
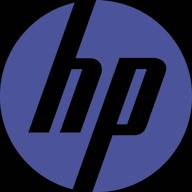



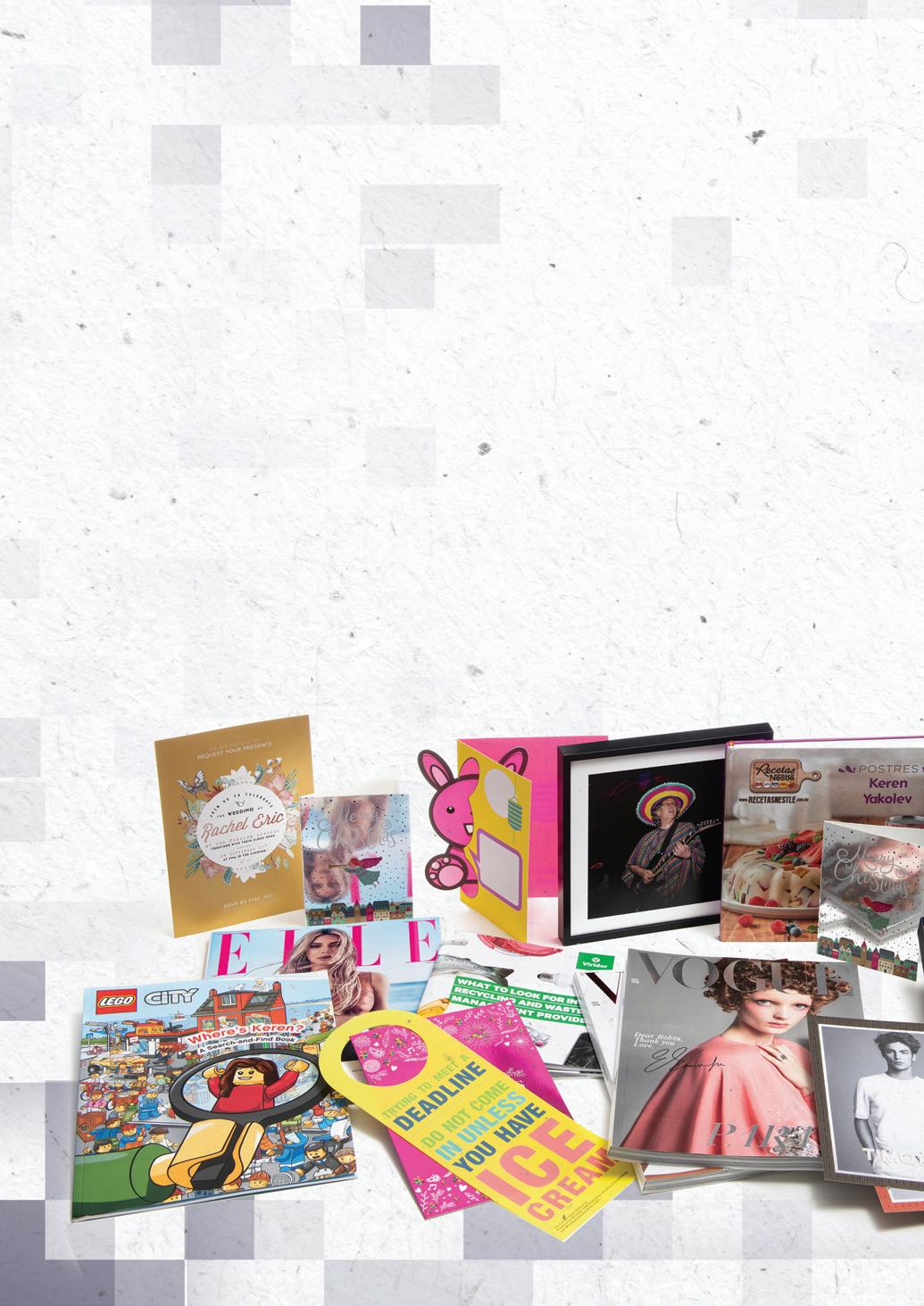
HP Indigo offers a wide range of digital press solutions for commercial, label and packaging printing. Regina Guslitzer, Sustainability & Application Business Manager, spoke to Hannah Barnett about where the company came from, where it is going, and the sustainability value of digital print.
Founded in 1977, in Israel, Indigo was always known for its innovation. In 1993, the company introduced the E-Print 1000 press, one of the earliest digital offset color printing presses. Indigo was acquired by technology giant Hewlett Packard (HP) in 2001, in recognition of the potential of digital printing technology, and became HP Indigo.
“We have been the innovation leaders in our industry for several decades,” said Regina Guslitzer, Sustainability & Application Business Manager. “We regularly break boundaries and open new opportunities for customers. The company has been granted more than a thousand patents for a host of inventions in hardware, software, ink and other supplies.”
HP Indigo also retains a 60% market share in digital printing, covering the commercial print market, labels, flexible packaging and folding cartons, software and service solutions. “Our install base includes 7,000 presses,” said Guslitzer. “And we have more than 4,000 global customers, ranging from small print shops with one digital press to large global print giants commanding hundreds of presses across several sites.”
HP Indigo’s worldwide workforce of 2,500 employees operates from a 41,000 square meter HQ in Israel, where it is one of the country’s top ten exporters, with additional sites in Barcelona, Spain, and Alpharetta, Georgia, USA, and a production plant and business site in Singapore.
The digital advantage
Digital print in general has a myriad of advantages, many of which contribute to sustainability. HP Indigo’s digital print maximizes sustainability benefits, including saving substantial amounts of media. Converters save 80-90% of setup media waste compared to analogue. The impact is dramatic, since media is the main contributor to the carbon footprint of print jobs. In fact, 60% of CO 2 emissions from printing stems from media usage.
“Another advantage of digital printing is on-demand delivery and no minimum
order requirements. This is particularly crucial vis a vis the rising trend of personalization (versioning),” explained Guslitzer. “With the proliferation of SKUs, forecasting poses a significant challenge. On-demand delivery and no minimum order policies empower CPG (consumer packaged goods) brands to enhance inventory turnover and mitigate packaging obsolescence.”
“We see it in action in a supermarket: brands can offer a wide variety of flavors of yogurt, each with different images on the packaging, without requiring the converter to change analogue plates. It’s a truly sustainable benefit for the customer,” Guslitzer said. “Of course, there are always challenges as well,” she added. “The main challenge of digital printing is that very long runs become less cost-effective. Therefore, HP Indigo’s new series of presses focuses on higher productivity at a low running cost to fulfil our analogue-to-digital transformation vision.”
Sustainable solutions
HP Indigo’s Sustainability Program was launched in 2006 and has expanded every year since, focusing on main sustainability KPIs such as CO 2 emissions and circularity. It started with a spare part and supplies take-back initiative to reduce waste and the circularity-driven, pre-owned press program, which remains very successful.
“Customers value the sustainability attributes of pre-owned presses and their significant cost-effectiveness,” said Guslitzer.
The company recently developed a carbon footprint calculator to help customers account for the CO 2 emissions of
each printed job – information now widely required by converters and brands. The calculation is based on main CO 2 contributors, such as media, process and supplies. Having the emission data per job enables customers to control parameters by choosing low carbon footprint media, energy efficient print modes, and a more efficient usage of supplies.
Durable HP Indigo presses continue to perform reliably for more than a decade
after installation, eliminating the need to build new presses more frequently. Furthermore, predictive care, along with other AI-based features like preventive maintenance, troubleshooting and virtual service support systems, significantly reduce travel by service teams and the environmental impact associated with it.
In addition to HP Indigo’s focus on press and process sustainability, the company invests continuously in print circularity compliance. HP Indigo printed products, labels, flexible packaging, folding cartons and commercial applications are certified for recycling and compostability by accredited institutions and associations such as Cyclos-HTP, TUV, and Certico, according to relevant standards in the U.S. and EU, and regularly updates compliance to new requirements and regulations across all printing segments.
HP Indigo has a history of impactful presentations at Drupa. In 2012, the company commanded the single largest booth at the trade show, which was brimming with printing presses, supplies and service solutions. At the 2016 event, data-driven software solutions were added to the leading press portfolio, creating a combined print ecosystem that enables exceptionally successful operations.
“For a company like HP Indigo, time elapses from one Drupa event to the next, because it is the largest printing exhibition,
and only happens every four years,” continued Guslitzer. “For companies in the printing business, Drupa is a milestone to work towards and from which to launch new products.”
In response to the need for high-quality digital printing at analogue speed, HP Indigo has launched its innovative LEP x technology, based on the company’s core LEP printing process, which now runs at a speed of up to 120 meters per minute.
LEP x seeks to put an end to the association of digital print with short runs and can achieve unprecedented productivity.
With LEP x , one HP Indigo press delivers the earning power of a few conventional presses, at a lower TCO. In addition, by bringing the value of digital print to any run-length job, converters can grow their revenues and competitive edge. LEP and LEP x will continue to coexist and evolve, enabling HP Indigo customers to grow and prosper.
“At drupa 2024, we will be showcasing the first LEP x technology representative, the HP Indigo V12 Digital Press, which provides brands with new opportunities to optimize their supply chain and reduce inventory obsolescence,” Guslitzer said.
HP Indigo continues to invest its R&D efforts in four main areas: versatility, automation, productivity and sustainability.“Regulations and sustainability guidelines are becoming more and more demanding, driven by governments and brands,” Guslitzer explained. “This sometimes requires modifications to our products, while maintaining print quality and versatility.”
But for Guslitzer, it is striving for solutions in the modern print world that make the job so dynamic. “I thrive on challenges,”
she concluded. “And I’m driven by the opportunity to help HP Indigo lead the way to optimal sustainability for the print industry,” she said.
“Our products influence many people around the world, either directly or through brands and businesses. My team’s role is to implement the changes that will reduce our environmental impact on our planet, and this both excites and engages me.”
HP Indigo’s leading partners include, but are not limited to, A B Graphic International, Karlville Swiss Sagl, Synaptik Lamination SL, Brotech, and Michelman.
“Over the years, we have developed close relationships with our suppliers and partners,” said Guslitzer. “We share similar goals, like reducing the environmental impact of our mutual customers. We are continuously improving supply chain management in raw materials, logistics and transportation, without compromising on quality and availability.” n