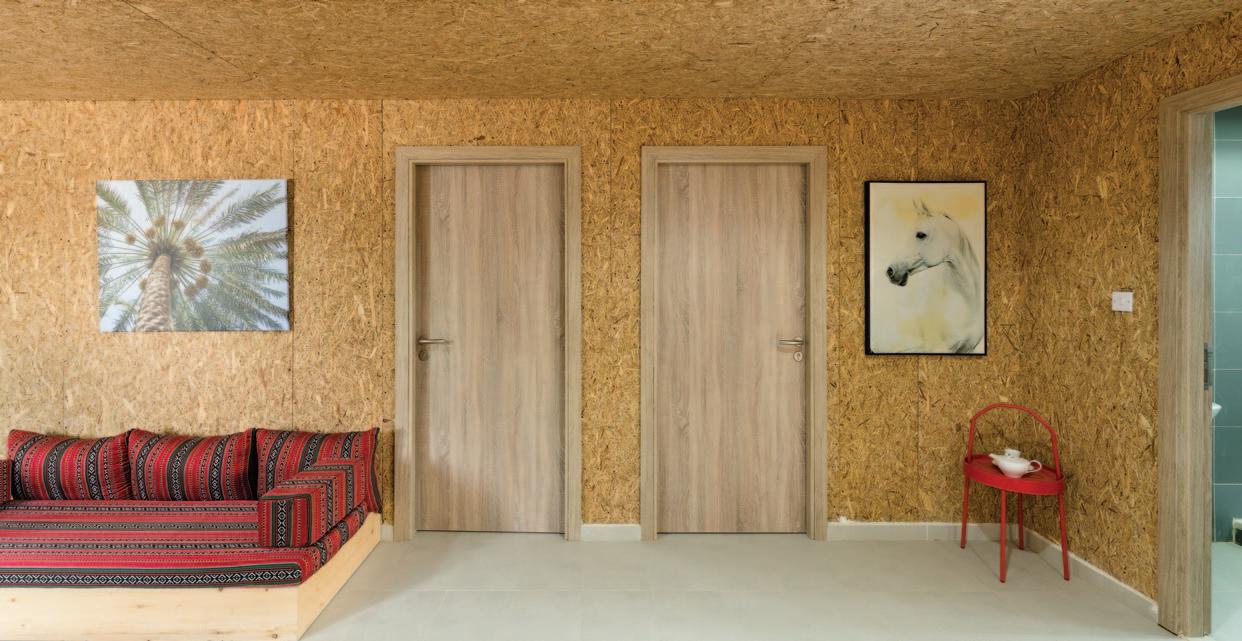

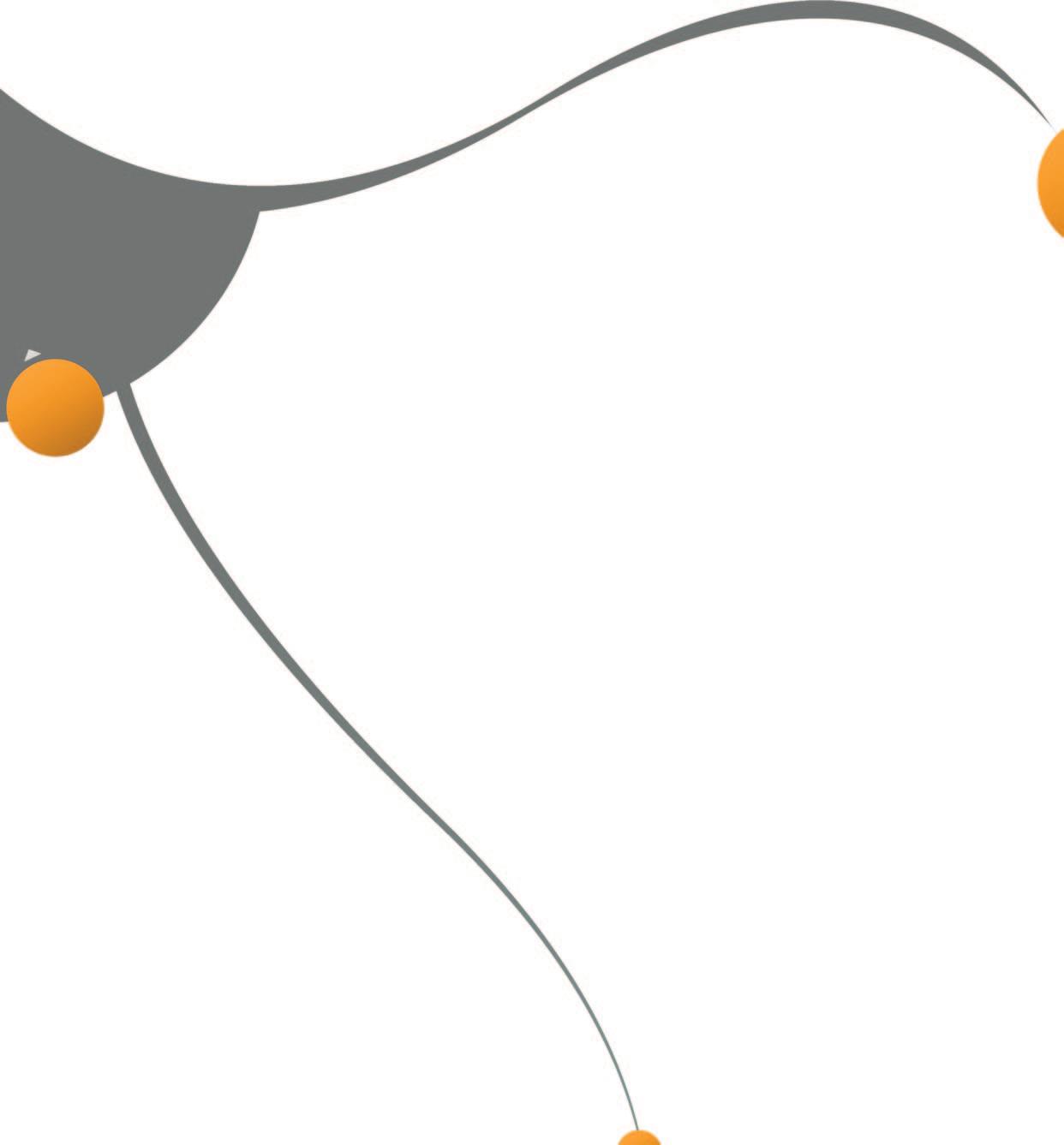

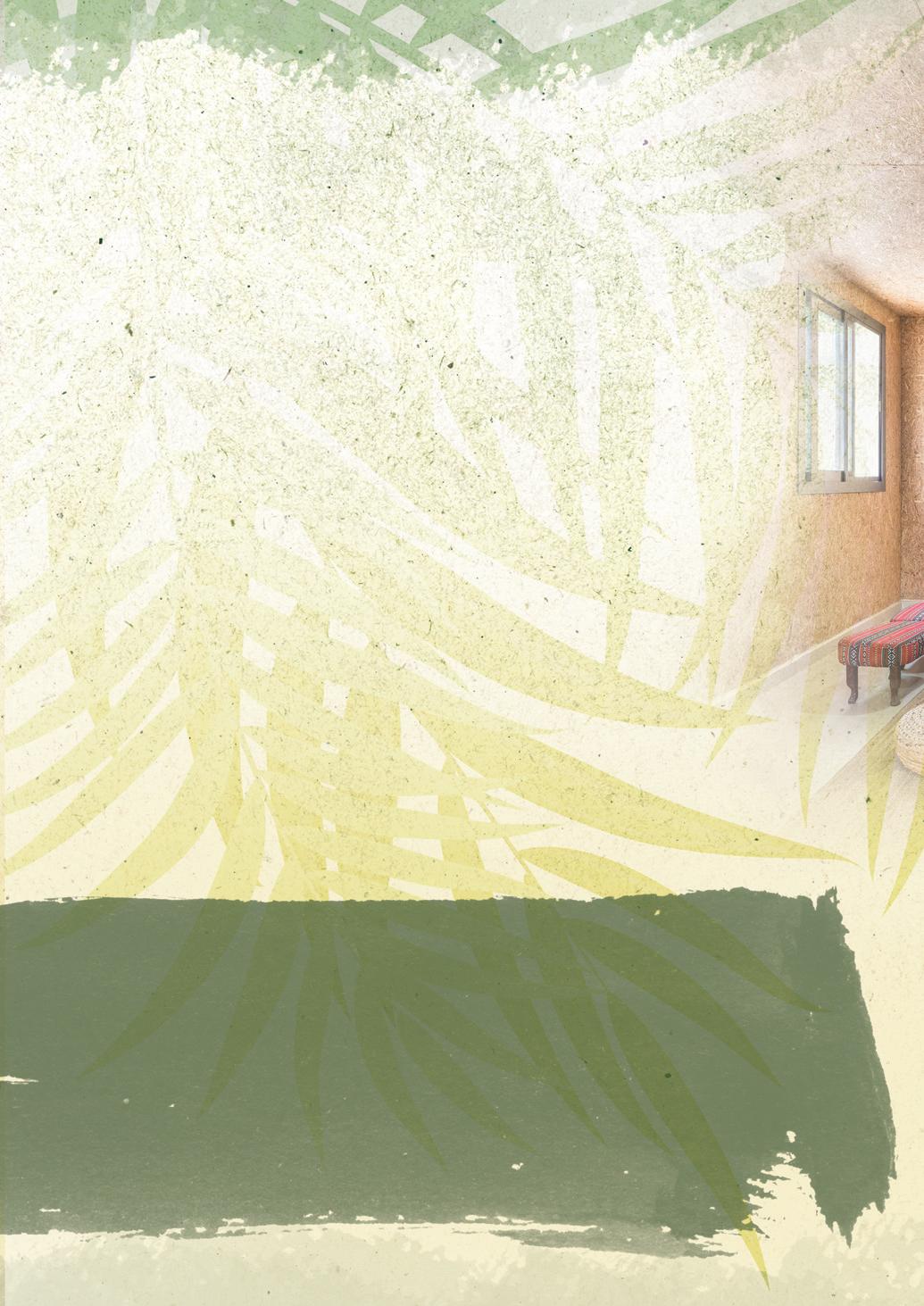
Desert Board is an exciting new company revolutionising the construction and living sectors with the world’s first engineered carbon-neutral wooden board, crafted from upcycled palm fronds. After making an impression at COP28, the UN Climate Change Conference, Director Kamal Farah explained how the UAE company is determined to showcase how sustainability can flourish by tapping into the heart of the desert. Report by Andy Probert.
Sheikh Zayed bin Sultan Al Nahyan, the late President of the United Arab Emirates and Ruler of the Emirate of Abu Dhabi, was a champion of conservation and safeguarding the environment for future generations.
While the national leader and visionary died in 2004, his inspiration and legacy live on in Desert Board, a young UAE company. It is determined to uproot traditional thinking by taking the lead
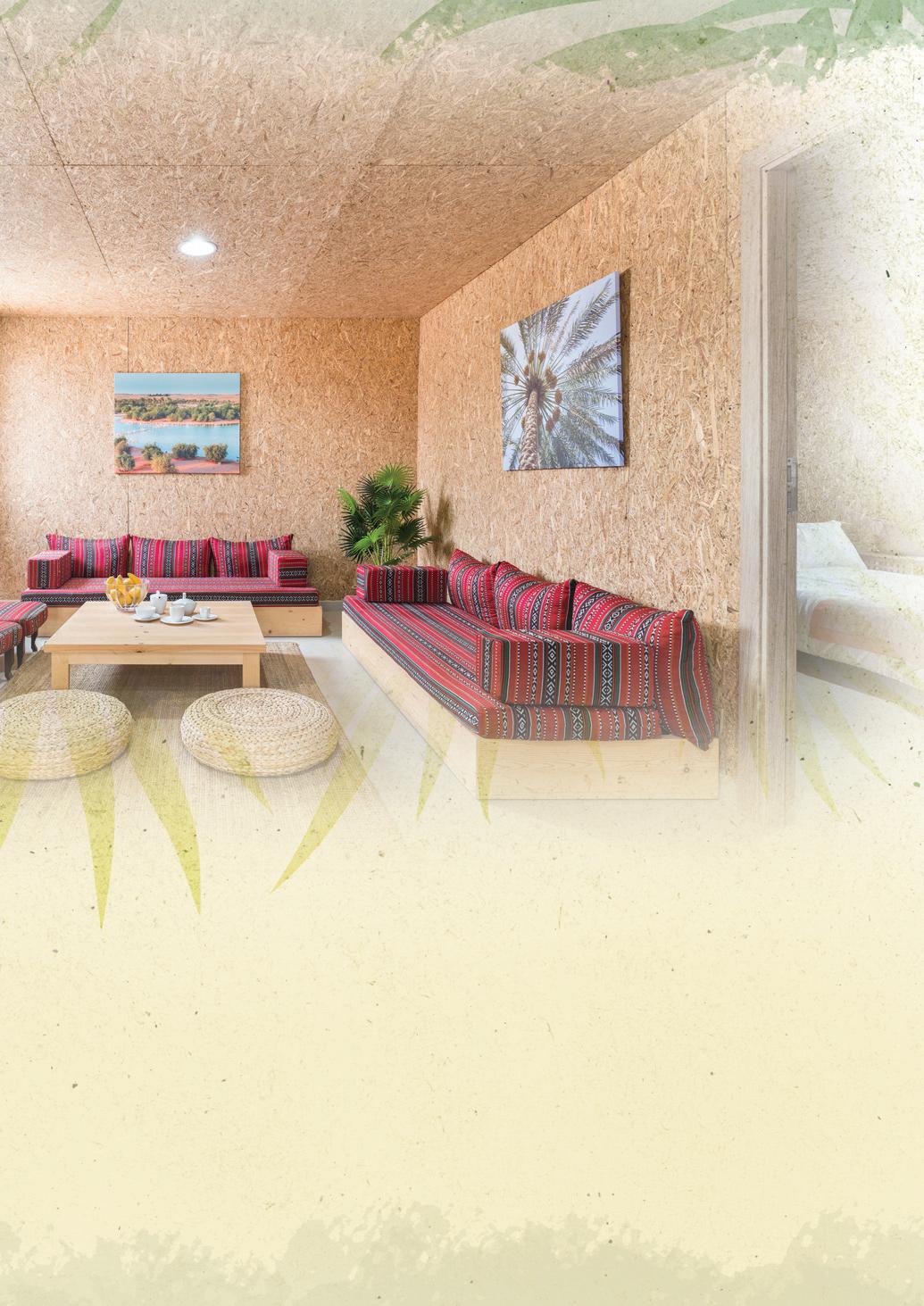
in empowering the decarbonisation efforts of the construction industry and transforming the built environment.
Desert Board has developed innovative, engineered, locally manufactured biobased Palm Strand Boards (PSB) from upcycled palm fronds. They are free of formaldehyde, a noted carcinogenic, and can be safely used indoors.
“Our PSB is the future of construction, it can be recycled up to 40 times,” said
Director Kamal Farah. “It is the equivalent of a standard Oriented Strand Board (OSB), but the key difference is that we don’t have to cut down trees to make them.”
Tech spec
PSB ® is an authentic nature-based construction material derived from the abundant palm biomass of date palm trees across the UAE. Desert Board sources the waste from municipalities and farming communities. At a state-ofthe-art factory in Kezad, Abu Dhabi, it utilises a patented manufacturing process to create durable and eco-friendly building materials.
“Our patented technology allows us to establish a circular economy,” Mr Farah explained, “meeting our goal to support environmental preservation efforts, uphold
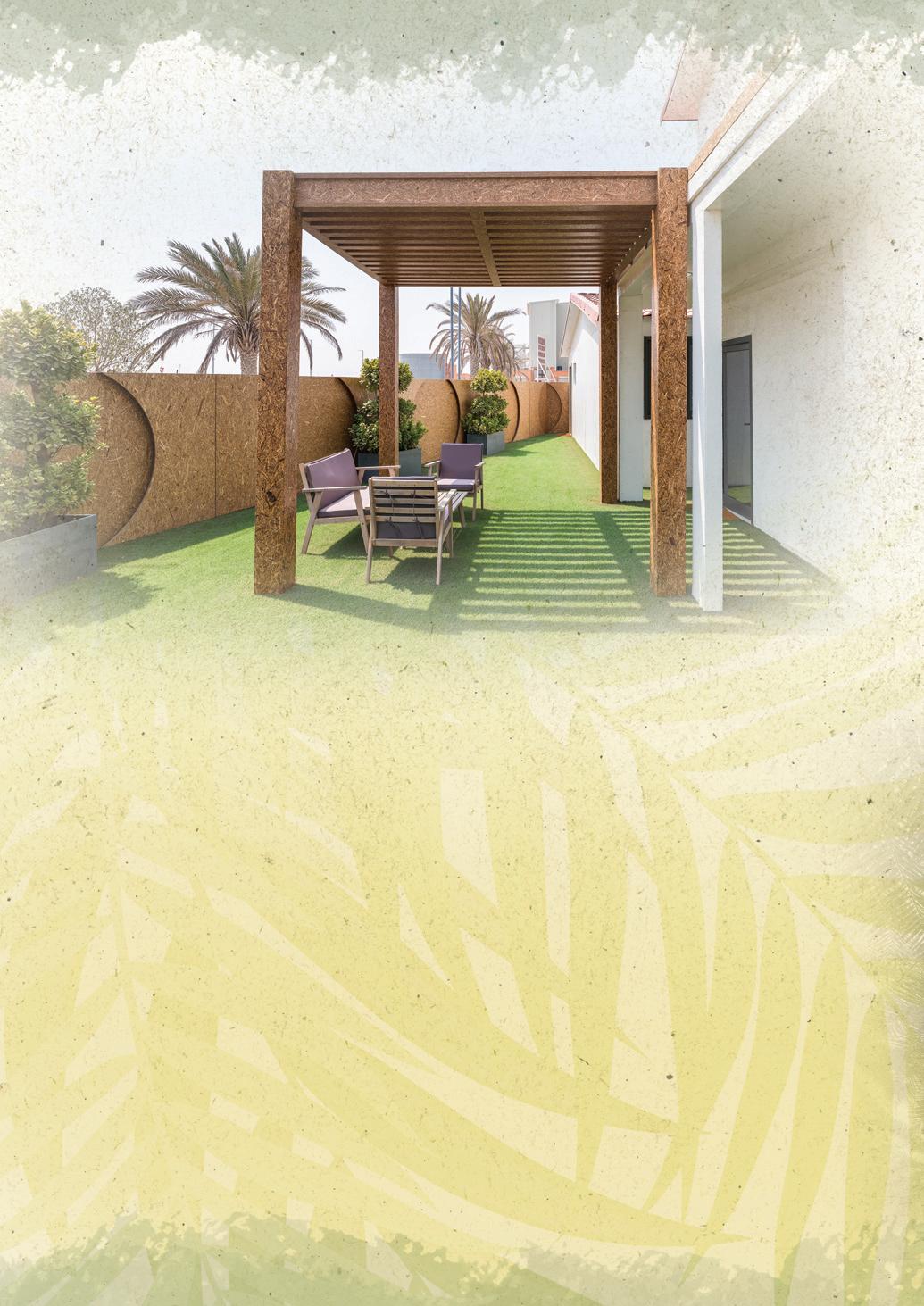
global sustainability agreements to protect our planet and facilitate healthier structures.”
The board, which can be fashioned in thickness from 9mm to 44mm, has a high mechanical strength equivalent to a traditional OSB. “You can build high beams and structures, including prefabricated h ousing units to fire prevention door cores , shuttering and construction boards,” Mr Farah said.
The concept was derived from Mr Farah’s father, Hatem, Chairman of ECC Group, a family-owned parent group renowned in the Middle East construction industry. The first PSB ® was created on December 14, 2021.
In a video created by The Climate Tribe, a UAE-based NGO championing sustainable businesses, Mr Hatem Farah explained:
“The palm tree has a lot of culture and history, and the people of the UAE were building houses and fences from that resource. As I am from construction, I never considered utilising this material.”
Circular economy
The Farah family was concerned on a number of fronts: palm waste was being thrown away, burnt or buried, polluting the atmosphere; spiralling importation costs, and the rise in carbon emissions, with construction accounting for up to 40% of global emissions.
“Around 11 per cent of emissions are from building materials, so Desert Board was born with the aim of replacing plywood for forming concrete,” continued Mr Kemal Farah. “After a long R&D period,
the board emanates from the desert environment. Because we are only utilising the palm fronds that are cut down, we are allowing the tree to continue living and capturing carbon.
“Our ancestors used to be sustainable and environmentally friendly because they used to take these palm leaves and build barasti houses and fences. Now we are crafting buildings from this board.” Desert Board produces around 110,000 cubic metres annually, or 340m3 daily.
The patented technology allows it to establish a circular economy meeting the goals to support environmental preservation efforts and uphold global sustainability agreements to help protect our planet for future generations while facili tating healthier structures.

“We have calculated internally that for every tonne of PSB® used, it is equivalent to capturing 400 tonnes of carbon,” said Mr Farah. “Key to that is how the board can be recycled and repurposed as part of the circular economy.”
PSB ® can be used to create fire-rated door cores that meet British standards for 60 and 90 minutes. It is being used as shuttering boards for casting concrete, as well as hoardings and scaffolding.
Desert Board is going further to use PSB ® to make furniture, such as kitchens,
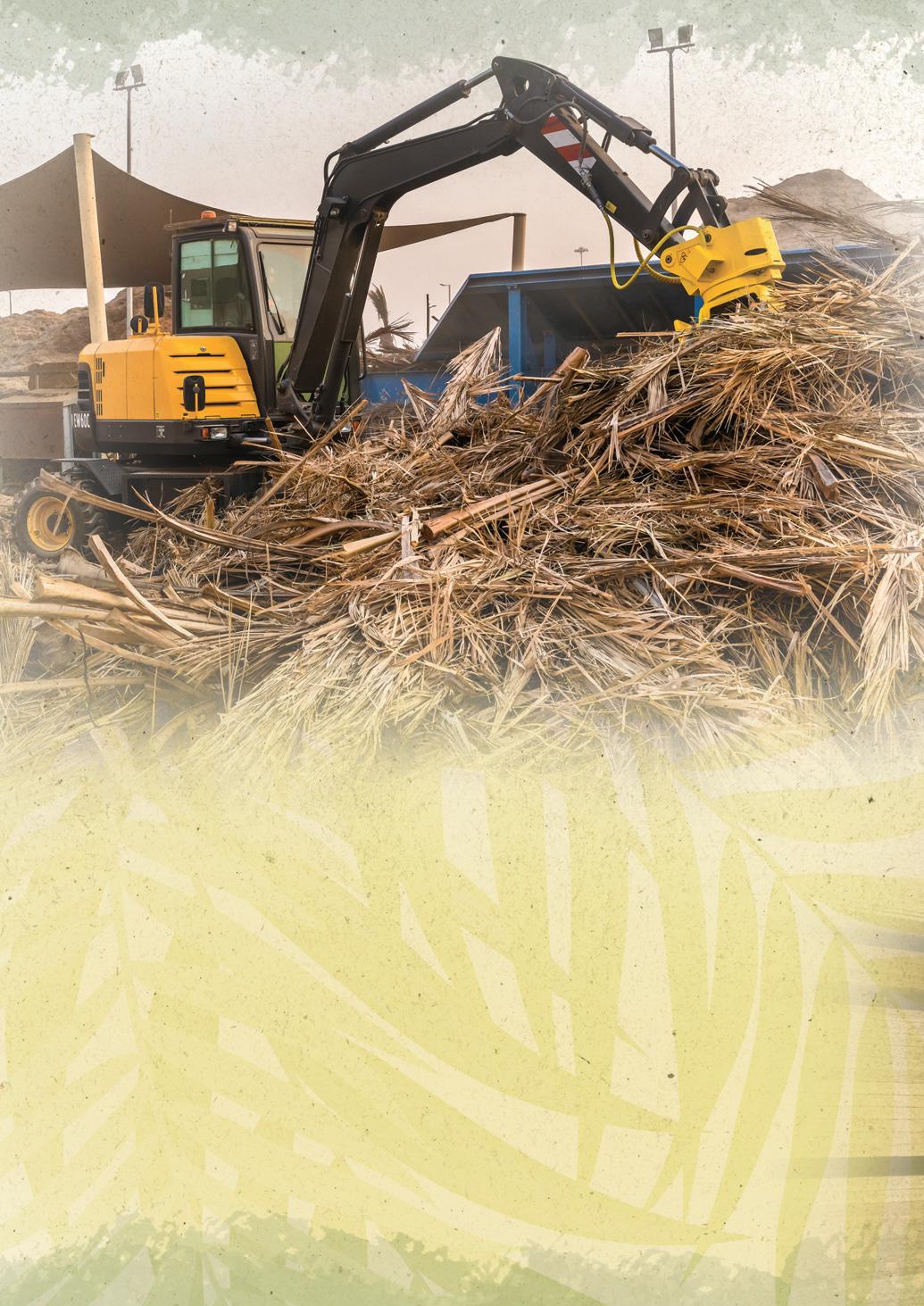
wardrobes and doors, and even built 25 homes for the Red Crescent to accommodate refugees. “We have built one and two-storey homes in our factory, created acoustic wall panelling for events , exhibitions and stands, and for prefabricated volumetric construction for projects in Saudi Arabia,” Mr Farah explained.
One significant step to raise awareness around PSBs was Desert Board’s invitation to provide products as part of a showcase for COP28, the UN Climate Change Conference, hosted in Dubai
from November 30 to December 12, 2023. The Climate COP meets in a different city yearly to demonstrate the importance of collaboration between nations to fight climate change.
The company also makes door core frames that are better than solid wood door frames and PSB® has excellent screw-holding capacities. PSBs are fully utilised by the UAE-based Abanos Interior Fit-Out & Joinery, one of several related companies under the ECC Group umbrella.
Desert Board also conforms to the Al Sa’fat Green Building System, which ensures PSBs contribute to environmentally friendly construction practices.
While the aim is to scale up production capacity, Mr Farah noted that the com -
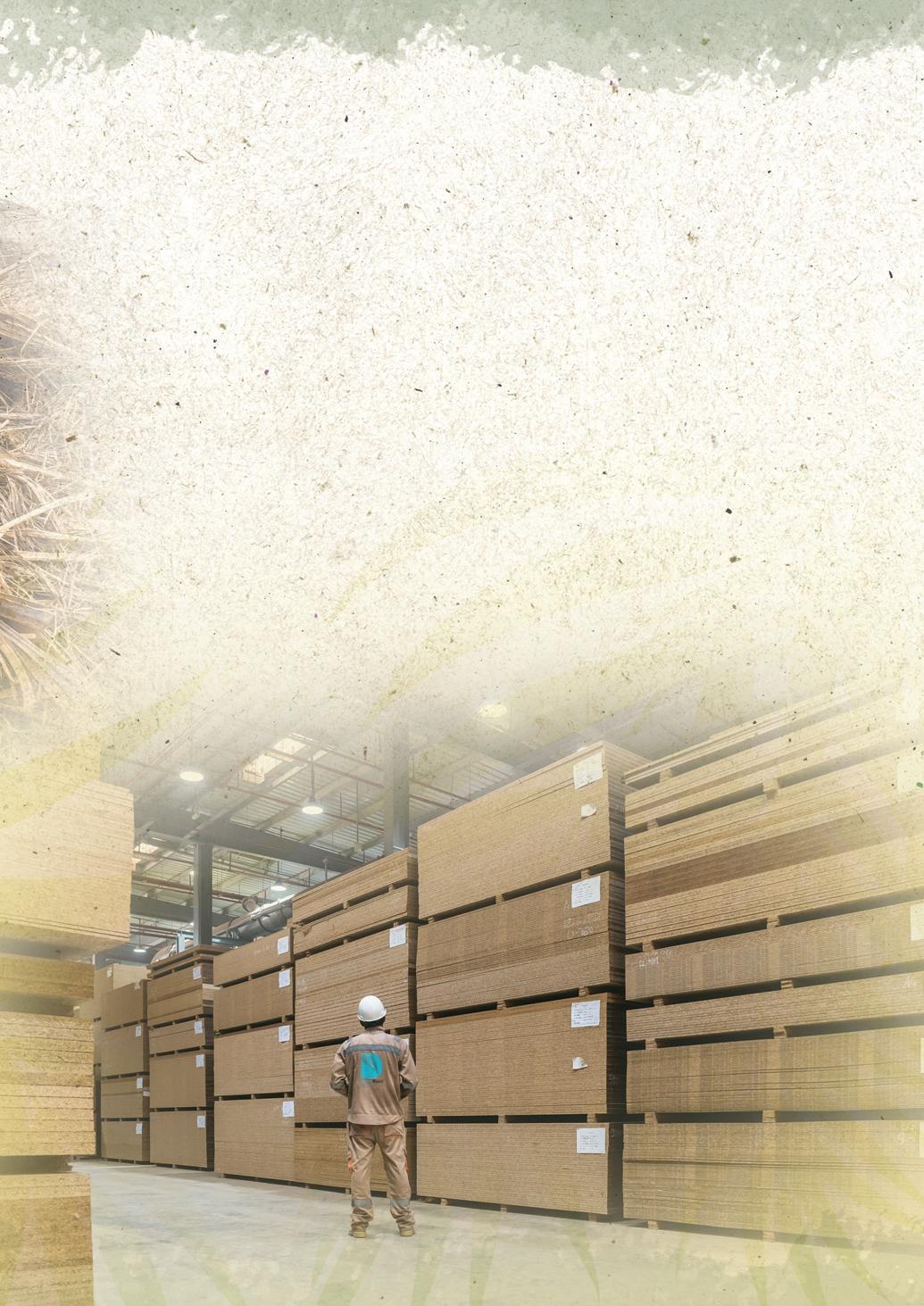
pany had eyes on enabling the boards to be used more for timber structures due to its inherent mechanical properties.
“There is enormous potential to build timber structures,” Mr Farah continued.
“We are also aided by a strong R&D team and the eight companies within the ECC Group. We are already using PSB shuttering boards for casting concrete and adding veneer to give it a wood look for furniture. It has also been used for raised flooring, and we intend to look at using it for floorboards.
“The challenge is to get traction and for the wider market to buy into what is a nature-based solution that can aid decarbonisation in the construction industry. It will take time, but we are on the right track.”
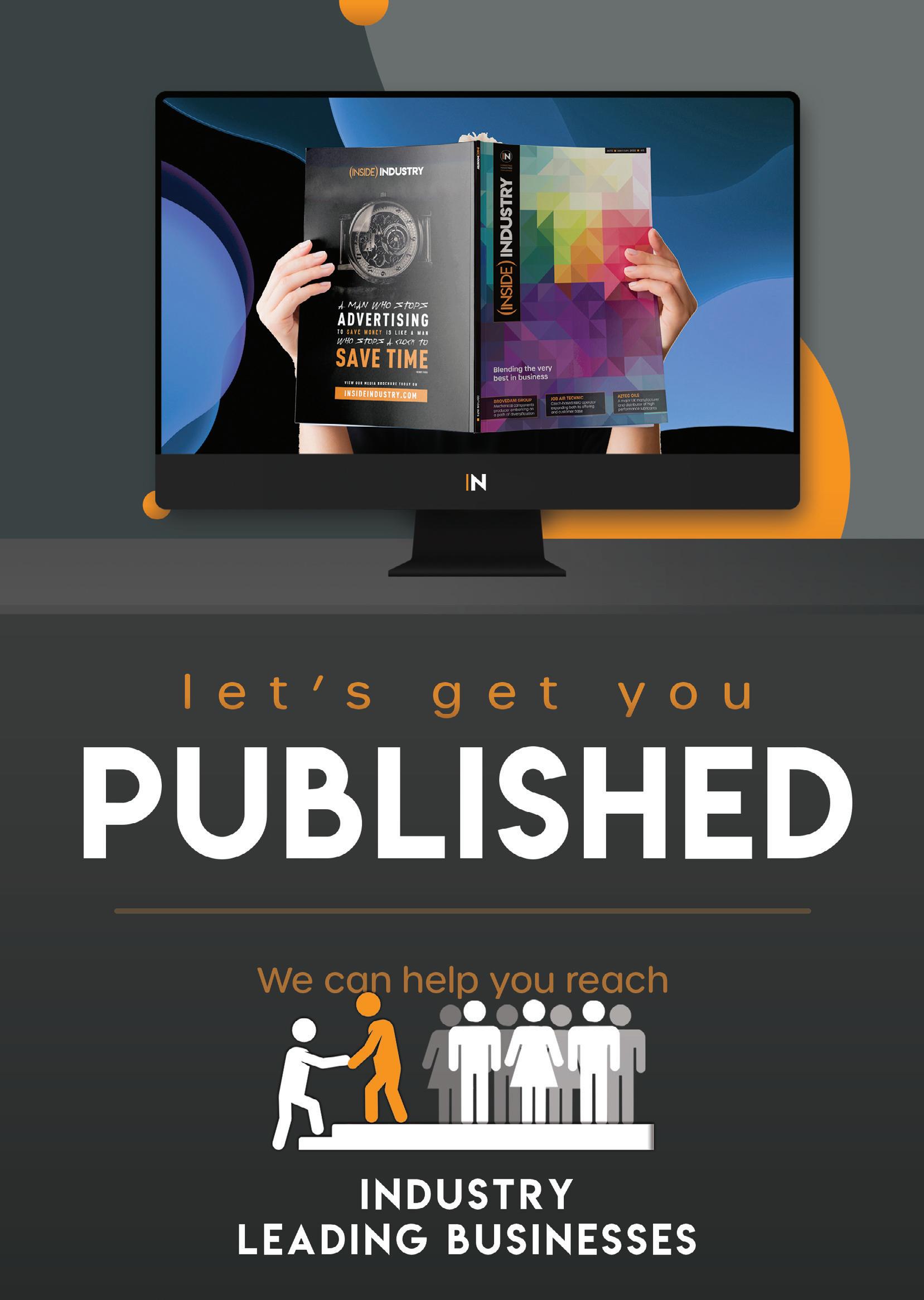
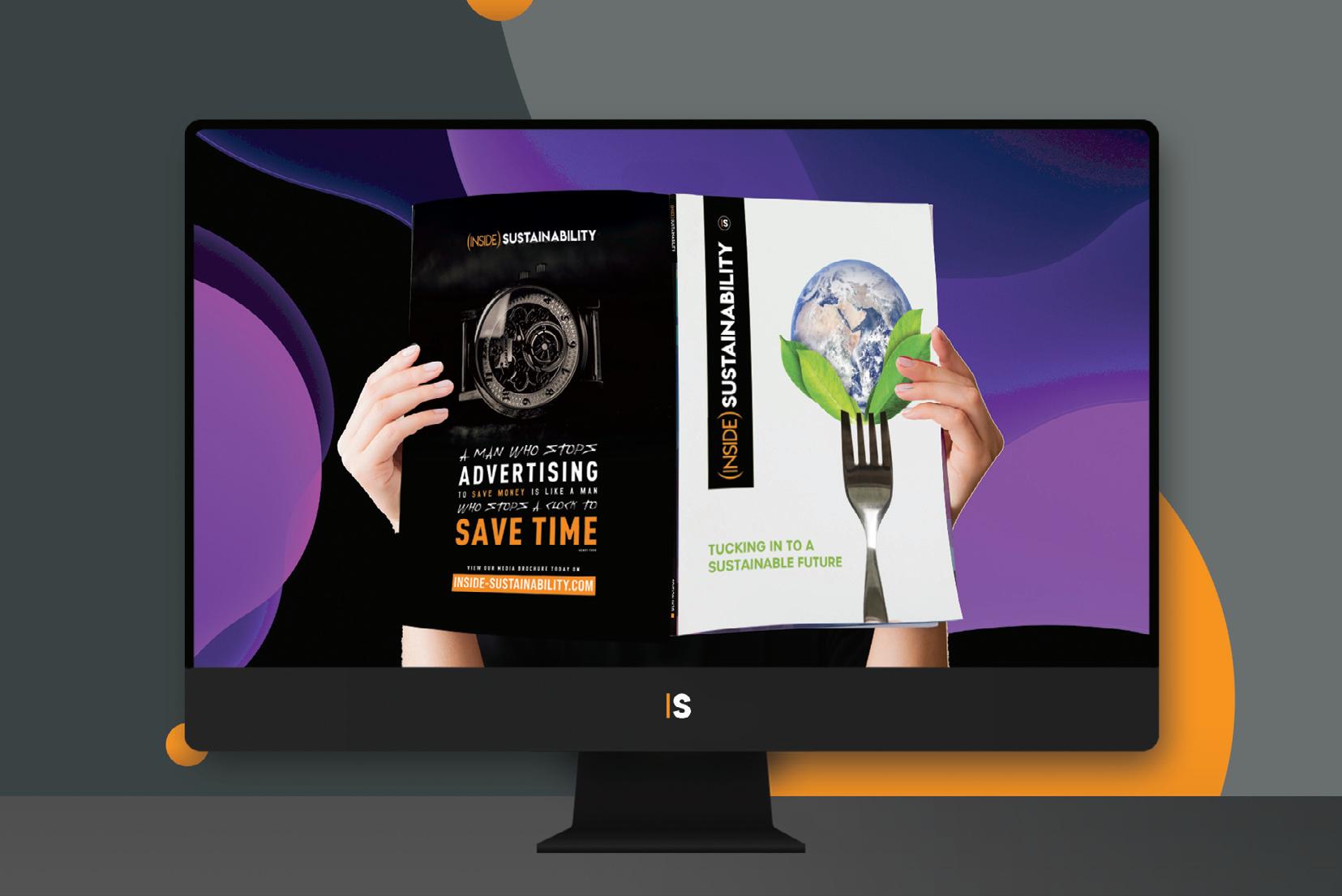