Renewables are not the cheapest yet, but we can give industry clear visibility on the cost of installation, maintenance and service: and the sun and wind are free resources for power, and thus a foreseeable cost.
“Rioglass Solar’s technology and service advancements have positioned it at the forefront to enable it to provide greater support to best work together and provide for our customers,” Mr van Schijndel said, in conclusion. “We aim to maintain our leading position as the largest supplier of products – focusing intensively on R&D with a strong patent portfolio – and to expand our new package of services to clients to provide more comprehensive solutions.” n
BES Ltd creates cutting-edge cleanrooms, laboratories and other sophisticated facilities for the pharmaceutical, life sciences, healthcare and other hi-tech industrial sectors, developing bespoke solutions to meet each client’s project-specific requirements. Its fully integrated service combines design, digital innovation and construction capabilities to provide a complete multidisciplinary offering. CEO Zeb Ahmed explained more to Hannah Barnett.
ASboth a design and construction company, BES has plenty to offer its clients.
“We pride ourselves on providing fast track, high value-added solutions that support the low carbon economy and meet stringent regulatory requirements for the industries we operate in,” said Zeb Ahmed, CEO. “We deliver projects in a highly innovative manner because we can influence both the design initially and
then implement modern methods of construction or hybrid methodologies.”
The company, based in Rochdale, was founded in 2002 and has grown to a team of more than 150 professionals. A key milestone was reached in 2021, when BES recorded a £100 million turnover. “We have seen a period of rapid growth and had a lot of success, becoming a leading brand in the sector we operate in,” Mr Ahmed reflected. “Reaching the milestone turnover two years ago was a high point, because within a 20-year span that’s quite impressive.”
BES remains highly profitable, with a turnover of approximately £60 million for 2023, due to its low-overhead structure and lean project delivery methods. In a competitive marketplace, the company offers sustainable bespoke solutions, with
products and services that are agile, value added, optimised and tailored precisely to our client’s needs.”
The full package BES offers turnkey lifecycle project solutions including front-end consultancy, detailed design, construction, commissioning, and validation, with an in-house team of 50 multidisciplinary design consultants.
“We take extreme pride in exceeding our client’s expectations, not only with demonstrating competitiveness of the project capital costs,” said Mr Ahmed: “we focus on the project and asset lifecycle costs to ensure our clients receive best value over the lifespan of the facility operation.”
As BES operates in high tech research, development and manufacturing sectors,
the company designs and builds within the context of highly stringent regulations, where the lifecycle of a building is typically around 20 to 40 years.
“Most of our competitors still focus on ensuring that a pharmaceutical facility satisfies product regulations, and that is it,” said Mr Ahmed. “We have added to that a low-carbon sustainability agenda. We have a unique business model, which we use to benefit our clients in terms of the overall lifecycle value to them, which now includes the ability to deliver low-carbon solutions.”
In 2017, BES acquired Norwood, a leading partition manufacturer, also located in the UK north-west, with an impressive portfolio of cleanroom modular systems.
The acquisition provided complementary faculties and gave BES control over a key part of its supply chain, ensuring installations are delivered to the highest standard while providing best value for money to clients.
“Norwood provides the internal panels, or the cleanroom fit out, for our projects,” Mr Ahmed explained. “The panels are constructed with steel, which is recyclable and reusable, and some of the coatings on other products are made from very environmentally efficient materials such as rapeseed oil.”
The company can also construct modular systems in-house. This means where traditionally materials are designed to be
assembled on site, parts can be prefabricated and made in the factory, significantly reducing carbon emissions.
“We also have prefabrication facilities within the group that deliver process, mechanical and electrical systems,” Mr Ahmed added. “This means when we do a project, we can prefabricate a large portion of what we’ve designed and install it, significantly reducing the overall carbon footprint. So, we have a strong internal capability to deliver sustainable, low-carbon projects.”
It is no surprise that the BES portfolio is made up of many technically challenging complex projects, with some of the world’s leading
research, development, and manufacturing organisations. This includes state-of-the-art facilities for AstraZeneca, GSK, Pfizer, Recipharm and Johnson and Johnson to name but a few: BES has been providing facilities with products that deliver life saving and life changing products and technologies. The company also played a part in the building the national vaccine manufacturing facility during the Covid pandemic, a noteworthy challenge. “This project required very fast delivery of the actual facilities,” said Mr Ahmed. “So, we incorporated a significant element of prefabrication including modular process plant skids, energy centre equipment and the cleanroom and laboratory fit-out panelling systems. With this prefabricated modular approach and other sustainable technology selection, we can reduce carbon intensity by around 20 to 40 per cent compared with published figures for traditional building methods.”
BES is also currently working on a project for a confidential client with a capital value of over of over £80 million. As part of the site master planning, BES suggested a more flexible sustainable solution supporting the circular economy model, which can be scaled up or down to meet a range of operating scenarios and product forecasts.
“Typically, the high-tech industries require basic buildings, industrial in nature, more like a factory; so we give them various options, from designing out materials, designing out waste and designing for flexibility, longevity and disassembly for reuse and recycling at the end of life,” explained Mr Ahmed. “For example, with regards to designing our materials, structural steel is a higher density material compared to
concrete, requiring less material to deliver the same structural integrity.”
Though the low-carbon solutions can be perceived to be more expensive from a capital cost perspective, they can offer a more sustainable lifecycle cost from a whole life carbon perspective, which, according to Mr Ahmed, is something BES’s clients are becoming ever more receptive to: “They’re more willing to consider the big question on the circular economy about how much it costs to both build – and more importantly operate, something over the facility or asset lifecycle and reuse. I think for the first time, the whole industry and supply chain are becoming aligned, to try and really deliver change, challenging and moving away from the linear economic model of take, make, use and dispose.”
The company is now reaping the benefits of the loyal relationships it has cultivated with its own supply chain, with some supplier partnerships stretching back 20 years.
“We work with a range of suppliers,” said Mr Ahmed. “It means we can incorporate open innovation and develop collaborative sustainable solutions. If they want to work with us, then they must be thinking about the concept of sustainability in their operations as well. It is through the adoption of the principles of Whole Life Carbon Assessment that we are trying to create tangible measures and carbon intensity performance benchmarks for warehouse, science and technology buildings: and we have evidence from clients that they are now looking at the benefits of doing the same.”
Indeed, it is this potential for, and focus on, innovation that drives BES, and the people who run it.
“What inspires me, as an engineer, is the potential to influence what happens in the industry and being part of the thought leadership, heralding change and transformation,” Mr Ahmed concluded. “That really supports the company’s vision of being the leader in the marketplace, by providing these regulatory-compliant, high value-added sustainable solutions.
“We are unique in our capabilities, and we have the opportunity to actually design, implement and evaluate these strategies and the solutions that we profess are the right ones. So, the journey ahead is extremely exciting.” n
EVENT PARTNERSHIPS
HOMEWARE & FOOD
PACKAGING & PAPER
CONSTRUCTION
SERVICES & TECHNOLOGY
BACK TO CONTENTS
one planet – one chance – one voice
An introduction to the engineering and manufacturing sectors, with innovations and news, followed by company profiles.
The latest company and industry related developments from the engineering & manufacturing world
Brusche Process Technology has secured a contract from the Austrian company OMV, a major player in the energy industry. Brusche Process technology will design and construct a process installation for OMV, aimed at capturing CO2 emissions from the company’s processes.
Limiting CO2 emissions is crucial to combat climate change and such a pilot installation is a significant interim step towards the necessary sustainability of the energy industry. The captured CO2 can be utilised for the production of sustainable raw materials and fuels.
The pilot installation will be designed and built at Brusche Process Technology in Almelo. Subsequently, the installation will be transported in parts to one of OMV’s sites in Austria. There, the installation will be assembled and prepared for commissioning by Brusche’s technicians. This final phase is expected to take place around March 2025. In total, this represents approximately 12 person-years of work for the Almelo-based company.
Brusche Process Technology
spe cialises in the development, engineering and construction of innovative sustain able process installations, including pilot and demonstration installations. The company has specialised knowledge in CO2 capture and reuse. It collaborates with universities and research institutions, such as the University of Twente.
Founders Ewald Kosters and Andy Roeloffzen have a vision to bring their knowledge and extensive experience to the market, coupled with an ambition to contribute to the energy transition and societal sustainability through innovative process technology.
“We want to work joyfully on beautiful innovations,” said Mr Kosters. “You can see that in the enthusiasm of our team and in the projects we are privileged to help develop.”
“It’s gratifying that in the third full year of our existence, we have already gained the trust of such a significant player as OMV,” Mr Roeloffzen added. n
West & Chester Council has approved groundbreaking plans by EET Hydrogen for the first large-scale, low-carbon hydrogen production plant (HPP1) in the UK, located at the Stanlow Manufacturing Complex in Ellesmere Port, Cheshire.
Consisting of two plants (HPP1 and HPP2), the hydrogen hub will enable local industrial and power generation businesses to switch from fossil fuels to low-carbon energy. This will help to reduce the North West’s carbon emissions by 2.5 million tonnes every year –the equivalent of taking 1.1 million cars off the roads.
The hydrogen will be used locally by the Essar refinery and other major manufacturers in the region, including Tata Chemicals, Encirc and Pilkington, to create the first low-carbon refining operations, glass and chemicals manufacturing sites in the world. The EET Hydrogen hub will help to secure and grow vital industries, create jobs
and unlock billions of pounds of related investment.
EET will develop the hydrogen hub in phases with the first plant (HPP1) at 350MW capacity, the second (HPP2) at 1,000MW capacity and an overall target capacity of 4,000MW+ by 2030. These plants are critical to meet the UK’s hydrogen and industrial decarbonisation targets and enable the critical hydrogen infrastructure.
The development is a key pillar of HyNet – the UK’s leading industrial decarbonisation cluster. Construction is anticipated to start on HPP1 in 2024 with low carbon hydrogen produced at the site by 2027 . n
A state-of-the-art tidal turbine blade has been manufactured in Scotland for the first time. Engineers believe this could reduce the cost of tidal energy.
HydroWing has designed an innovative new barge which will help drive down the cost of installation and maintenance for its patented tidal stream array technology.
HydroWing is designed to be a cost-effective and scalable solution to tidal streamenergy generation and was the largest tidal stream project in Wales to be successful in the UK government’s latest Contracts for Difference round, having been awarded a 10MW project at the Morlais tidal energy site in Anglesey.
Commercialisation of the tidal energy sector has so far been held back by high operations and maintenance costs. HydroWing’s next generation technology addresses that challenge head on.
The HydroWing technology offers a modular, reliable solution, based on its unique patented design. The wing system streamlines operations and maintenance by allowing for removal of sets of tidal energy turbines without the need to remove or work on the foundations. The new Quad Hull Barge is the latest innovation to the HydroWing system, which further increases productivity and drives down costs.
“By using four hulls connected by crossbeams and arch support beams, the limit to load width is dramatically increased,” said Richard Parkinson, MD of Inyanga Marine Energy Group, the parent company of HydroWing. “Where commercial vessels would typically need to place the load onto the deck with little to no overhang of the load, the Quad Hull Barge locks the load after lifting to the arch. This reduces offshore handling and makes the operation much safer. It means that the width of the load can be independent of the vessel width.”
The company has filed a patent application to protect its unique Quad Hull Barge design. n
As of 2024, the entire popular and high-performing Tundra range of refrigerant air dryers from Hi-line Industries will transition to R-513A, a refrigerant with zero ozone depleting potential that helps customers to enhance their sustainability credentials.
Although Hi-line attributes the success of the Tundra range in compressed air applications to its ultra-reliable performance, energy efficiency and reasonable price tag, the introduction of R513-A and its zero ODP means there really is no need to go anywhere else for refrigerant air dryers.
R-513A (Opteon™ XP10) refrigerant is a hydrofluoroolefin (HFO) based replacement for R-134a. Ideal for use in medium- and lowtemperature refrigeration products, such as Tundra air dryers, R-513A offers 56% lower global warming potential than R-134a, delivering long-term sustainability and F gas legislation compliance.
Notably, R-513A resides in the A1 (nonflammable) safety class, making it an ideal retrofit candidate for R-134a, while offering very similar cooling performance. R-513A also provides negligible temperature glide to ensure reliable performance day after day.
Despite the new innovation in refrig erant development, Hi-line intends to hold pricing for the Tundra range firm throughout 2024. This initiative will help customers combat challenging trading conditions and remain competitive in their respective industries.
Tundra refrigeration air dryers are in widespread use across UK industry, improving the quality of compressed air, protecting valuable assets and outperforming rival technologies in energy efficiency by minimising pressure drop and lowering absorbed power. Among further features driving Tundra’s energy-efficient characteristics is a patented single-cell heat exchanger, which delivers highly efficient heat transfer at low energy costs, and a link between the controller and condensate removal valve for minimum loss of compressed air during condensate discharge. n
Tummers Food Processing Solutions is the globally recognised leading specialist in the development and improvement of processes in the potato and tuber processing industry. Head of Sales Edwin Langbroek spoke with Richard Hagan about how the company’s latest investments will ensure its continued market leadership.
Tummers Food Processing Solutions, based in the Netherlands, specialises in the development, design, manufacture, installation and maintenance of processing equipment for the global potato industry. Selling to customers
ranging from major multinationals to family-owned companies and emerging processors, businesses around the world rely on Tummers’ machinery to reliably and consistently produce the highest-quality products every day.
The company offers a comprehensive package of products and services, all of which are sourced from within its manufacturing facility in Hoogerheide, in the province of North Brabant. This includes the whole scope of any project, from sales and project management through to engineering, production, shipping, installation and commissioning.
That immediately sets the company apart from the competition, according to Edwin Langbroek, Head of Sales: “We have the entire scope of supply in-house,
including all of the deliverables needed to support our customers from A to Z. This enables us to have full control on the quality of every step in the process.”
For its electrical controls, Tummers Food Processing Solutions trusts the Eltra Group
to provide it with the highest quality electrical control equipment for its various processing lines. Tummers’ relationship with Eltra extends back to the early days of both companies. “We grew together,” said Mr Langbroek. “We’re part of what they do and vice-versa; we’ve experienced mutual growth both in terms of volume and professionalism. It’s a great example of a successful partnership and it’s comparable to the way we partner with other companies as well.”
Tummers’ potato flake processing machinery has always made a substantial contribution to the company’s revenue. Potato flakes are a core ingredient in a wide variety of food products, including stackable crisps/chips, many different fabricated snacks, gnocchi, instant potato mash, soups, potato croquettes, sauces, thickeners and various other products.
“A lot of products in the supermarket that don’t have the shape of a potato or even the original texture of it, are made with potato flakes,” revealed Mr Langbroek.
The potato flake market has seen sustained growth and Tummers Food Processing Solutions has consequently continued to enjoy notable success in this area, particularly in developing economies. “There has been worldwide growth in processed foods such as snacks, but also in frozen products and ready meals,” said Mr Langbroek. “Growth in India and China has been especially strong.”
But Tummers’ continued growth in these and other markets is not left to chance; Indeed, it is by design.
At the start of 2024, Tummers Food Processing Solutions proudly opened the doors to its brand new, state-of-the-art research and development laboratory. The Tummers Innovation Centre has been specifically designed to allow the company to carry out advanced testing and prototyping for its customers – not only in terms of potato processing, but that of other food materials, too – including starches, proteins, yeast and algae.
“There are so many different potential applications of our technology that it’s very useful for us to have this facility,” explained Mr Langbroek. “It allows us to work with our customers to find the right application for drying their product.
“Our growth in markets such as China and India is due to our continued product development using the latest technology. Since 2019, we have really stepped up our development programme, and our highly skilled R&D department is our latest step to ensure that we remain the industry leader in these and other markets.”
In one of its latest and most significant technological breakthroughs, Tummers Food Processing Solutions has introduced a new evaporation process for its potato flake drum dryers. This E 2 E SteamClosure promises to vastly reduce the energy
required for potato mash evaporation. The groundbreaking new system captures, processes and reuses the vapour produced during the potato mash drying stage, resulting in energy savings of approximately 70% versus the traditional drum dryer system. The energy recovered from the reuse of the vapour is then used to generate steam to power the drum dryer.
“We believe that the conventional means of powering a flake line is not sustainable and won’t last,” said Mr Langbroek.
“By exploring this new method of running a flake line, we can drive the drying process with electrical energy instead of gas.
The energy required can be generated by renewable sources such as solar and wind. That’s how we see a factory of the future.”
In addition to this innovation in the evaporation process, Tummers offers a similarly revolutionary system for steam peelers, the E 2 E Condenser.
“We now have a system to recover the energy that is normally just lost and turn
it into usable hot water that we can reuse in the factory’s process,” continued Mr Langbroek. “We focused on the two biggest energy consumers in a potato processing line – the steam peeler and drum dryers. Now, by reusing as much energy as possible from the steam exhausts, we have been able to eliminate emissions, lower energy costs and generally drive more sustainable factories.”
Tummers Food Processing Solutions is happy to announce that in 2024 it will open its first sales office in the United States. Located in Boise, Idaho – the heart of America’s potato industry – the new office will open in partnership with Southern Fabrication Works, a local specialist in industrial food processing equipment. This physical presence in the important United States market promises to further increase Tummers Food Processing Solution’s own share in the US.
Simultaneously, Tummers will begin a joint venture in India with Food Processing Technologies India (FPT India). Tummers has enjoyed a long-term relationship with FPT India who have represented Tummers in the subcontinent for many years, and this JV is a natural extension of that successful relationship. The JV will initially see the opening of an Indian sales and service office, but it is also hoped that it will later incorporate a fabrication facility.
Concluding, Mr Langbroek emphasised the company’s high-quality offering: “We have the best flake lines in the world in terms of end-product quality, capacity, ease of operation and reliability. These are the most important reasons why customers choose Tummers.
“We truly are ahead of the competition. With that in mind, we look forward to continuing our growth worldwide.” n
Aeristech is renowned for its market-leading development of hydrogen fuel cell technology, and the company’s latest project is no different: as it helps to change the public transport scene, COO Luke Read explained more, in an exclusive interview with Inside Sustainability. Report by Imogen Ward.
With a knack for innovation, manufacturing and engineering firm, Aeristech is a prominent player in Project HEIDI, a consortium focused on the electrification of London’s public transport sector.
“Larger vehicles such as commercial, on and off highway and buses, are where hydrogen technology really shines,” said COO Luke Read. “Project HEIDI is an excellent test to show peopl e just how capable our technology is.”
Entering the automotive scene more than a decade ago, Aeristech was quick to build a reputation with those in the industry.
“The company evolved in 2010 from the idea of being able to spin up an electric motor very quickly, with speeds in excess of 100,000 rpm,” Mr Read explained. “This was accomplished using a patented method of controlling the motor. Initially, this technology was used to investigate fully electrifying a mechanical turbocharger, to
allow for easier downsizing of internal combustion engines, which would result in an emissions reduction.”
From there, the company went on to explore the electrification of superchargers, whilst continuing its development of downsized internal combustion engines. In 2015, following Dieselgate, development of internal combustion engines became less desirable, and Aeristech made the decision to reduce its R&D in this area.
“At that time, we noticed the emergence of hydrogen fuel cells, which, just like diesel engines, require a supply of compressed air,” said Mr Read. “Similarly, because they are also used in mobile applications, the fuel cell compressors also needed to be compact and power dense. Then in 2019, battery electric for passenger vehicles really came into its own.
“Now, we produce high-speed electric compressors for on and off highway commercial applications using our patented technology.”
When it comes to London, the city is known for a number of things, including Big Ben, the Tower of London and its iconic red buses. The latter are about to become even more iconic for a reason relating more to the colour green than red.
One of the UK’s most prominent ongoing projects relating to green hydrogen is Project HEIDI. An abbreviation of Hydrogen Electric Integrated Drivetrain Initiative, HEIDI is set to electrify London’s red doubledecker buses, and Aeristech is one of the companies making it happen.
Joined by Aeristech are the University of Bath, Equipmake and Bramble Energy, the
“As we look to the future, we would like to capitalise further on the platforms we are generating for the APC projects and start getting them out to a much wider audience”
likes of which will combine their knowledge and expertise to develop the hydrogenpowered buses ready for the 2026 deadline.
“Bramble Energy is producing the fuel cells, and we are developing the compressor to supply the air to the cathode side of the fuel cells,” Mr Read clarified. “With that, the main challenge for us is to produce a compact compressor that will meet the requirements of Bramble’s fuel cells, whilst allowing them to generate the power necessary to run the bus.”
This process is particularly challenging due to the requirement for oil-free compressors, meaning the systems are required to run at high speeds without the aid of lubrication. Thankfully, Aeristech has vast experience in developing oil-free compressors.
“When it comes to oil-free compressors, the bearing technology is key,” said Mr Read. “We use a foil-air bearing which allows the compressor shaft to sit on a cushion of air that acts in place of the lubrication.
“Of course, foil-air bearings bring their own set of challenges because they do not have the load capacity of more traditional bearing types. This becomes a real issue when looking at the axial force applied on the compressor, so further steps are required to make the system work. To overcome this, we have dedicated a lot of time to developing elements of thrust reduction into our designs.”
Aeristech is developing 40kW high-speed oil-free turbo compressors for Project HEIDI and expects the first prototype to be ready for delivery in April 2024. At this stage, the compressor is expected to hold a technology readiness level (TRL) of 3 – offering experimental proof of concept. Following the success of this prototype, the company plans to progress to TRL 5 in July 2025, with the validation of the technology in the relevant environment.
“Our 40kW turbo compressor prototype generates a significant amount of axial force,” Mr Read explained. “That’s on the higher end of what our competitors can achieve at the moment. So we have an exceptional handle on the force on our machines.”
Keen to remain on the cutting-edge of the industry, Aeristech exposes all its products to rigorous testing, ensuring it maintains some of the top speed units in the industry. To achieve this, the company relies on bi-directional power supplies which enable it to recover energy used during testing. This is then used to
supplement the company’s energy demand, and any excess is put back into the national grid.
According to Mr Read, the success of Aeristech can be attributed to the strong partnerships it has developed over the years. The company is proud to be part of the Advanced Propulsion Centre’s (APC) programme for accelerating the transition to a net zero automotive industry. Through APC, the company met Cummins Turbo Technologies, an important partner that has supported Aeristech’s exploration of prototype development.
“As we look to the future, we would like to capitalise further on the platforms we are generating for the APC projects and start getting them out to a much wider audience,” said Mr Read. “In the next 12 months, we want to be able to start supplying these on a more regular basis, especially to markets in North America and Asia. We also want to simplify the core of the product to make it more modular, allowing
us to address more markets and develop a simpler supply chain.”
The supply chain is, and will continue to be, an important element of Aeristech’s journey towards the mainstreaming of hydrogen fuel.
“There’s still some way to go – mainly when it comes to the supply chain and ensuring the technology remains reliable,” Mr Read concluded. “We are used
to technology being incredibly reliable, especially when it comes to internal combustion engines, so we must ensure that continues on to the next platform of technology. With that in mind, we are probably still around five to ten years away from becoming mainstream. Despite that, now is absolutely the time to begin integrating this technology, and it is an incredibly exciting time for everyone involved.” n
Carbody is a leader in the design and engineering of pedal, clutch and brake systems from technical plastics for automotive platforms. The dawn of the electric vehicle has given the 60-year old company added impetus, while breakthrough contracts from German powerhouses BMW and Audi have consolidated Carbody’s influence in the industry. Managing Director Stéphane Charre assesses the company’s performance in a discussion with Andy Probert.
ASa smart solutions provider, Carbody has always stood for safety and innovation. Those principles are the main drivers in its pioneering engineering approach to products made from plastic and rubber
for automotive platforms. The Reimsheadquartered entity’s core offerings include pedal systems, rubber hoses, steering column seals and insulation moulded parts to protect from fluids, noise, dust and heat.
“We not only manufacture parts, but design and test them,” Managing Director Stéphane Charre said, acknowledging Carbody’s growing recognition as a platform provider. Essentially, an automotive platform is a vehicle’s structural underpinnings, such as components, sub-assemblies and functions.
Carbody’s showcase products include complete pedal systems with clutch and brakes based on polyamide plastics. Air management components found in air extractors located in the body of a car – balancing the internal and external air pressures – are also manufactured from plastics.
Other products in Carbody’s portfolio include energy-absorbing and safety bump stops for bonnet and tailgate applications, body seals and plugs, and steering column seals or grommets for cables between the body and doors.
Carbody’s engineering competencies include material, structural analysis, seal design, acoustic and process development. Three factories in France and one in the Czech Republic provide manufacturing excellence in rubber, plastic and foam products, as well as assembly.
The company also has a presence in Turkey through three partnerships, and a subsidiary in Morocco with two partners.
Mr Charre elaborated: “These reflect Carbody’s strategic expansion of its geographic footprint to match customer expectations for platform businesses.
“As our name suggests, for a significant part of our product offering Carbody is primarily a platform provider, being more linked to automotive platforms than a specific model.
“Being a platform provider with good geographic coverage, Carbody offers scale savings as the client wants a single supplier: and for contingency reasons, they require two production locations. So, we had to expand, and we did that with the support of our partners in countries where we had no presence.”
Typically, these collaborations see Carbody handling the product design, client relations and the production on owned sites, while partners are responsible for managing production and quality by complying with Carbody’s standards.
Carbody has duplicated this arrangement by opening a commercial subsidiary in Germany to tackle the German automotive OEM market, and has clinched contracts with BMW and Audi. Mr Charre said: “We have been a supplier to BMW for steering column seals for the i20 electric model for a few years now.
“The breakthrough with Audi was only achieved this summer. This is against the tough period in which the automotive industry found itself. It is a testament to our capabilities, as Germany is a hard market to break into.”
One of Carbody’s critical successes has been to operate independently in the automotive sector, while being part of parent group Bavaria Industries. “Our parent group is immensely supportive while granting us a lot of autonomy in our areas of expertise,” Mr Charre explained. “That has enabled Carbody’s rapid reaction time.”
Over the past five years, Carbody has navigated the automotive industry crises of Covid, a raw materials shortage, spiralling energy costs and rising inflation. “It has been a very tough period,” he said. “Nevertheless, we have shown great flexibility and reacted fast to the fluctuating demands of the marketplace.”
This has included adjusting the opening hours of its factories on a weekly basis by responding to demands according to the orders received from its clients. Mr Charre reflected: “It has been destabilising, but
demand has dramatically fluctuated over the past three years. That agility is in our DNA and culture.”
While Carbody is financially sound, it continues to invest and achieve the right
balance by protecting the company without undermining its future.
The company has developed a lightweight solution for its brake pedal systems, with the brake pedal not being 100% metal. This is now progressively equipping one platform from Stellantis, a constellation of 14 iconic automotive brands and two mobility arms.
“Steering column seals have become very complex over the years and are facing another challenge with the dawn of electric vehicles,” Mr Charre said. “The first step of the product line was to deal with two contradictory constraints: to be fully watertight and as close to the intermediate driveshaft as possible, while not causing friction on the shaft or disrupting any sensors.
“That was a very technical compromise to find – to meet both criteria. It was a key challenge and a driver in developing this product and then to supply BMW.”
The other aspect was dealing with the acoustics in an electric vehicle, according
to Mr Charre: “We had to adapt the steering column seals to deal with the noise emissions of the EV, and we became a recognised expert in that space.”
The steering column seal was a ‘good summary’ of what Carbody represents. “These seals are made of rubber, plastic and foam, which are our core processes,” Mr Charre continued. “They come with strong acoustic expectations, another competency of ours. We now serve many German and French OEMs, plus Jaguar Land Rover, and we are recognised as a smart solutions provider. It is an increasingly important product for Carbody.”
A French government edict asking companies to reduce energy consumption by 10% over two years has been more than met by Carbody. “We will hit 10.8 percent energy savings by the end of 2023, one year ahead of target,” Mr Charre said. “That’s due to a combination of things, including new equipment, moving our hydraulic injection moulding presses to electric.
“The electric injection presses consume up to 70 per cent less electricity than hydraulic presses. Our sustainability journey is progressing very well.”
He reflected the company was primed to rapidly surmount the challenges it faces on a day-to-day basis, rather than worrying about the unpredictable: “OEMs know they can rely on Carbody for rapid reactions and agility. Meeting these engineering challenges has positioned Carbody at the forefront of its sector. Our culture is ‘we say what we’re gonna do and do what we said’.
Carbody is also where it is because of the commitment and dedication of its staff.”
The company is set to continue its expansion in Europe and is considering a presence in China and North America, given OEMs’ predominance to work as global automotive platforms.
He added: “Our challenges are tied with the rise of electric vehicles: the needs for heat and sound insulation are increasing, and new smart functions are required on existing solutions.”
Carbody is also focused on sustainability, energy-saving and maximising recycled materials use in some of its products. “We have very high technical competencies,” Mr Charre concluded. “We are driven by continuously looking at innovations and to develop our DNA as a smart solutions provider.” n
Denco Fluid Systems is renowned as a leader in the design and manufacture of systems including bespoke oil recirculation, heavy-duty grease, conveyor and chain lubrication, and cooling water. Hannah Barnett spoke to Ian Hussey, Sales Director, to find out more about the company’s decades-long history and recent rebrand.
The supplier of choice for numerous end-users and international manufacturers, Denco Fluid Systems provides high levels of professionalism, design competence, workmanship and specification-compliant products. This is backed up by experienced installation and commissioning services.
The company is a one-stop-shop for lubrication and cooling; priding itself on the full offering from design to drawing, contracting, manufacturing and aftercare spares sales for products: and Denco is staffed by the best in the business.
“We have, and retain, some of the UK’s leading experts in their respective disciplines,” said Sales Director Ian Hussey. “From the sales teams to design and application – including our 3D modelling and production engineering professionals – we provide a seamless service to our clients. This reinforces our continued repeat business.”
Denco was founded in 1948, and during the first 30 years the company specialised in worldwide lubrication tools. It also pioneered close-control air conditioning equipment and produced compressed air-drying systems.
Hydratech and Denco celebrate their 20-year partnership
Hydratech’s market leading heat transfer fluids, glycols, antifreeze, inhibitors and water treatment chemicals are proven to provide precise, stable, temperature control and comprehensive system protection. Hydratech brands such as Coolflow, Thermox and Purachem have become synonymous with the applications they're designed for – making them the go-to choice for Denco and many other industry leaders. Denco have trusted Hydratech’s products and unrivalled customer service for over 20 years.
“EVERYTHING WE PROVIDE HAS ENERGY CONSUMPTION AND EFFICIENCY AT ITS HEART: PARTICULARLY
THE COOLING WATER SYSTEMS, WHERE ENERGY CONSERVATION IS OFTEN PARAMOUNT TO THE CLIENT’S PROCESSES”
A management takeover commenced in 2000, when the Denco Lubrication Division was sold to Bijur Delimon, part of the family-owned IMCI Group.
“We have grown from humble beginnings, with a £3m operation, to where we find ourselves today, at a record turnover of £15 million,” said Mr Hussey. “The core of Denco has remained with our lubrication heritage, but it has not been the single contributing factor towards our growth.”
Indeed, the company has recently undergone a brand change to symbolise
the wider level of services on offer. “Our legal entity hasn’t change: we’re still Denco Lubrication Ltd,” Mr Hussey explained. “But we have altered our name and our logo and put wavy lines in front of the words Denco Fluid Systems. That is intended as a new message; the wavy lines represent the level of fluid handling we are capable of.
“We run lubrication systems on many of today’s major rotating machinery applications. But we also do fluid spraying systems for cooling purposes. So, this is a more focused brand name, as we think
it is really important for us to acknowledge that we do fluid systems too.”
The new name not only encompasses all the trades and services Denco is capable of, but ties in seamlessly with its partner company, Hellan Fluid Systems, based in Cleveland, Ohio. The two companies account for around £50 million of the £400 million portfolio of the IMCI Group.
As part of its ever-evolving path of collaboration and diversification, Denco is keen to promote its Hellan Strainer Division, which provides online cleanable strainers, reducing the manual process of cleaning baskets.
Another area that has rapidly expanded is the BDi Cooling Division, providing bespoke heat rejection cooling skids to a wide range of industries. Operating at the forefront of cooling technology, the
division offers design, manufacture, service and support for water, oil and specialist fluid-based cooling and chiller systems. Clients are located across multiple industries including steel mills, oil refineries and specialist manufacturers for aerospace and defence.
The Denco aftersales and spares department ensures that all products are maintained quickly and efficiently by keeping extensive records over decades. One of the company’s key strengths is its ability to provide spare parts for everything it produces.
Denco has been based in Herefordshire since the 1940’s. Over time, the growth of the company has seen the regular expansion of production facilities; from three small business units to two additional factory facilities. In line with this continued growth, the two factory units are about to expand to four. This demonstrates the
company’s continued success and the demand for its products.
“The recent approval for a premises extension has permitted further investment in our own tools and equipment,” said Mr Hussey. “This is another pivotal time in our development; making our selfdelivery services more sustainable and allowing us to be competitive in the markets we operate in.”
Representatives from Denco recently attended the FPSO World Congress in Singapore. This gathering of key industry stakeholders set out to explore best practices in strengthening the future of
FPSOs by navigating market and supply chain uncertainties to drive FPSO projects on-time and on-budget. Denco plans to exhibit more extensively in the coming years, bouncing back from the challenges brought about by Covid and its aftermath.
“Attending major shows such as the FPSO World Congress gives us direct contact with delegates and the ability to use physical models to demonstrate our products,” Mr Hussey explained. “Today’s world is often one of vendor portals, where human interaction is lacking. Communicating online only makes it harder to understand the true benefits of a different way of doing things. The show allowed us to meet over 70 delegates and to forge connections in that region far quicker.”
The company upholds a family ethos: that suppliers are an integral part of the efficient running of its business.
“We take great pride in our suppliers, and in return, they are paid on time, to the terms agreed,” said Mr Hussey. “The business supports this model to maintain our approved supply chain, and our credit ratings therefore remain to the best standards we can operate to.”
Denco is embracing its sustainable potential. The company has converted its facilities to LED lighting and maintains a policy of energy reduction where possible, with efficient heating and cooling systems. This principle is also passed on to client designs, with the most efficient solution for an application always highlighted, as well as the associated benefits in any sales activity.
“All of our systems are bespoke and r arely repeat in their designs,” explained Mr Hussey. “Everything we provide has energy consumption and efficiency at
its heart; particularly the cooling water systems, where energy conservation is often paramount to the client’s processes. This is no more apparent than with industries like power production where heat rejection must be as efficient as possible.”
With a focus on the continued growth of each of its divisions, Denco looks set for a sustainable and profitable future, driven by the skills of its staff.
“ Our diverse sectors represent the largest opportunity for increasing customers and business,” said Mr Hussey. “The company needs product design professionals in all areas and maintaining this skill set has sometimes been a challenge. We continue to offer apprenticeship s for our future engineers and support our home-grown talent through their career. This has worked for decades, and we are proud of our long-standing employees and the value they bring to our business.” n
As world leaders in loading solutions, Joloda Hydraroll has been supporting global logistics since 1962. Marketing Manager Gary Warner outlined how the focus on sustainability is driving growth at the company. Report by Phil Nicholls.
From reduced journeys to pro moting circular economy practices, the logistics solutions from Joloda Hydraroll help clients generate savings in efficiency, carbon and costs.
“For example, our loading solutions reduce the number of forklift trucks customers require by an average of 20 per cent,” explained Marketing Manager Gary Warner “This is achieved by installing our automated loading systems in clients’ warehouses, which removes the need for forklift trucks in the loading areas altogether.”
The company was founded as Joloda Transport in 1962 by Mr GB Johnstone, following his development of the skate and track trailer system. Since then, the company has been on an extraordinary journey, bringing innovative loading solutions to customers around the world. After several name changes, the company rebranded as Joloda Hydraroll in 2021.
Today, the company has nearly 250 employees, with offices strategically positioned across the UK, Europe, North America, South America and Asia. Joloda Hydraroll is headquartered in Liverpool, has its production facility in Anglesey, North Wales, and works with more than 30 distributors across five continents.
Over the years, Joloda Hydraroll has installed more than half a million loading systems worldwide and is currently ranke d 32 in the UK Fast Growth 50 Index for the North of England.
The team of experts at Joloda Hydraroll work as partners to find each client’s loading and unloading requirements. The team is on hand to automate, innovate and make every manual solution more effective.
Every product from Joloda Hydraroll is made to exacting standards, delivering solutions that are expertly designed and engineered to suit specific needs. The team works closely with each client to create the ideal solution to any loading problem, then helps the customer manage and maintain them too.
The company can develop customised solutions for automatic or manual loading options, or even a combination of the two. Joloda Hydraroll has experience in developing everything from production lines and warehouse solutions to truck loading and handling air cargo. Expert
engineers offer a full bespoke service to clients, including the design, manufacture, installation and service of innovative loading solutions.
With projects across many industries, from the automotive to FMCG sectors, Joloda Hydraroll provides loading solutions for all kinds of problems.
Loading solutions from Joloda Hydraroll help customers limit their carbon footprint, and maximise the efficiency of clients’ delivery operations – meaning improved deliveries and fewer trucks on the road.
“Our loading system and delivery optimisation also allow clients to increase efficiency and output using the same number of HGVs,” said Mr Warner. “On average, an automated system reduces loading time from 35 minutes to five minutes. This means a decrease in the number
of vehicles that our clients need to purchase, as well as a smaller fleet required to perform their operations.
“We have seen a reduction of more than half in the number of HGVs required by our clients to fulfil their quotas. Based on ou r estimated carbon savings and the average cost of diesel HGVs, we expect that for every HGV purchase avoided, our clients will save approximately 44.2t CO2e.”
Joloda Hydraroll embeds environmental stewardship in everything it does. For example, the company procures 100% of its electricity from renewable sources in Europe and at its UK Liverpool site. Joloda Europe’s carbon-neutral forklifts are powered by 100% renewable electricity and 40% of its UK models are electric.
The company procures sustainable materials such as those from Hydro Aluminium UK, that use 78% recycled aluminium, while Joloda’s batten blocks are
made from 95% recycled plastic. In 2022, Joloda Hydraroll attained carbon-negative status for the second year in a row, by investing in global sustainability projects.
“We are established as global leaders in loading solutions due to our 60-year heritage, proven engineering prowess and dedication to innovation,” Mr Warner continued. “Our commitment to tackling the climate crisis is another core pillar of Joloda Hydraroll’s business culture. We firmly believe we have a duty to society and the planet to provide efficient, carbon-lean solutions that meet the business demands of our clients, without compromising the needs of the natural world.
“Increasingly, we are seeing partners and clients ask for our support to reduce their emissions, and we are able to quantify for them how our systems and products can help achieve their reduction targets.
“Companies in the materials handling and intralogistics industry are making environmental changes, but the research we conducted showed that many felt external pressures to do so. We want to let companies know that with the right strategies, sustainable goals can be hit at the same time as achieving the essential improvements in performance needed to meet financial growth.”
Growth continues at Joloda Hydraroll with the new modular Powered Cargo Roller (PCR) system for the air cargo industry. The system is the first of its kind that can be retrofitted to any standard trailer due to its unique, low-profile design. With a PCR system, the loading and unloading of air cargo can be completely automated.
The new PCR unit is now available as part of Joloda Hydraroll’s range of Modular Rollerbed Systems (MRS). The MRS concept transforms any standard trailer into a rollerbed vehicle for handling all types of air cargo equipment, including PMC pallets and ULDs. Rollers are activated pneumatically so that air cargo can be rolled in and out of the trailer without the use of forklifts, helping road feeder service companies load and unload their vehicles more efficiently, sustainably and safely.
Modularity is a major advantage of all Joloda Hydraroll rollerbed systems, allowing for both easy installation and removal. The system is simply mounted on top of the existing floor of new-tobuild or existing vehicles, without the
need for civil works. MRS modules or MRS with PCR modules are delivered pre-assembled and ready for quick installation in workshops (or by trusted bodybuilders) within a matter of days. Additionally, this modularity ensures the system can be removed and reinstalled into another vehicle during fleet renewal, maximising the module’s longevity and value.
Joloda Hydraroll grew at the start of 2024 with the acquisition of Actiw Oy. Based in Finland, Actiw is a leading provider of automated loading solutions for the unmodified trailer market. This acquisition is an important milestone in Joloda’s Hydraroll’s growth strategy to increase global market presence by expanding its suite of loading and unloading solutions.
As growth and innovation continue at Joloda Hydraroll, the company remains dedicated to being a sustainable operation.
“We’re continuously looking at new ways to reduce our carbon impact across the business – from switching to renewable energy, to further decarbonising our fleet, ” Mr Warner said, in conclusion. “We have committed to formalising our net-zero strategy by March 2024.
“At Joloda Hydraroll, we strive to help lighten the load for businesses around the world, and regularly review how to solve our clients' problems. The company is continually optimising our existing portfolio and thinking of ways to innovate solutions. Additionally, the company is always looking to develop our presence in other, new global markets and we have exciting acquisitions in the pipeline that will help strengthen our portfolio and service offerings.
“We expect these to lead to many interesting projects for customers to and contribute further to our growth targets.” n
Utilising its reusable and eco-friendly bag seal, We Seal plays a vital role in keeping industrially produced bread fresh. Having successfully conquered this sector, the company is now turning its talents to table-top sealers. CEO Richard Hobson revealed more, in an exclusive interview. Report by Imogen Ward.
WESeal has taken sealing by storm with its innovative bread seals. Successfully holding 95% of the UK’s bread seal market, the Leeds-based company is in hot demand.
“Since 2016, we have more than tripled in size and turnover,” explained CEO Richard
Hobson. “We’ve successfully doubled our manpower, we are operating 24 hours a day, and we are now exporting to 21 countries in addition to supporting all the major household names in the UK.”
With roots dating back to the ‘70s, We Seal is well equipped to offer the market the very best resealable and recyclable bag sealing options.
“Our seals are 100 per cent recyclable, and they are also helping to combat food waste, purely through the retention of freshness,” Mr Hobson continued. “Our seals can add more than a day to the shelf life of bread.”
In 2016, the company proudly acquired the intellectual property for the machines that apply its seals to bagged bread. The company has made significant mechanical improvements since then, and, among other things, the machines are now capable of processing 10 times more seals than previous generations.
“As a result of several very tactical acquisitions, we own the intellectual property of our machines, which dates all the way back to the 1970s – when this style of packaging was first introduced,” Mr Hobson said.
We Seal’s machines are not the only element to receive a revamp: the company recently patented a new design for its seals, making them more user friendly.
“We have adjusted the way we cut our seals, to introduce an angled edge,” Mr Hobson continued. “From a consumer perspective this is a very simple idea, but
Innovia is a material science company and major producer of speciality BOPP (polypropylene) films using ‘Bubble’, Stenter and Cast technologies. It holds a leading global position in the markets for high-performance coated packaging, tobacco overwrap, graphic media solutions, label and security films.
Our films are sold to brand-owners, end-users and converters across the globe. They are used by some of the world’s best known brands across a variety of consumer goods.
Innovia employs over 1,400 people worldwide and has production sites in Australia, Germany, Poland, Mexico and the United Kingdom, all with a focus on high-quality value added products, Research & Development, and excellent service.
editorial mention
it is actually a very clever way to provide an easy lift edge, without completely redesigning the product.”
Following year-on-year success, the company is setting its sights on a new sector. Fully aware of the frustration that consumers face when trying to open freshly sealed produce from butchers and green grocers, the company has designed, developed and patented the easy to open Fresh Seal.
“Most people will probably be familiar with the torment of trying to open a bag of fresh produce that has a tape seal on it,” said Mr Hobson. “After wrestling with it the only solutions are to rip the bag or cut off the seal. We have recently patented an easy open & reseal solution that is polypropylene based, allowing it to be recycled with the bag. A lot of the tape currently used in this market is incompatible when it comes to recycling.”
Expected to hit the market by the third quarter of 2024, Fresh Seal joins the company’s growing portfolio of 100% reusable and recyclable seals.
Fully aware of the environmental impact that can be caused by an abuse of plastic, We Seal has worked hard to ensure its seals are environmentally friendly.
Following the introduction of new legislation in the UK, recycled content became a huge focal point for the pack -
aging industry. As a result, We Seal spent a lot of time researching chemically recycled plastics (CRP), with the hopes that this could be the perfect solution for its seals. After securing a deal with its supplier, the government guidelines were changed once again, and CRP was no longer a viable option.
“Following a lot of work on our end, the government decided there wasn’t enough CRP in circulation for it to be used as a recycled material,” said Mr Hobson. “CRP was pulled from the legislation at
the last minute, leaving us to seek out something else.”
Ever determined, We Seal did not give up and set to work implementing a different solution. With the government agreeing to the use of post-industrial recycled waste, We Seal decided this was the route to take.
“We have to follow the legislation: and of course post-consumer plastic is not food grade, so that’s why we landed on postindustrial recycled waste,” Mr Hobson continued. “This is waste material that is created within the manufacturing process: it then gets extruded and fed back into our products.”
Although this is the route currently being undertaken by We Seal, the company is open to adapting in the future. One area it is interested in is biopolymers. However, being a small manufacturer, We Seal understands that it is not in a position to drive market change this development would therefore depend on the direction of the market.
Implementing improvements
Always eager to advance its technologies and techniques, We Seal recently entered into a Knowledge Transfer Partnership with the University of Derby. The two entities will complete a partially government funded research project costing more than £250,000. It is expected to last around two years and will help We Seal find new ways to improve and innovate.
“We Seal operates with five main pillars: our employees, our supplier partnerships, our customers, the quality of the products we manufacture and our ability to innovate,” Mr Hobson explained. “We are constantly searching for new ways to innovate and make our products better, with the environment and the consumer in mind.
“In line with this commitment, we have been awarded a Knowledge Transfer Partnership with Derby University. This university will look at our current methodology and find ways to best improve our materials and techniques.”
There are several exciting solutions that Mr Hobson could see being offered as a result of this Knowledge Transfer Partnership: “There may be a way to incorporate composite materials into our machinery designs. Also, we would be interested to look at the orientation capabilities of our machines. When bread is packaged, it travels along a conveyor belt horizontally. Other produce, like apples for example, are sealed vertically, and our machines are currently incapable of doing this. We are very interested in adapting our machines to meet this need.”
Following the two year period, We Seal expects to be in a position to move to the next stage, where it will begin to implement initial improvements.
As We Seal gears up to tackle this new project, the company also hopes that 2024 will be a year filled with more export opportunities.
“Given that the growth of this business will be export, we are excited to be seeing
huge opportunities worldwide as more and more bakeries are putting sustainability first, and looking to move away from the old-fashioned sealing solutions which can’t be recycled,” Mr Hobson said, in conclusion. “When the time comes, we are ready to invest in local manufacturing, whether that be in the US, Canada or Australia. This will really enhance our presence and expand our capabilities.” n
Poole-based Parvalux Electric Motors Ltd made its name by manufacturing fractional horsepower electric motors to a high standard. In 2018, the company joined the maxon Group. Being part of the Swiss motor manufacturers operations has ushered in a new era of investment in people, machinery and facilities. Doug Sheppard, Managing Director, explained more about the company’s growth strategy to Hannah Barnett.
Parvalux is the kind of company that provides the full package.
“We have been designing and building geared motor solutions for over 75 years and have a vast knowledge base and expertise,” said Managing Director Doug Sheppard. “We work with customers as an extension to their engineering team; supporting the specification and development of a solution, customising geared motor solutions or designing them from scratch.”
Parvalux was first established in London in 1947 to provide motor rewinds and repairs. In 1957, the business relocated to
Bournemouth, where it started designing and manufacturing complete gear-motor units for industrial applications.
In 2008, Parvalux acquired Essex-based EMD Drive Systems, nearly doubling the company’s turnover in the process. The Clark Group’s longstanding ownership of Parvalux came to an end in December 2018 when maxon, a specialist for mechatronic drive systems, acquired the company.
Most recently, a new Parvalux House development project began in 2021 after purchasing the 8.75-acre site in Poole. The new site broke ground in January 2022, and opened in the summer of 2023. This has brought together three factories and offices under one roof, representing a £30m investment from maxon into Parvalux’s future.
A range of sectors
Parvalux geared motors are found in hundreds of applications, including healthcare, leisure, mobility and transport. The company’s decades of experience creating motors and gearboxes mean it can offer thousands of AC, PMDC and BLDC motor options.
“Anyone might have experienced the operation of a Parvalux motor without even realising it,” said Mr Sheppard.
“We are the force behind opening and closing automatic doors in buildings, operating windscreen wipers in trains, helping people retain independence in their own home via stairlifts and hoists, and our products even make light work of positioning the caravan on a family holiday.”
One particularly unusual application for the company’s geared electric motors is within a child-sized miniature electric car, the Firefly Sport, designed to give 4- to 10year-olds an insight into driving with the goal of instilling excellent road safety practises and driving skills early on.
Developed by UK-based Young Driver, the Firefly uses a twin rear mounted PMDC right-angle motor-one per rear wheel,
in combination with a Parvalux GB9 right-angle worm wheel gearbox, optimising torque control for an enhanced driving experience. “Young Driver selected Parvalux motors thanks to our exceptional performance, including high starting torque and controlled speed delivery,” Mr Sheppard added.
Parvalux has been striving to improve its sustainable practices. This means an approach to business that does not negatively impact the environment, community, or society as a whole. The company instilled this ethos into its new facility.
“As a manufacturer and employer, we have considerations to ensure a sustainable future for us and our customers,” said Mr Sheppard. “For the new factory project this meant targeting net zero emissions. The new development gave us an exciting opportunity to make a step change, so we set the goal for Parvalux House to be carbon neutral.”
Ultimately, the new building achieved an impressive 5 A+ rating for efficiency, meaning it actually performs five points better than carbon neutral.
The high rating is partly thanks to 1,500 solar panels on the roof; the largest single array on a building in the area. The panels generate all the energy requirements for the operation of the building, and air source heat exchangers provide heating and hot water without gas-powered boilers.
Other features include highly rated thermally efficient composite panels and energy-efficient glass, both critical components for achieving stable temperatures inside year-round. These flagship
features are underpinned with additional details like movement sensitive lighting and energy-efficient bulbs.
All these factors combine to deliver a 75% reduction in grid energy consumption, reducing CO 2 emissions by 343,857 kg per year.
Despite this admirable milestone, Parvalux does not look likely to rest on its laurels, as the commitment to sustainability is an ongoing one. “As we grow, we will keep looking at how we can continue to stay carbon neutral,” Mr Sheppard explained. “Surplus energy from the solar panels will be fed to over 50 EV and e-bike charging points to encourage the switch to electric transportation and support CO 2 emission reductions.”
With the company’s net zero emissions targets in mind, Parvalux was careful in the selection of both partners and mater ials when constructing the new facility.
“We chose architects with credentials and expertise in designing energy-efficient buildings, and selected contractors who shared our net zero goal to work together to identify materials and construction methods accordingly,” Mr Sheppard said.
By recycling 7,000 tonnes of bricks and concrete from the old structures as part of the foundations for the new building, a sustainable approach was established from the start.
The main challenge was balancing energy efficient materials with cost considerations, though Parvalux had the advantage of financial support from parent company maxon.
The composite panels were selected for their thermally efficient properties, to provide insulation and management of internal temperatures. They were also manufactured in the UK, at facilities powered by 100% renewable energy. The panels feature a hybrid insulation core
which is HCFC-, CFC- and HFC-free and were cut to size at the manufacturer to eliminate onsite building waste.
The new building remains the starting point for the company’s sustainability journey and heralds a bright and sustainable future for Parvalux.
“We are on a growth trajectory and by 2030 it is envisaged that we will double in size, which meant designing a building that could support that growth,” said Mr Sheppard. “It was designed for minimal external maintenance, and the ability to extend through seamless modular expansions into the land at the rear of the site.”
With numerous challenges facing manufacturers around the world, having an effective and loyal network of suppliers has proved key to ensuring success. The
Parvalux purchasing team works closely with its supply chain, to ensure materials and components are delivered to exacting standards within agreed timescales.
“Joining the maxon family saw a change to our sales operations,” concluded Mr Sheppard. “Our products are now supplied worldwide via the global maxon network, which means there are now local sales engineering representatives in almost every country in the world.
“The international sales force has significantly increased our reach, and demand for products is increasing. Where some manufacturers are seeing a slowdown, Parvalux has a strong order book, and we are continually improving processes. We are investing in people to keep pace with the strong demand, which looks set to continue throughout 2024 and beyond.” n
Thanks to innovation and acquisition, Panolam Surface Systems® offers the largest selection of integrated surface products. With more than 80 years’ experience, the company continues to grow and adapt to the evolving needs of the market. Senior Director of Marketing & Design Patricia Rongitsch, Senior Director of Environmental & Safety Jeff O’Hearn, and Creative Director Debbie Stach explained more, in an exclusive interview. Report by Imogen Ward.
Having been in the business for more than 80 years, Panolam Surface Systems has a rich history within the integrated surface sector.
Originally based in Canada, the company developed its brand Panolam® in the 1990s to promote particleboard and Thermally Fused Laminate (TFL). After moving the corporate office to the U.S. in 1999, Panolam purchased Pioneer Plastics which specialized in High Pressure Laminate (HPL) under the brand Pionite ® at its Auburn, ME facility, and its Conolite ® aircraft laminate at its Morristown, TN site.
Creative Director Debbie Stach further explained: “The business expanded once more in 2006 with the purchase of Nevamar ®, which, at the time, was a competitor of ours in HPL. The following year, we installed a new Fiberglass Reinforced Plastic (FRP) production line at our facility in Tennessee.” In 2015, Panolam consolidated its Nevamar and Pionite HPL products into the Maine facility.
Panolam’s distributor partners play a crucial role in reaching its target audience and ensuring the success of its products
These partners function as an extension of Panolam's sales force, bringing valuable
expertise and connections to diverse customer segments.
Distributors possess deep-rooted relationships with architects, designers, and fabricators – the key decision-makers in specifying HPL for various projects. This local market knowledge helps Panolam navigate regional trends and preferences, ensuring its product offering aligns with specific demands. Distributors are brand ambassadors, actively promoting Panolam's integrated surface solutions to their networks. They possess product knowledge and can effectively showcase the unique benefits and applications of Panolam's offerings, influencing buying decisions at the ground level.
Importantly, distributors also provide crucial logistical support. They stock inventory, allowing for faster deliveries and reduced lead times, which is vital in fast-paced construction projects. Additionally, they manage order processing, invoicing, and even offer value-added services like cutting and edge-banding, streamlining the buying process for Panolam's customers.
One important factor always considered at Panolam Surface Systems is sustainability. Since 2009, the company has been FSC certified, and it partners with paper suppliers who carry the same accreditation.
“We also ensure that our wood suppliers for our particle board production line are included in our FSC certification program,” Senior Director of Environmental & Safety Jeff O’Hearn said.
With many of its products being wood based, Panolam Surface Systems is proud to be saving wood fiber from being burned or landfilled. Currently, its TFL consists of 80-90% wood fiber, and its HPL is manufactured with up to 60%. These products also come with a life expectancy of 30 to 40 years.
“All our wood fiber to produce particleboard for our TFL process comes from secondary sources; we do not chop down any trees for the process,” Mr. O’Hearn explained. “This includes waste material from lumber mills and sawmills and
a portion of post-consumer material. We also recycle our cooling water so we don’t rely on a continuous supply of fresh water, and we have transitioned our facilities over to natural gas to help reduce our carbon impact.”
The wood dust generated from the company’s TFL process is also combusted for energy, to reduce the amount of waste going to landfill.
“Additionally, our HPL plant has invested in a new air compressor system,” Mr. O’Hearn continued. “This has reduced our energy usage significantly.”
Dedicated to reducing its carbon footprint even further, Panolam Surface Systems has spent the last year and
a half developing a new digitally integrated Decorative Surfaces Guide.
This system is designed to be an easy access alternative to wallboards and sample binders, reducing the need for unnecessary paper usage. As an additional bonus, the system also saves customers time and space, whilst also improving the sustainability of sample selection.
“The Decorative Surfaces Guide has been a huge undertaking for us,” Director of Marketing & Design Patricia Rongitsch explained. “We had noticed that many clients were shrinking their physical footprint, and a large wallboard was no longer practical for them.
Sustainability was also a huge deciding factor: we had countless binders filled with sample chips that were just sitting around, and it felt unnecessary.
“Of course, we still offer our physical chips to those that request them, but we really wanted to create this digital binder to provide our customers with a choice.”
The Decorative Surfaces Guide features all the company’s integrated surfaces, allowing designers to narrow down their choices digitally before requesting a much smaller range of samples. This has been available since Summer 2023 and has been extremely popular.
As Panolam Surface Systems is heading through what is set to be another successful year, the company is doing so with several new product launches.
Designed to bring people closer to nature, the company’s Walk in the Woods collection features eleven
new laminates (eight wood grains and three solid colors) which promote indigenous wood.
“The Walk in the Woods collection launched in November 2023 and was designed to spotlight not only indigenous species but also how laminate is made” said Ms. Rongitsch. “So, it tells a story about our raw materials.
“The paper that we use for our solids is sourced from the famous Arches Paper Mill in France. It is exceptional for its unique properties that allow pigments to
penetrate the cellulose fiber in an absolute wash of color. This color saturation is due in part to Arches’ ancient artisanal processes and the unique water properties of the spring-fed brook that runs through the mills land.
Another recent addition is the company’s new fingerprint resistant finish called Modern Matte. Currently taking the industry by storm, this type of finish has been incredibly popular; but Panolam Surface Systems’ stands out from the crowd in a unique way.
“Unlike other fingerprint resistant finishes on the market, which are typically only available in solid colors, our new product can be purchased with any pattern – woodgrain or solid – and in HPL and TFL,” Ms. Stach explained. “We are the first company in the U.S. to do this.”
The company has also been working closely with Material Bank (a US-based company that offers a wide selection of free material samples), which currently features Nevamar and Pionite samples.
“What we have found since collaborating with this company is that the number of overall requests has increased, but the number of sample requests has decreased, which has been a really positive outcome,” said Ms. Rongitsch. “Designers order samples with specific intent.”
Designers are creating design boards online and ordering samples that get shipped together, resulting in a saving of energy and fuel. These samples can also be returned to the company for reuse.
“This is just one of the ways that we are making a difference in 2024,” Ms. Rongitsch concluded. “To be able to help our end users in a positive way is incredibly important. There is a wonderful team working here at Panolam Surface Systems that is passionate and motivated to help make our customers’ visions a reality.” n
Founded in 1992 by three engineering partners with the goal of exploiting materials technologies and pushing the boundaries of what was possible with polymers, Advanced Plastics has since grown to become the largest privately-owned injection moulding business in the UK. Aided by its high-tech, high-efficiency sites across the UK, the company has steadily grown not only its production capabilities, but also its market share and its turnover. Group Sales Director Michael Hadfield spoke with Richard Hagan.
Following the company’s establishment by engineers Peter Thompson, Glyn Barrick and Rob Anderson, Advanced Plastics quickly found a niche with its ability to rapidly convert concepts into production jobs.
That would lead to the company’s successful penetration of the automotive sector only a year later, in 1993. This major milestone would go on to define a substantial part of the company’s journey, with projects over the years being completed for the likes of Ford (parts for the Fiesta and Mondeo models) and flagship Jaguar vehicles.
A further milestone was reached in 2006 when Advanced Plastics was sold to its original founder Rob Anderson and partner Chris Pearson (formerly Ford Business Unit Manager of Nifco). The company rapidly diversified into the HVAC and filtration sectors, all whilst continuing to prove its ability to develop technically challenging applications for its core automotive clients. Turnover, meanwhile, increased from £2.75m in 2006 to £38m in 2023, and its workforce grew to 317 staff.
Today, Advanced Plastics boasts highly automated, world-class manufacturing
facilities located in Hull, Fareham and Manchester. Across the three sites, the company owns 70 injection moulding machines ranging from 22 tonnes to 1,600 tonnes. The Hull facility boasts several fast-cycling high efficiency, low energy all-electric machines that specialise in high cavity, high volume mass production. The company continuously invests in the latest and most efficient machinery, delivering premium products from its three stateof-the-art facilities.
Across its machinery assets, Advanced Plastics is able to offer several speciality manufacturing services including Foam in Place (FIP) technology, within which it produces over 500,000 sealed mouldings per year, and over moulding and 2k
moulding, in terms of which it produces several million parts per year.
The company’s Hull facility is a particular highlight for its advanced Industry 4.0 technology. It features a fully integrated Enterprise Resource Planning system, real-time monitoring of production machines and six axis robotics on each machine, while offering significant assembly automation.
However; according to Group Sales Director Michael Hadfield, Advanced Plastics’ high-tech manufacturing capabilities are only half of the company’s secret to its success: “We recognise that people are the key to our ability to continue achieving the quality and performance demanded by our clients. Attracting talented individuals and developing them within the Advanced Plastics way, immersing them within our core values of Partnership, Respect, Integrity and Commitment is critical to our success.”
This combination of highly skilled and motivated staff and high-tech machinery was put on full display during a significant project involving the manufacture of parts for a consumer product, as Mr Hadfield explained: “Our team worked closely with the customer’s design team to establish cost-effective solutions to meet the client’s design and performance criteria for a new high efficiency gas boiler that the client wished to produce.
“The project scope included aesthetic and end user interface elements of the boiler, fluid and flue gas carrying systems with chemical resistance, heat and sealing performance requirements accounted for, as well as the integration of electronic components.
“In addition to injection moulding, complementary manufacturing processes had to be adopted including automated assembly, linear vibration welding, spin welding, Ceracon FIP sealing, digital and hot foil printing.”
The gas boiler project ultimately saw Advanced Plastics design and manufacture 36 injection mould tools ranging in size from 250kg to 7,000kg, (with the largest running in a 1,500t injection
moulding machine), and the integration of all downstream manufacturing processes.
“This significant project was delivered on time and within budget, clearly demonstrating our overall design, development and manufacturing capability,” said Mr Hadfield.
Amidst global concerns about plastic pollution and a general increased emphasis on sustainable industry, Advanced Plastics has embraced a number of sustainability programmes. One of these is a major focus on the use of recycled materials, especially at its Fareham and Manchester factories. “Wherever possible, we choose to use recycled resins and invariably that creates opportunities for reduced cost and improved environmental impact,” Mr Hadfield explained.
He highlighted an example of how the company’s sustainability programme substantially benefits one of its larger customers: “A major worldwide telecommunications customer traditionally used virgin polymer, reaching a peak of 800 tonnes in 2015. As of 2023, its use of virgin polymer has been switched for 90% post-industrial and post-consumer recycled materials,
all with the full knowledge and collaboration of the customer’s technical and commercial teams.”
Meanwhile, Advanced Plastics has become an industry leader in its ability to supply to customers the energy usage data and carbon footprint information for its polymers, for use with Environmental Product Declarations (EPDs). The EPD document transparently communicates the environmental performance or impact of any product or material over its lifetime.
“Many of our customers readily embrace this programme and supply the required data, increasing their market share and overall turnover,” Mr Hadfield said.
In September 2023, Advanced Plastics announced the appointment of a new Board of Directors, with majority shareholders Chris Pearson and Rob Anderso n becoming joint CEOs of the business. The new board, with collectively over 150
years’ worth of plastics industry experience, is developing a five-year business plan with the stated goal of driving Advanced Plastics to £50m turnover, which is set to be achieved organically and through site growth and strategic acquisitions.
The company expects organic growth to be partially driven by further diversification as well as continued investment in the latest manufacturing technology and automation, allowing the company to continue to offer its
customers the best and most competitive technical solutions.
In conclusion, Mr Hadfield reflected on the company’s prospects: “Our team is very confident about our future; we believe that our business covers so many market sectors that we’re well protected from major turbulence in individual ones. Our financial stability remains a major strength and we look forward to continuing to deliver excellent projects on-time to customers all over the UK and Europe.” n
Copper Alloys is a global-leading, UK-based engineering entity in metallurgical development constantly setting the standard in creating custom metals for diverse clients. As demand for sustainable manufacturing increases –particularly for mechanical equipment, the company is spearheading further innovation to create more high-integrity metals. Managing Director Ben Turner spoke to Andy Probert.
Copper Alloys can trace its history back over a century. While it has changed hands and countries in that time, a culture of transition through innovation is deeply enmeshed in everything it does.
From its first castings made from nickelaluminium-bronze to support the war effort
in the 1940s through to the development of wrought nickel-aluminium-bronze in the 1980s, its higher specification replacement, wrought copper-nickel-chromium, was developed in the 2010s.
Seeking to develop next-generation wrought versions of advanced cast alloys, Copper Alloys has spearheaded
the drive to create ever more reliable and high-integrity metals: some alloys have become the specified standard for marine and naval defence applications, others are set to become the next standard as metallurgical development continues.
The Staffordshire company, which employs over 50 people including renowned scientists and metallurgists , has excelled at bringing innovative alloys to scale for industrial use.
“Our business has always been forward-thinking in metallurgy; constantly pushing the boundaries in the metals that are available, developing new material technology and making new metals more sustainable and reliable,” said Managing Director Ben Turner.
Today, Copper Alloys makes 248 different alloys, with thousands of specifications, and nine Elite Alloys TM , offering game-changing material technology at
every conceivable level for industry, and always fit for purpose.
Copper Alloys also excels at controlling process technology to increase the engineering potential of these custom metals, the machining of highly complex parts and mechanical assemblies of vast numbers of components. This concept of ‘integrated engineering’ – having the engineering and metallurgy controlled by the same organisation, – risk is mitigated to unprecedented levels in the production of complex machined forgings.
“Our approach is one of absolute quality,” said Mr Turner. “With everything we make, people’s lives are at stake if something goes wrong. Over the last decade, we have achieved a classleading approach to controlling quality, traceability and transparency.”
The company works in partnership with aerospace customers such as Airbus and BAE Systems. It manufactured thousands of critical components for the likes of
Rolls-Royce Submarines for the Astute-class submarines. It now supports Governments, OEMs and leading design engineers worldwide to make sustainable, high-quality solutions to demanding applications.
“We have a culture of continuous improvement and naturally gravitate to the extremes: we have parts on the Mars Rover, components on submarines in oceans, and everything critical in between,” Mr Turner continued. “The common denominator is the drive for complex metals that are of high value, highly challenging and non-standard material technology.
“Our metallurgists and engineers love the complexities and challenges: from food technology to offshore oil rigs, landing gear on aircraft, downhole tooling and submarine components. At our core is setting quality standards and doing things better. Integrity and trust are stamped on every material we create.”
To genuinely affect sustainability, Copper Alloys is committed to considering what things are made from. The material technology has to be up to the challenge
of lasting the lifetime of the application in which it is being used.
“Indeed, one of the many concerns that our employees have is the carbon footprint they leave behind and the sustainability of the industries in which they work,” said Mr Turner. “We have identified six key markets where our material technology can improve how mankind treats the Earth.”
Power generation is one such industry: Copper Alloys is engaged in a long-running collaboration on a full-scale nuclear fusion project in France, according to Mr Turner: “The concept is a man-made sun. We have supported the design of critical parts that manage magnetism for the free movement of the engineered metallic system. This is a key enabler for true sustainability.
“The approach we adopt with the UK’s Ministry of Defence, the US Navy and others is that we enable engineers to design things to last by giving them access to better material technology. The issue is that the demand for the application is increasing: aircraft must fly longer, submarines want greater uptime over a longer period. There are huge strategic implications for new materials being used.”
This has driven Copper Alloys to develop the ‘fit-and-forget” alloy CNC-1, a high-strength, tough wrought coppernickel-chrome alloy composition which exceeds specification requirements. It offers excellent ductility together with outstanding seawater corrosion resistance.
The MoD first developed this material in the 1990s as a replacement for nickel-aluminium-bronze in seawater systems on submarines due to corrosion issues. CNC can last the platform’s lifetime, showing excellent performance, negligible corrosion and up to 10 times resistance. The MOD abandoned the project due to the inability to break through the technology gap of reliably producing the material that could withstand the hot working, or forging processes.
“Copper Alloys picked this project up in 2009 after working on T1000, its strongest cupro-nickel alloy specified on boats and applications worldwide,” Mr Turner explained. “We applied the lessons from T1000 to CNC-1, and we
forged it in a similar way. The results were unbelievable
“One benefit of CNC-1 is that it is a singlephase alloy; it is stable from an anatomic and galvanic perspective and five times tougher than replacement metals.”
Copper Alloys’ advanced melting, alloying and casting techniques, combined with a deep metallurgical understanding of hot working materials, allowed it to develop two forged alloy versions: the ‘standard’ CNC-1 and a higher strength version, CNC-2, applicable to bars to around 150mm in section.
The company embarked on a collaborative project with the British Corrosion Institute to do a comparative analysis of different types of metals in the same environment. “There are 36 grades of metal used in marine altogether, and three different test comparatives were conducted: CNC-1 bridged all the gaps
and was game-changing,” said Mr Turner “It can last a boat’s lifetime and is five times tougher.”
The MOD standard was released in 2019 and put into the public domain for engineers to consider CNC-1 as an alternative to traditional alloys and metals.
Copper Alloys has presented CNC-1’s capabilities to over 1,000 engineers worldwide, according to Mr Turner: “The interest in adopting this alloy is overwhelming. We have alloys that combine high strength, high conductivity and high corrosion resistance, and they are all inherent, so these alloys are low risk from an engineering angle. That is uniquely sustainable: things can be designed simpler, less replacements needed and a lower burden on the environment.
“Innovation is never stifled at Copper Alloys.”
While making the metal and machining components, Copper Alloys is committed to closing the loop by recycling swarf and scrap generated in the machining process. It also designs components with better metals
that last much longer than traditional metals, helping reduce carbon emissions and the consumption of energy and resources.
The company has several projects ongoing: developing alternative metal alloys for safer extraction of potable water, supporting high efficiencies in food processing machines and developing technology to improve the efficiency of flight. “We have also worked with Unilever, Airbus, Rolls Royce and Shell to help them move their decision-making processes and give them greater options,” he added.
The company is on a mission to drive forward more Elite Alloys TM and challenge engineers to do more with them in critical engineering and positively impact the next generation to make better sustainable decisions.
In conclusion, Mr Turner said: “We are completely focussed on quality and want to make a difference because it’s our driven purpose to set global standards. More actions than words will only define sustainability in the long term.” n
Andreas Lupold Hydrotechnik GmbH is one of the leading manufacturers of valves, pumps, control and regulating devices, and hydraulic lifting equipment. Thanks to the company’s innovative products and services, it can offer customers system solutions that are tailored precisely to individual requirements. Hannah Barnett spoke to Sales Director Rifat Cetin to find out more.
The core competence of Andreas Lupold Hydrotechnik GmbH is in hydraulics. Otherwise known as Lupold, the company offers a range of standardised and complex solutions in the field of stationary and mobile hydraulics and has been doing this successfully for over 75 years.
In 2019, Lupold became part of the Hydraulik Nord Group – a medium-sized corporate network of technology com -
panies – allowing the further expansion of its capabilities.
“The benefits of belonging to the group are clear; we can build a much bigger network in the hydraulic sector,” said Rifat Cetin, Sales Director. “It means we have access to both a wider customer and supplier network; and of course, there are capital benefits including a lot of investment into R&D.”
Lupold has always existed at the cutting edge, while working with some of the biggest players in the industry. “For the last 30 years, almost every pump from the market leader for piston pumps has used regulators from Lupold,” Mr Cetin explained. “We are a key supplier for them. If we speak about regulators in hydraulic, we have more than half of the complete market share.”
The company had a turnover for 2022 of €22 million, while the figure for the whole Hydraulik Nord Group is around €230 million.
Lupold has been able to test the potential of hydraulic innovation by developing a pioneering digital regulator, which may prove to be a ground-breaking product in the sector.
“Compared to the old-style standard regulators in hydraulics, we are going to save up to 95 per cent of energy usage with a digital regulator,” Mr Cetin explained. “We have developed this new system, known as Beyond Digital, and it is a very big milestone. It means we can save energy in all hydraulic systems, thereby helping to reduce the environmental impact of our customers and contributing to the fight against climate change.”
The digital regulator combines the advantages of digital technology with those of hydraulics to provide optimised pump management. The controller uses its own poppet valves (known as pulsed universal leak-free solenoid valves, or pulse
for short), which are leak-free, unlike a standard system, and can be switched in a few milliseconds. The basic controller type can be adjusted live to the system’s needs via pioneering software, meaning a change from a pressure controller to a flow or capacity controller is possible during operation. The flexibility of the system is increased enormously from standard models, and controller losses are also minimised.
Lupold launched this groundbreaking product at the 2023 Agritechnica show in Hanover, Germany.
“There is a similar system from a competitor on the market, but our system is more dynamic,” said Mr Cetin. “A customer using the Lupold regulator can see from their construction machinery that the system is reacting faster. Not only that, but the energy efficiency is better and there is only one system that can adapt the software to different pumps. In the
classic version, every pump needed its own regulator and a physical system to run it: the digital version allows for true standardisation.”
As well as helping its partners to improve their carbon footprint via more efficient products, the company is committed to sustainability in its own operations. Lupold is TÜV certified according to ISO 9001 and ISO 14001.
The company also introduced its first solar power plant, consisting of 246 modules, at the end of 2022. This commission marked not only a step towards a greener present, but also an investment in the future. In synergy with this, the Hydraulik Nord Group is also in the process of implementing photovoltaic systems at every location across the group.
Lupold also has on ongoing project to ‘digitalise’ its workforce. “This means the worker in the assembly area has their steps tracked by a digital system,” Mr Cetin explained. “So, we can monitor if the work is done to the technical requirements we expect in-house. The system is made by TULIP, part of DMG MORI, programmed and individually adapted for different applications and clients in-house, and is very innovative.”
The company is also looking to establish a retail presence online for its own range
of hydraulic systems, including lifting tables for various applications.
“I think we cannot maintain our market share in the classical hydraulic system, without making the step into digital –meaning we have to build up new systems,” said Mr Cetin. “And we are not the only ones thinking this way. It is inevitable that the future of hydraulics will be digitalised.”
Like many companies with decades of experience in its sector, Lupold has several long and loyal supplier relationships, some stretching back 40 years. However recent market turbulence has meant other partnerships are less certain. This is where being part of a larger group proves useful, once more.
“We have a commodity management system within the Hydraulik Nord Group,
where we can build up a network and check the best conditions for all of us and then make long term contracts through the group,” Mr Cetin explained. “It benefits suppliers too; they get a bigger share of orders and we, most of time, get better prices.”
In what is sometimes a demanding market, amidst fluctuating raw material prices, a shortage of skilled professionals and an ongoing transition to greener energy, it is clear that Lupold will continue to thrive on the basis of its commitment to innovation.
“I love a challenge,” Mr Cetin concluded. “That’s the main reason, I think, why I’m in sales. And I am inspired by the technical innovations within this group. Selling a product which everybody can make is not so exciting. But if you can go to the customer and offer a new solution, like our digital system, then that really motivates me.” n
For more than 20 years, SG Automotive has supplied the automotive industry with high quality PCBAs and LEDs. With a history of innovation and success, the company is preparing for a period of significant growth. Sales Director Juan Arrambide sat down with Inside Sustainability to explain more. Report by Imogen Ward.
Over the years, SG Automotive has worked hard to build a solid repu tation within the automotive industry. Today, it boasts an impressive turnover of €20 million and a quality rating of 2.0PPM.
“We have a long history making PCBAs, electronics and LEDs,” said Sales Director Juan Arrambide. “We actually pioneered the automotive industry with our LED technology for cars.”
SG Automotive’s origins date back to 1998, when its predecessor CMP Electronic was established as a specialist automotive wire harness manufacturer. The following year, after a change in direction that led to a joint venture with Alfred Schefenacker, the company was renamed SG Automotive, and its production focus switched to electronic components.
“ At the time, Schefenacker was a very well-known German automotive group,” Mr Arrambide explained. “We began collaborating on projects, and the partnership really evolved from there.
“Today, we are most well-known for manufacturing the turn light indicators for Mercedes Benz. We manufacture the PCBAs for the electronics and assemble and package the final product in house. This is one of our best products and has been for many years.”
After more than 20 years of success, SG Automotive has new goals for growth. Ever ambitious, the company intends to grow its turnover to €30 million by the end of 2025.
With a target on the table, SG Automotive began searching for the perfect partner to help accelerate growth. In 2023, it came to an agreement with UK-based contract electronics manufacturer Jaltek Systems. The partnership will support demand from new markets and is likely to lead to fresh opportunities.
“We signed the collaboration agreement with Jaltek Systems in October last year, to support demand from the European and UK
markets,” Mr Arrambide explained. “Both parties are happy with the outcome, and we are excited about the new opportunities it will bring.
“The partnership will give us access to the UK’s automotive sector but also other non-automotive markets such as medical , aerospace and defence. These are all new areas for us that we are looking forward to exploring further. We are confident in achieving our 2025 turnover goal, thanks to the support of Jaltek Systems.”
As a result of this partnership, SG Automotive is now active in the UK market (an area it was previously absent from) and is very busy generating projects and leads.
Whilst new doors open for SG Automotive in the UK market, the company has been busy diversifying away from its expertise in automotive. At the end of 2023, the company embarked on its first major project outside of the automotive sector.
“We have been working hard to diversify into other industries, because the automotive sector covers 95 per cent of our operations,” said Mr Arrambide. “This year, we are set to assemble approximately 200,000 PCBAs and control boxes for a smart furniture company. Off the back of this, the client has already placed an additional order for more than 185,000 units, which will be tackled later this year.”
Diversification is a major element of SG Automotive’s strategy: one that will not only help it reach its 2025 targets but will also help ensure it outlasts any potential market stagnation.
“The automotive industry is quite fragile at the moment,” Mr Arrambide continued. “In more recent months, we have witnessed a reduction in orders from this side of th e business. By diversifying into other
non- automotive markets, we are securing our current market-leading position and our future.”
Although orders from the automotive industry have reduced, SG Automotive is still experiencing a steady demand, especially when it comes to electronics requests.
Manufacturing PCBAs is not the only thing that SG Automotive excels in; the company has also been working to improve its environmental impact. One way it is achieving this is through the generation of electricity using the heat from its production processes. The company also minimises its waste as much as possible.
“Any solder waste we produce is recycled, and we try to avoid scrapping our PCB boards,” Mr Arrambide explained. “We also design all our electronics with efficiency in mind: we don’t use unnecessary amounts of material, and we try to avoid
using too many different types of material. By designing the products to be as simple as possible, we can keep our environmental impact to a minimum.”
At this stage in the process, SG Automotive also takes packaging design into consideration. Where possible, the company offers clients returnable packaging so that it can be reused for future projects. Although more expensive than the non-returnable alternative, SG Automotive favours this option for its circularity.
When it comes to sustainability, SG Automotive has more planned for the rest of 2024 and beyond.
“We are always working on our KPIs and measuring our performance indicators to assess where we can improve,” Mr Arrambide continued. “We endeavour to make our electronics as sustainable
as possible, and we are assessing new ways to do that every day.”
According to Mr Arrambide, SG Automotive intends to remain fully focused on its growth objectives for the foreseeable future: “We offer our customers transparency and flexibility when it comes to their orders. As long as we continue to provide that, whilst prioritising product quality, we will continue to grow closer to our target turnover.
“All our achievements past, present and future, would be impossible without the amazing team of individuals we have at SG Automotive. Each employee is dedicated to ensuring the very best products for our clients, and they are a joy to work with. I am looking forward to what the remainder of 2024 has to offer, because we have a lot of incredibly exciting projects lined up. ” n
STARTECH is an innovative Czech engineering company founded in 1996. It focuses on the precision machining of common and special materials using progressive CNC technology. Hannah Barnett spoke to Managing Director Jan Šildberger to learn more.
Though it may have been officially established in 1996, the origins of STARTECH stretch back much further. Originally beginning as a small locksmith and machining business in 1947, the rise of communism in Eastern Europe meant
the company was lost as a private holding for decades.
When ownership was returned in 1990, the son of the original founder eventually transformed STARTECH into a components business. Now, STARTECH specialises in
the medium, small-series and piece production of complex and precise parts for sectors including the petrochemical, food and aerospace industries.
Set across two sites, the company houses almost 50 CNC machines at its sophisticated facilities. To improve production capacity and satisfy customer demand, STARTECH plans to further develop new premises with a total area of over 28,000 square metres. Company operations are supported by a healthy turnover of €20 million and 194 employees.
Around the year 2000, STARTECH began supplying components for electron microscopes and established a niche in customer projects involving small batches and complex parts.
“We now supply the biggest electron microscope companies in the world,” said Managing Director, and grandson of the original founder, Jan Šildberger. “This has shaped our company because it involves very specialised work for high-tech customers. The electron microscope
manufacturers are always improving their products and introducing new ones, and we go with them. We have established very good relationships with these companies.”
STARTECH now produces components for spectrometers and laser interferometers, as well electron microscopes. As Mr Šildberger emphasised, these are not only highly technical pieces of equipment, but exceptionally powerful ones too.
“We are very proud to be in this business, because the products are so cutting-edge,” he said. “Using this equipment, a person could be on the International Space Station and take a look at a park bench. They would not only be able to see a man sitting there, but also to read his newspaper. This is the sort of resolution possible with an electron microscope.”
STARTECH runs on innovation, both internally and in response to customers. In recent years, like much of the industry, the company has been exploring the possibilities of automation. Almost 20% of production at STARTECH is now fully automated, using
commercial robotic systems. However; the type of manufacturing the company performs means a ‘one-size-fits-all’ system for automation is not always enough.
“We are driven by our customers to innovate and my colleagues, in turn, are very eager to do so,” Mr Šildberger explained. “I don’t have to encourage them. As we are a small batch production, we have to be especially innovative around automation. We do not produce millions of the same mechanisms again and again, we produce small, specialised components. It might just be 10 pieces, and then each time we need to reset the machine and restart production for quite different parts.”
In response to the challenge, STARTECH is working on a prototype of a robotic AGV system, in collaboration with sister company TG Drives.
The robot is equipped with actuators, has 13 controlled axes, weighs 900kg and can handle a load of 800kg. It moves around the production floor on magnetic strips, which provides considerable flexibility and easy system reconfigurability.
“We have completed the first prototype testing, and if everything goes well, by the end of this year we should be in production, once we have established certifications,” said Mr Šildberger. “This will allow us to fully utilise machines and decrease setup times. Sometimes we need to reset the machines several times a day, so it is helpful to be able to reduce times.”
The final frontier
True to its name, many STARTECH products have left the Earth’s atmosphere. For example, the company’s components are installed in the flight version of the ESA Solar Orbiter spacecraft, which was launched in 2020 to investigate the sun from close proximity (about 50 million km).
The company has also been part of the European Hera mission to the binary asteroid Didymos and the US OSIRIS-REx
project. And samples from the asteroid Ryugu were examined under TESCAN AMBER LYRA3 electron microscopes, for which STARTECH produced a number of mechanical components.
Back on Earth, another noteworthy project has involved producing laser system parts dedicated to the elimination of parasites living on salmon in the Norwegian Sea. Using a new MAZAK Variaxis i-700 CNC 5axis milling machine, the components are mainly made of aluminium and plastic, and protected with a thick coating to withstand the harsh saltwater environment.
“We are enabling the customer to kill parasites on fish using laser beams,” said Mr Šildberger. “They have a special device monitoring the salmon, and if it sees any parasites, it uses this green laser beam to shoot it off the fish: it’s like Star Wars.
“It is a very ecological way to get rid of pests. The Norwegian economy has suffered big losses because of parasites, and they were using products to treat them that were not very ecological. Now they have a special system which is harmless to fish. And, of course, it doesn’t pollute the sea either.”
Indeed, STARTECH is serious about sustainability and as a result, has equipped its buildings with PV panels. This enables the company to produce around 25% of its own electricity. Buildings are also equipped with heat pumps and the capability to reuse the energy wasted by machinery is being developed. The company also recycles certain materials, disposes responsibly of other more dangerous ones, and is looking to expand recycling to include the reuse of plastics.
Keen to continue to improve, STARTECH also recently registered with EcoVadis, and is pending the results of an audit, hoping to learn where to strengthen its sustainable credentials.
It is important to STARTECH to treat its suppliers like partners and maintain a relationship built on mutual understanding and value.
“For example,” said Mr Šildberger, “we work in close cooperation with Yamazaki Mazak, a Japanese company and the biggest producer of CNC machines in the world. We have used their equipment since 1996 and have a very loyal relationship. We have always helped each other, and they have even developed some machines according to our wishes.”
Indeed, as a result of its innovative workforce, STARTECH often works to develop new products with both customers and suppliers.
“Many companies that offer custom-made machining are just producers of parts according to the drawings of their customers,” Mr Šildberger explained. “They don’t offer any new ideas about how to improve their products. I think that is our strongest point. Our customers are always satisfied, and they stay with us because of the quality of our work.
“Sometimes I think about my grandfather, who died in 1995, and what he would say about the development of the company that he never had the chance to build up. I think he would be happy.” n
www.carbide.cz/en
Carbide s.r.o. specialises in the production and sharpening of HM and HSS tools, achieving a 2023 turnover of EUR 180,000. Carbide has enjoyed a close, personal relationship with Startech for almost 20 years. The Carbide tool service collects the tools, sharpens them within two to three days, or sends them for coating, before returning them by the given date.
Carbide also deploys its knowledge and experience to produce tools for Startech, both standard and bespoke items. This includes any special shapes or stepped tools, all manufactured according to the specific designs of Startech and delivered on schedule.