
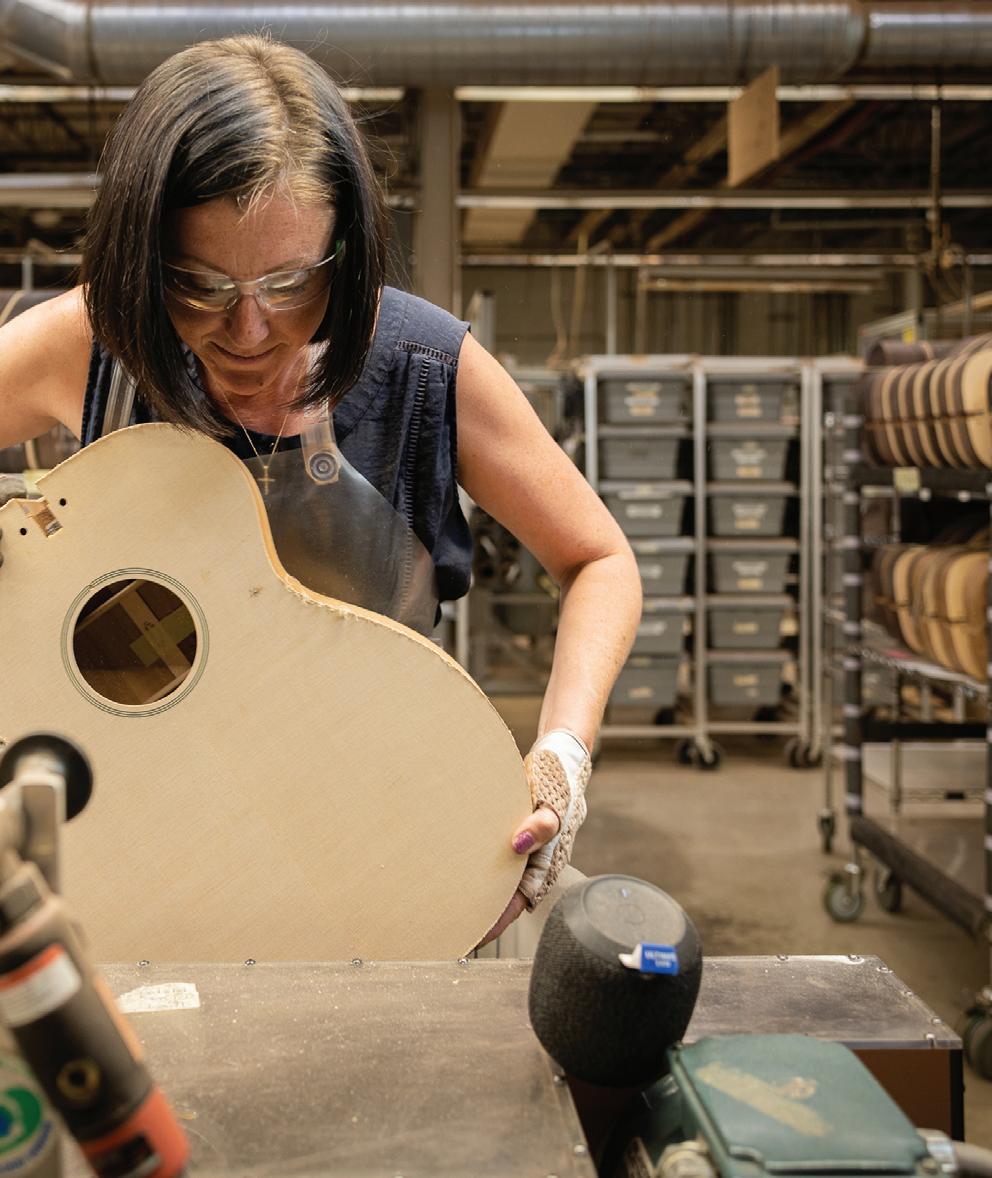
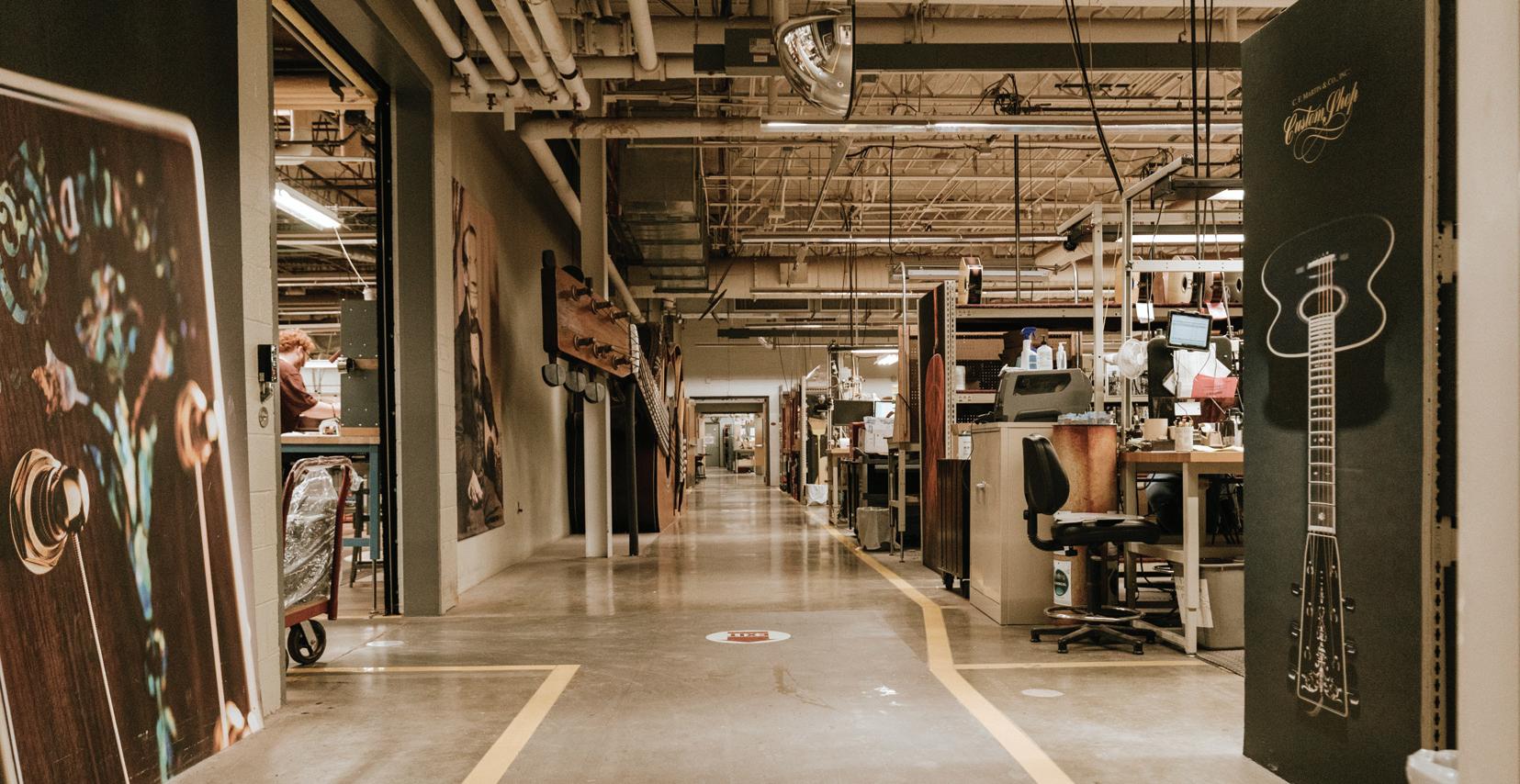

Six generations after the first guitar was produced on Christian Frederick Martin’s workbench in 1833, C.F Martin & Co has earned its place as a leading manufacturer of acoustic guitars and strings. Director of Supply Chain Management Frank Untermyer sat down with Richard Hagan and revealed how the company has forged a unique manufacturing process that combines the best of traditional, time-tested skills with modern machinery and a remarkable commitment to sustainable procurement.
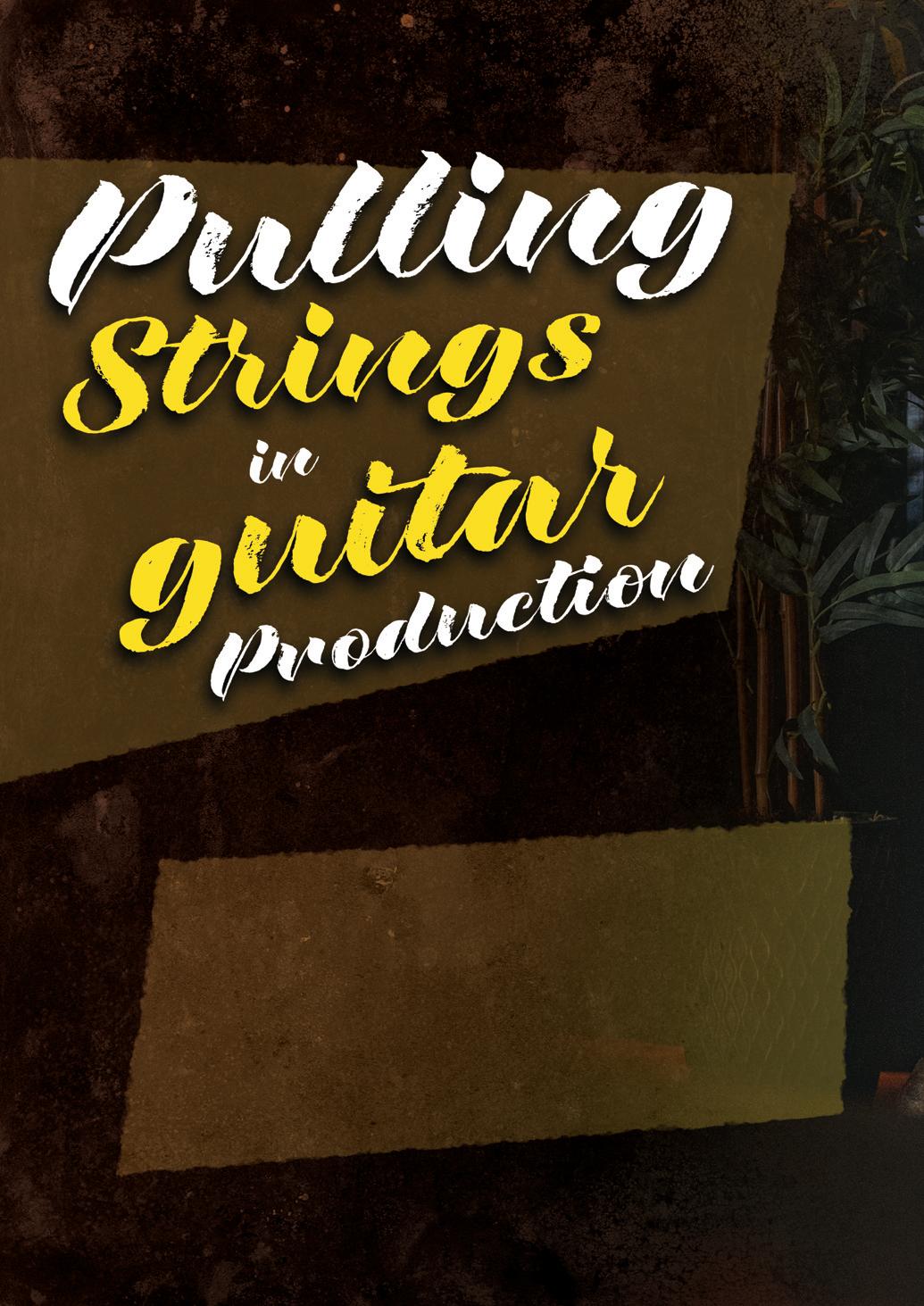

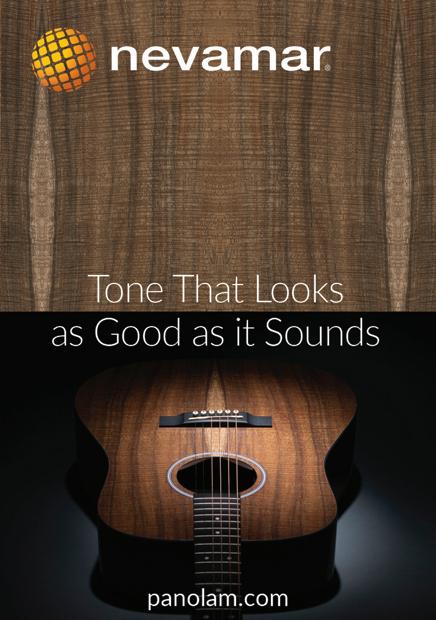
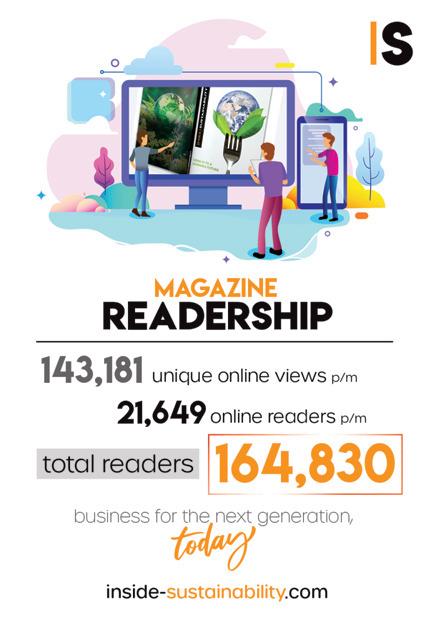
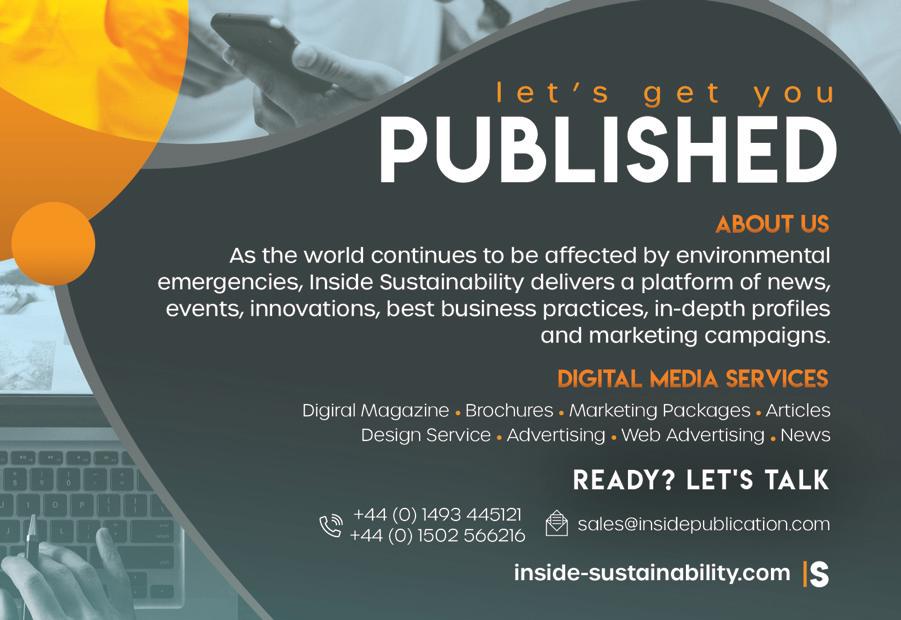
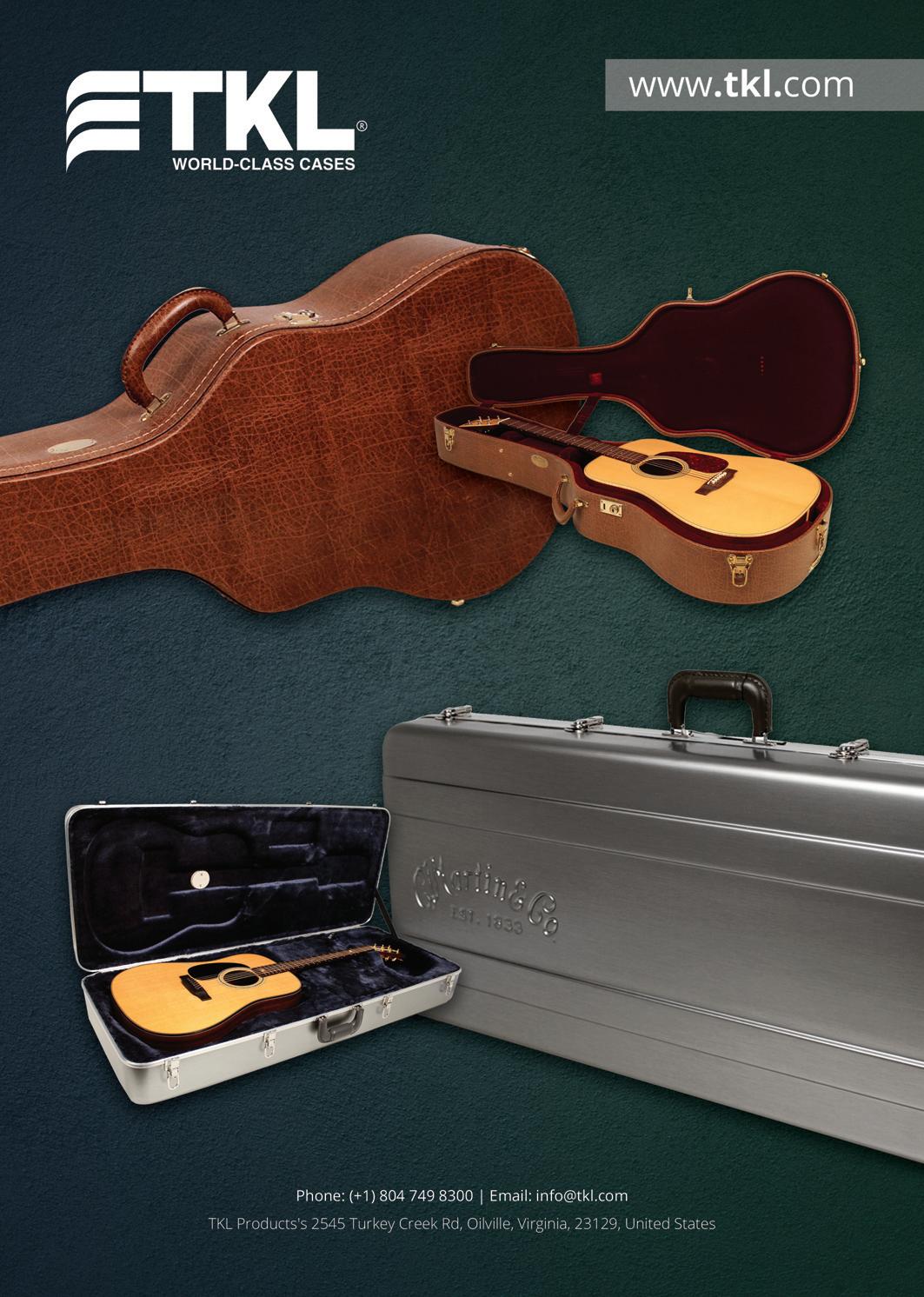
Martin Guitar, headquartered in Nazareth, Pennsylvania in the United States, manufactures a range of high-quality guitars and guitar strings. Founded in the early 19th century by Christian Frederick Martin, the company pioneered various manufacturing techniques and design philosophies that were so effective and successful that they quickly became industry standards.
Merging tradition & modernity
Martin Guitar’s main facility is also its headquarters, with an impressive footprint of 200,000 square feet, 146,000 of which is dedicated to manufacturing space and the remainder is offices and manufacturing support. Ten minutes from this facility lies the firm’s second property. Designed specifically for the company’s
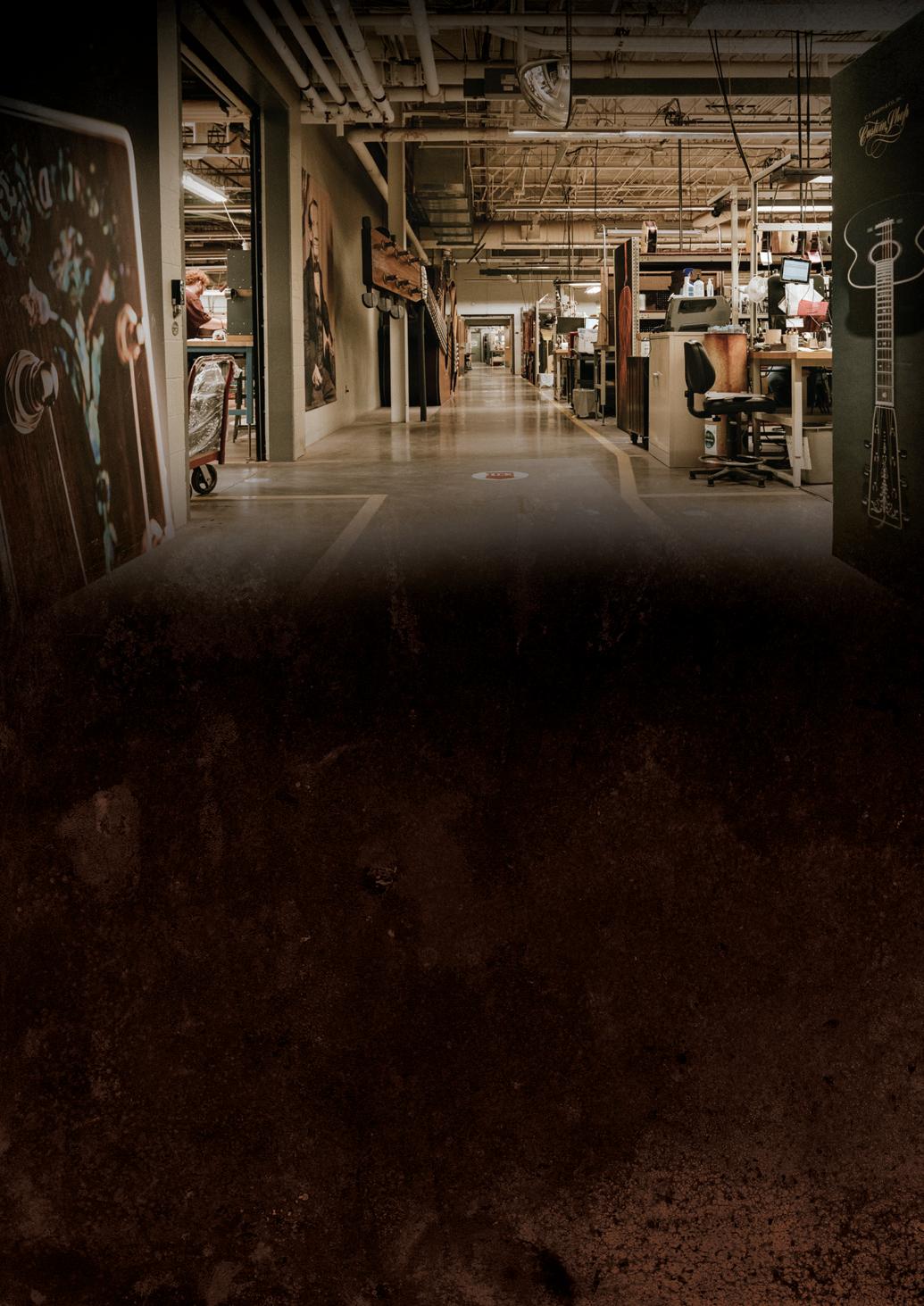
distribution needs, Martin Guitar occupies about half of this 200,000sqft facility, with the remainder leased out to others.
Finally, its third facility is located in Navojoa, Sonora, in Mexico. This factory is equipped to a similar level as its headquarters and is responsible for manufacturing. Across all three sites, the company employs about 1,000 staff.
Martin Guitar’s manufacturing philosophy is a fascinating blend of artisanal guitarmaking techniques - called luthiery - with ultra-modern machinery and capabilities, as Frank Untermyer, Director of Supply Chain Management, pointed out: “We strongly believe in continuous investment in the latest technology. We have machines that precisely cut a guitar’s dovetail neck joint, as well as CNC buffing machines. We also utilise automated
technology to set a uniform fret height on the fingerboards. Our spray booth is robotic, and we use CNC for precision inlay work.”
The company’s high-tech production capabilities contrast with its deliberate, continued focus on traditional luthiery skills, especially for its higher-end products. Martin Guitar’s custom guitar workshop is said to be the largest of its kind in the music industry, boasting a large number of skilled luthiers.

“We use chisels to hand fit necks to bodies, and hand files to dress the frets on the fingerboards,” said Mr Untermyer. “This workshop cuts inlays and sprays the guitars all by hand. Our capabilities in the custom shop match and exceed those found anywhere else. It’s a focus area of ours and it continues to grow.”
Making sustainable music
Sustainability is a core value at Martin Guitar, especially given its inescapable reliance on timber and other natural resources for manufacturing its products. For that reason, the company places a high value on the wood that its uses while also ensuring that it is responsibly harvested from sustainable sources.
“Wood is the lifeblood of an acoustic guitar and so we need the tonewoods to exist for generations to come,” Mr Untermyer explained. “Responsible harvesting methods guarantee a high monetary value for those woods, discouraging wasteful usage of such precious resources.”
Martin Guitar developed an ecological policy as far back as 1990 which subsequently saw the company receive Forest Stewardship Council ® (FSC ® Chain of
Custody certification (License code FSCC008304). Consequently, the company strives to procure FSC-certified wood wherever possible. For example, the company sources mahogany for its guitar necks and bodies from a certified source in Guatemala, and its ebony for its fingerboards and bridges from a similar source in the Republic of the Congo. Additionally, the company utilises the services of a specialist third party to verify the legality of the woods that Martin Guitar procures, and in certain cases, the company dispatches its own teams into the forest to confirm the actual source of the wood. “We are passionate about ensuring the sustainability of the forests and specifi c species that we use,” said Mr Untermyer.
Martin Guitar also actively embraces listings on the appendices of the Conference of International Trade in Endangered Species (CITES) which fosters the legality and traceability of the
tonewoods used in Martin Guitar manufacturing processes. To this end, Martin Guitar maintains close relations with the United States Fish & Wildlife Service –responsible for managing CITES in the United States – as well as many other CITES authorities all in addition to the Secretariat based in Geneva.
Reclaimed wood is another sustainable source for Martin Guitar. In Canada, the company routinely travels into the forests and disassembles old, disused logging bridges from which it produces guitar tops. Abandoned logs left behind on the forest floor are also fair game and to date, have gone into the production of 15,000 guitar tops without Martin Guitar having to cut down a single tree.
Chilling investments
Martin Guitar’s sustainability efforts extend to a substantial infrastructure investment to reduce its energy
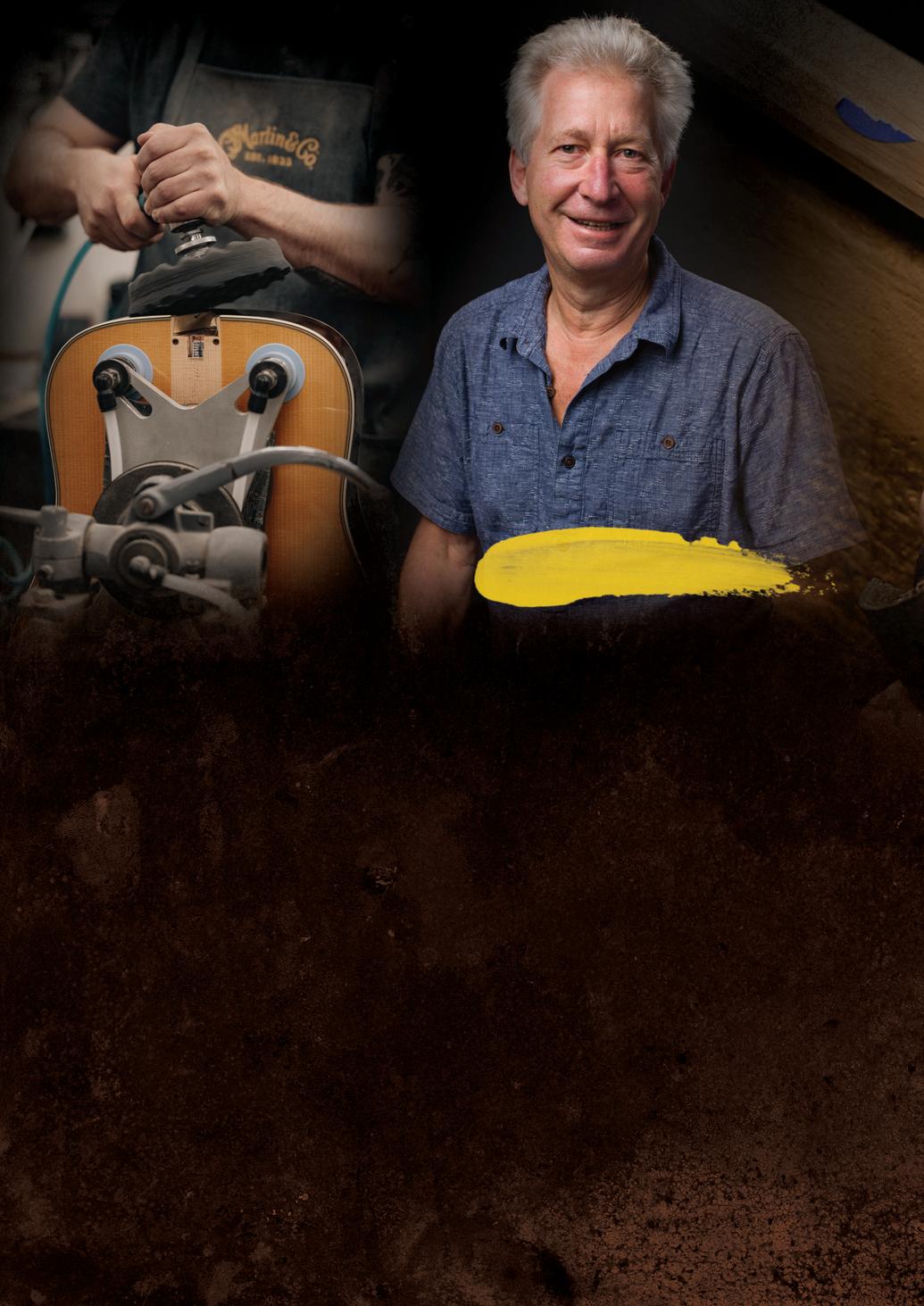
footprint. Several years ago, the company invested $8.85 million in a full retrofit of Martin Guitar’s Pennsylvania facility’s HVAC system. The new system now consists of three water-cooled chillers, while the heating system now includes three, low-temperature condensing boilers. This upgraded system reduced the company’s electrical and natural gas consumption by over 40% and 20% respectively, resulting in an annual cost reduction of $500,000.
Meanwhile, Martin Guitar partnered with guitar string manufacturer D’Addario to support that firm’s Playback world-leading string recycling program. With the aid of
string recycling receptacles at music stores around the country, Playback has recycled over 10.5 million guitar strings.
Looking ahead, Martin Guitar is focused on continuing to innovate the guitar market just as it has done for over six generations; and so in closing, Mr Untermyer explained the company’s vision: “We will continue to set the benchmark for acoustic guitar design, quality and playability. We hope that the instruments that we build, and the music that is made on them, will continue to inspire people. Music is the universal language; it brings people together. We need more people to live harmoniously . We all need more music.”

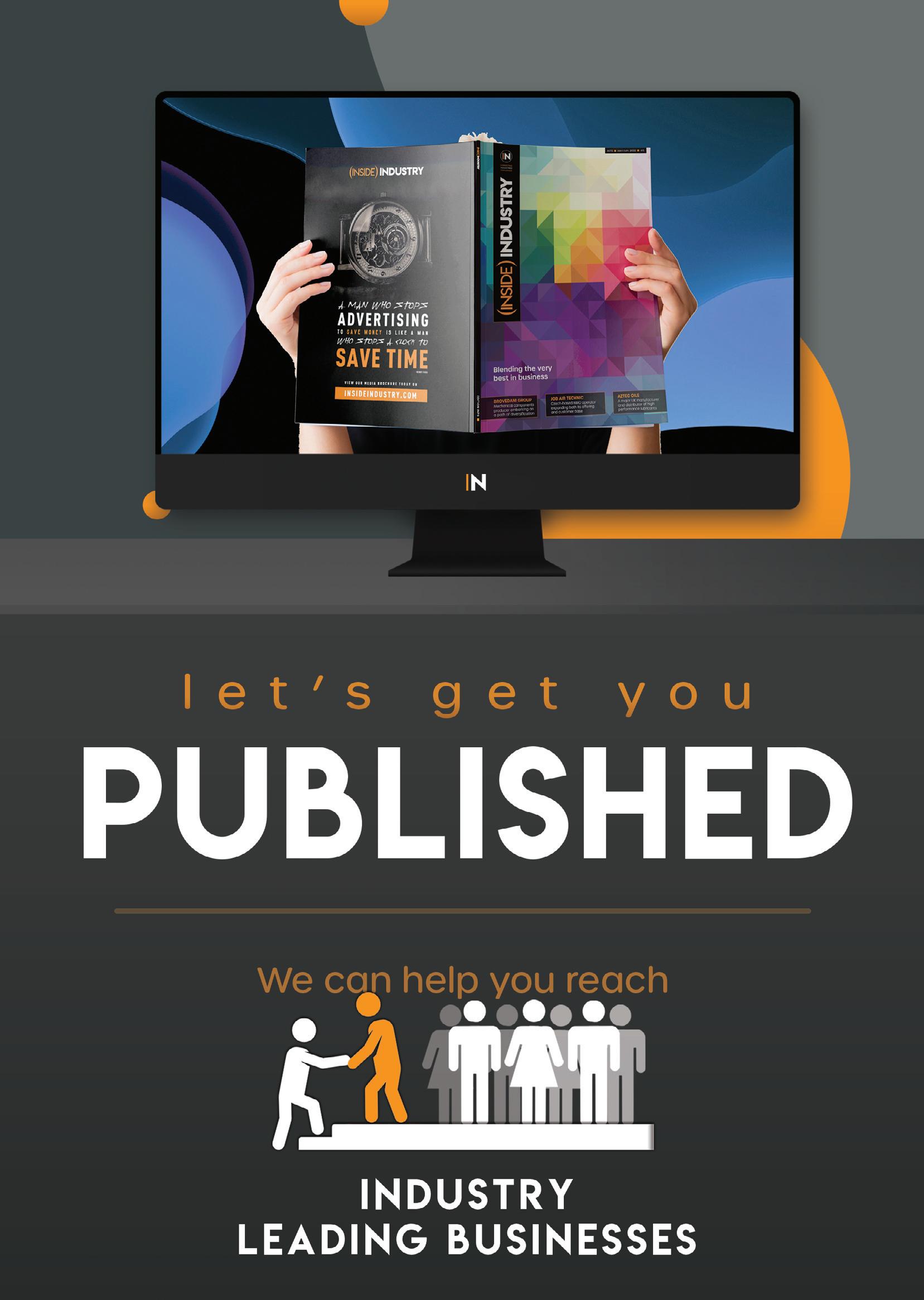
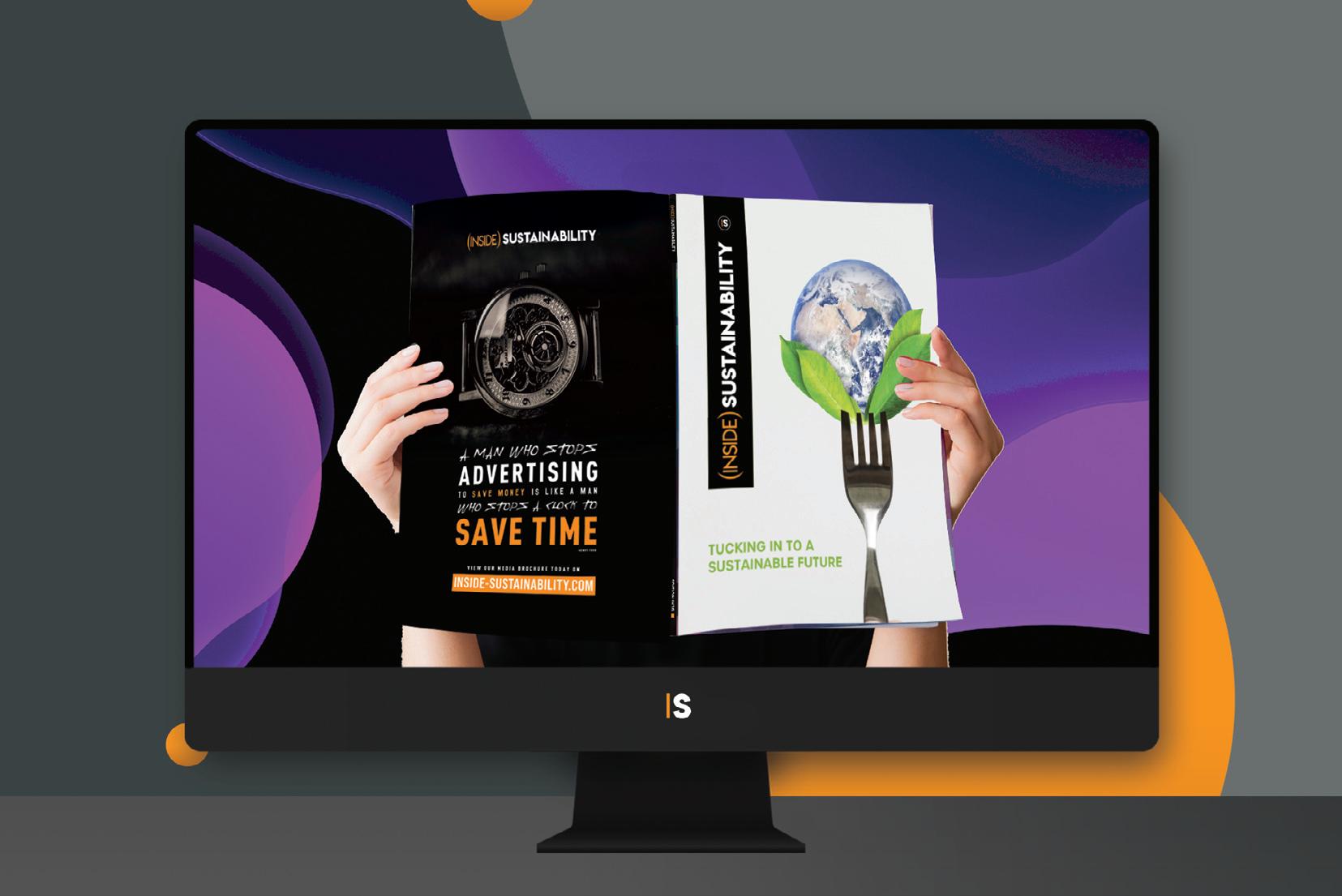