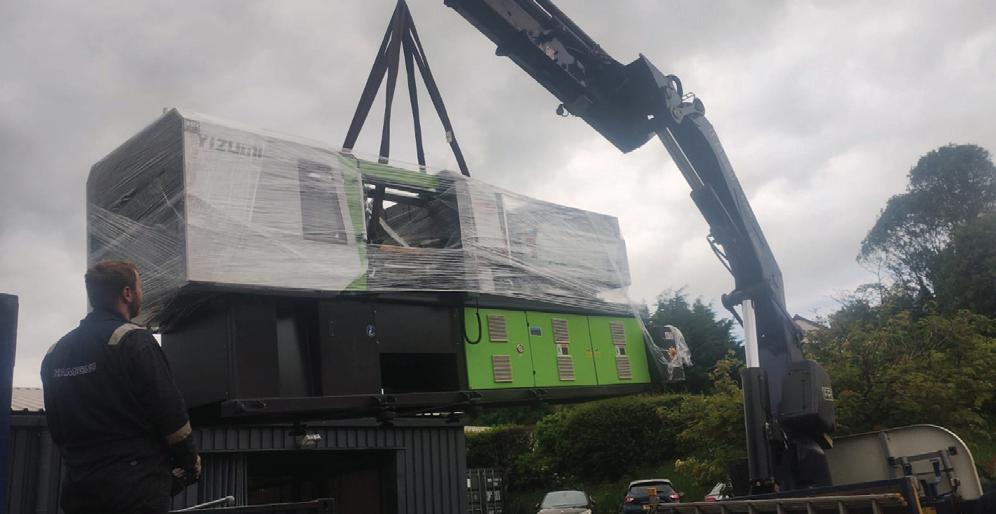
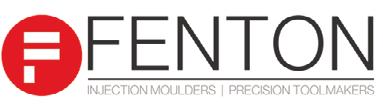
Fenton Precision Engineering specialises in precision tool making and injection moulding. From in-house concept design, CAD modelling and prototyping to manufacture, assembly and distribution, the company offers a comprehensive service to clients. Co-Owner Nicholas Skidmore discussed Fenton’s investments into sustainability, in conversation with Antonia Cole.
ASpart of Fenton Precision Engineering’s journey to becoming more sustainable, it has invested in new machinery, Co-Owner Nicholas Skidmore said: “We have the first electric Yizumi machine in the UK. This is exciting as it’s very efficient and will help us to reduce our energy usage for a more sustainable operation.”
With almost 50 years of experience in precision injection moulding and toolmaking, Fenton runs an effective operation generating an annual turnover of £7 million, a 5% growth from the prior year. The company is headquartered in Northamptonshire, UK, and has a second site in Leicestershire, UK. As well as UK markets, Fenton also supplies to customers in Europe and the rest of the world.
The company has two injection moulding facilities with presses that range from 22 to 500 tonne maximum clamp. Additionally, Fenton’s tool making facilities offer the in-house manufacture of new moulds up to three tonnes, plus refurbishments,
repairs and design changes for existing mould tools.
“There’s been a lot of investment that has gone into the company,” added Mr Skidmore. “We have an exceptionally talented team with great technical ability and we are continuously investing in their progression through training and guidance. On top of this, we have been working to modernise the company. By improving our marketing strategy and technology, we hope to evolve Fenton even further.”
The majority of Fenton’s services are c ompleted in-house, giving the company increased efficiency and flexibility. Consequently, Fenton is able to accommodate individual customer needs more effectively. The company’s facilities are fully equipped to manage a range of complex projects with specialised equipment.
For toolmaking, Fenton has a fully equipped toolmaking facility, EDM spark eroders, wire erosion machinery and high speed VMC milling centres, grinders, lathes and milling stations. Additionally, Fenton has the capability to injection mould components from 0.0005g to
2.5kg, as well as offering sonic welding, pressure testing, industrial sewing, high volume pad printing services and more.
“We’ve invested £1.8 million back into the business over the past seven years,” revealed Mr Skidmore. “By continuously upgrading and improving our facilities, we are able to operate more sustainably and provide better solutions for our customers. We have been very focused on improving our efficiencies so that we can serve clients quicker whilst limiting our environmental impact.”
As part of this investment Fenton is now using a new brand of material handling equipment from Piovan. After identifying the inefficiency of old equipment, Fenton decided to replace it with Piovan’s new technologically advanced machinery. This has resulted in significantly more productive operations for Fenton, whilst also saving energy.
In addition to this, Fenton has also invested in the UK’s first Yizumi 120 tonne FF electric/hybrid injection press. This new technology has recently been installed at the company’s site and is already offering faster and more reliable operations. The machine combines the benefits of electric drive with the practical features of hydraulic operation. Using servo motors for accuracy and a hydraulic drive for linear movements, the Yizumi is an accurate, efficient and reliable machine.
“We have advanced capabilities as a company,” explained Mr Skidmore. “A couple of years ago, we were approached by a company to supply reflective studs for the highways. It’s quite a challenging job that involved a lot of complex work. We redesigned the product for them, prototyped it, sourced the materials and then manufactured 1.6 million reflective studs for motorways in the UK. It was a great success and we achieved it in a very short lead time.”
Expanding upon investments into machinery, Fenton has also installed LED lighting across all facilities. LEDs convert 95% of energy into light, which is much more efficient and requires significantly less power than filament lighting. Additionally, the company has installed new equipment throughout facilities. The old appliances were around 15 years old, so water chillers along with desiccant material dryers and water temperature controllers have all been replaced over the past twelve months. A new energy saving compressor has been installed in June 2024.
In 2018, Fenton began to renew older machines. These machines were using 40 to 60kWh, but now the company’s new presses use between seven and 20kWh. Through this, Fenton has seen a reduction in power usage by approximately 75%.
“We have also installed a software monitoring system called Intouch,” said Mr Skidmore. “This software measures and records the efficiency of each machine and how much waste is produced. By having this data, we are able to fine tune our processes to become more sustainable. We can see where we’re creating too much waste,
in terms of both energy and resources, and work to minimise this.”
Fenton also works with LIMEX, a biobased composite material sourced from LXD (LimitX Group), derived from high quality, ultra-fine calcium carbonate (CaCO3). LXD has a vision of creating another source of CaC03 from carbon capture utilisation by 2025. LIMEX is recyclable and reusable.
By choosing LIMEX, Fenton lowers its reliance on petroleum-based resins and reduces CO2 emissions. When considering the entire supply chain emissions, LIMEX exhibits lower greenhouse gas emissions compared to other types of plastic.
Fenton is actively reducing its carbon footprint, exploring the options for installing solar panels at its facilities.
“As well as our own operations, we are helping our customers to reduce their carbon footprint,” continued Mr Skidmore.
“We collaborated with one of our healthcare clients to reduce the number of plastic bags in their operations. They were using over a million polythene bags a year, so we redesigned and trialled a new packaging design that saved on plastic waste.”
“We also launched a new range of point of sale, building and drinkware products earlier this year. These products are made using recycled polymers.”
Fenton has become more sustainable by working across the industry to implement new, more efficient machines into operations. The Yizumi brand was introduced
to the company by STV Machinery. Fenton has now been collaborating with STV for around six years and has replaced 11 moulding machines. This has saved on oil, time, repairs and energy in operations. Additionally, Fenton uses STV for servicing as part of a long-term partnership.
“We are the first UK company to use GÜNTHER Hot Runner’s Bluetooth technology,” said Mr Skidmore. “About two years ago we partnered with the company and started using its hot runner controllers and hot runner systems. They have been really beneficial for our operation and made us much more efficient.”
The company also works with Resinex, using its warehouses for storage and material call off, and Rocket Leads for online marketing. Over the past three years, Fenton has been upgrading its digital presence. Rocket Leads has collaborated with Fenton on introducing online advertisements and improving SEO strategy.
“I want to invest in more automation for our site,” added Mr Skidmore, in conclusion. “This will save on cycle times, scrap material and energy. We also want to add more efficient tools and technology to our tool room and make the company more sustainable. Also, we are developing our own range of recyclable products, which is really exciting. I’m looking forward to seeing where we can take the company in the next few years.” n