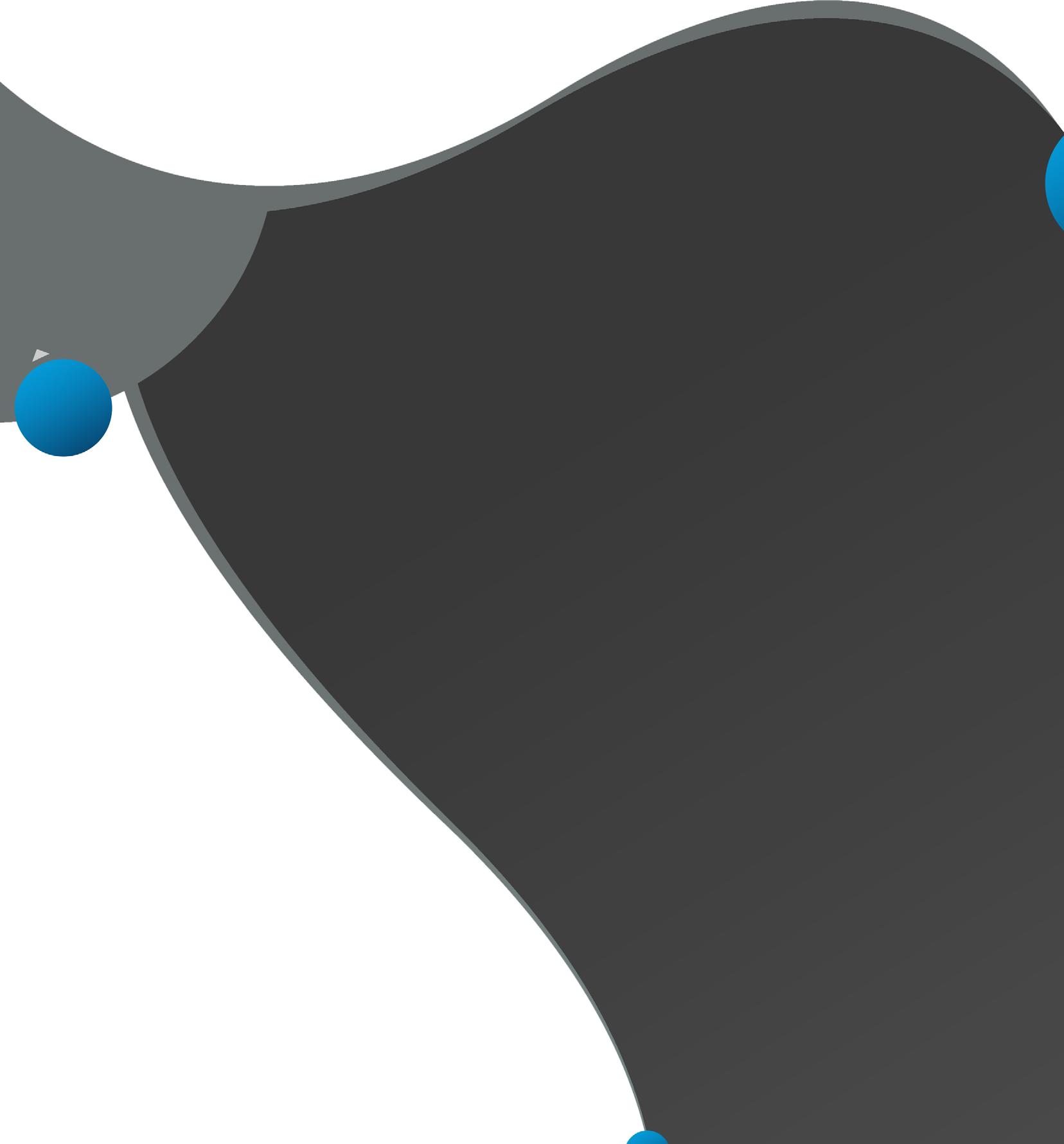
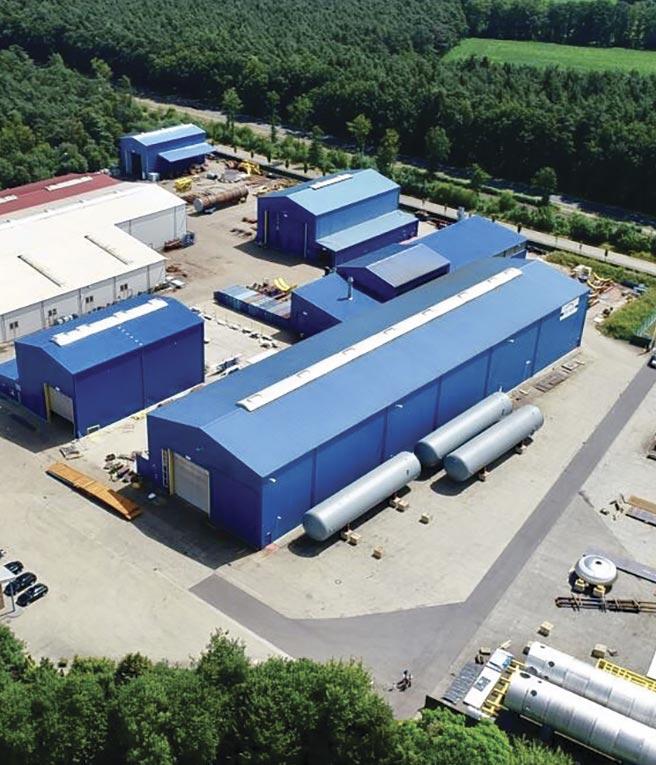
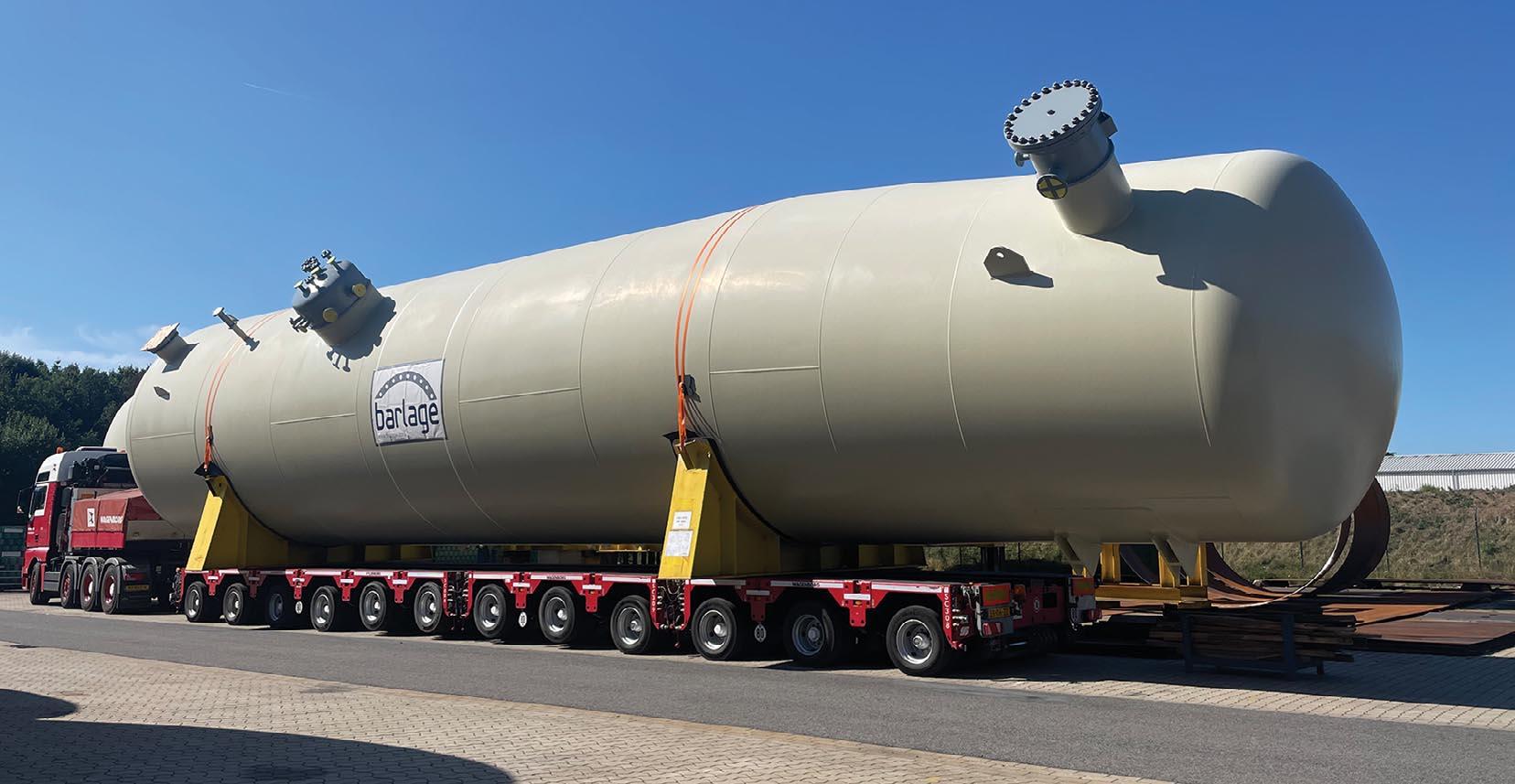

Barlage GmbH is prolific in the steel industry. The German company specialises in designing, manufacturing and delivering oversize welded structures such as pressure vessels, reactors, tanks and heat exchangers. Whether it is large components, special devices or production for conventional construction, Barlage has a solution. André Schöning, General Manager, explained more about what the company does to Hannah Barnett.
When the company was founded back in 1963, Barlage was a sheet metal construction business, mainly manufacturing dust filters, electrostatic precipitators and ducts.
At the end of the 1990s, Barlage shifted into operating as an equipment manufacturer, initially in order to serve the coal and gas industries. The sector transition was
complemented by an expansion into new facilities alongside its original location in Emstek-Halen, with an additional site in Haselünne-Flechum. Both are in Lower Saxony, in the northwest of Germany.
“In 2008, we took the next step and became a special equipment manufacturer,” recalled General Manager André Schöning. “In order to support this change, a large assembly hall was built at Europort in Haren, with a canal
connection leading directly to the factory. We have been building components for transportation by the inland waterway industry since 2017.
“We are now a one-stop shop for the manufacture and delivery of bespoke steel items. We can manufacture large cargo up to nine metres in diameter, and up to 90 metres in length.”
As a special equipment manufacturer, Barlage now serves the inland waterway, chemical, petrochemical and sludge industries. This involves making components for
power plant construction, the chemical or oil and gas industries, apparatus or aeronautics, shipping, agricultural technology, and the mining or pipeline sector. The company develops individual solutions to create optimal results.
Barlage attaches great importance to maximum safety and optimal conditions for the quality of its products, because some of the components are used in sectors where precision, durability and reliability are vital. As a result, the company ensures that the facilities where its items are manufactured are state-of-the-art. Barlage boasts approximately 200 employees across its two sites. The Flechum location has a workshop area of approximately 21,500 square metres spread over nine manufacturing halls with a storage area of approximately 90,000 square metres and a separate
stainless-steel production area. From there, it can move bespoke steel items up to six metres in diameter, 60 metres in length and 600 tonnes in weight.
The Haren site has a workshop of approximately 3,500 square metres and a storage area of approximately 10,000 square metres. From there, it can transport steel items up to nine metres in diameter, 90 metres in length and 900 tonnes in weight.
“The Haren location also focuses on shipment via inland waterway vessels or pontoons,” Mr Schöning explained. “That site has a huge logistical advantage due to its direct port connection. Since 2017, we have built over 100 tanks for the shipping industry, which is something we are very proud of.”
Nothing stands still in the steel industry, and as a result Barlage is looking to expand its Europort site in Haren with a recently opened new administrative building. “Alongside the upgrade of the office infras -
tructure, our machine park is constantly renewed in order to remain the state-ofthe-art facility it is,” said Mr Schöning.
Of course, any modern business must adapt and evolve in accordance with environmental concerns; Mr Schöning explained that Barlage has recently started using solar power rather than deriving all its electricity from the grid: “Our new PV system will self-generate nearly 50 per cent of the electricity needed for welding.”
Unsurprisingly, the company’s sustainability policy does not end there, with
a doubling of PV capacity planned in upcoming years. Barlage also has a district heating connection to a nearby biogas plant, as well as newly installed heat-meters in every manufacturing hall to monitor and control heat consumption.
Mr Schöning was clear that what sets Barlage apart from its competitors is also what will continue to propel the company into a successful future.
“We always ensure on-time delivery, which includes direct shipping,” he said. “And the size of a component does not matter – not even during transport. Thanks to our intelligent assembly and logistics concepts, we always deliver products on time, worldwide. Plus, offering the highest quality of product is vital to us. And we
can – and do – react flexibly to customer requests at any time.”
Indeed, as a business, Barlage is proud of its reliable, made-to-measure solutions, extensive staff knowledge and compliance with higher safety requirements. The company has been quality management certified for over 20 years.
Mr Schöning acknowledge that, like any business, Barlage does face challenges going forward. Firstly, there is a shortage of skilled professionals. “We intend to overcome that by forging close contacts with schools to increase the number of trainees,” he said.
Another challenge is inflation of costs, and a third is the energy crisis which the company is already striving to overcome with countermeasures like the new photovoltaic system. Mr Schöning also
acknowledged that Barlage has been impacted by supply chain delays and price concerns due to the Ukraine conflict, with especially large fluctuations in the cost of raw materials.
However, it is clear, that the future is bright for this dynamic, synergistic company. Always keeping an eye on evolution and development in the industry, Mr Schöning indicated that he thinks CO2 vessels will be the next big thing.
But for now, the challenges of the job are something that keeps the General Manager flourishing in the role. “Every project is different, no two days are the same,” he concluded. “And we very rarely build the exact same vessel components
again. It makes us so proud watching the whole journey; from the drawing board at our manufacturing site, to the delivery of the finished components.” n