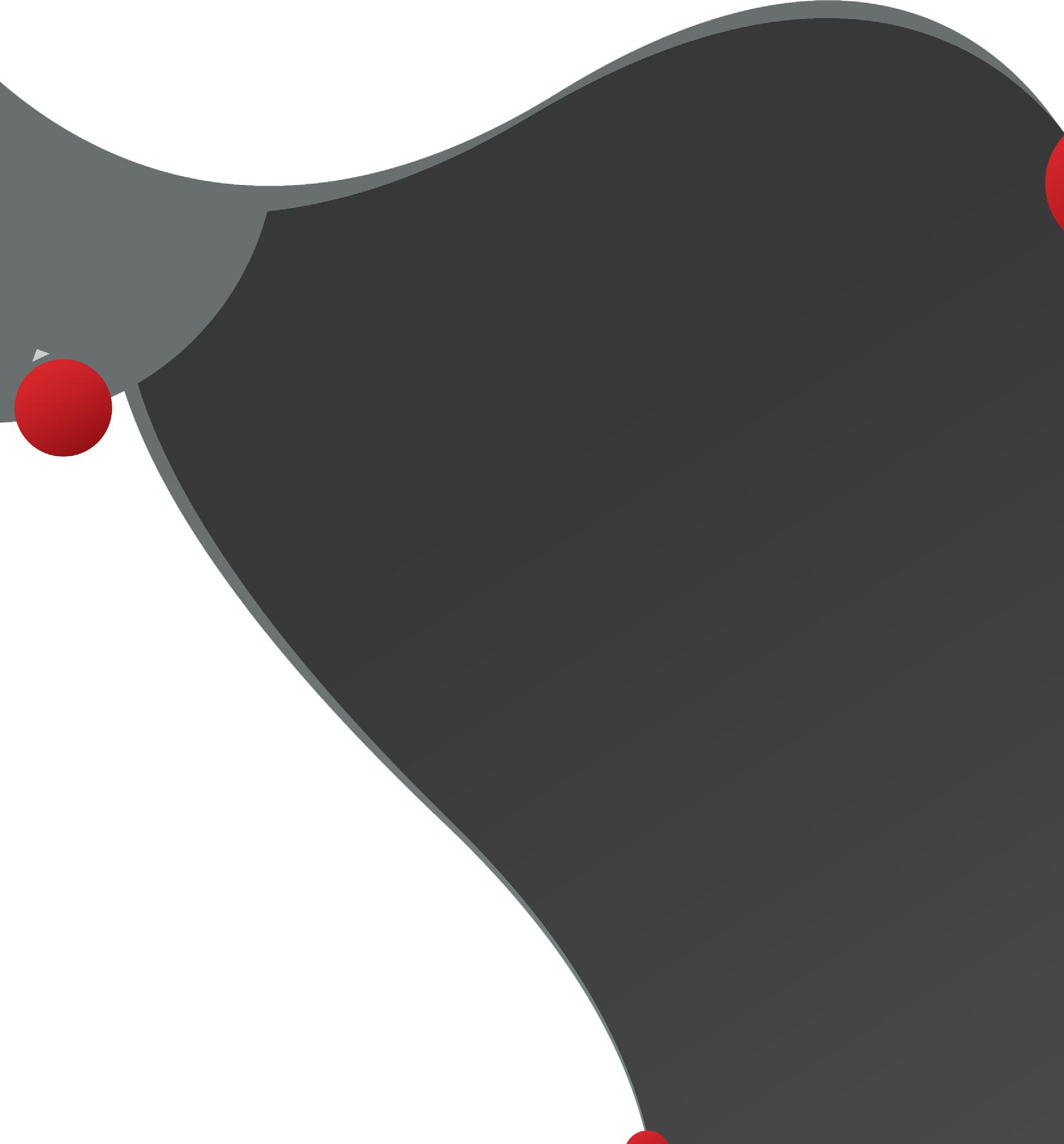
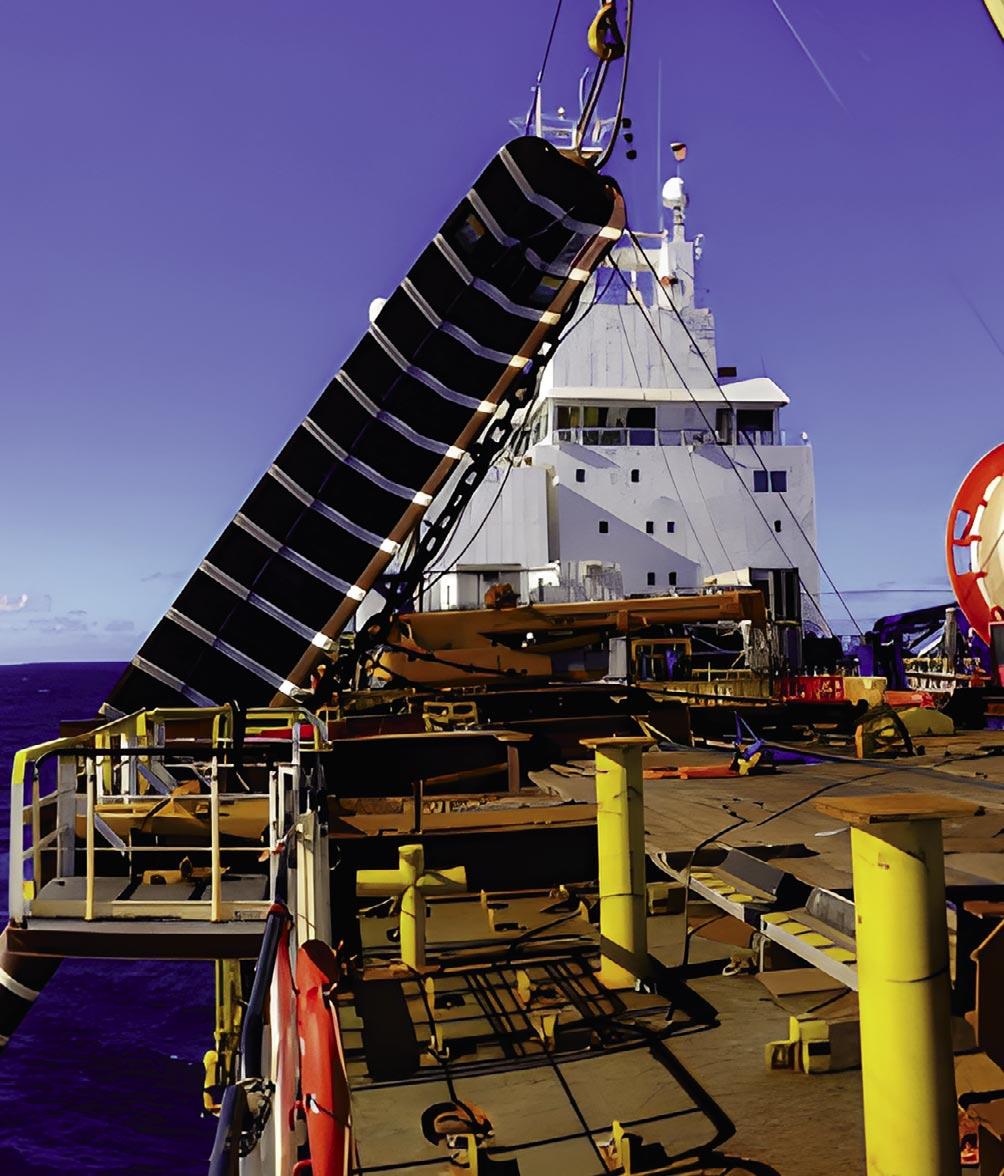
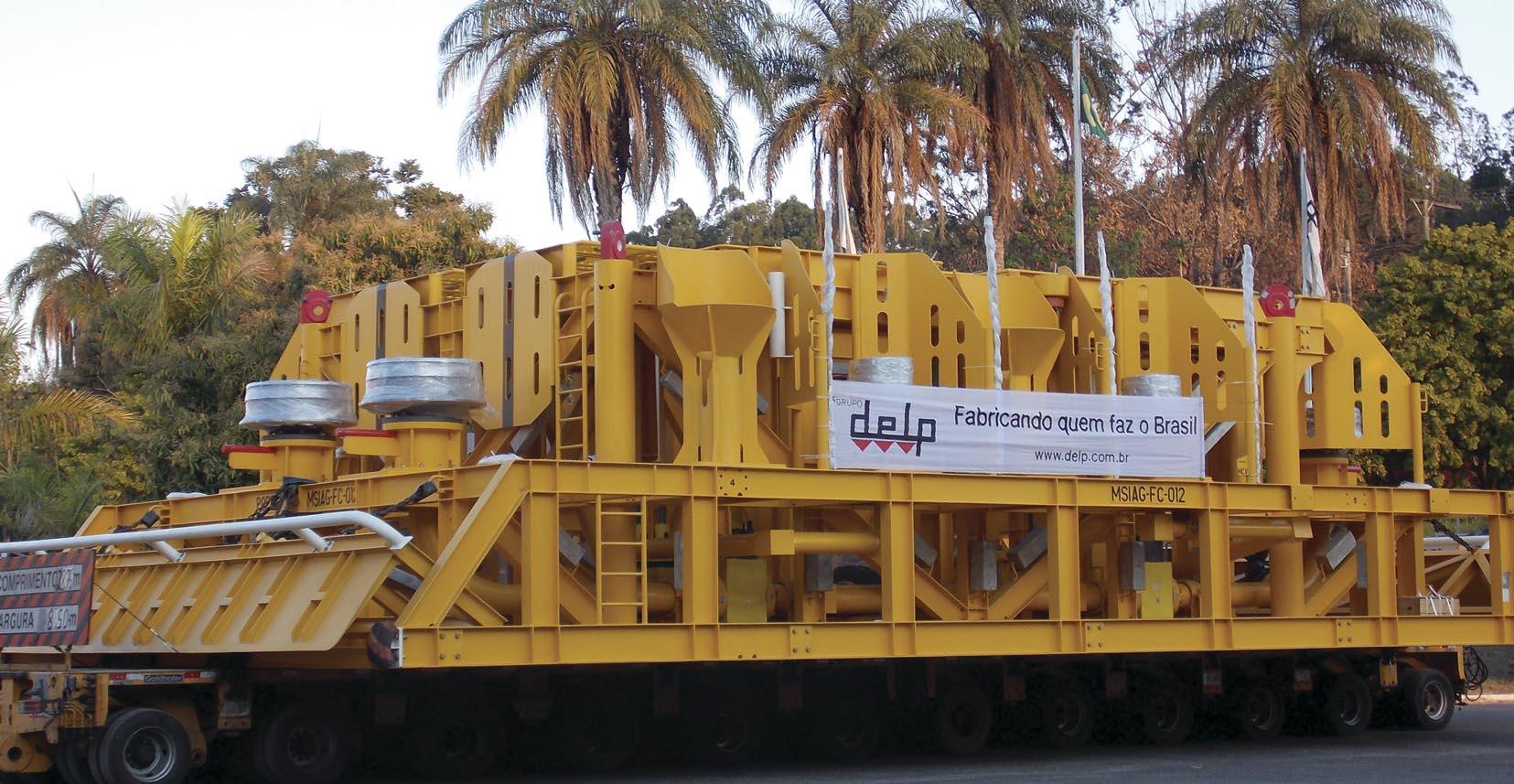

DELP Engenharia Mecânica is a leading engineering and manufacturing company in Brazil with significant ambitions to take its South American knowledge to new continents. Among its specialities is anchoring solutions for the energy and renewables sectors. Andy Probert caught up with Sales Director Cristiano Caldeira on the company’s strategy to pile in on its export potential.
Petronio Zica began his career from inauspicious beginnings with a simple nuts-and-bolts-making machine before going on to create one of Brazil’s foremost manufacturers, DELP Engenharia Mecânica.
Nearly 60 years on, his name still resonates across industry as a pioneer. Having dominated domestically, DELP’s ambitions now focus on building business growth overseas. Zica’s name could be hitting the heights in new countries as DELP’s products are piledriven into the ground.
The company has become an essential player in the petrochemical industry, providing equipment and solutions to various segments, from oil exploration and production to refining and gas production.
Its primary specialism is manufacturing huge torpedo piles that help anchor floating production storage and offloading (FPSO) units, located near offshore oil fields where oil is processed and stored. The piles are also used to secure flow and production of oil and gas pipelines and, latterly, to moor floating wind farms in deep sea with more than 100m in depth.
Its first torpedo pile was manufactured in 2005 when the company moved to a new 30,000sqm factory in Vespasiano, north of Rio de Janeiro. In April 2023, DELP will mark the manufacture of its 1,000th pile.
The evolution of what is now becoming DELP’s most important product was inspired by Petrobras, Brazil’s stateowned petroleum multinational. Sales Director Cristiano Caldeira explained: “The torpedo pile was invented and patented by Petrobras. When the patent ceased years ago, DELP developed the torpedo pile integrated solution.”
Having manufactured and supplied around 1,000 torpedo piles to Petrobras, DELP created Anchortec Solutions, a business unit specialised in integrated offshore anchoring systems. Anchortec Solutions’ core objective is to provide comprehensive solutions in pipeline anchoring for FPSOs, rigid risers and offshore floating wind installations, with a scope ranging from soil data analysis and equipment design to construction and installation.
“Importantly, Anchortec Solutions has a significant partnership with the two inventors of the Petrobras pile,” Mr Caldeira said. “They had retired but joined us and helped DELP create the unit. They have all the knowledge and experience (more than 2,000 torpedo piles) and helped hone our complete solutions package to clients. Their participation has been critical to DELP’s expansion.”
DELP has also partnered with renowned experts in geotechnics and offshore installation in pile anchoring, and participated in the development and deployment of the system. DELP’s accumulated experience enabled it to offer torpedo piles with high anchoring efficiency, low anchor costs, greater savings and on-time deliveries due to lean, automated processes.
It recently delivered 26 subsea torpedo piles for the anchoring system designed to keep Petrobras, last project in place for oil production – located 180km off the Rio de Janeiro coast, in ultra-deep waters.
DELP’s business development is a far cry from when Petronio Zica began producing nuts, bolts and machined parts from a small 180sqm space in Santa Efigênia, Belo Horizonte, a place known as ‘The Village of Vultures’. Operations consisted of three machines, but 21-year-old Zica soon teamed up with his three brothers to strengthen DELP.
Since the creation of the company, many changes have occurred, and the company has put together a history of
major accomplishments, marked by the continuous search for new markets, innovative technology and process solutions.
DELP, whose turnover is predicted to increase by 16% in 2023, now employs around 800 people at Vespasiano, providing mechanical engineering and detailing to manufacturing, industrial erection and equipment supply for the oil and gas, renewables, power generation, steel industry, mining, and services markets.
It has manufactured more than 160 manifold and subsea structure projects for oil majors such as Petrobras, Shell, Enauta and Equinor. A recent milestone was manufacturing 22 manifolds, each weighing 60-80 tonnes, for a five-phase project for ExxonMobil in Guyana.
The company, now led by Humberto Zica, ( the second generation of the family), has predicted that around 5,600 people have worked for DELP over its entire history, achieving over 46 million hours of work on
more than 2,000 projects, and delivered over 460,000 tonnes of equipment.
DELP has invested in developing compact centrifugal separators for produced water treatment for the oil and gas industry, and created a new facility at Port Do Acu to manufacture subsea jumpers for the oil and gas industry.
Mr Caldeira highlighted how the Vespasiano factory is equipped with heavy machinery and has the capability
of meeting clients’ demand for top-quality, high-end equipment for all downstream and upstream projects. The company also promotes a safe working culture for employees and has achieved six consec utive years without any lost time due to major incidents or accidents. It is also working towards further sustainable actions to minimise its environmental impact.
The company plans to increase its Vespasiano plant with a 7,000sqm hall, with completion scheduled in 2024. “This investment will enable us to increase production time from 55,000 hours per month to 65,000 hours,” explained
Mr Caldeira. “This will put us in good stead to drive our expansion abroad.
“One of the challenges is to take our technology abroad and partner with major oil players on their projects. Compared to our main competitor technology, our torpedo pile products’ manufacturing and installation costs are 40 per cent less than suction piles – the ongoing technology.
“We are now in talks with several oil producers about our technologies and hope to close out signings on projects by 2023. It is incredibly exciting to fulfil DELP’s true potential.”
DELP is also going into the offshore floating wind farm market with its reliable piling technology to offer deep-sea mooring. It has strengthened its network, establishing
a sales representation in Europe and Asia through Dutch-based Mooreast Holdings and with Strana for the USA market. Mooreast has a Singapore factory and is building a new facility in Aberdeen, UK, that could each accommodate DELP’s production.
“There are several projects at a very advanced stage in Japan, South Korea and elsewhere in Southeast Asia as well as in California that we are excited by,” Mr Caldeira said. “DELP is also looking at potential partners in the US to manufacture our torpedo piles. An offshore floating wind farm project could take 300 piles. Each pile can weigh 150 to 200 tonnes and be 25 metres high.
“We can produce piles from 24 to 200 tonnes, but the ones used in FPSOs and
offshore floating wind installations are from 120 to 200 tonnes. Ideally, DELP would need local facilities to manufacture such massive equipment. And the partners were already defined in the USA, Europe and Asia to do so.”
The company is also studying the opportunity to advance new monopile technology for bottom-fixed offshore wind farm structures; mainly as Brazil is approving such installations closer to shore.
“DELP’s present output is geared 90 per cent to the domestic market, but we would like to achieve 30 per cent production for export in the next five years,” Mr Caldeira concluded. “It is Brazil’s and the world’s foremost leader in torpedo piles. Our track record is beyond doubt, but we want to take our torpedo pile knowledge abroad.”n