HEAT EXCHANGE GROUP COMBATTING

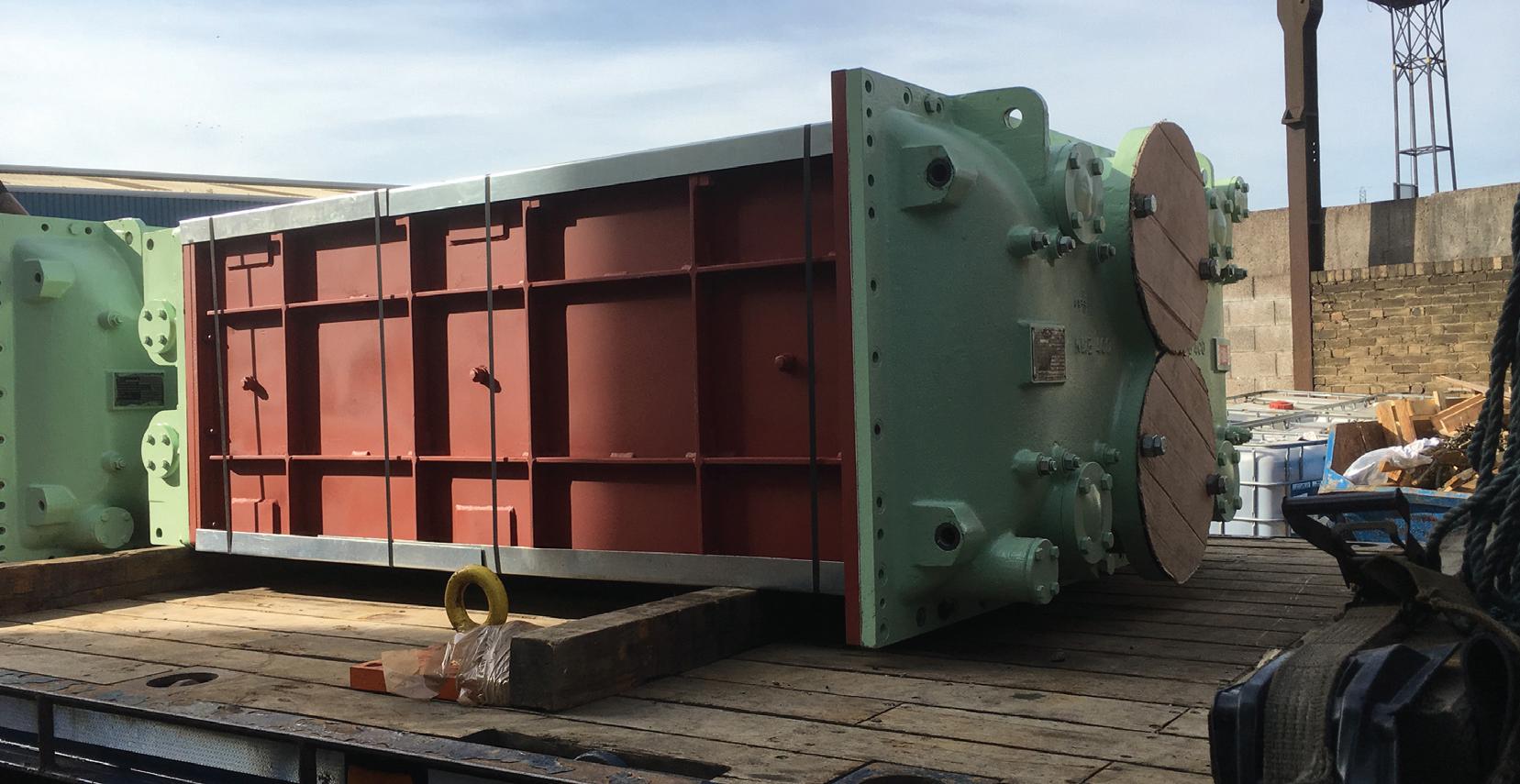
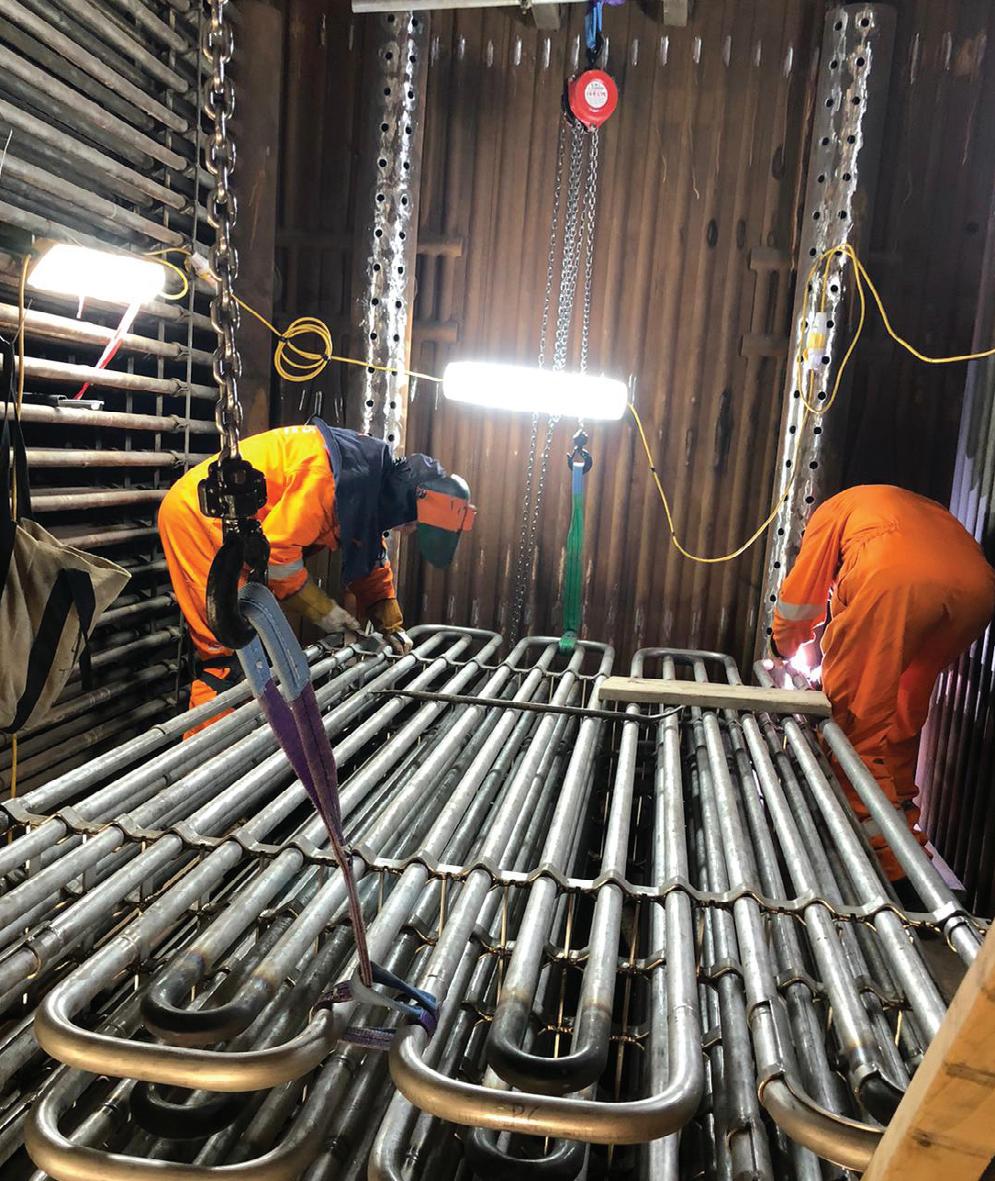
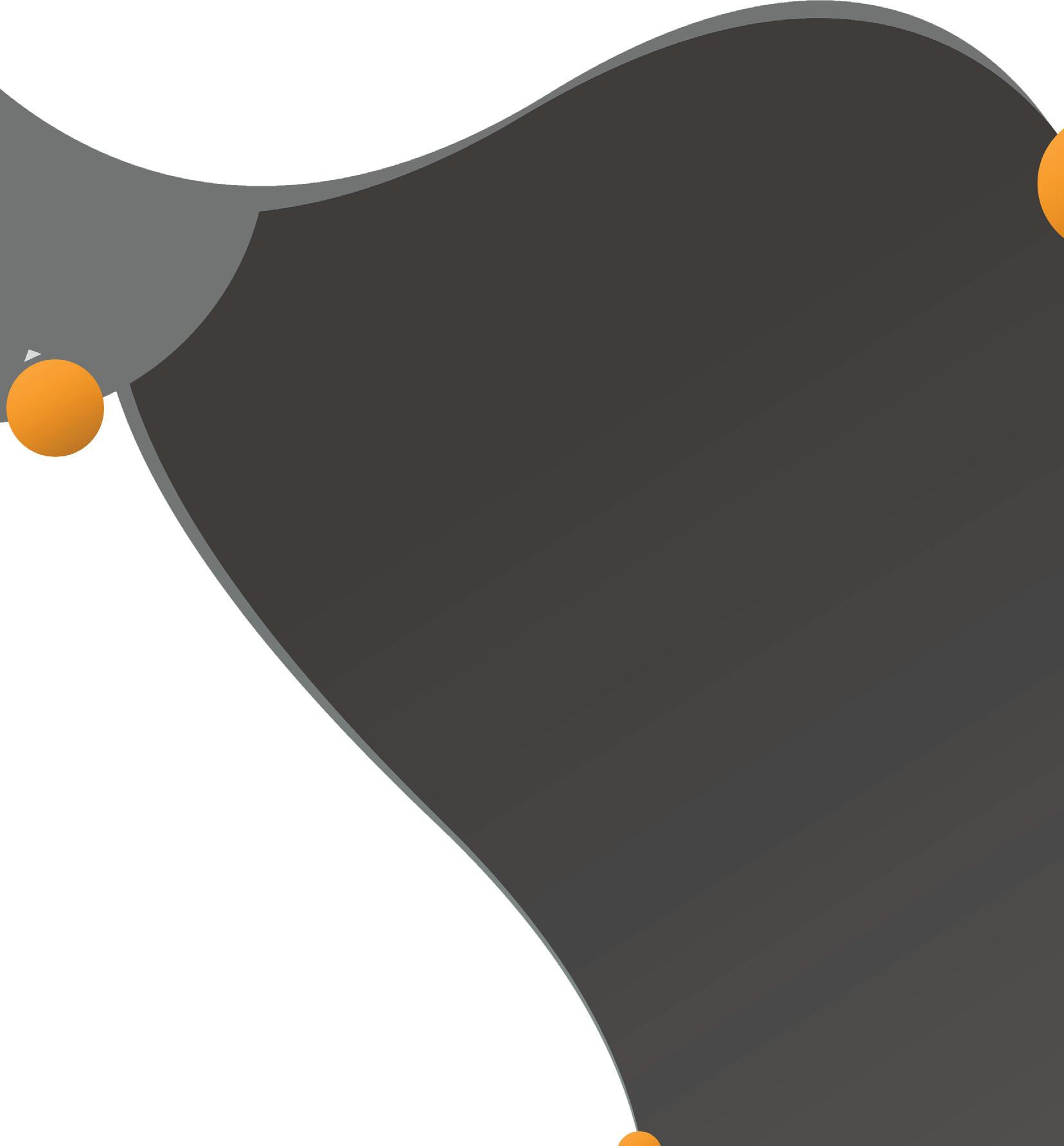
In 2020, Heat Exchange Group formed following the merger of Green’s Power and Thornhill Heat Exchangers. Now, with a focus on sustainability, the group is hoping to expand its presence within the oil and gas sector. Group Service Sales Director Neil Ford provided an update on the business’ latest operations, in a report written by Imogen Ward.
Heat Exchange Group offers a handson comprehensive service across all aspects of the business. From servicing and inspection to design and manufacture, the group has the needs of every customer covered.
“Our customers are more like partners, who we develop long term relationships with,” Group Service Sales Director Neil Ford said. “We design and manufacture the products for them, and we continue to support them once the project is complete. That’s something that really fills us with pride, because our customers know they can rely on us.”
With more than 200 years of knowledge and experience behind it, Heat Exchange Group has been working hard to make good use of its green roots.
The most recent development at Heat Exchange Group resulted in the acquisition of the intellectual property of Hunt Thermal – a UK-based manufacturer of complex heat exchangers. This really expanded the group’s capabilities. “Heat Exchange Group’s heat exchanger offering originated from Thornhill, and it was more focused on service, maintenance and repairs,” Mr Ford explained. “By becoming the OEM for Hunt Thermal, we have successfully expanded into the design and manufacture of large shell and tube type heat exchangers.
“This investment has also opened the doors to a larger variety of customers
and industries, including power, chemical, pharmaceutical and offshore. Not only did we grow our business model, but we also expanded our staff roster – recruiting some of Hunt’s key technical sales & support, design, and engineering staff.”
The group now offers a wide range of heat transfer equipment, from small heat exchangers to large shell and tube units installed on oil rigs and refineries, for example.
The group has also ramped up its service and repairs department: with a 24-hour service centre located in Prudhoe, UK, the group is fully prepared to accommodate any inspections, tests, repairs or services
needed on its systems. Employing more than 20 engineers that offer the service and repair of heat exchangers, steam boilers and economisers, Heat Exchange can also provide offshore assistance.
With the group’s presence in the sector growing rapidly over the past 12 months, it has five offshore certified service engineers and is currently working on several service agreements with oil and gas companies based in Aberdeen.
The eco-friendly economiser Heat Exchange’s best-selling product is its long-standing economiser. First manufactured in 1845, under Green’s Power, the product is commonly used to capture waste heat from boiler flue gas.
The group makes good use of all its facilities, including its own design program, Multi-Bank. Heat Exchange Group uses this software in collaboration with other programs, to provide highly flexible
designs. “Thanks to the years of collated data, we have been able to develop our own in-house design program,” said Mr Ford . “When using this system, we can input variables, such as temperature, mass flow rates, fin pitch and tube spacing, to ensure the product operates efficiently without any problems. By doing this, we can achieve the best rates of heat recovery from our economisers; and ultimately, the more heat our products can recover, the better the customers’ emissions will be further down the line.”
Working on a project for Metsä Fibre – a leading producer of pulp, sawn timber, bioproducts and bioenergy – Heat Exchange Group designed and manufactured four flue gas coolers for a new bioproduct mill in Finland.
“We actually manufactured flue gas coolers for two of Metsä group’s mills,” Mr Ford added. “These coolers have a H Fin heating surface, which maximises heat recovery without the risk of blockages. These particular flue gas coolers were so big that they had to be manufactured in parts, to ensure they could be transported along the UK road network.
“Both facilities use these products to reduce the temperature of the flue gas. The waste heat captured is absorbed by the water present within the coolers and can be redistributed throughout the factory as a source of heat.”
This project is not the first time that Heat Exchange Group has worked with a Metsä Group company. Valmet (a Finnish devel -
oper and supplier of technologies and automation systems) is one of Heat Exchange’s biggest clients.
The products made at Heat Exchange Group are effective in helping reduce customers’ emissions; however, the group’s eco-friendly efforts do not end there. Despite recent global supply issues, Heat Exchange Group is determined not to overstock on materials. “We only purchase what we need, as excessive purchasing often leads to material wastage, which is uneconomical,” said Mr Ford. “Wherever possible, we are also working with British suppliers to cut down on delivery times and reduce our carbon footprint.”
As part of its commitment to sustainability, Heat Exchange Group has prioritised the reduction of its scope one and two CO2 emissions. To help accomplish this, the group has invested in a wastewater treatment plant at its service centre in Prudhoe. All heat exchangers need to be chemically cleaned during servicing; this process results in effluent that needs to be treated and disposed of.
Previously, this was outsourced to other companies and picked up by tankers, but by constructing an in-house treatment plant, the group has successfully cut out emissions from wastewater transportation. With the plant up and running, Heat Exchange Group now reuses the treated water where possible and safely recycles the rest through drainage.
“We are always looking for ways to reduce our carbon footprint,” Mr Ford commented. “Firstly, we encourage hybrid working and are currently looking into electric cars to try and reduce the impact of our employees’ commutes. We have also recently invested in a new fleet of six vans; although they aren’t electric, they are extremely efficient –much more so than our old fleet, which is a brilliant step forward for us.”
Looking to the future, the group plans to continue improving its carbon footprint. Heat Exchange Group also hopes to create new and innovative products and services.
“Following the acquisition of Hunt, we plan to further develop our designs and the manufacturing capabilities of our heat exchangers,” Mr Ford said: “We also want
to increase our presence within the oil and gas sector, hopefully growing that side of the business to match our success in other industries.
“In a job like this, you spend a lot of time communicating with customers and collaborating, to provide them with the most beneficial proposals,” Mr Ford concluded. “Being able to find a solution that works for them, and winning the contract because of that, is incredibly satisfying.
“Our customer base is extremely varied: one day, we could be working with a multibillion-pound organisation, and the next, we are collaborating with a local factory that needs help with something small. No matter the size of the project, we are always on board to aid our customers in every way we can.”