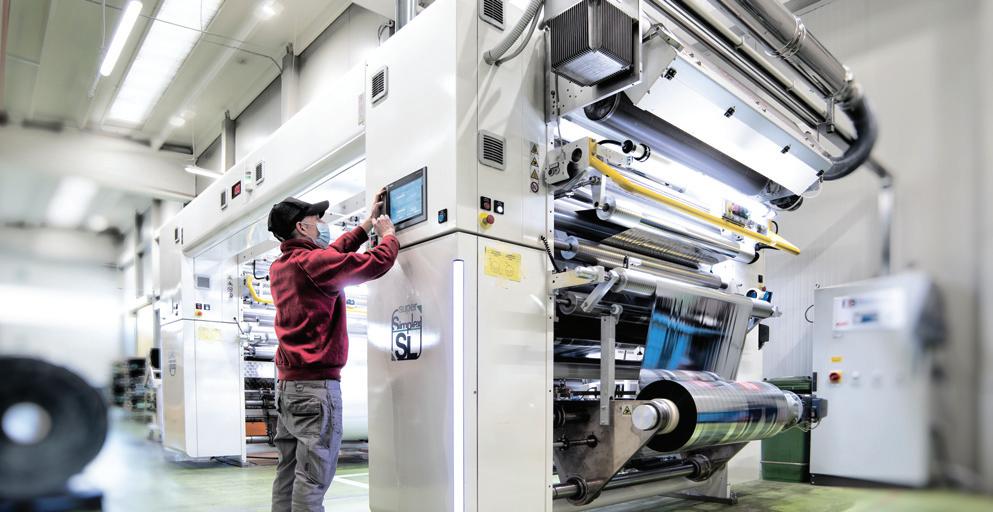


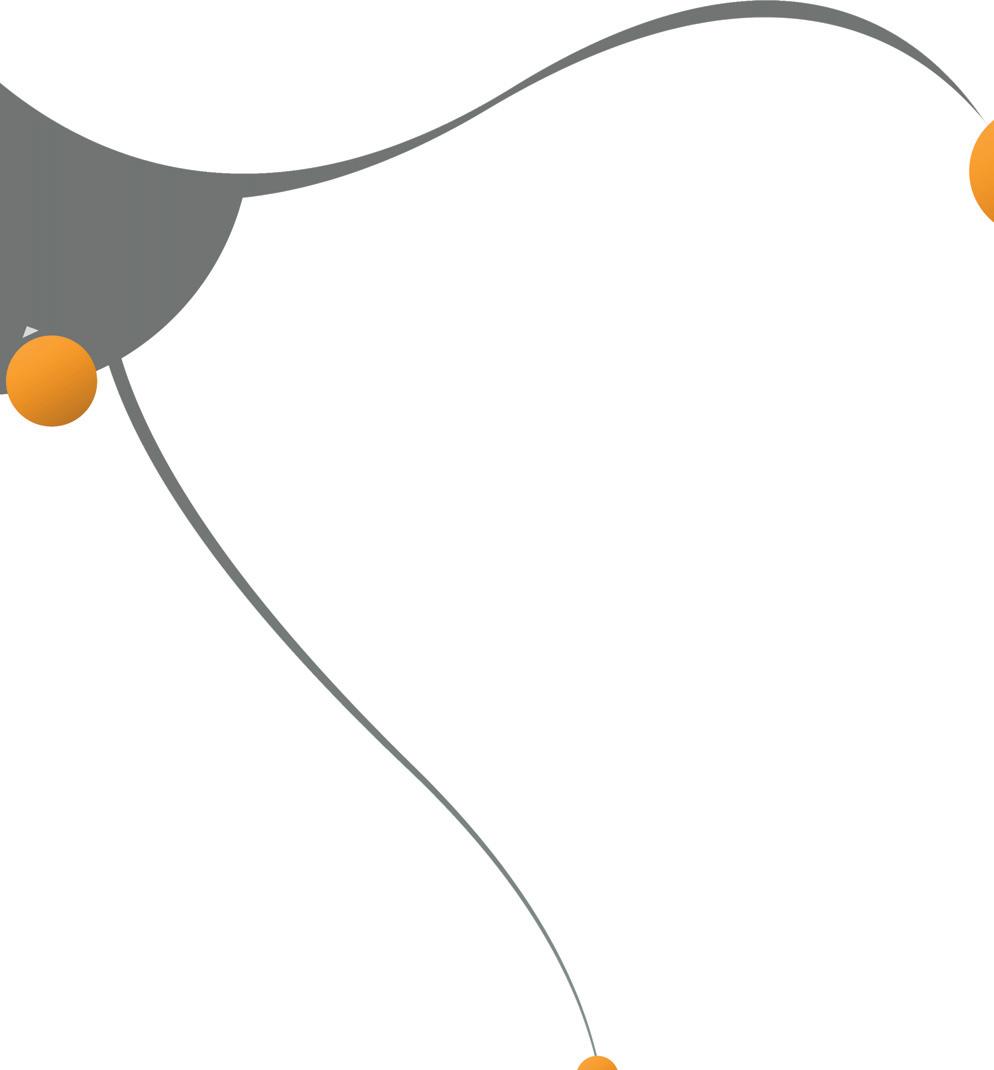

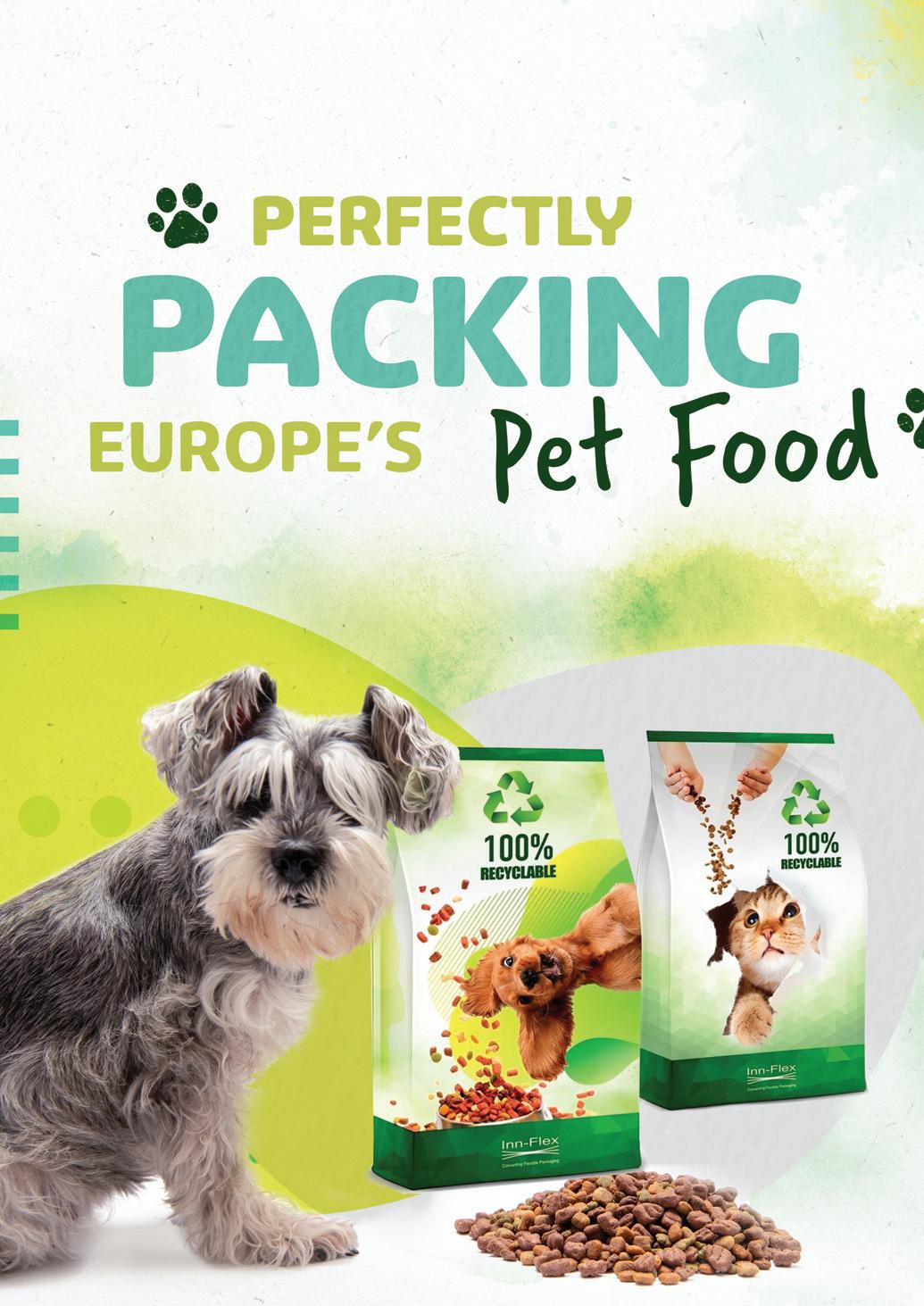
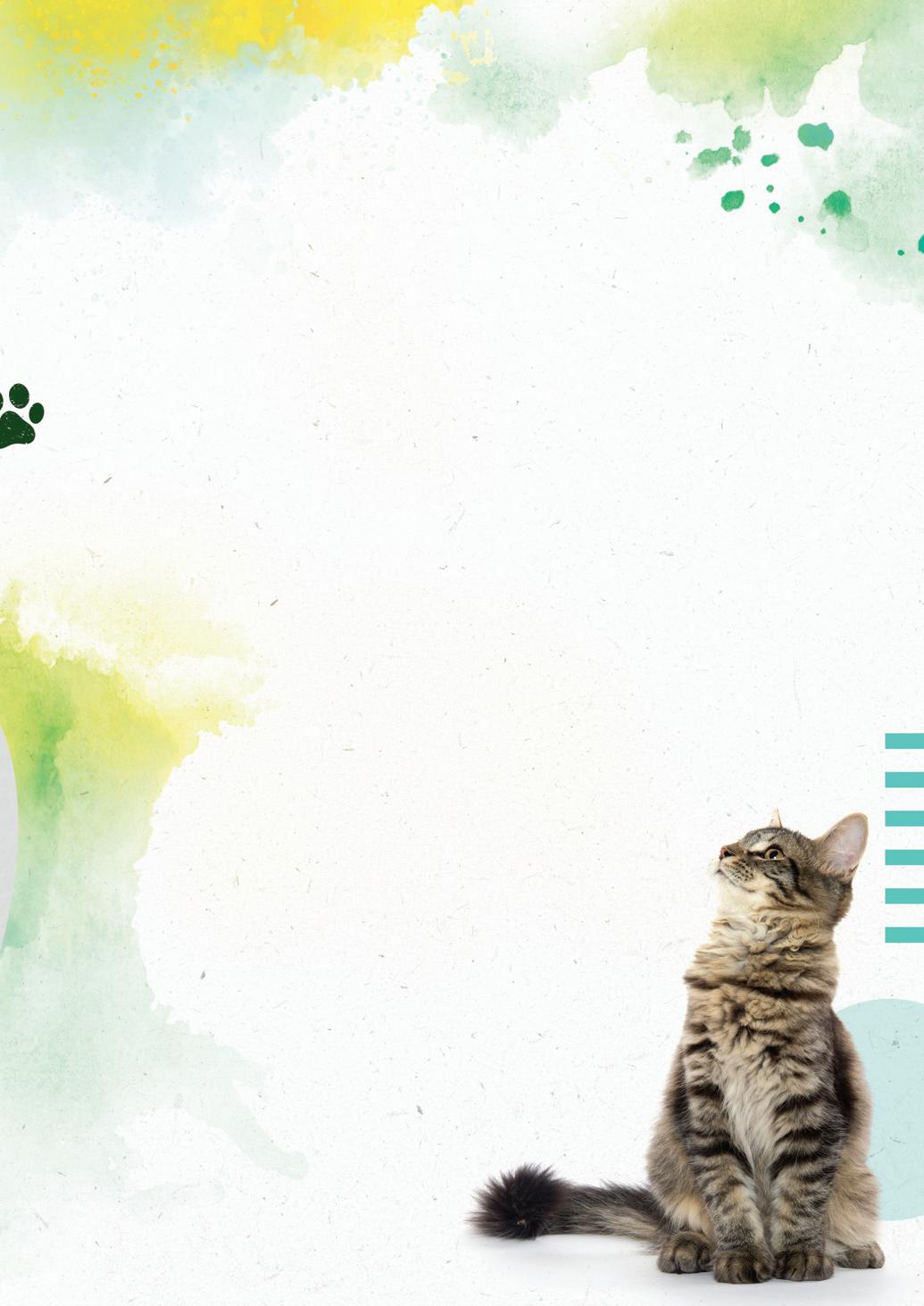
Founded in 2006 by a veteran team of packaging sector specialists, Inn-Flex is a packaging converter mainly serving the pet food industry. Richard Hagan spoke with Managing Director David Tomasin to find out about Inn-Flex’s innovative sustainability programme.
Inn-Flex is a specialist packaging producer and converter primarily serving pet food producers across Europe. It works directly with these companies to develop packaging for each brand’s specific needs. Thanks to its high-tech production facilities in Italy and Serbia and its substantially vertically integrated supply chain, Inn-Flex has developed sustainable packaging to make it the environment’s best friend, as the company packs the food for man’s best friend.
Inn-Flex prides itself on its direct relationship with its customers. This direct contact smoothly facilitates the packaging design process, in which the customer typically supplies a specification including desired dimensions and all of the graphics. Flowing from there, Inn-Flex’s teams generally provide technical input regarding material choices, construction methods and –crucially – sustainability advice.
Recyclable pet food packaging
According to Inn-Flex’s Managing Director David Tomasin, construction and sustainability are particularly on-trend in the industry right now: “Following Covid, the industry began talking again about plastic reduction and environmental impacts. Consequently, more and more packaging construction is moving towards 100 per cent recyclability. The final decision
regarding materials is, however, ultimately the customer’s because recyclable material is more expensive since the technology is not mature.
“There are fewer material options available in the market and the production process is slower compared to non-recyclable materials. We expect that in future, economies of scale will see the pricing come down, especially since clients are increasingly requesting a recyclable solution.”
Inn-Flex’s product range reflects the market’s shifting priorities towards recycling, too. “At the moment, 50 per cent of our products are recyclable, but we expect to achieve 100 per cent before the end of 2025,” Mr Tomasin continued. “We’re constantly testing and prototyping new solutions to improve the product’s performance. Recyclable bag performance
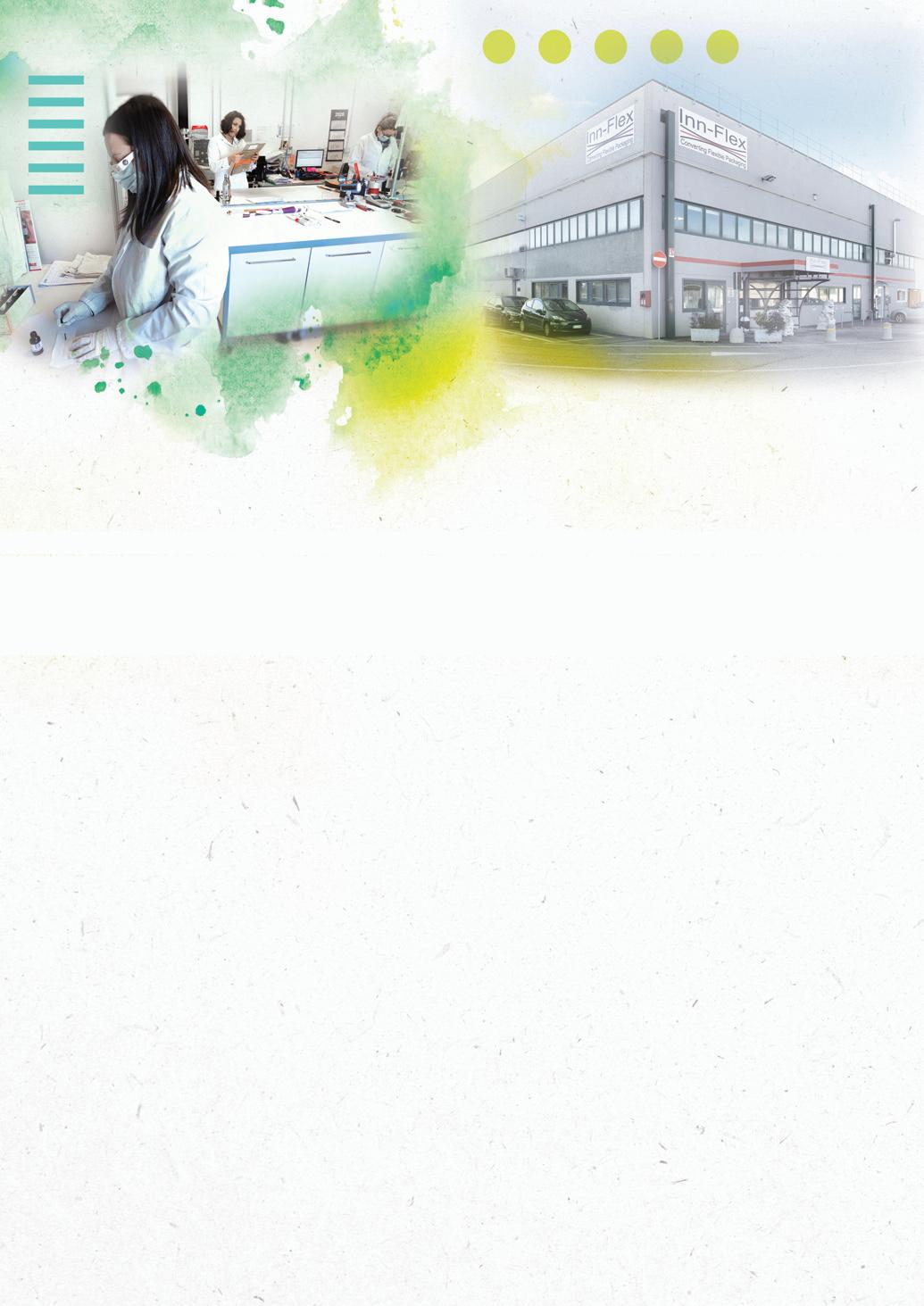
is cur rently not equal to non-recyclable bags, so we’re working hard to resolve that so that we can guarantee the same performance in terms of protection of the contents as well as mechanical resistance –for example if the bag is dropped.”
A family packaging business
Inn-Flex was founded in 2006 by the Volpato family with decades of prior experience producing industrial paper bags for the packaging industry. The founders established Inn-Flex with the specific goal to produce flexible plastic packaging for the pet food industry. At the time, less than 50% of the packaging in the industry was plastic, in comparison to the market today which boasts over 90% plastic packaging.
“They sold the industry the trend to move things to where they are today,” said Mr Tomasin. “It resulted in the company growing very quickly.”
Inn-Flex later opened a second plant in Serbia with the specific task of conversion production. That plant is deliberately strategically located close to the company’s key accounts. The Serbian site is mainly responsible for bag production which it delivers to customers in eastern and southern Europe.
All told, Inn-Flex’s operations today span 210 staff across four production facilities, with two in Italy and two in Serbia, with the Italian factories being the largest. Located in northeast Italy, close to Trieste and 100km from Venice, Inn-Flex is conveniently near the Slovenian and Austrian borders. The site is also close to the sea, enabling easy export operations to the north and east of Europe. By the end of 2023, Inn-Flex had recorded a combined €60 million in turnover across its group. That is especially impressive given the fact that Inn-Flex remains a family-owned and run business, with the original founder’s son and daughter continuing to run the business to this day.
Modern machinery
Inn-Flex owes part of its ongoing success to its high-quality raw materials, and its continued reinvestment into its modern, high-tech machinery and production lines, which Mr Tomasin was keen to detail: “Our production process starts from the PE granulate and runs all the way to the final premade bags,so it’s a long process, but it makes us competitive and allows us to maintain full control over the quality.”
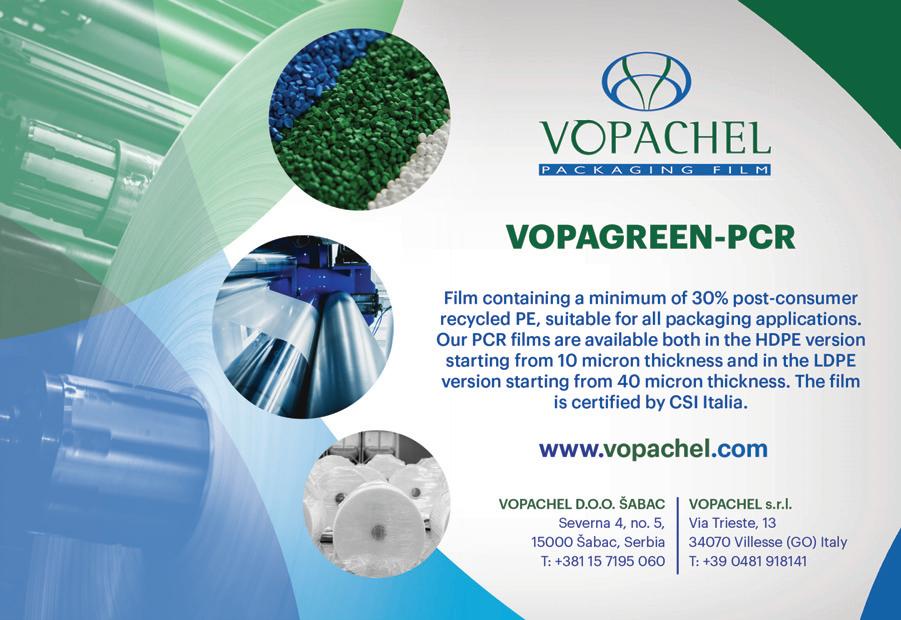
The factory floors boast a total of six extruders, three flexo printing machines, a laser cutter for pre-cutting film and four lamination machines. Finally, there are ten converting machines creating Inn-Flex’s premade bags. Most impressive of all is that all of this machinery is essentially brand new.
“We renovate and replace our machinery every three to eight years,” Mr Tomasin revealed. “Therefore, all of our machinery is practically new.
“In 2023, Inn-Flex installed a state-of-the-art flexo machine. It’s the best possible machine for this type of technology and it allows us to guarantee our clients a very high-quality level.”
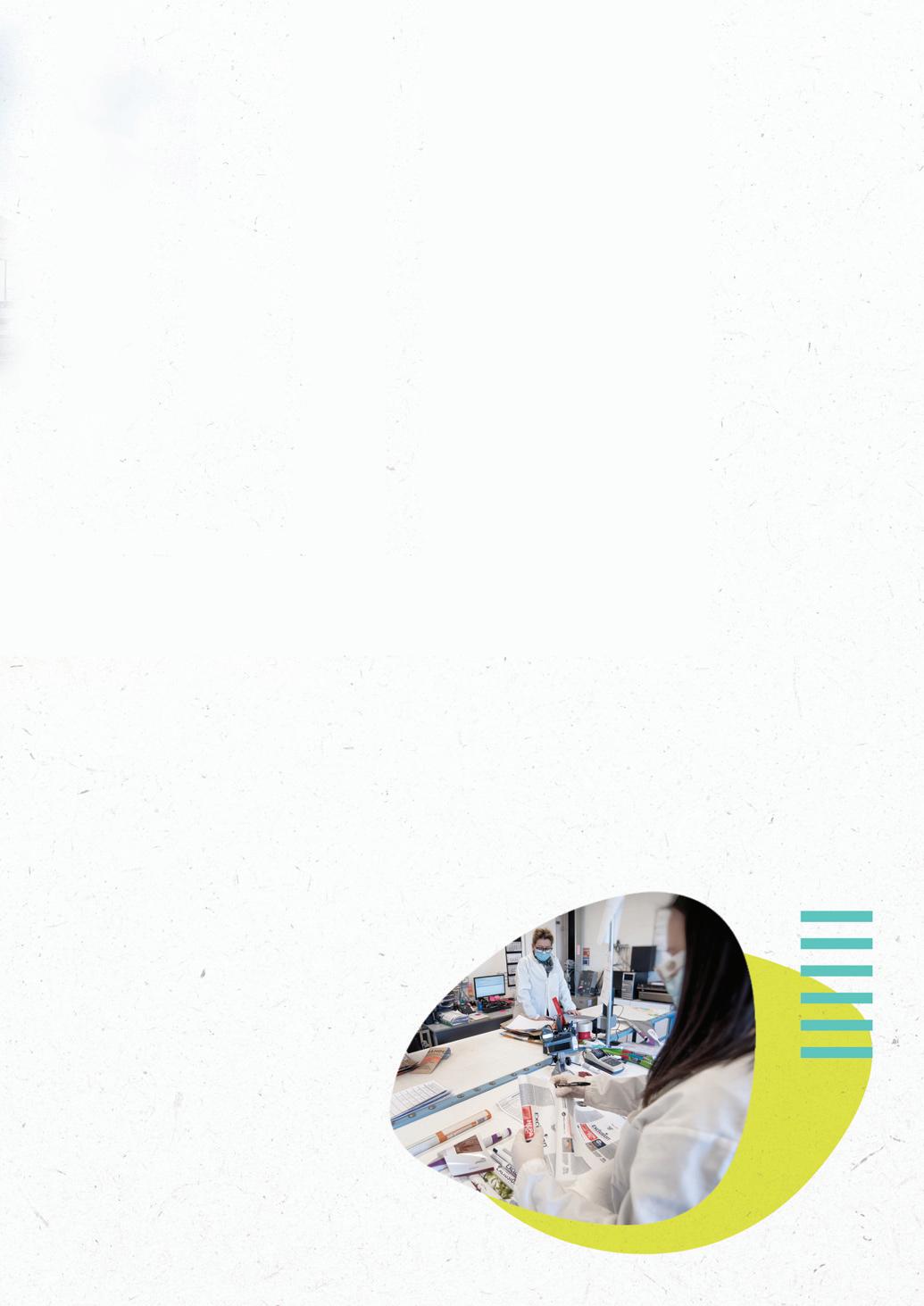
Inn-Flex’s expertise, technology and quality levels combine into a major selling point for the company, as Mr Tomasin noted: “We are a pioneer in the production
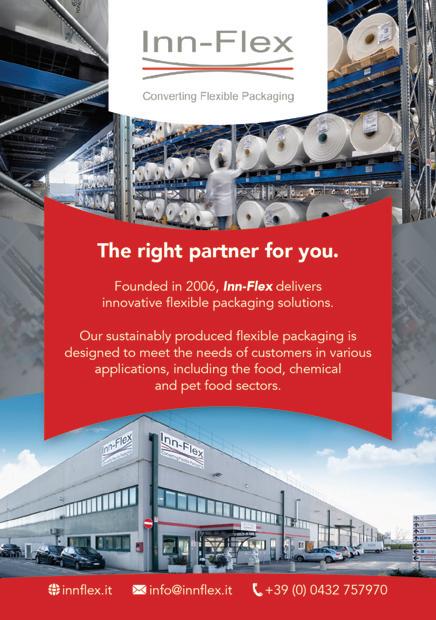
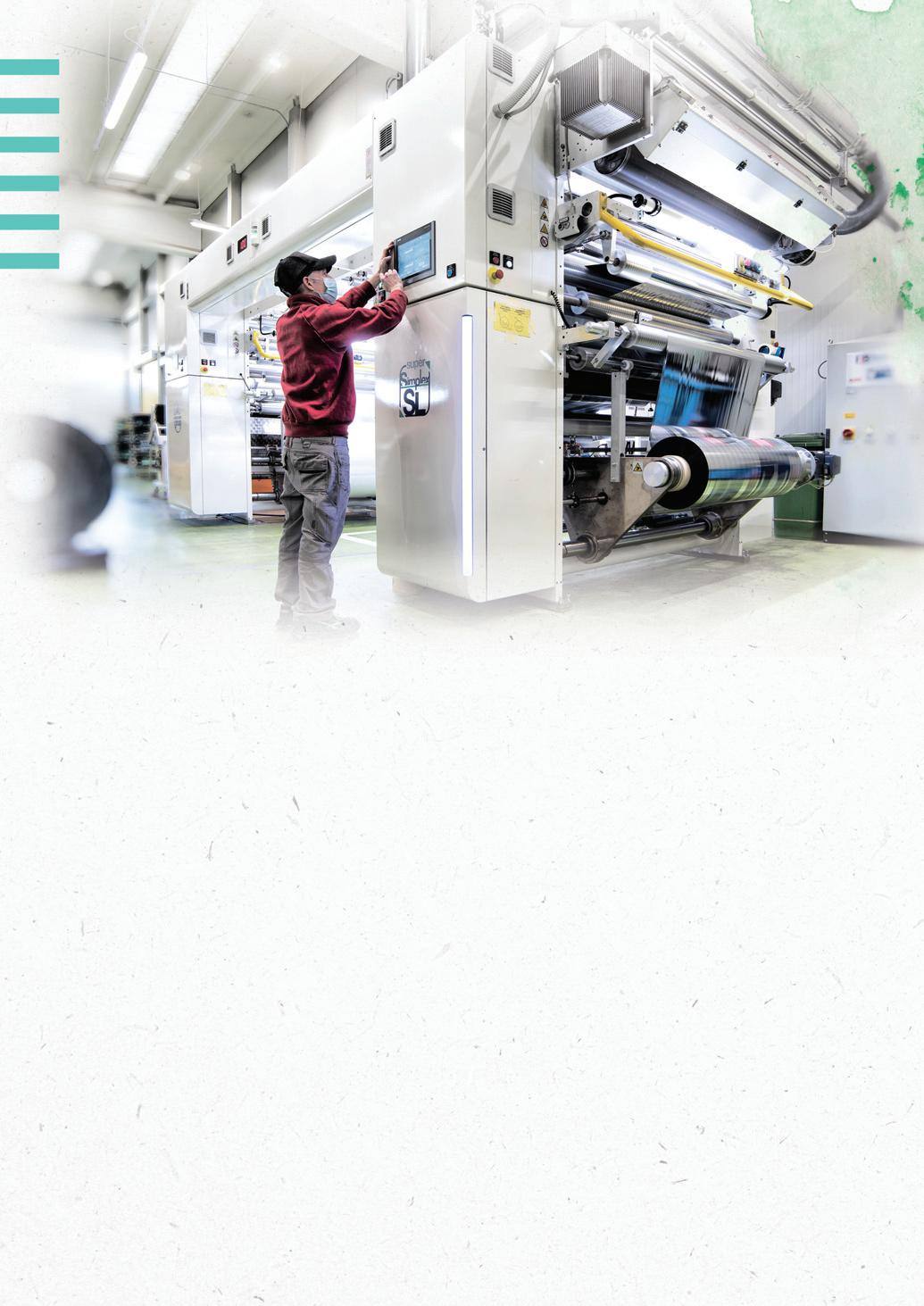
of premade bags for pet food, with deep knowledge and experience in this specifi c application. Our high level of integration also allows us to control all of the production phases and the delivery lead times for our projects.
“For example, if we have to print the packaging externally, then we lose control in the quality chain and we can’t control the delivery turnaround times. This is very important to us, because our clients appreciate our quality and our service.”
To deliver on this quality, Inn-Flex works closely with its suppliers of films and chemicals, especially for PE. The closest working relationship is with its main supplier Vopachel, Inn-Flex’s daughter company.
Sustainable manufacturing
During 2023, Inn-Flex finished construction of a large solar PV park. This 12,000sqm facility is capable of producing 1.3GW per year, enough to power 30% of the Inn-Flex’s production as well as 100% of its daytime energy needs and save 700 tonnes of CO2 annually.
Additionally, the company invested in a sophisticated system to reduce the waste inside its production lines. The system collects all of the offcut waste from the lines, then automatically sorts and deposits the waste into various marked receptacles, from which it is later collected by specialist recycling companies for processing. This inno vation will eliminate 100 tonnes of waste.
In closing, Mr Tomasin – who has been with the company

since its inception - reflected on his passion for the business: “When I look at the plant with so many people and families connected to it, I feel emotional and positive about the future. It encourages me to ensure that we grow and continue to create opportunities for the company and our staff.” n
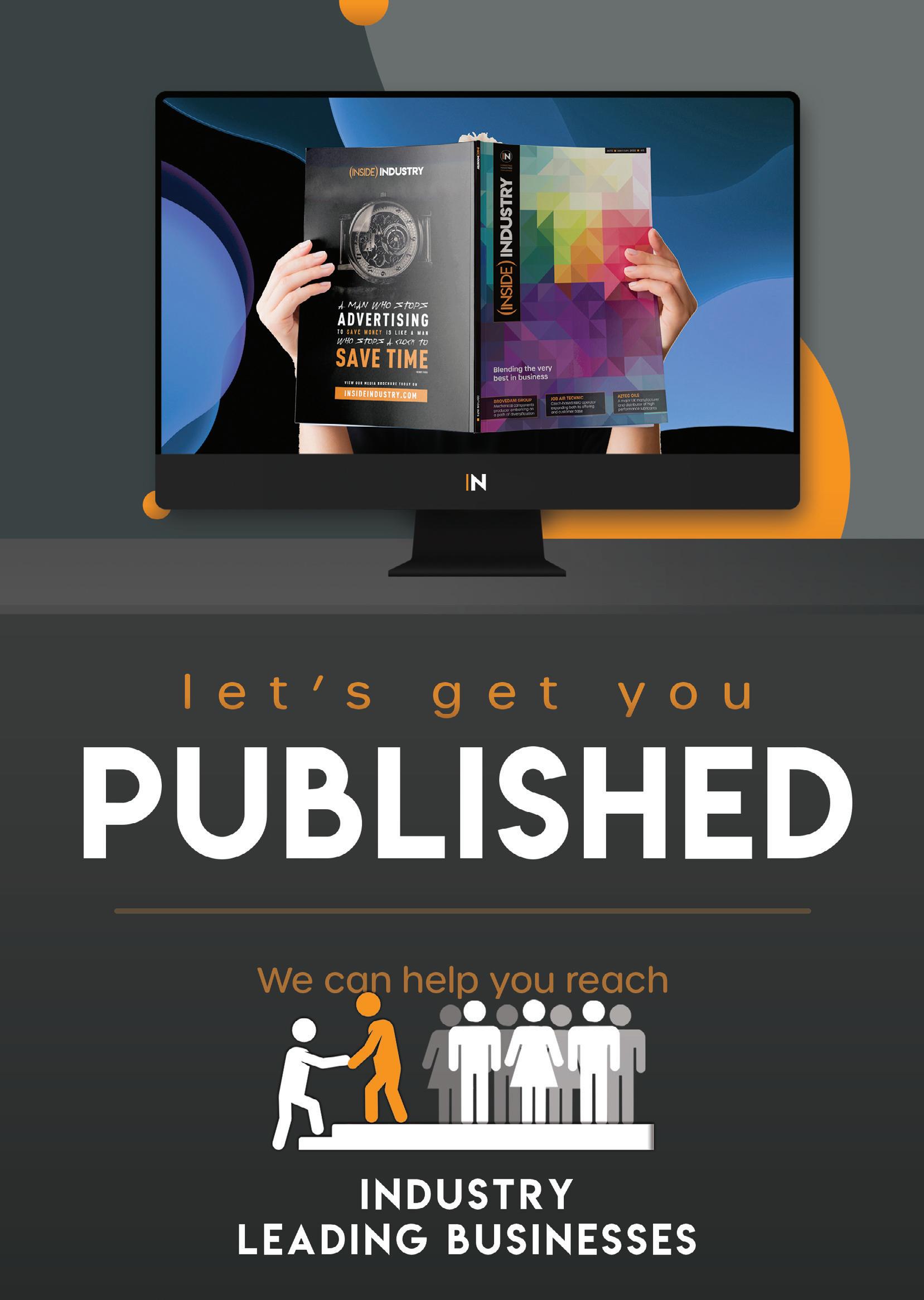
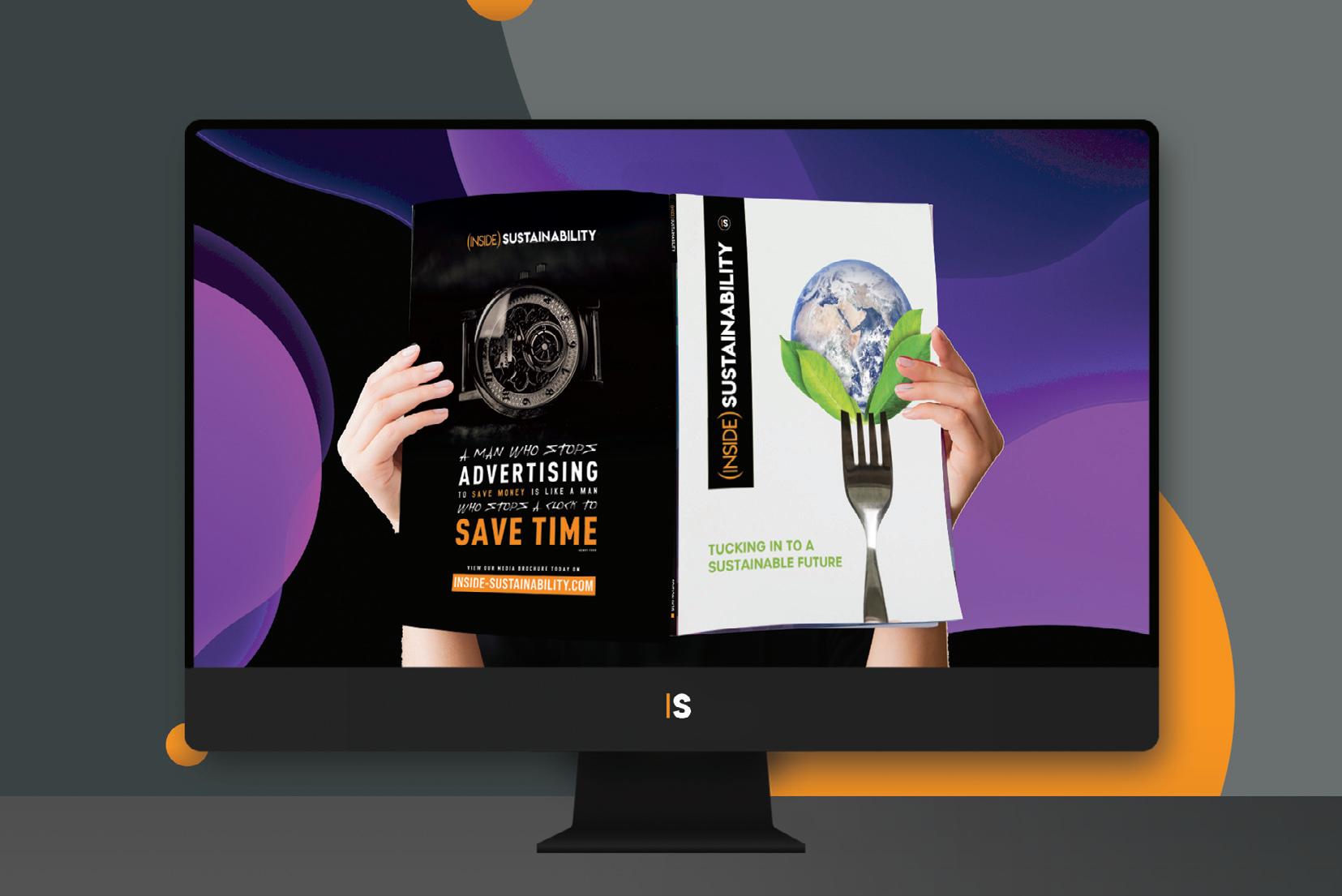